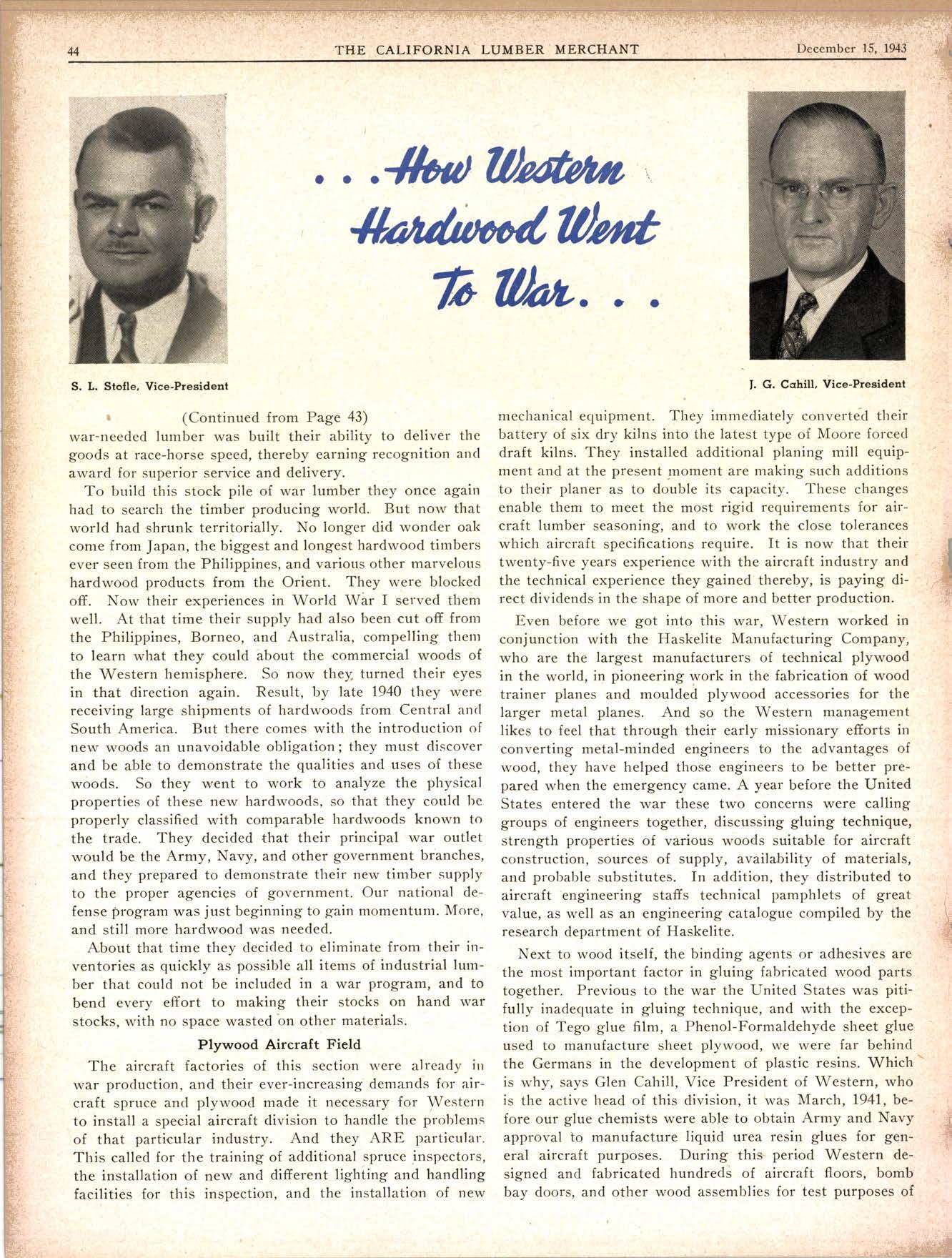
7 minute read
o..hlw llMllt,t fr llhrrL.
S, L. Stolle, Vice-President
r (Continued from Page 43) war-needed lumber was built their ability to deliver the goods at race-horse speed, thereby earning recognition a.rrcl award for superior service and delivery.
To build this stock pile of war lumber they once agairr had to search the timber producing world. But now that world had shrunk territorially. No longer did wonder oak come from Japan, the biggest and longest hardwood timbers ever seen from the Philippines, and various other marvelotts hardwood products from the Orient. They were blockecl off. Now their experiences in World Wlr I setved them well. At that time their supply had also been cut off from the Philippines, Borneo, and Australia, compelling thenr to learn what they could about the commercial woods of the Western hemisphere. So now they, turned their eyes in that direction again. Result, by late 1940 they were receiving large shipments of hardwoods from Central ancl South America. But there comes with the introduction of new woods an unavoidable obligation; they must discover and be able to demonstrate the qualities and uses of these woods. So they went to work to analyze the physical properties of these new hardwoods, so that they could be properly classified with comparable hardwoods known to the trade. They decided that their principal war outlet would be the Army, Navy, and other government branches, and they prepared to demonstrate their new timber supply to the proper agencigs of government. Our national defense program was just beginning to gain momentum. More, and still more hardwood was needed.
About that time they decided to eliminate from their irrventories as quickly as possible all items of industrial lumber that could not be included in a war program, and to bend every effort to making their stocks on hand war stocks, with no space wasted bn other materials.
Plywood Aircraft Field
The aircraft factories of this section were already irr war production, and their ever-increasing demands for aircraft spruce and plywood made it ne.cessary for Westelrt to install a special aircraft division to handle the problems of that particular industry. And they ARE particular. This called for the training of additional spruce inspectors, the installation of new and different lighting and handling facilities for this inspection, and the installation of new mechanical equipment. They immediately converted their battery of six dry kilns into the latest type of Moore forced draft kilns. They installed additional planing mill equipment and at the present -moment are making such additions to their planer as to double its capacity. These changes enable them to meet the most rigid requirements for aircraft lumber seasoning, and to work the close tolerances which aircraft specifications require. It is now that their twenty-five years experience with the aircraft industry and the technical experience they gained thereby, is paying direct dividends in the shape of more and better production.
Even before we got into this war, Western worked in conjunction with the Haskelite Manufacturing Company, who are the largest manufacturers of technical plywood in the world, in pioneering work in the fabrication of wood trainer planes and moulded plywood accessories for the larger metal planes. And so the Western management likes to feel that through their early missionary efforts in converting metal-minded engineers to the advantages of wood, they have helped those engineers to be better prepared when the emergency came. A year before the United States entered the war these two concerns were calling groups of engineers together, discussing gluing technique, strength properties of various woods suitable for aircraft construction, sources of supply, availa,bility of materials, and probable substitutes. In addition, they distributed to air,craft 'engineering staffs technical pamphlets of great value, as well as an engineering catalogue compiled by the research department of Haskelite.
Next to wood itself, the binding agents or adhesives are the most important factor in gluing fabricated wood parts together. Previous to the war the United States was piti fully inadequate in gluing technique, and with the exception of Tego glue film, a Phenol-Formaldehyde sheet glue used to manufacture sheet plywood, we were far behind the Germans in the development of plastic resins. Whichis why, says Glen Cahill, Vice President of 'Western, who is the active head of this division, it was March, l94l,before our glue chemists were able to obtain Army and Navy approval to manufacture liquid urea resin glues for general aircraft purposes. During this- period Western designed and fabricated hundredi of aircraft floors, bomb bay doors, and other wood assemblies for test purposes of the aircraft industry, assuming the financial obligations itself, mostly because of lack of early appropriations for that purpose in the air.craft plants. It was largely because of these pioneering efforts that they were able later to participate so generously in the business of the wood aircraft field.
Marine Division
The Navy demands for additions to its fleets of small boats came upon the boat builders of Southern California like a tidal wave as the war preparations increased. Western analyzed the things it must do to help serve this rapidly grorving trade, and immediately installed air-conditioning units in a special building where green bending oak could be properly protected from the rapidly changing humidity conditions prevalent in Los Angeles. They secured the services of an expert boat builder to train the personnel of their newly formed Marine Division so that they coulcl have first-hand knowledge of the problems which the boat building trade faced in the construction of wooden fighting ' ships, on many of which the designs were new and presented difficulties that must be overcome, both in materials and workmanship.
They prepared themselves to supply as r4uch information and assistance as possible to the users of their shipbuilding materials, as, for example, on the following woods: Honduras Mahogany and Port Orford Cedar for outer and , inner planking of PT boats, aircraft crash boats, and fast utility craft of one kind and another; long lengths in vertical grain Fir for planking and decking of sub-chasers and mine-sweepers, all specially selected for the purpose; large har'dwoods from Central and South America, such as Ararcang'a, Massaranduba, Itauba, Marina, Tatjuba, piquia, Albarco, etc., as well as our native Oak, all of these for keels, horn timbers, bumper rails, stem and stern posts, ' and many other items that go into making efficient fighting vessels. Other items of special quality are: Sitka Spruce for masts and jack staffs, selected for straight grain, ancl up to forty feet long; waterproof panels for bulkheads and joiner work. All these and many other items come under the jurisdiction of Western's Marine Division. Sterling Stofle, Vice President and Sales Manager for'Western, was largely responsible for the development and successful operation of this division.
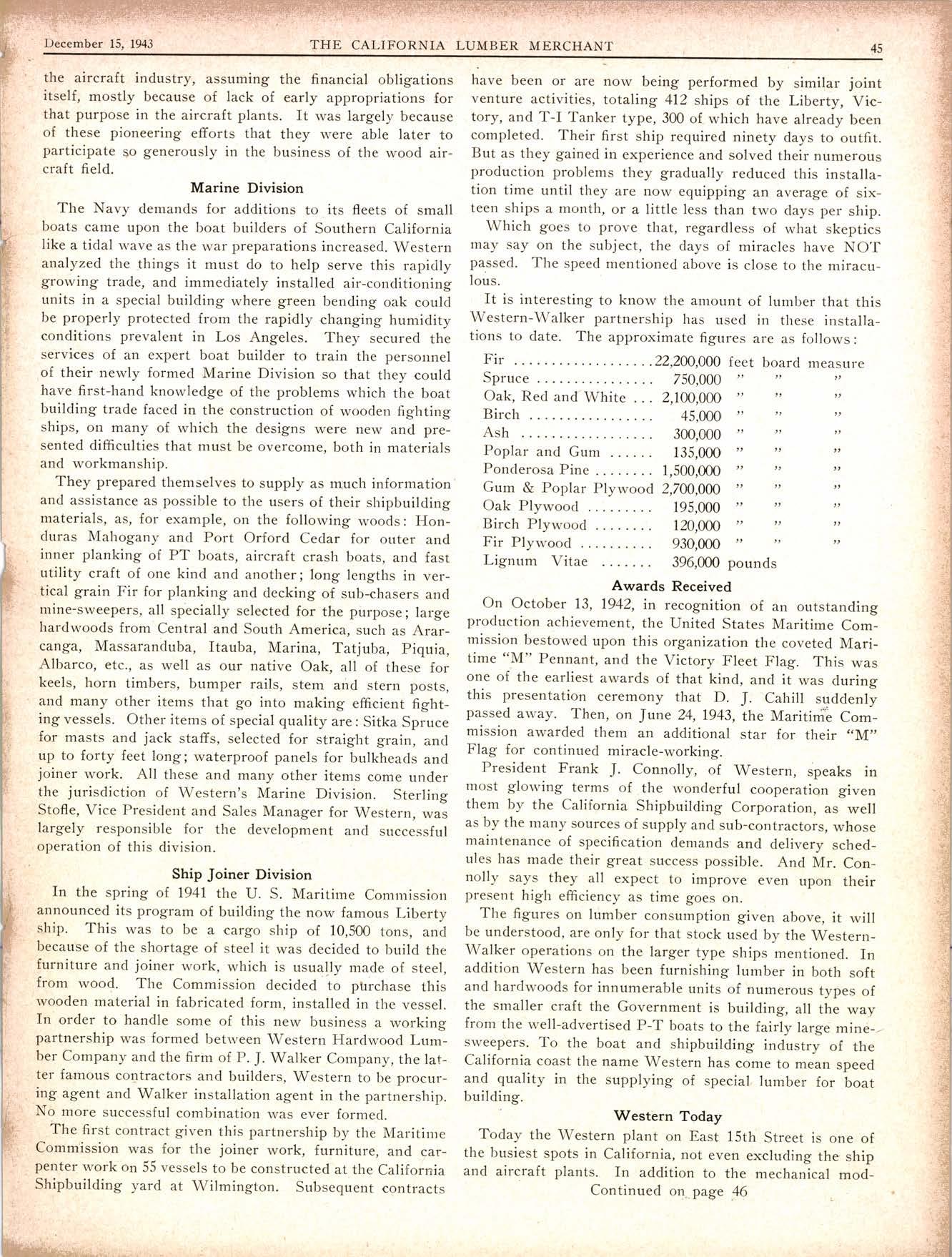
Ship Joiner Division
, In the spring of 1941 the U. S. Maritime Comrnission announce'd its program of building the now famous Liberty ship. This was to be a cargo ship of 10,500 tons, ancl because of the shortage of steel it was decided to build the furniture and joiner work, which is usually macle of steel, from wood. The Commission decided to ptrrchase this wooden material in fabricated form, installed in the vessel. In order to handle some of this new business a working partnership was formed betrveen Western Hardwood Lumber Company and the firm of P. J. Walker Company, the latter famous contractors and builders, Western to be procuring agent and Walker installation agent in the partnership. No more successful combination was ever formecl. The first contract given this partnership by tl-re Maritinte Comm'ission was for the joiner work, furniture, and carpenter work on 55 vessels to be constructed at the California Shipbuilding yard at Wilmington. Subsequent contracts have been or are now being performed by similar joint venture activities, totaling 412 ships of the Liberty, Victory, and T-I Tanker type, 300 of which have already been completed. Their first ship required ninety days to outfit. But as they gained in experience and solved their nuruerous production problems they gradually reduced this installation time until they are now equipping an average of sixteen ships a month, or a little less than two days per ship.
Which goes to prove tl.rat, regardless of what skeptics may say on the subject, the days of miracles have NOI passed. The speed mentioned above is close to the miraculous.
It is interesting to know the amount of lumber that this Western-Walker partnership has used in these installations to date. The approximate figures are as follows:
Fir ....,22,200,000 feet board measure
Spruce 250,000 ,' ,' ,'
Oak, Red and White 2,100,000 ,, ,, ,'
Birch . 45,000 " ,, ,,
Ash 300,000 " ,, ',
Poplar and Gum 135.000 ,, ,' ',
Ponclerosa Pine . 1,500,000
Gum & Poplar Plywood 2,7ffi,0N
Oak Plywood ... 195,000 " ', ,'
Birch Plywood .. 120,000 ', ,, "
Fir Plywood . 930,000 ', ,, ,'
Lignum Vitae 396,000 pounds
Awards Received
On October 13, 1942, in recognition of an outstanding production achievement, the United States Maritime Com_ mission bestowed upon this organization the coveted Maritime "M" Pennant, and the Victory Fleet Flag. This was one of the earliest awards of that kind, and it was during this presentation ceremony that D. J. Cahill suddenly passed away. Then, on June 24, 1943, the Maritime Com_ mission awarded them an additional star for their ..M,, Flag for continued miracle-working.
President Frank J. Connolly, of Western, speaks in most glorving terms of the wonderful cooperation given them by the California Shipbuilding Corporation, as well as by the many sources of supply and sub-contractors, whose maintenance of specification demands and delivery sched_ ules has made their great su,ccess possible. And Mr. Con_ nolly says they all expect to improve even upon their present high efficiency as time goes on.
The figures on lumber consumption given above, it will be understood, are only for that stock used by the Western_ Walker operations on the larger type ships mentioned. In addition 'Western has been furnishing lumber in both soft and hardwoods for innumerable units of numerous types of the smaller craft the Government is building, all the way from the well-advertised P-T boats to the fairly large mine_sweepers. To the boat and shipbuilding industry of the California coast the name Western has.come to mean speed and quality in the supplying of special. lumber for boat building.
Western Today
Today the Western plant on East lsth Street is one of the busiest spots in California, not even excluding the ship and aircraft plants. In addition to the mechanical modContinued on. page 46