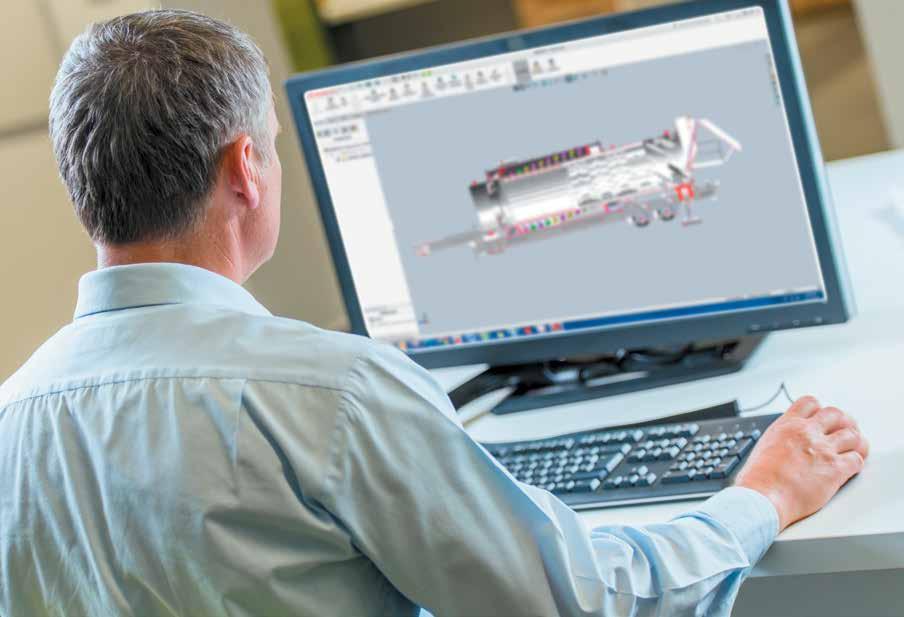
7 minute read
TRB Discusses Driving
TRB Discusses Driving Surface Aggregate Specs
The National Academies of Sciences, Engineering and Medicine Transportation Research Board (TRB) hosted presented the webinar Driving Surface Aggregate: Improv ing Performance and Sustainability in late 2019. Presenters Steve Bloser and Eric Chase of Penn State University and Bethany Kunz of U.S. Geological Survey provided an overview of driving surface aggregate (DSA) and how it can improve the performance and sustainability of unpaved, low-volume roads. While most AsphaltPro readers pave with asphalt binder mixes, some may be called on to place a DSA roadway in site-specific areas. Here’s how DSA works and some tips for its success, based on the Nov. 13 presentation.
At this time, counties and agencies use a wide variety of aggregates when surfacing unpaved roads, sometimes with no materials testing or formal spec. This results in suboptimal materials on the roadway and early failure or a need for extreme maintenance schedules. Of course, agencies aren’t using suboptimal surface aggregates out of apathy. Budgets are tight, some quarries aren’t set up to prepare this specific type of aggregate, and not all agencies understand—yet— that DSA is a necessity. The presenters explained that “most road aggregates in use today were created for drainage under pavements, and were not intended to be used as a driving surface.”
To solve all this, DSA is an aggregate spec designed to achieve maxi mum compaction and resist erosion. It includes requirements for gradation and other material characteristics and requirements for placement. T
Gradation
PERCENT PASSING Sieve Size DSA FP-14 SD LTAP 1.5" 100 1.0” 100 0.75” 65 to 95 100 0.5” 70 to 80 (5) #4 30 to 65 40 to 50 (7) 50 to 78 #8 37 to 67 #10 25 to 40 (6) #16 15 to 30 #40 15 to 25 (5) 13 to 35 #200 10 to 15 8 to 14 (4) 4 to 15 8 to 15
Values in parentheses are allowable deviations (+/-) from target values. FP-14: Standard Specification for Construction of Roads and Bridges on Federal Highway Projects. FP-14, U.S. Department of Transportation, Federal Highway Administration, Federal Lands Highway, 2014 SD LTAP: Gravel Roads Construction & Maintenance Guide August 2015, South Dakota Local Technical Assistance Program and the U.S. Department of Transportation, Federal Highway Administration Source: TRB
DSA MATERIAL REQUIREMENTS Bloser explained that the high humidity level ever-present in Pennsylvania means they don’t want a lot of moisture in the pavement. This affects the plasticity index (PI) that can be tolerated. Their spec calls for a maximum PI of 6. The DSA fines passing the #200 sieve must be crushed rock.
Pennsylvania requires the resistance to abrasion be less than 40 percent, as measured by the LA Abrasion Test. Soundness must be less than 20 percent loss as measured by the sodium sulfate soundness test. And the pH should rest between 6 and 12.5.
DSA PLACEMENT GUIDELINES It will come as no surprise that DSA must be placed at optimum moisture to achieve optimum compaction. The moisture will be measured by a standard proctor test; haul trucks must be covered. While the presenters spoke of the possibility of tailgate spreading and getting a smooth finish from a skilled blade operator, they agreed that placing DSA with a motor paver provides the uniform, controlled, well-mixed lift necessary. The tailgate spreading operation tends to segregate aggregate, and not all grader operators have the fine skills necessary to achieve the smooth slope of the perfect road.
For compaction, use at least a 10-ton vibratory roller. A minimum 6-inch lift will compact to 4.5 inches.
TWO TRIALS OF DSA Researchers took the DSA challenge to Muscatatuck National Wildlife Refuge in Indiana and Green Mountain National Forest in Vermont. In Indiana, they placed a limestone DSA with a paver in a single, 6-inch lift, compacted to 4.5 inches, for a 1.5-mile sec tion. In Vermont, conditions presented limited paver availability, grades up to 14 percent, few quarries in the vicinity and different parent material for the DSA (in this case: schist rock). They placed the aggregate via tailgate spreading in an approximately 6-inch lift, compacted to 4.5 inches, for a 0.75-mile section. They considered Green Mountain National Forest a “good test case for remote sites with similar challenges.” Twelve months after placement, they measured sediment runoff with a rainfall sim ulator and dust production with a vehicle-mounted particulate matter meter.
The rainfall simulator was a 100-foot-long piece of equipment with eleven 10-foot risers. Atop each riser were two rotary
Web Extra at www.TRB.org/Centennial: The Transportation Research Board celebrates its 100th anniversary this November. Congratulations to TRB from the AsphaltPro magazine family!
ENGINEERING CONSTRUCTION SERVICE & TRAINING
SERVICE & TRAINING
ENGINEERING CONSTRUCTION
ENGINEERING
ENGINEERING CONSTRUCTION
CONSTRUCTION SERVICE & TRAINING
SERVICE & TRAINING
SERVICE & TRAINING PARTS
ENGINEERING CONSTRUCTION SERVICE & TRAINING PARTS
ENGINEERING SERVICE & TRAINING PARTS CONSTRUCTION WE DO THIS... ENGINEERING CONSTRUCTION SERVICE & TRAINING PARTS
ENGINEERING CONSTRUCTION SERVICE & TRAINING PARTS
ENGINEERING SERVICE & TRAINING PARTS CONSTRUCTION The Astec engineering team draws on a vast knowledge pool that includes specialists in thermodynamics, environmental compliance, electrical systems and structural design. Their knowledge is grounded in years of experience in the asphalt mixing industry and they are ready to put their expertise to work for you when designing an asphalt plant.
ENGINEERING CONSTRUCTION SERVICE & TRAINING PARTS ENGINEERING SERVICE & TRAINING CONSTRUCTION ENGINEERING SERVICE & TRAINING CONSTRUCTION No other North American manufacturer offers more options than Astec.
ENGINEERING SERVICE & TRAINING PARTS CONSTRUCTION 4 DRUM OPTIONS Double Barrel / DBX / DBXHR / Dillman UniDrum ENGINEERING SERVICE & TRAINING PARTS CONSTRUCTION ENGINEERING SERVICE & TRAINING PARTS CONSTRUCTION
ENGINEERING SERVICE & TRAINING CONSTRUCTION ENGINEERING SERVICE & TRAINING CONSTRUCTION ENGINEERING SERVICE & TRAINING CONSTRUCTION ENGINEERING SERVICE & TRAINING CONSTRUCTION 4 BURNER OPTIONS Phantom / Talon II / Fury / Whisper Jet
2 BAGHOUSE OPTIONS Pulse Jet / Reverse Pulse ENGINEERING SERVICE & TRAINING CONSTRUCTION
ENGINEERING SERVICE & TRAINING CONSTRUCTION ENGINEERING SERVICE & TRAINING CONSTRUCTION ENGINEERING SERVICE & TRAINING CONSTRUCTION 2 SILO OPTIONS Long-term Silos / Dillman Silo Sytems
ENGINEERING CONSTRUCTION SERVICE & TRAINING PARTS
4 3 2 1 Total sediment produced (lbs) Traditional aggregate Driving surface aggregate (DSA) .8 .6 .4 .2 Average dust production (mg/m3) Sediment Runoff Dust Production
Traditional aggregate Driving surface aggregate (DSA)
0
Muscatatuck National Wildlife Refuge, IN Green Mountain National Forest, VT The bars represent average of three simulated rainfall events at 0.6-inches per 30 minutes per section. Source: TRB
.0
Muscatatuck National Wildlife Refuge, IN Green Mountain National Forest, VT The bars represent average of three runs per section. Error bars represent standard deviations. Source: TRB
Road Surface Condition
Washboarding Raveling Rutting Potholes
Site Section Mean depth (mm) Rating a Mean depth (mm) Rating Mean depth (mm) Rating Rating b Overall Rating
Indiana Traditional 0 10 17 6 8 8 10 8.5
DSA 0 10 10 7 8 8 10 8.8
Vermont Traditional 1.6 9 7 8 4 9 10 9
DSA 0 10 3 9 7 8 10 9.3
a All ratings on a scale of 0 to 10, with 10 being best condition b No potholes were observed on any section; therefore, all sections received a rating of “10.” NOTE: 25.4 mm=1 inch Source: TRB
nozzles that produced the equivalent of 0.6 inches of rainfall in 30 minutes. As seen in the graph, from the Muscatatuck National Wildlife Refuge, they collected nearly 3 pounds of sediment from the traditional aggregate surface and almost half a pound of sediment from the DSA surface in the test sections; from the Green Mountain National Forest, they collected approximately 1 pound of sediment from the traditional aggregate surface and almost half a pound of sediment from the DSA surface in the test sections. Kunz shared with the audience: “At Muscatatuck NWR, each mile of DSA-surfaced road could be expected to produce approximately 13 pounds of sediment per 0.6-inch rain event, while each mile of traditional aggregate would produce more than 143 pounds.”
To gather data on dust produced on the surfaces, researchers used a laser photometer mounted on the tailgate of a work truck. It measures particulate matter in five size ranges at one measurement per second. As seen in graph 2, the average dust production for traditional and DSA aggregate surfaces had a wider disparity at the Indiana site.
Researchers also evaluated the road surface condition of three 25-foot sub-sections for each DSA and traditional aggregate section for washboarding, raveling (loose material), rutting and potholes (see Road Surface Condition table). Researchers found the process of laying the DSA with a motor paver was superior to tailgate spreading; it assisted the DSA’s mixing, compacting and holding together. The researchers concluded: “A more intentional approach to aggregate selection and placement can reduce long-term costs and health/environmental impacts.”
“Site-specific considerations can help guide targeted installations of DSA to maximize benefits,” the presenters concluded. “Specifying higher quality aggregates, DSA or otherwise, and improving aggregate placement methods are critical for the long-term success of unpaved road networks.”
– BY ASPHALTPRO STAFF
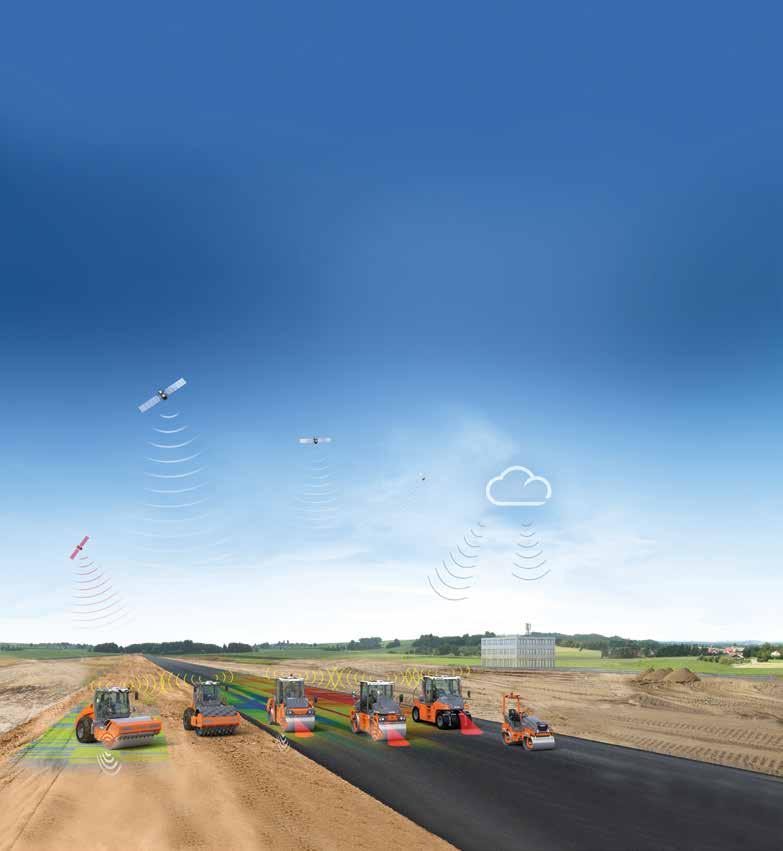