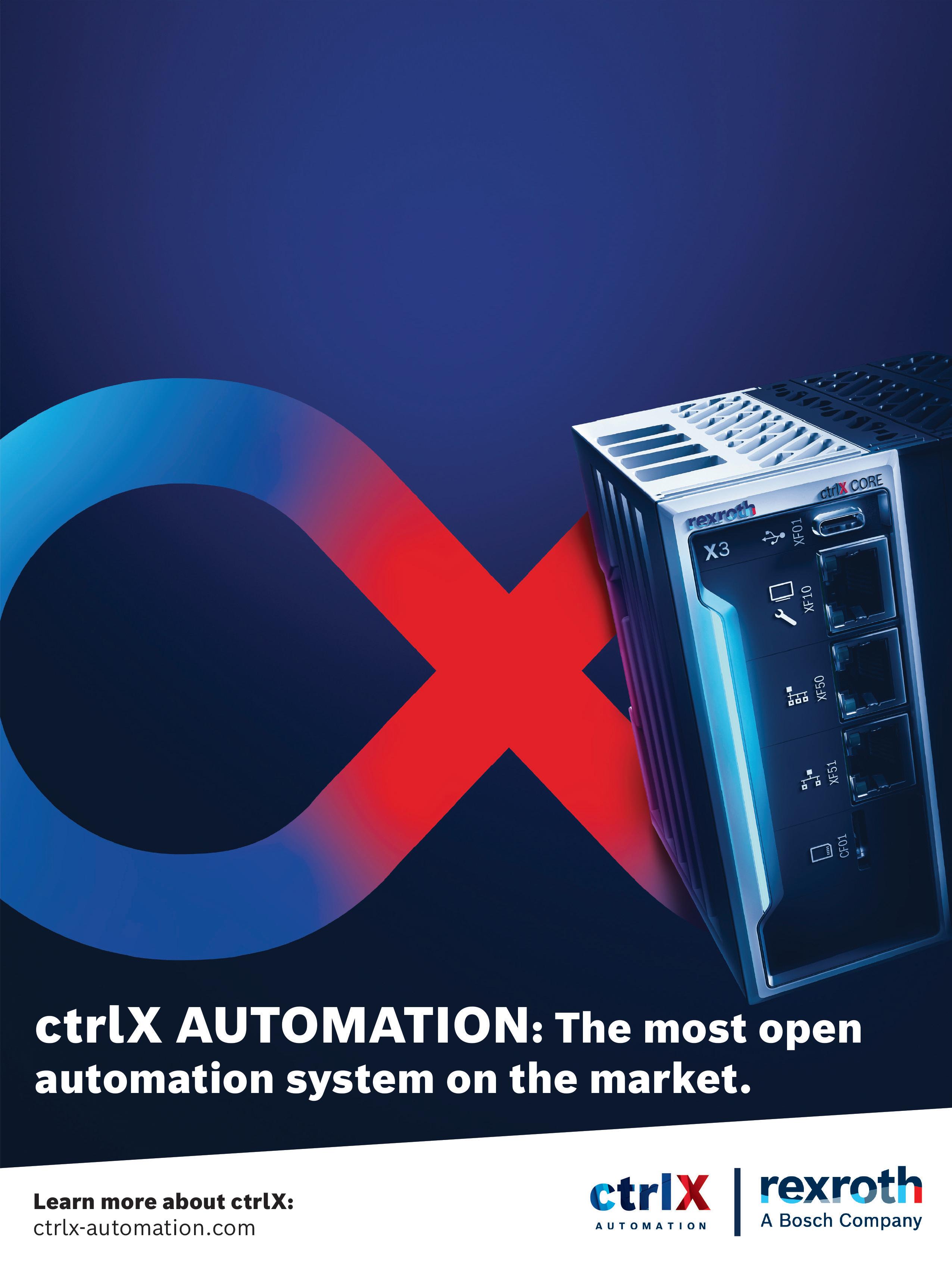
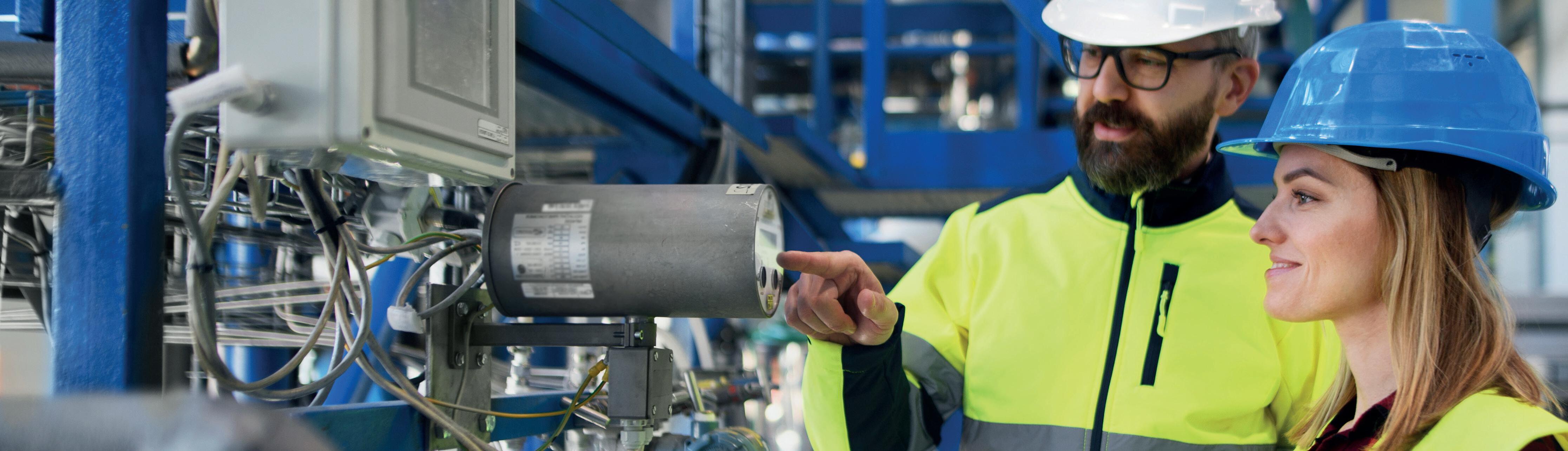
I can see exactly what needs repair
The FLIR T865 thermal imaging camera is a non-contact inspection tool with 180° rotating optical block that allows users to safely and comfortably assess the condition of critical electrical and mechanical equipment in utility and manufacturing applications.
With advanced features including unmatched temperature measurements down to -40°C, accuracy as good as 1°C/1%, 1-Touch Level/Span contrast enhancement, and laser–assisted autofocus, you’ll get highly accurate temperature measurements every time.
The on-board Inspection Route system helps you record temperature data and imagery in a logical sequence for faster troubleshooting and repair.
www.flir.eu/products/t865/
Editor
Oliver Batt oliver@cimltd.co.uk
Publication Manager
James Burke jb@cimltd.co.uk 01795 509105
Account Managers
James Davies jamesd@cimltd.co.uk 01795 509105
Jim Bearden jim@cimltd.co.uk 01795 509105
Design & Production
Grant Waters grant@cimltd.co.uk
James Taylor james@cimltd.co.uk
Administration Manager
Natalie Murray admin@cimltd.co.uk 01795 509103
Credit Facilities Manager
Gwen Lee creditcontrol@cimltd.co.uk 01795 509103
Marketing Manager
Lucas Payne lucas@cimltd.co.uk
Sales Director
Tom Woollin tom@cimltd.co.uk
Chief Executive
John Denning
© 2024 Cogent Multimedia Limited,1st Floor, Saphir House, 5 Jubilee Way, Faversham, Kent, ME13 8GD. No part of this magazine may be reproduced or stored in a retrieval system or transmitted in any form – electronic, mechanical or physical – without express prior permission and written consent of the publisher. Contributions are invited and when not accepted will be returned only if accompanied by a fully stamped and addressed envelope. Manuscripts should be typewritten. No responsibility can be taken for drawings, photographs or literary contributions during transmission or in the editor’s hands. In the absence of an agreement the copyright of all contributions, literary, photographic or artistic, belongs to Cogent Multimedia Limited. The publisher accepts no responsibility in respect of advertisements appearing in the magazine and the opinions expressed do not necessarily represent the views of the publisher. The publisher cannot accept liability for any loss arising from the late appearance or non-publication of any advertisement.
Welcome to the December issue of MEPCA magazine!
In every issue, we manage something remarkable: time travel. Our publishing calendar has us working at least a month ahead, with the year appearing to pass ever more quickly for us as a result. This issue, we embrace that phenomenon as we usher in 2025.
Given the rocky ride the manufacturing sector has experienced this year, it is reassuring to see confidence returning for 2025. With many businesses focused on the year ahead, our Business Operations section features expert advice on finance, recruitment, marketing and software to help our readers prepare for the coming year.
In this month’s cover story, we learn how Bosch Rexroth has increased efficiency at one of its key manufacturing hubs by leveraging an advanced control system. Elsewhere in this issue, we bring you the second part of Titan Enterprises’ turbine flow meter deep-dive, demystify B Corp accreditation, visit The Scalpel to learn about predictive maintenance, reveal our December Manufacturing Champion, and much, much more.
We hope you enjoy this issue and wish you a fantastic end to the year.
@Mepca-magazine
To subscribe to MEPCA visit our website www.mepca-engineering.com or scan the QR code.
Leading HVAC specialist, Jet Environmental, has recently launched a service and maintenance offering for businesses using non-Jet systems. This strategic expansion ensures that more companies across industries, such as warehousing, manufacturing and aerospace, can benefit from Jet’s unmatched expertise in temperature and humidity control.
Recognising that HVAC systems are often critical assets in controlling sensitive environments, Jet’s new offering is designed to enhance system reliability and performance. Their planned preventative maintenance programmes ensure minimal
disruption and reduce the risk of costly breakdowns.
Customers can also opt for 24/7 system monitoring, allowing Jet to detect and resolve issues remotely, often before they impact business operations.
Emphasising the importance of this initiative, Jason Hibbs, Jet Environmental’s managing director, said: “We understand that HVAC systems are the backbone of many businesses, particularly where climate control is critical.
“By extending our service contracts to non-Jet customers, we’re offering our extensive industry knowledge and cuttingedge technologies to ensure their systems operate at peak efficiency. We aim to build
long-lasting partnerships, regardless of the original system provider.”
jetenvironmental.com
Rushlift, the national fullservice provider of materials handling equipment (MHE), has opened a Centre of Excellence for training forklift truck maintenance engineers and drivers at its Northampton HQ. The investment provides state-of-the-art facilities, alongside highly skilled trainers, allowing Rushlift to open-up its training capabilities to businesses across the country.
As an Association of Industrial Truck Trainers (AITT) accredited training provider, Rushlift is now able to provide technical training courses and operator training for employees, apprentices, customers and businesses nationwide.
Steve Briscall, National Training Manager at Rushlift: “Efficient, reliable materials handling equipment is absolutely critical to the profitable running of many businesses. Keeping forklift trucks both safe and efficient takes skilled service engineers and qualified drivers that are fully in-tune with their equipment. That’s why in-depth training and gaining the right skills is so essential. I’ve attended and delivered many training courses during my 29 years in this industry,
and I’m proud to say that these are the best equipped training facilities that I’ve had the pleasure of working in.”
The new facilities include a spacious training room that can comfortably accommodate up to 16 trainees. A large screen TV for presentations, with computer tablets available to access technical information. The practical workshop area is equipped for technical training offering tooling, benches and diagnostic equipment for hands-on training. The area is also used for operator training, allowing trainees to
practice driving manoeuvres.
A core element of the investment is the training team itself. Along with Steve Briscall’s appointment to the role of National Training Manager in 2023, Sam Cook recently joined the team as Technical Training Manager bringing to the business 37 years of experience as a research and development technician, workshop supervisor, apprentice development officer and technical trainer.
rushlift.co.uk
Han-Modular ® Domino ModulesRobust technology for industrial transformation.
The first modular connector with a hybrid module configuration
■ Smaller and lighter connectors allow space savings of up to 50%
■ Compatible with components of the Han-Modular ® series, the market standard for modular industrial connectors
■ Flexible and scalable to the respective need
■ Sustainability through consistent modularisation
■ Reduction of installation times by combining several individual connections
One Range. No Limits: www.HARTING.com/domino
At WEFTEC 2024, the largest water quality event in the United States, ABB introduced the UviTec™ analyser product family. UviTec is the successor of the optical sensor technology by Real Tech, which ABB acquired in February 2024.
Based on patented and proprietary technologies, UviTec is a comprehensive optical-based water quality-monitoring platform. The platform includes optical sensors, controllers, a suite of add-on accessories and a data analytics and software solution.
UviTec uses spectrophotometric and fluorescence measuring techniques to deliver lab-quality water analysis results in the process environment. Through the power of UV/VIS technology, UviTec enables rapid detection of a wide range of water quality parameters and compounds in real
time. The UviTec Liquid Ai data analytics and software platform uses the obtained measurements to provide plant operators with actionable insights, helping improve how water and wastewater are managed across numerous applications.
“Unlike traditional water quality testing which can take days in lab conditions, the products in the UviTec family provide critical measurements immediately,” said Jon Penn, Global Product Line Manager, Continuous Water Analysis, ABB Measurement & Analytics. “The UviTec biochemical oxygen demand (BOD) and chemical oxygen demand (COD) analyser used for measuring organic levels in water delivers accurate results in five seconds, instead of five days like traditional lab-testing, saving time and money while improving safety and efficiency.”
With the introduction of the UviTec family, ABB can now help customers measure
an even wider range of water parameters, expanding its strong presence in the water segment.
In addition to introducing UviTec at WEFTEC 2024, ABB showcased its continuous water analysis portfolio, electromagnetic flowmeters, pressure and laser level transmitters, as well as recorders and controllers for the water industry.
new.abb.com
During the automotive manufacturing coating process, the height of the skid’s pick-up pins can vary due to factors such as acid and alkali corrosion, high-temperature baking, and mechanical impacts. If the height of the vehicle pick-up pins is too low, it can lead to potential vehicle body rollovers or other serious accidents due to the continuous application of gravity.
Traditional quality control methods involve manually transferring the skid off the production line to a tool platform for inspection after it has been in operation for a certain period. This approach incurs high-labour costs and low overall efficiency, making it difficult to ensure 100% inspection accuracy or meet long-term inspection needs. The reliability of skid equipment is crucial for controlling the upstream and downstream processes of the automotive production line, requiring meticulous 100%
inspection to ensure proper operation during production.
The FAW-Volkswagen Foshan Branch Intelligent Coating Digitalisation Team implemented a solution using two customised LMI Gocator 2540 laser line 3D sensors and a Master 810 sensor networking hub. This setup simultaneously collects 3D surface data from both the left and right steel beams of the skid, as well as the connecting points. The collected data then undergoes precise calibration and processing on board the sensor. After data collection, the system pre-processes, locates, and establishes a corresponding coordinate system. It then identifies surface
data characteristics, performs full-size measurements, and provides detailed inspection results.
“Gocator’s ease of deployment and advanced 3D profiling capabilities transformed our inspection process. The system’s precision and seamless integration have significantly enhanced our efficiency, reducing costs and ensuring 100% inspection. It’s a game-changer for the stable operation of manufacturing equipment.” — Tao Chen, Production Maintenance Engineer, FAW-Volkswagen Foshan Branch.
lmi3D.com/contact
MEPCA is delighted to be celebrating Rob Dando, Digital Marketer and co-founder of Finally Agency, as December’s Manufacturing Champion.
Rob Dando has been in digital marketing for over 25 years, developing strategies for a range of sectors. Having recognised that manufacturers and engineers face specific challenges when marketing their products and services, Rob co-founded Finally Agency to provide award-winning B2B strategies to technical and industrial companies.
MEPCA had the opportunity to ask Rob about his career and gain a better understanding of how industrial companies can reach their target audiences.
what ways have you seen industrial marketing change during your career as a Digital Marketer?
Digital marketing has seen many changes in my career. For instance, when I started building websites, paid advertising and social media did not exist, so the changes have been dramatic and have created entire economies.
In the industrial sector, I would say that the uptake and understanding of the power of digital marketing have been far slower. Only in the past three years have many companies begun to adopt and change their marketing spend.
The ability to target such specific audiences from anywhere in the world makes it the best channel for most industrial companies, opening their potential sales to an audience they could not have previously reached.
AI tools will only increase the speed of adoption, and provide companies with the opportunity to create new markets for themselves using these digital tools.
advice do you have for manufacturers and engineers struggling to promote their products and services?
My advice is to take a step back in the first instance. Look at what you are actually saying to the market, and be honest with yourselves. Are you highlighting benefits to the end customer? Are you speaking in the correct way to the target buyer?
You have to know who your customer is, as often, it will not be the person making the financial decision to purchase. So speak to your audience, educate them on how the product or service will benefit them; how it will help them do their job more efficiently, and what timesaving benefits it might bring.
Once you are doing this, you need to provide multiple touchpoints for each stage of the buying cycle: Awareness, Consideration, and Decision. Each stage requires different messaging and levels of detail to help people make the final decision to purchase.
When you have all of this worked out, choose the correct channel to get the
message out to your audience, test this across multiple channels to find what works best for your target audience.
During your 25 years in digital marketing, what achievement are you most proud of and why?
I am proud of building companies that have allowed me to employ and train so many people. It is a real honour to see people do something they love and work with amazing brands and clients across the globe.
We currently have a team of over 25 and were recently recognised by the UK Agency Awards as having the best culture, which was a very proud moment.
The work we do can sometimes be fastpaced. Often, we have no time to celebrate the achievements both internally as an agency and externally alongside clients, as the next project or campaign needs to be worked on. When I take a moment to reflect on what makes me proud, it is the recognition of my team, the success they have and the results they bring for clients. finally.agency
MEPCA toured The Scalpel, Lime Street, to see how a collaborative effort between CBRE, Turck Banner and Fletcher Moorland delivers condition-based maintenance to the cutting-edge skyscraper.
The Scalpel was purpose built as the headquarters for insurance company W.R. Berkley and completed in 2018. Designed by Kohn Pederson Fox to passive design principles, the building stands 190m tall (10m higher than the neighbouring Gherkin) has 42 floors and offers over 59,400 m2 of high quality, modern and sustainable mixed-use space.
MEPCA was invited by Turck Banner, specialist manufacturer of sensors and automation products, to find out how an innovative approach to asset maintenance has improved the facilities management of this impressive building.
CBRE, the company responsible for facilities management of The Scalpel, led the tour. It started and ended in the control room, out of which CBRE’s team provide The Scalpel with proactive, condition-based maintenance using the sensor and controller technology of Turk Banner and the software and support services of Fletcher Moorland.
John Dennis, Account Manager at CBRE, explained the benefit of the system they have in place: “You can see the knock-on effect of anything going wrong very early” and this enables them to deliver a “costeffective way of repairing the pump before it gets to the failure point.”
Importantly, as Matt Fletcher Managing Director of Fletcher Moorland was quick to point out: “The first thing to realise is condition monitoring doesn’t stop failures. It gives you data to make good decisions to stop failures.”
Before looking behind the scenes in one of the plant rooms, Tony Coglhan, Managing Director of Turck Banner, asked CBRE what the drivers were for choosing Fletcher Moorland.
Daniel Mayer, Engineering Manager
at CBRE, explained that, while Fletcher Moorland’s Meerkat solution “stood out,” it was actually “the value of the service, the engineering experience” that was most important.
In Plant Room B2, Tony Coglhan provided an insight into the technology involved: nodes attached to the pumps wirelessly transmit data to the Meerkat box, supported by Turck Banner’s controllers.
Using the Air Handling Unit (AHU) pump in front of us to illustrate, Daniel Mayer further explained that the sensors attached to it are on every pump in the building. The sensors monitor the pump vibrations and sends that data through the GSM network (provided by Turck Banner) to the Meerkat cloud server. If the vibration level breaches a set threshold it is communicated via the Meerkat dashboard. Increased vibration is an early indication that something is starting to go wrong: “as the bearings start to wear, the acceleration, the vibration velocity will start to increase”
After a visit to boiler room on floor 36, we ascended to the chiller room, the highest point of our tour. It was here that the Meerket system most recently demonstrated its value when a condenser pump failed.
The fault was picked up before catastrophic failure. From the vibration data collected, CBRE were able to determine that the bearing was failing prematurely. Advance notice of the issue provided CBRE with ample time to have the pump surveyed, order the parts and equipment needed, and schedule its repair.
This perfectly illustrates the benefit of the Meerkat solution; condenser pumps of this size cost between £20,000 and £30,000, on top of which there is the added cost of the seal kit and lifting equipment needed to carry out the replacement.
MEPCA are grateful to Turck Banner, CBRE and Fletcher Moorland for this insightful tour. It demonstrates the clear benefit of data-led predictive maintenance for all industries. As the method evolves, adding further metrics for proactively managing asset wear, it promises to extend asset life and reduce maintenance costs considerably.
turckbanner.co.uk/en fletchermoorland.co.uk/
Wayne Rose, Director and CEO of the British Pump Manufacturers Association (BPMA), urges businesses across the UK’s industrial sector to prioritise energy audits as a key strategy for improving operational efficiency, cutting costs and reducing environmental impact.
With energy prices continuing to fluctuate and sustainability becoming increasingly central to business operations, understanding how and where energy is consumed has never been more important.
Energy audits are an essential first step in identifying areas of energy waste and inefficiency. They provide businesses with a comprehensive assessment of their energy use, highlighting opportunities for improvement and offering actionable recommendations. For industries reliant on energy-intensive processes, such as manufacturing and production, these audits can lead to significant savings in terms of both energy consumption and cost, while also contributing to broader environmental goals. Most existing pump systems were not originally designed with energy conservation as a major consideration. However, if pump systems are designed on an energy efficient basis, with the pumps correctly sized and applied, the energy savings will often be in excess of 50%.
Central to this process is the BPMA’s Certified Pump System Auditor (CPSA) scheme, which offers a critical foundation of knowledge for conducting energy audits in systems involving pumps. Pump systems are often one of the largest consumers of energy in industrial operations, yet they are also an area where efficiency gains can be most easily realised.
Through the CPSA scheme, professionals are equipped with the expertise to assess pump systems thoroughly, identifying inefficiencies and providing solutions to optimise performance.
By undergoing a CPSA-accredited audit, businesses can ensure they are receiving expert advice tailored to the specific
challenges of pump systems. The knowledge provided by a certified auditor goes beyond identifying simple inefficiencies – it provides a strategic understanding of how to enhance overall system performance. This not only results in direct energy savings but also leads to improved reliability and reduced maintenance costs, driving long-term operational resilience.
Candidates carry out the Pump System Audit in accordance with ISO/ ASME 14414:2019, the standard that outlines the requirements for conducting and reporting the results of a comprehensive pumping system energy assessment. This assessment evaluates the entire pumping system, from energy inputs to the work performed, with the objective of determining the current energy consumption and identifying opportunities to improve system efficiency.
The value of an energy audit cannot be overstated. Pump systems are fundamental to the functioning of many industrial operations, but they also represent a significant opportunity for energy savings. The CPSA scheme is designed to provide the industry with highly qualified professionals who can deliver real, measurable improvements in energy efficiency. We urge all businesses to take advantage of this and make energy audits a priority.
As the UK strives to meet its energy reduction targets, the role of energy audits in industrial settings will become even more pivotal. The BPMA is committed to supporting businesses in their journey towards greater energy efficiency, offering not only the tools but also the expertise
needed to make a tangible impact.
Through the CPSA scheme, pump engineers are being trained to correctly assess the efficiency of pump systems, and to provide appropriate recommendations in order to improve the efficiency of those systems.
By adopting energy audits as standard practice, and by leveraging the deep expertise provided through the CPSA scheme, UK industry can unlock significant improvements in energy efficiency, reduce operational costs and contribute to a more sustainable future.
For more information on how to gain the skills and knowledge needed to conduct a full pumping system audit, please visit the dedicated website below.
bpma-cpsa.co.uk
With the UK dropping from 8th to 12th in the world for manufacturing output, robotics and automation have a way to go to improve this position. Oliver Selby, the new Chair of BARA, provides strategies for supporting automation adoption.
In my first piece for MEPCA as Chair, I should first say that I am delighted and honoured to have been elected by my peers for the post of Chairperson at the British Automation and Robotics Association (BARA). I have sat on the committee for the past three years as a general member representative and have seen quite a change occur in the way that the organisation is supported by the rebranded PPMA Group who are now Automate UK. I think the ambition of the three* trade organisations under the Automate UK banner is very exciting and really positive for the industry.
My ambition within the role is to strategically align and deliver value to the membership and all other stakeholders that the association supports. The new support structure put in place by Automate UK helps dramatically and we have already the big steps taken in the past 2 years with the delivery of Automation UK tradeshow that has gone from strength to strength and will again grow next year.
When we think about value that a trade organisation can deliver for its members, its sometimes difficult to appease everyone. We have large OEM’s as well as small SME’s, dealers & equipment suppliers, as well as education and Catapult engagement as members. With such a broad selection of those engaging with UK manufacturers in different ways, I hope we can unite those parties through the association and find some common value in the way we all work to increase the adoption of robotics and automation in UK manufacturing.
A common thread in conversations I have with my customers and Automate UK panel discussions is the fact that the UK falls some way behind our competition in Europe and globally for the number of robots adopted
into our manufacturing processes. Currently, we sit in the top 12 nations globally for manufacturing output, but down in 23rd for robotics density within manufacturing. There are many reasons for this disparity, but I hope to see that whilst we are behind the curve now, UK manufacturers will soon look to capitalise on the benefits automation and robotics will give them. Higher productivity, higher quality, and supporting challenges in the workforce are benefits that I am sure will drive the growth over the coming years.
I was recently asked what three factors support a higher rate of automation adoption, and I immediately looked to those that are already deploying best practice. I ended up with Ambition, Culture and Skills. The companies that are succeeding to implement automation here or elsewhere globally generally have one or more of these factors covered. Having the ambition to automate allows for growth and company development, it proliferates goodwill around investments within a firm. Inspiring a culture of continuous improvement and that automation of processes benefits all with a firm is paramount. A strong business rarely reduces headcount, as they expand and upskill loyal workers. Finally, they commit to education and skills across their internal stakeholders. From shop floor operators, to maintenance, engineering up to the leadership team, it’s important everyone understands automation and how it affects them and the business.
I hope that by strategically supporting our members, and becoming more visible to those manufacturers looking for the knowledge and best practice to improve their production, we can help. There are going to many ways we do that, and in future submissions to MEPCA I’ll look to outline those in more detail. Whether it be business case development, de-risking methods, workforce upskilling or finding a supplier, I’ll try and cover it!
www.automate-uk.com/ourassociations/bara/
*PPMA – Processing & Packaging Machineries Association, BARA – British Automation & Robotics Association, & UKIVA –UK Industrial Vision Association
By using an advanced control system at its Blaichach plant, Bosch has aligned production with rapid advances in the automotive industry. Bosch explains how the software’s open architecture supports its crucial manufacturing hub.
The industrial control system ctrlX CORE from Bosch Rexroth has proven to support the automated production of active driving safety products – at Bosch’s Blaichach site, all assembly cells as well as the Flexible Transport System (FTS) are equipped with it. Due to the open system architecture, ctrlX CORE enables seamless communication between stations, machines and the factory network, which allows more room for manoeuver and greater efficiency.
The Bosch Blaichach plant, located in Immenstadt and Blaichach, Germany, is a significant manufacturing hub for Bosch, specialising in advanced automotive technology. This site produces critical high-tech systems focused on enhancing
vehicle safety and supporting the transition to more sustainable forms of transportation, especially for electric vehicles. Key products include active driving safety systems such as Anti-lock Braking Systems (ABS) and Electronic Stability Programs (ESP), which help improve control and stability for drivers. Additionally, the plant manufactures brake boosters specifically designed for electric vehicles, which help in reducing braking distances while enhancing vehicle performance and efficiency. Bosch also produces sophisticated camera systems at this facility, used in Advanced Driverassistance Systems (ADAS) to enhance road safety through improved vision and object recognition.
With over 60 years of history, the Blaichach plant has grown into a
comprehensive site, integrating various technical and commercial operations. The facility is not only a manufacturing site but also a centre for research, training and development. Coordinating ABS and ESP production across eleven Bosch facilities globally, it serves as a model for best practices and process improvements in production, reinforcing the importance in driving forward Bosch’s automotive safety technology and innovations.
The automotive industry is undergoing a period of rapid and transformative change, driven by technological advances, evolving consumer demands, and the global shift toward sustainable and autonomous
mobility. The increasing adoption of Electric Vehicles (EVs), advancements in autonomous driving and stricter regulatory requirements for emissions and safety are putting pressure on automotive manufacturers to adapt quickly. This dynamic environment demands that production processes are not only efficient but also adaptable, scalable, and resilient. To stay competitive, manufacturers must be able to produce high-quality products at a fast pace, implement new technologies seamlessly, and ensure production continuity even as models and requirements evolve.
In this context, communication between machines, plants and systems becomes essential. This connectivity allows for real-time data exchange and decisionmaking across the entire production process, from supply chain and assembly lines to final quality checks. Effective machine-to-machine and system-tosystem communication enables seamless coordination of processes, optimised resource utilisation, and rapid response to any disruptions. For instance, if one station in the assembly line detects a fault, it can immediately communicate with the next station to halt production or reroute operations, preventing a cascade of inefficiencies and waste.
At Bosch Blaichach, these capabilities are vital, especially in the automated production of safety-critical automotive components such as chassis systems, active driving safety products, and personal safety equipment. To meet the demands of closely synchronised and precise manufacturing, Bosch relies on advanced industrial control systems that ensure smooth process control and operation of the FTS; this plays a key role in moving parts between stations with minimal delays, supporting just-in-time production while adapting to various product specifications.
These control systems and communication networks allow Bosch Blaichach to achieve tightly timed coordination across stations, enabling automated, flexible, and highly efficient production. They support predictive maintenance by monitoring equipment health and process performance, which reduces downtime and enhances Overall Equipment Efficiency (OEE). Through such sophisticated control and coordination, Bosch can consistently meet the high standards required in the production of critical automotive safety components, remaining agile and competitive in an industry that is constantly evolving.
Niels Wefers, Head of the Special Engineering department in Blaichach, explains: “In production, individual process stations are linked together to form one assembly line. Step-by-step, they produce, among other things, modules for brake controls for ABS and ESP safety systems in vehicles. The controls used for this purpose required adaptation because we needed better performance and a better ability to communicate.”
The long-standing cooperation already in place with Bosch Rexroth in the hardware area has been extended to include software options of the control system ctrlX CORE from the automation system ctrlX AUTOMATION. The control replaces an older generation of industrial PCs and uses modern technologies such as EtherCAT master, PLC licenses and Open Platform Communications Unified Architecture extensions.
“We were impressed by the open system architecture of ctrlX AUTOMATION, which is reflected in the ctrlX Data
Layer and in open interfaces. This opens numerous communication opportunities for connectivity. In addition, the solution measures up to our planned concept for data storage and data interfaces, for example regarding MES. Everything comes from a single source now, from sensors to the cloud,” says Niels Wefers.
With the use of ctrlX CORE, the plant in Blaichach takes advantage of the benefits of the operating system ctrlX OS and the ecosystem. While the previous industrial PCs were based on Windows 7, ctrlX CORE relies on Linux, meaning openness, extensibility and “secure by design”. The specially developed operating system ctrlX OS running on the control aims to achieve complete hardware independence.
“We’re impressed by the broad scope for action offered by ctrlX CORE with its associated app technology. This enables us to realise a wide range of applications, from simple process controls to highly automated assembly lines. So, we can always adapt the solution to our needs,” explains Niels Wefers.
The control system also increases the efficiency of the processes and offers greater scalability as well as cycle time advantages – in the ultra-short-term range, for example, by 10 percent. Cycle times of 1 second are also possible.
The significantly higher processing speed leads to greater availability of data and offers the ability to process more data. Overall, the control can be used consistently for the requirements of the future.
www.boschrexroth.com/en/gb
MEPCA examines growth strategies for 2025
P18: MEPCA prepares for 2025 with expert advice in finance, marketing and recruitment.
As the UK navigates its way through a challenging final quarter, MEPCA turns its attention to 2025 and considers how manufacturers can prepare for the coming year.
2024 has been rollercoaster ride for UK manufacturing. After a mixed performance at the start of the year, things picked up in Q2, but that momentum couldn’t be sustained throughout Q3, where output figures fell into the negative for the first time in 4 years*. While this is expected to improve in Q4, the sector is not predicted to fully recover until 2025.
The new Chancellor’s first Autumn Budget has provided some additional twists and turns. The cumulative effect of the raise to the National Living and Minimum Wages, the increases in Employer National Insurance contributions and changes to the related
thresholds, as well as the increased cost of apprenticeships, will cause a fiscal headache for many manufacturers.
More positively, however, the Government has shown a long-term commitment to growth for UK manufacturing in its Industrial Strategy, with a focus on investment stability,
and by showing its support of key initiatives, such as Made Smarter, as well as other measures to encourage innovation.
Despite the evident challenges, 2024 has seen numerous success stories in UK manufacturing, demonstrating that businesses remain confident, and, even
“Strong supply chains are also critical. Amid ongoing disruption, manufacturers that are diversifying suppliers and investing in local sourcing will mitigate risk and avoid any roadblocks to growth.”
– Dave Atkinson, UK Head of Manufacturing SME & Mid Corporates at Lloyds.
more importantly, that the resilience of the UK’s supply chain is starting to return post-Covid, even in the face of continued geopolitical unrest.
While still trying end in the best possible position this quarter, many manufacturers already have their sights set firmly on 2025, which is expected to see growth of 0.8%, according to Make UK’s Manufacturing Outlook Survey Q3.
To help companies prepare for optimising growth in 2025, we sought out expert advice on three key areas: finance, marketing and recruitment.
Making informed financial decisions will help safeguard growth in 2025 and ensure that companies benefit from the opportunities available to them. For advice on financial strategies, MEPCA turned to Dave Atkinson, UK Head of Manufacturing SME & Mid Corporates at Lloyds.
What financial strategies should UK manufacturers consider adopting to optimise growth in 2025?
David Atkinson: SME manufacturers are poised for growth. Recent reports from Make UK and the ONS are forecasting a positive 2025, with increased output and orders. To take advantage of opportunities and achieve sustainable growth, firms should have effective financial forecasting and cashflow management front of mind.
Regularly updated cashflow and profit forecasts allow for better strategic planning and informed decision-making when you are presented with growth opportunities, helps to ensure that your business has enough liquidity to meet its plans and avoid disruptions in production. Strong financial management also builds credibility with investors, lenders, and other stakeholders –all of whom can be critical to growth.
Getting this right can help manufacturers to invest in technologies that are driving growth across the sector, and to acquire, retain and cultivate the skill they need to implement them. Innovations like intelligent automation, robotics and AI are helping more firms to enhance productivity and reduce costs. Those at the forefront of adoption will be best placed for growth in the years ahead.
Strong supply chains are also critical. Amid ongoing disruption, manufacturers that are diversifying suppliers and investing in
local sourcing will mitigate risk and avoid any roadblocks to growth.
With the cost of doing business increasing, it is even more crucial that manufacturers reach their target audiences and ensure they are communicating clearly with their customers. MEPCA sought advice on how to approach marketing 2025 from industrial marketing specialist Sarah West of Full Fix Marketing.
Sarah West: It’s a great question, as 2025 looks like it could be quite an opportunity for UK manufacturers! With the UK and US elections behind us, growing consumer and business confidence may fuel manufacturing.
With fewer inflationary or supply chain pressures, successful marketing can once again focus on quality and capability – an area where UK manufacturers often outshine competitors.
With regards to which forms of marketing may be most effective next year, digital marketing will continue to play a key role. A business’s website is a likely stop-off point for anyone interested in what it delivers, so it
“With fewer inflationary or supply chain pressures, successful marketing can once again focus on quality and capability – an area where UK manufacturers often outshine competitors.”
– Sarah West, Full Mix Marketing.
has to create the right impression.
The growing importance of content marketing looks like it will continue in 2025, too, as customers look to businesses to demonstrate and prove their expertise through social media, articles and press coverage.
Direct marketing may remain a gamechanger for many manufacturers, particularly if competition continues to rise. If you know who you want to work with then going direct may be the quickest route to sales.
The growing skills shortage remains a major challenge for UK manufacturing that shows no sign of abating on entering 2025. Compounded by the increasing cost of hiring staff, it is ever more important that businesses place the right people in the right roles. To help manufacturers navigate their way through this challenging process, Russell Smith, Managing Director at Hunter Selection lends MEPCA his 30 years’ experience in the field.
What advice would you give UK manufacturers struggling to fill key positions?
Russell Smith: Firstly, you are not alone. The demand for skilled staff, whether that be Engineers or Manufacturing Professionals still outstrips supply. The rapid increase in salaries in some roles across the sector, noticeably in Maintenance and Automation
has made these areas very hard to recruit for. Thankfully, there are now signs of this cooling as inflation falls to more manageable levels and in turn wage expectations become more realistic.
As a hiring Manager, there are factors that you can control. When compiling your Job Specification, are you focused on the past or the future? Do soft skills and ‘trainability’ have as much value as experience and qualifications? Is your picture of the right candidate too narrow? Could you be more equitable and inclusive and attract a broader
pool of applicants that way?
Does the hiring manager know how to sell the organisation and the role, and what does the employee of 2024 expect? The vision, culture, values and flexibility of the employer business are becoming more and more important, above and beyond the salary and hours. The interviewee is picking their employer of choice, too.
It is important to move fast in a competitive employment arena. Taking too long to go through each phase of the recruitment process is a huge turn-off to
prospective employees and leaves you uncompetitive when good applicants will typically have 4 or 5 opportunities on the go at any one time. Ask yourself, can you make your recruitment processes quicker and more agile to get the competitive advantage?
Uncertainty can be worse than bad news for businesses. At least now, with the promise of post-election stability, the autumn budget delivered and the Government having laid out its intensions for UK manufacturing in its green paper (Invest 2035: The UK’s Modern Industrial Strategy), businesses are able plan
for the year ahead from a more informed position.
As demonstrated above, UK manufacturers also have a wealth of expert advice at their disposal, which will support them as they move into 2025.
* Make UK, Manufacturing Outlook 2024 Q3.
Often asked what the secret of successful marketing is for manufacturers, Sarah West of Full Mix Marketing, East Anglia’s leading B2B marketing agency, looks at why consistency is key.
One of the most common attributes of successful marketing campaigns is consistency!
The temptation is to attempt to be all things to all people by packing your marketing with every possible detail of what you deliver and frequently changing the focus. When increasing your marketing or targeting a new market, simply making others aware of what you do can be much more effective than bombarding customers with solutions to every challenge.
The more your potential customers see the same message, the more familiar they become and the greater trust they develop. Most marketing has just a split second to catch an audience’s attention, so a simple message is best.
The science of successful marketing is about making well-informed decisions and giving them the opportunity to deliver results.
If you’ve identified the right marketing methods and messages to reach your target customers, the additional ingredient needed is time.
Businesses respond slower than consumers and may only review their manufacturing relationships periodically.
Have faith and give your marketing adequate time to create success before altering the formula.
The greatest results typically come from a mix of marketing; customers don’t differentiate between different types of marketing, so seeing your brand in various locations soon helps drive sales. fullmixmarketing.co.uk
CRM tools can offer a solution to inherent inefficiencies in the manufacturing sales cycle by streamlining processes and enhancing collaboration, as SugarCRM explains.
Manufacturing sales cycles are typically complex, involving several stages, namely prospecting, lead generation, qualification, proposal, negotiation and closing. Many products are custom-made to meet each customer’s specific needs and requirements, which further prolongs these cycles, with tailored specifications requiring additional approvals and time to execute. Multiple stakeholders on both the client and manufacturer sides add further layers of complexity.
CRM (Customer Relationship Management) tools can simplify these processes by automating workflows, improving tracking and boosting communication, leading to more productive sales cycles and better customer experiences.
Modern CRM solutions like SugarCRM serve as digital assistants for sales teams, thanks to the integration of generative AI and predictive analytics. These technologies streamline the sales process by capturing and summarising critical customer information, making it easier for teams to track essential details across each stage of the sales cycle.
“CRM solutions, particularly those with advanced automation and AI capabilities, empower manufacturers to manage complex sales cycles effectively and deliver outstanding customer experiences,” explains John Maguire, General Manager for EMEA. “Manufacturers who harness these tools can offer a seamless service, anticipate customer needs, and ultimately gain a competitive edge.”
For manufacturers, CRM tools equipped with tracking and forecasting features are invaluable in managing long lead times. Predictive analytics helps companies forecast demand, plan production
schedules, and allocate resources efficiently. With this proactive approach, manufacturers can better identify potential bottlenecks and make adjustments before they impact timelines.
Use cases for CRM in manufacturing:
In manufacturing, customisation is often crucial to meeting specific client needs. CRM systems capture and integrate customer specifications, allowing relevant departments to access and act upon this information seamlessly. These systems also help with generating accurate quotes, encouraging collaboration, and reducing the potential for errors—ultimately leading to higher customer satisfaction.
Manufacturing sales cycles typically require multiple approvals from stakeholders, including sales managers, finance officers, engineers and executives. CRM tools simplify this process by automatically routing approval requests and centralising
all documentation. Not only does this streamline the approval process, but it also enhances transparency and accountability with a clear audit trail.
For manufacturing businesses, integrating CRM with ERP systems is essential. This integration enables seamless data flow across departments, giving sales teams real-time access to inventory data and other critical insights. With this information readily available, sales reps can avoid overpromising and ensure they meet delivery timelines.
In the intricate world of manufacturing, CRM tools like SugarCRM provide substantial advantages. By automating workflows, streamlining approvals and offering predictive insights, CRM solutions simplify the sales cycle and improve customer experiences. As John notes, “By investing in a robust CRM, manufacturers can stay competitive, proactive, and better equipped to meet their customers’ evolving needs.”
sugarcrm.com/manufacturing/
As detailed in Compass Business Finance’s insightful white paper, released September, Asset-Based Lending (ABL) can provide manufacturers with funding when they need it most.
Securing business funding can be notoriously challenging. This is especially so following a prolonged period of uncertainty impacted by a financial crisis, Brexit, a pandemic, a war in Europe, an energy crunch, rising inflation and elevated interest rates.
This doesn’t have to be prohibitive according to Compass Business Finance’s latest white paper on ABL. Unlocking Capital: Strategic Advantages of AssetBased Lending details how to leverage business assets for growth and stability.
Asset-based lending is comprised of a combination of two or more types of finance that together achieve the overall funding package required. The result is often access to significantly higher levels of working capital than conventional methods of funding. It is also especially useful for raising working capital for restructuring, acquisitions, management buyouts (MBOs), and management buy-ins (MBIs).
The white paper shares how assetbased lending is now supported by the British Business Bank through the Growth Guarantee Scheme (GGS). The ABL variant allows an increased percentage of loan to value (LTV) against key assets, combining the benefits of the existing term loan, revolving credit facility, invoice finance and
asset finance variants of the scheme.
The paper also demonstrates how ABL has been instrumental in the growth and success of a number of businesses. Below is one case study illustrating how a combination of a loan and asset finance was leveraged for growth.
Established in 2001, Browns Print Limited is a commercial B1, B2, B3 and digital printer, employing over 82 people, from its 30,000 sq. ft. freehold factory based in Greater Manchester.
The business was acquired by Tim Guest, Chairman, through his investment vehicle, Guest Investments Limited on the 1 October 2018. Tim’s other business interests include property and his business and equipment/ stationery business, Boss Direct Limited.
The Browns acquisition was a continuation of Tim’s investment strategy where he had to date acquired 5 previous businesses in the commercial print and related sectors. Before finding Browns, Tim Guest and David Bunker, Compass Director, had been discussing the need to find a suitable site when David introduced the idea of an M&A deal to acquire Browns Print Limited and floated the idea to both the seller, Andrew Brown, and Tim.
This quickly became an opportunity to acquire not only a good print business but a ‘one-site’ freehold factory with capacity for growth. The purchase price was agreed, and Tim used a mixture of private funds and an ABL facility including a loan and asset finance to refresh the plant in the factory. Following the acquisition, they set about introducing changes in the factory and bedding in the combined businesses. This investment enabled Browns to increase efficiencies and prepare for post-Covid revenues.
“Central to getting the most from an ABL facility is finding the right lender,” states David Bunker. “Since Compass’s inception in 2005, we’ve been coming alongside businesses as they select which finance product is right for them and accurately matching lenders and customers. As a lender ourselves and a broker to over 25 banks, we are able to put customers’ needs at the forefront of arranging an ABL facility. This white paper provides an overview of the funding options to choose from and some examples of how businesses have thrived after having identified their perfect mix. Compass Business Finance can be there from first contact to journey with you throughout the process.”
compassbusinessfinance.co.uk/ abl-paper
Manufacturing consultants Tim Grant (Business Solution Providers), David Altemir (Altemir Consulting), and Patrick Verryn (Move2Cloud) share common challenges experienced by small manufacturers.
A recurring challenge is managing and understanding BOMs, especially when dealing with products that have multiple variants, engineering changes, or complex assembly processes. This complexity can lead to errors and inefficiencies in production planning and inventory management.
“Many of our clients have gotten stuck when trying to create BOMs,” says Patrick Verryn.
“It is especially difficult to turn engineering BOMs into manufacturing BOMs, and transferring changes as the design evolves,” David Altemir adds.
Many small manufacturers struggle with keeping accurate inventory records. The consultants emphasize the need for transaction recording to manage inventory effectively. Without this, manufacturers face persistent issues with inventory discrepancies, which can lead to stockouts, overstocking, and increased operational costs.
“Not being able to keep accurate inventory is a common issue clients come to me with,” David Altemir states. “This always proves to be an operational issue within the company, most often a lack of transactional discipline.”
According to the consultants, small manufacturers have difficulty determining how much they can produce at any given time. This leads to customers being promised unrealistic lead times as production bottlenecks start to slow down processes. To mitigate this, manufacturers need solutions explicitly made to tackle these issues.
“Specialised software gives manufacturers an immediate understanding of what can be realistically accomplished within given timelines,” says Tim Grant. “Without it, small manufacturers will continue to struggle with their production and delivery schedules.”
Integrating various operational functions and eliminating data silos is essential for businesses that want to scale up efficiently. This integration, often involving several different applications, is crucial for improving efficiency and responsiveness in manufacturing operations. However, many small businesses are bogged down by legacy systems and bad data.
“Our clients know how to produce things; they are experts at that,” Tim Grant maintains. “But they also acknowledge their
lack of experience with software, especially when it comes to integrating multiple applications.”
Understanding your actual costs is critical for pricing products, finding financial sinkholes, and ensuring profitability. The process of actual costing calls for meticulous tracking of material lot prices, labour costs, and overheads. Maintaining such detailed records in spreadsheets, however, can soon become overwhelming.
“Often our customers don’t even realise that actual costing is possible,” David Altemir says. “That’s understandable because there aren’t many solutions available to small manufacturers that offer actual costing.”
Having completed hundreds of software consultation projects between them, Grant, Altemir, and Verryn have one thing in common: they all recommend manufacturing resource planning (MRP) software for overcoming common small manufacturing challenges. They also favour one solution in particular – MRPeasy.
mrpeasy.com
B Corp provides external accreditation for companies’ social and environmental achievements. Recruitment specialist Hunter Selection shares how it became part of the growing B Corp community.
The ever-growing focus on environmental, social and governance (ESG) issues has led many businesses to make net zero pledges and to sign up to diversity, equity and inclusion (DEI) initiatives.
B Corp not only gives businesses a global third-party validation of their ESG claims, but also enable them to strive for further positive change through a transparent commitment to evolve and improve. The principle behind B Corp is that organisations adopt a purpose driven approach to business and stakeholders that includes but is not limited to the profit needs of shareholders. Becoming a B Corp means that a business is meeting strictly verified
standards of performance, accountability and transparency, for everything from supply chain to treatment of workers, to its impact on the environment and the community.
There are currently over 9000 Certified B Corporations in more than 162 countries and over 100 industries worldwide with 3000 of these based in the UK. The latest Brand Awareness data shows that 1 in 4 consumers in the UK is now aware of B Corp and what it stands for and that the importance of this ethical purchase decisionmaking is most critical among younger consumers.
Hunter Selection, the manufacturing and engineering recruitment specialist, began its B Corp journey in early 2023, recognising that being a great company first and
foremost had always been the guiding vision, and that being a values-led business was engrained in the DNA of the organisation, but this proved hard to express or validate in a sector where everyone claims to be different.
In 2024, the company began the process of accreditation in earnest, supported by an excellent local consultancy in Bristol and nine months of collecting and collating evidence of performance in the five key areas of Governance, Workers, Community, Environment and Customers was underway. Corporations aiming for accreditation are required to demonstrate high standards in environment and social performance across these areas by achieving a score of at least 80 in B Lab’s B Impact Assessment
(BIA) and passing a rigorous risk review. Hunter scored a highly impressive 95 where organisations at large score 59 on average.
Russell Smith, founder & Managing Director, said, “Achieving B Corp certification is the culmination of 20 years of hard work, building a recruitment company that prioritises people, ethics, and sustainability. Being a great business to work for and a great business to work with. We’re proud to be part of a global community of businesses committed to making a positive impact.”
B Corp project lead and Director of Development Claire Torrington: “The process should not be taken lightly and is so far removed from the tick box exercise that some expect. The process is comprehensive and exhaustive, examining every aspect of our business operations and ethos. Only with the complete commitment of the leadership team to be better could we hope to be successful.
“B Corp hasn’t changed the direction our business was taking but it has validated so much of the good work we were doing and empowered us to strive to do more. The commitment to provide an annual impact assessment and to re-certify again in 3 years means we have the platform to showcase our journey and that no-one can take their eye off of the ball now,” she added.
Looking at some of the more challenging aspects of accreditation Russell Smith touched on the area of sensitive industries; those perceived to be at odds with values of a B Corporation.
While B Lab does not stipulate which industries or activities a B Corp can operate or engage in, applicants are required to ‘confidentially disclose potentially sensitive’ sectors and practices with which they are involved (such as the alcohol, firearms, tobacco, fossil fuels). However, as Smith explained: “Working with clients which operate within these disclosure areas is not an insurmountable obstacle and that transparency and the ambition to have a positive impact on these industries is key. We have always selected our clients carefully and by introducing best practise for equity, diversity and inclusion in the recruitment process for example we aim to keep adding value and moving all client employers in the right direction.”
Here are some questions to ask yourself before starting the journey:
• Are you ready to make lasting changes that positively impact your people, clients, and the environment?
• Does your business already meet some of the B Corp standards – and can you work towards the rest?
• Are you prepared for rigorous assessment and accountability?
If the answer is yes, then B Corp is more than just a certification – it’s a commitment to progress. It will push you to think about your long-term impact and build a business that’s truly sustainable.
Being a Purpose led business is not only a noble ambition but also makes great business sense too. Working with a recruitment supplier committed to the highest standards has to be attractive, whilst it gives employers the edge in a competitive labour market especially when culture, sustainability and respect consistently rate highest amongst the factors that determine where young people decide to ply their trades and build their careers.
Becoming a Certified B Corp has been one of the most rewarding challenges the company have faced. It’s made Hunter a stronger, more ethical business, excited about the future. If you’re thinking of starting your own B Corp journey, don’t be afraid to reach out to others who’ve done it. The B Corp community is full of supportive businesses willing to share their experiences.
Remember: Certification is just the beginning. It’s a commitment to ongoing improvement and a chance to be part of something bigger – a global movement of businesses that use their success to create positive change.
Find out more about the Hunter Selection B Corp journey by visiting the company’s website.
hunterselection.co.uk/b-corpcertification
Carl Eely, Product Manager of Industrial Automation, ABB, explains how modern Programmable Logic Controllers (PLCs) can help analyse and make sense of the vast amounts of data generated by modern plants, and use it to drive optimisation.
We’re frequently told that data is the key to unlocking a new era of productivity and energy efficiency. However, data itself is of little value unless you actually use it for something.
Manufacturers – including ABB – will often tell you that data will help to drive unprecedented gains in productivity, efficiency, reliability and safety. While this is absolutely true, for many plants, it’s also easier said than done, particularly in older plants that are some way behind the modernisation curve. Sensors fitted to devices, machines and processes generate constant streams of data; the difficulty is in making sense of all this data, and joining the dots between discrete systems to not only identify new energy saving opportunities across the plant, but to put them in context.
Advances in sensor and monitoring technology have allowed unprecedented insight into the condition of machines and processes either on an individual level, or for fleets of similar devices, but stitching the vast amounts of data generated into a seamless and cohesive whole has typically been a challenge. This is due in part to compatibility issues, the diversity of devices
and processes, and the sheer complexity of today’s sophisticated automation systems.
However, modern PLCs have some new tricks up their sleeve to help bridge the gap between operational data and enterprise planning, bringing in all data from every asset in real-time via the PLC. Once the data is aggregated, it is then turned into genuinely valuable information to inform decisionmaking, and help to optimise systems and processes.
ABB’s Ability™ zenon software is a SCADA platform that sits above the rest of the automation architecture. It takes data from all the various drives, motors, PLCs and every other data-generating device across the plant. What is innovative about this is the way it can bring everything together in one place, enabling better supervision, storage, control, data acquisition, scheduling and performance reporting. It helps to close the loop between automation and electrification by consolidating all data in one place, while facilitating remote condition monitoring, as well as remote access and troubleshooting to solve issues quickly and easily.
With more than 300 communication protocols and drivers, it is compatible with almost every type of electrical device. As well as measuring critical processes,
it also combines these inputs with data on water flow, electricity usage, heating and more, from all over the plant. It also connects greenfield and brownfield technology, regardless of vendor, and turns it into actionable insight across machines, infrastructure and production assets, in real-time.
This helps provide a more holistic view of plant operations, providing greater context for decision-making, and allowing energy saving opportunities to be identified in areas that previously would require discrete tools or device-specific software. Crucially, it requires no re-engineering of existing devices or processes, as it feeds off any data that can be transmitted from devices and combines it with additional data stored in the cloud.
ABB Ability™ zenon is an example of a trend of increased openness and compatibility in PLC and automation systems. Essentially, it can connect all of a manufacturers technology, regardless of vendor, and turn it into actionable insight across machines, infrastructure and production assets, in real-time. More information is available on the company’s website.
global.abb/group/en
Photoionisation detectors (PIDs) are commonly used to monitor hazardous compounds during remediation works, but as Rockall Safety explains, PIDs have a diverse range of applications.
PIDs are continuous, broad-spectrum monitors capable of detecting most volatile organic compounds (VOCs), ranging from simple compounds like methylene chloride (CH2Cl2) to complex ones, such as diesel fuel. Environmental contractors and consultants frequently use these devices to monitor the remediation of industrial waste sites and decommissioned military bases.
The detection ranges of these devices vary. For example, the MiniRAE 3000+ offers detection in the range of 0.1 to 15,000 ppm, while the ppbRAE 3000+ measures from below 1 ppb to 10,000 ppm, and fixed RAEGuard PIDs have a detection range of 0.01 to 100 ppm, 0.1 to 1000 ppm, or 1 to 1000 ppm.
0.1 to 15,000 ppm range PIDs are ideal for detecting BTEX compounds (benzene, toluene, ethyl benzene, xylene) and Total Petroleum Hydrocarbons (TPH) found in gasoline, diesel, and jet fuel. This makes it an excellent tool for headspace analysis to identify soil contamination from leaking underground storage tanks. Environmental engineers and professionals in the petroleum industry can deploy this instrument to monitor contamination at gas stations, industrial sites, commercial transportation refuelling areas, and defence facilities.
Environmental engineers and consultants often use these larger range PIDs for monitoring soil contamination at industrial real estate sites and former military bases.
These devices help determine whether soil contains VOCs, providing critical information before the sale of land. Conducting due diligence and environmental impact assessments ensures that land can be safely rezoned for homes, shops, or parks.
0.01 to 100 ppm range, fixed photoionisation detectors are commonly used at remediation sites to monitor effluent levels and assess the efficiency of treatments such as soil vapor extraction, incineration, and bioremediation. The RAEGuard PIDs, for example, provide 4-20 mA outputs for continuous data recording and feature two dry contacts for process control if concentrations exceed alarm thresholds. The MiniRAE 3000+, which can run continuously and stores up to 15,000 datalogging points, is suited for monitoring treatment effluent levels.
Leading PIDs are highly effective for determining VOC levels in drinking water. Hydrologists and environmental engineers use it to monitor chlorinated solvents (e.g., carbon tetrachloride) and VOCs (e.g., toluene) in groundwater at drilling sites, closed industrial plants, military bases, and nuclear facilities.
Headspace analysis can help determine contamination levels in soil or water. Samples are collected in jars, which are partially filled and sealed with aluminium foil and a lid ring. After the contents reach room temperature, PIDs can be used to measure VOC concentration by inserting the probe through the foil to assess contamination levels.
For hazardous waste monitoring, PIDs assist contractors, engineers, and industrial hygienists in detecting toxic vapours and VOCs. PIDs are particularly useful for identifying hazardous areas at old disposal sites, disused industrial plants, and former military bases, as well as during the transport of hazardous waste. They also help determine the appropriate personal protective equipment (PPE), such as SelfContained Breathing Apparatus (SCBA), required for worker safety.
Photoionisation Detectors (PIDs), such as the MiniRAE 3000+, UltraRAE 3000+, and RAEGuard models provided by Rockall Safety, play a vital role in environmental applications by detecting volatile organic compounds (VOCs) in a wide range of settings. Whether it’s identifying underground storage leaks, performing headspace screening for water and soil contamination, or ensuring safety at hazardous waste sites, PIDs offer a robust solution for environmental monitoring, ensuring accurate, continuous detection and reliable data for process control and safety assessments. rockallsafety.co.uk
Flexible, modular range of high efficiency, robust gearboxes with output torques up to 250kNm.
Available on short delivery times, same
Dust zone 21 cat 2D and zone 22 cat 3D
Gas zone 1 cat 2G and zone 2 cat 3G
IEC Ex, EAC Ex, CCC Ex, UKEX and specifications for North American market
In the second of the two-part turbine series, Titan Enterprises shares the five critical design features for Pelton wheel turbine flowmeters.
The design challenge for turbine flowmeters based on the working principles of this type of radial turbine is primarily straightforward: simple electronics versus complex precision engineering.
In developing a cost-efficient and reliable Pelton wheel turbine flowmeter, Titan Enterprises considers five critical design elements:
1. Excellent linearity and repeatability
2. Long operational life
3. In-line meter connections
4. Good chemical resistance of materials
5. Ease of manufacture
Good linearity and excellent repeatability are essential in any turbine flowmeter. One of the more subtle critical design areas is that of the radial clearance of the turbine in the housing. If the radial clearance is too small, there is a constant drag with the chamber wall that causes problems with linearity and changes in fluid properties. Too large a clearance and the chamber volume becomes unacceptable and the entrainment of gasses becomes problematic; the same is true with the side clearances. Fortunately, there are a series of solutions to turbine drag as the chamber velocities start to become laminar.
Titan use a hexagonal chamber that permits the formation of vortices, which reduces the drag and assists the linearity into the laminar flow region. Other turbine designs use square chambers or square chambers with posts in the four corners, effectively generating the space for eight vortices.
With known fluid properties and careful calibration techniques, variations affecting linearity and repeatability can be ‘calibrated
out’. Designing-out some of these issues to give good flowmeter performance prevents the resulting solution from becoming overly expensive.
Linearity and repeatability are also linked to the design of the bearings. Here, special care must be taken in both bearing design
and choice of materials to ensure long, reliable operational life. The most common fluids used in these devices are waterbased, but the poor lubricating properties of water increases the wear on many bearing materials, making them unsuitable for long-term use. Add to that the requirement of aggressive chemicals, and the bearing material options are further reduced. With low flow rates and the energy available from the fluid minimal, the bearings must also be of low friction and able to maintain the original level of friction for the operational life of the meter. For a domestic coffee machine for example, this may only be four hundred hours of use, so a simple metal spindle in plastic housing would be sufficient. Whereas the operational life of flowmeters used in medical equipment is more likely to be 4 years plus, so a more durable bearing material like sapphire or ruby would be more suitable.
The loads on the bearings can be quite high so there is a trade-off to consider between bearing life, low friction and the meter’s lifespan. A ball and cup bearing would give low friction and excellent low-end performance when new, but the wear on the extremely small contact area would soon result in turbine precession affecting linearity and repeatability.
Titan utilise a sapphire spindle and bearing arrangement, and together with their recommended installation, this ensures the flow devices continue to operate within specification for years.
With a rotating turbine, the lower density gasses tend move towards the spindle and can stay there under certain conditions, affecting the meter linearity and life of the bearings. One solution is to extract the fluid axially on the centre line of the turbine’s rotation, leaving the inlet and outlet connections at 90° to each other. This 90-degree inlet to outlet orientation is not always acceptable and can cause problems for installation. However, this can be solved with a complicated housing but this will result in a retained fluid volume increase, as well as compromising the bearing arrangement.
Some flowmeter manufacturers run the incoming stream at an angle so that it wraps its way around a wider than normal blade and exits at a corresponding angle to the inlet jet, one whole revolution later. Two hundred and seventy degrees of
wrap-around is also quite common but this tends to leave the inlet and outlet on the same ‘face’ of the device or requires the incorporation of a manifold system.
Titan chose the in-line radial design, i.e., the inlet and outlet are opposite each other, for 3 key reasons:
• Ease of installation for the customer
• Lower manufacturing costs which result in a cost-effective meter
• To minimise the pressure drop within the customer’s piping system
The turbine itself seems like a simple element, but it must also be carefully considered. Low mass is important, so a polymer is often used in turbine manufacture, and occasionally the turbine’s density is matched to the fluid to fractionally reduce bearing load at start-up. A potential issue here is that the turbine’s rotation must be detected somehow. Optical detection does not allow for mass increase to the turbine, but liquid measurement is restricted to optically clear fluids and any build-up of deposits on the optical path can stop detection.
Some manufacturers use curved or tapered blades on the turbine. If magnetic or inductive detection is required, a suitable magnetic material insert is necessary, and this should be over-moulded to protect it from aggressive chemicals.
Titan produce the majority of their turbine devices in NSF-approved PVDF (suitable for food and medical applications), and overmould the magnets to ensure long-life in the most corrosive chemical environments.
To ensure ease of manufacture, the design should integrate the latest innovations in moulding and machining technologies, accommodating various flow ranges and simplifying production. From the outset, components should be designed for easy interchangeability and made from highgrade materials to enhance durability and streamline assembly. This approach not only optimises manufacturing efficiency but also ensures consistent quality and performance.
To conclude, a Pelton wheel turbine is not just the simple paddle in a chamber; it is the perfect device for cost effective low-flow measurement, and the choice available is extremely wide, from the $1 meter for your coffee machine, through to a device costing tens of thousands for demanding industrial use.
As with all flowmeters, it is essential to ensure you are choosing the correct sensor for your application. When specifying a flowmeter, Titan Enterprises recommends the following considerations:
• Is the flow range, pressure, temperature and chemical resistance acceptable for your application?
• Is the flowmeter cost-effective over the lifetime of the installation?
• Does it have the performance required for the application and will it maintain that performance over the operational window?
• Are the suppliers/manufacturers knowledgeable in their technical capabilities and honest in their specifications?
Visit Titan Enterprises’ website for full technical information on Titan’s turbine flowmeters.
flowmeters.co.uk
Elevator encoders have a profound impact on elevator performance and reliability, but what exactly are encoders and why are they so important?
Elevator encoders are sophisticated devices integrated into elevator systems, providing precise controls and monitoring. These powerful components convert mechanical motion into digital signals, enabling elevators to achieve accurate floor alignment, controlled speed, and safe door operations. Encoders are vital for ensuring smooth operation in various elevator functions, particularly in motor control, door control, and positioning systems. Here’s a closer look at how they work in each of these areas.
In elevator motor control, encoders provide essential feedback about the position, speed, and direction of the elevator car. Encoders are typically installed on the elevator motor or drive system, allowing them to accurately determine the car’s position within the shaft. This is crucial for achieving precise floor levelling, ensuring safe entry and exit for passengers.
Encoders also monitor the motor’s rotational speed, which contributes to smooth acceleration and deceleration during travel between floors. This helps create a comfortable ride experience. Additionally, they provide feedback on the motor shaft’s rotation, enabling the control system to accurately determine the elevator’s direction.
Furthermore, encoders offer real-time data on the motor’s performance, facilitating proactive maintenance and troubleshooting. This minimises downtime and enhances the overall reliability of the elevator system.
Encoders play a significant role in elevator door control, ensuring their smooth and safe operation. They provide precise feedback on the position of the doors, which allows the control system to determine their exact opening and closing positions.
By regulating the speed of the doors,
encoders help ensure they operate efficiently, reducing the risk of sudden movements that could startle passengers. They also assist in controlling the acceleration and deceleration of the doors, making sure they start and stop gradually. This helps reduce wear on the door mechanism over time.
Safety features are another critical aspect of encoders in door control. They can detect obstructions or resistance in the door’s path, prompting the system to stop or reverse the doors to prevent accidents. Additionally, encoders ensure that the doors remain securely closed while the elevator is in motion.
Real-time performance data from encoders also aids in proactive maintenance and troubleshooting, which further optimises system reliability and minimises downtime.
In the context of shaft positioning, encoders ensure precise alignment of the elevator car with each floor. Typically mounted on the elevator motor or directly on the car, they measure the rotation of the motor shaft or the car’s movement within the shaft. These devices provide crucial feedback on the rotational position of the motor shaft or the linear position of the car, allowing the control system to accurately determine the elevator’s location. As the elevator approaches a floor, this feedback is used to
fine- tune the motor’s speed and direction, ensuring the car stops at the correct level.
If the encoder feedback indicates any deviation from the desired position, the control system can quickly adjust to ensure perfect alignment with the floor before the doors open. Encoders also play a key role in safety by continuously monitoring the elevator’s position, allowing for the activation of emergency brakes if necessary.
During installation and maintenance, encoders are essential for calibrating the elevator’s position, ensuring accurate floorlevel control.
In summary, encoders are fundamental components in elevator systems, enhancing functionality, safety and reliability across various operations. Their precise feedback mechanisms enable smooth journeys for passengers while ensuring the efficient and safe operation of the elevator.
encoder.co.uk
Total Cost of Ownership (TCO) is an economical method for the calculation and consideration of all costs incurred along the entire life cycle of investment goods. In a new white paper, NORD navigates the complexities of optimising TCO.
The term TCO was popularised in 1987 by the US consulting firm Gartner Inc., which highlighted the economic efficiency of IT investments with a self-developed model. In addition to the initial purchase price, it includes all ongoing costs associated with the operation and recycling or disposal. However, the concept behind it dates back even further. As early as 1927/1928, there is evidence for the first approaches and strategies that no longer made the initial purchase price the only purchase criterion for investment decisions.
The goal of a TCO analysis is to obtain an overview of all aspects of cost for the use of a product. A TCO analysis is an important tool for investment decisions and profitability calculations, as it reveals cost drivers in advance, uncovers hidden costs and shows savings potential.
The focus is increasingly on the followon costs, e.g., for electricity consumption, administrative processes, service and maintenance, spare parts stocking or the disposal. After all, they account for around 80 to 85 percent of the Total Costs of Ownership of drive systems. Why look at drive systems or technology? It’s simple: industrial electric motors account for more than 67% of all electrical usage in industry today. Thus, by introducing the latest technology with vastly improved efficiency levels, it has the potential to make significant savings on cost of running.
The two major factors to reduce the TCO are energy consumption and the number of drive versions used. However, there is a conflict of objectives between the approaches of
energy efficiency optimisation and version reduction. Planning a system with drives that are designed for the most energyefficient operating point leads to optimal investment costs and motors operating comparatively energy-efficiently, independent of their efficiency class. In return, many drive versions must be managed and serviced during the system’s entire life cycle.
While a drive concept mainly focusing on saving energy costs leads to a large number of versions, a version reduction has exactly the opposite goal, namely to provide the required torques and speeds in a system with as few different drive versions as is economically feasible. Thus, costs for administration, service and warehousing can be reduced, but the energy costs usually increase.
The major skill required here is to optimally bring in line the two conflicting areas “energy-efficient operation” and “minimum of drive versions” in the drive design. Achieving both is possible. Customised advice on individual version reduction can help to reach a system’s optimum without driving up the stocks.
The challenges of optimally planning the drive technology for a conveyor system are diverse. Conveyor belts in airports, warehouses and parcel centres are often designed for the expected maximum load and with corresponding safety factors. This often results in drives which are too large. However, in
real operation, such systems reach the maximum load only with a small proportion of the conveyed items. As a result of such designs, the drives only operate in the partial load range for most of the time.
With the introduction of new drive technology with increased efficiency levels it brings exciting new opportunities to really reduce TCO, NORD has been committed to introducing energy efficient drive systems since it was formed in 1965, having recently released motors that meet IE8 efficiency levels whereas currently minimum standards are IE3 and IE4. For more information on TCO and available technologies NORD have produced a white paper, which can be downloaded from its website.
nord.com
In a global first, Tom Parker Ltd, an authorised distributor of CEJN products for over 50 years, is thrilled to introduce the new 208 Detect range of FDA-approved blow guns.
The ground breaking Detect compressed air blow gun product range, a global first in the food and beverage industry, is poised to transform food production safety. These metal and X-ray detectable compressed air blow guns will reduce the risk of accidental contamination, product rejection and expensive recalls.
One of the most significant risks faced in the food and beverage industry is physical foreign body contamination, particularly from unwanted metal and plastic fragments. To address this issue and safeguard product integrity, CEJN has engineered an innovative, patented solution. The 208 Detect compressed air blow gun is the first metal and X-ray-detectable plastic blow gun available globally. It is manufactured entirely of food-grade plastic and materials, and all components are detectable, helping to dramatically minimise the risk of product contamination and waste in production.
The 208 Detect blow gun is engineered to provide comprehensive protection. Even if it is damaged, metal detectors and X-ray inspection systems can detect fragments as small as 2x2 mm (dependent on the system and sensor calibration). This next-generation product range also complies with many international food regulations, including HACCP, IFS, BRC, and GFSI standards like FSSC 22000.
The CEJN 208 Detect blow gun features
stainless steel AISI 303 (1.4305) valves that resist corrosion, high temperatures, and chemicals, including those commonly used in industrial cleaning and disinfection products typically used in food processing and manufacturing plants.
The 208 Detect blow gun has detectability features and shares the impressive qualities of the standard CEJN 208 blow gun. These include a high blowing force, precise flow control and a lightweight, ergonomic design for comfortable use. Its technical specifications ensure optimal performance and safety in food and beverage manufacturing. These specifications are a maximum working pressure of 232 psi, a minimum burst pressure of 928 psi, a temperature range of -20°C to +60°C, a flow capacity measured at 87 psi inlet pressure, and a pressure drop of 7 psi.
The CEJN 208 Detect blow gun is just one of over 30,000 products in Tom Parker Ltd’s 2024–25 product catalogue. With over 50 years of experience as an authorised distributor of CEJN products, Tom Parker
Ltd is one of the UK’s leading pneumatic, hydraulic, industrial and process product suppliers, including a wide range of product solutions suitable for food, beverage and drinking water applications. Their fully stocked warehouses enable sameday despatch of most stock items upon request, demonstrating their unparalleled commitment to customer satisfaction and efficient service.
tom-parker.co.uk
The EWO series is CEMBRE’s innovative family of split cable entry systems, marking a global leap forward in quality for this product category.
Thanks to the work and study of its technical team, CEMBRE has been able to design a new generation of cable entry systems. They are characterised by an ergonomic split frame, equipped with an over-moulded seal and compatible with grommets with a high degree of protection against the ingress of solid foreign bodies and the penetration of water.
Thanks to their compact design, they are slim and space saving. The absence of an outer seal makes EWO cable entry systems the ideal choice for countless applications, especially those in the field of industrial automation. CEMBRE cable entry systems are available in square, rectangular and circular shapes to meet all installation requirements and allow them to manage, easily and with precision, the passage of cables on switchboards, panels and machines.
Thanks to the efficiency and widespread coverage of the CEMBRE distribution network, EWO cable entry systems are the ideal solution because they are easily and quickly available to anyone, anytime, anywhere.
The frame of the EWO cable entry system is made of glass-fibre-reinforced PA6.6. With its slim and compact design, it is equipped with an innovative over-moulded seal, which allows EWO to achieve a high level of IP66 protection without the need for an external seal. The CEMBRE cable entry systems prove to be a versatile and practical product, suitable for every operational requirement.
The EWO cable entry systems can also be equipped with an additional external seal, which is suitable for supporting the fastening of the frame on particularly rough surfaces and those damaged by irregular drill holes, thereby guaranteeing maximum tightness and protection against weathering.
The stop plinth technology, which characterises the frame structure, protects the over-moulded seal from any risk of compression, ensuring effective IP66 protection at all times.
The demountable frame structure of the EWO cable entry system ensures great freedom and versatility in every wiring operation. Through the opening side of the frame, conveniently, it is possible to insert the protective grommets, modulating and configuring them according to the various installation requirements.
Designed to be as functional and versatile as possible, the EWO cable entry system can be conveniently fixed using galvanised stainless-steel screws, deep-drawn holes or rivets. The anti-fall system allows cable entry systems of the EWO series to be secured quickly and easily, even if the installed frame is pointing downwards. The accessory fitting of a Snap-on bracket increases the installation options of the EWO cable entry systems, satisfying every configuration requirement.
The EWO cable entry systems are equipped with the modern Plug&Fix system, which reduces wiring time and simplifies the entire installation process. The demountable side of the frame can be opened and closed easily by means of the convenient galvanised stainless-steel screws, implemented with an anti-fall system. This allows the grommets to be positioned and cables to be inserted at
any time with great ease.
EWO cable entry systems are tested to certify a high level of safety and complete IP66 protection against dirt and water. The innovative CEMBRE-designed over-moulded seal no longer requires the installation of a traditional external seal, thereby considerably reducing space requirements and installation time.
Because of the double side shaping of their design, the EWO grommets adhere perfectly to the frame, positioning themselves inside it without ever protruding, ensuring full IP66 protection against dirt and water and an effective cable seal in accordance with EN 62444.
EWO cable entry systems meet all installation requirements with versatility because of the wide variety of grommets, designed to create as many combinations as possible and adapt to every configuration need. EWO cable entry systems are designed to reduce installation time and costs.
Not only that, the revolutionary interchangeable faces of the EWO grommets have been specifically developed by the CEMBRE technical team to allow the grommets to be positioned without having to worry about the direction of installation, thereby offering a valuable and unique advantage in terms of time and convenience.
cembre.com
Cutting-edge component carriers have surpassed the capabilities of flexible printed circuit boards (PCB). MEPCA looks at how the construction of this technology is key to its advantage.
PCBs made of thin polyimide films have become established components in many products thanks to their adaptability. However, assembling and mechanically fixing these circuit boards is highly complex, so HARTING has developed a new component carrier solution based on 3D Mechatronic Integrated Devices (MID) technology, which simplify installation and deliver cost savings of up to 66%.
By employing this new HARTING development, electronic components can be fitted directly onto the component carrier, thereby replacing flexible circuit boards. The component carrier serves as a connecting element between the PCB and electronic components such as LEDs, ICs, photodiodes and sensors.
Component carriers are constructed using a process called Laser Direct Structuring (LDS), which applies electronic conductor paths directly onto plastic parts. The base body is manufactured using an injection moulding process and additives in the material are ‘activated’ by the laser, allowing the plastic material to accommodate the electrical conductor paths. It can then be assembled in a standard surface mount processes, like a conventional PCB, or soldered in a reflow oven.
As a result, electronic assemblies can be made in flexible, complex geometric designs and products such as smart phones, hearing aids and smart watches can become smaller and more powerful. LDS also enables the production of 3D-MID assemblies, meaning electronic components can be fitted directly onto a three-dimensional base body without the need for circuit boards or connecting cables.
Component carrier technology is suitable for various applications. It can be equipped with several sensors to take measurements
in three axes, and parts can be fitted simultaneously on two parallel surfaces as well as on the end face. As it is an extremely stable and reliable process, it has become established in quality-critical sectors, such as the production of safety-relevant components for the automotive industry.
Another recent application for LDS is security covers for payment terminals. The 3D-MID covers protect the internal components from unauthorised mechanical and electronic access, increasing the security of transactions and preventing theft.
However, it is within the field of medical technology that the latest advancements have taken place. MID technology allows designers to create devices with an even wider range of electronic functions that fit in the smallest of spaces. Mechatronics allows for the extreme downsizing or miniaturising of medical applications, enabling examination, sensing and monitoring from within the patient.
With such technology, medical devices can be designed to be much less invasive, leading to a significant improvement in patient care. Taking large medical machines and devices and putting them into a more compact package is a big part of what
MID brings to the table. It offers significant improvements by changing how medical devices are used.
One of the most important benefits of this technology is that it makes these advances possible without sacrificing quality. As 3D-MID continues to grow in popularity, it will open up new options for smaller and more effective medical devices, from hearing aids and implants to surgical and dental instruments.
Miniaturisation is one trend in healthcare that will dictate how mechatronics technology is used. The development of ever-smaller instruments, devices, and equipment enables less invasive treatment methods, allowing faster recovery times and much-improved patient care.
These micro actuators and miniature sensors also propel the development of small mechatronics systems for applications, including handheld diagnostics for use at the point of care, including ultrasound and blood testing, implantable devices that can be dynamically adjusted in-place, micropumps and auto-injectors for drug delivery products, and mobile miniature robots.
3d-circuits.com/en/
The Ecodesign Regulations had a decisive impact on the design of ventilation equipment. With a stricter iteration of the regulations now in place, Novenco Building & Industry, an expert in energy efficient ventilation, illustrates the benefits of using Axial flow fans over their plug counterparts.
On January 1st 2018, the Ecodesign Regulation 1253/2014 for AHUs (Air Handling Units) came into full force, affecting the design of AHUs ever since. The focus of the regulation was the reduction of energy in AHU optimisation. This applies in particular to non-residential systems with large air volumes.
In recent years, heat recovery has become very popular in solutions for energy saving and, with the tightening of regulations having a significant effect, much has been invested in this sector to further increase the efficiency. However, the range of fans that consume up to 60% of the electrical consumption of an AHU system remain unnoticed.
Just as the strengthening of the Ecodesign Regulation regarding the limitation of the power consumption (SFPlimit values) has changed the design of current AHU products, the Ecodesign Regulation 2024/1781 published in June of this year, replacing the prior regulations and ushering in far stricter sustainability obligations covering the entire lifespan of a product, will affect all future AHU concepts.
In cooperation with AHU producer Trubel Luft- und Klimatechnik GmbH, Novenco has conducted a comparative performance test in the TÜV Süd Test Laboratory. TÜV Süd is recognised as the world’s leading company for product certifications and approval tests.
The comparative test was a demand from one of Germany’s largest manufacturers of vehicles.
Both tests were conducted with identical
different fans: a premium plug fan from an unspecified fan manufacturer, and the ZerAx® axial flow fan from Novenco.
A framework of corresponding test series gave some very convincing results, where the ZerAx® fan was the unquestionable winner.
After a long test series, the results were clear: energy saving of 20%, 3 dB lower sound levels for the fan section and the complete AHU length more than 30% shorter than the comparative system with the plug fan.
Although the ZerAx® fan technology is a more expensive alternative, the ROI
expected 12-18 months. The answer to the comparatively big difference between the two solutions is in the way the ZerAx® fans integrate in the AHU and operate. The ZerAx® fans fit in very compact fan sections that transport the air to the duct with minimum loss. Although the plug fans also create high pressure, they do so after the airflow is slowed considerably. Hence, a lot of energy is lost and more is required to recreate and raise the pressure. The loss in the ZerAx® diffuser is at a minimum, as it delivers a much less turbulent airflow. Add to this the market-leading ZerAx® fan efficiency and the investment is a sound choice for years to come.
novenco-building.com
Rather than offering an alternative, 3D printing can be the optimal way of producing precision components for collaborative robots, as demonstrated in the following case study from Markforged.
Harvestance, a design and engineering services company, specialises in additive manufacturing. They provide 3D printing design solutions (DfAM) and services across various industries, including automotive, semiconductors, footwear and food tech. Harvestance received numerous inquiries for the design and manufacture of customised, lightweight and strong grippers for collaborative robots, aimed at automating production lines.
Traditional aluminum grippers, often heavy, limit the weight of workpieces that can be lifted and consume more energy. Harvestance’s customers, including collaborative robot users and robot system integrators, expressed several pain points:
• Collaborative robots are typically limited to small payloads of 20kg. Conventional aluminum grippers made by CNC machining usually weigh 1 to 2 kg or more limiting the weight of the work it can handle.
• Job site conditions vary, requiring customised grippers. However, the complexity of geometries and conditions makes customisation challenge for traditional manufacturing.
• Pneumatic grippers with multiple suction cups require numerous vacuum tubes, potentially causing interference with robot movement.
• Designing custom grippers for each set of usage conditions posed a challenge in maintaining price competitiveness.
“We were convinced that 3D printing could fully address these pain points. We chose Markforged composite 3D printing technology to reduce the gripper’s weight while improving its strength and stiffness, optimising performance,” explains Harvestance CEO Seungjae Leem.
Harvestance focused first on lightweight design, integrating vacuum channels from the compressed air source to the suction cups directly into the gripper body, enabling one-touch fitting without external tubes. They adopted various design methodologies to enhance the quality and efficiency of 3D printed parts, such as redesigning to minimise surface roughness and creating self-supporting internal vacuum channels. This approach improved quality and reduced time and costs.
Part material is critical for factory production tools like grippers. Mr. Leem and his engineering team tested various printers and materials including Fused Filament Fabrication (FFF), Stereolithography (SLA), Selective Laser Sintering (SLS), and Powder Bed Fusion (PBF). Only Markforged, with Onyx and Carbon Fiber Reinforcement, could meet the flexural and impact strength these parts required for certification.
Another Markforged advantage is superior surface quality. All of the other 3D printers Harvestance evaluated required post processing steps, such as melting away support structures, depowdering, washing and curing, or polishing, whereas Markforged printed parts come off the print
bed ready to use, without any delay or extra labour cost for post processing.
Harvestance turns to the Markforged FX20 when they need to print larger tools such as customised grippers for palletising and heavy pick and carry tools for large industrial robots. The faster FX20 also speeds up production 3 to 4 fold.
“Utilising Markforged 3D printing technology, we achieved an 80% weight reduction compared to standard commercial grippers and reduced delivery time from two weeks to two days, compared to conventional CNC machined grippers,” says Harvestance CEO Seungjae Leem.
By reinforcing the bottom of the gripper body with continuous carbon fiber and glass fiber, Harvestance created a strong, light gripper capable of supporting heavy workpieces without altering its shape.
“Markforged’s high-strength material (Onyx), Continuous Fiber Reinforcement, excellent surface finish, and easy postprocessing have been ideal solutions for us. Our engineers can focus entirely on their work, developing products without concerns about mechanical properties, postprocessing burden, or quality,” added Leem.
mark3d.com/en/
This November, the Princess Royal Training Awards will honour 52 recipients for their investment in training their people, resulting in exceptional organisational benefits. Read on for details of the companies celebrated this year and how to get involved in the 2025 awards.
The Princes Royal Training Awards, the ultimate symbol of excellence in learning and development (L&D), attract more and more organisations each year, eager to achieve this royal accolade.
2024’s Award-winning recipients will receive their Awards from HRH The Princess Royal, President of the City and Guilds of London Institute at a high-profile ceremony in London. They will also be invited to join a community of over 600 like-minded professionals who share a commitment to investing in L&D. Previous winners have also reported on the transformative impact of the Awards. As precision engineering organisation and Award recipient EDM Zone Ltd explained: “We have won lots of awards in the apprenticeship realm, but we believe this one to be the pinnacle of apprenticeship awards. It’s the best you can get.”
In a recent Alumni survey*, 93% of organisations reported a boost in employee engagement and wellbeing due to investment in learning, 91% saw an increased ability to demonstrate the value of skills to their organisation’s social value and 84% expressed enhanced confidence in their organisation’s culture and training approach.
The manufacturing and engineering sector has a strong history of participating in the Princess Royal Training Awards and 2024 is no exception, with an increase in both applications and Awards for the sector.
Achieving the standard in 2024 is steel producing company, Tata Steel,
which achieved the Award in 2019 for its apprenticeship programme, and has maintained a strong focus on training and developing its people. The company identified that 30% of its workforce was aged over 50 and it has recruited 1,500 trainees onto programmes ranging from levels 2 to 7, successfully creating sustainable talent pipelines. The company receives 1,500 applications for the 200-300 apprenticeships it has available each year.
Also recognised is Bentley Motors, commended for its outstanding training programme. In 2020, the organisation aimed to become the world’s most sustainable luxury car brand. To adapt to the pandemic, they transformed their Retail Academy into a digital platform, doubling UK retailer engagement in training to nearly 16,000 participants and significantly reducing costs.
These organisations – along with Lotus Cars, Monnickendam Diamonds Ltd, Sharing in Growth UK Ltd, Tecniq Ltd and Xtrac – join the many manufacturing and engineering sector organisations celebrated
for their training excellence over the years by these exceptional Awards.
This year, the Awards celebrate a decade of honouring training excellence. Organisations keen to be recognised for their dedication to training during this special year should register their interest on the Awards’ website. The Awards are open to all organisations in the UK and Ireland, regardless of size or sector, are free to apply from start to finish, and applicants receive unrivalled support throughout the application process.
Applications open on 2 December 2024. For more information, contact the Princess Royal Training Awards team. Awards are open until 31 March 2025.
princessroyaltrainingawards.com
*City & Guilds (2024), Impact Report 2024: The impact of skills on lives.
A trip to Southern Manufacturing & Electronics, to be held at the Farnborough International Exhibition & Conference Centre from 4th to 6th February 2025, will tempt visitors with much more than just the latest production technology.
Prior SM&E previews gave a taste of what awaits visitors in production equipment, consumables and subcontract manufacturing services in the mechanical, electrical and electronic engineering sectors. Now it is time to cover the plethora of general services that will be on offer to every area of manufacturing industry. It is just one more reason why this is an unmissable event.
Broanmain is a family-owned plastic fabrication company in Dorking offering polypropylene, polycarbonate, ABS and technical polymer moulding services, including high volume production runs, precision moulding, CNC finishing and assembly. The company utilises economies of scale, a secure storage facility and kanban to help OEMs maximise cost savings and boost profitability. It has a new, fully-automated, 320-ton Haitian injection moulding machine arriving shortly.
Custom plastic enclosures are designed and manufactured by Ortumex Systems to customers’ specifications, with no need for mould tools, thanks to its innovative fabrication process. The tool-free approach enables cost-effective, efficient production for low to high volumes, while also offering rapid prototyping within a few days. Trifibre will explain its ability to produce bespoke flight cases and injection-moulded waterproof cases, combined with CNCrouted foam inserts, to protect products during transportation.
Camberley Rubber Mouldings is a specialist manufacturer of bespoke rubber products, offering prototyping through to high volume production solutions for industrial, commercial and military applications across the UK, Europe and worldwide. Machines are available for
injection, compression and transfer moulding and the company provides a consultancy service to select the material that best suits any given application.
CIM Software is a leading provider of ERP software for manufacturers using Sage 50 and Sage 200. Modules included are stock control, bill of materials, works orders, planning, quotations, shop floor data capture and a graphical scheduler, allowing businesses to streamline their entire manufacturing processes. E-Max Systems will be offering its Cloud ERP solution with advanced material planning, cost control and scheduling capabilities along with easy-to-use reporting and analytics, and will show how systems can be designed to meet specific needs. Similarly, Epaccsys implements ERP Solutions that are flexible, scalable and tailored to an organisation’s requirements.
Exhibiting for the first time, Compass Business Finance will be urging attendees to think differently about finance to obtain optimised solutions for their business requirements. A fun highlight on the stand will be the Batak Reaction Game to test people’s speed and reactions, with prizes for winners. Whether companies are looking to invest in new equipment, increase working capital, move premises, embark on a new
project or even buy another company, the provider professes an ability to help.
Ecotile is a UK-made industrial flooring solution that can be fitted without causing disruption. The low-maintenance, interlocking floor tiles solve damaged flooring problems, has British Standard fire-retardant certification and are fully recyclable. ETA Logistics, with offices in London, Hong Kong, Germany, Singapore and Vietnam, specialises in freight forwarding services including marine freight, AOG logistics, and customs and trucking consultancy.
As well as showcasing the latest in adhesive and sealant technologies under its LOCTITE brand, the company will spotlight its semi-automatic, automatic and robotic equipment. It offers a free on-site line survey, which has the potential to increase productivity, improve reliability and simplify design.
There is free car parking at the Farnborough site, which is well served by road and public transport links. A regular, complimentary bus service runs between the two local railway stations and the showground. Admission to the exhibition is also free. Register today!
southern-manufacturing-electronics. com
Midlands 3D Printing
T: 01785 594389
E: sales@midlands3d.com
W: www.midlands3d.com
Fibet Rubber Bonding (UK) Ltd
T: 01282 878200
E: sales@fibet.co.uk
W: www.fibet.co.uk
CEMBRE Ltd
T: 01675 470 440
E: sales@cembre.co.uk
W: www.cembre.com/en
Nord
T: 01235 534404
E: GB-sales@nord.com
W: www.nord.com
Schmersal UK Ltd
T: 01684 571980
E: uksupport@schmersal.com
W: www.schmersal.co.uk
T-Mark
T: 0330 153 8320
E: sales@t-mark.co.uk
W: www.t-mark.co.uk
Jacob UK Ltd
T: 01694 722841
E: sales@jacob-uk.com
W: www.jacob-group.com/uk
Titan Enterprises Ltd
T: +44 (0)1935 812790
E: sales@flowmeters.co.uk
W: www.flowmeters.co.uk
Silverson Machines Ltd
T: +44 (0)1494 786331
E: sales@silverson.co.uk
W: www.silverson.co.uk
Brainboxes
T: + 44 (0) 151 220 2500
E: sales@brainboxes.com
W: www.brainboxes.com
Intoware
T: 0115 977 8969
E: hello@intoware.com
W: www.intoware.com
Axair Fans UK Limited
T: 01782 349 430
E: sales@axair-fans.co.uk
W: www.axair-fans.co.uk
ESI Technology Ltd
T: +44 (0)1978262255
E: sales@esi-tec.com
W: www.esi-tec.com
KUKA Robotics UK Ltd
T: 0121 505 9970
E: sales.uk@kuka.com
W: www.kuka.com
IFM Electronic
T: 020 8213-0000
E: enquiry.gb@ifm.com
W: www.ifm.com
PLUS Automation Ltd
T: 0121 58 222 58
E: Sales@PLUSAutomation.co.uk
W: www.PLUSAutomation.co.uk
BITO Storage Systems Ltd.
T: 02476 388 852
E: Info.uk@bito.com
W: www.bito.com
AMETEK Land (Land Instruments
T: +44 1246 417691
E: land.enquiry@ametek.com
W: www.ametek-land.com