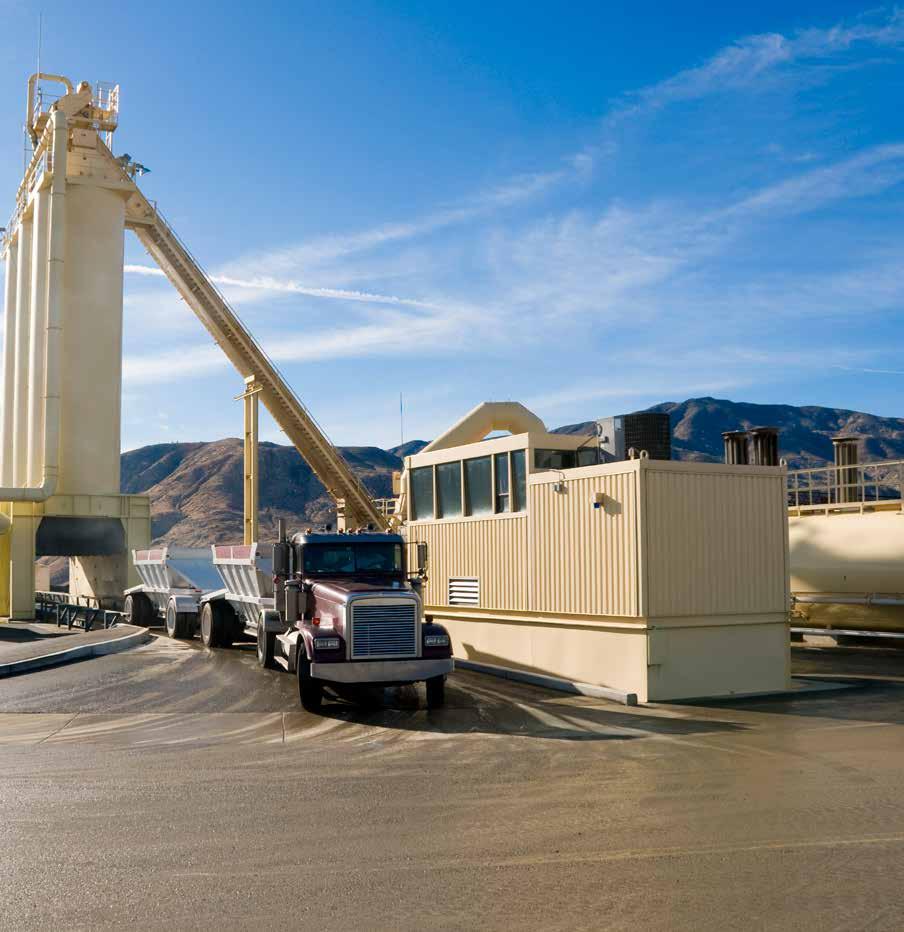
7 minute read
Financial Terms for the Plant Manager
Financial terms aren’t sexy, but knowing the basic ones makes your job as a plant manager easier. In today’s world, business is driven by financial language. As much as you might like to limit your talk to plant performance, repair needs or weather, at some point, you’ll need to talk in financial terms.
No matter your background or educational level, every plant manager needs a basic understanding of financial terms in order to discuss local plant concerns. When reading reports or participating in meetings, as the manager, you must be able to understand what is being conveyed. Is your plant in line with other sites? Are you controlling costs the best that you can? Whether or not you are directly involved in the negotiations of various cost factors relating to your plant, you need to understand the effects of the costs.
Let’s use this space to review some terms that may come up in your day-to-day decision-making. In the following descriptions of financial terms, we’re focusing on the needs of the local plant manager, starting with a definition of management. F
Management: Combined fields of policy and administration and the people who provide the decisions and supervision necessary to implement the owner’s objectives and achieve stability and growth
Amortized expenses: The costs for assets such as buildings and computers, which are expensed over time to reflect their usable life Second, capital investment refers to money invested in a business with the understanding that the money will be used to purchase fixed assets, rather than used to cover the business’s day-today operating expenses.
Cost: An amount that has to be paid or given up in order to get something. In business, cost is usually a monetary valuation of (1) effort, (2) material, (3) resources, (4) time and utilities consumed. One of the greatest champions of the practice of controlling costs was Andrew Carnegie, who is quoted as saying, “Watch the costs and the profits will take care of themselves.”
Direct vs. indirect costs: Costs that are directly associated to the manufacture of a product. • Indirect costs cannot be directly tied to a particular product. • Direct materials cost is the cost of the materials that are traceable to the product.
Direct labor: Represents the wages and fringe benefits earned by the individuals who are physically involved in converting raw materials into a finished product • Straight time: scheduled shift of time normally eight hours, paid at the straight time-rate • Overtime: request for additional time in addition to the straight time, paid at a higher rate than the straight time
Assets: Anything owned by the company having a monetary value; i.e., fixed assets like buildings, plants, machinery, and vehicles (As a plant manager, your focus is to manage local site assets. You keep the assets in good working condition, evaluate the plant for improvements and ensure all assets are in safe working order.)
Break-even point: The point when a business’s revenue equals its expenditure (In most cases, the plant manager will participate in the break-even point by providing data in the budget process. It’s important to have a sense of the break-even point in order to make your day-to-day decisions.)
Budget forecast: The amount of money the company plans to spend over the course of a period, usually a year
Budget variance: The difference between a budget forecast and actual expenditures
Capital investment: The term capital investment has two usages in business
First, capital investment refers to money used by a business to purchase fixed assets such as land, machinery or buildings. Depreciation: The method used to systematically move the cost of an asset from the balance sheet to the income statement over the course of the asset’s useful life
Fixed assets: Assets that are difficult to convert to cash, such as buildings and equipment • Inventory is an asset, and is found on the balance sheet under current sssets, as it is usually assumed that these parts will be turned into products and sold reasonably soon.
Financial reports: Reports issued by a company that describe the financial activities of the company • The financial statements are broken down into three different statements: • The income statement shows the income and expenditure of the company, including things such as depreciation, income tax, interest income, etc. These expenditures are then compared to revenue to determine gross profit. • The balance sheet statement is used to value a company and to show what it owns or owes. The balance sheet lists all assets, liabilities and shareholders’ equity attributed to the company. It is always a snapshot of one point in time. The balance sheet statement must always be in balance.
LOWER YOUR CREDIT CARD PROCESSING FEES
Focusing on the aggregates, asphalt supply and hauling industries
The Most Trusted Brand in the Payments Industry
Call Us Today! ph. (631) 923-2586 www.nccpgroup.com
• The cash flow statement is a summary of the actual or anticipated incomings and outgoings of cash in a firm over an accounting period.
Inventory: The value of materials and goods held by an organization (1) to support production (raw materials), (2) for support activities (repair, maintenance, fuel or other energy sources held), or (3) for sale (merchandise, finished goods, spare parts) • Inventory can be valued in three ways. • The first-in, first-out (FIFO), method says that the cost of goods sold is based on the cost of the earliest purchased materials, while the carrying cost of remaining inventory is based on the cost of the latest purchased materials. • The last-in, first-out (LIFO), method states that the cost of goods sold is valued using the cost of the latest purchased materials, while the value of the remaining inventory is based on the earliest purchased materials. • The weighted average method requires valuing both inventory and the cost of goods sold based on the average cost of all materials bought during the period.
Inventory shrinkage: Aggregates used in the production of hot mix need to be removed and be free of all moisture in the production process. Moisture will account from 1 to 7 percent of the total weight of the incoming aggregates. This loss may be up to 35,000 tons of material shrinkage over a one-year period. When accounting for aggregate inventory, we need to take into consideration the loss of moisture. In addition to moisture, you also need to account for any inventory that is not part of the final delivered mix.
Indirect labor: Employees or workers who do not directly produce goods or services, but who make their production possible or more efficient. Indirect labor costs are not readily identifiable with a specific task or work order. They are termed indirect costs and are charged to overhead accounts.
Manufacturing overhead: Includes all of the other costs incurred in the manufacturing activities. These indirect costs include repairs and maintenance, depreciation of the manufacturing equipment, utilities, salaries of manufacturing supervisors, etc.
Operating expenses: Expenses such as administrative employee salaries, rents, sales and marketing costs, that occur in operating the business
Operational annual budget: A plan for expenditures, to which most plant managers will be asked to contribute, required to maintain the functioning of a business
Overhead: An expense that cannot be attributed to any one single part of the company’s activities
ROIC: Return on invested capital is a calculation used to assess a company’s efficiency at allocating the capital, under its control, to
profitable investments. The return on invested capital ratio gives a sense of how well a company is using its money to generate returns.
Variable costs: Costs that are incurred in relation to sales volume; examples include the cost of materials and sales
To the non-financial manager, financial terms can be confusing. Many times, you’ll be asked to attend a meeting with the accounting department, which may cause you some stress. Don’t allow yourself to be intimidated; if you’re not sure what they’re talking about, ask questions. I cannot tell you how many times I have been asked to give a plant tour to a group of accountants or bankers. You would not believe the questions they asked. Never forget you are the expert at your plant. The accounting department houses the experts in the documenting of the cost of doing business.
As a suggestion, you may want to cut out this article and file it somewhere in your office. It can be used as a resource. When the time comes for a financial meeting, take it out and review the financial terms as part of your preparation.
Ken Monlux is an asphalt industry veteran with 30 years experience in all areas of operational management. For more information, see his ad on page 72 or contact him at (209) 495-1017 or kenmonlux@yahoo.com.
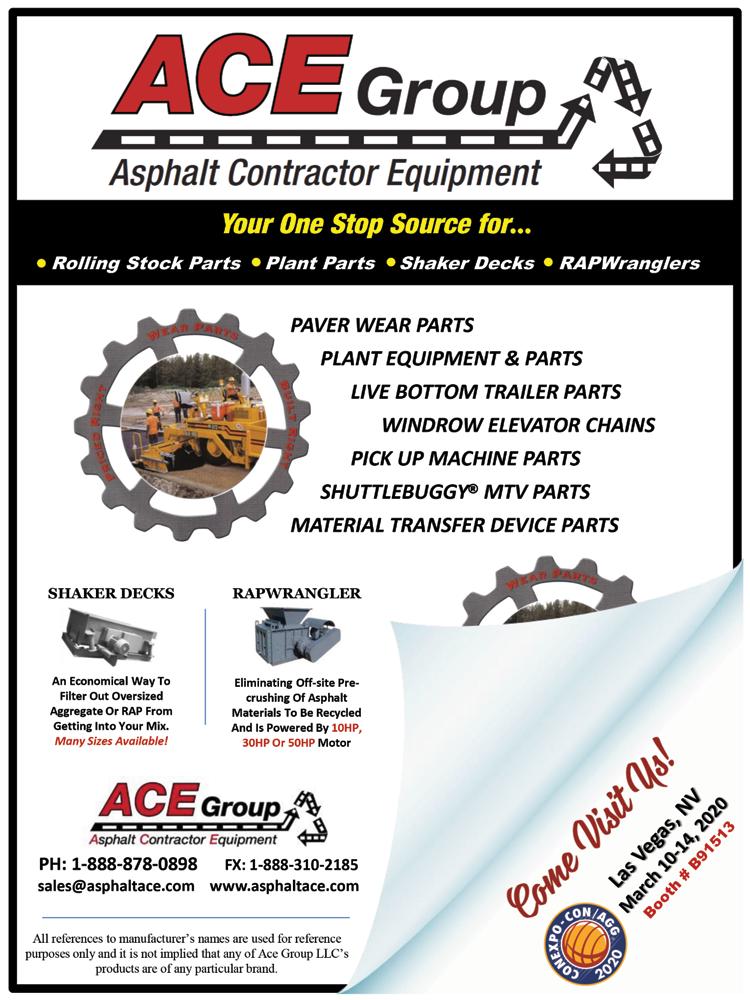