Whitepaper Building on Mycelium
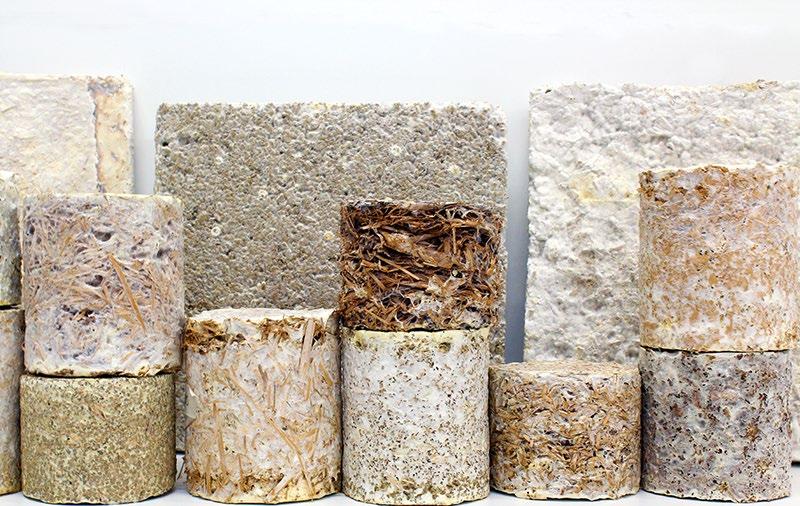
Date: December 2022
Authors: Ilse Rovers, Ilaria La Bianca, Shannon Peuling, Joost Vette - Centre of Expertise Biobased Economy
Wasabii Ng - Caradt, Jordi Pelkmans - University of Utrecht


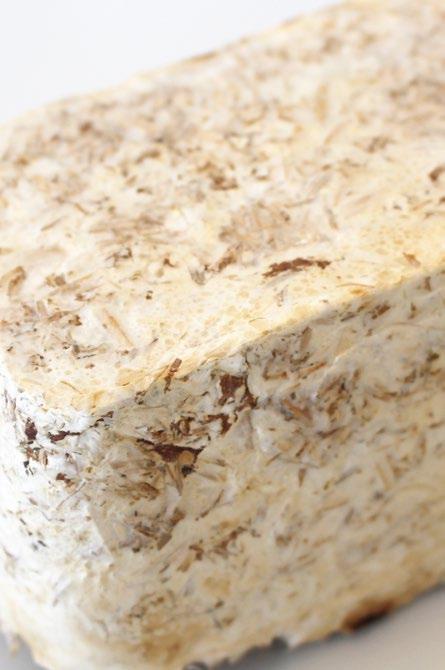

Date: December 2022
Authors: Ilse Rovers, Ilaria La Bianca, Shannon Peuling, Joost Vette - Centre of Expertise Biobased Economy
Wasabii Ng - Caradt, Jordi Pelkmans - University of Utrecht
In a rapidly changing world with raw materials depleting quickly and which therefore become more expensive, with environmental problems like climate change, pollution and waste, biobased materials are becoming more important. The building industry is more and more interested in circular (biodegradable) material alternatives. One of the promising fully biodegradable materials is mycelium biocomposite (MBC), which promise to decrease the high environmental impact of constructions.
Mycelium biocomposites are composed of substrate that is considered an agricultural residue, non-living material. The fungi that provide the mycelium are alive when producing the MBC, but after drying or baking are no longer alive. Interested how MBC’s are grown? See the movie.
In September 2021 The SIA RAAK-MKB Project Building on Mycelium, hosted by the Centre of Expertise for the Biobased Economy (CoE BBE) was finalised. In this project, research was done to rank mycelium biocomposite (MBC) for building purposes, divided in board and foam-like materials. The focus was on a combination of local available agricultural residue streams with fungi species that are originally found in Northwestern Europe. The MBCs should result in a material that has properties that are usable for indoor construction and furniture applications.
This paper shows the summary and all you need to know to introduce you to mycelium biocomposities for building purposes and to the project Building on Mycelium in particular. The links in the paper will guide you to the separate research document summaries (fact sheets and reports) after which you can dive in deeper in case you need to know more in detail. If questions still remain after that, please know that we are taking the research a step further as we speak (May 2022) into a further, market focussed, project on insulation products from MCB, called Mythic – Mytherials for thermal insulation in construction.
DIFFERENCE BETWEEN FOAM AND BOARD.
Foam-like materials are MBCs that are grown in solid state by mixing a substrate with a fungi species spawn and to naturally leave it to grow in a mould, so that you obtain a product. The derived product is generally fluffy and relatively light. Since no inner construction is used, the material was expected to be soft and relatively flexible.
Board materials started off as a foam-like materials, but are later pressed into a dense board. The pressing procedure can be done with or without a heated press, using a (partially) dried MBC.
Given that Mycelium Bio-Composites (MBC) are an innovative material which is still lacking production standards and protocols, Building on Mycelium was set up to determine the best conditions for producing MBCs for application in construction and/or furniture. The mechanical characteristics of mycelium based composites are highly dependent on the interactions of the specific fungus-substrate combination. The parameters considered to determine the optimal mycelial growth while testing the different types of MBC included temperature, moisture content, substrate and fungal species.
Five species and ten substrates were chosen to be investigated (see table below). We used a water contents of 80% (w/w) of the maximum water uptake of each substrate. More water did not show differences in growth.
1a. Rapeseed straw fibres
1b. Hemp fibres
1c. Hemp shives
1d. Reed fibres (from maintenance in natural reserves)
1e. Raw cellulose (from wastewater treatment
1f. Processed cellulose (from waste water treatments)
1g. Flax fibres
1h. SMS (spent mushroom substrate)
1i. Elephant grass
1j. Wood chips
2a. Trametes hirsuta
2b. Lenzites betulina
2c. Pleurotus ostreatus
2d. Strobilurus esculentes
2e. Ganoderma resinaceum
The MBC were produced at 30°C. After that, the fungal growth curves were assessed to conclude on the optimal fungus-substrate combinations for MBC production. The fungi which grew the fastest and most homogeneous were Ganoderma resinaceum, Trametes hirsuta, and Lenzites betulina (see top 10). The most favoured substrates were Rapeseed straw, hemp shive and fibres. Because the lower water content was used, the water use during production could be minimised. The following characteristics determined a satisfactory MBC for foam: aerial hyphae, shrinkage after drying, speed of growth, and density. The characteristics of each MBC type were tested and added to a multicriteria analysis (MCA). Board materials were assessed with an MCA considering bending test and speed of growth. This resulted in the best combinations which would be tested on mechanical and physical characteristics of both foams and boards. The top 3 for foams and for boards are shown below: > factsheet: Screening tests mycelium foams & boards
MATERIAL CHARACTERISTICS
After determining the best performing MBC’s for foams and boards, a selection of these combinations were put up to mechanical testing. Not all of the tested combinations result in the desired material properties, but the Mechanical testing determined which combination is most suitable as a material for application in construction or furniture.
Different mechanical and physical properties were used for foams and boards since they are also intended to be used for distinct purposes which each have specific requirements. Mycelium boards were assessed by testing the following:
TENSILE STRENGTH > factsheet
Determined through a tensile test, following NEN-EN 1607
BENDING STRENGTH > factsheet
Determined with a three-point bending test following ISO 178-3
FIRE BEHAVIOUR > factsheet
Samples are exposed to a small flame to indicate fire behaviour. This test is similar to ISO 11925-2:2020.
MOISTURE RESISTANCE > facsheet
The water uptake when exposed to moisture is measured.
DIMENSIONAL STABILITY > factsheet
The dimensional stability is the amount of deformation that occurs when exposed to humidity or water. The dimensional stability is measured following EN 2796
Foams were tested for the following properties:
COMPRESSIVE STRENGTH > factsheet
Determined with a compression test following NEN-EN 826
THERMAL CONDUCTIVITY > factsheet
The transient method (non-steady method) was used by following ASTM D5334-08 with a thermal needle probe (ISOMET model 2104) to measure the thermal conductivity.
SOUND ABSORPTION > factsheet
With an impedance tube the sound absorption at different sound frequencies is measured following ISO 10534-1:1996
WATER ABSORPTION/DESORPTION > factsheet
The water absorption and desorption behaviour describes how fast and how much water can be taken or released by the material when exposed to a change in humidity or submersion. Tests follows ISO 12571
MOISTURE BUFFERING VALUE > factsheet
The Moisture Buffer Value (MBV) indicates the amount of moisture uptake or release by a material when exposed to variations in relative humidity. In this project the NORDTEST method is used.
DIMENSIONAL STABILITY > factsheet
The dimensional stability si the amount of deformation that occurs when exposed to humidity or water. The dimensional stability is measured following EN 2796
The results proved the potential of MBC as foams and boards, but it also demonstrated that plenty of research can be done.. More homogenous samples are needed, while both materials’ and mechanical properties have to be improved.
MBC’s are very attractive material for bio-design: the material turns agro-industrial waste into innovative materials. The designing possibilities of the MBC’s were tested to investigate the possibilities to apply the material, like breaking and rejoining, pinning and nailing. Apart from being able to work with the material for applications in interiors, different phases are considered: the production of MBC (when the composite is still alive) and the using phase (when the composite is considered non-living). By looking at both phases, we consider the concepts of patching and mending: MBC’s can be built and assembled and afterwards also repaired and reappropriated to extend the lifetime of an application.
The healing abilities of the “alive” bio composite were tested by cutting different shapes in a MBC product, varying between a straight line and zig zag movements (see image below). The results showed better heal-ability on the more complex lines.
change 2D materials into 3D structures, of-fering an interesting alternative for further explorations like home-built products. The researched method-ologies allow for novel aesthetic expressions in repaired samples which occur with colour, texture and form variances.
This image below shows the varying aesthetics of different stages of growth in a mycelium composite. Two individual pieces of mycelium composites have grown and are embedded as a single unit. The edges of where the two pieces sit have seen no previous shadows that it was once separate pieces. The darker hues on the edges shows the aging of the mycelium composite in comparison to the edges that have seen new fungal skin growth.
The experiments with healing MBCs demonstrated that - when still alive - the fungus can fill in the material substrate to repair and reappropriate mycelium-based materials and extend their lifetime once applied.
> factsheet: Healing with mycelium
The healing abilities of mycelium also depended on the distance between the different pieces with the narrower gaps being more easily bridged.
The non-living MBC was also able to heal by using patching (with a small piece on top) or mending with living inoculum (liquid or solid). It is important to maintain favourable conditions for the material, for example by providing a sterile and moist environment during the healing process.
Stacking and folding of MBC was also part of the research, to
New materials cannot promise to be a sustainable alternative to existing materials without environmental proof. Also, the financial aspects of MBC determine whether they offer a sustainable replacement for conventional synthetic materials. However at this stage it is not possible to assess the economic and environmental cost of MBC’s, as there is insufficient data on large scale manufacturing. In this analysis the shadow costs of existing materials are defined, to display the boundaries for MBC’s to be a (more) sustainable alternative.
> factsheet: Feasibility analysis
In this analysis existing rigid insulation materials are compared based on their ‘shadow costs’. Shadow costs are the total costs of a product, considering not only the economic costs but also the costs of its environmental effects, expressed in euros. To calculate shadow costs, a Life Cycle Assessment (LCA) is required. Figure 2 shows the range of shadow costs of a square meter of material with an R-value of 3, for different insulation materials, based on the properties of the different materials and the Nibe database. The figure shows a clear distinction between biobased (straw and woodfibreboard) and non-biobased (PIR, EPS and XPS) products. At this stage it is not possible to calculate the shadow costs for MBC’s. The follow-up project MYTHIC will dive further into the total costs of MBC’s foams.
Figure 3 displays that the strength of the MBC’s measured in this project are within the range of OSB, particleboard and MDF. Figure 4 shows the shadow costs per kg material for mentioned conventional board materials. Although the shadow costs of MBC boards are unknown, in order to be a sustainable alternative for existing materials, they should be less than the values displayed in Figure 4.
> factsheet: Environmental analysis
The relative environmental impact of the mycelium materials was determined by looking at the foam MBC and boards and comparing those to currently used materials. Foam MBC were compared to XPS and EPS, and boards were compared to gypsum, MDF and particle boards. A multicriteria analysis (MCA) was performed to grade and compare the different materials. Nine criteria were chosen and divided in four categories as can be seen in Table 1. The results showed that MBC scored better than its alternatives because of the locally derived substrates and high durability in sense of waste prevention and re-used materials. Also, the financial aspects are favorable for MBCs. The study now is a quickscan, so more abundant and accurate information about the products would result in a precise result. Therefore it remains important to invest in developing and studying mycelium based composites to ensure a rapid transition towards a circular economy.
In March 2022 we learned the follow up project has been granted! Partners from Building on Mycelium agreed that research on developing an MBC insulation material is most promising. Therefore, the research in Building on Mycelium on the foam-like materials will continue in Mythic, which is an abbreviation for Mytherials for Thermal Insulation in Construction.
In this project, we want the production process to be more environmentally friendly by using less energy and water, while also meeting the legal and construction requirements for insulation materials in the building industry. In the project true pricing of biobased materials and design for indoor application get a profound place.
The research at CoE BBE could not have been done without our partners, who took the initiative to request for a joint project on MCBs in the building industry. The partners originate from different sectors: from agriculture to furniture and board developers.
www.coebbe.nl