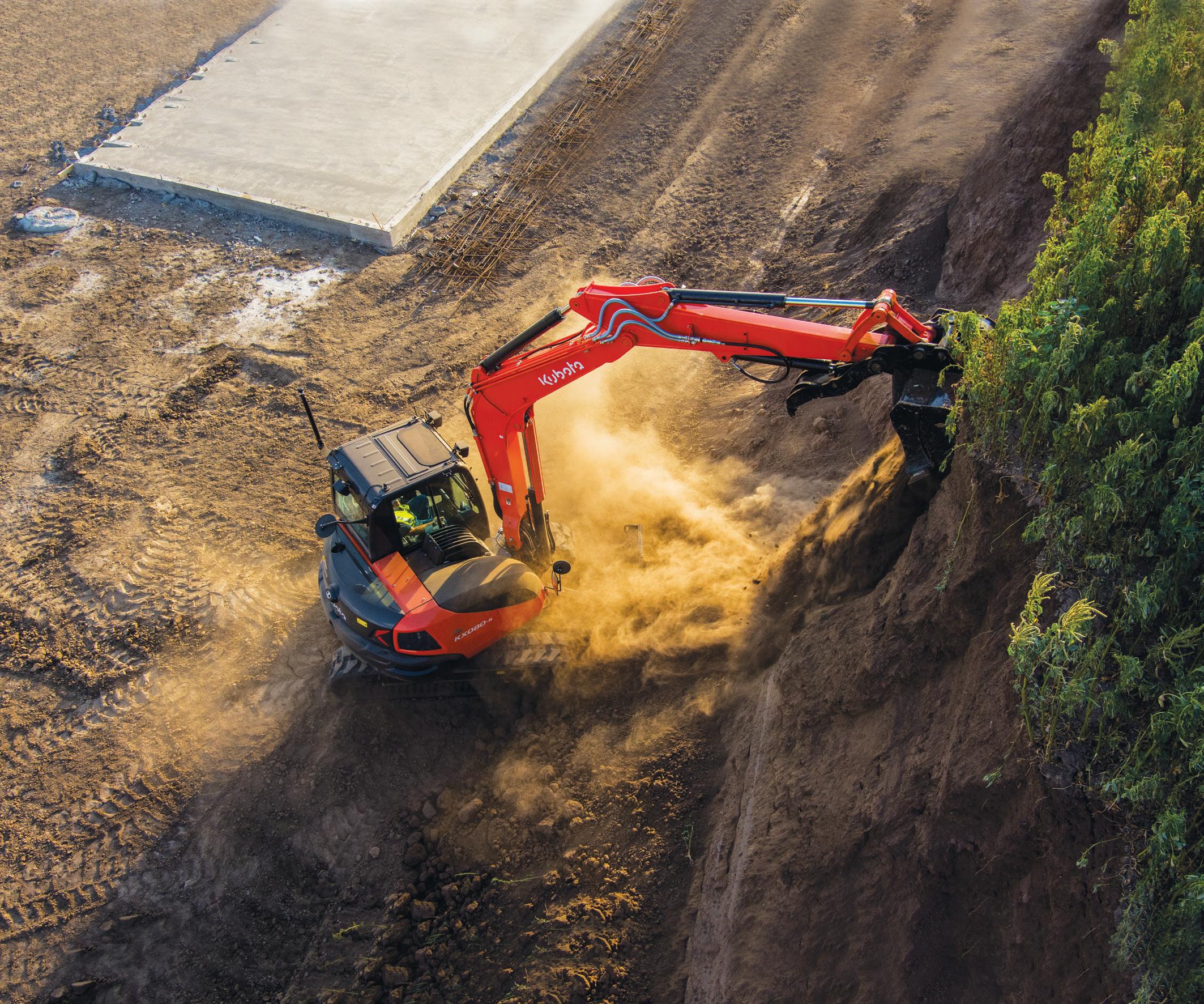
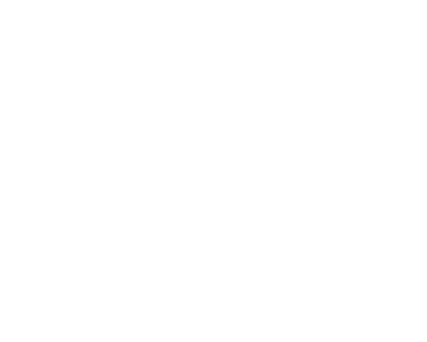
Introducing the new VHD
On the jobsite you need a truck that’s tough, safe, and smart. So, we built the new Volvo VHD to be the best-looking, most rugged vocational vehicle in the industry, packed with innovative ideas like Volvo Active Driver Assist and the revolutionary Volvo Dynamic Steering. Your toughest jobs just got easier. Learn more at volvotrucks.ca/en-ca/trucks/vhd/
All it takes for the challenges you face.
From the original compaction brand comes a full line of construction equipment designed to help you get the job done with efficiency, quality and comfort. Whether your challenge is to load, move or place material, compact soil and asphalt, or to provide light, heat, power or pumping on your job site, Wacker Neuson has the machines to get it done right. This includes zero-emission, battery-powered solutions to meet the demands of the construction environment today, as well as tomorrow.
Contact your local Wacker Neuson dealer today.
www.wackerneuson.com/ca
HEAVY EQUIPMENT GUIDE’S 2024 TOP INTRODUCTIONS
FUTURE
COVER PHOTO: KUBOTA’S KX080-5 COMPACT EXCAVATOR
Heavy Equipment Guide’s 2024 Top Introductions
Turn to page 28 .
YOU
Do you have a job site story, innovation, or industry concern that our readers should know about? We’d like to hear from you.
Contact: Editor in Chief Kaitlyn Till at ktill@baumpub.com or 604-291-9900 ext. 330
EDITOR IN CHIEF Kaitlyn Till ktill@baumpub.com 604-291-9900 ext. 330
EDITOR
Stephanie MacDonald smacdonald@baumpub.com 604-291-9900 ext. 335
SENIOR WRITER Meghan Barton mbarton@baumpub.com 604-291-9900 ext. 305
ASSOCIATE PUBLISHER Sam Esmaili sam@baumpub.com 604-291-9900 ext. 110
ADVERTISING PRODUCTION MANAGER Tina Anderson tanderson@baumpub.com 604-291-9900 ext. 222
DESIGN & PRODUCTION
Morena Zanotto morena@baumpub.com 604-291-9900 ext. 325
PRESIDENT/PUBLISHER
Ken Singer ksinger@baumpub.com 604-291-9900 ext. 226
VICE PRESIDENT/CONTROLLER Melvin Date Chong mdatechong@baumpub.com
FOUNDER
Engelbert J. Baum
Published by: Baum Publications Ltd.
124 - 2323 Boundary Road Vancouver, BC, Canada V5M 4V8
Tel: 604-291-9900
Toll-free: 1-888-286-3630
Fax: 604-291-1906
www.baumpub.com www.heavyequipmentguide.ca @HeavyEquipGuide
FOR ALL CIRCULATION INQUIRIES
Toll-free: 1-866-764-0227 email: heg@mysubscription.ca
Subscription: To subscribe, renew your subscription, or change your address or other information, go to: http://mysubscription.ca/heg/
Heavy Equipment Guide serves the Canadian engineered construction industry including: roadbuilding and maintenance; highways, bridges, tunnels; grading and excavating; earthmoving; crushing; trucking and hauling; underground utilities; trenching; concrete paving; asphalt paving; demolition; aggregates production; fleet maintenance; and asset security and management. The magazine is distributed to key industry personnel involved in these sectors.
Subscription Price: In Canada, CDN $91.00; Outside Canada, US$149. Heavy Equipment Guide is published eight times a year in January/ February, March, April, May/June, July/August, September, October, and November/December.
Heavy Equipment Guide accepts no responsibility or liability for reported claims made by manufacturers and/or distributors for products or services; the views and opinions expressed are those of the authors and not necessarily those of Baum Publications Ltd.
Copyright 2024, Baum Publications Ltd. No portion of this publication may be reproduced without permission of the publishers.
We acknowledge the financial support of the Government of Canada.
Printed on paper made of FSC®-certified and other controlled material. ISSN 1715-7013.
PUBLICATIONS MAIL AGREEMENT NO. 40069270
Return undeliverable Canadian addresses to: Circulation Dept., 124-2323 Boundary Road, Vancouver, BC V5M 4V8 email: heg@mysubscription.ca Toll-free: 1-866-764-0227
In the November/December issue of Heavy Equipment Guide we always like to reflect back on the year that was in the industry.
What were the hot topics of conversation and the broader trends in equipment and technology, and what are the pain points that these solutions address? We’ve done that again this year, and you can discover our 2024 Top Introductions in this issue. But throughout this issue we also take a broader look at the construction industry and its rapid evolution — and if you think the recent rate of change has been dizzying, you’ve seen nothing yet.
The construction industry is on the cusp of its most transformative era. Digitalization, autonomy, and decarbonization will change how you manage your job site, complete projects, and even who can work for you.
We revisit an inspiring vision presented by HD Hyundai at CES 2024, and take a look at a few exciting concept machines revealed this year, examining how technology can change construction for the better.
We recently attended Volvo Days 2024 in North America and BOMAG Innovation Days in Germany. At these events the OEMs presented cutting edge equipment for earthmoving and roadbuilding applications. Of course, we have heard plenty of understandable technology-related concerns from contractors, and we hope that our event reports will provide some insight into the value proposition that these OEMs have to offer, both in their latest hardware, and in their technology tools.
Finally, we sat down with senior leadership from Liebherr–Canada earlier this year for a far-reaching conversation. Liebherr–Canada celebrated its 50th anniversary in 2024 and is excited to look ahead to the next few decades. Leadership has already observed that the speed of equipment and technology development, from proof of concept to field validation, particu-
If you think the recent rate of change has been dizzying, you’ve seen nothing yet.
larly in the transition to zero emissions, is moving at the fastest pace the construction industry has ever seen. We think you’ll enjoy this conversation and the practical insights from a unique player in the Canadian market.
On behalf of the Heavy Equipment Guide team, thank you for spending another year with us, and we look forward to bringing you the latest equipment, technology, and perhaps more visions of the future in 2025.
Have a happy and safe holiday season.
Kaitlyn Till Editor In Chief
ktill@baumpub.com heavyequipmentguide.ca
Sized right for tight spaces. Steel-built for heavy-duty work. With groundbreaking power in a nimble package, Takeuchi Compact Excavators are proof positive that it’s not the size of the machine in the work, it’s the size of the work in the machine.
EXTENSIVE EXCAVATOR LINEUP: INCLUDES CONVENTIONAL TAIL SWING, SHORT TAIL SWING, SIDE-TO-SIDE (STS) OFFSET BOOM, HYBRID AND FULLY ELECTRIC MODELS.
Rokbak has partnered with Terapro Construction to distribute trucks across Eastern Canada. With 18 branches throughout the region, Terapro will cover the entire province of Quebec and parts of Ontario, focusing on selling and distributing Rokbak articulated haulers to construction contractors and general construction sites. Terapro aims to offer both Rokbak RA30 and RA40 ADTs by early 2025.
Terapro sees the addition of Rokbak haulers as a complementary expansion of its product line. It will enable the dealer to offer a complete package to its customers, having not had an articulated hauler in its portfolio before. North America is Rokbak’s largest market, both geographically and financially, and with this partnership, Rokbak looks to work with dealers who are perfectly placed to understand the needs of customers.
Terapro has already showed the RA30 at two key construction and forestry expos in Quebec — Expo Pelle and Demo International.
To help contractors in Eastern Canada, Terapro says it is positioning itself as more than a supplier. The company dedicated a team of experts to advise on how to maximize operational profitability of the Rokbak trucks. Additionally, Terapro offers customized, high-quality services designed to meet the specific needs of each buyer.
Rokbak provided comprehensive sales and technical training for the Terapro team, with ongoing support facilitated by a Rokbak service manager based in Ottawa, ensuring local expertise and availability.
Having grown through business acquisitions globally for 90 years, Nors Group is now uniting its portfolio of brands, including Canada’s Strongco and Great West Equipment, under one brand: Nors.
Nors will now cover more than 80 percent of the Canadian market, where it has a total of 37 branches and more than 750 employees. At a launch event held in Porto, Portugal, and broadcast to around 3,000 employees, Nors unveiled its new brand strategy.
“Nors’ brand embodies what we have been for over 90 years and our even greater ambition to be recognized for our exceptional quality service and teams, boosting future growth in all the geographies in which we are present,” said Tomás Jervell, Nors Group’s CEO. “This brand will be stronger, closer, and more sustainable, prepared for the future and for global transformations.”
This brand will replace the previous 17 brands of all Nors’ companies in seven countries on three different continents. They will be organized into five segments: Trucks and Buses, Construction Equipment, Agro, Aftermarket, and Ventures.
“The Nors brand has existed since 2013 in an institutional dimension. As of today, the launch of Nors in its commercial aspect is part of a process of evolution and growth, where international expansion stands out,” said Jervell.
Nors Group acquired Volvo dealer Great West Equipment in early 2024 and Strongco in 2020.
John Deere has expanded forestry equipment production at its John Deere Specialty Products facility located in Langley, British Columbia. Manufacturing of the 900-Series models will start later this year, followed by the 800-Series models in early spring 2025.
According to the company, the John Deere Specialty Products facility will serve as the centre of excellence for manufacturing purpose-built tracked forestry equipment. This increase in production aims to enhance services provided by John Deere to both North American and global forestry companies and strategically position tracked harvesters and feller bunchers in a key forestry region.
“All of us at John Deere Specialty Products are excited about this opportunity to grow at our location and provide customers with even more confidence through our commitment to the highest quality and durable products,” said Alan Tracey, factory manager at John Deere Langley. “We have a long tenure of forestry design and manufacturing experience, and we are passionate about working with our customers.”
The John Deere Specialty Products production facility currently employs 100 employees and produces tracked processors, road builders, and tracked log loaders for the global market. The business has been operating since 1998.
The most exciting and innovative new products and technology introduced in 2024.
Turn to page 28.
The Hitachi Construction Machinery Challenge 2024 solicited ideas from start-ups that fit within three themes;
“Construction Planning”, “Revolutionize Equipment: Information, Interface & Autonomy”, and “Transform Fleet Management”. The winners of the inaugural contest are Sodex Innovations, Teleo, and Veristart Technologies, who will join the Hitachi Construction Machinery exhibition area at bauma
2025 and explore the possibility of collaboration with the Hitachi Construction Machinery Group.
“Hitachi Construction Machinery is traditionally known as a company that provides mechanical items, but we are pivoting to also being a true technological solutions provider. For us, that means collaborating with innovative start-ups,” said Masahiro Yamada, Hitachi Construction Machinery vice president of the New Business Creation Unit. “This event is very important to us because it will show the world that Hitachi Construction Machinery is more than just excavators, wheel loaders, and mining trucks. We are also a technology company that listens to their customers’ needs and provides holistic solutions.”
Sodex Innovations won under the “Construction Planning” theme. Its product equips machines with a system that enables capturing terrain in real time. This allows job sites to keep track of their progress and report on it without the need to pause the job site for a survey. The solution creates digital twins of construction sites by equipping machines with laser scanners and cameras, giving construction machinery digital eyes. With Sodex Innovations’ winning solution, any machine operator can become a surveyor while getting the job done.
Teleo won under the “Revolutionize Equipment: Information, Interface & Autonomy” theme. Its supervised autonomous machine is a brand-agnostic solution that allows operators to operate multiple machines simultaneously from an office-like environment.
Veristart Technologies won under the “Transform Fleet Management” theme. Its solution is targeted at preventing
Frontline Machinery brings you a state-of-the-art custom crushing and screening unit meticulously designed to meet your unique needs. With the Astec K400 Cone Crusher at its core and an in-and-out chassis, this machine redefines efficiency and adaptability in the industry.
machinery theft by providing fleet managers with better control of their machines. The solution consists of a cloud application, a mobile application, and a hardware device that work together to give fleet managers precise control over who can operate their machines. Machine operators will receive an electronic key on their smartphone that allows them to start the vehicle.
John Deere product training experts are helping new operators take their skills to the next level with new in-person training courses. Through the company’s three-day training courses, contractors and equipment operators get hands-on operation time and focused training on John Deere earthmoving equipment.
“Our customers face daily challenges of operator shortages and attrition,” said Matt Nolte, manager, sales and customer training for John Deere. “When they have an opportunity to train new operators, they’re looking for not only high satisfaction from their new operators being trained, but also the right level of training to get them working efficiently, fast.”
The three-day training courses, which take place in Sacaton, Arizona, will teach operators how to conduct proper and thorough machine walkarounds, perform basic operations, and operate
all key equipment features on John Deere machines. In addition, each attendee will spend approximately half a day exploring various machine families, helping to advance knowledge and skills on pertinent job site equipment. This course is intended for new equipment operators with less than one year of experience.
The first in-person training session took place the first week of December 2024, and registration is open for the next two sessions, happening from January 14 to 16 and February 25 to 27, 2025. John Deere plans to roll out additional customer training sessions at various levels of skill at a later time, helping to enhance the performance of operators at all stages of their careers. Contractors looking for customized training can also request tailored solutions to match their needs, with Custom Training Sessions available by inquiry.
PRINOTH has opened its newly expanded production facility in Granby, Quebec. This $25 million investment, which nearly doubled the facility’s size, marks a major milestone in the commitment to innovation, growth, and sustainability for the future. A significant portion of the new space has been dedicated to custom project development, highlighting PRINOTH’s efforts to create tailored solutions for clients in a variety of industries.
Klaus Tonhäuser, president of the PRINOTH Group, emphasized the importance of the expansion to PRINOTH’s future plans: “Our investment in the Granby plant reinforces our unwavering commitment to investing in the future — not only for our company, but for our employees and the region. The relentless efforts and dedication of our employees have been the driving force behind this achievement, and we are proud to further establish Granby as a key hub for custom project development and innovation in the crawler carrier market.”
“PRINOTH’s many accomplishments would not have been possible without the hard work of its employees. Their continued commitment is the foundation upon which we build our success,” said Anton Seeber, president of the HTI group which owns PRINOTH.
The Granby facility’s expanded production capacity will allow the company to continue serving its customers worldwide, driving further innovation. With this expansion, the company aims to be better prepared to meet growing demand while also fostering a culture of continuous improvement and sustainability.
The next edition of the United Kingdom’s largest quarrying, construction, and recycling exhibition will take place from June 23 to 25, 2026, at Hillhead Quarry, Buxton. The 2024 event attracted more than 19,500 visitors and featured 600 exhibitors.
Takeuchi’s Moore employees signed the interior engine cover of the 10,000th CTL, and the milestone machine, a TL12R2 model, was shipped to Takeuchi dealer, Bennet Equipment & Supply. The Moore facility team is manufacturing all five of Takeuchi’s current compact track loader models. Since production started in September 2022, the team has increased the number of units produced each month.
The 10,000th compact track loader has rolled off the assembly line at Takeuchi’s Moore, South Carolina, production facility, just two years after the plant opened. It was Takeuchi’s first production facility outside Asia and represented a whole new venture for the company.
LIEBHERR–CANADA CELEBRATES 50 YEARS WITH A CANADA-THEMED EXCAVATOR WRAP.
BY KEN SINGER, PUBLISHER
Liebherr–Canada celebrating its 50th year is made doubly sweet by coinciding with the Liebherr Group’s 75-year anniversary. Earlier in 2024, I had the opportunity to sit down with the Liebherr–Canada leadership team: outgoing managing director, Tim Petersen; CFO Paul Robson; and new managing director, Tom Juric. In a far-ranging conversation, we reflected on the origins of Liebherr–Canada, current industry trends, and how the company is set to tackle its next 50 years.
This conversation has been edited and condensed for clarity.
KEN SINGER Congratulations on 50 years. Can you tell me a little about how things started at Liebherr–Canada?
TIM PETERSEN When Liebherr–Canada was founded in 1973, we were one of the first mixed sales companies in the Liebherr Group formed under the guidance of Mr. Willi Liebherr. The model brings all the different divisions togeth-
er, acting as one, finding the best solution for our customers, offering the proper product, and looking after that product with excellent service and support. That was the whole idea behind Liebherr–Canada and is the vision of the Liebherr family. Customer Service has always been the differentiator here in Canada, which we’ve always focused upon heavily with our customers.
PAUL ROBSON Canada is a unique marketplace. It always has had incredible opportunities, and that’s what Liebherr embraced early on. We have an extensive product portfolio which fit this marketplace, and that’s what Liebherr excels at, providing solutions to our customers. Tim has really lived that journey of how we brought products into the market. In the early days we were less than 50 people, primarily concentrated on excavators, and we didn’t have mobile cranes, we didn’t have foundation equipment. They’ve all come in at a series of timelines and that’s what working with customers allows us to build on. The more depth we have in our products, the greater the experience we have with our customers.
TP The key item for us at Liebherr–Canada is the service we bring and the direct from factory to customer model, without all the middlemen. That’s always been a key selling point for us. We’re representing the factory, we’re representing the owners; we’re direct to the customer, and it’s always an advantage when you take out the middleman.
PR For an OEM, that’s unique in Canada. There are no other direct OEMs. We bought the steel, we cut the steel, we designed it, we built it. For technicians, or for our customers, that’s a straight line back to the R&D, design, and production and the technology that Liebherr brings to the marketplace. That is a unique factor that we have really capitalized on to create enduring partnerships.
TP Our strength, from the beginning right till now, and it will continue to be so, has always been our staff and our people, the commitment from our people to the customer, and the commitment from the Liebherr family. That differentiates us from some of our competitors, and that’s been noticed by our customers. It’s always different when you deal with Liebherr. There’s a very strong commitment from our employees to the customer and to the company, that’s always been our strength in the past, and that will continue to be so.
TOM JURIC If you look at our hyper successful product categories, the reason they’re successful is because we built them with the industry, with the customer. We had some foundational customers that helped us to develop this product portfolio. The culture around building, not just a great asset from an engineering standpoint, but something that can be used, serviced, and utilized in the marketplace, fundamentally, comes
PR Close customer tie-ins have helped define how we bring products to market. For example, our rough-terrain crane models were specifically designed and inbuilt for this marketplace. We can really spot an opportunity and can very successfully develop the technology to deliver a solution for the right outcome. One of Liebherr’s strengths is this ability to listen to its market, listen to its customers, and then provide the correct solutions.
TJ We’re evolving from just listening to actively seeking customer input. We will go out, actively seek the input from the industry, from our customers, and even people that aren’t necessarily our customers today. We seek their opinion and we seek their input to improve our products and services — call it the Liebherr experience.
KS Technology, digitalization, and sustainability have been significant drivers in the construction industry across all product categories. How is Liebherr responding?
TJ If we look at the green space, the transition toward zero emission, the speed at which the industry has gone from conversation to proof of concept, and now field validation, it has been nothing like we’ve ever seen in a construction technology space. It has been so rapid. When we look at what Liebherr’s fundamental principles are on most of its equipment, we realize there’s no silver bullet to displace the diesel. Diesel has been an exceptionally critical fuel for the industry, and we’ve optimized it to within an inch of its life. To offset that with a direct substitute is proving to be difficult.
So what Liebherr has done, particularly in the mining space,
electricity. Hydrogen is another area of interest; it’s transportable and we can generate it cleanly. Fuel cells are still in their infancy — that’s probably the third option.
We’ve been electrifying large excavators for nearly 50 years with millions of operating hours. Electrification via tether cable is nothing new to us. We are investing heavily into the battery/ electric area. The investment, not just by our group, but as an industry, in looking for the next breakthrough in battery technology is astronomical.
People want a solution, but they want us to come up with it. But we are only one part of the equation. There’s a whole infrastructure that needs to be considered prior to whatever form of energy can be delivered into our vehicles. That’s stirred the concept of modularity because as much as people do want to electrify, the reality of the situation is we don’t have enough green capacity on the grid nor the infrastructure.
In mining, Liebherr has embarked upon the modularity concept. The products that we make today have to be capable of accepting the green technologies of tomorrow. So what we say to our customers is, if you have a requirement to decarbonize at some point in the future, what you can do is invest in our product, service, and technology today, conventionally with diesel power, and then in the future, when the infrastructure of alternative energy generation is ready, we can convert with you. That requires modularity and being an energy agnostic or a power agnostic OEM. Diesel will still factor in some way, but obviously the powertrains of the future will be some mixture of battery-, electric-, and hydrogen-based. This is one of the biggest technical engineering challenges that we’ve ever had.
KS The earthmoving division has been a big focus the last few years. Where do you see the opportunities in the years ahead?
TP We do earthmoving with good customers that trust us and work with us for the long term. We’ve never been the type of company to go after huge highway projects and try to sell a hundred pieces a year. We’re not trying to have the largest market share of earthmoving; we will continue to bring high-technology products, whether that be with a hydrostatic drive or all the different systems and the ruggedness and the uniqueness, for instance in our telehandlers, which offer far more flexibility and safety features on the job site.
When we talk about electrification, we’re starting with our smaller wheel loaders, and it’s only a matter of time until our telehandlers and other products follow suit as well. That’s where the market’s going; by 2035 we’re going to be astounded by what can be electrified.
PR As we brought new products in, like telehandlers and the TA230 ADT, we have more opportunities to work with new customers who are looking for a more rounded portfolio of equipment. The products are constantly being designed based on customer feedback and this drives the next model, features, or improvements.
TP Liebherr’s been an innovator throughout my whole career, whether it’s our hydrostatic drives or engines that burn much less fuel than our competitors’, it’s really exciting to watch the company keep evolving into this sustainable, hightech producer of equipment.
KS How are you approaching the shortage of skilled operators and technicians in the industry?
TJ Yes, there is a shortage of high-quality, experienced, and motivated operators and technicians across the country; it’s an extreme situation. While we believe that technology will alleviate some of those pressures, we’re still probably a generation away from automation being a viable alternative to people. The industry is not training enough people, we are conscious of the part we play in attracting people to the indus try. What we do is very complex, very sophisticated, and it can be a well-paying career.
Technology absolutely has to work for us, not against us. So, when talking about things like electrification, when we’re talking about these alternate fuels and the digitalization of the industry, as Paul has mentioned, we have to ensure that labour touchpoints are minimized. Because if we go making something that we cannot support, we may as well not start. Liebherr has invested a great deal of time and resources into how we make our equipment and our services user friendly and as light as possible from a labour ratio to ensure that we are not creating things that people can’t service.
We have an extremely unique business here, when you talk to our people, they want to work for us, they are genuinely excited, to be part of our group, part of our organization, and we’re the brand. There’s no doubt that one of the biggest business inhibitors that the industry is facing, is the lack of technically focused people in the next 10 years. That is our biggest risk.
PR We are practically doubling in size and revenue every five years, and that requires people, more products require more technical staff in the field, and we are working very hard to model out that career path. Not a job, a career. A highly valued, highly technical role. It’s on everybody in our industry to promote and to really demonstrate value to the young emerging workforce and say that this is a whole career pathway that opens up for them. We’re moving from a very mechanically focused/hydraulic focus into electronics/ diagnostics focus, which I think will make that a much more attractive career path for people.
TP One of the key aspects of Liebherr, in all my time with the company, is that it has maintained its core values. Everything we do now and into the future is about our customers and about giving them the highest quality at the right price. Liebherr will never change. The third generation of the family is fully committed to the core values, and I think the fourth generation will be the same way. They’re thinking long-term into the future, like Tom said, and that’s the exciting part of the company. It really is.
KS What is the most exciting opportunity in the years ahead?
TP I think the biggest opportunity in Canada for Liebherr over the next five years is mining, without a question. It’s super exciting.
PR The earthmoving division is a high-growth opportunity for us, which we’ve been sustaining year on year; the product portfolio is now more complete. But we should not neglect the highly successful products, such as crane technology, which we have to defend in our market. From a pure growth perspective, where we see huge potential is definitely the mining field.
TJ What excites me is that we are no longer a curiosity and people recognize us as more than just exceptional cranes. As Paul said, we are very, very strong in our cranes, and we must defend our cranes at all costs. But the beautiful thing is that now, as we’ve said, earthmoving is in a very similar position. As Tim said previously, we’ll never be like our competitors, but we do have a suite of customers and a suite of products that we will absolutely defend. What really excites me is the fact that we have matured to a genuine contender but still maintain the ethos and the entrepreneurialism that the Liebherr Group represents. The next 50 years is all about customer service: it’s at our core, it’s foundational. It gets us out of bed in the morning and tucks us in at night. HEG
Tim Petersen, former managing director, Liebherr–Canada
Tim started at Liebherr–Canada in 1986 with the earthmoving division. During his time with Liebherr–Canada, notable achievements include starting the Crane division in 1995, followed by the Foundations, Mining, and Maritime divisions. Tim took over as managing director in 2015.
Paul Robson, CFO, Liebherr–Canada
Paul has been with Liebherr–Canada for 12 years, previously working with Liebherr Group for 10 years in the UK and Ireland. Working from a corporate finance background, he has helped grow the company bigger, broader, and more appealing across the Canadian landscape.
Tom Juric, managing director, Liebherr–Canada
Tom has been with the Liebherr Group for 14 years. Prior to joining Liebherr–Canada he was the executive general manager for sales and marketing for Liebherr–Australia. In 2020 he had the opportunity to head the mining division in Canada. Earlier this year he became managing director, succeeding Tim Petersen.
When you’ve got a big snowstorm coming in and you’re just not sure if your existing snow removal attachments can handle it, you need a Blue Diamond solution. That’s where our all-new heavyduty snow blower comes in.
Ideal for skid-steer loaders, the new snow blower extends our full line of snow removal attachments and provides excellent performance under both wet and dry snow conditions.
HEAVY-DUTY SNOW BLOWER full line of snow removal attachments and provides excellent
Adding the new Blue Diamond heavy-duty snow blower to your attachment line-up, means you’ll be ready for anything. When the snow falls, Blue Diamond has your back. Choose Blue Diamond –where all we do is elevate everything you do.
BY KAITLYN TILL, EDITOR IN CHIEF & KEN SINGER, PUBLISHER
The construction industry faces many pressing challenges today: labour, tight timelines, productivity gaps, and decarbonization are a few. We regularly discuss OEMs’ solutions to alleviate these challenges, but construction has long been an inherently conservative industry. As a contractor, you need to know how technology and equipment solutions will help you meet your targets, retain your workers, and make you money today, next month, and next year. This is vital information for your business, but sometimes it’s also essential — and fun — to look at construction with a far broader time horizon.
In 2024, we were treated to a vision for the future of construction that not only addresses your pain points today, but incorporates a creative imagining of what construction can look like 10, 20, or 50 years from now. At CES 2024, HD Hyundai’s keynote address and booth demonstration delivered a vision of construction that is clean and efficient, incorporating emissions-free power, digitalization, and automation. And Hyundai isn’t the only OEM that is experimenting with a vision for the future of construction: In 2024 we saw more innovative, outside-the-box equipment concepts and continued advancement, and upsizing, of hydrogen-powered construction equipment development. As we move into 2025, lets explore what your job site could look like a little farther down the line.
HD Hyundai has a bold vision it calls a “living blueprint of what the future construction site will look like.”
Offering a sleek and inspiring glimpse of the future, HD Hyundai displayed two autonomous machines at CES 2024. A cab-less, autonomous electric excavator concept which, aside from being a remarkable design, featured an array of advanced technologies, including a safety system that, with radar and a smart AAVM (all-around view monitoring) 360 degree camera system, detects nearby obstacles and minimizes the potential for accidents while moving autonomously. The excavator concept is designed to be a versatile, modular robotic machine capable of performing various tasks in challenging environments. It features an interchangeable upper body and undercarriage modules, including
track systems and battery packs.
The machine is equipped with four independent adaptive track systems that enable it to climb steep hills and navigate difficult terrains, reducing the need for human operators in potentially hazardous sites. Key features include an operation status and working load indicator, an offset boom swing, and extended arm systems for flexible movement and long reach tasks.
Additionally, it has a rotator capable of accommodating various attachments, including an integrated tiltrotator, boom-integrated perception sensors for improved navigation and operation, and a combined auto-balancing counterweight.
Also on display was the DEVELON X2 dozer concept. Teleoperation, as well as an application concept for entirely autonomous machines, was presented as a solution to future skilled labour shortages.
We had the opportunity to talk with Young-cheul Cho, president and CEO of HD Hyundai Xite Solutions and Hyundai Infracore, who laid out HD Hyundai’s goal to become a leading global player in construction innovation. “Xite Transformation is HD Hyundai’s vision for future construction sites that aims to solve pressing industry challenges designed to improve safety on the job site, the environment, and job site productivity,” said Cho.
All areas of the job site need to be integrated with technology, and HD Hyundai is looking to combine multiple currently separate technologies together to unify both equipment and the entire job site.
“We are already connecting machine monitoring and machine control systems,” said Cho.
HD Hyundai plans on expanding these features across most of its product lines. The integration of technology is driving the greatest innovation at a time when, according to Cho, the construction industries are “facing difficulties, ranging from a lack of skilled operators, site safety, and an overall decrease in productivity.”
Bobcat has openly worked on some very cool futuristic construction equipment concepts for a couple of years and in 2024 advanced its RogueX platform with the RogueX2, an all-electric autonomous concept loader that uses some of the technology already commercially available on Bobcat’s unique-to-the-industry all-electric compact track loader.
Bobcat has pushed the possibilities of autonomy and electrification on the visually striking, futuristic cab-less tracked RogueX and wheeled RogueX2, which feature a lithium-ion battery, electric drive system, and electrically actuated lift and tilt kinematics with no hydraulics — the same kinematics already used on the electric T7X compact track loader.
Joel Honeyman, Doosan Bobcat vice president of global innovation, calls the RogueX platform a proving ground for Doosan Bobcat to look at designs and potential technology that could be applied to future work vehicles.
Taking the cab off a traditional loader allows for lift geometry experimentation that wouldn’t be possible on a machine with a cab. On the RogueX and RogueX2, that meant combining vertical-path, radial-path, and variable-path lift capabilities in one machine.
As Honeyman noted in conversation at CES, Bobcat’s legacy as the originator of the skid-steer loader makes this reimagining a particularly suitable project for the company.
“Our roots are in the skid steer. We invented the skid steer, so if we’re going to do a really cool future vehicle, let’s make it a skid steer.”
Kubota showed a cabless tractor vehicle for agriculture at CES
ment of another concept for a robotic all-terrain vehicle, KATR. Kubota North America has earned the Best of Innovation title in the Industrial Equipment and Machinery category ahead of the 2025 show.
This four-wheeled multi-functional robot is designed with advanced stability control that adjusts the robot’s four legs to maintain a level cargo deck, keeping the platform stable on uneven and sloped terrain in off-road construction and agriculture applications.
According to Kubota, a proprietary algorithm processes sensor data in real-time, then commands the robot’s four hydraulically actuated legs to extend or retract to maintain stability. Four independent motors provide robust all-terrain capability to navigate challenging environments.
KATR can be powered by either an electric or combustion engine, load capacity is 284 pounds (129 kilograms), and it can be controlled either remotely or via an on-board controller.
next two years.
To meet decarbonization goals, the wheel loader is powered by green hydrogen supplied by Energie Steiermark. Green hydrogen is produced without the use of fossil fuels via electrolysis, which uses wind or solar energy to break down water molecules into oxygen and hydrogen.
Hydrogen combustion engine development has been ongoing despite the significant hurdles to widespread viability at present. While access to hydrogen fuel is limited, engine OEMs, including JCB and Liebherr, have invested heavily in preparing for the day that robust fuel distribution infrastructure makes this technology widely viable.
In 2024, Liebherr advanced the size of hydrogen-powered earthmoving equipment with its demonstration of the world’s first hydrogen-powered large wheel loader, a 26-tonne L 566 H. Liebherr partnered with STRABAG to test the wheel loader at a quarry in Austria and will continue that testing program for the
It has become clear that combining these innovations — decarbonization, autonomy, and connectivity — will deliver the greatest transformation that the construction industry has experienced, and your construction job site 20 years from now may be almost unrecognizable from what it is today. Innovation, however, isn’t just a product of the future. Turn the page to discover the most innovative construction equipment and technologies introduced in 2024. HEG
BY KAITLYN TILL, EDITOR IN CHIEF
While revisiting equipment and technology introductions from the past year, three themes dominated: agility, efficiency, and the operator experience. These themes were common across sectors, including earthmoving, roadbuilding, lift and access, aggregates, and more.
In 2024, OEMs introduced machines and entered new equipment categories with an emphasis on maximizing versatility and utilization — whether through easy customization, ability for a single machine to do the job of two, compact design, or automation of functions. This attention to agility can give you the flexibility to respond to labour shortages, space-restrictive job sites, and timeline pressures.
While decarbonization via equipment electrification has remained a hot topic across the industry, and once again appears among our Top Introductions, in 2024 OEMs heavily emphasized making their diesel-powered equipment more efficient — a benefit for operators in the cab and for bottom lines. Optimized electro-hydraulics, hybrid drives, and machines and attachment solutions that reduce the need to reposition are all represented.
Retaining operators and training new ones remains an industry challenge, and OEMs have stepped up to make getting in the cab as attractive as possible. Many of our 2024 Top Introductions feature assistance technologies, emphasize a comfortable environment with excellent visibility, and have simplified, intuitive design that reduces fatigue for experienced operators and gives novice operators the confidence to excel.
Our picks for Heavy Equipment Guide’s 2024 Top Introductions represent a range of new solutions designed to respond to your pressures and pain points — we hope you enjoy exploring them with us.
Volvo kicked off the biggest update to its excavator line in 20 years with six medium and large models introduced this summer and added two more mid-size models in the fall. Optimized electro-hydraulics, a smart cooling system, and engine speed regulation all contribute to an increase in fuel efficiency and give operators what they need to complete precise, efficient work. Keeping those operators comfortable is more important than ever, and Volvo has made the new work environment attractive to retain them. New safety features, an improved interface, and the newest generation Co-Pilot combine to give operators confidence and comfort on long work days. In 2024, Volvo also introduced a specialized version of the L180H wheel loader targeted to aggregates applications. A long boom, new counterweight, and bigger tires give the L180 3-Pass Rehandler the ability to quickly and efficiently load trucks.
Takeuchi entered two new product categories in North America this year with its first crawler dumper and first wheeled excavator. Driven by the demand for agility, the TCR50-2 crawler dumper is designed for moving material on challenging terrain and in confined spaces and is versatile for both rough-terrain environments and urban use. The dumper bed rotates 180 degrees, reducing the need to reposition. Takeuchi’s first wheeled excavator available in North America is the 23,424-pound TB395W. Combining the power operators expect from a tracked machine with the versatility of roading between job sites gives contractors and municipal end users the flexibility to efficiently complete diverse tasks.
world’s biggest hydrostatic drive dozer. Liebherr remote control, LiReCon, provides the option for operators to work remotely, ideal for keeping them out of hostile environments. Previously available on Liebherr’s smaller dozer models, new Operator Assistance Systems for the PR 776 include “Free Grade” for active blade stabilization during fine grading and “Definition Grade” for automatic blade positioning on 2D grades. “Auto Blade Pitch” stores blade positions for the operator to recall with a button push.
Electric variable transmission (EVT) E-Drive on John Deere’s two new hybrid X-Tier production class wheel loaders replaces the torque converter and traditional transmission. Paired with a JD9 diesel engine, the E-Drive on the 744 X-Tier and 824 X-Tier provides instant power while simplifying operation. Hybrid E-Drive reduces fuel costs — an attractive benefit lowering the total cost of ownership over the life of the machine. In 2024, John Deere also significantly expanded its P-Tier compact loader lineup, introducing five new models of skid-steer and compact track loaders along with new powered attachments and new technology features. The new technology simplifies attachment management and improves the operator’s view from the cab.
Kubota’s flagship compact excavator received a big update in early 2024. The 8-ton KX080-5 has been redesigned to give operators a new, quieter cab environment that maximizes comfort on the job site. Smoother operation will reduce soil spillage. A two-pump load-sensing system allows operators to easily perform simultaneous operations, while auto-shift meets the needs of the terrain to provide smoother simultaneous operations when dozing and turning.
Dynapac’s 8-ton tandem asphalt roller, the CC2200 VI, is part of the company’s new range of 8- to 10-ton articulated tandem rollers. The vibration of compaction is loud and can be hard on the operator’s body when running a machine all day. Dynapac’s SEISMIC technology addresses this discomfort while maximizing compaction quality. Active on both drums, SEISMIC reduces vibration and energy consumption by automatically detecting the optimal frequency for the compacted material and constantly monitoring variations in the asphalt layer, adjusting to temperature conditions.
The first commercially available electric backhoe loader, the 580EV, minimizes energy and maximizes responsiveness, ideal for operators working in utilities installation and construction applications. Based on the 580SN diesel-powered model, CASE has considered every element of operation that would affect energy efficiency and has refined this electric backhoe to give operators the performance they expect from their machine. It uses an automotive charger and can deliver eight hours of run time on a single charge. It has four-wheel drive with two independent electric motors for the PowerDrive transmission and hydraulic pumps to feed the loader, backhoe, and steering systems to minimize energy consumption.
Quieter operation, a compact footprint, and simplified ease of use address common job site challenges for utility installation contractors. Vermeer’s redesigned D24 horizontal directional drill not only checks these boxes, but also features automated rod exchange (ARE) technology that reduces the operator’s workload and maximizes wear component life. ARE technology eliminates up to 19 manual steps and reduces the risk of human error. Operators can choose between 400 feet or 480 feet (122 m or 146 m) of 2.375-inch Firestick drill rod, and the D24’s stakedowns feature tiered shark teeth and a rotation speed of up to 60 rpm — nearly triple its predecessors.
Wirtgen’s new compact milling machine has a cutting width of up to six feet, ideal for milling applications in urban environments with limited room for manoeuvrability. A front loading design delivers high-performance on restricted job sites, and digital assistance and levelling systems ensure that a single operator
MEC’s unique DualReach 85-J boom lift can switch between telescopic and articulated operation to handle jobs that would otherwise require two separate machines. The flexibility to switch modes for different work-at-height needs reduces the number of machines needed on site, simplifying asset management. Both configurations have a 91foot working range.
Bobcat has entered the backhoe loader market in North America with the long-reaching B760. Intended to minimize footprint while maximizing reach in congested areas, this backhoe loader is friendly for novice operators with ease-of-use features including automatic return-to-dig, ride control, and pilot controls.
Hitachi introduced an extensive range of excavator updates across size classes and applications throughout 2024. New models include compact, medium, large, and super long front excavators. Hitachi has improved durability of the undercarriage and boom on the six models added to the ZAXIS-7 medium and large excavator line. Redesigned cabs reduce noise levels and improve airtightness, while nextgeneration hydraulic systems paired with Isuzu engines provide operators with reliable power while using less fuel.
DEVELON entered the CTL market with a powerful 115.3-hp model optimized for use with a range of powered attachments. Standard features, including ride control, return-todig and attachment positioner, bucket shake, auto self-levelling, torsion suspension, and a rear-view camera give operators a premium experience out of the box.
Power Curbers’ new enclosed cab option for the 5700-D curb and gutter machine gives concrete contractors a unique opportunity to provide their operators with a climate controlled environment that protects them from the elements. A glass floor insert gives the operator full visibility to the mold and the finished concrete. The cab reduces noise exposure for operators and shields the control panel, eliminating glare and maintaining a cooler temperature.
Manitou’s newest telehandler is designed for easy transportation between job sites and manoeuvrability in tight spaces with excellent visibility from the cab. Versatile for a variety of applications, this telehandler has a universal skid-steer quick attach system and full-power ground-engaging telescopic boom.
Tiltrotators are big investments and Steelwrist has recognized that not all contractors need full tiltrotator functionality, but can significantly benefit from the rotation capability. To that end, Steelwrist introduced its first rotor couplers as part of its complete tiltrotator lineup relaunch this year. The XR7 and XR20 give operators 360-degree rotation of the attachment without the need for a specialized tiltrotator control system. The XR7 is for four- to seven-ton excavators, and the XR20 is for 14- to 20-ton excavators.
Topcon’s MC-Max Asphalt Paving and MC-Max Milling solutions offer modularity, simplified configurations, and advanced feature sets for paving professionals. MC-Max is highly customizable and easy to upgrade as contractors’ needs change. The entry level 2D systems follow references, such as a string or curb, while the
KIOTI Tractor entered the robust CTL and SSL markets with the TL750 CTL and SL750 SSL. An open cabin design is standard on both machines while an enclosed cab is an available option. Both
Caterpillar has continued the complete relaunch of its compact loader line with eight more models including the first skid-steer loaders in the lineup. The new 285 and 285 XE are the biggest CTLs Cat has ever produced with lift height up to 146 inches, tilt breakout force of 13,920 pounds, and ROC of 4,719 pounds on the 285 and 4,816 pounds on the 285 XE, both with counterweight.
Komatsu has introduced a range of four demolition excavators, previously available in Europe, to the North American market. The 80-ton PC490HRD-11 features Komatsu’s K100 boom change system which makes set-up and switching between six different configurations easy. Oversized quick couplers on the hydraulic lines minimize back pressure and oil heating without restricting oil flow, while hydraulically powered pins inside the main boom structure reduce the risk of damage during reconfiguration.
JCB re-entered the North American tandem roller market with two new Vibromax models, the CT160 and CT260. JCB has focused on introducing simple-to-operate machines that will be intuitive for new operators or renters. Vibration turns off automatically at certain speeds so that inexperienced operators don’t over-compact. JCB has shaped the new rollers to make getting on and off the machine easier, to improve manoeuvrability and visibility,
Hyundai entered the dozer market with its first two models, the 10-ton HD100 and the 15-ton HD130. Operators will appreciate an unobstructed view to the blade on both dozers. The HD130 is available in two configurations, LGP (low ground pressure) or XL. A parallel ripper and towing bar are available for both machines, and a forestry cabin guard is available for the HD130.
The 3-tonne TH 3.6 is the smallest fixed telehandler in Magni’s lineup, providing an option for work in tight spaces while more than capable of handling uneven terrain. This compact telehandler features an LMI (load moment indicator) that continuously monitors the machine to prevent overload, and operators will appreciate the new compact cab that is based on Magni’s larger telehandler models.
Sakai introduced its Guardman safety technology to North America at World of Asphalt 2024, showing the technology on the new 79-inch SW884ND double-drum asphalt roller. Guardman is integrated into roller hydraulics during production and detects whether pedestrians or objects are behind or in front of the roller, providing alerts to the operator and automatically slowing and breaking the machine.
THE COMPANY’S FIRST BACKHOE LOADER IS DESIGNED TO MAXIMIZE REACH AND SIMPLIFY OPERATION
Bobcat has entered the North American backhoe loader market with its first model, the B760. Bobcat has previously offered backhoe loaders in Southeast Asia.
“The new B760 helps operators accomplish more on the job site with its dig, load, and carry versatility,” says Jamison Wood, Bobcat product development specialist. “The backhoe loader is designed for durability, easy operation, simple maintenance, and incredible performance. Its size keeps it accessible on sites with limited space, while its impressive travel speeds keep operators productive across large job sites.”
Applications for Bobcat’s first backhoe loader include excavation, site preparation, material handling, trenching, and snow removal.
BOBCAT B760 BACKHOE LOADER KEY
Bobcat’s first backhoe loader has a lift capacity of more than 2,200 pounds at full reach, digging depth of 18 feet 5 inches, and nearly 180 degrees of backhoe swing for less repositioning
This backhoe loader has been designed for ease of operation for novice operators.
and fast cycle times.
It comes with a standard-equipped extendable arm that provides up to 8 inches of additional dig depth compared to other machines of the same size, according to Bobcat. The front-end loader provides a lift capacity of 7,985 pounds with its standard general purpose bucket.
Powered by a turbocharged 3.4-litre Bobcat engine with DPF, the B760 delivers powerful, high-torque performance and efficiency. The power shift transmission provides quick
BOBCAT’S B760 BACKHOE LOADER COMES WITH A STANDARD-EQUIPPED EXTENDABLE ARM THAT PROVIDES UP TO 8 INCHES OF ADDITIONAL DIG DEPTH COMPARED TO OTHER MACHINES OF THE SAME SIZE.
direction changes while the backhoe loader’s quick travel speeds allow operators to minimize the need for a trailer.
According to Bobcat, this backhoe loader has been designed for ease of operation for novice operators. Contractors can choose either a canopy or a cab, and controls are thoughtfully laid out and easy to use. New operators can reach maximum productivity in less time while working in comfort. The 5-inch colour display panel provides full-featured machine interaction and monitoring capabilities.
• Ride control.
• Automatic return-to-dig positioning.
• Eight work lights.
• A 1.4-cubic-yard general purpose loader bucket.
• Pilot controls.
• Auxiliary hydraulics.
CONTRACTORS CAN CHOOSE EITHER A CANOPY OR A CAB.
BY KEN SINGER, PUBLISHER
Volvo Construction Equipment welcomed nearly a thousand customers and dealers to its North American headquarters earlier this fall for Volvo Days 2024 in Shippensburg, Pennsylvania. This exclusive event held every few years showcased dozens of new and existing products and offered a unique opportunity for visitors to see and operate the full range of Volvo Construction Equipment machines. Attendees participated in in-depth discussions with product managers, were given an overview of the latest job site technologies, and experienced a dynamic machine show and factory tour. The 2024 event showcased Volvo’s growing range of offerings in both conventional and electric power across the company’s equipment lineup.
“Providing an exceptional customer experience is something we’re focused on every day of the year, but Volvo Days gives us a special opportunity to celebrate our customers, strengthen relationships, and allow people to talk with our experts and test-drive machines,” said Scott Young, head of Region North America.
Several new products were introduced to the North American market including the SD125 soil compactor, the R60 and R70 rigid haul trucks, the L120 Electric mid-size wheel loader, and the new-generation EC230 Electric mid-size excavator.
Volvo Days was the first chance for many customers to experience the new Volvo F Series excavators introduced earlier this summer. The new range features electro-hydraulic controls which enable superior integration with Volvo CE’s Co-Pilot allowing further optimizations such as Dig Assist and other semi autonomous excavator functions. The new series includes several mid-size and larg-
er models, with more to be introduced in the coming months. It represents the biggest update to the Volvo CE excavator lineup in two decades.
“It’s critical that we give customers comprehensive solutions for their projects,” said Young, “And that means pairing the right machines with the right services to help them optimize their safety, productivity, and uptime.”
Designed and built at the Volvo CE North American headquarters in Shippensburg, the SD125 has been designed for medium- to heavy-duty compaction jobs. The 12-ton machine is the largest model in the Volvo soil compaction range with an 84-inch smooth drum and operating weight of 26,565 pounds (12,050 kg). The new model has an additional 935 pounds (424 kg) of mass on the drum, increasing the static load and eccentric force for a different amplitude profile than the current SD115.
As terrain and material depths change, the ability to adjust dynamic drum forces is as simple as the flip of a switch on the new SD125. Another switch adjusts the two drum frequencies to compensate for changing conditions, and a five-frequency feature is available as an option to further boost versatility and performance.
A heavy-duty axle is integrated into the drivetrain for an efficient rear wheel drive system. The No-Spin differential increases traction, eliminates tire slippage, and improves gradeability, performance, and productivity. A high-traction variant is available for demanding applications where additional torque is needed to tackle extreme slopes or thick
part of the DD25 already in the market, as well as the new TC13 Electric trench roller, its first ever offering in the prod uct category.
Volvo’s expanded rigid haulers line has expanded with the R60 with a body volume of 47 cubic yards (36 cubic metres), and the R70 offers 55.6 cubic yards (42.5 cubic metres), which makes them well-matched for the loading abilities of Volvo’s EC950 crawler excavator and the L350H wheel loader. The machines feature a V-shaped haul body for maximum load retention and minimal carry-back post-dumping. The dumping process itself is also speedy thanks to a fast-tip system.
VOLVO IS EXPANDING ITS LINEUP OF ELECTRIC MACHINES TO MIDSIZE MODELS INCLUDING THE L120 ELECTRIC WHEEL LOADER.
Providing real-time insights on payload, the optional on-board weigh ing system helps operators apply the industry standard 10/10/20 payload, where the machine can take 10 percent overload for 10 percent of the time but should not exceed 20 percent. Both the R60 and R70 are designed with a new adaptive retarder system that can automatically control the rear braking system when travelling downhill.
When it comes to grip, the high-drive axle multiplication ensures maximum traction while the high-torque engine reduces fuel consumption with an automatic adaptive gear selection called Volvo Dynamic Shift Control. The engine also has an ECO mode that defaults to the most efficient gear, while the auto engine idle reduces engine wear and boosts fuel efficiency. The haulers feature gear-de pendent speed control and a selectable brake or transmission retarder, which also helps reduce operator fatigue. Early feedback from aggregate and light mining customers has been extremely positive.
Volvo also showed a sneak peek of its next-generation articulated dump trucks, which are scheduled to be re leased in 2025.
Volvo has already established itself as having the largest offering of electric compact machines in the industry and is now expanding into mid-size electric machines with the L120 wheel loader and the EC230 excavator, designed to meet the growing demand for larger, more powerful equipment with reduced environmental impact and more sustainable power systems.
“These larger battery-electric models mark a significant advancement toward zero-emission solutions that can help businesses and government fleets meet sustainability and productivity goals,” said Dr. Ray Gallant, vice president — Sustainability and Productivity Services. “The electric excavator and wheel loader offer comparable performance to their diesel counterparts but with zero emissions, reduced noise, and lower maintenance costs.”
The L120 Electric wheel loader is a 22ton machine with 6-ton lifting capacity and a recommended rehandling bucket capacity of 5 cubic yards, giving it nearly identical performance capabilities as its
conventional counterpart.
Its 282-kWh lithium-ion battery system can run for five to nine hours on a single charge, depending on the application. Charging options include a 50-kW DC mobile charger that will charge the L120 Electric from empty to full in about six hours or a 150-kW DC fast charger that can charge it from empty to full in two hours.
The L120 Electric wheel loader is equipped with separate electric motors for propulsion and hydraulics. The system recoups deceleration energy to
extend battery runtime, reduce brake wear, and minimize the need for axle oil cooling. The loader also features active cooling and heating of the high-voltage batteries as well as passive cooling for the electric motors, transmission, and hydraulic oil.
It includes many of the same features as its diesel equivalent, including on-board weighing with the Volvo Load Assist system, torque parallel linkage, electro-hydraulic lever controls, and auto bucket-levelling functions. HEG
Loved for the features. Trusted for the performance.
Do more without feeling like it in Hyundai’s NEW HX355ALCR compact radius excavator.
• Engineered to redefine efficiency, comfort, and safety
• RH and rear camera (standard)
• AAVM 360° camera with ultrasonic system (option)
• LED lights
• Dozer blade (option)
• 8” touchscreen color LCD monitor (standard) and 2nd monitor (optional)
• Free Hi-MATE mobile telematics for 5 years
or na.hd-hyundaice.com. NEW MODEL
BY LYNETTE VON MINDEN
When you must haul heavy loads over rough or soft terrain, you need a crawler dumper. While a truck can do the trick on paved or hard-packed surfaces, a crawler dumper is invaluable when the ground is hilly or muddy and when your job site is too small to accommodate a truck’s turning radius. Because crawler dumpers are equipped with tracks, they can also tackle steep slopes with ease due to their low centre of gravity, using their tracks for better grip and stability and preventing them from tipping over.
“Crawler dumper tracks distribute the vehicle’s weight over a larger surface as compared with wheels,” says Lee Padgett, national product manager for Takeuchi-US. “This reduces their ground pressure and prevents them from sinking into soft ground — mud, sand, or any soft terrain where a wheeled vehicle might get bogged down and stuck.”
For all these reasons and more, crawler dumpers are ideal for use in the construction, mining, forestry, landscaping, and agriculture industries. These machines can move gravel, soil, and other materials across potentially unstable ground. They can also assist with site prep, create embankments, or level large areas.
“Because crawler dumpers are so versatile, they’re growing in popularity,” Padgett says. “They’re compact, yet powerful, able to operate in confined spaces and in fragile areas that can’t support a heavy dump truck. As more construction takes place in urban areas, and as governments increase infrastructure spending, we’re seeing more demand for crawler dumpers, which is why Takeuchi introduced the new TCR50-2 model to North America back in June.”
If a crawler dumper sounds like a machine you might want to add to your fleet, Padgett says there are some decision factors that can help you determine which model is best for your specific needs.
Payload capacity It’s important to determine the maximum load your dumper will need to carry. The machine’s payload capacity should align with the volume and weight of the materials it will need to transport.
may be less critical than stability and traction.
Bed rotation Crawler dumpers can feature beds that rotate, making it easier to more precisely dump material in any direction without repositioning the entire machine. This is especially useful in confined or narrow spaces where turning the entire vehicle is not feasible. Rotating beds also reduces wear and tear on tracks because the crawler dumper doesn’t need to pivot or make sharp turns as frequently.
Size and dimensions Larger dumpers may have larger payloads, but they could be more challenging to manoeuvre in tight spaces. You’ll also want to ensure you have adequate space to store your crawler dumper when it’s not in use.
Track width and durability Wider tracks help distribute weight more evenly and improve stability on soft or uneven ground. Be sure to assess the ground conditions where you’ll be working and choose a compatible track width for optimal performance and minimal ground disturbance.
“Tracks made from high-quality, wear-resistant materials are more durable and can withstand tough conditions and abrasive surfaces,” Padgett says. “Our TCR50-2 features a bogey-style undercarriage with double-flanged track rollers for better ride quality and less susceptibility to de-tracking. You also want rollers that are permanently sealed with metal face seals to prevent damage from dirt and other contaminants.”
Gradeability and stability High gradeability means that the
comfortable operator is a more productive operator.” Ergonom ic controls, good visibility, and even features like air conditioning and a radio can lead to safer, more comfortable operation over longer periods of time.
The most common mistakes Padgett sees people make when choosing a crawler dumper include focusing solely on the machine’s initial cost and failing to anticipate future needs. Choosing a crawler dumper based solely on its purchase price doesn’t give the full picture of its total cost of ownership. It’s important to consider maintenance, fuel efficiency, durability, and warranty. Purchasing a machine only for today’s needs means your machine may quickly become inadequate when your business grows, or you take on a larger project.
“You also want to investigate the manufacturer’s reputation for support,” Padgett says. “Does the company have a well-established dealer network? Are spare parts readily available? What’s their customer service like? You don’t want to end up with a machine that’s down all the time because you can’t get it serviced.”
Like all machines, regular maintenance is essential to keeping a crawler dumper up and running at top performance. Every manufacturer will provide a comprehensive maintenance schedule, and following that schedule will help prevent breakdowns, provide greater safety, and maximize the machine’s efficiency.
As more construction takes place in urban areas, and as governments increase infrastructure spending, we’re seeing more demand for crawler dumpers, which is why Takeuchi introduced the new TCR50-2 model to North America back in June.
Lee Padget National Product Manager, Takeuchi-US
Telematics systems, which can reduce downtime and control costs by providing maintenance reminders and much more, are a go-to feature on crawler dumpers, as they are on nearly every type of heavy equipment today.
“Telematics systems give owner/operators updates on machine health and condition, run time (hours), and machine location, as well as remote diagnostics, scheduled maintenance reminders, and customizable alert settings,” Padgett says. “Our system, Takeuchi Fleet Management (TFM), also gives owners the ability to geofence their machines, helping them protect and secure their investments. These machines aren’t cheap, so it’s important to take the extra step to make sure they’re available when you need them.”
In addition to the recommended daily, weekly, monthly, and quarterly maintenance, it’s a good idea to take your crawler dumper to your dealer’s service department for major service intervals, which may include checking out the engine, trans mission, or hydraulic components. Scheduling an annual inspection of the entire dumper is also a good idea to test those major systems and all safety features.
“Takeuchi also recommends keeping detailed records of your maintenance activities, repairs, and inspections,” Padgett says. “That will help you keep track of your dumper’s condition and any future maintenance needs.”
Operators should be trained on how to perform basic main tenance tasks and recognize the signs of any potential ma chine issues to prevent the possibility of damaging the crawler dumper. Operators should also be aware of how environmental factors can impact the machine’s maintenance needs and how to ensure it remains in good working order.
Wet conditions can cause mud to accumulate around the undercarriage, tracks, and engine compartment, which could cause overheating, corrosion, and premature track wear if not cleaned out regularly. Dusty, dry conditions can cause dirt to infiltrate various components like filters, cooling systems, and engine parts, making it necessary to clean or replace those components more frequently. Extreme weather can also take a toll on a crawler dumper if it’s not properly maintained.
“Extreme cold can affect fluid viscosity, making it harder for the engine to start and operate as it should,” Padgett says. “Use the right winter-grade lubricants and ensure the engine and hydraulic system are warmed up before operating the crawler dumper. It’s also important to remove any snow or ice to prevent additional load on the tracks and undercarriage.”
Hot weather requires frequently checking coolant levels, the radiator, and cooling fans to reduce the risk of overheating. Ensure operators are only using the crawler dumper within the recommended temperature range to prevent any related issues.
Crawler dumpers provide a unique combination of power, stability, and versatility, making them indispensable for any job
CRAWLER DUMPERS PROVIDE A UNIQUE COMBINATION OF POWER, STABILITY, AND VERSATILITY, MAKING THEM INDISPENSABLE FOR ANY JOB THAT REQUIRES MOVING HEAVY MATERIALS OVER ROUGH, SOFT, OR OTHER UNSTABLE SURFACES.
that requires moving heavy materials over rough, soft, or other unstable surfaces. By carefully considering factors like payload capacity, track width, and engine performance, you can ensure you’re investing in the right crawler dumper for your needs. Moreover, a proactive approach to maintenance will keep these machines in optimal condition, maximizing their lifespan and return on investment.
“The best crawler dumpers are compact, powerful, and built to last,” Padgett says. “By choosing the right machine for your needs and maintaining it diligently, you can ensure your crawler dumper will be able to transport heavy loads over challenging terrain for years to come.”
LYNETTE VON MINDEN is a senior public relations specialist with Swanson Russell.
Cardinal Scale’s ARMOR® digital truck scale with included free iSite remote monitoring means you can say goodbye to downtime with high-tech Cloud-based diagnostics.
John Deere has added the new 330 and 334 P-Tier skid-steer loaders and the 331, 333, and 335 P-Tier compact track loaders to its compact equipment lineup. The company has focused on offering a range of new cab comfort options, technology, and safety features, in addition to new powered attachments.
Prioritizing operator comfort and capability, the new P-Tier models have a larger redesigned cab. The cab is sealed, pressurized, and isolated from the frame to help improve operator comfort and productivity. Noise levels are reduced, and the new cab provides better protection from the elements. An eight-inch touchscreen display interface is available on the full lineup of P-Tier models and is standard on the 334 and
335 P-Tier. Additional features include new seats and hands-free Bluetooth.
Onboard Grade Indicate is standard on the new touchscreen display. It displays the cross-slope and main-fall of the machine in either degrees or percent and allows operators to use a relative benchmark to assist in maintaining grade.
The optimized joystick controllers enable more tasks to be completed with easy-to-reach and adjustable controls. The new 25 Button SSM puts all functions in one spot, eliminates rocker switches, and makes it easier to quickly make machine adjustments while operating.
Visibility has increased 20 percent over G-Series machines, improving the operator’s view out the front, sides, and to the back of the machine.
With a focus on serviceability, the new cab tilts up in one piece, giving
ground-level, all around access to the engine, drivetrain, and undercarriage. A single operator or technician can raise the boom and enable the mechanical lock out.
On Board Diagnostics are easy to navigate through a diagnostic and settings menu structure. The operator can look up detailed information on current machine settings and any active codes.
The 333 and 335 P-Tier compact track loaders can be equipped with SmartGrade Ready including 2D grade control or 3D SmartGrade with Topcon, and a new hydraulic system is designed to help operators maximize their efficiency.
John Deere is debuting two new technology features on these models: Attachment Manager and Surround View.
Attachment Manager, available as an upgrade on the 330, 331, and 333 P-Tier
machines and standard on the 334 and 335 P-Tier, takes the guesswork out of optimizing attachment performance by enabling preprogrammed flow and pressure for John Deere attachments. Key attachment parameters are displayed on the screen while running, and operators can save or select performance parameters depending on the tool. Operator confidence and productivity will improve, and this feature helps prevent damage to the attachment.
Surround View technology, available on all P-Tier models, stitches together views from around the machine to provide the operator with a bird’seye-view to the sides and rear of the machine. When reversing, the display will automatically switch to the rearview camera.
John Deere Operations Center will continue to be included on all largeframe CTLs and SSLs, enabling fleet managers to efficiently monitor machine location, codes, and fuel usage. Enabling data sharing with a dealer streamlines maintenance and repairs and can help prevent downtime.
In addition to updating its Quik-Tatch system with efficiency and design improvements, John Deere has added three more attachments to its extensive lineup for compact loaders.
Featuring Wirtgen Group milling and cutting technology, the CP40G cold planer is compatible with the 333, 334, and 335 P-Tier machines. Intuitive in-cab controls include tilt float activation for seamless pass matching across rolling terrain. It can slide horizontally from left to right for maximum control, and is designed for easy pick replacement. Visible indicators for side plate depth, tilt angle, and milling drum cut boundary ensure accuracy. An optional pressure gauge aids in monitoring milling performance. The optional water tank mounts within the cold planer frame to provide convenient filling and the nozzle kit effectively suppresses dust.
The MK76 and MH72D Mulching Heads are designed to work with the 333, 334, and 335 P-Tier models to take on land clearing needs. The optimized knife style head on the MK76 is ideal for fibrous vegetation. In addition, John Deere notes that these mulching head attachments produce the finest chip of all the company’s mulchers, broadcasting discharge to mitigate piles.
HANDS-ON DEMONSTRATIONS SHOWCASE THE LATEST EQUIPMENT & ADVANCEMENTS FOR TECH-DRIVEN ROADBUILDING
BY SLONE FOX, EDITOR
Nestled in the scenic town of Boppard, Germany, BOMAG’s global headquarters was the hub of this year’s Innovation Days which brought together more than 1,500 industry professionals from around the world to witness the company’s latest advancements in roadbuilding machines and technology.
Attendees toured BOMAG’s advanced production facilities — spotlessly clean and filled with robotic assistance — observing firsthand the meticulous assembly of everything from rollers to milling machines. With live equipment demonstrations, interactive sessions, and presentations focusing on technology and digitalization, BOMAG pulled back the curtain on its tech-driven mission.
Fun demos like a refuse compactor car-crushing showcase, motorbike stunts, and soccer freestyler performances
bridged the gap between technical discussions and attendee engagement, adding excitement and balance to the event. The interactive activities gave everyone a fresh and unique perspective on BOMAG’s capabilities in action — like an asphalt roller so precise that it removed the cap off a beer bottle — while also fostering networking by sparking conversations among attendees, making the event more than just a learning opportunity.
The event highlighted a range of innovations, with many following one of two distinct themes: minimizing emissions, and reducing the learning curve for new operators by making equipment and technology more intuitive to use. BOMAG has notably expanded its hybrid and electric lineup to meet sustainability demands, especially in compact equipment. This includes the
BW 120 AD e-5 light electric tandem roller, which was shown op erating without any tailpipe emissions and utilizing autonomous features designed to optimize compaction performance.
BOMAG also introduced the BW 177 BVO-5 PL single-drum roll er, which offers three compaction modes to handle a wide range of applications. High amplitude mode is ideal for deeper compac tion, tackling thick layers on materials like gravel and sand. The low amplitude mode supports lighter compaction, maintaining material integrity on subgrades that require a softer approach. Finally, the oscillation mode ensures gentle compaction for sensi tive projects, like those near buildings or over pipelines. Another highlight was the new generation of BOMAG’s radio remote-controlled BMP 8500 multi-purpose compactor. Two light strips on the machine show compaction progress in real time as part of BOMAG ECONOMIZER. The system warns against
over-compaction and identifies soft spots immediately, helping to avoid unnecessary passes. The radio controller — with a run time of 35 to 40 hours — also ensures frequencies don’t need adjusting, and if the original transmitter does get lost, pairing a replacement can be done quickly and with no special training.
During the facility tour, attendees participated in a live demonstration that showcased the company’s BOMAP technology in action. BOMAP tracked each tour group via GPS throughout the day, ensuring that every activity stayed on schedule. Attendees were also shown an example of the app’s use in a job site setting, complete with a map that tracks the number of passes in real time, monitors compaction levels, and visualizes progress so that operators can make instant adjustments and plan more efficiently.
Notably, BOMAG emphasized that the app works without any additional special hardware. BOMAP uses the phone’s internal GPS to detect the machine’s location and can document the compaction results of rollers from any manufacturer without requiring the operator to change settings.
Using a wireless GPS antenna, operators can achieve even more accurate data tracking, reaching an accuracy of up to 20 centimetres. The antenna can also be equipped with a correction feature for even finer precision, allowing it to reach a resolution of fewer than 5 centimetres.
Another noteworthy feature was BOMAP Connect, an advanced telematics platform integrated into BOMAG’s tandem rollers and pavers that lets operators monitor and optimize machine performance remotely. It has predictive maintenance features that alert crews to potential issues before they become a problem, ensuring that machines run smoothly and efficiently.
ASPHALT PRO and ASPHALT MANAGER were standouts at Innovation Days this year, quickly becoming favourites among attendees. With ASPHALT PRO, site managers can calculate mix requirements, pass on process changes, and communicate directly with mixing plants, allowing teams to proactively manage resources and materials. This new toolkit can optimize workflows, reduce downtime, and prevent miscommunication by allowing teams to address issues as they come up.
ASPHALT MANAGER intelligently adapts compaction based on real-time surface conditions, making adjustments automatically as the operator selects the layer to be compacted. Once set, the tandem roller optimizes its amplitude on its own, adjusting to the current compaction levels. This prevents issues like bouncing and over-compaction, allowing for more precise and efficient performance across different surfaces.
According to the company, combining ASPHALT MANAGER and ASPHALT PRO optimizes asphalt compaction, minimizing costly errors and ensuring precision — two major pain points attendees praised these tools for addressing.
As contractors consider adopting these technologies, several key concerns were voiced. Cost was at the forefront, as the upfront investment in machinery and software can seem daunting. Many worry that the financial returns may not justify the initial expense, making them hesitant to take the leap.
Integrating new technology into well-established workflows can also be challenging. Contractors need to find the right
FUN DEMOS LIKE A REFUSE COMPACTOR CAR-CRUSHING SHOWCASE, MOTORBIKE STUNTS, AND SOCCER FREESTYLER PERFORMANCES BRIDGED THE GAP BETWEEN TECHNICAL DISCUSSIONS AND ATTENDEE ENGAGEMENT.
balance between their current practices and their need for newer tools. Training is another factor — keeping pace in a fast-moving industry means lengthy learning curves can seem insurmountable.
During the event, BOMAG acknowledged these challenges and noted that it has implemented support measures to assist contractors by prioritizing ongoing support and resources, including specialized training, to help contractors maximize the return on their investments.
BOMAG Innovation Days 2024 combined technical innovation with engaging, hands-on demonstrations, allowing industry professionals to fully experience BOMAG’s latest solutions. This year’s event showcased advancements across sustainability, digitalization, and operator safety. BOMAG’s approach bridges technology and practicality, equipping contractors with tools that drive productivity while adapting to the evolving demands of modern road construction. HEG
BY JOSH SWANK
There are some things in life that make more sense, or simply become more useful, when paired together — milk and cookies, cars and heated seats, smartphones and an internet connection — the list goes on. Each of these items on their own provides some benefit. Add in the complimentary item to each of these though, and their benefit is elevated even more.
A similar anecdote could be applied in the aggregates industry when it comes to reducing weight and articulated truck bodies. Custom truck bodies are a significant investment and to truly realize the full utility of one — whether lightweight or standard — there are many factors producers must consider.
The first consideration when looking at lightweight bodies is whether a custom
solution to maximize productivity or an off-the-shelf solution is the right fit. For some operations, an off-the-shelf truck body does the job. For producers that want to truly optimize their operation, boost profits, and meet the growing industry pressure amidst the infrastructure boom, custom aggregates bodies offer what standard OEM bodies and other offthe-shelf bodies just can’t.
When deciding on a custom body, look for a manufacturer that focuses on increased stability and operator safety in the design of custom haul truck equipment. Custom bodies should be constructed with a low centre of gravity to ensure the best weight distribution and minimize vibration to the driver as well as impact to the truck overall. Customizing individual truck bodies to the operation’s specifications increases loading safety and greatly reduces the potential for loading damage by ensuring the truck body dimensions are correctly
paired with the loading tool.
Another consideration is maintenance, and to truly maximize productivity custom truck bodies should address this concern. Some manufacturers add four free-floating lifting eyes into the body rather than the sides, enabling fast and easy removal or installation of a body for maintenance from a lower overall height without needing to go outside and use a portable crane.
One of the key goals of a custom truck body is to maximize the amount of material an operation can haul with each pass. With a heavier payload and the weight of the standard body, maximum gross weight is reached very quickly in aggregate operations, limiting the amount of material hauled in each load. This creates a dilemma: add more trucks
to the haul fleet or utilize the existing fleet more efficiently.
Previously, manufacturers used a thinner steel to reduce the body weight, which directly translated to increased payload capacity. However, the lighter-weight steel brought with it a shorter lifespan, often leading to the term “throwaway” body. In other words, producers had to choose between increased capacity or durability. And for some producers, the sacrifice in wear life of the body was worth it for the ability to haul extra material. Eventually, the need to change out the body after just a few years would frustrate fleet managers, and they would return to purchasing the heavier bodies that offered longer life and less maintenance.
Quarry managers should not have to choose between maximizing haul loads and getting the best possible life out of their truck bodies. In addition to payload and wear life, producers should consider partnering with a manufacturer that looks at the big pic-
ture, including how the truck body fits into their operation, while maximizing operator safety.
If you give an aggregates producer additional payload capacity in the form of a lightweight truck body, they’ll probably want some durability to go with it. And that only makes sense.
JOSH SWANK is chief growth officer at Philippi-Hagenbuch.
These lightweight bodies offer increased wear life while adding 10 to 20 percent to payload capacity.
But what if producers didn’t have to choose between capacity and durability? It’s a question that drove some manufacturers to research, engineer and manufacture options that offer the full benefit of maximized capacity in the form of a lightweight body that lasts more than three years. Producers can distinguish these more durable options from the “throwaway” lightweight truck bodies by looking at the quality of the steel. Some of the most durable options on the market are manufactured with Hardox 500 Tuf steel, which increases abrasion resistance by three times compared to 450 Brinell steel.
These lightweight bodies offer increased wear life while adding 10 to 20 percent to payload capacity. In terms of wear life, bodies engineered with 500 Tuf steel offer up to 30 to 40 percent more life than traditional lightweight bodies, creating an ideal solution that maximizes capacity without the extreme sacrifice in durability.
HD Hyundai Construction Equipment North America has introduced two new large-frame excavators, the 82-ton HX800A L and the 100-ton HX1000A L.
The HX800A L is powered by a 528 net hp (389 kW) engine, while the HX1000A L is equipped with a 620 net hp (420 kW) engine. Each machine can be operated with various boom and arm configurations to match the material being excavated. The HX800A L supports buckets from 4.5 to 7 cubic yards (3.4 to 5.4 cubic metres) capacity, while the HX1000A L supports buckets from 7 to 8.9 cubic yards (5.4 to 6.8 cubic metres).
“These heavy-duty Hyundai exca vators are engineered to deliver peak performance in mines, quarries, and large-scale construction projects,” says Joe Hodges, product manager, HD Hyundai CE North America. “Both ma chines were built to ensure maximum productivity while reducing total cost of ownership.”
Bucket digging force ratings also reflect the machines’ suitability for heavy-duty applications, with the HX800A L delivering 85,098 lbf (38,600 kgf) and the HX1000A L delivering 88,185 lbf (40,000 kgf).
Both excavators offer selectable power modes and an electronic power-optimizing system for control over machine power and efficiency. The HX800A L also comes with an integrated smart power control system which monitors the excavator’s real-time performance data and automatically tunes the engine power and hydraulic flow to match the operational requirements for maximum performance.
Both excavators come with Hyundai’s warranty and five years’ unlimited access to Hyundai’s Hi MATE fleet management system.
Kleemann’s MSS 502 (i) EVO offers a generously dimensioned feed hopper, a screening surface of 5.4 square metres, and a wide main discharge conveyor that ensures good material guidance.
Well-designed hydraulics ensure high power transmission for lower costs. An optional electro-hydraulic Dual Power drive allows the machine to be run electrically for on-site emission-free operation. A load-controlled fan reduces noise levels and diesel consumption. Water sprays at the discharge conveyors cut dust emissions and improve working conditions around the machine.
All of the conveyor belts feature steplessly adjustable speed, and a simple conversion from two to three final grain sizes is possible, adding flexibility to the screener. The screen casing angle can be set from 15.4 to 20 degrees for a high screening capacity combined with very high product quality. This is complemented by a wide selection of screening media that can
handle everything from excavated earth to decorative grit.
A user-friendly operating system on the new MSS 502 (i) EVO features automatic mode for simple and fast production start. The mobile operating unit, optional radio remote control, and telematics solution contribute to improved planning, operation, and analysis.
A good view of transfer points and the material flow is always possible thanks to LED lighting. Easy ergonomic access to screen decks and components requiring maintenance improve safety and reduce downtime. Flexible refuelling from both sides of the machine and simple cleaning of the hopper discharge conveyor using a retractable chute also reduce downtime.
Compact transport dimensions and stepless drive control simplify transporting the screen. During set-up, joystick control on the mobile operating device combines with assembly-free folding out of discharge belts to allow easy and precise positioning.
There’s only one place you’ll find the heavy hitters of concrete and masonry this January: Vegas, baby — at World of Concrete 2025, the largest and only annual international event dedicated to your business. Be here to mix with industry giants. Get your hands on the latest technologies revolutionizing safety, performance and speed. And learn what it takes to not only claim a piece of our industry’s massive projected growth but dominate the field. Join the
EXHIBITS: JANUARY 21-23, 2025
EDUCATION: JANUARY 20-23
LAS VEGAS CONVENTION CENTER
TRUCK BUILDER MAKES IT EASY TO CUSTOMIZE A MACK TRUCK.
Mack Trucks’ Truck Builder is a digital platform that allows users to customize their dream Mack truck from the ground up. This tool is a comprehensive overhaul of Mack’s previous online truck customization experience.
“Our new Truck Builder isn’t just an upgrade — it’s a complete reimagining of how customers interact with our products,” says David Galbraith, Mack Trucks vice president of global brand and marketing. “We’ve created an immersive, user-friendly experience that brings the excitement of building a Mack truck to life in new and unprecedented ways.”
Users can personalize every aspect of their truck, and it covers the Mack Pinnacle, Mack Granite, Mack Anthem, Mack MD Series, and the Mack LR, including MD Electric and LR Electric models. Users can explore a full 3D rendering of both the truck exterior and the cab interior, including trim options. The exterior colour can be customized with an expanded palette. Control over component selection across body, powertrain, axles, suspension, and chassis ensures the truck meets the user’s needs. Multiple viewing angles, including studio view, 360-degree rotation, and
detailed hot spots, are available.
Truck Builder integrates Mack’s financing options and the Mack Connect fleet performance portal into the customization process, giving users a comprehensive view of their potential Mack truck ownership experience, and meets the specific needs of both over-the-road and vocational applications.
The Truck Builder also introduces users to Mack Connect, a unified dashboard that offers real-time performance data, location tracking, analytics, and diagnostic insights. This fleet performance portal enables future Mack truck owners to track performance, optimize routes, identify points of interest using location data, maximize uptime, and increase efficiency. The platform also highlights Mack’s warranty protection and service contract options.
Once a build is complete, the platform seamlessly connects customers with local Mack dealers who can refine the specifications and bring the custom truck to life. The builder saves configurations, allowing users to revisit and modify their designs at their convenience.
STELLAR’S TMAX 3T ALUMINUM MECHANIC TRUCK IS A LIGHTWEIGHT VERSION OF THE STEEL TMAX.
tellar introduced its new TMAX 3T Aluminum Mechanic Truck at MINExpo 2024. The tandem axle TMAX 3T Aluminum Mechanic Truck is a lighter-weight alternative to Stellar’s steel TMAX Tandem Axle Mechanic Truck and is available in 14-foot and 17.5-foot bodies.
“We are so excited to unveil the aluminum version of the TMAX 3T Mechanic Truck,” says Tim Davison, vice president of sales and marketing at Stellar. “This lighter-weight, corrosion-resistant aluminum model exemplifies our commitment to delivering cutting-edge solutions that minimize downtime and enhance operational efficiency and reliability in challenging environments.”
Suited for the demanding conditions of mining operations, construction sites, and more, this aluminum mechanic truck combines the benefits of lightweight construction with enhanced durability. The TMAX 3T Aluminum Mechanic Truck features increased payload capacity, superior corrosion resistance, and an extruded top rail for convenient mounting. It also includes a robust steel crane compartment and a torsion box to withstand the
With a weight reduction of 1,587 pounds compared to the steel model, Stellar says its TMAX 3T Aluminum Mechanic Truck maximizes payload and efficiency without sacrificing options or durability.
BY MEGHAN BARTON, SENIOR WRITER
Founded by Tom Foord in 1953 as a small automotive ser vice shop in Vernon, British Columbia, Kal Tire has since grown into a tire service industry leader with over 260 stores across Canada. Kal Tire’s steady growth and expansion into the mining tire space since the 1970s reflects a deep com mitment to innovation, safety, and performance in a rapidly evolving market.
Today, Kal Tire’s Mining Tire Group delivers tire management expertise, proprietary tools, and sustainable solutions to mining industry clients across five continents. Kal Tire teams manage more than 120,000 tire changes every year. Kal Tire’s growth is also measured by the creation of its forward-thinking Innova tion Centre in Vernon, a hub for solutions and product design. Launched in 2015 under the leadership of Peter Nilsson, innova tion and R&D manager, this centre is turning out products that enhance safety and productivity in the mining sector.
This dedication to innovation is exemplified by Kal Tire’s lat est breakthrough: WheelJaws, a game-changing and award-winning tire changing tool that has already gained industry acclaim. Part of the new KalPRO brand, a recently launched line highlighting the collection of Kal Tire’s proprietary mining tire products and technologies, WheelJaws redefines tire management and safety practices.
This hazardous aspect of tire maintenance sparked the idea for a tool to help technicians work more safely and efficiently.
In the heavy-duty mining and construction industries, the removal of massive earthmover tires is a high-stakes process with inherent safety risks. The standard procedure requires a tire technician to enter the narrow space between the wheel assembly and the tire manipulator to remove the final lug nuts. This step is critical yet dangerous. Human error or environmental conditions could cause the 8,000-kilogram assembly to tip, posing a severe threat to the safety of the technician.
WheelJaws is a groundbreaking solution to this age-old problem in mining tire management. The core innovation of WheelJaws lies in its design and functionality. Installed at the 3 o’clock and 9 o’clock positions on the tire, the WheelJaws device secures the wheel assembly before the final lug nuts are removed. This is achieved by attaching the WheelJaws onto specific studs, effectively gripping the tire assembly in place, so that the technician no longer needs to be positioned between the assembly and the tire handler during the riskiest part of the process.
Once WheelJaws is in place, the “jaws” hold the tire securely. The device operates through a remote control, allowing the technician to engage or release the jaws from a safe distance,
journey marked by iterative innovation and persistence. The project began with a simple concept aimed at addressing a spe cific safety gap in ultra-class tire handling and quickly evolved through several phases of prototyping and refinement. Early in the process, Kal Tire created a 3D-printed prototype to present to key stakeholders, sparking immediate interest and validating the need for this innovation in mining operations. However, the journey was far from straightforward.
In 2021, the team was forced to pause development due to COVID-19 restrictions, unable to test prototype number two at mine sites — a step critical to gaining real-world feedback. When restrictions lifted, the second prototype revealed signif icant issues that sent the team back to the drawing board. In total, Kal Tire went through four prototypes over almost three years, overcoming technical and logistical hurdles to ensure that WheelJaws would perform reliably and safely in demand ing mining environments.
As Kal Tire’s WheelJaws advances safety standards in mining tire management, the product has also garnered industry recognition. WheelJaws was honoured with the International Manufacturing Innovation: New Product Award at Electra Mining Africa 2024. This prestigious award is given to top new products in the global mining sector, celebrating technological advancements that drive safety, efficiency, and innovation in mining operations.
Another KalPRO product was recognized at the Electra Mining expo in 2018. The first time Kal Tire exhibited a product at Electra, the company was awarded first prize for the KalPRO GATR, its Gravity Assist Tooling Rig for weightless tool operation.
These wins for Kal Tire have underscored the importance and the value of the company’s investment in driving change through its Innovation Centre. As more organizations seek solutions that prioritize worker safety without sacrificing efficiency and performance, WheelJaws sets a new bar in tire management, reinforcing Kal Tire’s ingenuity in the mining tire sector.
Market adoption of WheelJaws has been swift and global, with the first units heading to mining sites in Zambia, Australia, and Chile. This widespread demand underscores the industry’s eagerness for innovations that enhance productivity and safety.
The impact of WheelJaws extends beyond safety improvements. By eliminating the most dangerous step in tire installation and removal, Kal Tire has also enhanced operational efficiency and reduced downtime. This reduction increases productivity on site but also results in substantial cost savings, especially over long-term operations where cumulative downtime can significantly affect profitability.
The development journey of WheelJaws has provided Kal Tire’s Innovation Centre with valuable insights that will shape future projects. One of the standout lessons learned was the importance of engaging field team members in the early stages of product development.
Through internal initiatives like the “Bright Idea” program, Kal Tire designates “Super Users” — global ambassadors in each market — who collaborate closely with on-the-ground team members to identify job site challenges and propose effective solutions. By involving those who would ultimately use and support the product at mine sites, Kal Tire secures vital buy-in, leading to a smoother acceptance of technologies like WheelJaws across its global operations.
“There is a certain pride among our team members when they feel they have a stake in a tool’s development and success,” says Nilsson. Recognizing this, Kal Tire sets a precedent for user-centred design and collaboration.
As WheelJaws expands to more mining sites worldwide, Kal Tire is assessing the logistics of global manufacturing and distribution. Although initially produced in Canada, scaling up production to meet international demand may involve partnering with regional manufacturers in heavy manufacturing hubs. This
I watched a tire tech enter the space between the tire and the wheel manipulator. We call it the ‘danger area’. I thought to myself, ‘There has to be a safer way’.
Peter Nilsson Innovation and R&D Manager, Kal Tire
approach could streamline distribution, reduce costs, and meet demand more efficiently as the popularity of WheelJaws grows.
Looking forward, Kal Tire’s Innovation Centre is actively exploring new concepts, guided by insights gained from WheelJaws. The development process now includes regular ops meetings that gather feedback from operational teams worldwide, helping refine ideas before presenting them to leadership.
As Kal Tire considers the future, the Innovation Centre continues to be a hub for ideas and strategies that create safer, more efficient work environments for tire technicians. With numerous exciting projects on the horizon, Kal Tire is well-positioned to bring forth even more transformative solutions that prioritize safety, efficiency, and global impact. WheelJaws is a testament to Kal Tire’s forward-thinking approach, one that values both innovation and the people behind it. HEG
EQUIPMENT-AS-A-SERVICE CAN HELP YOUR BUSINESS PAY AS YOU GO FOR MACHINERY YOU NEED NOW WHILE AVOIDING ONEROUS UPFRONT CAPITAL EXPENDITURES AND PROVIDING GREATER PREDICTABILITY.
BY NELSON ABELHA
This is where Fair Market Value (FMV) leases can offer significant cost advantages and flexibility. With an FMV lease, organizations can receive the full benefits of using the equipment while only paying for a portion of the machine’s value over the lease term.
An FMV lease is a type of operating lease that allows businesses to use equipment for a specified period while making regular payments. This structure is particularly beneficial for companies that need access to heavy equipment but don’t want to invest large amounts of capital up front.
At the end of the lease term, the business has the option to return the equipment, extend the lease, or purchase the equipment at its fair market value.
Additionally — and as mentioned previously — one of the biggest advantages of an FMV lease is that it allows businesses to use equipment without having to pay the full cost of ownership. This is especially valuable in the construction sector, where equipment is essential but not always needed long-term. Rather than tying up capital in equipment purchases, companies can allocate those funds toward other critical operational areas.
With an FMV lease, businesses only pay for the use of the equipment during the lease term and are not responsible for the total value of the machine, as they would be with an outright equipment purchase. The result is a more efficient use of financial resources, allowing companies to access the equipment they need while keeping their capital free for other investments.
The concept of “equipment-as-a-service” has gained popularity in recent years, and FMV leases are a prime example of this model in action. With equipment-as-a-service, businesses essentially rent the functionality of the machine rather than owning it outright. This approach offers several advantages.
Equipment-as-a-service allows businesses to control costs more effectively by only paying for the use of the machine rather than bearing the total cost of ownership, maintenance, and repairs. Companies can use the equipment for as long as needed and then return it at the end of the lease term, avoiding the long-term commitment and costs associated with ownership.
With an FMV lease, businesses can easily upgrade to newer models at the end of the lease term, ensuring they always have access to cutting-edge technology and the best tools for the job. This regular access to newer equipment can lead to improved efficiency, reduced downtime, and, ultimately, a stronger bottom line.
The ability to turn variable costs into fixed costs has a direct impact on a company’s cash flow and financial forecasting. When costs are predictable, it’s easier for businesses to allocate funds toward other essential areas such as labour, materials, and project development. This is especially important in an industry such as construction, where cash flow can be inconsistent due to the seasonal nature of the work and dependencies on supply chains and project timelines.
By returning equipment at the end of the lease and opting for newer models, businesses can also avoid the pitfalls of owning outdated equipment, which can become costly to maintain and less efficient over time.
THE CONCEPT OF “EQUIPMENT-AS-ASERVICE” HAS GAINED POPULARITY IN RECENT YEARS, AND FMV LEASES ARE A PRIME EXAMPLE OF THIS MODEL IN ACTION.
project. Instead of purchasing the machines outright, ABC opted for an FMV lease.
effectively shielded itself from potential financial losses tied to the resale of depreciated equipment at the project’s end. This savvy decision relieved the company from the obligation of paying the total value of the machines up front and eliminated burdensome maintenance costs.
Opting for a Fair Market Value (FMV) lease allowed ABC Construction to streamline its expenses into a single manageable monthly payment. This not only ensured consistent monthly costs covering the equipment but also included essential maintenance, repairs, and soft costs like installation. Such an approach not only simplifies budgeting but also enhances operational efficiency, making it a wise choice for any construction firm.
This strategic shift stabilized ABC Construction’s cash flow, providing the funds needed for critical areas like hiring skilled labour and procuring materials. As a result, the company boosted profitability and increased its capacity to take on more projects without the fear of unexpected financial burdens.
At the conclusion of the 24-month project, ABC simply returned the equipment, having only paid for its use throughout the lease. This method allowed them to expand its equipment fleet for the larger short-term project and return the machinery once it was no longer needed. Ultimately, this strategy put them in a prime position to upgrade to the latest models, ensuring the company always has access to cutting-edge technology for future projects.
By leasing rather than purchasing, ABC Construction avoided the costs associated with making payments on the full value of the machine, in maintaining that equipment and taking a loss on the eventual sale of this depreciated equipment at the end of its useful life. By opting for an FMV lease, ABC Construction was able to bundle all these variable costs into its monthly lease payment. Over the course of the lease term, the company enjoyed fixed monthly costs that covered not just the equipment, but also all associated maintenance, repairs, and soft costs such as installation.
This shift allowed ABC Construction to stabilize its cash flow, ensuring it had sufficient funds available for other important areas such as hiring skilled labour and purchasing materials.
during the lease term. ABC Construction was able to expand its ect, then return the equipment at the end of the lease, when it was no longer needed. Ultimately, they were able to upgrade to the latest models when their next project required more advanced technology.
For a $700,000 unit, the payment is $21,869.38 per month.
ABC Construction was also provided an alternative — a 36-month capital lease:
For the same $700,000 unit, the payment is $21,639.08 per month.
However, since the project is only 24 months in duration, with a 36-month capital lease, ABC Construction would be obligated to make an additional 12 months of payments for a machine it no longer required.
That is an additional carrying cost of $259,668.96.
FMV leases provide businesses with the flexibility and financial efficiency needed to stay competitive in the construction sector. By allowing companies to receive the full benefit of equipment without paying for its total value, and by offering the option of regular equipment upgrades, FMV leases are effectively turning equipment into a service that businesses can rely on.
An FMV lease provides more than just access to equipment — it offers financial predictability. By converting variable costs such as repairs, maintenance, and soft costs into fixed payments, construction companies can better manage cash flow, reduce financial risks, and make more informed business decisions. For greater financial stability in an unpredictable industry, an FMV lease is a valuable tool that is worthy of consideration.
NELSON ABELHA is the regional vice president of First Financial Canadian Leasing.
LAS VEGAS, NV | JAN. 21–23, 2025
World of Concrete has served the global concrete and masonry construction industries for over 50 years. This annual international event highlights the latest technologies revolutionizing safety, performance, and speed for these industries with indoor and outdoor exhibits, education programming, and demonstrations. worldofconcrete.com
LAS VEGAS, NV | JAN. 28 – FEB. 1, 2025
The ARA Show serves rental business owners, managers, and their teams with networking opportunities and the latest equipment and innovations aimed at the rental market. Attendees can come early to take advantage of education sessions and gain insights to maximize their business potential. arashow.org
ST. LOUIS, MO | MAR. 25–27, 2025
World of Asphalt/AGG1 is the largest industry event that brings together professionals working in the aggregates and roadbuilding sectors. Highlights include a robust roster of education sessions, live demonstrations, and networking opportunities. worldofasphalt.com
FL | JAN. 15–17, 2025
ON | FEB. 18–19, 2025
• See the latest equipment
• Learn best practices and techniques
• Improve your jobsite and business March 25-27, 2025 | St. Louis, MO
MINING Fortescue commits to “real zero” targets, plans to end fossil fuel use by 2030
Volvo CE and Heidelberg Materials advance partnership to decarbonize construction
Electric air compressor meets the precise demands of an artistic performance
eberspaecher-off-highway.com
No matter how challenging your needs, BKT is with you offering a wide range of OTR tires specifically designed for the toughest operating conditions: from mining to construction sites.
Sturdy and resistant, reliable and safe, able to combine comfort and high performance. BKT is with you, even when work gets tough.