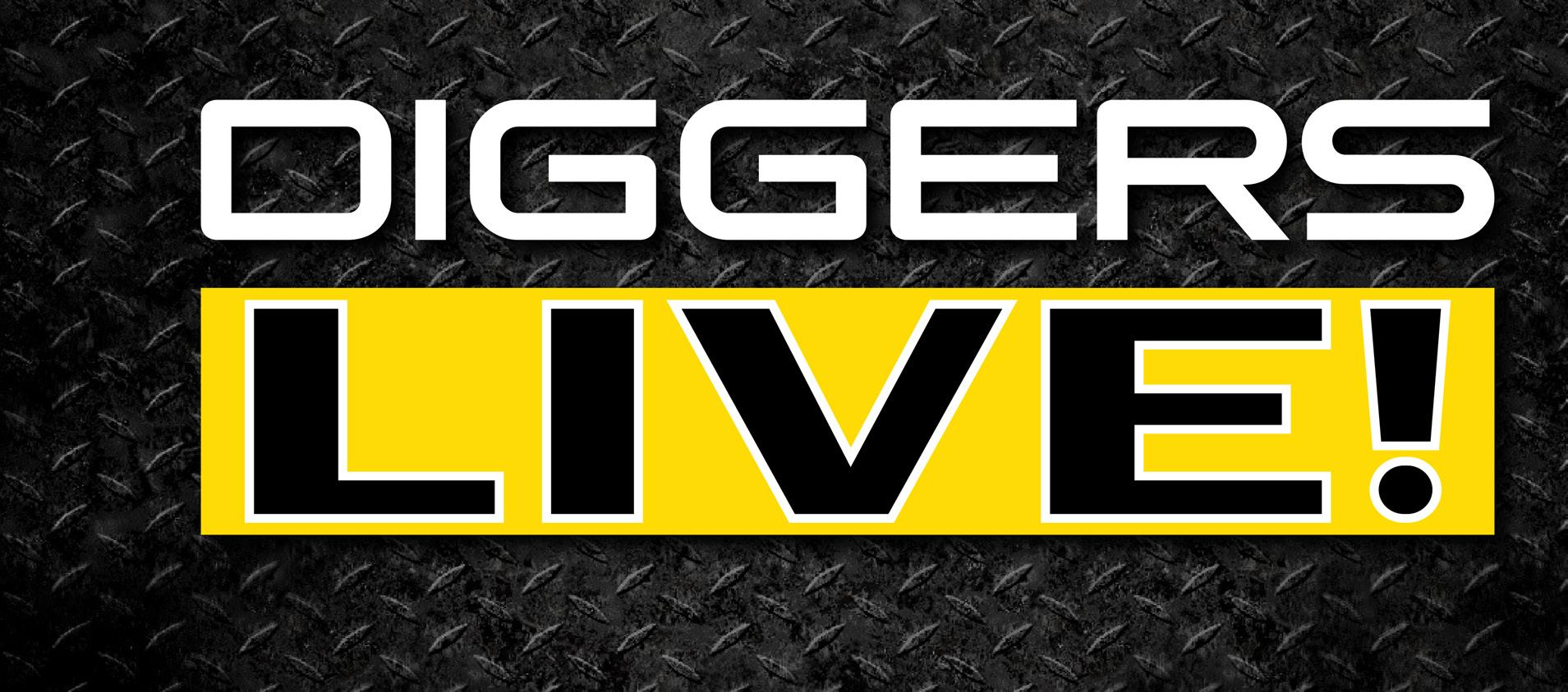
EQUIPMENT ENGAGEMENT
We speak with JCB’s Business Head –Excavators, Paul Swallow
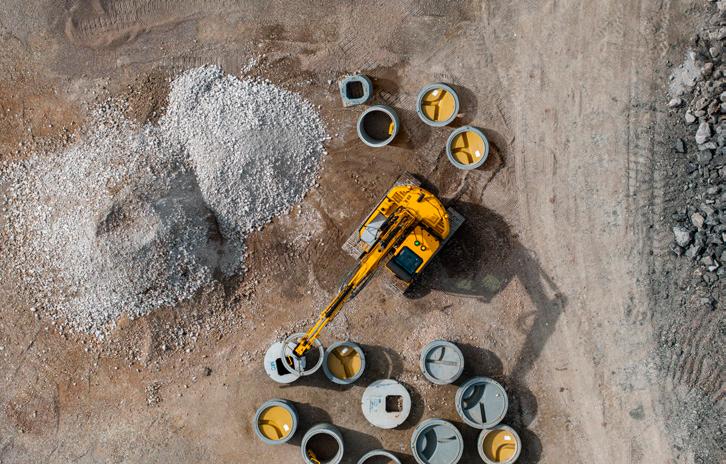
DATA DUMP
Packed feature devoted to Dumpers and Loaders inside
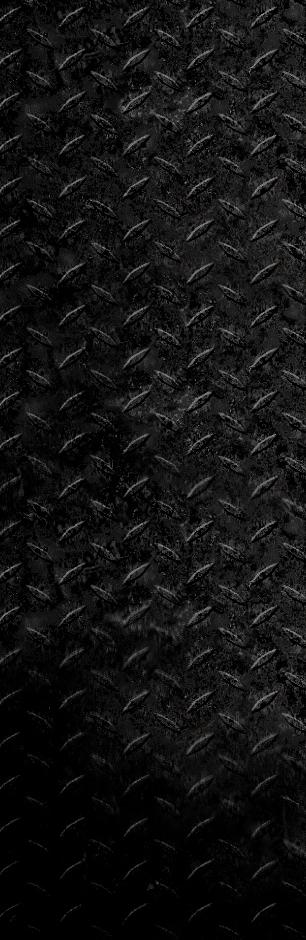
BUSINESS INSIDER
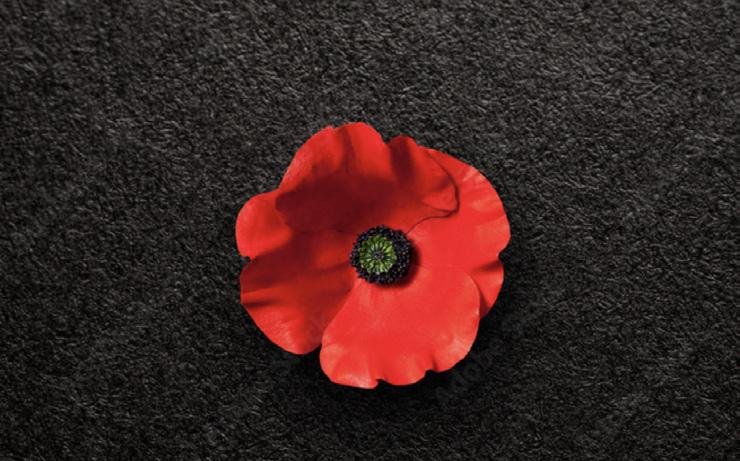
We salute owner of Machines on the Market and former Grenadier Guardsman, Richard Cross
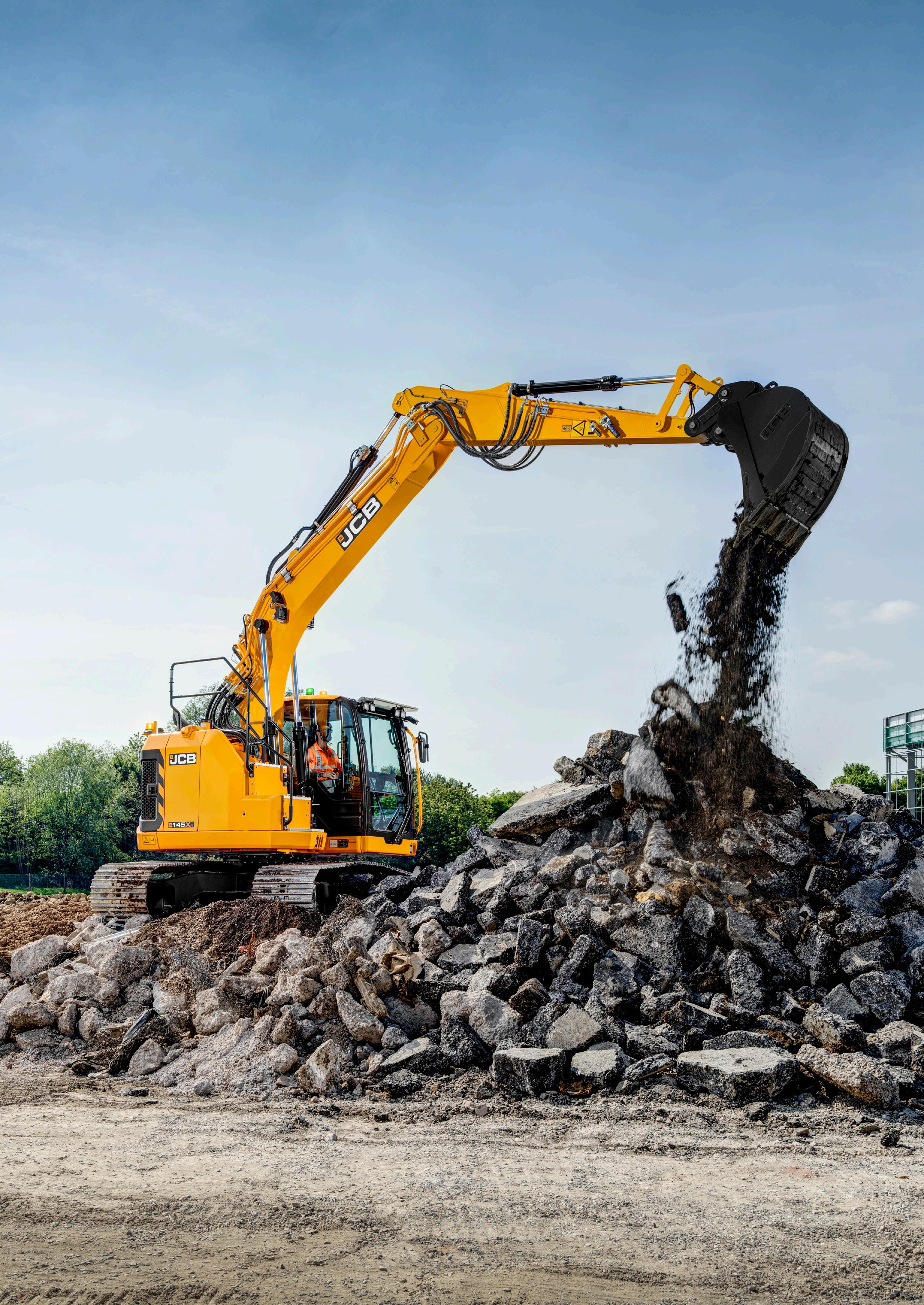
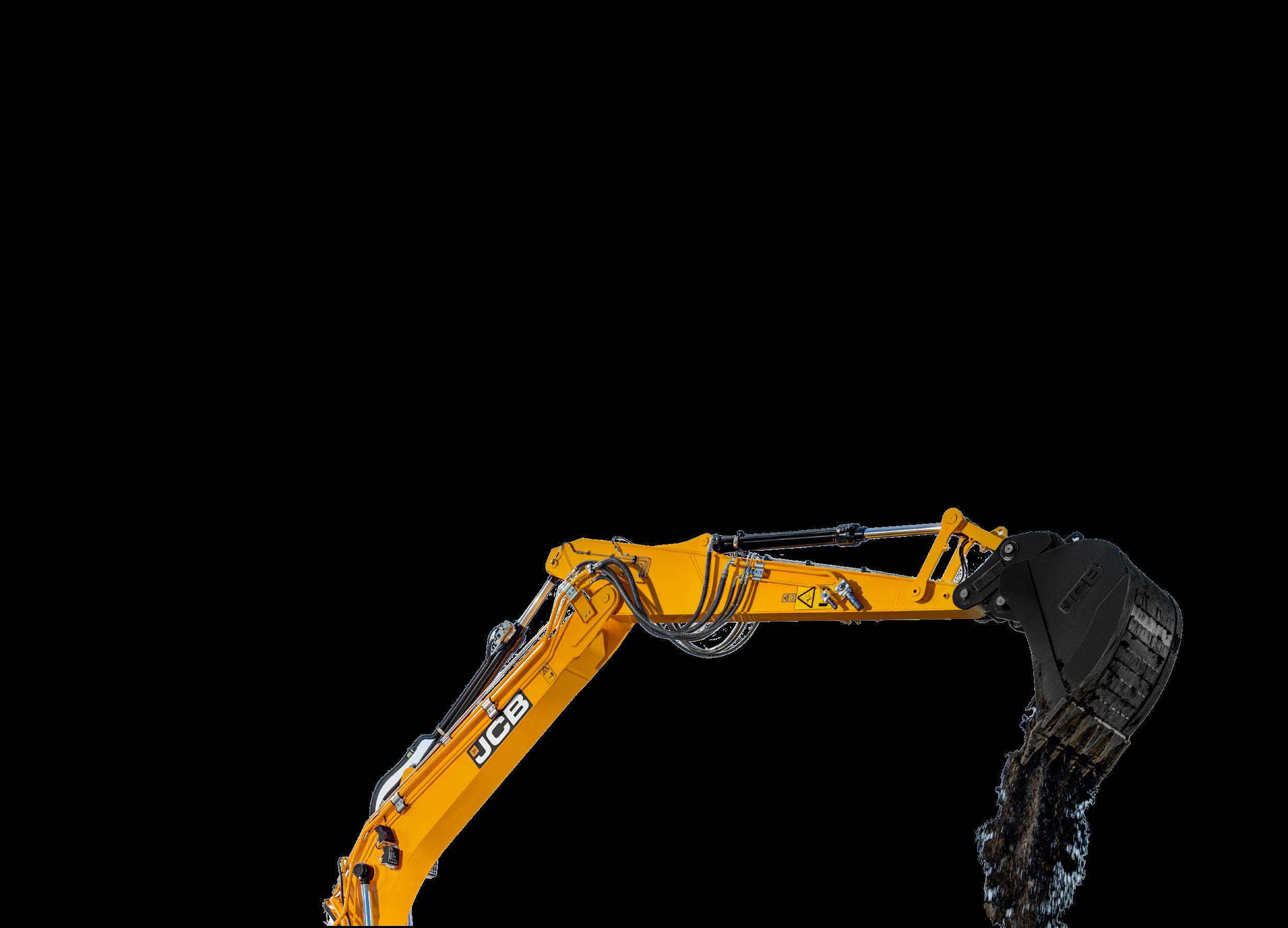
EQUIPMENT ENGAGEMENT
We speak with JCB’s Business Head –Excavators, Paul Swallow
Packed feature devoted to Dumpers and Loaders inside
We salute owner of Machines on the Market and former Grenadier Guardsman, Richard Cross
FROM 1.8 TO 95 TONNES THE ALL NEW F-SERIES BREAKS THE MOULD.
On the rare occasion that my social life is spent with non-industry friends, when the subject of work comes up it is invariably prefixed with the words “Oh, it’s JCB you promote, isn’t it?” Yep, still and almost every time when talking about any type of construction equipment.
This is definitely testament to the proud name JCB has built globally but also to its marketing over the years – I grew up seeing these yellow diggers along the motorways as I sat in the back of my parents’ car listening to Queen, Erasure and more shaping my musical tastes. JCB is without doubt a byword for a digger and although it took a while, this year in particular we have got closer to them with our Editor Toby being invited to a number of launches as well as having more and more news sent directly to us.
Now we can boast of a strong 2025 advertising campaign beginning in this very issue, check out the centrefold.
This closer relationship continues with JCB debuting in our regular supplier interview EQUIPMENT ENGAGEMENT, in which we spoke to Paul Swallow, Business Head – Excavators. It is quite the read.
Machines dominate our interviews as in BUSINESS INSIDER we talk to the owner of Machines on the Market, Richard Cross, regarding its three years in operation, its growth in that time, and with stats like 400 machines being on their books right now, some extremely impressive numbers. This alongside the revelation that he shares Las Vegas with me as a desirable destination.
It is also good to be able to support friends with such coverage as close friend Louise Bradshaw-Black happens to be doing an awesome job as the Creative Director there. Keep doing what you are doing MOTM – we and the industry are right behind you!
We bow out of 2024 with awesome memories of Hillhead, World of Concrete, RWM, The Executive Hire Show and the British Demolition Awards all indelibly implanted in our heads, as we put together this, the last edition of the year.
I want to thank everyone for being involved in this challenging but extremely rewarding year. It’s been a hell of year in every possible way and we cannot wait to be reunited in January in what will be our sixth calendar year as Diggers LIVE! Wow.
Have a brilliant end to 2024 – you know where we are.
v Ben Chambers, Publisher
EDITORIAL TEAM
PUBLISHER
Ben Chambers ben@chambers.media
EDITOR
Toby Wilsdon toby@chambers.media DESIGN Joe Chambers joe@chambers.media
Nicki Chambers GENERAL ENQUIRIES info@chambers.media 01903 952 640
Ben Chambers ben@chambers.media 01903 952 648
PRODUCED & PUBLISHED BY Demolition Hub Ltd
Suite 5 & 6 Chapel House 1-6 Chapel Road, Worthing West Sussex BN11 1EX ben@chambers.media 01903 952 640
Diggers LIVE! is published six times a year by Demolition Hub Ltd
Articles and information contained in this publication are the copyright of Demolition Hub Ltd and may not be reproduced in any form without the written permission of the publishers.
The publishers cannot accept responsibility for loss of, or damage to, uncommissioned photographs or manuscripts.
6
Industry leaders give their take on Rachel Reeves’ first budget
8
EQUIPMENT ENGAGEMENT
With Paul Swallow, JCB Business Head – Excavators
12
With Richard Cross, Owner of Machines on the Market
16
JCB unveils a series of new additions to its extensive range of construction equipment
28
• Dates announced for Hillhead 2026
• PlantWorx 2025: One year to go
• Rethinking Futures at PlantWorx 2025
34
• AUSA
• Bobcat
• DEVELON
• JCB
• Kramer
• Liebherr & Strabag
• Rokbak
• Komatsu Europe
With Abigail Scott, Operations Manager at Digger Delivery
CEA response to UK government’s industrial strategy –Invest 2035
SANY UK sells first 23-t electric excavator in UK to Explore Plant and Transport Solutions
Smarter fleet management from Bell Equipment
Peter Fitzpatrick Ltd futureproofs and expands with CDE investment
Distinctive Hyundai HX140A L blends into wildlife landscape
Doosan Bobcat to create synergy through vertical integration with Doosan Mottrol
Boliden and Komatsu accelerate on fast lane to a zeroemission mining site
Komatsu PC700 with special boom conversion for raw gravel extraction
The construction site of the future according to MB Crusher
Red Rhino crowned Family Business of the Year at the coveted Midlands Family Business Awards
Terapro Construction and Rokbak announce distribution agreement
Looking back on three years since the delivery of Rokbak #1
Bearing the emotional weight – focusing on World Mental Health Day, by Sarah Bolton CEO, Lighthouse Charity
Wacker Neuson introduces HVO as an alternative fuel
Hitachi transforms fleet management with CONNECT
Job stress affects 70% of construction workers, University of Cambridge study finds
CPA Appoints Decarbonisation and Sustainability Manager in Newly Created Role
SANY reinvents the eight-tonne excavator
Key figures in the construction plant and property law and finance sectors give their first reactions to the Chancellor, Rachel Reeves’s first budget, delivered on 30 October.
Following the Chancellor Rachel Reeves’ autumn budget, Steve Mulholland, Chief Executive Officer of the Construction Plant-hire Association (CPA) said:
“Today’s budget was an opportunity for the new government to show it is serious about providing the business community with stability and certainty. Despite not being part of the Industrial Strategy there appears to be an acknowledgement that infrastructure shall play its part in this new era of intended stability and growth with a commitment to spending on roads, rail, hospitals, schools, and homes.
“We welcome the news that fuel duty remains frozen, however it is disappointing that employers will have to pay more in National Insurance and that the plant-hire sector remains excluded from being able to take complete advantage of the Full Expensing
Allowance in its current form. We need further clarity on what fiscal conditions must be met before this can happen. We look forward to seeing more detail.”
Commenting on the budget, Viki Bell, Director of Operations at the Construction Equipment Association (CEA), said:
“This budget brings some positive developments for the UK’s engineering and construction sectors, especially with the £6 billion allocated to R&D in engineering. This investment, alongside the £520 million for a life sciences manufacturing fund and £20 billion committed to R&D, has the potential to support new technology, improve equipment safety, and encourage more sustainable practices – essential elements to keep UK construction competitive on a global scale. Such funding could open doors for both SMEs and OEMs as we work to meet the demands of modern infrastructure projects. The government’s renewed commitment to rail, road, and infrastructure development is a promising step for the construction equipment sector.
“The commitment to resume HS2 construction to London Euston, the pledge to invest and maintain hospitals and the investment in 300 new planning graduates all signal a strong focus on essential infrastructure and housing reform. This investment in the planning workforce is encouraging, but projects of this scale will still require sustained funding, coordinated planning and broader industry support to be delivered effectively and on time.
“The investment in 11 green hydrogen projects is another positive step, supporting the transition to cleaner energy and encouraging sectors like ours to consider alternative fuels. Despite these positive moves, it’s disappointing to see limited direct financial relief for construction firms.
“Doubling the employment allowance to £10,500 helps smaller construction equipment firms by reducing National Insurance liabilities, however, the planned increase in employer National Insurance from 13.8% to 15% in April 2025, coupled with the reduced secondary threshold from £9,100 to £5,000, is a double blow for firms. These added costs are likely to
strain budgets and limit opportunities for new hires or expansion, putting significant pressure on SMEs and OEMs at a time when stability and investment are critical. While we welcome the forward-looking approach, more targeted support is essential to help our sector fully contribute to these ambitious goals.
Sarah Fitzpatrick, Head of Planning and Jennifer Glasgow, associate at international law firm, Norton Rose Fulbright, said: “The key focus of the autumn budget is reform of planning policy and procedure with the intention of providing sustained long-term growth. We have already seen the draft amendments to the National Planning Policy Framework (NPPF), but the budget confirmed the government’s intentions for planning reform enabling the removal of barriers for growth. This will be aided through simplifying the planning system, developing a 10-year infrastructure strategy, which is currently expected to be published alongside the Phase 2 Spending Review, as well as increasing funding.
“The government has already started to progress projects through the planning system having approved six National Significant Infrastructure Projects (NSIP) since taking office – four of which related to green energy. The Deputy Prime Minister has also taken decisions on appeals below the NSIP threshold, within the 13-week decision period. This goes some way to support the government’s intentions they want to speed up the planning decision making process.
“The government is also focused on housing delivery and affordable housing. As the Deputy Prime Minster has previously set out, the government is committed to delivering 1.5 million homes and this was reiterated in today’s budget. The government’s remedy is its commitment to NPPF consultation, the New Homes Accelerator and New Towns Taskforce as well as over £6 billion of investment to promote affordable housing and support small housebuilders.”
Commenting on the budget and its impact across the housing market, Daniel Austin, CEO and co-founder at specialist independent property lender, ASK Partners, said: “Following today’s budget, there is good news for property developers. The promise of £5 billion of investment for new homes contained within today’s announcement will be warmly welcomed. Increased supply should buoy the market and level out values; a plus for first time buyers, who conversely will be hit by the new lower stamp duty thresholds.
“Further, it was encouraging to hear specific reference of help being offered to SME housebuilders, who can unlock smaller projects to revitalise towns and cities, and the help for cities such as Cambridge to meet its potential as an area rife for property development amidst key life sciences campus developments, and the homes needed for the workers this attracts.
“The decision to not include buy-tolet properties in the Capital Gains Tax increase will also be well received. The exodus of buy-to-let mortgage holders has been heaping pressure on the UK rental market causing prices to rise due to a lack of supply. However, the wave of private landlords selling off properties ahead of the budget may offer a short-lived upside
in supply of properties for sale. We have already seen a rise in mortgage approval rates back to levels previously seen before Truss’ mini-budget. The impact on the rental market should entice developers of schemes such as co-living and build-torent to fulfil the lack of supply, provided planning reforms allow.
Paresh Raja, CEO of independent bridging finance and residential and commercial buy-to-let mortgage provider Market Financial Solutions, said: “The government had warned of tax rises to fill the black hole in public finances, so there was apprehension across the property and finance sectors heading into today’s budget. Unlike previous budgets – think Kwarteng’s mini-budget – Reeves refrained from pulling any proverbial rabbits out of the hat, although the increase to Stamp Duty surcharge on second homes was unexpected. This approach should calm the lending and property markets, easing some of the uncertainty that has lingered in the leadup to this announcement.
“The government’s commitment to house building should stimulate activity across all segments of the housing market, creating a wide range of opportunities for buyers and investors. But people can be forgiven for listening to today’s budget pledges with a degree of scepticism –almost every budget includes promises to build more homes, but the devil is always in the detail.
“Reforming the planning system is clearly key, so the government’s focus on this area is welcome, with the rumoured additional planning officers being confirmed by the Chancellor today. It not only needs to be easier for new developments to get the green light, but also for investors and property owners to do more with existing real estate –conversions, renovations and extensions can do a lot to boost the national housing stock.
“It’s equally important that the government ensures new homes are delivered where demand is highest. If the location, type and quality of property is not high enough, there will be a struggle to attract buyers and renters, so there has to be a sharp focus on building the right properties in the right places.”
Interviewee: Paul Swallow
Role: Business Head –Excavators
Company: JCB
Paul Swallow is Business Head – Excavators at JCB. He joined the company in 2013 and has worked extensively on the development and promotion of the JCB X Series range of tracked excavators, now heading up the JCB excavators division
QTell us about the new JCB 145XR crawler excavator
One of the key products in JCB’s expanding X Series range is the brand new JCB 145XR crawler excavator, just launched. The JCB 145XR is a reduced tailswing model with compact dimensions yet maintains full-size performance and operator comfort.
QWhich sectors does it serve and what needs does it meet? What technologies are key?
The 145XR is designed for exceptional performance and productivity despite its reduced tailswing operation, making it ideal for confined applications such as housebuilding sites, highway carriageways or urban areas.
Key specifications and functions include:
• 27% shorter tailswing than a conventional 140X, making it perfect for working in tighter spaces,
• Optional TAB boom layout for improved reach and versatility,
• Full-size X Series cab with enhanced comfort features such as heated air suspension seats and climate control,
• The new JCB UX operator interface, which includes a 10" touchscreen display, customisable hot keys, up to 25 user profiles and mobile phone connectivity,
• Up to 10% improvement in fuel economy thanks to Auto-Stop
and Auto-Idle functions and an optimised engine speed of 1,700 RPM,
• Extended maintenance intervals, including a 250-hour greasing interval and fewer filter changes, reducing operating costs,
• JCB’s LiveLink fleet management system provides real-time data on performance, fuel consumption, and maintenance schedules, allowing fleet managers to keep operational costs low and productivity high and also enhance the security of the machine.
“The 145XR is designed for exceptional performance and productivity”
The 145XR is suited for sectors such as construction, urban development and highway maintenance, where space constraints require compact yet highperformance equipment.
QHow is the 145XR critical for potential users?
The 145XR is critical for users who require high performance in restricted spaces. It offers a reduced counterweight overhang and compact design, making it ideal for projects where space is limited but fullsized machine power is needed. Potential buyers will benefit from:
• Increased fuel efficiency: Up to 10% fuel savings,
• Reduced downtime: Faster cycle times and lower downtime thanks to intelligent hydraulic systems and robust engine designs,
• Lower maintenance costs: 24% fewer filter changes over 10,000 hours of service and extended greasing intervals up to
250 hours reduce operating and maintenance costs,
• Enhanced comfort: The full size JCB CommandPlus cab, which includes a heated air suspension seat and intuitive touch screen monitor, offers bestin-class ergonomics, reducing operator fatigue and improving productivity,
• Greater safety: Features like 360° cameras, impact detection and proximity alerts ensure peace of mind on site,
• Improved site accessibility: 27% shorter tailswing than a conventional 140X allows the 145XR to access tighter sites.
QTell us about the development of the 145XR
The development of the 145XR is part of JCB’s broader strategy to offer products that address the specific challenges of confined job sites. It builds on the success of the larger 245XR, delivering the
same level of performance in a smaller, more compact package. This approach represents an evolution of JCB’s X Series excavators, blending proven durability with new, advanced technologies and a more compact design to meet the growing demand for machines that can operate more efficiently in smaller spaces.
QHave you had any feedback?
The JCB 145XR itself is a brand new machine that is not yet with customers in the field. However, it benefits from all the hallmarks of the wider JCB X Series range which has proved hugely popular since its introduction.
With the X Series, JCB redesigned key elements, including the undercarriage, cab and hydraulics, based on feedback from operators across various industries bringing superb build quality and durability.
Testimony from users including contractors, hire firms and operators from across the industry confirm the X Series is a high quality excavator and a major step forward for JCB.
QBriefly introduce us to Machines on the Market and your role in it I’m the owner of Machines on the Market. com. We are a transparent worldwide sales platform where buyers and sellers are connected. Our website caters for waste and recycling, crushing and screening, construction and handling equipment, forestry and auxiliary parts.
Interviewee: Richard Cross
Role and company: Owner, Machines on the Market
Sector: Online plant marketplace
Geographical reach: Worldwide
When established: 2021
The website offers one of the most diverse selections of waste, recycling and handling equipment available and caters for all customer requirements. We are creating realistic residual values, whilst helping customers move machinery in a fast timeframe to reduce depreciation.
QTell us about your career progression
After an eight-year career in the Grenadier Guards, I moved into the waste industry in 1998 and through a variety of positions became Contracts Director for Cheshire West council, running the refuse and waste department. This further sparked my interest in recycling and two years later I took the step of creating and developing my first company, Future Recycling. The company was one of the first in the UK to start exporting waste materials around the world and was the beginning of my journey to Machines on The Market. I briefly
moved into the forestry side of recycling after this, before moving to a multi-brand UK dealership to handle the sales of large machinery. I appreciated the opportunity to expand my knowledge base into more areas and niches of the industry, something that has proved priceless experience for Machines on The Market.
QHow is what you do personally at Machines on the Market developing and how does that relate to the development and growth of the company?
I handle a general wide reach in the company, everything from customer visits and acquiring machinery to sales, handling export and closing sales. Both my personal and business values have always been that transparency is key and that way of working is something that I have been able to develop into a recognised corner of the industry.
Machines on The Market has developed its own organic following by offering a more transparent way so that both the customer and purchaser retain the true value of the machine. Unless specifically requested, all prices are visible for everyone to see. We don’t believe in hiding pricing, I believe the industry should be an open book where machines can be easily valued
and moved on as required.
Trading by this straightforward, uncomplicated business model takes all the cloak and dagger out of sales and gives us an uncapped potential for growth. We are taking on new customers daily and this growth is without a doubt down to the core values we trade and grow by.
QTell us about Machines on the Market’s growth path until now and into the future. Tell us about the rebrand
We’ve grown massively since the launch in 2021. The company has always been self-sufficient from day one and as it stands today, we currently have over 400 machines live on our books, with a value of over £36 million.
The aim has always been to be the largest resale site in Europe and that goal hasn’t changed. In order to achieve that end goal, I knew a plan for expansion was needed and in 2023. The first step of that expansion was Louise Bradshaw-Black coming onboard in the role of Creative Director.
Louise and I have now worked together for the best part of a decade and I knew she was coming onboard with a clear vision for developing the company image.
We rebranded in September 2023, giving the company a next level online presence. We are also working on the end stages of a very exciting project which will propel us further towards our goal. This will be announced in the coming months.
QGive us the sales pitch. What’s Machines on the Market for?
The company offers free evaluation, diverse and wide markets for all types of waste, recycling and handling equipment, regardless of condition or age. Construction, demolition, material
handling, we have a platform that needs your machinery.
QTell us about its range of services, how these relate to each other and how they relate to customers
We offer one of the most comprehensive sales packages in the industry with unrivalled marketing for maximum exposure. No matter the size or price of the machine, all customers receive the same level service. We don’t have any hidden fees and we don’t charge anything unless we sell the machine. We offer as standard:
• Listing of all stock on our website. We provide comprehensive descriptions of each machine, including its make, model, year of manufacture, operational condition and any maintenance records. Highresolution photos and, in some cases, video demonstrations and viewings are also available,
• Listing of all stock on multiple other platforms that we hold premium advertising accounts with. These platforms reach over 20,000 visitors per day,
• Expert, custom written SEO to place your items highest on search engines,
• Dedicated email marketing mail shots to our extensive CRM,
• Advertising on Facebook to over 250 groups,
• Premium advertising on our social media platforms,
• Word of mouth sales where we can offer items directly to customers as appropriate,
• Handling of all export as required (we charge this to the customer separately, making the sale hassle free for the seller),
• Arranging visitor visas as required if items are to be viewed and attending site with the visitors, including collecting them from the nearest airport.
QWhat are your criteria to sell on your marketplace?
Having a machine! If you have it, we will sell it. It doesn’t matter what age, condition, brand or location, we can match you with a buyer.
Q
What are Machines on the Market ’s USPs?
We often get machines with no plates or information and that feet on the ground experience definitely gives the company the edge over others where machines are being advertised by telesales staff for example, who often don’t have experience in custom or older machines.
We appeal to the broader market because we don’t cap ourselves by only selling certain categories. There is literally no machinery limit to what we will sell. If someone contacted us tomorrow with, say, tanks, we’d make new categories and put our full resources into expanding our product range. We are not scared of taking on anything out of the ordinary.
Q
Tell us about the working culture. Is there a fundamental company philosophy?
Transparency is our philosophy. Clear pricing, clear fees, clear T&Cs. We are also very open with our customers on pricing expectations against current market values.
QWhere does the knowledge base within Machines on the Market come from and how do you keep this up to date – in terms of machines, the market, marketing and any other business skills?
Experience and priceless contacts you build up through the years are the biggest assets any company in our industry can have. We have a lot of industry friends and as most people reading this will know, the industry is small enough for us all to keep up to date on what is going on. It also goes without saying that we are always learning as new machinery comes in and the general sales
process around it. Every machine teaches you a lesson that can enhance the next sale. Louise has a strong interest in analytics and SEO, as well as a distinctive marketing style and extensive brand experience. We run reports on all our machines so that we can give our customers accurate feedback on popularity, view counts etc so that if a machine isn’t moving as fast as anticipated, price point can be looked at, along with tweaking information and photo updates. We cover all aspects of marketing on an individual basis to keep us at the forefront of the resale market. At any point if a customer contacts us, we can tell them within minutes what number their machine is ranking on our website.
When and where are you happiest? Spending time with my two children, my daughter Alex who is 12 and my son James who is nine.
What would you do for a team building, money no object? Las Vegas!
What ’s your favourite cuisine? Any Asian cuisine, I love eating out and exploring different menus.
At a two-day launch event at its World Headquarters in Staffordshire, JCB unveiled a series of new additions to its extensive range of construction equipment. Infrastructure was on the agenda on day one as JCB launched the latest addition to its X Series range of tracked excavators.
With inclement weather forecast, day two opened in the comfort of the JCB Theatre where JCB’s pioneering
AI pedestrian safety system was demonstrated brilliantly on stage. The event then moved to JCB’s Kevin Quarry where the manufacturer showcased groundbreaking developments in technology, sustainability and safety alongside a new rotating Telehandler range that takes JCB’s world number one telescoping handler range to new heights.
Key features include:
• A 27% shorter tailswing than a conventional 140X,
• Reduced front swing and optional TAB boom layout,
• Full-size X-Series cab,
• Innovative JCB UX operator interface with 10” touchscreen display,
• Up to 10% fuel economy improvement,
• Extended maintenance intervals reduce operating costs.
JCB has expanded its popular X Series range of crawler excavators with the launch of the brand new 145XR – a second reduced tailswing model that delivers exceptional performance and productivity with compact dimensions and a full-size operator cab.
The 145XR reduced tailswing model builds upon the success of JCB’s larger 245XR, delivering impressive performance in a compact design with a minimal counterweight swing. The 145XR has a 27% shorter counterweight overhang than a conventional 140X, making it an ideal machine for working within a highway carriageway or on confined urban job sites.
The machine weighs in at 15-18 tonnes, depending on specification, and can be supplied with a monoboom or a two-piece triple articulating (TAB) configuration. The monoboom layout provides a maximum digging depth of 6,027 mm with a three-metre dipper, while the TAB boom has a maximum of 6,167 mm. Forward reach is up to 8,801 mm for the monoboom and 9,230 mm for the TAB specification.
Powered by JCB’s proven Stage V Dieselmax engine, the 145XR boasts an output of 81 kW. This features AutoStop and Auto-Idle engine functions, to reduce fuel consumption and emissions when idling. Engine working speed has been reduced to 1,700 RPM, increasing
fuel economy by 10% and cutting overall noise levels.
As with all JCB X-Series machines, the 145XR has undergone rigorous testing, to guarantee maximum durability and robust strength. The machine is built with heavy-duty track components, plates, bearings and features graphite bushings on key pivot points, allowing up to a 250hour greasing interval. Hydraulic filter changes are extended to 2,000 hours, meaning this new machine requires 24% fewer filter changes over 10,000 hours of service, reducing operating and maintenance costs.
As with all X-Series models, the 145XR benefits from the full-sized JCB Command Plus ROPS cab. As well as being one of the largest on the market, with 2.86 m³ of volume, the Command Plus cab benefits from a heated air suspension seat and a reduced in-cab noise level.
The cab is further improved with a new 10" touchscreen monitor, with the JCB UX interface. The switch panel incorporates customisable hot keys, allowing personalisation for the operator. Climate control, keyless start, and twin cameras for added visibility are all standard.
The JCB UX interface has up to 25 user profiles, which can be customised for the operator to set preferred joystick
configuration to meet their individual requirements. Mobile phone connectivity has been improved, with phone book integration via the monitor. The machine is easy to use and help guides are available within the monitor, along with ‘how to’ videos covering all of the features of the JCB UX system.
The 145XR is available with a range of options, to tailor the machine to an individual customer’s requirements. These include auxiliary hydraulic circuits with up to 15 attachment settings and a premium heated and cooled operator’s seat. LED lights are now standard, with options available to increase to up to 14 LED work lights. A bird’s eye 360 ° camera system, integrated within the 10" display, can also be offered, along with high visibility, all-round handrails.
JCB’s Business Head for Excavators Paul Swallow said: “The JCB 145XR delivers all of the performance that customers need in a compact design with an ultra-tight slewing radius. It is perfect for working in tighter areas, delivering best-in-class performance and ultimate operator control.”
Key features include:
• A 300 kg boost to 5,800 kg maximum lift capacity,
• Standard safety pack with side and rear cameras, white noise reversing alarm,
• New radio control system with real-time load parameter display,
• Standard heated air suspension seat and air conditioning,
• Available on 21-m and 26-m PRO models.
JCB is expanding its rotating telescopic handler range with the launch of the JCB 558-210R PRO and the 558-260R PRO. The range-topping machines feature increased lift capacity, a higher standard specification, a range of new options and attachments, plus a three-year warranty.
The 21-m lift 558-210R PRO and the 588-260R PRO, which offers a 26-m lift height, have a maximum lift capacity of 5,800 kg – an increase of 300 kg. The machines benefit from a range of upgraded components, including a hardened slew ring, to cope with the increased weight capacity.
With a revised colour scheme mirroring other PRO models in the JCB lineup, the two rotary telehandlers feature a range of option packs as standard. This includes a safety pack, consisting of side and rear cameras, plus a white noise reversing alarm. There is also a vision pack, of LED amber beacon and LED working lights on the cab and boom,
along with a storage pack that includes a front chain box and a side tool box.
Operators will welcome the standard comfort pack, incorporating air conditioning and a heated air suspension seat, along with the security pack’s keypad immobiliser. A maintenance pack comprises grouped greasing points on the front and rear of the chassis for reduced regular service work, while a handling pack includes JCB’s free-standing fork frame and 1,200 mm clear view forks, with a travel retention system built into the frame.
The 558-210R PRO and the 588260R PRO are powered by Stage V compliant JCB Dieselmax engines delivering 112 kW. This drives through a proven Bosch Rexroth two-speed hydrostatic transmission, delivering a top
speed of 40 km/h. The machines feature individually configurable X-style outriggers with one-touch deployment and retraction and the rotary telehandlers have +/- 8° degrees of chassis levelling capability.
A variable displacement hydraulic pump with proportional servo electric joysticks provides fingertip control to the operator and the two machines now come with an Autec remote control system, offering full remote control of all hydraulic functions. The control system has a display screen, showing real-time operating information. It comes with an easy stop/start system and a one-touch joystick unlock button.
A Clearview carriage with Radio Frequency Identification (RFID) attachment recognition makes it easier
for the operator to change between attachments. The machines are available with 5.8-tonne capacity forks, with a 5.5-tonne winch and a 2-tonne capacity 2-m jib winch. Attachments include a 5.5-tonne carriage-mounted hook and a 5.5-tonne capacity reduced height jib. The two telescopics can also be used with a 1-tonne capacity, 2.4 x 4.4-m access platform, or with a 400-kg capacity 4-m extension jib. If required, operators can work the machines with a 0.9-m 3 bucket or with 1.7-tonne capacity rotating forks.
The 558-210R PRO and the 588260R PRO will be supplied as standard with a new cost of ownership pack, which includes a three-year/2,000-hour warranty, providing peace of mind for customers and ensuring maximum uptime for end users.
Many wheel loader operations can, by their very nature, be repetitive. Driving into a stockpile, reversing back, tipping into a truck and repeat. For the operator that means plenty of repeated inputs, mainly twirling the steering wheel from left to right and back again.
Lever steer, or stick steer as some call it, is the most comfortable, productive alternative. Rather than using the steering wheel, many manufacturers offer a small servo lever to the left of the operator’s seat. This acts as a tiller, steering the machine left and right with fingertip control. The pod that contains the lever will usually also house a forward and reverse switch and a transmission kickdown button.
While it has been possible to have a JCB wheel loader converted to Lever Steer as an after-market option, the company has never offered the system as a factory option, until now. The company has developed a Lever Steer system that can be included on all 457 and 457 Agri models, along with any of the smaller 427 or 437 loaders.
The option includes a sidepod to the left of the operator’s seat with a short lever to steer the machine. There is a fingertip transmission selector, offering F/N/R positions and a kick-down button that drops the transmission to the lowest gear ratio for hard stock piling. The pod also includes the activation button, that switches from steering wheel to lever steering, along with buttons for the horn and the front windscreen wipers.
seatbelt as part of the installation. Operators may not realise how much they brace themselves with a hand on the steering wheel when turning and on rougher terrain. With no steering wheel to hold on to, the three-point belt provides far better location in the seat, boosting comfort and safety for the operator.
This allows the operator to drive the machine without needing to take their hands off the levers, with the right hand working the bucket and boom control. It also greatly reduces the effort required by the operator, as there is no need to constantly spin the steering wheel from side to side, it’s just a slight movement of the wrist to work the lever.
The steering lever is proportional, so the further you push to one side or the
other, the faster the machine will turn.
With JCB’s lever steer it is possible to make very gentle inputs and there is none of the jerkiness that could be found on some earlier after-market systems. The transmission control is also well placed for repetitive stock piling and loading operations.
While using the lever, the steering wheel can be pushed forward, increasing the feeling of space around the operator’s seat. Likewise, if you move to the steering wheel, the Lever Steer pod can be folded back out of the way, making it easier to access the seat or to leave the machine.
If Lever Steer is specified, JCB automatically includes a three-point
JCB is also boosting productivity for its wheel loader models, with the launch of Intelliweigh. Available across the 427, 437 and 457 models, the Intelliweigh Loadmaster 100 weighing system, can now be specified as a factory option. Offering both dynamic and target weighing, the system allows for multiple operator profiles and a range of attachment settings.
Intelliweigh can be used to load and weigh multiple vehicles on a site, using a split system. Individual target weights can be set for each truck, while maintaining the overall target weight for a contract. This allows for combined weight tickets, to provide customers with total material moved figures.
An on-board printer provides weight tickets for individual trucks from within the loader cab. The data can also be uploaded to a customer’s own in-house
system if required, to provide live updates on production and machine use.
Intelliweigh comes with a 7" touchscreen display with separate keys for regular functions. It is compatible with up to 10 attachments, including a range of buckets and pallet forks and offers a +/- 2% accuracy rating. The touchscreen can also be used as a reversing camera monitor if preferred.
The combination of Lever Steer and Intelliweigh enhances the productivity and performance of any 427, 437 or 457 JCB wheel loader, while reducing stress and fatigue for the operator. By having both systems available from the factory, there is no lost time during machine supply waiting for third-party installation.
• 270° Artificial Intelligence (AI) camera coverage around the machine,
• Visual and audible alerts for the operator and pedestrians in close proximity to the machine,
• Full integration with JCB’s LiveLink telematics system to allow data to be accessed from a single source,
• Machine and cloud data storage as standard,
• Customer data encryption and full compliance with data protection regulations,
• Industry-first OEM factory-fit solution,
• Covered under the machine standard warranty.
JCB’s product launch event saw a number of high-tech innovations that will boost the safety and security of machines on and off site.
Its new integrated pedestrian recognition system – JCB INTELLISENSE – is a factory-fit solution for JCB Loadall telescopic handlers.
It includes an onboard data storage facility with a telematics box to provide a back-up of events for site reporting that can be downloaded for playback. Unlike aftermarket systems, the JCB INTELLISENSE is fully integrated into the machine’s LiveLink telematics system, allowing users to remotely access the data,
making it the ideal risk management tool for fleet and construction managers alike. It is designed to drastically reduce the risk of harm and injury to workers on UK construction sites. It is made to be used on Loadall telescopic handlers to reduce the risk to workers of being struck by moving materials handling machines on construction sites. The system identifies, assesses, and mitigates risks on construction sites and enables contractors and operators to manage potential hazards around the machine and its operating environment.
The JCB INTELLISENSE system is initially being launched on two key
construction models, the JCB 540-140 and the 535-125 Loadalls, following calls from UK construction firms for pedestrian recognition systems on site. JCB is the first major OEM manufacturer to provide a factory-fit solution.
The system utilises four cameras, three of which are AI cameras (two side mounted and one rear-facing) as well as a forward-facing standard camera to improve visibility to the operator in line with the object detection and visibility aids standard ISO16001:2017. The system is designed to detect pedestrians within a pre-set proximity of the machine. When the system senses a pedestrian in that area, there are audible and visual warnings inside the cabin for the operator and externally to warn the pedestrian and other site workers. The system also provides an operator alert button as standard, where the operator has the capability to record a 10 second data segment that is automatically sent to and stored in, the cloud.
JCB has launched a new product to help customers monitor the location of all powered or non-powered equipment, regardless of its size, function, or brand.
The LiveLink Asset Tag is a small battery-powered, Bluetooth-transmitting device that can be fixed to any asset –from hand tools, machine attachments such as breakers, buckets, and sweeper
collectors, through to skips, powerpacks and site accommodation units.
The tag integrates with JCB LiveLink, a fleet management system, providing complete visibility and improving productivity by eradicating the time wasted locating misplaced equipment.
At 68 mm x 32 mm x 16 mm and weighing just 50 g, the tags are compact, discrete and lightweight. Attached by bolts or adhesive, they are strong and durable, achieving the highest IP69K rating for protection against dust and water ingress. This makes them capable of withstanding the rugged outdoor conditions typically found in the construction and agricultural sectors.
They function by transmitting a Bluetooth connection from any enabled LiveLink unit or partner units, to track the location of any piece of equipment registered within the customer’s LiveLink account.
LiveLink Asset Tag uses the latest Bluetooth Low Energy 5.0 technology and can be located within an 800-m line of sight range of the nearest enabled LiveLink unit or partner unit. The tags feature an impressive four-year battery life.
JCB Aftermarket Managing Director Mario Moser said: “By integrating with the JCB LiveLink system, customers can now benefit from a single, central source for all asset management. The JCB Asset Tag is another great addition to the LiveLink portfolio to help businesses maximise efficiency and drive productivity.
“Losing or misplacing any piece of equipment can be costly and result in unnecessary downtime. Designed to bridge the gap between larger machine telematics and the types of site equipment not typically monitored, the Asset Tag provides increased visibility and control over all assets.”
Launched in 2011 and now with over 500,000 machines monitored by the system, JCB LiveLink gives machine operators and fleet managers easy access to all data through an online portal and mobile app. Every aspect of fleet management is covered with features including service tracking, security geofencing, what3words global location, machine utilisation data and mixed fleet functionality.
JCB launched the new TLT 30-22E HL Teletruk, bringing a 4.4-m lift height option to its innovative telescopic-boom battery electric lift truck range. This compact, high lift industrial telehandler offers a maximum lift capacity of 3,000 kg up to the full lift height of 4,400 mm, opening up a range of market sectors to the opportunity of a battery-powered, telescopic boom machine.
Building on the success of the existing TLT 30-19E and the TLT 35-22E E-TECH models, the TLT 30-22E HL uses the same 80V battery driveline, allowing up to eight hours of operation on a single charge. The machine’s telescopic boom greatly increases productivity for customers, permitting single-sided loading and
unloading of a road-going trailer thanks to its extended forward reach.
With zero emissions and low noise output, the electric TLT trucks are ideal for 24/7 operation in urban environments, inside buildings and in noise sensitive areas. Their forward reach, low overall height and compact running circle, with a 90 ° spin turn possible on the TLT 30-22E HL, deliver maximum versatility.
Now, with the increased working height of the High Lift machine, that versatility and productivity is available to a new range of customers. The additional lift height will allow the machine to compete with larger diesel models, making it possible for a wider group of customers to transition from diesel to
electric power as part of their net zero targets.
In addition, the increased working height will be popular with agricultural applications, such as potato growers, where boxes are generally stacked four or five high. The waste and recycling sector should also find a variety of applications for the machine, as it can now load into hoppers and into high cube containers.
The TLT 30-22E HL retains all of the JCB CommandPlus cab comfort and security that customers have come to expect, with single lever electro-hydraulic control for all boom functions. LED working lights and an LED beacon are standard, along with a white noise reversing alarm and JCB’s proven Load Motion Control safe lifting system.
The countdown to the sixth edition of PlantWorx, hosted by the CEA (Construction Equipment Association), has officially begun. From 23 to 25 September 2025, the Newark Showground, a new venue for PlantWorx, will be the hub for the latest developments in construction equipment and technology. With an anticipated 400 exhibitors and over 15,000 visitors, this is the must-attend event for professionals looking to stay ahead in the construction industry.
For anyone serious about advancing their business, PlantWorx offers an unparalleled opportunity. Industry veterans and newcomers alike will find the latest machinery, groundbreaking technologies and live demonstrations designed to transform daily operations. The event goes beyond the traditional trade show, providing a hands-on experience that aims to inspire and equip professionals with the tools and solutions needed to stay competitive.
Major names like Takeuchi, RSP UK Suction Excavators Ltd, SANY Heavy Machinery UK Ltd, Sunward, Avant Techno, XCMG, Hydrema, Liugong, Mecalac, Kubota, Steelwrist, Hidromek, Rototilt, Worsley Plant, Merlo, Manitou, National Highways and many more are already confirmed. These companies will showcase their machinery through live demonstrations, providing an up-close look at how they tackle the industry’s everyday challenges.
Simon Frere-Cook, PlantWorx Event Director, said: “Technology is advancing faster than ever and PlantWorx 2025 is where these innovations come to life. We’ve designed this event to ensure that whether you’re a contractor, operator or business owner, you’ll leave with insights and practical knowledge that can transform your operations. It’s about preparing for the future as much as seeing what’s available today.”
Back by popular demand, the Operator Challenge will once again give attendees a chance to test their skills and compete with the industry’s best. This challenge remains a highlight of the event, offering substantial prizes, including a significant cash award for the overall winner.
For exhibitors, PlantWorx 2025 offers a platform to demonstrate innovations to an engaged audience. New features like the Shared Dig Zone will allow more companies to showcase their equipment without the need for a large demo plot. Whether a market leader or an emerging brand, exhibitors will have the chance to demonstrate their capabilities to thousands of industry professionals.
Simon added: “PlantWorx continues to be the go-to event for the construction industry because it offers a unique space where companies, large and small, can showcase their technologies in action, and visitors can engage with them directly.”
With one year to go, now is the time to ensure your participation in the event. Whether you’re looking to discover the latest innovations, network with industry leaders, or experience the future of construction equipment first-hand, PlantWorx 2025 promises to deliver.
For exhibitors, spaces are filling fast. For visitors, mark your calendars –PlantWorx 2025 is set to be one of the most anticipated construction events of the year.
For more information or to register your interest in attending or exhibiting, visit Plantworx.co.uk.
Rethinking Futures will make a significant impact at PlantWorx 2025, offering secondary school and college students aged 12 to 18 a unique opportunity to explore careers in construction engineering. This initiative provides a platform for young people to connect with industry professionals, experience new technologies and learn about the construction sector.
Addressing the skills gap in construction, engineering and mechanics, Rethinking Futures connects educational institutions with industry leaders to engage and inspire young minds. With a focus on apprenticeships, training and recruitment, the initiative aligns with government objectives and supports schools in meeting Gatsby benchmarks.
Local schools will participate in a practical engineering challenge, where students design, build and test machinery inspired by equipment such as grab lorries, excavators and cranes. Equipped with the necessary tools and materials, teams will gain hands-on experience
emphasising creativity, teamwork, and problem-solving. Their projects will be evaluated by judges from the sector, giving students a unique opportunity to present their work to experts and explore potential career paths.
“Rethinking Futures is about igniting a passion for engineering and construction in young people when fresh talent is crucial,” says Stuart Favill, PlantWorx operations manager and co-founder of Rethinking Futures. “We’re creating a memorable, hands-on experience that connects young people with current technologies and potential employers. It’s an invaluable opportunity for students and the industry alike.”
Vic Boneham, a school teacher and cofounder of Rethinking Futures, brings an educational perspective to the initiative. “As a teacher, I know how powerful hands-on experiences can be for students,” she says. “This initiative gives young people a chance to tackle real engineering tasks and see what a future in this field could look like. It’s all about helping them
connect what they learn in school with real opportunities and showing them that these careers are within their reach.”
John Morrison, who has served as the Principal of Lincoln University Technical College and Director of the Lincolnshire Institute of Technology for the past seven years, will be instrumental in bringing Rethinking Futures to Nottinghamshire schools. “This is going to be one of the most exciting competitions we have ever run with students,” says Morrison. “I have organised countless regional and international engineering challenges over the years. This project is so clearly and closely linked to our construction industry partners that it will feel genuine and relevant to the young people involved.”
The engineering sector offers a wide array of career opportunities, many of which often fly under the radar. Rethinking Futures aims to raise awareness of these diverse paths and showcase the industry’s potential to students. While Nottinghamshire schools will be the first to benefit, the initiative
will expand beyond the region, with plans to bring it to other events and shows in the construction and agricultural sectors. By connecting students directly with industry, Rethinking Futures aspires to cultivate a new generation of talent equipped to tackle the challenges of tomorrow.
With over 400 exhibitors expected, PlantWorx 2025 is set to be the UK’s largest live-action construction equipment exhibition, featuring cutting-edge technologies and leading OEMs. The event will attract experienced professionals and, through the inaugural Rethinking Futures initiative, inspire the next generation of industry talent.
Sponsorship opportunities are available for those looking to support this exciting initiative and help cultivate the next generation of construction professionals.
For further information, please get in touch with Stuart Favill ‘Rethinking Futures’ stuart@rethinkingfutures.org or call 07970 534 644.
The QMJ Group has announced that the next edition of the iconic quarrying, construction and recycling exhibition will take place from 23 to 25 June 2026 at Hillhead Quarry, Buxton. With the dates now confirmed, demand for the 2026 show is expected to be very high and new enquiries to exhibit should be directed to Event Manager, Harvey Sugden on +44 (0)115 945 4377 or harvey.sugden@qmj.co.uk. All enquiries will be contacted next spring with an update of the latest availability.
Diggers LIVE! magazine and all at Demolition Hub Ltd look forward to seeing you at Hillhead in 2026!
ELECTRIC
KHD Brokk Hire is the ‘one stop shop’ for all things electric plant, with a sustainable twist too! From electric diggers & dumpers to Brokk machines – we do it all! WE OFFER:
AUSA, the manufacturer of compact all-terrain industrial vehicles, is launching two new six-tonne articulated dumpers. These new models are being introduced to build on the success of their predecessors and are equipped with new features to improve their functionality and increase their safety.
The new rear styling combines design with practicality. The size of the bonnet has been increased to provide unrivaled accessibility to the engine and maintenance parts. Air, oil and fuel filters, radiator, tanks… everything is optimally positioned to keep downtime to a minimum.
The new EN 474-1:2022 and EN 474-6:2022 standards that are coming into force in February 2025 require all dumpers with an operating weight between 3,500 and 4,500 kg to be fitted with additional safety measures to prevent the operator from being thrown out of the vehicle in the event of a rollover. At operating weights of 4,500 kg and above, all dumpers must be fitted with
enclosed cabs.
In order to comply with these new regulations, AUSA provides three different configurations for its new sixtonne models: Folding ROPS protective structure with safety rails 96% larger than current models; open cab; and heated enclosed cab.
This means that AUSA has ensured that all its dumpers that are shipped from the beginning of 2025 will comply with the new regulations. In addition to the different driver cabs that are available, as standard the D601AHG+ and D601APG+ models will continue to be
equipped with additional safety features such as a seat with a presence sensor, seat belt with buckle sensor, negative brake and front view camera.
Reducing operator fatigue on the machine is also essential for the safety of the operator and the surrounding area. As standard, the new D601AHG+ and D601APG+ dumpers are equipped with a high-comfort seat with built-in suspension, ensuring comfort in the vehicle and reducing tiredness during long working days.
Bobcat has been selected as a Red Dot Award: Design Concept winner for RogueX2, an all-electric, fully autonomous concept loader.
The Red Dot Design Award is one of the most respected design awards in the world, with its Design Concept category identifying and celebrating new design concepts and innovations as the precursors of tomorrow’s great products.
“We are honoured to win the world-renowned Red Dot Award for Design Concept in recognition of the groundbreaking design of the RogueX2,” said Joel Honeyman, Vice President of Global Innovation at Doosan Bobcat. “This award is a testament to the dedication of the Bobcat teams who are passionate about pushing design limits and advancing innovation to redefine the machines of tomorrow.”
Key to the machine’s development
was the Bobcat Global Design Studio, which supported the project in collaboration with the Bobcat Global Innovation team.
On display at CES 2024, the RogueX2 is a powerful, smart machine that produces zero emissions and features a lithium-ion battery, electric drive actuated lift and tilt kinematics with no hydraulics.
Specifically designed and built without a cab, RogueX2 explores the idea of how work machines of the future can be designed and optimised for new technologies and enable an entirely new work experience. Designed with wheels to optimise the electric battery run time, the RogueX2 features axial flux motors, which give the machine incredible tractive effort.
The RogueX2 was built as a proving ground to advance Bobcat’s innovation
leadership and has garnered many new patents pending.
“To build a smarter, more sustainable and connected future, we must ask the questions no one else has thought to ask before and invent new solutions that previously did not exist,” continued Honeyman.
In the research and development stage, the award-winning RogueX2 is not commercially available.
The Red Dot Design Award is an annual international competition that recognises excellence in design and business. With around 20,000 entries per year, it is one of the biggest design competitions in the world. The Design Concept category features projects in varying stages of development ranging from concepts to prototypes, to almost or fully developed products which are ready for market.
Rother Valley Tree Services Ltd, a family business that covers Doncaster, Rotherham, Barnsley, Sheffield, Leeds, Wakefield and surrounding areas, has purchased a top-of-the-range Bobcat T86 compact track loader.
Delivering a higher engine and hydraulic output, the Bobcat T86 is the most powerful compact track loader the company has ever built. The T86 uses a well-proven Stage V-compliant 3.4-l Bobcat engine – producing 78 kW at 2,600 RPM. Just like all of Bobcat’s R-Series loaders, the engine is mounted in-line with direct drive, which improves the cooling capacity of the engine and hydraulic components.
One of the most exciting aspects of the T86 is that for the first time there is a choice of three different auxiliary flow outputs. There is a standard flow configuration providing 87 l/min for applications such as load and carry, or where low hydraulic flow attachments are used. Bobcat also offers two additional hydraulic performance functions using the new Electronic Displacement Control (EDC) Pump on the T86: a High Flow function giving 138 l/min and a new optional, industry unique Super Flow function taking auxiliary flow to 159 l/min.
As well as the Super Flow, the T86 purchased by Rother Valley Tree Services features an enclosed cab with HVAC, an air-suspension seat, 7" touch panel display, two-speed Power Bob-Tach attachment system, a reversing fan, premium LED Lights, keyless ignition and joystick controls.
Steve Smith, Managing Director of Rother Valley Tree Services, said: “I was intending to purchase the T770 model from Bobcat, but AMS Bobcat introduced us to the idea of the new T86 and its Super Flow output and the more powerful attachments it can power. Now part of our fleet, the T86 has more than matched what we were promised.”
Carl Chadburn, Plant Manager of Rother Valley Tree Services, added: “The many jobs we are
able to do are specialist, with only a few companies being able to offer these services in the UK. The T86, the new forestry cutter and the other Bobcat attachments we’ve purchased from AMS complement the rest of the vehicles and machinery in our fleet, giving us access to an even larger array of solutions to help complete even the most difficult of jobs.”
In a host of applications in construction, landscaping, agriculture, disaster relief and many other areas, there are no other machines that offer the combination of versatility and productivity that can be provided by compact track loaders such as the T86. This is due to their unique characteristics as tool carriers and the wide array of attachments that they can work with, from trenchers, augers, graders, soil conditioners, scarifiers and dozer blades to more specialist attachments such as forestry cutters and stump grinders.
As tool carriers, compact track
loaders offer many advantages over the comparable wheeled machines. They can provide increased productivity in many conditions with a lifting capacity approximately 25% more than the equivalently sized wheeled loaders.
Carl Chadburn continued: “Combined with the low centre of gravity of the T86, the traction delivered by the tracked undercarriage gives us advantages for climbing and working on steep slopes in diverse applications such as scrub clearance on motorway verges, which would be difficult to carry out with the other machines in our fleet.
“Approximately three times less than a wheeled machine, the low ground disturbance of the T86 allows it to work on delicate surfaces, such as established lawns or asphalt, minimising damage and reducing the need for tidying up after the job is complete. As well as being perfectly suited for working anywhere on uneven terrain, the T86 can also work well on snow extending work into the winter, due to its superior traction and flotation.”
“The low ground disturbance of the T86 allows it to work on delicate surfaces, such as established lawns or asphalt, minimising damage and reducing the need for tidying up”
DEVELON now offers a range of three articulated dump trucks (ADTs), comprising the DA30-7 and DA45-7 6x6 models, complemented by a new 4x4 version of the DA45-7.
The DA30-7 and DA45-7 6x6 models have payloads of 28 tonne and 41 tonne, respectively. The DA30-7 is powered by the Scania Stage V compliant DC09 nine-litre diesel engine providing 276 kW of power. The DA45-7 is driven by the Scania Stage V DC13 13-litre diesel engine with an output of 368 kW.
Also powered by the Scania Stage V DC13 13-litre diesel engine with an output of 360 kW, the 4x4 version of the DA45-7 ADT is intended to compete
with rigid dump trucks (RDTs) in the 40-tonne class.
The DA30-7 and DA45-7 feature an articulation hinge positioned behind the turning ring to provide equal weight distribution to the front axle even during maximum steer articulation. This combined with a free-swinging rear tandem bogie ensures equal distribution of weight to each wheel and guarantees permanent six-wheel contact and drive for equal power distribution and excellent performance particularly on difficult terrains such as soft ground, uneven
surfaces, very steep slopes, tight turns or a combination of all of these difficult conditions.
Collectively, the forward turning point, the unique tandem bogie and the sloping rear frame results in best in class rough and soft terrain capabilities. The unique body shape and sloping frame ensure equal load distribution on all the wheels making these machines the best haulers for soft terrain work. The design of the articulation also provides equal load distribution on the wheels on both the left and right hand side when turning, which is very important for the traction and stability of the machines.
Superior performance in difficult conditions compared to RDTs
In the new 4x4 ADT, the front truck and cab unit is the same as in the 6x6 models, with modifications being made on the rear dumper unit only. Featuring a ZF EP8-420 transmission, the 4x4 DA45-7 is a two-axle ADT with twin wheels at the rear, and with a dumper section similar to that on RDTs in the 40-tonne class.
As well as performing better in conditions that are tough for RDTs, the new 4x4 DA45-7 ADT has a width of less than four metres to avoid the need for special transportation and offers a better turning radius than a comparable RDT. The shorter turning radius and
the design of the rear dumper unit, which is more suited to carrying flat and heavy rocks, provide particular advantages in the mining and tunnelling industries.
The latter are growing markets for ADTs, and include pioneering, short-term mining projects, quarrying and contract mining industries, especially those in southern Africa, the UK and Australia. Construction and bulk earthmoving contractors involved in roads, dams, airports, landfills and development projects are also large users of ADTs. Together these areas make the ADT market a wide and varied one, thereby ensuring a large customer base.
Summarising the advantages:
• The 4x4 ADT can climb steeper inclinations than equivalent RDTs.
• The 4x4 ADT performs better than RDTs in wet and slippery conditions,
• In heavy rain, RDTs may need to stop working – DEVELON’s 4x4 ADT does not.
• Thanks to the short turning radius, the 4x4 ADT operates effectively on compact sites.
• The two axle 4x4 ADT design causes less ground disturbance than 6x6 configurations.
DEVELON used the recent Resource & Waste Management (RWM) show at the NEC in Birmingham to present for the first time a new design of wheel loader aimed at the waste handling industry.
Based around the successful DEVELON DL280-7 wheel loader model, part of the award-winning DL-7 range of wheel loaders from DEVELON, the new waste wheel loader preproduction model increases safety and efficiency for the operator.
The new waste wheel loader has a novel design featuring a strong, light weight loader frame and a unique and innovative lifting arm that minimises
the front end weight of the machine, providing an impressive super high lift and reach capability to deliver a higher dump height, whilst maintaining excellent manoeuvrability. The light-weight loader frame is designed to offer optimum strength and heavy duty axles contribute to the exceptional stability of the new waste loader.
The super high reach on the new DEVELON waste wheel loader is designed for loading material into high sided containers such as walking or moving floor trailers specially developed for transporting waste. For assured loading, the new waste loader is equipped
with a high tip bucket supported by two robust cylinders. The lower bucket pivot pins have internal greasing lines to prevent them being damaged by material carried by the loader.
The new loader incorporates a waste kit with heavy engineering and strength at its core, including an exoskeleton around the machine and further protection provided by mesh type windshield guards, articulation guards, belly protection and fuel tank guards. The unit also features an air intake mesh and the cab has specialised air filtration. Other features of the new waste loader include a reversible fan to clear the radiator, a heavy duty
radiator guard, rim covers for the wheels and solid tyres with suspension cut outs.
Safety features include high visibility chevrons on the rear of the machine and a fire suppression system, with internal and external actuation points on the front and rear of the loader.
Inside the spacious cab, the new waste wheel loader offers significantly enhanced operating comfort, with joystick controls and a leather type upgraded operator seat. The seat is equipped with fully adjustable horizontal and vertical suspension settings, a pneumatic lumbar function and seat heating as standard. There is a three-point safety belt with alarm icons on the 8" touchscreen monitor and on the gauge panel, which features a new layout and anti-reflective glass.
The operator can also benefit from an optional 360 ° camera system with AI person detection to ensure the safety of personnel in close vicinity to the machine.
The operator has an excellent field of vision from the cab, with the large glass window area minimising blind spots around the cab. The new waste wheel loader also offers the option of electrically adjustable rear view mirrors for added safety.
Full LED working lights are installed on the cab (four on both the front and rear as standard, with the option of six each at the front and rear). For higher pedestrian safety, the LED lights on the rear bonnet have an automatic strobe function to indicate when the wheel loader is reversing.
Included in the information at the operator’s fingertips on the touchscreen
is the feed from the optional weighing system, the HVAC controls (heating, ventilation and air conditioning), radio and bluetooth devices (music streaming, hands-free) and the operator help function.
Overall, the cab interior offers a large, quiet and more comfortable operator environment, which improves safety and productivity and helps the operator work with high concentration. The operator also has increased leg room, an enlarged storage area and cool-box position and an improved air conditioning system (with optimised air circulation).
JCB has expanded its electric site dumper offering with a three-tonne swivel tip model powered by lithium-ion battery technology. Designed to work indoors and in emissions and noise-sensitive areas, the 3TE electric dumper offers all the benefits of the one-tonne 1TE with a three times greater capacity.
Key features include:
• Zero emissions and low noise levels,
• Fast charge capability,
• Full shift operation in typical use,
• Swivel-tip skip design to enable loading and unloading in tight, confined spaces. The 3TE site dumper is a durable,
compact machine with a full steel skip and heavy-duty articulated chassis. The machine dispenses with the hydraulic pump and engine featured in the diesel powered 3T-2 model and comes with an electric motor that connects to a drop box, to provide full-time all-wheel drive.
A 22.3-kW electric motor delivers drive to the drop box, while a second 16.1kW electric motor powers the machine’s standard hydraulic circuit, for steering and skip lift, via a hydraulic pump.
The power is supplied by a 20-kWh lithium-ion battery pack, capable of providing full shift operation in normal use. The batteries can be recharged from conventional site electrical supplies, with 110-V and 230-V cables available.
In addition, the optional JCB Universal Charger can be used to rapid charge the batteries for extended operation.
Designed primarily for European and North American markets, the 3TE delivers zero emissions at the point of use and low noise levels, making it ideal for indoor, underground and emissionssensitive working sites. A ROPS frame is standard, along with LED amber and green lap-belt beacons. In low light conditions, powerful LED working lights provide maximum visibility when working, and additional lighting at the operator station allows for safe egress. The machine offers a maximum payload of 3,000 kg and a maximum load over height of 1,566 mm.
JCB has developed a fully glazed, heated ROPS/FOPS cab alternative for the 403E electric compact wheeled loader. The cab comes complete with heated front and rear screens, a heated seat, and an efficient three-speed heater with boost feature. It is also possible to pre-condition the cab while charging, to preserve traction battery power and potential operating time.
The 403E uses a 2.2-kW Positive Temperature Coefficient (PTC) heater system with three temperature settings. There is also a boost switch that can be used to rapidly increase the temperature within the cab for 10 minutes, before switching off to conserve energy. The heater is automatically disabled if the doors are open, to further preserve battery power.
In the warmer months, the operator can use the blower function, even if the doors are open, to circulate air within the cab.
Cab pre-conditioning allows the operator to warm the cab while the machine is being charged prior to the start of work. This time-based system uses a rotary dial and the main digital display in front of the operator to set the time that work will commence. With the start time set, the heater will activate 30 minutes before work commences and will de-activate 15 minutes after the start time if the machine has not been used. This feature will only function when there is more than 25% battery charge available.
The heated seat provides rapid warming for the operator, reducing the need to run the main cab heater, conserving electrical energy and prolonging run time. Heated front and rear windscreens also allow rapid defrosting in colder climates and demisting during wet weather. Again, this reduces the requirement for the heater to be run, preserving battery power for loader use.
The 403E is JCB’s first full electric compact wheeled loader. The machine boasts a 20-kWh battery pack, among the largest in the sector, allowing up to
four to five hours of continuous use in a mixed operating cycle. Even with the full cab, the machine weighs in at less than 2.6 tonnes, allowing transportation on a 3.5-tonne trailer, behind a 4x4 or a light commercial vehicle.
The machine has a 33.4-kW peak power drive motor for the wheels, with three driving modes. Drive is transmitted through a ZF drop box, to both axles, which can be supplied with open differentials or with differential locks. In addition, it uses a 20-kW peak power motor to drive the hydraulic pump for the lift arms and attachments.
The 403E is aimed at both agricultural and construction customers. It is proving particularly popular with those farming customers who have solar or
wind turbine power generation on their land and buildings. By harvesting this green renewable energy, it is possible to operate the electric loader while incurring virtually no fuel cost.
The machine is also proving popular in urban construction and paving work, where the ability to carry palletised loads with zero emissions and low noise levels is in demand. The addition of a fully glazed, heated cab will add to that appeal, particularly in countries with colder, wetter climates.
JCB X-Series excavators are leading the way in lowering fuel consumption. The 145XR now uses up to 10% less fuel than our previous model, the JZ140. We’ve made this possible by reducing the working speed of the engine from 2050rpm to 1700rpm, whilst maintaining performance by optimising the hydraulic system. We’ve also improved slew control and increased bucket tearout by 13% for smoother operating. Start saving today.
* £2000 saving is versus the JZ140 Stage V and is based on an
Kramer is expanding its portfolio with the new 5045 wheel loader, which impresses with its combination of low weight and high payload. With an operating weight of approx. 2,600 kg, the 5045, with a full cab including standard bucket and stacking device, can be easily transported on a 3.5-tonne trailer, which not only saves time but also significantly increases machine use.
The 5045 wheel loader is perfect for transporting standard paving stone pallets or stone packages and masters the loading and unloading of lorries effortlessly. Thanks to its high performance and compact dimensions, the 5045 is ideal for use in confined areas, such as underground car parks or multi-storey car parks.
Depending on customer requirements, the 5045 offers two engine variants: the wheel loader is equipped with a 19-kW engine as standard, while a 33-kW engine is available as an option, which enables a top speed of up to 30 km/h. There is also a choice of two full cab variants – a comfort cab with a height of 2.3 metres and a low cab with a height of 2.1 metres for maximum compactness. Both cabs offer excellent all round visibility and ergonomically arranged controls that ensure simple and intuitive operation.
Thanks to the undivided vehicle frame, high stability, manoeuvrability and constant payload, the machine is easy and safe to operate. In addition, the 5045 offers three different steering modes – all-wheel steering, crab steering and front axle steering –which make manoeuvring easier even in difficult situations.
Another highlight of the new wheel loader is the standard quick hitch, which is also used on the next larger models. For the customer, this means that existing attachments can be used even
more flexibly. The fully hydraulic Smart Attach quick hitch system is available as an option, which enables hydraulic attachments to be changed quickly and safely without the driver having to leave the cab. This innovative function saves time, increases productivity on the construction site and is unique in this machine class.
With the new 5045 wheel loader, Kramer is setting new standards in the 2.8-tonne class and offers a machine that impresses in terms of both performance and versatility. Whether in the construction industry, in landscape maintenance or in urban applications –the 5045 is the ideal partner for a wide range of requirements.
Together with STRABAG, Liebherr is taking important steps towards a decarbonised construction site. In a project that recently started at the Kanzelstein quarry in Gratkorn, Austria, STRABAG is testing Liebherr’s large hydrogen-powered wheel loader over a period of two years. Energie Steiermark will supply green hydrogen for its own hydrogen filling station at the quarry. The L 566 H wheel loader is the world’s first large wheel loader with a hydrogen engine.
Leonore Gewessler, Austrian Federal Minister for Climate Action; Clemens Haselsteiner, CEO of STRABAG; Martin Graf, Director of Energie Steiermark; and Jan Liebherr, Chairman of the Board of Directors of Liebherr-International, attended a special event at the Gratkorn quarry to mark the start of the project for the first test use of the large hydrogen powered wheel loader.
In addition to technical presentations
and a tour of the quarry, the hydrogenpowered wheel loader was demonstrated in operation. For the next two years, STRABAG will be testing the L 566 H prototype on a daily basis. A hydrogen filling station is being built to refuel the wheel loader directly at the quarry. The energy supplier Energie Steiermark will provide the green hydrogen required for this.
Leonore Gewessler praised Liebherr’s exemplary commitment to reducing greenhouse and other harmful gases and its cooperation with STRABAG on testing hydrogen technology: “I am pleased to see innovative companies pushing ahead with pilot projects, especially in forms of mobility that are difficult to electrify, such as those in the construction sector.”
The cooperation with STRABAG, one of the foremost construction companies in Europe, shows what an important and positive development the Liebherr drive technology is.
As one of the biggest manufacturers of construction machinery, Liebherr has provided STRABAG with the L 566 H prototype as a test machine. The large wheel loader with a hydrogen engine should save up to 100 tonnes of CO2 each year, corresponding to about 37,500 litres of diesel. “We want to be climate neutral by 2040. The only way to achieve this is by consistently and comprehensively saving CO2, for example, in the operation of construction machinery,” explains STRABAG CEO Klemens Haselsteiner.
The L 566 H from Liebherr is the world’s first prototype large wheel loader with a hydrogen engine. “The technology also enables large vehicles that are difficult to electrify due to their high energy demand to be operated without CO2,” explained Dr Herbert Pfab, Technical Director of Liebherr-Werk Bischofshofen GmbH. The hydrogen engines are manufactured by the Liebherr
components division’s own engine plant in Bulle, Switzerland. These engines will not only make it possible to emit zero greenhouse gases and almost no nitrogen oxides, but will also offer excellent efficiency.
With the pilot project, Liebherr and STRABAG are demonstrating how emissions can be reduced in a sector that is difficult to decarbonise by means of alternative fuels. Climate-neutral hydrogen produced with wind and water power or solar energy can be a key enabler for achieving the goal of climate neutrality set by Austria’s politicians. “Green hydrogen is an indispensable element of our future energy. As an important and valuable energy source, it helps replace fossil natural gas – especially in industry,” said Climate Action minister Gewessler. What makes the two-year test deployment at the Gratkorn quarry such a showcase project is, above all, the joint approach of Liebherr and STRABAG – two companies that are actively pushing decarbonisation forward.
Investing in an articulated hauler is a significant decision. Choosing the right truck can lead to increased productivity, more uptime and a safer working environment. Articulated haulers play a crucial role in various applications from commercial construction projects to quarries, mines and infrastructure developments.
The best ADTs offer efficient transportation of heavy loads across challenging terrain and easy manoeuvrability on tight, tricky sites. Before investing in an articulated dump truck, it’s essential to consider several factors to ensure that the machine aligns with your specific needs and operational requirements. With its trucks designed and built for the toughest jobs and roughest sites, Scottish articulated hauler manufacturer Rokbak outlines five key considerations that should be integral to your purchasing decision.
One of the primary factors to consider is the truck’s hauling capacity. You need to assess typical load capacity and weight to ensure that the equipment chosen can handle the demands of the specific application. Rokbak offers two hauler models, the RA40 is the largest with a gross power of 331 kW, a maximum torque of 2,225 Nm and a 38-tonne payload. It is a popular choice for major infrastructure projects, with its effective power to weight ratio enabling the fast movement of heavy-duty materials. Like the RA40, the 28-tonne RA30, with a gross power of 276 kW and a maximum torque of 1880 Nm, also benefits from a transmission retardation system, a fully adaptable drivetrain and easy maintenance to suit a variety of different job sites.
Consideration of the type and size of material being handled allows
the truck’s load-carrying body to be specified correctly to ensure optimum payload, load retention and longevity. Body options such as side extensions for lighter materials, tailgates for free-flowing material retention and additional liner plates for highly abrasive or large blasted rocks are all popular choices. Matching the hauler to existing complementary equipment ensures onsite efficiencies and safety.
Articulated haulers are designed to navigate challenging terrain, but the extent of their capabilities can vary. Both the RA30 and RA40 provide excellent performance in all hauling conditions, from muddy terrain to slippery slopes and the scorching heat to sub-zero temperatures. It’s important to evaluate the application and climate the truck will be used in, as well as consider the
materials that will be transported and the topography of the site, including slope gradients, ground conditions and potential obstacles. Rokbak trucks offer top-level off-road performance. Choosing a hauler that can handle the specific conditions of the site is crucial for optimal efficiency and safety.
Operating costs, including fuel consumption and maintenance, are significant considerations for any heavy equipment investment. Efficiency in the use of power is as important as having a high-performance truck. Rokbak articulated haulers are built to perform while also setting new standards for total cost of ownership and a commitment to sustainability as part of the Volvo Group’s journey to net-zero. A lean-burning, high-performing engine and responsive transmission shift control are good for low fuel consumption and environmental impact – as well as increased uptime and extended service intervals. An adaptable, perfectly balanced drivetrain provides performance and productivity in all hauling conditions, while meeting
worldwide emission standards with low cost of operation.
High-level, user-friendly retardation systems, as found in Rokbak trucks, facilitate control of the machine and allow the operator to manage the safety and speed of the hauler – increasing efficiency and reducing wear and tear with shorter cycle times on the haul route.
Machine owners should also look for strong after-sales support and assess the availability of spare parts and maintenance services. A well-supported machine will lead to increased uptime and lower operating costs throughout the equipment’s lifecycle.
The wellbeing of operators is paramount in any heavy equipment operation. Features such as ergonomic design, operator visibility and the quality of the cabin environment provide a comfortable and safe workspace that not only enhances productivity, but also contributes to employee satisfaction and retention. A planetary gear transmission – as found in the RA40 to deliver smooth, efficient gear shifting – also
increases operator comfort. Haulers equipped with safety features such as stability systems with traction control, body tip inhibits and advanced braking mechanisms help to ensure a secure working environment.
Modern articulated haulers often come equipped with advanced technology and telematics solutions. These features can provide valuable insights into machine performance, fuel efficiency and maintenance needs – helping machine owners to manage their operating costs. The RA30 and RA40 are linked to the Rokbak Haul Track telematics system, providing customers with complete visibility and control of the hauler, enabling you to monitor and manage fleets effectively.
Komatsu is proud to present its latest generation of wheel loaders, the WA47511 and WA485-11. These two new models are packed with state-of-the-art technology and offer great performance, efficiency and operator comfort.
At the heart of new Dash 11 generation wheel loaders is a new Komatsu diesel engine characterised by extremely high torque in the low speed range. This is combined with a Komatsu-designed hydro-mechanical-transmission (HMT), resulting in unmatched performance, power reserves, fuel efficiency and ease of operation for all transport and loading tasks.
The WA475-11 demonstrates a 14% improvement in fuel efficiency over its Dash 10 predecessor, while the WA485-11 achieves a remarkable 29% increase in fuel efficiency compared to its predecessor, the WA480-8.
Thanks to a constant variable gear ratio, the engine stays in a highly efficient fuel zone. Variable speed control makes it possible to individually adapt the machine’s
maximum speed to the requirements of the job site. The adjustable variable traction control effectively limits wheel spin in difficult ground conditions.
The WA485-11 is significantly upgraded in payload and bucket capacity compared to its predecessor. All components have been adapted to a permanent payload of 8,800 kg and can even be increased to 9,300 kg in an aggregate handling variant, reducing the number of loading cycles required.
The new wheel loaders’ advanced emissions control systems meet EU Stage V standards. On top of that, the well-proven Komatsu exhaust system includes a diesel particulate filter (KDPF) and, together with the Selective Catalyst Reduction (SCR) system, further reduces NOx emissions using AdBlue. These technologies, in conjunction with the particularly low-emission combustion, allow the diesel particulate filter to be replaced only every 8,000 hours; this interval can be extended even further by using particularly low-ash engine oils.
Another new feature is variable power control, which enables the lifting speed
to be controlled independently of the accelerator pedal. Never before has it been easier for an operator to find the right balance between traction and lifting power. The optimised Z-bar linkage offers up to 20% more lifting power and a higher production rate. Remarkable lifting speed and class-leading machine stability help to increase productivity, especially in tight V-shaped loading applications. In addition, the hydraulic response time and the tipping or lifting speed can be adjusted to specific application requirements.
The spacious new operator-friendly cab offers generous all-round glazing and has an interior noise level of just 70 dB(A); the heated rear window is angled, preventing dirt from sticking on the rear screen; the lever console has a new command control switch and is adjustable on a five-way axis for each operator; and increased internal air pressure prevents dust and other particles from entering the cab. For easy and safe entry and exit, both machines are equipped with a rear-hinged door, angled steps and large handrails.
A new air-suspended seat dampens
vibrations, ensuring a more comfortable driving experience; the seat-mounted electronic pilot control levers with a new ergonomic design improve operating comfort and reduce operator fatigue; and automatic bucket filling and other assistance functions help the operator maintain productivity even during long shifts.
A fully digital, high-resolution driver information system provides important machine measurements, including KDPF status and data on AdBlue levels and fuel consumption. Messages from the ECO control system are displayed in real time during operation and on the exit screen when the ignition is turned off. The ECO control menu allows the operator to check operating logs and fuel consumption – these records are useful for reducing overall fuel consumption and can be saved and sorted by the operator.
Another innovation is the new Angle-Feedback-Joystick-Steering (AFJS), which gives the driver feedback on the steering angle already achieved at any time via the position of the steering lever, making it very intuitive to use. Eliminating the steering column helps
improve visibility of the work platform and space.
The programmable engine management system automatically switches the engine off when idling or lets the engine run to cool down after leaving the cab and then switches off automatically later.
Cleaning and maintenance are easier than ever. The radiator fan swings out and automatic reversing function as standard.
An electrically tilting hood provides full access to the engine compartment. Additional side doors allow quick and convenient access for daily checks and maintenance. Full rear fenders are standard and an indicator on the AdBlue filler cap minimises overfilling.
KOMTRAX telematics and the Komatsu Care customer maintenance programme provide first-class fleet management and support, protecting the machine from misuse and ensuring maximum efficiency and uptime.
“These two new models offer great performance, efficiency and operator comfort”
Interviewee: Abigail Scott
Role: Operations Manager
Company: Digger Delivery
Location: Bristol
Geographic reach: National
Fleet size: 50
Independent or exclusive: Independent
Major brands: Kubota, JCB, Bobcat, Hitachi, HAMM (Wirtgen Group)
Q
Can you tell us a little about the background and current circumstances of the company?
Digger Delivery was founded with a commitment to providing reliable, highquality equipment for projects of all scales with a fast turnaround.
We have grown steadily by focusing on a service-oriented approach, meeting
the needs of contractors, ensuring our equipment is maintained to the highest standards and delivered quickly. “Need a digger today? No problem.”
QWhich sectors do you predominantly supply?
We primarily serve construction, landscaping and infrastructure, delivering machines suited for diverse tasks ranging from excavation to ground preparation and material handling.
QWhat is the scope of your hire offer?
Our hire catalogue includes mini diggers, excavators (Up to 15 tonnes), dumpers (up to 9 tonnes), attachments, rollers, telehandlers and loaders.
We aim to provide a range of options that meet the varying needs of projects,
from residential landscaping to large construction sites.
QWhat is the geographical reach of Digger Delivery?
Digger Delivery operates nationally with major current projects in Liverpool, Rotherham, Oxford and of course all over the south-west. Our focus on flexible, quick delivery has helped us establish a solid client base and we are looking to reach additional regions in the coming years.
QWhat are your biggest product lines or machine types?
Our most popular hires are mini diggers, excavators and dumpers, which are essential across most projects.
QWhat is the average age or working life of your machines?
Machines are typically rotated out after reaching a designated number of working hours, factoring in their maintenance record and demand in the market.
Condition and relevance to industry standards also play a role in our decisions, ensuring we provide our customers with reliable and efficient equipment.
QWhat do you do with expired machines?
Once equipment reaches the end of its rental lifecycle, we assess it for resale potential. Machines still in good working condition are sold with a detailed maintenance history and a limited warranty, giving buyers confidence in their purchase.
QDo you have any preferred manufacturers or brands? What attracts you to these?
We favour manufacturers known for durability and performance, such as Hitachi. Our focus is on quality, low maintenance and strong aftermarket support, all of which enable us to maintain high availability and quick servicing.
QWhat is your service offering?
Our services include short and long-term hires, same-day delivery and an option for operators upon request. We emphasise flexibility and quick replacement in the case of malfunctions, prioritising uptime for our clients.
Q
How has the hire market been developing in relation to contractors’ needs?
The hire market has been expanding as contractors seek flexibility and avoid the upfront costs of ownership. We’re observing an increasing preference for hire solutions, driven by the need for cost efficiency and evolving project requirements.
Q
Do you have any expansion plans?
Looking forward, Digger Delivery aims to broaden its machine lineup to include more specialised equipment and to expand into additional regions to meet demand. We’re also exploring partnerships with more manufacturers to bring the latest technology and eco-friendly solutions to our customers.
In mid October, the UK government unveiled Invest 2035, a comprehensive industrial strategy designed to drive sustainable economic growth across key sectors, including advanced manufacturing and clean energy.
The CEA (Construction Equipment Association) acknowledges this initiative and the potential it brings. However, the construction equipment industry’s critical role within these sectors deserves greater attention.
Speaking of how the construction equipment sector aligns with these growth areas and the importance of integrating its contributions into the government’s vision for a resilient economy, Viki Bell, Director of Operations at the CEA, said: “We’re pleased to see the industrial strategy, which aligns with our calls in the CEA manifesto. However, it’s disappointing that the construction equipment sector hasn’t been more prominently recognised, given its natural fit within Advanced Manufacturing and Clean Energy [specified sectors within the strategy]. Our sector generates over £15bn in revenue, supports over 44,000 jobs, and invests heavily in R&D – £250m annually. We’re
playing a leading role in advancing clean energy within our sector with sustainable innovations such as battery storage and hydrogen fuel, which are essential to the transition to clean energy.
“The CEA looks forward to working with our government to ensure the sector’s role as a major contributor to the UK’s economic resilience is acknowledged. Our industry is ready to fully engage in the consultation process to highlight how we advance within these critical sectors.”
“It’s disappointing the construction equipment sector hasn’t been more prominently recognised”
You wanted a versatile electric jobsite solution to dig, load and carry, inside or outside. We’ve delivered a super quiet, zero emissions, no heat, plug and play solution allowing you to work in even the most restricted environments with ease.
Build your cleaner and greener business with us.
Following its European debut in the Netherlands earlier this year, SANY is thrilled to announce the sale of its first medium sized electric excavator in the UK.
The first 23-tonne electric excavator, the SY215E, has been sold to Explore Plant and Transport Solutions, one of the UK’s largest and most diverse suppliers of equipment and services to the construction industry.
Leigh Harris, Business Development Director for SANY UK said: “We are incredibly proud to introduce SANY’s first 23-tonne electric excavator, the SY215E to the UK market, which highlights the growing demand for eco-friendly heavy machinery in our construction industry.
“Explore Plant and Transport Solutions is also the perfect partner for
this venture as like SANY they continue to invest in greener and more sustainable plant solutions to help their clients reduce their emissions and work towards zero carbon sites.”
As a global leader in construction engineering, SANY is dedicated to delivering high-quality, sustainable and emission reduction initiatives, introducing over 40 new electric products globally in 2023 and remains committed to supporting the energy transition in Europe.
With an operating weight of 23,200 kg, the SY215E boasts a rated power of 150 kW, always ensuring peak performance. It has a maximum digging height of 9,600 mm, a maximum digging depth of 6,255 mm and is available with a range of tracks from 600 mm to 800
“We are incredibly proud to introduce SANY’s first 23-tonne electric excavator, the SY215E to the UK market”
mm. In addition, the efficient and smooth Kawasaki main pump and valve block provides the precision electro-hydraulic controls to really maximise productivity.
The SANY SY215E has been tailored specifically for the European market, featuring the latest generation cab including a large 10" HD touchscreen, LED lighting, improved air suspension seat, enhanced air ventilation, intelligent fault self-diagnosis and a low noise working environment, all designed specifically with the operator in mind. This pure electric machine offers costsaving, convenient operation, excellent performance and numerous safety features.
With a rated battery capacity of 422 kWh, the SY215E has a battery life of six to eight hours. With the CCS2
charging option achieving a full charge in just 90 minutes, a full day’s work can be easily achieved.
Warren Wilkinson, Operations Director of Explore Plant and Transport Solutions said: “We are excited to be able to bring SANY’s first 23-tonne electric excavator to the UK market, I believe this latest addition to the Explore Plant and Transport fleet demonstrates our ambition and continued investment into the latest innovations and sustainable products across our plant and transport fleet.
“We want to ensure that our clients have access to the most efficient and sustainable products in the marketplace to reduce emissions across the industry. It has been a pleasure to work with the team at SANY and we are looking forward to putting this
machine out to work in the coming weeks.”
Explore Plant and Transport Solutions took delivery of the SANY SY215E this month. With more than 30 years’ experience and an extensive network of offices and depots across the UK, Explore Plant and Transport Solutions has built an excellent reputation as one of largest and most diverse suppliers of choice.
Fleetm@tic®, Bell Equipment’s South African-developed telematics solution, collects stores and communicates information in three key areas: machine productivity; machine utilisation; and machine condition: to enable fleet operators to maximise the value of their assets and the efficiency of their operations. Bell Equipment Product Manager, Brad Castle, explains.
Fleetm@tic is a purpose-designed telematics system for Bell Equipment machines that enables mining and construction operators to get the very best value from their assets. “By using Fleetm@tic to take ownership of the entire operational fleet on a mining or construction site, machine owners can keep projects on schedule, maintain machine health, reduce downtime and running costs, all while maximising productivity,” says Bell Equipment’s Brad Castle.
He says that today’s earthmoving industry faces the challenge of improving efficiency: doing more with less. Information is critical to meet this challenge and Bell has harnessed technology to be able to offer customers the right information at the right time, helping them to manage their fleets with
greater than ever precision and efficiency.
“Fleetm@tic is designed to be the eyes on the worksite, keeping track of every Bell machine in operation on a continuous basis – a fleet management partner that never sleeps.
“The cornerstone of our company is to provide lowest cost per tonne equipment solutions to our customers. Fleetm@tic adds this exciting dimension, enabling operators to maximise their return-oninvestment,” he says.
The appeal is that it is simple to use. Working machines can be watched via the Fleetm@tic website or WebApp from the comfort of a home or office, or even while travelling abroad. A confidential login and password is used for secure access, and automated reports are emailed to authorised managers on a daily, weekly or monthly basis, depending on the need.
“This keeps Bell Equipment owners in touch with their machines at all times. Accurate, up-to-date operational data, production data, fault data as well as the machine’s location and movements are all presented via user-friendly interfaces,” Castle assures.
Remote monitoring of Bell machines includes vital details such as fuel consumption, when and where a machine
is operating, vehicle speed, all aspects of machine health, driver access and much more. From a reliability perspective, not only is the machine being continuously monitored, but the embedded service indicator ensures that the closest Bell Customer Care Centre automatically receives notice that a service on a specific machine is due, thus avoiding machines running over their service hours.
The system is satellite based, driven by a series of satellites with worldwide coverage. Production, machine and precise location data is gathered and stored, then sent via a machine-mounted satellite modem to the Bell server. From there the raw data is analysed and compiled into reports that make it easy for users to access and understand.
A selection of reports are available for each machine, ranging from shift, daily, weekly or monthly, and including loading and event reports, amongst others. These can all be customised and the automated system will ensure that they are delivered promptly, providing detailed information that is always in time.
Fleetm@tic also includes a Driver ID Access feature that enables productivity and the driving style of each specific driver to be tracked, building up a use
history of how the machine is driven and used. This ensures that drivers take responsibility for the machine during their shift, while also highlighting training needs and productivity enhancement opportunities.
A significant differentiating feature of Bell’s Fleetm@tic system is onboard weighing, which has been a standard feature on all Bell ADTs for more than a decade. “With ongoing development to fine tune accuracy and reliability, our onboard weighing can now highlight exactly how much useful work a machine is doing and how much money it is earning,” adds Jones.
GPS tracking enables site machines to be configured for specific applications requiring extensive control. Sites can be segmented on Fleetm@tic, with vehicles made aware of their current location. Speed limits can be activated based on the vehicle’s current position, which ensures that the machine is driven at a safe and
legal speed in specific areas. A warning and limp mode will also be automatically activated should the vehicle leave a predefined geofenced area.
Fleetm@tic software is integrated into the CANBUS system of each machine, which collects vital information from the machine’s data receptors. GPS location and machine operational information from the CANBUS is stored in an onboard memory module ready for transmission.
Communication is key. A state-ofthe-art GPS antenna works in collaboration with a satellite modem and GPRS modem receiver to deliver repeatable high quality information. The satellite communication capability provides true worldwide coverage while the global SIM card allows large amounts of data to be communicated over cellphone networks around the world when the machine is within range – via one service provider that delivers worldwide coverage.
“Ongoing developments to fine tune accuracy and reliability now enable our onboard weighing to calculate exactly how much money each machine is earning. This, along with idle and unladen time tracking and shift summary reports offers managers insight into how to optimise daily production schedules, while offering a very clear perspective of operational costs,” Brad Castle points out.
Bell offers three Fleetm@tic packages, depending on the
preferred level of fleet management required: daily, per shift, per cycle, or even per minute with the premium package.
The Basic Package is available on all Bell-supplied machines and provides machine hours worked per shift, average fuel burn and a productivity report.
The Classic Package is standard on all new ADTs for two years from the date of delivery to customers. Thereafter it can be renewed at an additional charge. It supplies enough information to give a thorough understanding of how the machine is operating, measuring shift productivity, shift fuel burn, shift fault codes and numerous other metrics.
The Premium Package is available as an upgrade at any time. Geared for customers who need detailed operational information, this package offers similar information to the Classic package but for each individual laden-unladen cycle. Live tracking is also available on the Fleetm@tic website on a per minute basis. This function is used by some customers in their site control rooms to continuously track and manage their fleet operations.
“Fleetm@tic is a definitive management tool that adds real value to mining and earth moving operations. It can be customised to suit the needs of fleets of any size and to ensure that machines are used effectively and safely, that their asset value and operational life is maximised,” Brad Castle concludes.
Written by Peter Middleton and published courtesy of MechChem Africa magazine.
Peter Fitzpatrick Ltd, a family-owned quarrying and contracting company based in County Down, Northern Ireland, has been a key player in the quarry and asphalt industry for over fifty years. From its modest beginnings in the early 20th century, the company has grown into a dynamic business serving a broad customer base across various sectors.
Recently, Peter Fitzpatrick Ltd collaborated and invested with CDE to implement a cutting-edge wash plant to address the growing issue of excess crushed rock fines (CRF) and blinding from its greywacke processing operations.
Peter Fitzpatrick Ltd has historically faced challenges managing the byproducts of its quarrying operations. The primary issue was the accumulation of excess CRF and blinding material, which had been stockpiled with a view to future processing. As natural sand reserves become increasingly scarce, the need to efficiently process and repurpose these
by-products became more pressing. The excess material not only took up valuable space within the quarry but also posed environmental and operational challenges.
Additionally, the company recognised an opportunity to transform this byproduct into a saleable manufactured sand, which could alleviate some of the pressure on natural sand resources.
Paul Fitzpatrick, Managing Director at Peter Fitzpatrick Ltd highlighted the specific problems: “The fine dust, 4-mm material, which we didn’t have enough of an output of, in terms of what we had in the quarry, was becoming an issue. It started to take up a huge footprint within the quarry and we wanted a solution for dealing with that by-product. One of the more obvious things we were looking to address was how to turn it into sand.”
CDE proposed a comprehensive solution to address the challenges faced by Peter Fitzpatrick Ltd. The 130-tph solution centred around the installation
of a new washing plant that included the M2500 modular washing plant, the EvoWashTM sand washing system, and the AquaCycleTM thickener. This combination of equipment was designed to process the excess CRF and blinding material, transforming it into high-quality manufactured sand and other aggregates.
The M2500 mobile washing plant integrates feeding, screening, sand washing and stockpiling on a single chassis. The EvoWash system, specifically designed to remove the unwanted fines from the material, produces a consistent and high-quality sand product. The AquaCycle thickener recycles up to 90% of the water used in the washing process, significantly reducing the need for fresh water and minimising the environmental impact.
The team at Peter Fitzpatrick Ltd was invited to local sites that were already reaping the benefits of CDE technology to see the equipment in operation.
Paul Fitzpatrick commented: “It was impressive to see the CDE equipment. There is always a worry that the plant we are visiting is not the same as our plant, but seeing the material being processed gives you a lot of confidence. We had a conversation with Brendan Campbell, of Campbell Contracts, and were encouraged by what he had to say about their plant, the installation and his positive relationship with CDE.”
The implementation process involved detailed discussions and collaboration between CDE’s sales team and technical engineers and the team at Peter Fitzpatrick Ltd. They meticulously planned the design and location of the plant, considering factors such as power generation, water servicing, and the construction of silt ponds. The plant was strategically located to minimise civil engineering requirements and optimise operational efficiency.
The new CDE washing plant has delivered impressive results for Peter Fitzpatrick Ltd. By processing the excess CRF and blinding material, the plant was able to produce a consistent and high-quality sand product. This not only addresses the issue of stockpiled material and contributes to the conservation of natural sand reserves but has also created a valuable new revenue stream for the company.
Paul Fitzpatrick commented on the positive impact of the plant: “We now have a consistent sand product that we can provide to customers. We now have a product rather than the quarry dust coming from our crushing plant and being stockpiled with no prospect of getting to customers. We believe we have
a product that has promising sales value or can be used internally.”
The plant’s capacity to handle up to 100,000 tonnes of dust and another 100,000 tonnes of secondary blinding material per year has significantly reduced the footprint of stockpiled material within the quarry. This has not only freed up valuable space but also improved the overall efficiency and sustainability of the quarrying operations.
Moreover, the quality of the manufactured sand has attracted new customers, further expanding the company’s market reach. The integration of the new plant has also enhanced the company’s ability to meet the demands of its asphalt plant ensuring a steady supply of high-quality materials.
The strategic planning, innovative technology and effective implementation of the CDE solution has enabled Peter Fitzpatrick Ltd to optimise its quarrying operations and enhance the company’s
product offerings. The results speak for themselves, with significant reductions in stockpiled material, improved operational efficiency, and the creation of a new revenue stream through the sale of manufactured sand.
Des Crawford, Business Development Manager at CDE commented: “As Peter Fitzpatrick Ltd continues to build on the legacy of the company’s founders, this successful project exemplifies their commitment to innovation, sustainability, and excellence in the quarrying and contracting industry. The new CDE washing plant not only addresses current challenges but also positions the company for future growth and success in an increasingly competitive market.
“It is always rewarding to work with a company that shares our values of creating our best world, one tonne at a time, and we look forward to a long and fruitful relationship with the team at Peter Fitzpatrick Ltd.”
Specialist environmental construction, groundworks and landscaping
contractor WL Straughan & Son has added a very individual HD Hyundai 14-tonne excavator to its growing fleet. The machine, which boasts a full width painting by Mr Mural across its counterweight, is also the first excavator to be supplied to the company with a Rototilt tiltrotator.
The firm, based in Bedlington, Northumberland, specialises in environmental projects, constructing tracks and paths, creating wildlife habitats and conservation works, alongside groundworks, civils projects and operated plant hire. Based on a farm, the familyrun business also operates a green waste recycling company and an equestrian arena and livery stables.
WL Straughan has more than 25 excavators, from sub 1-tonne micros, through to a 15-tonne HX145A. The company also operates backhoe loaders, wheeled and tracked dumpers, dump trailers and a wide range of agricultural tractors and compact equipment. It even has a motorgrader, for forestry and windfarm access work. Half of the firm’s excavators are now HD Hyundai machines, supplied by local dealer Taylor & Braithwaite.
“We started buying Hyundais in 2014 and we’ve been changing three or four machines a year since then,” said Director Gary Miller.
“We’ve tried them all, but we always come back to Hyundai as one of our preferred brands. The service from Taylor & Braithwaite is second to none and
we’ve just never had any issues with the machines.”
Straughan undertakes a lot of work for the National Trust and the Wildlife Trust, but the company also works as a framework contractor for Scottish Power on wind farm construction and for Forestry England, where it is also a preferred contractor. To cope with these varied specialist contracts, the business operates its excavators with a wide range of attachments. This includes mulching heads, selector grabs, tree shears and flail mowers.
The HX140A L has been supplied with a Miller quick coupler, to cope with regular changes of attachment. However, this can be removed and replaced with a Rototilt attachment, supplied by local dealer Stephen Pigg. To cope with the
“There is no exact plan for the shape of the islands, John is just very creative and knows what’s needed,” said Mr Miller.
The new HX140A L, like all of the company’s equipment, is equipped with bio-oils, to prevent any concerns in the event of spillage on sensitive soils. Straughan also specifies a brightly painted boxing ring of upper-structure handrails, additional piping to power those attachments, additional work lights, flat beacons and 750-mm track pads. Mr Reed maintains the excavator in immaculate condition, even removing his work boots before entering the cab.
additional weight of the tiltrotator, Straughan has specified the shorter 2.5-m dipper arm on the machine, in place of the more commonly specified 3-m arm.
“It’s taking a bit of getting used to,” said operator John Reed. “But once you get the hang of it, it’s really good. You don’t have to relocate the machine as much, which really speeds things up on site.”
The tiltrotator also helps when creating landscaping features. The HD Hyundai machine is currently working near a giant rock and soil sculpture called Northumberlandia, Lady of the North. Working on a former opencast mine reclamation contract, the excavator is creating wetland ponds and islands within new lakes, for birds and other wildlife to settle.
“We normally change our equipment around at about 2,500 hours. John gets the latest excavators and then his older machines get handed down to other parts of the company, like the green recycling operation, for up to five years,” said Mr Miller.
As a specialist contractor working for such a variety of prestigious customers, WL Straughan has worked as far afield as Peterborough and Newquay, though the majority of its operations are in the northeast and Cumbria.
It is doubtful that all of the company’s new machinery will have such a distinctive appearance, but there seems little doubt that any additional excavators will be wearing an HD Hyundai logo and they will be supplied by Taylor & Braithwaite.
“Once you get the hang of it, it’s really good. You don’t have to relocate the machine as much, which really speeds things up on site”
Doosan Bobcat has announced that its vertically integrated subsidiary, Mottrol, which specialises in hydraulic components, is expected to relaunch as Doosan Mottrol.
Mottrol produces travel and swing motors, pumps, main control valves and other hydraulic components for construction equipment. In response to equipment electrification, Mottrol has also been developing E-Drive, a technology for inverters, and swing and travel devices that can electrically drive and control machines.
Doosan Bobcat stated on 15 October that its executives, including CEO and Vice Chairman Scott Park, visited Mottrol’s headquarters in Changwon, Gyeongsangnam-do, South Korea. This marked Doosan Bobcat management’s first official visit since it completed the acquisition of Mottrol on 4 October.
The executives toured the production plant in Changwon. Scott Park announced the new beginning at a town hall meeting attended by some 200 blue and white collar employees by declaring Mottrol’s name change to Doosan Mottrol.
At the town hall Park stated: “I am truly delighted and proud to welcome the employees of Doosan Mottrol to the Doosan Bobcat family, whose world-class quality has been well proven through many years of partnership. We aim to double Doosan Mottrol’s sales in the next five years by achieving win-win results and creating synergy.”
Doosan Bobcat acquired Doosan Mottrol to assure a stable supply of core components and enhance product
competitiveness through vertical integration. Doosan Mottrol expects to grow from product and regional diversification as it seeks to expand its target market from large construction equipment to medium and small construction, agriculture and logistics equipment.
Youngmin Kwon, President of Doosan Mottrol, remarked: “We are happy to take the first step towards becoming a global leading company alongside Doosan Bobcat. We will strive to improve quality standards further and accelerate the development of new products.”
Doosan Mottrol will continue independent management as a separate entity while seeking synergies for external expansion as a subsidiary of Doosan Bobcat, such as securing growth momentum as a global player.
“We aim to double Doosan Mottrol’s sales in the next five years by achieving winwin results and creating synergy”
Komatsu has announced a significant step forward in its commitment to sustainable mining, together with Boliden, a leading global mining and metals company with a strong focus on sustainable production. At MINExpo, Komatsu unveiled its all-new Power Agnostic 930E haul truck, built on Komatsu’s modular power-agnostic platform, this new generation truck allows customers to future-proof their operations with a versatile approach to decarbonisation.
Thanks to this modular poweragnostic platform, customers are able to start with conventional diesel engines and gradually transition to cleaner energy sources as needed. Whether adopting battery technology, hydrogen fuel cell technology or a combination of energy systems, the Power Agnostic 930E provides the infrastructure and adaptability necessary to meet evolving sustainability goals.
Following the exhibition, this preproduction haulage truck will make its way to Boliden´s Aitik mine – Europe’s largest and one of the world´s most productive open-pit copper mines. This marks a milestone moment as the truck will become the first of its kind to undergo field testing in production at a customer´s mine site including the ambition of conversion to battery technology.
This one-year field trial will take place within the Komatsu Greenhouse Gas (GHG) Alliance framework, where Boliden will work closely with Komatsu to gather first-hand insights and feedback
based on real-world applications. This collaboration will contribute to the advancement of Komatsu´s power-agnostic truck concept.
“We are excited to continue our partnership with Boliden in their Aitik mine, where the Power Agnostic 930E truck, showcased at MINExpo, will soon start the first field trials in a customer mine site,” says Jeroen De Roeck, Senior Manager Mining for Komatsu Europe.
“This milestone not only represents a major step forward in our decarbonisation strategy but also exemplifies our commitment to support our customers in achieving their sustainability goals. Together with Boliden, we are paving the way for a more responsible mining industry.”
As one of the founding members of the GHG Alliance, Boliden has
consistently demonstrated its commitment to ambitious carbon reduction goals within the mining industry.
In 2023, Boliden became the first company in Europe to implement Komatsu Frontrunner, an Autonomous Hauling System, on 17 haul trucks at the Aitik mine. This initiative aimed to optimise productivity and asset utilisation to meet increased transportation demands while maintaining world-leading cost competitiveness.
As the demand for essential minerals continues to grow, mining companies face increasing pressure to deliver these crucial resources productively and responsibly.
Komatsu is focused on supporting mining operations in meeting these challenges through innovative solutions that prioritise both productivity and climate performance.
The German construction company Kann GmbH Baustoffwerke required a customised hydraulic excavator to extract gravel from deep underwater deposits. Komatsu’s PC700LC-11E0, equipped with a long boom and 3D Machine Guidance was the ideal solution. The excavator has significantly increased productivity and safety at the Kann site, surpassing its target production of 1,000 tonnes of gravel per shift.
The production of concrete products is the core business of Kann GmbH Baustoffwerke, a family business founded in 1927 with 18 locations throughout Germany. The company obtains some of the raw materials it processes itself, while 50% of the raw materials obtained are sold externally. Around 500,000 tonnes of raw gravel are extracted annually at its site in Mülheim-Kärlich.
The most recent challenge at this site was the replacement of the over 40-yearold scraper bucket.
The special nature of the excavation area, with gravel deposits up to 12 metres below the water surface, places high
demands on the successor machine, which is to handle both the excavation and loading of the raw gravel. In the end, Komatsu sales partner BRR Baumaschinen Rhein-Ruhr was able to offer a customised PC700LC-11E0 hydraulic excavator that was ideally suited to the application.
The basic machine, including the lifting cylinders from the Komatsu factory in England, provides the necessary stability and lifting power. The steel construction of the boom and arm was customised by a third-party supplier so that the required length can be achieved when digging to reach the deep gravel below the waterline. The excavator also has a hydraulic ditching bucket and is equipped with GPS and Smart Construction 3D Machine Guidance. Due to the underwater use, BRR’s subsidiary AP Deutschland installed a special solution to protect the sensors and connections.
“The bucket’s movement options save us a lot of time, as we don’t have to constantly move the excavator and it can
work from the same spot. This is currently only necessary about once per shift,” says Technical Manager Frank Hergenroether. “Another advantage of the excavator is that it is still very mobile despite its size. This is not only a relevant aspect in this gravel pit, but also for the future, when the machine changes the extraction area, as the areas are becoming ever smaller and more urbanised,” Hergenroether continues.
Increasing urbanisation is both a trend and a challenge that runs through the entire construction industry. However, examples like this show that it is possible to grow and find future-orientated solutions.
The Komatsu PC700LC-11E0, which has been in operation at Kann since April 2024, is expected to produce 250,000 tonnes per year.
“The decisive factor in our decision to purchase the Komatsu hydraulic excavator was that, despite its length, the boom does not rest on the chassis to achieve the required depth, does not dig up the ground itself and can also maintain a
safe distance from the bank. In addition, BRR was a competent partner right from the start, understanding and realising our requirements,” explains Frank Hergenroether.
Machine operator René Münch sees further advantages: “The lifting power speaks for itself. In addition, the comfort during operation is impressive thanks to the superior cab suspension and low noise level. Overall, the machine is very clear, tidy and intuitive to operate. Within a very short time, all machine operators were trained to work safely on the excavator and were ready for action,” summarises Münch. “The length of the arm and how quickly we were able to achieve the required performance was
surprising. The target of being able to extract at least 1,000 tonnes of gravel per shift has already been exceeded,” says the machine operator.
“This is also thanks to the detailed on-site instruction and training provided by BRR and Komatsu on delivery,” adds plant manager Andreas Müller. “The increasing performance curve of the employees with the new PC700LC-11E0 is clearly visible.”
To summarise, a unique special construction project was implemented in partnership. The result is a machine that offers increased safety during operation thanks to its ability to keep its distance from the bank, while still being extremely efficient by reaching the required depth.
“The target of being able to extract at least 1,000 tonnes of gravel per shift has already been exceeded”
Not too long ago, excavators were simply digging machines. Today, these iron giants are evolving into multifunctional tools; whether large or small, construction machines are becoming the Swiss Army knives of the building site. They transition from crushing to screening, handling to loading with ease, all with just a change of attachment. By fitting an MB Crusher attachment to their arm, they can swiftly switch between tasks, making the construction site of the future a presentday reality.
A future without waste
On the construction site of the future, the concept of waste will be obsolete. Every scrap material will be recovered and
reused either on-site or in other projects – nothing will go to waste. MB Crusher units turn waste into valuable resources, eliminating the need for material transportation and reducing the necessity to purchase new materials.
The future site is one of pure efficiency, where every action is optimised, and every resource is used to its fullest potential. MB Crusher accessories streamline the recycling process, making resource reuse an integral, automated part of daily operations. With MB Crusher, every site becomes more efficient with less waste and faster operation.
A future with lower costs
In the future construction site, both costs and project times will be more
than halved. MB Crusher’s equipment installed on a heavy machine allows multiple tasks to be managed easily while saving on maintenance and management costs. Projects thus become more affordable, and the initial investment is reduced.
The future site is also safer, as the operator remains inside the excavator’s cab, effortlessly controlling the MB Crusher attachment. A quick-coupling change system allows for smooth transitions between tasks, enhancing both safety and efficiency.
And that’s not all – soon, we may see construction sites operated remotely, with operators monitoring and controlling machines from distant control centres.
Imagine the future – but start using it today
Some only imagine the future, while others are already living it – such as Roberto Mauro’s Italian company, which has integrated three MB Crusher attachments into its fleet to use on an eight-bucket, the MB-G600 sorting grapple and the MB-S10 screening bucket. This combo has enabled them to tackle a variety of jobs, from beach cleaning and coastal reclamation to waterpipes and road works, as well as demolition and construction.
Thanks to the versatility of MB Crusher equipment, the company has significantly reduced processing times and slashed operational costs. “I bring the machine to the site,” says Roberto, “and
with the quick coupling system, I mount the MB Crusher attachments in no time, and I’m ready to work.”
The future is now
The construction site of tomorrow isn’t a dream – it’s happening today. MB Crusher is leading the way with cuttingedge equipment that supercharges productivity, slashes costs, and reduces environmental impact. This isn’t about imagining the future; MB Crusher is already shaping it, one job site at a time.
“We may see construction sites operated remotely, with operators monitoring and controlling machines from distant control centres”
It was a night to remember for Lincolnshire crusher and screener manufacturer Red Rhino, after the team took home the Family Business of the Year award at the glittering Midlands Family Business Awards on 3 October.
The coveted annual ceremony shines a light on family businesses of all sizes from across a range of sectors, providing them with the opportunity to be recognised for their significant contribution to the region’s economy and its local communities.
Over fifty businesses were shortlisted across nine categories – including Sustainability, Property and Construction Excellence, Digital and Tech Innovation and Family Business of the Year.
Following a rigorous judging process, Red Rhino was named as the winner of the Family Business of the Year category. The judges recognised the team’s drive, passion and ability to embrace innovation, as well as its ongoing commitment to demonstrate excellence in business performance while fostering a culture of integrity, resilience and long-term vision.
The business is situated in Grantham and was acquired in 2009 by Winfield Engineering – a family owned and managed business with over 50 years of specialist engineering experience in the supply of agricultural and commercial fabrications.
Red Rhino’s product range includes crushers and screeners suited to small-scale construction and demolition projects, as
well as larger remote controlled crushers and screeners with the ability to crush and organise material such as concrete, brick and other building waste into reusable material.
The business, which manufactures its products in the UK, has enjoyed significant growth over recent years and continues to attract new customers in every corner of the globe – from the USA to central Europe.
For company director Laura Winfield it was a special occasion for the whole team and testament to the positive influence that family businesses have on the national economy: “This award means so much to us. It’s not just special for the Winfield family, it’s special for the entire Red Rhino team who make what we do so rewarding every single day.
“We pride ourselves on our
commitment to employing locally to transform the lives of people in our community. Everyone who walks through our doors – be they employees, customers or partners – are thought of as an extension of our family and I think it’s these embedded family values that allow us to think outside of the box, innovate and form long-lasting partnerships with organisations around the world.
“It is really encouraging to see the difference that family businesses make on a local and national level. Family businesses are the backbone of the economy and seeing so many in attendance fills me with immense pride. I would like to say a heartfelt thank you to everyone who has supported and believed in us, as well as a big congratulations to all of this year’s finalists and winners.”
THE DEMOLITION, ASBESTOS,
FOOTBALL, BOXING, TRAVEL, GENERAL KNOWLEDGE, SCIENCE, WRESTLING,
CONSPIRACY THEORIES, LITERATURE,
#01 Get Involved... The PowerPlant Podcast
Scottish articulated hauler manufacturer
Rokbak has partnered with Terapro Construction, a well-established equipment dealer, to distribute its trucks across Eastern Canada.
With 18 branches throughout the region, Terapro will cover the entire province of Quebec and parts of Ontario, focusing on providing Rokbak articulated haulers to construction contractors and general construction sites.
Terapro will offer both the RA30 and RA40 models of Rokbak ADTs. Terapro received its first RA30 in August 2024 and is expected to receive the RA40 by the end of October. Terapro aims to fully integrate Rokbak haulers into its offerings by early 2025, with a structured plan to promote and grow the brand’s market presence in the region.
“We are delighted to join forces with Rokbak,” says Terapro President Daniel Riendeau. “ This distribution agreement is a testament to our shared commitment
to excellence. By leveraging our combined expertise, we will drive transformative change and deliver cutting-edge solutions to our clients. We are confident that this alliance will pave the way for a brighter, more successful future.”
Rokbak articulated haulers are known for being robust, reliable, easy to operate and easy to maintain. The 38-tonne RA40 is designed to make light work of large-scale quarry, mine and construction jobs. The 28-tonne RA30 is made for the toughest jobs and roughest sites, from quarries and infrastructure developments to commercial construction projects. Both models offer high capacity and performance, delivering cost-effective productivity in the toughest conditions. Terapro, already a dealer for construction equipment such as loaders and excavators, sees the addition of Rokbak haulers as a complementary
expansion of its product line. It will enable the dealer to offer a complete package to its customers having not had an articulated hauler in its portfolio before. North America is Rokbak’s largest market, both geographically and financially, and Rokbak looks to work with dealers who are perfectly placed to understand the needs of customers.
Terapro has already showcased the RA30 at two key construction and forestry expos in Quebec – Expo Pelle and Demo International – where the hauler attracted considerable attention.
“The name and the look of the hauler turned a few heads,” says Steve Lalonde, Vice-President of Business Development at Terapro. “We expect to see these Rokbak trucks with general contractors, which is our focus area. We believe having these products in our portfolio is going to help us retain key customers and add new ones.”
An exciting partnership Terapro positions itself as more than a supplier. A dedicated team of experts is committed to sharing knowledge to help customers in Eastern Canada maximise their operational profitability. With a high level of professionalism and multiple branches throughout the region, Terapro offers customised, high-quality services designed to meet the specific needs of each customer.
“Rokbak wants to work with dealers who share our goals and who want to build constructive partnerships,” says Gregory Gerbus, Rokbak Regional Sales Manager. “Terapro certainly fits that remit. Rokbak has always been a face-toface company, and Terapro will help make even more customers in Canada aware of who we are and what exactly we can provide them.”
Rokbak provided comprehensive sales and technical training for the Terapro team, with ongoing support facilitated by a Rokbak service manager based in nearby Ottawa, ensuring local expertise and availability.
Terapro’s strong service reputation and dedication to supporting its customers will now be extended to the Rokbak brand, ensuring a seamless and highquality service experience in applications across east Canada. The partnership marks an exciting step for both Terapro and Rokbak in the competitive Canadian market for construction equipment.
In 2021, Easton Sales and Rentals became the first company to take delivery of a Rokbak truck. Fast forward three years and the US dealer is still enjoying its partnership with the Scottish articulated hauler manufacturer, calling it “one of the best decisions we’ve ever made”.
Houston, Texas, has been the focal point for some of the world’s most significant space launches. In 2021, it was the site of another significant launch, only this time earthbound – the introduction of the very first Rokbak articulated hauler.
After the Rokbak brand was officially unveiled in September 2021, a pair of RA30 ADTs were the first to be dispatched from the factory in Motherwell, Scotland, and sent to Houston-based heavy equipment specialist, Easton Sales and Rentals, marking the beginning of the Rokbak journey into the public arena.
The sand-coloured RA30 trucks arrived at the Easton depot and made an immediate impression.
“When they first hit the yard, everybody liked them,” reflects Jeff Udelson, Managing Principal of Easton Sales and Rentals. “Not one person had a bad thing to say about them. It’s such a good looking truck and the new colours really stood out. We knew we were onto a good thing. Today, Rokbak haulers are some of the most productive and competitive trucks on the market and we’re proud to say, ‘we got there first’!”
Easton Sales and Rentals is a key Rokbak dealer in North America. The US and Canada make up the biggest ADT market in the world and account for around 60% of Rokbak’s sales.
The company got off to a great start in the region, with Easton’s first RA30s immediately provided on a three-year lease to Texas-based Linco Construction, to help with earthworks, underground utility and clearing work
on the company’s projects. After the leasing agreement expired, Easton added the trucks back into its own rental fleet where they continue to deliver productive performance.
“We now rent out the trucks for big, high-profile dirt jobs,” says Jeff. “In Houston, these are typically excavation areas for detentions basins, tilt-wall construction and distribution centres.”
The RA30 articulated hauler is ideal for these types of applications in the tough Texas heat. The 28-tonne unit offers a heaped capacity of 17.5m 3 and is powered by a Scania DC9 engine, producing 276 kW and 1,880 Nm of torque at 1,400 RPM. Its fuel-efficient engine is emissions compliant and meets all North American T4F engine requirements. It’s also got a spacious, ROPS/FOPS compliant, pressurised cab with excellent HVAC for better operator comfort.
Reliable Rokbak relationship
Since taking on the dealership for the
Rokbak brand, Easton has continued to enjoy success. In 2023, during the CONEXPO event, the company was named Rokbak’s North American Dealer of the Year 2022, highlighting the team’s commitment to providing top-of-theline, heavy equipment solutions and exceptional customer service.
“From day one, we’ve felt the benefit of working with Rokbak,” Jeff reflects. “We knew we were investing in a brand that shared our values of quality, innovation and customer satisfaction. Looking back, it’s been one of the best decisions we’ve made.”
In the time since those first two RA30s made their way across the Atlantic, market awareness for Rokbak has significantly increased over the past several years. Trucks can be found in applications all over North America – from California to Canada and Tennessee to Texas.
“We’re proud that Easton Sales and Rentals acquired the first Rokbak trucks and have helped the brand develop such a strong reputation. We have a productive and reciprocal relationship, which we believe will sustain us long into the future,” says Daniel Meara, Regional Sales Manager for Rokbak in North America.
“We’re continuing to cultivate long-standing dealer partners in North America, and Easton’s enthusiasm for the brand and the product has been integral to establishing Rokbak as the industry benchmark for performance, power and reliability in this important market.”
“We knew we were investing in a brand that shared our values of quality, innovation and customer satisfaction”
World Mental Health Day always brings a focus on what more could or should be done to support our industry’s workforce. Greater awareness of some of the issues can only be a positive thing, but for the Lighthouse Charity, our work to improve the wellbeing of our construction community is continuous; every hour, every day, every month.
We are consistently advocating for a positive mental health culture, but the past few years have presented the industry with a number of external challenges. Whilst we anticipated the far reaching and ongoing financial effects of Covid, the enduring impact on our mental wellbeing has proven to be just as challenging. The pandemic affected us with changing roles, altered working practices and increased lone working, spotlighting the nation’s emotional wellbeing. Coupled with the inherent challenges of working in construction,
we’re confronted with numerous issues demanding attention.
So far this year we’ve seen a 33% increase in people contacting us for support. I see this as positive as it indicates that people feel less stigmatised and more able to reach out for the support they need; be that through our helpline, live web chat or text support service. Each person has a ‘presenting problem’ but things are never black and white. We know that poor mental wellbeing goes hand in hand with the vast majority of calls for help we receive and what can start out as a simple issue can quickly spiral out of control and seem insurmountable.
As well as continually reviewing our charitable services, one of the keys to improving our industry’s wellbeing is to have Mental Health First Aiders in the workplace who are trained to spot the early signs and symptoms of someone who may be struggling. With over 15,000 MHFAiders in our industry, the message of support can be amplified and simply starting a supportive conversation can have a life changing and a lifesaving impact.
But this is not a tick box exercise and having the right people in place and then ensuring they get the support they need is paramount.
Volunteers should be exactly that, not individuals nominated purely on their seniority in an organisation. A good mental health first aider is someone who
already demonstrates that they are a nonjudgemental listener who can empathise with others and offer hope and support.
Our MHFAiders deal with extremely sensitive information on a regular basis and bear the emotional weight of our workforce. So, the next critical element is to ensure that they too can access the professional support they need.
Our charity has always been at the forefront of providing expert proactive and reactive charitable services and this is no exception. We offer a unique programme of support for the industry’s MHFAiders that incorporates access to peer support networks, new resources and empowers people with the skills to monitor their own wellbeing. This programme of support has been developed through feedback from MHFAiders who have first-hand experience of the many challenges our workforce face.
Our peer support sessions are facilitated by a mental health professional and offer people the opportunity to share their experiences with other MHFAiders and receive encouragement in their role. It also offers updates on new referral pathways and resources so that they can signpost effectively.
If you or anyone you know is struggling, reach out for 24/7 free & confidential support. 24/7 helpline 0345 605 1956; Text HARDHAT to 85258; Live chat www.lighthouseclub.org.
We have the largest central stockholding in the UK, which is supported by a finely tuned stock control program, a highly organised warehousing system and carefully selected logistics partners. This allows Astrak to have the undercarriage parts that you need available when you need them, minimising machine downtime.
Once it’s on the machine, our extended warranty is the most comprehensive in the market place. Each of our rubber tracks come with an extended 24 month warranty as standard.
All of our undercarriage and wear parts are manufactured in IS0 9001 and OEM approved production facilities with rigorous quality control procedures.
Place your order prior to 4.30pm and it will be despatched for delivery on the next working day.
Our wide range of heavy-duty components will keep your excavators, dozers and tracked machinery working harder, for longer. Every hour of machine downtime incurs avoidable costs! This is why you need a reliable partner you can rely on. Stocking the widest range from bucket teeth, cutting edges and OEM quality undercarriage components through to custom made wear parts. Astrak providing you complete undercarriage and wear part solutions. The right part, to the right place, at the right time!
Hitachi Construction Machinery (Europe) NV has introduced a new all-in-one fleet management system –CONNECT – which is designed to empower its authorised dealer network and customers by streamlining their operations.
The CONNECT system will transform fleet management with instant access to performance data on Hitachi construction machinery and other brands of equipment, custom reporting tools focusing on key metrics, smart geofencing for precise productivity tracking, and convenient access from tablets and smartphones.
This latest development highlights the manufacturer’s commitment to helping customers overcome the challenges they face. “We understand that our customers require smart and efficient solutions to stay ahead in this evolving industry and we will continue to focus on digitalisation and innovation to meet their needs,” says Pooja Gupta, HCME Product Manager Solution Linkage.
Easy, streamlined access Dealers and customers will be able to access CONNECT using an existing Hitachi Global e-Service account.
CONNECT is also integrated with Hitachi’s ConSite service solution, so if an alert for an issue is triggered through ConSite, it will also be displayed on the CONNECT dashboard. This allows everyone in an organisation to track machines and promptly respond to
any issues, minimising unscheduled downtime.
reporting
CONNECT allows users to create sites at the project and location level, which can be customised according to customer objectives. The operation of machines at each site can be easily compared, ensuring optimal utilisation of equipment. Data such as idling, uptime, fuel consumption, CO2 emissions and system-generated alerts can also be shared.
Organising data by project, site, or other requirements enables overall operational management and analysis
through easy-to-understand graphs and tables. From office management to jobsite personnel, everyone will be able to maximise the performance of their fleet using a smartphone or tablet.
“For customers wanting to improve efficiency, manage their entire fleet more effectively or enhance the performance of their equipment, CONNECT is here to make it happen,” says Pooja.
“Available in 24 languages, it is a user-friendly platform that can be tailored to the needs of our customers. We look forward to seeing the positive impact that this solution will bring across the European construction industry.”
Since this year, Wacker Neuson has been offering customers the option to fill up all diesel driven machines with the alternative HVO fuel. With fuels made from hydro-treated vegetable oils (HVO), combustion engines can be operated with an almost neutral carbon footprint. The fuel is manufactured from renewable raw materials and burns with less emissions. It therefore has a better carbon footprint than fossil fuels.
With HVO it is possible to reduce CO2 emissions by 90% compared to diesel operation. All Wacker Neuson construction equipment and compact machines with a Stage V diesel engine produced from September this year are approved for use with HVO fuels following EN15940. This includes excavators, wheel dumpers, wheel loaders and telehandlers, as well as vibratory plates, rammers and rollers.
“We take our responsibility to provide an environmentally friendly and safe product range very seriously,” says Alexander Greschner, Chief Sales Officer of the Wacker Neuson Group. “With the option to use HVO instead of fossil fuels, our customers can improve their carbon footprint without great effort and they can work in a more future-oriented manner.
With this, we are offering our customers more flexibility, and as a manufacturer we are contributing to more sustainable construction sites.”
Almost all Wacker Neuson compact machines, with the exception of the tracked dumpers, will be initially fueled ex-works with HVO from September this year. As a result, Wacker Neuson is taking a consistent step towards a more sustainable future and is also encouraging customers to take this path.
As there are no significant differences in the chemical properties of HVO and diesel, the engine does not require any adaptions. There are also no additional requirements in terms of storage or use when compared with fossil fuels. While diesel only has a shelf life of approximately one year, HVO fuels have a shelf life of several years.
Even during use it is evident that HVO fuel does not harm the engine’s service life, maintenance intervals or emissions behavior. The customer can operate the same engine with either pure HVO, an HVO-diesel mixture or continue to use standard diesel.
Wacker Neuson is playing the role of a trailblazer with its innovative products and future-oriented solutions. For more than 10 years, Wacker Neuson has been working with electrically powered compact machines and construction equipment, always focusing on the best solution for the customer with these zero emission products.
With the zero emission series, including excavators, dumpers, wheel loaders and telehandlers, vibratory plates, rammers and an internal vibrator system for concrete consolidation, it is possible to operate an entire construction site without any direct exhaust emissions.
Wacker Neuson plans to double its range of zero emission machines within the performance class up to 40 kW or up to five tonnes by 2025 and all handheld construction equipment will be on offer as battery-powered alternatives by 2030.
Wacker Neuson even goes a step further and focuses on the whole zero emission ecosystem: from the charging infrastructure to specific services such as rental or financing offers as well as government subsidies and a life-cycle analysis of the battery.
A ground-breaking study conducted by researchers from the University of Cambridge has revealed that at least 70% of people in the construction industry report feeling stressed at work, and this not only has a negative impact on job performance but also personal life. The findings highlight the urgent need for effective strategies to combat workplace stress.
The construction industry is the largest in the world and is currently facing a mental health crisis. In the UK, construction employees are almost four times more likely to take their own lives compared to workers in other sectors. Poor mental health is a common experience in the construction sector and has significant implications.
Job stress is estimated to cost the UK economy a staggering £28 billion annually, while in the United States and other parts of the world, the financial toll is also high. Stress can lead to decreased productivity, increased sickness, and higher employee turnover. If left unmanaged, chronic stress poses serious risks to physical and mental health and can lead to chronic illnesses, such as cancer and heart disease.
The study, published in the Healthcare journal, gathered data from participants across 12 UK employers in the construction industry, the largest global economy industry, accounting for 13% of the world’s GDP.
Key findings indicate that 70% of people reported their jobs as being either
moderately stressful, very stressful, or extremely stressful.
Furthermore, 80% of people signalled that work stress can negatively impact their jobs, and 75% indicated that stress can negatively impact their personal lives. The major sources of stress were found to be high workloads, tight deadlines and situations not being under one’s control. Responsibility for the safety of others emerged as another stressor.
Dr Olivia Remes, co-author and a mental health researcher at the Cambridge Laing O’Rourke Centre at the Department of Engineering, emphasised the importance of effective coping mechanisms: “Opening up to family, friends, or colleagues about workplace stress can be helpful. Having
a robust support network acts as a buffer against stress and is beneficial for mental health.”
Some of the participants coped with the stress by “blocking it out” or keeping it to themselves. Dr Olivia Remes explained: “Blocking out or bottling up stressful problems may lead to feelings of helplessness and other negative consequences.
“Instead, connecting with supportive others during stressful times can be more effective. In fact, self-disclosure and sharing your thoughts with a close family member, friend or colleague has been linked to greater resilience.”
Co-author Rachel Blair Winkler, a University of Cambridge Construction Engineering Masters alumna and
MBA candidate at Oxford University advised on the necessity of tailored programmes that consider the individual, as well as the context. “It’s essential to consider various professional responsibilities, environmental conditions, and organisational cultures when developing wellbeing initiatives. This will be one of the next steps in the research,” she stated.
As workplace stress continues to rise, this study underscores the pressing need for construction organisations to prioritise mental health and implement effective strategies to support their employees. Taking decisive action in this area means creating a healthier work environment that significantly contributes to the UK’s economic growth.
“Job stress is estimated to cost the UK economy a staggering £28 billion annually”
The Construction Plant-hire Association (CPA) has appointed Luis Bassett in the newly created role of Decarbonisation and Sustainability Manager.
Luis joins the CPA from the London Borough of Merton, where he worked for over eight years. He has extensive experience in low emission solutions for the construction plant sector, as Luis’s main role at London Borough of Merton was in the Cleaner Machinery Team, who implement the London NRMM Low Emission Zone on behalf of 32 London local authorities.
Luis became the team’s Technical Lead on compliance queries, guidance documentation, training materials and emissions calculations. He represented fleet and site operators, taking the lead on supplier engagement, most recently specialising in low emission solutions to site power, including Stage V generators, battery solutions and Flybrid Technology.
CPA Chief Executive Officer Steve Mulholland said: “We are very pleased to welcome Luis to the CPA in this important role. Luis’s appointment will not only strengthen the CPA team, but also support the CPA membership to reach net zero targets. Luis will also liaise closely with other industry stakeholders on future technologies and manage expectations within government and local authorities on the timescales of what is possible in the short to medium term.”
Luis Bassett added: “I am really excited to join the CPA. Decarbonisation is a huge challenge for the sector, a tricky terrain to navigate and will require support and understanding from those who set environmental policies and targets. I am looking forward to getting to know CPA members and supporting them throughout this journey.”
“Luis’s appointment will not only strengthen the CPA team, but also support the CPA membership to reach net zero targets”
SANY is proud to announce the release of the reworked SANY SY80U compact excavator. Based on the success of its popular eight-tonne machine, this advanced version is designed to deliver enhanced operator comfort and productivity, features a new optional twopiece boom and like all SANY excavators comes with a five-year / 5,000 hour warranty for complete peace of mind.
The tried and tested Stage V vw engine remains as the centrepiece of this powerful machine, that has a digging depth of 4,535 mm, dumping height of 4,530 mm and digging reach of 7,290 mm. The optional two-piece boom increases reach and control, making it ideal for applications such as groundworks, drainage and preparing trenches for utilities. There is also a 260-kg counterweight option, while the two-piece boom model has a 400-kg counterweight as standard.
The new SY80U also comes with a next generation cab with the highest levels of comfort to ensure that the operator can achieve maximum productivity while working. Highlights include an upgraded, ergonomic and comfortable air suspension operator’s seat and a new sleek and intuitive 7" touch screen display that has been designed with high performance and ease of use in mind. The joysticks
with two proportional control circuits are also part of the standard specification and enable safe and precise control of the machine including all its attachments. Furthermore, the ergonomically positioned control lever for the blade with integrated operating position selector makes it even easier to adapt the machine to the relevant work situation, making operation even more effective.
Jonathan Smith, Product Manager at SANY UK said: “The upgraded operator’s cab and the addition of the optional twopiece boom further empowers operators to do more in less time, maximising productivity while delivering a superior user experience. This improved model is the result of feedback from our customers and our commitment to providing real solutions to the market.”
The SY80U is registered and protected with the CESAR Datatag Scheme and CESAR ECV for quick and easy verification of emissions category and also comes with EVI telematics as standard.
The new model is now available through SANY’s extensive dealer network across the UK and Ireland.
“The upgraded operator’s cab and the addition of the optional two-piece boom further empowers operators to do more in less time, maximising productivity while delivering a superior user experience”
Operators of Mecalac’s new Revotruck can now rotate the entire cab to keep their vision and focus on the job and a view of potential obstacles on the site The exclusive chassis with central oscillation ensures stability and traction in all conditions. The infinite cab positions of the Revotruck open up visibility in all directions