
2 minute read
Blaw-Knox's PF-7110B Asphalt Paver
Step 1
The operator extends the operator station beyond the paver deck for best visibility. Step 2
The haul truck charges the 13-ton-capacity hopper.
Step 4
The 10-foot paving width can extend up to 20 feet with the Ultimat screed from Blaw-Knox.
Step 3
Independent augers feed material to the screed. The Tier 4 Final engine offers 235 HP at 1,800 RPMS.
FFor highway class paving power, the 10-foot PF-7110B tracked asphalt paver from Blaw-Knox Corporation, Orlando, Florida, features a Tier 4 Final D8 235-horsepower (175 kW) engine designed to improve fuel efficiency by up to 5%. Here’s how it works:
First, the paver operator takes his or her position in the rotating and extending operator seat for 360-degree paving visibility, including unobstructed views into the auger tunnel and hopper.
He starts the Tier 4 Final D8 engine, which offers 235 horsepower at 1,800 rpms.
When the operator signals the haul truck driver to do so, he will charge the 13-ton-capacity hopper and the operator will push forward, paving at a maximum speed of 224 feet per minute.*
Material moves along the conveyor system, to the auger tunnel, where independent augers feed it under the screed. For the PF7110B tractor, several Blaw-Knox screeds are available, ranging in extendable widths up to 20 feet (with the Ultimat screed) and allowing mat depths of up to 12 inches, according to the manufacturer. *Best practices suggest paving speeds not exceed 25 fpm for typical projects. Monitor your speed to match the plant’s production or reliable haul truck delivery to minimize starts and stops during mainline paving.
For more information, contact sales@blawknox.com or (407) 290-6000.
SHOW US HOW IT WORKS
If you’re an original equipment manufacturer with a complex product, let us help you explain its inner workings to asphalt professionals. There’s no charge for this news department, but our editorial staff reserves the right to decide what equipment fits the parameters of a HHIW feature. Contact our editor at sandy@theasphaltpro.com.
CRUSH RAP COSTS
with the HONEY BADGER
From replaceable abrasion-resistant steel wear liners to a 1/2" steel pulverizing hopper, this machine is ready for wear and tear. And by reducing material handling and minimizing moisture, the Honey Badger increases production and saves on fuel costs. Average return on investment is 1/8 the cost of other crushing operations. Fully-equipped with max power, reliable operation, and easy maintenance, the Honey Badger is ready to crush your costs!
Reduced RAP moisture = lower fuel consumptions
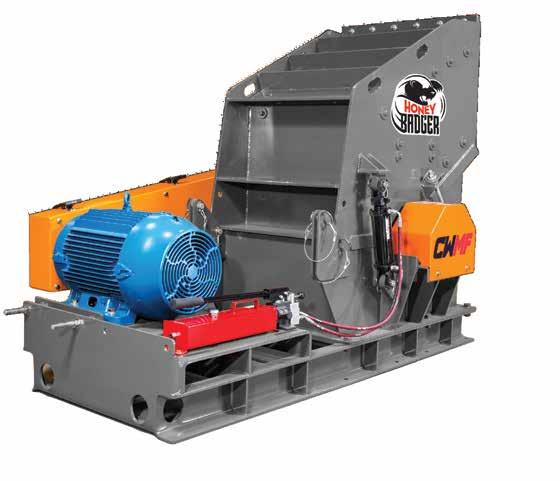
Reduce or eliminate crushing costs
Typical 6 month ROI
(300,000 ton/season plant)
Minimize material handling
STATIONARY PORTABLE
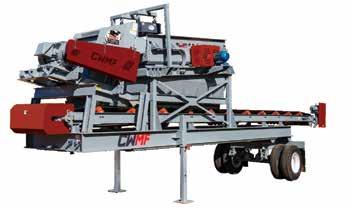
