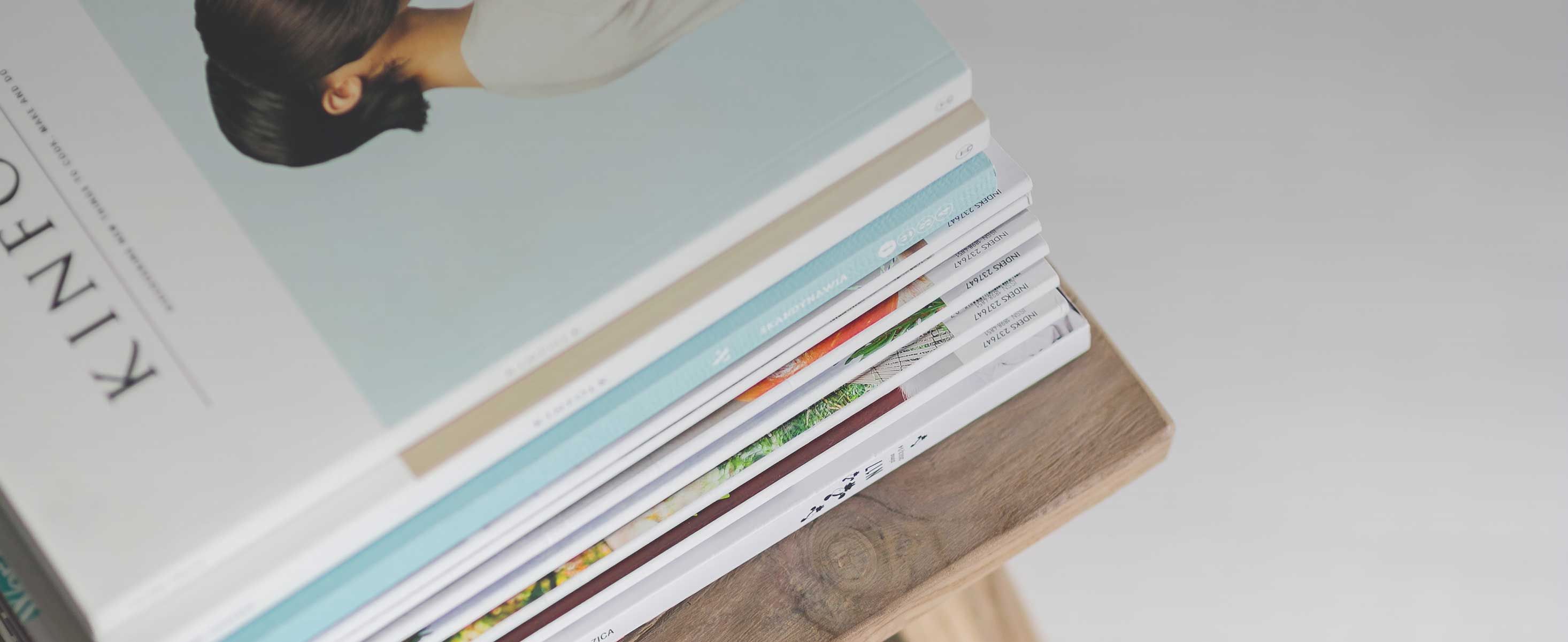
3 minute read
Millwork Cost Schedules
(Continued trom Page 22) cost records would sholv t\q relative costs of both methods the detail work contains the added risk caused by errors in design, layout machining and assemblihg which on the Jpecial work, rnade one at a time, may destroy thp possible profit for the job, whereas on standard work these risks ere practically eliminated because of the established practice in making. Furthermore in making detail work you are endeavorlng to fu!fill the ideas of architects who may not become critical and arbitrary over your interpretation of their intentions.
It is practical to set up an account on the ledger and determine the percentage of risk manufa-cturing detail work, defective allowance as it is called. This metlgd of measuring the element of risk has been thoroughly tested aq{ found to be thoroughly practical, not only in recording defective'work in the factory but in ill othei departments. The tenth axiom then is, "On detail production costs use a safety factor,"
Every millwork factory has about the same line of standard wood-working machinery rtt6 .,ach machine is capable of perform- ing only_-certain specific operations, so a systern of finding costs is _naturally determined by the kind and quantity of operati6ns re- quired to complete a given piece of work. Presuml that each machine is a complete manufacturing enterprise and that the essential problem is determining the production cost of that machine produc!1q its own particular kind of work. Then cost finding resolves itself into adding together the work of each machine iniolved to determine a complete cost.
The-. cost of operating each machine is not difficult to compute and the method of doing so i_s appended as a matter of record, though not actually pertinent to the subject at hand. To those interested the Timberman will doubtless furnish copies of my talk before this organization at the Santa Cruz Convention at which time the subject was treated in considerable detail.
.The problemthen is recording or charting the flow of any given piece of work through the factdry to determine the units of o-peralions required to produce it. flris charting serves several purpbses. It plans the routing of the wqfk through the factory in ihe-most economicat yay,.it permits analyzing the efficiency of each production proc_ess in detail, it measures production to the capacity of each machine and department and it enables the managemeni to intel- ligently go into the cfficiency of costs directly to the exact point of inefficiency.
This axiom then is required in Millwork Schedules, the ELEVENTH, "Build costs by units of value for each operation involved."
No intelligent millman will take another millman's record of costs as a basis for his own costs. If records were mutually obtained with the same system there -lnight be mutual confidence in the records. But at present such uniformity is practically absent. Wc can definitely say that all millmen come from Missouri and you have to show them.
Thus the obligation to prove costs used in Cost Schedules exists and the best way to prove a-nything is let every one prove thc thing themselves. If you cannot prove the value you cannot censure for each mal- having. ag opinion of his own. So this axiom goes in, the twelfth, "Enable every man to prove cost schedules in his own factory.'
The value of cost finding is -not for the purpose of setting prop€r price alone. Profit and loss_ statements, budgeting, production efficie_ncy, wage .incentives, inv-entory records, shipping- sirvice and il other lyays "knowing your costs" can be used io advantage. But the subject at- hand_ refers. mainly to the use of cost finding for estimating schedules. In applying prices it is necessary to group together units of costs to facilitate iapidity in figuring. Thesl .groups of -costs -m_ay take- -some liberty with the exact-costs by dealing with carefully considered average costs.
In building cost schedules it is necessary to consider three basic costs. These are cut stock base, machine base and bench base. Fach valued ?t F_actory Cost. Thus commercial burden, (warehousing, office and selling, and delivery) is an added cost.
Cut Stock Base includes costs of lumber either comptetety manufactured as finished, or partially manufactured for the sirop and is chargeable either to the customer or shop exactly as deterrnined by the operations incurred. For the customer thi further values of commercial burden and p1ofit would be added, for the shop the,factory cost would be charged.
Machining and Bench work in some instances would be grouped
(Continued on Page 32)