THE DIAL
A master dial-maker
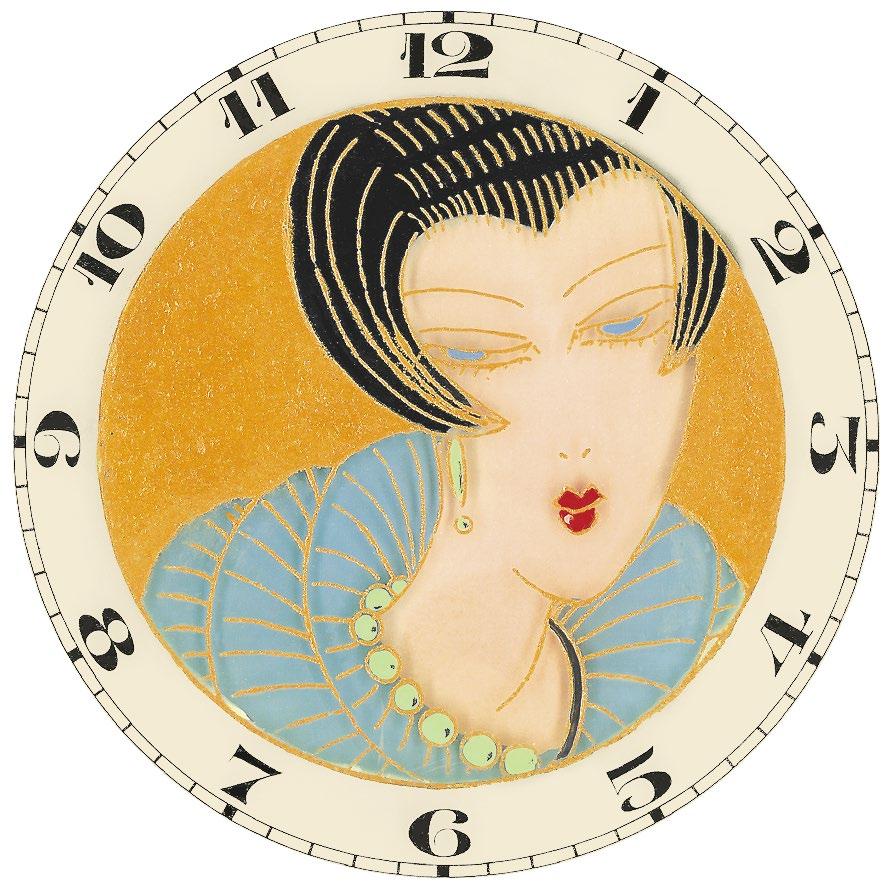
A master dial-maker
Le Cadran
C adran jauni sur un vieux mur
A ux rayons du soleil tu fixes l’heure
D éjà les rois vêtus de bure
R egardaient sur ta face le temps qui meurt
A ujourd’hui les hommes de ce temps
N e peuvent se passer de toi
S tern frères depuis déjà longtemps
S ’ingénie à t’embellir et te polir
T u es choyé comme il se doit
E ntre les mains des ouvriers
R egardons maintenant vers l’avenir, N oël est si vite passé
Georges Renand DiaboloThe fascinating story of the Stern dial company takes us deep into Swiss watchmaking territory and merges with that of the country's centuries-old watch industry. The family business was founded in Geneva in 1898 and survived until the month of June 2016 when it drew its last breath. Surprisingly, its last official mention in the state council registers went virtually unnoticed. Ignored even by the watchmaking press, it nevertheless signalled the demise of a prestigious name inextricably linked to an era of tremendous expertise.
Sadly, it also signalled a slow and gradual decline in traditional dial craftsmanship skills: a treasure-chest of knowledge synonymous with a name that had captured minds and hearts everywhere. To this day, there is not one collector who fails to refer to Stern, whether in New York or London, Moscow or Hong Kong, Singapore, Tokyo or anywhere else. The name remains intimately entwined with the world's most iconic watches. Stern was the go-to maker of dials for the likes of Rolex, Audemars Piguet, Vacheron Constantin, and many other great watchmaking houses, including, of course, Patek Philippe.
Beyond the prestige behind the name, the history of the Stern dynasty is, above all, a touchingly human story, one that unfolds as a series of personal ups and downs mirroring the developments in the global economy. Yet it is a story full of deeply human experiences, a mixture of tragedy and existential weakness, a story of courage and sheer will of character. No one, thus far, has attempted to articulate in such detail, or to such a documented extent, the intensely rich history of the Stern dial-making dynasty.
The luxury business, it will come as no surprise, has always been highly permeable to the influences of the general economic climate. An example that springs to mind dates from the late 19 th century when a huge number of pocket watches were manufactured in Switzerland for the Chinese and Turkish markets; the collapse of those markets took a heavy toll on the Swiss economy. Given the regular crises to which the luxury sector, and therefore high-end watchmaking, is susceptible, history often ends up repeating itself. In that sense, the luxury industry is like a boat sailing the high seas without a sail: the ship must constantly adapt to the whims of the waves, the turbulence of current events shaped by war and peace, tortured markets, fluctuating interest and currency rates, and so on. Some tides will bring the boat to shore, others will set it further adrift.
I'd nonetheless like to stress the fact that the dial manufacturing industry is so much more exposed to these trends and tribulations than the watchmaking industry itself. Literally, the initial face of the timekeeper, the dial is, in reality, a reflection of an era and its ever-evolving aesthetic and technological trends. So, if current dial preferences tend towards metal, rather than enamel, the company manufacturing the dials will inevitably need to adapt. Likewise, every era will have its own colour palette, size or finish preferences, or favourite materials, thus compelling the manufacturer to navigate the twists and turns of taste to survive the journey: or, to continue the climate metaphor, weather the economic squalls, showers and storms in order to reach the shores of success. Such was the entrepreneurial journey of a dynasty inextricably linked to the history of its country, the global watch industry and, above all, the manufacture of the most accomplished watch dials in the world.
In 1996, Orior Holding SA acquired all of the shares in Stern Créations and its subsidiaries.
The value of the transaction is estimated at 45 - 47 million Swiss Francs. The balance sheet published by Stern Créations in the Commercial Register of Geneva for 1996 was almost 50 million, which would indeed bear out the purchase price. The takeover included 260 employees.
The advantage of the 1981 restructuring operation was that the same people and employees were retained within the company. Stern Créations thus continued to benefit from their expertise in their respective fields of activity, whilst safeguarding the Stern family philosophy and business culture. André Colard's efforts were vital in this respect. They undeniably helped to preserve the company's historical, human and cultural values, which continued to be upheld following the company's acquisition by Orior SA.
The new owners of the company had no involvement or experience in the watchmaking sector. The buyers were, therefore, soon confronted with the complexities of the dial-maker's profession, realizing that the maison needed a manager with in-depth knowledge of the field. Despite this handicap, every endeavour was made to protect Stern's reputation and image as a traditional, leading high-end manufacturer. In one of the company's reports published in 1977, I came across these words by Maxime Manera, managing director at the time:
"We are virtually the only ones to manufacture jewellery dials with ornamental or semi-precious gemstones... "
He was referring to the fact that Stern produced hundreds of thousands of dials a year, a few of which were set with jewels and manufactured in limited series of a maximum of 20 pieces.
"We remain artisanal in our approach, although our industrial process is characteristic of what is going on in the luxury industry: it offers a very high added value; the knowledge of the mind that inhabits the hand that gives shape to the object. Our personnel are supremely specialised. Although age-old techniques form the basis of our skills, modernity is evident in our use of digital machinery and our access to the very latest technologies."
In late June 2000, Stern Créations was acquired by the Richemont Group. Highly active in the luxury industry, the group had a solid basis in the watchmaking world, in particular, and already owned brands such as Cartier, Vacheron Constantin, A. Lange & Söhne, Piaget, Jaeger LeCoultre and Panerai.
The new owner, known for its skills in the takeover and management of traditional brands, embarked on a restructuring exercise that incorporated the subcontracting companies already in its possession. It thus embarked on a redistribution of Stern's various departments and the significant task of transferring their knowhow to other units. In doing so, it brought a legendary entrepreneurial history to an end.
During the seventeen years following the acquisition, four or five different directors took the helm. Naturally, many customers of Stern Créations terminated their agreements, neither wishing to divulge their trade secrets to a competitor, nor to share projects protected by intellectual property rights, such as prototypes or special dials.
The number of outside orders thus gradually diminished, although Rolex continued ordering for some of its ranges for another ten years. It was a nice demonstration of loyalty, especially knowing that in the year 2000 Rolex was procuring its supplies from Stern's life-long competitor, the Beyeler factory.
Richemont adopted a new strategy and renamed the different Stern entities between 2012 and 2014. Stern La Chaux-de-Fonds became Procadrans and Stern Créations became Manufacture Stern 1898 before merging with the Manufacture Genevoise de Haute Horlogerie, a branch of Richemont dedicated to the production of watchmaking calibres aspiring to the Geneva Seal.
In 2015, Richemont decided to bring the 118-year-old history of Stern dial-makers to an end and in June 2016, Manufacture Stern 1898 was definitively no more. What have they thrown away? Oh God, oh God! was the lament of former Stern workers even in 2019...
Below is a list of the various company names adopted for a very particular jewel in Switzerland's watchmaking crown that history will always remember as "Stern Cadrans":
1898 - 1902 Atelier Henri et Louise Stern
1903 - 1905 Atelier Stern Frères
1905 - 1907 Fabrique de Cadran Charles Henri Stern
1907 - 1931 Stern Frères general partnership
1931 - 1981 Stern Frères SA
1981 - 2012 Stern Créations SA
1981 - 1996 Stern Créations SA (board members and watch brands)
1996 - 2000 Stern Créations SA (shareholder: Orior Compagnie SA)
2000 - 2012 Stern Créations SA (shareholder: Richemont Group)
2012 - 2016 Manufacture Stern 1898 (shareholder: Richemont Group)
More than 50 operations go into the making of a top-quality dial. If ever there was a watchmaking component that deserved an entire book in its own right, it is the watch dial. Complex to manufacture, requiring an understanding of aesthetic and dimensional constraints, the dial is the face of the watch and the first thing we see. It is therefore the raison d'être and main motivation behind this book. The aim is thus to demonstrate, with numerous richly illustrated explanations, the sheer complexity of the manufacturing process: a series of operations, each performed one step at a time, each more fascinating than the last. Age-old processes steeped in history and crowned by knowledge help us to track and date the technological developments that have typified this unique facet of watchmaking. Yet, as production volumes rose, skilled trades evolved into industrial processes, and traditional practices and standards acquired a new vocabulary for the new technical era.
All enthusiasts deserve new pastures to explore, new experiences to slake their thirst for knowledge. This book therefore invites them to discover an interesting period in Swiss watchmaking history. It lights upon some of the most iconic dial-manufacturers on the way, focusing on the fascinating and ingenious world of the dial-maker's craft and its magnificent creations. Although the dial holds the aesthetic and dimensional key to an initial appreciation of the wristwatch, the scant literature on the subject has always left the enthusiast craving for more. Only a handful of legendary dials can boast documentation commensurate with their rarity and value, among them the Patek Philippe Nautilus and the Audemars Piguet Royal Oak. Yet the literature available fails to cover the full spectrum of techniques employed and the myriad complex, delicate operations that have gone into the dial's manufacture throughout the ages.
The dial has travelled oceans of time. In Antiquity, artisans and artists (in those days the terms were intimately entwined) worked with metals and strove to master the immutable techniques of engraving and chasing. As guardians of this legacy, dial-makers naturally acquired a deep understanding of these processes; refining them and applying them to their own craft. The infinite pearls of wisdom shared by these artisans defy belief and command the utmost respect. I fear that some of these age-old skills will one day disappear due to the advancing age of their practitioners. It is this fact alone that gave me the courage to pursue my project. Fortunately, the craftsmen I met were still sharp-witted and more than eager to pass on their legacy to succeeding generations.
I am confident that today's inquisitive minds, no doubt tomorrow's aficionados, will find much food for thought inside these pages. I intended it as a common sense practical guide that offers key explanations and raises an awareness of the quality nuances among these diverse techniques. For example, how to discern an enamel from a lacquered finish, or a multi-polished layered lacquer from a matt varnish or single layer of lacquer, a chapter ring that is struck into the dial rather than assembled on its surface using gold, or coloured brass index appliques, or how to distinguish between hand-machining techniques and their automated numerical controlled equivalents. Technological advances in today's machines have made it virtually impossible to tell the difference.
The second section of this book invites you on a revelatory journey into the world of ingenious inventions and technical prowess, an insightful one-way trip to the heart of expert craftsmanship, a look back at the origins of elegance and the fine art of detail. This journey offers a more or less chronological overview of the main processes involved in 20 th century dial manufacture. Each one is a key element participating in the whole. One of the skills of the dial-maker is, in effect, the ability to plan the precise order of execution that will ultimately dictate the end result or even type of dial.
The dial manufacturing process may be divided into different stages comprising sub-stages. There can be many types of procedure, depending on the dial, the manufacturer and the choice of manufacturing method. At Stern, there were three main stages of dial manufacture.
The ébauche (blank) is the basic dial plate consisting, at this stage, of the main shapes and openings, i.e. the feet, the stamped blank in the required diameter, centring holes, counters where relevant, aperture and moon windows. This is the stage that precedes decoration. Roughly speaking, the blank stage relates to the phase in dial manufacture concerned with any form of operation designed to remove material or fragments of material.
Decoration is the term applied to a whole host of operations performed on a dial-blank in order to obtain a decorated dial. It includes any finishing process carried out on the dial's surface other than for removing material, such as graining, satin-finishing, or even the application of galvanic colour-coatings, varnish, or enamel, and, if necessary, a transparent protective layer of Zapon (cellulose) lacquer. This second stage might also include machining operations, such as milling recesses to obtain pearled markers, or drilling feet-holes for appliques.
Finishing is the term used to refer to the various final additions made to a dial: i.e. the transfer-printing of indications, or the securing of applied elements known as appliques (indices, Roman or Arabic numerals, cabochons, rings or apertures). Finally, it also refers to all the assembly or setting operations relating to these elements.
Polished and cambered blank for a Vacheron Constantin Patrimony dial: in this example, we can see the blank cut to diameter complete with centring hole, aperture opening and stamped bevel.
Decorated dial, here sporting a silver-coloured opaline finish and recessed pearled dots made with a burin.
Until the late 1990s at Stern, blanks, once polished, were routinely silvered using the electroplating process. The very fine layer of silver was more malleable than the dial's base material and therefore easier to work with for the dial-maker, resulting in a superior final decorative finish. Very fine decorative finishes come into their own when combined with colour-coatings just a few microns thick, such as those obtained by electroplating, or physical vapour deposition (PVD). In actual fact, the choice of decoration can significantly influence a dial's aesthetics, both in terms of ultimate colour or shade, and subtlety of effect, for example veering between matt and gloss, or light and dark.
A mirror polish involves polishing the surface of the dial-blank very gently to create a shine, but without affecting the pattern. This high grade of polishing, or high-end buffing, is one of the final operations sometimes performed on a finished dial.
In the 1950s, the mirror polish was combined with the épargne or galvanic resist technique for branding, minute-circles, or what is known as the mirror polish épargne hour-circle. Nowadays, such techniques are rarely used and are limited to small areas, given the increased risk of surface scratches in such an operation.
In its early days in 1898, the Stern workshop mainly made monochrome opaque enamel dials, like most other dial-makers elsewhere in Switzerland during this era. These dials were usually white in colour, or more rarely, black.
In 1957, Stern Frères adapted its production infrastructure to the demands of large-scale production and parted company with its enamelling department. During the period 1960 to 1990, workshop-crafted enamel dials were no longer fashionable. It was not until the 1990s that there was a renewed interest in enamel and it made a comeback. Interest grew and so in 2000 Stern Créations revived its high-end enamelling department.
The only operations conducted on the bon courant or "standard grade” monochrome enamel dial were the hole-piercings for the hour and minute hands, and the opening reserved for the seconds. The surface of the dial was left flat. One approach, normally considered a high-end technique, consisted in manufacturing the dial in several pieces. Complete openings were made in the dial-blank, then a separately baked enamelled piece was applied to the back of the dial to create the surround for a central recess or counter.
Different enamelling techniques proposed by Stern Frères between 1898 and 1985:
• Opaque monochrome enamel for large-scale production. Between 1898 and 1957, but later contracted out.
• The engraved-enamelled technique was practiced in the Stern workshops between 1898 and 1982. The dials were hand-engraved and, no doubt as of the 1950s, often by photogravure.
• Openwork cloisonné enamel or cloisonnéchamplevé enamel from 1940 to 1960. For these essentially one-off commissions, the enamelling was contracted out to an independent artisan, whilst all other work on the dial, such as blank manufacture and finishing, was executed by Stern Frères.
• Champlevé enamel and champlevé-cloisonné enamel between 1940 and 1982. The different manufacturing stages were organised as before.
• Translucent enamel on a guilloché (engine-turned) base or on basse-taille engraving between 1898 and 1985. These commissions destined for smallscale production were mostly executed in the Stern Frères Métiers d'art workshops.
• Miniature enamel painting between 1898 and 1960. For these essentially one-off commissions, enamelling and painting were contracted out to an artist, whilst the blank manufacture and finishing of the painted enamelled dial were executed in-house at Stern.
Old coal-fired kiln in which the dial plate undergoes several firings at temperatures of 700°C to 900°C. Document taken from a Flückiger brochure published for the dial-maker's 100 th anniversary. 5
Manufacturing an opaque monochrome enamel dial with the applied counter, method and steps involved
1. Copper plate with welded feet is deoxidised and trued after stamping.
2. Enamel-backing is applied to dial to counteract tensions. Master-craftsman, Louis Émile Millenet has this to say in his Manuel Pratique de l'Émaillage Sur Métaux (Handbook for Enamelling onto Metal): "Under the effect of the relatively high temperature required for bonding enamel to metal (temperature ranging from 600 to 900°C), both materials will expand at different rates, the latter far more than the former. On cooling, however, the enamel and metal contract, this time the other way around. This therefore gives rise to an imbalance, especially on larger metal surfaces resulting either in a totally warped object, or chipped or cracked enamel. (...) The French term "contre-émaillage" (meaning counter-enamelling) is an appropriate one here, as the metal is effectively imprisoned between two layers of enamel." 16
3. Opaque monochrome enamel is applied in several layers.
The critical firing stages can have undesirable consequences, for example oxygen can become trapped in the raw material causing tiny bubbles to form on the finished surface. The size of the bubbles depends on the quality of the raw enamel and the act of grinding. These visual imperfections were removed by the enlevé-repiqué process, to use the enameller's term, i.e. pricked away with a needle or even a small milling-cutter. Better still, they were often milled, then lapped and refired. Next, in order to fill the recessed areas, an additional fine layer of enamel was applied. Drawing on centuries-old know-how, the enameller
would complete the final milling operation using hand-tools made of wood and special stone, an operation that required the patience of a saint and extraordinary skill. He would ensure that the work was carried out in a dust-free environment to avoid even the minutest of scratches on the dial's surface. Following its relocation to the Place des Volontaires in Geneva in 1906, i.e. along one of the banks of the Rhône, the Stern workshop now had the benefit of hydraulic power. Stern thus set up a system of rotary boxwood discs driven by pulleys. These mechanisms provided a more efficient way of polishing the enamel dials and required, among other things, the regular application of specially calibrated sand and water.
4. Numerals and letters are either transfer-printed or hand-painted in coloured enamel.
5. Firing.
6. Optional layer of flux can be applied.
7. Dial is filed to appropriate diameter.
8. Hole pierced in centre.
Two paths are open to the enameller at this stage, each requiring a special technique. The first consists in piercing the dial prior to enamelling. This carries with it the increased risk of slight depressions forming around the pierced openings. The second technique, giving a higher grade of finish, entails piercing the dial once the blank has been enamelled. This operation requires a drill and diamond burs and the courage to risk the enamel cracking during drilling.
9. Seconds counter is cut out.
10. An applied enamelled counter is nested and welded to the dial.
Made by Stern Frères in 1953
In the 1950s, Rolex, together with Stern Frères in Geneva, made some of the most iconic wristwatches with a cloisonné champlevé dial. The dial pictured opposite with its Caravelle motif was one of them. This strikingly beautiful dial features a multi-coloured enamel painting of an ancient Greek ship riding the surf. The design was the work of the celebrated Genevan enameller Marguerite Koch, who had designed other famous champlevé enamel dials commissioned by Stern Frères for Vacheron Constantin and Patek Philippe. Interestingly, Madame Koch reportedly worked in-house for Patek Philippe for a while.
Some parts of the area to be enamelled on the flat blank are initially hollowed out (champlevé), then the yellow gold blank is given its domed shape. The back is struck with the code 103 389 corresponding to the customer code designating Rolex, the Stern Frères hallmark and the order number. The no. 29 roughly sketched into the enamel-backing relates to the Caravelle drawing produced by the enameller Marguerite Koch, taken from one of the four books of samples collated by Stern Frères for the benefit of its customers.
It should be noted that the enamel-backing is applied in such a way as to leave space for the attachment of the appliques and to allow for the index feet and Rolex crown to be two-point peened to the dial and not glued. The black patches are traces of calamine and oxidation resulting from the dial's numerous visits to the kiln during enamel firing. The two yellow gold feet on the dial are attached to the caliber by brazing.
The vast majority of the blank is sectioned into compartments using gold wires in the cloisonné champlevé technique in order to accommodate the enamel. The enameller painstakingly fashions the various wires into the required shapes for the desired motif, embedding them into a flux base layer. Then begins the enamelling, here performed in several layers. The pearled ring is circular satin-polished and the pearls are hand-milled. The two stars consist of gold spangles. A final layer of transparent enamel (flux) is used to glue them in place and protect the enamelled motif.
In this cloisonné champlevé dial (see p. 242), the interplay of colours and graduations is quite remarkable. I should add that master enamellers, being skilled in the superimposition of enamel layers among other things, were able to obtain highly nuanced, lively colours of a quality that nowadays would be difficult to achieve.
The large-format enamel seascape incorporates the hour-circle complete with Rolex crown and 11 pointed yellow gold indices with five lapped facets. See pages 140 and 141 for a similar example of cloisonné enamel, but in a smaller format. Note that the task of boring and setting required for attaching these appliques to the enamel inevitably incurred the risk of destroying all the work undertaken thus far. The SWISS and Rolex inscriptions are transfer-printed in black.
Enamel does not age and remains here in perfect condition.
Distinguishing features
• Large-format cloisonné champlevé enamel.
Made by Singer in 1970
Few vintage wristwatches are as sought-after by collectors as the Rolex Daytona Paul Newman with its characteristic Art Deco style dial. Originally named exotic dial, it was later renamed Paul Newman when aficionados discovered it to be the favourite model of the celebrated actor and distinguished racing driver. It should be noted that this Daytona model, with its atypical counter markings, was exclusively intended for the American market. However, having not met with the anticipated success, it was soon replaced by the classic model. Created in the early 1970s, the Cosmograph Daytona reference 6262 features technical adaptations including the introduction of the caliber Valjoux 727. This cult watch succeeds reference 6239.
Blank
The blank is in brass. The three counters are recessed and the minute-circle zone is inscribed into the dial on a slightly lower level than the silvered section. The two copper mounting feet are electrically welded on the back of the dial. The Singer hallmark and the SJ logo are also visible.
The two-tone decoration in galvanic black and galvanic silver is achieved using the resist technique. The entire surface, including the previously snailed counters, then undergoes graining.
Finishing
The inscriptions and scales on the dial are white transfer-printed, with the exception of the red DAYTONA. The applied hour appliques consist of flat-polished square studs probably in white gold, fitted with a single centrally peened foot. The luminescent hour-circle pearls are Tritium-based, as indicated by the transfer-printed T SWISS T inscription, and are deposited adjoining the stud hour markers.
Ageing
Protected by a layer of Zapon cellulose lacquer, the face of the dial has withstood the test of time particularly well, unlike the unprotected back which shows overall signs of oxidation. The luminescent dots have turned from their original white to a yellowish colour.
Distinguishing features
• Two-tone dial.
• Art Deco style design.
• Grained finish.