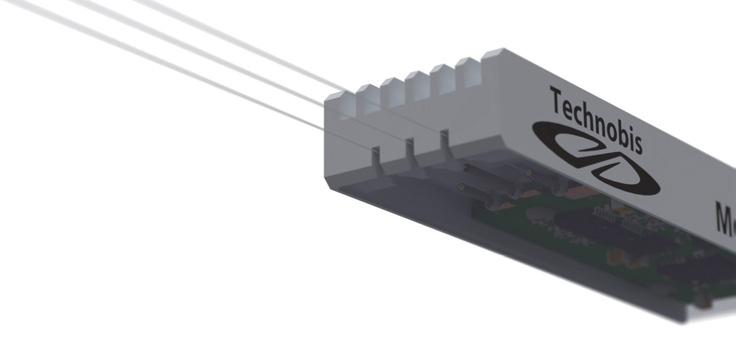
10 minute read
Reducing an optical sensor interrogator to the size of a memory stick
Fiber-optic sensing is gaining traction for accurate strain, shape and temperature measurement in aircraft, civil structures, high-tech machines and medical catheters and endoscopes. To support a higher market penetration, a cost and size reduction is needed. Technobis and Bruco Integrated Circuits have developed a memory stick-sized fi ber-optic measurement system.
Pim Kat Frank Vonk Marco Hagting Mark Gortemaker
Advertisement
Fiber-optic sensors have many appealing characteristics: they’re small, lightweight, inert to chemical substances, able to withstand high temperatures and immune to electromagnetic interference. As a result, they’re nding widespread use in a multitude of applications. For example, in structural health monitoring, the deformation and dynamic response behavior of objects are measured using optical bers that are mounted on or even embedded in the structure being monitored.
Successful applications have been shown and proven in the aerospace industry, performing standard strain and temperature measurement in the new generation of planes. In the medical domain, the technology is being applied in catheters, endoscopes and guide wires to gauge shape, temperature and pressure. ere, the number of systems sold typically varies from 1,000 to 50,000 pieces per year. Further market adoption requires a more compact and lower-cost solution, including disposables in medical and ber- optic battery monitoring systems.
Fiber-optic sensing
Over the last years, ber-optic strain sensors have been developed based on ber Bragg grating (FBG). With this technique, light is sent through a ber-optic cable and partially re ected by a microstructure inscribed into the ber core. Strain on, or a temperature change of, the ber causes a shift in wavelength of the re ected light, which can be measured very precisely and translated into strain or temperature values.
Current sensor detection devices, so-called interrogators, are mostly based on free-space spectrometry. An optical spectrometer (spectrophotometer, spectrograph or spectroscope) is an instrument used to measure properties of light over a speci c portion of the electromagnetic spectrum, typically used in spectroscopic analysis to identify materials. Free space means that in measuring the re ection, the light will move through air. is approach has fundamental limits, regarding device dimensions, measurement resolution, accuracy and power consumption, for example.
For improving the resolution, interferometry seems to be a promising approach. An optical interferometer can precisely measure characteristics such as length, refraction index and surface irregularities. It divides a light beam into a number of beams that travel unequal paths and whose intensities, when reunited, add or subtract – interfere with each other. For high-resolution wavelength
The Monadgator PCB module with SMD components
analysis, a fiber optics-based MachZehnder interferometer was developed, which makes the reflected light of the FBG interfere with itself, resulting in a phase change proportional to a wavelength change. However, since the system still has a free-space design, it has limited practical use for integration in demanding environments due to its high sensitivity and associated erratic behavior.
As fiber sensing matures, device dimensions, power consumption and costs need to be optimized to serve
Spectrometry measurement using optical fiber grating
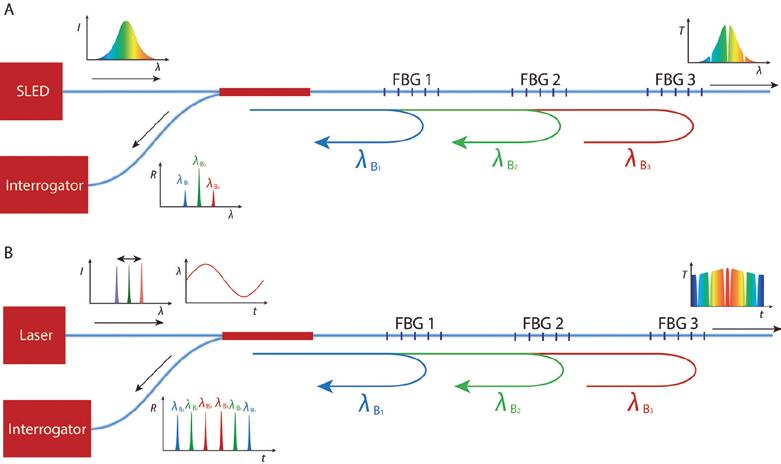
the increasing application requirements. Over the last ten years, new interrogators – spectrometer and interferometer based – have been developed using photonic integrated circuits (PICs), which combine multiple photonic functions in a single device. This second generation is on the market now.
Technobis has been working on fiber-optic sensing solutions for many years, with module assembly as a vital core IP. Its current interrogators are based on spectrometry
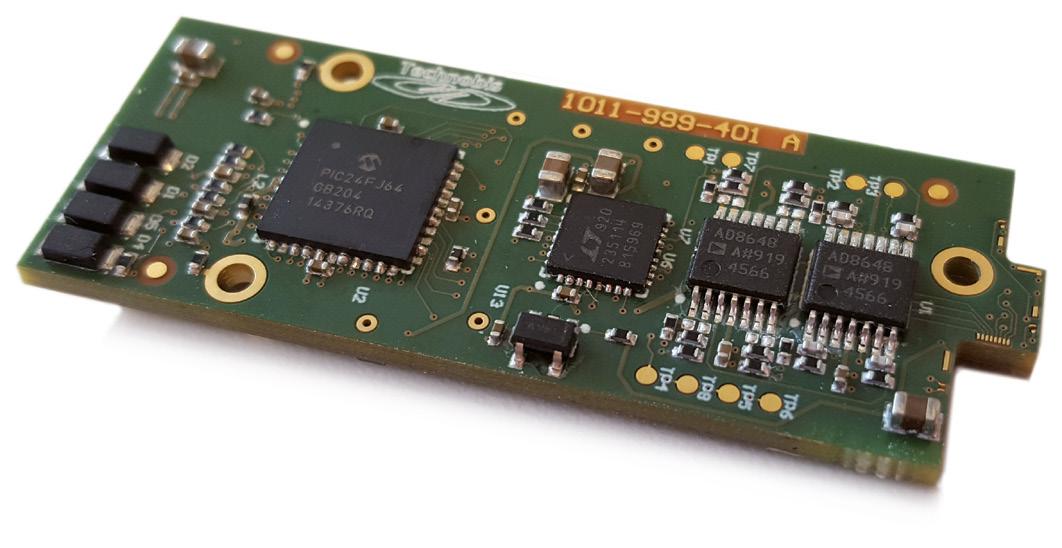
and interferometry on chip, capable of detecting wavelength shifts down to 10 attometers – corresponding to about 0.2 nano-strain. These second-generation systems, called Ladygator, are now in production or the design-in phase at OEMs. Main characteristics include a temperature resolution better than 0.001 degrees Celsius and 2,500 unique sensors per fiber. For a medical application, the tip position of a 2.2-meter-long catheter can be calculated with an accuracy of 1 mm. Responding to market demands for a smaller form factor, work is now underway on a third-generation measurement system the size of a memory stick.
Monadgator
Last year, Technobis already took first steps to bring down the cost of the system by reducing the cost of the light source, package and PIC. This only left the electronics to be optimized. Together with Bruco Integrated Circuits, Technobis has developed the Monadgator system – “monad” means “single” and “gator” is an abbreviation of “interrogator”. Following overall specs that have been jointly drawn up by the system architects of both companies, the device integrates a PIC with discrete off-the-shelf electronics. It can have a readout of 1-200 FBG sensors and it spits out raw serial sen
The memory sticksized Monadgator housing combines a PCB containing the electronics, and a photonic submodule with the fi ber-optic interconnections.
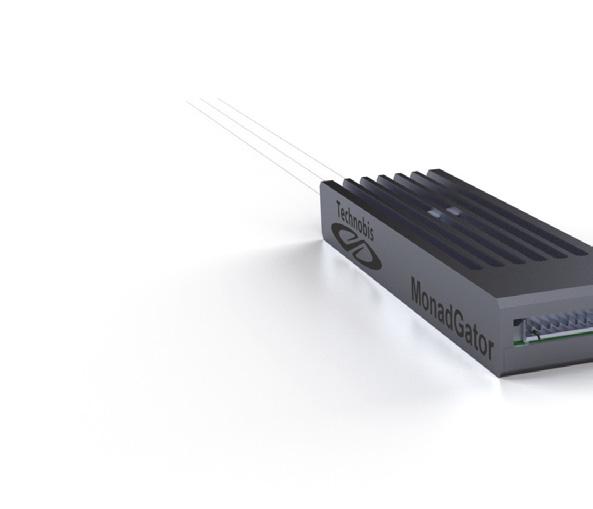
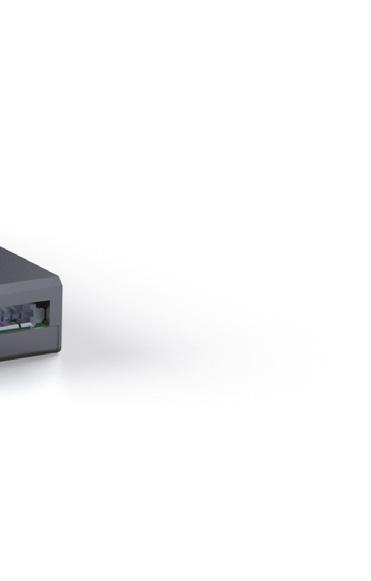
sor data to be processed in the main processing unit. e Monadgator combines a photonic submodule, developed by Technobis, and a printed circuit board containing the electronics, developed by Bruco. Everything is assembled by Technobis in a small box, measuring 60 by 12 by 5 mm. e photonic submodule holds two light sources and a spectrometer section including photodiodes, integrated on a PIC. To measure the temperature of these three parts, three thermistors have been added. e electronics submodule consists of circuitry to transfer the photodiode current measurements to a host. It also controls the light sources, one at a time, and gauges the local temperatures on both submodules. e temperature data is part of the output stream.

e memory stick-sized box detects the re ected light that’s coming in on the ber. e light originates from one of the two light sources inside the module, which inject it into the ber. e photodiodes register the re ections and the electronics ampli es, lters and digitizes their output current by sampling a current-related voltage with a rate of 4 ksample/s. e result is sent via a serial interface to a host that’s attached to the box’s output connector, in frames containing sixteen data samples and four temperature measurement channels. e photonics interface connects the optics to the electronics. To drive the two light sources, two current outputs are used. e light sources each have a thermistor connected to an input circuit on the electronics

The Monadgator block diagram
core. e photodiodes are connected to the inputs of a transimpedance ampli er (TIA), with a thermistor connected to a core input circuit. e physical interface is implemented by means of direct wire bonding instead of a connector interface. e host interface is used to control the Monadgator module, to power the complete device and to transfer sensor data and device information. is RS-485 interface also serves as a device control interface. To be able to load new rmware, a programming interface is included as well.
ASIC
e current Monadgator module is an intermediate step, generation 3A, aimed at delivering demonstrators and low-volume production samples to develop the market and customer base. Still, the bill of materials for the electronics is already ve times lower. e nal goal for the thirdgeneration system, generation 3B, is to go to an ASIC for high-volume application, which will reduce the BOM by a factor of 50. Developing an ASIC from scratch is very risky because of the large investments and long development time, but by working closely together at an early stage, Technobis and Bruco pave the way for a seamless e ort that mitigates the risks involved.
From idea to working prototype took four months, with intensive communication. e complete working measurement system will be delivered within three months. e rst industrial customer, from the oil and gas industry, has already shown interest.
Pim Kat is the founder and CTO of Technobis. Frank Vonk is a system architect there. Marco Hagting and Mark Gortemaker work at Bruco Integrated Circuits, as a system architect and the sales and business development manager, respectively.
Wim Bens is managing partner at Bens & Partners.

I’ve been involved in many hightech innovation cases, at different stages and in different roles. In some cases, I was present when the idea was still on the drawing board, in others when project proposals or subsidy applications were being drafted, and in yet others when the program, project, startup or spinoff was getting off the ground. I’ve seen successes, but unfortunately, in my experience only a limited amount of innovative ideas or technical inventions actually make it – by which I mean that controlled and cost-effective production is possible, customers pay for the product, money is earned, profit is made and (new) jobs are created.
You’d be surprised how many developers of great new technologies either have no plan at all, or if they do, a poor one. Having a plan doesn’t guarantee that there’s a business case (economic or social) underneath. Often, this is the kind of plan in which the technology or the invention dominates, and the rest is forgotten or underexposed.
Many inventors seem to think: my technology is superior and everybody wants it. They often get disappointed. Sometimes the essential competencies and partnerships, not only for engineering and production but also for after-sales services, maintenance, repair and recycling, aren’t properly considered. People sometimes tend to think they can do everything themselves.
Many factors determine the outcome, and if you can’t tick them all off, failure of technological innovation projects is a very real danger. On the other hand, failure every now and again isn’t all bad. However painful, it’s usually extremely instructive to evaluate and study a case or a project that failed. Take some time to do so! Those who had a part in it will for sure do better next time, so definitely don’t write these people off and don’t fire them! What they’ve learned needs to be put into practice in the next project. In other words, failure needs to be treated
Failure every now and again isn’t all bad
as a normal part of the innovation game. I would even go as far as including it in business cases. Eventually, the rewards will be huge.
There are many checklists available that sum up the elements determining success. These lists come in all shapes and sizes but generally contain the elements that need to be included in a sound project or business plan. Read one or two of these list, and you won’t ever again question why you actually need those plans. It takes time and energy, but you’ll find out, it will be worthwhile in the end.
However, an organization-wide, well-communicated and thorough plan is the basis for success – still no guarantee, but if you know how to tick off all the elements and communicate them properly in your team and in your project, you do have a reasonable chance for success. Make sure you can answer all “what if” questions – if you can’t, work on solutions, mitigating measures and necessary answers. Gather the necessary insights or organize help, otherwise failure will be lurking in the shadows.
If you find all this too much and too complex, I’d advise to at the very least focus on the outside-in aspect of the innovation project: gauge the market and competition and consider, or even better, involve the customer who’ll soon have to pay, and have an eye for the distinctive value (proposition) that you’re going to add. Don’t simply focus on the idea, the invention or the new technology – those are the worst to take as a starting point. It’s all about the product-market combination.
Technological inventions are not the outcome but the starting point. It takes a lot of steps and learning to get there. Success usually doesn’t come naturally; you really need to possess the right talents. Open innovation and co-creation may seem to be adding even more complexity and additional challenges, but take my advice: on your own you can go faster, but together you can go further.