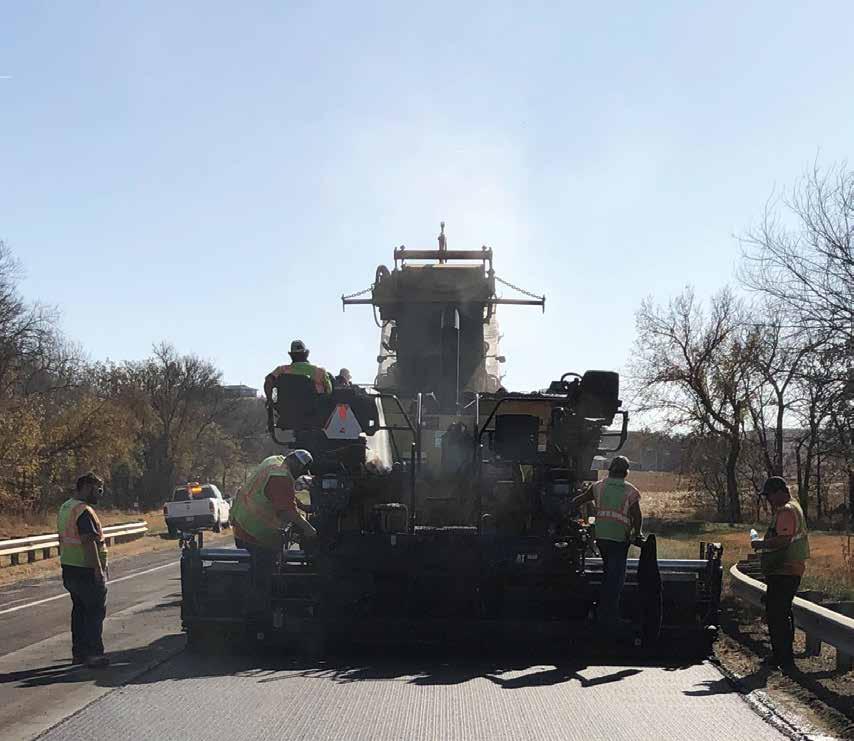
11 minute read
Shilling Construction’s Proven Screed
Shilling Construction’ Shilling Construction’S S Proven Screed Proven Screed
Shilling Construction has been testing out an innovative textured screed from AXENOX Construction Solutions since April 2020. During that time, the system has moved from social media curiosity to the crew’s favorite screed.
BY ASPHALTPRO STAFF
WWhen Travis Shilling, vice president of Shilling Construction Company Inc., Manhattan, Kansas, first saw a video on social media of a textured screed in January 2020, he was intrigued.
Shilling reached out to Stuart and Michael Frost, who invented the unique screed, and asked if he could buy one. The brothers agreed to send Shilling their new screed to help them test the design. When Shilling received his screed in April 2020, it was the first model in operation outside the Frosts’ own paving company, Mountain Construction Company, Powell, Wyoming. To date, only a handful of paving contractors have had the chance to use the Frosts’ screed system firsthand. The Frost brothers are third-generation paving contractors; their grandfather started paving back in the 1940s. Throughout their time in the industry, the brothers have performed a lot of their own equipment maintenance, learning how to fabricate, weld, engineer and eventually invent new machinery. “That’s how we learned so much about paving—through the school of hard knocks,” Stuart Frost said.
Although the brothers have had numerous inventions, this is the first time they’ve moved to commercialize one. “We felt this was too important of a technology not to share it with the industry,” Stuart Frost said, citing its potential to increase paving efficiency, reduce compactive effort, and even open up new opportunities in mat thicknesses and nominal maximum aggregate size.
They started AXENOX Construction Solutions and began posting eye-catching videos of their products—the OXCLAW textured screed and BULLOX conductor plate—in action on social media. Those videos included the one Shilling spotted.

SHILLING, SHUTTLE BUGGIES & SUPERPAVE
Shilling Construction is a family-owned business started by Shilling’s grandfather in 1965. It began as a small family business performing mostly commercial work and grew to a major player in the state of Kansas. Roughly 80 percent of the company’s paving projects are for the Kansas Department of Transportation (KDOT). The company also does its own milling and has three asphalt plants. As Shilling puts it: “We take care of anything asphalt.”
The company has a history of adopting new technology early and was one of the first to use a Shuttle Buggy in the 1990s. They also got into milling early on, purchasing some of the first Roadtec mills ever produced. Shilling, and the state of Kansas in general, was also early to use Superpave mix designs. “My dad was LEFT: As a result of its tests in 2020, Shilling’s main highway crew used the OXCLAW for the 2021 season. TOP: Although they were able to achieve the same density with both screeds on the Highway 18 job, Shilling said they were able to achieve consistently higher density behind the breakdown roller on the OXCLAW sections. BOTTOM: Shilling used the OXCLAW on a KDOT job on Highway 18, comparing it side by side to a traditional screed. At the end of the job, KDOT gave Shilling permission to use the OXCLAW on other projects as long as the district or area engineer approved.
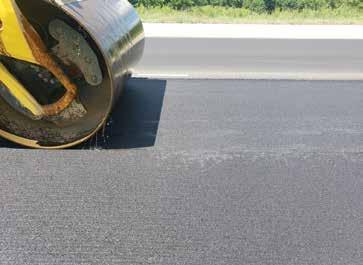
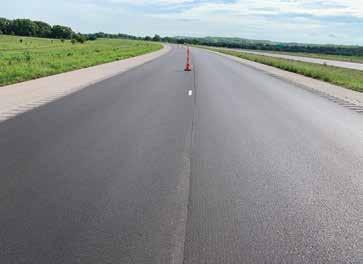
a pioneer in Superpave’s early days,” Shilling said. “We were one of the first to have a full-blown Superpave laboratory.”
Shilling was mainly interested in AXENOX’s system for its wear capabilities—the OXCLAW is made of chromium carbide—and the ability to change out screed plates quickly. When he saw the videos, his crews had been paving in western Kansas and were quickly running through screed plates due to the harder aggregates used on that side of the state.
Not only might the chromium carbide plates last longer, but screed swaps would be faster with AXENOX’s BULLOX conductor plate. The BULLOX is designed to remain on the screed for the lifetime of the paver, with the OXCLAW attaching via a silicone rope. This way, screed swaps take only one third the time as a normal screed swap.
Although the quick change screed system was a primary interest for Shilling, it was actually an afterthought for the Frost brothers.


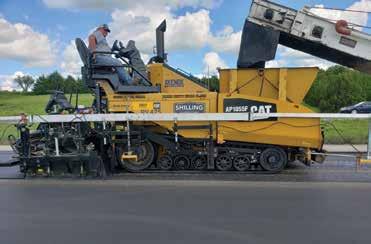
LEFT: “The first thing people ask when they see pictures is if the mat is textured,” Stuart Frost said, but he assures them it’s not. He compares the shadows to those left behind after mowing grass; the mower leaves behind a pattern, even though all the grass is 2 inches tall. TOP: The OXCLAW screed plate also has a diamond-shaped pattern on it, which aims to improve density behind the screed by applying multiple force vectors, locking the aggregate together. BOTTOM: Shilling’s local Cat dealer attached the BULLOX and OXCLAW onto its Caterpillar SE60v screed on its Cat 1055F paver
They realized that casting was their best option to manufacture textured screed plates economically, but this required creating the screed in two pieces: the textured screed plate (OXCLAW) and the conductor plate (BULLOX).
“The BULLOX system offers benefits even for contractors who want to run a conventional screed, because of the quick change system,” Michael Frost said. AXENOX also offers traditional flat screed plates in long-lasting chromium carbide, in addition to their textured screed plates.
Shilling thinks the OXCLAW could last his crew four or five years. Because most of Shilling’s paving operations are in eastern Kansas, where the aggregate is softer than the job in western Kansas that had originally piqued Shilling’s interest in the OXCLAW, he thinks the OXCLAW itself might even last the lifetime of the paver.
OXCLAW IN ACTION
After Shilling’s local Cat dealer had attached the BULLOX and OXCLAW onto its Caterpillar SE60v screed on its Cat 1055F paver, the company kept its new setup on jobs near its headquarters in Manhattan in case of any issues.
The first project Shilling used it on was a parking lot job at a rural high school. “The crew was pretty skeptical, especially seeing the shadows on the mat,” Shilling said.
The screed material and set-up isn’t the only thing that’s different about AXENOX’s product. The OXCLAW screed plate also has a diamond-shaped pattern on it, which aims to improve density behind the screed by applying multiple force vectors, locking the aggregate together. The end result aims to be a smooth mat with improved density; however, the OXCLAW does leave behind shadows that some mistake for a textured mat.
“The first thing people ask when they see pictures is if the mat is textured,” Stuart Frost said, but he assures them it’s not. He compares the shadows to those left behind after mowing grass; the mower leaves behind a pattern, even though all the grass is 2 inches tall.
“Anytime you organize things, it creates a pattern—sort of like looking down on a bunch of people at a concert versus a battalion,” Stuart Frost said. And that’s what the texture is doing: organizing the aggregates in such a way that they lock together. “If you imagine a traditional screed as a duck boat and ours as a V hull boat, our screed disrupts what’s in front of it, cuts through it and averages it out, leaving behind a smooth mat, whereas a duck boat-style screed is at the mercy of every little thing it hits and then skips across it.”
He said the texture also results in a smoother ride on the screed, a benefit Shilling has experienced firsthand. Although it might seem like mix would be more likely to stick to the textured plate, Shilling
One thing the Shilling crew has to keep in mind when using the AXENOX is that it requires less of a fluff factor. Instead of 1/4 of an inch per inch of the final lift, the crew only adds about 1/8 of an inch per inch of the final lift. “You have to keep that in mind when matching curbs or centerline joints,” Shilling said. Otherwise, he adds, it operates like any other screed.
SOLD ON TEXTURED SCREEDS
On the parking lot job, which was a single 4-inch lift, the crew was sold when they realized how good the density was right off the screed. “Normally when you walk on a lift that thick, it’s pretty soft and you leave behind a good footprint,” Shilling said. “With the OXCLAW, there was barely any indentation. The crew quickly saw something was different and it was for the better.”
This feature was actually illustrated in one of the videos Shilling saw on social media, which only reinforced his desire to have the OXCLAW on Shilling’s highway jobs where density bonuses were at stake.
With the mat being more stable directly behind the screed, the rollers are able to keep closer together. “The rollers are able to finish getting density at higher temperatures with less effort, so they’re less likely to be rolling cooler mats where they risk fracturing the aggregate,” Stuart Frost said. A more stable mat also means stronger unconfined edges with less shoving and even improvements in longitudinal joint density.
Throughout the first season with the OXCLAW, the crew tested it out on everything from parking lots to state highways, including two projects with KDOT. One of those jobs was a 1 ½ inch mill and overlay on Highway 18, between Manhattan and I-70, paved in August 2020.
Shilling began talking about the OXCLAW with KDOT in the spring and invited them to a parking lot job the crew was performing with the OXCLAW so they could familiarize themselves with the new design. After DOT staff saw the screed in action, Shilling asked if they could use the OXCLAW on the Highway 18 job and KDOT agreed, asking the crew to do a comparison with a traditional screed.
“Originally we were going to do half the job with the OXCLAW and the other half with a conventional screed to compare, but our crew liked the OXCLAW so much that we did three of the four lanes with the OXCLAW and only one with the traditional screed,” Shilling said, which still allowed them to compare the results of the two.
Although they were able to achieve the same density with both screeds, Shilling said they were able to achieve consistently higher density behind the breakdown roller on the OXCLAW sections. At the end of the job, KDOT gave Shilling permission to use the OXCLAW on other projects as long as the district or area engineer approved it. “Honestly, we haven’t run into anyone who’s said we can’t use it,” Shilling said. “So far, everyone has been receptive to it and sees the benefits.”
As a result of its tests in 2020, Shilling’s main highway crew used the OXCLAW for the 2021 season.
According to the Frost brothers, this is only the beginning.
Make It Last.
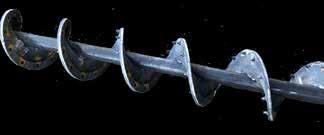
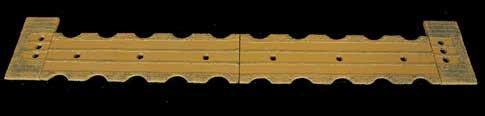
Protect your investment with Kenco wear parts.
Proudly manufactured in the USA since 1957, Kenco offers innovative products for the aggregate, asphalt and road building industries. Our products are designed to increase wearlife and reduce downtime on your plants and equipment.

Kenco Engineering, Inc
www.kencoengineering.com 800-363-9859


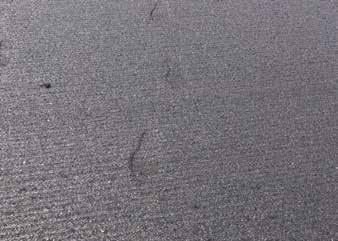
“We were very conservative with our first texture for testing,” Stuart Frost said, “because this is so new and we didn’t want to scare DOTs.” However, a good reception from the DOTs which have experienced the OXCLAW in action has encouraged them to experiment with different textures.
Although pending patents prevent them from going into much detail, the brothers have said newer versions of the OXCLAW are more in line with their original vision. “Our tests have been going better than we imagined they would, so we feel more confident to move forward with our initial vision,” Stuart Frost said. The ultimate vision is to have different patterns for different applications.
The brothers hope to launch new models for general sale for the 2022 paving season.
Meanwhile, AXENOX has added a new paving contractor to its lineup of trial users for the 2021 season: the biggest competitor to the Frosts’ own paving company. “They heard the hoopla about our new system and wanted to be on the cutting edge,” Stuart Frost said, adding with a chuckle, “We may have lost our advantage against them!”
PUGMILL SYSTEMS
We’ve been designing and manufacturing custom mixing solutions in Tennessee for nearly 40 years.
RCC • CTB • Pugmix • Stabilized Sand

Coldmix • Fly Ash • Salt Treatment
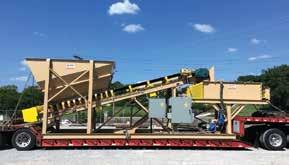
Rental Plants Available
Check out additional projects at: PUGMILLSYSTEMS.COM or give us a call at: 931-388-0626