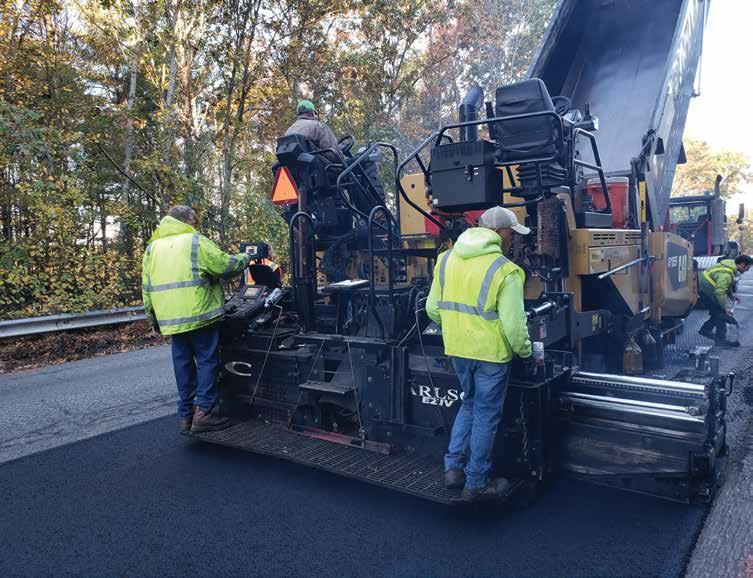
5 minute read
Selecting Your xD for
Mill-and-Fill Workflow
BY SARAH REDOHL
Many asphalt contractors have some level of familiarity with 2D asphalt paving technology. However, far fewer will be familiar with 3D technology.
At CONEXPO-CON/AGG 2023, experts from Topcon Positioning Systems, Livermore, California, and Trimble Inc., Westminster, Colorado, presented an education session titled “The Future of Asphalt Paving Technology,” during which 3D solutions featured prominently.
Here, we’ll explain the difference between 2D and 3D, the basic steps required for 3D, and best practices for incorporating 3D on your asphalt projects.
2D VS. 3D: THE DIFFERENCE
According to Kevin Garcia, general manager of Civil Specialty Solutions at Trimble, 2D milling or paving is usually performed or applied to a consistent thickness and/or slope, from the ground up. “What I mean by that is you’re referencing something on the ground, either with your sonic sensor hanging off the side of the paver or a sensor on your mill,” he said.
For example, if a 2D equipped paver is paving the right lane of a crowned highway with a 2% cross slope, the machine is going to hold the desired thickness to achieve that cross slope while referencing something on the ground, be it the contact sensor, sonic sensor, or similar.
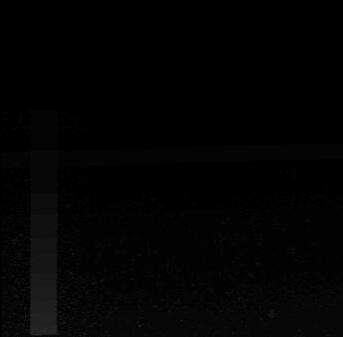


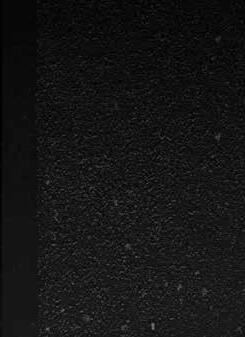
On the other hand, 3D is top-down in that material is placed or removed based on a purpose built model. “Basically, 3D [automated machine guidance] turns a big piece of equipment into a Roomba robot that goes where it’s told to go, based on the model, and it lays or takes away the thickness the model indicates,” Garcia said.
Milling in 2D, enables some level of smoothness, especially when using multi plex or averaging beams, Garcia said, “but if the road is bumpy in front of the mill and you’re just referencing that road to take 2 inches off, generally speaking that’s what it will look like behind the mill, only two inches lower. And that means the paver is going to have some varying thickness to that paving application if they’re trying to get an even smoothness on that surface.”
3D: THE BASICS
To perform 3D paving or milling, the contractor needs both the final desired design and the existing surface profile. “To 3D mill or pave rehabilitation projects, you have to collect information from the road surface,” said Mark Larranaga, senior manager of Software Business Development at Topcon. He said the collection of the point data required to generate the models is usually gathered via survey rover or robotic total stations.
However, new solutions such as vehicle-mounted LiDAR scanners like Topcon’s SmoothRide solution are emerging. “With [LiDAR scanners], you can have a vehicle driving down the road at highway speeds, picking up millions of points,” he said. Not only does this result in more (and easier) point capture, but it is also safer. “Once that data is gathered, it’s no different than data gathered by any other 3D systems.”
From there, modeling software is used to convert these point clouds into a model the machine can use to control the milling tooth or trailing edge of the screed. “The operator is still operating the machine— going forward, steering it—but the business end of the machine is fully automated,” Garcia said.
The model production is among the more challenging aspects of 3D versus 2D, however, it’s important that the model be done correctly. “If you have a model problem, it will show up in the field,” Garcia said. “If you spend time getting the model right, the application will go much smoother.”
Utilizing 3D technology also changes operations in the field, where total stations or similar solutions are required to collect vertical documentation needed to guide the mill or paver. Unfortunately, GPS doesn’t usually offer the accuracy required for milling or paving operations, Garcia said.
“It’s important to understand that GPS is only good to a certain accuracy,” Larranaga said. If you want to use GPS on high-accuracy paving projects, there are some tools available to do so. For example, MM GPS. “MM GPS uses GPS for the horizontal position and lasers for the vertical position so we can now use GPS in areas with open skies.”
“When we talk about GPS, we’re usually talking about golf ball accuracy,” he said. Total stations, on the other hand, offer millimeter accuracy—roughly the thickness of a quarter, Garcia said.
Deploying total stations does increase complexity on the paving train, not only in having someone trained to operate the machine but also in terms of project set up given the distance limitations of the total stations. The further the machine gets from the total station the less accurate it will be. “A general rule of thumb is around 1,000 feet,” Garcia said, “500 feet up to the instrument and 500 feet past it, and then set up another instrument beyond that.”
3D MILLING OR 3D PAVING: THE ANSWER
Both Garcia and Larranaga agree that it’s better to 3D mill whenever possible instead of 3D paving.
Garcia envisions 3D paving for high-spec jobs, like projects with an elevation spec, test tracks, race tracks, airport runways and sport surfaces. “We’re seeing 3D paving used for pickleball courts,” Garcia said, “where they have to have just a tiny bit of slope to shed water.”
Although he sees a number of use cases for 3D paving, Garcia said it’s easier to fix the road with 3D milling than 3D paving for several reasons, including that it’s easier to position the tooth of the mill very accurately than it is the floating screed on an asphalt paver. With the screed, there’s also more room for potential issues, such as a change in the angle of attack or if the auger box gets starved or flooded.
Garcia also gave a real-world example of a contractor who subbed out the milling to a company that did not use 3D milling and planned to resolve any issues with 3D paving. However, halfway down the project, the existing surface was higher than it was everywhere else and so the paver only placed the lift about ¼-inch thick, Garcia said. “The surface might have been at the desired elevation, but how long do you think that will last?” he said. “It may not even have survived compaction.”
That’s why Garcia recommends fixing the profile of the road with 3D milling, if possible. And Larranaga agrees. “We have a lot of rehab projects out there right now, and in this day and age we’re typically milling to a certain depth and the paver is trying to get that smooth surface,” Larranaga said. “If you did 3D with the mill, you’ve cut any bumps and dips out of the road…You can just pave to depth at that point.”
Garcia is frequently asked if the dirt work is done in 3D, can it be relied upon for paving. His answer? “If the profile of the dirt is the same as the profile of the final road, you can just vertically offset,” Garcia said.
Not only does 3D milling make paving easier, but it also makes it easier to calculate yield and manage trucking, Garcia said, because the length, width and depth are fixed. “I can tell the asphalt plant what I need, I can plan the trucking that I need. …3D milling also makes compacting easier, too. You’re not having to change energy to get density,” he said. “The whole day just goes smoother.”