

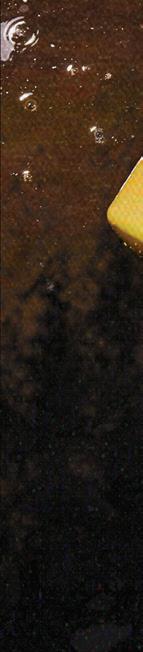
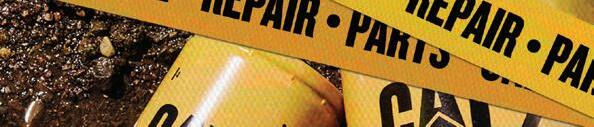
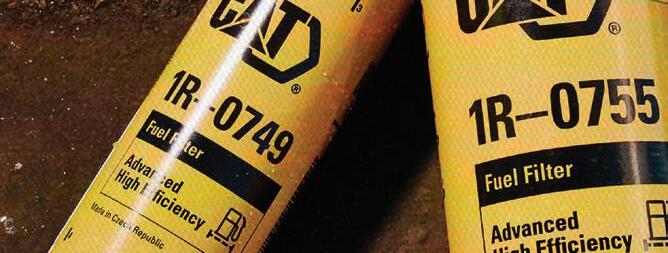
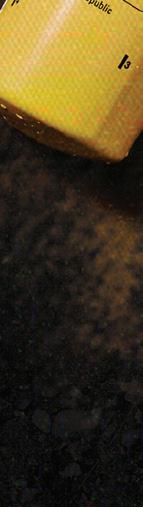

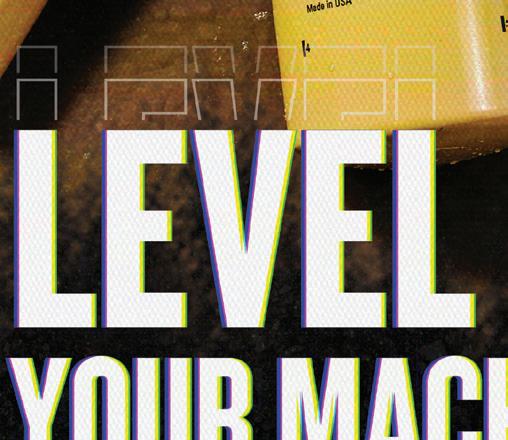
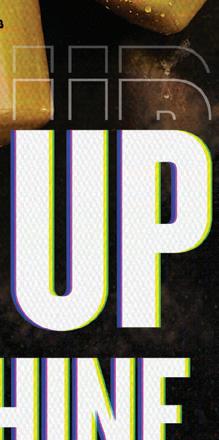
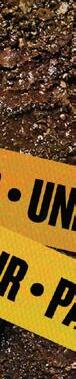
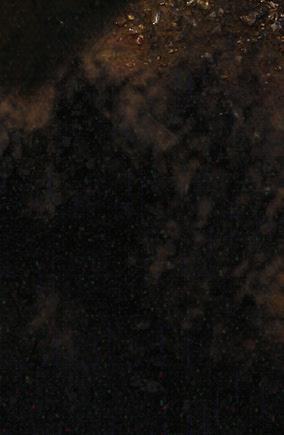

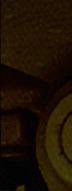
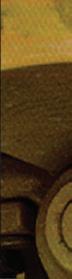

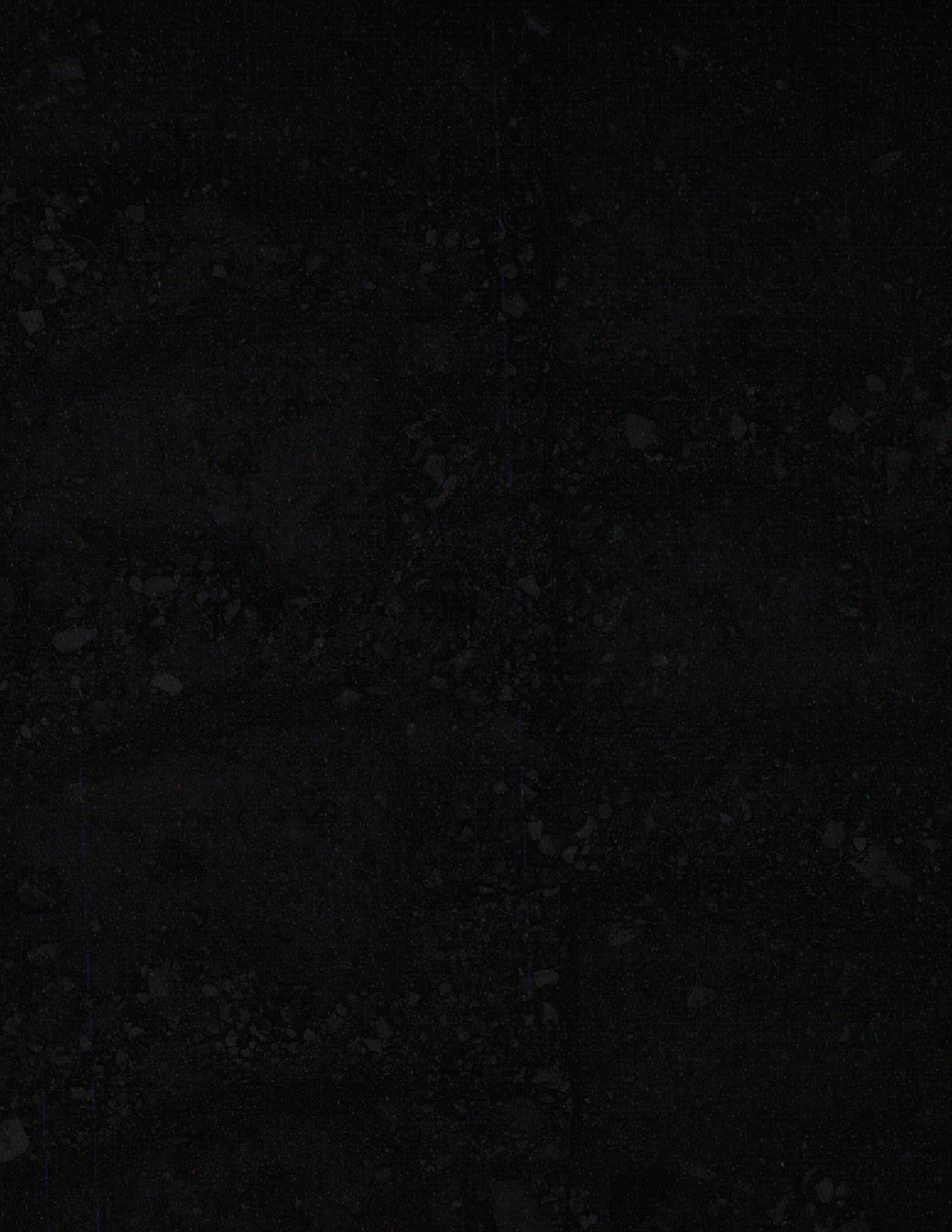
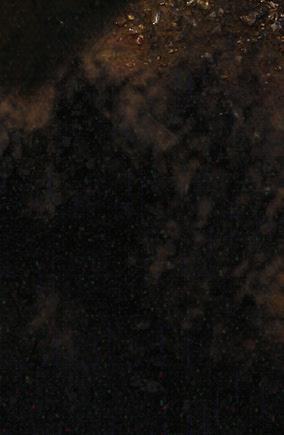
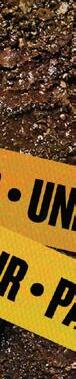
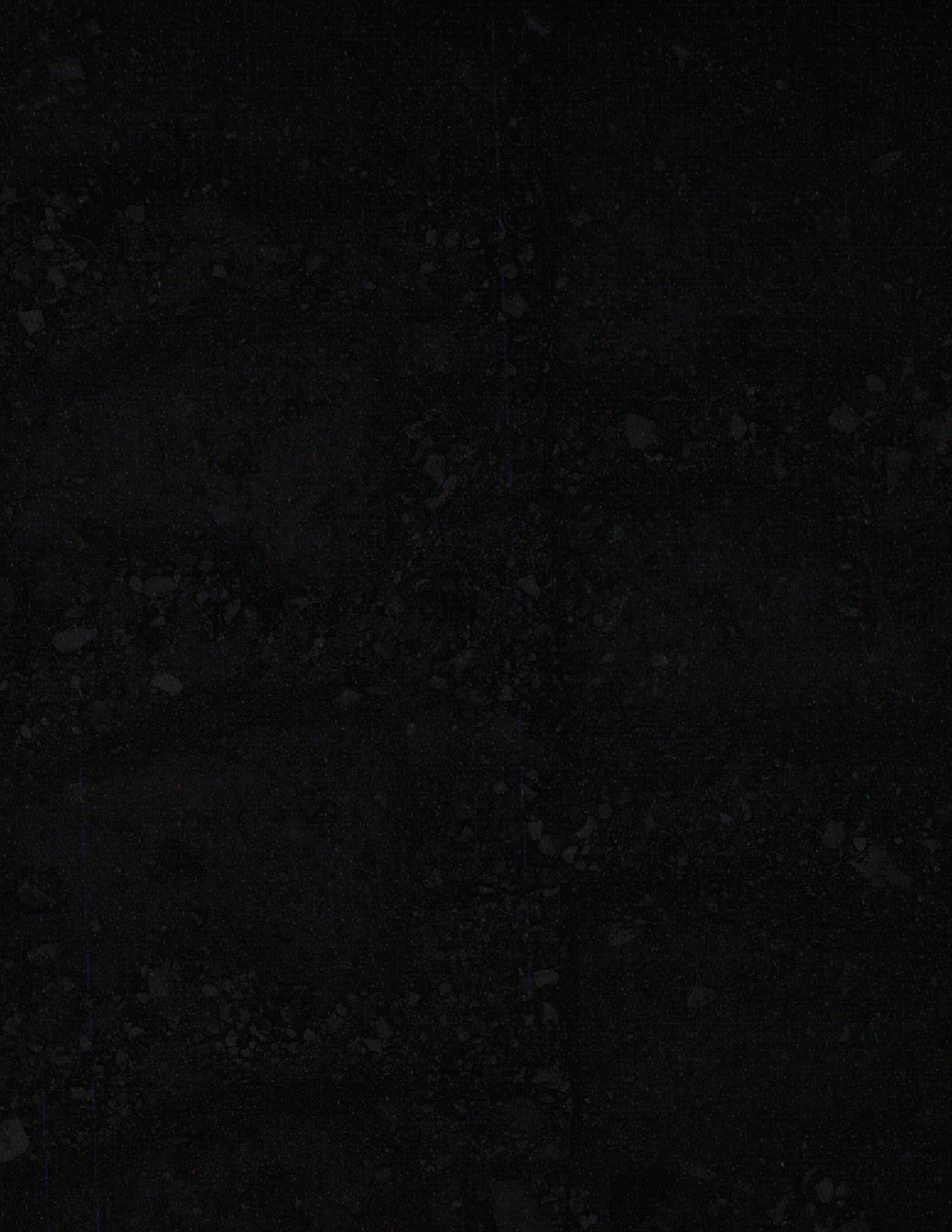


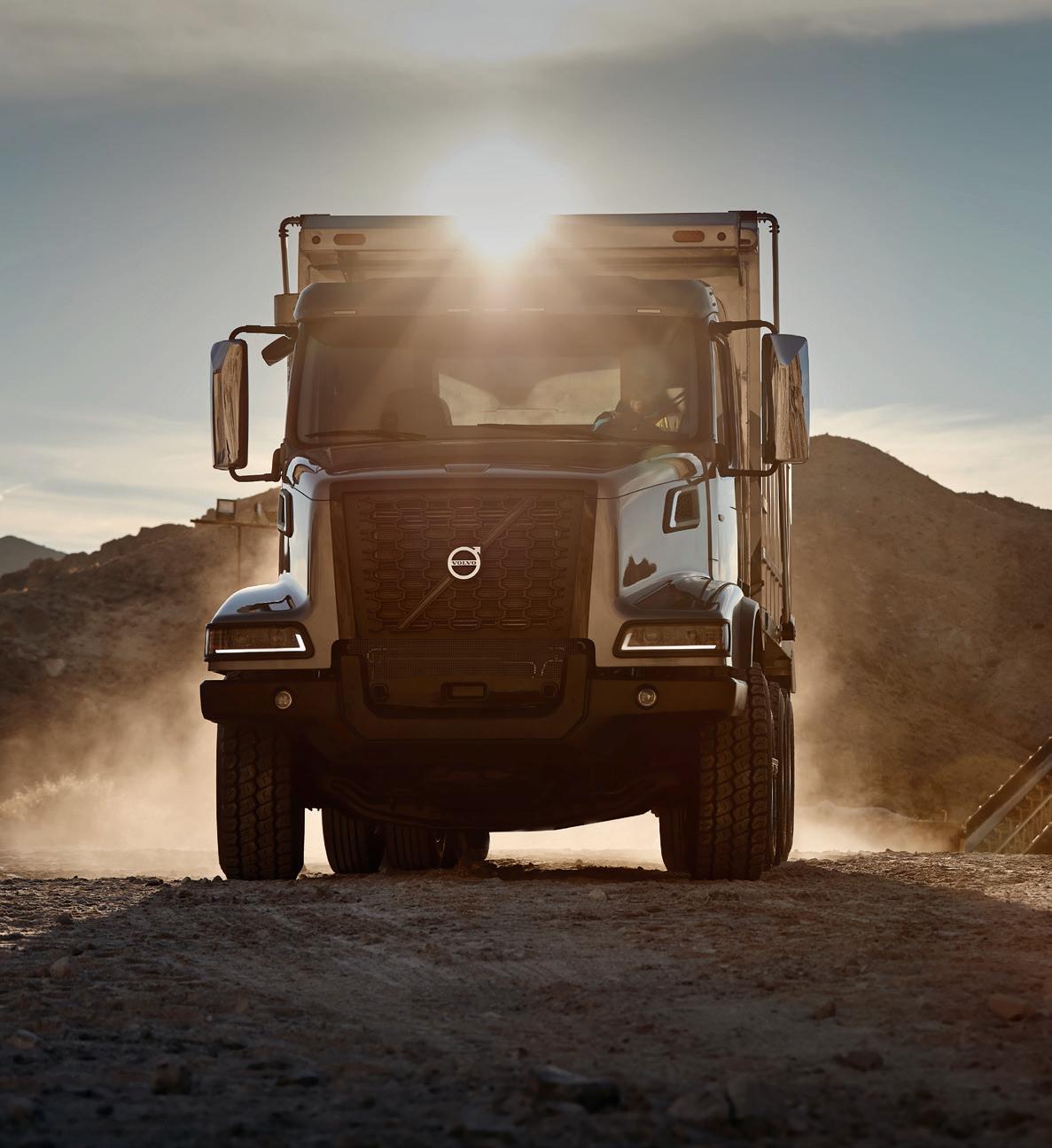

Introducing the new VHD
On the jobsite you need a truck that’s tough, safe, and smart. So, we built the new Volvo VHD to be the best-looking, most rugged vocational vehicle in the industry, packed with innovative ideas like Volvo Active Driver Assist and the revolutionary Volvo Dynamic Steering. Your toughest jobs just got easier. Learn more at volvotrucks.ca/en-ca/trucks/vhd/
Loved for the features. Trusted for the performance.
Do more without feeling like it in Hyundai’s NEW HX355ALCR compact radius excavator.
• Engineered to redefine efficiency, comfort, and safety
• RH and rear camera (standard)
• AAVM 360° camera with ultrasonic system (option)
• LED lights
• Dozer blade (option)
• 8” touchscreen color LCD monitor (standard) and 2nd monitor (optional)
• Free Hi-MATE mobile telematics for 5 years
No wonder so many first-time Hyundai users become longtime fans. See the Hyundai difference yourself at your local dealer, or na.hd-hyundaice.com NEW MODEL
FEATURE STORY THE DEEPEST DIGGING EXCAVATOR IN NORTH AMERICA
28 THE INDUSTRY’S FIRST ELECTRIC BACKHOE LOADER
30 38
HOW PROPANE CAN INCREASE PRODUCTIVITY
MINING EQUIPMENT, AUTONOMY & DECARBONIZATION
50
COVER PHOTO: LIEBHERR R 9150 MINING EXCAVATOR.
First Liebherr mining excavator in Eastern Canada goes to work at Quebec lithium mine Turn to page 38.
CONNECT WITH US @HeavyEquipGuide
WE’D LIKE TO HEAR FROM YOU
Do you have a job site story, innovation, or industry concern that our readers should know about? We’d like to hear from you.
EDITOR IN CHIEF Kaitlyn Till ktill@baumpub.com 604-291-9900 ext. 330
EDITOR Stephanie MacDonald smacdonald@baumpub.com 604-291-9900 ext. 335
ASSOCIATE PUBLISHER
Sam Esmaili sam@baumpub.com 604-291-9900 ext. 110
ADVERTISING
PRODUCTION MANAGER
Tina Anderson tanderson@baumpub.com 604-291-9900 ext. 222
DESIGN & PRODUCTION
Morena Zanotto morena@baumpub.com 604-291-9900 ext. 325
PRESIDENT/PUBLISHER
Ken Singer ksinger@baumpub.com 604-291-9900 ext. 226
VICE PRESIDENT/CONTROLLER
Melvin Date Chong mdatechong@baumpub.com
FOUNDER
Engelbert J. Baum
Published by: Baum Publications Ltd.
124 - 2323 Boundary Road Vancouver, BC, Canada V5M 4V8
Tel: 604-291-9900
Toll-free: 1-888-286-3630 Fax: 604-291-1906 www.baumpub.com www.heavyequipmentguide.ca @HeavyEquipGuide
FOR ALL CIRCULATION INQUIRIES
Toll-free: 1-866-764-0227 email: heg@mysubscription.ca
Subscription: To subscribe, renew your subscription, or change your address or other information, go to: http://mysubscription.ca/heg/
Heavy Equipment Guide serves the Canadian engineered construction industry including: roadbuilding and maintenance; highways, bridges, tunnels; grading and excavating; earthmoving; crushing; trucking and hauling; underground utilities; trenching; concrete paving; asphalt paving; demolition; aggregates production; fleet maintenance; and asset security and management. The magazine is distributed to key industry personnel involved in these sectors.
Subscription Price: In Canada, CDN $91.00; Outside Canada, US$149. Heavy Equipment Guide is published eight times a year in January/ February, March, April, May/June, July/August, September, October, and November/December.
Heavy Equipment Guide accepts no responsibility or liability for reported claims made by manufacturers and/or distributors for products or services; the views and opinions expressed are those of the authors and not necessarily those of Baum Publications Ltd.
Copyright 2024, Baum Publications Ltd. No portion of this publication may be reproduced without permission of the publishers.
We acknowledge the financial support of the Government of Canada.
Printed on paper made of FSC®-certified and other controlled material. ISSN 1715-7013.
PUBLICATIONS MAIL AGREEMENT NO. 40069270
Return undeliverable Canadian addresses to:
Contact: Editor in Chief Kaitlyn Till at ktill@baumpub.com or 604-291-9900 ext. 330 SEPTEMBER 2024 | VOLUME 39 • NUMBER 6
Circulation Dept., 124-2323 Boundary Road, Vancouver, BC V5M 4V8 email: heg@mysubscription.ca Toll-free: 1-866-764-0227
All it takes for the challenges you face.
From the original compaction brand comes a full line of construction equipment designed to help you get the job done with efficiency, quality and comfort. Whether your challenge is to load, move or place material, compact soil and asphalt, or to provide light, heat, power or pumping on your job site, Wacker Neuson has the machines to get it done right. This includes zero-emission, battery-powered solutions to meet the demands of the construction environment today, as well as tomorrow.
Contact your local Wacker Neuson dealer today.
The mining industry is an ideal proving ground for new technologies that can benefit the construction industry.
Sites are large and remote, and traditionally mining vehicles have been significant emitters of GHGs. Decarbonization and autonomy were hot topics in mining long before they came to construction sites and smaller quarries.
Mining operations are perfect for proving the efficacy of autonomy. Haul trucks travel the same routes; encounter a predictable, finite set of variables; and are completely removed from public spaces. As a result, autonomous hauling is now a proven technology for the mining sector, and haulers from major OEMs — including Liebherr, Komatsu, Hitachi, and Caterpillar — have achieved massive tonnage milestones on projects in conjunction with large mine operators.
While autonomy is a difficult proposition for trucks operating on more fluid construction sites, autonomous ADTs are now used by some quarry operations and development of the technology for more applications is ongoing. The continuing development of autonomous features to assist operators is vital for an industry that is struggling to attract and retain skilled labour.
The next step is combining autonomy with electrification to further decarbonize the mining process. Electric drive tech for mine haul trucks has been developed since the 1960s and is commonplace now. It is growing in availability on larger construction vehicles, such as dozers and wheel loaders. Mining has moved on to the next step in electrification for large equipment. Today, Liebherr, Caterpillar, and Hitachi are among OEMs that have tested 100 percent electric mining trucks on active mine sites around the world.
Trolley assist, which provides electric power to mining vehicles via overhead power lines along haul roads, has been explored since the 1970s. The use of trolley assist on mine haul roads is growing, and you can see Komatsu trucks using trolley assist in action starting on page 42.
Decarbonization and autonomy were hot topics in mining long before they came to construction sites and smaller quarries.
Battery-electric vehicles have been used in underground mining for more than a decade, and the mining industry is experienced with managing some of the challenges that the construction industry is now facing, such as how to maximize electric machine usage and how to optimize charging of electric machines via on-board charging or off-board charging with battery swapping.
We’ll be attending MINExpo at the end of September to learn more about the mining sector’s innovations designed to increase productivity and accelerate decarbonization. We will provide extensive coverage, including of Caterpillar’s major announcements, at heavyequipmentguide.ca during and after the show. For now, explore more mining innovation starting on page 38 in this issue.
Kaitlyn Till Editor In Chief
ktill@baumpub.com
heavyequipmentguide.ca
The Canadian Equipment Dealers Association (CEDA) will merge with the Associated Equipment Distributors (AED).
The merger is expected to be finalized by November 1.
“We are pleased with the outcome of the vote and look forward to the future with AED,” CEDA President and CEO Beverly J. Leavitt said. “CEDA board members carefully evaluated various factors before selecting AED. AED offers the best benefits and resources for our members going forward.”
“We are confident that CEDA members will see increased value with the merger of their organization into AED. CEDA has a long history of delivering outstanding service to its members and we look to build upon this strong foundation,” said AED President and CEO Brian P. McGuire. “The industry will be stronger as we unite as one organization.”
Leavitt will serve as vice president at AED and will be responsible for seeing a smooth integration of CEDA’s over 160 members into AED. She will also work on member recruitment for AED.
“CEDA has been a trusted resource for equipment dealers for over 78 years, helping them navigate the ever-changing challenges of running a dealership,” said CEDA Chairman Brian Osterndorff. “As we look ahead, it’s important for us to align with AED to continue providing the level of support our dealers expect. Our decision to enter into discussions with AED was based on the strong alignment of our values and the clear representation AED provides in Canada, making this partnership a natural choice. By joining forces with AED, we can ensure that our dealers have access to even stronger resources and support. Our priority has always been our dealers, and this partnership marks an exciting new chapter for us. We look forward to working with AED to keep serving our industry.”
“We are excited to welcome CEDA members into the AED family and are eager to support them in navigating the challenges of running successful businesses,” said AED Chairman John Shearer.
CEDA members will gain access to the full range of AED resources and benefits including educational conferences and seminars, online courses, multiple industry reports, and strong advocacy in Ottawa. AED will carry on CEDA’s representation at the provincial level in Ontario. The merger comes a year after the Far West Equipment Dealers Association merged with AED.
As part of an expansion plan into Canada, Procore has forged two new industry partnerships aiming to advance diversity and inclusion in the construction industry. According to the company, the partnerships with the Afro Canadian Contractors Association (ACCA) and the Canadian Association of Women in Construction (CAWIC) illustrate Procore’s commitment to supporting diversity, inclusion, and innovation within the construction industry.
The partnerships include training, technology solutions, and support to minority contractors, diverse-owned firms, and women in construction across Canada, including access to Procore’s construction management platform and discounted buying programs to eligible members.
The president of the Afro Canadian Contractors Association, Stephen Callender, said he is proud to work with Procore on this project.
He added, “This collaboration is a testament to our shared commitment to fostering diversity and inclusion within the construction industry. By providing minority contractors with cutting-edge technology and comprehensive training, we are equipping them with the tools they need to thrive in a competitive market.”
Procore, ACCA, and CAWIC will also collaborate on thought leadership initiatives, including webinars, articles, and industry insights.
“I am thrilled to see Procore’s commitment to diversity and inclusion within the construction industry,” said Lisa Laronde, president, Canadian Association of Women in Construction (CAWIC). “This partnership with Procore represents a powerful step toward providing women in Canada with the resources and opportunities they need to succeed. Together, we can break down barriers and foster a more inclusive and innovative construction industry.”
Caterpillar’s first-ever Global Dealer Technician Challenge celebrates the role dealer technicians play in the service experience. This challenge, for independent Cat dealers that choose to participate, showcases how skilled technicians have a high-tech, high-impact, high-demand career.
“This hands-on, skills-based competition will test the technicians’ agility, resilience, and versatility,” said Caterpillar global service vice president Henry Venneman. “These trained experts are on the front line of support, working to keep machines and engines up and running to help ensure our customers’ critical projects are completed.”
Cat dealers globally are offering growing opportunities for technicians. By the end of 2026, it is estimated that Cat dealers may need to hire more than 44,000 technicians. This competition is also designed to help raise awareness of the career opportunities in this field.
“There are thousands of opportunities available globally for those who are interested in a hands-on career,” said Venneman. “Cat dealers are often looking for individuals who are problem solvers, mechanically inclined, and tech savvy.”
The Global Dealer Technician Challenge will take place over a series of regional and semifinal competitions around the world. The top 10 finalists will have the opportunity to compete in the finals in March 2026 at CONEXPO/CON-AGG in Las Vegas.
BelPacific’s excavation for 1515 Alberni Street in downtown Vancouver required a customized excavator with the deepest reach in North America.
Learn more on page 30.
Longtime Mack Trucks dealer Vision Truck Group invested $20 million to open a new facility in Brantford, Ontario, in April. The Brantford site has 22 service bays and is a Mack Certified Uptime Dealer, meaning it received the accreditation because it has met stringent requirements to improve uptime for customers. The location is a natural-gas-certified facility, and the team is currently working toward becoming a Mack Certified Electric Vehicle Dealer. Vision will employ about 70 people at Brantford, building toward 40 technicians, with 12 master techs. The Brantford site offers $2 million in parts inventory.
VMAC announced its new High-Voltage Electric Vehicle (HVEV) air brake business in July. The project received over $3.1 million in funding from the Pacific Economic Development Agency of Canada (PacifiCan), through PacifiCan’s Business Scale-up and Productivity program.
VMAC’s HVEV business has also received funding and support from the National Research Council of Canada Industrial Research Assistance Program (NRC-IRAP), the B.C. Manufacturing Jobs Fund, and the Canada Trade Commission’s CanExport SMEs.
Brandt Tractor is now an authorized Canadian SharpGrade dealer. Family-owned and based in Hamilton, New Zealand, and Ohio, U.S., SharpGrade is a specialist design, manufacture, and export business known for building skid-steer grader attachments. According to Brandt, The SharpGrade addition is an exciting opportunity for the Brandt machine guidance product line. SharpGrade products will be available across Brandt’s 56 Canadian locations.
Liebherr has plans to build a new logistics distribution centre for spare parts for North and South America on newly-acquired 480,000 square metres of land in the Hive Business Park in Tupelo, Mississippi. In addition, the company intends to invest over $200 million to establish a campus on the site, where various business units from different product segments will operate in the future.
The continental warehouse of Liebherr-Logistics GmbH will handle logistics and service operations, such as warehousing, distribution, value-added services — pre-assembly, kitting, repackaging — as well as customs and export services. Liebherr-Logistics GmbH provides logistics services for the earthmoving machinery, components, concrete technology, tower cranes, and maritime cranes product segments.
Hillhead 2024 was the most visited show ever in terms of the volume of visits over the three days, with visitors spending more time at the show than ever before. The show even achieved a record number of attendees for more than one day. In total, there were 26,626 visits over the three days, which was eight percent higher than 2022.
In terms of unique visitors, with 19,577 attendees (6.2 percent higher when compared with 2022), this year’s show had the second highest-ever number of unique attendees (only 2018 was higher at 19,753, although that show had less volume over the three days).
June 26 was easily Hillhead’s busiest day ever with almost 10,800 people on site throughout the day.
www.heavyequipmentguide.ca
The R60, with a 55-ton payload, and the R70, with a 65-ton payload, are designed to reduce total cost of ownership while prioritizing operator comfort and safety. The R60 can carry a volume of 36.04 cubic metres, while the R70 hauls 42.4 cubic metres. Both have a V-shaped haul body designed for load retention and minimal carryback post-dumping. These haulers feature a fast-tip system for quick dumping, and an optional On-Board Weighing system allows operators to maximize the load.
High-drive axle multiplication ensures the haulers have plenty of traction, while a high-torque engine is supported by automatic adaptive gear selection offered by Volvo Dynamic Shift Control to help cut fuel use. A selectable Eco mode defaults to the most efficient gear, while the auto engine idle shutdown
reduces engine wear.
The haulers feature gear-dependent speed control and a selectable brake or transmission retarder. The gearbox also has overspeed protection and a neutral coast inhibitor for downhill work. Fail-safe braking and a secondary steering system keep the machine on the right track.
Access to the cab from both sides includes anti-slip steps. Inside, a large windscreen and low dashboard combine with a left-positioned operator station for good job site views. The 360-degree Volvo Smart View is optional.
An ergonomic seating position and air suspended seat, paired with independent suspension, give operators a smooth ride. Low-effort steering with an adjustable wheel makes driving simpler.
With its 700- by 500-mm jaw chamber and diesel-electric drive technology, EvoQuip’s Bison 170 jaw crusher is suitable for both natural rock and recycling applications and provides output of up to 110 tph. A fuel-efficient diesel-electric drive system with an on-board generator powers the plant. It can also be plugged in and driven from an external power source, such as mains power, which allows for zero-emissions processing. The engine and power unit can also be removed completely, allowing the plant to be powered from an external source with no combustion engine on board. The electric drive can run in reverse for asphalt recycling and also provides an unblock/jog function. The deflector plate, fitted as standard, provides belt protection by allowing uncrushable objects to pass through the crushing chamber safely and onto the discharge belt safely.
The versatile BPW wireless mobile column lifts for medium and heavy-duty vehicles are powered by a low-friction recirculating ball-screw mechanism, allowing for precise lifting control. A long battery life enables more lifting cycles per day, and technicians can move and reposition each wireless mobile column lift, increasing turnaround time and productivity.
Wireless mobile column lifts can be hooked up in sets of up to eight with a maximum capacity of 144,000 pounds, and each wireless lift supports up to 18,000 pounds. Eliminating wiring declutters work areas and reduces risks, and the recirculating ballscrew mechanism requires little maintenance, is lightweight, and does not have fluids that can leak. Self-balancing and automatic shut-off add protective measures.
Vermeer has updated the versatile RTX1250 ride-on tractor to improve efficiency and performance for a variety of tasks in installation of gas, fibre, water, and electrical utilities. It’s powered by a 127-hp Deutz diesel engine, and attachments can be switched out in as little as an hour. Options include a backhoe, backfill blade, or reel carrier attachment for the front of the machine and a vibratory plow, rockwheel, sliding offset rockwheel, sliding offset trencher, or trencher for the back end.
On-board technology includes TrenchSense electronic control system and EcoIdle engine control. These systems actively monitor the engine’s operations to promote smooth trenching, prevent stalls, and optimize fuel efficiency. The Productivity Zone feature and Auto Plunge technology determine the optimal operating range and ground speed for attachments in use and control the plunge rate for trencher or rockwheel attachments, respectively. The ride-on tractor can be outfitted with rubber tires or tracks.
Loader operators who need a little more reach will get just that thanks to two new telescopic New Holland small articulated loader models, the ML35T and ML50T. The flexibility of the telescopic booms allows operators to retract and extend the load as needed; these models are a good fit for sites with limited space thanks to their ability to deliver horizontal and vertical outreach. Both models have a hinge pin height of around 170 inches. They are powered by 65- and 74-hp engines respectively, and are built for durability with steel plates and reinforced booms.
The rear articulation position puts the operator toward the front of the machine, making for a more ergonomic and accessible cab, and the loaders can be manoeuvred closer to walls or in tight spaces with reduced risk of collision. The cab is also more stable thanks to the inclusion of zero-cab swing, which according to New Holland is unique to its small articulated loaders. Climate control and adjustable seating are included.
BY LEE TOOP
Asignificant barrier to the adoption of electric construction equipment by contractors is their lack of confidence that convenient, reliable charging will be available at job sites. You can charge a machine at the shop just fine, but put it on a remote job site, and you’re faced with a problem. If there are no grid connections available, you’re stuck with a diesel generator and its associated fuel costs plus emissions.
For Portable Electric, a Vancouver, B.C.–based producer of mobile power solutions for a variety of industries, working with Volvo Construction Equipment has resulted in a new solution for on-site charging of construction equipment. The solution developed by Volvo and Portable Electric — the PU130 mobile charger — has the power storage and connections necessary to charge electric machines while also powering tools and site structures.
Founded in 2015, Portable Electric has focused on areas like film and television with a range of products that provide battery-stored power which can be used silently and easily recharged as need-
ed — in some cases using solar panels right on site. The company’s Voltstack technology has been selected for tasks such as shoots in busy neighbourhoods where generators would be unwelcome. Or, in one case, built right into the set of a major Marvel movie — hidden by a train seat in the background of a tricky fight scene where no other power source could fit the bill.
Portable Electric’s Voltstack 30k towable BESS (battery energy storage solution) has “smart hybrid” capability, which provides versatile power for site use. If needed, it can be connected to a diesel generator. When the Voltstack 30k reaches a predefined depleted state of charge set by the user, it automatically triggers the diesel generator to recharge it. Then, once it reaches the pre-defined replenished state of charge set by the user, the Voltstack 30k communicates to the generator that it can shut down. This system ensures no waste of power and keeps the diesel genset running at the correct load, which reduces maintenance costs.
Keith Marett joined Portable Electric as CEO in 2023 after years of experience in the clean energy sector. He says that, as one of the early adopters of electrified equipment, Volvo was looking for power options to work with its dealer network, and later for partners to develop equipment charging solutions.
There is no industry standard for construction EV charging. “Currently there are two different voltage architectures used in the construction EV space — less than 96 volts or low voltage; and greater than 96 volts, usually around 400 volts, or high voltage,” says Marett. “Each of these solutions requires their own matching fast charging solution and in the case of Volvo, which utilizes a 48-volt architecture for their compact equipment, we had to design a specific low-voltage charging solution.”
Volvo isn’t the only OEM that Portable Electric has developed a charging solution with — the company worked with LeeBoy. Leeboy, however, leverages automotive high-voltage architectures and requires a high-voltage charger
tric’s experience working with Leeboy has helped inform its work with Volvo. The Voltstack 30k that was paired with LeeBoy’s 8520C E-Paver demonstrated that it could quickly charge the machine and keep it working. Portable Electric started work with Volvo exploring Level 2 charging options, which operate on currents of 12 to 80 amperes.
“The challenge we found was it was just taking too long on Level 2 — anywhere from six to eight hours to recharge that equipment,” Marett says.
“We call it low-voltage DC fast charging — it’s similar to what you’d find in a Tesla supercharger, but it’s done at low voltage capacity for construction equipment. That cuts the charge time down from what we were doing at Level 2, six to eight hours, down to a half-hour or less,” Marett describes.
Designed to power both electric construction machines and job site tools and structures, the PU130 has a storage capacity of 130 kWh and a low-voltage DC fast charging rate of 20 kW, combined with a 40 kW AC output. It uses LFP — lithium iron phosphate — batteries and this rugged unit can be towed across rough roads or into dusty, dirty environments and still operate smoothly. It also has a broad operating temperature range, including sub-zero.
“If you’re just doing straight equipment recharging, you can typically get six to eight pieces of equipment recharged off that. If you’re adding other loads, such as tools or lighting, that’s going to vary the capability,” Marett says.
Once the PU130 needs to be recharged, it can be trickle charged from low-amperage site power connections, swapped for another unit and recharged off-site, or paired with a traditional generator. During downtime, the generator runs long enough to quick-charge the battery unit, then shuts back down. The generator runs far less and produces less emissions when charging the battery than it would need to if charging machines directly. Typically it will take four to six hours to recharge the PU130 off the grid.
The PU130 is simple to use compared to generators — in fact, it’s a one-touch system, Marett says. Portable Electric’s PowerAi intelligent controller is built into each unit and manages the flow of power, automatically switching between AC and DC or running both simultaneously, depending on the needs of the user and application. PowerAi communicates with Portable Electric’s Neuron OS software
which allows for remote monitoring and provides re al-time data, analytics, and GPS tracking for the unit.
“If you’re a fleet manager you can see all the units deployed, the state of charge, the data from the field, and how often they’re being used,” Marett says. “Because these systems are reducing CO carbon capture or carbon offset calculations, which is a huge benefit.”
The PU130 eliminates the need for generators to idle throughout the day, and, when paired with zero-emission electric construction equipment, significantly reduces emissions on the job.
“From the pure CO2 and emissions standpoint, there is a lot of benefit to the electrified approach,” Marett says. “There’s also the silence — you can stand right next to our battery energy storage system and not even know it’s on, just like you can stand next to one of these Volvo excavators and not know it’s on. It makes job site communication way easier and way more effective.”
The PU130 provides Volvo and Portable Electric with an opportunity to demonstrate that produc tivity on an electrified job site is just the same as a diesel-powered site, with the added benefits of reduced fuel cost and carbon emissions.
“With the PU130, we’ve removed the productivity gap. Users should be much more willing and able to adopt electrified construction vehicles,” Marett concludes. HEG
komatsu.com/construction
How has the market for electric construction equipment changed since JCB introduced its first electric mini excavator, the 19C-1E, in 2019?
There has really been learning and growth with that machine. Obviously since that time we’ve launched additional electric models and taken that same technology and the learnings from the 19C-1E and all its success and we have incorporated that into the other products that we launched. It’s essentially a journey into this electric product world. Electric vehicles are commonplace and construction equipment’s catching up with that. We’re all on a journey together, really, in the Off-Road to Zero, as we call it. It’s been really well received in the market, and the 19C-1E has been extremely popular and I believe we’re well over a thousand machines in the field now, so it’s fantastic.
BY KEN SINGER, PUBLISHER
Over the past five years, JCB has stood out as a leader in electrification for the construction industry. Since the introduction of its first electric excavator, the 19C-1E in 2019, the company has expanded its E-TECH product line to include scissors, a telehandler, site dumpers, and more. Heavy Equipment Guide caught up with Lee Tice, senior product manager, at ARA to discuss electrification and it growth, the role of the rental market, and opportunities presented by the product line.
role does the rental market play in the growth of electric construction equipment?
We are at the rental show for an entirely new machine, the S1932ED electric drive scissor lift, which understandably is a different type of offering. Prospective customers are able to get their hands on the machine, try it out, and take that route of adoption through the rental channel. The rental market is extremely huge and valuable to those customers where it’s something that’s unknown. You hear about an electric product and think “it may not do what I need it to do.” Well, the rental sector is obviously a great opportunity to go out and try it and understand that there is no loss in performance by going to a zero-emission electric-powered machine. You’re not going to lose anything that you would have on the diesel counterpart. You just gain additional opportunities where you can use the machine and when you can use the machine. The rental market is extremely valuable
when it comes to getting this into customers’ hands. It makes it more obtainable. They’re not having to go out and buy the machine right off the bat. They can try it, say, “yes, this is right for me,” and then make the decision.
Are you surprised at the degree to which the large rental houses have embraced electric machines?
I don’t know if I’d say surprised, but it’s definitely a rewarding feeling that they have embraced it because it’s all like one team here. It’s not just us out here pushing these machines into the market. They have the same
goal that we have with Off-Road to Zero. It really feels like a partnership with it, where we’re not in this alone, fighting this battle, pushing electric machines into the market. They’re on board with us and they’re supporting us.
How many electric machines do you have operating in North America and what applications are they working in?
Over a thousand are operating in North America in the U.S. and Canada. So obviously the first thing everybody thinks of with an electric machine is “now I
and he was an “I’m gonna always burn diesel fuel” guy. He got a contract with a Walmart 24/7 retail store where he’s doing work while customers are in the store during business hours, so he went out, got an electric machine, and he loves the things it does. He’s got it in the store working around customers. They cord off an area and they can do utility work on the floor. Those unique applications are a really interesting, exciting part of that product and they continue to grow.
What is the role of regulatory requirements in driving the adoption of electric machines?
Some contractors are playing catch up and they’re caught off guard when they get hit with some of these regulations, but there are a lot of them that are pre-emptively saying, “Hey, this is coming. We need to get ahead of it and be prepared to lead that market.”
There is an increasing interest in tracking carbon emissions. Once that is tracked, the industry can put a metric to it.
In the Netherlands it’s a requirement now in your bidding documents to give the customer an estimated carbon footprint, including all of the diesel fuel you buy. I don’t think
ther these bid documents or actually regulating.
What else is important for people to know about electric machines?
The big one is instantaneous torque. You no longer have to
increase RPMs to get the pump spinning and increase the flow to the machine. It’s basically proportional off a joystick or the throttle pedal. It’s a well-received feature of the electric product. And then it’s understanding that there’s no loss in performance, at least for the JCB electric products. When we’re looking at these machines and we’re going through the design phases, we want this machine to be as close as possible to the diesel version. So from a lift capacity or a breakout force, eight hour runtime, that’s what all the machines are designed around, and that’s what we’ve delivered with all the electric products we have. We would like customers to know that you’re not going to lose anything by going to the electric product. You’re just getting a zero-emission, low-noise machine that opens up doors to work in different applications — maybe some places that you couldn’t work prior to having an electric machine. HEG
BY KAITLYN TILL, EDITOR IN CHIEF
CASE Construction Equipment’s first commercially available EV backhoe loader is a milestone machine introduction designed for municipal crews, utility teams, urban construction, and other contractors. The 580EV is the industry’s first electric backhoe loader and provides a unique, zero-emissions, low-noise solution for a wide range of job sites from overnight construction, to work in urban centres, or jobs in other environments where noise and emissions must be limited.
“With the 580EV electric backhoe loader, we took an industry staple and designed it as a purpose-built EV to help crews meet increasingly unique job site demands and win more contracts on projects that prioritize sustainability criteria,” says Terry Dolan, vice president, North America, CASE Construction Equipment.
The new CASE 580EV electric backhoe loader has the same loading and digging specifications and delivers the same breakout forces as the four-wheel-drive, 97-hp CASE 580SN diesel-powered model.
The company has made significant changes to the electric backhoe since revealing the original EV concept, Project Zeus, at CONEXPO 2020. That concept was based on CASE’s 580NEP model. According to George MacIntyre, product manager for backhoe loaders, the NEP backhoe is a lower volume model that is targeted at the rental market.
“We decided to go with our most popular model, which is the 580 Super N [580SN], which is in the heart of where the volumes are in backhoe sales,” MacIntyre says. “We didn’t step it up all the way to our 590 series because we also wanted to keep the
weight within a reasonable amount for a backhoe. Everyone knows that with EV machines, the more weight you have on there, you’re going to have more energy consumption because you just have more that you have to move. So it was an easy decision for us because the 580SN is our most popular model.”
CASE took customer feedback from the Project Zeus model and optimized everything from thermal management to operator controls in order to electrify a machine with comparable specs to the 580SN.
Powered by a 400-volt, 71-kWh lithium-ion battery platform that’s charged with the same type of Level 2 J1772 adapter found in automotive EVs. CASE says the backhoe can deliver up to eight hours of operational run time on a single charge, depending on the application. The battery platform also uses an advanced thermal management system with system-specific cooling circuits to better regulate temperatures and help maintain performance in hot or cold conditions.
The 580EV has four-wheel drive and uses two independent electric motors for the PowerDrive transmission and hydraulic pumps to feed the loader, backhoe, and steering systems to
minimize energy consumption and improve performance in loading applications.
The 14-foot backhoe also includes an Extendahoe to boost reach, while ProControl swing dampening, PowerLift/Pow erBoost, and electro-hydraulic controls improve precision. Electrification gives operators instant torque and peak torque at any RPM, so they don’t need to wait for an engine to ramp up to meet load demands.
Operators will appreciate the cab, including its energy-efficient heating and air conditioning, an 8-inch touch screen display, customizable work mode/sensitivity settings, push-button start, and operator security codes. The backhoe’s multicoloured, four-corner strobe lights let operators work safely and meet regulatory requirements; they have adjust able colours, strobe patterns, and an “always-on” feature for low-light conditions when strobes are not needed.
“We listened to what our customers wanted to see in an electric backhoe and purpose-built this machine to be an EV from day one,” says Stemper. “Instead of just simply retrofitting a diesel-powered machine, we considered everything that might impact energy efficiency. Through out the validation process, we continued to refine systems across the unit to optimize efficiency without sacrificing anything for lift, anything for digging, and anything for driving performance.” HEG
Two more CASE EVs will be commercially available in the coming months. The CASE CX25EV electric mini excavator and the CASE CL36EV electric compact wheel loader will extend the CASE EV lineup to five machines.
The 2.5-metric-ton CX25EV mini excavator includes hydraulic flow settings and up to three auxiliary circuits that can be paired with a variety of quick couplers and attachments. It’s equipped with electrohydraulic controls and a short-radius design, making it easy to manoeuvre in tight spaces.
CASE says the 3.6-metric-ton CL36EV electric compact wheel loader delivers the same power and performance as comparably sized diesel-powered loaders, along with simplified maintenance and lower lifetime TCO. It can utilize a full range of attachments and has a hinge-pin height of over 10 feet.
BELPACIFIC EXCAVATING & SHORING
LP USES CUSTOM-BUILT TELESTICK
EXCAVATOR TO EXCAVATE 120-FOOTDEEP FOUNDATION IN DOWNTOWN VANCOUVER
BY MACK PLOVIE
BelPacific has a long history of digging deep for projects that have made a significant contribution to the Vancouver, B.C., skyline, completing excavation and shoring work that ranges from 90 to 120 feet deep. These notable landmarks include the Wall Centre, Shangri-La tower, Telus Garden, and The Hudson at 610 Granville in downtown Vancouver, earning BelPacific a reputation as one of the premiere excavation and shoring contractors in Western Canada.
The contractor’s latest project, 1515 Alberni Street, took the company to its deepest depth at 120 feet below ground level — a project that required a unique custom-built telestick excavator that delivers the deepest reach in North America.
The company was formed in 1994 after a merger between BEL Contracting and Pacific Blasting. At the time, both companies were competing for market share in the deep excavation space, and it was in the owners’ best interests to start a limited partnership. BelPacific Excavating & Shoring LP was created, and operated as part of a group of companies under the NorLand Limited name. When BEL Contracting and Pacific Blasting merged, the combined management team brought 70 years of experience and a wealth of excavating, blasting, and shoring knowledge to the new company, all while continuing to operate with family owned values. The company began to thrive on emerging opportunities in the excavation industry. There weren’t many deep excavation contractors at the time, and BelPacific had a majority of the market share. BelPacific colours could be seen on any excavation and shoring job site for residential, commercial, or industrial development in Vancouver.
Since starting out with Caterpillar 235D excavators and air track drills for shoring work, the company has grown to deploy a modern fleet of Caterpillar and John Deere excavators. Today, BelPacific has two main divisions: excavation and shoring/ foundation. While the excavation team handles general earthworks on projects, the shoring/foundation division completes drilling, anchoring, micropiles, and shotcrete work.
AS HIGH RISES HAVE BECOME TALLER, EXCAVATIONS TO ACCOMMODATE THEM HAVE BECOME DEEPER. THE 1515 ALBERNI EXCAVATION HOLDS THE UNOFFICIAL RECORD OF VANCOUVER’S DEEPEST DIG AT 120 FEET VERTICAL.
As Vancouver’s downtown population has grown over the years to 662,248 people, according to the 2021 Census, the downtown core has densified with larger and taller buildings to accommodate population growth. Developers and architects continue to design taller and more unique high rises to creatively meet the needs of the city.
Downtown Vancouver’s newest residential tower development, 1515 Alberni Street, located in Coal Harbour on the corner of Alberni and Nicola Street, will stand tall at 42 storeys boasting 202 residences that provide an inspired alternative to typical urban towers. A team effort between Bosa Properties, Kingswood Properties, Büro Ole Scheeren, and Francl Architecture, the building will be characterized by glass enclosed cantilevers offering a three-dimensional downtown living experience. Nicknamed the “Jenga Tower,” its distinctive silhouette will maintain a small footprint at street level with larger protruding three dimensional structures above providing previously unrealized views of the harbour, North Shore mountains, and Stanley Park.
“This is a project I am really proud to be bringing to life as it meets my personal philosophy of quality over quantity,” says Lorne Segal, CEO of Kingswood Properties. The 1515 Alberni Street tower is German architect Ole Scheeren’s first North American residential building, fulfilling his ambition to reconnect architecture with nature and city surroundings.
As high rises have become taller, excavations to accommodate them have become deeper, and 1515 Alberni is no exception — it holds the unofficial record of Vancouver’s deepest dig at 120 feet vertical. These deep vertical excavations are primarily for underground parking to meet bylaw requirements based on the number of residences in large urban towers.
On the 1515 Alberni project, BelPacific’s scope of work began by partnering with Pacific Blasting & Demolition Ltd, also part of NorLand Limited, to demolish a commercial rental unit building, large water feature, and two and a half levels of parkade. One of the many advantages of NorLand Limited, which includes 12 different companies, is that various divisions can vertically integrate for projects. Deep excavation work in downtown Vancouver can be incredibly challenging; contractors have to navigate adjacent active roadways, ground water, vertical excavation walls, inclement weather, developer schedules, and surrounding high rises.
After the demolition of structures on site, BelPacific began excavation from surface level, excavators worked to remove earth and expose walls on the perimeter of the excavation for drilling, anchoring, and shotcrete work as part of the shoring process. In order to excavate vertically, excavation walls are reinforced or “shored” with long anchor bars, grout, wire mesh, and shotcrete to effectively stabilize and prevent the walls from collapsing inward. As the excavation advances in depth, the process of excavating earth and shoring vertical walls along the perimeter of the excavation is repeated until target depth is achieved. This type of shoring is only temporary until the developer builds the concrete building up against the shored excavation.
On these deep digs, efficiently removing earth from the excavation is key to keeping the project on schedule. In the upper portion of the dig, conventional excavators both excavate and load out material into on-highway trucks. However, as the excavation advances deeper, so do the excavators, which required BelPacific to deploy its long reach excavator, a Cat 336E
moved earth stockpiled by excavators within the vertical hole, and loaded tandem axle trucks and pups at street level. Earth excavated from the 1515 Alberni project was exported to a landbased disposal facility by conventional on-highway trucks.
A unique resource for BelPacific is its marine-based disposal facility. If excavated material meets a certain criteria, material exported from site can be sent to a central barge loading facility for disposal at sea by belly dump barges or relocated to another location that could use the material. BelPacific is one of the few deep excavation contractors in Vancouver that has a marine facility, allowing for faster removal of material as trucks don’t haul as far compared to land-based disposal facilities.
As the 1515 Alberni dig continued to progress, the long reach soon became ineffective due to its limited reach of 60 feet. To continue excavating material from the project, BelPacific brought in a custom-built Cat 349E L excavator with telescoping stick to excavate material to a final depth of 120 feet below street level.
“Our telescopic excavator’s overall performance allowed us to load trucks quickly and efficiently, thanks to the arm’s high-speed extension, retraction, and powerful pull-up force,” says Richard Christensen, site superintendent with BelPacific Excavating & Shoring LP.
The telescoping stick excavator, or telestick for short, was an instrumental part of the deep dig at 1515 Alberni. With a reach of 35 metres (115 feet), the machine sat adjacent to the vertical excavation. With an internal hydraulic ram it can extend a threestage stick vertically to scoop up 1.7 cubic yards of loosely piled earth with the stick-mounted clamshell bucket. The stick then retracts, and the excavator swings over to load tandem axle trucks staged in an active laneway. The telestick is the only machine that can reach such depths to excavate material, averaging 400 cubic
depth, the excavators that began the excavation at surface level and advanced it vertically downward were craned out. Overall, the 120-foot-deep excavation took a total of 15 months, removing 80,0000 cubic yards of earth to excavate for eight levels of parkade including elevator core and other building footings.
BelPacific’s customized telestick excavator is the deepest-reaching machine in North America. The decision to build a telestick excavator hinged off the reality that many of BelPacific’s projects are becoming deeper and require unique solutions to excavate material. Prior to building this telestick, BelPacific had rented a smaller Cat 336 excavator with telescoping stick for projects such as The Butterfly, a 57-storey luxury tower on the corner of Nelson and Burrard Street in Vancouver.
BelPacific’s telestick features a Cosben TA-3550 three-stage telescopic arm reaching 35 metres (115 feet). This set-up was installed onto a Cat 349E L excavator by Van-Ed Equipment, the dealer for Cosben products in Western Canada. Cosben SRL, an engineering and manufacturing company based out of Italy, is well-known for telescoping stick excavator attachments with some capable of reaching 42 metres (138 feet). The units are designed to be strong, lightweight, safe, and offer fast cycle times, making them ideal in these demanding deep excavation projects.
The Cat 349E L was prepped by removing the OEM stick and bucket, then Van-Ed Equipment installed the Cosben TA-3550 at its Port Kells facility in Surrey. The primary scope of work included installing the high- and low-flow hydraulic circuits for telescoping arm functions and clamshell bucket rotation
ONCE THE EXCAVATION WAS COMPLETED TO DEPTH, THE EXCAVATORS THAT BEGAN THE EXCAVATION AT SURFACE LEVEL AND ADVANCED IT VERTICALLY DOWNWARD WERE CRANED OUT.
respectively, Cosben wiring harness and control box, and hydraulic quick connects between the clamshell bucket and the telescopic arm.
An interesting safety feature was included in this work: Caterpillar OEM lock valves for the boom and stick cylinders. These valves lock the hydraulic cylinder in the event of a hydraulic system failure, such as a ruptured hydraulic hose. BelPacific’s Cat 349E L was also modified to accept the Cosben unit, receiving an additional 4,500 pounds of counterweight to balance the excavator when fitted with the telestick. This counterweight was designed and fabricated in-house by Van-Ed Equipment. Additionally, a secondary hydraulic tank known as a “surge tank” was added to accommodate the
higher volume of hydraulic oil required by the telescoping arm. This was again designed and built in-house by Van-Ed and adapted to work in conjunction with the Caterpillar OEM hydraulic tank.
For added visibility when excavating over a vertical edge, Van-Ed Equipment installed a Brigade Electronics Elite HD Camera with sound capability mounted to the telescoping arm, and a 7-inch monitor in the cab. Once all the modifications were completed, Van-Ed Equipment carried out on-site testing and calibration, in addition to safety and operational training sessions for BelPacific operators. The telestick was an instrumental component to BelPacific’s success at 1515 Alberni Street, reaching 120 feet below street level to excavate material, a task no other machine was capable of.
The 1515 Alberni Street project is just a taste of where the deep excavation market is headed in the coming decade as high rises get taller and larger, requiring deeper excavations to accommodate levels of parking and building structural components. BelPacific’s Cat 349 telestick excavator will be an essential tool, helping the company take on deeper digs than its competitors are capable of. With 30 years in the business of digging deep in Vancouver, a fleet of modern equipment, and a talented team of people in both the field and office, BelPacific Excavating & Shoring LP is well positioned as Vancouver ushers in a new era of high-rise building construction to meet the demands of a growing population.
• Maintenance-free vibratory system
• Maintenance-free steering joint
THE TB395W’S EXCELLENT REACH AND MANOEUVRABILITY CATER TO OPERATORS WHO NEED EASY MOBILITY FOR VERSATILE APPLICATIONS
BY KAITLYN TILL, EDITOR IN CHIEF
Takeuchi-US’ first wheeled excavator for North America, the TB395W, is now available. Previewed at CONEXPO 2023 and formerly available only in select global regions, the TB395W is a versatile new introduction for the North American market where there is increased interest in wheeled machines that deliver digging power, diverse attachment capability, and the manoeuvrability to navigate densifying urban centres.
“Wheeled excavators have become increasingly common in Europe over the years, and they’re gaining popularity in other regions as well,” says Lee Padgett, product manager for Takeuchi. “That’s one reason we’re introducing the TB395W to North America. It’s a high-performing excavator that provides all the unique benefits of a wheeled unit, including higher travel speeds and the ability to handle both on- and off-road applications.”
We had the opportunity to check out the TB395W at CONEXPO 2023, where Takeuchi’s David Caldwell noted that there is particular demand for this machine in the northeast of the U.S., as well as Toronto and Quebec, where higher-density urban centres need machines that have more manoeuvrability. The TB395W is ideal for road and bridge work, tasks on space-constricted job sites, and municipal applications that may require the machine to travel quickly between job sites and do roadside maintenance work.
“The mobility of this machine is really what sells it because we can get from Point A to Point B much quicker. This has a top speed of about 18 and a half miles per hour, so we don’t have to get a truck and transport it to another spot on the job. We can actually drive this,” said Caldwell.
The TB395W excavator weighs 23,424 pounds when equipped with outriggers and a blade. It is powered by a Tier 4 Final diesel engine delivering 114 hp at 2,200 RPM and up to 339 footpounds of torque. A closed-loop, load-sensing hydraulic system delivers smooth control of the work equipment and powers a range of hydraulic attachments.
OPERATORS CAN NAVIGATE OBSTACLES WITH EXCELLENT REACH AND MANOEUVRABILITY
The TB395W features two steering modes – 2WS (two-wheel steering) and 4WSC (four-wheel with crab steering). A two-piece boom with a long arm provides more clearance between the bucket and dozer blade due to the arm-mount position, allowing the operator to pull the bucket back to the dozer blade, which is ideal when working in narrow spaces or moving an obstacle out of the way. An auto cruise feature enables operators to set and adjust the machine’s travel speeds with a toggle switch. Auto cruise is also ideal when using attachments that require a consistent, repeatable travel speed, such as a mulcher, mower, or trencher.
The excavator’s 13-foot 5.2-inch digging depth and 27-foot cutting height make it particularly useful on construction sites. The TB395W offers a maximum bucket breakout force of 13,241 pounds, a maximum arm digging force of 8,925 pounds, and a traction force of 12,994 pounds. Three auxiliary circuits cater to different hydraulic requirements. The primary circuit delivers 32 GPM, ensuring ample power for use with hydraulic attachments. The secondary circuit provides 14.5 GPM. Additionally, the third auxiliary circuit is specifically designed for use with a hydraulic quick coupler.
“You may see [the TB395W] being used with a mulcher on it or a mower where they can go along the side of the road and mow the right of way,” Caldwell said at CONEXPO.
He added that a tiltrotator will be desirable for contractors who want to use the TB395W with a variety of attachments, including grabs.
THE TB395W IS IDEAL FOR ROAD AND BRIDGE WORK, TASKS ON SPACE-CONSTRICTED JOB SITES, AND MUNICIPAL APPLICATIONS THAT MAY REQUIRE THE MACHINE TO TRAVEL QUICKLY BETWEEN JOB SITES AND DO ROADSIDE MAINTENANCE WORK.
The TB395W’s cab features an 8-inch colour touchscreen monitor with integrated air conditioning and DAB radio functions. Using the machine’s intuitive jog dial, operators can easily navigate and control the monitor, including its HVAC and DAB radio functions. The TB395W includes a 270-degree camera to provide operators with a bird’s-eye view for increased safety.
One-touch control switches operate other machine functions, such as work lights; Standard and ECO working modes; primary auxiliary detent; low- and high-speed gearboxes; swing boom/second boom select; differential lock; manual
The new TB395W provides the power of a tracked excavator but with less disruption to existing infrastructure and the ability to travel efficiently.
Lee Padgett Product Manager, Takeuchi-US
regen/regen inhibit; and lift overload alarm. A high-back, air-ride suspension seat, adjustable armrests, pilot controls, a large flat floor area, and integrated footrests help operators remain comfortable.
The TB395W has a lockable, wide-opening rear engine service door and a right-side cover, both of which open overhead.
“We know from experience that machine owners are more likely to properly service and maintain their machines at the correct intervals when those tasks are simpler to perform,” Padgett says. “That’s why the TB395W’s design ensures easy access to key daily inspection points like the engine oil dipstick, engine oil filter, engine oil fill, and more.”
Takeuchi’s Fleet Management (TFM) telematics system comes standard on the TB395W.
“As the world becomes increasingly urbanized, excavator owners and operators must frequently work on projects near city streets and other developed areas,” Padgett says. “The new TB395W provides the power of a tracked excavator but with less
THE LIEBHERR R 9150 WAS DELIVERED IN JANUARY TO L. FOURNIER & FILS, A GENERAL CONTRACTOR WORKING IN THE INDUSTRIAL, CIVIL, AND MINING SECTORS.
Agigantic Liebherr mining excavator, the first to be commissioned in Eastern Canada, has been delivered for use at a lithium ore mining operation in Quebec.
The 130-tonne Liebherr R 9150 was delivered in January to L. Fournier & Fils, a general contractor working in the industrial, civil, and mining sectors. It will work in the Abitibi-Temiskaming region at the North American Lithium operation, part of the largest spodumene — lithium ore — reserve in North America.
Fournier first met with Liebherr–Canada at the 2023 CIM Expo in Montreal, and within seven months had become a customer. Tom Juric, divisional director of mining for Liebherr–Canada, credits the entire mining team for bringing Fournier aboard.
“It’s important to us that the Canadian mining industry understands we not only supply fantastic digging, hauling, and dozing solutions, but also products and services that can optimize the performance and longevity of our machines,” Juric says.
Fournier representatives were invited to Liebherr–Canada facilities in Alberta in October 2023, with visits to the Fort McKay service centre and the Acheson sales and reman centre. Gabriel Routhier, operations superintendent for Fournier and a lifelong
heavy equipment operator, was given the opportunity to try an R 9150, and the group also had the chance to see one at work in a limestone quarry.
“As soon as I started digging, I felt the power of the machine. It had the speed of a 50-tonne construction excavator,” Routhier says. “When we were at the quarry, it only took three cycles to confirm the speed I experienced. At the time, I was wondering how it was possible for the machine to perform so effortlessly because I could barely hear the engine. Following discussions with the operator and the VP of operations, I was fully convinced the Liebherr R 9150 was the right tool for us.”
Liebherr–Canada also showcased its ability to support customers across the entire life cycle of their equipment. Members of the company’s customer service team met with the Fournier delegation to discuss how they would support the customer with comprehensive machine inspections, troubleshooting, and problem resolution strategies to maximize uptime. The Acheson reman facility provided a look at how Liebherr–Canada supports customers with parts planning, remanufacturing, and service.
“After speaking with multiple members of the customer service team at Liebherr–Canada, I was thoroughly impressed
with their attention to detail, professionalism, and passion. Everyone from the service technicians to the customer service team and up to the managing director took time from their busy schedules to present the process from the point of sales to the detailed support plan,” says Jason McNicoll, mechanical general superintendent for Fournier’s mining operations. “Our visit to Alberta was an eye-opener for us and we believe this has the potential to be the beginning of a great partnership.”
Once at work, the R 9150 will be running round the clock, so for maximum uptime, a Liebherr–Canada mining service technician will provide full-time support to the customer, and an inventory of consignment parts and components will be maintained at the North American Lithium site.
“North American Lithium operation is six hours away from our closest sales and service centre, which means that orga nizing service for unexpected maintenance or repairs can take days, rather than hours,” says Dominic Bergeron, sales repre sentative for Liebherr–Canada. “By having someone on-site, we can ensure that Fournier will experience minimal downtime with their R 9150.”
Liebherr and Fortescue are collaborating to develop a fully integrated autonomous haulage solution (AHS). This development is an expansion of the partnership between the two companies; this zero-emission haulage solution utilizes Liebherr’s experience and Fortescue’s fuel cell battery and battery-electric technology.
The AHS will be integrated with the zero-emission haul trucks that the companies are currently co-developing. Both companies want the development to become the first AHS operating zero emissions vehicles globally.
In August 2023, Liebherr announced the deployment of a fleet of four T 264 autonomous trucks in Western Australia for on-site validation, which marked the next stage of Liebherr’s development of a new autonomous product for the mining industry. This on-site validation is currently taking place in partnership with Fortescue at its Christmas Creek mine site in a facility for validating zero-emission and autonomous haulage technologies.
Liebherr and Fortescue’s partnership to develop and validate the AHS was formalized in March 2023. Since then, the team has finalized the definition of the system and is now developing the system’s features and functionalities for validation.
As part of the AHS development, Liebherr and Fortescue will develop an integrated fleet management system and a machine guidance solution that are capable of being used independently on human-operated sites. Upon completion of system validation, the Autonomous Haulage Solution will be deployed across Fortescue mine sites.
The AHS including the fleet management system and machine guidance solution — will also be made available worldwide as part of Liebherr’s technology portfolio.
BY TANYA ANAND
As mining and construction operations face increased pressure to meet net-zero targets, many turn to their equipment dealers for solutions to reduce greenhouse gas emissions (GHGs) on their job sites. From real-time analytics to electric machines, the range of carbon-reducing options can be daunting. Dealers have a critical role to play in helping customers navigate the complexity and build short- and longterm decarbonization programs. And, as the industry evolves, this role is set to expand. But are dealers ready for both the opportunity and the challenge?
“Our opportunity as equipment dealers is to be the trusted advisor in identifying the equipment and technology solutions that will help customers reduce emissions across their operations,” says Mike Brown, executive vice president, Technology and Innovation at SMS Equipment. “In order to do that well, we need to understand which solutions are mature in the market and what’s on the horizon, then create a path for customers to transition.”
For a mid-sized construction operation, machine control that increases efficiency might be a short-term opportunity. For a mining company, multi-year partnership programs like trolley assist may be more appropriate. Selecting the right solution depends on a customer’s emissions reduction goals and timeline.
“Most decarbonization solutions are highly dependent on the operating environment,” adds Brown. “Once we understand a customer’s unique goals, we layer in considerations like location, operating environment, energy availability, and budget.”
At present, there are hundreds of technology solutions that help reduce GHG emissions from heavy equipment. Some are focused on the machine’s engine and working components. Others impact how efficiently a machine is utilized.
Brown divides these into two major categories: transitional solutions and step-change initiatives.
Transitional solutions provide incremental improvements on emissions. At the mechanical level, Tier 4 engine technology, which has become a global standard, reduces particulate matter and nitrogen oxides while improving overall fuel efficiency. Electric drive trucks (EDTs) use diesel to power an electric drivetrain, an important step toward electrification. Some
equipment, like the Komatsu PC8000-6 hydraulic shovel, can be directly connected to a source of electricity by tethered cable, removing the diesel engine, or engines, altogether.
Across the construction sector, a plethora of digital solutions drive equipment efficiency. Telematics provide important data on machine utilization so customers can hone their operations. Machine control increases productivity for dozers, excavators, and graders; by providing precise instructions on where and how each machine should operate, fewer machines are needed to complete the same work.
In the mining industry, a range of advanced technologies optimize fleet management, ensuring the right material is moved to the right location at the right time, avoiding added emissions caused by material rehandling. Others improve payload management, provide analytics on equipment health, and improve
overall productivity. Autonomous haulage systems offer precise GPS routing and consistent machine operation, among many other benefits; with this added efficiency comes significant emissions reductions.
“These are all important technologies that will help,” says Brown. “Many have even become best practice. However, when it comes to meeting ambitious GHG reduction targets like the ones we’re seeing in the mining sector, they alone will not get companies to 2030 GHG targets or the goal of net zero by 2050.
“We need bigger movers to drive the reductions. That’s where we look to the step-change, zero-carbon solutions on the horizon.
“Consider the analogy of a passenger vehicle,” he adds. “The addition of a catalytic converter to an internal combustion engine significantly reduced emissions. The electric vehicle eliminated them altogether.”
Once we understand a customer’s unique goals, we layer in considerations like location, operating environment, energy availability, and budget.
Mike Brown Executive Vice President, Technology and Innovation, SMS Equipment
IN THE MINING INDUSTRY, A RANGE OF ADVANCED TECHNOLOGIES OPTIMIZE FLEET MANAGEMENT, ENSURING THE RIGHT MATERIAL IS MOVED TO THE RIGHT LOCATION AT THE RIGHT TIME, AVOIDING ADDED EMISSIONS CAUSED BY MATERIAL REHANDLING.
One approach being explored by industry is to transition from diesel-powered engines to those that run on more sustainable fuel sources like renewable diesel or biodiesel. Work is in progress with OEMs and engine manufacturers to certify engine capabilities and performance for renewable fuels. Newer Komatsu equipment is already certified to operate on these alternatives.
“The current GHG benefits of renewable fuel solutions are largely due to credits and offsets connected to sustainable energy,” notes Brown. “Widespread adoption will be dependent on commercial-scale production of these fuels, which is still evolving. Even with significant investment in Canadian production facilities for renewable fuels, the expected capacity will not be enough to meet demand.”
Hydrogen, similarly, could replace diesel as a viable fuel source, whether in a direct combustion engine or in hydrogen fuel cells. Supply and safe storage are top considerations as prototypes are being developed around the globe for both mining and construction.
The most anticipated solution, according to Brown, is electrification.
“Powering fleets with electricity presents the greatest opportunity to our industry in the near-term,” he says. “The question is how we’ll use electricity across various platforms to help customers reach their net-zero targets.”
Pure battery trucks, static charging stations, and in-line charging, like trolley assist, are all new in their adoption, but rapidly evolving to overcome challenges such as battery weight, downtime for charging, and price.
Which option is best? The answer depends on a customer’s situation.
“The ideal customer solution takes advantage of a fuel source that’s local, abundant, and affordable,” advises Brown. “There
TELEMATICS PROVIDES IMPORTANT DATA ON MACHINE UTILIZATION SO CUSTOMERS CAN HONE THEIR OPERATIONS.
isn’t a one-size-fits-all strategy here. The answer will have a strong regional dependency.”
In B.C. or Quebec, for instance, electric equipment powered by hydroelectricity may have the most impact on emissions. Operators in the oil sands can take advantage of large natural
gas cogeneration facilities. For a remote operation in northern Canada, a diesel-powered machine with an electric drivetrain may be the most practical and efficient choice.
As decarbonization technology evolves and regional strategies become more defined, OEMs are developing equipment models that can adapt to the changing landscape.
“Power agnostic machines, like the trucks being developed by Komatsu, allow customers to best manage the power source that meets their needs on a common truck body,” shares Brown.
“The same truck that uses diesel to power an electric drivetrain today will be able to support the option of diesel or renewable diesel, trolley with diesel, trolley with battery, pure battery, and a hydrogen fuel cell with a battery. We’ll see these options roll out across mining and construction equipment over the next several years.”
An evolving industry provides growing opportunity for heavy equipment dealers to partner with their customers in their decarbonization programs. Understanding both transitional and step-change solutions that can help customers reduce their CO2 emissions is just the beginning, Brown advises.
“Decarbonization isn’t a mountain to conquer. It’s more of a mountain range with four peaks: the equipment, which we manage well today; the energy infrastructure, where we will need to forge new partnerships; the digital software, where we already have experience; and operational consulting, where we can best help our customers manage change.”
TANYA ANAND is principal of Covalent Communications.
Wirtgen surface miners and cross application miners work in open-cast mining operations and on infrastructure projects around the world. Cutting drums are at their core. The Wirtgen Group will introduce a new cutting drum at MINExpo 2024. It will enable cost-efficient extraction of resources with uniaxial compressive strengths of over 100 MPa UCS (14,500 psi).
The new cutting drum is equipped with HT14 toolholders and features a redesigned cutting geometry. The central-drum concept, which Wirtgen says ensures optimum utilization of the machine weight, and direct belt
drive that guarantees the transfer of high usable power to the cutting drum, also contribute to the ability of surface miners to profitably extract even very hard rocks and minerals, such as limestone, gypsum, or anhydrite.
The new cutting drum has been used on a limestone quarrying job in Nebraska. A 280 SM(i) surface miner extracted very hard limestone and also eliminated the need for drilling and blasting, making it possible to extract previously unexploitable limestone deposits. This extended the working life of the quarry and downstream production systems by several decades.
Terex has introduced a new brand targeting large-scale operations in quarrying, mining, recycling, and construction.
Terex says its new MAGNA brand will build on the company’s knowledge and experience across the Powerscreen, Finlay, and EvoQuip brands. MAGNA will offer a new range of high-capacity machinery designed for users who need larger output and volumes.
Terex says launching MAGNA supports its growth by expanding its offering with products that complement the existing portfolio and leverage the global presence of the company to provide high-quality solutions supported by a global network of skilled distributors.
“While we have a prominent position in the global market for compact and mid-sized materials processing equipment, MAGNA will position us to serve customers requiring higher output machines, via our renowned and extensive global distribution network,” said Pat Brian, vice president of Terex Aggre-
gates. “With an ambitious product road map and supported by Terex-wide engineering, manufacturing, marketing, parts, and service capabilities, MAGNA will provide significant growth potential for Terex.”
Neil McIlwaine has been appointed business line director for MAGNA. Previously working with Finlay, McIlwaine has completed assignments in China and South Africa among others, increasing Finlay’s distribution footprint and continued growth strategy globally.
“I am excited to leverage my experience to drive innovation, growth, and success for MAGNA,” said McIlwaine. “Large and robust crushing and screening equipment is essential for quarries and other operations that require high output and volumes. MAGNA truly is made for more, with equipment that is designed to have more power to handle more material throughput efficiently, ensuring more productivity and more cost-effectiveness for customers.”
JLG’s SkyTrak 8042 telehandler has been updated to reduce weight while maintaining performance and reliability. The new lightweight design with an optimized boom and frame structure allows two JLG 8042 telehandlers to fit on a single flatbed trailer. All-steel construction and maximum capacity are retained. Maximum lift height is 42 feet 4 inches, maximum reach is 29 feet 6 inches, and the operating weight is 21,200 pounds.
The improved cab provides a larger LCD display and single-page load charts to deliver the data operators need, while allowing them to stay focused on the job. The enclosed cab is available with optional air conditioning. The hydrostatic transmission provides operators greater control and ease of operation while allowing for inching. The multi-function electric-over-hydraulic joystick includes auxiliary hydraulic functions and attachment tilt capabilities. Improved boom speed is complemented by auxiliary hydraulic connections on the side of the boom head for quick, efficient attachment changes.
A new advanced control system provides more options like load stability indication (LSI), which senses forward load capacity and displays colour-coded visuals. Seatbelt engagement and operator presence (SEOP) technology is also available. Other options include a multi-reverse camera system, reverse sensing system, and white noise backup alarm.
Sinoboom has updated four models in its range of electric and diesel rough-terrain scissor lifts. According to the company, these updates improve off-road performance, the operating experience, and reliability while reducing weight and reducing energy consumption of the lifting and lowering cycle by 33 percent. Updated models include the 4389RD, 4389RE, 5389RD, and 5389RE.
For upgraded off-road performance, Sinoboom has increased the speed ratio with a 20 percent improvement in walking and
climbing torque. The wheelbase has also been enlarged, and the tires have a greater depth of tread and spacing for better grip. Single-tire ground pressure is reduced by 10 percent. These changes, combined with the advantages of the active oscillating function, which was already a feature of the previous generation, improve off-road performance and adaptability to complex ground conditions.
The extension platform has an optimized bearing mechanism for a smoother retraction and can be locked in any position. An optional 7.4-metre-long platform is available. In addition, outrigger span has been increased to boost stability.
With a three-tonne (6,613-pound) capacity and a lifting height of 5.8 metres (19 feet), the new TH 3.6 fixed telehandler can lift its maximum load to a height of 5.4 metres (17.7 feet). It can lift 2,500 kilograms (5,511 pounds) to the maximum height, and 1,100 kilograms (2,425 pounds) to a horizontal reach of more than three metres (10 feet). Its low-level design makes it ideal for tight spaces while retaining ground clearance for uneven terrain. Powered by a Deutz Stage V engine delivering 55 kW (75 hp), the TH 3.6 has a top speed of 35 km/h (21 mph). The four-wheel drive and steering, with hydrostatic transmission, provide excellent stability and manoeuvrability with three steering modes: front, concentric, and crab.
The new cab features an air-suspended seat, adjustable steering column, heating, and radio. On the 7-inch touchscreen, the MCTS (Magni Combi touch system) on-board software gives operators access to themed screens covering various functions, including load charts. Magni says that the TH 3.6 is the only machine equipped with a sophisticated, precise tipping protection mechanism. The LMI (load moment indicator) enables constant monitoring of the machine’s movements to prevent overload.
BY ROD STROMBERG
Several factors go into how a contractor chooses to power their job sites. The size of site, the number of workers, the length of the project, and the equipment and other materials being used must all be accounted for. Construction job sites can be complex ecosystems and are often a tough environment to work in. In Canada, cold winters pose many challenges. But what if there was a fuel that could help power your job site while keeping costs, emissions, and safety risks down while helping productivity remain high?
While there may be all sorts of propane tank myths floating around, propane is one of the safest and most versatile fuels on the planet. It’s most commonly used to provide temporary heat, but it has other applications as well — such as powering generators and other
equipment like aerial lifts and booms.
The biggest challenge is ensuring that the people who are carrying, maintaining, and installing the fuel are properly trained and/or qualified. Propane may be reliable and efficient, but it can be dangerous, and even deadly, if it’s misused. However, if you’re looking to reduce your costs and increase productivity all while keeping your workers safe, propane can be an easy and effective fuel solution that minimizes environmental impact and maximizes efficiency.
The use of propane-powered heating equipment can help ensure projects
finish on time and on budget. When it comes to the comfort and safety of workers, propane-powered heaters are also better at maintaining the ambient temperatures necessary for tasks like drywall or cement installation. No one holds budget to replace drywall or fix cracks in concrete that result from incorrect ambient temperatures. With new advancements in heat monitoring technology, contractors can also receive notifications for even the slightest change in temperature or humidity.
When it comes to safety, real-time monitoring can help with that too. Overheating is one of the most common winter hazards — especially in areas with a lot of combustible materials. On the other hand, lack of heat in the winter months can also be detrimental to your workers’ safety and productivity. We are
PROPANE’S NATURALLY ODOURLESS, NON-TOXIC, AND LOW COMBUSTION QUALITIES MAKE IT SAFER THAN DIESEL OR GAS-POWERED ENGINES.
Workers must know how to identify a propane leak and understand the importance of keeping propane containers away from ignition sources, combustible materials, air intakes, and building structures.
Propane can efficiently fuel your power generators and other equipment — all while lowering emissions and saving money, making it easier to finish projects safely on time and on budget. Since emissions regulations are getting stricter (especially for indoors and in residential areas) propane’s naturally odourless, non-toxic, and low combustion qualities make it safer than diesel or gas-powered engines. At Cooper Equipment Rentals, we
are seeing an increased investment in propane-powered generators to heat office trailers, thaw grounds, and heat job sites since they are quieter, cleaner, and more cost-effective than diesel generators.
We’re also seeing propane-powered scissor lifts, forklifts, and telescoping booms that are as reliable as diesel and gas-powered equipment but with lower fuel costs. The fuel savings goes far beyond the day-to-day fuel costs as propane-powered equipment is also typically less expensive to rent and has lower maintenance costs over its lifetime.
Propane is gas under pressure and can pose a significant danger when cylin-
ders are being transported, stored, and connected, or when people are working in areas with propane heaters and torches. Workers must know and follow the correct propane safety regulations. They must know how to identify a propane leak and understand the importance of keeping propane containers away from ignition sources, combustible materials, air intakes, and building structures. They should also be aware that propane tanks should never be below grade or near open excavations. Direct-fired heaters like propane have a low risk when used properly, but when placed next to combustible materials, they can be a serious fire hazard. They also have the added risks of releasing hazardous gases such as carbon monoxide, which is especially dangerous in areas that lack proper ventilation. Some people cannot smell
the chemical mercaptan that is added to propane — so those workers need to be especially vigilant.
Liquid propane is tied into a vapourizer and must be handled by a qualified gasfitter, so it’s important to know when to engage these individuals. Every propane supplier is governed by the Canadian gas code with dedicated procedures in place to support customers while ensuring crews are trained to work with this fuel source.
Propane is much easier and less expensive to compress, ship, and store. If you’re working with a reliable propane provider, they should be able to schedule delivery according to your needs — this is a big benefit for projects located in remote areas or outside of
major energy infrastructure. Look for a provider that can also offer both rental equipment for your job, and fuel delivery services – it will not only save time and costs but brings peace of mind knowing your propane solutions are coming from someone you trust with all the right equipment and propane supply you require.
Some providers are also starting to supply gas fitters, provide safety training for workers, and even apply for the necessary permits on your behalf. In Ontario, safety standards for fuel are overseen by the Technical Standards and Safety Authority (TSSA). Due to a number of serious accidents over the last few years, the TSSA has stepped up its enforcement of the law as it applies to compressed gases such as propane. This means anyone handling propane must have propane and/or N.G. awareness training and a current record of training certificate or they may be liable in the case of an accident and charged and/or fined. The Canadian Propane Association also provides industry training through its Propane Training Institute (PTI). PTI courses are recognized across Canada and have been designed to provide instruction on the safe handling of propane and propane-powered equipment.
When it comes to heating construction sites and powering equipment, propane’s benefits are clear — it’s abundant, affordable, and safe when following the correct procedures. The reality is, not all fuels are created equal — especially when it comes to costs, safety, and environmental impact. Propane has emerged as a low-carbon solution that can help maintain a safer environment without sacrificing performance. As energy demands, emissions regulations, and safety requirements continue to change, you may stand to gain from a better understanding of the safety benefits propane can bring to the job site.
ROD STROMBERG is the general manager, climate (Canada west) at Cooper Equipment Rentals.
TRACTION ATTACHMENTS FOR EXCAVATORS, COMPACT TRACK LOADERS, AND OTHER TRACKED VEHICLES IMPROVE SAFETY AND UPTIME
BY KAITLYN TILL, EDITOR IN CHIEF
When your equipment needs greater traction to work in challenging conditions, such as ice and packed snow, mud, rock, and on steep slopes, a track attachment is essential. TrackGrip offers a range of track attachments for compact equipment including mini excavators and compact track loaders, full-size excavators, and other tracked vehicles to give operators the best traction no matter what conditions they operate in. Options are available for machines with rubber or steel tracks, and, compared to cleats, lugs, or grousers, these bolt-on track attachments are faster to install and remove and don’t require any welding or drilling.
Crafted from high-tensile steel, MightyGrip’s heavy-duty additional wear plates and gusseting add strength for use on tracked machines in mud, snow, clay, rock, shale, and dense forestry. Compared to traditional grousers or cleats, MightyGrip spans the entire width of the steel tracks, promoting even weight distribution and eliminating side-to-side rocking to improve stability. The bolt-on installation and removal process takes just 30 minutes.
Confidence in better traction when operating on snow is essential for operators working through the winter. IceGrip is made from high-tensile steel with a heavy-duty design and is engineered to maximize traction on ice and packed snow, permafrost, and various challenging terrains. It takes 15 to 30 minutes to install or remove the equipment with no welding required. The IceGrip sits the full width of your track distributing weight evenly and offers excellent sideways protection, preventing your excavator or tracked vehicle from sliding on ice and other slippery surfaces.
The ChainGrip chain track attachment boosts traction, stability, and safety for excavators and other rubber-tracked vehicles. ChainGrip fits 95 percent of track widths and gives operators confident traction in a wide range of applications, including clearing parking lots and driveways of snow and on dirt slopes in farm and forestry terrain. With a simple bolt-on/bolt-off mechanism, ChainGrip can be installed or removed in 15 to 30 minutes.
Increase traction, stability, and safety of excavators and other tracked vehicles working in muddy conditions or on softer terrain with RubberGrip. The RubberGrip excavator track attachment provides a good depth and bite in ice, snow, mud, and forested environments.
Manufactured from high tensile steel, these attachments for rubber tracks assist with sideways protection and prevent sliding. The bolt-on RubberGrip can be installed or removed in 30 minutes. RubberGrip track attachments can also extend the life of rubber tracks and allow you to repurpose worn-out tracks.
With bolt-on traction attachments, operators of tracked compact and heavy equipment can get the best performance out of their machine year-round with more traction on a variety of terrain. When risk of sliding in steep and slippery conditions is mitigated, safety for machine operators is improved while benefitting on-site productivity and reducing machine downtime. HEG
BY LEE TOOP
Marco Goodridge is a busy man. As regional maintenance manager with Sterling Crane Canada, he and his team are responsible for around 900 pieces of equipment in Canada, and he needs to make sure that each of those pieces of equipment is being used correctly, is properly maintained, and is ready for work.
That’s a daunting task, to be sure. For the 16-year veteran with Sterling Crane, finding the right tools for managing that fleet has meant some trial and error. Today, taking advantage of technology solutions from Samsara, Goodridge and Sterling Crane have a fleet solution that works for everyone, from the operators to head office. That effort hasn’t gone unnoticed, as Samsara has named Sterling Crane its 2024 Connected Operations Award Winner for “Excellence in Systems Efficiency.”
Sterling Crane is part of Marmon Crane Services and has 15 branch offices across Canada. It has been providing heavy lift services to Canadian businesses since 1954, and its fleet of cranes has grown steadily. Today, it is a broad, mixed-manufacturer fleet.
“We have various makes and models of equipment — we have cranes manufactured in Japan, Germany, the U.S., all over the place. Our technicians need to be well-versed on troubleshooting this equipment, and any technology we use needs to be compatible with all our programs,” describes Goodridge. “They’re all cranes, but they’re all built a little differently.”
With that broad scope of equipment, it made sense to explore technology options for fleet management. Sterling started on that path around 2016 with several goals: tracking equipment, understanding utilization, and better capture of maintenance information.
“In the past we would rely on our operators to scratch down the engine hours on their timecards, and those paper timecards would go to the administrators who would update our preventive maintenance program. But the administrators were super busy with invoices, payroll, all that good stuff, and updating our hour meters was sometimes low priority,” Goodridge explains. “Our technicians had no idea when we needed to service our equipment.”
First attempts with GPS technology showed some promise, but issues quickly arose. An initial deployment worked in some equipment, but in others caused technical issues — in cranes especially.
“Did they plug into our rigging and supervisor trucks? Absolutely, no problem. When it came to a [mobile crane], well — you plug it in, and . . . the system would fail. We’d be stranded on the side of the road scratching our heads,” he recalls. “As soon as we unplugged it, the crane would be happy.”
Technology failures eventually turned into one more thing on service technicians’ plates, and that, among other shortcomings, sent Sterling Crane looking for a different solution that would work more smoothly with its fleet.
Goodridge was drawn to Samsara for the platform’s broad suite of solutions that encompass key areas like driver safety, telematics, and digital mainte-
nance tracking. Plus, he adds, it was a plug-and-play solution that worked with all of Sterling Crane’s equipment.
Since implementing Samsara on its fleet, Sterling Crane has introduced a number of initiatives to take advantage of the system’s range of capabilities, with the goal of improving efficiency across the board.
One deployment that has paid dividends thus far focuses on capture and analysis of driving data from Sterling’s fleet of onroad vehicles. Dual-view cameras and sensors on vehicles detect specific incidents, such as hard braking, and capture video both in the cab and in front of the vehicle, which can then be reviewed.
In the roughly one year since Sterling Crane integrated Samsara into its systems, the company has saved an estimated $2.5 million in major maintenance costs. Improved driver productivity and compliance adds up to $1.2 million, while more than 10,000 hours of technician time saved adds up to around $500,000.
Sterling’s unions at first had some concerns surrounding privacy and constant monitoring of members when the cameras were first discussed, and negotiations were required prior to launch.
“It has taken a lot of education on our part. We’ve communicated and have had multiple meetings with our unions in every province to discuss,” Goodridge describes. “We were a little hesitant at first to roll it out, but it’s been a game changer for us.”
Goodridge shared a look at the back end of the program with me to demonstrate the capabilities of the dual-view camera capturing inside and outside images. Video is captured when the system is triggered by a specific occurrence such as a hard braking. In some examples, the drivers are simply caught unaware. In others, they are either speeding or braking too abruptly.
For Sterling, it was all a reminder that the company needed to know more about its drivers and their habits — and
a way to improve their results. A rewards system has created good-natured competition to determine the safest driver, with small gifts handed out each month to those in top spot. Buy-in has risen among drivers, Goodridge says, bringing safety and efficiency along as well.
Another new initiative is digitizing Sterling Crane’s maintenance processing. Previously, technicians would have paper forms to fill out during inspections, indicating necessary main-
tenance to be performed. Those forms, Goodridge says, would then be scanned and emailed, sent through the regular mail — or not submitted at all.
“I could go to the branch for a visit and they’d have a pile of these [forms] sitting on a bench or in the office,” Goodridge describes.
Now, technicians and operators are receiving tablets and digital maintenance forms that they can fill out and transmit directly through Samsara. When a technician looks over a machine in Ontario and finds an issue, they can take photos, make notes, then send the form immediately to Goodridge in Edmonton, and maintenance can be scheduled and completed much faster.
“Our goal for Marmon Crane Services is to have 80 percent planned maintenance and 20 percent unplanned,” he says. “We don’t want to react to something on the side of the road. We are now fortunate to be able to keep our eyes on the equipment and get accurate hours in.”
Overall, the results of adopting Samsara on the Sterling Crane fleet have been eye-opening for Goodridge and the company as a whole. A few hours a week per driver, technician, and operator add up quickly to thousands of yearly hours that can be used for more important work.
Financially, in the roughly one year since Sterling Crane integrated Samsara into its systems, the company has saved an estimated $2.5 million in major maintenance costs. Improved driver productivity and compliance adds up to $1.2 million, while more than 10,000 hours of technician time saved adds up to around $500,000.
Those results are central to why Samsara has named Sterling Crane one of its 2024 Connected Operations Award winners, who use data-driven insights to work safer, more efficiently, and more sustainably.
“It’s incredible to see the tangible impact our technology has had on Sterling Crane, which has been serving Canadian customers for 70 years. At Samsara, we’re always looking for new ways to help our customers take data from every aspect of their operations — whether it’s driver safety, equipment monitoring, or employee workflows — and leverage it to solve complex problems,” describes Charlie Cubeta, head of growth, Canada with Samsara. “Sterling Crane is a perfect example of this in action, having achieved such significant gains in efficiency and compliance less than a year into deployment.”
Discover what’s new, visualize what’s next, and engage the future of work.
Experience the power of connection at Dimensions as you tackle the current and future challenges of the construction and geospatial industries. With a diverse range of sessions, an indoor and an Offsite Expo, and countless networking opportunities, Dimensions is the event of the year that you can’t afford to miss.
Register today at Trimble.com/Dimensions
BY NELSON ABELHA
turned, there are also no concerns about its condition at the end of the lease term. This is beneficial if the equipment is heavily used and may not be in a suitable condition for return.
Although both leasing options have their advantages, there’s a common misconception that capital leases offer greater flexibility. However, a closer look shows that FMV leases may actually be a better choice to provide the quintessential operational versatility that construction companies need.
Let’s take a closer look at each leasing type to debunk the myth of capital lease flexibility and highlight how and why FMV leases can provide optimal flexibility, making this lease type a far superior choice.
Capital leases essentially give the lessee (borrower) ownership of the equipment. The lease term typically covers most of the equipment’s useful life. At the end of the lease term, the lessee has the option to purchase the equipment for a nominal fee, usually $10 or $1. This type of lease is recorded as an asset and a liability on the company’s balance sheet, reflecting the equipment’s value and the obligation to make future lease payments.
1. Ownership benefits The lessee eventually owns the equipment, which can be advantageous if the machinery has a long operational life and is essential to the company’s core activities.
2. Depreciation Although I’m not an accountant, nor do I play one on TV, the company can benefit from tax advantages related to the equipment’s depreciation.
3. No usage restriction There is no limitation on how many hours a construction company can operate the machinery throughout the lease term. Since the equipment cannot be re-
At first blush, capital leases may seem to offer quite a bit in the way of flexibility, but there’s more to this story. Despite these advantages, capital leases may not be as flexible as they appear.
The perception of flexibility with capital leases often comes from the aspect of ownership. However, this ownership can limit flexibility in several ways:
1. Long-term commitment Capital leases require a longterm commitment to the equipment. This can be a significant drawback if a company’s needs change or technological advancements render the leased equipment obsolete. In an industry where machinery and technology evolve rapidly, being tied to older equipment can be a disadvantage.
2. Balance sheet impact Since capital leases are recorded as assets and liabilities, they increase a company’s debt-to-equity ratio — a key financial statement metric. This can affect the company’s financial health, potentially making it more challenging to secure additional financing or impacting borrowing costs, which can restrain growth.
3. Maintenance and disposal Ownership means the lessee is responsible for all maintenance and disposal costs. These costs can be substantial for heavily used construction equipment. Additionally, the company must manage the logistics of selling or disposing of the equipment at the end of its useful life, adding another layer of complexity. This often means the company must employ its own team of technicians.
Alternatively, FMV leases offer a different kind of flexibility that can be aligned with the dynamic needs of construction com-
FMV leases enable companies to keep up with technological advancements, manage cash flow more effectively, and avoid the pitfalls associated with longterm ownership commitments.
panies. Under an FMV lease, the lessee pays for the use of the equipment for a specified period, with the option to purchase the equipment at its fair market value at the end of the lease term. Alternatively, the lessee can choose to return the equipment or renew the lease, and in some cases, this can be on a month-tomonth basis.
1. Lower monthly payments FMV leases typically have lower monthly payments compared to capital leases. This is because the lessee is not paying for the full cost of the equipment, just for its use during the lease term. Lower payments improve cash flow, allowing the company to allocate financial resources to other critical areas.
2. Upgrade options At the end of the lease term, companies can return the equipment and lease newer models. This is particularly beneficial in the construction industry, where technology and equipment quickly become outdated. The ability to upgrade ensures the company always has access to the latest and most efficient machinery.
3. Maintenance and repairs Many FMV leases include maintenance and repair services. This reduces downtime and transfers the burden of maintenance costs away from the company while helping ensure the equipment remains in optimal condition throughout the lease term.
4. Flexibility at lease end FMV leases provide multiple options at the end of the lease term: The lessee can return the equipment, purchase it at fair market value, or extend the lease. This flexibility allows construction companies to adjust their equipment needs based on business conditions and project requirements.
Many people mistakenly believe that capital leases offer more flexibility due to the traditional association of ownership with control. However, in the fast-paced construction industry, where adaptability and financial agility are crucial, Fair Market Value (FMV) leases often provide superior flexibility. They enable companies to keep up with technological advancements, manage cash flow more effectively, and avoid the pitfalls associated with long-term ownership commitments.
While capital leases have their own benefits, they do not necessarily provide greater flexibility. For numerous construction companies, FMV leases present a more versatile and financially prudent option. Understanding the true nature of these leasing agreements can help companies make more informed decisions aligned with their operational needs and strategic goals. The real flexibility lies in the ability to adapt to changing circumstances — something that FMV leases facilitate far better than capital leases.
NELSON
ABELHA is the regional vice president of First Financial Canadian Leasing.
Held every four years, DEMO International is a unique event that takes place on an active forestry site near Ottawa/Gatineau. Attendees can get up close to see the latest tools for forestry in a working environment. demointernational.com
| SEPT. 24–26
MINExpo takes place every four years and is hosted by the National Mining Association in Las Vegas. It draws members of the mining sector from around the world to learn more about solutions and products for safety, drilling, engineering, and more. minexpo.com
VEGAS, NV | NOV. 11–13
Trimble’s yearly user conference provides attendees in construction, mining, infrastructure, and other industries with educational sessions on the latest in construction software and technology. The off-site demo area offers a first-hand look at new tools and solutions in real-world situations. trimble.com/en/our-company/events/dimensions/overview
• See the latest equipment
• Learn best practices and techniques
• Improve your jobsite and business March 25-27, 2025 | St. Louis, MO
Strong dealer relationship helps Alberta aggregates producer achieve consistent quality
18 Liebherr cranes involved in one of Germany’s largest bridge modernization projects
Komatsu surpasses 10 billion tonnes of material autonomously hauled
When installed on your carrier, it crushes any type of inert material.
Scan for the full range MBCRUSHER.COM +1 204 900 9931
iSlip
No matter how challenging your needs, BKT is with you offering a wide range of OTR tires specifically designed for the toughest operating conditions: from mining to construction sites.
Sturdy and resistant, reliable and safe, able to combine comfort and high performance. BKT is with you, even when work gets tough.
GOMACO offers the full range of concrete slipform pavers, curb and gutter machines, trimmers, placer/spreaders, texture/cure machines and bridge/canal finishing equipment. GOMACO equipment features our exclusive and proprietary G+® control system, created in-house by our software engineers from the wants and needs of contractors paving in the field. At the heart of GOMACO equipment is our passion for concrete and our commitment to our customers. We look forward to visiting with you about your upcoming paving projects and your concrete paving equipment needs. Our worldwide distributor network and our corporate team always stand ready to serve and assist you.