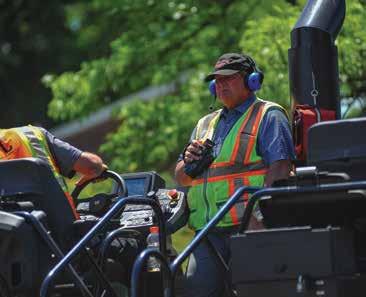
9 minute read
How Your Workers Grow a Successful Paving Operation
How Your Workers Grow a How Your Workers Grow a Successful Paving Operation Successful Paving Operation
YBY JOHN BALL You can read any number of articles about the financial side of starting and running a paving business. The Off the Mat department in this magazine is set up to help with that. But if you don’t have the right people with the right attitude committed to running the right equipment the right way, all that business work will stop there on paper. I’ve had the pleasure to work with many great companies over the years. I’ve seen some good laborers and good equipment operators grow into great workers—great workers who advance their careers while helping to advance the whole crew and company with an attitude of committing to excellence.
Let’s talk about how to nurture those employees at your company and grow your paving operation through training.
We’ll start with an assumption. Let’s assume you’ve worked with local agencies, your state asphalt pavement association (SAPA) and/ or trade schools to hire people who are interested in construction.
The researchers at the National Opinion Research Center at the University of Chicago have data showing us that construction workers have reported higher levels of job satisfaction than all other industries combined over the past four distinct economic cycles since 1974. You can see a detailed page of stats from the National Center for Construction Education and Research (NCCER) regarding “Job
Satisfaction in the Construction Trades.”
If you can pull the right folks into your company, you’ve won half the battle. But if you’ve hired someone who doesn’t really want to work in the construction industry or who doesn’t understand we have long hours during the height of paving season, you’re setting yourself up to lose that person. As soon as the weather turns hot enough, the worker who was never committed to the industry will walk away. So, let’s assume you’ve done your homework to make sure you hired the right people for this industry.
BRING LEADERSHIP ON BOARD
You know that building a safety culture in your company starts at the top, with the leadership. The same is true for building a quality mindset in your employees. You want to bring leadership on board with the idea of getting quality out of every project, which starts with every worker buying into quality. You want every employee from the laborers to the CEO to understand the importance of equipment maintenance, the paving process, best practices and safe operations.
Bringing everyone into the same headspace may look different for your company, but when I go to a client’s home office, I sit down with management and go over what we’re going to do to improve their entire operation—not just the project (or projects) we’re working on that week. I include leadership in the pre-plan and in the report at
Consultant John Ball oversees the project from the deck of the paver and is able to speak clearly to workers through the wireless headsets on this job. This photo courtesy of Intercounty Paving
the end of the week, so everyone is on board and buying into the mission to grow the whole operation.
It’s important to make sure everyone is on board with training for paving excellence—from the top down.
PLAN AHEAD
One of the factors in getting excellent quality is to plan ahead. Whether that’s in our pre-planning meeting at headquarters or whether that’s the gameplan the paving superintendent puts together before the first day of a paving project, you need to know where you’re going before you take your first step. (Check out the article titled “Train Paving Laborers to be the Best Superintendent Ever” on theasphaltpro.com for tips on how to help your superintendent pre-plan the job.)
The same is true for your training program. If you know ahead of time that you’re training Laborer A to grow into a foreman someday and Laborer B to grow into an estimator, they may both start with the same basic skills and information, but their paths will diverge. When and how they diverge is up to your training director.
Maybe you have two laborers with unknown skill sets and the decision to set them on different paths hasn’t been made yet. You know what your company needs to have in place next season, the season after and five seasons down the road. By planning ahead and watching the attitudes and aptitudes of the new workers today, you can guide them into the training programs for tomorrow.
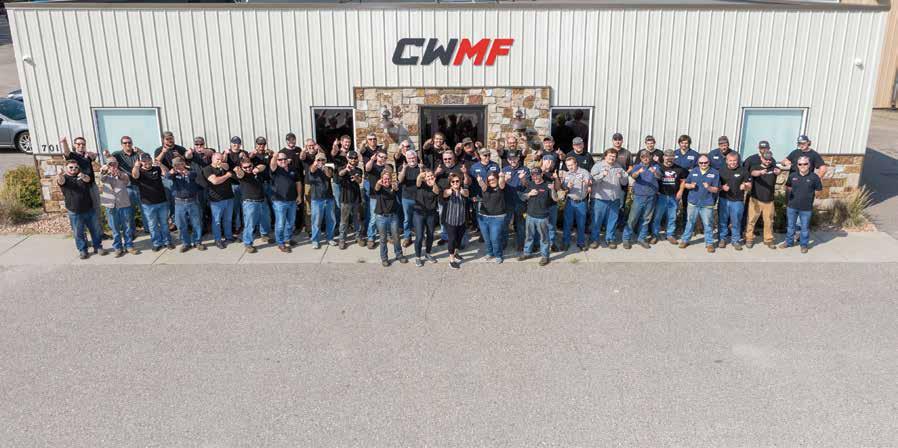

FROM THE TEAM AT
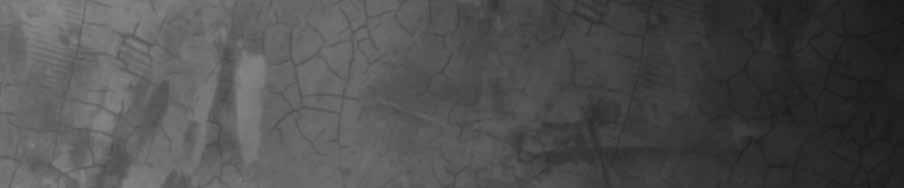
SELECT THE RIGHT EQUIPMENT
Picking out the right equipment for each project is just as important as choosing the right employees for your company. Think about your potential for success if you show up to a highway paving project with a paver, equipped with a hopper insert, and all the haul trucks arriving (whether they’re on time or not) are belly-dumps. You better scramble to get a pickup machine to the site in a hurry. (And look into what fell apart during pre-planning.)
Having the right pieces of equipment on the job gives workers their best chance at doing the job right. In the example above, the paver operator might be one of the best in the industry and might be fantastic at communicating with haul truck drivers and screed operators alike. But if you handicap him with a mess in front of the paver or trucks that can’t get material to the hopper, he can’t do his job. Imagine his frustration level as he sits there waiting atop a machine where he’s already input settings to get a full day’s work for a bonus-worthy mat.
Another element of getting the right equipment is having the correct compaction equipment on hand for projects. Wider is not always better if you’re watching your fuel economy. (Check out the article titled “How to Roll for Bonus: Part 2” on theasphaltpro.com for tips on selecting the right size and type of roller for the right job.)
At this time in history, contractors are being asked to retire machines that may or may not be at their end-of-life in an effort to remove older diesel-run engines (whether Tier IV Final or not) from the national fleet in favor of electric off highway construction vehicles (EOHVs). If you have the money to spend on the machine, its charging infrastructure, its best maintenance schedule and its replacement battery, this may be the time to prepare for upcoming bidding opportunities that will be reserved for contractors who have a set percentage of EOHVs in their fleets.
Beyond the heavy equipment, don’t forget the smaller technology that makes life easier for workers and could entice them to stay with your company and crews.
We all know our paving operations are hot and noisy. No matter how many battery-powered engines you put out there, the backup alarms, raising and lowering haul truck beds, passing traffic, vibratory rollers, plate compactors, and the like, will make noise for workers to shout over to be heard. If this shouting makes for a tense environment, do you think the new employee who has never experienced a real-world paving operation before is going to be excited to come back tomorrow?
Investing in a system of headsets that cancel some ambient noise while giving foremen and supervisors a clear line of communication with operators and laborers is an option. You can check out a number of articles about their positive use at theasphaltpro.com, including “Use Headsets to Communicate with Your Crew.” The team at Eartec Co., headquartered in Narragansett, Rhode Island, has released the self-contained EVADE headsets, which feature a compact, full duplex transceiver built inside the ear cups. The complete system, like many others on the market, relays digital signals to and from a “main” unit and “remotes.” For the Evade system, the team at Eartec says theirs link automatically without a hub or base station; the Evade connects up to nine users within a 400yard range. The point is to enhance coordination, productivity and safety.
Have you looked into the ergonomics of the operator cabs of your equipment? Your workers spend an 8-hour or longer shift in the machine’s cab. You want that environment to be one that’s comfortable enough for the worker to accomplish his or her tasks efficiently and with top quality while avoiding lumbar or other injuries due to repetitive motions. You want a healthy and happy worker to come back tomorrow.
I’m not suggesting the construction industry is coddling workers; just consider how excited you would be to return to a machine’s cab if it was made in the 1950s with a board bench for a seat. By offering your workers the best in class—or at least the best that you can reasonably afford— you're offering a work environment they’ll be more willing to return to day after day and a work environment that is more conducive to safe and quality performance.
ROUND OUT THE ATTITUDE
This takes us back to the initial hiring decision. When you bring a new worker to the crew, you’ll be able to tell how he or she is adapting to the job. You don’t want to assume that a person who hangs back and watches how things are done is going to be a lazy worker; this person might be learning by example. But if you see a trend of this person letting everyone else do all the work, maybe you’ve brought on someone who would be better off in a different position. You don’t want to assume that a person who shouts a lot on the job is going to be an argumentative or bullying team member; this person might be hard-of-hearing or might be trying to be heard above engine noise. But if you see a trend of this person shouting on and off the job site (or using improper language in front of customers), maybe you’ve brought on someone who would be better off working alone or in a different company.
By using mentors and supervisors to track new workers’ behavior and progress, you not only train the new workers more quickly, but you also have the chance to catch attitude patterns before they become problems. You have the opportunity to notice and nurture the workers who will grow their careers alongside your quality projects and your quality crew.
John Ball is the proprietor of Top Quality Paving & Training, Manchester, New Hampshire. He provides personal, on-site paving consulting services around the United States and into Canada. For more information, contact him at (603) 493-1458 or tqpaving@yahoo.com.
LEARN MORE
Who Did You Hire?
The person you hire today will move up the ranks to be tomorrow’s equipment manager, supervisor, estimator or other important leader in the company. The way to build a quality mindset throughout the entire company is to start with the workers who will carry a quality mindset through all those positions. You want to look for some common, positive traits in the workers you bring on board: • A positive attitude • Timeliness • A proactive nature • Willingness for teamwork • Willingness to learn • Personal responsibility • Safe, respectable clothing.