
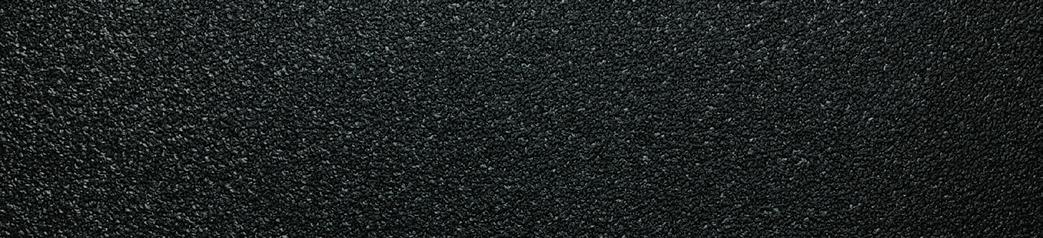
With the world watching, All States Materials Group, a CalAPA member, helps deliver a winning performance in Las Vegas
By Brian Hoover / Photos by BuildWitt and CMSAs any race car driver will tell you, it’s the little things that can add up to a winning formula. And having a solid team backing you up helps as well. The same is true of asphalt pavements.
All States Materials Group (ASMG), a CalAPA member, represents Zydex Industries, the manufacturer of a family of bitumen additives including ZycoTherm, NanoTac, DuraTac, TerraSil, and ZycoBond. All States Materials Group has over 65 years in the asphalt paving and construction industry with capabilities including the materials supply of liquid asphalt, asphalt emulsions, asphalt binder additives and specialty products, construction aggregates, hot mix asphalt, and ready-mix concrete, as well as a complete
range of pavement maintenance and construction services.
ASMG represents ZycoTherm, a product chosen to be included in the asphalt mix design for the Formula 1 Las Vegas Grand Prix racetrack. Formula 1 championship racing officially began in 1950, but its Grand Prix roots extend much further to the European Grand Prix championships of the 1920s and 1930s, when legends like Tazio Nuvolari raced alongside some of the world’s most prestigious motor racing drivers. The Fédération Internationale de l’Automobile (FIA) is the governing body for Formula 1 motorsport, which is currently owned by the US firm, Liberty Media. Formula 1 features 10 teams, with seven based in the UK, one in Switzerland, and two in Italy.
Each team must run two drivers who race at a top speed of 215 mph with an acceleration of 0 to 60 mph in 2.4 seconds. Currently, 23 events run from March to November in locations all around the world.
Some of the Formula 1 tracks utilize public roads, such as the street courses in Monaco or Singapore, and now the newest location in Las Vegas. The 2023 Formula 1 Heineken Silver Las Vegas Grand Prix (Las Vegas Grand Prix) was held on Nov. 18 on a temporary street circuit course that included several iconic sections of the Las Vegas Strip. The 2023 Las Vegas Grand Prix is a part of the 2023 Formula 1 World Championship, and practice runs began on Nov. 16 with qualifying
and the race commencing on Nov. 18, 2023.
Construction of the 3.8-mile racetrack began more than a year ago when the contractor, Las Vegas Paving, started removing select median sections, modifying intersections, and milling 6 to 10 inches of existing roadway to make room for a denser, stronger 7.5-inch base layer. Most of the paving was done at night, and after the base layer was complete, crews began laying a final high-performance lift designed for durability and longevity, with a specific design for Formula 1 race cars. The finished race route in Las Vegas is expected to last longer than an average asphalt surface, with a top asphalt lift layer that is specifically designed for safety, speed, and performance.
Rory Klinger is the VP of asphalt supply and specialty products for ASMG, and recently recounted the use of Zycotherm for the Las Vegas Grand Prix racetrack. “The performance of Zycotherm in both laboratory studies and field applications has been excellent and we are excited about the potential opportunities it can provide for contractors, agencies and road managers on future projects,” says Klinger.
Antistrip/WMA additive used in Las Vegas Grand Prix asphalt paving mix
Anti-strip and compaction aid additives play a crucial role in
enhancing the durability and performance of hot mix asphalt (HMA), making them an indispensable component in asphalt pavement technology. These additives work to mitigate the detrimental effects of moisture on the bond between asphalt binder and aggregate, a phenomenon commonly known as stripping. Moisture-induced stripping can compromise the integrity of the asphalt mix, leading to premature pavement distress, reduced durability, and increased maintenance costs. By incorporating anti-strip/compaction aid additives into the asphalt mix, engineers and pavement professionals can significantly improve the resistance of the asphalt binder to moisture, ensuring a robust and long-lasting bond with the aggregates. This ultimately enhances the overall resilience of the HMA, providing a reliable and durable surface that can withstand the challenges of diverse weather conditions and heavy traffic loads.
The Las Vegas Grand Prix course was paved in two lifts with a special mix design containing an anti-stripping/warm mix asphalt additive manufactured by Zydex Group (Zydex) and distributed by CalAPA member, All States Materials Group (ASMG). This asphalt additive was selected for use as an anti-strip/compaction aid additive in the paving mix for the street circuit racecourse. Additives
provide multiple benefits during the process of manufacturing, transferring, placement and compaction of HMA. According to ASMG, their additives can offer what is referred to as, “3C benefits,” (Chemical Bonding, Complete Coating, Consistent Compaction), when applied at low mixing and compaction temperatures, per Section 1.1 of Zydex Field Protocol.
Dr. Ajay Ranka, Founder & CEO –Zydex Group
Established in 1997, Zydex is a specialty chemicals company created for the purpose of maintaining a sustainable world through the conservation of resources. The company offers a diverse set of chemical technologies for the textile, painting, waterproofing, agriculture, pavement, and construction industries. Zydex is recognized as a world leader in the development of non-polluting and ecologically conscious technologies and chemical innovations that foster a safer, greener, and more resourceefficient future.
Dr. Ajay Ranka is the founder, CEO, and managing director of Zydex Group. “We pursue the sustainability goal because if we do not reduce our footprint on the planet, we are all in trouble. From maintaining bio levels to environmental protection, to limiting the resources which we
are consuming, the kind of footprint we are leaving behind is of great concern. Our company was founded on the principle that we innovate for sustainability,” says Dr. Ranka. “Our technology is chemically bonded, and it becomes part of the aggregate. That is why pavements that use these technologies tend to last longer and perform better. An added benefit includes reduced bitumen temperature for both mixing and paving. Maintaining a lower temperature and attaining higher or more consistent density is where our technology really shines.”
Brian Atkins – Business Development Manager, Zydex IndustriesBrian Atkins serves as the business development manager for Zydex here in the United States. “Formula 1 has its own specifications and special production methods for what they want in asphalt binders. A durable surface is of utmost importance for any roadway but imagine what would happen if a racetrack pavement failed during a race. This would be an absolute disaster during any race, let alone one as highly visible as the Las Vegas Grand Prix,” says Atkins. “A lot of time, money, and research have gone into the design of this
pavement for the Formula 1 Las Vegas Grand Prix to ensure the track is safe for the drivers and holds up to the rigors of moving at speeds in excess of 200 mph.”
Atkins goes on to point out that many pavements are going to have to use some sort of polymer to achieve exceptional durability and smoothness. “In the case of a Formula 1 track, particularly high levels of polymer are necessary. If you go from using unmodified asphalt to something using 3% to 4% polymer, that will result in a stickier mix design, which is ultimately and typically harder to work with out in the field,” says Atkins. “Formula 1 racetracks would be using a modified polymer at a rate of around 7% to 8%, which is more difficult to produce at asphalt plants and harder to get necessary and appropriate compaction. Therefore, from a Formula 1 perspective, having an additive that can address those concerns is of utmost importance.”
According to Atkins, Formula 1 has its own mix design, and they gave the parameters to the mix design company – PRI Asphalt Technologies, Inc. (PRI), a global leader in materials testing. “PRI helped tailor the pavement recipe for success and performed testing with our product, along with other additives. PRI has worked with our
materials in the past, and from their perspective, they felt that our product offered appropriate assistance to the contractor when placing the mix. Although we are less expensive than some other antistrip products, I don’t think that factored into the decision. It all came down to performance, and our product checked all the boxes,” continues Atkins. “After the decision to go with our product for the antistrip additive, the next step was to determine the dose, which was 0.1% by the weight of asphalt. We are proud that our product was chosen, and I think it speaks volumes about just how well this additive works.”
Another important feature of ZycoTherm is that it is typically added to the asphalt binder at a rate of around 0.05% by the weight of bitumen. “To put this into perspective, imagine a 6,000-gallon tanker load of bitumen at a plant being typically loaded with 25 to 30 gallons of traditional liquid antistrip additives. One of the benefits is that our dosage rates are substantially lower,” says Atkins. “We are typically on the high end going to be dosing at 0.1% by the weight of asphalt and in some cases as low as 0.05%. In reference to the 6,000-gallon tanker example, we
Above: Material transfer vehicle feeding hopper for paving machine on Las Vegas Strip.[ Continued from page 10 ]
would be adding anywhere from 3 to 6 gallons of our product.”
Additives are being used every day all over the world. “ZycoTherm went through more than 10 years of performance testing and qualified with Caltrans and other state transportation departments across the United States as well as other countries. Additionally, the cost is minimal at 1% to 2% of the cost of the overall mix for an additive that will help to add a 50% to 100% increase in pavement life,” says Atkins. “I think what Formula 1 is looking for is really no different than what a DOT or other agency wants. I think they want a smooth, durable surface that will hold up under the stress of heavy traffic flow. Whether that be for tractor trailers carrying 80,000 pounds of weight, or Formula 1 racing cars going 215 mph.”
Number: CP2C-2017-102
The California Pavement Preservation (CP2) Center Lab at the California State University, Chico is a California Department of Transportation (Caltrans) certified laboratory. CP2 conducted select tests on asphalt mixes using the ZychoTherm-SP product supplied by Zydex, Industries, Inc. The objective of these and other tests were meant to evaluate the
effectiveness of the product for use in prevalent Caltrans type mixes to aid in preventing moisture sensitivity issues in mixes. DingXin Cheng, Ph.D., P.E. is a professor in the Department of Civil Engineering at California State University, Chico. Additionally, Cheng serves as Director for the California Pavement Preservation Center and Director of the Tire Engineering Research Center. “Based on the laboratory performance testing including Modified Lottman Test, Hamburg Wheel Tracking Test, and Boiling Water Test, with the right dosage of the ZycoThem-SP, the additive significantly improved the performance of control hot mix asphalt, says Cheng. “For detailed information, please see our testing report on our website at https://www.csuchico.edu/cp2c/.”
Another CalAPA member, Knife River, a construction materials and contracting company, donated the aggregates and RAP from its Stony Creek plant in Orland for use in the testing. “Knife River Construction has a very good working relationship with the California Pavement Preservation Center Lab,” says Tim Denlay, QC manager, Knife River. “We are always happy to help them any way we can. The work the CP2 Center does to improve pavement preservation practices is very important to our Industry.”
Knife River also donated the binder for testing. The asphalt
binder performance grade tested was PG64-16. Control samples, along with samples with recommended dosage, were considered in the study per Section 4.1 of Zydex Laboratory Protocol. The binder was heated to the mixing temperature for the grade of AC being used (325ºF) before adding the additive. The ZycoTherm-SP was added with measured drop by drop by a lab technician while another technician continued stirring the mixture for two minutes to complete the mixing process. The dosage used was the percent by weight of binder, according to the recommendations.
The asphalt mix conformed to a prevalent mix design supplied by Knife River based in Chico.
Because Reclaimed Asphalt Pavement (RAP) was used in the mix and per Section 3.2 of Zydex Field Protocol, the base doses of ZycoTherm-SP were increased by 0.025% of the total binder weight, giving dose percentage of 0.075%. The aggregate and binder used in the mix design was the standard for the Caltrans District 3 involved, and the aggregates and binder were supplied by Knife River. Several tests were performed by the California Pavement Preservation Center - Califorina State University, Chico. Testing included gyratory compaction, tensile strength ratio, Hamburg wheel track and extended boiling
Right: Numerous vibratory compaction rollers compacting final F1 track surface lift.testing. Specifically, the following tests were performed on the dosed mix design and control: AASHTO T283: Resistance of Compacted Hot Mix Asphalt to MoistureInduced Damage, AASHTO T324: Hamburg Wheel-Track Testing of Compacted Hot Mix Asphalt and ASTM D3625: Effect of Water on Bituminous-Coated Aggregate Using Boiling Water.
Concerning the gyratory compaction testing by the CP2 Center Lab, when 0.075% ZycoTherm-SP (the additive) was added, the samples were easier to compact, easier to clean up the testing equipment and required a lower number of gyrations compared to the control sample. Tensile strength tests for each sample set were conducted by using the Toni Technik machine. The sample with 0.075% of the additive had the higher wet and dry strengths as well as higher tensile strength
100%, dull finish, more fines observed, dry looking
ratio than control sample. The Hamburg wheel track test revealed that the 0.075% type sample sets performed better than the control sample with the maximum passes of 25,000 being completed before reaching 0.5 inches rut depth with no inflection point. Details of the boiling water test concluded that all types of HMA material was observed to be fully coated after being subjected to one hour of boiling water as recommended in the task order. The control material did however appear dry and more crumbly after it dried for 24 hours. The HMA material with 0.075% percentage of the additive appeared shiny, more clusters of aggregates with less fines segregated out. The right amount of additive is important to improve the performance of the hot mix asphalt. For this particular Knife River mix design, 0.075% of the additive is a good dosage. The results of the Moisture Resistance test, Hamburg Wheel Track test,
100% coated: shiny coated aggregates, clusters stuck together, less fines observed
and Boiling Water testing all show benefits with the 0.075% dosage.
Come race day on Nov. 15, the asphalt track performed as expected, presenting a dazzling backdrop to the iconic images of the Las Vegas Strip and roaring race cars watched by a celebritystudded crowd and a worldwide TV audience. Max Verstappen from the Netherlands, with Red Bull Racing, took the checkered flag in the 50-lap race with a winning time of 1:29.08. It was a spectacle befitting the venue, and smoothriding asphalt was at the center of it all.
For more information on ZycoTherm or other Zydex products, please visit All States Materials Group online at www.asmg.com or call Rick Bird, All States technical sales manager at (775) 690-8513. CA
Brian Hoover is co-owner of Construction Marketing Services, LLC, and editor of CalContractor Magazine.