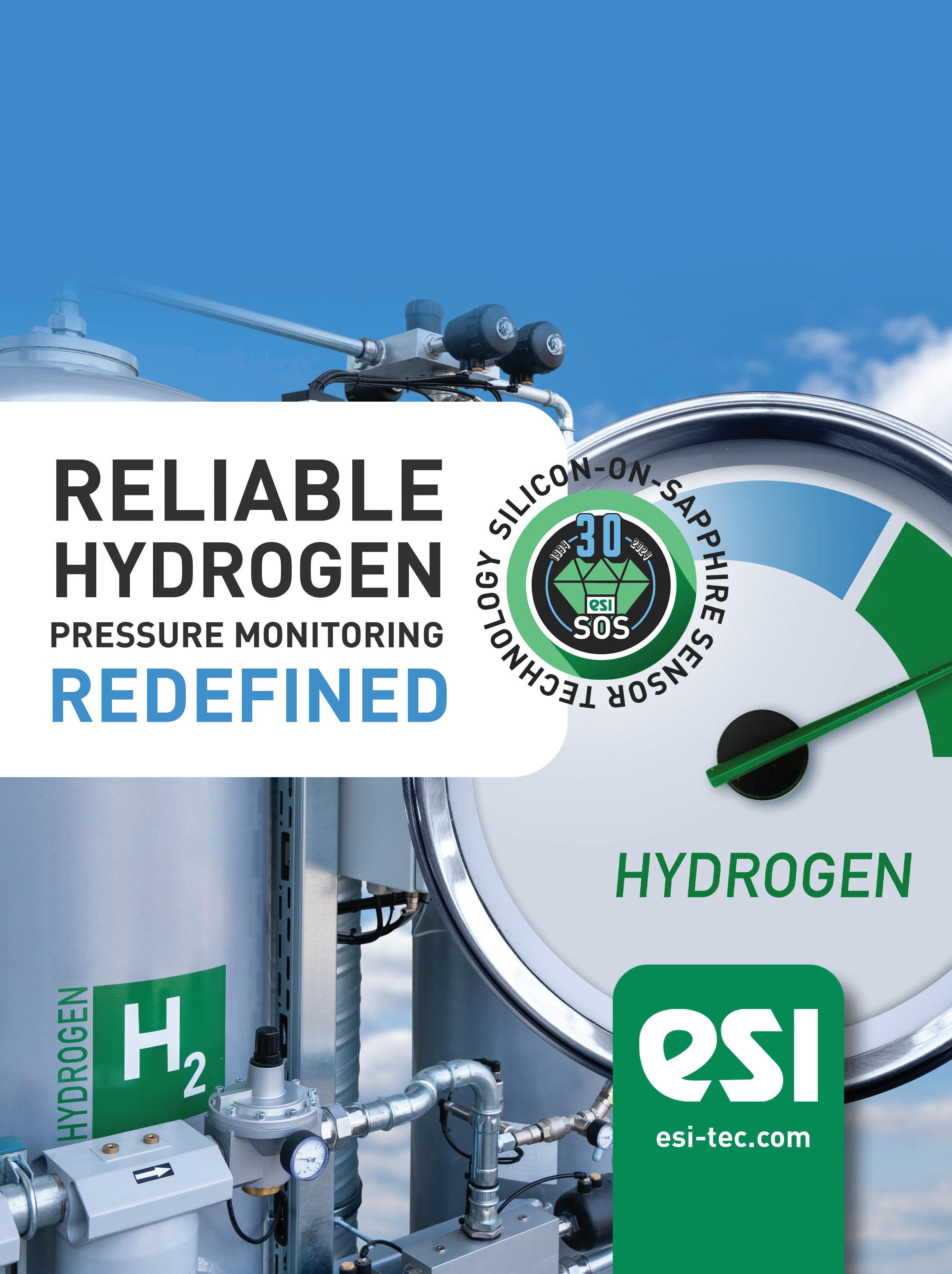
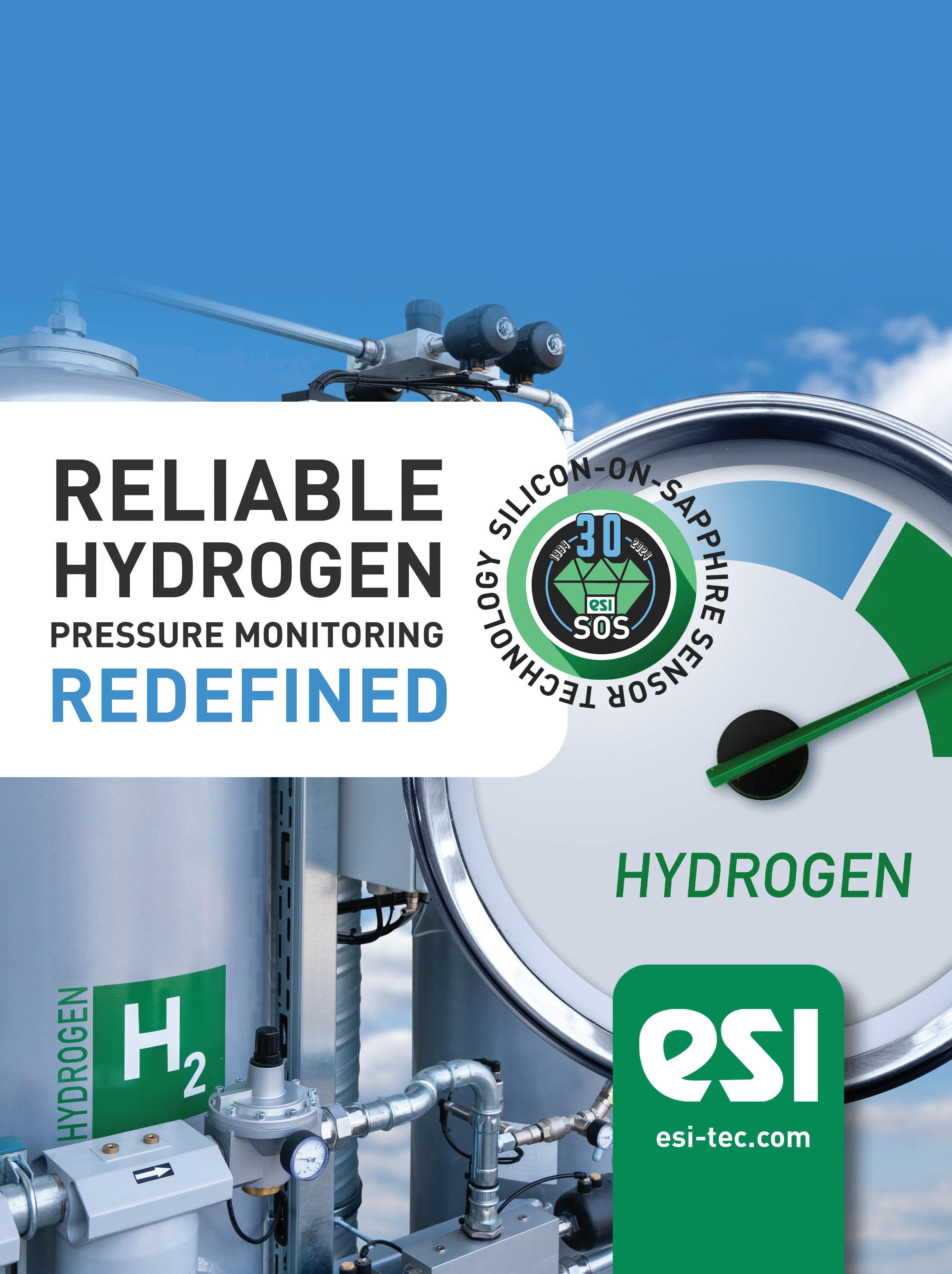
Automation software experts
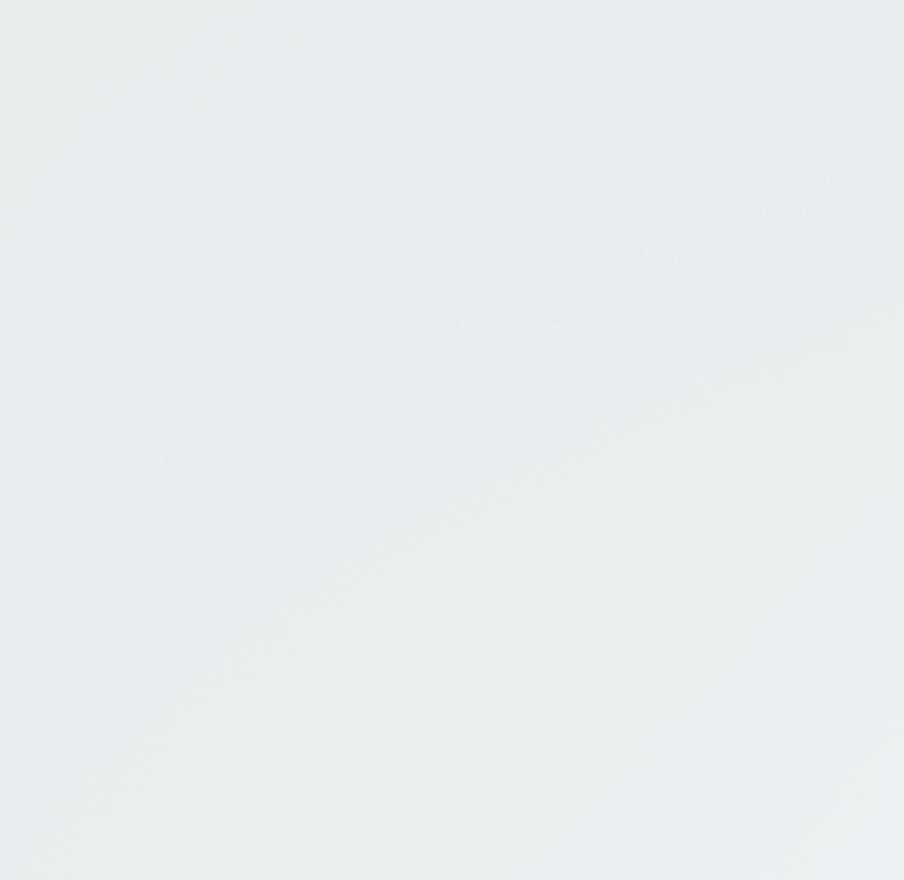
In a world of big data, our software simplifies its use.
From control systems for mobile machines to parameter setting for RFID read/write heads, we have software solutions that simplify your automation. We even have visualisation software for real time plant monitoring, from anywhere in the world.
Our software engineers remove the hassle of integrating automation solutions and ensure that you are getting all the usable data you can, providing actionable efficiency insights.
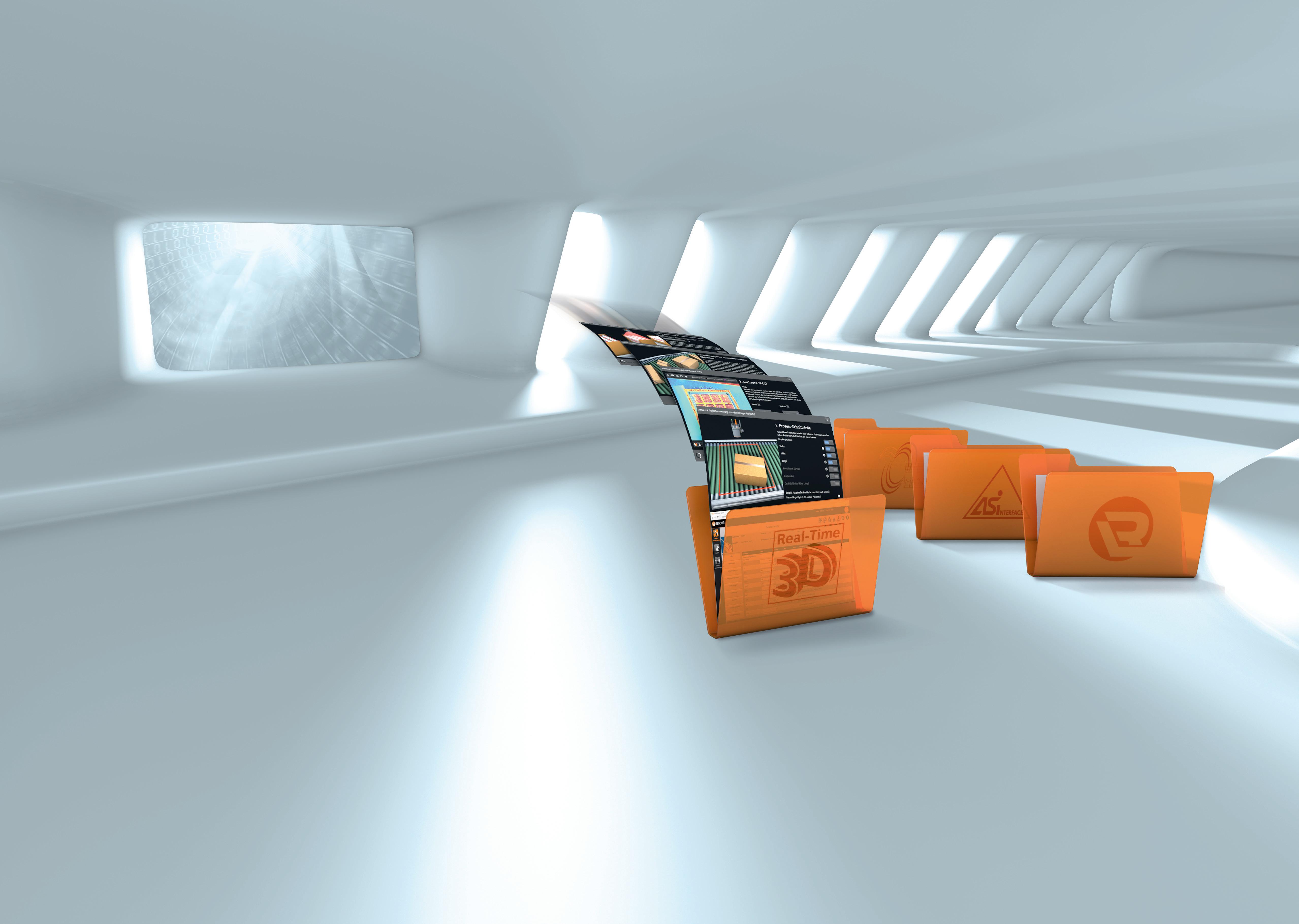

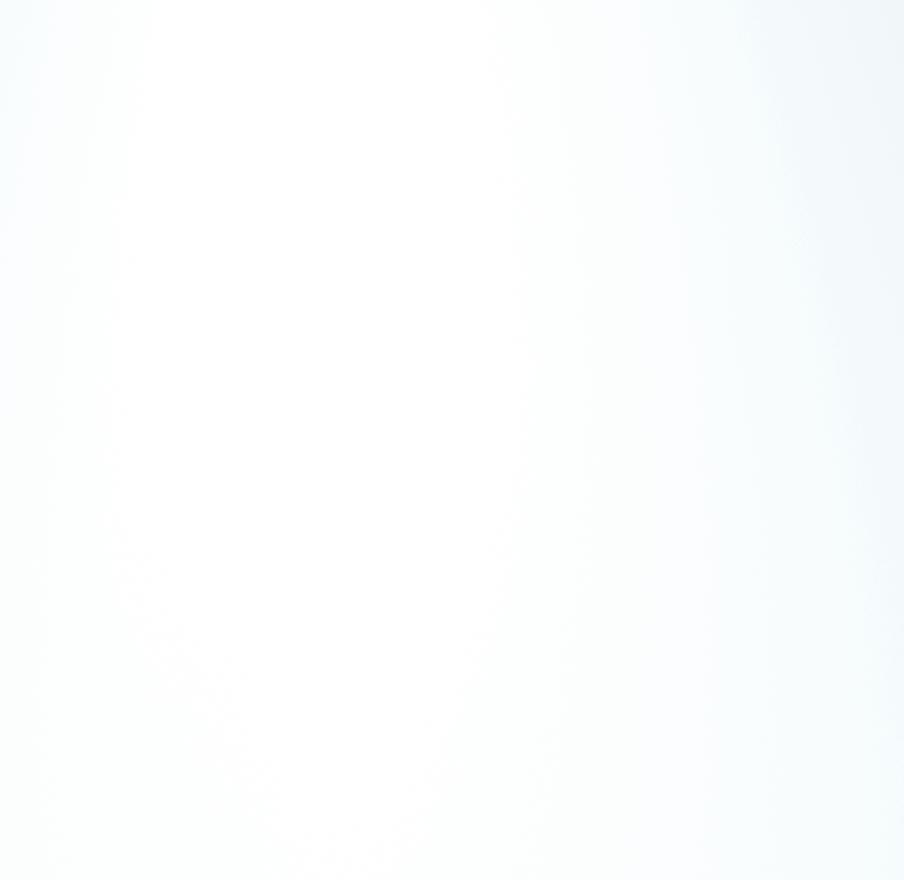
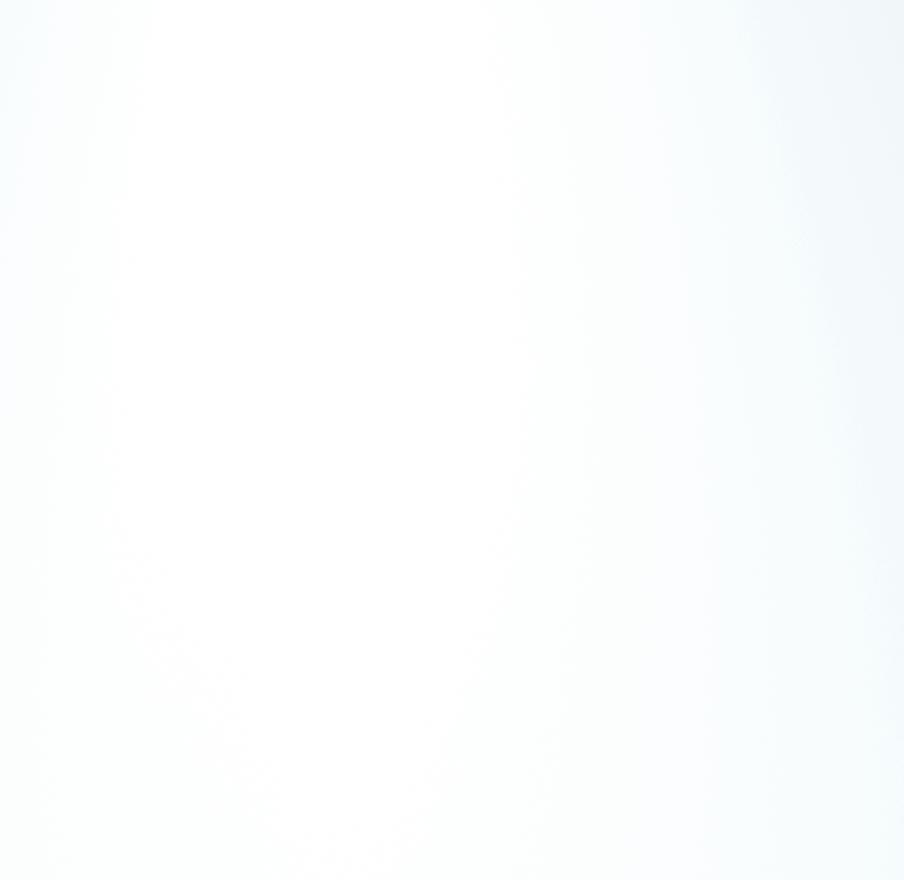


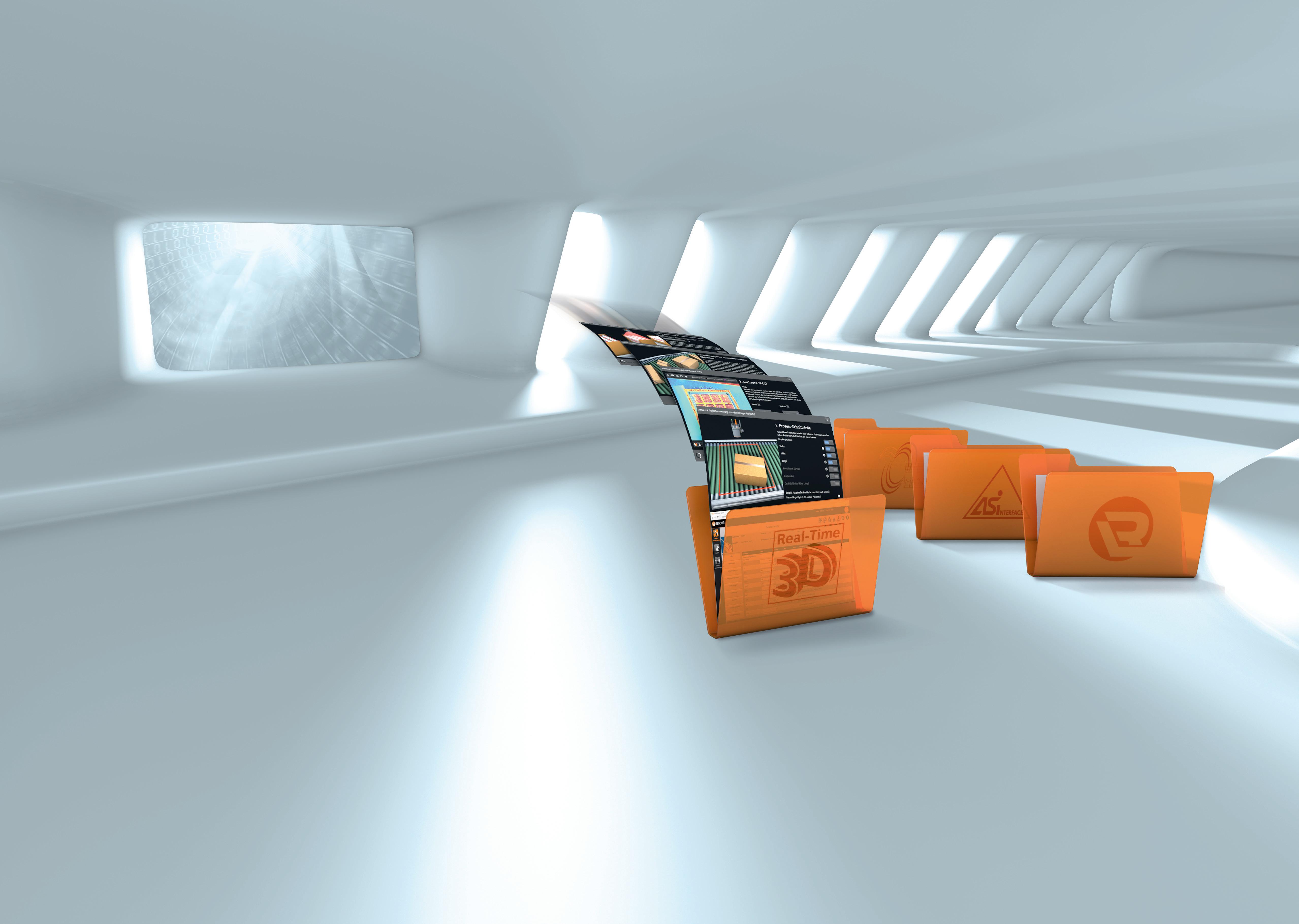
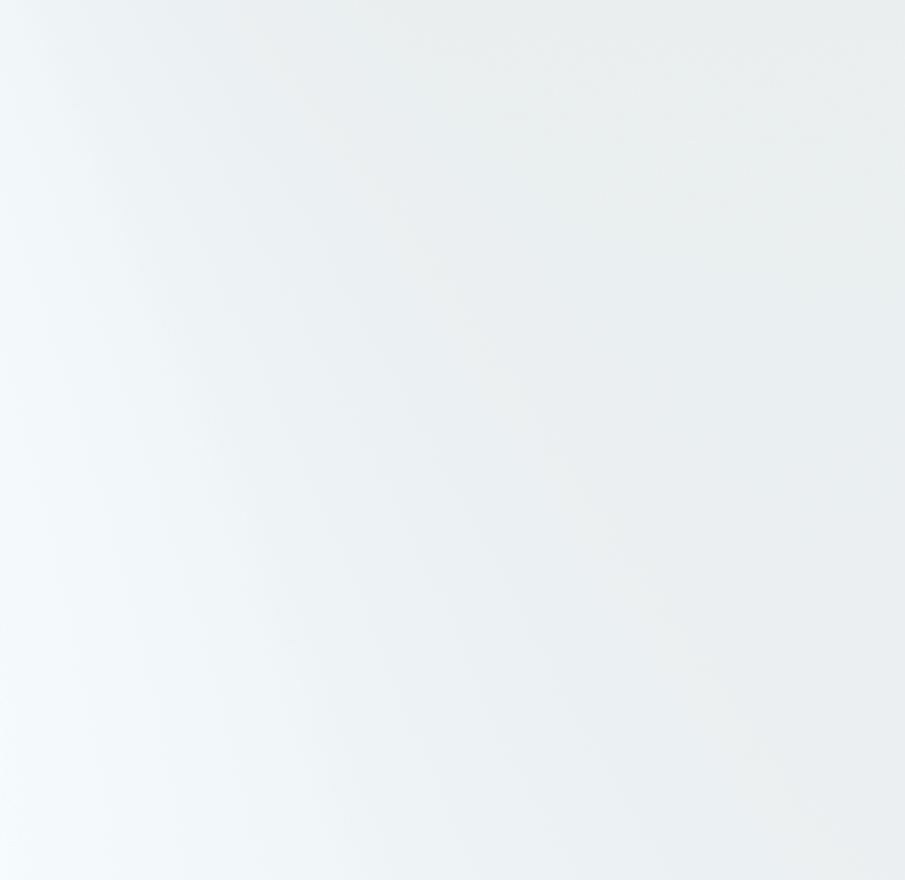

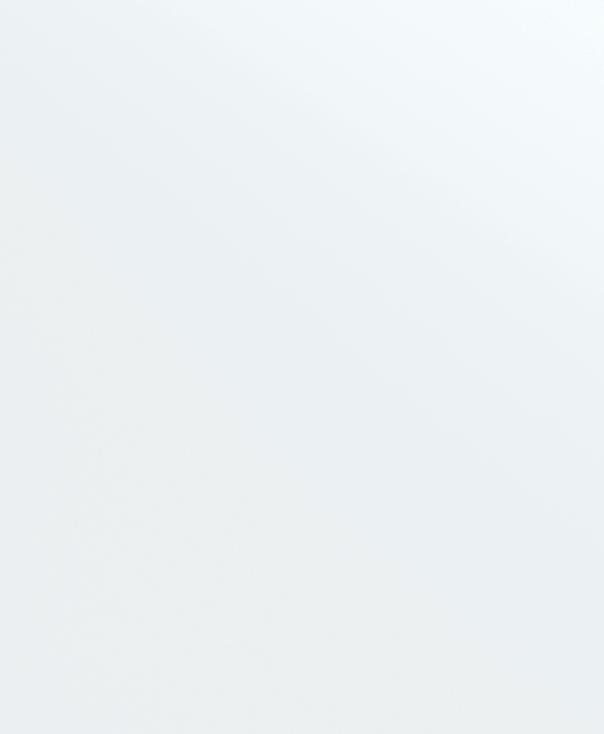
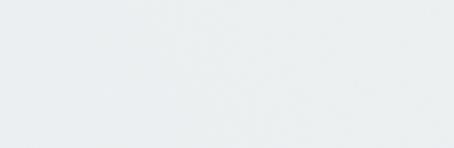
Editor
Chris Callander chrisc@cimltd.co.uk
Publication Manager
James Burke jb@cimltd.co.uk 01795 509105
Account Managers
James Davies jamesd@cimltd.co.uk 01795 509105
Jim Bearden jim@cimltd.co.uk 01795 509105
Design & Production
Grant Waters grant@cimltd.co.uk
James Taylor james@cimltd.co.uk
Administration Manager
Natalie Murray admin@cimltd.co.uk 01795 509103
Credit Facilities Manager
Gwen Lee creditcontrol@cimltd.co.uk 01795 509103
Marketing Manager
Lucas Payne lucas@cimltd.co.uk
Sales Director
Tom Woollin tom@cimltd.co.uk
Chief Executive
John Denning
© 2024 TGM Publishing Limited,1st Floor, Saphir House, 5 Jubilee Way, Faversham, Kent, ME13 8GD. No part of this magazine may be reproduced or stored in a retrieval system or transmitted in any form – electronic, mechanical or physical – without express prior permission and written consent of the publisher. Contributions are invited and when not accepted will be returned only if accompanied by a fully stamped and addressed envelope. Manuscripts should be typewritten. No responsibility can be taken for drawings, photographs or literary contributions during transmission or in the editor’s hands. In the absence of an agreement the copyright of all contributions, literary, photographic or artistic, belongs to TGM Publishing Limited. The publisher accepts no responsibility in respect of advertisements appearing in the magazine and the opinions expressed do not necessarily represent the views of the publisher. The publisher cannot accept liability for any loss arising from the late appearance or non-publication of any advertisement.

July 2024
The warehousing and logistics sector has undergone a profound transformation over the past few decades, driven by technological advancements, globalisation, and evolving consumer demands. Traditionally, warehousing was a static operation focused primarily on storage and inventory management. On the other hand, logistics dealt with the movement of goods from point A to point B. However, technology integration has blurred these lines, leading to a more dynamic and interconnected industry.

In the 1980s and 1990s, the advent of barcode scanning and warehouse management systems (WMS) revolutionised inventory tracking, reducing human error and increasing efficiency. The early 2000s saw the rise of globalisation, necessitating more sophisticated logistics networks to handle the increased volume and complexity of international trade. This era also marked the beginning of e-commerce, which has continued to reshape the industry.
Today, the sector is grappling with several challenges. The demand for faster delivery times has never been higher, pushing the limits of existing infrastructure. Labour shortages are accelerating the adoption of robotics and AI to maintain operational efficiency. While sustainability is another pressing issue as companies strive to reduce their carbon footprint amidst growing regulatory pressures and consumer awareness.
As the warehousing and logistics landscape continues to evolve, the ability to adapt and innovate remains paramount for industry leaders. The future promises further integration of cuttingedge technologies, but it also demands a proactive approach to addressing the multifaceted challenges of today.
Starting on page 17 of this issue, our Warehousing & Logistics focus explores just some of the ways organisations are rising to today’s challenges and preparing for the future.
Enjoy the issue.
@Mepca-magazine
To subscribe to MEPCA visit our website www.mepca-engineering.com or scan the QR code.
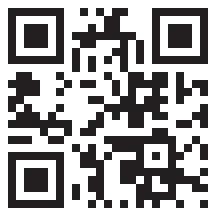
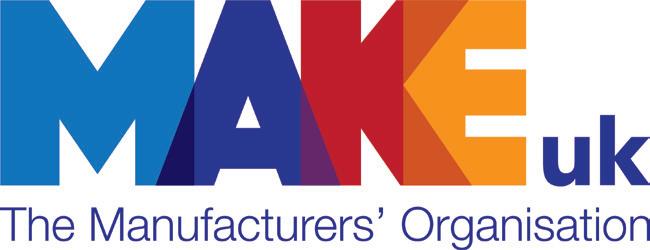

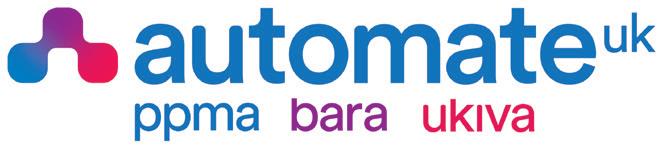

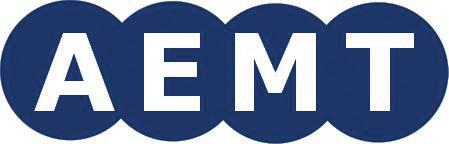
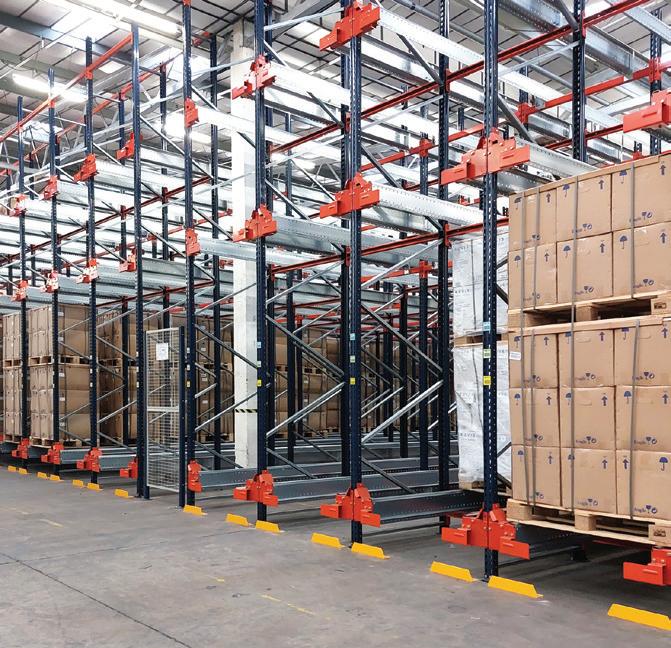
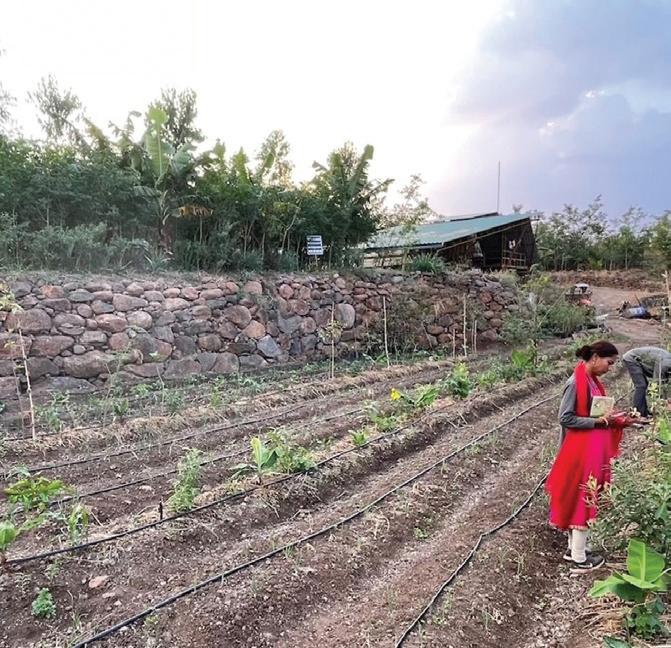
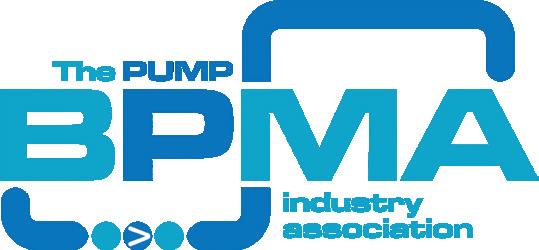
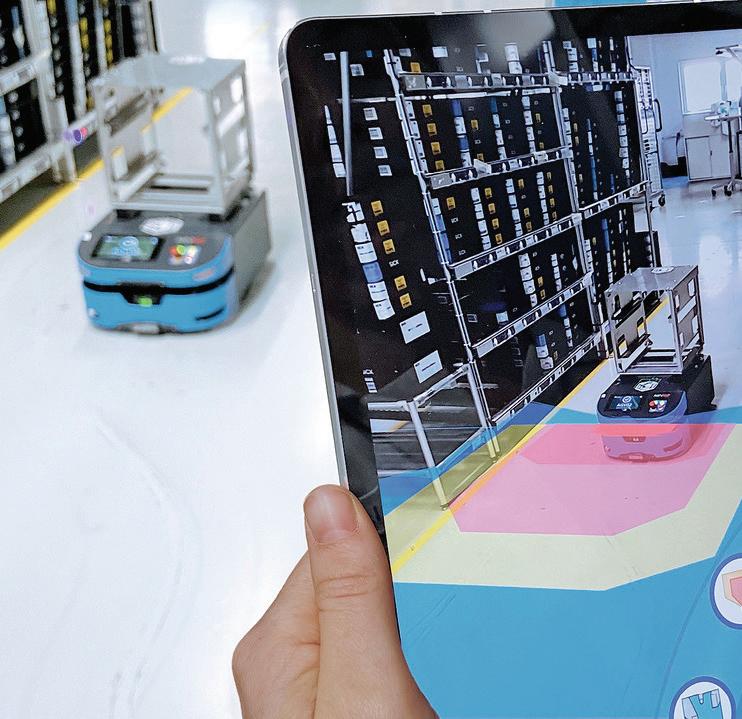
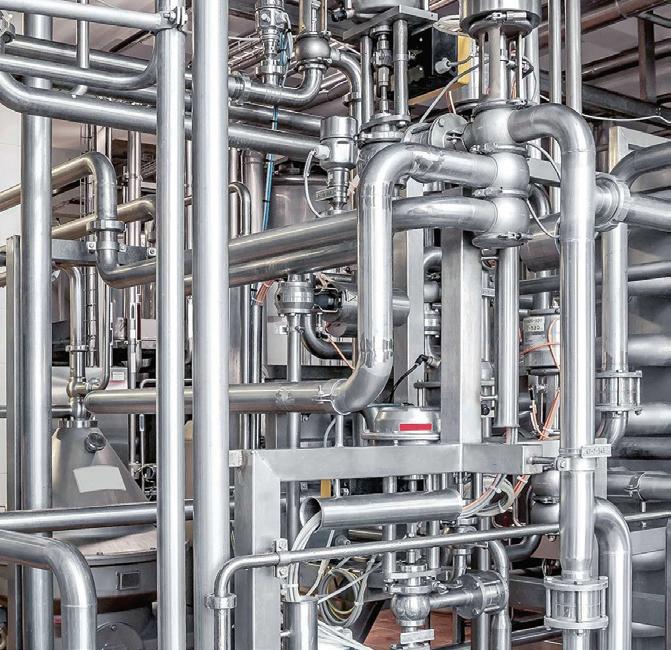

Flexible manufacturing roadshow proves a hit
OMRON’s Flexible Manufacturing Roadshow recently concluded its European tour with wellattended invitation-only events held across three days at the RAF Museum in Cosford.
Delegates learned about a wide range of solutions that are redefining flexible, efficient, and sustainable production for the factory of the future. Live demonstrations of technology at work – usually inaccessible beyond the factory due to its size and scale – allowed delegates to experience firsthand how robotics and automation are driving flexible manufacturing approaches across a range of manufacturing sectors.
Solutions on display included OMRON’s Mobile Manipulator (MoMa), a fusion of its autonomous mobile robot and cobot arm; its strongest HD-1500 mobile robot, ideal for heavy loads of up to 1,500 kg; a collaborative palletising cell; and IoT dashboard technology.
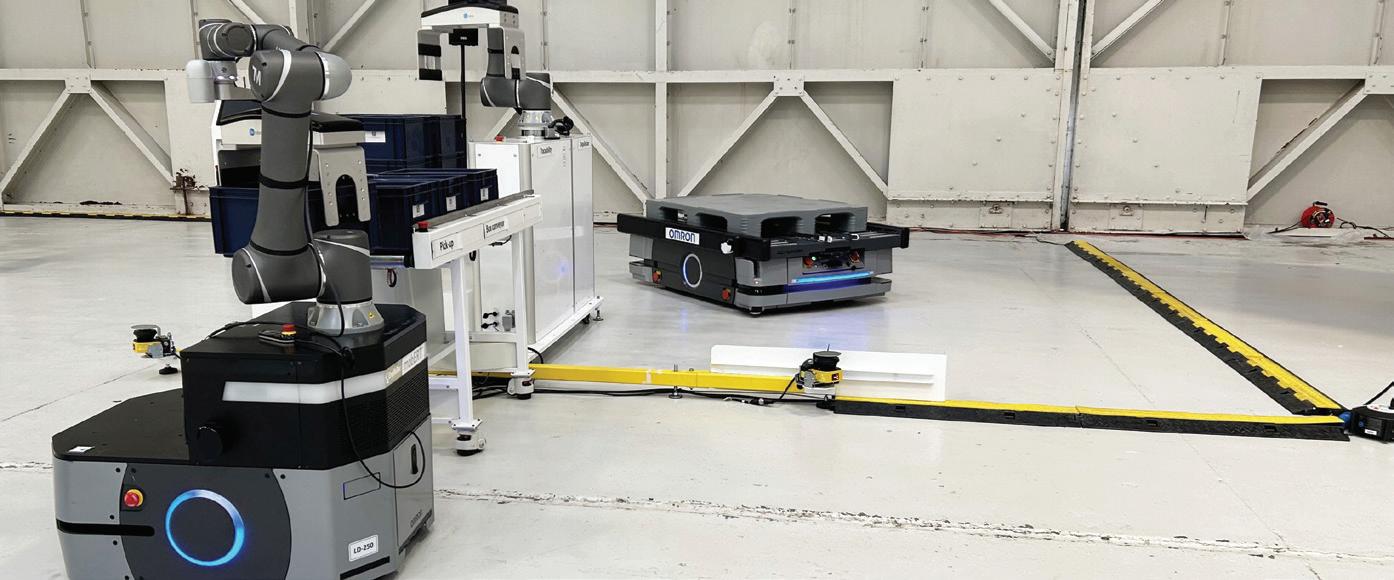
Delegates also heard from OMRON UK Marketing Manager Stuart Coulton on the social, environmental, and technology trends that are driving flexible manufacturing. Pointing to the need for customisation and short-run production to meet consumer demands, a shortage of skilled labour, and the need to enhance sustainability, Stuart explained how flexible manufacturing is not only essential but increasingly acts as a form of competitive differentiation for manufacturers.
The event also featured a number of OMRON technology partners, who had set up live demonstrations of realworld solutions that called on OMRON technology. Experts from Reeco Automation, Gripple Automation, Brillopak, Absolute Robotics, Hepco Automation and Factbird not only demonstrated their solutions but had experts on hand to answer questions about robotics, automation and the role of data in flexible manufacturing.
SKF UK announces ERIKS as its first maintenance partner for the UK
SKF UK has announced the launch of its SKF Maintenance Partner programme in EMEA and that ERIKS UK and Ireland will be the first SKF Maintenance Partner in the UK and Ireland. SKF Maintenance Partner status is a new level that recognises authorised distributors who can offer industrial customers more than just a traditional transactional relationship.
SKF Maintenance Partners have SKF’s support in implementing best practices, and always use SKF components for repairs. As a highly skilled service supplier, ERIKS uses its industry-specific knowledge to perform root-cause failure analyses and advanced troubleshooting. It is recognised by SKF as a knowledgeable advisor on maintenance matters, trained by SKF and with access to the very latest SKF technology.
ERIKS UK & Ireland has been appointed
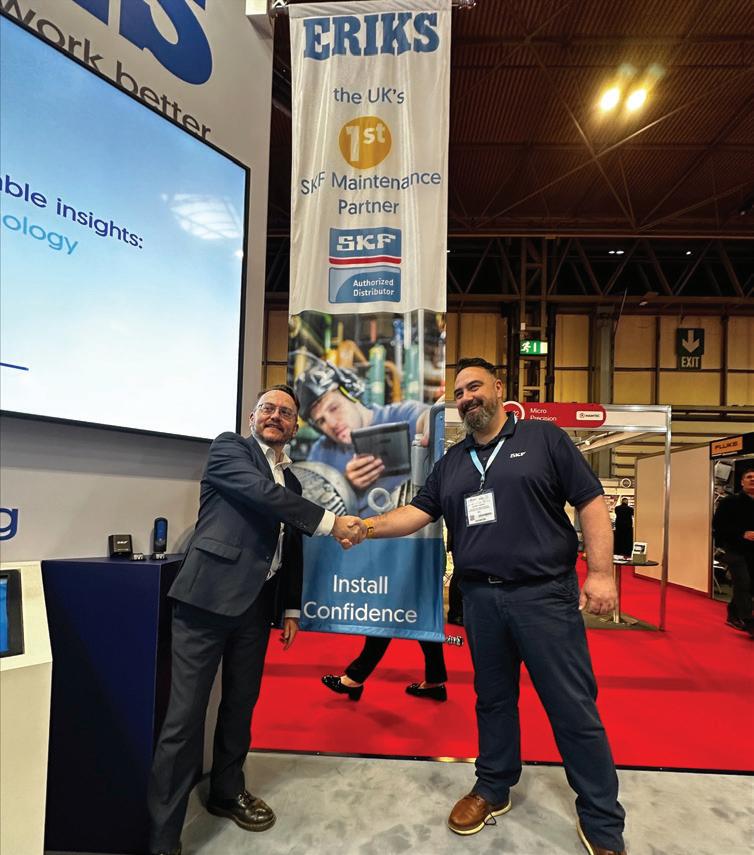
by SKF due to its investment in the SKF brand and its strategic alignment in adding long-term value to customers through engineering capability, innovation and knowledge and meeting the high-level criteria and accreditation process set by SKF. To support this partnership, ERIKS is extending the range of SKF products it stocks and will exclusively use SKF products in its UK repair facilities.
Speaking about the partnership, Pamela
Bingham, CEO of ERIKS UK & Ireland, said: “We are delighted and proud to announce this significant extension to our partnership with a world-leading company such as SKF. To become SKF’s Maintenance Partner, we have had to meet a stringent set of requirements, including support for the full range of SKF products and services in bearings, lubrication, maintenance products and condition monitoring.”
Global manufacturing industry recovery in 2025 to follow sluggish 2024
The global manufacturing economy will remain sluggish in 2024 and is forecast to expand by just 0.6% compared with last year. However, it looks set to recover in 2025, the latest data from Interact Analysis reveals. The market intelligence expert explains that, except for China, most territories will experience a slight contraction this year, but many will be better off than expected going into 2025.
Although Interact Analysis has lowered growth forecasts for 2025 in its latest Manufacturing Industry Output Tracker (MIO), this is the result of a slightly improved global outlook for the end of 2024, which will in turn see most economies finish the year in a stronger position. A slight dip in the growth rate is anticipated in 2026, but manufacturing output is expected to maintain a relatively steady positive trajectory out to 2028.
It is still unclear where the global manufacturing recovery will come from, and until there is an upturn, it is difficult to judge the potential strength. Despite optimistic signs for other territories, the latest MIO includes a slight downward revision for China compared with the previous edition, from 2.8% to 2.4%. China as ‘the factory of the world’ is responsible for almost half of the total manufacturing market value and any further reductions in the country’s forecast could well lead to a small contraction in the global MIO figure for 2024.
Consumer resilience, coupled with inflation and interest rates slowly starting to fall, is pushing up spending worldwide, and the US manufacturing economy is strengthening. The semiconductor industry has bounced back from a low point in 2023, boosting the outlook for parts of South Asia that are heavily reliant on the market sector, including Taiwan, Singapore, and South Korea. Dwindling order books and
the impact of the higher cost of living have constrained global demand, but there are signs of recovery in consumer spending, and post-COVID supply chain problems have eased considerably.
However, there are various economic indicators pointing to a more challenging environment for manufacturers. All four major European manufacturing economies are in a downward cycle, and sentiment for the year remains gloomy. Positive signals from the US may well start to manifest in other regions later in the year, but this has yet to be seen.
Although the overall outlook for manufacturing is expected to improve into 2025, the machinery market is in a slightly worse position. There are variations by machinery type, but underlying factors include persistently high interest rates pushing up the price of new machinery and low order intake in the last year, affecting current production figures.
Industry publishes manifesto for bold economic vision
Britain’s manufacturers are calling on the next Government to match their ambition for growth with a bold economic vision that puts the importance of the economy across every Ministerial portfolio.
Publishing its manifesto Make UK believes that the centrepiece of this vision must be a bold, long-term industrial strategy announced within the first hundred days, along with four other specific policy measures. In particular, this strategy must embrace a skills revolution throughout the education and training system to provide future talent, as well as the upskilling and re-training of the current workforce.
According to Make UK, such a vision is essential given the huge changes in the policy landscape, the need to shock the UK economy out of its anaemic holding pattern and, take advantage of the
opportunities provided by rapidly accelerating technologies, investment in infrastructure and the move to a greener economy.
The five specific measures Make UK is calling for in the first hundred days of the next Government are:
1. Announce a long-term modern Industrial Strategy to underpin all economic policymaking which has cross Government commitment. This should be backed by the re-introduction of an Industry Strategy Council and a new Cabinet Office backed Committee to ensure the implementation of the Strategy across Government.
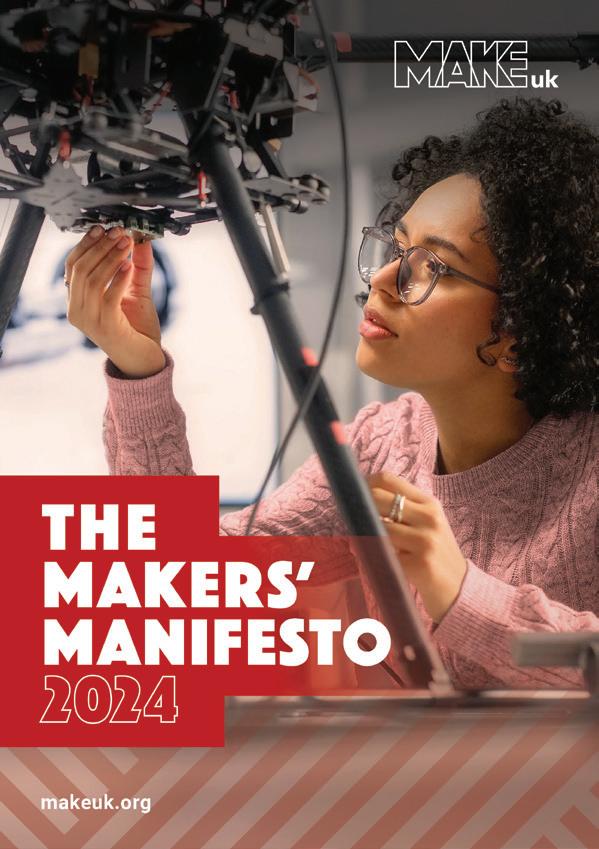
2. Align the UK CBAM (Carbon Border Adjustment Mechanism) with the EU CBAM in terms of timescale and design to provide a level playing field with the EU.
3. Commence a rootand-branch review of the Apprenticeship Levy as a funding mechanism, as well as the wider apprenticeship system.
4. Re-establish an updated, modern Manufacturing Advisory Service.
5. Establish a mechanism for ongoing and active consultation with industry to decide where it is appropriate to maintain alignment with EU regulatory changes or where opportunities for divergence might apply.
Flexible, safe, and economical material handling
Thanks to its inductive charging concept, the new KMP 3000P is ready for operation 24/7, bringing a new efficient dimension to intralogistics. The mobile platform, which can transport loads of up to three tons, expands KUKA’s AMR (Autonomous Mobile Robot) portfolio.
With the KMP 3000P, KUKA is launching a real heavyweight in the AMR sector. The mobile platform can transport loads of up to three tons and its omnidirectional drive ensures maximum flexibility in the tightest of spaces in intralogistics. The platform is always ready for operation thanks to its inductive charging concept, which enables flexible charging during the process.
The KMP 3000P builds on the success of its smaller sister, the KMP 1500P, and adds another one and a half tons of transport capacity. The ability to move up to three tons opens a wide range of possible applications
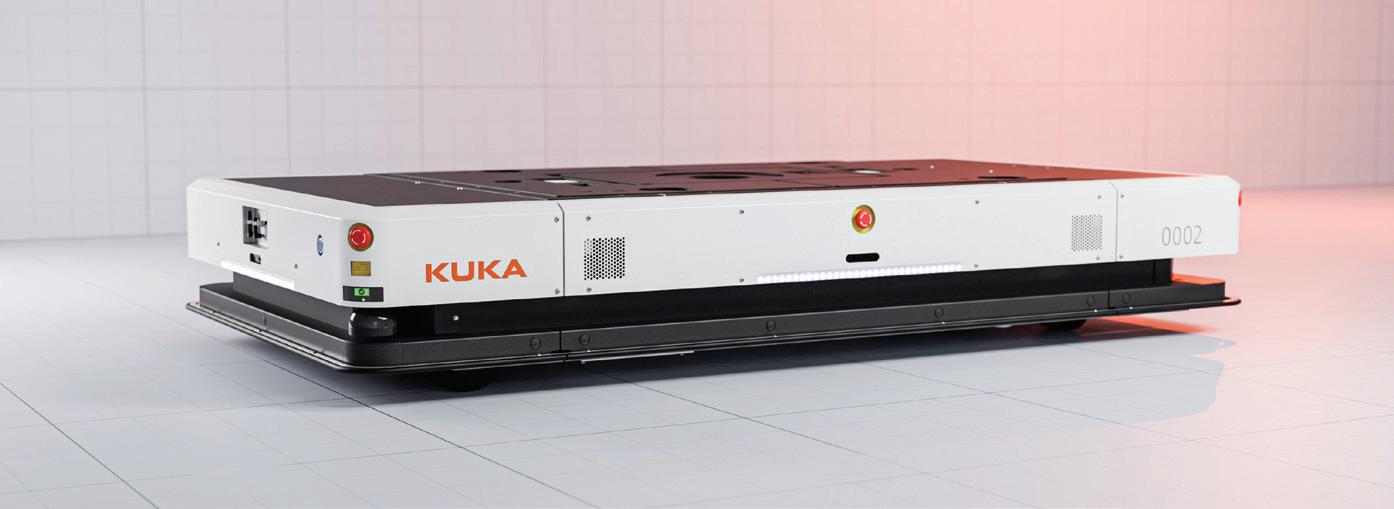
for various industries. Whether for material supply in production, process interlinking without conveyor belts or classic point-topoint transport – the KMP 3000P masters the transport of large, unwieldy, and heavy components without any problems. If the maximum payload exceeds three tons, the KMP 3000P also has the right features: with load-sharing, two platforms cooperate and can transport up to six tons in total. One of the two platforms becomes the master vehicle and sets the direction.
The KMP 3000P has an omnidirectional drive, which enables it to move in all
NOVA software platform gains its fastest camera yet
Machine vision solutions specialist SICK’s AI-powered NOVA platform now offers even more to customers with the launch of a new 2D smart camera.
NOVA is SICK’s unique, scalable and cost-effective foundation software for configuring machine vision solutions. Featuring a user-friendly web interface and capable of running on a wide range of 2D and 3D vision sensors, NOVA can leverage different imaging technologies to handle even the most challenging applications across many different industries.
Providing machine vision and non-vision experts with the opportunity to create bespoke applications and utilise readymade plug-ins, SICK’s NOVA platform simplifies the development process and makes it accessible to everyone. The
advanced AI functionality removes the need for complex manual setups by enabling users to teach through examples.
The newly launched, next-generation Inspector83x is the fastest camera on the NOVA platform, providing unparalleled capabilities in automated inspection and measurement. Combining the capabilities of the Inspector83x with the NOVA foundation software platform delivers a market-leading out-of-the box solution.
Designed to handle machine vision inspection tasks quickly and precisely, the Inspector83x is equipped with 5MP resolution, built-in illumination and a powerful quad-core CPU.
Nathaniel Hofmann, SICK UK’s Market Product Manager, said: “Our strength lies in providing full-spectrum machine vision solutions. We use our extensive expertise to meet customer needs, creating bespoke solutions for even the most challenging applications. The Inspector83x
directions. Four integrated 3D cameras and two laser scanners enable a 360° view, allowing the platform to recognise obstacles and drive around them effortlessly. This not only increases efficiency but also safety in various working environments.
The KMP 3000P is configured and controlled with the KUKA.AMR Fleet software platform. This enables process planning, comprehensive fleet management and peripheral monitoring all in one – without any programming.
/bit.ly/KUKAAMR
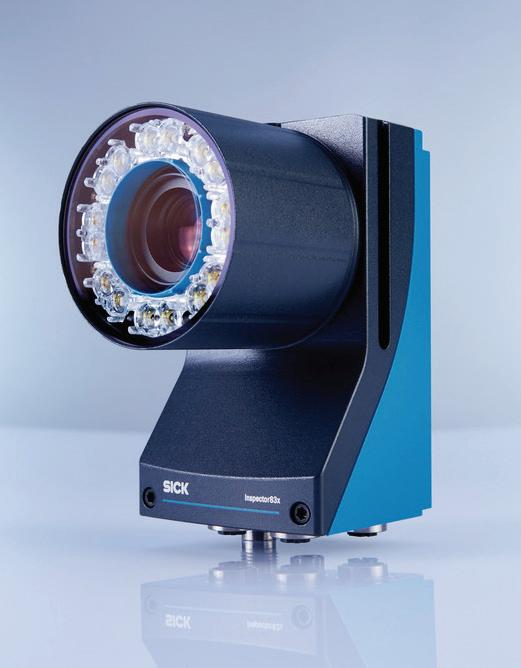
is a 2D AI smart camera designed to handle even the most challenging machine vision tasks.
“SICK’s legacy as a pioneer in machine vision, combined with our powerful NOVA platform and a complete range of 2D and 3D machine vision products, ensures we deliver top-quality machine vision solutions like the Inspector83x.”
www.sick.co.uk
The latest version of ABB’s
Ability OPTIMAX digital energy management and optimisation system, version 6.4, provides coordinated control of multiple industrial assets and processes for improved energy efficiency to reduce emissions and support decarbonisation.
The performance and usability upgrades to OPTIMAX include an AI module for improved fore-casting of load demand, energy generation and energy pricing without manual interaction. This significantly reduces day-ahead and intra-day nomination errors when feeding energy to the grid, which helps avoid rising penalty payments for operators.
“At ABB, we believe that the greenest energy is the energy you don’t use, so driving efficiencies across the entire energy value chain is key,” said Dr Sleman Saliba, Global Product Manager En-ergy Management and Optimization at ABB
Upgraded energy management system optimises industrial energy efficiency Sugar sugar for hard-working Borger pumps
Following the proven, ongoing performance of three rotary lobe pumps installed in a key process at a sugar refinery, a further two units from Borger are to be installed at the plant.
Two of the existing Borger pumps are utilised for white mass (sugar syrup with crystals), whilst the third pump also runs 24/7 (from August to May) but for a slightly lower grade of sugar. Both applications send the highly viscous solution (50-55% solids) to its final stage, where the syrup is spun off to reveal the end product of fine white sugar crystals.
Increasingly prohibitive maintenance bills (over £12,000 per overhaul, per pump) and lengthy downtime had prompted the sugar refinery to replace three of its pumps.
To further improve and streamline its pumping operation, the sugar refinery also ensured that the new pumps were all the same size (unlike the previous units)
Energy Industries. “OPTIMAX has been upgraded to incorporate the newest technology and address the latest market opportunities, enabling the acceleration of industrial decarbonisation to help preserve resources, as well as sector coupling to replace the use of fossil fuels across energy systems and industrial sectors.”

Combining digital technologies with modular solutions, presented in a simplified user interface, it delivers an updated optimisation environment for solving the energy management challenges fac-ing industrial enterprises and energy providers. In a complex steam and power plant in Germany, OPTIMAX led to an additional 1.5% reduction in energy costs in the first six months, enabling an ROI within one year for
the customer.
Modularised for easy installation, each component can be ordered separately and the modular platform enables automated and semi-automated updates and upgrades.
For the first time, ABB’s Channel Partner network will also be able to distribute OPTIMAX 6.4 due to enhance-ments in usability and code-free configuration.
new.abb.com
to reduce the cost of required spares.
A further four Borger pumps have also become an integral part of the sugar producer’s AD plant, which uses waste pulp beet as a feedstock for clean renewable energy.
At the AD plant that includes three digesters, receiving around 100,000 tonnes of pressed sugar beet pulp pa, the Borger pumps are utilised for the transfer of digestate.
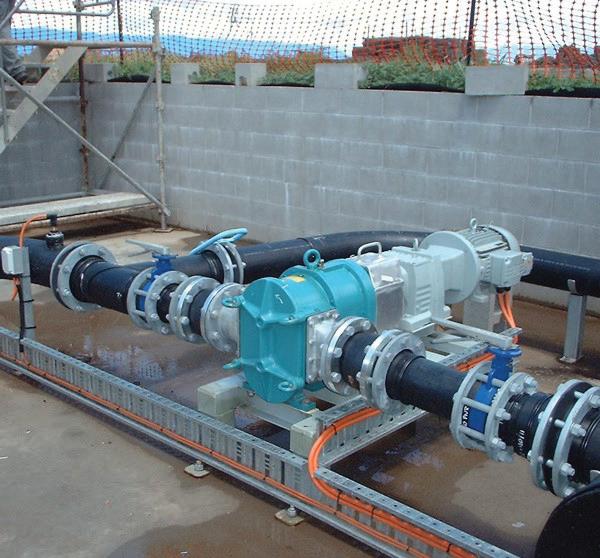
At a separate sugar-beet processing facility, a Borger BLUEline EL 1000 pump was installed after an old rotary piston unit failed. The Borger pump conveys massecuite (sugar crystals) with flow rates of 60–150GPM @ 52 psi.
And to complete a hat-trick of new orders in highly viscous and abrasive applications such as the processing of magma, sugar syrup, and liquid sugar, a Borger BLUEline EL 1000 pump has commenced its role in unloading molasses (10,000cP) from rail tankers. www.boerger.com
Let associations help you on your journey
Gambica’s Nikesh Mistry explains how working with trade associations and other knowledge transfer networks can help manufacturers embark on their digitalisation journey.
The beat of digitalisation has been echoing through every industry for a number of years, and manufacturing is no exception. Digital technologies are not new; rather, they are becoming more developed, more secure, and increasingly reliable. Yet, despite the undeniable benefits –increased efficiency, improved quality control, and enhanced agility – many manufacturers remain hesitant to embrace the digital evolution. As an association, we understand this reluctance stems from a number of different factors but includes a mix of fear, misunderstanding and uncertainty. I’d like to explain and attempt to debunk some common myths and explore how industry associations, knowledge networks and other corporations can bridge the digital divide.
Firstly, there is a perception that digitalisation requires a complete overhaul of existing systems, and this, to begin with, is a major deterrent. The reality is digital adoption is a journey, not a destination. Manufacturers can begin by focusing on specific points of improvement. Starting backwards by finding a problem they wish to solve and then finding the right technology to tackle that issue. Implementing a digital solution for inventory management or predictive maintenance, for example, can deliver immediate value without disrupting core operations. Similarly, there are many digital technologies that, with only a slight change, can begin to realise significant results.
Another myth I hate to hear is the fear of the loss of jobs due to digitalisation. Yes, there is an understandable fear of job displacement, and while some repetitive tasks will be automated, digital processes create a range of new opportunities with jobs existing today which didn’t ten years ago and equally the prospect of more rewarding jobs being created in the future. Workers have to transition from manual labour to roles
requiring technical expertise, data analysis, and problem-solving skills. Upskilling the workforce is crucial for capitalising on the digital advantage and, in actual fact, will generate a much better-equipped workforce and build a more competitive environment for the future.
The upfront cost of digital technologies can also be daunting, but the best approach is to have a long-term perspective. The cost savings as mentioned above, from improved efficiency, reduced waste, and optimised production processes often outweigh the initial investment. While sometimes difficult to realise initially, the rewards are certainly received. Additionally, government grants and industry initiatives can help manufacturers offset the financial burden.
Cybersecurity concerns are also another valid consideration. And yet again, there is a solution: modern digital solutions prioritise data security. Manufacturers can mitigate risks by partnering with reputable vendors and implementing robust cybersecurity protocols. Managing data on external servers and through cloud software is often allowing manufacturers to have a greater security.
Beyond these misconceptions, manufacturers we speak to tend to grapple with real challenges, such as a lack of in-house expertise, especially for some SMEs, the internal talent or understanding to implement and maintain digital solutions is often forgone. Coupled with this is the understanding or ability to integrate new technologies with legacy systems, which can often be complex and time-consuming if not understood.
Industry associations and knowledge transfer networks can be instrumental in helping manufacturers navigate the digital landscape. We help our members through not only our special interest groups but also through information on workshops, seminars, and online resources available which educate

manufacturers about digital technologies and their applications. Along with this we form a community of manufacturers where they can discuss their issues with one another and find solutions for best practice.
Networks like the Manufacturing Technology Centre, Innovate UK’s Knowledge Transfer Network, Make UK, GAMBICA and others help to connect manufacturers with peers who have already embarked on the digitalisation journey. These groups advocate for policies that promote digitalisation in manufacturing, such as funding for research and development and workforce training programs. And can often direct manufacturers to the right source of help.
Digitalisation is not only the past and present, but it is certainly the future of manufacturing. By demystifying the myths, understanding the challenges, and leveraging the support of industry organisations, manufacturers can transform fear into a competitive advantage. The path to digitalisation may seem intimidating, but by taking calculated steps, forging strong industry connections, and adopting a learning mindset, manufacturers can unlock a new era of growth, efficiency, and innovation.
Manufacturing: An underappreciated industry?
Dave Atkinson, UK Head of Manufacturing SME & Mid Corporates at Lloyds Bank, considers new data that reveals manufacturers’ fundamental role in the UK economy.
Launched at the MACH 24 exhibition, a report, titled The True Impact of Manufacturing, seeks to uncover the full extent of UK manufacturers’ contribution to the nation’s economy – and it makes fascinating reading.
Published by the Manufacturing Technologies Association and produced by Oxford Economics, the report takes a deep dive into decades of economic data to reveal how the sector’s impact is far bigger than is often appreciated.
Analysis states that manufacturers generated an estimated £184 billion in GDP during 2022, while directly employing 2.6 million workers; around 8% of the country’s total economic output and 7% of all jobs.
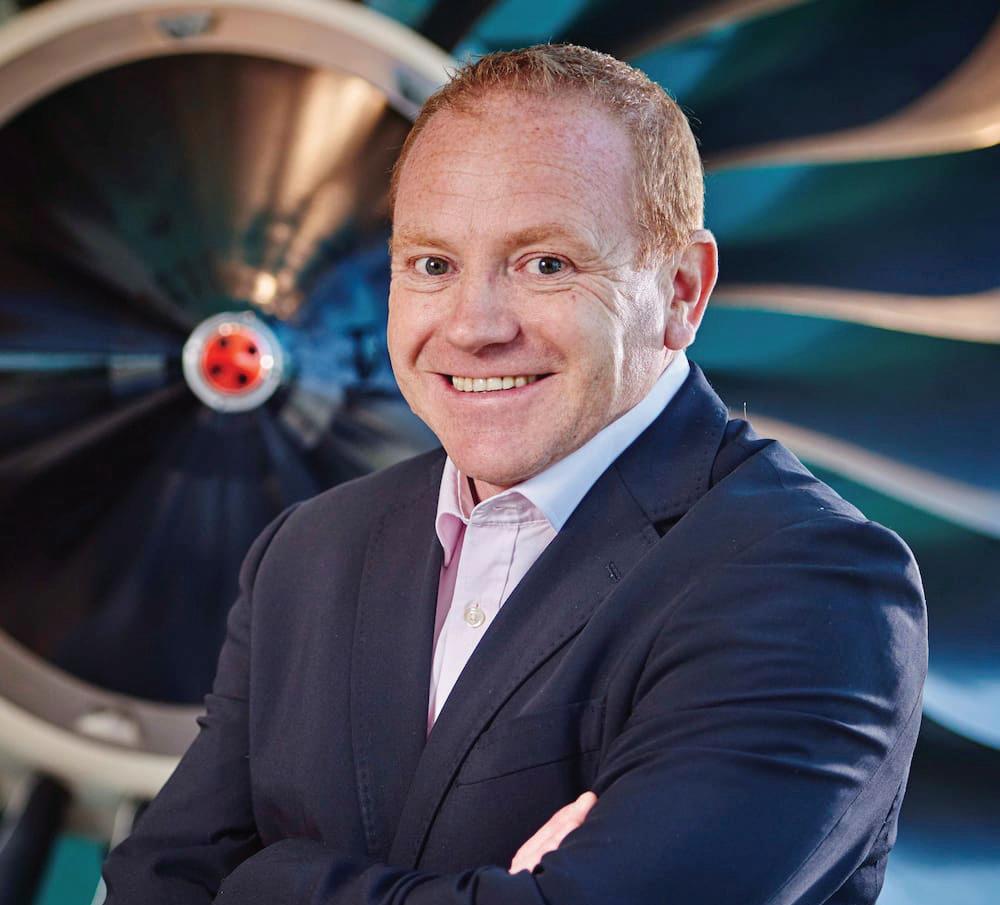
That’s impressive enough, but further investigation shows that the sector’s economic footprint is actually much larger.
Manufacturers support a network of suppliers, from food and drink to financial services, indirectly impacting all sectors of the economy.
That adds a further £164 billion and a further 2.6 million jobs to the manufacturing ecosystem.
And there is a third component known as induced impact; a measure of the amount everyone employed by manufacturers and their suppliers add to the economy when they spend their wages, which are 11% higher than the UK median average.
By combining the direct, indirect and induced effects of manufacturing, we get the true impact of the sector; £518 billion a year and 7.3 million jobs.
That means almost a quarter of the UK economy (23%) and over a fifth (22%) of all jobs rely in some way on UK based manufacturers.
Evolution and innovation
Manufacturing contributes so much more than just jobs and GDP; it’s a driver of future prosperity, accounting for 47% of all business R&D spend in the UK.
This innovative activity is happening in areas that represent some of the world’s most fundamental challenges, including health, defence and climate change.
As manufacturing becomes increasingly advanced, firms need practical and financial support to assist their evolution or risk being left behind.
This requires a joined-up effort, which must include policymakers, trade organisations, business, academia, lenders and more.
We recognise that, as one of Britain’s biggest banks, Lloyds Bank can be an important piece of that puzzle.
So, we’re on the front foot, bringing organisations together to provide the resources that manufacturers, particularly SMEs, need to transform.
Central to that is our support of the Manufacturing Technology Centre (MTC) in
Coventry, which we have backed with a £15m sponsorship through to 2030 to give the sector the much-needed confidence to plan long-term.
Strategic support
This partnership has two main aims.
To help fund the MTC’s state-ofthe-art training centre, creating a new generation of engineers and technicians who will help the UK realise its potential in advanced manufacturing. And to support firms in transforming their operations to be more productive, efficient, and sustainable.
SMEs can access the MTC’s subject matter experts and advanced manufacturing technical engineers who can help address a number of challenges; from adopting the right technology to new process development.
We’ve also worked closely with the Manufacturing Technologies Association for 14 years, including sponsoring the flagship MACH Exhibition.
Lloyds Bank wants to lead by example, and it’s heartening to see others doing the same.
The Government recently announced a £4.5 billion support package for strategic manufacturing sectors, for example, while there are countless examples of universities partnering with manufacturers to support their innovation.
These are the kinds of initiatives that create a more supportive UK-wide ecosystem for manufacturing innovation.
As this strategic collaboration becomes the norm, the true impact of UK manufacturing can become even bigger and better.
lloydsbank.com/manufacturing
The evolution of pressure measurement in the hydrogen industry
With hydrogen set to play an increasing role in the global energy mix, pressure measurement specialist ESI Technology outlines the advantages of silicon-on-sapphire technology for pressure measurement in the growing number of applications and systems emerging in this sector.
The hydrogen industry is on the brink of revolutionising the global energy landscape. As a clean and efficient energy source, hydrogen promises to reduce carbon footprints and mitigate climate change. One critical aspect of harnessing hydrogen’s potential is the correct and reliable measurement of pressure within various systems, from production and storage to transportation and utilisation. Silicon-onsapphire (SoS) pressure transducers and transmitters are playing a pivotal role in advancing pressure measurement technology in the hydrogen industry, ensuring safety, efficiency, and precision.
Silicon-on-sapphire technology
Silicon-on-sapphire technology involves the integration of a thin layer of silicon on a sapphire substrate. This combination uses the unique properties of both materials: silicon’s well-established semiconductor characteristics and sapphire’s exceptional mechanical strength and thermal stability. The result is a robust and highly sensitive pressure measurement device capable of performing in extreme environments.
The advantages Silicon-on-Sapphire pressure transmitters can offer include:
• High precision and sensitivity: SoS pressure transmitters show superior precision and sensitivity due to the excellent piezoresistive properties of silicon. This sensitivity is crucial in the hydrogen industry, where even minor variations in pressure can significantly affect safety and efficiency.
• Temperature stability: Hydrogen systems
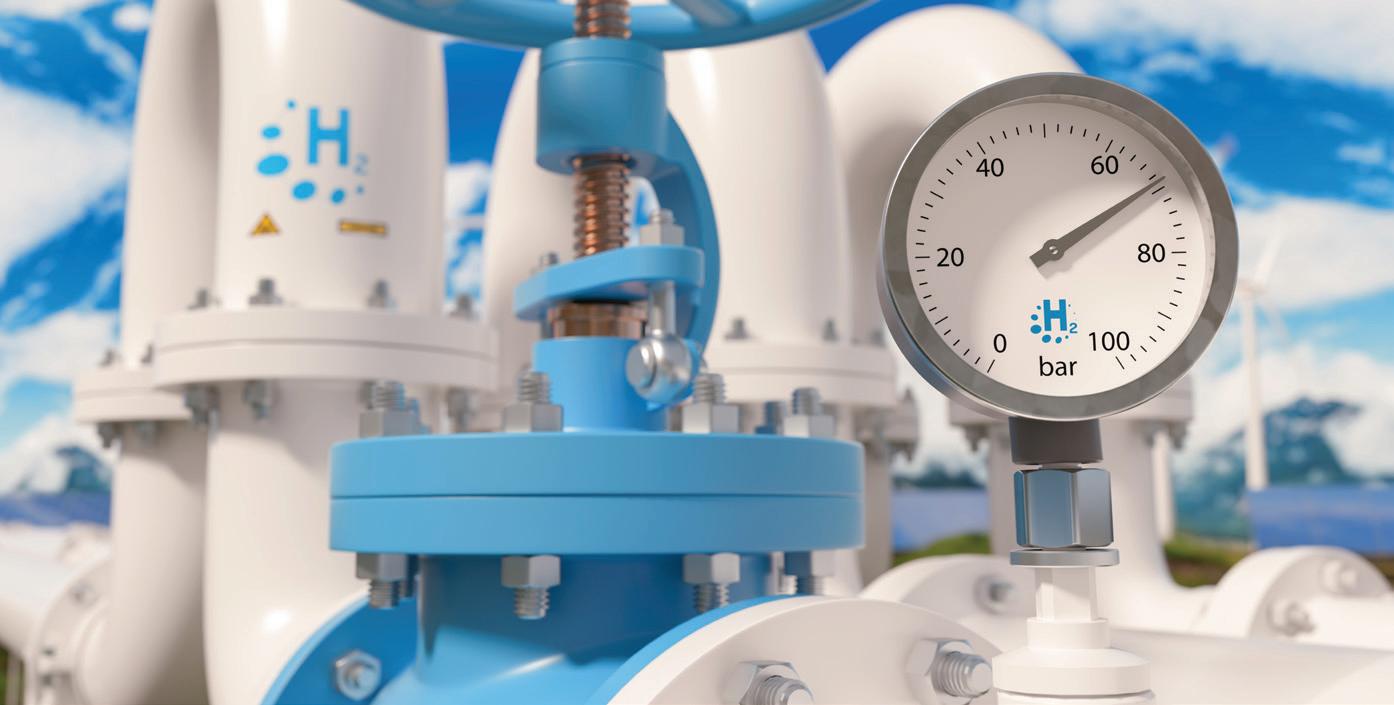
often run under extreme temperature conditions. SoS technology ensures minimal thermal drift, supplying accurate pressure readings across a wide temperature range. The sapphire substrate’s low thermal expansion coefficient helps keep measurement integrity, which is crucial for high-temperature hydrogen applications.
• Durability and corrosion resistance: Hydrogen environments can be harsh, with potential exposure to corrosive substances. Sapphire’s chemical inertness and mechanical robustness make SoS pressure transmitters highly resistant to corrosion and physical wear, ensuring long-term reliability and reduced maintenance costs.
• High-pressure capability: Hydrogen systems can involve extremely high pressures, especially in storage and transportation. SoS pressure transmitters are designed to withstand these highpressure conditions, making them ideal for hydrogen applications that demand robust performance under stress.
SoS pressure transducers can meet a number of challenges and deliver clear benefits in hydrogen industry applications, including:
• Hydrogen production: In hydrogen production, particularly through methods such as water electrolysis, maintaining precise pressure control is essential for efficiency and safety. SoS pressure transmitters provide accurate monitoring and control, ensuring optimal performance and preventing hazardous conditions.
• Storage and transportation: Hydrogen storage, whether in liquid or gaseous form, requires meticulous pressure management. SoS pressure transmitters are employed to monitor storage tanks and transportation vessels, ensuring they operate within safe pressure limits and alerting operators to any deviations that could indicate leaks or other issues.
• Fuel cells: Hydrogen fuel cells convert chemical energy into electrical energy, requiring precise pressure regulation for optimal performance. SoS pressure
transmitters help maintain the necessary pressure conditions within the fuel cells, enhancing efficiency and longevity.
• Hydrogen refuelling stations: Refuelling hydrogen-powered vehicles needs accurate pressure control to ensure safe and efficient transfer of hydrogen. SoS pressure transmitters are integral to the refuelling infrastructure, providing real-time data to manage the refuelling process effectively.
Enhancing safety
Safety is paramount in the hydrogen industry due to the high flammability and potential hazards associated with hydrogen gas. Reliable pressure measurement is, therefore, crucial for detecting leaks, over-pressurisation, and other anomalies that could pose risks. SoS pressure transmitters offer several safetyenhancing features:
• Leak detection: Accurate pressure monitoring enables the early detection of leaks, allowing for prompt intervention before the situation escalates. This capability is vital in preventing accidents and ensuring the safety of personnel and equipment.
• System integrity monitoring: Continuous pressure measurement helps maintain the integrity of hydrogen systems by providing real-time data on pressure conditions. This data is essential for identifying and addressing potential issues that could compromise system safety.
• Compliance with regulations: The hydrogen industry is subject to stringent safety regulations. SoS pressure transmitters provide the reliable and precise data needed to comply with these regulations, ensuring that hydrogen systems operate within the prescribed safety parameters.
Efficiency and sustainability
The use of SoS pressure transmitters also contributes to the overall efficiency and sustainability of hydrogen systems. By providing accurate and reliable pressure data, these devices enable:
• Optimal system performance: Precise pressure control ensures that hydrogen systems operate at their best performance levels, maximising energy efficiency and reducing waste.
• Reduced downtime: Reliable pressure measurement minimises the likelihood of unexpected failures and downtime. This reliability is crucial for keeping continuous operation in critical hydrogen applications.
• Lower maintenance costs: The durability and corrosion resistance of SoS pressure

transmitters reduce the frequency and cost of maintenance, contributing to the long-term sustainability of hydrogen infrastructure.
Real-world applications
Numerous real-world applications prove the benefits of SoS pressure transmitters in the hydrogen industry. For instance:
• Hydrogen refuelling stations in Europe: Several hydrogen refuelling stations across Europe have adopted SoS pressure transmitters to enhance the accuracy and reliability of their pressure measurement systems. This adoption has resulted in safer and more efficient refuelling operations, promoting the broader use of hydrogenpowered vehicles.
• Hydrogen production facilities in Asia: Leading hydrogen production facilities in Asia are utilising SoS pressure transmitters to monitor and control their electrolysis processes. The precise pressure data provided by these transmitters has improved the efficiency of hydrogen production, contributing to the region’s energy sustainability goals.
• Aerospace applications in the United States: The aerospace industry in the United States is incorporating SoS pressure transmitters in hydrogen propulsion systems for spacecraft. The reliability and high-pressure capabilities of these transmitters are crucial for ensuring the safety and performance of hydrogen-based propulsion systems in demanding aerospace environments.
Prospects and innovations
As the hydrogen industry continues to evolve, the role of silicon-on-sapphire pressure transmitters is likely to expand. Future innovations may include:
• Enhanced miniaturisation: Advances in microfabrication techniques could lead to even smaller and more sensitive SoS pressure transmitters, enabling their use in compact and lightweight hydrogen systems.
• Integration with IoT: The integration of SoS pressure transmitters with the Internet of Things (IoT) could supply real-time data analytics and remote monitoring capabilities, further enhancing the safety and efficiency of hydrogen systems.
• Advanced sensing capabilities: Ongoing research and development may yield SoS pressure transmitters with enhanced sensing capabilities, such as multi-parameter measurement (e.g., temperature, humidity), supplying comprehensive monitoring solutions for hydrogen applications.
Conclusion
Silicon-on-sapphire pressure transmitters are at the forefront of evolving pressure measurement technology in the hydrogen industry. Their high precision, temperature stability, durability, and high-pressure capability make them indispensable for a wide range of hydrogen applications, from production and storage to fuel cells and refuelling stations. By enhancing safety, efficiency, and sustainability, SoS pressure transmitters are driving the advancement of the hydrogen industry, paving the way for a cleaner and more sustainable energy future.
The continued innovation and adoption of SoS pressure transmitters will undoubtedly play a crucial role in realising the full potential of hydrogen as a key energy source, contributing to the global efforts to reduce carbon emissions and combat climate change.
esi-tec.com
Innovations beyond the standard
Although standard products from the binder portfolio suit most applications, they do not fit all of them. In such cases, the Neckarsulm-based manufacturer’s solution expertise comes into play in the form of exclusive connectors that are perfectly tailored to the application. Customers benefit from binder’s exceptional vertical integration as well as six decades of experience in design and engineering.
Binder, a leading supplier of industrial circular connectors, develops and manufactures specialised connectivity solutions according to customer requirements. The focus is on use cases with special demands that exceed the typical scope, so that none of the binder catalogue products meet all the criteria. Such applications can be reliably implemented with customised solutions from the Neckarsulmbased specialist. binder has extensive knowhow and more than 60 years of experience in the design and development of connectors –and has been creating individual connectivity solutions together with customers and according to their ideas for just as long.
Vertical integration and quality expertise
For the benefit of its customers, binder offers design, tooling, manufacturing, assembly, and automation from a single source. Through its affiliated companies, the manufacturer has additional expertise in stamped, turned, and cast parts as well as in galvanics, PCB design, and component assembly. Furthermore, binder’s customised products are qualified in the company’s own laboratory. With the help of Failure Mode and Effects Analyses (FMEA), critical design and production challenges are identified at an early stage. Sample assemblies and preliminary tests in the binder lab support the optimisation and quality assurance of custom products, as well as the monitoring and approval of pilot series production by the quality project managers. ISO 9001:2015, ISO 14001:2015, and EN ISO 13485:2016 + AC:2018 + A11:2021 certifications underline binder’s competencies in terms of quality and

environmental management.
The target markets for binder’s tailor-made products are as diverse as the company’s customers. Examples of applications can be found in sanitary and medical device technology, industrial automation, as well as metrology and controls. A typical requirement in medical device engineering, for example, is that connectors must not be identical. An interface has to be unique to prevent mismating. In addition, resistance to certain liquids can already be considered during the design phase when selecting the components’ materials. Potential medical applications include respiratory and dialysis equipment, instruments for ultrasound and electrotherapy, as well as infusion pumps and contrast agent injectors.
For applications in patient monitoring, binder has developed a modular 12-pin connector system consisting of a panel mount plug and eight panel mount sockets (970 series).
Reliability was the key design criterion. While the sockets were integrated into the housing of the patient monitor, the plugs were part of the pluggable parameter modules. Concentric arrangement of the contacts ensured the plug connection was centered automatically when mating – without the need of removing the protective cap.
When realising customer-specific development projects, all binder corporate divisions involved operate in a flexible and extremely customer-oriented manner. Thanks to their outstanding experience and technological capabilities, binder is able to develop and manufacture highly individualised connectors for different target markets according to customer specifications – providing excellent supply reliability and at the highest level of quality.
www.binder-connector.co.uk
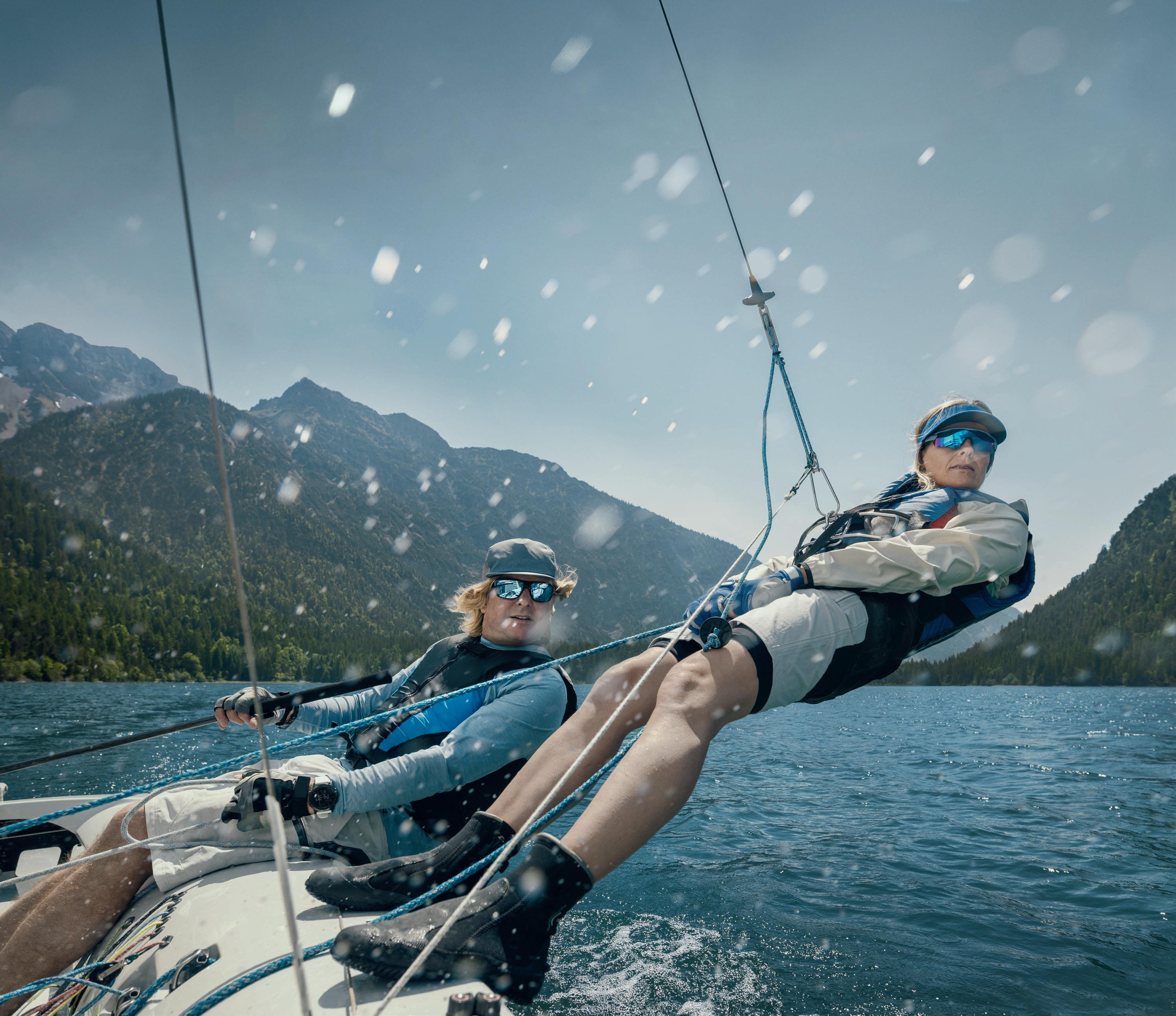
Process improvement is like sailing. With an experienced partner, you can achieve more.
Optimizing processes and maximizing efficiency is important to remain competitive. We are the partner that helps you master yield, quality, and compliance. With real-time inline insights and close monitoring of crucial parameters, we support manufacturers to optimize processes, reduce waste, and increase yield.
Pallet Shuttle: driving space efficiency and reduced costs in manufacturing
MAXIMISES YOUR SPACE UTILISATION BY REDUCING THE NUMBER OF ACCESS AISLES
INCREASES YOUR HANDLING RATES WITH AUTOMATED PALLET RETRIEVAL SPEEDS UP YOUR ORDER FULFILMENT AND IMPROVES BUSINESS CASHFLOW
2-WAY & 4-WAY SOLUTIONS 100% CUSTOMISED TO YOUR BUSINESS NEEDS
OPTION TO ADAPT YOUR EXISTING DRIVE-IN RACKING AND/OR RESTORE END-OF-LIFE SHUTTLES
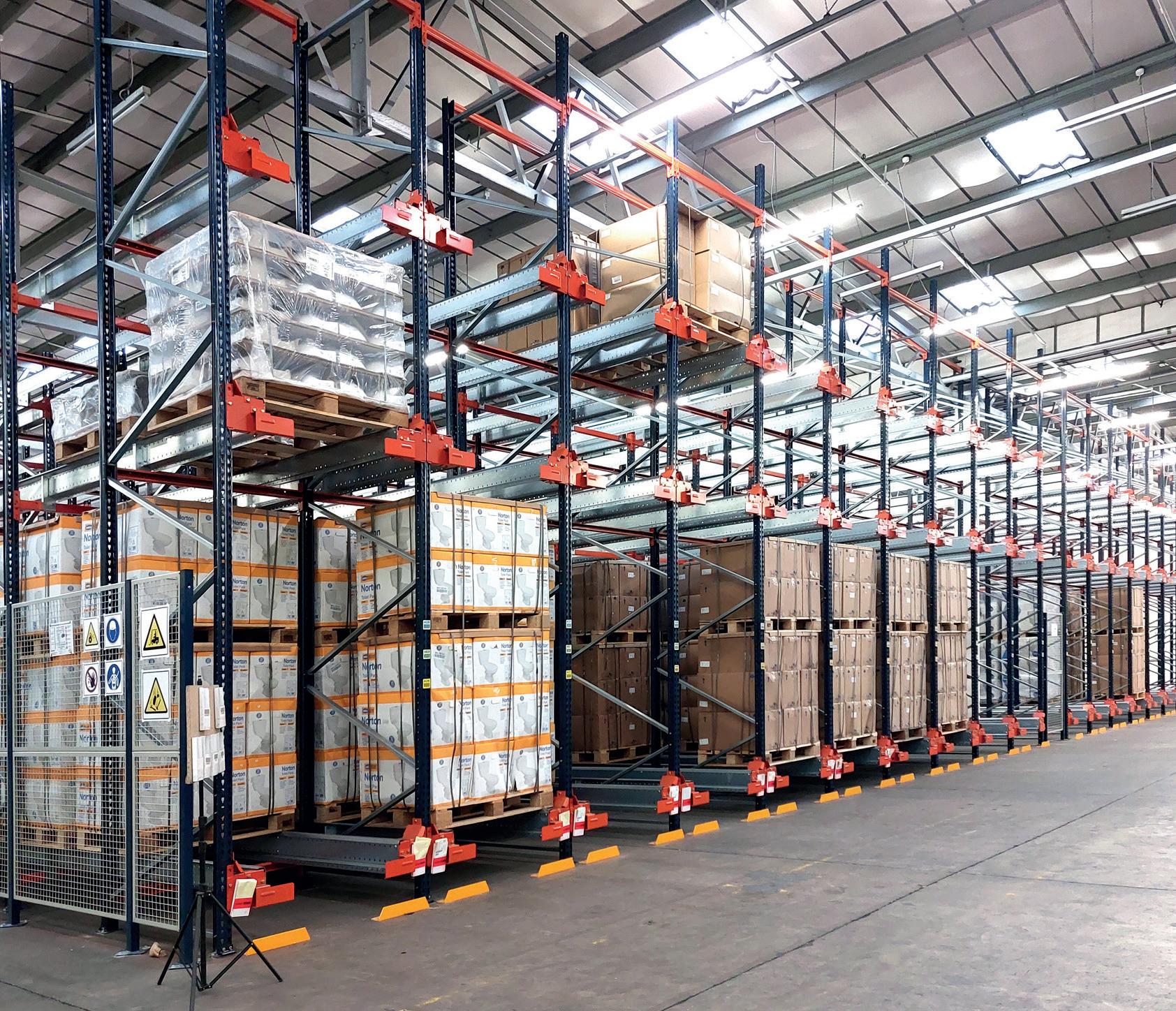
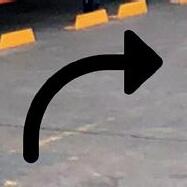

Warehousing & Logistics
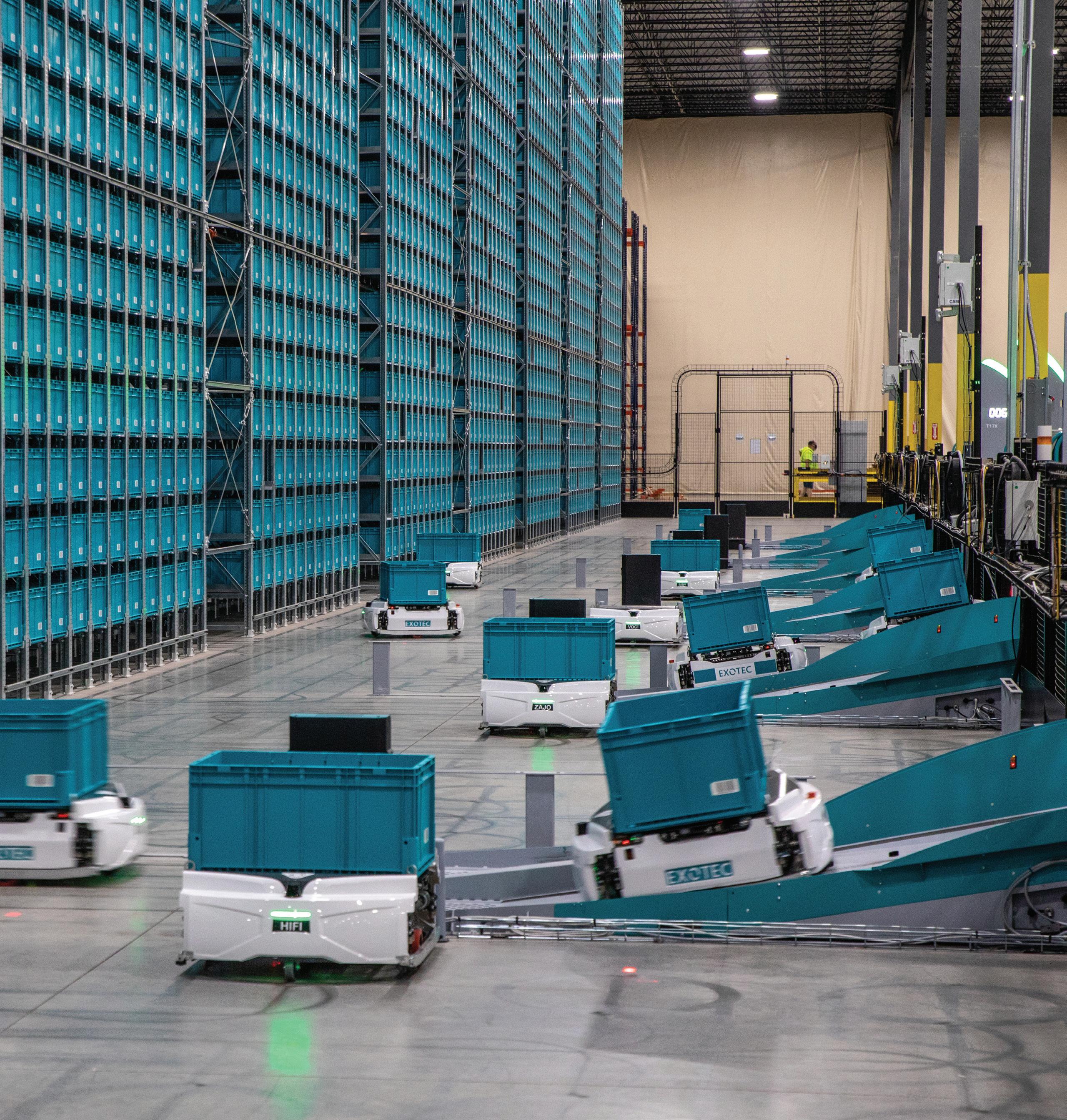
MEPCA explores the latest news, innovations and applications in warehousing & logistics
Avoiding a hangover
Simon Jones, Senior Sales Executive at Exotec explores the benefits and potential offered by warehouse automation in the alcohol industry.
British alcohol businesses have experienced a revolution in recent years with the rise of craft beers, artisanal spirits and nonalcoholic options. Meanwhile, consumers are shifting away from pubs and bars towards at-home drinking experiences, largely fuelled by e-commerce and rising prices. Alcohol wholesalers, manufacturers and distributors must find new ways to adapt to beat the competition, and it all starts in the warehouse.
Is trouble brewing?
In the UK, the wholesale market for alcoholic beverages is estimated to be worth £18.4bn, with home delivery services contributing to this post-pandemic. Many alcoholic beverage manufacturers and retailers have established an online presence to tap into this growing market, which is expected to increase by 5% each year between 2024 and 2029.
Brits are also turning to low- and noalcohol products, while customers are also spending time finding the ‘right’ product, choosing quality over quantity.
This is great news for established wholesalers who have been in the market for some time and are known for their premium products. However, the surge in options for consumers has created a competitive landscape for manufacturers, retailers and wholesalers alike, having a knock-on effect on big names who may be unable to adapt quickly.
Businesses need to prepare and distribute orders quickly, more efficiently and at a lower cost to maximise the opportunities the current climate presents, or risk falling short.
Uncorking the warehouse challenge
The answer to this is flexible warehouse automation. After decades of growth in an industry fuelled by ‘Franken-systems’ – which combine mechanisation, pick-and-packing and intensive labour to move heavy, fragile and expensive cases – alcohol distributors
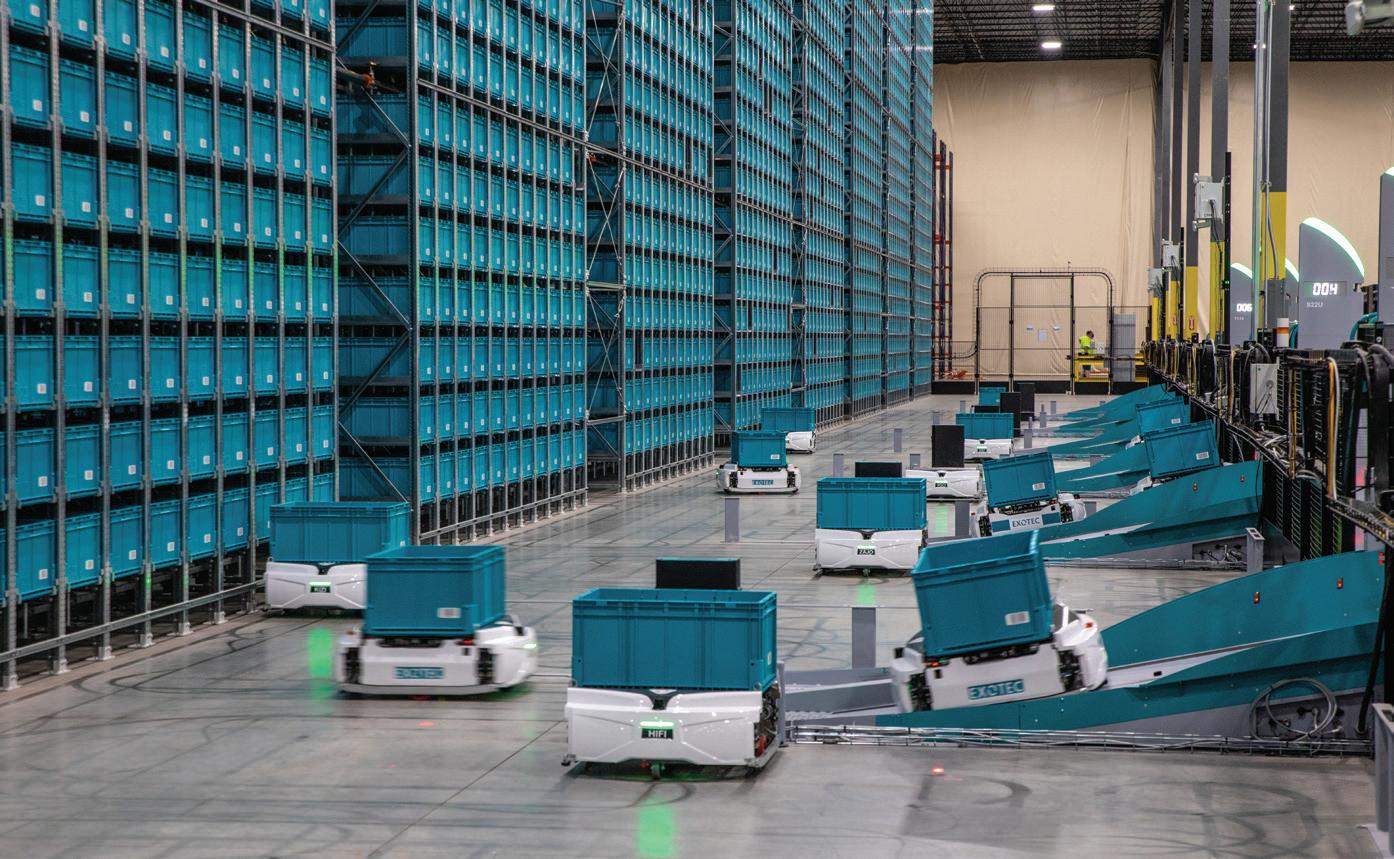
have hit a wall. Traditional warehouse operating systems need an upgrade, and there is pressure from all sides, including from labour shortages and the disruption caused to fulfilment operations driven by increases in direct-to-customer deliveries.
While automation isn’t a new concept in the UK, traditional automation is sized on anticipated volume and type of orders based on a long period of time. Subsequently, traditional picking technology and equipment is no longer enough to support today’s alcohol warehouse environment. Instead, robotics has huge potential to support the complex demands of customers in 2024 and beyond.
Serving up a treat
In a warehouse environment dealing with home delivery fulfilment as well as store deliveries, flexibility and the ability to scale is vital, while ensuring that order cycle times are minimised. This is important as many retailers offer same- or next-day delivery on mixed cases of wine, beer and spirits. Robotics can be instrumental here.
Fragile and heavy bottles come in all shapes and sizes, needing careful handling and attention. Picking bottles and cans manually is difficult because of their weight, and pushing a trolley stacked with them is an arduous task. This can lead to health
and safety challenges and exacerbate labour shortages in warehouses. Embracing robotics increases productivity by up to five times and improves staff satisfaction by eliminating these tasks.
For B2B wholesalers selling full cases of alcohol who need to shift towards direct-toconsumer sales, automation helps overcome the disruption caused in a warehouse where traditional picking methods are in use. This enables them to deliver mixed cases or individual items direct to the consumer.
Additionally, the same system can automate full case picking for stores, as well as mixed case picking for e-commerce, with the same levels of productivity. It’s this agility that sets smaller distributors apart from the incumbents.
Success on tap
Beer, wine and spirits distributors adopting robotic goods-to-person automation will continue to become more resilient against the challenges affecting the industry today. From reducing dependence on manual labour and boosting productivity to maximising space in the warehouse, these innovative systems position businesses to meet ever-changing market demands now and grow faster in the future.
www.exotec.com
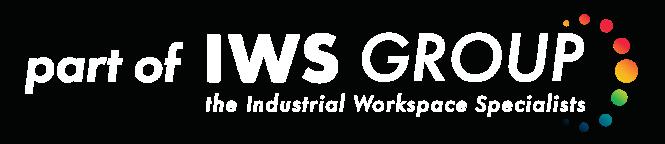
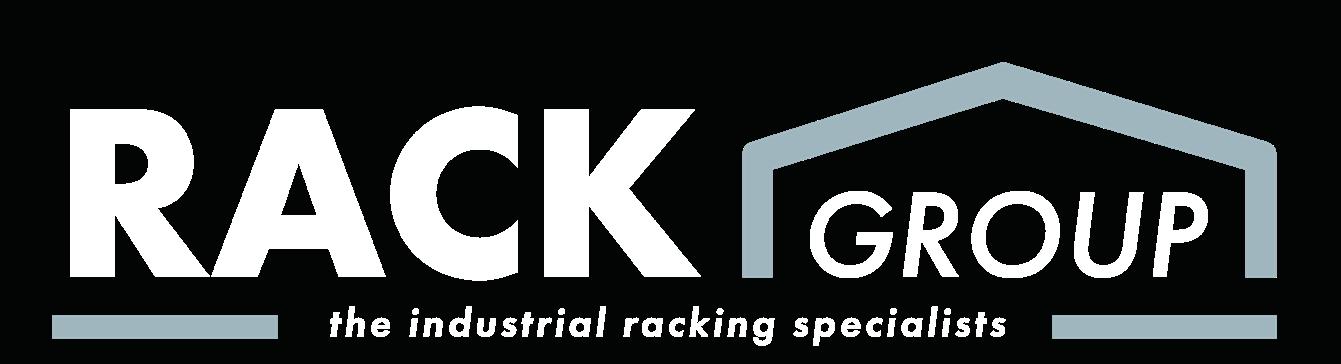
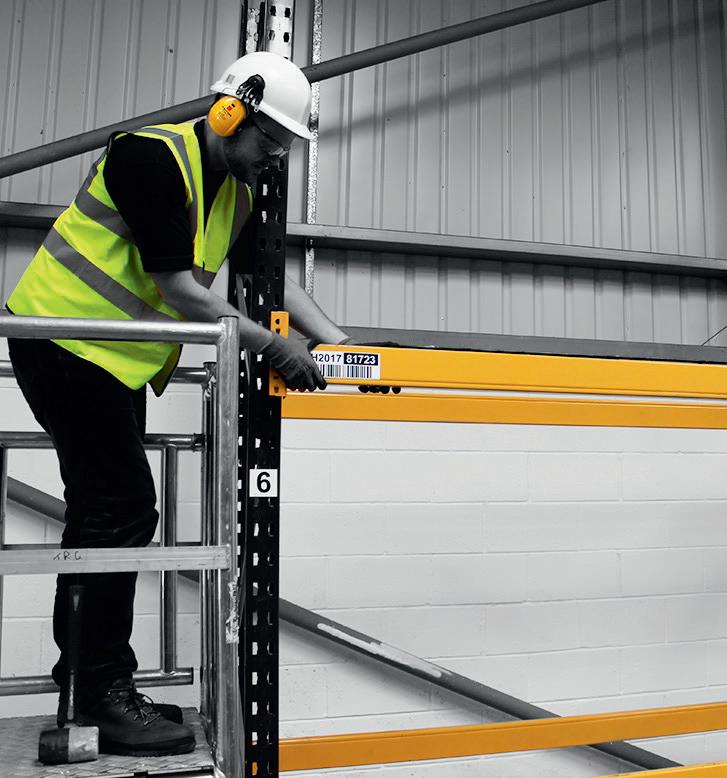


Maximising efficiency with pallet shuttle racking
Samuel Fry, Head of Business Development at Oakway Storage, explores the strategic advantage pallet shuttle racking can offer growing manufacturers.
Pallet shuttle racking systems represent a transformative solution for growing manufacturers seeking to optimise their storage capacity and improve operational efficiency. These dynamic systems utilise automated shuttle vehicles that streamline the storage and retrieval process, significantly enhancing productivity. The semi-automated nature of these shuttles allows for rapid transport of pallets to and from designated locations, controlled via a sophisticated radio-control system that ensures both performance and safety.
Maximise space
The structural design of shuttle racking systems is engineered to maximise vertical space while minimising aisle widths, thus increasing the overall storage density. This is particularly beneficial for manufacturers experiencing growth, as it allows for the accommodation of increased inventory without the need for additional floor space. Moreover, the integration with warehouse management software provides real-time visibility and control over inventory, facilitating a more efficient workflow.
Increased flexibility
One of the key advantages of shuttle racking systems is their compatibility with various inventory management strategies. Unlike traditional drive-in or drive-through systems that operate on a Last-In, First-Out (LIFO) basis, shuttle racking systems offer the flexibility of First-In, First-Out (FIFO) rotation, which is crucial for manufacturers dealing with perishable goods or items with expiration dates. This ensures timely access to inventory and reduces the risk of obsolescence.
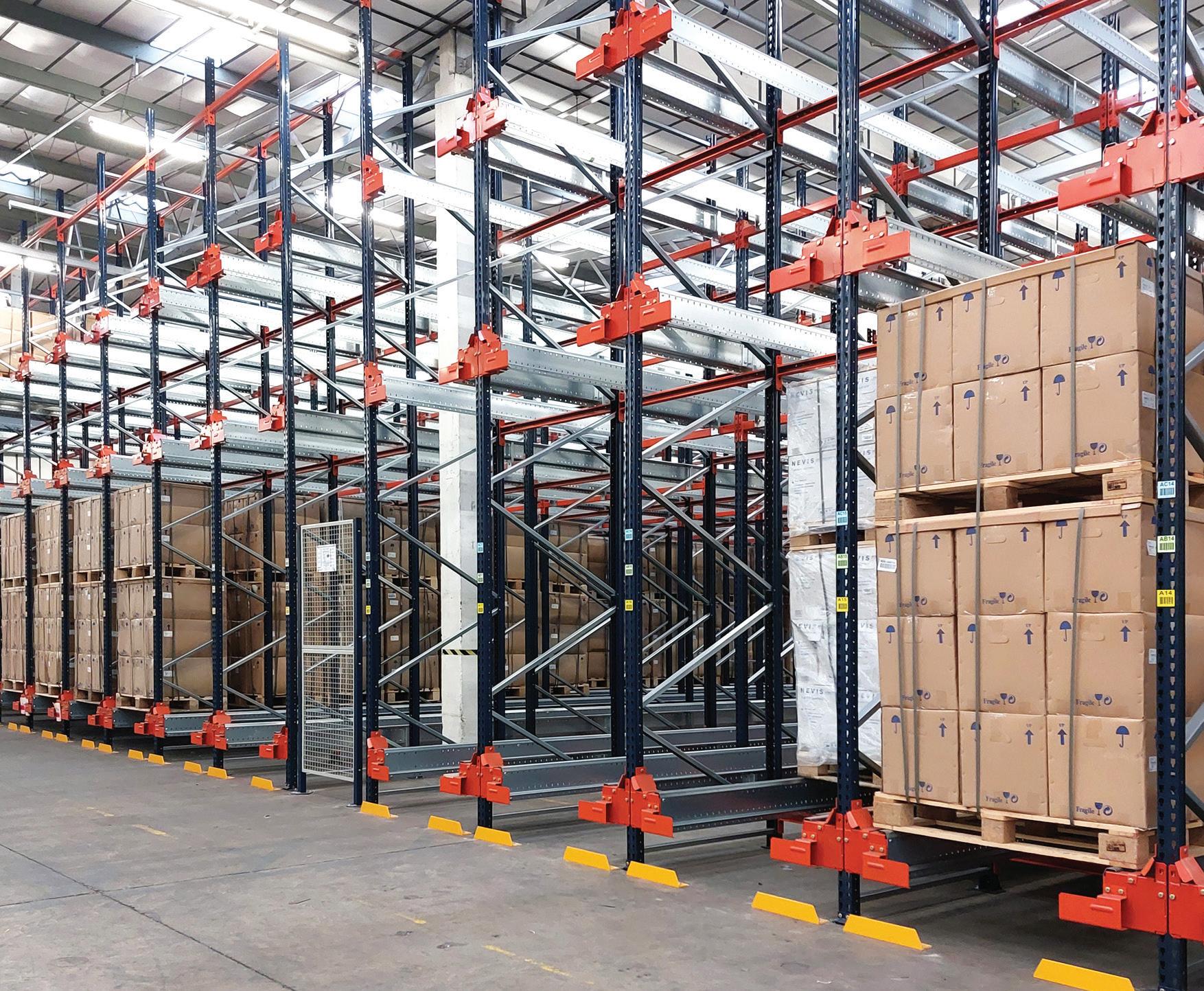
Improve productivity
Furthermore, the high level of automation inherent in shuttle racking systems translates to faster throughput times and higher productivity levels. This efficiency not only drives down operational costs but also supports scalability, allowing manufacturers to adjust to market demands without compromising on delivery times or product quality. The ability to perform repeat tasks with precision reduces the margin for error and enhances overall reliability in the handling and transporting of goods.
Competitive advantage
In the context of a competitive market, manufacturers must seek out innovative solutions that can provide a tangible edge. Shuttle racking systems offer just that, by delivering significant cost savings and operational benefits. They are an ideal choice
for industries such as food and beverage production, dairy products, and high-value SKUs, where fast-moving and low SKU products are the norm. The adaptability of shuttle racking systems also means they can be combined with other racking systems to maximise productivity and efficiency.
In conclusion, pallet shuttle racking systems are an excellent investment for growing manufacturers. They provide a scalable, efficient, and cost-effective solution for storage and inventory management, ensuring that businesses can keep pace with growth and market changes. With their ability to maximise space utilisation, improve inventory accuracy, and enhance operational efficiency, shuttle racking systems are poised to become a staple in the manufacturing industry.
bit.ly/3ydy8lR


A pre-Brexit export experience for British manufacturers
European road freight specialist Europa Road explains how it has developed a shipping service for British exporters to lower transit times and costs, with minimal administrative burden.
Despite being the fourth largest exporter in the world, trade experts at the British Chamber of Commerce believe that to keep the UK at the top table, we must still look at navigating the trade barriers with the EU.
With up to 90%of UK manufacturers still finding trade with the EU a challenge, innovative European road freight specialists are deploying new strategies to streamline their supply chains and ease the complexity on British businesses.
Solving this problem, European road freight specialist Europa Road has invested over £5 million in a shipping service for British exporters, called Europa Flow, to offer faster transit times, lower costs and no administrative headaches for UK manufacturers.
Adrian Redmile, Branch and Sales Director at Europa Worldwide Group, explained: “Many British manufacturers continue to express huge frustration with the complexity and costs involved with exporting to the EU in a post-Brexit climate.
“The administrative burden alone lengthens transit times, which has a domino effect for manufacturers relying on timecritical trade. Shippers need reassurance that their items will arrive by the agreed date. For many – particularly Just-in-time manufacturers – if deliveries are late or delayed, production at the destination facility might need to stop.
“Many manufacturers regularly export into EU countries but don’t necessarily have the customs infrastructure in those regions to tackle this extra administration. Europa Road recognises that brands need a cost-effective way of sorting customs clearance on both sides of the channel without necessarily having to hire specialist teams and customs brokers. So, we started investigating the technology to streamline the process.”
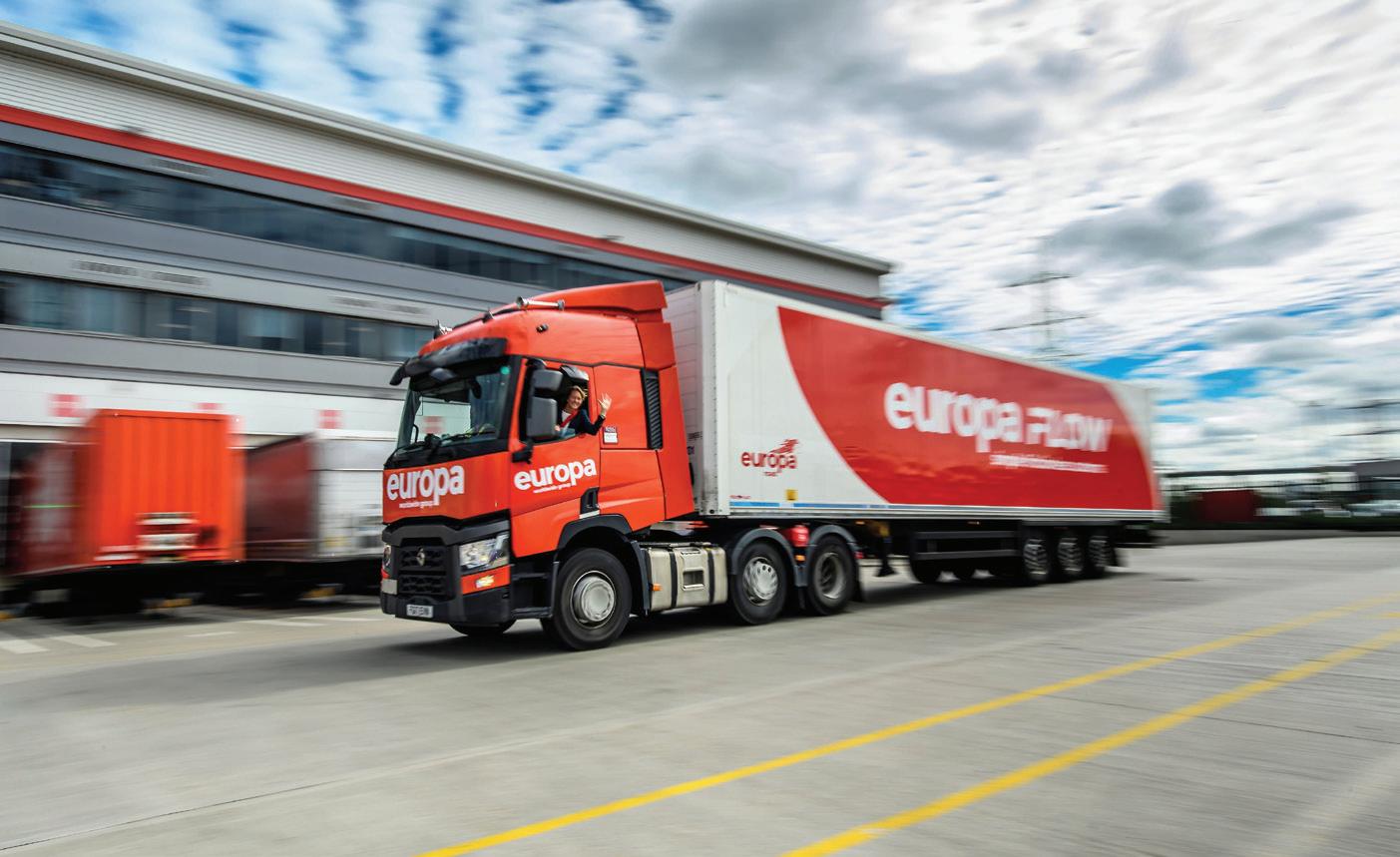
Europa Flow uses a combination of DDP incoterms, postponed VAT accounting and pre-logged declarations to manage all customs formalities so that manufactured goods are not delayed by additional paperwork or costs.
Adrian continued: “Immediately after Brexit, it seemed that many manufacturers would rather temporarily stop trading between the UK and the EU because of the additional complexity. Now, having moved more than 300,000 DDP shipments across the channel, we can officially say that there is a tangible, proven solution being used by manufacturers everywhere to speed things along.”
A manufacturer in Scotland recently welcomed the expansion of Europa’s DDP solution, Europa Flow, to Ireland. It stated: “The new DDP service from Europa has been well received by our current Irish customers, in that the admin burden imposed on them has significantly decreased. It has also reopened some customer conversations that have been closed since Brexit occurred.”
Europa Road, part of the UK’s largest independent logistics provider, Europa
Worldwide Group, also offers a moneyback guarantee option on all Europa Flow shipments. This unique offer will ensure full refunds for consignments not delivered on time.
The company received feedback from a just-in-time manufacturer in the Northwest, who said: “When we use Europa Flow, we are guaranteed a seamless flow of goods into EU countries without the hassle emanating from incomplete paperwork. Furthermore, with Europa Flow we are offered the company’s money-back guarantee, which gives us peace of mind, knowing that deliveries will meet an agreed delivery date.”
Europa Road, which operates Britain’s largest European groupage ‘1Hub’ in Dartford, now ships more than 56% of all network groupage exports using DDP. The 1Hub, which is strategically located close to the Dartford Crossing, provides scheduled, daily, road transport lines, which connect British customers’ shipments to its 42 partner hubs in mainland Europe.
www.europa-worldwide.com
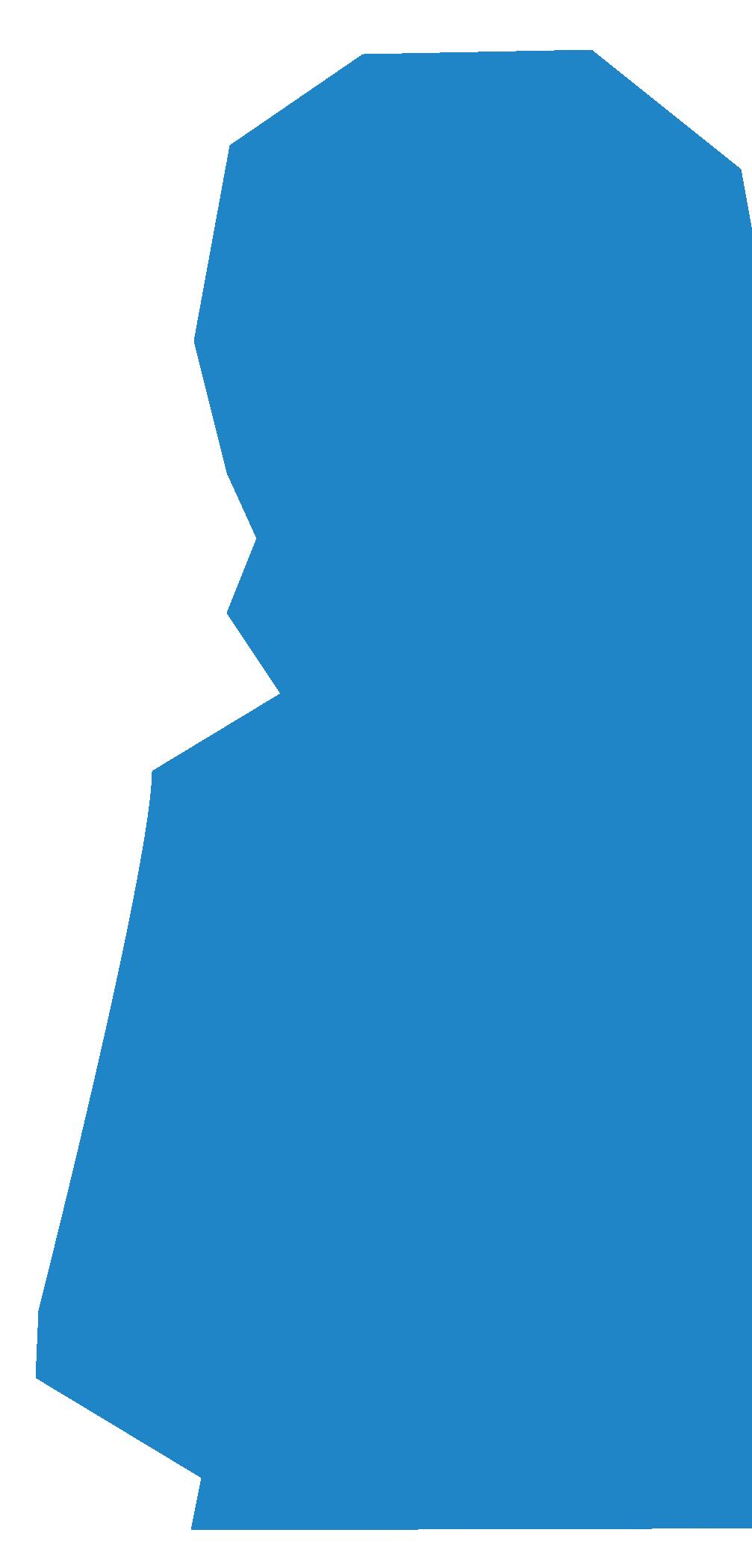
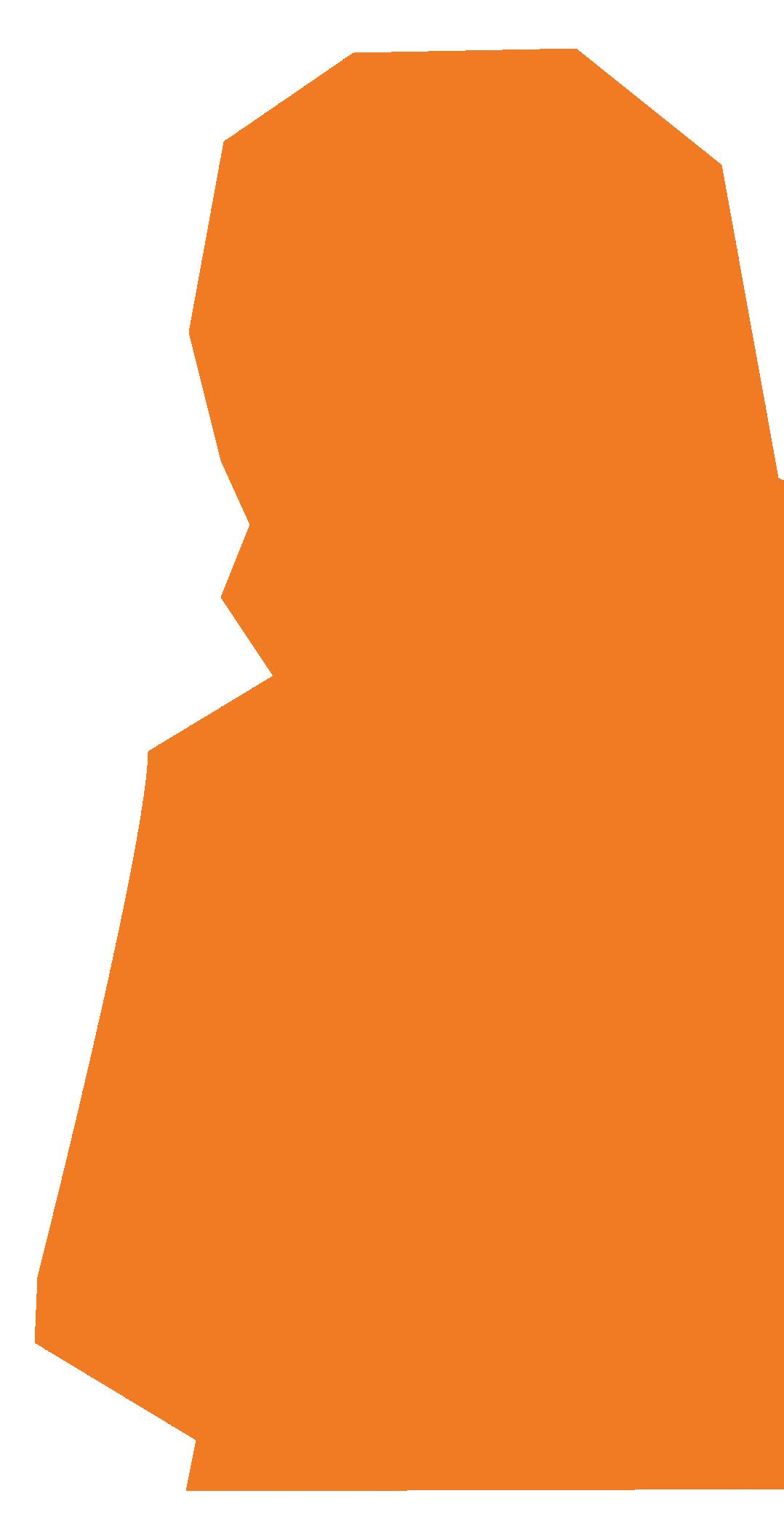

Animation series brings mixing to life
The Mixing Science series of videos produced by Silverson Machines uses animations to explain and demonstrate a range of mixing topics and terms, such as homogenisation and emulsions. The latest animation to be released in the video series explains the pumping capacity of high-shear in-line mixers.
When mixing continuously in larger batches, in-line mixing is often the method chosen by manufacturers to get the best results; it also offers greater energy efficiency over in-tank mixers as the mixer’s effort is concentrated on the small volume in the mixing chamber rather than having to circulate the entire volume in the tank.
But although Silverson in-line mixers are self-pumping, some people think that they will need a very powerful machine to recirculate the product back to the top of a large tank. The new animation debunks this by explaining how a Silverson in-line mixer can recirculate product in a large tank without the need for pumps or additional power.
Other videos in the series also focus on seals and sealant systems for Silverson in-line mixers. One animation explains why some applications require single mechanical shaft seals and why others require double mechanical seals on in-line mixers. The mechanical shaft seal contains the mix in the body of the in-line mixer, where the rotating shaft passes through the body. For many applications, a single mechanical shaft seal is all that is required to prevent liquid from leaking out of the mixing chamber.
But mixing materials that are abrasive or sticky in nature can cause problems where a single mechanical seal is being used. Abrasive materials cause the seal faces to wear, and sticky substances can solidify between the seal faces when the mixer is switched off; this can cause the seal rings to seize and break when the mixer is restarted. To avoid this a double mechanical seal would be recommended.
A double mechanical shaft seal can be two single mechanical seals mounted in a chamber
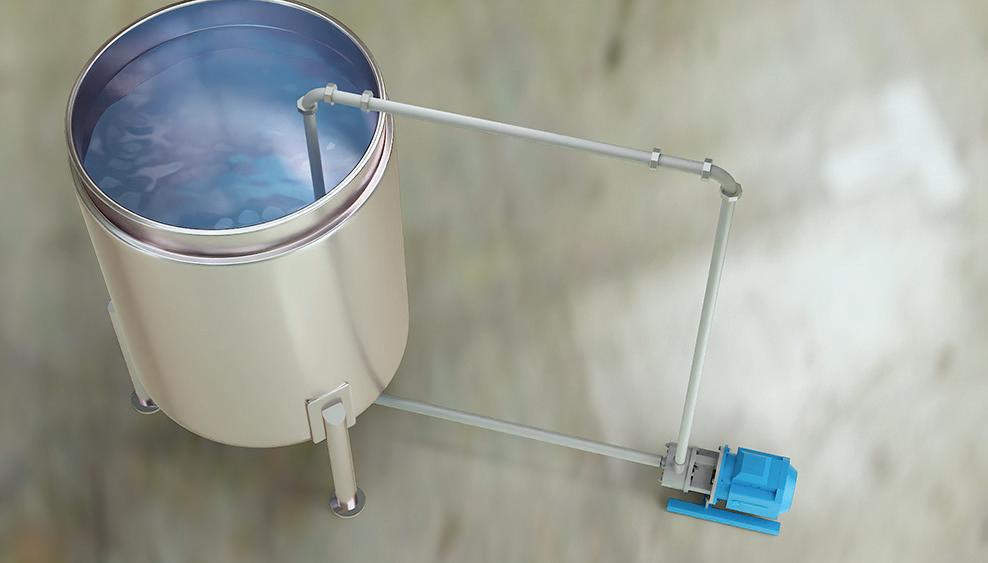
or a cartridge seal. The chamber between the seals needs to be flushed with sealant fluid, which is compatible with the product being mixed and preferably non-flammable. The pressure inside the double seal chamber must be higher than that inside the mixer. This forces clean, lubricating liquid between the seal faces to cool and lubricate them and prevents any of the product from inside the mixer from getting onto the inboard seal faces.
If you are flushing the double seals with liquid other than mains water, for example oil or glycerine, this is where a Thermosyphon system is often required, which is explained in another animation in the series.
Silverson also offers in-tank mixers and one animation in the series details how to use and get the best results from these mixers. Other animations include explanations of common mixing applications such as emulsions, homogenisation and deagglomeration.
One of the most popular videos in the series, ‘What is homogenisation?’ has almost 200,000 views on the Silverson YouTube channel. As the title suggests, this animation
explains what homogenisation is and why it is important to achieve a uniform particle or globule size in many products. Silverson Mixer/Homogenisers can achieve a globule or droplet size in the range of 2 to 5 microns, which is sufficient for the vast majority of products, including creams, ointments, sauces and pharmaceutical suspensions. Where sub-micron particle size is required, a high-pressure homogeniser would be needed, however, a Silverson mixer/homogeniser can help to improve the throughput by producing a uniform premix that will allow the high-pressure homogeniser to operate more efficiently, reducing process time and costs.
The ‘What is an emulsion?’ animation is equally popular, with nearly 150,000 views. Again, this animation explains what an emulsion is and how high-shear mixing can finely and uniformly disperse the two phases.
For more information or to watch the animations, visit the Silverson YouTube channel at: bit.ly/MixingScience
www.silverson.co.uk
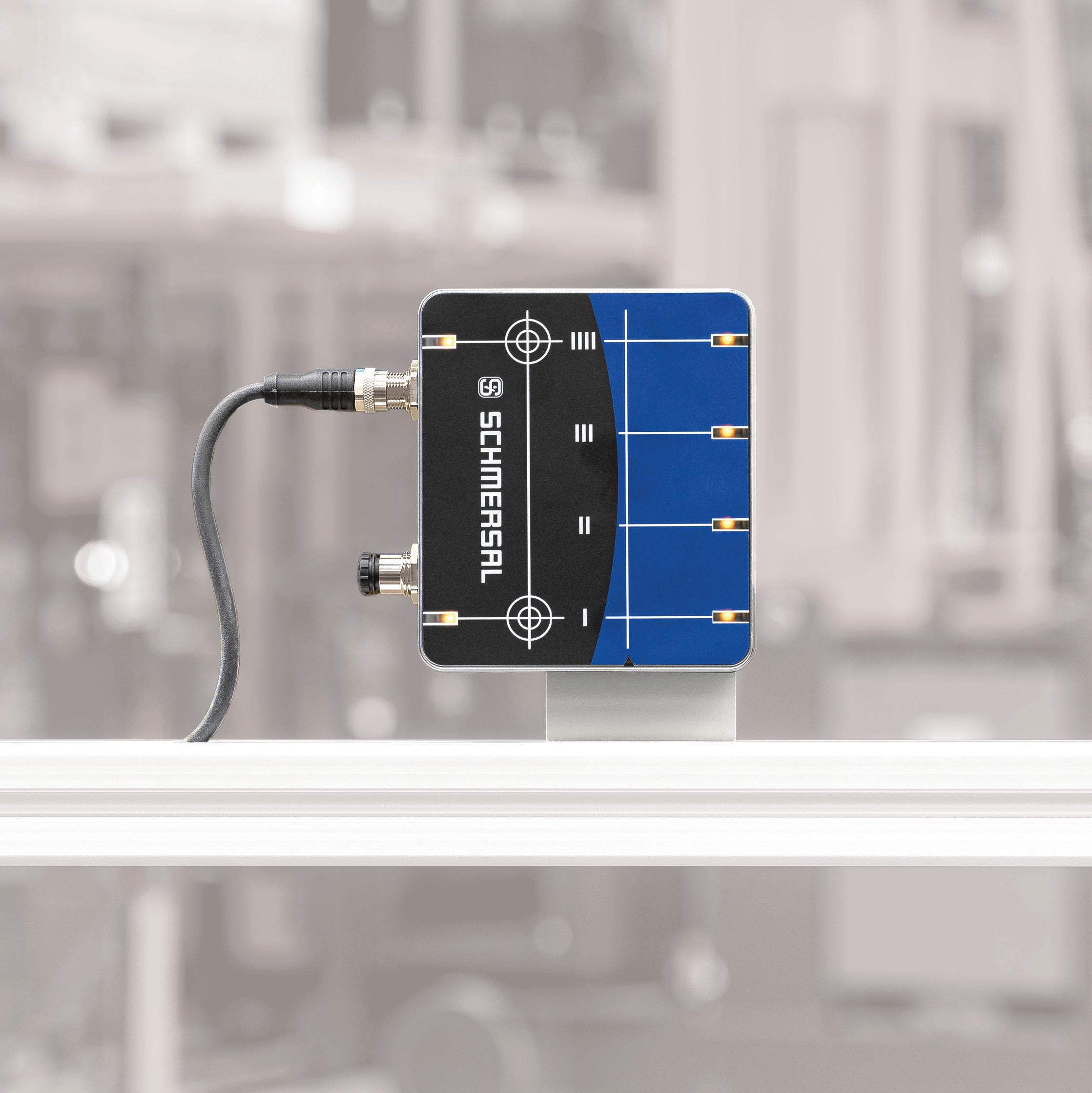
MAGNET TRACK SENSOR BOX: MAINTENANCE FREE PRECISION
Magnetic switches are used for positioning and control in electric monorail systems and in lift construction, they are characterised by wide-ranging wear resistance and tolerance in the event of misalignment.
A connected control unit uses the signals to determine the position and section of the sensor box and controls the speed and holding positions of the drive motor. In addition, two angle sensors enable fine positioning.
Electric monorail conveyors are used to transport workpieces, tools and other purchased parts in almost every industry. The SSB-R magnet sensor box is used to define route sections for speed regulation for electric monorail conveyors in a manner that is cost efficient and maintenance free. It also allows park positions to be approached with careful accuracy.
SCHMERSAL | Enigma Business Park
www.schmersal.co.uk
uksupport@schmersal.com

AR data visualisation and error analysis in your pocket
SICK UK has officially launched its SICK Augmented Reality Assistant (SARA), providing limitless data visibility and information via augmented reality – at the exact location it is needed – through handheld digital devices.
In June, SICK UK unveiled its SICK Augmented Reality Assistant (SARA) at Smart Factory Expo 2024. The intuitive augmented reality app provides data visualisation and error analysis by merging machine, sensor and diagnostic information with the real environment using technology most people carry in their pocket. With the unique SARA app, users can take data from any source and map it into the SARA augmented reality (AR) engine for review on a handheld device, such as a mobile phone, without requiring costly wearable devices or fixed HMIs. SARA provides visibility of information that can’t be seen with the naked eye, taking users directly to the site of the problem that needs maintenance.
Created in response to customer demand, SARA provides access to data and faults at the location where they arise, to accelerate commissioning, diagnostic, condition monitoring and maintenance activities. The engine empowers shop floor staff to diagnose faults and monitor the performance of machines to get the best results.
Tackling skills shortages
UK manufacturers and OEMs are experiencing significant skills gaps, and the problem is showing no signs of abating. According to the WorldSkills UK Manufacturing Excellence report, published last year, more than half (55%) of manufacturers questioned were experiencing shortages in advanced manufacturing skills and 61% in traditional manufacturing skills. Similarly, the Manufacturing Commission warned in October 2023 that labour shortages and skills gaps in the sector cost between £7.7 billion and £8.3 billion a year in lost economic output.
With the increasing use of automation, monitoring and maintaining machinery and preventing costly stoppages is more important
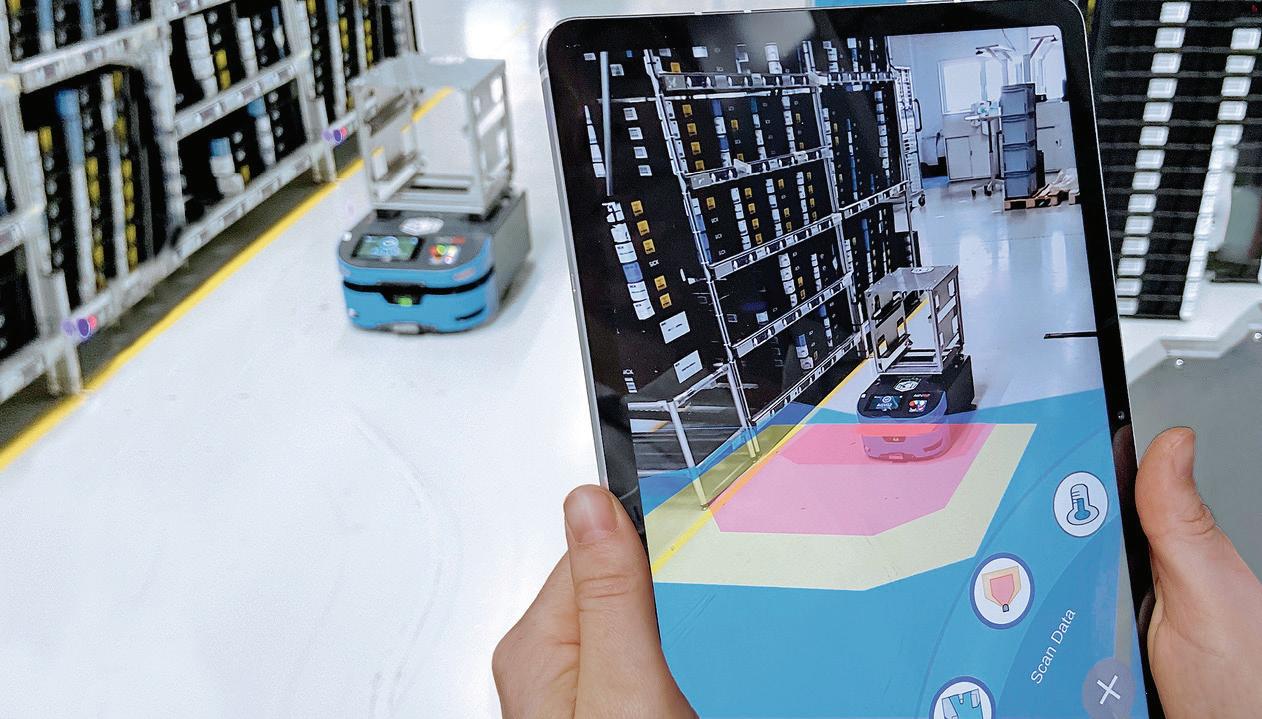
than ever. However, the skills and recruitment problems dogging the industry are particularly acute when it comes to qualified operators and maintenance technicians. As companies require more from employees on the ground, SARA offers the ideal opportunity to upskill existing staff and get new hires up to speed fast, empowering them to carry out more tasks, such as machine monitoring and basic maintenance. OEMs and equipment providers also report increasing numbers of callouts as end-users struggle to hire the maintenance staff and operators they require.
SARA was in action on the SICK stand at Smart Factory Expo 2024 as part of demonstrations of SICK products working harmoniously to deliver digital manufacturing solutions. These included one demo on the use of various SICK devices (load detection, line guidance, height measurement, safety laser scanners and barcode readers) to enhance the safety and performance of AGVs, and another showcasing the vertical integration of SICK smart encoders and sensors.
With such a wide range of potential applications, SICK has created various
licences (including LiDAR and robotics variants, in addition to the base licence) that unlock specific features of SARA to allow users to customise solutions for specific use cases. Plans are underway to develop further specialist licences in the future.
Charlie Walker, SICK UK Data Solutions Consultant, said: “SARA is a unique application, blending data visualisation with the real environment and delivering it via the technology you have in your pocket.
Using SARA, teams can reduce the risk of outages, increase machine availability, and boost productivity by ensuring that equipment performs optimally.
“SICK’s SARA AR app can bring employees up to speed with equipment quickly, to regularly monitor machines and to enhance safety. Codes can be scanned and linked to relevant documentation to provide access to critical information where and when needed. The possibilities and opportunities SARA can bring are vast and we are excited to officially launch it to the UK market to see how companies unleash its potential.”
www.sick.co.uk
Vision
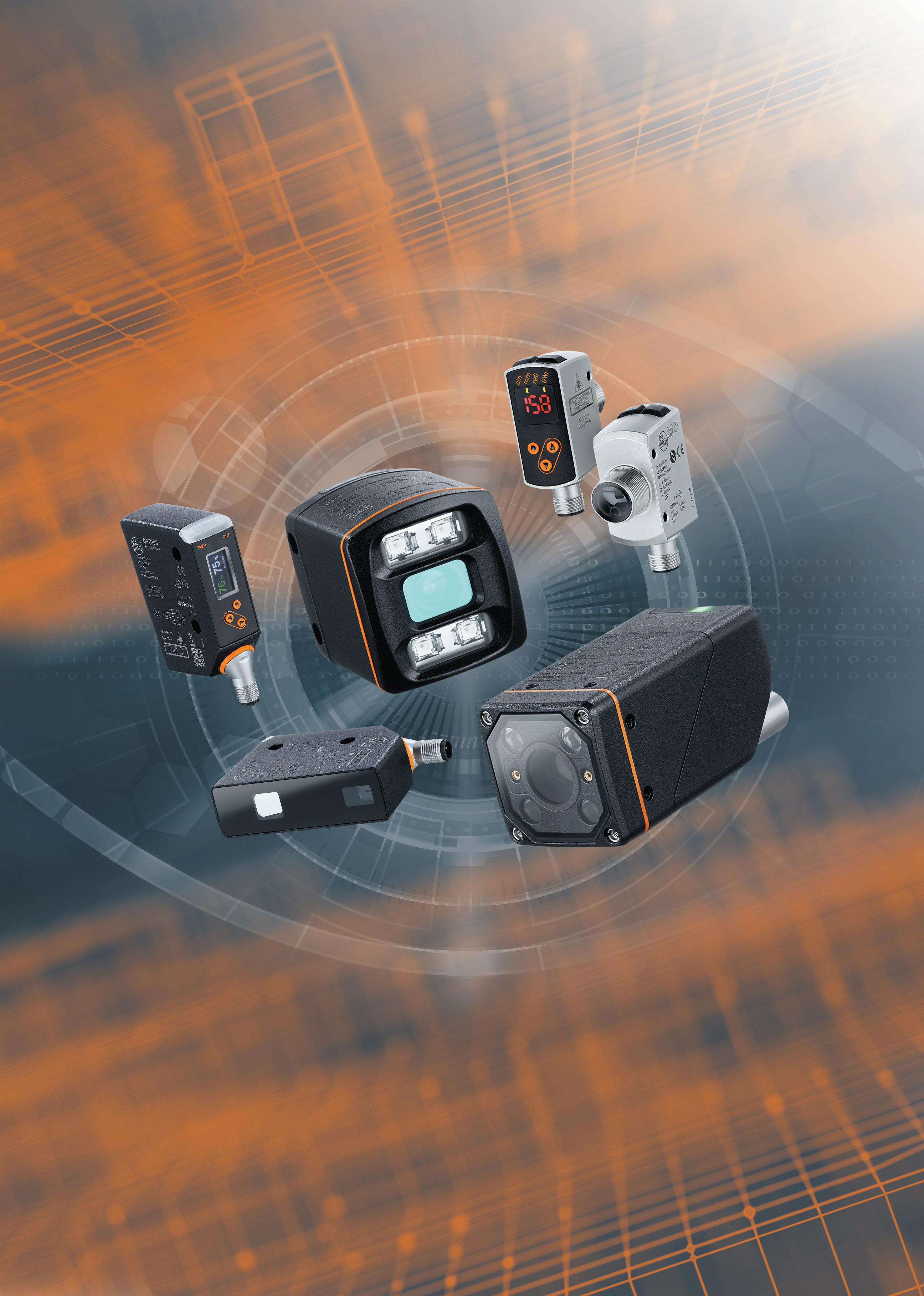
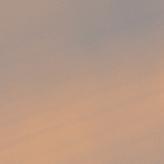
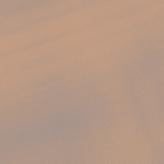
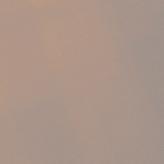
ifm Vision: from selective distance measurement to industrial imaging
Being a driver of industrial digitalisation, our mission is to make outstanding optical technologies available to companies of all sizes. This also applies to vision sensors, which, as the “eye” of Industry 4.0, play a significant role in the implementation of digital evolution. Our vision: cutting-edge technology, available to all!
A tropical paradise made possible
Pumps from specialist KSB are enabling a couple to live out their dream of running an ecological farm based on agroforestry principles in the tropics of India.
Antje Ute Bauer and Johannes Michael Nether have made their dream come true: an ecological farm in the tropics. Over 350 different species of plants grow in the area, including 90 varieties of fruit and vegetables such as bananas, papayas, passion fruit, mangoes, pomegranates and avocados. They want to avoid pesticides and artificial fertilisers through agroforestry – a form of agriculture that combines trees, shrubs and annual plants to provide shade, shelter and nutrients, improve the soil and provide food for animals. A sophisticated system of pipelines and pumps ensures that the plants are supplied with water all year round and can grow at record speed.
Having fallen in love with India in 2013, only six years later, the couple decided to move to their favourite country and buy a piece of land. To achieve their dream of running their own ecological farm, they needed water. The farm is located in an area with a semi-arid monsoon climate. During the rainy season, from July to September, there is an abundance of water – the rest of the year they have to contend with drought conditions. In order to have enough water available during dry periods, they had a reservoir blasted into the slopes of the farm and created an earth dam to increase its capacity to four and a half million litres. Three KSB well pumps supply the farm with water from surrounding wells and reservoirs via pipelines up to two and a half kilometres long, providing them with water all year round: “We generally manage to fully maintain our reservoir level from the end of the rainy season in October until the end of March,” explained Johannes Michael Nether.
An efficient water management system is the key, with drip irrigation enabling them to save water. The couple do not spray the plants, as a great deal of
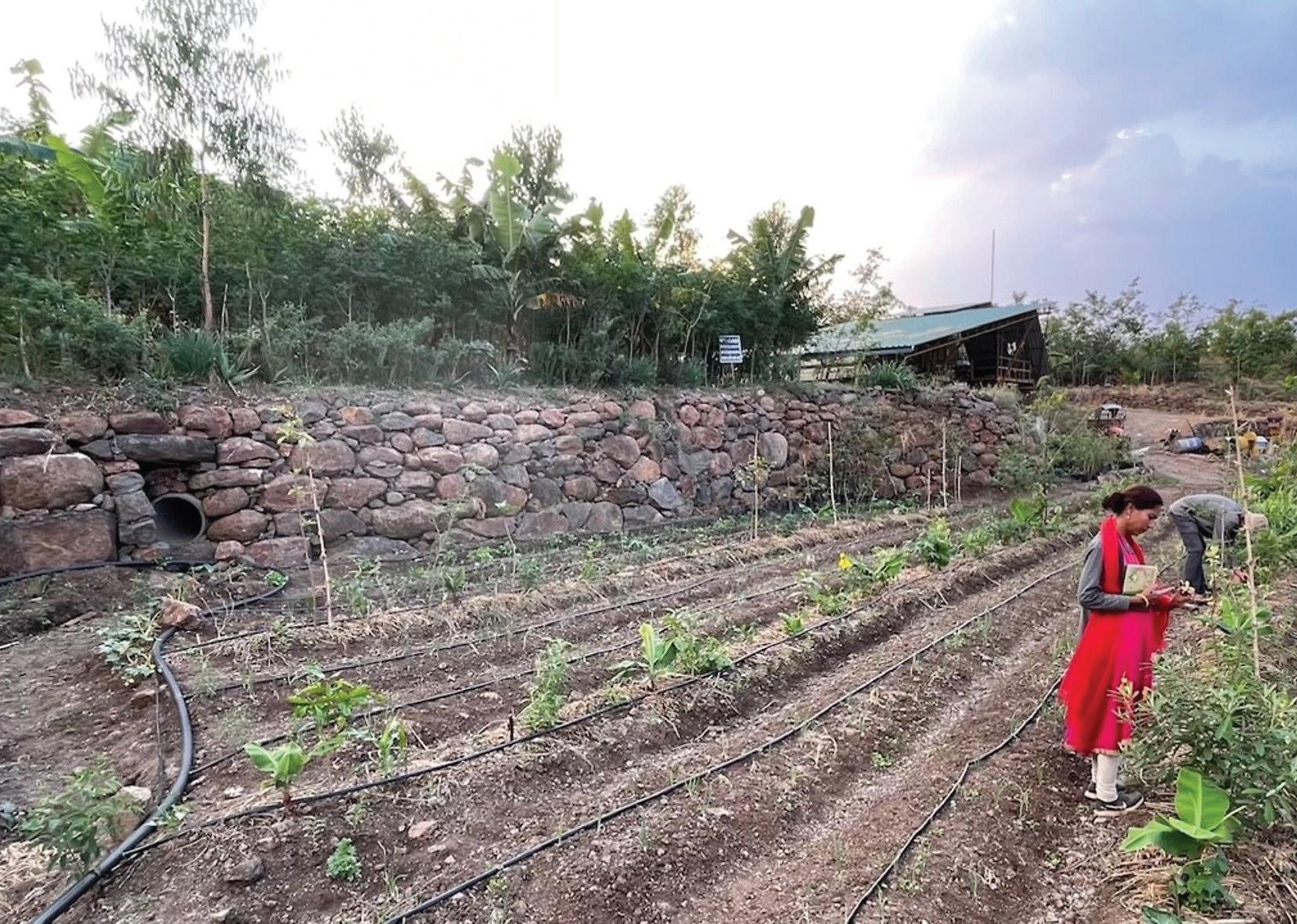
water would otherwise be lost through evaporation. Instead, after sunset, water continuously drips directly onto the roots of the plants through thin and flexible pipes. Approximately 14 kilometres of these driplines have been laid around the farm. “Driplines are the cheapest method of supplying water to large areas of land,” continued Johannes.
The water management system also minimises losses due to seepage from the water reservoir and wells. As the farm is located on a slope, water-bearing layers mean that the water seeps down into the valley. The resulting seepage water collects in several wells before being pumped back up to reservoirs and wells located on higher land. “We keep pumping it back up so the water stays on our land,” added Johannes.
The farm gets the electricity it needs for the pumps from solar panels.
When choosing pumps, Johannes immediately opted for KSB products. Twelve different submersible motor pumps
from KSB form the beating heart of the water management system. He uses KSB products because he is familiar with their high quality from his previous profession as a plant engineering consultant.
Today, three families live on the farm, which employs almost 30 people. Over the years, the couple and their helpers have planted 40,000 trees and shrub species. Not all of them are still growing there, as some are used as nitrogen binders to improve the soil. “We now have four years behind us, and the first phase of restructuring the soil is slowly coming to an end,” explained Johannes. “The soil quality is improving. We are now cutting clearings out of the jungle in order to plant future crops.”
But they are already seeing the first successes of their sustainable agriculture. They have planted 170 avocado trees so far, which have borne fruit after just four years. “That’s extraordinary because they usually take eight years,” Johannes concluded.
www.ksb.com/en-gb
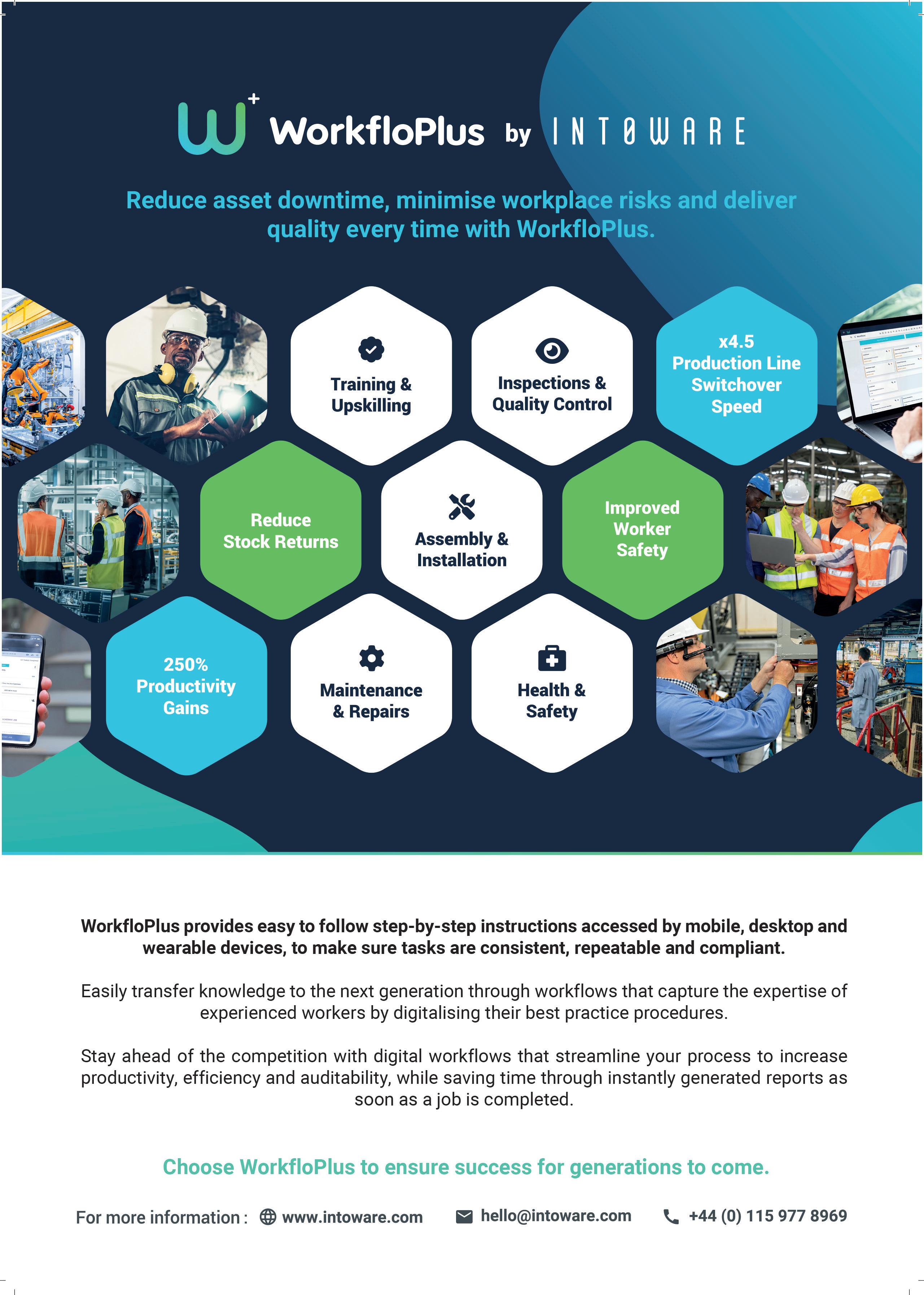
Satisfy the demands of HACCP cook and chill CCP validation
As part of any food processor’s HACCP (Hazard Analysis & Critical Control Point) program, validation of cook and chill processes is a critical and significant task, taking time, effort, and resources. PhoenixTM has developed a thru-process temperature monitoring technology specifically for this task, designed to meet the challenges of the food processing market.
PhoenixTM’s solution is ideal for the validation process for any new cook regime, new product, or annual process certification. Whether performing an oven survey, oven mapping to identify cold spots, or validating the cook under production conditions, the through-process profiling solution gives users the accuracy, efficiency, and reliability needed to satisfy the demands of HACCP.
As its name suggests, through-process profiling is the method by which product and or process temperature is monitored throughout the complete cook and chill process. The data logger makes the physical temperature measurement with multiple thermocouples and travels safely with the product through the process.
Protection from process conditions such as heat, steam, water, and oil is provided by a suitably designed thermal barrier. The thermal barrier provides robust protection to the data logger to prevent damage but also ensures that it maintains a safe operating temperature to give accurate temperature readings. Monitoring of continuous conveyorised linear and spiral ovens and semi-continuous or rotational batch cookers is feasible where the use of external recorders with trailing thermocouples is tedious, completely impractical, and possibly unsafe.
Employing the through-process principle, process monitoring can be performed under true production conditions without compromising line productivity.
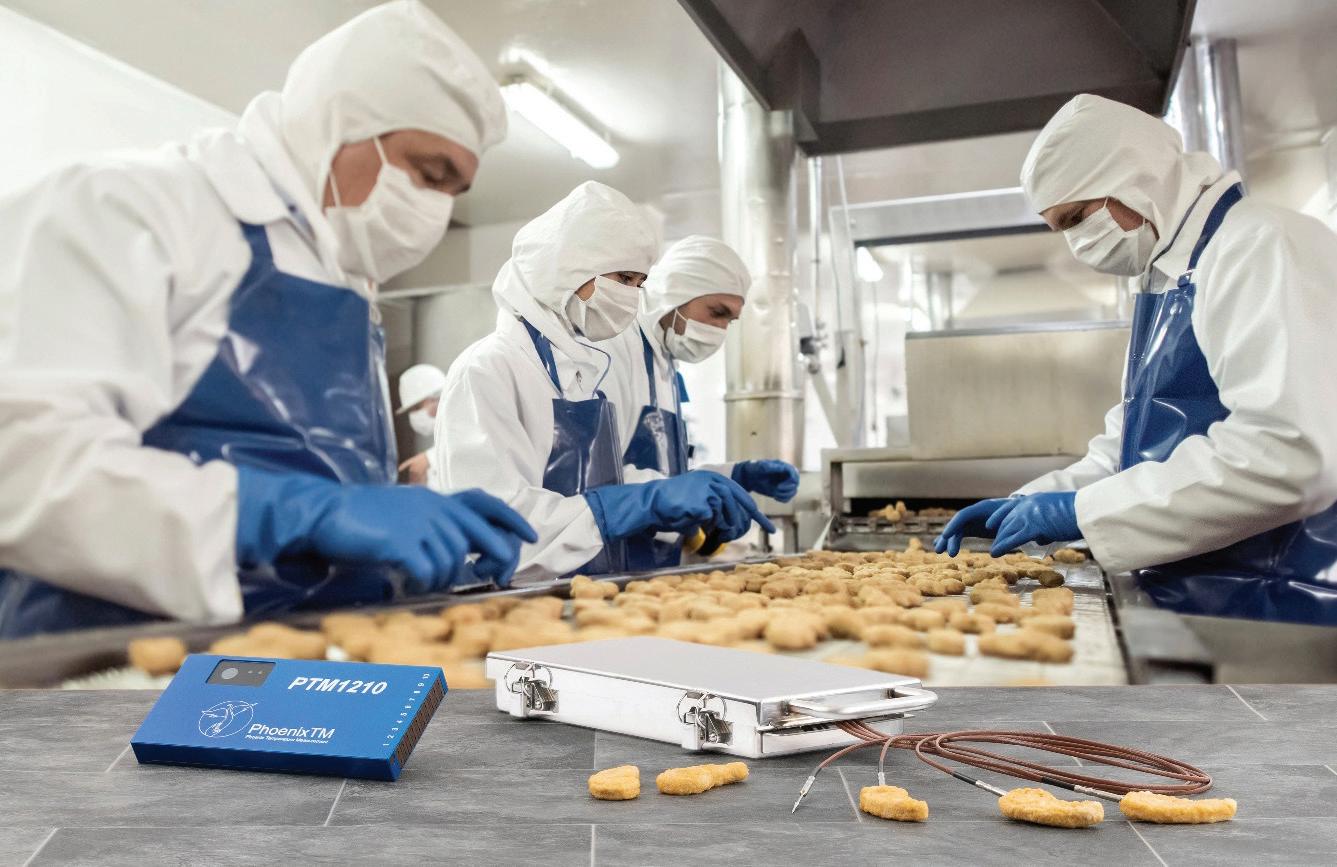
At the heart of the through-process monitoring system is the PhoenixTM data logger. The PhoenixTM NT data logger range has been designed specifically for the challenges of monitoring food processing applications with an IP67 case design protecting from moisture. Type K or Type T data logger options allow accurate measurement of both cook and chill processes (Type T measurement range is -200 to 400°C).
Data logger and thermocouple correction factors can be applied to the recorded data logger data to maximise measurement accuracy. PhoenixTM also offers a range of thermal barriers to suit the process type, duration, and temperatures. Even if a standard thermal barrier cannot meet the process
requirements, PhoenixTM can often custom design a unique solution to suit. Monitoring core temperatures of food products can be a challenge and getting it right or wrong can have a significant influence on the data collected and therefore any decisions or conclusions made. PhoenixTM offers a range of different thermocouple designs to suit different
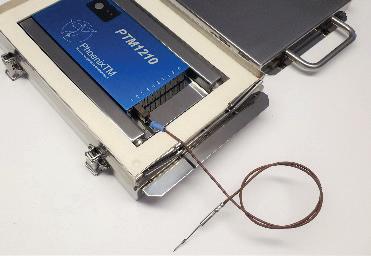
product types and sizes. The needle thermocouples ensure you can measure the true core or cold spot of the product accurately and repeatably. Fitted with standard miniature thermocouple sockets, the data logger is also compatible with other generic commercially available thermocouple designs.
Employing the thru-process temperature monitoring principle provides the food technologist with a complete temperature profile of the cook process from start to finish. This information is like the cook DNA giving full details of the product and or process temperature which is invaluable to allowing validation of the cook CCP (critical control point).
From a temperature profile, it is possible to accurately quantify product safety (pasteurisation) by knowing both the temperature of the product and the time spent at the temperature.
From the profile graph, you can see instantaneously the variation in product temperature at any point in the process, either at different locations on the product (for example, a whole chicken) or different
FOOD PROCESSING
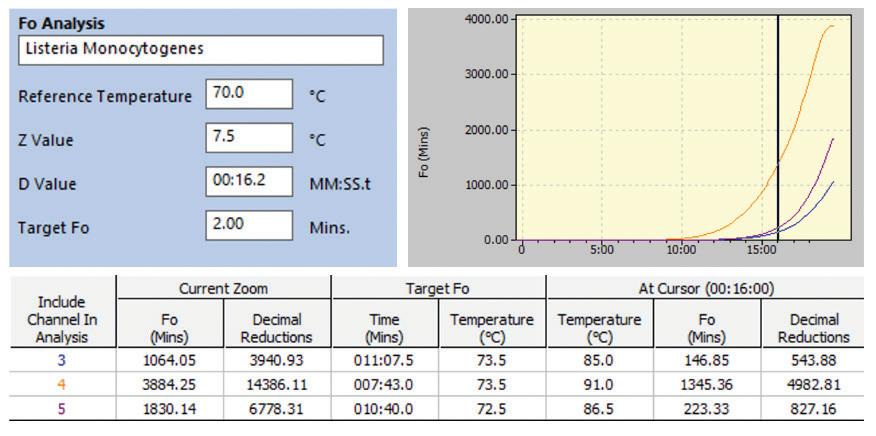
product positions within the cooker, cooking rack or across a mesh belt.
The PhoenixTM Thermal View Food Software provides a comprehensive suite of analysis tools to convert the raw profile temperature data into useful process information. The analysis tools include the ability to calculate Fo/Pu values for the process against target micro-organisms.
For a typical chicken cooking process the lethality parameters for Listeria Monocytogenes (Tref 70°C, Dt 16.2s
and Z value 7.5°C) can be input to automatically and accurately calculate for each monitoring point the number of decimal reductions of the pathogen achieved during cook to meet CCP limits.
The information gathered, further to process validation, can be used to allow informed process problem solving and optimisation to maximise product quality, yield, process productivity and efficiency.
www.phoenixtm.com
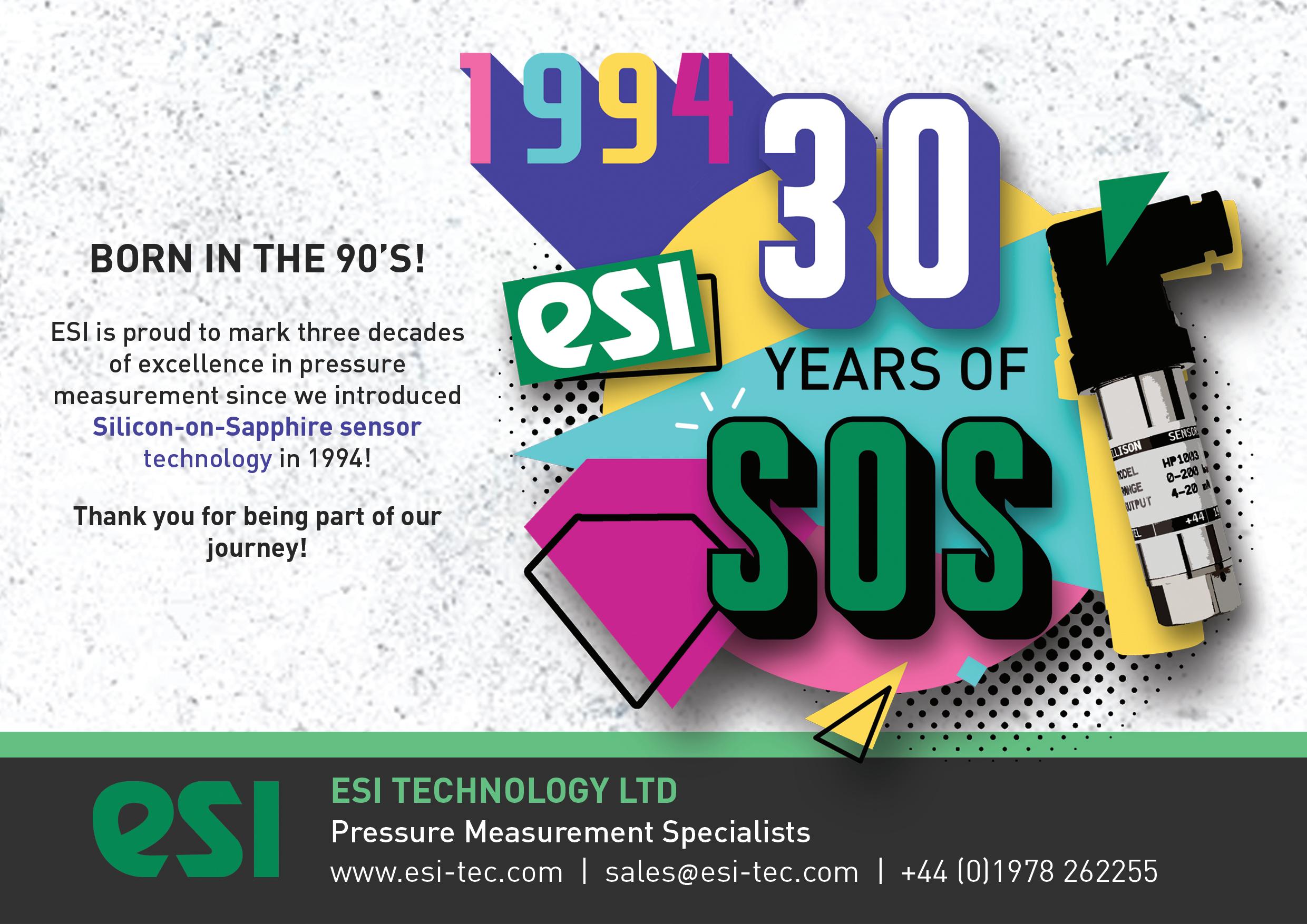
Peek inside the pipes
Today, processes in the food and beverage industries are usually comprehensively monitored. Nevertheless, most plants have a blind spot. Operators are well informed about what’s happening in vessels and tanks, but what’s going on in the pipework?
Andy Walker of ifm electronic explains how recent sensor developments make it easy to answer this important question.
Why do process plant operators in the food and beverage sectors need to know what’s going on inside their plant’s pipework? The first answer is that information such as a low flow rate or an unexpectedly empty pipe can provide early warning of developing problems, possibly in time to save expensive ingredients from going to waste. The second answer is that if the plant does develop a fault, knowledge of flow rates, temperatures, and the like is an invaluable aid to locating and remedying the cause, thereby keeping costly downtime to a minimum.
But what do the plant operators need to know? The most important parameter is the flow rate of the media in the pipe. There are, of course, many types of flow sensors, but it can still be difficult to find one that is suitable for hygienic applications, capable of consistently delivering accurate results and resistant to the rapid temperature changes and pressure surges often associated with food and beverage applications. There is, however, one sensor technology that dependably fits the bill: magnetic-inductive flow meters.
In a magnetic-inductive flow sensor, the media whose flow rate is to be measured passes through a magnetic field. As a result, a small voltage related to the speed of flow is generated in the media. The sensor accurately measures this voltage and uses it to determine the flow rate. Magneticinductive sensors based on this principle are not new, but the latest versions offer many advantages over their predecessors.
In the past, a significant limitation of this type of sensor was that it would only work with liquids that had a relatively high conductivity. The latest versions, however, deliver dependable results at conductivities down to just 5µS/cm, which covers the vast majority of media used in the food and

beverage industry.
The new sensors also have a high upper temperature limit of around 150 ºC, which is another important benefit in many applications, and they are highly resistant to damage. They are unaffected, for example, by rapid temperature cycling, which can be found in some cleaning and sterilisation processes. They are also impervious to pressure surges, high humidity and high levels of vibration, which might be experienced close to a large pump.
Of course, flow rate is not the only thing plant operators will want to know about what’s going on inside the pipework. The temperature of the media is also likely to be important, along with the total volume of flow, the flow direction, media conductivity and warnings if the pipe is not fully flooded. The good news is that the latest magneticinductive flow sensors, such as those in the SMF Foodmag range from ifm electronic, provide all this additional functionality. In many applications, this eliminates the need
for additional sensors, resulting in cost savings and reductions in plant complexity.
One issue remains: how to efficiently communicate all of the information provided by these new sensors to the plant control system. The answer is IO-Link, a versatile digital connection system that ensures errorfree transmission of sensor data and also supports easy-to-use options for setting up and testing the sensors.
It has been said that what’s going on inside the pipework is the last blind spot in modern process plants. With the latest magnetic-inductive flow sensors, this blind spot is finally eliminated, giving operators a truly comprehensive real-time view of everything that’s happening in their plant. Potential benefits include increased efficiency, fewer faults and reduced downtime if faults should occur. These new sensors are, without a doubt, a modest investment that can pay very big dividends.
ifm.com
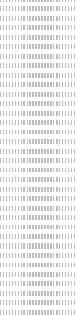
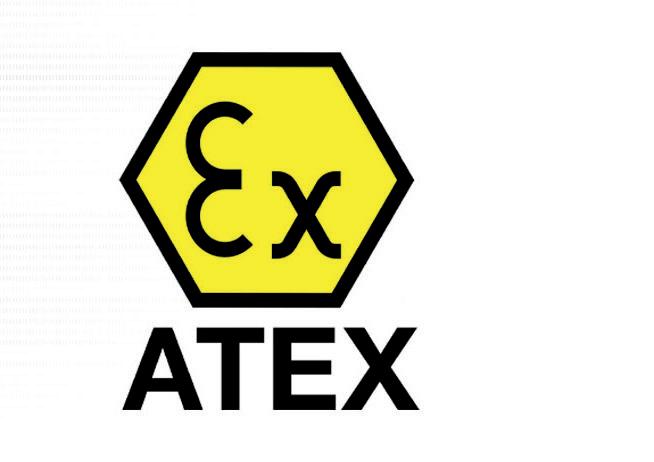
ATEX Hazardous Area Drive Systems
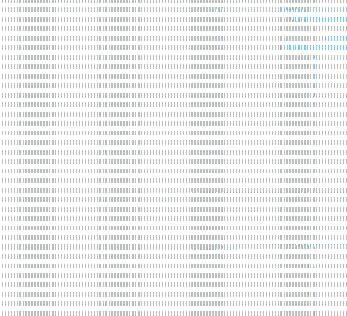
Flexible, modular range of high efficiency, robust gearboxes with output torques up to 250kNm.
Available on short delivery times, same

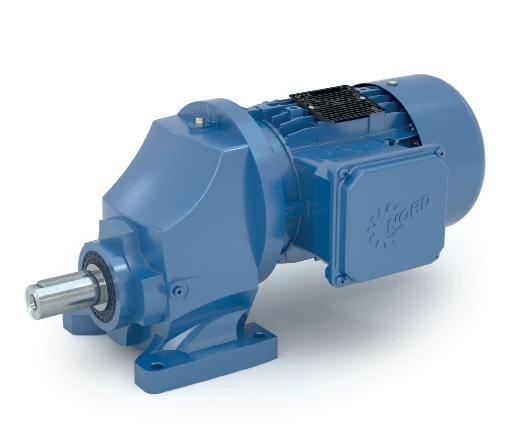
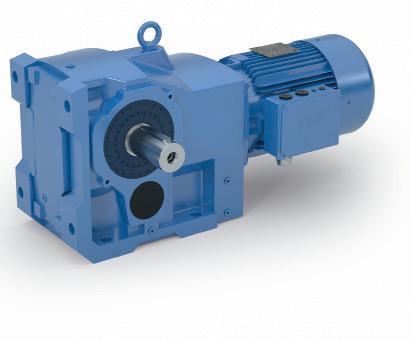
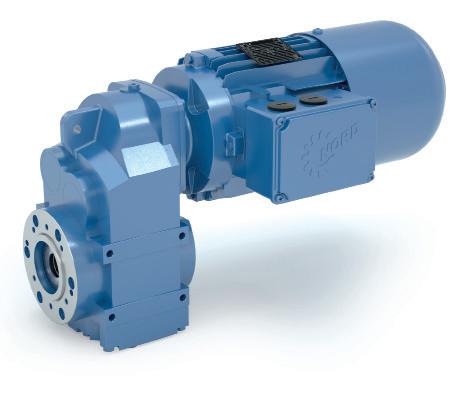
Dust zone 21 cat 2D and zone 22 cat 3D
Gas zone 1 cat 2G and zone 2 cat 3G
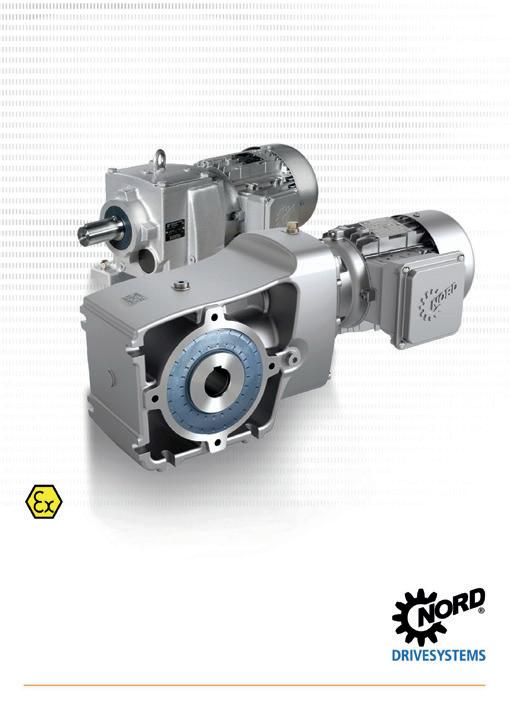
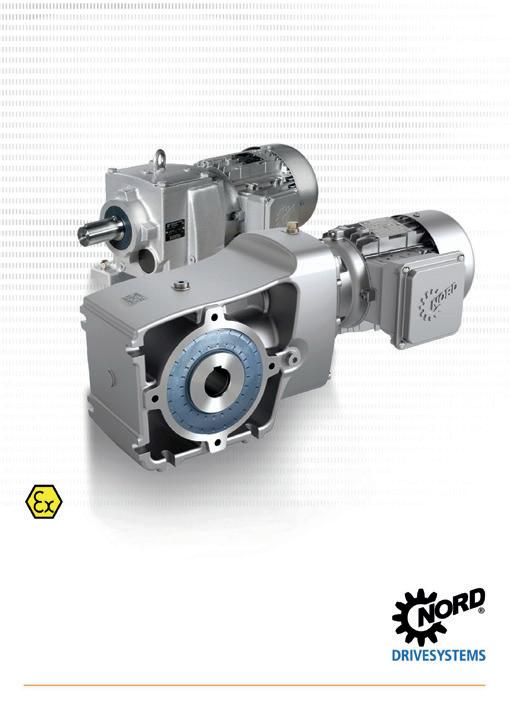
IEC Ex, EAC Ex, CCC Ex, UKEX and specifications for North American market
Flowmeters for ultrareliable dispense solutions
MEPCA discovered how Titan Enterprises’ robust flowmeter technology is helping beverage manufacturers solve sticky situations.
Soft drinks are typically formulated from a combination of water (which may be carbonated) and a syrup flavouring. Soft drinks manufacturers such as Coca Cola, use a twin dispense system to carefully combine and control each fluid to the exact concentration, ensuring the quality and consistency of flavour that their customers expect.
Dispense systems ensure consistent and accurate measures of syrup are supplied during the dispensing of each soft drink. For lowviscosity syrups or flavour additives and the diluent being dispensed alongside, both can be controlled and monitored using a turbine flowmeter. Titan’s NSF-Approved 800 series and Beverage flowmeters are widely used within the food and drinks industry for this purpose. These meters are the choice of many being both effective and reliable flow sensors, with some manufacturers also using them as low-cost alternative flow switches.
gear flow meters can also be calibrated specifically for the syrup type. Dispensing equipment software is then capable of switching between multiple calibrations for an individual flow measurement device, enabling multi-syrup dispense using a single oval gear ‘syrup meter’. So, although the temperature and viscosity of syrups are variable parameters, the flow rate of the syrup is ultimately of prime importance to the total
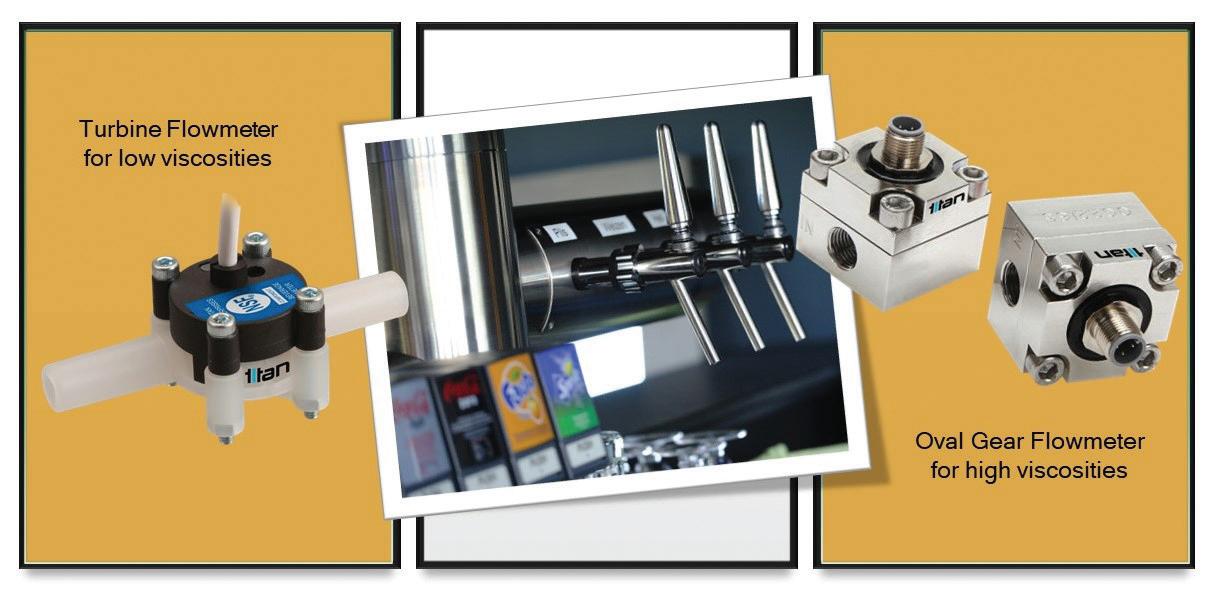
volume dispensed to ensure the correct flavour is achieved.
Typically, separate thick syrup and water lines are necessary for soft drink dispensing systems, requiring a flowmeter for each line. However, the beverage industry is evolving fast, with dispensing machines becoming more compact and modular and capable of adding flavours and CO2 at the point of sale rather than at the bottling plant. This lends itself to OEM designs incorporating the oval gear and turbine mechanics into one flow device designed to fit the space limitations of the customer’s equipment. Titan has developed dual-line flowmeters that provide a solution that suits smaller spaces, with a single unit able to measure both nonviscous and viscous liquids side by side at the point of dispense.
As syrup increases in viscosity, positive displacement oval gear flowmeters are used for accurate dosing. Due to the nature of syrup viscosities – for example, sugar-free syrup has a lower viscosity than full sugar syrup – oval gear flowmeters can address variable viscosity fluids to measure the rate of syrup flow. Where a higher level of accuracy is required, oval
Based on its OG2 model design, Titan Enterprises has developed a syrup meter against Coca-Cola’s OEM specifications for its multi-soft drink dispense machines. Manufactured in a polymer material as opposed to standard stainless steel, the syrup meter is a low-pressure, low-cost design alternative using food grade polymers. Titan’s oval gear range of flowmeters are capable of measuring flows from 0.01 to 500l/min, using the low differential pressure across the body to drive a pair of toothed oval gears, one of which contains chemically resistant magnets.
“These types of product developments can translate into big environmental and financial savings for the beverage industry”, said Neil Hannay, Senior Development Engineer at Titan Enterprises. “Higher viscosity concentrate of key ingredients requires less transport, energy and CO2 when diluted at point of sale to deliver a fresh end product.”
In addition to reducing transport and maintenance costs, venues are able to hold less stock, saving on storage and fridge space.
flowmeters.co.uk
8-pole bayonet locking
> 5000 mating cycles
Panel mount parts unplugged IP67
Solder and dip solder contacts
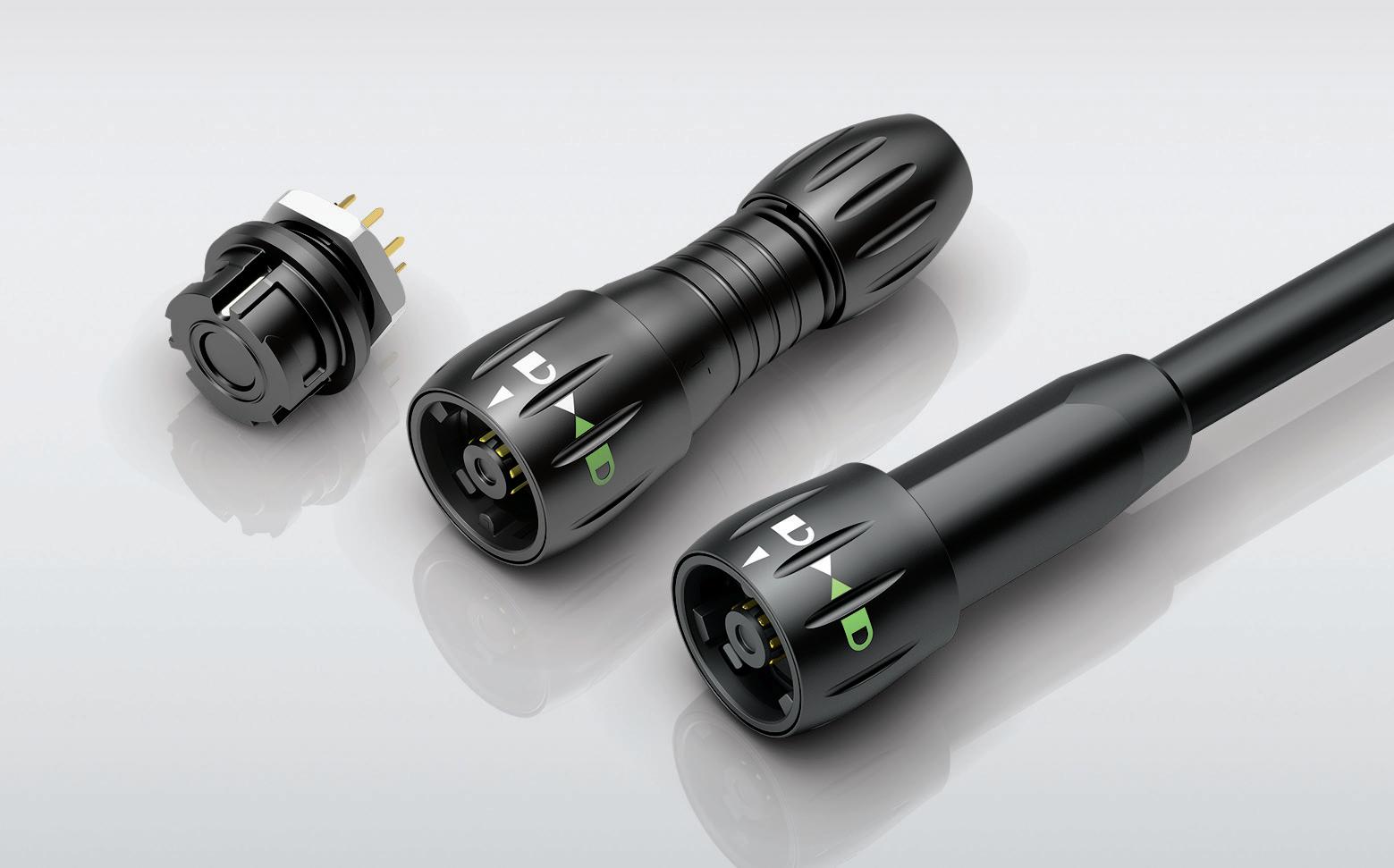
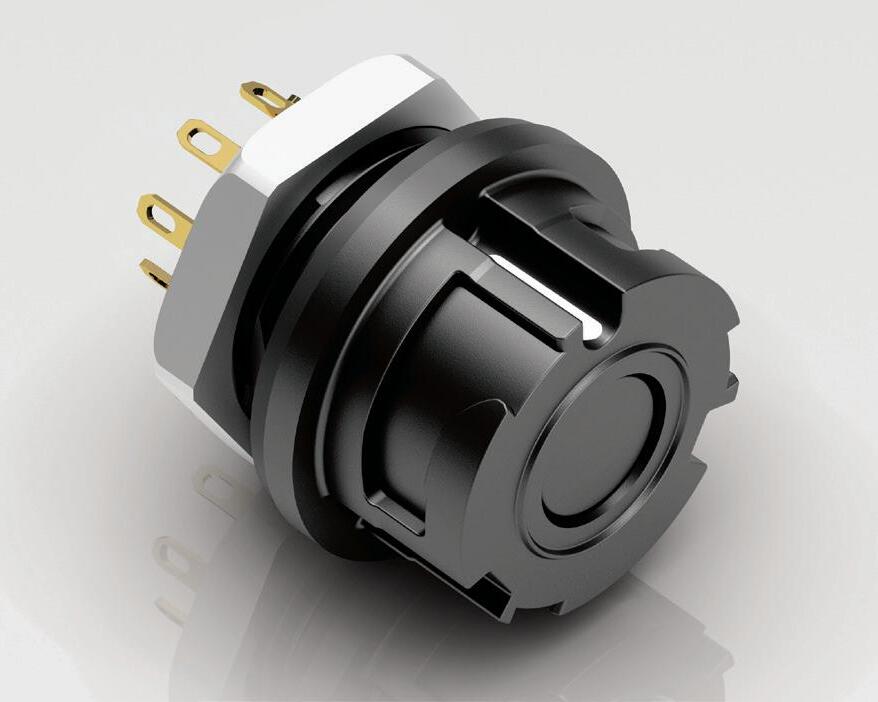
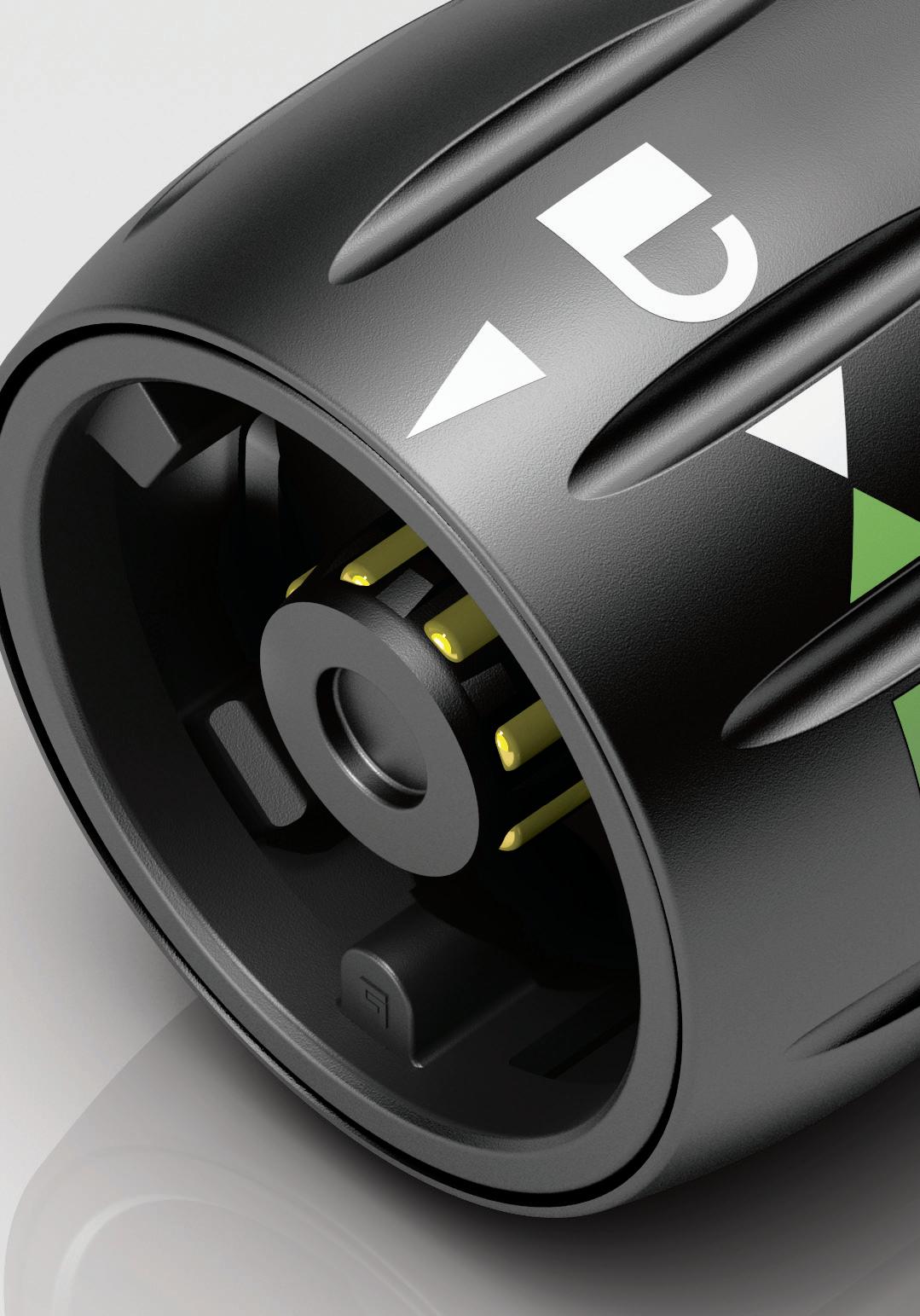
Know today what to expect tomorrow
Bosch Rexroth explains how its digital service assistant, CytroConnect, can revolutionise how maintenance is conducted in the industrial sector.
Maintenance engineers face a litany of daily challenges: sudden machine breakdowns, unplanned and costly maintenance, and the inefficiencies of predefined maintenance cycles. The traditional approach often leads to extended downtimes, inflated costs, and unpredictable operational disruptions. But what if you could know today what to expect tomorrow?
Digital solutions are transforming the service industry within industrial automation, driving significant improvements in efficiency, reliability, and predictive maintenance. By leveraging advanced technologies such as the Industrial Internet of Things (IIoT), machine learning, and real-time data analytics, digital solutions are enabling service providers to optimise their operations and enhance service delivery.
Predictive maintenance
One of the most impactful applications is predictive maintenance. Whereas traditional maintenance methods rely on fixed schedules or reactive responses to machine failures, digital solutions continuously monitor the health of your equipment through sensors and data analytics. By predicting potential failures before they occur, these systems allow maintenance teams to perform timely interventions, thus minimising unplanned downtimes and extending the lifespan of machinery and saving costs.
Real-time monitoring and data analytics are

also revolutionising the service industry. IIoTenabled devices collect vast amounts of data from various sensors installed on industrial equipment. This data is then analysed to provide insights into the operational status and performance of machinery. Service engineers can access this information remotely, enabling quick decision-making and efficient troubleshooting. Real-time monitoring ensures that issues are detected early, and corrective actions can be taken promptly, improving overall system reliability and reducing operational disruptions.
Increased operational efficiency
Automation and smart analytics streamline processes, reducing the need for manual interventions and lowering the risk of human error. For instance, automated diagnostics can pinpoint issues more accurately than traditional methods, and digital twin technologies allow for virtual simulations of equipment performance, enabling engineers to test solutions before applying them to real-world scenarios.
Enter Bosch Rexroth’s CytroConnect and its suite of service packages, designed to revolutionise how maintenance is conducted in the industrial sector. Bosch Rexroth’s digital solutions are tailored to address the specific needs of hydraulic systems. These solutions begin with basic data visualisation and can be expanded to include sophisticated rule-based condition monitoring and predictive analytics services.
Data visualisation
A foundational element that offers real-time insights into the current condition of hydraulic systems is data visualisation. By visualising operational data, maintenance engineers can quickly identify anomalies and address issues before they escalate into major problems. This immediate access to actionable information simplifies decision-making and enhances overall system reliability.
Rule-based condition monitoring
Rule-based condition monitoring utilises predefined rules and algorithms to analyse data and detect deviations from normal operating conditions. When potential issues are identified, maintenance teams receive alerts, enabling them to intervene early and prevent unplanned downtimes. This approach not only reduces the frequency of breakdowns but also extends the lifespan of machinery.
Predictive analytics
By employing advanced machine learning algorithms and historical data, predictive analytics can forecast future failures with high accuracy. Maintenance activities can then be scheduled proactively, minimising downtime and reducing maintenance costs.
Bosch Rexroth’s CytroConnect and its associated service packages are designed to simplify the daily challenges faced by maintenance engineers. By providing clear insights into the current state of machinery and predicting future conditions, these digital solutions enable more efficient and effective maintenance strategies.
Understanding that every industrial operation has unique requirements, Bosch Rexroth offers a modular approach. Whether users need basic data visualisation or a comprehensive predictive maintenance solution, the CytroConnect suite can be customised to meet a customer’s specific needs. This flexibility ensures that maintenance engineers can adopt the most appropriate solution for their operational challenges.
By knowing today what to expect tomorrow, maintenance engineers can mitigate the risk of sudden breakdowns, optimise maintenance schedules, and ultimately enhance the productivity and reliability of their operations.
www.boschrexroth.co.uk
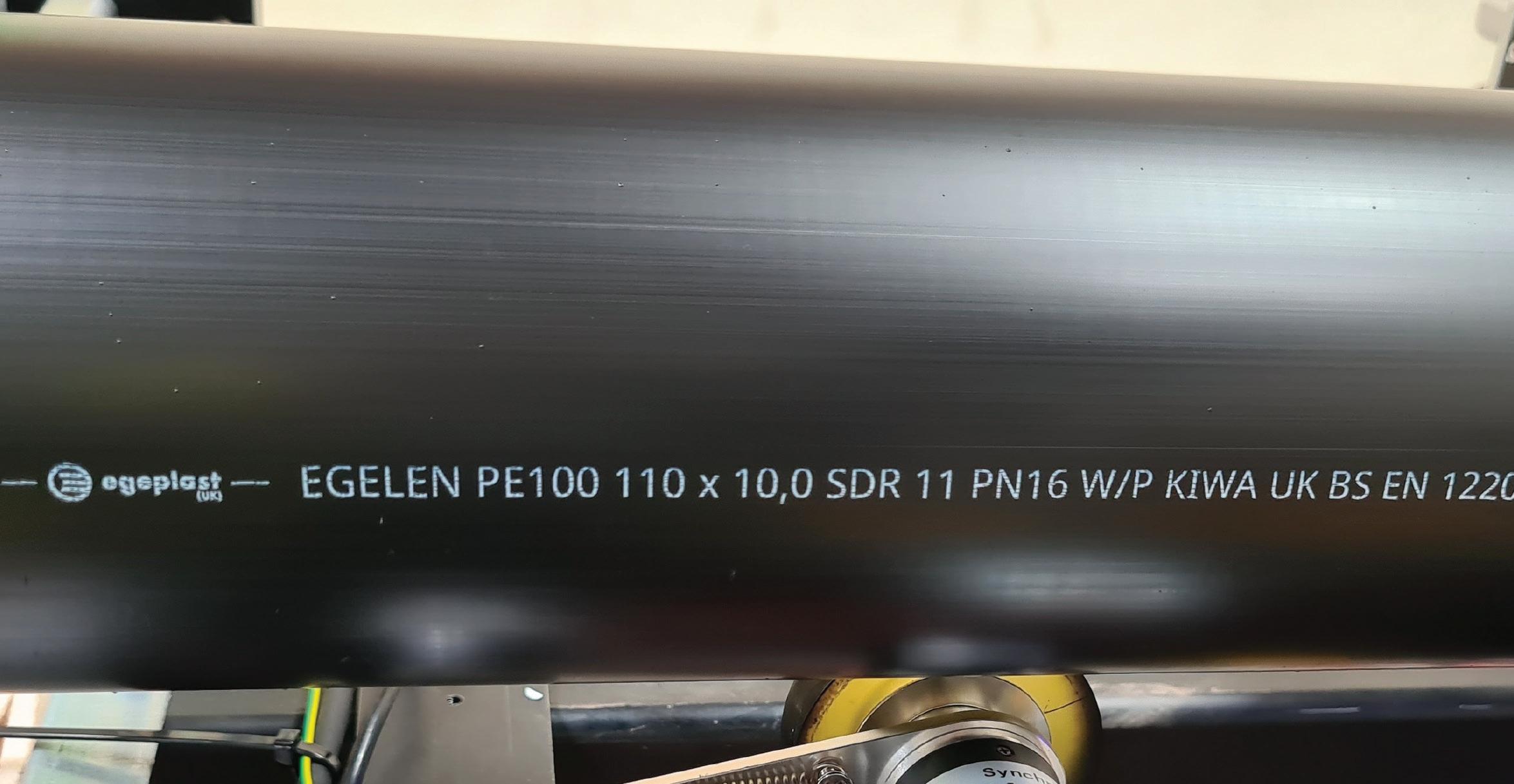

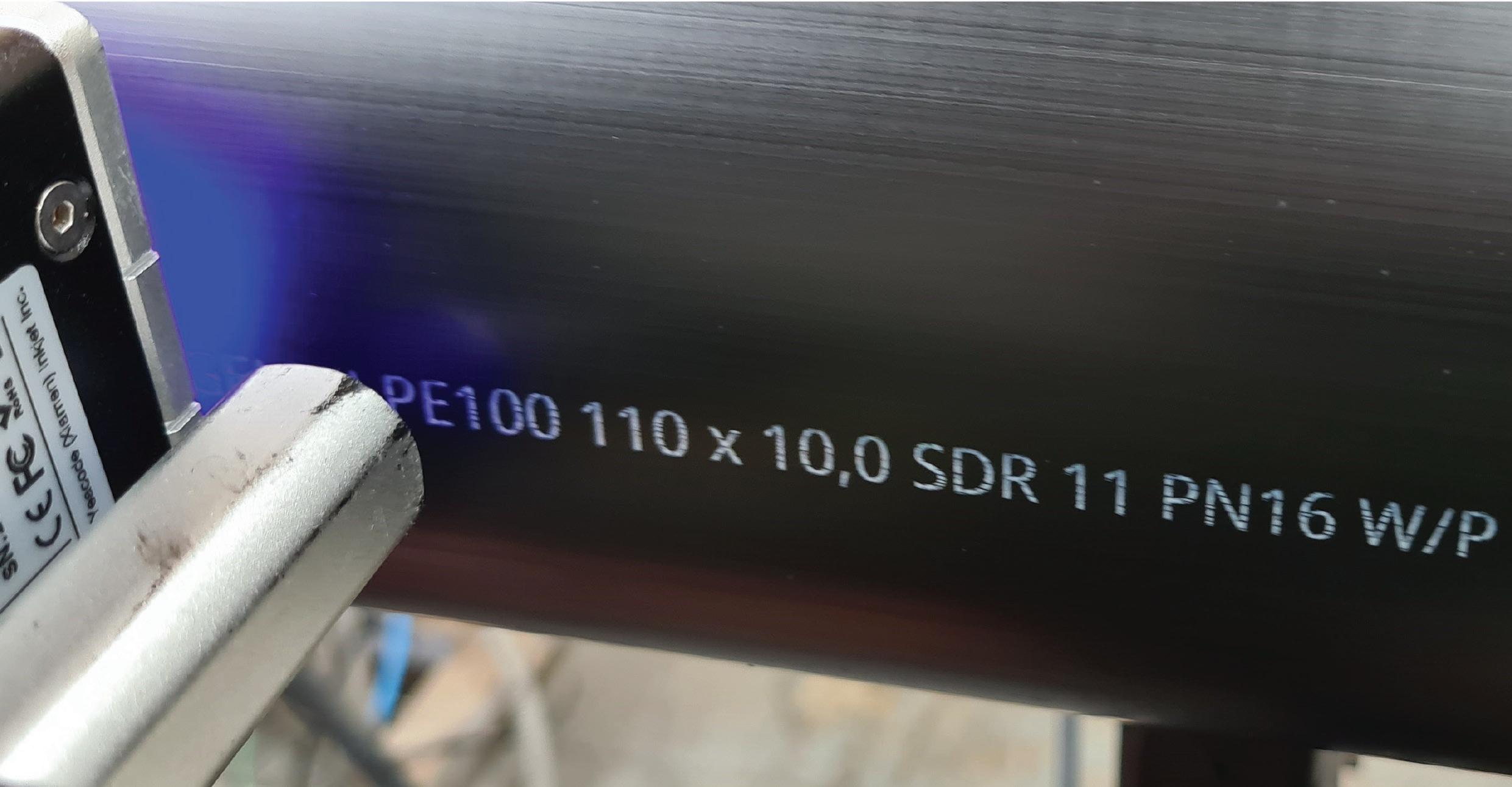
Accurate testing to meet strict Benzene exposure limits
The EU-wide 8-hour time weighted average (TWA) for benzene exposure recently changed from 1ppm, to 0.5ppm and a further reduction to 0.2ppm planned for April 2026. Safety equipment specialist, Rockall Safety, explains the background to these requirements and outlines a solution which can measure concentrations of benzine and other volatile organic compounds to help ensure compliance.
The EU sets occupational exposure limits (OELs) for hazardous substances like benzene to protect workers’ health. Adhering to these limits is not only ethically responsible but also legally required. Failure to comply can result in fines, legal action, or even closure of the workplace.
The EU-wide 8-hour time weighted average (TWA) for benzene recently changed from 1ppm, which equals a concentration of 3.25mg/m3 to 0.5ppm equivalent to 1.65mg/m3. This exposure limit will remain effective until April 5, 2026, after which it will be further reduced to 0.66mg/m3, equivalent to 0.2ppm.
Why is benzene so dangerous
Volatile organic compounds (VOCs) possess significant vapour pressure at ambient temperatures, leading them to evaporate readily. This makes it easy to breathe them in, absorb them through your skin, or even swallow them accidentally. The extent of their impact on workers’ health depends on the duration and level of exposure.
Similar to other organic solvents, immediate symptoms resulting from minor exposure to high concentrations (e.g., hundreds of parts per million) may include:
• Headaches
• Fatigue
• Nausea
• Dizziness
• Unconsciousness at high levels
From a long-term health perspective, both the World Health Organization (WHO) and the International Agency for Research on Cancer (IARC) classify benzene as a Group 1 carcinogen.
Prolonged exposure to elevated levels of benzene can lead to various forms of
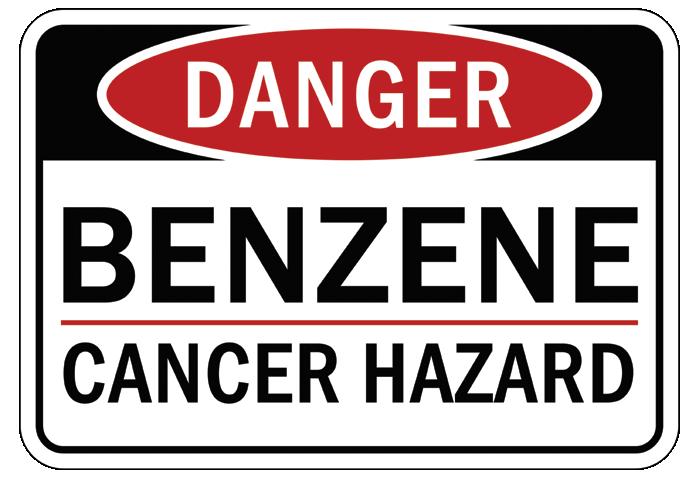
leukaemia and adversely affect red and white blood cell counts. Chronic effects may include myeloid leukaemia, lymphocytic leukaemia, non-Hodgkin’s lymphoma, multiple myeloma, and aplastic anaemia.
Why do we detect benzene?
Benzene exposure can arise during its manufacturing, transportation, and utilisation in the oil, chemical, and petrochemical sectors. The significance of exposure to this substance may vary, being crucial during both routine and non-routine operations (consult local regulatory guidelines, agencies, and hygiene specialists). Benzene is a known carcinogen, capable of inducing cancer.
Exposure to high concentrations of this compound, typically in the range of 10,000 to 20,000ppm, can lead to fatality. Moreover, Benzene is suspected to be harmful to several vital bodily systems, including cardiovascular, endocrine, gastrointestinal, immunological, neurological, and respiratory.
Findings from a National Occupational Exposure Survey involving over 400,000 individuals exposed to Benzene rank it among the top concerns out of approximately 12,000 exposure incidents.
Conclusion
The UltraRAE 3000+ available from Rockall Safety is a highly advanced Compound-
Specific Monitor renowned for its versatility and precision in detecting volatile organic compounds (VOCs), particularly benzene. With a specialised Photoionisation Detector (PID), it offers an extended detection range from 0.01 to 10,000ppm in VOC mode and from 10ppb to 200ppm in benzene-specific mode.
This wide range makes it suitable for various applications, including entry prescreening during maintenance at refineries and plants, hazardous material response, marine spill management, and downstream monitoring in refineries. Its dual detection mode enables users to choose between a 60-second snapshot or a 15-minute ShortTerm Exposure Limit (STEL) measurement, ensuring comprehensive assessment of benzene exposure over different time frames.
Moreover, the instrument’s high sensitivity to benzene reduces the risk of false alarms, thanks to its advanced speciation method, ensuring accurate detection and minimising unnecessary disruptions in the workplace. Additionally, the UltraRAE 3000+ offers a total VOC measurement mode, further enhancing its utility in assessing workplace
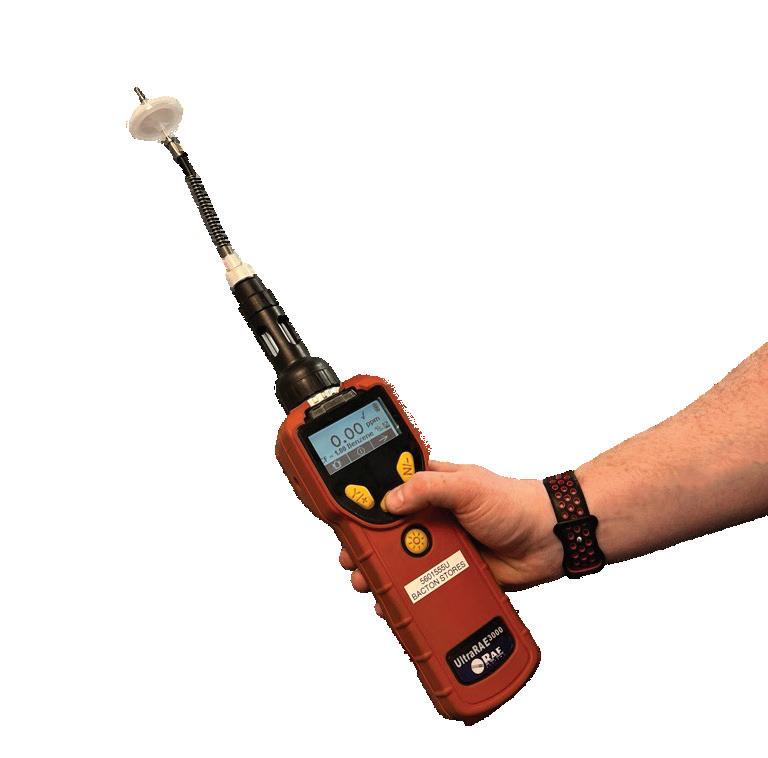
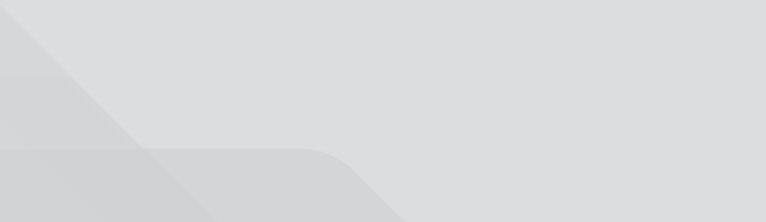
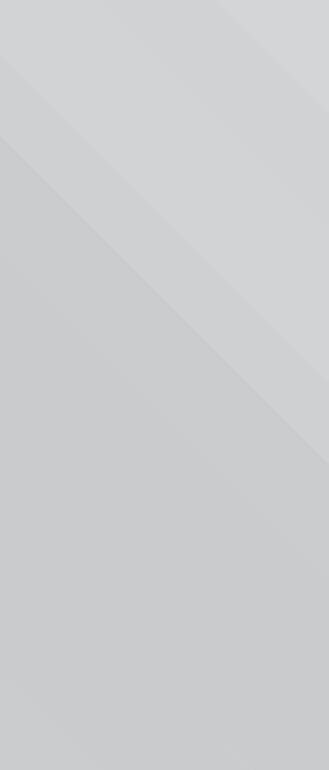
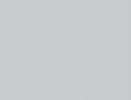

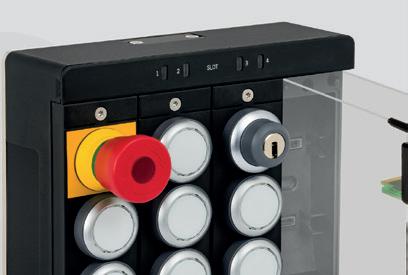

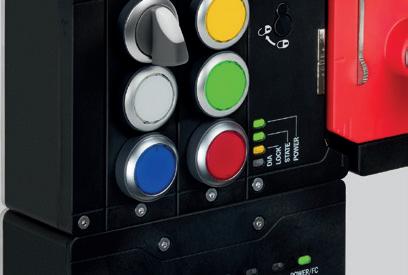
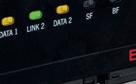
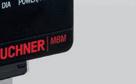

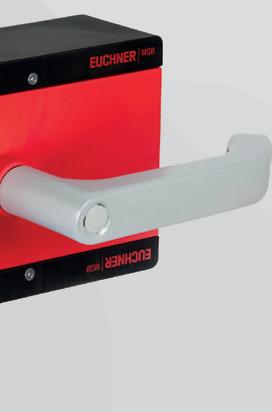

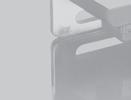
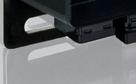


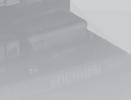
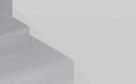


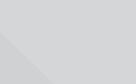
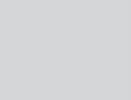
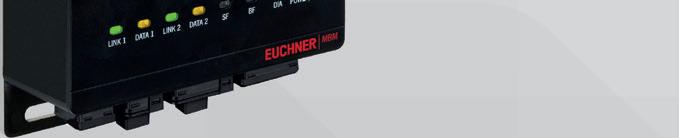


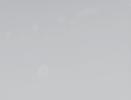
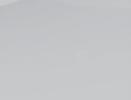
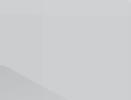

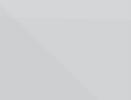
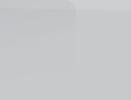


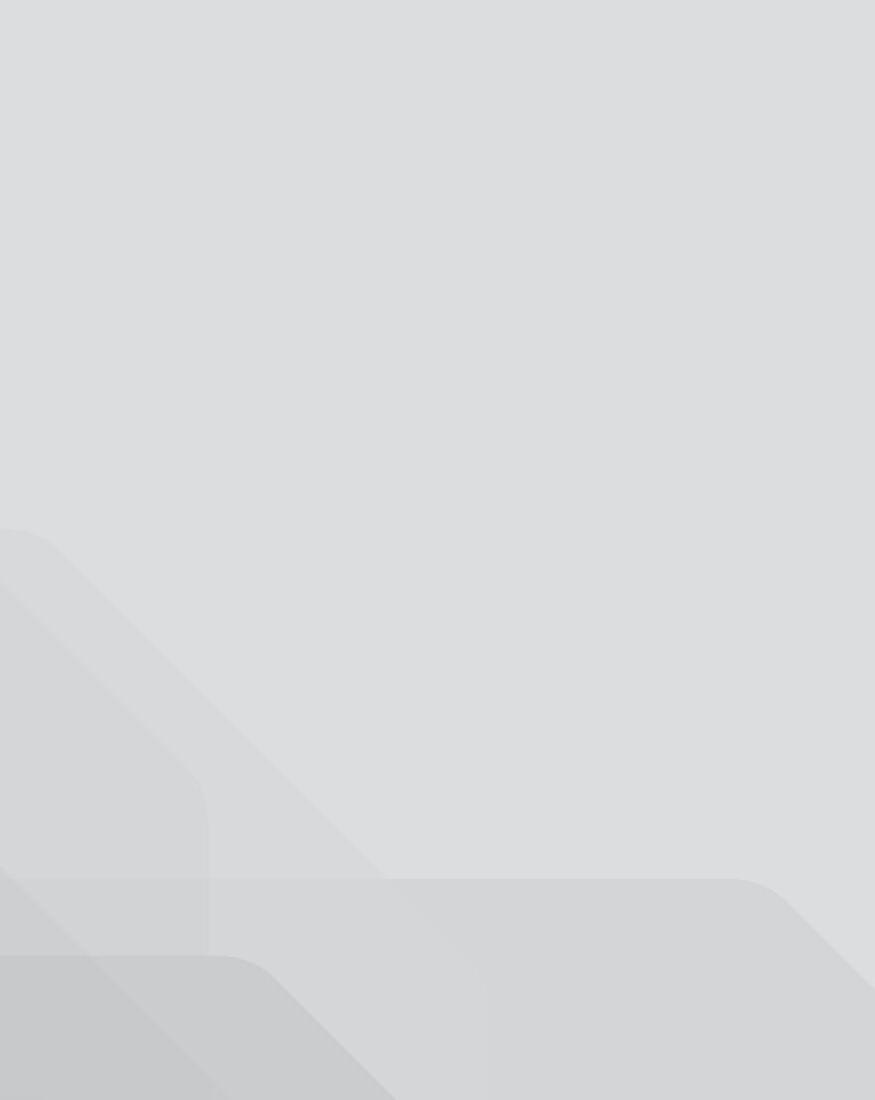
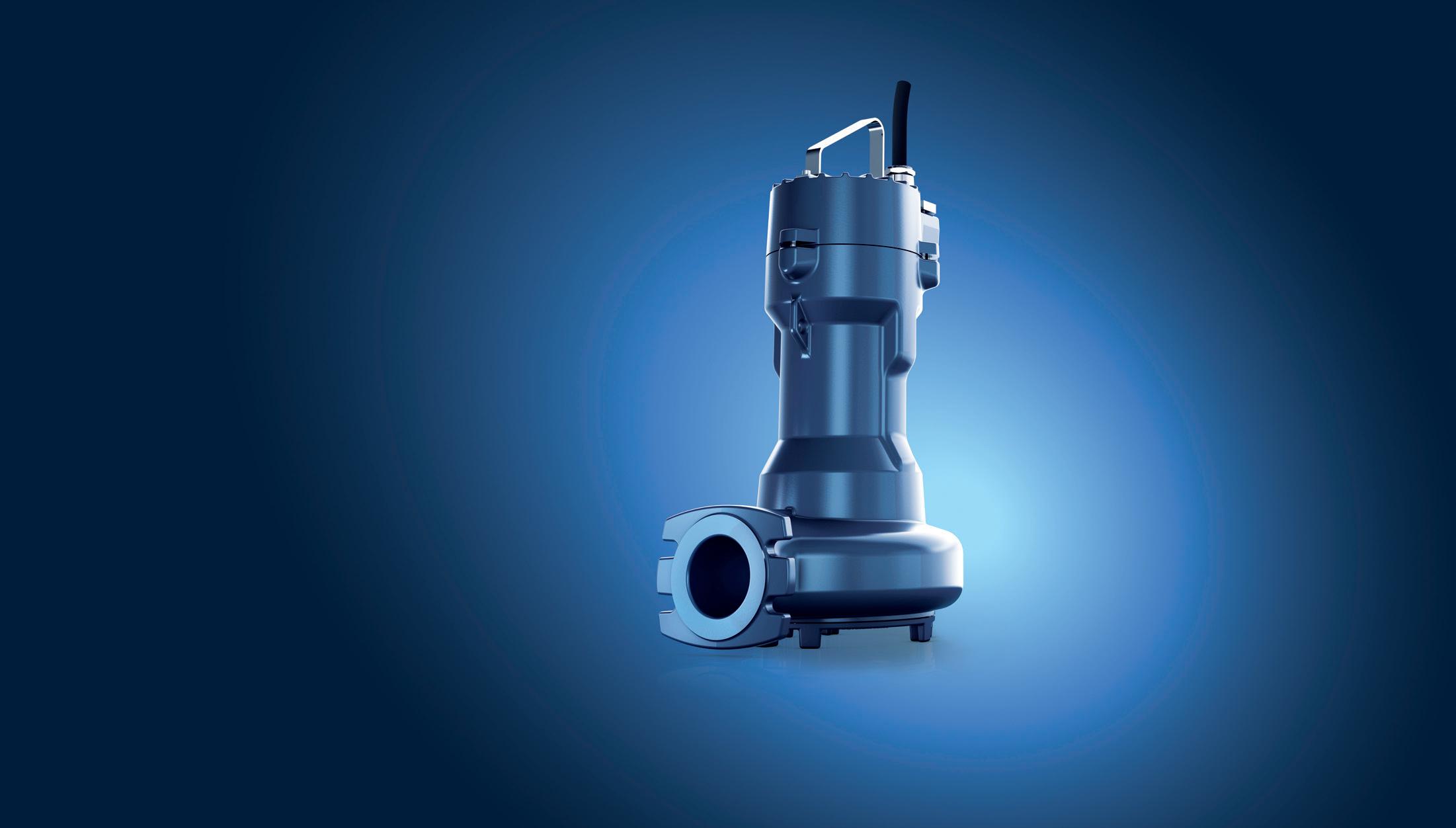
In-furnace thermal imaging
AMETEK Land, a manufacturer of high-end instruments for industrial infrared temperature measurement, has supplied a 28-camera system for one of the world’s largest ethylene producers.
Ethylene is produced via gas and liquid crackers that react steam and hydrocarbons (usually either ethane or naphtha) in coils designed to withstand high temperatures. The temperatures are measured, often daily, by inspectors with a handheld pyrometer. Once the temperature reaches a design limit, the unit is taken out of production for a decoke – that burns away carbon formed on the inner surface of the tubes. AMETEK Land manufactures the majority of handheld pyrometers for this purpose, including the Cyclops, but has witnessed an uptick in the interest in using fixed thermography to automate and enhance the data coming from the furnace.
The NIR-B-2K, AMETEK Land’s highdefinition thermal imaging system, addresses this challenge, which has led to the company being selected by one of the world’s largest ethylene producers for installation on multiple liquid-feed cracker furnaces.
Following extensive technical consultation to determine the optimum location for each camera, the end-user proceeded with LAND based on a simple, proven value proposition: high-definition imaging of the most critical areas of the furnace, combined with automated tube metal temperature measurement, allows for small increases in the furnaces run-length, reductions in decoking times, and improvements in firing efficiency.
LAND supplied 28 NIR-B-2K thermal imaging cameras to deliver highly accurate measurements to help optimise furnace uniformity, extend tube life and improve safety – all critical requirements for furnace operations.
With an outstanding resolution of up to 3 million pixels, the NIR-B-2K provides high spatial resolution of the entire measurement
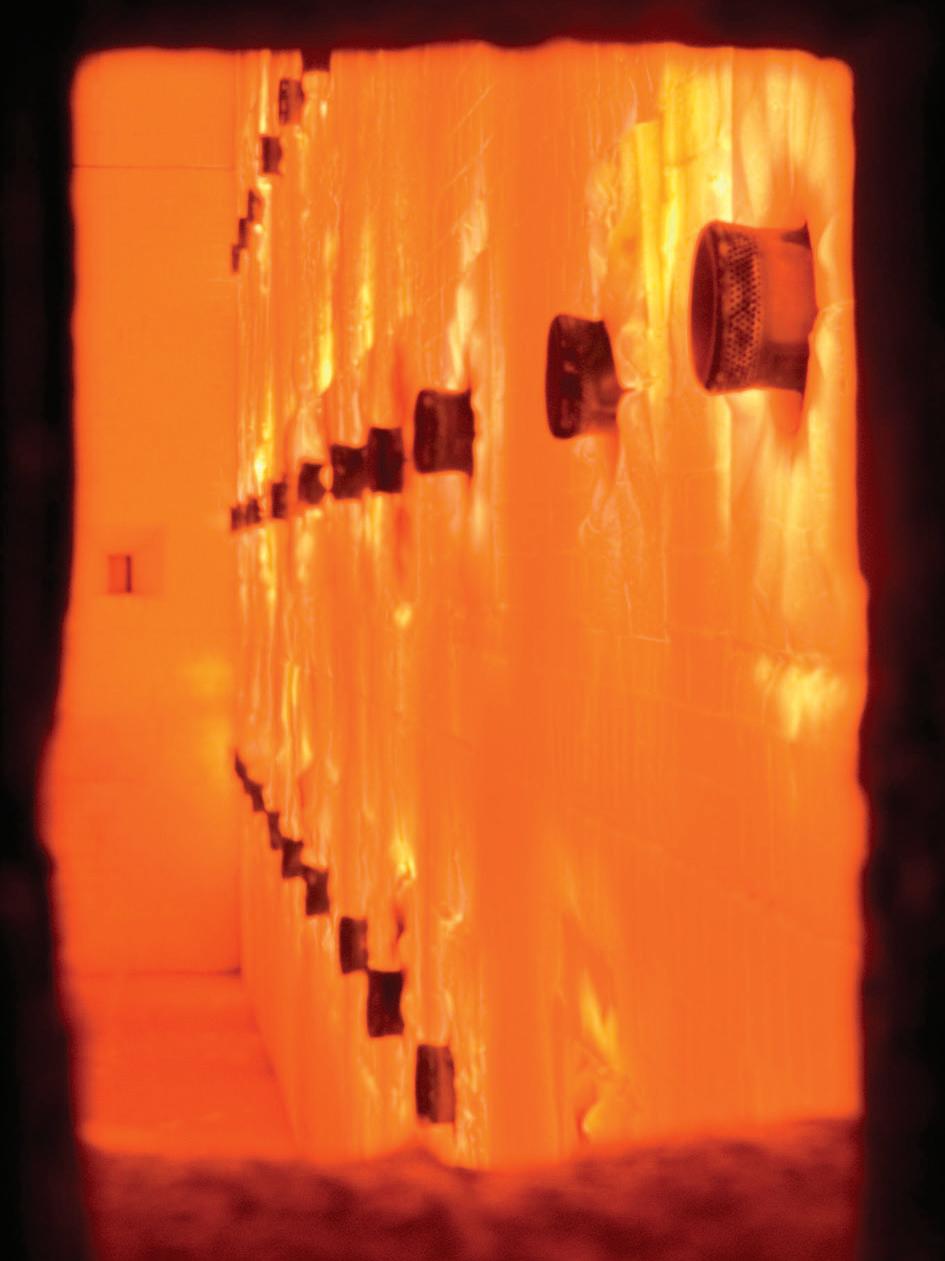
area, measuring temperatures in the range of 600 to 1800 °C.
The expected results are improved and optimised performance of the furnaces, enabling the operator to have better control over the decoking schedule.
Also, by delivering accurate and real-time temperature measurements, the tube and catalyst life will be extended, with early warnings of rising temperatures.
www.ametek-land.com
Efficient HACCP Cook & Chill CCP Validation
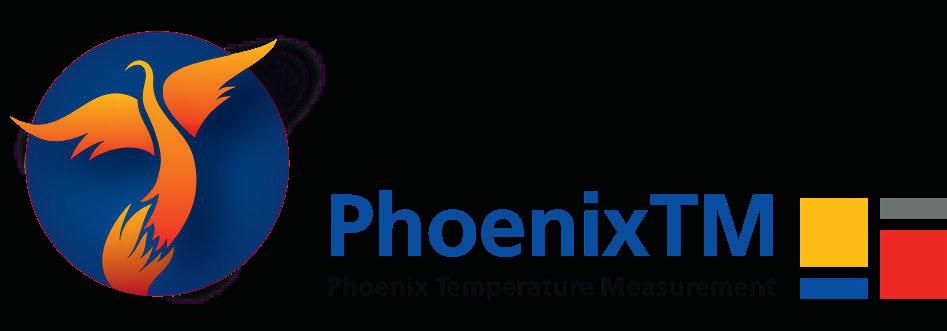
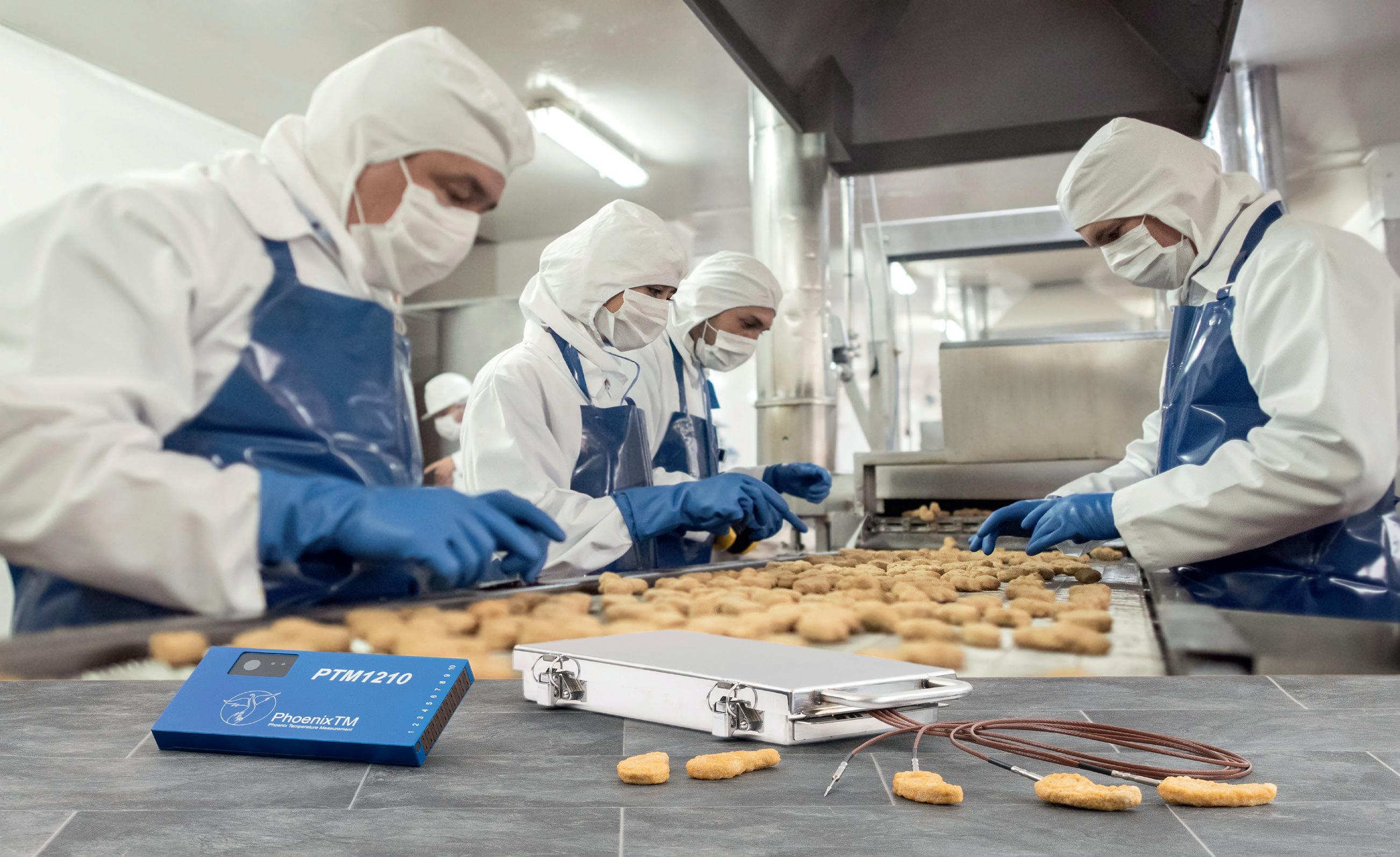
Product Safety
Process Efficiency
Improved Product Yields
Rapid Fault Finding
Full HACCP Certification
Thru-process temperature monitoring solutions for all your cook applications
PhoenixTM Technology
• Accurate IP67 data logger (Type K or T)
• 10 Measurement Points for full oven mapping
• Thermal barrier options to suit cook regime
• Comprehensive thermocouple range
• Standard miniature thermocouple plugs
• Calibrated thermocouple options
• Food trays and thermocouple jig options
• Full lethality (Fo/Pu) and reporting
• Real Time RF Telemetry options
• Local efficient calibration and service support
Phoenix Temperature Measurement
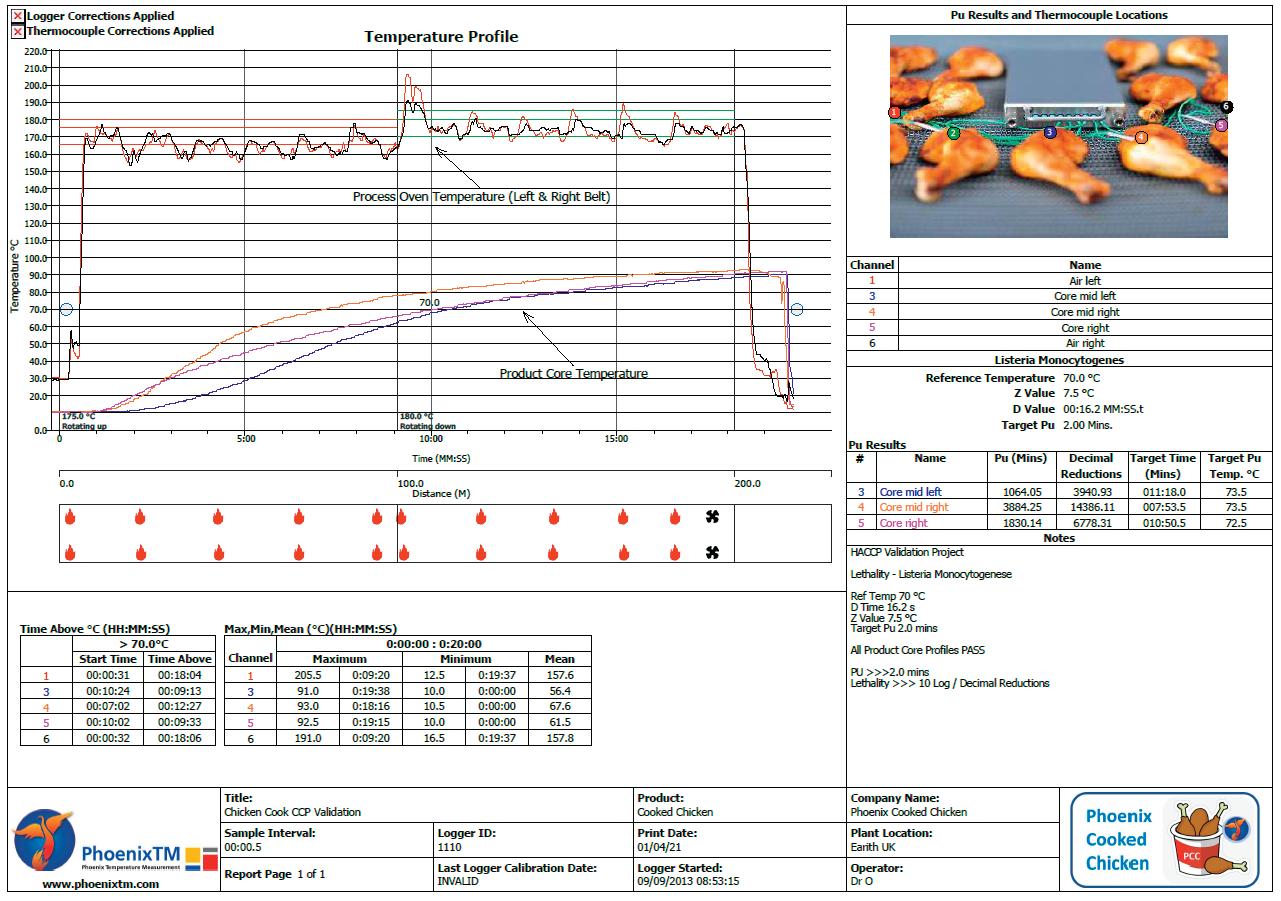
Robots unlock growth for a wider range of users
Julian Ware, UK & Ireland Sales Manager for ABB Robotics, explains how recent developments in robotics are helping automation tackle new applications for a wider range of users.
Faced with a continuing labour squeeze and the need to boost productivity in a sustainable way, manufacturers and distribution companies are increasingly turning to automation for answers.
The most recent World Robotics Report from the International Federation of Robotics (IFR) highlights a global increase in the rate of robot adoption, recording 553,052 industrial robot installations in factories around the world in 2023 – up 5% compared to 2022. What’s more, the IFR predicts that new installations will top 600,000 in 2024.
Developments such as artificial intelligence (AI) and machine vision are key drivers in this shift, paving the way for deployments in an expanded range of applications.
Today’s robotic solutions can be used to achieve highly automated end-to-end manufacturing, with options encompassing everything from low payload cobots and fast picking Delta robots to complete lines handling multiple operations. The development of smart AGVs and mobile robots (AMRs) enables the seamless transfer of parts or sub-assemblies between different production stations. Globally, the benefits of this increasingly joined-up approach are driving steady growth across a variety of industries, including food and beverage, pharmaceuticals, electronics, logistics and construction.
A new level of simplicity
Innovations such as cobots, and simplified programming and user interfaces, are helping to address many of the concerns that have deterred SMEs from investing in robotic automation, providing them with an easy and scalable way to integrate robotic automation into their operations. Cobots provide the opportunity for inexperienced users to tackle the low hanging fruit of simpler applications. Meanwhile, developments such as block-

based programming are making it much easier for first-time users to introduce robotic automation without the need for specialist programming skills. ABB’s Wizard easy programming software for its cobots and small IRB 1100 industrial robot uses Blockly, for example. This open-source visual coding method presents programming language or code as interlocking blocks, which can be used to quickly build robot application programs.
Tools such as digital twins, virtual and augmented reality viewers, offline programming, and simulation enable companies to develop and test different configurations before installing new solutions or changing existing ones. This is especially beneficial for industries subject to rapid changes in consumer demand, such as food and beverage and logistics, which must be ready to adapt fast to accommodate new products or packages.
Boosting productivity
Robots can enhance workforce productivity, taking on lower value, dirty or dangerous tasks, or providing additional production capacity. Developments such as vision, force
control and path following increasingly enable robots to plug the skills gap.
This is attracting new users in nontraditional sectors such as construction and healthcare, as well as manufacturing and logistics.
Preparing for a robotic future
With many companies citing a shortage of expert robot operators as a barrier to adoption, there is a need to ensure that both current and future generations of workers can access the training they need to be able to use robots. For this reason, robot manufacturers, including ABB, have devoted considerable effort to designing training programmes aimed at all levels of ability, enabling operators to develop their skills from basic through to advanced levels.
As the capabilities of robots continues to expand, new opportunities are being created for companies to find ways to grow by applying robotic automation to addressing their challenges.
new.abb.com
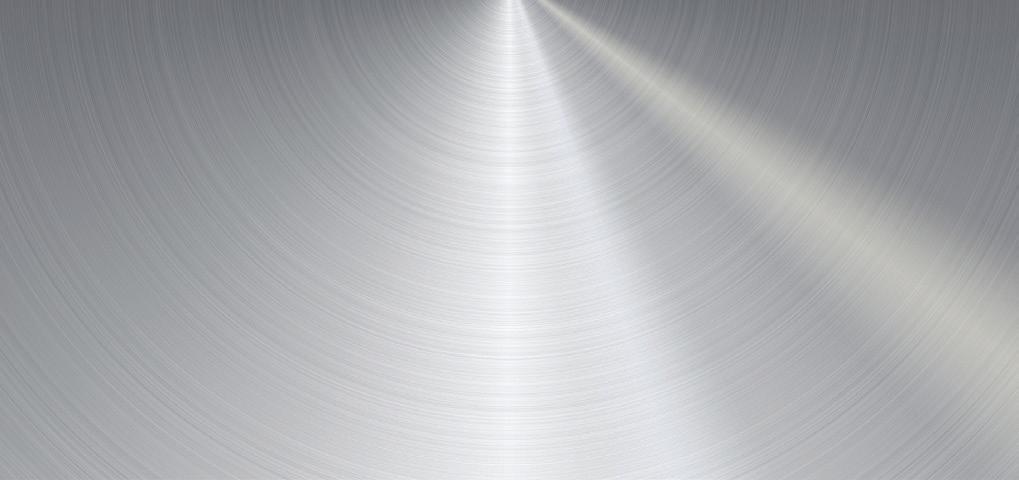
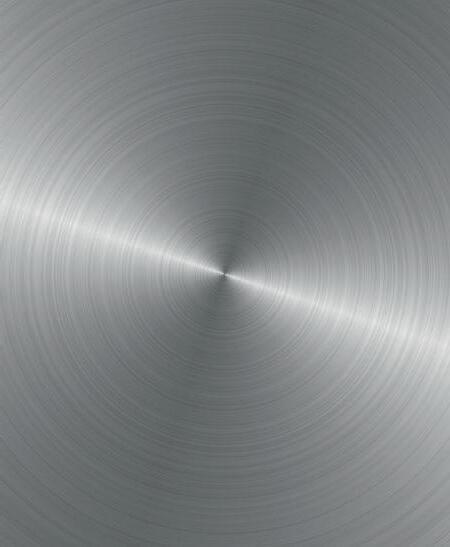



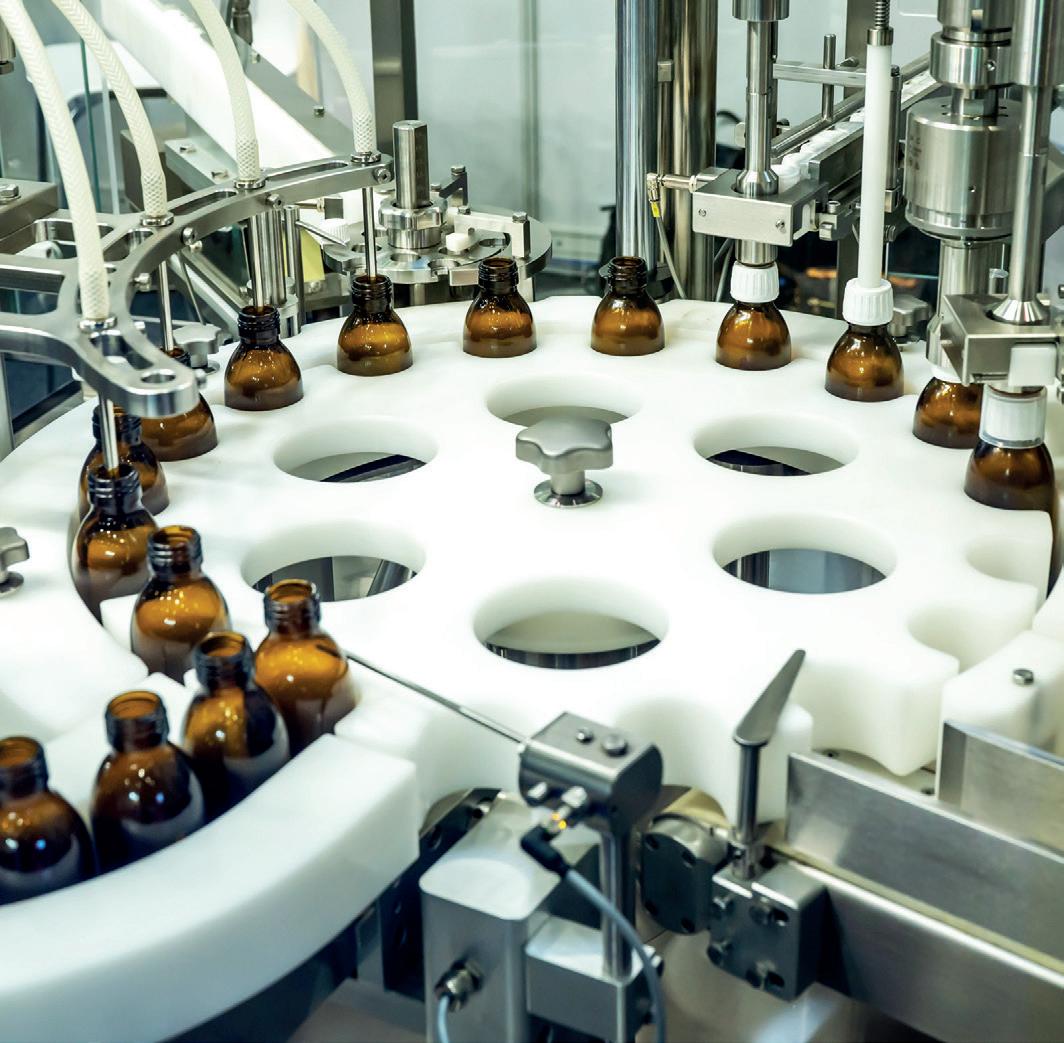
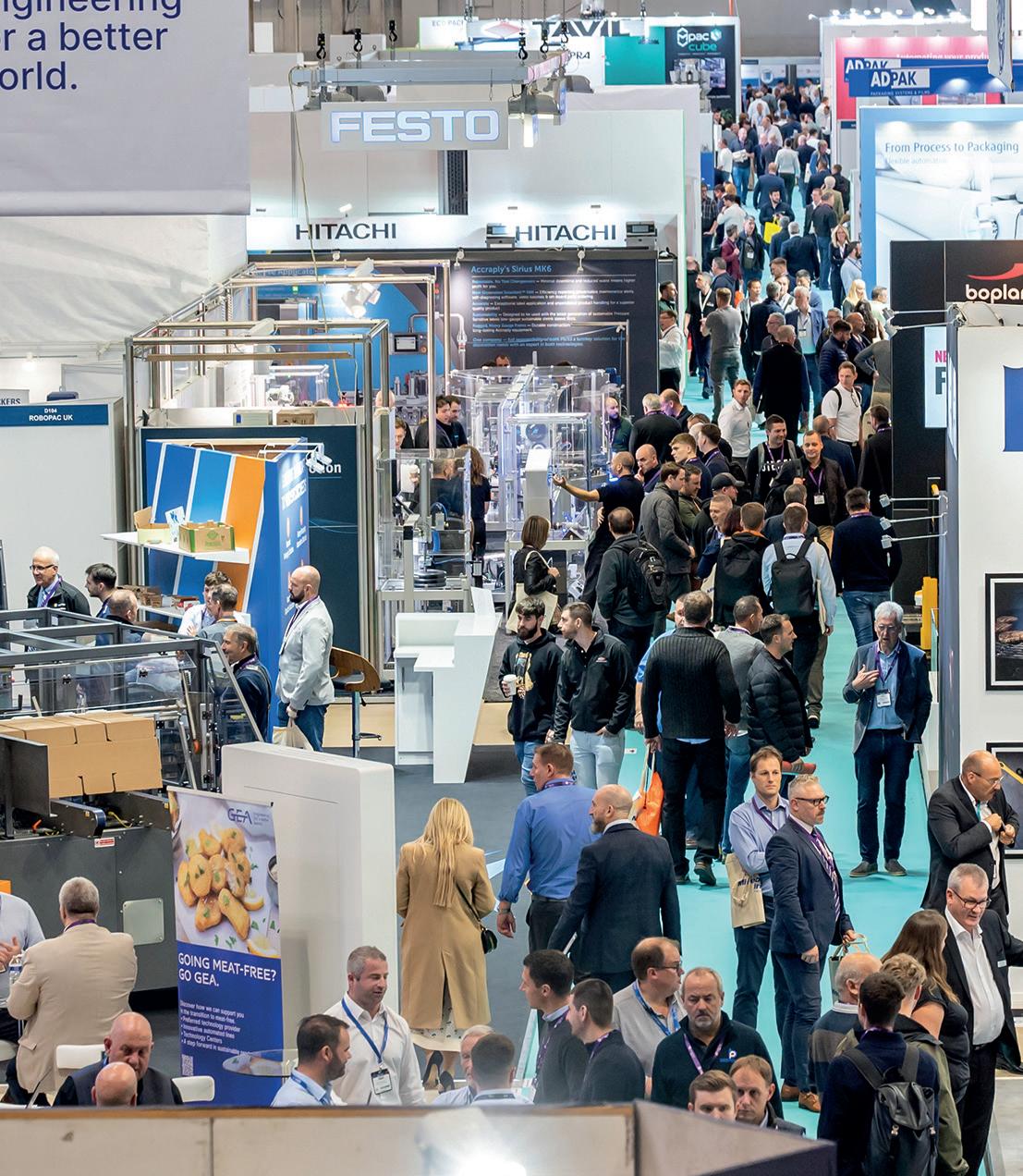
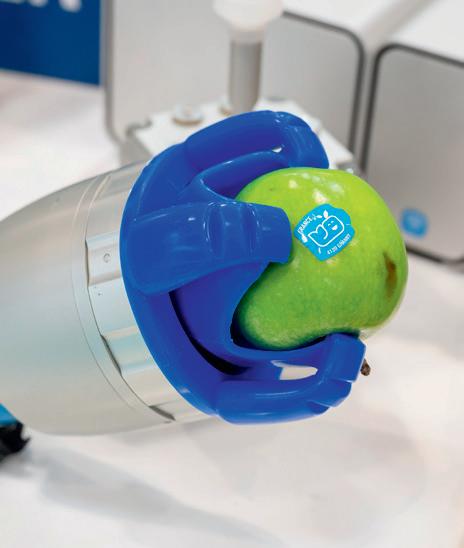

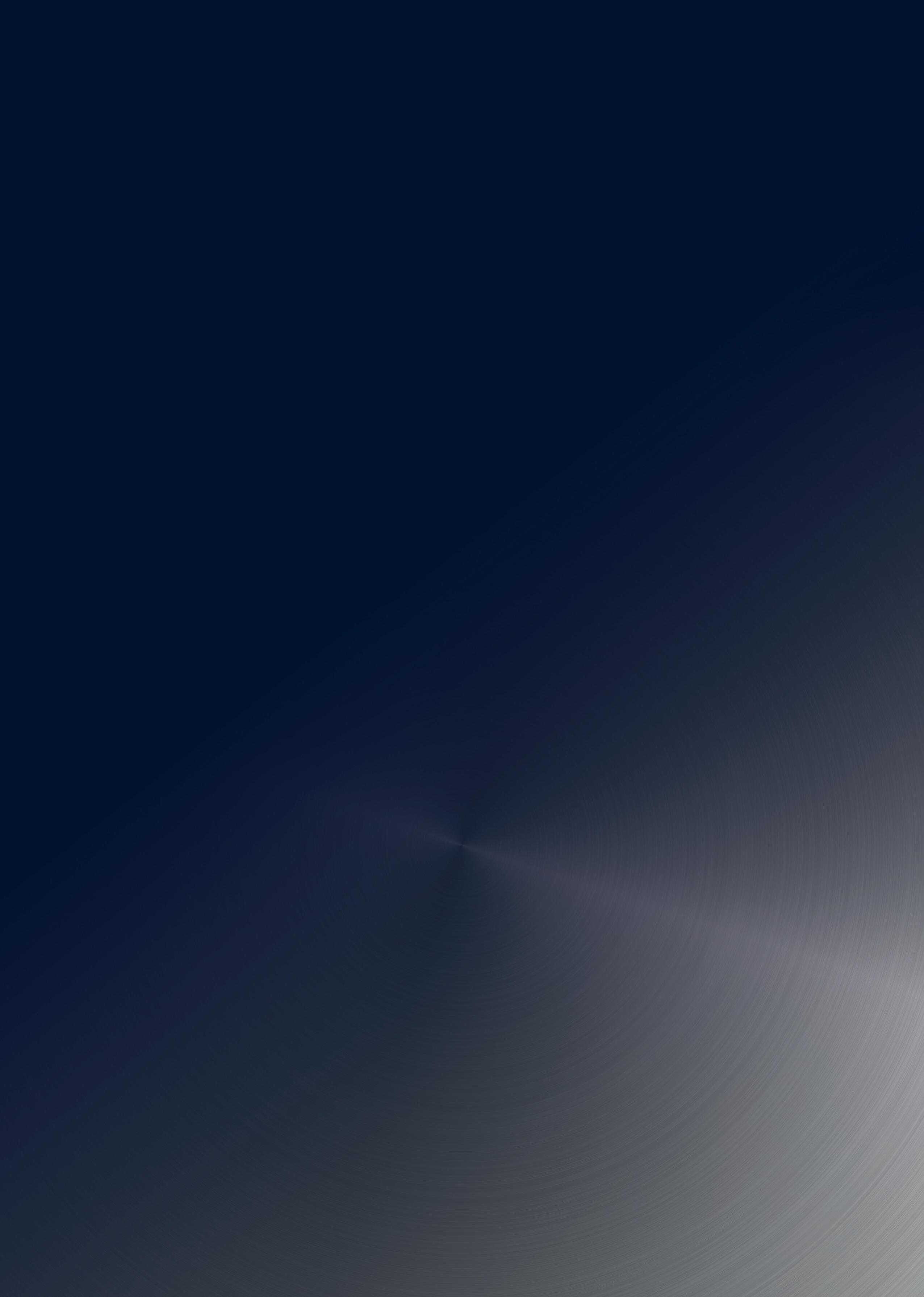
CHEMUK Expo achieves record attendance
CHEMUK 2024 opened its doors on 15 and 16 May at the NEC in Birmingham to a record attendance of 4641 visitors over the two days, representing a 17% increase rom 2023.
The total two-day attendance including both visitors and exhibitors at the CHEMUK 2024 was 6677. Commenting on this record attendance, CHEMUK show founder, Ian Stone, said: “Standing in the hall mid-morning on the first day was electric! So much volume and energy in the hall with our biggest concentrated audience ever, from literally every corner of the sector.”
“I think the seniority of attending technical, scientific, supply chain, and business visitors rocketed to a whole new level this year, one visitor badge after the next from the biggest names across the sector.”
Visitors to CHEMUK were invited to an exclusive pre-recorded address by Minister Mak, Minister for Industry and Economic Security at the Department for Business and Trade, and Minister for the Investment Security Unit at the Cabinet Office.
The address was supported by a comprehensive UK Government footprint at the show, with several government departments exhibiting this year, including the Department for Business and Trade, the Department for Environment, Food and Rural Affairs, the Health and Safety Executive, the Home Office, and the Department for Energy Security and NetZero.
CHEMUK redefined itself this year with the introduction of several sub-brands: the Chemical & Process Engineering Show, the Chemicals Supply Show, the Chemicals Management Show, and the Chemical Laboratory Show. The organising team was delighted to see not only an increase in the number of visitors but also an increase in the quality of visitors, which they largely attribute to the introduction of these more focused show zones.
Covering the big issues
Reflecting on the enormous CHEMUK 2024 speaker programme, Ian continued:
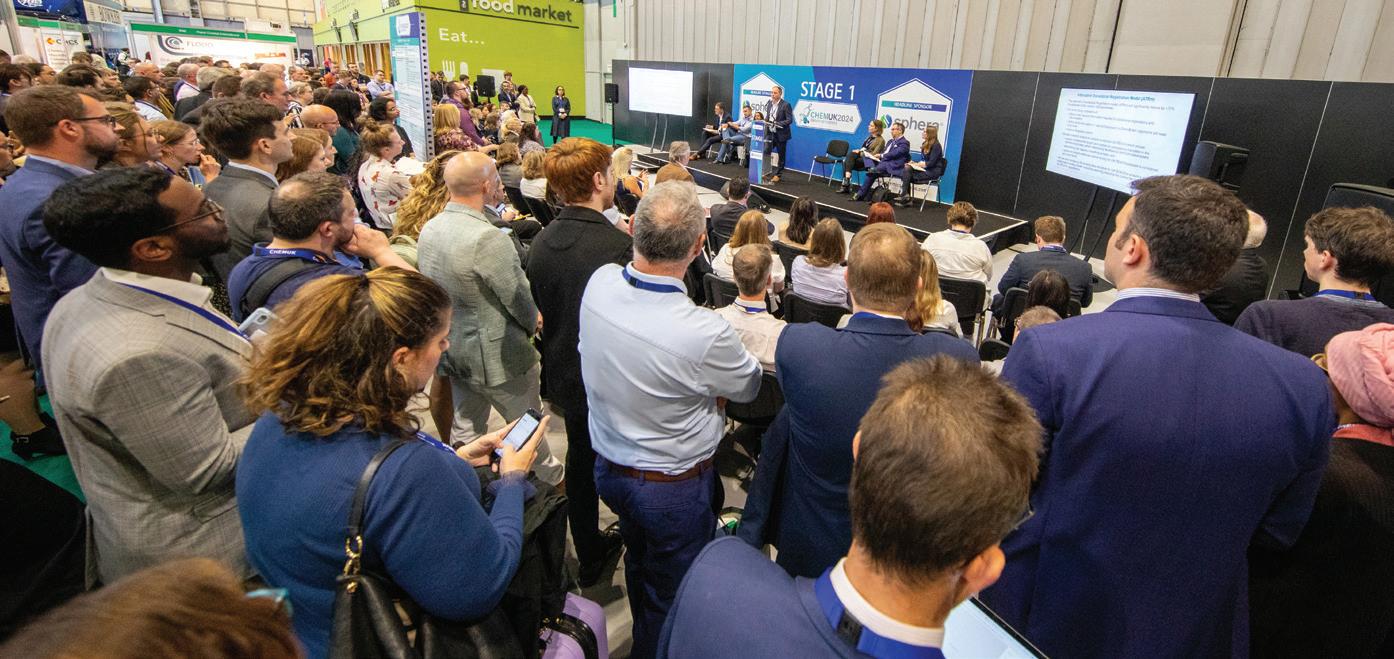
“CHEMUK24 was our most comprehensive conference programme to date and certainly our best attended, with standing room only at so many of the keynotes and panel programmes.
The drop-in nature of the CHEMUK conference stages carries so much appeal, giving instant access to senior figures, expertise, technology, innovation, and the most topical and lively debates around the BIG issues affecting and influencing the sector, whether Sustainability, UKREACH, Decarbonisation, Future Skills, Digitalisation, Bio-based Transition, Scale-Up and so much more.
“It’s pretty much a freeze frame of where the industry is each year and is invaluable in intelligence gathering, empowering all important directional and investment decisions.”
Partner support
The 2024 show welcomed several key new partners to the show this year who brought invaluable content and member groups to the show. The new partnering organisations included the British Plastics Federation, IMechE, ScotCHEM, CICA (Chemical & Industrial Consultants), and the CHCS (Chemical Hazards Communication Society).
The show’s success was underpinned by the continued support and input provided by their longstanding partner network, comprising the CBA, BCA, BASA, BVAA, BPMA, BioVale, BCMPA, BADGP, CPI, CCUK, IBioIC, GAMBICA, NEPIC, SIA, InnovateUK KTN, Chemicals Northwest, UKLA, and the UK & Ireland Spill Association, to name a few.
Looking ahead
In 2025, CHEMUK will introduce ‘The Formulated Product Manufacturer Show’.
Ian explained his vision for 2025: “CHEMUK is all about providing a single destination where all strands of the chemical industries converge through its individual show stream brands, and 2025 sees the introduction of a brand new fifth stream with the Formulated Product Manufacturer show.
Aimed squarely at the downstream consumer and industrial formulated product industries, from cleaning and disinfecting products to car care, from personal care and cosmetics to adhesives and sealants, coatings and paints, lubricants, oils and fluids, plastic compounds, etc., the list goes on.
CHEMUK 2025 is being held at the NEC, Birmingham, on 21 and 22 May, 2025.
www.chemicalukexpo.com
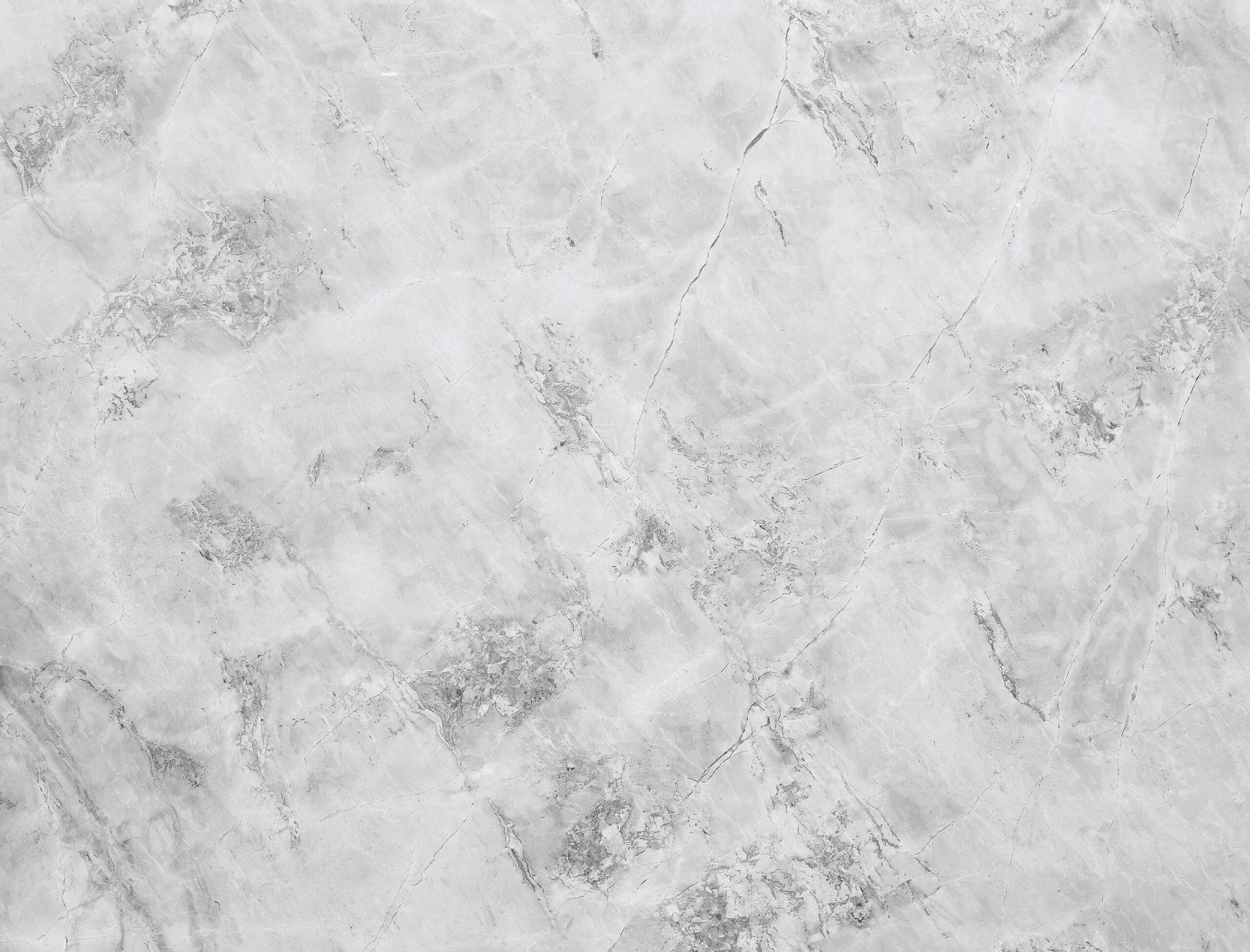

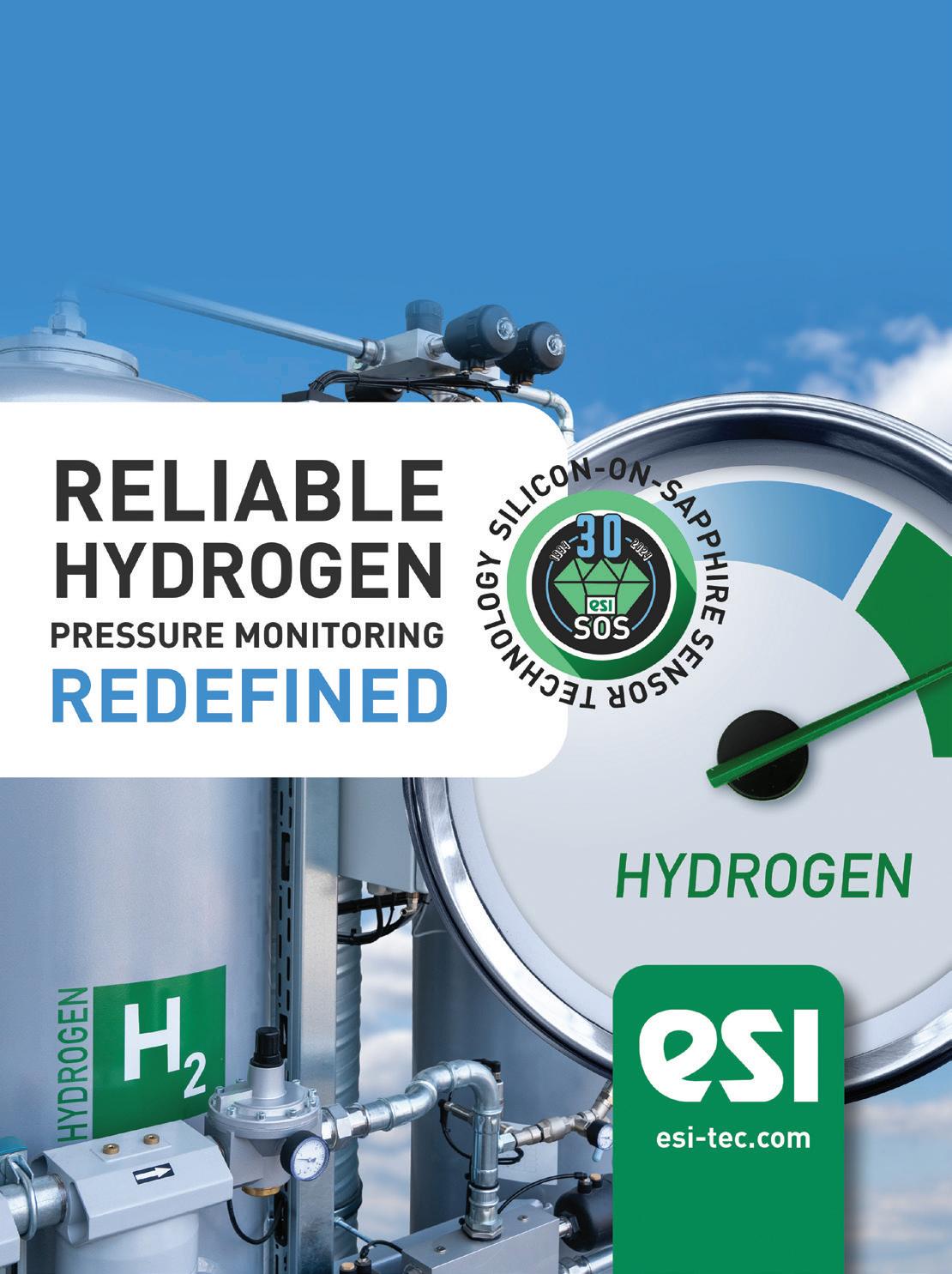
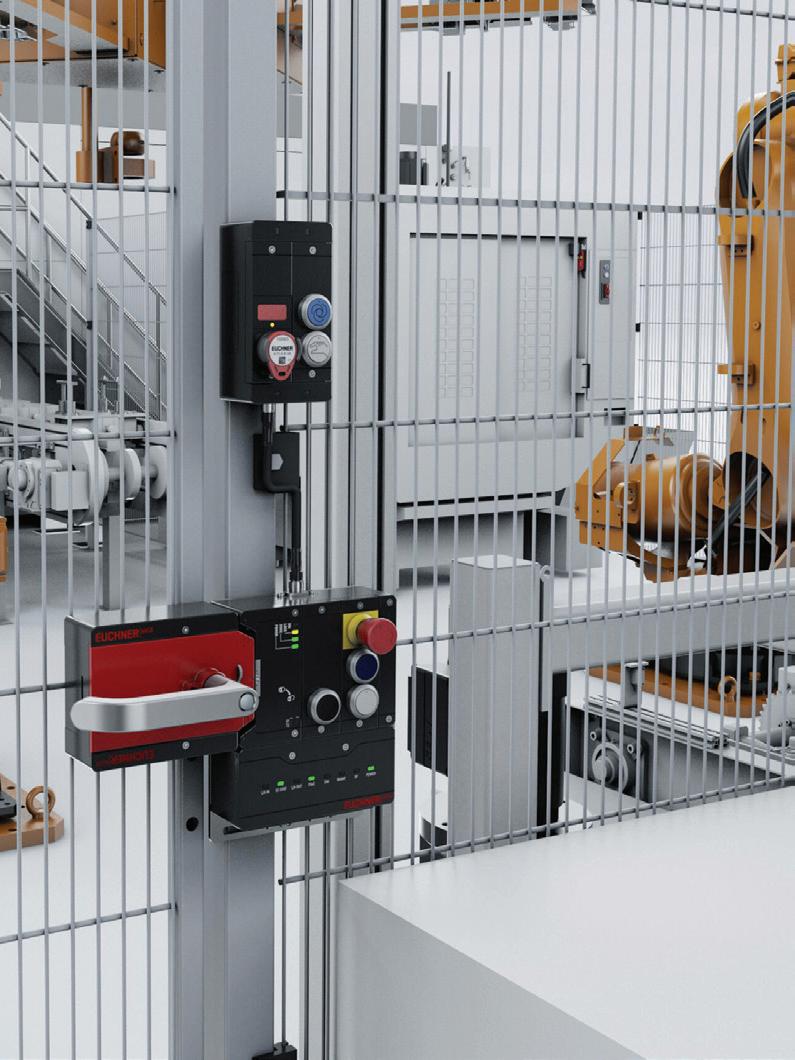

Embracing Innovation: Silicone Expo USA 2024
The world of silicone manufacturing is set to converge at Silicone Expo USA, A premier event that promises to showcase cutting-edge developments and foster crucial industry connections.
As anticipation builds, professionals, innovators, and enthusiasts alike prepare for what is poised to be a landmark gathering in the silicone industry.
Scheduled to take place on September 10 to 12, 2024, in Pittsburgh, PA, Silicone Expo USA serves as a melting pot of ideas and innovations, drawing participants from various sectors, including automotive, healthcare, electronics, and consumer goods. The expo highlights the transformative potential of silicone, an extraordinarily versatile material that plays a critical role in modern technology and everyday products.
Innovation and networking
One of the defining features of Silicone Expo USA is its comprehensive exhibition floor, which will host a multitude of companies demonstrating their latest products and technologies. From raw material suppliers to advanced product manufacturers, the expo provides a platform for the entire silicone supply chain to interact. This interaction is not only beneficial for business development but also crucial for the cross-pollination of ideas that drive innovation.
Attendees can expect to see pioneering advancements in silicone applications, ranging from medical devices that save lives to high-performance automotive components that enhance safety and efficiency. The expo will also feature a variety of interactive displays and live demonstrations, offering a hands-on experience that brings the latest technological breakthroughs to life.
Technical conference
In an exciting development, the details of the much-anticipated technical conference will be revealed in early July. This conference is set to be a highlight of the event, providing an invaluable opportunity for professionals to delve deeper into the scientific and
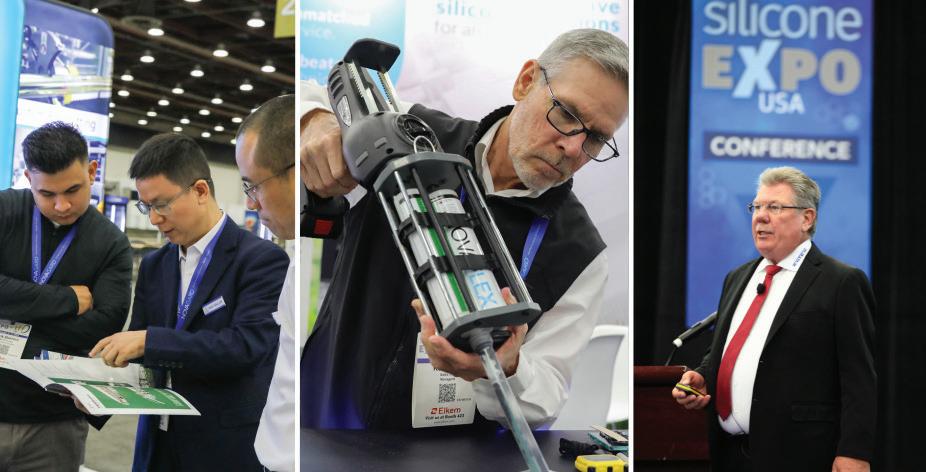
engineering aspects of silicone materials.
The technical conference will gather leading experts from academia, industry, and research institutions to share their insights and findings. Topics are expected to cover a broad spectrum, including advancements in silicone chemistry, processing techniques, and emerging applications. Attendees will gain access to cutting-edge research and practical knowledge that can be applied to improve products and processes in their own organisations.
Sustainability
A key theme at this year’s expo will be sustainability. As industries worldwide grapple with the challenges of environmental responsibility, the silicone sector is no exception. The expo will feature presentations and discussions on sustainable practices, highlighting how silicone products can contribute to a greener future. Innovations in recycling processes, the development of ecofriendly silicone alternatives, and strategies for reducing the environmental impact of silicone manufacturing will be prominent topics. Moreover, the expo will address future
directions in silicone technology. As industries continue to evolve, so too do the demands placed on materials like silicone. Participants will explore how the unique properties of silicone – such as its durability, flexibility, and thermal stability – can be leveraged to meet the needs of tomorrow’s technologies. From the burgeoning field of wearable electronics to advanced medical implants, the potential applications for silicone are vast and varied.
Silicone Expo USA is more than just a trade show; it is a convergence of minds dedicated to advancing the field of silicone technology. For industry professionals, it represents a rare opportunity to gain insights into the latest trends, forge new partnerships, and stay ahead of the curve in a rapidly evolving market.
As the countdown to the expo continues, the announcement of the technical conference details in early July adds an extra layer of excitement. Participants can look forward to an enriching experience that blends practical learning with strategic networking.
silicone-expo.com





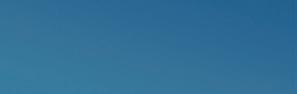




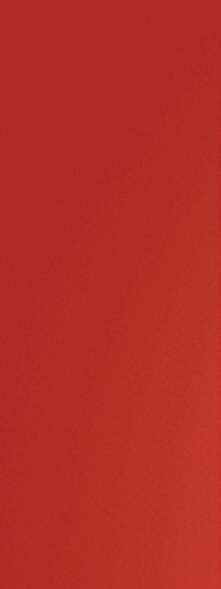
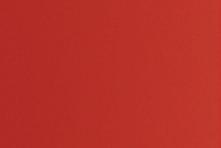


BITO introduces the next-generation LEO AGV
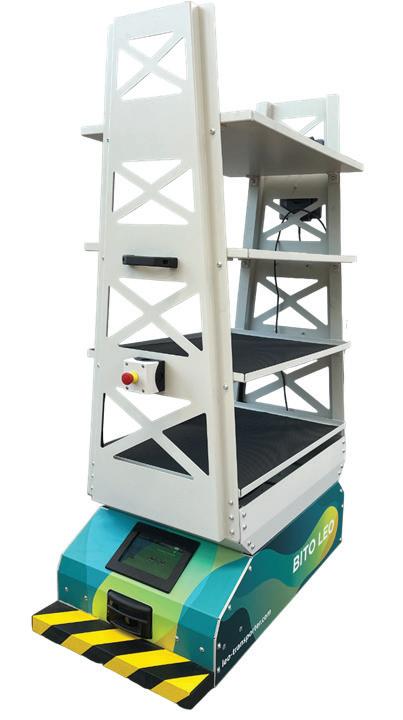
BITO’s new LEO Automated Guided Vehicle (AGV) provides an innovative solution for automating material flow in warehouses, fulfilment centres and factories. Less complex than more expensive AGVs, the new LEO flow and LEO carrier offer productivity advantages over manual handling and conveyor alternatives for transporting bins and containers, with a payback period often in one year or less.
Delivered in a box, all that’s required to get going is to lay a route marked by a 19 mm wide track line with tape or floor painting for the transporters to follow using optical navigation. Instructions are entered on a tablet and markers with printed QR codes guide LEO on destination points and tasks.
Users can implement simple systems themselves in just a few days, without the need of IT support. And they can be quickly and easily adapted, enabling rapid reaction to seasonal fluctuations and warehouse reorganisations. www.bito.com
Denso system repairs damaged factory coating at London railway terminal
Abitumen tape wrap system from Winn & Coales (Denso) Ltd was utilised for the repair of damaged pipework at the new HS2 terminus at London Euston train station.

Following damage to the existing factory coating, corrosion had already begun to inflict damage upon the pipe and had propagated underneath the coating itself, causing it to delaminate. To eliminate further damage, the Denso Bitumen Tape Wrap System was applied to not only protect the pipe from the effects of further corrosion, but to provide a large degree of mechanical protection too.
Winn & Coales (Denso) Ltd is a leading manufacturer and supplier of corrosion prevention and sealing systems. The bitumen tape wrap system supplied for the project was comprised of a bitumen-based primer (Denso Primer D), a heavy-duty PVC-backed bitumen tape (Densoclad 70 Tape), and a protective outerwrap (Denso Glass Outerwrap). The protective outerwrap offers exceptional mechanical and impact strength for buried pipes exposed to aggressive backfill conditions. Once applied and fully cured, the whole system provides a long-term protective coating that is ready for immediate service.
www.denso.net
Battery-powered vibration sensor
Ifm has introduced the VWV series of batterypowered vibration sensors. This advanced sensor series is poised to transform machine monitoring with its stateof-the-art features and seamless integration capabilities.
The VWV vibration sensor is designed to deliver comprehensive vibration and temperature monitoring, even in hard-to-reach spots, ensuring peak machine performance and proactive maintenance. Boasting a wireless design and intelligent mesh topology for efficient data transmission, the VWV sensor offers swift integration and reliable communication, making it a perfect fit for a diverse range of industrial applications.

Key features and benefits include measurement axes VWV001 (1 axis) and VWV002 (3 axes), measuring ranges for vibration (-16 to 16g) and vibration velocity (0 to 25mm/s), a frequency range from 10 to 1000Hz, an ambient temperature range of -30 to 80°C, and robustness and durability thanks to an IP68 rating.
The VWV sensor enables early detection of potential machine issues. Leveraging wireless technology and a long-lasting battery, the VWV sensor ensures uninterrupted monitoring for a minimum of four years, reducing downtime whilst maximising operational efficiency. ifm.com

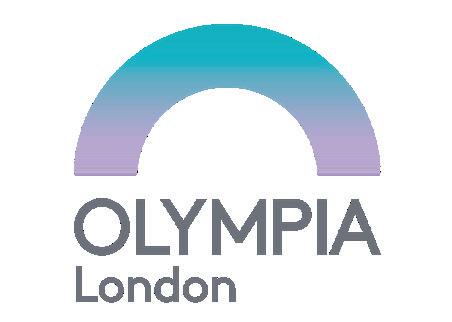


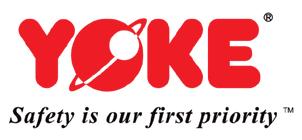
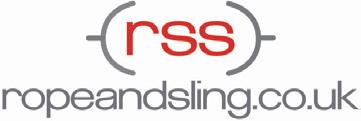
CONNECTIONS
3D Print Manufacturing
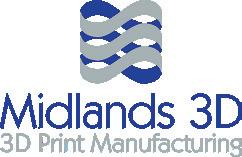
Midlands 3D Printing
T: 01785 594389
E: sales@midlands3d.com
W: www.midlands3d.com
Anti Vibration Products, Mounts & Bushes

Fibet Rubber Bonding (UK) Ltd
T: 01282 878200
E: sales@fibet.co.uk
W: www.fibet.co.uk
Connectors & Cabling Solutions
CEMBRE Ltd
T: 01675 470 440
E: sales@cembre.co.uk
W: www.cembre.com/en
Drives, Motors & Gears
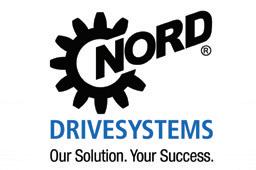
Flow Meters

Nord T: 01235 534404
E: GB-sales@nord.com
W: www.nord.com
Machine Safety
Schmersal UK Ltd
T: 01684 571980
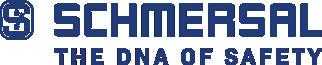
E: uksupport@schmersal.com
W: www.schmersal.co.uk
Marking Solutions
T-Mark T: 0330 153 8320
E: sales@t-mark.co.uk W: www.t-mark.co.uk
Pipework Systems
Jacob UK Ltd
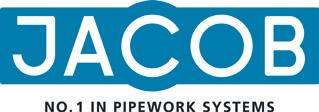
T: 01694 722841
E: sales@jacob-uk.com
W: www.jacob-group.com/uk
Pressure Measurement Specialists
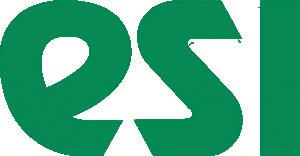
Titan Enterprises Ltd
T: +44 (0)1935 812790
E: sales@flowmeters.co.uk
W: www.flowmeters.co.uk
High Shear Mixing Equipment
Silverson Machines Ltd
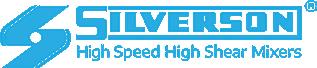
T: +44 (0)1494 786331
E: sales@silverson.co.uk
W: www.silverson.co.uk
Industrial Communications
Brainboxes

T: + 44 (0) 151 220 2500
E: sales@brainboxes.com
W: www.brainboxes.com
Intoware

T: 0115 977 8969
E: hello@intoware.com
W: www.intoware.com
Industrial Fans
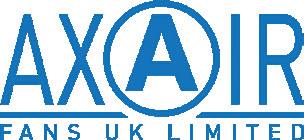
Axair Fans UK Limited
T: 01782 349 430
E: sales@axair-fans.co.uk
W: www.axair-fans.co.uk
ESI Technology Ltd
T: +44 (0)1978262255
E: sales@esi-tec.com
W: www.esi-tec.com
Robotics & Automation
KUKA Robotics UK Ltd

T: 0121 505 9970
E: sales.uk@kuka.com
W: www.kuka.com
Sensors
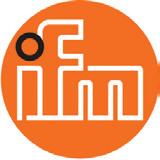
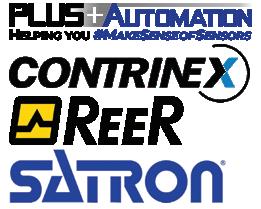
IFM Electronic
T: 020 8213-0000
E: enquiry.gb@ifm.com
W: www.ifm.com
PLUS Automation Ltd
T: 0121 58 222 58
E: Sales@PLUSAutomation.co.uk
W: www.PLUSAutomation.co.uk
Storage Solutions
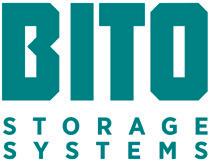
BITO Storage Systems Ltd.
T: 02476 388 852
E: Info.uk@bito.com
W: www.bito.com
Test & Inspection
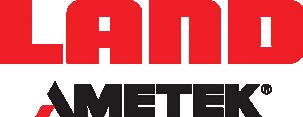
AMETEK Land (Land Instruments International)
T: +44 1246 417691
E: land.enquiry@ametek.com
W: www.ametek-land.com
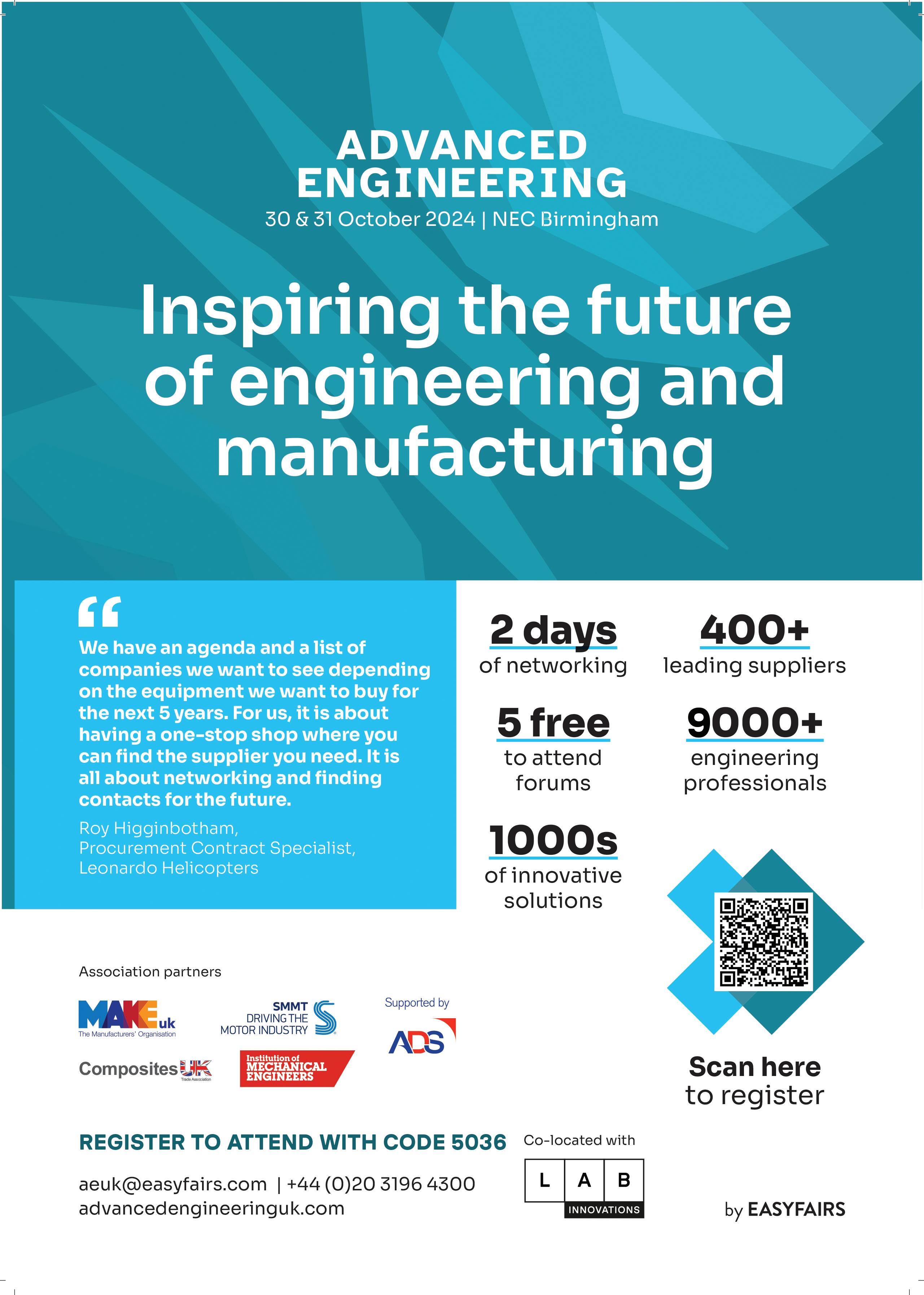
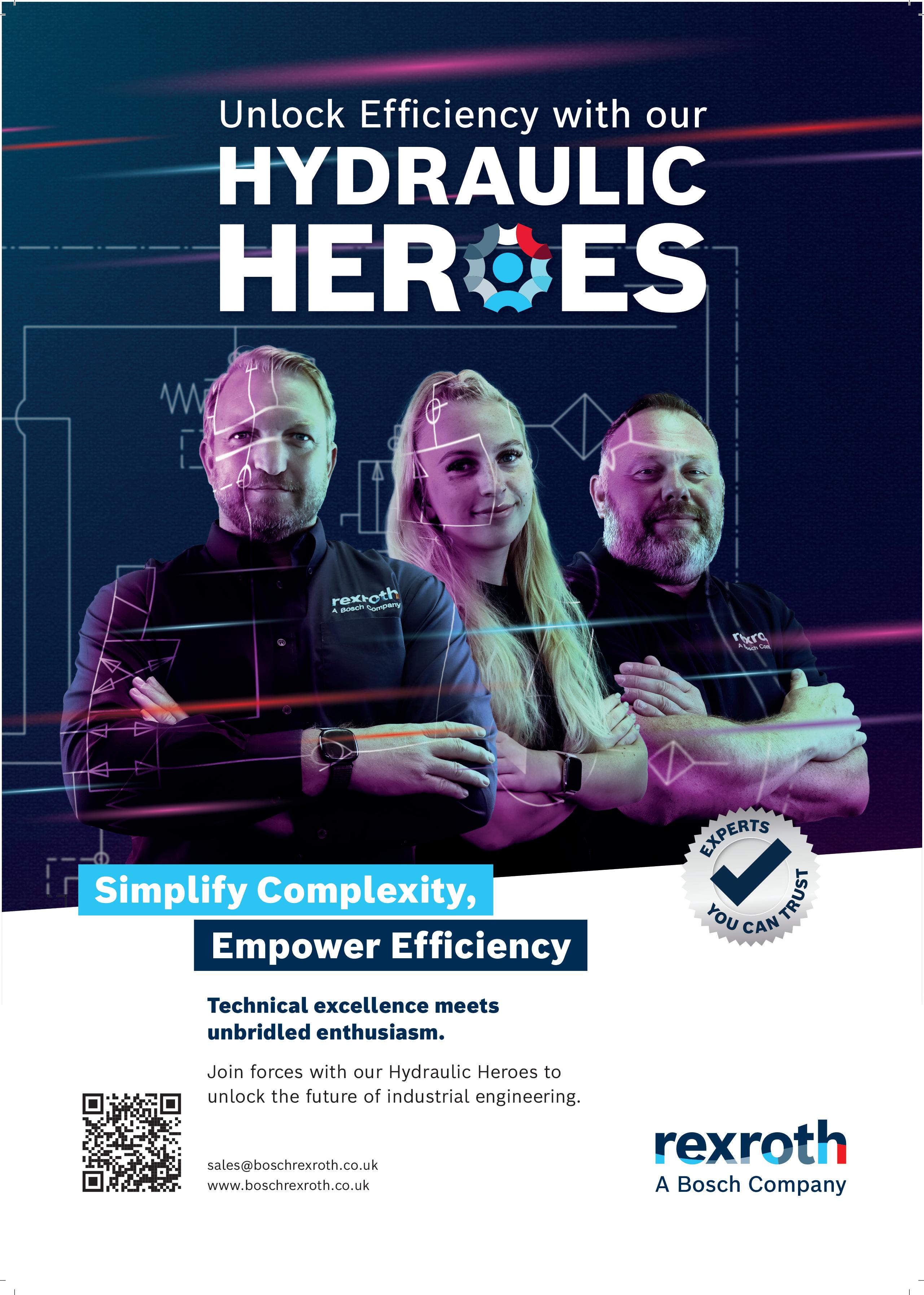