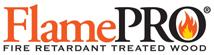
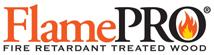
PRESSURE IMPREGNATED, CODE COMPLIANT FIRE RETARDANT TREATED WOOD
Surface applied re retardants like paints, stains, penetrants, and intumescent coatings ARE NOT building code compliant in applications where Fire Retardant Treated Wood is required.
2 Hour Tested Exterior Wall Assembly (120-02)
Max. Tested Load: 100% of Design Load
Fire Ratings: 2 hour load bearing rated from interior and 1 hour load bearing exterior. For details refer to ESR Report 4244.
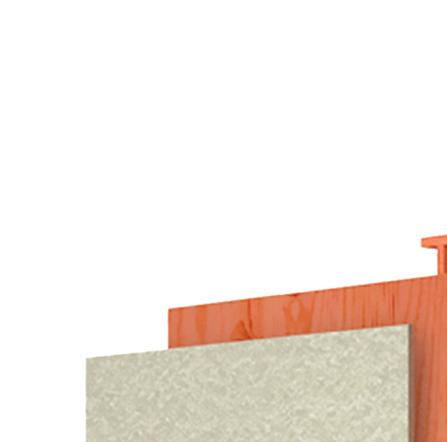



4. Exterior Facings (Required): Brick Veneer, 3/4” Cement Plaster (Stucco)

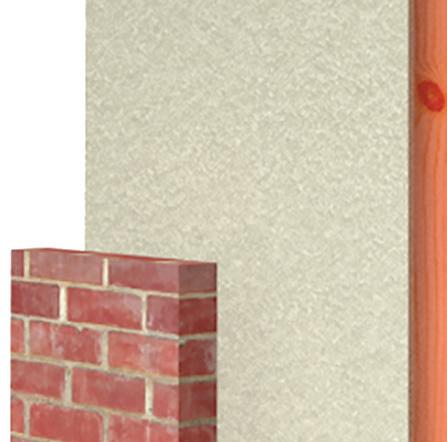



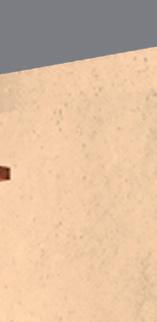

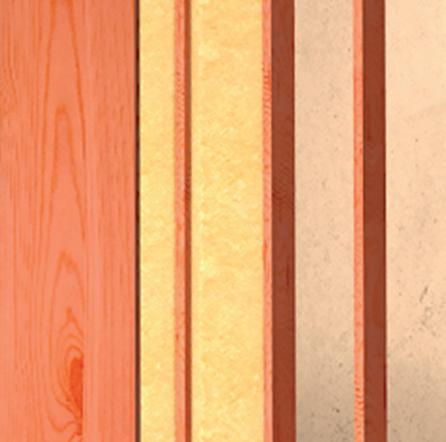

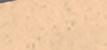
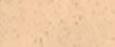
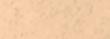
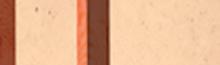

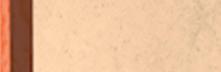


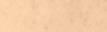



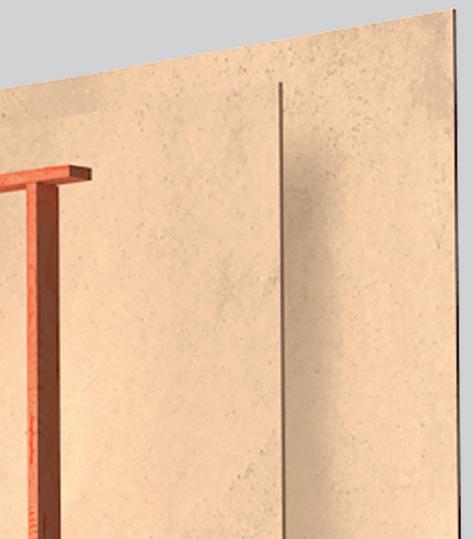
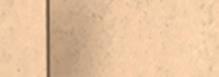
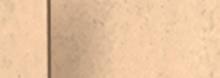

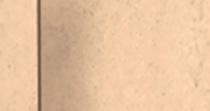
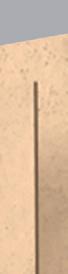
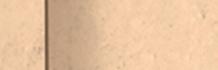

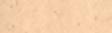
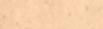

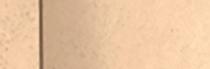

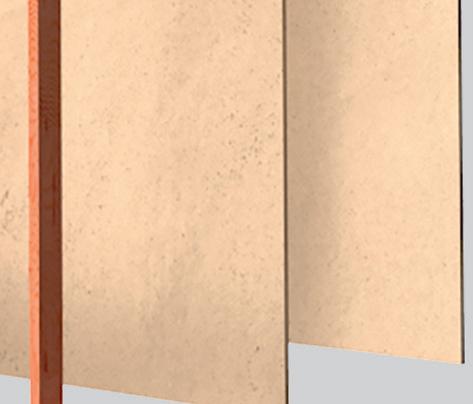


FlamePRO Fire Retardant Treated Wood is pressure impregnated, fully code compliant Fire Retardant Treated Wood. It is appropriate for use in all applications where Fire Retardant Treated Wood is required.
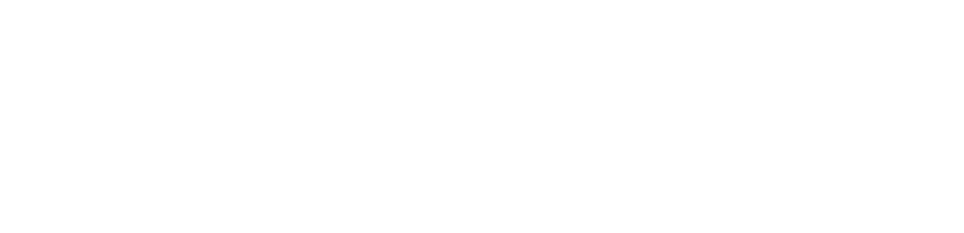
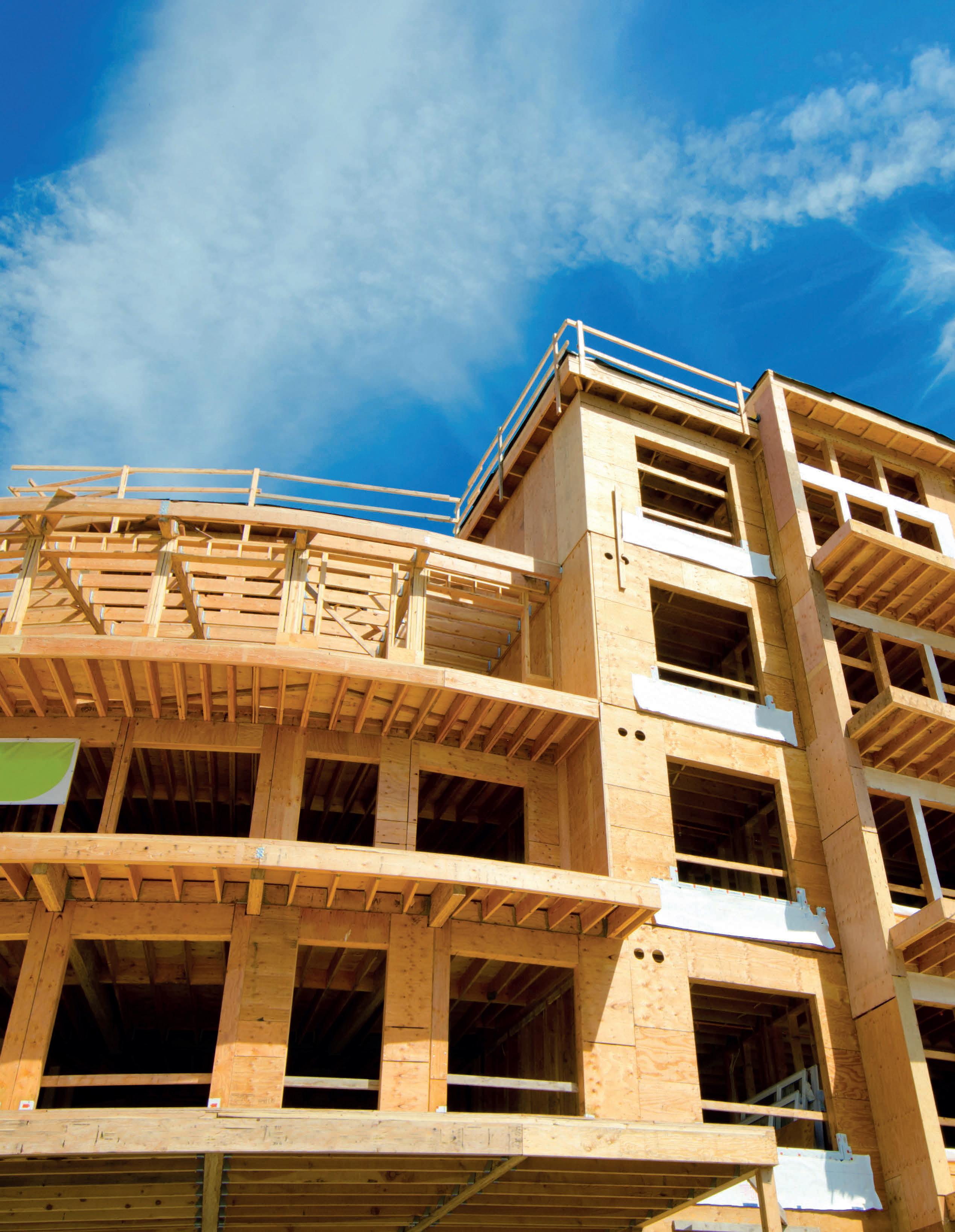

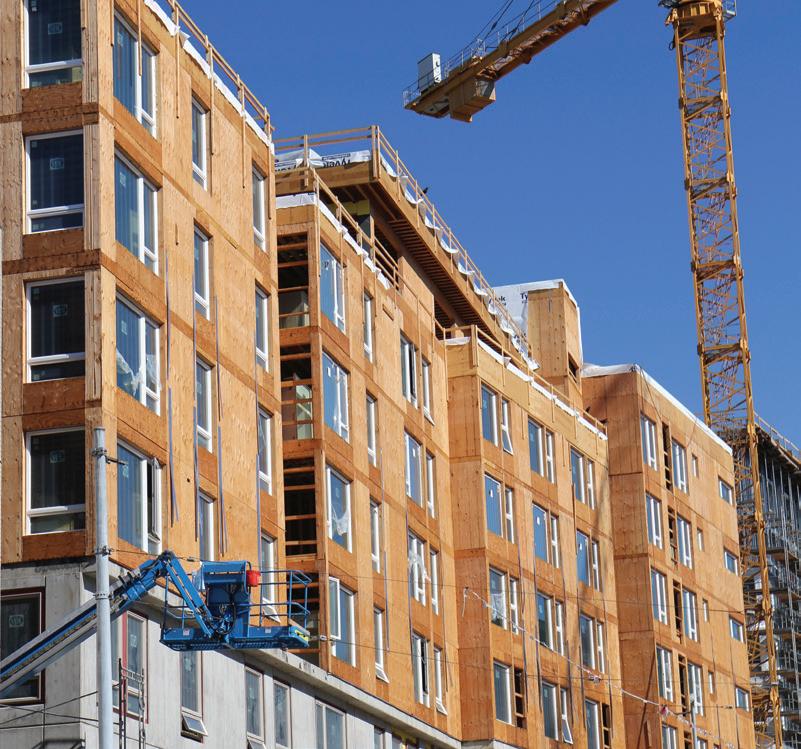
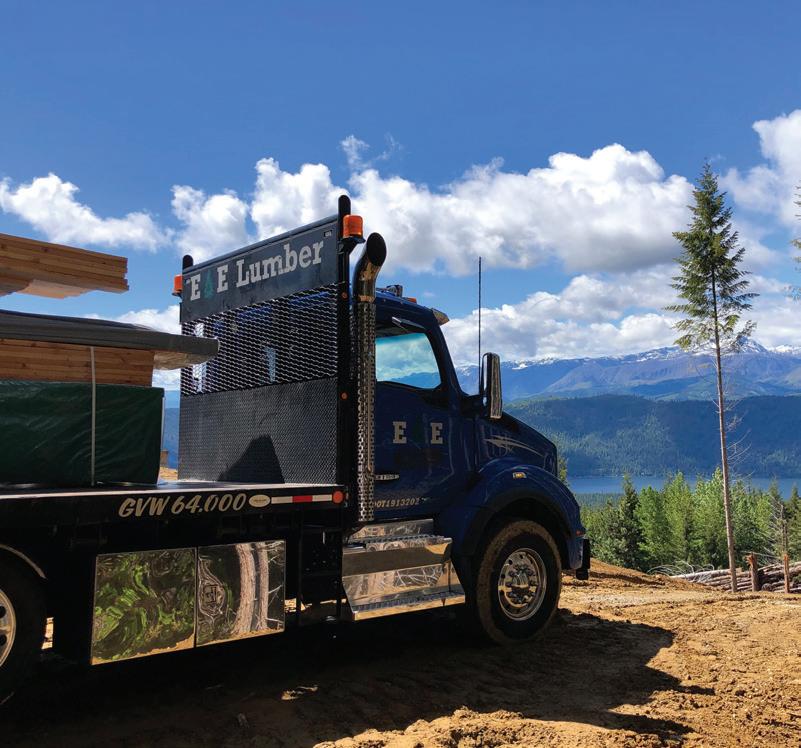
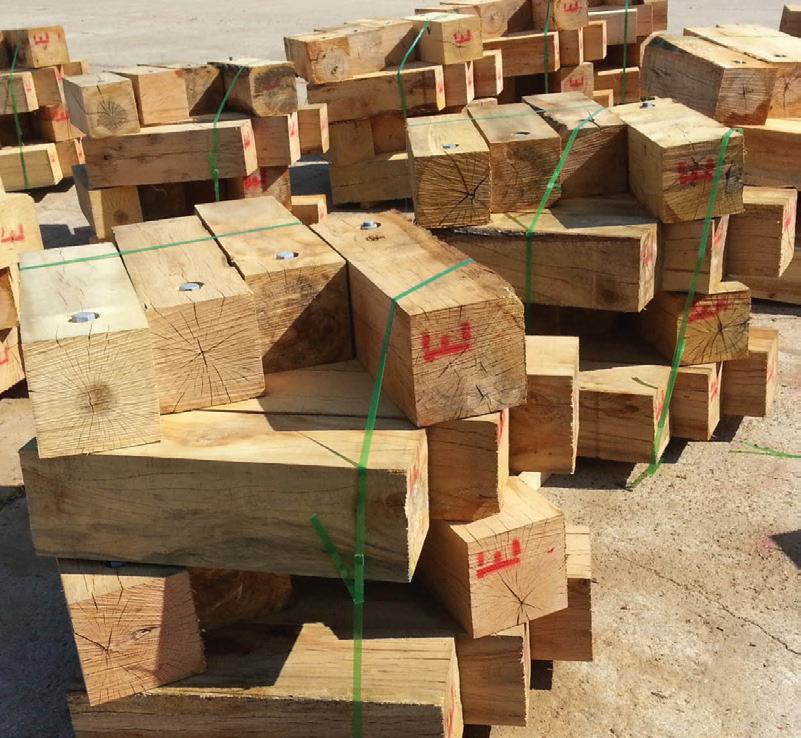



FEATURE
Mass timber is poised to expand the reach of engineered
Everything
•
•
•
•
•
The promising future of pressure treating hardwoods
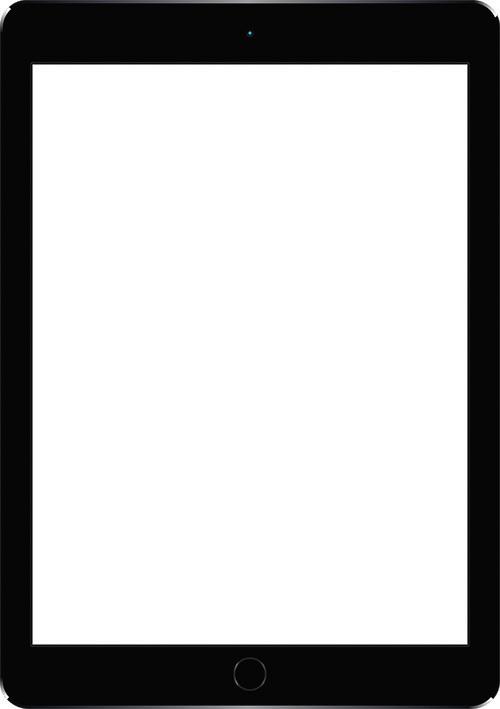




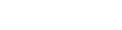
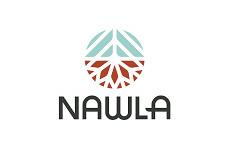
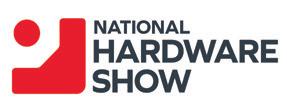
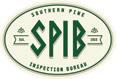
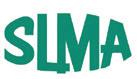
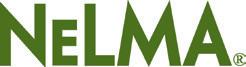

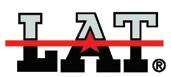
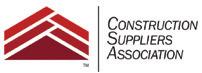
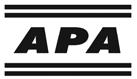

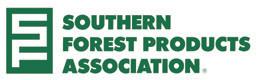
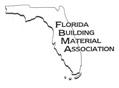

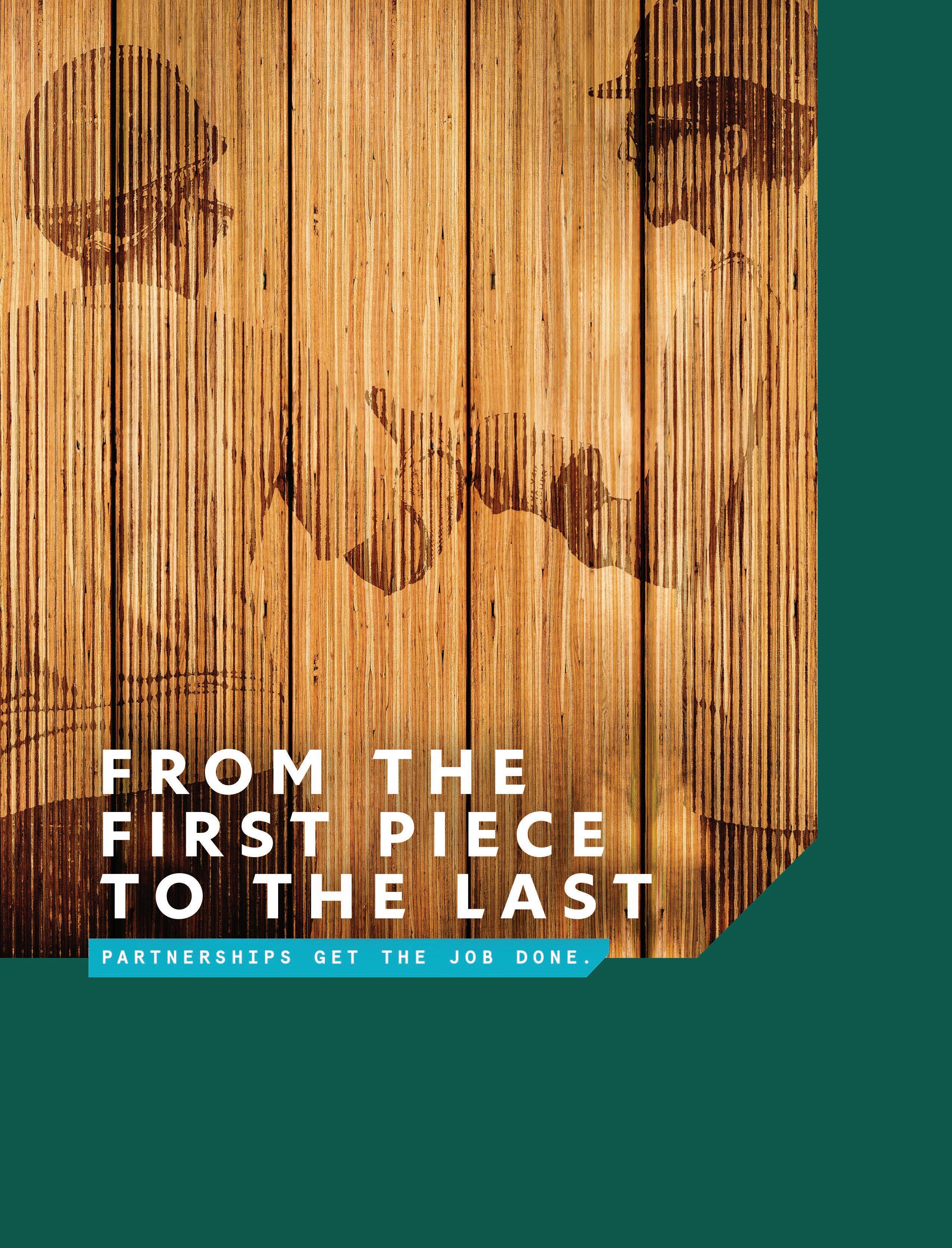
PRESIDENT/PUBLISHER
Patrick Adams padams@526mediagroup.com
VICE PRESIDENT
Shelly Smith Adams sadams@526mediagroup.com
PUBLISHER EMERITUS
Alan Oakes
MANAGING EDITOR
David Koenig • dkoenig@526mediagroup.com
SENIOR EDITOR
Sara Graves • sgraves@526mediagroup.com
COLUMNISTS
James Olsen, Kim Drew, Claudia St. John
CONTRIBUTORS
Dallin Brooks, Sarah Duenas, Jeff Easterling, Robert Fouquet, Joe K. Elling, Paige McAllister, Bill Parsons, Madison Stephens
ADVERTISING SALES
(714) 486-2735
Chuck Casey ccasey@526mediagroup.com
Nick Kosan nkosan@526mediagroup.com
John Haugh jhaugh@526mediagroup.com
DIGITAL SUPPORT
Alek Olson • aolson@526mediagroup.com
Josh Sokovich jsokovich@526mediagroup.com
CIRCULATION/SUPPORT info@526mediagroup.com
A PUBLICATION OF 526 MEDIA GROUP, INC.
151 Kalmus Dr., Ste. J3, Costa Mesa, CA 92626 Phone (714) 486-2735
BUILDING PRODUCTS DIGEST is published monthly at 151 Kalmus Dr., Ste. J3, Costa Mesa, CA 92626, (714) 4862735, www.building-products.com, by 526 Media Group, Inc. (a California Corporation). It is an independently owned publication for building products retailers and wholesale distributors in 37 states East of the Rockies. Copyright®2024 by 526 Media Group, Inc. Cover and entire contents are fully protected and must not be reproduced in any manner without written permission. All Rights Reserved. BPD reserves the right to accept or reject any editorial or advertising matter, and assumes no liability for materials furnished to it. Opinions expressed are those of the authors or persons quoted and not necessarily those of 526 Media Group, Inc. Articles in this magazine are intended for informational purposes only and should not be construed as legal, financial, or business management advice.
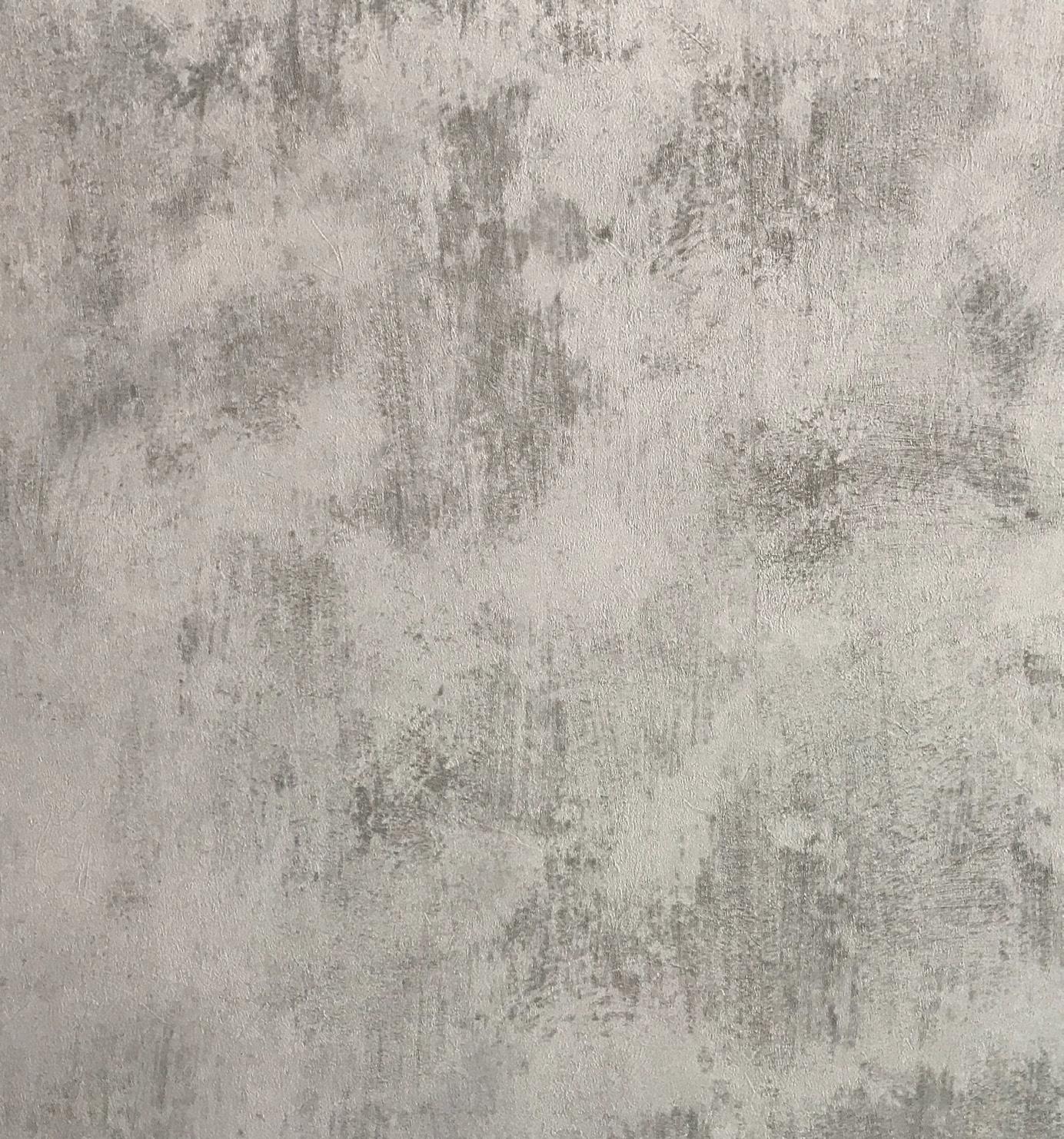
Update your subscription
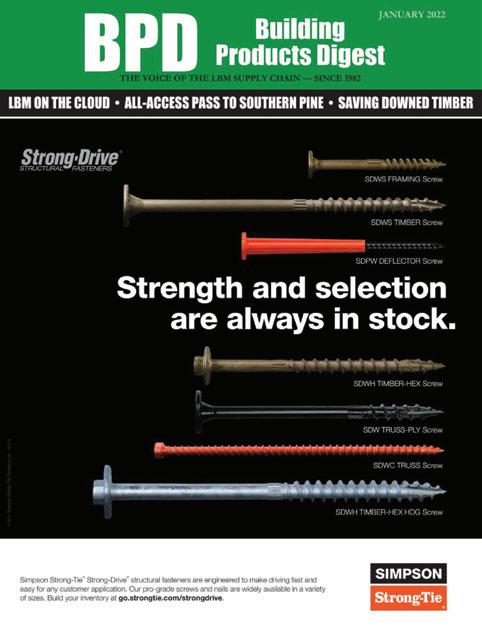
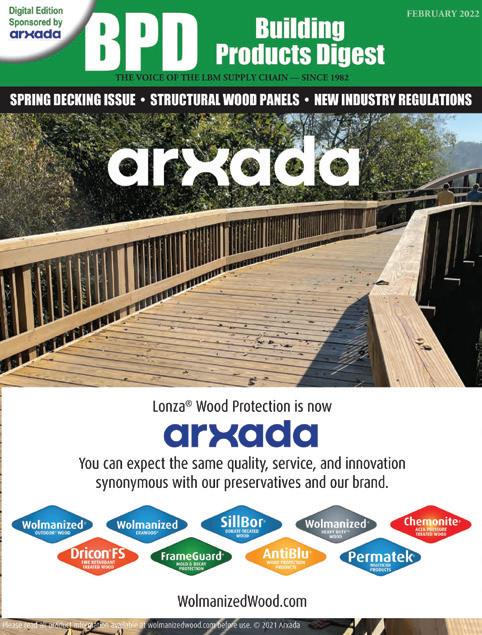
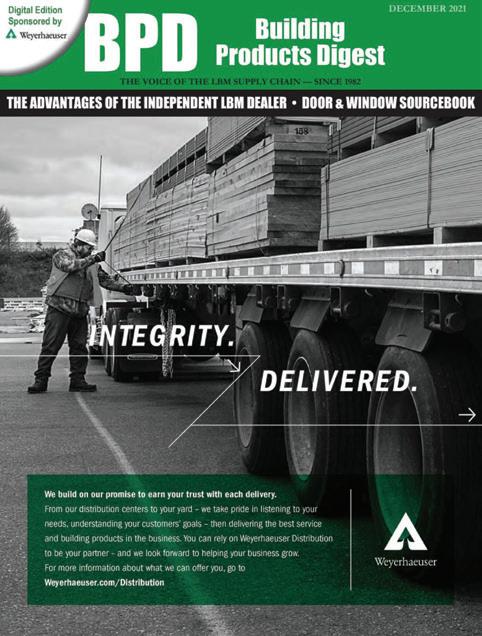

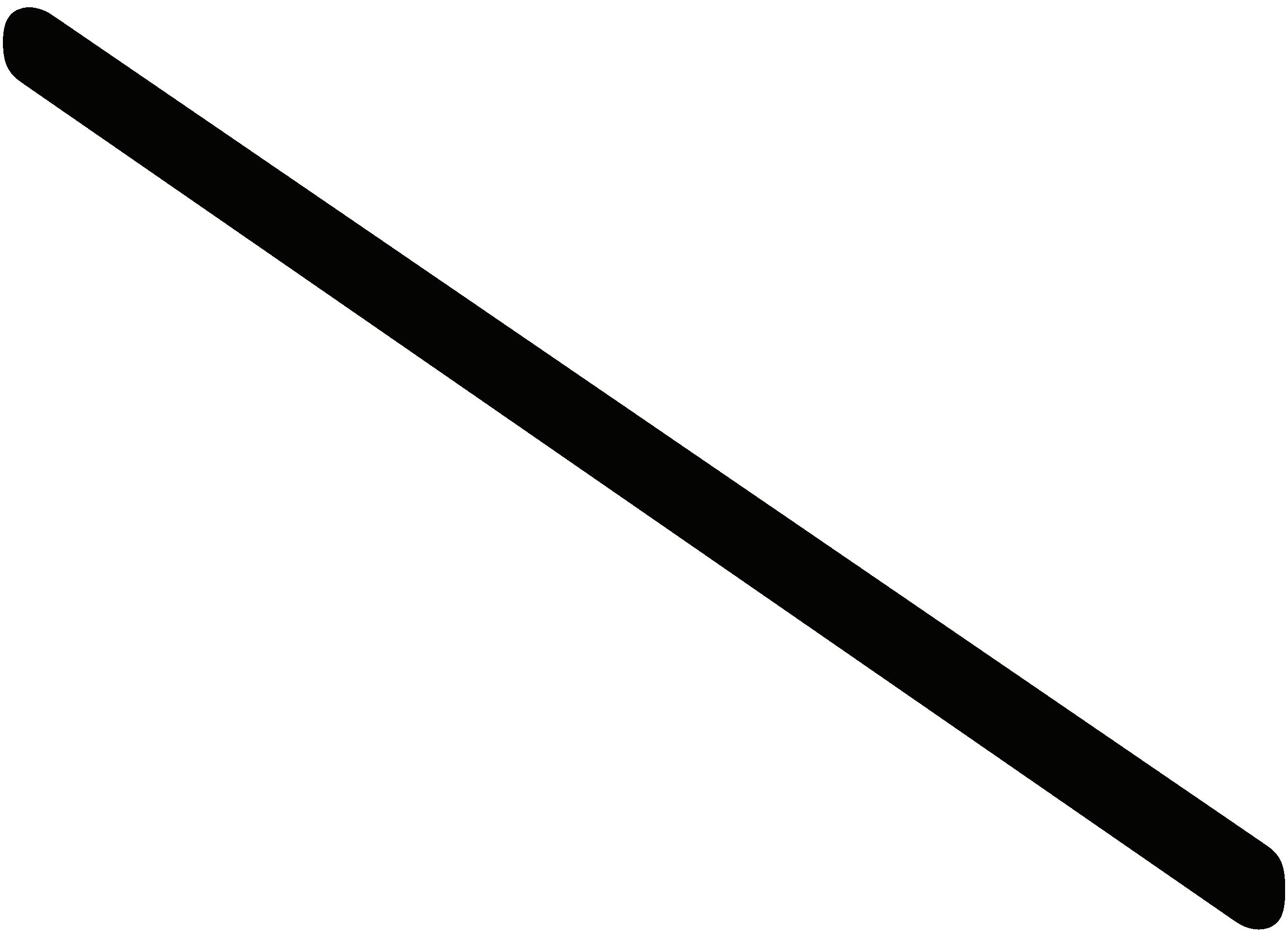
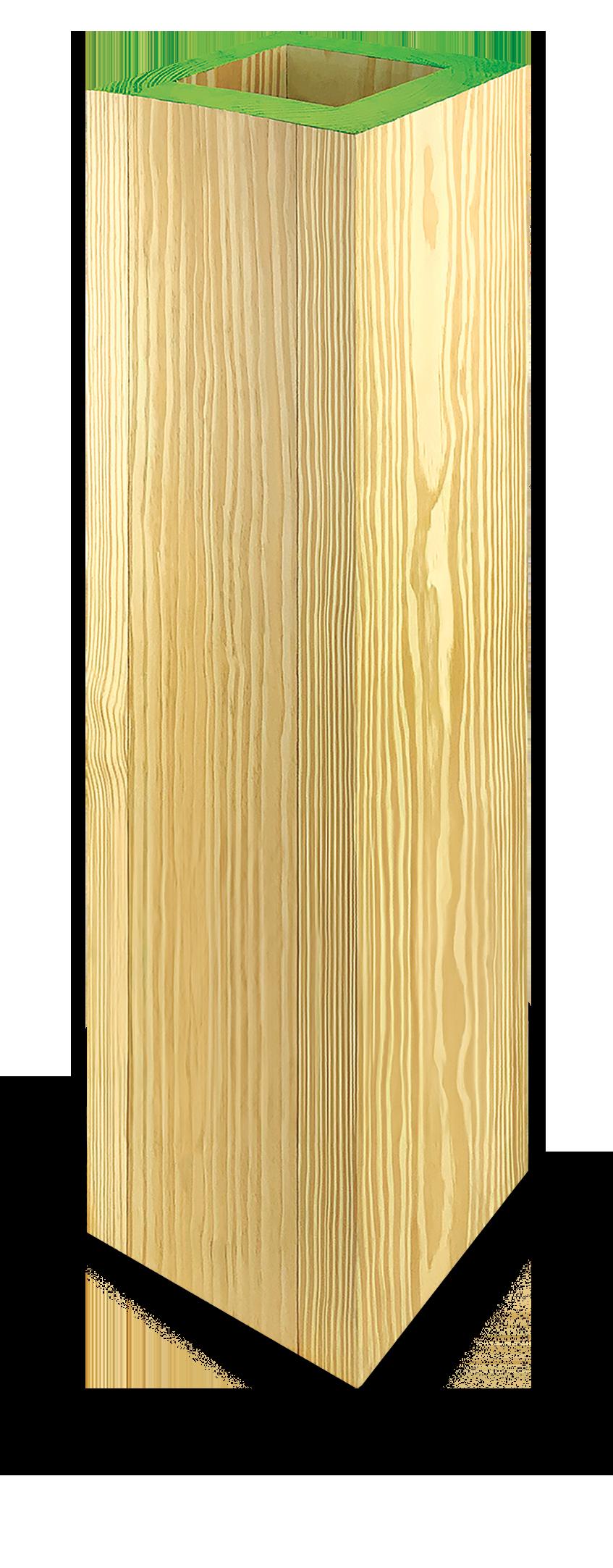
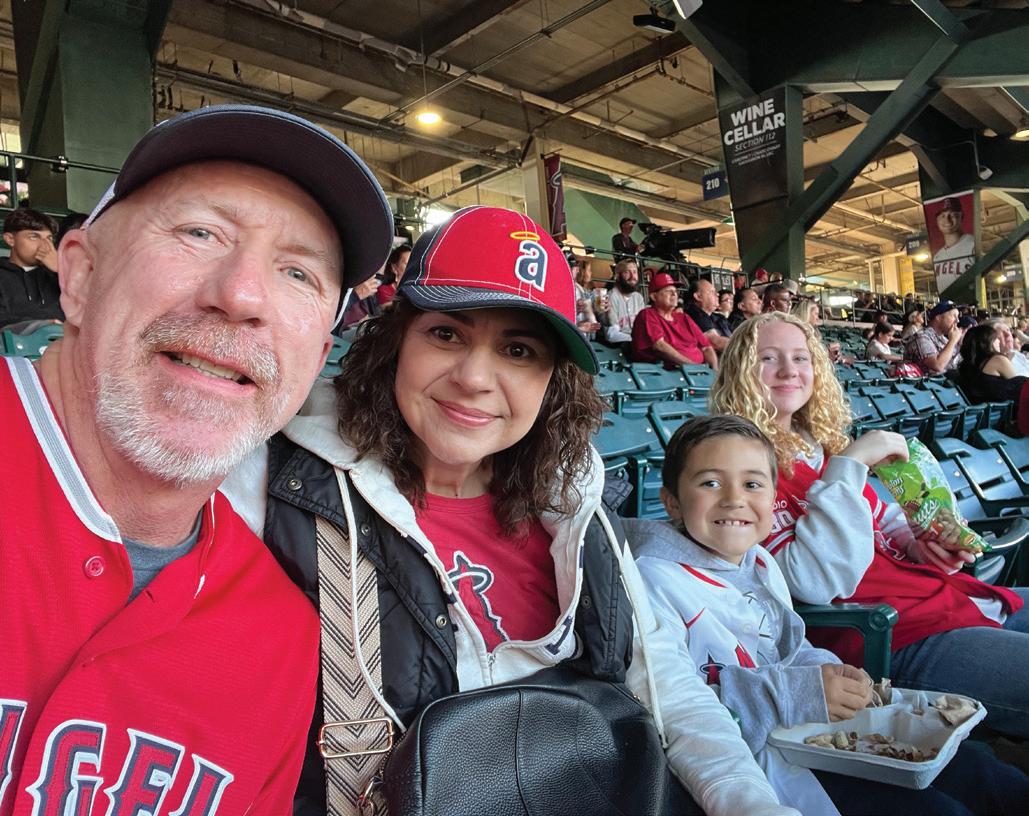
THREE PROMISES
------------ BY PATRICK ADAMS
IS LIFE TODAY more complicated, or does it simply appear that way as technology, media and other life distractions swirl around us on a 24/7 cycle? I think it’s easy to get caught up in this and believe life is more complicated.
I consider this frequently as it is my nature to constantly be gathering information around me, processing it in the background of my mind, and trying to gather meaning from it. Of course, there is a LOT more information to process these days than for generations past. It’s harder to discern what is accurate, or even real.
However, I suppose the question that gets complicated is, “Does more complicated mean harder?” Do we have harder lives now than past generations did? I think we’d all agree the answer is no. But are things more complicated? I guess that is the very root of my dilemma, which is what we choose to make complicated. (I know, very deep and philosophical this article).
Perhaps as a survival mechanism, or perhaps because with age comes wisdom, these days I find myself constantly seeking simplicity and things with solid foundations. As I reflect on the things that do not bring out the best in me and cause stress, I challenge whether they are truly necessary portions of my life and if not, strip them away. More and more, I seek peace and stability in my life often at the expense of so-called “opportunity.” If needs are being met, is the challenge of conquering another mountain truly worth the sacrifice of peace, my “best self,” and enjoying the moment?
I work hard these days to be my best self, for those I hold important and especially as a role model for my kids. It’s hard to believe that my “little girl” is already half past 13—two and a half more years until driving and five more until she starts college. Just five more years! In simplifying my life, I think about how to simply define me and what I stand for. My word means a lot to me and the promises I’ve made are like unnegotiable contracts. It takes a lot for me to utter the words “I promise.” I have made three promises in my life that I think about frequently:
1. I promised my father-in-law when I asked for his permission that I would take care of his daughter for the
rest of my life. And when we made our vows, I promised my wife and God that I would honor, love and respect her until death do us part.
2. I promised my grandmother, when she was the first person who said she believed in me, that I would never give up.
3. I promised God that if he gave me a chance at a better life that I would never stop trying to be the best man that I could be.
Each day when I say goodbye to my kids, we hug, we say we love each other, and I ask them, “What is the plan?” They each respond with sincerity, “To be better than yesterday.” I hold up my fingers with just a small gap in between and respond, “Just this much.” Because we each have a tendency to assess where we are, and where we want to be and feel like it is just too big of a gap to get there. But, “just this much” each day is progress and something to be proud of and eventually, will result in you being “there.”
I hope each of you finds “simple” in the complications that swirl around you these days, and in that search, spend some quality time with those most important this summer!
Now, in a follow up to last month’s teaser, you will notice an ad on page 51 for something new from us. In our constant pursuit of serving this industry, as well as evolving as the media landscape changes around us, we are trying something new! For a year, we have researched and curated some of the very best partners to bring you a product that we all deeply cherish every day—COFFEE! “Lumberman Coffee” has officially launched! We know you all start your day with it, and we believe why buy from a stranger when you can buy from a friend! Please, give it a try and give us your honest feedback. Like everything we do, it was done to serve you! If we’re in the service industry, why not serve you your first cup of coffee each day!
As always, thank you for your support and the opportunity to serve you!
PATRICK S. ADAMS, Publisher/President padams@526mediagroup.com

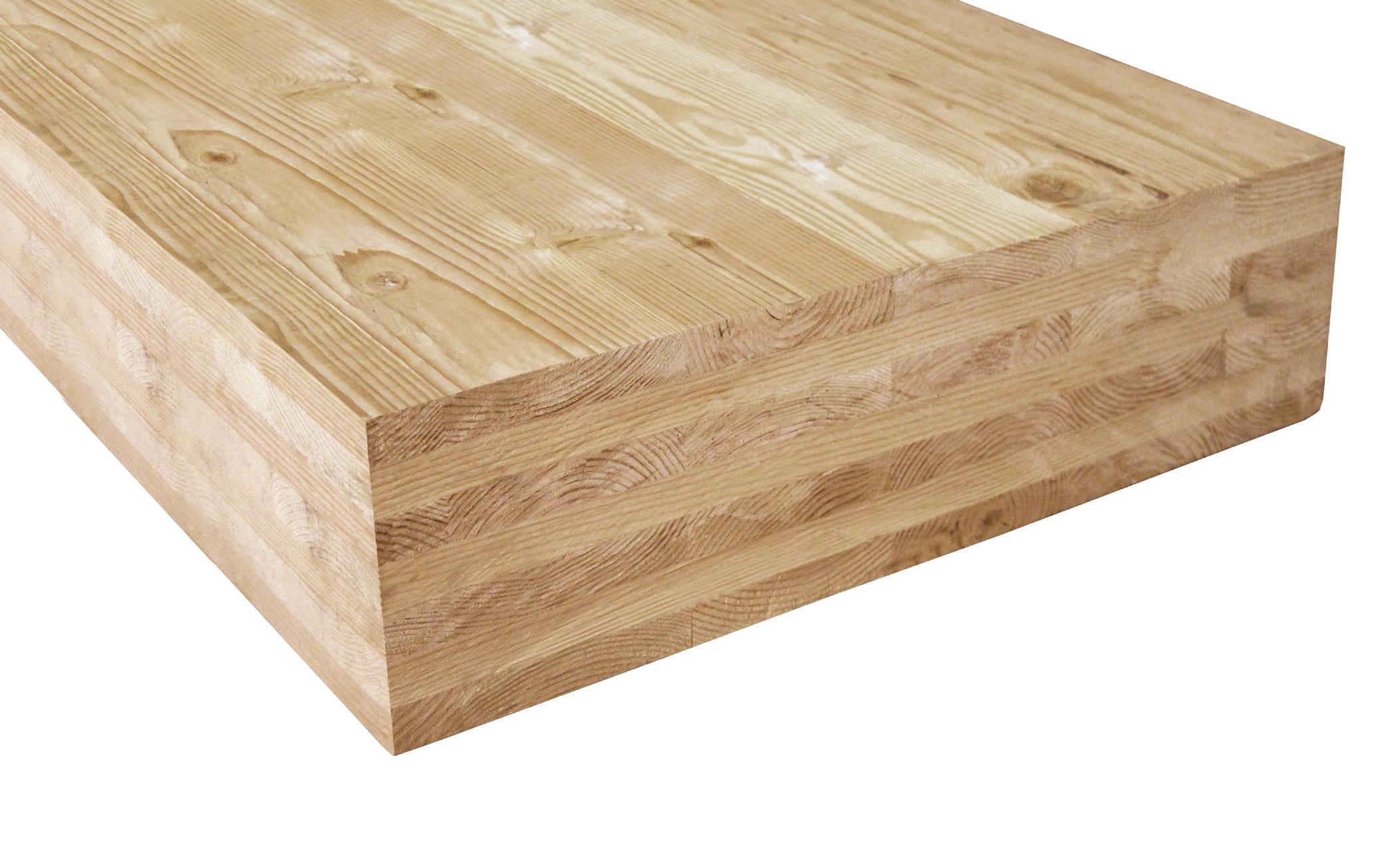
MASS TIMBER POISED TO EXPAND REACH OF EWP
------------ BY ROBERT FOUQUET
MASS TIMBER, an innovative construction material, has been gaining traction in North America as a result of its many benefits including its sustainability, minimal environmental footprint, structural performance, and aesthetic appeal. As a new form of engineered wood, mass timber complements traditional engineered wood products (EWPs) such as LVL, LSL, PSL and wood I-joists.
This article is divided into two parts. Part 1 provides a brief overview of wood I-joists and LVL, emphasizing their reliance on North American residential construction. Part 2 explores the history, development, and status of mass timber in North America, highlighting technological advancements, future prospects, and the potential for mass timber to extend the reach of EWPs in North American building construction.
Part 1: Traditional Engineered Wood Products
Engineered wood products (EWPs) have transformed the construction industry over the past 50 years, providing sustainable, high-performance alternatives to traditional solid wood. These innovative materials, made by binding wood strands or veneers with adhesives, offer remarkable attributes such as strength, uniformity, reliability, precision in manufacturing, and versatility in dimensions. These qualities have led to substantial benefits for the construction sector, resulting in significant
market share gains, particularly in residential building construction.
In 2022, 70% of wood I-joists (approximately 290 million ft.) were used for the construction of new single-family homes in the U.S., primarily as joists for framing raised floors—an area where I-joists have achieved an impressive 47% market share.
However, several factors challenge the continued growth of wood I-joists in this segment. These include the increasing use of parallel chord trusses, changes in fire codes, and a regional shift in construction toward the U.S. South. In this region, 60-75% of homes are single-story, and the slab-on-grade floor solution is popular among builders. These trends are contributing to a decrease in usage rates for wood I-joists.
Laminated veneer lumber (LVL) is renowned for its superior structural properties and dimensional stability, making it an excellent choice for applications requiring high strength, stiffness, and reliability. LVL is commonly used for beams supporting floor and roof assemblies, long-span headers like those for double garage doors, and as flange material for wood I-joists.
Like wood I-joists, LVL is widely used in new single-family and multifamily construction where stringent loading conditions and performance requirements govern. The structural capabilities of LVL, along with
its availability in long lengths and large cross-sectional dimensions, provide greater flexibility in design and construction. This flexibility is particularly beneficial for accommodating architectural preferences such as openspace designs.
LVL is also gaining popularity in light-frame, low-rise nonresidential buildings, a market segment where steel and concrete have traditionally been dominant. Market share gains for LVL are expected in emerging enduse segments as well, such as outdoor and industrial applications, which have the potential to increase LVL volumes in the future.
Overall, although the future of traditional engineered wood products like wood I-joists and LVL is closely tied to North American residential construction, there are expansion opportunities. In particular, the combination of LVL and mass timber in hybrid structures offers a significant opportunity for displacing steel and concrete in the nonresidential building construction sector, which we will discuss next.
Part 2: Mass Timber
Mass timber generically comprises panels such as cross-laminated timber (CLT), and glue-laminated timber beams and columns (glulam). These products are typically used together to create structurally efficient two-dimensional and three-dimensional assemblies for multifamily and nonresidential building occupancies, including institutional, offices, hotels, student housing and other nonresidential buildings.
Mass timber beams and columns can be made of glulam, LVL and PSL, although glulam is the dominant column and beam material in North America. Mass timber glulam differs from traditional glulam in that it is typically 3D modeled, manufactured to very fine tolerances and often includes imbedded connections which facilitate easy assembly on site. We refer to this glulam as MT-ready (mass timber-ready) glulam.
Mass timber panels include cross-laminated timber (CLT), nail-laminated timber (NLT), dowel-laminated timber (DLT), veneer laminated timber or mass plywood panels (VLT or MPP). The dominant mass timber panel product in North America is CLT, with 90% of total panel production.
CLT panels are formed by stacking and gluing successive orthogonal layers of dimension lumber under pressure. The lumber can vary in size and structural grade but commonly consists of 2x6 dimensional lumber of No. 2&Btr grade. The pressing can be done in either hydraulic or vacuum presses, although in North America, presses are hydraulic. The panels coming out of the press are produced in a variety of dimensions, typically up to 12” in thickness, 12 ft. in width and 60 ft. in length. They are then prefabricated (sized and shaped) by CNC machines into construction-ready elements that can be shipped to the job site for easy and quick assembly.
History & Development of Mass Timber
Interestingly, CLT was invented and first patented in Tacoma, Wa., in 1923. However, the commercial roots of mass timber can be traced to Austria, where CLT was
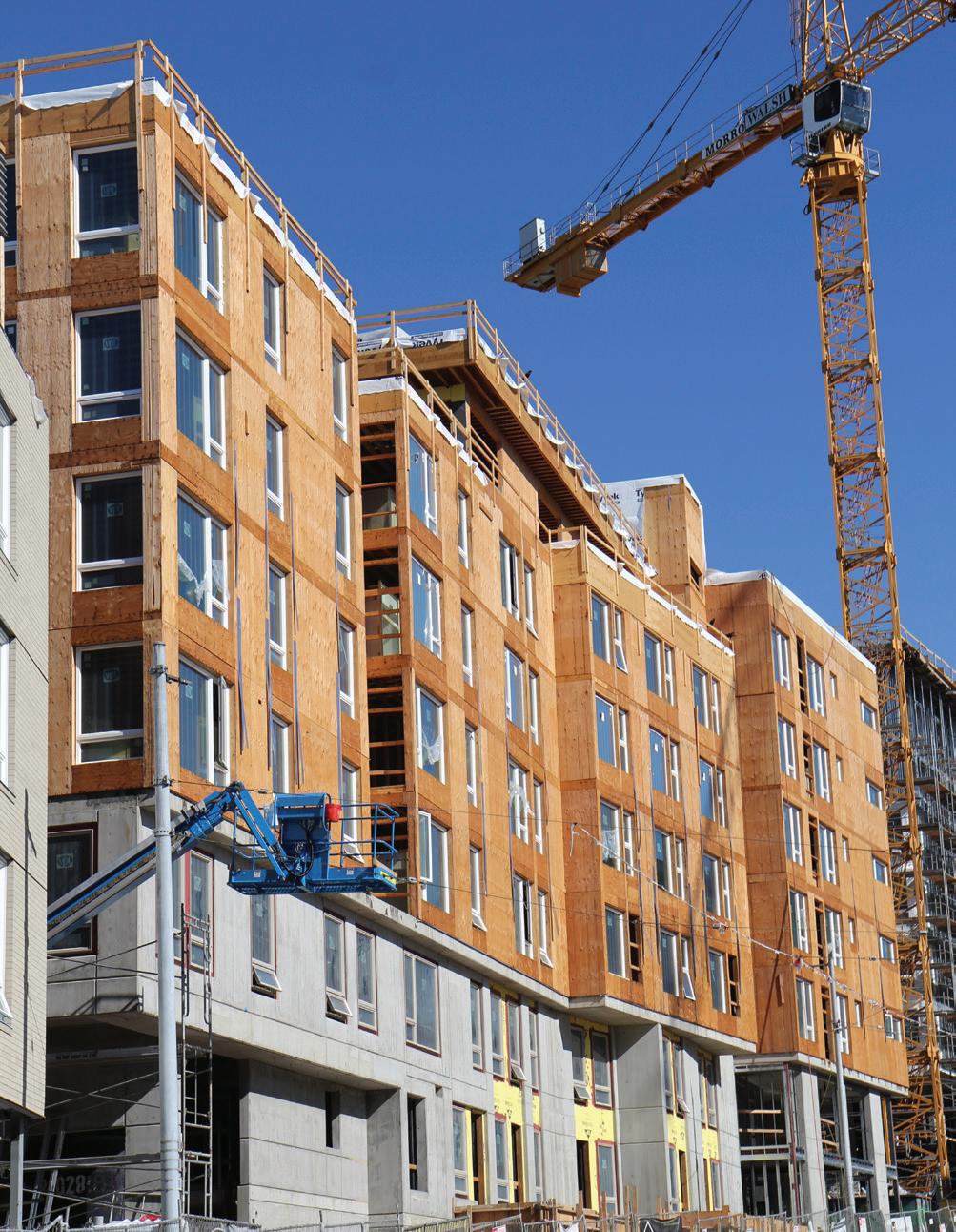
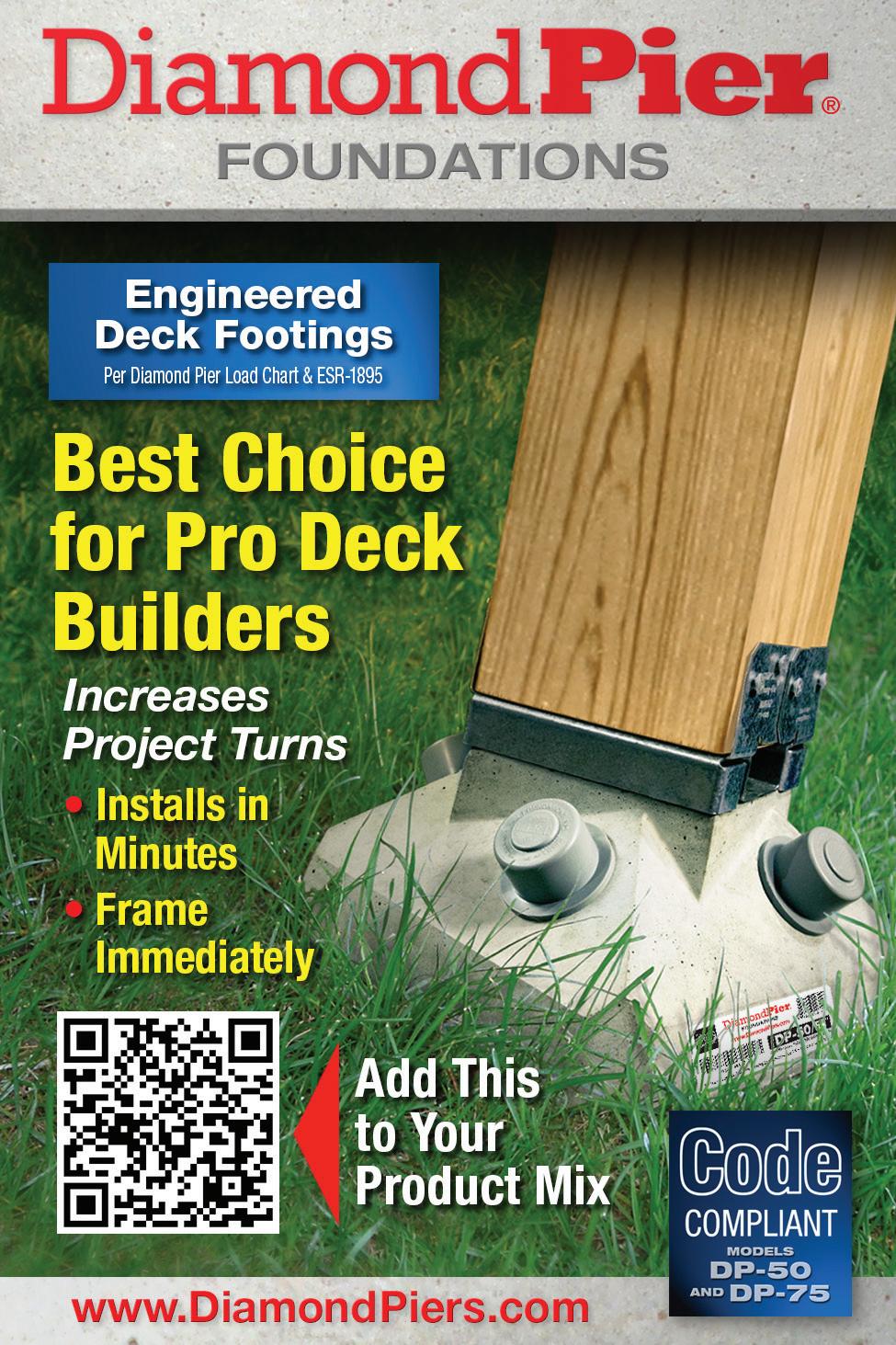
RISE IN MULTIFAMILY construction has been a boon to LVL and other engineered wood products. (Photo by APA)
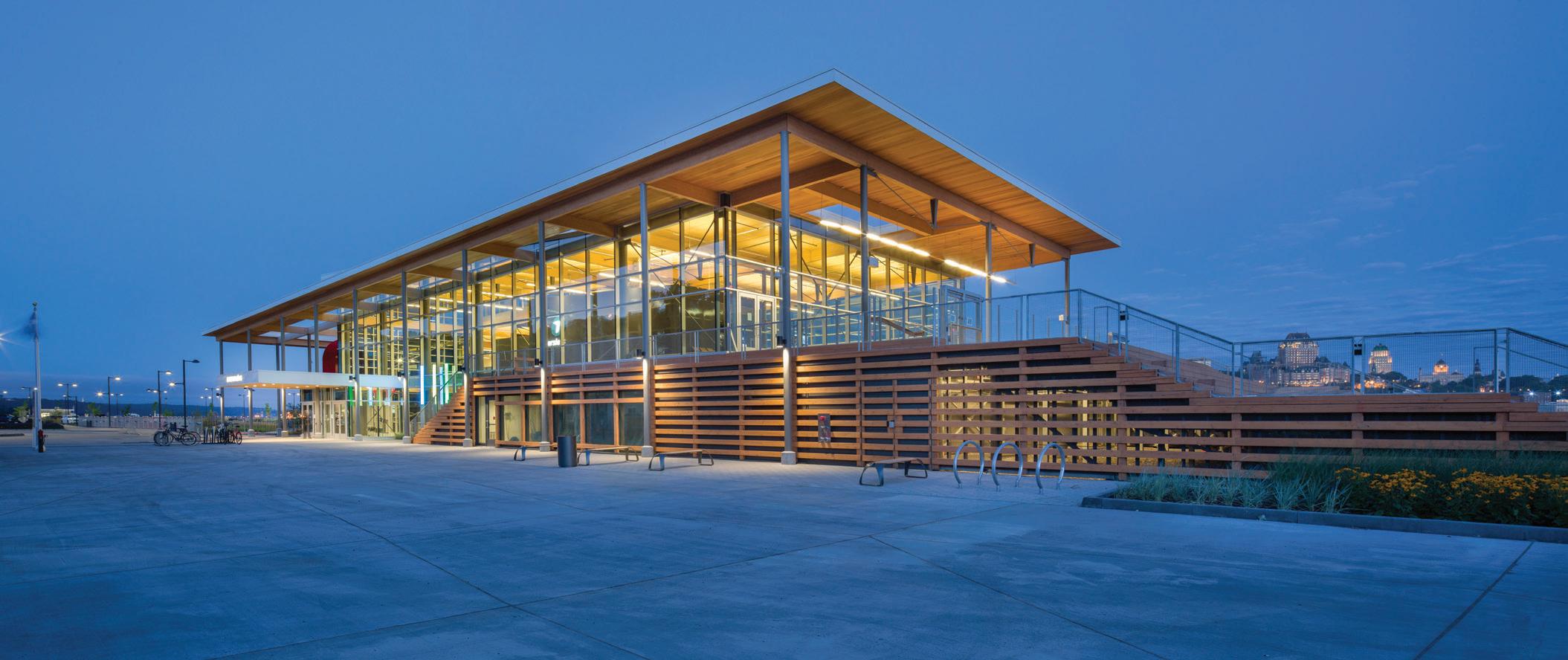
developed and first commercially used in the 1990s.
Cross-laminated timber has been in use in North America since 2010. The first few structures were built with CLT and glulam imported from Austria. Since 2013, with Structurlam (now Mercer) and Nordic leading the way, several companies have established mass timber manufacturing plants in the U.S. West and Southeast, and in both Western and Eastern Canada. There currently are 15 mass timber panel plants in North America, with a nominal press capacity of 26.9 million cubic ft. The effective manufacturing capacity is considerably less—approximately 65% of the nominal press capacity.
The big demand driver for mass timber is the environment and specifically climate change. Sustainability, carbon sequestration and reduced embodied carbon emissions are becoming ever more important with time and mass timber is demonstrably superior to steel and concrete on all of these metrics. Other demand drivers include cost certainty, lightweight, seismic performance, aesthetic appeal and biophilic advantages (health and well-being). Finally, mass timber elements are prefabricated, enabling structures to go up much more quickly.
Case in point: The Brock Commons student housing building on the University of British Columbia campus, Vancouver, B.C., in 2016 was a game changer. Scrupulous advance planning using Building Information Modeling (BIM) and prefabricated CLT components resulted in the onsite assembly of an 18-story building in just nine and a half weeks and with only nine skilled wood installers.
The growth of mass timber is also being driven by major U.S. corporations such as Walmart, Microsoft, and Google, which are building new corporate offices and—in the case of Walmart—a 2 million-sq. ft. corporate campus with 14 mass timber buildings. This trend is largely driven by the desire to enhance sustainability and advance environmental, social and governance performance. These flagship projects will undoubtedly
stimulate faster adoption among architects and building owners alike.
Future Prospects of Mass Timber
A final trend that will enhance the competitive position of wood-based solutions relative to concrete and steel is the growing interest in establishing additive manufacturing operations. These operations are situated between suppliers (such as producers of CLT blanks, glulam, EWPs, and conventional wood products, as well as manufacturers of MEP systems, kitchen, and bathroom pods) and projects. They can involve varying degrees of integration to capture both upstream and downstream value.
Additive manufacturing integrates the design process, including BIM, and a library of standard components (the “kit-of-parts”), streamlining manufacturing and planning for onsite construction. This approach ensures consistency, reduces errors and waste, and simplifies and speeds up the construction process, potentially leading to significant cost reductions. Intelligent City, Timberlab, Mercer, Kalesnikoff and Element5, for example, are all investing in additive fabrication/manufacturing.
The integration of additive manufacturing into mass timber construction and engineered wood holds great promise for advancing the industry. It can foster more innovative designs, greater customization, improved sustainability, and lower costs. As research and technology development continue, we can expect to see more applications of additive manufacturing, driving new possibilities in architecture and building design. BPD
– Robert Fouquet, partner, Forest Economic Advisors, has 40 years of experience in the lumber, panels and engineered wood products industries with a focus on North American, Asian and European markets. He assists FEA in analyzing new wood product technologies and uses, and expanding FEA’s analysis of emerging markets, particularly in Asia (getfea.com).
GARE FLUVIALE terminal in Lévis, Quebec, employed mass timber inside and out. Its Nordic X-Lam cross-laminated timber roof is supported by Nordic Lam glulam beams, which rest on steel columns (Photo by Nordic Structures)
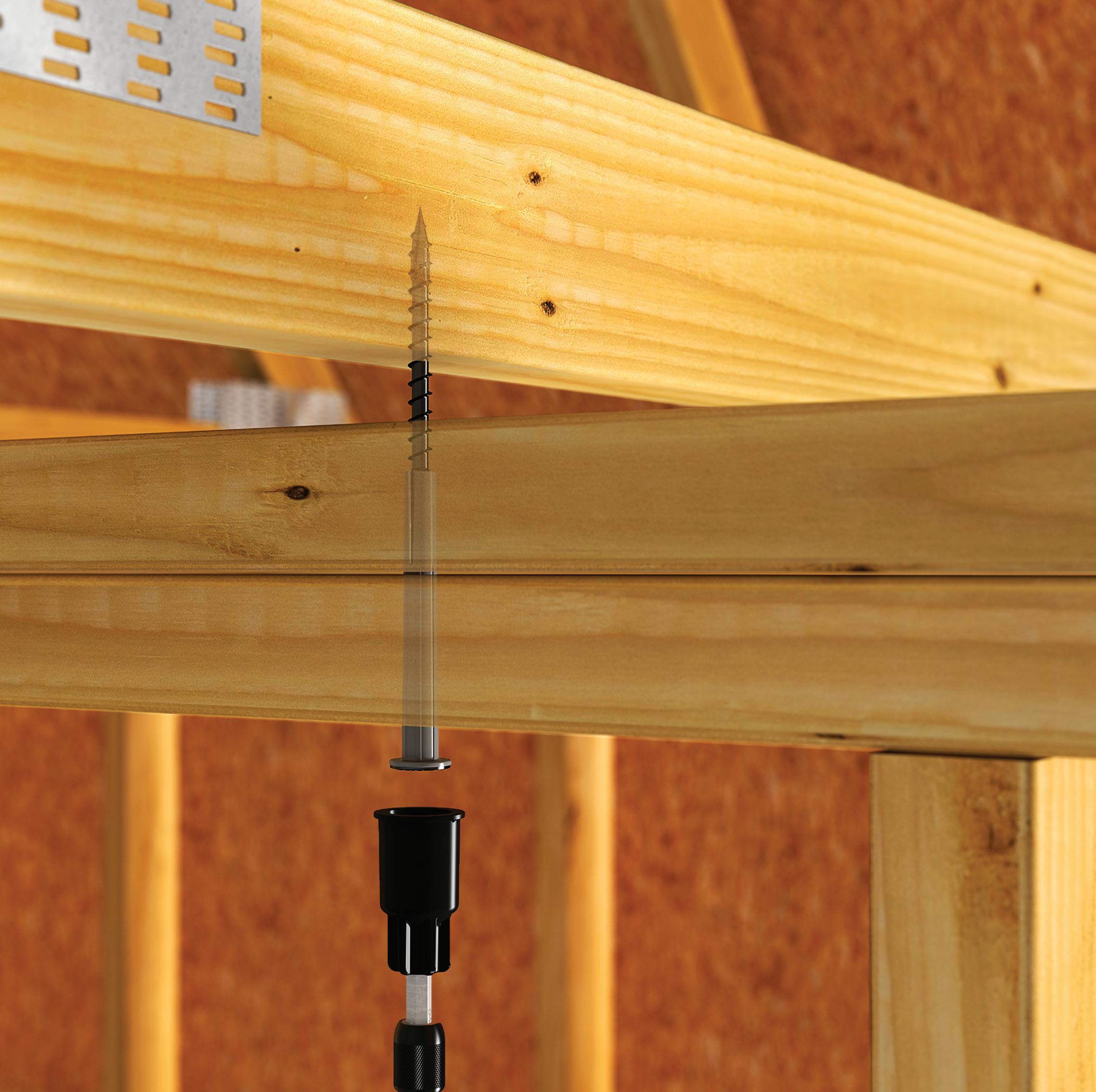
Introducing the Strong-Drive ® SDPW DEFLECTOR screw from Simpson Strong-Tie — a premium structural fastening solution that provides support for non-load-bearing, full-height partition walls and helps minimize squeaks and wall separation. Keep your shelves stocked with the high-performance fasteners your customers demand. Pair it with our Strong-Drive SDWC Truss screw for load-bearing walls to offer a complete wall-to-truss fastening solution.
For more on the Strong-Drive SDPW DEFLECTOR screw, visit our website at go.strongtie.com/sdpw or call (800) 999-5099.
A CASE FOR OPTIMISM IN 2024? APA MARKET OUTLOOK
------------ BY JOE K. ELLING
PURCHASES OF existing and new homes followed different paths in 2023. Quarterly sales of existing homes consistently fell through 2023 and totaled 4.09 million at the end of the year, down 18.7% from 2022. Higher mortgage rates certainly played a role in driving the sales decline. Also contributing was the historically small number of homes available for sale. In 2023, the number of existing homes for sale averaged 1.06 million at the end of each month, compared to an average of 1.82 million in the years 2016 to 2019.
New home sales rebounded in 2023, as home builders aggressively used incentives, most notably with mortgage buydowns and adjustments to their product mixes to make homes more affordable. As a result, new home sales rose 3.9% to 666,000 in 2023.
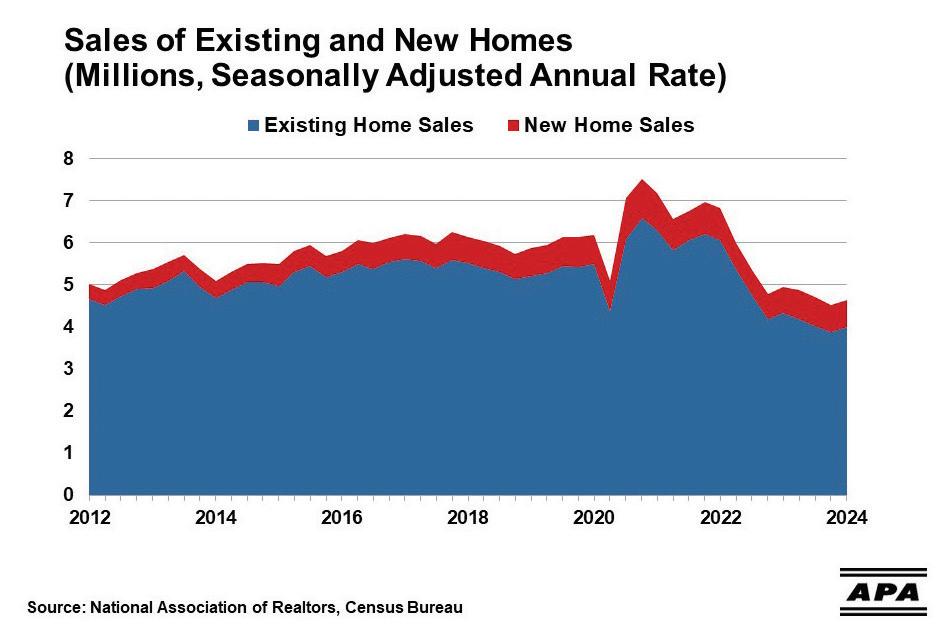
Still Not a Good Time to Buy
Each month, the research staff at Fannie Mae conducts a survey to gauge the public’s perception of the housing market. One question asks whether the individuals believe it’s a favorable time to buy a home. The answer largely depends on the level of mortgage rates, home prices and the time needed to find the desired home. Throughout 2023, just 18% of the respondents felt it was a good time to buy, while 82% felt the opposite was true (see following graph). There was effectively no difference in the January 2024 survey. Prospective home buyers and builders expect mortgage rates to fall over 2024. Based on statements made by Federal Reserve policymakers, it appears they might begin to lower the target range for the federal funds rate in the second half of 2024. However, the declines will be small, 25 basis points at a time, and spaced over two to three
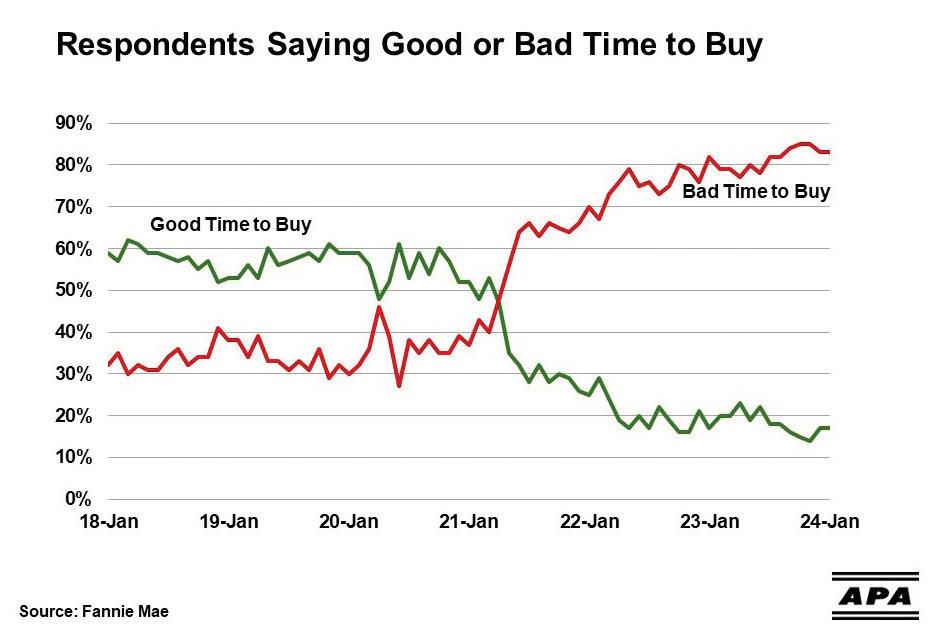
months each. This suggests that the rate on a 30-year fixed-rate mortgage could be near 6.5% at year-end.
Labor Shortage Easing
Periodically the research staff at the National Association of Home Builders surveys its members regarding labor availability. In the January 2024 survey, just over half of the home builders stated labor was in short supply, marking the lowest reported shortage of labor since 2017 (see graph below). This suggests the rate of increase in labor costs will slow in 2024. It also means construction time should improve, which will contribute to lower building costs.
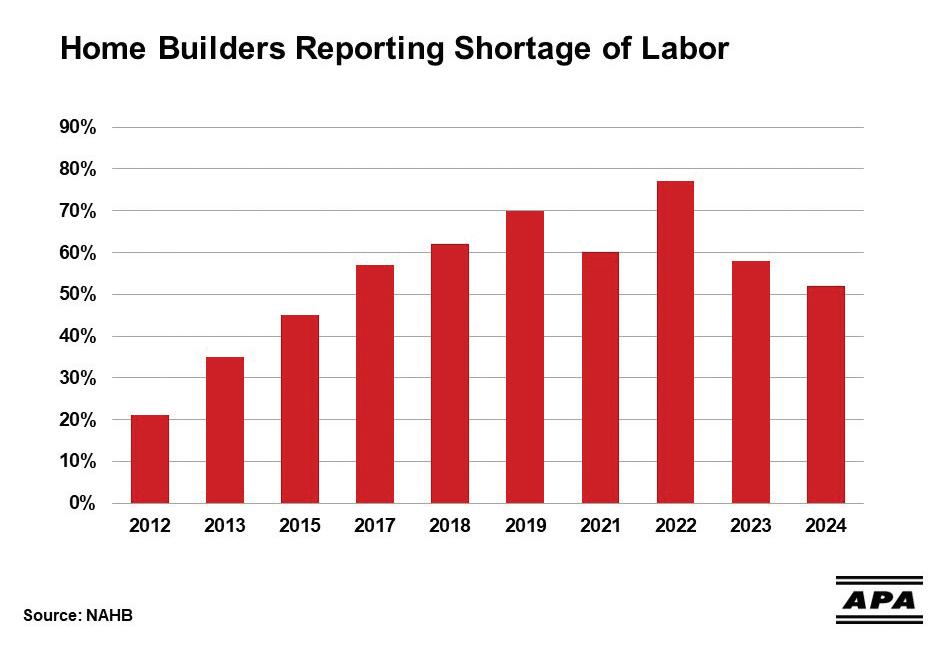
Multifamily Construction Historically High
At the end of January 2024, the number of multifamily units under construction totaled 996,000, down 22,000 from the July 2023 historic high of 1.018 million.
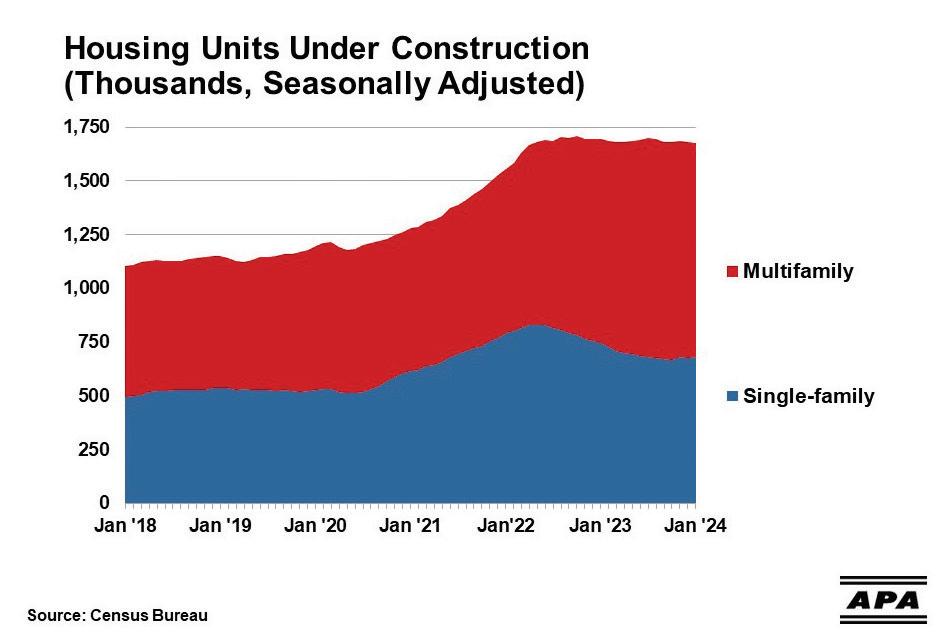
Roughly 95% of the units under construction are intended for rental. Investors in rental housing are backing off from the market due to rising vacancy rates, which are causing rents to either stagnate or decline. There is already evidence of this, as property owners are offering the first two months rent-free, reduced prices for parking and other incentives to attract tenants.
Starts Mixed in 2024
Housing starts totaled 1.42 million in 2023, down from 1.55 million in 2022. Single-family starts fell 6% to 947,000, while multifamily came in at 473,000, off 13.2%. The prospects of lower mortgage rates in 2024 point to another increase in home sales and, in turn, a rise in single-family starts to 1 million for the year. Rising vacancy rates, stagnant rents, and falling property values are expected to initiate a drop in multifamily starts to 380,000 in 2024. At 1.38 million units, starts will be less than what is needed to meet demand for new housing units.
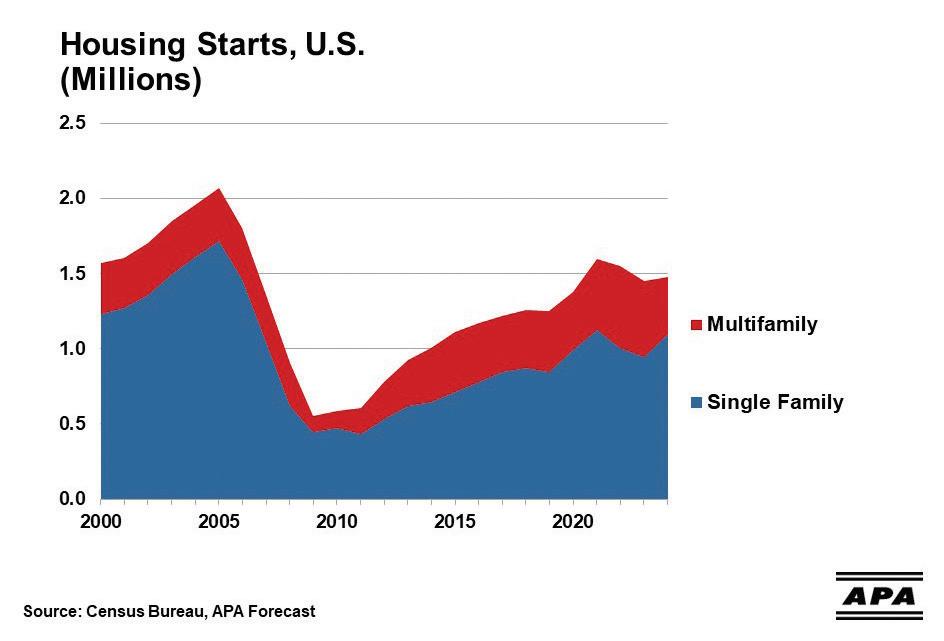
Home Size Down Again
The average size of single-family units started in 2023 was 2,411 sq. ft. (see next graph). This marked the lowest value for average size since 2010. The decline in the average size of single-family-unit starts was driven by home builders reducing size to improve affordability. The average size of single-family homes started in the fourth quarter of 2023 was 2,374 sq. ft. With sustained efforts by builders to enhance affordability, the average size of new homes started is projected to be 2,365 sq. ft. in 2024.
Repair and Remodeling Peaked in 2022
The availability of reliable data for estimating repair

and remodeling activity is very scarce. One indicator used to get a feel for the repair and remodeling market for wood products is the Census Bureau’s estimates of sales at building material and garden equipment dealers. The data are expressed in nominal dollars and not adjusted for price changes. As shown below, sales at these establishments totaled $499 billion in 2023, down 3% from 2022. Anecdotal reports from key players in this market were down on a per capita basis. Sales in January 2024 were reported to be down 4.1% from December 2023 and off 8.3% from January 2023. These two data points imply 2024 is going to be another down year for the repair and remodeling market.
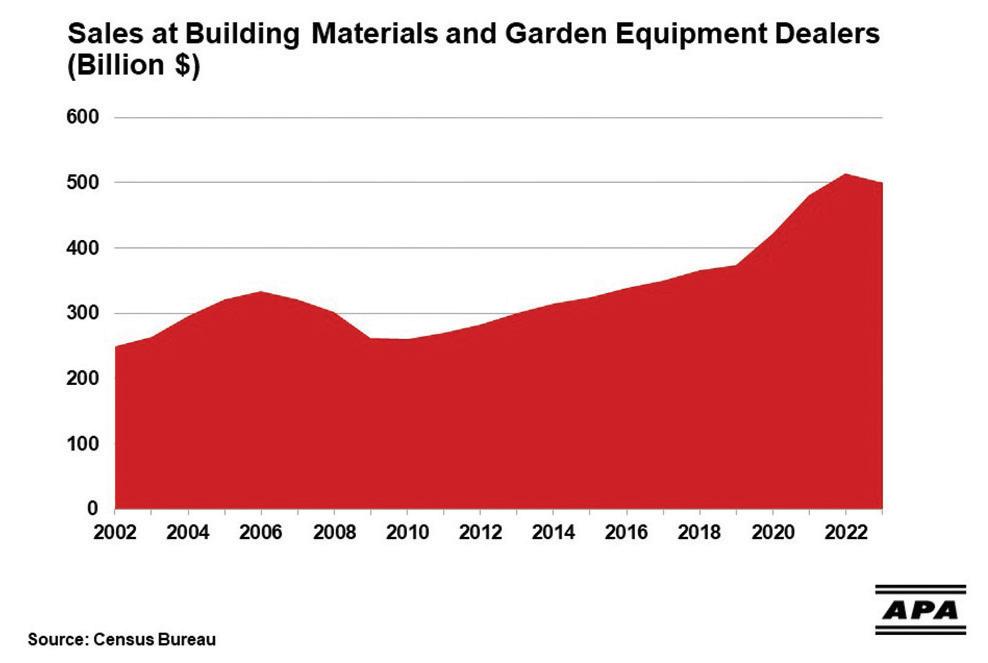
Answer to Opening Question: Probably Not
Despite the talk in the business media about the prospects for lower interest rates, 2024 is going to be a challenging year for those in the wood products industry. The degree of the decline in mortgage rates is likely to be slight. The reluctance of existing homeowners to move will sustain the competition in the existing home market, implying higher home prices. Home builders will again do what they can to generate sales, but the likelihood of smaller homes will partially offset the increase in wood products demand through an increase in single-family starts. Existing homeowners who would like to undertake a major remodel will remain frustrated by high financing costs, either through a direct loan or pulling equity out of their house via refinance at a much higher interest rate, significantly driving up their mortgage payment. BPD
– Joe K. Elling is the director of market research at APA –The Engineered Wood Association (www.apawood.org).
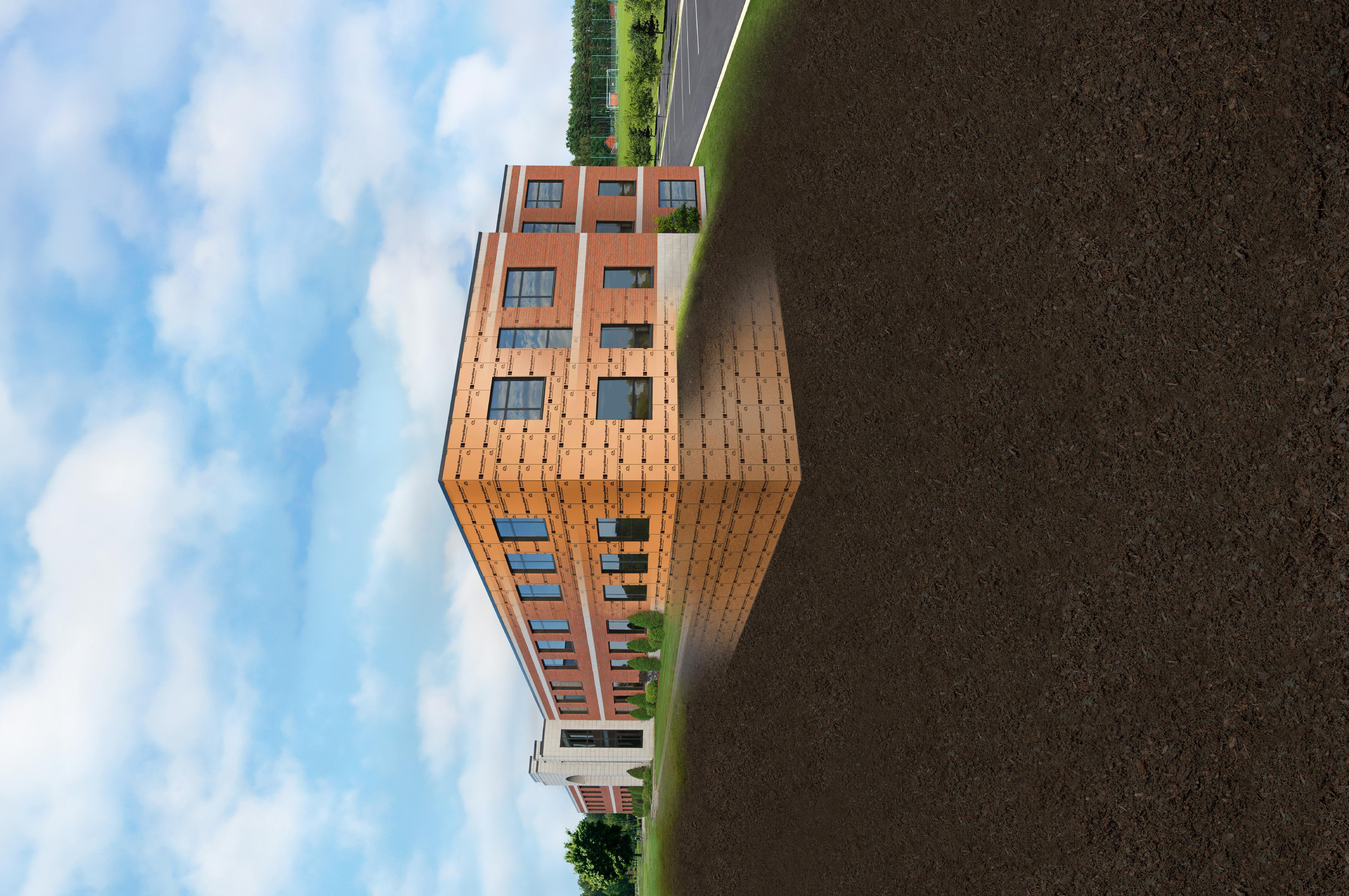
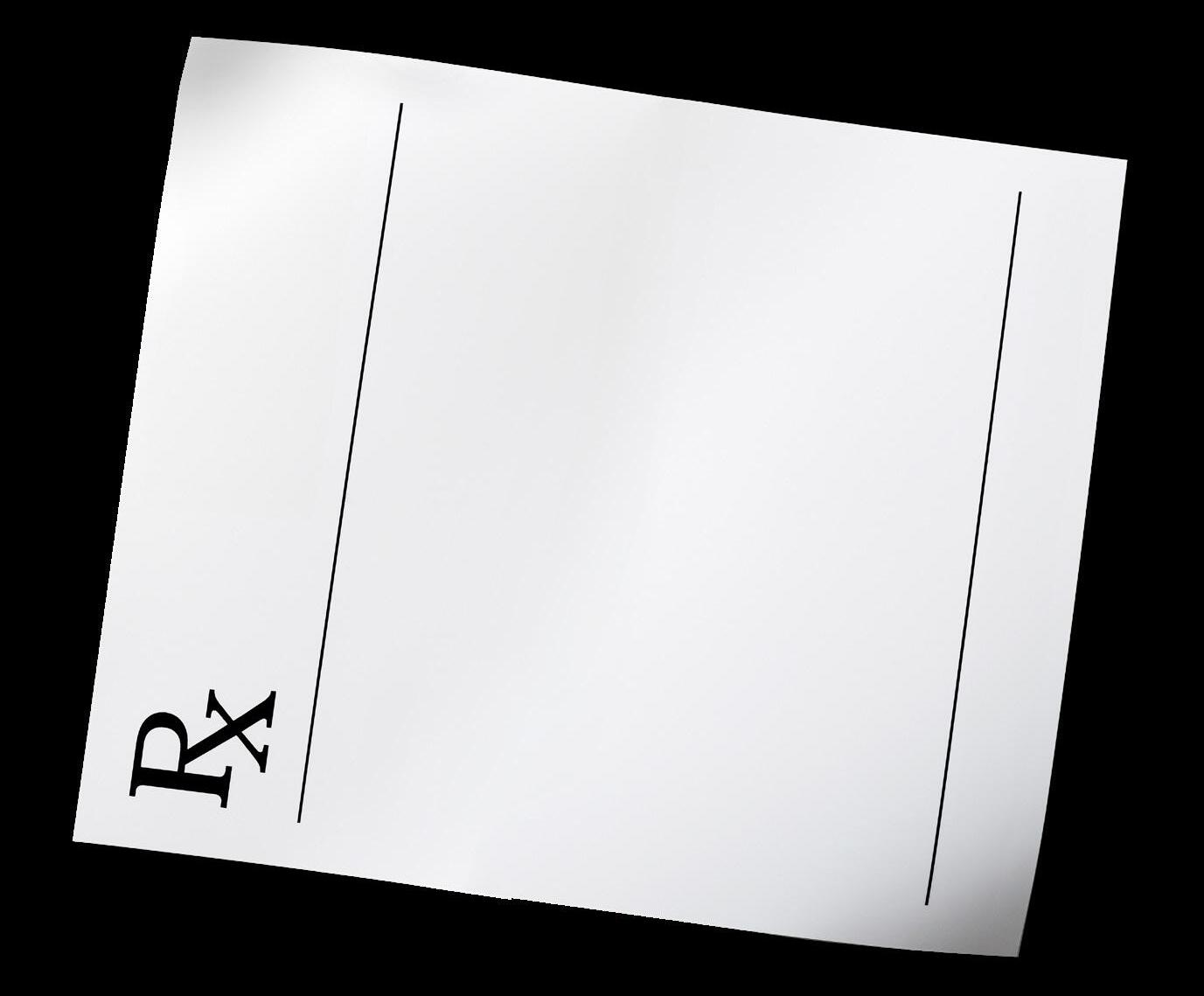
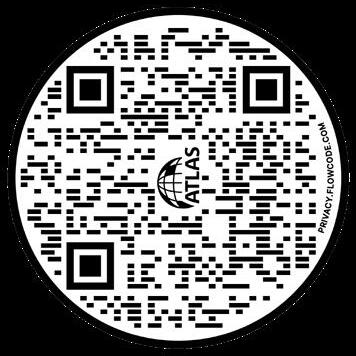
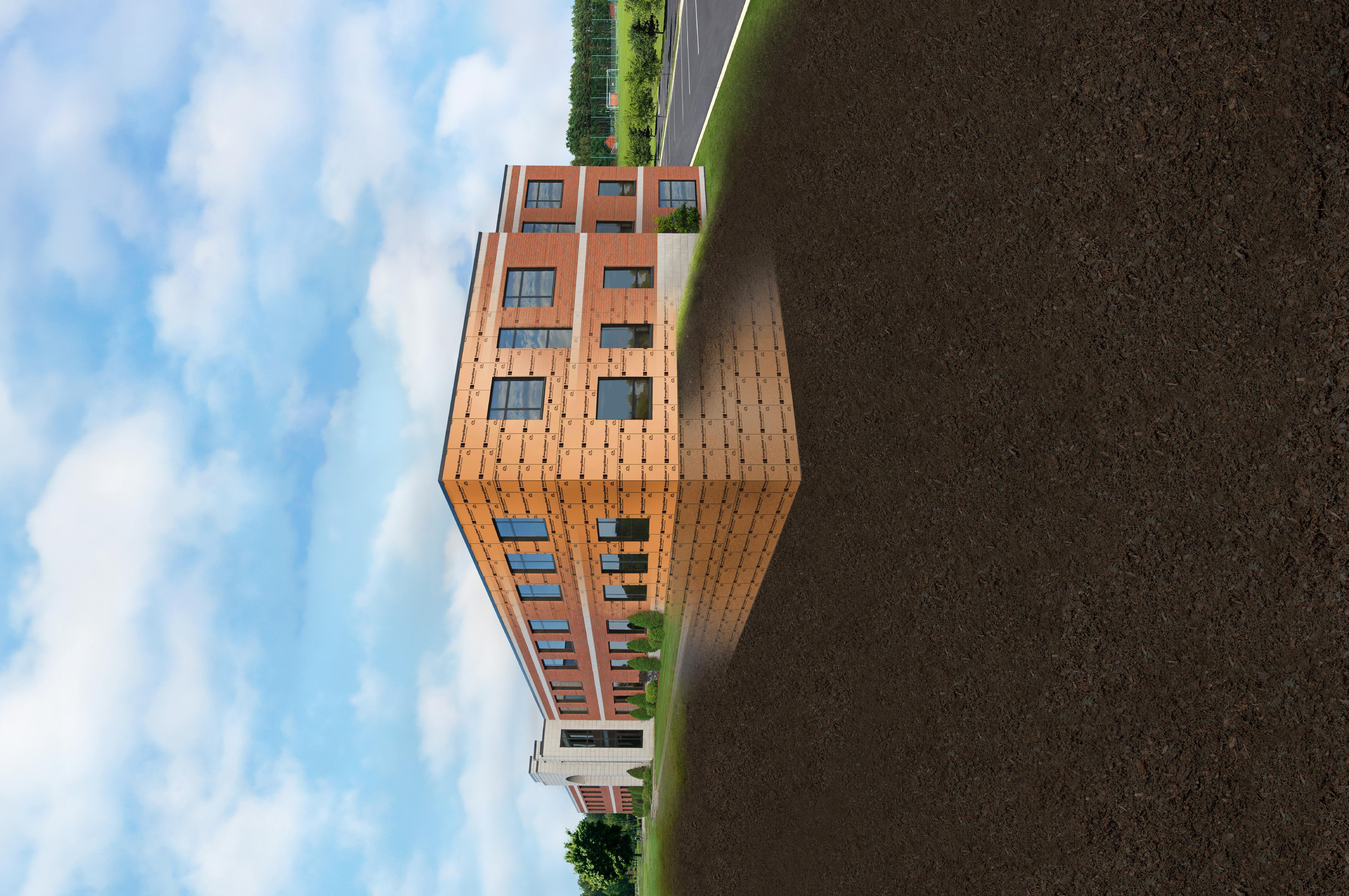
Do not take if you enjoy higher energy costs and other headaches.

MASS TIMBER: A SUSTAINABLE SOLUTION FOR AFFORDABLE HOUSING
------------
BY MADISON STEPHENS
AMERICA’S HOUSING stock is failing to keep up with the need for affordable housing and mass timber is a compelling new option for consideration in affordable housing projects across the country.
The National Low Income Housing Coalition estimates a shortage of 7 million affordable and available rental homes and nearly two-thirds of renters say they can’t afford to buy a home. Rather than the affordable housing complexes that come to mind in recent history, mass timber construction offers an efficient, sustainable solution to the current affordable housing crisis.
Using mass timber products has the potential to lower the overall project cost by up to 25% just through faster construction time and smaller crews, because mass timber arrives at construction sites as premanufactured panels, ready to be assembled. This speed of construction is an important factor in the ability to quickly address our massive housing shortage.
Affordable housing is more than just a safe, stable structure to live in, it is also a critical part of remediating inequality, addressing social problems and reducing unemployment. Cities on both the East and West Coasts have recently turned to mass timber to meet the physical and social needs related to affordable housing.
In late 2023, Seattle’s Heartwood, an eight-story mass
timber building that provides 126 workforce housing units, welcomed its first tenants. The 67,000-sq. ft. structure was built using cross-laminated timber (CLT) ceilings and glued laminated timber (glulam) columns and was the first tall mass timber (also known as Type IV-C construction) workforce housing building permitted in the U.S.
New Haven, Ct., followed Seattle’s lead and broke ground on a mass timber affordable housing project called 340+ Dixwell. The structure will include 70 units and rely on CLT for walls, including the elevator and stair core walls. In an effort to ensure access and equity, the project includes units that are dedicated to supportive housing for chronically homeless individuals and families at risk of homelessness in the New Haven area.
Before its inclusion in the national model building codes, mass timber was rigorously tested to demonstrate its fire performance. The wood boards that make up a mass timber product are glued or pressed together so tightly that oxygen is forced out preventing fire spread. Instead, the outside of mass timber panels char while the inner part of the panels remain unaffected, preventing a loss of structural integrity and creating a barrier of protection for the inside of the structure.
Along with its superior structural integrity and faster construction time, U.S. mass timber products are sourced
from sustainable working forests that sequester carbon from the atmosphere, and then store that carbon for the life of the product. As the worldwide climate crisis continues to be a motivating factor in how cities are built and maintained, mass timber is already prepared to meet the need for a truly climate-friendly construction material.
The American Wood Council (AWC) is highlighting mass timber at the federal level through advocacy, partnerships and showcases like the Department of Housing and Urban Development’s (HUD) Innovation Summit. Last year, AWC hosted the House Working Forest Caucus on the National Mall where legislators toured two modular mass timber buildings that were displayed as part of HUD’s Innovation Summit and were recipients of Wood Innovation Grants (WIG). Representatives heard from AWC’s president & CEO Jackson Morrill and Forest Service staff who emphasized the critical role WIG grants play in creating new markets for wood products. Both Republican and Democrat representatives heard how HUD is pursuing mass timber to help
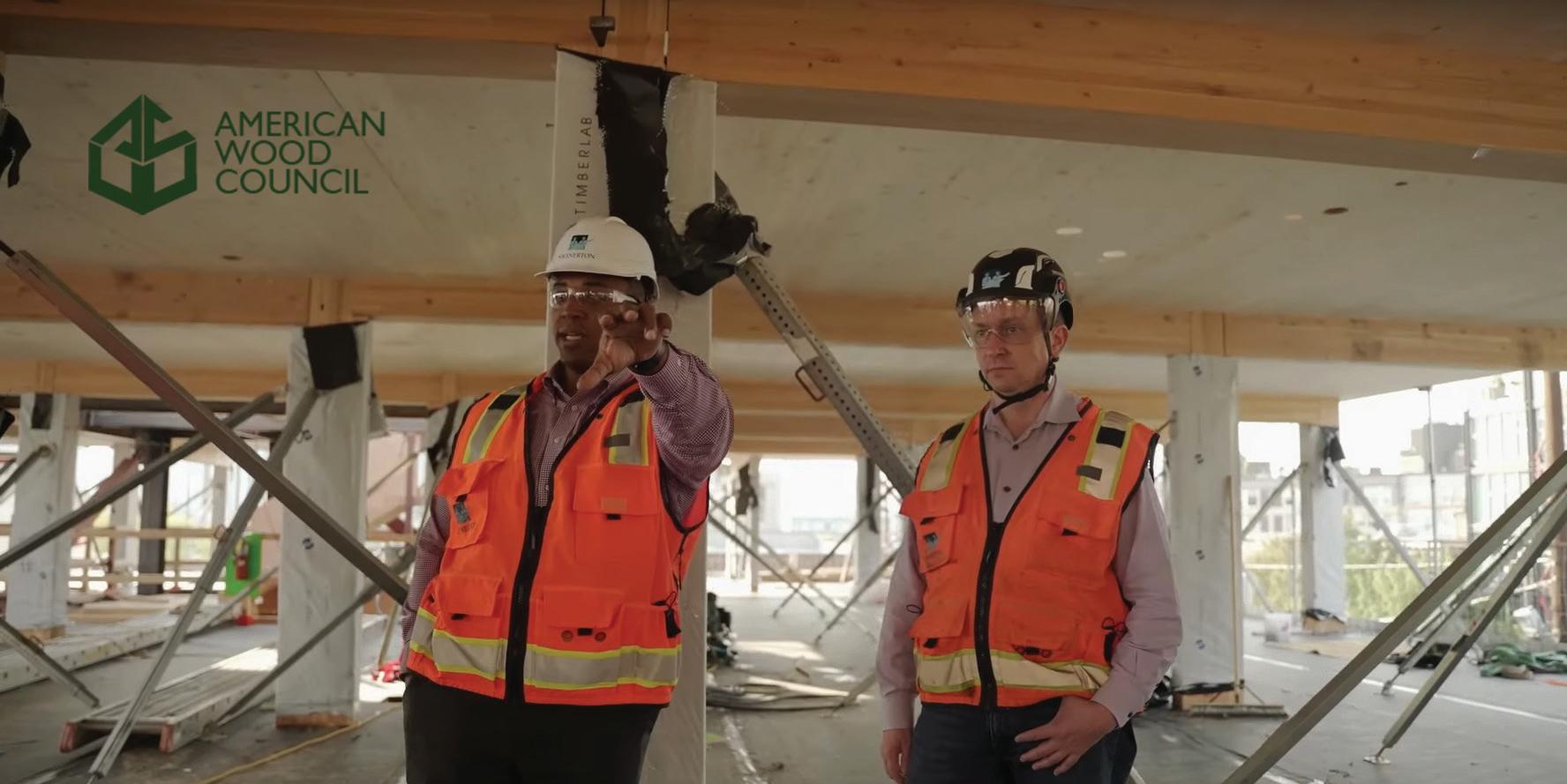
MASS TIMBER has tremendous potential to reduce carbon emissions and sequester carbon, as well as provide a better living environment for its occupants, particularly as a “green” solution for low-cost, affordable housing solutions. Learn about one such project in Seattle. Watch a short video on the Heartwood workforce housing project on AWC’s YouTube page at youtube.com/@AmericanWoodCouncil.
reduce housing costs nationwide. This year’s HUD Innovation Summit was held in June with AWC supporting the wood product exhibits and engaging key members of Congress and the public through exhibit tours.
Officials at the federal and state level are recognizing that mass timber quickens the construction process, can lead to a cheaper overall
project cost and is a more sustainable and climate-friendly building material. As a climate-friendly material that is also safe and able to withstand the increasing number of climate-driven disasters, mass timber is the right now solution to meet the critical need for affordable housing in the U.S. BPD – Madison Stephens is communications manager for the American Wood Council.
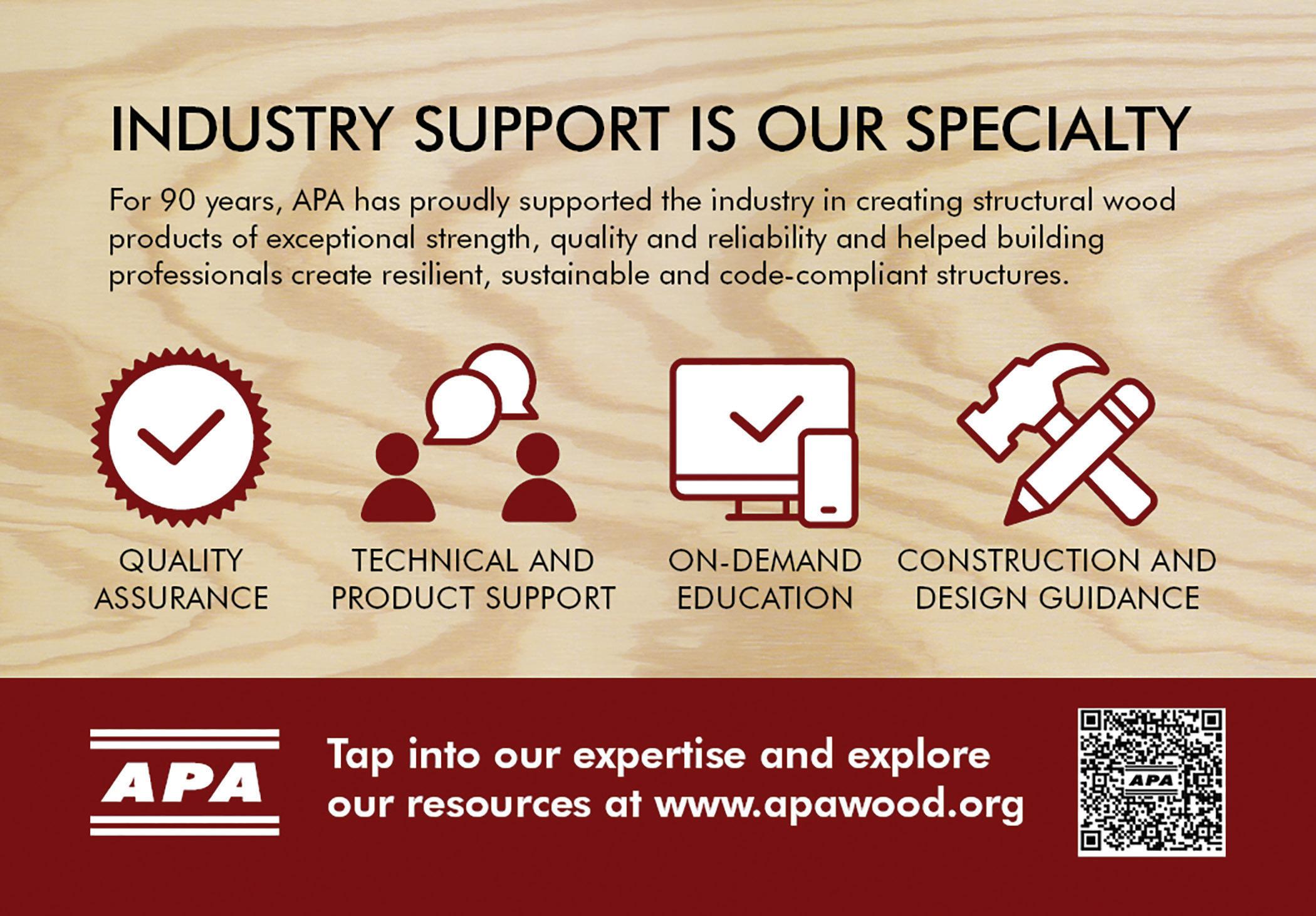
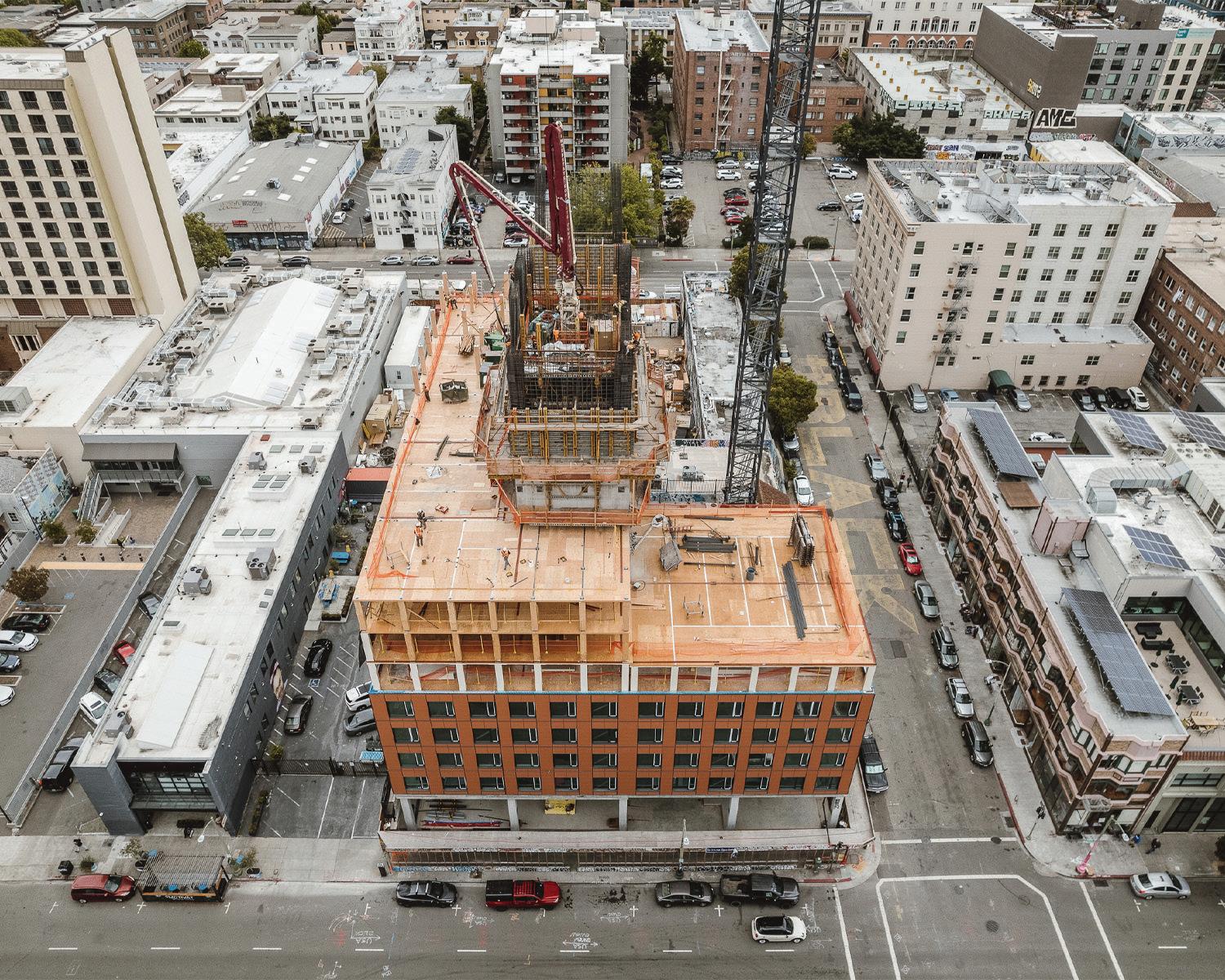
SNAPSHOT OF A GROWING MARKET
SHARED EXPERIENCE DRIVES MASS TIMBER ADOPTION
------------ BY BILL PARSONS
IN THE EVOLVING landscape of construction, mass timber continues to expand as a high-performance, sustainable structural solution for commercial, multifamily and institutional markets. Nearly two decades into the growth of the U.S. mass timber market, more design teams than ever have exposure to successfully built wood projects. New research, building code updates, and technical resources focused on mass timber continue to bridge gaps in knowledge, catalyzing growth and innovation. As of March 31, 1,006 multifamily, commercial, or institutional projects were underway or completed in the United States, with an additional 1,109 in the design phase.
The trend toward greater urban density as a means to address housing needs is driving multifamily devel-
opment, and developers are increasingly recognizing the potential of mass timber and hybrid solutions (e.g., mass timber floor and roof systems with lightframe wood walls, or a combination of wood and non-wood systems) to provide a differentiated product that offers sustainability and biophilic benefits, as well as greater leasing velocity, tenant retention, and return on investment. Approximately 75% of U.S. mass timber projects six stories or greater that are now in design are multifamily residential.
New models for tall timber construction have emerged since changes in the 2021 International Building Code (IBC) allowed for wood buildings up to 18 stories and amendments to the 2024 IBC increased the allowable percentage of exposed wood ceilings in buildings 12 stories or less. Tall mass timber projects
TREND TOWARD greater urban density is driving the rise in multifamily construction, including with mass timber.
(Photo by 1510 Webster / oWOW / DCI Engineers / Flor Projects)
like 1510 Webster in Oakland, Ca. (19 stories, 16 of which are mass timber); Bakers Place in Madison, Wi. (14 stories); and Heartwood Workforce Housing in Seattle, Wa. (eight stories), have leveraged the updated codes in groundbreaking designs. As of March, 15 tall mass timber building projects (both multifamily and office developments) were built or under construction in the U.S., and WoodWorks, which offers free technical support to design and construction teams, is currently assisting on 230 projects at that scale.
The performance capabilities of mass timber have led to growth in commercial and institutional market segments. Warehouse and manufacturing projects have experienced a surge in the last several years. The switch to mass timber on Janicki Industries Building 10 (a 188,000-sq. ft. aerospace manufacturing facility in Hamilton, Wa.) helped the project overcome supply chain issues and meet an ambitious construction timeline.
Education and student housing segments have also shown continued growth, with 173 projects under construction or built. While labs and life sciences buildings have been slower to adopt mass timber, pioneering projects like the Michigan State University STEM Teaching and Learning Facility are leading by example and pointing to the untapped potential for timber’s use in high-tech projects.
The International Mass Timber Conference (IMTC) serves as a barometer of industry momentum and collaboration. The 2024 IMTC saw a record attendance of 3,000 professionals and featured WoodWorks’ second live mass timber construction demonstration on the exhibit floor. Developers’ interest in mass timber was underscored with the addition of a new session track in partnership with the Urban Land Institute (ULI). Networking events throughout the week, including one hosted by the WoodWorks Innovation Network (WIN), brought together attendees to share their experience with mass timber products and highlight their growing project portfolios.
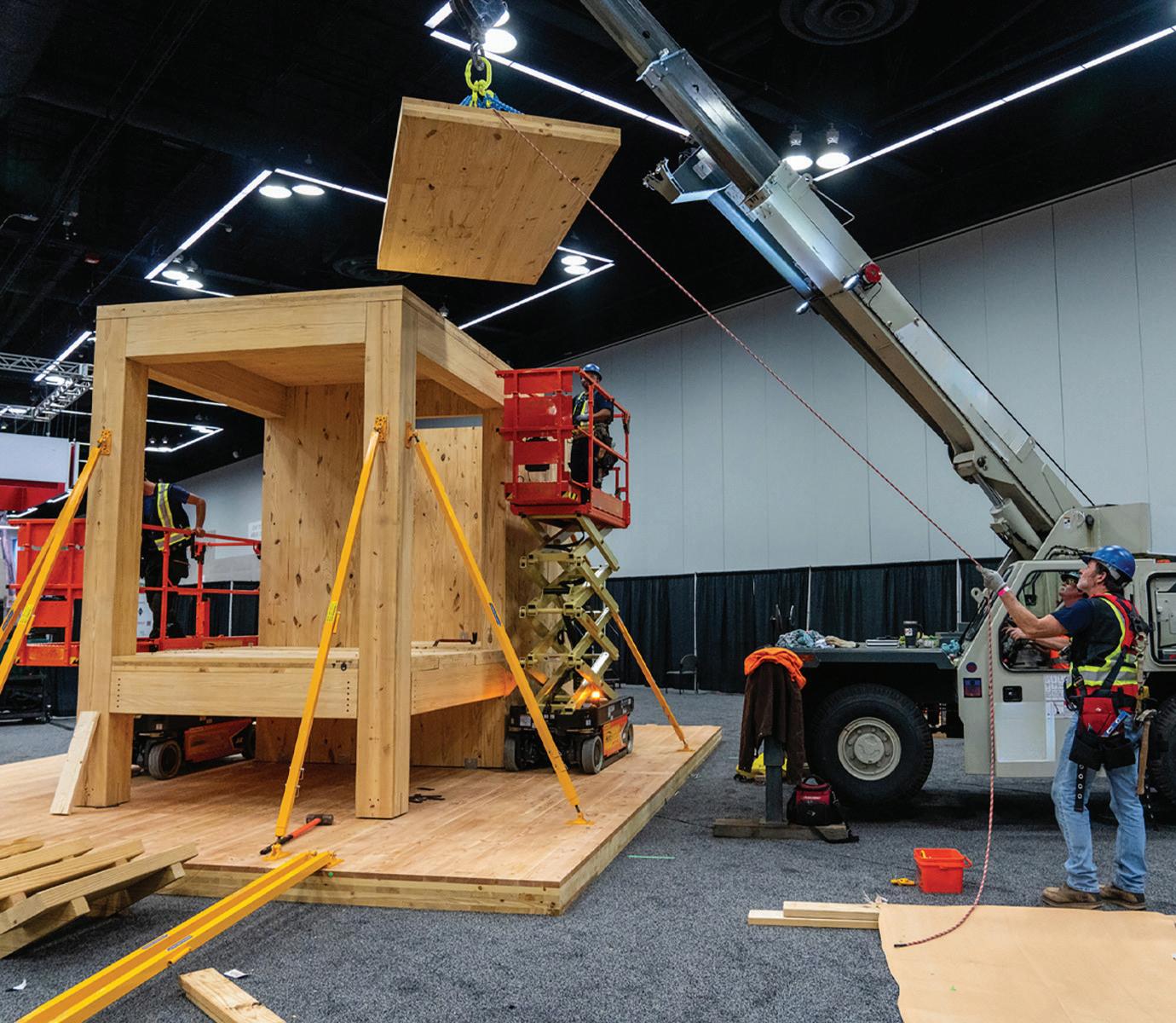
Major cities like New York, Boston and Atlanta have launched successful mass timber accelerator programs, helping projects move from concept to construction. The programs award grant money and technical support to teams whose project proposals meet community needs and sustainability goals. Additionally, mass timber project management and installer training is expanding across the country. To date, 28 training centers and four universities throughout the U.S. are using WoodWorks’ mass timber construction management training mock-ups and curriculum to educate tradespeople with experience in other building systems, along with the next generation of general contractors and installers.
The body of knowledge on mass timber continues to expand through cross-disciplinary collaboration. This year, WoodWorks partnered with an experienced mass timber construction professional to release a guide covering cost-estimating considerations for general contractors with an emphasis on minimizing whole project costs and maximizing the value of
mass timber projects. WoodWorks also collaborated with KL&A Engineers & Builders to release a Mass Timber Comparative Life Cycle Assessment series comparing the embodied carbon impacts and cost of mass timber buildings to functionally equivalent buildings.
Mass timber is unique among solutions addressing the needs of modern construction, as designers pursue wood products for their many benefits, from flexibility and sustainability to speed of installation. Backed by the proliferation of shared experience and widely available technical education across trades, the U.S. mass timber market is positioned to continue gaining in strength with increasing supply and popularity in the multifamily, commercial, and institutional sectors. BPD
– Bill Parsons, PE, is the chief operating officer at WoodWorks/Wood Products Council, a non-profit organization providing free project support for commercial and multifamily mass timber and light-frame wood buildings, a nationwide education program, and a wide range of published resources.
MASS TIMBER construction demonstrations took place right on the exhibit floor at the International Mass Timber Conference. (Photo courtesy International Mass Timber Conference)
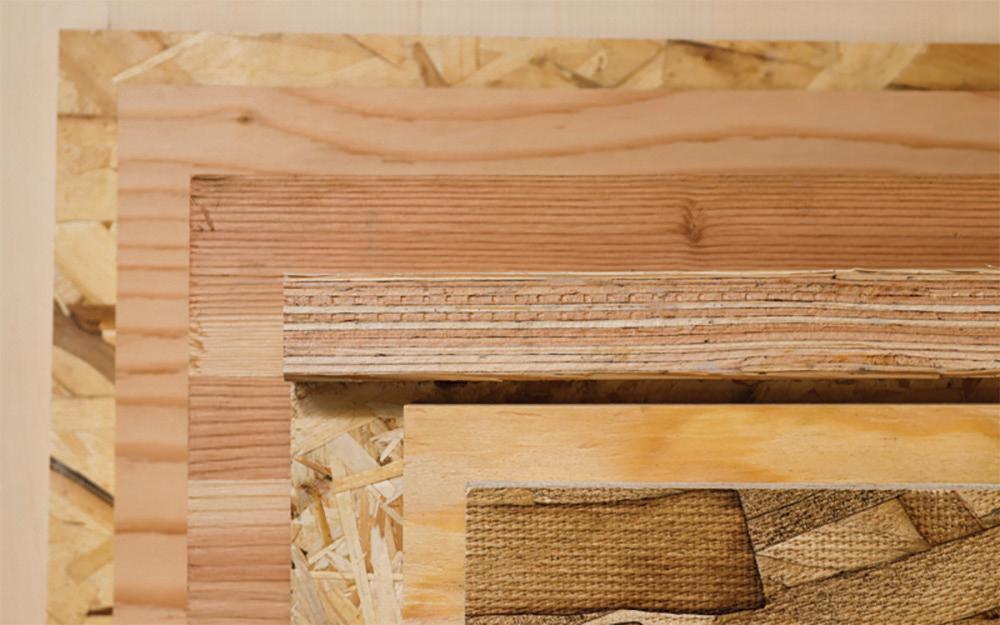
HOW TO SPECIFY ENGINEERED WOOD PRODUCTS
ENGINEERED WOOD
products are used in a wide range of construction applications. For low in-place cost, versatility and superior performance, engineered wood systems are simply hard to beat. Their various sizes and dimensions mean less construction jobsite waste and lower disposal costs. In completed buildings, they store carbon and deliver decades of strong, dependable structural performance.
Engineered wood products (EWP) that bear the APA trademark are manufactured in accordance with APA or national standards. The trademark is the manufacturer’s assurance that the product conforms to the standards noted on that trademark. APA members commit to a rigorous program of quality inspection and testing. Some EWPs are proprietary and use proprietary engineering service reports and APA Product Reports for their code recognition and product use and design information.
Below is a look into a few engineered wood products and specification factors to consider.
Wood Structural Panels
OSB and plywood, referred to as “wood structural panels” in the code, are manufactured with an alternating layer direction using moisture-resistant adhesive. The panels must pass wet and dry structural performance tests. Panels are available in Exterior and Exposure 1 bond classifications.
Specifying Wood Structural Panels
Specifiers should refer to APA’s Engineered Wood Construction Guide
Tips for writing the spec:
• Use “wood structural panel” rather than OSB or plywood.
• Call out panel “Performance Category” rather than thickness.
• Avoid the term “CDX.” Instead, use “rated sheath-
ing,” which refers to both plywood and OSB.
When specifying panels, designate the grade, span rating, bond classification, dimensions (Performance Category, width and length) and APA trademark.
Example Specification:
19/32 Performance Category, APA Rated Sheathing, 32/16 (span rating), Exposure 1, nominal 4’x8’ (either tongue-and-groove or square edge).
Exposure 1 panels are appropriate for applications that will be covered with finished materials. Exterior bond classification is used when the panel is going to be permanently exposed (like siding and concrete forms).
Structural I provides higher lateral resistance in engineered shear walls and diaphragms, most commonly needed where the panel strength axis will be installed parallel to supporting members, such as in panelized roof applications.
Other Considerations:
• 1/8” gap on all panel edges to accommodate expansion.
• Fasteners installed 3/8” from panel edges.
• The APA trademark on the panel should reflect what’s specified in the plans.
Glued Laminated Timber
Glulam is made with layers of 1-1/2” and 1-3/8” lumber face-bonded together by adhesives. The wood grain runs parallel to length. Glulam can be used for beams, headers and columns and is available in I-joist-compatible depths and lengths up to 60 feet. Glulam can be custom made in just about any shape or length.
Balanced or Unbalanced Members
Unbalanced are primarily for simple span applications and include “TOP” for proper placement. Balanced are
(Continued on page 24)
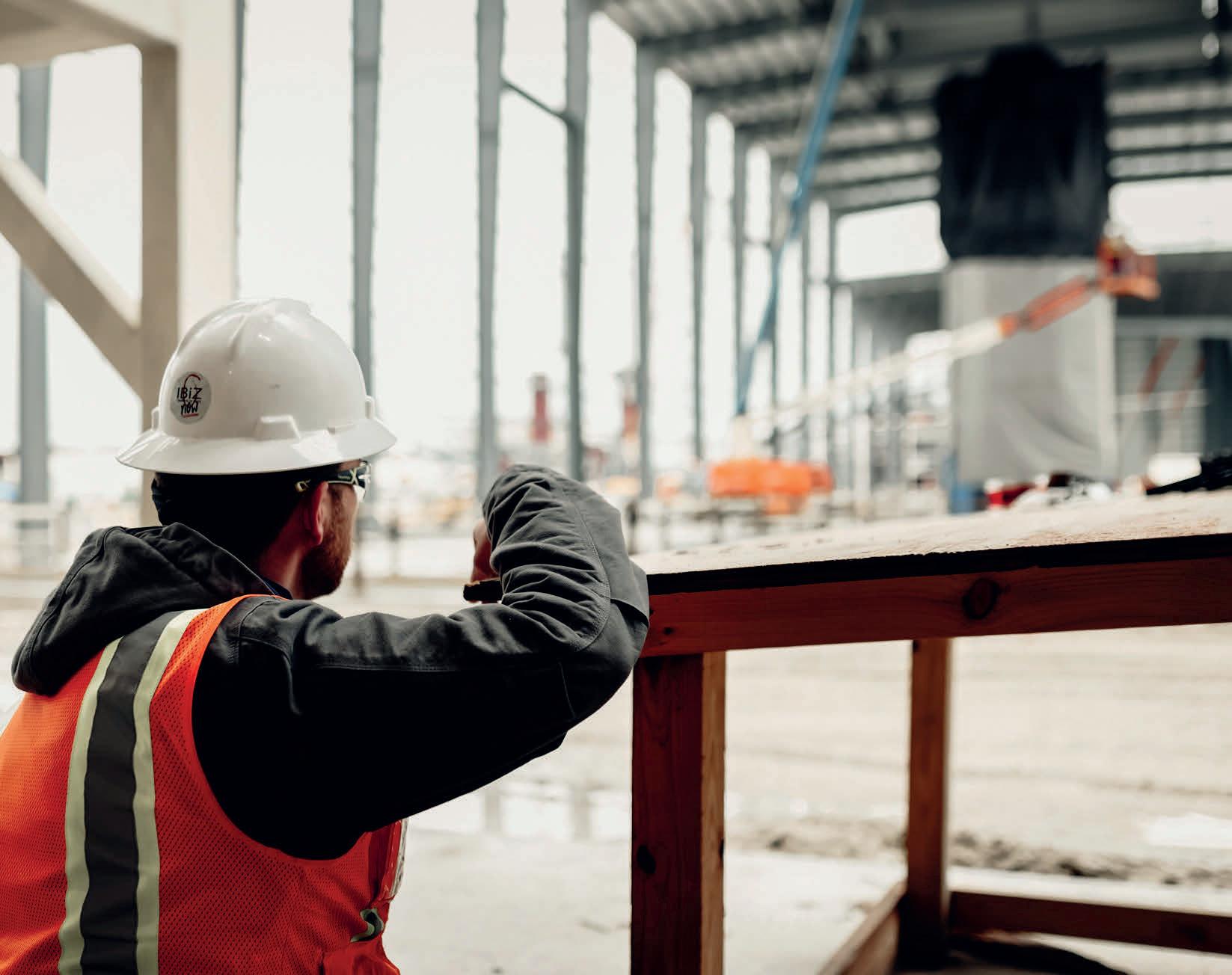
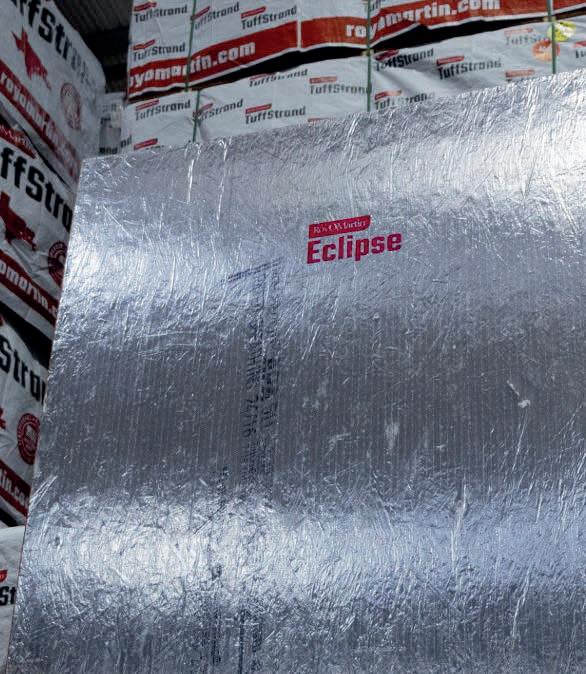
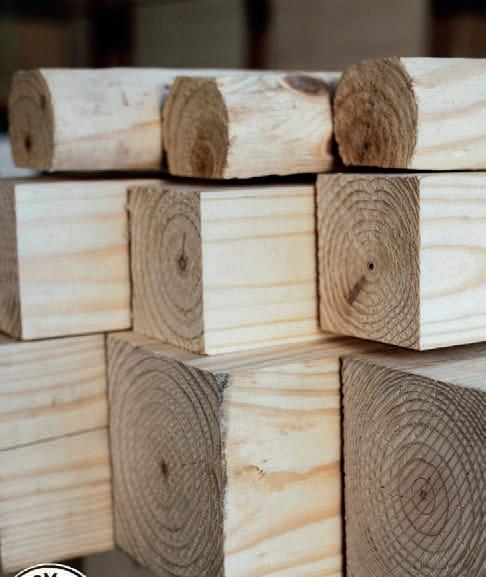

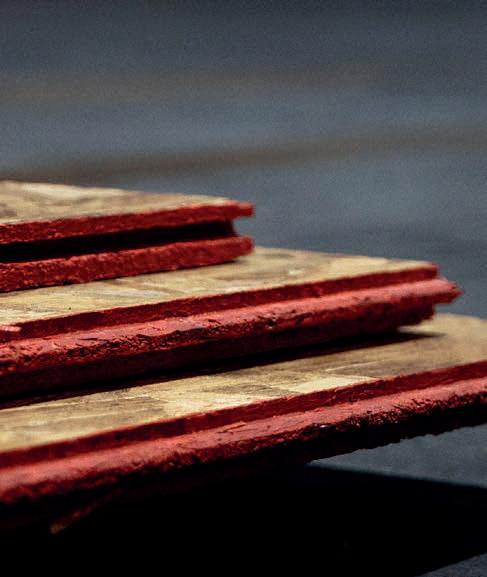

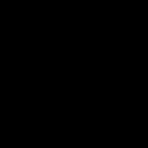

used in applications of long cantilevers or continuous spans. Glulam can also be used in column applications. See APA’s Design of Structural Glued Laminated Timber Columns
Allowable Design Properties
Bending stresses are typically specified on the basis of the maximum allowable bending stress of the member. Combinations are found in ANSI 117, Standard Specification for Structural Glued Laminated Timber of Softwood Species, used by APA glulam manufacturers for design stresses. Some can also produce glulams to ESR-1940. Some manufacturers have APA Product Reports for proprietary and commodity glulam layups.
Appearance Classifications:
Architectural, Industrial, Industrial-L, Framing, Framing-L. See APA Technical Note: Glulam Appearance Classifications for Construction Applications for details.
Outdoor Applications:
If glulam members are covered by a roof or other overhead weather barrier and the sides and ends are not subject to direct wetting from precipitation, the application is not considered as exposed. In that case, preservative treatment or naturally decay resistant species are not required.
Glulam subject to long-term direct exposure should be pressure preservative treated or produced from the heartwood of a naturally durable species like Alaska yellow cedar or Port Orford cedar. See APA Technical Note: Preservative Treatment of Glued Laminated Timber.
Exposed glulams can also be designed for one-hour or two-hour fire exposure. See ANSI 117-2020, Section 5.7, Fire-Resistive Construction and APA Technical Note: Calculating Fire Resistance of Glulam Beams and Columns.
Glulam Specification
When specifying glulam, refer to APA’s Engineered Wood Construction Guide, and ANSI A190.1-2022: Product Standard for Structural Glued Laminated Timber.
The APA glulam trademark contains several critical pieces of information you should know when specifying beams. The trademark identifies:
1. Allowable design stress
2. Appearance classification
3. Grading: Visual (V) or Mechanical (E)
4. Assigned combination number of lumber used to assign the design stresses
a. Shear, Modulus of Elasticity, etc.
5. Wood Species: Commonly Douglas fir (DF) or southern pine (SP)
While many stress classes are listed in ANSI 117, the most commonly available stock beam or column combinations are:
• Glulam beams: 24F-V4/DF, 24F-V8/DF, 24F-V3/SP, or 24F-V5/SP
• Glulam columns: Combination 2/DF or Combination 47/SP
• High-strength glulam beams: 30F-E1/SP or 30F-E2/SP
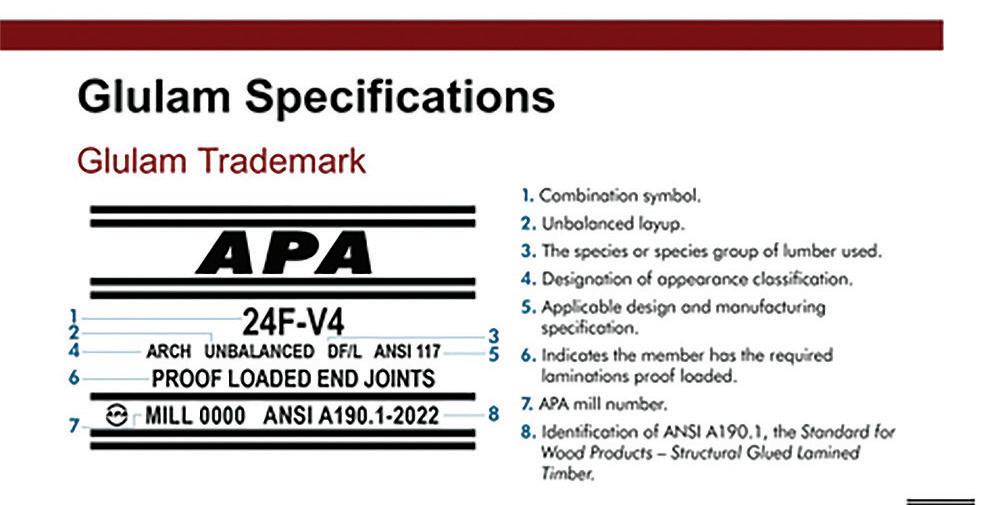
The trademark shown above tells us the allowable bending stress is 24F, which represents the allowable bending stress of 2,400 psi. The V tells us that the lumber used in this glulam was visually graded. The number 4 is the recipe for how the lumber layers were laid up, which is relevant only to the manufacturer. The trademark also tells us the appearance grade, whether balanced or unbalanced, the wood species, if it is cambered and the mill number.
Cross-Laminated Timber
Cross-Laminated Timber (CLT) panels are exceptionally stiff, strong and stable, handling load transfer on all sides. Panels can include precision cuts using state-ofthe-art CNC (Computer Numerical Controlled) routers. Finished panels are typically 2-10 ft. wide with lengths up to 60 ft. and thicknesses up to 20”. Wider widths and lengths are possible. Check with each manufacturer, as transportation restrictions might dictate size.
CLT offers superior acoustic, fire, seismic and thermal performance, is fast and easy to install, generates almost no on-site waste and offers design flexibility and low environmental impact. For these reasons, CLT is proving to be a highly advantageous alternative to materials like concrete, masonry or steel, especially in multifamily and commercial construction.
2021 IBC has expanded acceptance of CLT including buildings up to 18 stories. CLT in taller structures pertains to the requirements of the standard.
• Adhesives are required to be evaluated to ASTM D7247, Standard Test Method for Evaluating the Shear Strength of Adhesive Bonds in Laminated Wood Products at Elevated Temperatures.
• Moisture durability: Face-bond criteria is the same as glulam.
• Fire performance: Per the National Design Specification for Wood Construction (NDS) Chapter 16 including adhesive heat durability of PRG 320. New adhesives qualified to ASTM E119, and full-scale Compartment Fire Test specified in the standards.
Specifying CLT
To specify CLT, refer to APA’s free Engineered Wood Construction Guide, ANSI/APA PRG 320: Standard for Performance-Rated Cross-Laminated Timber (basic CLT grades) and APA Product Reports (custom CLT grades).
For custom products, a manufacturer should be pre-chosen in order to develop the most efficient design incorporating all the capabilities of the product. BPD
– Learn more on specifying EWP at www.apawood.org.
MORE PRODUCT SOLUTIONS FOR THE MASS TIMBER MARKET
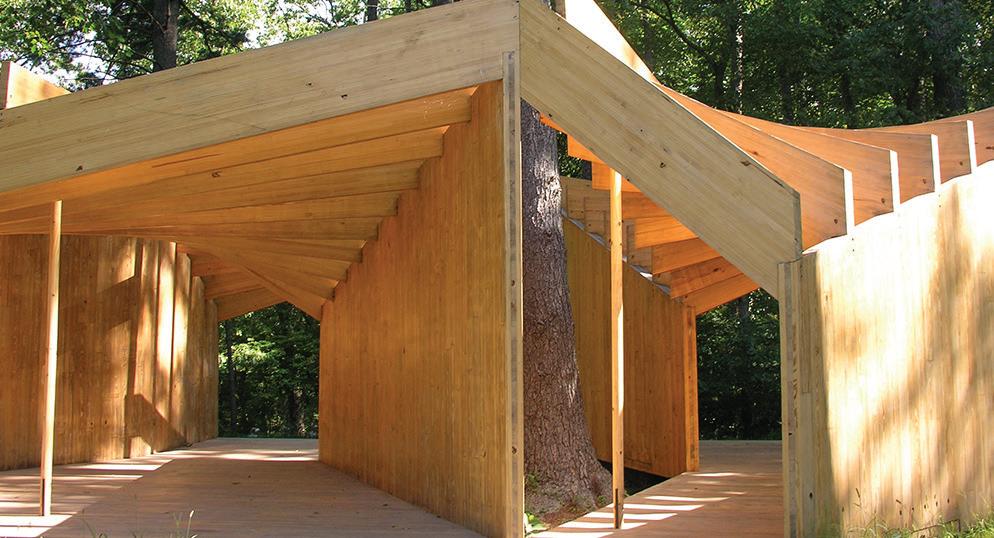
TOMORROW’S ENGINEERED WOOD -
• Cutting-Edge Equipment: New 48” technologically advanced glulam press and lay-up system.
• Versatile Production: Widths produced range from 2-7/16” to 10-1/2”, while depths range from 3-1/2” to 35-3/4”.
• Expanded Size Options: Finished Glulam Sizes up to 10 ½” x 35 ¾” x 60’.
• Diverse Applications: Available in various appearance classifications and strength grades for Commercial, Industrial, and Residential applications.
• Superior Quality: Manufactured with superior strength southern yellow pine MSR Lumber.
• Sustainability: Sustainable Forestry Initiative (SFI®) is certified for environmentally conscious projects.
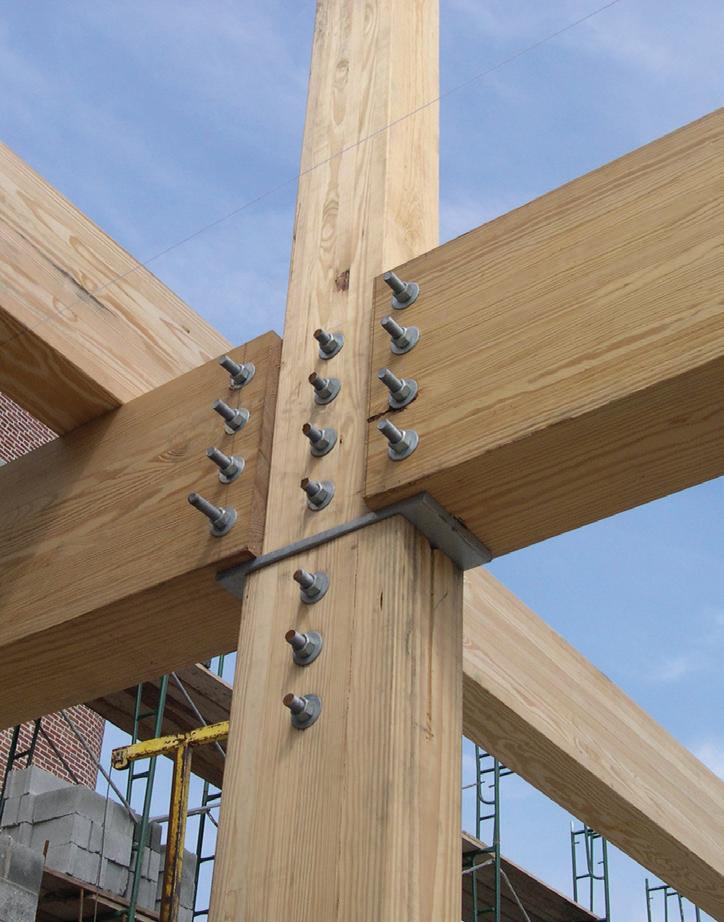
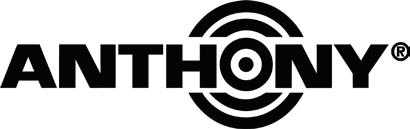
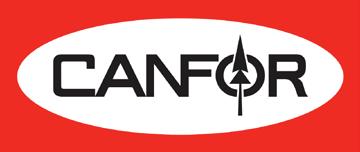
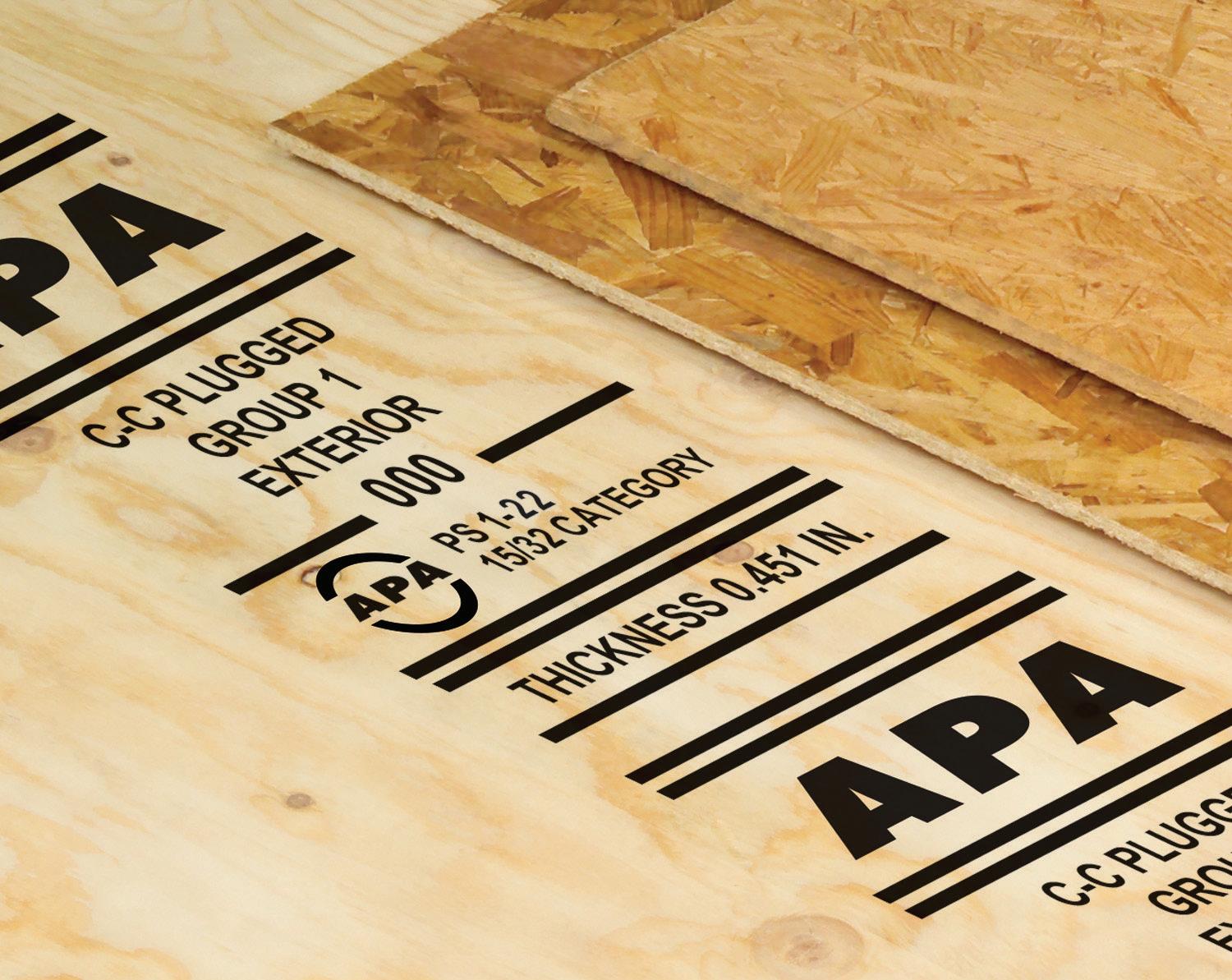
APA –THE MARK OF QUALITY FOR WOOD STRUCTURAL PANELS
WHEN ORDERING or specifying wood structural panels, it is important to receive the right panel for the application, and equally important that the panel is manufactured with the required quality. Wood structural panels trademarked by APA meet both criteria, based on qualification tests in compliance with PS 1 for plywood and PS 2 for plywood and oriented strand board (OSB), as well as ongoing quality assurance tests on every production period with a robust quality assurance system. In Canada, APA panels are trademarked to similar standards, which include CSA O121 for Douglas fir plywood, CSA O151 for Canadian softwood plywood and CSA O325 for OSB and plywood.
APA’s quality assurance system includes review of mill quality procedures, independent third-party audits of the mill quality program and regular independent testing that verifies the quality and performance of wood structural panels. APA’s quality assurance system has proactive steps to ensure any product quality issues are addressed promptly and properly in the manufacturing plant.
APA-certified products bear a trademark clearly identifying the appropriate standard and product application. The qualification and quality assurance system apply evaluation methods that are appropriate for many applications, including span ratings for roof, wall and floor construction, and for a wide variety of other uses, such
as in concrete forming, upholstered furniture frames, recreational vehicles and other products where materials with high strength-to-weight ratios, durable exterior adhesives and known mechanical properties are important.
Occasionally, imported wood structural panels are sold in North America. Those imported panels may be manufactured with foreign wood of low density or with adhesives of unknown durability, or they may be qualified by testing to a foreign standard that is not intended for North American markets.
In the past, APA has been asked to evaluate imported panels available in local markets by testing them with requirements specified in PS 1 and PS 2. In some cases, the panels were found to be lacking in stiffness and bond quality and emitting formaldehyde more than certified products conforming to North American standards. Specifying APA-trademarked panels from trusted manufacturers means getting the right product for the right application at a recognized quality level.
The APA Panel Trademark (Top Right) Explained
1. Panel grade — The term “grade” may refer to panel grade or veneer grade. Panel grades are generally identified in terms of the veneer grade used on the face and back of the panel (e.g., A-B, B-C) or by a name suggesting the panel’s intended end use (e.g., APA RATED SHEATH-
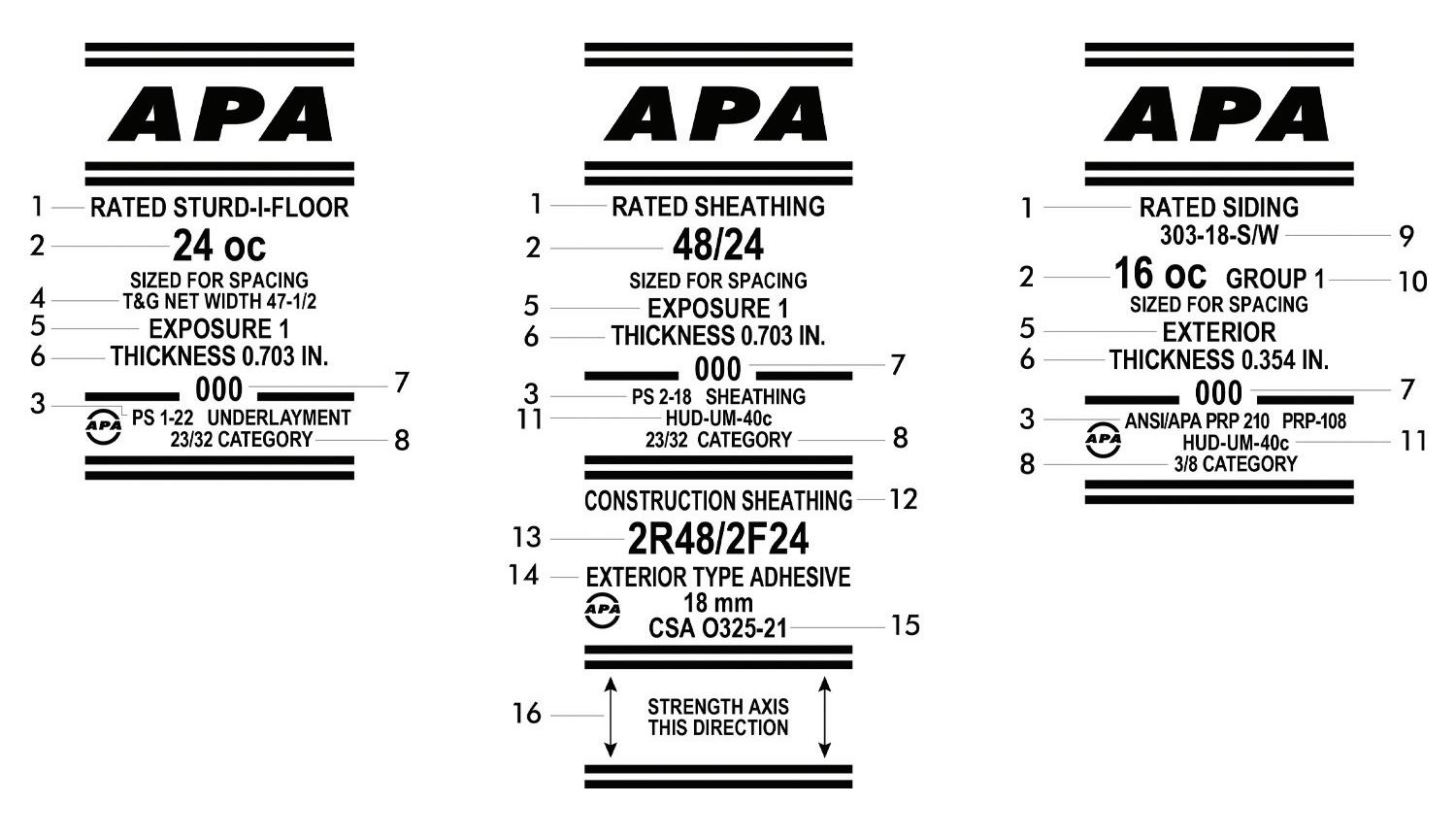
ING, APA RATED STURD-I-FLOOR, APA RATED SIDING, UNDERLAYMENT).
2. Span rating — Two numbers separated by a forward slash. The left-hand number is the maximum recommended center-to-center spacing for supports in inches when the panel is used for roof sheathing with long dimensions across supports. The right-hand number is the maximum center-to-center spacing of supports in inches when the panel is used for subflooring with the long dimension across supports. The span rating on APA RATED STURD-I-FLOOR underlayment and APA RATED SIDING panels appears as a single number. The span ratings for APA RATED STURD-I-FLOOR and underlayment panels, like those for APA RATED SHEATHING, are based on application of the panel with the long dimension or strength axis across three or more supports.
3. Product Standard — An industry product manufacturing or performance specification. Voluntary Product Standard PS 1, Structural Plywood, was developed by the plywood industry and the U.S. Department of Commerce. Voluntary Product Standard PS 2, Performance Standard for Wood Structural Panels, establishes performance criteria for specific designated construction applications. ANSI/APA RP 210, Standard for Performance-Rated Engineered Wood Siding, was developed by APA under the national consensus process of the American National Standards Institute (ANSI) to provide qualification and marking requirements during manufacture. APA PRP108, Performance Standards and Qualification Policy for Wood Structural Panels was developed by APA to provide qualification and marking requirements on APA RATED SIDING products.
4. Tongue-and-groove — A system of jointing in which the rib or tongue of one member fits into the groove of another. Tongue-and-groove edges eliminate the need for blocking beneath panel edges for support.
5. Bond classification — Exposure ratings for APA wood structural panels may be Exterior or Exposure 1. The classifications are based on the severity and duration of weather and moisture exposure the panels are designed to withstand, and the wood materials and adhesives used in manufacture.
6. Decimal thickness declaration — This value is generally at or near the lower tolerance specified in PS 1 or PS 2.
7. Mill number — Manufacturing mill identification number.
8. Performance Category — A panel designation related to the panel thickness range that is linked to the nominal panel thickness designations used in the International Building Code (IBC) and the International Residential Code (IRC).
9. Siding face grade — Grade identification of siding face, based on number of repairs and appearance characteristics.
10. Species group number — Classified according to strength and stiffness under manufacturing standard PS 1 into groups 1 through 5. Group 1 woods are the strongest, Group 2 second strongest, and so on. Typically used when no span rating is noted.
11. HUD recognition — Recognition of wood-based performance-rated panels is contained in Use of Materials Bulletin UM-40c.
12. Panel type, Canadian Standard — Some APA panels are manufactured to both U.S. and Canadian standards, and carry a dual mark, as shown in the RATED SHEATHING mark above. Other panels may carry a single mark for either the U.S. or Canadian standard.
13. Span rating, Canadian Standard — Span rating and end-use designation for use in Canada. In the Canadian span marking, the “R” signifies roofs and the “F” represents floors: 1F for single floor and 2F for subfloor.
14. Adhesive type, Canadian Standard — Adhesive type is required by Canadian building codes. Bond classifications Exterior and Exposure 1 meet Exterior Type Adhesive according to CSA O325.
15. Canadian Construction Sheathing Standard.
16. Panel face orientation indicator.
APA field representatives are available in many major U.S. cities and Canada and can answer questions involving APA trademarked products. For more information, visit www.apawood.org. BPD
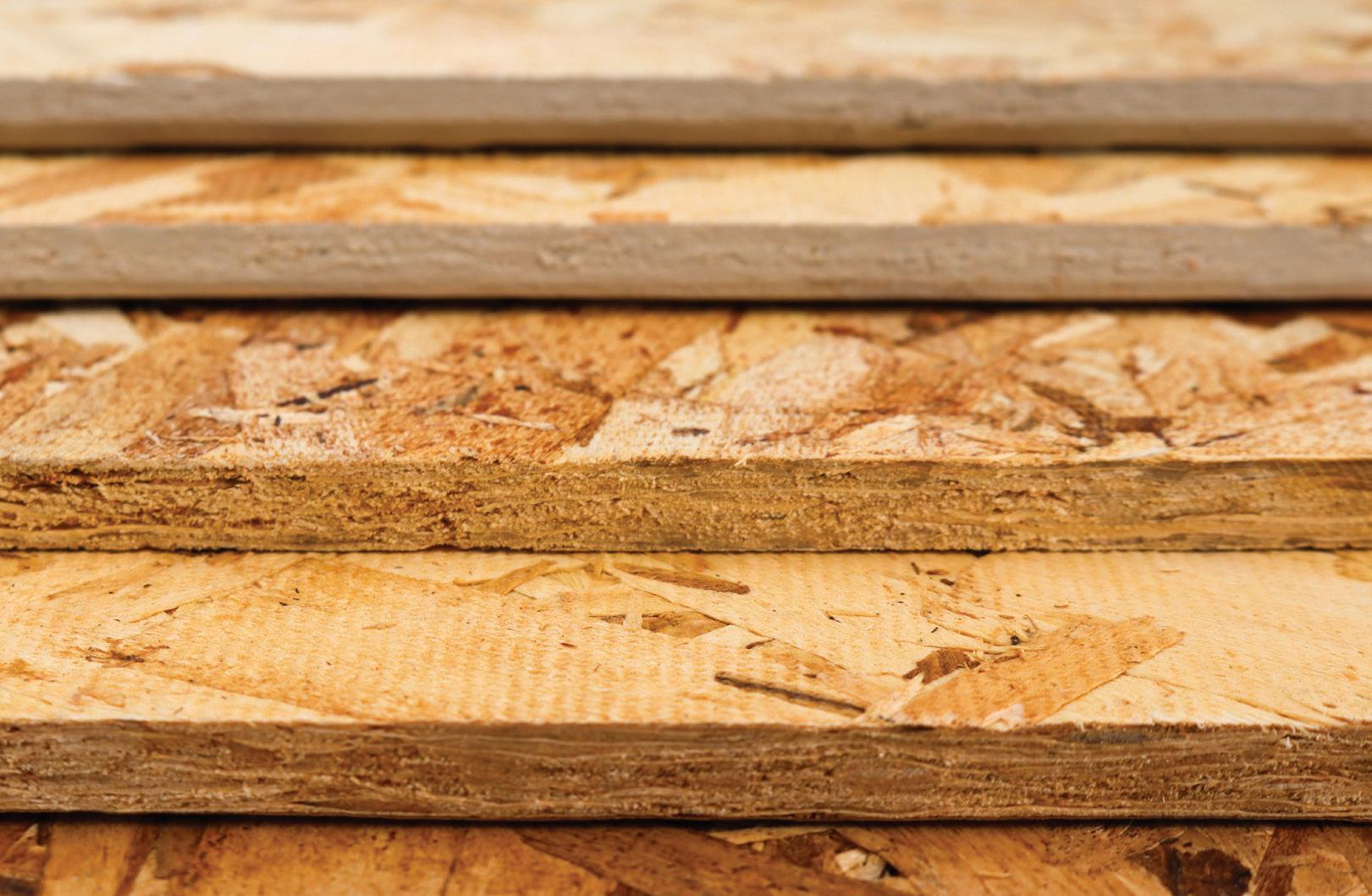
FAQs ABOUT ORIENTED STRAND BOARD
APA – THE ENGINEERED Wood Association answers some of the most commonly asked questions regarding oriented strand board (OSB) wood structural panels.
Buckling
Panel buckling occasionally results when increased moisture conditions cause expansion. Builders can significantly reduce the potential for buckling by assuring minimal moisture content increase in service and/or providing for its natural effects.
If the OSB panels are tightly butted during installation, there is no room left for expansion, and buckling can occur. APA recommends a 1/8” space between panel edges and between panel end joints. In moist or high-humidity conditions, wider spacing may be required.
Helpful Hint: Use a 10d box (0.113”x3”) nail to gauge the 1/8” spacing between panels. For roof applications, spacer-type panel edge clips may also be used.
Typical Fastener Recommendations
For roof, wall and floor applications, a minimum fastening schedule of nails at 6” o.c. should be provided at supported panel edges and 12” o.c. at intermediate supports. Fasteners should be 3/8” from panel ends and edges. Installing panel fasteners at a greater end or edge distance can lead to panel edge curling or missing the framing (shiners).
Surface Flaking
OSB panels exposed to moisture may exhibit a rough, uneven surface. Lifting or flaking of surface strands on OSB panels may also occur. Structural tests show that such surface degradation does not result in a loss of panel structural capacity after the panel dries to in-
service moisture conditions.
It is not uncommon for wood structural panels, including OSB, to be exposed to the weather for a month or more during construction. The panels’ surface often appears rough and discolored, but they generally remain structurally serviceable. The best way to preserve panel performance is to protect them from weather exposure. Only Exterior-rated panels are intended for long-term exposure.
Thickness Swelling & Edge Swelling
OSB panels exposed to excessive moisture conditions for extended periods may exhibit irreversible thickness swelling, typically near panel edges or ends and occasionally throughout the entire panel if exposure is severe. Tests show, however, that such swelling generally does not result in a loss of structural capacity of the panel after it dries to in-service moisture conditions.
The thickness swell of a panel exposed to moisture during construction may give the appearance of overdriven fasteners when, in fact, the panel has swollen while the fastener remains in place. This can be verified by measuring the thickness of panels where fasteners appear to be overdriven and comparing measurements where panels have been protected from the weather or to the decimal panel thickness included in the APA trademark. Nails overdriven into structural sheathing may not perform as expected.
Sized for Spacing
“SIZED FOR SPACING” is a notation often found in APA-Rated Sheathing, APA-Rated Sturd-I-Floor and
(Continued on page 54)
TUF-TRED®
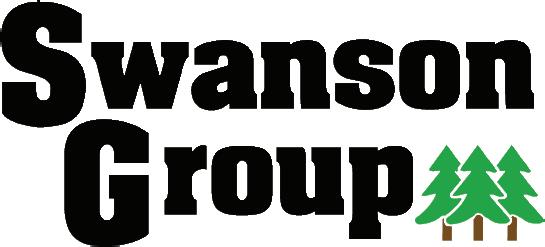
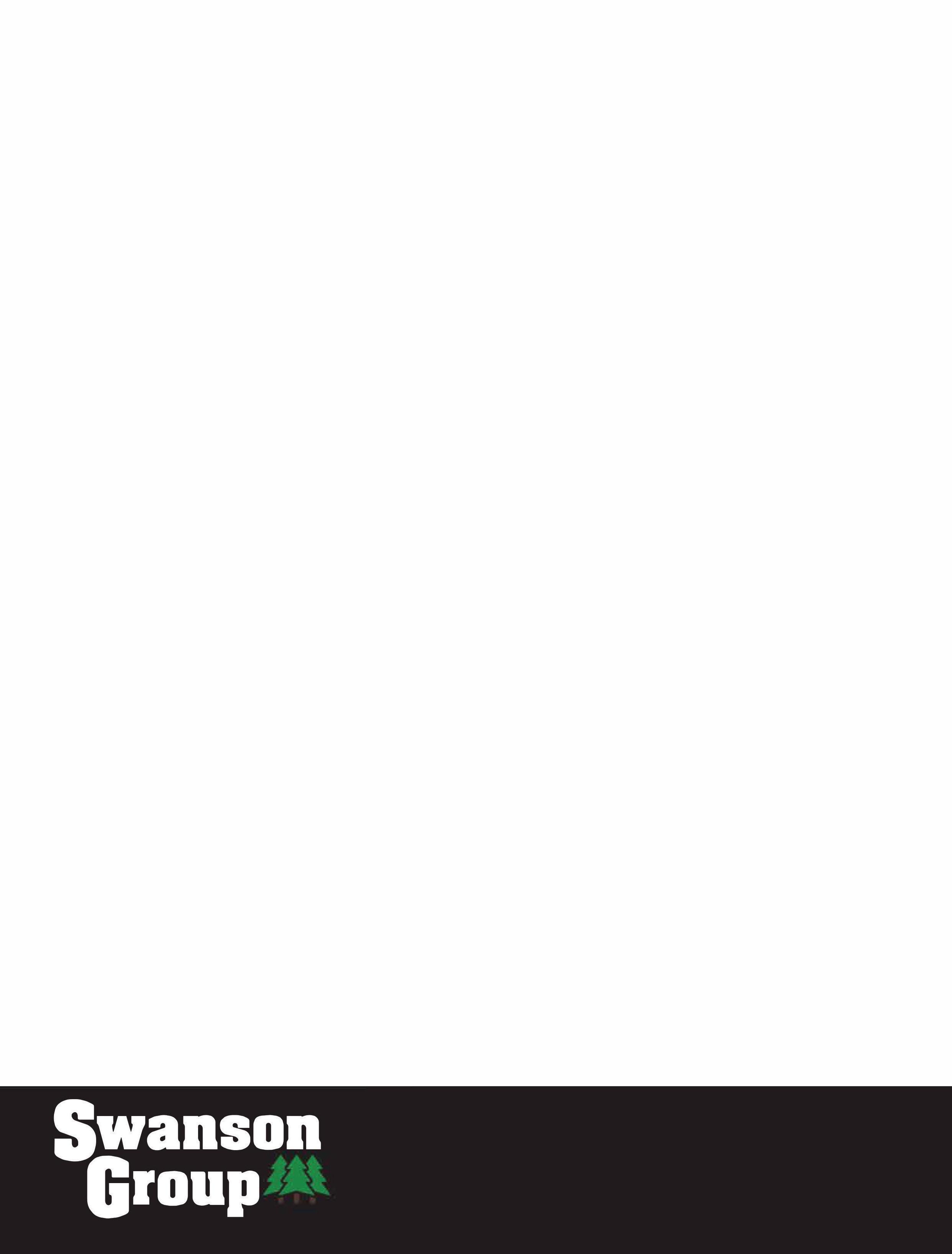
• Superior skid resistance
• Surface durability
• Weatherability
• Moisture resistance
• 4x8 panels, ¾" thick
• ADA Approved
Swanson Tuf-Tred is ideal for interior or exterior stair applications where skid-resistant surfaces are desirable.
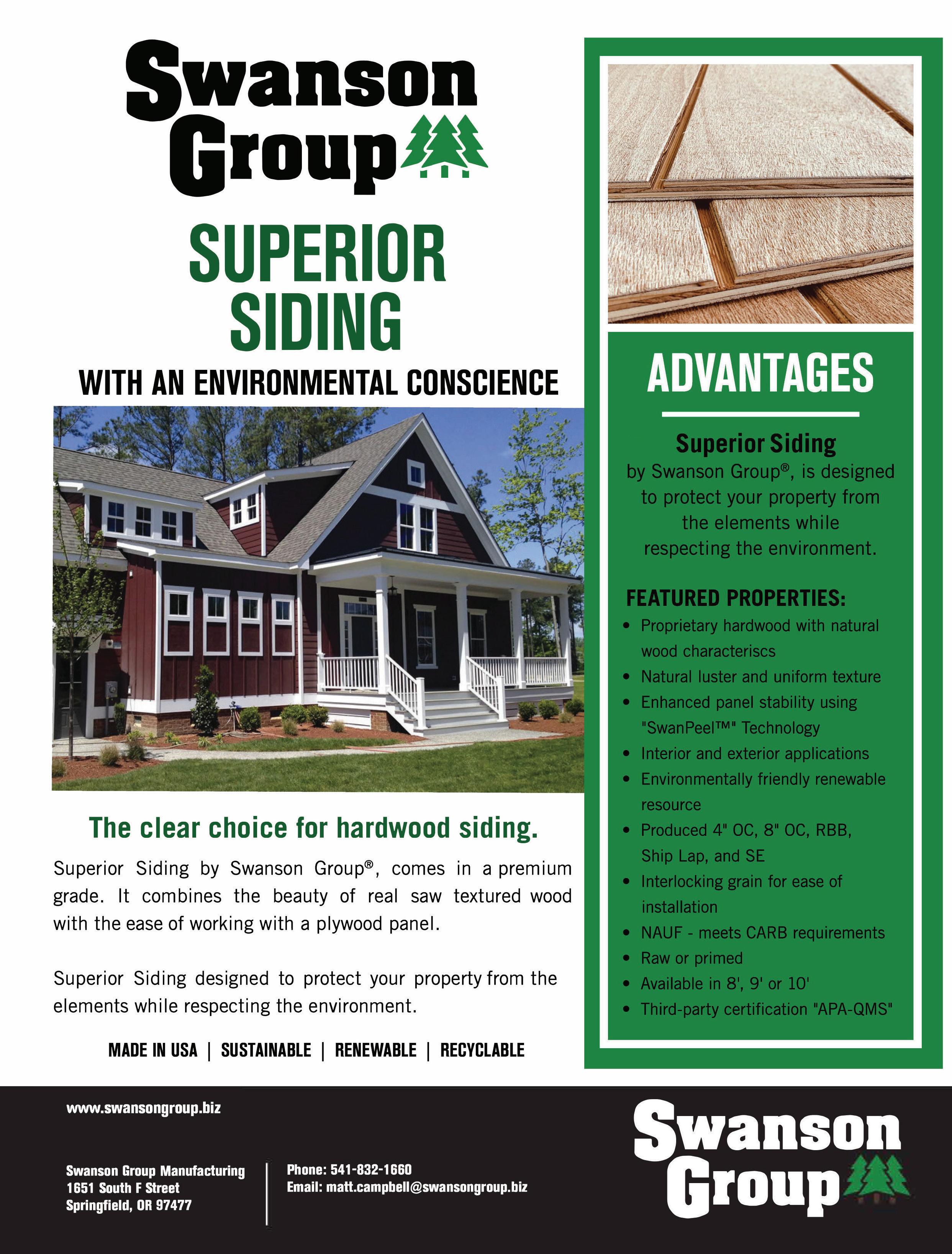
PASSING THE BATON
------------
BY SARA GRAVES
RELATIONSHIP. Loyalty. Commitment. These are the words that the folks E&E Lumber have lived by for 58 years. And the reason that they have remained a steady resource for the homeowners and contractors across Washington state.
“This whole business is relationship based, from the customer to the vendor,” says Brent Emory, VP of E&E, who started with the company at 16, then took over the family
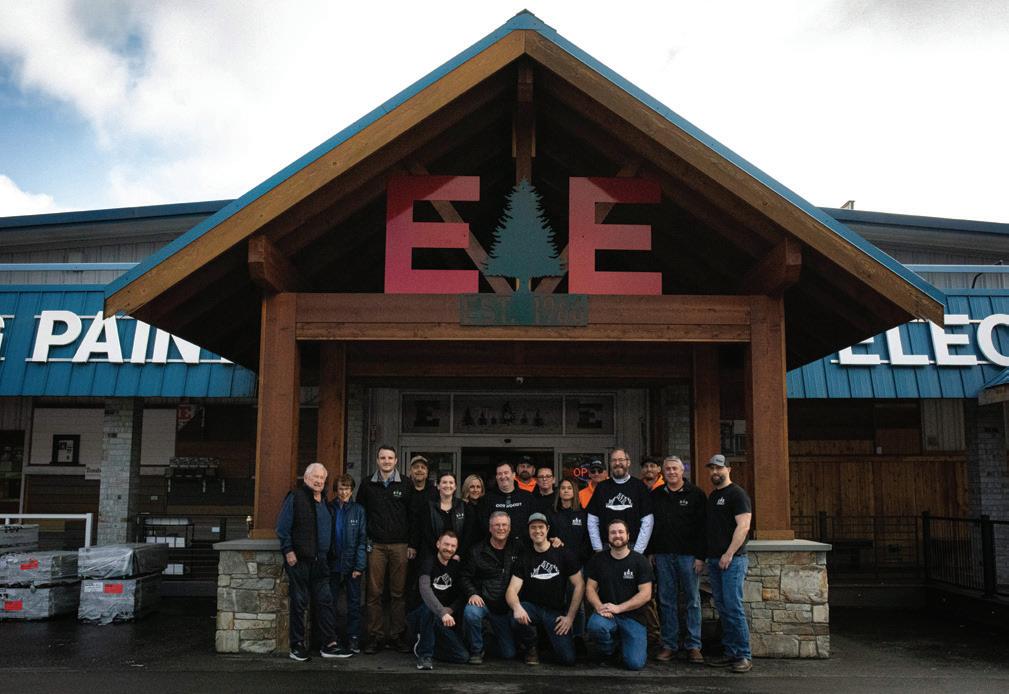
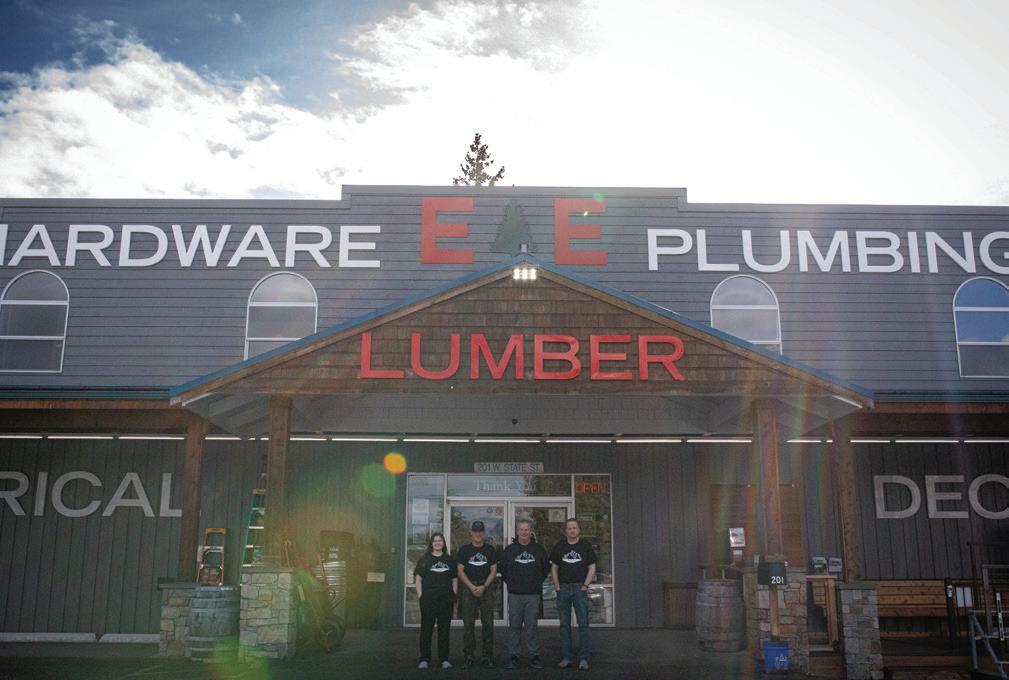
WASHINGTON’S E&E LUMBER LOOKS AHEAD
business 43 years ago at the age of 21. “That’s always been my philosophy growing up—and my whole life.” He equates it to a marriage: “It’s about talking about stuff, having good communication.”
In Emory’s 20s, he and his staff built many of their decades-long, customer relationships from their two Washington locations in Marysville and Sedro-Woolley. It’s why 75-year-old Ron Loop of Loop Construction still comes into the Marysville store 45 years later to buy his supplies.
Yet, as Emory is looking towards retirement, so too are a number of his longtime customers. He shared that one of his employees, who has been with the company nearly 40 years, has seen some of his customers retire that he used to work with every day. Emory says others are “phasing out, moving south, or unfortunately passing away.”
That’s why Emory has educated his children and younger staff on the importance of building their own relationships with younger clientele. “You do something long enough, there’s going to be change one way or another. The kids, the younger contractors, need to do their thing.”
He says relationship building is all about team building. He points to his family’s relationship with Mike Reimer, president of family-owned Western Wood Preserving Co., Sumner, Wa., and Mike’s two children, who enjoy motorcycle riding together.
Ultimately, Emory says, it’s about loyalty, quality, good service, and competitive pricing. “You want your customer to be loyal to you and vice versa. You always try to do the right thing with your customer. Hopefully, you’ll have them for 30 years or so like we did.”
Emory has taught his staff, including his son-in-law Kyle Rossnagle and daughter, Brooke Rossnagle, that quality and good service have been the keys to keeping E&E Lumber competitive despite the four box stores within five miles of their Marysville location and the two box stores within five miles of the smaller Sedro-Woolley location.
“People like coming to us because they get the quality help. All our people have been here 12 to 40 years. We give them that quality help, and get them the answers instead of just pointing them down an aisle.”
This, in turn, has kept their sales steady year over
E&E LUMBER is all about relationships at both its Marysville (upper photo) and Sedro-Woolley, Wa. (lower), locations.
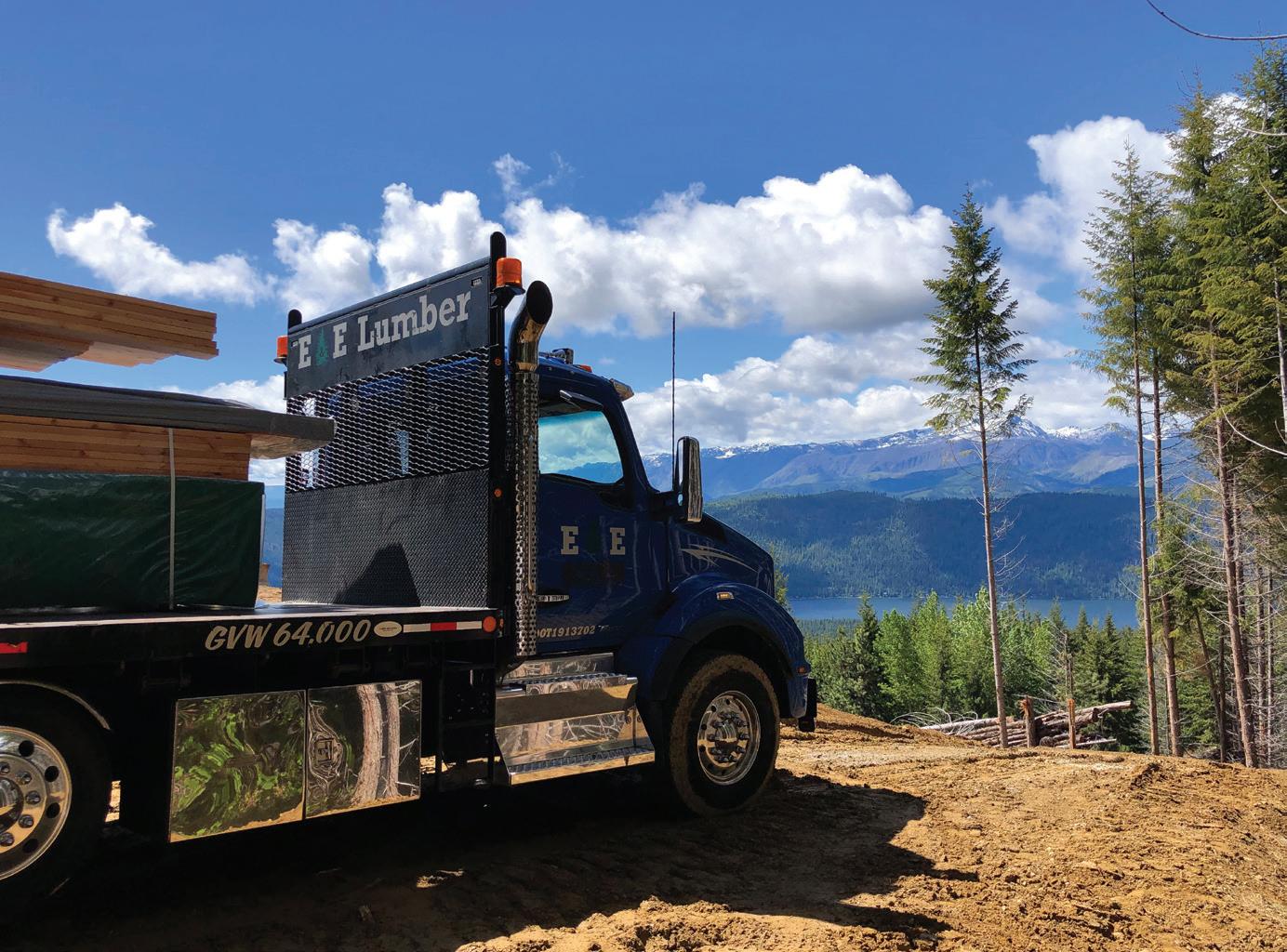
year. That and their fully stocked lines of decking including Trex and TimberTech. “We have really good suppliers that we work with. We get our products every day—next day if we special order it. The quality of the service is what keeps (the customers) faithful.”
They also stock premium Douglas fir purchased from Weyerhaeuser in Seattle, Wa., and treated products by Western Wood Preserving.
E&E, whose business is made up of approximately 20% treated wood, had been dealing with Western Wood Preserving for over 35 years, but made
them their primary treater during the pandemic when their previous treater wasn’t able to provide what they needed. Emory explains that one of Western Wood’s sales managers had been trying to get them to switch for 37 years. “Once we switch,” Emory explains, “we’re extremely loyal.” Western Wood Preserving makes stops at E&E three days a week.
“I feel if you’re loyal, you’re going to always be taken care of,” Emory adds. “The guys that aren’t browbeating (their suppliers) all the time for better pricing are gonna get—if the deal does come up—they’ll really hook you up, take care of you. I just feel the loyalty there at the end of the day—everything is long term, if you plan on being in business long term.” BPD
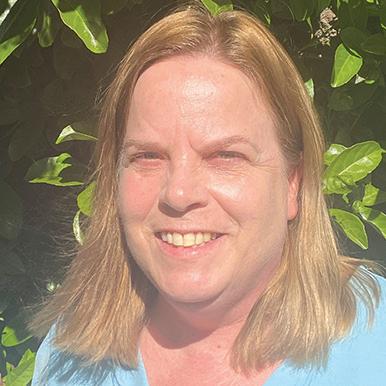
SARA GRAVES
Sara Graves, senior editor, is interested in your story. Contact her at sgraves@526mediagroup.com.
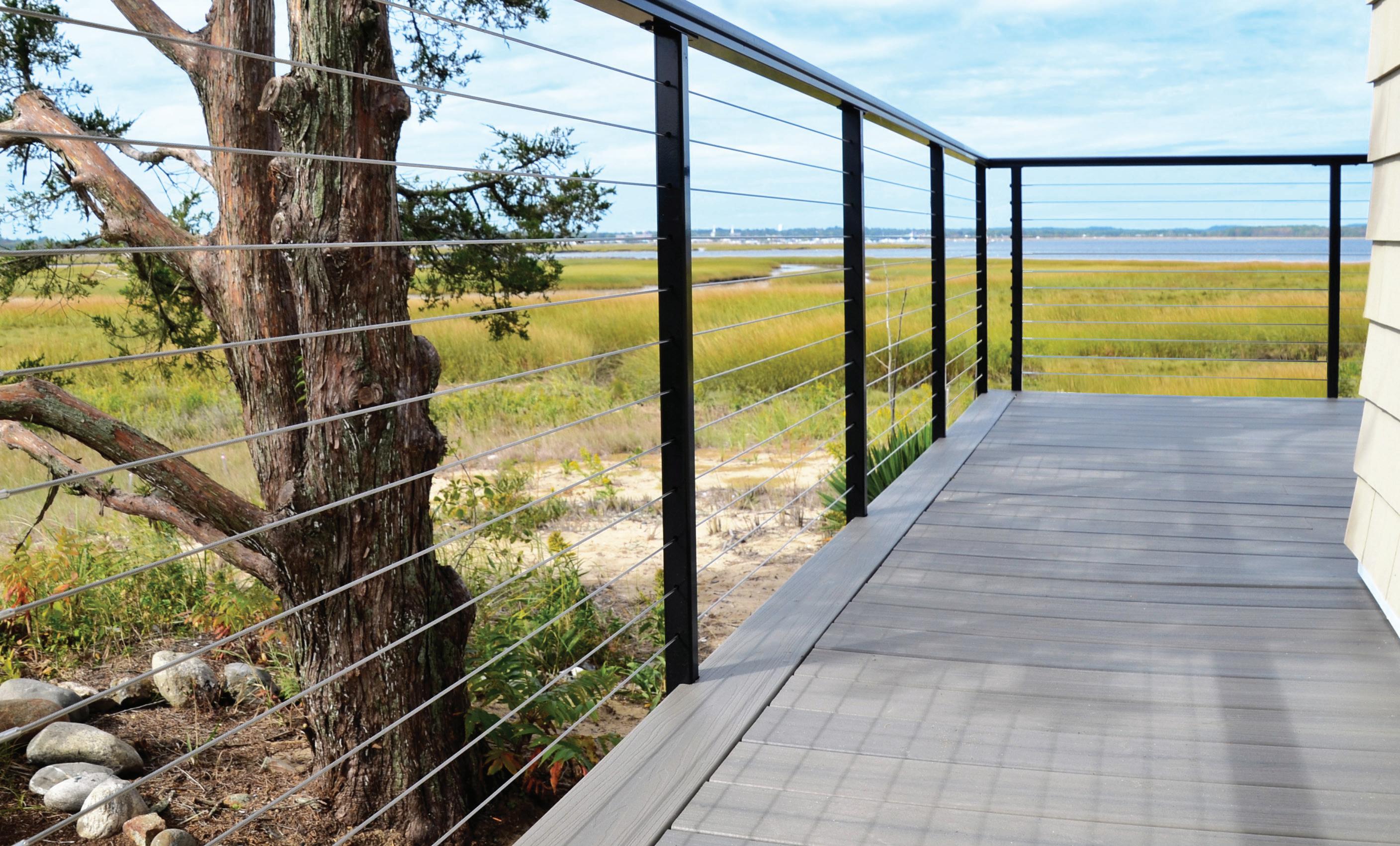
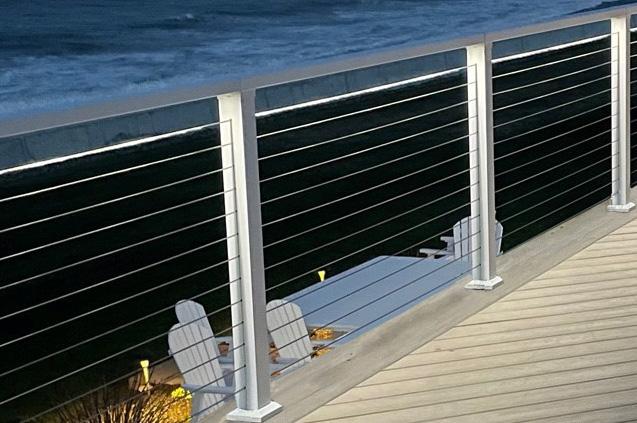
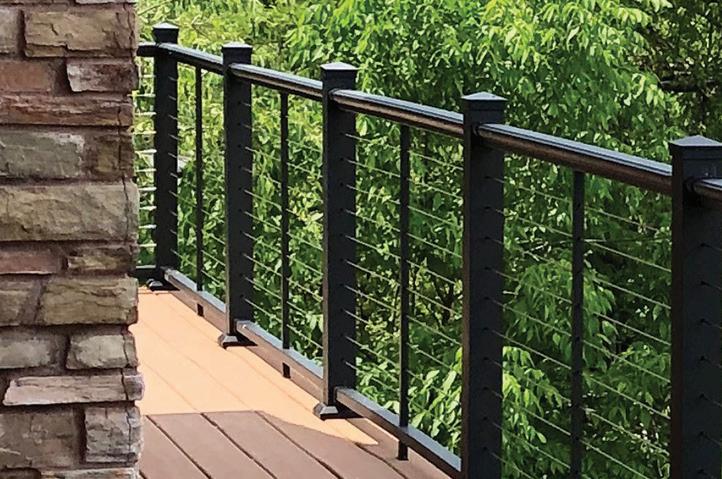




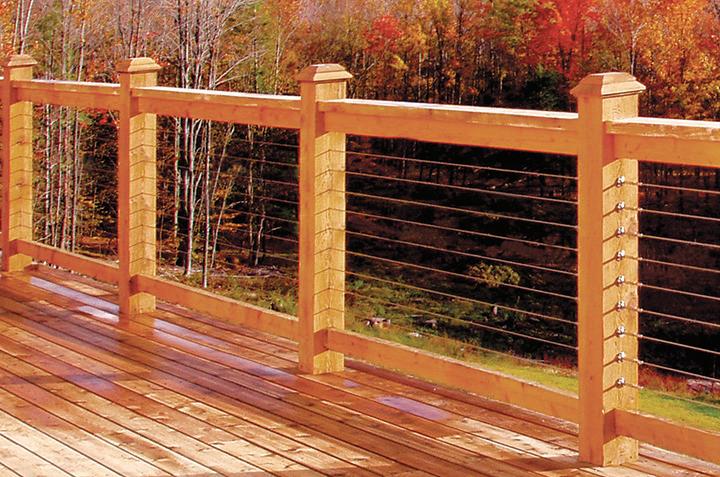

LOYALTY is ingrained toward E&E’s employees, customers and suppliers.
QUESTIONS
------------ BY JAMES OLSEN
MOST SALESPEOPLE
talk too much. The Master Seller knows how and when to ask questions.
Open-Ended Questions
Open-ended questions help customers engage. Many sellers “feed” the answer in the question, which leads to monosyllabic, non-engaged answers. Example:
Salesperson: You’re probably using southern yellow pine, right?
Customer: Yes.
Salesperson: Do you use random lengths or straight lengths?
Customer: Random.
Versus “open-ended”:
Salesperson: What species do you use?
Customer: We mostly use southern yellow pine in 2x8 – 2x12, but we use spruce in our 2x4 and 2x6 and our studs.
One Question at a Time
Another mistake is asking multiple questions in a row. This can be confusing to the customer and breaks rapport. Example:
Salesperson: How do you normally buy your lumber? Do you put out an RFQ or do you buy off offerings or do you do it after you do your inventory?
Better: How do you normally buy your lumber?
Simple, open-ended questions are better. Customers are more likely to give us a more detailed answer when we give them room to do so. “Fed” and multiple questions lead to short and non-detailed answers. Conversation will flow more when we give our customers space to elaborate.
Questions on Inquiry
Many sellers are in such a hurry to quote product that they don’t take a thorough inquiry. When we don’t take
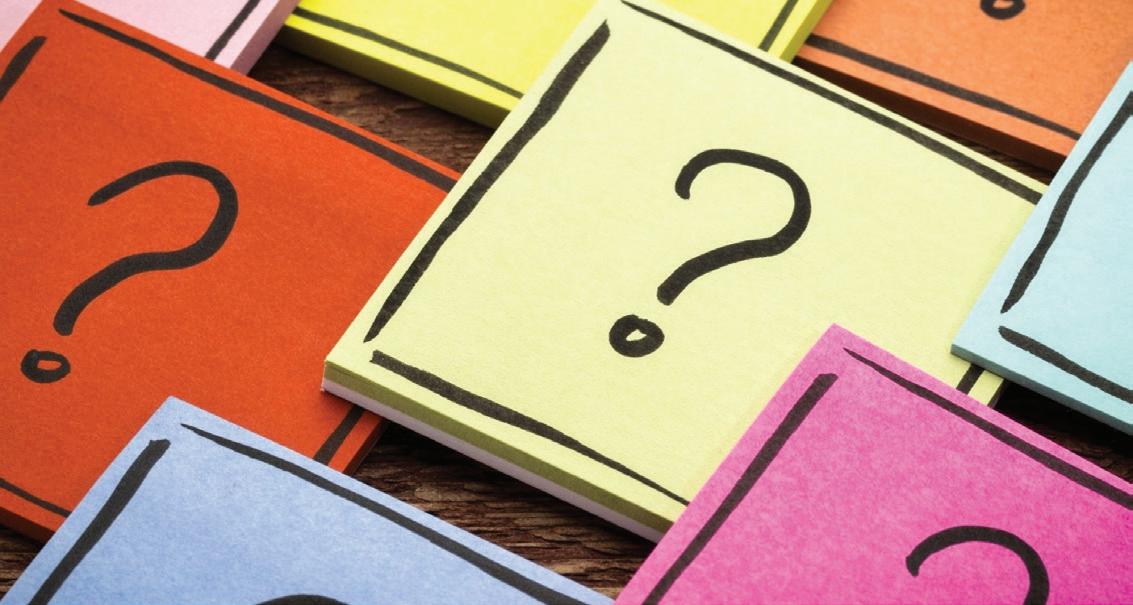
a thorough inquiry, we send the message “I’m just here for a quick order” which is easy to say no to. In addition, when we don’t ask enough questions, we often come back with the wrong item because we missed the nuance of what the customer wants. Example: Customer: I’m looking for a 2x4 random.
Salesperson: Okay, let’s go look for that and I’ll get back to you with a quote.
Better:
Customer: I’m looking for a 2x4 random.
Master Seller: When you say random, what kind of tally are we thinking?
Customer: 8 through 16, heavy 16.
Master Seller: When you say heavy 18, how heavy are we needing?
Customer: About 75% 16.
Master Seller: What would the rest of the tally look like?
Customer: Maximum one 8 and 10 foot, three to four 12s, and maximum two 14s.
Master Seller: What grade are we needing?
Customer: Euro premium.
Master Seller: Could we use a highline western or eastern spruce?
This extra question gives the seller more options to provide more value to the customer and more options to get the order.
Customer: I could use a highline western out of ABC or XYZ Sawmill.
Master Seller: When do we need it to ship?
Customer: Two weeks or sooner.
Master Seller: Could we live with three weeks?
Again, this gives the seller more options to bring value. There may only
be two mills that can do two weeks shipment and there may be 10 mills that can do it for three.
Customer: Yes, I can live with three weeks.
Master Seller: What are we thinking of paying on this?
Most sellers are too intimidated to ask this question because a lot of buyers won’t answer it. Master Sellers make price just another detail to be discussed between partners. They train customers to be open with them. It will take more time to get some customers to treat us like a partner, and some never will, but we must try with all of them, and most will over time. If the customer is thinking of an unreasonable price it is better to discuss early rather than doing a bunch of work and finding out later.
Asking for the Order
Somewhere between 80% and 90% of sellers fail to ask for the order. Most sellers present product and then wait silently for the customer to buy or give the price and ask, “What do you think of that?” The problem with both of these methods is that they work. They just don’t work as well as asking simply and directly for the order.
Master Sellers tell the customer why what they are offering is a good deal and then ask, “Can I earn your business on this?” There are many ways to ask for the order but asking is a must for success in sales.

JAMES OLSEN

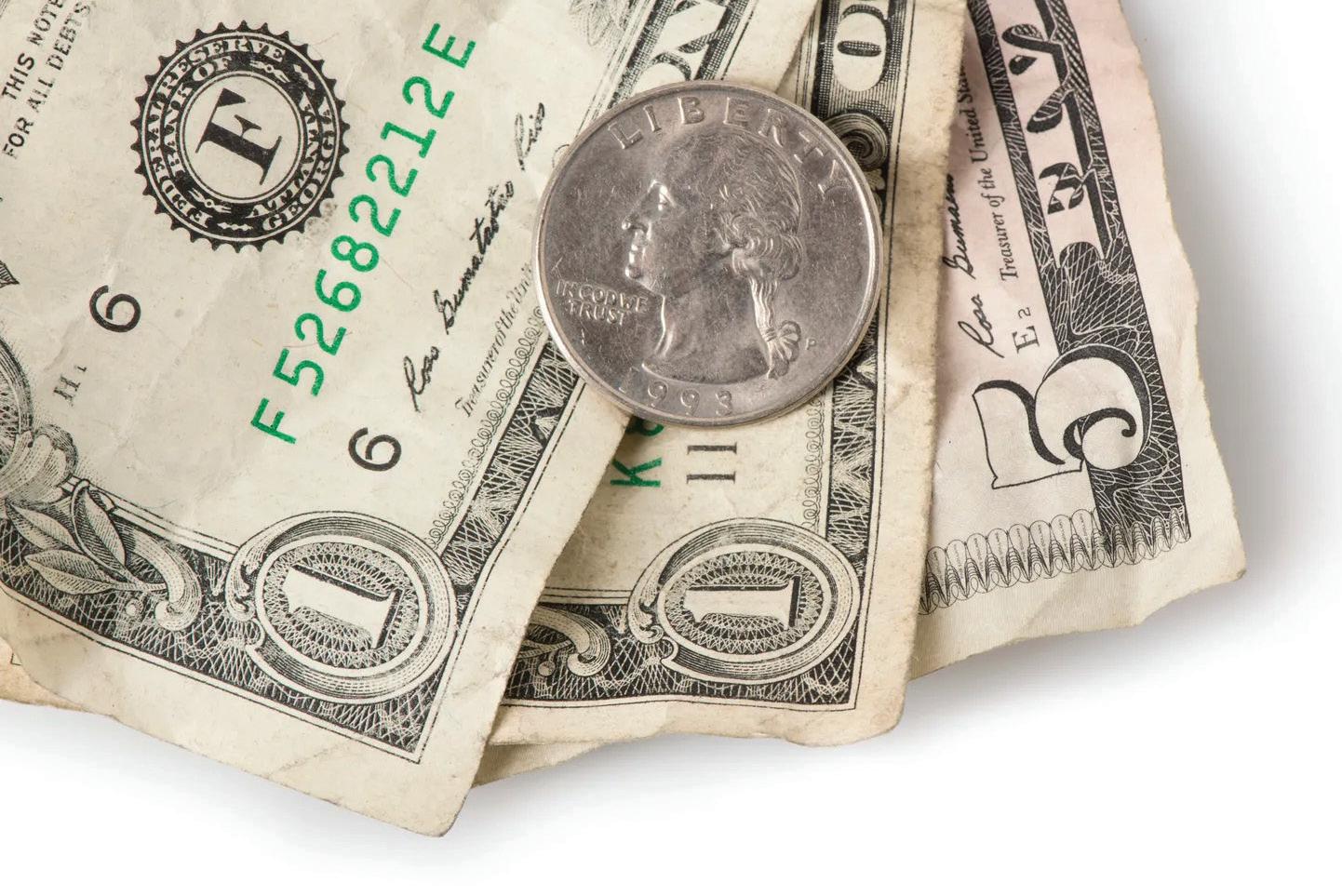
WHAT DO WE DO WITH THE NEW EXEMPT MINIMUM SALARY?
BY PAIGE McALLISTER
While legal challenges have been requesting an injunction until the question whether the U.S. Department of Labor (DOL) has the right to increase the salary threshold is determined, no such injunction has been issued as of this writing. Therefore, all employers must prepare their response to the new rule which goes into effect July 1, 2024.
IN APRIL, the U.S. Department of Labor (DOL) announced its long-anticipated change to the “white-collar” exemptions (Executive, Administrative and Professional, or EAP) and highly-compensated exemptions. The changes were published to its website.
Increasing the salary requirement reflects the overall growth of wages in general as well as the thinking that an employee with exempt-level responsibilities to be truly exempt should probably be making more than $17.10 per hour.
The DOL estimates that by January 1, 2025, the exemption of four million workers will be impacted unless their employers increase their weekly salary, while another 292,900 workers will be impacted with the increased Highly-Compensated salary.
First, the Basics
The Fair Labor Standards Act (FLSA) is enforced by the DOL and dictates several areas of labor law including minimum wage, overtime, compensable time, child labor, and independent contractors. FLSA also requires all employees to be classified as exempt or non-exempt according to its definitions and tests.
Non-exempt employees must be paid at least minimum wage for all hours worked and time-and-a-half their regular wage rate for all hours worked over 40 in a workweek (defined as a set seven-day period). To ensure
proper wage payment, records must be kept of their exact time worked within this seven-day period, although how time is tracked is left to the discretion of the employer. Non-exempt employees can be paid hourly or salary.
Exempt employees are not required to be paid overtime and do not need to track their exact time worked. While there are many categories, the main ones are Executive, Administrative, Professional, Computer, Outside Sales, and Highly-Compensated. To be classified as exempt, employees must pass three tests:
1. Be paid on a salary basis (defined as a wage guarantee) which is not reduced based on time worked or not worked;
2. That salary must be no less than the minimum salary threshold (This is the test under discussion now.); and
3. Meet the job duties test for their applicable category.
As with all labor laws, if an employee’s classification is uncertain under these tests, the employee must be classified as “non-exempt” as this is considered the most favorable to them.
New Minimum Salary Threshold
The “good” news: the DOL did not change the job duties test.
The “bad” news: the DOL announced a significant increase to the minimum salary threshold although they softened it by allowing for a two-stage increase. The EAP salary was calculated based on the 35th percentile of weekly earnings of full-time salaried workers in the lowest-wage Census region. The Highly-Compensated salary was based on the annualized weekly earnings of the 85th percentile of full-time workers nationwide.
The announced minimum salary threshold for EAP and Highly-Compensated exemptions will increase as follows:
Current $684 $35,568 $107,432 June 30, 2024
July 1 - $844 $43,888 $132,964 Dec. 31, 2024
Jan. 1, 2025 – $1,128 $58,656 $151,164 June 30, 2027
July 1, 2027 + every The salary basis will be recalculated based on a 3 years thereafter formula to be announced
What to Do Now
All employers need to review their payroll roster to determine which currently-exempt employees will fall below the higher salary threshold and then take one of the below steps for each:
• Keep those employees exempt: If you want to ensure the employee stays exempt, you will need to increase their salary to meet the above standards by the effect dates.
o If the increase is minor, consider making it their annual adjustment.
o If the increase is significant, consider explaining that this increase encompasses their annual increase for the next two to three years since the next increase will not be required until July 1, 2027.
• Reclassify those employees to non-exempt: Given the salary threshold is almost doubling by January 1, 2025, employers may decide that it is best to reclassify these employees as non-exempt to avoid having to pay the higher salary and to reduce misclassification exposure. If you choose this route, advise employees:
o of their non-exempt status;
o of their hourly rate or, if still salaried, effective hourly rate (weekly salary divided by the number of hours they will work, usually 40);
o how to track their exact work time;
o what is considered compensable time; and
o that they will be entitled to overtime.
Whatever you choose, notify employees in writing of all changes prior to the effective date.
Challenges
While some employers will absorb the increase with minimal impact, small employers and/or those in the lower-wage industries and/or Census areas (typically the South and Midwest) may find the salary increases difficult to budget for and sustain long-term. These employers may find it best to convert all but the highest-paid employees to non-exempt so they can more easily manage pay rates in line with the markets and trends of their area and/or industry.
Even companies that can manage the increases may then need to deal with resulting wage compression across the rest of their organization so all employees are paid fairly based on factors such as job duties, educa-
Q. We allow employees to have their personal cell phones at their desks while they work, but we have some who take advantage of this. One employee spends most of the day taking calls from her family and friends while another watches his favorite shows and TikTok videos while he is working. What can we do without penalizing those who use their cell phones only when needed?
A. Cell phones can cause major disruptions in the workplace. Ring and text tones can be loud and annoying; conversations or streamed content can be disruptive and not suitable for the workplace; and any time spent talking, texting or watching is time not working or being productive.
You can expect employees to perform their job duties with minimal personal distractions during their work time. Address those that are creating issues with their cell phone use. Explain that this use is keeping them from meeting expectations and creating distractions preventing others from working effectively.
You can also consider offering meal and rest breaks and defining these as the only times employees can make calls, send texts, or stream content. By offering these breaks, you can reduce the during-work-time use except in emergencies.
Hopefully by addressing the specific behavior and offering defined times for use, you can control disruptions without having to escalate to disciplinary action.
tion, and experience. Wage compression can cause low morale, result in high turnover, and lead to legal challenges. Employers facing wage compression issues could consider:
• initiating an across-the-board rate increase so employees are still paid comparable to their duties, experience, etc.;
• defining that the required increase will cover a longer period (i.e., two years instead of one), adjustable based on the percentage of increase; or
• offering employees impacted by wage compression bonuses, benefits, and/or perks (such as flexible scheduling, professional development reimbursement, or more PTO) to adjust their overall compensation.
Looking to the Future
The Workplace Advisors will continue to monitor this DOL change including clarification and legal decisions as they develop. We are here to answer questions and help you develop a plan to address this change and its impacts in the future. BPD
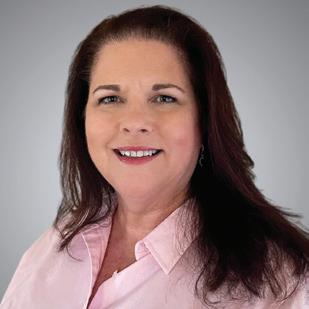
McAllister, SPHR, SHRM-SCP, is vice president for compliance with The Workplace Advisors, Inc. Reach her at (877) 660-6400 or paige@theworkplaceadvisors.com.
PAIGE McALLISTER
Paige
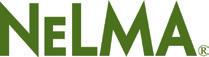
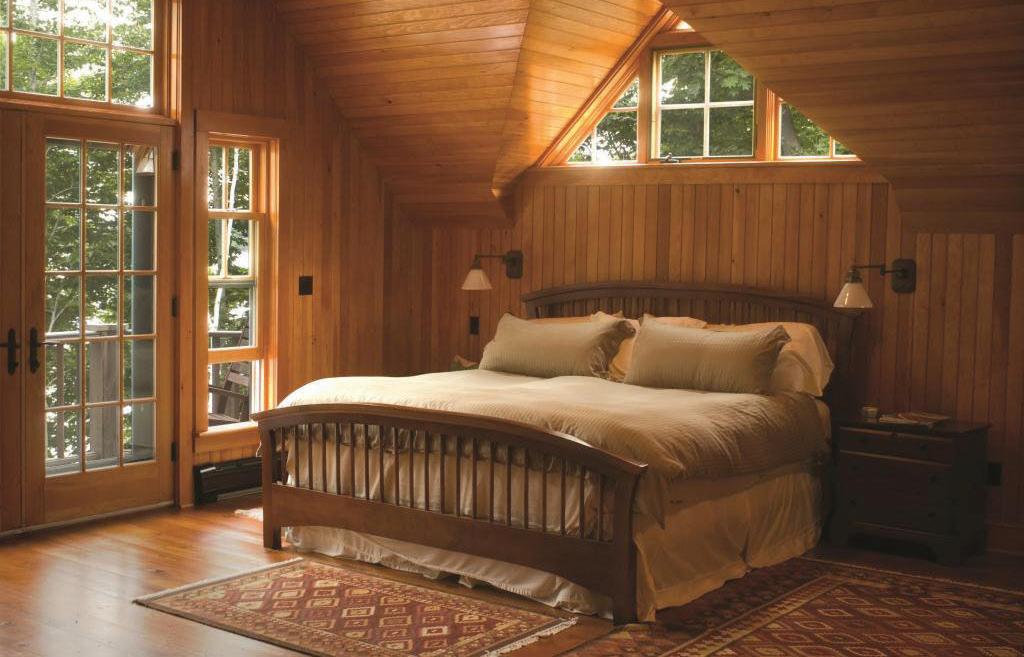
THE TRUTH ABOUT WOOD
------------ BY JEFF EASTERLING
“LOW MAINTENANCE.” “Natural looking.” “Real wood look.” “Environmentally friendly.” “Green.” Words and phrases such as these are used frequently to describe certain building materials, but here’s the funny part: the products they are describing don’t fit these descriptions at all. The truth is, descriptors like those above only fit one product across the board: real wood.
This isn’t new information. A 1960 brochure called “A Case for Wood,” written and shared with lumber dealers nationwide, was designed to educate via wood-selling tips. This published piece addressed myths and misconceptions about the use of wood head-on and refuted them with cold, hard facts. Topics addressed included dry rot, insects, fire safety, paint performance, and dimensional stability.
That was 1960. Even then, wood was under attack by alternative materials claiming to be better, stronger, cheaper, longer lasting. And yet—here we are in 2024, and wood is still the premier building material of choice. And once again, we are seeing lesser materials attempting to take down wood with outdated and incorrect misinformation. Wood has stood the test of time as the building material of choice for more than four centuries—we don’t think that will change anytime soon.
Have you ever stopped to take a look at the history of wood as a building product? Join us for a quick trip through time!
• Back in the stone age when dinosaurs roamed the earth (probably), man used wood for shelter, fires, heat, transportation of food and to carry their stuff to the next camp. Were dinosaurs used to harvest wood? We’re not sure, but we think so.
• Decades ago, archaeologists from the University of Pennsylvania unearthing a site in Ankara, Turkey, discovered huge wooden beams that had survived for about 2,700 years. The beams were hand-cut, sanded and smoothed in a beautiful fashion, and expertly fitted together in such a way that the joints could hardly be seen. The wood wasn’t treated with anything special—it was just wood that was strong enough to survive thousands of years.
• Fast-forward to the American Revolution. Across the beautiful original 13 Colonies… was wood. Homes and mills and businesses, all constructed with locally grown and harvested wood, still stand today and showcase the use of real wood in the early years of this great country. In fact: we at NELMA worked on a project in 2023 with This Old
House to renovate a Massachusetts home originally built in the 1720s—and much of the original wood was still intact and used throughout the home.
• The next several decades after the Revolution saw the expansion of America from the East Coast to the West, and what building material was used to develop new towns and homesteads? Easily accessible real wood. America was built on wood, and wood is the heart and soul of the genesis of the United States.
• About a century ago, the first wood associations came into existence, with the purpose of promoting the use of natural, renewable, gorgeous wood to lumber dealers, builders, and consumers across the country. Much of the work still done today by these associations (like NELMA) focuses on educating and re-educating the end user as to the value of wood. Why? Because we are a country that often falls victim to shiny, new products. We are led to believe that plastic decking will last longer than wood and be easier to maintain—but this isn’t true. We are led to believe that concrete is somehow more environmentally friendly than wood—take a quick look at how concrete is made and even a small child will tell you that wood is friendlier to the earth.
Too often, we see these new products failing down the road or being touted for uses for which they are not approved. No surprise, this leads to failure. Misinformation campaigns are rife across the industry today, as anyone attending a building industry trade show can attest. But it doesn’t matter what the alternative materials say, it doesn’t matter how loud they yell, it doesn’t matter how much money they spend—the truth is the truth.
Wood is renowned for its beauty, its lasting quality, its ease of use, it’s strength, its durability and so much more. No other building material requires so little care and maintenance. No other building material brings the level of carbon sequestration to the table that wood does. Wood is the original green building material: always has been, always will be. The wood industry is backed by data, by life cycle assessments that tell the tale of wood vs. alternative materials, and by facts. Do your research, read and learn, and you’ll see the true picture.
So, bring on the fake, alternative, earth-destroying products: wood isn’t going anywhere, and we’re backed by the truth. See you in another thousand years. BPD
– Jeff Easterling is president of the Northeastern Lumber Manufacturers Association (www.nelma.org).

MINNESOTA’S SIMONSON LUMBER
PURCHASED BY KODIAK
Kodiak Building Partners, Englewood, Co., has acquired Simonson Lumber and its six operating locations in central Minnesota. Simonson has yards in St. Cloud, Alexandria, Baxter, Crosslake and Hutchinson, Mn., and its corporate headquarters in St. Cloud.
“Great Odin’s Raven, that escalated quickly,” said Kodiak CEO Steve Swinney. “Simonson Lumber’s deep-rooted presence in their community and commitment to quality resonates with Kodiak’s goal of empowering local businesses to thrive. Together, we are poised to meet the escalating demand for housing and construction solutions in Minnesota, leveraging Simonson’s expertise and Kodiak’s resources to create lasting value for our customers and communities.”
The partnership between Simonson and Kodiak opens new avenues for growth and innovation on multiple fronts, leveraging Kodiak’s network and capital expertise to fuel expansion. Founded in 1913, Simonson is positioned to emerge as the preferred partner for family-run lumberyards across Minnesota, harnessing Kodiak’s support and resources for accelerated growth.
The acquisition ensures the continued success and legacy of Simonson Lumber in the Minnesota market. By prioritizing a people-first mentality, Simonson Lumber remains committed to its core values of fostering relationships beyond transactions and navigating the industry’s evolution alongside its customers and suppliers.
RP ACQUIRES MISSOURI’S THORNE
R.P. Lumber Co. has purchased Thorne Lumber Co., with three locations in northwestern Missouri.
The Thorne Lumber locations in the Missouri communities of Chillicothe, Cameron and Plattsburg bring R.P. Lumber’s total location count to 87, including 20 in Missouri.
“Strategically, this is the right decision,” remarked Pat Thorne, owner of Thorne Lumber. “Susan and I have been contemplating our next move for a few years now. We have worked very hard and very diligently to make sure we made the
best decision and, as we have gotten to know R.P. Lumber and their team, this made the most sense for our employees, our customers, and the communities we serve.”
CARTER EXPANDS IN LOUISVILLE
Carter Lumber, Kent, Oh., has opened a new full-service lumberyard in the Louisville, Ky., market.
In 2020, Carter began servicing builders and remodelers in Louisville through a downtown showroom, focusing primarily on cabinetry and millwork. The success of this showroom and growing demand from customers prompted Carter to expand its services to include a full-service yard, which officially opened on June 1.
Nate Christie, a seasoned professional with over 20 years of experience assisting builders in Louisville, is managing the new location.
LESTER GROUP PURCHASES VIRGINIA BUILDING SUPPLY DEALER
The Lester Group has purchased Custom Builder Supply Co., Williamsburg, Va., as its sixth retail location.
As Lester Group CEO Jay Dickens noted, “Custom Builder Supply Co. has built a great brand in Williamsburg and James City County over the past nearly 40 years. We strongly believe in the role of the independent lumberyard and the decisions of our store management are always made closest to the customer.”
Custom Builder Supply will continue to operate under its established name and staff, maintaining the trust that customers have come to know and rely on. George Lester, co-chairman, said, “We’re not just adding a business, we’re welcoming a brand that shares our values and commitment to quality and service into our family. This union will strengthen our commitment to serving the community and fostering enduring business relationships. The best is yet to come.”
Lester owns real estate, treating (Fortress Wood Products), door manufacturing (Fortress Door), forestlands, and retail stores, including Lester Building Supply, Martinsville; Jim Carpenter Co., Fredericksburg; Taylor Bros., Lynchburg; New River Valley Building Supply, Christiansburg; and Building Supply of Manassas.
DEALER BRIEFS
Discount Lumber, Centre, Al., suffered extensive damage from a May 31 blaze.
Zuern Building Products purchased 148-year-old Saeman Lumber, Cross Plains and Madison, Wi.
LeNoble Lumber Co., Long Island City, N.Y., has opened a new distribution center in Edison, N.J.
McCoy’s Building Supply opened a 15,000-sq. ft. store with drive-thru lumberyard in Lockhart, Tx. (Zach Dauer, mgr.). A board-cutting ceremony is set for July 11.
Bond Lumber & Hardware, Norris City, Il., was destroyed in a June 2 fire.
Harrison Lumber, Harrison, Mi., held a grand opening May 23-24 to show off its recent remodel.
Outdoor Warehouse Supply, Plano, Tx., added a branch in Lewisville, Tx.
Sunshine Ace Hardware will open a 20,190-sq. ft. store early next year in North Naples, Fl. The presently 10-unit chain will also add stores in August in Ave Maria, Fl., and in 2025 in Babcock Ranch and Golden Gate Estates, Fl.
Mains Hardware Supply hosted a grand opening celebration at its new location in Kenner, La.
Northfield Ace Hardware, Northfield, Mn., held a grand opening June 1-9 (Josh Listul, mgr.).
Revell Ace Hardware held grand reopenings at its refreshed stores in Pearl, Clinton, Byram, Florence, Madison and Jackson, Ms.
Owatonna Ace Hardware, Owatonna, Mn., held a grand opening June 14-16 (Tyler Swenson, mgr.).
Bests’ Ace Hardware held a June 20-22 grand reopening celebration at its recently relocated storefront in Lewes, De.
Cross Ace Hardware, Jacksonville, N.C., was opened by Matthew Cross, with a June 15 grand opening.
Aubuchon Ace Hardware opened a branch in Naples, Me. (Christopher Smith, store manager).
Curt’s Ace Hardware has added stores in Abingdon and Lebanon, Va. Eikenhout Inc., Grand Rapids Mi., now offers Tando Composites’ Beach House Shake and TandoStone from its 10 locations in Michigan.
REDWOOD
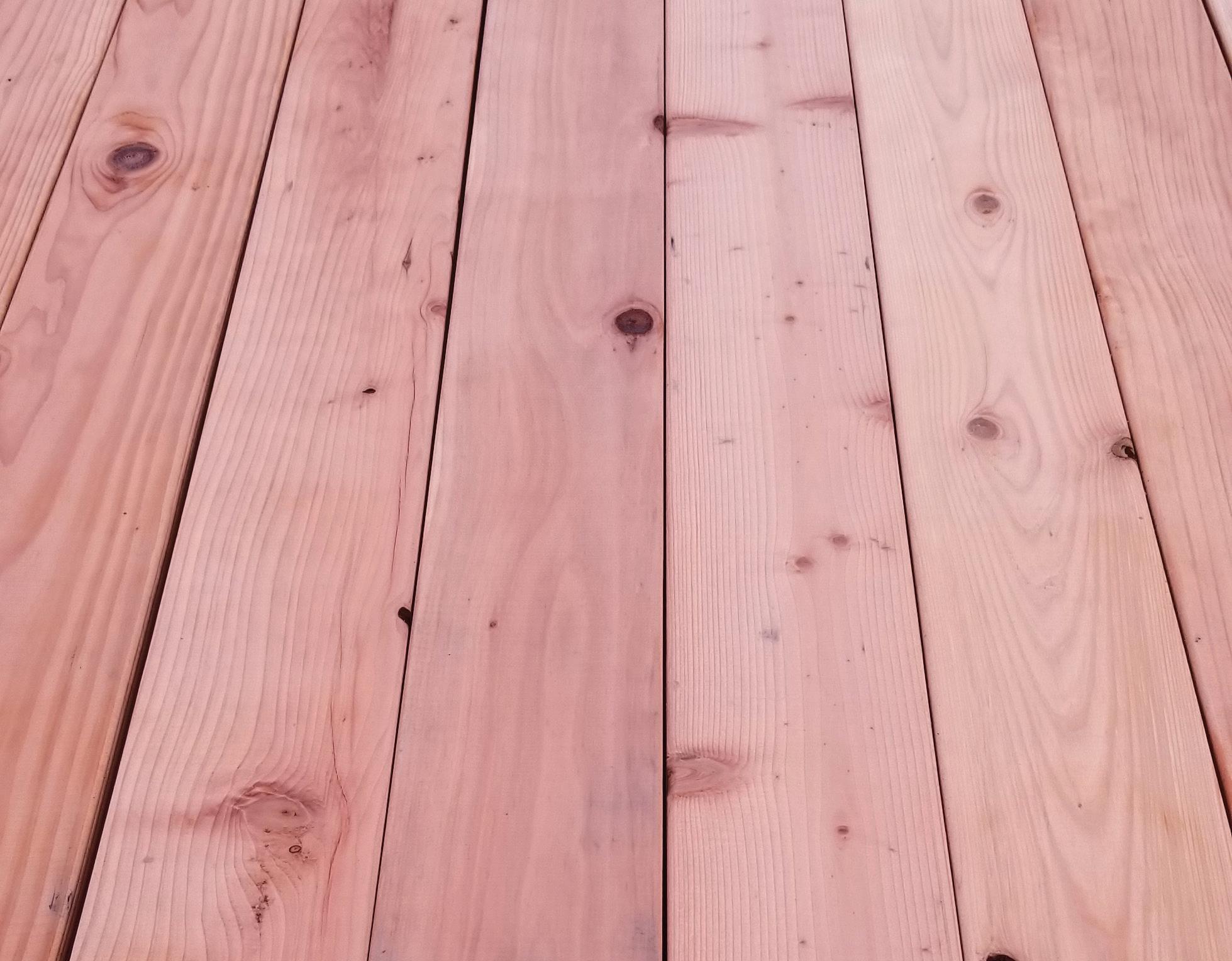
Like the foods we buy, when it comes to decking, we want natural and real. Redwood is always available in abundance of options. So stock the shelves! Unlike mass-produced and inferior products, Redwood is strong, reliable and possesses many qualities not found in artificial products. They maintain temperatures that are comfortable in all climates.
Redwood Empire stocks several grades and sizing options of Redwood.
CAMERON ASHLEY ADDS MILWAUKEE DC
Cameron Ashley Building Products has opened a new Milwaukee-area distribution center in Franklin, Wi.—its third in Wisconsin. The Milwaukee distribution center will stock fiberglass batts, blow and board, cellulose, spray foam, insulation accessories, and mineral wool.
“We are thrilled to open our newest distribution center and this location allows us to service Milwaukee, west to Madison, south to Kenosha, and north to Green Bay and Appleton,” said regional vice president Steve Knutson. “We are thrilled to be able to more efficiently service this area and provide FAST Delivery to our customers in eastern Wisconsin.”
NATION’S BEST ACQUIRES REECE’S OF VIRGINIA
Nation’s Best, Dallas, Tx., has acquired Reece’s Building Supply in Narrows, Va., representing its 58th location nationwide and its second in Virginia.
“Reece’s Building Supply is a perfect fit within the Nation’s Best model,” said Chris Miller, president and CEO of Nation’s Best. “The entire Reece family—Philip, Tanya, Keith, and Marcia—have worked hard to build an exceptional home center to serve their community. And we’re excited to now have them as partners leading our growth in Virginia.”
Founded in 1999, Reece’s Building Supply has effectively adapted to the changing needs of the Giles County area over the last quarter century. With their dedicated team, a full-service delivery fleet, and a deep selection of building products, they have become the go-to supplier for area builders and remodelers.
As part of Nation’s Best’s strategy, Reece’s Building Supply will maintain operations under their existing name with its key management team, including Philip Reece, overseeing operations alongside Nation’s Best, which will provide the strategic and financial support necessary to drive optimal growth and profitability.
SIMPSON STRONG-TIE TAKES OVER CSD
Simpson Strong-Tie, the leader in engineered structural connectors and building solutions, has acquired Canada-based Calculated Structured Designs, a software development company providing solutions for the engineered wood, engineering, design and building industries for North America, Australia, and the United Kingdom.
CSD is committed to creating state-of-the-art software solutions for architects, designers, engineers, and builders, selling and distributing its iStruct products across the U.S., Canada, Australia and the U.K.
“This acquisition helps Simpson Strong-Tie better serve our customers using EWP products, as well as steel and dimensional lumber,” said Noah Daniels, Simpson Strong-Tie senior VP market development–digital solutions. “CSD has been a longtime partner of Simpson Strong-Tie, with their iStruct solution perfectly combining 3D layout, member design, and material reporting.”
Sean Nason, CSD president and CEO, said, “The past 15 years for CSD has been one spectacular ride. I am very proud of everyone and humbled to have worked
and grown friendships with this amazing group. I know the combined Simpson Strong-Tie and CSD team will take EWP software to even higher levels.”
COOPER BUYS THOMASVILLE, AL., SAWMILL
Cooper Lumber, Mobile, Al., has acquired Thomasville Lumber Co., Thomasville, Al.
Owned and operated by James Dixon since 2001, Thomasville produces 4/4 and 8/4 rough and dressed pine lumber for sale in domestic and export markets.
The mill facility that became Thomasville Lumber in 2001 was developed in 1966 as a small lumber mill under R.R. Bedwell. The facility continued to expand operations until 1975 when Bankhead Hardwoods bought the facility. In 1979, Coastal Lumber Company acquired the location and converted it to a pine mill in 1988.
------------| SUPPLIER BRIEFS
L&W Supply opened a new location in Jacksonville, N.C., managed by Thomas Hightower.
Beacon has added branches in Attleboro, Ma., and Terrell, Tx.
Mill River Lumber has indefinitely shuttered its sawmill in North Clarendon, Vt.
Westlake Royal Building Products closed its vinyl window plant in Carrollton, Tx., consolidating operations in Dallas, Tx.
Pallet Distributors, Inc. will invest $5.9 million to expand capacity at its ePallet plant in Byesville, Oh.
Koppers Utility & Industrial Products held a ribbon cutting ceremony for its new utility pole peeling and drying facility in Leesville, La.
White Cap has acquired fabricator/distributor Rebar Solutions, LLC, Mount Crawford, Va.
Capital Forest Products, Annapolis, Md., is now the exclusive distributor of Copper Cat roofing.
Snavely Forest Products has expanded its distribution of Trex decking and railing into Oklahoma City, Ok., through its Mid-States Wholesale Lumber subsidiary.
Momentum IRG, Florida City, Fl., is now repping IKO Commercial roofing, waterproofing and insulation products in Florida.
Toyota Material Handling has broken ground on a $1-million, 295,000-sq. ft. electric-forklift manufacturing plant next to its Columbus, In., headquarters.
MasterBrand Cabinets agreed to acquire Supreme Cabinetry Brands, Howard Lake, Mn., from GHK Capital Partners for $520 million.
Trex has appointed Paragon Stairs, the largest producer of spiral stairs in the U.S., as the exclusive supplier for its Trex Spiral Stairs collection.
US Lumber Brokers, Austin, Tx., has rolled out a new Prime Line Softwood collection, including western red cedar, Douglas fir, and southern yellow pine.
Domain Capital Group and its subsidiary Domain Timber Advisors, LLC, Atlanta, Ga., have acquired five forestland assets totaling 5,800 acres in Mississippi, Alabama, Virginia and Georgia.
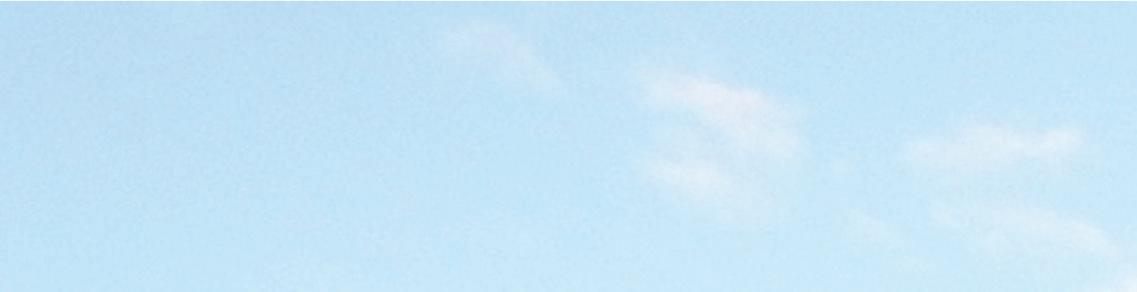
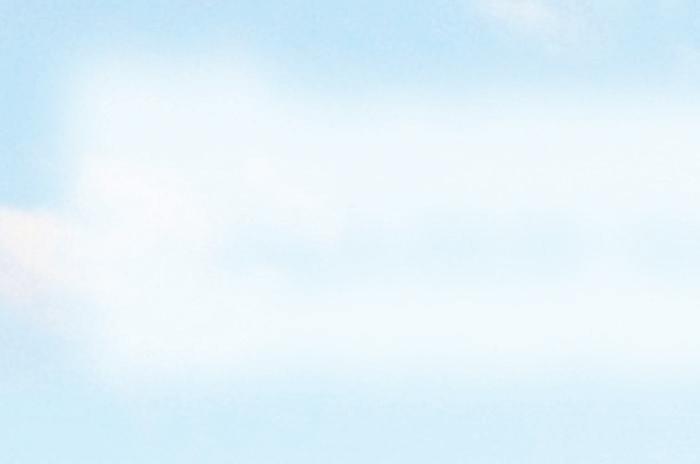

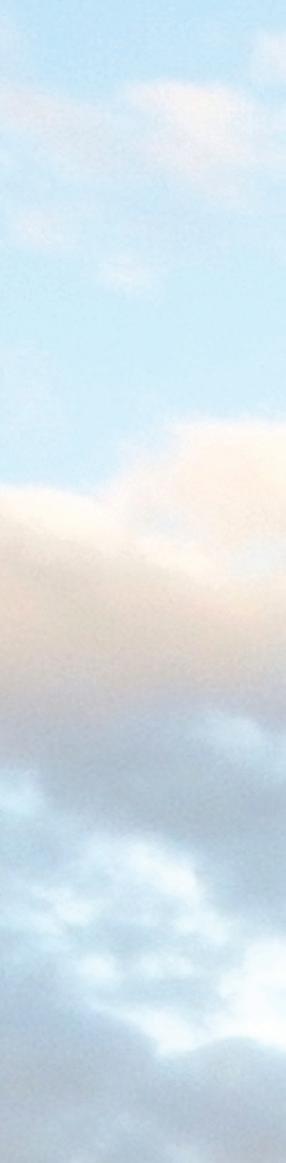
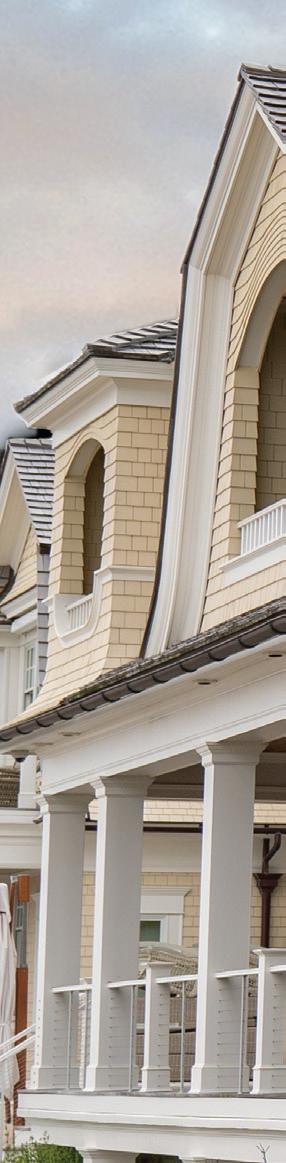


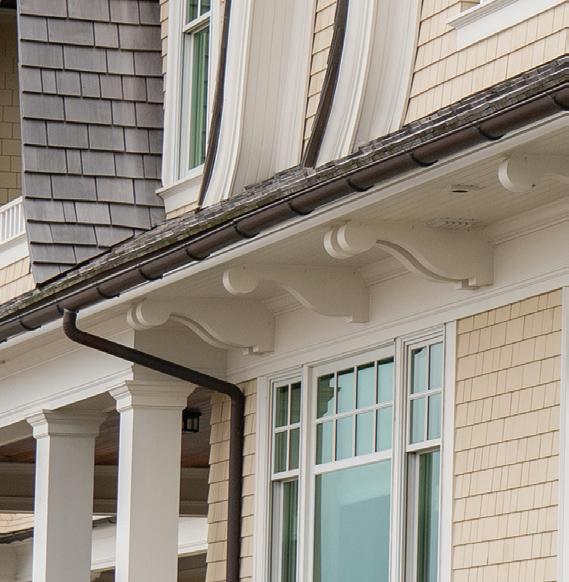

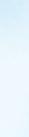

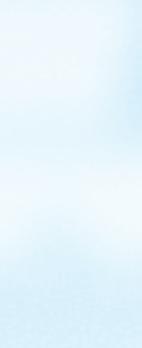

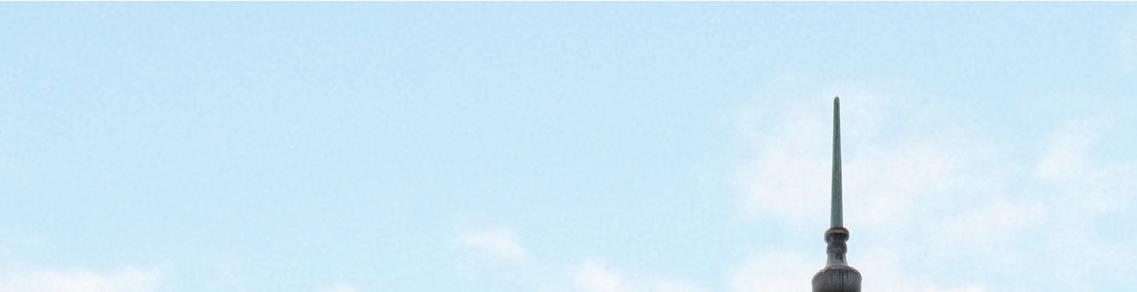
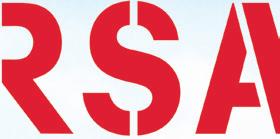
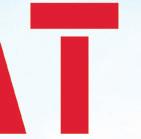

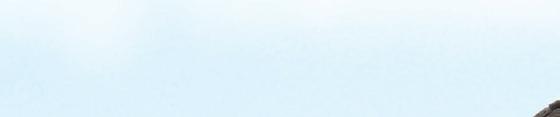
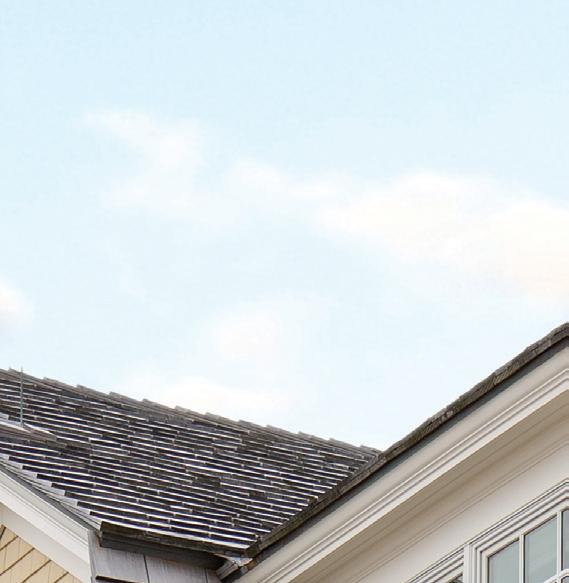
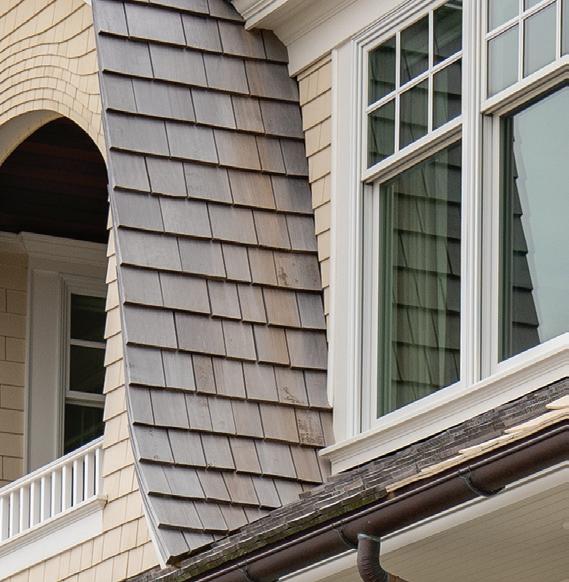


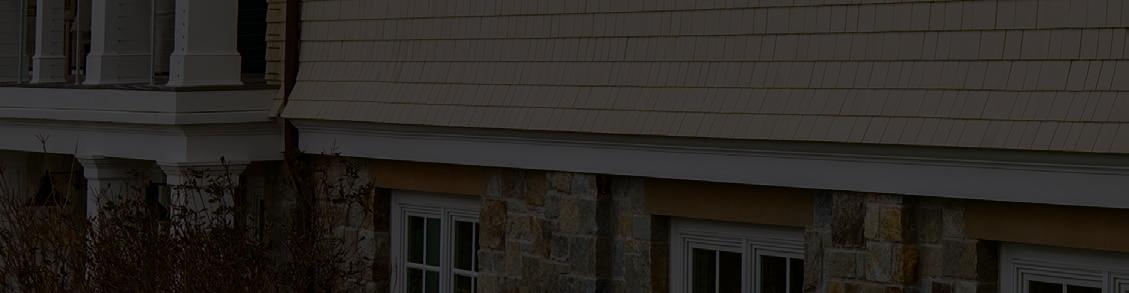
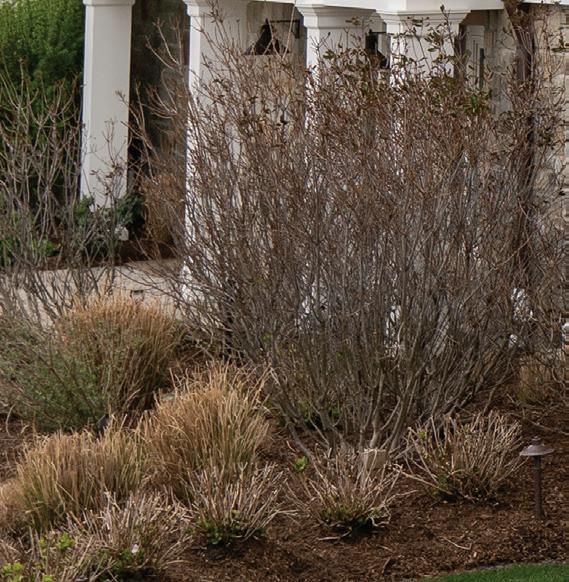





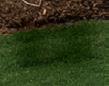




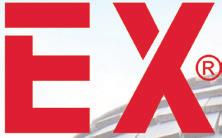
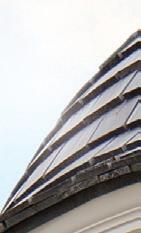



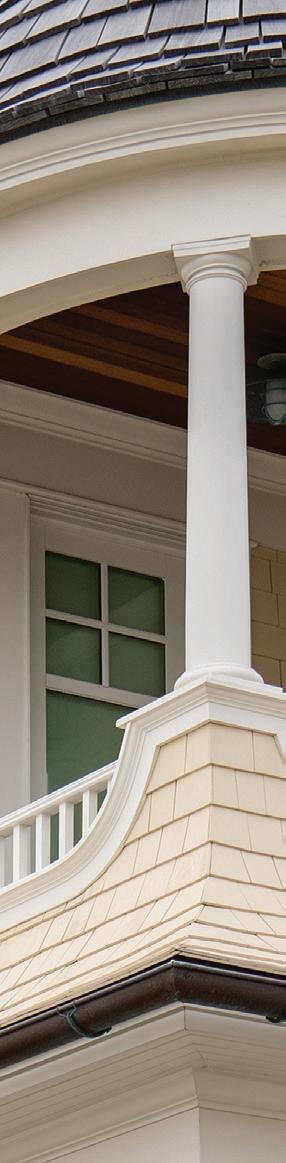
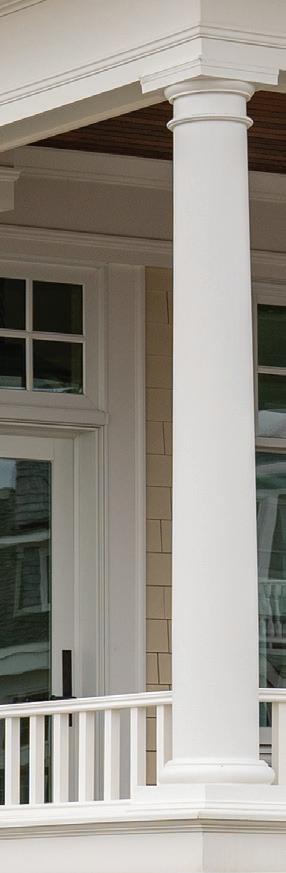
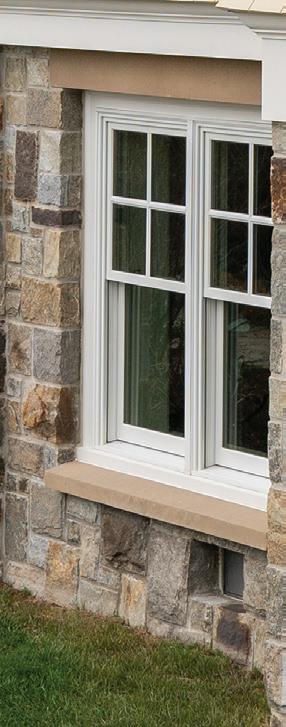
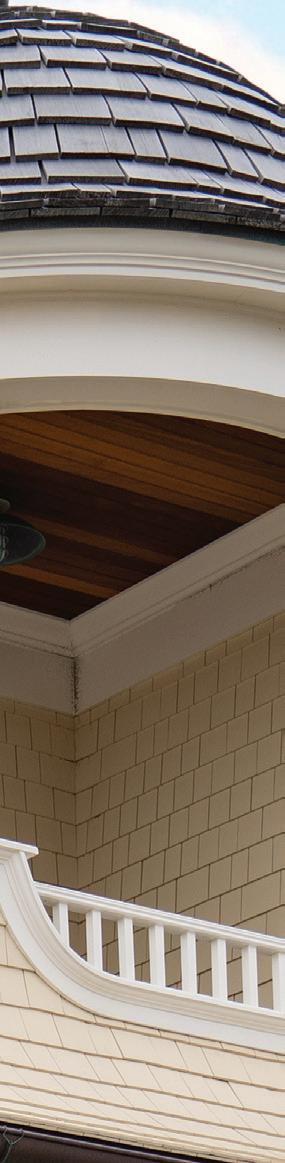
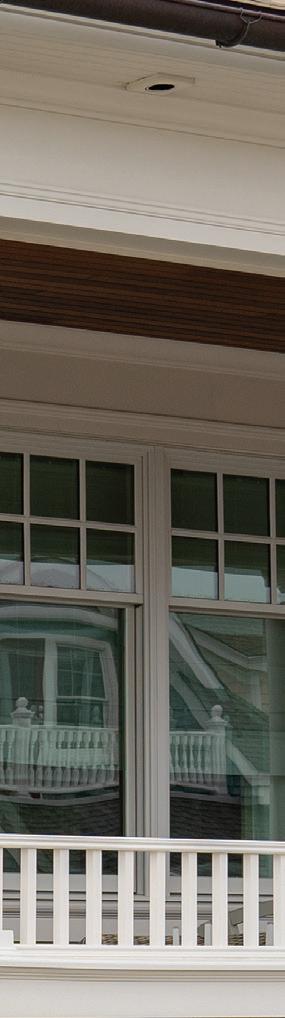


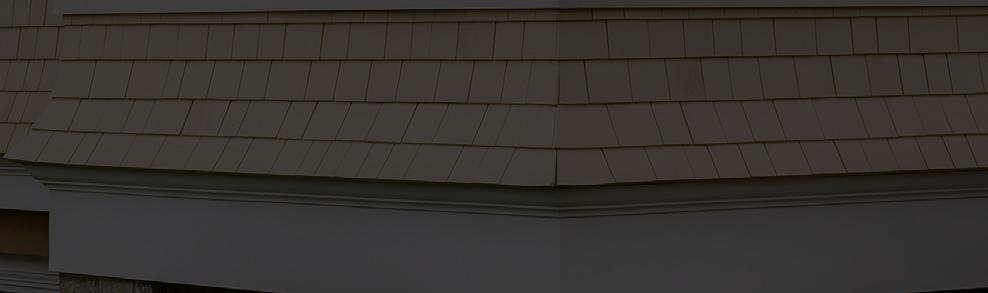
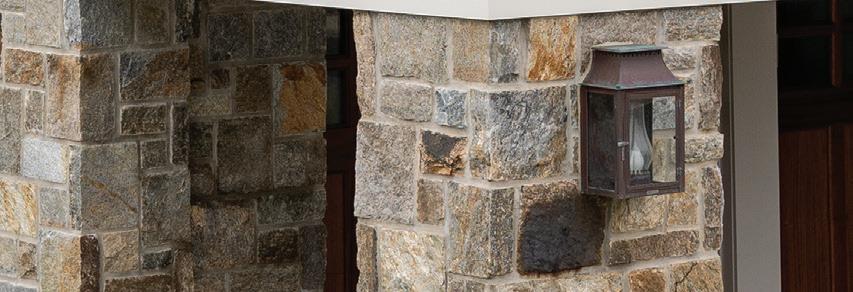

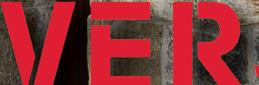
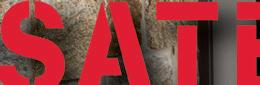

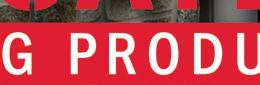

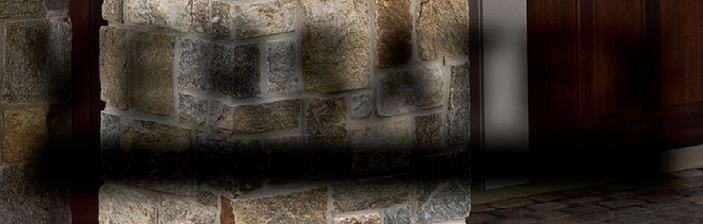
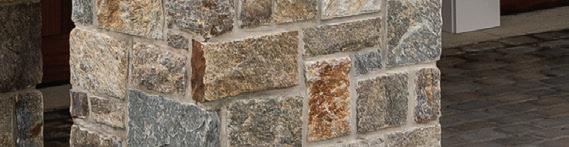
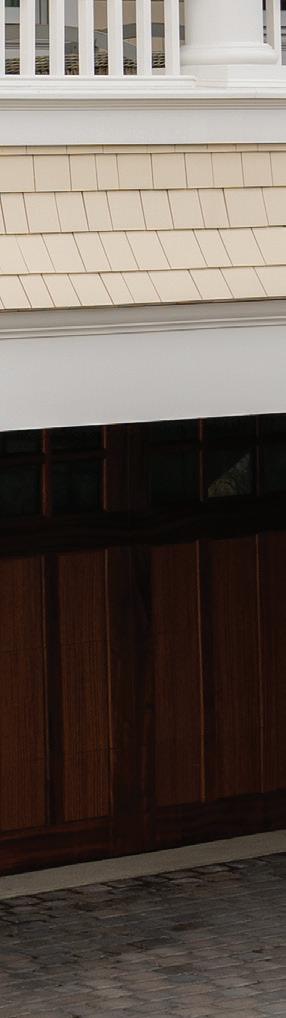
MOVERS & SHAKERS
Gordon Staley, ex-Spahn & Rose, was appointed VP of sales & marketing for Wilson Lumber Co., Huntsville, Al.
Nathan Honea, ex-Swift Supply, has been named store mgr. of Gulf Coast Building Supply, Robertsdale, Al.
Ryan Connolly has been promoted to sales mgr. at Boise Cascade, Detroit, Mi. Justin Brown is new to field sales-national accounts, based in Oklahoma.
Joe Woods, ex-Metrie, has been named president and general mgr. of Professional Builders Supply, Mooresville, N.C., a division of US LBM.
Beth Blount, ex-Roseburg, is a new national account mgr. with Aperture Solutions/Cornerstone Building Brands, Matthews, N.C.
Anthony Kolodziej, ex-Tampa International Forest Products, is now trading for Lumber One, Tampa, Fl.
Gary Magee Jr., ex-Brand Vaughan Lumber, is new to outside sales with Four Corners Building Supply, Hardeeville, S.C.
Chad Wester has been appointed director of sales operations at Southern Lumber Supply, Dothan, Al.
J’Vaughn Vega has been promoted to general mgr. of 84 Lumber, Horseheads, N.Y. Wayne Wright has rejoined 84 Lumber as general mgr. in Wellford, S.C. Colby Tart is new to outside sales in Hickory, N.C. Melody Chancellor-Hackett is now director of sales & business development in Richmond, Va. Tanner Ivy is a new mgr. trainee in Charlotte, N.C.
Adam Grody is new to Guerry Lumber, Savannah, Ga., as purchasing mgr. & sales analytics.
Carlos Quiroz is the newly named marketing director at NewTechWood, Houston, Tx.
Matt Vigna has been promoted to location mgr. of Shelly’s Supply, Bethlehem, Pa.
Nikke Mathe, ex-Lowe’s, is new to MoistureShield, as territory sales mgr. for Georgia.
Mark Smith, ex-Ware-Butler, is the new general mgr. of Hancock Lumber, Damariscotta, Me.
Lauren Ludewig, ex-MoistureShield, is now a territory sales mgr. with Westlake Royal Building Products, based in Nashville, Tn.
Zachary Thompson has joined the sales force at Holmes Lumber, Columbus, Oh.
Alex Gonter-Dray, ex-Goodfellow, has been appointed director of sales for Church & Church Lumber Co., Wilkesboro, N.C.
Daniel Villasenor has been promoted to VP of sales at Oak Creek Wood Products, Oak Creek, Wi.
Bishop Biddix, ex-LBM Advantage, and Sean Nuedling, ex-Boise Cascade, are new business development mgrs. with PWT, Burlington, Wa., covering the mid-Atlantic and Eastern regions, respectively.
Maria Guillen is new to inside sales at Lumber Plus, Houston, Tx.
Joe Stubler has been promoted to division mgr. for Envision Outdoor Living Products, Mount Joy, Pa., supporting the company’s sales teams in the Great Lakes, Midwest, Rockies, and South-Central regions. Mikhail Mikhailov is now senior regional mgr. in the Southwest and Pacific Northwest.
Tad Collins, ex-Fiberon, is now in sales with Garden State Lumber Products, West Columbia, S.C., covering N.C.
Josh Travis is the new general mgr. of Ward Lumber Co., Jay, N.Y.
Sam Bell “Tres” Steves III was named CEO of Steves & Sons, San Antonio, Tx., succeeding Edward Galt Steves Doug Gartner is now president, and Scott Lovett chief operating officer, replacing Sam Bell Steves II. The two elder Steves will continue as co-chairmen of the board. Gloria Galt Steves is now vice-chair of the board.
Danielle Schneider, ex-BNSF, has joined the outside sales force at Teague Lumber Co., Fort Worth, Tx.
Tom Hodson was promoted to VP-marketing & sales for Kyocera Senco Industrial Tools, Cincinnati, Oh. He succeeds Dave Moore, who retired after 17 years with Senco.
Matt Borden has been appointed CFO for Ware-Butler Building Supply, Waterville, Me.
Rachel Schukar is a new designer/sales specialist at Chic Lumber/Design Center, St. Charles, Mo.
Jordan Broggi has been promoted to executive VP of customer experience and president of online for The Home Depot, Atlanta, Ga. He will succeed Matt Carey, who will retire Dec. 31 after 16 years with the company.
Russell Tiejema has been named executive VP and CFO of US LBM, Atlanta, Ga. He succeeds Patrick McGuiness, who retired from the company last year.
Skyler Slack, American Lumber, Bryan, Tx., was promoted to associate sales mgr.
Jennifer Wilson has been named senior vice president, chief marketing officer for Lowe’s, Mooresville, N.C.
Lydia Schloskey is a new designer with Nelson Lumber & Home, Hayward, Wi.
Bill MacDonald has joined Sightline Commercial Solutions, Minneapolis, Mn., as senior preconstruction mgr.
Michelle Brundige was named regional human resources mgr. for Ambassador Supply, Fort Wayne, In.
Steve Schulz is now senior territory sales mgr. for the Midwest with Tando Composites, covering Minnesota, Wisconsin, Illinois, Iowa, Missouri, Nebraska, Kansas and the Dakotas.
Scott Voss has joined Miki Forest Products, Santa Rosa, Ca., as Texas-based president of sales.
Jeffrey D. Smith is the new CEO of Crystal Windows, Queens, N.Y.
Thomas Tornillo has been appointed product management & claims mgr. for Garnica, Wilmington, De. Jack Naish is now inside sales mgr.
Catherine Courage, Google VP, has been appointed to the board of directors at MasterBrand, Beachwood, Oh.
Jay Hilsenbeck, Arxada, was elected president of the American Wood Protection Association during its recent annual meeting in Portland, Me. He succeeds Andy Kudick, Intec Services. Paul Merrick, LouisianaPacific, is the new 1st VP; David Jones, Timber Products Inspection, 2nd VP; Bill Buczek, UFP Industries, 3rd VP; and Jonathan Moyes, Viance, treasurer.
Kyle Evans, Mullican Flooring, Johnson City, Tn., was elected Decorative Hardwood Association chairman of the board during the group’s recent annual meeting in Scottsdale, Az. Garrett Keil, Murphy Co., Eugene, Or., is the new vice chair, and Rocky Boucher, Columbia Forest Products, Newport, Vt., immediate past chair.
Earl Lee Riser is the new opening-shift foreman at Mungus-Fungus Forest Products, Climax, Nv., report co-owners Hugh Mungus and Freddy Fungus.
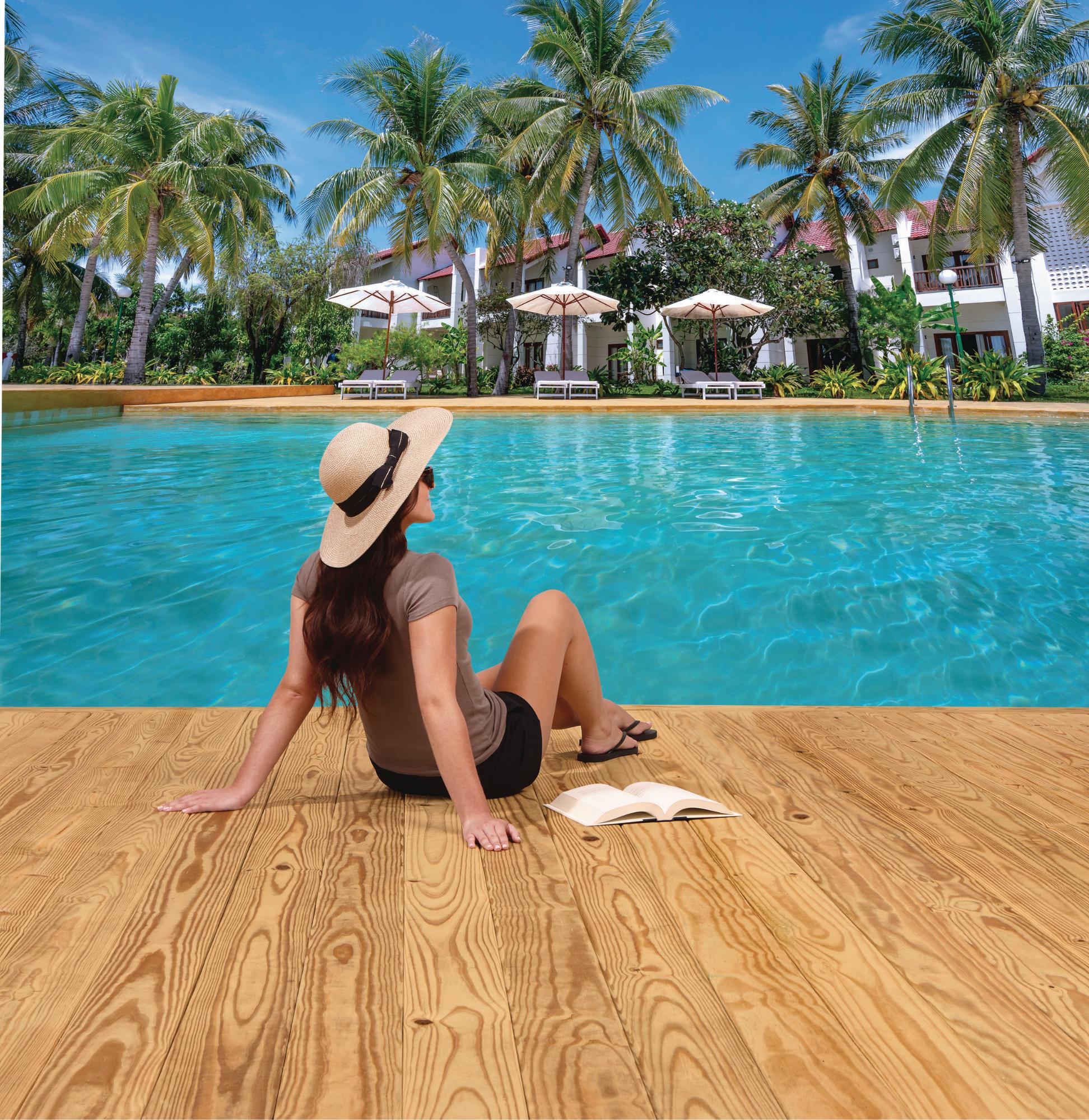
Take outdoor living to a new level with Select Cut®. Trusted by professionals for its superior appearance, Select Cut blends quality, durability, and the beauty of real wood. Select Cut is the ultimate choice for building exquisite outdoor living spaces that reflect first-class craftsmanship.
F�� w�en appearances matter.
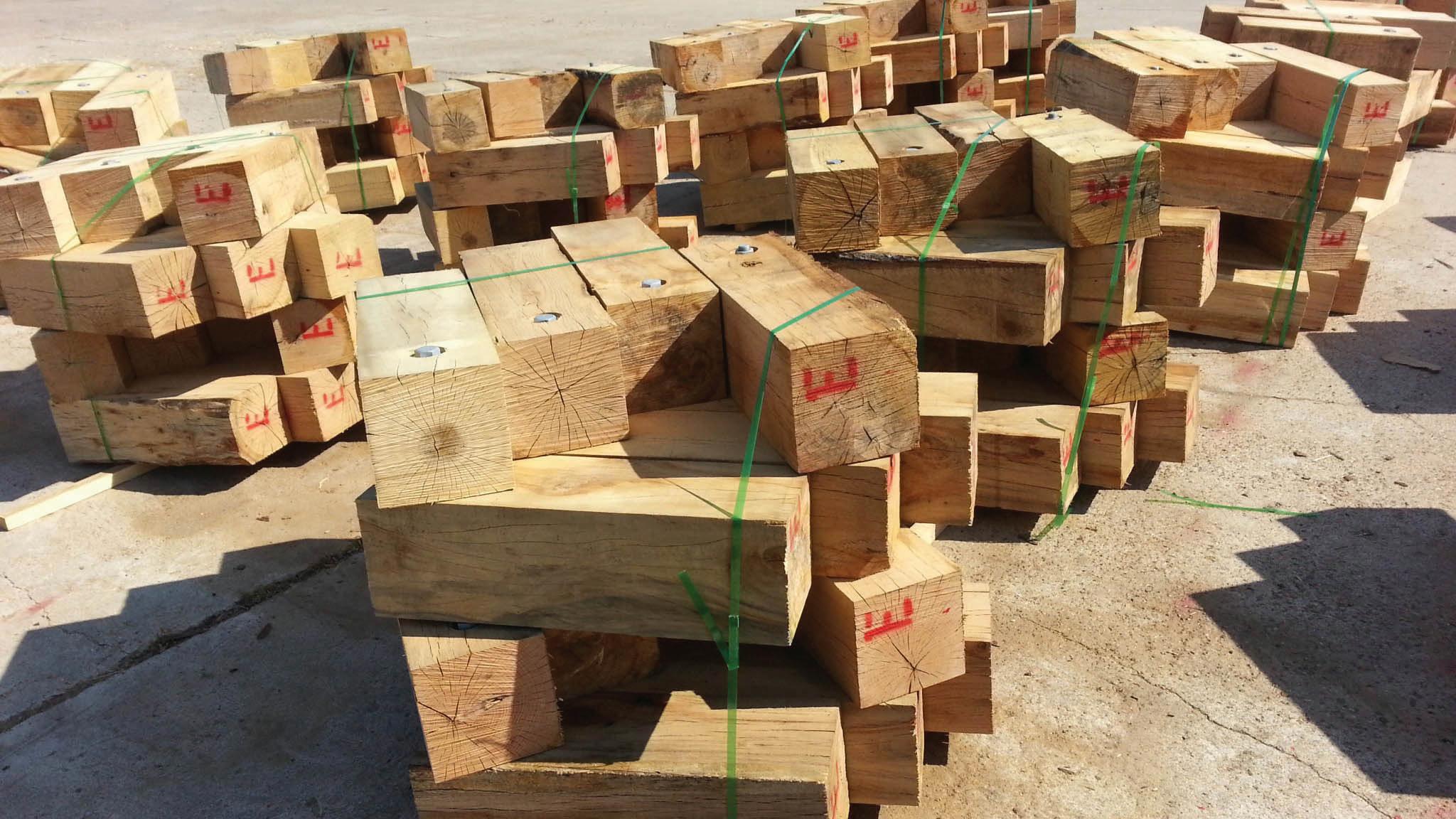
THE FUTURE OF PRESSURE TREATING HARDWOODS
------------ BY DALLIN BROOKS
WHEN WE DISCUSS pressure-treated or preserved wood, the automatic assumption is that we are talking about softwoods. That’s fair enough, considering that 50% of [SYP] lumber is pressure treated in the South and East, while along the West Coast, the refractory species have about 10% of their production preserved. Hardwoods are preserved, mostly in railway ties, but other options exist.
Today, hardwood markets focus on infrastructure and yield-graded (appearance) lumber. The demand for pallets, ties, and crane matting use in infrastructure has stayed static at around 5 billion bd. ft. since 1999. However, graded lumber markets have dropped from highs of 6 billion bd. ft. in 1999 to 2 billion bd. ft. after the 2008 crisis and remain at 2 billion today. The hardwood lumber industry has never recovered from this drastic drop in U.S. consumption of flooring, millwork, cabinets and furniture, as substitute products have taken over these traditional hardwood markets. The hardwood industry must shift into structural and preserved markets to help grow and stabilize production and pricing.
So, why aren’t there hardwood posts or hardwood decking? There are some, but they are minimal, and you must look for one if you want it. There are several rea-
sons for the limited availability of preserved hardwoods. It is not because hardwood is not treatable. Just like softwoods, some species treat better than others, but there are plenty of permeable hardwood species, such as alder, poplar, maple, red oak, and sap gum, to name a few. It is not because hardwood costs more. High-appearance grades have lots of value, but plenty of lowgrade stock goes into pallets and ties that can meet the structural requirements and are ideal for preserving. It is not because of lower strength and grading. Hardwoods are often stronger than softwoods, and there are structural grades for many hardwood species.
The reason you don’t see a lot of treated hardwood lumber is due to limited supply. Undoubtedly, the hardwood industry has not gone after these markets for a while, and thus, it has not met the needs and might not be able to shift back to structural and preserved applications quickly. The limited supply is also due to variable sizes. Hardwood mills produce random widths that don’t work for structural and preserved applications where fixed sizes fit together. However, more than the above reasons, the shortage of available pressure-treated hardwoods is due to a lack of knowledge between
(Continued on page 46)
PRESSURE-TREATED hardwoods today are mostly used in industrial/commercial applications such as pallets, ties and industrial blocks. (Photo by American Pole & Timber)
Unrivaled dealer support comes from understanding a high-quality product means nothing if it means headaches to get it on your shelves. For five decades now, we’ve built a trusted reputation for going above and beyond to deliver on the extras that make a difference. Like near-by facilities for timely product deliveries. A seasoned sales support team. Or stand-out advertising that drives higher demand for products. That’s just the beginning of a very long list that only we do. See all the other ways the YellaWood® brand has your back. Visit yellawood.com/for-dealers
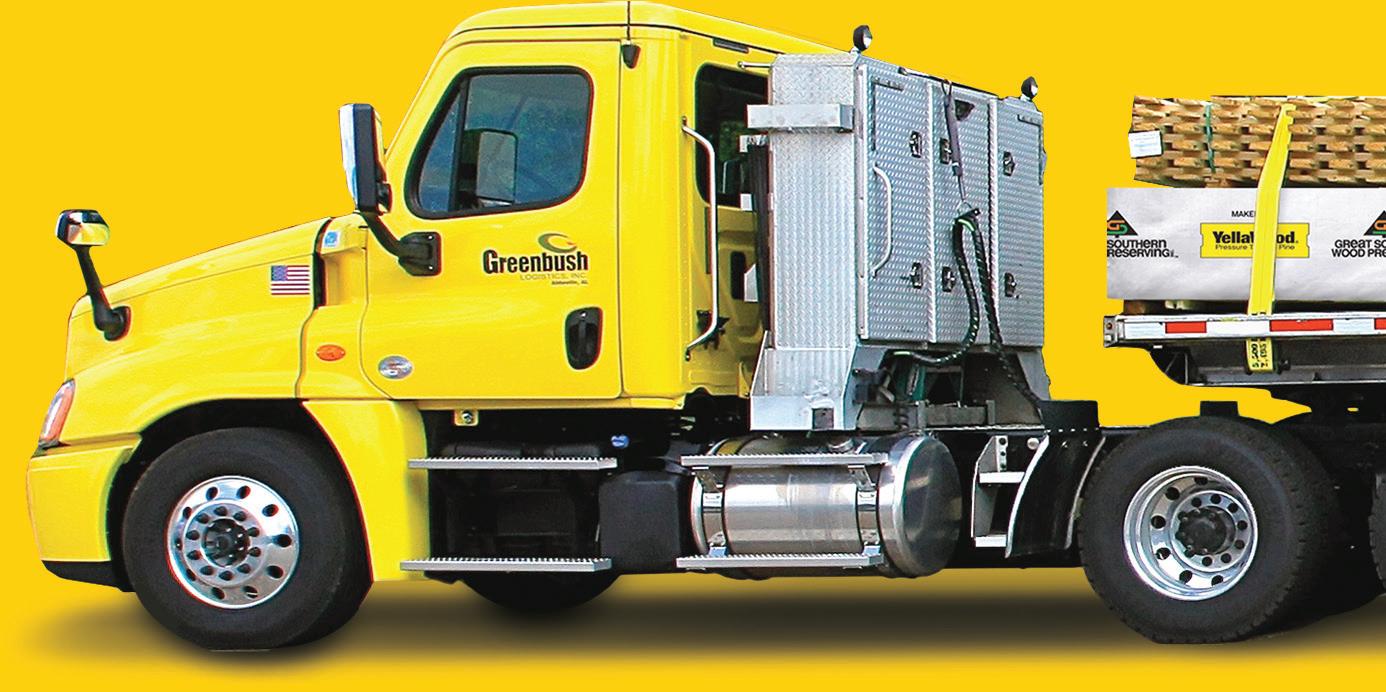

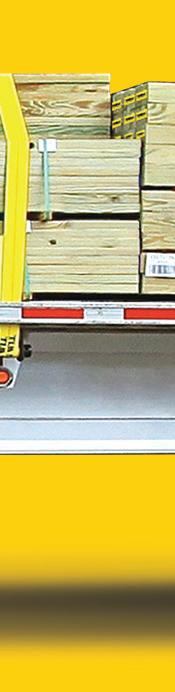
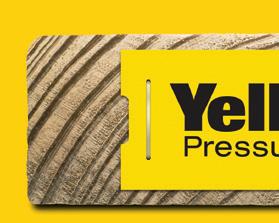
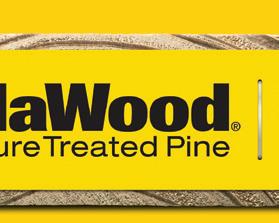
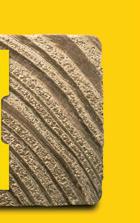
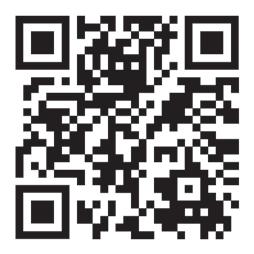
FUTURE OF PRESSURE TREATING HARDWOODS
(Continued from page 44)
the hardwood and the wood preservation industries on the other capabilities. Hardwoods are able and available to be pressure treated. Now, we just need to grow the market.
For the hardwood industry to be innovative and build market share, it needs to capitalize on the overlooked markets of the softwood industry. Hardwoods should focus on exterior fire retardants and preservatives in applications like hardwood mass timber (CLT and glulam), profiled decking, thermal modification, preserved siding, preserved square posts, and other areas the softwood market has mostly ignored.
The good thing about hardwoods being late to the game is that they don’t have to recreate the wheel, and it is easy to differentiate Real American Hardwoods (RAH) from tropical hardwoods and softwoods. The RAH campaign promotes hardwoods to consumers, architects, and designers and can easily incorporate exterior applications. The existence of thermally modified hardwoods will continue to push the exterior stories and open markets for preserved hardwoods. Check out the campaigns at RealAmericanHardwood.com for consumers and RealAmericanHardwood.pro for designers and architects. The Softwood Lumber Board has ignored the pressured-treated market; thus, the treaters should look to capitalize on the hardwood industries’ interest.
For the preserved wood and FRTW industries, the status quo, and the high cost of the search for the perfect chemical has ignored the perfect wood. Simply put, if you want increased fire resistance, then increased density should be welcomed in preserved and FRT hardwoods. Concerns for wood use in the Wildland Urban Interface (WUI) should lead to a lot of opportunities for hardwood to be used instead of wood-plastic composites (WPC) and other substitutes for softwood. The concerns for tropical hardwoods and WPCs should encourage treaters to look at other ways to compete on the higher end markets. Profiled hardwood decking offers a great alternative. The trend is coming, and almost every deck board in Europe is profiled. Research has shown that profiling the deck board offers increased visual appearance and smaller checks. The softwood market has not picked up on this trend, but hardwood hopes to.
The NHLA strongly recommends that the hardwood and wood-preserving industries unite in a collaborative effort to conduct research and testing. This is not just a suggestion; it’s a call to action to expand new markets, prevent the loss of wood markets in the WUI, and from substitute products. The research must be done anyway, so why not on pressure-treated hardwoods?
Nothing changes overnight, so it will take time for treaters and hardwood producers to find a match and create a good relationship. Lumberyards should encourage this to differentiate from box stores and capitalize on higher-end opportunities. A lumberyard representative told me that they make more money on the markup of WPC than a softwood board, no doubt, but you can
make more profit on hardwood and don’t have as many competitors.
The future of pressure treating hardwood lumber is not just uncertain, it’s full of potential. Hardwoods are still responsible for the shipment of your goods, the table you eat on, the floor you walk on, the cabinet you store in, the chair you sit in, the sports you watch, the music you play, and so many more possibilities; if treated properly, the potential of pressure-treated hardwoods is limitless. BPD
– Dallin Brooks is executive director of the National Hardwood Lumber Association (www.nhla.com).
MORE YOUNG ADULTS CHOOSING TRADES OVER COLLEGE
A shortage of skilled labor coupled with a growing distaste for big student-loan debts has led to a rebound in the number of high-school graduates opting to go to trade school instead of traditional college.
The news could be a boon for the forest products and the construction industres, which have suffered from labor shortages in recent years.
According to the National Student Clearinghouse, the number of students enrolled in vocational-focused community colleges increased 16% from 2022 to 2023. Meanwhile, the number of students studying construction at two-year undergraduate programs has risen 12% since 2021.
The Morning Brew’s Cassandra Cassidy explains why: “Four-year schools used to seem like the most straightforward path to a high salary, but with their costs going up, they also lead to a lot of debt. Meanwhile, a shortage in skilled workers has driven up workers’ earnings.”
She notes that, according to payroll provider ADP, median pay for construction workers rose more than 5% last year to $48,089, compared to $39,520 for new hires in professional services such as accountants and IT workers.
A recent study of young adults suggested that blue-collar jobs seem more secure than white-collar jobs due to fears that developments in generative AI technology could render some jobs obsolete.
Indeed, the trend has caught the eye of the Wall Street Journal, which over the past four years has run about a dozen articles like “More Students Are Forgoing College for Apprenticeships,” “Not Everyone Should Go to College,” “College Doesn’t Need to Take Four Years,” “Apprenticeships vs. College,” “Is This the End of College as We Know It?,” “Stop Calling It ‘Vocational Training,’” and “Why Americans Have Lost Faith in the Value of College.”
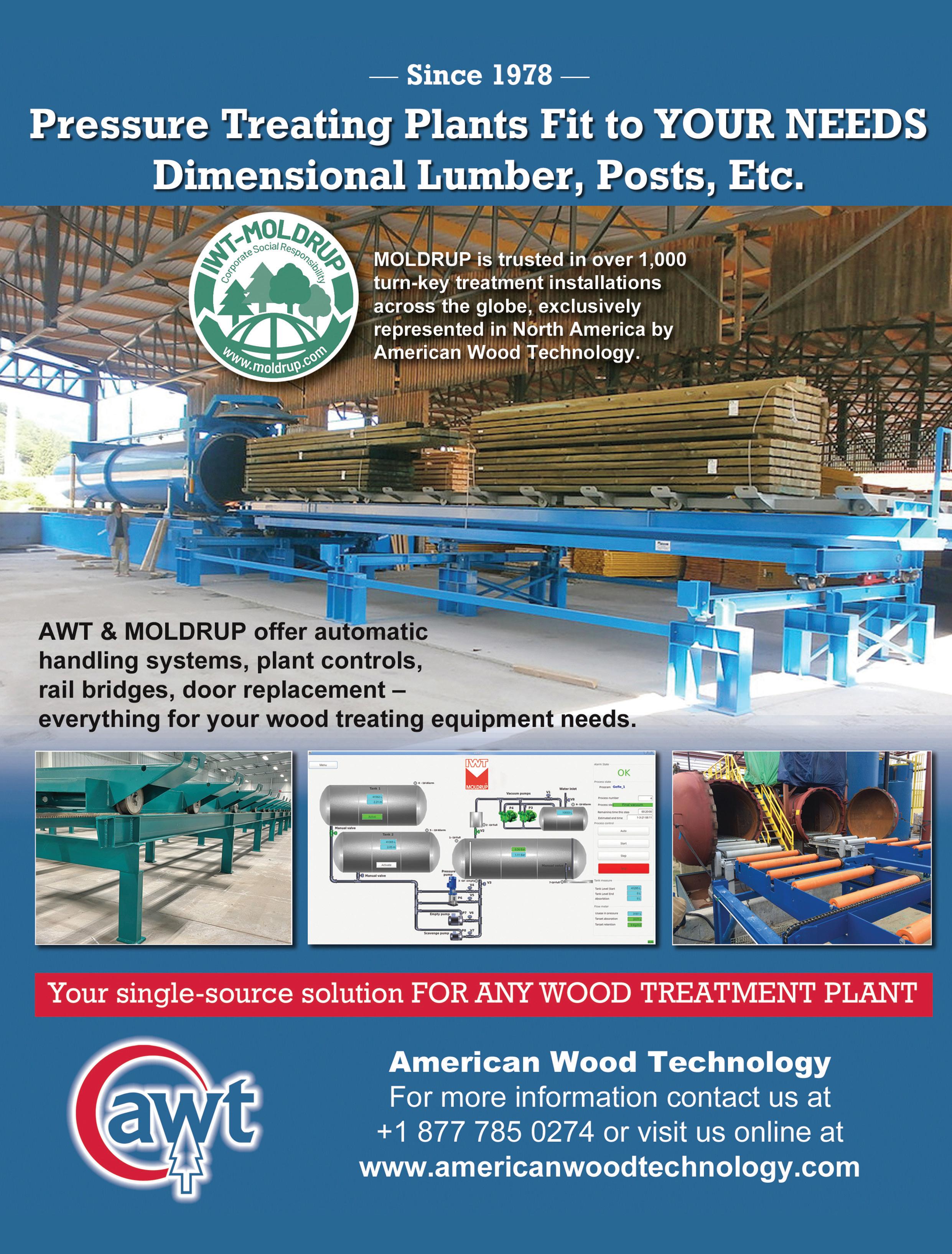
BARRETTEOUTDOORLIVING.COM (877) 265-2220 ,
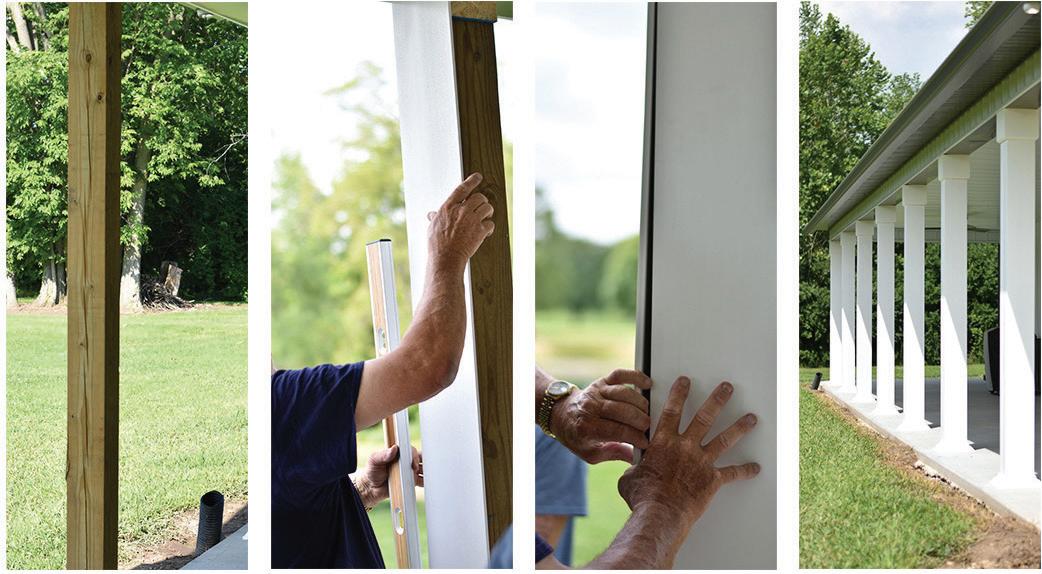
QUICK COLUMN WRAPS
Snap-Tite PVC Wrap-Around Column Wraps from Superior Aluminum Products, which snap together for quick and easy installation with no glue or adhesive, are now available in either a smooth or woodgrain finish. The product shaves 30 minutes off installation time for traditional PVC columns that require mitering, gluing, and clamping-in-place while the glue is curing. Long-lasting cellular PVC is available in 6” or 8” widths, with lengths up to 10 ft.
SUPERIORALUMINUM.COM (937) 526-4065
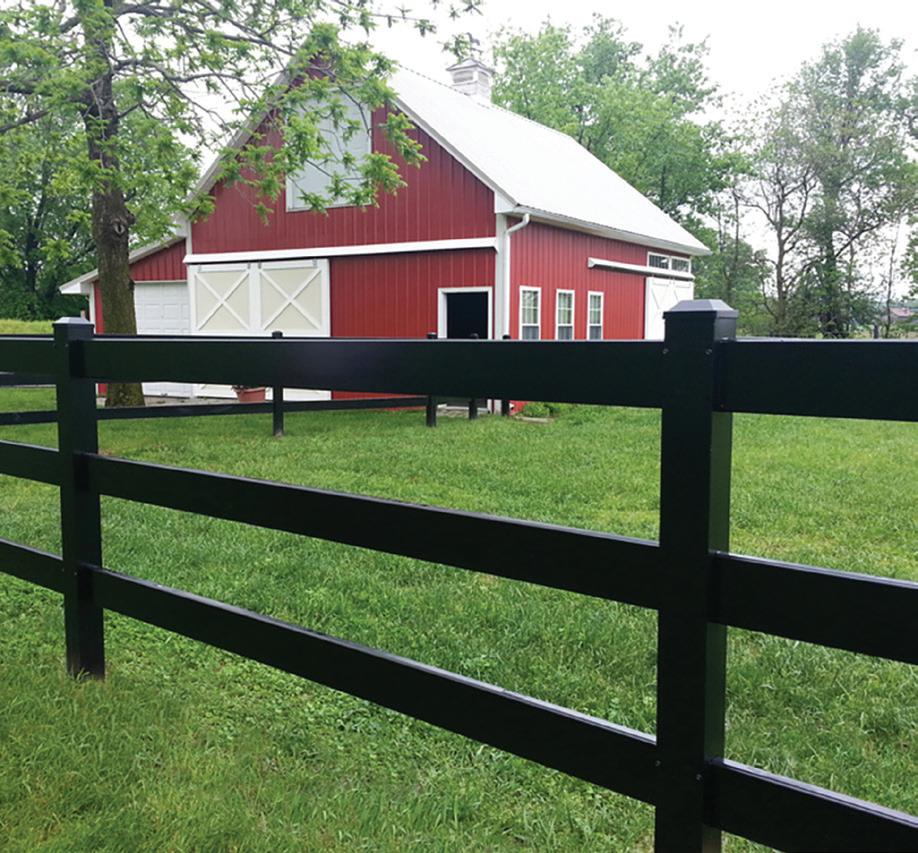
POST AND RAIL FENCING
Barrette Outdoor Living’s new Aluminum Post and Rail fencing features a premium powder coat that meets and exceeds AAMA 2604 standards and is available in seven colors—including Black and Matte Black. Unlike steel or wood, aluminum won’t rot or rust over time. Styles include two, three and four rails in heights of 3, 4 and 5 ft. and widths of 8 ft. as well as three-cap options.
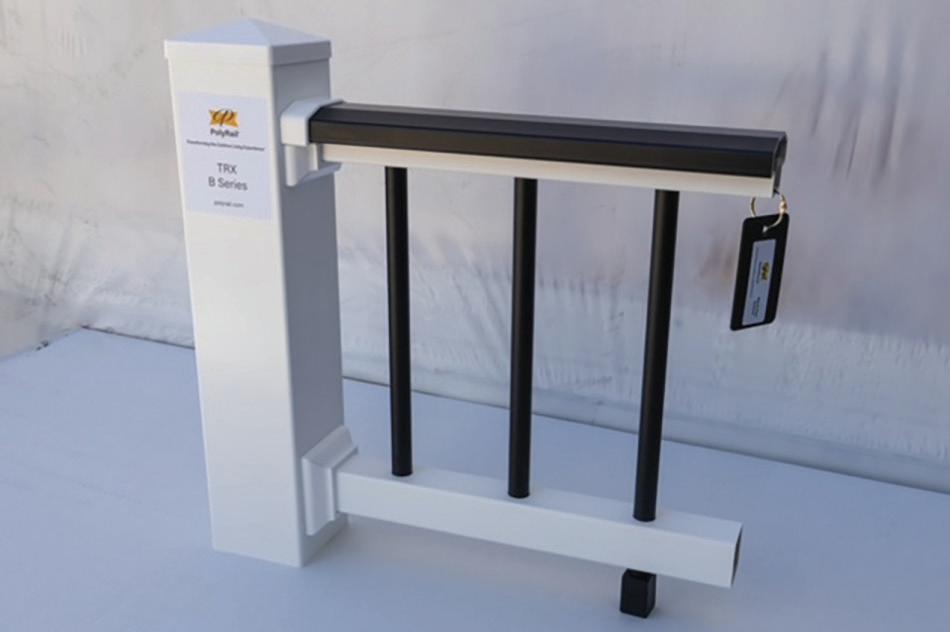
BLACK ONYX TOP RAIL
Digger Specialties Inc. is adding a stunning new color option to the PolyRail TRX B-Series vinyl railing system. The exclusive look of Black Onyx top rails accompanied by 3/4” round black aluminum balusters is contrasted with white vinyl posts, caps, and bottom rails.
The elegant tuxedo inspired color combination provides upscale curb appeal to residential and commercial properties. This eye-catching design enhancement is achieved by applying a sleek black onyx wrap to the white top rail of TRX B-Series railing.
The TRX B-Series system incorporates proprietary laminated black top rail surfaces that are highly resistant to fading. Durable black aluminum balusters are available in a choice of satin black or black fine texture finishes. The B-Series railing comes in 4’, 5’, 6’, 7’, 8’, 9’, and 10’ straight and stair sections in 36” or 42” heights.
DIGGERSPECIALTIES.COM (800) 446-7659
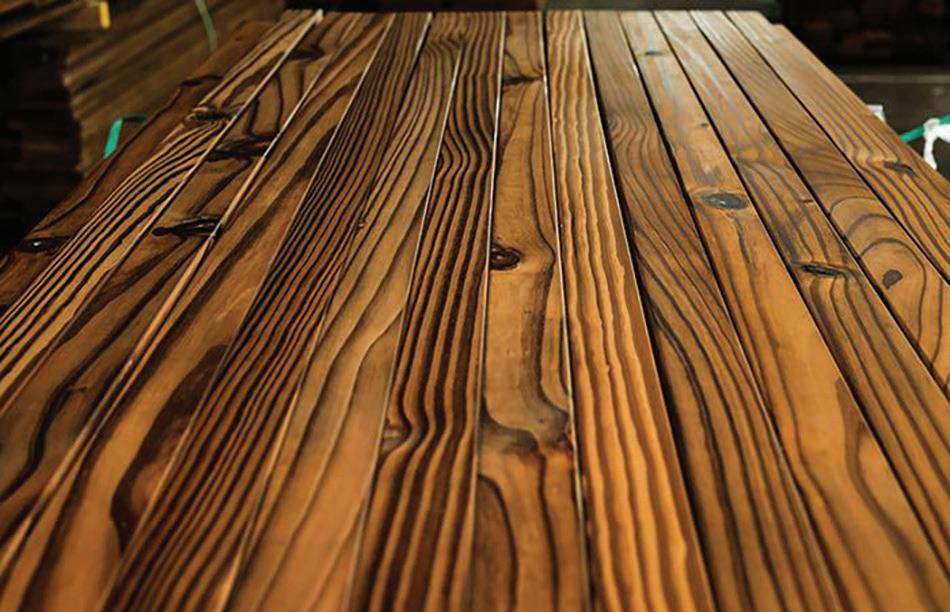
MODIFIED CLADDING & DECKING
Spartan Forest Products has launched ThermaPro Wood, a collection of thermally modified, prefinished, installation-ready building materials that are entirely sustainable, weatherproof, and devoid of chemicals.
The ThermaPro line include prefinished T&G nickel gap wood cladding and prefinished decking, all presealed with CUTEK Extreme Wood Oil. A complete line of coordinating trim, moulding, railing, and other finishing components is also available.
SPARTANFOREST.COM (336) 574-0111

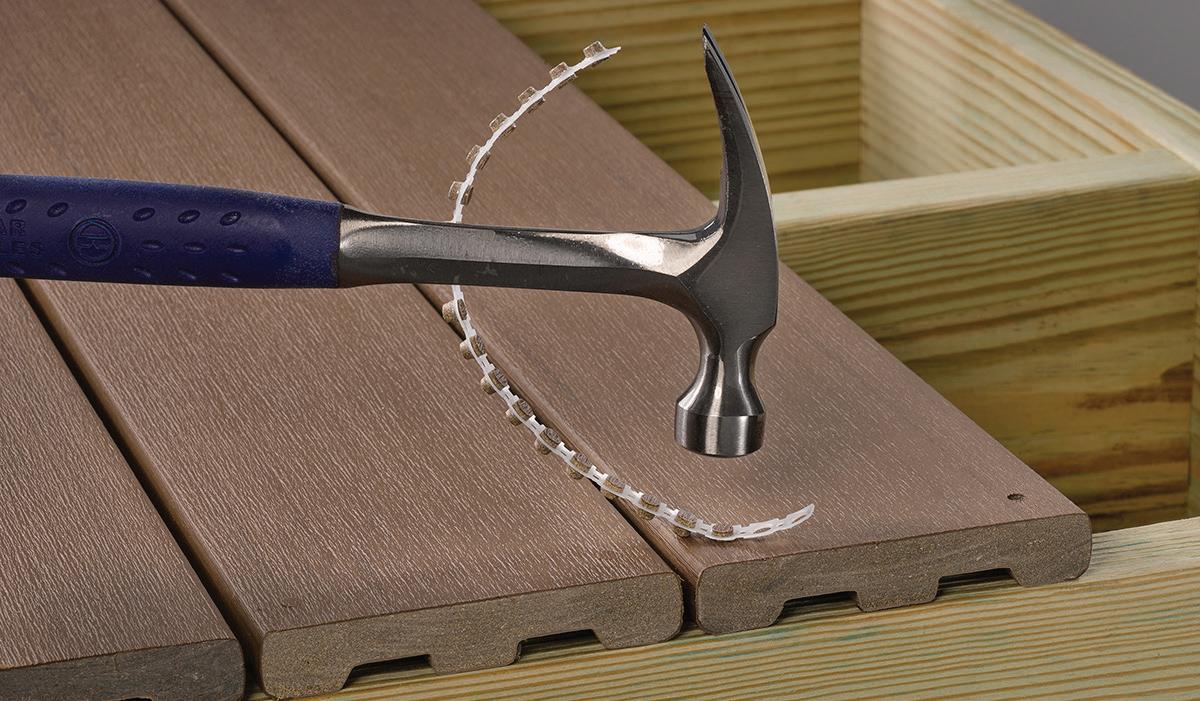
COLLATED PLUGS FOR COMPOSITES
FastenMaster’s Cortex hidden fastening line is now available with an easy-to-use hand guide for scalloped TimberTech boards.
The hand guide helps installers properly align the fasteners through the thickest portion or ‘pillars’ of the scalloped boards for maximum engagement and strength. The new plugs and hand guide are available for TimberTech Terrain+ boards, including Natural White Oak, Weathered Oak, and Dark Oak.
The new-colored plugs come on collated strips in 100 linear ft. and bulk 300 sq. ft. configurations. Each package includes enough fasteners and plugs to install the requisite linear or square footage of decking, assuming two fasteners installed 16” on center. The 100LF pack includes two setting tools and one alignment guide; the 300-sq. ft. pack has six setting tools and two guides.
FASTENMASTER.COM (800) 518-3569

TWO CONTAINMENT TAPES IN ONE
FrogTape Double-Sided Poly-Hanging Containment Tape provides two tapes in one to create a cost-effective and efficient solution for hanging poly-sheeting and creating high-performance containment systems. With a premium grade painter’s tape adhesive on one side and an aggressive adhesive on the other, the tape securely holds poly-sheeting and ensures protection of surfaces, helping to tackle jobs with speed and ease. Because it offers two tapes in one, it’s 50% faster compared to standard poly-hanging methods and removes quickly and easily, with 21-day clean removal. The tape is ideal for a variety of surfaces, such as painted walls, woodwork, glass, metal and vinyls.
SHURTAPETECH.COM (800) 321-0253
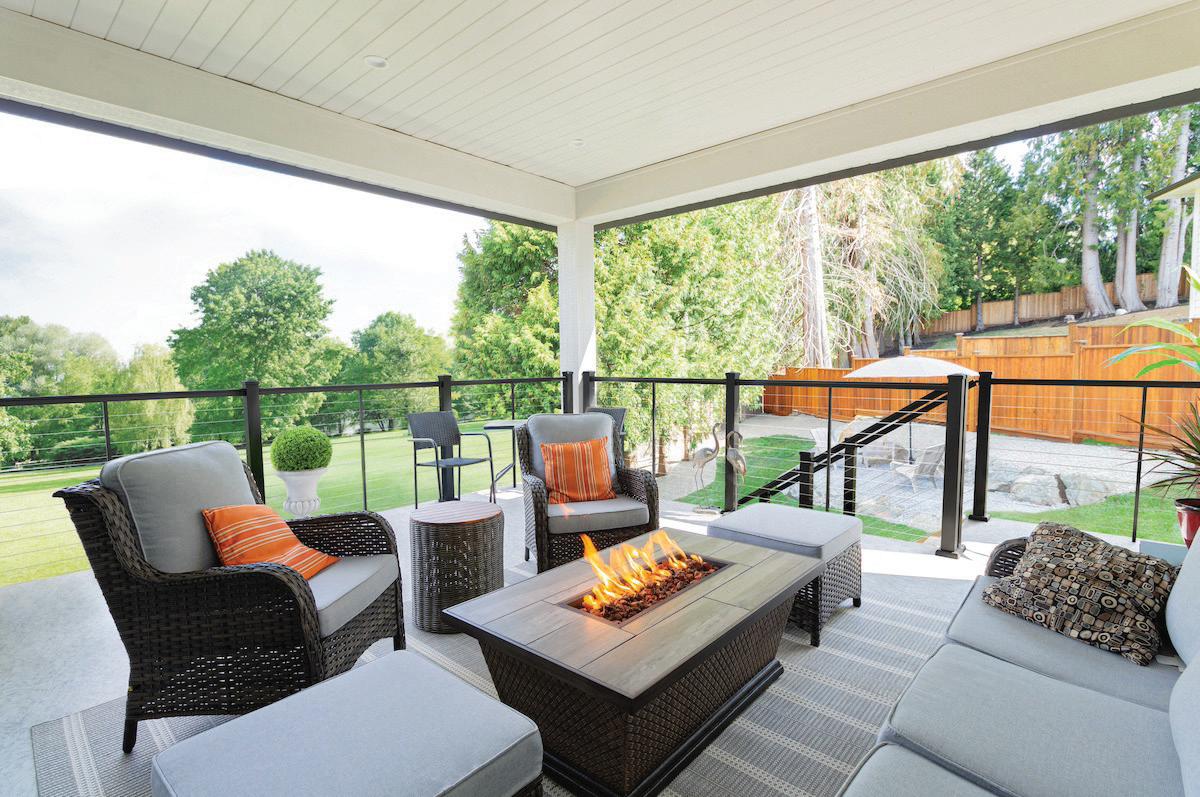
VERSATILE RAILING SYSTEM
The new RailFX Oasis Railing System makes it easy for contractors and homeowners to create beautiful outdoor living spaces by offering a blend of style and simplicity in aluminum railing systems.
What makes the system unique is its versatile infill options, including picket or horizontal cable infills to match diverse aesthetic preferences. It also features 3” posts, which are available in 36” and 42” railing heights. The posts can be spaced up to 8 ft. apart with a cable brace. For cable railing installations, the posts are predrilled, ensuring cable runs are perfectly aligned, evenly spaced and level.
Tension-fit balusters make it easy to secure the railing systems together tightly to prevent rattling.
Railings are made of extruded aluminum that will never rust and exceeds IBC and IRC requirements to provide the structure you need. Single corner posts maximize cable runs and reduce the overall project cost.
RAILFX.NET/OASIS (206) 453-1123
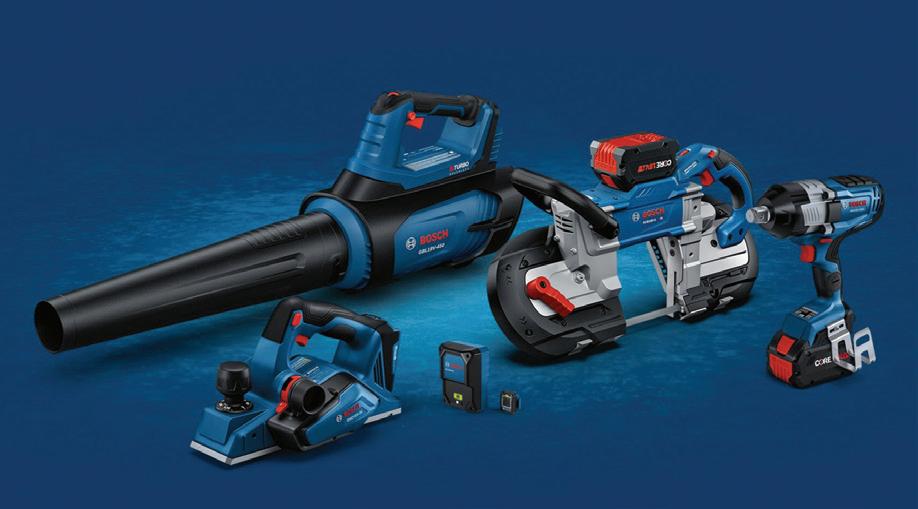
TOUGHER TOOLS FOR TRADESMEN
Designed to help make hard workers’ efforts on the jobsite simpler and seamless, Bosch Power Tools has expanded its line of 18V cordless tools for tough cutting, drilling and debris removal.
New are an 18V Brushless 5” Deep Cut Band Saw, 18V Brushless Planer with fast blade-changing technology, ProFactor 18V Connected-Ready 3/4” Impact Wrench with Friction Ring and Thru-Hole, and 18V BiTurbo Brushless Blower.
BOSCH.US (877) 267-2499

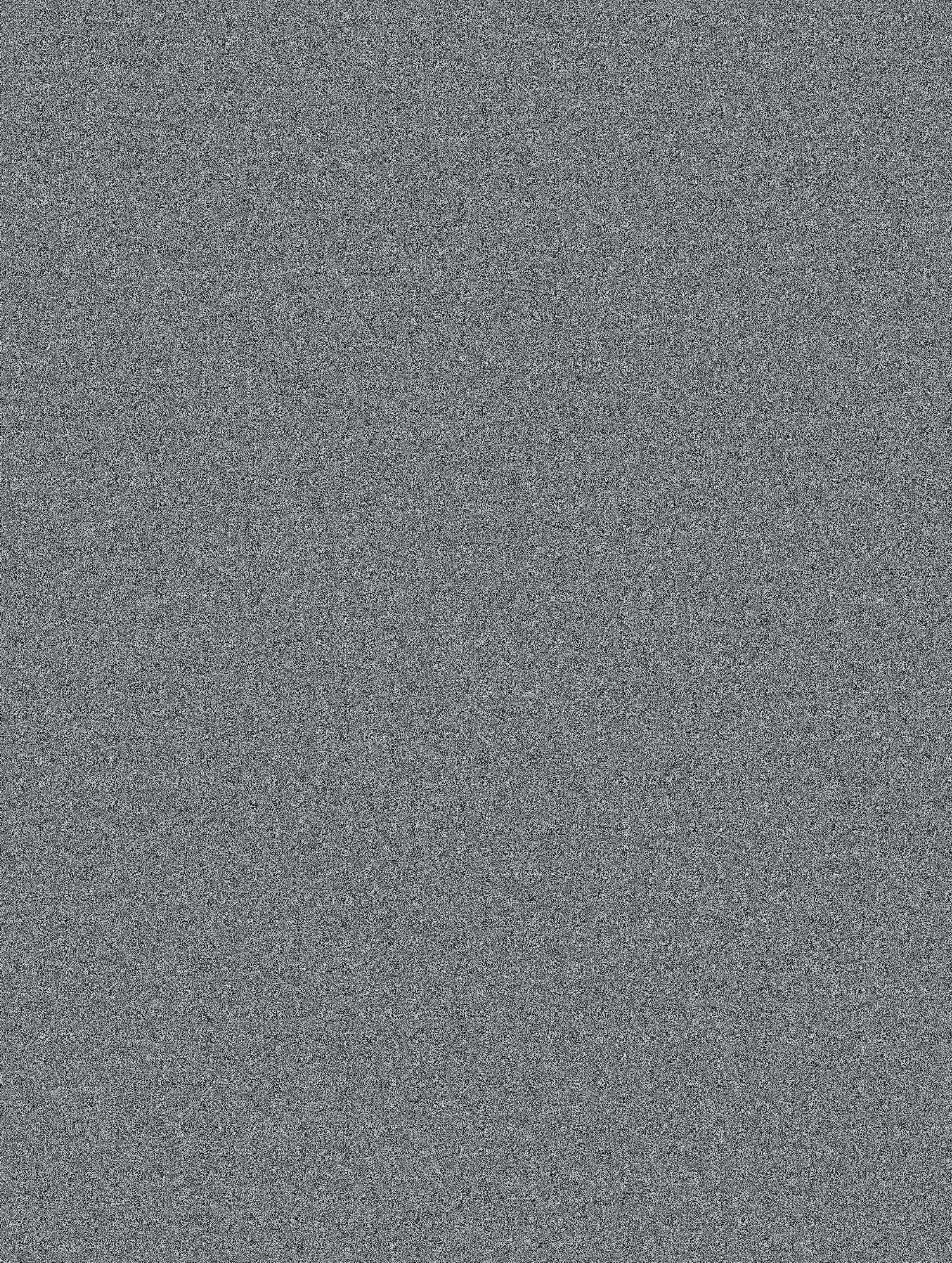

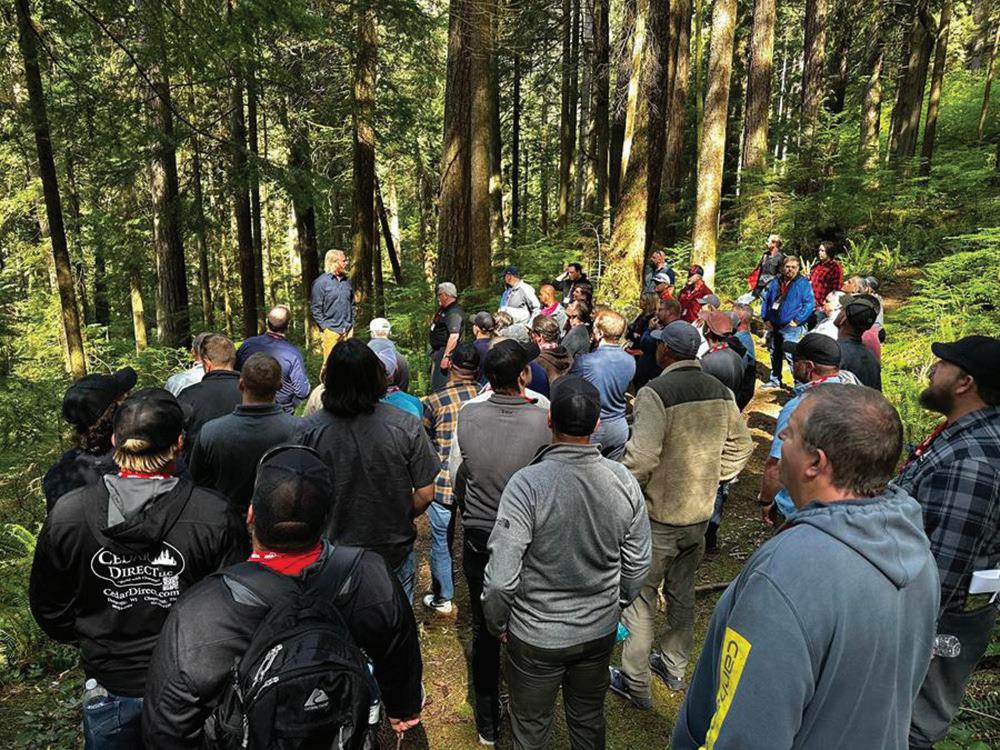
WRC IS THE STAR OF ANNUAL CEDAR SUMMIT
OVER 180 ATTENDEES, including delegates and Cedar School students, traveled to beautiful Whistler, B.C., to celebrate the 70th anniversary of the Western Red Cedar Lumber Association and participate in the annual WRCLA Cedar Summit.
Held May 15-17, the Cedar Summit featured a series of events including a golf tournament at the Fairmont Château Golf Club, receptions, dinners, speakers, business sessions, and the AGM & board meeting.
Keynoters included architect Brett Farrow on “Western Red Cedar Makes My Work Stand Out” and Forest Products Association of Canada’s Kerry Patterson-Baker and Justin Veale on “Forests Can Save the World.”
This year’s Cedar Champion Award was given to WRCLA’s Paul Mackie for his distinguished service not only to western red cedar but also to the WRCLA. The association also saluted Jake Power for his service as one of the longest standing chairman of its board of directors. This year, Power handed the reins to longtime WRCLA member Ben Meachen, OrePac Building Products.
A highlight was WRCLA’s Cedar School, which educated students on the benefits and uses of western red cedar. The program offered the opportunity for students to learn about the full circle of the species, from the forest to finished product. Courses included manufacturing, grading, installing, finishing, marketing and more. The school sold out this year and it is recommended that future students sign up early in 2025.
Cedar School kicked off in Richmond, B.C., with a seminar by master grader and quality control expert consultant Rob Johnson. His course included a tutorial on manufacturing and details on the primary mill that

the students visited at Terminal Forest Products. The mill’s access to deep water allows efficient transport, sorting of logs, grading and scaling. The tour included a look at the beginnings of the manufacturing process after harvesting.
The primary mill tour was followed with a hands-on grading course by Johnson that taught the students to understand grading rules and identify grades.
On day three, a woodlands tour at the University of British Columbia’s Malcolm Knapp Research Forest facility gave students a look at a large working forest. From reforestation to harvesting, they learned about sustainable practices used to keep forests in good health.
The final stop was PowerWood Corp. for a tour of its remanufacturing mill. PowerWood specializes in producing a broad range of customized cedar products such as timbers, decking, siding, paneling and trim.
In all, it contributed to a most satisfying event. BPD
WRCLA’S 2024 Cedar School included a grading course... ... AS WELL AS a Malcolm Knapp Research Forest Tour....
AND A TOUR of PowerWood’s remanufacturing plant.
DATE BOOK
Listings are often submitted months in advance. Always verify dates and locations with sponsor before making plans to attend.
Rhode Island Lumber & Building Material Dealers Association – July 10, golf outing & clambake, Green Valley Country Club/Kempenaar’s Clambake Club, Portsmouth, N.H.; www.nrla.org.
Construction Suppliers Association – July 17-18, DOT workshop, Tyrone, Ga.; www.gocsa.com.
New York & Long Island Lumber Association – July 18, fishing outing, Captree State Park, Bayshore, N.Y.; www.nrla.org.
Appalachian Hardwood Manufacturers – July 20-23, summer conference, Omni Grove Park Inn, Asheville, N.C.; appalachianhardwood.org.
Southeastern Lumber Manufacturers Association – July 21-25, annual conference, JW Marriott Marco Island Beach Resort, Marco Island, Fl.; www.slma.org.
Southeast Building Conference – July 24-25, Orange County Convention Center, Orlando, Fl.; www.sebcshow.com.
Building Material Suppliers Assn. – July 25-28, summer conference, Westin Chattanooga, Chattanooga, Tn.; www.mybmsa.org.
Florida Hardware – Aug. 2-3, dealer market, Ocean Center Convention Center, Daytona Beach, Fl.; www.floridahardware.com.
BLD Connection – Aug. 5-7, Pinnacle roundtable, Sheraton Minneapolis West, Minnetonka, Mn.; members.bldconnection.org.
Orgill – Aug. 5-18, fall online buying event; www.orgill.com.
Garden Center Show – Aug. 6-7, Rosemont, Il.; gardencentershow.com.
International Woodworking Fair – Aug. 6-9, Georgia World Congress Center, Atlanta, Ga.; www.iwfatlanta.com.
Midwest Building Suppliers Association – Aug. 8, Sycamore Scramble, Anderson Country Club, Anderson, In.; www.thembsa.org.
Ace Hardware – Aug. 8-10, fall convention, McCormick Place, Chicago, Il.; www.acehardware.com.
North American Young Lumber Employees – Aug. 15, summer outing, Saratoga Race Course, Saratoga Springs, N.Y.; www.nrla.org.
Western New York Lumber Dealers Association – Aug. 15, summer board meeting, Irondequoit, N.Y.; www.nrla.org.
Mid-States Distributing – Aug. 20-22, Fall Rendezvous, Phoenix Convention Center, Phoenix, Az.; www.msdist.com.
American Wood Protection Association – Aug. 21, summer executive committee meeting, Grand Rapids, Mi.; www.awpa.com.
Construction Suppliers Association – Aug. 21, HR workshop, Tyrone, Ga.; www.gocsa.com.
Independent Home Improvement Conference – Aug. 27-29, JW Marriott Resort, Marco Island, Fl.; www.ihiconference.org.
National Hardwood Lumber Association – Aug. 28-30, intro to hardwood grading course, Memphis, Tn.; www.nhla.com.
Midwest Building Suppliers Association – Aug. 29, White Pine Classic, Tullymore Golf Resort, Stanwood, Mi.; www.thembsa.org.
FAQs ABOUT OSB
(Continued from page 28)
APA-Rated Siding trademarks, indicating that the manufacturer has produced the panel to a size slightly less than the traditional nominal 48” by 96”. This is done to facilitate proper panel spacing during construction. The size difference could vary from something other than 1/8”. The standard recognizes that a manufacturer may target the width and length to be less than that specified
by the customer to allow for moisture-related growth and recommended panel spacing. The vast majority of OSB sheathing is sized for spacing.
Limited Exposure
All engineered wood products that bear the APA trademark are manufactured to standards that require moisture-resistant adhesives. Moisture-resistant adhesives are known to provide bond strength stability over time, despite fluctuating moisture conditions.
APA trademarked panels may be produced in two moisture-resistant bond classifications—Exterior and Exposure 1. The bond classification is defined by the applicable standard and relates to the moisture resistance of the glue bond.
Exterior panels have bonds capable of withstanding repeated wetting and redrying or long-term exposure to weather.
Exposure 1 panels are suitable for uses not involving long-term exposure to weather. Panels classified as Exposure 1 are intended to resist the effects of moisture on structural performance during construction or other conditions of similar severity. Exposure 1 panels may also be used outdoors if protected from direct exposure to weather and precipitation. However, only Exterior panels should be used for long-term exposure to the weather.
Conditioning & Acclimation
Helpful Tips:
• Reduce panel buckling by conditioning the panels to the building environment before installation. Including this step can reduce the amount of additional moisture absorption after panels are installed.
• Temporarily nail panels with a nail spacing of 12” or 24” o.c. at ends, edges and intermediate supports during the framing phase of construction. With this lighter-than-specified nailing schedule, panel edge gaps more readily accommodate panel expansion.
• Complete final nailing after panels acclimate to job site moisture conditions and immediately prior to covering with siding or roofing.
Mold, Mildew & Moisture Management
Mold and mildew grow when conditions have ample moisture, darkness or low light and stagnant airflow. Mold and mildew grow easily in a temperature range of 68°F to 86°F. As an organic material, mold grows on wood when the moisture content exceeds 20%. Mold and mildew affect only the surface of OSB and does not cause any structural degradation.
The first step in mold remediation is to identify and eliminate the source of moisture that caused the mold.
Helpful Tip: Mold can be removed or cleaned with commercial mold/mildew removers or with a solution of one part household bleach (5% sodium hypochlorite) mixed with three parts warm water. However, if the conditions that caused the mold are not removed or improved, mold can return.
Find additional information regarding frequently asked questions about OSB in APA’s Technical Topics: FAQs About Oriented Strand Board, Form TT-133 BPD
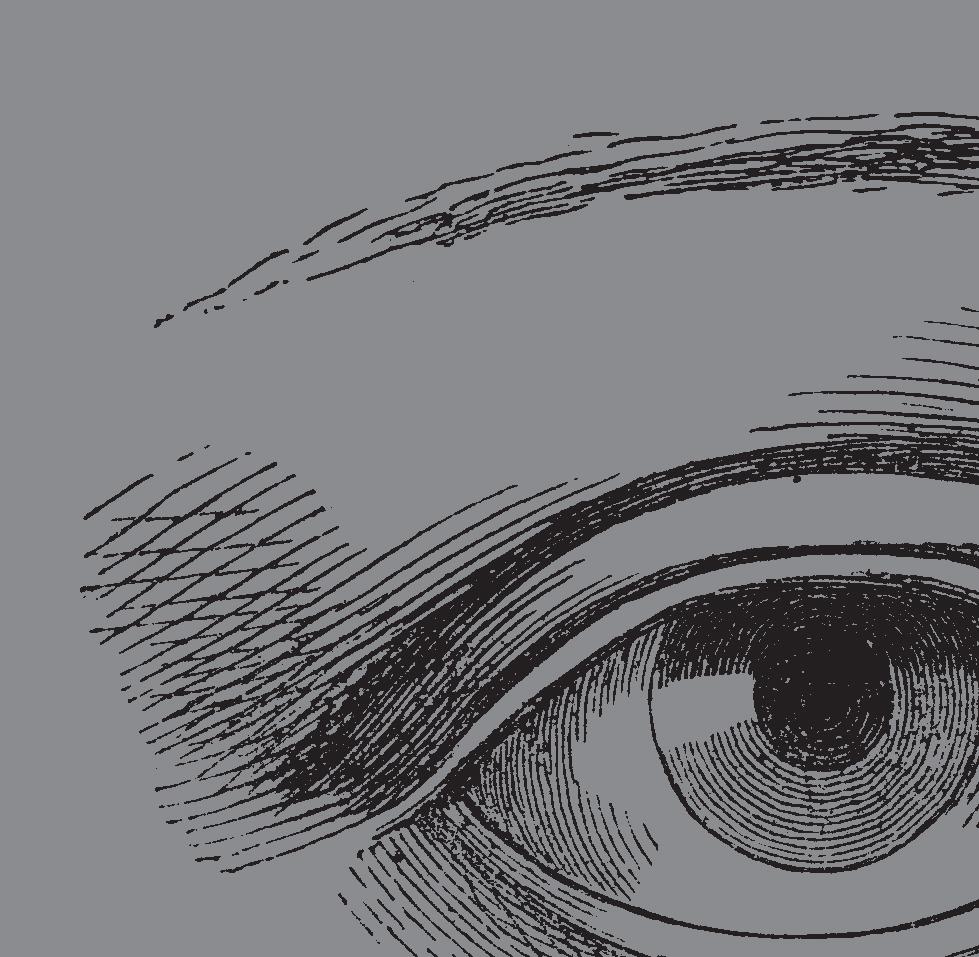
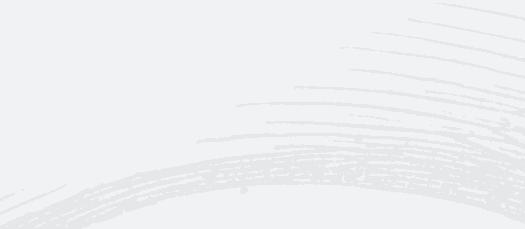

Read grade rules, span details, and get new promotional ideas for your business.

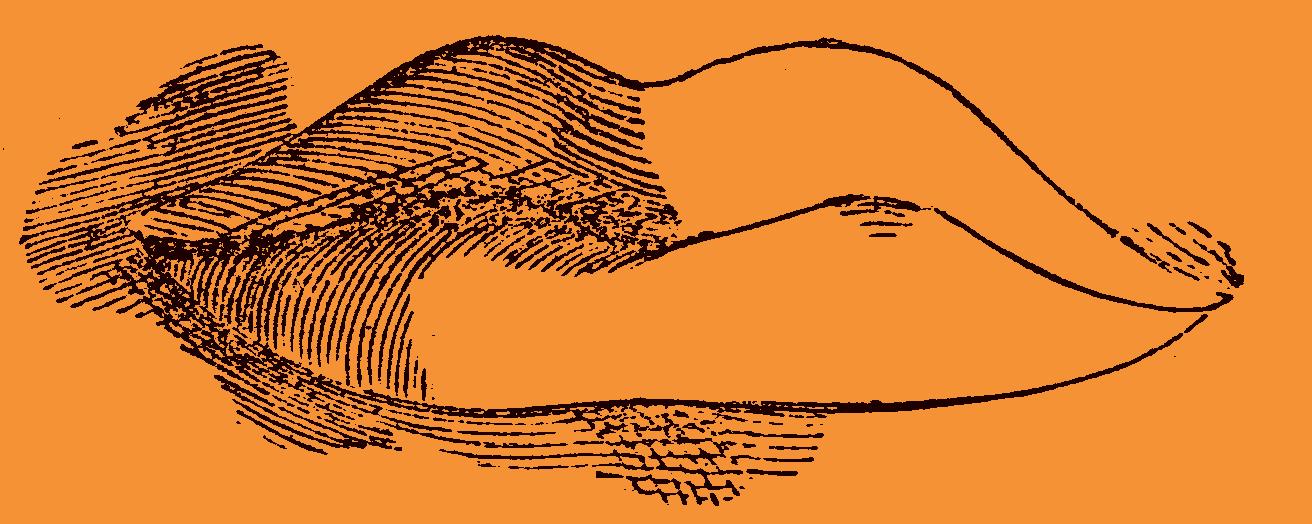
Sample the variety and versatility of eastern white pine.
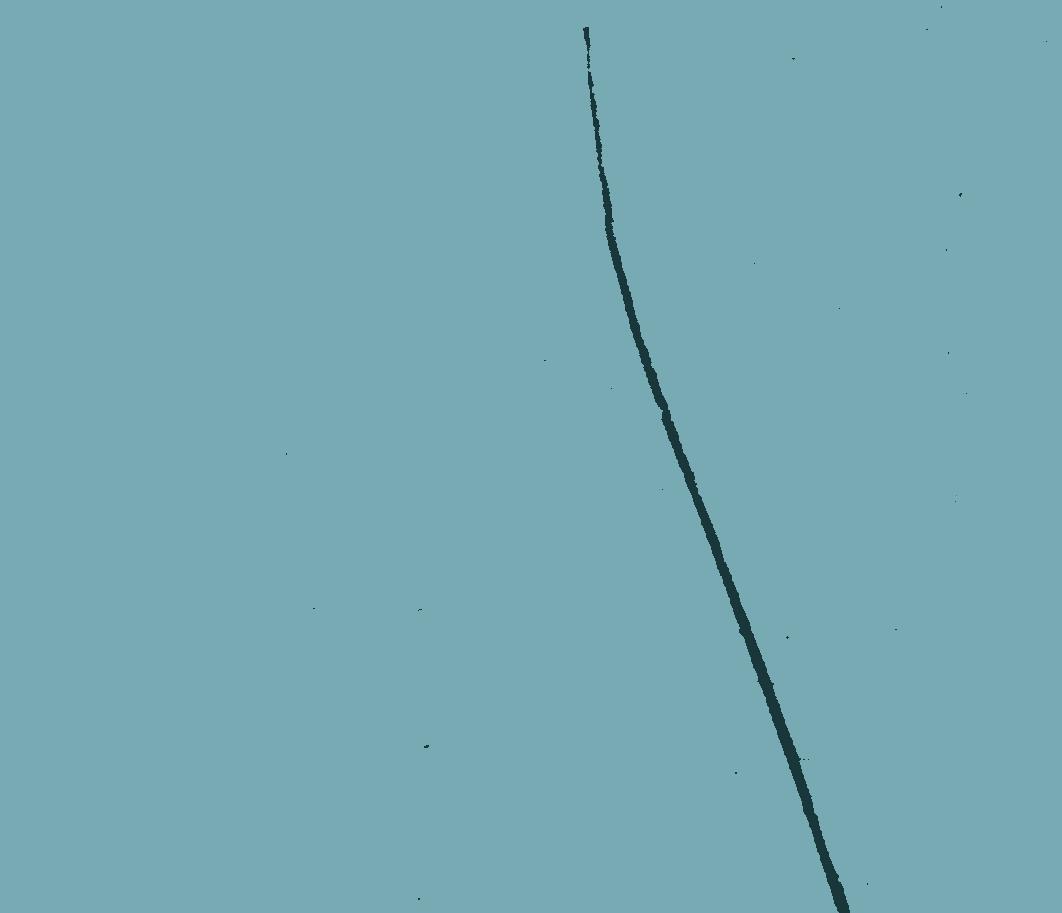
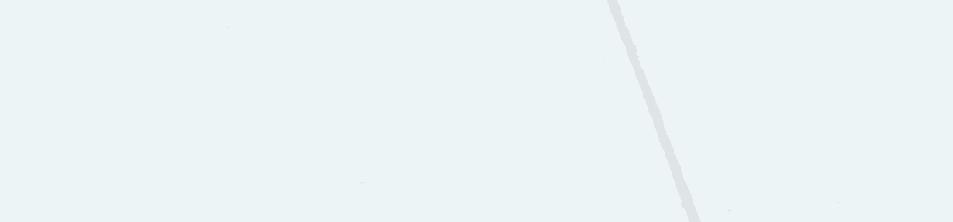
Plastic, concrete or pine? Learn why consumers prefer natural over fabricated.
Reach more customers by getting listed on NELMA’s Retailer Directory.
Listen to and watch product installation and comparison videos, plus grade representations.

Use all your senses. Visit nelma.org for all things eastern white pine, spruce-pine-fir and other softwood species grown in the Northeast and Great Lakes region.

Ever see a paint swatch for wood grades? Scan here to see it. Simply open the camera on your smartphone or tablet, and hold it over this image.
@NortheasternLumberMfg
@WoodInspiration
@wood_inspiration1933

------------| CLASSIFIED MARKETPLACE
WANTED TO BUY
WANTED TO BUY

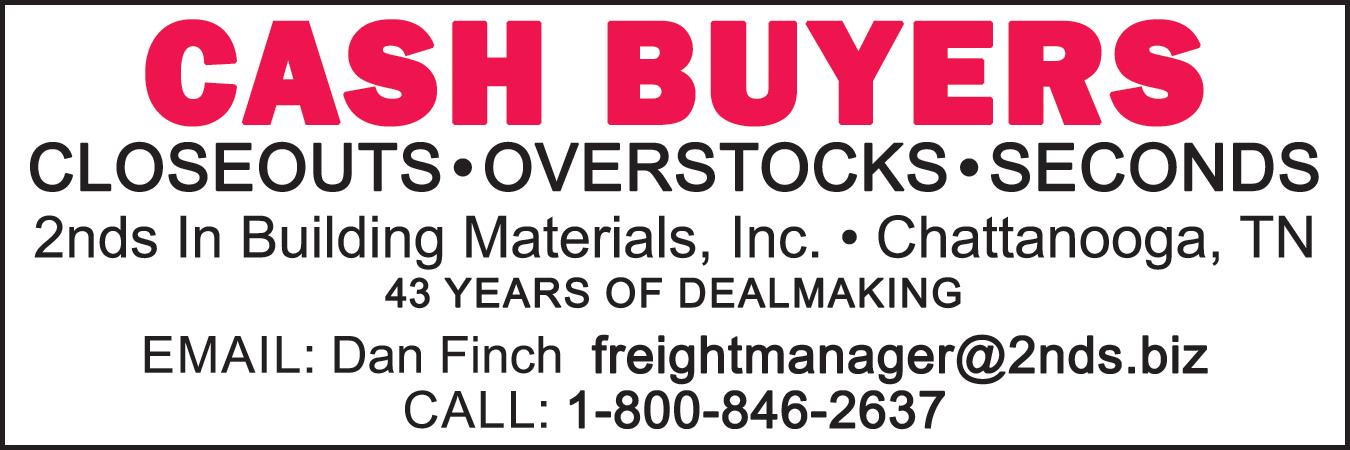
IN MEMORIAM
Gerald “Jerry” Stein, nicknamed the “Godfather of Treated Wood,” passed away May 8 at the age of 98.
After serving in the U.S. Navy, he attended the University of Wisconsin, Madison and then became a lumber broker. He joined wholesaler Lentin Lumber Co., Chicago, Il., in the 1960s and it was in 1974, while serving as sales manager for Lentin, that he teamed up with the old Koppers Co. to launch the first sales/marketing program for dealers to promote Wolmanized treated wood in residential applications.
Jerry remained active in the lumber business until his 90s, representing Mid-States Wood Preservers to Chicago-area lumberyards.
William S. McNamara, 83, former vice president of Osmose Wood Preserving, Buffalo, N.Y., died on April 19.
William graduated with a forestry degree from the University of Massachusetts in Amherst, Ma., in 1962; a Master’s degree from the University of Idaho in Moscow, Id., in 1964; and a PhD from North Carolina State in
Raleigh, N.C., in 1969. He was a college professor at UMass from 1969 to 1973. In 1973, he joined Osmose as director of laboratory, and was promoted to VP and director of research in 1977. He retired in 2000.
William was a member of the International Research Group on wood preservation (IRG), and 1994-1995 president of the American Wood Preserving Association, receiving AWPA’s Award of Merit in 2003.
Ronald Dean Hees, 92, a pioneer of the hollow core flush door, died on June 5 in Gaylord, Mi.
Ron served in the U.S. Marine Corps from 1952 to 1954. He would later found Downriver Forest Products, Wayne, Mi., and Custom Forest Products, Grayling, Mi., and Sparta, Tn.
Howard Lee Jones Jr., 85, owner of J.M. Jones Lumber Co., Natchez, Ms., died on May 28.
In 1960, after graduating from Louisiana State University with a degree in forestry, Lee became a third-generation employee of J. M.
Jones Lumber. He would become sole owner in 2001.
Lee served two terms as chairman of the American Hardwood Export Council. In 1998, he was the first chair to host an AHEC convention in China.
James Fred Robinson, owner and operator of Newark Lumber Co., Newark, De., died on May 24. He was 92.
Ray Timothy “Tim” McClain, 69, retired vice president and partner in Mauldin Lumber Co., Greenwood, S.C., died on June 10.
Palmer Tobias Wetzel Jr., 92, owner and operator of Wetzel Lumber Co., Jersey Shore, Pa., died on May 30.
John Paul “Johnny” McIntosh, Jr., 70, retired owner of McIntosh Lumber Co., Star, N.C., died on June 1.
Upon graduation from high school, Johnny and his sister Claudia took over the sawmill from their parents. He also operated Thick n’ Thin Sawmill.



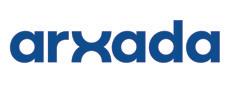
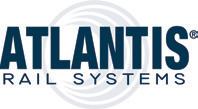
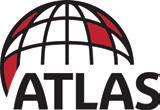
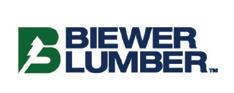

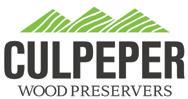
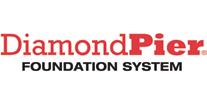
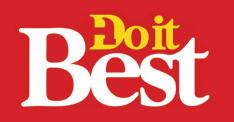
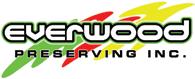
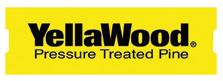


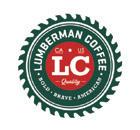
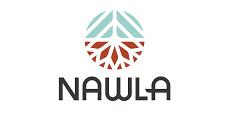
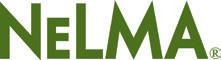
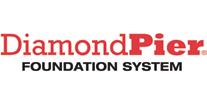
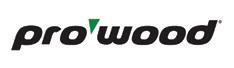
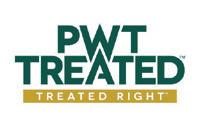

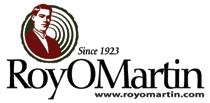
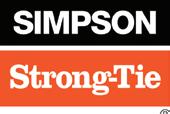
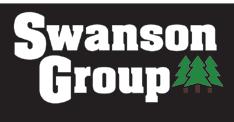
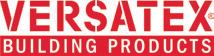

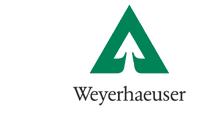
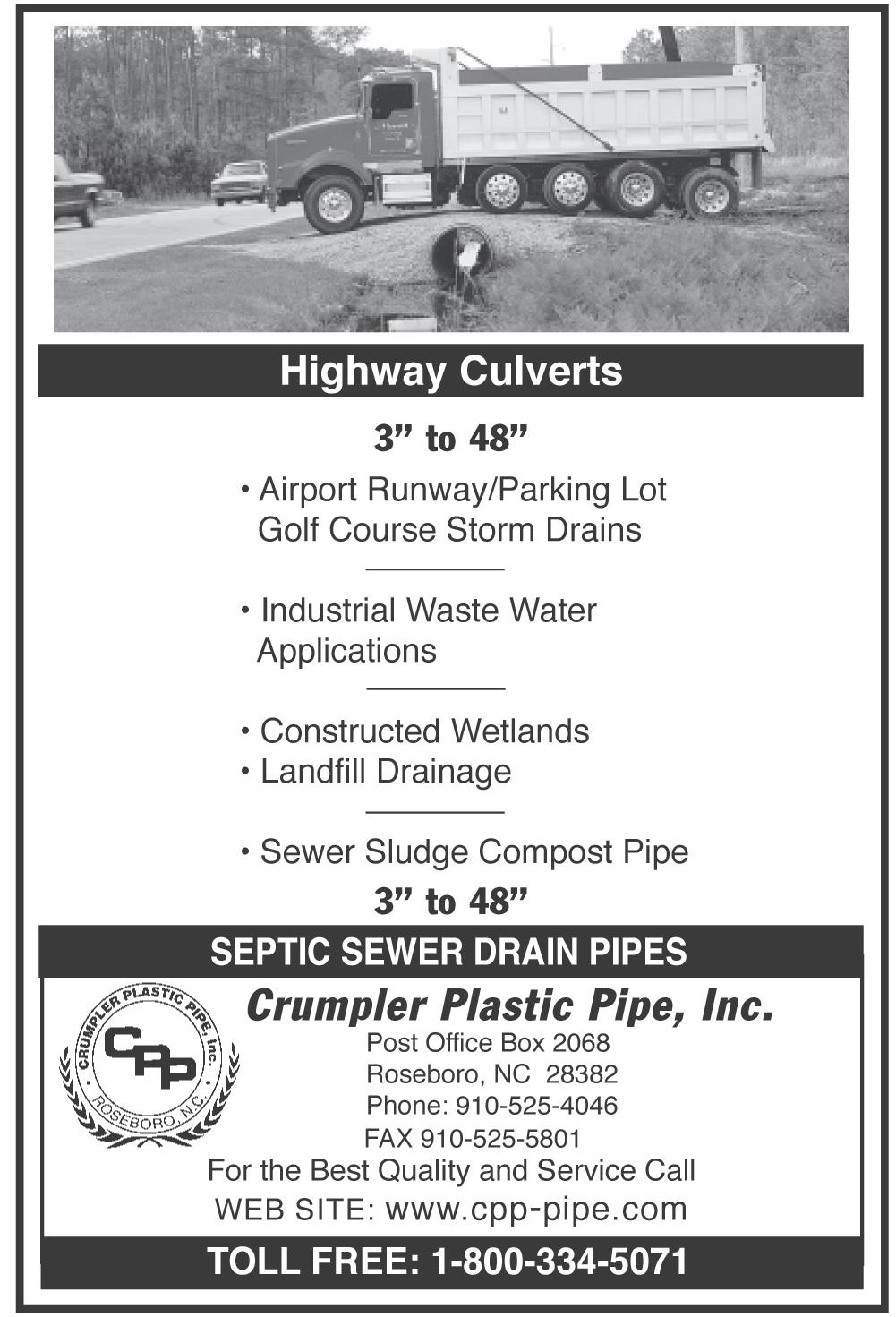
FLASHBACK: CALL TO YOUTH
EVERYTHING IS CYCLICAL.
Sixty-five years ago this month, BPD’s sister publication, The California Lumber Merchant, reported on the 67th annual meeting of NAWLA (today’s North American Wholesale Lumber Association), which gathered over 350 members in New York to discuss topics as critical today as they were back then.
The most urgent was a “Call to Youth,” recognizing that the pioneers were passing or retiring, and the industry desperately needed a new generation of skilled youngsters to take their places. (With perfect timing, NAWLA’s secretary manager/ executive vice president, Sid Darling, announced he too was calling it quits after nearly 30 years of service.)
Attendees were encouraged to “develop a program for recruiting forces of outstanding men and training them in the art of manufacture and sale of forest products. We must compete
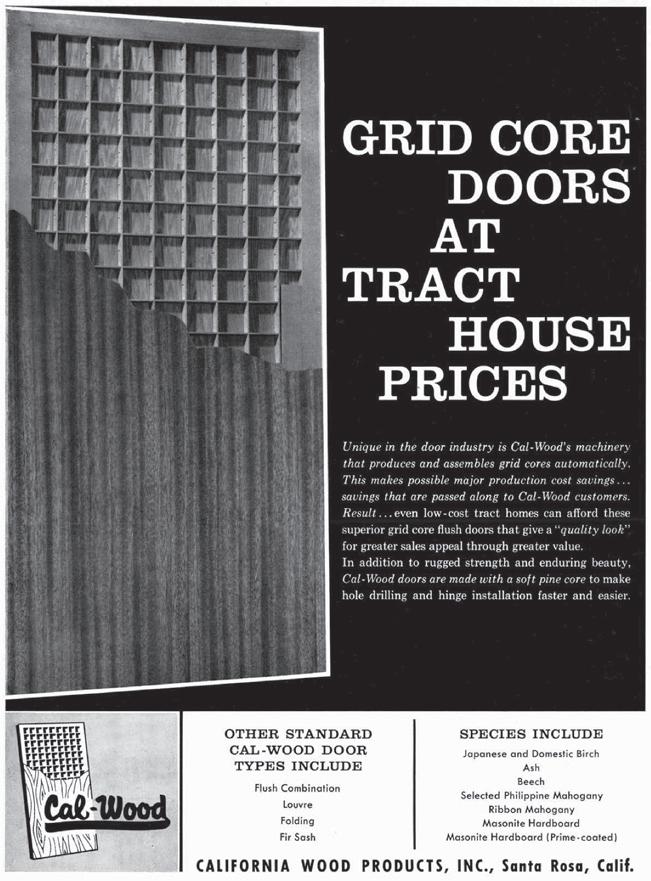
with other industries for new talent, and we are not going to get good talent for peanuts.” *
In California, the trend had been “out with the old”—but minus “in with the new.” The same July 1959 issue of The Merchant reported that the historic Woodhead Lumber on West Pico Blvd. in Los Angeles announced it was ceasing operations after 43 years, effective June 30, 1959. Shutting down would allow president Hal A. Brown to retire to his recently built home on the cliffs above Malibu Beach.
At the time, Brown was serving as president of the Southern California Retail Lumber Association (a forerunner of today’s West Coast Lumber & Building Materials Association).
The news was the latest closure by a Southern California lumber giant— including Patten-Blinn, the Hammond Lumber chain, Fox-Woodsum Lumber, and E.K. Wood—which had all weathered the Great Depression and World War, but ran out of steam by the end of the 1950s.
With its eye on the growing $2.5 billion-a-year small boat industry, Matzley Corp., San Francisco, Ca., had begun importing plywood leisure
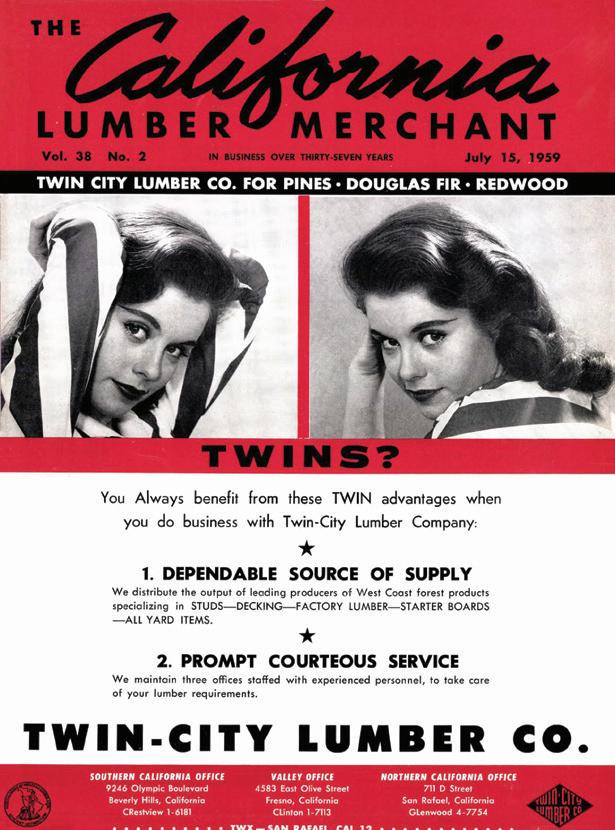
The cover of the July 1959 edition continued the Twin-City Lumber Co.’s ad campaign featuring sets of attractive twins.
crafts from Japan to be sold at retail lumberyards.
The new line, manufactured in a variety of different models ranging from 14-ft. runabouts to 21-ft. cabin cruisers, were “reasonably priced” and “of equal quality” to domestically produced vessels. They would be constructed from Philippine mahogany marine plywood, complete with fiberglass bottoms, and outboard motors.
Consumers would place their orders at their local lumberyard, it would be custom-built to their specs in Japan, and Matzley would oversee the overseas delivery. Matzley’s initial shipment included two cabin cruisers and one runabout.
Unfortunately, Matzley—which had only been founded the prior year— found few takers and soon abandoned the strategy. BPD
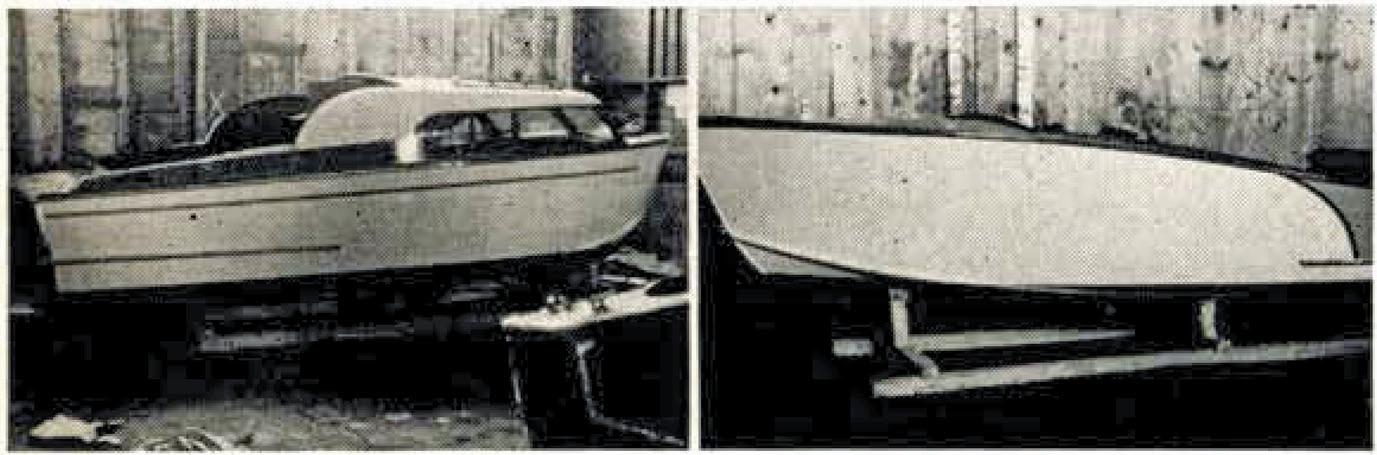
IN THE LATE 1950s, California Wood Products, Santa Rosa, Ca., began advertising its wide range of flush doors.
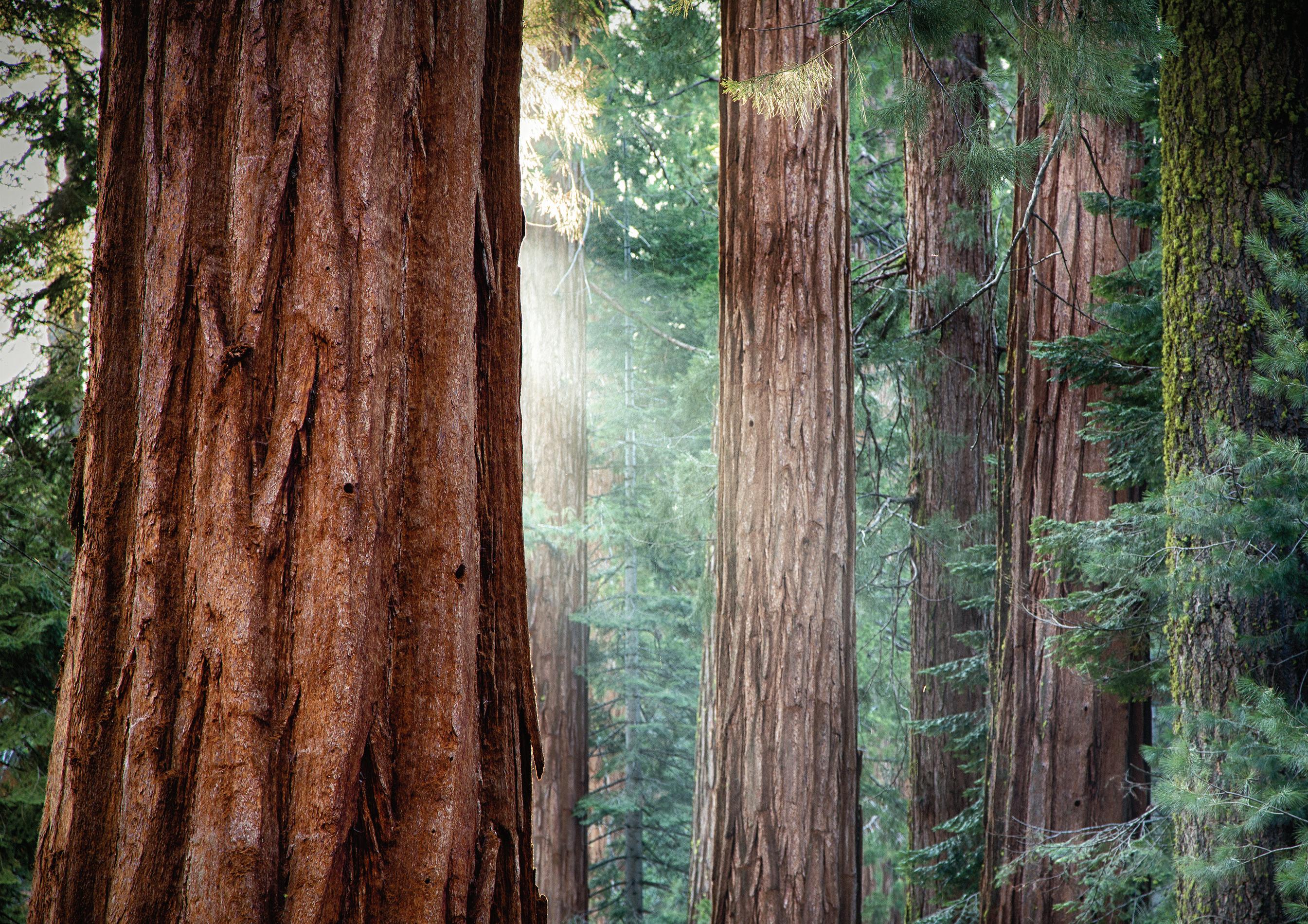
Re Reddwwood i ood is
thrives in some of the most productive timberlands in the world. Redwood is known for its timeless durability without the use of chemicals. Due to its flawless formation, there has never been a Redwood recall. There is a grade of Redwood for every application, every budget, and every customer.
“Growing beyond measure.”
Call or visit us today. Our family of Redwood timberland owners will continue to be your reputable and reliable source of Redwood.
Change Service Requested
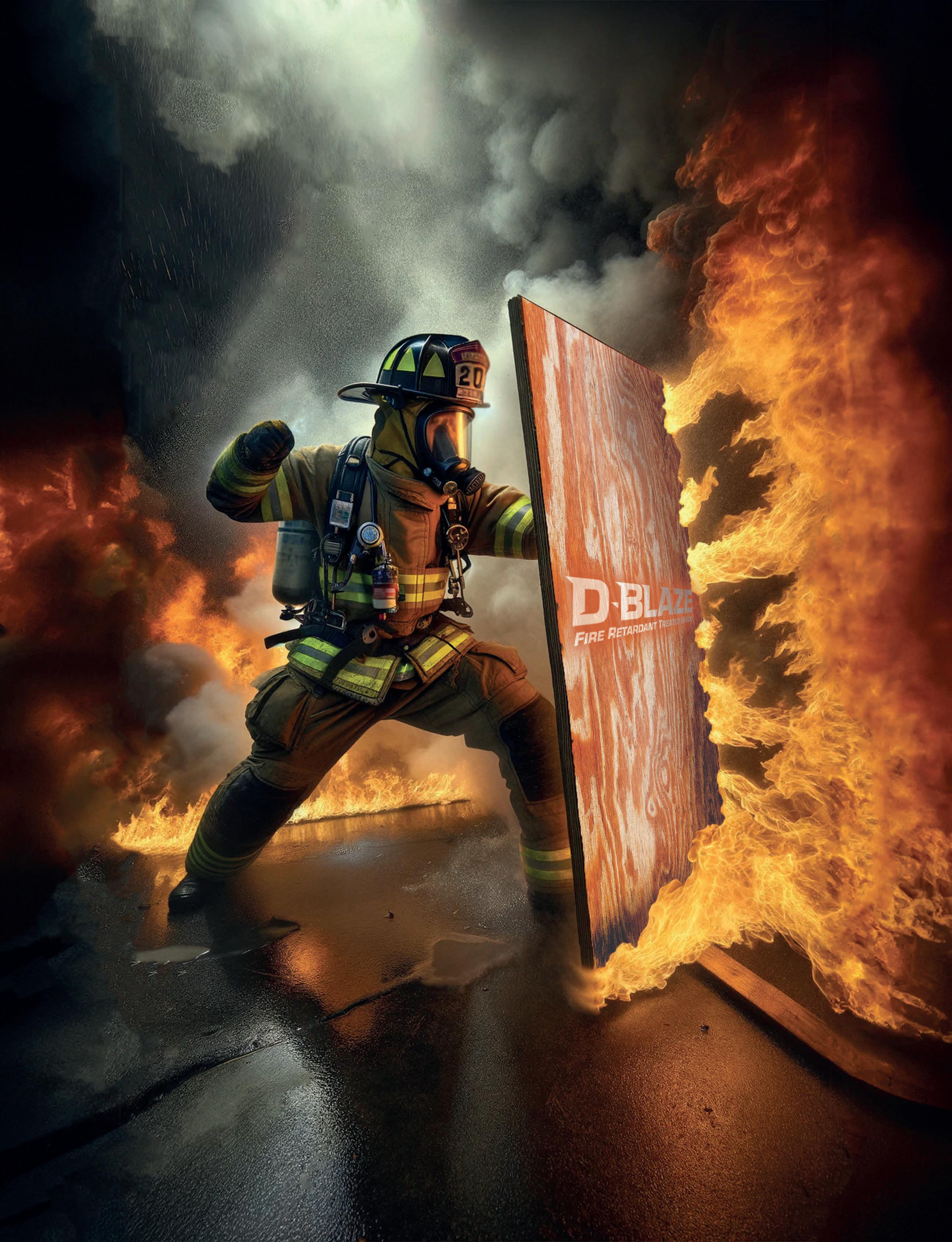
It’s simple: when you’re responsible for meeting building codes, you want to slow the spread of flames from the ground up. That’s why D-Blaze fire retardant wood has been the choice of builders from the Sears Tower to the One World Trade Center. It’s so good at its job, you’d think an army of firefighters was defending your building.