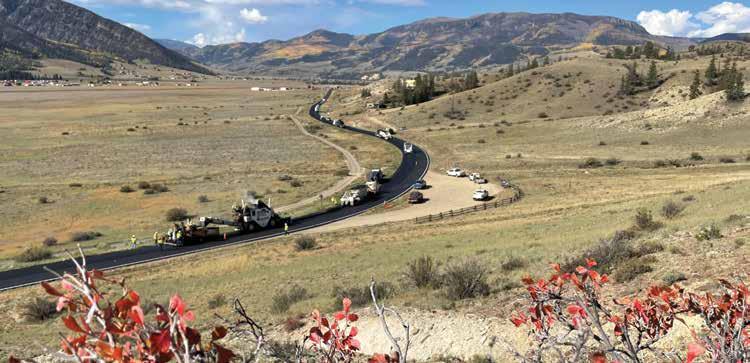
15 minute read
Scenic Mountain Road Gains Smoothness with CIR
A recent project to rehabilitate 41 miles of a scenic mountain highway in Colorado reaches new heights of smoothness following one of the largest cold in-place recycling treatments in the west.
BY SARAH REDOHL
Prior to 2022, the 43-mile section of Colorado’s State Highway 149 between Creede and Lake City had not seen any pavement surface treatments in more than 20 years, and up to 40 years in some sections.
After passing through the historic mining town of Creede, CO-149 winds through the San Juan Mountains before passing through Spring Creek Pass (elevation 10,901 feet), Gunnison National Forest and Slumgullion Pass (elevation 11,361 feet) and descending into the town of Lake City.
However, the existing pavement of the scenic highway had reached the end of its useful life. According to Colorado Department of Transportation (CDOT) Region 5 Materials Engineer Tim Webb, the pavement consistently contained at least ¼-inch wide and 4- to 5-inch deep cracks (primarily transverse) throughout the 43-mile span between Lake City and Creede.
“The driveability life of this stretch of highway was zero to one year,” Webb said, based on a condition-based index system within CDOT’s statewide pavement asset management approach of quantifying several surface distress criteria. “The resulting existing ride was not smooth and there was no useful life remaining in the existing surface.”
When CDOT received special senate bill funding for rural roads, Webb’s Region 5 teamed up with neighboring Region 3 to pool funds to repair a large section of CO-149 across the border of the two regions.
“We don’t always have such funds for a rural road like this, but that enabled us to cover a significant number of miles on this one project,” Webb said. With a fairly short paving season and the harsh winter conditions in Colorado, Webb said CDOT prefers to complete projects in one construction season, “especially in mountain passes like where this project is.”
With such a large project and limited time, CDOT opted to perform cold in-place recycling (CIR) on this job. “A faster construction method like CIR helped us achieve that goal because it allowed us to resurface 40 plus miles in a single construction season,” Webb said.
CIR is a process that cold mills and recycles the top 2 to 5 inches of asphalt using a continuous train operation. According to the Pavement Preservation & Recycling Alliance (PPRA), CIR reduces construction times by anywhere between 20 and 40% compared to conventional reconstruction methods.
Furthermore, the conditions of the existing pavement were a perfect fit for CIR as a treatment. “When you have older pavement that has cracks that are primarily top-down but are pretty severe, that’s a perfect candidate for CIR,” Webb said. The CIR on CO-149 recycled the top 4 inches of the existing pavement, “basically eliminating all of those cracks,” Webb said.
The sustainability aspect of CIR was another selling point to CDOT, as the process reuses 100% of existing materials and can reduce greenhouse gas emissions by up to 90%, according to PPRA.
“We strive to use recycling methods when it fits the existing roadway conditions,” Webb said. Webb shared that using the existing materials in place negated the environmental impact of a project that would transport new materials to the site from a remote location.
ABOUT THE PROJECT
The two sections of the project included 22 miles between the town of Lake City and the north side of Slumgullion Pass and 19 miles south of the pass to the town of Creede, for a total of 82 lane miles. The project was divided in two sections because the section of the road passing through Slumgullion Pass had received a more recent resurfacing treatment.
United Companies, Grand Junction, Colorado, a subsidiary of CRH North America and the midwestern extension of Staker Parson in Utah, was the prime contractor on the project.
“The majority of CIR bids on the western slope are installed by my crew,” said United Paving Foreman Ramon Chavez. When United won a bid on its first CIR project eight years ago, Chavez’s crew was the one tasked with the new challenge. “At that time, we thought we drew the short straw, but it turned out to be the long straw.”
To date, his crew has performed six CIR projects in the last eight years. “My crew is probably the most experienced crew in western Colorado with this process.”
United subcontracted the recycling portion of the project to Coughlin Company Inc., St. George, Utah. The 101-year-old company has been milling asphalt since 1992 and expanded into asphalt recycling in 2006. Today, Coughlin has 23 roto-mills and three recycling trains that travel throughout the western United States, including Arizona, California, Colorado, Idaho, Nebraska, New Mexico, Nevada, Oregon, Washington, Wyoming and Utah.
Coughlin frequently works with United, said Coughlin Safety Manager Stephen Steed. “They’re a great outfit to work with,” he said. “We can’t compliment them enough.”
Recycling on the project began in May and the new asphalt overlay was completed in October. Coughlin milled to a depth of 4 inches at a full-lane width of 12 feet, 6 inches wide with a production rate of 23 to 25 feet per minute with its Astec (Roadtec) RX 900e. “We have quite a few of those,” Steed said. “They’re very powerful, dependable machines.”
In total, Coughlin recycled approximately 86,000 tons of material.
Coughlin injected a lime slurry into the cutting drum of its roto mill at 1.5% based on weight of dry recycle. “We put lime slurry in there as well to help with the conditioning of that asphalt to be like new again when it’s laid that back down,” Webb said.
Next came Coughlin’s recycle unit, an Astec (Roadtec) RT-500. The impact crusher within the 100% enclosed unit crushed the recycle to size, 1 inch minus, before running it up through the machine’s weighbridge. The material is then dropped into the pugmill where the rejuvenating agent (AC emulsion) is introduced and mixed before it’s dropped out of the pugmill into a windrow where it can be picked up by the paver on the other end of the recycling train.
The RT-500’s onboard computer helps determine the amount of emulsion based on specifications. For the CO-149 job, Coughlin operated in the 3.2 to 3.4% emulsion content range.
“To be successful with the recycling portion of the project requires you to go in and calibrate all the different components to make sure you’re putting the specified amount of emulsion, lime or other additives on the job,” Steed said. “You can’t meet the specification if you don’t get the calibration done right.”
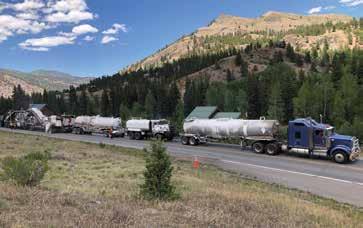
Coughlin located unused gravel pits midway through both ends of the project to use as its staging areas. It set up a couple tanks of emulsion at those sites that could be brought to the recycling train with transfer trailers. Lime slurry was mixed at the staging area and transported to the recycle train by supply tankers.
In total, the project on CO-149 recycled approximately 86,000 tons of material and required 64,000 tons of the SX HMA.
Coughlin was assured of the importance of the project to local residents when the recycle train pulled into Lake City. “We had shop owners coming out telling us how excited they were to see the road getting fixed and how much it means to them,” Steed said.
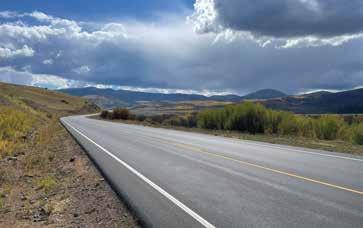
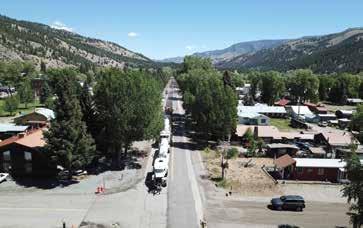
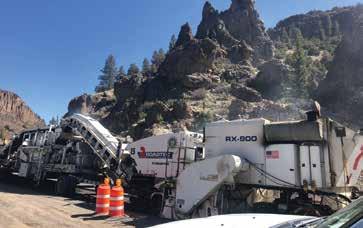
United subcontracted the recycling portion of the project to Coughlin Company Inc., St. George, Utah.
Steed said the most unique aspect of the job to him is its location. “It’s beautiful country out there,” he said, adding that the crew even saw a moose on the side of the road. “The scenery is just unbelievable. You just can’t ask for a better place to work.”
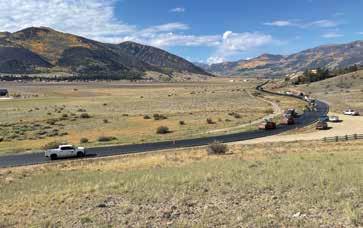
LOCATION-RELATED CHALLENGES
According to Webb, CDOT doesn’t perform many CIR projects, but the lion’s share of CIR jobs in Colorado take place on the state’s western slope due to its remoteness.
“The project took a lot of coordination and logistics to get the material out there,” Steed said, adding that teamwork is key to the company’s success on the project. Although using CIR reduced the number of trucks needed to get the required materials to the job site, Steed said “it can still be a challenge when you have to move even the amount of material we did need (emulsion, lime, etc.) at that distance.”
Coughlin located unused gravel pits midway through both ends of the project to use as its staging areas. It set up a couple tanks of emulsion at those sites that could be brought to the recycling train with transfer trailers. Lime slurry was mixed at the staging area and transported to the recycle train by supply tankers.
The remote job also spanned a number of challenging road conditions, including portions that are narrow, winding and steep. Steed said the south end of the project was fairly easy because it was relatively straight and flat without a lot of sharp turns. However, the northern side had many narrow areas where Coughlin had to stop traffic entirely to give the train enough room to maneuver.
“There wasn’t much room for traffic on those mountain roads alongside that CIR train,” said United QC Manager David Fife. “The traffic going through some of the canyons was a challenge.”
At one point, the road became so narrow, the recycle train resulted in a one-hour delay to the traveling public. Although it was unfortunate for the traveling public in the short term, Coughlin was assured of the importance of the project to local residents when the recycle train pulled into Lake City.
“You don’t see a recycling train going through the main street of a town very often,” Steed said. “We had shop owners coming out telling us how excited they were to see the road getting fixed and how much it means to them.”
COMPACTING COLD IN-PLACE
Because the material changes throughout the project as it’s milled up, the rolling pattern must also change, Chavez said. “With a traditional HMA job, you can fine tune everything on the test strip,” he added. “With CIR, it’s like the mix design is changing throughout the entire project.”
Results from the modified Proctor tests performed on material from the project ranged from 110 to 130 pounds per cubic foot. “It’s easy to get density on 130 pounds, but it’s harder to get density on 110 pounds,” Chavez said. “It seems counter-intuitive, but if you’re not able to get heavy densities with the hammer, it tells you that material doesn’t compact well.”
The modified Proctor test is a CIR mix design method (in accordance with AASHTO T 180, Method D) where loose material is put in a cylinder and struck a preset number of times with a 10-pound weight to determine optimum moisture content (OMC) at peak dry density of the material.
To compact the rejuvenated asphalt behind the recycle train the crew started with a breakdown roller (Volvo DD140) running two full passes on the edges and one in the middle, followed by two rubber tire pneumatic rollers (Bomag BW27RHs) until the breakdown roller finished the next section. “That might result in 15 or 16 passes,” Chavez said. Then, United’s Volvo DD120 finish roller passed through to achieve final density, which must be 100% of lab compacted density in accordance with Colorado Procedure 53 (CP-53).
“There was a bit of a learning curve early on, but once we got going the process went pretty well,” Fife said. “With CIR, you shoot for different densities based on where you are on the project, so we were monitoring densities behind the rollers with a nuclear gauge to make sure we were compacting to the appropriate percentages.”
This is where the unexpected weather the crews faced became particularly challenging. Although the weather was often good for the first twothirds of the day, it would get overcast, humid and cool most afternoons and frequently rain, shutting down that day’s production, Chavez said.
“Achieving compaction in such a constantly changing climate was the biggest challenge we faced,” he said, adding that CIR is dependent on
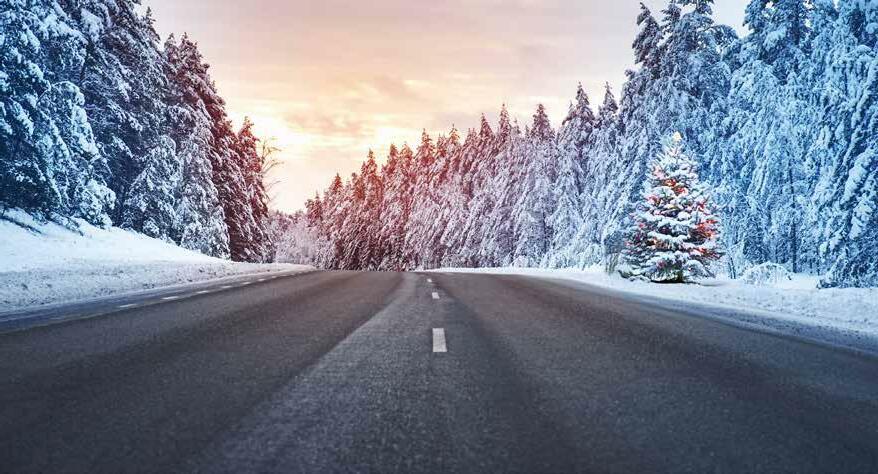
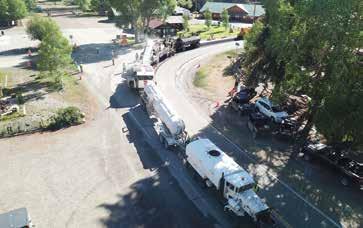
The project spanned a variety of road conditions, from straight and flat roads on the south end of the project, through the town of Lake City, and many narrow, winding and steep areas on the north end of the project.
temperature. “It’s difficult to get good densities in the types of weather we were working in.” Chavez said his crew’s expertise was critical to overcome these weather-related challenges.
“When it comes to traditional HMA jobs, you have this trigger telling you have a certain window to achieve density,” he said. “But with CIR, there’s no set amount of time. So much depends on the weather. You have to understand how the material works to know how and when to roll it. Most of my guys know based on the color of the mat and the feel of it from the rollers if it’s the right time. And that’s what my guys did, and they were able to get compaction throughout the project.”
“We thought the weather might give us problems with raveling, but in actuality, we had very little raveling despite the rain,” Steed said. He attributes a large portion of this to the performance of the AC emulsion used on the project.
“The emulsion we used was an awesome emulsion,” Steed said. “At the end of the day, we could put traffic on that road and it looked like a regular hot mix paved asphalt road even though it was recycled.”
EMULSION MASTERS
To determine the chemistry of the emulsion, cores were taken from the road to develop a mix design for the project. Arkema-Road Science, Tulsa, Oklahoma, provided the surfactant, ArrTekk 800 series High Performance chemistry, to make the engineered emulsion used on this project.
During the design phase, several high performance specialty tests outlined in the specification were conducted to establish predictability of the mix for long term performance. The tests included Lottman test CPL 5109 on freeze/thaw, Marshall stabilities, indirect tensile strength for crack resistance and raveling tests to indicate cure time of the emulsion itself. “Ultimately, these tests determine what emulsion content and chemistry is appropriate for the climate conditions of the project,” said Arkema-Road Science Account Manager Jeff Weitzel.
“The raveling test is very important,” Weitzel said. “The raveling test (ASTM D 71 96) is a short-term strength test that must result in less than 2% raveling. This indicates if the material will cure fast enough to allow traffic rolling on it without raveling. You don’t want to build a road out in the middle of nowhere that you can’t put traffic on for a week. You want to put traffic on it that same day the CIR was done.”
Weitzel said Arkema-Road Science recommended that CSS special asphalt emulsion be used on CO-149 based on the emulsion’s early strength build and cure. “This chemistry enables maximum emulsion dispersion throughout the mix itself and provides heavy film thickness, while lowering void content, delivering better rut resistance and better thermal and fatigue cracking resistance,” Weitzel said. “Even with all the thunderstorms and varying temperatures in this mountain region, we still had no raveling or rutting issues.”
The cure time following the CIR portion of the project was a minimum of 10 days, however, poor weather struck again. “We generally like to be paving on it within a couple weeks, but a ton of bad weather up here held us up,” Fife said. However, he added, the CIR still held up really well. “Instead of paving on top of a crumbly old road, CIR gave us a really nice product to pave on top of that I think will be a really nice road for years to come.”
Even without the wearing course, Fife said the CIR alone drastically improved the smoothness of the road. The Coughlin crew agreed. “The level of smoothness we were able to achieve with the CIR left a much easier job for the paving crew to come back through and pave,” Steed said.
As soon as the weather allowed, United’s paving crew returned to the jobsite to place the asphalt overlay with its Cat 1055F paver. The overlay consisted of a 1-inch leveling course on the Creede side, an ST mix with PG58-28 and a ⅜-inch nominal maximum aggregate. On both sides, the crew placed a 1.5-inch wearing course, an SX mix with PG58-34 and a ½-inch nominal maximum aggregate. The Lake City side contained 30% RAP coming out of United’s pit in Gunnison, Colorado. “On the Creede side, we didn’t have RAP available to us, so that’s a virgin mix,” Fife said.
In total, the project required 64,000 tons of the SX HMA.
SMOOTH & SCENIC
Ultimately, both companies and CDOT are pleased with the results of the project. “We were able to remove the severe cracking in the roadway, place a recycled pavement surface without cracks, top it with two lifts of fresh HMA, and give the traveling public a very smooth ride,” Webb said.
By eliminating those cracks, the CIR will not only improve rideability but also the longevity of the roadway by preventing water from infiltrating the pavement, Webb added. PPRA estimates CIR adds 15 to 20 years of life to that pavement. “They’ve gained quite a few years by putting down CIR under the asphalt overlay,” Fife said. “The CIR and overlay combined should result in a nice road that should last a long time.”
“The job turned out really well,” Steed said. “It’s definitely a big improvement on ride quality.” The average IRI for the north segment of the project was 185 before construction began, and now has an average IRI of 65.
In addition to the success of the project, this may be the one of the largest, if not the largest, CIR project in the western United States. “I’ve been doing this for 30 years, and it’s definitely the largest I’ve ever seen in this region,” Weitzel said.
“I’ve always taken pride in my crew’s expertise with CIR,” Chavez said. “To know we’ve been involved in such a history-making project fills me with gratitude.” Steed agreed: “It’s an honor to be able to have been involved in a project of this size, and it’s a very successful project to boot.”