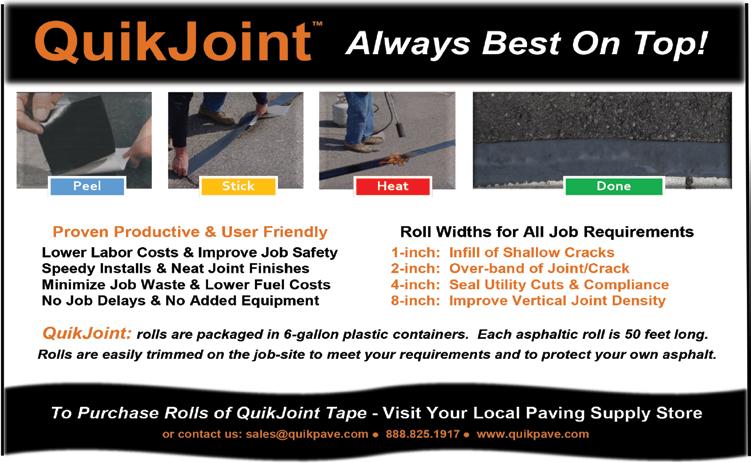
6 minute read
Solve Low Volume Lots I
In an Asphalt Pavement Alliance webinar, Mike Skinner, P.E., director of pavement engineering for the Colorado Asphalt Pavement Association, shared his best practices for the design and construction of low volume and commercial parking lots.
Of the 9 million tons of asphalt produced annually in Colorado, Skinner said about 25% is supplied to the commercial market, which includes commercial and office buildings, restaurant and retail, and also residential new development.
“There are a number of factors as to why asphalt is the answer [for commercial pavements],” he said, which include aesthetics, design, speed of construction, performance, cost, and sustainability. “With a lower upfront construction cost, asphalt is a win-win for industry, property owners and constructors alike.”
Let’s take a closer look at some of the factors that need to be considered for low volume commercial paving applications.
Subgrade Solutions
“As far as performance for a subgrade goes for a parking lot, granular materials (sands) have better performance than cohesive materials (clays), but as pavement engineers, we have to work with the material we have on site,” Skinner said.
To determine the type of soil on the project, the geotechnical engineer will run Atterberg Limits and -200. However, it’s valuable to understand the basics. Skinner said soil has three components: solids, water and air voids.
“When you start to apply some compactive effort to the material, you start to rearrange the particles and get grain-on-grain contact and the strength of compacted materials increases,” Skinner said. The subgrade may also require additional moisture to fill that void space to reach optimum moisture content. “Construction specifications will generally say, depending on the soil type, +/-1 to 4%.”
“When you reach optimum moisture content, if you continue to add moisture, you’ll start to push those grains apart and you start to lose grain-on-grain contact,” Skinner said. “That’s why saturated soils pump and lose stability. A general rule of thumb is when a soil reaches 5% beyond its optimum moisture con-
By Sarah Redohl
tent, it’s generally considered to have lost its structural capacity.”
Skinner said it’s also important to identify the strength of the existing subgrade, adding that there are several different ways to do so, including running R-Values, California Bearing Ratio and the Resilient Modulus.
Some particularly low quality subbase materials may require excavation and replacement with more suitable material, but there are some workarounds to low quality subbase, Skinner said, in the form of either mechanical or chemical stabilization. Common chemical stabilizers include lime, cement and fly ash tilled to a depth between 8 and 12 inches to achieve around 160 psi. “More is not better here,” Skinner said. “We don’t want to exceed 200 psi because it could cause reflective cracking [of the asphalt pavement].”
Skinner reminds us to be aware of soluble sulfates found in some subgrades, as calcium leaching out of lime, cement or fly ash can react with the sulfates in the subgrade to create a mineral called ettringite. “That can result in significant swelling and isolated areas of heaved subgrade,” he said. If there are soluble sulfates, a double application of the chemical stabilizer may be required, such that the subgrade is treated, water is added to create the chemical reaction and heave the subgrade, which is then knocked down with a pulverizer prior to a second application of chemical stabilizer.
Mechanical application is another option, which includes sub excavation of the problematic material and importing cleaner material or aggregate base course using reinforcement. “Reinforcement, like geogrid, can offset the cost while increasing performance as a way to optimize your design,” Skinner said.
Factor for Traffic
Another factor is the anticipated traffic for a given parking lot. “Traffic is its own unique beast as it relates to low volume and commercial applications,” Skinner said, adding that this is a difficult number to determine in commercial applications because a civil site designer doesn’t have anticipated traffic loads for these parking lots.
The anticipated traffic loads are often based on the number of design stalls, Skinner said, but this approach has its own flaws. Skinner points out that a car has a load factor of 0.0007 ESALs, while a loaded 18-wheeler is 1.35 ESALs and a loaded 68-foot articulated bus is 5.11 ESALs. “One [18,000 pound axle] truck driving across your parking lot is equivalent to 1,929 cars driving over that same spot,” he said.
“If you were to put a tube counter down for a driveway or an entranceway and you find 97% is personal vehicles and 3% is truck traffic, the 97% is irrelevant because it has such a minimal impact on the structural section I have to design,” Skinner said. “Most of the traffic is inconsequential; we’re only designing for the heavy stuff.”
Skinner indicated it’s general practice to use the following ESAL average ranges when designing for parking lots:
- Automobile stalls: 21,900 to 36,500
- Secondary drives: 36,500 to 58,400
- Primary drives: 58,400 to 73,000
- Loading docks: 73,000 to 182,500
“We can take these ESAL values, expand that into a 20-year service life and put that into our equation,” Skinner said. However, he added, “traffic is as much an art as it is a science when it comes to pavement design.”
So, how does one perform structural design for parking lots? Skinner recommends the tool PaveXpress, which incorporates AASHTO’s empirical pavement design. “This is the go-to for any kind of commercial application for a parking lot,” Skinner said.
With this tool, a user can input the required data and receive a pavement design including the desired structural number and optimized layer thickness based on the structural coefficients entered for those materials to be used on a design consideration.
Pavement Section Alternatives
Skinner said that when it comes to low volume commercial applications, there are a number of pavement section alternatives. “We can build a full-depth section directly on the prepared subgrade,” he said, usually 4 to 6 inches thick. “If the section needs to be more than 10 inches thick, which would be very rare, it would make sense to incorporate an aggregate structural section.”
Another option, he said, is adding a flexible section, which is a thinner section of asphalt built over a composite section of aggregate base course placed on the subgrade, sometimes with composite, sometimes with geotextile or similar to increase structural capacity of the subgrade. He said a good rule of thumb is to build these at a ratio of 2:1. For example, 3 inches of asphalt over 6 inches of base course.
“When building a composite section, you have to be careful that you’re addressing drain- age because you have that layer with increased void space in the aggregates down below the asphalt pavement,” Skinner said.
Mix Design
When it comes to mix design for low volume commercial applications, Skinner highlights three things: asphalt binder, mix gyrations and aggregate size.
As binder use varies from state to state, Skinner recommends reaching out to your local asphalt pavement association for guidance on their preferred binder for commercial applications. His recommendation for mix gyrations is a bit more direct: “Do not exceed 50 gyrations.
“When we’re talking about low volume commercial applications, most stresses are going to be the result of aging and environmental impact,” Skinner said. “Our biggest concern for performance in commercial applications is maintaining flexibility, so a softer material that will allow for flexibility and movement over time will be critical for longterm performance.”
Given that the number illustrates the number of gyrations to compact that material, Skinner reminds us that a 50-gyration mix will be less dense than a 100-gyration mix.
“Putting down a 100-gyration mix in a parking lot will be stiff and brittle and will accelerate distress,” he said.
The third factor in commercial mix design is aggregate size. He recommends ½-inch aggregate for commercial applications. “People call us on occasion to ask if they can use ¾-inch aggregate on a surface lift of a parking lot, but it doesn’t have the same aesthetic and it won’t have the same performance because of the void structure,” he said. “With commercial applications, you ought to live in the world of 50-gyration mix with ½-inch aggregates.”
Maintenance Considerations
A very common question when designing a commercial parking lot is that of maintenance. Specifically, “What should we be budgeting for maintenance?” According to Skinner, the predominant distresses found on low volume pavements are raveling, oxidation and low temperature thermal cracking.
Skinner gives the following example of a football stadium parking lot with a total surface area of 6,500 square yards and an asset value of $453,530. “The FHWA has provided some guidance for maintenance and has recommended that a property owner budget 2 to
3% of their total asset value for annual maintenance,” Skinner said. In this example, that would be up to $13,605 a year. “Based on my experience, I’ve never found an agency that budgets that high. It’s more typical to see an agency budget at about 0.5%.” In the above example, that would be $2,268 per year.
However, Skinner says it’s important to discuss the cost of deferred maintenance with your clients. “Deferred maintenance can quickly escalate and impact the long-term performance of the parking lot,” he said.
Skinner offered the example of a local church whose parking lot required around $5,000 in crack sealing and selective patching. The church opted to wait on the maintenance and when it called back five years later, the cost to repair the lot had increased to $35,000. “They were kicking themselves for not addressing it sooner.”
Contractors paving low volume parking lots should not only utilize best construction practices, but they also have to be a partner to their clients to determine the best solution and budget for initial construction and maintenance costs.The contractor that can do all this not only builds a dependable asphalt pavement, but also the industry’s good name.