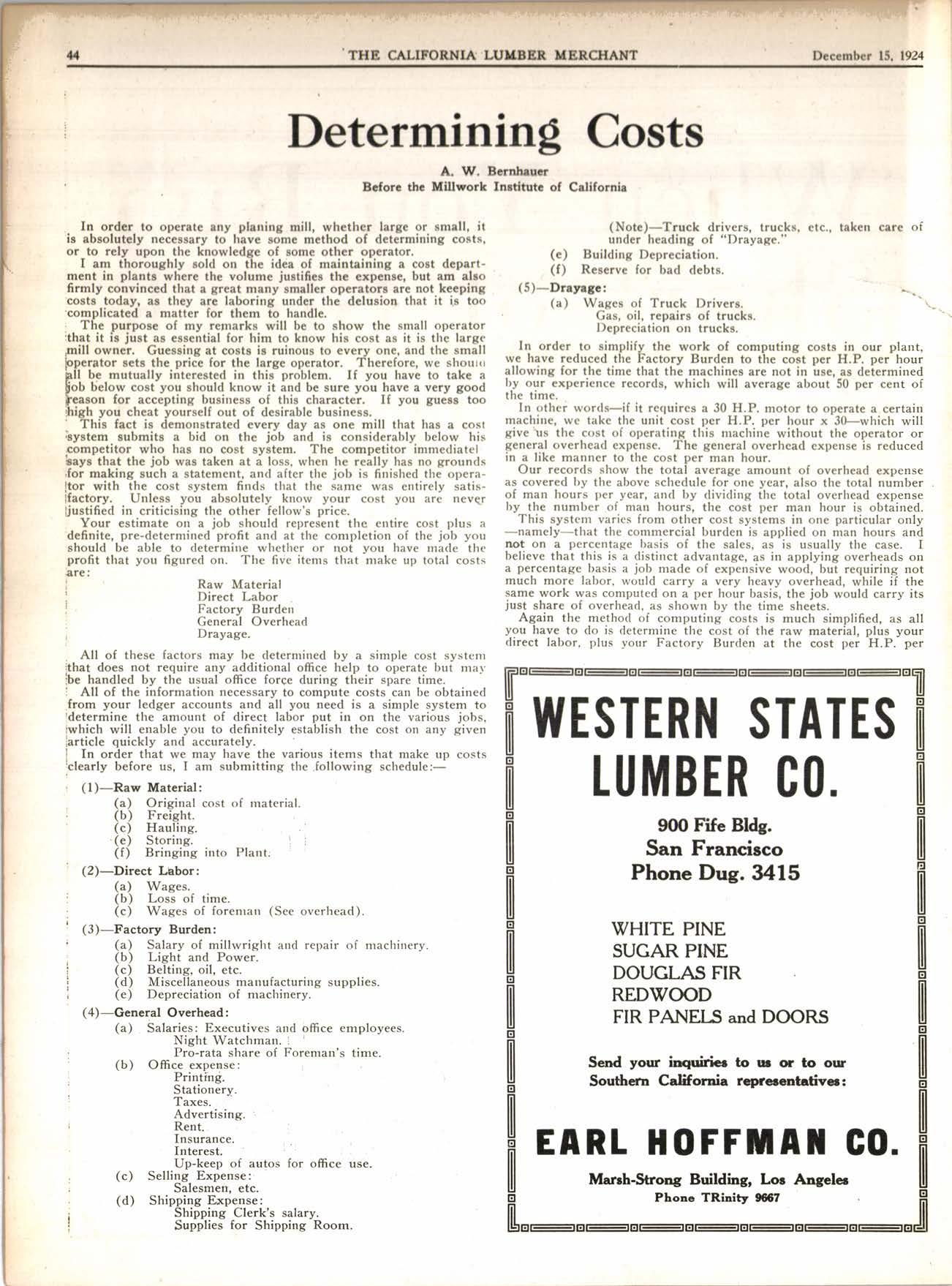
3 minute read
Determining Costs
A. W. Bcrnhrucr Bcforc thc llilhork Inrdtutc of Crlifornle
In order to operatc any planing mill, whether large or small, it is abeolutely necessary to have some mcthod of determining costs, or to rely upon the knowledge of some other opcrator. I am thoroughly eold on the idea of maintaining a cost dcpartment in plantr where the volume justifies thc expense, but am alro firmly convinccd that a great many smeller opcrator! are not kccping 'costs today, as they arc laboring undcr the dclueion that it is too 'complicated a matter for them to handte.
' The purpose of my remarks will be to show the small operator :that it is just as essential for him to know his cost as it is the large ;nill owner, Guessing at costs is ruinous to every one, and the small loperator sets the price for the large operator. Therefore, we shourrr iall be mutually interested in this problem. If you have to take a lob below cost you should know it and be sur€ you have a very good feason for accepting business of this character, If you gueas too high you cheat yourself out of desirable business.
' This fact is demonstrated every day as one mill that has a cost ibystem submits a bid on the job and is considerabty below his competitor who has no cost system. The competitor immediatel 'eays that the job was taken at a loss, when he really has no grounds 'for making such a statement, and after the job is finished the operaltor with the cost system finds that the sanre was cntirely satislfactory. Unless you absolutely know your cost you arc nevqr ljusti6ed in criticising the other fellow's price.
Your estimate on a job should represent thc entirc cost plus a definite, pre-deternrined profit arrd at the completion of the job you should be able to determine whether or not you have ma<le the profit that you figured on. The five itenrs that nrake up total costs
Raw Material
Direct Labor
Factory Burden
General Overhead , Drayage.
All of these factors may be deternrined by a sirnple cost systenl ithat does not require any additional office help to operate but ma)' ibe handled by the usual office forqe during their spare time. : Atl of the information necessary to compute costs can be obtained .from your Iedger accounts and all you need is a simple system to Idetermine the amourrt of direct labor put in on the various jobs, which will enable you to definitely establish the cost on any given iarticle quickly and accurately.
I In order that we may have the various items tl-rat make up costs 'clearly before us, I am submitting the.following schedule:-
(l)-Raw Material:
(a) Original cost of material.
(b) Freight.
(c) Hauling.
(e) Storing. I
(f) Bringing into Plant;
(2)-Direct Lhbor:
(a) Wages. :
.
(b) Loss of time.
(c) Wages of forenran (See overhead).
(3)-Factory Burdcn:
(a) Salary of millwright and repair of machinery.
(b) Light and Power.
(c) Belting, oil, etc.
(d) Miscellaneous manufacturing supplies.
(e) Depreciation of machinery.
(4)-General Overhead:
(a) Salaries: Executives and office employees. Night Watchman. i Pro-rata share of Foreman's time.
(b) Office expense:Printing. Stationery.
'
Up-keep of autos for office use.
(c) Selling Expense: Salesmen. etc.
(d) Shipping Expense: Shipping Clerk's salary. Supplies for Shipping Room.
(Notc)-Truck drivers, trucks, etc., tsken care of under heading of "Drayage."
(c) Building Depreciation.
(f) Reservc for bad debts.
(5)-Drayegc: l)epreciation on trucks.
(a) Wages of Truck l)rivers. Gas, oil, repairs of trucks.
In order to simplify the work of computing costs in our plant, we have reduced the Factory Burden to the cost per H.P. per hour allowing for the time that the machines are not in use, as determined by our experience records, which will average about 50 per cent of thc time.
In othcr worcls-if it rcquircs a 30 H.P. motor to operate a certain machine, wc take the unit cost pcr H.P, per lrour x 3G.-which will give \rs the cost of operating this nrachine without the operator or general overhcad expensc. The gerreral ovcrlread cxpense is reduced in a like manner to the cost per man hour.
Our records show the total average amount of overhead expense as covered by the above schedule for orre ycar, also the total number of man hours per year, an<l by dividiug thc total ovcrhead expense by the number .of marr hours, the cost per man hour is obtained.
This systcrrr varics from other cost systems in onc particular only -nanrely-that thc commercial burderr is applied on rnan hours and not on a pcrccntage basis of the sales, as is usually the case. I believe that this is a distinct advautage, as irr applying overheads on a percenta!{e basis a job nrade of expensive wood, but requiring not much morc lallor, would carry a very heavy overhead, while if the same work was conrputed on a per hour basis, the job would carry its just share of overhead, as showrr by the time sheets.
Again the mctho<l of computing costs is much simplified, as all you have to do is determine the cost of the raw material, plus your direct labor, plus your Factory Burden at the cost per H.P. per
9m Fifc Btds. San Frar,rcirco
Phone Dug. 34l$
WHITE PINE SUGAR PINE
DOUGLAS FIR
REDWOOD
FIR PAI.IELS and DOORS