
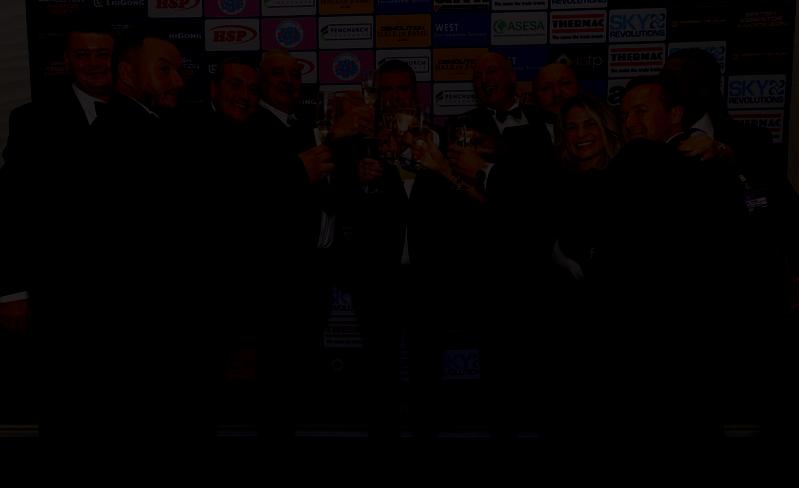
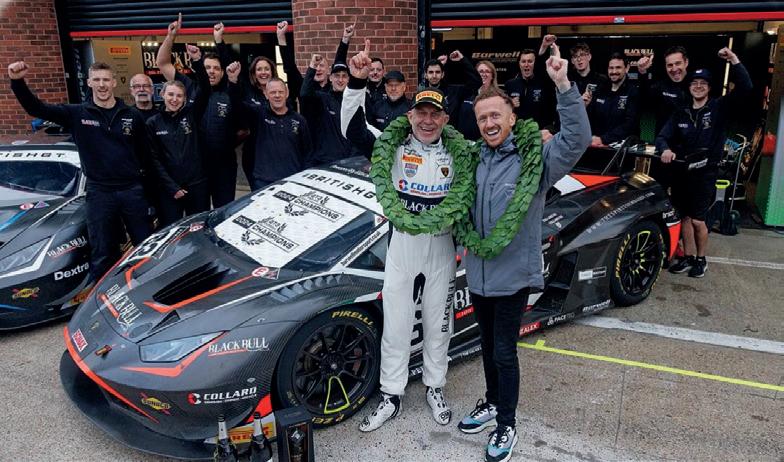
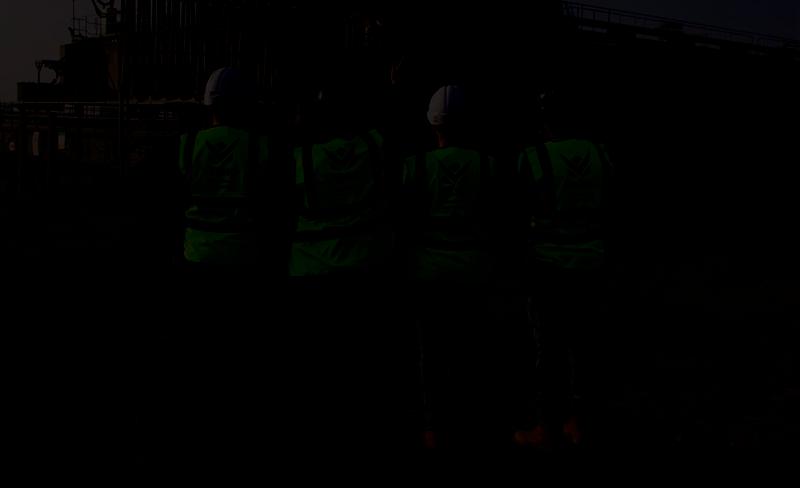
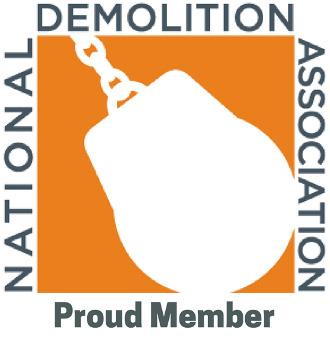
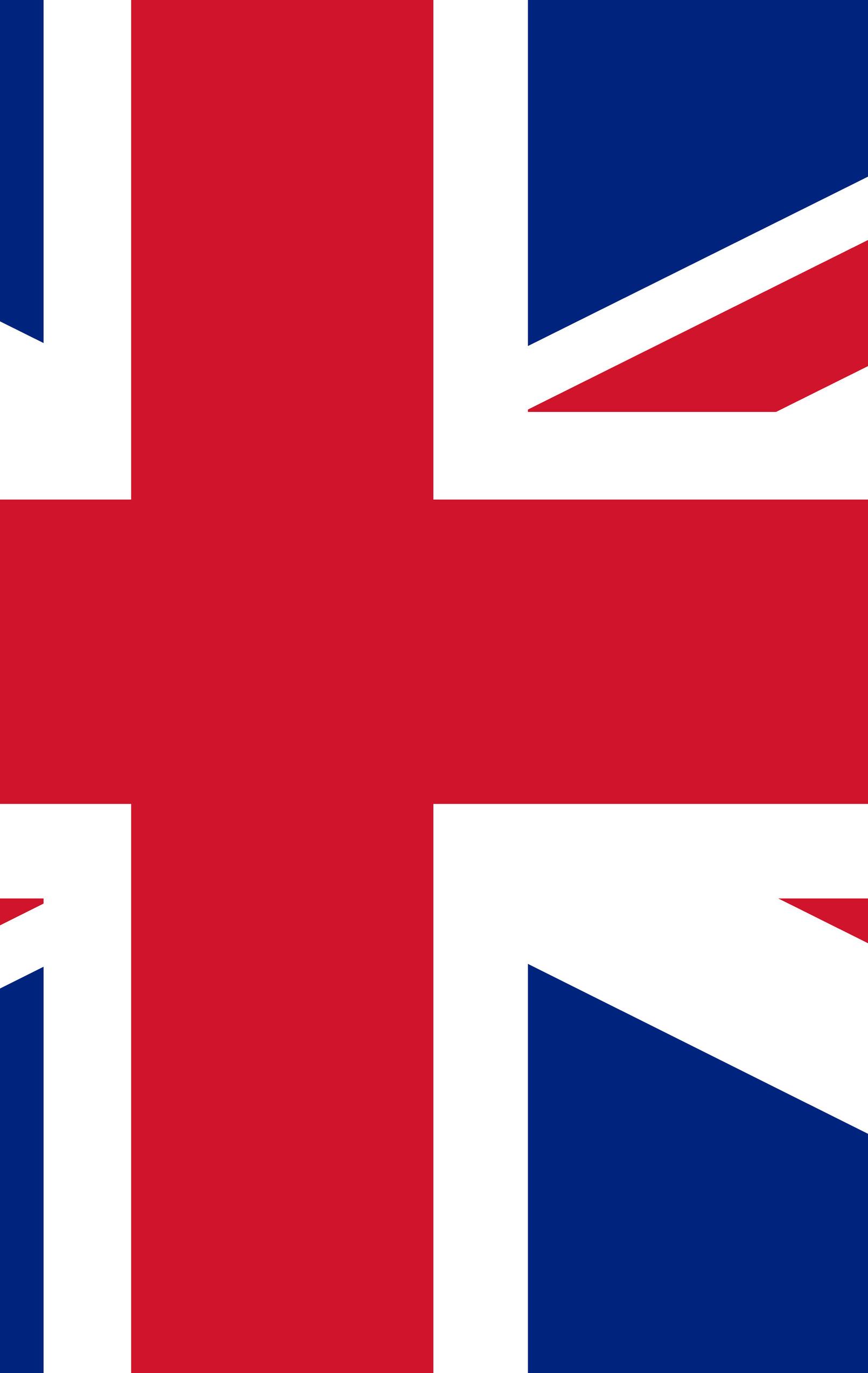

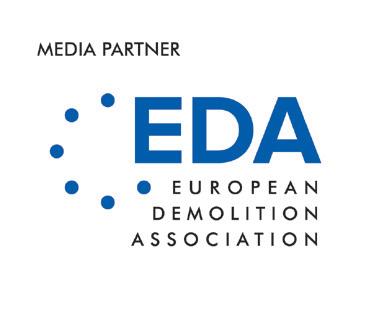

It brings me great delight to present issue #25 of Demolition Hub Magazine, a special edition that marks our fourth anniversary, arriving just after the incredible success of the 6th annual British Demolition Awards.
As our patriotic front cover comes emblazoned with the Union Flag in recognition of British triumphs, we are so very proud that roughly 400 professionals came together to network, celebrate and recognise the achievements of this remarkable industry in Great Britain. Your support has been invaluable and as we move into our fifth year, we’re more committed than ever to shining a spotlight on this vibrant sector.
This issue features comprehensive coverage of the event that was, in every sense, a true celebration of demolition excellence. Held in early September, the evening was a veritable jamboree of industry talent. We were thrilled to co-host the British Demolition Awards alongside the British Asbestos Awards and the 3rd annual Demolition Hall of Fame – all under one roof in the heart of London. From the winners to the inspiring stories shared that night, you’ll find everything you need to know in this issue of Demolition Hub. It was an unforgettable evening, and we’re already looking forward to what’s in store for next year.
In between producing the magazine and organising events, I’ve managed to squeeze in an impressive 30 site visits this year, inching closer to my ambitious goal of 50 by the end of 2024. If you’re looking to have your site featured or want to discuss how your company can be better represented, don’t hesitate to reach out – I’m always keen to meet more of the industry’s key players.
In this milestone issue, we’re particularly excited to feature a true legend of British demolition and a notable name on the racetrack: Rob Collard, CEO of Collard Group. Rob joins us for an engaging Demolition Discussion with our editor, Toby. Together, they explore Rob’s illustrious career, the history of Collard Group, the current state of the industry and what lies ahead for demolition in the UK. Not to mention, there’s some talk of some ridiculously good-looking, fast cars!
With so much packed into this issue, and only one more left to wrap up 2024, I can’t wait to see where the time will take us next! Enjoy the read!
Ben Chambers Publisher, Demolition Hub
PUBLISHER
Ben Chambers ben@chambers.media 01903 952 648
EDITOR
Toby Wilsdon toby@chambers.media 01903 952 645
COLUMNISTS Howard Button
Dolman
ADVERTISING SALES
Ben Chambers ben@chambers.media 01903 952 648
Daniel Christmas dan@demolitionhub.com 01903 952 642
DESIGN
Nicki Chambers nic@chambers.media
Joe Bers joe@chambers.media
PRODUCED & PUBLISHED BY Demolition Hub Ltd Suites 5 & 6, Chapel House, 1-6 Chapel Road, Worthing, West Sussex BN11 1EX demolition@demolitionhub.com 01903 952 640
Hub is a proud member of the National Demolition Association
Demolition Hub is the media partner for the European Demolition Association and the Indian Demolition Association
Demolition Hub is published six times a year. The subscription rate is £60 per year. Subscription records are maintained at Demolition Hub Ltd, Suites 5 & 6, Chapel House, 1-6 Chapel Road, Worthing, West Sussex BN11 1EX
Articles and information contained in this publication are the copyright of Demolition Hub Ltd and may not be reproduced in any form without the written permission of the publishers. The publishers cannot accept responsibility for loss of, or damage to, uncommissioned photographs or manuscripts.
EDA participates in 2024 CECE Congress
Insight on new EU Asbestos at Work Directive and more in EDI Special Publication 2024
EDA and EDI Think Tank returns
Statement about recyclable construction and demolition materials and REACH
European Decontamination Industry Report
2024 out now
EDI and EDA at NFDC annual conference in Rome
Dutch demolition and asbestos removal industry opens doors to public
EDA welcomes its newest member, MEDRA
From coal to clean – Bierlein Companies consigns James DeYoung Generating Station to history
Taking the sky road – J.R. Vinagro’s rapid removal of bridge crossing interstate highway
Spirtas Wrecking selectively demolishes Blunt Hall at Missouri State University while preserving brutalist architectural heritage
by
Howard Button
With Rob Collard, Managing Director of Collard Group
Feedback from attendees and all the winners at the British Demolition Awards 2024
Howard Button reflects on the Circular Steel structural steel recycling summit
52 PROFILE
Viking Demolition & Construction: A rising force in the industry
58
BRITISH DEMOLITION AWARDWINNING CASE STUDIES
Rhodar Specialist Enabling Works: Rank Hovis Premier Mill
Total Reclaims Demolition Ltd: Botanic Place, Cambridge
70 OUT AND ABOUT
Snapshots of Ben and the Demolition Hub team’s activities between issues
76 PROFILE
Sustainable asset disposal by Kevin Gardner, Commercial Manager at BPI Asset Disposal Solutions
80 INDUSTRY
Sir Robert McAlpine partners with Datatag ID to enhance security and combat tool theft
82 OPINION
Richard Dolman
Richard Vann: How to compile a decommissioning bid package
Terry Lloyd: Policy implementation can’t come soon enough
Demolition Hub is the media partner for the European Demolition Association
The European Demolition Association (EDA) is pleased to be attending the CECE Congress 2024, held from 17 to 19 October in Madrid. This year’s theme, Reindustrialising Europe, offers an exciting opportunity to explore the evolving role of construction equipment in shaping Europe’s industrial landscape.
At the Congress, the spotlight will be on how Europe can view its industrial revolution as an opportunity for growth rather than a challenge. Discussions will centre around the revitalisation of manufacturing within the construction sector, its critical role in economic growth and the essential link between the mining sector and Europe’s raw material supply. These topics are of high relevance to EDA’s members, as they relate directly to sustainable resource management and the future of construction practices across Europe.
Key discussions will also focus on the trajectory of construction equipment and how it can
drive innovation, efficiency and sustainability. The Congress will bring together business leaders, EU decision-makers and experts to discuss how advanced machinery and digitalisation can align with Europe’s broader goals for smart urban development, economic resilience and environmental stewardship.
EDA is proud to participate in these discussions as an attendee, recognising the importance of understanding where the construction and demolition industries are headed. The Congress provides a valuable platform for connecting with industry leaders and staying at the forefront of technological advancements that will shape the future.
We invite our members to attend the CECE Congress. It is a unique opportunity to engage directly with industry experts, explore the latest trends, and contribute to the conversations that are defining the future of construction equipment and demolition across Europe.
The much-anticipated EDI Special Publication 2024 is now available, offering a comprehensive collection of technical articles and case studies focused on the decontamination of hazardous substances. The 2024 edition spotlights two critical areas: asbestos removal and the decontamination of various hazardous materials.
The publication features expert content created by EDI’s working groups, composed of industry professionals, providing valuable insights and discussions on essential topics in the decontamination sector. An insightful article addresses the critical issues surrounding asbestos decontamination in light of the new EU Asbestos at Work Directive that came into effect on 1 December 2023. The updated Occupational Exposure Limit (OEL) is now 10 times stricter than previous regulations,
representing significant progress in worker safety.
The article provides a thorough analysis of the challenges posed by asbestos, particularly in older buildings that contain significant amounts of the hazardous material. Key topics include the health risks associated with asbestos exposure, its role as the leading occupational killer and the importance of removing asbestos to protect workers and building inhabitants. The article highlights the need for replacing old asbestos cement roofing with modern solutions like solar panels, while also pointing out the importance of proper training and protection for
those involved in asbestos removal.
The article also raises critical questions about the handling and disposal of removed asbestos, emphasising the need for innovation in asbestos destruction techniques, which could make the resulting materials safe and recyclable.
With its in-depth coverage of these pressing issues, the article offers valuable insights for professionals across the decontamination and demolition industries, contributing to the broader goal of creating safer, healthier environments across Europe.
Released in both digital and hard copy formats, the EDI Special Publication 2024 offers an excellent opportunity for industry players to share experiences and solutions. Don’t miss your chance to take a look at this year edition.
MAXIMUM PERFORMANCE
LOWEST OPERATIONAL COSTS
HIGHEST RELIABILITY
The EDI is thrilled to announce its partnership in the EDA Think Tank, set to take place in Brussels on 9 October. The EDA and EDI will bring together industry leaders and experts for face-to-face discussions on critical topics shaping the demolition sector.
The event is specifically designed to share ideas and best practice in the industry, fostering direct communication between stakeholders, create a debate and share experiences, common challenges, risks and possible solutions related to those topics.
EDA Think Tank 2024 will tackle two main topics: Construction and Demolition Waste Management Protocol and Guidance; and Audits Before Demolition and Renovation Works. These topics are at the
forefront of industry innovation and sustainability efforts, making the event essential for stakeholders seeking to stay ahead in their field.
The event’s structure emphasises close contact and direct interaction, distinguishing it from traditional conferences. It offers attendees unparalleled opportunities to engage with peers, exchange ideas and gain valuable insights into industry best practices.
We encourage all stakeholders interested in advancing demolition practices to join us in Brussels for what promises to be a transformative event. Registration for EDA Think Tank 2024 is now open. Registration is free of charge and anyone can participate, but you must sign up in advance.
The Think Tank is divided into
two sessions, with roundtable discussions among contractors, engineering companies and asset owners.
General themes
• Presentation of the EU Construction and Demolition Waste Management Protocol and Guidance,
• Building a collaborative framework between all parties involved in the process for more efficient waste management protocol and audits before demolition and renovation works,
• Strategies for integrating circular economy principles into construction projects,
• Best practices in audits before demolition and renovation works,
• The impact of new technologies applied to the Construction and Demolition Waste Management Protocol and Guidelines.
Programme
8.30: Registration
Debate session 1: New Construction and Demolition
Waste Management Protocol
Presentation of the EU Updated Construction and Demolition Waste Management Protocol and Guidance by Florian Flacheneker and Philippe Moseley, of the European Commission
Themes:
• Current practices in construction and demolition waste management across Europe,
• Common obstacles the EU is trying to solve with the protocol update and how this is helping the industry. Challenges faced during the revision of the protocol,
• Innovations and technological advancements with this new protocol,
• How recycling and reuse can be maximised on construction sites.
Panelists
Liesbet Van Cauwenberghe, TRACIMAT (Belgium)
Florian Flacheneker, European Commission
Stefano Panseri, NADECO (Italy)
Katrin Mees, Deutscher
Abbruchverband (Germany)
Marco Camboni, RPA EUROPE
(Risk and Policy Analysts Europe)
Coffee and networking
Debate session 2: Guidance for resource audits before demolition and renovation works
Presentation about best practices in audits before demolition and renovation works in Europe by Johan D’Hooghe of TRACIMAT
Themes:
• Important procedures when conducting thorough audits before demolition and renovation,
• Common challenges and solutions during work audits. Regulatory and safety challenges,
• Innovations and new tools or technologies in audits and automating these processes,
• Environmental and safety considerations.
Panelists
Thomas Kasper, BRV –Österreichischer BaustoffRecycling Verband (Austria)
Philippe Moseley, European Commission
Johan D’Hooghe, TRACIMAT (Belgium)
Duncan Rudall, NFDC
13:00 – Closing Remarks by EDA president, Stefano Panseri
Lunch and networking
A joint statement by the European Quality Association for Recycling (EQAR), the European Demolition Association (EDA) and the European Decontamination Institute (EDI), calls on the European Commission to ensure that recycled mineral construction materials remain exempt from the REACH regulation.
Authored by Martin Car, Secretary General of EQAR, the statement highlights the vital role of recycled materials in the circular economy and the potential negative impact if they were subjected to REACH.
Recycled construction materials, primarily derived from mineral waste like concrete, bricks and asphalt,
The European Decontamination Industry Report 2024 is now available for online consultation. This biennial publication collects data of high value for decontamination professionals across Europe. It provides an overview of the current situation of the sector.
This study, like those that precede it, includes a series of comparisons with the results of the previous editions. It will also give its readers forecasts for the current
have been successfully used for over 30 years and represent a significant opportunity to reduce reliance on primary raw materials.
These materials meet stringent national and EU environmental and technical standards, with thorough pre-demolition audits ensuring harmful substances are removed before recycling.
The statement emphasises that subjecting recycled materials to REACH would increase costs, reduce competitiveness with primary materials, and potentially threaten the EU’s target to increase recycling rates.
EQAR, EDA and EDU argue
that the current system effectively safeguards health and the environment, making additional REACH requirements unnecessary and detrimental to the industry.
Recycled construction materials have proven to be safe and environmentally friendly, and the statement calls for their continued classification as products, not substances, under the REACH regulation.
year. The results of the study were obtained from the responses of contractors and suppliers.
Since 2020, EDI has been working on creating this document annually.
The European Decontamination Industry Report 2024 includes general industry data, information on company activity, turnover, investment and industry forecasts for the current year.
It is therefore an extremely valuable tool for professionals in the
deconstruction and decontamination sector. If you want to keep up with market trends and perspectives you can’t miss it.
The NFDC Annual Conference 2024 in August brought together key players in the demolition industry at the iconic Rome Cavalieri Hotel.
With panoramic views of Rome and St Peter’s Dome, the event created a perfect setting for insightful discussions, networking, and collaboration among professionals from across Europe.
José Blanco, General Secretary of both the EDI and EDA, actively contributed as a panellist, offering his expertise on current trends and the future of the demolition sector. His participation emphasised the growing importance of decontamination and sustainability in demolition, resonating with the industry’s commitment to innovation and environmental responsibility.
Highlights:
Industry discussions: José Blanco’s participation in the panel showcased the EDA and EDI’s continued efforts to lead conversations on critical issues like sustainable practices and innovative solutions for the demolition and decontamination sectors.
Networking opportunities: The conference also provided an excellent platform for the EDA and EDI to strengthen ties with the NFDC and its members, fostering a collaborative spirit that will undoubtedly lead to future joint initiatives.
Cultural and networking experiences: Attendees were
treated to a blend of business and cultural experiences, enjoying Rome’s rich heritage while engaging in meaningful discussions on the future of the demolition industry.
As the event drew to a close, the collaboration between the NFDC, an active member of both the EDA and EDI, was further reinforced. The conference highlighted the shared commitment of these organisations to shaping the future of the demolition and decontamination industries, with a focus on sustainability, safety, and innovation. This continued partnership sets the stage for exciting developments and joint initiatives in the years ahead.
We invite everyone to continue the conversation on these important themes at upcoming events, including the EDA Think Tank, EDA Study Tour, EDA Annual Convention and the NFDC Annual Event in 2025. These gatherings will offer further opportunities to discuss the future of the demolition and decontamination sectors, with a continued focus on innovation, sustainability, and collaboration.
On Saturday 21 September VERAS, the trade association for demolition contractors and asbestos removal companies in The Netherlands, hosted the fourth Demolition Day. This unique event offers the public an inside look at the demolition industry, allowing visitors to explore project sites and company locations across the Netherlands.
VERAS members highlighted the important role demolition plays in the circular construction economy,
showcasing how materials are recovered, recycled and reused to promote sustainability. Visitors also had the chance to learn about career opportunities in demolition and asbestos removal, making it an excellent event for anyone interested in the industry.
A key highlight was the Dutch Nail Pulling Championship, a symbolic competition showcasing the craftsmanship required in demolition work. Skilled
professionals demonstrated how they remove nails from wooden beams, preparing them for reuse – a perfect reflection of the industry’s dedication to sustainability.
MEDRA, the Malta Excavation, Demolition and Recycling Association, stands as a pivotal organisation within Malta’s construction sector, advocating for regulation within the industry while providing a platform for its members to voice concerns and suggestions.
Established with a mission to foster sustainable development and industry best practices, MEDRA plays a crucial role in shaping policies and standards that govern the construction landscape in Malta.
One of MEDRA’s key strengths lies in its proactive engagement with regulatory bodies and governmental agencies.
By securing a seat at the table during critical discussions, the association ensures that the voices of its members are considered in the formulation of policies that impact the construction industry. This strategic positioning allows MEDRA to influence decisions that affect everything from safety standards to environmental regulations, thereby safeguarding both the interests of its members and the broader community.
Furthermore, MEDRA serves as a knowledge hub and resource centre for industry stakeholders, providing valuable insights, training programmes and educational opportunities.
The association fosters continuous learning and professional development among its members. By staying abreast of emerging trends and regulatory changes, MEDRA equips its members with the tools and knowledge needed to thrive in a dynamic and competitive market environment.
In a monumental step towards environmental responsibility, the James DeYoung Generating Station in Holland, Michigan, has been successfully demolished. Operated by the Holland Board of Public Works, this coal-fired power station was a significant landmark in the city but its demolition represents a stride toward modernisation and sustainability.
Constructed in 1939 as part of the New Deal’s Public Works Administration, the James DeYoung Generating Station was a symbol of industrial development during a challenging period in American history. Over the years, the plant expanded, with additional units built in the 1950s and 1960s. However, as societal and
environmental priorities shifted, the plant ceased coal-burning operations in 2016, paving the way for a greener future.
The replacement, Holland Energy Park, embodies the city’s commitment to reducing carbon emissions and enhancing efficiency. By leveraging modern technology, this new facility aims to cut carbon emissions by 50%, aligning with broader efforts to combat climate change.
Leading the charge in this ambitious endeavour was familyowned and operated demolition contractor and NDA member Bierlein Companies Inc. Following a rigorous bidding process that considered factors such as approach, safety record and price, Bierlein Companies Inc. was awarded the project.
The demolition process commenced in January 2023 and spanned 11 months, culminating in the successful removal of the ageing power station. Notable equipment included a Caterpillar 395 excavator with a Genesis 775 shear attachment and a Cat 385 ultra-high demolition machine with a 23-metre boom and shear attachment. In addition, a Cat 349, Cat 340 and multiple Cat 330 excavators were used on site. The power plant also required the use of Caterpillar loaders and skid steers.
The project involved meticulous planning and execution, beginning with asbestos abatement and conventional demolition techniques to prepare for the engineered explosive felling. “The project started with asbestos abatement of the entire plant,” says Jeramey Bierlein of Bierlein Companies Inc. “Conventional demolition techniques exposed the skeleton of the entire structure. Peeling the brick walls and shearing through the steel of
the boiler house and boilers was necessary in preparation for the explosive felling.
“A mechanical felling (engineered cable pull) was implemented to bring a 20-metre silo to the ground, which was then torch cut, sheared and processed. Months of planning and preparation were required before the explosive felling could take place. Subsequent to the successful explosive felling, the Cat 395 excavator sheared through the steel debris and processed it for recycling. To wrap up the project, the crew demolished small buildings and performed site work and restoration.”
One of the project’s most memorable moments was the explosive felling, which drew widespread public attention.
Situated in the heart of Holland, the demolition site attracted crowds eager to witness the landmark event. To ensure public safety, authorities coordinated with the US Coast Guard, Sheriff Marine Patrol, police and first responders, underscoring the significance of the occasion.
“Using this felling technique significantly reduces the amount of man hours needed to raze the structure,” Bierlein says. “Less man hours means decreased risk of safety-related incidents, and that is our number one priority.”
Despite the challenges posed by the project’s public exposure and the harsh winter conditions near Lake Michigan, the team remained steadfast in their commitment to safety and efficiency. With a crew of 10 individuals, Bierlein Companies Inc. navigated each phase of the demolition with precision and professionalism.
Upon completion, the project yielded impressive statistics, with
7,300 tonnes of scrap and 6,600 tonnes of miscellaneous materials recycled. This commitment to sustainability underscores the broader environmental objectives driving the transition from traditional power generation to renewable alternatives.
“The project has been deemed a huge success,” Bierlein says. “The project’s scope and objectives were achieved through the crew’s continual safe and diligent work.
Like each job Bierlein Companies Inc. is associated with, the safety of the employees is priority number
one, and that goal was achieved. The successful coordination during the high-profile explosive felling allowed the people of Holland, Michigan to witness something that you wouldn’t typically get to see every day.”
As the dust settles on the James DeYoung Generating Station, Holland looks toward a future defined by innovation and sustainability. The successful demolition of this iconic structure serves as a testament to the city’s unwavering commitment to progress and environmental stewardship.
The thunderous echoes of jackhammers and the orchestrated precision of heavy machinery marked the urgency surrounding the demolition and replacement of the Wellington Avenue Bridge that carried I-95 over Cranston, Rhode Island. This task fell into the capable hands of NDA member J.R. Vinagro, a renowned demolition company selected for its proven expertise in rapid bridge replacement.
J.R. Vinagro, a site development and demolition company, was chosen to carry out the Wellington Avenue Bridge demolition. The selection was based on the company’s proven track record in performing expedited demolition for rapid bridge replacement and a competitive bid price.
The project commenced in August 2023 and the demolition was
carried out over four consecutive weekends to minimise disruption. The equipment used included excavators with hammers and shears, with multiple machines staggered on the bridge deck to maximise efficiency. Loaders and additional excavators were stationed below the bridge and a fleet of dump trailers removed debris as the demolition progressed.
The demolition process began
with a saw cut to separate the section of the bridge being removed from the structure that would remain. Working from the centre out, excavators removed the concrete bridge deck and subsequently the bridge beams. After the beams were taken down, the substructure saw cutting began. All concrete and steel debris was processed and recycled within the company’s yard in Johnston.
Aetna Bridge Company was the general contractor for the project. The J.R. Vinagro crew consisted of six operators and approximately 10 labourers, with additional saw cutters from subcontractor Pinnacle Concrete Cutting Corporation.
The project’s biggest challenges included the rapid timeframe from contract signing to demolition initiation, as well as the strict 12-hour window for each of the four consecutive weekends. Despite these challenges, the project was completed successfully, with no injuries and the efficient demolition work allowed the general contractor to complete its work ahead of schedule, opening the highway earlier than required.
“We completed our work within the timeframe allocated within our contract with no injuries,” the company said. “The timely demolition work helped the general contractor to complete their work with time to spare, opening up the highway earlier than their contract required.”
Spirtas Wrecking Company’s selective structural demolition of Missouri State University’s Blunt Hall in Springfield, Missouri, was a Category 1 ($0-$1m) finalist for the 2024 Excellence in Demolition awards. The project was a vital preconstruction phase in the addition and renovation of the university’s College of Natural and Applied Sciences – a cornerstone of Missouri State’s modernisation efforts.
The Blunt Hall project required meticulous planning and execution. NDA member Spirtas Wrecking Company was tasked with carefully demolishing specific areas of the existing building while preserving the structure’s integrity for a new 77,000-sq ft laboratory and science
building. The project’s goals included integrating the new addition with the historic campus and ensuring minimal disruption to ongoing university operations.
The demolition scope involved two distinct areas: a one-storey auditorium foyer and a four-storey east entry vestibule. Both required specialised techniques due to the unique structural elements and the building’s historic designation. To safely perform the work, Spirtas Wrecking Company employed a combination of hydraulic shear demolition and saw-cutting techniques, reinforced by sacrificial
shoring to support the remaining structure during demolition.
For the auditorium foyer, Spirtas Wrecking Company first separated the demolition zone from the rest of the building by saw-cutting a 30-cm relief joint. Using a concrete processor attachment, the team efficiently broke down the structure while segregating concrete and rebar for recycling. The transition to the four-storey vestibule involved similar precision, with concrete components being cut into manageable sections and safely lowered via telehandler.
Blunt Hall, originally constructed in 1971 in a brutalist architectural style, is a significant piece of Missouri State’s history. Its eligibility for historic status added layers of complexity as Spirtas Wrecking Company had to navigate stringent permitting and preservation requirements without delaying the project. The project team also relocated campus sculptures and other site features to protect the university’s heritage during the demolition phase.
Sustainability was a critical focus for both the university and the demolition team. The project achieved a 94.12% landfill diversion rate by recycling all concrete and metal debris. On-site processing allowed for the reuse of crushed concrete, further reducing waste and supporting the university’s sustainability goals.
Executing the demolition within a sixweek schedule while the rest of the building remained fully operational for teaching and research required seamless coordination among all parties. Spirtas Wrecking Company worked closely with general contractor Whiting-Turner and other subcontractors, conducting twice-weekly “pull planning” sessions to synchronise efforts across the multi-employer site. Up to four subcontractors were on site simultaneously, yet the demolition zones remained carefully controlled to ensure safety and efficiency.
The project’s success was bolstered by Spirtas Wrecking Company’s commitment to inclusive daily briefings, hands-on management involvement and robust safety practices. Weekly safety toolbox talks and monthly sitewide safety lunches kept communication open and prioritised worker wellbeing.
The Blunt Hall project also created opportunities for community involvement and workforce development. Missouri State and Whiting-Turner implemented construction management internships, providing students with hands-on experience in a live construction environment.
Spirtas Wrecking Company’s crew, comprising both regular employees and local union hall personnel, included a noteworthy 30% female staffing by hours worked. Younger staff members gained valuable skills through on-the-job training, learning from seasoned veterans in areas like scaffold installation and telehandler operation.
by Howard Button
Following years of negotiation and testing of hundreds of samples, the Environment Agency has released confirmation of its revised position on the disposal of wood waste.
I would like to personally thank everyone involved in this mammoth project, which has thankfully come to a workmanlike conclusion.
The following statement has been issued by the Wood Recyclers Association detailing the current position.
In a huge victory for the waste wood sector, the Environment Agency is set to classify all amber waste wood items from both the HWRC and demolition waste streams as nonhazardous.
The decision follows six years of work involving more than 1,000 tests, led by the Wood Recyclers’ Association (WRA), and is expected to save the industry millions in hazardous waste disposal costs
and red tape.
Up until now, certain treated “amber” waste wood items including fence posts and decking from households and ten items from demolition* have been deemed “potentially hazardous”. These are currently subject to Regulatory Position statements RPS249 and RPS 291, which were due to expire at the end of September and are now in the process of being withdrawn.
Following a meeting with the WRA on 4 September to discuss the latest test results, the Environment Agency said it was satisfied that the amount of hazardous waste wood in both the HWRC (Household Waste Recycling Centre) and demolition waste streams was negligible and reducing.
This means that, even after the RPSes are removed, these items can be moved and processed as non-hazardous provided they are destined for panel board manufacture or Chapter IV biomass,
with no requirement for further testing.
Wood from heavy industrial buildings is an exception and will still need to be assessed and tested to WRA02, now the recognised standard for hazardous waste wood by the Environment Agency.
Howard Leberman, Senior Policy Advisor at the Environment Agency, said: “We are very pleased to have reached a risk-based and proportionate outcome through great collaborative working with the WRA. We are therefore happy to remove RPS 249 and RPS 291 and will take the necessary steps to withdraw them before their expiry at the end of September.”
Vicki Hughes, Technical lead on the WRA Board, said: “We are absolutely delighted that all our hard work has paid off and that the Environment Agency has recognised that the hazardous waste wood content in these waste streams is tiny and diminishing.
“While we knew the hazardous content was low, we needed the evidence to prove it so a massive thank you to all those organisations who took part in sampling and testing and in particular to WRA members, who really led the charge.
“This outcome will be hugely beneficial for our sector and is testament to our close collaborative working with the Environment Agency, SEPA, NRW and NIEA and also our project partners at the NFDC, UROC, ESA and CIWM Construction & Demolition Forum.”
Duncan Rudall, CEO of the NFDC, said: “We welcome this news which will significantly reduce the regulatory burden on those working in the demolition sector and potentially save our sector millions of pounds a year in testing and hazardous waste disposal costs. A big thank you to the WRA for leading this important project.”
Following the decision, those accepting treated waste wood onto
their sites should update their Acceptable Materials Guides to reflect those changes.
The WRA will be updating its WWC Toolkit to include the new position. Alongside the NFDC, it will also be reviewing and updating the household and construction and demolition waste wood classification guidance documents.
The Environment Agency’s position relates to England and it is hoped that a similar position will be adopted in Scotland, Northern Ireland and Wales, although the WRA is still awaiting confirmation.
Richard Coulson, WRA Chair, said: “I wish to pass on my sincere thanks to all involved in the Waste Wood Classification project for their time and diligence over many years to ensure we continue to make the best use of waste wood in a compliant manner. I’d especially like to thank and recognise Vicki and Julia’s work, who have been instrumental in successfully delivering this project.”
* Amber waste wood items from all buildings built between 1950 and 2006 include:
• Roof timbers
• Tiling and cladding battens
• Timber frames and joists
* Amber items from buildings built between 1950 and 1995 also include:
• Barge boards, fascias and soffits
• External timber cladding
• External doors
• External windows
If you have something to say and would like to submit a column for publication in Demolition Hub, please email: toby@chambers.media
Interviewee: Rob Collard
Role:
Founder and CEO
Company: Collard Group
QTell us about the 30 year history of Collard Group I started in demolition when I was about 15 years of age, working for my father. He had a waste recycling and small scale demolition business, which is something I used to really enjoy. I left when I was about 22 years of age and set up as a small, independent sole trader, RJC Services, going around repairing
people’s diggers and lorries as a mobile mechanic.
Then I got a workshop, I got an old lorry, and then I bought an old JCB digger. Just over 30 years ago I set up what’s now Collard Group doing small demolition projects. I had a couple of tippers and was operating out of an old farm that I used to rent. That’s where the journey started.
It took a good five or six years, maybe even nearer to 10 years before I started to get to see any significant momentum. And from that point onwards, it’s really blossomed. To this day I cannot believe where we are now. We’ve got roughly 440 people full time on the
books, 150 trucks, 100-odd diggers, nine recycling centres and we turn over just close to £70m.
People don’t see everything we do. There’s a lot more to the Collard Group than meets the eye.
One of our high reaches is working for a demolition company in Wales, the big Volvo is up in the north east of Scotland decommissioning an oil rig. There’s another Volvo 750 80-tonne machine doing some demolition in Inverness. We’re doing a million tonnes a year of recycling – we facilitate a hell of a lot of the demolition industry even when we’re not doing the demolition. They all use our facilities for wood, for scrap metals,
for hardcore. We bring a lot of the material back to our crushing yards and recycle it, grade it, wash it to go out a single size – 10, 20, 40 mm stone, or we blend it in with our ready mixed concrete.
QWas there anything in particular behind the blossoming of the business?
Any successful organisation or has to build a team and I’ve been very lucky that as my company has grown we’ve been able to recruit, maintain and develop talent. We have some very long standing people here who have been very loyal to me and I’ve been very loyal to them. That, I think, is a major key to our success.
We do everything it says on the tin. We own all our equipment, we maintain our own equipment, we demolish, we recycle and then we deliver that material back to site. So we’re a one stop shop for any developer or contractor doing any form of building in the south of England. We do go nationwide –we’re up in Scotland at the moment – but we predominantly facilitate most of the south east.
QYou do a broad range of jobs and own all your own equipment, so you must have a wide range of equipment Yes, absolutely. We do everything from soft strip refurbing of buildings, so we’ve just completed a 500 bedroom strip out at the Imperial Hotel at Russell Square in London. And we took the whole top floor of the hotel off. So we had Brokks on the top, mini diggers inside, Bobcats running around inside as well as all the manual demolition and asbestos removal.
We’ve got 20, 30, 40 and 50-tonne excavators, demolition shears, rotating grabs, munchers, that sort of stuff. Then we’ve got four high reaches. We’ve got 28-metre arms on Hitachi 490s, then we’ve got Volvo 750s with a 20-metre reach, and then a 40-metre telescopic arm to fit that machine as well. So we’re one of the few in the UK with a 40-metre telescopic demolition machine. That machine is actually working up in Scotland at the moment, decommissioning an oil rig.
So we’ve got a very comprehensive range of equipment. Demolition and remediation go very much hand in hand these days so having a fleet of dump trucks, bulldozers, screeners and crushers very much complements the demolition arm.
We are finding a lot of enquiries for hire at the moment. With the industry so tight at the moment you can see quite a few companies are holding back from buying equipment. We don’t operate as a
hire company, but we will hire high reach, or crushers or dedicated demolition machinery to people that we know and are competent contractors.
We’ve got very comprehensive assets and the skillset to look at any form of demolition. I think we sometimes fly under the radar a little bit – people don’t know the comprehensive equipment and facilities that we offer.
QTell us about the team culture and career development
We’ve got more than 440 people here plus 100 agency staff but I very much try and get to know everybody.
I’m out on site a lot; I try to get around the recycling depots and the demolition jobs.
We invest heavily in our people and training and like to promote from within. We’ve had guys who started as site labourers become machine drivers, machine drivers become general foremen or move up to contracts managers, and we’ve got contracts managers who have become directors. We’ve got a lot of people who are second and even third generation – we have an apprentice welder whose grandfather still drives a digger here.
We do a lot with the NDTG, bringing people through site manager courses, supervisor
courses etc. We sponsor people to do the demolition Master’s degree, and we’ve got quite a few apprentices coming up through the Bircham Newton Construction Skills College. We’ve brought mechanics out of Basingstoke college – we have a workshop that works 24 hours a day, seven days a week.
Then we’re doing health and safety training, NEBOSH training, we’ve done some directors courses and we’re doing a wellbeing course for senior office people. We’ve brought in the Aston Martin health and wellbeing coach, who I know personally through the motor racing. He’s looking at 15 people in the senior management team doing
cholesterol testing, blood pressure, diet, looking at sleep patterns and general wellbeing.
It’s an expensive investment, but if after 30 years we can’t give something back like that to our people, we’re doing something wrong. If they’ve if they’ve slept better, they have a better diet, their blood pressure’s lower, their blood sugar’s correct, they’ve hydrated properly and their performance is one or two per cent better – it’s a very good investment.
QAre there any standout projects for Collard Group?
For nearly a year we’ve been doing the soft strip and high-level
demolition of a hotel in Russell Square in London – a £3m+ contract that was two years in the planning. They were going to extend the hotel upwards so we had to take the top floor off as well as doing a lot of work in the basement and quite a bit of cut and carve. That was an interesting project because it was a full soft strip right back to the bare shell.
The logistics of working in Russell Square, just off Oxford Street and a stone’s throw from Great Ormond Street Hospital pushes us and it’s proved that we’re able to complete that job on time, on budget and make a profit. That’s quite a significant milestone.
QHow do you acquire contracts?
I think we’ve built a good reputation, so a lot of tenders come to us. Naturally, we have a work winning team, three full time estimators, commercial lead and a bid writer. Anything that’s a bit out of the ordinary or a large job, I would go and look at it with one of the team. I haven’t got the time to put a tender together these days, so I’ll go and look at it and then the work winning team put it together.
We’re on certain frameworks with local councils, we chase the planning portals, try to make early engagement with the with the developer or the client. And then we’ve built up a reputation in the south east, with a lot of house builders. If something’s needed with the tender they would come to us in some form.
And then we’ve got the small developers who come to us repeatedly with individual houses. We still do that type of work because it’s very handy for cashflow. We wouldn’t go 50 miles to knock a house down but if something’s relatively close to one of our recycling depots, getting the hardcore and the rubbish from the building feeds work into the recycling centres.
QTell us about your engagement in the community
We do as much as we possibly can with local communities. If we have an open day we bring the schools into the recycling depot and we also take our trucks into the local primary schools. We sponsor quite a few people that ride horses, compete on motorbikes, cars. We’ve been a big sponsor of Aldershot Town Football Club for many years and also sponsor Eastleigh FC and Fleet Town FC.
We’ve had stakeholder open days with companies like Balfour Beatty where they’ve had 20 or so people turn up wanting to walk around and see where the waste from any sort of construction site goes. We’ve helped educate them about the cradle to grave journey of waste. We specialise in taking a waste product and turning it back into a usable commodity, whether that’s crushed concrete, sand, stone, soils, glass, scrap metals, or wood from a demolition site.
QHow do you see the industry developing over the next few years?
Clients and developers are pushing more and more responsibility onto the demolition contractor as Primary Contractor. If I went
back 25 or 30 years ago, most demolition contractors just knocked it down to slab. At no point did anybody really go down into the ground. That’s something that’s become the norm over the last 15 years – service diversions rather than disconnections, moving transformers, laying cables, slab removal, foundations out, reduce level digs, remediate, lay piling mats and sometimes put in temporary access to the highway, just putting more and more work into the demolition package.
So we have to have a bigger skillset. There are opportunities if you’re prepared to take them, but with that comes the risk that you could do a successful demolition but get something wrong in the ground. Some people don’t want to do it, but I think forward-thinking companies will flourish in the long run.
QWhat technological developments do you foresee?
The efficiency improvements in hydraulic excavators are just outstanding. You now have machines barely ticking over, delivering great power on very low RPM. You very rarely see the plumes of black smoke that you used to and the hydraulics are much more efficient.
Obviously hybrid and electric power are coming. I’m waiting to find out how reliable it is before we switch. I see a massive fire risk with electric vehicles – we’re seeing so many fires from lithium batteries in power tools, cars, electric scooters. Once you start charging vehicles overnight inside or outside buildings, they’re catching fire everywhere. I think we’re moving too quickly, the technology is not proven or reliable enough.
QHow about hydrogen internal combustion engines?
I see hydrogen coming in to play a lot more. In motorsport hydrogen is happening with big races like Le
At Romax Solutions, finding the best candidates is our driven desire and passion, we aim to meet the recruitment needs of a diverse range of clients within the construction & demolition industry, leaving them happy, everytime. Romax Solutions is also fully accredited by the Recruitment and Employment Confederation and the National Federation of Demolition Contractors.
With a depth of knowledge, our experienced and trusted staff are on-hand to deliver a bespoke service, supplying reliable and talented staff of all levels both nationally and locally. Specialising to demolition contractors to NFDC guidelines. As Members of the NFDC we offer Internal training to all our candidates whether starting their career in demolition or to help further their skill set.
Mans and 24-hour endurance races. Manufacturers like Toyota, Audi, Ferrari are all moving cars over to hydrogen. So I’m waiting to see. I’d rather buy a hydrogen combustion engine than an electric motor.
QAnd so to the racing. It’s a multi-generational thing, a family pursuit. What does that mean to you?
We’re very passionate about our motorsport. My father raced for many years. He was British, European and world champion on the short ovals. He was very well-
known back in the 80s and had a huge following.
I followed in his footsteps, starting on the ovals. I was British and European Champion and then moved away and went into circuit racing. In my early days I raced Formula Ford with people like Mark Webber and Jensen Button before doing British Touring Cars for a number of years. I was a contracted driver to BMW for 10 years. We won multiple team championships, constructors championships and I was regularly top five in the overall British Championship.
Now I’ve moved away from touring cars and gone into British and European GT racing. I won the British GT Championship for Lamborghini in my first year in 2020. We won the Spa 24-hour and we also won the Silverstone 500, a historic race won by Stirling Moss in his day.
We’re having a stellar year. I’ve teamed up with my eldest son, Ricky and we’re currently leading the British Championship by 24 and a half points. We’ve got the final round this weekend at Brands Hatch. On top of that I am second in the European Championship, with the final round in Barcelona, on the 11th and 13th of October.
Stop press: Rob and Ricky won the British GT Championship on Sunday 29 September, making Rob only the third driver in history to be multiple champion in the series, and together they are only the second father and son pairing to claim the crown.
QSo what is it that you actually drive?
It’s a Lamborghini Huracan GT3.
QHow do you see Collard Group in 5 or 10, years?
I’m obviously very keen to continue the progression of the company. I think we’ll be at £75m turnover either by end of this year or definitely next year. And the aim is to get it to £100m; that is my goal.
We don’t want to go out and just buy turnover without profit, otherwise you just end up being a casualty of another casualty in our industry. Anybody who looks at our books will see that since the first day of trading as R Collard Limited 30 years ago we’ve never gone backwards. We’ve only ever grown every year and we’ve always made a decent profit.
The hardest thing is just to continue being successful. People can be successful for a week or a month or a year, but then take their eye off the ball. I started as a one-man-band; I didn’t get given
anything, I built everything from a box of spanners in the back of a van. And looking forwards, my eldest two sons both work in the business. At the right time I’d like them to come in and work at a senior management level so I can perhaps take my foot off the gas a little.
QSo do you have any retirement plans?
No. I’d like the management team to continue to grow and develop and, yeah, maybe take over one day with the guidance of my two sons. But no, I get too frustrated, I can’t sit still. I’m very much an outdoors person who lives and breathes demolition. Diggers, tippers, recycling on a practical scale, outside, rather than sitting at an office desk learning about compliance.
What would you be in an alternative life?
An eagle as I would love to fly and be free
QAre we going to see you at the British Demolition Awards next year?
It’s a great event. I’m gutted I wasn’t able to come this year because I was racing at Magny-Cours in France but if it doesn’t clash I will definitely come. Our industry needs to continue doing this sort of stuff because it’s very much about family businesses.
Who is your favourite artist? Oasis
What do you do for fun? Running and cycling
When and where are you happiest?
When I am wearing my crash helmet
What gets you out of bed in the morning? To achieve
What’s the most expensive non-essential thing you’ve ever bought?
My carbon fibre bike
What’s your favourite food? A fillet steak
What’s your tipple of choice? G&T ...
It was an honour to host and stage what may well have been the most significant global celebration of the demolition industry to date this past September at the Royal Leonardo Hotel, St Paul’s in London.
The 6th annual British Demolition Awards brought together approximately 400 industry professionals for an unforgettable evening of recognition, camaraderie and celebration of the sector’s finest achievements.
The night’s spotlight shone on Brown & Mason, specialists in power station decommissioning, who clinched the prestigious Demolition Contractor of the Year award for the first time. In the supplier category, Worsley Plant took home the top honour, following a heartfelt nomination by Rotar’s director, Louis
Broekhuizen, who commended Sean Herron and his team for their exceptional contributions to the industry – a sentiment echoed by the judging panel, who praised them as the deserving winners.
The evening also celebrated the broader demolition and asbestos industries, with a total of ten awards distributed. Additionally, three new inductees joined the prestigious Demolition Hall of Fame, which Demolition Hub established in 2022. Liz Darlison, CEO of Mesothelioma UK, was named Asbestos Pioneer for her tireless dedication to supporting those affected by the disease. From across the Atlantic, Scott Laird, former NDA convention organiser and a key figure at Independence Demolition in the United States, was honoured for his lasting impact on the industry.
A particularly poignant moment occurred when Robin Powell, the former Managing Director at DSM, was posthumously named Demolition Person of the Year. The entire room fell silent in respect as his family and former colleagues took to the stage to accept his place in the celebrated annals of demolition history, followed by a standing ovation – a powerful tribute to his legacy and influence.
With the demolition and asbestos industries coming together under one roof for a night of mutual celebration and reflection, it was a reminder of the strength, resilience and unity that define our industry. Here’s to the future of demolition and to the seventh edition next September. Join us and make sure you are involved…
Ben Chambers
Fireward were delighted to not only attend the recent British Demolition Awards evening but win the award for Safety Innovation of the Year for our Dual Agent Automatic fire suppression systems that protect heavy plant and machinery from the devastating risks of fire.
As a critical safety supplier into some of the harshest working environments, this award is reward for the hard work and development that goes into the design, manufacture and supply of our systems. Fireward proudly supports the demolition industry, protecting people and assets not only nationally but globally; and to be recognised at prestigious awards events such as the British Demolition Awards is testament to the hard
work and dedication that goes into protecting our customers. From small beginnings in Chelmsford to supplying major clients the world over, Fireward continues to strive for engineering and critical safety excellence every day and to be recognised by industry peers for the work that would do is both a proud and humbling experience. We look forward to further developing fire safety across the industry and working with leading demolition businesses in the future. Thanks again go to Demolition Hub, Ben Chambers and his team, for a superb event and their dedication to championing the demolition industry and dedicated professionals operating in it for the innovate and forward-thinking market sector it is.
At Worsley Plant Limited, we have been at the forefront of the attachments industry for over 25 years, establishing ourselves as experts in all aspects of grabs, shears, pulverisers, hammers, crushing and screening buckets and quick couplers. Our commitment to excellence has made us the industryleading plant sales and hire company we are today.
In 2011, we proudly became the exclusive UK distributor for Rotar, the renowned Dutch manufacturer specialising in attachments tailored for the demolition, recycling and scrap metal industries. Rotar’s innovative designs are developed with the operator’s needs in mind, resulting in reliable equipment that maximises performance with excavators and wheel loaders. This dedication to quality makes Rotar the preferred choice for attachments.
Along with Worsley Plant’s
technical advice, skilled expertise and efficient lead times nationwide, we are proud to provide an outstanding service to our customers. Our team is dedicated to understanding the unique needs of each client, ensuring that we deliver tailored solutions that enhance their operations.
Because of the strong partnership between Worsley Plant Ltd and Rotar, we have been able to thrive in the demolition industry, progressing from strength to strength. This collaboration has allowed us to leverage Rotar’s innovative and highquality attachments, enabling us to meet the diverse needs of our clients effectively.
We were thrilled to be recognised in the industry by winning the Demolition Supplier of the Year award. This achievement is a testament to all our hard work and dedication at Worsley Plant Limited. It reflects our commitment to providing exceptional service and quality products in the attachment industry. Thank you to everyone who has supported us on this journey.
We are proud to have received the Environmental Innovation of the Year award for our efforts at Edmund Street, Birmingham. Throughout the project, we reached a remarkable 98% recycling and redistribution rate for all materials and proudly donated several tonnes of unwanted materials to support the development of the new community centre by Nightlife Outreach. This collaboration reflects our dedication to local
communities and sustainable practices. By fostering a circular economy, we minimise waste and emissions, allowing organisations like Nightlife Outreach to focus their resources on other key priorities. We are pleased to be have been recognised for this project as it highlights the significant value of community collaboration and our commitment to cultivating impactful partnerships.
We are very proud of our team for the work they have put in over the last year. To once again be recognised with awards is truly humbling. We hope that the awards and commendations for individuals and projects can inspire our wider team to strive for the same recognition next year and many years to come.
Gheorghe Tomozei said: “The British Demolition and Asbestos Awards was absolutely amazing. The people I met were so kind and respectful to me and I enjoyed every moment of it. I’m doing my best at every single job, but it was unexpected to win the Asbestos Operative of the Year award. I’m thrilled for myself and the company I work for and really thankful to them for nominating me. My family is very proud that I won the award.”
This is the first time Rhodar has submitted an entry into the British Demolition Awards so to win the Demolition Project of the Year Over £1m category in such esteemed company felt very special. This was particularly the case, as several of our project team, who delivered this project so successfully and diligently, were able to attend and enjoy the celebrations. The awards process itself has also proven to be an excellent opportunity for us to showcase the innovation and professionalism displayed by our team during the demolition of the former Rank Hovis Flour Mill. This high-profile project, delivered in the heart of London’s historic Royal Docks, will help to pave the way for the wider £3.5bn regional regeneration scheme to develop 6,500 new homes, arts, dining and leisure facilities, along with creating around 2,000 jobs.
We are thrilled that Windsor Waste Management has been named Waste Provider of the Year for the second year in a row at the British Demolition Awards. This prestigious accolade is a proud moment for our entire team and highlights the dedication, innovation and hard work that goes into providing the highest standard of asbestos and hazardous waste management services for the demolition industry. Being recognised at such a significant event is not only an honour but a reflection of our ongoing commitment to excellence. From day one, our goal has been to offer reliable, compliant and tailored waste disposal solutions that help our clients tackle even the most challenging projects. This award reinforces our belief that our efforts in problem-solving, customer care and compliant practices are truly making an impact in the industry.
The British Demolition Awards provided an outstanding platform to celebrate industry achievements and innovation. Attending the event alongside so many respected professionals was an inspiring experience. We were able to reflect on how far we’ve come as a business while also looking ahead to the future of demolition and waste management.
We take immense pride in our team, whose dedication is at the heart of everything we do. Their expertise, attention to detail and passion for delivering exceptional service have been pivotal to our success. This award is a testament to their hard work, as well as the trust our clients have placed in us over the last 24 years.
Looking ahead, we are more motivated than ever to continue evolving and enhancing our services. As we adapt to the
Demolition & Enabling Works
Our unique capability to repurpose virtually all construction and demolition waste from site helps our public sector, local authority, commercial and residential clients achieve zero-to-landfill targets.
Demolition
Structural alterations
Site clearance
Soft strip
Asbestos management
Remediation
Earthworks & civils
Temporary works
& Concrete
Total Reclaims Demolition Ltd is proud to have been awarded the prestigious Demolition Project of the Year 2024 – under £1m at the recent British Demolition Awards. This accolade was awarded for our work on the Botanic Place project in Cambridgeshire, a development set to provide 300,000 sq ft of cutting-edge office space.
The Botanic Place project is not only an innovative and ambitious undertaking but also a first for the city of Cambridge, achieving BREEAM “Outstanding” certification, and showcased our commitment to sustainability and excellence. This project presented a unique set of challenges, from the complexity of the site to the strict sustainability goals, but our team’s dedication and expertise ensured its success.
We are incredibly proud of our team, whose hard work, innovation and attention to detail were critical in delivering such a complex project, within budget and to the highest standard. This award is a testament to the skill, quality, professionalism and teamwork that Total Reclaims Demolition Ltd. brings to every project.
Winning this award reinforces our position within our industry, and we are excited to continue delivering exceptional results on future projects. We would like to thank both our client, Railpen, for trusting us with our appointment and Demolition Hub for this recognition, as well as our incredible team and suppliers who made this achievement possible.
Since joining in 2022, Kayleigh has gone from strength to strength. In her nomination, Kayleigh’s Site Manager praised her journey so far: “Having closely worked with Kayleigh over the past year and a half, I am immensely impressed by her exceptional performance and dedication to her work. She consistently demonstrates a strong work ethic, exceptional problem-solving skills and outstanding leadership potential. She has become an invaluable asset to our team, consistently delivering results and exceeding expectations. I have no doubt that she will continue to excel to make significant contributions in her future endeavours.”
On top of excellent technical skills, top-end qualification results and tackling any challenge that comes her way, Kayleigh has become integral to her team above and beyond her daily role. As a mental health support worker, she has been crucial in fostering a supportive, inclusive, and collaborative team dynamic.
Kayleigh shows that demolition is a rewarding and exciting career for anyone, and it’s a career based on merit where hard work is recognised. This sentiment is at the heart of Brown & Mason – we’re passionate about what we do and as such build teams filled with people who share that passion.
Kayleigh is a credit to herself, to her team, and to the whole company. She is committed to our values, such as hard work and expertise, while looking for ways to innovate and continuously develop. We are thrilled that this is recognised not only within the company, but at an industry level at the British Demolition Awards as Apprentice of the Year.
how our teams give back to local communities, through initiatives like school visits, which inspire the next generation of demolition engineers.
Brown & Mason is a company made up of people just like Kayleigh –across all parts of the business. This is what makes winning Contractor of the Year such an important achievement for us. It shows the strength of the whole business. Our achievements are the culmination of bringing together dedicated experts in their own fields to build winning teams that allow Brown & Mason to deliver excellence in everything we do.
We’re delighted that the judges recognised our expertise, professionalism and ability to
handle highly complex projects for a long list of satisfied clients.
The client testimonials we submitted with our nominations highlighted our “extremely robust Social Value Delivery Plan,” our “strong determination and commitment” and the fact that clients felt they could “always rely on unambiguous and immediate action”.
It holds particular significance to us that outside of technical excellence, the judges also shared our belief that social value is worthy of recognition. We’re proud of
We’re no strangers to awards, record-breaking achievements and accolades, having collected a wide range of them over the company’s 60+ year history, but we celebrate each award as if it’s the first one.
We’re driven to constantly achieve excellence and continuously develop – as individuals, as teams of experts and as a company. From the board of directors to every single operative on site, we’ve got our eyes firmly set on the future and how we can go above and beyond on every project – and this award is another step on that journey.
The British Demolition Awards made for a wonderful evening. Everything about the night was top notch, from the class of champagne to the photographer taking great pictures, and the ballroom was a one-of-a-kind setup.
Being chosen as the Demolition Hall of Fame Class of 2024 International Personality was a moment of great honour for me. When Ben informed me about the award, I was shocked but the feeling of honour quickly overshadowed it. I immediately made plans for my wife Karen and me to attend the event. To my delight, I discovered that two of my colleagues and friends from Independence Demolition, Justin King and Steve Wilk, and their wives would join us in London.
The food was excellent and it all went very quickly for me once the evening started. My speech was a blur, so I had to watch some videos
to ensure I came off ok, which I did. The event ended on the rooftop bar, with old and new friends enjoying a cocktail against the backdrop of St Paul’s Cathedral, a picture I will never forget.
The British demolition family is a loud and lively bunch of professionals. I love how their passion for the industry moves us forward, and at all costs to do it safely, because we must do the best job possible to keep our workers safe every day. Once again, I am proud to be
in their Hall of Fame.
Lastly, I want to thank my family Zoe, Katie and Matthew; my mum, who at 84 took the train from Glasgow to be with me; and my colleagues who have supported me and allowed me to become the demolition guy I am.
So, I leave you with this: dream it and it can become a reality. I did and look at what happened to me –a member of the Demolition Hall of Fame.
Warrior and a great friend to both the charity and to me, personally.
“Mesothelioma UK are often asked by people living with mesothelioma to do all we can to raise awareness and prevent other people being put at risk of exposure.
Demolition workers are at the forefront of managing the UK’s dreadful asbestos legacy through their amazing and important work, and we’ve found that linking with them and the wider asbestos industry is one of the best ways to achieve what these patients want. I feel honoured and tremendously grateful for the continuous warm welcome that I receive from people across the industry, as they work to make the UK a safer place.
I would especially like to thank the team at the British Asbestos Awards for this remarkable recognition. I am honoured to be following in the footsteps of previous recipients – Dr Yvonne Waterman, Founder of the European Asbestos Forum and the late Mavis Nye BEM, President and Co-Founder of the Mavis Nye Foundation, a real Meso
From patients, families and charity workers, through to support groups, healthcare professionals and the asbestos industry, we all want the same thing – a safer, asbestos-free UK to prevent future generations succumbing to this national healthcare nightmare.”
Liz has served as the Chief Executive of Mesothelioma UK, the national charity for anyone affected by mesothelioma, for more than 20 years, while also caring for patients at Leicestershire hospitals. Mesothelioma is a form of cancer that is caused by exposure to asbestos in around nine out of ten cases.
More than 2,700 people are diagnosed with the condition every year in the UK.
The charity exists to support people with mesothelioma to live better and live
longer and to prevent mesothelioma happening to future generations. It does this by advocating for better treatment and care, enhancing quality of life, supporting research and amplifying the patient’s voice.
The team includes over 30 specialist nurses based in NHS trusts across the UK, striving to help everyone affected by mesothelioma access the expertise, care and support they need they need – no matter where they live.
For more information, visit www.mesothelioma.uk.com, email info@mesothelioma.uk.com or call the freephone information line on 0800 169 2409 (Monday to Friday 9am – 4pm).
I had a fantastic time at the British Demolition awards representing 360 Recruitment. It was an honour to receive the Highly Commended Demolition supplier of the year award and I look forward to growing my network further within the demolition industry over the next year. See you again next year!
Elle Marchetti, Recruitment Consultant, 360 Recruitment
HSP were proud to both attend and sponsor the awards, which continue to get better every year. Congratulations to all involved in organising this event, the venue was excellent and the company even better; we cannot wait for next year!
Dean Clark, Director of Business Development, HSP Site Supplies
One of the most professionally run events that I have attended in a long time. I was very impressed with not only the organisation, but the extensive industry leading attendees present, all of whom make the demolition sector one to be proud of. Fireward will certainly be attending again and thanks go to those at Demolition Hub who make the event possible.
Fred Dulwich, Head of Sales, Fireward
Fireward won the Safety Innovation of the Year award
What an incredible night at the British Demolition Awards – we were thrilled to take home the Demolition Supplier of the Year award. A huge thank you to the Demolition Hub for organising such an enjoyable event and bringing the demolition industry together.
Sean Heron, Managing Director, Worsley Plant
Worsley Plant won the Demolition Supplier of the Year award
We are a ‘one-stop shop’ for the Asbestos Removal, Demolition & Construction industries, dedicated to customer satisfaction backed by our extremely fast delivery service and highly trained sales team.
Asbestos Removal Consumables
Sacks and Bags, Disposable Suits and Protective Work Wear, Adhesive Tapes, Signage, Polythene Sheeting and more.
Site Tools & Equipment
We stock a wide range of industrial tools, machinery and equipment for the construction and aerospace industry
Plant Hire
From Excavators, Dumpers, Loaders to Decontamination Units for Hire. We also provide plant maintenance service, test and repair.
PPE & Janitorial Materials
High quality Janitorial, Traffic Management, Catering, Respiratory and Personal Protective Equipment
Attending the British Demolition Awards and British Asbestos Awards was fantastic. The atmosphere was electric and we were in good company with such a broad spectrum of industry players there supporting each other. We’re keen to come back again next year and would be excited to put forward our new company Viking Demolition & Construction as a nominee. Thanks to all involved, it was a great night full of great people.
Ben Batchelor, CEO, Viking Group Attachments
The British Demolition Awards this year was an honour to attend. It provided a wonderful opportunity to recognise and appreciate the outstanding achievements across our industry. The evening was exceptional, it allowed us to reconnect with valued partners and forge new relationships, showcasing the innovation and dedication that drive our field forward. It truly was a who’s who of the demolition industry both from the UK and the world. Well done everyone at Demolition Hub.
William Crooks, Managing Director, Cawarden
Cawarden won the Environmental Innovation of the Year award
This unique awards evening provided a great opportunity for us to learn about and celebrate a range of achievements from right across the demolition sector over the past year, highlighting a host of projects and people deserving of recognition. Hosted at a brilliant venue, the event itself had a packed agenda and was well organised. The combination of awards, fundraising for charity and special recognitions proved to be a successful formula. Special thanks go to Ben and all the team at Demolition Hub for the hard work put into making the event so enjoyable.
Ian Spence, Group Strategic Development Manager, Rhodar
Rhodar won the Demolition Contract of the Year Over £1m award. For further details of the project see their case study in this issue.
There’s only one place you’ll find the heavy hitters of concrete and masonry this January: Vegas, baby — at World of Concrete 2025, the largest and only annual international event dedicated to your business. Be here to mix with industry giants. Get your hands on the latest technologies revolutionizing safety, performance and speed. And learn what it takes to not only claim a piece of our industry’s massive projected growth but dominate the field. Join the power players of concrete and masonry.
EXHIBITS: JANUARY 21-23, 2025
EDUCATION: JANUARY 20-23
LAS VEGAS CONVENTION CENTER
We had an incredible time attending the British Demolition Awards this year. Winning Waste Provider of the Year is an absolute honour and a testament to the hard work and dedication of our team. The event was a fantastic opportunity to connect with industry leaders and celebrate innovation in the demolition industry. We’re excited to continue delivering best-inclass service to our customers.
Tony McPartland, Group Managing Director Windsor Waste Management and Zest Recycle
Windsor Waste Management won the Waste Provider of the Year award
As representatives of the Swantest team we were thrilled and honoured to be part of the prestigious British Demolition Awards. The event was an exciting and enjoyable experience, bringing together likeminded professionals from across the construction industry. We look forward to being part of the 2025 event for another fantastic evening.
Liam Dixon, Operations Director and Mihai Chelmus, Operations Manager, Swantest
Rotar International was proud to be present at the British Demolition Awards in London earlier this month. The event was exceptionally well organised and we were delighted by the positive atmosphere and the high calibre of the attendees. We were particularly impressed by the well-deserved recognition given to the winners. It was an inspiring evening and we look forward to participating again in the future.
Louis Broekhuizen, Commercial Director Attachments, Rotar
I had an amazing time at the British Demolition Awards, I felt welcomed from the moment I arrived and was able to finally meet some familiar faces from LinkedIn in person, which made the night even better. The event was well organised with good food and I’m already looking forward to the next one!
Riley Pond, Contract Manager, The Labour Desk
We attended another fabulous British Demolition Awards night. Great hospitality, great fun and some great auction prizes. Thank you to Ben and Demolition Hub. We’re looking forward to next year’s event already!
Melvyn Cross, Director, Total Reclaims Demolition
Total Reclaims Demolition won the Demolition Contract of the Year Under £1m award. For further details of the project see their case study in this issue.
Brown & Mason had a fantastic time at the Leonardo Royal London St. Paul’s for the 2024 British Demolition Awards. We were proud to take home not only the title of Contractor of the Year but also that one of our rising stars, Kayleigh Gerrietty, was named as Apprentice of the Year.
Brown and Mason
Brown and Mason won the Demolition Contractor of the Year award and Demolition Trainee/Apprentice of the Year
Attending the British Demolition Awards in London was a fantastic experience for Dragon Equipment. We were proud to be recognised among the best in the business, receiving a highly commended award in the Demolition Supplier of the Year category. The evening was thoroughly enjoyable and provided a great opportunity for us to network with other industry leaders in the world of British demolition.
Jeff Haines, Director, Dragon Equipment
We had a great night – the Demolition Hub team were fantastic as always.
Ben Gorham, Managing Director, Sky Revolutions
We were excited to attend the British Demolition Awards for the first time this year, marking our entry into one of our new target markets for our tree services. The event was exceptionally well organised, providing a great opportunity to connect with industry professionals. We left with a deeper understanding of the demolition sector and established some valuable new contacts. We’re looking forward to being a part of this fantastic event again in the future.
Juliet Perrett, Marketing Manager, Artemis Tree Services
Clifford Devlin had a brilliant time at the event, which turned out to be both memorable and rewarding. A special thank you goes out to Demolition Hub, Asbestos Hub and Ben Chambers for putting together such a well-organised event. It was a fantastic atmosphere that brought people together, fostered networking and highlighted key industry insights.
Liam Hennessy, Head of Group Operations, Clifford Devlin
Gheorghe Tomozei, Supervisor, of Clifford Devlin won Asbestos Operative of the Year
As we draw ever closer to the conclusion of the ASBP Disrupt II steel reuse initiative, the team were presented at the Circular Steel 2024 conference in London on 10 September, which was attended by more than 150 delegates ranging from contractors, project managers and clients.
This insightful and collaborative event was dedicated to advancing the reuse of structural steel in the construction industry. With over 90 companies represented, the event was a key moment for professionals to share knowledge, explore practical challenges and drive forward innovation in the circular economy. The agenda was structured around five panel discussions, each addressing critical aspects of steel reuse.
This session, led by industry champion Holy Price of Keltbray, explored fundamental questions such as how and when to deconstruct buildings for optimal steel recovery, whether there is a real demand for reused steel and whether incorporating reuse into demolition tenders increases costs. Contractors and project managers detailed various projects completed with direct steel reuse and donation to rebuild projects while balancing cost. The group shared their thoughts on this rapidly emerging market commenting that significant changes have already been seen since the
steel 2023 seminar. The discussions shed light on the strategic considerations that developers and contractors must weigh when planning for steel reuse.
The second session, Writing the Brief, led by Will Arnold of IStructE, tackled some of the common pitfalls that can lead to missed opportunities for steel reuse. Panellists discussed changes to procurement guidance and how clients and developers should better frame their project briefs to encourage reuse, asking the right questions early on and aligning the project team’s approach to ensure that reuse opportunities are maximised and that reuse of steel becomes standard practice rather than “a cottage industry”.
In Buying the Stock, chaired by Rob Mumford of Gardiner & Theobald, the conversation turned to the practicalities of sourcing reusable steel. Key topics included potential contractual and insurance considerations, the importance of designing with reuse in mind and whether these factors might affect project timelines. This session also delved into the logistical realities of incorporating reused materials into project planning.
The technical challenges of steel reuse were addressed in Testing &
Fabrication, led by Jonathan Davis of William Hare Group. Following a short video of steel fabrication works, discussion focused around the process involved and the need for quality control of the production line feed emphasising that reused steel was currently unsuitable for automated fabrication.
With the panel including Roy Fishwick of Cleveland Steel and Tubes, Tom Howarth of EMR Reusable Steel and Michael Sansom of British Structural Steelwork Association (BCSA), panellists discussed how reclaimed steel is refabricated, noting the differences between this and systems optimised for new steel stock. Some interesting debate followed around quality issues and the possible consequences of electric arc furnace steel production coming online.
Special measures and fabrication times were highlighted as important considerations when working with reused materials, giving the audience a practical understanding of how these factors impact the construction process.
Finally, Lessons Learned, chaired by Brogan MacDonald of Ramboll UK, wrapped up the day’s discussions by sharing real-world examples of successful steel reuse projects. This session allowed for a broader reflection on the insights gained from the day and highlighted the tangible benefits of incorporating steel reuse into future projects.
The lessons were clear. Much more needs to be done to ensure the message for steel reuse is communicated with clear industry guidance to maximise the substantial carbon savings, while embracing project challenges as learning opportunities.
Throughout the day, attendees had the chance to explore case study boards displayed around the venue that showcased innovative steel reuse examples. These case studies are already available on the Circular Steel website and recordings of all the panel sessions will soon be made available online for those who were unable to attend.
The event’s success was made possible by the support of its sponsors, with special thanks to the platinum sponsors, Keltbray and Excess Materials Exchange.
Reflecting on the event, organiser Steve Gilchrist said: “Circular Steel is all about knowledge sharing, connecting people, and pushing the industry forward. The conversations and energy levels in the room were fantastic and so collaborative, and they just go to show that reuse is happening and steel is leading the way.”
The event concluded with networking drinks, giving attendees the opportunity to continue their discussions and build connections in a more relaxed setting.
For more information, visit: www.circularsteel.co.uk
Co-founded by Ryan Son and Ben Batchelor, Viking Demolition & Construction is quickly carving its name as a versatile and reliable player in the demolition and construction sectors. As part of the larger Viking Group, the company benefits from a unique structure that allows it to offer a broad range of integrated services, with a focus on recycling, metal reuse and contributing to the circular economy. These efforts have become integral to the company’s approach, ensuring environmentally responsible practices are at the core of its operations.
Reflecting on his partnership with Ryan, Ben says: “The reason I was drawn to Ryan was his ambition. I saw that he was incredibly good at his job, but he was in a position where he was underutilised.” It wasn’t just Ryan’s talent that caught Ben’s attention. “Ryan also introduced me to his dad,” Ben continues. “His dad, Darren Son, was a straight shooter, and I quickly realised that Darren was excellent at what he does.”
Ben saw the potential for collaboration early on: “Not everyone is great at their work, but Ryan truly was.” Ben adds: “We each have different strengths and it became
clear that Ryan, his dad and I together could complement each other’s approaches to business.”
A foundation built on family and experience Ryan’s journey into the world of demolition began almost as soon as he could walk. “Demolition has always been a part of us,” he recalls. “I have videos of me at eight years old on a private yard in Romford, operating an excavator. My dad was always working and I’d spend time on site, learning the ropes.”
Ryan’s father, Darren Son, a self-made man in the demolition world, instilled in him a strong work ethic from a young age. Growing up, Ryan balanced school and his burgeoning career, working with his father during school holidays, stripping copper and reclaiming materials, experiences that laid the groundwork for his future.
“My dad always emphasised that you have to start from the bottom. ‘You’re never going to be a good manager if you haven’t done all the different roles,’” Ryan explains. That advice guided him through the years, shaping his approach to the business. Even after finishing school with a solid set of qualifications, Ryan chose a different path, opting
to travel and work rather than head straight to university. His travels took him as far as Australia, where he continued labouring and building his construction and life skills.
Returning to the UK, Ryan joined his father’s company, which had landed major contracts like the British Museum and Chelsea Barracks. But his father’s unexpected injury left Ryan with a sink-orswim situation. “My dad was in the hospital for a year, and it was up to me to keep things going,” he says. Balancing multiple sites, working long hours, and managing a team, Ryan learned firsthand how to run a company. “It was tough, but it taught me everything I know about management, operations, and the pressure of getting things right.”
After his father’s recovery, Ryan took the opportunity to expand his experience by working for several other demolition firms, progressing to become a Project Manager at a very established Tier 1 demolition company. It was during this time that Ryan truly honed his skills. “I wouldn’t be where I am today without the guidance and mentorship I received under my Operations Director,”
Ryan reflects. “He taught me how to foresee problems before they happen, and I learned how to overcome different obstacles that would arise throughout projects, both commercially and operationally. I also learned the importance of how crucial the paperwork side of things are to a job, even though I was terrible at it.”
One of Ryan’s standout projects at the Tier 1 company, was a complex demolition job involving a tube line beneath the building and a live UKPN substation. “There were so many constraints – party walls, a Grade II listed wall with a mosaic attached to it, and we had to keep fire exits live throughout the demolition,” Ryan explains. “It was a massive learning curve, but we finished on time and it helped shape how I approach complex projects today.”
Despite his success at previous demolition companies, an unexpected opportunity arose that would change the course of Ryan’s career. While project managing large-scale demolition projects, Ryan met Ben Batchelor, Director of Maldon Metals, the company responsible for handling metal and salvage. They became acquainted and ideas and visions for collaboration began to flow.
“I was happy where I was, I had no intention of leaving,” Ryan says. “But Ben and I saw that there were many opportunities to take on jobs that larger companies weren’t interested in due to the package values. And the idea to start Viking Demolition took root.”
After months of deliberation, Ryan took the leap to co-found Viking Demolition. “It was a big decision, I didn’t want to burn any bridges but I knew if I stayed I wouldn’t have the same opportunity to work for myself,” Ryan explains. With Ben’s support and partnership, Viking Demolition was able to quickly grow, taking on projects
that required both demolition and construction expertise. As part of a group of companies, we were able to offer a full turnkey package, from demolition, substructure, super structure and fit-out, saving time and money for our clients and making us more competitive.”
One of Viking Demolition’s early successes has been its ability to secure major projects while maintaining an agile, client-focused approach. Ryan attributes much of this to the strategic hires he’s made,
including the addition of Joe Gott, an incredibly focused and hard-working Quantity Surveyor.
Joe, a commercial management professional with a solid foundation in high-level mathematics and engineering, joined Viking shortly after its launch. Having worked on prestigious projects such as Battersea Power Station, his five-plus years of experience have made him a key player. “Joe’s analytical skills and attention to detail have been crucial in delivering projects on time and within budget,” Ryan notes.
Joe’s dedication to the company’s success is evident in his words: “I
believe that the key to successful commercial management lies in the perfect blend of technical skill, clear communication and focus on continuous improvement.”
Pushing the boundaries: sustainability, safety and accreditation
Today, Viking Demolition & Construction is not only at the forefront of sustainability in the demolition industry but also leads in health and safety standards. With Maldon Metals, a sister company, the team is committed to recycling industrial metals efficiently, reducing their carbon footprint by keeping materials in the UK.
“Sustainability is something we take very seriously,” Ben says. “When doing the demo side of things, we have to cut up the steel, put it into cargo containers and send to smelters overseas. Currently in Merthyr Tydfil in South Wales, they are changing their smelting units from a traditional smelting to an arc reactor, which will enable us to manage green steel more effectively. In the meantime, the most effective way of lowering your carbon is
the reuse of the steel rather than the recycling of the steel. This is a selling point for us and something we actively strive to achieve on every job. If I bought a lintel from a demolition contract it could cost us a fraction of the new steel costs. If you go and buy it would be around £300. It’s about reintroducing materials back into the industry. And that’s what we are trying to do in every regard. Be it reusing the steel or reclaimed material we take from sites such as cobblestones and making the most of it rather than send it to waste, this significantly reduces the potential environmental impact from demolition projects.”
Ryan says: “We’ve recently brought in a new Head of HSQE (Health, Safety, Quality, and Environment), Angelica Stoica, who has worked for multiple high-profile Tier 1 contractors on significant projects across central London, and is working diligently on acquiring top-level industry accreditations.”
Under Angelica’s leadership the company has already passed the Stage 1 audit for BSI (ISO) 31000: Risk Management; BSI (ISO) 9001: Quality Management; BSI (ISO)
14001: Environmental Management; and BSI (ISO) 45001: Health & Safety Management, with Stage 2 scheduled for October. “Angelica is so qualified we had to create a new signature template to fit in ‘CMIOSH PCQI MIIAI MIIRSM MCMI MIoL AaPS,’” Ryan laughs.
But Viking hasn’t stopped there. “We’ve also just obtained Achilles and Construction Line Gold certifications,” Ryan adds. These achievements not only demonstrate Viking’s commitment to meeting the highest standards but also open up new opportunities for securing larger, more complex contracts.
Angelica’s work has been crucial in positioning Viking Demolition & Construction as a fully accredited leader in both safety and environmental responsibility. “These certifications validate the rigorous processes we’ve put in place,” Angelica says. “They allow us to confidently take on top-tier contracts, knowing that our clients can trust we’re working to the highest industry standards.” I would like to be better innovative, to try more environmental, health and safety techniques that out there on
the market.”
Angelica, who leads sustainability and safety at Viking Demolition & Construction, highlights the company’s proactive approach to environmental responsibility and worker safety. “When it comes to sustainability, we’re committed to increasing our use of electric vehicles and HVO (Hydrotreated Vegetable Oil) fuel to lower our carbon footprint. We’re also focusing on having a dedicated BREEAM AP (Accredited Professional) on board, which is a significant advantage, particularly in places like London where BREEAM targets are a priority.”
Discussing health and safety, Angelica adds: “Our employees are always our top priority. For example, we are working to introduce more mechanised equipment, such as remotely operated Brokk robots for smaller demolition tasks. This minimises operatives’ exposure to dust, vibration and other hazards, as they can control the machinery from a safe distance.”
Angelica also mentions the use of advanced technology to safeguard workers: “We’ve introduced HVS watches, which are incredibly helpful. When a worker approaches their exposure limit, the watch sends an alert, allowing them to pause and step away, ensuring they stay within safe working limits.”
Looking towards the future, Viking Demolition is embracing digitisation as part of its sustainability initiatives. “Over the next year, we’re aiming to digitise everything to reduce paper usage and move towards being as paperless as possible. We’re also focusing on using recycled PPE and setting up recycling stations on our sites.”
Angelica emphasises the
importance of giving back to the community: “Engaging with the local community is a priority for us and over the coming year we plan to work more closely with charities, especially those supporting children, as they represent the future of the country. We’ll also be engaging with schools by offering apprenticeship programmes and work experience opportunities to inspire the next generation.”
In addition to its environmental and safety efforts, Viking Demolition & Construction also places a strong emphasis on quality. Angelica explains: “We are constantly working to understand our customers better by conducting surveys to gauge their needs and expectations. Customer feedback plays a key role in identifying areas for improvement, which in turn helps us enhance the overall quality of our products and services.”
Building trust is essential, she notes: “Clients are more likely to work with a company they trust, and that trust is built on delivering consistent, high-quality outcomes.”
The company recognises the value of customer retention, Angelica adds: “It’s more cost-effective to retain existing customers than to acquire new ones, and a good quality management system focuses on enhancing the customer’s experience with our products and services.”
The company is also investing in the future, with apprentice Bella Munday being a prime example. Initially joining the company for business administration, Bella quickly developed an interest in the projects themselves. With a keen interest in becoming a quantity surveyor, Bella is now enrolled in a Level 3 Surveying Technician apprenticeship, with the
goal of progressing to studying at University. Bella is learning to use waste management tools like Smart Waste, helping the company meet all levels BREEAM standards for environmental sustainability.
As Viking Demolition & Construction enters its second year, the foundation has been set for even greater achievements. “This first year has been all about laying the groundwork,” Ryan explains. “We’re predicting a turnover of £2.5 to £3 million, and with the projects we’ve secured and the tender lists we’re on, I expect next year we’ll be somewhere between £5 and £7 million.”
The company’s vision is clear – growth, innovation and a commitment to sustainability and quality. With strategic partnerships, the right team in place and the full support of Viking Group, Viking Demolition & Construction is poised to make an even bigger impact in the industry.
And for Ryan, it all comes back to the values instilled in him from day one – hard work family, and dedication to doing the job right. “I’ve always believed in earning your place in this industry,” Ryan says. “And with Viking, we are doing everything we can, as best as we can to earn our place at the table. This is just the beginning.”
Project: Rank Hovis Premier Mill
Structure: Former roller flour mill, derelict for more than 30 years
Site area: Over one hectare
Scope of works: Asbestos removal, full structural demolition, waste management and site clearance
Contractor: Rhodar Specialist Enabling Works
Client: Greater London Authority
Other stakeholders: Avison Young, Lendlease, Environment Agency, Natural England
Start date: 17 October 2022
Completion date: 22 November 2023
Techniques: A range of advanced techniques, including super high-reach demolition, precise hand separation, diamond cutting, track sawing, stitch drilling, plus mist cannons and direct suppression methods. Cantilevered scaffolding and pontoons were used to protect the watercourse and ensure safe access at the water’s edge,
Future use: Part of a £3.5bn regeneration project of London’s Historic Royal Docks to develop 6,500 new homes, arts, dining and leisure facilities,
Resources: Heavy equipment: Komatsu 30-m high-reach excavators; 25 and 30-tonne excavators; super high-reach cherry picker; three Dust Busters to control particulate matter,
Scaffolding and water management: Specialist cantilevered scaffolding to safeguard building integrity, adjacent structures, and prevent debris falling into the waterfront; Aqua Dock Pontoon System to prevent debris from entering the waterway and enable construction of the scaffolding,
Safety and monitoring equipment: Advanced security surveillance; noise barriers and mist cannons to reduce environmental impact on surrounding community.
Located in the heart of London’s Docklands in close proximity to the City Airport, the demolition of the Rank Hovis Premier Mill represented a significant milestone in the £3.5bn regeneration project of London’s Historic Royal Docks.
Originally a flourishing flour mill, the Rank Hovis structure had been out of use since the 1980s and was further damaged by a fire in 2019. Given the building’s compromised structural integrity and prime location opposite the London ExCeL alongside the Royal Victoria Dock, the demolition was both necessary and challenging.
Following the competitive award of the project, Rhodar not only focused on dismantling the structurally compromised building but also piloted innovative designs and created solutions that supported the principles of the circular economy.
The scope of the project, which spanned a site of more than one hectare, included:
• Structural demolition: Complete removal of all building and sub-surface structures,
• Asbestos removal: The safe removal and
disposal of asbestos-containing materials,
• Innovative scaffolding design: Development of bespoke scaffolding design and pilot programme designed to use specialist cantilevered scaffolding and a floating water pontoon to protect the Royal Victoria Dock,
• Waste management: Separation and recycling of over 2,000 tonnes of concrete and 800 tonnes of steel,
• Ecological mitigation: Implementation of ecological mitigation measures to protect local wildlife,
• Historical preservation: Safe removal and storage of artefacts, such as steel flour mill spirals and other industrial equipment,
• Community and environmental safety: Minimise the impact on the nearby residential community and the local environment,
• Regulatory compliance and coordination: Close collaboration with local authorities and environmental agencies to ensure regulatory requirements and safety standards,
• Site clearance: Ensuring a clear site for subsequent redevelopment phases.
During an initial survey of the site, Rhodar discovered a bat population roosting within the mill. As protected species, these bats required careful handling to comply with conservation laws.
Rhodar collaborated closely with Natural England and a team of ecological experts to develop a comprehensive bat mitigation strategy. This included conducting extensive ecological surveys and thermal imaging equipment to map the locations of bat colonies and identify their preferred nesting sites. The demolition was delayed until alternative habitats were prepared, including specially designed bat boxes placed around the site. The roosting sites were carefully dismantled while ensuring minimal disturbance to the bats.
The building contained significant quantities of asbestos and other hazardous substances. Rhodar’s asbestos removal teams followed stringent safety regulations, employing containment measures to isolate hazardous zones and using air filtration systems to ensure no asbestos fibres contaminated the air.
Negative pressure enclosures were created to contain asbestos debris during removal and the material was carefully doublebagged and disposed of in compliance with hazardous waste regulations. Continuous air monitoring ensured that the workplace remained safe throughout the project.
The building’s structural integrity had been severely compromised by fire damage and years of neglect, increasing the risk of uncontrolled collapse into the dock that ran adjacent to the building. Rhodar used various techniques to mitigate these risks.
• Structural assessment: Engineers conducted comprehensive structural assessments using advanced techniques like groundpenetrating radar and 3D scanning to map weak points and potential hazards across the building,
• Pontoon and scaffolding: Rhodar implemented a strategic demolition plan involving a custom-designed 70-m pontoon system and protective sheeting that acted as a barrier to prevent debris from entering the water. Counterbalanced scaffolding cantilevered off the building provided a secondary layer of protection for the dock and workers,
• Temporary support structures: Additional temporary supports were installed to reinforce critical structural elements and maintain stability during the demolition process,
• Phased demolition: The demolition was phased strategically, starting from the most unstable sections and progressing in stages. This gradual reduction of structural load minimised the risk of an uncontrolled collapse with the scaffolding being dismantled as the waterside section of the building was demolished from the top down,
• Precision equipment: Highreach excavators equipped with precise demolition
attachments and controlled by experienced operators dismantled the building in a selective and controlled manner. This approach minimised debris and ensured that hazardous materials were handled safely and efficiently,
• Dust suppression systems: Mist cannons and water sprays were employed extensively to minimise airborne particulates. The team also monitored water quality to ensure the dock remained uncontaminated throughout the project.
Managing logistics in a densely populated urban area was difficult due to space constraints and heavy traffic. Rhodar developed a comprehensive traffic management plan to control and coordinate deliveries, minimising traffic disruption and ensuring maintained access for local businesses and residents. The proximity to residential and commercial areas required careful management to minimise noise, dust, and disruption. Rhodar maintained regular communication with the local community through informational meetings and project updates. Noise and vibration control measures included scheduling work during less sensitive hours, using low-noise machinery, and employing acoustic barriers to shield nearby areas.
Delays due to slow issuance of permits and licenses such as the bat licence threatened the project timeline. We maintained flexible scheduling and constant communication with regulatory bodies to expedite permit and license processes and adjust project timelines efficiently.
See the project video here: www.youtube.com/watch?v=exFn3IH3mEY&t=28s
The Rank Hovis Premier Mill demolition was executed over 56 weeks and divided into distinct phases, each carefully timed to optimise efficiency and safety. The project delivery was detailed in the following key phases:
• Preparation and setup: Works commenced with initial site setup, including the installation of robust perimeter fencing, temporary infrastructure/offices/welfare, security measures and comprehensive ecological surveys, with a focus on bat mitigation due to the presence of the protected species,
• Mobilisation and demolition notification: Formal notifications and approvals were swiftly managed, ensuring all regulatory compliances were met before demolition commenced,
• Zone fencing and site investigation: A comprehensive site investigation was carried out to identify any potential hazards, followed by strategic zoning and fencing to secure various sections of the site,
• Asbestos removal and hazardous material management: Focused removal of asbestos and other hazardous materials was conducted early in the schedule to mitigate health risks, followed by ongoing management throughout the demolition process,
• Pontoon and scaffold protection installation: Installation of protective measures, including a pontoon to safeguard the adjacent waterway and cantilevered scaffolding
to protect the site and surrounding areas was installed,
• Structural demolition: The main phase of structural demolition was methodically executed using super highreach excavators and other specialised machinery. This phase was divided into several sub-phases to manage different sections of the building efficiently,
• Arisings management and waste segregation: Concurrent with demolition, rigorous waste management protocols were enforced, focusing on the segregation and recycling of debris to maximise sustainability,
• Final site clearance and demobilisation: Removal of all scaffolding, site clearance, and demobilisation of equipment marked the final stage, preparing the site for handover,
• Handover: The project concluded with the formal handover of the site on the specified completion date, ensuring all specifications were met and the site was ready for redevelopment.
Throughout the project, Rhodar maintained stringent adherence to safety and environmental standards, facilitated effective communication across teams and ensured minimal disruption to the surrounding community. This holistic approach to project delivery not only met but exceeded client expectations and regulatory requirements, showcasing Rhodar’s excellence in managing largescale demolition projects, including:
• Regular coordination meetings: Weekly site meetings with the client and daily briefings with the project team to ensure alignment and address any emerging issues promptly,
• Safety and quality controls: Continuous monitoring of safety practices and quality of work, with periodic reviews to adapt to any necessary changes or improvements,
• Community engagement: Ongoing communication with the local community to keep them informed and engaged, ensuring that their concerns were addressed and the project’s impact on their environment was minimised.
As one of the most high-profile demolition projects of 2023, the Rank Hovis Premier Mill was a substantial undertaking, generating significant quantities of waste. Detailed planning and rigorous waste management procedures were applied to minimise environmental impact and promote sustainability. This included:
Total waste generated
• Concrete and brick: Approximately 2,000 tonnes of concrete were recycled onsite, contributing to the new development’s foundation and landscaping features,
• Steel: Around 800 tonnes of steel were recovered and sent to recycling facilities, where they were processed for reuse in various construction applications,
• Timber: 291 tonnes of timber were recovered and sent for recycling and repurposed into new wood-based products or biomass fuel,
• Miscellaneous nonhazardous waste: Included plaster, glass and other mixed demolition debris.
Hazardous waste
• Asbestos-containing materials: Specific procedures were in place to safely remove, handle, and dispose of asbestos-containing materials, ensuring they were segregated from other waste streams and treated as per hazardous waste regulations.
• Other hazardous substances: Included paints, solvents and chemicals, which were carefully handled and disposed of in compliance with strict environmental standards.
Waste management strategy
• Segregation and recycling: All waste materials were meticulously segregated at the source to maximise recycling potential and reduce landfill use,
• Reuse of materials: Wherever possible, materials were processed and reused on-site or in the local community, supporting the circular economy ethos and reducing the carbon footprint associated with transporting materials,
“ As developers for the significant redevelopment of London’s Historic Royal Docks, we faced the task of choosing a demolition contractor who could manage the challenging demolition of the Rank Hovis Premier Mill. This project required a high level of technical skill, consideration for the environment and sensitivity to local community needs. Rhodar was selected for its outstanding reputation and commitment to safety and sustainability.
Right from the start, Rhodar’s professionalism and thorough approach were evident. They tackled the demolition with a clear, strategic plan, focusing not just on efficiency but also on minimising environmental impacts and ensuring community safety. Their innovative use of specialised scaffolding and a custom pontoon to protect the Royal Victoria Dock was impressive, demonstrating their commitment to environmental care.
Rhodar provided excellent communication throughout the project, keeping us well-informed with regular updates and detailed
• Contractor collaboration: Rhodar worked closely with certified waste management contractors who specialised in recovery and recycling of construction and demolition waste.
This focus on waste management reflects Rhodar’s commitment to sustainability and responsible demolition practices. It showcases our ability to manage large-scale projects while adhering to the highest waste reduction and recycling standards.
reports. Their adept handling of challenges, such as the presence of protected wildlife and hazardous materials, showcased their expertise and compliance with regulatory standards.
The completion of the Rank Hovis Premier Mill demolition by Rhodar was a vital step in our redevelopment effort. It was carried out with outstanding precision and an understanding of its historical and community significance. Rhodar’s work has set a strong foundation for the next stages of our project and we are truly appreciative of their partnership in this challenging project.
We wholeheartedly recommend Rhodar for any demolition project where professionalism, expertise and a commitment to the environment, community and circular economy are valued. We look forward to future projects with their exceptional team. ”
Harry Chinn, MRICS Surveyor, Building Consultancy Avison Young
Project: Botanic Place, Hills Road, Cambridge
Structures: Betjeman House (three-storey, former BBC Cambridgeshire); Ortona House (three-storey office block); Francis House (three-storey office block) and a multistorey car park
Site area: 1.07 ha
Scope of works:
Asbestos removal, soft strip, waste diversion, hand and mechanical demolition, substructure removal and site remediation, protection of the adjacent Cambridge University Botanic Gardens
Contractor: Total Reclaims Demolition Ltd
Clients : Railway Pension Nominees Limited (client-appointed development manager)
Start date: November 2023
Completion date: August 2024
Future use:
300,000 sq ft of zero-emission, all-electric, naturally ventilated, water and energyefficient adaptable workspaces achieving BREEAM Outstanding, a first for the city of Cambridge. Public realm benefits include a pub, cafe and restaurant at ground floor level, extensive landscaping and a new public square with views of the Cambridge University Botanic Gardens
Resources: In-house personnel: TRD Demolition Design Team (DDT) including four demolition engineers; two H&S managers (NEBOSH); one CSCS/CCDO site manager; one CSCS/CCDO site supervisor; 100% CSCS-CCDO/CPCS site personnel
Machinery: State-of-the-art demolition machinery, including semi-high reach and normal demolition rigs with specialist attachments for precision demolition
On-site crushing: TRD’s in-house mobile crusher unit utilised, reducing the need for waste transportation and minimising carbon footprint
Safety equipment: All personnel were equipped with the latest PPE, with regular safety briefings conducted to maintain high safety standards
Welfare: Eco welfare facilities including solar, PIR, thermostatic heating, self-closing doors and dry urinals
The project involved the stripout and demolition of Betjeman House, Ortona House, Francis House, and multi-storey car park. Additional works included asbestos removal, disconnection of services, and the removal of existing hard standings and paving.
The site, spanning 1.07 hectares, is located at the junction of Hills Road and Station Road in Cambridge, adjacent to the Cambridge University Botanic Gardens and close to other university and city centre facilities. Minimising disruption to the public was therefore a key
consideration together with the planning condition for BREEAM outstanding, required stringent attention to environmental, planning conditions, stakeholder considerations, waste diversion and safe demolition methodologies.
Total Reclaims Demolition’s in-house Demolition Design Team (DTT) was crucial to achieving approved project design, documentation production, programming, and resource assignment. We allocated both a CCDO Demolition Site Manager and Site Supervisor, supported by top-
tier management to manage the delivery of the works with agreed work activity sequences that considered the different localities and stakeholders. Sequencing involved the installation of security measures, hoarding and protective demolitionspec scaffolding to enable safe demolition operations abutting the Botanic Gardens’ boundaries and surrounding highways. This was followed by asbestos removal, demolition by both hand and mechanical techniques and major sub-structure removal operations before the final crushing phase.
Total Reclaims Demolition implemented stringent environmental controls, including containment scaffolding and hoarding, dust suppression and noise monitoring, ensuring full protection to the flora and fauna and minimisation of disruption to the gardens and their users.
Working within the busy city centre with high pedestrian and cycle traffic
We registered with the Considerate Constructors Scheme (CCS) and achieved an Excellent performance level rating. We also engaged closely with stakeholders to minimise disturbance, installing full public protection to all site boundaries. There were no complaints received throughout the project.
TRD established dedicated access routes, permitted timings for demolition traffic and launched an awareness campaign for cyclists, ensuring safety and minimising traffic disruptions. Cycle parking was maintained to minimise disruption to surrounding facilities.
to environmental standards while maintaining efficiency
We met very stringent environmental requirements set by the local authority, with no reported incidents or violations. On-site dust controls included at-source damping down/remote fine spray units throughout strip out, demolition and crushing operations, which resulted in full containment and minimised impact on surrounding environs.
Total Reclaims Demolition maintained an exemplary safety record throughout the project, with zero reportable incidents. In-house and external health, safety and environmental audits were carried out to ensure compliance. Real-time vibration and noise monitoring equipment was employed to ensure we met very stringent environmental standards.
All asbestos removal was carried out in accordance with HSE guidelines, with timely notifications and approvals and we implemented 24/7 site security measures, including physical security personnel and CCTV to safeguard the site and surrounding areas.
We conducted a detailed predemolition waste audit to identify materials for recovery, reuse and recycling, which was fed in to and monitored against the BREEAM report. This resulted in the following:
• Computer flooring – reused in a London refurbishment project,
• Cycle store – donated to a local church,
• Carpet tiles – sold for reuse,
• Kitchen and bathroom fixtures – donated to a TRD employee for use in their first home,
• Windows and brickwork –removed by hand and preserved for reuse in the newbuild phase,
• Crushed arisings – clean, inert materials were crushed on site according to WRAP protocol for reuse within the new scheme,
• Statistics – 98% of waste was reclaimed, reused or recycled, contributing to the project’s sustainability goals.
BREEAM Outstanding: On target for the Botanic Place project, reflecting TRD’s commitment to sustainability,
Scheme: Excellent performance rating, showcasing our dedication to minimising disruption and maintaining high standards of site management and personnel welfare,
ISO certifications: ISO 9001, 14001 and 45001 certified through BSI, demonstrating our commitment to quality, environmental management and occupational health and safety,
NFDC membership: As members of the National Federation of Demolition Contractors, we adhere to the highest industry standards,
Social value: We have met our set targets for Social Value initiatives for the scheme with local suppliers, local employment, homeless initiatives and links formed with local social enterprises.
Total Reclaims Demolition is committed to pushing the boundaries of what is possible in the demolition industry. With a focus on sustainability, safety and client satisfaction, continuous learning and adaptation were key to overcoming the challenges faced on the project.
We refined our waste management processes and enhanced our stakeholder engagement strategies, setting new benchmarks for future projects. Using HVO to replace fossil fuels for heavy machinery, together with on-site crushing and the salvage of materials for integration into new projects demonstrated our innovative approach to demolition and sustainability.
The Botanic Place project exemplifies TRD’s commitment to excellence in demolition, sustainability and client satisfaction. Through innovative techniques, rigorous safety standards and a focus on environmental stewardship, we delivered a project that not only met but exceeded client expectations.
Our work on the Botanic Place project is a testament to our industry leadership and our unwavering continued investment and commitment to quality, environmental, sustainability and personnel development. Winning the Demolition Project of the Year Under £1m award is a recognition of our team’s hard work and dedication to delivering the best possible outcomes for our clients and the community.
“The team at TRD exceeded our expectations in every aspect of the project. Their innovative waste management strategies and dedication to environmental protection were key to the continued project’s successes”
Andrew Boyle,
Construction Director, Socius
Developments
Snapshots of Ben and the Demolition Hub team’s activities between issues
by Kevin Gardner, Commercial Manager at BPI
As with many businesses that rely on specialist equipment, demolition contractors often accumulate unwanted machinery. This surplus can arise for many reasons, including downsizing, business closure, a slowdown in the market or simply project completion. Disposing of these unwanted assets sustainably, efficiently and profitably requires a strategic approach. Kevin Gardner, Commercial Manager at BPI Asset Disposal Solutions, looks at why demolition contractors are choosing to partner with commercial asset disposal specialists
As demolition projects progress, assets such as machinery, equipment, vehicles and tools play a vital role in ensuring overall success. However, when they are no longer needed these assets need to be disposed of properly. By efficiently disposing of unwanted assets, demolition contractors can achieve multiple benefits that contribute to the overall health and success of their businesses.
Unwanted equipment represents tied-up capital. Selling surplus assets frees up cash that can be reinvested in the business, used to fund new equipment purchases or cover unexpected expenses.
Demolition equipment also requires significant storage space.
Selling surplus assets frees up valuable space and may also remove the need for costly storage facilities.
Maintaining a large inventory of equipment can be expensive.
Unused machinery still requires regular maintenance to prevent deterioration, as well as insurance. Selling unwanted assets eliminates these ongoing maintenance costs, resulting in significant cost savings.
It’s worth bearing in mind that by selling unwanted demolition equipment while it’s still in good condition contractors can unlock the value of their equipment and maximise the return on their investment.
Asset disposal is a great way to achieve environmental objectives
and contribute to the circular economy by repurposing used machinery and equipment. This reduces the need for raw material extraction and minimises waste going to landfill.
The benefits of asset disposal are clear. However, disposing of surplus demolition equipment also presents a unique set of challenges.
Demolition projects require a diverse array of equipment, each with specific functionalities, conditions and resale values.
Accurately identifying and appraising this varied inventory demands an indepth understanding of demolition equipment and its market. Inaccurate evaluation can lead to significant financial losses, either by undervaluing your equipment or missing out on opportunities to maximise its worth.
There’s also the size issue to consider. Demolition equipment can be extremely large, making shipping
a costly logistical nightmare.
In addition, demolition projects are notorious for tight schedules and limited resources. Disposing of equipment efficiently under these constraints can be difficult, especially when managing multiple sites. Coordinating asset disposal, managing logistics and ensuring compliance while minimising disruption to ongoing projects requires meticulous planning and execution.
This is why we would always recommend that you work with a specialist. They can handle the entire process, freeing you up to focus on your core activities.
It’s not just about saving time and reducing hassle – partnering with a specialist provides a wealth of additional benefits that can maximise the return on your surplus equipment.
Commercial asset disposal specialists have the skills and experience required to accurately appraise the asset based on market conditions, specifications and age. This expertise ensures that demolition contractors receive fair value for their assets during the disposal process.
Reputable asset disposal companies have cultivated extensive networks of potential buyers and investors specifically interested in the demolition industry. This targeted approach connects you with parties actively seeking your type of equipment, significantly increasing the chances of finding the right buyer and achieving a competitive price. Unlike trying to sell equipment on your own, a specialist ensures that you’re not just reaching a broad, non-targeted audience; you’re reaching a pool of qualified buyers ready to make a deal.
Some asset disposal specialists offer auctions and will handle the entire auction process on your behalf. This includes cataloguing your equipment with detailed descriptions and photos, strategic marketing to targeted buyers, managing the
bidding process and even finalising post-sale logistics. This ensures a smooth and hassle-free experience.
Auctions are live 24/7 for the duration of the sale, have an extensive worldwide reach and often generate higher returns than traditional methods.
Auctions also offer a significant additional benefit – the freedom to keep your machines on site during the sales process, saving time and money and reducing the environmental impact associated with transportation. This approach can be hugely beneficial to sellers who can then avoid the hassle and expense of moving the equipment themselves.
Additionally, you can set reserve prices to ensure your equipment doesn’t sell below a minimum acceptable value. This combination of reach, control and specialist expertise can maximise your return on investment.
High standards are vital in any industry and asset disposal is no exception. ISO standards provide a framework for achieving this. We currently hold ISO 9001:2015, the globally recognised standard for quality management. To achieve this a company must adhere to rigorous
requirements including monitoring customer satisfaction, addressing risks, working to a consistently high quality and maintaining reliable services.
By partnering with an ISO 9011:2015 certified asset disposal specialist, demolition contractors can be confident that their systems and processes are robust.
The demolition industry is subject to strict environmental and health and safety (HSE) regulations. Partnering with a reputable asset disposal specialist ensures you navigate these regulations with confidence. They’ll guide you through the proper disposal processes to minimise environmental impact.
There’s a growing focus on responsible asset management at the end of a product’s life cycle. By choosing refurbishment, repurposing or responsible recycling whenever possible, demolition contractors can significantly reduce waste and conserve resources. This not only benefits the environment but can also enhance your brand image by demonstrating a commitment to sustainability – a factor that’s increasingly valued by clients and partners in today’s ecoconscious market.
Effective asset disposal is crucial for maximising value, minimising environmental impact and ensuring a healthy cashflow. Working with a commercial asset disposal specialist is one of the best ways of accessing these benefits, while at the same time streamlining the disposal process.
For many demolition contractors being able to hand this to an asset disposal specialist allows them to concentrate on what they do best – delivering successful demolition projects on time and in budget.
For more information on BPI Asset Disposal Solutions visit: www.bpiassetdisposal.com
Sir Robert McAlpine, one of the leading UK construction and civil engineering companies, has partnered with Datatag ID, a specialist in forensic marking, to enhance security and combat tool theft in a unique event designed for contractors. Tool theft is a significant issue in the UK, costing companies millions annually and causing delays in project timelines. The collaboration between Sir Robert McAlpine and Datatag, following a recent high value theft of tools, highlights their commitment to safeguarding tools and reducing criminal activity on their sites.
The special event hosted onsite, saw contractors introduced to Datatag’s cutting-edge forensic marking technology which combines invisible markers, microdots and tamper-evident warning labels to mark tools with unique identifiers that can be easily traced by the police. Once applied, these markers are virtually impossible to remove, offering a lifetime solution for
“Tool theft is a significant issue in the UK, costing companies millions annually and causing delays in project timelines”
identifying stolen property. The unique identifier is registered in Datatag’s secure database, which can be accessed by law enforcement, making it easier to identify stolen goods and prosecute criminals.
The event was not only an opportunity for contractors to get their tools marked on the day but also to learn about the importance of tool security and theft prevention. Representatives from Datatag demonstrated how the technology works, explaining its benefits and effectiveness in deterring theft.
By proactively marking their tools, contractors reduce the risk of theft and mitigate the losses often associated with it.
Martin Cunningham, Site Manager said: “The effect on the site following the theft has been considerable in term of disruption to workflows and obviously morale with the team so we felt we had to do something. We approached Datatag as the obvious choice as specialist in security marking assets and have been really pleased with the takeup from the contractors on site.”
Dave Luscombe, Special Projects lead at Datatag commented “We’ve long known about the issue of tool theft and its recent rise has been well documented in the press and on social media. We were very happy to help McAlpine’s forward thinking efforts in tackling this and the constant stream of contractors coming through was encouraging, showing as it did a willingness to have tools marked and a belief in the deterrent that this sees.”
The collaboration with Datatag reflects McAlpine’s commitment to using advanced technology to solve real-world challenges faced by its workforce. The company recognises that preventing theft not only protects assets but also enhances productivity by reducing downtime and project disruptions caused by the loss of essential tools. Adding warning signage provided by Datatag to all access points clearly announces that McAlpine sites are no-go areas for criminals.
by Richard Dolman
The demolition industry is at a pivotal moment following the recent guidance issued by the Health and Safety Executive (HSE), which advises against the use of scaffolding during machine and high reach demolition. This position comes in response to several major scaffolding incidents, marking a critical shift in safety protocols.
In the wake of this guidance, our industry has taken significant
steps to embed these changes into standard practice. At AR, where I am Director, we have long voiced our concerns over the safety of using scaffolding in such contexts and many within the sector are familiar with our stance. The HSE’s directive is a watershed moment that reinforces the need to elevate safety standards within demolition, once again.
The question now is whether we are truly championing this guidance within our operations and across the sector. Have we effectively communicated these new standards to our clients, ensuring they understand the expectations and benefits? Pushing for client awareness is crucial, as it not only expedites the implementation of the new guidelines but also ensures a level playing field for everyone involved.
Some within the industry have already made strides in addressing these safety concerns and the HSE’s
position serves as both vindication and a call to action. It challenges us to question whether we should have needed such a directive to prioritise safety, and more importantly, it should inspire us to continue driving improvements.
As we move forward, it is imperative that we embrace these changes collectively, share information and raise discussion points through the correct channels such as the NFDC. By fostering a culture of safety and continuous improvement, we can ensure that the demolition industry not only meets but exceeds the new standards, safeguarding the wellbeing of all those involved.
If you have something to say and would like to submit a column for publication in Demolition Hub, please email: toby@chambers.media
Swantest can provide a wide range of test solutions for all aspects of a project. This can include structural tests on the superstructure, substructure and geotechnical tests on the substrate of any project. Our range of structural tests include:
Load Capacity Tests: Used for determining the load capacity of various structures, fixings and materials. We can load test structural slabs, marine structures, lift beams, pile foundations and more.
Anchor Tests: We can carry out pull tests and shear tests on all types of bolts, fixings and fasteners. From small fixings supporting a few kilograms up to large diameter bolts supporting significant loads.
Geotechnical Tests: In-situ site tests for verifying pile mats, formation layers, subgrades and other materials. These include; Plate bearing tests, CBR tests, shear vane tests, dynamic cone penetrometer test and light drop weight tests.
Balcony and Barrier Tests: Various types of horizontal load tests to check and verify the safe use of; Balcony handrails, balustrades, insert panels, sports ground barriers, bridge parapets, edge protection systems and more.
For more information call us on 0370 950 7707
Website: www.swantest.co.uk Email: info@swantest.co.uk 52-54 St. John Street, Farringdon, London, EC1M 4HF
by Richard Vann
Richard Vann, Managing Director at RVA Group, uncovers the critical components of a well rounded bid package, exploring how this foundational step can make or break the success of a demolition project
In the highly specialised field of demolition, accuracy and thoroughness at every stage counts –not least when it comes to the bid package, which can often be the deciding factor between project success and costly oversight.
The best prepared tender documentation doesn’t just outline the technical, contractual and financial aspects of the project. Serving as a critical communication tool between the client and contractor, it also sets clear expectations, manages ongoing risks and streamlines the delivery of the project. So, what makes the perfect bid package?
A robust HSE plan is a statutory requirement in most regions and a hallmark of industry best practices. While the specifics of this document will differ from one country to the next, it effectively details actual
and potential residual process hazards, ensuring all risks are clearly identified and addressed in line with minimum mitigation standards. By prescribing the regulatory framework that governs the project, it also outlines essential site rules and incident reporting procedures to maximise HSE excellence throughout the project life cycle.
Providing this information at the tender stage allows contractors to fully assess the project’s requirements, ensuring appropriate methods and resources are allocated for safe execution.
The technical specification of works is where fine detail truly matters. This document outlines the client’s detailed requirements for the contractor’s design, clearly stating what must be delivered. Serving as the bridge between the HSE regime, scope of work and the commercial elements, it prescribes the sequence and programming of operations – from monitoring regimes and reporting processes to quality standards and auditing protocols – to control and streamline the project delivery. With a flexible range of options, it also accommodates for potential adjustments as the works progress.
This element represents the contractor’s formal offer, encapsulating the financial and legal commitments of the project. Typically, it will define the contract total, including provisional sums, day-to-day works and any identified asset credit allowances. More than a financial summary, it also confirms compliance with client specific clauses (such as anti corruption and modern slavery regulations), outlines required insurance levels from Employer’s Liability (EL) to Professional Indemnity (PI), and covers essential bonds and securities.
Acknowledging the importance of clarity, documentation should also declare which subcontractors and professional advisers will be assigned to the project, alongside a comprehensive overview of the organisational structure and key personnel. It must specify any exclusions or deviations from the overall tender package, ensuring all aspects are clearly understood and agreed upon.
As well as providing a structured and standardised framework for evaluating tenders, the pricing schedule demonstrates the
contractor’s understanding of the work scope by detailing costs for tasks like hazardous material removal and structural dismantling.
The schedule also facilitates accurate pricing for different scope options, such as methodology variations, working hour relaxations, programme adjustments, etc. It acts as a tool for tracking expenditure and managing progress payments, helping control credit and debit balances. And, should any valuing variations or additional works arise, it ensures all financial adjustments are clear, justified and fair.
No two projects look the same on a technical level and naturally, the financial arrangements will vary too. The commercial framework lays out key financial details, outlining aspects such as the payment structure and schedule, and clarifying when and how payments are to be made throughout the project. It also covers debit and credit sums, settlement terms and key milestones, making sure progress and finances align smoothly.
Beyond that, it includes elements such as scrap gainshare, bonds, deposits and security mechanisms to protect all parties involved, as well
as penalties and forfeiture criteria to handle any potential issues. It may also include clauses for resale and buyback options, along with incentivisation and bonus schemes to encourage top performance.
When it comes to contractual terms and conditions, the form of contract – whether NEC, ICE, FIDIC, or a client-specific version – needs to be appropriate for the type and scale of the works. It should offer the client and their delegates adequate control over the project, ensuring smooth management and oversight.
For decommissioning projects, the contract may need to be adapted or amended to address specific requirements. However, it’s crucial the contract remains clear and straightforward, avoiding unnecessary complexity or excessive administrative burdens. The goal is to keep it clean and efficient, providing necessary control while minimising bureaucracy.
Supporting information provides essential material in a clear, accessible format – including client and site rules, corporate standards documentation and relevant surveys
and reports. Relevant drawing registers and plant information are also included to ensure all technical aspects are covered, supporting a smooth and compliant execution of the project. And, to address any potential impacts on the project, HSE regulations and local authority requirements – including planning and decommissioning conditions, discharge consents and other statutory compliance issues – are detailed.
While these components provide a strong foundation, this is by no means an exhaustive list. By compiling a bid package that’s truly tailored to the specific scope of works, project managers can set the stage for successful tender list selection and a more effective, well informed bidding process that brings safe and compliant bottom line benefits.
If you have something to say and would like to submit a column for publication in Demolition Hub, please email: toby@chambers.media
Terry
Since July, the new policies proposed by Labour have been a hotly discussed topic.
From the new National Wealth Fund to the reintroduction of mandatory housing targets, many businesses in the construction and demolition sectors have been wondering how these new plans might impact them.
As discussed in my last column, the industry has generally reacted positively to the policies as the overall impact is expected to benefit the sector significantly.
The reintroduction of mandatory housing targets and the aim to build 1.5 million homes over the next five years will likely boost demand for construction and demolition services, especially as the new government has outlined an emphasis on grey-belt and brownfield sites being redeveloped.
This is crucial for the demolition industry, as these sites often have abandoned industrial buildings or need extensive clearing. For housebuilders, it’s beneficial too, with government and local councils likely to want to collaborate and upcoming planning reforms set to
support more developments in the coming years.
However, despite the positive news of the new policies being announced, the expected influx of work can’t start soon enough for some.
Statistics released by the Office of National Statistics (ONS) in September show that the UK economy experienced no growth during the month of July, with construction output falling by 0.4%.
This decline in activity during the summer months shows the need for more work within the industry. It emphasises the importance of Labour’s new policies taking effect at a quicker pace to enable the industry to benefit from these plans.
It’s important that the confidence bounce following the election is maintained too and there could be some bumps in the road there. After a summer of the Labour government talking about the black hole in the nation’s finances and the autumn budget looming, many are anxious about what is to come on 30 October for personal finances.
There’s been talk of tax hikes –particularly around Capital Gains
Tax – and cutbacks, and while the talk of economic growth hasn’t been completely forgotten, the rhetoric coming out of Labour today is on the difficult decisions that need to be made to get the economy back on track.
While it’s a necessary task, for many in the industry, it’s not what they want to hear after a few difficult years.
Ultimately, the mandatory housing targets and use of grey-belt and brownfield sites should support the construction and demolition industry in the long term, but for many, the policies can’t become reality soon enough.
If you have something to say and would like to submit a column for publication in Demolition Hub, please email: toby@chambers.media
KHD Brokk Hire is the ‘one stop shop’ for all things electric plant, with a sustainable twist too! From electric diggers & dumpers to Brokk machines – we do it all! WE OFFER: