
4 minute read
Industry Again Iroolrs to Plywood
Prefabrication Reaches Maturity-Now, Plywood is "Down on the Farm"
By Charles E. Devlin Director of Publicity Douglas Fir Plywood Association
for food, renewed high prices for farm products and with the government favoring betterment of farm facilities, building in rural areas is expected to be heavy. Thp effects of plywood experimental projects undertaken during the past year and a half at various agricultural schools are being felt, and farmers are becoming familiar with the material.
4. Plywood construction will continue to gain favor in the home construction field. Paneled walls finished in the light stains developed for plyrvood are increasingly popular. Advantages of "dri-bilt with plywood" construction, speed and economy with durability, are more clearly defined than ever before.
5. Plywood is not on the list of critical materials. There is every indication at the present time that the material will remain free from such restriction.
While acute shortages in certain metals partially account for the renewed attention on plywood for industrial uses, there are other equally important contributing factors. As a result, there is definite reason to believe the new applications for the material expected to develop in the near future will be established as permanent uses for plywood no matter what the turn of world events. Manufacturers right no\\' are being put to a different kind of test of efficiency -the test of maximum capacity.
Barrels, Boxes, Bulkheads
Plywood contributes to the geared-up output simply because of its exceptionally high strength-to-weight ratio and because it comes in big panels which can easily and quickly cut to desired dimensions and patterns; it can be bent to minimum radii and still retain its rigidity. Because of these qualities, fir plywood may soon be used for bomb doors in thousands of the hard-hitting, high-flying planes being built for United States and England; already it forms certain parts of many planes, is being tested for seaplane pontoons.
Other recently developed industrial uses are for crates or boxes in which to ship airplane motors, propellers, parts. A major tobacco company is curing its leaves in plywood barrels because they are stronger, cut costs due to increased a full grown industry of perhaps 75 or 100 firms capable of manufacturing thousands of houses a day.
Prefabrication Refinements
Most of these firms use plywood as the primary structural material. An average of 5,000 square feet of the panels are used for inside and outside walls, sheathing, roof sheathing and subflooring. Many of the systems call for glued-up or stressed skin construction with the plywood panels glued ' to light framework and bearing part of the structural load. The sizes and types of the shop-built house sections vary according to systems employed, but all have accent on speed construction. Prefabrication is the fastest way to build and prefabrication and plywood are so interrelated they are almost synonymous.
Two important improvements are expected in the system of speed building during the coming months. First, greater attention is to be given to architecture to improve exterior re-uses. Railroads build boxcars and refrigerator cars inside and out of plywood; truck lines do the same. Fishing boats, coastal patrol boats have bulkheads, compartments, cabins of plywood. Fruit canners have learned plywood trays cost less, last longer than trays built of any other material; factories use plywood for air ducts.
Startling example of the abuse that plywood will take is that presented by the shock absorbers now used in the driving of piling. Some contractors use a thick chunk of plywood between the top of a wood piling and the metal driving hammer to prevent splitting of the piling.
The versatility of plywood long has been recognized; industrialists now are grasping for new materials, new methods and they have their eyes fixed on plywood to do more and more different jobs.
Construction news of. l94l has been almost entirely centered in prefabrication; the interest has been justified because its growth has been phenomenal. At the beginning of 1940, prefabrication was a dwadling infant in the building field. Soundness of prefabrication had been demonstrated in the all-plywood house built by the U. S. Forest Products Laboratory engineers five years earlier, but there seemed to be no need for the system, no impetus to push forward the handful of prefabricbtors. The frantic call for housing facilities for defense workers and their families planked down the need; overnight prefabrication became
For cut-outs, signs like thig one, plywood is c lqvoritE matericl. It is ecrsy ,""r1Tn;["":lprool, ccn be re-us€d appearance; finer interior finish is expected. While government needs may account for the vast majority of the shopfabricated structures, increasing percentage of the privately built homes are destined to be prefabricated.
In the farm buildings construction field, plywood already has appeared as an ally of the farmer who does his own building, of the builder and of the prefabricator who shopbuilds ,small (and often portable) farm structures. Aided by J. D. Long, agricultural engineer of the Douglas Fir Plywood Association, engineers at agricultural schools in every part of the nation already have completed enlightening experiments with plywood buildings. Such structures as circular and rectangular grain storage bins, corn hoppers, range shelters, brooder shelters, dairy barns, g'reenhouses, hog houses, poultry buildings, silo linings and septic tank forms are being tested.
At the same time farmers already are utilizing the big panels to do an endless number of jobs in the improvement of their facilities. First they are remodeling or building their homes and farmers give more attention to the convenience, attractiveness of their homes than ever before with the big panels. They are lining barns, milk houses with the panels to provide a clean, smooth surface, eliminate drafts and dirt infiltration and strengthen the buildings.
Furniture Flattery
The "Dri-bilt with plywood" system of home construction was introduced just four years ago; since then it has been firmly entrenched as the outstanding advancement of the type during the period. The system includes use of plywood for exterior siding, sheathing, subfloors, roof sheathing and interior walls. Advantages are listed as speed of erection, lower labor costs, extra strength, exceptional strength and susceptibility to any architectural design, any desired interior finish.
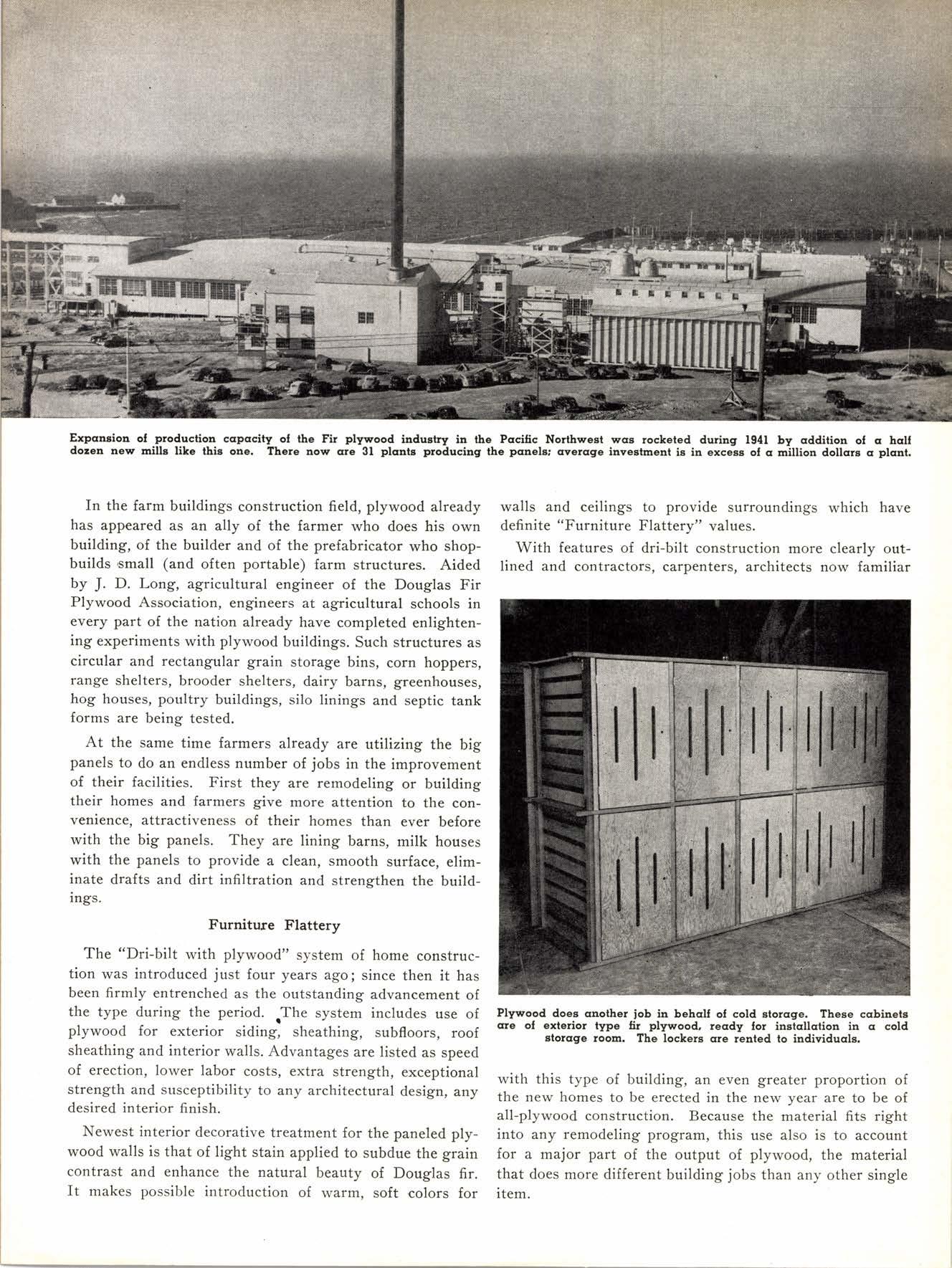
Newest interior decorative treatment for the paneled plywood walls is that of light stain applied to subdue the grain contrast and enhance the natural beauty of Douglas fir. It makes possible introduction of warm, soft colors for walls and ceilings to provide surroundings which have definite "Furniture Flattery" values.
With features of dri-bilt construction more clearly outlined and contractors, carpenters, architects now familiar with this type of building, an even greater proportion of the new homes to be erected in the new year are to be of all-plywood construction. Because the material fits right into any remodeling program, this use also is to account for a major part of the output of plywood, the material that does more different building jobs than any other single item.