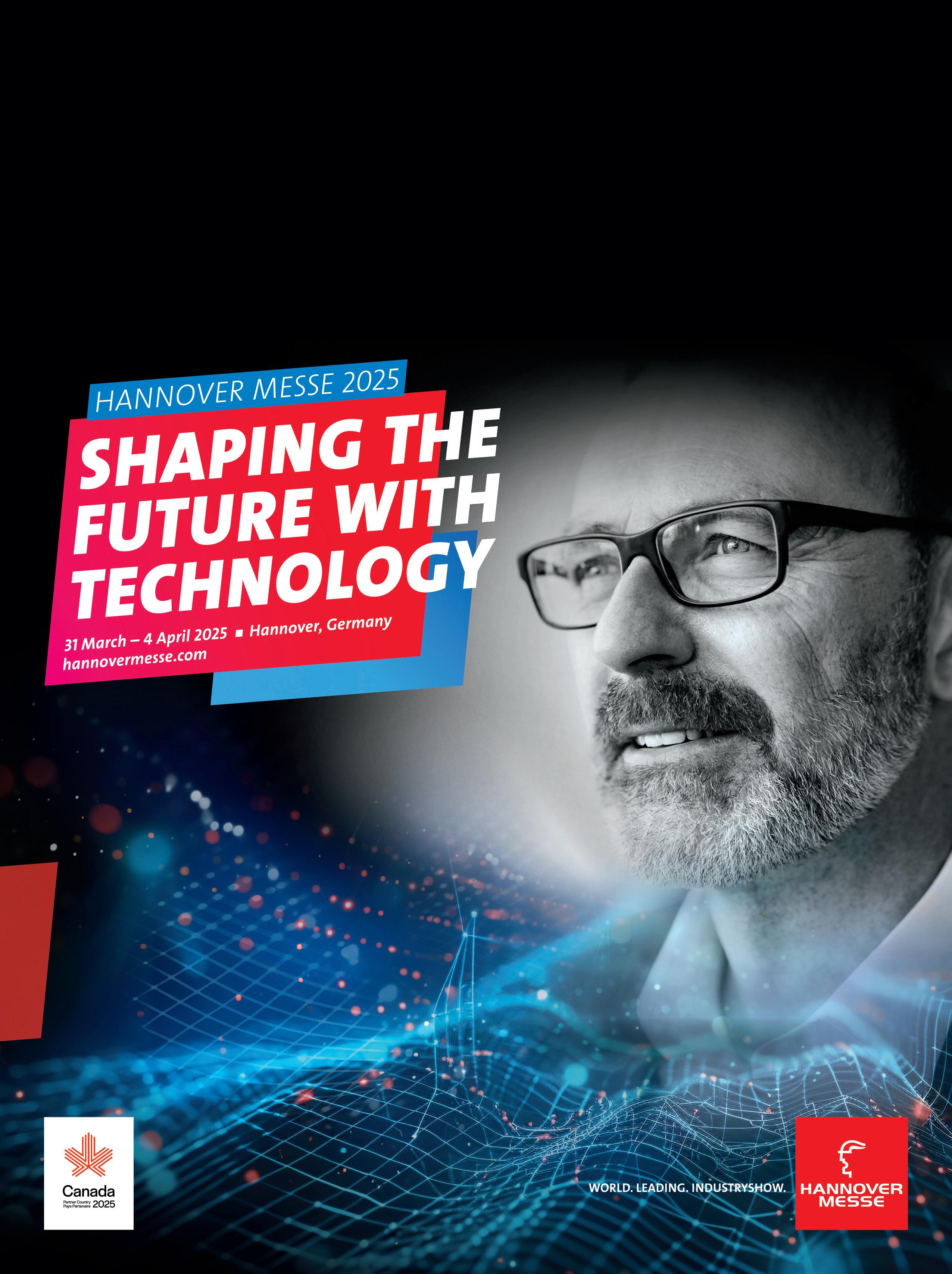
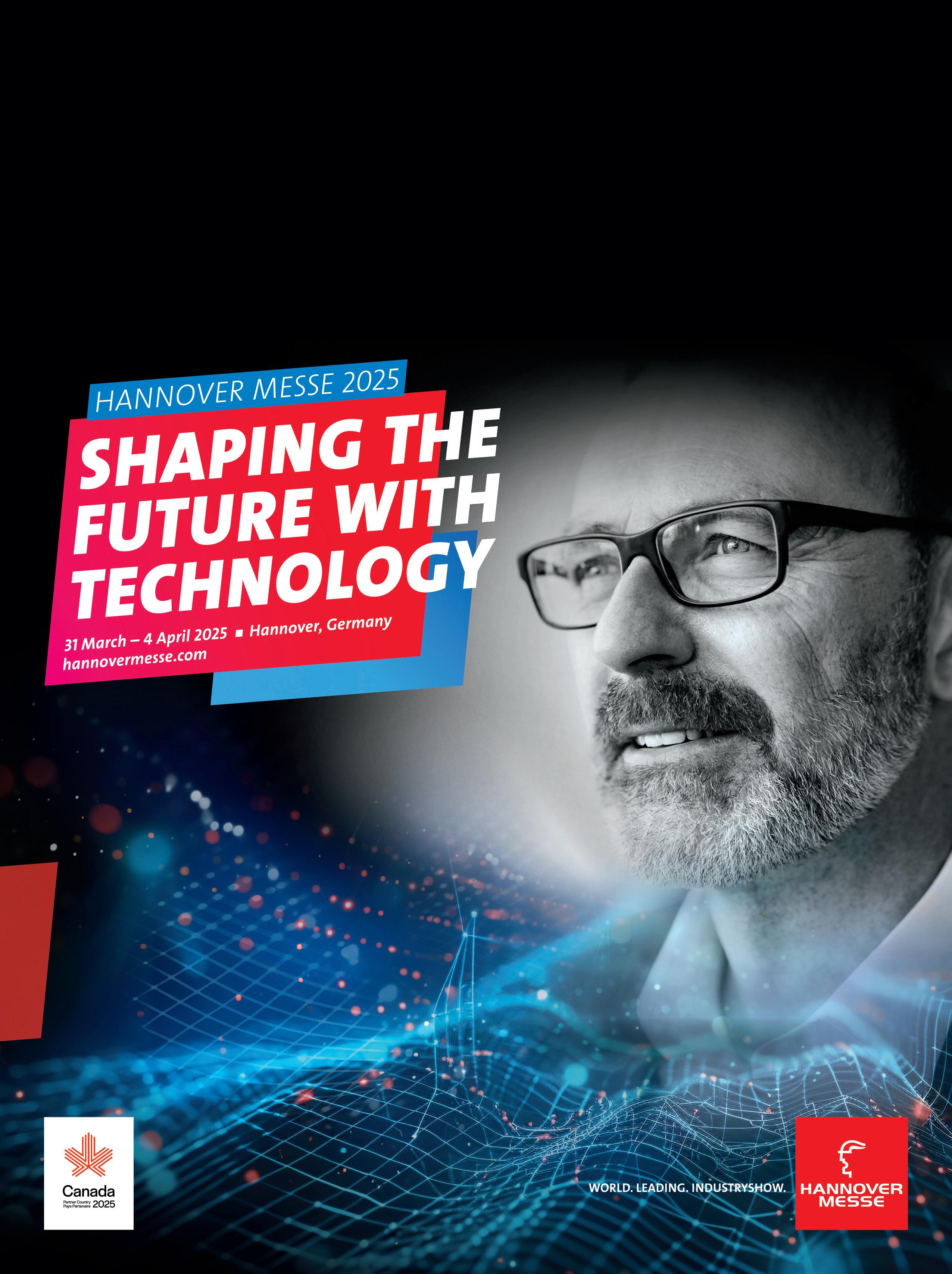
Anomaly Detector
Powered by GoMax and AI
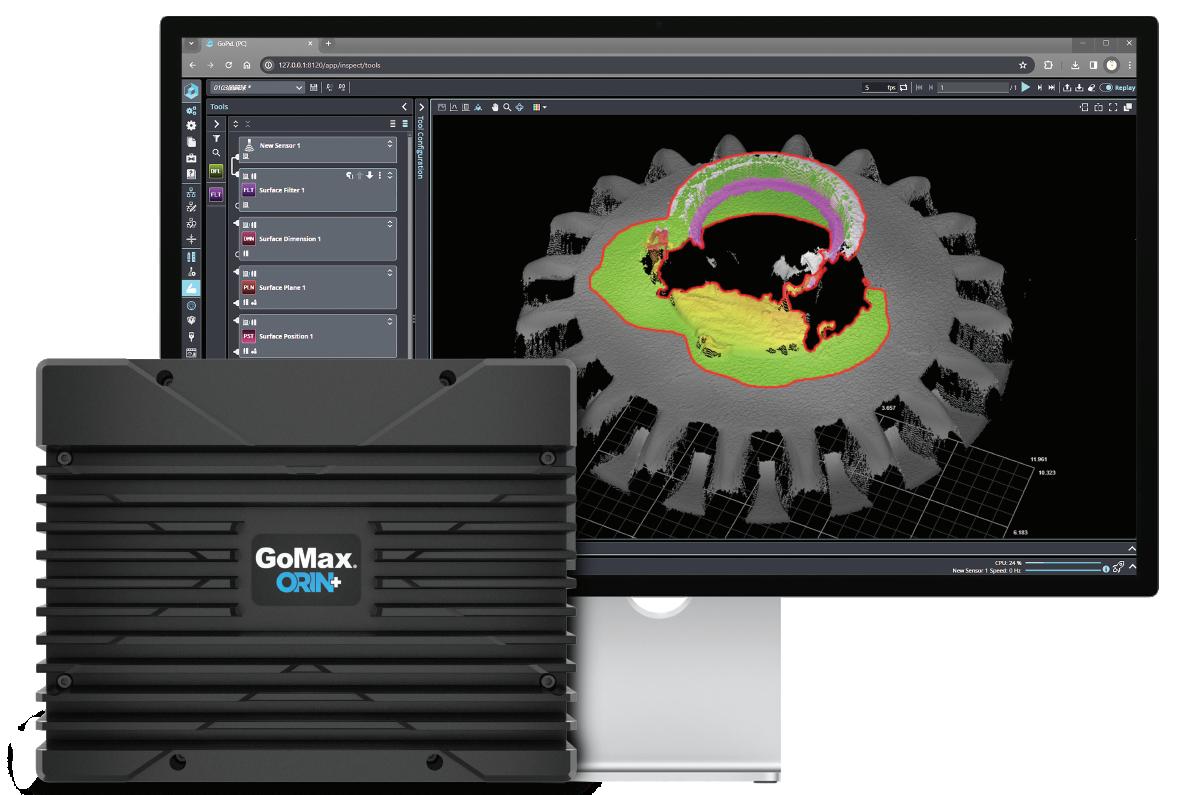
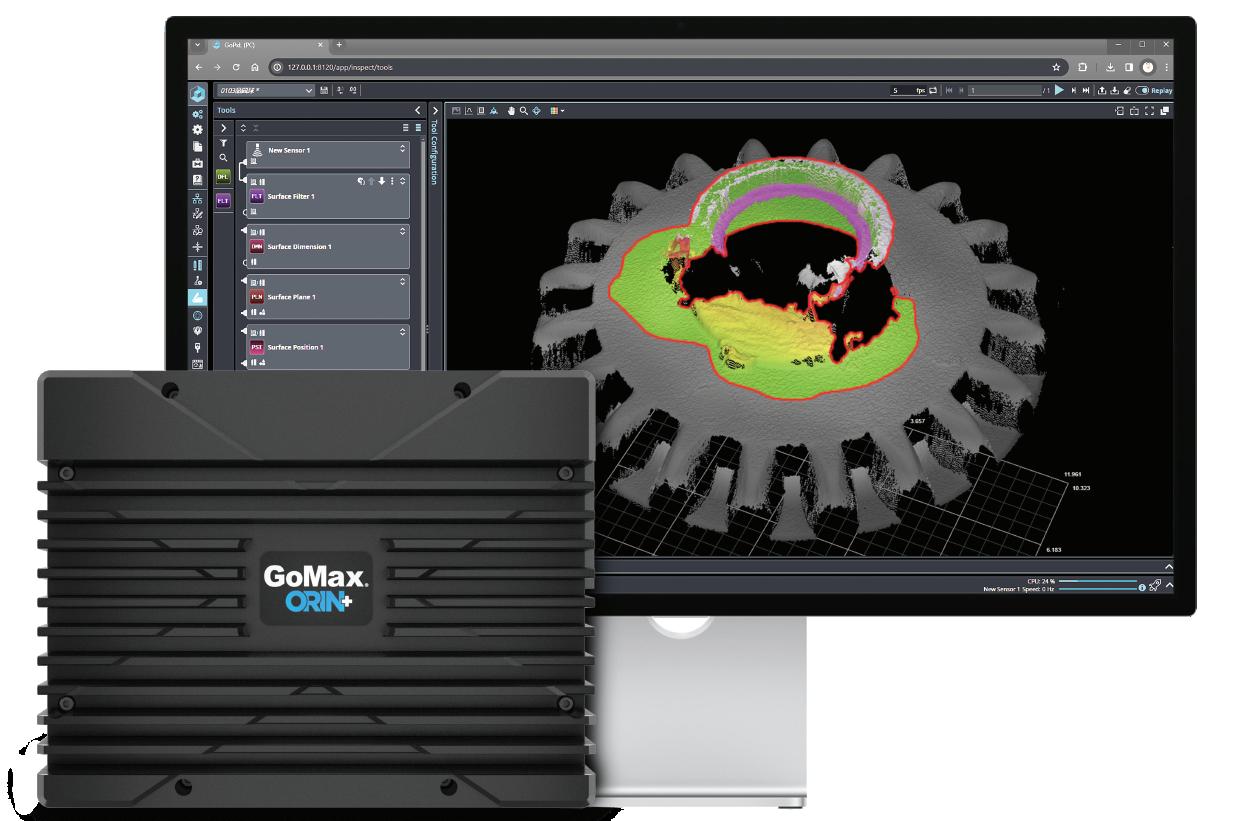
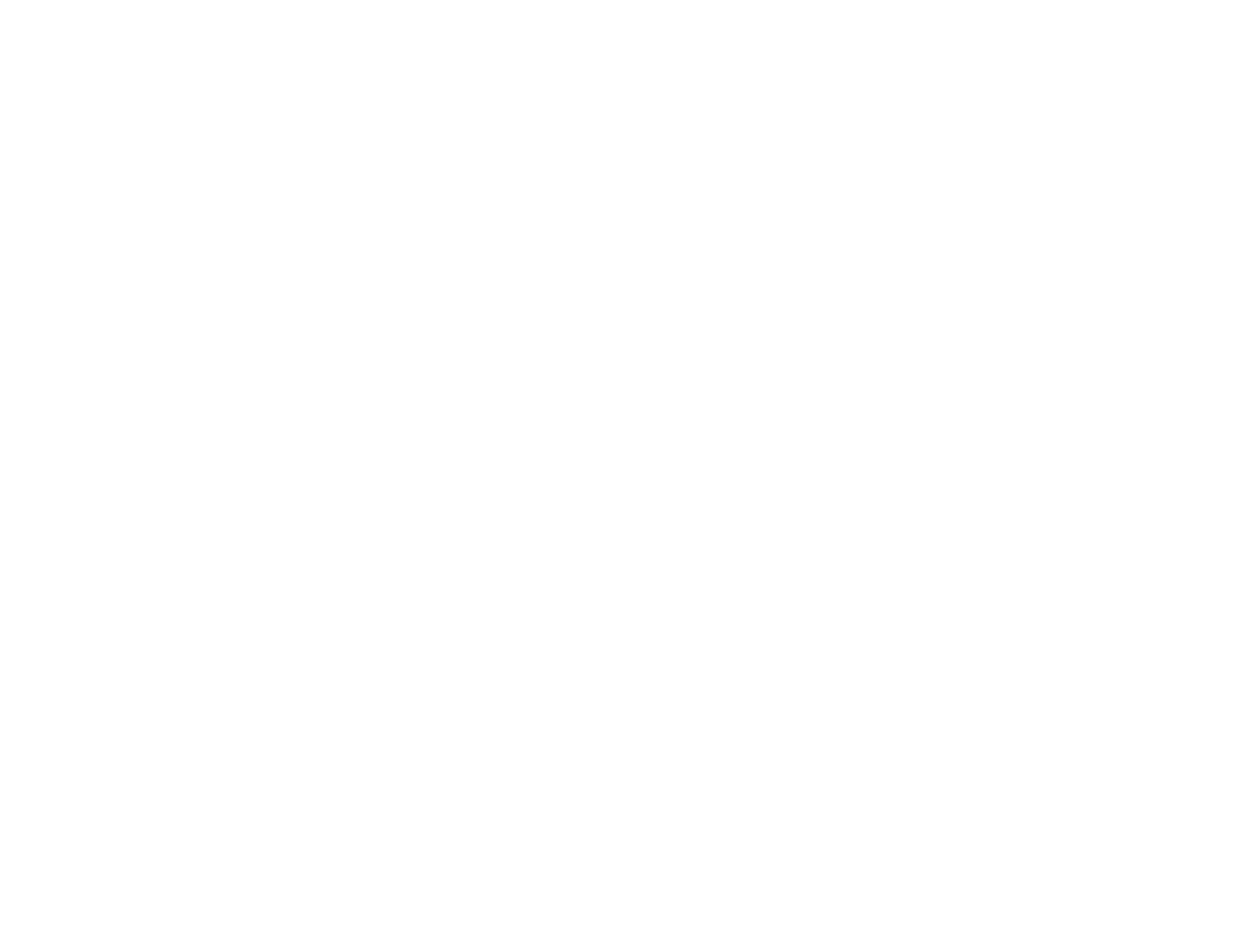
Deploy AI-Powered Anomaly Detection into Your Production Line.
GoPxL Anomaly Detector leverages traditional and AI-based tools in GoPxL to provide powerful 2D/3D defect detection for challenging applications in the production of parts for the automotive, food, building material, tire, and many other industries. Anomaly Detector runs on all Gocator Line Profiler, Snapshot, and Line Confocal Sensors when accelerated with GoMax.
Example Applications
Part Inspection
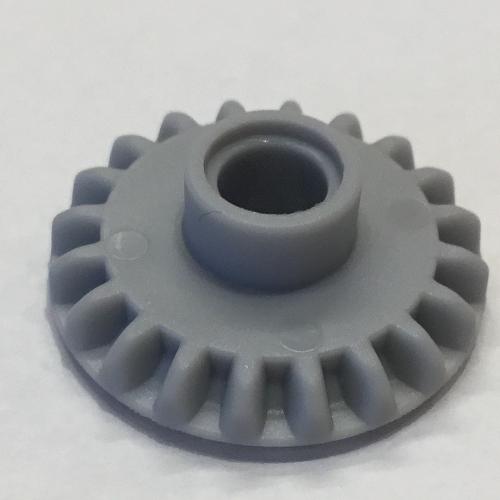
Surface Inspection
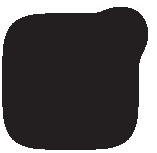
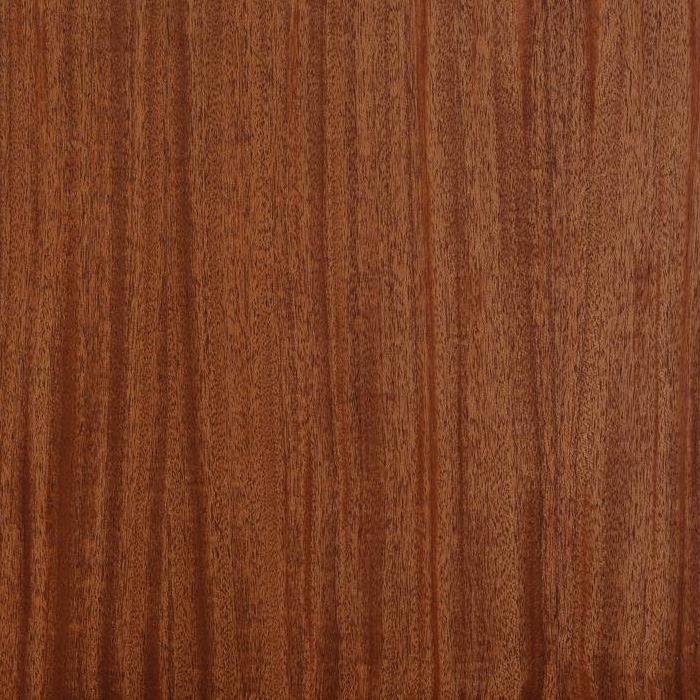
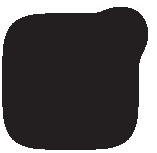
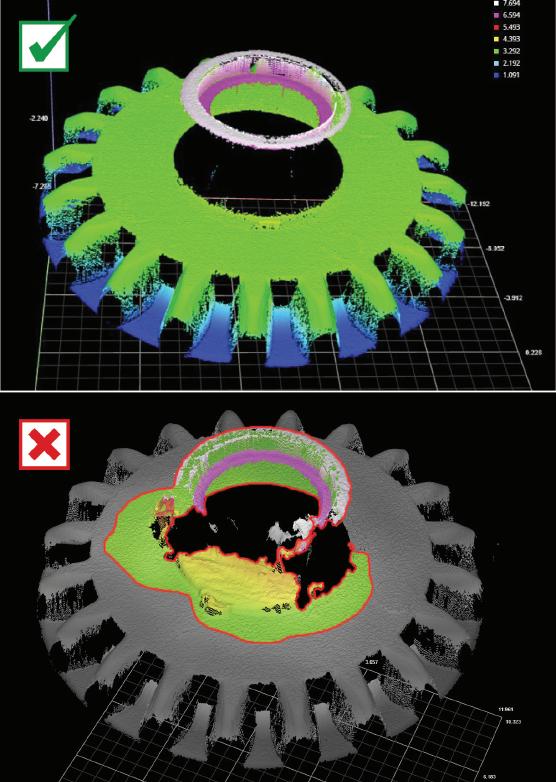
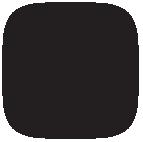
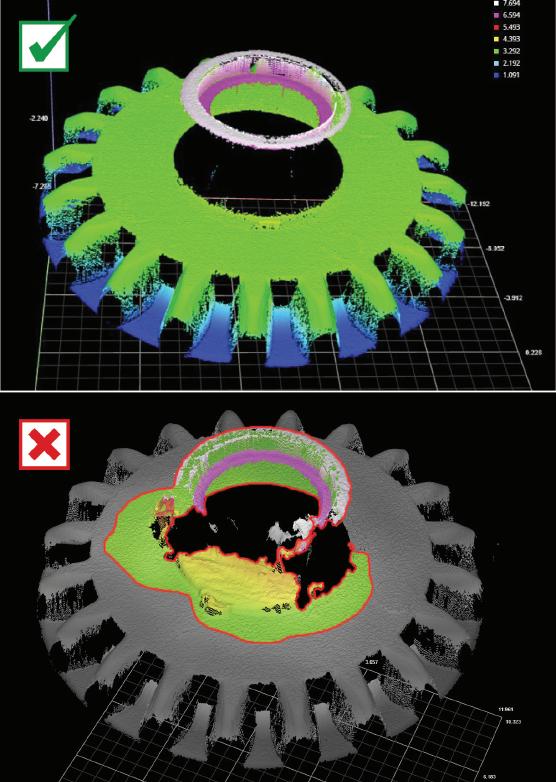
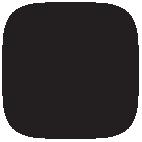
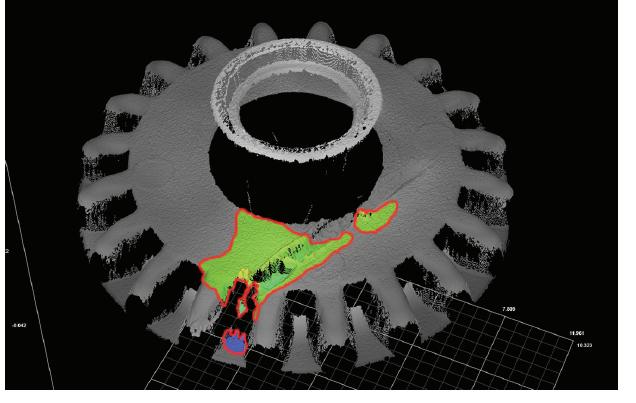
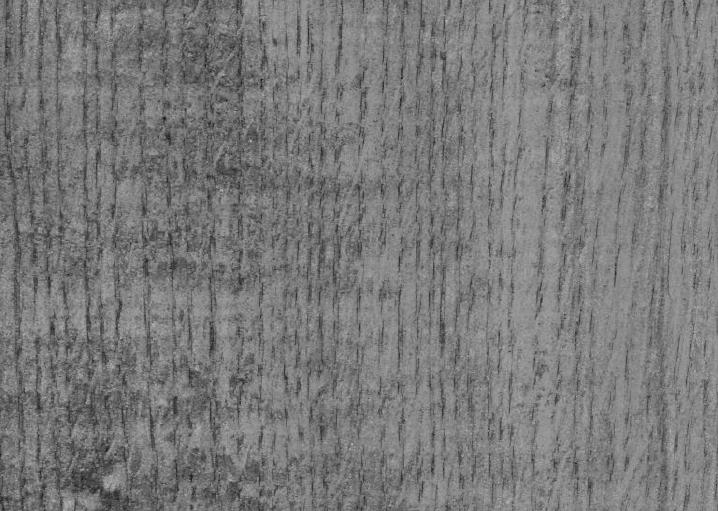

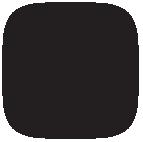
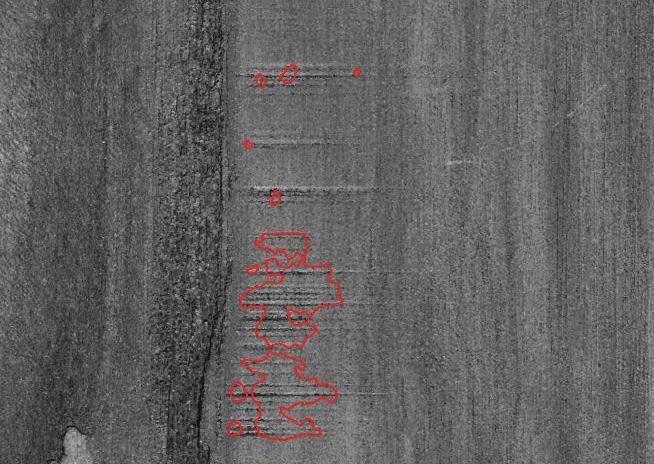
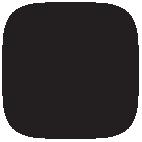
Key Benefits
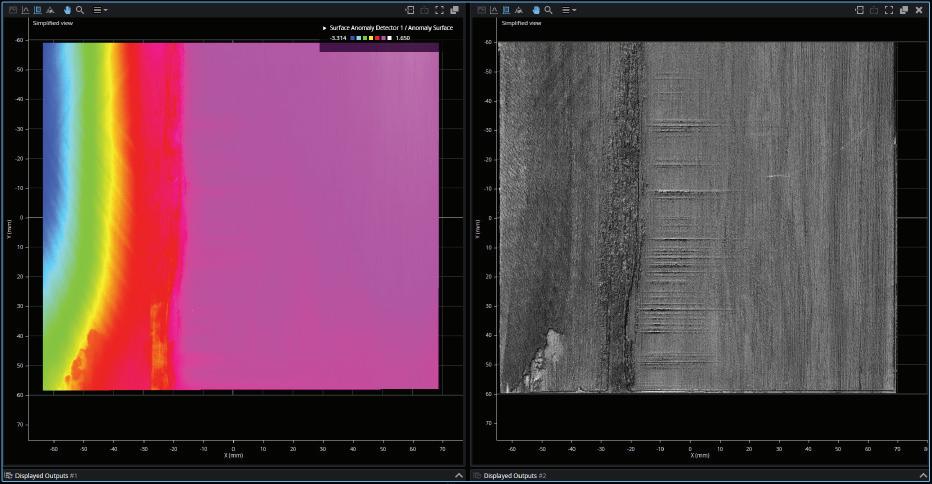
Train on 2D intensity or 3D height map data
Scan parts with intensity and surface data, select the best option during training, and use a 3D visualizer to enhance labeling accuracy.
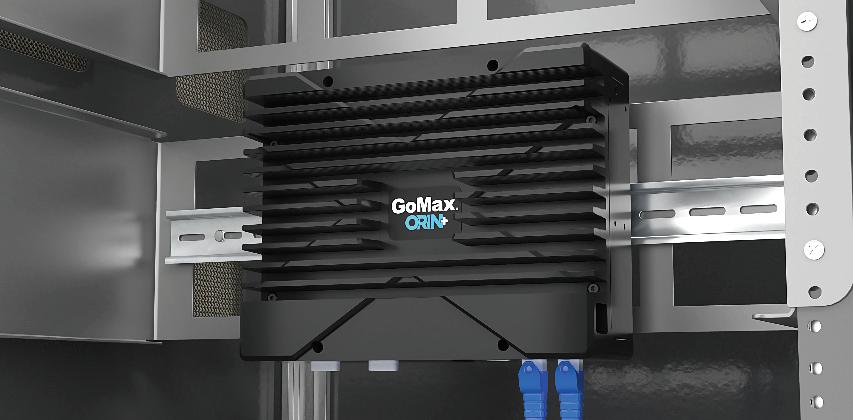
Train on the production line
Train data directly on GoMax to save time, cost, and security risks, with seamless model updates using the same license.
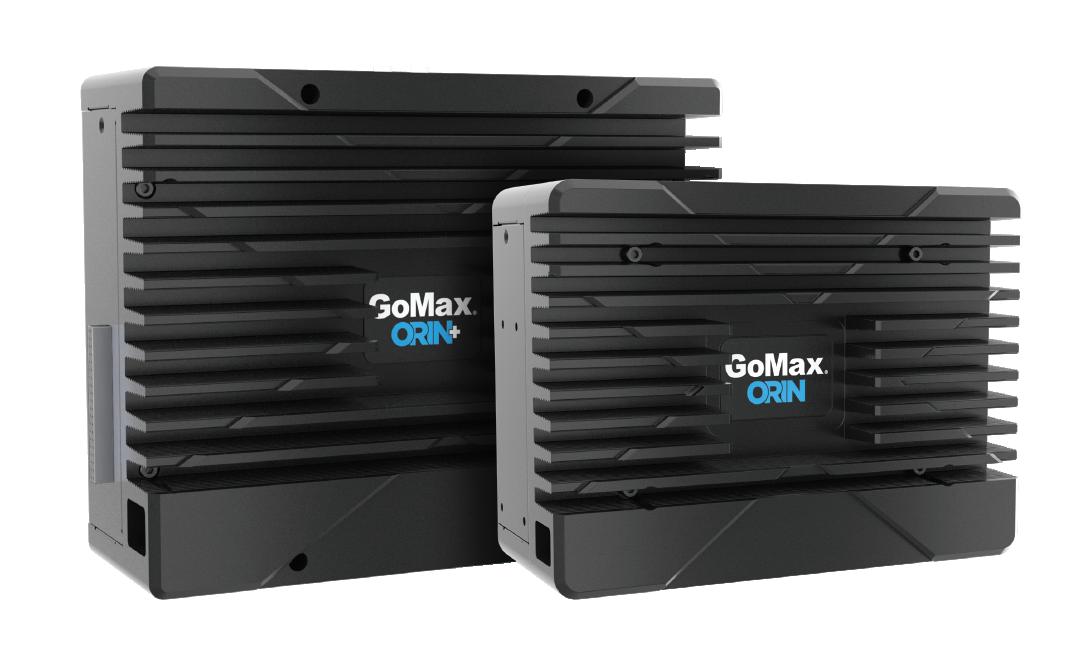
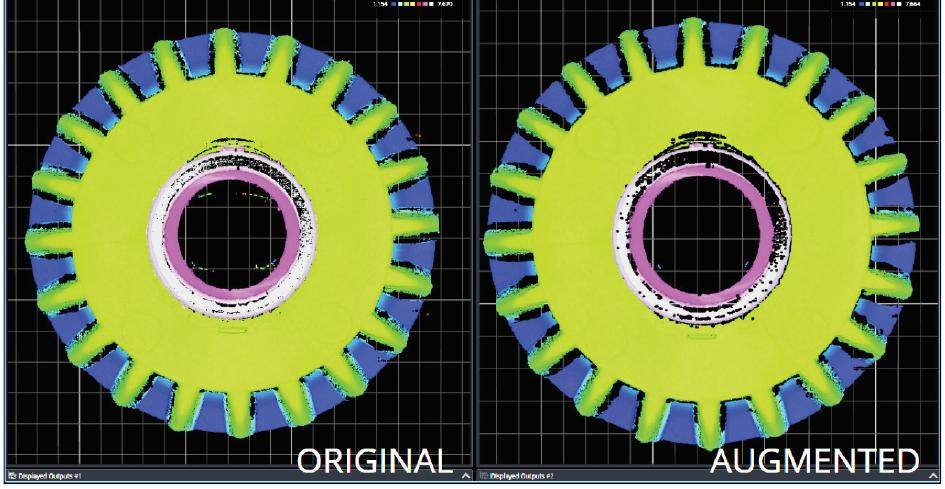
Generate synthetic and augmented data
Reduce training images by integrating synthetic defects and augmented frames to boost model performance.
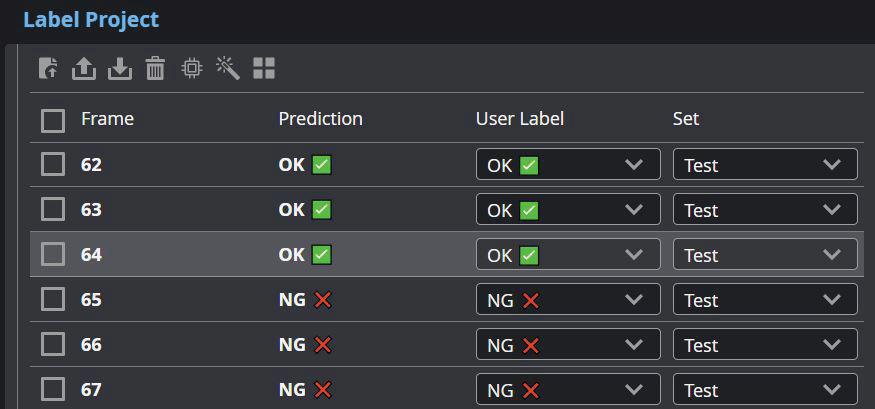
Use Prediction to label new production data
Use assisted labeling after initial training for fast and easy iteration.
GoMax ORIN/ORIN+ SMART 3D VISION ACCELERATORS
Users train and deploy the Anomaly Detector solution all onboard GoMax ORIN/ORIN+ without relying on cloud or additional GPU for initial and subsequent model training.
Editor
Oliver Batt oliver@cimltd.co.uk
Publication Manager
James Burke jb@cimltd.co.uk 01795 509105
Account Manager
Jim Bearden jim@cimltd.co.uk 01795 509105
Design & Production Grant Waters grant@cimltd.co.uk
James Taylor james@cimltd.co.uk
Administration Manager
Natalie Woollin admin@cimltd.co.uk 01795 509103
Credit Facilities Manager
Gwen Lee creditcontrol@cimltd.co.uk 01795 509103
Marketing Manager
Lucas Payne lucas@cimltd.co.uk
Sales Director
Tom Woollin tom@cimltd.co.uk
Chief Executive
John Denning
© 2025 Cogent Multimedia Limited,1st Floor, Saphir House, 5 Jubilee Way, Faversham, Kent, ME13 8GD. No part of this magazine may be reproduced or stored in a retrieval system or transmitted in any form – electronic, mechanical or physical – without express prior permission and written consent of the publisher. Contributions are invited and when not accepted will be returned only if accompanied by a fully stamped and addressed envelope. Manuscripts should be typewritten. No responsibility can be taken for drawings, photographs or literary contributions during transmission or in the editor’s hands. In the absence of an agreement the copyright of all contributions, literary, photographic or artistic, belongs to Cogent Multimedia Limited. The publisher accepts no responsibility in respect of advertisements appearing in the magazine and the opinions expressed do not necessarily represent the views of the publisher. The publisher cannot accept liability for any loss arising from the late appearance or non-publication of any advertisement.
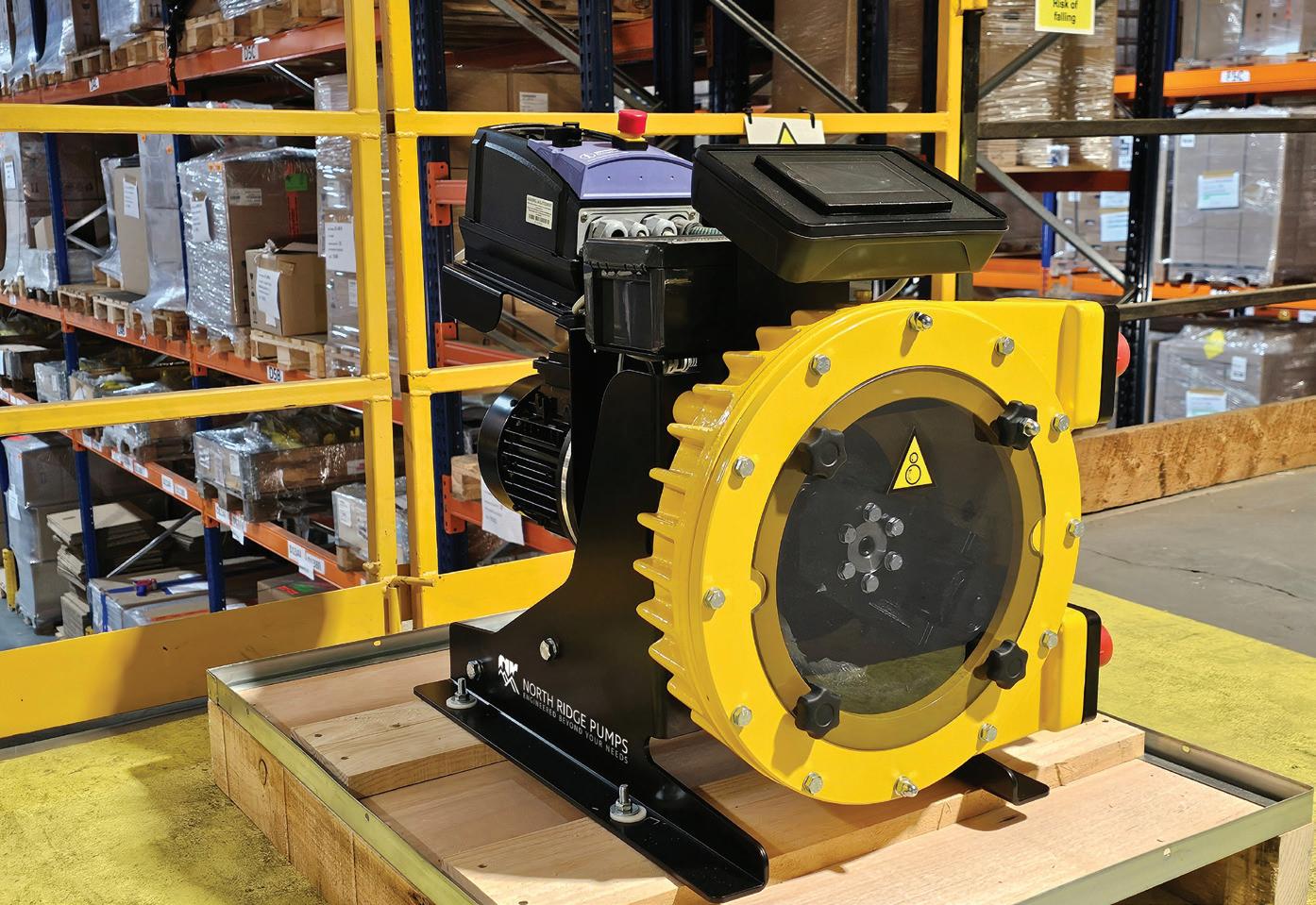
March 2025
Welcome to the March issue of MEPCA magazine. In the past few weeks, I have experienced some firsts; I attended Southern Manufacturing & Electronics for the first time, a ram-packed show with an overwhelming concentration of fantastic companies, at which I took part in my first video interview, covering a Vision Engineering product launch. Video content is a new one for me (and somewhat outside of my comfort zone), and also new to MEPCA, but we will endeavour to bring you more very soon. Watch this space. Comfort zones are meant to be stepped out from.
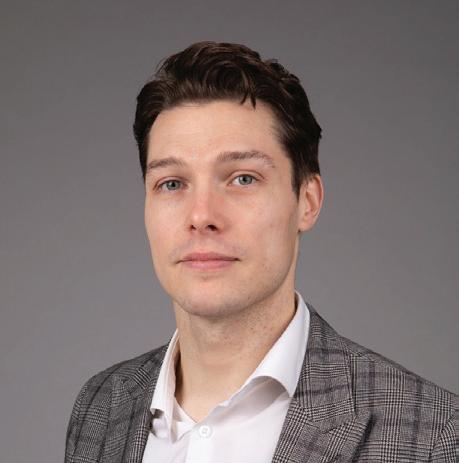
On to what we have in store for you in this issue. In this month’s Cover Story, I attended the HANNOVER MESSE Preview press event to bring you details of what to expect from this remarkable show. Delving further into this issue, you’ll find our extensive Food Processing Focus, in which we look at trends impacting the industry in 2025 and examine the efforts towards circular economy in package recycling. Also included in the Focus, Silverson Machines introduce its new mixing guide, North Ridge Pumps explains why peristaltic pumps are favoured by the industry, MRPeasy highlights the importance of tracking actual costs, and much more.
Elsewhere in the issue, we have expert opinion pieces from Hunter Selection, BPMA and GAMBICA; Murrelektronik Canada takes an optimistic look at advances in machine building; we look at how machines ‘see’ with Axiomtek UK; Titan Enterprises shares its expert insight on liquid flow measurement; we announce our March Manufacturing Champion, and introduce you to the latest industry news and solutions.
I hope you enjoy this issue.
@Mepca-magazine
To subscribe to MEPCA visit our website www.mepca-engineering.com or scan the QR code.
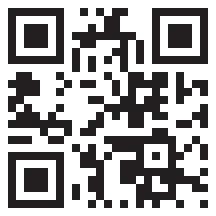
Oliver Batt, Editor
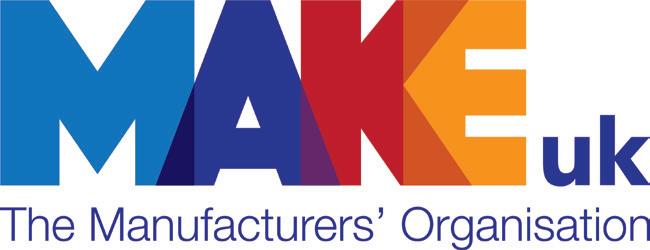

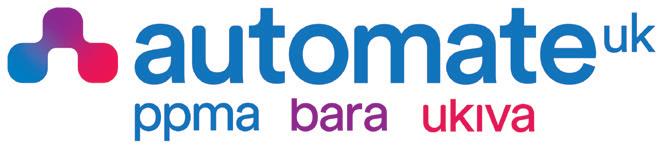
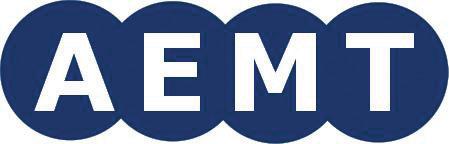
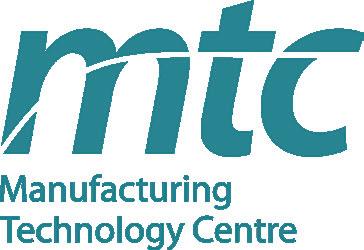
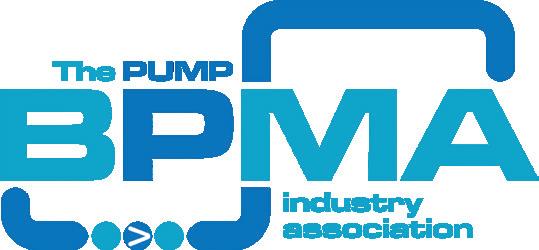
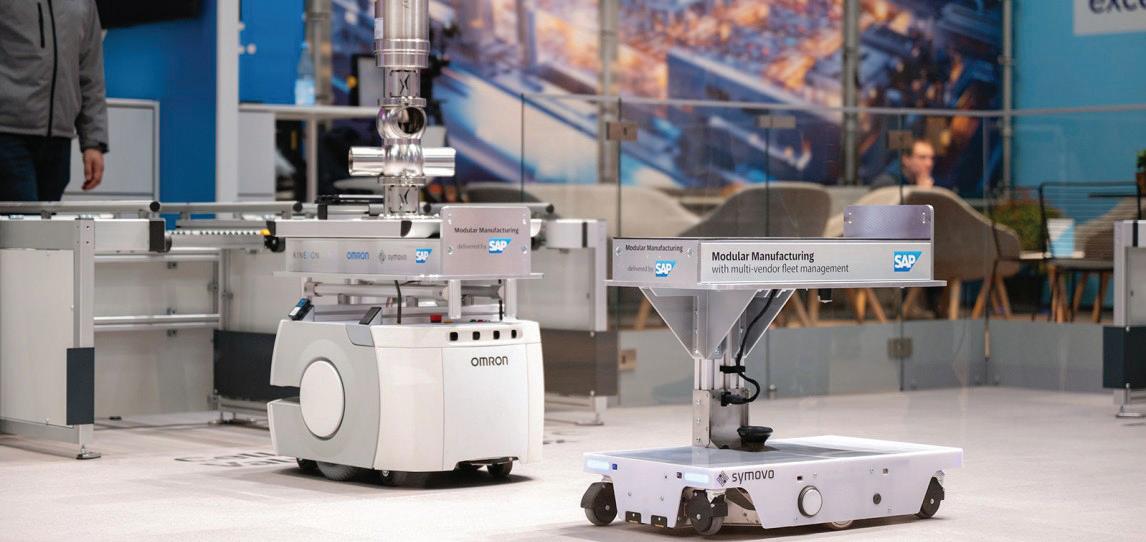
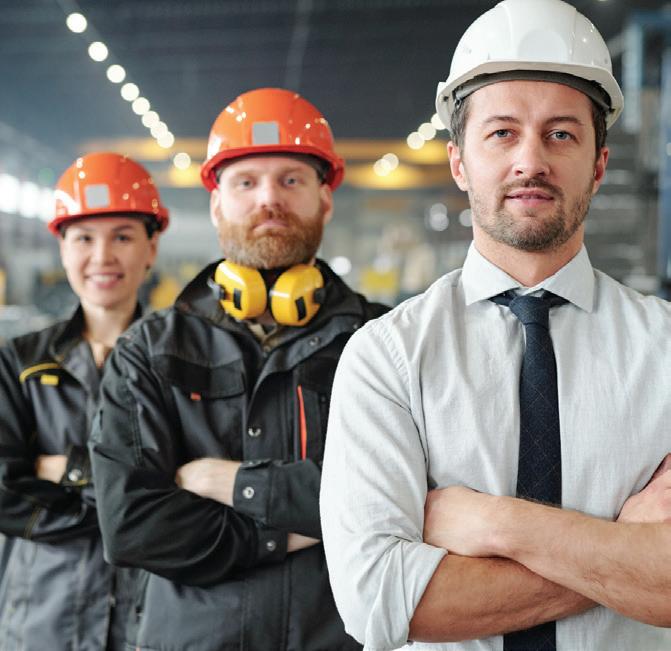
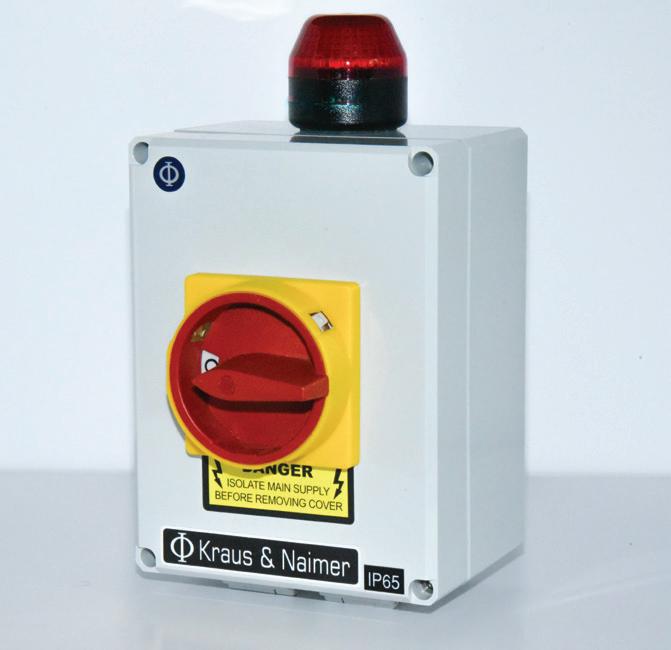
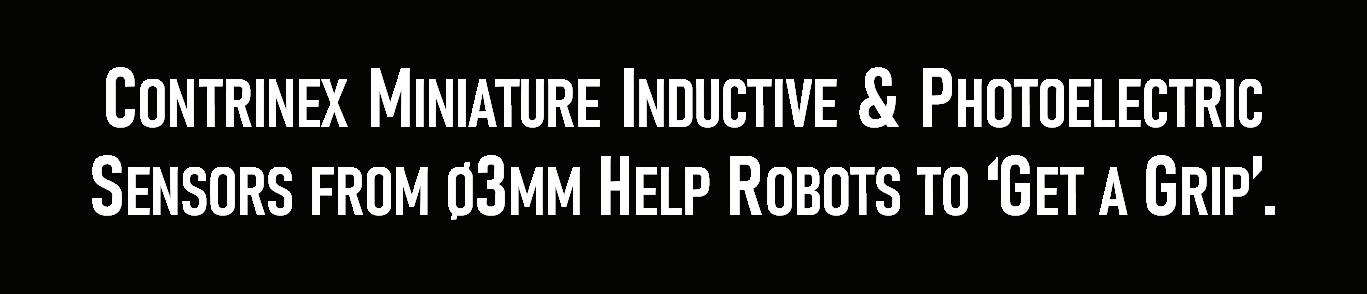
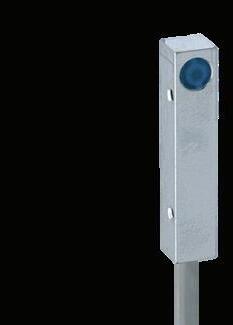
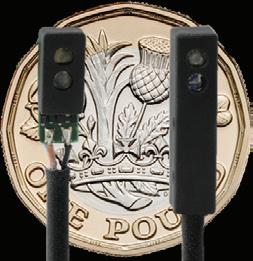

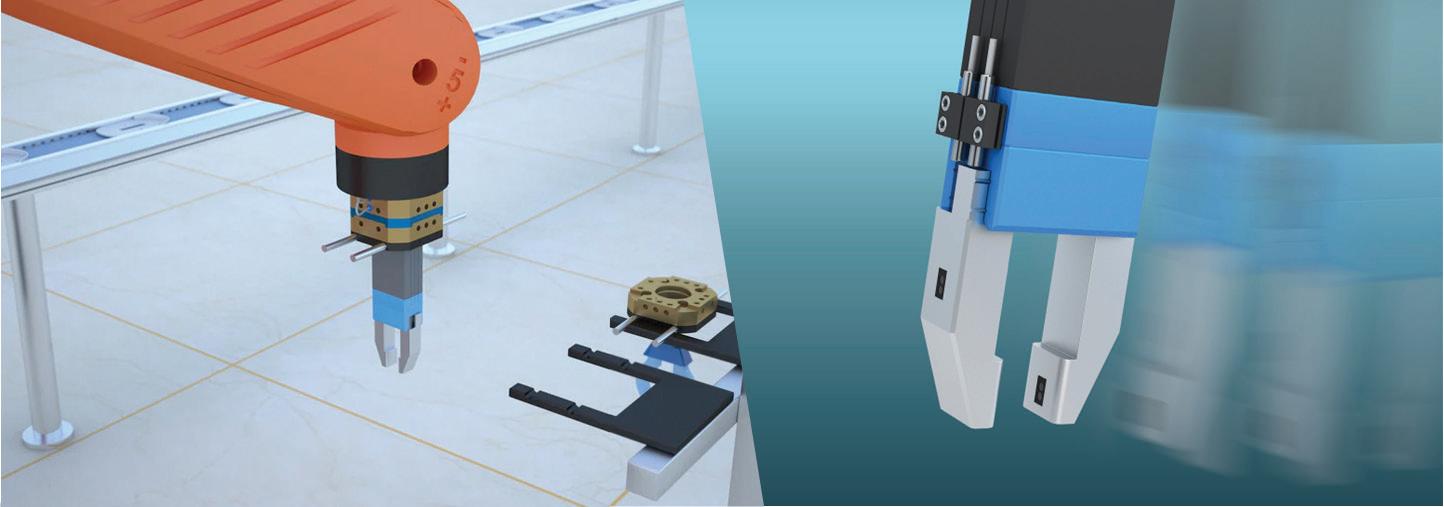
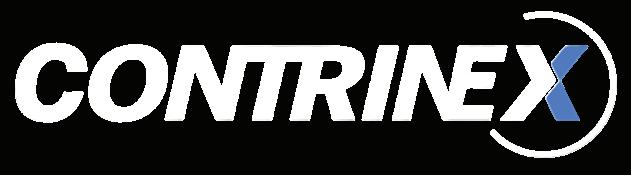



‘HALO’ 4K Digital Inspection Microscope
Vision Engineering, a UK based manufacturer of ergonomic microscopy and digital 3D visualisation technology unveils the EVO Cam HALO, a new 4K digital microscope that redefines the standard for clarity, precision and consistency in inspection and measurement tasks.
Suitable for a wide range of inspection applications,
EVO Cam
HALO combines stunning 4K image quality with advanced, adaptive illumination, and new intelligent software, empowering users to capture the most challenging details with unparalleled accuracy.
HALO’s key features include 4K resolution, which reveals previously obscured details with remarkable clarity, ensuring nothing escapes the user’s view. A super-wide Dynamic Range ensures the user captures images with exceptional brightness and contrast, even in challenging lighting conditions. Additionally available with HALO is a new enhanced Illumination package, including a quadrant light, panel light and white/UV light, to optimise illumination for a variety of inspection needs.
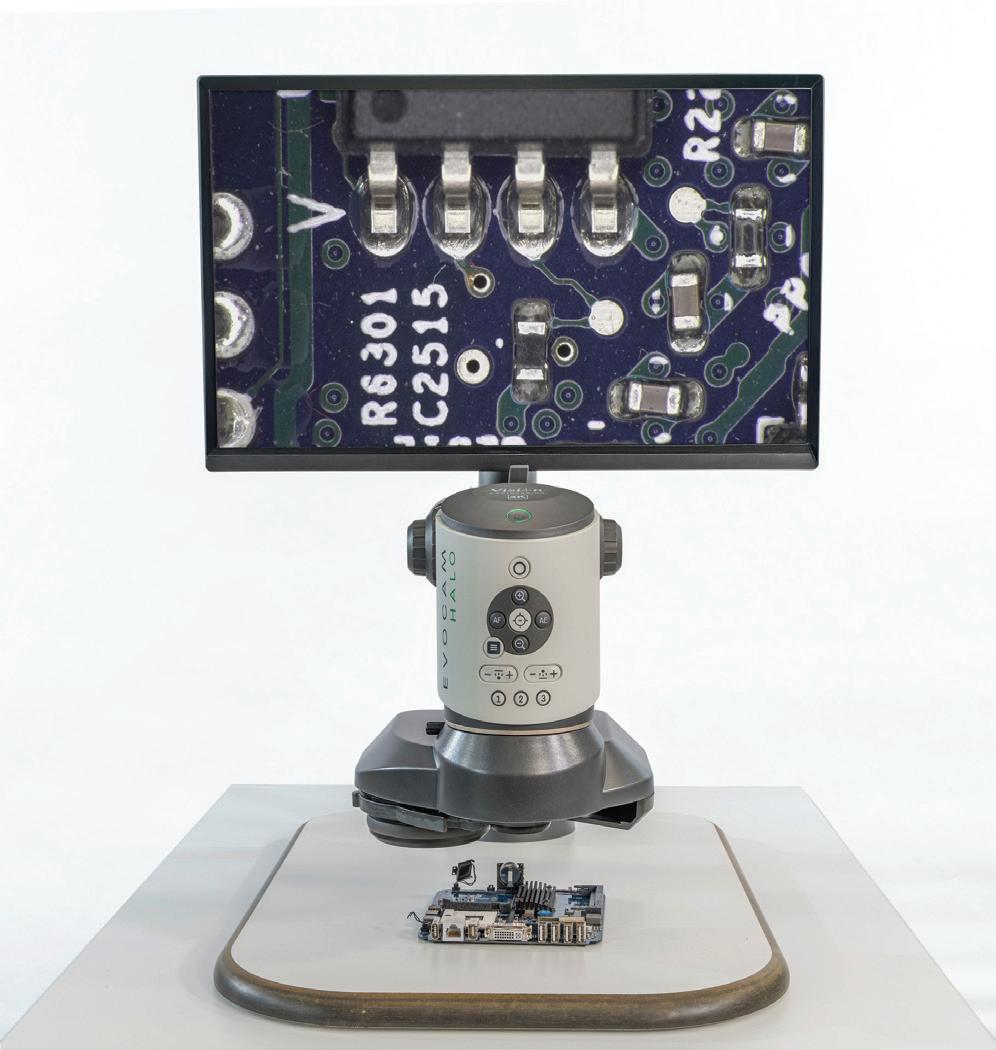
components with enhanced clarity and accuracy.
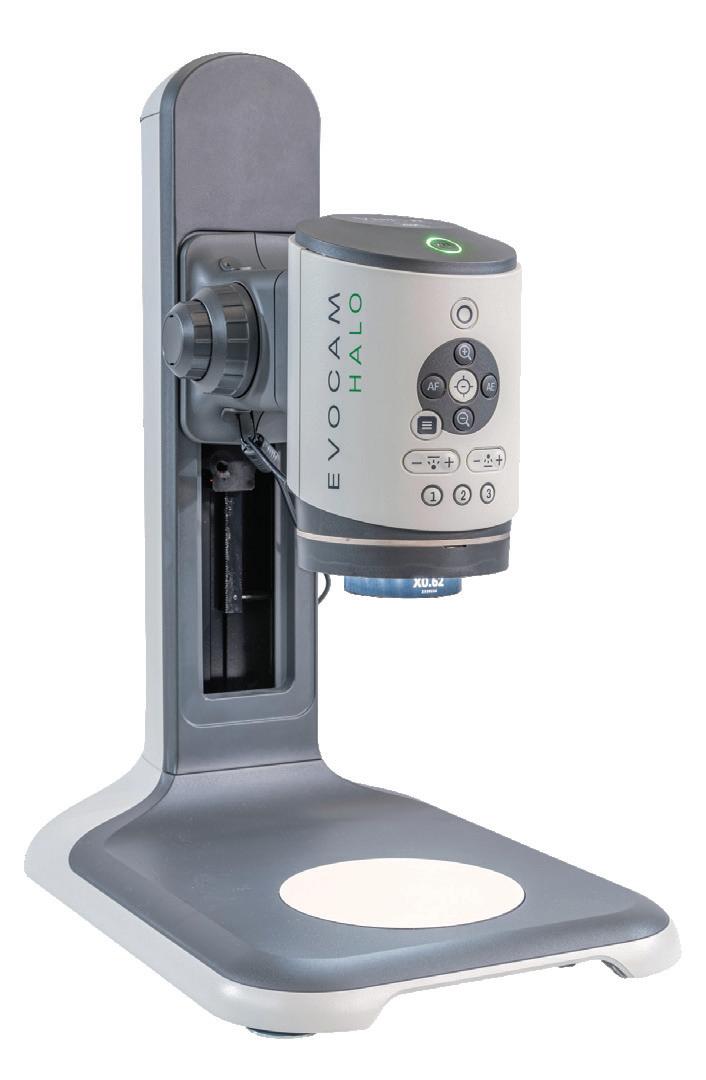
New intelligent hardware and software automatically detects lenses and adjusts magnification settings, ensuring seamless workflow and accurate results. Real-time insights are available providing intuitive image capture, measurement, and analysis tools, enabling faster and more informed decisionmaking. Vision Engineering’s popular 360 Direct/Oblique Viewer also works with HALO, enabling users to inspect details from different angles, revealing hidden features that would otherwise be inaccessible.
HALO is suitable for a wide range of applications, including medical device manufacture and testing, especially in the practices of inspecting translucent tubes, electro-polished devices, and other medical
It is also effective at capturing fine details on small, reflective metal parts for precise inspection and quality control – perfect for micro mechanics. In the laboratory HALO cam improve the examination of Petri dishes with translucent samples, enhancing contrast and clarity for detailed analysis, and in industrial manufacturing, intricate assemblies, solder joints, and other components are inspected with much improved precision and efficiency.
Pricing and availability
EVO Cam HALO is available for purchase now, with configurations starting at 6,500GBP.
Commenting on the launch, Paul Newbatt, Group Sales and Marketing Director at Vision Engineering, said, “We are delighted to bring
EVO Cam HALO to market, confirming our reputation for innovation, whilst improving the inspection performance available within digital microscopy. 4K image quality plus fully controllable lighting and flexible software available in multiple configurations means that our customers in a wide range of sectors can easily choose the most accurate and consistent digital system for their inspection requirements.”
MEPCA’s editor interviewed Stephen Sanderson, International Product Manager of Vision Engineering, at the Southern Manufacturing & Electronics show, on the HALO launch day. The full interview can be found on MEPCA’s website under “MEPCA TV+”. For further information on the product, please visit the company’s website. visioneng.com
Digitalisation Trends Impacting I/O Modules
Introducing a new breed of I/O module to meet the fast-growing need for decentralised data processing. Schneider Electric’s Dave Sutton, Product Marketing Manager for Industrial Automation, explores how businesses across industrial applications from simple to the most demanding can improve performance at the I/O level.
As industry adopts distributed control systems, there is a need for decentralised input/output (I/O) devices to process data closer to the source, providing a way for businesses to make informed decisions at the machine level. At the same time, businesses are deploying more IoT devices, which is furthering the need for I/O modules to translate data between machines and their control systems. New generation I/O systems deliver greater scalability and flexibility. In turn, industrial businesses can adapt to market needs, simplify digital transformation, and save on valuable engineering time.
OEMs, system integrators and end users should make the I/O level work for them, by adopting a cutting edge I/O solution that holds the key to delivering a reduction in total cost of ownership and robust cybersecurity. Integrated diagnostics, as well as simpler design and wiring will cut down complexity from pre-sales all the way to operation. Advancing at the I/O level empowers businesses to keep up with rapidly changing consumer and market trends, quickly introducing new assets or adapting processes without barriers. Intelligent I/O solutions can also streamline cybersecurity concerns, playing a vital role in the protection of the network as the facilitator of data transfer. Each of these capabilities offers value to entire manufacturing supply chain.
Creating a strong foundation
A new generation of I/O modules has been developed to play a significant role in the digital transformation of industry, as
businesses can only achieve the benefits of digitalisation when they can rely on secure, scalable and flexible data transfer. The key is to adopt new I/O solutions that are capable of seamless integration of data across assets and devices regardless of what is already installed. Seamless integration ensures that even facilities operating legacy assets can realise efficiency improvements through analytics.
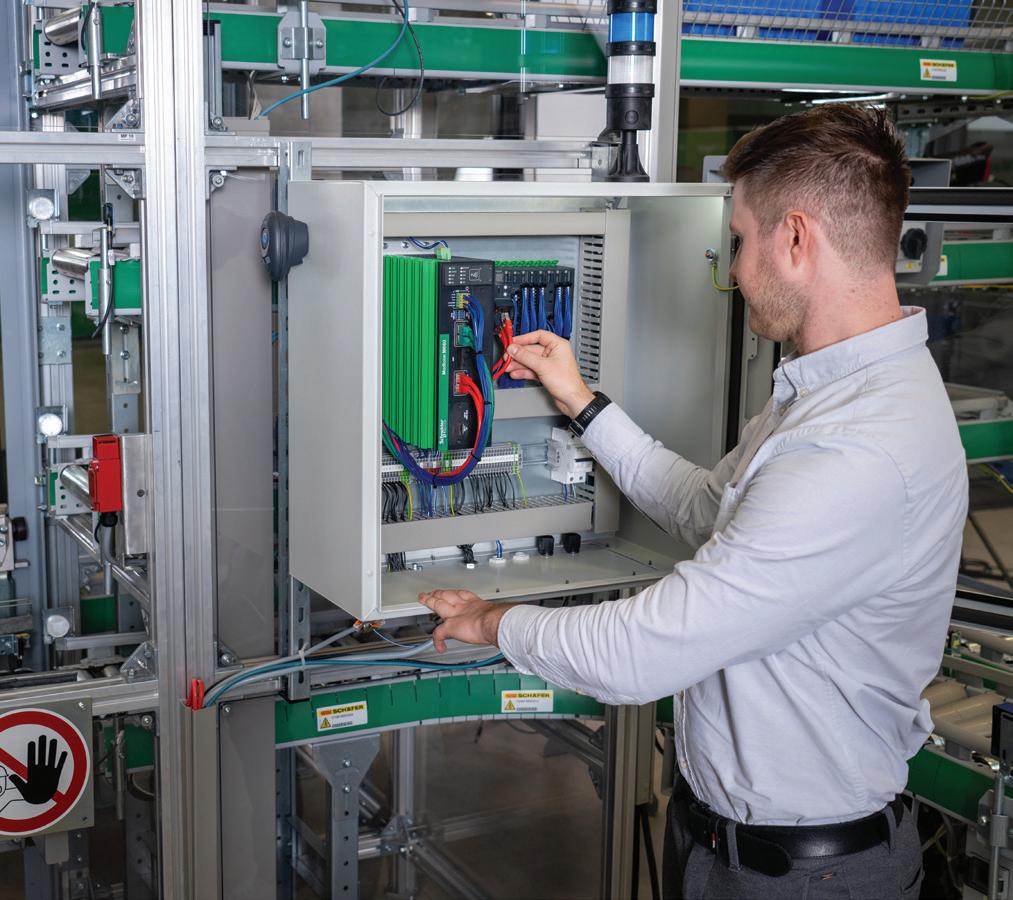
Communication and future-proofing
Compatibility with open industry standard Ethernet protocols, such as Ethernet/ IP, Modbus TCP and OPC-UA, provides interoperability and future-proofing as it lays the foundation for a new generation of connected products.
24/7 operations
The latest type of I/O solution can also cut downtime and its associated costs due to hot swap capabilities. This means that plant managers, maintenance teams and OT professionals can react to issues by replacing a module (or slice) immediately, therefore minimising the impact of unforeseen maintenance and ensuring availability, whether an application is simple or demanding.
Data continuity
That same modular design also provides flexibility to add new machines and adapt processes without extensive reengineering. These I/O capabilities deliver scalability for businesses of all shapes and sizes, ensuring the solution can not only grow with a business but also provide flexibility for the future.
As industrial manufacturers adapt their hardware and software to take advantage of digital transformation, they need I/O technology that is flexible, scalable and protects the valuable flow of data. The latest I/O modules, such as Schneider Electric’s Modicon Edge I/O Network Terminal Slice (NTS), represent a smart solution that prepares industrial operations for the datadriven future. OEMs, systems integrators and end users can meet the needs of any application within a single I/O family. se.com
Manufacturing Champion of the Month
MEPCA is thrilled to announce Rolf Schweizer, CEO of the Hidrostal Group, pioneers in pumping technology, as our Manufacturing Champion for March. In our Q&A, Rolf shares how to improve wastewater management and why it is important.
Headquartered in Switzerland, Hidrostal is a leading manufacturer of pumping solutions, operating in over 100 countries. Rolf Schweizer is a Swiss native with an industrial B2B background, having worked at the likes of Bühler Group, Sulzer, General Dynamics, StadlerRail and Voith.
Since joining Hidrostal Group as the CEO in 2022, Rolf has led the group in its crusade to improve global wastewater management, which he says, is not working.
What key hurdles must the UK overcome to improve wastewater management?
A working water and wastewater system is essential for the wealth and health of a country. The key challenge within the UK wastewater industry is fundamentally a lack of investment. Putting aside the political public versus privatisation debate, more investment into a sector that struggles with an aging infrastructure compounded by a rising population, along with a disjoint in new house building legislation, is vital to update the assets to meet increasing demand. Climate change will also have an impact in future. Increased rainfall and flooding overwhelms the sewage systems and leads to the pollution discharges that constantly hit the headlines. This results in huge fines, and in turn, less money for investment. It effectively culminates in an ever-rotating circle.
The UK aren’t alone in this, of course. I would go so far as to say that globally, wastewater isn’t working as around 50% of global wastewater volume is still not treated at all. In some countries, public private partnership might be the way forward. I can’t say for sure that would work in the UK, but the one thing that is certain is that intelligent
investment needs to be made into the aging wastewater infrastructure, along with the continued education of how we can play our part with regards to what we are flushing.
When it comes to asset performance, how does a lack of understanding of Total Cost of Ownership (TCO) impact the industry?
Basing a purchase decision on upfront costs rather than lifetime costs leads to far higher long-term expenses. Purchase price, energy use and scheduled maintenance of a pump over its lifetime are easy to quantify and track, but they don’t tell the whole story when it comes to TCO. Often overlooked are the energy costs that arise from a loss of efficiency due to blockages or wear, and the resulting costs of unscheduled maintenance. The value of these, alongside lost output, will quickly dwarf all the other elements. And in industrial applications it can easily happen that a single unplanned downtime or production process interruption costs the plant more than the original CAPEX investment of a reliable pumping solution. TCO is a significant focus for the industry for AMP8 and Hidrostal is best placed to assist with this. Our pumping solutions are highly efficient but also fit for purpose and durable. Whilst high efficiency is important, it should never be attained at the cost of compromising on the pumps ability to handle solids, rags and fibre.
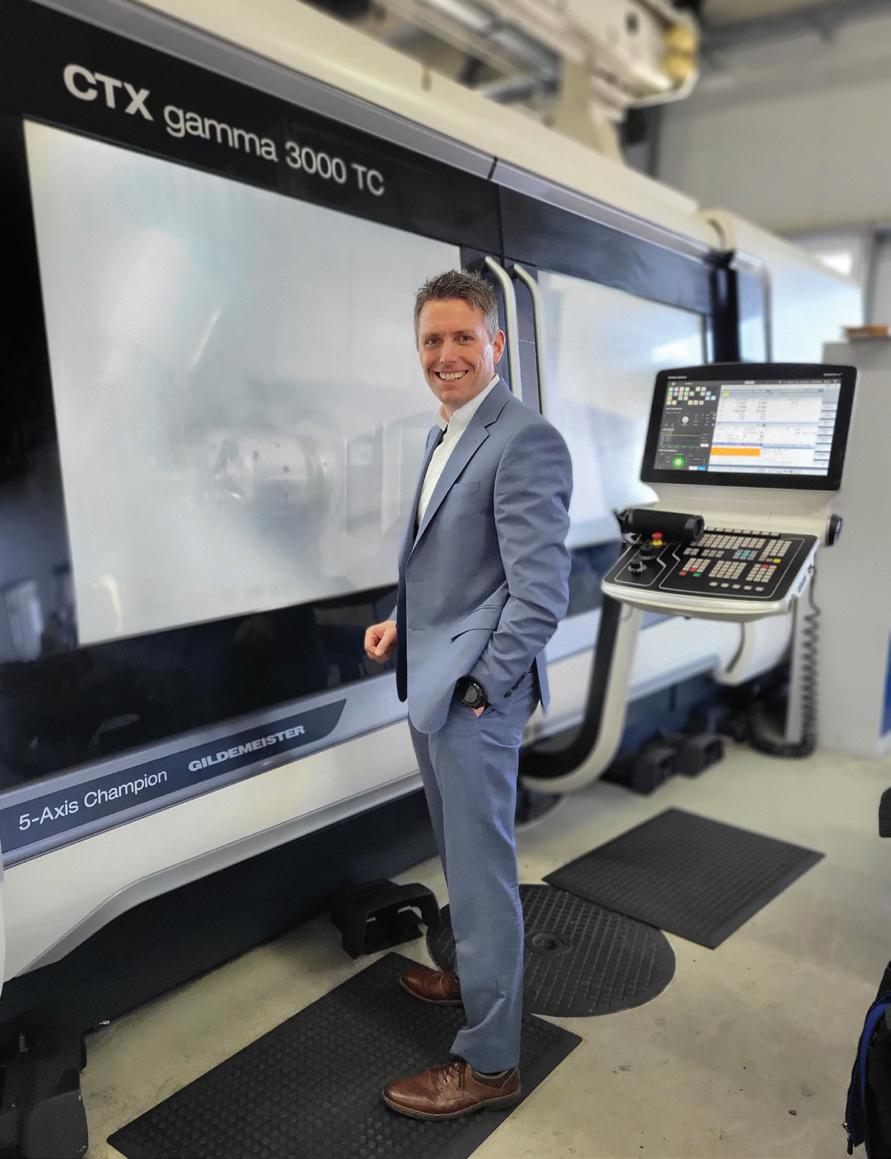
Reflecting on 2024 what company achievement are you most proud of and why?
Last Autumn we formally released our new Group Strategy “Together to the Peak” – the result of an 18-month collaboration amongst the Hidrostal senior leadership team. Our vision is to be the world’s preferred provider of screw centrifugal pump solutions for fluidsolid handling. I am proud and privileged to lead this team and to see how the process has enabled us to grow stronger together behind our new joint vision. The most fulfilling aspect so far is to see our strategy execution gaining momentum and already providing the first improvements and results. hidrostal.com
Contract or Permanent Work?
Russell Smith, Managing Director at recruitment specialist Hunter Selection, offers his expertise to engineers on the benefits and pitfalls of contract versus permanent work.
We often receive enquiries from engineering professionals considering a move from permanent to contract employment, usually attracted by the higher rates of pay. While the decision ultimately depends on personal circumstances and preferences, we believe it’s important to outline key factors to help guide your decision between contracting and permanent roles within the Engineering, Manufacturing or Technology sectors.
Benefits
1. Flexibility
of contracting
Contracting offers a significant level of autonomy, allowing professionals to choose the projects they work on and when and where they work. This flexibility enables contractors to take breaks between assignments for personal commitments, travel, or skill development—flexibility that is harder to gain in permanent role.
2. Variety
For those who may feel restricted or uninspired by long-term employment with a single company, contracting provides the opportunity to work across various organisations and industries. This variety keeps the work dynamic and prevents the stagnation that sometimes arises in permanent positions.
3. Potential for higher earnings
Contractors often have the potential to earn higher hourly or daily rates compared to their permanent counterparts. However, this increased compensation typically comes without the benefits package associated with permanent roles, such as healthcare, pensions and paid leave. The rate you can command depends on several factors, including your experience and skillset the contract duration, IR35 status, sector and
market conditions.
4. Expanding your professional network
With each new contract, contractors quickly expand their network by working with different companies and colleagues. This growing professional network can be valuable, providing opportunities for future contracts or career advancements as your reputation and relationships grow.
Drawbacks
1. Lack of security
As a contractor you have to be prepared to look for new work regularly and this can often lead to gaps between contracts with no income. You also need to be prepared to be replaced or let go once a project is completed or earlier if there is a change in the client’s requirements or financial situation.
2. Administration and finances
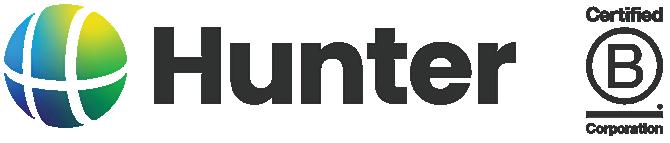
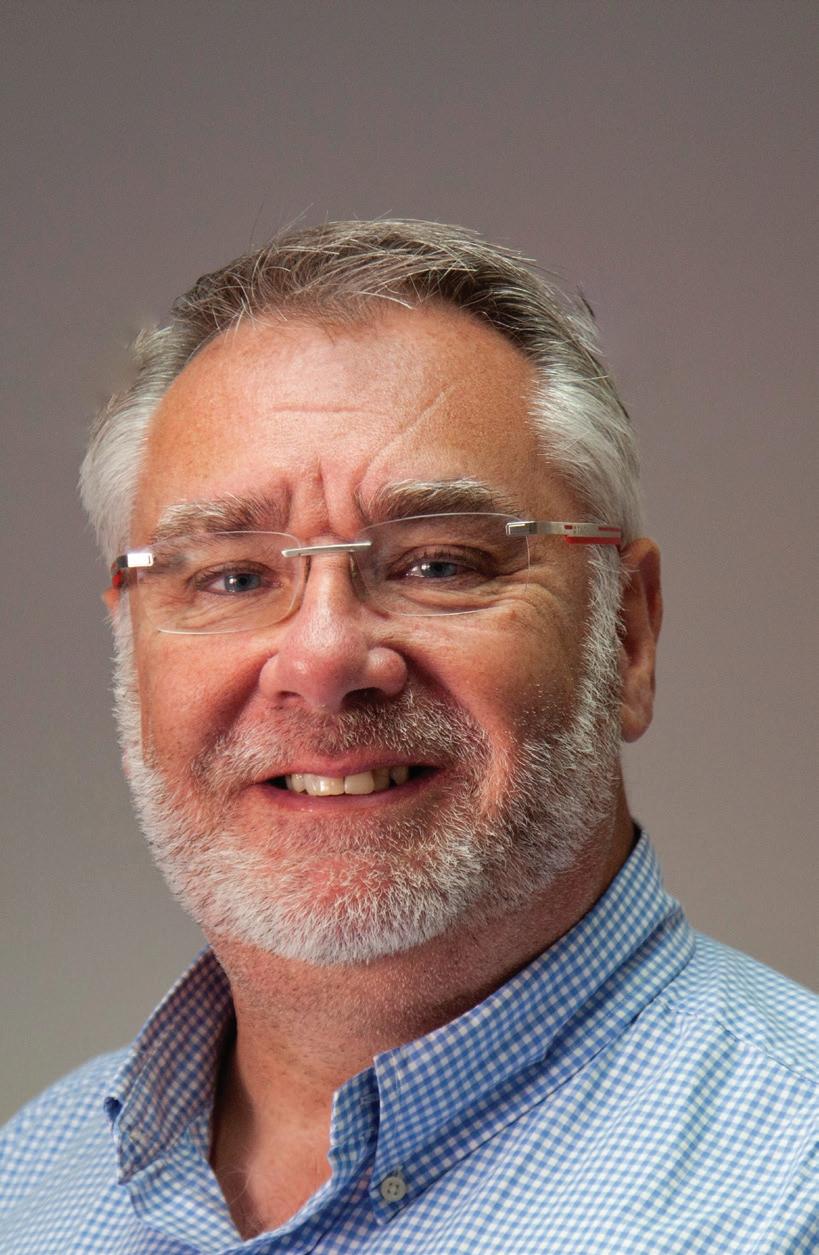
As a contractor you will either need to set up and manage your own limited company or employ an umbrella company to do this for you. Whilst this can be done with good guidance, it’s something else that needs to be considered. The admin that goes along with this includes managing your own taxes, accounting, invoicing, and legal responsibilities, including insurance.
3. Lack of training
As a contractor, the opportunity for training and development can be rare in comparison to permanent employees – as a contractor the expectation is usually that you will do this in your own time at your own expense.
4. No additional benefits
As previously mentioned, contractors will expect to receive a higher basic rate of remuneration, but then will have to make
their own provision for pension and life assurance and may not receive other noncontractual bonuses and perks which are made available to permanent employees.
5. Expectation in the role
Permanent employees are normally afforded a longer period of time to settle into a new role, but the expectation of a contractor is normally that they would need to ‘hit the ground running’. This means that the pressure to perform exists from day one. If you are looking for a permanent or contract engineering role, or looking to fill a position and would like some additional advice and support of our experienced Consultants in Bristol, Cardiff or Stafford would be pleased to help.
hunterselection.co.uk
Harmonising Standards
Wayne Rose, CEO of the British Pump Manufacturers Association (BPMA), a key member of Europump, shares his perspective on the critical role of international standards in shaping a safer, more efficient and sustainable future for the pump industry.
In today’s global landscape, where safety, reliability, energy efficiency and sustainability are priorities, international collaboration on standards is crucial. Pumps are vital to industrial processes, utilities and building services, making stringent and harmonised regulations essential for safety, performance, and reduced environmental impact.
Ensuring safety and reliability
In manufacturing environments requiring precision and reliability, pumps are essential for seamless operations. Whether transporting hazardous materials or regulating temperature-sensitive processes, pump performance directly affects system safety and efficiency. This highlights the need for globally recognised standards that establish best practices for pump design, installation and maintenance.
Standards form the backbone of industrial safety and reliability. By adhering to global regulations, the pump industry ensures optimal performance across sectors, protecting both people and processes.
Enhancing energy efficiency
With increasing emphasis on reducing energy consumption and carbon emissions, the pump sector offers significant opportunities for efficiency gains. Pumps account for around 20% of global electricity consumption, and inefficient systems contribute to substantial energy waste. Strict energy efficiency standards are vital in lowering industrial energy demand and supporting the transition to a greener economy.
Energy efficiency standards help achieve climate goals. Standardised testing and labelling allow businesses to make informed decisions, adopting the most energy-efficient technologies while reducing costs and environmental impact.
Through its involvement with Europump, the BPMA has helped shape and enforce
energy efficiency standards. Working with industry stakeholders, it ensures that policies like the EU’s Eco-Design Directive align with industry needs, helping businesses cut operational costs and improve sustainability.
Driving sustainability
Sustainability is now an essential consideration for industries worldwide. Clear environmental performance standards help the pump industry lead the shift toward greener operations.
Standards provide a structured framework for reducing resource use, emissions and waste. As industries move towards sustainable operations, harmonised regulations ensure sustainability remains a core manufacturing priority.
The BPMA and Europump actively define life-cycle assessments for pumps, embedding sustainability principles throughout a product’s lifespan—from raw material sourcing to end-of-life disposal.
Fostering innovation and global competitiveness
Beyond safety and sustainability, international standards encourage innovation. By setting clear performance benchmarks, they drive the development of advanced pump technologies that enhance efficiency and sustainability while ensuring fair competition.
Standards help foster technological advancements and maintain a level playing field for manufacturers worldwide.
Encouraging global collaboration
The BPMA, in collaboration with Europump, urges governments, regulatory bodies, and industry associations to work together in harmonising pump standards globally. While Europe has made significant progress, broader international adoption of best practices is key to achieving universal safety, efficiency and sustainability.
Standards should not be confined by regional borders. Global collaboration is
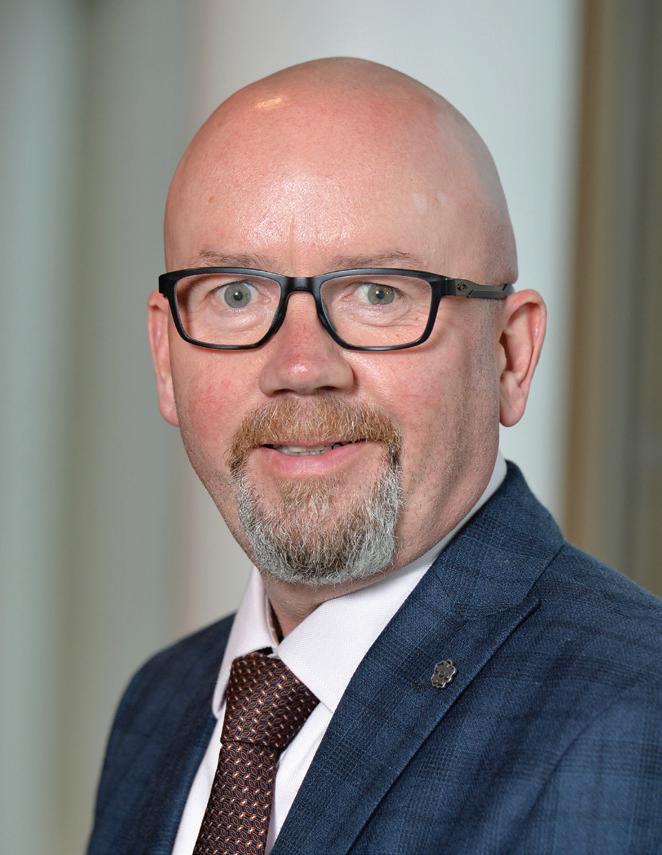
essential to ensuring ongoing industry progress. Harmonised regulations allow manufacturers to meet diverse market needs while delivering consistent benefits in safety and sustainability.
Europump and the BPMA work closely with international organisations such as ISO (International Organization for Standardization) and IEC (International Electrotechnical Commission) to promote global alignment of pump standards. This ensures that regardless of where a pump is manufactured or used, it meets the same rigorous quality, safety and environmental criteria.
Building a stronger future with standards
As industries evolve, the need for robust international standards has never been greater. Safety, efficiency, and sustainability are not just industry goals but global imperatives, and strong regulations provide the foundation for achieving them.
The future of the pump industry depends on continued commitment to internationally recognised standards. By championing best practices, the industry can build a safer, more efficient, and more sustainable world. bpma.org.uk
The Strategic Value of Sustainability
While environmental considerations and regulatory pressures initiated the UK food industry’s sustainability ambitions, there are other factors driving it forwards. As Nikesh Mistry, Sector Head of GAMBICA, explains, adopting more sustainable practices also makes good business sense.
As the world continues to grapple with climate change and environmental degradation, the food industry in the UK faces mounting pressure to adopt sustainable manufacturing practices. For manufacturers, this shift is not just a moral priority but also a strategic business decision.
Embracing sustainability can lead to increased profits, enhanced efficiency, and a stronger competitive edge. Coupled with the integration of digital technologies, sustainable manufacturing offers a pathway to a thriving future for the UK’s food industry.
In practice, manufacturing sustainability involves minimising waste, reducing energy consumption and optimising resource use. By implementing these practices, food manufacturers can achieve significant cost savings. For instance, reducing waste not only lowers disposal costs but also allows for the recovery and repurposing of valuable materials. Additionally, energyefficient technologies can lead to substantial reductions in utility bills.
Beyond cost savings, sustainability can enhance brand reputation and customer loyalty. Today’s customers are influenced heavily by societal changes and news released in social media, and they are increasingly conscious of the environmental impact of the products they purchase. By positioning themselves as environmentally responsible, manufacturers can attract a growing segment of eco-conscious consumers. This, in turn, can drive sales and foster long-term loyalty.
Moreover, regulatory compliance is becoming a critical factor for businesses. Governments around the world, including
the UK, are enacting stricter environmental regulations. By proactively adopting sustainable practices, manufacturers can avoid potential fines and penalties, ensuring smoother operations and uninterrupted market access – becoming more sustainable now will help manufacturers prepare for future legislations.

To help manufacturers, the integration of digital technologies plays a pivotal role in achieving sustainable manufacturing in not only the food industry but all sectors. IoT devices and sensors enable real-time monitoring of production processes, optimising waste reduction. Most manufacturing equipment has been using a form of Artificial Intelligence (AI) for many years already. What used to be machine learning has now developed into more complex generative AI, and manufacturers can utilise the vast amounts of data collected to identify patterns and predict outcomes. This can help with supply chain management, forecast demand accurately, and ensure consistent product quality.
By leveraging contacts within Trade Associations, Knowledge Transfer Networks, Catapults, and more, businesses can discover relevant case studies and likeminded individuals with similar problems, helping them to tackle their issues and minimise waster and energy consumption. These success stories can demonstrate the tangible benefits of integrating sustainability and digital innovation.
Looking ahead, the potential for
sustainable manufacturing in the UK’s food industry is immense. As technology continues to advance, manufacturers will have even more tools at their disposal to optimise processes, reduce environmental impact and maximise profits. This makes it even more important for schools and colleges to be made aware of the technologies available, and to make them more attractive to the future workforce, as it is they who will be the future leaders championing these technologies to reach the potential of the industry.
GAMBICA have been building our NextGen council to promote exactly this, as STEM ambassadors to ensure that the future generations are equipped with the knowledge and value of what it means to work in a STEM career and how pivotal they will be to our future. To learn more about food processing, GAMBICA are supporting Appetite for Engineering, 20th March 2025 at the MTC in Coventry, and later in the year is Food Manufacturing live at the National Agricultural Exhibition Centre on Wednesday 15th October. Sign up now to get involved! gambica.org.uk
Transforming Industry: HANNOVER MESSE 25
MEPCA’s editor attended the HANNOVER MESSE 2025 Preview to learn how this globally renowned trade show encourages industrial transformation. Read on for details of what to expect from this year’s event.
The world leading trade fair HANNOVER MESSE is set to return 31 March – 4 April, Hannover, Germany. This year, more than 4,000 exhibiting companies from the mechanical engineering, electrical, digital and energy industries will come together under the event’s overarching theme of “Industrial Transformation” to showcase solutions for production and energy supply. The main exhibiting areas for 2025 will be Smart Manufacturing, Digital Ecosystems, Energy for Industry, Compressed Air & Vacuum Technology, Engineered Parts & Solutions, Future Hub and International Trade & Investment. The event also boasts a conference program featuring around 1,600 speakers.
Presenting at the HANNOVER MESSE 2025 UK press event, Hubertus von Monschaw, Global Director Trade fair and Product Management, Deutsche Messe AG, explained that the faster the industry evolves, the more challenges it must overcome, and HANNOVER MESSE provides an ecosystem of solutions by connecting thought leaders from across industries and territories towards common goals. Indeed, as he went on to explain, the show has an outreach like no other in the industry, with circa 150 nations participating in the event.
During the HANNOVER MESSE press event, the idea of creating ecosystems of innovation and collaboration was a common theme, with the speakers highlighting how the cross-pollination of ideas is not just crucial to the success of the event, but also offers far-reaching, tangible benefits for the industry. In anticipation, we look at just some of the ecosystems that will be present at HANNOVER MESSE 2025.
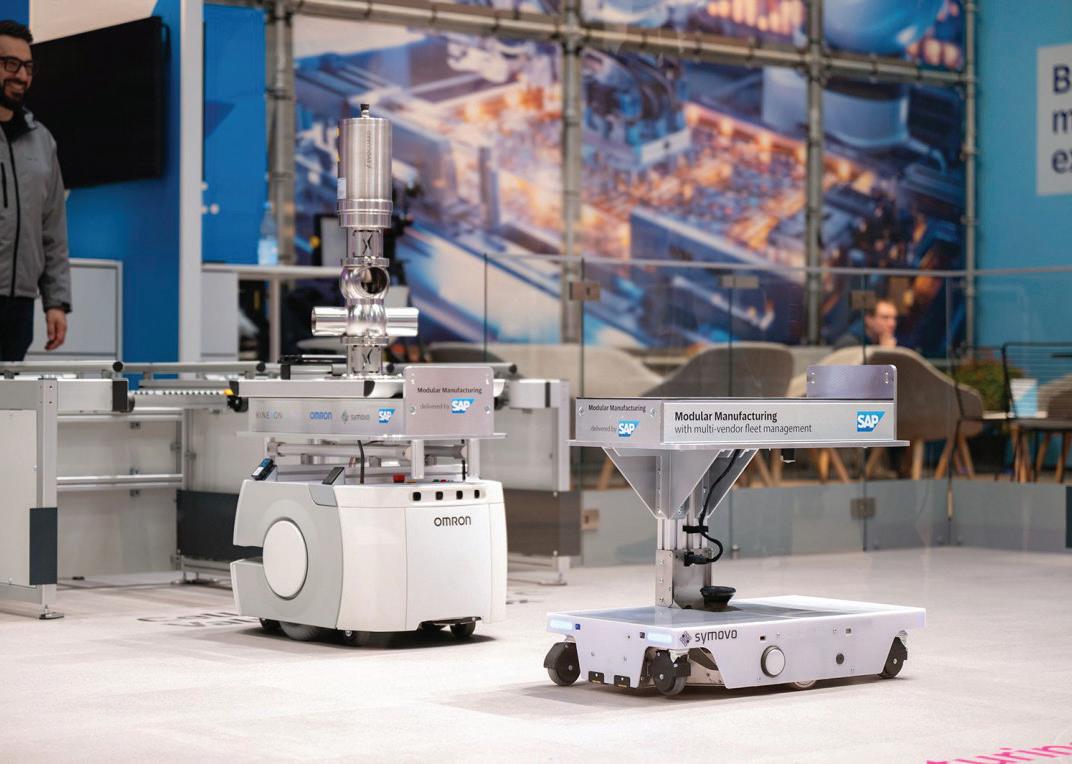
Application Park
With new and exciting robotics applications, the Application Park will be one of the highlights of HANNOVER MESSE for many attendees. There, it will be possible to view intelligent robot systems, autonomous driving devices in operation, the latest AI applications in robotics, image recognition tools and virtual platforms.
Modern robots are increasingly taking on high-precision tasks that require maximum accuracy. Thanks to the use of artificial intelligence, they are becoming increasingly flexible and intelligent. Around 30 companies will be presenting exciting and modern applications at the Application Park. AI-enabled robots will be in action, demonstrating how they learn to perform tasks and adapt dynamically to changing production environments.
One example is the French company Inbolt, which will be presenting an intelligent,
adaptable solution for robot guidance: with a 3D camera mounted directly on the robot, AI-powered algorithms allow it to instantly locate and position parts in real time, while smoothly adjusting its movements on the fly to achieve the best results.
Digital and AI
The Digital Ecosystems exhibition area at HANNOVER MESSE will offer visitors first-hand insights into the future of digitally networked industry. Over 600 companies will present sample applications and use cases, from intelligent machine networking to the digitalisation of supply chains, right through to innovative business models based on big data or AI. New features for exhibitors and visitors at HANNOVER MESSE are the Digital Transformation Conference Stage and the Masterclasses.
The organisers of HANNOVER MESSE maintain that the future of industry lies in
intelligent networking and the application of Artificial Intelligence (AI). Digital ecosystems enable companies to collaborate across platforms, securely share data and drive innovation collectively. Exhibitors this year include, Accenture, Aleph Alpha, Altair, Autodesk, AWS, Capgemini, DELL, Google Cloud, Ericsson, Hexagon, Formlabs, HPE, Microsoft, PTC and SAP.
Artificial intelligence and machine learning, as well as big data, data analysis or cloud computing, are other topics featured in the exhibition area.
Energy for Industry
By showcasing solutions for industrial energy supply, the event hopes to shape the future of industrial energy supply, bringing together numerous manufacturers and solution providers from the fields of hydrogen and fuel cells, Energy 4.0 and power engineering, under the theme “Energising a Sustainable Industry.” Visitors from industry, science and politics gain an in-depth understanding of topics such as digitalisation, decarbonisation, energy efficiency, electricity self-generation, cost reduction, price volatility, and resilience.
Exhibitors in the exhibition area “Energy for Industry” – which includes Hydrogen + Fuel Cells EUROPE, Europe’s leading hydrogen event – will present the latest products and services in the sectors Hydrogen and Fuel Cells, Energy 4.0 and Power Engineering. The energy halls feature exhibits, presentations and networking events that showcase the latest technical solutions for energy generation, management, distribution and storage.
International corporations, small and medium-sized enterprises and startups from all over the world will exhibit. They include familiar names such as GP Joule, Janitza, Wöhner, PreZero and EMKA as well as large group exhibits from Baden-Württemberg, Schleswig-Holstein, Brandenburg and the European Union.
Smart Manufacturing
The Smart Manufacturing exhibition area at HANNOVER MESSE will be focused on intelligent and sustainable production. In seven halls, companies from all over the world will showcase how state-of-the-art technologies, components, integrated Industry 4.0 solutions, and artificial intelligence is set to help make production processes even more effective and sustainable.
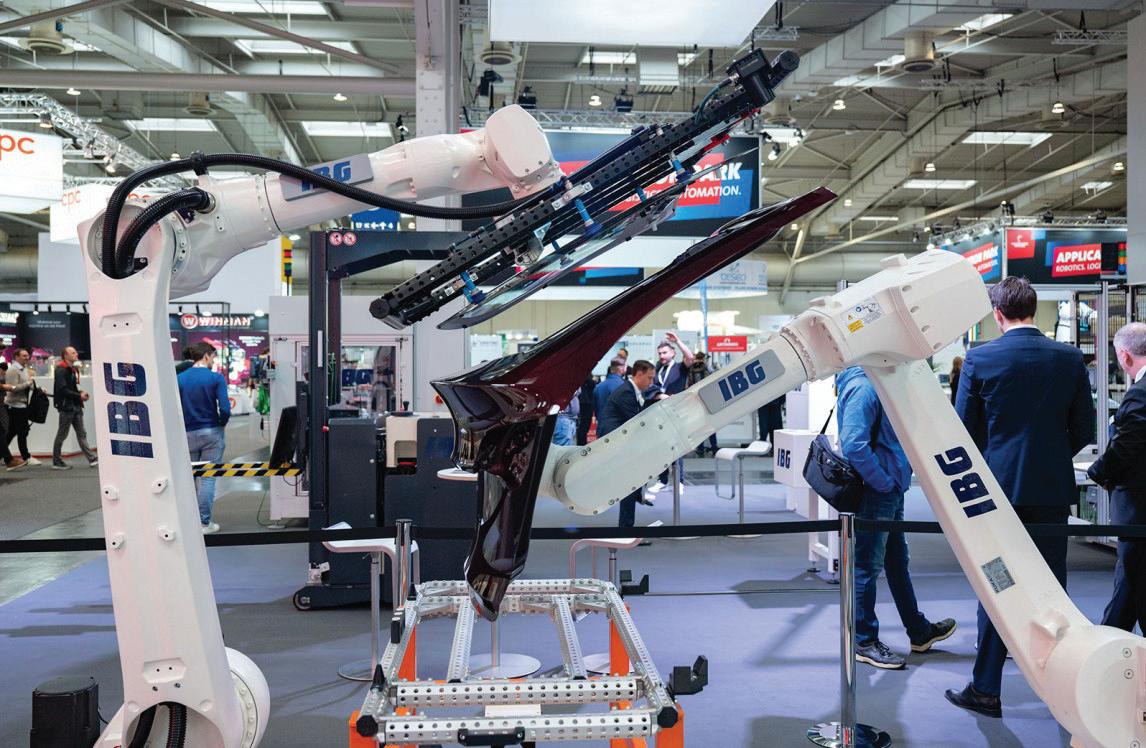
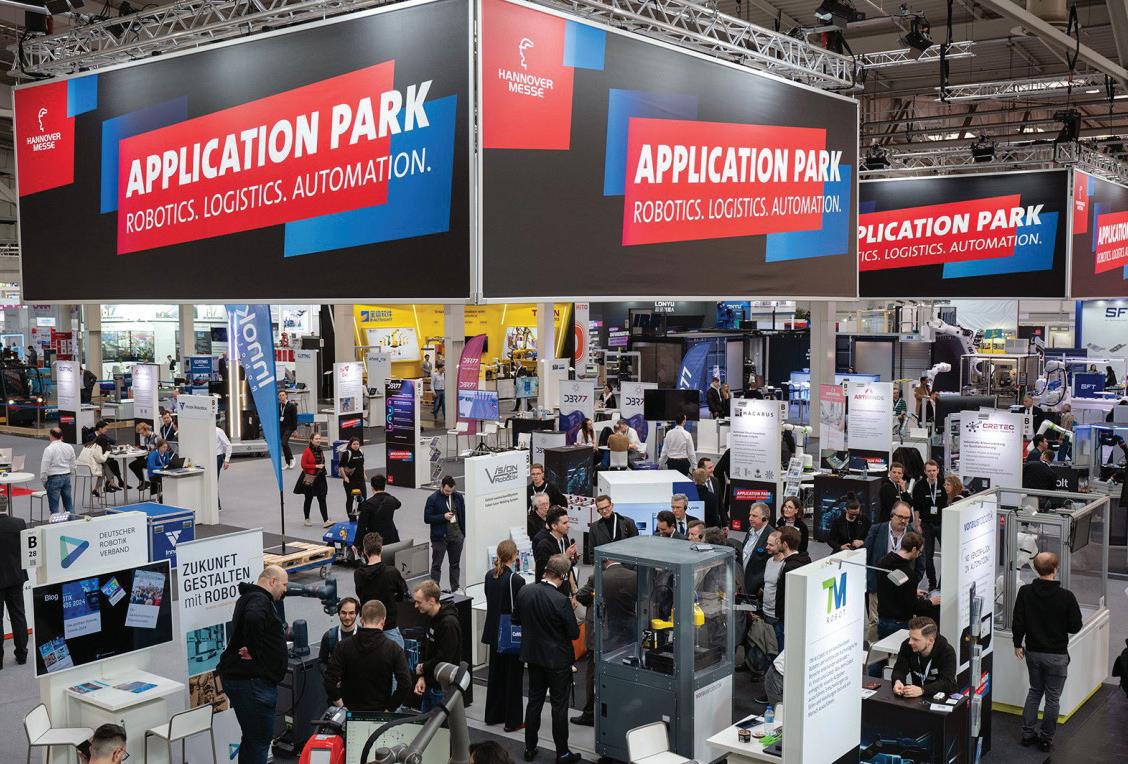
In particular, it will feature the topics of automation and sensor technology, robotics and logistics automation, as well as drive and fluid technology. Exhibitors in the Smart Manufacturing area will include, Aignep, Beckhoff, Bosch Rexroth, Cantoni, Delta Electronics, Emerson, Festo, Flender, Harting, HAWE, ifm electronic, I.M.M. Hydraulics, Lapp, Pepperl+Fuchs, Pilz, Phoenix Contact, Rittal, Schaeffler, Schneider Electric, SEW-EURODRIVE, Siemens and Turck.
AI-enabled robots will be in action at Application Park, demonstrating how they learn to perform tasks and adapt dynamically to changing production environments, for example.
“With HANNOVER MESSE, we are offering all exhibitors in the Smart Manufacturing area the opportunity to
be embedded in a unique industrial innovation ecosystem, in which German and international companies from the general engineering, electrical and digital industries as well as the energy sector present efficient and sustainable solutions for industrial value creation now and in the future. This mix of research, business, startups, and political topics will provide a unique opportunity to connect with top-level decision-makers, technology scouts, experts, and media representatives from throughout the world,” says von Monschaw, HANNOVER MESSE 2025 takes place 31 March – 4 April, at The Hannover Fairground exhibition area in the Mittelfeld district of Hannover, Germany. To attend this inspiring event, register now using the website below. hannovermesse.de/en/
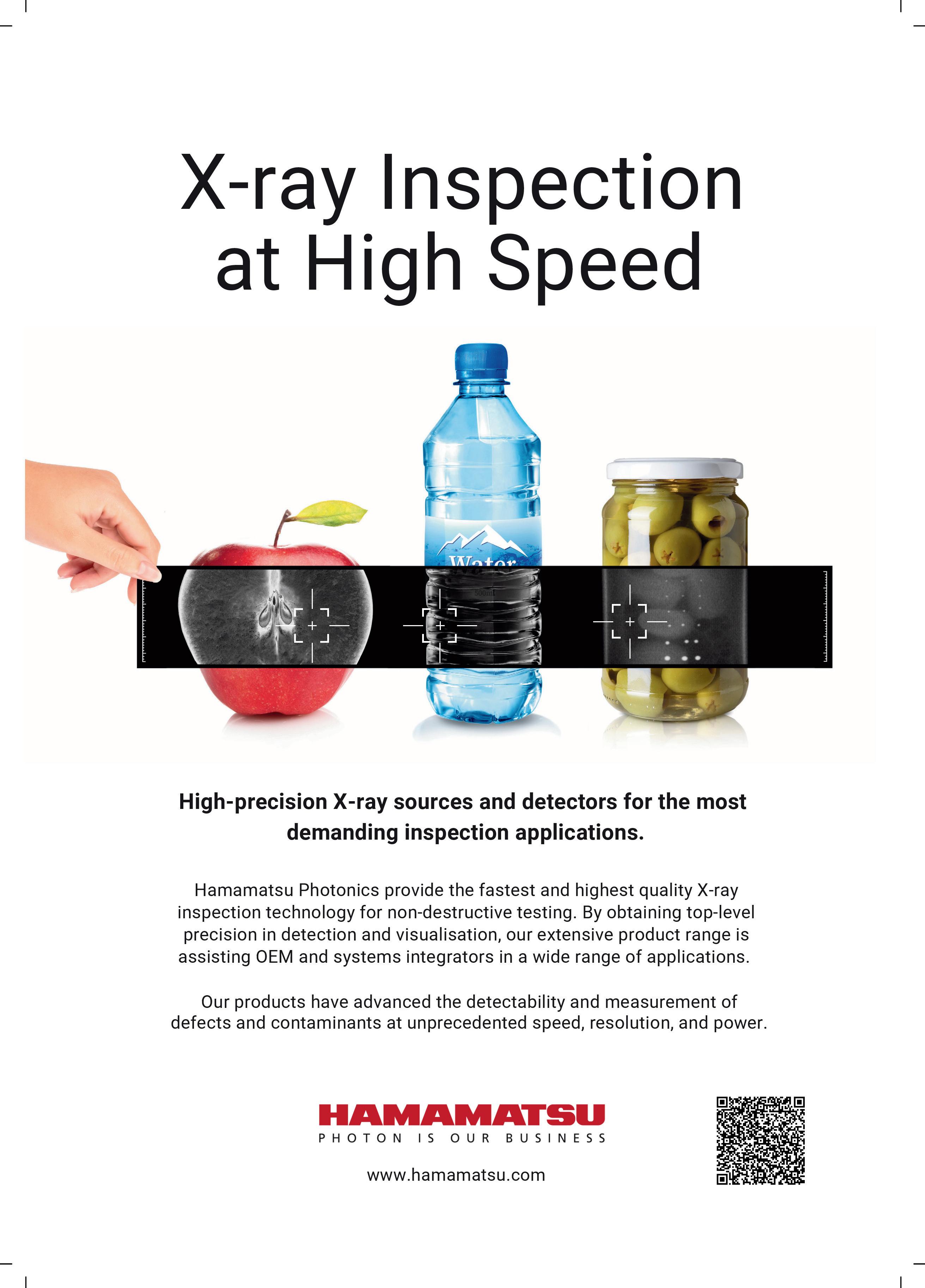
Focus On: Food Processing
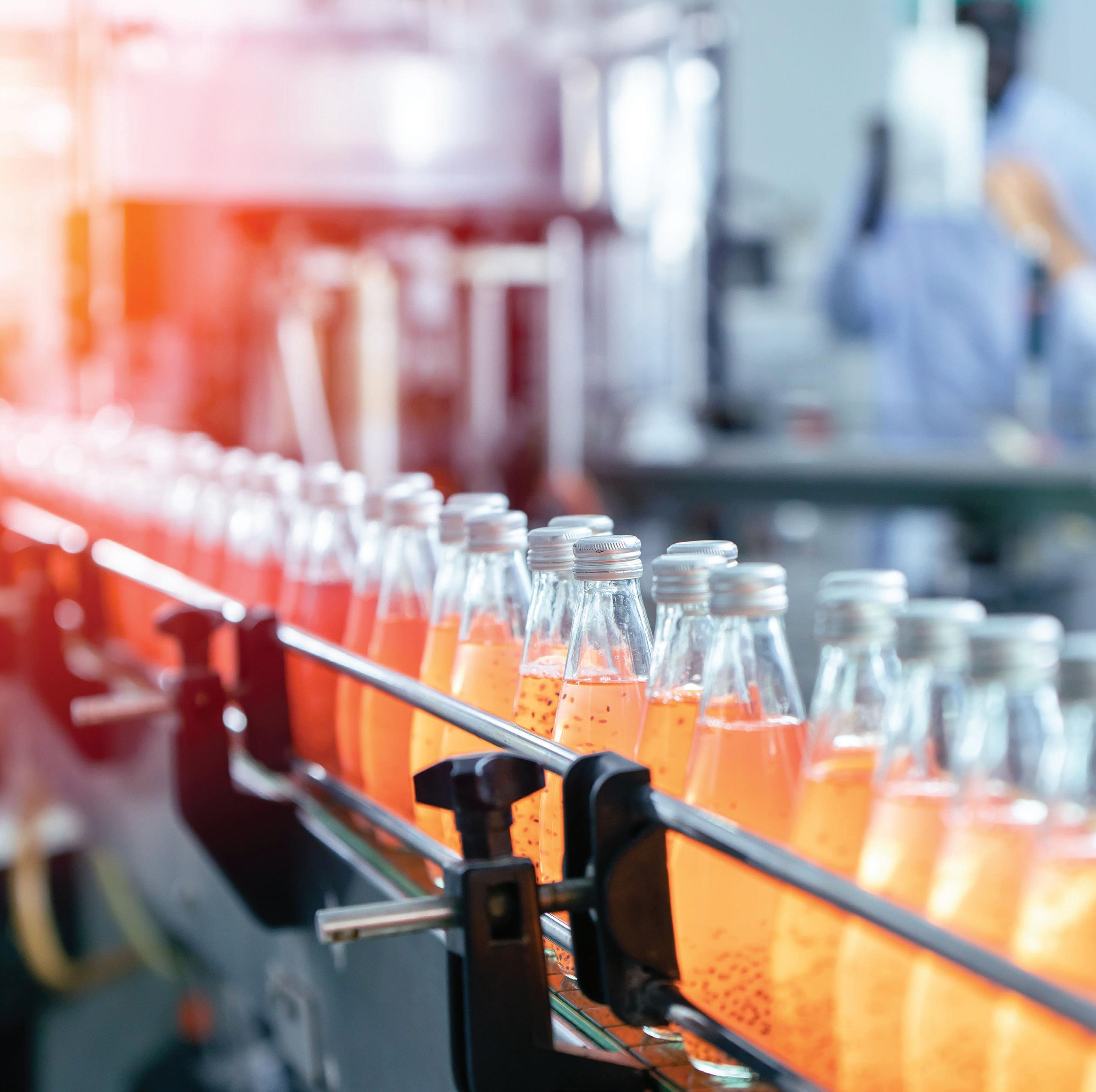
P18. MEPCA looks at 5 trends that will shape Food Processing in 2025.
In Ever Increasing Circles
Aluminium recycling is a circular economy success story. As a permanent material, aluminium can be recycled indefinitely, making it the perfect material for packaging and containers. In this feature, MEPCA looks at the potential of circular economy in food and beverage packaging and beyond.
Of all the aluminium ever produced worldwide, 75% of it is still in circulation.
I came away with this incredible fact after visiting the House of Commons to learn more about circular economy in the aluminium industry, at the tail end of the last year, courtesy of Alupro.
Alupro is an industry funded, not-for-profit organisation representing the UK’s aluminium packaging industry. The organisation works tirelessly to assist the aluminium industry in fulfilling its obligation to meet recycling targets. It does so by partnering with local authorities, the waste management industry and the wider metal packaging sector. All of whom were represented at the House Commons event, aimed at raising awareness of the continued progress in aluminium recycling towards achieving a true circular economy.
The event was sponsored by Dr Rupa Huq MP, Labour MP for Ealing Central and Acton, who also spoke at the event, referring to herself as the “Aluminium Woman”, due to her unwavering support of the aluminium recycling and the principles of circular economy. Sam Jones, head of climate and sustainability at Coca-Cola Europacific Partners (CCEP) was also one of the speakers, showing that even industry giants are aware of aluminium recycling’s pivotal role in the supply chain.
Tom Giddings, executive director at Alupro, explained that while Aluminium recycling rates increased in 2024, policy and industry must work in tandem to enable aluminium recycling to achieve its potential by improving on collection volumes and material quality.
One of the key challenges to improving aluminium recycling in the UK is the devolution of waste management. This leads to an inconsistency in the practice of kerbside collections, making it more difficult to ensure that all aluminium recycling is collected.
By raising awareness of challenges and encouraging MPs across parties and territories to show their commitment to supporting the industry, Alupro hopes to dismantle the barriers in policy and practice that are preventing the aluminium industry achieving true and lasting circular economy.
Why aluminium?
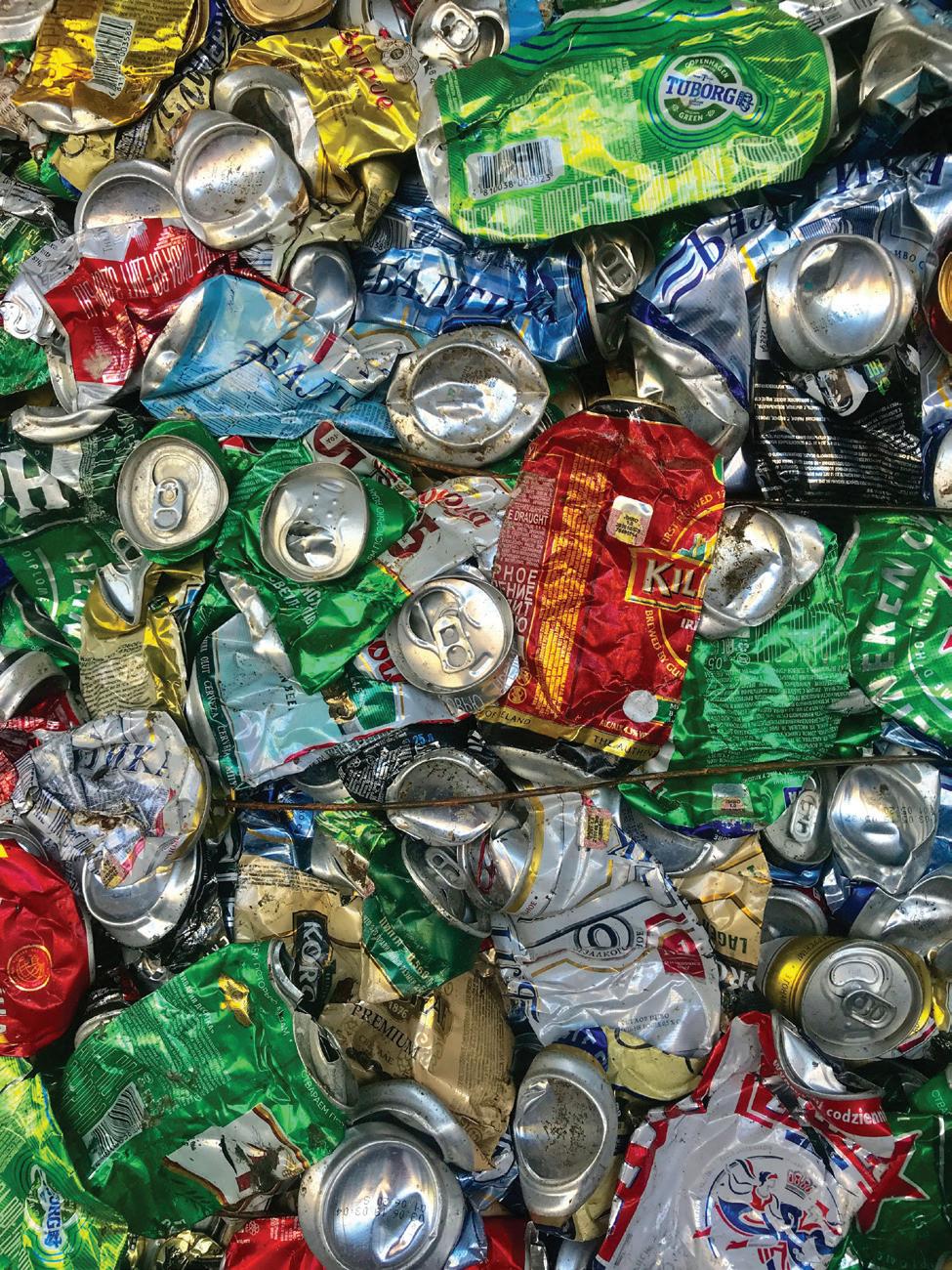
Of all packaging materials, what makes aluminium such a suited material for circular economy?
Aluminium has a high-strength-to-weight ratio, making it a lightweight yet study material, with properties that make it ideal for preserving, protecting and transporting food and beverage products. It is also a highly workable material, meaning that it is easy to machine and create products from.
Virgin aluminium is produced through a process of grinding and refining aluminium bauxite ore before separating the alumina from bauxite using electrolysis. The process
of electrolysis uses a considerable amount of energy. In contrast, producing new aluminium from recycled material uses 95% less energy and emits less than 10% of the greenhouse gases1
Not only is it better for the environment to produce aluminium from recycled material; it is significantly cheaper to do so.
When we consider the success of recycling in aluminium, both in terms of sustainability and economically speaking, it is natural to wonder why other prevalent packaging materials aren’t reaching similar levels of circularity. A particular material that
springs to mind is plastic, and specifically, PET (polyethylene terephthalate).
PET spiral
Plastic bottles are almost exclusively made from PET, which is the most circular of all recycled plastics.
However, unlike aluminium, PET is not a permanent material. While there are efforts to increase circularity, compared to the circular economy model of aluminium, PET’s recycling trajectory is more reminiscent of a spiral. On the outer spiral, the product begins its journey as a new bottle produced from raw material. Through recycling, the material transforms into poorer quality products, such as trays and films, which are not typically recycled.
According to a report published in 2022 by Zero Waste Europe2, despite the best of intentions, improvements in circularity of PET can only be achieved by making significant strides in how PET products are designed and recycling is managed. This would include significantly enhancing bottle collections; designing all bottles to be clear rather than coloured or opaque, as recycling coloured material is more difficult; prioritising bottle-to-bottle recycling to prevent the material falling out of the circle and applied to other PET products; and advances also would need to be made in chemical depolymerisation, the method by which polymers and returned monomers, i.e., back into its raw material.
PET recycling is far behind aluminium, but there are success stories that highlight its potential. With recycling plants in Germany and Mexico, global packaging specialist ALPA has reported that its recycling process, which uses state-of-the-art technology, can reliably produce rPET (recycled PET) with 87% reduction in carbon3
Circular economy beyond packaging
Circular economy is a model of production and consumption driven by the principles of repair, refurbish and recycle.
Where the traditional, linear economy model takes raw materials and makes products to be consumed and then discarded, circular economy aims to extend the life cycle of all products and mitigate waste at every step of the process.
In a working circular economy model, resources flow in closed loops where all waste is repurposed.
The Ellen MacArthur Foundation4 is a
FOOD PROCESSING
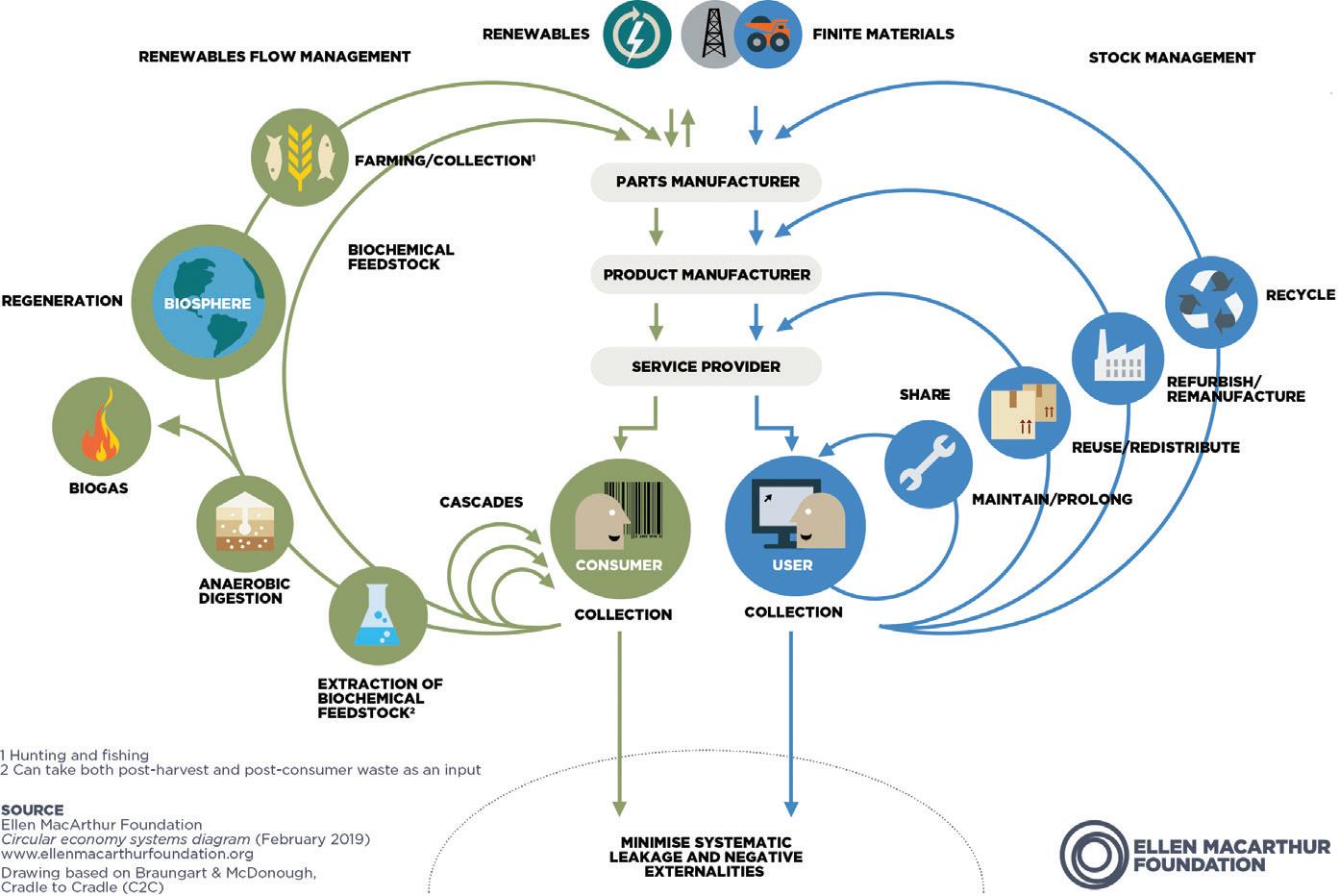
non-profit organisation set up to develop original, evidencebased original research on the benefits of a circular economy. According to the organisation out three principles of circular economy as:
• Eliminate waste and pollution
• Circulate products and materials (at their highest value)
• Regenerate nature
At a time when we are increasingly aware of the finiteness of our resources, a linear economy model, which by nature relies on the availability of cheap raw materials and energy, is increasingly unsustainable.
In the coming years as governments seek to achieve zero carbon, the principles of circular economy will affect all facets of food processing, with developments such as edible food packaging, water recycling irrigation systems, biodegrading waste, prioritising plant biomass. As well as being better for the environment, it also makes economic sense; every industry tries to reduce waste and minimise the consumption of resources. Seamlessly looping resources and waste is, in every sense, the perfect economic model.
Circular economy butterfly diagramellenmacarthurfoundation. org
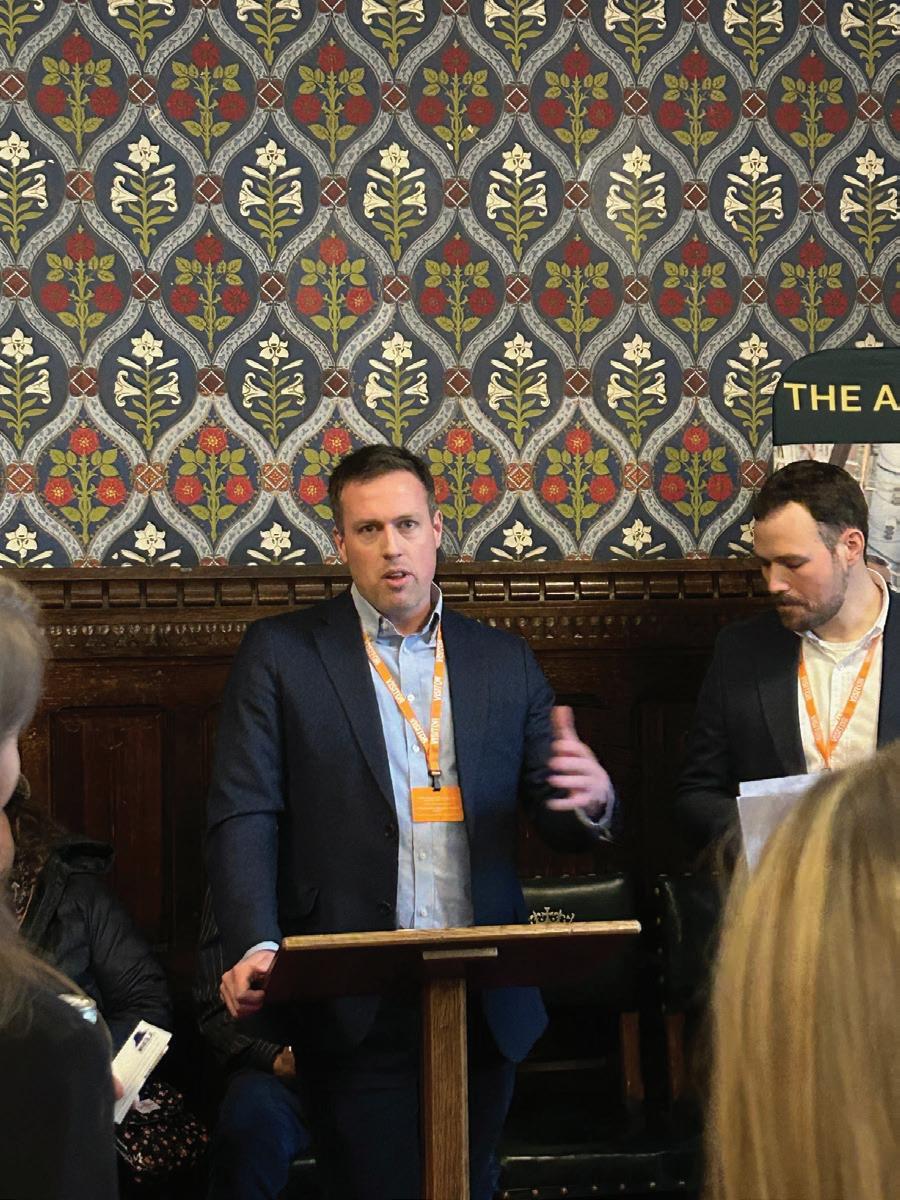
Sam Jones, head of climate and sustainability at Coca-Cola Europacific Partners (CCEP) and Tom Giddings, executive director at Alupro
industries making tangible improvements in line with circular economy principles along the way.
It is worth noting that, to date – unless something remarkable happens between now and this issue being published – no industry has yet achieved a 100% circular economy. Instead, it remains something to strive towards, with companies and whole
You can expect to see more coverage relating to circular economy, in relation Food Processing and other manufacturing sectors, within MEPCA in the coming months. If you are interested in learning more on this topic, links to resources are included below.
1.alupro.org.uk/sustainability/fact-sheets/carbon-footprint/
2. zerowasteeurope.eu/library/how-circular-is-pet/
3. blog.alpla.com/en/press-release/newsroom-recycling recycled-plastic-reduces-carbon-consumption-87-cent/11-23
4. ellenmacarthurfoundation.org/
Top 5 Food Processing Trends for 2025
From health and nutrition to navigating tariffs, MEPCA takes a look at 5 trends that will shape the UK Food Processing industry this year.
Health and nutrition
Whether it drives our food habits or not, we’re all more conscious of health and nutrition. According to the Food Standards Agency (FSA), while there is a correlation between ultra-processed foods (UHPs) and negative health implications, it is important to point out that the link is not supported by a strong body of scientific evidence, and the term UHP is ambiguous of often misapplied. FSA instead encourage focus on the actual nutritional content of our food over how it is produced. However, both these factors are driving consumer-purchasing habits in 2025.
Traceability
In spite of the cost of living crisis, consumers are increasingly aware of the origins of their products and the journeys. For food manufacturers, the challenge is one of global standardisation. The EU is leading the way in traceability, but the credibility of other territories is wanting. Where a product may be produced using a range of ingredients come from a variety of sources and may involve complex supply chains, upholding standards of traceability becomes more challenging. Fortunately, advances in digital traceability systems will make it easier to track and demonstrate the provenance of products, helping companies meet consumer expectations.
Tariffs
Uncertainty around US tariffs is affecting UK manufacturing sector, and food processing is no exception. Whether directly affected by the tariffs, or indirectly due to the effect on global supply chains, a negative impact is expected. However, UK manufacturers aren’t waiting around for the worst to happen; instead they are diversifying their markets, seeking opportunities, locally and globally. Resilience is key, as many companies learned following Brexit and Covid.

Plant-based
A demand for more ethical protein-rich foods is transforming consumer habits and encouraging companies to innovate. Despite this, the plant-based boom that characterised the start of the decade has declined, with several plant-based companies going into administration. The perception plant-based foods being UHP and therefore unhealthy, despite not being entirely accurate in comparison to other processed foods, has been blamed, but market saturation could also be a factor. Plant-based food remains a strong market and an area of burgeoning innovation.
Automation and digitalisation
In line with other industries, Food Processing has been impacted by a dwindling labour pool; and like other manufacturing sectors, it has adopted automation and digitalisation technologies to mitigate this while improving efficiencies and output. From the automation of food production tasks, such as robotic mixing, to automated palletising and conveyors, the food-processing environment is transforming, albeit slightly behind other industries. Alongside this, increasing digitalisation and digitisation is improving quality control, inventory management and supply chain transparency.
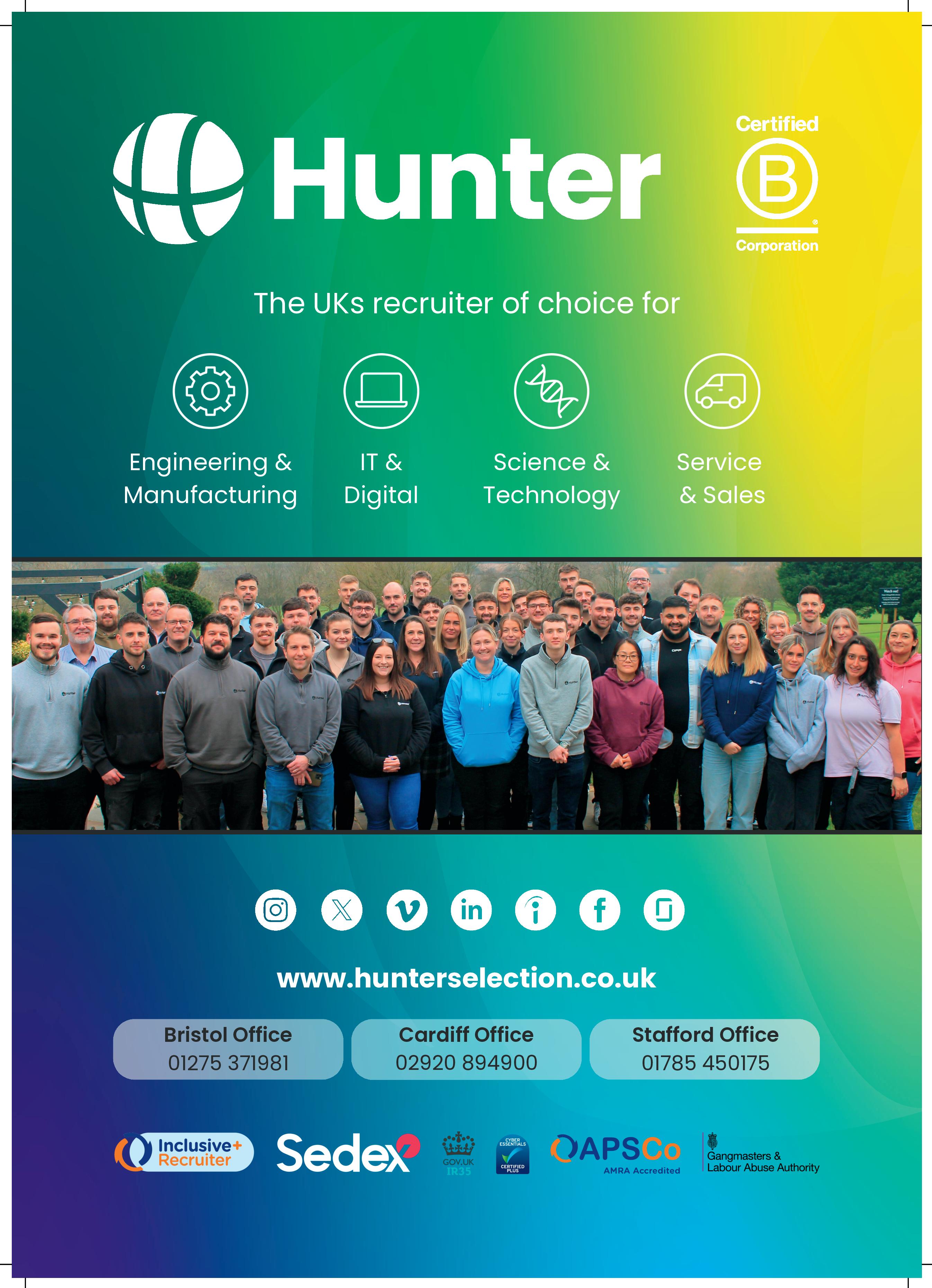
30 Second Mixing Guides From Silverson
Silverson Machines has recently added more 30 second mixing guides to their series of ‘Shorts’ available on the Silverson YouTube channel. These videos quickly demonstrate common mixing problems in a range of applications across food, cosmetics and chemicals.
One of the first ‘shorts’ to launch was a 30 second guide on Mixing Xanthan Gum, which now has over 85,000 views. Many food applications rely on the properties of gums and thickening agents such as xanthan gum, pectin, or CMC (also available in the 30 second series) to give the end product the characteristics the manufacturer desires. Gums such as these provide stability and can improve the “mouth feel” and texture of the end product. However, they can cause a number of problems during the manufacturing process and can be difficult to disperse and hydrate correctly and efficiently.
As highlighted in the mixing guide, one of the most common problems with processing Xanthan gum is the formation of agglomerates when the gum is added to liquid. These agglomerates make it difficult to obtain full yield, resulting in poor quality and inconsistency between batches. Traditional agitators struggle to effectively disperse these agglomerates, as they merely wash the surface, prolonging the hydration process and requiring extensive mixing times. As a result, many formulations contain unnecessarily high levels of gums to compensate for the poor yield, which increases raw material costs.
In the 30 second mixing guide the difference in performance between conventional mixers and High Shear mixers is clearly demonstrated for the viewer. Silverson high shear mixers utilise specialised rotor/stator technology to generate extremely high shear rates, creating a powerful suction effect that continuously draws materials into the high shear zone. This high shear action swiftly disperses powders, disintegrate agglomerates and expose a large surface area to the surrounding liquid, resulting in a

uniform, agglomerate-free solution.
In another of the 30 second guides, Silverson explain how their high shear mixers can be used to manufacture Mayonnaise on a small and large scale.
The mixing equipment used for the manufacturing process has a significant impact on the quality of the finished product. The challenge comes from needing a mixer that can complete several mixing processes. For example, mayonnaise is an oil-in-water emulsion, so the mixer must be able to form a stable emulsion, but it must also be able to maintain movement in the vessel during oil addition when the viscosity begins to increase. Oil addition must be controlled because if it is added too quickly this can cause the emulsion to break. In low-fat formulations where gums and thickeners such as starches are added to enhance mouthfeel, the mixer needs to incorporate and hydrate these ingredients without forming agglomerates. These tasks are beyond the capabilities of conventional
mixing equipment such as agitators or stirrers.
The Silverson Mayonnaise plant can carry out the entire mayonnaise manufacturing process. The egg (either powder or liquid) is added to the vessel and is rapidly wetted out and dispersed. The Mayonnaise plant uses a separate hopper for oil addition and when the oil feed valve is opened, oil is drawn down from this hopper into the aqueous phase at a controlled rate. The aqueous and oil phase ingredients pass directly into the workhead of the In-Line mixer, where they are subjected to intense high shear. This finely disperses the oil into the aqueous phase, immediately forming an emulsion.
As well as Mayonnaise, Silverson High Shear mixers can also be used for the production of other sauces including Hummus, on which there is another 30 second mixing guide.
To see how Silverson high shear mixers overcome these and other challenges, visit the Silverson YouTube channel. youtube.com/@silversonmachines
Processing xanthan gum with a Silverson high shear mixer

Revolutionising the Pumping Process
Peristaltic pumps are favoured in food processing for their non-clogging operation and ease of maintenance. Despite the established design, there is room for improvement, as trusted pump manufacturer North Ridge Pumps demonstrates with its new integrated control function.
When it comes to the dosing, metering or transfer of aggressive chemicals, flavourings, or abrasive solid laden mixtures, there is often only one logical choice – a peristaltic pump.
With innovations in pump technology being few and far between, operators have often been left to create their own control functions, integrate logic and separate custom control panels for pump control.
However, a new locally mounted integrated control function available on the range of peristaltic pumps supplied by North Ridge Pumps is helping to revolutionise pump operation.
Serving users ranging from small-scale start-ups that don’t have the time, expertise or resource to set up and configure additional controls, to non-technical operators where the simplicity in design, operation and adjustment means that users are far more likely to use such equipment without causing damage to their pump or interruption of process.
Peristaltic technology
Peristaltic technology is well known for its ease of maintenance, which can be readily undertaken by non-technical personnel with very little or no training. Its ruggedness due to the lack of internal seals and dry run capability make it very difficult to damage, and its slow working motion ensures it is barely affected by abrasive, dry liquids that contain suspended solids.
Peristaltic pumps offer various advantages over other designs of pumps. Due to their simple hose design, it enables the precise metering of gaseous, viscous, and shearsensitive media, containing particles with ease without the use of valves, or seals prone to blockage, leakage or wear. It is

ideal for liquids ranging from thin syrups, to abrasive tomato paste and aggressive chemicals.
The new control function panel is available fitted and Integrated across the full peristaltic family of pumps and can be installed on both new and existing peristaltic pumps. Specifically, it offers the following functions:
Metering Method: modes can be set to alter how the pump meters from amounts dosed over a set amount of time (timed metering), to volume proportioning to meet a required concentration based on feedback from an external probe, or sensor connected directly to the pump automatically adjusting the volume of chemicals for PH correction.
Operation: start and stop can be controlled remotely via external input such as a float switch on a tank, a control signal from process, or 4-20 ma analogue control directly connected to the unit.
Access & Control: menu functions can have access limited by passcode, or functions hidden, with the unit accessed remotely. It can be controlled by industry leading process control systems such as PROFIBUS®/Profinet /CANbus as well as being IoT capable.
Built In User Interface: eliminating the need for separate Human Interface (HMI), the locally attached display enables full control of the pump via intuitive touchscreen displaying current flow, operating pressure, warnings in case of hose rupture, as well as stopping the pump prior to pump leakage. Should maintenance be required, it visually guides users on how to replace the hose.
Reduced maintenance time & points of failure
Using this type of pump means reduced down time due to its simplicity of design, enabling it to be serviced by users with little expertise in a short amount of time.
Its design eliminates points of failure in processes through the elimination of external accessories as non-return or pressure loading valves are not required, while the predictive flow can eliminate the requirement for an external flowmeter, and the user interface removes the necessity of a control panel.
For more information visit North Ridge Pumps’ website. northridgepumps.com
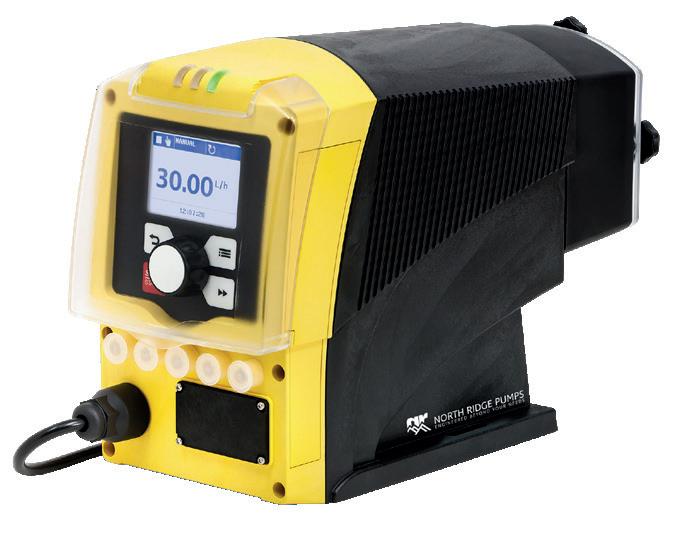
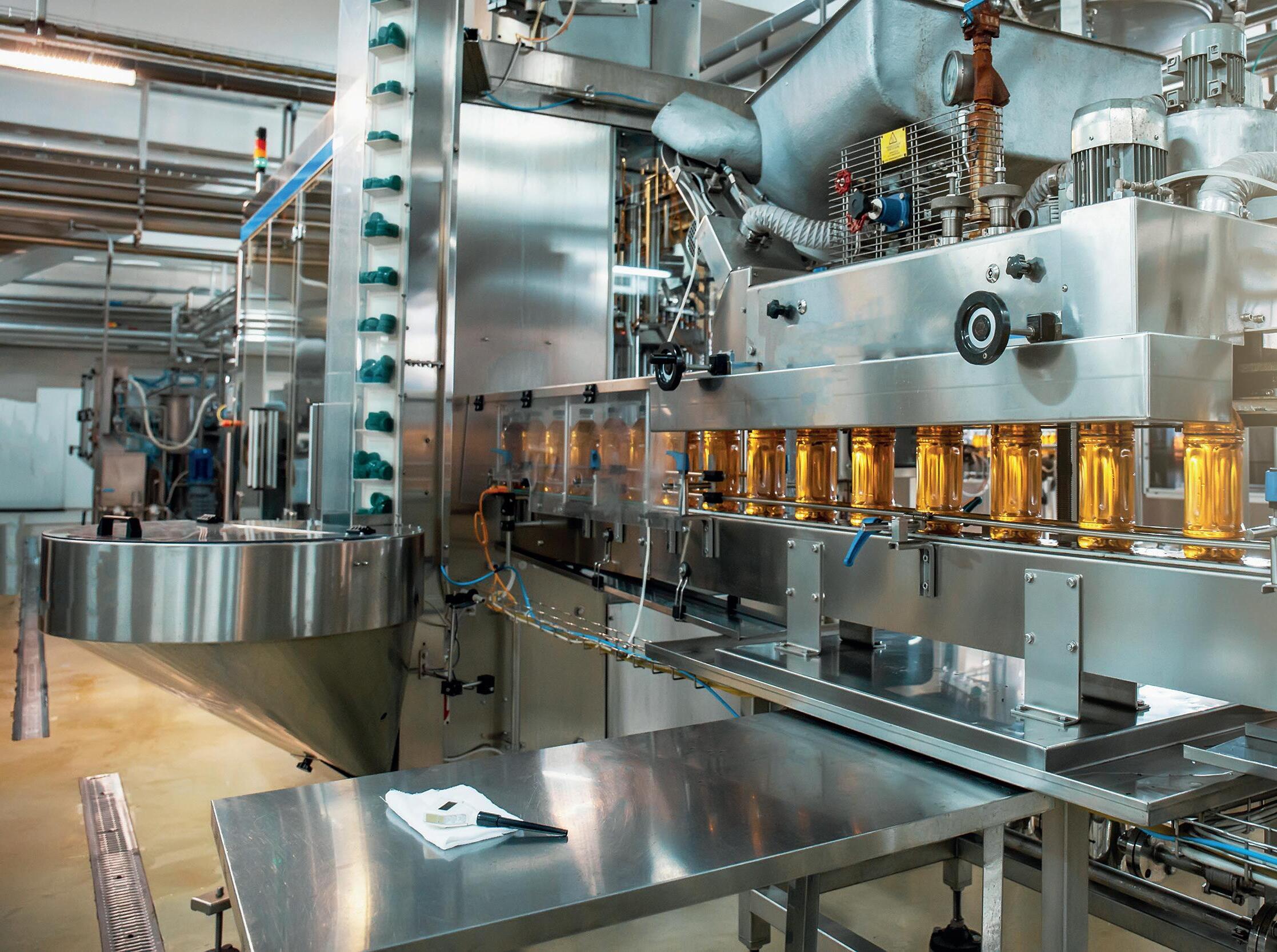
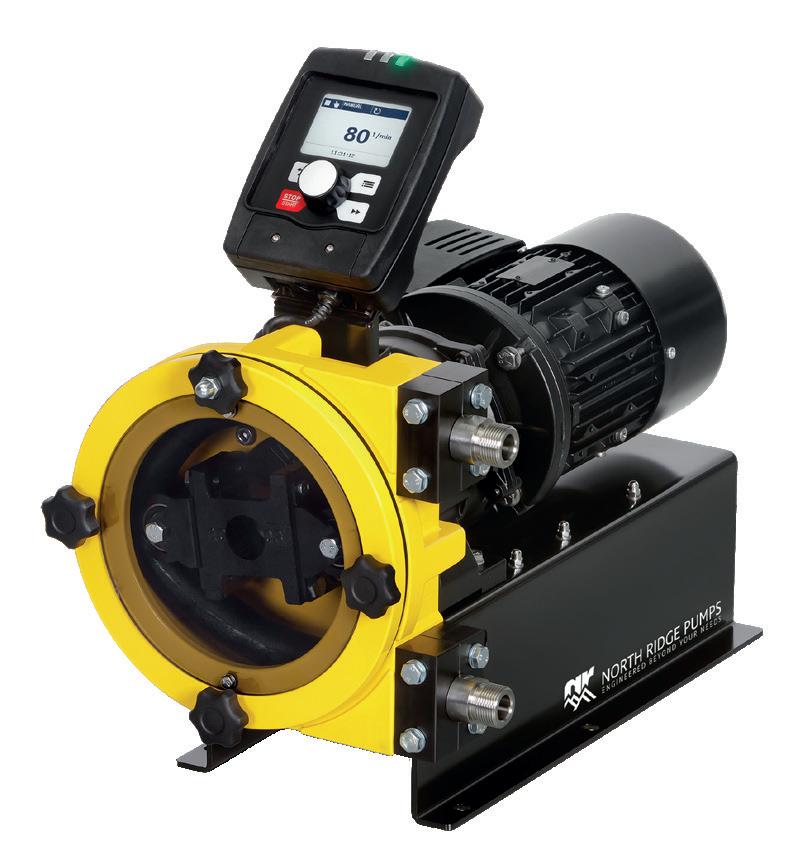
In fact, we have a whole range of non-clog metering pumps which will give you incredibly precise measurement of gaseous, viscous and shear-sensitive fluids without any loss of flow.
We’re North Ridge Pumps, the UK’s largest pump supplier with over 25 years’ experience. We’re expert at specifying exactly the right pump for every client – not just an off-the-shelf, one-size-fits-all solution.
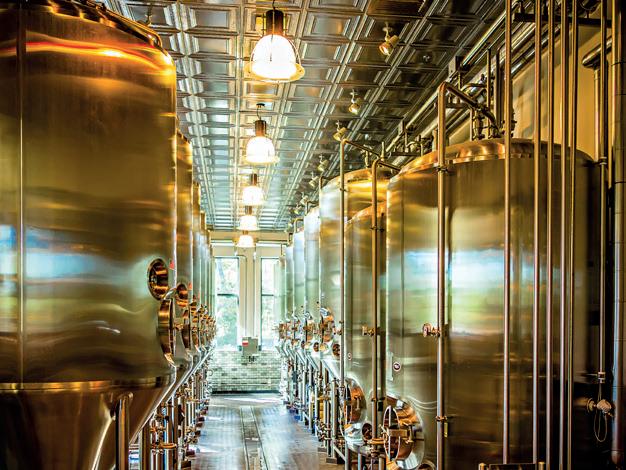
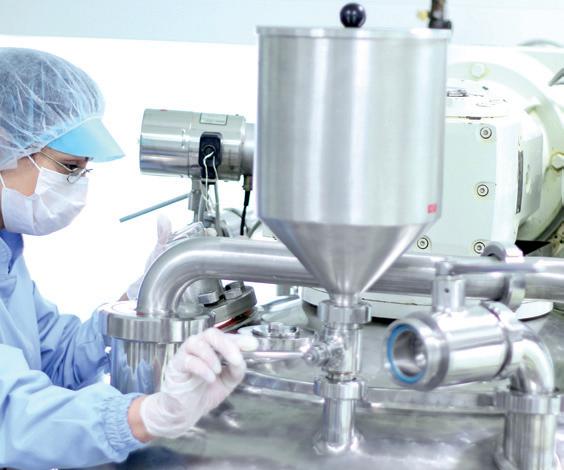
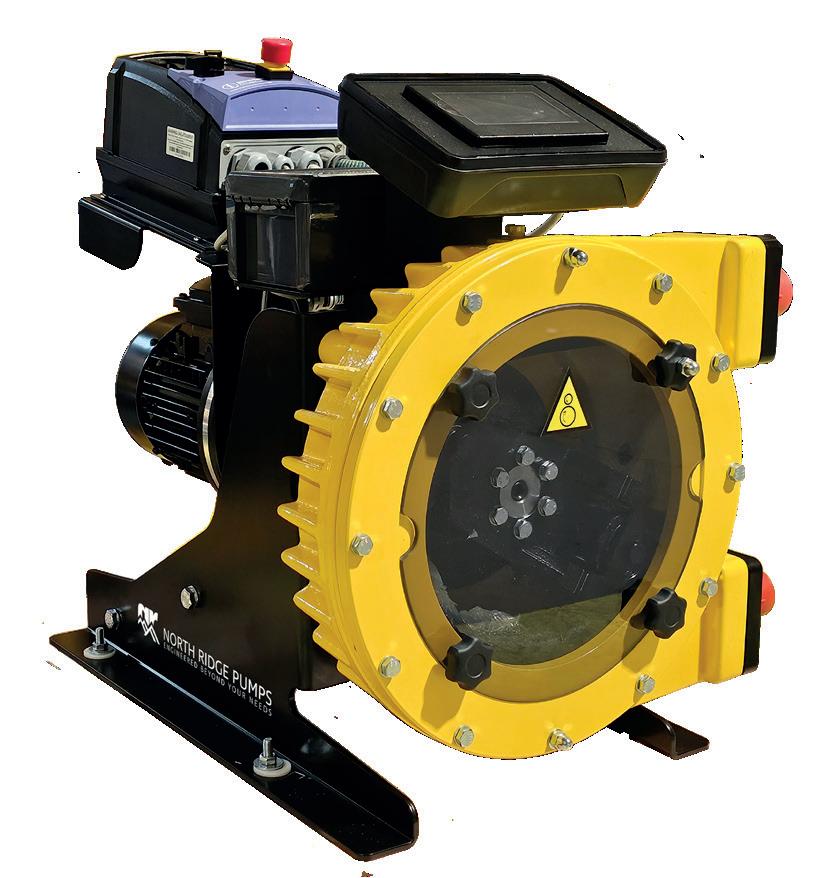
That’s probably why we’ve completed over 2,000 successful projects for clients all around the world. You can read case studies at www.northridgepumps.com
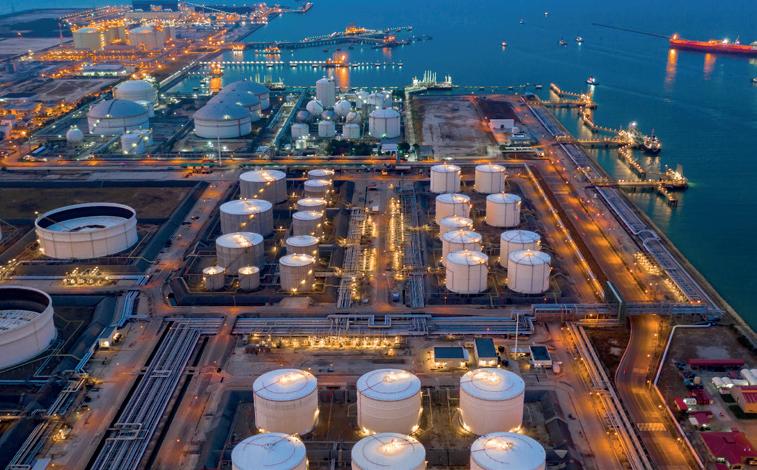

Tracking Actual Costs in Food Manufacturing
Keeping track of actual costs is vital for ensuring profitability, especially in industries like food processing where ingredient prices can be volatile. MRPeasy, manufacturing software specialist, demystifies actual cost tracking and explains how leveraging the right software can make all the difference.
As opposed to standard costs that are forecasted ahead of time to plan financials, actual costs are the real costs incurred during production. These are recorded after the fact and can vary from the estimated standard costs due to ingredient price fluctuations, production inefficiencies, or changes in overhead costs such as utilities. For a food manufacturer, understanding actual costs is critical for pricing products, finding financial sinkholes and ensuring profitability.
Tracking actual costs in spreadsheets
Actual costing in spreadsheets involves meticulously recording the costs of materials, labour and overheads, and tying these to specific products, batches and orders. This process can be highly complex and gets even more complicated as variable expenses fluctuate and a product portfolio grows.
It requires structured spreadsheets that capture the cost factors for each product batch. Calculating labour and overhead costs for a batch, based on the hours put into the production run, is straightforward. However, the complicated aspect of actual costing is associating each product batch with specific ingredient lots and their respective prices.
To effectively manage this complexity, each ingredient lot used in a product batch must be recorded with precise details about the quantity used and the price paid. This detail is crucial because price fluctuations in raw materials can significantly affect the overall cost of production.
For example, if a batch of bread uses flour from two different lots purchased at different times at different prices, the cost calculation must accurately reflect the proportion of flour
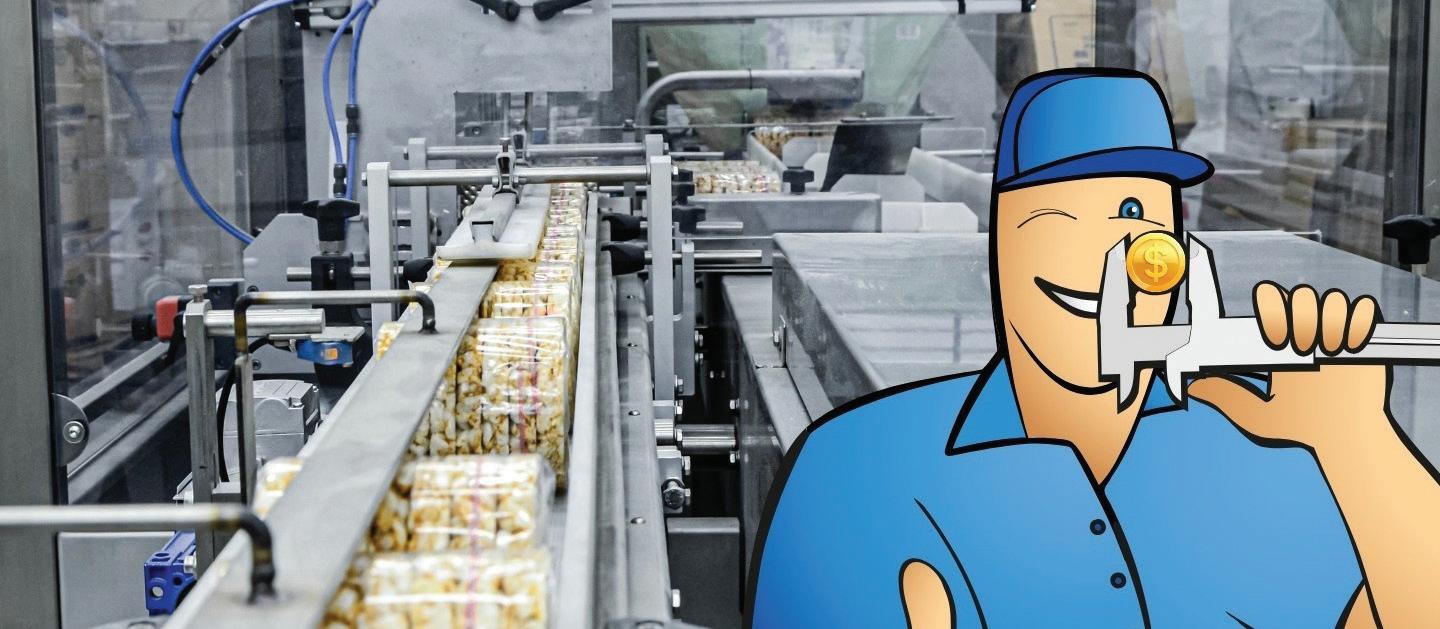
used from each lot to determine the true cost of the bread.
This level of detail in tracking is not just about financial accuracy; it also supports operational decisions such as determining the most cost-effective ingredient lots to use or identifying potential cost savings by switching suppliers. Furthermore, in case of quality issues, knowing exactly which products contained contaminated ingredient lots can be critical for effective response strategies, including targeted product recalls.
However, maintaining such detailed records in a spreadsheet can become unwieldy and error-prone as the volume of data grows. Spreadsheets lack the dynamic capabilities required for real-time updates and integration with other business systems, such as inventory management and procurement, which are essential for modern manufacturers.
Using manufacturing software for actual costing
Growing food manufacturers need specialised software that would enable full traceability and integrate all critical aspects of their operation. Here, manufacturing resource planning software such as MRPeasy stands out. Unlike many other
systems, MRPeasy is a manufacturingcentric solution that caters specifically to the needs of growing manufacturers. This includes cost-tracking capabilities that are often missing from other systems.
From ingredient suppliers through production to the customer, modern MRP software helps manufacturers record each direct and indirect cost, material handling transaction, inspection, and other events, helping company’s achieve full traceability as well as transparency. The software automates much of the data entry necessary for maintaining records and provides valuable reports to make impactful business decisions.
“We are more profitable now because we know exactly what it costs us to make our products, and we can increase or decrease our prices as we go along,” says Karen Addenbrook, Sales Manager at Tait Farm Foods, an MRPeasy client since 2022.
In addition, food manufacturers can use MRPeasy to:
• Manage product recipes
• Get complete visibility into their inventory
• Quickly forecast material requirements
• Automatically schedule production
• Track expiry dates mrpeasy.com
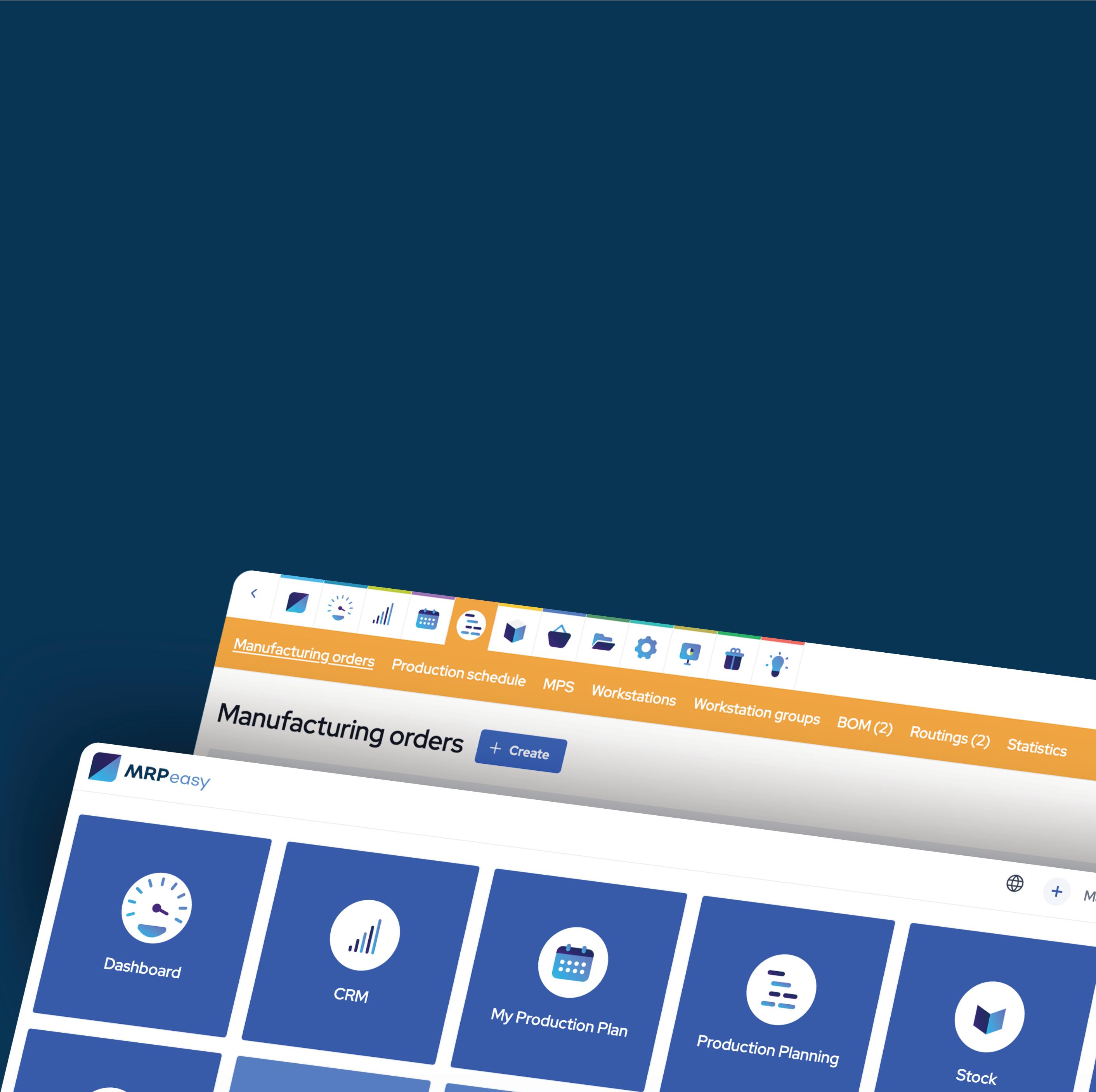
Setting the Standards in Apprenticeships
Apprenticeships are a crucial strategy for bolstering the industry’s pool of skilled professionals. Here, MEPCA introduces FDQ, a leading awarding organisation, specialising in qualifications and training for the Food and Drink industry.
FDQ provides a wide range of regulated and accredited training programmes, including Food Manufacturing, Engineering and Supply Chain Management. Working closely with employers, training providers, and industry experts, FDQ ensures its products and services meet the latest industry standards and regulatory requirements, helping individuals develop skills and progress their careers. FDQ is also an approved Endpoint Assessment Organisation (EPAO), offering independent assessment services for apprenticeships in the Food and Drink industry. The organisation’s EPA services ensure apprentices meet industry standards, providing fair evaluations to support workforce development.
Food and drink apprenticeships in the UK have evolved significantly, reflecting the industry’s needs for skilled professionals. From traditional craft and manufacturing based training to modern, employer-led apprenticeship standards, the sector has continually adapted to changing demands. FDQ has played a key role in this transformation, working closely with industry leaders to develop high-quality qualifications and robust assessment standards. Historically, apprenticeships focused on hands-on learning, but today, they encompass a broader range of skills, including Supply Chain Management and Food Manufacturing. The introduction of End-point Assessments (EPAs) under the Apprenticeship Reform further strengthens the system by ensuring apprentices meet industry benchmarks before certification.
As an approved EPAO, FDQ has been instrumental in upholding assessment standards, supporting both employers and apprentices in achieving excellence. By aligning training with industry needs, FDQ
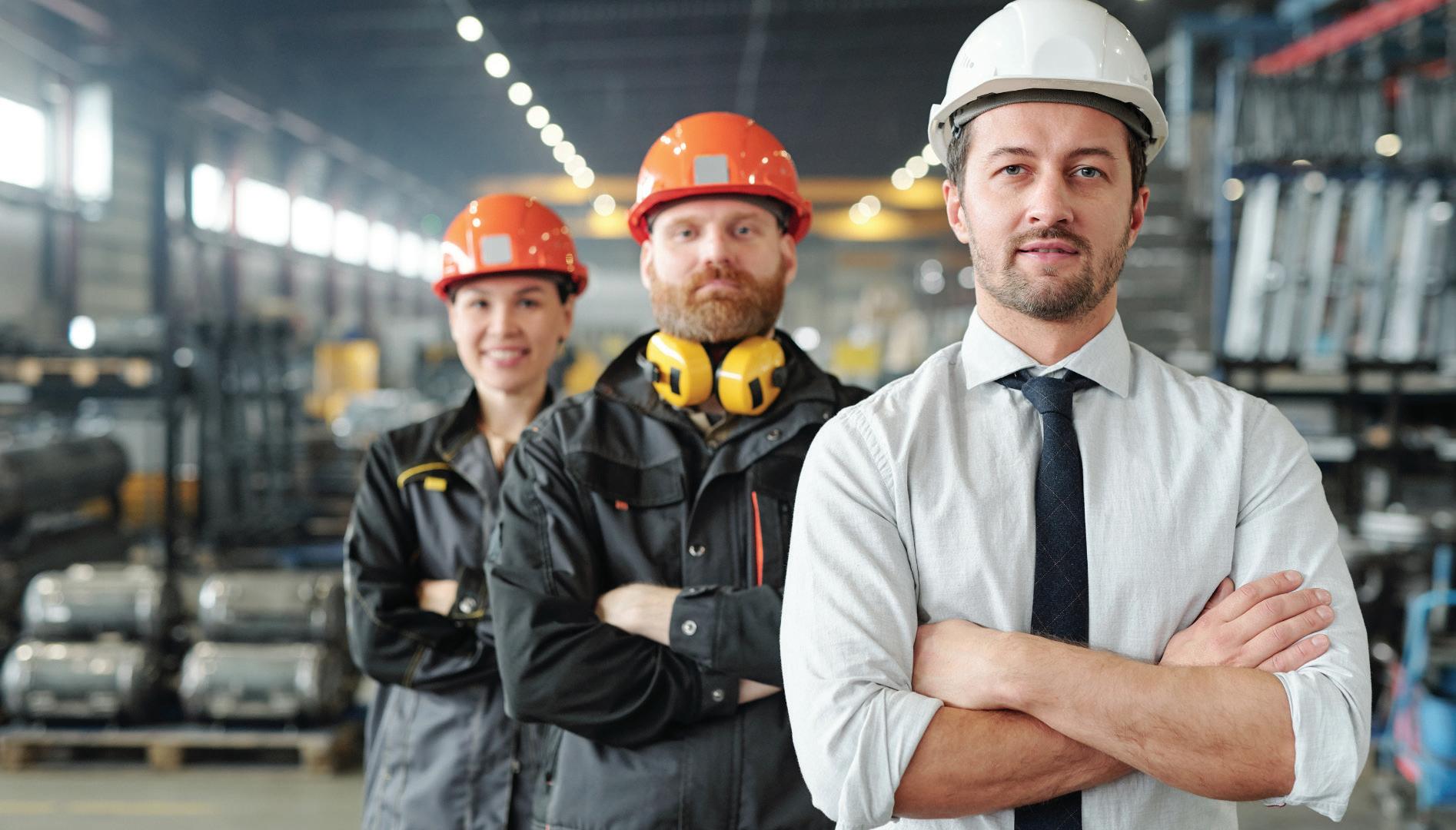
continues to drive the future of Food and Drink apprenticeships in the UK.
FDQ’s Head of Business Development, Matthew Bell, states, “Apprenticeships serve as a valuable pathway in the Food and Drink industry. They combine hands-on experience with structured learning, offering practical skills and industry knowledge. For newcomers, they provide entry points into careers. While for current staff, they offer professional development and career progression opportunities”. Employers benefit from a highly skilled workforce and improved staff retention. By supporting apprenticeships, FDQ plays a crucial role in developing the next generation of Food industry professionals, ensuring that businesses and employees alike thrive in a competitive and growing market.
FDQ provides comprehensive EPA services for Manufacturing, Engineering and Processing apprenticeships within the Food and Drink industry, ensuring apprentices are fully equipped to meet industry standards. FDQ’s manufacturing-tailored EPAs cover key apprenticeships such as Food and Drink Maintenance Engineer, Metal Fabricator,
Food and Drink Process Operator, and Food and Drink Technical Operator. The apprenticeship levy is a tax that all businesses with an annual pay bill over £3 million pay into. This levy pot supports workforce development by enabling businesses to invest in apprenticeship training. Unused funds from a company’s apprenticeship levy pot are returned to the Government after 2 years. For non-levy employers (annual payroll under £3 million), apprenticeship funding provides a costeffective way to train staff. The Government covers 95% of apprenticeship training costs, with employers paying just 5%, and in most cases, full funding is available for apprentices under 21. Employers can access funding via the apprenticeship Service platform and are exempt from Class 1 Employer NICs for apprentices under 25.
FDQ provides expert guidance on industry recognised assessments and qualifications to employers, training providers and apprentices alike. More information is available on the organisation’s website. fdq.org.uk
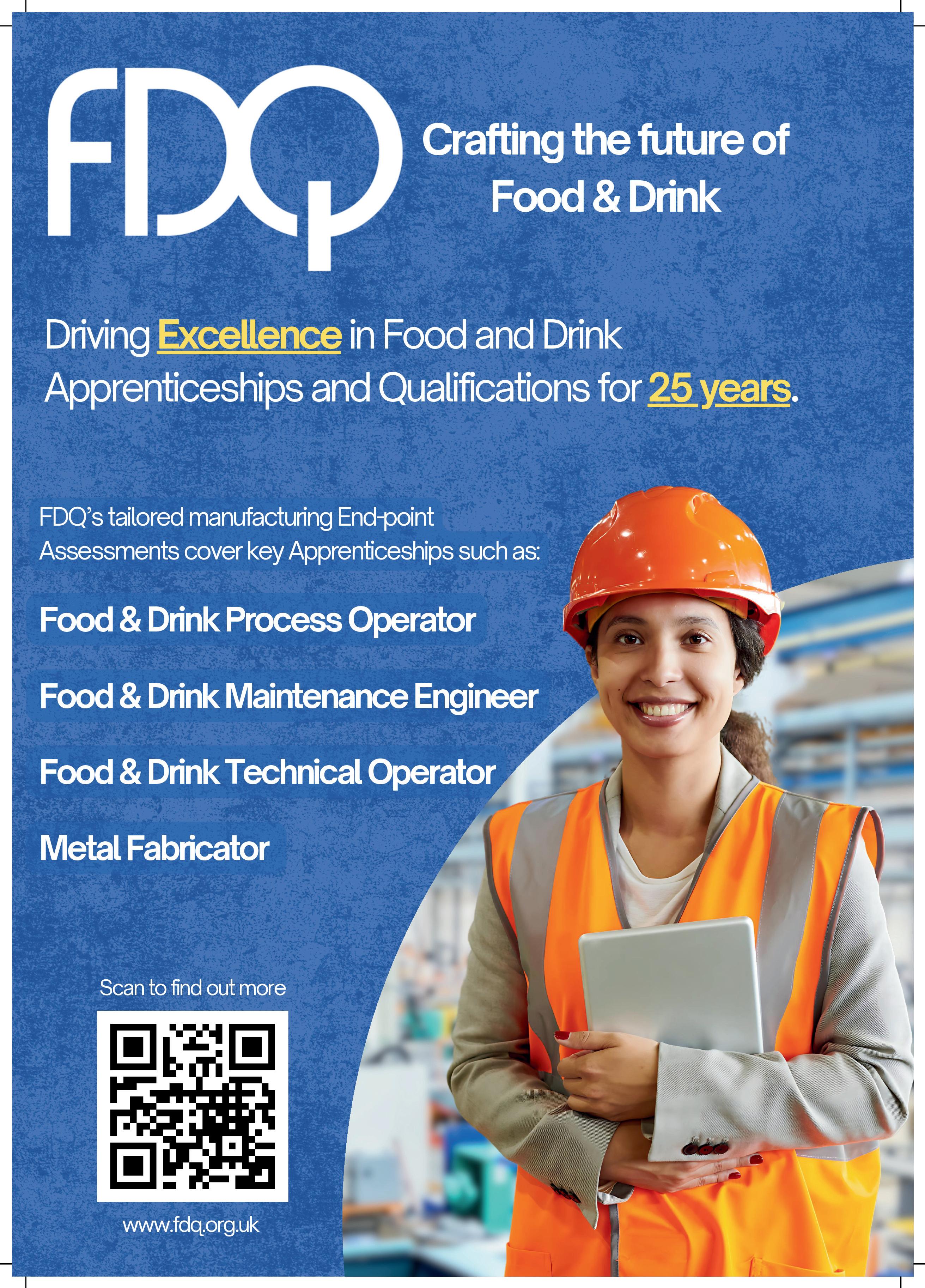
A Sober Look at Automation
Driven by the growing demand for low- and no-alcohol products, food and beverage manufacturers must rethink their production strategies. Here Stephen Hayes, Managing Director of automation and control specialist, Beckhoff UK, explains how automation can help.
According to data from IWSR Drinks Market Analysis, global sales of non-alcoholic and low-alcohol beverages are expected to grow at a CAGR of 6 per cent between 2023 and 2027, with alcohol-free beer being the main driving force. In the UK, the revamp of the alcohol duty is likely to encourage growth in lowalcohol products — drinks below 3.5 per cent ABV now qualify for a new lower rate of duty which, per litre of alcohol, is typically less than half of that imposed on drinks over 3.5 per cent.
In tandem, the Dry January movement has witnessed exponential participation. The first edition in 2013 saw 4,000 people take part. Skip ahead to 2023, and over nine million people planned to give up alcohol for the month. These figures highlight a clear pivot towards health-conscious choices and the desire for alcohol-free options.
How to adapt
This shift presents both an opportunity and a challenge for manufacturers. Producing alcohol-free drinks isn’t as simple as removing alcohol from a recipe — it involves balancing taste, quality and production efficiency. Traditional production methods for alcoholic beverages rely on fermentation, which inherently produces alcohol. Removing it while maintaining the beverage’s flavour profile often requires complex processes like vacuum distillation or reverse osmosis.
Brands like Heineken and Guinness are prime examples of companies leveraging innovation to thrive in the alcohol-free space. Heineken 0.0, for example, uses a proprietary process to brew and remove alcohol while preserving the beer’s traditional taste. Similarly, Guinness gently removes the alcohol through a cold filtration method that
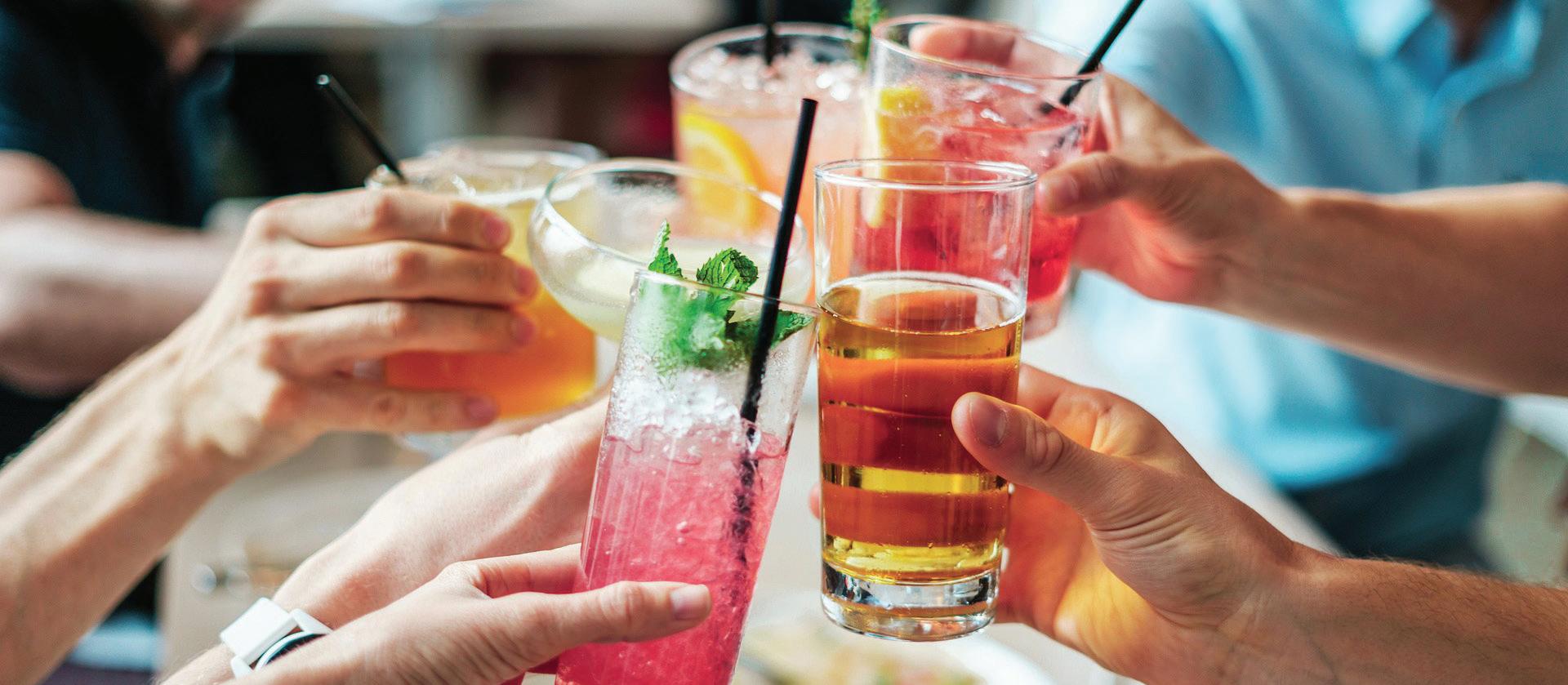
preserves the beer’s taste and character. These brands illustrate the potential for combining innovative production methods with consumer-centric product design to achieve success. However, they also demonstrate some of the key challenges that manufacturers must overcome to make the most of this move towards low- and noalcohol alternatives.
The need for flexibility
Traditional production lines are often designed with specific products in mind. Adapting these lines to produce alcohol-free alternatives requires equipment capable of quick changeovers and multi-functionality.
Automated systems equipped with modular hardware and software can be easily reconfigured to handle different production processes. For instance, a single production line could seamlessly switch between producing non-alcoholic beers, spirits and soft drinks maximising efficiency.
Maintaining quality
Manufacturers must also consider the impact that switching to low- and noalcohol beverages will have on their product range. Technologies like advanced motion control and real-time data analytics ensure precision in mixing, bottling and packaging.
Maintaining consistent quality is critical for alcohol-free beverages, as even minor deviations can alter taste or shelf life.
By using digital twins — virtual models of production lines — manufacturers can go one step further and simulate processes, test recipes and troubleshoot issues without disrupting operations. This accelerates the development of new alcohol-free products and optimises production efficiency.
Finally, alcohol-free drinks must adhere to strict labelling and production guidelines, which often differ across countries. This necessitates adaptable systems for tracking and ensuring compliance.
The alcohol-free trend is more than a passing fad — it reflects a profound change in consumer preferences. Beyond Dry January, demand for low- and no-alcohol drinks is likely to grow year-round as more people prioritise health and wellness. Food and beverage manufacturers must invest in technologies that allow for flexible, efficient and high-quality production.
For manufacturers ready to adapt, the opportunities are immense. The era of zeroalcohol innovation has arrived, and those who embrace it will shape the future of food and beverage production. beckhoff.com/en-gb/
Transforming Drive and Order Preparation
In the following case study, Luxembourg-based food retailer Auchan Retail demonstrates how deploying the right warehouse automation can revolutionise e-commerce operations.
Present in Luxembourg since 1996, Auchan Retail offers various formats of food retail with three hypermarkets, seven Auchan Drive pick-up points, countrywide delivery via Auchan Drive, 16 MyAuchan convenience stores in partnership with Aral, and 3 Mondial Relay lockers. Today, it employs over 1,200 staff.
Auchan Retail operates in 13 countries. To build a competitive and modern retail experience, Auchan Retail places its customers at the heart of all its decisions: discount prices, a wide and diverse product range, quality service, and adaptation to local markets.
The challenge
Since 2006, Auchan Luxembourg has relied on a “master” warehouse in Dudelange, in the south of the country, to prepare and distribute its e-commerce drive-through and home orders; the company also aims to develop in-company delivery. Stocked in four different temperature zones – dry, fresh, frozen and fruit & vegetables – products of all sizes are stored and prepared here, before being dispatched to the various order distribution points.
Automating the Dudelange warehouse is the final building block in a wide-ranging overhaul of Auchan Luxembourg’s e-commerce processes and tools, following a new website, a new ERP a and new WMS (MAGISTOR). The project aimed to densify storage, rationalise preparation and dispatch operations, and reduce hard, repetitive manual work for employees.
After a period of consultation with various companies, Auchan Luxembourg turned to Exotec, attracted by the “all-inclusive” aspect of Exotec’s Skypod system (including the modularity of the system, integration of specific software and machines, and
integrated maintenance).
“We benefited from a 100% turnkey service”, explained Martin Delattre, Logistics Operations Manager at Auchan Retail Luxembourg.
Exotec’s proven experience with other major retail companies, and its ability to understand the business issues at stake in pre-sales, deployment and maintenance, and to provide solutions to the specific problems encountered by Auchan Luxembourg, was also important.
“Right from the pre-sales phase, we were dealing with people who not only had a perfect grasp of the system, but also of our problems, having encountered them at other customers in the sector. This made the workshops very productive”, added Delattre.
The solution
Exotec’s Skypod installation included:
• 37 robots
• 3 picking stations
• 2x 15,300 bins
• 915 bins per hour
• 749 m² floor area.
The results
1. Performance improvement
• Capacity to handle up to 915 bins per hour, optimising order-picking times.
• Centralised picking and restocking operations, reducing inventory errors and improving stock accuracy.
• Flexibility of stations, allowing preparation and reception to be carried out on the same workstations, increasing operator versatility.
2. Reducing hard, repetitive manual work
• Automation eliminates repetitive manual tasks and physical constraints.
• Improved working conditions: pickers no longer have to handle heavy products or work in uncomfortable positions.
• Reduced internal travel for preparation
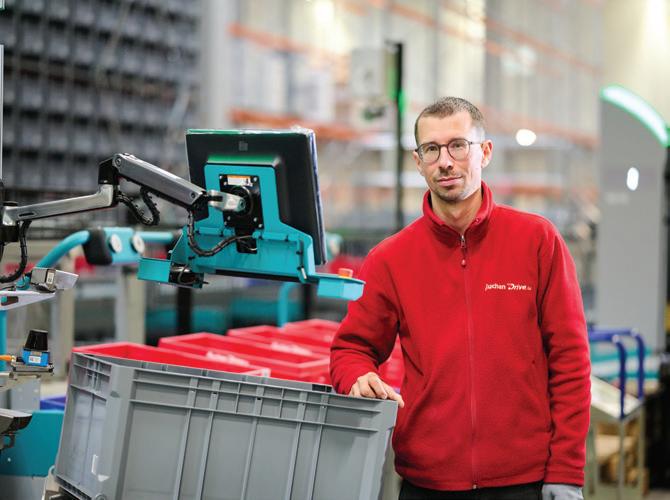
staff, increasing efficiency and reducing fatigue.
3. Turnkey solution
• Complete integration of system, machines and software, ensuring uninterrupted operational continuity.
• Maintenance included, with options such as system cleaning, allowing Auchan to concentrate on its core business.
• Team support and training by Exotec, facilitating rapid adoption of the new system.
4. Storage densification
• Optimisation of available space, enabling an increase in the number of references stored.
• A flexible, scalable system, designed to absorb future stock increases and manage seasonal or promotional variations.
• Use of specific Auchan bins for preparation and delivery, maximising logistical efficiency.
5. Efficient returns management
• Simplified management of customer returns with a multi-reference storage system.
• Automatic prioritisation of returned items for rapid reintegration into active stock.
• Reduce inventory errors and optimise receiving productivity.
Delattre summarised: “Exotec’s turnkey system, coupled with a keen understanding of our specific needs, simplified our transition to automation.”
exotec.com
100 Years of Cycloidal Gears
In a fascinating look at its heritage, Sumitomo Drive Technologies, trusted provider of quality power transmission solutions, examines how modern drive technology originated in 1925 owing to the vision of a German engineer.
Sumitomo Drive Technologies celebrates 100 years of cycloidal gears and thus a century of German engineering that continues to significantly influence the world of drive technology today. Since the invention of the Cyclo® principle by Lorenz Braren in 1925, this technology has stood for precision, reliability and efficiency – qualities that have not only revolutionised industrial automation but also had a lasting impact on robotics.
An invisible revolution: the Cyclo® principle changes the industrial world
There are groundbreaking technologies like the automobile, the steam engine, the printing press, or even the telephone and the internet, which everyone knows and which have had a lasting impact on society. The Cyclo® principle, also known as cycloidal gears, is less visible but has revolutionised the industrial world in the background and is now an indispensable part of modern drive solutions.
The cycloidal gear, the centerpiece of Sumitomo Drive Technologies’ product portfolio, has changed drive technology with its unique design. Unlike conventional gears, the Cyclo® principle distributes the load evenly over several pins and discs. This construction minimizes wear, increases load capacity, and significantly reduces maintenance effort.
Thanks to these outstanding properties, cycloidal gears are indispensable in a variety of industries today:
• Robotics and automation: as backlashfree precision gears for maximum accuracy and efficiency.
• Machine tools and medical technology: for applications requiring the highest precision.
• Intralogistics and production: in autonomous mobile robots and driverless transport systems that require reliable and compact drive solutions.
Historical milestones:
From the Cyclo® principle to a global brand
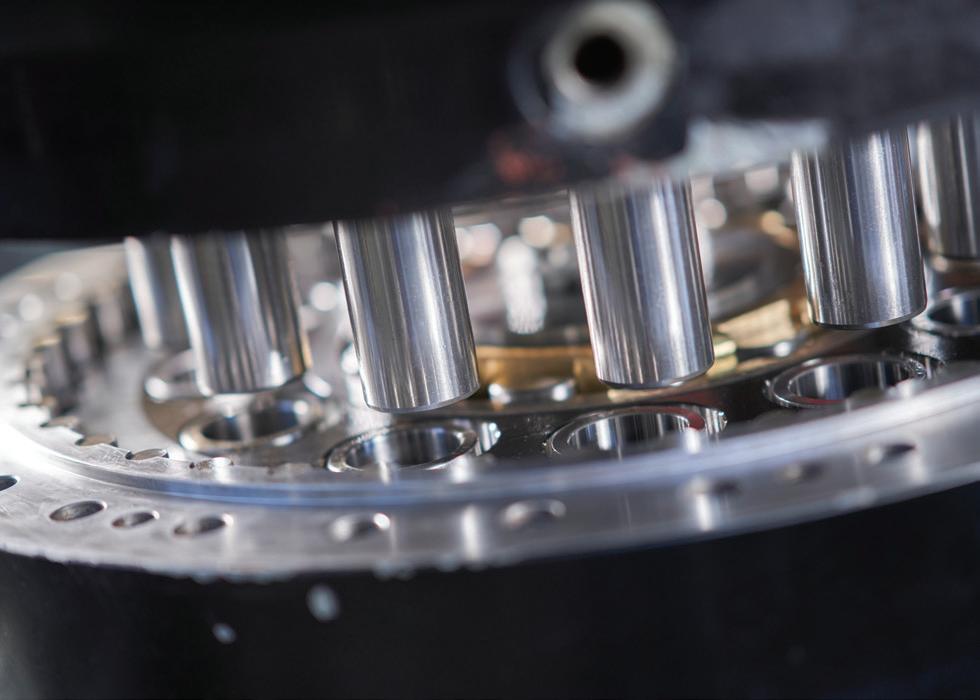
With a spirit of innovation, Lorenz Konrad Braren laid the foundation for the success story of cycloidal gears in 1925. The engineer, born in 1886 on the North Frisian island of Föhr, drew on his experience gained in the USA, Germany, and as chief designer at the company Friedrich Deckel in Munich. Inspired by Deckel’s precise “COMPUR” camera shutter, he developed a new gear technology characterised by the highest precision and reliability.
After Braren’s invention in 1925, his visionary work led to a cooperation with today’s Sumitomo Heavy Industries in 1932, which acquired a license to build the Cyclo® gear in Japan. Despite language barriers, the shared fascination for technology established a lasting alliance.
Today, Sumitomo Drive Technologies unites all activities in the field of drive technology under a recognised brand.
With recent acquisitions, such as the Lafert Group and Invertek Drives, Sumitomo Drive Technologies has evolved from a component manufacturer to a complete provider of motion control solutions. The portfolio consists of precision gears, industrial gears, centrifuges, actuators, motors, variable frequency drives and connected solutions for Industry 4.0.
Looking to the future: sustainability and social contribution
Sumitomo Drive Technologies sees innovation as the key to a sustainable future. The integration of the latest technologies not only enables more efficient industrial processes; it also makes a positive contribution to society and the environment.
The corporate culture, characterised by a passion for technology and a strong team spirit, offers room for continuous development. The needs of customers always remain in focus – with customised solutions for the challenges of modern industry.
“We are proud to have been moving and improving industrial processes worldwide for 100 years. This anniversary is a milestone that underlines both our innovative strength and our commitment to quality and sustainability,” says Florian Butzmann, CEO of Sumitomo Drive Technologies EMEIA.
You can find more information about the history of the Cyclo® principle on the website below.
cyclo100.com
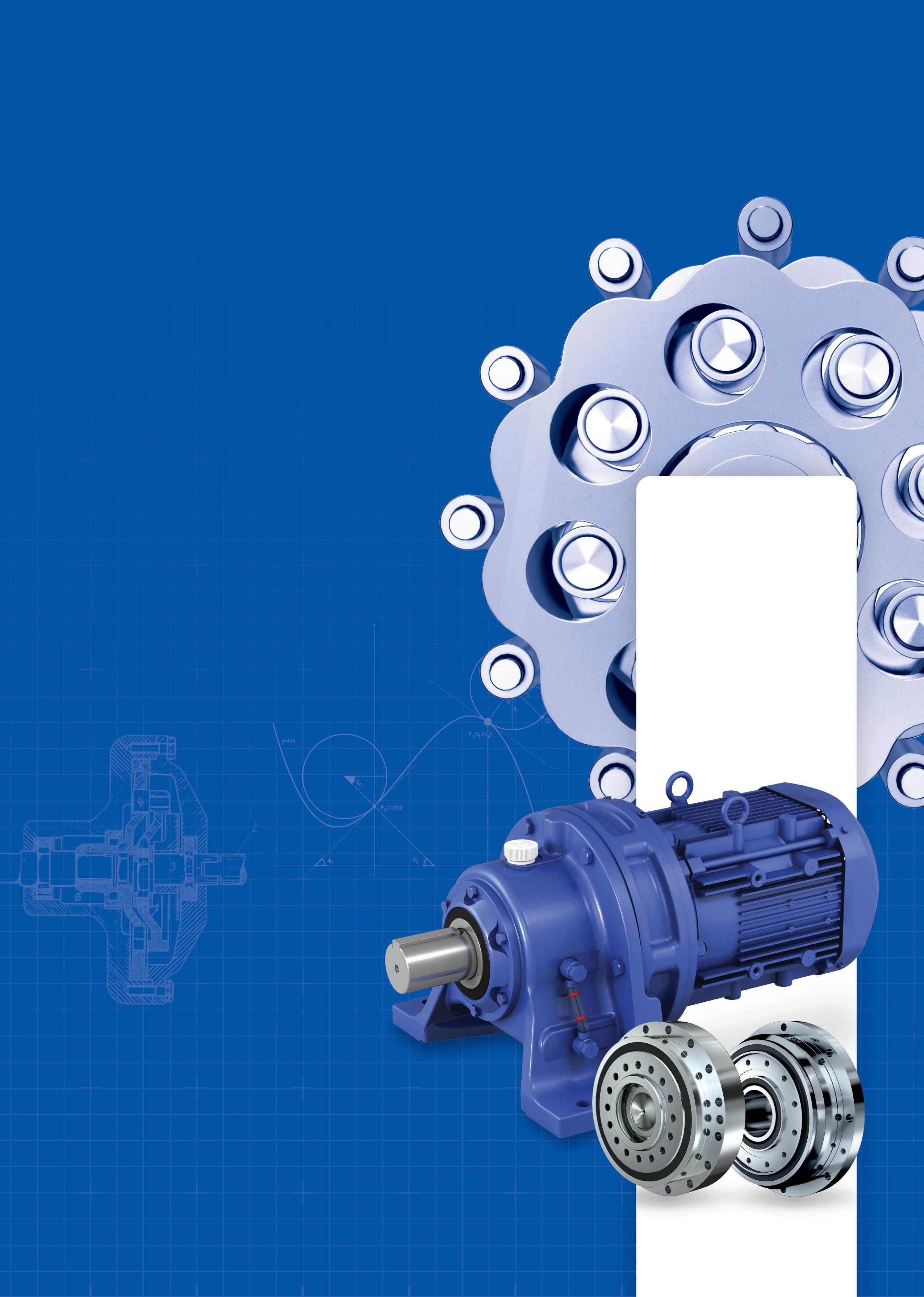
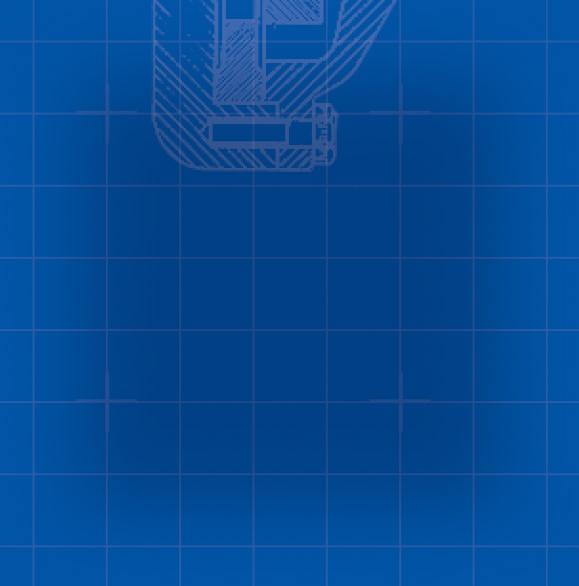
Flexibility Meets Functionality
STOBER introduces the new compact SB6 drive controller for stand-alone applications, designed for engineers and manufacturers requiring precision and flexibility in motor control.
Abrand new addition to the STOBER range, the SB6 stand-alone device is suitable for applications with up to four axes and is characterised by its excellent control performance. The extra-compact, economically attractive drive controller features numerous configuration options, which enable perfect motion control via CiA 402 and PROFIdrive. The SB6 is designed with manufacturers of special machines in mind who need to react flexibly to the changing requirements of their clientele.
With the new SB6, engineers will always have the right drive controller at hand for applications with one to four axes. The stand-alone solution has numerous configuration options. The series is available in three sizes for low to medium power ranges. Both linear and rotational synchronous servo motors and lean motors can be controlled.
The new controller is particularly impressive due to its compact dimensions: it fits into control cabinets with installation depths as low as 210 mm. The drive controller can also be extended by the safety standards STO and SS1 via Fail Safe over EtherCAT (FSoE) and PROFIsafe up to SIL 3, PL e (category 4). A safety module
for control via digital inputs and outputs is also available. The SB6 is available with an optional operating unit consisting of a text display and buttons.
Another special feature is the number of digital and analogue inputs and outputs. As such, STOBER offers a functional, flexible drive controller that companies can use in various applications. For fast automated commissioning and uncomplicated servicing, an SD card can simply be inserted into the drive controller as an application memory, allowing configurations to be transferred.
In combination with the One Cable Solution (OCS) and EnDat 3, the new SB6 reliably supports cable lengths of up to 100 metres. STOBER developed the hybrid cable together with encoder manufacturer HEIDENHAIN. In combination with its geared motors, STOBER offers a fully coordinated system from a single source. For connection to PLC or Motion Controller, a firmwarebased EtherCAT and PROFINET interface is standard.
Concludes Martin Preece, Head of UK
Subsidiary: “If you’re looking for a powerful drive controller with outstanding control performance that can be configured flexibly for individual solutions, look no more!”
For more information, please visit STOBER’s website. stober.co.uk

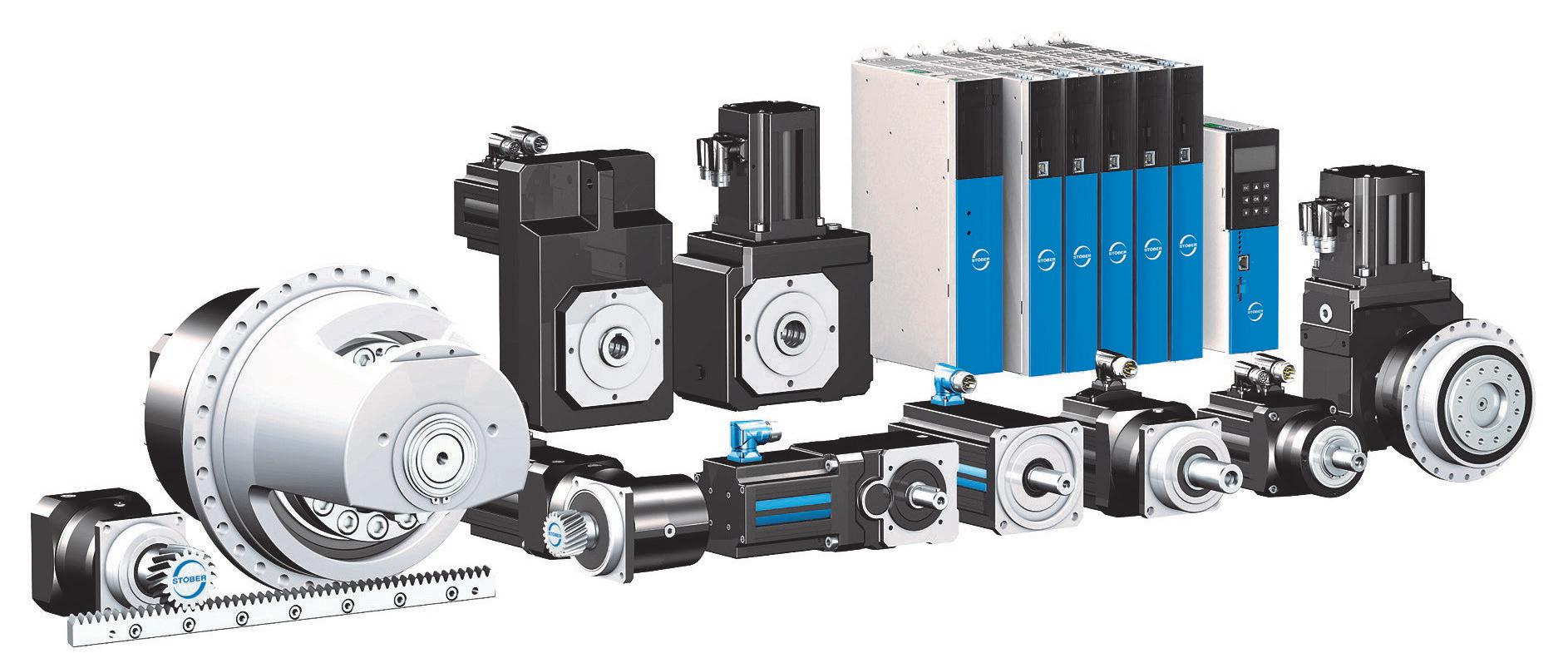
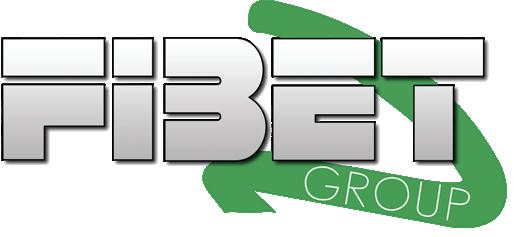
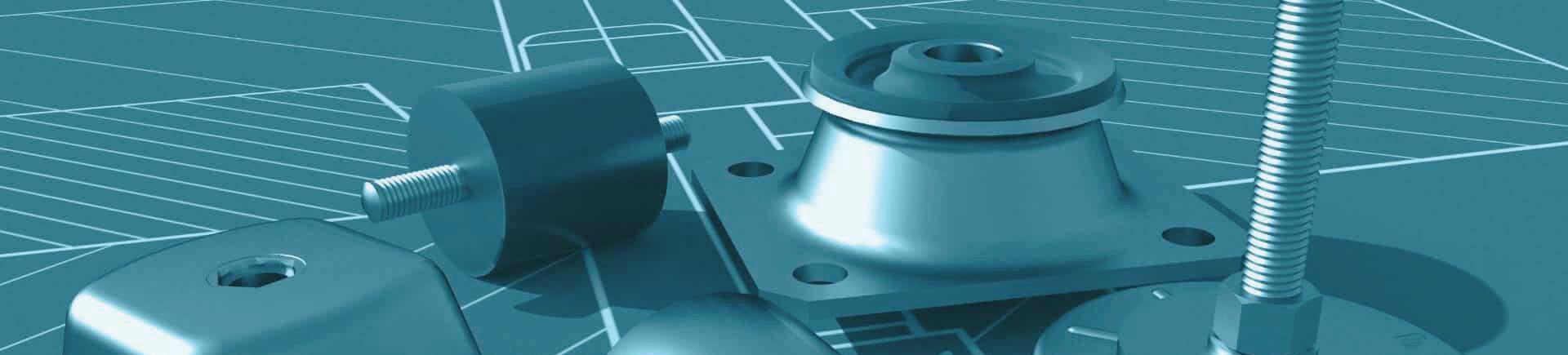
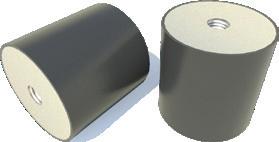
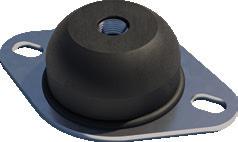

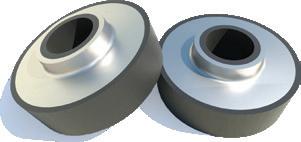
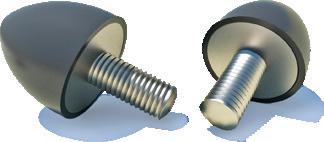
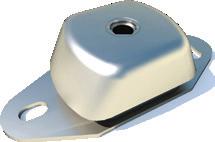
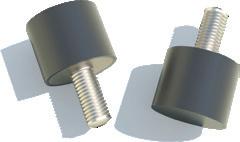
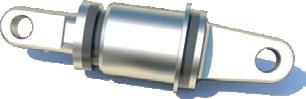
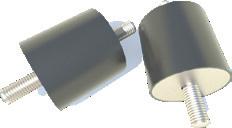
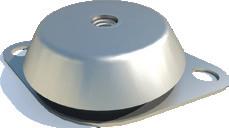
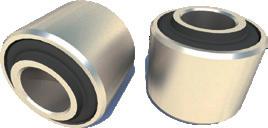
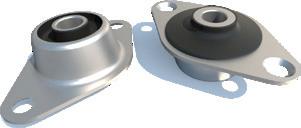
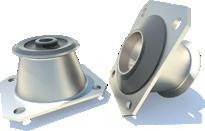

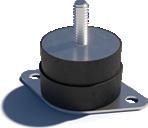
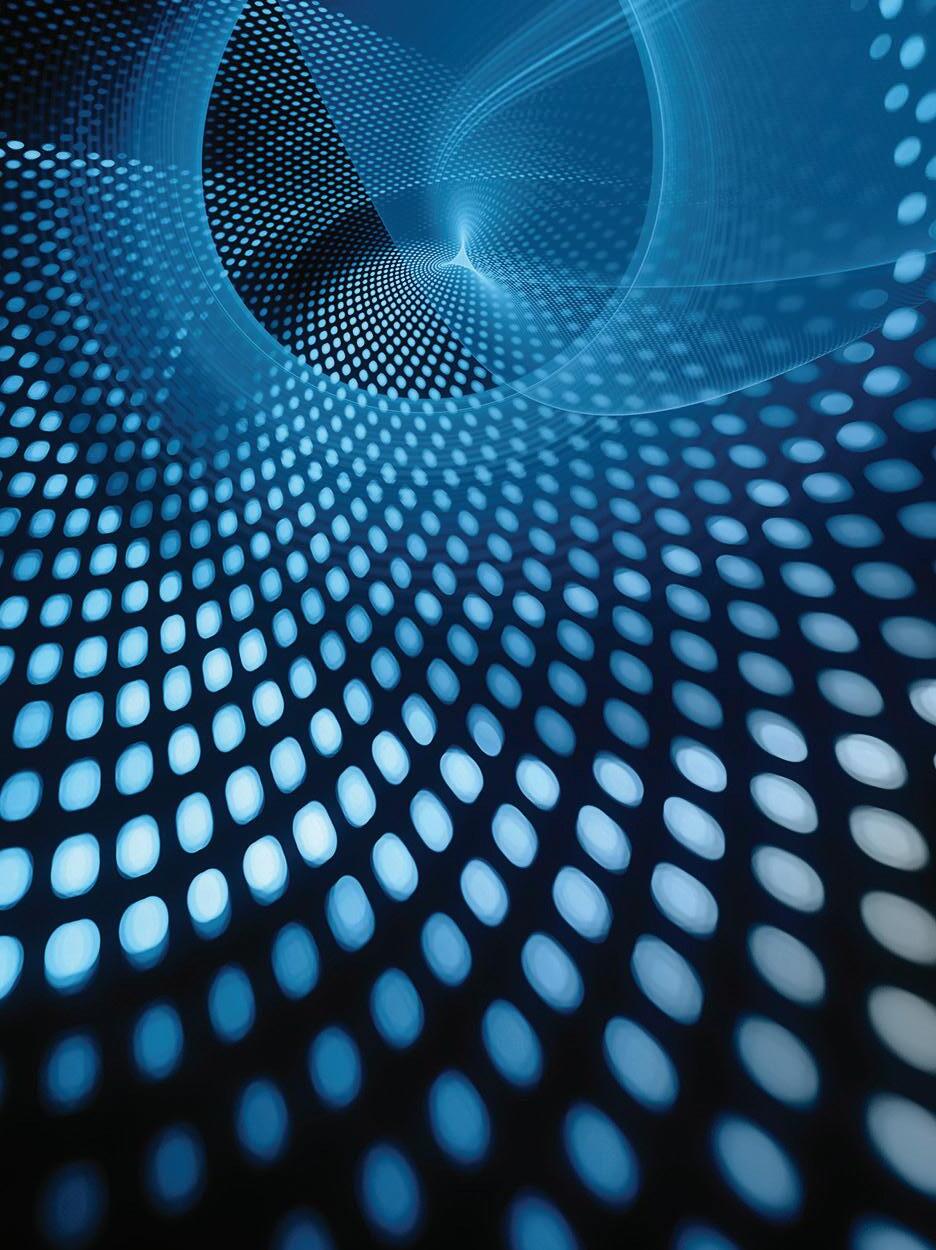
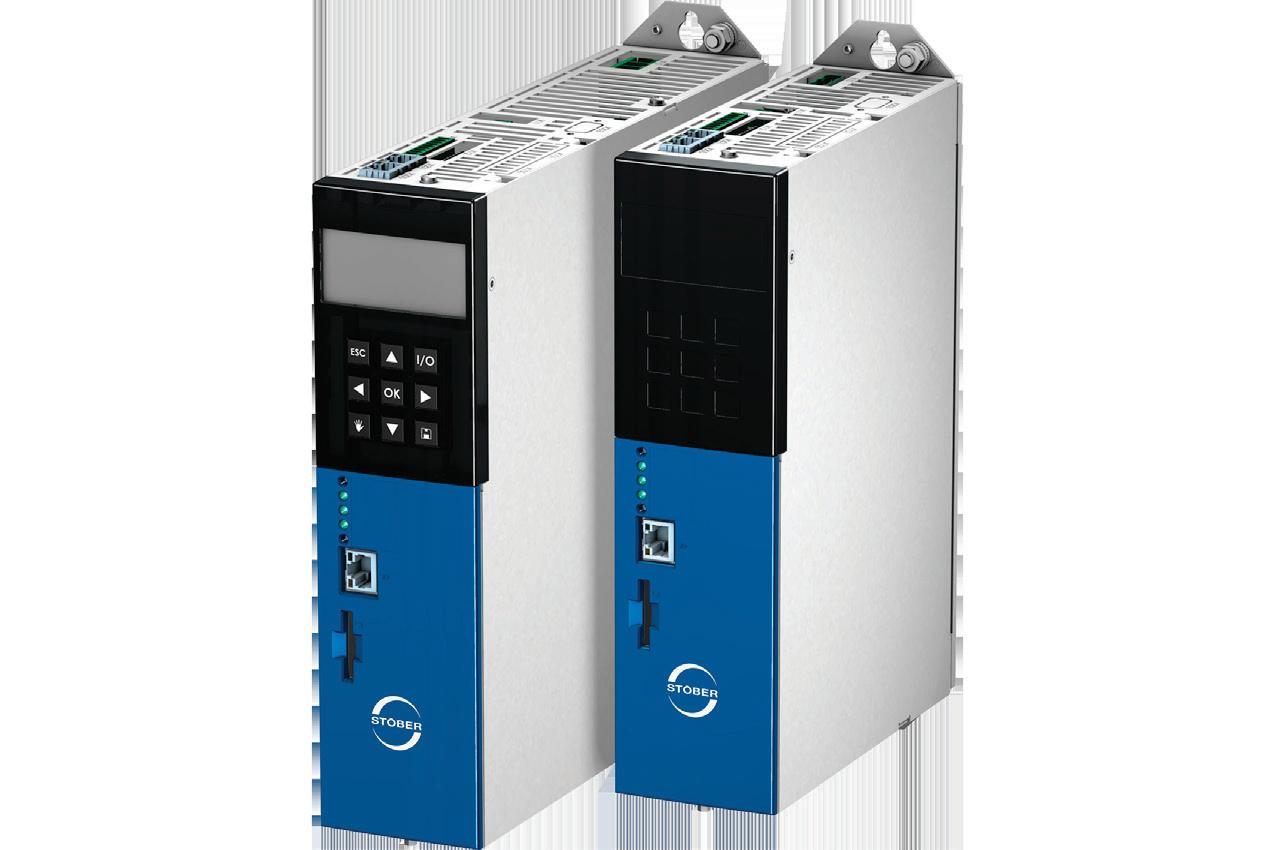
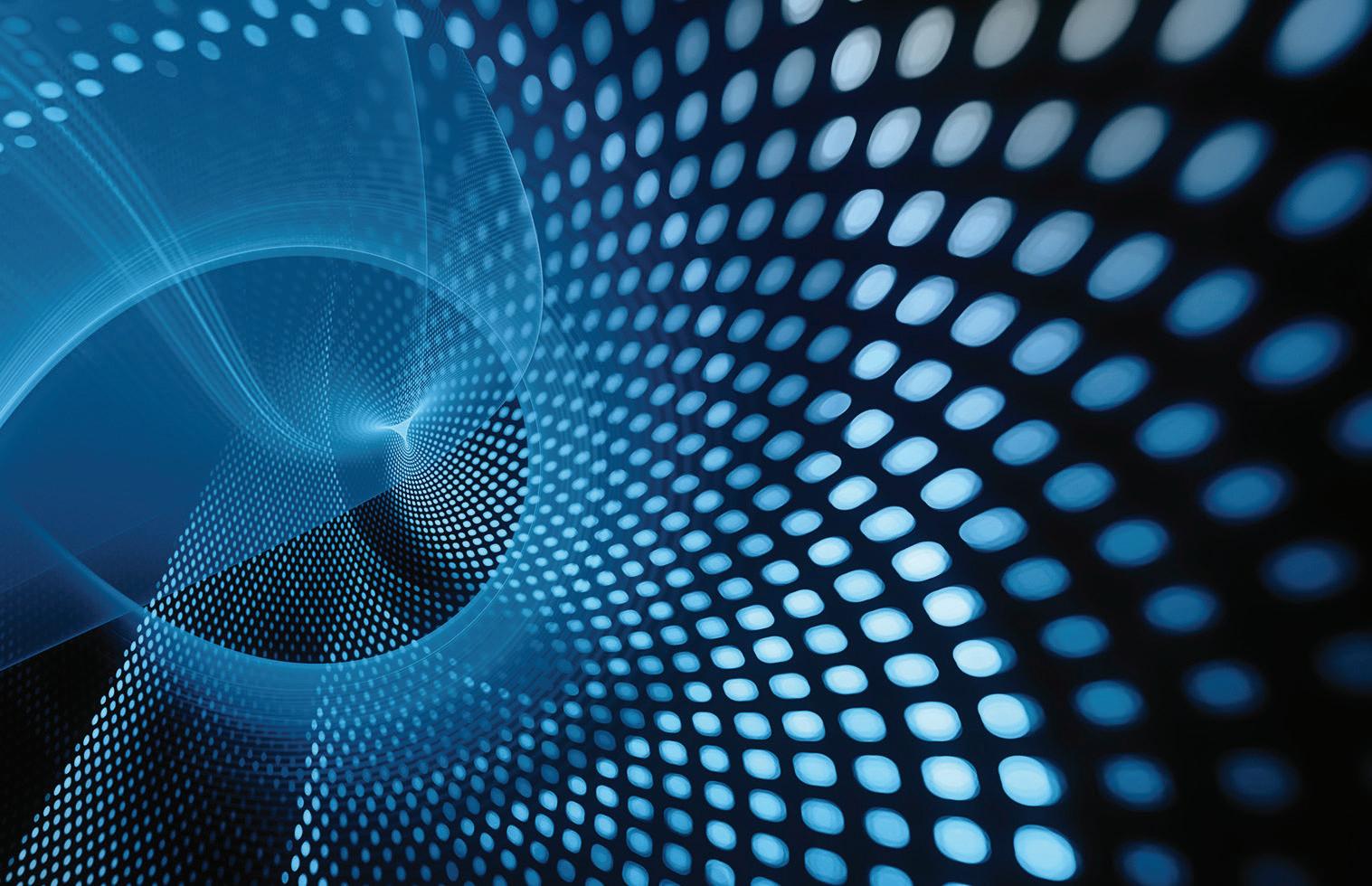
The Importance of Switch Customisation
Switchgear manufacturer Kraus & Naimer shines a light on the growing demand for flexible switch solutions before demonstrating the benefits of bespoke switch enclosure design.
The range of switch applications is vast and ever changing. For manufacturers today, enabling customers to personalise a switch with a variety of add-ons and choice when it comes to an enclosure, including the size, the material used, and the number of switches/devices contained within it, is a must.
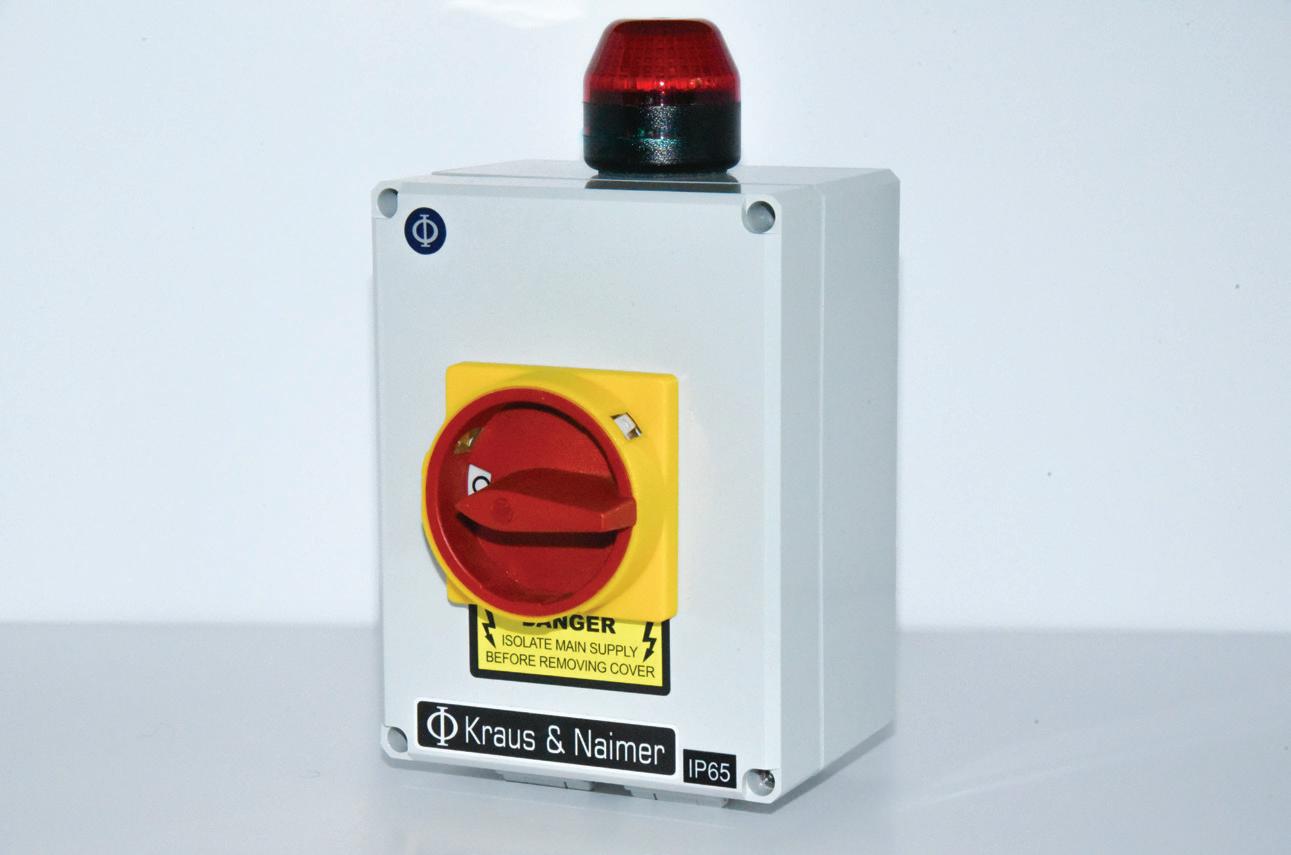
The ability to combine multiple devices in one enclosure can save installation time and is useful where space is of a premium, which is often the case in busy production facilities. It can also provide a more cost-effective overall solution.
When selecting an enclosure for switches, it is important to understand the environment in which the equipment will be located and what protection is required.
In food processing, the dairy industry, or anywhere hygiene is of concern, stainless steel enclosures are often the preferred choice. Not forgetting that where protection against liquids or fine particulate matter is needed, equipment with an appropriate IP rating to match is crucial.
For extremely harsh environments, where equipment may be subject to heavy impacts, e.g., mines, metal enclosures are recommended, or an IK10 rated GRP enclosure may also be suitable. For general industrial applications (e.g., packaging, assembly factories or warehousing) often plastic enclosures are sufficient, however, it may also be necessary to consider UV resistance or protection from chemicals. By factoring in the environmental conditions,
equipment size and compatibility, and the appropriate NEMA (National Electrical Manufacturers Association) accreditation or IP ratings, a company can select appropriately.
Specialists in bespoke switch assemblies
At Kraus & Naimer, flexibility is a core competency. Knowing that every application has unique requirements, the company not only offer standard switches but also tailored solutions for specific needs.
The sales team at Kraus & Naimer was recently approached by a customer to provide a bespoke solution for their machine control application.
The requirement was for a lockable 20A 2 pole Off-On switch with a momentary start position and spring return to the On position. A signalling beacon was also required, both to be housed in a suitably sized enclosure with a captive hinged lid. The environment where the assembly was to be located was not particularly abrasive, so an IP65 polycarbonate enclosure was considered suitable.
Although not part of the Kraus & Naimer standard product portfolio, this is the type of requirement that the technical sales and assembly teams are adept at providing solutions for.
Utilising one of their high-quality single hole panel mounted 20Amp switches from the CA10 range, the technical team were able to source an appropriately sized polycarbonate enclosure, offering the facility to provide a hinged lid along with the requisite signalling beacon. Once the designs for the assembly were complete, including drawings of the layout of the switch and beacon in the enclosure, the job was handed over to the skilled workshop team to assemble and ship out.
The complete assembly saved the customer time and effort in sourcing their own components and putting the assembly together. They were simply able to mount the enclosure adjacent to the machine, complete the cabling necessary between the machine, the incoming power supply and the signalling beacon with little hassle, safe in the knowledge that the assembly reflected the experience and expertise of the Kraus & Naimer team.
With its technical department and workshop based in Newbury, Kraus & Naimer is able to design and supply a variety of customised enclosed control switches & mains isolators, tailored to a customer’s specification and usually on a quick turnaround.
Krausnaimer.com/gb_en





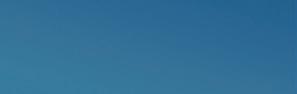

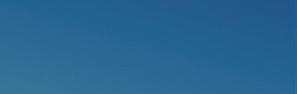
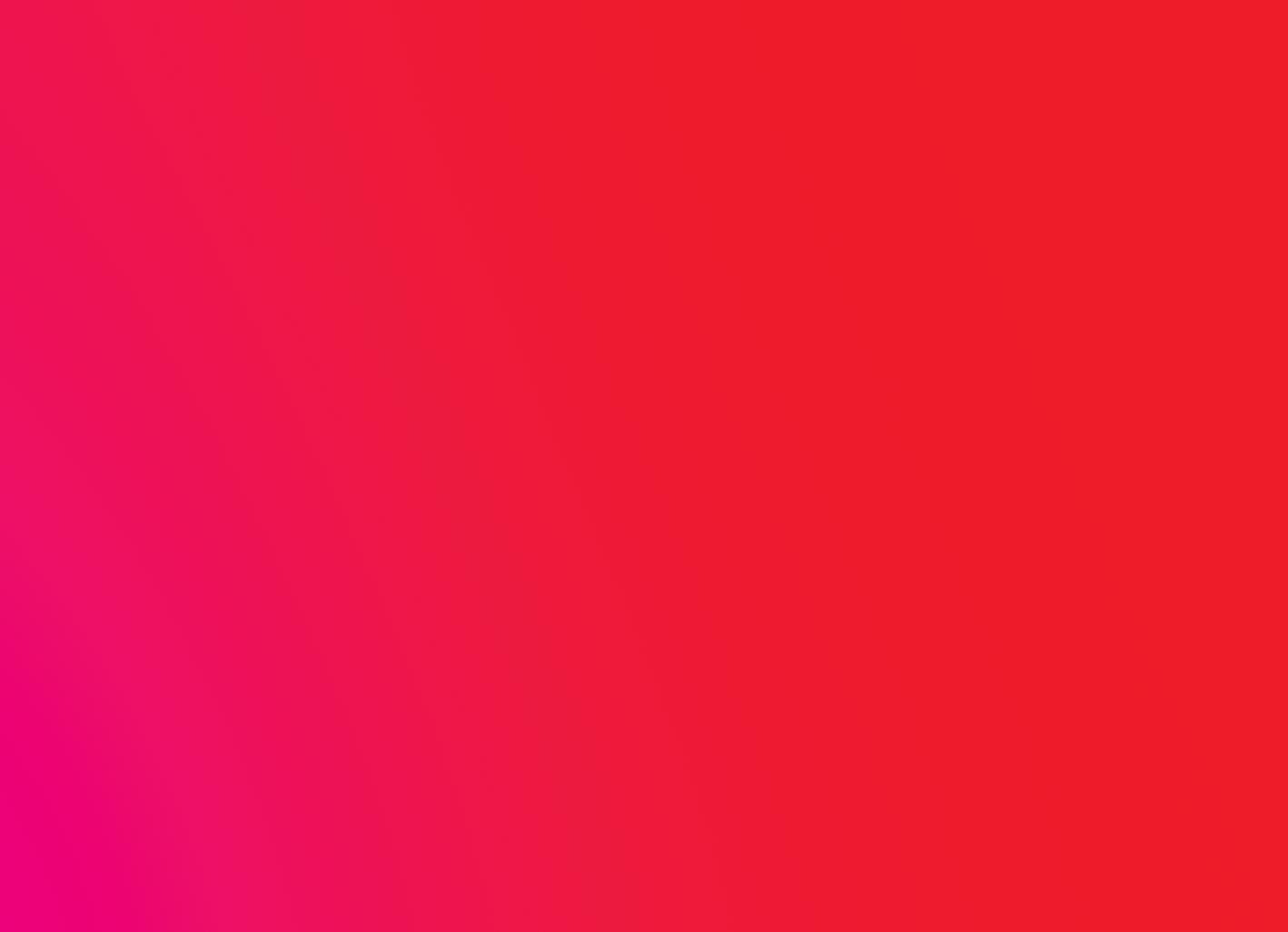


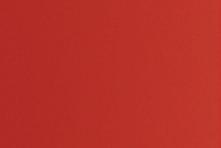
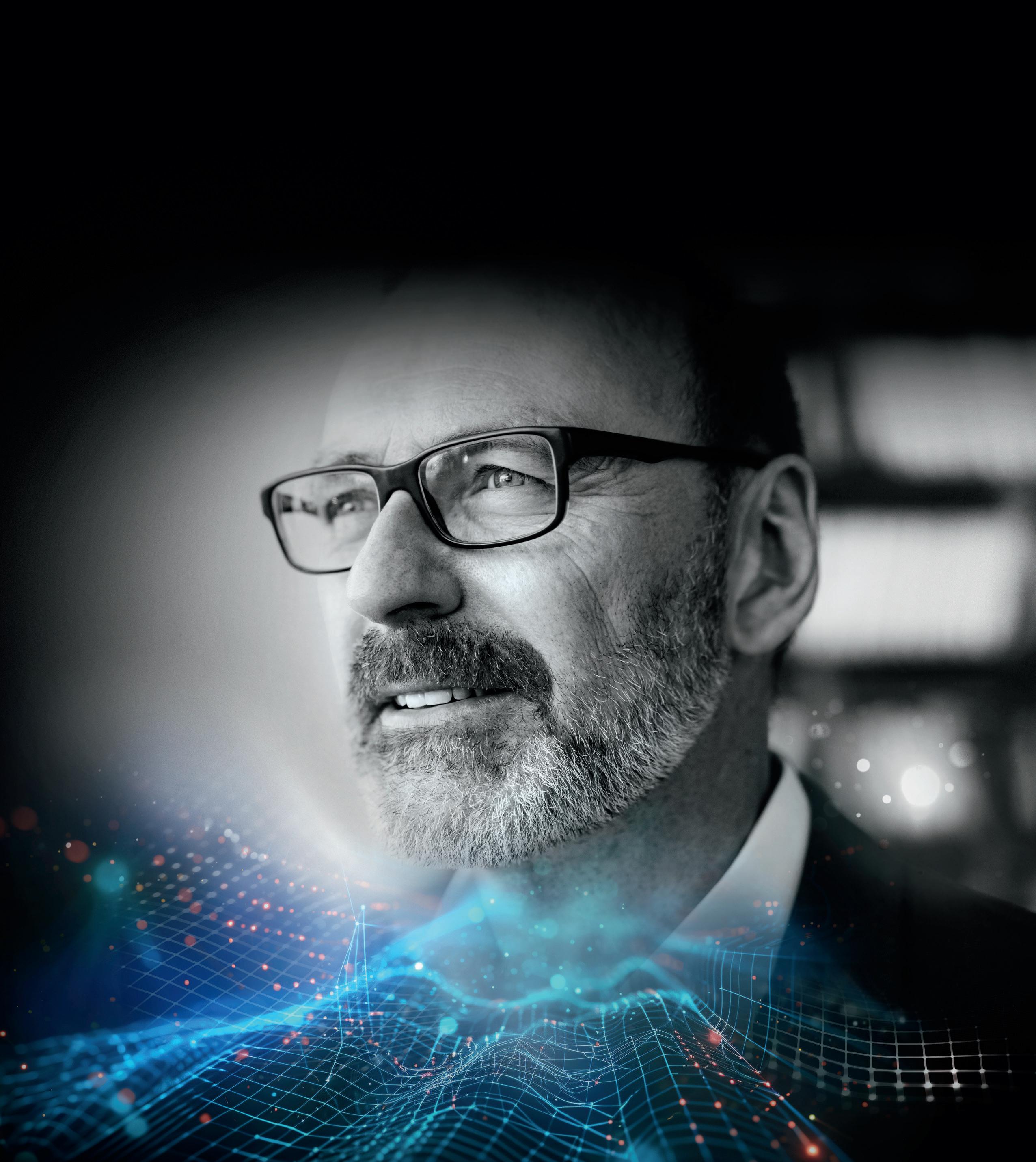

Revolutionising Machine Building
In this optimistic look at the year ahead, Colin Cartwright, Director of Business Development at Murrelektronik Canada, examines how machine building is becoming a smarter, sustainable and collaborative industry.
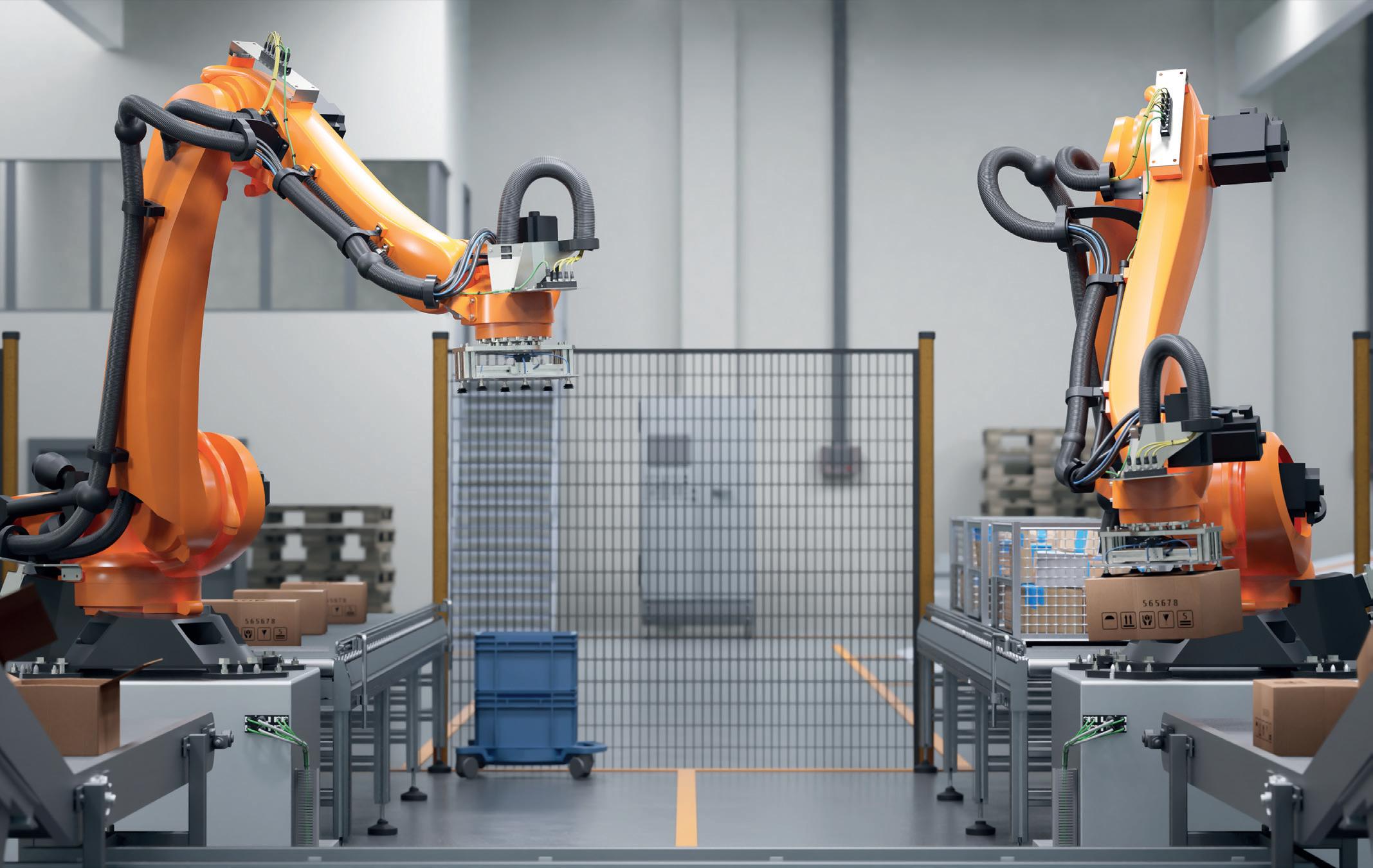
As we enter 2025, the machine-building industry is experiencing a major transformation. Artificial intelligence (AI) has moved from theory to practice, fundamentally altering how machines operate and adapt. AI-driven predictive maintenance is reducing downtime by 30%, while machine learning-powered quality control is cutting defect rates by 25%. This shift is not just evolution but a revolution, with AI anticipating issues, adjusting in real-time, and optimising production schedules.
The automotive sector is particularly
impacted by the rise of electric vehicles (EVs). Production lines now need to handle both EV and traditional powertrains seamlessly, with adaptive systems that switch between modes quickly, reducing changeover times by 60%. As battery and drivetrain configurations evolve rapidly, AI-driven quality control ensures critical components, such as battery cells, meet safety and performance standards. Manufacturers are also partnering with innovative suppliers of advanced technologies to lower the total cost of ownership (TCO), reduce installation times and improve diagnostics.
The logistics sector is also benefiting from AI and smart automation. Autonomous Mobile Robots (AMRs) are optimising warehouse workflows, boosting productivity by 200% and reducing energy consumption by 30%. These robots dynamically redistribute workloads to ensure smooth operations, even during peak demand. Quality control powered by AI ensures precise sorting, reducing errors and improving efficiency. Collaborative automation, where humans and robots work together, enhances operational efficiency, blending precision and flexibility to redefine what’s possible in logistics.
The food and beverage industry is undergoing a technological leap as well. AI and advanced automation allow modern production lines to switch seamlessly between product formats in minutes, with vision systems detecting inconsistencies with 99.98% accuracy. These systems ensure consistent quality at high speeds. Additionally, sustainability initiatives are being integrated with innovation, with energy monitoring systems reducing utility costs by 25% and intelligent cleaning solutions optimising water use and minimising waste. This combination of precision, flexibility and sustainability is helping manufacturers stay competitive while meeting consumer demands.
Sustainability is now a business necessity. Green initiatives like energy-efficient systems and waste-reduction technologies are driving measurable results. Manufacturers are partnering with suppliers to develop systems that use AI to optimise energy consumption, saving costs and reducing carbon footprints. These collaborative relationships are becoming essential, as suppliers with advanced diagnostics and streamlined installations help reduce TCO and improve long-term ROI.
The skills gap in manufacturing is being addressed through technology as well. Augmented reality (AR) is transforming training by allowing technicians to learn through interactive, on-the-job guidance. Collaborative robots (cobots) are complementing human workers, creating safer, more efficient production environments. These advancements foster human-machine collaboration, attracting younger, tech-savvy workers while retaining experienced talent.
Decentralised automation is also providing solutions to the labour challenge. With IP67-rated connectivity, manufacturers are moving control points directly onto machines, eliminating the need for complex wiring and centralised terminal blocks. This approach reduces installation times and simplifies troubleshooting and maintenance, enabling less experienced workers to operate flexible machines. Modular, plugand-play systems designed with IP67rated connectivity make it easier to build adaptable control systems without relying on specialised staff.
Strategic partnerships between machine builders, component suppliers, software developers, and AI specialists are crucial to speeding up innovation. These collaborations are reducing implementation times by 40% and accelerating advancements in predictive maintenance, process optimisation, and sustainability. Forward-thinking manufacturers recognise the value of these partnerships in driving transformative results.
As manufacturing systems become more connected, cybersecurity is a critical concern. Securing these networks against cyber threats requires encrypted communications, real-time threat detection, and robust employee training. Manufacturers who integrate security at the design stage are better positioned to protect their operations and maintain customer trust.
Future-proofing is now a central principle of machine design. Scalable automation systems and modular architectures allow manufacturers to adapt to evolving needs without requiring massive reinvestments. AI-ready designs ensure equipment can evolve alongside emerging technologies, helping manufacturers stay ahead of market demands while minimising disruption and cost.
MACHINE BUILDING
The digital thread is revolutionising machine building by enabling continuous data flow across design, production, and maintenance. Digital twins are being used for virtual commissioning, reducing development time, costs, and errors. The ongoing feedback loop between machine builders and end-users drives innovation, allowing for rapid adjustments to meet changing requirements and improve performance.
To all in the industrial automation space, the mission is clear: embrace intelligent systems, prioritise sustainability, and collaborate with partners and suppliers. By moving beyond cost-focused negotiations and exploring ways to reduce TCO through collaborative design, we can create machines that work smarter, not harder. With decentralised automation and smarter connectivity solutions, we can address labour challenges and shape the future of manufacturing.
Here’s to a year of bold innovation, strategic partnerships, and meaningful progress. Let’s make 2025 a defining moment for our industry.
murrelektronik.co.uk

Machine Vision and Its Growing Popularity
Machine vision technology underpins automatic imaging-based inspection and analysis. Put simply, it allows machines to ‘see’. In the following article, Axiomtek UK, the industrial PC field expert, examines the reasons for machine vision’s growing popularity in a diverse range of industries.
Machine vision can be the key contributing factor for successful machine-to-machine (M2M) communications, quality control applications and machine and deep learning. For quality control, it supports accurate detection of measurements, inspection of parts, the guidance of assembly robots and correct ID reading, all of which can be done real-time. Machine vision can also enhance machine learning (ML) processes, from delivering the collections of visual data to facilitating M2M communications
An embedded system for machine vision
The machine vision-based embedded systems address critical industrial IoT needs, including monitoring of various conditions during the production process. For example, machine vision is used to detect defects and anomalies during the production process in a factory environment. The results are better product quality, control as well as productivity improvements. It is also used for predictive maintenance and helps facilitate the machine learning process.
For instance, eBOX671B, a fanless embedded system designed to provide high-speed connectivity for on-premise and cloud servers, enabling real-time hosting of industrial machine vision systems. Purpose-built for smart factory applications, eBOX671B offers extensive I/O connectivity options for multi-camera imaging applications and supports multiple display interfaces, including two HDMI, one DisplayPort, and up to five display outputs for greater flexibility.
This industrial-grade embedded system also features dual DDR5 SO-DIMM,
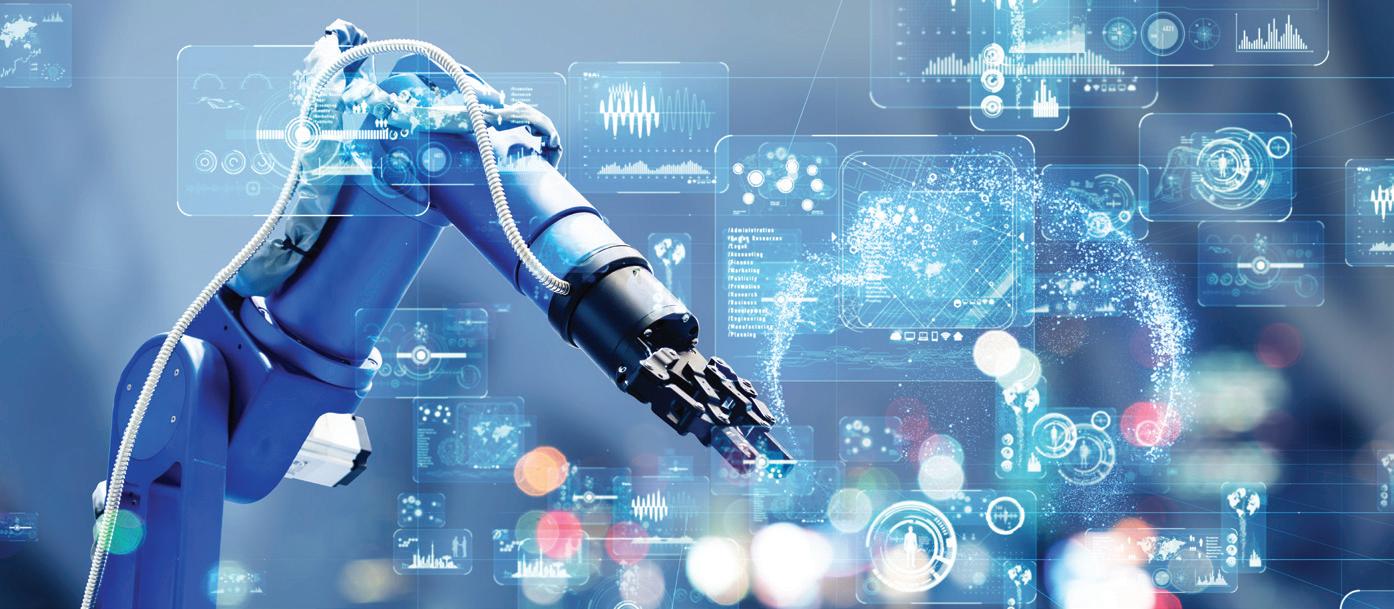
supporting up to 64GB of memory, ensuring enhanced storage and graphics capabilities to accommodate various cameras, lighting, and controllers tailored for diverse inspection requirements. Equipped with Intel® R680E chipset and optional MXM 3.1 Type A, it harnesses the latest graphics technologies, making it an excellent choice for demanding machine vision applications.
More importantly, this robust embedded computer plays a crucial role in high-speed image acquisition and processing. It is particularly vital for machine vision systems managing robotic operations, where safety and precision are paramount in avoiding human-robot collisions.
Axiomtek’s eBOX671B is highly scalable, offering 14th/13th/12th Gen Intel® Core™ i9/i7/i5/i3 or Celeron® processors. These processors provide ample capacity for handling multiple simultaneous data collection streams while delivering an immersive visual experience with 4K Ultra HD graphics support.
ML applications demand reliable highspeed connectivity with sensors, on-premise servers, or cloud computing environments.
The eBOX671B’s 3 x 2.5 GbE* LAN and 1 x 1GbE LAN, with optional PoE support, offer an ideal solution for seamlessly connecting
sensors and cameras. PoE technology eliminates the need for additional power sources, simplifying the integration of edge sensors and actuators while ensuring efficient M2M and machine-to-server communication. Additionally, PoE reduces networking costs by consolidating backup power and transmitting both data and power over a single Ethernet cable.
The eBOX671B provides four PoE options (IEEE802.3at, up to 60W), ensuring uninterrupted power delivery for continuous camera operation in machine vision applications such as automated optical inspection (AOI).
What the future may bring
As machine vision continues to evolve, its role in industrial automation and ML will grow significantly. With advancements in realtime data processing and IoT connectivity, production lines will become more efficient, quality control will improve, and M2M communication will be more seamless. These innovations will pave the way for smarter, interconnected systems that boost productivity and drive progress across various industries.
axiomtek.co.uk
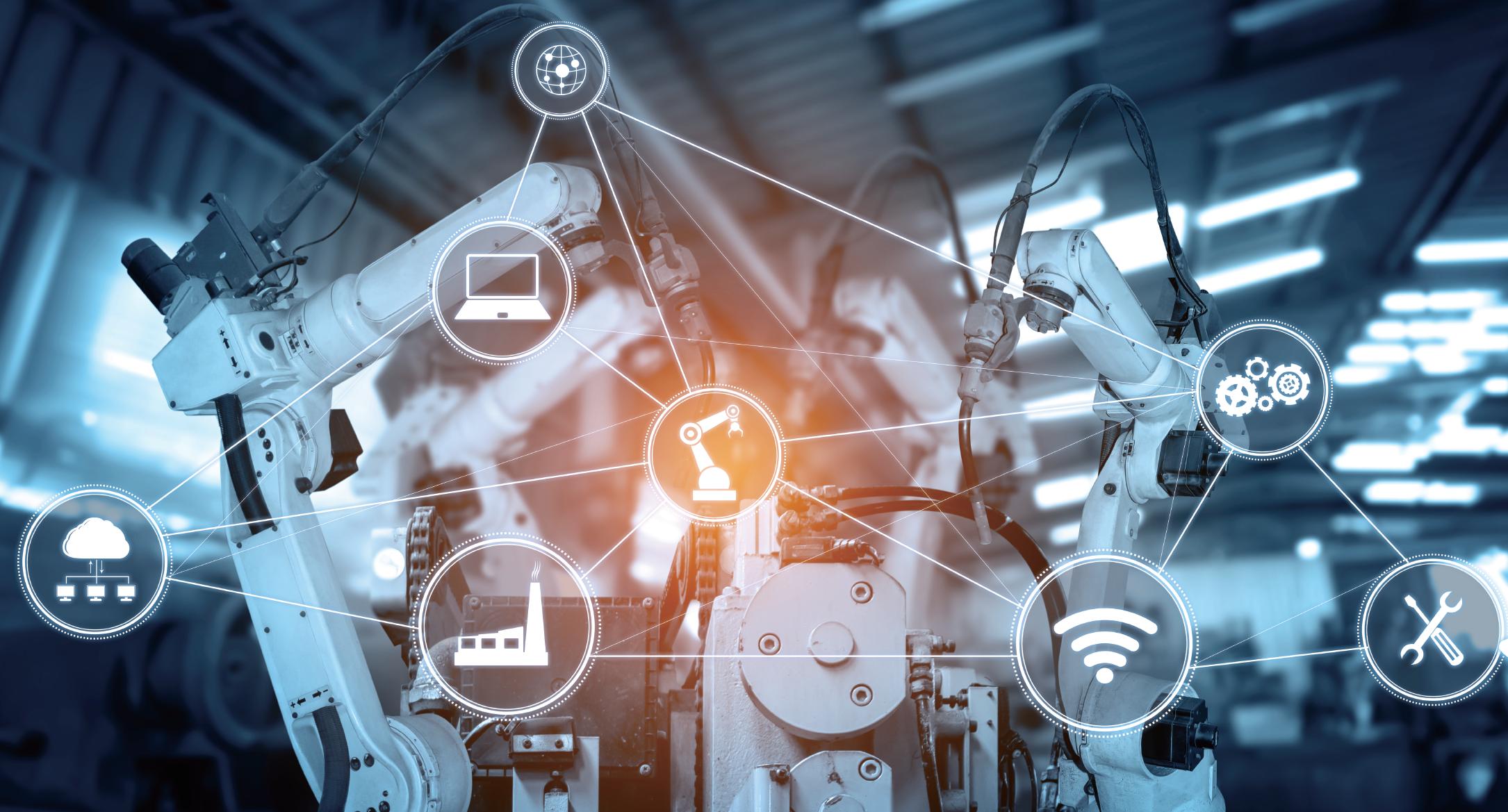

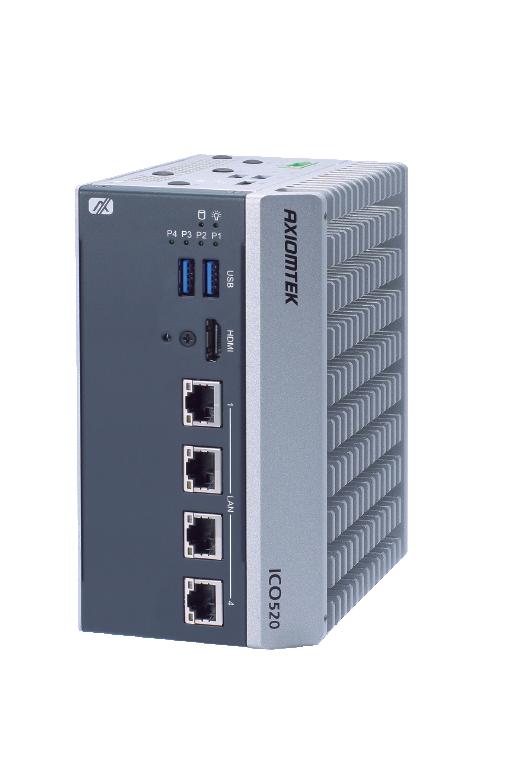

Wide Voltage Range for Diverse Applications
When it comes to operating and servicing control cabinets and enclosures, reliable illumination is crucial for safety and efficiency. STEGO, developer and manufacturer of innovative control cabinet climatisation products, introduces the new LED 025 M Enclosure Light, designed to provide optimal illumination for a wide range of applications.
Glare-free daylight illumination, a multi-wide voltage design, and effortless installation—the new LED 025 M (24 to 240 V AC/DC) from STEGO offers flexibility and efficiency for control cabinets and enclosures, simplifying material management while ensuring optimal lighting conditions.
Lighting that enhances safety and efficiency
Proper lighting isn’t just about convenience it’s a key factor in workplace safety. Poor visibility in enclosures can lead to miswiring, operational errors, and safety hazards. The LED 025 M addresses this by delivering glare-free, daylight white illumination (6,000 - 7,000 K), creating a clear and comfortable workspace.
For added convenience, the LED 025 M is available with a traditional switch or an automatic motion sensor, ensuring the light turns on only when needed, perfect for when an enclosure door is opened.
A universal solution for any voltage requirement
Electrical enclosures operate under varying voltages and current types, which often complicates planning and procurement in addition to stocking. The LED 025 M eliminates this challenge by supporting a multi-wide voltage range of 24-240V AC/ DC (min. 20V, max. 265V) with 50/60 Hz frequencies, making it suitable for a vast array of industrial and commercial applications.
With a power consumption of just 4.5 W, it emits 560 lumens with a 120° beam angle, providing bright and efficient illumination. Built for extreme conditions, it operates
flawlessly in temperatures from -40°C to 60°C and up to 90% relative humidity.
Effortless installation and long-term reliability
Enclosures come in various shapes and sizes, which is why the LED 025 M is designed for quick and flexible installation. It includes mounting options for magnetic, screw, and din-rail installations, while preassembled connection and extension cables simplify the electrical setup.
For larger setups, up to 10 lights can be connected a daisy-chain connection. With a lifespan of 60,000 operating hours, the LED 025 M is a long-term lighting solution that minimises maintenance and downtime.
Certified quality
The LED 025 M meets high industry standards and holds multiple certifications, including CE, UKCA, EAC, UL, VDE, CCC, and ROHS, ensuring compliance with global regulations.
Discover more
For detailed specifications, available variants, accessories and complementary products, visit the company’s website. stego-group.com/en-gb
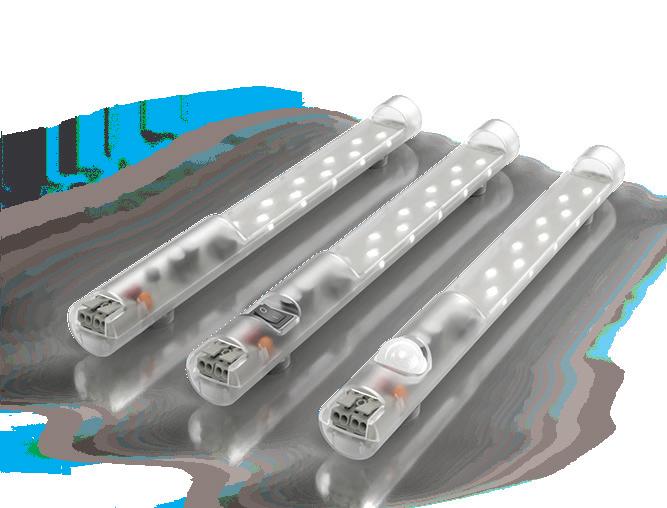
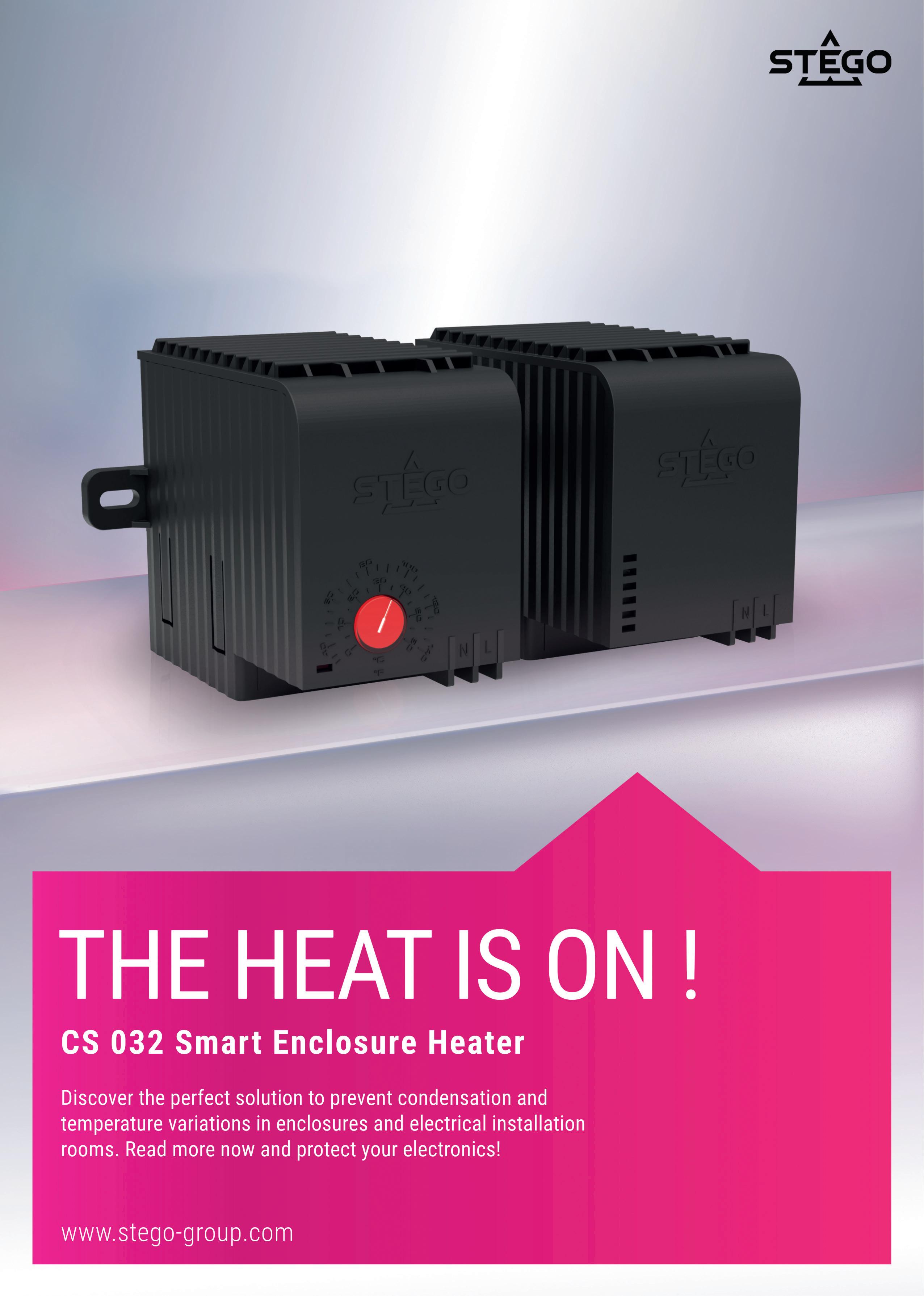
Master Liquid Metering for Batching Precision
Titan Enterprises shares key insights to help engineers and operators navigate the challenges of precision batching to ensure accurate measurements and smooth process operations.
Metering batches of liquids may seem straightforward at first glance – install a flowmeter in the product line, connect it to an instrument, control the measurement with on-board software, wire in a valve, enter the required volume, press a button and the right amount of liquid is dispensed into the vessel. However, real-world applications reveal a host of complexities.
Today’s advanced process and liquid handling systems demand highly precise flow measurement. From adding water to food production mixers to handling aggressive chemicals, even slight inconsistencies in system design can lead to inaccuracies, wasted product, or disrupted processes.
For batching systems, the critical factor is repeatability. To achieve this, the system should maintain consistent process conditions. However, this is not always feasible. For instance, temperature fluctuations throughout the day can alter fluid viscosity and volumetric flow measurements. Similarly, a decrease in the feed liquid tank level supplying the process pump can reduce the dispensing rate, impacting the accuracy of the flow meter and the flow control valve. Therefore, batching system designs should aim to minimise as many variables as possible within a reasonable cost. Equipment can then be selected to effectively compensate for any parameter variations.
Titan’s NSF-Approved Beverage Flowmeter is designed specifically as a flow measurement solution for the drink dispensing market.
Applications of liquid flow measurement and control in batch processes
Batching ingredients in juice processing
Fruit juice production relies on accurate flow measurement of small quantities of ingredients to maintain product quality. High-precision flowmeters provide repeatable measurements, indispensable for maintaining product consistency.
Liquid batch dispensing in beer walls

Incorporated as part of an installed beer wall, the valves and flowmeters count and control the dispensing of beer at the bar taps. Titan’s low-cost beverage turbine meters are used to accurately measure and control dispensed beer at self-serve counters.
Flow switching in bottling operations
In bottling operations, reliable liquid flow indication prevents costly disruptions. Inline flow switches detect and manage critical scenarios such as product flow loss, ensuring efficient operations.
Critical considerations for liquid batching systems
1. System repeatability
Air pockets in the line can lead to dynamic flow situations, causing volumetric errors in delivery. Ensuring a hydraulically locked system eliminates such variability and enhances repeatability.
2. Stable process conditions
Changes in pressure, temperature, or flow rate can push flowmeters into unpredictable operational zones, affecting calibration and accuracy. Maintaining consistent conditions is vital for reliable performance.
3. Pulsating flow management
Selection of the pump type is important to avoid pulsating flow. Pulsation from certain pumps can disrupt flow rates, especially in aggressive chemical applications. Pressure
regulators and pulsation dampers should be incorporated into flow systems to achieve a smooth and constant flow.
4. Strategic placement of flowmeters
Positioning the flowmeter just before the dispense valve minimises fluid inertia and improves measurement accuracy.
5. Understanding flowmeter resolution
Low-resolution meters, such as those with one pulse per litre, may lack precision in small batch applications, while too high a resolution is an unnecessary expense.
6. Valve selection and calibration
The type of shut-off valve used can impact delivery accuracy. Fast-acting solenoids are ideal for smaller pipelines, while larger setups benefit from solutions like multi-stage shutoff systems to fine-tune results.
7. Optimising electronic flowmeters
High-performance batching meters (such as Titan’s ultrasonic Atrato® flowmeter) can predict stop signals in advance, ensuring consistent delivery even at high speeds. By accounting for these factors during system design and commissioning, engineers can eliminate common pitfalls in liquid metering and achieve extremely good accuracy. Investing in the appropriate flow measurement technology for the application will ensure that the batching system performs with precision and consistency. flowmeters.co.uk
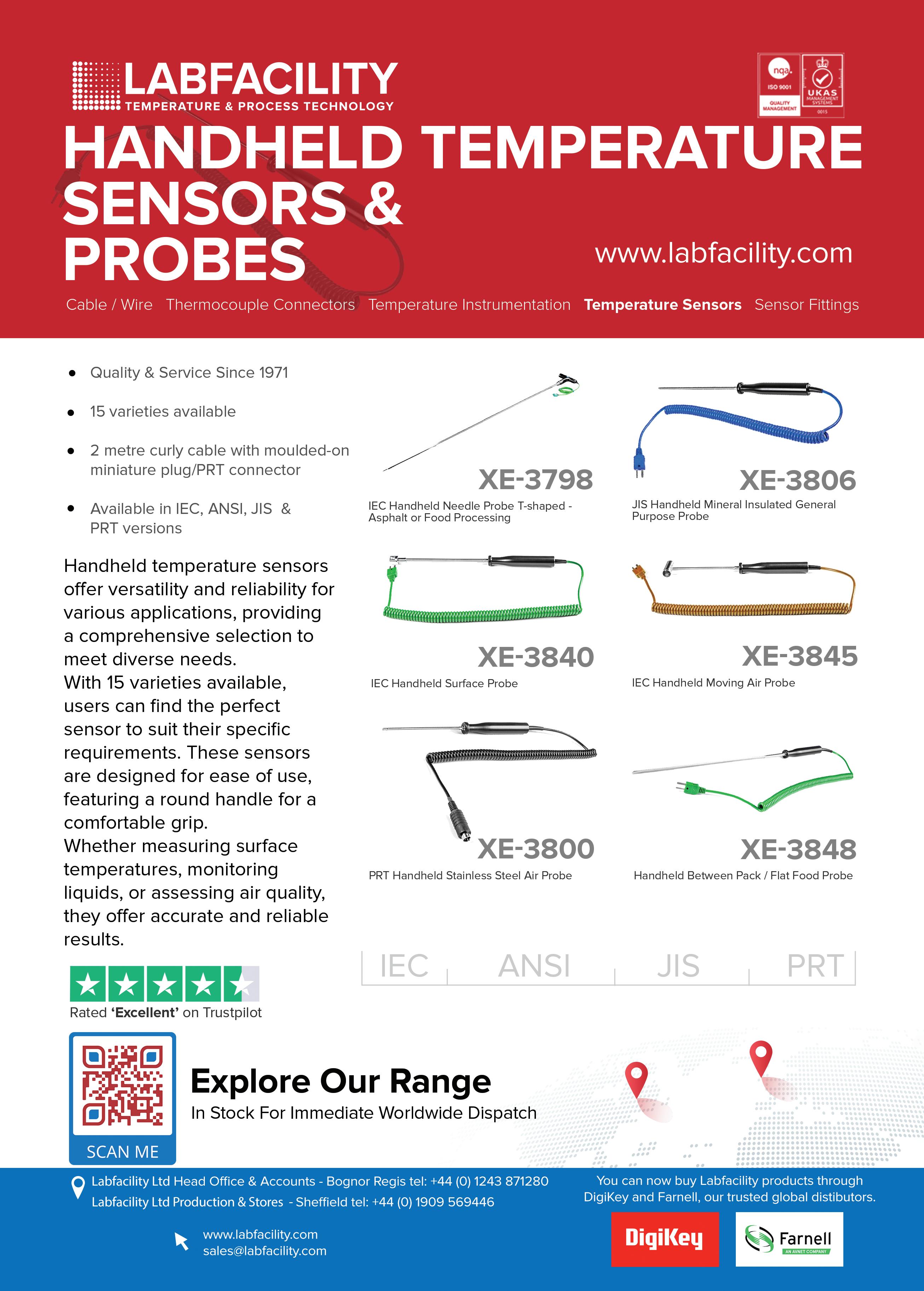
From Revolt to Results
Andrew Jones, the Technical Director at Axair Fans, talks about their most recent disruptive campaign; We’re Revolting, and specifically how their revolt has led to better results for customers in the industrial fan industry.
I’ve gone into the reasons for our revolting images being scattered around everywhere over the last 9 months, and over that period I’ve spent a considerable amount of time discussing the positive outcomes of the messaging while out on customer visits.
You see, it’s one thing to say something, but getting all those ducks in a row and delivering on them is another, entirely different beast. It takes a companywide collaboration on optimising sales processes, enquiry escalation, technical support hierarchies, and setting achievable service level agreements that every employee commits to.
Firstly, let’s discuss response times, an inherently unrecognised pain point for most customers in all industries. The meatiest enquiries are replied to and actioned, the small but profitable fish are handled a few days later, while those deemed too small are ignored, discarded with no response to even highlight to the customer that the supplier is unable to give a commercial offer. It’s a bit like applying for a job when you’re 16, if you have 10 years’ experience in coding at 16, you’ll be replied to, but a school leaver with no experience is ghosted, losing motivation and self-esteem with every failed application. When a simple reply with feedback on why they were unsuccessful would go a long way on improving CV quality, or encourage them to volunteer to bolster experience, for example.
Our proactive response times have been recognised wholeheartedly by our new and existing customers; the positive feedback is far greater when the issue is pointed out through visual messaging. It has made customers recognise the value immediately when compared to what they’re used to.
Secondly, I’ll touch on one of the most important aspects: technical support. I won’t blow my own trumpet, but I consider myself to be one of the few fan men with a unique and natural affinity for physics, and air or fluid movement. Just generally engineering problem solving, it gets me in my flow –meaning it’s where my energies lie best. Not
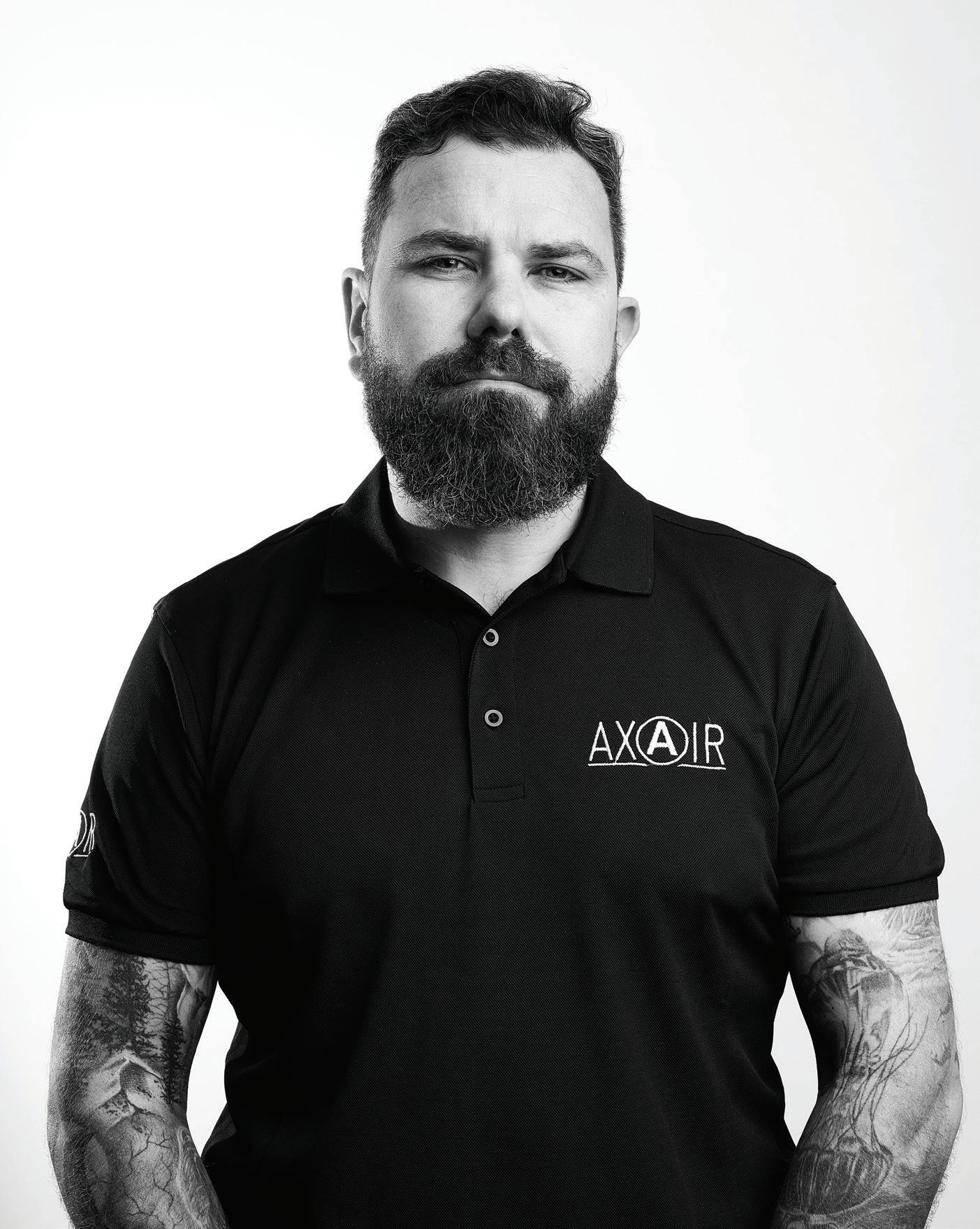
in spreadsheets or analysing sales figures. In a strong man competition, I’m going to liken our pre and after sales technical support to the Stoltman brothers; consistent and likely to lead, you can place your bets and know you’ll probably win backing one of them. Customers recognise this too, and they’ve gained a huge amount of trust in our team, which creates barriers to entry for competitors who can only rely on price negotiation. What use is a product without the reliable backup of presale’s accurate selection, after sales technical and a team committed to service level response times
on issues? It’s the difference between saving a few quid on each component, against getting a unit on site back up and running within a day compared to 6 or more weeks.
I’d call it a result when we’re getting phone calls and emails requesting our “revolting service”, or when compliments from brand new enquiries expressing how impressed they are that a simple, yet highly important aspect of response times has been identified and actioned for customer benefit flood in. Learn more by visiting our site. axair-fans.co.uk
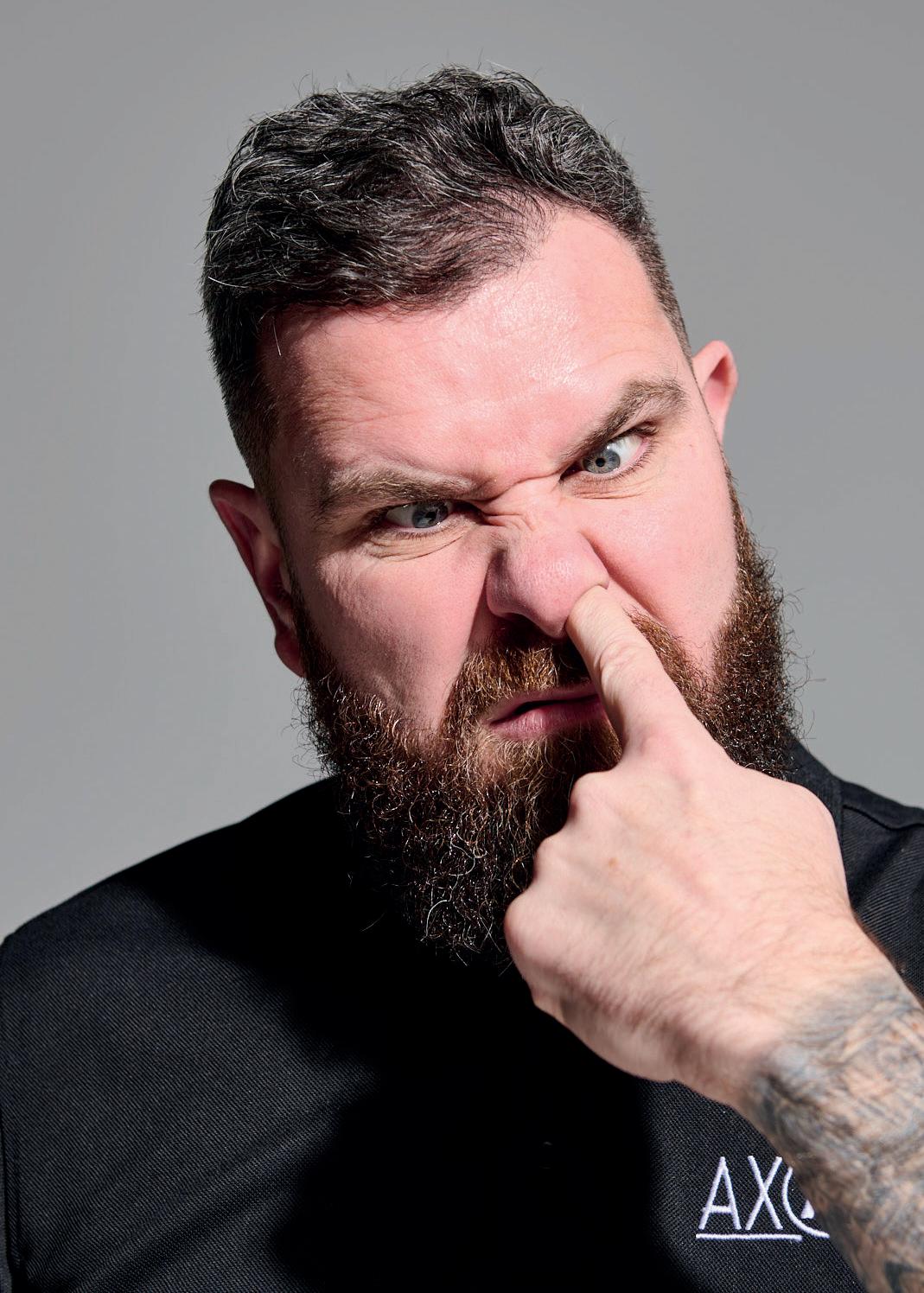
Revolting For A Reason. Technical support that disrupts your existing behavioural norms.
Just like AJ in the picture, we’re revolting! We’re changing the rules of the game, breaking the mould. Response times that take some companies days, only take us minutes. Pre-sales and after-sales support is based around your needs not ours, because our job is to empower you. So as they say in Stoke, viva la revolution! Join us now.
Axair. Revolutionary Fan Expertise.
Andrew Jones (AJ) Technical Director
High-Efficiency Circulator at ISH 2025
Among the innovations on display at ISH 2025, the world’s leading trade fair for HVAC and Water, Frankfurt 17 to 21 March, KSB Group will showcase its new high-efficiency circulator for building services applications. Here, the company shares details of this energy efficient and affordable solution.
Atechnical highlight at ISH 2025 will be the KSB
Group’s Calio Pro Plus type series – an extension to its programme of high-efficiency glandless pumps with continuously variable speed control. The new pumps reach efficiencies that exceed the requirements of the current energy efficiency regulations.
Thanks to the integrated intelligent Dynamic Control program, energy savings of up to 40 percent more can be achieved compared with conventional proportionalpressure control. As the function is purely based on software, no additional costs will be incurred by further sensors or actuators. The pumps automatically gather all required information from their internal signals. This patented technology practically rules out undersupply in changing system conditions.
The pump offers comprehensive connectivity options for flexible integration into building management systems. A Modbus RTU interface is integrated as standard, enabling direct connection. Additional plug-in modules provide extended compatibility with all common building management systems. Two parameterisable relays are available for operation and fault messages. Connectivity is rounded off by a configurable digital input and an adjustable analog input.
Installation and commissioning are straightforward. All operating modes, functions and setpoints in metres are fast and easy to adjust directly at the pump or via the Bluetooth interface. An energy meter helps monitor and optimise consumption. Also, the pumps offer practical functions such as an operating point display, a calorimeter and a vent function. A dualpump variant Calio Pro Plus Z is available for
dual-pump operation. Suitable for operation with one pump redundant or with both pumps running during maximum load, this model is designed with an energy-efficient changeover behaviour.
Commissioning is swift with the intuitive KSB FlowManager app. The app helps users configure all electrical connections in a flexible and user-friendly way. All pump information is quickly accessible in the app’s Favourites menu. A clear overview of process values is also displayed in a graphical diagram. Integrated motor protection ensures high operating reliability. The maintenance-free motor is fitted with a carbon fibre reinforced plastic can. The integrated filter system provides reliable protection against contaminants, such as magnetite.
The pumps of the Calio Pro Plus type series are designed for universal use and cover the pressure classes PN 6, PN 10 and
PN 16. New and enhanced characteristic curves offer an extended operating range. The new type series is available in 46 sizes and can handle flow rates of up to 28 m3/h at a maximum head of 16 mWC. The fluid temperature range from -10 to +110 °C makes the new pump sets suitable for a wide variety of applications, from heating water to coolant transport and industrial recirculation systems. The pumps are also available in a twin pump configuration as Calio Pro Plus Z.
To assess the product’s environmental impact over its entire life cycle, the pump manufacturer performed a life cycle impact assessment (LCIA) in accordance with the standards ISO 14040 and 14044. ksb.com/en-gb
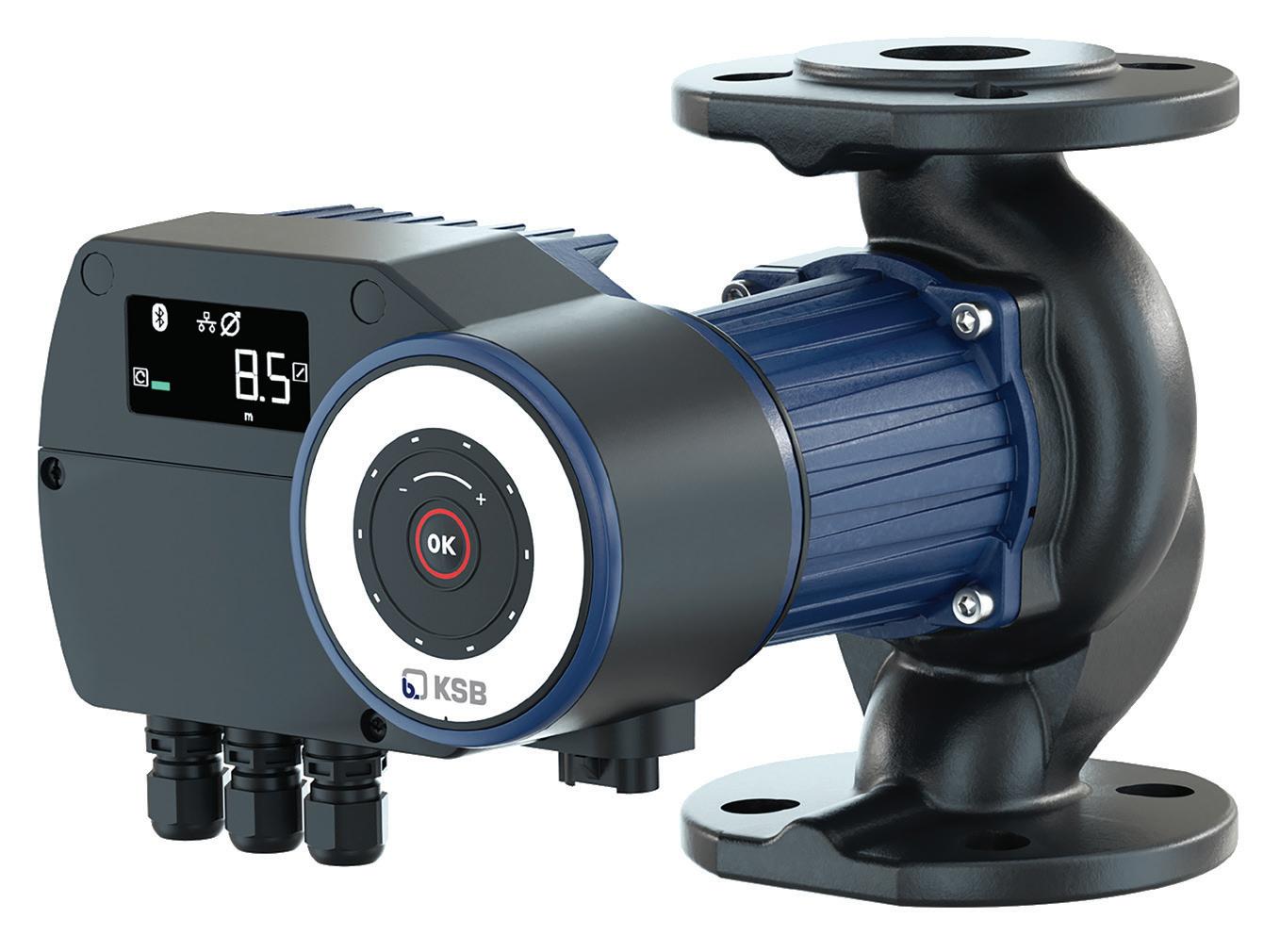
PROVEN PUMPING POWER OVER AN ENTIRE LIFE CYCLE.

Versatility and adaptability – KSB products deliver the perfect mix to maximise your system’s efficiency and lower your total cost of ownership. We’re exhibiting at CHEMUK 2025! Find us at stand C44 on 21-22 May 2025.
Find out more at www.ksb.co.uk - 01509 231872 - sales@ksb.com
We’re exhibiting at CHEMUK 2025 in May!
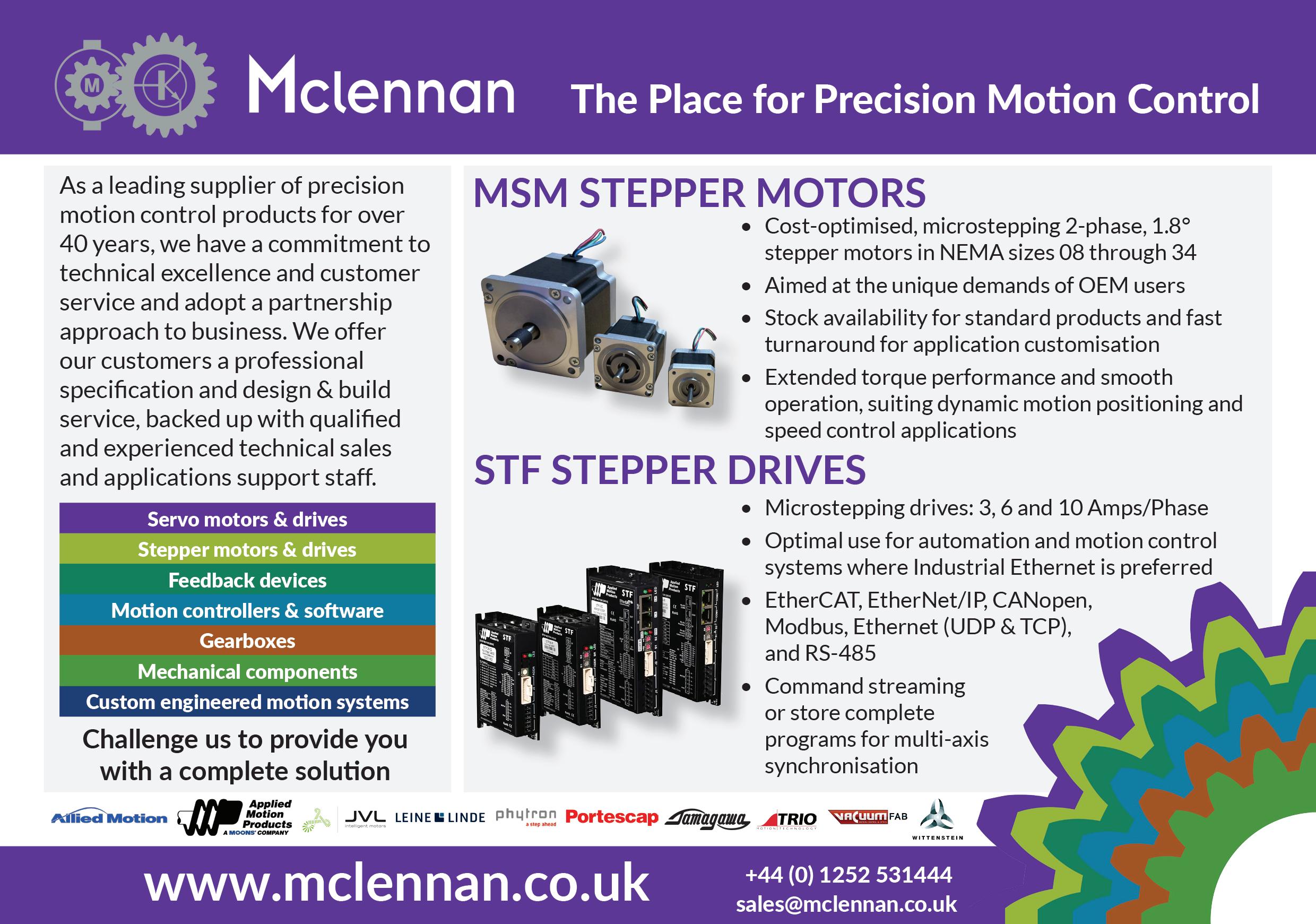
Countdown to TCT 3Sixty 2025
The anticipation builds as TCT 3Sixty, the leading event in the UK for 3D printing and additive manufacturing, draws near. Scheduled for June 4-5 at the NEC Birmingham, this two-day event promises to unite industry pioneers, innovative brands and the latest technological breakthroughs.
TCT 3Sixty provides a crucial platform for networking, learning and exploring advancements in the additive manufacturing sector.
Unlocking opportunities for manufacturing professionals
With over 150 exhibitors and an expected attendance of more than 5,000, TCT 3Sixty 2025 is tailored for professionals eager to explore, implement, or enhance 3D technologies in their operations. According to Charlotte Penny, Group Marketing Manager at Rapid News Group, the event is invaluable: “It offers a significant opportunity for attendees to uncover innovative solutions that enhance productivity and address common manufacturing challenges. Whether you’re considering technology for the first time, ready to invest in new equipment, or looking to optimise existing systems, TCT 3Sixty will provide the guidance you need.”
Strategic initiatives to accelerate additive manufacturing adoption
The 2025 edition of TCT 3Sixty will host various meetings, events and initiatives helping to unlock AM’s transformative potential across industries.
• TCT User Group: this meeting brings together UK users of additive manufacturing technologies across a breadth of industries for a deep dive into the roadblocks hampering AM adoption and optimisation. The day provides a range of opportunities for debate and knowledge exchange, with the aim for participants to share experiences and begin to find routes to possible solutions to these roadblocks, whether for individual
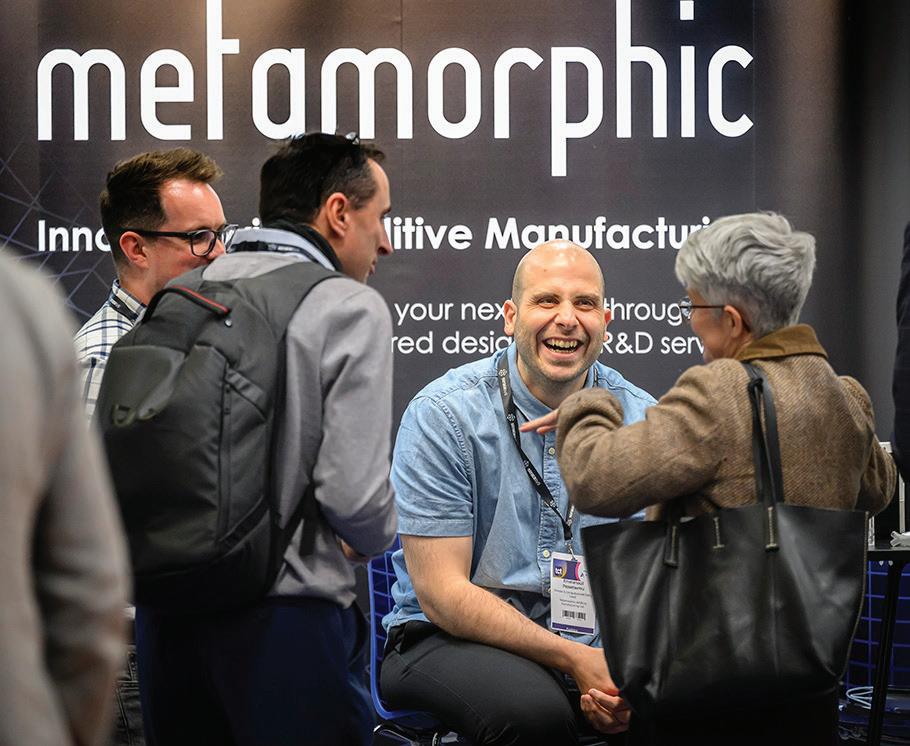
cases or for the broader issues additive faces. Attendees should register their interest via the TCT 3Sixty registration form at www.tct3sixty.com.
• MOD’s Project Tampa: project TAMPA was created by the Chief of Defence Logistics & Support in 2021 to accelerate the use of Additive Manufacturing technologies within the UK Defence Industry. The aim is to contribute to a step change in platform and equipment availability and readiness. The project holds regular working groups throughout the year and the second meeting for 2025 will be alongside day 1 of TCT 3Sixty enabling Project TAMPA contributors to look firsthand at the UK AM sector. Register for TCT 3Sixty for more information about this workshop.
• TCT Knowledge Bar: powered by Additive Manufacturing UK (AMUK), this distinctive feature on the show floor will provide complimentary one-on-one consultations. Attendees can receive expert advice from a group of specialists in 3D printing and additive manufacturing, helping them tackle specific challenges and discover customised solutions for their projects.
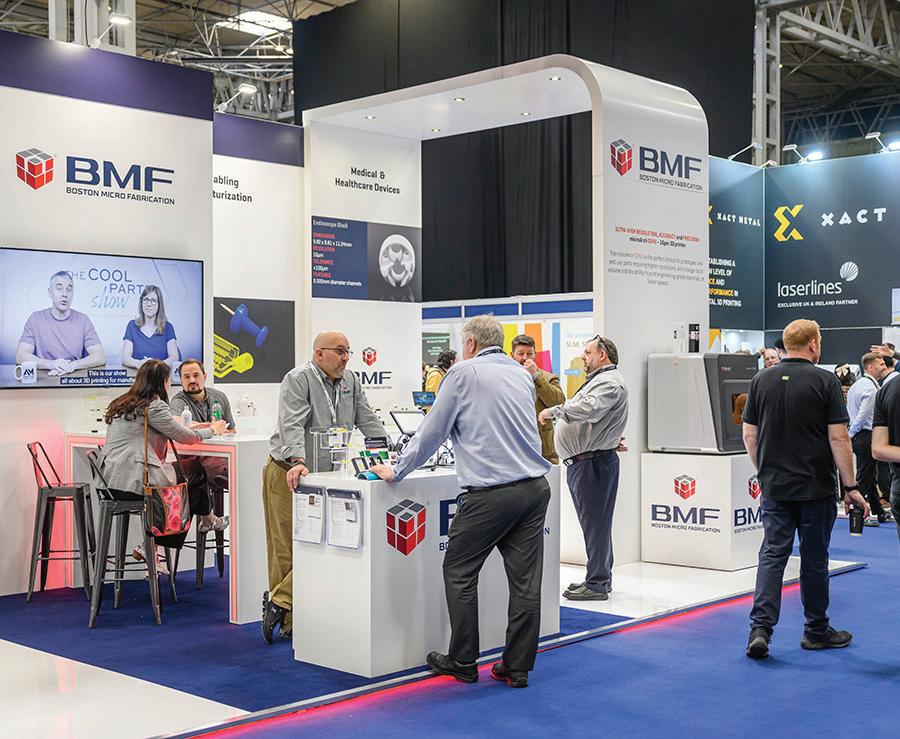
Educational opportunities for industry leaders
A highlight of TCT 3Sixty 2025 is its extensive educational agenda, featuring over 50 complimentary talks and interactive sessions. With two upgraded conference stages—the TCT Insights Stage and the TCT Innovation Stage—industry experts will cover a wide array of topics, from aerospace and healthcare to sustainability and return on investment. Attendees will also gain insights from leading R&D sectors, including renowned universities and innovation hubs like the Manufacturing Technology Centre.
Honouring innovation and building connections
On June 4, 2025, the TCT Awards will take place, celebrating the most remarkable innovations and applications in 3D printing and additive manufacturing worldwide, along with recognising outstanding individuals in the industry through the TCT Hall of Fame and the Women in 3D Printing Innovator award.
Use the website below to register today for a complimentary pass and start planning an itinerary through the TCT 3Sixty Event Hub and app. tct3sixty.com
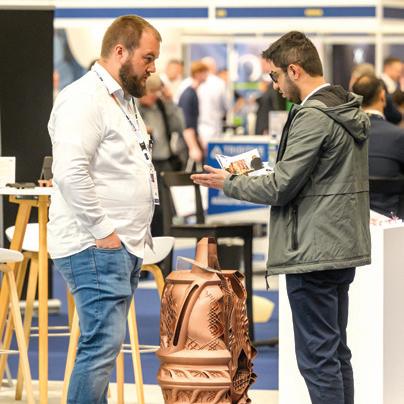
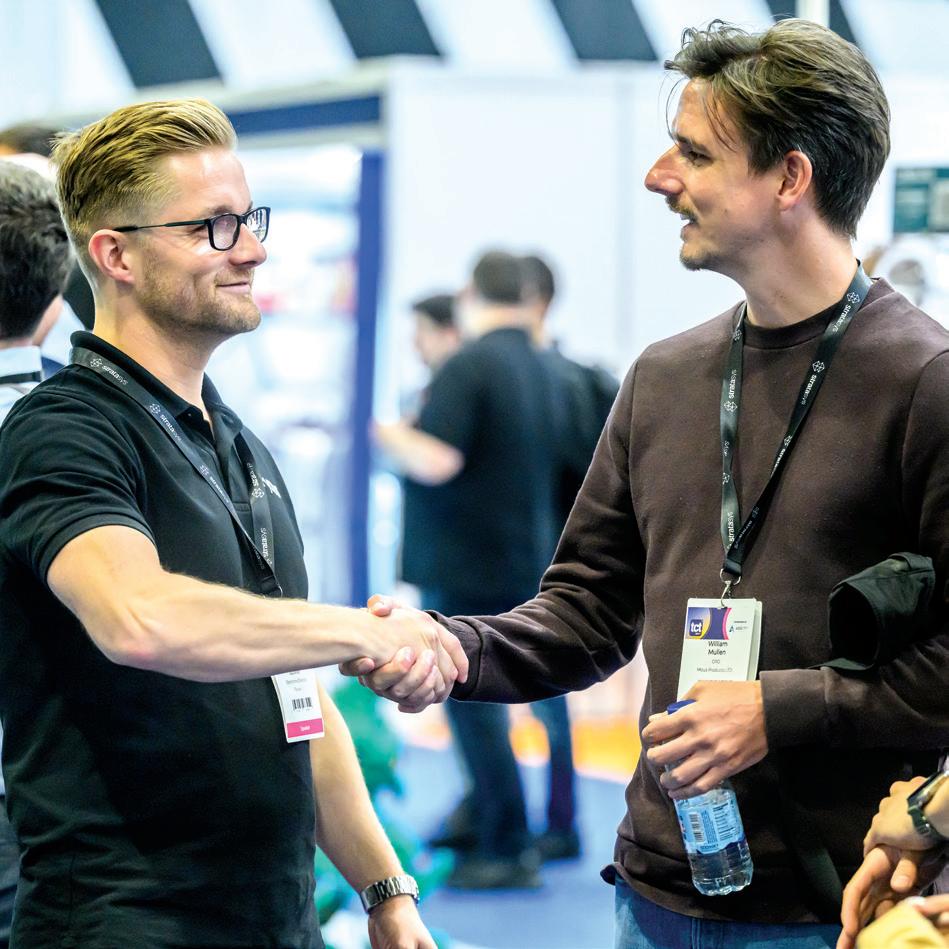
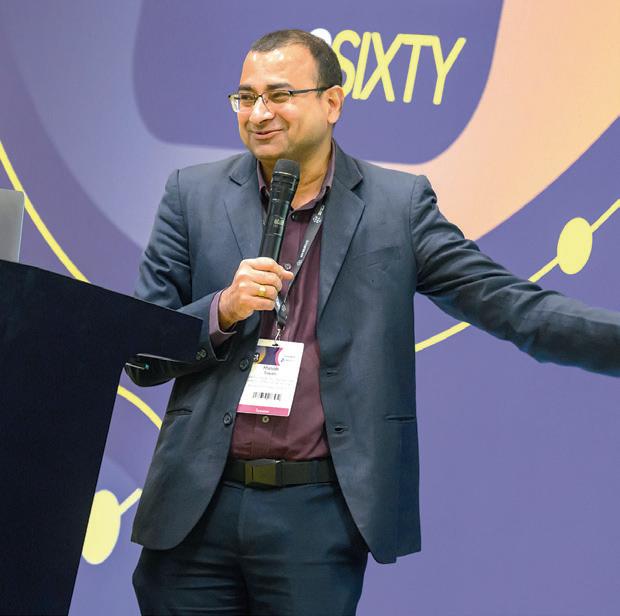
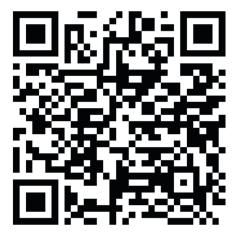
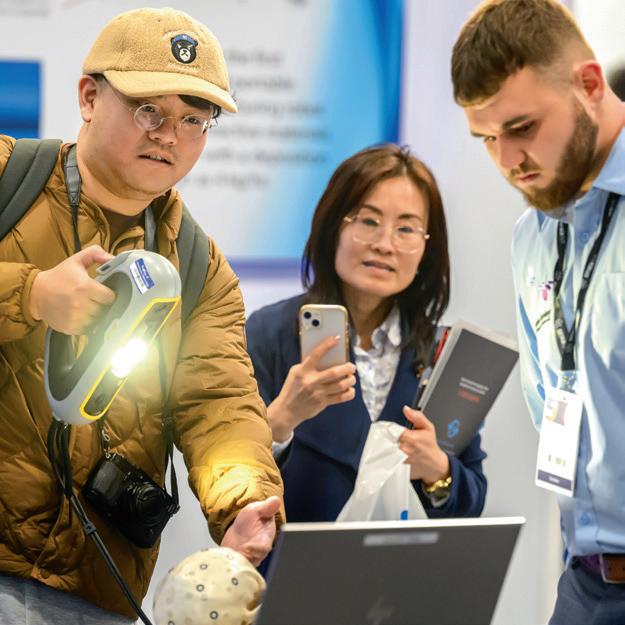
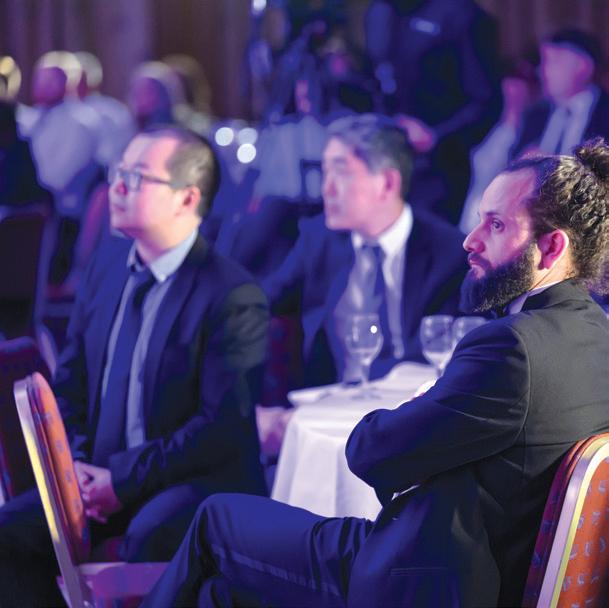
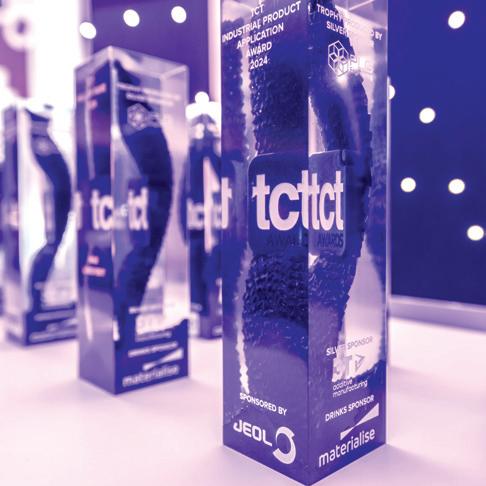
SCAN ME
Subcon 2025 Returns to Birmingham
The much-anticipated trade show Subcon 2025 returns with MEPCA as a show partner! The event which hosts subcontractors and outsourced engineering service providers will take place from the 4th – 5th June 2025 at the NEC, Birmingham.
Subcon is known to attract manufacturers and buyers across the engineering and manufacturing sectors hoping to advance the capabilities of the supply chain. Key sectors attending the event range include aerospace, automotive, defence and security, and the medical industries.
Over 170+ exhibitors will be attending the trade show. Innovations and solutions will be showcased, ranging from CNC machining, metal fabrication, electronics and component parts. Other solutions on show include additive manufacturing and metrology solutions, frictionless bearings and cables and controls.
Dynamic conference programme
Attendees can also participate in interactive CPD-accredited workshops and product demonstrations. This event will focus specifically on the future of manufacturing such as sustainable practices, clean mobility and the emergence of co-bots. Speakers at the event will range from Rolls Royce, Lego Group, Siemens and JLR.
Themes at the conference will revolve around:
• Current approaches to connected manufacturing – how implementation of innovative technologies into evert manufacturing aspect is helping enhance capabilities.
• The power of data and AI for smarter manufacturing – exploring topics such as leveraging machine learning to enhance condition-based maintenance and reducing downtime.
• Robotics and intelligent automation –how are manufacturers moving beyond automating individual, narrow tasks toward automating complex end-to-end processes.
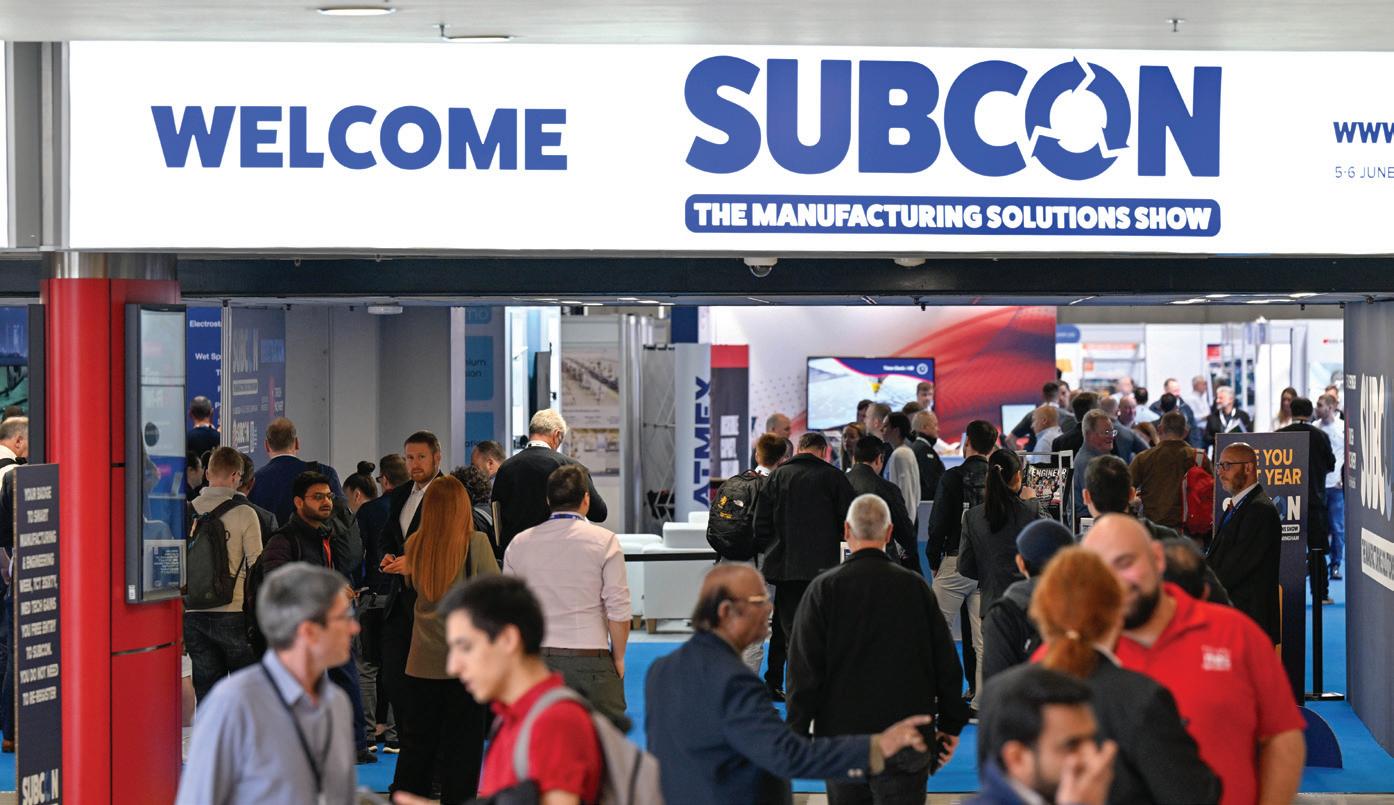
• How to attract more young talent to the manufacturing sector – speakers will outline the current issues hindering a strong pipeline of future talent and the measures needed to tackle this.
What’s on?
Subcon 2025 will have three main areas/ forums: the Innovation Zone, Workshops and Learning Space, and the Manufacturing Insights Theatre.
The Manufacturing Insights Theatre is a forum that will focus on presentations and panel discussions.
The Workshops and Learning Space will provide roundtable sessions with peer-topeer meetings – addressing specific industry challenges as well as allowing visitors the chance to network.
In addition, the Innovation Zone is where attendees and exhibitors alike can see hands-on demonstrations of the newest technologies and products.
Other features include a game zone featuring Formula One racing simulators, with the chance to win a PalmerSport driving day experience. As well as an all-new ‘Chill
and Charge’ area for visitors to relax and catch up on meetings and work.
There will also be a networking and drinks reception hosted by Subcon 2025, on the first day of the show commencing at 4.30pm.
The Manufacturing Solutions Show Awards
The Manufacturing Solutions Show Awards will take place within the exhibition on the 6th June.
The awards, which is a free-to-attend event, will celebrate the best in the industry and is open to all visitors.
The award categories include:
• Start-up of the Year
• UK Manufacturing Partner of the Year
• International Manufacturing Partner of the Year
• Product Innovation of the Year
• The Rising Star Award
• Lifetime Achievement Award
Registration is free for all visitors. Visit the website for more information.
subconshow.co.uk
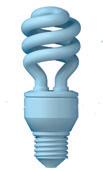
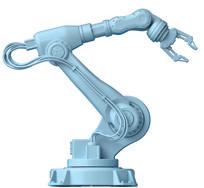

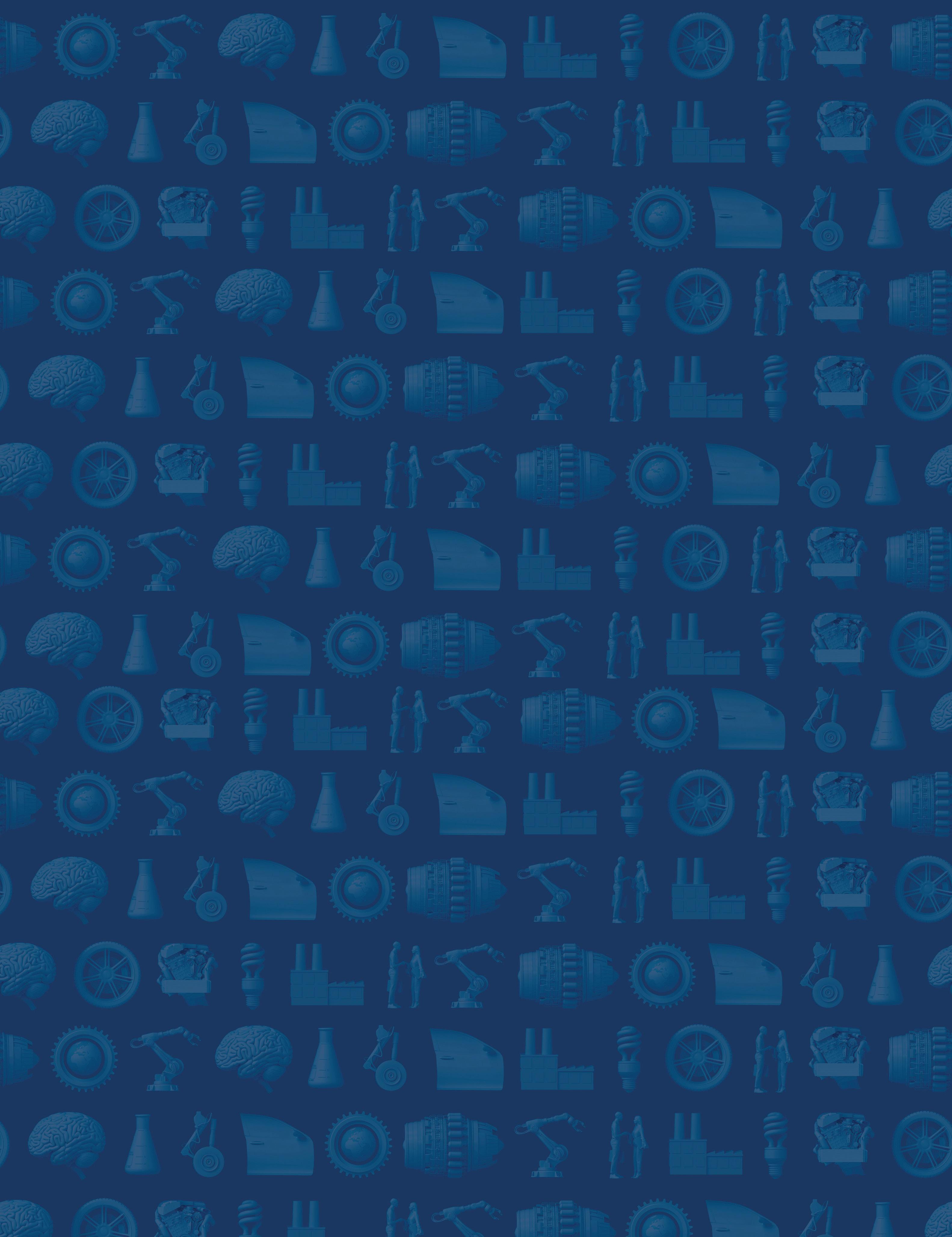
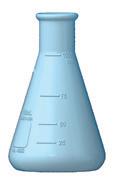
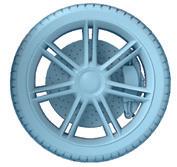
UK Metals Expo 2025
The UK’s premier metal manufacturing trade show returns this September. UK Metals Expo 2025 is set to build on the success of last year’s event, with even greater expectations.
In just three years, the UK Metals Expo has become a cornerstone of the metals and manufacturing sectors, attracting over 300 exhibitors and more than 7,000 professionals from 51 countries. The event has created a valuable platform for companies, buyers, supply chain partners and industry peers to connect, collaborate and drive innovation across the entire metals supply chain.
Scheduled for 10-11 September 2025 at the NEC Birmingham, UK Metals Expo offers Directors, Senior Managers, and Engineers from various sectors—including production, maintenance, operations, procurement, quality, inspection, safety, toolmaking, and test and measurement— the opportunity to discover new solutions, explore emerging trends, and engage with the latest technologies shaping the future of manufacturing and metals.
Showcasing leading innovations
UK Metals Expo 2025 will feature industry leaders such as Tata Steel, British Steel, Outokumpu, and Hadley Group, showcasing advancements in material innovation and decarbonisation. Welding and fabrication specialists like Selmach Machinery and John Winter will present the latest in CNC technology, metal processing and surface finishing innovations.
Attendees will have access to ground breaking technologies, materials and sustainable practices that are transforming the sector.
The event will also attract attendees from major organisations such as Rolls-Royce, Jaguar Land Rover, Siemens, Airbus, JCB, and AECOM. This diverse mix of professionals ensures high-value networking opportunities, allowing exhibitors and visitors to form meaningful connections and explore new business opportunities.
A comprehensive platform for industry professionals
Alongside the exhibition, UK Metals Expo 2025 offers a comprehensive seminar
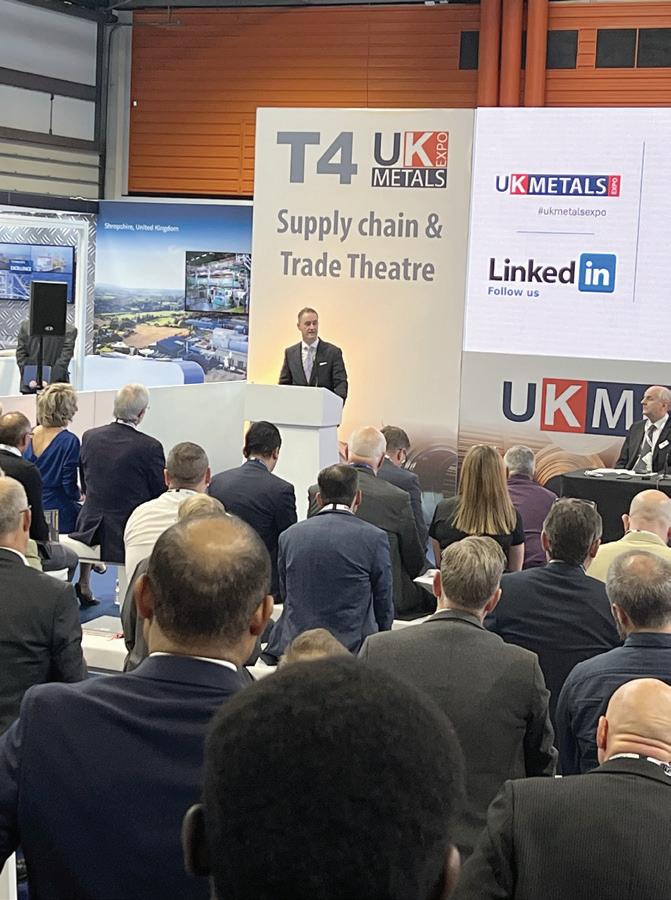
programme, giving professionals the chance to explore everything from advanced CNC machinery and automation systems to sustainable manufacturing practices. The event serves as an ideal space for learning how these innovations can be practically applied to meet the growing demands of industries such as aerospace, automotive, energy, and infrastructure.
Attendees will also gain critical insights into industry trends, expert opinions, and updates from government and trade bodies. Whether you’re focused on improving efficiency, reducing costs, or integrating the latest technologies, UK Metals Expo 2025 is the key event for staying ahead of the curve.
Networking and business development opportunities
UK Metals Expo fosters a collaborative environment, offering valuable networking and business development opportunities. It’s the perfect platform for both seasoned professionals and newcomers to deepen their understanding of the industry, forge new partnerships and tackle sector-specific challenges. For those seeking to grow their business, build key relationships and stay at the forefront of the metals and manufacturing industries, UK Metals Expo 2025 is a mustattend event.
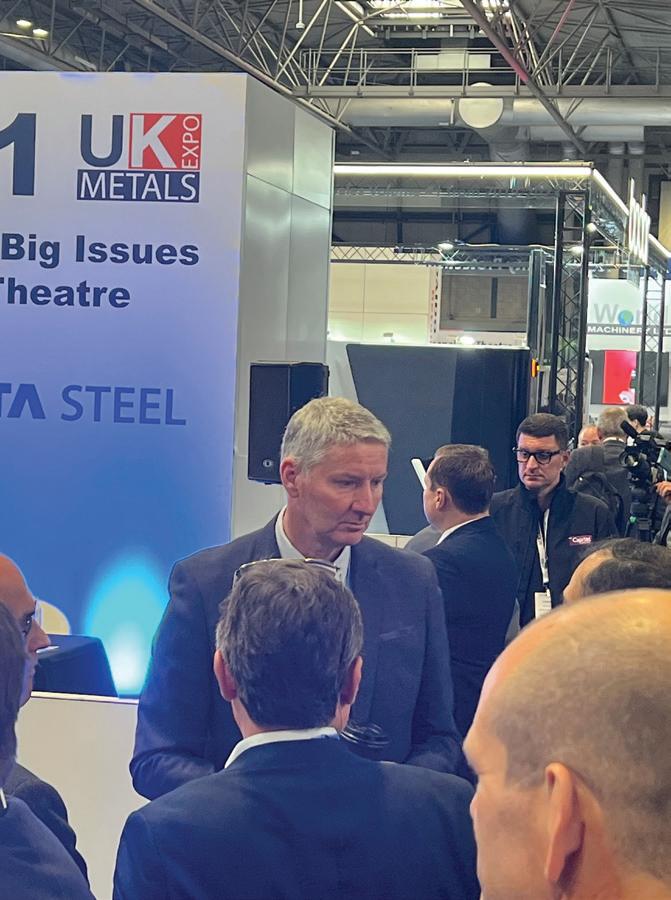
Exhibiting: a unique opportunity for suppliers
Exhibiting at UK Metals Expo presents a unique chance for suppliers to showcase their latest innovations and expand their market presence. With direct access to professionals across the value chain, exhibitors can engage with potential customers, position themselves as leaders and identify new business opportunities.
“A really impressive and uplifting event with so many businesses represented. It’s a great opportunity to bring our customers here, talk to our suppliers, and find new opportunities that can help each other’s businesses,” said Tata Steel UK’s CEO, one of the 2024 event speakers.
Now part of the Easyfairs family, UK Metals Expo offers greater reach across the UK and Europe, giving you access to a broader, more diverse audience.
Mark the date and secure a spot
Exhibitor spots for UK Metals Expo 2025 are filling up fast, so businesses are encouraged to secure their place early. This is an unmissable opportunity to be part of an industry-leading event that will shape the future of metals and manufacturing. ukmetalsexpo.com
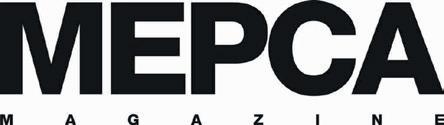
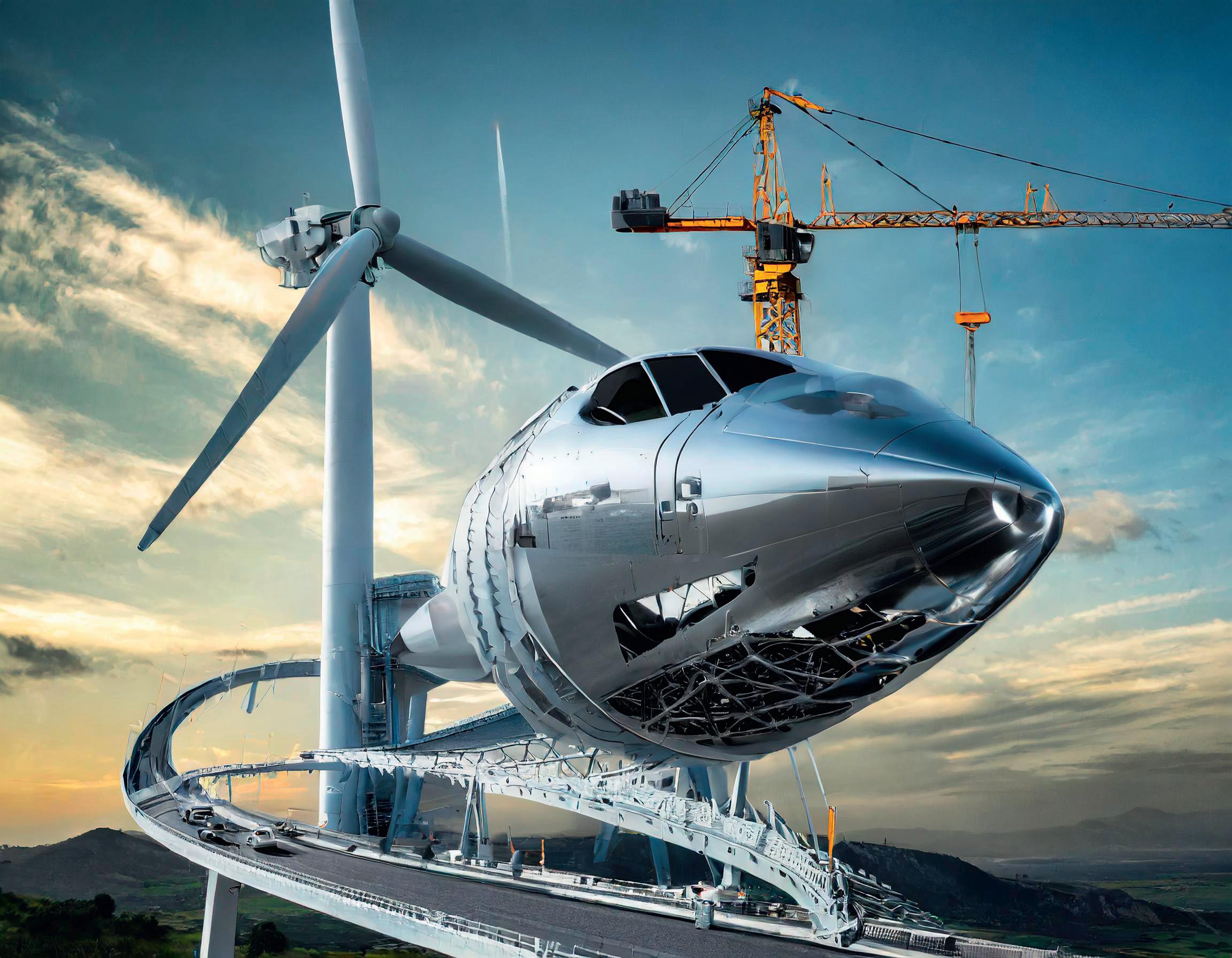


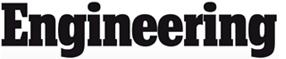

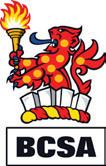

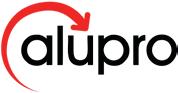

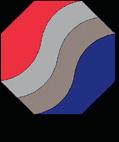
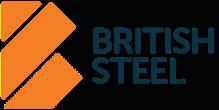
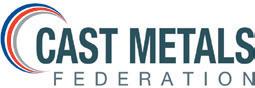
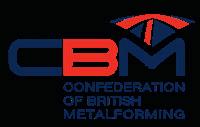

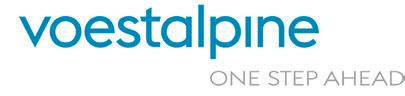
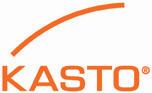
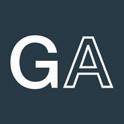

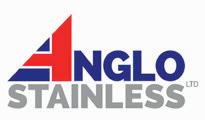
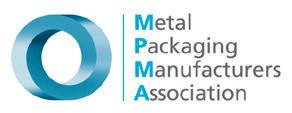
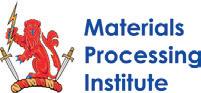
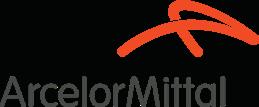
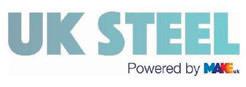
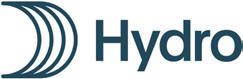
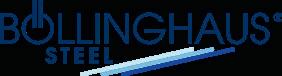
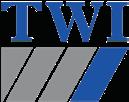
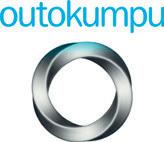
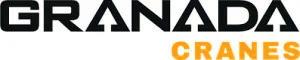

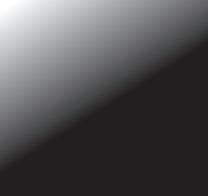
3D Print Manufacturing
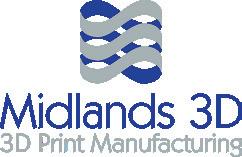
Midlands 3D Printing
T: 01785 594389
E: sales@midlands3d.com
W: www.midlands3d.com
Anti Vibration Products, Mounts & Bushes
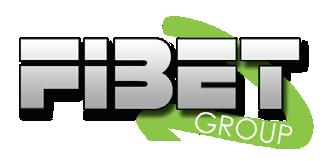
Fibet Rubber Bonding (UK) Ltd
T: 01282 878200
E: sales@fibet.co.uk
W: www.fibet.co.uk
Connectors & Cabling Solutions
CEMBRE Ltd
T: 01675 470 440
E: sales@cembre.co.uk
W: www.cembre.com/en
Design-In Power Supply Solutions
Ideal Power
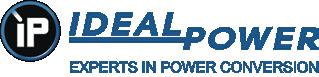
T: 01733 309865
E: salessupport@idealpower.co.uk
W: www.idealpower.co.uk
Drives, Motors & Gears
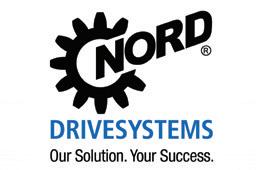
Flow Meters
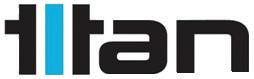
Nord
T: 01235 534404
E: GB-sales@nord.com
W: www.nord.com
Industrial Fans
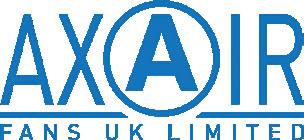
Axair Fans UK Limited
T: 01782 349 430
E: sales@axair-fans.co.uk
W: www.axair-fans.co.uk
Machine Safety
Schmersal UK Ltd
T: 01684 571980
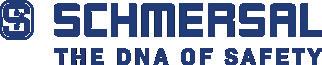
E: uksupport@schmersal.com
W: www.schmersal.co.uk
Marking Solutions
T-Mark
T: 0330 153 8320
E: sales@t-mark.co.uk
W: www.t-mark.co.uk
Pressure Measurement Specialists
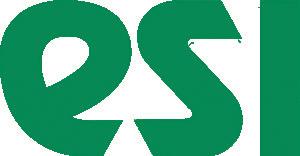
ESI Technology Ltd
T: +44 (0)1978262255
E: sales@esi-tec.com
W: www.esi-tec.com
Robotics & Automation
KUKA Robotics UK Ltd

T: 0121 505 9970
E: sales.uk@kuka.com
W: www.kuka.com
Sensors
Titan Enterprises Ltd
T: +44 (0)1935 812790
E: sales@flowmeters.co.uk
W: www.flowmeters.co.uk
High Shear Mixing Equipment
Silverson Machines Ltd
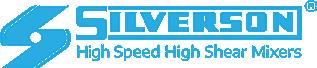
T: +44 (0)1494 786331
E: sales@silverson.co.uk
W: www.silverson.co.uk
Industrial Communications
Brainboxes

T: + 44 (0) 151 220 2500
E: sales@brainboxes.com
W: www.brainboxes.com
Intoware
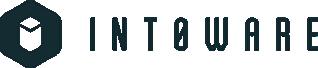
T: 0115 977 8969
E: hello@intoware.com
W: www.intoware.com
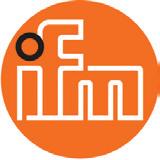
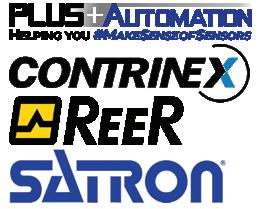
IFM Electronic
T: 020 8213-0000
E: enquiry.gb@ifm.com
W: www.ifm.com
PLUS Automation Ltd
T: 0121 58 222 58
E: Sales@PLUSAutomation.co.uk
W: www.PLUSAutomation.co.uk
Storage Solutions

BITO Storage Systems Ltd.
T: 02476 388 852
E: Info.uk@bito.com
W: www.bito.com
Test & Inspection
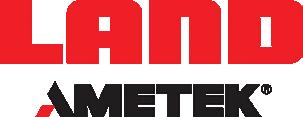
AMETEK Land (Land Instruments International)
T: +44 1246 417691
E: land.enquiry@ametek.com
W: www.ametek-land.com
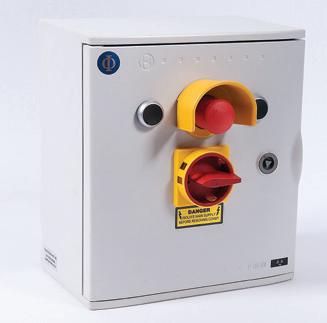

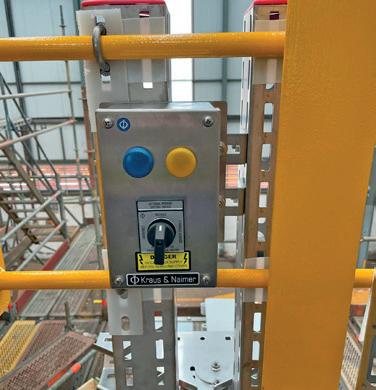

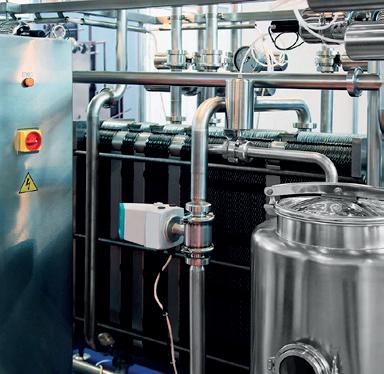
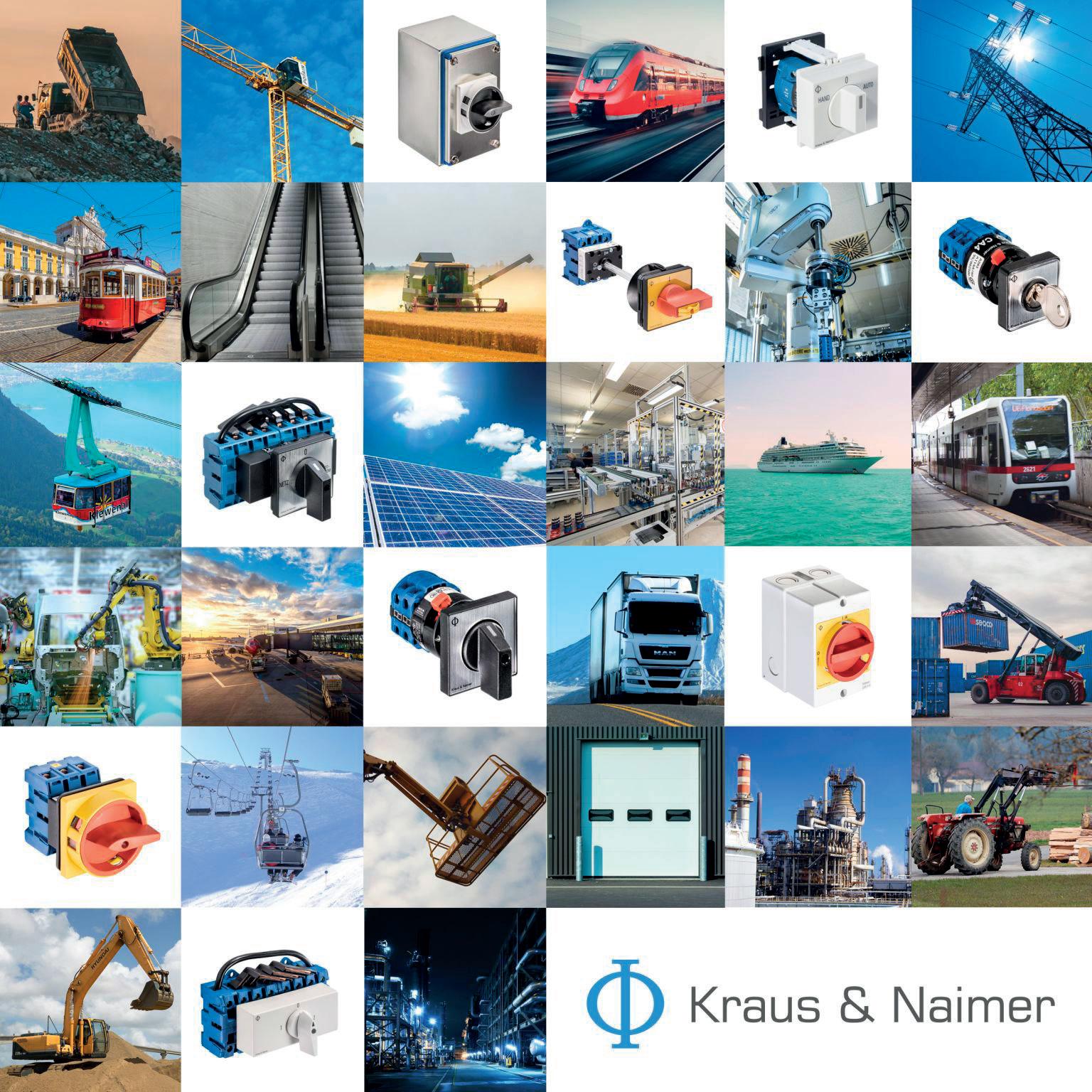
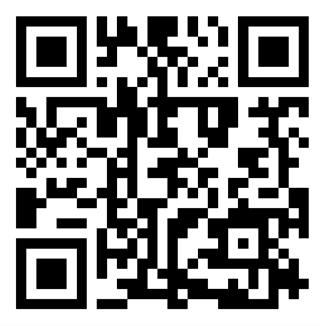
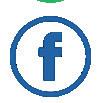
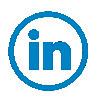
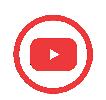
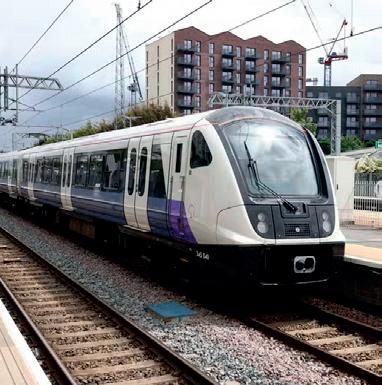
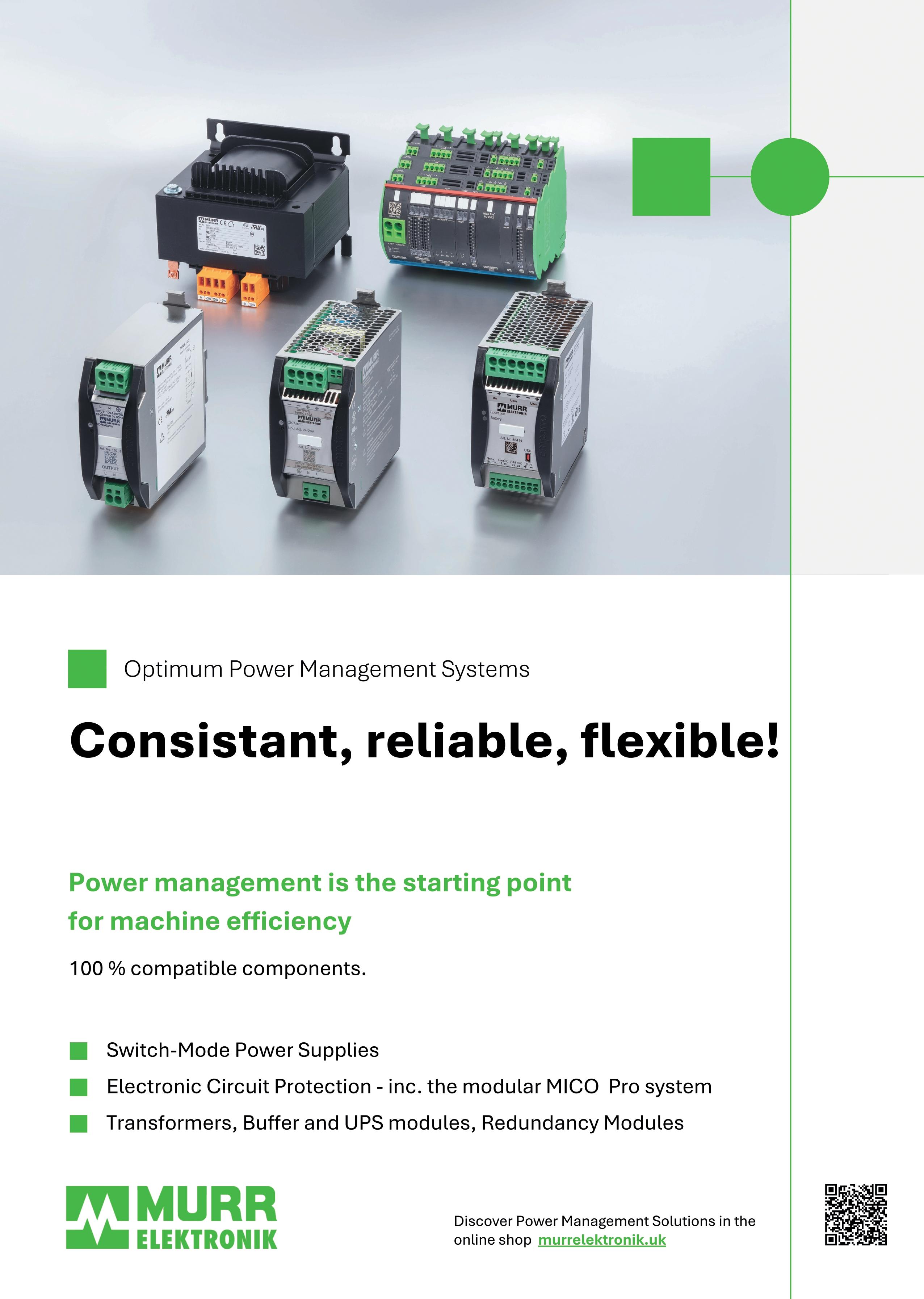