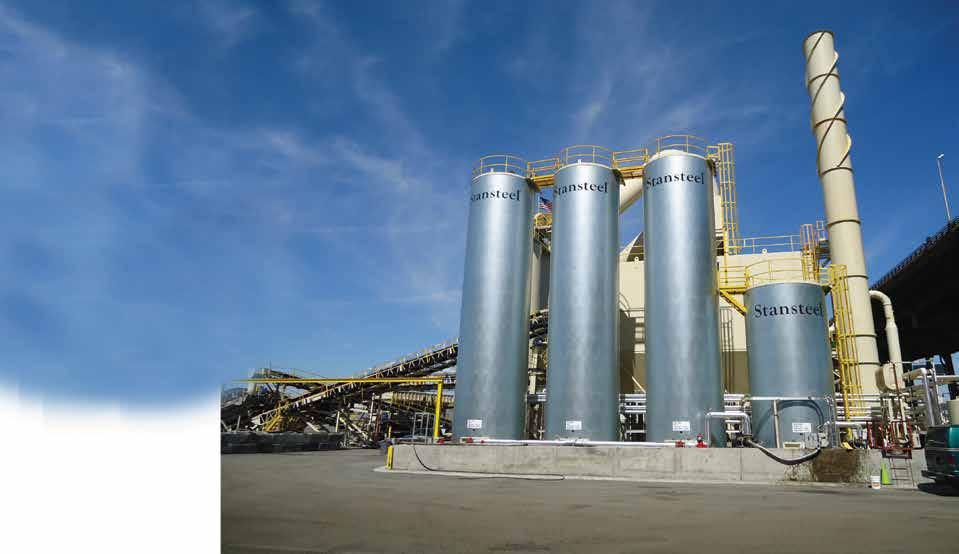
9 minute read
Military Airfield Testing Introduces December Lab Equipment Gallery
FROM DYNATEST
Dynatest A/S, headquartered in Copenhagen, Denmark, delivered a heavy vehicle simulator to the U.S. Army in September. The Danish-American company also has a department in Gainesville, Florida, and develops, manufactures, and services equipment and software for testing and evaluating pavement on roads and runways.
“When the giant C17 military aircraft lands, enormous forces hit the ground,” Dynatest CEO Jesper Rantala said. “This requires a runway built for that purpose. When it comes to U.S. defense equipment, nothing is left to chance. Everything is thoroughly tested. This also applies to the pavement on the runways that the defense has at its disposal.”
Jesper Rantala became CEO of Dynatest in 2019 when the company became part of the Danish technology group Eltronic Group.
The heavy vehicle simulator has been nicknamed Titan, which emphasizes that it is the largest of its kind. The machine is 150 feet long and weighs 125 tons, and Dynatest engineers spent two years developing, producing and delivering it. Now, it is up and running at the military base in Vicksburg, Mississippi, where the U.S. Army Development Department, U.S. Army Engineer Research and Development Center (ERDC) will be using it in their research.
Jeb Tingle is senior scientific technical manager at the U.S. Army ERDC’s Geotechnical and Structural Laboratory. Tingle said, “The heavy vehicle simulator, Titan, built in partnership with Dynatest, is a critical research tool to evaluate new materials, design methods and construction techniques to optimize transportation infrastructure facilities. It has been a long process to get us where we are today, and with this new capability added to the ERDC toolkit, we will be able to discover, develop and deliver solutions to the Warfighter and nation much more quickly.
“We are also proud to claim that the Titan has the ability to apply a dynamic impact load to simulate impact loadings from aircraft touchdown and vertical takeoff and landing aircraft,” he continued. “No other heavy vehicle simulator is capable of performing these critical tests. The Titan also has some first-of-their-kind features to help ERDC support military transportation needs.”
THE PENDULUM WHEEL
With a wheel that goes back and forth, the task of the heavy vehicle simulator is to imitate the forces of a military aircraft and thereby test the strength of the runway.
“It is not possible to determine whether a runway is worn out just by looking at the surface,” Rantala explained. “The pavement consists of several layers, all of which must be in good condition to ensure that
“THERE IS NO DOUBT THAT WE ARE ‘NERDS’ IN OUR FIELD. WE HAVE A STRONG FOCUS ON IMPROVING DETAILS AND FURTHER DEVELOPING OUR EQUIPMENT.”—JASPER RANTALA
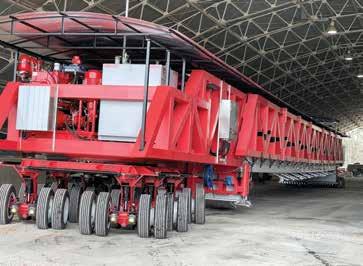
Titan weighs 125 tons, and is 150 feet long, 16 feet wide, and 17.5 feet high. All photos courtesy of Dynatest
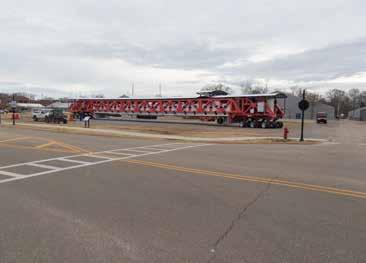
For more than 46 years, Dynatest has manufactured equipment and software to evaluate runways and roads. Over the years, the company has supplied equipment to more than 70 countries.

Titan includes a pendulum wheel to imitate the forces of a military aircraft and thereby test the strength of the runway.
the load-bearing capacity is strong enough. With the heavy vehicle simulator, you can test how 20 years of use affects the pavement in just three months. It provides an accurate and realistic picture of the condition of the runway, and in this way, you get the opportunity to develop better runways.”
CONTROLS
CONTROLS S.p.A., headquartered in Milano, Italy, presented, among other products, its new range of electromechanical compact universal testers at Bauma Oct. 24-30 in Munich. The company shared: “We’ll be unveiling our new range of multipurpose premium testers—all using the electromechanical technology and fully automatic, with an integrated advanced controller.” The manufacturer was unable to provide further information prior to press time.
For more information, visit the IPC Global website.
GSSI
GSSI has released the PaveScan® RDM 2.0, which is an asphalt density assessment tool designed to provide real-time measurements to ensure pavement life and quality. The company unveiled PaveScan RDM 2.0 for the United States and Canada at the Transportation Research Board 2020 Conference in January.
PaveScan 2.0 incorporates a new sensor design built specifically for the extremes of the asphalt paving environment, foldable deployment arms with high-visibility for work site safety and has a warm-up time of under one minute when ambient temperature is over 70° F. The manufacturer states it PaveScan RDM is ideal for uncovering problems that occur during the paving process, including poor uniformity and significant variations in density. By avoiding these problems, PaveScan RDM helps avoid such premature failures as road raveling, cracking and deterioration along joints.
This system automatically measures the dielectric value to identify anomalies in real-time. In addition, the dielectric values can be used as a means to correlate percent voids and density in new pavement. The technology enables users to obtain critical density data for quality control/quality assurance (QC/QA) of new pavements.
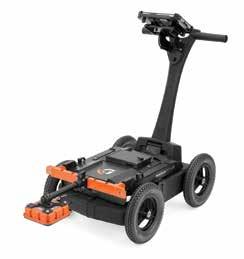
The PaveScan RDM 2.0 from GSSI measures the dielectric value to identify anomalies in real-time.
Integrating with GPS systems, PaveScan features a flexible, modular design that facilitates easy and efficient operation and data collection, according to the manufacturer. It is offered as a single sensor or a three-sensor cart-based configuration.
As of April 2019, this pavement density measurement technology is an accepted American Association of State and Highway Transportation Officials (AASHTO) specification, PP 98-19.
For more information, visit www.geophysical.com.
IDOT
A new 1-mile test track in Clinton County will help the Illinois Department of Transportation (IDOT) Bureau of Research calibrate equipment used to assess pavement condition. Under construction at press time, the track will be one of only four of its kind in the nation when it is completed in 2022.
“What makes our track unique is that it will have all pavement types—continuously reinforced concrete pavement, full-depth hotmix asphalt pavement and jointed plain concrete pavement—for certifying equipment,” said John Senger, engineer of pavement technology in the Bureau of Research. “Additionally, this track will offer various textures to challenge the capabilities of the equipment to ensure it is working properly.”
Located along the south side of U.S. 50 between Breese and Trenton, the track covers multiple disciplines in pavement testing, including ride, friction and structural assessment. It also will offer at least six different textured surfaces for skid testing correlation, as well as copper plates for ground-penetrating radar testing.
“The goal was to make the facility as multifunctional as possible to maximize the return on our investment,” Senger said. “We anticipate other states and private companies paying to use the track as well.”
IDOT regularly tests state highways for ride quality, friction availability and structural integrity. Data collection vans are used to collect various metrics every year. To ensure accuracy, each test vehicle must be certified annually. Certification—and any necessary calibration—will be completed on the test track, which will not be part of the regular roadway or be open to traffic.
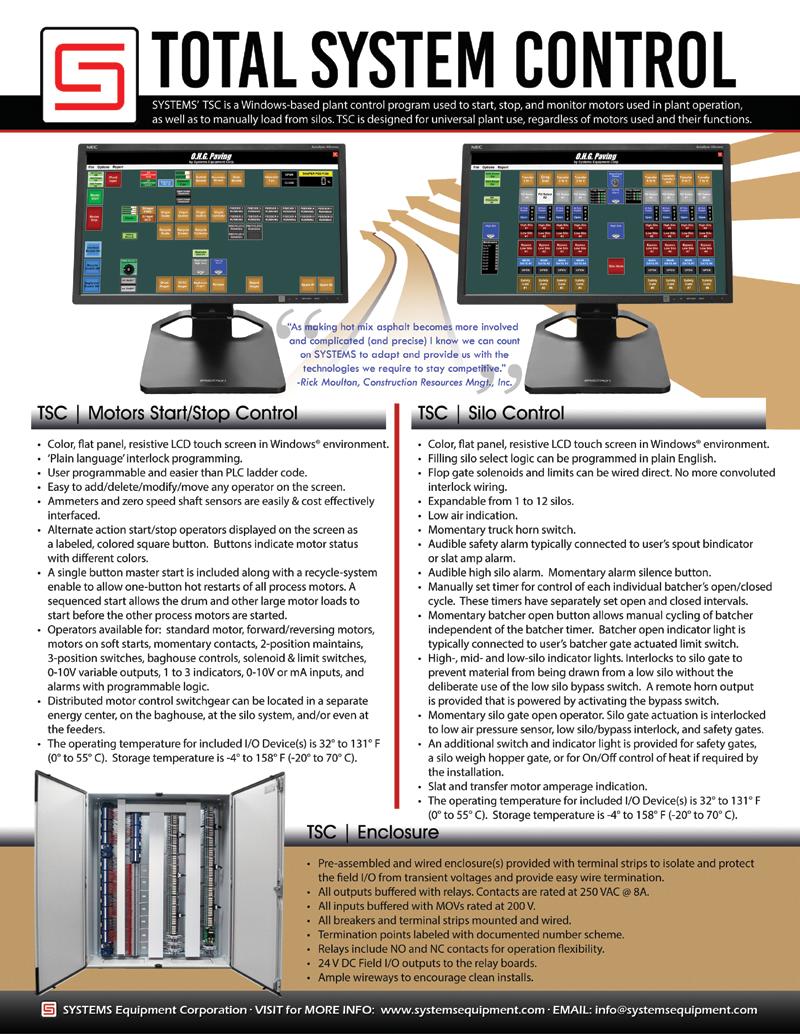
SRIPATH
Sripath Technologies, Mahwah, New Jersey, recently established an agreement with VA Asphalt Pavement Technologies, for Vince Aurilio to act as a technical advisor for Sripath Technologies in Canada. Sripath® develops, manufactures and markets a range of innovative additives used to enhance performance of bitumen and asphalt mixes. Sripath is a global company with offices, affiliates, agents and advisors in the United States, Canada, India, Australia, United Kingdom, Brazil, and South Africa.
Aurilio, owner and president of VA Asphalt Pavement Technologies, has 40 years of experience in pavement design and materials engineering for roadways and airports in both the private and public transportation sectors in Canada. His area of expertise includes: hotmix asphalt technologies, testing and design; warm-mix additives, high-RAP mixes, stone matrix asphalt mixes, mix plant production, paving quality control and assurance, in-place pavement recycling, and full depth reclamation. He is an active leader within the asphalt paving and roofing industries in Canada.
“Vince brings decades of technical and business development expertise to our team and provides us with a valuable leverage to pursue and develop new opportunities within Canada. We are thrilled to have him on our team,” said Deepak Madan, chief marketing & business development officer of Sripath.
For more information visit sripath.com.
STANSTEEL
To ensure the accuracy of your plant’s liquid asphalt metering system, hot mix producers should periodically run a calibration check. Liquid asphalt cement (AC) can be calibrated and weighed by a separate holding vessel, which is supported on multiple load cells and calibrated with a known weight. The team at Stansteel Hotmix Parts & Service®, Louisville, Kentucky, offers the Stansteel Automatic A.C. Calibration System.
With the Stansteel Automatic A.C. Calibration System, AC can be diverted from the run line on the plant directly to the calibration tank (using the proper piping and valving). The tank is loaded with a specific amount of material and then stopped with a weight registered on the electronic digitizer located in the control house. After the material is weighed, the process can be reversed and pumped back to the AC storage tank so that no waste occurs.
According to the manufacturer, this offers the benefits of: • Reduced man hours; • Accurate calibration; • Quick and easy installation to the current system; • Vertical, horizontal and portable options; and • Prompt delivery of units in stock and ready to ship.
For more information, visit: https://stansteel.com/asphalt-plantcomponents/asphalt-calibration-system/
TRANSTECH
TransTech Systems invented an innovative use of capacitance technology and has continuously developed and improved it over the course of 25 years for the use of non-nuclear technology for quality control in determining in-process asphalt density. A quarter of a century ago, TransTech Systems invented and patented the use of a well-established electrical technology for a new purpose: characterizing asphalt during construction and determining its density in a matter of seconds.
The first prototype for this technology, developed for determining the density of longitudinal joints, became the Pavement Quality Indicator, or PQI 100. Since this first commercial unit was introduced to the marketplace, TransTech has continuously made advancements to its flagship product in order to improve its accuracy, reliability, ruggedness and user-friendliness for a wide variety of mixes and conditions, according to the manufacturer.
The latest fourth generation Model 380 features items such as a GPS status display, the ability to download files to/from the PQI via USB drive, a touch screen GUI, and an advanced data management system.
The PQI is now used worldwide, and the company has distributors in over 87 countries. When combined with the Soil Density Gauge, TransTech has over 5,000 units in use every day.
For more information, visit http://transtechsys.com/products.
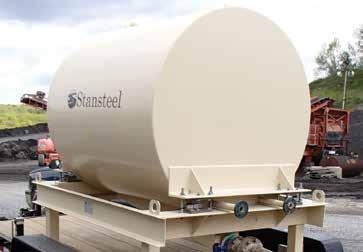
The Automatic A.C. Calibration System from Stansteel-Hotmix Parts & Service is designed to improve the plant’s accuracy, cost savings and safety. TransTech Systems offers the PQI 380, a non-nuclear pavement quality indicator.
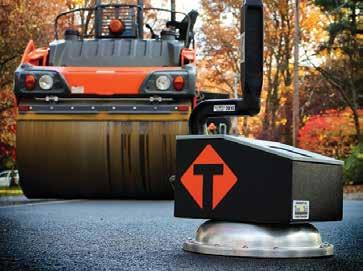
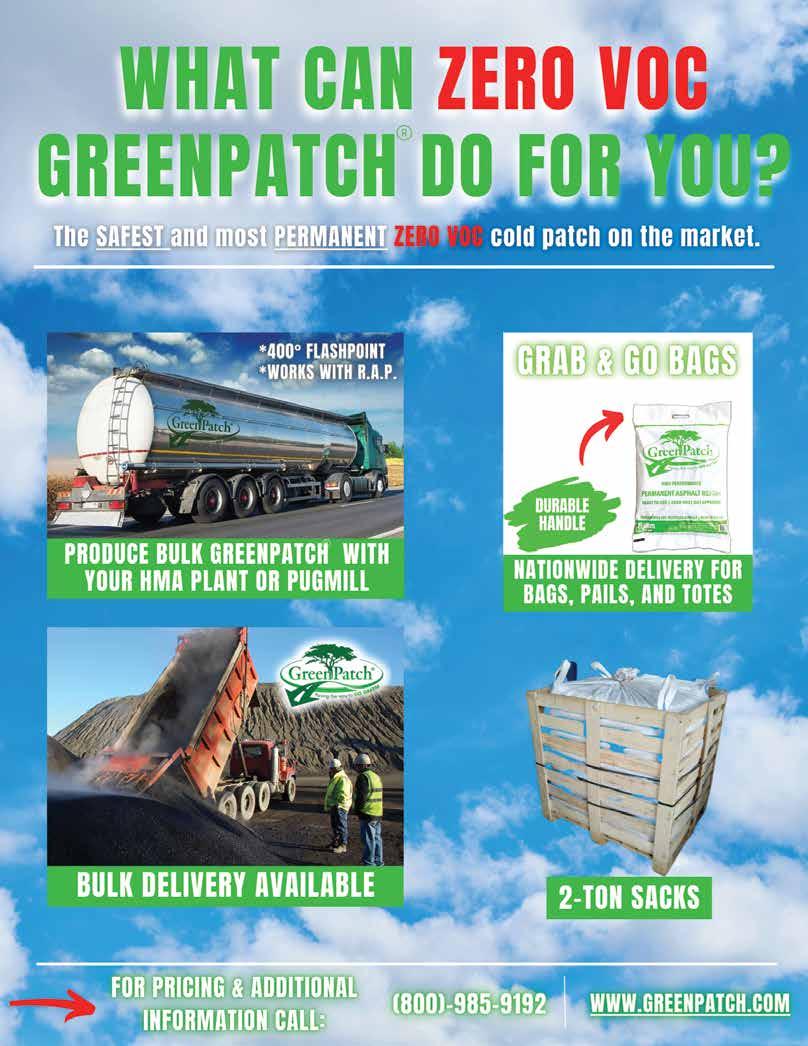