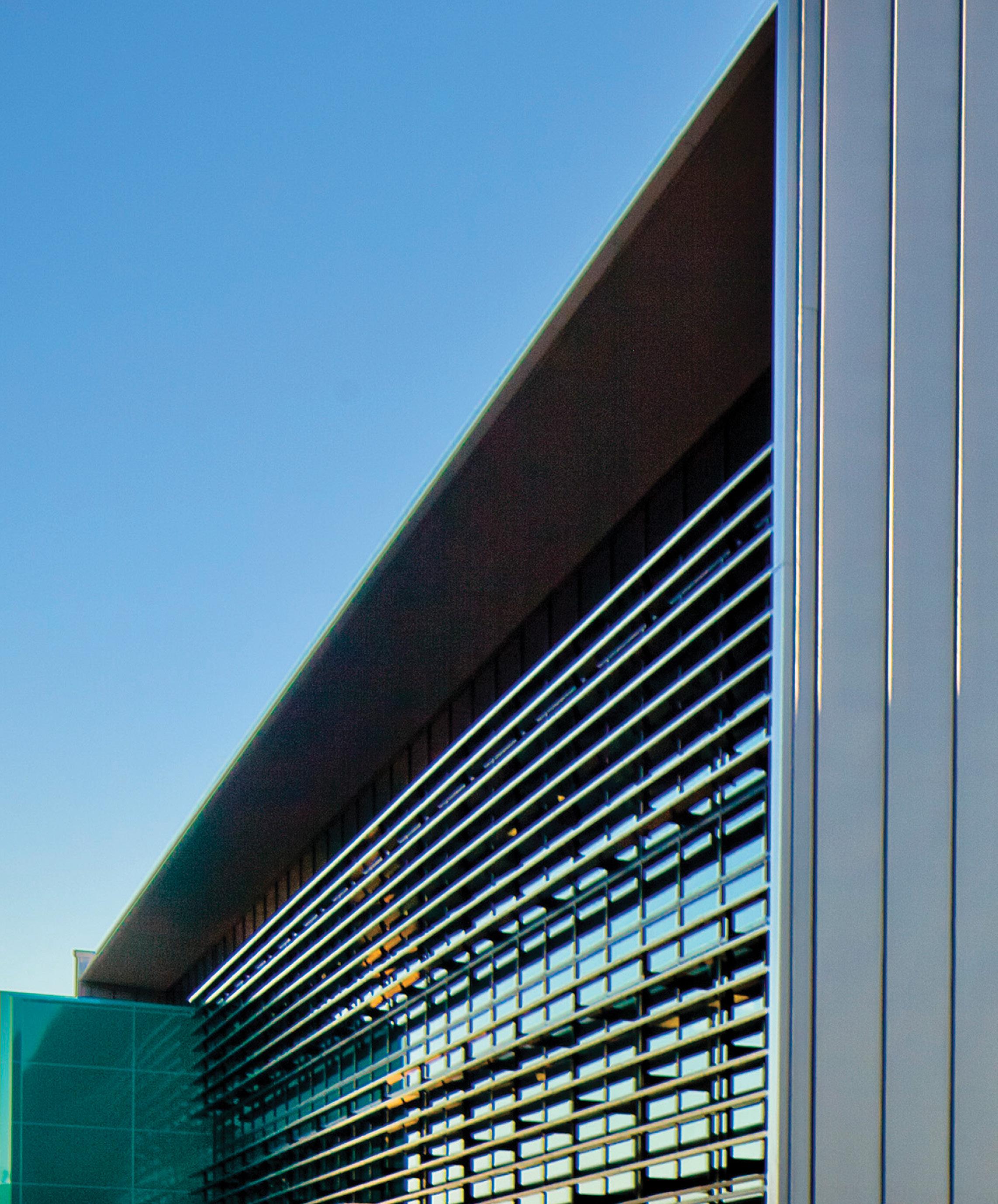
13 minute read
INDUSTRIAL
INDUSTRIAL PROPERTY
+ AS THE CALL FOR QUALITY DESIGN AND INNOVATION INCREASES, MORE IS BEING ASKED OF THIS GROWTH SECTOR. INDUSTRIAL BUILDINGS ARE EXPECTED TO WORK FOR STAFF WHO SPEND SO MUCH TIME IN THEM, AS WELL AS DELIVER TOP RESULTS.
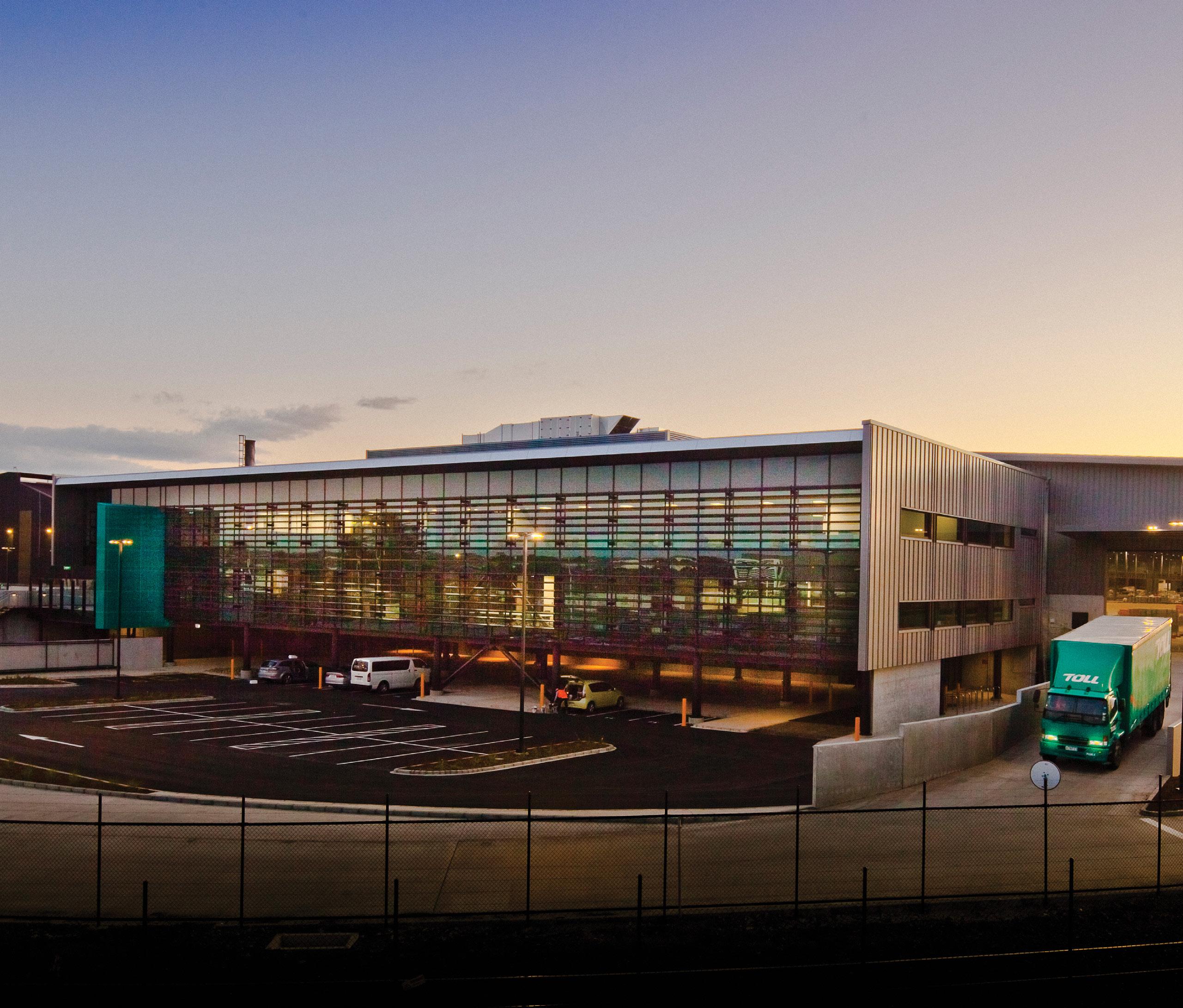
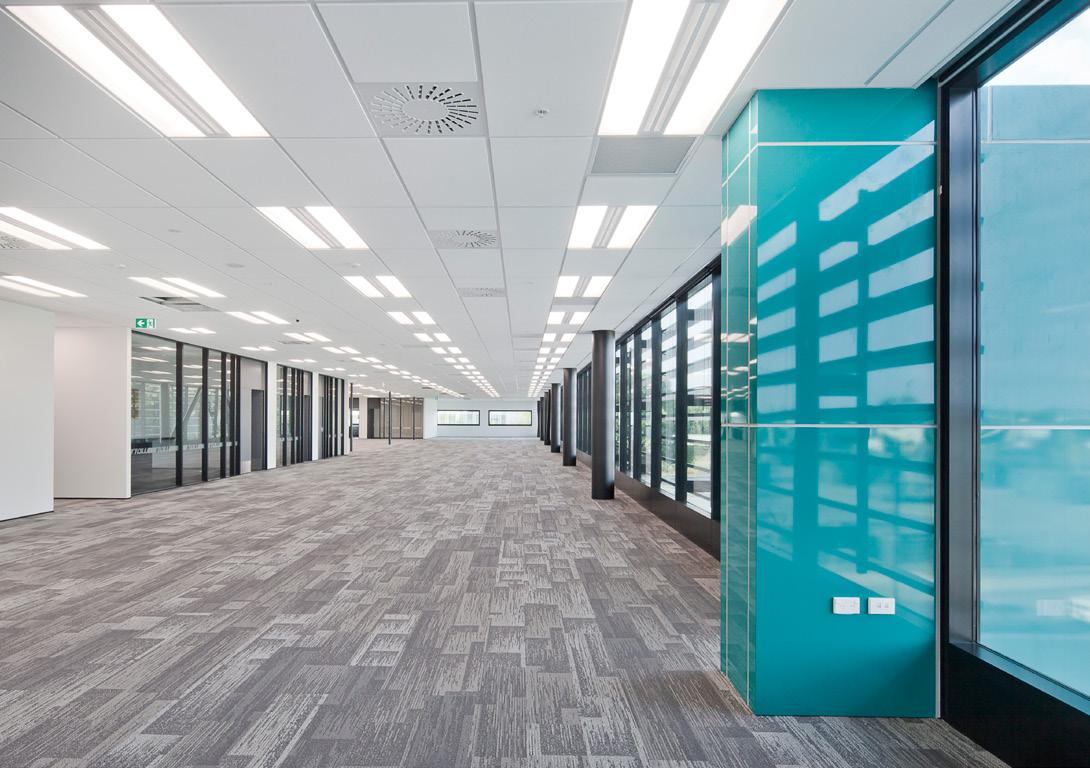
When Toll Group replaced four facilities around Auckland with one central hub, the building had to satisfy many objectives.
The building has light, bright work environments, plenty of space for workers to dine and relax in, and a handsome, striking frontage.
WHERE FOUR GOES INTO ONE BEAUTIFULLY
Macrennie Commercial Construction and RDT Pacific had a big job on their hands. The contractor and project management firm were hired to develop a new facility for logistics company Toll Group, which wanted to bring three separate freight-forwarding depots, plus a national head office, together on a single site in Ta -maki Makaurau Auckland. Macrennie and RDT Pacific contracted Williams Architects to come up with a design.
The resulting purpose-built facility ticks every single box – no small task when you consider that the Auckland depots form the backbone of the freight company’s New Zealand operation. They contribute about 40 per cent of the group’s total domestic road and rail freight revenue and represent a critical node for nationwide business growth.
Achieving the goal involved finding a suitable site, which was close to Toll’s customer base and the rail network. After a long and detailed assessment of
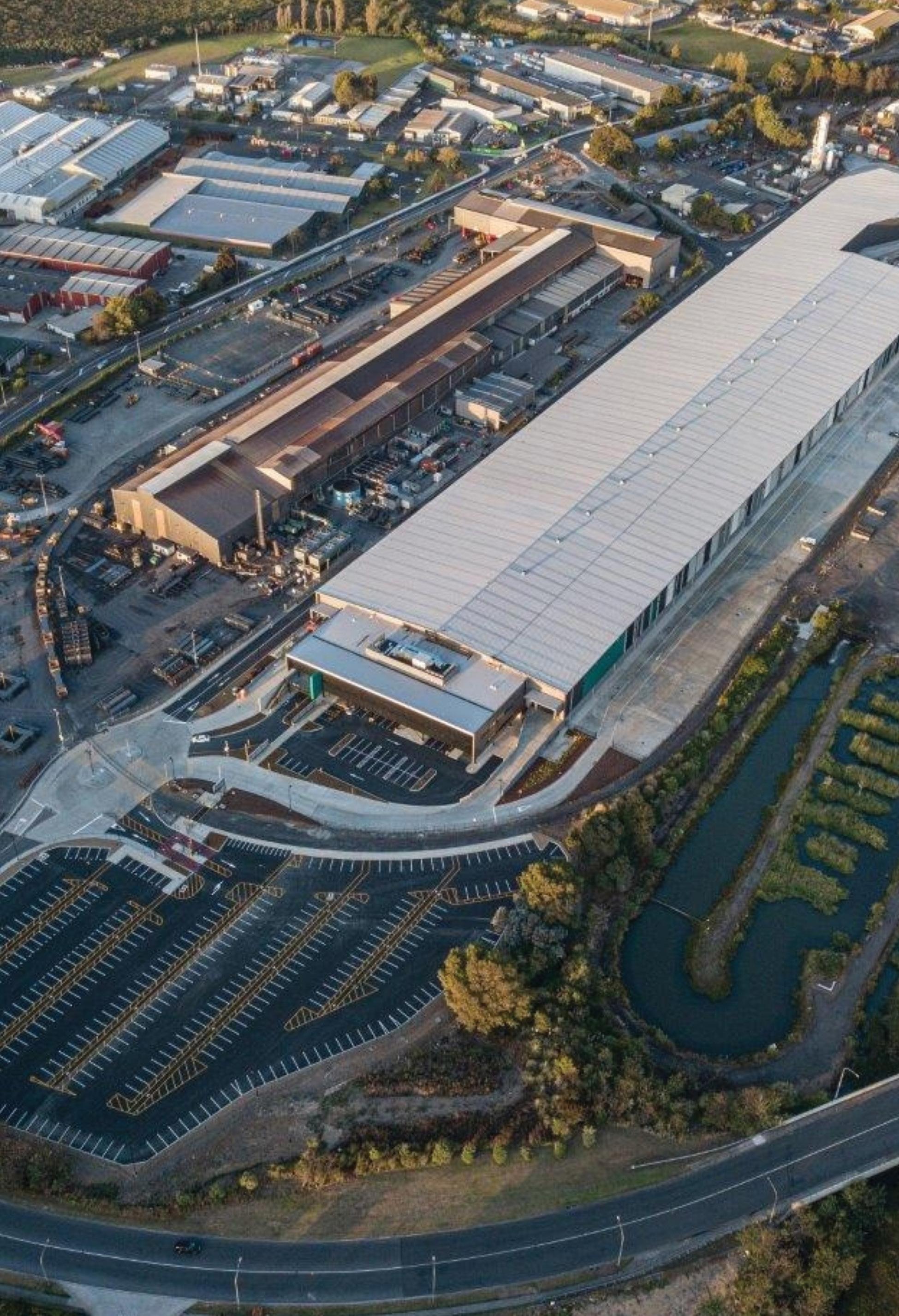
locations during 2015, the company found what it was looking for on James Fletcher Drive in Favona, South Auckland.
Toll then had to reach an agreement with the vendor so it could get cracking on preparing the land. A subsequent land swap with a neighbouring owner was then negotiated to optimise the layout of the new complex.
In order for the exchange to take place, Toll had to construct a new water treatment plant and then satisfy resource consent conditions. After these conditions had been met, work on the beautiful new two-storey building began.
The overarching principle applied to the project was to create a place, rather than just a building. The result: a development that positively adds to the precinct with a high-quality design in an industrial environment. The complex represents a collaborative effort between Toll Group, Macrennie, RDT Pacific, the team of architects and contractors.
“The main innovation is the way we have adapted and utilised standard construction methods and materials to create a very special building,” says Simon Williams, director of Williams Architects, the company responsible for the striking design, which includes a 24,800sqm warehouse.
The corporate office component of the building, an eye-catching structure that delights in colour and linear forms, is sited near the street to engage directly with the public. It has also been built to Toll’s corporate office specifications and makes full use of the north-westerly aspect, creating a pleasant working environment with ample natural light.
Extensive discussions between the parties highlighted the need for ‘positive’ facilities for workers, particularly during breaks. So there is an expansive cafeteria for staff meals, and an outdoor area so they can be enjoyed alfresco. All of the available space upstairs was devoted to these staff-focused areas. The office has
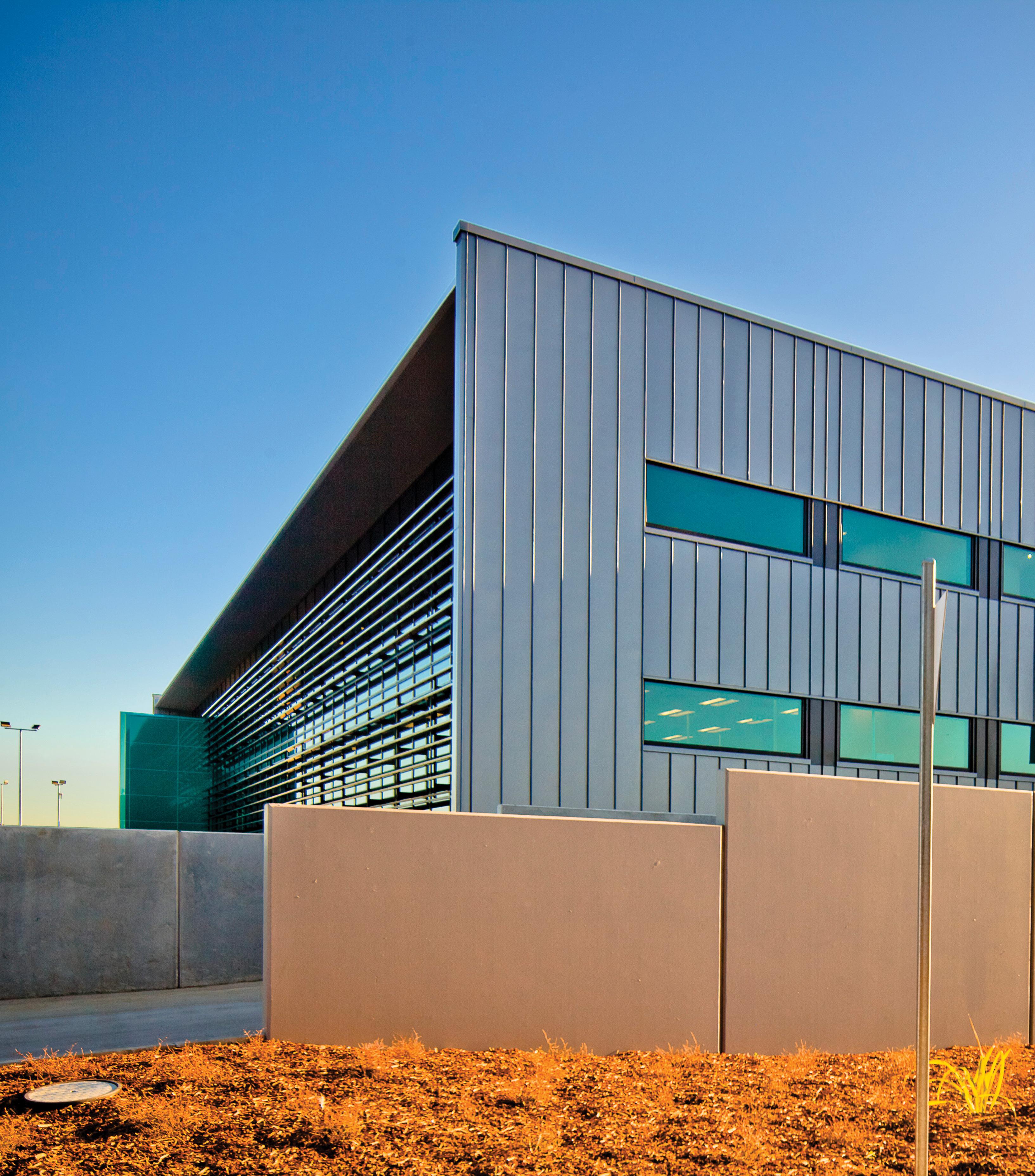
Materials were chosen for their durability, low maintenance and ease of installation, but also to make the building an attractive addition to the industrial neighbourhood. suspended ceilings; exposed soffits; and carpet tile, vinyl, rubber and honedconcrete flooring. Glass partitions capture natural light and ensure visibility, while maintaining confidentiality and noise control.
A central elevated walkway links the office to the rear of the transport facility. Natural light filters through to both areas.
Exterior materials, such as trough-profile metal cladding, boarded precast concrete and aluminium windows and framing, were chosen for their durability, low maintenance, value and ease of installation. They will retain their appearance over time.
This development is the fulfilment of an objective born six years ago. Three out-of-date depots and a national corporate office have been replaced with a single purpose-constructed building that will suit Toll and its workers for years to come.
“Toll has been able to combine its freight-forwarding palletised services
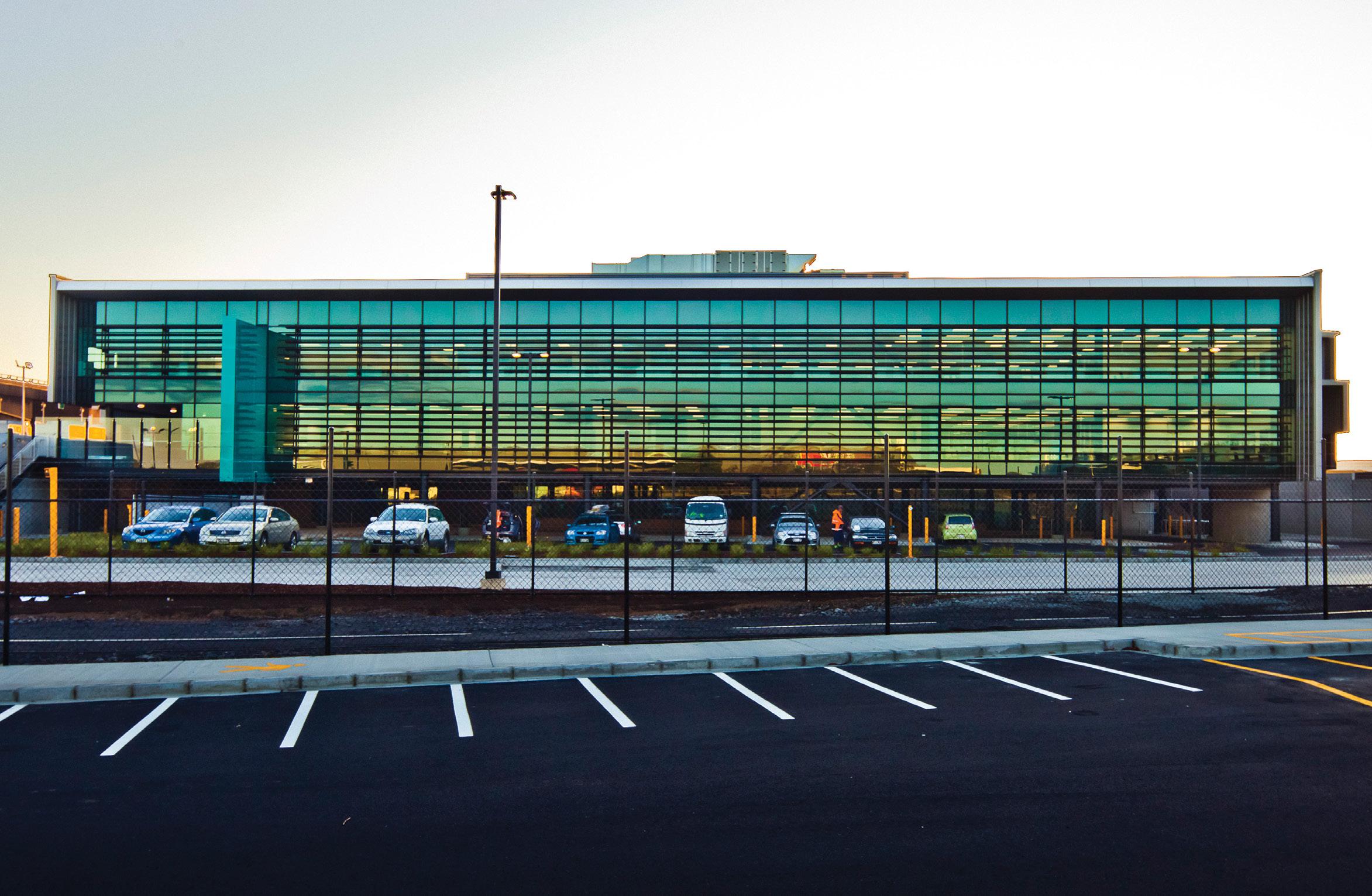
The front of the complex is devoted to office space, including Toll’s New Zealand corporate headquarters. A central walkway links the office to the rear of the transport facilities. and the parcels business unit into one facility – ultimately improving its speed and consistency of services throughout the North Island, and making full use of the New Zealand rail network through a dedicated rail spur for north-south containerised freight connections,” says Daniel Taylor, national property development manager of Toll Group. +
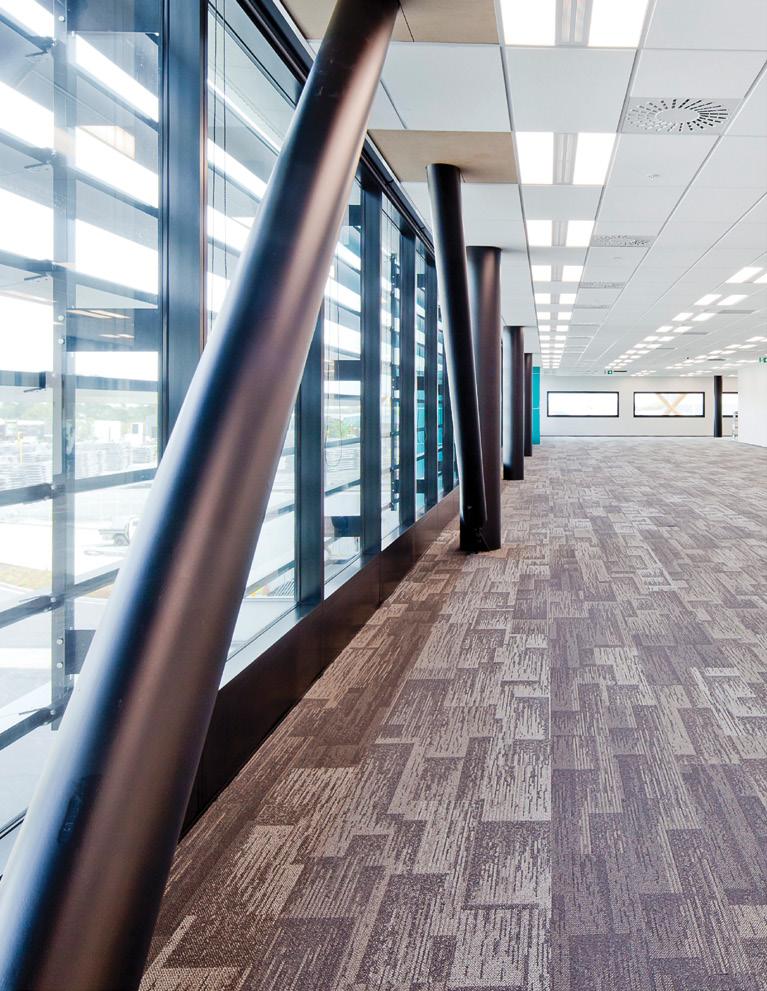
TOLL TAMAKI FREIGHT FORWARDING FACILITY
223 James Fletcher Dr, Favona, Ta - maki Makaurau Auckland OWNER, DEVELOPER TOLL NETWORKS (NZ) CONSTRUCTION MACRENNIE COMMERCIAL CONSTRUCTION ARCHITECT WILLIAMS ARCHITECTS SERVICE ENGINEER, MECHANICAL ENGINEER WSP/OPUS STRUCTURAL ENGINEER DAY CONSULTANTS QUANTITY SURVEYOR BQH PROJECT MANAGER RDT PACIFIC OTHER CONSULTANTS SOIL & ROCK CONSULTANTS, ECS
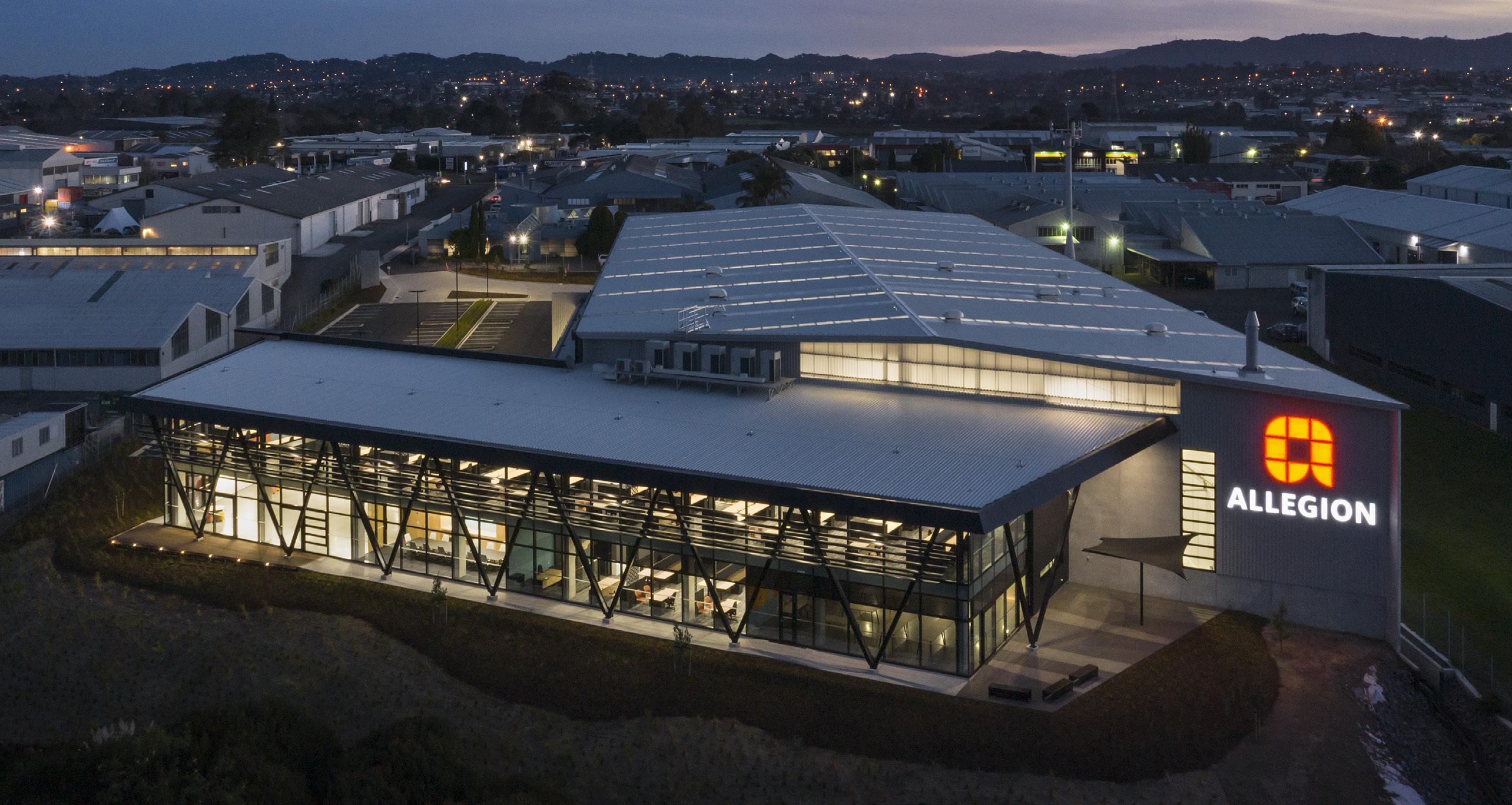
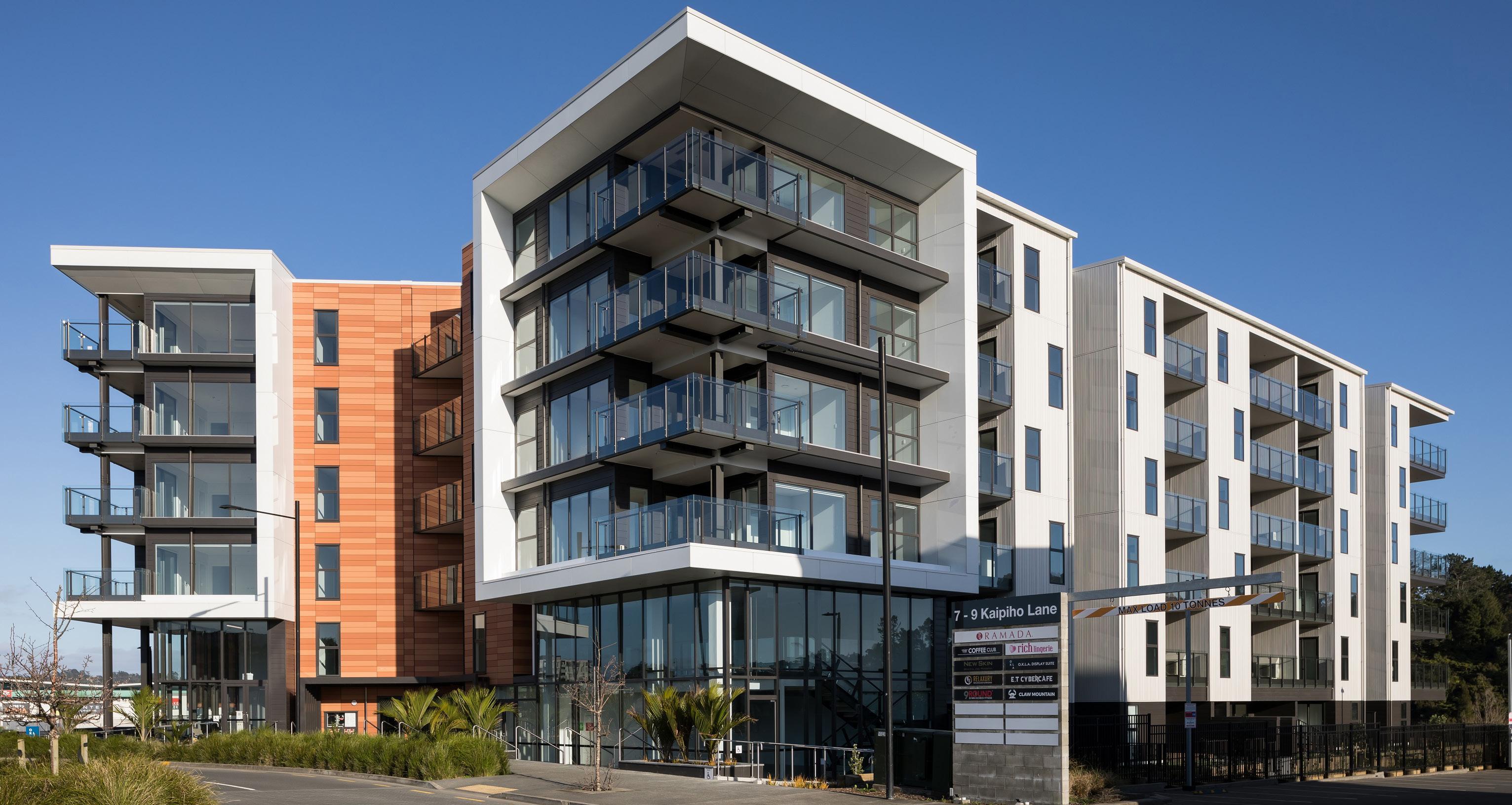
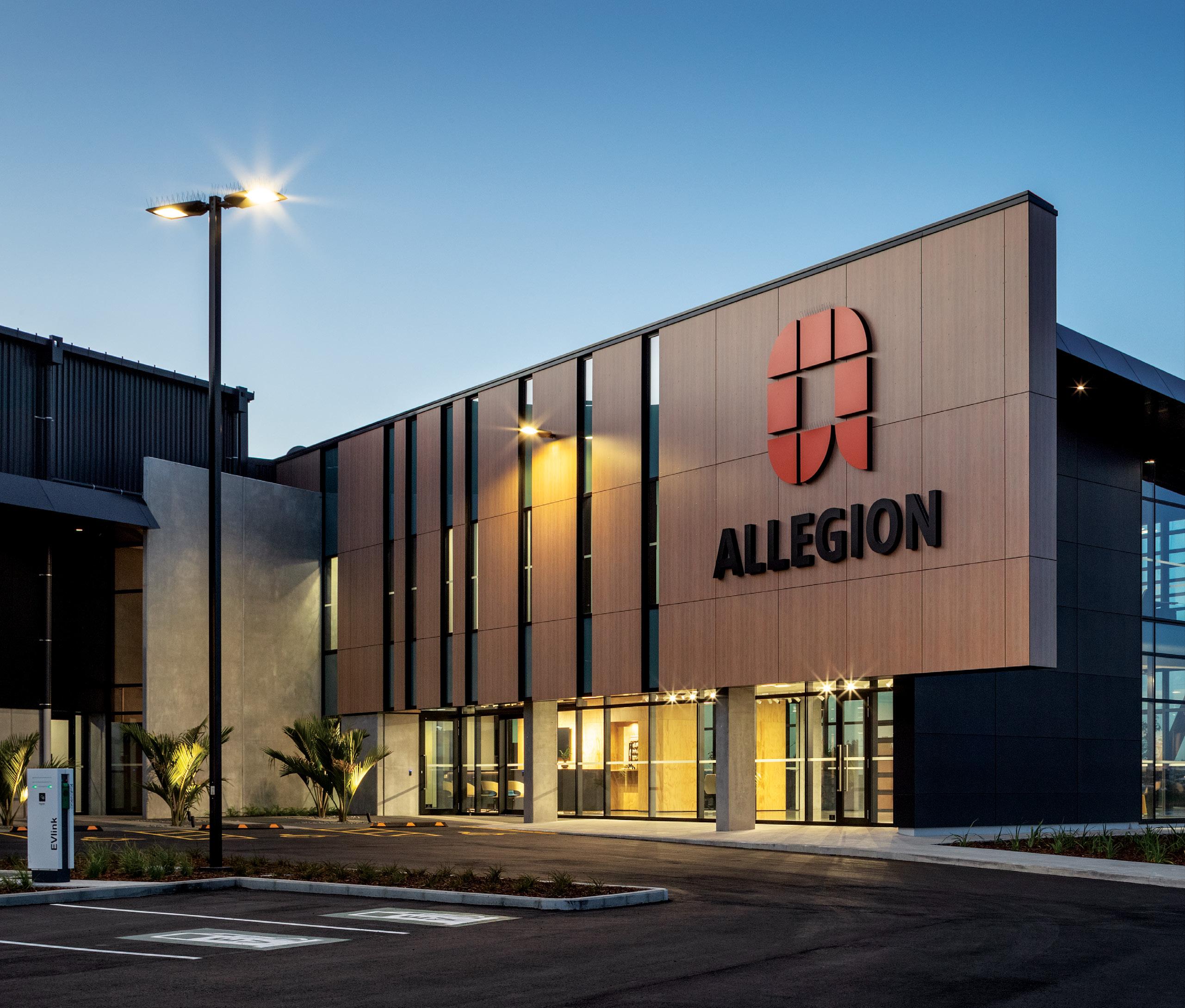
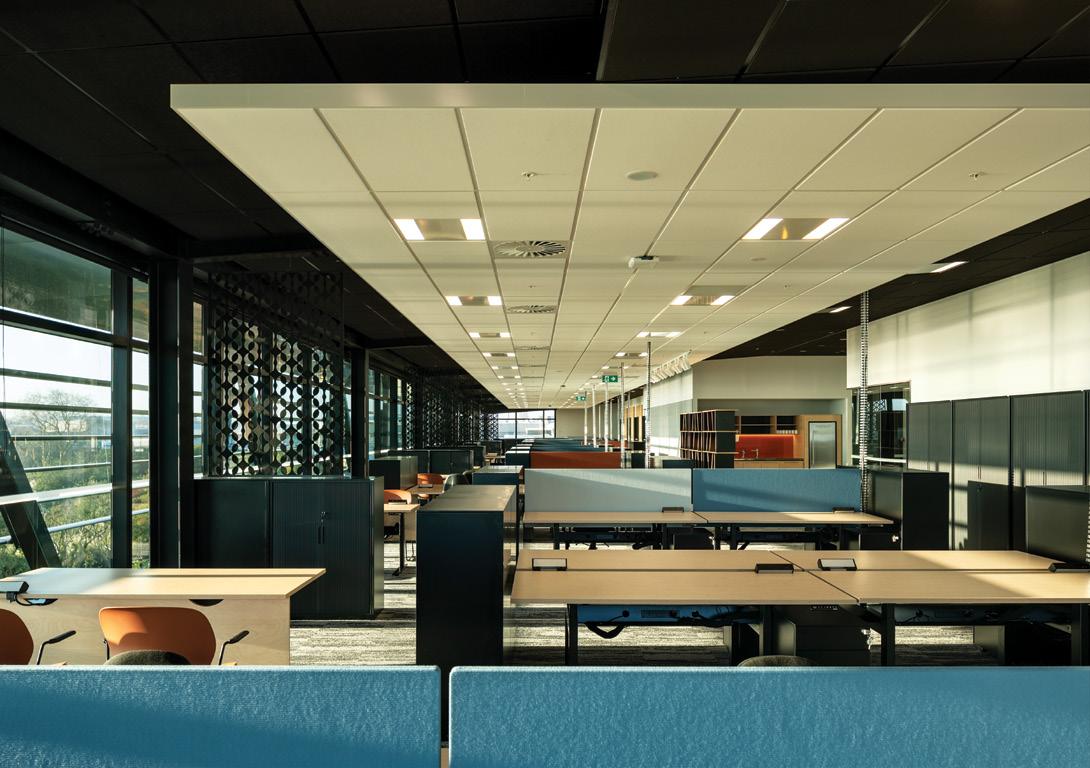
Environmental sustainability strongly influenced Allegion’s building design and the scope of site- improvement works. Natural light and increased levels of ventilation create a pleasing work environment within the offices and on the factory floor.
A TEAM BASE WITH A LEGION OF FANS
The company motto is ‘One Team, One Allegion’. Add to that 11,500 native plants and the remediation of land on which this new complex sits, and you have something special in the industrial space.
The facility in Avondale, Ta -maki Makaurau Auckland, is owned and developed by security product and solution company Allegion. The building comprises offices, a warehouse and a factory on a 14,346sqm site. Designed by Williams Architects and built by Haydn & Rollett, the development provides a connected and inspiring work environment that’s conducive to innovation – something that reinforces the company’s culture.
Allegion’s original factory was built in the 1970s and no longer met the company’s needs. The business had outgrown the office area, there was too much non-productive factory space and the low-stud warehouse was highly inefficient.
The decision was made to develop a new, bespoke facility on vacant land at
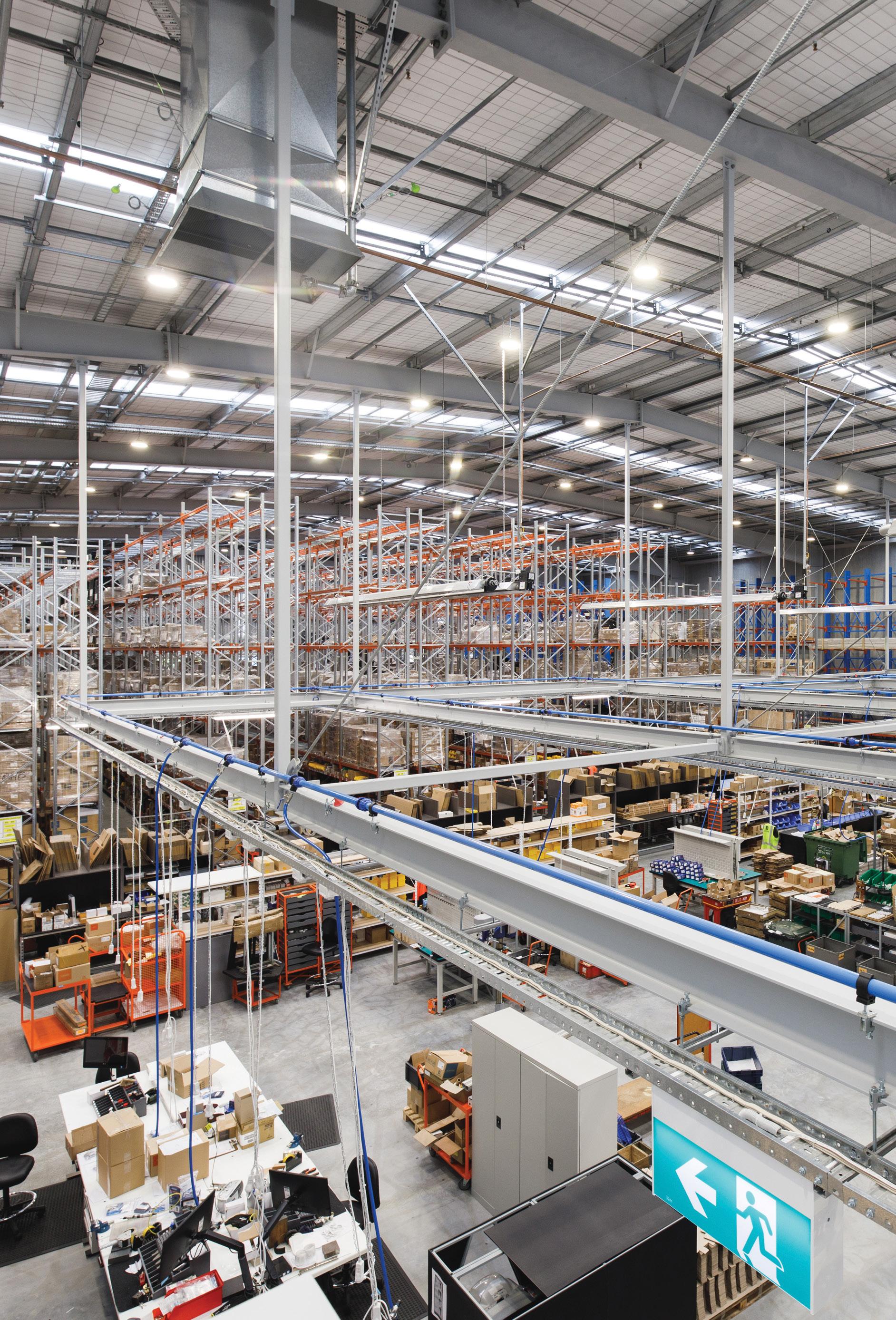
the rear of the existing site. The objective was to future-proof the business, allowing for growth of local manufacturing, sales and distribution.
As well as creating a pleasant and stimulating environment for its workers, the owners also wanted a building with “spirit” that would serve as a showpiece for the construction industry.
Other requirements included maximising the site’s potential (with opportunities for expansion), following sustainable principles and guidelines, and using quality, low-maintenance building materials.
Within the work environment, there had to be natural movement flows and connections throughout (for both people and functions) and a visual connection between the office and factory.
Environmental sustainability and corporate social responsibility strongly influenced the building design and scope of site-improvement works.
Improving the low-ecological value of the land to set a new benchmark for the area was both a significant undertaking and achievement. Erosion was uncontrolled and the coastal margin was overgrown with noxious weeds and undesirable trees. This called for extensive groundwork and regeneration.
And the result? “Full-site remediation addressed all the issues and included planting 11,500 native plants to create an area for wildlife and the wider community to enjoy,” says Brendon Simpson, managing director of Allegion.
Both the factory and warehouse have been designed so that staff can operate in an open and vibrant workplace. The majority of the office areas have indirect lighting, which provides lower levels of glare and improves comfort.
Bright colours and timber finishes provide a warm and welcoming feel. On the factory floor, the new look delivers a comfortable environment, achieved with a high level of natural light, coupled with natural and forced ventilation.
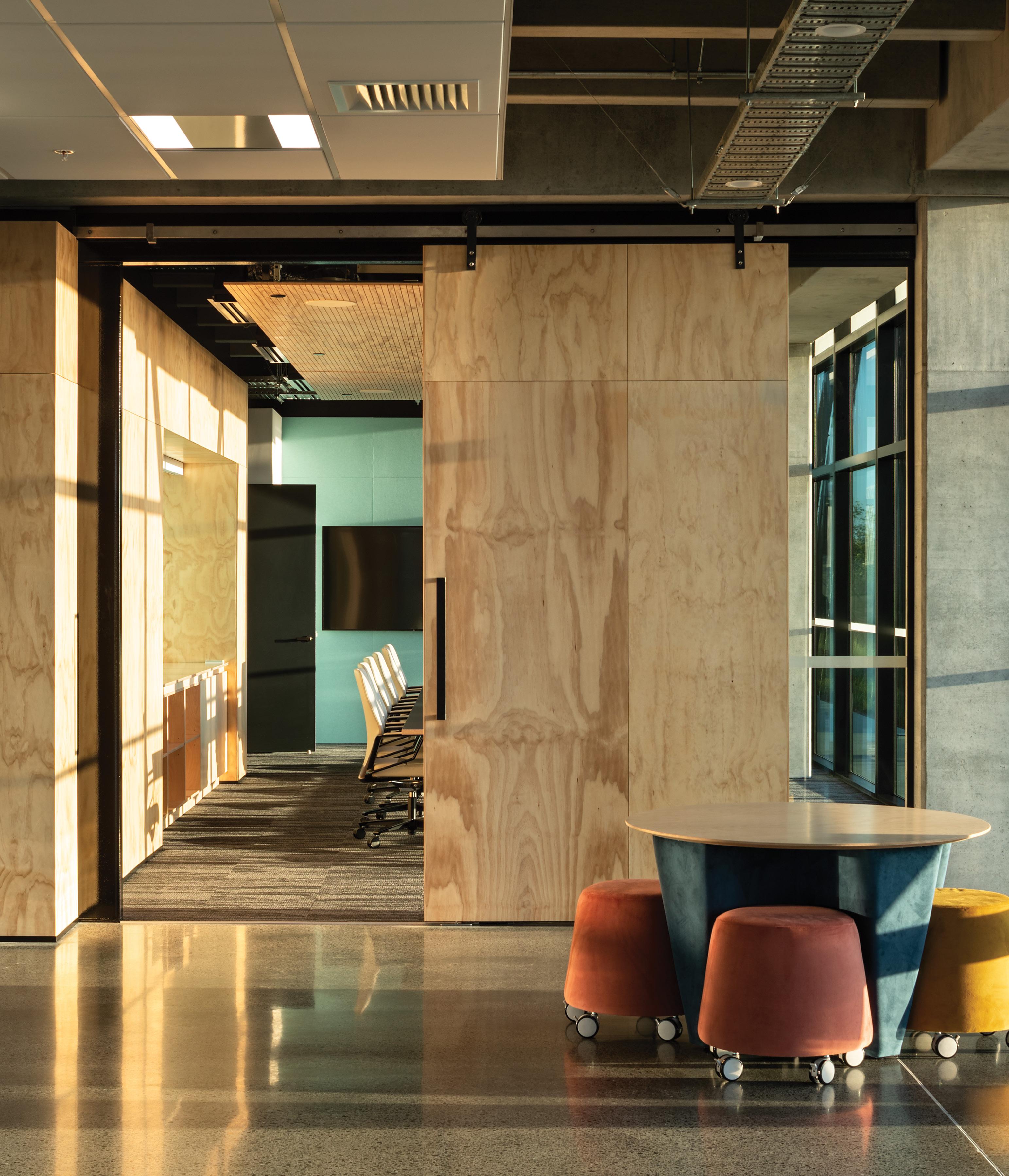
Above Plywood finishes and rich colours result in a warm and welcoming interior. Clear roofing panels provide ideal levels of natural light, reduce heat loss, but don’t allow the space to overheat in summer. The results are a significant improvement when compared to the old complex.
The factory has performed extremely well through the seasons, with staff comfort levels achieved and the benefits recognised. Services and plant rooms are easily and safely accessed.
The new warehouse footprint is smaller than the previous one, but has 50 per cent more pallet storage capacity. This has been achieved with more efficient six-pallet bay high racking, compared to the previous warehouse that had a low stud and only allowed three-pallet bay high racking.
Exterior lighting is controlled by photocells and sensors, which ensure
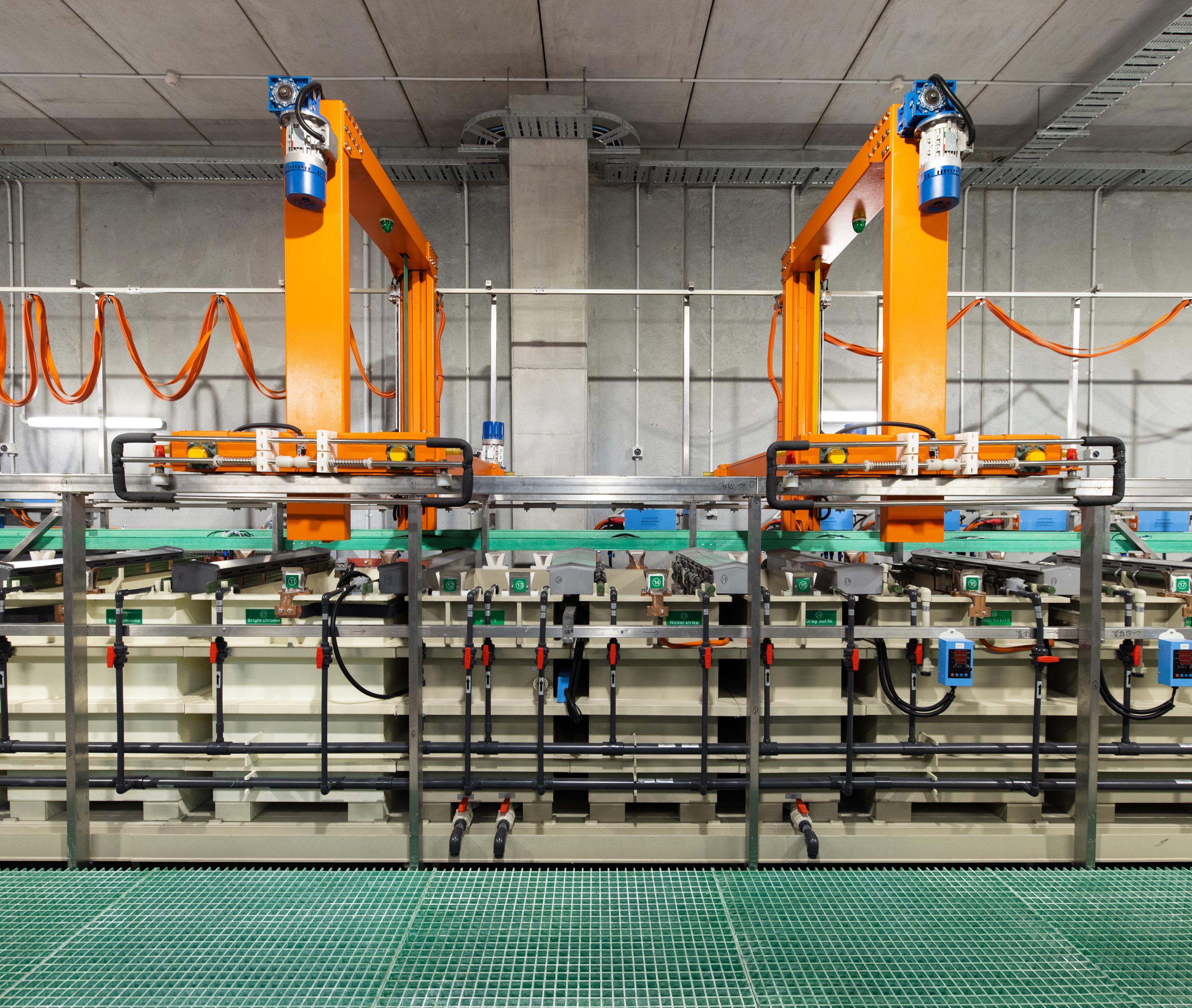
Above Local manufacturing is a key focus with the introduction of a fully automated electroplating plant. Below Bright, new kitchen facilities are just some of the advantages for workers in Allegion’s new warehouse and office space. lighting is in operation only when the site is active, or in darkness. Other nods to the future include the installation of electric-vehicle chargers.
“The entire building has many environmentally sustainable development features and a strong emphasis on creating an enjoyable work environment,” says Simpson.
On completion of the complex, the owners were delighted that all the elements of the brief had been met or exceeded. +
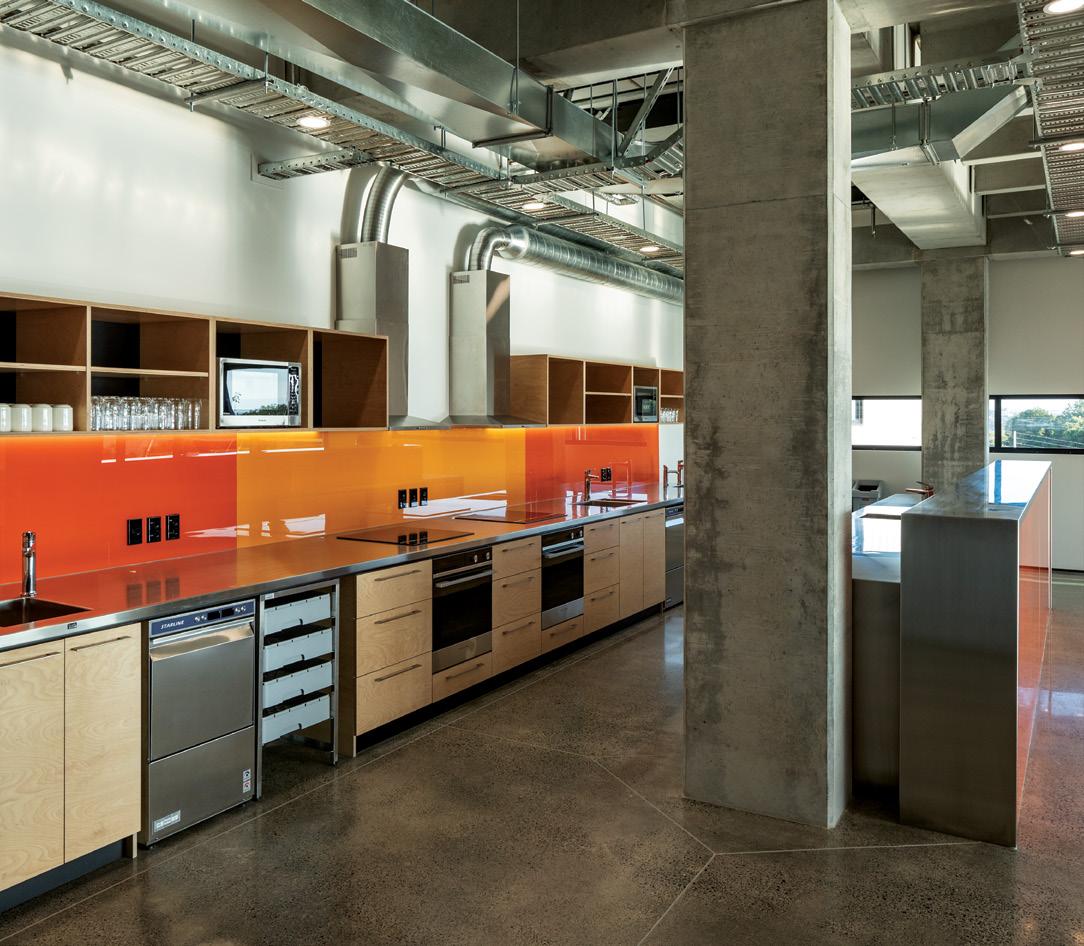
ALLEGION WAREHOUSE AND MANUFACTURING FACILITY
437 Rosebank Rd, Avondale, Ta - maki Makaurau Auckland OWNER, DEVELOPER ALLEGION CONSTRUCTION, PROJECT MANAGER HAYDN & ROLLETT ARCHITECT WILLIAMS ARCHITECTS SERVICE ENGINEER ECS STRUCTURAL ENGINEER MSC CONSULTING GROUP MECHANICAL ENGINEER THURSTON CONSULTING QUANTITY SURVEYOR HAYDN & ROLLETT, ALLEGION OTHER CONSULTANTS ENGEO, PLANNING FOCUS
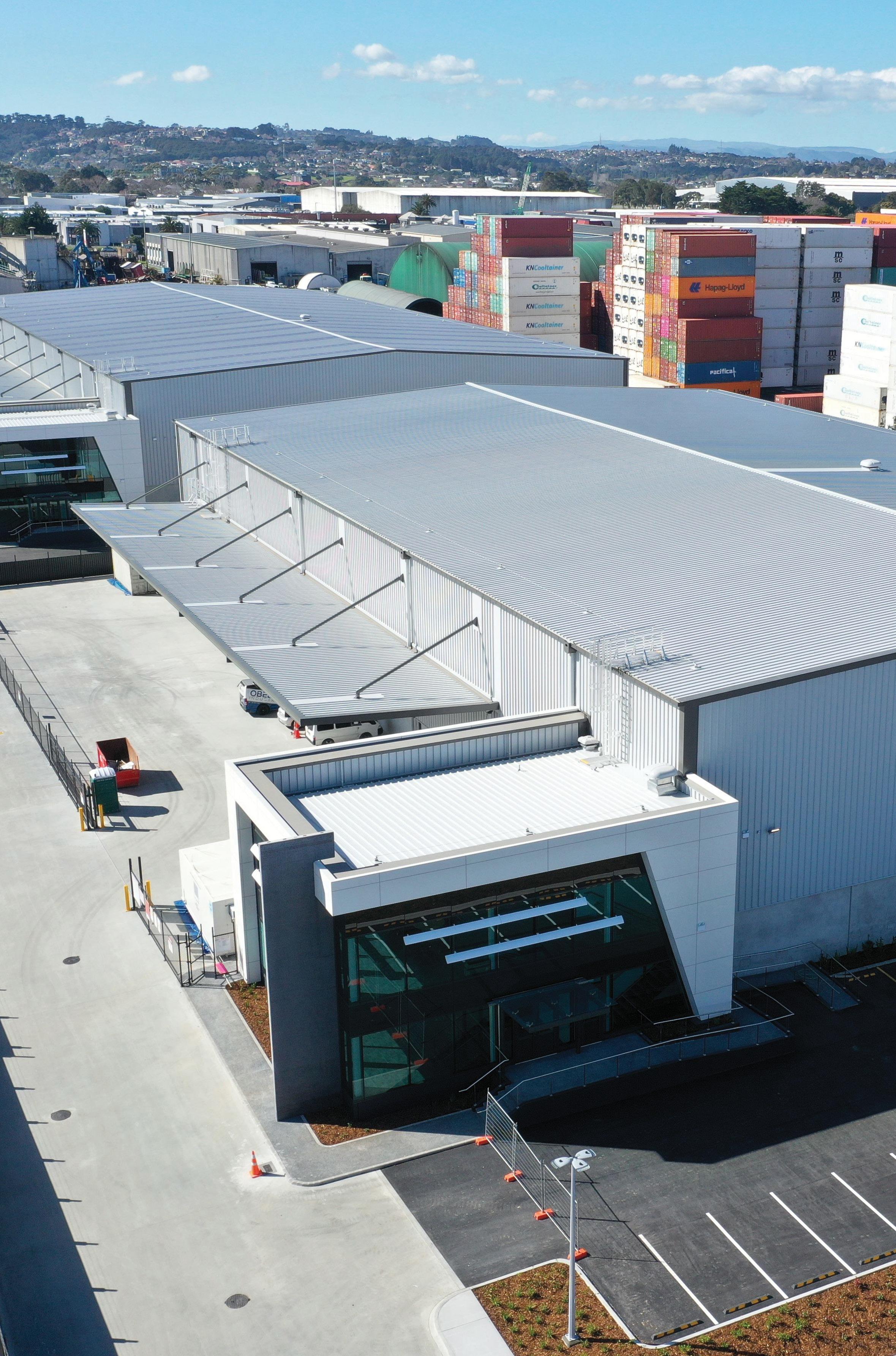
The architects took an innovative approach to designing the property and specified quality materials in the build.
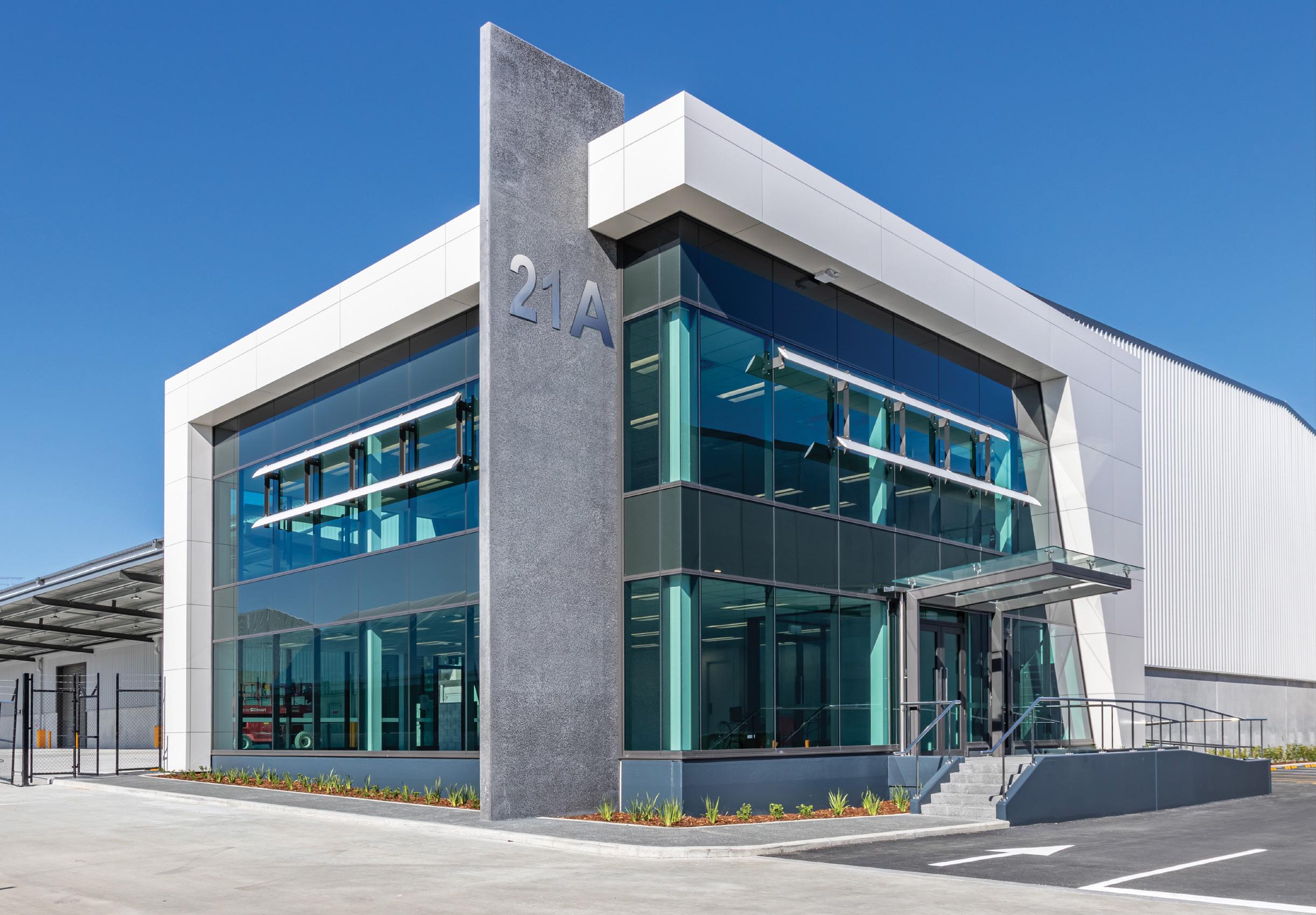
GREAT OAK GROWS WITH TIME & CARE
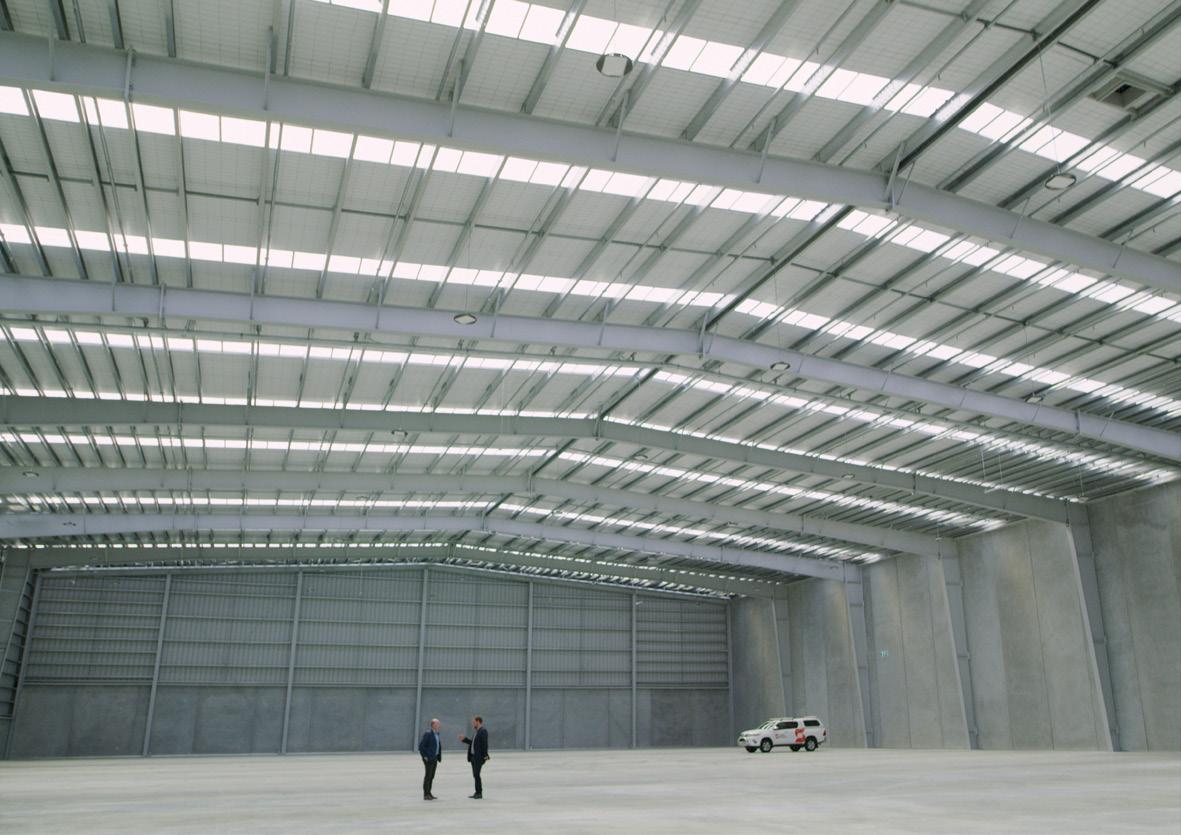
The vision was to create a high-value industrial business park that generates strong returns over time. It was a plan that looked like it could be easily realised when land came up for sale next door to the owner’s property in an industrial precinct in Wiri, Ta - maki Makaurau Auckland.
Then came the hard part: the complex matter of multiple resource consents. “It’s far easier to build on greenfield land than on a site that requires improvement,” says David Chafer, general manager of owner and developer Chalmers Properties. The company worked through the consent processes and Oak Industrial Park is the impressive result. It is a modern, master-planned estate with two state-of-the art office and warehouse facilities and a blue-chip tenant on a multi-decade lease.
Sustainability, efficiency, low energy, low maintenance and long-term are words that underpin all the owner’s projects – achieved through the design, build and maintenance of their assets. At Oak Park, materials were chosen for their life cycle, cost efficiency and ease of installation, even if the initial cost was greater. For example, you’ll find concrete yards and driveways instead of asphalt, and premium Alucobond pre-finished cladding rather than cheaper cement-board, which needs ongoing painting.
Choosing an architect and design team was integral to taking a creative approach to this 185 per cent New Building Standard development.
A post-tension warehouse slab and fibre-reinforced yard were selected for durability and floor loadings. Other features include a double-pitch roof that maximises height; polycarbonate material that lets light in, but not too much heat; and horizontal aluminium louvres on two sides for shade.
Tenants played a big part. “Key to our tenants’ requirements were accessibility and during tenant fit-out, the ability to add specialist plant, plant rooms, service ducts, monitoring and control equipment – all to meet exacting standards,” Chafer says. +
OAK INDUSTRIAL PARK
21A Oak Rd, Wiri, Ta - maki Makaurau Auckland OWNER, DEVELOPER CHALMERS PROPERTIES CONSTRUCTION CALDER STEWART CONSTRUCTION ARCHITECT WOODHAMS MEIKLE ZHAN ARCHITECTS SERVICE ENGINEER HYDRAULIC SERVICES CONSULTANTS NZ STRUCTURAL ENGINEER CALIBRE CONSULTING MECHANICAL ENGINEER THURSTON CONSULTING QUANTITY SURVEYOR CONSULT QS PROJECT MANAGER OCTA ASSOCIATES OTHER CONSULTANTS ECS, BARKER & ASSOCIATES
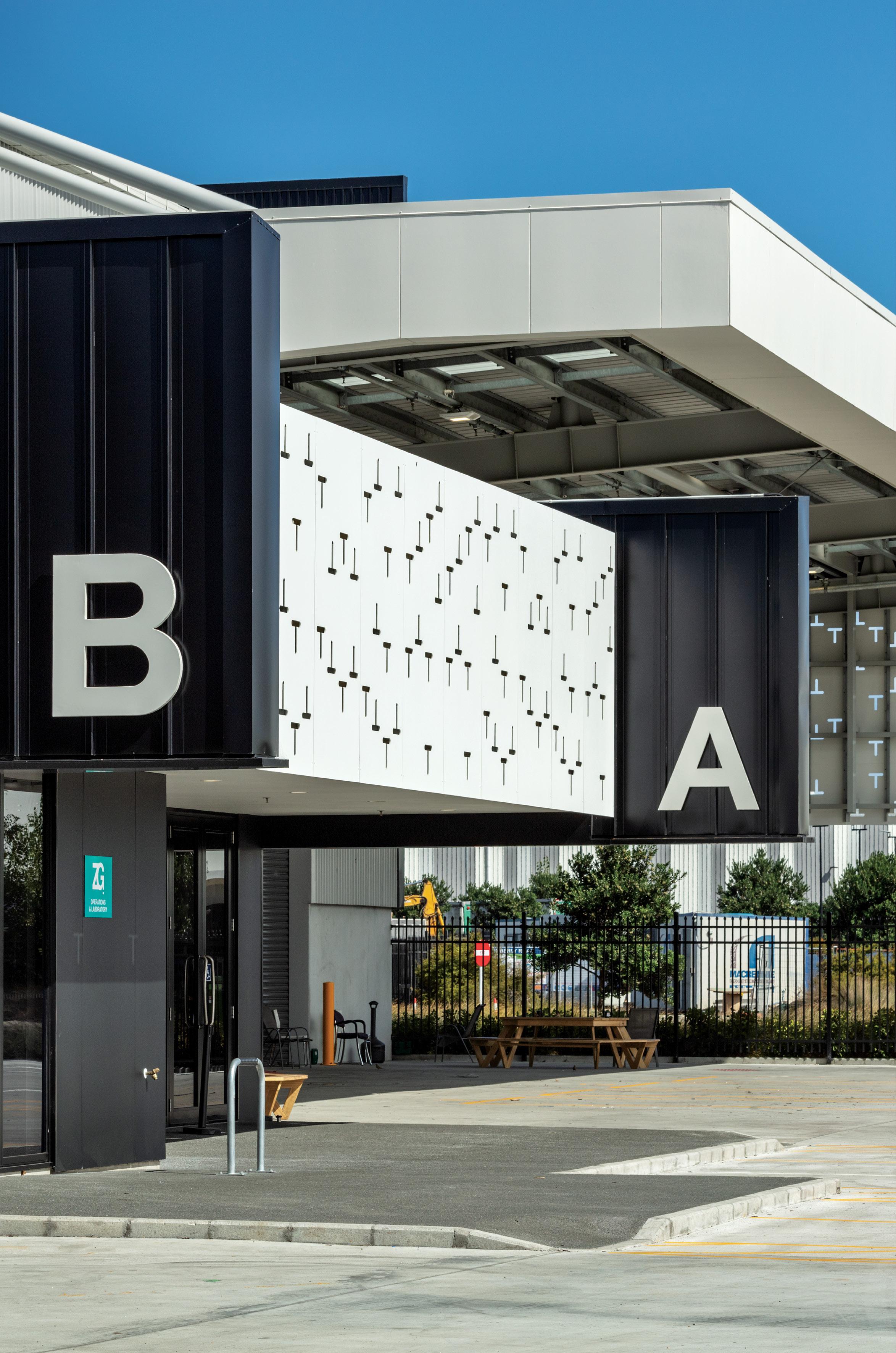
Auckland Airport has transformed challenging sites into investments by developing land and attracting top-shelf tenants. Zeta, a healthproduct exporter, has set up its base in several units at one such site at 27 Timberly Rd.
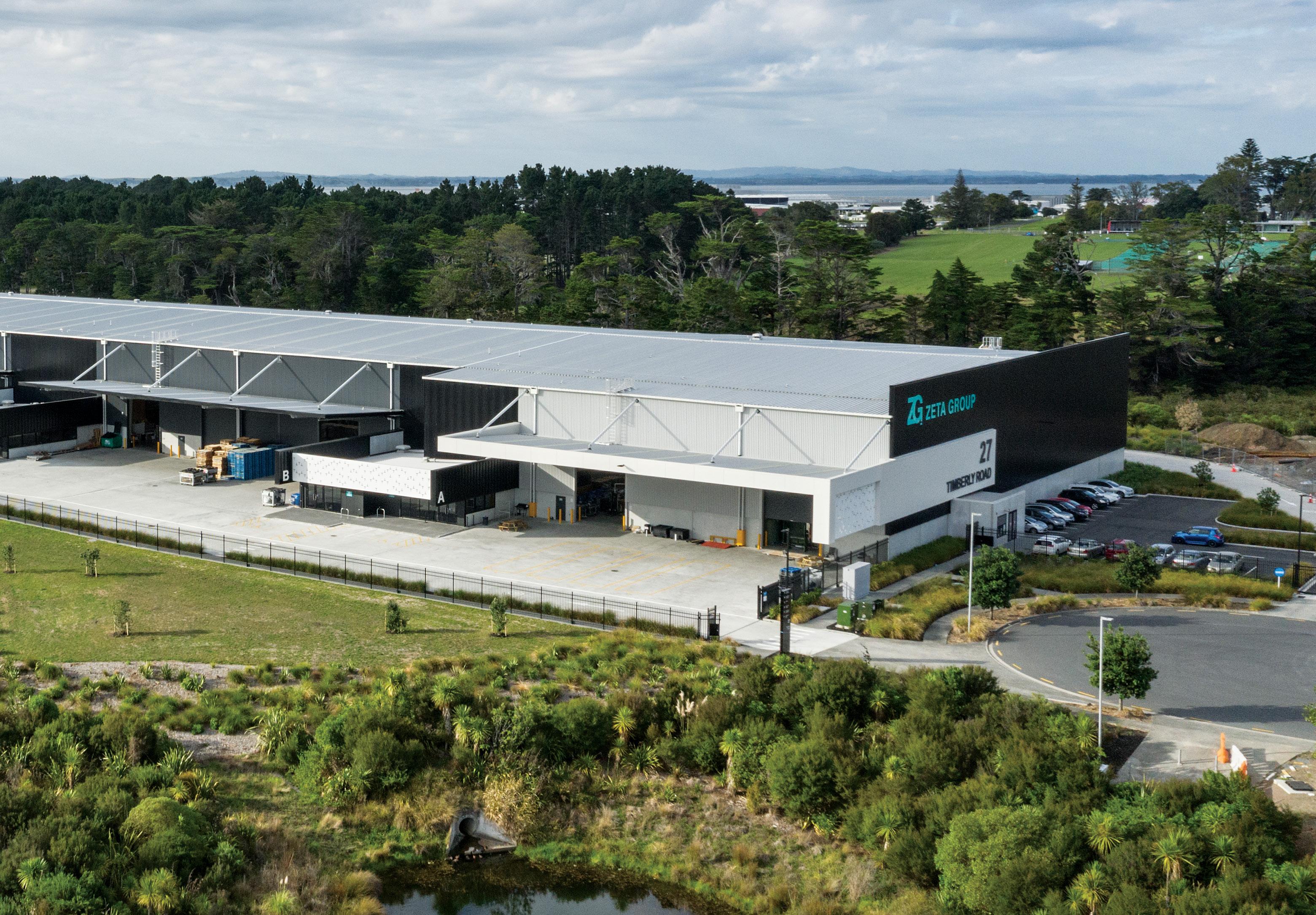
PROOF POSITIVE OF AIRPORT’S PROJECTS
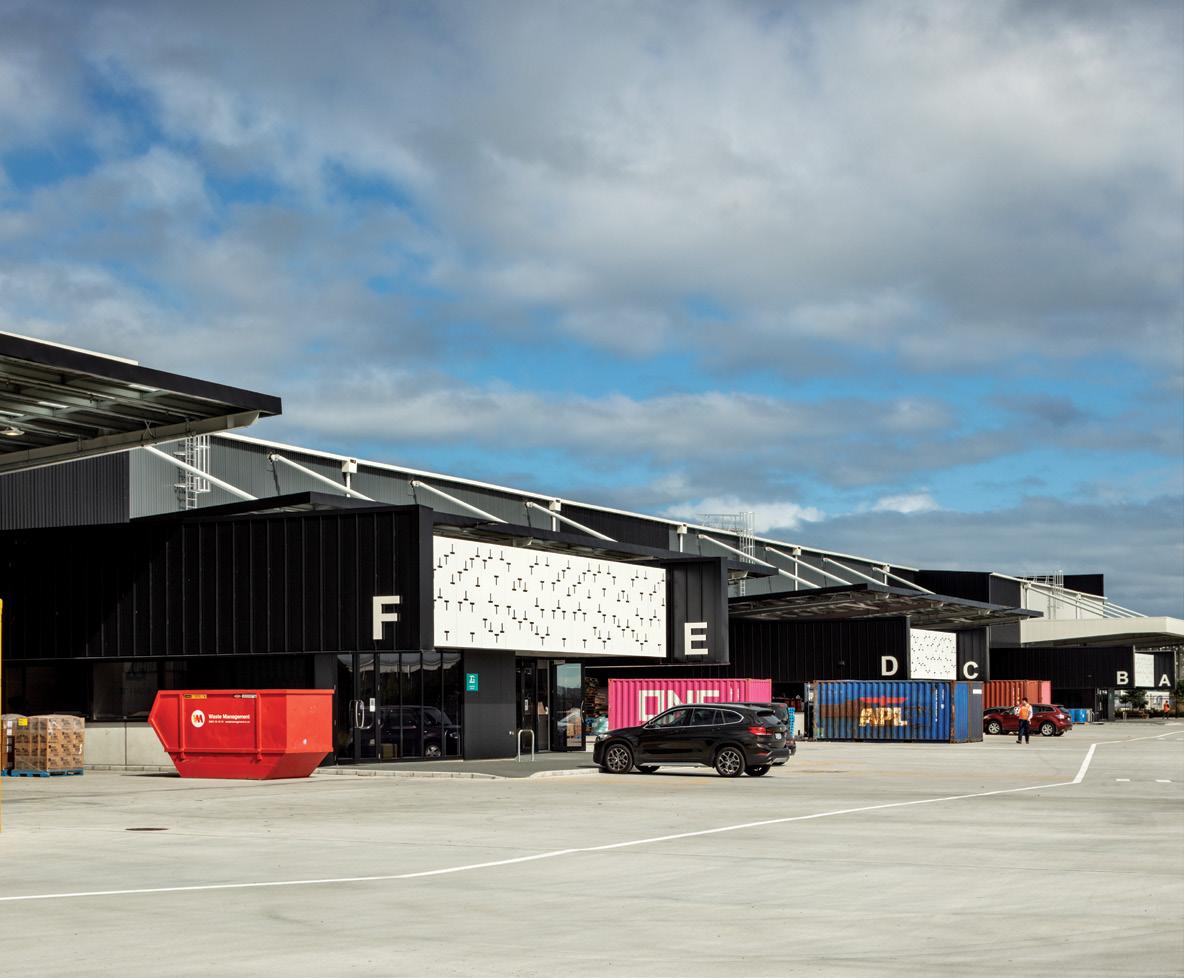
It was a difficult site and a difficult time, but the 27 Timberly Road development has turned two negatives into one very positive outcome.
The purpose for undertaking the development was to add to Auckland International Airport’s established speculative build programme. Here, difficult sites – generally due to complicated shapes – are ‘solved’ by undertaking speculative build projects during strong market conditions.
The 23,000sqm greenfield site is finger-shaped, located on a peninsula overlooking an inlet of the Manukau Harbour. The primary design consideration was for the development to integrate with its surroundings.
The brief was also to create a general-purpose, multi-unit facility that could be adapted for a variety of tenants, while delivering an aesthetically striking working environment for employees and visitors. That prescribed a 9700sqm clear-span warehouse and 1000sqm of ancillary office space. The narrow 200m-long building was subdivided into six units. Stretching from west to east, the architectural design maximises site coverage, while reducing visual impact to the northern suburban areas, including Pukaki Marae.
While design resolved the problems the site presented, then came Covid. However, from this emerged the ideal tenant – Zeta Group, which occupies five units. The business manufactures health-related products for export, and experienced exponential growth throughout 2020 due to the pandemic. The development’s adaptable style is a perfect fit for Zeta, which uses each unit for a different manufacturing function.
The offices utilise precast concrete, metal and composite claddings, and aluminium windows. All construction materials are durable, long-lasting and low-maintenance.
The warehouse has precast concrete with pre-painted metal cladding in standard colours, which can be readily recycled. Translucent polycarbonate roofing on the warehouses and canopies maximises natural light. Completion of this development shows how quickly the subdivision has matured since the land was originally purchased.
Daniel Byrne, Head of Property Development, Auckland Airport says: “Timberly Road subdivision has been rapidly developed since the land was
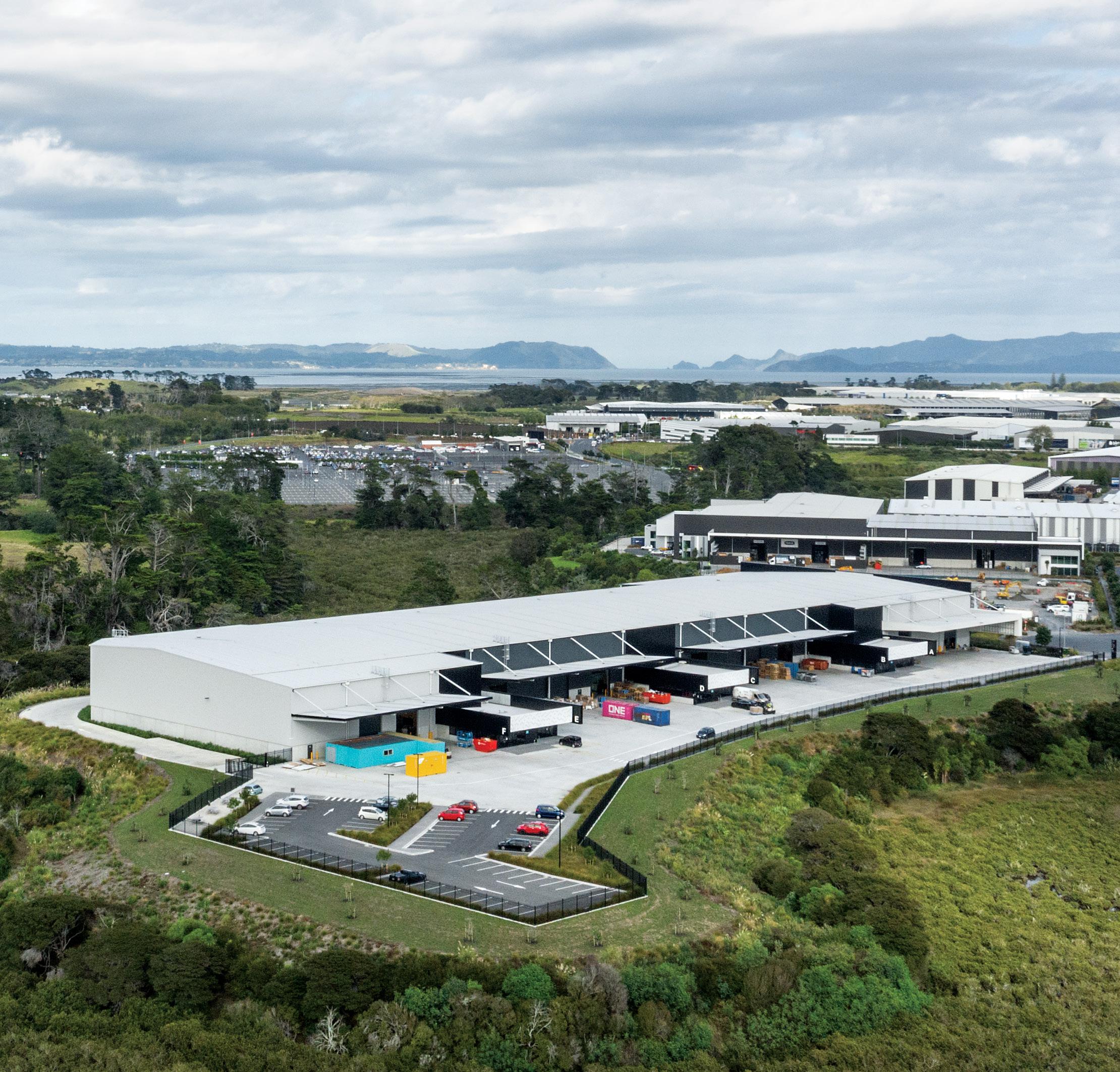
The 200m-long building is located on a peninsula, overlooking wetlands on a Manukau Harbour inlet. purchased nine years ago and is now home to household brands Fonterra and Coca-Cola, among others. With 27 Timberly Road now complete, there remains only one site and this was recently signed up by international freight company Geodis Wilson.”
More positives have emerged from this original concept. The brief also called for efficient construction costs and durable materials to maximise the build’s longevity. The highly desirable ‘A grade’ industrial investment asset was delivered 3.5 per cent under budget and ahead of programme. +
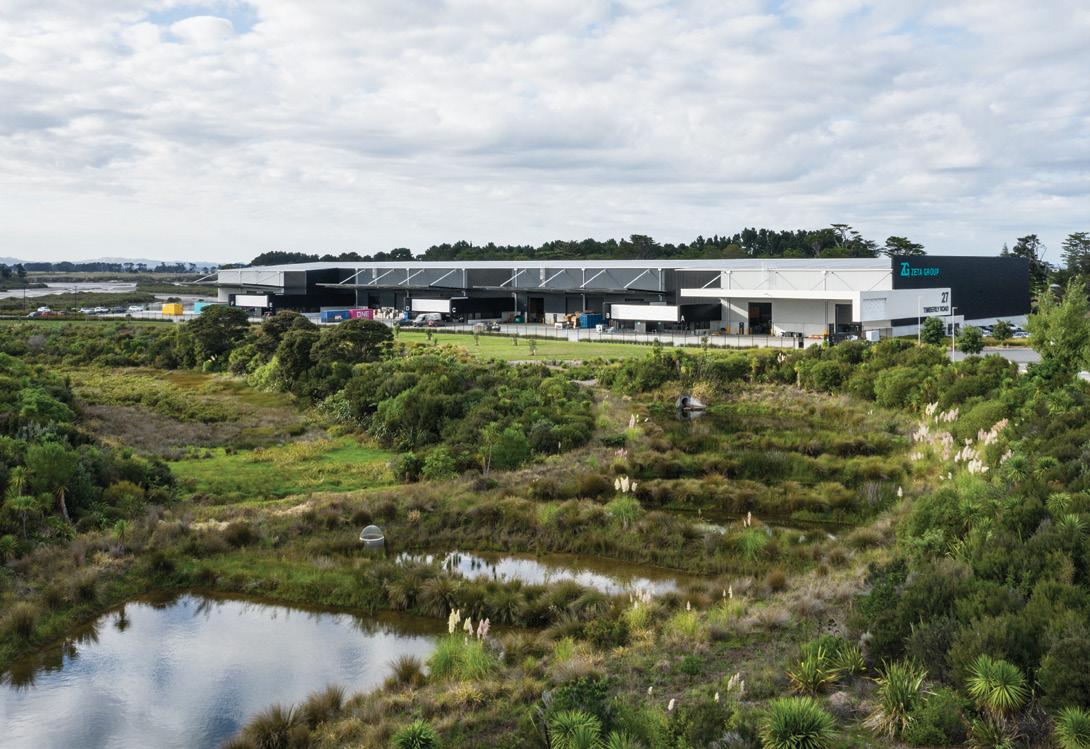
27 TIMBERLY ROAD
27 Timberly Rd, Ma - ngere, Ta - maki Makaurau Auckland OWNER, DEVELOPER AUCKLAND AIRPORT CONSTRUCTION MACRENNIE COMMERCIAL CONSTRUCTION ARCHITECT ECLIPSE ARCHITECTURE SERVICE ENGINEER ECS STRUCTURAL ENGINEER DAY CONSULTING MECHANICAL ENGINEER THURSTON CONSULTING QUANTITY SURVEYOR BQH PROJECT MANAGER RTD PACIFIC OTHER CONSULTANTS PROTECH, CROSSFIRE