
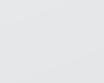
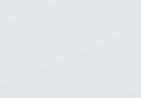
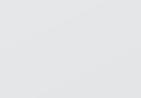
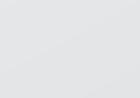
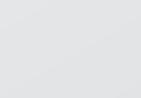
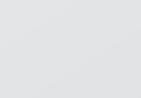

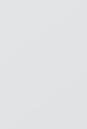
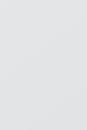


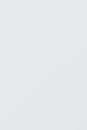
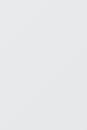
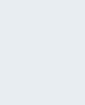

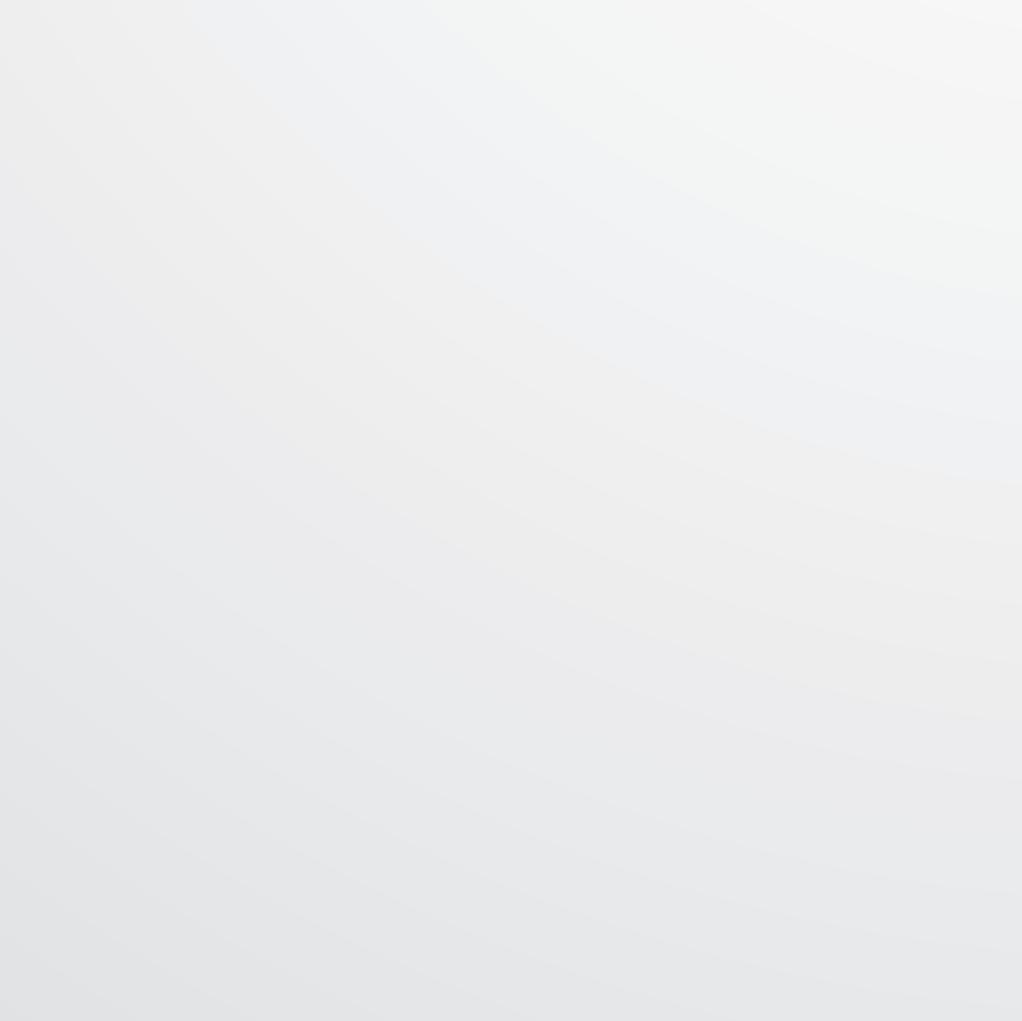

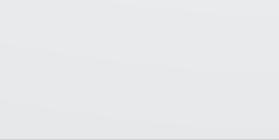
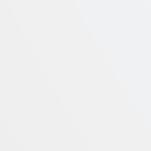

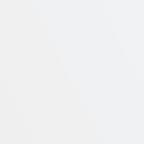
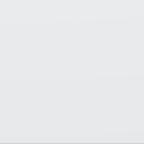
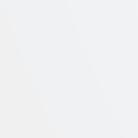
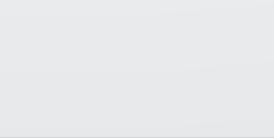
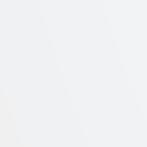


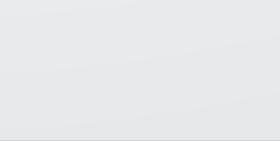





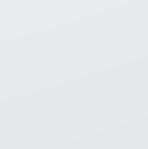
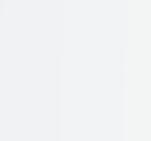
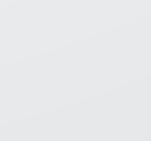












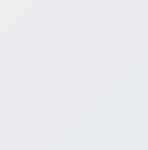

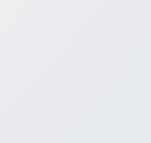
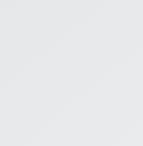
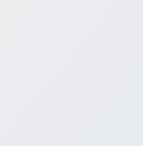

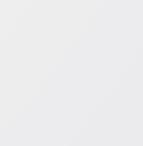
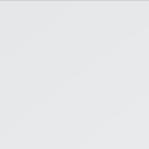
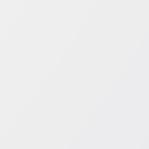
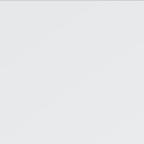
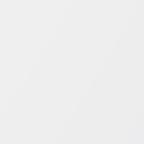
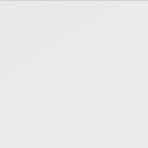
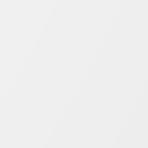
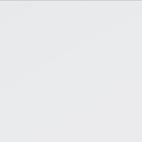
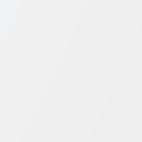
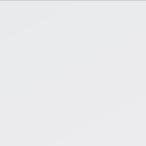

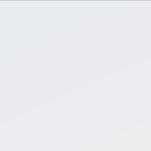

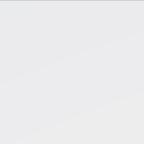
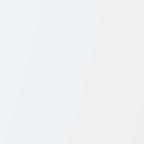
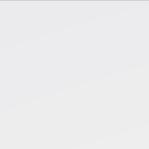
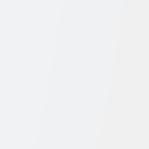
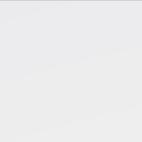
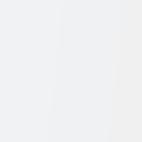
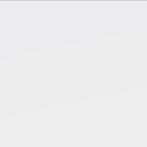
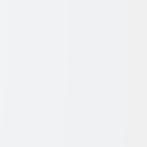
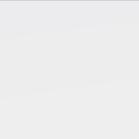
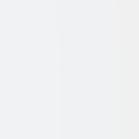

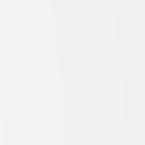
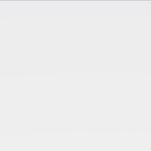
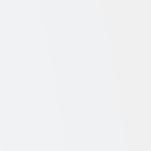
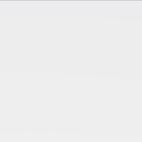


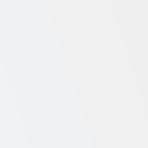
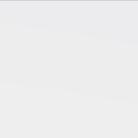
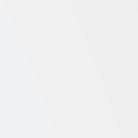
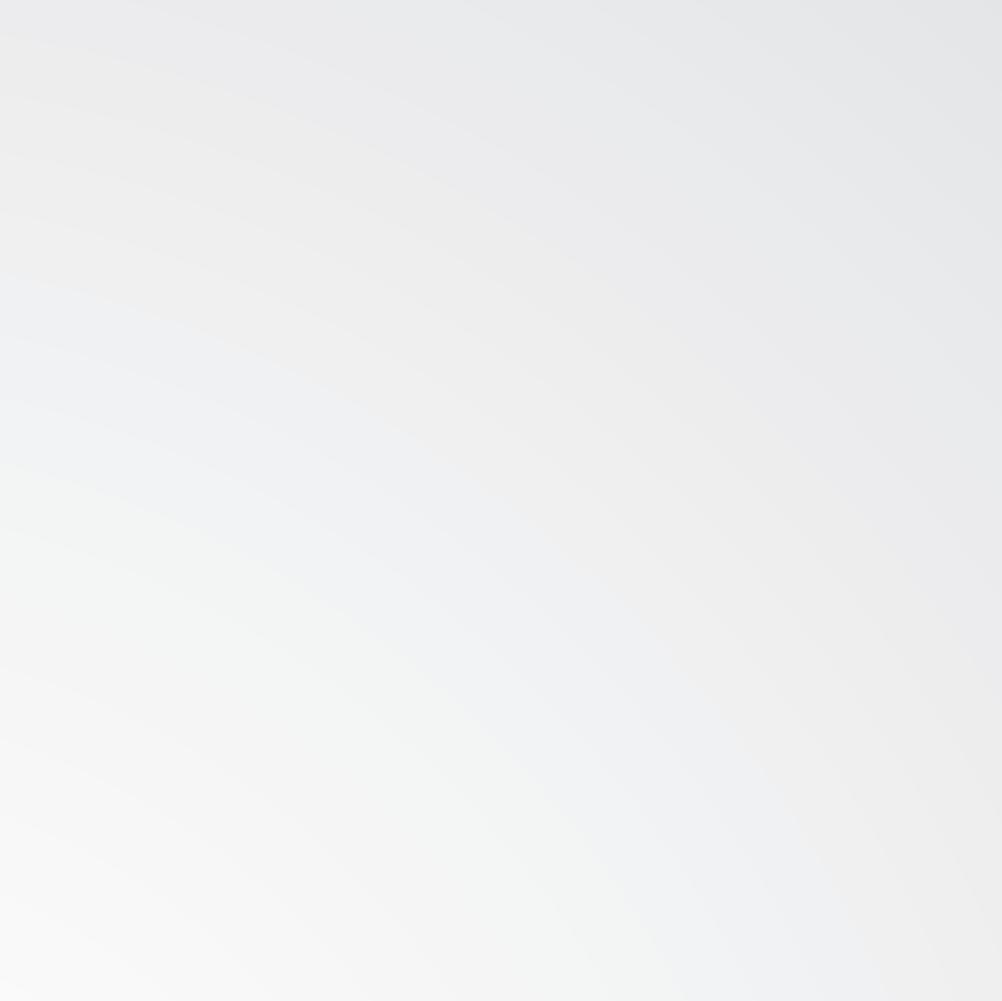
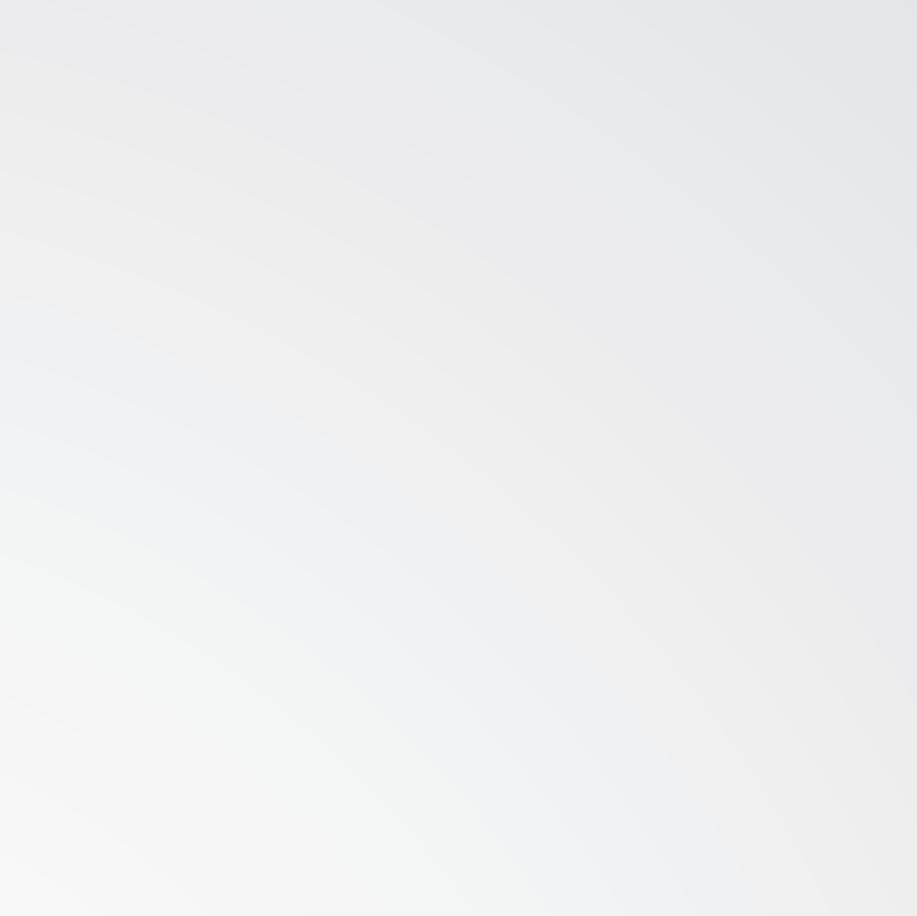
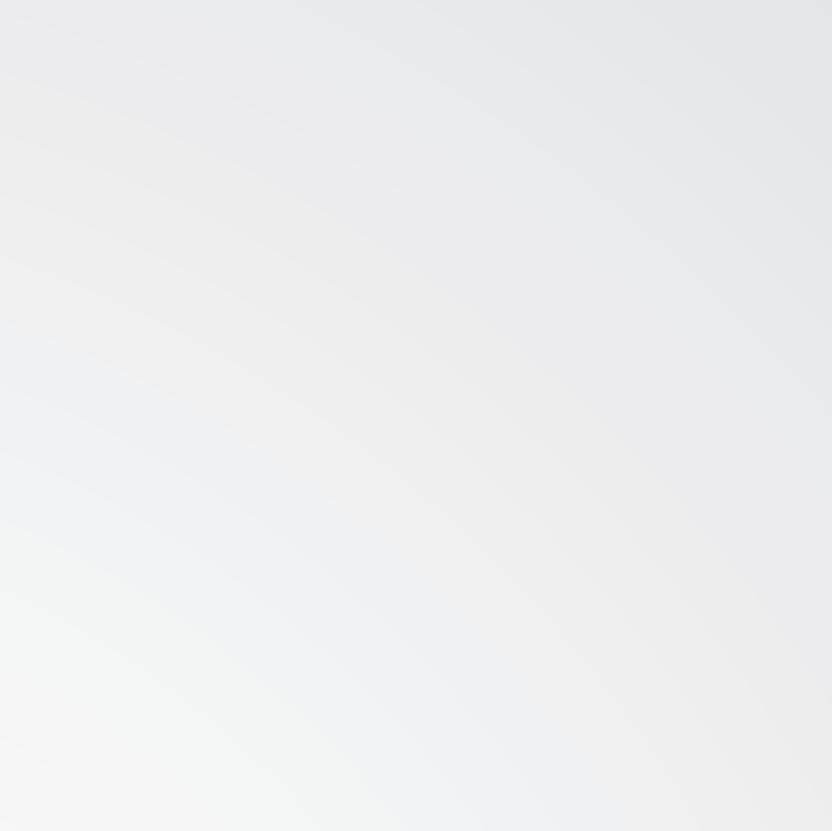

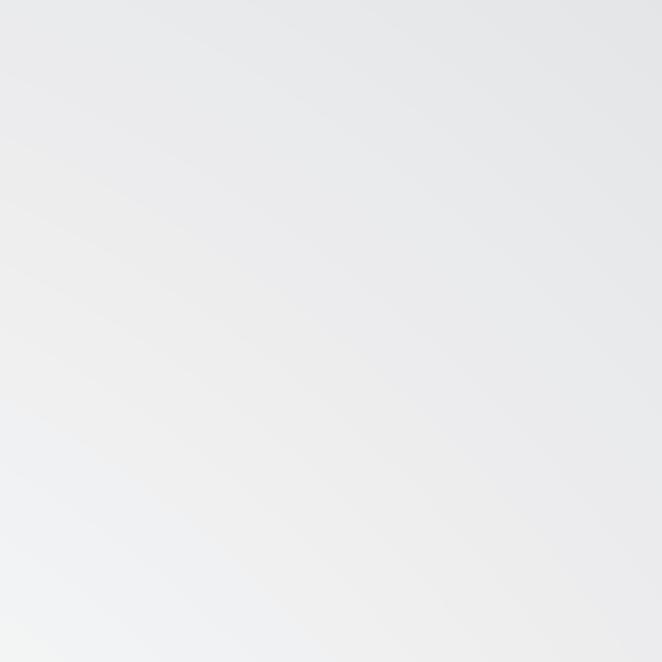

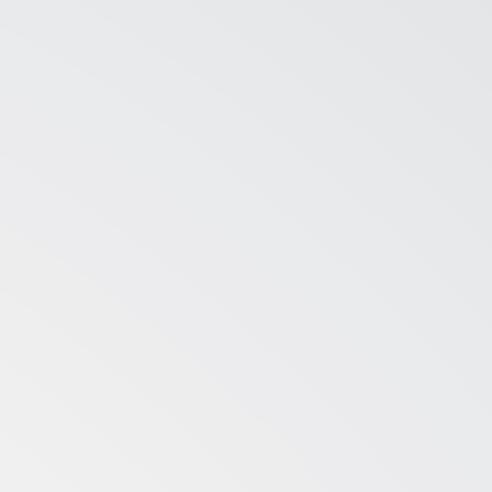

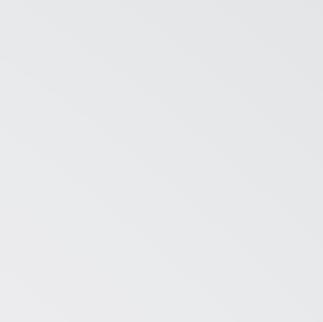
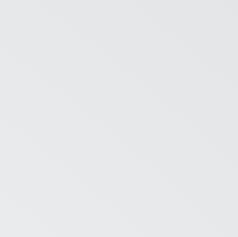
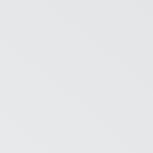








































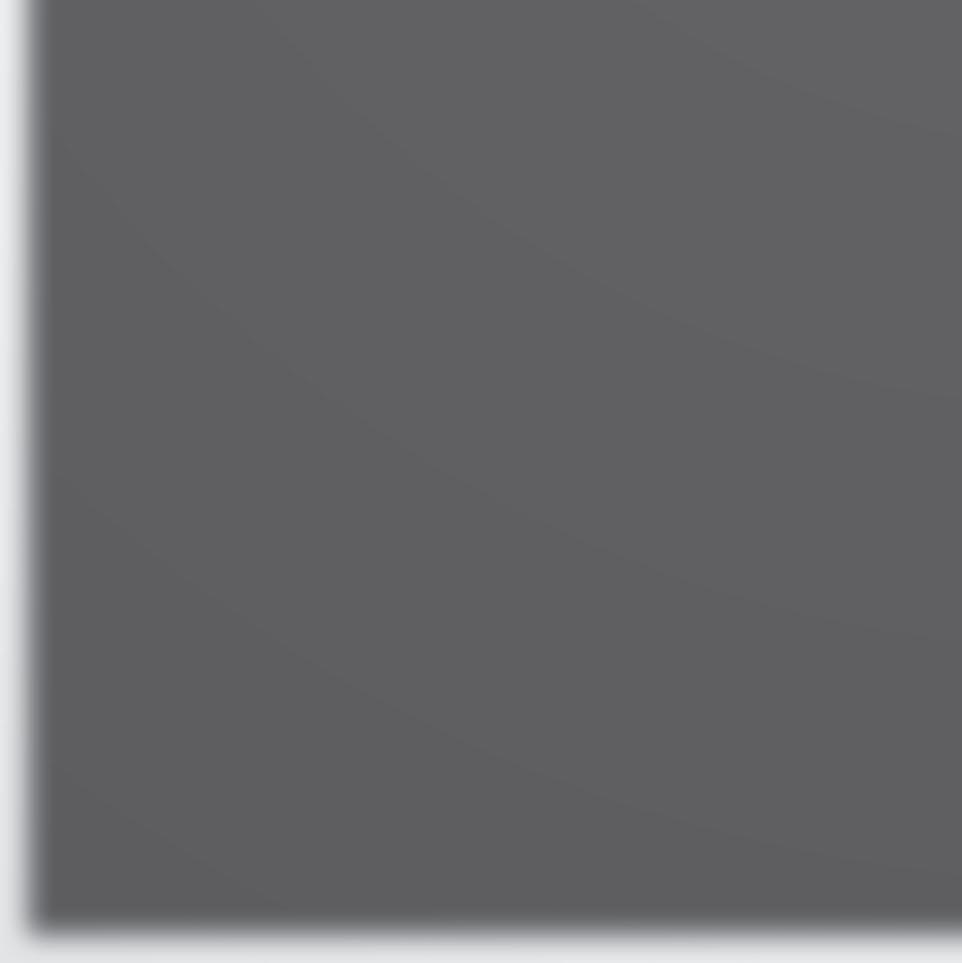
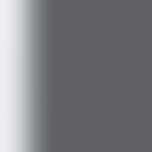
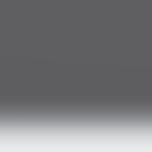

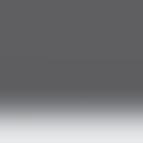
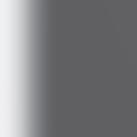
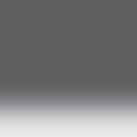
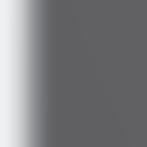
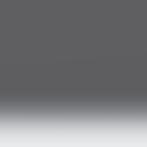
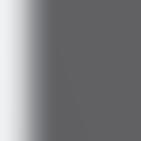
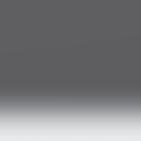
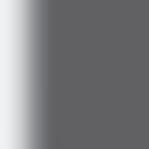

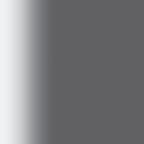
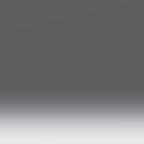
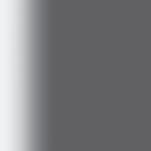
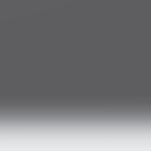
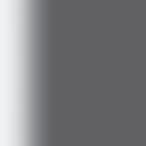

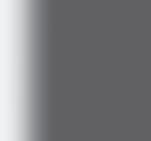
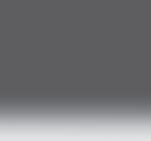































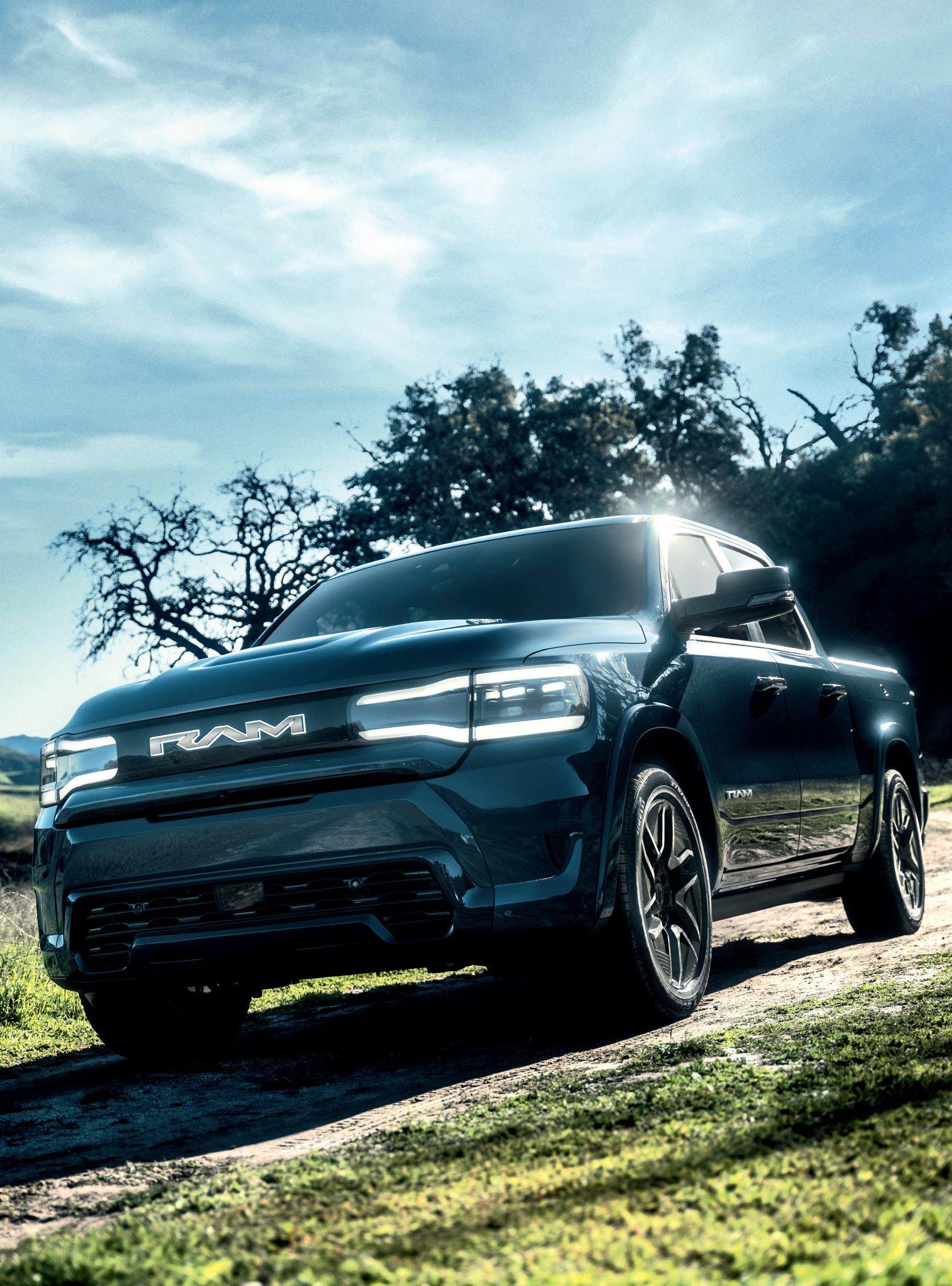























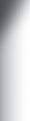














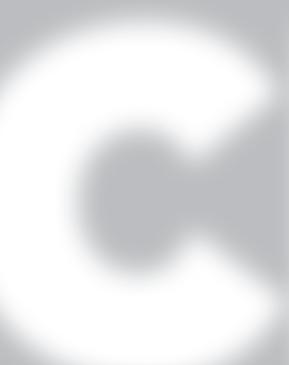



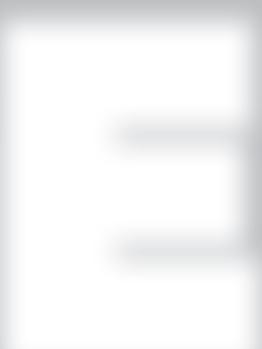

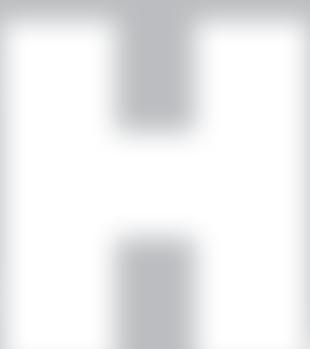


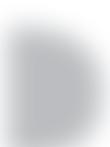

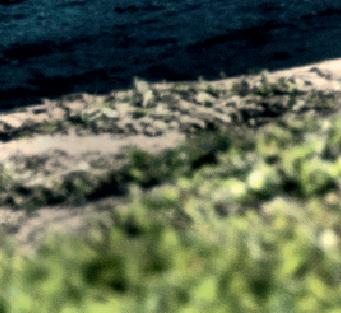
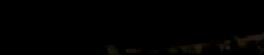

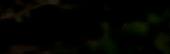


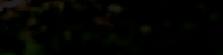
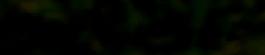
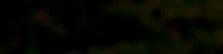
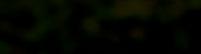
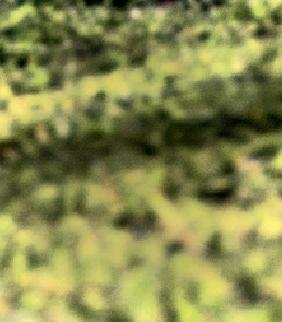
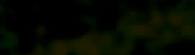
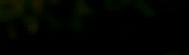
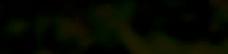
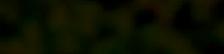


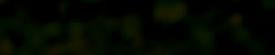

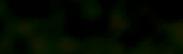
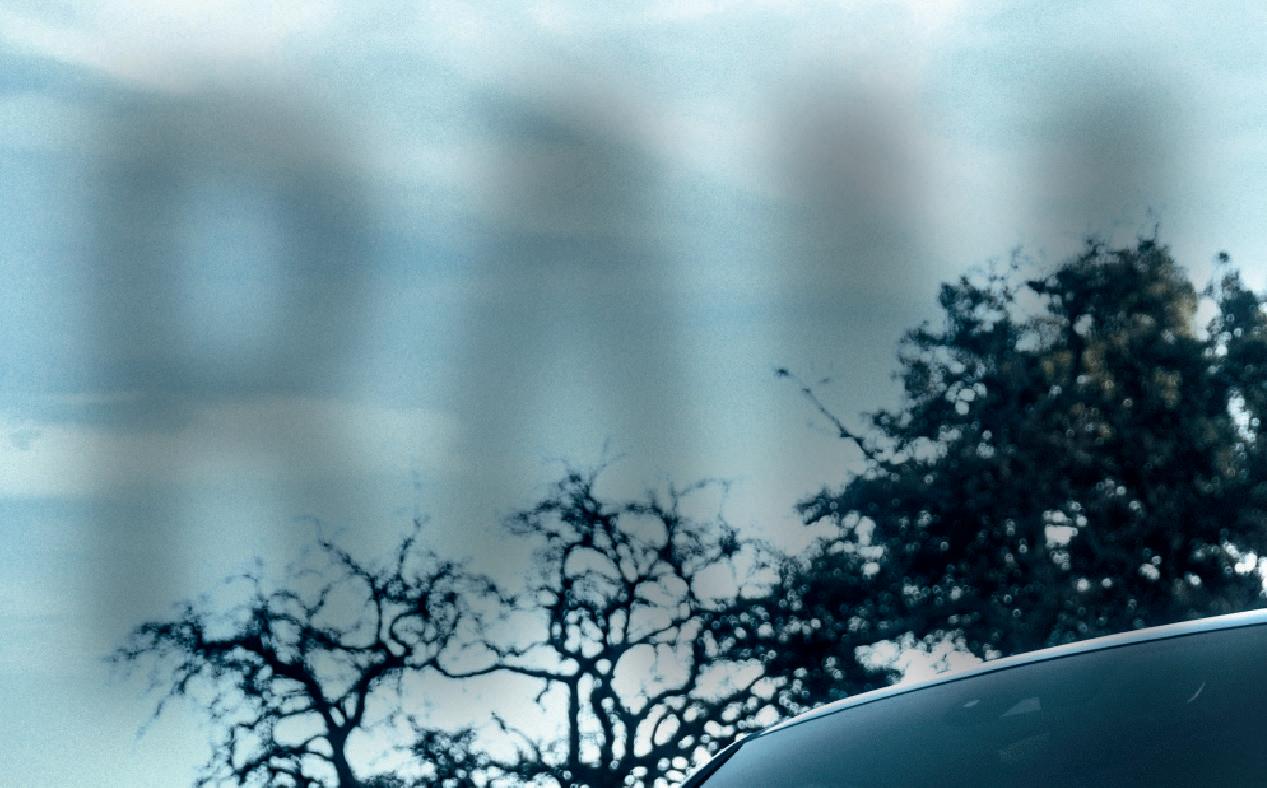


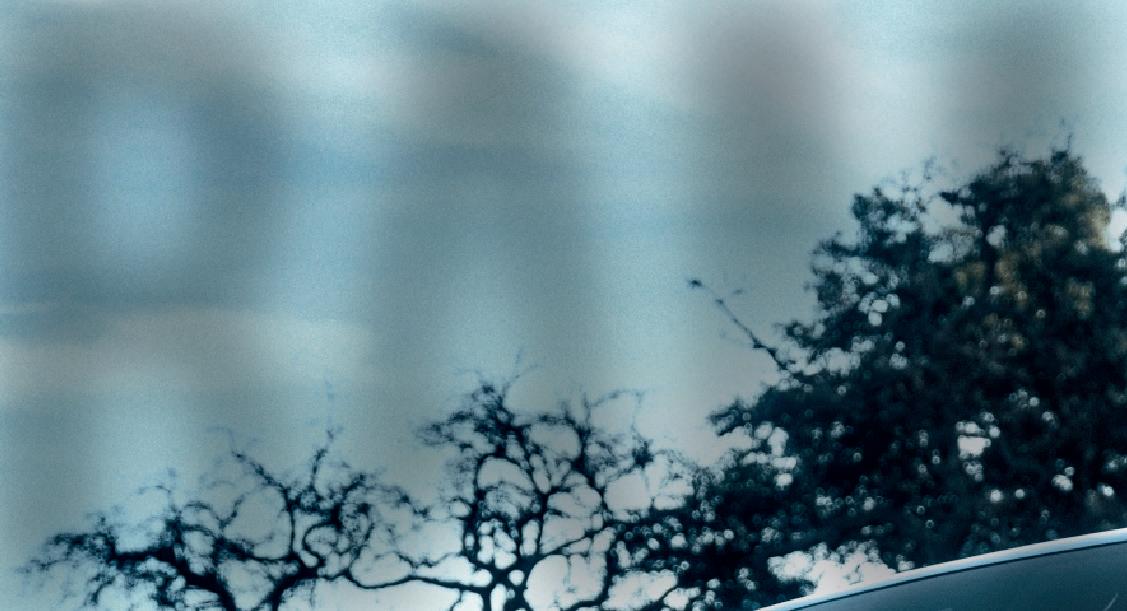
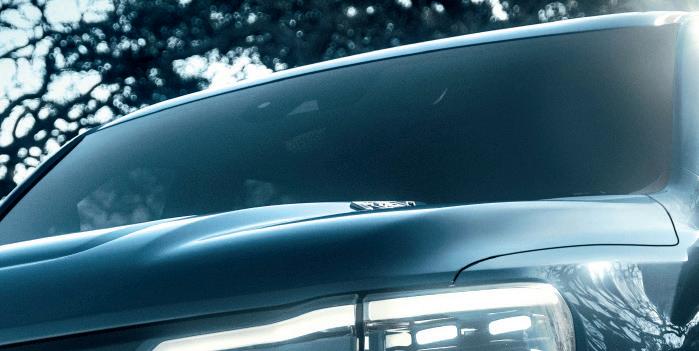

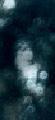
FLEXIBLE, HIGH PRECISION SOLUTIONS FROM R&D TO END OF LINE
Battery cell, module and pack level charge/discharge cycle testing solutions designed to provide high accuracy measurement with advanced features. Regenerative systems recycle energy sourced by the battery back to the channels in the system or to the grid.
Battery simulation for testing battery connected devices in all applications to confirm if the device under test in performing as intended. Battery state is simulated which eliminates waiting for the charge/discharge of an actual battery. Real time test results include voltage, current, power, SOC%, charge/discharge state and capacity.
To learn more about our Battery Test Solutions visit chromausa.com
Rheinmetall receives 250-million-euro order for 900-volt EV contactors
Infinitum unveils Aircore Mobility electric motor with PCB stator technology
Kia EVs to use onsemi’s silicon carbide power module for traction inverters
Wolfspeed and ZF partner to develop silicon carbide semiconductors
Marposs offers a new system for checking pouch cell battery welds
Proterra begins producing EV batteries at new South Carolina factory
Renesas launches new generation of automotive Intelligent Power Devices
Rincon Power launches new 600 A, 1,000 V manual battery disconnect
Rice University announces new process to revive lithium-battery anodes for reuse
Hyundai-Kia lauds Eaton’s Breaktor technology
ZF reaches milestone: two million EV motors produced
MAHLE receives 1.4 million euros in e-compressor orders
KMD launches constant-velocity driveshafts for EVs
Maserati’s first fully-electric car powered by three Marelli 800 V motors
Cummins tests new ePowertrain on track at Millbrook Proving Ground
LEM’s new UL-certified bidirectional DC meter for fast EV chargers
Tesla to open up its US Supercharger network, double the number of chargers
Electrify America will power its entire charging network with solar energy
Emporia Energy unveils new low-priced Level 2 charger
ABB E-mobility announces new Terra Home residential charger
TravelCenters to deploy 1,000 Electrify America fast chargers at 200 locations
AMPECO raises $16 million for its EV charging management platform
EverCharge’s load balancing enables large-scale EV charging at Houston airport
Volkswagen and Enel X Way to deploy 3,000 high-power charging points in Italy
EV charging station data provider Eco-Movement closes Series A funding round
Electreon to deploy public wireless EV charging road in Germany
Shell to acquire EV charging network Volta for $169 million
Enphase Energy demonstrates bidirectional EV charger technology
Leviton’s new EV charging stations integrate with smart home tech
Publisher
Christian Ruoff
Contributing Writers
Jeffrey Jenkins
Charles Morris
For Letters to the Editor, Article Submissions, & Advertising Inquiries Contact: Info@ChargedEVs.com
Associate Publisher
Laurel Zimmer
Senior Editor
Charles Morris
Account Executives
Jeremy Ewald
Cover Image Courtesy of Special Thanks to
Christian Ruoff
John Voelcker
Stellantis
Kelly Ruoff
Technology Editor
Graphic Designers
Jeffrey Jenkins
Tomislav Vrdoljak
Sebastien Bourgeois
ETHICS STATEMENT AND COVERAGE POLICY AS THE LEADING EV INDUSTRY PUBLICATION, CHARGED ELECTRIC VEHICLES MAGAZINE OFTEN COVERS, AND ACCEPTS CONTRIBUTIONS FROM, COMPANIES THAT ADVERTISE IN OUR MEDIA PORTFOLIO. HOWEVER, THE CONTENT WE CHOOSE TO PUBLISH PASSES ONLY TWO TESTS: (1) TO THE BEST OF OUR KNOWLEDGE THE INFORMATION IS ACCURATE, AND
(2) IT MEETS THE INTERESTS OF OUR READERSHIP. WE DO NOT ACCEPT PAYMENT FOR EDITORIAL CONTENT, AND THE OPINIONS EXPRESSED BY OUR EDITORS AND WRITERS ARE IN NO WAY AFFECTED BY A COMPANY’S PAST, CURRENT, OR POTENTIAL ADVERTISEMENTS. FURTHERMORE, WE OFTEN ACCEPT ARTICLES AUTHORED BY “INDUSTRY INSIDERS,” IN WHICH CASE THE AUTHOR’S CURRENT EMPLOYMENT, OR RELATIONSHIP TO THE EV INDUSTRY, IS CLEARLY CITED. IF YOU DISAGREE WITH ANY OPINION EXPRESSED IN THE CHARGED MEDIA PORTFOLIO AND/OR WISH TO WRITE ABOUT YOUR PARTICULAR VIEW OF THE INDUSTRY, PLEASE CONTACT US AT CONTENT@CHARGEDEVS.COM. REPRINTING IN WHOLE OR PART IS FORBIDDEN EXPECT BY PERMISSION OF CHARGED ELECTRIC VEHICLES MAGAZINE.
Our 70 years experience in Surface Treatment is ready for the E-Mobility market.
Research, innovation, development. In 70 years, our vision towards the future has never stopped. Today, Tecnofirma provides quality to the electric market which is the most evolving technology in the automotive industry. Our impregnation, cleaning and painting plants are the result of the constant commitment to o er cutting-edge solutions and products anytime, anywhere.
e EV news is coming so hot and heavy these days that we can hardly keep up with it. (We’re making a valiant e ort—you’ve probably noticed that we’ve added more online feature articles and expanded our coverage.)
Chinese EVs are becoming common sights on the streets of Europe, and they’re headed for the US (see this issue’s Charging Forward column, page 82). A Vietnamese automaker is also delivering product, and hopes to establish production in the States. Tesla has begun to open its Supercharger network to all brands in the US—and by the way, announced plans to support bidirectional charging, hinted at a future wireless charging option and said it will build a new Gigafactory in Mexico. e US Postal Service, a er years of dithering, has placed a substantial order for electric delivery vans. ere are signs that industry laggard Toyota may nally begin to electrify. Game-changing V2X technology is on the cusp of moving from the pilot phase into commercial deployment (see our feature on e Mobility House in this issue, page 72).
Every one of these recent news items is a blockbuster, with huge potential to advance the cause of electri cation. However, the biggest ongoing story of all is the massive support that Western governments are getting ready to funnel into electri cation and renewable energy. e US In ation Reduction Act and Bipartisan Infrastructure Law (silly names, but nobody asked us), along with similar legislation in the EU, seem to be a part of every conversation about EVs these days. Large pots of money are available for public charging infrastructure, school bus electri cation, battery production and much more—and companies are moving quickly to take advantage of the opportunities.
One important—and controversial—aspect of policies on both sides of the pond is a major push to establish domestic extraction and processing of raw materials for batteries. is is a global earthquake—automakers will have to rebuild their entire supply chains—and these goals won’t be achieved quickly, or without pain. However, when the dust settles, the auto industry will be far greener and more resilient.
Is this all too good to be true? Could changes in Washington shut down the EV revolution in the US? Certainly the anti-EV forces are powerful (and they have allies in both parties), but we’re cautiously optimistic that at least the main initiatives set in motion by the IRA/BIL will continue to move forward. If there’s one thing that politicians of all stripes love, it’s JOBS, and the scramble to establish domestic battery production promises to create plenty. Billions worth of investment is headed for the Battery Belt, which runs through southeastern deep red states, and local politicians are happily cutting ribbons and hailing the new technology. (One study found that red states are slated to receive far more in per-capita climate investments under the IRA than blue states.)
Another promising sign that EVs are getting depoliticized: All 50 states quickly established Electric Vehicle Infrastructure Deployment Plans, unlocking $1.5 billion in funding under the National Electric Vehicle Infrastructure (NEVI) program. at’s something that doesn’t always happen with federal programs (Medicaid expansion, for example). Another small but symbolic victory: A Wyoming bill that would have banned the sale of EVs was soundly rejected, with nary a Democrat in sight.
At Charged, we’ve always believed that EVs make much better cars, in many different ways—and advancing the best technology by encouraging new engineering breakthroughs should never be a partisan political issue.
German automotive and arms manufacturer Rheinmetall has received an order for contactors worth over a quarter-billion euros from an undisclosed German automaker.
Contactors ensure that EVs can be safely switched on and o , especially in emergencies like an accident or system failure.
Rheinmetall has a new type of contactor that’s designed for the coming 900-volt generation of EVs, and it will be available starting in 2025.
e new 900-volt technology poses challenges for the contactors’ design, particularly concerning the cut-o performance under high short-circuit currents.
e company says its new product platform combines low weight with high performance, and that low contact resistances guarantee lower power losses. Rheinmetall’s contactors function without volatile quenching gases, which reduces production costs, improves longevity and enables higher operating temperatures with a signi cantly lower risk of bursting.
Electric motor manufacturer In nitum introduced its new electric traction and propulsion motor, Aircore Mobility, at CES 2023.
Aircore Mobility is an axial ux motor designed to power a wide range of electric vehicles. It’s engineered to operate with high e ciency over a wide range of speeds and load conditions, expanding vehicle range and reducing energy loss in the process, according to In nitum.
e Aircore Mobility motor replaces the heavy iron found in traditional units with a lightweight, printed circuit board (PCB) stator that’s 10% more e cient, 50% smaller and lighter, uses 66% less copper, and is ten times more reliable, according to the company.
In nitum says Aircore Mobility can achieve up to four to ve times the current density of a conventional liquid-cooled motor, using a liquid cooling technology that allows the coolant to be in direct contact with the stator, mitigating heat across a larger surface area, enabling high overload capability and extended life.
“Our Aircore motor topology eliminates core losses and delivers a broader range of speeds and load conditions in which the motor can operate at high-e ciency levels,” says Paulo Guedes-Pinto, VP of Technology for In nitum. “ e Aircore Mobility motor o ers a new avenue in extending the range for Class 1-8 vehicles, aerospace, marine, construction and agricultural machines.”
onsemi has announced that its EliteSiC family of silicon carbide power modules has been selected for Kia’s EV6 GT model.
onsemi says its power module enables high-e ciency power conversion from the DC 800 V of the battery to the AC drive for the rear axle. It also delivers package technology to minimize parasitics and thermal resistance, and o ers package reliability using interconnects. ese innovations, says onsemi, lead to reduced power losses in DC-AC conversion, as well as reduced size and weight of the traction inverter, potentially improving performance and EV range by as much as 5%.
e company reports that it plans to continue collaborating with Hyundai and Kia to use the EliteSiC technology for the automakers’ upcoming EVs based on the Electric Global Modular Platform (E-GMP).
PyroThin cell-to-cell barriers can perform as combined fire barriers and compression pads.
Tunable platform to meet thermal, compression and thickness requirements.
Ultrathin and lightweight to support maximum volumetric cell-to-pack ratio
US silicon carbide specialist Wolfspeed (NYSE: WOLF) and German automotive supplier ZF have announced a strategic partnership that includes the creation of a joint innovation lab and the construction of silicon carbide device fabrication facility in Germany. Both the lab and the fab are planned as part of the Important Project of Common European Interest for Microelectronics and Communication Technologies framework, and are dependent upon state aid approval from the European Commission.
e joint research facility will focus on e-mobility and renewable energy. e goal of the collaboration is to develop breakthrough innovations for silicon carbide applications, covering the full value chain from chips to complete systems. Additional partners will be invited to participate, with the goal of establishing an end-to-end European silicon carbide innovation network.
Also, Wolfspeed plans to build a fully automated 200 mm wafer fabrication facility in Saarland, Germany. ZF will support the project by making an investment “in the hundreds of millions of dollars” in exchange for Wolfspeed common stock.
“ ese initiatives are a signi cant step towards a successful industrial transformation,” said Dr. Holger Klein, CEO of ZF. “ ey strengthen European supply resilience and support the European Green Deal and the strategic goals for Europe’s Digital Decade.”
“ZF brings industry-leading experience in scaling components for electric mobility as well as the aptitude to accelerate innovation in silicon carbide systems and power devices,” said Gregg Lowe, President and CEO of Wolfspeed. “I am con dent this partnership will li silicon carbide semiconductor technology to a new level of global impact.”
Marposs, a designer and manufacturer of measurement, inspection and testing products, has announced a new system for checking the welding joints of pouch cell batteries within the production process, consisting of interferometric sensors and the company’s NCG (non-contact gauge) controller.
e system works by splitting light into two beams that travel di erent optical paths and are later combined to produce interference, which can identify refractive changes and surface irregularities.
Pouch cell batteries are typically sealed using impulse or contact welding (heat sealing), which fuses the plastic layers together. e thickness of this joint is a key indicator of the quality of the seal, and must be measured while the material is still so . Marposs says its system is able to check the thickness right a er the welding process using the non-contact interferometric technology.
e solution can measure thin external plastic layers starting at 1 µm, and can accommodate thickness variations due to the presence of the tabs in parts of the welding seam. It comes with a measuring snap with two interferometric sensors that enable the simultaneous measurement of the total thickness of the welding seam and the thickness of the two external plastic layers. Each sensor has a measuring eld of 900/1.8 mm and o ers a repeatability range within 1 mm of the application thickness.
Proterra (NASDAQ: PTRA) is a commercial electric vehicle OEM, and it has two related businesses: Proterra Energy, which o ers turnkey charging services to eets; and Proterra Powered, which provides battery packs to other vehicle manufacturers.
Now the company has produced the rst Proterra Powered EV battery at its new Powered 1 battery manufacturing plant in Greer, South Carolina. Proterra expects to begin deliveries of Proterra Powered battery systems from the new factory in the rst quarter of 2023. Powered 1 has also started production of drivetrains and other ancillary systems such as high-voltage junction boxes.
Powered 1 brings battery production closer to Proterra’s customers on the East Coast and in Europe, and to its own electric bus manufacturing operations in Greenville, South Carolina. e 327,000-square-foot battery plant will eventually have “multiple gigawatt-hours of annual production capacity.”
“Achieving this important milestone at Powered 1 a little over a year a er announcing our plans for the factory is a re ection on the talent, innovation, and collaboration of our incredible team,” said Proterra CEO Gareth Joyce. “At full scale, we believe Powered 1 will be the largest battery manufacturing facility in the US dedicated exclusively to electric commercial vehicles.”
at’s a laudable ambition, but Proterra might just have some competition for the “largest” title—so many new battery plants are planned for the US Southeast that some are starting to call it the Battery Belt.
Japanese semiconductor manufacturer Renesas Electronics has revealed a new automotive Intelligent Power Device (IPD) that’s designed to safely and exibly control power distribution within vehicles.
e new RAJ2810024H12HPD is available in a small TO-252-7 package and reduces the mounting area by about 40% compared to the conventional TO-263 package product.
Renesas also says that the advanced current detection function of the new device allows highly accurate detection of abnormal currents such as overcurrent. Since the new IPD detects abnormal currents even at low loads, it allows engineers to design power control systems that can detect even the smallest abnormalities.
Key features of the new RAJ2810024H12HPD IPD:
• Single-channel high-side IPD
• Small TO-252-7 package (6.10 x 6.50 mm, excluding pins)
• Low on-resistance (Ron) of 2.3 mΩ at 25° C (typical)
• Highly accurate current detection at low loads
• Built-in charge pump
• Self-diagnostic feedback by load current sense
• Protection functions such as load short-circuit, overheat detection, sense current output and GND open protection
• Supports 3.3 V / 5 V logic interface
• Low standby current
• Battery reverse connection protection with self-turnon
• Compliant with AEC-Q100 and RoHS automotive standards
Electronic parts manufacturer Rincon Power has announced a new line of battery disconnect switches, the HVBD6Axx series. is hermetically sealed switch serves to isolate a high-voltage system in a compact and robust package.
According to the company, the HVBD6Axx o ers 600 A continuous current carry in applications ranging from 12 to 1,000 V DC. e single-pole, single-throw switch features optional auxiliary contacts which can be used as part of a high-voltage safety circuit. Low contact resistance (averaging less than 0.1 mΩ) ensures limited heat generation and energy losses.
e hermetic seal allows the unit to be operated in virtually any environment, while also ensuring that there is no contact oxidation over the life of the switch. e handle features a lock-out hasp for OSHA-complaint lock-out/tag-out functionality.
“Our 600A HVBD Battery Disconnect o ers an attractive solution for physically isolating high-voltage systems while allowing for a visual indication that the switch is turned o ,” said Markus Beck, Rincon Power’s VP of Sales. “ e HVBD series has been successfully implemented in a wide range of applications including electric buses, o -road equipment, electric marine and a wide range of high-voltage battery systems.”
Rice University scientists have reported what they believe to be a partial solution to the mounting disposal problem of worn-out lithium-ion batteries. It relies on a unique “ ash” Joule heating process they have developed to produce graphene from waste.
e lab of Rice chemist James Tour is said to have recon gured the process to quickly regenerate graphite anode materials found in Li-ion batteries, removing impurities so they can be repeatedly reused. Powdered anodes from commercial batteries are “ ashed” for a few seconds with a jolt of high energy, decomposing their inorganic salts, including lithium, cobalt, nickel and manganese, which can then be recovered by processing them with dilute hydrochloric acid. e reported cost is about $118 to recycle one ton of untreated anode waste.
“We’re claiming our process can recover critical metals and recondition anodes in a far more environmentally and economically friendly manner,” says Tour.
Hyundai-Kia has named Eaton’s Breaktor circuit protection technology “Best Technology” in its electri cation category.
Power management company Eaton developed Breaktor as a circuit protection system for EVs that combines the functions of fuses, pyro switches and contactors into one coordinated device.
“Our technology lls a unique need in the growing EV market,” said Kevin Calzada, Eaton’s Global Product Strategy and Marketing Manager.
According to Eaton, as EV power levels increase, its proprietary technology solves the coordination challenge between fuses and contactors and provides fast, reliable protection for high-power battery, fast-charge and inverter systems.
Our trusted Gocator smart 3D laser profilers solve a wide range of universal EV Battery manufacturing quality control applications including scanning electrode coating thickness; cylindrical and prismatic battery surface inspection; cell, module, and pack dimensional measurement (LxWxH); battery weld seam inspection; and final battery installation inspection.
Powered by Silicon Mobility OLEA® T222 FPCU & OLEA® APP INVERTER Software
3-Phase SiC MOSFET Intelligent Power Modules
• Up to 1200V/350kW
• Integrated SiC Gate Driver
• Low-ESL DC-Link Capacitor
• Reference Liquid Cooler
Motor Control Board & Software
• ISO 26262 ASIL-D
• OLEA® T222 FPCU chip
This optimal mechanical & electrical integration of a 3-Phase Silicon Carbide MOSFET Intelligent Power Module from CISSOID together with OLEA® control solution and application software from Silicon Mobility accelerates the development of Compact and Efficient e-Motor Drives! www.cissoid.com
• Advanced control algorithms & software libraries for e-motors
is year, automotive supplier ZF reached the milestone of two million electric motors produced.
To keep pace with the global increase in demand for EVs, the company has been continuously accelerating production at its lead plant in Schweinfurt, Germany. It has also commissioned major production lines in Serbia and China. Another plant in North America will go into operation in 2023.
Recently the company has begun focusing on a new technology: hairpin winding, which enables wires to be packed tighter together, resulting in increased power, speed and torque while using the same amount of space.
According to ZF, there is even more innovation potential for electric motors—for example, sophisticated cooling solutions.
“Currently we are developing a solution with oil owing past—to directly cool the copper wire, which is the main heat source in electric motors,” explains VP Roland Hintringer. e company also develops electric motors with magnets that are almost free of heavy rare earth metals. Another potential future technology: separately excited electric motors that don’t need any magnets at all.
In view of globally increasing volume and the high demand for electric powertrain technology, ZF expects to reach the next production milestone soon. “Our order books are well lled,” says Hintringer. “ e next two million units of electric motors will probably be produced in less than two years.”
German auto parts manufacturer MAHLE is increasingly becoming an e-mobility supplier. e company says its electric AC compressor is particularly sought-a er thanks to its peak power of 18 kW, which makes it the most powerful e-compressor on the market at the moment.
e company says it has already secured numerous series orders in the passenger and commercial vehicle sectors, amounting to approximately 1.4 billion euros.
E-compressors are one of the key components in EV thermal management. ey regulate the temperature of the electric drivetrain, and are thus crucial for the service life, charging speed and cruising range of the battery.
In addition to e-compressors for e-mobility, MAHLE develops and produces electric actuators, auxiliary components, engine accessories, auxiliary aggregates, electronics and so ware, as well as entire thermal management systems. According to the company, between 2022 and 2026, more than 20 electri ed vehicle platforms from leading passenger and commercial vehicle manufacturers will be launched on the market that rely on its technology and products. MAHLE says it already generates over 60% of its sales independently of ICE vehicles, a share that it hopes to increase to 75% by 2030.“MAHLE will continue to expand its role as a complete system supplier for air conditioning in EVs,” said Arnd Franz, CEO of the MAHLE Group.
Kalyani Mobility Drivelines (KMD), a manufacturer of driveline components, has introduced a lineup of constant-velocity (CV) drivesha s for EVs and other specialty vehicles.
KMD’s CV drivesha s are designed using high-strength steel for optimal performance under high torque generated by EVs, military, specialty and motorsports vehicles, and are engineered for a range between 7,000 and 16,000 Nm of torque at speeds up to 8,000 rpm.
e company says its drivesha s o er design exibility with no need for the equal angle alignment required by cardan designs.
ey’re also designed to provide smooth operation and long life, even under the most extreme operating conditions faced by military and specialty vehicles.
“EVs and other vehicles that create high torque put tremendous stress on driveline components. We engineer our CV drivesha s to survive under loads that would cause other drivesha s to fail,” said Dave Moore, Engineering Manager at KMD.
Italian automotive supplier Marelli developed and manufactured the three e-motors used in the new Maserati GranTurismo Folgore, and also provided its proprietary Adaptive Driving Beam Matrix LED headlamps and Telematic Control Unit connectivity system.
e 800 V motors, which were developed over a twoyear span and produced at Marelli’s Modugno plant in Bari, Italy, supply a total installed power of 1,200 hp in a compact pro le. ere are two motors mounted on the front axle and one on the rear, and they deliver a powerto-weight ratio of 9.2 kW/kg and total torque of 1,350 Nm.
Cummins, which has been building diesel engines for heavy-duty vehicles since 1919, is methodically moving into the electric age. Now the company has successfully demonstrated a new ePowertrain for heavy-duty vehicles, using a test truck at Millbrook Proving Ground in Bedfordshire, England.
Solid conductors in the hairpin windings of the stator, Marelli says, result in improved electromagnetic and thermal performance and a greater than 80% lling factor. e company also says that its choice of rotor geometry and the use of speci c segmented magnets, as well as optimized skew of the laminate stack, reduce noise, vibration and magnetic cogging. Its cryogenic cooling process used in rotor production, reaching about -200° C, ensures perfect t of the sha into the stack.
e integrated 17Xe ePowertrain, developed by Meritor (now part of Cummins) with Advanced Propulsion Centre (APC) consortium partners Editron and Electra, features output capacity of 430 kW continuous power. It’s designed to power heavy-duty trucks and buses in 6×2 or 4×2 con gurations, and is available in a range of ratios and with three-speed transmission capabilities. Danfoss’s Editron division developed and supplied the electric motor and silicon carbide inverter powering the axle. e motor is based on a patented architecture and thermal management methodology that exceeds the APC’s 2035 Roadmap targets for power density. As a result, only one motor will be required in the electric powertrain—Cummins says current alternatives usually need two motors to meet this product segment’s power requirements.
APC Senior Project Delivery Lead Sunil Maher called the demonstration a major milestone. “Seeing this prototype vehicle in operation is a signi cant step to addressing net-zero transport challenges in the UK. I look forward to the next stage of development, which will see technical improvements and further product variation, to deliver solutions for heavy-duty and commercial vehicles.”
e public charging industry is moving towards per-kilowatt-hour (as opposed to time-based) billing, and manufacturers will increasingly be required to incorporate certi ed DC meters into their charging stations.
To meet this need, electrical measurement specialist LEM has introduced the DCBM, a UL-listed bidirectional DC meter for fast EV chargers.
e DCBM “will enable makers of EV charging stations to accelerate their certi cation for DC metering requirements following Certi ed Test and Evaluation Professional/National Type Evaluation Program (CTEP/NTEP) certi cation,” says LEM. “ e DCBM will simplify the process of the manufacturers having to qualify their own charging stations for UL certi cation and, for extra peace of mind, will undergo a fresh audit every quarter.”
e new meter is capable of monitoring current, voltage, temperature and energy usage, and has been designed with data security and exibility in mind. e DCBM 400/600 complies with the UL 61010 and UL 810 standards in the FTRZ category for EV applications. To achieve this certi cation, the meter had to pass reinforced insulation tests, temperature testing of all its components and sub-assemblies, testing for protection against electric shock, durability of markings tests, equipment temperature limit tests, and resistance to heat/ re risk tests.
e DCBM is designed for DC chargers from 25 kW to 400 kW, and integrates the signed billing data sets according to the Open Charge Metering Format (OCMF) protocol. It can be retro tted to existing charging stations, and has a moveable measuring element for use with any type of charging station architecture. It is accurate in temperatures of -40° to 185° F, and has an IP20-rated casing.
Other features include Ethernet support and bidirectional energy metering, which makes it compatible with V2G (vehicle-to-grid) and V2X (vehicle-to-everything) applications.
“ e US and Canadian markets for EVs are continually expanding, but this growth could be held back by insu cient access to rapid DC charging stations,” said Claude Champion, General Manager at LEM USA. “LEM understands exactly what the sector needs, and has worked closely with EVCS manufacturers and installers when developing solutions like the DCBM 400/600.”
In my very rst article for Charged over 10 years ago, I opined that the Switched Reluctance Motor, or SRM, would eventually come to dominate the EV traction market, if for no other reason than the fact that it is almost as cheap as dirt to manufacture. I won’t sprain my shoulder patting myself on the back for a prediction that took 10 years to (partially) come true, but it does seem that the days of the Permanent Magnet Synchronous Motor, or PMSM, and the AC Induction Motor, or ACIM, dominating EV traction applications are coming to a close, with both Toyota and even stalwart ACIM fan Tesla introducing reluctance motors into the mix (albeit not ones that purely employ magnetic reluctance, but more on that below).
Despite the fact that the PMSM and ACIM types dominate the EV traction market, neither technology
is particularly well-suited to the job, mainly because of their limited overload and starting torque capabilities. Torque is a function of the magnetic eld strength of the motor’s eld structure, and that is obviously xed in a PMSM, because its eld is being supplied by literal magnets, but it is also limited in the ACIM, because its eld is induced into its rotor via transformer action, and like any electromagnetic structure employing a high-permeability core material, it is subject to saturation, or the point at which a further increase in current fails to increase the magnetic eld strength thus developed. Since traction applications require maximum torque at 0 rpm (to overcome both the inertia and static friction, or stiction, of the load), having a hard and fast torque limit is de nitely a downside. Furthermore, the PMs invariably employed in the PMSM are rare earth types—which, as the name implies, tend to be
expensive—and most avors of these magnets—particularly the neodymium type—have a very low upper temperature limit before they start to lose their ability to resist demagnetization (in some cases as low as 80° C), an especially unfortunate weakness, because the only way to extend the constant power speed range of a PMSM is with eld-weakening, in which an opposing (i.e. demagnetizing) eld is applied to the eld magnets to reduce the back EMF, or the voltage produced by the rotation of the rotor, to below that of the battery voltage. at brings up another potential downside to the PMSM: since BEMF is proportional to rpm, if the rotor is spinning fast enough to require eld-weakening
and the inverter shuts down (or misjudges the timing of the stator currents) for any reason, then it (and possibly the motor) will almost certainly be destroyed from the huge jump in BEMF causing an equally huge jump in current from the now rapidly-braking motor (a situation that is somewhat euphemistically termed uncontrolled generation). is failure mode can’t occur with the ACIM, of course, because the rotor’s eld can only exist through the action of the stator currents (and a di erence in the relative rpm of both), but the ACIM is much less power-dense than the PMSM (especially the interior PM version), so achieving a given power output requires a much larger motor, and that’s a signi cant drawbacks itself in an EV traction application. With all these downsides of both technologies, it’s fair to wonder how the PMSM and ACIM ever came to be used in EVs in the rst place—much less how they became the most popular choices—and a good chunk of the reason is that they both use the same inverter hardware that has been used to control the speed and torque of industrial motors for decades, with only minor di erences in the so ware and rotor position feedback to better adapt them to traction service.
e least-radical alternative motor type—and one which has already been used by BMW, in fact—is the wound-rotor synchronous motor, or WRSM. ere
The permanent magnets invariably employed in the Permanent Magnet Synchronous Motor are rare earth types—which, as the name implies, tend to be expensive—and most flavors of these magnets have a very low upper temperature limit.Interior Permanent Magnet Synchronous Motor, or IPM-SM Rotor Stator Stator Winding Permanent Magnets
is some irony in this, both because supplying current to the rotor requires brushes and a slip ring, which is almost anathema to those EV purists who shun the king of all traction motors, the series eld DC type, because of its brushes and commutator (to be fair, the latter wears out far more quickly), but also because it is downright ancient technology, predating even the induction type. Basically, the PMs of the PMSM are replaced by electromagnet coils in the rotor, which means the strength of the eld can be directly controlled, something that isn’t possible with xed-strength permanent magnets, of course. is makes eld-weakening to achieve high rpms a non-event, rather than something akin to juggling chainsaws, and makes minimizing the amount of reactive current that would otherwise slosh back and forth between the inverter and motor possible (this current does no useful work, but does use up some of the RMS current rating of the inverter’s semiconductor switches and cause heating from I2R loss). e downsides to the WRSM are a somewhat lower power density and a higher assembly cost for the rotor (a lower material cost, however, since copper is likely to remain much less expensive than any of the rare earths used in high-strength magnets). Also, of course, the eld needs a separate power stage to supply it, and the controller so ware is a bit more complex, but this is well-established technology, and the WRSM is eminently suitable for 4-quadrant traction applications (i.e. motoring and braking in forward and reverse).
Being able to use the rich ecosystem of existing electronic components, so ware and knowledge behind every industrial variable frequency drive, or VFD, is a huge advantage that cannot be overstated, and this is no doubt one of the major reasons that the axial- ux variation of the PMSM has received any attention, because it is de nitely a contender for the “most expensive way to construct a motor” award. As the name implies, the
axial- ux PMSM orients its eld magnets parallel to the output sha on a disc that is sandwiched between the stator phase windings (and the “back iron” to complete the magnetic path, if necessary). is naturally results in a motor with a relatively large diameter-to-length ratio, and since torque is proportional to the square of rotor diameter, but only directly proportional to rotor length, a wide-in-diameter but short-in-length motor—a disc shape—is optimal for high-torque applications, such as EV traction. Securing the eld magnets in a disc-
The least-radical alternative motor type—and one which has already been used by BMW, in fact—is the Wound-Rotor Synchronous Motor, or WRSM.Wound-Rotor Synchronous Motor, or WRSM AXIAL FLUX Flux is produced axially along the axis of the rotor RADIAL FLUX Flux is produced radially along the sideways of the rotor DC supply (slip rings) Rotor 3 phase supply
shaped rotor requires some form of banding on the circumference of the disc, so it is arguably about as prone to disintegration at high rpm as the surface PM construction, but it is undeniably less e ective than burying the magnets, as in the IPM construction. Furthermore, the push and pull of the magnetic elds from the stator poles exert torsional, or wave-like twisting, forces on the axial- ux rotor, and resisting these forces is not the strong suit of a disc shape. Consequently, the parts of the rotor that hold the eld magnets in place must have a very high strength-toweight ratio, which basically means using exotic (read: expensive!) materials like woven carbon ber composite. e combination of exotic construction materials and rare earth magnets in the rotor is the reason that the axial- ux con guration is one of the most expensive types being considered for EV use, and there doesn’t seem to be much that can be done to lower its cost in the future. For a more in-depth explanation of the axial- ux PMSM construction, see my article in the May/June 2020 issue of Charged. For those wondering if there is an axial- ux analog to the ACIM; well, it’s theoretically possible, but doesn’t really o er any compelling advantages over its conventional radial- ux counterpart.
Another alternative motor construction that leverages the existing VFD ecosystem is the Interior Permanent Magnet-Synchronous Reluctance Motor
Multiphysics simulation helps in the development of innovative battery technology by providing insight into mechanisms that impact battery operation, safety, and durability. The ability to run virtual experiments based on multiphysics models, from the detailed cell structure to battery pack scale, helps you make accurate predictions of real-world battery performance.
» comsol.com/feature/battery-design-innovation
(IPM-SynRM), which combines the buried magnets of the Interior PM Synchronous Motor (aka IPM-SM) with the rotor structure of the reluctance motor. Basically, the IPM-SynRM behaves pretty much like the IPM-SM as far as the inverter is concerned, but with a signi cant contribution from reluctance torque (more on what that is below). In both the IPM-SynRM and IPM-SM, burying the rotor magnets also partially shields them from heat as well as demagnetization from the stator (during overloads and eld weakening) and also eliminates the risk of being ung o the rotor at high rpm, as is the invariable case for the surface PM construction (that, to be fair, is rarely used in EVs these days). Both Toyota and Tesla have reportedly started using this type of motor, albeit not exclusively.
Moving along the continuum from the pure synchronous motor to the IPM-SM, then the IPM-SynRM, we nally come to the pure reluctance motor, which operates only on the attraction between electromagnets in the stator and a magnetically-so iron or steel rotor. Reluctance is the magnetic analog to resistance, so a magnetic circuit with minimum reluctance occurs when magnetic eld lines can freely ow from the North to South poles. is condition occurs in a reluctance motor when a diametrically-opposed pair of electromagnets on the stator align with a matching pair of projecting teeth on the rotor (maximum reluctance occurs when the rotor teeth are between two pairs of stator poles). By constructing the rotor with fewer teeth (or salient poles)
than the stator (e.g. 4 rotor poles to 6 stator poles), it can be ensured that when some salient poles are aligned with the stator electromagnets, some will be in between them. Sequentially energizing the stator electromagnets—switching from one pole pair to the next, hence the more common name of Switched Reluctance Motor—will cause the rotor to rotate in much the same fashion as in a PMSM or ACIM. One crucial di erence in the SRM, however, is that the stator electromagnets are supplied with a trapezoidal but unipolar (DC) current waveform, rather than a bipolar (AC) one. is means there are no iron losses in the rotor, which is a huge plus, but the torque output has a lot of ripple, and this subjects the rotor to immense tension and compression, which can then cause vibration and noise. It also means that the classic half-bridge power stage used for each phase in an inverter/VFD isn’t the best choice here; rather, a two-switch, two-diode power stage is preferred,
One crucial difference in the SRM is that the stator electromagnets are supplied with a trapezoidal, but unipolar (DC), current waveform, rather than a bipolar (AC) one.
as it can rapidly increase the winding current, and just as rapidly decrease it (while recycling any energy still stored in the winding inductance back to the battery).
Another issue that has hampered the adoption of reluctance motors until recently is the fact that the current through the stator electromagnets must be ramped up rapidly and with precise timing as a given rotor pole pair comes into alignment with a stator pole pair, then held at a de ned level for a few degrees of rotation, and then rapidly ramped down again as that rotor pole pair rotates out of alignment. is requires very accurate knowledge of the rotor position, which generally means a relatively expensive (and relatively delicate) absolute encoder, and as if that weren’t enough, the inductance of the stator electromagnets increases as a rotor pole pair comes into alignment (because the reluctance drops, and inductance is inversely proportional to reluctance), which makes increasing the current that much more di cult, especially given the fact that the dI/ dt (i.e. rate of change in current over time) must be carefully controlled for optimum torque production. is requires a lot of computing power, but fortunately, modern microcontrollers and Field-Programmable Gate Arrays (FPGAs) have more than sucient grunt for the task. Consequently, the SRM is bound to be the dominant EV traction motor of the future… Any day now, I’m sure…
Power levels in electric vehicles are increasing. EVs need to drive farther and charge faster. What does this mean for system safety? Expertise is critical when managing, distributing and protecting electrical systems. Eaton’s advanced battery disconnect units (BDUs) feature integrated Breaktor® circuit protection technology, enabling EV manufacturers around the globe to deliver the safest vehicle systems possible.
Because that’s what matters.
Engineering firm NI has been significantly expanding its EV battery testing capabilities over the past few years. The company reports an industrywide recognition that test data is an underutilized asset and that many systems need to be rebuilt to take better advantage of very rich data sets.
Tpalpable as it undergoes the transition to EVs. Governments have been implementing stricter emissions regulations for about a decade now and, more recently, they’re upending supply chain plans and forcing automakers to source and build locally. ere is also a growing sense that a few EV winners could take all. Whoever can iterate the fastest to deliver popular and pro table products could gain an insurmountable competitive advantage and reap all the rewards, leaving behind those who fail to adapt fast enough. e EV shi represents a signi cant challenge for the legacy industry, and requires a rethinking of everything, including design protocols, manufacturing processes, supply chains and business models.
One of the biggest bottlenecks to iterating in the EV
space is—obviously—batteries. From building up battery development and validation labs to securing raw materials supply to massively expanding production lines, there is an enormous amount of work to be done.
One company at the center of many of those new challenges is NI (formerly known as National Instruments). e Austin-based company—widely known for its engineering so ware platforms such as LabVIEW, and hardware products including data acquisition devices— has been making a lot of headlines as it announces new EV test solutions and acquires other companies in the battery testing industry.
Charged recently chatted with NI CEO Eric Starklo to learn more about the company’s expanding EV-testing focus.
Q Charged: We’ve been writing about EV battery testing technology for over a decade, and in the past few years, we’ve noticed a lot of new activity from NI. When did you decide to lean into the EV space?
A Eric Starklo : We have broad-based technologies that serve many things related to electrical and mechani-
cal engineering, so automotive has always been a segment for us for the long history of the company. About ve or six years ago, we started transitioning our strategy as a company to be more application-oriented.
e idea was to take that broad-based technology that we’ve built up over so many years and tune it to applications where our customers needed more complete capability. And in automotive, that was active safety systems and electric vehicles.
If you think back six or seven years ago, the prevailing point of view was that autonomy was closer than electrication. But then that ipped. We heard that loud and clear from our customers and we started to see them really accelerate EV plans. ey began making commitments externally for new models of EVs and trying to build up their battery and electronics technology, so we rapidly increased our organic investment.
And then, over the last couple of years, we augmented that with a series of acquisitions. We found that there were a lot of companies that have been around for a long time with some of the technologies that were now being used for EV testing. For example, very high-voltage stimulus and measurement—those products have been around for decades in other smaller industries, like the electric grid or certain aerospace testing applications. But then that technology intersected with a much bigger and rapidly moving industry in automotive. So what we’ve been doing is building our own technology, augmenting with these acquired companies to build system-level capability that helps our customers accelerate their paths to bringing EV technology to market and building it.
I can disclose that this is the fastest growing part of our company, and it’s an area we’ve done a lot to improve in, so it’s very exciting from our business point of view. And, personally, I’m almost 10 years into owning EVs. I’ve been a believer in the technology over that period and have seen it personally develop as a consumer, but also we’re working with all these leading-edge companies and we see how things are progressing. It’s a cool space.
Q Charged: You’ve been with NI for a large part of your career, correct?
A Eric Starklo : Yes, I’m an electrical engineer by education and background, and came to NI 25 years ago as a support engineer. I supported our customers here in the US and Sweden for a while, and then went into
product management and built up some of our early set of products. I launched PXI, which is still going strong these days as a modular hardware platform, and created the PXI Systems Alliance, which is the consortium that still governs that speci cation twenty years later. I also spent a lot of my time on our so ware products. And then I’ve had roles all over the company—sales and marketing, R&D—and created some business units to get more focused on vertical applications for our customers. en in 2020, right as COVID took hold, I took over as CEO. It’s an amazing company and I’m proud to lead it.
Q Charged: Five or six years ago, when you started to build up the EV testing vertical, what were some of the big problems you found that you thought you could solve for the automotive world?
A Eric Starklo : A couple of things. One is that our specialty as a company is really around automating measurement systems, and more and more of what you do with the data. e two principal things that we’re solving for, which really line up well with this industry, are predominantly about quality and performance. So our products and systems are typically used in validation and R&D to ensure the quality and performance of a design.
And then e ciency and cost. We typically associate that with manufacturing. Our systems—and the automation of our systems—are used to improve the e ciency of production, which helps scale the cost down. And we’re involved in this area as well.
To give you some other examples on the production side, we’re involved in very high-volume applications like semi-electronics, where we test in production the products that are sold in billions. And also in consumer electronics, the highest volume of consumer electronics products that we all use, we’ve been involved in that kind of testing for a long time.
So what we saw in the EV area was that the intensity of
development is the highest with batteries. e need for customers to get more high-quality data in validation to use to improve quality and performance is really intense. And the automation and measurement technology we have is right at the center of that. And over time we’ve added high-voltage electronics that are needed when you’re dealing with hundreds of amps and thousands of volts, that’s a di erent kind of front-end technology that’s needed.
And then, increasingly, we’re focused on data analytics. We found with batteries, as we’ve seen in other industries, it’s all about the data. If you look at the quality and performance side, for example, our customers are trying to gure out, “How’s our battery design going to perform in a variety of operating conditions? How’s it going to perform over di erent charge and discharge cycles? What are the best ways to charge and discharge the battery to improve its range and longevity?”
All the answers to those questions are in the data that comes from the test systems that we create with our customers. at’s what’s used for feedback into the design of the vehicle, it’s used to create the speci cations to ensure a long life on that battery, etc. All of those really, really critical things for the vehicle owner.
A massive amount of data comes from those tests, and being able to store, manage and analyze it has become more and more critical. You may have seen that we’re collaborating with GM, for example, on their data storage and management and analytics, and they’re really leaning into that point, as are others. But, broadly, for most other companies, it’s still a big problem. We’ve
surveyed our customers and found that more than half of them don’t even collect the data in a way that lends itself to determining the kind of information and insight that they want to get from that data. More than half of them really aren’t able to use that data upstream to improve the design, which is the ultimate goal. So we think there’s a huge amount of opportunity and innovation, especially as this EV application scales as is expected at a tremendous rate over the next few years.
Q Charged: We’ve interviewed quite a few people recently who have said that building new battery labs quickly is a big problem for many companies. Are you nding that as well?
A Eric Starklo : Right now, most of the intensity in our industry is exactly that. It’s building labs to be able to test all kinds of di erent variations at the cell, module, pack level, to determine the performance and other important characteristics. It’s kind of a gating capability to the ultimate competitiveness of EV platforms versus each other and versus non-EV platforms.
As time goes on, the challenges will change, and the speed of being able to produce cells, modules, packs, that’s going to be more and more important. To do things like scale the costs down, measurement is a big part of that. e time it takes to do a measurement, for example. We’ve seen this play out in other industries in the past. Like with semiconductors, because that’s such a high-volume industry, the optimization that’s occurred over the last couple of decades to ensure the quality, and test semiconductor devices, has been tremendous. And it’s been required, because, again, that becomes a gating function to the speed of producing semiconductors and the cost. In some semiconductor applications, half the cost can be testing costs.
I think in EV components, as they scale up to very high volumes compared to where they are today, that’s going to become a more and more important characteristic, the speed of testing and how it ts into manufacturing e ciency.
Q Charged: When you say that half the production costs can be testing the semiconductors, do you mean end-of-line testing to validate that the unit is working perfectly?
We’ve surveyed our customers and more than half of them don’t even collect the data in a way that lends itself to determining the kind of information and insight that they want to get from that data...to use that data upstream to improve the design, which is the ultimate goal.
”
A Eric Starklo : Yeah, that’s for end-of-line testing. As I said, most of the intensity for us right now is still in the earlier-stage battery validation labs, like what we’re doing with GM and others. Over time, we expect production testing to grow, and at the cell production level, that’s a particularly challenging area that has sort of massive scale and parallelism. And we are working on some innovative things there that we can talk more about in the future.
e value that we’ve delivered in production testing to other industries is in test time. e instrumentation that we build, because we’re an automated test-focused company, it’s optimized for the speed of the measurement, from everything from how quickly data goes over a backplane to how quickly you process the measurement data. And then the other area that has become more and more important is the integration of data analytics and the measurement system itself. A lot of times we think of data analytics as improving the design, where we take insight from the battery pack performance data to gure out how to improve its design. at’s classically done in validation.
In production, however, what we’re doing in the highest-volume applications is using the real-time data on a measurement system to improve the speed of the measurement system itself. So there are real-time optimizations that you can do based on the data that continue to make the automated system perform better, and it uses all the fancy technologies that people talk about, like machine learning, to ultimately improve performance. So those are the kind of technologies we invest in to improve performance and end-of-line production.
Q Charged: Is the challenge with the data—in battery validation, for example—the amount of it? Or do most people just not know how to analyze it? Or does it take too long to process it all?
A Eric Starklo : Yeah, it’s multiple things. It starts with many companies having a lot of unstructured data in lots of disparate systems. ey have measurement data, but it’s in di erent formats and stored in di erent places. So obviously, there’s this vision that I’d love to be able to take simulation data from my design, and take real-world measurements, and even take in-use data, and I’d like to be able to see deltas and patterns across those. at, itself, is quite challenging.
Data in di erent systems in di erent formats is not easily associated across a ow. Now, we have technology that helps do that, that can help create ingestion and structure so that those data sources can be brought together, and then you can start to do great things. Like comparing my actual performance to my design, that should be a base-level simple thing, but for a lot of people, it’s not easy to do that. en, of course, there are more sophisticated analytics, like anomaly detection and looking for patterns and data that might not be clearly obvious to the engineer that is looking at it manually.
In our opinion—informed by lots and lots of work with customers on this—the data challenge starts with acquiring the data itself, the quality of the acquired data, the way that it’s processed and stored. As I mentioned, more than half of the people we surveyed industry-wide said that the way that they capture and store data limits their ability to actually get insights from it. So the data problem starts there in the system that’s acquiring it.
But then beyond that, everyone I talk to in the industry recognizes that the test data is an underutilized asset. ey’ve got to be able to get more information from this very rich set of data about all the performance characteristics of their battery or their inverter, for example. So that, I believe, is one of the challenges in the industry that’s fairly nascent still. And the amount of data that’s being produced is going up exponentially because of the ramp-up of the technology. And everyone is asking themselves, “How do we incorporate all this data—billions of points of in-use data? How can that help us improve our processes and our technology, and so forth?” I think that’s the number one issue.
And then as I alluded to, the speed of automation as this industry scales, and we’ve seen it happen time and time again, e ciency becomes more and more important, how e ciently you can produce something. And in
I’d love to be able to take simulation data from my design, and take realworld measurements, and even take in-use data, and I’d like to be able to see deltas and patterns across those. That, itself, is quite challenging.
our industry, that typically means the speed of a measurement system is the thing that contributes to e ciency. So we think that our automation framework is an important thing we bring to help try to solve that.
Q Charged: Can you give us details of your recent acquisitions in the EV testing space, and how they t into your system?
A Eric Starklo : Yes, we’ve done a few. I’ll actually go back to one that people think of as outside this space— back in 2020, we acquired a company called Optimal+, which is a very sophisticated data analytics company that was, at the time, primarily focused on semiconductors. Most of the world’s semiconductor components that are produced, the data from those components runs through this system to enhance the performance of their production and ensure quality and yield. Our logic in buying that company was actually to use the technology as a general-purpose data analytics platform. So we are extending that technology, along with some of our own organic technology, to help solve this issue of data storage and analytics. e basis of those technologies is used in what we’re doing with GM, for example, for battery analytics. So that’s an acquisition we did that complemented some internal technology.
Another acquisition that is classically thought of as very EV-focused is NH Research. ey’re in the area of high-voltage electronics testing. We were already partnering with NHR in those kinds of applications and we were doing the lower voltage, or what we call the signal-level measurement and core so ware for a lot of those combined systems. So this acquisition enabled us to deliver to a customer a holistic capability that goes from the signal coming into and out of the battery, for example, all the way through the measurement and quality and so ware. So that was the rst company in this space.
Around the same time, we also acquired a carve-out of a German company called Heinzinger that is in a similar space, and served more of the European market with similar capability, while NHR served North American and Asia. Many of our customers want to have standard solutions with a big global scale. ey want to build battery labs in lots of di erent places and have systems that can support that. So bringing those technologies together was important. Both of those companies give us this system-level capability that goes all the way from very high-voltage stimulus and measurement all the way through the measurements and the so ware and the data.
And then the last company that we acquired was the test systems business of Kratzer Automation, also a German company. Kratzer was in the same ecosystem, with application-speci c EV so ware and integration capabilities. ey would integrate the full system consisting of a cycler, the high-voltage cycler from a company like Heinzinger or NHR. It will include measurement components from what NI has delivered. And then in addition, Kratzer has some unique so ware speci cally for running test programs around batteries speci cally. ose systems will o en have a battery pack that is going through temperature cycles and charge/discharge cycles, and characterizing its performance over that full range. e so ware is designed to run through those ramp pro les and control all of the equipment and deliver that. And Kratzer was already working with many of the large European OEMs, but also already had a footprint in North America and China with some of that capability.
So we are continuing to expand to be able to serve customers building these full integrated systems, particularly for battery labs. You can think of it as Kratzer building integrated systems that consist of all of those components that we’re bringing together and the soware and analytics.
Q Charged: How do you decide to acquire one of these companies versus building up the technology inhouse?
A Eric Starklo : We have a really disciplined process on that, and the term we use is a “strategy accelerator.” It iterates over time, because markets change, but we have a clear view of, “Here’s what we think are the most important customer problems that we have unique technology
to help solve. Here are the gaps between where we think the needs are going and what we currently have today.” And then we go to ll that. We are an engineering company with hundreds of millions of dollars spent each year on R&D, so nine times out of ten, our development roadmap and most of our investment goes into our own engineering.
But when there’s an opportunity to accelerate the roadmap by acquiring existing capability and expertise, that’s when it’s kind of a build-versus-buy decision for us. And accelerating the plan is especially important in a space like EVs, where the speed and the urgency of our customers is really high to get this technology ramped and at a high quality. And o en the conversation begins because we had some existing relationship with the companies because we were partnering with them on a gap that they were lling, and then we decided that we could get there much faster through acquisition.
It’s not just the products they have today, but they have the engineering expertise to do these things. e high-voltage design is a kind of unique expertise in the Kratzer case. ere’s some very specialized expertise. Kratzer had people, now we have the people, that are onsite engineering teams with the large OEMs that are e ectively the validation experts for their battery technology. at’s a really important and very unique skill set. So in large part, we’re acquiring the skills that would take us a lot longer to build if we were to do it organically. at is how we make that call.
Any space where you’ve got this high degree of urgency on technology development, the value of integrated capability is very, very high. In other words, a higher-level starting point so that I can rapidly get this battery lab up and running becomes very, very important. A core tenet of our value proposition is actually the openness of the system. Because of our customer’s urgency, they want a pretty complete solution-level capability, because they don’t have a lot of time and talent to put the systems together. ey also fully recognize, because of the speed of the market and the technology, the openness and exibility of the platform becomes very critical, because they can’t anticipate the new cell technology that they’re going to want to put in. ere are new innovations happening at module and pack level and battery control systems. So their system has to be able to be upgraded and expanded over time, and that’s our core value proposition. Open interfaces in so ware,
open interfaces in hardware, third-party components can be integrated. It’s not a bespoke system where the only way you can change it is to come back to us.
Recently, one of our battery supply customers, Northvolt, shared the criticality of owning their test strategy to achieve their sustainable goals. By working with an open technology partner like NI, they’re able to quickly implement the features they need in order to challenge the existing supply chain.
So having that integration capability is really important. And having a company at our scale that can deploy and support those kinds of systems all around the world is something that is really important to big automotive companies that are making a bet on EVs.
Q Charged: Can you talk about your test systems for other EV systems? Are you in the development lab for EV motors and power electronics? Are you in production testing?
A Eric Starklo : We’re a pretty ubiquitous kind of measurement platform—we do a little in all of those applications. e battery’s the biggest focus area. e next would be the inverter. A lot of this has to do with, “What are the most important technologies to our customers? Where are the critical things that de ne the performance of the vehicle?” at inverter system is really important, so we do both validation and production testing on the inverter system.
And then charging infrastructure as well. We’ve released a new capability fairly recently for charging infrastructure testing. You can imagine there’s some similar technology because to test a charger, you have to behave like a battery; to test a battery, you behave like a charger. It’s a little more complicated than that, but there is symmetry in the technologies. So that’s another application that we now serve with ramping volumes.
Accelerating the plan is especially important in a space like EVs, where the speed and the urgency of our customers is really high to get this technology ramped and at a high quality.
”
Thermal runaway occurs inside a battery cell through a fault, a crash scenario or some other defect that causes the cell to release thermal energy through chemical reactions. That thermal energy increases the temperature of the cell, the increased temperature drives faster kinetics, and more heat is released, further driving up the temperature.
Eventually, you can get to a tipping point and, essentially, the cell catches on re. ermal propagation occurs when that rst cell in thermal runaway causes its neighbors to also tip over into thermal runaway, which then spills over into the cells next to them.
Speaking at the recent Charged Virtual Conference on EV Engineering, John Williams, Vice President of Technical Services at Aspen Aerogels, gave an excellent overview of cutting-edge techniques to delay or prevent thermal propagation scenarios.
First, a little background. In China, the standard for thermal propagation delay is ve minutes, explained Williams. What that means is that, from the moment of detection of a hazardous situation in the battery pack, you must have a ve-minute delay before there’s a dangerous situation in the passenger compartment. ose ve minutes allows the driver to nd a place to park, exit the vehicle, and get a safe distance away.
“A ve-minute thermal propagation delay is essentially the table stakes now for manufacturers of electric vehicles,” said Williams. “As electric vehicles become more common, that ve minutes will almost certainly ratchet up to longer durations until, eventually, we would reach the promised land of having no thermal propagation at all.”
e ultimate goal is that one cell can go into thermal runaway and that’s it. It will be a maintenance event and
not a safety event. But we’re not there yet, and Williams explained why.
e physics of thermal propagation involve multiple pathways for heat to transfer from a cell in runaway to its neighbors, Figure 1. e rst and most important is cellto-cell conduction, and Williams is an expert in this particular pathway. Aspen Aerogels manufactures a barrier material, called Pyro in, designed to prevent cell-to-cell conduction. But that is not the only thermal pathway. ere is also gas release, both primary combustion, in which the reactants come from within the cell, and secondary combustion, in which the fuel inside the cell reacts with the external environment. ese gas ows and reactions drive a lot of the behaviors inside a pack
Better C2C insulation extends time-at-temperature
Secondary combustion (internal & external reactants): depends on gas-management
during a thermal propagation event. ere are also hot particulates being ejected during the initial phase of the thermal runaway. ere are secondary conductive pathways, such as busbars, cooling plates and structural interconnects between cells. ese are essentially thermal bridges—conductive pathways around a cell-to-cell barrier. Also, heat may be transferred through natural convection across air gaps that allow hot gases to spread throughout the battery pack.
“Active cooling can help draw down the energy of a cell in thermal runaway,” explained Williams, “although many times you can’t count on it, especially a er a crash scenario.”
A thermal barrier material between the cells can reduce heat transfer through cell-to-cell conduction. Barriers in prismatic and pouch packages serve two purposes: mechanical and thermal. e ideal barrier acts as both a mechanical compression pad and a thermal insulator, but there’s a trade-o : materials that make very good compression pads o en provide little thermal resistance, and those that act as good thermal and gas barriers tend to be
“A fi ve-minute thermal propagation delay is essentially the table stakes now for manufacturers of electric vehicles.”Figure 1: Heat transfer mechanisms during a thermal runaway
too sti to serve as compression pads.
Cells will swell as they age, and breathe as they go through charge-discharge cycles. Compression pads absorb the resulting cell movement. Swelling with age occurs over extended time scales, but the breathing that occurs over a short time interval has to be absorbed by the cell-to-cell barrier in order to maintain consistent pressure. Polyurethane and silicone foams are very e ective compression pads, but, as low-temperature materials, they simply cannot withstand thermal runaway situations. ey may delay thermal propagation a bit, but rarely enough to achieve even the ve-minute standard, and certainly not more than that. A good barrier is a exible material that’s also capable of withstanding high temperatures. ose two attributes— exibility and high-temperature tolerance—are o en mutually exclusive.
Figure 2 shows potential cell-to-cell barrier materials, with the Y-axis representing the maximum exposure temperature that a material can withstand and the X-axis indicating how much strain energy a material can absorb.
e right-hand side of the graph shows that materials commonly used as compression pads, such as silicone foams and polyurethane, can absorb a lot of strain energy, but their temperature tolerances max out around 100-300° C. On the le side of the graph, we see that metals and mica sheets are very resistant to high temperatures, but aren’t good at absorbing mechanical energy. e Holy Grail of barrier materials would reside in the upper-right corner of the graph, providing heat resistance ve times greater than silicone foam and mechanical absorption four orders of magnitude above that of mica sheets. According to Williams, Aspen Aerogels’ Pyro in ts the bill.
“ e universe of possible things that can live in that neighborhood is very, very small,” said Williams. “One of them is an aerogel such as our Pyro in, which is engineered speci cally to be a unitary material inside a cell-to-cell barrier, providing both the mechanical function of a compression pad and the thermal function of a re barrier.”
Aspen Aerogels has been in the aerogel business for more than 20 years, primarily focused on optimizing energy e ciency and passive re protection for industrial energy facilities. e company is now transferring its experience to the EV segment, with the goal of developing
The ideal barrier acts as both a mechanical compression pad and a thermal insulator, but there’s a tradeoff: materials that make very good compression pads often provide little thermal resistance, and vice versa.
the world’s best cell-to-cell barriers. Aspen’s testing shows that a two-millimeter sheet of Pyro in material can withstand exposure to a propane torch at 1,000° C, and absorb the strain energy from cell breathing and swelling. Williams claims that Aspen’s aerogels are the thinnest insulating materials available, and that they o er the best possible thermal insulation properties.
An aerogel is produced when complex polymer chains of silica molecules form through a sol-gel process. is process is similar to making gelatin, but using silica and ethanol instead of sugar and water. A wet phase of suspended silica starts out with the viscosity of water; in about two minutes, the suspension turns gelatinous. In the process, the silica self-assembles into long polymeric chains, which house tiny nano-pores.
“ at nano-porosity is the secret in an e ective thermal insulation material,” said Williams. “An aerogel’s pores are 10,000 times smaller than that of any other insulation material. In that four orders-of-magnitude di erence,
the physics completely changes. Now you have a material that has a thermal conductivity lower than still air, which means that when you compress it and squeeze out the air, the thermal conductivity can actually get better, [see Figure 3]. Under the same conditions, almost every other insulation material will get worse.”
Figure 4 shows the relationship between compressive stress and strain—the area under the curve represents the amount of strain energy the material can absorb reversibly. Williams says that Aspen’s newer M-grade materials will continue to absorb strain energy over the life of a vehicle with minimal compression set or fatigue.
“An aerogel’s pores are 10,000 times smaller than that of any other insulation material. In that four ordersof-magnitude difference, the physics completely changes.”
To test how materials behave during a thermal event, Aspen’s engineers subject the materials to mini-module testing. For example, they put a thermal barrier between two cells and triggered one cell with a heating pad to see if the barrier would prevent thermal propagation from one cell to the other.
e test setup in Figure 5 includes two o -the-shelf prismatic cells compressed inside of a jig, allowing the experimenters to control the cell-face pressure. e pressure at the end of a cell’s life tends to be higher than at the beginning of its life, so Aspen conducts a worstcase scenario test by arti cially creating higher pressure inside the jig. e graph on the right shows that the elevated temperature of the trigger cell (right) is absorbed by the barrier material, keeping the temperature of the adjacent cell (le ) at a safe level.
is mini-module experiment has limitations, however. In a real battery pack, other pathways—secondary conduction, hot particulates and convection—also a ect the system. is test merely demonstrates that thermal
runaway can be stopped at the cell-to-cell level, allowing designers to focus on isolating the other mechanisms. Pyro in has about the same density as urethane foam, but the latter isn’t a thermal barrier. Urethane foam coupled with a thermal barrier will typically be heavier than a comparable part that’s made with Pyro in alone. Because Pyro in is both lighter and thinner than other thermal/mechanical barriers, battery designers can pack more cells into the same space, increasing vehicle range.
Apsen’s customers include General Motors, which has chosen PyroThin as the cell-to-cell barrier for Ultium, the modular battery and drivetrain platform that will power more than 30 new EV models.
Aspen concentrates on Li-ion cells in prismatic and pouch packages because the aerogel material naturally lends itself to at, rectangular objects. In cylindrical cells, the interstitial space is a lot more complex, so other materials may perform better than Pyro in as cell-to-cell barriers. In those situations, Williams says that Pyro in is still suitable for pack covers, sidewall covers and other at geometries.
Some of the company’s customers have successfully used Pyro in with lithium-metal batteries, which tend to burn hotter than Li-ion cells, sometimes reaching 1,200 to 1,400° C. Lithium-metal batteries employ di erent grades of Pyro in, depending on the temperature requirement.
Aspen Aerogels currently o ers consulting services through its global engineering support team, which includes engineers in Asia, Europe and North America who will answer questions about battery pack and barrier designs. e company’s customers include General Motors, which has chosen Pyro in as the cellto-cell barrier for Ultium, the modular battery and drivetrain platform that will power more than 30 new EV models.
To learn more about thermal barriers, check out Aspen Aerogel’s presentation at the Charged Virtual Conference: ChargedEVs.co/AA-Webinar
Electric transit buses are becoming increasingly common sights on US streets. A new report from clean transport consultancy CALSTART found that there are some 5,480 full-size zero-emission buses in operation in the US—an increase of 66 percent since 2021—and another 859 in Canada.
e entire US eet of full-size transit buses numbered about 72,700 in 2019.
Federal incentives and—particularly in California— state programs have been a major enabler for transit agencies to phase out fossil fuel-burning buses. e Infrastructure Investment and Jobs Act, which became law in November of 2021, has made historic levels of funding available. In 2022, more than $1.6 billion was allocated to 150 transit eets throughout the US through the FTA’s Low and No Emission Grants and the Bus and Bus Facilities Grants.
“ e federal incentive has been a signi cant bene t, and will continue to be,” said Jarrett Stoltzfus, Senior Director of Government Relations and Public Policy at electric bus OEM Proterra.
Stoltzfus added that battery-electric buses are proving far more popular with transit agencies than hydrogen fuel cell buses. In 2022, there were about 5,269 battery-electric buses in operation or on the way, along with 211 fuel cell buses.
Hydrogen buses have the advantage of longer range, but the gap is shrinking as BEV technology continues to improve. Drawbacks of hydrogen include a lack of refueling infrastructure, and above all, costs.
“ e cost of a hydrogen fuel cell bus is quite a bit higher on average,” said Stoltzfus. “ ere’s a use case where hydrogen makes sense, but we found with the vast majority of transit customers…battery-electric is the only player.”
However, Mike Hynes, Electric Bus Program Manager at CALSTART, said, “A transit agency must weigh many factors and ultimately make the choice that is right for them. It is reasonable to think that some agencies may deploy both technologies.”
California remains the centerpiece of the electric bus market—there are nearly 2,000 e-buses in use by transit agencies around the state.
Tesla’s Nevada Gigafactory is quite a place—since its 2014 opening, the company has invested $6.2 billion in the region, and the 5.4-million-square-foot, 11,000-employee facility has produced some 7.3 billion battery cells, 1.5 million battery packs and 3.6 million drive units.
Now Tesla has announced plans to invest an additional $3.6 billion, hire 3,000 more team members, and add two major new operations at the site: one to build 4680-format battery cells at an annual capacity of 100 GWh (enough for around 1.5 million electric vehicles); and another to build the new Tesla Semi electric Class 8 truck.
Tesla originally announced that the expansion would consist of “two new factories,” but later made it clear that the plan is to build out the existing Gigafactory building to its originally-planned dimensions in order to accommodate the new cell and Semi production.
According to Benchmark Mineral Intelligence, Tesla’s total annual battery capacity could be as much as 439 GWh by the end of the decade, nipping at the heels of China’s BYD, the world’s largest EV battery producer with some 546 GWh of forecast capacity. (Tesla has been talking much bigger numbers—500 GWh a year in Nevada and 1,000 GWh total).
Tesla has been increasing production of its 4680 cells in California and in Texas, tripling production in the third quarter of last year from the previous quarter. Benchmark believes the company’s goal is to bring its cell-level cost down to $70 per kWh.
It’s unclear whether Panasonic, which currently makes battery cells at Tesla’s Nevada Gig, will be involved in the next round of expansion.
Meanwhile, Tesla’s earnings announcement for Q4 2022 brought the news of the company’s “best year ever on every level.” In 2022, Tesla delivered over 1.3 million cars and achieved a stellar 17% operating margin.
“On a full-year basis, revenue increased over 50%, operating income doubled, free cash ows increased over 50%, and our margins remained industry-leading,” said CFO Zach Kirkhorn.
Dutch electric bus and charging infrastructure manufacturer Ebusco has announced its new Ebusco 3.0 18-meter electric bus.
e company has used lightweight composite materials to keep the e-bus’s starting weight down to 14,500 kg (32,000 lb). In combination with 350 and 500 kWh LFP battery packs, such a lightweight frame should give the new electric bus a range of 700 kilometers (435 miles), according to the company. e bus has a maximum capacity of 150 passengers. e company adds that the lightweight structure enables the Ebusco 3.0 18-meter to utilize a single-tire axle con guration, making it possible to create an extra-wide aisle for people with physical disabilities and for prams.
“I am immensely proud that we are presenting this 18-meter bus today,” said Peter Bijvelds, CEO of Ebusco. “With about a third of our workforce working in R&D and engineering, we continuously manage to develop at high speed.”
Logistics company Schneider has ordered 92 Class 8 electric trucks for its intermodal operations in Southern California.
A er the rst order of 62 Freightliner eCascadias, manufactured by Daimler Truck North America, Schneider’s second order of 30 additional units brings the total to 92 Class 8 EVs.
Schneider says electric trucks are crucial to meeting its sustainability goals of reducing CO2 emissions by 7.5% by 2025 and 60% by 2035. Schneider states that it has already achieved more than half of its 2025 goal by reducing per-mile emissions by 5%.
e new eCascadias have the potential to avoid emitting over 81,000 pounds of carbon dioxide per day compared to conventional ICE trucks.
“ e integration of nearly 100 electric trucks is an important milestone for Schneider as we are moving beyond the electric truck testing phase to running an operation at scale,” said Schneider President and CEO Mark Rourke.
GM and its subsidiary BrightDrop have opened an EV manufacturing plant in Canada a er completely retooling the CAMI Assembly plant in Ontario.
e automaker began retooling CAMI for EV production in May 2022, and in just seven months, the team installed entirely new production equipment covering two million square feet.
BrightDrop will now use the CAMI plant to manufacture its Zevo 600 electric delivery vans, and DHL will be its rst Canadian customer.
“ e BrightDrop Zevo is a prime example of GM’s exible Ultium EV architecture, which is allowing us to quickly launch a full range of EVs for our customers,” said GM President Mark Reuss.
e state of New York has allocated $23 million in new funding for transportation electri cation initiatives. e total includes: $8 million under the Direct Current Fast Charging program to install EV infrastructure in Bu alo, Rochester, and Syracuse, including in underserved communities; $7 million in DCFC awards to ChargePoint and EvGateway to improve access in upstate New York; and $8 million for electric school buses and paratransit buses under the New York Truck Voucher Incentive Program.
e initiatives support the state’s goals under the Climate Leadership and Community Protection Act to reduce carbon emissions by 85 percent by 2050 and to direct at least 35 percent of the bene ts of clean energy investments to disadvantaged communities.
If you can’t measure it, you can’t manage it, as the saying goes. e J.D. Power EV Index is a new analytics tool designed to track the growth of the EV market in the US. Each month, the index arrives at a single number (on a 100-point scale) that represents the progress towards parity of EVs with legacy ICE vehicles. Sub-category numbers represent various roadblocks to parity.
Metrics are available at the national, regional, state and Designated Market Area (DMA) levels, and can be broken down by segment, brand and model.
e latest EV Index score is 47 (as of November 2022). Some categories improved and others declined during the 12-month pilot period.
J.D. Power aggregates millions of data points into six speci c categories to make up the EV Index:
Interest—Potential commitment to purchasing an EV based on customer data. e Interest score is currently 32, up 8 points from a year ago in the pilot phase, due largely to the growing number of EV models available or soon coming to market.
Availability— e proportion of new-vehicle buyers who have an EV purchase option that meets their buying needs. e Availability score is 30, up 12 points compared to a year ago.
Adoption— e proportion of new-vehicle buyers who purchase an EV. e Adoption score is 22, down 4 points from a year ago.
A ordability— e total cost of ownership of an EV compared with the ICE segment average (considering incentives, operating costs and residual value). e A ordability score is 84, down 12 points year over year, as EV prices have increased and 15 models lost eligibility for tax credits beginning in August when the IRA’s North America manufacturing criteria kicked in. e A ordability score is expected to change dramatically for January as the manufacturers’ volume cap is li ed. Infrastructure—Availability, location, speed and reliability of EV charging. e Infrastructure score is 27, down 4 points, primarily because the volume of EVs in operation is outpacing the rate of charger installations.
Experience—Owners’ overall satisfaction with their EVs, including appeal, quality, durability, range, and the sales and service experiences.
e Experience score is 89, down 2 points from a year ago.
“Vehicle electri cation has industry leaders grappling with billion-dollar decisions, and hyper-detailed data and analytics will help guide their decision-making,” said Elizabeth Krear, VP of Electric Vehicle Practice at J.D. Power. “We’ve created a smart and dynamic way to capture how the EV marketplace is performing in relation to gas-powered vehicles, and the index provides a heightened level of detail never seen before in this arena.”
EV manufacturer Envirotech Vehicles (EVTV), working with aviation refueling equipment maker Garsite, will deliver an electric aircra refueler to Atlantic Aviation in Colorado.
Phillip Oldridge, CEO of EVTV, said: “We are proud to deliver the rst all-electric aircra refueler to Atlantic Aviation and further plan to continue ful lling the aviation industry’s demand for more sustainable ground support equipment through our partnership with Garsite.”
e newly delivered vehicle is an aviation gasoline (avgas) truck with a 900-gallon capacity and an EV chassis.
“ anks to our relationship with EVTV, we have been able to develop an a ordable and reliable green alternative for aviation refueling,” said Teresa Montgomery, VP and GM of Garsite. “We have been purposeful in building a vehicle that is similar to operate as our traditional combustion engine refuelers so that our ground support teams can easily and intuitively shi to these electric models with minimal additional training.”
omas Built Buses and Proterra unveiled their Saf-TLiner C2 Jouley electric school bus back in 2018 , and there are now more than 300 units on the road. Now the companies have announced that the Jouleys have driven more than one million miles for school districts across North America.
is may be just the beginning. School buses, with their light duty cycles and predictable schedules, are o en cited as an ideal use case for electri cation, and unprecedented amounts of federal funding will soon become available under the EPA’s Clean School Bus program.
e Saf-T-Liner C2 Jouley uses Proterra Powered’s battery technology. It has total battery capacity of 226 kWh, and o ers up to 135 miles of range.
TBB and Proterra o er school bus operators a comprehensive, turn-key EV program that includes planning and funding consultation, electric school buses, charging systems, and charging infrastructure design and installation.
“Reaching one million miles with our C2 Jouley is a testament to the continued success of our best-in-class electric product and partnership with Proterra,” said Nick Rini, Director of the Freightliner Specialty Vehicles eMobility Group. “Together, we are paving the way for a cleaner and more e cient future for our kids, communities and the transportation industry.”
e iconic cement mixer truck, which fascinated so many of us in our childhood, is considered one of the most challenging vehicle classes to electrify, due to heavy loads and the need for continuous mixing of the concrete. However, Volvo Trucks and global construction materials company CEMEX have been working together since 2021 to make it happen, and they now have a fully electric heavy-duty mixer truck on the road.
e Volvo FMX Electric concrete mixer truck features two motors with total power of 330 kW, an I-Shi gearbox, and four battery packs with total capacity of 360 kWh. e mixer body is powered by a hydraulic system that gets its power from a traction battery.
e electric mixer truck is now in operation at the Berlin Spandau ready-mix plant in Berlin. It can be used for a full day’s work with a single top-up charge, says Volvo.
“Both our companies have committed to ambitious sustainability targets and collaboration is the way to get there,” said Volvo Trucks President Roger Alm. “Our electric trucks are zero-emission, and their silent operation also provides a better environment for people working at construction sites, as well as for residents.”
Volvo Trucks is developing a comprehensive electric line-up, including vehicles from 16 to 44 tons, in every segment from city distribution to refuse handling to urban construction and regional haulage. e company hopes to make half of its total sales of new trucks electric by 2030.
EV manufacturer VIA Motors has received a purchase order for 2,000 Class 3 VIA electric cutaway chassis cabs from Pegasus Specialty Vehicles to build Type A school buses, electric shuttles and paratransit buses.
A Pegasus bus on a VIA cutaway will feature all-wheel drive, low oor height and a small turning radius. e gross vehicle weight rating (GVWR) will range from 12,500 to 14,000 pounds, while the electric motors will generate 400 horsepower and will be able to transport a payload of 7,000 to 8,200 pounds within a range of 180 miles.
Swedish commercial EV manufacturer Volta Trucks has received its rst orders for over 300 units of its medium-duty urban delivery electric truck Volta Zero, with associated revenue of more than €85 million.
Series production Volta Zeros are expected to start rolling o the line of the company’s contract manufacturing facility in Steyr, Austria, in early Q2 2023.
Volta says it will reveal customer details “later.” e company claims to have pre-orders for 6,500 trucks.
“Volta Trucks is poised for a successful rst year of sales and production. We are con dent and focused on delivering on our strategic ambitions and purpose to decarbonize and improve the safety of city centers,” said Essa Al-Saleh, CEO of Volta Trucks.
Despite a showy concept, Ram’s EV pickup doesn’t look that different than its gasoline versions. Is following Ford’s lead the right move?
By John VoelckerIt was clear that the striking Ram 1500 REVolution Concept, unveiled at January’s Consumer Electronics Show (CES) in Las Vegas, foreshadowed a production electric Ram 1500 within the next couple of years. Ram is the last of the three Detroit makers to reveal a batteryelectric full-size pickup, and the concept stole the show with many tantalizing features. ese ranged from a lengthwise pass-through tunnel running bumper to bumper, for long lumber, to a mid-gate that allows the back of the cab to be used as an extension of the bed.
Surprisingly, the production version of the electric Ram 1500—due in Q4 of 2024—didn’t debut at February’s Chicago Auto Show. Instead, it surfaced days later in a cheeky Super Bowl ad addressing “Premature Electri cation,” and hinting that the Ram 1500 REV would be the right treatment for that ailment.
When the chuckles died down, the striking concept truck was revealed as just that: a concept. e production Ram EV pickup will be considerably more conventional on the outside—with, of course, entirely new underpinnings. Aside from a blanking plate over the grille and di erent headlights, taillights and wheels, even truck fans might be hard-pressed to tell from the side that it isn’t just another trim variation on the gasoline Ram 1500.
at came as a disappointment to some critics. It’s “not the game changer we expected,” said Car and Driver. “No design revolution,” sni ed Green Car Reports.
But in that respect, Ram has followed the lead of the Ford F-150 Lightning. Both use instantly recognizable cabs, pickup beds and pro les of their makers’ latest combustion-powered pickup trucks. at puts Ram and Ford in contrast to the approach taken by General Motors.
at company’s upcoming Chevrolet Silverado EV and GMC Sierra EV pickups unite the cabin and bed in a single structure, with a mid-gate that allows use of the passenger cabin for extra storage ahead of the bed. It’s reminiscent of nothing so much as the 2002-2013 Chevy Avalanche four-door unibody pickup.
Pickup a cionados will debate the merits of the two approaches for years to come. GM says it expects its
Even truck fans might be hardpressed to tell from the side that it isn’t just another trim variation on the gasoline Ram 1500.
EV lineup to be “additive” rather than “substitutive,” meaning it believes it will gain new customers who’ve not previously driven its trucks. Ford and Ram, conversely, appear to be targeting and reassuring existing customers, by highlighting the similarities of their electric trucks to their combustion-engine siblings.
Giving truck buyers what they want Ram clearly feels that pickup buyers want trucks that appear very similar to its current models. e looks are deceptive: An entirely new architecture, STLA Frame, sits beneath that familiar body. It’s intended solely for body-on-frame EV models, a genre largely con ned to North America.
Ram also con rmed that it will o er a range-extender version with a gasoline engine. In a late February media roundtable in New York City, Stellantis CEO Carlos Tavares clari ed that this truly meant a way to extend the range of a batteryelectric pickup truck—not just a Jeep-style plug-in hybrid with perhaps 40 miles of electric range.
Few technical specs are available to date—unsurprising, considering that the Ram 1500 REV won’t go into production for more than a year. Interested buyers can provide a refundable $100 deposit on a web site called RamREV.com, where further information is promised in due course.
ere’s little question that the former Fiat Chrysler has lagged on electri cation. rough the 2010s, it sold only the California-only Fiat 500e, while then-CEO Sergio Marchionne regularly highlighted the com-
Few technical specs are available to date—unsurprising, considering that the Ram 1500 REV won’t go into production for more than a year.
The looks are deceptive: An entirely new architecture, STLA Frame, sits beneath that familiar body. It’s intended solely for body-on-frame EV models, a genre largely confi ned to North America.
pany’s loss of $14,000 per vehicle. It launched a plug-in hybrid version of its Chrysler Paci ca minivan in 2017, and followed that with the Jeep Wrangler 4xe and more Jeep PHEVs to come.
GM has sold cars with plugs in volume since 2011. It now has bold plans for a dozen or more electric models built on its Ultium architecture. ose include the Chevy Silverado EV full-size pickup that debuted at last year’s CES, which is supposed to enter production this year— eet models rst, then consumer versions.
As for Ford, a er it red a CEO for lack of progress on electric vehicles, it launched the surprising and successful Mustang Mach-E electric SUV, the E-Transit commercial delivery van, and the wildly popular F-150 Lightning electric full-size pickup truck. All are now in production.
Stellantis steps up—Jeep, Ram lead in US CEO Tavares said his company will have announced eight battery-electric vehicles for North America by the end of this year. e rst three to hit the roads will be an electric version of the Ram ProMaster commercial van, followed by the entirely redesigned Fiat 500e and the Maserati Grecale Folgore, all by the end of 2023. Following that next year will be two Jeep EVs and the production Ram 1500 REV, plus two more.
ose are a subset of the global portfolio of EVs being launched by Stellantis—the company had 23 separate models at the end of 2022, expects 32 by the end of this year, and 47 by the end of 2024. Many of those are small European models from brands not sold in North America, including Citroën, Peugeot and Opel/Vauxhall.
Jeep’s rst three all-electric models were revealed last September. e subcompact Avenger went into production in October and is now on sale in Europe, where it was named 2023 European Car of the Year—a surprise
CEO Tavares said his company will have announced eight batteryelectric vehicles for North America by the end of this year.
honor. But it’s an entire size class smaller than the smallest Jeep sold in the US, the Renegade, so we won’t see it in North America. However, both the sleek, luxurious Wagoneer S and the upright, square, off-roading Recon will be sold around the world. Built in North America, those two will go on sale in 2024.
Asked about the practicalities of devoting scarce capital to a new EV that could really only be sold in North America, CEO Tavares told Charged , “We see strong demand for what Ram has to offer. People all over the world are buying the US lifestyle, the power. We will have news on that front soon.”
Does that mean that the Ram 1500 REV itself will be sold globally, or that the Ram brand will expand outside its current North American market? Tavares suggested that “Ram has some opportunities globally,” as Jeep did 10 years earlier, but that “the whole world
is not moving at the same pace on EVs” as Europe and North America.
If we had to guess, we’d suggest that means you may see Ram pickups sold in Europe and elsewhere—but they’re likely to be smaller than the Ram 1500 REV, and perhaps not electric.
We see strong demand for what Ram has to offer. People all over the world are buying the US lifestyle, the power. We will have news on that front soon.
Stellantis CEO Carlos Tavares ”
Vehicle Electrification Expo will bring together the entire supply chain involved in electric and hybrid vehicle development showcasing the very latest technologies for this rapidly growing market.
Join
Co-located with:
e White House announced that Tesla will move forward with plans to open its Supercharger network to non-Tesla EVs in the US. Tesla, which rolled its own charging standard back in the early days as other automakers dithered, has been moving towards opening up its Superchargers for some time. It has little choice but to do so, as subsidies for public chargers in the EU, and now in the US, are available only to companies that make their charging stations available to all drivers.
Tesla has already opened hundreds of stations in most of its European markets, where it was already using the standard CCS connector, but here in North America the company fell behind schedule—it had announced plans to open up by the end of 2022.
Making Superchargers available to non-Teslas may be a bit more challenging in the US, where the company still uses its own proprietary connector. However, Tesla has a new CCS adapter called the Magic Dock, which can be retro tted to existing Supercharger stalls (hopefully with a longer charging cable).
e Bipartisan Infrastructure Law will make some $7.5 billion in funding available for public chargers that serve all brands of EVs. Assuming that Tesla moves quickly to open up access, it stands to earn a sizable chunk of that pot of funds. e company has also announced plans to “more than double” the number of Superchargers in the US by the end of 2024. e o cial White House announcement reads, in part:
Tesla, for the rst time, will open a portion of its US Supercharger and Destination Charger network to non-Tesla EVs, making at least 7,500 chargers available for all EVs by the end of 2024. e open chargers will be distributed across the United States. ey will include at least 3,500 new and existing 250 kW Superchargers along highway corridors…and
Level 2 Destination Charging at locations like hotels and restaurants in urban and rural locations. All EV drivers will be able to access these stations using the Tesla app or website. Additionally, Tesla will more than double its full nationwide network of Superchargers.
If the past is any guide, the transition may not happen as quickly as advertised, and a number of important questions remain. Will opening the network increase congestion at Superchargers? Will Tesla have to change the layout of its stations to accommodate EVs that have their charge ports in other locations? Will it be allowed to charge non-Tesla drivers a higher rate for charging?
Over the longer term, will opening up prove to be a positive or a negative development for the EV trend-setter? Some have opined that Tesla risks losing one of its major competitive advantages. e Supercharger network is widely considered to be the “gold standard” of charging. Will allowing the thundering herd into the walled garden cause standards to slip?
Well, Tesla may not be great at meeting deadlines, but the company has proven to be good at rolling out large numbers of Superchargers (it currently has around 17,700 in the US, in addition to 10,000 Destination Chargers). Reliability is o en simply a numbers game—if a site has 20 charge points, it’s no big deal if 2 or 3 are out of order. Furthermore, back in 2021, Tesla’s CEO said that non-Tesla EV owners will use the Tesla smartphone app to manage and pay for their charging sessions. at sounds like a golden brand-building opportunity—and brand-building was historically another Tesla specialty.
Charging network operator Electrify America has entered into a 15-year virtual power purchase agreement (VPPA) with developer Terra-Gen to build a solar photovoltaic project in California’s Mojave Desert.
e Electrify America Solar Glow 1 project is expected to have a peak capacity of 75 MW, and estimated annual energy production of 225,000 MWh—enough to more than o set the energy delivered to Electrify America’s EV charging customers. e project is targeted to be operational by mid-2023.
Electrify America says its charging network is already backed by 100% renewable energy, through the purchase of environmental certi cates from existing renewable generation. By entering into a VPPA, Electrify America will support the key sustainability goal of additionality, which is to say that the project will create new, additional renewable energy generation.
e solar project may also be expanded at the option of Terra-Gen to include a co-located battery energy storage system. is would add to EA’s ongoing e ort to deploy over 30 MW of co-located behind-the-meter energy storage systems at its charging stations across the US.
“Electrify America’s business model—and purpose—have always been at the forefront of e orts to reduce emissions through enabling electric mobility,” said Giovanni Palazzo, CEO of Electrify America. “Our commitment to customers and to a sustainable future go hand-in-hand, which is why we are investing in renewable energy generation to commit to a net-zero carbon footprint associated with the energy delivered to our customers.”
Emporia Energy, a Colorado-based provider of home energy management technology (see the feature article in our January-March 2022 issue), is pushing the EVSE price envelope with a new Level 2 charger priced at $399.
“Competing chargers with similar specs, warranty, safety certi cations and customer ratings are selling on Amazon for as much as $750,” said Emporia CEO Shawn McLaughlin. “ ere is no reason consumers should be paying that much for a Level 2 EV charger. Heck, when you combine our charger with our Energy Management System, we o er added features like excess solar charging and peak demand management that our competition cannot o er, and we are still less expensive.”
When combined with the Emporia Smart Home Energy Management System, the Emporia Level 2 EV Charger o ers the ability to optimize energy use through automations that schedule charging based on utility time-of-use rates, excess solar generation and the user’s selected peak demand goals.
e Emporia system provides up to 48 amps, and comes with a generous 24-foot cable. It’s designed to t smoothly into Emporia’s energy management ecosystem, which includes a home battery system, energy monitor, smart plugs and third-party thermostat integration.
e new unit is ENERGY STAR-certi ed, which means that it uses 40% less energy in standby mode than non-certi ed products. Emporia notes that households and property managers using an ENERGY STAR-certied charger may qualify for special energy bill savings and rebates o ered by some states and local electric utilities.
ABB E-mobility provides products and services in every segment of the EV infrastructure eld. e multinational electronics giant unveiled a new home charging solution at the recent CES 2023 in Las Vegas.
ABB E-mobility’s new Terra Home is set to go on sale later this year. It features a stylish, minimalistic design that can be personalized to t into di erent home decors, as well as the ability to automatically prioritize the use of electricity from renewable domestic sources.
Plug and Charge, an intelligent feature that’s increasingly o ered by public chargers, enables instant and automatic user authentication. Using the ABB E-mobility charger app, owners can ensure that only they can connect to their Terra Home. Interactive lighting features indicate the state of the charging session. A cloud connection between the Terra Home and ABB E-mobility allows the charger to be remotely serviced, while remote rmware updates are designed to ensure a future-proof experience.
“O ering unprecedented user choice, the new Terra Home provides the exibility for an even greater number of people to simply and stylishly embrace the transition to electric mobility,” said Leon van de Pas, SVP for ABB’s Destination Charging business line.
TravelCenters of America (Nasdaq: TA), which operates a network of 281 travel centers (truck stops, to use the old-fashioned term) in 44 states under the TA, Petro and TA Express brands, is working with Electrify America to deploy DC fast charging at select TA/Petro locations.
TA aims to install some 1,000 chargers at 200 locations along major highways over ve years. Electrify America will provide its branded DC fast chargers, and will install, operate and maintain the charging stations through its Electrify Commercial business unit. EA will manage the entire process, obtaining permitting approvals, providing warranty and support services, and conducting on-site maintenance.
e EA chargers feature charging speeds of up to 350 kW, and support the Plug and Charge seamless payment standard. Customers will be able to locate and pay for charging through the Electrify America app. e rst stations are to open later this year.
“TA’s large locations with expansive amenities are attractive to EV motorists, and we are committed to expanding our EV charging infrastructure to accommodate this growing number of EV drivers,” said Jon Pertchik, CEO of TravelCenters of America. “Our agreement with best-in-class Electrify America provides an unmatched o ering of excellence in locations, service and support.”
“Electrify America is pleased to collaborate with an industry leader like TravelCenters of America to provide the critical infrastructure needed for EV drivers of today and tomorrow,” said Giovanni Palazzo, President and CEO of Electrify America. “Our combined strengths allow us to take bigger steps toward our shared vision of a more sustainable future.”
EV charging management platform AMPECO has raised $16 million in venture capital investment a er closing a $13-million Series A funding round led by BMW i Ventures. e round also included LAUNCHub Ventures, Cavalry Ventures and a number of angel investors.
e company o ers a white-label, hardware-agnostic EV charging management platform that covers public, private and home charging and currently serves 120 customers in 45 markets, representing over 62,000 charging points in Europe and North America.
AMPECO says it plans to use the new funding for expansion in North America and for building the company’s engineering and product innovation teams there as well as in the UK, France and Germany.
“ ere is an incredible opportunity for EV charging providers to build and scale a pro table business using innovative technologies,” says AMPECO CEO Orlin Radev. “ is is exactly what AMPECO o ers—we give them the exibility to use our so ware platform by integrating it closely with their existing systems and providing them with complete control of their business, from customer relationships to payment ows.”
EverCharge, an SK Group company, will deploy “a signi cant number” of EV charging stations at Houston’s George Bush International Airport for Avis Budget Group. e stations will power Avis and Budget’s rental eet of plug-in vehicles at the airport.
Intelligent load balancing allows eet operators to install more charging stations without straining the existing electrical grid or requiring costly utility upgrades. EverCharge’s patented load balancing so ware, SmartPower, is designed to enable large-scale, networked EV charging by analyzing charging patterns and intelligently allocating available power based on the needs of each individual vehicle.
“An optimal charging infrastructure is a necessary condition to support a seamless transition to an electri ed eet,” said Joe Ferraro, CEO at Avis Budget Group. “We are committed to o ering the best possible experience for our customers and this requires investing in technology that integrates with the diverse EV eet that our OEM partners will deliver.”
“EverCharge is on a mission to enable the widespread adoption of EVs by providing intelligent so ware and hardware charging solutions that leverage the capabilities of existing electrical infrastructure,” said Jason Appelbaum, CEO of EverCharge.
Following the launch in Houston, Avis Budget Group and EverCharge plan to extend their partnership to additional airport locations this year.
e Volkswagen Group and Enel X Way, the Enel Group’s company dedicated to electric mobility, have launched a joint venture called Ewiva, which aims to build a high-power charging (HPC) network of 3,000 charging points across Italy.
At the moment, Ewiva boasts some 750 chargers, either in operation or awaiting activation, in 233 locations, and Enel X Way operates approximately 17,000. e joint venture is expected to expand the number of locations to 500 by the end of 2023, and aims to reach 3,000 charging points, each with up to 350 kW and powered by 100% renewable energy, by 2025.
Ewiva expects to operate more than 800 sites focused on city centers, suburban areas and main roads used by commuters and tourists.
“ e expansion of charging infrastructure plays a key role in the success of e-cars. Enel and Volkswagen, two strong partners from di erent industries, have now joined forces to tackle this task in a targeted manner, thus advancing e-mobility in Italy,” said omas Schmall, CEO of Volkswagen Group Components.
Eco-Movement, a Netherlands-based provider of EV charging station data, has closed a Series A funding round. Investors included Dutch VC rm Ponooc and business news outlet Dow Jones.
As an independent B2B data platform, Eco-Movement provides charge point location and pricing information to navigation providers, online maps and eet operators. Clients include Tesla, TomTom, Shell, Apple and HERE. Many EV-related companies need accurate and complete data on public charging stations in North America and Europe. Eco-Movement “helps solve this challenge by working together with charge point operators to aggregate their data, including price and real-time availability, into a uniform, accurate and complete database.”
Roderick van den Berg, CEO of Eco-Movement, said, “ e relevance of our data is increasing every day. With the support of both Ponooc and Dow Jones, we will further improve our product to help charge point operators with their visibility on mobile and in-car maps and support the EV industry with the best data possible.”
“Our investment in Eco-Movement is a strong complement to our existing expertise in the renewable energy and sustainability arena,” said Almar Latour, CEO of Dow Jones. “Dow Jones’s commitment to increasing expertise in this arena will help our customers make informed decisions as they navigate major energy-related changes in the world as well as their own energy transitions.”
Z a f e r S a h i n o g l u W e s l e y P e n n i n g t o n
T e r r y A l g e r
I T E C c r e a t e s s p a c e f o r h i g h l y p o s i t i o n e d e n g i n e e r i n g p r o f e s s i o n a l s t o n e t w o r k , c o l l a b o r a t e a n d e x p e r i e n c e c u t t i n g - e d g e e l e c t r i f i c a t i o n t e c h n o l o g y o f t r a n s p o r t a t i o n . C o m e w a l k t h e e x p o t o f i n d s o l u t i o n s r a n g i n g f r o m h i g h v o l t a g e t e s t e q u i p m e n t t o c o m p o n e n t s , s i m u l a t i o n s a n d c o m p a n i e s s h o w c a s i n g t h e i r l a t e s t i n n o v a t i o n s N e t w o r k w i t h d e c i s i o n - m a k e r s a n d i n f l u e n c e r s i n t h e t r a n s p o r t a t i o n e l e c t r i f i c a t i o n i n d u s t r y ! H i g h l i g h t s o f e x h i b i t i n g :
E x h i b i t o r b o o t h s s t a r t a t $ 2 , 6 5 0 0 0
1 4 u n i q u e b r a n d i n g o p p o r t u n i t i e s
4 0 0 + a t t e n d e e s a r e e x p e c t e d t o v i s i t t h e e x p o t h a t c o m e f r o m
i n d u s t r i e s s u c h
a s H E V / P H E V ’ s , F a s t C h a r g i n g / E x t r e m e F a s t C h a r g i n g , a n d B r e a k i n g
T h o m a s W a l l n e r F a b r i z i o M a r t i n i E u g e n e C h o i
A b o u t U s :
I T E C i s a i m e d a t h e l p i n g t h e i n d u s t r y i n t h e t r a n s i t i o n f r o m c o n v e n t i o n a l v e h i c l e s t o a d v a n c e d e l e c t r i f i e d v e h i c l e s . T h e c o n f e r e n c e i s f o c u s e d o n c o m p o n e n t s , s y s t e m s , s t a n d a r d s , a n d g r i d i n t e r f a c e t e c h n o l o g i e s , r e l a t e d t o e f f i c i e n t p o w e r c o n v e r s i o n f o r a l l t y p e s o f e l e c t r i f i e d t r a n s p o r t a t i o n , i n c l u d i n g e l e c t r i c v e h i c l e s , h y b r i d e l e c t r i c v e h i c l e s , a n d p l u g - i n h y b r i d e l e c t r i c v e h i c l e s ( E V s , H E V s , a n d P H E V s ) a s w e l l a s h e a v y - d u t y , r a i l , a n d o f fr o a d v e h i c l e s a n d a i r p l a n e s a n d s h i p s
C o n t a c t U s : h t t p s : / / i t e c - c o n f . c o m / i n f o @ i t e c - c o n f . c o m
T e c h n o l o g i e s ( H y p e r l o o p , a u t o n o m o u s v e h i c l e s , d r o n e s ) .
L o c a t e d i n t h e a u t o m o b i l e a n d e n g i n e e r i n g h u b o f D e t r o i t
Electreon, a developer of wireless EV charging technology, is building a public wireless road project in Germany, which will power a public electric bus.
In collaboration with EnBW, a provider of EV charging infrastructure, Electreon will be deploying 1 km of Electric Road System (ERS) along a stretch of road in the city of Balingen, together with two static charging stations. is project follows a successful pilot of Electreon’s technology in the city of Karlsruhe, where an electri ed road was installed at the EnBW training center, powering a local public bus at peak hours.
Electreon will receive up to €3.2 million in public funding for the project.
“ e aim of this project is to open up wireless charging to the public in Germany and develop a tool that will assist public transportation planners in choosing where to install the inductive infrastructure for a speci c town or region,” said Dr. Andreas Wendt, CEO of Electreon Germany. “We have already shown in our joint Karlsruhe project with EnBW how e ective, safe and easy to deploy wireless dynamic charging is.”
e oil giants, ush with cash a er a year of record pro ts, are on a buying spree in the EV charging space. e latest company to be gobbled up is Volta Charging, which will be acquired by Shell USA in an all-cash transaction valued at approximately $169 million.
Shell USA will acquire all outstanding shares of Class A common stock of Volta at $0.86 per share. As part of the agreement, an a liate of Shell will provide loans to Volta to bridge the company through the closing of the transaction.
Volta’s public charging stations feature large video screens that can be used to display advertising or other information through the Volta Media Network.
Volta says that, following the acquisition, there will be no immediate change in driver experience, capabilities available to advertisers, or services provided to commercial properties and retail locations.
“Shell recognizes Volta’s industry-leading dual charging and media model delivers a public charging o ering that is a ordable, reliable, and accessible,” said Volta Interim CEO Vince Cubbage. “While the EV infrastructure market opportunity is potentially enormous, Volta’s ability to capture it independently, in challenging market conditions and with ongoing capital constraints, was limited. is transaction creates value for our shareholders and provides our employees and other stakeholders a clear path forward.”
Enphase Energy, a supplier of microinverter-based solar and battery systems, has successfully demonstrated a bidirectional EV charger that enables vehicle-to-home (V2H) and vehicle-to-grid (V2G) functionality. It also allows energy generated from solar panels to be sent directly to an EV battery.
e new product uses Enphase’s grid-forming IQ8 Microinverters and Ensemble energy management technology to seamlessly integrate into Enphase home energy systems. Enphase’s bidirectional EV charger supports both the CCS and CHAdeMO charging standards. Enphase has made details of its demonstration available in a white paper and a video.
“ e new bidirectional EV charger, along with Enphase’s solar and battery storage system, can be controlled from the Enphase App, empowering homeowners to make, use, save and sell their own power,” said Raghu Belur, Enphase co-founder and Chief Products O cer. “We are working with standards organizations, EV manufacturers and regulators to bring this charger to market in 2024.”
“ e Enphase bidirectional EV charger is the next step on our roadmap to building a solar-powered, all-in-one home energy system that further unlocks electri cation, resilience, savings and control for homeowners,” said Mohammad Alkuran, Enphase Senior Director of Systems Engineering.
Leviton sells both residential EV chargers and wireless smart home technology. Now the company is bringing these two product lines together with the launch of a new line of charging stations that are compatible with the My Leviton app.
e new EV Series product line, which will be available this quarter, includes 32-, 48- and 80-amp Level 2 charging stations that are designed to be easily integrated into the My Leviton ecosystem, which enables users to “take control of their entire homes with a single app, including EV chargers, lighting and load centers.”
Using the My Leviton App, users can remotely view the status of the charging station, and can be noti ed if any fault occurs during a charging session.
e My Leviton app for iOS and Android can also be used to control the Leviton Smart Load Center and the Decora Smart WiFi product lines, letting users perform actions such as viewing real-time load center energy consumption and scheduling lighting scenes.
Leviton’s EV Series charging stations feature a sleek look, an Energy Star rating and a water-resistant enclosure rated NEMA Type 3R. ey can be installed in indoor or outdoor locations.
In addition to the My Leviton app, the EV Series can easily integrate with other Leviton electrical infrastructure solutions, including surge protection devices. Leviton has a dedicated EVSE support team to assist customers with installation requirements, local codes, and rebates and incentives.
ew York-based Revel is riding two timely trends. Because rideshare vehicles log so many miles, electrifying them can deliver outsize emissions reductions—and drivers for the likes of Ly and Uber will need strategically located urban charging hubs. Meanwhile, millions of drivers in dense cities like New York live in locations where, unlike suburban drivers, they don’t have the possibility of installing chargers at their homes.
It’s easy to see that there’s a connection between ridesharing and urban public charging, but as Revel COO Paul Suhey recently explained to Charged , the synergies run much deeper than are apparent at rst glance—and Revel’s approach could prove to be a model for advancing EV adoption in cities around the world.
Q Charged: You’re doing three different things in New York City—you have fleets of electric scooters and Tesla rideshare vehicles, all in highly visible blue, and you also have a large public charging station called the Superhub in Brooklyn, with ambitious plans for more around the city. What’s the overarching business plan that ties all these related activities together?
A Paul Suhey: The primary challenge that we’re focused on is enabling EV adoption in cities. All of the challenges and opportunities, technology, regulatory issues, business model issues that are associated with enabling EV adoption at scale in major urban markets, that’s where we’re focused. From there, every business line sort of ladders up to that core mission. I think the two most important things that we’re doing right now are: enabling the build-out of fast charging in major urban markets; then, as we build out that infrastructure at scale, thinking about how we ensure that EVs can actually be integrated into that infrastructure in a way that enables or supports a reliable grid.
Sort of a dual challenge: How do you execute and put chargers in the ground today? Then, how do you think three, four or five years ahead to the time when EV adoption really starts to pick up, and the types of innovation that we’ll need to see, and how can we be on the ground
floor of driving that innovation today? As that relates to our general business models, I think one of the things that makes us different is we’re not just an infrastructure company and we’re not just a mobility company. We think it’s important at this stage in the industry that we’re integrated under the same roof. We’re very familiar right now with building fast charging, but to make a business case for that, you have to be confident that you have a certain level of utilization to justify the CapEx of putting those expensive chargers in the ground.
So having this infrastructure business integrated with our rideshare business, that gives us confidence that we have this captive source of demand, and if we build out this infrastructure, we have confidence in the level of utilization that we’ll see from our rideshare fleet. We build out that infrastructure, utilize it with our rideshare business, but then also make it completely publicly accessible. So if you’re a consumer, or if you’re another business such as
You have a certain level of utilization to justify the CapEx of putting those expensive chargers in the ground.
“ ”
a rental car company, you start to have con dence that there’s infrastructure available for you to charge. So that sort of solves the initial business model challenge of building infrastructure and then, whether it’s vehicle-to-grid or dynamic smart charging, beginning to pilot various elements that we think will be essential as this industry continues to grow to ensure that we’re supporting a reliable grid.
Q Charged: e chargers themselves are Revel-branded chargers, but who’s the equipment manufacturer?
A Paul Suhey: We have a strong partnership with an OEM called Tritium. We work closely with the charging market, sourcing chargers from various vendors. If you really focus on fast charging, there are probably ve or six major players.
Q Charged: What’s the advantage of having a Superhub as opposed to distributing public chargers in ones and twos around the city?
A Paul Suhey: I think one of the key di erences with the types of sites that we’re building compared to what’s been common in the industry is building sites at scale. Typically, outside of Tesla, the normal fast charging station maybe has two plugs on average. We’re building sites that have 10 to 25 plugs.
e main di erence from a technical perspective is that when you have two plugs, it’s what I refer to as an all-in-one unit. You have AC-to-DC conversion happening within that one unit. It’s 50 kW, 75 kW, that’s it. With bigger sites, you’re able to do that AC-to-DC recti cation in a central location, and then power-share across dispensers, so you can be much more intelligent around what charger is getting what speed at what time. It allows you to be more e cient with grid connections, and it allows you to be more e cient with your CapEx costs.
Q Charged: At your Superhub, you have several companies involved in managing the chargers, including AMP Control and EV Gateway. Sometimes it’s a little hard to sort out exactly what these di erent companies are doing. Can you explain how the pieces of the puzzle t together?
A Paul Suhey: Maybe one way to describe it is just the
di erent components of the general ecosystem. On the Amp Control side, it’s really about load. We’re able to look at what vehicles we have due out at certain times, how much energy we expect them to use, what constraints we have on how we want to manage our peak load, and then how we ensure that we intelligently charge our eet at the right speed to ensure that vehicles can make it out for their shi s on time—that they have enough energy and we minimize costs as much as possible. It allows us to minimize our electricity costs without impacting system reliability at all.
EV Gateway is more about connectivity to the chargers themselves—ensuring that you can connect the vehicle, initiate a charge session, authorize charge sessions—the backend system that enables that connectivity is where that comes into play.
Because this industry is so new, there’s a lot of interesting upstart companies. It’s a very disaggregated space. You have a lot of companies in the so ware space, some working in hardware, and there’s a lot of exciting technology development happening.
Q Charged: Your Superhub in Brooklyn powers your own rideshare vehicles and also is open to the public. Do you have di erent chargers designated just for your drivers?
A Paul Suhey: All the same chargers. All of them have either Tesla connectors or CCS connectors and we also have a few remaining CHAdeMO chargers. But all 25 chargers are completely open to the public as well as to our eet.
at’s one of the interesting synergies with our use case of combining these two di erent demand pro les—combining public charging with rideshare charging—because
With bigger sites, you’re able to do that AC-to-DC rectification in a central location, and then power-share across dispensers... It allows you to be more efficient with grid connections, and...your CapEx costs.
“ ”
it allows us to interplay those two pro les to maximize the station utilization. General public charging, you’ll have certain demand pro les throughout the day. Maybe you have a peak in the morning, it goes down in the a ernoon, you have another peak in the evening. We can control when and where our vehicles are charging, so when we know that we have more dead time at chargers, whether it’s overnight or it’s early in the morning or in the a ernoon, that’s when we will charge our vehicles. Combining those two demand sources really allows us to maximize our station utilization more than just being a standalone public charging business.
If you take the very simple use case of overnight, that’s when there’s very little, if any, demand for charging. at’s also when there’s very little, if any, demand for rideshare, so then we can take those vehicles o the road, charge them primarily overnight, then during the day, that’s when they’re doing rides. When they’re doing rides is when the public is primarily using the site. at gives you one example, but there’s a lot of blocks in the middle of the day when there’s less demand on the road for rideshare vehicles, and you can charge your vehicles.
at’ll change over time as well, because the demand pro le of a station in a residential neighborhood might be di erent than the demand pro le you might get on a major thoroughfare that’s connecting between a residential and a primary commercial district. So it really will depend on the site that you’re looking at.
Q Charged: You started a V2G pilot last August involving Fermata, another company that we’ve covered quite a bit.
A Paul Suhey: Yes. If you take a step back and think about V2G, I think the primary focus to date has tended to be on residential V2G or school buses. Both use cases make sense. School buses, you have a vehicle that is utilized nine months out of the year, not really utilized during the summer when the grid tends to be more stressed.
Residential, one of the primary challenges has been that it’s confusing enough to convince consumers to go electric and teach them about charging and everything that goes along with it. So try doing that at the same time that you’re trying to teach them about selling energy back into the grid, why they should care or how it should work. It’s complicated. With us, I think we see a big opportunity.
A: We’re focused in major urban markets, and those tend to be environments where the grid is more stressed and there’s more opportunity to participate in grid services and provide a valuable service to the grid.
And then B: We’re talking about operating a eet that we own and operate and control. It’s much easier for us as a business to make these strategic decisions and investments when we control the vehicles. You don’t have to worry about individual consumers making individual decisions.
Combining public charging with rideshare charging...allows us to interplay those two profiles to maximize the station utilization.Image courtesy of Revel
But the use case that we see is participating in V2G operations the ve to ten times a year when the grid is most stressed. So, unlike a school bus where you’re exporting energy every single day of the summer for weeks at a time, what are the ten times throughout the year when we can get a signal from the utility that there’s an opportunity for us to export energy back into the grid for a four-hour period? What that allows is at scale, as we control these EVs, we can make the determination: should this vehicle be doing rides via our rideshare business or should it be dispatched to a certain station at a certain time to send energy back to the grid?
Q Charged: So you might take a vehicle out of rideshare service if it’s more pro table for it to act as a battery for the grid at a particular time?
A Paul Suhey: Correct. And then it’s important to keep in mind that the times that we’ve wanted to do that is maybe ten times a year—certain locations on the grid, certain networks will have signals at di erent times. So maybe at one location there’s a need from noon to 4:00 PM. At another location it might be 6:00 PM to 10:00 PM. So the number of vehicles that we need to take out of our service to provide a lot of value to the grid does not materially impact the quality of our rideshare service.
All of the backend ride operations, the determination of where vehicles should be used is our in-house so ware. Just the one-to-one V2G tech is what we’ve partnered with Fermata on.
Q Charged: You have plans to open ve more of these Superhubs in New York City over the next few years. I spoke to another company recently, called Beam Global, and they told me that it can take up to
two years in New York City to get through the whole process: permits, environmental impact, getting the power hooked up. Does that sound about right or are they exaggerating?
A Paul Suhey: It’s spot-on. ere’s a big window of uncertainty depending on the nature of the site, how much power you’re bringing, a lot of di erent factors. But it can be anywhere from a year, if you’re lucky, to three years. Two years is a safe average.
Each site that we look to build, before we sign a lease, we’re working with the utility, we’re going through the engineering process to understand the estimated timeline to bring power to the site. at’s what gives us the con dence of where we’re focusing, depending on how long we’re projecting those development timelines to be.
One thing to keep in mind when you’re dealing with the amount of load that you would have for a typical fast charging site at scale, that’s the type of load that usually goes in a major commercial building. e utility is used to working on much longer timeframes because if you’re working on a massive ground-up development process, that’s a four- or ve-year build process. A utility taking two years, that’s not a major constraint in the general construction and operations of the building, but this is a major constraint for our charging site going live. So working through the process that typically takes two years or three years and trying to say, “Hey, we need this done faster,” you’re kind of working in a way that the utility hasn’t really done before. It’s a kind of new time crunch.
We de nitely have a very strong relationship with Con Edison, the utility here in New York City. ey’ve been very open and transparent about their process, how things need to improve, what they’re working on. We give them suggestions. But the reality is on both sides, whether it’s
A utility taking two years, that’s not a major constraint in the general construction and operations of a building, but this is a major constraint for our [charging] site going live.Image courtesy of Revel
the customer or the utility, we’re working through these issues together for the rst time. is is new, so until you actually go through the process and do it, it’s going to be di cult to say how long it takes to bring power to a site. I think each side gets more e cient as we work together.
Q Charged: At the moment, your Superhubs are just planned for New York?
A Paul Suhey: Just in New York, but de nitely looking to expand that network to other major cities soon. Our primary focus is on New York City. at’s where we’re based, that’s where we’re founded. at’s the market that we know the best, where we think there’s a massive gap in opportunity. But infrastructure, you have to think in a time scale of years, so if we want to build infrastructure in X City in 2027, you almost have to be thinking about that now.
Q Charged: Tell me about the other users of your Superhub besides your own rideshare vehicles. Have you also partnered with some other rideshare providers or eets?
A Paul Suhey: Yeah, of the third-party users that we get, meaning non-Revel usage, I’d say about maybe 50% tends to be from other taxi or rideshare customers—EV drivers that are driving for Uber and Ly , or driving a yellow taxi that are going electric. And I think that’s a trend that we’ll continue to see because those are the drivers that are putting the most miles on their vehicle, can see the most bene ts of going electric and operating cost savings versus an internal combustion engine. And then the remaining 50% is general consumers looking for somewhere to charge, leaving the city for a weekend, coming back, doing small trips. We’ve also seen a lot of people that are buying an EV or leasing or renting an EV because we’re in their neighborhood, they’re con dent that they actually have somewhere to charge. at’s also our hope as we build infrastructure, make it more publicly accessible, you start to give consumers more con dence that they can make the switch to electric because they will have somewhere to charge.
Q Charged: When it comes to public chargers, a lot of people are appalled at how o en they’re out of order. I’ve talked to a lot of people about this and nobody
seems to know exactly what the problem is. Why can’t companies keep those darn things working?
A Paul Suhey: A lot of answers to that. And it depends on if I’m talking fast charging or Level 2 charging. First and foremost, it’s hard. e technology is new, hardware is new, things break, growing pains. But I think there are a couple of challenges at play.
For Level 2 in particular, there can be di ering business models on how those charging installations get installed. O entimes you might have a municipality or a grocery store, a location that wants to install that charger as an amenity. Charging company comes along, sells the hardware, and that’s it. ey make money on the hardware sale, but they don’t really have to worry too much about ensuring utilization. And you’re bringing revenue through that utilization. You don’t have the right incentives—the store operator or whoever owns that real estate, they don’t care too much, they’re not making a bunch of money o of it. So no one’s really incentivized to ensure the uptime of that charger.
en from a fast charging perspective, I think one of the challenges that we hope to solve is that, when you have two or three chargers, if one charger is broken, that means that half or a third of the chargers in that site are down. But if you have 10 or 20 chargers, if one charger goes down, two chargers go down, you’re able to x that without materially impacting the customer experience and the reliability experience.
As we focus on building out a dense network within one location or one city, that allows us to concentrate our service and our spare parts network in that location. As opposed to if you’re a company where you have chargers here, a hundred miles over here, it can be di cult to stand up the service network, the spare parts network, to really support that operation, especially when you’re dealing with new technology where you’re not always certain which part is going to break.
We want to be the largest and most reliable fast charging network in major cities. e major component of that is thinking really hard about the maintenance in cities, spare parts operation, warranty with the manufacturer, timeline of getting things xed, communication. It’s a whole operation to ensure that you understand when you have issues, which is a problem in and of itself, and then you pinpoint the root cause of those issues and x them on a timeframe that keeps that experience where it needs to be.
If there’s one topic that everyone in the EV infrastructure eld is talking about these days, it’s charge management. As organizations of all sizes electrify their vehicles, they o en nd that power consumption is a major constraint. Charging stations, especially those that serve large eets and/or heavy-duty vehicles, can suck up vast amounts of power, and simply plugging an array of chargers into the wall (so to speak) is not a good option. Using charge management to manage power levels and charging times enables a eet or charging provider to limit its peak power usage and thus lower its electricity bills, but it also o ers several other bene ts. Managing charging times can ensure that vehicles are charged with renewable energy as much as possible. Planning infrastructure projects with charge management in mind can allow companies to get their charging done with fewer and/or lower-power chargers, and it can help to avoid long delays in getting new electrical service set up by the local utility. e Mobility House provides charge management systems to a wide variety of customers in Europe and in
the US, including eet operators, car dealerships, multifamily housing and workplace charging projects. Charged spoke with Business Development Manager Sam HillCristol about how charge management works, how it can address the di erent needs of various types of customers, and how emerging technologies such as vehicle-to-grid and micro-grids t into the picture.
Q Charged: As far as the terminology, I see charging management, load management, load balancing, smart charging...Do these have some speci c meanings, or are they di erent terms for the same thing?
A Sam Hill-Cristol: I’m not sure that everyone agrees, but we say charge management system (CMS), or charging and energy management—we usually throw energy in there to communicate that we’re controlling power ows. Some of those other terms refer to functions that a charge management system should provide. A useful CMS is a so ware solution that can provide load management, load balancing and even dynamic load management, which is a situation where the chargers are on the same meter as a building load, and we’re actually monitoring the building load and adjusting the charge limit based on the building load.
Q Charged: I’ve heard a lot about charge management systems, but I’ve never seen one. What’s the physical layout at a vehicle depot or a charging hub? Are there some servers in a shed that are connected to all the charging stations?
A Sam Hill-Cristol: It varies. ere are versions of charge management that are pretty invisible on the site. ese are cloud-based and/or within the chargers themselves. ey might do something simple like share power equally between a few chargers on a single circuit, depending on how many vehicles are plugged in. A more robust charge management system—something that is more of a t for eets or multi-family, and can really help us attack the distribution grid limitations—that system has some hard-wired components and a local controller. A little controller, probably the size of your palm, sits on-site inside a weatherproof box. It has a 120-volt power supply and a switch, or maybe multiple switches, so you can connect a bunch of chargers to it. at controller is hard-wired with Ethernet cable into
every charger. It’s not daisy-chained from one charger to another—there’s no line where if you break communication with one charger, then you lose everything else down the line. We have what we call a ChargePilot kit, which is basically what I described, and we can just send that out to a site. And we typically work with an engineer or an EPC [engineering, procurement and construction] rm that knows our system. ey can just install it, and it’s pretty straightforward. ere’s also a router, so we can send data from our controller up to the cloud, to a user interface that the eet can log into and see data and a live view of what’s happening on the site.
Q Charged: Is the so ware that makes all this work something that e Mobility House provides, or could that be a commercial product that’s available from di erent vendors?
A Sam Hill-Cristol: Certainly there are options, but yes, e Mobility House provides that so ware. What I just described, all of those physical components are relatively o -the-shelf, but the so ware is what’s proprietary and where all the intelligence lies. at’s what allows us to optimize charging based on whatever the available power is, whatever the limit is that the grid has, or a sub-panel has, the schedules of the vehicles and the cost of electricity. Now those are the three big things that we’re paying attention to, but how that’s optimized and which chargers are told to turn on when and how much, that’s the so ware that lives on the controller. Of course we can push updates to it from the cloud, but if you were to lose connectivity, you would still have that intelligence, and that charging management would still occur.
at’s the architecture of e Mobility House’s system, ChargePilot. It’s not the architecture of every system, but that’s what we see as a best-in-class charge management system, and that’s what you need from a reliability perspective.
We’re starting to see more RFPs that are just for charge management, that are isolating that as an individual category.
Q Charged: Is there such a thing as a standalone, off-the-shelf software package that somebody could go out and buy?
A Sam Hill-Cristol: There are third-party charge management companies like ours that are selling software as a service, and we do a lot of work with partners. Someone could come to us and say, “I want to buy your system and roll it out on a bunch of sites and resell it.” We do a lot of reselling work. I think that is a good model. There’s also in-house charge management software that a charger manufacturer makes. The downside of that is that it only works with the chargers that that company makes, so you kind of get locked in as a fleet and you don’t have any flexibility to go buy new chargers, because then your new chargers won’t talk to your old chargers.
Q Charged: What kind of RFPs do you usually see? Do most customers want a full turnkey system, or do some mix and match products and services?
A Sam Hill-Cristol: We’re starting to see more RFPs that are just for charge management, that are isolating that as an individual category. And if you are a sophisticated customer, like a transit agency, we see a lot of piecemeal procurement—we’re going to get the buses, we’re going to get the chargers, we’re going to get charge management, and we’re going to put a solution together that works for us. We’re increasingly starting to see that, and seeing charge management broken out as its own RFP.
Even on some of the smaller municipal fleets, we’re starting to see this, as opposed to one RFP that’s for everything, or it’s just for chargers and they don’t even really talk about charge management. I think the industry’s getting a little more educated on that, but we still see the old type of RFP where they just say “Hey, let’s buy some chargers,” and don’t really think about the software at all.
That’s why we created our RFP Guidebook for charging and energy management. We saw that many fleet operators didn’t know the full set of questions to ask about what their charge management could or should do for them. There were actually several RFPs that went out in the last couple of years that didn’t evaluate or differentiate for charge management comprehensively, and they had to start over and try again.
Q Charged: e classic story is that a eet buys a few EVs, they buy a few chargers, and a er a while they realize that they need expert help to get their system organized. Would you say that’s a thing of the past, or are you still seeing eets that don’t understand the need for charge management?
A Sam Hill-Cristol: I would say it’s still there, but it’s changing, and a lot of our job has been market education. Certainly in the school bus space, transit space, municipal space, I think we’re starting to see a shi towards a more complete approach—people kind of learning from the rst wave and thinking a little more critically about all the pieces of the puzzle.
Q Charged: Would you say that charge management is analogous to a company’s IT department in the sense that a smaller company might buy a turnkey system, whereas a larger, more sophisticated customer might have their own in-house people that run the system?
A Sam Hill-Cristol: I would draw that parallel more about the whole charging ecosystem. I don’t think there’s any eet out there, as sophisticated as they are, that’s putting together their own charge management system. I think the sophisticated eets are putting together their own charging ecosystem of vehicles, chargers and charge management, and they’re picking and choosing vendors. Whereas yes, a smaller eet might say, “Just give me the whole ecosystem. You give me the chargers, you give me the so ware, all turnkey from one provider.” We don’t see anyone building a charge management system from components from the ground up. at just doesn’t make sense. We’re always selling a whole system, we’re always selling so ware as a service, but for more sophisticated eets, we’ll sell just charge management. For others, we might tack on some chargers for them if they ask for that.
From an IT perspective, we certainly see more demanding security requirements from larger eets. ey’re more involved in that sense, but they’re still buying the whole turnkey so ware solution. ey just might buy that separately from charging hardware.
Q Charged: Vehicles, chargers, charge management— could we call those the ree Pillars of an electri cation project?
A Sam Hill-Cristol: Yeah, I would say those are the three most important, and I would say that charge management was not considered as one of the three pillars until recently. It was seen as within the chargers themselves, and now it’s starting to be seen separately.
Q Charged: Some of the chargers do provide some rudimentary charge management.
A Sam Hill-Cristol: Exactly. It’s sort of a spectrum of charge management from what I would call load sharing on a single circuit to a more advanced sort of site-level optimization that can look at schedules, costs, power limitations across a whole site, multiple sub-panels, multiple types of chargers; and even provide some ability to integrate with solar and storage, or a micro-grid, or talk to a depot management system that’s calculating
I would say that charge management was not considered as one of the three pillars until recently. It was seen as within the chargers themselves, and now it’s starting to be seen separately.
schedules. You start to get to a pretty advanced level with di erent integrations. But it is a spectrum and there is a very sort of simple version that I think works when you have only a couple chargers.
Q Charged: So, the main goal is to control our energy consumption. Can we put some numbers to that? Let’s say I have a eet of 50 trucks or buses. How much power capacity am I going to need, and by what factor can I reduce that requirement by using charge management?
A Sam Hill-Cristol: It really depends on the duty cycle of the vehicle, but if you say it’s a larger, mid-mile delivery truck, maybe you’re looking at a 50-kilowatt to 100-kilowatt charger minimum, and a 250 kW or even 350 kW charger could be needed. If you need that for every vehicle, you’re looking at 2,500 kilowatts, 5,000 kilowatts minimum. For school buses, o en we’re looking at 19.2 kW charging stations. So if you had 50 of those, that’s about 960 kilowatts. And that’s what you would expect to see if you just plugged in all of the vehicles at the same time.
With charge management, we can see anywhere from a 15 to 20% reduction in that peak, all the way up to maybe 60% for school buses in some cases that we’ve modeled. School buses are a use case that has a huge potential for charge management because their schedules are not very demanding. You might be able to bring that 960 kW peak
down to 200 kW, because you’re spreading that across the whole night. For commercial trucks, it may be somewhere in the middle. en for a transit agency, where you have really demanding duty cycles, the vehicles are on the road a lot, maybe you only see a 10-15% reduction. But even then, for a eet of 50 transit buses, you’re looking at at least 5 megawatts or something in an unmanaged scenario, so even that relatively smaller reduction can have some pretty big cost implications.
Certainly that has operating cost implications—if you can reduce your peak by 50 to 60%, you’re going to save money on demand charges and reduce your electricity bill. But I think it also can have implications for the capital costs if you know what charge management can do for you up front. One thing I like to point out, which I think is not always talked about, is: What’s your ratio of plugs to power capacity? Because if you’re reducing your peak and maybe instead of 960 kW, you only need 200 or 250 kW, you might be able to buy fewer chargers. And if those chargers are of the type where you have 3 or 5 plugs for every power cabinet, you can still plug all the buses in.
You still get 50 plugs, but behind that is less power, and that’s a lot cheaper. We talk a lot about vehicleto-charger ratio, but I think the right charging management system makes you think about your plugto-power capacity ratio, and that might lead to a cheaper capital solution because you have that so ware control.
Q Charged: It sounds like school buses are at one end of the use-case spectrum and transit buses are at the other end.
A Sam Hill-Cristol: Yeah, I think that’s right. It’s about how much the vehicle is on the road. What are the duty cycles? What’s the dwell time? Do you have any exceptions to standard routes? If you’re a municipal eet you may have some emergency response—sometimes you need to respond to a snowstorm with your plow trucks. You can certainly get complicated and think about the edge cases, but generally, you have school buses or municipal vehicles that only operate during the day, they sit all night. And that really provides a ton of exibility in terms of how many chargers you might need and how much you can optimize the charging, how low you can push the peak by staggering the charging. But for a good management system, the key overriding parameter is operation of the vehicle. You can never sacri ce that. You get into the transit world, for example, you have a bus that’s running multiple routes a day, maybe it’s charging multiple times a day, you have to respect that. And so sometimes you say, “I actually can’t delay charging. I’d like to, it’s going to be expensive right now, but I have to charge.” e right charge management system pays attention to vehicle routes rst and foremost, and then everything else ows from there.
Q Charged: It sounds like there’s quite a lot of consultation with a customer involved before they ever buy any chargers.
A Sam Hill-Cristol: Yes, there can be. Maybe this makes us unique in the charge management world, I’m not sure, but we o en come in on a consulting basis, provide some modeling simulations, guide the customers through. We’re not tied to any hardware, so based on a simulation of what we think their optimized charging schedules will look like, we come up with a 15-minute interval basis. And we can look at that in a lot of detail and say, “ is is how many vehicles are going to be charging at one time. is is how many vehicles are going to be plugged in at one time, based on our assumptions around when the vehicles are operating. Here’s how many chargers we think might make sense, and here’s a couple hardware options.” We o en provide that to all types of customers, but certainly to ones that have less capacity in-house, maybe less money to hire a large engineering rm that’s going to do a full feasibility plan for them.
Q Charged: I’ve talked to a number of people recently who say that getting electrical service hooked up takes a long time, and that can be a big bottleneck.
A Sam Hill-Cristol: I think those people are right and smart. We are seeing a big crunch in a lot of the country, California being one big example. We’re hearing from customers about limitations in power capacity, about utilities saying, “We need two or three years to give you the power that you need.” We try to bridge that gap. We try to say, “First, maybe you don’t need as much power as you think you do.” at’s part of our work with the charge management system.
If you know what your charge management system can do, then you can actually have some con dence to say, “Hey, I thought I needed a megawatt of power but now I only need 300 kilowatts, so maybe I can start
my electri cation sooner, and use charge management to bridge the gap between when I want to put these vehicles on the road and when the utility is ready to upgrade my service.” And then I can iterate. “Two, three years from now, I can raise the limit. Maybe my utility nishes construction, and now instead of 300 kilowatts, I have that megawatt I originally wanted, and I can shi my charge management system, change the limit that it has, and unlock more power.”
We see our system as enabling that sort of phased approach—it future-proofs the eet so they can start now, they don’t have to wait. I have an example of a customer in New York City that is getting a bunch of buses through the EPA Clean School Bus Program, and the utility said, “We have under 100 kilowatts for you to use on our system.”
We put that in our model, and we tell them how many buses we think they can charge on that limited power, and then that gives the customer the tools to plan their deployment. ey say, “Okay, I can put 18 of my 25 buses at this site with the power limitations, and the rest need to go to my other depot.” Otherwise, those buses would show up and they would try to put the chargers in, and they would run into a big issue. It can be hard to get that information from the utility, but once you have that knowledge, then you really have a constraint, and the charge management system can maximize that situation, as opposed to, in our previous example, 19 kilowatts per bus, that might only be 3 or 4 buses without the charge management.
Q Charged: So they can modify their plan and stretch out their procurement, but still move ahead.
A Sam Hill-Cristol: Still move ahead, and not stretch it out as much as they would have had to otherwise. 18
buses is signi cantly more than 3 or 4, and you can take advantage of that limited power, maximize it the best you can. And then again, you don’t have to pull the charge management system out, you just change the settings when you have more power.
Q Charged: What about solar and storage? Is that something that could be part of your system?
A Sam Hill-Cristol: We don’t develop solar and storage on our own, but we enable the chargers to talk to those other resources. If you just have solar, our system can interface with the solar and maximize charging based on the solar output. It can monitor that load. en if you have a full micro-grid—solar, battery storage, a generator—our system talks to the micro-grid controller, and says, “Right now the micro-grid is producing this much power, so we have this much power for charging.” We are kind of a layer of intelligence that enables the chargers to interface with other distributed energy resources, but we work with partners to develop those. I can share an example in Silver Spring, Maryland. ere’s a transit depot down there that we worked on that has a full micro-grid, so it can charge a bunch of buses when the grid’s down, and we’re a piece of that puzzle.
Q Charged: I know that you’ve been involved with some vehicle-to-grid pilots. Are you doing that on a commercial basis, or is that still mostly in the pilot phase?
A Sam Hill-Cristol: I would say that we’re at an in ection point between pilot phase and commercial. We’ve done 10 pilots around the world, all of them in Europe and Asia. We are moving forward with two projects that we’ve announced that are going to be bidirectional in the US, and we hope to scale that using industry standards such as OCPP, open charge point protocol. But there’s not a big market for bidirectionality right now in the US, so we’ve done pilots elsewhere. We don’t want to keep doing pilots, but we also can’t get ahead of the market. In the next two years I think we’ll start to see more commercially viable V2G projects that are scalable, that aren’t just a proprietary system that you build for one project. Because you can’t roll that out across the country.
For a good management system, the key overriding parameter is operation of the vehicle. You can never sacrifice that.
For more info about advertising visit: www.ChargedEVs.com/Advertise
JUNE 14–16 2023
■ Charging the future of mobility: Markets, business models and trends
■ Experience innovations: Smart charging systems, e-vehicles and mobility services
■ Knowledge2Go: Conference, exhibition forum, guided tours and much more
■ Industry meeting point: Meet 85,000+ energy & mobility experts and 1,600 exhibitors at four parallel exhibitions
Today’s global auto industry neatly illustrates the axiom (attributed to William Gibson) that the future is already here, but unevenly distributed. In places such as Norway, Holland and California, the electric future has more or less arrived. In much of the developing world (and parts of the US) it remains a vague rumor.
Of course, this probably isn’t news to you, dear readers. Plenty of pundits have ponti cated on the relative prospects of the planet’s auto-producing polities, and you may be tired of reading about the “lunch” that China’s poised to eat, “eulogies” for the UK auto industry, and the “tsunami” that’s headed for Japan.
A glance at 2022’s sales gures shows that the trends these metaphors describe are very real—and they’re worrisome for those who want to see a speedy global transition to e-mobility (and to those who hate to see their own regions falling behind). On the streets, however, the situation is far more complex than on the metaphorical racetrack. Just as pro-EV and anti-EV factions exist in the executive suites of every major automaker (save one), progressive and regressive forces are at work in all the world’s auto markets, and they interact with economic and political trends in complex ways. Contradictions and ironies abound.
Chinese automakers hope to use EVs a lever to pry their way into the global auto market, and this strategy is beginning to show results—China-made EVs from BYD, Xpeng, Polestar and other brands are roaming the streets of Europe, and they’re headed for the US. BYD has been producing electric buses and trucks in California for some time, and Polestar hopes to establish US production in 2024.
Domestic automakers fear the dragon—Stellantis CEO Carlos Tavares (among others) recently warned that European OEMs need to increase the pace of innovation or risk ceding the low-priced EV market to the Chinese. Since Mr. Tavares spoke, the future of the trade situation with China has become even more unpredictable. He opined that anti-China protectionism would be a non-starter, because German automakers are making bank from their Chinese JVs. However, if geopolitical tensions continue to grow, new trade restrictions could be in store.
Meanwhile, China’s domination of the mining and (especially) processing of key raw materials is a pressing problem for the global EV industry. In the US and Europe, governments are pushing automakers to develop domestic supply chains.
ere’s a growing (and refreshing) sense of urgency about “onshoring” battery production. e European Battery Alliance recently warned that the Continent’s battery industry is in “crisis,” and called for billions in “emergency” investments.
Almost every press release we see these days mentions the Biden Administration’s IRA and BIL, both of which include strong incentives for automakers to source raw materials and components from the US and trade partners. It’s working— Atlas Public Policy estimates that $73 billion of investment in US battery plants was announced in 2022. e EU’s Battery Law has turbocharged a similar wave of gigafactory construction.
By Charles MorrisSome European players seem intent on starting a pointless ght between the US and Europe over the Buy American provisions of the IRA/BIL, but the bills’ authors never meant to disinvite Europe from the party—they meant to snub China. As the details of the new rules are worked out, they’ll surely be brought into harmony with existing free-trade agreements. American and European companies will continue working together.
Subsidies are a hot topic everywhere. Australian rm Recharge Industries has bought defunct battery maker Britishvolt and hopes to resurrect it, but the rm’s collapse set back hopes of UK battery production by several years at least. Many place the blame for the debacle on the UK government, which turned o the subsidy tap in the name of free market ideology. As one commenter put it, ideology may work when other countries play the same game, but they don’t, and won’t—China has generously supported its EV industry, and now the US and EU are following suit.
Some economists believe that economic competition among nations is a myth, perpetuated by populist politicians, and the auto industry provides some evidence to support that view. German, Japanese and Chinese OEMs are building EVs in the US, and their factories and dealerships support thousands of American jobs. Meanwhile (for now) Western brands are still busy in China, and Chinese suppliers are participating in the global coopetition—CATL’s plans to build new battery plants in Europe (for Mercedes et al) and the US (Ford) are just a couple of the many pending transcontinental partnerships.
Political theories may be important to pundits and politicians, but businesspeople (and voters) are more interested in doing business and creating jobs. Decisions about subsidies, tari s and tax policy need to be made on a case-by-case basis with an eye on real-world results rather than rigid ideologies.
It’s critical for Western automakers to build up domestic supply chains, for both geopolitical and sustainability reasons, and that’s going to require government support. Subsidies may be distasteful in theory, but in the real, rapidly warming world, we can’t wait for some theoretical free market to bring everyone together in a Kumbaya circle.
If the threat of competition from other regions (realistic or exaggerated) is what it takes to convince governments to support electri cation, then so be it. However, scal conservatives correctly point out that subsidy programs can create perverse incentives (see PHEVs). ey should be narrowly aimed at promoting innovation, not at preserving politically powerful industries (see hydrogen).
ere’s also an elephant in the room, poised to stomp on politicians’ dreams of job creation: electri cation is going to cause not just layo s in some areas, but the extinction of entire industry segments. Policies should ultimately be aimed at helping humans, not corporations. Decision-makers need to help displaced workers to nd new places in the clean energy economy, and the auto industry needs to start making EVs accessible to lower-income drivers.