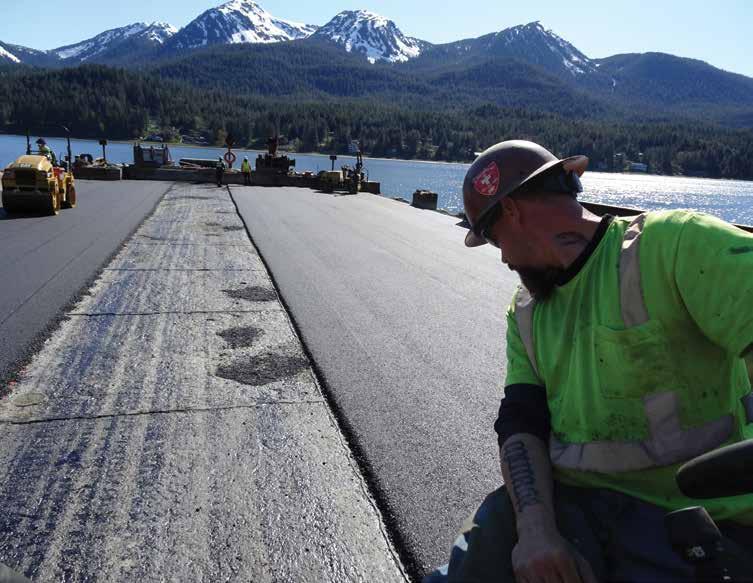
11 minute read
How to Pave on a Moving Surface
The crew paved three passes on the right, two passes on the left, a stub on the left, and in this photo they’re backing into place for the last pass out.
From environmental stewardship to compaction tips, here’s how one professional crew managed an aggregates barge paving project
EEarlier this summer, I worked with the fantastic SECON crew in Alaska to help them fine-tune existing skills and develop new skills to enhance their overall performance. The company asked me to observe and assist the crew during its execution of a paving project on a barge in Gastineau Channel, and it started with a curve ball that the crew handled with professionalism. Let’s look first at the oversized trench the crew took care of, then walk through the steps to pave on a not-sosteady surface for top quality paving. Check out the pictures on the next few pages for a deep dive into the details.
FILL THE TRENCH
Part of a working dock system is the electronics. For this project, the owner needed an electrical trench completed. Originally, they thought it would be a little extra mix in a trough. Not so much. When the crew arrived, the owner had put a large electrical cable in deep trench and filled in 2 inches of aggregate. That left 10 inches for us to fill with hotmix asphalt (HMA). It took about 20 tons. • First, we hand-swept and cleaned off the dirt and dust with a leaf blower to get the sides of the trench clean. • Next, because the distributor truck we had on the project was not equipped with a spray wand, we heated up tack in a kettle and used this to tack the sides.

From left: Mark Davies, Jake Ritter, Eddie Sandifer, Dustin Jacobsen standing behind Vickie Brown, Foreman Daniel Gradin and Kevin Sandifer make up the SECON crew that performed the barge deck paving project.
The crew matches the joint beautifully. With the leveling course down, compaction is the final touch.

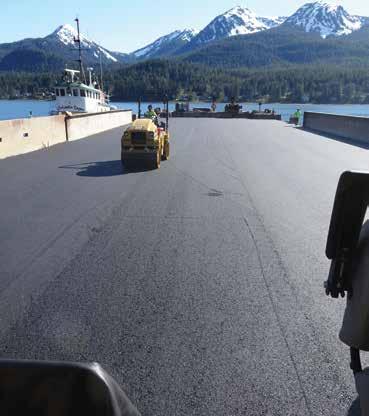
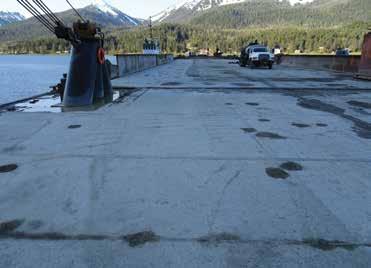
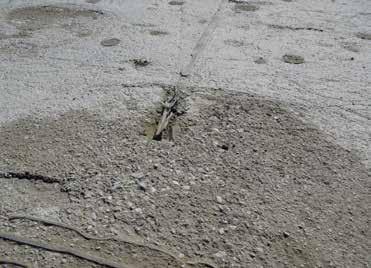
The deck before tacking or paving shows lips of the concrete slabs and squares that the new asphalt pavement needed to level out. The exposed and damaged steel girder had to be cut down flush with the surface before we could pave over it.

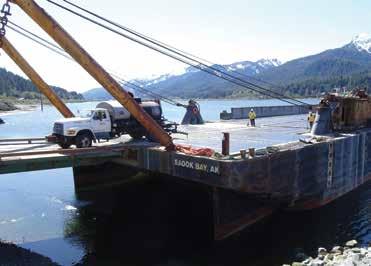
A special note to think about is we also swept the ramp leading onto the barge so trucks didn’t contaminate the surface—the tack or the leveling course— with dirt as they approached the paver. This is a good practice for commercial lots or new residential roadways where trucks can bring all manner of dirt and clay onto the surface to interfere with asphalt’s adhesion to the surface. To be good stewards of the environment, we used a push broom to move dirt to the middle of the deck, then brought a vacuum broom in to suck up the dirt. A leaf blower dried water used in the sweeping process.
• Then, we used an attachment from
Road Widener on a skid steer to convey HMA into the trench. We placed it 5 inches deep and compacted that lift with a plate compactor. • Finally, we used that same attachment to place the top 5 inches and compacted that with a tandem steel-drum roller. • For this trench-fill, Roller Operator
Vickie Brown pinched both sides of the trench, sealing the sides, before rolling down the middle for final compaction.
You can read more about Brown in the
October Women of Asphalt feature.
PREP THE DECK
One of the first steps to any quality paving project is to clean the surface to be paved, and this was true for the barge deck in Gastineau Channel as well.
Unlike a typical paving project, we had to be extra careful with the material we swept up to ensure no dirt accidentally fell into the water. To get the deck clean in a safe way, we carefully broomed all dirt, dust, leftover aggregate, and so on into rows. Next, we brought in a skid steer to scoop up and carry away material. What material the skid steer couldn’t carry away, we captured with a vacuum sweeper.
Water was an integral part of keeping dust down, so blowing the deck dry was the final step before tacking the surface.
A surprise that made this deck different from a parking lot was the steel girder sticking up from the floor. Over the years, the concrete deck had worn and spawled to the point the steel had been exposed to the wheel loader buckets that moved material on and off the barge. Sometimes, that equipment would snag on exposed steel and cause the unsafe protrusion of
THE TANK
100 YEARS OF DOING IT BETTER
WE ARE A UL-142, ASME SECTION
VIII AND API APPROVED TANK
MANUFACTURER. Our facility is quality control inspected by
Underwriter’s Laboratories four times per year.
WE ARE A LICENSED MANUFACTURER
FOR THE STEEL TANK INSTITUTE (STI). We are the recipient of STI’s
Quality Award 16 consecutive years and inspected two times annually.
ALL ASPHALT TANKS ARE BUILT
TO THE UL-142 CONSTRUCTION
CODE. We keep records of the steel purchases, welding practices, pressure tests and other quality control measures.
WE USE 6” INSULATION ON TOP
AND SIDEWALLS OF OUR TANKS.
The bottom of our tanks are insulated with foam glass block.
ALL OF OUR SHELL JOINTS ARE
DOUBLE BUTT WELDED AND NOZZLE
JOINTS SEAL WELDED INSIDE AND
OUT. 100% Welded - The strongest union of two pieces of steel possible.
WE ARE CONSTANTLY IMPROVING
OUR TANK DESIGNS. The only way to keep our tanks better than any other tank on the market!
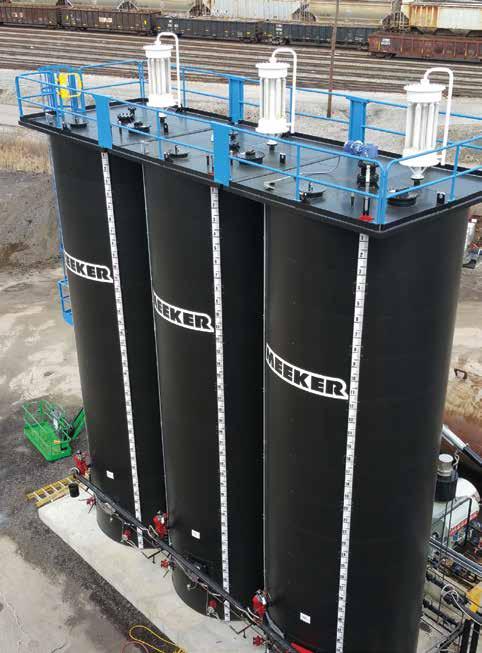
Call us toll free! (888) 333-0323
www.meekerequipment.com
Your Preferred Asphalt Equipment Resource Contact Information
Meeker Equipment Headquarters 4381 Front Mountain Road Belleville, PA 17004 Phone: (717) 667-6000 Fax: (717) 935-2389 E-mail: info@meekerequipment.com
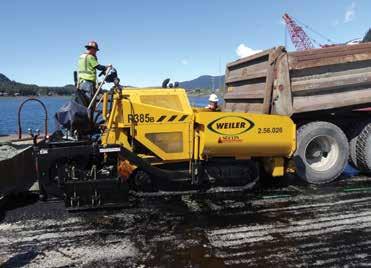
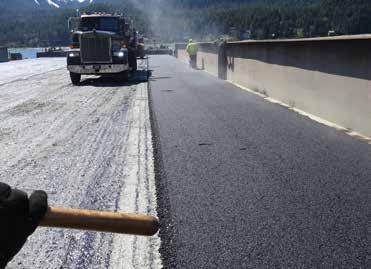
LEFT: The crew used their brand new Weiler P385B paver for the project. They extended the 8-foot screed to 10 feet for six passes across the 60foot by 280-foot deck. RIGHT: After the first pass, the operator backed the paver for the second pass. Take a look at that smooth straight line for matching the joint. Before paving began, we lined out the job with green paint on top of the tack. We marked out the 4-foot starting pad and ending point to ensure everyone, including truck drivers, knew exactly how to perform for a top quality paving job.
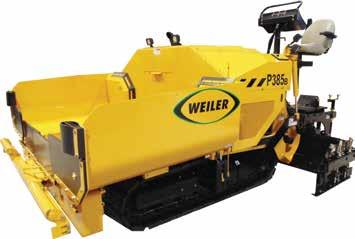

LEFT: The tracked paver SECON used on this project was brand new. While it’s not a full-size highway paver, it’s “beefy” for a commercial paver. The 8-foot, front-mount screed weighs 3,700 pounds and is hydraulically extendable up to 15 feet, 8 inches, although we only needed it out to 10 feet for this project. The tractor is 14 feet, 5 inches long and the 9-ton hopper capacity gave us plenty of working space, too. RIGHT: In this photo, Brown shows us the welding tip cleaner that can be used to clean the nozzles of roller spray bars. They’re an inexpensive tool for roller operators to keep on hand.
girders. To keep that from causing a dangerous situation, we cut it flush with the surface with a saw.
Just as you would with a parking lot, we mapped out the best way to apply tack to avoid tracking or overcoating. We tacked the deck in long passes from the back of the barge toward the front, stopping at obstructions. We then tacked across the front from the sides toward the center to make sure all areas including the front loading area were tacked. The final pass with the tack wagon moved from the center straight off the barge.
This is the same basic layout we used to pave a leveling course and then a top lift of asphalt.
PAVE IT BLACK
The leveling course required approximately 2 inches of HMA, which we placed with a brand new 8-foot Weiler P385B tracked paver. We extended the screed to 10 feet and pulled six passes across the 60-foot deck of approximately 210 tons. I say “approximately” because this was a base course that needed to fill in some holes and crevices where the concrete had failed or where the concrete plates were not level with one another. This course lived up to its name as “leveling.”
The 2-inch surface course required 210 tons of HMA.
In almost every article I share with you, I remind you to double-check the slope and levelness of your mat with a four-foot level.
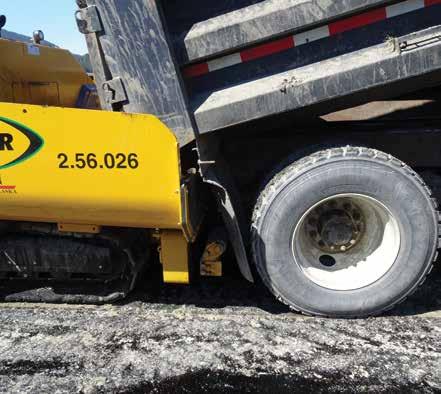
When this truck arrived, we noticed a pindle hook on the back end. This is a problem because it prevents the paver operator from bringing the push rollers all the way to the tires. The pindle hook basically holds the truck away from the paver a few inches. This can be a pricy problem if mix spills out.
The solution, at first, is to dump the truck slowly. You have to let the mix dribble into the hopper slowly so the truck doesn’t fall out of the hopper from the sudden shift of weight.
The final solution is to tell the driver he’s off the job. We told this driver we couldn’t use him anymore and sent him off the job. In the heat of production, you might not notice a specific truck’s return and you might start charging the hopper of the problematic truck without realizing it’s setting you up for an expensive, timeconsuming mess. It’s better to solve the problem before it starts.
For the barge deck project, we started with five trucks hauling material. Even going down to four trucks, we never had to wait on material. The plant was about 10 minutes from the project and the team stayed in communication with the plant operator sending material to us at 300 degrees F.
Make your RAP piles pay for themselves.
Use ReLIXER™ to maximize RAP content while meeting project specifications.
Engineered, high-performance rejuvenator for High RAP & RAS mixes
Rapidly penetrates and rejuvenates. Reduces the virgin asphalt requirements in the mix. Allows increased RAP & RAS content while aiding compaction Improves low temperature performance, fracture toughness, aging & fatigue 100% RAP mixes with no virgin AC added are viable with outstanding performance
ReLIXER™ • NuMIXER™ • ReNUBIT™ • PGXtend® • PGXpand® • SriCote™
1-800-562-6276 1-201-721-7562
Learn More At Sripath.com/piles
Make Asphalt Better
1 2
3
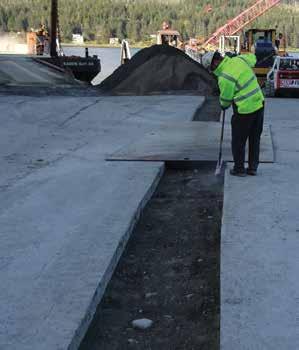
Before filling in the trench, the crew swept the sides, cleaned it with a leaf-blower, and tacked the sides with tack heated to 160 degrees F.
The crew used a Road Widener attachment with conveyor belt in its hopper, affixed to the front of a skid steer, to put two 5-inch lifts of HMA on top of a 2-inch lift of gravel to fill in the electrical cable trench. Roller Operator Vickie Brown used a plate compactor to get the first lift compacted in the 3-foot-wide trench. To complete it, Brown used the steel drum tandem roller to pinch both joints of the trench before compacting right down the center.
Special Note: Keep bottles of biodegradable release agent on hand to keep equipment free of asphalt buildup, as you see in this final picture. Also notice that the team had been cleaning and tacking the bridge deck in the background while the trench project took place. That’s the kind of teamwork that keeps a job on schedule.
4 5
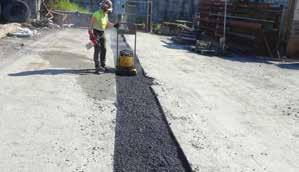

6 7
The electrical trench required more mix and more work than we anticipated, but the crew got it done ahead of deck paving.
When you’re on a ship docked on the water, this isn’t possible. Even with “calm seas,” there’s movement that will affect your instruments. For example, the tide rose while we were paving, lifting the barge. In this situation, you trust your equipment and your teammates to perform at their best. You can read about best practices for starting the paving day at https:// theasphaltpro.com/articles/how-to-trainnew-operators-to-pave/ or take a full online course for back-to-basics paving at https://training.theasphaltpro.com/p/asphalt-paving-101 .
COMPACT WITH CARE
To achieve compaction on a concrete deck above a hollow ship’s hold, we elected to use oscillation in the breakdown rolling position and static rolling for all other compaction. The Cat CB34B that Brown used has a 51-inch drum and achieved compaction beautifully. Look at the smoothness and lack of lines this crew achieved. You can find more tips about sensitive rolling zones at https://theasphaltpro.com/ articles/roll-bonus-part-2-ideas-perfectcompaction/.
When all was said and done, paving on a barge took attention to details like ambient temperature, extra environmental stewardship, removing broken rebar, carefully lining out the job, achieving density over a hollow ship, and so on. But the crew was up to the task and have the pictures to show how it can be done.
– BY JOHN BALL
John Ball is the proprietor of Top Quality Paving & Training, Manchester, New Hampshire. He provides personal, on-site paving consulting services around the United States and into Canada. For more information, contact him at (603) 493-1458 or tqpaving@yahoo.com.