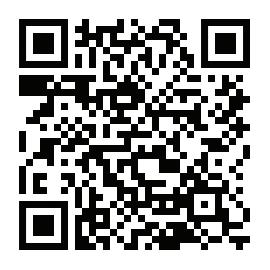

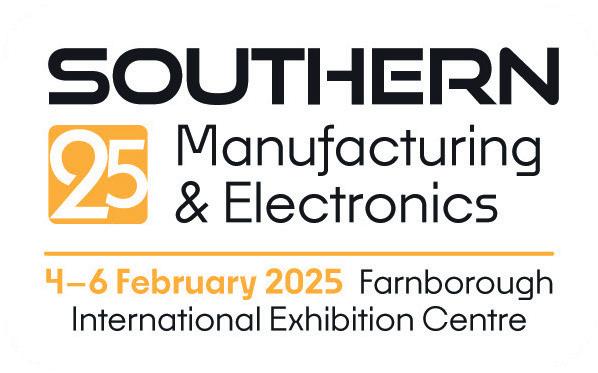
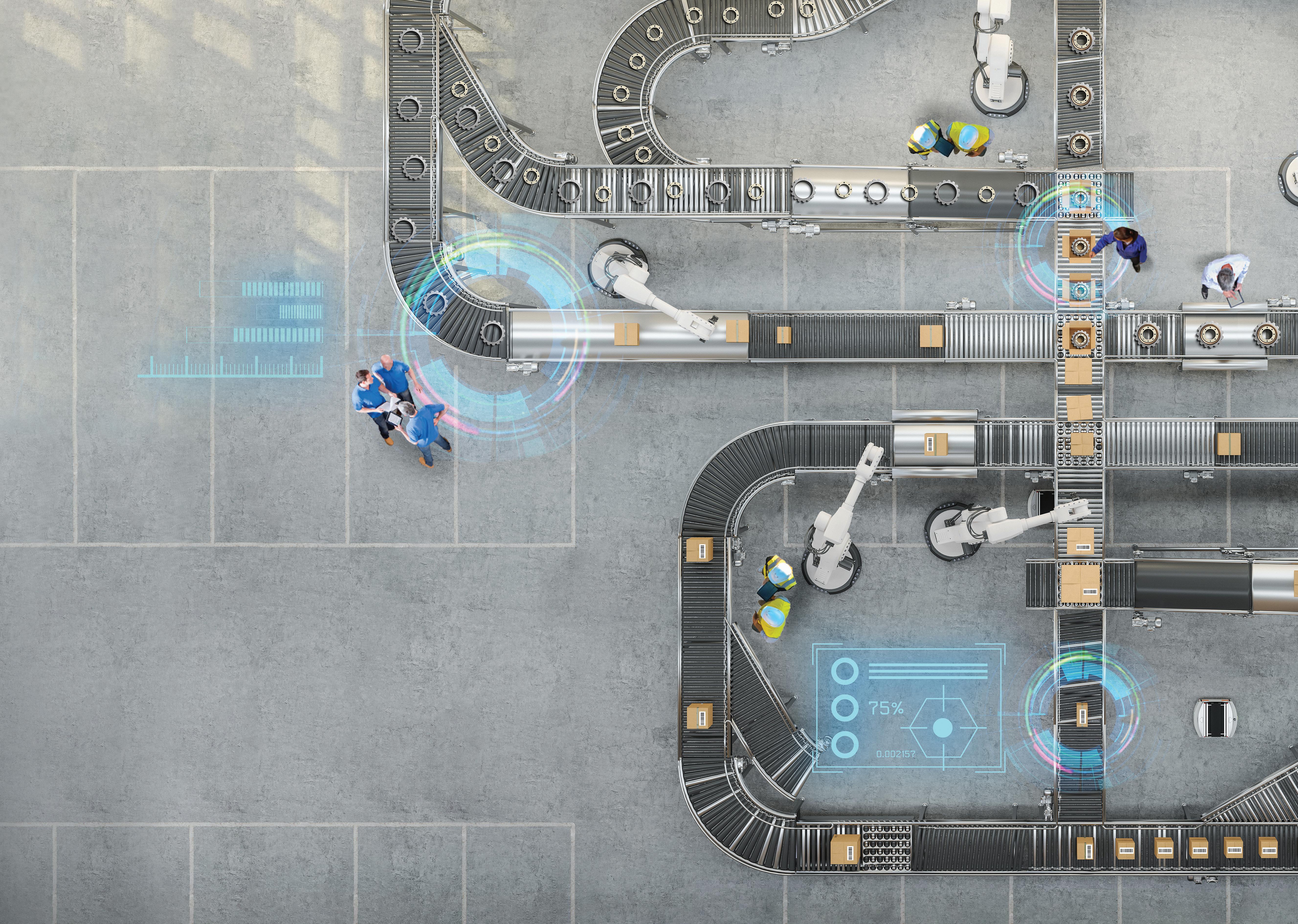
The Matrox Imaging solutions you know and trust just got better, and they are now available through Zebra.
More choices from the widest portfolio
More agility to scale and adapt in the moment
More interconnectivity via easier integration
More savings with streamlined solutions
Editor
Oliver Batt oliver@cimltd.co.uk
Publication Manager
James Burke jb@cimltd.co.uk 01795 509105
Account Managers
James Davies jamesd@cimltd.co.uk 01795 509105
Jim Bearden jim@cimltd.co.uk 01795 509105
Design & Production
Grant Waters grant@cimltd.co.uk
James Taylor james@cimltd.co.uk
Administration Manager
Natalie Murray admin@cimltd.co.uk 01795 509103
Credit Facilities Manager
Gwen Lee creditcontrol@cimltd.co.uk 01795 509103
Marketing Manager
Lucas Payne lucas@cimltd.co.uk
Sales Director
Tom Woollin tom@cimltd.co.uk
Chief Executive
John Denning
© 2024 Cogent Multimedia Limited,1st Floor, Saphir House, 5 Jubilee Way, Faversham, Kent, ME13 8GD. No part of this magazine may be reproduced or stored in a retrieval system or transmitted in any form – electronic, mechanical or physical – without express prior permission and written consent of the publisher. Contributions are invited and when not accepted will be returned only if accompanied by a fully stamped and addressed envelope. Manuscripts should be typewritten. No responsibility can be taken for drawings, photographs or literary contributions during transmission or in the editor’s hands. In the absence of an agreement the copyright of all contributions, literary, photographic or artistic, belongs to Cogent Multimedia Limited. The publisher accepts no responsibility in respect of advertisements appearing in the magazine and the opinions expressed do not necessarily represent the views of the publisher. The publisher cannot accept liability for any loss arising from the late appearance or non-publication of any advertisement.
Happy New Year and welcome to the January issue of MEPCA magazine!
The success of e-commerce has transformed our expectations as consumers. Where once we were content to wait weeks for products to arrive, we now expect them nearinstantly. Rarely do we pause to consider the efforts involved in fulfilling our orders. Every year, the pressure that consumer expectation places on warehousing and logistics is exponentially increasing, which in turn forces businesses to find new ways to improve efficiency.
In this issue, we delve into warehouse automation, examining how it can help alleviate these pressure points. Assisting us in this is Dexory, the warehouse automation specialist; in two insightful articles, Dexory explains how to leverage data-insights for improved manufacturing logistic and highlights current trends in warehouse automation. Proceeding on from this, we look at the factors involved in implementing automation and why the UK is leading the way. Also contributing to this month’s Warehouse Automation Focus, we have Lucas Systems and Joloda Hydraroll.
This month’s Cover Story will whet the appetite for the most essential industry event of early 2025: Southern Manufacturing & Electronics. Elsewhere in this issue, we announce our first Manufacturing Champion of 2025, Kraus & Naimer answers our questions, we look at how additive manufacture can make supply chains more resilient with WAAM3D, and provide an array of other industry news, solutions and insights.
Enjoy this month’s issue as you seize 2025.
@Mepca-magazine
To subscribe to MEPCA visit our website www.mepca-engineering.com or scan the QR code.
To mark the company’s 60th anniversary, the lubrication-free igus:bike is travelling through at least 16 countries over a twelve month period to raise awareness for the circular economy of plastics.
The igus:bike marks the beginning of a new chapter in sustainable mobility, made using recycled ocean plastic waste. The ultimate goal with the igus:bike is to establish local production near waste plants worldwide and therefore close the plastic recycling loop. After three and a half years of development, the dream of an urban bike made from plastic waste became a reality. Initially produced using 50% recycled ocean plastic from discarded fishing nets, the igus:bike is the world’s first bicycle made using recycled plastic. “The igus:bike is a permanent development project. When you see an igus:bike on the road, you know that something completely new is being explored and with that comes constant changes and improvements.” says the managing director of igus® in the UK, Matthew Aldridge.
In the future, igus® plans to make the bike available all over the world. Even countries where there is a lot of waste, igus® wants to set up local production lines for the bike. As well as helping with plastic waste recycling, this will also create jobs.
“As a company that has been manufacturing industrial components from plastic for 60 years now, we are committed to driving the transformation to a sustainable circular economy of plastics. The igus:bike is a significant milestone on this path,” says Aldridge. “As the bike travels with us through the UK, we hope to inspire many companies and customers to get involved.”
Plastic waste from landfills all over the world could become the raw material for the igus:bike in the future. igus® manufactures the individual components using rotational and injection moulding – from the frame to the bearings and drive crank. Since the start of development, the material researchers have succeeded in gradually increasing
the percentage of recycled plastic– and the trend is rising. This makes it possible to process discarded fishing nets, shampoo bottles and other plastic waste into recycled pellets for rotomoulding machines, turning these into a valuable resource.
The green light was given for the igus:bike to begin the world tour and it set off from the igus® factory in Cologne, Germany. October marked the 60th birthday of igus®, and to celebrate the occasion, the bike will travel the world for a whole year. The urban bike highlights the many advantages of igus® “motion plastics” products, endeavouring to bring industry partners, media representatives and consumers closer while showing how the transformation to a sustainable circular economy of plastics can succeed. This bike does not rust, does not need oil and is almost entirely maintenancefree. Components such as ball bearings, crank and freewheel do not require any
lubrication at all, as they are made of igus® high-performance plastics.
Over the next year, the plastic bicycle will be travelling across at least 16 countries – including Germany, Italy, China, and of course here in the UK. The aim is to show industrial customers, recycling partners, the press and consumers that plastics do not have to end up in incineration or landfill and instead can help shape the transport of tomorrow. As it travels to each igus® subsidiary, the bike will visit various customer factories. Once it reaches the UK, expected to be summer 2025, the bike is set to travel across the country, sightseeing and highlighting customer applications along the way. With this worldwide tour, igus® hopes to make customer stories come alive at every stage.
Follow the igus:bike’s journey on the company’s website for live updates. blog.igus.eu/rcyl-tour/
SensoPart introduces the latest addition to the renowned vision sensor lineup: the VISOR® XE. This groundbreaking hardware platform sets new benchmarks in industrial automation, addressing the growing need for speed and efficiency.
The VISOR® XE stands out with its exceptional speed and performance, particularly when tackling complex tasks using artificial intelligence. With the VISOR® XE, SensoPart offers an innovative solution that significantly outperforms conventional vision sensor models.
The VISOR® XE operates four times faster than previous models, thanks to its advanced multi-core processor architecture. For example, the VISOR® Code Reader vision sensor can read codes in less than 40 milliseconds, even at a high resolution of 5 MP.
Installation of the VISOR® XE is streamlined and simplified, featuring an additional LAN interface that allows multiple vision sensors to be efficiently connected. When using several cameras on a robotic gripper, only a single cable is needed for robot control.
The XE series can also be set up and operated using the proven VISOR® software, ensuring compatibility with configurations from previous VISOR® models. The setup process and PLC interface protocols remain unchanged, providing seamless integration into existing systems.
Featuring the signature VISOR® family housing design, the new vision sensor is distinguished by its striking red partial housing.
The new XE series boasts AI algorithm classification speeds eight times faster than its predecessors. With a processor
featuring integrated hardware acceleration for deep learning, users are well equipped to handle current and future image processing challenges. This is especially beneficial for swiftly detecting numerous small details within large fields of view.
sensopart.com
ReeR Safety’s ATEX (Ex) certified Safety Light Curtains are now complemented by a new range of ATEX-certified versions of the company’s Mosaic safety controllers.
These new Mosaic RV controllers expand ReeR’s solutions for industrial environments with potentially explosive atmospheres. The versatility of the Mosaic RV range makes it suitable for a wide range of industrial applications:
• Chemical and Petrochemical Plants: providing safe control in environments with explosive gases or vapours.
• Industrial Automation: ideal for regulated sectors such as pharmaceuticals and food, where safety and productivity must go hand in hand.
• Maritime and Offshore Applications: designed to withstand harsh marine environments.
ATEX Zone 2 and HazLoc certifications,
the RV versions offer compliance with international regulations and protection against explosive gases and vapours to ensure reliability even in extreme conditions.
The Mosaic RV range integrates seamlessly with the main and expansion modules of the broader Mosaic series, offering unparalleled flexibility:
• M1S RV: Advanced master unit for comprehensive safety control, compatible with a wide range of expansions.
• M1S COM RV: the most advanced master unit, featuring dual RJ45 interfaces for Fieldbus connections and remote management, ideal for complex and highly integrated systems.
• MI8O4 RV: expansion module with digital inputs and outputs.
• MA4 V: expansion modules for analogue inputs.
• MBC V: field-Bus interface modules for diagnostics and data transmission.
The modules are the latest addition to ReeR’s MOSAIC Safety Controller range, which features 3 master units and the ability to connect up to 14 expansion modules. It’s modularity provides flexibility and allows it’s adaptation to diverse applications of all sizes, from small machinery to complex production lines.
plusautomation.co.uk
MEPCA looks to academia for 2025’s first Manufacturing Champion: Dr Chukwuma Ogbonnaya, a lecturer and registered engineer, whose current research includes renewable energy technologies.
Dr Chukwuma Ogbonnaya teaches at Wolfson School of Mechanical, Electrical and Manufacturing Engineering, Loughborough University, UK. He is the module leader of Lean Operations and Supply Chain Management (UG), and Lean and Agile Manufacturing (PGT) modules. His current research interest focuses on manufacturing renewable energy technologies using systems thinking, lean and agile methodologies to provide the sustainable energy needed to realise Sustainable Development Goals. Dr Ogbonnaya is also the Co-Director of Equity, Diversity and Inclusion at Wolfson School and Co-Chair of Race, Ethnicity and Cultural Heritage (REACH), a University-wide staff network for racialised minorities.
In the following Q&A, Dr Ogbonnaya provides his insights on the UK’s road to net-zero, tackling the skills shortage, and how universities and industry can work together to commercialise research.
What barriers must the UK manufacturing sector overcome to achieve its net-zero
Reflecting on our recent publication in Energies titled “Manufacturing Strategies for a Family of Integrated Photovoltaic-Fuel Cell Systems”, there are two potential barriers that UK manufacturing sector should be proactive about as efforts are geared towards achieving the net-zero ambitions. First is how to achieve “lean manufacturing” of renewable energy technologies so that components or whole renewable energy systems can be manufactured in the UK at the lowest ownership cost, and at the highest quality compared to global competitors. The second barrier is how to enhance the agility of supply chains of renewable energy technologies to
facilitate security, flexibility, dependability and mitigated supply chain risks. For instance, Lithium is a key raw material in battery technology. By securing the highest stake in the mining of Lithium by Chinese companies, manufacturing of Lithium-ion batteries in China for electric vehicles, renewable energy storage, computers, and other electronics are positively impacted.
How can universities and other educational institutions address the skills shortage?
As a Co-Director: Equity, Diversity and Inclusion at Wolfson School and a CoChair: Race, Ethnicity and Cultural Heritage (REACH) Staff Network at Loughborough University, I believe that women should be encouraged by the UK government, universities and colleges to study manufacturing and engineering courses. I included government because choosing to study manufacturing and engineering by students starts with their experiences in STEM subjects at the basic level. Therefore, there should be deliberate, systemic and systematic STEM education policies by the Government, as well as effective implementation strategies by higher education institutions to motivate girls to study STEM subjects and pursue STEM careers. More should be done to attract women to manufacturing and engineering so that the workforce for sustaining national productivity and economic growth will be diverse and inclusive.
What might improve the transition between academic innovation and its commercial implementation?
I believe that the “trilogy of industrialisation”
in any economy includes the co-creation of products and services by Government, Research Institutions and Companies. Government deliberately set the tone for innovation ecosystems through policies and funding of cutting-edge research. Research is better done in research institutions. Commercially viable results from research and innovation activities are either absorbed by existing companies or commercialised by spin-off companies. I think that the UK thrives as an industrialised country because government fund research through different bodies such as UKRI, Royal Society, RAEng, EPSRC, etc. A good example of the trilogy in action was how the UK government supported Oxford-AstraZeneca partnership during the COVID-19 pandemic. As a result, UK was among the first countries to start mass-producing vaccines, which helped to save lives across the globe. Deliberate design to commercialise research will remain the cornerstone of any productive economy.
Verity Davidge, Director of Policy at Make UK, puts a spotlight on the UK’s readiness for digital transformation, the driving force behind the next industrial revolution.
UK manufacturing is on the cusp of a significant digital transformation. With recent advancements in Artificial Intelligence (AI) applications, Machine Learning (ML) and the rapid acceleration of Large Language Models (LLMs; Generative AI), we are witnessing levels of innovation not seen since the invention of the steam engine. We are entering a new and exciting digital age that has the potential to bring about numerous benefits to the manufacturing sector.
These technologies are transforming industries by automating tasks, optimising production and revolutionising the way we approach problem-solving – just as the steam engine did, as it overcame the limitations of using people and horsepower to do the grunt work – to speed factories along at a pace never before seen.
As AI, automation and robotics continue to evolve and speed up processes on the factory floor and elsewhere, their potential to drive economic growth and reshape industries is becoming increasingly clear, and the manufacturing sector and its factories of the future have a central role to play. The sector brings stability and economic resilience to the economy, and provides the jobs and goods needed to ensure that communities across the country thrive.
However, despite being a major contributor of growth to the UK, the manufacturing sector faces a significant challenge when it comes to productivity and automation adoption. Just 7% of the companies we surveyed as part of this report regarded themselves as “very knowledgeable” about AI, and we remain behind in many global rankings when it comes to metrics, such as robot density, where the UK ranks 24th with 111 robots per 10,000 employees.
According to data from the International Federation of Robotics, the UK uses just 0.5% of the world’s robots in manufacturing compared to 1.2% in France and 1.6% in Italy, both of whom have similar-sized industrial bases. Less than a fifth of companies (16%) operate them with almost a third (29%) not considering using them and only four in ten (38%) considering using them.
There is also a large discrepancy between large and small companies, with large companies more than twice as likely as SMEs to be applying AI (71% and 28% respectively). The barriers to adoption include a lack of knowledge of how to apply AI and limited access to technical and digital skills. Consequently, lower adoption rates among SMEs are preventing them from realising the benefits of increased profits seen by almost a quarter of large companies and an ability to take on further work reported by almost a third.
Yet there are huge financial gains to be had. For example, the AI industry in the UK is expected to contribute $1 trillion to the economy by 2035. As an economy, and as a manufacturing sector, the UK has the potential to realise these gains. After all, manufacturing contributes some 47% of all private R&D spending in the UK.
It’s clear that factories could look very different in five, ten or twenty years’ time, by adopting already existing digital technologies to transform them into the factories of the future, and to help boost efficiency and productivity, not just on production lines, but also in other areas such as decarbonisation and occupational health and safety.
As the Government moves to develop its industrial strategy, digital technologies and digital skills must be at the heart of it. Two hundred years after the industrial revolution took root, the fourth one is bringing the zeroimpact factory within reach. makeuk.org
In this fourth preview of Southern Manufacturing & Electronics, the UK’s leading annual engineering trade fair – held 4th to 6th February 2025 at the Farnborough International Exhibition & Conference Centre – Easyfairs, the show’s organiser, highlights the prominence of quality control this year.
Asignificant number of companies will present advanced and novel equipment for test, inspection and measurement at the event. These quality control procedures are applicable to both the mechanical engineering and electrical/electronic sides of the show, which are covered in approximately equal measure.
Founded in 1989, the family-owned Carfulan Group will show metrology products offered by three of its five member companies. OGP UK provides multi-sensor systems for inspection and others designed for measurement using a scanning probe, Vicivision UK specialises in systems for quality control of turned components, while Zoller UK focuses on cutting tool inspection and measurement to ensure the accuracy and quality of mills, drills and turning tools.
CDG 3D TECH offers products for scanning, including stationary and mobile options, manufactured by various global companies including Evatronix and Shining 3D. It also has in its portfolio industrial 3D scanners from Faro, suitable for largescale applications such as scanning entire vehicles or large machinery. In addition to laser scanners, the range extends to photogrammetry systems, which use multiple cameras to capture images from different angles to create 3D models.
Offering both equipment and services, Central Scanning is a reseller for several brands of scanner including Artec 3D, GOM and Zeiss Optotechnik. In addition to 3D scanning, services include inspection for quality control and reverse engineering. The company’s offerings are widely used across industry, including sectors like aerospace,
medical, automotive, toolmaking, R&D and even sculpture and the arts. There will be demonstrations of new Artec Scanners, the Leo and RAY II, as well as the Zeiss T-Scan Hawk 2 and GOM Scan 1.
Hexagon Manufacturing Intelligence will explore its full suite of cutting-edge solutions tailored to enhance efficiency, accuracy, operational consistency and productivity across various manufacturing processes. Metrology solutions will include precision measurement devices designed to optimise quality control in complex production environments, from portable measuring arms and laser trackers to handheld laser scanners. Visitors will also learn about the firm’s production software for streamlining manufacturing workflows. The solutions integrate seamlessly with its hardware, providing data-based insights that drive
productivity and reduce lead times.
British co-ordinate measuring machine (CMM) manufacturer LK Metrology will show an Altera C HA high-accuracy series model equipped with its new EcoAir function, an energy-saving device that automatically stops delivery of compressed air to the CMM after a period of inactivity, reducing consumption by up to 95% when the machine is idle. New also will be LK’s own CMM laser scanner, the SLK25 VIVID, and the company’s modular tool storage and change racks for tactile probes, laser scanners, extension bars and other sensor accessories. On show will be a thirdgeneration LK FREEDOM arm, now supplied as standard with a 4.5 inch rather than a 3.5 inch diameter mounting ring to allow the unit to sit on a larger base for increased stability and accuracy. Additionally, there will be an opportunity to experience LK’s new Interactive virtual reality showroom featuring 10 CMMs running inspection programs.
MJ Allen Precision, an arm of the MJ Allen group, specialises in high-precision tooling, metrology equipment and component manufacturing. Its involvement in measurement centres on the sale of Verdict Gauge products, including precision gauges, dial test indicators, lever indicators, depth gauges and bore gauges. The products, known for being robust, reliable and of high quality, can be supplied in bespoke configurations for special applications. Customisations may include adjusting the measurement range, increasing or decreasing the resolution for finer or coarser measurements, customising the dial layout or markings for enhanced readability, different mounting options, and adapting the product for use in demanding applications.
Established for over 50 years, RDP Transducers & Instrumentation is a UK company that designs and manufactures general-purpose and harsh-environment transducers for measuring position, pressure, force and torque. With a dedicated engineering team and in-house manufacturing facilities, it has the ability to tailor products to suit customers’ requirements and applications. They are frequently found in the nuclear, renewables, oil & gas, marine, subsea, aerospace, automotive and rail sectors. A vast variety of transducers is offered, with displacements from 0.5 mm to 940 mm, operating pressures from full vacuum to 20,000 psi, PT rating from IP68 to 2.2 km, and operating temperatures from -220 to 600°C.
Printed circuit board (PCB) test cells from Absolute Robotics are configured with one or more Omron/Techman TM S Series collaborative robots for automated depanelling/ breakout/singulation, labelling, programming and testing, for almost any size and shape of PCB. Sub-assemblies and complete units may be tested and existing manual or semiautomated fixtures may be integrated. Built-in machine vision reads barcodes and checks components, including LED colour and intensity. Conveyor infeed/outfeed is provided for Euro storage trays and/or SMT magazine racks. Having a solid customer base requiring automated PCB testing, the company has coupled its experience of delivering efficient solutions with a flexible, modular approach to reimagine the future of PCB testing.
NTD Shielding Services is a leading designer, manufacturer, project manager and supplier of high-performance shielding solutions for electronic equipment, such as EMC, EMI, antenna, RF, Tempest and HEMP chambers, Faraday cages, 40GHz mmWave 5G solutions and EMC test and measurement equipment. The company also provides RF shielded tents, bench top RF boxes and mobile shielded rooms, as well as EMC facility maintenance, service and shielding effectiveness testing. The integrated solutions are configured with practicality, user friendliness, high performance and cost effectiveness in mind. Based in northwest England, the company also hires to its UK and European customers electromagnetic compatibility test and measurement equipment. A large range of EMC and antenna absorbers, ferrite tiles and both new and reconditioned boards are stocked, alongside a variety of high-performance RF filters, specialist pipes, penetrations, attenuvents and RF/EMC/ chamber components, plus entire RF/EMC reconditioned facilities.
Micro Precision is a leading global provider of calibration, repair, maintenance, validation, asset management and test equipment solutions. Serving a range of applications and industry sectors, the firm offers extensive electrical, RF, microwave, optical, mechanical, dimensional and temperature
calibration solutions. Headquartered in California, it has more than 30 laboratories worldwide and provides customers with equipment management solutions through localised service outlets.
As a manufacturer of automated test equipment, Yelo focuses particularly on laser diodes, LEDs, vertical-cavity surface-emitting lasers and other photonics components. For example, its systems measure the performance parameters of laser diodes, including output power, wavelength and modulation response. Other instruments measure the light-current-voltage characteristics of laser diodes, providing insights into their efficiency and reliability. The company offers extensive expertise in providing bespoke solutions for simple or complex needs. It designs and builds both final functional and bed of nails test fixtures for PCBs and provides comprehensive test solutions from its software and electronic departments. The company will present various customisable test fixtures on its stand, and its experts look forward to connecting with visitors.
There is free car parking at the Farnborough centre, which is well served by road and public transport links. A regular, complimentary bus service runs between the two local railway stations and the showground. Admission to the exhibition is also free. Register today using the address below.
https://bit.ly/3OPLSbF
Warehouses need the capability to sense and respond quickly and cost efficiently as the supply chain, market, and customer demands change. We can help equip your operation to sustain growth and resilience now and in the future. Contact us today to learn how.
Double productivity and eliminate congestion by reducing travel using AI-based batching and pick-path optimisation.
Improve accuracy and safety in hands-on tasks with JenniferTM voice-directed mobile applications.
Increase ecommerce efficiency and throughput with waveless order streaming without changing your WMS.
Sponsored by
P14: Dexory examines how leveraging data insights can improve speed and accuracy.
Speed and accuracy are the lifeblood of modern manufacturing logistics. Dexory, the warehousing automation specialist, examines how leveraging data insights can improve the speed of warehousing logistics.
Today, manufacturers face mounting pressure to deliver on tighter schedules, adapt to fluctuating demand, and navigate global disruptions. With the rise of eCommerce, just-in-time production, and customer expectations for near-instant delivery, the manufacturing industry is shifting to prioritise agility and precision like never before.
Recent global events, such as the pandemic, have exposed vulnerabilities in traditional supply chains. Manufacturers now need robust logistics operations that can withstand these challenges while maintaining efficiency. Rapid data-driven decisionmaking is essential to ensure that raw materials, components, and finished goods move seamlessly through the supply chain.
Timely insights, enabled by real-time data, robotics, and advanced analytics, form the backbone of this transformation. This article explores how manufacturers can leverage cutting-edge technologies to achieve the speed and precision required to meet today’s demands while driving operational excellence.
The integration of robotics in manufacturing logistics is revolutionising how factories and warehouses operate. Robots enhance speed, precision, and cost-effectiveness, making them an indispensable tool for manufacturers striving for operational excellence.
Key benefits are:
1. Round-the-clock efficiency: Robots operate tirelessly, allowing 24/7 production and logistics. This eliminates downtime, significantly increases throughput, and
ensures raw materials and finished goods flow smoothly through the manufacturing process.
2. High precision and consistency: Robotics achieve accuracy rates exceeding 99.9%, minimising errors in inventory tracking and component handling. This is
especially critical in industries like automotive and electronics, where even small inaccuracies can disrupt production.
3. Cost-effective adoption models: Subscription-based solutions, like Robotsas-a-Service (RaaS), make it easier for manufacturers to adopt robotics
without heavy upfront investment. Rapid deployment, often within a week, means immediate operational benefits, including reduced waste, fewer errors, and lower labour costs.
4. Flexibility and scalability: Modern robots can adapt to fluctuating production volumes and integrate seamlessly with existing systems. For manufacturers managing seasonal peaks or unexpected demand shifts, this scalability is invaluable.
5. Improved safety and compliance: Robots handle hazardous tasks, such as moving heavy materials or working in hightemperature environments, reducing risks for human workers. Their advanced sensors and AI capabilities also ensure they operate safely around staff and comply with industry safety standards.
6. Data-driven insights: Beyond physical tasks, robots serve as data collection tools, providing real-time insights into production efficiency and inventory levels. These insights enable manufacturers to optimise workflows, reduce bottlenecks, and make informed decisions.
Examples of robotics in logistics:
• Material handling robots: Streamline the movement of raw materials and components between production lines.
• Stock-scanning robots: Provide precise inventory tracking, ensuring raw materials are available when needed.
• Collaborative robots (cobots): Work alongside human operators to enhance assembly line productivity.
While collecting data is important, its true value lies in turning it into actionable intelligence. This requires a combination of robust data collection systems and advanced analytics tools tailored to the manufacturing environment.
1. Digital twins in manufacturing Digital twins, virtual replicas of physical assets, allow manufacturers to simulate production scenarios, identify bottlenecks, and test solutions in real time. By integrating data from IoT devices and sensors, digital twins provide unparalleled visibility into the production process.
2. Predictive analytics
Predictive analytics use historical and realtime data to forecast demand, optimise inventory levels, and anticipate disruptions. This proactive approach minimises risks and keeps production schedules on track.
3. AI-powered decision-making AI tools can sift through vast amounts of data to identify patterns and trends, enabling manufacturers to make smarter, faster decisions. For instance, AI can optimise production schedules based on real-time demand or suggest adjustments to improve efficiency.
1. Start small with pilot projects: Test new technologies in a specific area, such as
inventory management or material handling, before scaling up. This approach minimises risk and provides valuable insights.
2. Invest in aligned solutions: Focus on technologies that directly address your operational challenges. For example, IoTenabled devices can enhance real-time visibility, while AI tools can improve demand forecasting.
3. Foster a data-driven culture: Encourage your team to embrace data insights in daily operations. Provide training on analytics tools and emphasise the importance of data accuracy.
4. Prioritise data quality: High-quality data is essential for reliable insights. Regularly audit data streams and invest in tools that clean and validate data in real time.
Manufacturing logistics is undergoing a profound transformation, driven by the dual imperatives of speed and data intelligence. By adopting technologies like robotics, IoT, and AI, manufacturers can streamline operations, reduce costs, and exceed customer expectations. By turning data into actionable intelligence, manufacturers can navigate the challenges of today’s fast-paced environment and unlock new opportunities for growth and innovation. dexory.com
Warehousing is on the brink of transformative change. From the rise of consumer expectations to advancements in automation and robotics, the logistics landscape is evolving faster than ever. Dexory share the five most significant trends set to redefine warehousing in 2025.
Consumers are driving a seismic shift in warehousing. AI-powered tools make smarter purchasing decisions instant, creating heightened expectations for rapid delivery, seamless returns, and real-time stock availability. Simultaneously, sustainability is becoming non-negotiable, with consumers demanding traceability and eco-friendly practices.
Warehouses must evolve to keep pace, adopting advanced inventory planning, realtime data platforms, and automation. These technologies enable them to meet consumer expectations efficiently while managing limited space and capital. For instance, robotics paired with AI-driven analytics can optimise operations while reducing environmental impact.
Automation is moving from a luxury to a necessity. While only 10–15% of warehouses globally currently use robots, adoption is accelerating as automation costs fall. Robots not only increase operational efficiency but also reduce the need for costly relocations by optimising existing spaces.
In the short term, retrofitting warehouses with Automated Guided Vehicles (AVGs) and other robotic solutions offers a cost-effective path to partial automation. Long-term, new builds will incorporate designs tailored for robotics, think higher ceilings and smoother floors. Flexible funding models like Robotsas-a-Service (RaaS) are also making automation accessible to companies of all sizes.
Digitalisation is reshaping the thirdparty-logistics (3PL) industry. Traditional
relationship-driven models are giving way to agile, data-driven platforms that operate like the “Airbnb of warehousing.” Concepts such as On-Demand Warehousing (ODW) allow companies to book space as needed, reducing reliance on long-term contracts.
AI plays a key role here, forecasting space availability and optimising resource allocation. For businesses, these platforms offer greater transparency and trust through ratings and reviews, akin to consumer platforms. With increasing mergers and acquisitions, a more consolidated and specialised 3PL ecosystem will emerge, driven by data and efficiency.
As warehouses automate, the role of workers is evolving. Entry-level roles will remain vital for social mobility, but upskilling is essential to support hybrid roles that blend technical and operational expertise. Engineers monitoring warehouse systems remotely or workers operating cobots (collaborative robots) are becoming the norm.
Training programs, such as digital certificates and multilingual courses, will equip workers for these changes. The gig economy may also introduce dynamic shift
models, allowing workers to choose their schedules across competing warehouses. Companies that embrace workforce diversity and upskilling will gain a competitive edge.
5. Warehouses will prioritise sustainability and worker well-being
Tomorrow’s warehouses will be larger, greener, and more human-centric. Developers are integrating sustainability into designs with features like solar panels, advanced HVAC systems, and community engagement initiatives such as rewilding nearby green spaces.
Worker well-being is also a priority. Facilities will include gyms, training hubs, and affordable childcare to attract talent. Integrated Building Management Systems powered by IoT and AI will create safer and more comfortable environments, dynamically managing lighting, ventilation, and security.
The future of warehousing is a blend of automation, sustainability, and humancentric design. By adopting these trends, companies can not only meet evolving demands but also build resilient, efficient, and future-ready operations. dexory.com
MEPCA navigates the isles and racking of warehouses and distribution centres to understand the increasing requirement of automation and the effect it is having on this highly pressurised sector.
The successes of e-commerce and its continual evolution has caused a fundamental change to consumer expectation.
In the past two decades, consumers have grown accustomed to increasing speed and accuracy in order fulfilment, while Artificial Intelligence (AI)based tools provide them with access to a limitless variety of goods, in real time.
In response, warehousing has also had to evolve. The likes of Amazon have revolutionised warehousing, order fulfilment and logistics processes, but in doing so, they have ingrained a service expectation that is challenging for the industry to meet.
The pressure placed on businesses as a result is immense, leading to a perpetual striving towards efficiency and process improvement. Automation and digitalisation are therefore high on the agenda for many business involved in warehousing and order fulfilment. As demonstrated in the other articles in this month’s warehouse automation focus, there are many different strategies, tools and solutions available for optimising processes.
MEPCA consulted with warehousing automation experts to gain an understanding of the factors involved. Contributing to the discussion, Simon Brennan, senior business manager, Specialist Printing Solutions at Brother UK; Simon Houghton, director of Sales UKI, EMEA region at Geek+; and from Exotec, Renaud Heitz, co-founder and CTO, and Bassem Awada, VP of Business Development.
Simon Brennan: “Firms have a chance to gain a competitive advantage by investing
“Forecasting growth is essential when choosing an automation system that not only meets current operational needs, but has the ability to scale to handle increased demand.”
Bassem Awada, VP of Business Development at Exotec.
in automated labelling solutions that improve sustainability and efficiency in the warehouse and logistics sector.”
“One innovation that will help deliver these benefits is linerless labelling. By removing the non-recyclable backing paper from the equation, linerless labels help operations become more sustainable by reducing the amount of waste that’s sent to landfill. No backing paper also means more labels per roll, so staff don’t have to refill their label printers as often, reducing downtime and boosting productivity. Another way to boost
efficiency and sustainability is using more durable devices.”
Bassem Awada: “A useful benchmark for determining the right time to implement robotics systems is when operations exceed 400 lines per hour and show consistent year-on-year growth.
“Forecasting growth is essential when choosing an automation system that not only meets current operational needs, but has the ability to scale to handle increased demand. While upfront costs may seem daunting, companies should view this
as a strategic long-term investment that enhances efficiency, reduces costs, meets customer demand and delivers a return on investment within five years.”
Further to this, as Simon Houghton pointed out: “Many businesses see ROI within two to three years due to benefits like faster order processing, reduced errors, and lower operational costs. Hence, viewing automation as a strategic investment rather than a disruption can help organizations align expectations with achievable outcomes –improved efficiency, improved accuracy and better working environment.”
One important thing to consider when implementing any warehouse automation solution is how to manage the impact on staff.
Renaud Heitz: “There are two important areas that companies should consider when managing the impact of automation on employees: safety and ergonomics.
“Safety: before integrating any automated warehouse system, a provider should conduct rigorous risk analysis and worstcase scenario testing on all products. Systems should be built to minimise risk for both people and products. Safety should not just be a responsibility, but a core value.
“The introduction of automated robotics systems means that warehouse workers no longer need to walk long distances. In the past, workers would need to walk around 15 kilometres a day, but now, warehouse work is less strenuous and more efficient, while better supporting the overall health and wellbeing of workers.
“Ergonomics: automated warehouse robotics providers are putting operators at the centre of their designs to make warehouse work easier, smarter and more efficient. Systems stations, touchscreens and scanners can be adjusted to worker height, exceeding ergonomic logistics standards while maintaining high picking performance.”
Simon Houghton: “Companies can ensure a smooth transition by investing in upskilling and reskilling programs to equip staff for new roles, such as operating and maintaining automated systems. Including employees in planning and deployment discussions ensures their concerns are addressed. Training on the new technologies and offering safety awareness courses help staff adapt. Redesigning workflows to emphasise human-robot collaboration can maximise productivity.”
The UK is set to be market leading in warehouse automation in 2025 . Given that the UK’s uptake in robotics and automation overall is lower than its competitors in Europe and the rest of the world, this is encouraging, but what factors are contributing to the UK’s uptake of warehouse automation?
Necessity appears to be a key driving factor. According to Interact Analysis, the combination of a long-established e-commerce market and a relatively high wage cost has meant the UK embracing warehouse automation.
Simon Houghton also highlighted the impact of labour shortages, demand and other expectations of warehousing: “The UK’s adoption of warehouse automation is driven by increasing labour shortages and rising wage costs. E-commerce growth has intensified demand for faster and more accurate order fulfilment. The need to maximise space utilisation in urban areas with high real estate costs makes high-density storage solutions attractive. Additionally, sustainability goals and regulatory pressures are encouraging companies to adopt energy-efficient and environmentally friendly technologies, further boosting automation adoption.”
Without warehouse automation, several UK sectors would struggle to grow given the limiting factors of labour, space availability and demand. Bassem Awada: “In particular, sectors including e-commerce, grocery, pharmaceuticals and automotive industries are poised for significant yearon-year growth. The reason being that their human-intensive workload can largely be replaced with autonomous systems which fulfil fast-moving orders and boast high storage density and throughput, all whilst
guaranteeing high performance.”
Further to this, as Simon Brennan explained: “Recent data from business advisory firm BDO shows renewed confidence in the UK logistics sectorii, with three quarters of firms (73%) looking at ways to control costs and increase market share. This is encouraging businesses to invest in their operations to boost efficiency, reduce errors and make cost savings.
“Manual labelling mistakes can lead to lost sales, delayed shipments, and customer dissatisfaction, with 69% of consumers likely to stop shopping with a retailer if their order isn’t delivered within two daysiii. Investing in automation to optimise labelling technology reduces errors, enhances customer satisfaction, and allows workers to focus on more critical tasks.”
The grip that hyper-efficiency has on warehousing and logistics is showing no sign of alleviating. Indeed, as e-commerce technology continues to advance, businesses on the front lines of order fulfilment must keep pace, leading to an automation feedback loop. It is therefore reassuring to see that the UK is embracing warehousing automation as we head into 2025.
MEPCA would like to thank all the contributors for their insightful commentary. For more information, visit the companies’ websites.
brother.co.uk
exotec.com/en-gb geekplus.com/en/
i. www.interactanalysis.com/insight/why-the-uk-is-set-tobecome-europes-largest-warehouse-automation
ii. www.bdo.co.uk/en-gb/insights/advisory/mergers-andacquisitions/logistics-confidence-index
iii. www.websitemagazine.com/ecommerce/the-impact-oflate-and-inaccurate-deliveries-on-customer-loyalty
Smarter automation choices allow warehouse operations to scale and respond to business demand. In the following case study, Andrew Southgate, V.P. of Business Development, EMEA, at Lucas Systems, illustrates the benefit of adopting a more dynamic approach to automation.
Adapting warehouse operations to support business growth and fluctuating demands does not always require replacing or upgrading an entire warehouse management system (WMS) or adding large, capital intensive, equipment-based solutions. Instead, many distribution centre (DC) operators are achieving world-class performance by integrating artificial intelligence (AI)-based process optimisation tools and advanced execution software alongside their existing processes, equipment, and WMS.
This approach is not only faster, but also more cost-effective, flexible and nimble. In short, a more dynamic automation strategy. To illustrate this concept, we focus on alternatives to the replacement of the WMS,
one of the core automation investments for many operators.
At its core, a WMS manages essential warehouse functions such as inventory control and order management. However, these systems are not always equipped to handle the dynamic requirements of modern warehouses. By adopting modular, best-inbreed execution and optimisation software, businesses can extend the capabilities of their current WMS. This WMS enhancement strategy offers several advantages:
• Reduced risk: operators avoid the potential disruptions associated with a full-scale WMS replacement.
• Accelerated transformation: integrating
supplemental solutions speeds up the digital transformation process.
• Improved flexibility: modular tools allow for scalable improvements tailored to evolving business needs.
• Immediate access to technology: companies can quickly implement advanced tools to stay competitive.
This approach is particularly beneficial for businesses aiming to modernise their operations without discarding significant investments in legacy systems.
A notable example of this strategy in action involves a Lucas Systems customer— a leading multi-channel retailer specialising in women’s apparel and lingerie, with over
$1.75 billion in annual revenue, established a state-of-the-art fulfilment centre spanning more than 650,000 square feet to bolster its direct-to-consumer operations. This facility was equipped with cutting-edge automation, including conveyors and sorters for both inbound and outbound operations, as well as a newly implemented warehouse management system (WMS).
While their new WMS included voicepicking capabilities, the solution provided by the WMS vendor lacked the advanced functionality needed to meet their complex operational requirements. To bridge this gap, they partnered with Lucas Systems to implement a comprehensive warehouse optimisation solution. This solution offered customisable user workflows, robust assignment management, and real-time reporting tools, seamlessly complementing their existing WMS and driving measurable improvements across their operations. With the Lucas solution in place, picking accuracy was enhanced 8-12% and productivity increased 15-20% throughout the DC, and the time and expense associated with returns handling were slashed.
Lucas Systems’ extensive experience with more than 100 customers and over 400 DCs, underscores the transformative impact of integrated solutions in DCs. These tools empower businesses to achieve significant operational gains by addressing key challenges in a cost-effective and efficient manner. For example, integrated solutions enable standardisation across multiple DCs, allowing companies to implement best practices even when operating with different WMS platforms.
In addition, these tools can extend the lifespan of an aging WMS, providing muchneeded functionality and delaying the need for expensive system replacements. They also facilitate seamless transitions when a WMS upgrade becomes unavoidable, acting as a bridge that minimises disruptions and risk. This flexibility ensures that DCs can optimise their operations without incurring the substantial costs and operational risks typically associated with large-scale WMS changes, offering a practical path to sustained efficiency and performance.
For many businesses, the decision to
supplement rather than replace a WMS is driven by practicality. Replacing a WMS can be a lengthy and expensive process, often requiring significant downtime and training. In contrast, adding advanced optimisation tools provides:
• Cost savings: businesses can preserve their existing WMS investment while gaining new capabilities.
• Faster implementation: modular solutions can be deployed more quickly than a full WMS upgrade.
• Reduced risk: avoiding the complexities of a complete WMS replacement minimises potential disruptions to operations.
By supplementing their existing systems with specialised tools, DC operators can achieve immediate improvements in efficiency, accuracy and productivity—all while maintaining operational continuity.
In an increasingly competitive market, distribution centre operators face the dual
challenge of adapting quickly to shifting demands while keeping costs under control. Instead of replacing their warehouse management systems (WMS), many businesses are discovering the advantages of exploring targeted alternatives. By pursuing this approach, companies can accelerate their digital transformation journey, reduce the operational risks that often accompany large-scale system changes, and achieve faster returns on investment through focused, incremental improvements.
The key to success lies in adopting best-in-class solutions that integrate seamlessly with existing systems. These solutions enable businesses to optimise their operations without incurring unnecessary expenses or disruptions. By embracing a scalable and flexible approach, warehouses can maintain the agility required to compete in today’s dynamic supply chain environment. This strategy positions them to tackle emerging challenges while staying ahead in an ever-evolving industry.
lucasware.com
Wouter Satijn, Sales Director at Joloda Hydraroll, explains how automating the loading process can improve employee experience.
In a world of robots and automation, suggesting people are a company’s most important asset might seem counterintuitive. However, given the unabating labour shortages, that is surely the case. According to stats from the Office for National Statistics (ONS), between August and October 2024, 33,000 vacancies in the UK transport and storage sector remained unfilled.
Improving pay is one way to help attract staff and retain them. However, safety and job satisfaction are also important considerations. When it comes to the loading and unloading of goods, why would employees choose to work in a cold and potentially dangerous unloading bay? Or sit for hours in a warehouse car park waiting for a slot to load or unload when they no longer need to – not to mention while they’re on the clock?
As manufacturers look towards the factory of the future, they need to continue finding ways to make more effective use of their scarcest resources and improve their working experiences. Automating the loading process at the end of the production line is an often-overlooked opportunity to do so, while also improving efficiency and productivity.
Manually unloading and loading trailers is physically demanding, often requiring winches and ropes to move heavy items. Forklift trucks are also heavily relied upon, posing another risk to health and safety: on average, forklifts are involved in a quarter of all workplace transport accidents.
Automating this process makes it safer for employees to unload heavy loads. Fewer forklift trucks and operatives are needed, which minimises the risk of accidents and product damage, while cutting costs. The
entire operation is faster and more efficient –achieving in two or three minutes something that typically takes between 30 and 45 minutes manually.
Another way an automated loading system helps businesses increase output is by reducing the space needed for storage in the loading dock area. For staff, it can also mean more opportunities to take up roles that are better paid, or that they find more enjoyable.
Truck drivers are another limited resource. Yet it’s not uncommon for them to experience long delays as they wait for unloading or loading slots to become available. As mentioned, on average, it takes between 30 to 45 minutes to load or unload a trailer, but drivers often have to wait significantly longer.
Automating the loading and unloading process can dramatically improve their experience, reducing driver wait times by 85% . As a result, drivers have more time on the road and less uncertainty and stress
associated with meeting delivery deadlines or a set number of shuttle runs within restricted hours. A more efficient and reliable process saves costs as it requires fewer trucks and drivers to transport products. With trusted time slots for drivers, there is no need to build in contingency or for extra trailers to cover idle time.
What’s more, with a more streamlined operation and greater confidence in delivery timelines, manufacturers have the resources to pursue other improvements, such as environmental goals. Incrementally improving efficiency, reducing the number of forklifts, and cutting emissions generated from idling trucks can provide a noticeable boost to environmental performance.
Automating the loading process helps companies get the best from their most precious resource while improving working experiences at a time of staff shortages and high turnover. An automated loading system yields rapid returns and helps to future proof the business through greater efficiency, agility, and reduced costs.
joloda.com
Make loading and unloading processes more efficient and effective. The Joloda Hydraroll Group are a one-stop-shop loading solutions provider with a complete range of manual, semi-automated, or fully automated solutions for modified and non-modified trailer or container applications.
It is unsurprising that in today’s fast moving, competitive world, a large number of manufacturing companies practice elements of predictive condition monitoring as part of their preventative maintenance strategy. Teledyne FLIR, manufacturers of thermal and acoustic cameras, examines this trend.
In the 1980s, huge strides were made in oil monitoring techniques that enabled users to identify specific components within a piece of machinery, as lubricant marketers and original equipment manufacturers sharing lubricant additive composition and component metallurgy respectively. These databases allowed wear trends to be built up over time, and showed exactly where wear was taking place, but also the condition of the lubricant and the amount of active ingredient still present in the product.
During this time, companies were increasingly adopting alternative strategies to improve the bottom line, with Just In Time (JIT) manufacturing practices becoming commonplace. Unfortunately, many were finding out the hard way, that JIT manufacturing was fine when it worked according to plan, but when breakdowns happened, it was not only production that stopped, but also customer deliveries came to an abrupt halt, with disastrous financial consequences.
Wind the clock forward 40 years and many of the manufacturing strategies introduced back in the 1980s are etched into industry practice and taken for granted. Holding large stocks of raw materials and finished product doesn’t make for good fiscal policy, and holding replacement parts and equipment for production lines is also an expensive practice that must be balanced with the likelihood of component failure.
Condition monitoring is a multi-faceted practice in today’s industrial environment. As well as oil monitoring, vibrational and thermal analysis can reveal a lot about a piece of equipment and its condition. More recently, huge strides in acoustic camera technology
have enabled maintenance engineers to obtain accurate data from plant equipment, helping to avoid catastrophic failure.
With Fortune 500 companies still losing
hundreds of billions of USD every year due to unscheduled breakdowns, clearly there is still a lot of work that needs to be done to improve production and reduce downtime.
For this reason, Teledyne FLIR, a leader in the research and development of thermal and acoustic imaging cameras, have introduced a new range of handheld devices that provide the maintenance engineer with instant, easy to understand data regarding the condition of equipment and plant. A big advantage of these handheld portable devices is that they are non-invasive; in other words monitoring takes place without production being affected or halted.
The latest range of instruments includes the FLIR E96 advanced thermal imaging camera. It represents the top-of-the-range model in the FLIR Exx range and contains several advanced features to make life easier for the user. It has the highest IR resolution of any model, 640 x 480px, and a larger, 1-8x continuous digital zoom.
The FLIR E96 camera also has a thermal sensitivity of 30mK (at 30°C with a 42° lens) and can measure temperature to an accuracy of ±2°C/2%, supporting the following temperature ranges:
• -20°C to +120°C
• 0°C to +650°C
• 300°C to 1500°C
The UltraMax® Enhancement function can be used to increase the number of measurement points to 1.2 megapixels. The function captures a series of radiometric images, which are combined without compromising data, using an algorithm and FLIR analysis software. This function is particularly useful when inspecting small or distant components as it increases the camera’s distance-to-spot ratio.
Of course, any engineer will tell you that taking one reading at a single point in time doesn’t really tell you very much about the condition of a component. Trend data is therefore very important, and by taking regular weekly or monthly readings, abnormalities can be identified and explored further. To this end, FLIR have introduced on board software that enables users to establish a set route of inspection. Termed ‘Route Creator’, it allows an experienced engineer who is familiar with the manufacturing process to load the route into the camera and then people with less experience can simply follow the instructions on the camera to carry out a full inspection on a regular basis, allowing experienced
personnel to conduct other duties.
‘Route Creator’ also allows users to add reference images to a survey, so thermographers can always see the original thermogram to match their current images precisely, which is hugely important for the analysis of thermal images when trending.
However, the FLIR E96 is just one of a vast range of thermal imaging cameras from FLIR. There are cameras to suit every application and every budget.
It is not only in thermography where huge advancements have been made. Condition monitoring using acoustic techniques is now increasing commonplace in industry. The techniques can be utilised to assess the condition of moving parts, as components such as bearings, gears, pumps and motors emit very specific frequencies of sound as they operate. Abnormalities in those sounds can indicate mechanical problems that need addressing. Acoustic cameras can also be used to detect leaks from gaseous systems. Most industrial facilities will have compressed air lines running around site to operate presses or pneumatically operated machinery. A fortune is wasted every year by compressed air escaping through leaks in centralised systems. As the compressor compensates for these leaks, it uses additional electricity, resulting in higher energy bills and a detrimental
carbon footprint for the company. The latest handheld acoustic camera from FLIR is the FLIR Si2-LD.
Following hard on the success of its predecessor, the Si124, the latest model can detect leaks down to 0.0032 litres per minute at a distance of 2.5 metres. Even at a distance of 10 metres the sensitivity is an impressive 0.05 litres per minute. Difficult to reach areas of a production plant are often dark or dimply lit. For this reason, the FLIR Si2 comes complete with two extremely powerful LED lights that illuminate the area, allowing specific gas lines to be identified and analysed.
These are not the only benefits the new camera brings to the party: the operator can view the results on a sharper, brighter fiveinch 1280 x 720 screen which brings alive the images captured by the 12MP camera with its 8x zoom lens.
A key feature of the FLIR Si2 is the camera’s ability to not only detect the gas but to quantify the leakage rate and calculate the economic penalty. Termed ‘Industrial Gas Quantification’, the incorporated software can calculate financial losses for a variety of gaseous systems including ammonia, nitrogen, helium, hydrogen, argon, carbon dioxide and compressed air.
To out more about the extensive range of thermal and acoustic imaging cameras from FLIR, visit their website. flir.co.uk
Manufacturers often struggle to reconcile manual processes with digital insights. DataFlowIQ –specialist in data-driven manufacturing – examines the potential of digitising manual production environments.
In an era where digital transformation drives efficiency across industries, manufacturing faces a unique challenge: bridging the gap between manual processes and the digital insights needed for operational excellence. While much focus has been placed on automation, there is untapped potential in digitising manual production environments. A well-implemented Manufacturing Execution System (MES) can provide deeper insights, uncover root causes of delays, and enable smarter decision-making on the shop floor.
Manual production environments rely heavily on human input and expertise, but this reliance can make it challenging to track real-time progress, identify inefficiencies, and react quickly to disruptions. Traditional paper-based workflows and siloed data exacerbate these issues, leading to:
• Delayed responses
• Limited insight into root causes
• Suboptimal resource use
These challenges highlight the need for a centralised platform to capture, visualise and analyse shop-floor data in real time.
An MES bridges the gap between manual shop-floor activities and actionable insights. It combines data captured through human input with automated data from IoT-enabled devices to provide a comprehensive view of operations. Key capabilities include:
1. Real-time data capture
MES solutions digitise task tracking, machine performance monitoring, and energy usage. Operators log activities while IoT sensors automatically monitor parameters like energy consumption or machine status, ensuring accurate and consistent data.
2. Root cause analysis
Data captured through the MES provides
a clear picture of inefficiencies. Tracking downtime reasons, for example, helps manufacturers identify recurring issues—whether equipment-related or process-driven— and address them systematically.
3. Enhanced visibility Dashboards and live reports give managers a holistic view of production. Trends and anomalies can be identified quickly, enabling proactive decision-making.
4. Energy and resource efficiency
Sustainability is a growing priority. By monitoring energy consumption through IoT sensors, manufacturers can identify optimisation opportunities, such as reducing idle machine time or rebalancing resourceintensive tasks.
Adopting an MES in a manual production environment doesn’t have to be daunting. To ensure a smooth transition:
Assess Current Processes: identify inefficiencies or data gaps where an MES can provide value, such as downtime tracking or energy monitoring.
Start Small: pilot the system on a single production line or shift to adapt and refine the approach before scaling up.
Engage the Workforce: operators are key in manual production. Involve them in the process, provide training, and emphasise how the MES supports their work rather than replacing it.
Integrate Seamlessly: choose an MES that integrates with existing systems, such as ERP or quality management tools, to avoid creating data silos.
MES solutions in manual production
environments are enablers, not replacements. They enhance human expertise with data-driven insights, combining manual input with automated data from IoT devices. This blend allows manufacturers to achieve greater efficiency and resilience while maintaining the flexibility that manual processes often provide.
Digitising manual production is no longer a question of “if” but “how.” The right MES can transform shop-floor operations, providing the tools to achieve better visibility, address inefficiencies and support sustainability goals.
For manufacturers seeking such a solution, DataFlowIQ’s MES, OpsIQ, offers a practical and scalable platform. Combining real-time data capture, root cause analysis and energy monitoring, OpsIQ bridges the gap between manual workflows and digital decision-making. By integrating IoT-enabled automated data capture with intuitive operator tools, OpsIQ exemplifies how MES can transform operations while empowering the workforce.
Manufacturing leaders who embrace this approach will not only improve their operations but also lead the way toward a more sustainable and competitive future.
dataflowiq.com
Within additive manufacturing (AM), next generation machines are pushing the boundaries of what is possible. Dr Filomeno Martina, CEO and co-founder of WAAM3D, examines wire arc additive manufacturing (WAAM) and the capability of next generation machines to improve supply chains.
AM is an important tool for manufacturers looking to achieve more resilient supply chains, thanks to its ability to create customisable components that can be printed locally, with a high degree of material utilisation, minimum fixed costs and environmental benefits. Metal additive manufacturing in particular is growing at a significant pace and has come a long way since the first patent was granted for the manual deposition of superimposed layers of metal by arc welding in 1925 . The sector was valued at US$ 2.90 billion in 2022 and is expected to reach around USD 40.1 billion by 2032, growing at a CAGR of 30.3% from 2023 to 2032 .
When it comes to creating medium- to large-scale metal components, WAAM has been shown to demonstrate significant potential for time, cost and environmental savings in both component fabrication and repairs. At present, advanced materials and machine learning in WAAM are being explored, alongside technological convergence, to maximise the processes’ potential and optimise efficiencies.
WAAM can significantly reduce the amount of material wasted on component creation compared to traditional forging; for example, the BTF ratio for aero engine components can be as high as 25 , and WAAM can reduce that ratio to <2. WAAM has long been used to repair structures, extending the life of components, and delivering significant energy and CO2 emission savings.
WAAM also reduces pre-machining and spare part wastage and requires no tools – apart from the clamps needed to fix the starting feedstock – so design changes can
be made whenever needed, eradicating additional geometry waste. It also opens the door to on-demand manufacture, helping process, control and plant engineers to resolve spare part production and repair issues, quickly and as cost-effectively as possible.
WAAM3D is pleased to be taking mediumto large-scale WAAM production forwards with the launch of its next-generation, metal 3D printing, fully integrated system – RoboWAAM® XP (which has a build envelope of 2 x 2 x 2 metres and a maximum payload of 2.1 tonnes). Compared with the company’s existing WAAM systems, the latest development is up to five times faster, thanks to patented Cold-Wire Metal Inert Gas (CWMIG) welding technology. A genuine build rate in excess of 100 kg per day is now possible without compromising on quality. This increased productivity reduces lead times for customers and cuts operating costs by at least 50% because of the highly energy-efficient deposition technology.
When manufacturing parts from steel, the RoboWAAM® XP system has a deposition
rate of up to 15 kg/h, in comparison with the existing RoboWAAM Advanced system that deposits 4 kg/h. Substantial productivity improvements are also achieved when manufacturing parts from aluminium, titanium, nickel, nickel aluminium bronze and Invar. To demonstrate the speed and versatility of the 8-axis RoboWAAM® XP system, WAAM3D has built a slurry agitator, T-section and rocket stage. The three parts demonstrate the use of a range of materials, show repeatability of ±0.05 mm and savings in both cost and lead times.
For those manufacturers wanting to build in more resilient supply chains, this next generation of WAAM machines opens the door to even more cost-effective and sustainable medium- to large-scale metal component fabrication. waam3d.com/hardware/robowaam-xp
Baker R. (1925), Method of Making Decorative Articles, U.S. Patent US1533300A. VoxelMatters, (2023), Metal AM, A comprehensive analysis of the state of the market and 10-year forecast.
Allen J. (2006), An Investigation into the Comparative Costs of Additive Manufacture vs. Machine from Solid for Aero Engine Parts.
Elevate your manufacturing potential with the cutting-edge RoboWAAM® XP system, driven by the groundbreaking Cold-Wire Gas Metal Arc (CWGMA) technology.
Delivering exceptional deposition rates of up to 15 kilograms per hour, it redefines efficiency without sacrificing precision or quality.
Benefits:
• Patented CWGMA process for 5 x process speeds
• Includes also MIG, MAG, CMT
• Printing more than 100 kg in a day is now a reality
• Build parts of up to 2 m x 2 m x 2 m (configuration dependent) and 2,100 kg
• Celebrate geometrical complexity with 8 axes of motion
• Alloys of iron, aluminium, nickel, and copper
• Energy, space, marine, mining, repair
• Monitoring of melt pool, wire feed speeds, current, voltage, pre-deposition temperature, layer height and shape, air quality
• User friendly software package with WAAMPlanner® for tool path planning and WAAMCtrl® for monitoring, ensuring a uniform workflow across all WAAM3D integrated systems.
• Discover the next level of manufacturing with RoboWAAM® XP
• Boost production capabilities, achieve exceptional quality, and transform large-scale fabrication with ease
• Embrace the future of manufacturing excellence.
Switchgear is crucial for the control and protection of power systems. Kraus & Naimer, one of the oldest manufacturers of electromechanical switch technology, talks to MEPCA about its apprenticeship programme, the use of its switches on an historic vessel, and more.
Kraus & Naimer is a market leading switchgear manufacturer. Founded in Vienna, Austria in 1907 by Franz Kraus and Lorenz Naimer, the company now has six factories and operates worldwide. In the following Q&A, the company shows how it strives for innovation without losing sight of its origins.
What is the most interesting or unusual application of a Kraus & Naimer
We have supplied switches to many different industries and sectors over the years. One application that we were particularly pleased to be able to help with was the World’s Last Sea-Going Paddle Steamer, the Waverley.
Named after Sir Walter Scott’s first novel, built on the Clyde in 1947, the Waverley replaced the 1899 Waverley that sunk off Dunkirk during active war service in 1940.
The main engine telegraph and its bell are located both in the engine room and on the navigation bridge. A responsible officer from each of the departments handles the telegraph from these locations.
An additional telegraph was required for use in the event of a problem with the main telegraph, with the parts being sourced from various locations to keep the visual authenticity. This in turn created the need for a one-off switch for the selection by the bridge officer to indicate the direction and speed required of the main engine. In conjunction with the Chief Engineer, our inhouse technical team were able to design a bespoke 12 position control panel switch to meet the requirement, and we were happy to be able to donate the finished switch to enable this historic vessel to continue offering unique cruising experiences between the picturesque Scottish Isles.
How committed is Kraus & Naimer to innovation and the development of new
Kraus & Naimer have always been at the forefront of electromechanical switch technology. From pioneering the use of bakelite during the early 1900s to the introduction of world’s first modular cam switch (model C15) to the market in 1948, we have been market leaders.
The smallest cam switch in the world (model CA4N) also comes from Kraus & Naimer, so you can see innovation has always played a strong part. Even if the focus is on manual operation of the switching devices, trends in the industry such as automation and digital applications are also closely monitored at Kraus & Naimer.
We have always maintained our pioneering spirit and the pursuit of perfection. We are happy to accept the challenges of the future and continue to rely on technology, specialisation and know-how to provide new products and innovation to meet our customers’ increasingly complex requirements around the world.
Kraus & Naimer held its 3rd annual Apprenticeship Day in October. How important are apprenticeship programmes to Kraus & Naimer?
Extremely important to us as a company.
The apprenticeship scheme takes place in our headquarters in Austria every year and always attracts a high uptake. We strongly believe that today’s apprentices are our skilled workers of tomorrow – in many cases they eventually become our department heads. It is particularly important for us to provide apprentices with the best possible support on their professional path.
Our goal is to keep motivated and well-trained employees in the company permanently after completing the skilled worker examination by providing support for higher qualifications during their educational path towards the master craftsman examination or HTL (Höhere Technische Lehranstalt) engineer.
More than half of former apprentices are still employed by the company in key positions.
krausnaimer.com/gb_en
Conveyor systems form the backbone of process automation in manufacturing and production. AdaptTech, the sole distributor of mk products in the UK and Ireland, introduces two improved conveyor products.
mk has been working intensively to further develop its conveyor technology offering. With a range of innovative products and expansions, the company is responding to the growing needs of the market. Its latest developments are focused on enhancing efficiency, versatility, and environmental sustainability.
Discover more about the launch of the new mk products below; all designed to offer businesses maximum flexibility and reliability in process automation.
mk has given its tried and trusted GUF-P MINI small conveyor an overhaul.
The GUF-P MINI small conveyor series offers versatile solutions for transporting small and light products in systems with limited installation space. With widths ranging from 50 to 300 mm and lengths from 350 to 3,000 mm, it provides flexibility and can be used in reverse, accumulated and cycle operations.
Thanks to its low installation height of circa 35 mm including belt, the GUF-P MINI is ideal for the immediate output of products in applications, such as injection moulding machines or automatic small parts stores.
The small conveyors are equipped with a head or lower belt drive tailored to a variety of speed and load requirements as standard. The right motor is available for every application, from asynchronous AC motors, to 24 V DC motor variants, and 48 V stepper motor options.
The crowned driving and idler rollers simplify belt adjustment and ensure that the conveyor belt runs in the centre of the conveyor frame.
The T-slots running along both sides with a 10 mm slot width enables easy integration of the conveyors into existing machine frames or attach stands, side rails, initiators and other accessories via standard T-nuts.
mk has expanded its workpiece carrier system, Versamove, with fully electric functional units. For efficient and environmentally friendly process automation, the lift-and-transfer conveyor HQZ, the lift-and-rotate unit HDE, the lift-and-locate unit PE, and the stoppers SU/SD are now also available in fully electric variants. This completely eliminates the need for a compressed air supply and means they can be retrofitted into existing Versamove systems with ease.
Benefits of fully electric modules:
• Environmentally friendly
• Pre-assembled cabling (plug-and-play)
• Energy efficiency
• Quiet operation compared to pneumatic alternatives
• Low-maintenance
• Flexible control
• Quick commissioning
• No compressed air required
Versamove standard is the most compact of the Versamove systems. It offers fully electric functional units and affordable curve modules. Due to the specially developed 45 mm aluminium profile for the basic structure of the entire system, it is also compatible with other systems and workpiece carriers available on the market.
Versamove standard transports workpiece carriers from 240 x 240 to 400 x 400 mm, with custom dimensions or dimensions in 80 mm intervals possible. The system can move
pallets weighing up to 40 kg. The special feature of this system is its affordable curve modules, which are equipped with a flattop chain or, for compact curves in tight spaces, with a round belt.
As the sole distributor of mk products in the UK and Ireland, AdaptTech is the only place that these new products can be purchased. Visit their website now to find out more and to download a free brochure for each of the products.
adapt-tech.co.uk
Nylon is a material that is becoming increasingly popular across a range of industrial applications, from vehicles to fashion and interior design. Permabond, developer and manufacturer of engineering adhesives, examines the inherent challenges of bonding nylon.
Nylon’s versatility, affordability and excellent chemical resistance make it a highly sought after material in industry, which has presented adhesives manufacturers with a challenge – coming up with a product that can effectively bond this material. Firstly, what is nylon and what makes it so hard to bond?
The word ‘nylon’ has become a catch-all for different kinds of polyamide, a synthetic, thermoplastic polymer that was patented in the 1930s by DuPont and given the name ‘Nylon.’ The original DuPont product was PA6, whereas now there are other forms of polyamide such as PA6.6 and PA12, which, being pedantic, technically aren’t ‘Nylon’ – but industry calls them as such regardless. The different numbers of PA refer to the number of carbon atoms present in the material’s repeating unit, with higher numbers being harder to bond with adhesives.
Nylon has the characteristics of being both hydrophobic and hygroscopic. The former means that a liquid won’t spread out evenly on its surface, instead bunching together in small pools, and is a result of nylon’s low surface energy. The latter pertains to nylon’s tendency to absorb moisture from the air around it. Both of these factors present problems for an adhesive – a hydrophobic surface is very difficult for an adhesive to wet, and therefore effectively bond. A hygroscopic material, absorbing moisture as it does, further adds to this problem by making the surface inherently ‘wetter,’ competing with any adhesive present.
Therefore, before bonding nylon extensive surface preparation measures are usually needed. Wiping the surface before bonding isn’t enough, as moisture will swiftly return
to the surface thereafter. Abrading or grit blasting are usually required to remove the issue of hydrophobicity, whereas putting the nylon into an oven at 60°C for several hours (or even better, overnight) deals with its hygroscopicity by drying out the nylon from within. The alternative to doing all of this preparation is to use advanced engineering adhesive, Permabond TA4550.
There’s a reason why TA4550 is considered a revolutionary product. Whereas other adhesives for bonding nylon have all required some form of the aforementioned laborious surface preparation before they can be used, the TA4550 doesn’t – in fact, the surface needs only to be wiped beforehand. Not only this, but TA4550 achieves a far stronger bond on nylon than other products, often resulting in substrate failure of the nylon during product testing.
The way in which this structural acrylic adhesive is able to
achieve such an outstanding bond strength on many forms of nylon – 6, 6.6 and even on 12 – is via a process known as interdiffusion. Once TA4550 has been applied, it effectively ‘swells’ the surface of the nylon and causes a reaction whereby the polymer chains from the adhesive intermix with those of the nylon, resulting in a truly remarkable adhesive bond that offers incredible strength and flexibility. It achieves a peel strength of between 250 and 270 N/25 mm and an elongation at break of 130%.
TA4550 not only bonds nylon exceptionally well, but also many metals used in manufacturing, such as stainless steel, as well as the majority of plastics. For manufacturers and engineers working with bonding nylon of any kind, this adhesive really is one to have in the toolbox. Further details of Permabond’s array of adhesives can be found on its website.
permabond.com
Lifting safety professionals and people using or procuring lifting equipment from a range of industries, including Manufacturing and Engineering, gathered at Olympia in London 16th to 17th October 2024 for a busy and bustling LiftEx 2024.
Visitor registrations to the flagship event of the Lifting Equipment Engineers Association (LEEA) were higher than ever and the event generated discussions and content ideas, which will be explored further by LEEA and supporting partners over the coming months.
RiConnect UK, the Headline Sponsor of LiftEx 2024, was demonstrating its powerful software, “RiConnect”, to streamline equipment management and ensure regulatory compliance and traceability. This innovative solution seamlessly integrates with digital tags and NFC (Near Field Communication)-enabled mobile devices. Speaking at the show, the company’s Sales Director, Leanne Whitehurst-Maiden, said: “LiftEx is really important to us. It’s a flagship event for LEEA, which is also very important to us for guidance and we rely on it for technical assistance. We’d like to continue with sponsorship in the years to come because we really believe in LEEA and in LiftEx.
“As a company we do about 52 exhibitions every year globally. LiftEx is different because of the people that we meet and the quality of the leads. Every important company within the Lifting Industry is here, so it is a fantastic event with great networking opportunities. Brand awareness is key for us as we are still a relatively new
company and want to get our name out there, so being associated with LEEA and LiftEx is crucial.”
Yoke Lifting manufactures lifting fittings for chain, wire rope and webbing slings. Speaking at the show, the company’s Managing Director, Andy Charlesworth, said: “LiftEx offers us, as a manufacturer, the opportunity to showcase new innovations that we have brought out, as well as standard products. It’s very much in tune with our business, being focussed solely on the Lifting Industry. It gives us an opportunity to discuss lifting matters in detail with other experts and to see end users.
“We decided we wanted to be a sponsor of the event this year because we are big believers in LEEA and all that it can do. We are a global brand and we recognise that LEEA is also global and out there promoting
safety in the industry. It’s very important for us that we get that message across: that we can do things the correct way, working with like-minded people to provide the industry with what it needs.”
Sponsoring exhibitor Rope and Sling Specialists (RSS) was able to showcase the lifting equipment it manufactures, supplies and hires. It also provides servicing and repair as well as proof load testing and thorough examination. Its Operations Director, Paul Glover, commented: “We’re the largest independent lifting company, and as an independent it’s important to support LEEA and to expand our customer base with new and existing customers. We’ve looked at other exhibitions but LiftEx is lifting specific and we get to target our lifting customers, so it’s very important that we come here. We need to let people know we are expanding our depot locations – from 12 to 14 next year – and our offering.”
In addition, the LEEA Accredited Training Scheme (ATS) seminars delivered well-attended, free training sessions and presentations.
LEEA thanks the LiftEx 2024 visitors, exhibitors, speakers and sponsors for their support and looks forward to LiftEx 2025, which returns to the Exhibition Centre in Liverpool on 18-19 November. Watch this space for details, and visit the LiftEx 2024 photo gallery.
events.leeaint.com/liftex-london-2024
From 31st March to 4th April 2025, the world’s leading trade fair for industrial technology, HANNOVER MESSE, will transform the Hannover Exhibition Grounds, Germany into a global hub of innovation and sustainability. Read on for why it is an unmissable event.
Under the theme “Energising a Sustainable Industry,” HANNOVER MESSE will spotlight the technologies and strategies driving digital transformation, smart manufacturing, and green energy adoption across industries.
A comprehensive showcase of innovation
HANNOVER MESSE 2025 will feature over 4,000 exhibitors, presenting cutting-edge solutions across diverse sectors. Highlights include:
1. Smart Manufacturing: explore advancements in automation, robotics, and sensor technology that are revolutionising production and logistics. This exhibition area will demonstrate how intelligent systems improve efficiency and adaptability in industrial processes.
2. Digital Ecosystems: the Digital Transformation Conference Stage will debut this year, offering a platform for exploring topics such as artificial intelligence, big data, cloud computing, and cybersecurity. Visitors will witness practical applications of these technologies, from machine networking to real-time data-driven decision-making.
3. Hydrogen and Energy Innovations: with over 500 exhibitors, the focus on green hydrogen as a sustainable energy source will take center stage. Presentations will highlight hydrogen’s versatility, including its applications in mobile systems, industrial production, and renewable energy integration.
4. Engineered Parts & Solutions: this segment will showcase breakthroughs in materials, additive manufacturing, and lightweight design, which are paving the way for new possibilities in industrial engineering.
5. Future Hub: a dedicated space for startups and research initiatives, the Future
Hub will highlight emerging technologies, including quantum computing and sustainable solutions.
This year’s Partner Country, Canada, will highlight its innovative capabilities under the theme “The Future’s Here.” Canadian companies will demonstrate leadership in fields such as renewable energy, artificial intelligence, and eco-friendly manufacturing. Through this collaboration, HANNOVER MESSE emphasises the importance of international partnerships in advancing industrial transformation.
HANNOVER MESSE 2025 will feature a robust conference program, including sessions led by 1,600 expert speakers. The event will address pressing industry topics, such as:
• Sustainability and carbon-neutral production.
• Industry 4.0 and the role of digital twins in optimising manufacturing processes.
• The integration of additive manufacturing into supply chains.
New for 2025, the Masterclasses will offer hands-on workshops and deep dives into specific technologies, making it an essential learning opportunity for industry professionals.
Sustainability will remain at the core of the event. Key themes include the deployment of green hydrogen to replace fossil fuels, advancements in energy efficiency, and innovations enabling carbon-neutral production. Digital twins—virtual replicas of physical systems—will also be showcased
for their ability to enhance efficiency, minimise costs, and drive eco-friendly industrial practices.
HANNOVER MESSE also highlights the importance of cybersecurity in the industrial context. The Industrial Security Circus will demonstrate cutting-edge solutions for protecting systems from cyber threats—a growing concern in digitally connected industries.
The event offers unparalleled opportunities to:
• Discover: see ground-breaking technologies shaping the future of industry
• Learn: gain actionable insights from expert speakers and hands-on sessions
• Network: connect with global professionals, innovators, and policymakers
• Collaborate: explore potential partnerships and cross-industry synergies
HANNOVER MESSE 2025 stands as the ultimate destination for those seeking to understand and embrace the next wave of industrial transformation. Whether an industry leader or an aspiring innovator, this event offers tools and inspiration to shape a sustainable future. Register for a complimentary ticket now using the code qMcvM.
hannovermesse.de/en/
“attendees
exhibitors
This has been absolutely fantastic—far beyond our expectations! The turnout has been incredible, with more visitors than we ever anticipated. We’ve attended other shows across Europe in recent months, and this one is by far the largest. The energy has been amazing right from day one, with a constant flow of enthusiastic visitors. We’re thrilled with the outcome!
Agnieszka Radecka Regional sales manager, TME
Meet the power behind UK manufacturing industry and see live demonstrations and new product launches of machine tools & tooling, electronics, factory & process automation, packaging & handling, labelling & marking, 3D print technology, test & measurement, materials, composites & adhesives, rapid prototyping, ICT, drives & controls, plastics & polymers and laboratory equipment.
Free industry seminar programme available online. The exhibition is free to attend, free to park and easy to get to. Doors open at 9.30am on 4th February.
Smart Manufacturing Week is set to make its grand return 4th to 5th June 2025 at the NEC in Birmingham, promising to be the ultimate festival of advanced manufacturing & engineering.
As the UK’s premier event for manufacturing and engineering professionals, this year’s Smart Manufacturing Week is expected to attract over 13,500 attendees and feature 450+ exhibitors, showcasing cutting-edge technologies, solutions and insights to drive the industry forward.
The event will once again unite the sector’s brightest minds, forward-thinking businesses and key stakeholders under one roof, offering a unique platform for collaboration, inspiration and innovation. Smart Manufacturing Week serves as the epicentre for a wide range of themes that define the future of the manufacturing and engineering sectors: innovation, digital transformation, maintenance, sustainability, people & skills, cyber security, supply chain, automation & robotics, industrial data, and AI.
Smart Manufacturing Week is renowned for its comprehensive approach to addressing the challenges and opportunities facing modern manufacturers. Across its four colocated sub-shows — Smart Factory Expo, Design & Engineering Expo, Maintec, and Drives & Controls — attendees can explore a diverse array of cutting-edge solutions and gain insights from industry leaders.
The exhibition floor will host more than 450 exhibitors, providing visitors with a first-hand look at ground-breaking technologies and services designed to enhance productivity, sustainability, and competitiveness. From intelligent automation systems and predictive maintenance tools to advanced robotics and transformative industrial data applications, Smart Manufacturing Week delivers something for every professional in the sector.
In addition to the exhibition, Smart Manufacturing Week will also host several significant events during the same week. The Manufacturer Top 100 Award ceremony, celebrating the heroes of UK manufacturing and recognising their contributions to the sector, will take place on the show floor. Furthermore, the Manufacturing Digitalisation Summit will focus on the application of digital technologies to enhance the processes, efficiencies, and outcomes within the manufacturing industry, making it a must-attend for those keen on digital transformation.
Smart Manufacturing Week 2025 stands out for its comprehensive approach to the critical issues driving the future of manufacturing. Through dedicated solution and content theatres, attendees will explore cutting-edge advancements in digital manufacturing, highlighting how businesses are harnessing technology to maintain a competitive edge in a rapidly changing marketplace.
Sustainability and maintenance will also take centre stage, with solutions focused on improving energy efficiency and implementing innovative maintenance strategies for enhanced operational performance and a greener future. In conjunction with this, Smart Manufacturing Week have partnered with Forest Nation to help make the event carbon neutral; planting one tree for every attendee and exhibitor to the show.
Sessions will address workforce development, with a focus on upskilling teams and creating digital talent pipelines, as well as safeguarding operations, global supply chains, automation, robotics and AI.
Smart Manufacturing Week goes beyond
a traditional trade show by fostering meaningful connections among attendees. Whether it’s through informal meet-ups, exclusive networking lounges, or engaging roundtable discussions, the event offers countless opportunities for professionals to exchange ideas and collaborate on solutions to industry challenges.
The team behind Smart Manufacturing Week is committed to curating a world-class event that empowers the manufacturing and engineering communities. By gathering the sector’s leaders, innovators and disruptors, the event offers a unique platform to shape the future of manufacturing and engineering. Don’t miss your chance to be part of the conversation in 2025. Register your interest now and stay ahead of the curve as registration officially opens very soon. For more information, visit the Smart Manufacturing Week website.
smartmanufacturingweek.com
Midlands 3D Printing
T: 01785 594389
E: sales@midlands3d.com
W: www.midlands3d.com
Fibet Rubber Bonding (UK) Ltd
T: 01282 878200
E: sales@fibet.co.uk
W: www.fibet.co.uk
CEMBRE Ltd
T: 01675 470 440
E: sales@cembre.co.uk
W: www.cembre.com/en
Nord
T: 01235 534404
E: GB-sales@nord.com
W: www.nord.com
Schmersal UK Ltd
T: 01684 571980
E: uksupport@schmersal.com
W: www.schmersal.co.uk
T-Mark
T: 0330 153 8320
E: sales@t-mark.co.uk
W: www.t-mark.co.uk
Jacob UK Ltd
T: 01694 722841
E: sales@jacob-uk.com
W: www.jacob-group.com/uk
Titan Enterprises Ltd
T: +44 (0)1935 812790
E: sales@flowmeters.co.uk
W: www.flowmeters.co.uk
Silverson Machines Ltd
T: +44 (0)1494 786331
E: sales@silverson.co.uk
W: www.silverson.co.uk
Brainboxes
T: + 44 (0) 151 220 2500
E: sales@brainboxes.com
W: www.brainboxes.com
Intoware
T: 0115 977 8969
E: hello@intoware.com
W: www.intoware.com
Axair Fans UK Limited
T: 01782 349 430
E: sales@axair-fans.co.uk
W: www.axair-fans.co.uk
ESI Technology Ltd
T: +44 (0)1978262255
E: sales@esi-tec.com
W: www.esi-tec.com
KUKA Robotics UK Ltd
T: 0121 505 9970
E: sales.uk@kuka.com
W: www.kuka.com
IFM Electronic
T: 020 8213-0000
E: enquiry.gb@ifm.com
W: www.ifm.com
PLUS Automation Ltd
T: 0121 58 222 58
E: Sales@PLUSAutomation.co.uk
W: www.PLUSAutomation.co.uk
BITO Storage Systems Ltd.
T: 02476 388 852
E: Info.uk@bito.com
W: www.bito.com
AMETEK Land (Land Instruments
T: +44 1246 417691
E: land.enquiry@ametek.com
W: www.ametek-land.com