C. A. RASMUSSEN, INC. Constructs World’s Largest Wildlife Crossing While Celebrating 60 Years of Construction Success in 2024
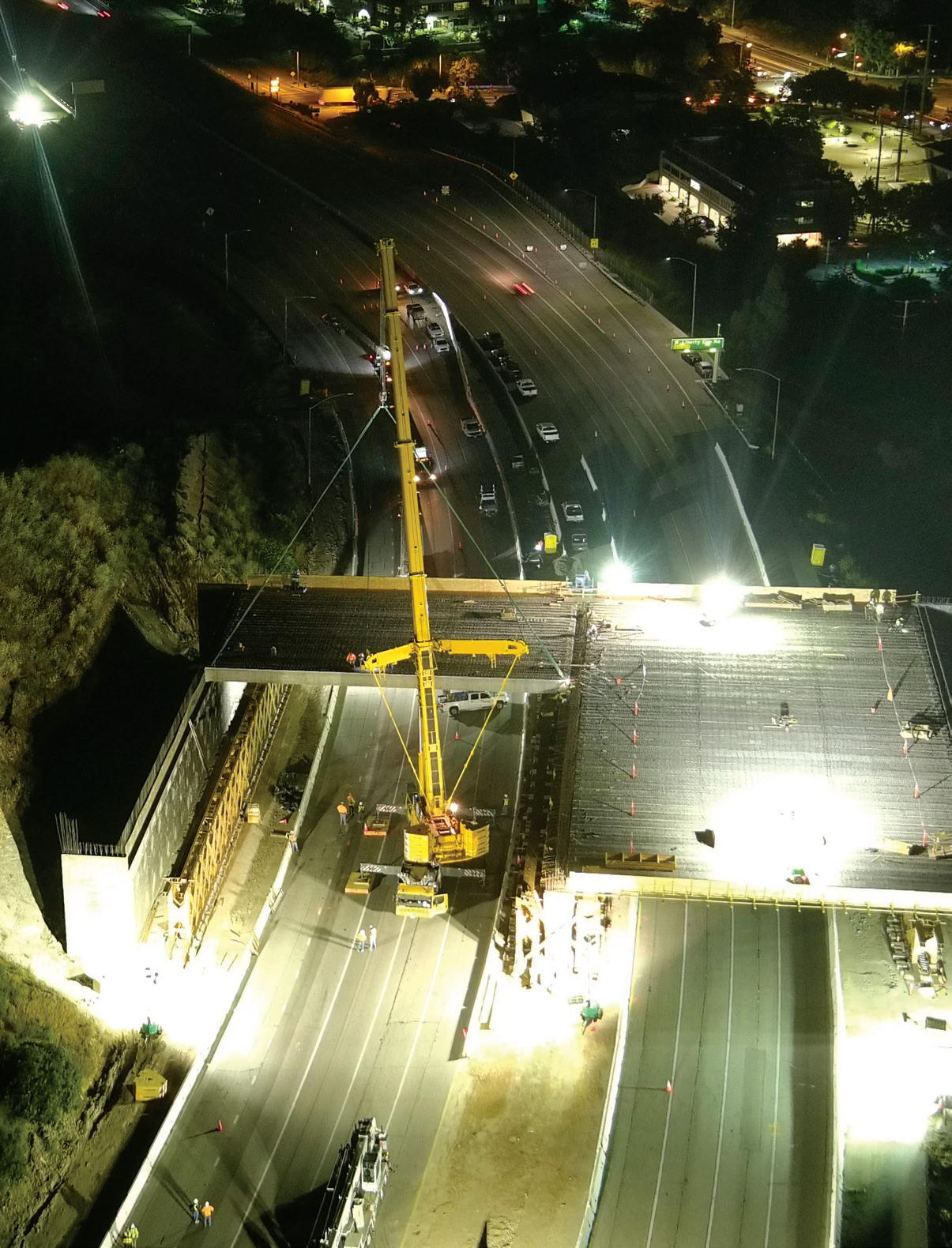
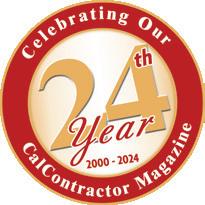
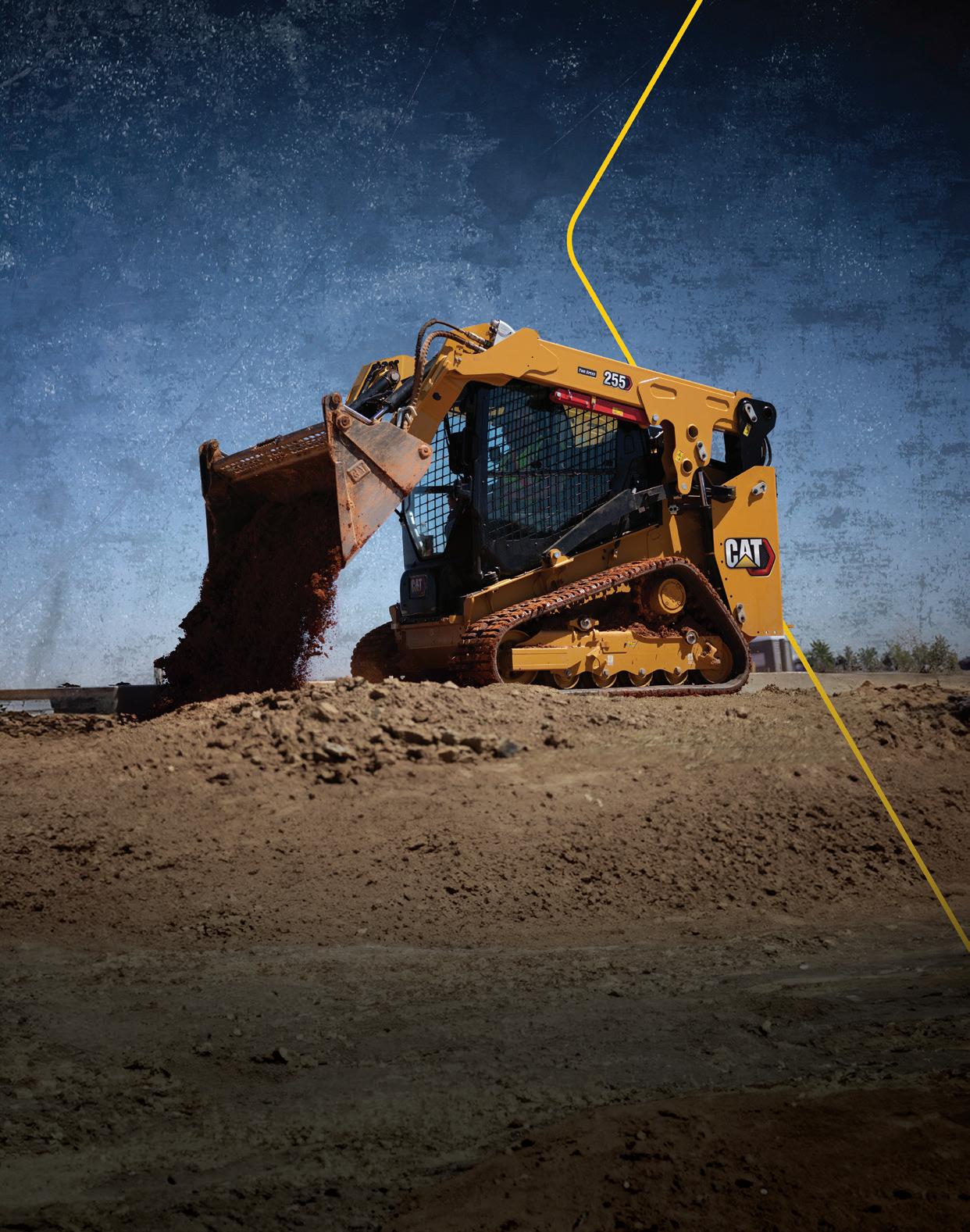

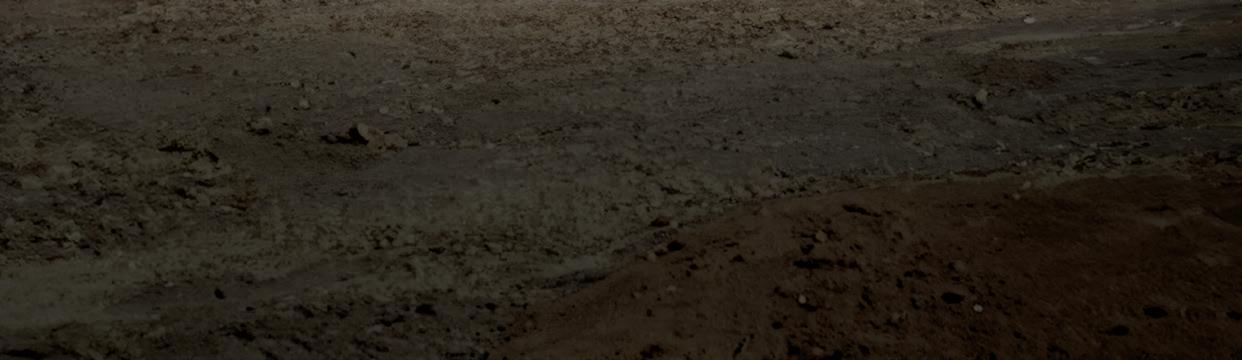
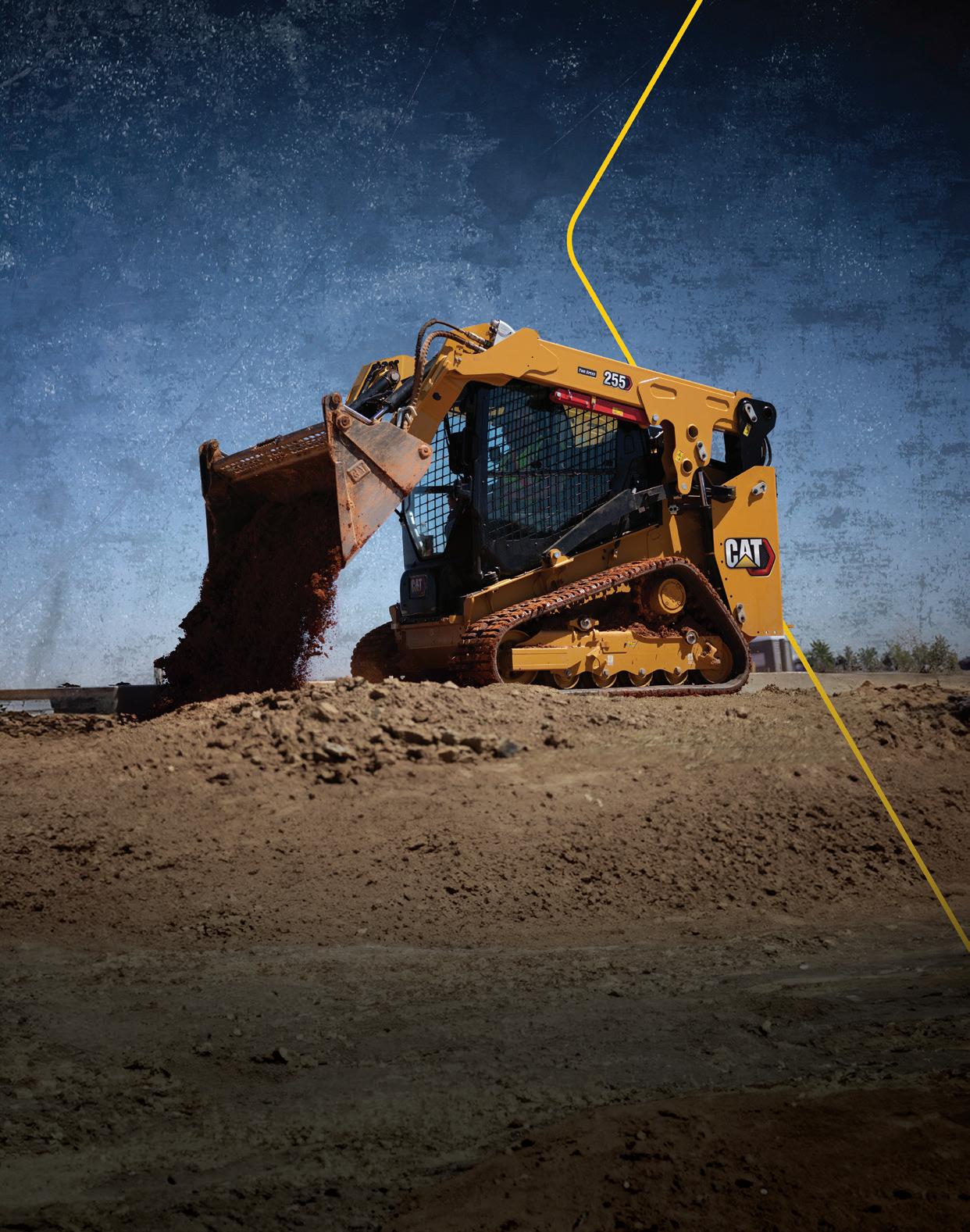
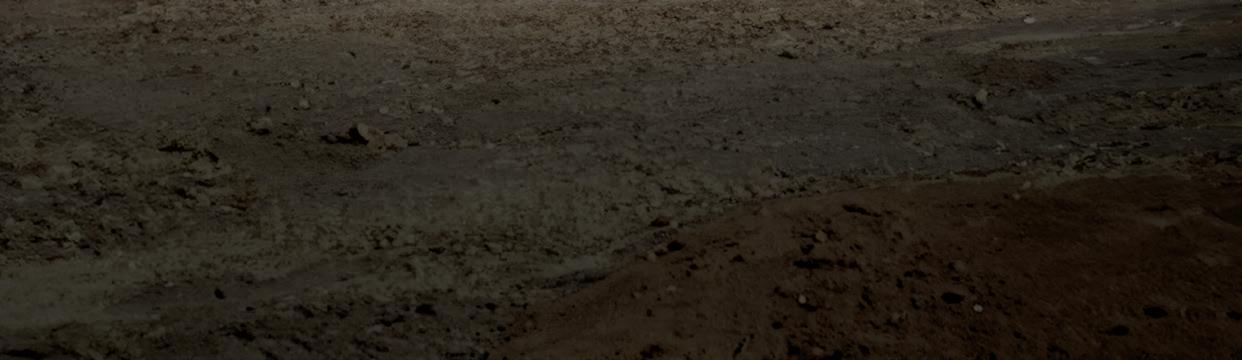
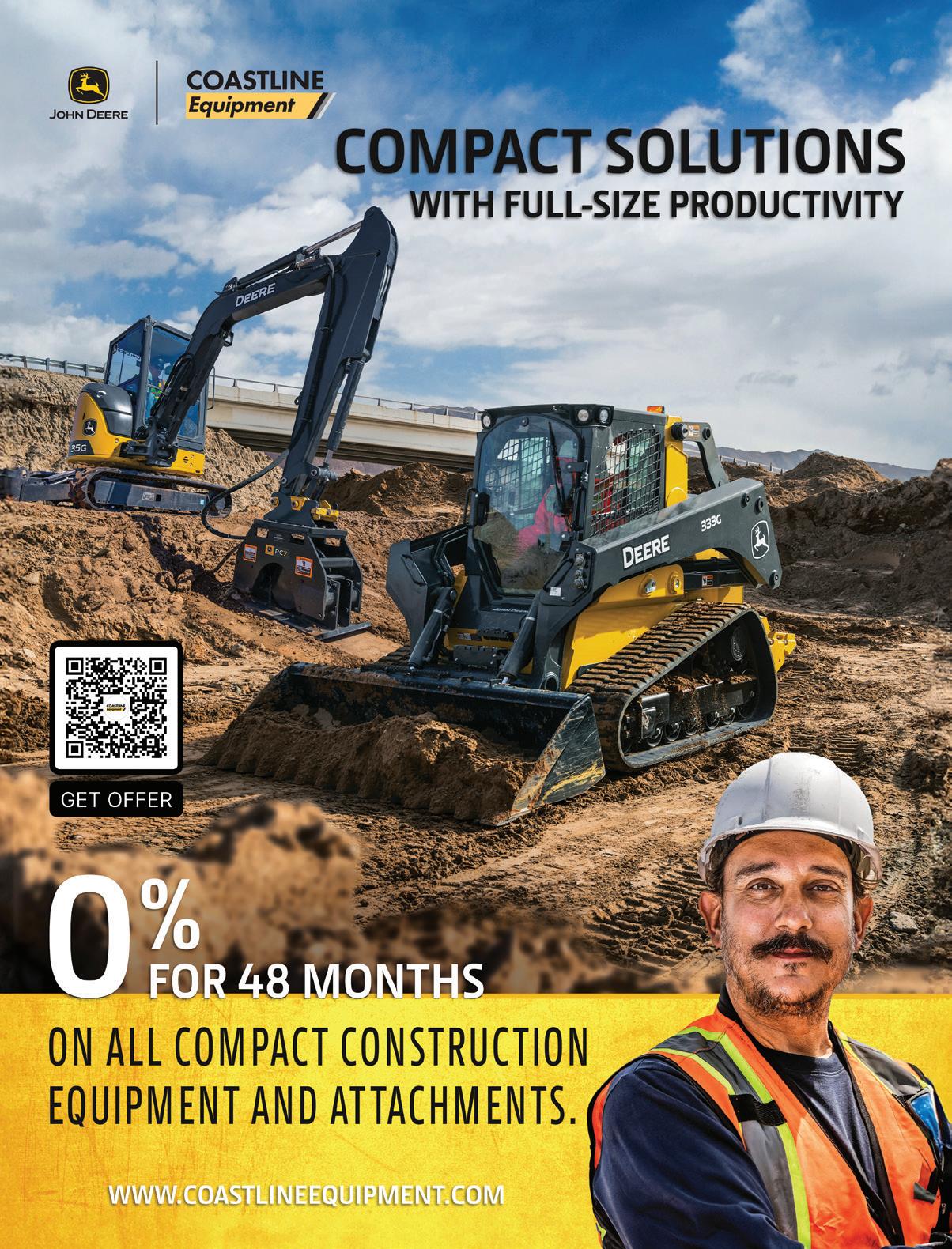
C. A. RASMUSSEN, INC. Constructs World’s Largest Wildlife Crossing While Celebrating 60 Years of Construction Success in 2024
Responsibly remove concrete 25x faster than jackhammers.
Light footprint.
Hydrodemolition uses a highpressure water jet to blast concrete and preserve rebar. Our solution includes an automated water treatment system that allows contractors to safely recirculate or release water.
Low labor
High production
On-site water treatment
Distributed by Brokk Inc. 1-360-794-1277
vcesvolvo.com
C. A. Rasmussen, Inc. (C. A. Rasmussen) is celebrating its 60th anniversary in 2024, marking six decades and three generations of family vision and leadership.
Carl A. Rasmussen started C. A. Rasmussen in 1964 after serving in World War II and then leaving the family farm in Colorado to pursue construction work in Southern California. Carl began as an owneroperator before going to work for
L.M. Wilson Construction Company for 13 years, and then eventually starting C. A. Rasmussen in 1964.
Over the years, C. A. Rasmussen expanded and reduced their operations statewide according to opportunity, the economy and whatever it would take to keep the company sustainable. Founder, Carl Rasmussen announced his retirement in 1977 and sold his shares to his three sons, Dean, Larry and Charlie. Dean served as President, Larry, Vice President
Above: C. A. RASMUSSEN , INC. subcontractor, Mr. Crane, placed a total of 82 (126 to 140 ton) pre-cast box girders on the Wallis Annenberg Wildlife Crossing Project using their 500 ton Liebherr LTM1400-7.1 with 152’ Main Boom Y-Guy & 264,600 lbs of CWT.
and Charlie oversaw fine grade and concrete construction. Sadly, Carl Rasmussen passed away in 1989 from ALS. By 2002, Dean and Larry had retired from the family business, leaving Charlie as the President and sole owner of C. A. Rasmussen. Adam Rasmussen now owns and operates the company as President and CEO. Adam earned his degree in construction management from Arizona State University, and immediately returned to work in the family business. Adam came up through the ranks just like his
father, estimating and serving as a field engineer and project manager on numerous and diverse jobsites. He was named Vice President of C. A. Rasmussen in 2016, eventually taking over the reins on September 13, 2021.
Now firmly in its third generation of family leadership, C. A. Rasmussen primarily serves Los Angeles, Ventura, and Kern counties with most of their projects being public works and approximately 10 percent in private construction. C. A. Rasmussen has built roads and bridges all over California for the past 60 years. Once known for their mass excavation abilities, the company is much more diversified today, able to take on more complex projects. Adding the ability to selfperform a larger scope of work, such as laying asphalt, building structures, and pouring concrete, has helped the company grow and added value to its customers.
C. A. Rasmussen is making their mark once again with the Wallis Annenberg Wildlife Crossing Project located at Liberty Canyon and the 101 Freeway. At a cost of approximately $92 million, the crossing will connect the Santa Monica Mountains and Simi Hills, spanning 10 lanes of traffic. If you are not yet aware of this project, just drive north of downtown Los Angels on the 101 Freeway near Agoura Hills and you will see the massive bridge crossing. The wildlife crossing is expected to be completed in 2026.
Rasmussen broke ground on this project during the 2022 rainy season, which made excavating around the 101-freeway difficult. “We designed and installed a shoring system for the abutment excavation. Once complete the crews went to work on constructing the center bent, which
Top Left: Adam Rasmussen discussing construction of over two miles of concrete barrier and sound wall on I-210 in Pasadena.
Left: C. A. RASMUSSEN, INC. crew using Palfinger truck crane to place metal forms in preparation of a night pour.
Above: Completed section of concrete barrier and sound wall.
are the columns located in the center of the 101 freeway,” says Rasmussen. “This section included 10 columns ranging in size from 20 to 25 feet in height. The abutments came next, 35 feet tall and 175 feet in width. All the concrete is colored with a beautiful architectural finish.”
To continue to paint the picture of the enormity of this project, the bridge crossing itself is 174 feet wide and 210 feet in length. 82 Massive pre-cast concrete box girders, provided by Coreslab, weigh in at 60 tons each and over 100 feet in length. Subcontractor, Mr. Crane, used a 500-ton crane to set the girders. All 82 of the boxes were placed in 24 days. “At completion C. A. Rasmussen will have poured over 3,500 cubic yards of concrete and placed one and a half million pounds of reinforced steel,” Rasmussen explained.
Above: C. A. RASMUSSEN, INC. paving a roadway in Victorville with their new Roadtec RP190 paving machine being fed by a Roadtec SB2500 Shuttle Buggy. C. A. RASMUSSEN, Inc . owns and operates Roadtec RP175 and RP190 paving machines and Roadtec SB2500 and SB3000 Shuttle Buggies. They also recently took delivery of a brand new Roadtec RP195 Highway Class Asphalt Paver from Herrmann Equipment.
C. A. RASMUSSEN, INC. using their Cat CB10 double drum roller purchased from Quinn Cat.
{ Continued from page 8 }
With over 12,200 daytime commuters per hour, C. A. Rasmussen performed the majority of the work at night to minimize the impact to the public. “We used our crews to take lanes each night to support our grading, structures and concrete operations. Self performing all this work allowed us to control the schedule and avoid any additional impacts to daily drivers,” continues Rasmussen.
Other challenging aspects of the crossing include the falsework “which is amazing,” Rasmussen said. 11,000 3/4” bolts and 100,000 board feet of lumber are a piece of the massive temporary support that was designed after the project was awarded. Both Rasmussen and Caltrans committed to a partnering process before the work even
started. “This process has proven to be successful several times,” Rasmussen said. The falsework, he said, is one example of such a partnership. After several months of working together, the team agreed to a final design and went to work. The falsework will remain in place until the deck is poured and all segments are tied together.
The Annaberg Wildlife Crossing is considered an earthen and vegetated bridge. Although considered a wildlife crossing, a pedestrian path will be constructed on either side of the bridge with a 20-foot concrete wall creating separation from wildlife. After the concrete deck is poured, waterproofing and drainage is installed allowing the concrete to be covered in dirt and landscaped to attract wildlife. Griffith Company and Pacific Waterproofing are the
subcontractors on this portion of work.
Rasmussen says the amazing crew and management team have already put in over 34,000 man-hours and that number will double before the project is complete (without including subcontractor hours). “We have a great team working on the crossing,” he said. Dave Dubois is the Project Manager and has been with C. A. Rasmussen for 28 years. Daniel Gonzales is the Project Engineer, Ismael Polanco is the Structures Foreman and Manhal (Mike) Sweden, is the Structure Superintendent. “Everyone on their crew deserves recognition for working so diligently on such an important project,” continues Rasmussen. “I also want to thank and recognize our subcontractors:
Malcolm Drilling, Integrity Rebar, Coreslab, Comet Electric and Griffith Company.”
The Wallis Anneberg Wildlife Crossing is a public-private partnership that has leveraged the expertise and leadership of dozens of organizations and institutions The core partners include Caltrans, the National Park Service, the Santa Monica Mountains Conservancy, Mountains Recreation and Convention Authority, Resource Conservation District of the Santa Monica Mountains and the National Wildlife Federation.
“This is truly an amazing project that will serve as the largest wildlife overpass in the world and protect wildlife such
as mountain lions, coyotes, deer, bobcats, gray foxes and rabbits while helping to restore area habitats and ecosystems,” says Rasmussen.
C. A. Rasmussen is made up of heavy construction specialists with capabilities to handle even the most complicated engineering problems. “Although the Rasmussen family has owned and operated this company for 60 years now, it has always been about the people. The individuals that choose to work here each day and give it all they have to get the job done right. We go to great lengths to find and maintain a
strong and talented workforce. We focus heavily on recruitment and retention of our team members. We have long term veterans working here and a mentorship program that ensures that they pass on their amazing talents and skills to the younger workforce,” concludes Rasmussen. “My grandfather Carl had a saying, ‘you can buy all the equipment you want, but none of that matters without the right people in the seat. They are the key to our and their own success.’ We all move forward together toward mutual success. We bring everyone in and up the Rasmussen Way. That is what it is all about now and for the next 60 years.” Cc
By
Growing up with a grandfather and father deeply rooted in the general civil engineering construction business, led Gavin Wakefield into an immersive world of building and craftsmanship. The sounds of machinery, the sight of blueprints, and the pride in a job well done were woven into the fabric of Wakefield’s childhood. Wakefield’s grandfather (Jim Hundley) and father (Dave Wakefield) were both contractors and developers right here in Southern California, developing major portions of Orange County, Lake Elsinore and Temecula. Following in their footsteps felt like a natural progression for Wakefield, not just as a career choice, but also a way to honor their legacy. While their teachings and values helped to guide Wakefield, he knew, that it would take a lot of tireless work to achieve his dream of one day owning his own construction firm.
Wakefield’s journey would begin by performing odds and ends small construction projects straight out of high school, and eventually earning a business degree from Grand Canyon University in 2014. After college, Wakefield went to work for a tilt-up construction developer out of Lake
Elsinore, before moving on to larger companies performing public works and prevailing wage projects.
“I grew up around private construction, but after going out on my own and experiencing the construction world for myself, I realized that my construction passion leaned more toward public works,” says Wakefield. “As I gained more experience, first as a project
engineer and then a project manager for public works firms for five or six years, I finally decided to go for my B contractor’s license in September 2019, while also making the decision to start Wakeco Construction, Inc. Then in December of 2021, I got my A license to begin work as a general contractor specializing in public works, working on government
contracts for schools, parks, municipalities and anything bond funded.”
Wakeco Construction hit the ground running after Wakefield’s controller helped him get his books together for the surety company. “Our first bond was for $500,000 and we were bonded out after just two jobs. We kept our nose to the grindstone and grew Wakeco from
Above: KGG Concrete, Inc. pouring structural foundation for retaining walls at Fallbrook Unified, and pouring in place walls for City of Beaumont.
a two to three-person office to 20 within a relatively short period, and advanced to a $20 million bond limit,” says Wakefield. “We are growing quickly and sustainably, doing around eight million last year and on track to do $20 million by the end of 2024.”
Wakeco specializes in government contracts for schools, parks, municipalities and general packages like ground up and tenant improvements. The company is currently performing a ground up classroom building project in Fallbrook and a greenhouse
and restroom facility project, also for Fallbrook Unified School District. Additionally, Wakeco is on a contract at this time where they are redeveloping the Ontario Police Department, after recently completing a new fire station for the City of Ontario. “We are right on track here at Wakeco due to folks like our VP of Construction, Steve Stehrenberger, our Preconstruction Estimator, Anna Velazquez, our Controller and Compliance Director, Lucy Testerman, our Assistant Project Manager and Training Development
Director, Melissa Ison, and of course my wife and partner in Wakeco, Kristen Wakefield.”
Wakeco Construction is a pure general construction firm and does not self-perform any of the trades on their projects. However, that does not mean that Wakefield does not have the desire to be a self-performing contractor. Quite the contrary. He has long had a passion and desire to for the concrete construction business. { Continued on page 18 }
“I have always liked and was intrigued with the concrete construction trade but had not found time in the past to pursue that interest,” continues Wakefield. “Now that Wakeco is firmly situated with a strong foundation, and a huge backlog of work on the books, I have found time to further pursue my love and passion for concrete construction.”
Wakefield rolled out his new company, KGG Concrete, Inc. in January 2024. The name KGG was named after, represents and honors Wakefield's three children, Kinsley, Gunner and Graham. “I got my first hands-on experience with concrete in the tilt-up industry and wanted to enter this specialty. Concrete is a solid trade and quite frankly the margins are better. KGG is all about and only about concrete and we are already making our mark,” says Wakefield. “I hit the ground running in January and brought on Rick (Ricardo) Martins as our Director of Construction and Estimating. Rick has a heavy background in both concrete and asphalt and has been estimating for the past 12 years. He has done an amazing job, growing KGG from
two to 18 people since March with a $3 million backlog.”
Gavin Wakefield has never been accused of cutting corners or underpaying his workforce. “I have been told in the past, from our accountant and business advisors, that my overhead can look a bit heavy at the beginning. I reply by telling them to ‘trust the process. Trust the system,” says Wakefield. “I invest in the best people and therefore get the best result. I took this same philosophy from Wakeco over to KGG and went after the best people out there with the most experience and it has proved me right both then and now.”
KGG Concrete, Inc. (KGG) primary focus right now is on concrete flatwork and smaller structural work like curb & gutter, sidewalks and pouring foundations. “Our concrete work is focused primarily on public works. We are currently working on or have completed projects for numerous school districts, cities, and counties, on a prevailing wage basis. We are on a job right now for the City of Beaumont doing concrete work on their public works facility, as well as constructing and pouring slabs for Fallbrook Unified.
Additionally, we are on a good-sized concrete project for Victorville Unified School District,” explains Wakefield. “Most of our work is from San Diego to Victorville, with jobs ranging from just a few weeks to six months, like the job we are on in Fallbrook right now. With people like Rick Martins and Jeff Brown, our Field Superintendent with 30 years in the concrete industry, we have set ambitious goals for KGG, including reaching $20 to $25 million within the next five years. Our talented team and signature hires for both Wakeco and KGG has put down an amazing foundation for the future. We are building generational companies, not only for my children, but also for our employees and hopefully their children. We are in this for the long haul with dreams of one day competing and winning bids against the largest concrete and general construction firms in the industry.”
Wakeco Construction, Inc. and KGG Concrete, Inc. are headquartered in Temecula. For more information, please visit www.wakecoinc.com or call (951) 200-5758. Cc
By
Founded in 1989, Largo Concrete, Inc. is a leading full-service concrete contractor renowned for its expertise in constructing complex and high-profile concrete structures across the Western United States. Headquartered in Tustin, California, Largo is a familyowned enterprise that has grown into one of the most respected names in the industry. Known for its ability to tackle challenging projects with precision and efficiency, the company's services encompass a wide range of sectors, including commercial buildings, residential developments, parking structures, healthcare facilities, and public infrastructure projects such as bridges and transportation hubs.
Largo Concrete is recognized for its innovative approach to construction, often employing advanced techniques like posttensioning, high-performance concrete mixes, and complex formwork systems. In addition to its technical expertise, Largo Concrete
is also well known for its collaborative approach, working closely with architects, engineers, and general contractors to deliver projects on time and within budget. Over the years, Largo Concrete has been involved in the construction of iconic structures, including highrise buildings, sports arenas, and large-scale urban developments, solidifying their status as a key player in the concrete construction industry. In this article, we will
feature two of Largo’s projects, one recently completed, and the other in final stages. Chris Wills has been with Largo Concrete, Inc. since 2003 and today proudly serves as one of their senior project managers. Wills was responsible for overseeing construction on both the 735 Apartment Unit Project on 5420 Sunset Boulevard and the Alloy Art District High-Rise project on 525 S. Santa Fe Avenue. in Los Angeles.
Hollywood has been experiencing a transformation with new residential developments catering to professionals and creatives who are drawn to the area's dynamic lifestyle. The 5420 Sunset Boulevard project is anticipated to contribute to the area's growth, blending urban living with the cultural and historical significance of Hollywood. The recent construction of 735 apartments at 5420 Sunset Boulevard in Hollywood marks a significant addition to the vibrant Los Angeles neighborhood. Located in the heart of Hollywood, this development is part of the ongoing efforts to meet the increasing demand for housing. The apartments are expected to offer modern amenities and are strategically placed to provide residents with easy access to Hollywood's entertainment industry, dining, and shopping venues.
The 735-unit apartment project is part of a larger mixed-use complex at the intersection of Sunset Boulevard and Western Avenue in Hollywood. Located on the former site of a 6.7-acre Food4Less-anchored shopping center, the property is being
redeveloped by American Commercial Equities. New construction will feature 735 studio, one-and-two-bedroom apartments, up to 95,000 square feet of commercial space and 1,400 parking stalls.
Largo began their work on the 735 apartment Sunset Boulevard project on July 1, 2023, and officially topped out on July 31, 2024. They still have three to four months of work left to wrap up the curbs, pads, cleanup and repairs. Largo is self-performing the structural concrete and managing subcontractors for the shotcrete, masonry and rebar concrete reinforcement. Senior Project Manager, Chris Wills says that the project is situated on a large 265,000-square-foot area, allowing for several crews to work at the same time. “This particular structure did not require enormous footings or big mat pour foundations, due to its smaller vertical size. We installed regular, conventional spread and continuous footings, but by simple sheer volume size of the site, we still poured more than 55,000 cubic yards of concrete provided by CalPortland. This included pouring concrete for two subterranean levels of parking space, one ground level of parking and retail, and a set of decks going up 25 feet on one side, and 15 feet on the other side.
From there, the structure was wood framing and went up four more stories,” says Wills. “Our crews used a standard three-piece deck system with as much as 150,000 square feet of formwork on site at one time. This job was not fancy or atypical. It was just massive and required a lot of close management and coordination. We had three crews working in one area and two crews working in another. If we weren’t pouring a deck, we were pouring vertical on almost every day. Luckily enough, we had an exceptionally knowledgeable ownership group in place that assisted us every step of the way. Additionally, the architect, TCA, maintained an office on-site, and the structural engineer, VSM2, was on everybody's speed dial. With their help, we finished the project on time and on schedule.”
Wills explains that the 735-apartment-unit project on Sunset Boulevard utilized post-tension concrete design and approximately 15,700,000 pounds of rebar. “The post-tension and steel reinforcement work was performed by our subcontractor, Pacific Steel Group (PSG). This included the slab, footings and all 800,000 square feet of elevated deck,” continues Wills. “We had three of our placing booms onsite and six placing boom locations.
1
Booms were consistently being moved around to give our crews the appropriate place to pour. To add to all this movement, we also had to maneuver around the numerous trades, like the electricians, plumbers and framers who were hard at work throughout the jobsite.”
Largo was also responsible for placing the perimeter shotcrete walls, going through 3,000 yards of concrete in the process. The contract also called for more than 100,000 square feet of nonstructural masonry walls to support the electrical and generator rooms in the parking garage and other areas. “This project made use of just about every imaginable trade, including earthwork. We moved around 10,000 yards of dirt for our footing construction alone, requiring the use of backhoes, skip loaders, wheel loaders, telehandlers and numerous Putzmeister pumps. There were also two Liebherr tower cranes from Maxim Crane,” says Wills. “I think at peak, we had three placing booms onsite with probably a half mile of system everywhere. Additionally, we had around 150 individuals working onsite between all of the laborers, carpenters and ironworkers.”
2
3
4
The Alloy Development high-rise at 525 S. Santa Fe Avenue in Los Angeles is set to be a landmark project in the Arts District, encapsulating the neighborhood's evolution from an industrial area to a vibrant, mixed-use urban environment. The 35-story high-rise represents a significant milestone in the transformation of the Los Angeles' Arts District. The high-rise will be a mixed-use tower, combining residential, retail, and designed to meet the growing demand for housing and amenities in this vibrant part of the city.
The Alloy development, which is being built by San Francisco-based Carmel Partners, replaces a late 1980s industrial facility. The completed project will include a total of 475 live/work apartments, 105,000 square feet of office space, approximately 18,000 square feet of street-level shops and restaurants, and parking for 650 vehicles. The visual centerpiece of the mixeduse complex is a new 35-story, 390-foot-tall tower, which will rank as the tallest building in the Arts District at completion. The tower
will share a podium with a smaller mid-rise office building to the west, which will front Mateo Street.
Largo’s work on the Alloy Arts District high-rise began in February 2022 and topped out on September 23, 2023. “This project required a mat foundation that was already fully excavated 35-feet in depth to accommodate three levels of subterranean parking. We began by pouring a 3-inch rat slab over an 85,000 square foot area. The rat slab was necessary to support the rebar and for the waterproofing and installation of a methane barrier,” continues Wills. “Next, we started with the rebar reinforcing work, again subcontracted to PSG. We went through 20,500,000 pounds of steel to support the entire 35-story structure, including a mat slab that was 3-feet to 13feet thick. The elevator pit had the thickest section of concrete of 13-feet to support the main tower. In all, we poured 75,000 yards of concrete provided by Associated Ready Mix, with the mat foundation
{ Continued on page 24 }
alone requiring 15,000 cubic yards. The mat called for a total of five pours, the largest being 8,500 yards that took 14 hours, 850 concrete trucks, eight pumps and one placing boom to accomplish.”
Wills says that his crews relied on two placing booms, one for the residential tower and the other for the adjacent office tower. Although the job is referred to as a 35-story high-rise, there is actually 39 floors, with the 35th floor containing the penthouse level with amenities like the pool, spa and gym. From there the 36th and 37th floors are roof levels, the 38th is where the elevator ends and the 39th is a 20-foot by 25-foot elevator doghouse. “We went 390 feet vertically and poured 1,100,000 square feet of elevated deck. In the interest of time and efficiency, we utilized a self-climbing core on the tower with specialized formwork with a dedicated placing boom on top. So instead of moving the formwork with a tower crane, level by level, the formwork was attached together utilizing a DOKA super climber platform with six long hydraulic rams attached to the core. You simply push a few buttons, and the entire wall core climbs up the inside while we slide the outside forms in place on the residential tower,” continues Wills. “We used a three-piece
decking system to pour 8-inches of concrete on all levels of both buildings. The office building was eight stories tall and also had its own dedicated placing boom.”
Beyond the structural concrete, Largo was also called upon to construct architectural board formed structural walls, columns, ceilings and decks. “We selfperformed the board form work on a normal cycle and production rate. Our Senior Superintendent, Gary Schulman has a lot of experience with this art form and helped us to provide several mockups to the owner,” says Wills. “This work was performed on the southwest side columns, the office building columns and office entrance, and some roof soffit, and tree planter area. It turned out really nice with uniform consistency throughout, all with our people in production mode.”
As Largo Concrete, Inc. continues to play a pivotal role in shaping the skyline of Los Angeles, their commitment to excellence and innovation in concrete construction remains unwavering. The successful execution of both the 735 Apartment Unit Project on Sunset Boulevard and the Alloy Arts District High-Rise exemplifies the company's ability to handle large-scale, complex developments with precision and efficiency. Chris Wills and his team have not only contributed to the
architectural transformation of these neighborhoods but have also set a high standard for future projects in the region. Largo’s dedication to quality, collaboration, and sustainable construction practices ensures that they will remain a leading force in the concrete industry for years to come, continuing to build the foundations of tomorrow’s urban landscapes.
For more information on Largo Concrete, Inc., please visit www.largoconcrete.com or call their Tustin, California headquarters at (714) 731-3600. Cc
xtreme Pressure Systems, Inc. began its journey in 2002 when Jeff Koval, Jack Burns, and Tom Navarro partnered up and decided to work out of Koval’s garage with a desire to provide surface preparation solutions to general contractors, developers and other end users within the construction industry. In the beginning, Extreme Pressure Systems, Inc. (EPS) specialized in ultra-high waterblasting (up to 40,000 psi) with vacuum recovery. They worked primarily with abatement companies who needed asbestos and lead removal. EPS also found a niche in removing rubber marks from airplane tires on runways at California airports.
As their business evolved, they recognized the additional need that general contractors had for surface preparation services. This included hydrodemolition services where they began using hydrohigh-pressure devices to remove concrete. EPS has two distinct surface preparation divisions, mechanical and hydrodemolition. The two divisions take care of all
kinds of surface preparation from concrete polishing, coating removal, shotblasting, waterblasting and hydrodemolition.
Tommy Niemerow has been with EPS for 10 years, overseeing sales and helping to manage overall operations. “At EPS, we are very specialized in what we do and offer. For example, Caltrans may request a special demolition process on a bridge deck because they do not want a hydraulic hammer being used as it can create spider cracking (micro fractures) throughout the rest of the surface and damage rebar. Hydrodemolition also washes the surface clean and removes any debris around the rebar. So, they will call for bids from companies like EPS to use hydrodemolition that will remove specific sections of concrete without damaging the rest of the structure,” says Niemerow. “We recently purchased a new Aquajet Aqua Cutter 750V to perform concrete removal for cities, counties, and other government agencies, as well as for construction firms. Our Aquajet always gets a lot of attention on a jobsite, and
everyone is amazed at the speed and precision we get from this machine. We recently completed a bridge deck removal job that had several damaged sections right along the bridge joint. The area in question was 18 inches wide and 40 feet in length. This contract may have taken a conventional crew six or seven days to complete, where we were able to have everything wrapped up in four hours with our Aquajet.”
Niemerow says that EPS has a large fleet of specialty equipment and attachments for any sized project. “Our surface preparation and hydrodemoliton fleet is the largest and most diverse in California. Jeff Koval (co-owner) does a lot of research on what is available to ensure that we always have redundant pieces of equipment in every category, size, and power type for all possible applications,” says Niemerow. We strive to always put the right tool on the job therefore saving all parties time and money. “All of this state-of-the-art equipment is of course meaningless without the best crews and operators to run
The Aqua Cutter 750V
can work on flatwork, overhead, and on walls. They offer many accessories to reach concrete in challenging locations.
them. Most of our team members have been with EPS for more than seven years, with several key members celebrating 10 to 15 years. Our employees and pride in our craft is what makes us the best in our business.”
According to Niemerow, the Aquajet 750V has numerous tasks and functions it can take on that make removing concrete cleaner, faster, more efficient, and with no operator fatigue. This includes piers, roads, bridges, reservoirs, tunnels, silos, tanks, walls, roof decks, foundations floors, airport runways, walls and other concrete structures. “We recently completed a project for LAX where we were tasked to remove 12 inches of concrete near a runway. During repairs it is very difficult, if at all possible, to get a hydraulic hammer through three layers of rebar. So, we went in with our Aquajet 750V and performed hydrodemolition on the 12 inches of concrete, down
to the base rock. The contractor was then left with the best possible surface to pour back the new concrete and make a solid connection with the existing rebar,” continues Niemerow. “We also remove the rubber buildup from aircraft tires on all California airports. This, however, is accomplished using our ultra-high waterblasting compact vacuum rigs. Over the past 10 years, we have removed around 20 million square feet of rubber each year, from just about every non-dirt airport runway in California.”
The most high-profile project to date that EPS has used their Aquajet 750V on would most definitely be the work they did for prime contractor, Security Paving Company, on the I-10 Fire that damaged 450 linear feet of the elevated freeway bridge section. This happened in the early hours of November 11, 2023, when a two-acre scrap yard fire beneath the I-10 freeway in Los Angeles did so much damage
that it prompted an immediate closure and a declaration of a state of emergency. By 11 a.m. the following morning, Security Paving Company and Griffith Company were contracted to stabilize the supporting structure of the affected burned bridge section. After the freeway was successfully shored up and reopened, Caltrans engineers analyzed core samples of burned columns and bridge deck and determined that it could be repaired rather than demolished and replaced. “During a fire, concrete becomes dehydrated, soft and crumbly, losing its structural support. Security Paving Company asked us to remove 2 ½ inches of concrete on the underside of the elevated I-10 freeway bridge,” says Niemerow. “We removed over 22,000 square feet of concrete under the affected I-10 freeway bridge section so the gunite contractor could shoot concrete up and under the existing rebar. Imagine attempting this with a hydraulic hammer, upside down and risking spider cracking, and stress fractures, while taking way more time in the process.
Getting as much of the concrete off of the rebar is key, and using our Aquajet 750V unit with its proprietary and patented infinity pattern helped expedite the process. This allowed the operator to set the angle of the nozzle to come up and over the rebar, removing the maximum amount of concrete for a better bond. Caltrans and Security Paving Company were great partners and easy to work with on this important project. They worked hard to create a teamwork mentality that allowed us to finish ahead of schedule.”
AQUA CUTTER 750V HYDRODUMOLITION ROBOT
Niemerow points out that the Aqua Cutter 750V Hydrodemolition Robot from Aquajet has a 20-foot expandable mast with multiple heads. EPS inverted the head under the bridge, using the patented Infinity Oscillation System and next generation Evolution Control System that automatically calculated optimal settings. “The Aquajet allows our operators to
program different shapes that they may encounter and want to target right into the system. This helped out immensely on the I-10 bridge and other projects where we are able to go right around obstacles and avoid stopping and resetting,” continues Niemerow. “We spent several years researching and testing several manufacturers before purchasing the Aquajet. In the end, it really came down to service and support, and who was going to help us retain clients through speedy response time. The support we have received from Aquajet before and after the sale has been amazing. They always responded quickly, with helpful and intelligent answers. We are also impressed with their parts and supply network. We carry a lot of parts internally, but when we need something from Aquajet, we get it the very next day.”
EPS has used their new 750V on several other applications since purchasing in January. These include specialized wall projects like the one they recently completed at a high school in Northern California. “We have
worked on stripping sections of concrete walls for school districts in the past and we typically use a lance gun to shoot water at 40,000 PSI to remove the surface. But on other projects, like the one we just completed, we are working on four separate buildings, utilizing scissor lifts or scaffolding at heights of up to 19 feet. Holding a heavy spray device for 8 hours a day at 40,000 PSI is exhausting. The ability to automate the process with an Aquajet robot allowed us to achieve better production time, work more efficiently and make the process easier on our team members,” continues Niemerow. “We have yet another project coming up soon where we will use our Aquajet 750V on the structure where chemicals have deteriorated the concrete. We will use the 750V to remove six to eight inches of concrete to get down to the solid, unaffected concrete behind. This will require a different head attachment than we would use on a bridge deck project and also a vacuum recovery system.”
{ Continued from page 28 }
Beyond waterblasting and hydroblasting, EPS also performs shotblasting. “Shotblasting also has its place for concrete removal. We used this method to remove concrete on a 2-million square foot job in the Bay Area on the San Mateo Bridge. We were able to complete 100,000 square feet each night utilizing five machines. We also use this method to remove material while leaving the wall intact, and to create a concrete surface profile (CSP). However, when it comes to removing concrete 6, 7, 8 or even 12 inches, with rebar or other structural components present, water is indiscriminate and will keep removing until it finishes. After all, water is the most powerful natural resource. It is the better choice for many applications, but every job has a solution and EPS has the equipment, the people and the know how to get it done safely, efficiently and on time,” says Niemerow. “In addition to our waterblasting and hydroblasting tools, we also own and operate high pressure pumps from
companies like NLB Corporation. Our engineers perform calculations to determine the pressure and water flow needed for each application. Sometimes we are running 40 gallons per minute, or 12,000 gallons of water per shift, and others, like the I-10 job, we will run 10 gallons per minute, which is only like 4,000 gallons per shift.
Dave Burns oversees sales, project management and overall operations for Extreme Pressure Systems. “Surface preparation is what we do, and we do it all from hydroblasting (water), shotblasting (metal pellets), grinding, polishing and scarifying (milling concrete). Every job is different, and no slab of concrete is ever the same,” says Burns. “You have something difficult or seems impossible? That is where we shine. Every job requires a special, custom solution, and we have the people and the equipment for everything and anything when it comes to concrete surface preparation and demolition. From a small room to massive bridges, we have the right tool for the job, every time.
Concerning the Aquajet Aqua Cutter 750V Hydrodemolition Robot, Burns has this to say, “I love our new Aquajet robot and I don’t think there is anything better for certain applications. It was the perfect machine for the I-10 bridge job where we wanted to maintain our high quality standards yet were under tight time constraints,” continues Burns. “Using our Aquajet on this project allowed us to meet the deadline with the best possible results, all at a reasonable cost. It is a very efficient, portable machine that I am proud to have in our fleet and at our disposal.”
A question that always seems to come up concerning hydroblasting services is the question of what is done with the wastewater. Some contractors choose to truck the wastewater away for treatment, while others choose to contain and treat the water onsite. Aquajet’s EcoClear water treatment system enables the operator to safely discharge wastewater back into the environment or recirculate it back into the robot without the need of constant fresh water, an
extra water reservoir, or a thirdparty source to collect and truck off the water. With EcoClear, the collected water is pumped into an inlet chamber where a flocculating agent is added, before flowing into a second chamber that introduces carbon dioxide, rather than mineral acid to reduce pH levels. The solid particles settle into the storage hopper and is removed while the water continues to another chamber for a second pH adjustment. The water is then ready to be reused or flow back into the environment.
Adam Weiss wears multiple hats, working for Extreme Pressure Systems each day. He is the company’s hydro specialist and works with operators and technicians to make sure the right machine is being utilized properly on each job. “The Aquajet Aqua Cutter 750V Hydrodemolition Robot is the perfect addition to our fleet for many reasons. For the I-10 job, the mobility and it’s mast reach allowed us to go vertically over 20 ft unassisted, which is a huge benefit and
advantage. The Aquajet also has its patented infinity head pattern with continuous motion. This provides a much more consistent profile. Another great feature is the shape function which helps to target specific areas more precisely, which we used a lot on joints and detail work,” says Weiss. “In addition to many features, I especially value the Aquajet’s durability and dependability. We did not have one breakdown on the I-10 job, other than blowing a hose which is normal wear and tear.”
Weiss says that Extreme Pressure Systems currently utilizes vacuum recovery systems on their jobsites but have recently been looking at Aquajet’s EcoClear system. “EcoClear is a fully automated water recovery system that will both reduce labor and provide a treated water to be returned to the environment or recycled back into the equipment. As California is very water conscious this is something that makes a lot of sense on a jobsite,” continues Weiss. “I also want to take a moment to talk
about NLB Corporation and their water pump system. We use NLB pumps to pressurize the water for our hydroblast systems. Like the Aquajet, the NLB pumps are hardworking units with many technological advantages. We are able to sync our NLB pumps with the Aquajet robot using an electronic clutch that allows our operators to control the pressure from the Aquajet’s main controls. We love efficient technology and both the Aquajet robot and NLB pumps have been great additions to our fleet.”
Extreme Pressure Systems mission is to solve client surface preparation issues by having the correct piece of equipment, properly trained professional crews with project managers that work hard to understand the client’s needs. They serve all of California with projects in Nevada, New Mexico and other neighboring states as needed. For more information on EPS, please visit, www.extremeprepandpolish.com or call their Camarillo headquarters at (805) 482-0101. Cc
Powerful performance, increased productivity
Get power and ef ciency in a big package with a hybrid excavator designed to reduce fuel consumption while driving performance. When swinging, all available hydraulic power is sent to the boom, arm and bucket for improved cycle time and increased production.
All hybrid components are covered by a 7-year/15,000 hour fully transferable warranty.
Models range from:
• 60-90 hp • 1,600-3,400 lb
The multifunctional slipform paver paves a wide range of monolithic profiles up to 2.0 m high. It can be used to easily pave concrete surfaces up to a paving width of 3.5 m using both the inset and offset methods (cannot be combined with all options).
One or two hydraulic parallelogram swing arms at the front and two hydraulically telescoping crawler units at the rear make it possible to pave concrete in an extremely flexible manner.
The intelligent, electronic steering and control concept means the machine can be driven through very tight turning angles and is highly adaptable to any building site situation. The machine can be precisely controlled via stringline scanning, without a stringline using WIRTGEN AutoPilot 2.0 or via 3D applications.