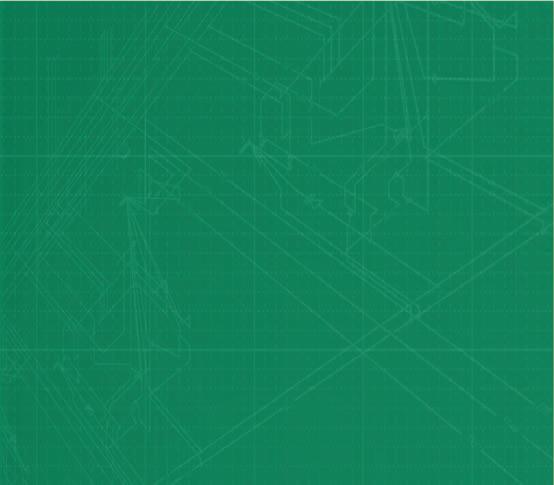
5 minute read
The BPMA can help you achieve the desired result
BPMA Job Seeker Service
Attention – Are you currently seeking a career within the pump industry?
BPMA has launched a new service for talented individuals seeking a career in the pump industry. Our members have interesting positions to fulfil within their company structures.
Simply forward your CV to s.smith@bpma.org.uk and we will do the rest.
A profile and details of the career you are looking for will be posted on our website free of charge for a maximum of three months. No personal details will appear, only a reference number. We will also include your profile on our weekly News-link bulletin which is circulated to key personnel at member companies.
The Hazards of Blocked Pipes in Slurry Pumping
By: Simon Jones of Weir Minerals Europe
The transport of solids in the form of slurry in pipelines using centrifugal slurry pumps is a common practice. Slurry is defined as any mixture of solid particles and a fluid (normally water) and under certain operating conditions it is possible for the flow through the pipeline to reduce to low or zero flow rates. In the worst scenarios, this can cause particles to block the slurry intake and discharge.
• Inadvertent closing of both the intake and discharge valves on the pump.
To minimise that risk, it is necessary to review all the hazards associated with application, system, pipeline, system controls and type of pump construction. Weir Minerals has been working with end users to assist with risk minimisation devices.
A range of Warman® metal lined slurry pumps has been fitted with a pressure relief failure ring mounted at the back of the shaft seal chamber. The pressure acting over the large area of the seal chamber causes a high force on the shear lugs on the failure ring.
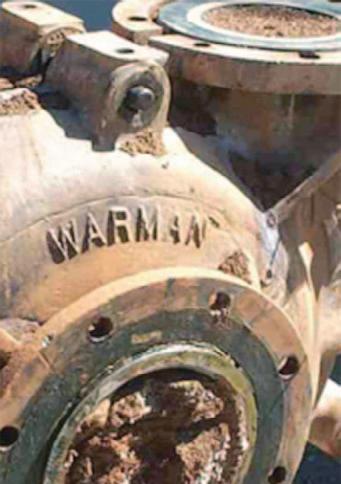
The ring is designed to fail in shear at a pressure of approximately 1.2 times higher than the pumps maximum allowable working pressure (MAWP), ensuring the failure occurs at a safe pressure and allows fluid, steam and slurry to escape out the back of the pump.
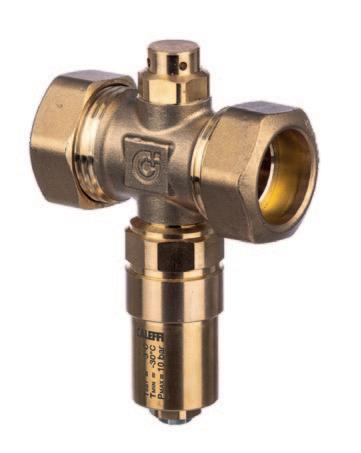
The escaping fluid and steam is contained within the pump by guarding and discharged downwards to the ground between the pump casing and the base.
As advances are made, pressure relief devices will assist to reduce the potential risks of pump explosion. These devices are simple and applicable to a wide range of applications. Further development is being undertaken to make these devices applicable to rubber-lined pumps. ■
For more information, Phone: +44 (0) 1706 298 476
Email: europe.minerals@mail.weir
If the slurry pump continues to operate in this condition, the energy input to the water inside the pump causes the water to heat up and generate steam. The pressure build-up from the steam can lead to a potentially dangerous situation and may result in the pump exploding.
The majority of slurry pumping applications occur in the mining and dredging industries. Slurry properties and particle sizes vary greatly from low to high concentration and from silt to gravel sizing.
The slurry is typically mixed before entering the centrifugal slurry pump, but as it travels along the pipeline, the velocity gradient in the pipe and/or the slope of the pipeline can change causing density gradients within the pipeline. As the solids start to settle, the particles become stationary on the bottom of the pipeline causing stationary dunes or even plugs to form. The plugs in the pipeline can partially or totally block the pipeline causing the flow to decrease to very low flow rates and, in the worst case, to drop to zero. In this case, the pipeline can become totally plugged with solids.
It’s possible to design a slurry system in which the conditions that plugs may form in a slurry pipeline are minimized, but the risk of blockage cannot be entirely eliminated. There are generally different causes of blockage, such as:
• Operation of the pipeline at subcritical velocity
• High solids concentration above the system design
• Large debris
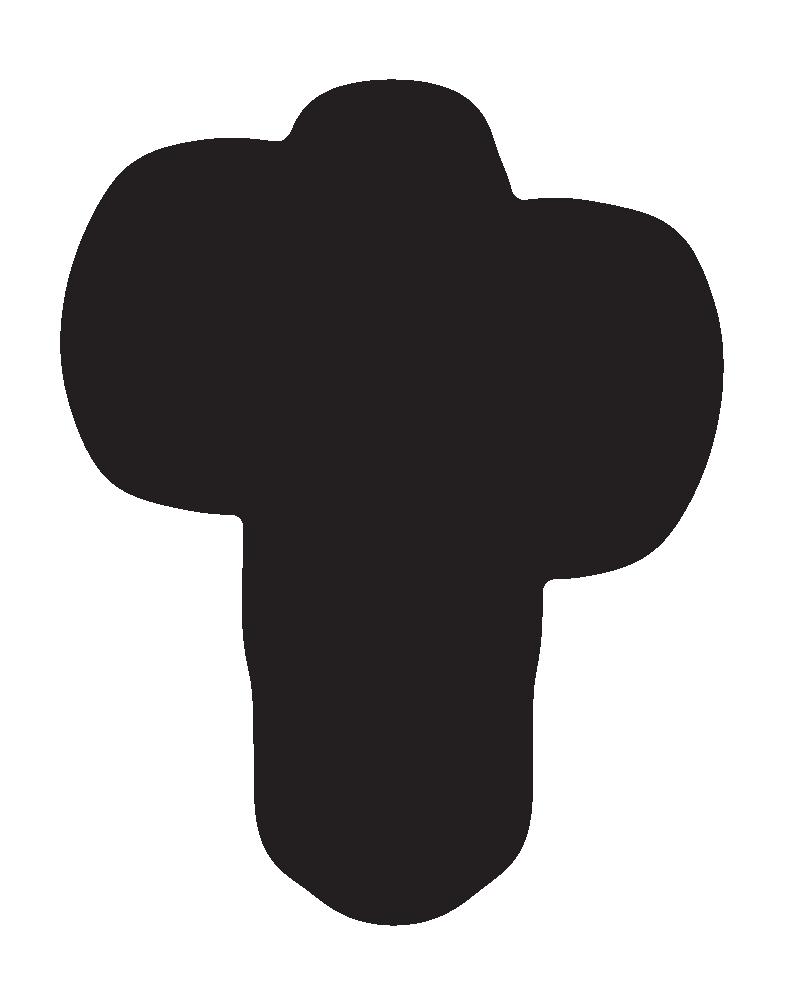
• Pipeline starting and stopping
• Pipe liner collapse
• Reducing pump speed below the level that causes particles to settle out in the pipeline
Prevents ice from forming in heat pump systems, avoiding potential damage to the heat pump and to the pipes
Pump Performance Curve & System Curve
By: Tony Dashwood of Crest Pumps Ltd
What is the system curve? This plots the head in terms of the static head (that does not change) in addition to the pressure loss through the system that will increase as the flow rate increases. This is a key element of the system curve as friction loss through pipework, elbows, valves, etc.
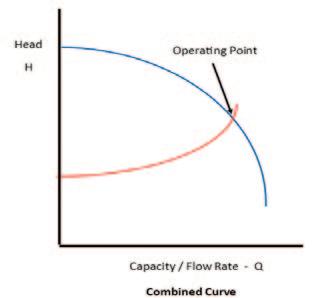
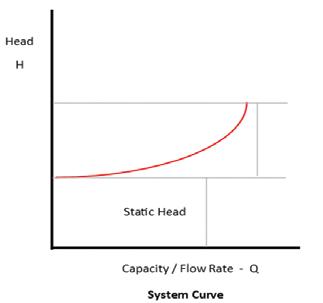
Performance Curve
Here is a simplified pump performance curve

Showing (as usual) head on the vertical axis and flow on the horizontal axis.
BPMA Membership Whether you are a pump user, supplier or manufacturer...
...the BPMA can help you achieve the desired result
System Curve
And now a System curve. The system line will start at the Static Head point at zero flow and gradually rise as friction head increases with flow. The static head is the actual height the liquid needs to be lifted, as the flow increase there will be more friction loss through the pipework and fittings so that the overall head rises.
Combined Curve
Finally, if we combine the two curves we can see the intersecting point between the curves which will be the operating point. If the two curves do not intersect then the pump is not suitable for your application.
Pump manufacturers, contractors, distributors, seal, bearing, motor, castings suppliers etc involved in the UK market for pumps and pumping equipment can all participate as members of the trade body for the UK pump industry (BPMA). Keep abreast of technical standards and EU directives affecting the industry, participate in industry events and marketing initiatives, access free membership services. Invest in business support for your company by taking advantage of introductory offers for membership of the BPMA.
For more information go to the BPMA website www.bpma.org.uk and download the latest BPMA membership benefits brochure or contact:
British Pump Manufacturers Association Limited (BPMA) National Metal Forming Centre 47 Birmingham Road West Bromwich West Midlands B70 6PY
Tel: +44 (0) 121 601 6350
Fax: +44 (0) 121 601 6387 E-mail: enquiries@bpma.org.uk
BPMA MEMBERSHIP – AN INVESTMENT, NOT A COST!
A Point to Note
All centrifugal pumps will have a best efficiency point (BEP) that is usually marked on the performance curve, it is important to select a pump that is as close to the BEP as possible, usually within 20% below and 10% above. Running a pump close to the BEP will ensure a longer and trouble free life as well as lower operating costs. A pump can have its impeller trimmed to bring it closer to the BEP if required. ■
For more information, Phone: +44
(0) 1425 627700 Email: info@crestpumps.co.uk
High-performance seals for rotary, reciprocating & static applications
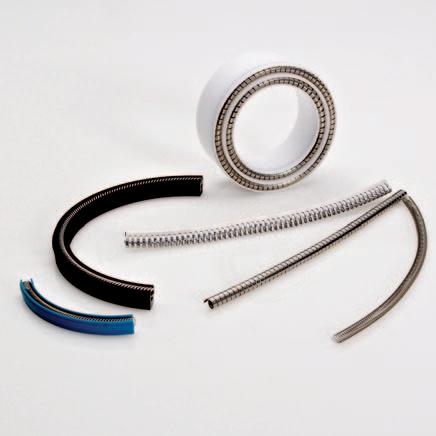
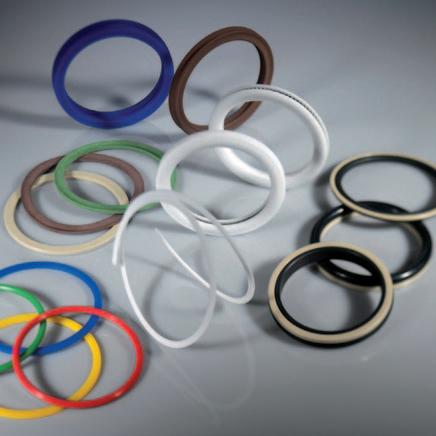
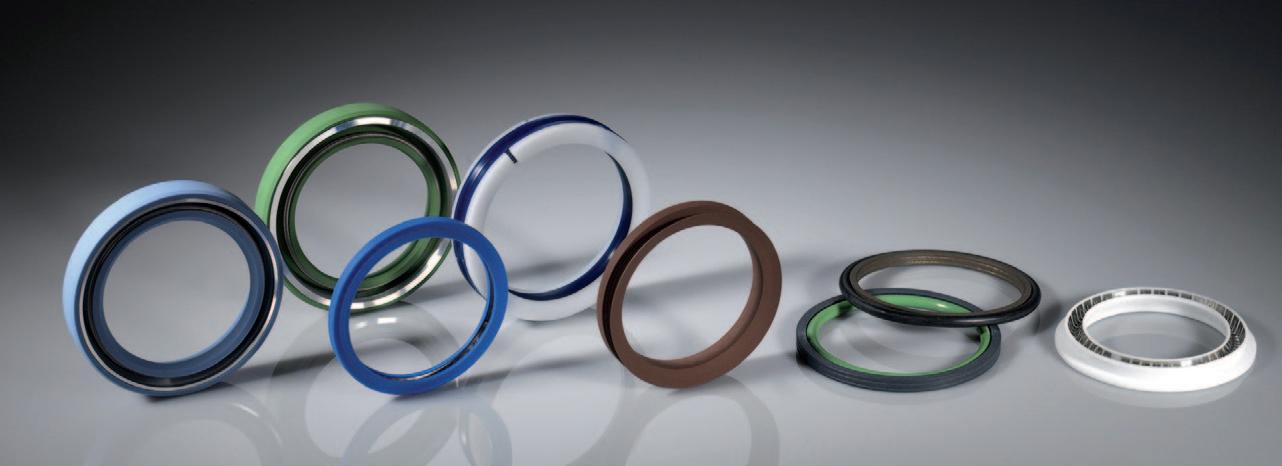
All specification, design and manufacture carried out in-house in our 24/7 manufacturing facility
Over 253 different seal profiles
OEM engineered seal design – typically 3-5 days versus 8-10 weeks industry standard
Responsive to urgent seal demand - sameday or next day where possible
Over £2.5m of semi-finished material and finished sealing products kept in stock
Rapid turnaround in quotations with access to extensive stockholding of industry-standard products