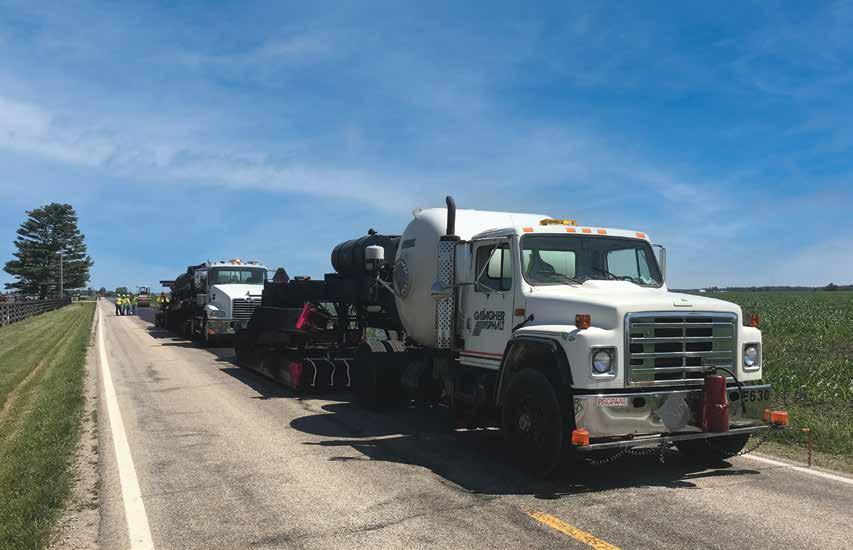
9 minute read
Gallagher Paves Ohio Hot In-Place
BY SARAH REDOHL
HHot in-place recycling (HIR) is a pavement preservation treatment where an asphalt pavement is heated and remixed on-site and inplace reusing 100 percent of the existing materials.
According to the Pavement Preservation and Recycling Alliance (PPRA), HIR reduces greenhouse gases by up to 30 percent and costs anywhere from 20 to 40 percent less than conventional rehabilitation techniques while offering same-day return to traffic and extending pavement life by seven to 15 years. And, the treatment option is growing in popularity.
“It seems to us we are doing more and more HIR with each passing year,” said Patrick Faster, national sales director at Gallagher
Asphalt Corporation, Thornton, Illinois. Today, the company has six sets of HIR equipment and dedicated HIR crews performing jobs in more than 20 states around the country.
Faster thinks demand is increasing both as a result of the increasing cost of asphalt and increasing interest in sustainability. He compares HIR to cold in-place recycling (CIR) and full-depth reclamation (FDR), the common denominator being the use of existing material in place to minimize hauling and use of virgin materials.
“HIR fits the niche in a roadway’s life cycle where it doesn’t quite need CIR or FDR,” Faster said. That was exactly the case on two recent projects Gallagher performed for Delaware County, Ohio, where HIR was used to level out the roads and improve rideability at a reduced cost compared to a mill and overlay.
Gallagher’s custom-built hot in-place recycling equipment includes two preheaters and a process machine. HIR is often an attractive option for roads without significant depth, “where the last thing you want to do is mill anything out,” Faster said. “Instead of milling and hauling off a couple inches and then paving on a couple inches, you can use HIR on the existing pavement and then add a couple inches of new asphalt on top of it. Then, it’s a net gain in terms of strength while also reducing tonnage.” HIR can also appeal to parts of the country where aggregate is particularly expensive, as well as for agencies who rely heavily on chip seal. “Many agencies use chip seals on lower volume roads, but there comes a point where chip seal won’t cut it anymore,” Faster said. “That’s where HIR can go in first, and then the agency can go back to chip sealing the road.” Faster said HIR is ideal for roads with poor ride quality, heavy rutting and surface degradation. However, Gallagher is particular about the roads on which it performs the process. They take cores of prospective roads and simulate the HIR method in the lab to see if the treatment works well on that prospective road. “The lab results dictate whether or not that road will be a good candidate for HIR,” Faster said. Gallagher doesn’t perform HIR on pavements with drainage issues and requires that the road be structurally sound, since HIR itself doesn’t enhance a road’s structure. “We’re only working the top 1.5 inches or so,” Faster said. “If you have a deeper problem, you’ll need to look at another treatment method.”
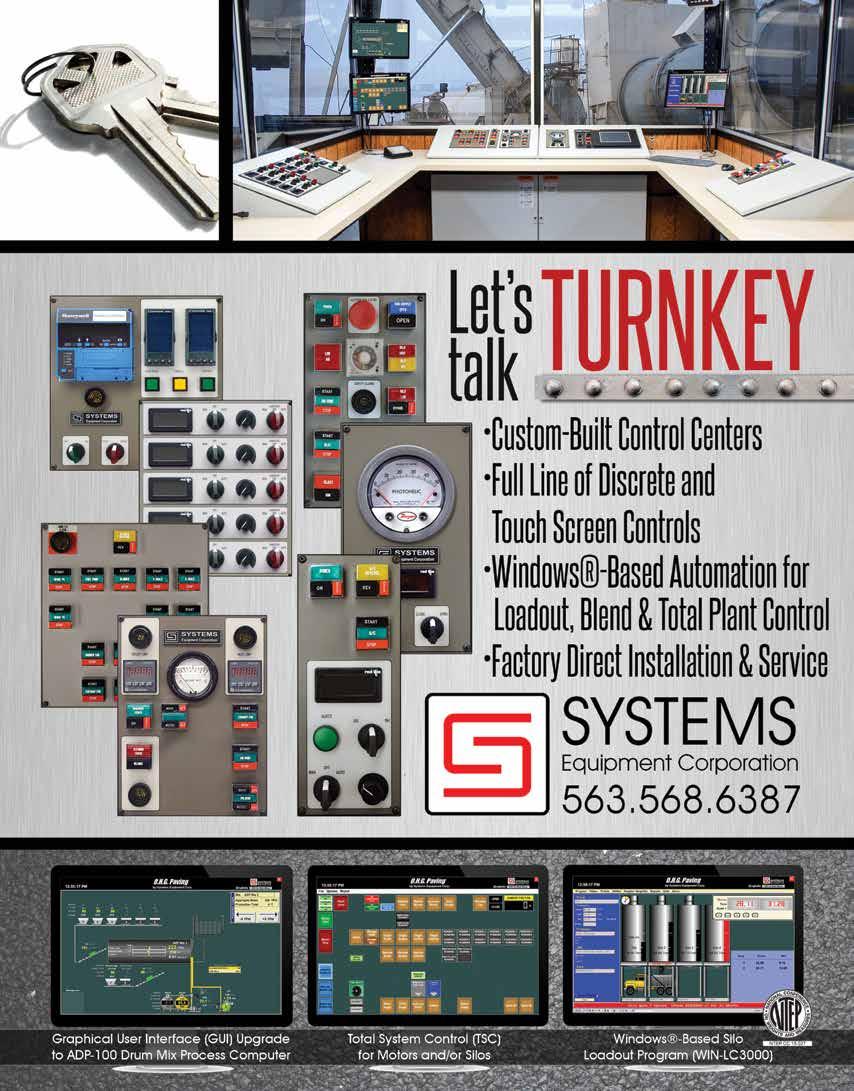
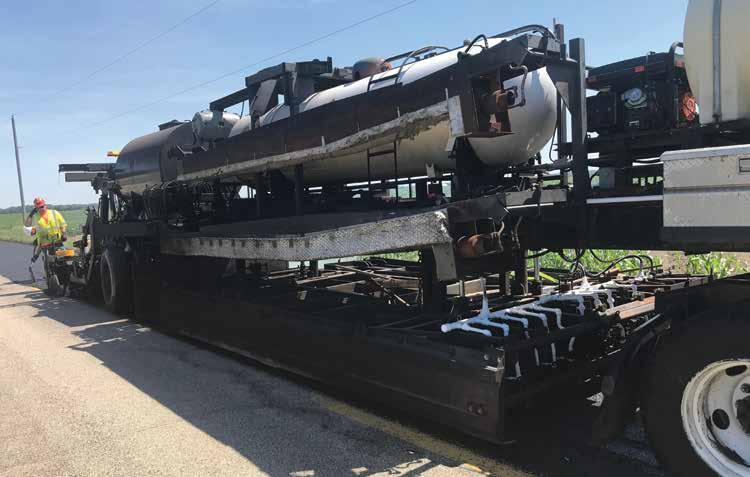
ABOVE: The preheaters are basically semi-trucks towing 300-degree oven decks above the pavement to transfer heat into the pavement, following closely one right after the other. BELOW: The process machine, which follows closely behind the two preheaters, consists of a third semi pulling a smaller oven deck followed by hydraulic tines, a rejuvenating agent distribution system, augers and a screed at the very back of the semi.
Depending on the depth and extent of the issues, CIR or FDR might be attractive alternatives, Faster added.
Most roads that are good candidates for HIR are up to 12 years old, he estimates, and face moderate issues. The roads in Delaware County had some aging, rutting, and issues with rideability that HIR could address.
“When we found a couple roads that were earlier in their life cycles that didn’t have deeper problems and the lab found to be good candidates for HIR, Delaware County was excited to try it,” Faster said. “They’re very forward thinking.”
The two two-lane country roads in Delaware County included Troy Road from the city of Delaware to Norton Road, a total of 90,000 square yards of pavement, and Ostrander Road from US-36 and State Route 257, a total of 50,000 square yards of pavement.

HIR IN OHIO
Gallagher began its work in Delaware County June 14, 2021. However, its preparations started much earlier.
The company strives to minimize bouncing its crews back and forth across the country, so smart scheduling throughout the season is key. It’s also common for Gallagher’s crews to work HIR jobs on multiple roads for one agency, like they did in Delaware County.
In the 2021 paving season, it had three crews traveling around the country to perform HIR projects. Along with the crew, Gallagher uses four lowboys to send its HIR equipment, most of which was built at Gallagher’s own shop, around to each job.
Gallagher uses the heater scarification HIR method, which requires them to heat the pavement to soften it before scarifying it and introducing a rejuvenating agent and remixing.
Gallagher’s custom-built equipment includes two preheaters, which are basically semi-trucks towing oven decks above the pavement to transfer heat into the pavement, following closely one right after the other.
“We want to pump as much heat into the pavement as we can, since pavement has a tendency to cool quickly,” Faster said. Its heaters follow closely behind one another and usually run at 300 degrees Fahrenheit, but never more than 320.
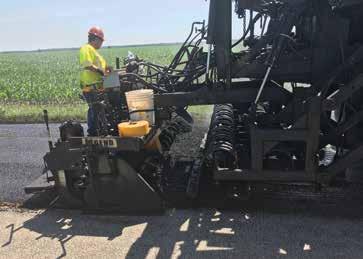
Following the two preheaters is the process machine, which is a third semi pulling a smaller oven deck followed by hydraulic tines, a rejuvenating agent distribution system, augers and a screed at the very back of the semi. “From the screed on, it’s just like a standard paving operation,” Faster said. They follow paving best practices, develop a rolling pattern, and compact the mat like they would for any paving job.
The crew averages 10,000 square yards of pavement per day, however, this depends on ambient and surface temperature and wind speed. “If we’re working in St. Louis in August, we can move more quickly,” Faster said, estimating around 22 feet per minute. “But if we’re in Minnesota in May, we might cover 10 feet per minute.”
He said the crew moved at about 15 feet per minute on the Delaware County job, finishing the 150,000-square-foot job in 15 working days.
“Our foremen are instructed to get as deep as they can with the tines and then go as fast as they can,” Faster said. “Depth first, then speed.”
Most jobs’ specifications, including those in Delaware County, require the tines to get 1.5 inches deep into the existing asphalt, and Faster said 2 inches is the maximum. “If you can get to 2 inches instead of 1.5 inches, you’ll retard negative characteristics on the pavement for longer,” Faster said.
Behind the tines are several augers to mix in the rejuvenating agent. “I think there’s some concern that applying heat to the pavement will burn the asphalt and prematurely harden it,” Faster said. “But with this process, we make it harder before we soften it with the rejuvenating agent. So, if the asphalt cores we send to the lab have a softness of say eight, it’ll be closer to a 30 when we’re done with it.”
Gallagher blends its own rejuvenating agent and applies it at the rate dictated by its lab, usually one tenth of a gallon per square yard. The older the road, the more rejuvenating agent it will require. However, the crews take care not to apply too much rejuvenating agent to prevent bleeding.
“The lab always gives us an approximate shot rate, but it’s always up to the back end guy to turn it up a bit if they see any white rock behind the screed,” Faster said. If the road has been previously chip sealed, he added, they may use a little less rejuvenating agent.
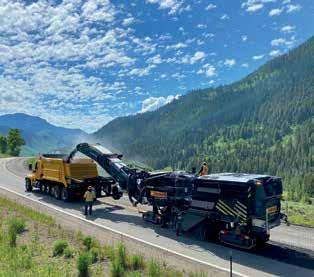

Behind the screed, Gallagher’s crew develops a rolling pattern and compacts the HIR mat like any standard paving job.
“It seems to us we are doing more and more HIR with each passing year.”—Patrick Faster
Behind the rejuvenating agent application and remixing comes the screed. “From the screed back, we’re laying asphalt like it’s virgin material,” Faster said. “It’s just that the source of the material is different.”
Although an HIR-treated road can open to traffic almost immediately, a surface treatment must be applied within 14 days. Common surface treatments include chip seal, micro surface and overlays, depending on traffic needs and budget.
Shortly after completing the HIR process in Delaware County, the roads were capped with 1.5 inches of asphalt.
Gallagher finished the job July 5, 2021. “Not only did the roads look great, but they were leveled out and left behind a very smooth ride for the residents,” Faster said.
The Delaware County jobs may also lead to more HIR work for Gallagher in the state of Ohio; representatives from more than 45 agencies came to see the process firsthand.
“When they see the pavement before and after, they’re impressed,” Faster said. He estimates that 90 percent of agencies who have roads ideal for HIR later reach out to Gallagher when planning the following year’s work after coming to see one of its jobs in action. “Our best sales tool is bringing people from surrounding counties out to a current job to see the machines work.”
Faster said Gallagher continues to perform more and more HIR jobs in Ohio year after year. The Ohio Department of Transportation having its own HIR specification, as do many states, helps give local agencies confidence in the process. However, it can still be an uphill battle sometimes.
“The number of people who haven’t heard of HIR still amazes me,” Faster said. “It’s an ongoing education.”
Faster said Gallagher’s good name in the asphalt industry also helps, “even if we’re bidding HIR work in places where they may not be familiar with the Gallagher name. If they look us up, they’ll find we pass the test every time.”
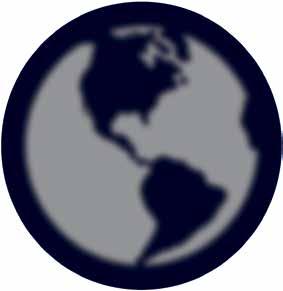
Drum mixers
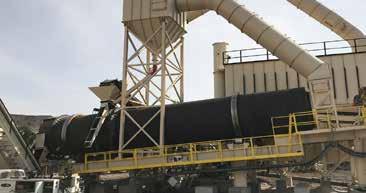
www.tarmacinc.com
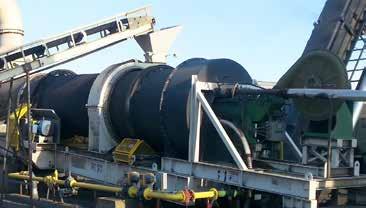
contact tarmac at 816-220-0700 or info@tarmacinc.com

