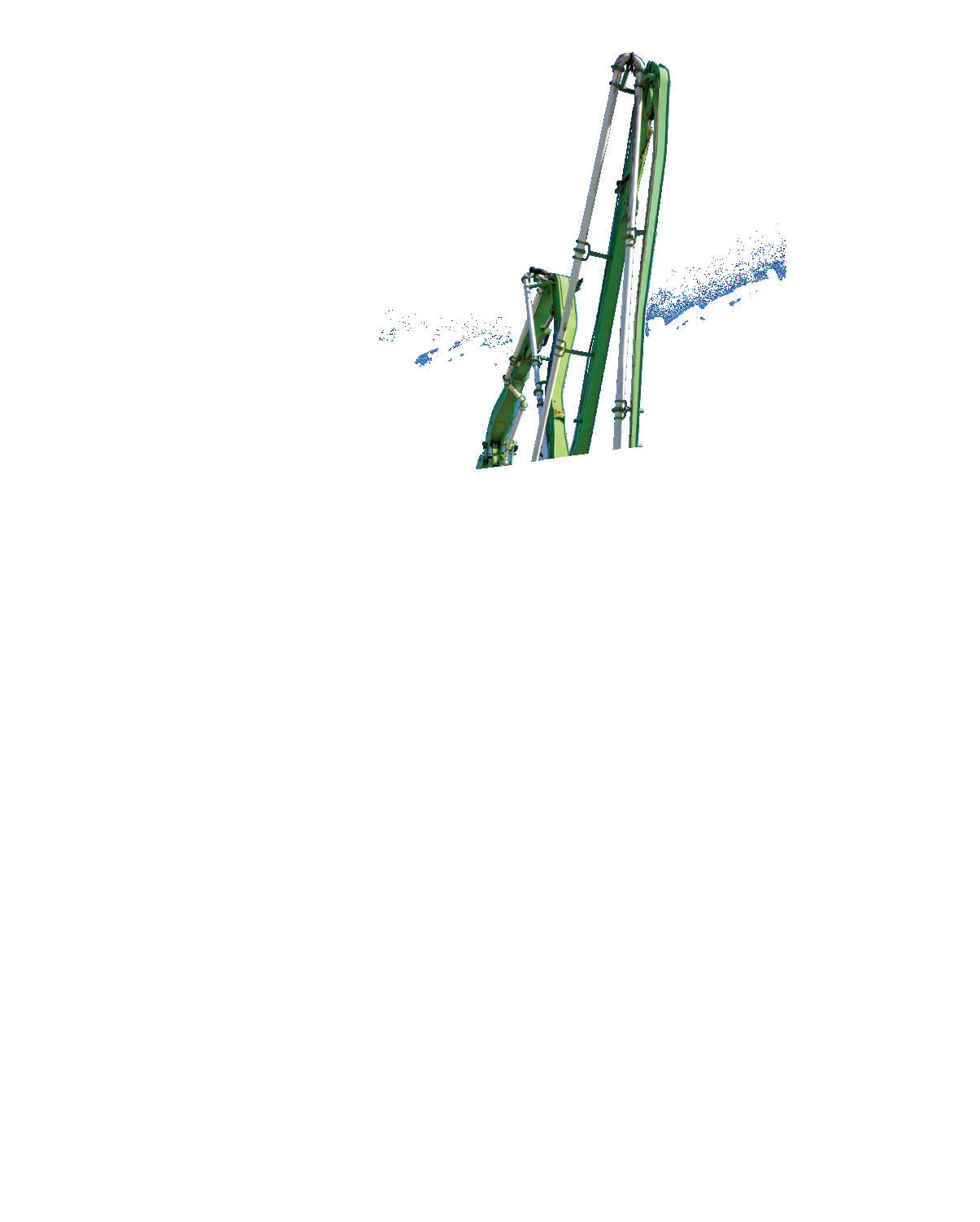
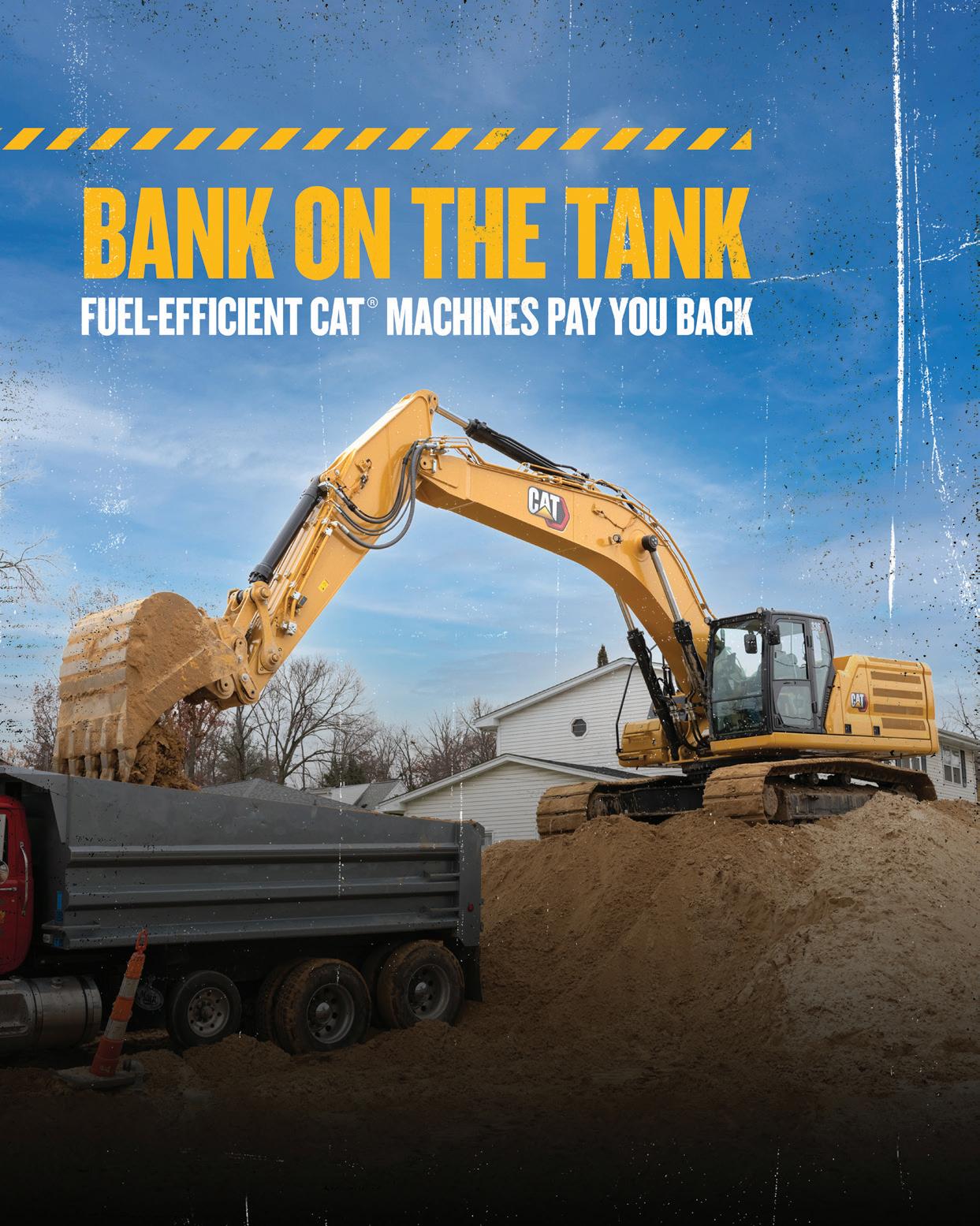
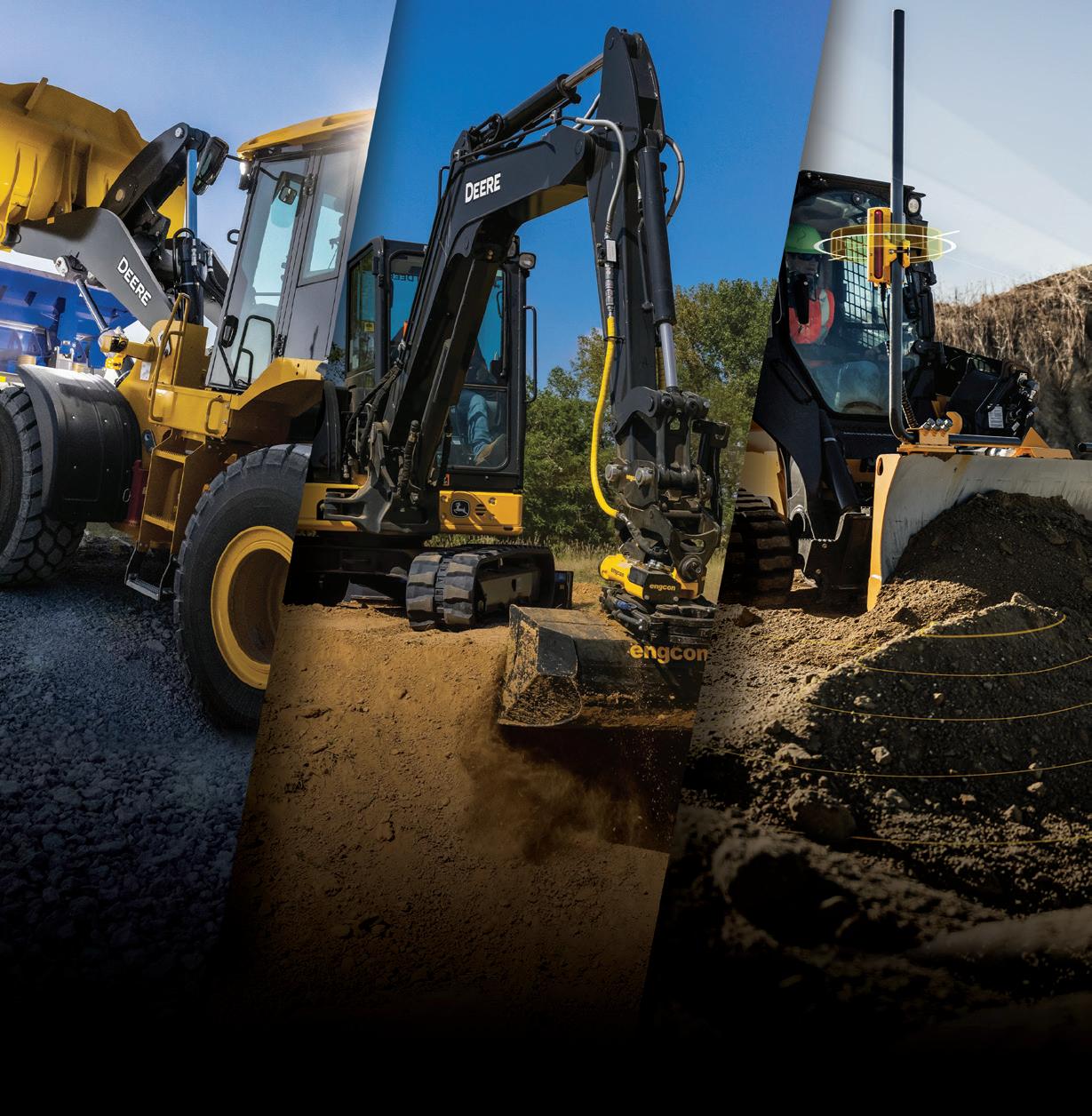
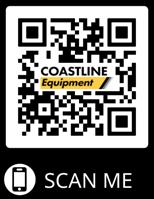

PUBLISHER: Kerry Hoover khoover@calcontractor.com
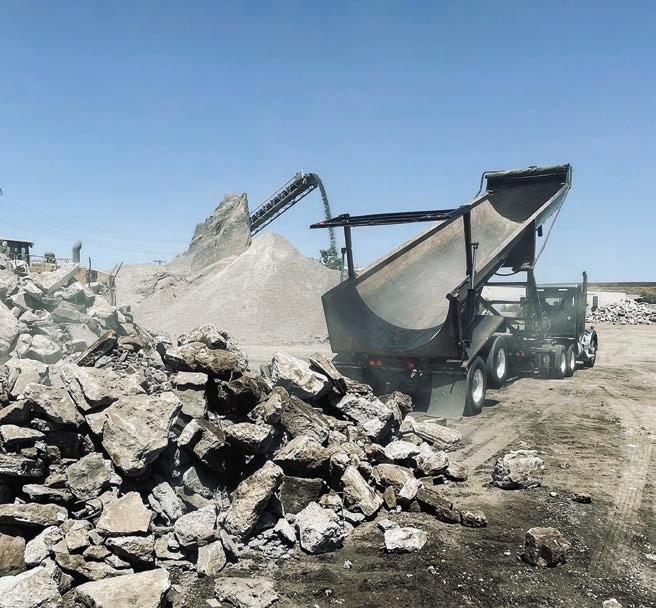
GRAPHIC DESIGNER: Aldo Myftari
EDITOR: Brian Hoover Senior Editor

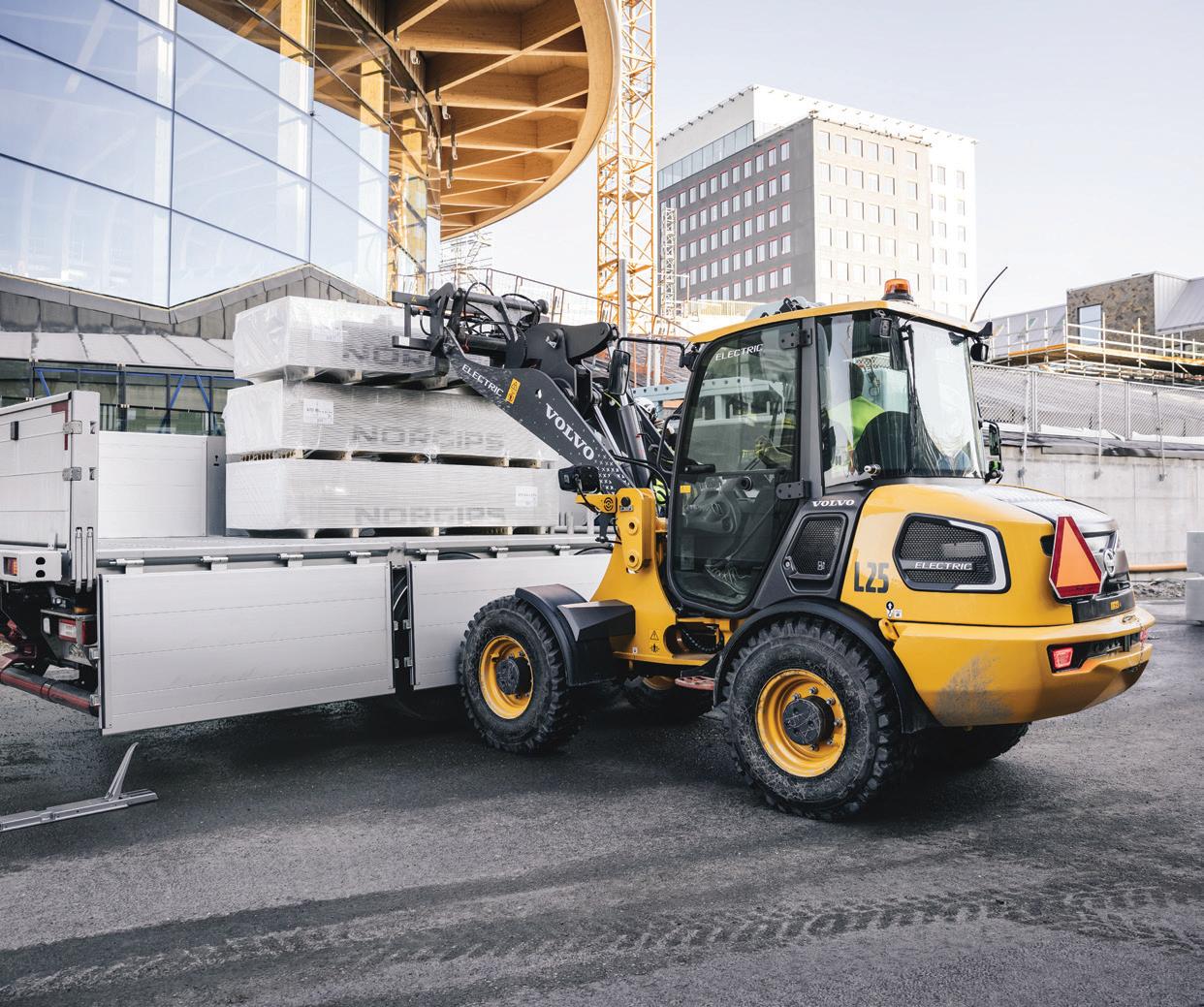
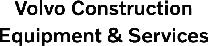
PUBLISHER: Kerry Hoover khoover@calcontractor.com
GRAPHIC DESIGNER: Aldo Myftari
EDITOR: Brian Hoover Senior Editor
The Coachella Valley is one of Southern California’s magical gems, visited each year by millions of tourists seeking adventure, inspiration, solitude, and serenity. Bordered by the San Jacinto, Santa Rosa, and San Bernardino mountains, the area’s
nine cities include Palm Springs, Desert Hot Springs, Cathedral City, Rancho Mirage, Palm Desert, Indian Wells, La Quinta, Indio, and Coachella. Each city has its own distinct history, personality, and unique offerings, all of which depend on a consistent supply of
water. However, excessive water from events like Tropical Storm Hilary can lead to catastrophic flooding.
The Coachella Valley stands as an arid desert region with an annual rainfall of under three inches. Nonetheless, the nearby
mountains experience significantly more precipitation, resulting in erratic and hazardous flash floods in the Coachella Valley. These unexpected floods can cause significant damage and even loss of life. In response, the Coachella Valley Stormwater District (renamed the Coachella Valley Water District, CVWD, in 1918) was established in 1915 to manage flooding on a regional scale. During the 1970s, numerous modern facilities were either constructed or improved through collaborative efforts with municipalities and other organizations. Many of these aging structures now require replacement to continue protecting the 590 square miles of the Coachella Valley from flooding. Within the jurisdiction of the CVWD, there are 16 stormwater protection channels. The entire system encompasses approximately 135 miles of channels built along the natural courses of dry creeks
that flow from the surrounding mountains into the Whitewater River. The backbone of this stormwater protection system is a 50-mile storm channel running from the Whitewater area north of Palm Springs to the Salton Sea. Known as the Whitewater River / Coachella Valley Stormwater Channel, this flood protection facility was designed to withstand a standard project flood (greater than 100-year floods), equivalent to a flow of around 80,000 cubic feet per second.
To further shield homes and land from regional flooding, the CVWD is actively working to remove approximately 2,700 acres of land within North Indio from a designated Special Flood Hazard Area. This initiative, part of the North Indio Regional Flood Control Project, involves constructing a 3.5-mile-long series of concrete flood control channels. These waterways will connect to existing
Below Left Page: Sukut is reconstructing a 3.5-mile-long series of concrete flood control channels, making this the largest project in CVWD history.
Below: The project requires over 100,000 cubic yards of concrete placement.
channels, starting in Sun City Palm Desert and flowing through North Indio to channels in Sun City Shadow Hills that ultimately link to the Coachella Valley Stormwater Channel. With a cost of $110.2 million, this marks the largest project in CVWD history. Upon completion, the North Indio project will facilitate the construction and connection of other stormwater facilities providing regional flood protection to Thousand Palms and northern Cathedral City. Moreover, this work will eliminate the need for residents in the area to maintain flood insurance, as previously mandated by FEMA.
Sukut Construction (Sukut) was awarded the North Indio Flood Control Phase 2 Project by the CVWD. Ground was broken in December 2021, and the project is anticipated to conclude by July 2024. Sukut is responsible for constructing 16,000 linear feet of flood control
channel, necessitating more than 100,000 cubic yards of concrete placement and over one million cubic yards of excavation. This new channel traverses six existing public streets and entails the construction of reinforced concrete box culverts, utility relocations, and street reconstruction. The project requires 2,500 linear feet of reinforced concrete box culverts, 8,700 linear feet of concrete-lined trapezoidal channels, 3,200 linear feet of rectangular concrete channels, and 1,600 linear feet of concrete channel transition structures.
Nathan Rodriguez, the Project Manager overseeing the North Indio Flood Control Phase 2 Project for Sukut explains, “We are essentially merging two separate flood control systems into a unified three-and-a-half-mile concrete channel. The design plans refer to the project as Phase 2, which consists of the Main, South, and
Middle Channels. Here, we are integrating the existing Channels 1A, 1B, and 2 with the Phase 2 channels to connect the flood control channel from Mountain Vista Golf Club at Sun City Palm Desert to Shadow Hills Golf Club in Indio,” says Rodriguez. “I mention these golf facilities because the golf courses are situated within flood zone areas, capable of temporarily storing water and acting as basins to receive water from the adjacent mountains and hillsides.”
Sukut’s grading crews have moved over one million cubic yards of dirt, of which 750,000 cubic yards were exported offsite. “Constructing these concrete channels involves excavation to create a flowline or void beneath the current elevation. Consequently, not all of the excavated material can be used on site, but around 250,000 cubic { Continued on page 10 }
yards were utilized as backfill or for grading adjacent properties. Additionally, water, sewer, and gas utilities have been relocated at various impacted roadway intersection sites through an excavated siphon that goes underneath the utility box and then returns to the original level. To date, we have relocated 12 water lines, four gas lines, and four sewer lines.”
Rodriguez emphasizes that the North Indio Flood Control Project is essential for safeguarding the Coachella Valley’s large and growing population. “This new flood control project primarily protects the people living, working, and visiting the Coachella Valley. It also safeguards numerous properties and assets, capable of handling flows even greater than 100-year flood capacity,”
says Rodriguez. “Our construction process takes the community into consideration. Residents and buildings are often just 50 feet away, so we implemented two traffic control detours to minimize disruptions to the local community and our on-site workers.”
According to Rodriguez, the Coachella Valley flood control project demanded extensive coordination, planning, and synchronization. “From the outset, we knew that this project required meticulous planning and close coordination with the County, cities, local businesses, and residents to ensure safe and timely execution,” Rodriguez affirms. “Weinitiated the project by addressing the mainline trap channel work not located around intersections. The work progressed sequentially, moving from one end to the other. After excavating
a phase or section, we promptly installed the steel-sheeted forms and proceeded to pour the concrete. Due to the rapid desert deterioration of exposed surfaces caused by wind, it’s crucial to pour as soon as possible to avoid additional work. The most significant challenge is maintaining ongoing efficiency.”
During the last eight months, Sukut completed a substantial portion of the dirt and concrete work, and the project is now about 70% complete concerning poured concrete. “During last summer and the first year of work, we poured between 2,000 to 3,000 yards of concrete every other week, averaging about 1,500 yards a week. Currently, the project has transitioned to more strategic, piecemeal work. There might be a three- to fourweek period without pouring,
followed by several weeks of pouring around 1,000 yards a week.”
Rodriguez notes that Sukut is utilizing five crews for the North Indio Flood Control Phase 2 Project, including four concrete crews and one grading crew. The concrete crews begin their workday at 1:00 a.m. and conclude between 8:30 and 10:30 a.m.
“The early morning hours for our concrete crews are due to the heat, which still reaches 95 to 100 degrees around midnight. By noon, temperatures soar from 115 to 120 degrees. Safety is paramount, and that includes ensuring the protection of our workers while continuing to maintain the highest quality product possible,” Rodriguez explains. “At the peak of this project, we had 85 to 100 team members, including approximately nine on the grading crew. Our
equipment includes Cat 374 excavators and double-bottom dump trucks for hauling. We also employed Cat 637 and 657 scrapers for cut and fill areas at the site.”
Regarding the 100,000 cubic yards of concrete being poured, Rodriguez clarifies that 75% is for open channel work, with the remainder at intersections. “The substantial trap channels are approximately 85 feet wide at the bottom and 120 feet wide at the top,” Rodriguez continues. “We also poured concrete boxes up to four cells wide, with each cell measuring 20 feet in width by 15 feet in height. These serve as mini bridges; around 2,000 linear feet have been poured, with another 1,000 feet remaining.” Our team has been doing an exceptional job, and we are on schedule to achieve substantial completion by year’s end. The channels will be fully
functional, thanks to the teamwork, planning, and coordination between our crews, the community, CVWD, and other involved cities and agencies. This is a truly collaborative effort!”
The CVWD provides domestic and irrigation water, agricultural drainage, wastewater treatment, and reclamation services, regional stormwater protection, groundwater management, and water conservation. It serves approximately 108,000 residential and business customers across 1,000 square miles, primarily located in Riverside County, along with portions of Imperial and San Diego counties. For more information on CVWD or the North Indio Flood Control Phase 2 Project, please visit CVWD.org. For more details about Sukut, please visit www.sukut.com. Cc
ww w.gomaco.com | info@gomaco.com
®
At the hear t of GOMACO equipment is our passion for concrete and our commitment to our customers We look for ward to visiting with you about your upcoming paving projects and your concrete paving equipment needs. Our worldwide distributor network and our corporate team always stand ready to ser ve and assist you
Riverside, California
(909) 879-1438
Sacramento, California
(916) 388-2480
Las Vegas, Nevada (800) 350-9230
Your authorized GOMACO distributor for California, western and southern Nevada, and the Hawaiian Islands
The Santa Clara Valley Water District (SCVWD) constructed miles of concrete-lined channels and other flood control systems to provide protection for County residents in response to repeated and large-scale floods throughout the 1950s. Many of these channels have reached the end of their life cycle and require major rehabilitation or full replacement. While the channels were successful at managing flood risk, in some cases, they also served to reduce the hydrologic and geomorphic functions in streams. These reductions can adversely affect aquatic ecosystems and
cause erosion and other damage to the infrastructure. Several sustainable hardscape and vegetative resolutions to this problem exist, and the Hale Creek Pilot Enhancement Project is one of the solutions currently under construction and review.
The Hale Creek Pilot project aims to increase channel flood capacity and improve the ecology of the creek system. It serves as a model project that takes a natural approach to flood control and protection, with methods that could potentially be applied to restoring other concrete channels throughout California.
The concrete channels along Hale Creek (in Santa Clara County) were originally built in the early 1960s. A structural stability study conducted in the early 2000s identified sections of Hale Creek in danger of structural failure in the near term. The SCVWD Board of Directors awarded the $6.4 million Hale Creek Pilot Enhancement Project to McGuire and Hester, a heavy civil sitework and landscape contractor headquartered in Alameda, Ca. Starting in May 2022, McGuire and Hester performed the earthwork, pile installation, and demolition of the existing
{
bridge. The earthwork involved removing approximately 650 feet of the existing concrete trapezoidal channel bank and invert lining from upstream in the City of Mountain View to downstream in the City of Los Altos. With the channel’s concrete lining removed, steel sheet piles were driven into place and vertically aligned with SCVWD’s right of way to form the outer walls of the new channel. Additionally, a 500-foot middle section of the channel was replaced with a geomorphically appropriate vegetated earth channel with hardened outside retaining walls. The remaining 150 feet upstream and downstream now serve as a transition zone consisting of an earthen bottom channel with rock banks. The entire flood-prone area available to the stream was
widened to restore the natural channel bank. Several other areas were cleared, including trees, shrubs, storm drain outfalls, access ramps, curbs, pavement, and gas lines, along with existing wood and chain-link fences. McGuire and Hester also removed the existing 30 ft. x 15 ft. bridge that spanned the area from the Seventh-Day Adventist Church parking lots to make room for a new bridge. The Hale Creek project was designed for construction over an approximately 650 linear feet section of the channel between Marilyn Drive and Sunshine Drive.
Although McGuire and Hester performed most of the earthwork and pile installation, they subcontracted the new concrete and new bridge erection work to
Casey-Fogli Concrete Contractors. Andrew Vasconi, the President of Casey-Fogli Concrete Contractors, was closely involved with every step of construction on the Hale Creek Pilot Enhancement Project. “Our team poured approximately 170 cubic yards of concrete for the construction of the pedestrian bridge and the new concrete ramp access that will allow small boats and canoes from agencies like the California Department of Fish and Wildlife to perform their measuring and testing,” says Vasconi. “CaseyFogli was also responsible for the closure pours between the sheet
pile and soldier pile shoring, in addition to the construction of the outfall structure that connects the new cobble invert of the creek to the existing concrete invert of the adjacent up and downstream channel.”
Casey-Fogli’s contract totaled approximately $600,000, including the erection of the new 30-foot x 12-foot prefabricated steel bridge spanning between the east and west banks slightly downstream from the previous bridge structure location. Vasconi states, “Our work began in July 2022, and we were on a fast-paced schedule that required completion by October 15,
2022. Our aim was to finish before the onset of the rainy season. However, due to delays in the approval procedure and the necessity to coordinate with the church’s schedule, our work hours were restricted to Monday through Friday, from 8:00 am to 4:00 pm. SCVWD and the California Department of Fish and Wildlife were understanding of delays that were beyond our control and graciously gave us a few extra weeks, and we ended up wrapping everything up by the end of October.”
In addition to the constrained working schedule, Casey-Fogli had to contend with tight working
conditions with zero to four feet of access along each embankment. Vasconi explains, “The only real access point was the parking lot at the Latter-Day Saints church. The tight working environment was primarily due to the homes that bordered the back of the creek. Our crew did an outstanding job minimizing the impact on our production. Our Superintendent, Carlos Maldonado, and Foreman, Edgar Rodriguez, did a great job keeping everything running safely and smoothly.”
Vasconi notes that the Hale Creek Pilot Enhancement Project was completed primarily with
Above & Left: Pile drives to support the installation of outside channel walls.compact equipment, such as a Kobelco excavator, a smaller-sized Cat skid steer loader, and a mini-reach forklift. A Cat excavator equipped with a Giken Silent Piler attachment was used for drilling the 24,000 square feet of sheet piling. “The ramp and retaining wall for access in and out were the last things we constructed on this job,” continues Vasconi. “This meant that we did not have drive-in access to the channel, so we craned in all of the machines until the final stage.” Other noteworthy quantities and specifications included 2,590 linear feet of galvanized soldier pile, 6,600 square feet of pre-cast concrete lagging, and 172 yards of ¼ ton rock for rock slope protection.
The Hale Creek Enhancement Pilot Project has received praise and recognition from several agencies, associations, and organizations. This includes The
American Public Works Association (APWA), which named SCVWD’s Hale Creek Enhancement Pilot Project the APWA Silicon Valley Chapter’s 2023 Project of the Year in the Environment/Parks category.
Casey-Fogli Concrete Contractors has been in business since 1906 (as H.E. Casey Company), initially starting as a material supplier and playing a role in rebuilding the Bay Area after the great San Andreas Earthquake. The company transitioned from a material supplier to a concrete contractor in the late 1960s. In 1972, the company was purchased by Pete Fogli, leading to the name change to Casey-Fogli Concrete Contractors. After Fogli’s passing in 1978, Vince Ippolito assumed the presidency. Before retiring in 2020, Vince chose to bring the Casey-Fogli family under the umbrella of Harbor Linx, a premier 100% employee-owned merger
and acquisition company in the Bay Area. Andrew Vasconi, an employee-owner at Harbor Lix, brings a wealth of leadership experience from the concrete industry. He has taken on the position of President at CaseyFogli, leveraging his industry insights and experience to lead the company forward.
Casey-Fogli primarily engages in place and finish, decorative, and package and site concrete work throughout Northern and Central California in both the private and public works sectors. For more information on the Hale Creek Enhancement Pilot project, please visit, www.valleywater.org. For more information on Case-Fogli Concrete Contractors, please visit www.caseyfogli.com or call their Hayward offices at (510) 887-0837. Cc
Above: New vegetated earth channel.Cooper Engineering, Inc. is a DBE-certified subcontractor that primarily builds concrete barrier rails for roads, highways, and bridges on both small and large-scale projects throughout Southern and Central California. Delivering successful projects under a variety of production methods, CEI delivers with unmatched efficiency and quality standards. The company was founded by Howard (Hod) and Denise Cooper in 1987 and has since become a leader in barrier wall construction, a detail-oriented trade that must be carried out skillfully, efficiently, and carefully. Now, 36 years since its inception, CEI is beginning the transition into the next generation of leadership with Hod and Denise’s sons, Chance and Mitchell Cooper.
Chance Cooper serves as a Vice President for Cooper Engineering, and Mitchell Cooper is also a Vice President for the family enterprise. CalContractor magazine has covered job stories for Cooper Engineering in the past, but this time the interview was with a second-generation stakeholder, Chance Cooper. Like so many other construction entrepreneurs’ children, Chance watched his parents’ business grow from the very beginning. “Cooper Engineering started out in our garage, and my brother and I got a first-hand look at how hard our parents worked every day,” says Chance. “I remember learning to weld in middle school and continuously working to keep the shop and yard clean. Then there were summers and other school breaks when I would spend my days welding and fabricating
for the various machines in the shop.”
Later in high school, Chance moved on to learn the administrative side of the business, particularly in the estimating department. Opportunities continued to become available as Chance began working as a laborer for a year and a half, eventually becoming a foreman and then moving back into the office to begin managing the daily schedules, and other job management duties. “Our company began adopting new machine guidance protocols for our new state-of-the-art slipform paving machines. I began taking on that responsibility, sort of by default and immersed myself in the new technology. I have always been a bit of a techie with computers, and this transition was both natural and enjoyable,” continues Chance. “There are
always new developments with these slipform paving machines, especially with the new wireless controls. I am now very involved in the machine control end of our business, which includes getting machines ready for specific jobs and applications.”
Flatiron West was awarded a four-year, $127 million contract from the California Department of Transportation (Caltrans) to rehabilitate 77 lane miles of distressed pavement sections. Some of the project details called for Flatiron to remove and replace approximately 400,000 square yards of pavement slabs, replace approach slabs at 16 bridges, and complete more than 900,000
square yards of diamond grinding along 9.7 centerline miles of the 210 Freeway. Additionally, the job called for the installation of more than 8.5 miles of freeway barrier, and Flatiron turned to Cooper Engineering for this detailed work. “We worked day and night on the 210 Freeway for Flatiron, from August 2021 to June 1, 2023. We were contracted to place 45,000 feet (8.5 miles) of concrete barrier in the median and shoulder from Sunland Blvd. to the Rt. 5 interchange on the 210 Freeway,”
says Chance. “Many of these walls were water-carrying barriers, meaning they have a large 18” drainage pipe located directly under the barrier. We created drainage slots in the bottom of these wall sections, allowing the freeway to drain efficiently.”
Chance points out that the project was not only unique due to its obvious length and the immense amount of barrier constructed but also because most of the wall called for a specific architecturally designed pattern. “We utilized our own patented method where we roll the desired stamped pattern into the concrete barrier wall directly behind the slipform paver while the concrete is still in its green, plastic state,” explains Chance. “My father, Hod Cooper, one of our owners and founders, played an integral role in inventing this method with a company by the
Left L-R: Chance, Hod, Denise and Mitchell Cooper golfing at the SCCA golf tournament at Pelican Hill Golf Club. Right: CEI stamped concrete barrier on the 210-freeway constructed using CEI’s patented slip stone method.name of Slip Stone. Our method allows our crews to pour the barrier with the same high quality, while also allowing for the optimum control we need to ensure excellent pattern results.”
According to Chance, the primary machine used on this project was a Wirtgen SP 25i offset slipform paver. “We have four differently equipped Wirtgen SP 25i slipform pavers that we purchased from Nixon-Egli Equipment Co. We have developed a very close relationship with Nixon-Egli and Wirtgen and have collaborated with them to help engineer and design our machines to be as versatile as possible. Due to the limited access on this project, we utilized our wireless technology to avoid the need for a stringline,” says Chance. “We had around 15 team members on this job. I want to thank everyone for doing such a great job on this complicated project, including Oscar Arellano, Flatiron’s Senior General Superintendent. We have worked with Oscar on other projects, and he always does an incredible job at coordinating the work and driving subcontractor production.”
The Coachella Valley Alternative Transportation Route (CV Link) is a 40-plus-mile bicycle, pedestrian, and low-speed electric vehicle pathway that is being built along the Whitewater River, providing a continuous transportation and recreation route connecting the Coachella Valley cities. The Coachella Valley Association of Governments (CVAG) awarded the $52.7 million contract to the low bidder, Ames Construction, Inc., and Cooper Engineering was subcontracted to perform the placement of around 14 miles of the pathway. “Our contract began in February 2022, and we are still currently on the project. We had originally bid the job to solely perform the concrete paving work,” says Chance. “However, we realized that we had more to offer when we figured out a way to use our Wirtgen paver with a custom wide trimmer to fine-grade the entire pathway. Designed specifically for this project, our slipform paver
allowed our 15-person crew to grade quickly and accurately, saving both time and money on the project.”
All projects have their challenges, and Chance explains that wind, heat, and a limited time schedule continue to be the real challenges on the CV Link Project. “We cannot control the weather, and our work has been restricted and even shut down a few times due to the heat and wind. Then there are the limitations due to the surrounding general public, limiting when and where we can work,” continues Chance. “Since the pathway is almost always near houses or businesses, we were limited to paving during the day, and since the average temperatures are well above 100 degrees, our hours of work are within a smaller window.”
Although Cooper Engineering is performing the fine grading and paving of this 14-mile CV Link pathway, they did not do any of the forming work. “We will place around 12,000 cubic yards of concrete with our Wirtgen SP 25i slipform paver,” explains Chance.
“The technology available with our Wirtgen pavers has allowed us to make up a lot of lost time. Another thing that has helped us to keep our schedule on this project is the great job that our concrete supplier, Hi-Grade Materials, has done in keeping us supplied in a timely manner.”
Atkinson Construction (Atkinson) was contracted for a $112 million contract from Caltrans to improve six miles of the 210 Freeway, adding an additional lane in both directions from Sterling Avenue to San Bernardino Avenue in the cities of San Bernardino, Highland, and Redlands, as well as an unincorporated portion of San Bernardino County. In addition, Atkinson widened 21 bridges,
constructed sound and retaining walls, replaced existing pavement, and developed drainage, sewer, and water systems. Cooper Engineering was subcontracted to perform top white paving, v-ditch drainage, and multiple types of PCC curb work. “We were on the 210 Freeway project from September 2021 to January 2023. We started the job at the 10-freeway interchange and moved north to Sterling Avenue,” explains Chance. “Our work consisted of placing 14,232 cubic yards of top white paving, followed by 1,205 cubic yards of v-ditch, and then closed the job placing 207 cubic yards of PCC curb,” says Chance. “This was also a tight access job, and we used our Gomaco paver for the top white paving, and two different Wirtgen SP 25i slipform pavers to do the v-ditch drain and curb work.”
Chance makes it clear that it is all about knowledge, experience, teamwork, equipment, and
especially partnering that makes the difference on any project they decide to take on. “We are successful because of the combined efforts of every person at Cooper Engineering. Knowing that the end product is the result of teamwork from all levels in an organization, the management at Cooper Engineering recognizes the importance of its employees along with clear communication and commitment on all issues,” continues Chance. “The best analogy I can use is one that we constantly talk about internally. Hod and Denise implemented this analogy from the book ‘Boys in the Boat.’ Our company is like a finely tuned ‘crew’ team. Each person has a specific place in the boat, and each is equally important. The key is for all to be in sync and always cooperating with one another.”
Chance is quick to give credit to all the great employees who have worked tirelessly over the years at Cooper Engineering. “None of this would, of course, have been possible
Above: CEI crews placing concrete pavement slabs for Atkinson Construction on the 210-freeway project near Sunland Blvd and I-5. Right: CEI places final curb for Atkinson Construction on the 210-freeway for the Highland Lane Edition project using their Wirtgen SP 25i curb slip form machine.without the hard work of Hod and Denise over the years. However, it has been everyone collectively that has allowed us to grow to new and exciting heights. I wish I could recognize everyone, but I will take a moment to thank and recognize my brother, Mitchell Cooper (Vice President) for the planning and execution he brings to the table every day. I also want to recognize Paul Loll, our Superintendent, and Lane Loll, our project manager, who are always there to help out Hod and myself with the organization and innovation that is needed on our job sites every day.”
The equipment a company chooses to use out in the field is also of great importance to Cooper Engineering. “It seems like we are constantly dialing in our machines and very much in the mindset that our growth and success depend on continually reinventing ourselves in our people and our equipment,” says Chance. “We appreciate the engineering and design that goes into manufacturing these complicated machines. Specifically, we appreciate and acknowledge the team from Wirtgen and Nixon Egli Equipment Co.”
Chance explains that everyone at Nixon-Egli and Wirtgen work together to service the needs of Cooper Engineering.
“We receive 24/7 support from both the manufacturer and distributor and have never had an issue that Wirtgen and Nixon-Egli have not been able to solve. They have stood by every Wirtgen purchase, and in this business, it all comes down to support after the sale,” continues Chance.
“We have worked closely with Wirtgen and their engineers over the years, and they are always
open to input and suggestions about functionality and design. Constantly improving upon these machines and keeping them dialed in is the key to our success here at Cooper Engineering.”
Chance Cooper points to Nixon-Egli Equipment Co. as Cooper Engineering’s main point of contact. “Jay Rosa is our Nixon-Egli sales representative, and he and Nixon-Egli have impressed us with a different and surprisingly refreshing type of service and support. The attention and respect we all receive from the entire team at Nixon-Egli are on a different level, and we very much appreciate their continued support.”
The importance of partnering is not just a trendy phrase or ideology for Cooper Engineering. “One of our highest priorities is choosing who we work with, and that is one of the main reasons we have been so successful. We are partners with everyone on every project we take on, and not just a subcontractor getting on and off a job for a paycheck,” concludes Chance. “Our company has been built from the beginning as a family, and that goes beyond genetics and birthright. Hod and Denise have created such an amazing company and operation that allows us all to be successful and thrive for generations to come. With the guidance and leadership of Hod and Denise, the second generation is now stepping up. Our core values and way of operating will continue to fulfill the legacy that has been created during these past 36 years. We will never stop innovating, creating, and improving as we continue to evolve into a bright and prosperous future.” Cc
POWERFUL
Responsibly remove concrete 25x faster than jackhammers. Hydrodemolition uses a highpressure water jet to blast concrete and preserve rebar. Our solution includes an automated water treatment system that allows contractors to safely recirculate or release water.
Low labor
Distributed by Brokk Inc. 1-360-794-1277
GOMACO is building on the success of the GP360, the industry’s first combination concrete slipform paver and placer/spreader on two tracks. GOMACO recently introduced the GP460 for widerwidth operations. As a placer/ spreader with a 60-inch belt, the GP460 will accommodate widths up to 50 feet wide. As a concrete slipform paver, the GP460 will pave widths up to 40 feet wide.
It’s built on the framework of the GOMACO two-track GP4 slipform paver with the ability to convert the prime mover into a concrete placer/spreader. The prime mover is equipped with vibrator circuits for paving and auger drive circuits for placing. Controlling the new technology is made possible with
the GOMACO-exclusive G+ digital control system. G+ seamlessly handles the controls conversion needed for each application while also bringing onboard Machine to Machine (M2M) communication, sonic sensors, 3D machine guidance, and more.
The GOMACO GP460 is powered by a Caterpillar C7.1 turbocharged diesel engine to efficiently drive the conveyor belt and distribute concrete across the grade. The high-volume, 60-inch conveyor belt can be mounted on either the left or right side, depending on jobsite conditions and the location of the haul road. It has a discharge speed of up to 492.5 feet per minute (150 mpm) for fast and efficient concrete placement. A controllable material deflector directs the flow of concrete at the discharge end of the conveyor for placement accuracy. A dual-drive auger system moves the material to the center or outer areas and across the strike-off. Cc
Expanding the product line, the new Cat® RM600 and RM800 reclaimer/stabilizers offer the power, performance and productivity needed to efficiently complete full-depth reclamation and soil stabilization projects. These versatile machines compete at the high end of the reclaimer/ stabilizer size class with an all-new adjustable height design capable of cross-slope cutting. Their powerful turbocharged Cat C18 engine gives the RM600 up to 17% more power than the RM500B. The RM800 delivers up to 42% more power than the
RM500B and up to 23% more power than the RM600.
These reclaimer/stabilizer models adopt key rotor system components from Cat cold planers for dependable cutting and mixing.
Featuring a belt driven rotor drive system, the machine is capable of flush-cutting on the right side. The new System K rotor uses the same cold planer fastener-free, dual-taper toolholder and base block components to deliver superior material quality on a range of projects. Exit and return-to-cut features simplify operation, save time and ensure the machine maintains a consistent depth of cut.
More information on the Cat RM600 and RM800 reclaimer/ stabilizers can be found by contacting a Cat dealer or visiting www.cat.com. Cc
NEW CAT® RM600 AND RM800 RECLAIMER/STABILIZERS OFFER MORE POWER, PERFORMANCE AND PRODUCTIVITY FOR FULL-The new GOMACO GP460 is an up to 50 foot wide placer/spreader and up to a 40 foot wide slipform paver.
Whether you're gearing up to lay a foundation or facing the challenge of demolishing old concrete, our machines are your ultimate allies. From precision excavation and seamless concrete removal to efficient material handling, our equipment empowers your team to work with speed and finesse.
www.wirtgen.com/concrete-paving
SP 15(i): The compact WIRTGEN slipform paver paves a wide range of monolithic profiles of up to 1.3 m high and concrete surfaces up to 2.2 m wide with highest precision. It is predestined for use on construction sites that demand a high degree of maneuverability and maximum flexibility. The mould can be flexibly positioned on either side of the machine. The machine can be precisely controlled by stringline sampling, without a stringline with WIRTGEN AutoPilot 2.0 or with 3D applications. Take advantage of the innovative solutions from the tech nology leader in the road construction segment. www.wirtgen.com
General Line Construction