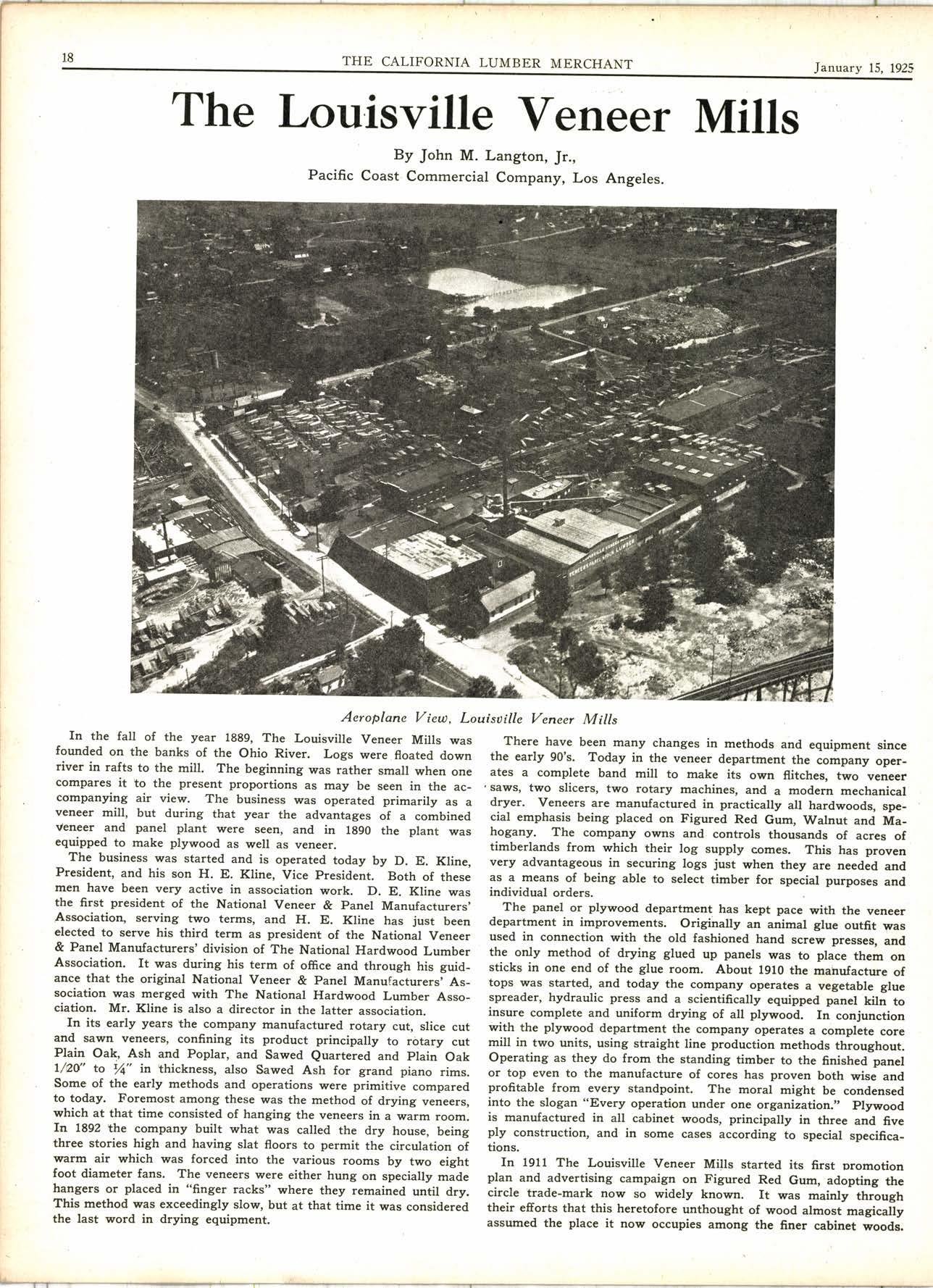
4 minute read
The Louisville Veneer Mills
By John M. Langton, Jr., Pacific Coast Commercial Company, Los Angeles.
Aeroplane Vieu, Louisuille Veneer Mills
fn the fall of the year 1889, The Louisville Veneer Mills was founded on the banks of the Ohio River. Logs were floated down river in rafts to the mill. The beginning was rather small when one compares it to the present proportions as may be seen in the ac_ companying air view. The business was operated primarily as a veneer mill, but during that year the advantages of a combined Veneer and panel plant were seen, and in 1990 the plant was equipped to make plywood as well as veneer.
The business was started and is operated today by D. E. Kline, President, and his son H. E, Kline, Vice president. Both of these men have been very active in association work. D. E. Kline was the first president of the National Veneer & panel Manufacturers' Association, serving two terms, and H. E. Kline has just been elected to serve his third term as president of the Nationar veneer & Panel Manufacturers'division of The National Hardwood Lumber Association. It was during his term of office and through his guid_ ance that the original National Veneer & panel Manufacturers' As_ sociation was merged with The National Hardwood Lumber Association. Mr. Kline is also a director in the latter association.
In its early years the company manufactured rotary cut, slice cut and sawn veneers, confining its product principally to rbtary cut Plain Oak, Ash and Poplar, and Sawed euartered and plain Oak I/QO" to /a" in lhickness, also Sawed Ash for grand piano rims. Some of the early methods and operations were primitive compared to today. Foremost among these was the method of drying veneers, which at that time consisted of hanging the veneers in a warm room. In 1892 the company built what was called the dry house, being three stories high and having slat floors to permit the circulation oi warm air which was forced into the various rooms by two eight foot diameter fans. The veneers were either hung on specially made hangers or placed in "finger racks" where they remained until dry. This method was exceedingly slow, but at that time it was considered the last word in drying equipment.
There have been many changes in methods and equipment since the early 90's. Today in the veneer department the company oper_ ates a complete band mill to make its own flitches, two veneer 'saws, two slicers, two rotary machines, and a modern mechanical dryer. Veneers are manufactured in practically all hardwoods, spe_ cial emphasis being placed on Figured Red Gum, Walnut and Ma_ hogany. The company ourns and controls thousands of acres of timberlands from which their log supply oomes. This has proven very advantageous in securing logs just when they are needed and as a means of being able to select timber for special purposes and individual orders.
The panel or plywood department has kept pace with the veneer department in improvements. Originaly an animal glue outfit was used in connection with the old fashioned hand screw presses, and the only method of drying glued up panels was to place them on sticks in one end of the glue room. About l9l0 the mah'facturc of tops was started, and today the company operates a vegetable gluc spreader, hydraulic press and a scientifically equipped panel kiln to insure complete and uniform drying of all plywood. In conjunction with the plywood department the company operates a complete core mill in two units, using straight line production methods throughout. Operating as they do from the standing timber to the finished panel or top even to the manufacture of cores has proven both wise and profitable from every standpoint. The moral might be condensed into the slogan "Every operation under one organization.,, plywood is manufactured in all cabinet woods, principally in three and five ply construction, and in some cases according to special specifica_ tions.
In 1911 The Louisville Veneer Mills started its first promotion plan and advertising campaign on Figured Red Gum, adopting the circle trade-mark now so widely known. It was mainly through their efforts that this heretofore unthought of wood almost magically assumed the place it now occupies among the finer cabinet wood,s.
D. E. KLI NE, Pr'esidenl
ert)ice !
Everybody wants it, de' serves it, and insists upon it.
It takes a lot of it and the right kind, to keep everybody happyl ln t923 when Walnut came into popular favor, especially in -the finishes, the Huguenot or French-gray, Jhis-company entered-into i "amoiien to pr-omote and advertise their Blue Limestone Walnut. ihese'lois weie obtained from the old limestone districts still exista;t in-this state, and the veneer produced contained the coveted nitural gray. This wood is still hishly popular and almost daily cuttings lre necessary to supply the demand.
Mostly a matter of being able to serve well, uanting to, and actually gioing service.
So widety has this company become known as- Specialists in Figrged Red Gum Products, trhat they are universally recogruzed as -l'he Home of Figured Red Gum.- Almost from the b-9gilnirg, it has been the cusibm of this company to retain intact all of the veneers cut from choice logs and eien- trees, thereby enablqls their- customers to obtain e-normous quantitiei of veneer similar in figure design, uniform in color and the same texture.
The Louisville Veneer Mills have not only kept pace in the forward march of progress, but hawe contributed generously to- ttte welfare of the two great industries that the-y have so successlully combined under a coinmon roof. Through the process of- time, th-e refinement of men and materials, this company is today in a position to fulfill thc most exacting requirements in veneers and plywood' and all throuch one organization. To be nationally known an iecosnirea as -specialistS ln two industries is no mean achievement'
H. E. CLI NE, Vice President
Nicolai Doors are made by an organization big etnugh to serye well. Production is on ao vast a gcale that Nicolai musl serve efficiendy, dependably and satisfactorily.
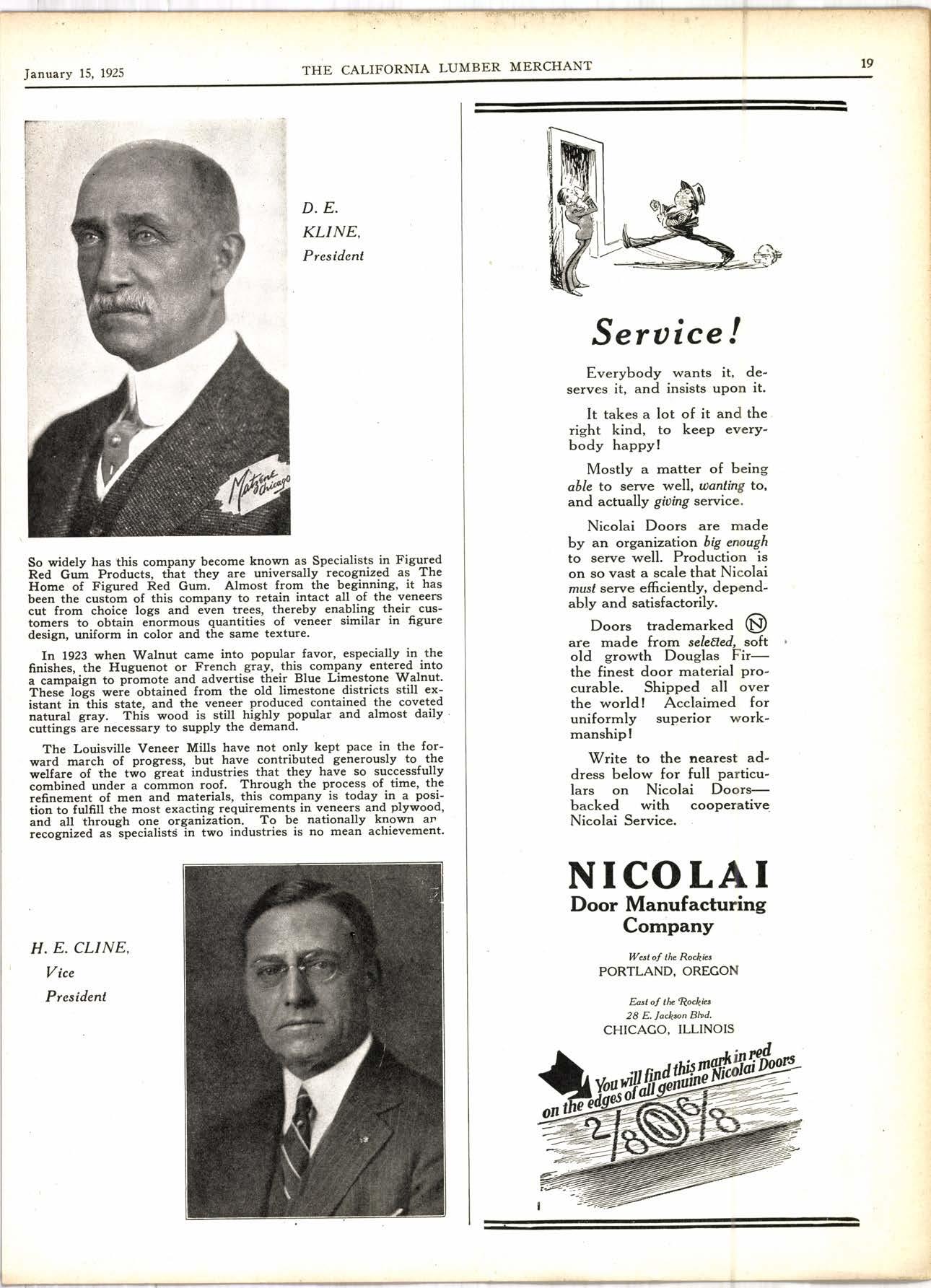
Doors trademarked @ are made from seleded, soft old growth Douglas Firthe finest door material procurable. Shipped all over the worldl Acclaimed for uniformly superior workmanshipl
Write to the nearest address below for full particulars on Nicolai Doorsbacked with cooperative Nicolai Service. #,fifu