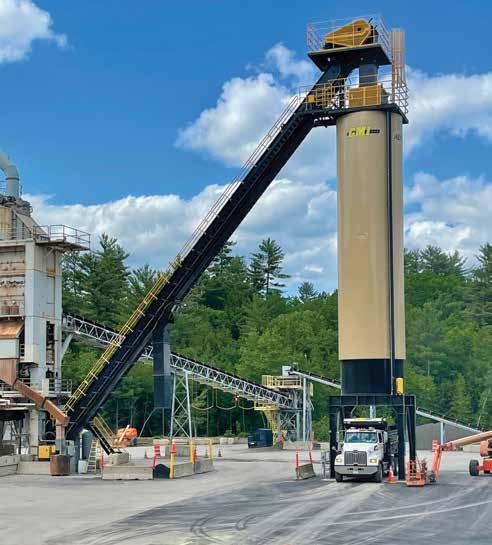
11 minute read
GMI Maximizes Trucks, Fuel, Labor
GMI Asphalt has invested in a new drag, silo and flop chute from ALmix to improve haul truck cycle times and reduce fuel and labor costs.
BY SARAH REDOHL
Every five or so years, GMI Asphalt, Belmont, New Hampshire, has made at least one major investment in the growth of the company. From buying other construction companies and acquiring its quarry and sand pit in Boscawen, to purchasing its 6-ton Barber Greene batch plant in Franklin, the company only seems to know one way to go: forward.
“We bought the plant to be more competitive in our market and to take the next step in GMI’s growth,” said Neil Arruda, general manager of GMI Asphalt’s materials division. “With our quarry, sand pit and asphalt plant, we now control the whole process and are able to price ourselves accordingly.”
Through each investment, GMI Asphalt has kept the end goal in mind regardless of the challenges they may face—and they have faced their share of challenges.
“When GMI bought the plant, it had only made 40,000 tons of mix total,” Arruda said. “I can’t even begin to describe the problems we faced in order to get the plant up to state spec and capable of producing 200,000 tons of consistent mix a year.”
For example, GMI invested in a fugitive dust fan to manage high dust content in the mix, as well as a blower and airlock to further control dust content, and a reclaimed asphalt pavement (RAP) system. “It’s been a continuous process of improvements,” Arruda said.
Having its own plant has enabled GMI to compete for state work, which was particularly important during the height of the COVID-19 pandemic when the municipal and private work that makes up the majority of GMI’s work was delayed or canceled. Arruda estimated that 15% of GMI’s book of work in 2022 has been for the New Hampshire DOT.
Then, in October 2021, GMI made perhaps the most significant investment in its plant: a 300-ton silo, 500 TPH drag conveyor and custom flop chute from ALmix, Fort Wayne, Indiana. “We made those investments so we could produce more mix at the plant and also increase our production and trucking efficiencies,” Arruda said.
BIG SILO, BIG BENEFITS
Having the silo allows GMI to distribute mix from two points, at the batch plant tower drive-through and the silo. And, for the first time, the plant can store mix as needed.
“The silo allows the plant to run continuously and enables us to fill the silo in the morning or the night before,” Arruda said. He’s also noticed a number of cost savings related to GMI’s latest investments. First and foremost, in terms of trucking.
“We went from an average time for a truck in the yard of 35 minutes to less than 10 minutes,” Arruda said. “Just loading the truck used to take 7 minutes from the batch plant. With the silo, we’re at 1 minute, 5 seconds to fully load a truck. That has been particularly
GMI Asphalt's new drag, silo and flop chute from ALmix enable the company to distribute mix from two points, at the batch plant tower drive-through and the silo. And, for the first time, the plant can store mix as needed.

This dual-chain, 36-inch x 116-foot drag conveyor was shipped from the factory to GMI Asphalt March 31, 2022, along with a new hot mix storage silo system.
beneficial during the current truck shortage because it enables us to run with fewer trucks. A line at the plant to get loaded is just wasted money.”
Arruda has also noticed savings related to labor costs as having the silo has enabled the operators to make what they need for the day, store it in the silo, and start shutting down the plant a bit earlier than before.
He also estimates that GMI has saved 5% on its total fuel and electric bills by reducing startups and shutdowns. “Being able to continue to produce mix even if there’s not a truck in the yard also allows us to produce a more consistent mix.”
Around the same time that GMI installed the new drag, slat and chute, the company also installed a Libra Self Service Kiosk from Command Alkon so truck drivers don’t have to get out of their cabs to grab their tickets. “That was planned in conjunction with the silo because we needed to get the final location of the silo to see how traffic was going to flow before we could build the building and stand in which the printer sits,” he said. “That’s also reduced our truck times by a few minutes.”
A TALL ORDER
Although the investments have brought big benefits, GMI’s plant location and its timing goals brought on additional challenges. This included difficulties with the layout of the plant, limited space between the batch plant’s legs for the flop chute, and a short timeline to complete the installation.
In fact, Arruda said GMI had signed a contract with another OEM who ended up backing out of the project when it couldn’t figure out how to make the flop chute work. “Then we talked to ALmix, and they were willing to find a way to make it work while offering a competitive price and delivering within our time constraints,” he added.
“We wanted a 300-ton silo because it’s the only one we were installing,” Arruda said, adding that the silo itself is 85 feet. But GMI also wanted a weigh batcher on the bottom of the silo because the layout of the plant made it impractical to install a truck scale.
“That left us with two ways to approach the problem,” said Ryder Harman, ALmix’s sales and marketing manager. “Either we could put the whole silo on load cells or we could build a weigh batcher into the silo.”
Ultimately, GMI opted for the weigh batch silo, and ALmix designed an 8-ton, fully lined weigh pod built on top of three load cells beneath the silo. As the silo discharges mix into the weigh pod, the pod weighs it and then discharges it into the truck below while safeguarding against mix segregation. It was the more economical option, but it added an additional 8 feet of height to the silo.
The total height of the silo (91 feet, 6 inches) called for a 36-inch by 116-foot drag conveyor. “We’re no stranger to drags this large,” Harman said, adding that although the con-
veyor wasn’t the largest the company has ever made, it is among the largest in recent years. The drag conveyor is powered by a 150-horsepower drive system, allowing it to feed the 300-ton silo at top production rates.
Instead of being supported by stiff legs located midway up the conveyor, this drag conveyor is constructed using cambered bridge beams. “The drag expands and contracts due to the changes in temperature depending on if the plant is running or not, and when you have those legs attached, they don’t allow the drag the range of motion it needs,” Harman said. That’s why ALmix opts for cambered bridge beams on drags of this size. “They're a more expensive approach to constructing drag conveyors, but the strength and cambering of the beams allows for the conveyor to be quite long and not sag over time without the need for stiff legs.”
The strength of the silo is derived from structural steel legs, and the 1/4-inch, 100% double welded silo tube is housed within the frame supports. The silo walls are insulated and covered with pre-painted aluminum sheeting to keep heat loss at a minimum. Silo top decks are insulated with 10 inches of high-density insulation and covered with diamond decking, toe kicks and OSHA approved handrails. A caged ladder is provided to access the bird’s nest on the main drag. ALmix also built the silo with 6-foot railings at the top, which is standard for the company’s silos.
GMI's plan to install additional silos in the future meant that even more height was added to the new silo setup. To account for the future addition, ALmix included a chute where a future transverse conveyor can be installed, allowing mix to be diverted to the new outboard silo, making the future installation an easier process for GMI.
“When it comes to adding silos and drags to batch plants not originally designed for them, we have a lot of experience with these projects,” Harman said. “We also manufacture a complete line of batch mix plants, so we are quite familiar with engineering

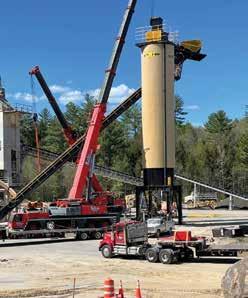
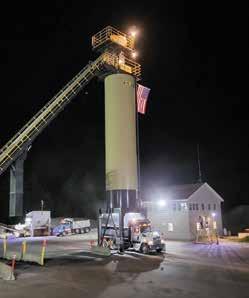
LEFT: In early spring, GMI took advantage of rainy days and scheduled any work installing the new equipment that might have otherwise shut down the plant for those days, and as the season progressed, on nights and weekends. MIDDLE: Throughout the installation process, GMI’s batch plant only had to be shut down for one day, the day the flop chute was installed. RIGHT: With the latest additions at GMI’s plant, average time for a truck in the yard went from 35 minutes to less than 10 minutes, with loadout dropping from 7 minutes to 1 minute, 5 seconds.
around them. We’ve faced enough challenges in the past that we knew our tenured staff of engineers would be able to solve these problems, with enough information from Neil and enough elbow grease.”
Around 90% of the mix GMI produces is for its own projects.
A FOLDABLE FLOP CHUTE
GMI wanted to continue to use its batch plant after adding the silo so it would have dual loadout ability. This was particularly challenging to achieve, given the drag conveyor’s width of 36 inches and the 40-inch clearance between the batch plant’s legs. GMI was also looking to limit any modifications to the original plant, including the tower legs where the drag would need to be positioned.
“We could see right away why other companies might have been scared off by the flop chute in particular,” Harman said. However, ALmix’s engineers were up to the task, landing on a flop chute design with two folding functions.
First, the flop chute folds out from between the batch plant’s legs. Then, the chute extends using pneumatic cylinders allowing the chute’s opening to expand up to the discharge gates of the batch tower to catch the mix. The flop chute can fold up and into the side of the drive-thru area, allowing trucks to load out from the batch tower when the chute is not in use.
“Being a larger batch plant, the discharge opening is quite a bit larger and you have to of course cover that whole opening,” Arruda said. “They also had to make sure the chute could take the larger drops that come out of a 6-ton batch plant and funnel it down into a 30-inch opening.”
With the photos and measurements Arruda provided, “everything ended up fitting perfectly without any modifications to the existing plant,” Arruda said.
“[Arruda] was a champ,” Harman said. “He got us every single measurement we needed and helped us every step of the way to ensure that our designs would meet GMI's needs and that everything would fit perfectly.”
Arruda has worked at GMI for 15 years. “I started as a truck driver and have grown my way through the company since then.”
A TIGHT TIMELINE
In early spring, GMI took advantage of rainy days and scheduled any work installing the new equipment that might have otherwise shut down the plant for those days, and as the season progressed, on nights and weekends.
It was also a struggle to find subcontractors to perform some of the work related to the installation of the silo. “In the end, we ended up self-performing a lot more than we had originally intended,” Arruda said. This included the concrete work, dirt work, plumbing, and erecting the silo and drag. “We had a tight timeline and didn’t want to wait for labor to become available once we got our permits in place. Doing that work ourselves gave us more control.”
Once all was said and done, the batch plant had only been shut down for one day, the day the flop chute was installed. “Other than that, the plant was running the whole time the silo and drag were being erected,” Arruda said.
“This was a fun project for us to be a part of,” Harman said. “We like to be involved in the decision making process, see the challenges they’re facing, and build custom solutions. Being able to design and build bespoke asphalt equipment and facilities is what we’ve become known for.”
As GMI continues to grow, Arruda and the rest of the leadership team is equipped to tackle whatever challenges that may present. “Our owners, Warren Colby and Mark Bourgeois, are very driven and focused on year over year growth. I don’t see that changing anytime soon. Our hope for the future is that we continue to grow.”