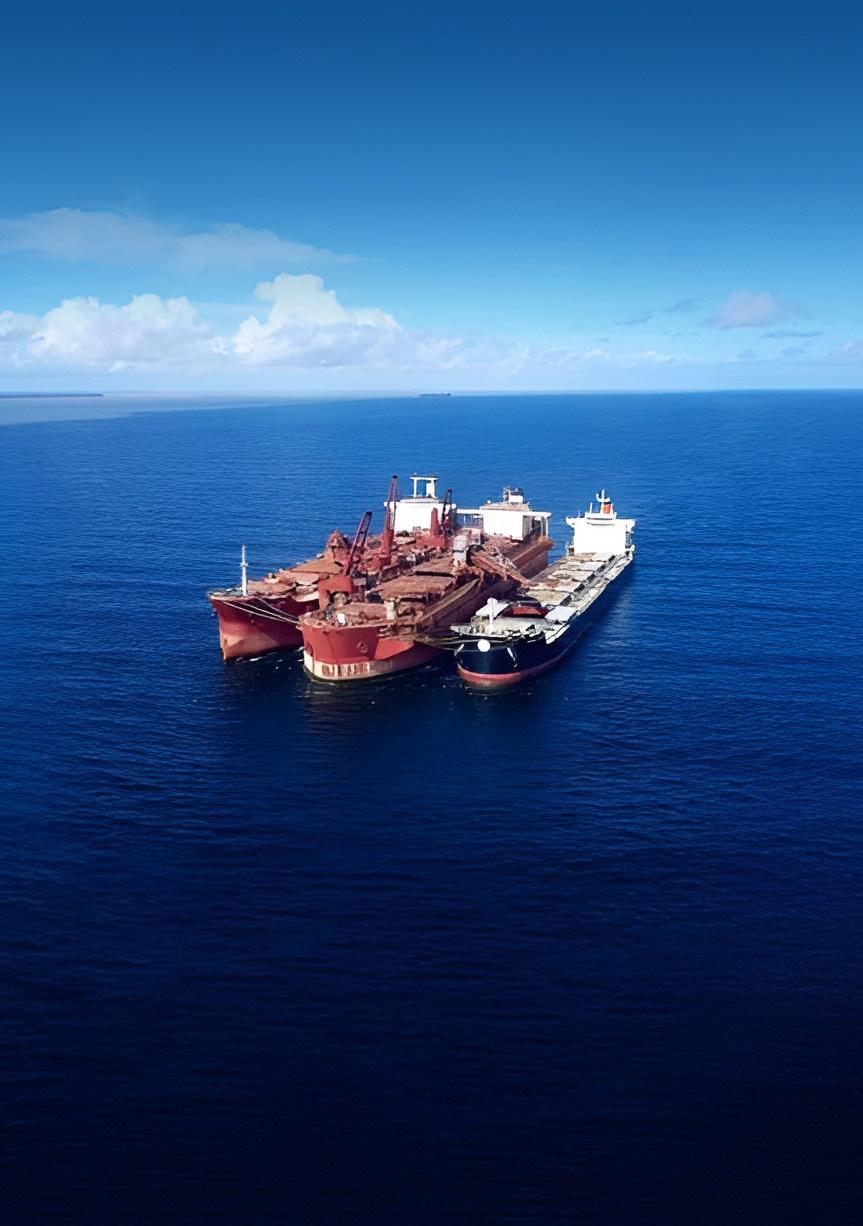
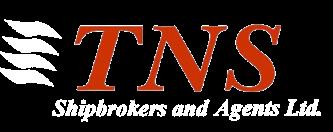
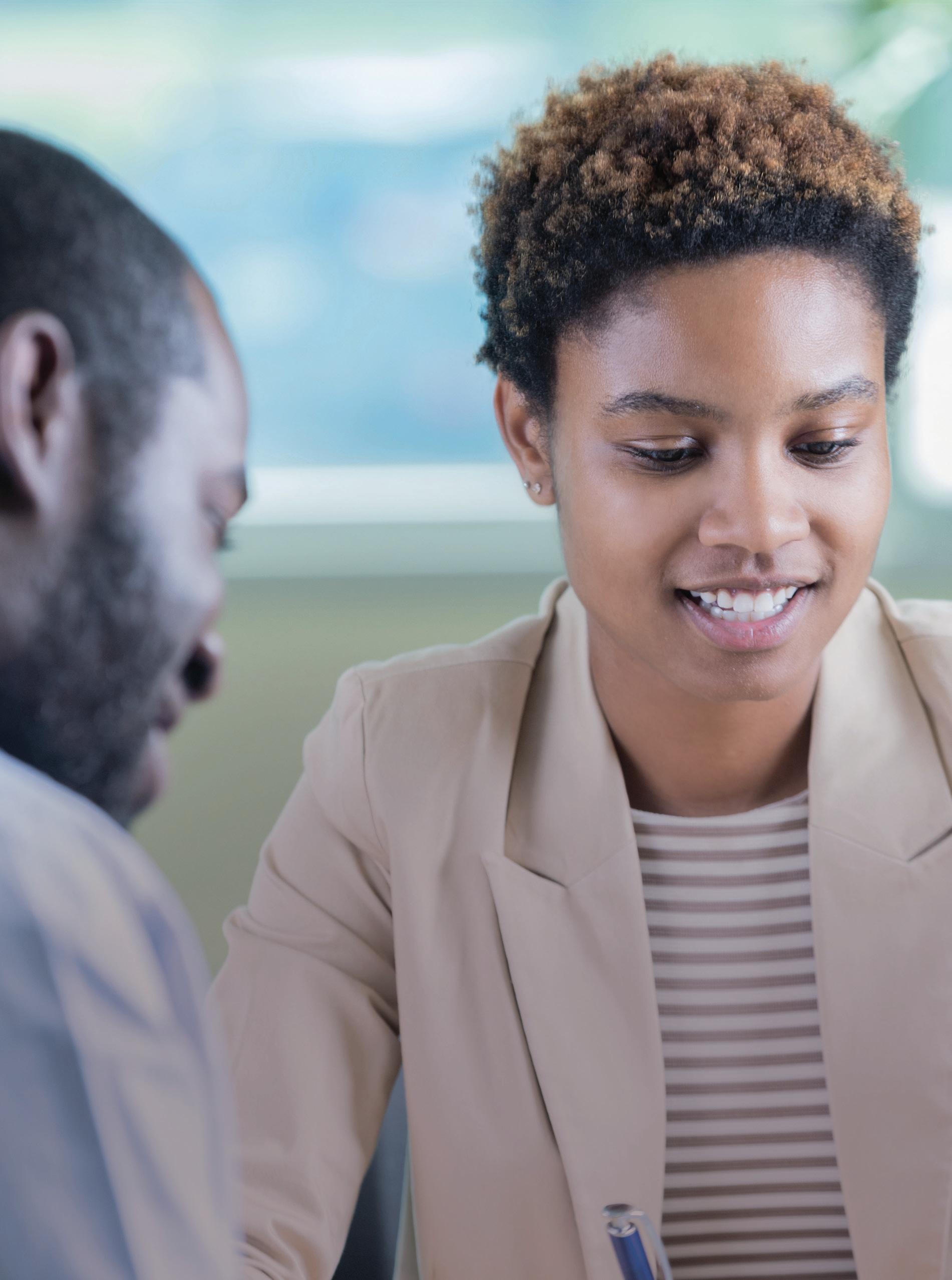
That’s how we help.
Switching your business is one of the most important decisions you’ll ever make. This is why we proactively manage the transition for you, to ensure minimal disruption to your business. We take end-to-end accountability until your business is fully banked, and a Business Banker is in play to look after the day-to-day relationship. It takes a bank that does more to help you start, run and grow your business.
For more information, contact:
Fathima Rahman
Email: frahman@fnb.co.za I Call: 087 328 0280
Eloise Heyduczek
Email: eloise.heyduczek@fnb.co.za I Call: 087 335 6859
Global Business Pursuit
Published and Distributed by Business Industry Publishing Ltd
For any enquires contact info@business-pursuit.net
Production
Donnie Rust Editor donnie@business-pursuit.net
Charles Brown Business Development Manager charles@business-pursuit.net
James Smith Operations Manager james@business-pursuit.net
Harry Lewis Accounts Manager harry@business-pursuit.net
Simon Poulton Project Manager Simon@business-pursuit.net
Design Felix Baldwin Design Assistant felix@business-pursuit.net
Harvey Tarlton Graphic Design harveytarlton.co.uk
www.business-pursuit.net
If you would like more information about ways in which Business Industry Publishing can promote your business please call +44 (0)20 32878 795 or email | charles@business-pursuit.net. Business Industry
Publishing does not accept responsibility for omissions or errors. The points of view expressed in articles by attributing writers and/or in advertisements included in this magazine do not necessarily represent those of the publisher. Any resemblance to real persons, living or dead is purely coincidental. Whilst every effort is made to ensure the accuracy of the information contained within this magazine, no legal responsibility will be accepted by the publishers for loss arising from use of information published. All rights reserved. No part of this publication may be reproduced or stored in a retrievable system or transmitted in any form or by any means without the prior written consent of the publisher.
© Business Industry Publishing Ltd 2024
Industry Publishing
In this issue of Global Business Pursuit, we dive deep into the intricacies of three industry titans making waves on the global stage. From maritime logistics to renewable energy and international shipping standards, these companies are shaping the future of business.
Ashley Group Shipping, a name synonymous with maritime excellence, shares insights into their latest endeavors, showcasing their commitment to innovation and sustainability in the ever-evolving world of logistics.
Lake Turkana Wind Power, a beacon of clean energy in East Africa, sheds light on their remarkable journey, highlighting the transformative power of renewable energy in driving economic growth and environmental stewardship.
BIMCO, a leading voice in the shipping industry, provides valuable perspectives on the challenges and opportunities facing the global maritime sector, emphasizing the importance of collaboration and standardization in ensuring a sustainable and prosperous future for all.
As you delve into these captivating stories, I invite you to ponder the question: How are these industry leaders shaping the future of business, and what lessons can we learn from their successes and challenges?
Join us as we explore the dynamic world of global business, where innovation, sustainability, and collaboration are the keys to unlocking a brighter future for all.
Donnie Rust
Global Business Pursuit – Editor
Ashley Group Shipping
Donnie Rust
To keep a business operating for over one hundred years requires a tremendous amount of focus, a gymnast’s ability to pivot, the foresight of a chess master and a lot of real-world grit.
Under its three subsidiaries, Ashley Group Shipping, offer a range of services including logistical shipping, chartering management and other services relating to the movement and sale of cargo along their worldwide network of regional partners. A legacy company Ashley Global Shipping is also a family owned and run business with the Mann family being involved in the shipping industry for over a century.
Although, with such a long legacy it would be easy to assume that the Ashley Group can do no wrong, it isn’t how they look at things.
Understanding that in business there are seldomly do-overs, the company holds itself to a high standard of performance and have developed meaningful relationships and ongoing agreements with regional partners worldwide. These allow the group to draw on the experience of experts in the various fields which allow them to make informed decisions.
“We are always looking for new and innovative solutions to complex logistics issues, whether the loading area is heavily draft restricted, or some other geographical factor is hindering freight,” says managing director Roddy Mann, “There is always a way to get it right.”
Perhaps one of the reasons their success continues is their attention to the lessons of the past and their methodology of putting those
lessons into practice. The Mann family first got into this industry in the pre-1914 ‘golden age’ of shipping when half of the World fleet had the ‘red duster’, or UK flag. Through hard work and grit, by 1930, H G Mann Shipping Ltd founded Buries Marks Ltd, and between 1932 and 1934 they managed The Cedrus, their first vessel which was purchased second hand.
This ship owning company situated in the heart of the London shipping market was acquired by Louis Dreyfus, and in 1938 ordered the company’s first new vessel, the diesel powered La Pampa (being Christened in the background picture above), at the Gothenburg yard where Louis Dreyfus had already launched its first two modern Procacci type vessels.
Two of H G Mann’s sons were active in the business, John Ashley Mann (1915-1982), and Philip Ashley Mann (1919-), but it was John who went on to be CEO of Buries Marks, whilst Philip ran Mann & Son, maintaining the Bethlehem Steel/Joshua Henty connection and Venezuelan iron ore, before becoming involved with important and innovative Scandinavian owners. At this stage they also developed their own specialised UK port which is still active more than fifty years later. Philip’s eldest son Christopher Ashley Mann has continued the family business into Ashley Global Shipping Ltd.
Having worked with his father Philip, and for Mann & Son post the ownership-change, another Peter Ashley Mann, Christopher’s brother, joined fellow Wallenius Lines close-associates Cobelfret as director of the Ro-Ro Agency for the Cobelfret Lines services from Purfleet to Continent, until he retired.
It is no co-incidence that Ashley Global Shipping Ltd maintains the Mann family
We were one of the first agents to serve the Ashley Group for fixing their cargoes and ships for the dry
connection to Cobelfret more than half a century on, and that Ashley Global Shipping has operated many Cobelfret vessels as disponent owners.
With clients relying on Ashley Group Shipping for a range of services, the years have taught the group that focus, and attention cannot be overspread. So, to make sure that they offer the right level of attention, the group conducts business through three subsidiaries.
While most of Ashley Global Shipping’s business concerns are centred on long-term supply contracts, where strong foundations and longevity nurture good business relations, they additionally provide logistical services to the group’s trading activities, as well as to trusted third parties.
Owning and operating a range of modern, economical bulk carriers ranging from Supramax to Kamsarmax vessels, which suit the needs of their long standing and international charterers across the globe, Ashley Chartering Ltd provide shipping and logistical solutions to third party charterers internationally. Handling much of the management of the groups traded activities. The subsidiary follows the same mantra as the group, offering a reliable and competitive service to all their global customer base.
Born out of a need to control the cargoes for the Group’s shipping activities, Alfa Commodities now facilitate the movement and sale of cargo on four continents. Their business model is very closely based on its shipping heritage. Where their word is their bond. By maintaining a reputation for reliability, the cost of transactions is greatly reduced, allowing for more competitive pricing both on sales and the netback passed to producers.
Good services come from weathered experience, and Ashley Group Shipping, as mentioned previously, have taken notes on the lessons of their past. As such there are some key services that the group offer to customers which stand out as their defining offerings.
There are many opportunities for innovation and change to be found within the practicalities and ton-mile efficiencies of transhipment. Bulk raw materials require economies of scale to compete in World markets, four generations of the Mann
shipping family lie behind the continuation of this philosophy that was first embodied via earlier generations creating the first low-draft vessels to serve the Venezuela/USA port WW2 boom market from 1947. To fuel demand, the US producers like Bethlehem Steel needed steel for which new supplies of iron ore were essential.
Ashley Global Shipping have implemented logistical solutions in draft-restricted areas around the world, taking advantage of economies of scale on freight costs to improve netback to producers.
As members of the Baltic Exchange, Ashley Global Shipping follow the same motto of “our word is our bond” and they operate in full compliance with all recognised international, IMO regulations whilst keeping the safety of the crews, the vessels, their cargoes, and the protection of the environment as top priorities.
All of Ashley Global Shipping operates all its vessels in compliance with classification and flag state rules, and applies recognised industry standards as appropriate, always including a readiness to respond to emergencies and establish safeguards against all identified risks. Not just lip service, they continue to evolve their operational techniques and expertise to maintain a record of excellence in cargo solutions and international trade.
Today’s trading, sea-fairing world cannot be compared to what is often depicted on the silver screen. The reality of operating in the most volatile market of them all, shipping, is that the number one priority is the mitigation of risk to ensure that the company experiences steady growth and is shielded from market shocks. Not appreciating this significance or being ill prepared for it can be the shortfall for many customers. However, the use of financial instruments both on the freight and on the commodity trading aspect of Ashley Group Shipping’s business is vital to the longevity and reliability of their provision of service.
Diversification of portfolio asset classes is important in reducing any over-exposure to one market and to get the most value-added for our controlling shareholder, Ashley Global Shipping attempts to enter projects as far upstream as possible, adding value through early-stage financing and expertise.
“And you cannot argue with the presence of our own global fleet,” says Roddy, “we operate a fleet of modern, eco bulk carriers ranging from Supramax up to Capesize.”
Located in Marsabit, Kenya, Lake Turkana Wind Power Project is a 310.25MW onshore wind power project that entered commercial operation in June 2018 after four years of development and construction.
The Importance Of Wind Power
As it has no carbon emissions and requires no human input to be generated, wind power offers a cleaner energy source compared to methods that require burning coal or fossil fuels. As a result, wind turbines can produce substantial power, while simultaneously contributing to climate change mitigation and providing access to affordable energy for accelerated economic development.
Lake Turkana Wind Power
Comprising 365 wind turbines, each with a capacity of 850KW and a high voltage substation, LTWP is connected to the Kenyan national grid through a 438 kilometre associated transmission line constructed by the Government of Kenya through the Kenya Transmission Company (KETRACO).
Through this collaboration, LTWP provides reliable, low-cost energy to Kenya’s national grid, accounting for approximately 17% of the country’s installed capacity, which can be purchased at a fixed price by The Kenya Power and Lighting Company PLC (Kenya Power) over
a 20-year period in accordance with the Power Purchase Agreement (PPA).
Six shareholders own LTWP. These include Anergi Turkana Investments Limited, Milele Energy Ltd, Vestas Eastern Africa Limited, Finnfund – the Finnish Fund for Industrial Cooperation, Danish Climate Investment Fund I K/S; and Sandpiper Ltd. The company’s management team is headed by chief executive officer Max Schiff.
Max Schiff has a wealth of experience in management and operations within the energy industry and has a background consisting of senior regional Business Development and General Management positions, principally in Eastern and Southern Africa. During his time, he has managed multiple power projects and demonstrated strong capabilities in building capital strength, improving shareholder value and overseeing effective strategy implementation.
His expansive career has seen him provide strategic advisory and leadership to businesses in Tanzania, Zimbabwe, Kenya, and Egypt as well as having management oversight for high value power projects in Malawi, Sudan, and Eritrea.
His most recent role was at Aggreko, a global leader in the provision of temporary and distributed power solutions, where he filled senior roles as head of sales and
general manager for Africa and Eastern Africa respectively. Max’s contribution at Aggreko included numerous subsidiary business turnarounds that earned him a track record of being able to improve regional financial performance for existing key power projects. Today, as CEO, Max leads the operational and leadership arm of LTWP, providing strategic direction and oversight to all business functions within the organization.
The Economic Impact Of The Project Since inception, LTWP has dedicated itself to ensuring that the local communities benefit from the Project. As part of this commitment, they established Winds of Change (WoC), through which sustainable community development projects are undertaken throughout Laisamis Constituency, which is the project’s area of Influence. WoC is registered in Kenya as an NGO and has been operational since June 2015.
“The primary focus of WoC is to enhance access to education, health and water, as well as support miscellaneous community development activities,” says Max.
As the largest wind farm in Africa, LTWP is also the largest private investment in its history at a cost of €625 million, but through its presence and functionality, as an energy provider, it has generated many additional opportunities for the
country to benefit from incoming investment and peripheral developments. LTWP is also the largest private employer in Marsabit County and currently employs 329 people, of whom 85% are local, 14% come from other parts of Kenya and 1% from outside of the country.
Through LTWP, over 208 km of road from Laisamis to the wind farm site has been upgraded and these road infrastructure developments have significantly reduced travel time from Nairobi to the Windfarm from 3 days to 12 hours, and between Sarima and Laisamis from 7 hours to 3 hours, respectively.
Additionally, the project has led to enhanced security in Marsabit County by fostering peaceful co-existence between communities. Inter-ethnic conflicts fuelled by cattle rustling and competition for water resources have significantly dropped due to the new opportunities now available to community residents. This can be attributed to the establishment of the different LTWP projects and CLO conflict resolution mechanisms that have been instigated since 2015. The introduction of more police officers on site has further contributed to reduced cases of illegal activities in the area.
Electricity generated by LTWP has reduced the country’s reliance on fuel imports from neighbouring countries. Kenya has saved more than €281 million between 2018 and 2021, due to reduced fuel imports, enabling continued economic growth of the country.
Through LTWP’s registered NGO, Winds of Change, the community has benefited from approximately €2.5 million since 2015. These funds have been used to enhance employability, improving access to health, access to water and other community activities (e.g. drought and food relief programmes).
Healthcare, or lack thereof, is a huge issue in the area and thanks to LTWP’s support, access to healthcare services has improved dramatically. As an example, the
LTWP support to Burri-Aramia dispensary has improved hospital maternity birth rates from an average of two to three hospital births per month to over 40 births per month. This has decreased the need for home births and lowered infant mortality rates. Equally, the hospital has been able to increase vaccination programmes for children and adults in the region.
Education and schooling have also seen changes, with water tanks, piping systems and the construction of laboratories increasing retention of students and teachers. These investments create an environment more conducive to learning and have improved performance of girls in the Girls Secondary Schools in the area.
“These kinds of developments make huge strides not only for the community but for the overall development of Kenya,” says Max, “Safeguarding the future of the country.”
It is also worth keeping in mind that another benefit being offered to Kenya, is that it has put the country on the global map for renewable energy. Be this a precedent or an example to be followed, it has established a standard for African involvement and development within this sector which could be the driving force to further economic and industrial benefits for the country.
Wh en coming from the world’s largest shipping organisation, it’s easy to see how BIMCO’s charter parties are the gold standard for transportation. Occupying an integral position in the industry, the organisation has a handson approach to developing international standards for all ranges of applicable contracts, producing documentation that is used by the entire industry and offer services for over three quarters of the international maritime industry.
BIMCO’s real power lies in the strength of the data gleaned from the expertise of its 2100 members spread across 130 countries. With open communication with ship owners, operators, managers, brokers, and agencies their information sources include the front lines and the offices.
Another benefit is being able to accurately understand the trends and priorities of the industry, the ‘business acumen’ of the times, allowing their contracts to be informative, comprehensive and on-point.
Contracts reflect the real-world priorities of an industry, and when that industry spans hundreds of countries and thousands of international businesses dealing with millions of cargo tonnage, the more information that
is available for detail, the better. The same information pool is used to keep members informed on the pressing industries matters, allowing individual members to make informed decisions based on real facts. This has made BIMCO the real-world practical voice of shipping.
As CEO and Secretary General of BIMCO, David Loosley explains, facilitating trade is at the very heart of their business, and since 1905 they’ve helped their members keep world trade moving.
“It’s our job to help our members with their businesses,” he says, “BIMCO members cover sixty two percent of the world’s tonnage and consist of local, global, small, and large companies.”
From offices in Houston, London, Copenhagen, Athens, Brussels, Singapore, and Shanghai the group aims to continue to build a resilient industry in a sustainable future whilst protecting world trade.
“We do this by finding practical solutions for our members to help them manage risk in a changing world,” David says, “And this plays a big role in both our contracts and our charter parties.”
Contracts
In a nutshell, BIMCO create and deliver
maritime contracts, and this is something they’ve done since the beginning in the first years of the twentieth century. They rely on a standardised method to create equality, fairness and to best support business.
Thanks to a library of over 300 contracts and clauses the organisation has the tools ready to help members of any size across all shipping sectors. And their constantly evolving clauses enable members to be responsive, and proactive, when necessary, to a world that is as shifting as the oceans they ship across.
“We are always exploring and progressing every aspect of the maritime industry, planning for the future and seeking practical solutions,” explains David, adding, “Our regulatory work promotes transparent and non-discriminatory standards and harmonisation within the shipping industry.”
He goes on to say that they are ambitious but realistic as their voice represents their members across the global regulatory space, such as the International Maritime Organization.
As a membership, the whole grows stronger by the individual strength of the members, and BIMCO provide practical business services, training, information, and market insight to their members to help them commercially
navigate to a sustainable future. From training, events, publications, news and insights to market analysis, port information and voyage planning.
“Our members are the catalyst for everything we do and why we do it,” says David, “We represent shipping without borders, we are fair, and we believe in the power of togetherness.”
BIMCO charter parties have become the gold standard for cargo transportation. Widely used throughout the shipping industry, according to The Maritime Executive, it’s estimated that seventy-five percent of maritime transactions involve the use of BIMCO contracts.
Like the contracts and clauses mentioned
“We represent shipping without borders, we are fair, and we believe in the power of togetherness.”
earlier, BIMCO charter parties are regularly updated to reflect changes in the market and in the law. For example, the clause for time charter parties regarding infectious or contagious diseases clause updated to 2022 version to replace the previous 2015 clause to provide the industry with a contractual solution that addresses the practical and commercial realities.
One of the key advantages of BIMCO parties is that they are based on the principle of freedom of contract. This means that the parties to a charter party are free to agree on any terms and conditions that they wish if they are not illegal or contrary to public policy. However, BIMCO charter parties provide a valuable starting point for negotiations, as they cover all the essential elements of a charter party in a clear and concise manner.
Another advantage of BIMCO parties is that they are supported by a global network of maritime lawyers and experts. This means that if a dispute arises under a BIMCO charter party, there is a wealth of expertise available to help the parties resolve the dispute quickly and efficiently.
BIMCO offers a wide range of parties for different types of cargo and different types of voyages. This includes charter parties for dry bulk cargo, liquid cargo, containerized cargo, and project cargo. BIMCO also offers charter parties for voyage charters, time charters, and bareboat charters.
As a result of their many advantages, BIMCO charter parties are the preferred choice for many shipowners and charterers and become essential for cargo transportation. They provide a fair and balanced basis for the contract between the
shipowner and the charterer, allocate risk fairly between the parties, and are widely understood and accepted by the shipping industry. BIMCO charter parties are also supported by a global network of maritime lawyers and experts.
Keeping Updated Information
Information is not only on the checks-balances and law-following of contracts but can and does involve more pressing dangerous situations such as the recent Somali pirate attacks that have emphasized the importance of ship self-protection. In recent months, Somali pirates have repeatedly attacked and hijacked several merchant vessels in international waters. These incidents serve as a grim reminder of the critical importance of BMP5 (Best Management Practices to Deter Piracy and Enhance Maritime Security in the Red Sea, Gulf of Aden, Indian Ocean, and Arabian Sea) in the shipping industry.
On 14 December 2023, the Maltaflagged handymax bulk carrier MV Ruen fell victim to a Somali pirate attack and subsequent hijacking. Similarly, the Bangladesh-flagged handymax bulk carrier MV Abdullah was hijacked on 12 March.
These two incidents have occurred during a time when maritime security has once again become a priority. In the southern Red Sea and the Gulf of Aden, the Houthis have been launching attacks on shipping vessels, alleging a link between international shipping and the ongoing conflict between Israel and Hamas.
Despite the focus on Houthi missile attacks, the activities of Somali pirates have not gone unnoticed. While mainstream commercial ships like the MV Ruen and the MV Abdullah have been attacked, the recent increase in attacks by Somali pirates has predominantly impacted fishing dhows and appears to stem from a fishing dispute with domestic political implications. Further complicating the situation are indications that Somali pirates might be collaborating with the Houthis or criminal networks in Yemen. This suspicion was further supported when, after an attempted hijacking of the tanker MT Central Park on 26 November 2023, the pirates escaped towards Yemen, not Somalia.
The rising security concerns in the southern Red Sea, the Gulf of Aden, and the northwest Indian Ocean underscore the pressing need for ships in these regions to implement self-defence measures as outlined in BMP5.
While not all BMP5 guidelines apply to every vessel, the majority are relevant to most. BMP5 advises owners to conduct a comprehensive, ship-specific, and voyagespecific security risk assessment, report movements and observations to military authorities, and make it more difficult for pirates to detect and board the ship.
In conclusion, joining BIMCO offers invaluable benefits and opportunities for individuals and businesses alike. From access to industry expertise and networking opportunities to advocacy and support, BIMCO membership equips members with the tools and resources needed to thrive in the dynamic maritime industry landscape.
Buzzi, formerly Buzzi Unicem, has evolved over a century into a significant multinational player in the production of vital building materials. Its operations extend across the Atlantic and reach from the Russian Urals in the east to the Mediterranean Sea and the Middle East in the south. Despite its expansive reach, the company retains its roots as a family business, boasting a rich history in cement, ready-mix, and aggregate production.
The manufacturing of concrete, cement, and aggregates plays a pivotal role in sustaining our modern world, underpinning countless aspects of daily life. Concrete, a versatile material composed of cement, aggregates, and water, serves as the foundation for essential infrastructure. Roads, bridges, and buildings rely on concrete for strength and durability, facilitating transportation and urban development. In housing, concrete provides stability and resilience, shaping the landscape of residential communities worldwide. Factories and industrial facilities utilize concrete for flooring and structural components, ensuring operational efficiency and safety.
Moreover, the importance of concrete extends beyond traditional construction. In IT server rooms, concrete flooring provides a stable foundation for equipment and helps regulate temperature fluctuations,
safeguarding critical data infrastructure. Without concrete, the fabric of modern society would unravel, disrupting transportation networks, impeding urban growth, and compromising technological advancements. Thus, the manufacturing of concrete, cement, and aggregates is indispensable, anchoring the infrastructure upon which our interconnected world thrives.
In March 2024, Buzzi Unicem USA and Lehigh University secured a $2 million grant from the US Department of Energy Industrial Efficiency and Decarbonization Office (IEDO). Their joint endeavor focuses on developing low-carbon non-ordinary Portland cements to drive decarbonization efforts in industries by advancing low-temperature calcined clays. Cement production contributes significantly to carbon dioxide emissions, primarily during the heating of limestone and other materials in kilns, which releases CO2 as a byproduct. Additionally, the curing of concrete also emits CO2 over time. Annually, cement and concrete production account for approximately 8% of global CO2 emissions, with buildings being a major contributor, totaling around 2.8 billion metric tons of CO2 emissions per year.
The decarbonization project initiated in
2023 aims to incorporate calcined clays as an alternative concrete binder, achieving durability through clay beneficiation. Calcined clays present a promising low-CO2 supplementary cementitious material, boasting a 50% lower carbon footprint than traditional cement.
This grant aligns with a broader initiative announced by IEDO, totaling $171 million in funding for 49 projects aimed at reducing industrial greenhouse gas emissions and accelerating the development of innovative decarbonization technologies.
These efforts coincide with the release of Buzzi’s 2023 Sustainability Report, which highlights the Group’s performance in environmental, social, and governance domains.
In 2023, Buzzi made further reductions in CO2 emissions, aligning with the objectives outlined in the “Our Journey to Net Zero” roadmap for 2030 and 2050. Simultaneously, the company increased its use of renewable energy, including self-produced energy from photovoltaic systems.
With a commitment to environmental stewardship, Buzzi engages in projects aimed at monitoring and preserving biodiversity in quarries, often in collaboration with academic institutions like the Università del Piemonte
Buzzi made further reductions in CO2 emissions, aligning with the objectives outlined in the “Our Journey to Net Zero” roadmap for 2030 and 2050
Orientale (UPO).
Through the publication of a new Health and Safety Policy, the company aims to achieve its “zero injuries” goal by fostering a more inclusive, widespread, and engaging health and safety culture. Furthermore, results from analyses conducted in 2023 on practices and activities for the protection of Human Rights are presented to assess the company’s maturity level and identify areas for improvement.
The cement industry is dynamic, characterized by constant evolution across various stages, from the chemical composition of cement products to machining, manufacturing, and application processes. Acknowledging this fluidity, Buzzi places particular emphasis on applied research, conducting extensive experimental activities to explore potential innovations in both production processes and products.
Buzzi actively participates as an industry partner in national and international research projects, contributing to the development of new materials and technologies while fostering knowledge exchange with esteemed scientific research institutions.
Five strategic areas guide the company’s research and development efforts:
• New Hydraulic Binders: Exploring alternative binders to traditional ones, including technologies for reusing waste and alternative materials in Portland cements.
• High-Performance Concretes: Researching new classes of binders with superior mechanical performance levels, focusing on strength, elasticity, and durability.
• Multi-functional Construction Materials: Investigating construction materials
with photocatalytic, self-cleaning, and self-repairing properties to enhance sustainability and performance.
• Improved Construction Materials: Developing new classes of construction materials with enhanced durability, mechanical strength, and unique characteristics such as lightness, thermal insulation, and resistance to aggressive chemicals.
• Innovative Production Processes: Technological processes that could impact the properties of cement and concrete and develop solutions to capture, store and/or convert CO2. Due to its complexity, this type of project is considered as pre-competitive research activity which is conducted by task forces in collaboration with other companies in the sector, such as the ongoing collaboration through the ECRA (European Cement Research Academy).
Quality serves as the cornerstone of Buzzi’s business culture, guiding all aspects of their operations. The company establishes quality targets that not only comply with local regulatory standards but also meet customer requirements across all products—whether cement, concrete, or aggregates—at every production site.
At the production level, Buzzi employs advanced control techniques and instruments to ensure the consistency and achievement of quality targets. Additionally, they offer technical assistance to support customers and address their needs effectively.
Buzzi’s diverse product line caters to various sectors, including the oil and gas industry (Oil Well cements), ready-mix, and high-performance segments (Solidur, Variodur, Nanodur, Next binders), and the broader construction industry.
To meet evolving market demands, Buzzi invests in research and development, maintaining two state-of-the-art research laboratories in Italy and Germany. These facilities support both production control laboratories and conduct research on new products or industrial processes, often in collaboration with academic and industrial partners.
By embracing innovation, sustainability, and quality, Buzzi continues to shape the future of the cement industry while advancing global efforts toward environmental responsibility and excellence in construction materials.
Donnie Rust
Trucking is synonymous with the North American spirit and as the country continues to experience a return to domestic manufacturing, there is a growing focus on reliable logistical services. Within manufacturing, the heart and soul of a country is found, and supply chains are the arteries.
From the tiny city of Centreville, New Brunswick, which has a population of just under 550 people, one enterprise has established itself as the premier manufacturer of specialty trailers. Over fifty five years old, one of Atlantic Canada’s most successful manufacturing enterprises and heading up an equally successful continentspanning dealer network, BWS Manufacturing is a business that has left many others trailing behind.
Like many businesses, BWS sprouted from modest beginnings. It began as a small welding shop owned by Burney MacDougall in 1967 as ‘Burney’s Welding Shop’ that catered to local potato farmers. Potato giant McCain was headquartered just eleven kilometres away, and this proximity fuelled early growth that was further boosted by Burney’s experience in the forestry sector. Opportunities and projects in one, allowed investment projects into the other and from there he carved out the speciality niche.
As the company expanded, the variety of projects continued to grow. By 1975, the rebranded firm was manufacturing snow and ice equipment, truck bodies, and final-stage trailers for a variety of sectors that only eight years earlier would have seemed unlikely.
“We started in agriculture and forestry, and fifty-five years later, we cover many market sectors,” explains Scott MacRae, Vice President of Sales and Marketing, “We are very diverse and the company’s trailers serve the gravel, agriculture, forestry, oil, and gas, nuclear, and even consumer products industries.”
In 2017 the company was purchased by Quebec business magnate Hugo St-Cyr, which marked a new chapter for them. Today, the company boasts over 220,000 square feet of production space for the manufacturing of their trailers, as well as a continental network of over seventy dealer locations across the U.S. and Canada.
Last year’s production was sold out prior to the start of 2023, as new purchasing trends have outpaced production. MacRae estimates the current increase in trucking will continue for several years and dismisses rumours of a recession on the horizon.
“Everything you see around you has been on a truck at one point in its life,” he says.
“Transportation is always something that is going to be necessary, so it is always going to be there.”
BWS offers the fairly new practice of zinc coated galvanizing as an option to most models of its trailers. This is an expensive but often advantageous procedure for the harsh winter environments of Canada and the northern U.S. Their trailers are designed to be dipped into a molten zinc finish at 845 degrees Fahrenheit during which the zinc actually permeates the steel and gives it a secure coating.
The results speak for themselves with MacRae explaining that a trailer that may only have a painted finish will offer a ten year period of reliable usage, but with the zinc finish that lifespan is extended to over twenty.
“This is the kind of return on investment that we offer our clients,” he adds.
As a caveat, not all trailers are made equal and the process requires each trailer to be designed to accommodate the unique properties of the zinc treatment. The process also adds an extra day to the trailer assembly, but the benefits still outweigh the costs on most ledgers.
In addition to its extensive product line, BWS maintains a close working relationship with its dealer network across the continent.
Trained product specialists visit dealers regularly, ensuring sales professionals and customers have comprehensive and accurate information on the company’s products. “We have to ensure that they have the start-to-finish and follow-up of a complete sale package,” MacRae says, “The goal is to ensure that customers know everything possible about their new trailer before they leave the dealership.”
Every BWS dealer is responsible for warranties, so any of the company’s trailers can be driven to one of those dealers and receive repairs. “We can honestly say we have a warranty network, from coast to coast, in Canada and throughout the U.S. as well,” MacRae says proudly.
They also maintain a close working relationship with their affiliated company, Stargate Trailers which is based in Ontario. This relationship is relatively new, having begun in 2020 when Hugo St-Cyr purchased Stargate, but the siblings have a naturally complementary relationship. BWS is an all-steel manufacturing company and Stargate is all-aluminium.
Additionally, the two companies have similar business models that enabled them to work together on their outreach as well, with each of them benefiting from a network overlap that has significantly increased their reach. As part of this working relationship, the companies enjoy a reciprocity in parts as many are interchangeable across models which allows them to streamline logistics. The purchasing teams have been combined and there is further inhouse cooperation with the production teams of both companies working closely together and applying the best practises of each.
A prime example of the collaboration between the two comes with BWS’s pony trailers, which are designed to be towed by dump trucks. The trailers’ long central pole assembly and chassis would be made with BWS steel; these are then shipped to Stargate, which will complete the trailers with aluminium.
MacRae explains that after the pandemic BWS took a good look at their supplier network with the aim of balancing costs and quality. In selection however, unlike many companies, relationships were very important to them. As
“We just got tired of waiting and decided to take it into our own hands,”
new suppliers are always being considered, BWS has to consider its hard-earned reputation for quality and has to avoid the siren song of cheaper, imported parts. There is always a cheaper option, but you get what you pay for.
And the company is not afraid to try something new. On their last recruitment drive, after growing tired of trying to recruit locally and getting little to show for it, they sent a human resources representative to the Philippines, where she recruited approximately forty-five skilled workers who the company then brought to Canada.
“We just got tired of waiting and decided to take it into our own hands,” explains MacRae, “I’s a great opportunity for us and for the immigrants. We are growing beyond our BWS and Stargate family.”
As it looks to the future, BWS is also experimenting with emerging technologies such as artificial intelligence (AI) and robotics and how they may be integrated into its business model. Yet while the company sees itself as forward-thinking, MacRae is quick to point out that they are not out to eliminate jobs.
“We’re not looking at robotics or AI systems to replace our workers, only to complement who we have here now,” he says, “Our business is here because of our people. We are here because of the people that work with us and for us.”
Just last year, Calibre Mining’s Valentine Gold Mine, was awarded the John T. Ryan National Safety Trophy for an outstanding safety record, by The Canadian Institute of Mining, Metallurgy and Petroleum. More than a mere accolade, this award reflects an outstanding safety performance in the 2023 calendar year with a reportable injury rate of zero. Further to this the company is involved in ongoing contributions to improving the industry’s safety record. Business Pursuit investigates.
According to Darren Hall, Calibre’s President and Chief Executive Officer, the award would be a proud achievement for any mining company, signifying the dedication they have to the sector. Winning it, puts Calibre in an altogether different class of company. He goes on to explain that achieving zero injuries required (and requires) a comprehensive approach encompassing stringent safety protocols, training programs and constant vigilance.
“As a core value,” he says, “We foster the culture of health and safety among our workers through communication, empowerment, and the understanding that safe practices play a pivotal role in preventing accidents. We share a unified vision of responsibility toward safe and responsible mining practices, safeguarding the lives of all personnel.”
Calibre is a Canadian-listed, Americas focused, growing mid-tier gold producer with a strong pipeline of development and exploration opportunities across Newfoundland and Labrador in Canada, Nevada and Washington in the USA, as well as Nicaragua. Focused on delivering sustainable value for shareholders, local communities and all stakeholders through responsible operations and a disciplined approach to growth. Leveraging a strong balance sheet, a proven management team, strong operating cash flow, accretive development projects and district-scale exploration opportunities Calibre will unlock significant value.
A company of this level requires the leadership of someone with an intuitive understanding of the industry. As that leader, Darren Hall offers over 35 years of experience in the mining industry with a track record of increasing production, reducing costs, improving capital effectiveness, and promoting health, safety, and business excellence as core values.
Having previously served as Chief Operating Officer of Kirkland Lake Gold, which acquired Newmarket Gold, (where he also served as the Chief Operating Officer). Paramount to his current “know-how”, Darren spent thirty years working for Newmont Mining
Corporation, climbing the ranks through roles of increasing responsibility to his final position there. Prior to that he graduated with a Bachelor of Mining Engineering (Hons) from the Western Australia School of Mines in Kalgoorlie, while mining is a specialist role that few people fall into nowadays, Darren is clearly a man who had his mine set on a specific industry.
Darren’s influence can be seen further with Calibre attaining its Year 3 conformance with the World Gold Council’s Responsible Gold Mining Principles (“RGMPs”). Darren explains that this significant milestone underscores Calibre’s unwavering commitment to ethical, sustainable, and responsible mining practices.
The World Gold Council’s RGMPs serve as a benchmark for the gold mining industry, emphasizing key areas including environmental stewardship, social responsibility, and robust governance practices. Calibre’s achievement of Year 3 RGMP compliance reaffirms the company’s dedication to upholding these fundamental principles across its operations.
“We were pleased to announce our Year 3 conformance with the World Gold Council’s RGMPs in May,” says Darren, “This achievement underscores our pursuit of excellence in sustainability and ethical mining practices
We are a specialized company in the implementation of construction sites and underground mining operations with emphasis in the exploration, development, preparation and extractions of minerals, as well as supplementary contract services. We operate in Peruvian territory with international certifications
ISO 14001 (Environmental Management System), ISO 45001 (Occupational Health and Safety System) and ISO 9001 (QualityManagement System) which guarantee the compliance of our operations with national and international standards. Our policies of safety, occupational health and environment are the basis of our integrated management system. Additionally, we count with the equipment and technological support to fulfill our objectives.
Mining Services
• Construction Of Tunnels
• Mineral Exploitation
• Support Or Fortification Services
• Complementary Mining Services
• Mine Closure
Civil Works Services
• Construction: Infrastructure (tunnels, roads, drainage)
Rural development (paths, roads)
• Utilities: Sewer/wastewater & Drinking water IN PERU:
Telephone: (511) 717-2709 E-mail: hcanchanya@cis.com.pe
NICARAGUA: Telephone: +505 57947921 E-mail: contactenoscis@cis.com.ni
I am confident the Valentine gold property has district-scale potential,
and reflects our commitment to fostering positive impacts on the environment, engaging with, and supporting local communities, and upholding rigorous governance standards.”
The Producing Assets
LIMON MINE & MILL: a wholly owned mining and milling site in Western Nicaragua, producing 500,000 tonnes of gold per year utilising open pit mining at the Lim Central and three underground mines , the Santa Pancha, Panteon and Veta Nueva.
LIBERTAD MINE & MILL: a wholly owned open and underground gold mining site in Central Nicaragua. Making use of Limon Mill Feed, the Pavon Norte and Pavon Central Open pits and Jabali underground.
PAVON GOLD MINE: a wholly owned open pit gold mining site in Northwest Nicaragua using open pits, Pavon North, Pavon Central
EASTERN BOROSI GOLD-SILVER: Calibre owns 100% of the Eastern Borosi Gold-Silver Property (“EBP”), located in the northeastern Nicaraguan low-sulphidation, epithermal district that hosts numerous high-grade, goldsilver vein systems.
PAN GOLD MINE: a fully owned gold mine in Nevada, The Pan Mine is a Carlin-style, open-pit, heap-leach mine in east-central Nevada, approximately 28 km southeast of the town of Eureka, on the prolific Battle-Mountain – Eureka gold trend.
Valentine Gold Mine, which has won them their reward is taking on centre stage however, as in May 2024 Darren revealed that the construction of their fully funded Valentine Gold Mine was 64% complete. Additionally, he announced that they were progressing detailed engineering to 98% from 60%, with the later having formed
the basis of the previously disclosed Marathon Gold capital estimates.
“With the first gold pour scheduled in Q2 2025,” he says, “The delivery of Valentine is a paradigm shift for Calibre as we transition to a quality mid-tier gold producer unlocking significant value for all stakeholders.”
Darren elaborates that since acquiring Valentine in January 2024, they have rebaselined the project schedule, advanced detailed engineering, awarded major contracts, connected the site to permanent power, delivered critical path items such as mills and motors, hired the operations leadership team, and started pre-commissioning and commissioning activities.
This project optimization and derisking efforts, combined with accelerating a portion of Phase 2 expansion capital, has resulted in an initial capital cost of C$653 million, which is a C$145 million increase over Marathon Gold’s that was highlighted in the third quarter of 2023. With a C$279 million cost to complete as of April 30, 2024, and approximately C$400 million of cash and restricted cash. Making the project fully funded with substantial cash flows from operations
“I am confident the Valentine gold property has district-scale potential, and we anticipate accelerating our exploration efforts in the near term,” Darren says, adding, “The Valentine Gold Mine and surrounding property offers a robust resource base and significant discovery opportunities with an extremely prospective array of exploration targets with similar geology to the prolific Val-d’Or and Timmins camps in the Abitibi gold belt.”
With first gold production scheduled for the second quarter of 2025, the company is clearly keen to get underway on digging deep and producing. However, they are approaching it with the mindset of safety first. Over his multiple decades handling many different levels and seeing the industry from multiple perspectives, Darren is adamant and assured that the best way to produce in the mining industry is to make sure workers are well paid, well equipped and above all kept safe.
“Calibre’s dedication to safety is exemplified through our comprehensive sustainability initiatives,” he says, “Our efforts extend beyond regulatory compliance, focusing on continuous improvement to minimize our environmental footprint, as well as transparent and extensive community engagement to create a positive impact in the regions in which we operate. But our people always come first.”
Foylan Rhodes
Flow Management Devices (FMD) is the leading provider of small volume meter provers for custody transfer applications in the oil and gas industry worldwide. Committed to providing their customers with the highest quality products, competitive pricing, unmatched service, and technical support available in the industry, they are a company that allows their product to speak for them.
As a leader in the industry, FMD have found that the best way to set themselves apart from the competition is to be better than any others. Founded in 2007 with the goal of improving liquid measurement technology, they have used their patented Small Volume Unidirectional Captive Displacement Meter Proving technology to blast away from the crowd.
Their products and provers are used by some of the largest oil and gas companies in the world, and they have helped to improve the accuracy and efficiency of custody transfer measurements. Producing demonstrative results for their clients. This capacity to have their products determine their reputation with their clients is important, as in this industry, the proof is not in the pudding but in the ability for the product to perform reliably and accurately.
A Small Volume Prover serves as a crucial instrument in the oil and gas industry, primarily designed to ensure the accuracy and reliability of flow measurement systems. By meticulously calibrating and verifying metering devices, such as flow meters, the prover validates their performance against known standards. This process is essential for maintaining compliance with regulatory requirements and industry standards. Additionally, Small Volume Provers enable operators to detect and rectify any discrepancies or inaccuracies in flow measurement, thereby enhancing operational efficiency and optimizing resource allocation. Overall, the purpose of a Small Volume Prover is to guarantee precise and dependable measurement of fluid flow in oil and gas operations.
Customer driven, FMD is committed to providing excellent customer service and have a team of knowledgeable and experienced engineers, sales representatives, and technicians available to answer any queries from new and current customers. Open and detailed communication is key and their customer facing teams are on hand to help with any problems that maybe encountered. Additionally, they offer a variety of training,
maintenance, and support programs to help customers get the most out of their FMD prover.
The way that customers are treated by the front line services makes or breaks an experience. Customer service operatives must possess comprehensive industry knowledge to anticipate and address customer inquiries effectively. Understanding the intricacies of their industry enables operatives to identify pertinent questions customers should be asking to obtain accurate information and solutions. This depth of understanding allows operatives to provide informed guidance, troubleshoot issues efficiently, and offer tailored recommendations. By anticipating customer needs and proactively addressing concerns, operatives foster trust and confidence, enhancing overall customer satisfaction and loyalty. Ultimately, a thorough grasp of the industry empowers customer service operatives to deliver exceptional support and ensure customers receive the right answers to their queries.
FMD In Focus
Delivering the highest quality small volume provers to the oil and gas industry takes dedication, great engineering, manufacturing prowess and keenness to deliver on time. This has been incorporated into the company’s
FMD can help you keep your prover running smoothly and accurately for years to come
vision according to their website where FMD provides world class proving solutions for all applications, whether simple or complex. Their commitment is to “Continuously Improve Liquid Measurement Technology”.
For over fifteen years the company has a proven track record with all meter and application types. Flow MDs patented line of small volume provers, provides an accurate, repeatable, and fast measurement with minimal product displacement, while being compatible with almost all liquid flowmeter types. Their unique and compact meter prover design utilizes pulse interpolation electronics, a patented drive end, a motor driven piston with durable carbon fibre belts, a smooth bore cylinder, a poppet valve, and optical position sensors. The Flow MD line of Small Volume Unidirectional Captive Displacement Provers incorporates Double Chronometry as recognized by API 4.6 and is compliant with API 4.2 Direct Master Meter Proving. Some of their other services are covered below:
Flow Management Devices (FMD) provides application specific meter provers tailored to you application needs, no matter how simple or complex. Our versatile Small Volume Provers can be tailored specifically for a variety of applications, including pipeline, custody transfer, FPSO, near shore, onshore, ball prover replacement, renewable fuels, cryogenic, LNG, mass proving, high temp, high pressure, and low pressure. With over 15 years of experience providing advanced proving systems, FMD has the expertise to meet your needs. Whether your application is straightforward or highly complex, we can provide the ideal proving solution.
FMD small volume meter provers are designed to be used in the field to calibrate flow meters in custody transfer applications. They meet strict quality standards and provide accurate, reliable measurements with minimal product displacement.
FMD provides prover accessories that enhance prover functionality and tailor your FMD meter prover to your application needs. FMD also provides spare part kits for your FMD small volume provers as well as seal kits for provers built by other manufacturers. These kits contain all the necessary parts to repair or replace any damaged or worn parts on your prover. With our wide range of prover accessories and spare parts, FMD can help you keep your prover running smoothly and accurately for years to come.
Reliability in manufacturing is paramount for ensuring consistent product quality, meeting customer expectations, and upholding brand reputation. Reliable manufacturing processes minimize defects, reducing the likelihood of product recalls and costly rework. This fosters customer trust and loyalty, crucial for sustaining long-term business success. Additionally, reliable manufacturing enhances operational efficiency by minimizing downtime and maximizing throughput. It instils confidence in stakeholders, including investors and regulatory bodies, ensuring compliance with industry standards and regulations. Ultimately, reliability in manufacturing underpins competitiveness in the market, driving profitability and enabling sustainable growth for companies across various industries.
Bridget Marks
Having become an important component to the longevity of businesses in the oil and gas, marine and container shipping industries, Hempel’s financial results from 2023 have proved that the company’s approach of “earning trust” from their clients is just as important to their bottom line as the products and services they provide.
The Denmark company, now headquartered in Kongens Lyngby near Copenhagen, was founded in 1915 and develops and manufactures coating solutions for the protective, decorative, marine, container, industrial and yacht segments. With these coatings minimizing maintenance costs, improving aesthetics, reducing waste, and increasing energy efficiency for their clients, the company’s ultimate secret is simply a matter of focus and interest.
As Michael Hansen, Group President and CEO of Hempel A/S explains, they partner with their customers and research institutions to find new ways to solve existing problems with the approach of constantly challenging themselves to create evermore efficient and sustainable solutions. And, through this long term approach, they are trusted to ensure that their customers’ assets last longer and perform better across their entire service lives.
“We believe that trust is earned,” he says, “And we earn this trust every day through the superior performance of our products and technical service. And by helping shape a brighter future for customers and the world in general.”
According to Michael, the company’s success is a direct result of the team they’ve built and fostered. As a company they live and work in many different countries, speak many languages and have different skills and areas of expertise but are all part of the Hempel family, which is a team of more than 6,500 people. He further explains that, with such responses from clients and such weathered evidence of their product’s value, it is easy for the staff number to be united in the belief that our coatings can make our customers’ businesses stronger and their world safer and longer lasting.
“Hempel is a growing business, both geographically and in its fields of work,” says Michael, “This gives us unique opportunities to develop our skills and explore different ways of working. Whatever we do, we constantly work to earn the trust of our colleagues, customers, and external stakeholders. We value collaboration and innovation, and back ourselves to succeed.”
In 2023, Hempel achieved record-breaking financial results with an organic revenue growth of 13.7 percent, by delivering revenue of EUR 2,351 million which is an increase on 2022 of EUR 192 million. A result that Michael attributes to their Double Impact strategy which has driven strong performance across the business.
“Hempel delivered record-breaking results in 2023. We set ambitious targets, and we surpassed our expectations,” says Michael, “The strong results were thanks to a stellar performance across our business.”
In 2023, Hempel maintained sharp focus on innovations to develop more sustainable solutions that meet its customers’ needs, enabling them to lower their CO2 footprint, while protecting and beautifying their assets. This focus was reflected in growth across all four of Hempel’s customer segments, with Marine and Energy delivering double-digit organic revenue growth of 26.2 per cent and 18.6 per cent, respectively. The Decorative segment maintained its position as Hempel’s largest customer segment in terms of revenue, delivering EUR 792 million for the year. The Infrastructure customer segment expanded sales by 9.6 per cent through innovative solutions that supported their various
At the heart of this growth expedition lies the synergy between Hempel’s highly skilled people and extensive global presence
customer sustainability plans.
“At the heart of this growth expedition lies the synergy between Hempel’s highly skilled people and extensive global presence,” says Michael, adding, “We are determined not to let ourselves slip this year and the 2024 outlook is expected to see singledigit organic revenue growth and an EBITDA margin around fifteen per cent.”
Hempel’s Double Impact strategy has proved very robust and effective. As such, in 2023, Hempel’s Board of Directors and Executive Group Management further committed to the principles of the strategy to guide the business beyond 2025.
“In 2020, we launched Double Impact aiming to deliver innovative, sustainable solutions that create a significant positive impact for our customers and society at large. Initially, our strategy had one clear goal: doubling our revenue within five years, something that we are well on our way to deliver on,” says Michael.
He goes on to explain that last year they added ‘Scalable Operations’ as a pillar in their strategy to drive a more harmonised global setup, enabling smarter use of resources across functions and segments. The aim is to generate higher sales, without seeing an equal increase in costs, through more effective and efficient ways of working together.
To support this, Hempel’s new stateof-the-art Chinese factories in Yantai and Zhangjiagang are now up and running and are poised to accelerate growth in the years to come. A growing business maximises the
positive impact that Hempel, its people and its owner, the Hempel Foundation, have on the world.
At Hempel, sustainability leadership means being frontrunners within the paint and coatings industry; working with material topics such as climate, biodiversity, resource depletion and diversity. Hempel’s sustainability framework, Futureproof, has been instrumental in driving this work.
In 2023, Hempel made significant progress towards delivering on its sciencebased targets and ESG commitments, decreasing its combined Scope 1 & 2 emissions by 51 per cent compared to its 2019 baseline. In May of that year, the Carbon Disclosure Project (CDP) recognised Hempel’s efforts to engage its supply chain on climate issues, awarding Hempel an A in its 2022 Supplier Engagement Rating. Hempel was, for a consecutive year, awarded B by CDP for good environmental management in its 2023 environmental disclosure and scoring process.
“Putting sustainability at the heart of everything we do means we not only focus on lowering emissions from our operations and reducing the resources we use, but also continue to develop products and solutions that support our customers on their sustainability journeys. For example, our high performance hull coatings helped customers in the maritime industry reduce their CO2e emissions by 6.5 million tonnes in 2023 alone. This is an improvement of 16 per cent compared to 2022,” concludes Michael Hansen.
Cassidy Blanks
Based in West Columbia, South Carolina, Lexington Medical Center Extended Care, is a 607 bed teaching hospital that anchors a health care network comprising of six community medical centres and employs a staff of more than 8,000 health care professionals. A leader in short, mid, and long term care, they demonstrate how people heal people.
Ranked best hospital in the Columbia Metro and #2 hospital in South Carolina by U.S. News & World Report, Lexington Medical Center was also named one of the “Best Places to Work in South Carolina” by SC Biz News, in partnership with the South Carolina Chamber of Commerce and Best Companies Group.
The centre cannot be properly understood as a location, instead it is best referred to as a network of medical centres, each with a team of their own professional staff. As a network, they are accredited as a Cancer Center of Excellence and have a clinical research and education affiliation with MUSC Hollings Cancer Center.
In addition, the network includes a cardiovascular program recognized by the American College of Cardiology as South Carolina’s first HeartCARE Center and an occupational health centre, the largest skilled nursing facility in the Carolinas, an
Alzheimer’s care centre and more than 70 physician practices.
Lexington Medical Center operates one of the busiest Emergency departments in South Carolina, treating nearly 100,000 patients annually. Over and above this, the hospital delivers more than 4,000 babies each year and performs more than 25,000 surgeries.
Considered by many a review as “the best place to have a baby in Columbia”, as well as one of the top twenty five hospitals to work in the United States, Patrick Bonds, the LMCEC’s director believes that these accolades are entirely a result of the calibre of the staff that work at the hospital. Elaborating that in his experience it is people who heal other people.
“All of our honours have been made possible by our dedicated, talented team of health care professionals and staff,” he says.
Opened as a nonprofit hospital in 1971, what was originally Lexington County Hospital quickly became a healthcare leader and over fifty years later, their name may have evolved, their technology and medicine may have developed, but their approach to care has remained the same and they continue to serve their community as a local, independent, nonprofit hospital.
The hospital has a solid history of
pioneering the use of sidewise thinking to enhance their medical care. They were the first area hospital with satellite health facilities and were the first to establish a community health education department. They opened the state’s first satellite outpatient facility with services including surgery, urgent care, lab, radiology, and physical therapy. At the time, this was revolutionary thinking but today is considered standard practice for many other healthcare organisations following suit.
By the 1980s, the now-called Lexington Medical Center offered community programmes including education on managing disease and learning healthcare skills, such as newborn care and home nursing.
In the 1990s, they established four community medical centres in small towns around Lexington County to provide residents with easier access to top-notch healthcare. In 2001, they opened their largest community medical centre in Lexington which was larger than the hospital was in 1971.
To keep abreast with the pace of which modern medicine develops, Lexington makes sure that they are a technology based complex, here patients have access not only to advanced technology but the leading edge techniques that come with it. The aim today is the same as
All of our honours have been made possible by our dedicated, talented team of health care professionals and staff
it was in 1971, to provide quality health services that meet the needs of the communities dependent on them.
“We’re dedicated to providing nothing short of the best care for our residents,” says Bonds, a former Marine who draws from his military experience in field artillery. “We tip our hat to our healthcare workers who uphold the highest standards every day across our system, putting us among the best in the nation.”
Recently, Lexington Medical Center has opened two new facilities to better serve growing communities in the Midlands, these are the Lexington Medical Park Forest Acres and LMC Lexington Medical Park 2.
Lexington Medical Park Forest Acres is a 22,300-square-foot building that houses Lexington Family Practice Forest Acres, South Carolina OB/GYN Associates Forest Acres, and an imaging centre.
“We are excited about the opportunity to have imaging services available in Forest Acres,” said Lara Lott Moore, vice president of Operations. “This facility allows our patients from the area to receive the services they need close to home.”
Lexington Family Practice Forest Acres has exam rooms and provider offices, X-ray, a laboratory, and consultation and dictation rooms. At this new practice, Sarah S. Cottingham, MD, and Kate Gordon, MD, provide comprehensive care for patients of all ages, including same-day sick appointments, preventive care and well visits.
“We have wanted to bring Lexington Family Practice to the Forest Acres community for several years, and we’re happy to open the doors on our 13th location at this new facility,”
said Terri Dooley, vice president in Physician Network Administration. “The staff and providers at Lexington Family Practice Forest Acres look forward to caring for those who live and work in this growing area.”
LMC Lexington Medical Park 2 is also now open. It’s adjacent to LMC Lexington at 103 Thompson Street in Lexington. It houses Lexington Paediatric Practice, Internal Medicine Associates and Lexington Women’s Care Lexington. All three practices relocated to this three-story, 33,612-square-foot building.
“By combining our West Columbia and Lexington locations at this stateof-the-art facility, patients throughout Lexington County have improved access to comprehensive outpatient care at Internal Medicine Associates,” said Kate Zannella, vice president in Physician Network Administration. “Our new location enhances patient experience and improve efficiencies for our providers and staff.”
Internal Medicine Associates has exam rooms, provider offices, injection and blood draw rooms and a laboratory, and Lexington Women’s Care Lexington has exam rooms, shared provider offices with dictation space, ultrasound, a laboratory, and procedure and nonstress testing rooms. Lexington Paediatric Practice features colour-accented exam rooms, provider offices, a laboratory, and dictation and conference rooms.
“We are here to meet the needs of the community, whatever they might be, to give patients a comfortable, safe and dignified place to stay,” Bonds says, “The team never loses sight of the fact that these people are our friends, neighbours and family, and that means something to us here and we will continue to grow and develop to meet their needs.”
Daemon Sands
Following a successful series of developments including the acquisition by Bettcher in November last year (2023) and the subsequent acquisition by Fortifi, MHM Automation is one step further to revolutionizing product handling across all conceivable sectors. We explore.
As part of the Fortifi Food Processing Solutions brand, MHM Automation has become part of a major endeavour to launch their unified platform of global leading brands and products, working within food processing equipment and automation solutions. This platform in turn connects them to business contingents in fifteen countries spanning five continents. As the overall owner, Fortifi provides solutions across the food industry including applications in protein, dairy, and fruits and vegetables. And, at the same time, their technologies enhance productivity, maximize yield, and improve worker safety for customers around the world.
As their Chief Executive Officer, Massimo Bizzi explains, Fortifi’s strategy is centred around a relentless focus on innovation, unparalleled customer service, and expansion through continuous improvement and complementary acquisitions of other leading brands and capabilities. He adds, “As a strategic partner to our customers, we strive to offer a full portfolio of solutions across the
food processing value chain.”
As he notes, the closing of MHM Automation’s acquisition and the incorporation of the New Zealand-based provider of postharvest processing, protein processing, and packaging solutions is expected to further strengthen Fortifi’s capabilities. Their innovative, reliable systems and equipment will no doubt improve safety, optimize product quality, and extend their automation and robotics capabilities across a host of industries. In joining the group MHM have opened many new doors to new opportunities and developments.
Additionally, Fortifi has also signed definitive agreements to acquire two other businesses based in Europe. LIMA France which is a France-based supplier of meatbone separators, deboners and grindersdesinewers, and Reich Thermoprozesstechnik GmbH which are the oldest Germany-based manufacturer of thermoprocessing food systems, both of which are expected to join Fortifi in 2024.
Still a fairly young organisation, the formation of Fortifi began in 2021 when investment funds affiliated with KKR, a leading global investment firm, acquired Bettcher Industries who remain a leading provider of innovative protein processing tools. The following year, Bettcher acquired Frontmatec,
a global supplier of automated pork and beef processing equipment, forming an end-to-end provider of protein processing solutions.
MHM’s recent addition brings interesting capabilities across new food processing segments and applications, including dairy and fruits and vegetables, and further expands Fortifi’s global reach by establishing an even stronger local presence in the AsiaPacific region.
“I am thrilled to welcome MHM into the Fortifi portfolio, and I look forward to welcoming LIMA and Reich as well,” said Dan Daniel, Chairman of the Board of Fortifi. “The global footprint, technologies, and expertise these brands bring will help Fortifi continue to serve its customers with excellence.”
Mhm Automation In Focus
When it comes to the backstory of MHM Automation, one has to note the power of hard earned, entrepreneurial style business building. The value of this can’t be understated and it shapes much of this company’s narrative. MHM’s story began in 1884 in Christchurch, in the South Island of New Zealand. Founded and ultimately driven by innovation, continuous improvement and hard work, the company quickly evolved into a technology and automation led business, designing and
As a strategic partner to our customers, we strive to offer a full portfolio of solutions across the food processing value chain
delivering systems to many of the leading food processing companies globally.
The tale behind the New Zealand’s own growth is one of elite primary production. As a small country the inhabitants and their businesses had to learn to capitalise on every margin. When their arable lands and agricultural prowess proved viable, the close of the industrial revolution in the country marked the beginning of global expansion. Today, little has changed in this regard and New Zealand’s export industry is still focused on products from the primary sector.
As a company whose history spans more than 140 years MHM’s tale runs parallels to that of New Zealand’s development. MHM Automation exists to support the global food processing sector, through the design and supply of innovative, world-leading processing and handling equipment.
Their company’s legacy brands have helped shape the New Zealand and Australian engineering and manufacturing sectors. Years of acquisitions, growth, milestones, and perseverance saw the original group of businesses move to a single focused organisation known as MHM Automation.
Now, as part of the global Fortifi Food Processing Solutions group, the company has a further chance to continue to be involved in proper chain helping to provide full-lifecycle automated solutions to Fortifi’s extensive clients. Working collectively with Fortifi, MHM believe they can improve a single line or automate an entire food processing plant, anywhere in the world, according to their website.
Even as a member of a larger organisation, MHM Automation is still a business built on a constant drive to innovate, which is one of the reasons they were acquired in the first place. This outstanding quality keeps them pushing to develop solutions that can enhance efficiency and drive growth in businesses. It’s this kind of initiative which is why MHM have been able to provide automation solutions in so many varied sectors. As such, MHM Automation bring to the table expertise in the whole food industry including meat and poultry, dairy, food and beverage processing and fruit and vegetables. Then, timber and sawmilling, agriculture, grain and feed, logistics, industrial and work in Antarctica! They’ve created stainless steel fabrication for sculptures and architectural features for domestic and commercial properties, automated storage and retrieval systems including ASRS shuttles and elevators, custom designed storage tanks for chemicals and acids, autonomous mobile robots for pallet and crate automation and bataprep gusseters which, in case you didn’t know, are the specialised machine used to prepare bagged cheese blocks for vacuum sealing.
What this proves is that while the requirements for different industries differ greatly, at their base the approach and procedures, the “circuitry”, if you will, is the same. Almost everything can be automated, and automation is key to progression, development and growth.
Daemon Sands
Adriving force behind Canadian real estate projects at the cutting edge of design, performance, urban planning and occupant wellness, MONTONI is a recognised name when it comes to sustainable building. Known for generating client value while safeguarding the environment and communities of their projects, the company is a pioneer in their industry and as such, do not follow conventions. Instead, as it says on their website, they seek to build the real estate heritage of tomorrow on the foundation of their convictions today.
With over 700 projects under their belt, MONTONI’s portfolio represents over 30 million square feet of industrial, commercial, institutional, and residential construction, with another 25 million square feet under development. Especially impressive considering that these are almost exclusively across Québec.
Although not always required, a company will usually find managing external projects easier when they have their own house in order. Taking this to heart, MONTONI is proudly one of Canada’s Best-Managed Companies and has held this title for nearly 25 years. They have committed themselves to making ESG criteria a permanent strategic reflex.
Over 4.2 million square feet of LEEDcertified buildings have been completed and, among many of their current projects they are targeting LEED certification for close to 7 million square feet. Additionally, it is in the process of acquiring zero-carbon building (ZCB) certification for nearly 2 million square feet of further project space.
Using their own HQ as an example of their capabilities, Groupe Montoni and Sid Lee Architecture recently unveiled the developer’s new headquarters, Maison MONTONI. The new space is housed in Espace Montmorency, a recent project in a bustling Laval neighbourhood, developed by MONTONI in collaboration with Fonds immobilier de solidarité FTQ and Montez Group and designed by Sid Lee Architecture. As the new centrepiece of downtown Laval, the site offers a range of services and is connected via a tunnel to the Montréal métro system for convenient commuter transit.
The MONTONI head office was imagined as a home, inspired by the belief that a company’s workplace should reflect its values and culture. The goal is to promote collaboration and wellness at work by providing spaces
to socialize, work, and unwind. This philosophy aligns with MONTONI’s broader vision for post-pandemic workspace design. MONTONI’s dynamic offices are a microcosm, offering employees an inspiring space planned around their day-to-day work. This focus comes directly from the company founder, Dario Montoni who says, “We want to offer our team a customized environment that serves as a catalyst for ideas and innovation; a space where people want to go, where they feel at home.”
He adds, “Seeing our teams bringing life to these spaces and making them their own makes me proud of what we’ve been able to create.”
Further to the above, Montoni’s forward thinking makes its headquarters a model of sustainable real estate development. The office tower is targeting Platinum LEED Core and Shell certification and is connected to the Espace Montmorency energy loop. This technology is responsible for a major feat— cutting the complex’s energy consumption by more than half and reducing greenhouse gas emissions by nearly 90%.
Also, the MONTONI offices are targeting WELL certification, which is intended to create an integrated environment to improve
its occupants’ nutrition, physical fitness, mood, sleep, and performance. The reference in occupational health and wellness, WELL is based on seven key pillars—air, water, nourishment, light, movement, comfort, and mind.
Sid Lee Architecture drew inspiration from the codes of the construction industry to design MONTONI’s new headquarters. Translated in the use of concrete, aluminium, exposed structures, and a series of finishings including high-visibility orange powder coats, the design principle pairs with the architecture to showcase SLA’s expertise.
A curved aluminium counter custom designed by Sid Lee Architecture greets team members and guests as they enter the lobby of the developer’s headquarters which occupy the second and third floors of the office tower at Espace Montmorency. This mechanical object adds an industrial accent to the space while a virtual reality dome offers visitors a tour of the developer’s projects.
Near the entrance, large wells provide a view of the different levels, enhancing a sense of interconnection between the space’s different functions. Two floating staircases connect the levels, their glass encasing creating an expansive effect. The first is suspended from a black steel frame and the other is made of concrete and supported by a steel structure. To unify the disparate elements, a walnut-panelled ceiling and Venetian plaster walls add a touch of warm texture to the raw minerality of the offices.
“We drew inspiration from the codes of the construction industry in creating the new offices. Guided by the builder’s innovative approach, every aspect of our design reflects our commitment to crafting offices that are unique, and honouring of our client’s legacy,” says Jean Pelland, Architect and Senior
Seeing our teams bringing life to these spaces and making them their own makes me proud of what we’ve been able to create
Partner, Sid Lee Architecture.
The Agora on the second floor serves as a gathering space for team members to eat, relax and mingle. Full-height windows and an impressive staircase suspended above a lush garden and movable platforms allow employees to take full advantage of the relaxed atmosphere. A few steps away, teams can enjoy a moment on a balcony terrace overlooking the complex’s flourishing outdoor courtyard.
The kitchen area is divided into two distinct spaces. The main kitchen visible from the Agora showcases gorgeous matte-black and olive-green Italian furniture as well as bespoke walnut and aluminium counters designed by SLA. A sculptural light fixture designed to resemble steel construction scaffolding floats above the bright orange stools. Tucked behind a wall of blue lacquered cabinets, the second communal kitchen is designed to reflect MONTONI’s sense of hospitality.
Maison MONTONI
Like a home, the headquarters are built to create spaces for socializing, collaborating, unwinding, learning, and refuelling. Collaborative work areas dot the space while each individual workstation can be adjusted for seated or standing work. Frame-like structures interlock to accommodate electrical and mechanical components while dividing and organizing the space. Small areas for employee coffee breaks are interspersed with informal meeting spaces and a training room, gym, multimedia room and conference rooms are available for use. With its focus on the wellness of its users, Maison MONTONI epitomizes the office for our times and is a perfect catalogue portfolio for clients to witness the scope and diversity and possibilities that this company offers.
Aa construction management partner of choice, Old Town Construction, a subsidiary of Old Town Companies, are reshaping the central Indiana community by insisting on a new standard of workmanship. The drive to rise to the challenge of beating modern mediocrity and in doing so, hoist up the industry standards with them, stems from their parent company who are an awardwinning, Central Indiana-based home building, land development, commercial real estate and construction company that is recognized in the industry as one of the premiere custom home building groups in Indiana, working on the founding principle of “Outstanding Location and Timeless Designs” which has become the cornerstone by which the company has evaluated, planned, and executed development projects since it was founded in 2009.
Steve Jansen serves as the President of Old Town Construction and is responsible for providing overall leadership and strategic planning for all Old Town projects. He maintains the culture of the business, through which the company’s relationships with clients, trade partners and employees are nurtured and strengthened. Holding a management degree from Indiana Wesleyan University, IN, Steve spent thirty years in commercial construction
where he worked his way from the grass roots to becoming general superintendent before joining Old Town. It was during these cheek-to-the-grinder years where he established a stalwart belief that a business should never accept a “that’ll do” standard when one could excel.
What distinguishes the company is their attitude to perfection. They are primarily problem solvers who approach challenges with a zest and the highest standards. And be the projects residential areas or office and retail units, Old Town Construction understands that buildings are more than just bricks and mortar. Not only do they provide security and location for people and businesses, but they also shape a legacy for both.
Unlike other industries, construction is scrutinised over periods of years and decades by the people who either live or work within the buildings. Old Town Construction design and build their projects to withstand this scrutiny and their strategy to accomplish this begins with a careful, scrupulous attention to the small details and a fundamental refusal to accept any other standards than their best.
This approach to standards, is reflected in the company’s core values which Steve ensures shape the decisions from top to
bottom. Comprised of the five fundamentals of: Modelling Integrity, Showing Dedication, Being Growth Minded, Practising Joyfulness and Showing Appreciation, these items help guide the company. It also demonstrates the culture of the business. Where other businesses may focus on values that showcase and highlight their projects and their onsite prowess, Old Town Construction’s focus is on their people.
“Our work, the long term relationships that we have with existing clients and the nature of our reputation speaks volumes for us,” says Steve, adding, “We work with construction professionals who apply themselves to their roles and are responsible for the level of work we produce. Our immediate job is not simply to build property, but to build the people we work with.”
He adds, “Old Town has a passion for people and the communities in which we work. We hire like-minded team members who can bring a passion for excellence, great work ethic, and a positive, can-do attitude to our team.”
The nature of Old Town’s approach to business is epitomized in the Provenance project which the company has just entered the second phase of their eight phase development strategy.
Provenance at Discovery Park, in partnership with Purdue Research Foundation,
Old Town has a passion for people and the communities in which we work
is a neighbourhood that combines a variety of housing types in a new walkable village-like environment. Provenance provides upscale apartments that are mere minutes from Purdue’s campus and nearby Schweitzer Engineering Laboratories, Rolls Royce, and Saab Aerospace.
Purdue Research Foundation selected Old Town Companies to master develop a mixed residential neighbourhood within its Discovery Park District. A unique, traditional neighbourhood development with a new urbanism twist, Provenance consists of a mix of single family detached homes, three-story town homes, multifamily rental apartments and light retail areas. Future development phases include condominiums, a senior residential development, and the potential for a school. Currently entering the second phase, Old Town’s eight-phase development strategy is expected to be implemented over the next eight
to ten years.
The work takes into consideration the history of the location, with careful consideration given to already established landmarks with an existing heritage. The aim being not to replace what is already there but to develop the area to safeguard it. The work includes open air walks, facets of local history, aesthetically appropriate design and layouts.
The project’s early phases involved the upgrading of existing ground works as well as the development of new ones to support the remainder of the construction phases. Phase I of the Old Town construction project was completed in late 2023 and involved crews replacing a water main under the CN railroad tracks on Eastern Avenue, Phase II of the project in Plainfield began in September 2023 and saw the replacement of water mains and storms sewers under Center Street, Amboy Street, Bartlett Avenue, and Evans Street. This part of the project is anticipated to be finished in early summer 2024 and is essential because underground works such as these have the task of supporting the growing communities in the properties built and need to take into consideration the potential growth of an area. Multiple project phases need to be conducted in time, because areas such as these that support business and homes, are built in layers.
“Clients like these rely on Old Town because we have the experience to be mindful of those little details that are addressed in the early phases that need to accommodate the later ones,” Steve reveals, “Each phase is interconnected and while we build them one phase at a time, you have to keep in mind how future construction will fit together.”
Donnie Rust
In this issue’s focus covering maritime engineering, Business Pursuit took a good look at Thecla Bodewes Shipyards of Kampen in The Netherlands, where we investigated what it takes to keep a business in the family for seven generations.
For over three centuries, the shipyard has specialized in supplying future-proof smart ships designed for emission-free shipping through innovative sustainable solutions. With over 200 newbuild vessels delivered to satisfied customers—25 of which are diesel-electric, LNG-electric, and hydrogen-electric—and more than 15 years of experience with diesel-electric propulsion systems, the shipyard consistently meets the highest standards. In addition to innovative multi-purpose short sea vessels, Thecla Bodewes Shipyards also constructs shallow water tugs and pushers, modern dredgers, and specialized vessels. The primary service categories offered are rental, lengthening, and ship repair, we cover these below.
Rental
In Harlingen, Thecla Bodewes Shipyards rents out various yard facilities, including halls, offices, and storage space. The halls, suitable for multiple purposes, are ideal for refit, (finishing) construction, maintenance, or conversion of ships. The yard’s location by open seawater, with a ship lift, ensures easy
accessibility for all types of vessels.
Their halls feature heavy-duty overhead cranes and indoor workshops, with offices available for rent in the adjacent main building, which also houses the canteen. When renting the halls, they provide various facilities to support the work, including a ship lift (120 x 20 meters), indoor and outdoor storage space, a warehouse, project management, and optional support for the work to be carried out.
Extending a ship’s length involves cutting the main frame and inserting a section between the two parts, thereby increasing the vessel’s overall length. Lengthening existing ships is increasingly common, primarily due to the removal of penalties associated with raising the ship’s tonnage. Constructing new fore and midships is also becoming more popular. If interested, contact the locations or use the general telephone number.
The sharp increase in knowledge and experience accumulated in this area is significant. This means that Thecla Bodewes Shipyards can give precisely what the customer wants – trustworthy and reliable, customised workmanship. Good ol’fashioned Dutch shipbuilding expertise, combined with the use of certified steel,
together guarantee an optimal product.
Alongside innovative activities and new vessel construction, Thecla Bodewes Shiprepair handles all types of repairs, maintenance, and conversions at the yard. The shipyard features a 110-meter transverse slope, allowing even larger vessels to be repaired in an ideal working environment. The Meppel shipyard specializes in repairs and has a fully equipped workshop with machinery for all types of welding and construction, as well as steel working, machine repairs, and finishing.
According to the company’s CEO Thecla Bodwes, the company recently celebrated the successful launch of the 7.280dwt vessel, MV Vertom Anette, for the Vertom Group. The Vertom Group currently operates a modern fleet of over a hundred vessels with a loading capacity ranging from 1,500 to 12,000 DWT. With almost 50 years of experience, the Vertom Group has built a strong track record in the Short Sea Shipping market by working with reliable suppliers and the launch marks a significant milestone in the ongoing partnership between Thecla Bodewes Shipyards and Vertom Group, showcasing their commitment
to innovation and excellence in the maritime industry.
The launch ceremony, held at Thecla Bodewes Shipyards’ facility in Kampen, witnessed the culmination of months of meticulous craftsmanship, innovation, and dedication. MV Vertom Anette stands as a testament to the exceptional engineering prowess and unwavering commitment to quality that both Thecla Bodewes Shipyards and Vertom Group embody.
MV Vertom Anette is the fifth vessel in the successful LABRAX series and, like all her sisters, is a masterpiece of maritime engineering and environmentally friendly design elements aimed at improving operational efficiency using a diesel-electric propulsion system.
The innovative LABRAX series was designed by Groot Ship Design and engineered by Thecla Bodewes Shipyards. The series marks an important milestone in the development of sustainable shipping solutions and is therefore fully in line with the ambitions of both the Vertom Group and Thecla Bodewes Shipyards to make a substantial contribution to the transition to an emission-free shipping industry.
Thecla Bodewes, CEO of Thecla Bodewes Shipyards, expressed her pride and gratitude on this momentous occasion saying that the successful launch of MV Vertom Anette underlines their shared commitment to deliver a series of vessels to the market that far exceed expectations.
“We are honoured to have partnered with Vertom Group to build these remarkable vessels and look forward to delivering the next vessels in the series,” she said.
Congruently, Arjan de Jong, CEO of Vertom Group told us that they were continually impressed with Thecla Bodewes Shipyards delivery, with this being the fifth vessel out of twelve in their order.
“We continue to be impressed by the craftsmanship and outcomes achieved by Thecla Bodewes Shipyards and our Vertom newbuilding team,” he says, “Our gratitude extends to all maritime suppliers for exemplifying the importance of Dutch expertise in shipbuilding. The performance of the four previously delivered vessels is beyond our expectations. The order of twelve vessels in total provides Vertom and Thecla Bodewes Shipyards with the opportunity to continue improving for more sustainable solutions.”
MV Vertom Anette is the fifth vessel of the successful Labrax series and was designed by Groot Ship Design and engineered by Thecla Bodewes Shipyards. The Labrax series marks an important milestone in the development of sustainable shipping solutions and is therefore fully in line with the ambitions of both the Vertom Group and Thecla Bodewes Shipyards to make a substantial contribution to the transition to an emission-free shipping industry.
The order of twelve vessels in total provides Vertom and Thecla Bodewes Shipyards with the opportunity to continue improving for more sustainable solutions
The LABRAX series have been specifically optimized to achieve the lowest possible Energy Efficiency Design Index (EEDI). Although not mandatory for diesel-electric propelled cargo vessels the EEDI of the Vertom Anette performs 38% under the current phase 3 EEDI requirements as required under the IMO MARPOL Convention.
The diesel-electric propulsion system on board of MV Vertom Anette, in combination with the advanced power-management system, minimizes energy losses, reduces overall fuel consumption and reduces CO2 emissions. This desired result has already been proven in the performance of the other LABRAX newbuild vessels. In addition, the installed propulsion power on board MV Vertom Anette is considerably lower compared to ships of equal cargo capacity and with conventional propulsion. With a length of 118.60m, a width of 14.30m and a full-box cargo hold of 329,700 cuft (7,280 dwt), the Labrax 7,280dwt series offers competitive transport solutions.
The launch ceremony featured the traditional christening, as MV Vertom Anette was named and blessed by her Godmother, Mrs. Anette Ruttmann, wife of Jürgen Ruttmann, former CEO of MST and former member of Vertom’s supervisory board, marking the vessel’s readiness for its maiden voyage. The event was attended by the Godmother’s friends and family, representatives from Vertom Group, Thecla Bodewes Shipyards, and other key stakeholders, all sharing in the excitement of this significant achievement.
Allianz Insurance is one of the largest general insurers in the UK and part of the Allianz Group, who are one of the leading financial services providers globally.
With around 147,000 employees worldwide, the Allianz Group serves over 100 million customers in more than 70 countries. Allianz Insurance handles Commercial, Engineering, Legal Protection and Premierline Business on their business insurance section. Meanwhile Petplan, Petplan Equine and Allianz musical insurance on their personal insurance section.
At the heart of the business is the focus on their customers and guided by the principles of their parent group, Allianz Insurance strives to be a trusted partner for their customers and to put them centrestage. By working to continually improve the quality of their service, incorporating sustainable and responsible business practices into their products and services, and combating insurance fraud, they aim to meet the needs of their customers now and into the future.
“We want to build relationships with our customers that are based on trust, so that they recommend us to others,” says Graham Gibson, chief claims officer of Allianz Insurers.
He goes on to explain that along with this customer centric approach is their management of customer feedback be it in the form of reviews or complaints. Swift action
being the top priority for them. He says, “We ensure that Group-wide quality standards are met in handling complaints and that our customers are treated fairly. We also regard complaints as another important source of customer feedback, so we analyse them to implement improvements.”
Offering peace of mind through their products and services allow the customers to know that, in moments that matter, Allianz deliver on their promises. Along with this, they maintain solid underwriting practices and ensure that insurance transactions in 13 sensitive business areas are screened and assessed for ESG risks.
Additionally, every employee must complete annual compliance training and regulatory testing to uphold the ethical standards and behaviours required of all of them to carry out their day to day business.
Graham says, “We ensure our products are clearly explained and honestly marketed so our customers and their broker partners can make informed decisions and choose solutions that are relevant to them.”
Interestingly, the company also does all it can to support a low-carbon society and social inclusion. In 2021, Allianz had over 162 sustainable insurance solutions globally including their products in the UK covering
An Allianz partner for over 15 years.
Ensure the resilience of your business with our expert consultancy services. At Glen Abbot, we understand the importance of preparedness in today’s dynamic business landscape. Our tailored solutions are designed to safeguard your operations against any unforeseen disruptions, keeping your business running, no matter what the circumstances.
Our Services include:
• Comprehensive Risk Assessment
• Business Impact Analysis
• Continuity Planning and Implementation
• Crisis Management Strategies
• Training and Education Programmes
• Testing and Exercises
• Pandemic Planning
• ISO 22301 certification and support
Why choose us?
• Over 25 years in business – we have developed an extensive portfolio of world-wide clients in many different sectors of business from small local firms to professional services and multi-national oil and gas suppliers
• Experienced Consultants: Our team consists of seasoned professionals with extensive expertise in business continuity management.
• Tailored Solutions: We customize our services to fit the unique needs and challenges of your organisation.
• Proven track record – we have a long history of successful implementations from simple business continuity plans for SMEs up to full ISO 22301 certification for global clients.
Don’t leave your business vulnerable to disruptions. Contact us today to strengthen your continuity strategy and help safeguard your future
renewable energy instalments. Globally the business supports emerging customers through their micro insurance products, giving protection to 62.2 million customers in 2021, in the poorest 60% of developing countries in Asia, Africa, and Latin America.
It is Graham’s belief that by supporting employees, they become resilient both at work and in their personal lives. He wants their employees to be able to come back from life’s setbacks stronger than ever and to have the courage to move forward. This makes the business stronger, and employees who are proud to work for a company are always going to be better brand ambassadors when serving customers.
As part of the above, Allianz Insurers believe that the difference in their people makes the difference to their business and they embrace the uniqueness of their employees because they understand the strength of their business lies in the diverse contributions everybody can make.
“We’re inspired to create a workforce which reflects our community and customers,” says Graham, “We champion environments where we celebrate diversity Glen Abbot Ltd
David.hutcheson@glenabbot.co.uk 01738 580580 www.glenabbot.net
We want to build relationships with our customers that are based on trust, so that they recommend us to others
and people are encouraged to share their thoughts and ideas with confidence to help us arrive at excellent solutions for our customers.”
This includes equality of opportunity where they are committed to creating a fair environment where people can succeed regardless of race, gender, age, disability, religion, sexual orientation, or ethnic background.
Providing personal development and career fulfilment for all employees is a top priority for the company management. Allianz invested 106.3m euros in training of their employees across the globe in 2022 making sure they are equipped with the skills and knowledge to carry out their role and to take on new responsibilities in the future.
Developing their inhouse talent is a very important success factor for their business, both locally and globally. Their internal talent programmes help to move people up through the business using performance management, succession planning and leadership development while their external recruitment activities help them find the best people for critical roles through search agencies and market mapping.
In 2022 across the Allianz world, they invested €719 per employee in development and training, each employee averaged 45.2 hours of training and the company had 83,529 learning users who logged into their AllianzU platform.
Insurance consultancy Gracechurch has awarded Allianz Commercial its Service Quality Marque (SQM) for the eighth year in a row and is the only insurer to receive this accolade.
Insurance consultancy Gracechurch has awarded Allianz Commercial its Service
I’m thrilled to secure this award for the eighth year in a row, which is a significant achievement and I’m proud of the team.
Quality Marque (SQM) for the eighth year in a row and is the only insurer to receive this accolade.
Run annually, the independent research found Allianz to be particularly strong for its personalised service, with the commercial insurer striking the right balance between expert assistance and online capability through its Claims Hub and Live Chat functionality.
The net promoter score (NPS) for Allianz is at its highest since 2018, with a marketleading position maintained throughout 2023 retaining its number one spot throughout the year according to the Gracechurch survey.
“I’m thrilled to secure this award for the eighth year in a row, which is a significant achievement and I’m proud of the team. Our aim is to constantly improve the service we provide, and our strong customer-first focus in claims management has strengthened our relationships with broker partners,” says Graham, “With a strong team of claims experts and a mixture of digital services, our people and service make a difference and winning this highlights that. However, this doesn’t mean we won’t rest on our laurels, as we constantly strive to maintain and improve how we support our broker partners in the best way.”
Byrne-Mech
Cassidy Banks
With a diverse customer portfolio spanning various industrial sectors, Byrne-Mech, a wholly Irish family owned business that was founded in 1977, is a trusted leader in their industry. Specialising in the design, prototyping, manufacturing, and validation of sheet metal components and assemblies they are the first port of call for many industry-leading companies not only in Ireland and the UK but also across Europe and further afield.
A Kaizen Approach In Ireland
At the core of Byrne-Mech is an unwavering commitment to quality which acts as the driving force for everything they do. This dedication has earned them certification to ISO 9001:2015 and recognition as a “Gold Standard Supplier” for their high-quality, precision components, assemblies, and fabrications that they have delivered to leading manufacturers over the years.
Embracing a culture of continuous improvement, the company supports its staff by providing them with the best tools for their trade. Consistent investment in the latest technology allows them to maintain a competitive edge and enables swift adaptation to change in product specifications and customer demands. Consequently, they offer short lead times
which gives their customers the agility needed to thrive in today’s dynamic markets.
Consistently Exceeding.
Businesses need direction and according to Byrne-Mech’s website, their mission is to be a total solution provider in the design and manufacture of sheet metal products for their varied and discerning customers. While aiming to maintain a reliable level of consistency, they strive to exceed the expectations in terms of quality and service, empowering their clients to maximize their own market share. This is achieved through delivering exceptional products at competitive prices.
The family line runs deep within the business, with multiple generations working through its ranks and today with over 100 staff members, the company has grown into something of a local icon. Known for their advanced expertise and capabilities as well as their custom-centric approach, they have established the kind of long term partnerships with clients that would be expected in a country known for its strong family ties and bonds of friendship.
With many engineering services able to bridge gaps between industries, Byrne-Tech’s portfolio nevertheless includes quite a range.
Their catalogue of successful in-industry partnerships includes aerospace, automotive/ transport refrigeration, custom engineering solutions, and even construction and mining. It isn’t easy to be sustainably good at a range of different industries, many businesses have tried and failed, but Byrne-Mech stands out as an oddity. The one problem that other companies face which they do not, is the understanding that each sector has unique, nuanced needs and so require their own comprehensive solutions to meet their specific requirements. Byrne-Mech’s approach, and it would appear, the key to their success is the level of research put into each industry. They do not overstep until they have fully researched and experimented and, combined with a proactive approach for exploring new parts of the sector, they’ve been able to provide solutions to both complex engineering projects and simple component manufacturing to meet the distinct demand of these industries. Another element, as mentioned earlier, is their keen interest in new technologies. Leveraging state-of-theart equipment and advanced technology allows them to cover the main criteria of any engineering project: precision.
A Gold-Star supplier to the aerospace
It isn’t easy to be sustainably good at a range of different industries, many businesses have tried and failed, but Byrne-Mech stands out as an oddity
industry. A leading engineering provider to the automotive and transport refrigeration industries. A metal fabrication solutions provider to the construction and mining industries with further endeavours in the quarrying and recycling industries, ByrneMech’s overall services are recognised by the following.
Accountability, traceability and flexibility, crucial abilities to stay ahead of competitors. Prioritizing cost-effectiveness and transparency and making use of inhouse research and development to fill in any gaps in their supply chain such as their in-house market leading powder coating capabilities for the automotive industry and their design services, PPAP (Production Part Approval), VAVE Service (Value Analysis/Value Engineering), prototyping, and high-volume production.
Their one stop shop and bespoke design and manufacturing is a universally valued service, where the creation of the precision engineered components is supported by a team of skilled designers and experienced engineers. This includes on-demand scheduling and taking client ideas from concept to delivery.
When customers are making decisions, price comes into it, but quality speaks for itself. A ‘Lean Business Principle’ upholds ByrneMech’s steadfast commitment to excellence and kaizen (continuous improvement) and their in-business culture always seeks innovative ways to enhance efficiencies, reduce waste, shorten lead times, and
elevate their quality standards.
Having engineered a fine reputation for so many decades, the company seems to have found a key to customer success. A challenged and empowered workforce. The approach is simple, by looking after their staff, their staff look after the customers. Afterall, maintaining the highest quality standards is easy when your team are motivated and on the same page.
Their team consists of highly skilled and experienced professionals who are dedicated to delivering top-notch engineering solutions. Their expertise ensures that every project meets the highest standards of quality. This makes increasing production efficiencies far simpler because no matter how newfangled your technology may be, without the human element you’re going to lose all the creative zest and motivation of a driven staff contingent.
It is unlikely that, being a business that has grown within a family atmosphere, in a country known for its people-centric warmth, ByrneMech could ever lose the human element that so distinguishes them. Not only does the human element provide a warmth to the cold mechanisms of engineering, but it offers the flexibility required to handle the individual client’s needs and requirements. The ability to pivot and act creatively to come up with unorthodox solutions that not only provide solutions but also opportunities. Human ingenuity is beyond the current capabilities of machines and if that ever changes, it will be because the machine would have become more human and not the other way around.
Some say that engineering will take the production of greatness away from human hands, but we say that Byrne-Mech is proof that this is not the case.
Canfornav
Cassidy Banks
The Canadian Forest Navigation Co Ltd (often abbreviated as CanforNav) is a Canadian company that specializes in forest management, timber harvesting, and related activities. CanforNav primarily operates in British Columbia, which is known for its vast forests and timber resources. The company participates in logging, processing timber, and manufacturing wood products. President and CEO Knud Jensen takes us through the story.
CanforNav plays a significant role in Canadian forestry, contributing to both the economy and the sustainable management of forest resources. As with many forestry companies, CanforNav likely faces challenges related to balancing economic interests with environmental conservation and community needs, which they have instituted many systems to counteract.
Established in Montreal in 1976 as a ship operator, initially serving the Canadian forest industry with their exports of lumber and paper products from Eastern Canada and the St. Lawrence to destinations in Europe and the Mediterranean. In the nineteen nineties came a change of strategy and a diversification plan to rebrand their shipping activities and operations under the name of Canfornav, with a view to change any perception that the company was involved only in carrying forest products.
In the following years, Canfornav expanded by chartering in larger ships, thereby giving the group access to a larger Great Lakes market with imports of steel and raw materials, as well as to the export of grain and grain products. Today, Canfornav carries approximately eight million tonnes of cargo (grain, agricultural products, fertilizers, steel, concentrates and more) and performs around 350 voyages annually, providing an integral service to its customers and to the global trade.
According to Jensen, Canfornav is expanding its fleet with a series of Japanese bulk carriers on long term charters. M/V Woody, the first vessel, was delivered to Canfornav at the end of 2019, a further three vessels were delivered within 2021 with further deliveries in 2022, 2023 and 2024.
“Canfornav provides a world class service to our customers,” Jensen says, “And by developing and maintaining long lasting relationships we’ve earned their trust and our investments into additional vessels demonstrates the longevity of our intention.”
Currently, their focus is the Atlantic handysize market linking the Great Lakes and St. Lawrence to ports around the world. The company is focused on innovation, and providing a dependable, reliable and sustainable service to their customers.
“We are actively engaged and involved in environmental initiatives to foster a greener maritime community,” he adds.
Speaking of longevity, the company is almost fifty. From a simple start up in 1976, the company has managed to keep pace with an expanding market. What began as a ship operator, today, CanforNav controls 35 handysize bulkcarriers,
own 29 of these vessels with the remaining six being on long-term Japanese charter. An additional six more vessels on long-term charters will enter the fleet over 2024 and 2025.
“The market is not slowing down,” says Jensen, “But with our strong foundation we are optimistic for the next couple of years.”
Persistence and old fashioned grit have played a powerful role in the company’s success over the years. Recently, during the pandemic years, CanforNav continued sailing and progressing in their sustainability upgrade programme. Jensen explains that while the approaches may have changed the plan remained the same, as did their deadlines.
“We moved forward,” he says, “To meet the challenges of IMO decarbonisation strategy.”
This came into effect at the start of 2023, with the Energy Efficiency Existing Index (EEXI) and Carbon Intensity Indicator (CII) that was applied to all vessels. This impacted operational measures as well as reducing emissions and required the upgrading of vessels with electronic flowmeters to reflect more accurate consumption figures for their fleet.
Currently, CanforNav is conducting a pilot project named Storm Geo 6, involving six vessels under trial. They assert that digital technology holds significant potential in addressing this challenge. The CanforNav fleet benefits from various energy-saving devices, including the latest duct and propeller bossfin, designed to enhance performance. Furthermore, the company is engaged in a computational fluid study. This study aims to facilitate the acquisition of classification approval, potentially enabling CanforNav to integrate the findings into forthcoming ExICI calculations. Regarding ballast water testing, CanforNav is pleased to resume collaboration with research scientists from Fisheries and Oceans, a branch of the Government of Canada, following a hiatus of over two years due to COVID-19. This year, CanforNav conducted a BW test energy using one vessel in a Great Lakes port.
Test results indicate that the sampled ballast met the D2 IMO standard. All vessels operated by Canadian Forest Navigation Co Ltd (CanforNav) trading in the Great Lakes are equipped with Alpha Laval PureBallast systems. This UV system is effective even in cold and turbid waters typical of the Great Lakes.
We are actively engaged and involved in environmental initiatives to foster a greener maritime community,
Navigating troubled waters during the COVID-19 pandemic, CanforNav had to primarily rely on platforms like Skype and Zoom for communication Now, transitioning to a hybrid work model has been beneficial for everyone’s mental health and well-being explains Jensen. “Company staff spend three days per week in the office and two days working remotely,” he explains, “This setup has proven successful, and CanforNav has enjoyed a profitable period, particularly in the lucrative handysized market over the past 18 months.
In conclusion, Canadian Forest Navigation Co Ltd (CanforNav) has demonstrated resilience and adaptability in its nearly fifty-year history, evolving from a ship operator to a significant player in forest management, timber harvesting, and maritime transportation. Through strategic diversification and expansion, CanforNav has positioned itself as a key contributor to the Canadian forestry industry and global trade, operating a fleet of handysize bulk carriers and implementing innovative solutions for sustainability and efficiency.
The company’s recent initiatives, including the expansion of its fleet with Japanese bulk carriers and participation in environmental initiatives, underscore its commitment to growth and responsible stewardship. Despite challenges posed by the COVID-19 pandemic, CanforNav has continued to navigate troubled waters and embrace digital technologies to enhance its operations and workforce well-being.
Amulti-billion dollar project that is ambitious and historic, the City Rail Link in New Zealand, aims to better connect Auckland’s entire rail network. Not only does this connection promise to improve transportation times but it is also the largest transport infrastructure project New Zealand has ever built.
This project involving the construction of twin tunnels spanning 3.45 kilometres each, reaching depths of up to 42 meters beneath Auckland’s city centre, seeks to establish connectivity between downtown at Waitematā Station (Britomart) and the revitalized Maungawhau on the Western Line. Congruently, the introduction of two new underground stations, Karanga-a-Hape, accessible via entrances at Mercury Lane and Beresford Square, and Te Waihorotiu, situated at Victoria and Wellesley Streets in midtown, is expected to significantly enhance central city accessibility.
Funded jointly by the Crown (NZ Government) and Auckland Council the construction of the stations and supporting rail infrastructure is expected to be completed by their construction partners, the Link Alliance, by November 2025. At that point, following the end of the construction programme, CRL Ltd will hand over the completed infrastructure to KiwiRail and
Auckland Transport, who will then carry out the additional work required to open the CRL to its first passengers.
And it isn’t only about the functionality for the link that is so important. As much as it is an effort to streamline transportation and lessen the woes of inner-city commuters, it is also a representation of the aesthetic of the city. The distinctive designs for the CRL, which have been designed in collaboration with Mana Whenua, for the stations and the outside spaces, reflect the city’s unique cultural history. Additionally, the Mana Whenua Forum have gifted the station names and the New Zealand Geographic Board Ngā Pou Taunaha o Aotearoa has formally adopted the proposed names.
There will be four stations along the line. These include the following:
Maungawhau Station: A redeveloped station at Eden Terrace / Mt Eden where the CRL connects with the North Auckland (Western Line)
Karanga-a-Hape Station: A new station just off Karangahape Road - with entrances at both Mercury Lane and Beresford Square.
Te Waihorotiu Station: A new mid-town station with entrances at Wellesley and Victoria Streets
You may be doing a small residential lighting job. Or working on a major scale data upgrade. Whatever the scale of the job, youll find the products you need, right here.
Waitematā Station (Britomart): The station at the bottom of Queen Street is being transformed into a two-way through station that better connects the city’s rail network.
A Very Busy 2024
Big projects like this always come with their own cache of hurdles and challenges. Many can and are calculated and prepared for but there has never been a construction project in history that has gone exactly according to plan. The City Rail Link has produced its very own series of interesting challenges.
After four years of shovelling dirt, work to remove a large sloping hill in Eden Terrace cleared the way for construction of the southern tunnel portal connecting CRL with the new station and the North Auckland/ Western rail line. The hill has now been restored and most of the heavy construction hidden underground.
“In many ways the hill was CRL’s ‘Everest’ – a mountain of a job completed successfully with larger-than-life high-tech machines and wonderful innovation that demonstrate the huge size of CRL’s work and all the complexities and challenges that come with that,” said City Rail Link’s Chief Executive, Dr Sean Sweeney, adding, “This was building for Auckland’s future on a grand
We maintain high stock levels in all our branches, so you don’t have to wait. It’s a comprehensive range that covers all of your residential, commercial and industrial applications. You’ll find products from leading brands, including Signify Philips, Schneider Electric, Nexans and Prysmian Cables. We carry innovative solutions from the smaller players too, so you can think outside the square for your customers. On the off-chance that an item isn’t in stock, we can source it for you. Or our knowledgeable teamcan suggest an alternative that will do the job just as well. If you can’t make it to your local branch, we’ll get the products to you. Phone us for an order and we can have it to you within four hours if you’re local - or within the day if you’re further afield.
0800 001 244 sales@scottelectrical.co.nz scottelectrical.co.nz
The area has been transformed, reshaped, and filled back in again
scale and all the materials w used can be measured by the tens of thousands.”
The project was by no means a simple one. To begin with, a historic colonial cottage perched above the hill was safely relocated after which the first spades of dirt were removed from the hill at an official sod turning ceremony in February 2020. Spades quickly gave way to heavy machinery and in the months that followed more than 130,000 cubic metres of material was carved away by CRL’s main contractor, Link Alliance.
In the space that the hill originally occupied, a line of 71 concrete piles between 42 metres and 8 metres long were driven deep into the ground to anchor a sweeping curved retaining wall 127 metres long and 25 metres high. Then a buttress of concrete and steel to support CRL’s southern portal and the streets above it was added. One of the most celebrated ‘visitors’ to the portal was Dame Whina Cooper, the project’s tunnel boring machine. From there it launched its two underground drives into the heart of Auckland’s midtown to excavate the rail tunnels.
Cut and cover tunnel construction was completed last October, clearing the way for the next massive programme of work – restoring the hill. For this, on average a convoy of 45 trucks a day transported backfill spoil from quarries in south-east Auckland to the Maungawhau site. Measured monthly, the amount of spoil was the equivalent of 13,000
cars, or 100 blue whales.
Link Alliance Project Director Francois Dudouit says:
“The area has been transformed, reshaped, and filled back in again. Much of this extraordinary achievement is hidden from view as 85,000 tonnes of dirt now cover the complex and significant structures built below. I am proud of the teams involved in achieving this enormous milestone, as the two hundred workers have spent four years in the tunnel preparing it.”
Dudouit adds that each layer of backfill was carefully compacted to ensure the restored hill was safe and secure for future use. Compaction has prepared the restored hill for future use by Eke Panuku, Auckland Council’s urban regeneration organisation. A street above the hill will also be re-aligned back to its original shape.
Dudouit is quick to point out that, that as new construction projects reshape urban landscapes, it is imperative to tread carefully, mindful of the heritage they may disturb. While progress is essential, minimizing damage to historical sites and structures should be a paramount concern.
“By employing meticulous planning, employing advanced technologies, and engaging with local communities and preservation experts, developers can ensure that their endeavours like this leave as little impact as possible on cherished heritage.”
Daemon Sands
Considered as one of the world’s leading innovators in material sciences, Corning Pharmaceutical Glass, have over a century and a half worth of experience in the field which has blessed then with unparalleled expertise. Daemon Sands investigates.
Serving an international clientele, Corning have built a reputation for innovation in glass and ceramic science, optical physics, deep manufacturing and engineering in an effort to develop category-defining products that transform industries and enhance people’s lives.
Their success comes through sustained investment in research and development, a unique combination of material and process innovation, and deep, trust-based relationships with customers who are global leaders in their industries.
Over the 170 years that the company has been active, Corning have maintained a versatility and synergy, allowing them to evolve to meet changing market needs, while also helping their customers capture new opportunities in their dynamic industries. Looking at the industries that the company works in today, Corning’s customers stem from optical communications, mobile
consumer electronics, display, automotive, solar, semiconductors, and life sciences. Glass is the ideal material for pharmaceutical applications and Corning Pharmaceutical Glass is uniquely suited to supply high-quality pharmaceutical glass tubing to meet the rigorous needs of the pharmaceutical packaging industry. Corning Pharmaceutical Glass operations in the United States and Europe manufacture a variety of clear and amber borosilicate glass tubing, which is converted by our global customers into glass vials, cartridges, ampules and syringes for drug storage and delivery.
Advanced Glass, originating as early as 2000 B.C. in ornamental bead form, has historically served as the go-to material for everyday essentials like containers and windows. The predominant glass in global production is of a conventional variety, largely comprising soda-lime compositions geared towards cost-effective mass manufacturing.
In contrast, Advanced Glass embodies a fusion of scientific expertise and glassmaking artisanry. Through extensive research, persistent experimentation, and ongoing innovation, scientists delve into the molecular intricacies of glass, unlocking its potential for addressing
complex industrial challenges.
Illustratively, a decade ago, the electronics sector faced mounting pressure to adopt eco-friendly LCD glass, devoid of heavy metals that could harm the environment upon disposal. This posed a significant hurdle for pioneers in advanced glass production, such as Corning, as it necessitated the removal of antimony, barium, and arsenic—formerly crucial components in LCD substrate fabrication. Leveraging toptier scientific acumen, Corning engineered a novel glass formulation compliant with the new standards, while maintaining exceptional visual clarity. Equally critical was the development of an impeccably precise melting technique. The outcome: EAGLE XG® glass, marking a milestone as the inaugural eco-conscious glass for the LCD domain.
Scientific exploration of glass and the ensuing evolution of advanced glass remain relatively nascent endeavours. Despite glass’ 4,000-year tenure as a material, scientific intervention in glassmaking commenced scarcely 350 years ago, pioneered by 17thcentury alchemists. Substantial intervals separated noteworthy breakthroughs in specialized glass formulations.
The paradigm shifted with corporations like Corning spearheading dedicated
Robert
Gary E. Forosisky, Founder/Executive Advisor 2316 South Main Road, Vineland NJ 08360 Phone: (856) 691-4371 | Fax: (856) 692-2175
Advanced Glass embodies a fusion of scientific expertise and glassmaking artisanry
research and development initiatives. This concerted effort catapulted advanced glass solutions into the forefront of industrial advancement, catalysing transformative impacts across sectors and enhancing livelihoods.
Corning has maintained its status as a reliable supplier to the healthcare and pharmaceutical sectors ever since the introduction of PYREX® glass in 1915. Currently, it stands as a frontrunner in life sciences laboratory equipment and products, cell culture solutions, bioprocess vessels, and specialized surfaces. Additionally, Corning contributes to enhancing access to medication through its groundbreaking glass packaging designed for drug storage and delivery.
In the pursuit of safe and efficacious medicines, individuals seek products that contribute to longer, healthier living. Corning’s Life Sciences assumes a pivotal role in facilitating this endeavour. Across myriad life sciences laboratories globally, scientists depend on Corning’s offerings to propel the advancement of medical breakthroughs. Leveraging its industry acumen, Corning is reshaping the landscape of conventional glass pharmaceutical packaging. The innovative Corning Valor® Glass technology provides enhanced drug protection compared to prevailing industry norms, thereby safeguarding lives.
With a century of experience in Life Sciences, Corning has emerged as a significant ally for researchers. Collaborating closely with scientists, Corning aids in addressing their unique obstacles. Renowned brands like PYREX® glass, Falcon® products, and Axygen® products, trusted for their quality, consistency, and reliability, are utilized in over 100,000 laboratories worldwide. Corning’s technology facilitates scientists in harnessing the potential of cell therapy for disease treatment, and its pioneers’ life sciences tools for 3D cell culture, bioprocessing, and genomics research.
In the realm of pharmaceutical packaging, medications reside within packaging materials crafted decades ago. Traditional pharmaceutical packaging has not progressed alongside advancements in drug formulations and high-speed processing equipment. Valor Glass emerges to fulfil the necessity for modernizing pharmaceutical packaging.
Applying their expertise in optical physics, vapor deposition, precision forming, and extrusion, a team developed a 21st-century glass container tailored to
safeguard modern drugs. This innovation, known as Valor Glass, marks a significant advancement in pharmaceutical glass packaging technology. It improves the storage and distribution of contemporary drug formulations, ensuring more dependable access to vital medications for public health. Valor Glass notably diminishes the risk of contamination from particles, fractures, and fissures, while also boosting efficiency for manufacturers. Collaborations between Corning and leading pharmaceutical firms aim to introduce this innovative life sciences technology to patients.
This is a company that is built to last, a company that continually produces innovations that enhance people’s lives
Their century-long journey in life sciences traces back to the inception of a revolutionary cake dish. In 1913, Bessie Littleton crafted a cake using a piece of heat-resistant glass, gifted by her Corning physicist spouse. This glass formulation evolved into PYREX®, an enduring range of cookware and scientific tools. PYREX labware played a crucial role in the mass production of penicillin during World War II and in the development and manufacturing of the polio vaccine in the 1950s. Corning subsequently introduced advanced technologies to expedite vaccine creation and facilitate cell-culture research. Since then, their cell culture vessels have become the global benchmark for drug discovery and development. Their latest groundbreaking advancement in life sciences, Valor Glass, holds the potential to transform pharmaceutical packaging as we know it
As Wendell P. Weeks, chairperson and chief executive office of Corning says, “This is a company that is built to last, a company that continually produces innovations that enhance people’s lives and can transform industries. But most importantly, one that lives its values and makes a real difference in the world.”
Daemon Sands
CRP Subsea specializes in crafting premium protective equipment, ancillaries, and buoyancy housing for subsea cabling and pipelines, catering to the global offshore oil, gas, and wind energy sectors. With the company’s recent acquisition and increased engagement in the renewables industry, CRP Subsea is primed to advance and capitalize on emerging opportunities, as affirmed by John Drury, CRP Subsea Managing Director.
For over four decades, CRP Subsea has been a cornerstone of the traditional energy industry, leveraging its expertise to capitalize on the vast potential offered by diversification into the renewable sector. According to John, buoyancy, both as a concept and as a trait, epitomizes CRP Subsea’s ethos. This sentiment succinctly encapsulates the comprehensive portfolio of products and the prevailing mindset of the workforce at its Skelmersdale, UK facility.
The company’s stature received a significant boost following its acquisition by Gloucester’s AIS in 2022, uniting two industry stalwarts into a global entity capable of delivering a myriad of subsea solutions to safeguard client assets
This unification offers a new chapter in CRP Subsea’s evolution as a polymer and synthetic foam-based product leader. Innovations such
as buoyancy floats and bend protection from CRP Subsea perfectly complement the subsea cable protection, insulation and buoyancy module products offered by AIS.
As per John’s assessment, AIS and CRP Subsea are cut from the same cloth, embodying forward-thinking and innovative ideals. Their amalgamation substantially enhances their capacity to address the energy industry’s global demands. With significant growth anticipated in the offshore market, the acquisition enables both entities to take advantage of opportunities presented by the current oil and gas cycle, navigate the energy transition leveraging combined resources, and better serve clients with an expanded array of subsea solutions.
Since their inception in 1978, CRP Subsea has specialized in large-scale polymer and composite components and offered products specifically designed for the unique needs of projects. Their first job was supplying polymer lifebuoys for ports and harbours, and this gave them an insight into how the subsea environment entails a challenging combination of conditions. This encouraged them to advance the technology available so they could provide high integrity solutions to project infrastructure including subsea pipelines, umbilicals and cables for the oil and gas industry.
CRP Subsea boasts an unparalleled record
in providing dynamic fatigue protection for safety-critical flexible risers, damping vortexinduced vibration to mitigate riser fatigue, and offering solutions for preventing overbending of cables. The company made history by supplying the inaugural dynamic bend stiffeners in 1996, with over 1500 installations to date, all operating without any in-service failures.
Additionally, in collaboration with Trello Burke Offshore, CRP Subsea pioneered the world’s first rotating buckle mitigation buoyancy innovation and developed buoyancy modules featuring integrated smart sensor technology.
“We are really excited about this new chapter for CRP Subsea as we join the AIS family,” John says, adding, “The move enables us to accelerate our growth ambitions towards the offshore energy sector, and the synergies between CRP Subsea and AIS will allow us to bring even greater value to our customers around the world. “
CRP Subsea boasts extensive expertise in oceanic environments, spanning decades. Originating in the 1970s, the company focused on safeguarding marine structures by pioneering products for secure oil and gas exploration in increasingly deeper waters. Today, their repertoire extends to offering solutions for offshore renewables projects.
We are really excited about this new chapter for CRP Subsea as we join the AIS family,
Specializing in this domain globally, CRP Subsea navigates diverse projects, including offshore renewables, oil and gas drilling, subsea operations, marine hose systems, subsea cables, and marine vessels. Their proficiency encompasses operations from the water’s surface to the seabed, positioning them as leaders in the industry.
Recently, they secured a contract with an energy technology company to supply its distributed buoyancy modules (DBMs) to a deepwater oil field project in the presalt Santos Basin offshore Brazil. In this project, CRP Subsea’s DBMs will be utilized on a flexible production riser transporting oil from the subsea facility to the FPSO vessel above.
Specifically engineered, CRP says the DBMs will establish a dynamic subsea lazy wave configuration to mitigate the top tension on the FPSO. They feature a high-capacity compliant internal clamp, designed to ensure controlled and uniform circumferential clamping pressure around the riser. This is designed to maintain the position of the DBM as well as eliminate the risk of pipeline damage, contributing to the prolonged lifespan of the field.
Manufactured at CRP Subsea’s manufacturing facility in northwest England, project engineering works are set to begin imminently, with delivery scheduled for June this year (2024).
In addition, CRP Subsea was awarded multiple contracts last month by a major oil and gas original equipment manufacturer to supply four of its solutions to a deepwater oil and gas field offshore Angola.
CRP Subsea’s integral buoyancy modules will be attached to two dynamic umbilicals to establish lazy wave configurations. An integral compliant clamping technology will be used to ensure a uniform clamping pressure around the umbilicals, thereby eliminating the risk of damage to them.
Additionally, hold back clamps will be provided to support the main dynamic umbilicals, ensuring that they hold in position. Uraduct also has been chosen for subsea crossing protection during the laying of the umbilicals on the seabed. Uraduct is designed to give the umbilical’s superior abrasion and impact resistance as well as reduces the risk of dropped object damage. Finally, bend stiffeners will be engineered to cater to the requirements of the umbilicals where they connect to the FPSO vessel.
Manufactured at CRP Subsea’s manufacturing facility in England, project engineering works were scheduled to begin soon, and final delivery is expected in the second quarter of this year.
“We are thrilled to be chosen for this important project. Leveraging our group’s wide range of technologies, we were able to offer a comprehensive technical solution. The urgency of the delivery requirements associated with this contract highlights our customer’s confidence in our ability to deliver quality products on time,” says John. Who goes on to add that by being able to fulfil this urgent requirement, they have assisted a key customer and ensured the project’s success and are looking forward to future partnerships and the opportunity to make further project contributions.
Foylan Rhodes
In 2021, the renowned London-based security firm G4S experienced an acquisition by Allied Universal®, a prominent provider of security and facility services celebrated for its proactive security strategies and cuttingedge smart technology. This acquisition has empowered the delivery of customized, comprehensive security solutions. Foylan Rhodes of Business Pursuit and Tim Kendall, Managing Director of G4S Secure Solutions UK, delve deeper into this development.
This acquisition signifies a substantial broadening of Allied Universal’s reach and operational framework, on both a global and local scale. Leveraging its expansive workforce of around 800,000 personnel, Allied Universal stands ready to introduce worldclass standards across diverse communities worldwide. With revenues nearing $20 billion, the company enjoys the advantages of efficient procedures and resilient systems made possible by its considerable size, thereby enabling the realization of its local mission: safeguarding individuals to nurture flourishing communities.
The “what” of G4S UK, is a multi-layered question. As Tim describes, they provide integrated security services and products for a wide range of organisations and events
across the UK. He adds, “And as a worldleading security system supplier, G4S combine innovation and quality guarding to provide a full end to end solution combining cutting edge technology with high-class manpower services.”
This involves cash solutions/safety and management, care and rehabilitation services, facility management, health services and employment services. But at their core and certainly what makes them the unique and valuable organisation they are is not the “what” but rather the “who.”
G4S Secure Solutions (UK) has been certified as a 2024 Top Employer by the Top Employers Institute, who are the global authority on recognising excellence in people practices. This certification showcases an organisation’s dedication to a better world of work through the demonstration of excellent HR policies and people practices.
If one were to close their eyes and envision a security officer, would the image likely be that of a man? With only approximately 11% of frontline security officers in the UK being women, it’s probable that this mental image would indeed lean towards a male
figure. However, G4S foresees a shift in this perception in the coming years. The company is actively promoting initiatives to foster diversity and inclusivity within the security industry. Their aim is to create a workforce that better mirrors the communities it serves, thereby enhancing the profession’s ability to safeguard all individuals effectively.
According to G4S, over the next few years, the security industry will be one that places great value on communication, interpersonal skills, diversity and uses innovative technology. The security officer of the future will be more emotionally intelligent and will rely on people skills rather than physical attributes of strength. Even the ability to speak additional languages will become more important in our multicultural society.
According to the first ever World Security Report, 67% of Chief Security Officers (CSOs) in the UK say emotional intelligence will be extremely important for frontline officers. In fact, the research found that, for nine out of ten respondents, people skills in frontline security professionals are more important than physical attributes of strength.
Fiona Walters, CEO of G4S UK, and Ireland explains that in their role, they perform a key part in society, safeguarding their communities. With this in mind it is important to have the right people for the job and for
We are committed to putting practical actions in place to drive positive change
security to reflect the demographics of the societies that they work in. She reveals they have an ongoing drive to improve and increase the percentage of women who not only are joining the industry but who are also getting promoted and pursuing careers.
“The fact is that women can have a fulfilling career in security that allows them to leverage their skills,” she adds, “We need to break down the stereotypes. As our recent World Security Report showed, the softer skills are often actually more effective, and, in many markets, increasing numbers of corporate security leaders are women.”
In the UK & Ireland, G4S sets its recruitment targets to increase the number of women hired, compared to previous years.
Perception is key, and unfortunately, many people still perceive security to be a poorly paid, dangerous career that provides limited career development. G4S believes that this is not the case, and the industry needs to address the perception issue. It’s also worth considering that for some women, traditional shift patterns and long hours can be a barrier to working in the sector, as they are more likely to also be juggling caring responsibilities outside of work.
G4S is working with clients, such as Yusen Logistics UK, who are committed to providing equal opportunities, achieving full inclusivity, and eliminating all forms of discrimination. Yusen Logistics believes that providing improved development opportunities for women will help to redress the gender imbalance across the logistics industry. The company runs internal campaigns raising awareness of genderrelated topics and challenges faced by female colleagues and has recently improved its
maternity and paternity pay policy. Along with hybrid working options for many roles, Yusen Logistics’ Flexible Workforce programme offers a solution for both men and women who need work flexibility, and women now also account for 58% of the company’s apprenticeship programme.
While there are some instances where flexibility is difficult, there are already many roles that offer office hours, split shifts, or other shifts that may suit candidates. Security in certain sectors, such as retail, can offer flexible options. G4S is working closely with customers to understand and provide that flexibility to help attract a more diverse workforce.
Naturally, recruitment is a focus. Head of Resourcing, Fran Watts explains to us that recruitment of women is a priority for G4S, and that they are looking at how they can target women more effectively and communicate that security can offer them a positive and rewarding career. To support this, they ensure that their recruitment advertising does not include words or imagery that makes it appear biased towards one gender and they have created videos and campaigns that make it clear that security represents a viable career choice for women.
“We recognise that the recruitment process can take longer than many other sectors, so G4S also runs women-only video calls where potential new recruits have the opportunity to talk to women already working at G4S, to find out about their experience and ask questions.”
Tim Kendall, leans in, “We are committed to putting practical actions in place to drive positive change. We have a key strategic objective to improve DE&I across our business and we are supporting industry change by collaborating with the DE&I Forum endorsed by the SIA and Forum members for the Private Security Industry.”
Foylan Rhodes
With an important location that provides crucial shipping route for cargo and workforce from a remote jurisdiction, Kapuskasing Airport is the gateway to Canada’s north. Not the biggest airport in the world by any means, it is nevertheless one of the most useful for those living and working in the region.
The area was named Kapuskasing (bend in the river) by the Cree people who were the original settlers. It has changed face multiple times since then. In the 1900s the Bureau of Colonization of the Ontario Department of Agriculture sent parties to survey the region north of the Canadian Pacific Railway between the Quebec border and Lake Nipigon. This became a lumber town, officially founded in 1911 after the National Transcontinental Railway, the forerunner of the Canadian National Railway, was built in the area.
A beautiful but rugged landscape, Kapuskasing lies in the heart of an area of Northern Canada called the Great Clay Belt and is characterised by its flatness, which has created numerous small lakes and muskeg bogs, and Boreal Forest. All the rivers here drain North to James Bay instead of East to the Atlantic or West to the Pacific. Thickly forested by stands of black spruce that have had a
historic value as commercial pulpwood.
A vibrant community of 8000 people, Kapuskasing boasts all the amenities associated with an urban centre but is still a lumber town that continues to grow in all segments of its commercial, industrial, and tourism sectors. Providing important opportunity for this growth is the Kapuskasing Airport which is used as a hub to ship much-needed supplies and goods to remote communities while also serving as an economic driver for the city and the surrounding area.
As Rock Robitaille, airport manager at Kapuskasing Airport explains, this is the closest airport to the North Coast and serves the people on the James Bay coast by hauling freight out of Kapuskasing to three communities up the coast, Attawapiskat, Fort Albany, and Kashechewan.
“We also host evacuees in the springtime due to flooding in these communities,” he adds, “We have hosted five to six hundred evacuees here each spring for the last 13 years. We had commercial air traffic through Bearskin Airlines, but the demand dropped below what is sustainable for them, and now we are mainly a cargo airport.”
With a is 5506 by 100 feet asphalt runway, an administration building, as well as a cargo
terminal, Kapuskasing Airport was run by Transport Canada until 1997, when the airport was decommissioned, and ownership was transferred to the city.
By this stage in the story, Robitaille had climbed the ranks from ground crew to administration to the director. In the Canadian system, only a commissioned, passenger airport qualifies for government funding and so the last few years have seen a focus on what is needed for cargo and continued economic growth.
“We have to keep an eye out for business opportunities,” says Robitaille, “We’re in a good location and are accommodate almost any request. We are self-sufficient with our own hangars, private outfitters, mechanics and even a crematorium out here at the airport,” he adds, although he does not elaborate on what this would be useful for.
Located on the field is a General Motors Cold Weather Development Centre. Since opening in 1973 GM has used this facility to assess over three hundred vehicles a year to determine how they function in the extreme cold. The facility sits on 272 acres and includes 30 Cold Cells that can recreate -45-degree Celsius weather.
Facilities And Business Growth
With roots in the bush plane business of hauling
hunters in and out of the woods, North Star Air grew from a couple of de Havilland Beavers to a fleet that now includes DC-3 Cargo planes. Headquartered in Thunder Bay, The Kapuskasing Facility has its logistics, pilots, and maintenance employees. North Star now serves the cargo needs of 54 remote Northern communities with its fleet of 18 aircraft and 280+ dedicated employees.
“Covid grew our business,” explains Robitaille. “As the communities became more dependent on cargo being shipped in there was an increase of approximately 30 percent. This meant we were seeing a lot more flights in and out which means when it comes to maintenance and upkeep, we are probably going to have to do an upgrade of our runway within the next five years.”
Kapuskasing does not have any government funding for what ends up being millions of dollars in restoration and maintenance fees, so the airport relies on the partnership with North Star as well as fuel sales to balance their budget. North Star, roughly speaking, flies three cargo loads a day for six days a week.
And the airport is busy for one of its sizes: seeing over 2,000 cargo movements each year. This puts fuel sales around 1,000,000 litres (792,516 gallons) per year and Robitaille points out that there are often
As the communities became more dependent on cargo being shipped in there was an increase of approximately 30 percent.
other companies doing business who use the airport as well. Such as a hydroelectric project that is using the airport for staging right now who are flying in and out a few times a week.
“Some of the other initiatives we are looking at for the new year are based around the idea of improving the quality of the airport. An example of this would be doing a complete mill and overlay of the apron, which for the last few years has been repaired as needed, leaving a combination of old and new pavement. That project is slowly in the works,” says Robitaille.
“When you are depending on only one source of funding you must prioritize, and sometimes it is hard to convince a city that they should spend a million dollars on an apron or five million on a runway. We must justify expense over benefit,” Robitaille notes.
Looking ahead to the future of the airport and to the job that Robitaille has prospered in for decades, he points out what he believes are the essentials needed for success.
“You have to love what you do,” he says, “I’m lucky that I do. I enjoy coming to work every day and I love how there is always something new to deal with. No two days are alike, and it makes things interesting, which is the key to making your days fulfilled.”
Kent Shaffer Homes
Cassidy Banks
Building a home is more than just constructing walls and roofs; it’s about crafting a sanctuary where dreams are nurtured, memories are made, and legacies are forged. For homeowners, the significance of building a home transcends mere ownership; it encapsulates the essence of stability, security, and belonging.
For nearly 30 years, Kent Shaffer has set the gold standard for custom home construction in Central Indiana. A secondgeneration builder, Kent began his career over three decades ago as a certified electrician and has since built over 250 premier homes in sought-after neighbourhoods. Using topquality materials, experienced craftsmen, and meticulous attention to detail, Kent Shaffer continues to attract new clients while also building new homes for previous satisfied customers. Kent Shaffer Builders is a member of the Builders Association of Greater Indianapolis and the National Association of Home Builders and holds an A rating with the BBB.
Carrying on the Shaffer Family legacy of crafting exceptional homes, Kent now partners with his daughter Kristen in the business. As the third generation of builders in the family, Kristen brings her expertise to the table, having graduated from Purdue University’s esteemed Construction Management
Program. With a background of growing up on job sites and experience gained from Ryland Homes, Kristen upholds the tradition of meticulous attention to detail and exquisite artisanry, infusing a fresh perspective into the design and construction process.
Building a house versus purchasing an existing one in America involves a nuanced decision shaped by financial considerations, personal preferences, and long-term investment goals. While purchasing a prebuilt home offers convenience and immediacy, building a house from the ground up presents unique advantages that extend beyond mere ownership.
As Kent outlines, one of the primary considerations is cost. Various online studies, including research by the National Association of Home Builders (NAHB), suggest that building a new home can be more costeffective eventually compared to purchasing an existing property.
“Despite the upfront expenses associated with construction, such as land acquisition and building materials, new homes tend to be more energy-efficient and require fewer repairs and maintenance, leading to potential savings over time,” he says, “Additionally, homeowners have the flexibility to customize
their home to suit their specific needs and preferences, potentially avoiding the expenses of renovations or modifications down the line.”
He also adds that building a house offers the opportunity to incorporate the latest advancements in construction technology and design, resulting in a home that meets modern standards of comfort, safety, and sustainability. From eco-friendly features like solar panels and energy-efficient appliances to smart home automation systems, new construction allows homeowners to futureproof their investment and reduce long-term operating costs.
“Beyond financial considerations, building a house embodies a sense of ownership and creative expression,” he says, “It’s a deeply personal endeavour that enables individuals to shape their living environment according to their unique vision and lifestyle.”
From selecting architectural styles and floor plans to choosing interior finishes and fixtures, every decision reflects the homeowner’s taste, values, and aspirations. This level of customization fosters a deeper sense of connection and pride in one’s home, enhancing the overall satisfaction with the living space.
Realistically, while purchasing a house in America offers immediate gratification, building a house presents compelling
advantages in terms of cost-effectiveness, customization, and long-term value. Kent Shaffer Homes allows potential clients to leverage online studies and resources, to make informed decisions that align with their individual financial goals and lifestyle preferences.
“The right decisions lead to a more fulfilling and rewarding homeownership experience,” he says.
The Kent Shaffer Process
Kent explains that their process begins when a client selects where they want their dream home to take shape. The company has built extensively in the Villages of West Clay (Carmel), Stonegate (Zionsville), Austin Oaks (Zionsville), and downtown Indianapolis in the Historic Herron Morton Neighbourhood. Kent Shaffer Builders also builds on custom lots that clients have purchased.
And, if a client is looking for an individual lot outside of a neighbourhood Kristen Shaffer, as mentioned above, can help with that, as she is a certified Realtor/Broker with Century 21 and is in the perfect position to consider and help the individual needs of clients.
After the location is selected, clients can either design their custom home from exterior elevation to interior finishers or choose a move-in ready home where available. If they choose to build, Kent and Kristen endeavour to walk them through the entire process and, believing that a personalise approach makes all the difference and should extend into the smaller details as well, clients who call into the
office with questions can expect to speak to Kent or Kristen directly.
After the consultation period, the next step is the creation of the house. A stepby-step process managed by their team of architects, interior designers, and trim carpenters who are the best in the business. Excelling at making the dream home into a reality, the process and quality of their homes thus far speaks for itself. And, when you consider that Kent, on multiple occasions, has built homes for both repeat clients and their children, the message is clear: they put their hearts into their work.
Members of the Building Association of Greater Indianapolis, BBB Accredited Business, Indiana Builders Association and the National Association of Home Builders, Kent Shaffer Homes can be found everywhere. Especially in thriving communities such as Zionsville, Carmel, Westfield, Noblesville, Indianapolis and Brownsburg, but their approachability is not limited to these regions. Areas where location to schools, shopping centres, dining areas and modern conveniences of modern city life are available but without the hectic pace. That’s where you’ll find them.
“We’re flexible in our approach and ready to build dream homes wherever a client needs them,” Kent says, “If their location is not on our site that isn’t a problem, or if a client doesn’t have a specific community in mind that doesn’t matter as we offer several beautiful neighbourhoods for which to choose.”
Foylan Rhodes
Mazda Toyota Manufacturing, U.S.A., Inc., a collaborative automobile factory in Huntsville, Alabama that is jointly owned by Japanese carmakers Mazda and Toyota, recently underwent a change in leadership and reached a new employee-related milestone.
We took a deeper look.
First off, Plant President Masashi Aihara, who took the helm of the new MTM plant in 2018 as part of his 40-year career with Mazda Motor Corp stepped aside in March this year for Mazda veteran Mitsunobu Mukaida who is now the plant president.
Having departed at the end of March 2024, Masashi Aihara said, “It has been a great challenge to start an automotive facility of this size from cotton fields, to where MTM is now. We received much support from the local governments, communities, suppliers, our team members and other stakeholders that has led to our success which included two new lines, two shifts and the production of two vehicle types. My hope is to leave the same kind of positive impact on MTM and Alabama, that they have had on me and on my family over the past five years.”
Mukaida, who has succeeded Aihara, has been with Mazda for thirty five years, most recently as executive officer in charge of global production has also served as
CEO and president of Mazda Powertrain Manufacturing in Thailand.
“My mission at MTM as a joint venture plant is to further realize the synergy between Toyota and Mazda through their respective strengths,” he said, “And to develop it as a ‘best in town’ facility that is loved by our team members and the local community. I will continue to work with determination to settle in Huntsville.”
There is a lot of excitement in the air, and the change of leadership comes a year after the company reached an impressive employee based milestone.
In March last year, Mazda Toyota Manufacturing (MTM) reached its 4,000-employee commitment and todate the company continues to expand its workforce. Last year’s additions which involved a second shift on the Discovery assembly line, which began producing the Mazda CX-50 in January 2022, were the final push that was needed to tip them over the hiring goal. Incidentally, surpassing the goal makes them one of the largest employers in the area.
“We were thrilled to start our second shift on the Discovery line,” says Jessica Luther, external affairs specialist for MTM,
adding that the ramp up to full production also included introducing a second shift on the Apollo assembly line less than a year after the Toyota Corolla Cross started production in the fall of 2021.
MTM is the sole manufacturer in North America of both the Mazda CX-50 and Toyota Corolla Cross. The parallel production lines, Apollo and Discovery, honour Huntsville’s contribution to the U.S. space program. And, as of March 2023, Mazda and Toyota have invested $2.3 billion in their jointly owned and operated Huntsville plant. The 3.7 million-square-foot facility can assemble up to 300,000 vehicles annually, split evenly between the two manufacturers. Last year, MTM earned Gold Certified status from the Wildlife Habitat Council for its conservation and stewardship efforts.
MTM began production in 2021 with the Corolla Cross, Toyota’s inaugural crossover vehicle. This compact SUV comes in three grades and offers both front-wheel and allwheel drive options. The model is available to dealerships across the continental United States and four U.S. territories and is also exported to Canada and Mexico.
In January 2022, the first-ever Mazda CX-50 rolled off the Discovery Line, marking the debut of Mazda production at the Huntsville plant. This mid-size crossover
SUV comes in eight packages with two engine options, featuring all-wheel drive and various drive modes for different conditions. It is available to dealerships across the continental United States and is exported to Canada, Mexico, and Colombia.
In addition to achieving production and employment milestones, MTM marked its five-year groundbreaking anniversary in November 2023. Coinciding with this and the Community Foundation of Greater Huntsville’s (CFGH) Giving Tuesday event, the MTM Grant Fund donated $110,000 to 20 local nonprofits: Arts Huntsville, Athens-Limestone County Public Library Foundation, Big Brothers Big Sisters of the Tennessee Valley, Calhoun College Foundation, Enable Madison County, Christmas Charities Year Round, Crisis Services of North Alabama, the Food Bank of North Alabama, Huntsville Community Drumline, Limestone County Career Technical Centre, Madison City Schools, New Futures Inc., Still Serving Veterans, Thrive Alabama, United Cerebral Palsy of Huntsville & Tennessee Valley, the United Way of Madison County, the United Way of Morgan County, Village of Promise, Wellstone, and Women’s Foundation of Alabama. Ten organizations received $1,000 each, and ten received $10,000 each.
That round of funding came on the heels of MTM awarding $150,000 to 12 local nonprofits in June 2023. Grant recipients included Huntsville Hospital Foundation, Family Services Centre, NCAC, Heals Inc., KTECH/Kids to Love, ELM Foundation, Girls Inc., Kid ONE Transport, The Care Centre, Huntsville Botanical Gardens, Still Serving Veterans and Cap & Gown Project.
The MTM Grant Fund, which is hosted on the CFGH platform, has awarded $340,000 in funding since 2022. The company has also developed three internal workforce training and development programs: the LEAD
We have learned so much from our parent companies at Mazda and Toyota
Academy, the NAVIGATE Academy and the Production-to-Maintenance Program.
Navigate Academy
“We have learned so much from our parent companies at Mazda and Toyota,” says General Manager of Administration Jason Pickering, “But we recognized that it was time for MTM to develop our own training and development programs that fit the needs of our company and of our team members. It is important to our team that we develop pathways for growth and invest in our team.”
MTM’s LEAD Academy provides a fourweek leadership development program for team leaders and a six-week program for group leaders. The classes emphasize training and leadership skills, including understanding the plant from other leaders’ perspectives, sharing challenges and strengths, raising mental health awareness, and learning about the legal aspects of leadership.
The NAVIGATE Academy is a selfpaced leadership fundamentals training program targeted to assistant managers. The Production-to-Maintenance Program is a collaboration with the Alabama FAME (Federation for Advanced Manufacturing Education) Advanced Manufacturing Technician Program at Calhoun Community College. MTM opened applications to production team members who would like to transition into a skilled labour role, and from those who applied, MTM chose 12 to complete the program this year.
MTM will continue to provide full wages and benefits to these team members as they split their time between working part-time at MTM and attending the FAME Program part-time each week for two years. Upon completing the FAME Program, they will graduate and transition into new roles within MTM’s maintenance or tool-and-die departments, with eligible earnings ranging from $28 to $40 per hour.
Founded in 1982, with the acquisition of Totem Ocean Trailer Express, the Saltchuk Marine family of companies has continued to grow and today includes Foss Maritime, Young Brothers, Cook Inlet Tug & Barge, AmNav and Starlight. Together they continue to lead the industry in harbour services and marine transportation solutions, proudly servicing Alaska, Hawaii, US West coast, and the burgeoning offshore wind industry on the eastern seaboard. Business Pursuit explores.
Through a series of intelligent acquisitions since that first purchase, the company has since acquired more than 30 companies organized in six operating groups: Air Cargo, Marine Services, Energy Distribution, Domestic Shipping, International Shipping and Logistics. Their policy on use of technology is to keep themselves as UpToDate and familiar as possible with proactive research and development and with a family-owned company with a long term outlook, their most important asset is their team of seven thousand extraordinary people that work across the family of companies.
“Saltchuk is poised to contribute to our industries and communities for generations to come, so for us there is no choice than to invest in our operations and let our values drive our acquisition strategy,” says CEO Jason Childs, “Which includes a number of key points.”
According to Jason, it is their shared culture of safety, integrity, and ethics that is the ultimate key to their success. They’ve set the goal to achieve a zero-injury workplace and require all their companies to maintain the same level of safety and environmental standards that they would deem acceptable for their own children.
“We have found that our most successful acquisitions have been companies that share our values,” he says, “Therefore culture is a key element of our investment strategy. It is also only with a single culture that a company can be expected to stick together during hard times and good.”
He goes on to explain that that, like farmers tilling the soil to ensure good crops, Saltchuk offers their companies the capital and resources to support reinvestment and growth.
“Our marine, truck and air fleets are among the newest in the industry,” he says, “And we continually reinvest in our equipment and have a strong track record of reaching beyond environmental requirements to set new standards for our industries.”
With industry knowledge and closely held ownership that allows them to facilitate faster
and offer a less intrusive due diligence process, Saltchuk’s experienced professionals can make decisions quickly. Most of their acquisitions have been family-owned companies, and Jason understands the importance of the transition process.
They work with the sellers to jointly develop a post-acquisition plan for the company, its employees, and its partners. By agreeing to a plan, they have found that they are able to create a smoother transition process for all the parties involved and are better able to achieve the objectives that led both the buyer and seller into the transaction.
“Acquiring businesses and welcoming in fully formed teams of expertise, experience and perspectives has become a part of big business,” Jason says, “It enables businesses to grow stronger together.”
In 2019, Lisa Sundborg of Alaska Petroleum Distributing and her siblings were looking for a way to keep growing the family business when they decided to join NorthStar Energy and the Saltchuk family of companies. She reveals that the process of acquisition was less about relinquishing control and more about being supported. For anyone who has a family business, keeping it as a family business is often a priority. Family businesses are built
At CSO Marine Group, we support the full marine and offshore renewables project lifecycle.
From ship brokerage and vessel support services to turnkey project engineering and offshore recourcing, our specialist teams can support you with a solution to overcome your challenges.
Data-driven ship brokerage
Offshore Resourcing
Turnkey Project Engineering
Vessel Support Services (modification, mobilisation, management)
csobrokers.com
cso.group
differently and have a soul, which is a tragedy to lose into the maul of big corporates. But as Lisa testifies this was not the case.
“At the start, they really made us feel that we were going to stay a family-run business,” she explains, “And years later it is still the same. We are a small family business with an HR department, a legal team, an environmental team, and a safety team all standing by to help us. When you get as big as we were independently, we had to do all that on our own. We still have a desire to be successful but we don’t have the constant stress that we used to.”
I admire and appreciate the work ethic, commitment to customers, and culture of the Carlile team
Lisa Sundorg and her sibling’s story segways neatly into how the Saltchuk approach to business was forged and how they’ve managed to retain their own soul. In 1982, eight investors came together to form a new partnership for the purpose of acquiring Totem Ocean Trailer Express, a domestic ocean-liner service to Alaska.
In their first decade, they grew by adding two other marine transportation companies, including a ship management firm based in Philadelphia and Foss Maritime, an iconic Pacific Northwest tug and barge operation.
In the 90s, as they entered their second decade, they established themselves as a strong Pacific Northwest-based maritime business and continued evolving by establishing an investment holding company office and acquiring additional companies that grew their maritime operations geographically and allowed them to diversify and expand into real estate.
By their third decade, in the 00s, they were clearly defined as a transportation company to watch, and they welcomed air cargo and energy distribution companies and divesting assets unrelated to their core transportation and distribution business to partner.
The 2010s saw the business further diversify by adding international shipping operations throughout the Caribbean and creating a stand-alone business unit for logistics operations. And finally, in this decade they’ve enjoyed continued growth in all areas of the business, including expansion of their energy distribution in the Western U.S. and support of U.S. offshore wind development on the East Coast.
Maintaining that family spirit that has so
benefitted companies like Alaska Petroleum Distributing, is that of the six original investors, four of their families remain partners today. These families share a core set of values, a multi-generational investment time horizon, and deep trust with one another. Over the company’s history, together, they have repeatedly put the needs and interests of Saltchuk ahead of their own.
Promotion and internal development are also key components to holding a business together. One of the many examples is of Krista Williams becoming the new CEO of Carlile, Alaska’s leading trucking and logistics company, in 2023. Founded in 1980, in recent years, Williams led Carlile’s continuous improvement and strategic growth initiatives as the Chief Operating Officer for Saltchuk Logistics –Carlile’s parent company. Now, Williams reveals that she plans to further position Carlile to meet expected surges in demand for transportation and logistics support in Alaska and beyond. Having worked alongside Carlile’s executive team during the last two years to prepare the company for future developments, she says that there are tremendous growth opportunities in natural resource development, retail, government, and other sectors of Alaska’s economy.
“I admire and appreciate the work ethic, commitment to customers, and culture of the Carlile team,” she says, “I look forward to building on the company’s success in future years. This is an exciting and promising time for transportation companies in Alaska.”
While Carlile gears up for growth in the marketplace, Williams explains that the company will continue its legacy of delivering safe, innovative supply chain solutions and service excellence to our customers.
Williams joined Saltchuk in 2018 after working in continuous improvement and developing strategic programs at Toyota, Kaiser Permanente, and Whirlpool. Williams earned a Mechanical Engineering degree from RoseHulman Institute of Technology and a master’s degree from Seattle University.
Williams joins Terry Howard, who has served as Carlile’s president since 2015 and will remain with the company through 2023.
“Terry Howard’s steadfast leadership has helped guide the company through many challenges in recent years. His commitment to our employees and to the safety and success of our operations leaves a legacy of respect, teamwork, and commitment to the Carlile brand,” says Williams.
Carlile was established in 1980 and operates terminals in AK, WA, TX, and Canada. With more than 390 employees, Carlile specializes in trucking and logistics solutions connecting the world to Alaska.
As a demonstrative example of how businesses can grow and expand off the drive and effort of a unified workforce who are emboldened and driven to succeed, Saltchuk Marine will no doubt continue to grow into the future. And remain a family through it all.
Shannon Valley
Daemon Sands
Established in 1991 as a plant hire company, Shannon Valley Group is a family-owned business that has quickly expanded and diversified. Today, it stands as one of Ireland’s largest and most progressive civil engineering and plant hire companies, handling construction and civil engineering projects both domestically and internationally.
Michael English founded the company over thirty years ago and it is currently controlled by his three sons who are equal partners: Mick, David, and Dermot. With up to forty projects in operation around Dublin and further afield, Mick and Dermot take responsibility for the sites while David looks after the maintenance of the construction machinery.
The company’s base of operations is the Shannon Valley Centre in Donabate, Dublin; a building they were responsible for constructing in 2005 as part of a mixed retail, office, and industrial site with eleven units and an area of over 20,000m2. Dermot English explains, “Shannon Valley constructed the buildings from ground to roof level and the office contains a four storey block giving us the capability to house all necessary functions of running the business.”
As such, the buildings include car parks, a plant maintenance yard and a sizeable truck parking area, administration, meeting rooms, a state of the art engineering and surveying section, health and safety, commercial and a department for transport and parts. Quality assurance and quality control, human resources and legal, and of course IT and cyber security.
Ranging from projects costing millions of euros to small and medium sized projects, the scope of work undertaken by the civil engineering and plant hire company Shannon Valley varies in type and size across all industry sectors. Projects include the construction of motorways, regional and local roads, tunnel works (such as the Dublin Port Tunnel), coastal defence works, tidal works, hospitals, and water attenuation systems. Additionally, various types of groundworks are undertaken, including deep large diameter drainage, utility installations, site clearance, commercial, industrial, and residential development works, landfill facilities, major earthworks, rock breaking, and processing materials for reuse.
On the other side of the coin, Shannon Valley is also involved in bringing stuff down. This includes quarry works, demolition and plant hire as well as recycling works. The company owns a comprehensive and modern fleet of civil
engineering machinery, equipment, and lorries.
Covering the full spectrum of civil engineering needs, their fleet provides the essential flexibility needed to meet the daily demands of projects nationwide. But the real essence of the company is in the people, as Dermot explains.
“Beyond hardware, we employ high-calibre individuals from a broad skills base,” he says, “Selecting and assigning individuals with the precise mix of skills and experience required by each project. This approach of combining the best people with the best equipment has helped us carve out a reputation for professional excellence, delivering projects on or ahead of schedule without compromising quality or safety.”
Conscientious And Punctual.
Dermot goes on to explain that with their dedication to quality, efficiency, and client satisfaction, Shannon Valley consistently completes projects to the highest standards, on time and within budget. According to him, innovative solutions, adherence to the highest safety and quality standards, and professional construction management are the hallmarks of Shannon Valley.
Services
As one of the largest civil engineering contractors in Ireland, Shannon Valley’s services have a wide range of applications. Whether as an
onsite sub-contractor or principal contractor, the company brings unrivalled expertise to all facets of the modern construction environment, delivering tailor-made and application-specific solutions to each individual project they undertake. Their civil engineering division projects include site development, top-down construction excavations, bulk basement and underground car park excavations, coastal and flood defence works, motorways, regional and local roads, and infrastructure work with watermains and attenuation tanks as well as storm and foul water projects.
“We provide a quality, innovative and professional service to all our clients in a timely and safe manner,” says Dermot, adding, “Our portfolio’s scope of successful projects demonstrates to current and new customers the untapped potential of the company while also giving them a glimpse of how our company has grown.”
The evolution of Shannon Valley is mapped as a clear chain of decisions. Each one representing a moment when the company explored a different opportunity to make use of their skillset and experience and discovered peripheral areas of research and development. Over time these areas of development became areas of expertise and in turn became services to offer. This is how businesses with their ear to the ground evolve and grow.
Shannon Valley has the unique position to have been granted permission from the Irish Aviation Authority to use drones within Irish Airspace and are able to conduct site surveys and inspections and aerial photography and cinematography. Not only does this give them the chance to offer an insightful perspective to the planning stages of their projects it also puts them in a comprehensive class. There are a number of important benefits to drone usage.
Dermot explains that with the use of the drones,
They can generate highly detailed 3D models that can be perceived from every angle instead of the traditional ground control points
they can generate highly detailed 3D models that can be perceived from every angle instead of the traditional ground control points. This technology has proved ideal for tracking digging progress, large no-vegetation OGLs (original ground levels) and stockpiles. Additionally, they can create 2D geolocated orthophoto maps (orthostatic) that can be attached to the software as background references. These are perfect for as-builts, such as areas of tarmac, locations of inspection cover, water meters, sluice valves, and for recovering trench locations or allowing visibility of ducts in open trenches.
The use of drones also cuts down surveying time and enables the team to cover large areas in relatively short time while keeping earthwork-grade tolerances, from the aerial perspective things can be taken from a birds-eye-view enabling a more thorough and accurate inspection, quicker.
Thanks to the forward thinking of the three brothers and the use of new technologies like this, Shannon Valley continues to offer their clients something beyond what they get from competitors. Their approach has delivered a level of safety, transparency and traceability to civil engineering that has raised the standards of the whole industry. Their father would be proud.
Stolle Machinery Company
Donnie Rust
Stolle is the foremost provider of machinery for manufacturing two-piece cans and can ends in the canmaking sector globally. Renowned for their highspeed capabilities, Stolle’s machines serve as the cornerstone of canmaking operations worldwide, renowned for their demonstrated productivity and unwavering reliability.
Offering comprehensive solutions at every scale, whether individual machines, line modules, or swift service with OEM parts, to the conception, construction, and initiation of entire facilities, Stolle’s technical expertise ensures clients consistently receive equipment featuring cutting-edge engineering advancements and enhancements. Canmakers globally rely on Stolle to bolster their productivity and profitability with many acknowledging the company’s unwavering support.
Legacy Of Innovation, Vision,
Value Stolle Machinery takes its name from Ralph J. Stolle, the founder of the predecessor company, The Stolle Corporation, established in Sidney, Ohio, in 1961. Mr. Stolle notably refined the high-speed production method for easy-open (pop-top) beverage ends, alongside other significant technical accomplishments. He also established a business philosophy that has steered the company through
more than six decades. This philosophy is straightforward: to develop and deliver the most dependable solutions and cutting-edge technologies to enhance the functionality and aesthetics of metal, particularly aluminium, packaging for their customers.
The utilization of aluminium in can manufacturing was a paramount development for several reasons. Firstly, aluminium is exceptionally lightweight, contributing to reduced transportation costs and energy consumption. Secondly, its corrosionresistant properties ensure prolonged shelf life and product integrity. Thirdly, aluminium’s recyclability makes it an environmentally sustainable choice, with recycled aluminium requiring significantly less energy for production compared to virgin aluminium. Additionally, aluminium’s malleability allows for intricate designs and easy shaping, enhancing branding opportunities. Lastly, aluminium cans are impermeable to light and oxygen, safeguarding the contents from deterioration, thereby preserving flavour and freshness.
Powered by innovation and guided by experience, Stolle has maintained it’s leading position in technology by delivering high-speed, precise, and safe packaging solutions. Such solutions that promote the brand experience through sustainability,
colour, shape, texture, and ease of use and by “Serving the world” by being seen as a local provider in each market.
“Along with the principles of good business and service, the values of the group are simple but applicable and festooned within the company’s core,” says Michael Larson, Chief Operations Officer for Stolle, “Safety, quality, sustainability, technology and customer happiness.”
Leadership
Over the last six decades it has been seen repeatedly that good leadership makes all the difference and often what makes or breaks a brand is who is out front. At the centre of their roadmap for the next century is how to find the right people for the job and provide them the right tools.
Now, at the heart of the company is the Stolle management team who offer a collective experience reaching across both industry and globe. From previous experience in managing global relationships, technology, and finance, they are well positioned to help continue the leadership of Stolle internally as well as internationally. With a focus on technology and a dedication to continuing Stolle’s globalization, each team member brings an invaluable perspective to the company. These experiences blend seamlessly into a vision for
the future that include the highest levels of customer satisfaction and the development of revolutionary new technologies that will advance the industry.
As their yellow “wave of innovation” has indicated for years, Stolle is committed to advancing metal packaging through a constant flow of sustainable innovations and technology that will benefit customers. From some of the strongest and most metal-efficient tab designs available, to brilliant new equipment upgrades, to revolutionary new equipment poised to impact the next generation of can making, Stolle continues to make significant investments of personnel and funding to R&D in every area of can making. Stolle’s global technical centres are dedicated facilities that develop the advanced software and hardware that future industry leaders can come to rely on while producing the sustainable machinery features that today’s customers expect.
As if to prove this point, Stolle has been designated a Platinum OEM Partner by Rockwell Automation. Companies at this level have met the product design, marketing, and business relationship criteria of Rockwell Automation technology across their entire company. Having occurred in 2022, Rockwell’s strategic partnership will further help Stolle to develop innovations in advanced software and hardware across their product line. Rockwell Automation evolved its OEM Partner Program globally, establishing levels of participation based on need and output. As a Platinum OEM Partner, Stolle Machinery takes advantage of a true partnership approach with Rockwell Automation with executive-level engagements and alignment with strategic growth opportunities along with various services for digital transformation.
“Rockwell Automation is pleased to welcome Stolle Machinery as a Platinum OEM Partner to our growing OEM Partner Program,” said Johannes zu Eltz, Vice President of Global Market Access, “Not only does this Platinum designation help Rockwell Automation partner with Stolle on initiatives, but it also adds diversity to our stable of partners, delivering unrivalled co-marketing opportunities, coordinated market planning with our sales force, and improved customer engagement with co-managed objectives.”
With its expanded range, which facilitates greater market access, streamlines processes, and standardizes product integration for manufacturers, the enhanced offering empowers stakeholders to maximize the benefits of Rockwell
The partnership excites us particularly because of Rockwell’s deep knowledge in the food and beverage industry
Automation technology. Anticipating an influx of platinum level partners, alongside numerous gold, silver, and bronze members, the company foresees the program becoming a premier opportunity for original equipment manufacturers on a global scale.
“The partnership excites us particularly because of Rockwell’s deep knowledge in the food and beverage industry,” said Michael Larson, Chief Operations Officer for Stolle. “With a long history of innovation, we’ll partner with Rockwell Automation to develop new machinery and technology to make production faster and more efficient for our customers.”
Stolle is committed to advancing their customer needs through ongoing innovation and technological advancement, backed by substantial investments in resources and personnel. Expert engineering teams collaborate with seasoned technicians at the company’s R&D Technical Centres to explore new ideas and concepts, integrating cutting-edge technology and materials as they become available in the market. Often, teams initiate projects from scratch, devising equipment that addresses industry demands for functionality, speed, and efficiency, even if it requires pioneering solutions. The Stolle R&D Technical Centres afford the company the flexibility to experiment and validate new concepts during their developmental stages. Strategically located within several assembly facilities worldwide, these centres facilitate seamless collaboration. Additionally, Stolle collaborates with various independent engineering firms to access specialized expertise when necessary.
As Veolia continues its meaningful expansion across North America, they are making a name for themselves through decisive partnerships that are affecting real change to the waste management landscape. Global Business Pursuit’s Cassidy Blanks investigates a pair of projects that they’ve wasted no time in pursuing.
New Orleans. Wastewater Treatment. First up, is a collaboration with the Sewerage and Water Board of New Orleans (SWBNO). The pair are spearheading a transformative initiative in wastewater treatment in the historic American city. The partnership is poised to redefine the paradigm of wastewater management, aiming not only to elevate the efficiency of treatment processes but also to convert wastewater byproducts into valuable environmental assets. At the heart of this endeavour lies a shared commitment to enhancing New Orleans’ environmental quality and, by extension, its residents’ quality of life.
It has also been projected to yield substantial economic benefits for the city, with an estimated annual saving nearing $2 million. However, the significance of this partnership transcends financial gains, encompassing substantial environmental
dividends as well. Among the key strategies deployed to achieve these benefits is the implementation of an advanced, on-site oxygen system, poised to curtail chemical expenses and energy consumption by a minimum of 10%, while concurrently slashing greenhouse gas emissions by approximately 12 metric tons monthly.
Karine Rougé, CEO of Veolia North America’s Municipal Water division, expresses profound pride in Veolia’s involvement in supporting the endeavours of this highly respected city to modernize its wastewater treatment infrastructure over the last three decades.
“Veolia is proud to support New Orleans’ dedicated efforts to modernize its wastewater treatment infrastructure since 1992,” she says, “And our partnership is now focused on implementing a new generation of physical and process improvements that reimagine this vital city service. We are glad to partner with SWBNO to envision a forward-thinking plan that is a major step toward delivering newer infrastructure and better public service.”
Against the backdrop of recurrent flooding challenges that have long plagued New Orleans, the importance of effective wastewater treatment assumes heightened
significance. As a city prone to inundation, New Orleans relies heavily on robust water management systems to mitigate flood risks and safeguard public health. For residents, access to clean water is not merely a convenience but the cornerstone of a healthy lifestyle, underlining the critical role that wastewater treatment plays in sustaining community well-being.
Ghassan Korban, Executive Director of the Sewerage and Water Board of New Orleans, emphasized the transformative potential of this partnership in bolstering the efficiency and efficacy of the city’s wastewater treatment plants.
“As part of our utility’s commitment to infrastructure reliability and resiliency, as well as technology modernization, this investment will make our East Bank and West Bank wastewater treatment plants far more efficient and effective,” he says.
Additionally, Veolia’s collaboration with SWBNO will introduce state-of-theart digital monitoring and analysis tools, aimed at optimizing the performance of New Orleans’ wastewater system. These digital upgrades will enable real-time monitoring of wastewater treatment processes, facilitating agile responses to evolving conditions and enhancing operational efficiency across treatment facilities. This digital transformation
Environmental Products • Solid & Liquid Waste Transportation • Roll-off Box Rentals
Remediation • Disposal & Recycling Options
Heavy Equipment Operations
Hine Environmental Services (HES) is a full service environmental company striving to satisfy industries’ needs.
HES can assist your company whether it’s supplying products such as absorbent pads & boom, containment boom, various sized drums, spill kits, profiling your waste for disposal, transportation of your solid/liquid hazardous or non-hazardous waste, finding the best disposal/recycling options for your waste, or renting various sized roll-off boxes.
The HES family will work diligently to assure the best interest of your company is met. Let Hine Environmental Services be your Total Solutions Provider (TSP).
Veolia is proud to support New Orleans’ dedicated efforts to modernize its wastewater treatment infrastructure since 1992
aligns seamlessly with Mayor LaToya Cantrell’s vision of leveraging infrastructure as a catalyst for sustainable growth and renewal in the city.
Beyond its core mission of environmental stewardship, Veolia is deeply committed to supporting community, educational, and environmental initiatives across New Orleans. Over the past two years, the company has contributed $35,000 to various community groups, supporting initiatives such as the New Orleans East Festival and the establishment of the Sankofa Wetland Park and Nature Trail in the Lower Ninth Ward. Veolia’s employees actively volunteer with community organizations like Sankofa, epitomizing the company’s ethos of corporate citizenship and community engagement.
Furthermore, Veolia has forged strategic partnerships with educational institutions such as Delgado Community College and the Southern University System, fostering innovation and talent development in the region. These partnerships provide invaluable opportunities for students to gain practical experience in environmental science and engineering, nurturing a pipeline of skilled professionals poised to contribute to the region’s sustainable development. Moreover, Veolia’s internship and apprenticeship programs offer students a pathway to join the company’s workforce, further bolstering New Orleans’ local economy.
In the windy city and the city with all those 90’s law shows, Tradebe Environmental Services and Veolia North America have announced a strategic commercial agreement ensuring guaranteed access for the former to Veolia’s state-of-the-art facility. Opening next year in Gum Springs, Arkansas, this decision addresses the pressing demand for additional capacity for hazardous waste treatment in the affected areas.
Veolia’s facility at Gum Springs is expected to set a new industry standard for the safe, efficient, and reliable treatment of waste materials, and the agreement with Tradebe – which comes a year before the facility opens – will go far to help both companies stay ahead of the curve in meeting the needs of the market.
This pioneering move in the sector illustrates the aligned strategy of Tradebe and Veolia to provide cutting edge solutions to support sustainable growth for industrial players in the U.S. hazardous waste market. Already a leading company in the hazardous waste treatment sector in the U.S., Veolia has an ambition to continue to expand its footprint to address growing demand.
“Veolia North America is pleased to enter this partnership with Tradebe, which is an example of how business can work collaboratively to address environmental waste challenges. With thermal treatment demand growing across the country, a forward-looking vision is necessary to meet the needs of the future, and that’s what this partnership provides,” said Veolia North America President and CEO Fred Van Heems.
In parallel sentiments, Oriol Mateu, CEO of Tradebe Environmental Services U.S., echoed this sentiment, stating, “This partnership marks a significant milestone in our commitment to innovation and customer satisfaction. By leveraging each other’s expertise, technology, and resources, we will provide customers with seamless end-to-end services, resolving existing inefficiencies and gaps in the market. This collaboration promises customers enhanced accessibility, reliability, and innovation. Together with Veolia, we are poised to achieve remarkable results and lead the way in shaping the future of recycling.”
Aligned with both companies’ shared commitment to sustainability, Veolia’s new facility will employ environmentally friendly technology for self-powering operations. The high-temperature thermal treatment will use energy generated from a solar farm, presenting a more sustainable option for the market and the environment. The agreement begins in 2024 to provide a seamless transition in 2025.
Looking ahead, Veolia remains steadfast in its commitment to leveraging its global expertise to support sustainable growth initiatives in the United States. The partnership with SWBNO and Tradebe Environmental Services stands as a testament to Veolia’s dedication to environmental stewardship and community empowerment, exemplifying the company’s capacity to drive transformative change in wastewater management for the betterment of Americans as they continue to expand its footprint in the United States. Delivering innovative solutions that address the evolving challenges of environmental sustainability and resilience.
Donnie Rust
Despite the dynamic evolution that Portsmouth Aviation has undergone over the 95 years since their founding, the values of this family-owned engineering powerhouse are forged in steel. Cost effective engineering and manufacturing solutions, a deep sense of community and belonging and a focus on employee development and growth, these values have shaped this business for almost a century.
Beginning as an air ferry innovator in 1929, Portsmouth Aviation’s present status as a leading engineering service manufacturer is a direct result of their unwavering commitment to delivering top-notch engineering solutions. Diligently standing by their clients, as they monitor every detail throughout every stage, from design conceptualization to seamless production, ensures a collaborative and supportive partnership.
What makes a business work well, especially to last for almost a hundred years, has less to do with the product than the team behind it. Having cultivated an environment that encourages continuous learning, growth and progress, the company’s workforce is creative and innovative. And there is no surer way to
decide how a company looks after their clients by how they look after their staff.
“Our dedicated team of skilled professionals are not only enthusiastic about their work but also driven to achieve excellence,” they said.
Commercial pressures.
In recognizing the commercial pressures faced by businesses today, Portsmouth Aviation has positioned itself carefully as a dependable business partner. Their focus on immediate customer needs has solidified their reputation for prompt deliveries, product improvement and comprehensive, cost-effective solutions to manufacturing challenges and new product introductions.
This commitment to efficiency is reflected in their in-house approach where they manage the entire manufacturing process, from innovative CAD design to purpose-built test facilities. This integrated approach not only ensures a comprehensive solution for their clients but also minimizes project timelines, reduces costs, and eliminates the inaccuracies and errors that can sometimes happen when production is spread across multiple businesses. Also, importantly, this in-house approach means that if something does go
awry, the problems can be corrected at once.
Their Story
“We take great pride in our ability to provide the high level of quality products produced and using the state-of-the-art inspection and test equipment, ensure the customer’s needs are always met or exceeded,” says Pete Vaughan, Quality Manager Portsmouth Aviation.
To be state-of-the-art one must be continually pushing against the boundaries of the tried and tested and the company is constantly evolving and modernizing, using their experience and knowledge of the industry to inform how they continue to develop as a company.
Technical Services: At Portsmouth Aviation, Technical Services are an integral part of their business model. Their bespoke approach can be a game changer for a client’s project, but innovation does not mean disregarding traditional manufacturing capabilities, but by using their wide range of core technical service competencies, they are able to ensure that their position at the forefront of precision engineering industries is secure.
CNC Machining: one of the main in-house
We take great pride in our ability to provide the high level of quality products
capabilities. Their ultramodern equipment and wide-ranging ability set them apart in the industry. This has included ensuring their CNC machining equipment is of outstanding quality, keeping their ability to provide efficacy and quality to their valued customers. The experienced team comes with a comprehensive knowledge of CNC machinery, ensuring that customers receive the best possible final product at the best time.
Metal Fabrication: fabrication and manipulation is an area of expertise that is essential to many of the projects undertaken by the company. Their specialist engineers have a multitude of experience in metal fabrication and their ability in welding is clear in the quality of their work.
Metal Finishing: Portsmouth Aviation has the power to enhance the performance, durability, and protection of the components they produce, enabling their process technicians to create reliable and longlasting protective coatings that can withstand challenging environments and operational demands.
Paint & Finishing: these services at Portsmouth Aviation play a crucial role in ensuring the quality and durability of their engineering products. With meticulous attention to detail and the use of advanced coating technologies, these services ensure the longevity and best performance of critical components, reinforcing the company’s commitment to delivering high - quality and reliable solutions to its customers.
Qualification, inspection and Testing: Qualification, inspection, and testing are critical processes aimed at ensuring the reliability, performance, and compliance of engineering products or systems. These processes involve assessing and confirming the design, manufacturing, and functionality of various components, materials, or entire systems. These processes help find potential
issues, weaknesses, or deficiencies early in the development or manufacturing stages, allowing for necessary improvements, adjustments, or corrective actions. Ultimately, qualification and testing contribute to delivering safe, reliable, and high - quality engineering solutions that meet industry standards and customer needs.
“Our state-of-the-art facilities and comprehensive expertise are channeled to our customers via our people and teams; working in close collaboration with our customers, we listen, challenge, and innovate, adding value and reducing risk throughout the project.”
Simon Escott, Managing Director.
Recently, Portsmouth Aviation was named NHS medical equipment manufacturer of choice, after they designed and manufactured a number of Bedside Chart Trolleys for the NHS. They were approached by the University Hospital Southampton during the first wave of the Covid-19 pandemic to create the Bedside Chart Trolley’s to support patient care in hospitals.
Thanks to their work, the NHS staff on hospital wards that are experiencing dramatic surges in admission and treatment, have been able to provide critical care efficiently and effectively to those in need. Hospital equipment is relied upon so heavily every day and has an immense impact on how medical care is provided.
“During this most challenging period, you very quickly learnt which companies stepped forward and those who did not. Whilst nurses, doctors and support staff worked around the clock providing care for the most vulnerable, it was heartening to know that there were people out there like Portsmouth Aviation, working just as hard to support us,” says Asa Thorpe – Senior NHS Manager in Charge of Critical Care, Theatres and Anesthetics
Our fully compliant, temperature-controlled vehicles provide secure and reliable distribution of medical and pharmaceutical deliveries, including time-sensitive cold chain parcels. With over 40 hubs across South Africa, our state-of-the-art and fully integrated technology and logistics infrastructure solutions makes us the perfect partner for the medical and pharmaceutical industry. Paperless, secure and timeous, our online track and trace system also makes it easy to follow your vital parcel journey from start to finish.