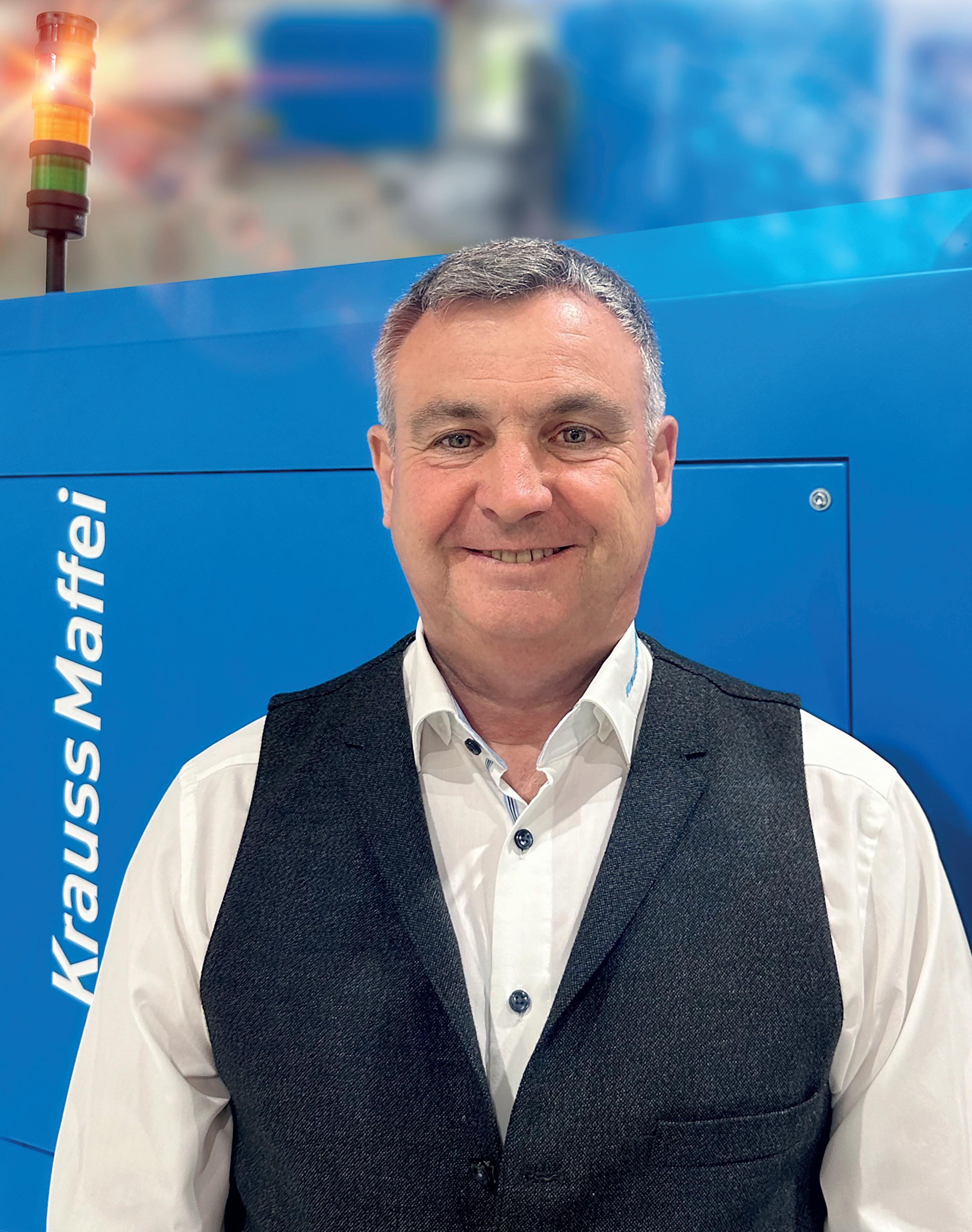
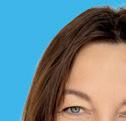
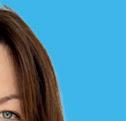
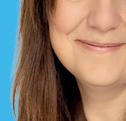

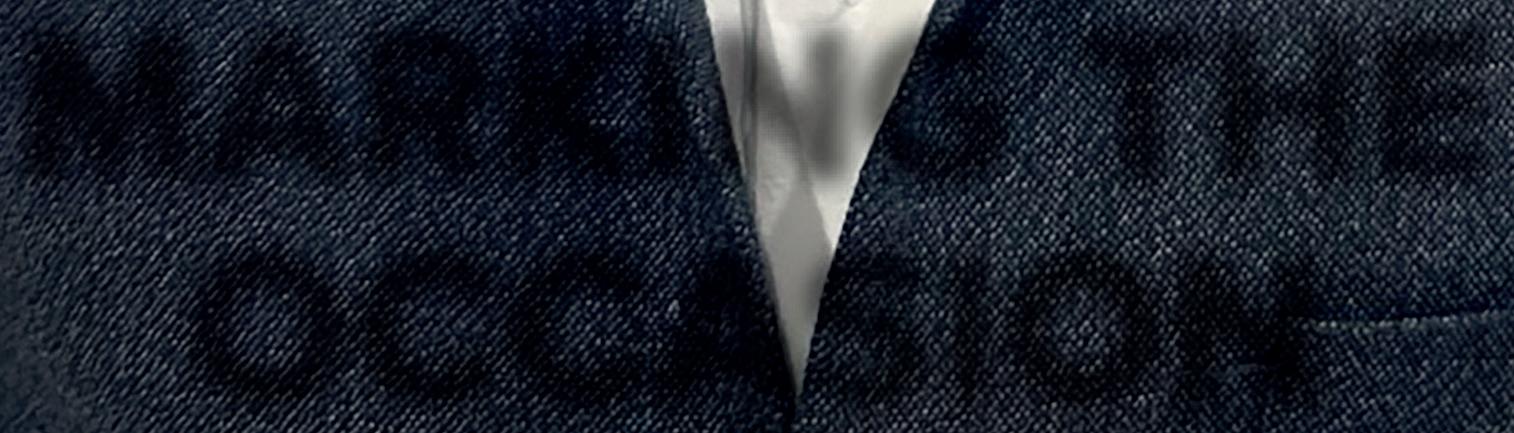
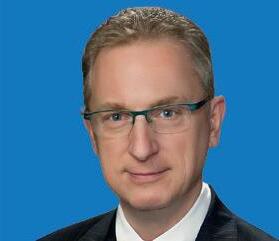
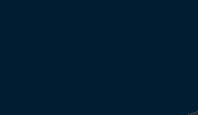
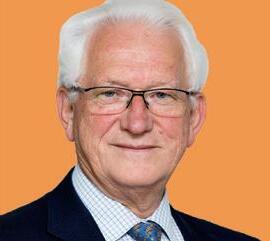
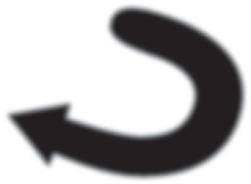
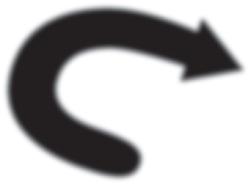
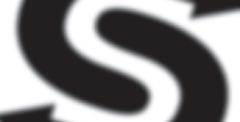
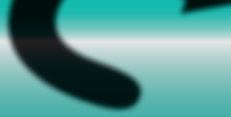
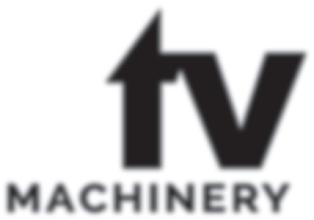

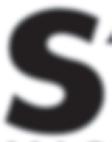

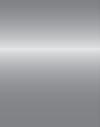
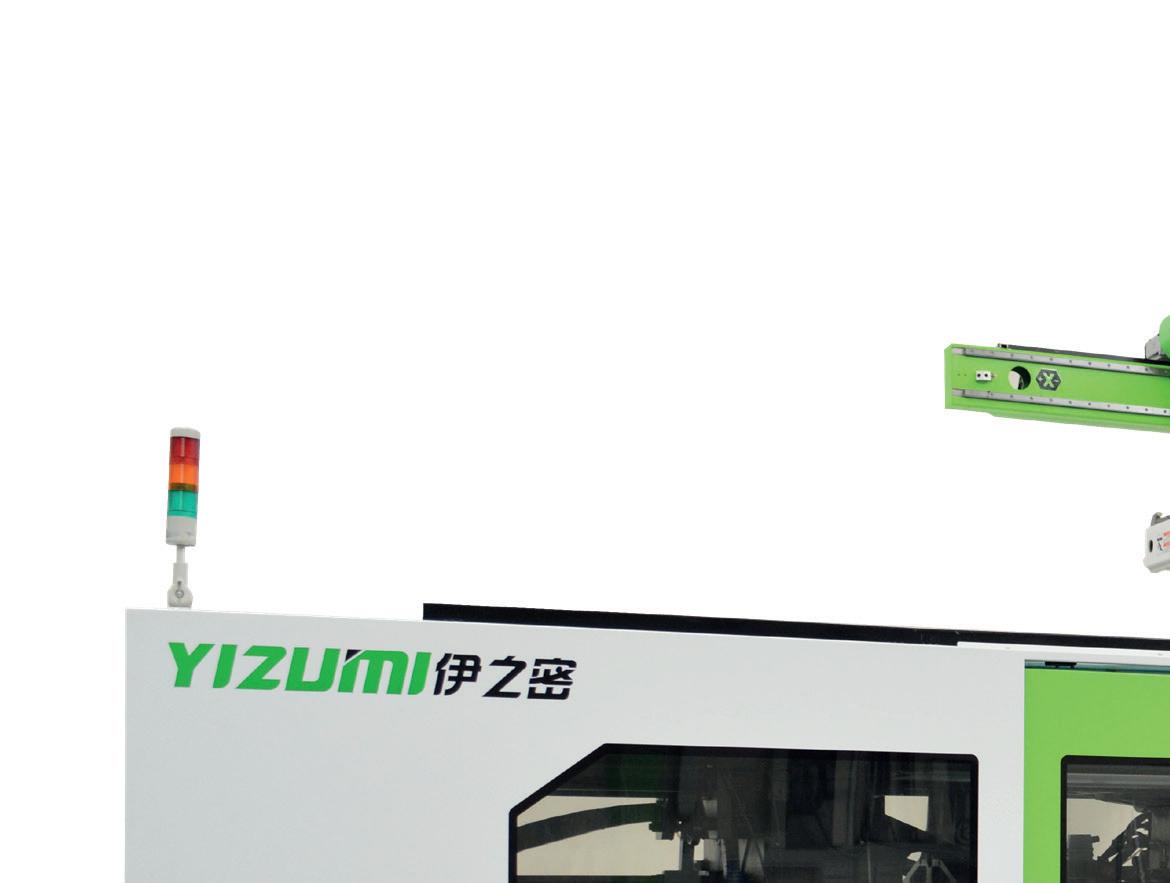
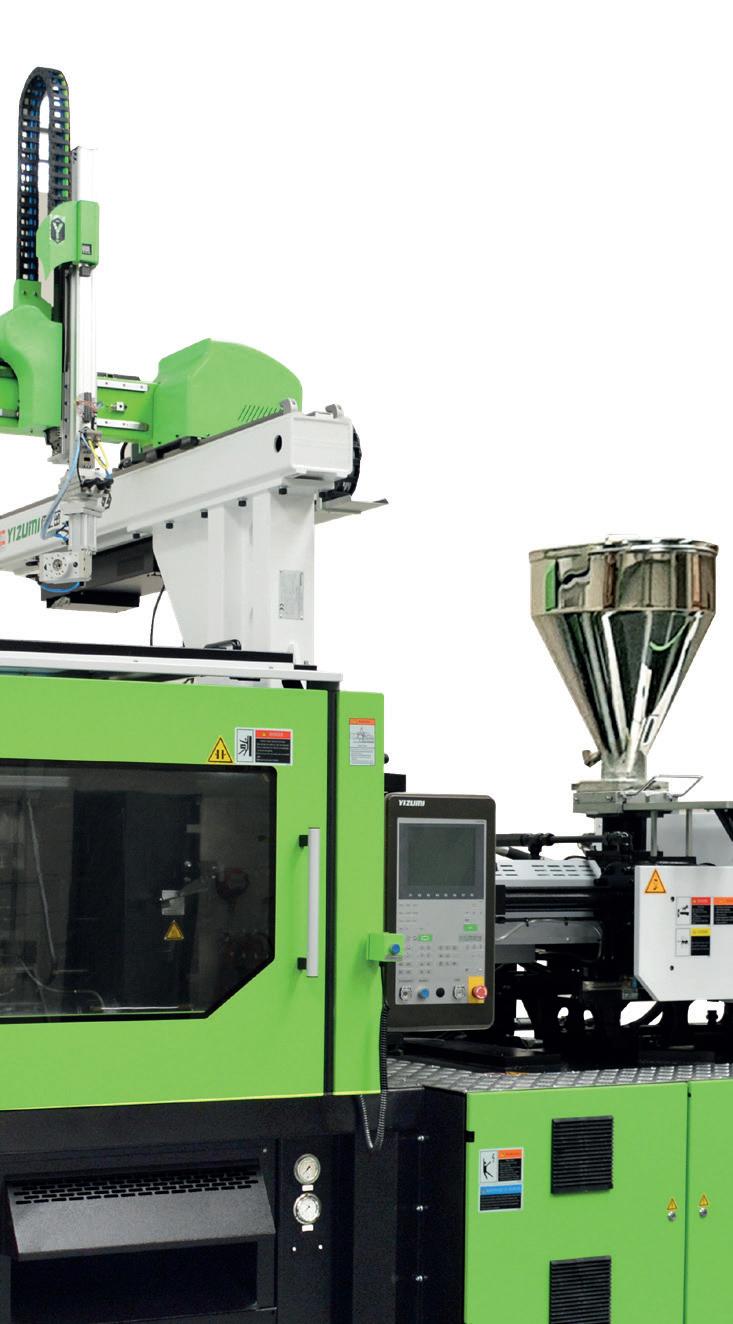
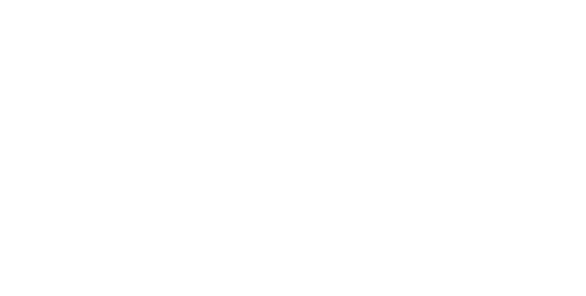

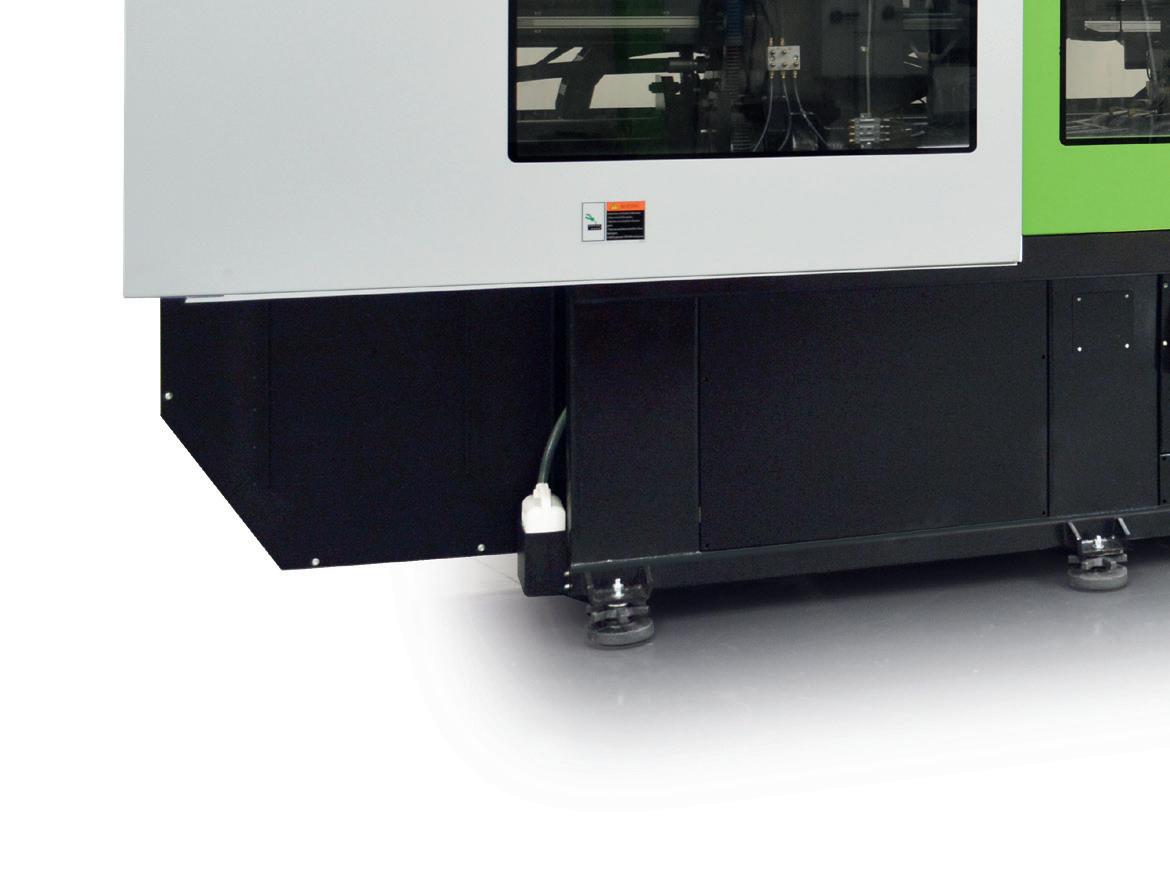
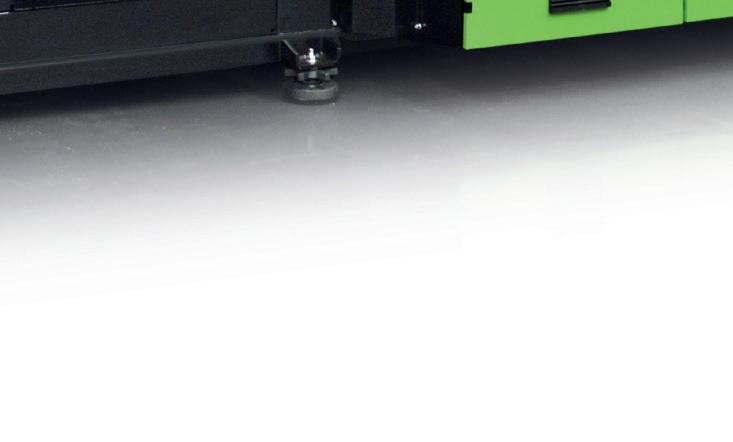
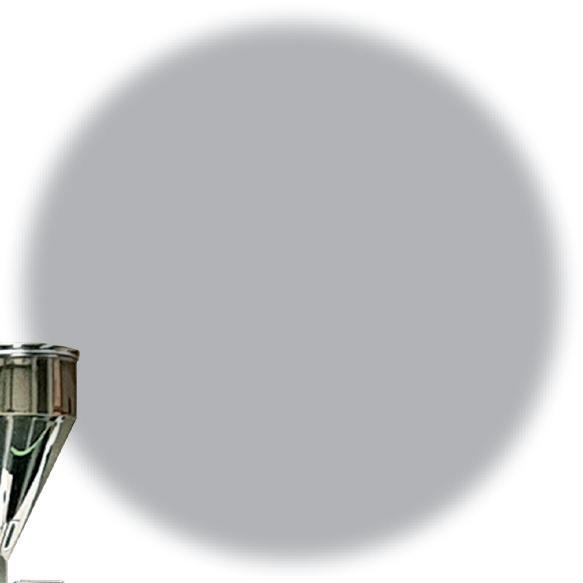
www.interplasinsights.com
Head of content: Dave Gray
T: +44 (0) 1244 680 222
E: david.gray@rapidnews.com
Junior editorial content producer: Daniel Ball
T: +44 (0)1244 680 222
E: daniel.ball@rapidnews.com
Head of sales: Mandy O’Brien
T: +44 (0) 01244 952 519
E: mandy.obrien@rapidnews.com
Portfolio sales manager: Gareth Jones
T: +44 (0) 1244 952 370
E: gareth.jones@rapidnews.com
Portfolio sales manager: Kelley Jo Gwatkin
T: +44 (0) 1244 952 375
E: kelleyjo.gwatkin@rapidnews.com
Head of studio: Sam Hamlyn
T: +44 (0) 1244 680 222
E: sam.hamlyn@rapidnews.com
Subscriptions:
T: +44 (0) 1244 680 222
E: subscriptions@rapidnews.com
Publisher: Duncan Wood
T: +44 (0) 1244 680 222
E: duncan.wood@rapidnews.com
Print subscription: Qualifying Criteria UK – Free Europe – £249 ROW – £249
FREE digital issues available to view and download online
British Plastics & Rubber is published monthly (8 times/ year) by Rapid Plastics Media Ltd, Carlton House, Sandpiper Way, Chester Business Park, CH4 9QE
T: +44 (0) 1244 680222 F: +44 (0) 1244 671074
© 2023 Rapid Plastics Media Ltd
While every attempt has been made to ensure that the information contained within this publication is accurate the publisher accepts no liability for information published in error, or for views expressed. All rights for British Plastics & Rubber are reserved. Reproduction in whole or in part without prior written permission from the publisher is strictly prohibited.
ISSN 0307-6164
Incorporating Polymer Age and Rubber and Plastics Age.
It’s with great pleasure that I’m able to open this edition of British Plastics & Rubber with the news that we have launched a dedicated editorial advisory board for both the magazine, and its sister website, InterplasInsights.com.
So why now, and why these particular individuals? Earlier this year, we launched our first reader survey – you may have received it in your inbox. I wanted to learn more about what you want from the UK’s only dedicated plastics industry magazine. The response rate was really encouraging, it’s a privilege to have such an engaged audience for the work we do. You told us that while most of you feel the level of technical expertise featured in our news outlets is about right, you’d still like to see more engineeringfocussed content. In particular, comments showed an appetite for more on R&D into material and processing developments. Technical guides to common processing problems seem to be the most appreciated article types – and so we’ll strive to bring you more of those.
That’s why I’ve approached a select group of individuals, who between them are experts in either R&D, or plastics processing. The hope is that they themselves will be able to contribute occasional works, but also that they will help uncover potentially common challenges the industry is facing – and suggest authors and experts who can work with the magazine to provide useful, problem-solving content.
This kind of knowledge sharing is where this industry really shines. As competitive as it clearly is, the UK has a great network of process engineers looking to share their experiences and help one another out. My hope is that the introduction of the board will help BP&R, and InterplasInsights.com become an even more useful sounding board for these minds. See page 12.
Elsewhere in the news, Lidl have now followed Co-Op and Sainsbury’s’ lead
in switching to vacuum packing its mince. However, consumer response has been mixed. While many see the benefits of the longer shelf life and reduced transport emissions, others have been concerned that the product quality is suffering – simply because it doesn’t look the same. This response threatens to stymie progress for brand owners hoping to re-design their plastic products for environmental benefit. And of course, the fact remains that although the all-flexible packaging is recyclable in stores (Tesco and Sainsbury’s offer it for free), most consumer behaviour is still geared towards disposal at home –which for most flexibles is of course not an option. It’s something of a quandary for an industry doing its best to keep up with public and legislative demand for greener packaging, when large swathes of the public are reluctant to depart from aesthetics and behaviours they know and are used to.
“It’s something of a quandary for an industry doing its best to keep up with public and legislative demand for greener packaging, when large swathes of the public are reluctant to depart from aesthetics and behaviours they know and are used to.”British Plastics and Rubber
Who are you and what do you do?
As a multinational company, Plasmatreat is facing up to its responsibility to protect the environment through its atmospheric Openair-Plasma technology.
Our customers benefit from our high degree of technical expertise, extensive experience, and global network of international partners. Preventing greenhouse gas emissions, cutting energy consumption during pre-treatment, reducing CO2 emissions, and avoiding effluent discharge and hazardous waste during industrial cleaning processes: these are some of the many benefits that make Openair plasma a key future technology.
Openair-Plasma technology is used in automated and continuous manufacturing processes in almost every industrial sector. Examples include the automotive, electronics, transportation, packaging, consumer goods and textile industry, but the technology, cost and environmental advantages of the plasma technology are used in medical technology and in the renewable energy sector as well.
Hall 4, Stand H14Why is Interplas important to you?
Today, at a time of great change in the plastics industry, Interplas is more important than ever to Plasmatreat UK Ltd to ensure that the innovation and technology we offer reaches the UK market.
What is the key feature of these innovations?
The key feature that Plasmatreat offer is a VOC-free controlled and consistent surface treatment, prior to bonding or printing.
What challenges are your customers facing?
For reasons of productivity, cost, and the environment, companies are increasingly abandoning the use of chemical substances or “primers” as bonding agents. Plasmatreat offer reliable, and cost-effective alternative treatment
of the substrate surface with atmosphericpressure plasma. Pre-treatment with Openair-Plasma from Plasmatreat increases the adhesion and wettability of surfaces, thus enabling the use of more cost-effective material alternatives while maintaining the quality of the end products.
How can your technology help solve them?
The plasma process is dry, non-contact, selective in location, and fast. It cleans the surface with microfine precision and activates it at the molecular level. The technique uses a comprehensive process-control system and is fully robot-compatible and inlinecapable. Production speeds are often increased many times over, reducing manpower, and increasing productivity. For more specific requirements, functionalised coatings can be applied to the surfaces of materials using the special PlasmaPlus process. With the PT Bond coating process, even plastics that were previously difficult to bond can be bonded directly and permanently with elastic adhesives. Replacing primers that are harmful to the environment and health.
• Plasma technology offers practically unlimited possibilities for designing safe and reproducible processing.
• Plasma technology helps manufacturers achieve significant CO2 savings, replacing traditional flame treatment.
• Innovation using recycled plastics. Plasma technology from Plasmatreat for surface pretreatment makes non-polar (recycling) plastics susceptible to adhesion processes and ensures that the different, sometimes even incompatible materials are firmly bonded.
• VOC free process for surface treatment.
At Interplas 2023, Sumitomo (SHI) Demag UK & Ireland will show how a 50% increase in output can be attained and more using its fully-integrated and automated entry-level “handle&box” injection moulding production cell.
Enabling manufacturers to increase production yields by letting automation pick-up extra unsupervised night shifts, Sumitomo (SHI) Demag will also reveal how existing and prospective customers can reduce overheads and unlock untapped profit opportunities.
Premiering to the UK & Ireland market, and designed for trade moulders and SMEs, the linear 4-axis robot with cartesian kinematics for standard applications, offers a compact production unit with efficient handling functions, and fully-integrated robotic controls.
The full turnkey cell – measuring as little as 3.95m x 2.4m- features the highly efficient all-electric IntElect75 with the company’s new SAM-C5. Also included in the cell is a storage and conveyor system with buffer and integrated boxing unit. Every element was engineered by Sumitomo (SHI) Demag’s automation experts in-house. The technology can give moulding firms the technology and tools needed to confidently operate ‘ghost’ workflow shifts with minimal human intervention.
“Making the night shift an additional source of processing production value, the Interplas 2023 exhibit in Hall 4, Stand C40, also highlights the reduction in operative errors and the efficiency improvements.”
Rather than operate split shifts or keep people in the factory until late at night, the reliable 75-ton IntElect turnkey cell being showcased at Interplas demonstrates to trade moulders and SMEs the potential untapped after-hours production opportunities. Additionally, day-shift teams benefit from the augmented workflow process by automating mundane and repetitive tasks. This frees up people’s time to focus on more creative and business-enhancing responsibilities. Resulting in more motivated and engaged employees.
Making the night shift an additional source of processing production value, the Interplas 2023 exhibit in Hall 4, Stand C40, also highlights the reduction in operative errors and the efficiency improvements. Equipped with a tool from Germany, visitors to Interplas 2023 can witness the moulding of a precision slide gauge.
The tool-dependent buffer system is available with or without optional robot removal. The conveyor belt technology is designed to transport standard-sized industrial containers.
Catering to moulders manufacturing FMCG, automotive and electronic
components, this “handle&box” solution is especially suitable for injection moulding machines within the 75 to 280 ton clamp force range. For ease of operation, the SAM-C robotic system is fully integrated into the IntElect machine control system.
Reinforcing the importance of relieving workforce pressures, incumbent UK managing director Nigel Flowers said: “Our new SAM-C robots fill an important gap in the processing market and help moulders to increase production capacity of standard components while simultaneously addressing the skills and labour challenges. Customers benefit from process and system technology from a single supplier source, complete with hardware and software control integration and robotic mechanics fully customised to Sumitomo (SHI) Demag machines.”
Sumitomo (SHI) Demag will also present to Interplas visitors its new productivity whitepaper. Revealing how the combination of automation, digital tools, remote diagnostics, expert field tests and processing adjustments and workforce training, can culminate in an extra 168 days of production; equating to approximately 50 percent boost in productivity.
Who are you, and what do you do?
Plastics Machinery Group buys and sells Plastics Equipment including Thermoforming, Blow Molding, Injection Molding, Extrusion, Grinders, Shredders, and more! Plastics machinery group also has a rebuild program for used machines and in January of 2023, PMG launched its new Mergers & Acquisitions division. Find out more at www. Plasticsmg.com!
Why is Interplas important to you?
PMG is always looking for ways to expand its market. Already, we have partners in Europe, naturally, the UK is the perfect halfway point to begin establishing a stronger presence across Europe. Additionally, we have seen a positive impact for our customers here in the US regarding the machines and services we provide, and we are eager to offer solutions to companies across the globe. This is why Interplas is so important to us; it’s a unique opportunity to establish our name and connect with likeminded people, excited to solve
Hall 4, Stand H82
INSET: Don Kruscke, CEO
industry challenges head on, far and wide!
What challenges are your customers facing, and how can you help solve them?
PMG differs from other brokers and dealers as we are a dealmaker (Partnering with a variety of OEMs such as Amut Comi and Meccanoplastica) with the offering of having new and used machines on the floor, available for immediate delivery, which helps us tackle a common industry wide issueextraordinary lead times! Another innovation we are excited to showcase
at Interplas is our rebuild program. Another unfortunate problem the industry is facing is the loss of business to “green alternatives” due to the negative misconceptions of plastics running rampant in pop media. With the demand for green/responsible production increasing all the time, along with the rising cost of new equipment, PMG has placed immense value in the refurbishment of used equipment. Not only do we breathe new life into used machines for the sake of affordability and renewability, but we also offer brand new machinery with a zero-carbon footprint patent, by Meccanoplastica, to help move your company toward a greener initiative. Overall, we hope to provide the industry with shorter lead times through our OEM relationships and diverse stock, as well as providing affordable alternatives to a greener production model. We want for others the same things we want for ourselves; increased production, lowered cost, reasonable lead times, and a sustainable future for generations to come. the end of the lease term, the borrower can choose to either return the asset or continue leasing it.
Who are you and what do you do?
Robafoam Ltd is a specialist company whose technology and expertise are focused on the automatic application of foam seals. With over 30 years of industrial adhesive and sealant experience, we represent a significant resource in this field.
Our core focus is to provide precise, robotically applied foam seals on both 2D and 3D parts that achieve high IP ratings on parts from a range of different industries. The technology and service are also applicable for NVH requirements, bonding, potting, and encapsulation.
What innovations will you bring to Interplas?
At Interplas 2023, we are bringing our advance foam sealing innovations. Our Contract Gasketing service applies high-performance foam seals directly to customer parts using flexible 6-axis robot systems. We offer customizable foam hardness, adjustable bead widths, and rapid heat curing. Additionally, our 1K foam application systems integrate 3D foam seals within productions lines. We provide technical support, from concept
Hall 4, Stand C79
design to full production integration. Our innovations transform gasketing processes, ensuring optimal sealing effectiveness and durability for diverse industries.
What challenges are your customers facing?
Our customers face challenges relates to consistency, accuracy, efficiency, and customisation in their sealing processes. Manual application of seals can lead to variability in gasket thickness, resulting in potential leaks and quality issues. This inconsistency presents a challenge for ensuring reliable and effective seals. Moreover, manual application is timeconsuming, leading to lower production rates and higher labour costs, especially in high-volume applications. Additionally, the ability to customise seals of different shapes and sizes is crucial for meeting
diverse design and manufacturing requirements. Overcoming these challenges is vital for our customers to enhance their sealing performance and optimise their production processes.
How can your technology help?
Our technology effectively addresses the challenges faced by our customers in their sealing processes. It ensures consistency and accuracy by placing the foam precisely, resulting in uniform gasket thickness and improved sealing performance. By eliminating manual application variability, it minimises leaks and quality issues. Additionally, our technology offers increased efficiency with faster sealing, leading to higher production rates and reduce labour costs. In addition, it enables customisation, allowing easy programming of gaskets in different shapes and sizes. Our 6-axis robot systems can apply foam to diverse substrates, from plastics to metals and glass. With our technology, customers achieve reliable seals, improved efficiency, and design versatility, enhancing product quality and competitiveness.
Robafoam Ltd is a specialist company whose technology and expertise is focused on the automatic application of foam seals. As a business our sealing services cross virtually all industry types. Our core focus is to provide the precise, robotic application of 2D and 3D compression joints, ensuring high level IP rated watertight seals. The technology and service is also applicable for NVH, bonding, potting and encapsulation.
A unique process to convert single part materials into closed-cell foam.
The foam systems at our facility mean customers can introduce high spec seals, without the need to invest.
Robafoam use and supply a range of 1K materials for their foaming process.
With over 30 years of sealing experience Robafoam is a valuable resource for component designers.
ENGEL‘s digitalization strategy is perfectly aligned with the life cycle of your products. From part design and mold sampling to production and maintenance & service. We have the right digital solutions to help you utilize the full potential of your injection moulding machines and sustainably reduce your carbon footprint.
Read more: engelglobal.com/inject-4-0
Most waste management schemes rely on mechanical recycling — a method that Greenpeace argues “will always fail” for plastics because they are “virtually impossible to sort.” Here, Stephen Harding, managing director of Gough Engineering, argues companies must invest in processing equipment to recover and gain value from their recycled products, such as plastics masterbatch, to meet the European Commission’s goals.
The EC has ruled that EU states must reduce packaging waste by five per cent by 2030. These rules cover both packaging design and waste management. Greenpeace is right to address the shortcomings of current mechanical recycling when dealing with plastics. The organisation’s Circular Claims Fall Flat Again report also highlights that plastic recycling rates declined to about 5 per cent in 2021, down from 8.7 per cent in 2018. The report suggests that a lack of recycling infrastructure has impeded how companies deal with plastic waste.
Frankly, we agree. Today’s
Let’s look at the example of a recycling company in Norfolk, UK, that required a screening operation to separate quality classifications of glass fibres. In this instance, Gough Engineering recommended using the Vibrecon GVC5 separator.
The system is designed to order and is used to remove
recycling processing centres are not equipped to deal with the influx of recycling they receive — let alone the ability to meet ambitious new targets. What’s more, these centres must resize inconsistent shapes of various materials into a consistently-shaped final product. The answer to these challenges is to invest in shredding/granulation, sieving and sorting equipment.
Industrial sieves are used across almost all sectors to classify and sort products. Vibratory sieves are often used to sort raw materials such as powders and ingredients through different mesh aperture sizes, ensuring the end-product is of a uniform size.
For recycling, sieves are used in a multitude of ways. A common method is to sort polyethylene terephthalate (PET) bottles. Collected post-consumer PET bottles are delivered to recycling centres to be mechanically separated from other materials and sorted by colour for specific applications or pricing.
In addition to this application, industrial sieves and screens can be used to separate everything from scarce metals in electronics, right through to elements of household and construction waste. In fact, greater investment in this kind of equipment could solve a plethora of recycling challenges — as well as reducing, or avoiding altogether, land fill charges for certain products.
Because there are so many potential configurations for sieves in recycling applications, it is always best to consult an expert. Gough Engineering boasts decades of experience in manufacturing bespoke sieving and screening equipment for industries around the world — including a large number of customers in the recycling sector.
In addition to bespoke equipment, Gough’s own Vibrecon vibratory screening systems differ in size for a variety of applications, starting at 610mm up to 1,630mmin diameter.
Greenpeace’s Circular Claims Fall Flat Again report is right to highlight the shortcomings of mechanical recycling in dealing with plastic waste. However, sieving and screening equipment are a solution to these problems.
Recycling companies will understand the challenges of separating materials, and should work with at trusted material handling equipment partner in order to tackle their material separation challenges.
The new PPWR ruling places more pressure on recycling centres to increase the effectiveness of their separation. Investing in equipment to improve these processes should be a first step towards meeting the EC’s ambitious targets.
fine particles, separating oversize and agglomerates and conveying between processes. Multiple screening decks can be also included in a single system to separate product into two, three or four decks.
For the recycling company, the system was supplied with two decks constructed in the
stainless steel grade 304. The Vibrecon classified glass fibres at 750 kgs per hour. The top deck discharges any oversized particles, and the bottom deck is designed for easy discharge of particles that are fine or undersized, which leaves the middle deck for ejecting good material.
Using this method, the
recycling centre could ensure that all particles are separated effectively. As well as recycling glass fibres, The Vibrecon circulatory vibratory separator is widely used to recycle a variety of other materials. This includes several decades of use in plastics, polymer, chemicals, powders and ingredients separation.
British Plastics & Rubber, and its digital outlet, InterplasInsights.com, are delighted to introduce an all-new editorial advisory board. The board will help to steer the future direction of the magazine, for the benefit of the industry, as well as contributing articles, research, guest authors and more.
Richard is currently running his consultancy R J Consulting and is also the Projects Director at Sierra 57 Consult, both roles offering the injection moulding industry support, training, and consultancy services.
Prior to this he was Managing Director for RJG Technologies (previously G&A Moulding Technology), the Operations Director at the Hi-Technology Group and Managing Director of Hi-Technology Mouldings Slovakia.
He is the Chairperson of the Polymer Committee for the Worshipful Company of Horners, a judge for the Plastic Industry Awards and Chairperson of Judges for Design Innovation in Plastics student design competition.
Dr Beken holds a degree in chemistry and a doctorate in polymer technology. She founded and is the lead for the UK Circular Plastics Network which hosts an annual conference Global Research and Innovation in Plastics Sustainability.
Prior to Innovate UK KTN she worked in the medical industry formulating polymeric materials to support the Montreal protocol enabling the protection of the Ozone layer from harmful CFCs, and her formulations are still on the market today.
She sits on the board for the Sustainable Material Innovation Hub in Manchester, The Centre for Enzyme Innovation in Portsmouth and as a Fellow at IOM3 on both the Polymer and Elastomer Group boards.
Robin has been involved with polymer processing since 1971 and has worked as Technical Director for several major plastics processing companies in the UK and Europe. He has published over 500 technical and management papers on plastics and windows, and 10 books on plastics processing. He is recognised as the leading authority on energy management in plastics processing and has carried out energy surveys and assessments on over 500 companies worldwide. His typical survey work identifies an average of 30% reduction in energy use and carbon footprint. Robin has a B.Eng.(Hons.) in Materials Engineering from Monash University (Australia) and a Ph.D. in Polymer Physics from the University of Surrey. He is a Fellow of the Energy Institute, a Chartered Engineer and a Chartered Energy Manager.
Professor Carmen TorresSanchez is the lead of the Multifunctional Materials Manufacturing Lab at Loughborough University. She designs and manufactures multifunctional polymeric structures and materials with tailored properties to meet specific in-service requirements (e.g., structural, acoustic, thermal, bio-mimetic). She has developed lightweight composites with optimised local properties for applications in the automotive, construction and medicine sectors. Her sonication technology is used to make foams with a bespoke cellular structure. She has attracted >£10M to support her research and has published 60+ papers in her areas of research and innovation.
I believe I can be a good ambassador for BP&R magazine providing inspiration and advice, utilising the knowledge and expertise I have amassed working in the polymer industry.Dr Sally Beken Knowledge Transfer Manager – Polymers Innovate UK KTN
I hope to bring insight into the future sustainable manufacturing processes and products within the UK and wider polymer value chain.Robin Kent Managing Director Tangram Technology
Energy and sustainability management are not only good for the planet but are also some of the most profitable things that you can do.Dr Carmen Torres-Sanchez Reader in Multifunctional Materials Manufacturing Loughborough University
I look forward to showing examples of R&D in the science and manufacture of materials and structures using polymers, rubbers and composites that could be taken from a research lab to production.
Dr Michael Junior Hopkins studied mechanical and polymer engineering. From there he moved to a position within the national polymer processing centre where he was tasked with overseeing all injection moulding-related projects. He went on to work with several large medical device manufactures in Ireland, on devices for multiple therapy areas, including Ostomy, Urology, Cardiology and Neurology. He holds a wealth of experience in managing and processing a range of complex polymer materials and device designs from drug loaded, resorbables, shape memory polymers etc. He has since co-founded, and is the current MD of Ross Polymer Services Ltd which specialises in innovative injection moulding technologies.
Pravin S Mistry has 45 years of experience in the polymer and other manufacturing industries. Over the course of his lengthy career, he has served as divisional managing director and CEO for various multinational companies, including RPM Inc and PolyOne Inc (now Avient). His work has seen him take on management of global projects in the automotive, aerospace, and medical sectors, restructuring loss-making companies into profitable business, and overseeing acquisitions. He also set up a global composite plant in India from scratch, and introduced new technology to a Detroit-based OEM supplier to Ford, Chrysler, and GM.
Professor Kosior’s expertise in the plastics recycling sector spans 48 years, split between 23 years as an academic and 25 years working in plastic packaging recycling. Reducing the world’s polymer waste and carbon footprint by developing new innovations is the driving force to his founding the science-based sustaintech organisation, Nextek.
Professor Kosior has designed numerous modern recycling plants and he has achieved a number of patented recycling breakthroughs. Some of his most recent transformational projects include NEXTLOOPP, the award-winning global multiparticipant project to close the loop on post-consumer plastic packaging and turn it into highquality food-grade recycled polypropylene (FGrPP) and award-winning COtooCLEAN, a unique technology to recycle soft plastic films back to foodgrade compliance.
Thomas is currently a Research Fellow for the Sustainable Materials Innovation Hub (SMI Hub) within the Henry Royce Institute at the University of Manchester, where he manages the delivery of a portfolio of consultancy and laboratory research projects as a senior technical expert. He is also R&D manager for ReCon² Ltd, a company developing a methodology for tracking and quantifying recycled content in plastics and packaging using fluorescent markers. A graduate chemist with a PhD in materials science and polymer chemistry, Thomas specialises in leading R&D projects in areas including materials selection, synthesis, product development, and research translation.
I hope to bring a mix of youthful enthusiasm and vast experience in medical device product development.Pravin S Mistry Global CEO PREA Ltd.
I’m excited to be bringing my 45 years of experience in plastics, rubber, compounds, adhesives, composites – as well as hands on experience of formulating, processing, and running companies globally.Professor Edward Kosior CEO and Founder Nextek
My experience developing recycling plants around the world, through to working with brand owners to develop tailored sustainability solutions, shape the insights I will bring to the editorial board.Dr Thomas Bennett Research Fellow University of Manchester
I’m bringing a genuine passion for plastics as a force for good in our society, and an enthusiasm to share new R&D developments with the plastics community.
Wittmann says it owes its beginnings to a successful automation strategy – created specifically for “real life” moulder needs. At K 2022, the group presented the Sonic 143 “chess robot”, a robot palletising solution and unveiled the radical new design of the WX128 robot – a versatile and compact system that is now set to take over from the W818/W918 series.
The WX128 benefits from the technology developed for the group’s larger WX138 - already available in today’s market. The new robot features a newly developed compact control cabinet on the horizontal Z axisshortened by 30%.
This is useful for small injection moulding machines, as it makes for a compact protective housing, achieved by positioning the drive unit and connection cables on the inside.
The Wittmann WX128 relies on a belt drive concept on all linear main axes. Wittmann says the result is a high level of dynamism. The vertical axis can accelerate at roughly four times the gravitational
acceleration rate. The predecessor model of the WX128 was equipped with an external rack on the demoulding X axis.
Despite the colour and livery changes, last year’s K 2022 trade exhibition proved successful for the Wittmann Group – not least in terms of its offerings in robotic solutions for injection moulders. The group will bring its latest launch to Interplas 2023.
The WX128 was designed to create an easily accessible, compact and low-maintenance design – and future proofing it with flexible upgradeability. As
to equip the WX128 with up to two additional rotational servo axes. This extension can be implemented either at the time of purchase, or as a retrofit later on without having to make any alterations to the control cabinet. At K 2022, Wittmann presented the WX128 robot with an A-C servo axis equipped with an illuminated gripper.
The new WX128 features a nominal load capacity of 6 kg, offered exclusively with the current Wittmann R9 control system.
At Interplas 2023, visitors to
the Wittmann Battenfeld UK stand – its biggest space yet –will be able to see the WX128, as well as Wittmann’s various other automation solutions. Wittmann Battenfeld UK joint managing director, Dan Williams said: “We are happy challenging any moulder to witness how Wittmann robotics and automation can instantly improve a business –including operations, energy saving, reliability and price/ performance. It’s not a cliché – Wittmann has an automation solution for every moulder. Our robots can be fitted on any machine, regardless of age, make or size.”
Tracy Cadman, joint MD added: “We encourage all in UK injection moulding to use the Interplas forum to make a date with us. Robotics and automation already play a key role in many mouldshops across the industry and Wittmann has been in the vanguard of this movement for decades. The exhibition always provides a convivial atmosphere and many opportunities for networking, learning and profiting.”
Williams added that connectivity and automation in injection moulding is only set to increase further as manufacturers take on more and more complex and challenging technical projects: “Relying on Wittmann repeatability and control will give any moulder complete peace of mind throughout the whole project process. I warmly encourage you to visit us at Interplas and see for yourself how we can support you from a simple pick and place solution to a fully automated multi-insert moulding application with full camera measurement and downstream automation.”
“Interplas always provides a convivial atmosphere and many opportunities for networking, learning and profiting.”
a result, it is possible
Need to invest in Injection Moulding equipment, but concerned about the impact of the electricity crisis?
BOLE Injection Moulding Machines incorporate the latest Servo Motor technology and patented designs to help reduce your exposure to an ever-changing market.
Worried about delivery times? Don’t be.
We have stock of machines between 50t – 1000t from our EKS, FE and DK ranges which are backed up by our team of in house engineers and a 3 YEAR WARRANTY on non-consumable mechanical parts that can be delivered within 5 days from order.
Contact us to find out about our Part Exchange scheme.
Back in 2003, we spotted an opportunity to offer clients something unique. An innovative and comprehensive manufacturing solution that combined the benefits of British standards and values with Chinese manufacturing efficiency and precision. That’s why we created Sino.
Fast forward 20 years and our experienced British designers, engineers, and management work alongside the team in our fully equipped 54,000-squarefoot factory in Shenzhen to offer clients high quality with keen cost efficiency, swift turnaround times, and stressfree project management.
Our unique infrastructure and experience set us apart from traditional Chinese toolmakers. We are a British and Chinese company with a 50% shareholding held by Rob Harris and 50% by Li Xie.
As a truly hybrid solution, our Western/Chinese structure is the DNA of our business and the secret to our manufacturing excellence. It enables us to design, manufacture, and deliver a huge range of high-performance mould tooling and components for leading companies across the globe. Plus, our British creative and technical knowhow ensures professional project management and communication throughout the turnkey process.
Our manufacturing ecosystem means clients can rely on us for everything from concept to delivery. To help customers with complex product design solutions, we’ve worked with a UK design agency that specialise in solving mould design problems for over a decade. They work closely with our in-house mould designers in Shenzhen to finalise the work
For 20 years, one particular company in the moulding arena has been offering a hybrid manufacturing model. Robert Harris, Executive Chairman & Founder, Sino Group, explains why he feels his approach offers the best of both worlds when it comes to sourcing tools.
in China and produce finished tooling GAs for our customer’s engineering team to approve. This international approach means we can solve most technical issues and can work in all CAD software packages.
When it comes to the manufacturing process, our UK-managed factory in China contains everything from a comprehensive CNC machine shop, spotting presses, and overhead cranes to a fully equipped quality and metrology department for ISIR & PPAP reporting and mould tool maturation.
The end result is mould tools that are equal to or better than Western companies in terms of quality & technical excellence.
Our solid reputation of offering clients all upside and no downside is thanks to the 20-year business relationship between Rob Harris and Li Xie. Two very different people with one united goal: Making things better.
• Rob Harris, Executive Chairman, 65, is a trained product designer with engineering degrees from North Staffordshire University & De Montford University. His 40+ years of experience in the plastics and plastics-related industries includes working for Glasdon Ltd, McKechnie Group, Plastic Omnium, and family injection mould & tooling business HSS Precision Moulds Ltd.
• Li Xie, CEO, 52, studied Mechanical Engineering at Shandong University. His 30 years of diverse experience includes The Small Business Incubation Centre, a Chinese Tractor manufacturer in Argentina, a Real Estate company in Hong Kong, and Circast, a PCB manufacturer in Leamington Spa, UK.
When you are running a business on two continents that are 6,000 miles apart, excellent communication and outstanding project management systems are key.
For this reason, we have adopted the English language for all communication between customers and in-house management and engineering staff. To facilitate this, we set up an English language lessons programme in our Shenzhen factory delivered by Sam Hemming, who is married to our Technical Director, John Hemming.
To help meet customer’s needs no matter where they’re based, our newly formed sales team in Shenzhen (headed up by Elena li with Myra Huang & Monica Wang) covers the UK and world markets, and Jon Harris is our Vice President and manages new business development.
Alongside our first-class Chinese manufacturing facility, we have set up a supporting infrastructure in the UK to offer customers a complete service from purchase order to delivery. This allows us to act fast and swiftly turn around modifications, warranty work, and repairs so that our customers can meet their customers’ delivery expectations.
Customers with limited storage onsite can make use of our warehouse in Redditch, Worcestershire where mould tooling and engineering components can be stored either bonded or non-bonded for onward delivery within the UK.
We also have a registered office at Frome Business Park, but since the Covid pandemic have encouraged staff to work from home. It’s fair to say that Microsoft Teams has revolutionised the way we communicate and project manage as we can now instantly bring customers and Sino team members together across different time zones.
“To help customers with complex product design solutions, we’ve worked with a UK design agency that specialise in solving mould design problems for over a decade.”
Together, their skills and experience and trust and understanding have shaped Sino into the thriving company that it is today.
In the fight against high bills and climate change, UK industrial SME’s need consumption insights to help target effort and investment to best effect, as well as to track improvements. Put simply, companies need the ability to stop treating electric bills as a large single ‘lump’ cost, and to start breaking them down by department or machine, as they already do for other major costs, such as raw materials.
But how can this be achieved in a mid-sized industrial setting?
It is true that measuring electricity at departmental or process level has been expensive. Add in the complexity of gathering all the data and processing it into a meaningful format, and the task became formidable. For these reasons, it has only
A complete ‘end-to-end’ package for UK industrial companies to understand and reduce their electricity consumption in a structured way. Sensors are placed to continuously monitor consumption in departments or by key machines as well as at the main ‘incomer’. The wireless sensors are easy for any electrician to quickly install and come with all necessary connections. No connection to your IT is required, as all the data goes over the mobile network. No setup is required – just plug in & the data starts streaming through the air.
The supplied online dashboard features world-class capabilities such as :
been feasible for large industrial companies to achieve the goal of managing electricity as a ’direct’ cost. Everyone else has been stuck with lumping the whole bill into the ‘overhead’ category.
Until now !
A brand new ‘Plug–n-Play’ package has been developed by UK startup Lora-Sense Ltd to bring these game-changing possibilities to SME’s, and it is launching now.
How much saving is possible ?
Implementing an energy management package can enable ‘quick win’ savings of up to 10% and point the way to further savings in excess of 20% -- all with >100% ROI.
Target your eff ort, by seeing breakdowns of where the energy & money is being used.
Measure the results of each improvement your team makes.
See KPI's like consumption per unit of production
As soon as they are installed and the receiver is plugged in you get real time information on the power being consumed by those machines.
The reporting within Wattics was easy to understand and enabled us to monitor and compare similar machines and different machines running similar product even to the point of cost per Kg of production by linking to the tonnage reports from our production recording system.
What became clear to us was how different the consumption was on different machines – even across machines of the same tonnage.
Andrew at Lora-Sense has proved to be a very knowledgeable person within engineering / manufacturing and has developed a very powerful tool which will identify areas of significant cost saving potential.’
Andy Thompson (founder) comments
• Monitor by KWh, cost or production KPI’s.
• Simulate alternative tariffs before switching, by running ‘what ifs’ on historic data.
• Easily spot ‘quick wins’ such as abnormal out-of-hours usage.
• Compare different machines by cost or KWh per unit of production.
• Evaluate results of investments.
• Share favourite graphs to colleagues or display screen.
• Analyse power factor, voltage variation, kVA demand as required.
Mark Cuthbert at Talisman Plastics comments
‘Here at Talisman Plastics we are always on the look-out for ways to improve our productivity, reduce costs and to improve our Carbon footprint. We trialled the equipment and reporting package (Wattics) on a number of moulding machines alongside our compressors and a chiller. The kit was quick and easy to install and came with clear installation instructions which meant little or no downtime as they could be fitted at convenient times to the business.
‘For too long, only large companies have been able to implement decent energy management systems, due to their complexity and high cost. Now this capability is available to all UK industrial companies. Lora-Sense is proud to be offering this game-changing package to UK industrial companies of any size.’
Expensive ?
No ! – just a few ‘quick wins’ will pay for it all.
Temporary or permanent ?
The package is not designed to be a ‘one-off ’ exercise – rather it is meant to be a permanent feature to enable continuous monitoring and cost reduction.
To mark its 185th anniversary, KraussMaffei is offering a special edition of its CX series. Dave Gray caught up with Mike Bate, MD, KraussMaffei UK, to find out what’s special about the machine, and what the group has in store for Interplas.
A new version of the CX is just one of many activities the group is undertaking in this milestone year. A live exhibit at Interplas, two new machine ranges and a new HQ are all set to create a buzz for KM customers in the months ahead. The machine maker’s anniversary edition CX comes with a package of additional features that are normally subject to a charge - but are now integrated at no extra cost. These features allow for a clamping force range from 500 to 4200 kN, while at the same time aiming to reduce operating
costs. I asked Bate about his plans for the rest of the year, as well as current business conditions…
DG: Why is this an important milestone – and how is the company celebrating?
MB: KraussMaffei is proud to announce our 185th birthday. We have 185 years of pioneering spirit which we are continuing in our birthday year by making some amazing offers with
both new machines purchased between now and November 2023 and our Digital Service Solutions. We have introduced “special” editions of our famous CX-Range (RelaCX) with numerous attractive features for energy saving and part optimisation.
DG: Where is KM’s business coming from in the UK?
MB: UK business is coming from a variety of market sectors. Medical has been very buoyant since the pandemic and the building and trade moulders have stayed loyal but we see the automotive market gearing up again. Recent Tata Group’s news about the UK winning the battery plant will be a massive boost to the economy. In recent years our Extrusion and Polyurethane businesses have enjoyed great success with outdoor composite decking and other composite products. KMGUK is not all about injection moulding – our successful extrusion business can only increase with the amalgamation with Berstorff. KraussMaffei Extrusion can enhance the portfolio of pipe and profile with rubber, compounding, and recycling. We have moved into a new facility in
DG: Can you talk about powerMolding and precisionMolding machines that came to Europe for the first time at K? Where do you see the interest for these in the UK market?
MB: As you say, we first launched the two machine ranges at K 2022. They are high quality manufactured machines made by KraussMaffei. This is an exciting time as it will open doors to new potential markets and new customers that would not normally think to look at a KM due to cost. The machines will not have all the options of our established machine ranges, so we can build them more efficiently and be more cost effective. We are happy to say we have received our first precisionMolding machine in Warrington which is available for customers to visit for demonstrations.
DG: And the company recently moved its Munich HQ – what does this mean for UK customers? Will there be an opportunity to visit?
MB: It was very sad, working for KraussMaffei for 34 years, Allach was like a second home to me, but we haven’t only
produce our injection moulding complete ranges and our polyurethane machines and plant. Initially, an Open House was planned for 2023 but this will be postponed to 2024.
DG: Energy e ciency is the top priority for moulders now – what can your team do to help moulders optimise their machines?
MB: This has been a hot topic with many of our customers over the past 12 months and has certainly kept our Sales4Service team very busy. In addition to APC+ and smartOperation previously mentioned, socialProduction is a valuable tool to remotely check on the machine’s performance and with the added option of liveCare. The customer can view wear of machine components, helping to reduce machine downtime. Our UK S4S team will be happy to give more information on these topics.
DG: Finally, you’re returning to Interplas this year – what’s the plan for your exhibit?
MB: It is great to be back, and be a part of the advisory board; it is promising to be a great show for the UK plastics industry from which we can all hope for a successful future. We are looking forward to presenting
Laatzen, just outside Hanover. It is a 97,000m2 facility for the manufacture of all our extrusion plant and machinery.
DG: What are the trends you’re seeing in customer requests lately?
MB: For many years major conversations have centred around lightweight composite products. The automotive sector has worked on this for many years. Now we are seeing more interest from other sectors, like aerospace and medical. The Ukraine crisis has focused everybody on energy. We are constantly striving to make our machines as energy efficient as possible, but there are other ways to help our customers optimise their process. We can already offer APC+ which can optimise the process from shot-toshot no matter the changing environmental or material conditions. smartOperation, developed to enable a single button to start the machine in the same configuration every time, will help many customers with machine set-up. We are happy to demonstrate these valuable options on our machines in Warrington. Our growing Digital Solution department are working on many more solutions to make the supplier/customer experience more enjoyable.
moved in Munich. At the end of 2022 we moved our Extrusion Division from Hanover to just outside Hanover – Laatzen. This is a unique site for all our Extrusion portfolio. The 97,000m2 facility is only surpassed by our Parsdorf facility on the outskirts of Munich, a 125,000m2 state-of-the-art technical centre and production facility to
demonstrations from all our technologies including our Additive Material division. Not wishing to give too much away at this stage, it is fair to assume, there will be a precisionMolding machine producing parts over the three days. Let’s leave it at that and let the plastics industry come to the NEC 26th–28th September to see a great show.
• BluePower servo drive that optimally controls the pumps according to current demand or energy requirements. This aims to significantly reduces electricity requirements and thus lowers operating costs as well as CO2 emissions from production.
• BluePower insulating sleeves, which are placed around the plasticising cylinder, stabilize the temperature profile there and thus improve process stability. They also reduce warm-up time by up to 30 percent, resulting in corresponding energy savings.
• The APCplus (Adaptive Process Control) machine function, which continuously analyses the injection moulding process and quickly and accurately compensates for material- and environment-related fluctuations in melt viscosity. KraussMaffei claims that this enables zero-defect production. APCplus will be integrated into the #185 special edition CX series at no cost when a contract is signed within 185 days of the start of the campaign, which was on May 9, 2023.
• The smartOperation machine function, which enables intuitive control of the entire injection moulding process, even without in-depth application expertise. Companies can thus ensure a standardised and error-free process as well as high system availability even without a designated operator. Here, too, the offer of free integration applies if the order is placed within 185 days.
“This is an exciting time as it will open doors to new potential markets and new customers that would not normally think to look at a KM due to cost.”
We’re giving away a FREE TT-181 All you need to do to enter is follow us on LinkedIn, Like & Share our ad and email us how you plan to use our unit, should you be our lucky winner.
The draw will not take place until September 2023. All participants will be entered into a random draw. You must be based in the UK or Ireland to WIN, and must work at a company who has a requirement for this unit on site. No cash alternative is available.
We look forward to hearing from you, and how you plan to use this unit.
Veronica Edmunds, business development manager at Haitian - Premier Moulding Machinery, reflects on the changing landscape for moulders in recent – and not-so-recent –times.
As we pass the 1st anniversary of Russia’s invasion of Ukraine it is natural to look back on a turbulent year for the economy, households and businesses.
Some changes in life are gradual, the newly aching knees, the stronger glasses prescription, the slipping down the leagues of once great teams. We get time to adjust to the new reality of age or fading form and it makes it easier to accept. But the modern world is fast paced, instant access, full connectivity, no time to waste, in your face.
So, when Russian tanks moved on Kiev, we discovered first that it was called Kyiv, and secondly that the World economy was a fragile structure. We needed Ukrainian grain and Russian gas to keep the wheels turning, and our mortgage rates low. Who knew?
When Premier Moulding Machinery (PMM) entered the UK market for injection moulding machines almost 20 years ago, it was a quiet introduction of the Haitian brand. Little was known of Asia’s market leader on these shores, or what advantages they would bring to their customers. PMM were perhaps the perfect vehicle for Haitian, time served plastics engineers, determined to offer the best service to the sector that had
Phil Marshall from JC Moulding in Wales remembers “When PMM first knocked on our door in 2017, I must confess I didn’t know about Haitian. It’s crazy that we weren’t aware of the World’s biggest supplier of machines, but it’s very easy to miss the world changing when you are so engrossed in your own business. I liked the PMM approach and the different way they said they do business, but I was still sceptical about whether we could afford to buy new machines”. JC Moulding is a small but fast growing business so as general manager, Marshall is used to fulfilling many roles within the business. “It was genuinely great to have a supplier who brought expert knowledge and insights to us, without wanting to charge us for it”, he added.
The energy savings alone from the new Haitian machine were greater than the finance JC Moulding paid on it each month. “We literally had more cash in the bank from day one, and our first new machine”. Phil credits this lightbulb moment with transforming his outlook on the business. “We now have 12 Haitian machines, all saving us money on power, spares, servicing and scrap. We have been able to reinvest the money in the business and the changes have generated even more work”.
nurtured them. Nowadays the PMM team refer to their quest to add value to their customers as being “Pleasantly disruptive” in a marketplace that had lost sight of the needs of the customer.
With unpredictable economic times in our midst, it’s important for businesses to invest in the best available technology to maintain and grow competitive advantage. Whilst the current mood
music maybe one of caution and restraint now is the time to invest to negate the high energy costs and take advantage of low shipping costs.
has invested in a new twin platen 750 ton Jupiter machine and Hilectro robot from Haitian International for the firm's ICM Rochester site. Due to an upturn in business and a desire to ensure the best return on investment, Merriott Group took delivery of a new 750 tonne Jupiter machine from Haitian International. This machine extends the current capacity over the Rochester and Crewkerne sites to 46 machines ranging from 25 to 1100 tonnes, alongside a further 34 compression machines. The new machine will predominantly run a new cable junction shell but with the capacity for new work too.
Andrew
The decision was made to join with Haitian by a willingness to look outside of the conventional European suppliers. With many customers reshoring tools and a need to reduce energy costs, a quick return on investment was essential. The Haitian business model of cost-centered spare parts and engineer visits plus the low initial purchase price (all backed by an extensive UK service team) made this an easy decision.
The polymer price rollercoaster ride is never ending, and given that prices never stay at the top or bottom for more than a few weeks, typically one of the following conditions apply:
1. Prices rising quickly.
2. Prices rising slowly.
3. Prices falling quickly.
4. Prices falling slowly.
It is easy to comprehend that the preferences of polymer suppliers and polymer converters are diametrically opposed, with sellers preferring prices rising quickly, as this maximises gains on unsold inventory, and converters preferring prices falling slowly as this reduces input costs on existing orders with a lower risk of either being undercut by competitors or from end customers pressing for dramatic price cuts based upon their knowledge of crashing polymer prices.
As depicted in the graph the past 39 months have provided a significant amount of price volatility, with a substantial drop as the Covid-19 pandemic hit the Western World, followed by price hikes as demand for plastics soared and availability of petrochemical feedstocks was limited by low oil refinery output rates and after a period of slowly increasing prices came the Russian invasion of Ukraine, which caused a rapid an unexpected peak in pricing; subsequently prices started to fall away as concerns relating to severe energy cost inflation caused fear of a significant global economic slowdown.
The implications of polymer price volatility on polymer producers are one of profitability and whilst key input costs such as Naphtha, which closely tracks crude oil, the moderation of these costs, has been less significant than the recent fall in polymer prices. Polymer production is energy intensive and as with other manufacturing sectors this has also impacted production costs. The current reality
is that many polymer producers are loss making and this situation will styme future investment and will likely result in reduced output rates; the inevitable outcome will be a shortage of supply and the consequence of increasing prices again.
Another serious effect of low polymer pricing is on the viability of recycling, where the contrasting cost model of mechanical recycling becomes increasingly challenged due to the relatively high variable costs involved in this activity. Furthermore, low virgin polymer prices and more specifically low off-grade or wide-specification polymer raw materials tend to lead to substitution of recycled products as producers factor higher performance and increased productivity into cost calculations.
For now, at least, the direction of travel remains towards prices softening, albeit that the rate of price reduction is much more moderate and on this basis prices are likely to start moving upwards before too long.
www.plastribution.co.uk | www.pieweb.com
"The implications of polymer price volatility on polymer producers are one of profitability and whilst key input costs such as Naphtha, which closely tracks crude oil, the moderation of these costs, has been less significant than the recent fall in polymer prices."
The report warns that the window of opportunity to secure a livable and sustainable future for all is rapidly closing. We will never again have this time, where we know what the situation is so conclusively. This scientific consensus, combined with the fact that the majority of climate solutions to avoid the worst consequences of climate change exist, provides a unique opportunity for us to address the gaps and take action.
Achieving the 1.5 degree limit is still possible so long as immediate action across all sectors occurs. Transitioning from ‘business as usual’ must escalate immediately.
The plastics and packaging industry can make a very significant contribution by boosting efforts to reduce the CO2e associated with their sector. Each tonne of recycled plastic saves at least one tonne of CO2. In the case of food-grade recycled Polypropylene (FGrPP), an estimated 1.6 tonnes of CO2e can be saved compared with virgin Polypropylene resin. As such a 20 ktpa plant would save 32.000 tonnes of CO2e.
The easiest and most direct way to achieve this is to increase the rate of recycling of plastics and packaging as soon as possible.
Whilst this means disruption for an industry that has longstanding and cost-efficient practices that did not consider CO2 emissions, these kind of critical choices and actions will have impacts now and for thousands of years to come. But these actions must be implemented immediately because adaptation options that are still feasible today will become constrained and less effective with increasing global warming.
Which is why, within the context of plastics packaging,
The latest report on the climate crisis by the Intergovernmental Panel on Climate Change (IPCC) is a sobering reminder of the dire consequences if we don’t drastically address the issue of CO2e in our atmosphere. Professor Edward Kosior of Nextek and NEXTLOOPP writes.
we must invest in design of easy-to-recycle packaging that has circularity at its heart with a clear focus on CO2e.
Right now if we applied our very best current practices of collecting, sorting and recycling, we still could recover at least 60 percent of our plastic packaging which is a big step forward over what we currently achieve.
Instead of trying to align with what brand owners and supermarkets put back into the waste stream for recycling, we need to go back to the packaging design drawing board and produce packaging that can be recycled simply and productively by recycling businesses. We can no longer afford the “luxury” of “difficult to recycle” packaging. By optimising the composition, such as low or no pigmentation, monomaterial construction through to readily removable adhesives, labels and inks we can already make an impactful difference.
With the fate of the world hanging in the balance this is no tall order, so let’s unpack this further.
The biggest market for consumer-focused plastics is food packaging - as such food-grade compliance for recycled materials is crucial. To achieve this we must simplify recycling rather than look to over-complex technologies to solve our challenges. Without the need to go down any sophisticated, costly route there are four components in packaging that could transform the way packaging is recycled.
In the true sense of a circular economy one can only recycle what is put out by the retailers and adhesives, labels, inks and pigmentation limit re-use as food-grade recycled materials and therefore impede true circularity. These might seem like small details when in fact all four play a pivotal role in whether a pack is recycled back into high-quality packaging or turned into lowvalue recyclates or worse, sent to energy recovery or landfill.
The aggressive glues with a range of additives are particularly an issue for recyclers of PET, PP and HDPE packaging as these materials can accumulate in the recycled materials as non-intentionaly added substances (NIAS). Some options such as selfpeeling labels that remove the adhesive and the label during washing stages of recycling are already on the market.
Going further we need to ensure the inks on the labels don’t bleed into the water used in the washing stages of recycling. The labels themselves need to be readily separated by logical separation steps such as sink/ float systems and recycled to avoid any unwanted waste.
Less is more
Coloured recycled plastics have a lower value and are much less likely to be recycled into food-grade packaging due to the colour matching needs for specific packaging. Yet, as mentioned earlier, food packaging is plastics’ biggest market so it stands to reason that if we can readily differentiate food from non-food packaging we can have a huge impact on recycled plastics.
One simple solution would be to use colours to speed the process up. Pigments are possibly the most contentious yet easily reversible element of today’s packaging and we need to flip the way we use them. Instead of using colours to tell a brand story and create on-shelf standout, colours could be put to better use if they were to define which category the product contained within belongs to.
In this scenario all foods would be contained in natural or white packaging. Non-foods would be in pastel coloured packaging that would use a smaller concentration of pigments and all hazardous products would be in black (carbon black or detectable black) plastic.
Sorting by transparent, pastel and black would simplify recyclers lives as they could use their well-established, accurate and low-cost automatic sorting technology that relies on the Near Infra Red (NIR) and visible light spectrum and cameras for detection.
If we focus on these four elements we will already make great in-roads. What we don’t need is more time-consuming research that is not connected to current problems and tasks that need resolution. We literally don’t have the time. We now need to apply common sense and the effective technologies we already have to hand.
Despite the many good innovations coming on stream it would be fair to say that the majority of packaging is still being designed to be processed only once and this needs to change. Recycling-friendly formulations are needed and reducing pigments along with recycling-positive labels and adhesives, will have a transformational effect.
Of course we also need to enhance collection of recyclable packaging to divert it from leakage into the environment and the growing waste-to-energy destinations. We need to streamline and update the numerous administrative blockages stopping effective and safe recycling of food packaging given
the advances of technology that have recently taken place. Still - we can’t wait for the perfect moment when everything falls into place - we need to keep pushing forward with what we can do today.
As the IPCC report points out, apathy is our biggest enemy. If we stand back and observe, every increment of global warming will continue to intensify numerous and concurrent hazards. Yet by making simple and cost effective changes we can already make significant differences. We can’t afford to put future generations in jeopardy as they will increasingly struggle to adapt to a far hotter and profoundly different world to the one we currently know.
What if we told you that you can make savings of £20,000 in electricity consumption on just one production line?
Not to mention helping your sustainability goals by reducing CO2 emissions by up to 30%? Better believe it – all you need is SMC’s brand-new Compressed Air Management System. and
Those figures are real: that’s what the new SMC Air Management System just achieved for one of our UK end-user customers by simply reducing air consumption by 50%. We are certain that improvements can be made, regardless of the size of your facility and complexity of production lines. With electricity prices having rocketed in the last 12 months, seriously affecting profitability, can you afford to ignore this opportunity?
So how does it work? Quite simply, by precisely monitoring the air flow into a production line and, when systems or sections of a system are idle, reducing or halting the supply of air to that section. State of the art sensors mean there’s an instant return to full flow once manufacturing restarts. Think of it like a modern car that switches off its engine when stopped – and immediately restarts once the traffic is moving again.
An added bonus is the reduction in downtime and savings on maintenance costs as the air supply system is not running continuously. The Air Management System is a standalone unit that can be programmed via a button on the hub or the webserver – no need to connect it to a network, no need for a PLC or Edge device, meaning it’s super user-friendly.
For a deep dive into the technical details, keep reading.
It all started with one of our customers – a global blue-chip company - looking for a solution providing high-resolution data to assist in monitoring the air use (pressure, flow, and temperature) of its machines, while also providing economic control of the air supply. The solution had to be suitable for retrofitting onto existing machinery as well as being compatible with new machines. Further
requirements included easy access to data and simple commissioning. Based on these prerequisites, our team of engineers set about developing the Air Management System.
We work closely with our customers to develop solutions based on real-life projects that, for example, align directly with their goals. This approach provides SMC with a solid foundation for the development of optimal solutions, one that we ultimately roll-out to benefit the wider industry.
One end-user customer had a production line comprising of 10 different machines handling a minimum of 180 bottles per minute. Each machine performed various operations using compressed air, including air blowing and vacuum holding, resulting in high air-use and of course high energy costs. Due to the wide differences between each machine, the concept for our Air Management System centred on universal machine conditions such as stop, run, wait, and error. PackML provided the definition for those conditions.
Consider a bottle unscrambling machine lying idle because of an issue with the bottle labelling machine down the line. Previously, the unscrambling machine would continue consuming air. However, the Air Management System uses the machine’s ‘wait’ signal as permission to do something positive. For instance, if the wait signal exceeds a customerdetermined duration, the Air Management System regulates to a lower secondary pressure, such as 4-bar instead of 7-bar primary pressure. As a result, the flow rate drops,
typically by more than half, providing a dramatic reduction in air consumption, energy use and CO2 emissions.
SMC’s Air Management System also has an optional valve for a full isolation mode (compressed air isolation). Upon exceeding a secondary customer-determined duration, the
into other services such as computerised maintenance management systems (CMMS) or AI machine learning packages.
The savings from deploying our Air Management System are instant. In addition, over the course of a machine’s annual duty cycle and multiplied by several machines and production lines, this end-user customer achieved
same machine can completely stop any unnecessary use of compressed air, further reducing energy requirements.
Take control of your air management
When it comes to connection options the Air Management System is extremely flexible: it is possible to deploy either a wired connection or, using our proprietary wireless connectivity, you can utilise one wired connection to a base unit that collates data from up to 10 remote devices. You can also choose to connect it to your fieldbus network, or simply use the device’s integrated OPC UA server interface, negating the impact and complexity of communicating with machines featuring different fieldbus protocols.
In all applications involving the Air Management System, there is no need to access your machine’s PLC. Instead, the near plug & play nature of the system works with each machine individually and universally, requiring just one 24 VDC signal. Digital integration is also easy as one Air Management System wireless hub allows you to connect to 10 remote units, within a 100m radius, providing a more economical cost and reduced integration outlay.
The system is entirely ‘dark factory ready’, providing you with the opportunity for decentralised control and monitoring. Aside from energy savings, data analysis forms the basis for defining efficiency gains and preventative maintenance activities.
Our Air Management System facilitates the collection of high-resolution data (10Hz), enabling users to trend the pressure, flow and temperature of each machine equipped with the product. Thus the customer can measure and monitor their assets and make informed decisions on when to maintain their machines. Users can also pass the data
an exceptionally fast return on investment (ROI), saving £20,000 on energy costs in the first year alone. We are confident this will be similar for other customers adopting the Air Management System.
A further example from the food industry: an OEM was experiencing significant air loss during production. It turns out they were wasting significant amounts of air without realising – from seal wear, air blow and continuing to run the vacuum generator whilst the production line was idle. Enter SMC’s new Air Management System and they saved over 50% of air losses immediately. Following the successful trial, this OEM’s design concept was completely revolutionised going forward.
So don’t compromise. Whatever your size, whether you’re an end-user or an OEM, the system’s affordable price point and rapid ROI enable you to instantly make energy savings and boost your bottom line.
Call: 01908 563888 Email: sales@smc.uk
We develop amazing colours and special effects for some of the leading brands across the globe. With Performance built-in and cost designed out, no one gets closer. To discuss the addition of antimicrobials, please contact any of our experts.
Pentagon delivers a full turnkey solution for plastic injection moulding from one site of UK Manufacture.
With over 50 years’ experience you can be confident that your Bespoke Moulding project is in the hands of the experts for both mould tooling and repeat production.
DG: What do you mean when we speak of a circular model for plastics?
DJ: Today, there’s no denying that the plastics sector is at an unprecedented inflection point. For plastics producers and brand owners alike, sustainability is now a key priority given that the transition to a circular plastics economy is an integral element within the overall effort to achieve net zero.
In a world filled with finite raw material resources, developing and maintaining a comprehensive circular ecosystem will require us to keep existing resources in use for as long as possible to minimise waste generation. Following on from this, an effective circular model would then allow the recovery and regeneration of valuable materials and products at the end of each service life.
As a model of production and consumption, a circular model functions by driving materials consistently around a closed loop system. This allows the system to maintain the value within rather than discarding it, or allowing it to leak into the environment surrounding us – in theory, reducing material waste to minimal levels.
Dave Gray speaks to Dewey Johnson, Chemical Market Analytics, to find out how far the plastics industry really is from achieving true circularity.
Left unchecked, the status quo facing us is quite stark. Recent Chemical Markets Analytics data suggests that, global plastics waste production could reach as much as 320 million metric tons per year by 2030. This could elevate the current environmental challenge that plastics waste poses to new heights, and for years to come.
DG: What are the key challenges to moving beyond a linear model?
DJ: Our work at Chemical Market Analytics has highlighted a number of disruptive truths that require attention from stakeholders across the circular plastics value chain.
For example, our recent modelling has shown that the quantity of plastic waste is projected to increase by 60-70% over the next 30 years. Currently, around 9% of this is recycled. And while this figure could reach 15-17% by 2030, this will require meaningful investment into infrastructure and recycling technologies.
Our research also highlights that a significant portion of the projected waste increase will come about as a consequence of growth in population and living standards in less economically developed regions, for example, Africa, India and SouthEast Asia. These regions are currently characterized by low collection, recycling and recovery rates when it comes to plastics, which means large volumes of plastic waste are leaking into local environments, polluting landfills and water supplies in some of the most globally vulnerable regions. Many collection systems are overwhelmed with waste volumes of all materials and do not currently drive effective economies of scale. This also includes those located in the Global North.
Much of this waste is being generated at a significant distance from where the plastics demand centres are located. For example, production of petrochemical plastics typically happens in North America, the Middle East, Europe and China, but the associated waste is projected to appear in regions far from where the source materials originate. As
regulatory efforts accelerate and investment into improving plastic waste infrastructure increases, the ability to monitor evolving risks, costs and emissions will prove increasingly pivotal to achieve meaningful change.
DG: How can technology help us bridge the gap?
DJ: Over the past halfcentury, multiple plastic recycling technologies have risen to prominence. Take mechanical recycling for example. Such an approach has existed since the 1950s and works by non-chemical means to process plastics waste into secondary raw materials for use in new contexts.
Given the maturity of the technology, focusing on a mechanical recycling approach holds significant advantages from a CAPEX and operating costs perspective. This consequently enables stakeholders to achieve break-even economics sooner on investment. Additionally, mechanical recycling of plastics by definition avoids the need to tamper with the chemical make-up of plastics, which minimises the amount of CO2 released in the recycling process. However, there are potential drawbacks. Mechanical recycling reduces the quality of plastics as they pass through the process, reducing their efficacy and potential use cases over time. A lack of feedstock is also a potential barrier, as there are currently stringent quality specifications that limit the types of plastic waste to which mechanical recycling technologies can be applied.
To move beyond the degradation problem, chemical and other recycling technologies such as pyrolysis and gasification,
Mechanical recycling of plastics by definition avoids the need to tamper with the chemical make-up of plastics, which minimises the amount of CO2 released in the recycling process”
source chemical
as well as depolymerisation and solvent solution and dissolution, are often proposed as alternative solutions. Pyrolysis and gasification in particular can effectively break down low-quality plastic waste feedstocks, but the nascent nature of these technologies means that in the short term, they require significant CAPEX requirements, pushing breakeven points well into the future. At Chemical Market Analytics, we track more than 120 different recycling technologies in varying stages of development, which illustrates the significant complexity involved in selecting the appropriate technology for each use case.
DG: How pressing is plastic circularity for businesses and key stakeholders? Are we making much progress?
DJ: It cannot be denied that there are currently different perspectives on
urgency, depending on the audience. Plastic producer attitudes often differ from the brands that use their products. For example, consumer goods companies such as Coke and Pepsi are on the record with public pledges to drive reusable packaging and plastics by 2030 given consumer demand. Regulatory scrutiny
is also accelerating with the UK’s Extended Producer Responsibility (EPR) reporting requirements and the U.S. government’s EPA Draft National Strategy to Prevent Plastic Pollution driving increased scrutiny on brands when it comes to their attitudes about recycling plastics. Plastic producers, on the other hand, may not feel the same pressure, attracting less media and regulatory scrutiny as plastic feedstock suppliers.
Increased attention on global logistics issues when it comes to circularity in plastics is also an ongoing concern. The issue of plastic waste generation being located at a significant distance from where recycling and reuse can take place means that global supply chains need to adapt to drive cost efficiency. This requires careful consideration of whether it may make economic sense to carry out chemical recycling pyrolysis at a small modular
installation in one location before transporting the pyrolysis oil to petrochemical centres for further processing. Such additional complexity is a key concern for plastics producers and brands alike.
Ultimately, the plastic value chain as a whole must align itself with government regulation as it evolves to ensure progress on circularity is achieved in a strategic, cost-efficient fashion. The current discrepancy between global manufacturing and delivery of traditional plastics versus the development and scaling of “reverse” plastics highlights the need to effectively track progress and promote investment in these technologies to drive change.
DG: Will plastics really move the needle when it comes to overall sustainability efforts?
DJ: There’s no denying that urgent action is needed on the issue of plastic waste and driving increased uptake of the circular model. Currently, the “plastics end-of-life” challenge is expected to get worse before it gets better. In both the short and long term, it is important for stakeholders to carry out comprehensive life cycle analyses on an ongoing basis to maintain visibility on current priorities.
For meaningful action to be achieved, a global alignment of government policies, stakeholder values, financial support and application of transformative technologies must be prioritised across the entire plastics value chain. Achieving meaningful progress when it comes to circularity in plastics will require organisations to be increasingly nimble when adapting to change and have the right data and business intelligence at hand to make informed decisions.
“Ultimately, the plastic value chain as a whole must align itself with government regulation as it evolves to ensure progress on circularity is achieved in a strategic, costefficient fashion.”
With specialist industry knowledge and tailor-made support, we offer a range of finance options which can:
• Unlock the value of your existing assets
• Let you invest in new equipment
• Create positive cash flow for your business
Contact us today, we’re here to help
closeasset.co.uk/bpr
Products and services are subject to eligibility, status, terms and conditions and availability.
All lending is subject to status and our lending criteria. The right to decline any application is reserved.
BOOK REVIEW:
232 pages. Hardcover
Copyright: February 2023, Hanser/Hanser Publications
ISBN: 9781569907009 (print)
ISBN: 9781569907016 (ebook, PDF)
total usage is small compared to that of the commodity plastics (e.g. PE, PP, PS, PVC), and also to the engineering plastics (PA, PC, POM, PBT). However, they are much higher priced than both these two groups of products resulting in a market size of approximately USD 3bn. Moreover, they are used in the automotive industry, aerospace, electrical and electronic, medical and many other industries in applications that cannot be met by other plastics or conventional
This book, Specialty Thermoplastics, is particularly timely given the ever-increasing demand for improved performance in so many new and existing applications throughout industry. These demands are often being driven by the need to save weight or withstand various environmental factors.
The work pulls together in one convenient volume a wealth of information on four main types of specialty plastics. These four polymer types are defined by the author as amorphous or semicrystalline polymers that can withstand high temperatures, usually higher than 150 °C. The four are polyaryl ether sulfones (PAES), polyether imides (PEI), polyphenylene sulfide (PPS) and polyaryl ether ketones (PAEK). By the definition given, the four are also considered to be “hightemperature plastics”.
A chapter is dedicated to each of these polymer groups covering their producers and capacity, followed by their manufacture, processing, properties and applications. These are preceeded by a very useful introduction, in which it is pointed out that at 220–240 ktpa the
materials. The introduction also describes the market volume of each of the four groups and details the producers, their location and capacity. In common with other parts of the plastics industry, the ownership of some of these products, their plants and business have changed hands through acquisitions and divestitures. These changes are also described in the introduction.
The chapter on the PAES (polysulfone (PSU), polyether sulfone (PES) and polyphenylene sulfone (PPSU)) is the second most extensive (after that on the PAEK). It outlines the chemical structures of the monomers and subsequent polymers, followed by a description of the production methods. After outlining the processing techniques and conditions used, there is an extensive section on the properties of the polymers and their compounds. Much of the data relates to polymers made by Gharda Chemicals, the author having led the Gharda business in these products.
This section is followed by one showing typical applications for PSU, PES and PPSU. A number of these demonstrate the important property of transparency available with these amorphous materials.
This same format is used in the chapters on PEI, PPS and PAEK.
Interestingly, as pointed out, while PEI was commercialized in 1982, there has until now been only one source, viz, Sabic (previously GEP). As reported in the book, this is about to change with Gharda Chemicals’ PEI plant coming on stream in India. After describing the chemistry of PEI and its manufacture, there
Bernard Lanham, director, BJL Consulting
Processors, for example, moulders, extruders, AM users and other convertors, currently handling these materials, or considering using them, will find this book very helpful.
is an extensive section on its properties. Under processing, there is a striking picture of a part manufactured by AM (3D printing) which demonstrates the complexity that can be achieved. In fact, throughout the book, while the main manufacturing processes of injection moulding and extrusion are well covered, other processes like AM, film production and fiber spinning are also described where appropriate.
PPS, described as having the largest sales volume at about 90–110 ktpa, is also the lowest priced polymer of those covered by this work. As pointed out, it differs from the other polymers in that for most uses it needs to be reinforced or filled to have useful mechanical and thermal properties. It is suggested that, including the filled compositions, the total volume might be as high as 150–160 ktpa.
The most extensive chapter is devoted to the PAEK group of polymers covering PEEK, PEK, PEKEKK and PEKK, and some other less commercially important polymers. The introduction gives an insight into the history of the development of these polymers by various companies. It outlines the early work carried out by Union Carbide and DuPont and the crucial part played by ICI in the development and commercialization of PEEK. This section also shows the present line up of PAEK products by today’s producers (and some discontinued ones) together with their key thermal properties. The chemistry of the manufacture of the PAEK products is well covered in the following section. Blends of PAEK products with each other are described, together with novel blends of PEEK with PBI and PEK with ABPBI. The more conventional, and more significantly commercial, blends with PTFE are also described, highlighting the enhanced wear and friction properties of these compounds.
The processing section for PAEK materials includes compounding, which for these semi-crystalline products is highly important, as the enhancement of mechanical and thermal properties is significant and a large proportion of the volume used is made up of compounds. The methods of 3D printing applicable to PAEK products are described with a number of examples including the remarkable cranial implant in PEKK (also shown on the cover).
The properties of PAEK products is extensively covered as are the diverse applications.
The author is uniquely qualified for presenting this work as he has been instrumental in establishing the Gharda PAES and PEEK plants and managing the business (now part of Solvay). He now leads the Gharda polymer business,
in establishing a PEK and PEKK plant and most recently doing the same for their PEI plant.
Technologists, whether with a polymer producer, compounder, OEM, or in academia concerned with these specialty thermoplastics, will find this book pulls together in one volume a wealth of data and information. Processors, for example, moulders, extruders, AM users and other convertors, currently handling these materials, or considering using them, will find this book very helpful.
It will appeal to sales and marketing people with an interest in this sector of the plastics industry. This work is also applicable as a textbook for special courses on polymer science and engineering for graduate and undergraduate students.
In common with other parts of the plastics industry, the ownership of some of these products, their plants and business have changed hands through acquisitions and divestitures. These changes are also described in the introduction.
The shortlisted candidates for the final of the 2023 Design Innovation in Plastics (DIP) competition have just presented their products to the judges in an intense but fascinating day of discussion and scrutiny.
DIP is the longest running plastics design competition of its kind for university undergraduates in the UK and Ireland. Supported by the Institute of Materials, Minerals and Mining, and the Worshipful Company of Horners, it is industry headline sponsored by Covestro, a global supplier of premium polymers.
Answering this year’s brief of ‘Design for the kitchen or bathroom’, each candidate was asked to bring a prototype of their product and
ELECTED
explain the research, product development and material selection, along with key issues such as how it meets innovation and sustainability criteria.
Chairman of judges, Richard Brown, said: “This year’s candidates benefited from a bespoke training course delivered by new DIP sponsor Sumitomo Demag on manufacturing and materials from which the finalists were able to bring the knowledge learnt when preparing their final presentations. This has
made their selection of plastics more focused and also the way in which they will be processed.”
The results of the judging will be announced at the DIP award ceremony on Friday, July 07, at Painters Hall in central London. Students are competing for a top prize of £1,000. There are supporting cash prizes for all finalists, and work placements with leading design and industry sponsors, who include Brightworks, Innovate Design, and PDD.
The six award candidates are:
• Freddy Blake – Bournemouth University - ‘Bubble Buddy’, a bathroom aid for encouraging children to wash their hands.
• Kyle Farquhar – Edinburgh Napier University – “PlateMate – a foldable plate which teaches children how to prepare a variety of Mexican dishes.
• James Forrest-Smith – Northumbria University –‘Kitchen Helper’ – a height adjustable step which enables children to participate in kitchen activities
• Christopher Kenny – TU Dublin – ‘Flossie’ – a brand new tool which makes teeth flossing much easier
• Scott Rutherford – Edinburgh Napier University‘Rotary Bottle Opener’ – a solution for people with limited dexterity to open twist bottle caps more easily.
• Teresa Zheng – Loughborough University –Sianel - ‘Pocket Operation Panel’ – a portable, hygienic shelf to facilitate changing a colostomy bag.
experience will bring a fresh perspective to the BPF Skills & Education Committee.
From addressing the stigma that polymer engineering offers limited career pathways, to the corporate commitment required to invest in training and development, Davis, like many of her committee peers, is a staunch advocate of sharing best practice to address the skills shortfalls. Davis said: “Culturally, the plastics industry is quick to adapt. The pandemic was testament to this. Yet, the recruitment and retention pain points for employers remain evident to all. Solving the skills shortages requires collaboration from across the entire industry stakeholder group.”
engineers, as well as prioritising equipping existing personnel with transferrable new skills to support career progression,” explains Jo.
The BPF says that the scale of the challenge cannot be underestimated. Particularly when considering that the UK plastics industry turns over £23.5bn annually, employing a manufacturing workforce of around 170,000 professionals, at all levels. All too familiar with the compounding issues of balancing growth with skills shortages, succession planning, investing in development and maintaining morale, Davis hopes that her
Participants in this BPF committee represent all aspects of its Membership. Comprising of training providers, awarding organisations, plastics processors and raw material suppliers, The BPF claims that this spread enables the Committee to consider all the secondary, apprenticeship and technical educational needs, as well as a deeper appreciation on how to balance diversity and promote people from within their business.
Rather than focusing purely on apprenticeships, Davis is eager to expand the development framework to drive continuous learning and upskilling: “This can include recruiting from nontraditional labour pools, for example military
Pointing out that there’s no ‘one size fits all’ approach to bridge the skills gap, Davis cites how Broanmain, as an SME, successfully navigated this by supporting two of their Gen Z senior team with a blend of external course, mentoring and structured development programs. Now, apprentice Kamil is running the engineering department, while Monika is overseeing production. Both originally joined the company as temps in the assembly team.
The Zero Waste Bag is designed to offer consumers a simple and convenient way to recycle 14 common waste streams which are not collected in council kerbside recycling collections, meaning they are usually destined for landfill, incineration or the natural environment. The accepted waste streams include plastic packaging, crisp and snack packets, cosmetic products and packaging, and medicine blister packs.
The company says that the latest household waste recycling rates released by the Government show that Wales is the only UK nation currently recycling more than 50 percent. Yet new research reveals some 92% percent of Britons believe recycling has a key role to play in combating the waste crisis, with more than 9-in-10 UK residents already recycling at home.
The Zero Waste Bag is a paid for solution and comes in two sizes priced at £25 for a small bag and £39 for a large, with discounts available for bundle purchases.
The price of the Zero Waste Bag covers the cost of delivery to the consumer, shipping of the full bag of waste back to TerraCycle via InPost and the cost of processing the returned waste and turning it into a reusable material that can be incorporated into new products.
Due to the mix of materials these items contain, the processes required to recycle them are complex which means that the recycling process costs more than the value of the recycled material. This is the reason why councils cannot accept these items for recycling.
X-Rite, a colour science and technology company has announced new capabilities of the MA-T12 multiangle handheld spectrophotometer and the PANTORA desktop software that the company says enables automotive, electronics, and durable goods customers to measure and visualize a broader range of materials, including plastics, leather, fabrics, and structured coatings.
The company claims that the new updates make it easier and more affordable to capture and digitize colour and appearance characteristics of complex materials using one measurement device. With this solution, the company says that customers can transform a physical material into a digital twin or virtual prototype for remote visual approval, minimizing the need to ship samples between design teams, suppliers, and partners.
“The use of effect finishes and textures to improve a product’s aesthetic appeal have expanded beyond automotive paints to vehicle interiors,” said Matthew Adby,
Designed to withstand high filling pressures, the new compact stack mould, engineered by the hot runner manufacturer Oerlikon HRSflow for thin wall packaging applications, is equipped with the new Xd nozzle series. The company claims that the patent-pending solution, soon available on the market, enables
fast injection and cycle times in a stable process with high part weight consistency. Oerlikon HRSflow says assembly and maintenance are simplified and highly efficient thanks to a plug-and-play installation thus avoiding long and costly downtime. The system fits a maximum plate thickness of 220 mm and a minimum
distance of 260 mm from gate to gate of coaxial nozzles. A demo tool equipped with this new technology is available in the Oerlikon HRSflow Test Lab. Customers can run product trials with their most challenging polymers. The Test Lab is equipped with six injection molding machines – from 50 to 1000 tons – this aims
Product Management Director, X-Rite. “The new capabilities in the MA-T12 and PANTORA enable automotive manufacturers to measure, visualise, and control colour on both interior and exterior components using one handheld device. It eliminates the need for multiple devices and can be used anywhere from the design centre to the assembly floor, streamlining the digital design and quality control process.”
The MA-T12 measures effect finishes and complex materials with 12 angles of measurement and a calibrated camera. It is claimed that this allows manufacturers to verify colour, sparkle, coarseness, and surface texture. MA-T12 measurement data and PANTORA
In addition to effect paints, the combined solution now characterises a range of
to offer customers the possibility to define the best hot runner configuration for their specific applications. The tool has been designed to produce a 210 ml single-serving cup in R-PP with a weight of 6.3 g and a thickness of 0.3 mm. The mosaic frame on the part walls - patented by Collomb – allows for a robust structure despite the part weight reduction.
materials used across automotive, electronics, and durable goods. This includes:
• Plastics and Injection
Moulding – Digitally communicate how a moulded or textured plastic material looks to meet tolerance and reduce variances in appearance that lead to added rework and cost. This creates a more sustainable process with less waste and downtime.
• Leathers and Fabrics
– Measure and visualize natural or embossed leather and textured fabrics for precise virtual prototyping and improved quality control.
• Powdered Coatings –Accurately visualize the color and appearance of applied textured powder coatings to a final product and track product variances for remote approval.
The combined MAT12 and PANTORA solution supports digital workflows aims to accelerate the design to manufacturing process. Designers can use the solution to visualise product designs and digitally communicate colour and appearance requirements across a global supply chain.
The company claims that the new Xd nozzle series ensures a stable injection process and the maximum productivity at a lower cost per unit.
PMMDA Chairman Dave Raine reflects on Mental Health Awareness Month –and asks, what can the plastics industry do to support its people?
Speaking to colleagues and peers within the plastics industry recently, the general feedback I’ve received is that people are busier than ever, with enquiries and activity levels higher than they’ve been for some time. However, as with all things, there will be those seeing the opposite of this, or maybe even just a stabilisation, or stagnation if you want to call it that, of business. What is clearly a common by-product of any of these three states is increased anxiety, be it from feeling that work pressures are increasing and outside of our control because of the upturn in enquiries, or conversely, because of the lack of activity.
Anxiety is a normal emotion in us all, but sometimes it can get out of control and become a mental health problem, and as I write this article, I wonder how many of us were aware that May 2023 is Mental Health Awareness Month.
Lots of things can lead to feelings of anxiety, including work pressures, relationships, starting a new job (or losing one) or other big life events. We can also get anxious when it comes to things to do with investments and staff security, but also because of more fundamental issues such as personal financial and relationship issues. The important message here is that anxiety can be made easier to manage.
Focusing on anxiety for this year’s Mental Health Awareness Week is aimed at increasing people’s awareness and
understanding of anxiety by providing information on the things that can help prevent it from becoming a problem, and this awareness needs to translate into the business sector if we are to protect our most valuable asset – our people.
One area I personally am keen to ensure is monitored closely is remote working and its impact on employees. The plastics industry field sales & service sector is male-dominated, and men are less likely to seek help for mental health problems. This can lead to potentially easily solvable issues going untreated, which can have serious consequences for both the individual and the company. Providing access to mental health resources and creating a positive and supportive work environment is essential. Offering training courses and development programmes can also help staff members to gain confidence and self-awareness, both of which contribute to greater work efficiency. Companies who encourage open conversations about mental health and make resources available to their employees are more likely
to retain motivated staff who are focussed on improving their performance, achieving greater success, and building a sustainable future.
By taking measures now, companies can combat the longterm effects of poor mental health in their organisation and create an ethical workplace culture for the benefit of all, and as part of the PMMDA, I for one am committed to ensuring we make support and access to it as simple as possible, with no stigma attached to any request.
For more ideas on how to support your staff’s mental wellbeing at work, Mind has put together useful guidance on how organisations can take care of their staff: www.mind.org.uk/ workplace/mental-health-at-work/ taking-care-of-your-staff.
“
The plastics industry sales & service sector is maledominated, and men are less likely to seek help for mental health problems”
Our beats for your cavity.
OUTSTANDING CONSULTATION ON EVERYTHING TO DO WITH YOUR CAVITY
Consultation, service and support
» Support and advice from our trained professionals
» Wizards, configurators and selection guides in the web shop and offline shop
» The right product for every application
CURIOUS? WATCH THE VIDEOS NOW:
www.meusburger.com/ cavity