
13 minute read
Koss Construction Builds Perpetual
Koss Construction performed the second designed perpetual pavement project on US-69, containing five lifts of asphalt totaling 14 ¼ inches.
Koss Construction Builds Perpetual Pavements in Oklahoma
The goal of every pavement project is to build a high-quality roadway that will offer a smooth, safe ride for as long as possible. The concept of a perpetual pavement puts a hard number on that goal: 50 years.
According to the Asphalt Pavement Al liance (APA), a perpetual pavement is defined as “an asphalt pavement designed and built to last longer than 50 years without requiring major structural reha bilitation or reconstruction, and needing only periodic surface renewal in response to distresses confined to the top of the pavement.”
To construct a road built to last half of a century—or longer—the Oklahoma De partment of Transportation awarded the winning bid to Koss Construction, Tope T
ka, Kansas, for the state’s second perpetual pavement project.
The $24.5 million would utilize the per petual pavement concept on a 5-mile section of US-69 south of Eufaula, Oklahoma. US-69 has an average daily traffic count of 16,000. As a major trucking route between Kansas City and Dallas, one third of US-69’s ADT is truck traffic.
Koss Construction was founded in 1912. More than 90 percent of Koss Construction’s jobs are for government agencies, the majority of which are state DOTs. The company operates throughout the Midwest, in Arkansas, eastern Colorado, Iowa, Kansas, Missouri, Nebraska and Oklahoma. “Perpetual pavement is something we are very interested in, as an agency,” said ODOT Division Engineer Jamie Malmstrom. “It makes a lot of sense from a maintenance standpoint.”
PERPETUAL PAVEMENTS: A BRIEF HISTORY Although the term “perpetual pavement” wasn’t introduced until 2000, pavement engineers have been producing long-lasting pavements since the 1960s. Many of these pavements, APA said, were the products of full-depth or deep-strength asphalt pavement designs.
In fact, Oklahoma has its own history with long-lasting HMA pavements. According to a pamphlet produced for APA in the early 2000s, two sections of Interstate
“We tend to work in rural areas where there isn’t a high volume asphalt plant nearby. To reduce drive distance and to operate at the volumes we deal with, a portable plant works best for us.”—Mark Haines
Permeable Friction Course, PG 76-28 (1.25”)
Stone Matrix Asphalt, PG 76-28 (2”)
40 in downtown Oklahoma City offered early examples of the benefits of perpetual pavements.
First constructed in 1967, the sections withstood heavy traffic for more than 30 years. “Each of the sections has been overlaid, but the base course structure has not been touched,” the pamphlet reads. “Although they are 33 years old, they look like new.”
Oklahoma’s first designed perpetual pavement project was completed in 2006 on SH-152. “That pavement is working and it’s changing minds,” said Larry Patrick, executive director of the Oklahoma Asphalt Pavement Association (OAPA). “SH152 is coming on 14 years old, and outside of a slide area and bridge approach issues caused by subgrade issues, the pavement has not needed any maintenance at all.”
The perpetual pavement concept is one OAPA has been working hard to promote. “New ideas take time,” Patrick said. “There’s more interest in perpetual pavement than ever before in the state.”
Since Koss began the state’s second perpetual pavement project, Oklahoma has already seen the start and completion of its third perpetual pavement project, on the Kickapoo Turnpike east of Oklahoma City. The Oklahoma Turnpike Authority created the new turnpike to connect I-44 Turner Turnpike to I-40 to alleviate traffic in Oklahoma City.
FULL DEPTH ASPHALT According to the National Asphalt Pavement Association (NAPA), the perpetual pavement concept relies on the use of multiple layers of asphalt to extend the useful Base Mix, PG 64-22, 25 Percent RAP (4”) Base Mix (Polymer - Modified Asphalt), PG 76-28 (3.5”)
Base Mix, PG 64-22, 25 Percent RAP (3.5”)
Local endangered wildlife limited Koss’ time frame to natural daylight hours.
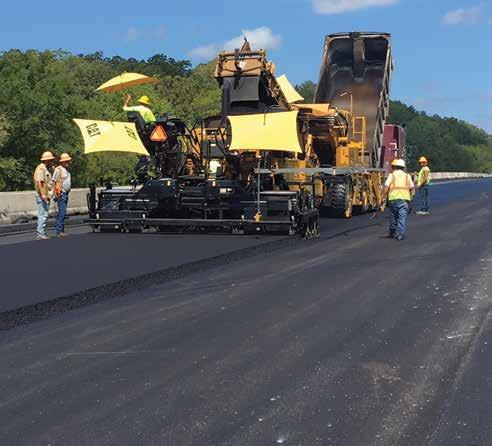
life of a roadway: “The pavement design begins with a strong, yet flexible bottom layer that resists tensile strain caused by traffic, and thus stops cracks from forming in the bottom of the pavement. A strong intermediate layer completes the permanent structural portion, and a final layer of a rut-resistant asphalt mix yields a surface that lasts many years before scheduled restoration.” For US-69, this was achieved in five lifts. The first lift was 4 inches of base mix with PG64-22 and 25 percent RAP, followed
ENGINEERING CONSTRUCTION
ENGINEERING
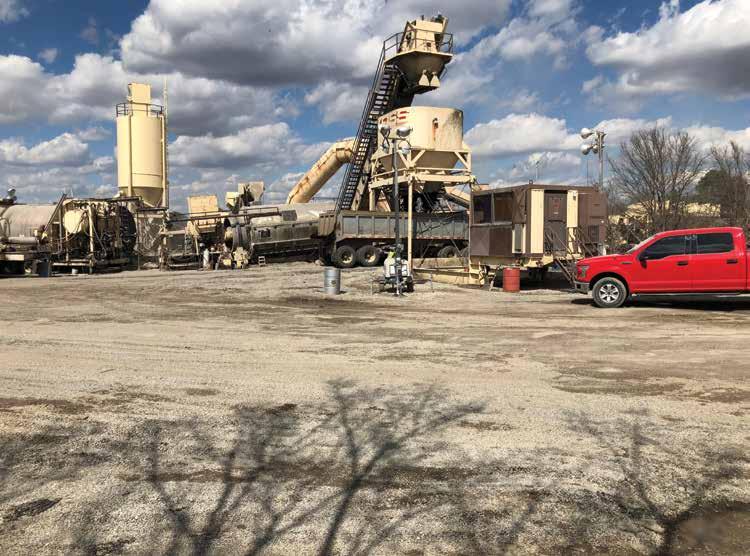
CONSTRUCTION SERVICE & TRAINING
ENGINEERING CONSTRUCTION SERVICE & TRAINING
ENGINEERING Koss Construction made 214,000 tons of asphalt for the project with its 400-TPH portable asphalt plant from Astec Inc.
CONSTRUCTION SERVICE & TRAINING
by 3 ½ inches of base mix with PG64-22 and 25 percent RAP, and then 3 ½ inches of base mix using polymer-modified asphalt (PG76-28) with 28 percent RAP. The fourth lift was 2 inches of stone matrix asphalt (SMA) with PG76-28, and the final lift was 1 ¼ inches of permeable friction course (PFC), also with PG76-28. The top two lifts contained no RAP.
The project spanned 4.9 miles across four travel lanes—two in each direction—for a total of 19.6 lane miles.
According to Koss’ Chief Engineer Mark Haines, the primary difference between this and traditional paving jobs was the sheer volume of material. “The volume of rock, sand and asphalt cement to pave that thickness, versus a pavement of 8 or 9 inches, is substantial,” Haines said.
Koss Construction made a total of 214,000 tons of asphalt for the project with its 400-TPH portable asphalt plant from Astec Inc., Chattanooga. Haines said the project’s volume of material required very active management of materials in and out of the plant site.
Under normal circumstances, Haines said a daily check of what materials are on hand is enough. On this job, Haines had to be more acutely aware of what materials were on site, checking stockpiles by the truck-load.
“Dealing with two different grades of liquid AC and four different mix designs while managing our stockpile of materials was a
ENGINEERING SERVICE & TRAINING CONSTRUCTION challenge,” Haines said. “We had to be very tuned in with our production demands.”
The use of SMA was also new to Koss Construction. The SMA for US-69 utilized warm mix, but did not contain cellulose fibers.
“SMA isn’t very common in Oklahoma, but it’s being used more and more often,” Haines said. Koss looked to EST Inc., Oklahoma City, for its SMA mix design, in addition to doing some test batches and trials with SMA in its own lab. Koss does all of its own internal quality control and testing.
The final lift was a permeable friction course. According to Patrick, the use of PFC is common on Oklahoma’s high volume roads. Its 20 percent in-place air voids allow water through so it leaves the surface quickly. “With the climate in Oklahoma, we can
SERVICE & TRAINING PARTS
SERVICE & TRAINING PARTS ENGINEERING CONSTRUCTION SERVICE & TRAINING PARTS
ENGINEERING

CONSTRUCTION SERVICE & TRAINING PARTS
SERVICE & TRAINING PARTS
ENGINEERING CONSTRUCTION SERVICE & TRAINING PARTS
AND WE DO THIS... ENGINEERING SERVICE & TRAINING CONSTRUCTION ENGINEERING SERVICE & TRAINING CONSTRUCTION PARTS PARTS
PARTS
When you call, we answer. Your call links you to the world’s largest inventory of in-stock parts for asphalt plants. It links you to a seasoned team of experts, ready to help. It links you to world-renowned service, ready to deliver. It links you to Astec.
ENGINEERING SERVICE & TRAINING CONSTRUCTION ENGINEERING SERVICE & TRAINING CONSTRUCTION No other North American manufacturer offers more options than Astec.
ENGINEERING SERVICE & TRAINING PARTS CONSTRUCTION 4 DRUM OPTIONS Double Barrel / DBX / DBXHR / Dillman UniDrum ENGINEERING SERVICE & TRAINING PARTS CONSTRUCTION ENGINEERING SERVICE & TRAINING PARTS CONSTRUCTION
ENGINEERING SERVICE & TRAINING CONSTRUCTION ENGINEERING SERVICE & TRAINING CONSTRUCTION ENGINEERING SERVICE & TRAINING CONSTRUCTION ENGINEERING SERVICE & TRAINING CONSTRUCTION 4 BURNER OPTIONS Phantom / Talon II / Fury / Whisper Jet
2 BAGHOUSE OPTIONS Pulse Jet / Reverse Pulse ENGINEERING SERVICE & TRAINING CONSTRUCTION
ENGINEERING SERVICE & TRAINING CONSTRUCTION ENGINEERING SERVICE & TRAINING CONSTRUCTION ENGINEERING SERVICE & TRAINING CONSTRUCTION 2 SILO OPTIONS Long-term Silos / Dillman Silo Sytems
ENGINEERING CONSTRUCTION SERVICE & TRAINING PARTS
The existing pavement on the job had included concrete travel lanes and asphalt shoulders. They crushed the concrete on-site for use as an 8-inch-thick aggregate base beneath the 14 ¼ inches of asphalt. The 36,000 tons of RAP milled from the shoulders was used on the project.
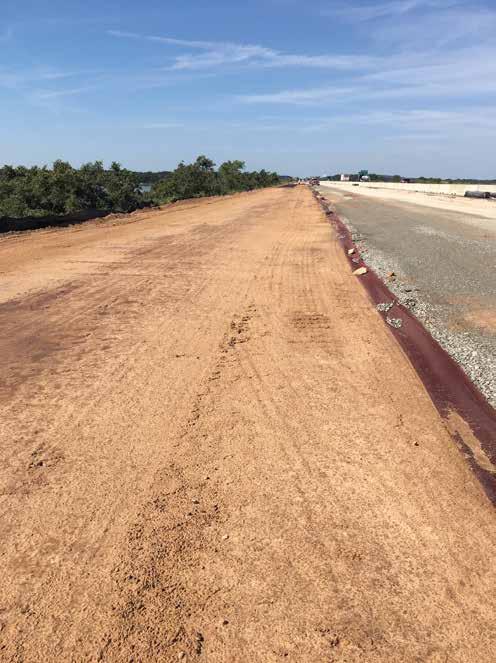
see extremes throughout the year,” he said. “Spring rain and tornadoes, extreme heat in the summer, and winter snow and ice. One worry was the PFC may not like a snow plow or that the deicing effort would plug up the pavement, preventing proper drainage, but neither of those issues have been observed.” “The permeable friction course is amaz ing,” Malmstrom said. “When it’s raining, you don’t get any spray, there’s no hydroplan ing, and the stripe still looks fantastic even when it’s pouring.”
ONE PROJECT, TWO PAVING SEASONS Koss began work on US-69 in June 2018 and completed the project just before Christmas in 2019. The only task left to complete is the placement of permanent striping when the weather warms up in Oklahoma this spring.
The existing pavement on the job had in cluded concrete travel lanes and asphalt shoulders. “The road was severely faulted and had a lot of random cracking,” Haines said. “It was in poor shape.”
In 2018, the Koss crew placed a temporary 2-inch overlay across the northbound travel lanes and part of the shoulder to accommo date north- and southbound traffic, divided by a temporary concrete barrier. “The pave ment was in such poor condition, we didn’t think it could make it through another year of traffic,” Malmstrom said in regards to the temporary overlay.
The crew could then begin work on south bound US-69. They first milled the asphalt shoulder with a Wirtgen W2000 milling machine. The 36,000 tons of RAP used on the project was the same material that was milled from the shoulders.
They crushed the concrete on-site for use as an 8-inch-thick aggregate base beneath the 14 ¼ inches of asphalt. Because ODOT had specified the placement of geotextile beneath the aggregate base, Koss had to manipulate the material to the side so they could excavate down to the project’s grade lines and place the geotextile.
As they did so, Koss determined that some of the existing subgrade wasn’t stable and would require stabilization. ODOT is sued Koss a change order to stabilize isolated areas with Portland cement.
“We only stabilized about 10 percent of the subgrade, but it was enough to be a big headache,” Haines said. Koss was working under a tight timeline and isolated subgrade instability would hold up the crew’s progress. “We tried our best to manipulate the material to dry it out, but during Oklahoma’s rainy season it would rain before we could get it dry enough to work with. Getting that change order allowed us to get that stability back and also expedited construction.”
After those isolated areas had been stabilized and the geotextile and aggregate base was placed, the crew could begin paving the southbound lanes. During the 2018 season, the crew placed the first four lifts of asphalt. In 2019, the crew moved all traffic to the southbound lanes to repeat their efforts on the northbound travel lanes and 18-footwide median. “We were definitely under the gun getting the final lifts on,” Haines said.
ARTIFICIAL HEAT MEETS DEADLINES To meet its deadline while meeting ODOT’s specs, Koss Construction hired Dustrol Inc., Towanda, Kansas, to artificially heat the pavement for the fourth lift on the northbound side and the 1 ¼-inch final lift across the whole project.
“The spec for SMA and permeable as phalt requires a surface temperature of 60 degrees or higher,” Haines said. “That’s hard to get in Oklahoma in the second half of November and early December.”
Dustrol used the large propane heaters it uses in its own hot-in-place recycling oper ations to bring the surface temperature of US-69 up to spec.
“They can’t do hot-in-place recycling at that time of year, so this is a way they can keep their people busy and help us meet our specification requirements,” Haines said. “It isn’t something we’ve done in the past, but we’ve known others who have used arti ficial heat to do this.”
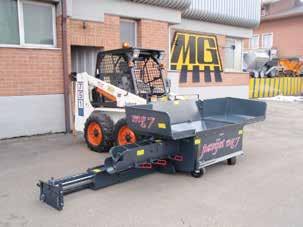
According to Koss’ Field Operations Manager Shane Griggs, the distance be tween the heater and the paving train depended on a number of factors, including cloud cover, ambient and overnight tem peratures, and pavement temperatures.
“It would be as close as 50 feet and as far away as several hundred feet,” Griggs said. “Our target was 60 degrees Fahrenheit. If the ambient temp was 40 degrees and the sun was out, the heater would get the pave ment up to 60 degrees and the sun would maintain that heat. Paving at ambient temps below 40 wasn’t an option.”
Local wildlife also presented a challenge to the crew’s timeline. The location is in habited by the critically endangered American burying beetle. When temperatures dip below 60 degrees Fahrenheit, adult beetles bury themselves in the soil until tempera tures rise above 60 again and they can begin mating. The beetles are also nocturnal crea tures, meaning nighttime light could disrupt their activities. “We weren’t allowed to use any artificial light before sunrise or after daylight hours,” Griggs said. This limited both Koss’ ability to fire up the plant early so mix would be ready at 7 a.m. and site clean-up and equipment maintenance time at the end of the day. “We had to be very efficient with our daylight hours.”
Koss Construction performed all aspects of the project, sub-contracting out only traffic control, striping, erosion control and some assistance with soil excavation. The same crew performed all paving work throughout the project’s two-year span.
US-69 may have been Koss’ first perpetual pavement project, but Haines hopes it won’t be the last. “This was a good-sized job for us, but not too big to handle,” Haines said. “It’s the type of job we’d like to see more of.”
“If we’re going to be doing full depth re placements, I think we’re going to be looking toward perpetual pavements,” Malmstrom said.
– BY SARAH REDOHL
Come visit us at Booth #S6828!

AND YOU KNOW WE DO THIS...
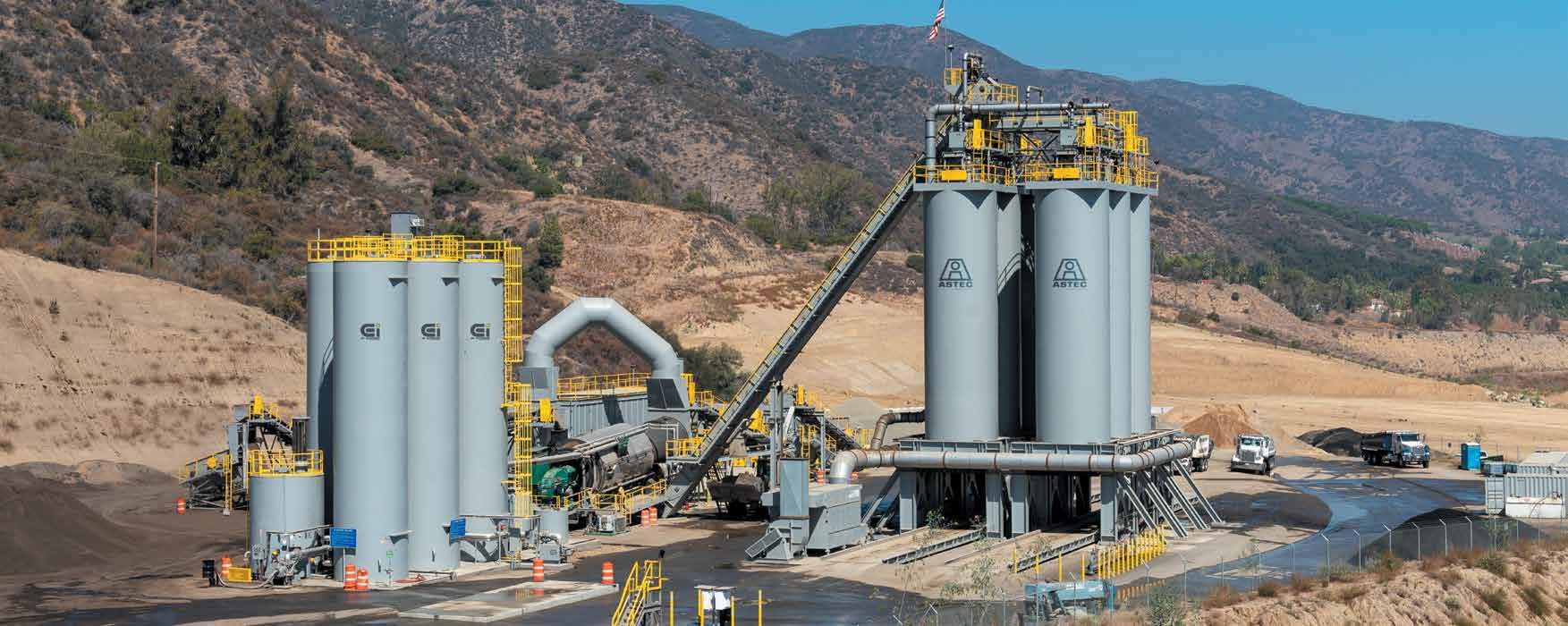
You know Astec for durable, reliable equipment with proven performance. A pioneering team with decades of experience and a culture committed to putting the customer first has culminated in a range of options including drum styles, baghouse styles, and silo styles which allow you to configure the precise plant for your needs. Only Astec offers a complete line of portable, relocatable and stationary asphalt plants from 80tph to 600tph. Astec manufactures both Astec and Dillman brand equipment.
ENGINEERING CONSTRUCTION
ENGINEERING CONSTRUCTION SERVICE & TRAINING
SERVICE & TRAINING
ENGINEERING CONSTRUCTION
ENGINEERING
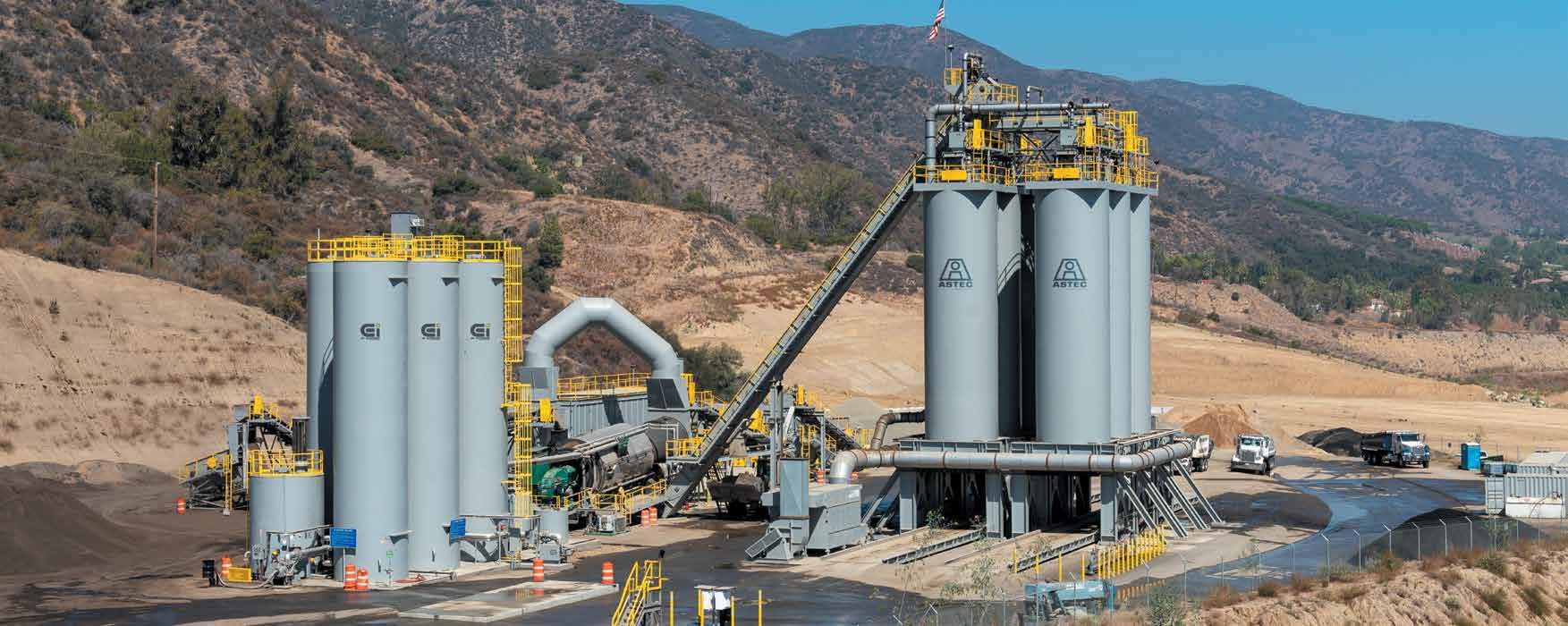
ENGINEERING CONSTRUCTION
CONSTRUCTION SERVICE & TRAINING
SERVICE & TRAINING
SERVICE & TRAINING PARTS
ENGINEERING CONSTRUCTION
ENGINEERING CONSTRUCTION SERVICE & TRAINING
SERVICE & TRAINING
ENGINEERING CONSTRUCTION SERVICE & TRAINING PARTS ENGINEERING ENGINEERING
CONSTRUCTION CONSTRUCTION SERVICE & TRAINING SERVICE & TRAINING
CONSTRUCTION CONSTRUCTION SERVICE & TRAINING SERVICE & TRAINING
ENGINEERING SERVICE & TRAINING PARTS CONSTRUCTION ENGINEERING SERVICE & TRAINING PARTS CONSTRUCTION 4 DRUM OPTIONS Double Barrel / DBX / DBXHR / Dillman UniDrum
2 BAGHOUSE OPTIONS Pulse Jet / Reverse Pulse
ENGINEERING ENGINEERING
CONSTRUCTION CONSTRUCTION SERVICE & TRAINING SERVICE & TRAINING PARTS PARTS ENGINEERING SERVICE & TRAINING CONSTRUCTION ENGINEERING SERVICE & TRAINING CONSTRUCTION 4 BURNER OPTIONS Phantom / Talon II / Fury / Whisper Jet
ENGINEERING SERVICE & TRAINING CONSTRUCTION 2 SILO OPTIONS Long-term Silos / Dillman Silo Sytems
ENGINEERING ENGINEERING
CONSTRUCTION CONSTRUCTION SERVICE & TRAINING SERVICE & TRAINING PARTS PARTS ENGINEERING CONSTRUCTION SERVICE & TRAINING PARTS