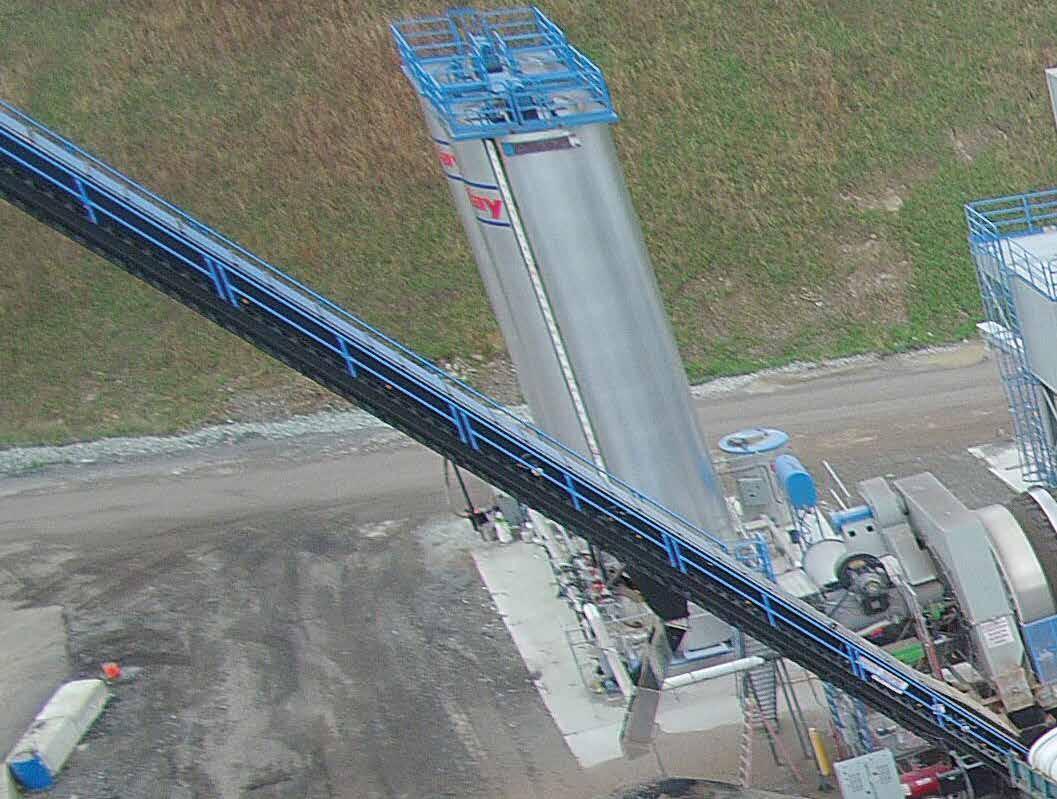
9 minute read
Start Your Asphalt Plant Motors
How to warm up, start up your HMA plant in sequence for the day’s best productivity
Start Your Asphalt Plant Motors Start Your Asphalt Plant Motors Step five is to start up the slat conveyor. With this component running, open the control house door or step outside and listen to it running. Listen for anything that sounds “off” or “different” from other mornings. All photos courtesy of Eagle Crusher, Galion, Ohio, and Tresco Companies, Mount Pleasant, Pennsylvania
WWith the proliferation of automation and robust plant controls, a newbie plant operator should be able to step into the control house and click the mouse over the button labeled “Startup Plant” to make the day begin. But there are steps he needs to make sure have happened first.
Most asphalt plant controls manufacturers and plant original equipment manufacturers (OEMs) who build controls into their systems will have the series of motors coming online in a logical pattern that keeps your operator from sending dry rock to the silo or blowing up the baghouse, but does your operator know why? Does he understand that the asphalt cement (AC) pump should warm up and circulate before delivering liquid to ensure there are no slugs of cool AC traveling around?
There’s theory and logic behind starting up an asphalt plant. Bringing the air compressor up before throwing a flame in the drum matters. Whether you’ve customized the controls so plant startup requires multiple clicks of the mouse—giving your operator time to listen to components and feel the vibration of slingers and conveyors—or you’ve purchased a system that starts with one click and moves through the startup protocol on its own, you BY A.J. RONYAK
want to know why you’re warming one piece before another. You want to know the method behind the madness.
Let’s pretend you have a plant with blending automation. That’s downright essential these days. What we’re going to focus on with this article is getting all the mechanicals going, and then go to the computer for the mix design.
Depending on the weather, time of year, area of the country you’re in, and so on, your start-of-day will fluctuate. You may be turning the lights on in the control room at 3 or 4 a.m., depending on whether or not you had rain or frost the night before. Thinking about the night before, if the RAP bin isn’t enclosed, it should have been emptied. I’m one who believes you never leave the RAP bin full overnight. The recoverable AC in the RAP congeals with condensation and other elements. Depending on how fine the RAP is, it could develop a crust that your ground man will have to break up. Throughout these steps, we’ll look at a couple other tips for shutting down the night before, but let’s focus now on the morning startup.
Step One. Turn on the air compressor to build up air throughout the plant. You shouldn’t see a surge of power here unless you’ve got a bad belt or something else the mechanic should take a look at. Back in the day, I had three different air compressors for the large plant I ran. One was dedicated to the baghouse, one was dedicated to the silos and gates, and one was dedicated to the rest of the plant. You get the air compressor going to get the plant full of air.
Step Two. Turn on the AC pump to circulate liquid back into the tank you’re pulling from. You’re putting the pump in circulation mode at this time. When you turn it on, watch the amperage. It should spike and then level off. If the needle peaks and stays buried, something’s wrong. A cold AC pump requires attention from the ground man. The newbie plant operator has no business running around trouble-shooting componentry so, send the ground man to the pump with an infrared or space heater, depending on safety regulations for your operation, if the AC pump has a tough time getting going. He just needs to put some heat around the pump; he’s heating the cast iron metal.
You’ll want to make sure you have hot oil at this point as well. The hot oil pumping through jacketed lines is the lifeblood of the plant.
Step Three. Turn on the screen decks for both virgin and recycle material. When shutting down the plant the night before, you should have emptied the decks, but some stray material might be waiting to shake off. When starting up these big motors, you’ll see a power surge.
Web Extra at TheAsphaltPro.com: Check out the article “Vary Your Energy Use, Increase Your Utility Savings.”
When you start the burner, set it on “low fire” at first to slowly warm up the drum, ductwork and baghouse. Earlier start-up steps will have ensured the drum is empty of sand or dry aggregate from the night before. Now you’re warming the plant to bring it up to production temperatures.
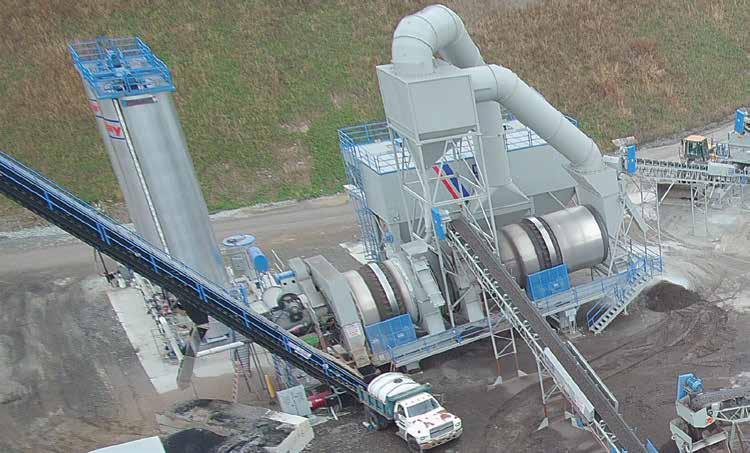
Step Four. Turn on all conveyor belts including the collector, in cline and weigh scale belts. With this step, you’re warming up the conveyor belts; you want them fairly dry and you want the weigh conveyors zeroed out. If the belt is soaking wet, guess what happens to material you feed to it? That mate rial will slide off the incline and your whole operation goes to crap. Get the belts warm and dry.
Whatever little bit of material was laying on the belts from the night before needs to move on to the screens at this point. This is why you’re starting up in a particular sequence. Move old material along. Then zero out the virgin weigh scale belt and the RAP weigh scale belt. (You’ll zero them out again right before making mix.)
Step Five. Start up the slat conveyor or bucket elevator. These are big motors again. Make sure you listen to the conveyors. Physically open the control house door and listen to the conveyors out there. When you start up the slat conveyor, listen to it. You can hear if a bearing’s going out or if a slat’s about to tear off. Learn the sounds of your plant when it’s running smoothly and you’ll be well aware of a sound that’s “not right.”
If you see a funky amp reading on the screen, you need to call for the ground man’s help. It’ll be natural to see an initial spike because some material might have been left in the tail end of the slat conveyor the night before. Sometimes it takes a little effort to “bust loose” and move, so you’ll see that initial peak. If the plant operator made a mis take shutting down the night before and buried the slat’s tail in mix, you’ll probably trip a breaker trying to start this motor. Moral of the story: Empty the slat before shutting down.
If you have multiple silos, also start your crossover conveyors at this time. Check the flop gates. Open and close the batchers to make sure everything is operating correctly. Listen to the flop gates going back and forth. When switching from filling silo 1 to filling silo 8, a malfunc tioning flop gate means you’ll have mix piling up on top of the silos. That’s an expensive, potentially dangerous, mess you can avoid if you listen for proper operation now.
Step Six. Open and close silo gates. Bring the loader operator or a dump truck over to pull a plug of mix out of full silos to make sure HMA is flowing correctly. You might think a silo is empty, but a portion of mix that fell out of a batcher in the night could be sitting in the bottom of the silo, waiting to cause a quality con trol problem. Dump that into the back of a truck for the RAP pile.
Step Seven. Start the exhaust fan. This involves a pair of giant motors. As I mentioned with other amp indicators, if you see the amps peak without recovering, something’s going wrong. The folks at Libra Systems Inc., Harleysville, Pennsylva nia, have their PlantWise drum mix control system set up so you can pull up a screen that monitors 32 analog inputs in a color-coded range. If you’re in the red range, you know something’s going wrong and you
Your final step before turning to the blending controls is to top off the cold feed bins and RAP bins.
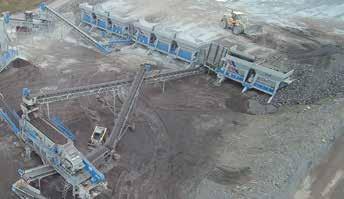
ASPHALT PLANTS AND COMPONENTS
have the option of clicking on the component on the screen to see what’s happening. You have the option of making notes for mainte nance or shutting down if it’s something serious.
Step Eight. Start the drum. You’ll start the drum or drums with the discharge chute in the dump or “on the ground” mode. If it was emptied last night, all is well, but you might have some dry rock and sand in there. Being in “dump” mode means the sand or dry material cycles out without contaminating future mix in the silos.
Step Nine. Set the drum burner on “low fire.” This step is to slowly heat up the drum and baghouse. You’re sending warmed air through the ducts and into the baghouse. This step is vital. You don’t want any moisture in that baghouse. You want dry dust in there.
Step Ten. Top off and zero out. At this point, the loader operator should top off the cold feed bins and fill the RAP bin(s), and the plant operator should zero out the virgin and RAP weigh scale belts again.
With your 10 steps in sequence to starting up the asphalt plant, you’ll finally look at your screen(s) in the control house to ensure everything is up to the proper temperature for making today’s mix. Make sure you’ve selected the appropriate silo to accept product and turn your attention to the blending system. By following a consistent, logical pattern for plant startup each day, the successful plant operator moves air, heat, and energy through the system without missing vital steps or sending material to a road block.
Of course, there are controls systems on the market that will start components in a sequence with the push of one button. Plant operators still need to understand what they’re doing and why. They need to understand the need to empty slats at the end of Thursday to make startup painless on Friday, and so on. They need to learn to listen for smoothly flowing bearings when specific motors begin moving the slat conveyor. And so on. These 10 steps for starting the HMA plant take the plant operator back to the basics for best plant operation.
A.J. Ronyak is the proprietor of Asphalt Solutions, Cape Coral, Florida, and a veteran asphalt plant operator. For more information, contact him at (623) 853-2273 or nosmellasphalt@msn.com.
www.tarmacinc.com
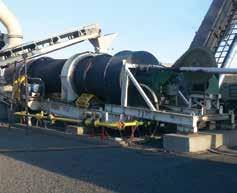


IMAGINE YOUR DREAM

YOUR BUSINESS STARTED AS A DREAM, TO GROW AND PROFIT. To get the personalized attention you want to help you on your way. The customization you need to meet your business’s specific production goals. Consult with one of our specialists today to help configure just the right asphalt plant for you. Start your custom plant design today.
VISIT US AT BOOTH S5455 CONEXPO-CON/AGG MARCH 10-14, 2020
IMAGINE YOUR DREAM
