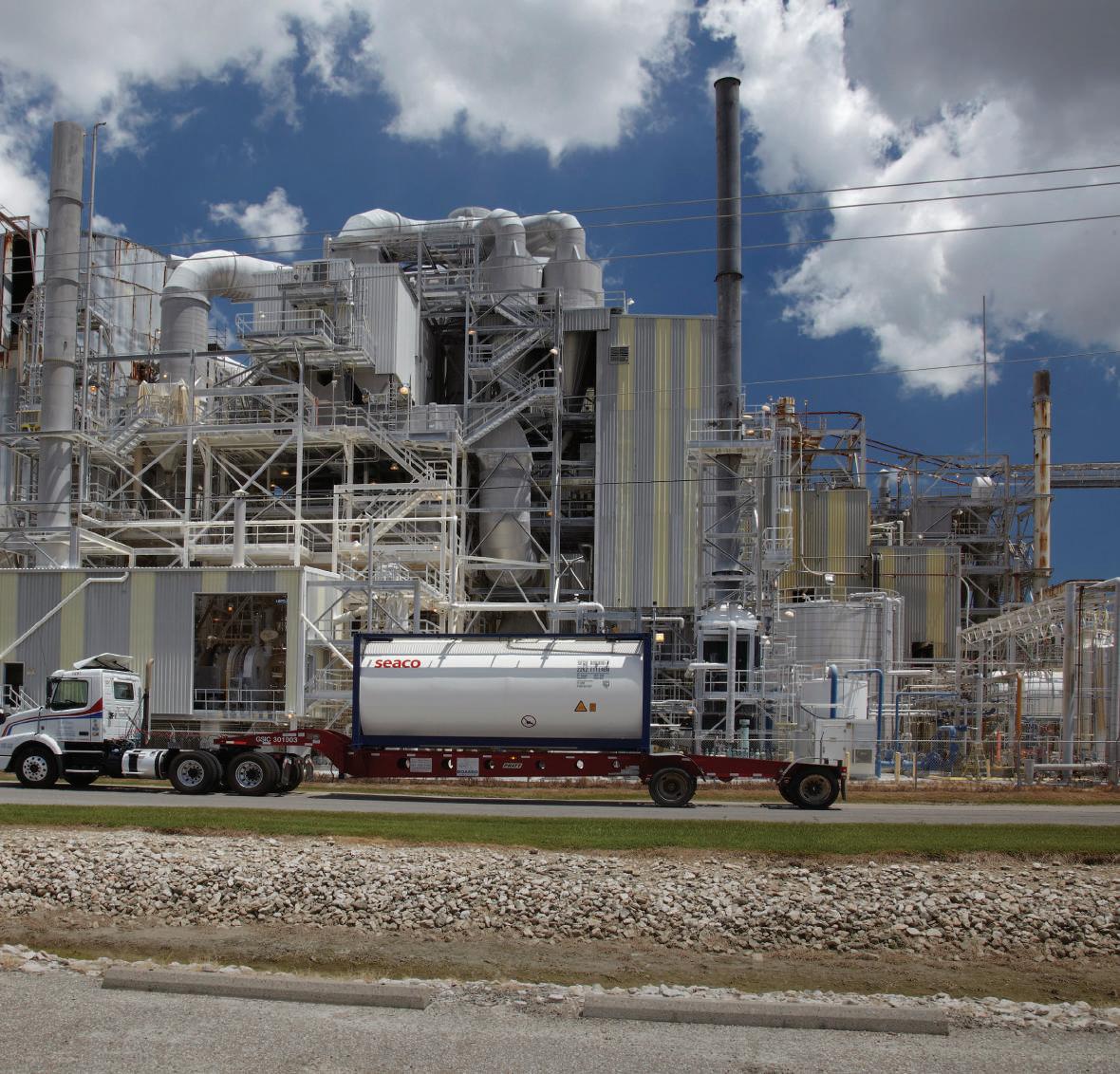
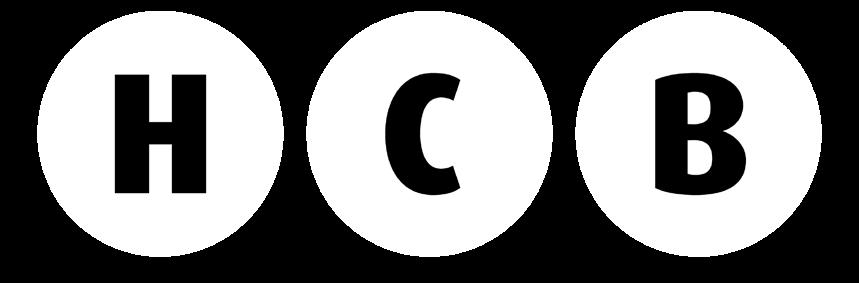

Our PFA Lined Cleanlift, bottom discharge valve has a shear groove (unlike some of our competitors). The shear groove is not a dance music classification, but a significant feature of these types of valve. It protects the tank in the case of an impact or incident, and complies with EN 14433:2014. Ideally suited for tank containers where space is limited in the ISO frame, with the PFA lining offering maximum protection against highly corrosive cargos, it’s simple to maintain and uses many of the components to be found on our standard footvalves - making spare parts supply much, much easier. We know accidents can, and will happen. Successful and profitable tank operation relies upon the technical integrity of each and every component. That’s why we ensure precision throughout, so that you can rely on the performance of our valves and your tanks.
FORT VALE. FOLLOW THE LEADER. Visit us at www.fortvale.com
December traditionally offers the ideal time to look backwards and assess the year just about to end. And 2022 has been an – ahem – interesting year, with many of those in the chemical logistics arena who have ridden its choppy waters coming out of it very nicely, while others have flailed and failed.
One salient feature of the year has been a great shift in values. The value of oil and gas in the ground remains high, leading the big integrated energy firms to record multi-billion dollar quarterly profits – much to the annoyance of motorists who only see their brands when they fill their fuel tanks with high-cost gasoline and diesel. Expensive assets – such as oil tankers and LNG carriers – have seen their secondhand values rocket, with newbuilding slots scarce and uncertainty over future marine propulsion choices in light of environmental legislation. Even the chemical tanker market has been enjoying a welcome recovery this year.
Those container liner operators who filled their boots in 2021 seem to have learned how to manage the market better and have brought down ocean freight costs, the better to keep hold of their market. But some of them have also been using their windfalls to expand aggressively, both within and outside their existing spheres of operation. Supply chain disruptions over the past two years have shown the value of cargo – it is the life blood of all logistics operators, after all – and the importance of being able to better control access to that cargo.
It will be interesting to see how that plays out over the course of 2023; recent pronouncements by analysts indicate that the current global economic gloom is likely to keep demand depressed, hitting trade volumes. Operators will probably
respond by idling existing tonnage, even at a time when the orderbook is large by historic standards.
Others who have benefitted over the past year include engineering firms, suppliers and logistics providers with expertise in handling those products that present options in the path towards decarbonisation, notably ammonia, hydrogen and methanol but also carbon dioxide, the latter in terms of capture and sequestration or re-use. Those have involved, for instance, industrial gas specialists such as Air Products and Air Liquide, LPG tanker operators (Exmar, Navigator Gas and many others), methanol specialists (Methanex, Waterfront Shipping, MOL, Proman and its partner Stena Bulk, etc) and bulk liquid terminal operators, many of which have been looking to adapt or expand capacity.
There is an awful lot of work going on, at enormous cost (some of which may be covered by grants) but it will be necessary if the UN’s Sustainable Development Goals are to be met. For northern Europe, to take one example, that will mean developing the infrastructure and supply chains necessary to deliver the new clean fuels into the region at a reasonable price; existing infrastructure, developed to handle imports of traditional liquid hydrocarbon fuels, took decades to mature but the new energies will need to leapfrog that process.
This has all been new stuff but I think it is time we retired use of the word ‘unprecedented’ from the pages of HCB – it has been over-used this year, and I suspect there have been many times in the past when pestilence, war and hunger have coincided. Maybe a less interesting 2023 is what we need.
Peter MackayVOLUME 43 • NUMBER 11
Letter from the Editor 01
30 Years Ago 04
Learning by Training 05
Let’s talk tanks
ITCO members get back together 06 Back to basics
Goodrich provides tank training 10
Foot in the door
Bertschi opens up in China 11
News bulletin – tanks and logistics 12
SUSTAINABILITY
The green carrier
Amsterdam plans LOHC network 14
Driven to be clean
Hoyer grasps the nettle 15 Washing whiter
Treating ship waste ashore 16 News bulletin – sustainability 18
Low slung
BASF, Stolt address low water 20 A rising tide
Odfjell enjoys market upturn 21 News bulletin – tanker shipping 22
The quarterly magazine of the Tank Storage Association
Getting tougher
CBA reports weakening market 25 Pressing ahead
Brenntag extends transformation 26 News bulletin – chemical distribution 28
INSURANCE
Work that data
Munch Re works with NCB, USCG 30 Keep it open
Reinvigorating Lloyd’s Open Form 31
SAFETY
Incident Log 34
Splash and burn
TT Club alert on lithium batteries 36 Use it or lose it
Avoiding containership fires 37
REGULATIONS
A clean slate
Joint Meeting gets back to work 38 Small change
What’s new in the IMDG Code 45
NEXT MONTH
What’s new in storage terminals Building an alternative supply chain North American regulations Industrial packaging update
Email: peter.mackay@chemicalwatch.com
Tel: +44 (0) 7769 685 085 Advertising
Email: sarah.smith@chemicalwatch.com Tel: +44 (0) 203 603 2113 Publishing
Email: sarah.thompson@chemicalwatch.com Tel: +44 (0) 20 3603 2103
ISSN 2059-5735 www.hcblive.com
HCB Monthly is published by CW Research Ltd. While the information and articles in HCB are published in good faith and every effort is made to check accuracy, readers should verify facts and statements directly with official sources before acting upon them, as the publisher can accept no responsibility in this respect. ©2022 CW Research Ltd. All rights
THE DECEMBER 1992 issue of HCB appeared just prior to the arrival of the European Single Market, which raised both promise of easier trade and concerns over what it might mean for chemical producers and logistics operators in the UK. However, HCB had chosen this month to run a special focus on North America, with the cover declaring: ‘Product stewardship in, Cowboys out’.
That comment of course reflected the growing attention being paid to Responsible Care and ISO 9000 but also changes in the structure of the emerging tank container (or ‘ISO tank’ in the local parlance) sector in the region. In particular, many of those companies that had invested heavily in one-stop-shop tank repair and cleaning stations had found their new facilities under-utilised and rationalisation was on the cards – perhaps not something that would help support the growth of the tank container concept.
Attention was also being paid more closely to raising safety and operational standards in the bulk liquids terminalling sector, and HCB reported on some presentations on the subject during the ILTA International Operating Conference in Houston in June. HCB noted that legislation was “being used as an uncompromising tool” in forcing safety improvements but also that, while new legislation was generally accepted as providing a common standard, “many argue that plain common sense and good housekeeping have as much to do with accident prevention” as environmental legislation.
The US was also providing much-needed work for deepsea chemical tankers at the time, given that freight rates were still recovering from a lengthy lull, and rising exports and, more particularly, imports of chemicals were giving some support. Here too, though, legislation was beginning to generate problems, with many operators concerned
in particular at the lack of uniformity in new rules, especially the unilateral US initiative of the Oil Pollution Act of 1990, which followed the Exxon Valdez incident in Alaska.
EV Vine of Dorval Shipping commented that, while industry could appreciate the difficulties states were working under, especially in light of the public’s perception of environmental risk, “it would be helpful if countries, particularly the US, could harmonise their legislation with the requirements agreed internationally by bodies such as the IMO”. Quite aside from OPA 90, the US had introduced stricter requirements for vapour control systems and slop disposal ashore, and shipowners were facing additional insurance costs, particularly for the carriage of persistent oils.
It was not just in the US that such moves were taking place; atmospheric emissions controls were just a part of a series of recent environmental legislation to have taken effect in Europe and storage terminals across the region were busy investing in vapour control equipment. While vapour combustion was being preferred by US terminals, especially those handling gasoline, in Europe a wider range of technology was being investigated, including carbon scrubbers and filters, adsorption units and condensation systems.
In those days, HCB’s December issue celebrated the coming Christmas break in many forms, including the popular Yule Log feature, which wrapped up some more-or-less hazardous incidents from the year. In 1992 one item from the Philippines reported on a police action against smugglers, whose ship arrived with 100 tonnes of contraband garlic. Not only were the usual sniffer dogs not required, customs officials had to approach from upwind.
Men dying and women crying If you breathe air, you’ll die Perhaps you wonder the reason why? Are you ready?
Sound familiar? Recently, when Russia retaliated for the attack on the Crimea bridge, people died and were maimed. Is this good or not good? You will know the answer. Perhaps you add; ‘but the Russians are terrorists’, or you can argue, ‘what about the harm done to the Russian speaking population in the Donbass by the Ukrainians?’ Was that good or not so good?
My column for this month is about collateral damage caused when a so-called tipping point has been reached beyond the point of no return. The only way left to go is downhill at an accelerating speed. Based on an objective observation the Western world is collapsing in its own footprint. The school of Athens had four main goals: “Seek Knowledge of Causes”, “Divine Inspiration”, “Knowledge of Things Divine”, “To Each What Is Due”. We will explore the first one.
Let’s seek the cause for the war in Ukraine. Because of the constant fake and false news, the propaganda machine by the mainstream media, it is very difficult to decide what is true or untrue by the general public. So, the first question philosophers of this school would ask: ‘Cui Bono?’ Who benefits? When you analyse and answer this question it becomes more easy to do so.
A second question asked would be: ‘Is it good or bad that collateral damage is ignored by politicians?’ I use the rhetorical questioning
method on purpose so your conscience automatically will answer. Perhaps your energy company is the one ‘Cui Bono’ by taking advantage of the current disturbance in the gas and electricity supply markets? Ordinary people and businesses are billed more than they can afford which results in poverty and business closures. Is that good or bad business for the long term? When an energy supplier destroys their own client base because of charging too much, the inevitable result will be self-destruction because when there can’t be any more buyers, there can’t be any more sales.
A philosopher from the School of Athens would ask: is it honourable or ethical to destabilise the social contract and cohesion? I believe your conscience will answer that question too. Jean Jacques Rousseau wrote about the social contract: “It follows that when any government usurps the power of the people, the social contract is broken; and not only are the citizens no longer compelled to obey, but they also have an obligation to rebel.”
Social Cohesion enables us to live together in a just and equal society. The wise thing to do is not taking away the basic comforts of life for the 99 per cent. What we now observe is that through an amalgamation of media, big business and authoritarian politics, even the last cents of ordinary man are being taken from him. Is eliminating the vulnerable social contract good or not so good for business?
This is the latest in a monthly series of articles by Arend van Campen, founder of TankTerminalTraining, who can be contacted at arendvc@ tankterminaltraining.com. More information on the company’s activities can be found at www.tankterminaltraining.com.
MEETING REPORT
THE APPETITE AMONG tank container professionals to get together again after the easing of Covid restrictions was evident from the crowd of more than 200 people who gathered in Amsterdam on 25 October for the annual Members Meeting of the International Tank Container Organisation (ITCO), the first in three years and the largest conference organised by the Organisation in its 24-year history.
And there was plenty for attendees to see and hear, with a range of presentations covering all sides of the tank container business. After an introduction by Patrick Hicks, ITCO’s secretary, Reg Lee, its president, gave an update on recent developments. He noted that he had visited the Shipping Training College (STC) in Rotterdam the week before the meeting, to finalise arrangements for including tank containers in its curriculum.
STC was planning a training day on 20 December, with 80 students given the opportunity to have classroom training and to see a tank container close up. Hoyer’s demonstration tank was being taken to the college and all 80 students were to take ITCO’s e-learning course.
The programme at STC mirrors that already established at Shanghai Maritime University (SMU) but, due to ongoing Covid restrictions in China, that is currently not being delivered. The situation is to be reviewed after the Chinese New Year in late January 2023. Jarno Weps, maintenance and repair manager, Europe, for Exsif Worldwide, himself a former STC student, gave some more details of the new course in Rotterdam as part of his presentation on ‘Inspiring a New Generation’.
The tank container industry, like many others, is suffering from an ageing workforce and a
lack of new entrants – as well as a lack of appropriate training. It makes sense, therefore, for industry to help colleges promote the sector.
First up to give his views on the current industry was Hans Augusteijn, installed this past February as president of Stolt Tank Containers, who sketched in the business environment this year, with its overheated demand, increasing costs, labour shortages and global conflict. This has come at a time when customer expectations are getting tougher, while there is a new focus on decarbonising supply chains and the need to invest in the digital transformation.
On the upside, Augusteijn felt there is still plenty of potential for more business for tank containers. Containerisation in general has proven itself over the last five decades, to the point where 99 per cent of non-bulk cargo is carried in freight containers; that figure is around 90 per cent for refrigerated goods but only some 25 per cent for liquid bulk cargo –there is plenty of conversion left in this sector.
That potential has certainly been recognised by industry; Augusteijn noted that the global tank container fleet has grown by an average of 10 per cent per year for the past decade,
SECTOR IS FACING SOME SERIOUS CHALLENGES. ITCO’S MEMBERS MEETING HEARD ABOUT SOME INITIATIVES THAT COULD BE OF HELP TO THEM ALL
As one of the world‘s leading logistics services providers in handling and transporting liquid products, we are the first point of contact for the chemicals, gas, mineral oil and foodstuffs industries. By road, rail and sea, from road tankers to IBCs, from equipment leasing to intelligently networked Smart Tanks, we will find the optimum solution for you. We do this by using our expertise to pioneer our own new pathways that take you forward in a customised way. How can we help you?
www.hoyer-group.com
twice the rate of dry containers, while the number of active operators has tripled over the same period to more than 310. Somewhere between 2.3m and 2.8m tank container shipments are made every year, again growing at an annual rate of more than 10 per cent. He predicted that the sector will continue to outpace chemical production growth as the shift from bulk to tanks goes on.
The future will not be plain sailing though and there are some uncertainties and challenges coming. “Adopting new strategies, tactics and innovative technologies will be essential to overcome challenges and capture opportunities,” Augusteijn concluded.
Challenges are also being experienced by service providers to the sector and Colin Garnett, senior vice-president, mergers and acquisitions at Boasso Global, gave some indication of how operators are responding. The most pressing problem is the shortage of drivers – Europe (including the UK) is short by around 500,000 drivers right now, and the US needs another 240,000. In response, haulage firms have increased salaries – with the support of shippers – and introduced more flexible working conditions and better training. It is not just drivers, though – Garnett noted that industry needs to work together to attract new entrants to work as maintenance crew, engineers, operators and office staff.
Looking ahead, there may be more changes for tank service providers; the tank depot sector remains highly fragmented, with plenty of small and often family-owned operators, and may present capacity constraints as development lags behind demand growth; there is now the need for change – which presents opportunities.
The afternoon session, moderated by consultant (and HCB contributor) Paul Gooch, focused on safety in the tank container industry, with four panellists drawn from different sides of the business reporting on their initiatives and activities to encourage and promote the safe use of tank containers.
Benjamin Reinke, technical manager at Bureau Veritas (BV) Industry Services, outlined safety procedures for working in third-party premises such as tank depots, and how BV trains personnel for tank entry and those who issue tank cleaning documents, including tank entry permits. A clear message from his presentation was that all those who see unsafe practices should stop working and get the situation rectified.
Roger Gloor, deputy head of Bertschi’s technical department, explained that all the company’s tank containers are equipped with full walkways and handrails and also went
into Bertschi’s ‘Stop at Risk’ policy. This is based on a training programme, covering behaviour-based safety, along with defined actions to achieve uniform safety and quality principles across the company. Internal safety and quality processes are regularly monitored and assessed, with the evaluation feeding into an action plan according to the principles of ISO audits and SQAS assessments to improve safety and quality protocols.
Across the Bertschi group, that approach results in more than 3,500 staff training days, 60 driver training days and 3,000 safety checks each year.
Jonas Fiers, QESSH manager at Van Moer Logistics, presented a case study on the relationship between safety culture and safety performance; for example, while every company should provide effective fall protection, it must also inculcate a safety culture to ensure that its personnel understand the importance of that protection and use it correctly, all the time. Van Moer uses visualisation techniques to reinforce the safety message and has an ongoing QESSH dashboard to track safety performance.
This approach has this year delivered a very significant reduction in the number of accidents at Van Moer’s sites and also a sharp fall in the severity of those accidents. The next step is to spread that safety culture to newly acquired businesses and to external drivers, review the key performance indicators and set targets for 2023.
Finally, Mike Yarwood, TT Club’s managing director of loss prevention, explained what operators can look for from their insurance provider in terms of promoting safe tank operation. He also explained the concept of ‘insured risk’ and gave advice on operational and contractual risks in terms of insurance cover.
The final session of the day was given over to David Bailey, design and development director at Fort Vale Engineering, who gave an update on the work that ITCO and its members are doing to head off the problems that could arise if the regulatory authorities in Europe and North America carry through with their
plans to restrict or ban the manufacture and use of perfluoroalkyl and polyfluoroalkyl substances (collectively known as ‘PFAS’). For the tank container sector, the main issue would be in terms of seals and gaskets, which rely on PFAS materials for their operational performance across a wide temperature range as well as their compatibility with most substances carried in tank containers.
ITCO has now put together a case study on the subject (reviewed in HCB October 2022, page 10), which has been submitted to the authorities and calls for PFAS used in seals and gaskets to be designated as ‘materials of essential use’. ITCO has also initiated a pilot project being undertaken at Stolt’s Moerdijk depot on the disposal and, it is to be hoped, recycling of used sealing elements and Bailey appealed for other operators and depots to join in.
The meeting concluded with a toast to the memory of David Jenkins, who as head of Multistar had been one of the founding members of ITCO in 1998 and who died earlier this year. His commitment to the organisation and to the industry in general was recognised by Reg Lee.
Looking to 2023, ITCO’s four divisions will hold meetings online in February and the Organisation is planning a number of other webinars over the course of the year covering such topics as sustainability, safety, efficiency and technical developments. The next big gathering will take place in May, when ITCO will once again take its ‘Tank Container Village’ to the Transport Logistic event in Munich. The Village will comprise 64 stands, of which 46 had already been reserved by the end of October. www.itco.org
TANK CONTAINERS TRAVERSE the world by all modes of transport; along the way they need to be repaired, maintained and cleaned, while being operated to a consistently high standard. The concept of the tank container appears fairly straightforward, but it is important to understand how a tank must be handled and operated.
Goodrich Maritime, the Mumbai-based international logistics firm, certainly takes its tank container operations seriously. Its liquid cargo activities include the operation of tank containers for foodgrade, chemical and gaseous products, as well as swap bodies for domestic operation, alongside chemical storage and blending facilities, tank container
cleaning and flexitank business. Keeping those assets moving, whether it is on international trade lanes by container vessel, land transport within India and the Middle East, or multimodal routes into central Asia and Africa, is vital to its market position.
This past October, Goodrich organised a week of ‘DG Training on Technical, Safety and Regulatory Requirements for Operation of an ISO Tank’ for its employees and clients in Mumbai. The event was also attended by members of the Indian Chemical Council (ICC) and Nicer Globe, ICC’s initiative to promote Responsible Care and the establishment of standards for chemical transport safety, security and emergency response. The
facilitator for the week’s proceedings was Paul Sireci, a seasoned professional in the sector who has worked with Goodrich on similar programmes in the past, the latest being in 2019 at Baroda, Gujarat.
The week was split into two halves, beginning with a theoretical session for Goodrich’s own chemical logistics employees on the first two days, which was repeated for the company’s clients on the next two. This session covered a variety of topics, including the design and construction of tank containers, safety, common hazards, industry standards, dangerous goods transport regulations, the International Maritime Dangerous Goods (IMDG) Code, CSC certification under the International Convention for Safe Containers, tank compatibility, filling, cleanliness, testing and other matters.
On the final day of the event, both groups, numbering more than 50 people, were taken to the Oceanglobe tank container depot in Taloja in Navi Mumbai, where Paul Sireci introduced the ‘Goodrich Training Tank’ to employees and customers.
Interacting with Paul, who has nearly 50 years of experience in the tank industry, proved to be highly captivating to the majority of those in attendance, who included customers as well as Goodrich personnel from its factory, logistics and supply chain department and other offices, including many ‘young Goodrichians’. They also enjoyed a brief tour of the Oceanglobe depot, with demonstrations of tank container cleaning and maintenance.
The week’s programme is only part of the process to improve tank container safety within the Goodrich organisation. “This is simply the beginning of another long journey for the Goodrich chemical logistics team,” the company says. goodrich.co
TRAINING • THOSE INVOLVED IN TANK CONTAINER OPERATIONS AND MAINTENANCE NEED TO KNOW WHAT THEY ARE DOING. GOODRICH IS PROVIDING ITS EMPLOYEES WITH THE TOOLS THEY NEED
CHINA • BERTSCHI’S NEW CHEMICAL HUB, ITS LARGEST INVESTMENT TO DATE, HAS STARTED WORK AND IS RAMPING UP TO HELP THE COMPANY FURTHER DEVELOP ITS CHINESE TANK CONTAINER BUSINESS
THE FIRST TRUCKS aarrived at the Bertschi Zhangjiagang (BZJG) chemical hub at the end of August. Switzerland-based Bertschi has invested some $45m in the new site, which covers some 62,400 m2 and includes a large tank container storage and heating area, a drumming facility and warehouses for all classes of dangerous goods, allowing it to offer a fully integrated logistics service to its local and international chemical clients.
The location in the Yangtze River International Chemical Park, close to Shanghai, puts the BZJG liquids hub in close proximity to several existing and other
potential customers for Bertschi’s services. The company aims to offer its clients an international door-to-door service and having this regional hub is a cornerstone in its global network, which now numbers 30 intermodal terminals around the world.
Zhangjiagang is also an important location in terms of domestic transport, making intermodal connections with inland waterways. Jemmy Wu, managing director of the Bertschi Group in China, notes that this mirrors company facilities elsewhere in the world, such as that at Duisburg. And having the ability to move dangerous goods on the
water avoids the need to move them by road through the densely populated and congested Shanghai area. Wu also notes that the local authorities in Zhangjiagang have a lot of experience with the chemical industry and a good understanding of the importance of having an integrated chemical logistics hub.
In the Chinese market, being able to offer an integrated service is important for European shippers; without facilities such as this, chemicals are likely to move from Europe to China in drums or intermediate bulk containers (IBCs) for domestic distribution. The BZJG hub now allows them to move product in tank containers, which offer a higher payload per 20-foot container slot, and then to store the tank container prior to onward delivery to the consignee or to decant the product into drums or IBCs.
This offers efficiency gains for Bertschi’s clients but it is also cost-effective and improves service quality. Having product in storage close to the end customer provides security of supply and ensures on-time delivery, while repacking as late as possible in the supply chain avoids unnecessary costs. Overall, for the client, this means the end-to-end cost is reduced and flexibility is increased.
But Bertschi has got a lot to do if it is to spread the word about the efficiencies offered by intermodal transport within the Chinese market. As Wu points out, rail transport is not yet widely used for the domestic movement of chemicals in China, although Bertschi has been actively involved in the ‘Belt and Road’ project, having been moving chemicals by rail from China to Germany since 2015.
Furthermore, rail operator Hupac, in which Bertschi is a significant shareholder, opened its own operation in China, Hupac International Logistics (Shanghai), in 2016 with the aim of developing traffic between Europe and China.
BZJG is unlikely to be Bertschi’s last investment in China; Wu says the company’s strategy in the country is long-term but also that the BZJG hub will become the benchmark for the chemical logistics sector in China and create a solid foundation for further growth.
www.bertschi.com
Grammer Logistics, an Indiana-based transport and logistics firm specialising in chemicals, ammonia, industrial gases and other hazardous materials, has acquired Logistics Management Resources (LMR), which provides transport services to a similar clientele from its base in Baton Rouge, Louisiana. The deal significantly expands Grammer’s footprint, service offering and operational capabilities, continuing its growth under the ownership of Stellex Capital Management and Mill Rock Capital.
“LMR is a highly-respected leader in the chemicals logistics market,” says Scott Dobak, CEO of Grammer. “We are thrilled to welcome their team into the Grammer family. This acquisition supports our strategy of providing a diversified offering of both asset and non-asset services to our growing customer base. We believe this integrated approach is the future of chemicals logistics.”
LMR’s personnel will remain with the operation and its president/CEO, Heston Hodges, will lead Grammer’s transport
management division. He says of the deal: “By combining the expertise of both companies, it creates a win-win combination. All stakeholders will benefit from the additional services that LMR and Grammer will jointly offer to the marketplace. Our clients gain access to an internal fleet of highly specialised drivers and equipment, and the strong carrier relationships we have developed over years will be further supported by the additional opportunities available through the combined platform.”
www.grammerlogistics.com
Neele-Vat has commissioned a new warehouse and distribution centre in Hazeldonk in southern Netherlands, close to the Belgian border and midway between Rotterdam and Antwerp. The 11,000-m2 facility will, the company says, support its growth strategy for warehousing, customs, air and sea freight and European distribution. The brownfield development is also said to complement
Neele-Vat’s other distribution facilities at the same business park. www.neelevat.com
Rinchem is nearing completion of its first dangerous goods warehouse in Malaysia and its third in the Asia-Pacific region. The new 4,200m2 facility, due to open for business in the second quarter of 2023, will have 3,100 pallet positions and offer multiple temperature zones.
“As the semiconductor industry continues to experience immense growth in response to various global governmental incentives, Rinchem is uniquely positioned to support both chemical and semiconductor manufacturers’ expansions,” says Matt Jensen, Rinchem’s vice-president of warehousing operations. “Rinchem has over 45 years of experience in managing the most complex supply chains in the world – every warehouse we build is optimised for safety and efficiency in accordance with our global standards.” www.rinchem.com
Talke has added two CNG-powered trucks to its vehicle fleet in Germany, as part of its broader aims to reduce its CO2 emissions. Talke says it has opted for CNG over the currently fashionable LNG option as the price of CNG is much more stable. It burns more cleanly than diesel, reducing CO2 emissions by up to 20 per cent, while bio-CNG, which is becoming more widely available, can cut CO2 emissions by as much as 90 per cent.
“We have been dealing with alternative drive technologies for a long time. On the one hand, we want to have a positive impact on our own carbon footprint and, on the other hand, we want to support our customers in achieving their climate targets,” says Christoph Grunert, who is responsible for sustainability on the
Talke management board. “We are aware that gas-powered trucks are not yet the final solution to today’s challenges. Nevertheless, CNG is indispensable today as a practical bridging technology.” www.talke.com
Wibax has rebranded its operations in Finland, following the acquisition of Baltic Tank and JJ Kuljetus over the past two years. Those two deals brought the Swedish company’s full service offering to Finland for the first time, as Tero Väyrynen, CEO of Wibax Finland, explains: “Wibax’s unique concept of storage and transportation means that we can offer our customers cost-efficient logistics solutions. It of course feels great that we can now show our true colours. The continued expansion in Finland means that we will also be recruiting new staff, both administrative staff and drivers. Wibax’s total solutions concept has been well received on the Finnish market and we see continued potential for major growth.”
Wibax Finland operates 15 vehicles, which are all being given a makeover. www.wibax.com
VTG has decided to discontinue its Russian business activities, which include wagon leasing
and project logistics, and has sold them to international investors. “We have reached a geopolitical turning point that is bringing terrible suffering to the people of Ukraine, but that is also bringing fundamental change on the global political stage and to the world’s economy. As a company, we too must face up to this new reality,” says Oksana Janssen, COO Eurasia & Far East at VTG. “It is important that we play our part in upholding the founding principles that define the European Union as a place of peace, democracy and human rights, and that this commitment is also reflected in our business activities.” www.vtg.com
Heniff Transportation Systems has acquired Coal City Cob Company, continuing its growth in the chemical transport sector in the US. The acquisition includes 230 drivers and 500 trailers operating from nine terminals across the country, along with a “significant” rail-to-truck bulk transfer yard and tank wash facility at Coal City Cob’s headquarters site in Waxahachie, Texas.
“Given the complementary nature of the two operations, we believe strongly that this combination will create value for all our stakeholders and offer real service enhancements to our respective customers,”
says Bob Heniff, founder and CEO of Heniff Transportation.
Alan Goldstein, president of Coal City Cob, adds: “As we enter this new relationship, I could not be more convinced that both companies are committed to preserving the same shared values, which start and end with taking care of people. I’m excited for our organisation to join the Heniff team and improve our abilities to provide our customers with creative solutions and excellent service. Of equal importance, I believe our existing drivers will discover meaningful economic opportunities by gaining access to Heniff’s expansive footprint and uniquely diversified service offerings.” www.heniff.com
Quantix, a leading provider of chemical transport services in North America formerly known as A&R Logistics, has further expanded its footprint in the Gulf Coast region with the acquisition of five fleet owner companies and the appointment of a new agent, LD McCloud Transportation. Altogether, the deals add more than 140 trucks and ancillary equipment to the company’s liquids and plastics transport division.
The acquired companies are Dobbins Enterprises, C&S Express, Chancelor Transportation, T&K Chancelor Enterprises and Templet Transit. “Quantix continues to scale our services in Texas and the Gulf Coast regions, and these new assets strengthen our ability to do so,” says Chris Ball, president/ CEO of Quantix. “Greater capacity means better service for our customers, which remains the guiding purpose of our continued growth.”
These latest acquisitions follow from the purchase in October of G&W Tanks, which specialises in tank container transport, repair, cleaning and storage (HCB November 2022, page 14).
quantixscs.com
toluene can be handled like a fossil liquid fuel within existing infrastructure, at ambient pressure and temperature. After dehydrogenation, it can be reused many hundreds of times to bind hydrogen.
The realisation of a LOHC import terminal and a plant for the continuous, large-scale release of hydrogen are important additions to other planned activities in the port. Such activities include the development of the regional and national backbone and various planned projects for hydrogen production in the North Sea Canal Area.
The next phase of this initiative will focus on exploring the spatial, infrastructural, and financial requirements to establish the terminal over the next years. The objective is to have the first plants for delivery of hydrogen to local off-takers in operation before 2028, with the potential of further upscale. In total, the handled LOHC volumes will be at least 1m tonnes per annum.
THE PORT OF Amsterdam has signed a Memorandum of Understanding (MoU) with tank storage provider Evos and liquid organic hydrogen carrier (LOHC) pioneer Hydrogenious, with the aim of developing large-scale hydrogen import facilities in the port. The plan includes an LOHC dehydrogenation plant to produce between 100 t and 500 t per day, as well as related storage and handling facilities. All three parties to the agreement are founding members of the H2A platform, which focuses on the development of green hydrogen import infrastructure in the port of Amsterdam.
“We have been building and supporting the H2A platform from the beginning, working with our partners on green hydrogen imports via the port of Amsterdam,” says Ramon
Ernst, managing director of Evos Amsterdam. “We see a promising future in LOHC technology as it is intrinsically safe and fits with the port’s existing logistics infrastructure. We operate two large tank terminals that are perfectly suited for the storage and handling of LOHC. We are delighted to have teamed up with two exceptionally strong partners and look forward to working on concrete next steps.”
The liquid organic hydrogen carrier used by Hydrogenious, thermal oil benzyl toluene (LOHC-BT), is already well established in the industry as a heat transfer medium and, the partners say, has ideal properties for safe handling in ports. Due to its characteristics as a flame retardant and non-explosive carrier with a high volumetric energy density, benzyl
“The location of the port of Amsterdam, and the companies operating here and in the wider North Sea Canal Area, make our port ideally suited for such a terminal and plant,” says Koen Overtoon, CEO of Port of Amsterdam. “This region also offers large potential for offtake, with our connection to Schiphol Airport and the presence of large industrial clusters. Additionally, we collaborate with duisport to facilitate the distribution of hydrogen to the German and European hinterland, further increasing the offtake potential. We are thrilled about this new, key step, which will strengthen the position of the port of Amsterdam as a hydrogen hub, for import, storage, transhipment and distribution to the wider hinterland.”
“The H2A consortium has focused on LOHC technology that can rely on existing oil handling and storage capacities and significantly reduces potential risks of handling molecular hydrogen or other derivatives,” adds Dr Daniel Teichmann, founder and CEO of Hydrogenious. “For a port and industrial region like the Port of Amsterdam, that is located very closely to the city, this is of paramount importance.” www.portofamsterdam.com
HYDROGEN • NORTH-WEST EUROPE WILL NEED HYDROGEN IF IT IS TO MEET EMISSIONS REDUCTIONS TARGETS. AMSTERDAM IS LAYING PLANS TO PROVIDE AN IMPORT ROUTE FOR LOHC
TRANSPORT • LOGISTICS FIRMS ARE TAKING SUSTAINABILITY SERIOUSLY, NOT JUST FOR THEMSELVES BUT ALSO FOR THEIR CUSTOMERS. HOYER EXPLAINS HOW IT IS GOING ABOUT REDUCING ITS ENVIRONMENTAL IMPACTS
“FOR HOYER, SUSTAINABILITY aspects play an essential role at all stages of the supply chain,” says Björn Schniederkötter, CEO of the Hoyer Group. “With solid improvements over the last ten years, we have already achieved good progress towards our goal of minimising our carbon footprint.”
Last year, for example – and for the first time in the company’s history – more than 80 per cent of the kilometres travelled by Hoyer vehicles were undertaken using intermodal transport, a less CO2-intensive mode of operation. And for the remainder, 95 per cent
of Hoyer’s truck fleet is powered by lowemission Euro 6 engines.
For a company like Hoyer, with its pedigree of family ownership and leadership, “thinking in generations” is quite normal. “Keeping an eye on our employees’ welfare and managing the company sustainably and in the long term are self-evident for the Hoyer Group,” says Schniederkötter. “We will play a leading, forward-looking role in overcoming the current ecological challenges. Our solid financial situation enables us to continue making long-term strategic decisions and investments that support our sustainable vision and the values and business strategies of the Hoyer Group.”
The company has now defined some ambitious new medium- and long-term emissions and safety targets for 2025 and 2030. Meeting those targets will require a
strategic mix of measures, including testing further alternative fuels and the creation of a New Energies project group.
By 2025, transport-related CO2 emissions, which have already been reduced by 29 per cent since 2010, are targeted to reduce by at least a further 10 per cent - and emissions from non-transport operations to reduce by 27 per cent. The logistics company aims to reduce its transport-related tank-to-wheel CO2 emissions by a further 15.6 per cent to a total 25.6 per cent reduction by 2030.
To achieve its medium- and long-term sustainability goals, Hoyer has opted for a mix of measures that will involve further optimisation of logistical and operational processes throughout the whole company. In road transport Hoyer already has additional CNG and LNG trucks in operation and has started trialling HVO biodiesel. Earlier this year Hoyer said it was already testing alternative drive systems and it is in constant dialogue with well-known truck manufacturers to examine new developments.
A specifically composed project group with internal experts keeps a constant eye on the direction in which research into new energies is developing - so the international business has a finger on the pulse of the times. Furthermore, the logistics specialist is switching to electricity from renewable energy sources in plant operations in its non-transport sector.
Sustainability is, though, more than just about counting emissions. Taking care of the planet is one thing but people need to be protected and nurtured too – especially when it is so difficult to recruit and retain drivers.
Hoyer now offers training sessions and further education courses to honour its social responsibility, with a special focus on driver training. That includes preventative driving skills, derived from analysis of forward-facing safety cameras in the cabs that allows the company to get an insight into the risks facing its drivers every day. This and other training initiatives have helped to reduce the accident rate by more than 40 per cent over a ten-year period, Hoyer says.
www.hoyer-group.com
WASTEWATER • ALL SHIPS, PARTICULARLY TANKERS, CREATE WASTE DURING THEIR OPERATION. TWO PROJECTS SHOW THAT THERE ARE WAYS TO RECOVER AND TREAT THIS WASTE ASHORE
STOLTHAVEN TERMINALS HAS been operating onsite biological wastewater treatment plants at its terminals in Houston and New Orleans for more than 20 years, initially for its own use but, after an expansion and modernisation that was commissioned in 2018, for third parties as well. The treatment plants operate around the clock, using bacteria and other microorganisms to degrade organic contaminants to produce readily usable water that can be safely released into waterways.
Now, in a pioneering move, Stolthaven has set up a partnership with its sister company Stolt Tankers for the removal and sustainable treatment of wastewater from ships docked in Houston. Stolt Tankers was looking for a way to achieve its own sustainability targets and fulfil its commitment to the UN Sustainable Development Goal 14 to conserve and sustainably use the oceans, seas and marine
resources. Discharging washwater ashore rather than at sea is one step towards that commitment. This is not a legal requirement, other than for washwater from toxic cargoes.
“This idea was initially thought to be too complicated, expensive and, ultimately, unworkable,” explains Paul O’Brien, deepsea operations manager at Stolt Tankers Houston. “But we are passionate about this topic and started thinking about how we could do it and we knew where to start: Stolthaven Houston has a state-of-the-art treatment facility and, better yet, they’re part of the same company.”
In June 2021 the two companies began a pilot programme to identify and balance the challenges, costs and benefits of treating washwater from ships at the Houston plant. There was one obvious cost saving: until that
point, Stolt Tankers’ ships, like all others, would dock in Houston, discharge their tanks and then steam back down the Houston Ship Channel to clean their tanks and discharge the washwater, before returning to the port to reload.
On the flip side, there was the very real possibility that demurrage costs and delays to onward journeys could be incurred due to the extra time spent at dock to discharge the washwater. “Essentially, we were adding a dock to each ship’s time in port, which is counterintuitive to anyone in the shipping or logistics business,” says O’Brien. “The trick was to figure out how we could manage that without adding any time or costs. We had to think differently to find the savings – or at least the break-even point – for this to be feasible from a business perspective.”
Daniel Styrdom, general manager of Stolthaven Houston, explains: “Stolt Innovation was our first vessel and she discharged approximately 1,700 m3 of washwater. The initial calculations showed that we could execute the discharge within the vessel operations window and that it made sense financially. Since then, we have received multiple vessels and – through a lot of testing and data analysis with Stolt Tankers – we can see the benefits to both
businesses from a financial, operational and environmental perspective.”
During the first year, the project in Houston reduced the amount of washwater discharged to sea by more than 8,000 m3, saved more than 200 tonnes of fuel and reduced CO2 emissions by some 600 tonnes.
“Both businesses have been highly committed to this project,” says O’Brien. “It has all been additional work on something that is not mandatory but done for the sake of doing something good. The great news is we have been able to do it at no additional cost and people have happily invested their time because this benefits the marine environment.”
One factor that was important in the project was the logistical benefits of having a spare dock at the Stolthaven Houston terminal. Dock 11 was commissioned in 2017 but, as yet, does not have any shore tanks alongside. “Eventually, of course, our plan is to expand our storage facilities to this space, but for now, the dock is not in regular use,” explains Henrik Olsson, regional commercial manager,
US for Stolthaven Terminals. “When we started this project with Stolt Tankers, we knew that it could be the ideal layby space for ships to discharge wastewater.”
Stolt Tankers is now looking to expand its onshore discharge programme to other ports that have wastewater or water-reclamation facilities. “We are currently rolling out training to our port teams around the world and having conversations with operators in other regions,” says O’Brien. “We’re looking to extend the project to Stolthaven New Orleans next and, wherever possible, we will look to use Stolthaven Terminals’ facilities.
“From Stolt Tankers’ perspective, this has been one of the best cross-business projects we have worked on. Together with Stolthaven Terminals we have pooled our expertise and innovative thinking to achieve something new in the industry and positive for the environment. We have proven this is a method of opportunity for shipping and terminals.”
Styrdom adds: “This has been, and will continue to be, a successful partnership. Stolthaven Terminals and Stolt Tankers are now leading the way in terms of using our
facility to discharge and treat washwater onshore. Just as importantly, we have integrated our teams and operations to make a positive impact on the environment.”
Stolthaven Terminals is not the only terminal operator looking to use its expertise to help reduce the impact of vessel operations.
Spain-based Exolum has announced a plan to invest €30m in the construction of a hydrocarbon treatment and recovery plant in Algeciras, which will handle oily water from ships, minimising the environmental impact of these products in the oceans and also recovering and recycling hydrocarbons so they can be re-used. Exolum has set up a new subsidiary, Garbium, to develop the project and is collaborating with Bilbao-based shipping company Naviera Murueta.
The plant will have the capacity to treat 550,000 tonnes of product per year and is expected to be operational at the beginning of 2025. The project, which has already obtained environmental approvals and is currently in the detail engineering stage, will occupy a 21,500m2 plot where the receipt tanks for the residue consisting of 90 per cent water and 10 per cent hydrocarbon waste will be built. The plant will also be equipped with settling tanks for oil/ water separation, as well as end product tanks from which the recovered fuel will be dispatched. A water treatment unit will also be installed for the treatment of recovered water, thus ensuring it is delivered in compliance with environmental quality requirements.
With this project, Exolum intends to provide a service that is in high demand by the ships that operate in the area by enabling them to comply with the provisions of the International Convention for the Prevention of Pollution from Ships (MARPOL). By using high-capacity resources that offer an outstanding performance, they will be able to use these services without incurring excessive delays.
Furthermore, for Exolum it is part of a broader strategy to develop the circular economy, minimise toxic emissions and waste and increase the lifecycle of products treated at the plant.
exolum.com www.stolt-nielsen.com
Hafnia has announced a collaboration with Clean Hydrogen Works (CHW) to explore the development of a global-scale clean hydrogen/ ammonia production and export project, Ascension Clean Energy (ACE), to be located on the Mississippi River in Ascension Parish, Louisiana. The project will aim to capture up to 98 per cent of CO2 emissions from its processes and will also explore additional technologies that could result in zero-carbon or even carbon-negative production.
The partners are targeting first production by late 2027, with first exports to commence in 2028.
Mikael Skov, CEO of Hafnia, says: “As the world’s leading product tanker company transporting energy worldwide, Hafnia is well positioned to transport this clean fuel safely and efficiently to markets across the globe. We look forward to our continued collaboration with CHW and its partners in bringing this transformational project to Louisiana – in a strategically significant initiative aligned with furthering our overall sustainability objectives.”
“We are proud to work with project shareholder Hafnia, the world’s leading product tanker company, to bring the Ascension Clean Energy project to Louisiana,” adds Mitch Silver, COO of CHW. “An industry leader and proven innovator, Hafnia’s established track record of transporting hydrocarbons safely and sustainably around the world, as well as its stated priority to reduce carbon emissions, are fully aligned with ACE’s goals to meet the world’s growing demand for clean and affordable energy.”
hafniabw.com
ETT, VTTI’s terminal in Rotterdam, has picked up a contract to store sustainable aviation fuel (SAF) for one of its customers.
“The contract marks ETT’s further diversification into low-carbon fuels, and builds on the terminal’s ambition to become a key hub for the handling and storage of SAF, enabling the energy transition and helping to build the emerging renewable value chain in the Port of Rotterdam,” says VTTI. “Handling and storing
SAF is a perfect fit for VTTI as the company scales up its efforts to help achieve decarbonisation and moves towards reducing greenhouse gas emissions.”
www.vtti.com
Martin Midstream Partners has agreed to take a 10 per cent holding in the DSM Semichem joint venture alongside Samsung C&T America and Dongjin USA, to produce and distribute electronic-grade sulfuric acid (ELSA). Martin Midstream will use existing assets in Plainview, Texas and additional facilities as needed to provide feedstocks to the new production plant as well as provide land transport of finished product through its affiliate Martin Transport. The ELSA produced by the partners will be used by semiconductor manufacturers.
“We are excited to partner with Samsung C&T America and Dongjin USA in this unique opportunity to capitalise on the diverse and complementary skillsets, operating expertise, and vast market knowledge of the three parties,” says Bob Bondurant, president/ CEO of Martin Midstream. “The new facilities will incorporate technology currently being utilised to produce ELSA in Taiwan, which exceeds the quality of sulfuric acid being produced in the United States today.
“This strategic alliance allows the Partnership to capitalise on our existing asset base to participate in the manufacturing and transportation supply chain of the most advanced and power-efficient chip technology to date,” Bondurant adds. “ELSA supply presently sourced in the US does not meet current domestic demand, and with announced new fabrication and existing fabrication facility expansions, we anticipate an attractive market for the ELSA produced in Plainview.” mmlp.com
Furetank’s dual-fuel tanker Fure Valö has performed the first voyage using a new fuel blend, supplied by charterer Equinor, that contains 30 per cent used cooking oil with standard marine gasoil. Based on early indications of the test voyage, the fuel maintains the same level of performance as conventional gasoil.
The initial voyage involved a round trip between Mongstad in Norway, where the bunkers were supplied, and Reykjavik, Iceland. Another five or six round trips are planned on the same route to prove performance in the harsh weather experienced in the North Atlantic, as well as the fuel’s handling over time.
“Acting as test pilots for this new loweremission fuel is an important and honourable mission for us,” says Furetank CEO Lars Höglund. “Even if we primarily run our dual-fuel vessels on LNG/LBG or gasoil today, they are designed to be flexible, future-proof and easily converted to run on any fuel that will prove to be the right choice for the future.” www.furetank.se
Mitsui OSK Lines (MOL) and JERA have signed a memorandum of understanding to launch a study into the transport of ammonia for use as fuel, including shipments to JERA’s ammonia-fuelled power station due to open in Aichi prefecture, Japan in the late 2020s. MOL notes that, at present, ammonia is used mainly as a raw material for fertilisers and there is an established maritime trade, but as ammonia emerges as a next-generation clean energy source, large-scale demand for ammonia and for its transport by sea is expected in the future.
MOL and JERA will now look to develop a large ammonia carrier design, suitable for serving thermal power plants and receiving terminals; install and operate propulsion
systems using ammonia as a marine fuel; and work with related parties to foster the development of rules for the reception of fuel ammonia.
Greater use of ammonia as a marine fuel is one element of MOL’s environmental vision to achieve net-zero greenhouse gas emissions by 2050, under which it has targeted the introduction of some 110 net-zero oceangoing vessels by 2035. www.mol.co.jp
Leading specialty chemical and ingredients distributor IMCD Group has become a member of Together for Sustainability (TfS), a member-driven initiative that aims to raise standards of corporate social responsibility throughout the chemical value chain.
“The sustainability challenges we face today can only be tackled in collaboration. It is about working together, being transparent and
sharing knowledge,” says Marcus Jordan, COO of IMCD. “We believe that joining TfS brings us a step closer towards improving our sustainability performance and accelerating the sustainability journey of our customers and suppliers. We are looking forward to working closely with TfS and its members to create solutions and share knowledge and expertise in the supply chain.”
“I am very proud to welcome IMCD Group to the TfS family,” adds Bertrand Conquéret, president of TfS. “The arrival of IMCD Group expands our reach and increases our impact on the sustainability performance in chemical supply chains around the world. As the need for sustainable businesses only intensifies, TfS is the crucial enabler to make supply chains and businesses at large more sustainable and resilient, and contribute to developing a better world.” www.imcdgroup.com www.tfs-initiative.com
THE HULL OF The new inland tank barge Stolt Ludwigshafen has arrived in Rotterdam after a seven-week sea voyage from its building yard, Mercurius Shipping in Yangzhou, China. It will now be fitted out and, once the engine, electrical systems, wheelhouse, piping and crew accommodation are finalised, it is due to go into service in the spring of 2023.
The arrival of the new vessel marks a milestone in a plan hatched by BASF three years ago, after it had experienced difficulty moving its products on the Rhine as a result of
low water – a phenomenon that happened again this year. Along with Stolt Tankers, BASF developed a concept for a tank barge that would be able to operate even in extreme low-water conditions and ensure that the transport of its products, especially between its major production sites in Ludwigshafen and Antwerp, would not be affected by future low-water events.
Uwe Liebelt, president, European Verbund Sites, for BASF, explains more: “Following the unprecedented low water levels of the Rhine
in 2018, I am pleased that, with our robust contingency measures already taken, we were able to manage the challenges of this year’s low water period quite well. The innovative design of the new Stolt Ludwigshafen will be another crucial element for further increasing the supply security and thereby competitiveness of our largest manufacturing site in the world.”
The main objective of this project was to create a barge with a high load-bearing capacity and a shallow draught, while always ensuring safe operations and full manoeuvrability even in extreme low-water situations through the use of a hydrodynamically optimised hull shape and an adapted propulsion based on three electric motors fed by high-efficiency diesel generators.
The new tank barge is 135 metres long with a beam of 17.5 metres, considerably larger than traditional tank barge designs. It will have a transport capacity of some 2,500 tonnes in ten stainless steel tanks, again much larger than standard designs, and under extreme low water conditions it will still be able to pass the critical point in the Rhine near Kaub while carrying 650 tonnes of product.
The concept was put together by BASF in collaboration with a consortium consisting of Duisburger Entwicklungszentrum für Schiffstechnik und Transportsysteme (DST), Technolog Services and Agnos Consulting, which specialise in various aspects of shipbuilding. The detailed design was completed in partnership with Stolt Tankers, which then placed the order for the barge and will operate it exclusively for BASF.
“I am proud of what we have achieved during this exciting partnership with BASF, which supports our commitment to developing new technologies and ship designs for a greener maritime industry,” says Lucas Vos, president of Stolt Tankers. “Our team is primed and ready to start the next, crucial stage of the building process. We are looking forward to operating the Stolt Ludwigshafen exclusively for BASF and seeing a considerable period of planning and preparation brought to life!” www.stolt-nielsen.com
THE CHEMICAL TANKER MARKET AS IT EMERGES FROM A LONG DOWNTURN. ODFJELL BELIEVES THERE IS FURTHER UPSIDE POTENTIAL
ODFJELL HAS REPORTED timecharter earnings from its tanker shipping operations of $171.3m in the third quarter, up from $159.9m in the previous period and $125.0m in third quarter 2021. “We are pleased to report another strong quarter for Odfjell,” says CEO Harald Fotland. “The results are driven by a robust chemical tanker market. We continue to perform well both operationally and commercially, capturing the ongoing momentum in our markets. The improved cash flow generation enables us to strengthen our balance sheet and also secures attractive returns to our shareholders. We expect continued strong spot rates across most trade lanes, and foresee slightly improved TCE results in fourth quarter 2022.”
Along with an improved contribution from Odfjell Terminals, Odfjell achieved a net profit of $50.2m in the third quarter, continuing an upward trend over the past year and contributing more than half the $91.2m made in the first three quarters.
Commenting on the results, Odfjell says that there has been further reduction in the volume of swing tonnage working in the core chemical and vegoil trades; moreover, less sophisticated chemical tonnage has been swinging into clean petroleum products (CPP), leading to tight supply across the market.
“The ongoing energy crisis is also driving strong demand for energy-related chemicals and biofuels,” Odfjell adds.
Odfjell has responded to the improving chemical tanker market by reducing its participation in pool arrangements, a plan it announced along with its half-year figures.
That has had the effect of reducing the overall volume of cargo carried and, following the re-delivery of coated pool vessels, an increase in the proportion of chemicals in the cargo mix, which further boosted the company’s returns.
More pool vessels are due for re-delivery in the fourth quarter, which will also result in the
closure of the Handy pool. Given the state of the market right now, Odfjell does not expect this to have a significant impact on its earnings.
Odfjell is also taking advantage of high freight rates to reap benefits in the contract of affreightment (COA) segment; it renewed 6 per cent of its COA portfolio during the quarter at an average increase of 9 per cent. Odfjell also reports increasing demand from charterers to enter into COAs, while there is limited availability in the market. As such, it expects continued strong momentum in contract rates during the peak renewal season in the fourth quarter.
To compensate for the loss of pool capacity, Odfjell is also actively looking to grow its fleet; it will take eight 25,000-dwt stainless steel newbuildings on timecharter, the first two of which have already been delivered, with the last due to arrive in 2025. Overall, the chemical tanker orderbook remains remarkably low, considering the high freight rates being earned in the current market; newbuilding prices are high and there is uncertainty over future environmental regulations and what that will mean for the choice of propulsion systems and sailing speeds.
That means, Odfjell says, that the market can be expected to remain very strong in the near term and, over the next three years, growth in tonne-mile demand will exceed fleet growth, leading to a strong chemical tanker cycle. That will support the spot market and the appetite for COAs and Odfjell expects a further increase in earnings in the fourth quarter.
www.odfjell.com
Seapeak has struck a deal to acquire gas shipping specialist Evergas from Jaccar Holdings for some $700m in cash. Evergas owns and operates two very large ethane carriers (VLECs) and eight ‘Multigas’ carriers, all on fixed-rate timecharters to Eneos and all dual-fuel; it also controls six LPG carriers under leases that expire in 2024.
“Acquiring Evergas is another big step in Seapeak’s evolution as a leading owner and operator of liquefied gas carriers,” says Mark Kremin, Seapeak’s CEO. “Just as we’re bullish on LNG, we’re also bullish on NGLs, especially given the even greener nature of NGLs. Already a world leader in NGLs, Ineos is now growing in LNG, and we are thrilled to be adding them as a key customer, further diversifying our portfolio. Together, Ineos and Evergas are vital to America’s liquefied gas export story and their collaboration to develop CO2 carrier trades will be vital to decarbonising Europe.”
“At Evergas we are pleased to complete the sales process and become part of Seapeak – one
of the gas industry’s biggest players, which also brings us significant financial strength,” adds Steffen Jacobsen, CEO of Evergas. “This will provide a solid platform on which we can continue to grow our businesses in NGLs and CO2, where we see outstanding potential for growth.”
For Jaccar, the sale of Evergas is part of its deleveraging plan agreed with its creditors. The sale is subject to standard closing conditions and is expected to close by the end of this year. www.seapeak.com
Petredec has formed a new company, Fortitude Shipping, to take over its 11 handysize LPG carriers. The fleet comprises eight ethane/ ethylene-capable vessels, two semi-refrigerated units and one fully refrigerated ship. With an average age of four years, the Fortitude fleet is, Petredec says, the youngest and most fuelefficient in the sector.
The London-based company will focus on the transport of ethane, olefins and ammonia as well as the group’s core LPG trade. Petredec
says Fortitude is also well placed to benefir from the emerging transition to cleaner marine fuels.
“The majority of the Petredec Group’s verticals have each achieved a level of scale that now warrants operation as standalone business units to better focus on performance and growth,” says Giles Fearn, Petredec Group CEO. “The latest of these, Fortitude Shipping, is our wholly owned subsidiary dedicated to the movement of NGLs, which includes the second largest and youngest ethane/ethylene capable fleet in the sector. With an efficient modern fleet and industry-leading team operating the business, Fortitude is well placed going into an exciting period in shipping as we navigate towards a low-emission society.” www.petredec.com
Furetank and Algoma Central have doubled the size of their joint venture, FureBear, adding another four dual-fuel product tanker newbuilding contracts at China Merchants Jinling. Two of the four Vinga-series ships were ordered by Furetank in September and will now transfer to FureBear; the two additional orders are due for delivery in 2025.
“The expansion of our FureBear investment with Algoma is exciting news”, says Lars Höglund, CEO of Furetank. “This is yet another endorsement of the environmental benefits and innovative design of our Vinga series. I look forward to delivering on these benefits with our partner and working together to fulfil the need for modern and efficient tonnage in the markets we serve.” www.furetank.se
Kirby Corp has reported third quarter revenues of $745.8m, up from $598.9m a year ago, with net earnings rising from $10.3m (adjusted for
one-off items) to $39.1m. David Grzebinski, president/CEO of Kirby, says: “I am pleased with Kirby’s third quarter results and the improvement in both of our segments. During the third quarter, our inland marine transportation business delivered strong results with significant sequential and year-over-year improvement in profitability. Tight market conditions in inland led to sequential increases in spot market rates in the high single digits, and term contract pricing that continued to push higher. Overall, higher demand and pricing improvements helped to improve inland operating margins into the low double digits during the quarter.
“Coastal marine transportation also delivered improved financial performance with steady gains in revenue and operating income,”Grzebinski adds. “Market conditions were favourable in the quarter, with our barge utilisation in the low to mid-90 per cent range and modest increases in spot prices. These factors coupled with continued cost discipline resulted in further improvement in operating income for our coastal business during the third quarter.”
Grzebinski is also bullish about the near term outlook: “Refinery activity remains at high levels, our barge utilisation is strong in both inland and coastal, and rates are steadily increasing. While we expect some near-term headwinds related to record low water conditions on the Mississippi River, increasing delay days due to normal seasonal weather conditions, and high levels of shipyard activity in coastal, our outlook in the marine market remains strong.”
kirbycorp.com
Exmar has reported third quarter revenues of $95.6m, down from $136.1m for the same period last year, largely due to the sale of its Tango floating LNG unit. Exmar’s shipping
activities have been on the firm side of stable all year, with average timecharter equivalent rates higher during the first three quarters than they were in 2021.
Prospects for the midsize gas carrier market, where Exmar is a major player, look positive for the rest of the year despite uncertainties in the ammonia trades resulting from the conflict in Ukraine. Higher LPG production in the US and alternative ammonia exports from the Middle East and Far East are adding to tonne-mile demand, which should help soak up the large number of newbuildings due to enter the fleet next year. In the pressurised markets, refinery cuts and demand destruction in the Far East put pressure on rates but the sanctioning of Russian LPG exports in Europe once more increased tonne-mile demand and continues to support market rates. exmar.be
BW STAYS STRONG
BW LPG has reported third-quarter timecharter equivalent earnings of $130.0m, 24
per cent up on last year, with EBITDA ahead by 42 per cent at $92.8m and after-tax profit up 58 per cent at $46.4m. The improvement reflects higher spot rates in the LPG market along with improved fleet utilisation following the completion of the dual-fuel propulsion retrofitting programme.
BW LPG’s planned acquisition of Vilma Oil’s LPG trading operations, announced in August, has now received regulatory approval and is expected to be completed by the end of the year. During the third quarter BW LPG also sold and delivered the 2007-built VLGC BW Prince to new owners, generating some $44.2m in cash and a net book gain of $2.3m.
Looking ahead, BW LPG remains optimistic for 2023, despite growing macroeconomic concerns and continued geopolitical uncertainties. The US is delivering record volumes of natural gas production and there has been significant growth in LPG exports from the Middle East, helping meet strong demand in Europe. www.bwlpg.com
Insight is published by the Tank Storage Association, the voice of the UK’s bulk storage and energy infrastructure sector.
To contact the editorial team, please email info@ tankstorage.org.uk
TSA Insight Team
Peter Davidson, Jamie Walker, Nunzia Florio
CONNECT WITH US @UK_TSA TSA
Tank Storage Association @uk_tsa
CONTACT
Tank Storage Association
Devonshire Business Centre Works Road Letchworth Garden City Herts. SG6 1GJ United Kingdom
Telephone: 01462 488232 www.tankstorage.org.uk
TSA has used reasonable endevours to ensure that the information provided in this magazine is accurate and up to date. TSA disclaims all liability to the maximum extent permitted by law in relation to the magazine and does not give any warranties (including any statutory ones) in relation to its content. Any copying, redistribution or republication of the TSA magazine(s), or the content thereof, for commercial gain is strictly prohibited unless permission is sought in writing from TSA. Claims by advertisers within this magazine are not necessarily those endorsed by TSA. TSA acknowledges all trademarks and licensees.
Peter Davidson Executive Director, TSAWelcome to the winter edition of Insight. November saw world leaders gather in Egypt for the 27th session of the Conference of the Parties (COP 27) with a view to building on previous successes and paving the way for future ambition to effectively tackle the global challenge of climate change. The bulk storage and energy infrastructure sector in the UK has been vocal in its commitment to supporting the achievement of the Government’s climate neutrality targets. In this issue, we explore our sector’s ambitions, innovations and transformative journey as it plays its part to ensure the UK can meet its Net Zero target. We also explore the role of education and training as we prepare for the future and ensure that future skills needs will be met. I hope you enjoy this new edition of Insight and don’t forget to follow us on social media for all our latest news.
David McCausland, Head of Rating at Farebrother, examines the Autumn Statement and 2023 Rating Revaluation.
06 Reducing oil storage terminal emissions through digitalisation
Remote thief hatch monitoring helps terminals identify any unsealed hatches quickly, which can significantly reduce emissions.
10 UM Terminals passes quality audits with flying colours
Continually meeting customer expectations is firmly at the top of the agenda for UM Terminals’ dedicated team.
12 Understanding natural hazards risks to your site
RAS Safety Consultants explore risk reduction and preparedness for natural hazards.
14 Stanlow Terminals is transforming for tomorrow and is ready to lead the energy transition: in conversation with Michael Gaynon
Michael Gaynon, Chief Executive Officer at Stanlow Terminals, discusses the energy transition and future opportunities for the bulk storage and energy infrastructure sector.
17 Celebrating 20,000 process safety champions
The UK and global high hazard industries celebrate a significant milestone.
18 Benefits of NonDestructive Testing (NDT) for lead based coatings
Integrity Support Solutions explore the benefits of NDT for lead based coatings.
21 GRP – the alternative to steel grating
Marine applications create a wide array of challenges for construction materials.
22 How new career pathways will ensure bulk liquid storage drives our greener future
There has never been a more pressing need to give apprentices and employees alike transferable, futureproof skills.
25 UM Terminals appoints new Managing Director Phil McEvoy takes up the role of Managing Director at UM Terminals.
26 Mobile and environmental-friendly emissions reduction services for every application
ENDEGS explains how reducing industrial emissions requires modern and reliable technologies.
News:
Ita sundit adit accabo. Nequas et, te laut vent, voluptas dellatibusa volo qui abo. Caeptam fugit, que volorecabo. Ut verum in reicae nim qui consequ assunt.
The following meetings will take place online:
Volupta exerate verovit lita sequas re etument pliti berrore iciati quiaeperiae volupta tatate nonem. Ro issi consequis parum aut liamusam exerae cuptum, untis dem re quidem eaquuntota sum nos acias dit aut eatem earum quatemporem aped quatquaes dunt eumquibus, as et que nonsequis dit venia vid qui sererorro blametur? Ehenisquasim veni doloreroremo blatur?
• 6 December 2022: TSA Energy Transition Committee
• 8 December 2022: TSA Council
TSA’s
• 15 December 2022: TSA SHE Committee
Obist, architatur? Qui re deritas volore necum imporisqui doluptate porem exeris endi dolenihilia de et fugiaspient.
For more information on TSA’s meetings, write to info@tankstorage. org.uk
Business Rates bills are all based on the product of a Rateable Value and a Multiplier. On 17th November 2022 in his Autumn Statement, Chancellor Jeremy Hunt confirmed that the 2023 Rating Revaluation in England and Wales would proceed, with a valuation date of 1st April 2021. This is the first Revaluation since 2017, which had a valuation date of 1st April 2015. This six-year gap is very unfortunate. The proposed 2022 Revaluation was changed to be from 2021 which was then cancelled altogether due to the Covid pandemic. The Devolved Administrations in Scotland and Northern Ireland are now expected to confirm their own 2023 Revaluations.
New Rating Assessments come into force from 1st April 2023, but there are important differences in the valuation dates. In England and Wales, the valuation date is 1st April 2021, a date chosen by the Government to allow the impact of the Covid pandemic to be considered. This followed a law change ruling out any Rating Appeals citing Covid as a “Material Change in Circumstances”. In Scotland, the valuation date is 1st April 2022. In Northern Ireland, the 2023 valuation date is 1st October 2021, with their last Revaluation having taken place in 2020, with a valuation date of 1st April 2018.
“It is an important principle that (rates) bills should accurately reflect market values” said Mr Hunt in his Autumn Statement. This is widely agreed. A Rateable Value is an estimated annual rental value. For most properties such
as shops, offices, and warehouses, there is rental evidence available to set Rating Assessments. The big winners from 2023 are the Retail and Hospitality sectors, where Rateable Values have come down, reflecting the drop in retail rental values, and where there are also further support measures. The good news in England, for all ratepayers including TSA members, is that the 2023/24 mulitiplier is frozen at the 2022/23 level, a reduction of over 10% in Rate Liability. The Industrial and Logistics sectors have seen rental value increases, resulting in higher draft 2023 Rating Assessments. The industrial theme applies also to the Bulk Liquid Storage sector. There is no rental evidence, so Rating Assessments for Bulk Storage terminals are set using a Depreciated Replacement Cost approach, combined with a Decapitalisation Rate which is set by each Devolved Administration.
Replacement costs for Rateable plant and Machinery, and commercial property values, increased from 1st April 2015 to 1st April 2021. The Welsh Assembly invited representations regarding the setting of the Decapitalisation Rate for the 2023 Revaluation, which included a submission from this practice. The Welsh Assembly correctly decided to reduce the Decapitalisation Rate, by 11%. A quick study of TSA member terminals in Wales indicates 2023 Rateable Values rising by no more than 20%. In England, no consultation took place about the Decapitalisation Rate,
with the same figure retained from the 2017 Revaluation. This is incorrect and too high. Representations are now needed to seek to correct this for the many industrial businesses affected, including TSA members. For England, draft 2023 Rateable Values are typically 30% up on the 2017 Rateable Values. The good news is that next year’s rates bills are limited to a cap of 30% above this year’s bill, and with no 10% inflation factor. No significant changes are expected next year in Northern Ireland, with the 2023 Revaluation following on soon after the 2020 Revaluation. Final thoughts though are on Scotland which has a valuation date of 1st April 2022, so there are seven years of cost and land value increases to consider! At the time of writing, 18th November, no further details for Scotland, Wales, or Northern Ireland are known.
AuthorDavid McCausland is Head of Rating at Farebrother Chartered Surveyors. He is a known specialist in the bulk liquid storage sector, a member of the UKPIA Rating Panel, and a guest lecturer for the RICS Rating Diploma course (Plant & Machinery Module).
Remote thief hatch monitoring helps terminals identify any unsealed hatches quickly, which can significantly reduce emissions.
The European Union has ambitious emissions reduction goals. The European Climate Law seals the EU’s commitment to reduce greenhouse gas emissions by at least 55% from 1990 levels by 2030 and become carbon neutral by 2050. Additionally, the United Kingdom has its own goal to reduce emissions by 78% compared to 1990 by 2035 and reach net zero by 2050. Naturally, these goals affect all industries, the oil terminal industry included. Efforts to reliably reduce energy consumption and emissions will require clear visibility into operations — not guesswork — powered by innovation and new monitoring technologies.
Digitalisation and the data-driven decision-making it empowers are not new to the European tank storage sector. By integrating connected technologies throughout terminals, businesses have received many advantages, including lower costs, greater reliability and lesser risk. One of the elements in the terminal to recently receive greater digital capability is the thief hatch.
Almost half of all emissions in major oil basins are from storage tanks, and a primary way that emissions escape is through open thief hatches. Storage tanks are typically located on remote sites that can cover many kilometers. They may go days without a site visit and physical inspection. If thief hatches are accidentally left unlatched, they may go undetected — and release fugitive emissions — for a long time. Remote thief hatch monitoring helps terminals identify any unsealed hatches quickly, which can significantly reduce emissions.
Minimising emissions through thief hatch monitoring
Thief hatches have several important functions. They serve as a tank’s maintenance access hatch and the primary level of pressure protection for venting and vacuuming. Thief hatches have historically allowed producers to check tank levels and media properties required to complete custody transfer; however, because of fugitive emissions and worker safety, this is a practice the industry is trying to move away from.
During site visits, thief hatches are frequently accessed by a variety of personnel measuring the contents of storage tanks, transferring fluids to and from the tank or testing the thief hatch seals. Unintentionally, hatches may be left fully open or, more frequently, closed without being securely latched. Without reliable monitoring, days or weeks
may pass before personnel notice an open or unsealed hatch and close it. As chemicals evaporate, the vapors escape through the open hatch and enter the atmosphere.
As a sealing element, thief hatches are inherently subject to leakage. While manufacturers and producers have long collaborated to develop better, tighter sealing thief hatches, no seal can account for a failed closure. A newly built, closed and properly sealed thief hatch can limit emissions, but a hatch left open or not fully sealed allows emissions to continuously vent out into the atmosphere. Not only is this an environmental concern, it can also result in lost product.
Monitoring solutions help terminal operators to confidently know that a hatch is sealed. The latest technology can provide precise data that includes how long each hatch at a terminal is open and confirmation that it’s closed and securely sealed after access, which can allow for measurement of total site emissions.
While thief hatch monitoring solutions have been available in the past, these early designs had a consistent issue — false signaling. The first monitoring systems sometimes made no distinction between a latched and unlatched thief hatch switch, which resulted in a false trip. A false trip can have substantial consequences. Since the thief hatch may display
as open when it is, in reality, closed and latched, operators may invest unnecessary time manually checking thief hatches.
Another challenge is the sheer range of thief hatch designs in the field. There can be thousands upon thousands of thief hatches in terminals, from brand new to decades old. It’s essential that a monitoring solution easily installs on and fits multiple models and designs. Mounting patterns, latch positions and angles differ from product to product.
There are now advanced solutions that address the biggest challenges in thief hatch monitoring. The latest monitoring technologies reliably sense a thief hatch is properly latched
Emerson’s AVENTICSTM Series AF2 Sensor continuously monitors air consumption in pneumatic systems and provides insights that can help terminal operators quickly detect and address leaks. (Image courtesy of Emerson)
and easily install in the field on both new and existing thief hatch models. Producers can receive these solutions in modular mounting kits that allow them to retrofit their thief hatches in the field using only simple tools.
The kits include an ultra-reliable, sophisticated proximity sensor and easy-to-install wireless transmitter that precisely and continuously monitor hatch position in real time, allowing operators to confidently ensure that hatches are fully sealed when not being accessed.
The precision position sensor is specifically designed to signal only when a lid is fully latched. Proven in mission-critical, process applications, it features a robust bracket design that guarantees no false signaling will occur. The sensor is designed to reliably operate in high- and lowtemperature extremes and highpressure and potentially explosive environments.
Like a proximity switch, the sensor has no moving parts and uses magnets to detect a ferrous metal or magnetic target. Like a limit switch, it provides highly precise readings. By combining these features, the sensor requires far less maintenance than traditional limit switches and performs within harsh environments that often prohibit the use of other technologies, such as inductive or capacitive sensors.
The sensor can connect to the
wireless transmitter, which offers control system access to discrete points that are otherwise not connected due to wiring costs and lack of input/output. The transmitter automatically keeps a time-stamped record of each time the thief hatches are open and closed. Operators can access a 24-hour automatic log of thief hatch status, which reduces the need for visual tank inspections. Since the connected sensor doesn’t draw power, optimising the battery life of the wireless transmitter, both devices are certified for global explosionproof applications.
The simplicity and sophistication of the design allow producers to easily install the system on both old and new thief hatches and remotely monitor their status without false trips. This helps ensure that emissions readings are accurate and reduces personnel trips to the field.
In addition to thief hatches, there are many other opportunities in oil terminals to reduce emissions. If left unchecked, pneumatic systems can use more energy than they need, resulting in excess consumption and higher carbon emissions. By optimising the energy consumption that pneumatic systems use, terminals can reduce emissions levels.
One way to optimise the energy use of pneumatic systems is by detecting
and addressing compressed air leaks. Compressed air production can be responsible for a considerable percentage of a terminal’s energy use. If there are leaks in the line, more air than necessary must be produced to compensate for what’s lost. Advanced air flow sensors can continuously monitor air consumption in pneumatic systems, and the visibility can help terminals reduce energy use as well as unplanned downtime. These stand-alone sensors are more than flow meters — they provide diagnostic data and insights that help operators quickly detect and address leaks and perform predictive maintenance that can prevent leak formation. Sensors can also interface with digital control and other systems and be retrofit on an existing pipeline up to 50 millimeters.
Another way to reduce energy consumption and, in turn, emissions is to replace solenoid operating
valves (SOVs) with lower-wattage models. There are now Ex d directacting valves available that use less than 2 watts. This can save more than 10 watts per SOV compared to standard models, which translates to a savings of 87.4 kilowatt hours. This may not sound like much, but terminals can have hundreds of SOVs that can usually last 10 years before replacement. Plant-wide energy savings and emission reduction can be significant.
Some terminals may use smaller valves commonly controlled by a rack-and-pinion actuator. These are usually NAMUR-interfaced and controlled via a NAMUR SOV. The latest valves feature Piezo technology and operate at 0.0007 watts, the lowest of any ATEX SOV.
As the process industry responds
to climate neutrality, reliable monitoring is a critical step toward emissions reduction, as well as digital transformation. The latest thief hatch and pneumatic solutions are essential tools for achieving both.
Whether terminals are just starting out or have mature digital transformation programs in place, it’s important that they have an expert partner to support them. Technology providers like this offer a comprehensive portfolio of intelligent solutions, from valves and sensing technology to software and services, that can help reduce emissions while optimising the safety, reliability and performance of a terminal’s most demanding applications.
It’s critical to monitor and confirm that terminals have no issues, like open thief hatches and pneumatic leaks, that could contribute to carbon emissions. By implementing reliable monitoring systems, terminals have greater asset and system visibility, giving them the power to make informed decisions that can address — or altogether prevent — emissions.
Author Mike Howells is the marketing manager for process in Europe, the Middle East and Africa for Emerson. He has been with Emerson for 25 years and understands the importance of digitalisation and sustainability in the industry. To know more, contact Mike. Howells@Emerson.com. For more information, visit www.emerson.com/ en-gb/automation/asco.
Audits carried out include the Universal Feed Assurance Scheme [UFAS], FSSC 22000, the certification scheme for Food Safety Management Systems, for its Regent Road and Gladstone Dock sites, and the Halal certification for Regent Road.
Continually meeting customer expectations is firmly at the top of the agenda for UM Terminals’ dedicated team.
Continually meeting customer expectations is firmly at the top of the agenda for UM Terminals’ dedicated team.
An integral part of achieving this goal involves ensuring the business is meeting the labyrinth of quality standards and industry accreditations. During recent weeks, UM Terminals has undergone an intensive programme of external audits –something that would usually be spread across a year but could not happen due to various unforeseen circumstances. It was also the first time in over two years that on-site audits had been possible due to the Covid-19 pandemic.
Responsibility for preparing for the audits lies with Jo Winning, UM Terminals’ Quality, Performance & Development Manager, along with Karl Pass, who was recently promoted to the role of National Operations Manager. Jo and Karl are further supported by the various terminal managers across the company’s eight sites and other key members of the team.
The company’s ISO9001:2015 quality management accreditation was also audited.
Jo said: “We received excellent feedback from the auditors regarding our planning and performance, including the high quality of our operations and Client Central Services teams. As a business, we pride ourselves on our capability to manage change. One recent example of this was how quickly we flexed to meet the new requirements of a Scandinavian customer which took a much larger tank that has been specially converted to store an AdBlue product. From day one of this project, everything went according to plan thanks to our forward planning, engineering expertise and attention to detail. As a business, we are only as good as our people and during recent months we have developed new terminal managers to ensure we have the right people in the right places. Karl’s promotion to National Operations Manager has also been an important step forward. We were particularly pleased with the FSSC 22000 and Halal audits as these accreditations have only been in place since last year.”
Further audits, including the Fertiliser Industry Assurance Scheme [FIAS], will take place before the end of the year.
UM Terminals and other companies owned by UM’s holding company W&R Barnett will also be scrutinised for their sustainability credentials via the Energy Savings Opportunity Scheme [ESOS] which assesses energy usage, including boiler efficiency.
Jo added: “The audits are important for our customers, staff and other stakeholders. We want our customers to know we are committed to excellence in everything we do, and our success is a real morale booster for our teams. We welcome the new audits around sustainability. We are committed to an ongoing programme of investment in our assets, and this includes enhancing our energy efficiency which is good for us and our customers. We also never rest on our laurels. We have already embarked on a calendar of internal audits and continue to invest in the training of our people, ensuring the training is appropriate to each of our facilities.”
Vic Brodrick, UM Terminals’ Interim Managing Director and Commercial Director said: “We are committed to a continuous programme of investment to guarantee that UM Terminals is best placed to meet the needs of our customers today and tomorrow. Thanks to the sterling work of Jo Winning, Karl Pass, our terminal
managers and other members of the team, the business has come through a series of highly intensive audits with flying colours.”
UM Terminals operates out of 8 terminals, strategically located across the UK, handling over 40 different products. It currently has a capacity of over 300,000 cubic metres of bulk liquid storage, but the plan is to grow this to over 400,000 cubic metres.
Product solutions include vegetable oils, industrial, food and feed, chemical, fertiliser, fuels, biofuels and base oils.
The company rebranded from UM Storage to UM Terminals in 2020 to better reflect the broad range of services the company offers its clients. It is part of the UM Group which has a distinguished history stretching back almost 100 years.
UM Terminals provides storage facilities for a wide range of products including vegetable oils, industrial, food and feed, chemical, fertiliser, fuels, biofuels and base oils.
For more information, visit www.umterminals.co.uk.
needs careful consideration.
Natechs (Natural Hazards Triggering Technological Accidents) refers to accidents initiated by natural causes, including earthquakes, lightning and flooding, all of which have the potential to impact high hazard industrial sites. Major accidents have the potential for catastrophic consequences to people and the environment as well as business reputation and sustainability. Such natural hazards can both trigger major accidents and weaken safeguards in place to prevent, control and mitigate them.
For this reason, the risk posed by Natechs needs careful consideration.
Natural hazards can be broadly categorised as seismic, hydrological and meteorological (e.g. earthquakes, flooding and wind storms respectively) and will have different likelihoods, severities, warning times and consequences. Generally, natural hazards will impact widespread areas. Climate change also plays a role, typically increasing the likelihood and severity of hydrological and
meteorological events. An example of a Natech accident in recent history is the floods that occurred in Central Europe in August 2002. In total, 232 lives were lost and one site, in the Czech Republic, was struck particularly hard. Large volumes of chlorine gas were released from pressurised storage tanks. The flood itself was a one in five hundred year event and as such, the severity was unprecedented, with the hundred year water level of the site being exceeded by 1.3 metres. Whilst it may not be practicable or justified to implement safeguards for events of unprecedented scale and severity, consequences involving the loss of containment of hazardous substances are still possible during lesser events, highlighting the importance of robust safety measures. Since the consequences of Natech events are often severe, just being aware of them is not enough and the duty holders of hazardous sites must be proactive in their approach to understanding, assessing and managing the risk.
Risk reduction and preparedness for natural hazards is something which is often overlooked. There is a requirement under the COMAH Regulations and the Seveso directive for sites to understand their risks from natural hazards, with some other countries having specific laws/ programs regarding the protection of people from earthquakes and/ or tsunamis. There is however a shortage of dedicated methodologies and guidance for assessing and
The risk posed by Natechs (Natural Hazards Triggering Technological Accidents)
managing Natech risks. In addition, for some natural hazards there is a limitation to the measures which can be implemented, and other measures may be deemed too costly, especially if considering the likelihood of the natural hazard event at the site versus a non-Natech major accident hazard event. Many measures in place to prevent a major accident hazard may not work in a Natech incident, meaning that crediting these barriers needs to be done with caution.
The use of hazard mapping, such as flood maps, may be useful for understanding the current risk, and can include inundation areas in the event of sea level rise and climate change. In New Zealand, GNS Science have provided vulnerability and evacuation maps to the government, authorities and private industry which focus on the possibility of a tsunami. The maps show the areas in the most danger and provide vital information for evacuation planning. These types of maps can also be available for other natural hazards such as volcanoes and can be used to help inform site emergency response plans, as well as the emergency response plans for the local authorities. It should be noted however that in a Natech event, there is a reasonable chance that emergency response teams would not be able to reach the site(s) requiring support. This may be due to damaged access roads, services being overwhelmed by the public, or the services themselves being affected by the hazard. This may
reduce the resources available to sites in an emergency and should be considered in response planning.
There is no ‘one size fits all’ when it comes to specific sites and hazards. Therefore, duty holders need to understand the risks posed by Natech events to their specific site and then ensure they are informed of what equipment may be impacted, how, and what to do in the event of a natural hazard. Although there may be a low likelihood, natural hazard events can often be a case of ‘when’ not ‘if’, and so we must be prepared for their eventuality.
RAS Ltd is an independent firm of risk specialists established in 1993. RAS are founded on a set of simple principles: recruit the best people in the industry, only work in our areas of expertise, and work with our clients, not for them. It’s an approach that has seen them grow from being a handful of specialists in the North West to a rapidly developing company working with the leading companies in the oil & gas, pharmaceuticals and specialist chemical sectors across the world.
The RAS team has worked on some of the biggest and most influential projects in the industry, and continues to expand their specialist knowledge.
For more information, visit www.ras.ltd.uk
Michael Gaynon, Chief Executive Officer at Stanlow Terminals, discusses the energy transition and future opportunities for the bulk storage and energy infrastructure sector.
Michael Gaynon, Chief Executive Officer, Stanlow TerminalsLocated on the south side of the Mersey Estuary, near the major cities of
Liverpool and Manchester, Stanlow Terminals owns and operates the largest tank storage facility in the UK, with over 3 million cbm of capacity within its portfolio.
The UK’s largest independent bulkliquid storage terminal can boast unrivalled connectivity to domestic and international markets through road, barge and jetty connectivity, plus access to key national distribution pipelines such as the UK Oil Pipeline (UKOP) and the Manchester Jet Line.
The location is strategically significant, serving the UK energy corridor and including major population centres, key regional airports and accounting for 16% of national transportation fuel demand.
Stanlow Terminals has a clearly defined long-term vision to lead the charge in the development of changing energy infrastructure. Tell us more about your vision for the future.
Against the background of a changing energy industry and as we develop innovative ways of creating sustainable energy, the supporting storage and transportation infrastructure needs to evolve. At Stanlow Terminals, we are not only transforming for tomorrow, but we are ready to lead the energy transition. We are investing to create the UK’s largest bio-fuels hub and playing our part to ensure that the UK can meet its Net Zero targets. Our strong geographical position and experience in the energy sector enable us to provide solutions based on the ability to safely handle energy products to meet the needs of society’s Net Zero goal.
In this transformative journey, Stanlow Terminals is primed to lead the national charge in the storage and distribution of hydrogen by diversifying current assets to accommodate the UK’s Net Zero target and by delivering in line with sustainability objectives through our multimodal logistics operations.
Stanlow Terminals operates at two locations, one being a deep-water terminal at Tranmere, which receives some of the largest vessels in the world via the Irish Sea, and the other along the banks of the Manchester Ship Canal, which provides excellent multimodal connectivity. The business can also call upon reliable road, rail and water links, along with connection to UKOP and the Manchester Airport Jet Pipeline.
And we are now set to expand our current operations through increased connectivity via road, pipeline, rail and shipping. These enhancements support our strategic objective to become the UK’s largest bulk liquid storage and energy infrastructure solutions provider and complement the developing hydrogen economy.
In this context, we are supporting HyNet by developing the storage and distribution facilities that will be required to provide a multimodal hydrogen transport hub.
The UK Government has set out its strategy to decarbonise the economy over the next 30 years and we are committed to playing our part in helping to achieve that. This vision for the future is shared with our sister company, Vertex Hydrogen, and our parent company, Essar: we are united in our goal to lead this transition.
Stanlow Terminals has also announced it will make investments over the next three years to develop the UK’s largest biofuels storage hub. Tell us more about this project and how you see the UK biofuels market developing in the future.
Stanlow Terminals is developing the UK’s largest new biofuels storage hub located in the North West of England which will deliver 300,000 cubic metres of capacity to support our customers in delivering the UK’s Net Zero transition.
The new facilities at the Stanlow
Manufacturing Complex and Tranmere Terminal will allow customers to store, blend and distribute biofuels suitable for use in the energy transition including as drop-in replacement transport fuels for road, aviation and marine. While we already provide biofuels storage capacity for customers through dedicated supply and delivery infrastructure, this new customer-led investment will support the growth of initiatives such as sustainable aviation fuel (SAF), sustainable hydrotreated vegetable oil (HVO) and will include waste-based feedstock import facilities, blending and capacity expansion for existing bio-ethanol and bio-methanol.
Indeed, the market for energy from renewable sources in the UK is expanding rapidly, driven by legislative obligations to encourage lower carbon fuels. And these investments reflect the growing demand from both our partners and our customers seeking storage facilities and expertise in future fuels handling, as businesses across the economy look to decarbonise and operate in a more sustainable way.
Against this background, we have also completed the International Sustainability and Carbon Certification (ISCC) sustainability accreditation for our storage terminals. ISCC is a global leading certification for sustainability and traceability which aims to facilitate and improve the environmental, social and economic
aspects of sustainability in biomass value chains. Products which are certified ISCC are becoming a fast requirement in the current storage market.
We have a clear vision to further accelerate sustainability in the North West region and ambitious plans to embrace our strengths to deliver on this ambition. We are therefore fast tracking a number of developments to be able to support future change and are on target to meet our objectives.
At Stanlow, the company hosts a well-resourced infrastructure portfolio. As the bulk storage and energy infrastructure sector looks to the future, how can it ensure that the opportunities of tomorrow are seized?
In order to seize the opportunities of tomorrow, it is critical to always think ahead as well as to build successful partnerships to drive future strategies.
At Stanlow Terminals we have recognised important investment opportunities to expand on our current offering. In the longer term, accessibility into new markets will undoubtedly be at the heart of our strategy. Our aim is to lead by example: we want to both contribute to the growth of the North West of England, where we are based, and be recognised as global leaders in the low carbon energy sector.
As the breadth of products and services provided by terminals evolve, there are always challenges but opportunities too. However, working and thinking proactively are key to ensure that operators in the bulk storage and energy infrastructure sector are able to identify and solve problems early, as well as capture important opportunities in order to seamlessly support customers as their needs change.
For example, heated tanks for biofuels, as well as ethanol tanks, are still hard to find and in high demand. The transition to E10, from a storage and logistics perspective, has resulted in increased demand for ethanol storage to ensure supply can keep up with consumer demand. These tanks require specialist linings to avoid corrosion and to manage HSSE requirements. At Stanlow Terminals, we worked with coatings specialists to develop a suite of linings for multiple biofuel components to re-life existing infrastructure for these new greener fuels. This allowed the repurposing of unused infrastructure originally built to handle products like fuel oil.
It is therefore by working and thinking proactively that we identified an opportunity in this context and gathered regular market intelligence reports to ensure that we are best placed to meet our customers’ needs today and as we look ahead towards our energy transition.
The company has a robust HSE management system in place
and has achieved ISO 45001 accreditation. Tell us more about this important recognition.
We are committed to meeting the highest standards in our environmental performance and, in May of this year, we were awarded the ISO 14001 Environmental Management System accreditation and the ISO 9001 Management System. This certification covers all of the environmentally sensitive aspects of our business, including how we manage and distribute crude products, refined petroleum products, petrochemical products and biofuels.
As our business grows, protecting people and the environment will always be our top priority, and this accreditation provides independent verification that we have the right management systems in place.
For more information about Stalow Terminals, visit www.stanlowterminals.co.uk
Author Michael Gaynon is Chief Executive Officer of Stanlow Terminals. He has 21 years of experience in the sector, having previously held senior roles globally with Essar Oil, Shell and SGS.
Responsible process safety training success has been achieved by over 300 UK and global high hazard companies, celebrating the fact that since 2010, 20,000 delegates have now adopted the Process Safety Management (PSM) industry framework training standards.
Listed in the HSE COMAH guidance document, the PSM standards are benchmarked to COMAH / SEVESO III competence and compliance requirements - to help improve all businesses’ operational integrity, safety and reduce the risk of a Major Accident Hazard to people, assets and the environment.
Developed for industry by the Process Safety Management Competence Programme Board, including representatives from the Health and Safety Executive, the PSM training standards are delivered by Cogent Skills, via the following 1 or 2-day courses:
• Process Safety Leadership for Senior Executives for Senior Executives and Board Members of major hazard facilities
• Process Safety Management Foundations for Managers, Supervisors, Safety Personnel, Senior Contract Employees and Junior Engineers
• Process Safety Management for Operations for Operators, Maintenance Technicians and Long-Term Contractors
• PSMO - Train the Trainer (License
to Train) deliver approved course content in-house under license
Peter Davidson, Executive Director of the Tank Storage Association, said: “The TSA is an active member of the Process Safety Management Competence Programme Board. The work of the board in developing and maintaining training standards for process safety is critical in providing the tools necessaryto allow business leaders, asset managers and operators to safely manage their plant and processes. These training standards have been developed jointly by industry, the Competent Authority and UNITE the Union, and the learning objectives within the standards represent the very latest knowledge and best practice. The TSA fully supports this important initiative and will continue to actively contribute as industry looks to the future.”
The 20,000 PSM delegates represent over 40 global major accident hazard sectors – from Chemicals, Nuclear, Energy, Utilities, Manufacturing, Upstream and Downstream Petroleum, to Explosives, Distribution and Storage, across the following site classifications:
• 36% Upper Tier COMAH
• 15% Lower Tier COMAH
• 49% Non-COMAH
For more information, visit www.cogentskills.com
its compounds including lead alkyls; and
• lead when it is a component of any substance or material.
The lead must also be in a form in which it is likely to be:
• inhaled, e.g. lead dust, fume or vapour;
Matt Wadie, General Manager of Integrity
Support Solutions, discusses the benefits of nondestructive testing for lead based coatings.
Matt Wadie, General Manager, Integrity Support Solutions GroupThroughout the tank storage industry, there is already a well-established practice to undertake lead declassification of fuel storage tanks based on the Energy Institute “Guidance on the declassification of tanks previously in leaded gasoline service”.
However, we often find that external coatings for tanks and associated pipework and infrastructure from a range of industries can also contain lead-based paints, often with a high lead content, which can be overlooked during project planning and works, potentially leading to non-compliance with the Control of Lead at Work Regulations 2002 and Health and Safety Legislation.
The Control of Lead at Work Regulations 2002 applies to any type of work activity, e.g., handling, processing, repairing, maintenance, storage, disposal etc which is liable to expose employees and any other person to lead as defined in Regulation 2, i.e., to:
• metallic lead, its alloys, and all
• ingested, e.g. lead powder, dust, paint or paste; or
• absorbed through the skin, e.g. lead alkyls or lead naphthenate.
Breathing or ingesting lead dust or fume from hot works can cause serious occupational ill health problems like kidney, nerve and brain damage or infertility.
What do employers/site owners have to do?
The Regulations require employers to:
• make a suitable and sufficient assessment of the risks to the health of employees created by the work to include whether the exposure of any employees to lead is liable to be significant;
• identify and implement the measures to prevent or adequately control that exposure; and
• record the significant findings of the assessment as soon as is practicable after the assessment is made.
As part of your legal duties and risk assessment, lead paint inspection and testing should always be
required as part of due diligence prior to maintenance works, repair, refurbishment or demolition of any structure, pipe, tank or surface that you own on site, unless you can prove that there is no risk or lead present. The duty the Regulations place on every employer to prevent or adequately control the exposure of employees to lead applies irrespective of the source of that exposure. For example, the exposure to lead may result from work with lead or leaded compounds being carried out by the employer’s own employees, or incidental exposure arising from work nearby being carried out with lead or leaded compounds by another employer’s employees.
Traditionally the method of sampling was to take a bulk sample of surface coating and submit it to an accredited laboratory, but this has a number of issues associated with it. The sample needs to be large enough to ensure sufficient analytical limits of detection can be reached, it needs to be full depth down to the base material, its time consuming in both the sampling and analytical turnaround and can be costly depending on the number of samples obtained.
Use of NDT lead detection instruments such as hand-held X-Ray fluorescence analysers can offer a range of benefits from rapid field testing with each sample
taking less than a minute, instant results and ability to take full depth measurements through many years of coating, without damaging the integrity of the surface material.
A full site register can be generated, from single survey, which contains all of the site assets containing lead-based coatings to enable the information to be available for any activity from simple works through to be included in any CDM or preconstruction information.
As X-ray fluorescence (XRF) spectrometry equipment becomes more commonplace, it is imperative to ensure that the users are familiar with the hazards and requirements of working with ionising radiation. XRF equipment can produce very high levels of radiation at the aperture, and it is important that the correct precautions are implemented to protect individuals working with or near the system.
Where paint or bulk material samples are to be obtained, care should be taken to ensure that the sample methodology is robust and has steps to prevent cross contamination of samples by cleaning the tools, using disposable materials and most importantly has a risk assessment in place to minimise the risk of lead contamination onto the workplace during sampling.
All sample analysis should be carried out by a laboratory that holds UKAS accreditation for lead analysis.
If the plan is to use an XRF analyser
for NDT the user should be trained and also ideally be a Radiological Protection Supervisor as a minimum requirement.
Where advice is to be given with regards to possible occupational exposure and suitable and sufficient control measures then a competent Occupational hygienist should be contacted, via the British Occupational Hygiene Society Directory of Consultants. Integrity Support Solutions have a wealth of knowledge on the methodology required to support companies through their risk assessment process to assess where exposure to lead or leaded compounds may occur.
For more information, visit www.integritysupportsolutions.co.uk
Author Matt Wadie is General Manager of the Integrity Support Solutions Group Ltd.
Marine applications create a wide array of challenges for construction materials. The salt air can cause corrosion resulting in accelerated wear on anything that is not highly resistant. In addition, the moisture can make surfaces slippery creating potential accident areas. Weight can also be an issue in dockside and marine settings, and GRP is a material that is light weight whilst still durable, and requires little in the way of maintenance.
Its resistance to corrosion and erosion, coupled with its light weight and anti-slip properties, make it an excellent material for the fabrication of platforms, walkways, and step-
GRP marine walkway (Image courtesy of JBP)
overs in the fuel storage environment. GRP is UV stable, it is non-conductive, and resistant to most chemicals.
TSA’s Associate Member JBP (a major supplier of Pipe, Fittings, Flanges and Valves) has long experience in the provision of fabricated access equipment, and holds the largest stocks of GRP grating and structural products in Scotland. From their Inverurie fabrication facility, JBP have produced a wide range of bespoke walkways, bund and drain covers, stepovers, landing platforms, mezzanines, and access stairs.
For more information, contact Kelly Thurston at kthurston@core-6.co.uk
operators with the right knowledge, allowing them to truly take off.
Why now? Because many with the wisdom and insight that has to be passed on have already retired, and potential recruits are skipping the sector entirely – enticed by offerings from “cleaner” green industries.
There has never been a more pressing need to give apprentices and employees alike transferable, future-proof skills to help move the bulk liquid storage sector forward.
There has never been a more pressing need to give apprentices and employees alike transferable, future-proof skills to help move the bulk liquid storage sector forward. Done right, we will see out the last days of any unnecessary fossil fuels while assisting the industry and its businesses in moving to a greener future.
To achieve this, we need to be a part of the UK’s evolving energy solutions and pass on decades of our collective expertise to the next generation.
That way, we can play an essential role in the UK’s future success story.
An urgent but exciting time Correct implementation will guarantee the most exciting time I will have experienced in my 30-plus years in the industry. But, to truly make the most of our position in this change, both businesses and training providers need to create a runway which will equip our next generation of engineers and
But despite successful overtures from fledgling green sectors, this brain drain causes problems for both the legacy of bulk liquid storage and the renewable energy providers. This is because although it is often called a green “revolution”, it is far from it. It has been a gradual, evolutionary process, and it will continue to be so.
Developing sustainable green technology has taken time, and much of it is still in its infancy – or at least some way off seizing its full potential. This gradual growth of technology (like carbon capture and hydrogen production), as well as different dependencies on fossil fuels, means that there will be no day when someone flicks a switch and everything is powered by green energy. This is as true for the UK’s vast, varied facilities as it is for the fleets of vehicles on our rail and roads.
The reality is that although we need to make sure the next generation is well-equipped for the new energy era, fossil fuels are also going to be around for some time. There will,
though, be a transition between the two that will gain momentum. So, we need an army of apprentices to take the torch from our retiring generation in bulk liquid storage. We need them to shepherd the country – and those our storage solutions serve – from fossil fuels to a landscape that includes greater use of renewables. We need their vigour, drive, and commitment to help us shape our future and lead in this transition.
If the energy industry is not careful, this transition will be choppy at best: supplies of fossil energy products will struggle without wellmaintained infrastructure. Likewise, major green projects will stall if their engineers and operators don’t have the right competencies –green energy will need production, transportation, and storage, and with that, new skills to ensure these storage and product conditions are maintained.
Although green energy rightly gets positive press, this excitement is not always tempered by the reality that these new, world-saving fuel sources are often high-hazard products with increased risks if not managed appropriately. So, moving and storing this product needs at least the same level of expertise as its fossil fuel forbears.
Only generations of understanding, then, can prepare for the challenges that come ahead. Innovation
shouldn’t be built on hope and naivety. It should be delivered on the back of sound technical understanding and built on the shoulders of hard lessons many have learnt to great cost in years past.
To get there, we cannot work as we have always done. We need to think differently.
As an industry, we need to create a standard pathway of qualifications to build a competent workforce. These qualifications will see people unchained from narrow specialisms and free to share universal expertise as their career inevitably moves from a starting point working with more traditional fuels and chemicals to something well-calibrated for Net Zero.
The new generation of apprentices is more transient. It didn’t grow up with ‘jobs for life’, and has to be more loyal to bright, inspiring ideas than tried-and-tested, handeddown notions. The technology they grew up with was obsolete before they left school, and the fuels they will be working with haven’t been fully determined or even endorsed yet at a government level.
But we can pass them our knowledge, our competencies, and our craft: a craft in setting out procedures, appreciating safety, and applying good problem-
solving know-how built on the fundamentals of process safety. Something that will put young people in a strong position for life. Providing apprentices with industryspanning qualifications will allow our young people to do one other thing: challenge the status quo many of us helped shape. At the dawn of green energy, we will teach them the rules so they can reshape them. Perhaps the reason why no green energy fuel type has been singled out as the “way forward” by the government is that none have enjoyed runaway success... yet! Only people with technical insight, who change what we think is possible, will be able to make the necessary leap beyond convention.
The first steps towards this future have been taken. Cogent, the TSA and other members of the industry are building on excellent qualifications like the Level 2 Diploma in Bulk Liquid Operations and Level 3 Diploma for a Bulk Storage Operator Technician –developing national occupational standards (NOS) for production, storage, and distribution of hydrogen.
Underpinning this must be a clear apprenticeship pathway that attracts talent but also gives career structure beyond that provided by individual organisations. That way, we can ensure bright minds have a bright future in our industry at a
time of major change. But all this needs buy-in at the right levels of the industry.
We must do this now Convincing the world we needed renewable energy sources took decades. Those were decades of lost time when we could, as an industry, have been in a position to transfer our know-how. As it is, some of the biggest green initiatives and projects are only just getting underway, and some haven’t even happened yet.
We need to focus our efforts as a sector looking to the future. Engineers, operators, planners and project managers understand this. The specialists working at the face of the energy transition know they need the talent to put wind in their sails.
It’s the next levels of leadership that need to be inspired now: at the corporate level, heads of industry must be made aware of the time, effort and finance needed. They must get the message urgently and release the shackles often placed on senior leadership teams to invest in
our future. They need to incorporate it into their vision and strategy as soon as possible.
Apprentices cannot be seen as just another cost; they need to be seen as an investment, an asset that will, if nurtured correctly, reap dividends and drive the sector forward as we transition – because the cost to the wider industry is greater if we do nothing to train them now, and the environmental cost, because of lost time, could be irreversible.
Health and safety isn’t expensive, it’s priceless. Developing the knowledge and skills of workers, after all, manages the day to day risks which are central to your businesses’ prosperity. That’s the approach we take at Reynolds Training Services when helping workplaces and industrial sites create fully compliant environments. Good workplace safety, after all, doesn’t happen by accident.
For more information, visit www.reynoldstraining.com
One of the UK’s leading bulk liquid storage specialists has appointed a new Managing Director.
Phil McEvoy takes up the role at UM Terminals after having held several senior roles in the UK and Europe. Most recently, Phil was Operations Director for the UK, Ireland and Northern Europe at global chemicals distributor Univar Solutions. Prior to that he was Group Operations Director for Argent Energy, a specialist in renewable fuels. He has also previously been responsible for Engineering and Asset Management at Manchester Airport Group. Phil replaces Vic Brodrick who has been combining the roles of Interim Managing Director and Commercial Director since the summer. Vic will continue as Commercial Director.
Phil, a chartered mechanical engineer, said: “This is an exciting time to join UM Terminals. While we are not the biggest company in our sector, we believe our unrelenting customer focus, ability to flex and add value sets us apart. We are also committed to the storage of a diverse portfolio of products, a portfolio that will continue to evolve as we meet the requirements of our customers, not least in the area of energy transition.”
A recent example of the company meeting the needs of one long-term
customer in the chemicals sector saw UM Terminals invest in the region of £2 million, enabling the Scandinavianheadquartered client to take a much larger tank that was specially converted to store and blend a range of AdBlue NOx reduction products.
UM Terminals operates out of 8 terminals, strategically located across the UK, handling over 40 different products. It has its head office in Liverpool. It currently has a capacity of over 300,000 cubic metres of bulk liquid storage, but the plan is to grow this to over 400,000 cubic metres. Product solutions include vegetable oils, industrial, food and feed, chemical, fertiliser, fuels, biofuels and base oils.
Phil added: “We are carrying out a strategic review of our assets, ensuring they are best able to continue meeting the requirements of our customers today and in the future with further investment being made where appropriate. UM is ideally placed to serve customers across multiple sectors due to the strategic location of our terminals, excellent transport links and range of storage options.”
For more information, visit www.umterminals.co.uk.
No-worry package for degassing, turnaround services, nitrogen services and rental of a remotecontrolled robot for tank cleaning.
Kai Sievers, CEO and founder ENDEGS GroupReducing industrial emissions requires modern and reliable technologies. That is why we at ENDEGS have specialised in various environmentally friendly services and offer a worry-free all-inone package when it comes to industrial emissions reduction! Our aim is to see that fewer emissions that harm environment and people get into the air. We further want to contribute to reducing the global greenhouse gas footprint. In 2008, we have developed the first fully equipped, autonomously operated, trailer-mounted vapor combustion unit (VCU) world-wide – thus, making mobile emissions treatment possible for the first time ever. More than 15 years of experience have given us the necessary expertise for the degassing of VOCs (volatile organic compounds) and HAPs (hazardous air pollutants). The various ENDEGS services also include the degassing of a broad range of components during refinery turnarounds as well as the mobile nitrogen services for liquified gases under pressure. We further rent out the remote-controlled ATEX Zone 0 robot for safe tank cleaning.
The ENDEGS mobile vapour combustion units burn all kinds of gases, gas compounds and vapours of the hazard groups IIA, IIB and IIC with a combustion rate of more than 99,99 % and no open flame – making us the only company operating in Europe being able to do so. We have successfully carried out more than 1.400 degassing projects internationally and offer the degassing of all types of containers, tanks, pipelines, ships, inland barges and vessels. Some of those projects have lasted up to three years and involved the degassing of hundreds of components. ENDEGS operates mobile combustion units with four different combustion powers – 3, 5, 10 and 20 MW –, so that they can be used in different scenarios and applications. The 3 MW unit, for example, is ideally suited for shortterm projects and emergencies, while the units with a larger combustion power are able to burn more complex products at a high efficiency.
The ENDEGS mobile vapor combustion units are also ideally suited for degassing projects during refinery turnarounds. We can degas all types of components on Seveso sites like vacuum trucks, mobile liquid storage tanks, decanters and more. During the degassing carried out by ENDEGS, downtimes of the facility
are reduced to a necessary minimum and daily operations can continue undisturbed or with only minimal interference. Our VCUs are also capable of replacing vapor recovery units (VRU), vapor treatment systems and flares in refineries temporarily so that there are no interruptions of operations and business for our customers during a downtime –whether it be caused by malfunction or regular maintenance – of a vapor treatment system.
Over the summer 2022, we have carried out one of our biggest projects yet – in fact, when it comes to the number of materials we used, it was probably the biggest ENDEGS project so far. For over two and a half months, we carried out the degassing of a broad range of columns, heat exchangers, mobile liquid storage tanks and more – degassing around 80 equipments simultaneously. For this project during a major turnaround, we used a total of three VCUs: two units with a combustion power of 10 MW and one with 5 MW. We also applied a total of 1,9 km of piping.
Since the beginning of 2022, we have added a fleet of mobile vaporizers with nitrogen tanks to our portfolio. The vaporizers are ideally suited to purge and render insert systems and system components handling flaming liquids and gases. Therefore, our nitrogen vaporizers are ideally suited for working with liquified gases
under pressure – complex products like LNG/CNG, hydrogen, ammonia or butane.
With our vaporizers, ENDEGS can offer nitrogen services for tanks, ships, barges, vessels and pipelines. Recently, for example, we carried out the degassing of inland barges containing butane and ammonia to prepare them for regular inspection and maintenance. For these projects, we used a combination of a mobile vapor combustion unit and a nitrogen vaporizer. The challenge when working with those pressurized products is that an efficient degassing and purging process with a minimal usage of N2 is necessary. The ENDEGS nitrogen services can provide just that!
Rented ATEX Zone 0 robot as safe alternative to manual tank cleaning ENDEGS further rents out the ATEX Zone 0 robot for the cleaning of industrial tanks. The robot as a rental service enables a safe cleaning in the dangerous ATEX Zone 0: it is remotecontrolled and can be operated from a safe distance. Previously, when cleaning industrial tanks manually, employees had to work in this hazardous area and, despite safety suits and masks, were exposed to a significant health risk. Compared to manual cleaning, leveraging the remote-controlled robot for tank cleaning is not only safer, but much more efficient and cheaper as well. The operator controls the robot out of a cabin via a control panel with two
joysticks and a monitor shows every movement of the ATEX zone 0 robot in real time.
Due to its small size, mobility and versatile robot arm movements, the ATEX Zone 0 robot can be used in many industries for a wide variety of materials. For example, the robot can be used, among many other applications, for:
• pit cleaning,
• petro-chemical cleaning,
• chemical cleaning,
• decommissioning cleaning,
• cesspit and septic tank cleaning,
• vacuuming applications.
We at ENDEGS rent worldwide and take care of getting the equipment to and from the site – wherever it is. Our personnel can also train the customer’s operators on-site. The work itself is carried out by the customer.
About ENDEGS ENDEGS is the European expert for the mobile and safe degassing of tanks, containers, tank cars, pipelines, ships and suction trucks in Europe.
For more information, visit www.endegs.com
Tank Storage Association
Devonshire Business Centre Works Road Letchworth Garden City Herts. SG6 1GJ United Kingdom www.tankstorage.org.uk T. +44 (0)1462 488232 info@tankstorage.org.uk
unanimous expectation is that this is not going to improve for the remainder of 2022.”
The numbers are even worse for sales margins, where only 11.5 per cent have seen an improvement since the second quarter, compared to 40.4 per cent saying they have got tighter. Expectations for the fourth quarter are gloomier yet, with only 8 per cent optimistic of an upturn.
Despite this outlook, prospects for employment look brighter, with 38.5 per cent of respondents expecting to increase their headcount by the end of the year, and only 7.7 per cent expecting a reduction in their labour force. That may turn out to be optimistic, given the current nature of the UK labour market.
Over the past year, CBA has also been collecting evidence of the impact of broader logistics issues on the chemical supply chain in the UK. CBA reports that the shortage of ocean freight containers experienced in 2021 and early 2022 appears to have eased significantly and that ocean freight costs are also coming down, though many members say that these issues are still problematic. Meanwhile, although the available capacity for road haulage has improved in the UK, little change has been noticed in the EU. That comment is relative, though, as 62 per cent of CBA members still feel that UK road haulage capacity is getting worse.
THE UK CHEMICAL Business Association (CBA) polls its members at the end of every quarter to gauge their opinions of the current market and short-term outlook. Its latest survey, conducted at the start of October, offers some grim reading. Not only have conditions worsened since the first half of the year, but they do not look like improving soon.
For instance, only 15.4 per cent of respondents reported an improved orderbook
compared to the position at the mid-year point, while 34.6 per cent said they have got worse. This shows some deepening in pessimism since the second quarter survey, which was also fairly downbeat, and reflects, CBA suggests, some impact from the Russian invasion of Ukraine.
A similar discrepancy is revealed in responses concerning current sales trends, with 17.7 per cent seeing an improvement but 31.4 per cent reporting further declines. Looking ahead, a significant 40.4 per cent expect sales to fall still further in the fourth quarter. “Sales and margins continue to stagnate and possibly worsen compared to the previous nine months,” CBA says. “The almost
CBA itself has been working hard to help its members navigate these difficult times and will continue to do so, especially as it has lately taken on some new staff. During the first quarter of 2023 it will hold a number of webinars and training sessions, covering Responsible Care, the CLP Regulation and general awareness of dangerous goods regulations. It will also hold a two-day refresher course for those dangerous goods safety advisers (DGSAs) sitting their recertification exam in late February.
One item that should definitely be in the diary is the annual ‘Floggers’ Lunch’, taking place on 26 April, which will also mark the start of CBA’s centenary celebrations.
More details on all the events and training sessions can be found on the CBA website at www.chemical.org.uk/training-and-workshops/.
TRENDS • CBA’S LATEST QUARTERLY SUPPLY CHAIN TRENDS SURVEY SUGGESTS THINGS ARE GOING TO GET A LOT WORSE BEFORE THEY GET ANY BETTER, WITH THE OUTLOOK CONTINUING TO WEAKEN
were key to the company’s success and were highly valued by its customers.
BRENNTAG HAS CONTINUED to perform well, despite a macroeconomic environment that remains highly challenging. “Severe geopolitical uncertainties, regional Covid measures, rising energy costs and inflationary trends add to the continued pressure on global supply chains and subdued growth in China and Europe,” the company says.
Nevertheless, during the third quarter Brenntag Group achieved sales of €5.10bn, up 36.4 per cent compared to the same period a year ago, with operating EBITDA ahead by 34.1 per cent at €459.7m and after-tax profit rising by 54.5 per cent to €248.8m.
“In the still highly challenging environment of the third quarter of 2022, Brenntag strongly grew its operating EBITDA, more than doubled its free cash flow and increased its EPS by 57 per cent,” says CEO Christian Kohlpaintner. “We successfully continue our growth path due to our excellent business performance and the hard work of all Brenntag employees dedicated to our customers day by day. Maintaining supply despite the most adverse conditions and to provide products and services to our partners globally stays our prime focus.” During the quarter, product availability and prompt and reliable delivery
Both of Brenntag’s operating divisions have recorded solid growth during the course of 2022. Brenntag Specialties, which builds on Brenntag’s position as the largest specialty chemicals and ingredients distributor worldwide, grew operating gross profit by 16.8 per cent compared to the third quarter 2021, with operating EBITDA up 17.8 per cent. The life sciences segments, including nutrition, personal care and pharmaceuticals, performed very well, though the materials science segment was weaker in the face of slower demand from the construction industry.
Brenntag Essentials, which markets a broad portfolio of process chemicals across a wide range of industries, reported exceptional
performance and growth in the third quarter of 2022. Its size and range helped it to maintain supplies to customers during a period of highly volatile supply and pricing. Operating gross profit was 18.6 per cent up on the previous year and operating EBITDA was ahead by 30.4 per cent. This performance was almost entirely driven by organic growth in the EMEA, North America and Latin America regions, with EBITDA in the Asia-Pacific region affected by Covid-related restrictions in China.
Brenntag’s financial performance has also been boosted in recent years by the outcome of its transformation programme, ‘Project Brenntag’. The company reports that, up to the end of the third quarter, this has contributed some €230m in additional annual operating EBITDA, which is already ahead of the target set for the 2023 financial year, with more to come.
Brenntag has announced the next stage of its strategic growth plan, ‘Strategy to Win’, with new medium-term targets running to 2026. Explaining the move, Kohlpaintner says: “Brenntag is the undisputed and resilient leader in an attractively growing and highly fragmented, indispensable market. We have now defined how to strengthen and expand this position. We aim to foster growth in our global divisions with clear differentiated strategies. Moreover, we build a comprehensive digital and data framework and architecture to better serve our global customer base and achieve the next level of operational efficiency, growth and excellence.”
The new strategy sets goals for both of Brenntag’s divisions. Brenntag Specialties will increase its value-added service offering, command the most comprehensive and sustainable portfolio, expand its global footprint, focus on high-growth customers and industries, and accelerate acquisitions. Brenntag Essentials, meanwhile, will strengthen its local and regional distribution networks and optimise its last-mile delivery capabilities, enhance its global expertise by reinforcing global sourcing market intelligence capabilities and expanding global terminal capabilities at strategic ports, and will put a focus on capturing new market potential through mergers and acquisitions
and by increasing its portfolio for sustainable products and supply chain solutions.
An important element in ‘Strategy to Win’ is Brenntag’s promise to invest strongly in its Digital.Data.Excellence growth driver (DiDEX). This aims to make Brenntag the easiest chemical distributor to do business with, unlock the value from its data, modernise its digital business architecture and build capabilities to attract and retain talent. Brenntag is partnering with key technology companies, including Salesforce and AWS, to improve and build its digital business infrastructure.
Ewout van Jarwaarde, Chief Transformation Officer, says: “We are thrilled about the capabilities Salesforce will enable across our global organisation, quickly expanding how we engage with our customers and supply partners in every interaction and leverage our data for even more targeted insights. The solutions will also benefit our internal teams’ daily work and services by providing streamlined end-to-end processes, transparency and accelerated insight, and easy access to relevant data.”
Brenntag has gone further than this, with a new ‘Purpose and Vision 2030’ commitment. “As Brenntag, we have a clear understanding why we are important for our customers, supply partners, and basically for everyone,” Kohlpaintner says. “We connect with products, knowledge, and innovation to foster a sustainable future and care for human needs.
We have the vision and the capabilities to shape the future of our industry by empowering our partners within networks, driving collaboration, excellence, and shared success.”
The most visible element in this commitment is a new global branding, acknowledging a new era for the company. “The new brand is the visible expression of Brenntag’s refreshed identity including an inspiring purpose and vision, ambitious and digitally driven growth strategies for its two divisions, as well as its strong corporate culture and engaging values,” the company states. The new branding will be rolled out gradually over the next few months in a staged approach at each of Brenntag’s 700 sites and thousands of internal and external touchpoints across Brenntag assets worldwide.
Brenntag is, though, not totally focusing on internal processes. It has recently acquired Texas-based Tech Management, a leading solutions provider for proprietary formulations and on-site services directly to operators in the energy sector in the Permian Basin. The acquisition will, Brenntag says, foster its “resilience in this market against the background of shifts on the global energy market and will accelerate the creation of a dedicated energy service platform”.
Steven Terwindt, CEO of Brenntag Essentials, says: “I look forward to welcoming our new colleagues from Tech Management (dba) to the Brenntag family. The company’s formulation expertise and state-of-the-art laboratory facilities are a welcome addition to Brenntag’s Energy Services business in North America, providing a further pillar to our resilient market offerings in the energy sector and filling a vital support role in a region critical to global energy security.”
Also in the US, Brenntag has opened a new production and warehouse facility in Upton, Massachusetts, designed to solidify its position as a leading chemical distributor in the north-east. “Upton provides a perfect location to improve service levels and grow volumes with the existing customer base in the region,” says Scott Leibowitz, regional president at Brenntag Essentials. “In 2017, we invested in this area to expand our capabilities by opening a warehouse in West Boylston. Upton adds packaging capability in the region, enabling us to service our customers in a reliable and cost-efficient way.”
Brenntag has also expanded is operations in Australia and New Zealand with the acquisition of Ravenswood’s life sciences and coatings distribution business. “Brenntag Specialties customers rely on us to provide solutions and services to very specific needs on a global and regional scale.
For us, expanding our operations with the capabilities from Ravenswood, especially with the expertise in blending, will be a great addition for our customers in the APAC region,” says Henri Nejade, COO of Brenntag Specialties. www.brenntag.com
DKSH has acquired Terra Firma, a leading distributor of specialty chemicals in North America. The move expands the platform of DKSH’s performance materials business unit to cover the US and Canada and is, the company says, “an important step in DKSH’s strategy to build a global distribution platform for specialty chemicals and ingredients”.
“Expanding our presence in the North American market has been a strategic focus for our Performance Material business,” says Stefan Butz, CEO of DKSH. “Terra Firma’s teams operate coast to coast and will accelerate our expansion into the North American specialty chemical distribution market, while we will provide their clients access to our global network. The Terra Firma acquisition is a milestone in the transformation of DKSH Performance Materials to becoming a global player.”
Tim Fetters, CEO of Terra Firma, adds: “Terra Firma has earned an excellent market reputation by delivering value and significant growth to its customers and suppliers. By joining DKSH, we will be able to leverage our
growth platform further and increase our presence in life sciences.”
Terra Firma currently has a team of some 100 professionals operating from offices in Los Angeles, Baltimore, Dallas and Toronto, and projects net sales of some $240m for this year. The transaction values the business at $360m and is expected to close towards the end of the year. DKSH will acquire at least 80 per cent of Terra Firma, with the remainder held by the current management team.
www.dksh.com
Bodo Möller Chemie Group has acquired Spanish adhesives specialist General Adhesivos (above), expanding its business footprint in the Iberian peninsula and adding a second adhesives laboratory.
“This merger is an essential component for us to demonstrate our own expertise on the Iberian Peninsula. Moreover, we expand our overall know-how through the team and the laboratory of General Adhesivos, pursuing a pan-European approach and a general organic
growth strategy in this way solely through the two laboratories in Poland and Spain,” says Frank Haug, chairman of the board at the Bodo Möller Chemie Group.
Bodo Möller Chemie has also acquired Portuguese distributor Anmapi, an established partner of Henkel, to expand its Iberian operation and its own existing partnership with Henkel. “By taking over Anmapi, we significantly expand the European business of our group and moreover acquire a partner that can be regarded as a true asset for us in Bonderite® application know-how,” says Haug. “While we have built up the loyalty to Henkel and other manufacturers in Central and Eastern Europe, Anmapi has taken over this task since it was founded in Portugal in 1999.”
Bodo Möller established its subsidiary in Spain in 2020. Following the recent acquisitions of General Adhesivos and Anmapi, the group now has offices in Madrid, Tarragona and Porto as well as warehouses in Tarragona, Barcelona and Porto. “The expansion by our new colleagues in Portugal is a strategic addition after expanding the business in Spain – thanks to Anmapi now also with an own laboratory for surface technologies,” says Alex Matosas, managing director of Bodo Möller Chemie Spain. bm-chemie.com
Safic-Alcan has established a presence in South America through the acquisition of Proquimil Produtos Quimicos, a Brazilian chemical distributor specialising in rubber and plastic polymers and additives. The integration of the firm will be led by Luiz Maranho, who has recently joined the company as general manager of the newly established Safic-Alcan Brasil.
“The establishment of Safic-Alcan Brasil, the acquisition of Proquimil and the onboarding of Luiz are major steps towards our goal for
ongoing geographical diversification,” says Yann Lissillour, CEO of the Safic-Alcan Group.
Safic-Alcan Brasil has already taken steps to expand, having acquired Sarfram, a Brazilian chemical distributor specialising in the personal care, perfumery and cosmetics sectors. “I am so happy and proud to welcome Sarfam´s team to the Safic-Alcan Group,” says Maranho. “This is an exciting moment for all. From Safic-Alcan’s perspective, this enhances its position in the Brazilian distribution market and its global place in cosmetics, a strategic market for the group. We welcome Sarfam’s employees to the entrepreneurial team of Safic-Alcan.”
Safic-Alcan has also expanded an existing distribution agreement with Nouryon, for which it already handles its crosslinking peroxides in the UK, Ireland and Portugal, to cover the rest of Europe as from 1 January; the deal does not yet cover Germany and the Benelux countries, which will be added at a later date.
“We are pleased to extend our distribution partnership with Safic-Alcan across several European countries,” says Alain Rynwalt, senior vice-president of Nouryon Polymer Specialties. “Safic-Alcan is a clear leader in providing solutions to the rubber and crosslinking market. Nouryon’s customers will benefit from the combination of highly trained sales and technical teams, formulation support, comprehensive regulatory know-how, and exceptional quality and service.” www.safic-alcan.com
Barentz has acquired Texas-based Viachem, a leading specialty chemical, food additive and ingredient distributor. By combining a dedicated market research function and digitally enabled sales and marketing capabilities, Viachem represents a market growth engine for Barentz and its principal
suppliers, Barentz says. Viachem’s founder, Mike Efting, will stay on to lead the team.
“Viachem has developed sales and marketing capabilities that are unique in the industry and we’re thrilled to welcome Mike and his team into the Barentz organisation,” says Hidde van der Wal, group CEO of Barentz. “By combining these capabilities with Barentz’ global scale, technical expertise, and extensive digital infrastructure, we see significant opportunity to expand market share for our customers and principal suppliers.” www.barentz.com
Caldic has agreed to buy Betaquímica, a supplier of raw materials for industrial applications, located near Barcelona. It specialises in additives, stabilisers and modifiers for polymers and rubber.
“We are delighted to welcome the Betaquímica team aboard Caldic,” says Laurent Pasqualini, CEO of Caldic Europe. “Betaquímica has a strong foothold in Iberia and many other countries where Caldic is present, and it is recognised for its innovative solutions and customer-centric way of doing business, which is perfectly aligned with Caldic’s culture. The highly complementary portfolio, but more importantly the
Betaquímica professionals, will be a valuable asset to the Caldic organisation. Their expertise will enhance our ability to inspire value-add solutions across various applications and support further growth in the industrial formulation markets.” www.caldic.com
IMCD has agreed to acquire Shanghai Sanrise Industries & Development (below), one of the leading distributors in the personal care market in China. IMCD will take 70 per cent of the company now and the remaining 30 per cent in 2025; in between, Sanrise’s founders will continue to lead the company.
“The acquisition will provide IMCD with a comprehensive portfolio from leading global suppliers and elevate our technical expertise with the addition of a fully equipped technical centre, putting us in a strong position in the Chinese market,” says Andreas Igerl, president of IMCD Asia. “This is a significant milestone to accelerate our growth momentum by complementing our existing life science portfolio and business.”
The transaction is subject to customary closing conditions and regulatory approval; it is expected to close in the first quarter of 2023. www.imcdgroup.com
THERE HAVE, ACCORDING to the International Union of Marine Insurance (IUMI), been an unprecedented number of cargo fires aboard ships over the past five years. In addition to loss of life and serious injuries, damage to property and the vessels themselves has fallen on underwriters. That is not to forget environmental damage and probably uninsured reputational losses arising from subsequent supply chain disruption.
IUMI also says that the single largest cause of these fires is improperly shipped dangerous goods in containers, whether due to improper packaging, placarding and stowage aboard the vessel or to unintentional or fraudulent mis-declaration.
National Cargo Bureau (NCB) and the US Coast Guard (USCG) conduct more container inspections than any other country and, as a result, both have captured significant amounts of data and information. Both organisations
are looking to leverage this information to allow potentially problematic shipments to be identified more easily and targeted for inspection.
NCB and USCG have been looking for partners with predictive analytical capabilities to analyse their data. They have now found a partner in Munich Re, which is offering them value-added data analysis and modelling to better inform their strategy and decision making in terms of cargo and vessel inspection at ports, allowing them to expand the data fields they are both viewing. Munich Re can also identify certain trends and make recommendations for meaningful data capture.
Janet Wesner, head of analytics at Munich Re US, explains more: “Analytics starts with data and understanding the data. We worked with both the USCG and NCB to define risk scores
based on deficiency types and severities that could serve as proxies for how dangerous the results of an inspection are. From there, by questioning the data and having a dialogue with experts who knew which conclusions were real insights versus artifacts of the data collection process, we were able to provide recommendations into areas to explore further and ways to enhance future data capture.”
“Our global marine expertise and reputation for innovation and investments in data analytics will greatly benefit those in the in the marine community,” adds Sean Dalton, Munich Re’s head of marine underwriting in North America. “It is impossible to inspect all containers, as it would cause massive delays. Any improvements that target ‘higher interest’ shipments hold a huge potential. Our collective, ultimate goal is to prevent improperly shipped dangerous goods from being loaded aboard a vessel.”
That goal will come closer once data from NCB-owned Exis Technologies, which has been specialising in this field for 35 years, is integrated with the inspection data.
“We are delighted to be working alongside USCG and Munich Re to better understand the important data we are generating from our container inspection activities,” says Ian Lennard, president of NCB. “To promote our not-for-profit mission of Safety of Life and Cargo at Sea, we feel it is critical that predictive analytics is incorporated into our work, not only to enhance safety but to ensure that safety becomes more efficient. Through the application of analytics, we allow for a more economical use of industry resources in the prevention of high-risk containers loading onto vessels.”
“Our collaboration with NCB and Munich Re in this specific initiative to deep dive into containerised shipping data alongside cargo and predictive analytic professionals has been extremely influential toward our best efforts of promoting a more widespread safety culture in the world of containerised hazardous material cargo shipping that will ultimately benefit the entire supply chain,” adds John Hillin, USCG’s New York Safety and Security Division chief. natcargo.org
INSURANCE • THERE IS PLENTY OF DATA OUT THERE ABOUT BADLY SHIPPED DANGEROUS GOODS BUT MAKING SENSE OF IT IS NOT SO EASY. MUNICH RE IS OFFERING ITS HELP TO NCB AND USCG
SALVAGE • USE OF THE LLOYD’S OPEN FORM CONTRACT FOR SALVAGE HAS BEEN IN DECLINE BUT, AS UNDERWRITERS ARE BECOMING AWARE, ITS USE OFFERS BENEFITS IN THE EVENT OF A CASUALTY
THE WORK THAT salvors do is not only dangerous to life and limb – and the environment – but also financially perilous.
Salvage companies need to invest in assets that may be used only intermittently, but those assets need to be available – and at short notice – in the event of a casualty at sea. There are still plenty of casualties, usually in bad weather, and response needs to be fast, with little time to be arguing over the details of a salvage contract.
As such, salvage companies have long relied on the Lloyd’s Open Form (LOF) approach but, in recent years, it has been used less regularly, much to the concern of salvors themselves. But it has come to the point now where underwriters are becoming
worried; in July this year, the International Group of P&I Clubs (IG) published the results of an independent review carried out by Hugh Shaw, the former UK Secretary of State’s Representative for Salvage and Maritime Intervention, into the potential for delays in the contracting and engagement of salvage services.
That report found that delays are occurring, with more than 80 per cent of stakeholders feeling that avoidable delays in the engagement of salvage services can open up a casualty to escalation to a point where significant damage, loss and/or danger to life might occur.
“Any delays in decision making may not only have a detrimental effect on the safety of life
of those onboard but may ultimately determine the fate of the vessel and its cargo, with the potential for consequential damage to the environment,” the IG report notes. “The consequences of delays in requesting or agreeing salvage services can be disastrous, especially if there is damage, or the potential of damage, to the marine environment.”
Hugh Shaw made a number of recommendations in his report, particularly about the role of LOF in minimising delays in contracting. His comments arrived at an opportune moment since Lloyd’s had been considering closing its salvage arbitration branch. The International Salvage Union (ISU), which represents the majority of the major salvage companies, reports that momentum is now building to reinvigorate LOF and that Lloyd’s has now initiated a programme of work, along with key stakeholders, to encourage greater use of LOF.
The work has been grouped into three streams: linking LOF to the Environmental, Social and Governance (ESG) agenda that is of increasing importance to business, including the shipping and insurance sectors; promoting greater use of LOF contracts in Asia and the Far East; and looking at the awards and costs associated with using the form. Central to all the work streams is consideration of the importance of spreading awareness and understanding of LOF.
The three work groups are made up of a wide range of interested parties, including ISU members. Initial sessions have taken place, with the Lloyd’s salvage group expected to consider their outputs before the end of the year and take into account the independent review report published by IG.
ISU is clear about the benefits of LOF, saying: “Few casualties improve with age and delay can lead to worsening of the situation with the potential for increased risk of loss of property – sometimes even total loss – and damage to the environment. Rapid intervention and full cooperation in the interests of the owner is always the best approach.”
www.marine-salvage.com www.igpandi.org
NISTM
DECEMBER 6-7, THE WOODLANDS
15th Annual National Aboveground Storage Tank Conference & Trade Show www.nistm.org
GPCA Forum
DECEMBER 6-8, RIYADH
16th annual meeting of the Gulf Petrochemicals & Chemicals Association www.gpcaforum.com
CDG General Awareness Workshop
JANUARY 17, CREWE/ONLINE
Workshop to update dutyholders on regulatory changes www.chemical.org.uk/training-and-workshops/ cdg-general-awareness-workshop-2/
JANUARY 23-27, SAN ANTONIO
Annual conference of the Cooperative Hazardous Materials Enforcement Development (COHMED) programme cvsa.org/eventpage/events/cohmed-conference/
Argus Clean Ammonia Middle East
FEBRUARY 14-16, ABU DHABI Conference for pioneers in the new energy sector
www.argusmedia.com/en/conferences-eventslisting/clean-ammonia-middle-east
Internationale Gefahrgut-Tage Hamburg 2023
FEBRUARY 27-28, HAMBURG
38th annual conference on dangerous goods transport (German language) www.ecomed-storck.de/Veranstaltungen/ Internationale-Gefahrgut-Tage-HamburgVeranstaltung-Hamburg-27-28-02-2023.html
International Energy Week
FEBRUARY 28-MARCH 2, VIRTUAL/LONDON
Annual week of meetings, conferences and seminars (formerly ‘IP Week’) www.ieweek.co.uk
Intermodal South America
FEBRUARY 28-MARCH 2, SÃO PAULO 27th annual international exhibition on intermodal logistics, cargo transport and international trade www.intermodal.com.br/en
Battery Recycling Europe
MARCH 1-2, LONDON Conference for the battery recycling and manufacturing sectors www.wplgroup.com/aci/event/battery-recyclingeurope/
Hazardex 2023
MARCH 1-2, HARROGATE Conference and exhibition on hazardous area operations and personal protective technology www.hazardex-event.co.uk/
PPC Spring Meeting
MARCH 5-7, SAVANNAH
Bi-annual meeting and tradeshow of the Petroleum Packaging Council www.ppcouncil.org/upcoming-meetings.php
Hydrogen
MARCH 8-9, LISBON
6th annual conference to discuss innovations in hydrogen and fuel cell technology, production and transport www.wplgroup.com/aci/event/hydrogen-fuel-cellsenergy-summit/
BADGP
MARCH 9, COVENTRY
Annual AGM and seminar of the British Association of Dangerous Goods Professionals www.badgp.org/
ChemCon The Americas 2023
MARCH 13-17, SAN FRANCISCO
Global conference on chemical regulation https://chemcon.net
LogiChem
MARCH 14-16, ROTTERDAM
Chemical supply chain and logistics conference http://logichem.wbresearch.com/
FETSA Annual Conference
MARCH 14-16, ROTTERDAM
Annual conference and AGM of the Federation of European Tank Storage Associations https://fetsa.eu/annual-conference/
StocExpo 2023
MARCH 14-16, ROTTERDAM
The main annual exhibition and conference for the European tank terminal industry www.stocexpo.com/en/
LNG Congress Russia
MARCH 15-16, MOSCOW
Ninth annual congress and exhibition on developments in Russian and Arctic LNG www.lngrussiacongress.com/en
World Petrochemical Conference
MARCH 20-24, HOUSTON
WPC 2023 provides an outlook on petrochemical supply chain, feedstocks, sustainability and more wpc.ihsmarkit.com/index.html
International Transport & Logistics Week (SITL)
MARCH 28-30, PARIS
Annual transport event, including hybrid and in-person conferences and workshops www.sitl.eu/en-gb.html
NISTM
APRIL 12-14, ORLANDO
National Institute for Storage Tank
Management’s 25th annual international aboveground storage tank conference and trade show www.nistm.org
Date
1/10/22
2/10/22 Pietermaritzburg, road tanker oil Road tanker with unspecified oil cargo overturned on N3 highway near Peter Brown Interchange; tanker Sowetan KZN, South Africa caught fire, driver died; Durban-bound lanes closed during response and cleanup, causing heavy congestion Live
3/10/22 Jaipur, road tanker LPG Truck crashed into LPG tanker making u-turn on Ajmer-Jaipur Highway; crash damaged tank valve, leaking Times of Rajasthan, India LPG but did not ignite; cab, tyres of tanker were on fire; highway closed while LPG was transferred India
6/10/22 Bilhaur, road tanker carbon Gas tanker overturned after swiping truck on GT Road, causing CO2 to start leaking from tank; police closed Times of UP, India dioxide road while fire crews plugged leak, removed vehicles; both drivers suffered minor injuries India
6/10/22 Ilo Awela, road tanker gasoline Road tanker overturned while ascending slope on Abeokuta-Lagos expressway, possibly due to mechanical Vanguard Ogun, Nigeria defect; leaking fuel caught fire, which spread to several other vehicles; two people killed, three injured
6/10/22 Wax, road tanker fuel Key Oil Co rigid tanker exploded while delivering unspecified fuel to convenience store; blast blew off rear WAVE Kentucky, US part of tank; thought that only one compartment contained fuel at the time but cause of blast not known
7/10/22 Palghar, road tanker chemicals Road tanker carrying chemicals used in dyes overturned on Boisar Chillar road in Warangade village, cause Times of Maharashtra, India unknown; no leak reported and no injuries but road had to be closed for two hours while wreck was removed India
7/10/22 Sandusky, freight train paraffin Ten cars of 101-car Norfolk Southern train derailed on bridge over Columbus Avenue; some cars leaked WTVG Ohio, US wax paraffin wax, which solidified, posing no danger; engineers found bridge sound but road work needed
15/10/22 Aligarh, road tanker gasoline Thief took road tanker and sped off, chased by driver and assistant on motorcycle; tanker overturned, spilling TNN UP, India gasoline into ditch; thief fled; locals ran to collect fuel; one minor injury but no fire
20/10/22 Aguascalientes City, road tanker fuel Road tanker crashed into overpass by rail line, probably due to excessive speed, caught fire; up to 1,000 locals Reuters Mexico evacuated; driver arrested; only one minor injury; initial reports said truck had hit a train, though not the case
20/10/22 Sagamu, road tanker gasoline Road tanker overturned after being hit by speeding truck on Lagos-Ibadan expressway; spilling gasoline Premium Ogun, Nigeria caught fire, tanker exploded; at least ten people killed, five vehicles destroyed in blaze Times
21/10/22 Bhopal, road tanker gasoline Seven people injured by blast during filling of road tanker at Bharat Petroleum depot in Bakania district; News 18 MP, India six of those hurt were HPCL drivers; police suspect explosion was caused by a short-circuit
23/10/22 Lufkin, road tanker baryte Fire broke out in engine of cab hauling tanker (?) carrying baryte (barium sulphate), used in oil drilling fluids; Lufkin Texas, US driver suspected hose had come loose, splashing oil onto engine; trailer with baryte not badly damaged Daily N’s
23/10/22 New Smyrna Beach,road tanker gasoline Vacuum tanker caught fire while pumping gasoline from underground tank at filling station; three people Daytona Florida, US injured in fire; likely that generator running nearby ignited vapours; fire department investigating Beach N-J
25/10/22 Delray Beach, road tanker fuel Tank truck with unspecified fuel overturned after being hit by car on I-95, exploding in fireball; five people WPTV Florida, US injured; car driver cited; widespread damage to road, barriers; locals reiterated safety concerns over highway
26/10/22 Khargone, road tanker fuel Road tanker with unspecified fuel overturned, caught fire; tanker exploded while locals were collecting fuel Times of MP, India spilling from tanker; one person killed on the spot, nine more died later in hospital India
5/10/22
Sea TSS Pearl
8/10/22 Georgetown, Tradewind
Major fire broke out in containers aboard containership heading from Jeddah to Aden; thick black smoke FleetMon engulfed superstructure; all crew rescued; vessel later sank, with several reports of containers drifting
Product tanker (7,740 dwt, 2008), heading up Demerara River to Guyoil pier, struck floating bridge that closed FleetMon Guyana Passion before all of convoy had passed through; bridge seriously damaged, some damage to tanker
8/10/22 Bangkok, Smooth Sea 18 fuel Product tanker (7,450 dwt, 2014), in load with unspecified fuel and heading upstream to terminal, lost control FleetMon Thailand after passing tug and barges, dropped anchor; brought to a stop close to riverside restaurant, scaring off diners
15/10/22 off Wuqui Island, Kelsey 2 oil, Product tanker (8,420 dwt, 2002), with cargo of oils, chemicals from Hong Kong to Gunsan, sank in Taiwan FleetMon Taiwan chemicals Strait after reporting water ingress in aft section; one crew died, all others were rescued
26/10/22 Singapore Strait Young Yong crude oil VLCC (306,400 dwt, 2001), with 284,400 t crude oil cargo for Mozambique, grounded near Batam close to Splash gas pipeline; no spill reported; refloating had to be cautious due to risk of rupturing pipe, took two weeks 247
Date Location Plant type Substance Details
Source
2/10/22 Clayton, oil depot kerosene Some 2,000 gal (7,500 litres) spilled to creek behind high school; though that winds from Hurricane Ian had WRAL N Carolina, US caused damage at TR Lee Oil & Gas facility; hay bales deployed to soak up spill
4/10/22 Kazanlak, weapons fireworks One killed, one seriously injured, two missing after explosion at Arsenal weapons plant in unit preparing Novinite SZ, Bulgaria factory material for fireworks; workshop destroyed in blast; prosecutor filed charges for failure to follow safety rules
4/10/22 Chirchik, chemical fertiliser Fire broke out in synthesis shop at Maksam-Chirchik plant, leading to explosion that injured two employees; Urdu Uzbekistan plant no off-site impact; other units at site were not damaged and continued work; investigation underway Point
15/10/22 Westlake, chemical chemicals Fire broke out in Ziegler alcohol synthesis unit at Sasol’s Lake Charles chemical complex; brief shelter- KPLC Louisiana, US plant in-place order but no off-site impact recorded; no injuries; Sasol investigating cause
20/10/22 Morena, house fireworks Four killed, six injured by explosion that demolished house being used to store firecrackers at Banmor Naga; NDTV MP, India officials investigating whether the explosion was initiated by gunpowder or by a gas cylinder
22/10/22 Malik, Syrdaria, military ammunition 16 people were injured by an explosion in a Ministry of Defence warehouse, presumably due to initiation of kun.uz Kazakhstan warehouse stored ammunition; nearby homes, shops suffered damage; military experts investigating incident
23/10/22 Vijayawada, shops fireworks Fire broke out in cluster of shops set up to sell firecrackers for Deepavali festival; two people killed in fire, PTI AP, India said to be workers sleeping in the shops; locals worried that shops were allowed to set up opposite fuel station
27/10/22 Pengerang, oil refinery oil Fire broke out in pipework at Petronas refinery in Pengerang Integrated Complex, followed by explosion; NST Johor, Malaysia Petronas fire crews responded, dealt with blaze; no casualties reported
27/10/22 Kaohsiung, oil refinery gas Explosion, fire in CPC’s Dalin refinery was seen from several kilometres away; fire started in hydrotreater SCMP Taiwan in desulphurisation unit during maintenance, possibly due to gas leak; no injuries reported
3/11/22 Sta Maria, Bulacan, fireworks fireworks Ten people, eight of them employees, were injured by explosion in fireworks factory in residential area of Sun Star Philippines factory Sitio Manggahan; police said that factory lacked the necessary permits to operate
THE HAZARDS POSED by lithium batteries during transport were first identified in the aviation sector; protecting aircraft and those in them from those hazards has been a major driver in the developing regulation of lithium batteries. However, after a number of shipboard fires during the course of this year, the maritime sector is also waking up to the threats posed by lithium batteries in containerised goods, whether they are properly declared or not.
To raise awareness of the hazards that such batteries present, Thomas Miller’s two mutual insurance businesses, TT Club and UK P&I Club, have worked with scientific consultant Brookes Bell on a white paper that outlines many of the numerous challenges facing the shipping industry and the potentially catastrophic situation that can be caused by battery failure. The three parties hope that this will help in correcting the widely held perception in the maritime community that risks in the supply chain of such products are relatively small.
“Recently, serious and sometimes catastrophic incidents involving lithium-ion batteries have become more commonplace, with fires reported in all modes of transport – ocean, air and land - as well as in warehouses and where such consignments are at rest,” notes Peregrine Storrs-Fox, risk management director at TT Club.
The topics covered in the white paper include details of the science behind lithium-ion batteries, the dangers they can pose during transport and the reasons for those hazards, such as insufficient testing and incorrect declaration. The paper also provides a review of current regulatory provisions, focusing on the International Maritime Dangerous Goods (IMDG) Code, with recommendations for change or further work. The final section of the paper discusses the current state of the firefighting provision and changes that could be implemented.
“The consequences of battery failure and the resultant thermal runaway must be clearly
understood and the correct procedures for handling them adhered to throughout their lifespan,” comments Stuart Edmonston, loss prevention director at UK P&I Club. “The dangers can exist no matter the status of the battery; charged, semi-charged, used, second-hand or scrap, and whether present in devices and vehicles or packaged separately.”
The white paper does not limit itself to the cause of lithium battery thermal runaway but also offers advice on extinguishing fires and puts forward suggestions and guidelines for helping to pre-empt dangerous goods incidents through correct classification and declaration. Safe and effective packaging, mandatory markings and labelling, uniformity of regulations regarding testing and suitable storage environments while batteries are awaiting transport can all play a part in reducing risk and should be encouraged.
The white paper also calls for action in various areas, some of which are already being addressed by the relevant regulatory authorities, such as the provision of the lithium battery test summary to parties along the supply chain and the classification and marking of electric vehicles during their transport. The authors suggest more guidance would be valuable on how to prevent short circuits and that the 30 per cent state of charge limit imposed for air transport should be picked up by the other modes.
With ongoing technical development and massive growth in the volume of batteries being transported as the world seeks ways to move away from carbon-heavy energy sources, the risk during transport is also growing. Dr Karwei So, managing scientist at Brookes Bell, says: “While increased industry awareness is crucial and technology to monitor and restrict fires is advancing, the increased capacities of batteries and the expected rise in trade volumes means regulations are potentially not fit for purpose, having been slow to catch up.”
The joint white paper can be downloaded free of charge from the TT Club website at www.ttclub.com/news-and-resources/ publications/lithium-batteries-whitepaper.
CONTAINER FIRES • CONTINUED VIGILANCE IS NEEDED IF THE SHIPPING INDUSTRY IS TO BE ABLE TO LIMIT THE NUMBER OF CONTAINERSHIP FIRES. TT CLUB HAS PLENTY OF TOOLS TO HELP ENVIRONMENTAL IMPACTS
THE FREIGHT TRANSPORT and logistics insurance specialist insurer TT Club is continuing its battle to convince cargo interests, supply chain professionals and enforcement agencies that the responsibility for mitigating containership fires is shared by numerous entities across the entire global supply chain. The estimated 60-day average occurrence of serious fires was been maintained recently by the Zim Charleston fire in August and the TSS Pearl in the Red Sea in early October. TT Club is once more urging a more comprehensive approach to arresting the trend.
“There were significant lessons coming from the sad incident on the MSC Flaminia, which cost the lives of three seafarers,
TT CLUB IS LEADING EFFORTS TO ERADICATE THE SCOURGE OF FIRES ABOARD CONTAINER CARRIERS
particularly from the subsequent legal proceedings that adjudged the shipper and NVOC responsible for root cause errors,” says TT Club’s Peregrine Storrs-Fox. “Despite the biennial updates to the IMDG Code, including multiple arising from this particular incident, the judge’s assessment that the regulations merely set the ‘baseline’ for good practice remains utterly true today.”
Ensuring compliance with the latest mandatorily applicable version of the International Maritime Dangerous Goods (IMDG) Code is essential as a minimum standard for all those shipping dangerous goods by sea. But the liability judgment in the MSC Flaminia case made it clear that regulations merely set the baseline. “This is an important statement to which any entity inclined to rely solely on the letter of the law when consigning dangerous goods, would do very well to pay heed,” comments Storrs-Fox.
TT Club advocates a comprehensive approach, striving to bring an understanding of all the factors contributing to these fires to all those involved in the movement of cargo in containers and underlining their responsibilities for safety. Errors, misunderstandings, mis-declarations and inadequate packing and securing lie at the heart of many significant incidents, both at sea and in storage facilities. Attention to accurate classification and declaration are critical to improve certainty of outcome from end to end. This requires truth as much as awareness of regulations and sound safety practices.
TT Club, along with its sister insurer the UK P&I Club, has worked hard to disseminate awareness and knowledge; most recently, they have updated the guideline publication Book it Right, Pack it Tight, which provides key insights for all those involved in the shipment of dangerous goods by sea. Closely related but with a broader applicability, and as part of the industry-wide Cargo Integrity Group, TT Club has contributed to the ‘quick guide’ to the IMO/ ILO/UNECE Code of Practice for Packing of Cargo Transport Units (CTU Code). While this Code is non-mandatory, it is referenced in the IMDG Code and, as the MSC Flaminia case showed, industry standards are just as important as regulation when it comes to assigning liability.
TT Club’s campaign to influence industry will continue with a series of webinars in early 2023 on the subject of containership fires and the ongoing efforts to prevent them. The intent is to attract awareness and debate, particularly around innovations that could materially improve the risk profile. These online forums will contribute further to the valuable weight of knowledge and expertise in the arena.
“The complexities of the global container trades increase rather than diminish,” concludes Storrs-Fox. “No one entity can surmount the dangers of these horrific fires, as a consequence it is essential that the entirety of the risk faced should be embraced by all involved through the supply chain if they are to be successfully reduced.”
HCB will alert readers to the upcoming webinars; meanwhile, they will also be announced on the TT Club website, www.ttclub.com.
THE AUTUMN SESSION of the Joint Meeting of the RID Committee of Experts and the Working Party on the Transport of Dangerous Goods (WP15) of the UN Economic Commission for Europe was held in Geneva from 12 to 16 September 2022, with Claude Pfauvadel (France) in the chair and Silvia Garcia Wolfrum (Spain) as as vice-chair.
The purpose of the Joint Meeting is to maintain, insofar as is possible and desirable, harmonisation between the modal regulations covering the transport of dangerous goods by rail (RID), road (ADR) and inland waterway (ADN) in Europe, and with the international regulations for transport by sea and air. The September session arrived after the finalisation of the amendments to those regulations that will enter into force in January 2023 but before the final meeting of the biennium of the UN Sub-committee of
Experts on the transport of dangerous goods; the parent Committee was only due to adopt the latest set of amendments to the UN Model Regulations this month so it was premature of the Joint Meeting to take those into account.
It was, as a result, a relatively short agenda that faced the delegates who met in Geneva or attended the meeting online. The UN office in Geneva is aiming to return to ‘business as usual’ from 2023, with the next sessions expected to be in-person only. For this meeting, 23 countries were represented as full members, along with the European Commission, EU Agency for Railways (ERA) and 19 non-governmental organisations represented in a consultative capacity.
The International Union of Wagon Keepers (UIP) rehearsed earlier discussions – going
back as far as 2014 – about the use of digital inspection reports and tank records, which had not delivered a provision to accept such electronic documents. It is now the case that digital versions, including a ‘simple electronic signature’, are the only copies provided by accreditation bodies; UIP returned to its 2014 proposal to add a note to recognise this alternative.
As time has gone by, it would appear that the experts had become more comfortable with the idea, although some concerns were raised about the ambiguity of the words ‘suitable’ and ‘secure’ in UIP’s proposal. In the end, on a majority vote, a slightly amended version was adopted as a Note to 4.3.2.1.7:
The tank record may alternatively be maintained in electronic form.
The UK followed up on discussions at the previous Joint Meeting on the use of level gauges and, in particular, whether sight glass gauges meet the requirements of 6.8.2.2.11. At that time, the general feeling was that such gauges should not be allowed for tanks subject to Chapter 6.8 but are suitable for those of Chapter 6.10 (vacuum-operated waste tanks).
The experts agreed the need to clarify the provisions in 6.8.2.2.11 but could not reach an agreement and, taking note of the diverse
MULTIMODAL • NOW THAT THE 2023 REGULATIONS ARE AGREED AND PRINTED, ATTENTION IS TURNING TO THE NEXT ROUND OF REGULATORY AMENDMENTS DUE TO ENTER INTO FORCE IN 2025
technologies available for tank level gauges, it was decided to defer discussion to the next session. The Working Group on Tanks was invited to consider the subject in detail.
The UK also followed up on the proposal at the previous session to develop a standard for relief valves on tank vehicles carrying dangerous goods other than petroleum products and LPG. At present, the requirements for such relief valves are found in several paragraphs in ADR and, as a result, some manufacturers have developed their own testing procedures or used inappropriate standards. The UK has put a proposal to the relevant technical committee of the European Committee for Standardisation (CEN), which was due to meet in November.
The Joint Meeting welcomed the UK’s input and felt it would be best to be able to include a reference to an existing standard in Chapter 6.8; it encouraged CEN to develop such a standard. It may be that other development work by CEN and/or the International Standardisation Organisation (ISO) will be relevant (see below).
The remaining papers on topics relating to transport in tanks were remitted to the Working Group on Tanks, which met concurrently with the plenary session under
the chairmanship of Arne Bale (UK). Its deliberations resulted in two specific proposals.
Firstly, Russia proposed a clarification for calculating the shell thickness of P22DH tanks for the transport of chlorine (UN 1017) and phosgene (UN 1076), as the existing text makes no reference to the calculation pressure for Class 2 gases. It offered three options for amendments, of which the Joint Meeting chose the addition of “or in the table of 4.3.3.1.1” at the end of the definition for ‘Pc’ in 6.8.2.1.17.
Secondly, the UK returned to the issue of the accreditation of inspection bodies for the authorisation and surveillance of in-house inspection services; it had been decided at the March 2022 session that this should be addressed during the next biennium, for which the September session was the first meeting. The purpose of the work would be to improve the precision of the wording relating to such matters and to take into account the relevant clauses in EN ISO/ IEC 17021-1:2015 and the work of the European Cooperation for Accreditation (EA), particularly the EA Document on Accreditation for Notification Purposes.
Following discussion of the UK’s paper by the Working Group on Tanks, the UK offered to
develop a short proposal to better set out what is expected of an inspection body when assessing the competence of an in-house inspection service in relation to the requirements of 1.8.7.7.2(a) of RID/ADR.
CEN provided the Working Group on Standards with an update of its work on those standards of relevance to the transport of dangerous goods, including some new work items and reports on the progress of others already in the pipeline. The Secretariat also noted that revised versions of EN 14025 and EN 13799, which had already been adopted by the Joint Meeting, had not been published in time to be notified for inclusion in the 2023 texts of RID/ADR. It proposed therefore that they should be added to the list of amendments for the 2025 texts.
As a result of those reports, the Joint Meeting adopted several changes. Firstly, in Table 4.1.6.15.1, reference to EN ISO 11114-2:2013 is updated to the 2021 edition.
In the table ‘for design and construction of closures’ in 6.2.4.1, a new row is added at the end for EN 13799:[2022] LPG equipment and accessories – Contents gauges for Liquefied Petroleum Gas (LPG) pressure vessels.
In the table in 6.8.2.6.1, under ‘For design and construction of tanks’, the existing row for
EN 14025:2018 + AC:2020 will now expire on 31 December 2026 and a new row is added for EN 14025:[2023].
In the same table, under ‘For equipment’, the existing row for EN 14432:2014 will now expire on 31 December 2016 and a new row is added for EN 14432:[2023]. The same change is made for EN 14433:2014. A new row is added at the end for EN 13799:[2022].
Finally, in 6.8.4(d), TT11 in the paragraph after the table, ‘EN 14025:2018’ is replaced by ‘EN 14025:[2023].
The RID Committee of Experts’ standing working group had considered including a reference to EN 14841 in the 2023 text of RID but felt that this would be premature, as it is not expected to be published until well into 2023. Moreover, even though its use would be voluntary, the standing working group felt that there were problems in its contents and the nature of its development.
CEN reported back on an issue raised by France a year earlier concerning the difficulties experienced when applying EN ISO 11118:2015, as referenced in 6.2.4. Those issues had been forwarded to the relevant ISO Technical Committee, which in October 2021 agreed to establish a Task Force of experts to review the points that had been raised. That Task Force acknowledged that some improvements and clarifications could be
made without affecting the scope or content of the standard. The matter was to be discussed by the relevant Technical Committee in October 2022 and it is to be hoped that a revised version will be made available during 2023.
Germany came back as promised with a formal proposal to add a new special provision for damaged or defective lithium batteries. At the previous session, it had noted that special provision 376, which was brought into RID/ ADR from the UN Model Regulations, with some amendment, differentiates between batteries that are liable to react dangerously under normal conditions of carriage and those that are not prone to such a reaction.
However, SP 376 does not provide full information on the transport category, which is crucial in RID/ADR for the application of the small load relief in 1.1.3.6.
Recalling that the Joint Meeting had already agreed to the need for change, the experts opted to add a new special provision 677:
Cells and batteries which, in accordance with special provision 376, are identified as damaged or defective and liable to rapidly disassemble, dangerously react, produce a flame or a dangerous evolution of heat or a dangerous emission of toxic, corrosive or flammable gases or vapours under normal conditions of carriage, shall be assigned to transport category 0. In the transport document, the words “Carriage in accordance with special provision 376” shall be supplemented by the words “Transport category 0”.
This new special provision 677 is assigned to UN Nos 3090, 3091, 3480 and 3481 in column (6) of the Dangerous Goods List in Table A of Chapter 3.2.
In addition, the last sentence of SP 376, which reads “In both cases the cells and batteries are assigned to transport category 0.”, is deleted. Delegations were invited to submit proposals for any further amendment they deemed necessary.
Germany had also been doing some research into the assignment of packing instruction R001 to the two entries under UN 1308 for zirconium suspended in a flammable liquid, PG II. This is inconsistent with the
assignment of special packaging provision PP 33, which allows only combination packagings, while R001 refers to light-gauge metal packagings, which are single packagings In addition, the first entry for UN 1308 has a vapour pressure more than 11 kPa at 50°C, which is not allowed in packagings conforming to R001.
The European Chemical Industry Council (Cefic) volunteered to look into the background of packing instruction R001 to the second entry for UN 1308 and, while the Joint Meeting agreed on the rationale for its removal from the first entry, it was decided to resume consideration of the subject at the next session.
The Council on Safe Transportation of Hazardous Articles (COSTHA) came back to its two queries on home deliveries, which had been raised at the previous session and also at the summer meeting of the UN Subcommittee of Experts. The first of these looked at the challenges posed by direct-tocustomer delivery services, which may involve the transport of dangerous goods such as aerosols, corrosive cleaning products, organic peroxides, flammable liquids and lithium batteries. When consumers buy these goods at the store and take them home, they
are in retail packaging and also exempted
delivered by the retailer’s own vehicles, do the provisions apply? If not, should this not be made clear? COSTHA offered an additional paragraph for 1.1.3.1, based on existing UK
There was some support for COSTHA’s proposed amendments were too broad in consider potential loopholes. There were also questions about some of the terminology used in the proposal and, indeed, some felt that the issue was best dealt with at the national level. Nevertheless, the Joint Meeting agreed to resume consideration of the subject at its next session, possibly on the basis of a revised
COSTHA also raised the issue of the use of handling devices by parcel delivery and postal
parcels within a delivery vehicle. These bags could be regarded as overpacks, as they may well contain dangerous goods, most likely in limited quantities. However, their contents do not remain constant throughout the delivery route and it would be difficult to ensure that
Tel: +44 (0)870 850 50 51 Email: sales@labeline.com www.labeline.com
the bag is correctly marked at all times.
COSTHA had also noticed that the definition of overpack in RID/ADR/ADN differs from that in the UN Model Regulations, whereas the international air and sea regulations and domestic regulations in the US and Canada are in alignment with the UN. It offered some options to harmonise the different provisions.
Once again, there was no agreement on the proposal, with some delegates observing that the definition of overpack in RID/ADR/ADN had been deliberately chosen to allow for differing practices. There were also those who felt that the change would be too broad and may have unintended consequences. The proposal also kicked off a discussion as to whether two- and three-wheeled vehicles are covered by ADR. The Joint Meeting will, though, pick up on the subject again at its next session, once more potentially on the basis of a revised proposal from COSTHA.
The impending expiry of the transitional period in 1.6.1.44 that relieves consignors of the duty to appoint a safety adviser (DGSA) has
concentrated the minds of many in the industry. The UK also observed that the existing exemption in 1.8.3.2(b), which applies to undertakings for which their main or secondary activity does not include the carriage or handling of dangerous goods, applies to carriers, packers, fillers, loaders and unloaders, but not to consignors. In an informal document it asked whether this should not be rectified.
The Joint Meeting had no hesitation in agreeing to the change and, having renumbered the relevant paragraph as 1.8.3.2(c) in ADR and ADN to mirror that in RID, decided in all cases to insert “consignment,” before “carriage”, twice.
Cefic raised a similarly urgent issue, which is the expiry of the transitional period under 1.6.1.46 on 31 December 2022; after then, the exemption in 1.1.3.1(b) for dangerous goods in machinery and apparatus will disappear. While some new provisions relating to the carriage of articles (in particular UN 3363 and UN 3537 to 3548) include an appropriate
alternative, industry is concerned that they do not address all current operations, especially those involving the transport of articles, machinery and apparatus for repair or maintenance.
Some delegates agreed on the urgent need to review the relevant provisions; while a new special provision might offer a solution, in the meantime a multilateral agreement could be initiated to resolve the urgency of the matter.
Liquid Gas Europe alerted the Joint Meeting to the need to discuss revising the definition of LPG in light of the introduction of ‘bioLPG’ and other renewable fuels such as renewable dimethyl ether. It sought to open a discussion prior to putting forward a formal proposal at the next session. Liquid Gas Europe, in collaboration with the World LPG Association, was also planning to submit a similar paper to the November/December session of the UN Sub-committee of Experts.
Most delegates who took the floor supported the initiative in principle and were keen to learn more in future about the percentage of blends with dimethyl ether. The Joint Meeting underlined the need to coordinate any amendments with the UN Model Regulations, while Germany offered the suggestion that a new special provision might be a more elegant solution. Liquid Gas Europe said it would consider that option and will also return with an official document at the next session, bearing in mind the outcome of discussions by the UN Sub-committee.
The European Federation of Waste Management and Environmental Services (FEAD) sought a revision of 4.1.1.22 to include reference to liquid waste classified under 2.1.3.5.5, for which the testing for chemical compatibility with plastics packagings is, from a practical point of view, difficult or impossible.
The Joint Meeting was not opposed to the suggestion, though it was felt an amendment of 4.1.1.21 might be preferable. FEAD invited interested delegates to send written comments so that it can prepare a new document for the next session.
FEAD had a similar query about the transport of packaged waste in combined packaging. When original products are so
Who do you contact for the latest DG compliant
You need Labeline.com
packaged, the inner and outer packagings are specifically tested for that purpose; however, when waste is collected, it is most common for only the inner packaging to be available. Nevertheless, the waste must be sorted according to its hazardous properties and be packaged in compliance with the regulatory requirements. There is currently no simple way to do this and, in the absence of such rules, some countries have developed their own national derogations, although this does not help if an international movement
FEAD offered an amendment in the form of a new 4.1.1.5.3, though the UK in particular raised concerns about the proposals. Delegates were again invited to send written comments to FEAD, which will prepare a new
the training requirements in Chapter 1.3, specifically about the training of ‘consignees’ when those are persons at private homes or small businesses where heating oil, LPG or similar products are being delivered. Are such individuals considered ‘consignees’ according
Labeline is the leading worldwide “One Stop Dangerous Goods Service” for Air, Sea, Road, and Rail
We serve Freight Forwarders, Shippers, Airlines, DCA’s, Port Authorities, Petrochemical industry and the Pharmaceutical industry.
Labeline is one of the world’s leading regulatory services and product provider; we hold comprehensive stocks with a fast worldwide delivery service.
We are one of the very few authorised Multi-mode providers worldwide and described by industry as a pro-active organisation, our name is recommended by many leading authorities and a world class service providers.
When it’s time to order your DG products and services, Labeline will be your “One Stop Service”
Compliant with IATA, ICAO, ADR, IMDG, RID, DoT
Tel: +44 (0)870 850 50 51 Email: sales@labeline.com www.labeline.com
FEAD also raised the question of the disposal of household waste, such as empty aerosols or packagings for corrosive products, in the general waste stream. It felt that new text could be added to 1.1.3.1(a) to clarify the exemption of such waste. Again, it was felt that more work was needed on the proposal
France had a query about the applicability of
Opinion was divided; some said that anyone taking delivery of dangerous goods should be considered as a consignee, others that those at a private home should be differentiated from businesses, whether small or large. It was, though, acknowledged that some consignees would not be able to meet the training requirements. France offered to prepare a more detailed document for the discussions of the informal working group on the carriage of molten aluminium (UN 3257). This product is carried in bulk in accordance with special provision VC3, which provides for the competent authority of the country of origin to specify conditions of carriage. The result of the work involved a proposal for a new alphanumeric code AP 11 in 7.3.3.2.7,
Tel: +44 (0)870 850 50 51 Email: sales@labeline.com www.labeline.com
Tel: +44 (0)870 850 50 51 Email: sales@labeline.com www.labeline.com
setting out uniform minimum requirements for carriage.
The Joint Meeting welcomed the report and there was support for the proposed provisions. After discussion, Germany invited written comments and said it would aim to submit an updated proposal for the next session.
A report on the first meeting of the informal working group on e-learning was provided by Germany and the International Road Transport Union (IRU). The meeting had received several presentations and comments about existing e-learning and online training courses, while noting that the legal standing of such courses differs significantly between countries. It was widely agreed that e-learning is suitable for refresher training (though not for practical elements) but there were mixed opinions about initial training. Some felt that the decision should be left to national competent authorities, though others noted that, were e-learning to be accepted as an alternative to in-person training, then appropriate
provisions should be included in Chapter 8.2 of ADR.
The informal working group was due to meet again in October and expected to hear from other training institutes. The Joint Meeting invited the group to develop any necessary amendments to ADR/ADN for consideration at its next session.
FEAD presented the minutes from the fifth meeting of the informal working group on the transport of hazardous waste, which had taken place in June 2022. The Joint Meeting welcomed the group’s conclusions and noted its intention to meet again to finalise a draft proposal for the transport of asbestos in bulk for consideration by the Joint Meeting at its next session.
ERA provided a progress report on the informal working group on the improvement of the Transport of Dangerous Goods occurrence report, ahead of the anticipated adoption of the Common Safety Methods on the Assessment of Safety Level and
Performance of Railway Operators (CSM ASLP) by the European Commission later this year or early in 2023. As a result, it would be beneficial to align the accident reporting requirements in 1.8.5 of RID with those in the CSM ASLP, which are somewhat more streamlined. There are several other points on which the two systems diverge and ERA is continuing to coordinate work ahead of a planned proposal of amendment to RID/ADR/ ADN for consideration at the next session.
Four informal documents were presented on the topic of the use of electronic freight transport information (eFTI) and the work of the Digital Transport Logistics Forum (DTLF). The current data model, developed in the context of the EU Regulation 2020/1056, do not take account of the specifics of dangerous goods transport and an informal working group on telematics has been investigating the differences in architecture principles. It was stressed that eFTI and dangerous goods experts need to work together to ensure close cooperation and resolve any potential issues.
The EU stressed that the DTLF work was still ongoing, in particular on the datasets, data models and architecture models for the transport of dangerous goods, and that input from the Joint Meeting would be valuable.
In terms of the UN’s Sustainable Development Goals, the Secretariat advised the Joint Meeting that the terms of reference of the Inland Transport Committee (ITC) have been revised and that it will be looking for the Joint Meeting to report back on aspects of its work related to the circular economy. Delegates were invited to contribute to the discussion. The Joint Meeting agreed that this topic should form a new agenda item to ensure regular discussion.
Claude Pfauvadel and Silvia García Wolfrum were re-elected to serve as chair and vice-chair, respectively, for the meetings scheduled in 2023. The chair announced that he is planning to retire shortly and will not be available to serve the Joint Meeting from 2024. The next session of the Joint Meeting is scheduled to take place in Bern from 20 to 24 March 2023.
THE LATEST UPDATE to the International Maritime Dangerous Goods (IMDG) Code, Amendment 41-22, was adopted by the International Maritime Organisation (IMO) earlier this year and will take effect on 1 January 2023. As usual, there is a one-year transitional period to the end of 2023, during which time the current version, Amendment 40-20, may still be used.
Amendment 41-22 takes account of the changes that appear in the 22nd revised
edition of the UN Model Regulations but includes also some mode-specific changes, particularly in terms of stowage and segregation. The regulators, both at the UN and IMO, have been affected by the Covid pandemic just as much as anyone else, and the number of changes included in Amendment 41-22 are fewer in number than is often the case; there are also no major changes for dutyholders to deal with. Nevertheless, they do need to pay close
attention to the details of the Amendment if they are to remain compliant.
Exis Technologies has once more published a detailed summary of the changes that appear in Amendment 41-22, which can be downloaded free of charge from its website at https://existec.com/hazcheck/imdg-codefree-summary-of-changes-41-22/. HCB is grateful to Exis for doing the work and for allowing us to provide the following precis.
The UN experts picked up on a number of changes introduced by the International Atomic Energy Agency (IAEA) in its SSR-6 document for transport safety; these have been transposed into the IMDG Code as appropriate, notably in 2.7, 5.1 and 6.4.
There are also a number of new and amended definitions in 1.2, particularly affecting inner vessels, pressure receptacle shells and service equipment. In addition, some changes have been made to the security provisions in 1.4.3.2.3 specific to highconsequence dangerous goods (HCDG) to clarify their applicability.
As usual, there are many new and amended self-reactive substances and organic peroxides; a change has also been made to avoid confusion in the selection of control and emergency temperatures for these substances, clarifying the applicability of packing instruction IBC520 and tank code T23.
Also important are various changes in Part 6 concerning the design, construction and testing of packagings and tanks. In most cases these clarify the meaning of the requirements and the terminology used, though they also have consequential amendments. IMO has also adopted the new 6.10 dealing with portable tanks with shells manufactured of fibre-reinforced plastics (FRP) materials, which has led to some changes in 6.7.
In Part 2, the introductory notes to 2.6 now include UN 3462, covering solid toxins from plant, animal or bacterial sources, or toxins contained in substances that are not themselves infectious substances; liquids under UN 3172 are also considered for classification.
MARITIME • IMDG CODE AMENDMENT 41-22 IS AVAILABLE FOR USE FROM 1 JANUARY. ALTHOUGH THERE ARE FEW MAJOR CHANGES THIS YEAR, USERS NEED TO BE AWARE OF THE DETAILED UPDATES
There are updates to 2.8.3 on the classification of corrosives, relating to the assignment of packing groups to substances and mixtures. A note is added to 2.9.3.4.3(a) and 2.9.4.7 to extend the exception to the lithium battery test summary requirements to cover button cells installed in equipment.
There is only one new entry in the Dangerous Goods List: UN 3550 Cobalt dihydroxide powder, containing not less than 10 per cent respirable particles. The two entries under UN 1169 are deleted and consolidated into UN 1197, renamed Extracts, liquid, for flavour or aroma.
The entry for UN 1439 Ammonium dichromate is amended, with the word “strong” deleted and the properties and observations column now reads merely “acids”; SG75, which applies to strong acids, has been replaced by SG35 in column 16b. Similar changes have been made to a number
THE LITHIUM BATTERY MARK WILL NO LONGER NEED TO SHOW A PHONE NUMBER, AS NONE OF THE REGULATORS COULD RECALL WHY IT WAS THERE OR WHAT INFORMATION SHOULD BE PROVIDED BY THE SHIPPER
of other entries. Similarly, all entries assigned SGG1a now have SGG1 instead.
The entry for UN 1891 Ethyl bromide has been changed, so that it is now Class 3 with a Division 6.1 subsidiary hazard; the LQ, EQ and EmS values have been amended and the flashpoint is added to the properties and observations column.
The UN experts corrected one mistake applicable to UN 3208 and 3209 Metallic substance, water-reactive; in UN 3208 PGII, E0 is replaced by E2 and in UN 3209 PGII, E2 is replaced by E0. For polyester resin kits (UN 3527), PGII and III, ‘E0’ is replace by ‘See SP340’, which provides more guidance.
The relatively new entry UN 3538 Articles containing non-flammable, non-toxic gas, nos is assigned a new special provision 396, which specifies the conditions under which ‘large and robust articles’ may be transported with connected gas cylinders and open valves.
There are two more new special provisions. SP397 is assigned to UN 1002 and makes it clear that this entry can apply to mixtures containing not more than 23.5 per cent oxygen by volume when no other oxidising gases are present. SP398 applies to UN 1012 and clarifies its applicability to certain isomers of butylene.
There are amendments to SP188, to remove the elapsed marking provisions, and SP225,
which has a new note clarifying that it applies equally to portable fire extinguishers shipped without the necessary components required for them to function.
There are some important changes in Part 4, including a new sentence added at the end of 4.1.3.3 relating to packagings that do not need to meet the design type test as per 4.1.1.3 and that are authorised in various packing instructions and special provisions. This clarifies that these packagings are not subject to the mass or volume limits of Chapter 6.1, unless otherwise indicated in the packing instruction. Therefore, authorised packagings may exceed 400 kg. Notes to that effect have been added to a number of packing instructions and special packing provisions.
There are a number of other amendments to the packing instructions, especially P200, where special packing provisions ‘d’ and ‘z’ have been revised and the LC50 values for UN 1008, 2196, 2198 and 1052 have also changed. More packaging options are now available for UN 2196 and 2198. P621 also now has more packing options for drums and jerricans. An additional requirement (i) is added in P911 to address consignments of multiple batteries and multiple items of equipment containing batteries, with similar amendments in LP906.
In the intermediate bulk container (IBC) packing instructions, special packing provision B15 in IBC02 has been amended; the new special packing provision B40 is added to IBC07 to provide for the use of flexible IBCs (13H3 and 13H4) with the new UN 3550 entry.
Elsewhere in Part 4, there is a new note to 4.1.1.15 to clarify that the period of use for composite IBCs refers to the date of manufacture of the inner packaging. The maximum size of salvage pressure receptacles in 4.1.1.9.2 has been increased from 1,000 litres to 3,000 litres. In 4.1.6 there are several small amendments to the special packing provisions for Class 2 gases and reference to tanks and IBCs is removed from 4.1.9.1.4.
Chapter 4.2 has several changes that reflect the inclusion of provisions for FRP tanks in the new 6.10. A new sentence is
unravels the mystery
Built around an ecosystem of shared knowledge from every industry and every step of the supply chain, SciveraLens® delivers on-demand certified toxicological information through an intuitive user interface that lets you save time and money while taking a proactive approach to your chemical management.
TAKE CONTROL OF YOUR CHEMICAL MANAGEMENT. SCHEDULE A DEMO AT SCIVERA.COM.
we know chemical management can feel like this
added at the end of the portable tank instruction table for T1 to T22 to clarify that the instructions for FRP tanks apply to substances of Classes 1, 3, 5.1, 6.1, 6.2, 8 and 9. TP32 has been updated to include a reference to FRP material.
IMO followed the UN’s lead in removing the requirement for an emergency phone number on the lithium battery mark, as no one could remember why it was there in the first place and it is not clear what information should or could be provided.
There are several changes in Chapter 5.4, notably relating to the use of the words ‘molten’, ‘stabilised’ and ‘temperature controlled’, as appropriate, as part of the proper shipping name in documentation. In addition, 5.4.1.5.3 is replaced with new text to
CHANGES TO STOWAGE AND SEGREGATION PROVISIONS WILL IMPACT CARRIERS, WHO WILL HAVE TO UPDATE THEIR SYSTEMS TO ENSURE THAT THE REVISED REQUIREMENTS ARE REFLECTED IN THEIR OPERATIONS
clarify that the documentation requirements for approved salvage packagings and receptacles also applies to any other appropriate packagings used. Significantly, 5.4.1.5.17 is no longer specific to ‘Engines’ but has been broadened to apply to all instances where a special provision requires additional information to be included in the transport document.
There are quite a lot of changes in Part 6, especially in Chapter 6.2 (and not just the usual amendments to references to updated and new standards), largely for clarification; and the new 6.10 is added to deal with FRP portable tanks. Those in Chapter 6.2 cover a wide range of containments, including pressure receptacles (as well as specific changes for acetylene cylinders), service equipment, closed cryogenic receptacles, bundles of cylinders and aerosol dispensers.
There are some minor edits in 6.3.2 on the provisions for packagings for infectious substances of Division 6.2, Category A. Chapter 6.5 has been revised to reflect ongoing product development in the IBC market, with changes to 6.5.1.1.2, and the
increasing use of recycled plastics material in the manufacture of IBCs (in 6.5.2.1.2 and 6.5.5).
IMO has removed the distinction between ‘acids’ and ‘strong acids’, so the segregation provision SGG1a is deleted from 7.2.5.2; SG75 is also deleted from 7.2.8, as it refers to stowing ‘separated from’ strong acids.
In 7.3.7.2.3.1, the word ‘Stabilised’ is replaced by ‘Temperature controlled’. And in 7.9.3, which gives contact information for the main national competent authorities, reference is now made to using IMO’s Global Integrated Shipping Information System (GISIS) to access up-to-date information.
In the Emergency Schedules (EmS), for UN 1891 Ethyl bromide, ‘F-A, S-A’ is replaced by ‘F-E, S-D’. This follows on from the reclassification of this substance. The new UN 3550 entry for cobalt dihydroxide powder is given ‘F-A, S-A’ schedules.
In the Annex, there are several changes to the Recommendations on the safe use of pesticides in ships applicable to the fumigation of cargo transport units.
Our new membership gives you and your colleagues unlimited use of our new class-leading platform, featuring:
Our new membership gives you and your colleagues unlimited use of our new class-leading platform, featuring:
Timely, in-depth, impartial and easy to understand global coverage from our award-winning team of industry journalists to inform your product safety strategy.
Timely, in-depth, impartial and easy to understand global coverage from our award-winning team of industry journalists to inform your product safety strategy.
Leveraging our unique network of contacts, we dig deeper into the issues, developments, challenges, and drivers to give you a thorough overview of the topics important to you and your business.
Leveraging our unique network of contacts, we dig deeper into the issues, developments, challenges, and drivers to give you a thorough overview of the topics important to you and your business.
Regularly updated, practical directories and databases so you have the data you need on-hand, plus the latest job opportunities, industry events and company news to promote you and your team’s development.
Regularly updated, practical directories and databases so you have the data you need on-hand, plus the latest job opportunities, industry events and company news to promote you and your team’s development.
Bespoke materials and insights for you and your organisation from our dedicated analyst team, as and when you need it, so you can make throughly informed decisions in your product safety strategy.
Bespoke materials and insights for you and your organisation from our dedicated analyst team, as and when you need it, so you can make throughly informed
An extensive range of resources saving time and arming your team with the intelligence you need, including:
An extensive range of resources saving time and arming your team with the intelligence you need, including:
• Comprehensive reference library of legislation, guidance, and translations
• Strategic global compliance tools
• Practical compliance resources
• Comprehensive reference library of legislation, guidance, and translations
• Expert analysis, horizon-scanning and interpretation
• Strategic global compliance tools
• Practical compliance resources
• Expert analysis, horizon-scanning and interpretation
Meet our influential network of industry experts at our regular conferences, workshops and webinars, and maintain your professional skills through our training and eLearning courses.
Meet our influential network of industry experts at our regular conferences, workshops and webinars, and maintain your professional skills through our training and eLearning courses.
Navigate content by regions, topics, sectors and substance groups, save personalised content views, and create collaborative groups – quick and easy access to the information and resources you need.
Navigate content by regions, topics, sectors and substance groups, save personalised content views, and create collaborative groups – quick and easy access to the information and resources you need.
Empower your business and create safer products with the new Chemical Watch
Visit our new website to find out more: chemicalwatch.com
Visit our new website to find out more:
Empower your business and create safer products with the new Chemical Watch
Global Contract: NO.159 Chenggang Road, Nantong, Jiangsu, China 226003 Tel: 86-513-85066022(Sales), www.cimctank.com E-mail: tanks@cimc.com
Europe contract: Middenweg 6 (Harbour nr.397-399) 4782 PM Moerdijk Tel: +31 880 030 860 www.cimctankcontainers.nl E-mail: info@cimctankcontainers.nl
BURG SERVICE B.V. Service Deport in Europe
Middenweg 6, 4782 PM, Moerdijk, The Netherlands
Tel: +31 88 00 30 800 Fax: +31 88 00 30 882 www.burgservice.nl E-mail: info@burgservice.nl