
4 minute read
Counties Expand Pavement Life with ESCS in Chip Seal Applications
By Vernon Mortensen
Asphalt pavement preservation helps maintain safe and beautiful roads. It can also save cities, counties and state departments of transportation (DOTs) money by extending the service life of roads and highways. In fact, asphalt maintenance experts estimate that every two dollars spent on pavement preservation can save four to 18 dollars on future costs.
When it comes to preventive maintenance, sealing cured asphalt can bolster a road’s resistance to UV oxidation and damages caused by the ingress of water, oil and salt. As such, sealing is a worthwhile investment for aging asphalt roads that are still structurally viable. For this type of preventive maintenance, contractors generally have two options: sealcoating or using an asphalt chip seal.
Merely a surface treatment, sealcoating prevents water and chemical penetration and must be applied every other year or so. It cannot repair cracks and other forms of distress. On the other hand, asphalt chip seal provides similar protection and offers a new, more robust wearing surface on more distressed pavements. It can also last up to five times longer than sealcoating, according to the Expanded Shale, Clay and Slate Institute (ESCSI). When contractors use lightweight aggregates like expanded shale, clay or slate (ESCS), they can expect several cost and safety benefits in addition to a longer service life.
The Secret of Lightweight Aggregates
Asphalt chip seal made with ESCS can provide a cost-effective surface treatment that both repairs slightly distressed roads and improves their safety and durability. Its ability to do this comes from the aggregates’ structure, specifically the network of unconnected voids and highly regulated aggregate size that result from the production process.
The highly regulated aggregate size supports the even placement of asphalt chip seal. The unconnected pores increase the surface area of the aggregates for a strong bond with the asphalt emulsion. They also decrease the overall weight of the aggregate, which requires fewer trucks to haul and increases the square yard per ton coverage ratio. Further, these voids help ESCS resist polishing for a long-lasting high skid resistance rating. These qualities benefit both DOTs and constituents.
Benefits
Because ESCS aggregates resist polishing for long-term skid resistance, they can support road safety in both wet and dry conditions. Whereas the skid numbers of common sealcoating treatments hover between 20 and 30, asphalt chip seal made from ESCS can achieve a skid number over 60. According to a 1996 survey of state skid control practices, only a skid number greater than 34 is acceptable to high traffic roads. Further, ESCS retains a similar rating after millions of vehicle passes.
In addition, these voids lower the aggregate density, reducing the force of dislodged chips. After using lightweight aggregate chip seal to repair I-80 and I-84, representatives from the Utah Department of Transportation (UDOT) stated they did not have a single complaint or claim for a broken windshield or vehicle damage. They continue, “This is unheard of for a chip seal.”
All these qualities support safer and smoother roads for motorists without requiring further processes and labor. As such, it can contribute to more satisfied taxpayers and fewer complaints to DOTs.
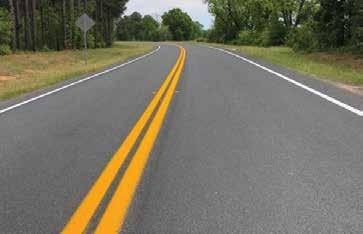
Due in part to the increased bond strength between ESCS and emulsion, asphalt chip seal can last up to 10 years. Further, the increased bond strength improves the retention rate of the aggregate. This reduces costs associated with replacing unretained chips. As an example, a 2017 return on investment report from Utah’s Carbon County Road Department found that using ESCS increased the retention rate from 30% to 99%, resulting in a significant reduction of application costs.
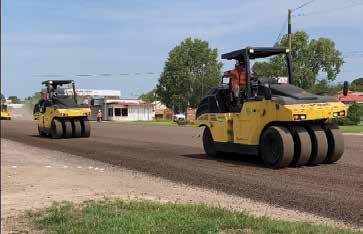
Because the voids lower the overall weight of the aggregate, DOTs can expect greater per ton coverage than conventional aggregate. This not only reduces the amount of material needed for coverage but also decreases the loads required to seal a road, both of which contribute to cost-effective maintenance programs. The Carbon County report concludes that using asphalt chip seal made from ESCS resulted in over $300,000 in savings annually.
To optimize the cost-effectiveness of asphalt chip seal made from lightweight aggregates, contractors and DOTs should adhere to the following best practices. Doing so will not only reduce potential misapplication but also ensure all parties have clear expectations of the process and results.
Site Prep and Placing Chip Seal
Before placing chip seal, it is important to survey a site’s level of structural integrity and degree of distress. While chip seal can repair some damage, it is not recommended for unsealed cracks greater than a quarter of an inch, rutting deeper than 1 inch, and medium- to high-severity alligator cracking. For sites with these damages, repairs will need to take place three to six months prior to the placement of asphalt chip seal, depending on the repairs used. This timeline allows these repairs to cure fully.
On the day the chip seal is to be placed, the ambient temperature should be at least 55 degrees Fahrenheit (F) and the pavement’s surface should be 70 degrees F and rising. Also, mud, dirt and debris should be cleaned from the road and the surface should be dry. Once these preparations have taken place, contractors can place the chip seal.
First, contractors should dial in the proper shot rate of emulsion based on site conditions—generally between 0.33 and 0.38 for type A—or ⅜ inch—chips and 0.42 and 0.48 for type C—or ½ inch—lightweight chips. After spraying the emulsion, contractors can place the chips in a uniform, single layer. Rubber tire rollers will then be used to ensure proper embedment and lodge the aggregate into the binder.
Post Placement Care
After the chips have been placed and rolled, contractors should lightly broom or sweep the loose chips from the top of the chip seal within
24 hours. Waiting longer, especially if the chips have been placed too heavily, will result in crushing.
For highways and non-curbed streets, the brooms can sweep the aggregates off the side. ESCS lightweight aggregates are chemically inert and free draining, so they will not cause harm to neighboring ecosystems, according to the ESCSI. For guttered streets and residential areas, the brooms should be able to vacuum or pick up the chips into a box rather than side casting them into the gutter.
Extending the Life of Roads and Highways
When used as preventive maintenance, asphalt chip seal made from ESCS can provide a smooth and long-lasting surface to highway and municipal roads—extending the service life of most asphalts by five to 10 years, depending on traffic and environmental conditions. As such, asphalt chip seal presents a cost-effective alternative to sealcoating for pavements that are still structurally sound but showing signs of aging.
Vernon Mortensen is an aggregate salesperson at Holcim Lightweight Aggregates, Utelite, with over a decade of experience in the lightweight aggregate industry. He is active in the Expanded Shale, Clay and Slate Institute (ESCSI) asphalt committee and has served as the committee chairperson.