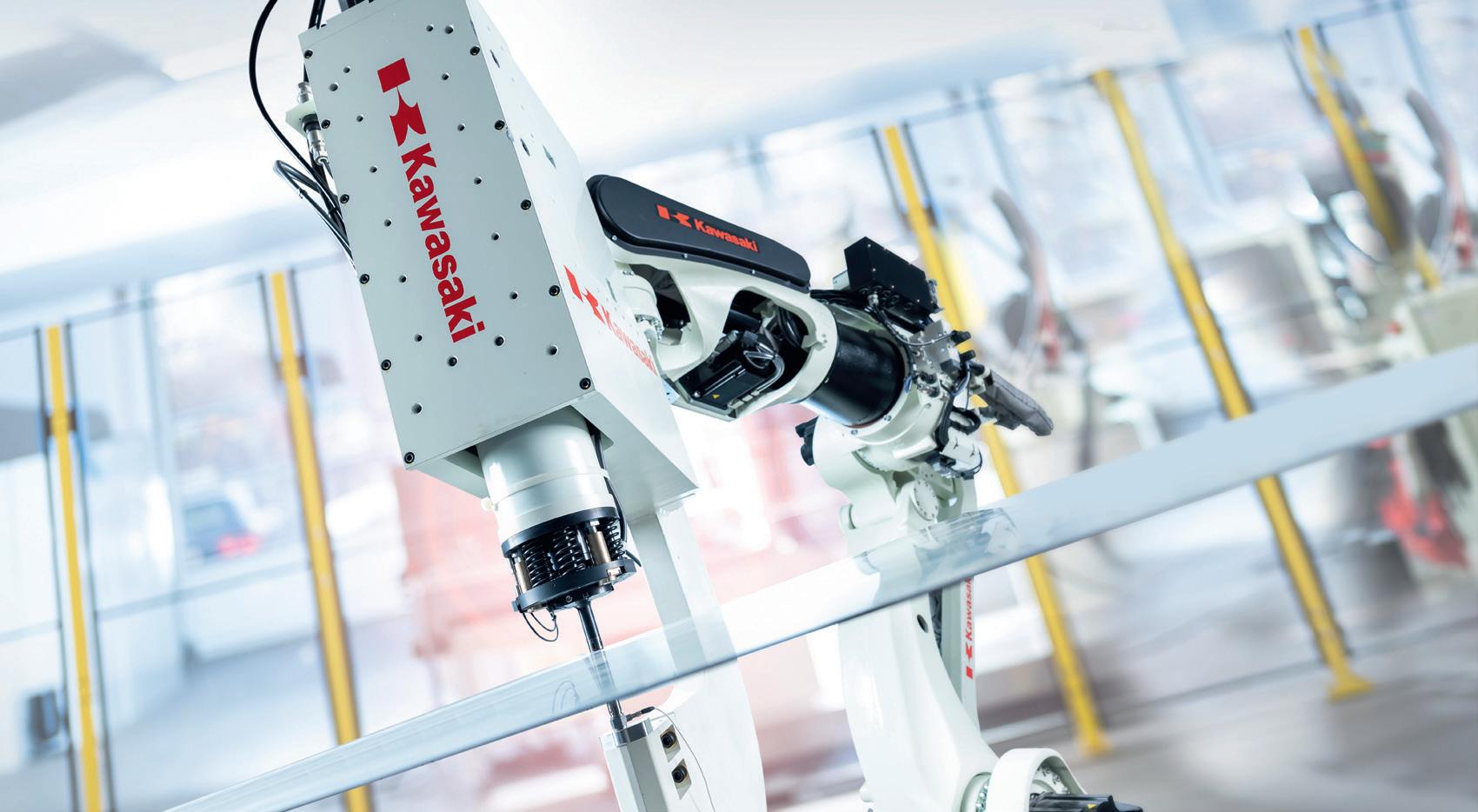
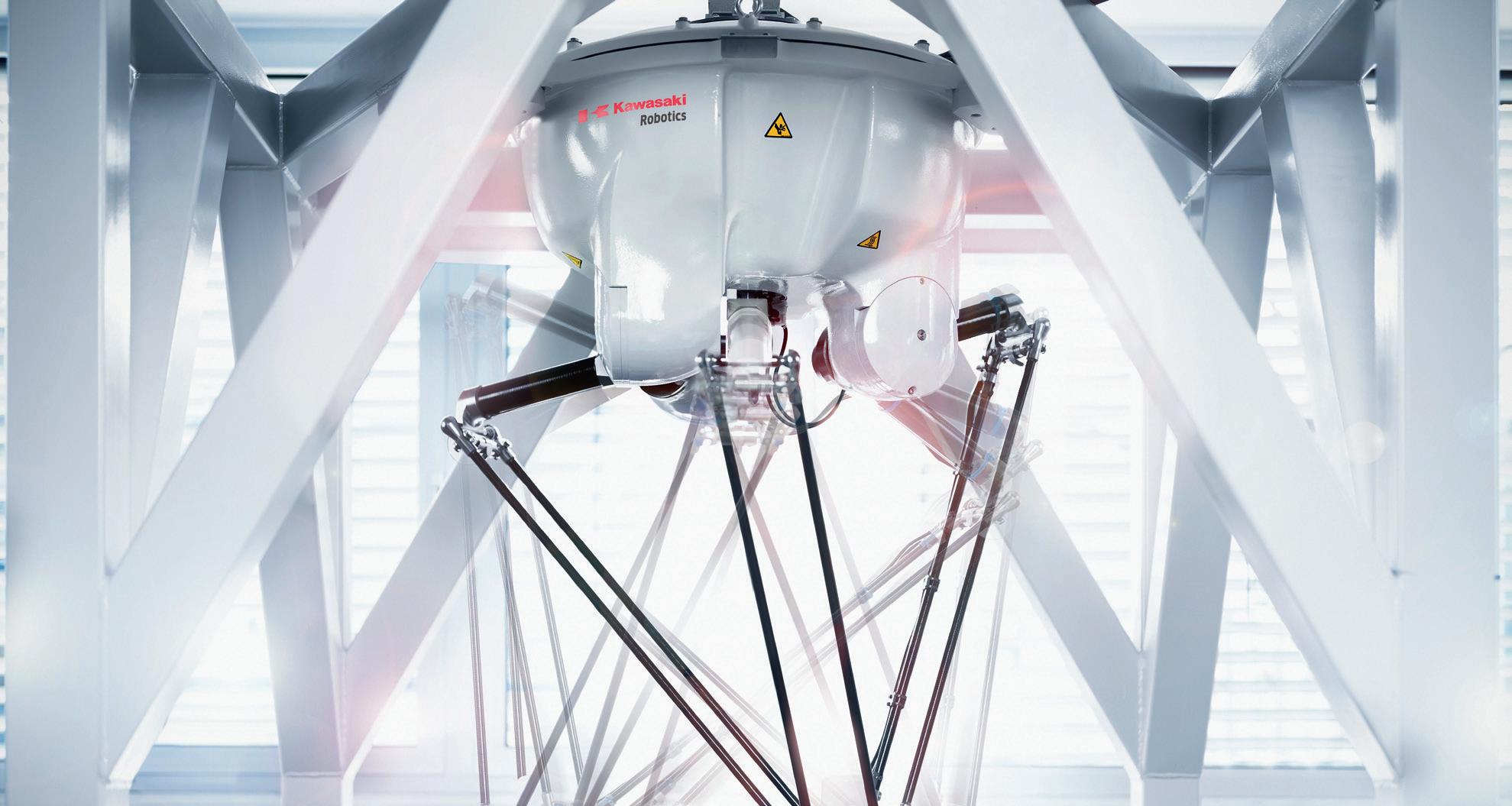

a highly flexible control cabinet-free automation solution robust, water- and dust-proof design (IP67 protection rating) plug-and-play with pluggable function modules for IPC, coupler, I/O, drive, relay and system standardized connectors for transmission of data and power EtherCAT communication tried-and-tested connector for the field level reduces engineering work high time and cost savings integrated diagnostic functions
Find out about
world of control-cabinet free automation!
Editor
Chris Callander chrisc@cimltd.co.uk
Publication Manager
James Davies jamesd@cimltd.co.uk 01795 509105
Account Manager
Hannah Moody hannah@cimltd.co.uk 01795 509115
Account Manager
James Burke jb@cimltd.co.uk 01795 509105
Design & Production
Grant Waters Grant@cimltd.co.uk
James Taylor james@cimltd.co.uk 01795 509108
Credit Facilities Manager
Lauren Sharpe creditcontrol@cimltd.co.uk 01795 509103
Sales Director
Tom Woollin tom@cimltd.co.uk
Chief Executive
John Denning jdenning@cimltd.co.uk
www.mepca-engineering.com
© 2023 TGM Publishing Limited,1st Floor, Saphir House, 5 Jubilee Way, Faversham, Kent, ME13 8GD. No part of this magazine may be reproduced or stored in a retrieval system or transmitted in any form – electronic, mechanical or physical – without express prior permission and written consent of the publisher. Contributions are invited and when not accepted will be returned only if accompanied by a fully stamped and addressed envelope. Manuscripts should be typewritten. No responsibility can be taken for drawings, photographs or literary contributions during transmission or in the editor’s hands. In the absence of an agreement the copyright of all contributions, literary, photographic or artistic, belongs to TGM Publishing Limited. The publisher accepts no responsibility in respect of advertisements appearing in the magazine and the opinions expressed do not necessarily represent the views of the publisher. The publisher cannot accept liability for any loss arising from the late appearance or non-publication of any advertisement.
Over recent weeks, several people have asked me if I think tools such as ChatGPT will put me and other technical magazine editors out of a job.
Generative AI does have the potential to assist or automate certain aspects of a technical magazine editor’s job, but it is unlikely to completely replace the role in the foreseeable future. While AI technologies, including natural language processing and generation, have made significant advancements, they still have limitations in terms of creativity, judgment, and understanding nuanced context.
Technical magazine editors are responsible for various tasks, such as curating content, ensuring accuracy, maintaining editorial standards, and making subjective decisions about the quality and relevance of articles. These tasks require a strong understanding of the subject matter, industry trends, and the target audience. While AI can generate content based on patterns and existing data, it may struggle to fully comprehend complex technical concepts or adapt to rapidly evolving trends.
However, AI can support editors in several ways. It can assist with tasks like fact-checking, grammar and style suggestions, automated formatting, and even generating preliminary drafts based on provided information. And in some instances, these AI-powered tools can also enhance an editor’s efficiency and accuracy. However, I believe the final decision-making and creative aspects of the job are likely to remain in human hands.
Ultimately, the integration of generative AI in the field of technical magazine editing is more likely to augment and streamline the editorial process rather than completely replace the role of an editor. Human expertise, creativity, and judgment are still highly valued in the editorial world and are unlikely to be replaced by AI alone.
Recalling a well-known saying, a marketing contact at a leading supplier of orange sensors put it well during a similar conversation at an exhibition recently. Knowledge is knowing that a tomato is a fruit. Wisdom is knowing not to put it in a fruit salad.
I’ve never likened my role to making fruit salad before.
Chris Callander, Editor @Mepca-magazineABB Robotics is continuing to close the global education gap in automation and prepare students for the future of work with the launch of a ready-to-use education package. Comprising a GoFa collaborative robot (cobot), teaching materials and a globally recognised technical qualification, the package is part of ABB Robotics’ global campaign to help workers thrive in a new era of au-tomation.
The ABB Robotics Education Package has been created to ensure educational establishments can provide highly skilled young people for companies looking to benefit from robotic automation. Although some 80% of global educators see automation shaping employment in the next ten years, only one in four education institutes incorporate robotics into their curriculum, according to ABB’s 2022 education survey. Barriers include the lack of teachers trained in robotics and automation and the difficulty in incorporating robotics training into the curriculum seamlessly.
The heart of the package is the Education Cell, which features a fully functional ABB GoFa col-laborative robot. Mounted on a compact tabletop, the award-winning ABB GoFa is an easy-to-use cobot that helps
students learn real-life industrial applications such as pick and place and 3D printing. Students as young as 15 can use the robot, with no need for any prior engineering knowledge, thanks to ABB Robotics’ leadthrough and ABB’s Wizard Easy Programming.
A comprehensive suite of material gives teachers everything they need to guide students through 12 lessons at basic and advanced levels, taking them from the fundamentals of robotics to more advanced applications and programming. Industrial level training material has been adapted by teachers into a student-friendly format, enabling them to easily grasp robotics concepts. A total of 56 hours of content is provided, including videos, interactive online exercises, 400 test ques-tions, and lab exercises with ABB’s RobotStudio offline programming tool, which is used by companies worldwide to plan, simulate and develop real-life robotic solutions in a virtual envi-ronment.
The third part of the package is a unique, globally recognised STEM certification for both teach-ers and students supported and
authenticated by educational research and credentialing organisa-tion STEM.org. This allows teachers to be certified by ABB and then certify their students as competent to use robots. It also provides students with an accepted qualification that can be shown to employers in over 80 countries as proof of their ability to work with robotic automa-tion.
The launch of the Education Package marks the latest step in ABB’s ongoing drive to help stu-dents develop the skills they need to thrive in a world where robots will be as common as laptops in the workplace. ABB currently works with educational institutions in over 40 countries to en-sure that students are able to learn the fundamentals of robot programming and operation.
Delegates trialling the Association of Electrical and Mechanical Trades, AEMT Training Academy at recent beta testing sessions have highlighted the ease of use and positive experience as the Association moves towards a summer launch of its new platform.
The AEMT Training Academy is a project under development with funding from Innovate UK to support a Knowledge Transfer Partnership (KTP) with the University of York. The two-year project began in 2022 and aims to transition the Association’s in-person training courses to a virtual learning and assessment environment where delegates can ‘handle’ virtual machinery and equipment.
The beta testing, which ran in January and March 2023, comes ahead of the planned launch of the first stage of the AEMT Training Academy by the summer of this year. The first stage will see the platform offer delegates an online version of the Association’s popular Ex Repair theory training course, drawing on over eight hours of video-based content backed up by interactive quizzes to track progress. The course, which covers basic concepts, the repair standard and identifying and recording data, has previously only been available in a classroom format, requiring the lecturers and delegates to travel significant distances at a significant financial and environmental cost.
Thomas Marks, Secretary and General Manager of the Association, explained:
“Our hazardous area, or Ex, courses are delivered across the globe, and historically we have delivered face-to-face training in 20 countries, to delegates from 40 countries, many of which have had to travel significant distances.
“To be able to reduce the carbon footprint and increase the accessibility to this vital training is significant and something we are delighted we will be able to do.”
Looking ahead, the team developing the AEMT Academy to focus on developing the 3D virtual twin functionality, which will allow delegates to interact with the equipment they are learning about. This is the project’s ultimate aim and will enable the virtual assessment of the knowledge and techniques taught in the training.
Mike Russell has joined KUKA Systems UK as Chief Strategy Officer and Head of R&D with a focus on developing welding portfolios and overseas channels.
With an impressive background of business development in advanced welding and a passion for cultivating strategic partnerships, Mike brings a wealth of experience and expertise to KUKA, supplemented by formidable academic credentials that include a Master’s Degree in Materials Engineering and a PhD in the ‘Development and Modelling of Friction Stir Welding’.
Mike has a proven track record of driving growth and establishing successful collaborations in diverse markets that will elevate KUKA’s presence in the international advanced welding arena. With a deep understanding of market dynamics, coupled with his innovative approach, Mike will enable KUKA to identify and capitalise on new opportunities overseas.
Jeff Nowill, KUKA Systems UK CEO, said
of Mike’s appointment: We are thrilled to have Mike on board, and we are confident that his contributions will propel our company towards greater achievements in the advanced welding solutions marketplace. His keen eye for identifying emerging trends and consumer demands will guide our company’s portfolio development, ensuring that we remain at the forefront of the industry. Advanced welding is a rapidly growing market due to several factors that have contributed to its increased demand and adoption. One of the key drivers is the advancement in technology, which has led to the development of innovative welding techniques and equipment – Mike’s proven experience and deep understanding of these techniques, their features and benefits, will enable us to navigate new, international
markets”.
Advanced welding finds application in a wide range of industries where the joining of highperformance materials is crucial, and the demand for high-quality, energyefficient welding solutions is paramount. Rotary friction welding, linear friction welding, and friction stir welding are much sought after, with demand arising from the need for stronger, lighter, and more durable materials in sectors such as automotive, aerospace, energy, construction, and manufacturing. These industries also require welding solutions that can support the transition to Net Zero manufacturing via the efficient fabrication of high-performance components and the tailoring of products by incorporating dissimilar materials. Solid phase joining processes have unique capabilities in this field.
Recent findings by the Chartered Institute of Procurement & Supply (CIPS), found that the downturn in UK manufacturing accelerated at the end of 2022. Moreover, the rate of decline was among the steepest during the past 14 years.
Companies reported that recent output had been scaled back due to declining intakes of new work and disruption caused by stretched supply chains and material shortages.
Long lead times prove to be a huge challenge for businesses attempting to source genuine parts for equipment and machinery. That’s why Obso Global has launched a new guide, which outlines five simple steps operators can take to help source and stock new and refurbished parts for production, helping to mitigate the risk of unplanned downtime and maintain productivity.
Available to download from bit.ly/ObsoPlan, the five-point plan guides operators through
the key steps to take to reduce the impact long lead times are having on businesses. It includes guidance on the importance of an operational strategy for parts procurement, developing contingency plans or using a thirdparty provider for bonded stock holding.
The plan has been compiled using insight from Obso’s experienced technical team, which has helped many customers across
the world combat the stresses of ongoing supply shortages and parts availability.
The supplier of hard-to-find and obsolete automation spare parts also plans to launch a series of blog articles discussing – from personal experience – how longer lead times and rising costs have affected the business over the past few years and what steps the team has taken to overcome this.
SICK has unveiled its nextgeneration family of large-bore hollow-shaft incremental encoders, the SICK DGS80. An innovative design concept has opened up versatile integration possibilities for the DGS80 across wideranging industrial automation applications, aided by a radically-streamlined specification process and easy installation.
The SICK DGS80 incremental encoder spans a broad range of shaft diameters up to 42mm, all within an extremely compact and rugged IP65-rated 81mm diameter housing. Starting with standard 30mm or 42mm diameter bores, the shaft size can be reduced with a large range of speciallydesigned insulated collets to ensure a secure connection to the application.
SICK’s new large bore hollow-shaft encoder family, therefore, gives end-users and machine builders the confidence of
universal machine compatibility while stocking minimal inventory. The DGS80 is also ideal for AC asynchronous motor feedback applications, capable of measuring speeds up to 3,600 revolutions per minute, with a resolution of up to 8,192 pulses per revolution. The plastic collets also offer the advantage of isolating the bearings from the motor current, ensuring long encoder life.
Installation time is kept to a minimum by a choice of two slotted encoder stator couplings that enable users to bolt the encoder at the right position onto any machinery, so there is no need to custom-make mounting brackets. Designed to Nema motor frame standards, the stator couplings also facilitate flexible mounting to the drive shaft of an AC motor. Once mounted on a shaft, the SICK DGS80’s clamping ring makes it easy to tighten the
encoder in place using a single set screw. The DGS80 is ideal for use as a replacement for existing encoders. Customers no longer need to engineer a cumbersome connection to a smaller encoder shaft; the same encoder can be adapted to many machine designs.
www.sick.com
Vision Engineering, leading provider of innovative inspection, metrology, and digital 3D visualisation solutions, has announced the launch of Mantis 3rd Gen, the latest addition to its best-selling and award-winning range of ergonomic optical stereo microscopes. Mantis is in use in tens of thousands of R&D, manufacturing and analytical sites around the world. Mantis 3rd Gen incorporates the latest developments in optics, digital cameras and fully adjustable LED lighting to keep Mantis at the forefront of stereo imaging.
Mantis is designed for precision engineering, electronic engineering, medical device manufacture, and a wide range of other applications that require high-quality images and superior ergonomics. It features a unique, patented, eyepiece-less design that delivers a large, high-quality optical stereo image directly into the user’s eyes,
making it more comfortable and easier to view than traditional microscopes.
Manipulative, rework and restoration tasks need stereo images to allow easy hand-to-eye coordination and depth perception. Mantis 3rd Gen combines stereo optical images with highresolution camera options for manipulation and recording.
Mantis 3rd Gen features long working distance and excellent depth perception, now with a choice of 3 magnifications, making it ideal for a wide range of applications. It also now comes as standard with five different ways to illuminate your subject, giving you the flexibility to adjust the lighting to get the perfect image for your needs.
In addition to its outstanding image
quality and ergonomics, Mantis also features a powerful digital imaging system that allows you to capture, review, and share highresolution images. This makes it easy to share your work with colleagues, document your findings, and train new
Substantial R&D has resulted in a new range of stand options to allow flexibility, stability and
“As our customers have told us for the last 28 years, Mantis is an ideal solution for anyone who needs to perform precise work with small objects,” said Mark Curtis, Managing Director at Vision Engineering. www.visioneng.com/mantis
The smart worker assistance system. No frills at all.
High assembly variance, personnel fluctuation and complex process sequences lead to a permanently high need for training in manual production – combined with an equally high commitment of resources when the experienced colleagues support the new ones with advice and assistance.
Unless you rely on the new ifm mate worker assistance system in the future. A system that is so simple in design, so easy to use and so smart without bells and whistles such as trackers or VR glasses – and yet helps you to reliably ensure quality, save time and generate more added value more quickly. How do we know that? We have developed and tested it ourselves. For us. For you. ifm – close to you.
With cybersecurity attacks on the rise in the manufacturing sector, machine builders are now designing industrial equipment with secure communication protocols in mind. This involves using encryption techniques to protect data transmission between equipment and other systems, as well as implementing secure authentication processes to prevent unauthorised access.
TwinCAT, from automation and control technology specialist Beckhoff UK, provides secure communication protocols in manufacturing by implementing the latest encryption technologies and authentication mechanisms to ensure data confidentiality, integrity and availability. It also supports various industrial communication standards, such as OPC UA and MQTT, which are known for their high level of security.
One of the most significant risks to industrial equipment is unauthorised access. Machine builders are now designing equipment with
access controls to prevent unauthorised personnel from accessing critical systems. This can include using biometric authentication methods or smart card access systems.
Machine builders are also considering network segmentation when designing industrial equipment. This involves separating equipment into different networks, each with its own security protocols and access controls. This approach helps prevent cyber-attacks from spreading across the entire plant network in the event of a breach.
Networks are often split into zones, such as production, management and guest, and firewalls and access controls are being implemented to limit communication between these zones. Additionally, manufacturers are implementing security protocols such as encryption, multi-factor authentication and regular security audits to ensure their systems remain secure.
It’s clear to see how a cyber attack that starts off small can soon spread across an entire organisation and cause severe damage. Beckhoff’s control technology, which can be used by both machine builders and end-users, incorporates various measures to enhance cyber security, such as secure communication protocols, access control mechanisms and encryption techniques. These measures aim to prevent unauthorised access, manipulation, or theft of data and ensure the safe and reliable operation of industrial control systems. beckhoff.com.
Winn & Coales (Denso) Ltd, a leading manufacturer and supplier of corrosion prevention and sealing systems, recently supplied its abrasionresistant outerwrap (ARO), Denso BoreWrap, for use on sections of a new 2.7km natural gas pipeline constructed to service Kilroot Power Station, situated on the north shore of Belfast Lough. The contract, secured by GMC Utilities Group with its joint venture partner Rayden Engineering, is part of a £600m decarbonisation scheme to transform the coal-fired power station and create a new low-carbon energy park.
The welded steel pipeline from the Marshallstown above-ground installation (AGI) to Kilroot AGI was mainly installed by open-cut methods, but at road crossings, including one on the A2, the pipe was installed by horizontal directional drilling (HDD). To ensure that the integrity of the
anti-corrosion coatings on the pipe was maintained, Denso Bore-Wrap was applied to these sections prior to pulling the pipe under the roadways. Once pulled through, the ARO showed no signs of damage,
indicating no damage to the coatings underneath and clearly demonstrating the exceptional mechanical protection offered by the system.
www.denso.net
I’ve just returned from UKIVA’s annual Machine Vision Conference (MVC) –where we did things a bit differently this year.
For the first time, the event ran across two days; it was also co-located with Automation UK, a new show organised by our sister organisation, BARA. The increasing convergence of vision and robotics has led to greater overlap between the technologies. Co-locating our events allowed visitors to see how best to apply vision and robotics to their own businesses.
Despite the obvious synergy between the events, they’re very different in nature. Automation UK is a technology-focused expo; MVC remains an educational and technical conference at heart, supplemented by a compact exhibition. As always, all booths at MVC were identical in size.
The larger venue gave MVC exhibitors more space to display machine vision solutions. Visitors had more scope – and time – to explore the technologies. The twoday format also enabled a new conference format. The one-day programme was repeated on day two – in a different order – allowing visitors to see any presentations they had missed on day one.
This year’s keynote speaker, Jeff Burnstein, is president of A3 – a North American trade association for both vision and robotics. He offered critical insight into vision trends and applications – and discussed future applications of vision systems.
Collaborating with an organisation like A3 – and, for that matter, BARA – is critical for UKIVA. A collaborative mindset will help the vision sector to expand – as will the programme of change that we have recently formulated.
As well as having a new committee, UKIVA has created a strategy focused on four key areas, the Machine Vision Conference (MVC), membership, education and training, and Vision in Action (ViA) and marketing. Each committee member –supported by the chairman or vice-chairman – will take responsibility for one area.
UKIVA’s new committee – seen in the photo, from left to right – comprises Simon Hickman – vice chairman; Paul Wilson (responsible for membership); Allan Anderson – chairman; Mark Williamson (MVC); Ian Alderton (ViA/marketing). Paul Cunningham – not pictured – is responsible for education and training.
Our plan to keep improving MVC will see it continue to expand in size – and attract more delegates. We took our first step this year by extending the event to two days. We want MVC to become the event for the industry: we’ll achieve this by building a diverse audience of OEMs, machine builders, end users and academics. Maintaining MVC’s traditional conference programme – with its focus on education and technology – will be vital in this.
Another goal is to grow UKIVA’s member base – by extending the benefits that membership offers. These benefits include preferential rates to exhibit at MVC, media exposure through Vision in Action, and discounted rates for training. We also plan to create a machine vision community –where ideas can be exchanged in dedicated networking sessions. This way, we are confident we can expand from 50 to 70 core members within two years.
Education and training underpin
professional development. We intend to explore a UKIVA-certified scheme for vision solution providers – and look at options to introduce UKIVA machine vision training courses. Schemes like this will make membership more attractive – and further boost numbers. To support certification and training schemes, UKIVA members will offer live online STEM sessions – creating good publicity and highlighting the vision industry as an employer.
Vision in Action (ViA) is the main route to market for many members. In future, UKIVA will expand its size and reach. A variety of initiatives – ‘ask the expert’ sessions, an increased digital presence and live-streamed discussions – will enhance the magazine and offer members an improved product. Raising ViA’s quality – in both the print and digital versions – will help expand its readership. In addition, enhancing our presence online and through social channels will further boost UKIVA’s reach and influence.
Machine vision can help industry to raise its competitiveness by banishing repetitive tasks and speeding up processes such as inspection and packaging. With its new strategy, UKIVA will make it easier for members to boost sales of their products and services – and extend the use of machine vision in the UK.
UKIVA’s new committee has devised a plan to encourage greater use of vision systems –which began with the recent success of its expanded Machine Vision Conference, says UKIVA Chairman Allan Anderson.Members of UKIVA’s new committee include (from left to right) Simon Hickman (vice chairman), Paul Wilson, Allan Anderson (chairman), Mark Williamson and Ian Alderton.
Gambica’s Sector Head for Industrial Automation and Test & Measurement, Nikesh Mistry, explains how, with the support of products supplied by the association’s members, manufacturers can fine-tune the operation of their equipment to reduce costs and improve competitivity in the current challenging environment.
The UK manufacturing sector has faced significant challenges due to soaring energy costs. These increases have placed tremendous financial pressure on businesses, compelling them to seek innovative solutions to reduce energy consumption. As a result, energy monitoring applications, preventative and predictive maintenance sensors and technologies such as Variable Speed Drives (VSDs) and soft starters are gaining popularity across the manufacturing landscape.
The manufacturing process typically requires substantial amounts of energy to power machinery, equipment and facilities. As energy prices escalate, manufacturers face higher operating expenses, reduced profit margins, and heightened global competitiveness. The knock-on effects of these price increases began causing businesses to rethink their strategies and business plans, and with the UK’s Net Zero target also in mind, ensuring that manufacturers develop their processes to maximise energy efficiency.
For many manufacturing businesses, energy expenses now represent a significant portion of their overall costs. This has prompted companies to reevaluate their energy consumption patterns and seek ways to optimise efficiency. Implementing energysaving technologies has become a priority to mitigate the financial burden and remain competitive in the market.
VSDs are pivotal for reducing energy consumption in manufacturing. They regulate motor speeds by adjusting the frequency of the electrical power supplied to the motor. By matching the actual demand of the machinery, a VSD is capable of reducing energy wastage by avoiding excessive power consumption. Another technology gaining prominence in
the UK manufacturing sector is soft starters. Traditional motor starts often require a significant amount of energy to initiate, leading to high peak demand and associated costs. Soft starters, on the other hand, limit the inrush current, reducing stress on the electrical grid and minimising energy consumption.
By mitigating the strain on electrical systems during motor startup, they help prevent voltage fluctuations and equipment damage contributing to a smoother operation and extending the lifespan of motors and other connected equipment.
Other technologies being implemented by GAMBICA members are preventative and predictive maintenance strategies. Manufacturers using these methods can efficiently reduce energy waste and prevent unplanned downtime.
Preventative maintenance involves regular inspections, servicing, and repairs of equipment to prevent breakdowns and ensure optimal performance. With a structured maintenance schedule, manufacturers can identify potential issues and rectify them before they lead to costly breakdowns or excessive energy consumption. Regular cleaning, lubrication, and calibration of machinery help maintain its efficiency and reduce unnecessary energy losses.
Moreover, preventative maintenance allows manufacturers to detect and replace worn-out components promptly. Faulty or inefficient equipment often consumes more energy than necessary, leading to increased energy costs. By proactively addressing these issues, manufacturers can optimise the performance of their machinery and reduce energy waste.
Predictive maintenance takes a datadriven approach to maintenance by utilising advanced monitoring techniques and analytics. By collecting real-time data from sensors and equipment, manufacturers can
predict when maintenance or repairs will be required. This proactive approach helps prevent unexpected breakdowns and allows for more efficient scheduling of maintenance activities.
Predictive maintenance leverages the power of machine learning algorithms, which then look at data patterns and help identify potential equipment failures. By detecting anomalies or deviations from normal operating conditions, manufacturers can address underlying issues before they escalate, saving both energy and downtime costs.
These solutions and other Industry 4.0 technologies allow manufacturers to optimise their equipment’s performance through the fine-tuning of operational parameters. Manufacturers should identify the areas in which they are consuming the most energy and then look at which technologies can be implemented most successfully with the greatest effect on reducing their energy consumption which will, in turn, reduce their costs and wastage, freeing up capital for other investments.
As energy costs continue to rise, the adoption of energy-saving technologies is poised to play a vital role in sustaining the competitiveness and profitability of UK manufacturers.
Han® F+B - Hygienic and robust.
Connectors for the food industry
■ Easy-to-clean design especially for the spray zone
■ Reliable connections ensured, even with daily cleaning
■ Protection against water jets and aggressive cleaning agents
■ IP69K rated, Ecolab approved and complies with EHEDG guidelines
One Range. No Limits: www.HARTING.com/UK/en-gb/connectors-food-industry
Tanaka Iron Works Co, based in Kobe City, Japan, manufactures precision machined parts for industrial robots, medical devices, aircraft and nuclear power plants. The company had already constructed a production system that operates unmanned 24 hours a day in its plant for cutting processes using dedicated machine tools. However, it had not been able to automate its finishing process, where the main work is performed manually. When exploring what could be done to introduce industrial robots into a space where people are performing the main part of the work, the company turned to the duAro collaborative type dual-arm SCARA robot from Kawasaki, as MEPCA discovered.
Tanaka Iron Works is a professional in the field of precision metal processing.
The company started business in 1938, with the production of the main landing gear for the Kawanishi N1K fighter plane. For more than 80 years since, it has continued to produce precision processed components that are used in aircraft, medical devices, nuclear power plant components and the like.
It also built up a relationship early on with Toa Medical Electronics Co., Ltd. (currently Sysmex), which developed the first automatic blood cell counter in Japan.
Components from Tanaka Iron Works are used in the current blood cell counting inspection equipment from Sysmex.
The company has also been a supplier to Kawasaki Robotics since 1977 and has delivered the mechanical components for the arms, etc., which can be described as the heart of industrial robots.
The strength of the company is its flexible multi-product variable quantity production, which merges 17 machining centres with skilled craftsmanship.
The company is engaged in the everexpanding businesses of industrial robots for manufacturing automobiles, semiconductors, and medical device components. President Yoshinobu Tanaka explained: “In recent years, we seem to be operating in a 120% utilisation situation, and we have really struggled with a shortage of labour.
For this reason, we have always been searching for work that robots can perform instead of people.”
The first floor of the two-story plant is filled with dedicated machinery where the cutting processing for precision processed components is performed unmanned 24 hours a day.
On the other hand, people are mainly performing the work on the second floor, where finishing processes are performed.
When President Tanaka looked at that workplace, where there were multiple technicians in front of workbenches silently performing the final processing work, he thought there must be some elements that could be automated.
However, introducing an industrial robot
to a workplace where human workers are the main element requires large-scale improvements, such as the installation of safety fences.
President Tanaka continued: “If you ask what the biggest issue is for a small factory, it is, of course, space. This is why the majority of locations where industrial robot use is possible are large-scale manufacturing lines, such as in the automobile and semiconductor industries. I had never considered that we would be able to introduce one to our factory.”
That was until President Tanaka came across the duAro collaborative type dual-arm SCARA robot launched by Kawasaki in 2015.
“I heard that it is a robot that can be
outside of a fence and coexist with humans, so I thought that it might be something that we could use.
The installation was only possible because of duAro,” added President Tanaka.
Precision and reliability
At Tanaka Iron Works, duAro performs the assembly work for critical components used in Sysmex products. Specifically, the work is to press fit two parallel pins made of stainless steel into aluminium blocks about the length of the back of a human hand.
President Tanaka explained that: “In recent years, the production (for these components) has been increasing. The production used to be 2,000 per month, but it increased to 5,000 per month three years later. When making 5,000, the pin pressfitting requires 10,000 points.”
The pins have a correct up/down orientation and must be inserted in the correct direction, at the correct pressure, and to the correct depth. It seems to be simple but requires skilled techniques. In addition, it is monotonous, repetitive work, so it is also a process where human errors can easily occur.
“If we prioritise speed, then people are faster at inserting them. However, it was not speed we required; it was precise and reliable work,” President Tanaka added.
The first idea was for a simple system where a human worker places the pins in a line, and the duAro would pick them up and insert them into the blocks.
President Tanaka examined that idea and had doubts because there was more preparation work by people than originally thought.
In response to this, he consulted Yasuhiko Hashimoto, then General Manager of the Robot Division, Precision Machinery and Robot Company (currently President of Kawasaki Heavy Industries, Ltd.). The response was quite clear. ‘Please make the robot work harder.’
A pin press-fitting robot system that combined the seven elements was developed. The elements comprised a supply unit to set the pins in the correct orientation, a surface area sensor to double check that the orientation of the pins is correct, duAro to set the blocks and pins on jigs, a press-fitting unit, a load cell to measure the press force, a contact type sensor to measure the height to check that the pin has been inserted to the correct depth, and a system to store the inspection records for all products.
The supply unit has a mechanism that exploits the profile of the pins, where one end is rounded, and the other end is flat.
First, pins that have been placed in a receptacle shaped like a funnel go down into the tube one at a time.
There is a dividing plate placed at an angle part-way along the tube. If the lower end of the pin that comes down is flat, then it will not tip over when it hits the dividing plate. The dividing plate opens, and the pin goes straight down as it is to the discharge port and is set.
However, if the pin comes down upside down, the rounded end of the pin hits the dividing plate, and the pin falls over. It then branches off to the side route as it changes
direction to the correct orientation. Air is used to send it off from there, and then it is discharged.
In preparation for the small possibility that a pin with the wrong orientation may pass through, a double-check mechanism is installed. A surface area checker reads the profile of the pin end and removes it if there is a doubt.
The failure rate by manual work was 0.05%. However, through automation, 100% of errors in pin orientation, pressure failures and insertion failures have been eliminated. Between 2016 and 2021, around 100,000 pieces went through the manufacturing process, but there have been zero defects.
President Tanaka says that more than anything else, it is significant that having duAro take on simple work tasks makes it possible for the employees to engage in more sophisticated and skilful work.
The business creed of Tanaka Iron Works is ‘a company is its people’. duAro helps the company put that principle into practice.
To develop this project, Tanaka Iron Works collaborated with the system integrators Nanbokusangyou Co., Ltd. and KSS Co., Ltd. President Tanaka believes that the existence of the integrators was essential in making the automation of the pin pressfitting a reality.
“A lot of the specialist terminology related to robotics is impossible to understand unless it is explained in a way that even we can understand. The system integrators are something like an interpreter, connecting the company installing the robots and the robot manufacturer. If you have somebody to act as a bridge like that, then I think that there are still a lot of opportunities for robots to spread in small factories,” he concluded.
Today, right next to a technician who is concentrating on the delicate work at hand, the duAro is quietly working monotonously on the pin press-fitting work.
President Tanaka believes they should be able to use duAro to automate the processes before and after the pin pressfitting work too. For example, the block masking processing and the inspections of components before shipping. Furthermore, there is also now a possibility of introducing duAro for lens assembly work.
The planning for these developments is well underway.
kawasakirobotics.com/uk
MEPCA found out how Bosch Rexroth, a leading provider of drive and control technologies, is pushing the boundaries of the off-highway sector with its innovative end-to-end high-voltage portfolio, the Rexroth eLION platform.
This eLION solution from Bosch Rexroth aims to accelerate the electrification of mobile working machines, offering manufacturers the tools they need to develop both partially and fully electric off-highway machinery. By combining advanced electrification technologies with intelligent software, eLION delivers enhanced efficiency, superior performance, and complete compliance with functional and electrical safety requirements.
As the world embraces the urgent need for sustainable practices, the off-highway sector, which encompasses industries like construction, agriculture, and mining, is undergoing a significant transformation. Traditionally powered by internal combustion engines, off-highway vehicles are transitioning towards electrification to reduce carbon emissions and comply with stringent environmental regulations.
Recognising this industry shift, Bosch Rexroth is actively driving the electrification of mobile working machines through its cutting-edge eLION platform.
The Rexroth eLION platform encompasses a wide range of high-voltage components that form the building blocks for electrifying mobile working machines. It includes electric drives, inverters, energy storage systems, and power distribution units. These components are designed to handle the demanding requirements
of off-highway applications, ensuring robust performance and longevity even in challenging environments.
In addition to efficiency, the eLION platform delivers powerful performance. The high-torque electric motors offer instant acceleration and precise control, enabling operators to manoeuvre heavy loads with ease. These vehicles maintain their productivity and functionality while operating quietly and emitting zero tailpipe emissions, creating a healthier and more comfortable working environment for operators and nearby communities.
Beyond its hardware offerings, eLION leverages intelligent software solutions to maximise the efficiency and performance of electrified off-highway machinery. By integrating control algorithms and machine learning capabilities, the platform optimises energy consumption, power delivery, and system responsiveness. This not only increases overall machine efficiency but also enables precise control and enhanced operational safety.
Safety is paramount in the off-highway sector, and Bosch Rexroth places great emphasis on ensuring that its eLION platform complies with functional and electrical safety requirements. By adhering to these regulations, the platform provides essential safeguards to protect operators, machinery, and the environment. With the eLION platform, manufacturers can have peace of mind knowing that their electrified off-highway machinery meets all necessary safety standards.
The platform is at the forefront of driving the electrification revolution in the offhighway sector. By equipping vehicles with this innovative high-voltage portfolio, the company is enabling manufacturers to realise both partially and fully electric off-highway machinery, furthering the goal of sustainability. With a comprehensive range of high-voltage components and intelligent software solutions, the eLION platform offers increased efficiency, powerful performance, and compliance with functional and electrical safety requirements. Bosch Rexroth’s commitment to providing
environmentally conscious solutions while maintaining productivity and reliability makes it a key player in shaping the future of the off-highway industry.
Bosch Rexroth’s mission is to contribute to the sustainability of our planet. With each vehicle it electrifies using the eLION platform, it says it moves closer to achieving its goal of providing solutions to an environmentally conscious world. By embracing electrification in the off-highway sector, Bosch Rexroth believes it can significantly reduce carbon emissions, noise pollution, and dependence on fossil fuels.
Moreover, the eLION platform enables manufacturers to meet increasingly stringent environmental regulations and supports their efforts in building a more sustainable brand image. Customers, stakeholders, and end-users are increasingly demanding eco-friendly solutions, and by adopting the eLION platform, manufacturers can position themselves as leaders in sustainability.
www.boschrexroth.co.uk
With compliance understandably high on every manufacturer’s agenda, Keith Tilley, CEO at Intoware Ltd, looks at the ways digitalisation can help companies ensure they are fulfilling the required rules and regulations.
Regulation has never been more important. In today’s complex world, it can feel like there are endless boxes to be ticked and hoops to be jumped through. Industry standards and supplier protocols can be overwhelming and call for thorough systems and processes to be put in place to ensure each requirement is met in the right way, at the right time, avoiding nonconformity penalties.
Moving these compliance checks over to digital formats can also feel overwhelming. Many companies are still reliant on paper trails and manual checklists to ensure processes have been followed.
But, with the right approach, digitalisation has the power to make sure manufacturing businesses meet their compliance requirements more efficiently and effectively.
Regulation is constantly changing, with industry standards, rules and regulations being reviewed and updated all the time.
For manufacturers, staying aligned with these ever-changing requirements is a mammoth task, and one we frequently hear causes headaches for businesses.
Digitalising critical procedures and guidelines allows businesses to easily update and distribute instructions in realtime, ensuring employees are notified of changes promptly and can always access the most current information. In turn, this helps organisations to stay aligned with evolving regulatory requirements and promptly address any necessary changes, reducing the risk of non-compliance due to outdated documentation.
Equally, compliance often requires adherence to specific processes and protocols. Employees often have developed their own methods and shortcuts for tasks over time, but these deviations, however small, can risk compliance issues later down the line.
Digital work instructions serve as a powerful
tool for standardising workflows and ensuring consistent execution of tasks across the workforce, providing clear step-by-step instructions to minimise the chances of errors or deviations from the established procedures. This standardisation helps to maintain regulatory compliance and avoid penalties resulting from non-conformity.
Compliance often requires employees to undergo specific training and hold relevant certifications. Digital work instructions can be used to create training programs, so companies can track and manage what training has been completed by each employee.
By monitoring training progress and certification validity, businesses can ensure that only qualified personnel perform tasks that require specific qualifications. This tracking capability also provides assurance that regulatory compliance is upheld throughout the workforce.
Detailed audit trails can be difficult to maintain in paper form. Lengthy documents and extensive filing systems can cause confusion and, again, run the risk of non-compliance later down the line.
Digital audit trails, however, are much easier managed and maintained.
Often, digital workflows can incorporate features that capture and record details such as who has accessed the instructions, when they were accessed, and any changes made. By maintaining a comprehensive record of activities, companies can demonstrate compliance during audits and regulatory inspections, providing transparency, accountability, and traceability, enabling businesses to validate their adherence to regulatory requirements.
By collecting data throughout manufacturing workflows, organisations can identify trends and recognise potential compliance risks, allowing for remedial action to be taken before a problem occurs.
Automated reporting systems and notifications can highlight errors or steps that have been missed, allowing processes to be improved or made more efficient quickly.
By doing so, manufacturers can rest assured that by embracing digitalisation, they are maintaining a culture of compliance excellence: not just by ticking the boxes they need to but by proactively recognising and reviewing the processes and protocols they have in place across the business to create trust and confidence among regulators, stakeholders and customers alike.
www.intoware.com
MEPCA explores a range of topics for the food processing sector
Products such as mechanically separated meat (MSM) and meat emulsions are commonly used in a wide range of products, including sausages, chicken nuggets, patties and some minced meats. While different meat sources and products will have different processing and cooking requirements, it is important that the methods chosen minimise the energy use involved, saving money and reducing greenhouse gas emissions.
Meat emulsions, slurries and reformed meat products have been used globally since the early 1970s. Around the world, there are strict rules both about the raw materials used for the production of MSM, but also how it is processed and labelled. Similar cooking, handling and cooling methods are also used for other food products, such as ground (minced) meat and soups, and these products can also benefit from the same approach to choosing cooking systems.
The European Food Safety Authority (EFSA) advises that ‘Microbiological and chemical hazards associated with mechanically separated meat derived from poultry and swine are similar to those related to non-mechanically separated meat (fresh meat, minced meat or meat preparations). However, the risk of microbial growth increases with the use of high-pressure production processes.’ In addition, ‘High pressure mechanically separated meat must be immediately frozen and can only be used in cooked products.’
These products are often cooked in batches prior to final product formation, often using large steam-powered kettles or pressure vessels. Some companies processing large volumes of product may have ten or more vessels in various states of operation at one time. This is because,
while these vessels are an effective method of cooking and pasteurising a range of products, including MSM, they are limited in their capacity because it is important that the product is cooked thoroughly. Because each vessel must be heated from scratch for every new batch of product, and the heat used is then lost when the vessel is emptied, this is an incredibly inefficient method of cooking such products.
A much more energy-efficient method is to cook a continuous stream of product using a scraped surface heat exchanger such as the HRS R Series or Unicus Series. The HRS R Series uses a rotating action to scrape the tube surface and a helix to ‘push’ material through the heat exchanger, ensuring thorough mixing and heat distribution. It provides an economical solution for situations where product mixing is a benefit in processing or where physical integrity is less important than heat transfer. For example, it is ideal for MSM, meat emulsions and co-products (such as materials which are destined for the pet food market).
In some situations, however, the robust
mixing action of the R Series can damage the product. For example, some minced and ground meat products, or products containing definite pieces of product. In this case, the HRS Unicus Series is preferred. This patented design uses a reciprocal action to prevent fouling of the heat exchanger by the product and to ensure thorough heating of the product to the required temperature. Importantly, once the unit has reached the required temperature, the heating medium is only required to maintain the temperature as the heat is not lost between processing batches. This continuous processing saves large amounts of energy compared to a batch approach.
The same is also true of the equally important cooling process, which must be conducted in a timely manner. In fact, this cooling allows for the use of heat generation, where the heat removed by the cooling process is not lost but can be returned to the start to pre-heat the product so that less energy (for example, steam) is required for heating. Further economic savings are also achieved by reducing the need to fill
and empty separate cooking vessels, and the fact that cleaning-in-place (CIP) can be performed when required, rather than simply between each (smaller) batch.
HRS has provided clients with continuous processing solutions to replace batchcooking and cooling systems. One Colorado-based manufacturer of sauces and soups replaced their batch-based system with a continuous process based on a number of HRS products in order to increase their manufacturing capacity to meet increasing demand.
HRS complete systems not only include the HRS R Series and Unicus Series scraped surface heat exchangers for cooking and then cooling the product, but also transfer pumps, balance tanks, other heat exchangers for pre-heating and precooling, and auxiliary equipment such as CIP systems and steam-powered hot water sets. Such systems are designed to have simple intuitive controls and to occupy the smallest possible footprint in order to fit within existing production facilities.
www.hrs-heatexchangers.com
HRS Heat Exchangers operates at the forefront of thermal technology, offering innovative and effective heat transfer products worldwide, focusing on managing energy efficiently
Pasteurisation
Sterilisation
Aseptic Filling
Direct Steam Injection
Evaporation
CIP Systems
Process Skids
Juice Crusher & Remelter
Flow metering solutions specialist, Titan Enterprises, explores the key factors to consider when selecting a flow measuring device to meet batching control needs, ensuring a smooth and efficient batching process.
While a recent white paper (bit.ly/TitanHSB) from Titan Enterprises reviews the application of ultrasonic flowmeters in high-speed batching, here we focus on the broader aspects of batching systems, highlighting five essential considerations to help users make an informed choice for a flowmeter that suits a batching process.
Batch filling systems are commonly associated with the food and beverage industry, dispensing product directly into a glass, bottle or other type of vessel. Batching systems are also integral to the pharmaceutical and medical, chemical and oil industries. Applications such as additive injection or chemical dosing necessitate the precise control of liquid dispensing, making flowmeters indispensable in such processes.
Repeatability is essential for a productive batching process: Multiple uncertainties can change the amount of liquid being dispensed, causing a negative effect on the repeatability of the system. Controlling as many process variables as possible will help to ensure the accuracy and repeatability of flow measurement. Flowmeters, such as Titans’ mini turbines, boast repeatability of 0.1% or better when operating under consistent conditions.
The physical properties of the batchfilled liquid will dictate equipment requirements: The choice of flowmeter may be limited by the properties of the liquid, such as viscosity, volatility, corrosiveness, flammability, or particle contamination.
For high-viscosity liquids like syrups or mayonnaise, a precision-engineered oval gear flowmeter is ideal, the oval gears generating a greater driving pressure across the gears. Almost immune from the effects of liquid viscosity, the measurement accuracy of Titan’s Oval Gear flowmeters improves with
increasing liquid viscosity. Titan’s specifically designed gears are provided for high viscosity liquids above 1000cSt to facilitate the additional flow of the liquid.
Whereas Titan’s NSF-Approved 800-series or Beverage turbine flowmeters accurately monitor and check the flow of lower viscosity beverages – beer, spirits, wine, coffee, and soft drinks – being dispensed through batch delivery systems such as bar taps, bottling processes and within the distillery process.
Maintaining constant process conditions: Changes in flow rate, temperature and pressure may cause a flowmeter to function in an unpredictable dynamic way. Although maintaining stable operating parameters is optimal, this may not always be feasible. Fluctuating flow rates, for example, can be compensated for by using a higher specification measuring device, like Titans’ Atrato ultrasonic flowmeter, that will help to mitigate negative performance effects.
Constant liquid flow or pulsations? Maintaining a steady overall flow and avoiding any pulsations within the
batching system will prevent aliasing and incorrect flow readings over the batch operating cycle. If pulsation is inherent, inline pulse dampening is required and choosing the right flowmeter becomes critical in reducing the undesirable effects of pulsations.
Limiting system inertia: System inertia is the delay in response within the system from stopping/starting the liquid dispense following the control signal, which affects the accuracy of dispensed volume. Simple adjustments to the batch system design, such as control valve specification, reducing pipe lengths, and the positioning of the flowmeter, can help to offset the effects of inertia.
Selecting the most suitable flowmeter for a batch system can be a complex task. Titan Enterprises is dedicated to assisting you in finding the most appropriate flowmeter solution for your process and plant.
Connectivity specialist, HARTING, explains the requirements for connectors used in the food and beverage industry and explains how its products are able to deliver a solution.
Hygiene and safety are critical in the food processing industry. Machines and equipment must be easy to clean to prevent dirt particles and bacteria from accumulating and meet strict requirements for usage in the food industry. Standards such as EN 1672- 2 are intended to ensure that processed food is optimally protected against contamination.
The EN 1672-2 standard defines three distinct zones for food production, which differ in terms of contamination risks and the number of cleaning cycles required. Zone 1 is the food zone, where components come into direct contact with foodstuffs. Connectors are not designed to come into direct contact with food and are rarely positioned in this zone.
Zone 2 is the splash zone, which includes all facility parts and components that come into direct contact with food which does not return to the production process. Components here must be cleaned regularly using high-pressure washing and chemicals to avoid contamination. HARTING focussed on the hygiene requirements for this zone during the design and manufacture of the Han F+B range of connectors.
There are several innovations which make the F+B range the ideal solution. Firstly, all hoods, housings and seals are IP69K rated, so the connections are fully protected and resistant to the water jets used to clean equipment. They also have large nooks and surfaces in accordance with the guidelines of the European Hygienic Engineering & Design Group (EHEDG), which allows cleaning and disinfecting agents to flow unhindered.
The F+B range is also Ecolab-approved, meaning it is resistant to the highly aggressive cleaning agents used in the food and splash zones. As the housings are constructed from polypropylene, they conform to the directives of FDA 21. The entire portfolio can also function in a wide temperature range from -40 to +125°.
Connectors in the food and beverage sector must not react to detergents or other antimicrobial chemicals used during rigorous cleaning as they could affect the smell or taste of food, or even be harmful to health. Therefore, they must be corrosion-resistant, mechanically stable and constructed so that the surface of the material cannot be damaged.
The most common material used for connectivity in the food and beverage industry is high-alloy stainless steel, which is offered by the Han-INOX series. Plastic connectors must comply with the provisions of the regulation 1935/2004/EC, the Plastics Ordinance 10/2011 or the directives of the FDA 21.
The surfaces must have a high surface smooth finish to prevent bacteria and microbiological impurities from accumulating. Small nooks and crevices should be avoided because they reduce the flow rates of the cleaning and disinfecting agents, creating a hygiene risk. Finally, it’s important to undertake regular inspections of machinery to ensure there is no damage to seals, cabling or conduit caused by mechanical stresses.
As well as hygiene and safety considerations, plug-and-play connectors also help manufacturers keep production line disruptions down to a minimum and embrace flexible manufacturing.
In the past, a manufacturing floor was static. Machines were placed with the intention that they would perform the same tasks for the duration of their useful life. Now, manufacturing floors are frequently repositioned so customised products can be produced for customer-specific needs. With the addition of modular connectivity and machinery, floors can now be reorganised quickly to manufacture entirely different products.
Plug-and-play connectors make flexible manufacturing possible as machines can be disconnected and reconnected quickly without the need for skilled labour and with no risk of miswiring. Manufacturers no longer need to spend an entire day disconnecting a machine now that plug-and-play solutions exist.
bit.ly/HartingF-B
8-pole bayonet locking
> 5000 mating cycles
Panel mount parts unplugged IP67
Solder and dip solder contacts
www.binder-connector.co.uk
Robots can answer many of the food industry’s biggest challenges. In addition, the barriers that have previously prevented many food companies from investing in robotics are also being stripped away. Taken together, these ‘push’ and ‘pull’ factors look almost certain to usher in a robotic revolution in food.
Sales figures suggest that it’s already started, with the British Automation and Robot Association (BARA) finding that sales to British food and beverage businesses rose by 35% in 2020, compared to 7.5% for industrial robots overall. That took the food and beverage industry to second place in terms of the number of robots installed, second only to the automotive sector. More widely, Allied Market Research reported last year that the value of robots sold into food and beverage globally is expected to grow by more than 10% every year to 2031.
This growth has clearly been accelerated by the pandemic, but the underlying issues of labour shortages and rising costs remain a long-term challenge for food companies globally.
Increasingly, cobots that can work safely alongside people make mixed production and packing lines a viable option. Meanwhile, robots are becoming smarter and can be equipped with AI-based machine learning and vision systems to handle the kind of unstructured sorting, picking and intralogistics tasks that would previously have been possible only with human operators. They’ll also tackle the most boring or unpleasant tasks, improving working conditions for human operators and supporting employee recruitment and retention.
With food companies facing growing pressure from regulators and consumers to promote sustainability and a Circular
Economy, the tireless, repeatable precision of robotic systems also minimises reworking and optimises waste reduction, as well as boosting product quality and food safety.
Adaptability is the other key benefit.
It is becoming progressively easier to program robotic systems to carry out new tasks as production needs change. This is increasingly important for food companies looking to respond quickly to the latest trends and consumer preferences, whether that’s plant-based, free-from, or simply the latest limited-edition flavours.
The ability to manage and apply robots more easily is a major consideration for food companies, many of which have previously been deterred from investing in automation by a lack of expertise.
Suppliers have responded with easy interfaces that can be used by those with little or no previous experience with robots. For example, ABB’s Wizard easy programming software for its cobots and small IRB 1100 industrial robot uses Blockly. This is an open-source visual coding method that presents programming language or code as interlocking blocks and allows users to program in different applications without the need for specialised training.
Developments in the field of digital twinning software, such as PickMaster Twin and RobotStudio, are also transformative. These allow users to build software simulations of a
robot or series of robots and test them before making changes on the real production line. This ability to program and test new configurations offline shortens the time to market for new products, enabling users to confidently install, commission and scale up production lines without the risk of running up against unforeseen problems.
A cloud version of RobotStudio enables developers to support users in real-time from any web-enabled device around the world, while PickMaster Twin users have the option to connect the simulation directly to production operations, allowing the picking process to be optimised at almost the same time as the process is being implemented.
Again, simplified user interfaces are designed to democratise the user experience by enabling the software to be used by operators at all levels of expertise.
These and other developments in robotic automation, including the availability of dedicated hygienic options, are helping to convince a growing number of food and beverage producers to make a switch to robots. www.abb.com/robotics
• Easy setup without image processing knowledge
• AI technology in a robust vision sensor, made for industrial automation
• Train the detector with a few images on your PC
• Reliable results with strong varying processes and products
Consider a highly automated logistics centre with fenced-in robots and storage and retrieval machines, conveyor systems and pallets as far as the eye can see. How can companies keep their employees safe from accidents inside the warehouse while maintaining a smooth material flow? EUCHNER explains how its new CKS2 key system will greatly simplify handling for the safe starting or stopping of dangerous machine movements.
With the CKS2 key system, intralogistics system integrators can benefit from a highly flexible, customisable and scalable system that does away with complicated key exchange boxes. This safe RFID solution is a great complement to the MGB2 Modular safety door system.
Whether for consumer goods, e-commerce, beverages, fresh foods or pharmaceutical products – automating warehouse and intralogistics processes is becoming more important and safety priority is a big part of the story.
The MGB2 Modular has proven its worth over many years in sectors as diverse as the automotive and logistics industries, where it secures safety doors and fences on machines and installations during dangerous machine movements. This modular safety door system from EUCHNER consists of a locking module, integrated submodules with controls and indicators for pushbuttons, selector switches, key-operated rotary switches or emergency stop buttons, any required expansion modules, and various bus modules for connecting to PROFINET/ PROFIsafe or EtherCAT P/FSoE. It works especially well when combined with the CKS2 safe key system, enabling many new applications.
The new CKS2 key system can be used for machine and installation lockout and starting, for assigning authorisation to select an operating mode, or as a key transfer system. The system guarantees maximum safety
thanks to its highly coded RFID keys. The CKS2 can be used in an installation either individually as a compact system with integrated evaluation electronics or separately as a submodule in the MGB2 Modular door locking system. This opens up a host of new applications to users as well as numerous combination options.
The CKS2 system is readily adaptable to individual requirements. Depending on the specific application, the key can be left in place or removed during automatic operation. When the system is used for locking out, the installation cannot be started without the key, for example. In other words, the key stays in the key adapter station during operation. The key is removed to stop the installation. Only then will a dangerous zone become accessible.
When the CKS2 is used with the additional access restriction function, operators must insert the key before entering the installation. One example is the application in an automated logistics centre where the MGB2 Modular’s safety door system secures the long transport aisles. The CKS2 is integrated as a submodule in an MGB2 locking module, along with a pushbutton for starting or stopping the machine. If a product package falls off a rack in a transport aisle, the person responsible can stop the installation behind the safety fence by inserting the key into the key adapter and pressing the push button to request access. This pushbutton is an
integral part of the MGB2 door-locking system and sends a signal to the connected control system, which stops the machine in a safe position. Only then does the employee withdraw the key and open the door to return the package to the right place. The installation can be restarted once the person has left the danger zone. This person then inserts the key into the key adapter from the outside and presses the pushbutton to activate the door locking.
“Intralogistics customers also use the CKS2 as a key transfer system,” said Xabier Antolin, Product Manager at EUCHNER. “The RFID keys are simply taught-in at several key adapters for this purpose. The same key can then be used in another key adapter of a machine or robot in the interior to perform manual work there, for example. When the user has finished their work, they remove the key again, leave the interior, re-insert the key into the MGB2 key adapter on the outside and start the installation in the interior by acknowledging with the pushbutton.”
www.euchner.co.uk
In order to fulfil the continually increasing and changing safety requirements in modern production facilities, Automation24 is continually expanding its range of safety technology. The recently added safety edges and bumpers from manufacturer ASO Safety Solutions ensure the safe stopping of systems and guarantee safety at pinching and shearing points. Both components can be configured in Automation24’s online shop and adapt perfectly to customers’ in-house conditions. In addition to this service, customers at automation24.co.uk have access to additional information in the knowledge area.
The safety contact edges from the SENTIR edge series serve to protect people and equipment at potential pinching and shearing points. Available in various designs, the edges feature resistance loops, which are bridged upon contact, thus bringing automated gates and machines to a stop in work areas that must be safeguarded. At automation24.co.uk, the safety edges can be configured to within
an accuracy of 1mm and are made to order. The edges are produced in-house at Automation24 and can be quickly delivered. A similar principle also underlies the safety bumpers from the SENTOR series by ASO Safety Solutions. The bumpers consist of a foam core with a moisture-resistant cover and are triggered by means of simple compression. Automation24 offers a simple solution by which to initiate an immediate top of all movements within a system. With various designs in different sizes, the bumpers can be individually configured to suit on-site conditions.
“With a diverse, continually expanding product range featuring strong and innovative brand manufacturers, we offer our customers
solutions for almost every standard safety application. The safety edges and bumpers from ASO Safety Solutions are required to cover specific areas in terms of their functionality. For this reason, we have made it possible to order this product in precisely the right size in our shop,” explained Adrian Gniwotta, Safety Technology Portfolio Manager at Automation24.
automation24.co.uk
Murrelektronik believes that the future will be completely cabinet-free, so decentralised solutions are a core aspect of its technology. Often, going cabinet free is perceived as a radical overhaul of a complete system – this is not the case. Murrelektronik’s range of decentralised solutions has been designed to offer maximum flexibility and ease of integration.
Solutions include fieldbus modules, switches, power supplies, IO-Link, cables and connectors, all working together to make automation easier and simpler. When needed, the company’s Application Engineers can assist with planning, design, test and integration into existing systems. This can save installation and design time, which in turn saves money and resources.
IO-Link is recognised as the standard industrial communications protocol that connects sensors and actuators to high-level controllers. IO-Link offers a huge advantage and is a gateway to smart manufacturing as it allows for all types of data (service/ process/event) to be transferred at high speed to and from controllers and devices. This means more efficient and agile processes, greater machine availability and permanent data access (for identification, diagnosis and configuration).
Korina Parker explained: “The IO-Link Pro system is a universal installation system, perfect as a starting point for digitalisation and, at the same time, delivering a futureproof IIoT concept.
“Its advantages include the easy integration of smart devices, transparency from the device level to the cloud and easy access to data for analysis.
“IO-Link masters, hubs and analogue converters can be integrated into an existing system or be the core of a new system or machine. Another great advantage is that our Application Engineers are specially trained in IO-Link technology, helping customers to plan and install IO-Link and
make end-to-end signal communication as easy as possible.”
Advancing industrial image processing technology is revolutionising machine vision applications. Vision systems are becoming increasingly important in industrial manufacturing and logistics. When it comes to Industry 4.0 technologies, industrial image processing cameras are a crucial component.
“Murrelektronik’s plug-and-play solution enables quick connection of power supplies and signal/data management supporting the smart networking of cameras in industrial production, processes and logistics applications. This modular, scalable and flexible solution means that switches, distributors and power can be mounted on the machine. This minimises the installation effort required and maximises performance for both new and existing machines and systems,” continued Korina.
As the need for machine and system communications increases, industrial networks become the lifeline for data. For successful digitisation, powerful and reliable network technology is required.
“Murrelektronik’s network technology ranges from basic switches all the way up to the latest in POE technology,” Added Korina. “The new Xelity 10 TX IP67 managed
switch offers new possibilities for smart data management that can be decentralised and field mounted. With up to ten gigabit ports and its high level of robustness and variety, it represents the new benchmark for the industrial switch market. The compact, robust metal housing with the high degree of protection IP67 allows the switch to be used even in extremely harsh industrial environments, while the M12 L-coded power connectors ensure an easy connection with power transmission.”
The plant automated by Vario-X has a digital twin right from the start. A movable 1:1 image of the real plant, which contains all functions and parameters of the later system – and this is all in the project phase before even the first mechanical component has been ordered or assembled.
Karina explained: “The Vario-X is a modular, flexible and stand-alone automation system, which has the ability to communicate to high-level systems, as well as other PLC systems. Vario-X is networked, pluggable and cost-efficient. With seamless integration of servo drive technology, it ensures reliable voltage, signal and data management directly in the field. This means that, for the first time, all automation functions can be implemented without a panel in sight.”
Murrelektronik UK, outlines how the company is focused on providing workable solutions for advances in digital transformation, Industrial Internet of Things (IIOT) and Industry 4.0, which are easy to integrate and offer long-lasting advantages.
UK motion specialist Trio Motion Technology has launched a new motion controller for up to 64 axes with high speed EtherCAT control. Trio’s new Flex-X Nano Motion Coordinator is designed to increase machine productivity while optimising motion precision. Powered by a 1.2GHz, 64-bit Dual Core ARM Cortex A55 Processor, Flex-X Nano runs EtherCAT cycle times down to 125μs. Just 147mm high and 17mm wide, the new pocket-sized Flex-X Nano Motion Coordinator fits within an extremely compact footprint.
The new motion controller has been designed for applications that demand multiaxis servo control performance, including packaging, manufacturing automation, material handling, pick-and-place, CNC cutting machines, and gantries.
The Flex-X Nano Motion Coordinator
advances on Trio’s existing Flex-6 Nano controller to further enhance machine productivity and quality. Adding a 64-bit chip, the new Flex-X Nano increases processor speed by 20%, raises Ethernet TCP communications speed by 10% and boosts programme execution speed by 25%. The new controller also features 1.2GHz clock frequency, IEEE 457 Double maths precision, and a motion command execution benchmark of 125 lines/ms. These advances achieve faster multi-axis motion coordination, from 2 to 64 axes, with EtherCAT cycle times down to 125μs.
The Flex-X Nano can simultaneously control machines, robots, and motion axes. The advantages of integrating a single controller, instead of using a PLC plus an
additional robot controller or motion controller, include faster set up, reduced space, and increased reliability for the end
Complex programmes can run from Flex-X Nano’s 1GBit DDR3 memory and 1GBit fast serial flash memory, and a Micro SD card slot further extends this capability.
OEMs can also add functionality, including I/O and device integration via Trio Flexslice modules that communicate over EtherCAT.
The controller can be programmed via Trio’s easy-to-use, Windows-based Motion Perfect software with either IEC 611313 languages, PLCopen, or Trio’s core programming option.
triomotion.com/flex-x_nano.
Multifunctional Gate Box MGB2 Modular
u Safety system with guard locking device
u Modular layout for maximum flexibility during operation
u Bus module with PROFINET/ PROFISAFE/ EtherCAT with FSoE
u Expansion module MCM for even more functions
u Category 4 / PL e according to EN ISO 13849-1
Precision sensor manufacturer Micro-Epsilon has extended its confocal sensor system portfolio with the new, innovative high performance series, confocalDT IFD2410 and the confocalDT IFD2415.
Each of the new systems introduced by Micro-Epsilon combines both sensor and controller together to save space and simplify installation in production lines and machines, as no fibre optic cabling is needed between the sensor and controller.
The confocalDT IFD241x series is the only one in the world that combines high precision and a compact design with integrated Industrial Ethernet. Comparable models from other manufacturers only offer Industrial Ethernet via a separate external module.
One of the key advantages of confocal technology is its ability to measure on any surface including highly polished and even transparent materials. Despite its compact size, the confocalDT IFD241x is still capable of displacement and distance measurements, and is also suitable for thickness measurement of transparent materials.
The new confocal sensor system is available in two versions, each with three measuring ranges. The entry-level version, the IFD2410, offers an attractive price-performance ratio and single layer transparent thickness measurements. The high performance version, the IFD2415, is best-in-class for high precision distance, thickness and transparent multi-layer measurements.
The IFD2410 is ideal for high precision distance and thickness measurements in industrial series applications such as production lines and plants. An adjustable measuring rate of up to 8kHz and submicrometer resolution down to 12nm make the IFD2410 suitable for a wide range of measurement tasks. The active exposure
time regulation of the CCD array enables high speed, stable measurements on various surfaces. The sensor is available in measuring ranges of 1mm, 3mm and 6mm. Typical applications include inline inspection and coordinate measuring machines; inline thickness measurement of flat glass and container glass; and inspection of electronic components.
For those applications where higher distance and thickness measurement precision is required, the IFD2415 is ideal. Based on the sensors from the IFS2405 range, the sensors have precision lenses and wide numerical apertures that allow high degrees of tilt from reflective surfaces and can be used with transparent materials for multilayer thickness measurements of up to five layers. The active exposure time regulation of the CCD array enables high speed, stable measurements on difficult, changing surfaces, even in dynamic processes up to 25kHz. The measuring system is also characterised by high luminous intensity. Therefore, the IFD2415 can measure quickly and reliably, even on darker surfaces. The sensor is available in measuring ranges of 1mm, 3mm and 10mm. Typical applications include inline inspection and coordinate measuring machines, robotics and 3D printers.
The combined sensor and electronics in one compact housing offers greater flexibility for system integrators and machine builders,
as there is no longer any need to route or connect fibre optic cables. The confocalDT IFD241x series has an integrated Industrial Ethernet (EtherCAT) interface, which simplifies integration with PLCs. Ethernet/ IP and ProfiNET will also be available shortly. This enables real time measurement data without time delays and reduced installation effort. The connection is established automatically. After the power supply is switched on, the sensor boots in EtherCAT mode by default. Using the multi-function button on the controller, the IFD241x can also boot in Ethernet mode and can then be controlled via the intuitive web interface. Parameter set up is simple: settings made are stored and applied directly to the EtherCAT mode on the next boot process. This eliminates time-consuming setting effort in the programming environment.
In addition to Industrial Ethernet, RS422 and analogue outputs are also possible. For those who wish to synchronise measurement data with positional information, the controller can also accept up to two incremental encoder signals directly without the need for additional interface hardware.
www.micro-epsilon.co.uk
Benedict Yelf, Machine Vision and Automation Engineer at Optimal Industrial Automation, discusses the opportunities as well as what to consider when developing a successful robotic application coupled with machine vision functions.
Combined robotics and vision systems are pushing the boundaries of industrial automation applications and enhancing their capabilities. These advancements are enabling end-users to considerably improve their operations when it comes to speed, performance and accuracy. Creating valueadding automated machines that leverage both robotics and vision systems, however, requires expert skills.
The role and prevalence of robots are continuing to transform shop floors worldwide, enabling companies to create ever more efficient industrial environments to satisfy increasingly ambitious market demands. Machines involving robotics can offer a wealth of benefits to their users, conducting repetitive tasks for prolonged periods with high reproducibility and speed. At the same time, they are helping to improve the wellbeing of operators, taking on potentially harmful tasks, e.g. handling
heavy items or operating in hazardous areas. Furthermore, collaborative solutions can be deployed to directly assist employees in their activities within shared workspaces. While robots can truly complement automated machines and lines, even their most advanced models have limited spatial awareness and lack a level of cognition about their surroundings. This limits their potential, specifically in areas where precision is required, or the environment changes around them. Applications such as pick and place within the pharmaceutical industry or processes with a tight tolerance, such as drilling within the aerospace industry, would be conventionally difficult and would greatly benefit from robot vision. Thanks to the latest developments in this field, it is possible to overcome these challenges and create extremely powerful and versatile solutions. These not only improve conventional solutions involving robotics, but also expand the potential uses, supporting more processes with highly flexible setups.
The most common pick-and-place systems include examples where visionenabled robots can sort, load, pack, assemble or discard items. In addition, companies can benefit from their glueing and dispensing solutions, machines for inprocess quality checks, as well as scanning and code reading units. Furthermore, as the latest robots and vision systems are easier than ever to integrate with additional hardware, such as sensors, laser scanners, PLCs and mobile devices, the seemingly impossible can be turned into reality. This can be seen when looking at the rise of autonomous mobile robots (AMRs) and autonomous guided vehicles (AGVs). These can navigate around the factory floor, moving products and inventory, seeing and acting accordingly to the world around them.
This expansion of possible robotics applications requires high levels of automation expertise to design, develop and
implement valuable solutions.
A key aspect when looking to adopt vision-enabled robotic systems is defining the most suitable components. In addition to typical considerations on budget, payload, processing rate, space available and type of gripper, other parameters need to be factored in. These include illumination and ambient light (environmental lighting), image processing speed, properties of the objects that are to be assessed by the vision system as well as the compatibility of the different machine components.
In practice, it is important to look for a vision system that can reliably identify the items that the robot needs to interact with while considering its impact on the overall investment. For example, when handling elements that vary greatly in terms of colour and/or shape, solutions can range in complexity. These may involve changing the angle of the lighting or using advanced lighting options, such as a multi-coloured ring light, to enhance the optical spectrum that the system can detect.
This can provide more accurate colour description, resolution and contrast, as
well as reduce any noise in the image. Even more, such a system can incorporate LEDs for UV and IR lights, expanding detection capabilities beyond the visible spectrum. In effect, users can benefit from a vision tool that has access to more than 1000x the number of colours available from a standard camera can detect whilst offering 3x the level of physical resolution. Of course, the benefits of more detailed imaging solutions need to be balanced with the feasibility of the processing power required.
Other important aspects include the identification of the ideal height and the calibration of the cameras. If the field of view is not scaled to the environment correctly, the robot may not be able to locate or position the right item, which would lead to poor quality results, reworks and, ultimately, higher costs.
Moreover, ensuring proper lighting and background at any time while the system is in operation is fundamental. This can be more challenging than expected if the machine is exposed, even partially, to ambient light, which can change throughout the day. Similarly, the presence of forklifts or other
pieces of equipment featuring lightbulbs or other sources of artificial lighting that operate near vision-enabled robots has the potential to influence the robot vision system.
Finally, the integration of vision systems, robots or any other potential element should be seamless to support optimised, reliable operations. These key factors and a broader knowledge of what should be considered make experienced automation system integrators more important than ever.
By partnering with specialists who have a proven track record of successful implementations that combine robotic and vision systems, such as Optimal Industrial Automation, companies can benefit from high-quality solutions that address their needs. As a result, end users can maximise the gains they can achieve from innovative automated systems and enhance their competitiveness in a demanding marketplace. www.optimal-ltd.co.uk
CHEMUK 2023 opened its doors on May 10 and 11 at the NEC in Birmingham to a record attendance of 3,956 visitors (excluding exhibitor staff) over the two days, representing an increase of 41% from the 2022 edition. The total two-day attendance (visitors plus exhibitors) was 5,559.
Summing up this year’s event, CHEMUK show founder, Ian Stone, said: “The industry is now responding to the single’ destination experience’ of CHEMUK providing deliberately segmented zones of specialist industry capability and solutions, supported with unmissable intelligence, whilst at the same time uniting the entire UK chemical industries’ value chain’ under one giant roof annually”.
A dedicated video address from the Minister of State at the Department for Science, Innovation and Technology, George Freeman, underpinned a comprehensive UK Government presence and input across the two days, with show floor presence and vital conference input from the Department for Business and Trade, the Department for Environment, Food and Rural Affairs, and Health and Safety Executive.
Sustainability was the common thread across the event this year, with progressive energy and emissions reduction solutions, process optimisation and greater operational efficiency of petrochemical-based plants, through to a wealth of coverage on developing ‘green chemistry’ innovation supporting the transition towards bio-based chemicals and downstream products.
Industrial Biotechnology and Bio-process innovations were reflected across all three zones and extensively through the conference programmes.
The 2023 show saw the Institution of Chemical Engineers (IChemE) join an already impressive line-up of supporting industry and trade bodies both on the show floor and hosting crucial intelligence and keynotes across the integrated CHEMUK conference. This included the likes of CBA, BCA, BASA, BioVale, BCMPA, BPMA, CPI, CCUK, IBioIC,
GAMBICA, NEPIC, SIA, and InnovateUK KTN, to name a few.
CHEMUK has become the destination in the UK where all the key bodies, major companies, and industry stakeholder groups embracing organic and inorganic synthetics, formulation chemistry, analytical and materials chemistry, industrial biotechnology, and chemical and process engineering are ‘predictably’ in the same ‘time’ and ‘space’, under one giant roof, alongside a wealth of downstream chemical-dependent industries.
Plaudits came from visitors and exhibitors alike. Commenting on the event, the Operations Director at Eternis Fine Chemicals UK Ltd said: “There is nothing like this in the UK, and it is a must for anyone working in the chemical industry. It is an opportunity to find out what is happening in your area and others, discuss opportunities with exhibitors showing
their novel ideas and also to meet up with old and new connections.” While another visitor likened the event to ‘Disney for Chemists’.
The General Manager of exhibitor SAFI UK said: “The show was a great success for SAFI Valves – this was our 3rd year in a row exhibiting, and the show gets better and better each year for us.” With fellow exhibitor, a Sales Engineer at Marshall Pumps, adding: “The show was buzzing from the first morning, and we hardly stopped for breath. People looking for pump system builders and solutions to the more difficult pumping applications visited us in their droves. It already feels like another successful CHEMUK show for us, which is why we did not hesitate to sign up again for next year.”
CHEMUK 2024 is scheduled to run on May 15 and 16, 2024, at the NEC, Birmingham.
www.chemicalukexpo.com
Exhibitors at HANNOVER MESSE, and the event’s organisers, have reached a strong conclusion that the world’s leading industrial trade fair demonstrated that the technologies for competitive and, at the same time, climate-neutral industrial production are already available. The next step, they said, involves the need to make consistent use of all the available solutions.
The core topics at HANNOVER MESSE included artificial intelligence, hydrogen, energy management, connected and intelligent production, and the new Manufacturing-X data ecosystem.
“A spirit of optimism permeated the halls at HANNOVER MESSE,” reported Dr Jochen Köckler, Chairman of the Deutsche Messe Managing Board, at the closing press conference for HANNOVER MESSE 2023. “Our event managed to exceed the already high expectations of exhibitors and visitors”.
More than 4,000 exhibitors presented their solutions for a digital, connected, sustainable industry, welcoming 130,000 visitors from around the globe to Hannover. “The past five days of the trade fair have made clear that the technologies for competitive and climateneutral industrial production are available – now it is just a matter of developing the necessary speed and determination in their implementation,” asserted Dr Jochen.
At the same time, he said, it was clear that climate protection required the help of industry in the form of a supplier and user of technologies that enable CO2-neutral production. According to Dr Jochen:
“HANNOVER MESSE is the global platform for networking among industry, government, research and society as a whole. And it has never been more important than today to share knowledge and ideas. The technological solutions for climate-neutral production are already present. However, in order to secure the competitiveness of industry and our prosperity in the long term, bureaucratic obstacles need to be overcome, opportunities fuelled, and transnational cooperation agreements concluded.”
The rate of international attendance was commensurately high: 43% of visitors came
from abroad to find out how they could make their production fit for the future. After Germany, the top visitor nations were the Netherlands, China, Korea, Poland and the United States.
“Visitors were able to see the process of industrial transformation live, in practice, in the exhibition halls,” Dr Jochen explained. Visitors were treated to displays of high-end industrial products for climate-neutral production, new hydrogen technologies, inspiring ideas for connected production processes incubated by startups, voice-controlled robots using AI, solutions for efficient energy management and the launch of the new Manufacturing-X data ecosystem, which is intended to pave the way for digital business models, especially for industrial SMEs.
ZVEI President and Chairman of the HANNOVER MESSE Exhibitor Advisory Board, Dr Gunther Kegel, summed up the view of exhibiting companies as follows: “Electrification, digitisation and automation: these three trends have shaped this year’s Hannover Messe and are already leading to solutions for achieving effective climate protection. And it is precisely the interplay of these trends that demonstrate that the energy turnaround must also usher in a turnaround in energy efficiency. This tradeshow confirms our optimism for the electrical and digital industry and our forecast of 1 to 2% real production growth this year. At the beginning of the year, we were still assuming a lateral trajectory, even if at a high level. But now, industry is on the upswing.”
Thilo Brodtmann, Executive Vice President
of VDMA, added: “Climate protection and sustainability are now at the top of the industry agenda throughout the world. In order to achieve the targeted climate neutrality, new, intelligent technologies and solutions are needed for resource conservation and efficient production across all areas of life.
“Here at HANNOVER MESSE, we have sensed the great interest of customers in the solutions that the mechanical and plant engineering sector is providing for this. That’s why this year’s show was a complete success for our industry and an important sign that intelligent and connected production can solve the major challenges of our age.”
Dr Jochen concluded: “For the companies who exhibited here, HANNOVER MESSE is a WIN-WIN-WIN tradeshow. First, they are able to meet visitors from all over the world. Second, they benefit from doing business with the other 4,000 exhibitors. And third, they have access to more political decisionmakers and delegations than at any other show.”
The next HANNOVER MESSE will be hosted from 22 to 26 April 2024.
www.hannovermesse.de
According to the event’s organisers, at Silicone Expo USA, taking place in Detroit on October 4 and 5, innovation, technology, and limitless possibilities will converge. As they gear up for another exciting edition, they showcase the remarkable crossover between the silicone, tape, and film industries.
Recognising the interplay between the silicone, tape, and film industries, it became evident to the organisers that co-locating Silicone Expo and Tape and Functional Film Expo was a relevant and natural move forward. With a focus on collaboration, immersive experiences, and incredible offerings, this year’s event promises to be a transformative platform for industry professionals and enthusiasts alike.
The intertwining nature of the silicone, tape, and film industries has given rise to exciting opportunities and innovation. By converging these sectors, Silicone Expo USA provides a platform for knowledge exchange, collaboration, and exploration of new possibilities. Industry leaders, experts, and exhibitors from all three domains will converge to showcase their latest advancements, products, and solutions. This convergence opens up avenues for cross-pollination of ideas, fostering innovation and driving the development of cutting-edge technologies. From adhesive solutions and functional films to silicone-based applications, attendees will have the chance to witness the powerful synergy that lies at the intersection of these industries. This unique amalgamation offers a comprehensive and holistic perspective, paving the way for groundbreaking advancements and transformative partnerships.
In its commitment to providing an unforgettable experience, Silicone Expo USA has partnered with Visit Detroit to create an immersive journey in the Motor City of Detroit. Working alongside this incredible organisation, the organisers aim to offer interactive experiences in the exhibition hall that showcase the vibrant spirit and
rich history of Detroit. From guided tours to special attractions, attendees will have the opportunity to explore and embrace the unique essence of this dynamic city.
Additionally, early registration for Silicone Expo USA has its perks. Anyone registering before September 15 will automatically be entered into a giveaway to win a night’s stay in Detroit, along with a pair of tickets to a Detroit sporting event of their choice. This exclusive offer adds an extra layer of excitement to visitors’ participation and rewards their proactive approach. However, even those who haven’t already registered can rest assured that they are still eligible for this exciting opportunity. And the organisers are urging delegates not to miss their chance to be part of this incredible giveaway and seize the opportunity to immerse themselves in the vibrant energy of Detroit while attending the premier silicone event of the year.
To ensure a seamless experience for all attendees, the newly renovated Cambria has been selected as the HQ hotel for this year’s Silicone Expo USA. Located in the heart of downtown Detroit’s bustling core, this contemporary hotel offers
a prime location just three blocks away from the Huntington Place Convention Center. The Cambria stands proudly within the vibrant central business district, providing easy access to all the city has to offer.
With a focus on sophistication, the hotel features a range of upscale smart guest rooms designed to provide maximum comfort and convenience. Complimentary WiFi is available throughout the entire property, allowing guests to stay connected effortlessly. Culinary enthusiasts can indulge in exquisite dining experiences at the hotel’s fine Mediterranean restaurant, while panoramic city views await at the rooftop bar.
As Silicone Expo USA approaches, the organisers are eagerly anticipating the convergence of the silicone, tape, and film industries, fostering innovation and collaboration. With the partnership with Visit Detroit, exciting giveaways, and the new HQ hotel, this year’s event promises to be a transformative experience, propelling the future of these industries forward.
www.silicone-expo.com/home1
TouchPath has released ‘TouchCount’, a new inventory cycle counting technology that live-counts production, warehouse and logistics inventory with no costly and timeconsuming production stoppages or disruption to warehouse product flows. This represents a major advance on traditional ERP inventory cycle counting and enables the system to pay for itself in six to nine months through time savings and continuity of supply.
TouchCount collects live inventory information from data capture devices, including scanners and mobile computers, while enabling operations to continue uninterrupted.
It can run on an existing browser, either standalone or integrated with an ERP system, and can be customised in line with user company rules and practices.
www.touchpath.com
ABB has inaugurated a process flowmeter calibration facility in its Minden factory in Germany. The new calibration hall, which houses water and air calibration rigs, will strengthen the company’s calibration capabilities and provide customers with high levels of quality and accuracy in process flowmeters.
The new capabilities will enable plant operators across industries, such as chemical, oil & gas, battery, hydrogen and power, to accurately measure in and outflow as well as raw and produced materials, controlling their processes in a more precise and efficient way as a result. The new facility will also significantly reduce time to market and streamline production.
“This is an important milestone for us. We are trusted by our customers to make some of the toughest measurement challenges easy,” said Jacques Mulbert, Division President, ABB Measurement & Analytics.
“The new calibration hall is a great example of how we streamline our manufacturing capabilities to deliver the best products at the best price to our customers.”
The new hall houses two water calibration rigs for various process flowmeters, such as Coriolis, Swirl and Vortex flowmeters, with a calibration accuracy of less than 0.1%.
It also includes a density calibration rig for Coriolis flowmeters and air calibration rigs for the thermal mass flowmeter series. In the 1200 m² hall, 375 m² are available for air calibration and 525 m² for water calibration. www.abb.com
Industrial gases supplier Air Liquide has benefited from the ii910 Precision Acoustic Imager, designed by Fluke to make it easier, faster and safer to carry out high-sensitivity detection of gas, corona and partial discharge (PD). With minimal training, the point-andshoot device can also detect compressed air, gas and vacuum leaks, making it ideal for detecting leaks in gas distribution systems.
With a frequency range of 2 to 100kHz and 64 digital MEMS microphones, the ii910 makes it possible to locate leaks rapidly, detecting a 0.005 cubic feet per minute leak at 100PSI from up to 32.8 feet.
The acoustic imager incorporates a 1280 x 800 resolution LCD display and offers a battery life of more than six hours in the field. bit.ly/FlukePAI
LUCID Vision Labs has launched the 5.4 MP Triton HDR camera featuring the AltaView oncamera adaptive tone mapping engine.
The Triton HDR TDR054S utilises the Sony IMX490 (BSI) back-illuminated stacked CMOS sensor, allowing for simultaneous 120 dB HDR imaging and LED flicker mitigation thanks to its sub-pixel technology.
Employing the AltaView adaptive tone mapping engine delivers real-time tone-mapped image output directly from the camera, producing data-rich 8-bit images with enhanced details in the shadows and highlights.
The optimised AltaView output offers perceptually equivalent lower bit depth HDR images, reducing CPU/GPU resource requirements and eliminating the need to create a custom tone mapping algorithm on a host.
www.thinklucid.com
Midlands 3D Printing
Units 6-7 Emerald Way, Stone Business Park, Stone, Staffordshire, ST15 0SR
T: 01785 594389
E: sales@midlands3d.com
W: www.midlands3d.com
Fibet Rubber Bonding (UK) Ltd
Unit 9 Dale Mill, Hallam Road, Nelson, Lancashire, BB9 8AN
T: 01282 878200
E: sales@fibet.co.uk
W: www.fibet.co.uk
Beckhoff Automation Ltd
The Boathouse, Station Road
Henley-on-Thames, Oxon RG9 1AZ
T:+ 44 (0)1491 410539
E: info@beckhoff.co.uk
W: www.beckhoff.co.uk
Impact Technical Services
3 Kingsley Street, Leicester, LE2 6DY
T: 0116 244 8855
E: enquiries@impactts.co.uk
W: www.impacttechnicalservices.co.uk
Titan Enterprises Ltd Unit 2, 5A Cold Harbour Business Park, Sherborne, Dorset, DT9 4JW
T: +44 (0)1935 812790
E: sales@flowmeters.co.uk
W: www.flowmeters.co.uk
Silverson Machines Ltd
Waterside, Chesham, Buckinghamshire, HP5 1PQ
T: +44 (0)1494 786331
E: sales@silverson.co.uk
W: www.silverson.co.uk
Brainboxes
T: + 44 (0) 151 220 2500
E: sales@brainboxes.com
W: www.brainboxes.com
Axair Fans UK Limited Lowfield Drive, Wolstanton, Newcastle-under-Lyme, ST5 0UU
T: 01782 349 430
E: aj@axair-fans.co.uk
W: www.axair-fans.co.uk
Schmersal UK Ltd
Sparrowhawk Close, Malvern, Worcestershire, WR14 1GL
T: 01684 571980
E: uksupport@schmersal.com
W: www.schmersal.co.uk
Pipework Systems
Jacob UK Ltd
Laundry Bank, Church Stretton, SY6 6PH
T: 01694 722841
E: sales@jacob-uk.com
W: www.jacob-group.com/uk
Robotics & Automation
KUKA Robotics UK Ltd
Great Western Street, Wednesbury, West Midlands, WS10 7LL
T: 0121 505 9970
E: sales.uk@kuka.com
W: www.kuka.com
Rotation Monitoring Equipment
Rotech Systems
Unit 57, Canal Bridge Centre, Ellesmere Port, Cheshire, England, CH65 4EH
T: +44 (0)151 356 2322
E: sales@rotechsystems.co.uk
W: www.rotechsystems.co.uk
Sensors
Carlo Gavazzi UK Ltd
4.4 Frimley Business Park, Frimley, GU16 7SG
T: 01276 854110
W: www.carlogavazzi.co.uk
IFM Electronic
Efector House, Kingsway Business Park, Oldfield Road, Hampton, Middlesex, TW12 2HD
T: 020 8213-0000
E: enquiry.gb@ifm.com
W: www.ifm.com
Cupio Services Ltd
T: 01256 262800
E: info@cupioservices.co.uk
W: www.cupioservices.co.uk
Interested in advertising within future issues of MEPCA?
Please call 01795 509105 or email hannah@cimltd.co.uk for more details.