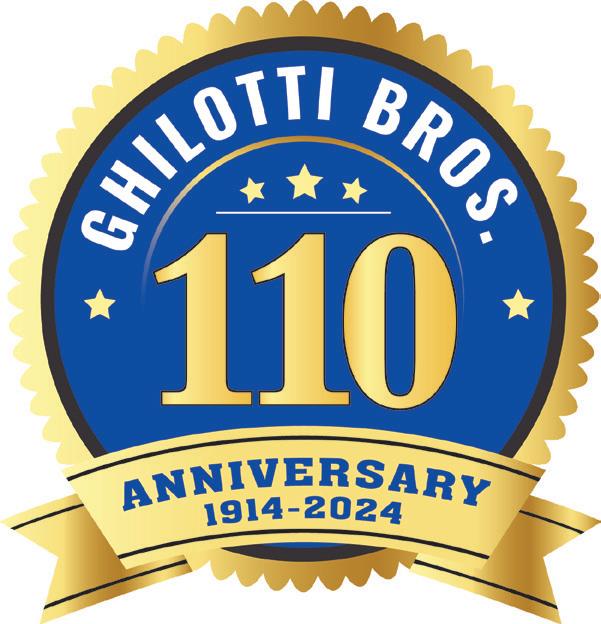
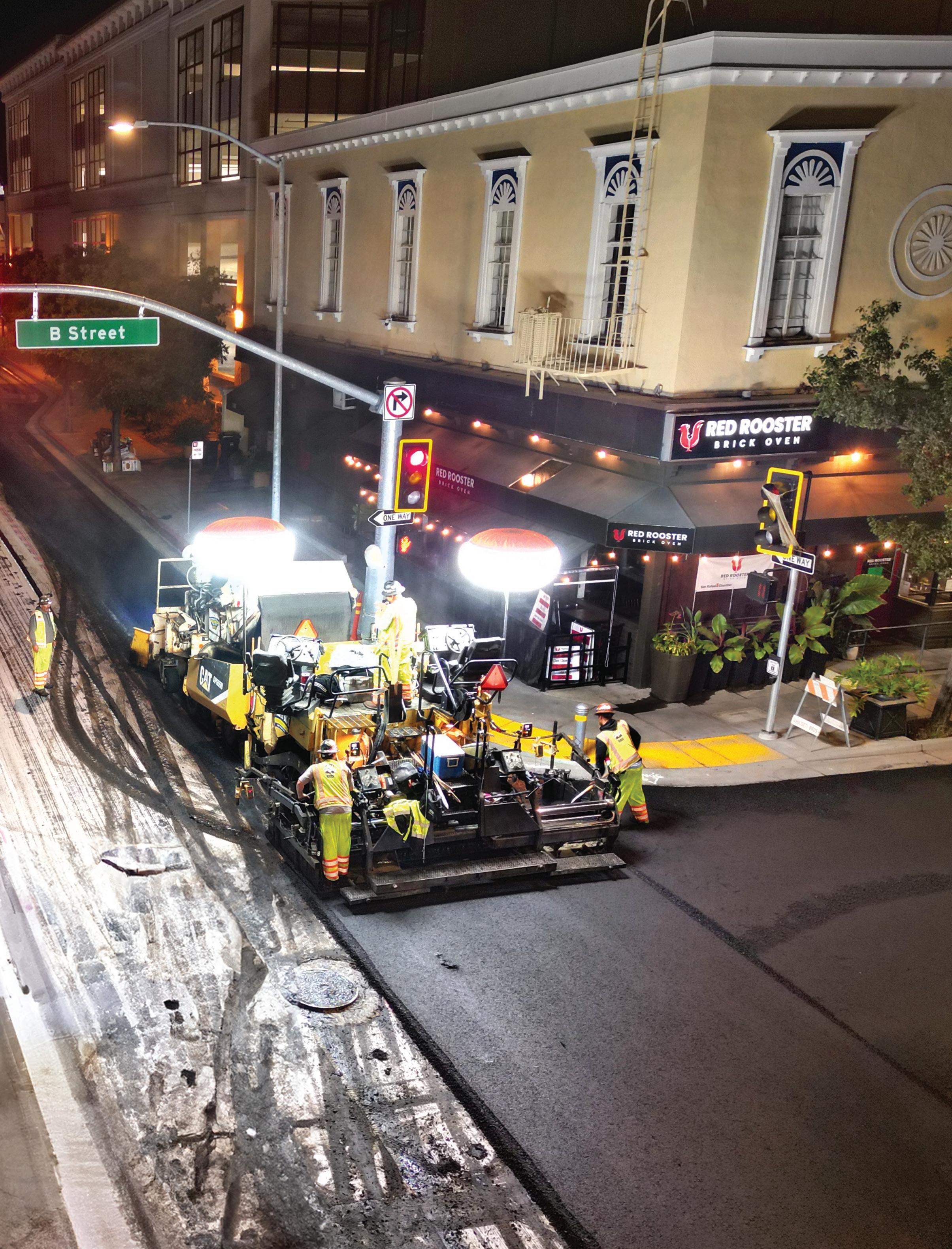
Celebrates 110 Years of Family-Owned Construction Success
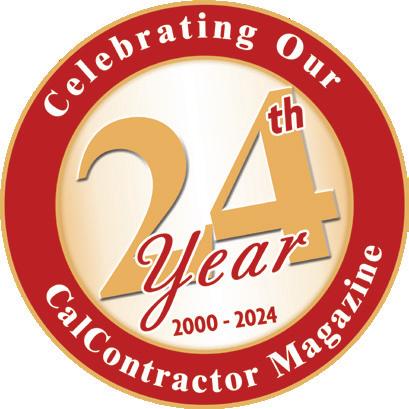

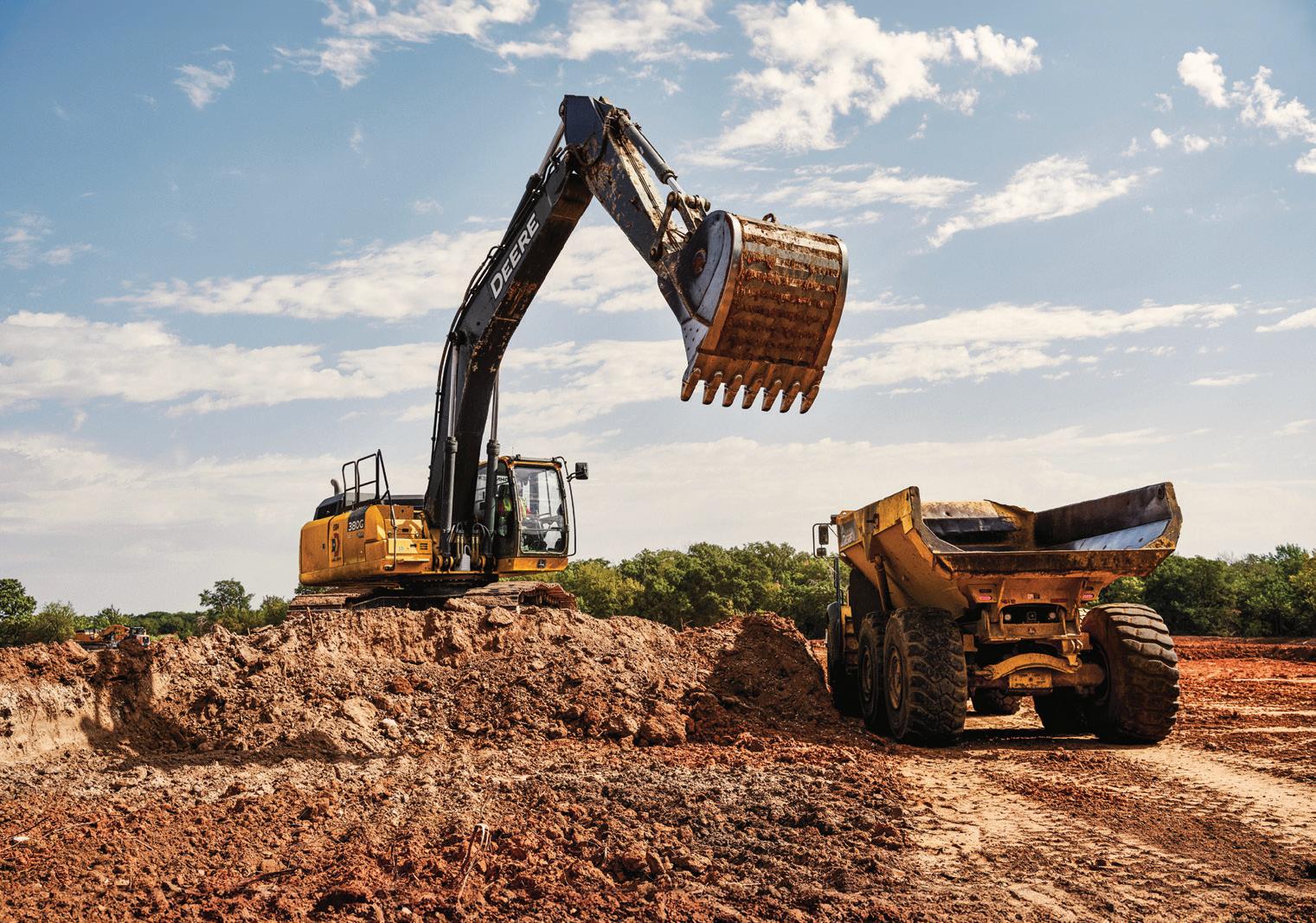
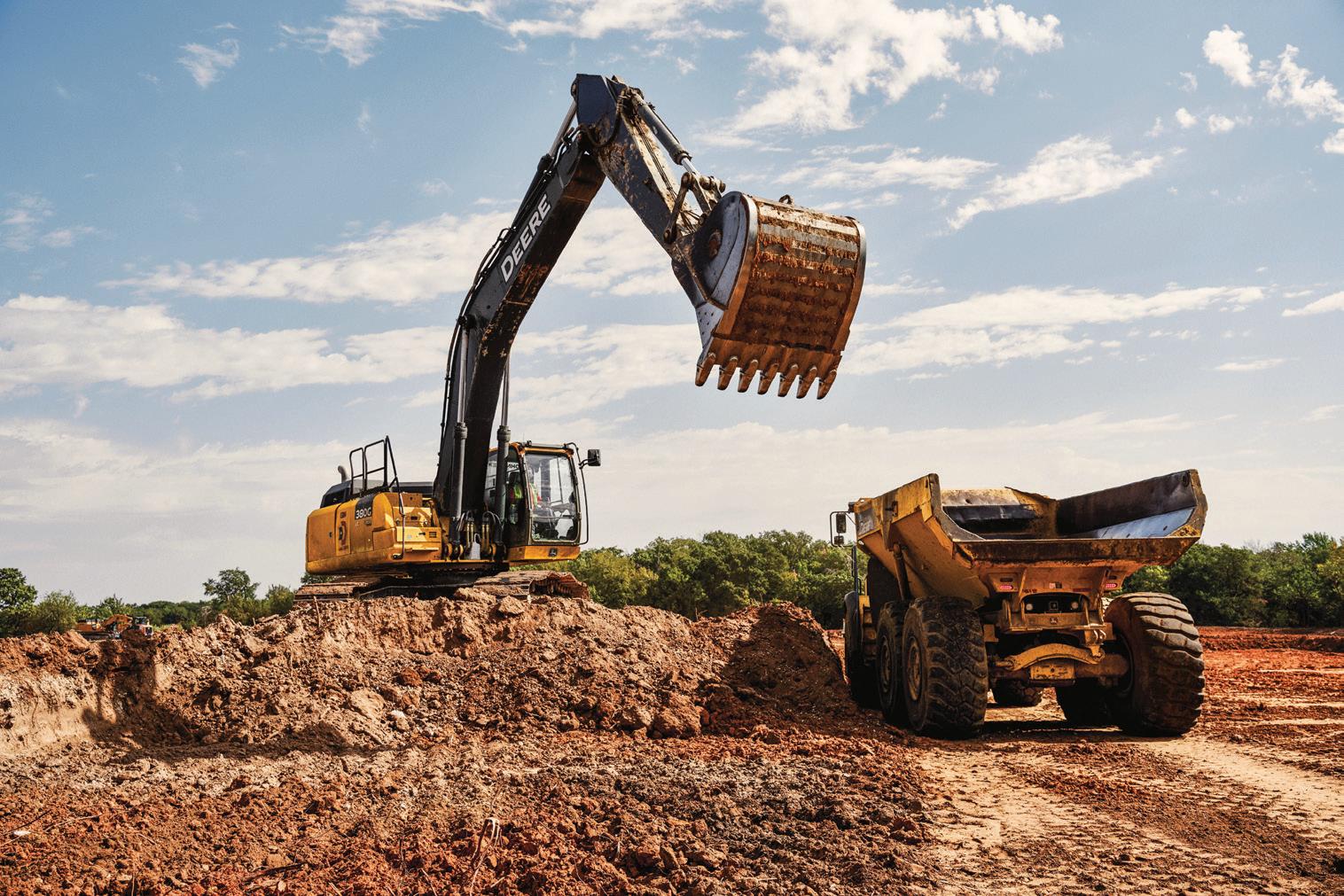

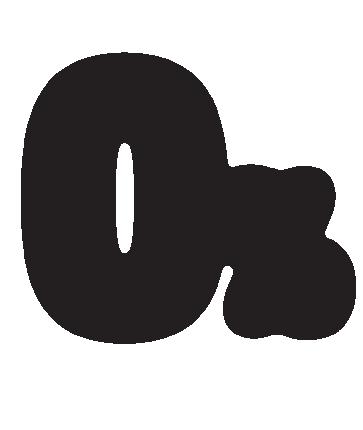
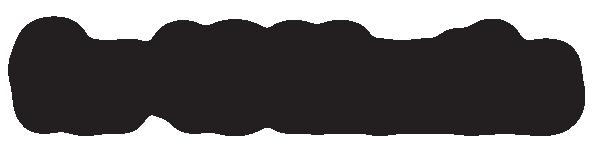
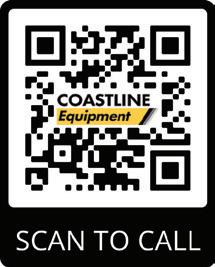
Celebrates 110 Years of Family-Owned Construction Success
06
Legacy of Hard Work and Excellence: Ghilotti Bros., Inc. Celebrates 110 Years of Family-Owned Construction Success
Paving the Way: Caltrans is Taking the Lead on Sustainable Road Innovations with Cold Central Plant Recycling Pilot Projects in California
20 GRANITEROCK
Constructs California’s First Turbo Roundabout in San Benito County for Caltrans District 5
PUBLISHER: Kerry Hoover khoover@calcontractor.com
EDITOR: Brian Hoover Senior Editor
GRAPHIC DESIGNER: Aldo Myftari FOR ADVERTISING INFORMATION: Please call: (909) 772-3121
26
Rebuilding Paradise by Overcoming Challenges and Restoring Hope After the Camp Fire
The Ghilotti family represents one of many Italian immigrant families who have played a significant role in shaping America's construction industry, especially during the late 19th and early 20th centuries. Drawn by opportunities for work and a better life, many Italians arrived in America with skills in masonry, carpentry, and other construction trades. Their expertise and strong work ethic quickly made them sought-after workers, contributing to the construction of iconic buildings, bridges, and infrastructure projects across the country. From the skyscrapers of New York City to the highways of California, Italian immigrants left their mark on America's built environment, leaving a legacy of craftsmanship and determination that continues to be celebrated today.
Ghilotti Bros. turns 110 years old this year, and they are looking better than ever. The Ghilotti Bros. business chronicle began with James Ghilotti, who spent his youth learning the art of stonemasonry from his father and grandfather. Once James turned 18, he began working in the diamond mines in South Africa with his two uncles. James worked hard and was able to save some money during this time, and after four years, he returned to Grosio, Italy, to work as a stonemason. Times were hard, and customers began wanting to pay with goats, sheep, and milk. James made it clear that he only worked for “soldi” (money), as it became abundantly clear that he had to make some drastic changes in his life.
James Ghilotti still had some money saved and decided to visit his uncle in San Rafael, California. He immediately found a job in stonemasonry as work was plentiful due to the recent 1906 earthquake. James eventually returned home to Grosio, Italy, where he met and married his wife, Amalia. James couldn’t shake his love of America and so he asked his wife to go with him, back to San Rafael, to make a life together with their infant son, William. Amalia agreed, and once again, James was crossing the great Atlantic Ocean in hopes of a better life in America. He found work hauling rocks by horse-drawn sled while also performing masonry
5
work wherever he could find a job. James added concrete construction to his offerings and constructed the area’s first concrete retaining walls and concrete patios, some of which still exist today.
Time moved on, and the business grew, along with their family as James and Amalia eventually had five sons and one daughter, including William (Willie), Dino, Dante, Henry (Babe), Mario, and Nancy. Dante sadly died at a young age, while the other four boys went on to eventually work in the family business. In 1935, the company name was changed from James
Ghilotti Construction to James Ghilotti and Sons to honor the boys' hard work and dedication. All four boys went on to serve their country in World War II, returning home with new skills to help the family business grow. As their knowledge grew, so did their construction disciplines as the company began taking on small grading and paving projects and eventually concrete tilt-ups, mass excavation, demolition, underground, and heavy highway construction. This diversification brought about great success as James made the decision to sell the family business to his sons in 1950. Sell, not gift, so they would all truly appreciate the great opportunity they were being offered.
1. James Ghilotti first logo circa 1914. 2. Four brothers enlist WWII, Willie (left), Dino, Mario and Henry. 3. Mario Ghilotti President 1967- 2000. 4. Early James Ghilotti family circa 1928.The brothers changed the name to Ghilotti Bros. to better represent their partnership, and they all prospered together for the next ten years. These were very dynamic and energetic times with four redblooded Italian men and brothers working together to make the most of their opportunity. Willie was the oldest and the glue that held all the brothers together during any arguments or differences of opinion. When Willie passed away in the early 60s, internal differences led to Henry (Babe) deciding to manage a new startup the brothers had by the name of Shamrock Concrete. Soon after, the brothers bought out their brother, Henry, as he went on to form Maggiora and Ghilotti with his new partner, Elmo Maggiora, and Ghilotti Bros. continues to compete with them to this day.
Mario and Dino remained great partners until 1990 when Dino passed on and left his share to his son Richard. Mario and his wife, Eva, remained the other half of the partnership, along with their sons, Michael (Mike), and Dante Ghilotti. The new situation did not last long as Richard (Dick) moved on to start Ghilotti Construction Company in 1991. Then, in 2005, the last two of generation three of Maggiora and Ghilotti split up with one starting Team Ghilotti. So, today, there are four Ghilotti companies, all using the Ghilotti
family name. All four related, but none affiliated.
Mike and Dante Ghilotti eventually purchased the company from their mother and father in 2000. Today, Mike Ghilotti is Ghilotti Bros.’ majority stockholder with his son, Gino, also being a shareholder. Mike Ghilotti serves as President and CEO of Ghilotti Bros. and received his bachelor’s degree from St. Mary’s College Moraga in 1984, and his MBA in Construction/Project Management from Golden Gate University, San Francisco in 1987. Like everyone else that has risen through the ranks of Ghilotti Bros., Mike Ghilotti started out with a broom and shovel in his hand. “We have many proud traditions at Ghilotti Bros. and one of them is that everyone earns their place here and is rewarded for their hard work and dedication. There are companies that do not look for the next generation to step in but instead backfill leadership positions by individuals they feel have the credentials and are a proven commodity. Others might send their son or daughter to work for another company for several years and come back after they experience things elsewhere,” says Mike Ghilotti. “I consider it a blessing that my son, Gino, has stepped up and demonstrated the talent and ability to be the next
in line, and everyone at this company supports and rallies around Gino. He started like the rest of us, pushing a broom and working a shovel and has now grown, matured, and developed over the years. We are two years into a seven-year transition plan and things are right on schedule. In the meantime, I will continue to steer the ship and mentor Gino and the rest of our management team to help ensure that Ghilotti Bros. sees another 110 years of service and success.”
Ghilotti Bros. Fourth Generation
Gino Ghilotti represents the Fourth Generation of Ghilotti Bros. operation and ownership. Gino is currently serving as Manager of Organizational Development, and succession planning is a part of the development program. “Each generation of Ghilotti stewardship has faced its challenges. We have been using a family business consultant to help with our seven-year transition plan. This is important to everyone involved because we have other children to consider,” says Mike. “Gino’s brother, Mario, worked for the family business before deciding to start his property development business, and we continue to work with him and support his ventures by partnering on projects. I am very proud of all our children, as well as our family heritage.”
{ Continued on page 10 }
{ Continued from page 8 }
Gino Ghilotti earned his Business Economics degree from the University of San Diego, immediately joining the family business after graduation. Like his father and uncles before him, he started out as a laborer and worked his way through the ranks. “Family is very important here at Ghilotti Bros., and so is maintaining a family-like atmosphere for every hardworking team member. This industry has undergone a change in the ownership landscape, with many deciding to go with an ESOP (Employee Stock Ownership Plan) as its only alternative. This seems to be in response to the current limited workforce. Offering ownership may, for some, increase an employee’s desire to remain with a company,” says Gino. “At Ghilotti Bros., we recognize all the noise and distractions and do what we can as a team to remain missiondriven and keep what is important to us at the forefront. We place enormous value on every team member and recognize that they are on the front lines and are the ones who have made reaching a 110-year milestone possible. We can talk about ownership and succession plans, but without our amazing staff, both in the office and field, there would be nothing to succeed in or pursue. We will always do everything we can to retain our team members and make sure that their career experience is the best in the industry.”
Mike Ghilotti echoes Gino’s thoughts on gaining and retaining laborers, operators, management, and administrative staff and adds one other important company focus. “The only thing more important than keeping our team members
happy and thriving is keeping them safe. We are at 910,000 hours without a lost time incident right now and hit over one million hours in the past,” says Mike. “All accidents are preventable, and accidents do not just happen. Distracted drivers, worksite intrusions, working around heavy machinery, and so many other potential hazards are there on the job site every day. There is nothing more important than the safety of our team members, and we have worked hard to put together safety plans and procedures to get them home safely to their families every day.”
Mike points out that many contractors and agencies have lost an entire generation of knowledge. “It is clear that we have lost institutional knowledge in our industry that is very difficult to replace. We are, however, blessed here at Ghilotti Bros. in the fact that we do have the longevity and family culture where people stay with us for many years. We just experienced the passing of Frank Palagi, who we affectionately refer to as the fifth brother from the second generation. Frank was with us for 68 years, and he was one of a kind. He mentored Dominic Nuccio, a great human asset who recently retired after 48 years with the company,” says Mike. “At Ghilotti Bros., we have retained most of the knowledge and expertise, but many other
contractors and agencies have lost an entire generation of knowledge. We are so fortunate to have people like Troy Simning, our V.P. of Project Management, who has been instrumental in our growth and progress for the past 28 years. We have Mike Llamas, who is our Heavy Highway and Alternative Delivery (APD) Vice President, and Dave Cantor, our V.P. of Estimating. We have so many experienced veterans who work as division managers out in the field. Scott Silvestri is our Business Development Manager, and he manages and maintains major projects for companies like Google and Station Casino. We also have Stephanie Taylor our Talent Development Manager and Nicholle Henning our V.P. of Finance.”
Tom Barr is another longtime veteran at Ghilotti Bros. who has moved up the ranks over his past 38 years with the company to become the firm’s Chief Operating Officer (COO). “We are a vertically integrated construction firm and whenever possible, we bid on projects where we self-perform all or most of the work. As an example, we recently completed work for Swinerton Construction in Modesto where we self-performed everything from grading, concrete work, base rock, and asphalt paving. The value here is that both
Swinerton and officials at Kaiser Hospital can work with just one company, reducing subcontractors from four to five, down to just one competent company,” says Barr. “Having said this, we also often bid and work on projects with just one discipline like underground utilities or concrete work, but our specialty is to bid and work on jobs with multiple disciplines. Practically speaking, we are more apt to bid on a job with underground construction as a component of other work such as grading and paving.”
Over this past century, plus 10, Ghilotti Bros. has self-performed numerous heavy-highway, site development, aviation, rail, marine, and other major infrastructure projects throughout the Bay Area. If you have ever passed through in the Bay Area, then you have driven on a roadway graded and paved by Ghilotti Bros. Some of these projects, like the new Chase Warriors Center, include architectural concrete work. Other legacy projects include the 28-acre recreation of Crissy Field along the shoreline of the San Francisco Bay, the installation of the moveable median barrier on the Golden Gate Bridge, and the resurfacing of the original 1922 Lombard crookedest street in the world. Other recent major projects include Phase 3 and 4 of the Graton Casino expansion where Ghilotti Bros. relied on all of their trades over a very large footprint. Additionally, there is the Highway 84 paving project
Left: Frank Palagi Sr. The fifth Ghilotti “Brother.” 68 years of loyal and dedicated service.
from Woodside to Highway 101 in Redwood City. This included grinding, paving, the restoration of 115 wheel-chair ramps, and the placement of 60,000 tons of hot mix asphalt pavement. Ghilotti Bros. is also involved in a joint venture project with Stacy Witbeck on the SMART commuter rail system project in Petaluma, allowing for diversification when partnering.
“Probably 70 percent or more of our work right now is on public works projects. This is a quick turnaround as far as payment is concerned, and the rules of engagement are fairly straightforward. We especially like working with progressive agencies of choice who are fair, responsive, and enjoy partnering to achieve the best possible results. The idea of partnering has led to our desire to take on more public works projects where many agencies are now leaning toward working with construction manager/general contractors. This is where we can come in early as a partner and help design and then begin negotiating a contract,” says Mike. “Then there is the private side of the business where we are working to enhance our vision for the future of our company by finding owners and clients that value our culture and what we bring to the table. We want to work with owners and shareholders that are interested in mitigating one another’s risks.”
Mike Ghilotti describes Grady Kimball as the company’s new shining star, as he also represents the second generation of his family working at Ghilotti Bros. “Grady runs the field operations and brings a new dynamic spirit and interest
to the field construction part of our business,” says Mike. “We are fortunate to have Grady and other young, ambitious individuals working here at Ghilotti Bros., as they represent the future.”
Grady says that Ghilotti Bros.’s four main disciplines are concrete work, asphalt paving, grading, and underground construction. “We primarily work as far north as Fort Bragg, south to Gilroy, and east to Sacramento. We perform everything from decorative concrete to heavy highway paving, to mass and deep cut excavation and underground construction. We are proud of our vertical integration that provides our clients with the opportunity and convenience of working with one team for all on-site services,” says Grady. “Things are changing in our business and technology is coming on strong. This can be a hindrance to those who fight it or refuse to adapt but a great tool for those who choose to embrace it. Things like going paperless or using technology to track machinery or access data points and quantities on a job site. These all make a difference and make our jobs easier, more
detailed and accurate. We use Trimble System Grade Control on all of our Cat machines, Topcon Sonar on our paving machines, and Total Station on the larger pad grading projects. Programs like these offer us built-in tolerances and laser technology instead of GPS for more precise elevation measurements.” With more than 200 pieces of heavy machinery in their fleet, Ghilotti Bros. relies on Peterson Cat for most of their yellow iron and companies like Nixon-Egli for other equipment such as Wirtgen milling machines.
James Ghilotti’s legacy for hard work and determination lives on today through his descendants. “We have 31 fundamentals that we live and work by that we call the GBI Way. Number 31 is “Work Hard/Play Hard.” Nobody works harder than the fine individuals here at Ghilotti Bros. Our industry demands long hours and hard work. This is an honest, straightforward industry full of genuine people who respect labor and what the guys in the field go through every day. Over the years, we have evolved
into an organization of excellence, structured for continuous improvement with the ability to adapt through out-of-the-box thinking and diversification,” concludes Mike. “I know that my grandfather (James) would be so proud of what has been accomplished over these past 110 years. In order to continue to teach the hard work ethic and ideals that my grandfather began so many years ago, we have established GBIU (Ghilotti Bros., Inc. University), a fully automated online program where employees are properly trained with classes that teach and shore up skills. Employees are able to realize several levels of achievement, including the designation of ‘High-Performance Employee.’ Our vision for the future is to expand on the rich history of Ghilotti Bros. Our time tested tradition, family culture and hard-work ethic, combined with the world-class craftsmanship of our loyal and dedicated employees, will go a long way to strategically support another 110 years of top-tier performance and success.”
Caltrans (California Department of Transportation) is at the forefront of sustainable pavement initiatives, prioritizing environmental stewardship and innovative practices. Committed to reducing the carbon footprint of transportation infrastructure, Caltrans has implemented several pavement engineering strategies, including incorporating recycled asphalt pavement (RAP) into its road maintenance and construction projects to promote sustainability and cost efficiency. By using RAP, Caltrans reduces the demand for new materials, decreases waste in landfills, and lowers greenhouse gas emissions associated with asphalt production and transportation. These efforts not only minimize waste and energy consumption but also improve the longevity and performance of roadways. Through collaborative research and advanced technologies, Caltrans continues to lead in creating sustainable, resilient pavement solutions that support California's long-term environmental, economic and equity goals.
Recycled asphalt strategies focus on reusing and repurposing existing asphalt materials to create new pavements, reducing the need for virgin materials and minimizing environmental impact. Techniques such as cold central plant recycling,
It is our mission to provide a safe and reliable transportation network that serves all people and respects the environment. By utilizing innovations like Cold Central Plant Recycling, we aim to reduce waste and minimize our carbon footprint while continuing to rebuild and maintain California’s vast highway system.”
Diana Gomez, Director, Caltrans District 6
and partial and full-depth recycling are employed to enhance sustainability and cost-efficiency in road construction and maintenance projects. In 2019, Caltrans established the Pavement and Materials Partnering Committee (PMPC) to work with the pavement industry on the development of new specifications and test methods. One of the committee’s subtask groups, the Recycling Subtask Group, recently developed and made available Cold Central Plant Recycling (CCPR) non-standard specifications (NSSP). These CCPR specifications have been tested on three projects located in San Bernardino County on Route 18, Tulare County on Route 63, and most recently in Kings County on Route 41. A fourth CCPR pilot project recently bid and will be
completed later this year in Siskiyou County on Route 161.
(CCPR)
CCPR is a sustainable engineered process where existing asphalt materials are milled to the required depth, transported to a nearby cold central plant, processed with an engineered bituminous reagent, transported back to the road, and then laid with a paver. This process can be used for both partial and full-depth recycling, as well as new construction with previously stockpiled recycled materials. Because of the “cold” nature of the recycled asphalt, multiple lifts can be placed and compacted in a day’s production. If necessary, chemical subgrade stabilization of the underlying base and/or subgrade, such as cement or lime stabilization, can be performed as part of the rehabilitation process to increase structural capacity without increasing the grade elevation of the pavement.
Granite Construction (Granite) won the bid for the rehabilitation of an eight-mile section of State Route 41 in Kings County near Kettleman City from 0.1 mile south of Quail Avenue to Nevada Avenue. The $15,045,175 contract included the use of CCPR on a one-mile pilot section of southbound State Route 41. Highway 41 near Kettleman City is a common route for people from the Fresno area headed to the
Brian Hoover, Senior Editor / Photos by: Pavement Recycling Systems, Inc.&
coast for destinations like Pismo Beach, Morro Bay, and San Luis Obispo. Caltrans was looking for a lower-volume highway section and a district maintenance engineer interested in testing the CCPR. This section of State Route 41 had distresses throughout the majority of its existing depth and was a good candidate for the CCPR process. Granite began the rehabilitation of State Route 41 on February 26, 2024. Their work began with the milling of the roadway by subcontractor Pavement Recycling Systems, Inc.
Pavement Recycling Systems, Inc. Performs Milling and CCPR Production
Michael Concannon serves as a pavement engineer for PRS and helped oversee the State Route 41 CCPR pilot project near Kettleman City. “Granite was the prime
Granite and PRS have worked together to successfully deliver many pavement preservation projects to Caltrans over the years and this project was an example of another opportunity to utilize innovative pavement rehabilitation strategies and project staging to deliver an improved roadway for Caltrans and the travelling public,” says Grimm. “CCPR, used in the right application, provides a great opportunity to rebuild our infrastructure in a sustainable way by minimizing unnecessary truck trips, waste, and cost which is in alignment with Granite’s core values.”
Jeff Grimm, Area Manager, Granite Construction
contractor on this pilot project, and we performed all of the milling over the eight-mile section and the milling and manufacturing of the recycled asphalt pavement for the one-mile CCPR test section,” says Concannon. “Our PRS team members milled the existing pavement for the conventional remove-and-replace areas down to 13 inches to accommodate the new pavement section. On the CCPR section, we milled from 8 to 12 inches, depending on the depth of the pavement. Our work on the CCPR section began on April 25 and was completed on May 1. Beyond the milling, we functioned primarily as the CCPR material producer. Granite hauled the material to and from our portable plant to their paving machine located just six miles from our plant.”
According to Concannon, the CCPR process has been around for decades and used by many California agencies and DOTs across the United States. Caltrans has utilized several pavement recycling strategies over the years and is now doing their testing and due diligence to standardize the CCPR process once the pilot programs are evaluated and complete. “Having completed over 100 Cold Recycling projects, Caltrans has utilized Partial-Depth Recycling (PDR) to rehabilitate, in-place, the upper 3 to 5 inches of deteriorated asphalt pavements. When the pavement distresses exceed this depth, CCPR can be implemented to rehabilitate the deeper distressed sections to a greater thickness in multiple lifts. The existing cracks, deterioration, and other distresses in the pavement on the State Route 41 CCPR pilot section went deeper than what can be processed with PDR. This is what made this particular highway section such a good candidate for CCPR,” says Concannon. “Caltrans completed the non-standard special provisions for CCPR in 2022, and
these four pilot projects represent the first CCPR projects in Caltrans history using modern specifications. Eventually, the tests and evaluations will be completed by independent sources such as University of California Pavement Research Center (UCPRC) in Davis, CA and Aragon Geotechnical, Inc., the company responsible for the CCPR mix design, quality control testing and inspection. This will soon come out of the pilot/testing phase; however, the specifications will not become standard for probably another year or two while they continue to monitor performance.
Partial Depth Recycling (PDR) took 15 years to become standardized, but we anticipate that CCPR will become a specified recycling solution much faster.”
The reconstruction work on State Route 41 near Kettleman City started this past February with the milling of the existing roadway. The milled asphalt spoils were then stockpiled six miles away at the chosen CCPR site location. By the end of April, the CCPR process was ready to begin feeding the one-mile southbound pilot section of SR 41. “The CCPR mix was in accordance with the design
formulated after testing the existing field samples in the laboratory. The CCPR plant is calibrated in compliance with the Caltrans MPQP program and to the same accuracy standards as any hot mix plant, in full compliance with all air quality standards. After milling the area at up to 13 inches in depth, the stockpiled grindings were fed into a recycling machine which is a combination screening and crushing unit. The material is screened and crushed to one inch maximum sizing and mixed in proportion with the 2 ½ percent foamed asphalt recycling agent and then cement is added at 1 percent in accordance with the mix design. The recycled asphalt is then loaded into Granite trucks and transported six miles back to the recently milled paving area,” explains Concannon. “Because Granite was paving to a depth of 10 inches, the recycled pavement was put down in three separate lifts, one on top of another. The overall finished multilayer sections function as one single layer. A total of 2,900 tons of HMA was placed over the CCPR section consisting of 2,150 tons of Type A and 775 tons of open grade friction { Continued on page 18 }
Above & Top Right: PRS' CCPR recycling plant with conveyors and cement silo is approximately 80 feet by 80 feet and can be mobilized and set up in half a day once it arrives onsite.{ Continued from page 16 }
course material. Each CCPR lift was compacted using a 10-ton steel drum roller and a 25-ton rubbertired roller to achieve 95% relative compaction. We completed between a quarter-and half-mile section each day, amounting to around 1,400 to 1,800 tons per day. In all, we processed 11,720 tons of RAP during the construction of the CCPR one-mile pilot section.”
Marco A. Estrada, Director of Business Development, has been with Pavement Recycling Systems, Inc. (PRS) for more than 23 years, and he has watched these asphalt recycling solutions grow and mature from the beginning. “Caltrans uses the term rehabilitation for these recycled asphalt projects, but due to the thickness of these CCPR sections, we are effectively reconstructing the entire roadway. Typically CCPR projects of greater than 5,000 tons see the benefits of the economies of scale,” says Estrada. “CCPR has been used by agencies here in California on low traffic neighborhood streets and in high traffic urban areas. The four Caltrans CCPR pilot projects have been or are going to be completed in rural areas, which offers even more savings in construction related trucking and fuel costs. When you put a calculator to the savings of trucking miles, you realize the true impact and savings of CCPR.”
For the hot mix asphalt remove and- replace sections on the State Route 41 project, the material was delivered from Granite’s Coalinga plant located around 35 miles from the jobsite. “Our plant was located six miles away for a total of 12 miles
By embracing solutions like in-place recycling, we can reduce the costs and environmental impacts of our pavement maintenance and rehabilitation projects while reducing the disruption to the traveling public. This approach aligns perfectly with our vision of a transportation system that is safe, efficient, and environmentally responsible. Let us continue to lead the way in promoting in-place recycling as an industry best practice. Together, we can create a safer, more accessible, equitable, and sustainable California for all.”
Tony Tavares, Director, California Department of Transportation (Caltrans)
round trip. So, that is a difference of 58 miles per truck round trip. So, when you calculate nearly 750 trucking round trips, you will see that there is a savings of 43,500 miles of trucking and an untold reduced number of exhaust emissions and traffic congestion along the way.”
Estrada also points out that CCPR, by definition, is a portable plant. “The CCPR recycling plant itself is 40 feet in length and 11 feet
wide. With the conveyors, and cement silo, the overall footprint is only around 80 feet by 80 feet and can be mobilized and set up in half a day once it arrives onsite,” continues Estrada. “Actual cost savings will depend on several factors, including how far away the hot mix plant would be located, potential conventional trucking travel costs, and what additives are used in the CCPR process.”
For Caltrans and other agencies, there are many other benefits of going with CCPR, such as minimizing the impact of trucking and emissions on travelers, businesses, and residential communities. Then there is the safety factor that is elevated by removing these trucks from the roadway. As Caltrans Director, Tony Tavares, continues to move forward with meeting Caltrans sustainability goals, the agency will undoubtedly consider and even rely on solutions such as CCPR and PDR to maintain their roads and highways economically. Anytime you can recycle as much as 100 percent of material on a construction site, there will be great interest by not only government entities but also the tax-paying residents of California. Cc
Right: PRS performing one-mile CCPR pilot section on southbound State Route 41 for Caltrans District 6.The Roundabout Revolution
Intersections are critical points in the transportation network where different traffic flows converge, making them hotspots for collisions. In the United States, intersectionrelated crashes account for a substantial portion of traffic accidents. According to the Federal Highway Administration (FHWA), over 50% of the combined total of fatal and injury crashes occur at or near intersections.
Roundabouts have been recognized as an effective measure to enhance intersection safety. Unlike traditional intersections, roundabouts use a circular layout where traffic flows counterclockwise around a central island. This design minimizes the points of conflict and encourages lower vehicle speeds.
The turbo roundabout is a relatively recent innovation in traffic management, first conceptualized and implemented in the Netherlands in the 90s by Dutch engineer Lambertus Fortuijn. Recognizing the limitations of conventional roundabouts, particularly the issues related to lane-changing conflicts and the resulting accidents, Fortuijn aimed to design a roundabout that
could better manage high volumes of traffic while significantly improving safety. The first intersection of this type was built in the Netherlands in 1998.
Following the success in the Netherlands, the concept of turbo roundabouts began to spread to other countries in Europe and beyond. Countries such as Germany, Poland, Slovenia, and the United Kingdom started experimenting with turbo roundabouts in the late 2000s and early 2010s. Today we count approximately 390 turboroundabouts worldwide, with the first in the United States being constructed in Jacksonville, Florida in 2022, and the second being right here in California in 2024.
Implementing roundabouts requires agency and stakeholder buy-in and support, which can sometimes be difficult to obtain, even with their proven safety performance record. Caltrans made the decision to build the state’s first turbo roundabout at the intersection of highways 25 and 156 in San Benito County in an effort to cut
down on collisions while maintaining traffic efficiency. This particular intersection was chosen due to statistics that showed a pattern of broadside and rear end collisions that amounted to more than twice the number as similar intersections in California. The intersection is located between Gilroy and Hollister, and was originally two lanes in each direction, consisting of northbound/ southbound 25 and eastbound/ westbound 156 with a light signal at the intersection.
Kevin Drabinski serves as the Public Information Officer for Caltrans District 5. “This location had a history of serious collisions that was higher than the state standard. This is the first Turbo Roundabout in the state of California and we were able to access highway safety funds for this project,” says Drabinski. “One of the design features and benefits is that it calms the speed at which people are negotiating the roundabout. As drivers are approaching the roundabout, they are seeing signs overhead that are suggesting lanes to get into determined by whether you want to go right, straight or make a left. We
Above: Mark Hurley Jr., Project Manager, Graniterock.have done a lot of outreach and have created instructional videos in both English and Spanish to publicize and assist in educating those who have or will be negotiating the roundabout. We have installed a live camera onsite and you don’t see the backups that you did before. Overall, this is and will continue to be an incredible benefit to the community. We can learn from this first Turbo Roundabout construction process and possibly use it as a model for other future locations throughout California.”
Graniterock Wins Bid to Construct California’s First Turbo Roundabout
Mark Hurley Jr. (Hurley) was the Project Manager for Graniterock overseeing all phases of construction on the new turbo roundabout in San Benito County. “The Turbo Roundabout Project was awarded in the winter of 2021 before going through winter suspension until Spring 2022. The original contract value was $9.9 million, but by the end of construction, that number went up to $10.4 million. We began the construction process by paving a temporary shoulder section to
push traffic over in June 2022. Next, we performed miscellaneous grading and fill work before officially beginning the first of five stages,” says Hurley. “There was a temporary traffic signal component to this project that presented a challenge as the electrical plans called for five separate stages. We took a closer look at the plan and pole locations, and worked with the subcontractor and Caltrans to develop a new plan that would allow for one installation process without any additional moves or changes for the duration of the project. This is what we call a Value Engineering Change Proposal (VECP), and we came up with a more efficient way to install the temporary traffic signals that saved Caltrans and the taxpayers a lot of money, but also took up most of the summer of 2022. We were able to get the K-Rail for Stage 1 installed in November 2022, and then a solid month of production before the rains came in December. Everything was wrapped up and fully open to traffic in February 2024.”
According to Hurley, the Highway 25/156 Turbo Roundabout Project was constructed in five phases, and within those phases, Graniterock
Above & Left: Graniterock night paving 20,400 tons of hot mix
performed 19,492 cubic yards of roadway excavation, and milled off approximately 7,140 square yards of asphalt pavement. “Stage 1 began with the northeast roundabout lane and then moved clockwise through the remaining stages. During each stage, our crews milled off three to four inches of existing asphalt pavement. Our next step was to pulverize another 8 to 10 inches of base and subbase material and then transport everything to the staging or laydown area just 800 feet away. This pulverized material was then screened and brought back to the site for use as subgrade along with around 5,000 cubic yards of imported Class II aggregate,” says Hurley. “We then installed 27,100 square yards of subgrade enhancement geogrid on all roadway sections. Finally, our professional crew members began paving what would eventually amount to 20,400 tons of hot mix asphalt that arrived from Graniterock’s Aromas plant.”
Hurley says that production varied by how much his crews could grind out and put back in a single shift. “The paving operation was completed in four separate lifts to achieve a final one-foot-thick
section in each of the four lanes. There was a good amount of asphalt and crushed base material that was not recycled back into the job, and those spoils were left for later use by the local farmer who allowed us to use his land for our stockpiles and screening equipment,” continues Hurley. The paving of one single lift per section required around 1,200 tons of hot mix asphalt, and that was what our achievement goal was each night. We utilized our Cat 1055F 10-foot paving machine, with our Cat 655F 8-foot paver onsite for use as a backup. We also utilized steel drum and rubber tired rollers, along with skip loaders and other support equipment.”
The process that was used on Phase 1, was repeated through the next three phases of asphalt pavement construction, followed by the fifth phase which included the construction of the center of the roundabout itself. “The work within each phase was nothing new to Graniterock, as we focused on assuring that our crews and the traveling public remained safe throughout the entire construction process,” says Hurley. “I know living in Hollister, I would see traffic backed up all the way to Highway 101 on State Route 25 southbound in the afternoon. Traffic flow and
efficiency is important to everyone, but the most important thing to have in mind when constructing modern roadways is safety.”
Unlike conventional roundabouts, turbo roundabouts have physically separated lanes that guide vehicles through the roundabout. These lanes are often marked by raised curbs or delineators, ensuring that vehicles stay within their designated paths. “There are around 925 feet of highway lanes leading up to the roundabout in all four directions. 335 cubic yards of A1-6 curb was installed leading up to the turbo roundabout, and in-between the curbs our crews installed a rock blanket that acted as a lane divider to keep the lanes separate,” continues Hurley. “In all, we placed 46,300 square feet of rock blanket that took our cement masons and laborers around one month to complete. The concrete was poured and then the cobble rock material was wet-set in place by hand, which although tedious, presented a nice and interesting aesthetic appearance.”
Hurley explains that once all of the lanes were complete, Graniterock crews began work on Stage 5 which included the construction of the middle of the turbo roundabout. “The construction of the turbo
Left: California's first Turbo Roundabout located at Highway 25 & 156 in San Benito County for Caltrans Distict 5.
roundabout section was made more challenging by the live traffic that continued to flow during work. The heavy truck traffic called for the concrete center section to be built with JPCP (Jointed Plain Concrete Pavement),” says Hurley. “This is a 240-foot diameter, 12-inch thick, concrete section with a D4 type curb sloped up to meet the CPCP for the trucks to use when maneuvering their wide semitrucks and long trailers. Colored concrete was used along with exposed aggregate and more of the cobble stone rock blanket.”
Hurley says that although the construction of the turbo roundabout lanes and center island were fairly straightforward for Graniterock, there were several external challenges that made the job more complicated. “All of the paving was done at night, which along with the sequencing, staging and traffic control, made for a more challenging project. Traffic control during the day was more manageable with the K-Rail in place and working within our closed off quadrant,” says Hurley. “However, moving from one stage to the next, and pushing traffic to the other side, was where it got trickier. We setup four flaggers in all four directions and brought traffic to a stop. We then reversed the traffic control, letting one direction go at a time.”
Hurley makes it clear that this successful, first in California, turbo roundabout project was a group effort, made only possible by the hard work and cooperation of many individuals and agencies.
{ Continued on page 24 }
936E, 936F, 950E & 995F
909ECR, 913FCR, 915E, 915FCR, 922F, 926F, 933E (Stage II), 933E (Stage IIIA) 9018F, 9027FZTS, 9035EZTS, 9051FZTS & 9057FZTS
835Hv, 838Hv, 848H (Stage IIIA), 848H (Stage V), 848Hv, 856H (Stage II), 856H (Stage IIIA), 856H (Stage V), 856H-E MAX & 856HV 877H, 890H & 890HV
“We answered to the resident engineer and inspector from Caltrans District 5, who were both great to work with. We also need to thank and recognize the Council of San Benito County Governments who were also heavily invested and helpful in the design, construction and implementation of this turbo roundabout project,” says Hurley.
“I would also like to thank all of our team members on this project, including Brandon Cole, our main foreman overseeing the grading, grinding, prep and paving on this project, Nick Delatorre (Paving Foreman), Marco Lopez (Paving Foreman), and Ray Espino, our labor foreman who helped to close out the job with all of the punch list and subcontractor work.”
The work at the SR 25 and 156 interchange is part of a long-range improvement plan named the SR 25 Expressway Conversion Project. Prior to Measure G being passed, funding for the widening and the interchange was not available. The Caltrans State Highway Operation and Protection Program (SHOPP), which funds safety projects, identified the need to address safety at this location in the interim. The proposal to place an interchange at this location will not be finalized, under best case scenarios, until 2028. In the short-term, Caltrans chose the turbo roundabout solution until the long-range plan of an interchange can be implemented.
“Motorists are still getting acclimated to the new turbo roundabout at the SR 25 and 156 interchange and there has been plenty of criticism both in the news and on social media. However, this is a roadway engineering concept that has been proven over and over again in many countries. As people become more accustomed and realize the safety and traffic flow benefits firsthand, the concerns will more than likely diminish,” concludes Hurley. “Successful implementation of turbo roundabouts requires effective driver education to ensure that all road users understand the new system and how to navigate it correctly. I am excited to see if more of these turbo roundabouts pop up throughout the state of California.”
The Paradise Fire, also known as the Camp Fire, was one of the most devastating wildfires in California's history. Igniting on November 8, 2018, in Butte County, it rapidly spread due to strong winds and dry conditions, ultimately destroying the town of Paradise. The fire burned over 153,000 acres, claimed 85 lives, and destroyed nearly 18,000 structures, making it the deadliest and most destructive wildfire in California to date. The aftermath highlighted significant issues in wildfire preparedness and response, leading to increased efforts in fire prevention, improved infrastructure, and emergency management practices. The Paradise Fire stands as a stark reminder of the destructive power of wildfires and the ongoing need for vigilant wildfire management in vulnerable regions.
Damon
Weston Hutchings oversee the new Bomag CR 1030 T in action on Alpine Court as part of the 2023 Roadway Rehabilitation Project in Paradise.
In the immediate wake of the fire, the community faced immense devastation, with most homes and infrastructure reduced to ash. Financial assistance and grants have been crucial in aiding the recovery. Efforts to rebuild have been multifaceted, involving local agencies, non-profits, and significant support from Federal Emergency Management Agency (FEMA) funding. Required matching funds of $446,225 (6.25%) were also funded through the Town’s Community Development Block Grant-Disaster Recovery (CDBGDR) Infrastructure Allocation. In addition to support from FEMA and other agencies like Caltrans, utility companies and construction firms were mobilized to aid in the rebuilding efforts.
The Paradise Town Council adopted a resolution approving the plans and specifications for the Off-System Roadway Rehabilitation project on November 7, 2022. Through the Public Assistance Program, the Town of Paradise approved $38,290,000 for the overall project. The first step in the construction recovery process involved assessing the extent of the damage. The intense heat and flames had severely damaged the road surfaces and compromised the structural integrity of many underground utilities, including water, gas, and sewer lines. Pavement scaring occurred due to car fires, and unusually heavy truck traffic during debris removal
By Brian Hoover, Senior Editor Photos by: Hat Creek Construction & Materials, Inc.further damaged the already compromised roadways. Initial efforts focused on clearing debris and stabilizing the ground. During the CALOES Debris Removal effort, over 3.7 million tons of material was removed, equivalent to approximately 300,000 truckloads. Once the debris was cleared, temporary repairs were made to allow for emergency and construction vehicles to navigate the area. During this same period, PG&E, Comcast, and AT&T restored the distribution infrastructure. Additionally, approximately 140,000 trees were removed by PG&E and through the FEMA-funded Category 3 tree removal project.
Hat Creek Construction & Materials, Inc.
Hat Creek Construction & Materials, Inc. (Hat Creek) was awarded the road rebuilding segment of Phase 1 of the Paradise 2023 Roadway Rehabilitation Project. Hat Creek’s initial contract amount was $5,756,809. Repaving the roads in Paradise was a multi-phase process that required excavation and removal of damaged roadway sections in some areas. Subgrade rehabilitation and preparation were necessary in other areas to ensure a long-lasting, stable new asphalt surface layer.
Clayton Poore (Poore) is serving as the Project Manager responsible for overseeing Hat Creek’s road repair and paving efforts. “Our contract began on September 18, 2023, and was scheduled for completion in May 2024. Our amazing paving crew will have placed more than 30,000 tons of hot mix asphalt supplied by Knife River Construction’s Hallwood Plant in Marysville,” says Poore. “Before the placement of hot mix asphalt could proceed, we performed variable subgrade treatments, mill and fill operations, dig outs, base backs, along with standard pulverization and a small
amount of cement treated base treatments.”
According to Poore, Paradise pavement conditions were affected by many factors besides the obvious fire damage. “You could see gatoring and cracking on existing roads, plus many of the underground utilities had been moved and repaired, which required new roadway construction. The reconstruction and paving solutions differed and were dependent upon the condition of the existing subgrade. We milled and paved around half of the streets and roads and performed full-depth pulverization, stabilization, and paving on the other half,” says Poore. “We worked last season (2023) and then went through a winter suspension period before returning in the Spring of 2024. In all, we replaced close to 50 roadway sections within a 5-to10-mile radius of the town of Paradise. It was all very segmented and primarily consisted of 20 to
30-lane miles. Most of our work was done on 20 to 25-foot-wide residential streets that included the paving of some driveways and 18 cul-de-sacs. We also repaired and paved thoroughfares like Nunneley Road and Kibler Road.”
Hat Creek subcontracted the milling operations to ABSL Construction, headquartered in Hayward, with additional offices in Sacramento and Visalia. “We were asked to mill off approximately 52,910 square yards of existing asphalt per the bid documents, but by jobs end, that number came in closer to 80,000 square yards at 0.5 to 0.80 in depth. This was followed up with the placement of 0.25 or three inches of new asphalt pavement. The asphalt spoils in these sections were either used as part of the base material in other areas or hauled off to Knife River and other asphalt suppliers for recycling purposes,” continues
Above: Hat Creek Construction & Materials’ Astec/Roadtec SB-3000 Shuttle Buggy material transfer vehicle operates in tandem with their Bomag CR 1030 T on Harrison Road in Paradise.Poore. “We also constructed five new ADA ramp sections with approximately 39 cubic yards of concrete, along with some shoulder backing and striping work.”
Hat Creek subcontracted the pulverization and stabilization work on this project to Pavement Recycling Systems, with headquarters in Jurupa Valley and additional locations in San Diego, Escondido, Colton, Santa Pauzla, Bakersfield, Sacramento, and Carson City, Nevada. “Approximately 48,860 square yards of pavement was pulverized in place at a depth of 0.80. Then, at a preconstruction meeting, I was handed a change order to pulverize an additional 40,000 square yards of roadway due to the condition of the pavement section. At the moment, we are around 14 change orders deep, as this project continues to show a lot of variable conditions. So, in these areas, we pulverized in-place, regraded, compacted, and then paved over these sections with, again, 0.80 or 3-inches of hot mix asphalt,” says Poore. “We also
had an increased number of digouts on this project due to the native red clay soil in the area. These sections were affected by the existing groundwater, springs, and a combination of burned or lack of vegetation that contributed to the excess amount of surface water and general dampness of the subgrade. We performed the digouts, replaced the section with a Class II base, compacted, and moved on. We also had a change order on Nunneley Road to go with FDRC, which is Full Depth Recycling with the addition of a small percentage of cement. This was a 3,100 by 2,400 (74,400 square feet) square foot section on only half of the specified roadway section. It was determined that the other half did not require FDRC; however, when the time came to pave that section, it appeared that it also had some subgrade issues. We are currently awaiting a directive from the town of Paradise officials.”
The Hat Creek Paving Crew Hat Creek is running a 10-person crew on the Paradise Off-System Roadway Rehabilitation Project. The crew was lucky enough to receive a brand new Bomag CR
1030 T 10-foot tracked paving machine from Herrmann Equipment. “This was the very first job for our new Bomag 10-foot paver equipped with a new Topcon sonar tracking system for better smoothness and rideability. We already owned this exact same paver, and we are currently using that one as our backup on this project. We liked it so much; we bought another one,” says Poore. “But it’s not just the paving machine that we like so much, it is also the unmatched service we get from Herrmann Equipment. If there is ever an issue, Matt Herrmann has a mechanic, and often times himself, onsite within 24 hours. In addition to the Bomag pavers, we also purchased an Astec/Roadtec SB-3000 Shuttle Buggy material transfer vehicle from Herrmann Equipment. We are using the Shuttle Buggy on this project for windrow pickups and back transfers. This machine has saved us a lot of time and fewer runs to the paver on the narrow roadways.” { Continued on page 30 }
Below: Hat Creek Construction crew members utilize their Bomag CR 1030 T for paving on Trafalgar Square, supported by their John Deere skip loader.
{ Continued from page 28 }
Poore points out that the Paradise Off-System Roadway Rehabilitation project was not without its challenges. “There were the usual challenges of working within an active residential area, but in this case that was magnified many times over due to what these residents have gone through these past several years. There has been construction almost constantly here in Paradise for the past six years, and we wanted to ensure that our crews were doing everything they could to make folks’ lives a bit easier while working hard to provide them with the best roadways possible,” says Poore. “Perhaps the greatest physical challenge, beyond keeping the residents happy, was working on these narrow roads like Honey Run Road from Chico to Paradise. The original roadway was 9.5 feet, but we paved it back at 10 feet,” continues Poore. “Our crew had to back the transfers down the road a mile and a half to the paver with only a couple available pullout sections. There was minimal room for error to avoid cleaning up a mess with a wheel loader or skid steer loader. All the equipment had to be staged in the correct order as we worked on this 7,500-foot road and other narrow sections.”
Poore wanted to make sure that he had a chance to thank and recognize everyone who worked so hard and helped manage this important project. “Everyone from the Paradise Town Council to Caltrans and the Paradise Irrigation District has been so accommodating and great to work with on this job. Then there is our incredible Hat Creek paving crew, superintendent, and foremen that make it all go
so smoothly,” concludes Poore. “I want to give a special shout-out to Damon Moore, our Paving Superintendent and Foreman, who deserves a lot of praise for an exceptional finished product. Then there is Jamie Anthony, our Dirt Superintendent and exceptional blade hand, and Aaron Canfield, our Dirt Foreman, whose attention to detail is much appreciated. It is always a group effort here at Hat Creek, and I want to thank everyone for being such exceptional professionals.”
Hat Creek will complete Phase 1 of the Paradise Off-System Roadway Rehabilitation Project in May 2024. Although the project's challenges were significant, the successful completion marks a major milestone in the ongoing recovery and rebuilding efforts in the town of Paradise. The collective efforts of Hat Creek, its subcontractors, and the entire community demonstrate the resilience and determination to restore and improve the town's infrastructure, ensuring a safer and more secure future for its residents.
Hat Creek Construction & Materials, Inc. is a verticallyintegrated, family-owned company based in Burney, California. Established in 1972, they produce raw materials (rock products, asphalt, and concrete) and construct public, environmental, and commercial projects throughout California.
Many operations remain in-house. Hat Creek owns quarries, crush rock, process and produce various rock products, and deliver the aggregate on their trucks to their construction projects. Their competitive advantage is also rooted in making business decisions based on the core values of Teamwork, Pride, Respect, Reputation, and Community, ensuring they deliver quality that meets customers' demands. Active in the community, they support local events and organizations that build character, work ethic, and entrepreneurship.
Learn more at HatCreekConstruction.com and connect on Facebook, LinkedIn, and Instagram. Cc
From versatile, job-dominating power to swift, smooth, smart product features, CASE backhoe loaders will help you ingeniously command the jobsite.
With Sonsray, you're not just buying a machine; you're investing in a partnership built on trust and expertise. Our team is dedicated to providing unparalleled support every step of the way, from helping you choose the right backhoe for your needs to ensuring its continued peak performance through maintenance and service.