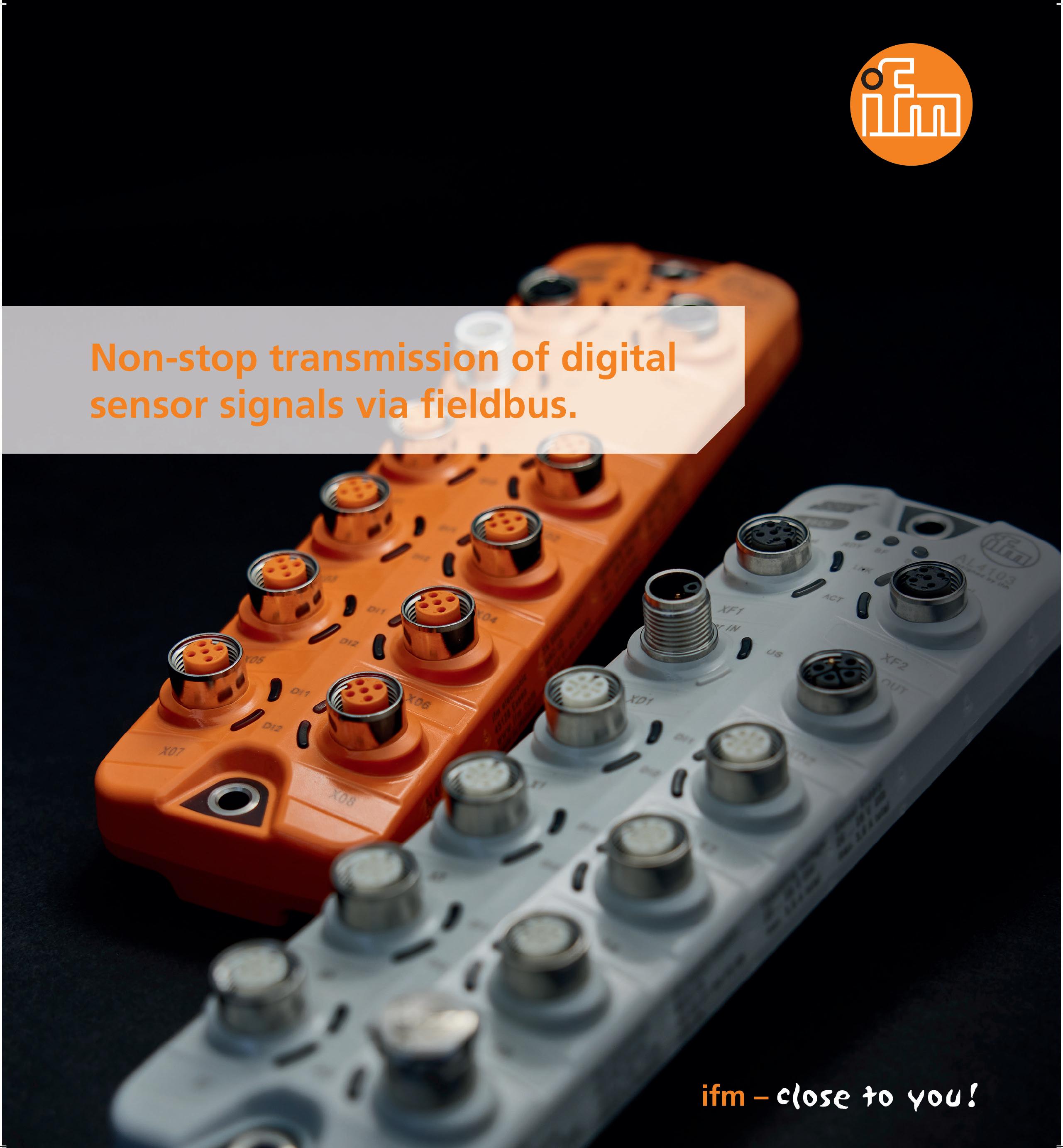
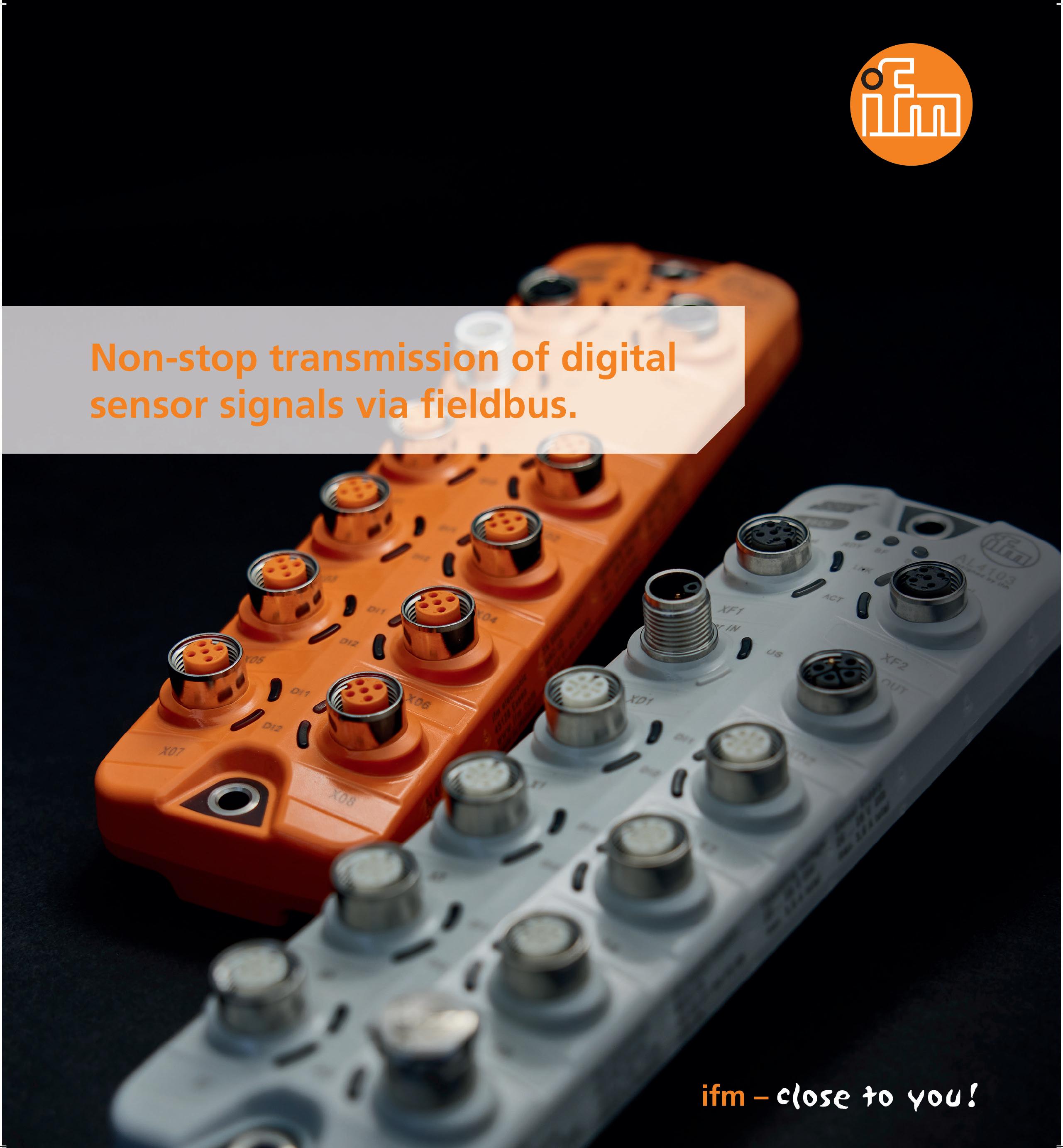
: Levitating, contactless, intelligent!

Free 2D product movement with up to 6 degrees of freedom

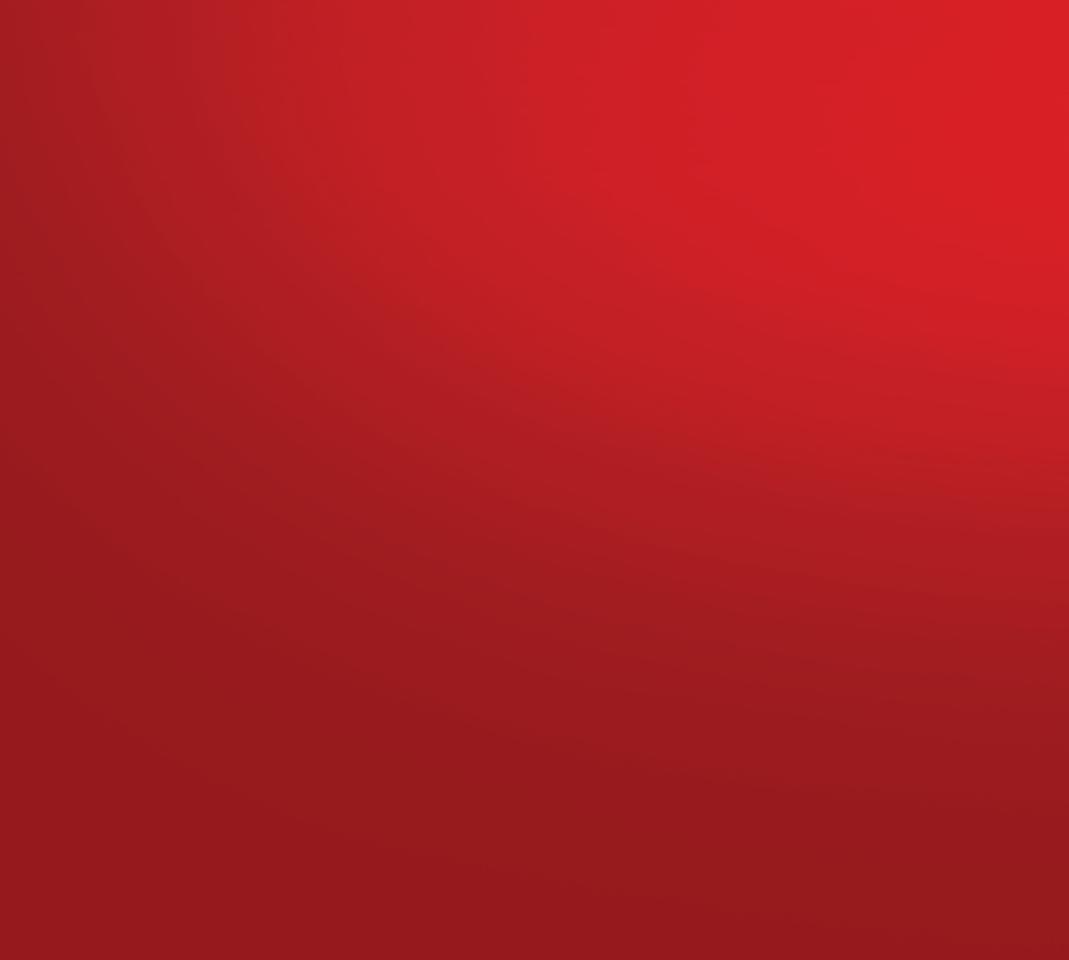
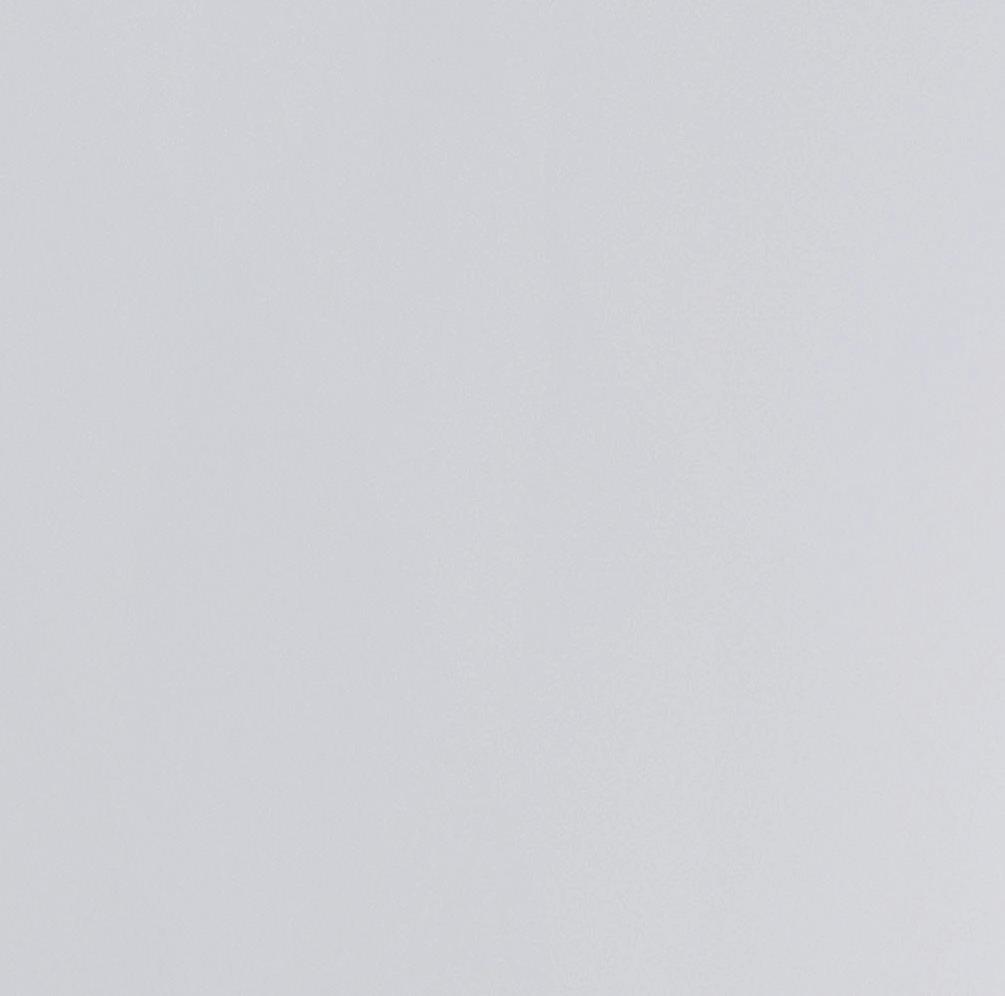
XPlanar enables new degrees of freedom in product handling: Levitating planar movers
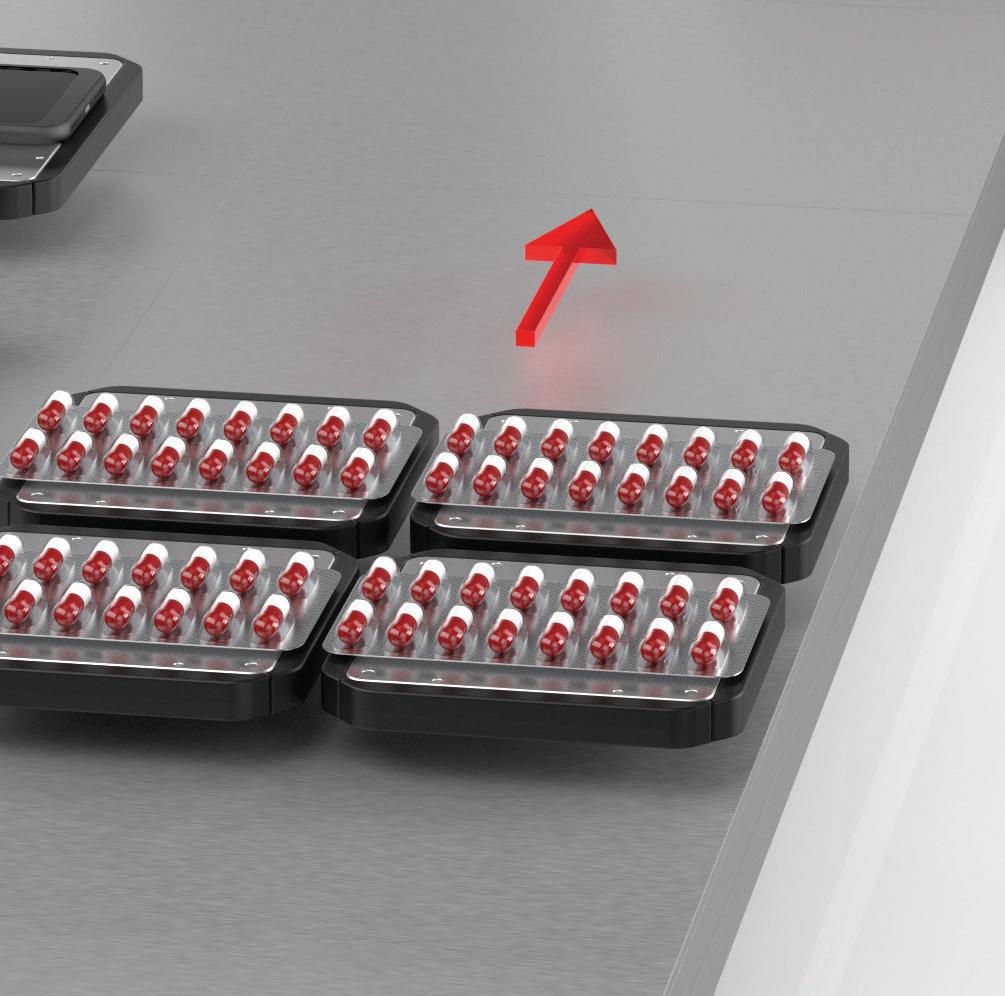
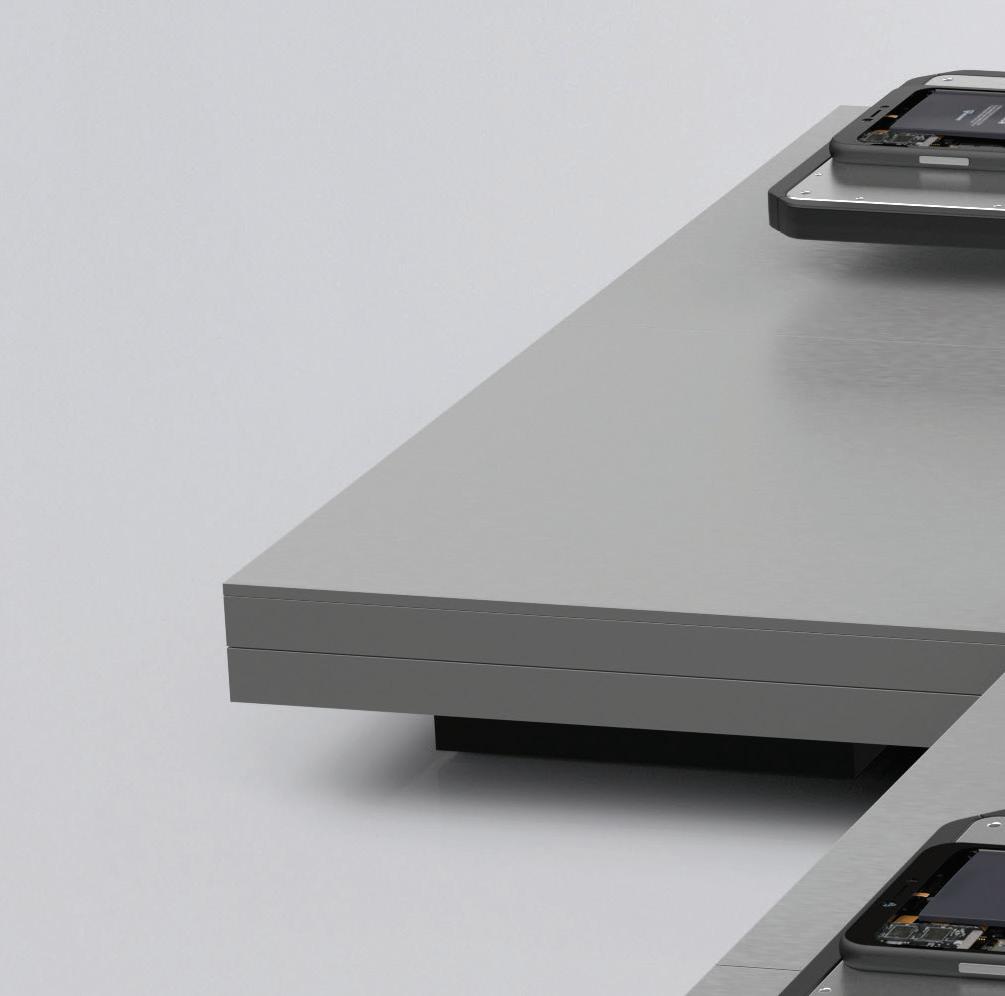

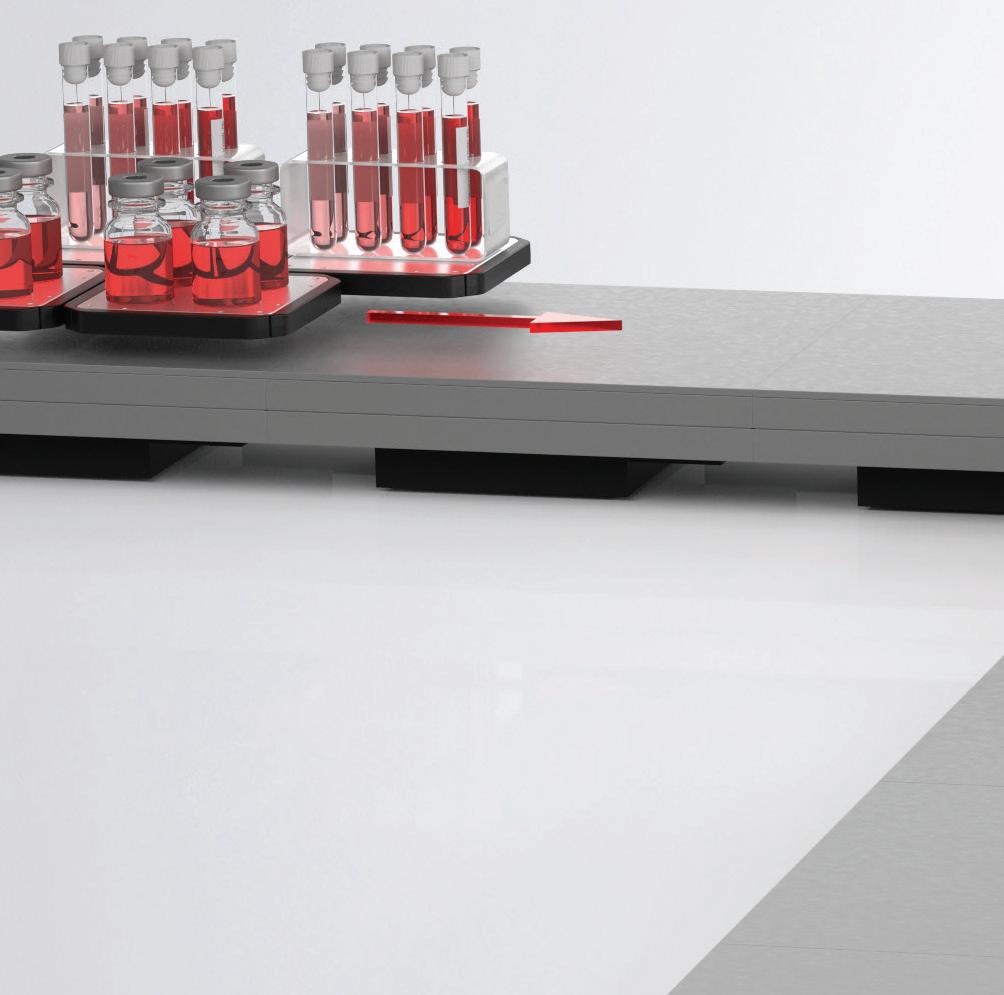

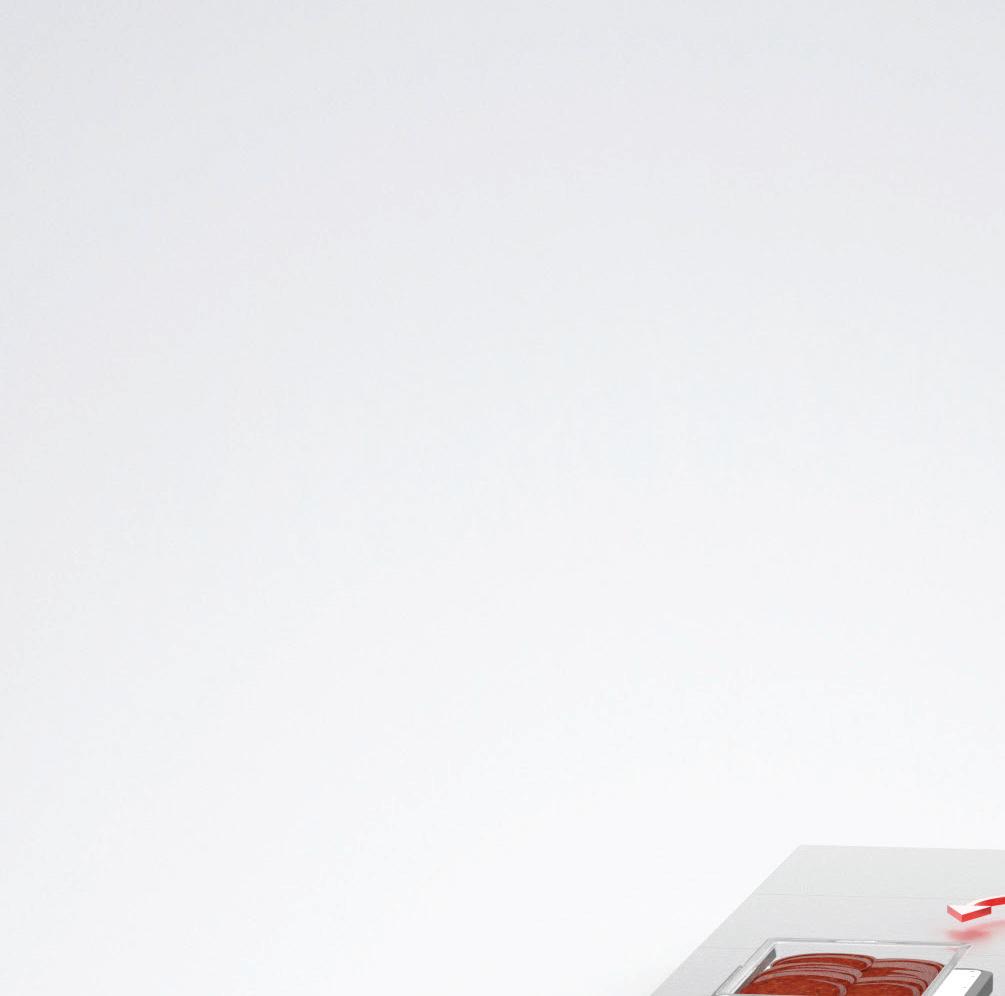
float over individually arranged planar tiles on freely programmable tracks.
Individual 2D transport at up to 2 m/s
Processing with up to 6 degrees of freedom
Transport and processing in one system
Wear-free, hygienic and easy to clean
Free arrangement of planar tiles enabling customized machine layout
Multi-mover control allowing parallel and individual product handling
Fully integrated into the powerful PC-based Beckhoff control system (TwinCAT, PLC IEC 61131, Motion, Measurement, Machine Learning, Vision, Communication, HMI)
For use across all industries: assembly, food, pharma, laboratory, entertainment, …
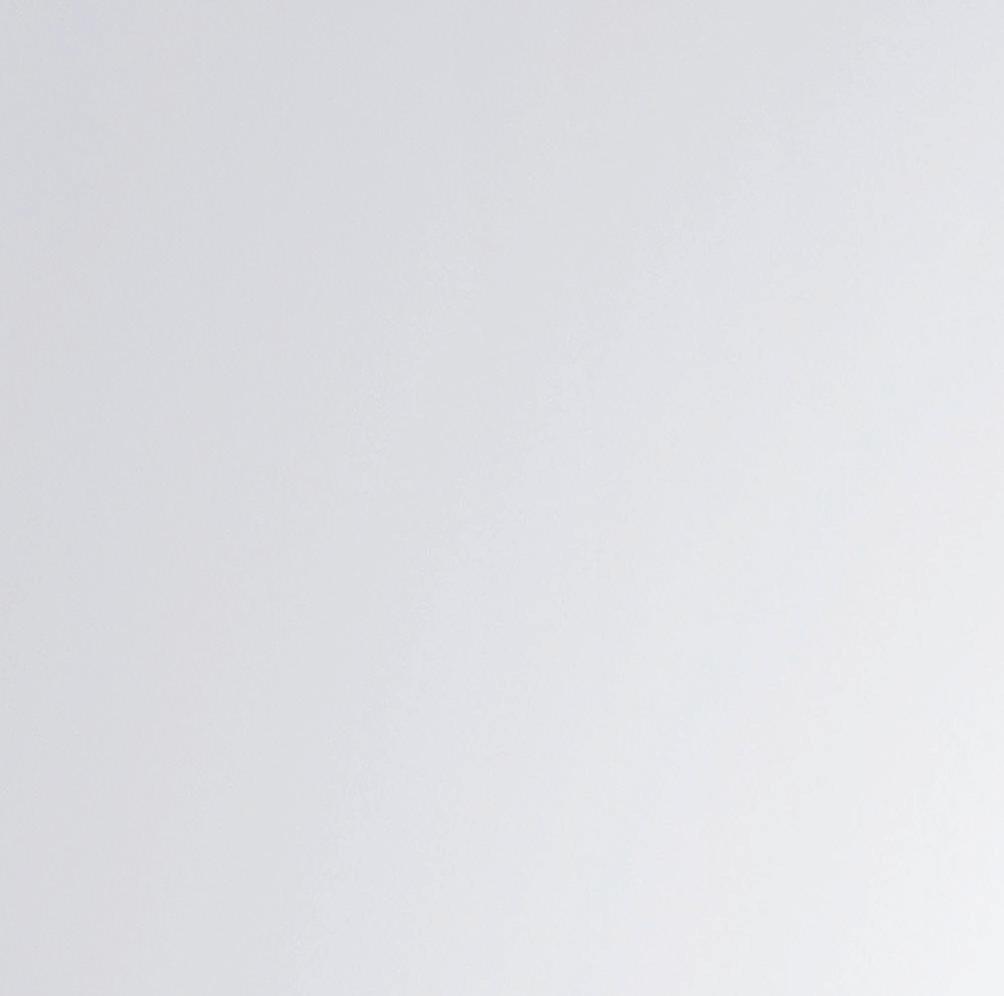
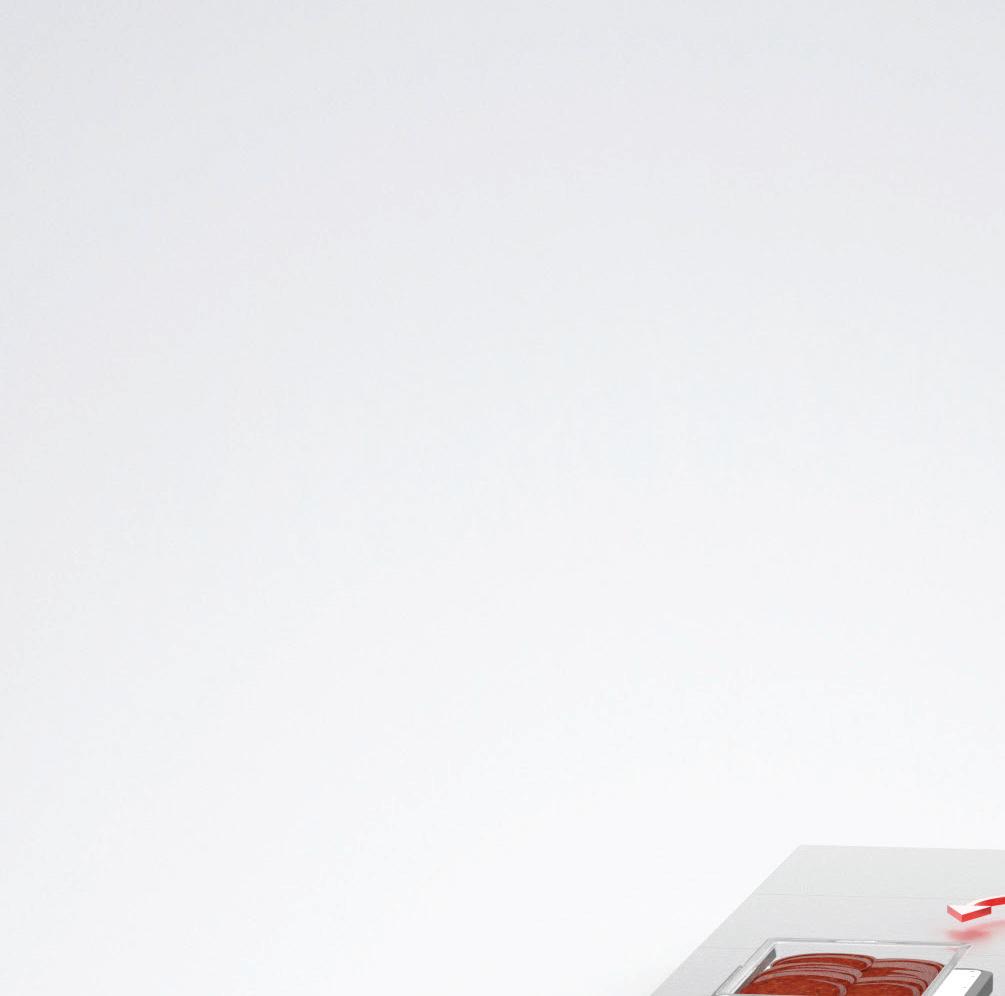


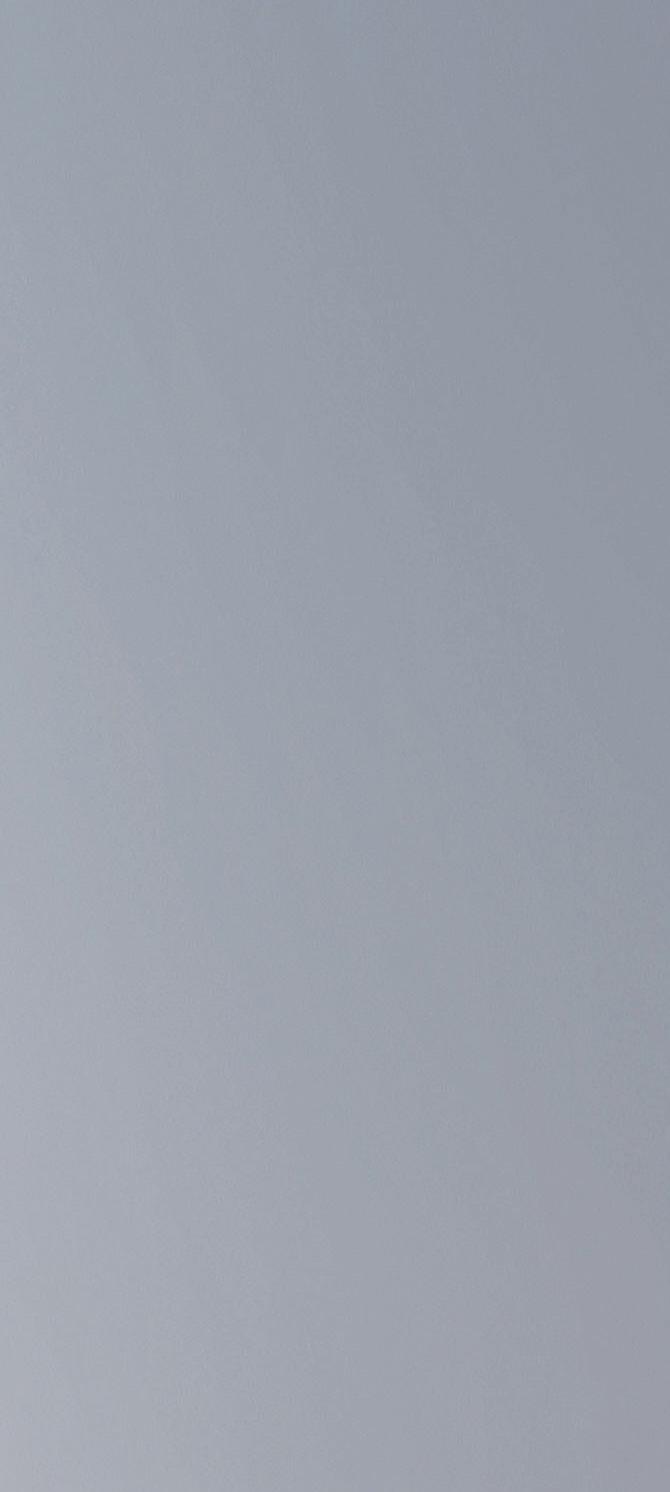

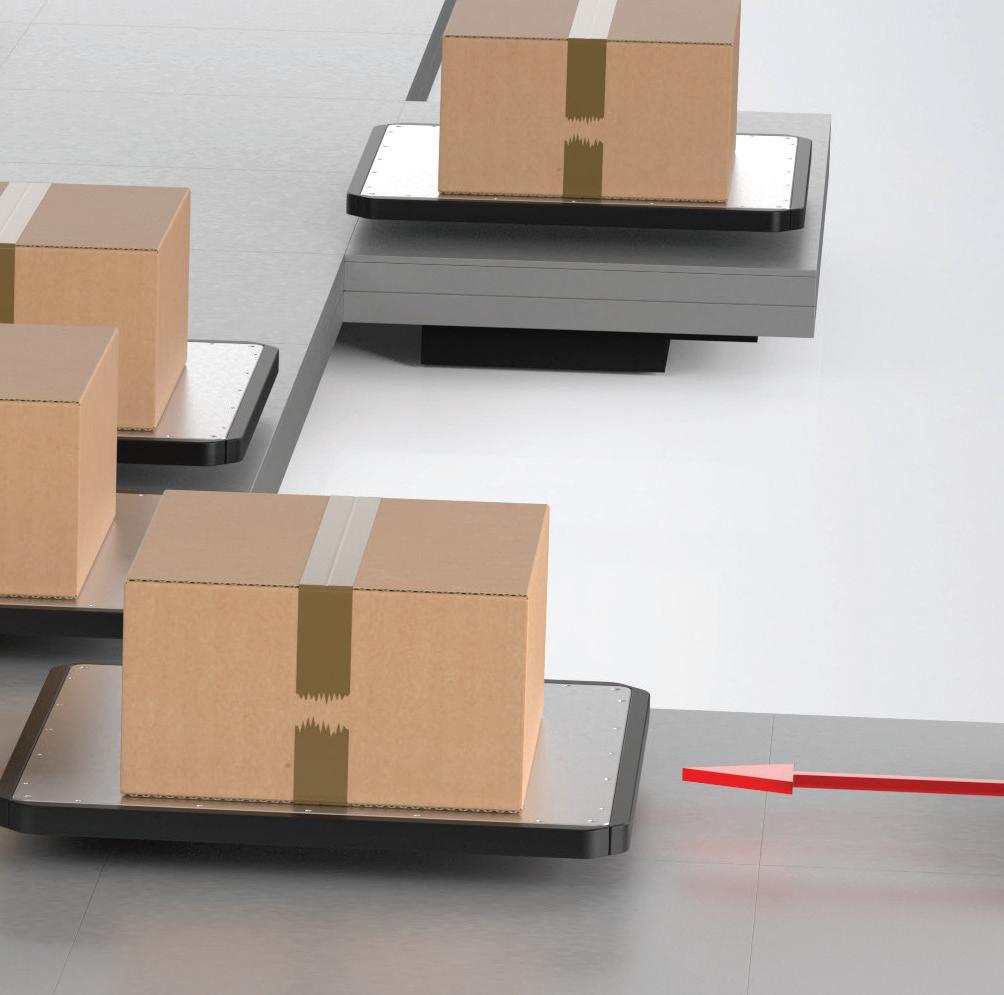

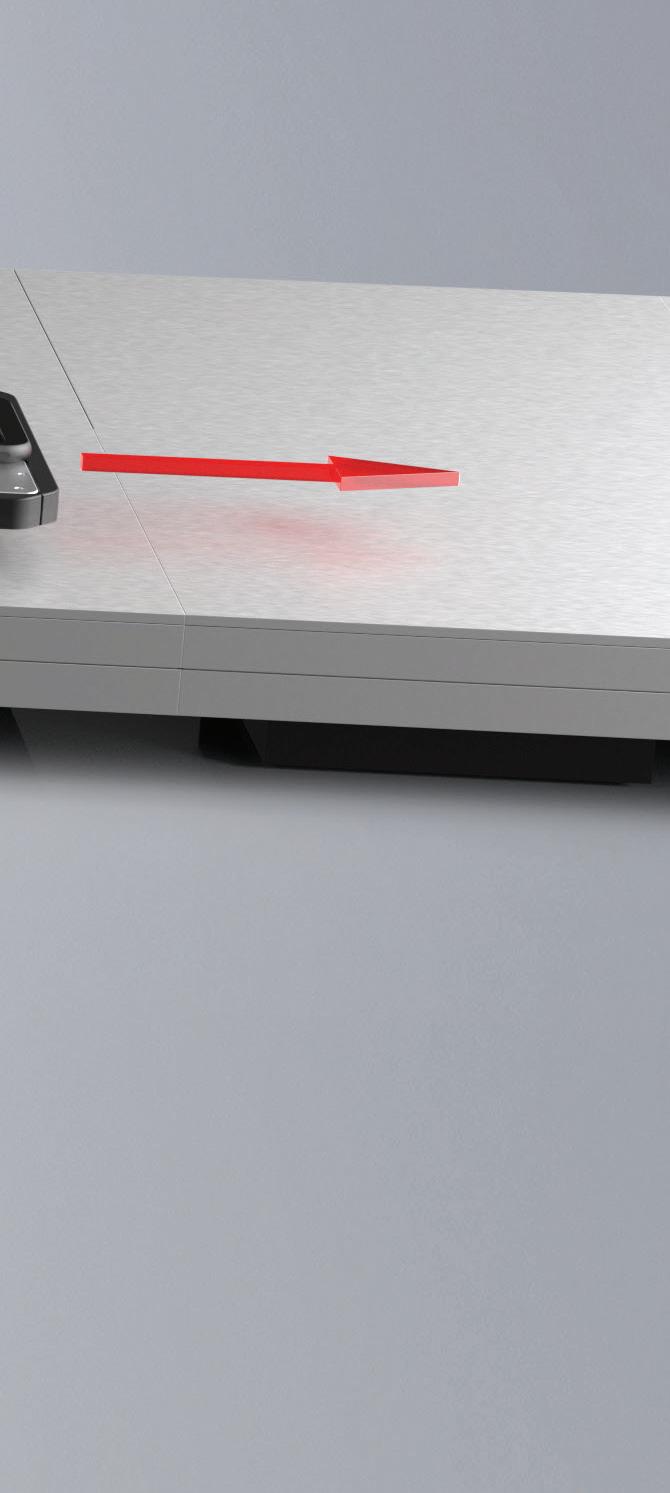
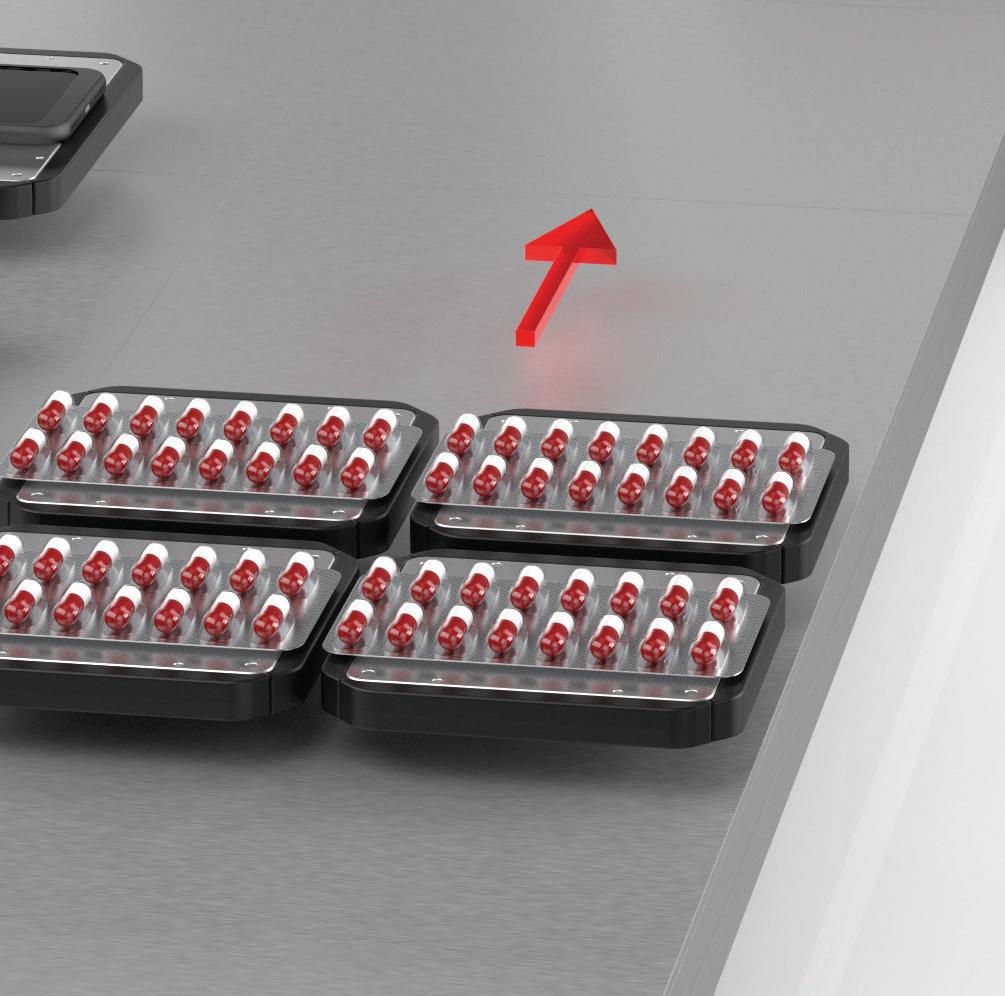

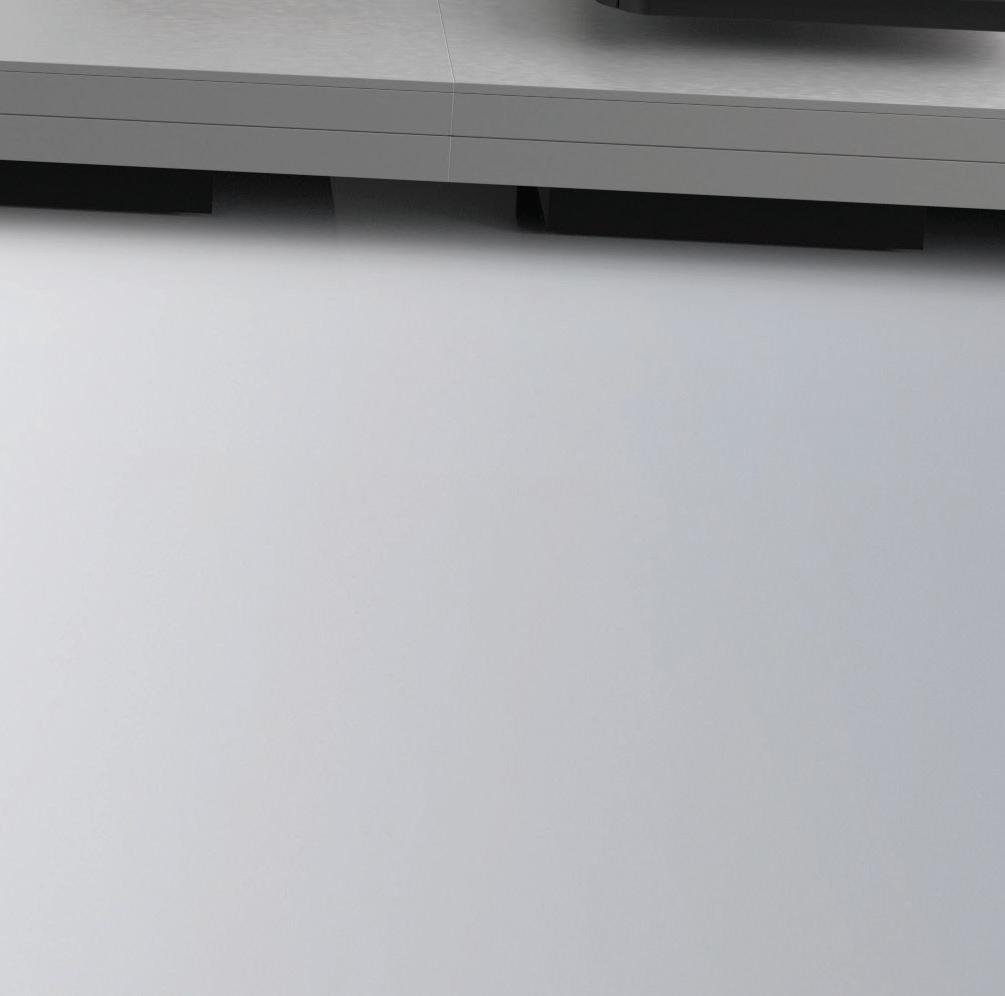

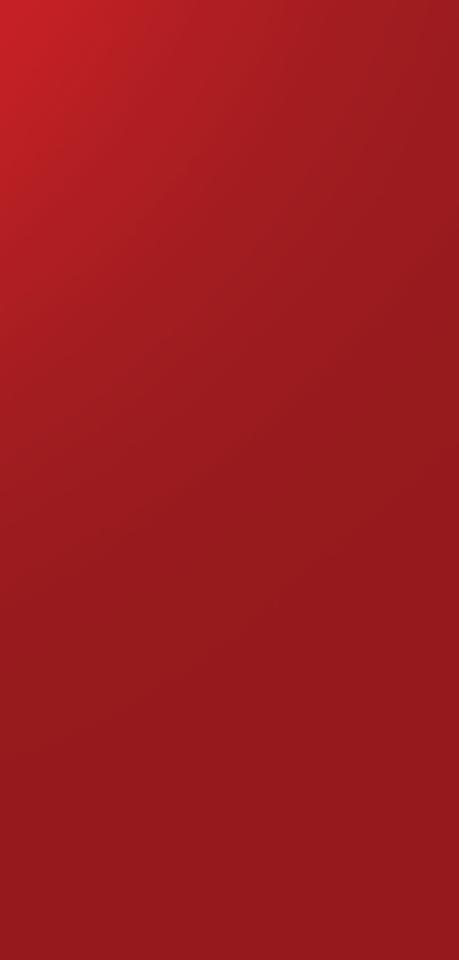
Editor
Chris Callander chrisc@cimltd.co.uk
Publication Manager
James Davies jamesd@cimltd.co.uk 01795 509105
Account Manager
Hannah Moody hannah@cimltd.co.uk 01795 509115
Design & Production
Grant Waters Grant@cimltd.co.uk
James Taylor james@cimltd.co.uk 01795 509108
Credit Facilities Manager
Lauren Sharpe creditcontrol@cimltd.co.uk 01795 509103
Administration Manager
Natalie Murray admin@cimltd.co.uk 01795 509103
Sales Director
Tom Woollin tom@cimltd.co.uk
Chief Executive
John Denning jdenning@cimltd.co.uk
www.mepca-engineering.com
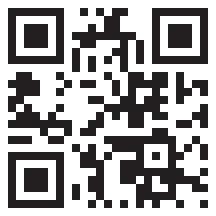
© 2023 TGM Publishing Limited,1st Floor, Saphir House, 5 Jubilee Way, Faversham, Kent, ME13 8GD. No part of this magazine may be reproduced or stored in a retrieval system or transmitted in any form – electronic, mechanical or physical – without express prior permission and written consent of the publisher. Contributions are invited and when not accepted will be returned only if accompanied by a fully stamped and addressed envelope. Manuscripts should be typewritten. No responsibility can be taken for drawings, photographs or literary contributions during transmission or in the editor’s hands. In the absence of an agreement the copyright of all contributions, literary, photographic or artistic, belongs to TGM Publishing Limited. The publisher accepts no responsibility in respect of advertisements appearing in the magazine and the opinions expressed do not necessarily represent the views of the publisher. The publisher cannot accept liability for any loss arising from the late appearance or non-publication of any advertisement.
May 2023
In this issue of MEPCA, we have our first connectivity focus. Connectivity is essential in a manufacturing or process environment because it enables the smooth flow of information between different systems, machines, and processes. It is arguably the most important aspect of today’s production environment and has evolved significantly over the last 40 years.
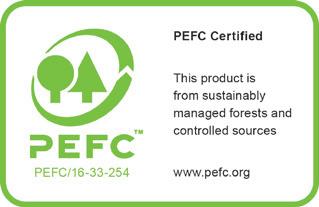
In the early 1980s, factory automation and connectivity were in their infancy and communication between machines and systems was limited. In the late 1980s and early 1990s, PLCs became widely used for factory automation, enabling the control and monitoring of machines and systems using a single, programmable device. In the 1990s, emerging industrial networks enabled machines and systems to communicate with each other, allowing for greater control and automation. Then in the late 1990s and early 2000s, Ethernet became widely used to connect machines and systems to each other and to central servers, allowing for real-time data collection and analysis.
In the last decade, the evolution of the Internet of Things (IoT) has transformed factory connectivity. Devices connected to the internet have enabled real-time monitoring and control from anywhere in the world. This capability has led to the latest development, Industry 4.0, characterised by the integration of digital technologies into all aspects of manufacturing, from design to production to supply chain management. This integration enables factories to operate more efficiently, with greater flexibility and agility.
Thanks to connectivity in manufacturing and processing, today we benefit from real-time monitoring and control, predictive maintenance, data analytics, safety, and supply chain optimisation like never before. And that is why it is such an important topic, and this won’t be our last connectivity focus.
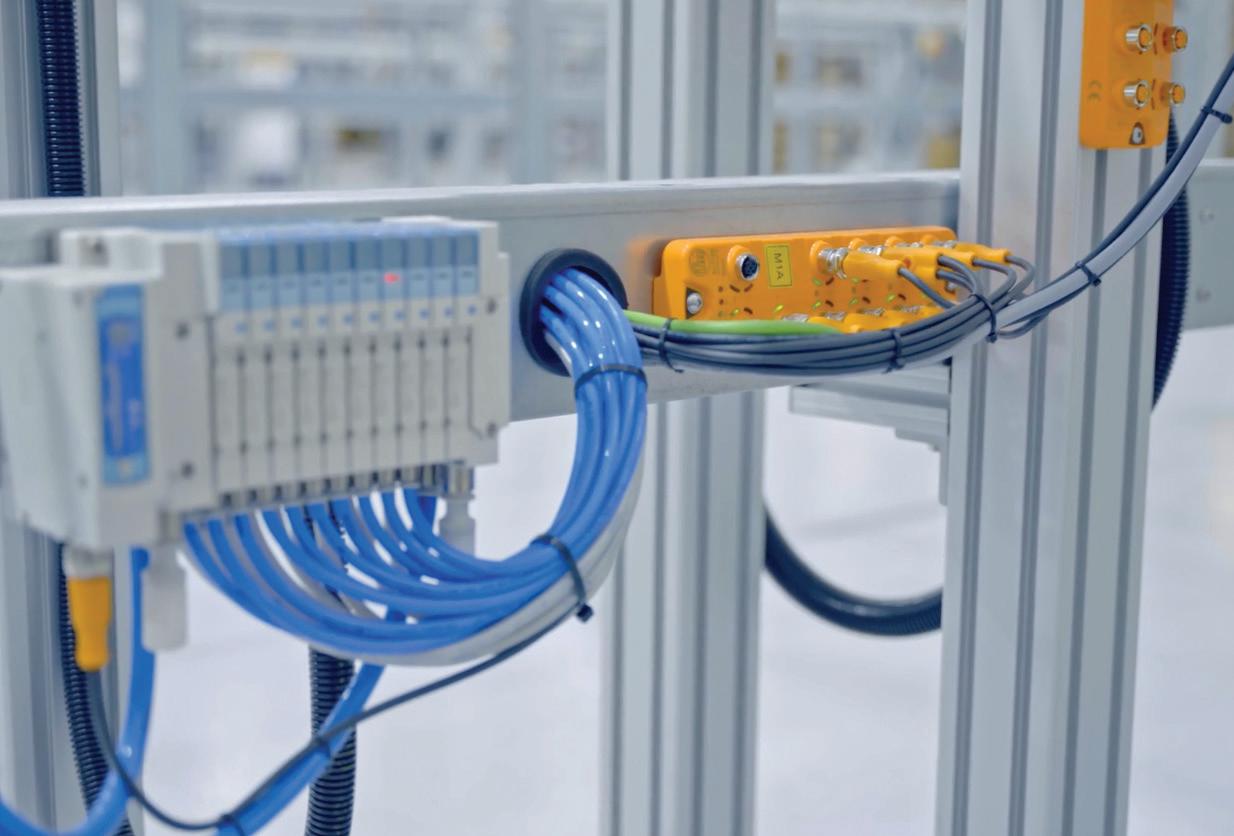
Enjoy the issue.
Chris Callander, Editor @Mepca-magazine
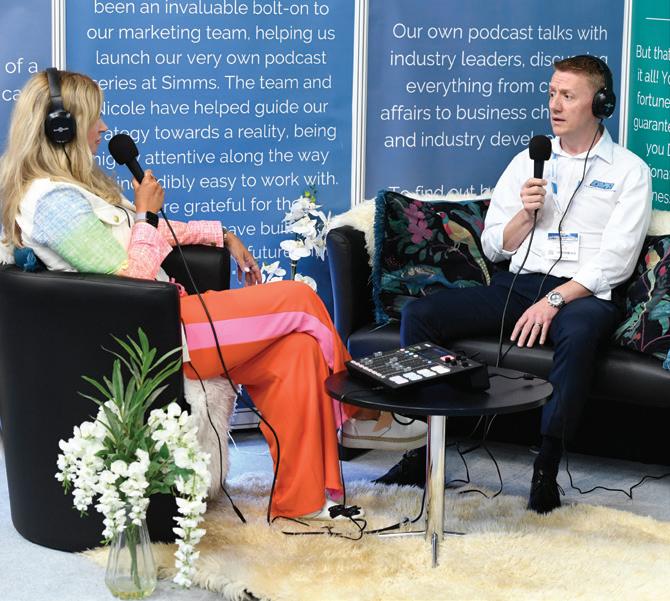
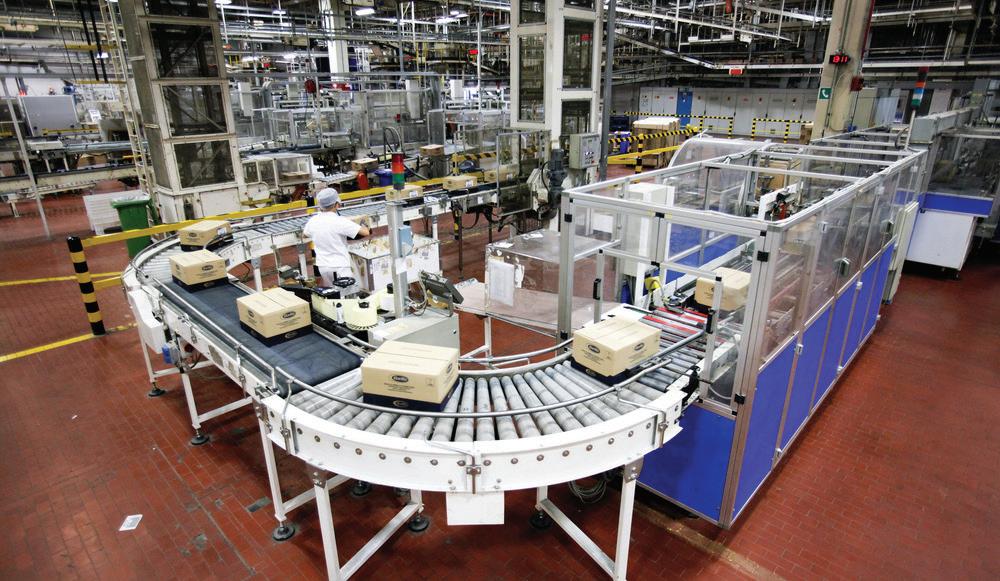
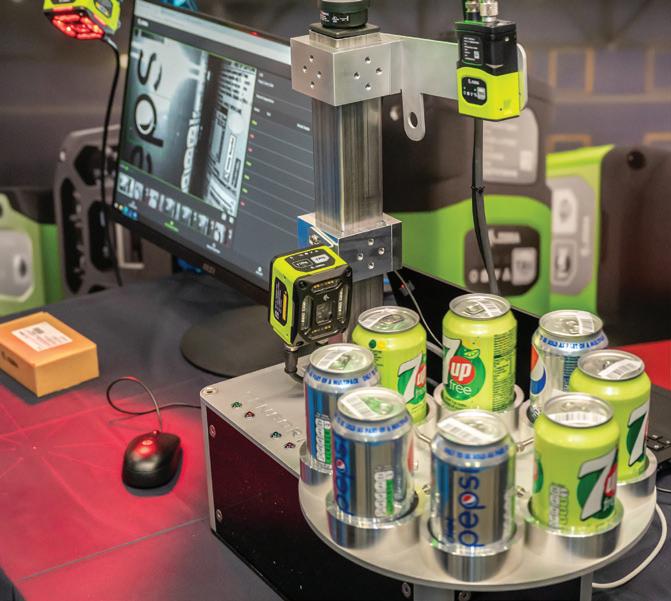
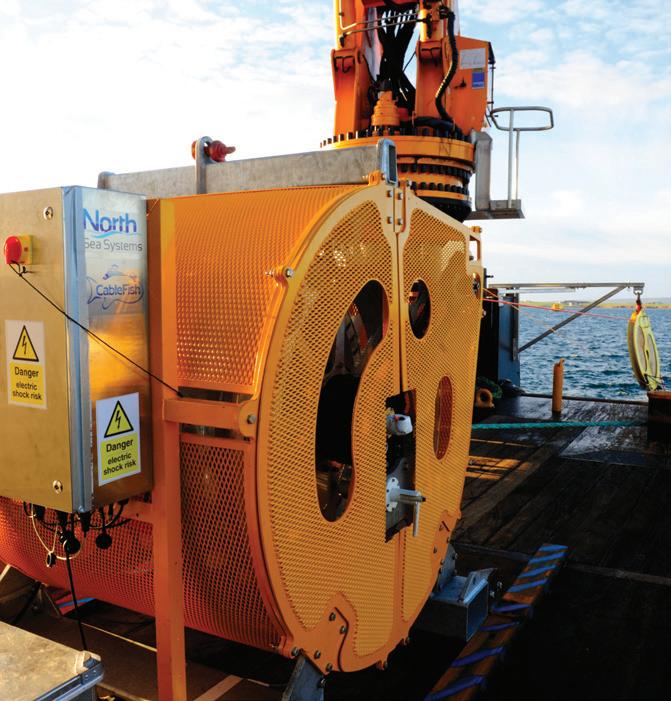

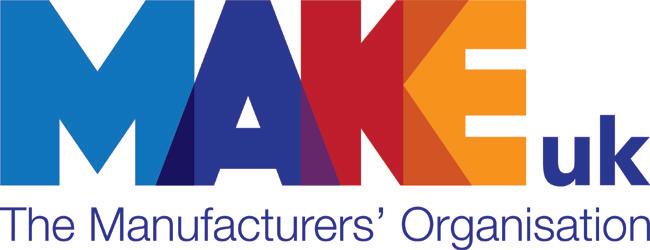
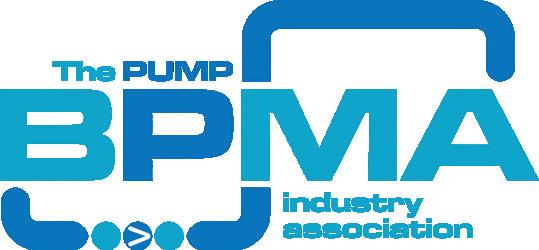
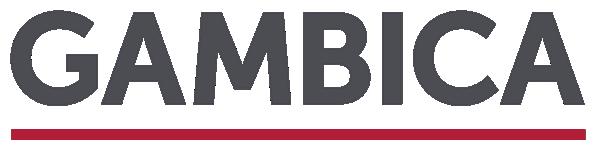
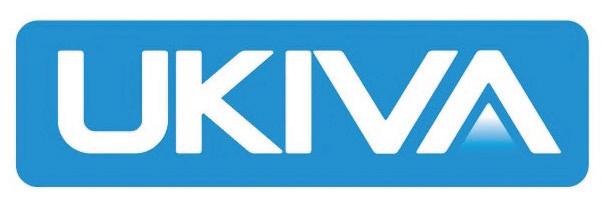
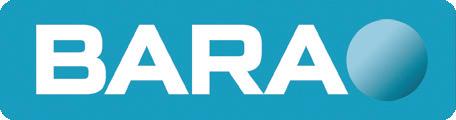
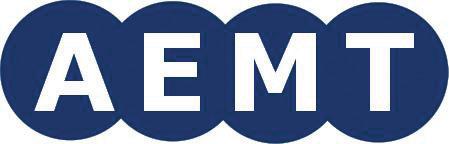

Manufacturing bounces back as clouds lighten
Britain’s manufacturers are seeing a rebound in activity in the first quarter of the year as the domestic and global markets have improved, easing fears of a significant recession for industry this year, according to a survey published by Make UK and accountancy and business advisory firm BDO.
The findings in the Make UK/ BDO Q1 Manufacturing Outlook survey show a marked pick up on the picture in the final quarter of 2022. The figures echo the gradual improvements in other data, such as the UK and European PMIs, which are now only just in negative territory, as well as a strong pick up in demand from China.
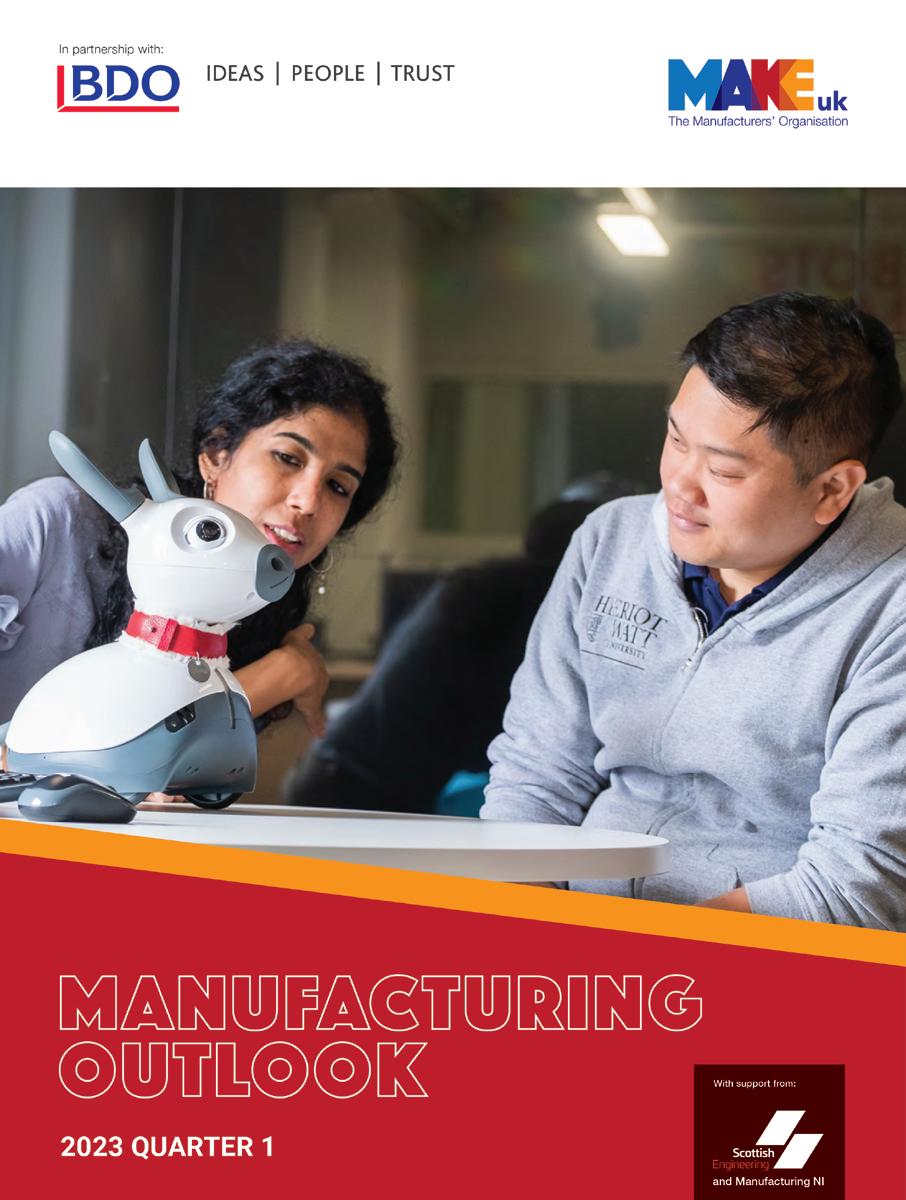
Most notably, the improvement is being largely driven by strong demand in the electronics and mechanical equipment sectors, with the balance of orders in the electronics sector in particular (+64%) extremely strong.
According to Make UK and BDO, this could be due to several factors, including companies investing in digitalisation and extra capacity to counter labour shortages or, to take advantage of the final period of the super deduction scheme, which ends this month. Demand for electronics goods is especially strong from overseas (+67%), in particular the EU.
The survey also shows a significant improvement in the investment balance overall, even before the positive announcement on full expensing in the recent Budget Statement. However, given the average investment cycle in manufacturing is around seven years, Make UK believes that for the measure to make a real and lasting difference to business investment levels, the measure needs to become permanent.
However, despite the improvement this quarter, Make UK and BDO caution against the worst of conditions being over and are forecasting a contraction for manufacturing in 2023 as the substantial challenges the sector is facing show few signs of abating.
Fhaheen Khan, Senior Economist at Make UK, said: “Manufacturers have seen a rebound at the start of the year as conditions have improved in their major markets and business confidence has improved. However, one swallow doesn’t make a summer, and it is far too early to say the worst has passed given the significant challenges the economy faces. However, the recent Budget should help boost investment in the short to medium term although ideally, full expensing should be made permanent to better reflect the investment cycle for manufacturers.”
According to the survey, the balance on output improved to +21% from +5% and is expected to gather strength in the second quarter to +32%, a significant improvement. Total orders also rose substantially from +6% to +28%, although the next quarter is slightly less positive at +23%.
In line with this improved picture, UK orders increased to +20% from +2%, while export orders also saw a rise from -6% to +12%, reflecting better conditions in overseas markets.
The scramble to attract and retain talent also shows no signs of abating, with recruitment intentions increasing from +3% to +19%, improving substantially to +31% in the next quarter. Investment intentions also rose substantially from -5% to +14% potentially reflecting manufacturers’ intention
to take advantage of the final quarter of the super-deduction scheme before it ends this month.
The Make UK/BDO survey showed that inflationary pressures are still very evident for manufacturers, with increased costs still being passed on. UK and export prices were both at balances of +52% picking up slightly from last quarter.
In terms of overall output, this year Make UK and BDO are forecasting a contraction of -3.3% (a slight improvement from the -4.4% forecast at the end of last year) and growth of just 0.8% in 2024.
The survey of 338 companies was conducted between 15 February and 8 March.
Wayne Rose has officially become the new Director and CEO of the British Pump Manufacturers Association (BPMA) following the retirement of his longstanding predecessor, Steve Schofield.
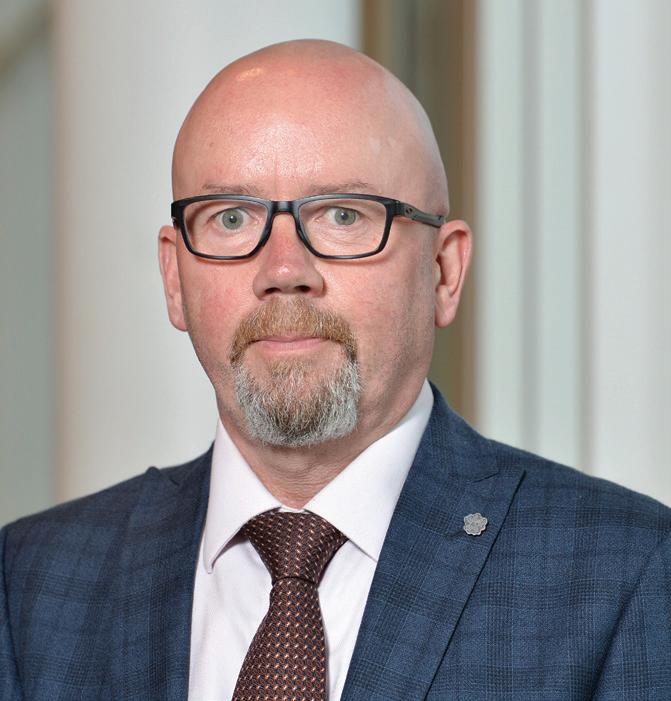
Having previously spent 24 years in various management roles at Manchesterbased Armstrong Fluid Technology, Wayne brings with him a wealth of pump industry experience. With over 1,200 employees worldwide and operating eight manufacturing facilities on four continents, Armstrong is known around the world as a leader and innovator in the design, engineering, and manufacturing of intelligent fluid-flow equipment. That depth of knowledge will undoubtedly serve him well as he helps to guide the BPMA through its
next chapter and ensure the Association continues to serve the interests and needs of its members.
Reporting to the Board, Wayne will
New Director and CEO for BPMA Manufacturing excellence boost for the west midlands
An agreement has been signed between the Manufacturing Technology Centre (MTC) and the Herefordshire-based New Model Institute for Technology and Engineering (NMITE), leading the way to regional partnership and industrial and educational growth.
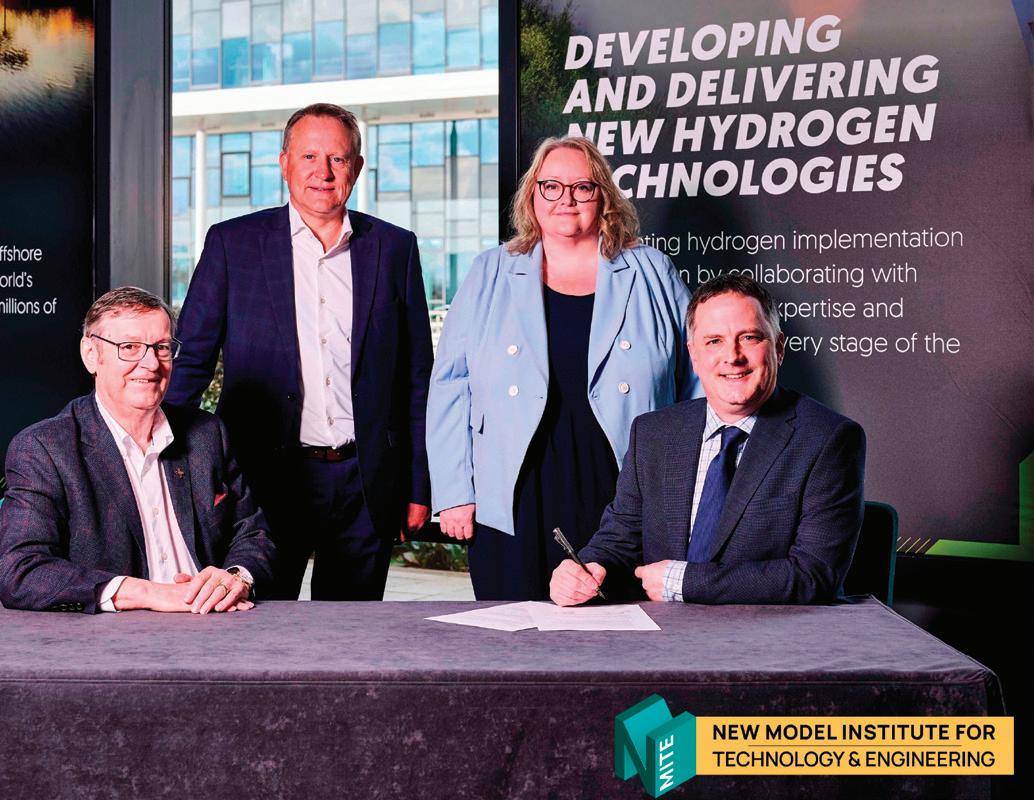
The agreement, signed by the CEOs of both organisations, marks a collaboration that will build on the strengths of each – the advanced technologies of the MTC and the academic quality and distinctiveness of NMITE – providing students with handson access to the latest in manufacturing equipment and techniques. The MTC@ NMITE, as the partnership has been named, will also work with local businesses in transferring and adopting knowledge to boost manufacturing productivity and sustainability.
The MTC aims to provide a competitive environment to bridge the gap between university-based research and the development of innovative manufacturing solutions, in line with the Government’s manufacturing strategy. The partnership
with NMITE will complement the MTC’s existing training offering, which offers professional qualifications up to post-graduate level to redress skills gaps in the highvalue manufacturing sector. NMITE offers a breakthrough, interdisciplinary model of higher education which equips students with the diverse and creative problem-solving skills needed in an everchanging world.
The MTC@NMITE is part of NMITE’s Centre for Automated Manufacturing (CAM), which was founded to boost regional productivity in the manufacturing sector and to impart the skills required for the delivery of Industry 4.0. CAM’s mission is to support the growth of a modern, productive, sustainable and competitive
assume commercial responsibility for the day-to-day running of the organisation whilst also engaging with the elected members of the BPMA Council.
Commenting on Wayne’s appointment, current BPMA President, and Managing Director at KSB, Dale Croker, said: “The BPMA Board and Council are delighted to have secured the engagement of Wayne as a successor to Steve, who had been with the BPMA for a good many years. Indeed, he has left some big shoes to fill, but we know Wayne will bring his vast experience to bear and play a key part in the future development of the Association and the important service delivery it offers to members.
“We are enormously grateful to Steve Schofield for all that he achieved on our behalf, and we wish him a long and happy retirement.”
regional manufacturing industry which will be achieved through offers for part-time, fulltime, and professional education learners, as well as degree apprentices. CAM will support companies in understanding how automation can support the next stage of their growth and also target affordable and appropriate automation for companies that may be smaller, working with more legacy equipment, or in lower volume.
Additional Denso corrosion protection for the Craigavon Bridge
In 2013 Winn & Coales (Denso) Ltd. supplied its Steelcoat 100/400 System to protect a gas pipe on the Craigavon Bridge in Derry City. The successful application led to the use of the same system by Northern Ireland Water to protect 281m of a wastewater pumping main, including flanges and support brackets, on the same bridge in 2022.
The Steelcoat 100/400 System has been used by water companies throughout the UK to provide effective, long-term protection from corrosion to exposed and aboveground pipework. The ease and speed with which the system can be applied, alongside minimal surface preparation requirements, also helped to reduce traffic disruption on the bridge during the works. The final layer of Denso Acrylic Topcoat was also supplied in the same shade of blue to match the colour already featured on the bridge structure.
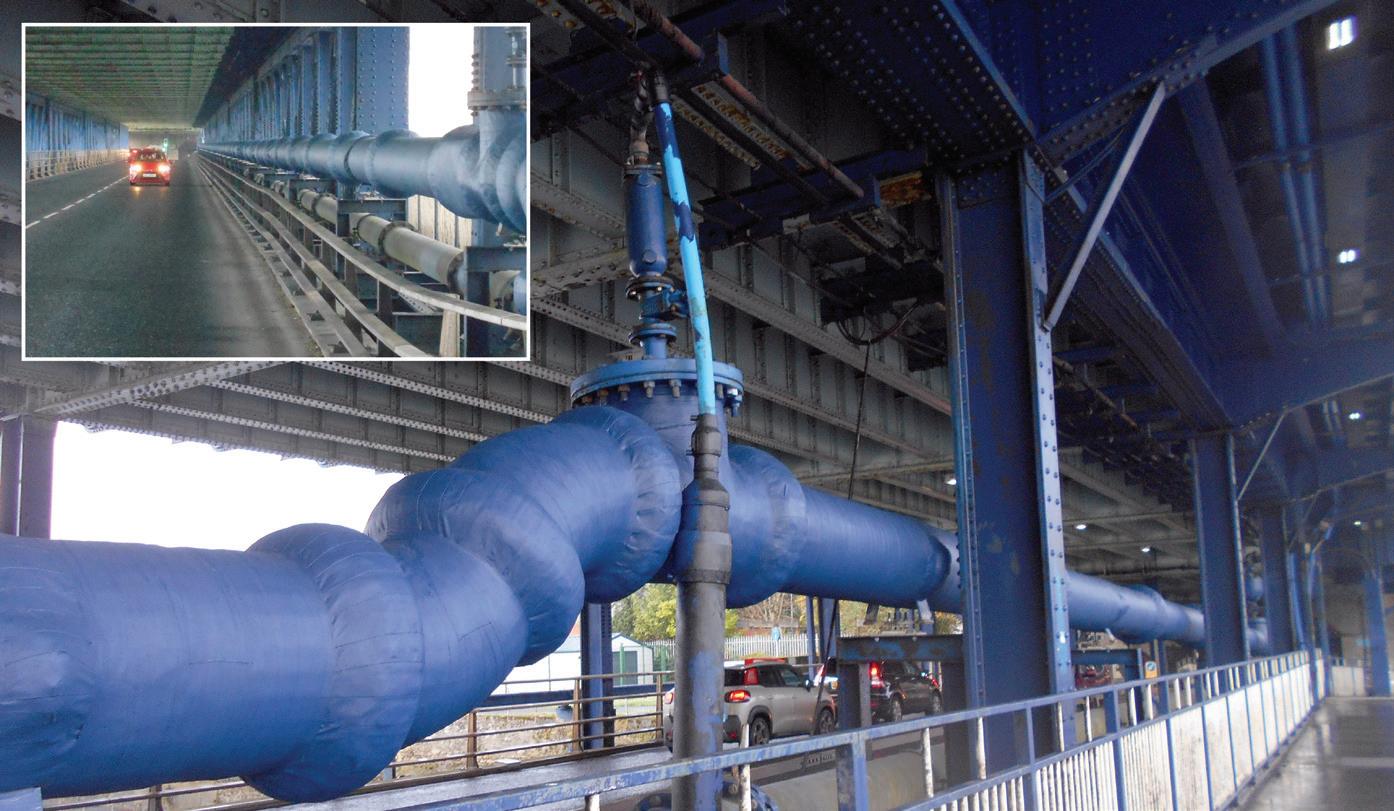
Winn & Coales (Denso) Ltd. provided training and site support during the application, which was carried out by BSG Civil Engineering Ltd and O’Kane Civil Engineering over a ten-week period. The
World’s first 3D camera with certified safety
SICK has launched the safeVisionary2, the world’s first compact 3D time-offlight camera with safety certification performance level c, in accordance with ISO 13849.
The safeVisionary2 represents a new milestone in safety technology. It uses 3D time-of-flight technology to monitor a three-dimensional space, offering exciting new possibilities for certain applications, particularly for increasing the availability of Automated Guided Vehicles (AGVs) and other mobile robots, as well as improving the productivity and versatility of human-robot collaboration.
In Automated Mobile Robots (AMRs), by scanning in three dimensions, SICK’s safeVisionary2 offers enhanced protection where there is a risk of collision with objects or people that are higher than the field of a standard 2D safety laser scanner. In addition, perception to the sides of the AMR
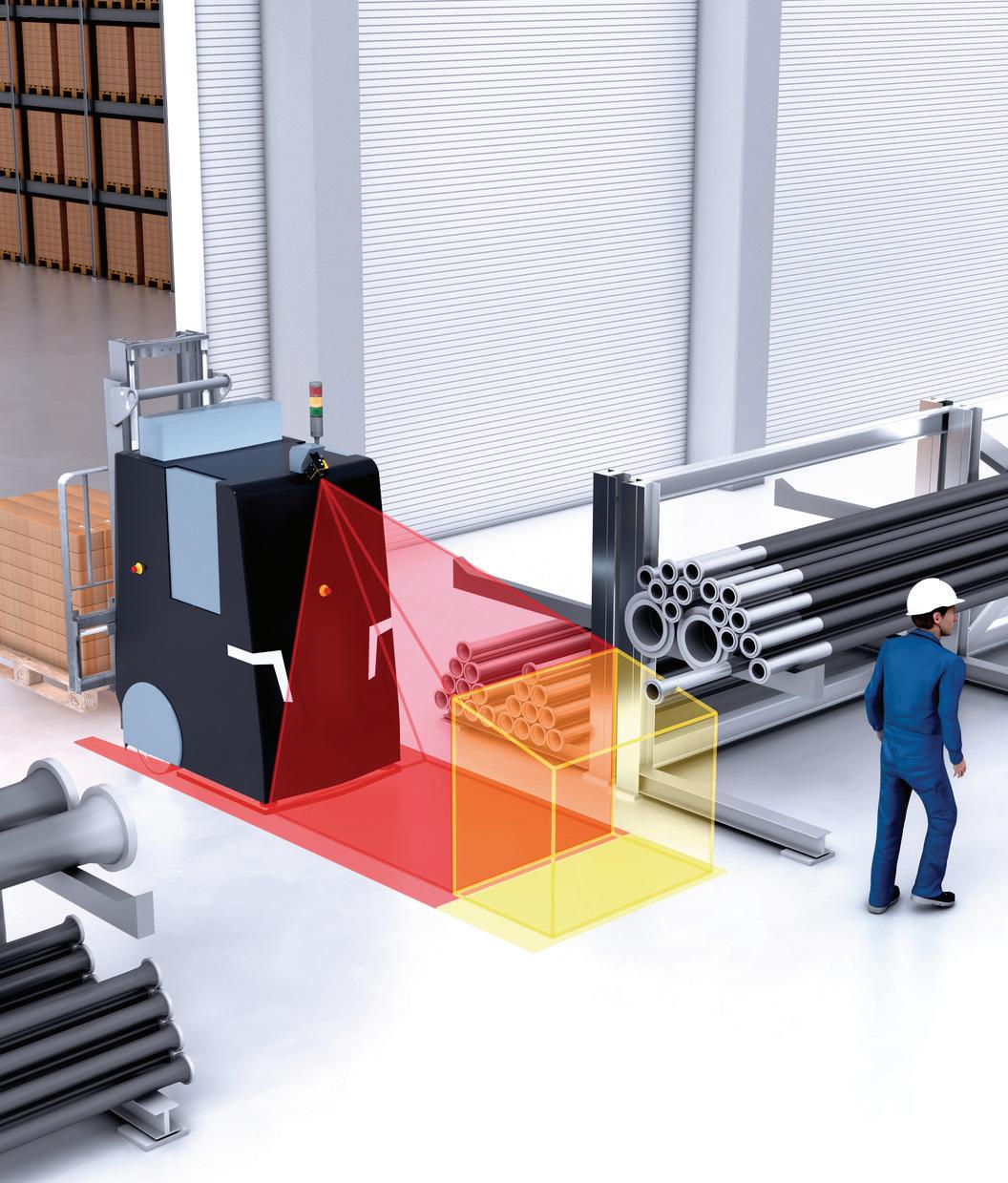
provides more protection to people when the vehicle is turning or rotating, for example after loading and unloading operations.
The safeVisionary2 also ensures greater levels of safety when using mobile service robots. As well as monitoring protective and warning fields in the robot’s travel path, the camera has a contour detection field that can reliably identify cliff hazards, such as stairs or ramps.
The safeVisionary2 enables more true collaboration between robots and workers with fewer stops and reduced safety distances in stationary applications. The camera can detect people’s upper bodies and, therefore, dangers such as reaching or leaning into hazardous areas. Protection of the robot work area at human head height
www.denso.net
is also extended, so robots can continue to operate safely with reduced force and speed.
In addition to its safety functions, the SICK safeVisionary2 can also output precise 3D measurement data for automation tasks.
www.sick.co.uk

Whether it be consumer goods, medical technology or 3D printing: Countless small parts need to be moved precisely and cost-effectively. This is now much easier.
Handling small parts is found in a wide range of sectors, including the consumer goods and packaging industry, semiconductor and battery production, 3D printing, the automotive sector, medical technology and mechanical engineering.
Many of these applications require a high repeatability of up to ±0.005mm with low to medium dynamics. And if the design is compact, robust and requires little maintenance – all the better. The new SMS linear modules from Bosch Rexroth meet exactly these requirements and help to reduce system and life cycle costs. They also welcome an alternative to pneumatically driven axes and provide a good opportunity for electrification with all of the associated benefits.
The compact SMS (Small Modules Screw driven) modules with ball screw assembly are manufactured to the usual Rexroth quality standards and impress with their flat aluminium profile, offering integrated, precise guidance. In addition, a magnetically fixed steel cover strip protects the components inside.
To ensure the shortest possible delivery times, the SMS linear modules can be ordered from stock. The five tailored sizes range from 30 to 120mm and are suitable for travel ranges of up to 1,200mm. They can be selected and ordered easily from the Rexroth online shop with the help of a product selector. Optional attachment sets for popular servo motors are available as a belt side drive or a flange coupling. Naturally, a choice of motors and drive controllers from Bosch Rexroth is available too.
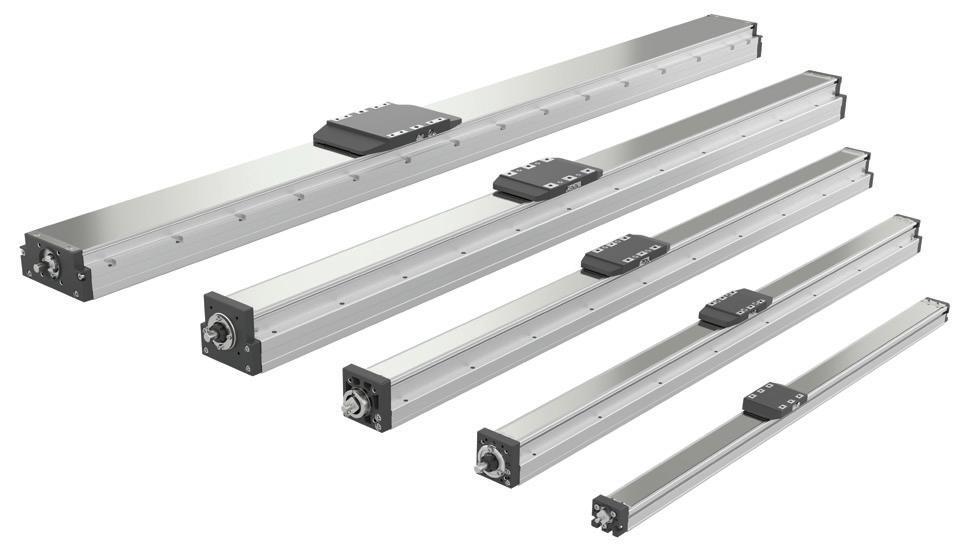
The SMS linear modules expand the range of linear axes, adding an ultra-compact series with a particularly flat design offering excellent value for money. Simple positioning and delivery tasks can thus be carried out economically – and at short notice. This opens up an attractive electrification path for greater precision, flexibility and energy efficiency in production – two key qualities in the factory of the future.
www.boschrexroth.co.uk
Handling small parts the easy way Schmersal to showcase Time-of-Flight technology for the first time
At the Hannover Messe 2023, the Schmersal Group will, for the first time, present a 3D camera for the automated acquisition of digital process data in real time in Hall 09, Stand D09. The AM-T100 is a Time-of-Flight camera (ToF), which uses a Sony DepthSense sensor to create 3D depth images with millimetre accuracy. The camera uses ToF technology, i.e., runtime measurement of emitted light pulses in the infrared range (850Nm), which are reflected off the objects being captured. This enables high-speed creation of a 3D image of the scene with millimetre accuracy that is available as a point cloud.
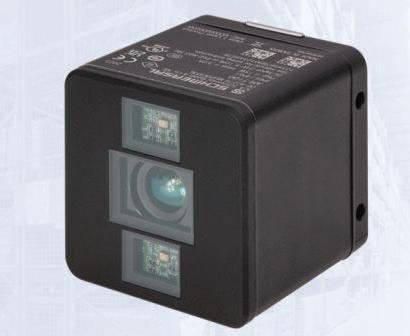
The high image rate of up to 60fps allows efficient use in industrial manufacturing processes as well as in logistics and robotics. The camera can be used for tasks such as packaging support, box filling, stacking, volume detection and labelling in logistics and packaging to boost the
efficiency and accuracy of processes.
The camera can also look into containers or large load carriers to detect their current fill level. In addition, the camera facilitates volume determination of general cargo and birds-eye monitoring of staging areas in production, assembly, storage and order picking. Other uses include the capture of dimensions and surface quality. With highperformance IR illumination and an image resolution of 640 x 480 pixels, the AM-T100 achieves a visual range of 67° x 51° at a range of 6m.
The image data is made available over the standardised GenICam data interface and can be edited with common image processing software. An Ethernet interface enables rapid and comprehensive data transmission, as well as a 24V power supply if required (Power over Ethernet).
The AM-T100 comes pre-installed with the CONSAM-T configuration software. This software allows the camera to be configured
to monitor complex and individually defined 3D zones. If it detects an object within the zone, it will switch digital outputs. In addition, digital inputs allow for switching back and forth between different 3D zones. An integrated software development kit supports software developers and system integrators with software configuration and application creation.
www.schmersal.co.uk
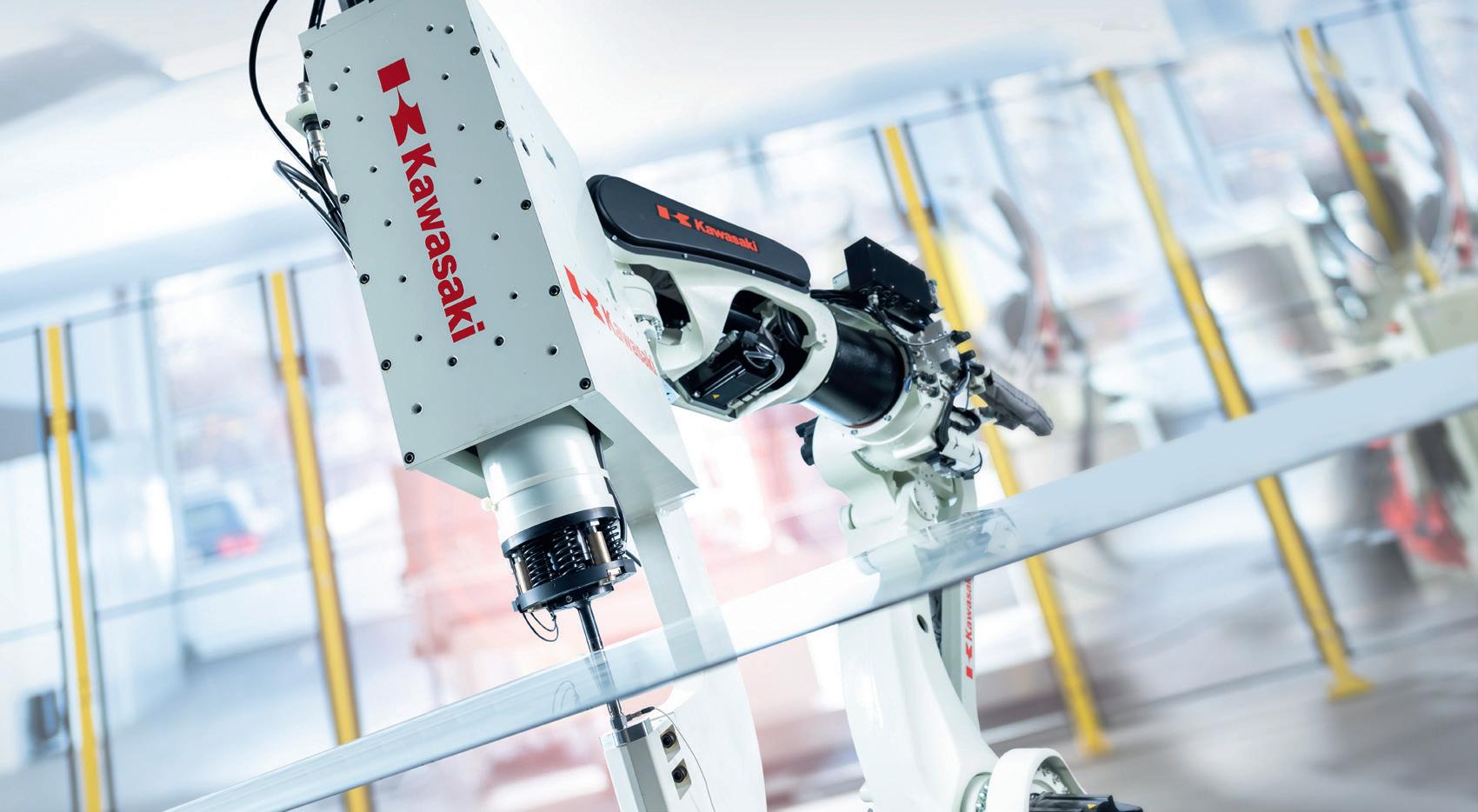

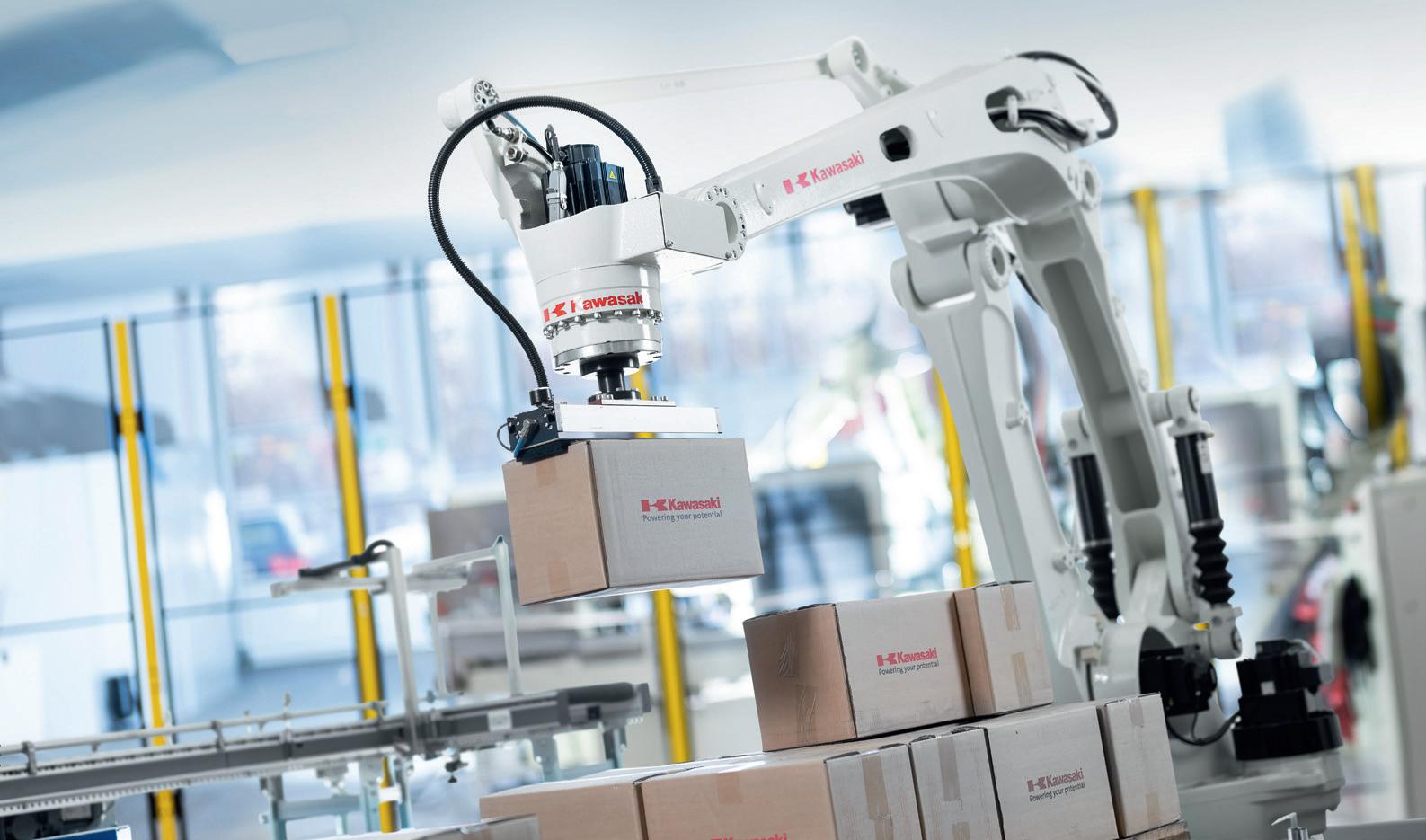
Automation: there’s still work to do
BARA
Chairman, George
Thompson,
believes automation systems and solutions
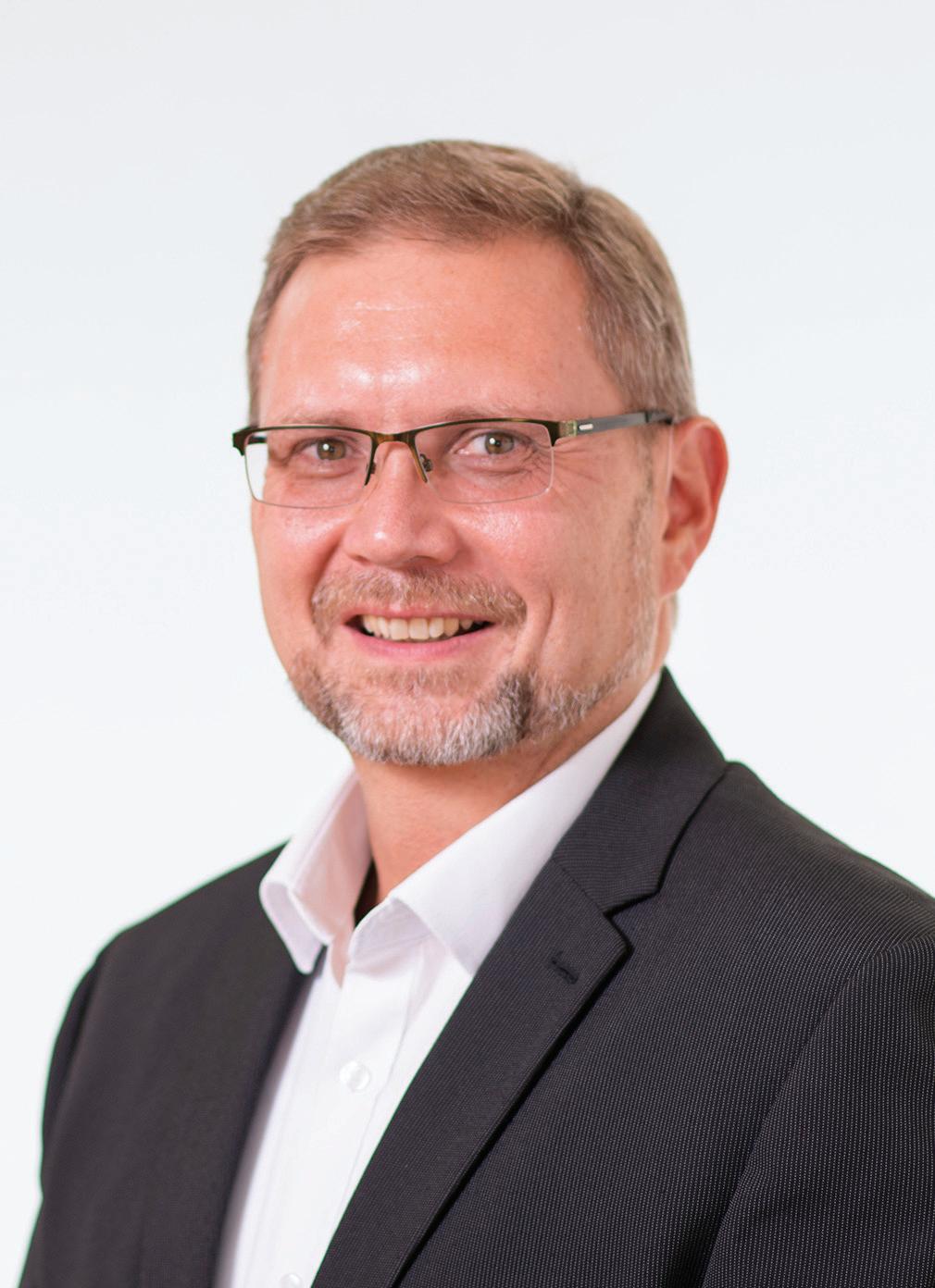
providers have more work to do to introduce the benefits of adopting automation to as wide an audience as possible.
Irecently took part in an interview for a trade publication where I was asked a series of questions about robotics and automation and how I thought they could be used within a specific industry sector. I answered one question with a question of sorts. The opening topic was about the latest developments in robotics, and my answer was, ‘That depends on how much the reader understands about robotics and automation’.
If they are early in their automation journey, everything is cutting edge. Whereas if a company is already experienced in at least the basics of automation, the answer is very different.
If a company is looking to dip their preverbal toe into the incredible world of automation, perhaps a collaborative robot could be a good starting point. One word of caution would be that despite what some may indicate, collaborative robots are subject to the same set of legislation as all other industrial robots and ignorance of the rules is never a valid form of defence in a court.
This led me to a discussion about what rules apply, and there are many, but the major ones are the Robot Standards (ISO 10218-1:2011 – Robots and robotic devices and ISO 10218-2:2011 – Robot Systems and Integration) and The Machinery Directive (Directive 2006/42/EC). In addition to this, there are others, such as the HSE Manual Handling Operations Regulations, which ask questions about how to reduce hazardous manual handling – specifically around the possibility of using automation or mechanisation to reduce the instances of manual handling. The topic of reducing manual handling risks to operatives could be a topic for another article all by itself. All of this got me thinking about how
we, as automation providers, need to find a way of reaching a larger audience to introduce the many benefits of adopting automation. There is so much that automation can offer, whether it is simple improvements to production efficiency or waste reduction, quality improvements or improvements to operative safety, just to name a few. There are also softer benefits like improving workplace morale by offering better jobs to operatives by automating the menial or low value-add operations and leaving the higher value-add tasks to the humans.
You knew I couldn’t resist banging on the sustainability drum again, so here goes… If existing and new equipment are interconnected and controlled by a central PLC, then the individual processes can increase or decrease production based on what is happening elsewhere within the production facility. For example, if the production facility has ten production processes for simplicity’s sake, and station seven has an unplanned stoppage, stations eight to ten will eventually be starved of product while stations one to six will be oversaturated. The big issue with this is if one or more of the stations has a time-sensitive component for this process, or perhaps the product itself is time sensitive; then there is the risk of the product or component effectively becoming waste. One possibility would be
to purge dispensing tubes of components that may be approaching their critical time or increasing or decreasing temperatures to extend the life of the product or components. Although this may seem like it could be increasing waste, it is more likely to prevent the entire batch from needing to be purged by only wasting a small amount of the component to save the larger amount.
If you would like to start your automation journey but don’t know where to begin – I would highly recommend visiting AutomationUK and The Machine Vision Conference, which are both being held at the Coventry Building Society Arena in Coventry on 20 – 21 June. I hope to meet you there at the BARA stand.
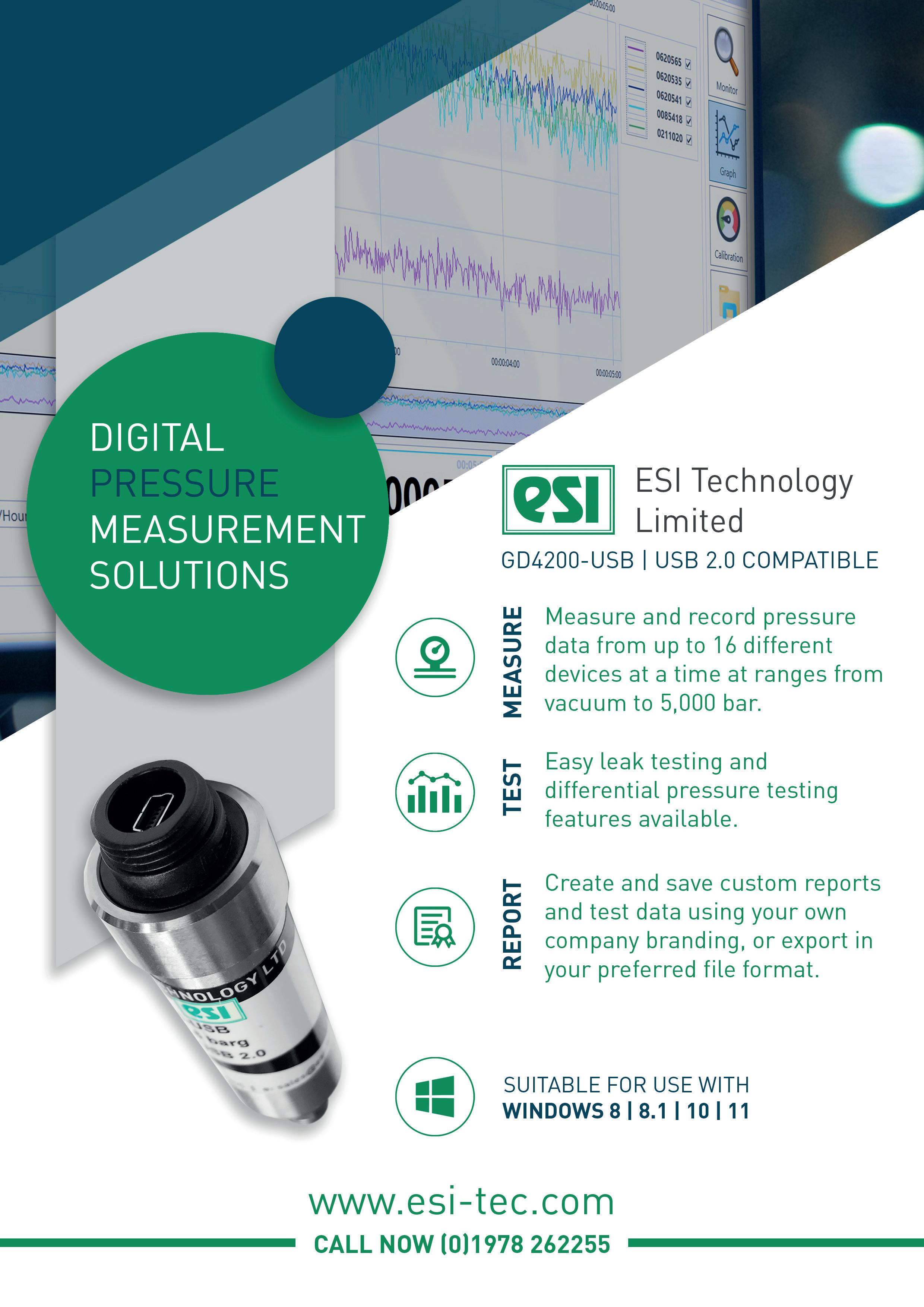
A new vision for robotics
Robots boost productivity, yet their use in the UK lags that of many competitors. Reversing this – and pairing robots with vision systems – can help raise UK competitiveness, as UKIVA Chairman Allan Anderson explains.
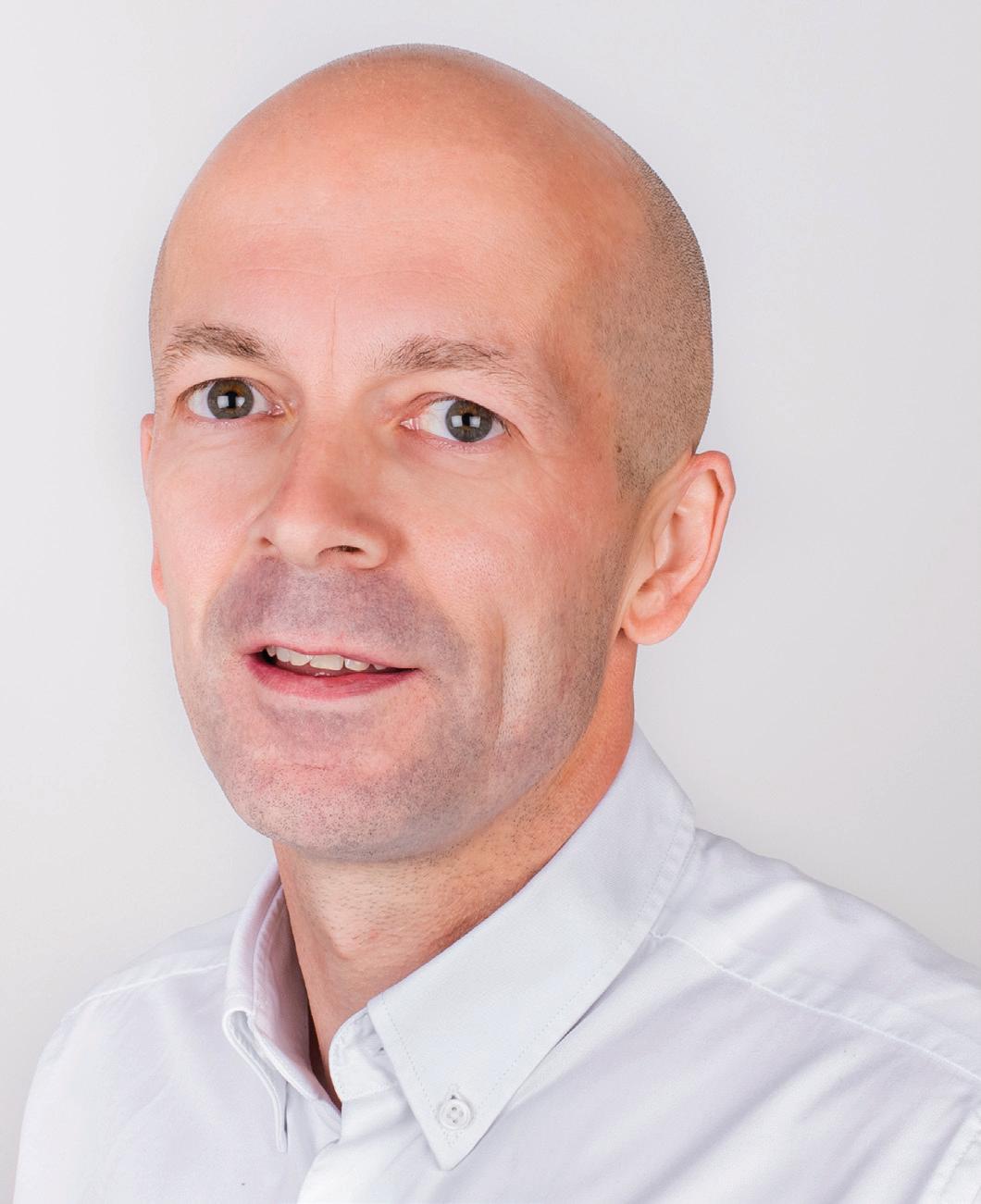
Robots, like no other piece of industrial machinery, encapsulate the idea of modern manufacturing. They are deployed widely across industry – on car assembly lines, in packaging, food production, logistics and elsewhere.
Despite the UK’s reputation as a manufacturing leader, our use of robots is very low. In its recent annual report, the International Federation of Robotics (IFR) estimated the 2021 ‘robot density’ for a range of countries. South Korea heads the list, with 1,000 robots installed per 10,000 workers. Further down the table, Germany has 397, the USA has 274, and France has 163. The UK languishes in 24th place –between Hungary and Norway – with 111 robots per 10,000 employees.
This figure varies according to the industry: the UK car industry, for instance, uses 824 robots per 10,000 employees. For comparison, the figure for Germany’s car industry is 1,500.
‘The UK has a strong manufacturing industry that has surprisingly low annual robot installation,’ the report states. ‘The automotive sector – and general industry –need to invest in automation technology to keep up with international competitors.’
The picture is hardly improving. UK robot installations in 2021 were down 7%, and annual installations hovered around the 2,000-unit mark between 2018 and 2021. It’s a far cry from the high watermark of 2012 – when the UK installed close to 3,000 robots. It’s vital for UK plc that we reverse this. We already suffer from poor productivity, and these figures show other countries investing in automation more quickly and heavily.
It’s not all doom and gloom, though, because this is both a problem and an opportunity. The problem is this: the UK lags behind many of its industrial and economic peers. At a time when we need to be more productive and competitive – and overcome a labour shortage – our lack of
investment in this critical technology is holding us back. However, it’s an opportunity because it offers the chance to reboot and embrace the benefits of automation. Starting from a low base means that even a modest extra investment in automation could have a noticeable effect.
Peter Williamson, CEO of UKIVA’s parent organisation, PPMA, says investment in robotics can raise manufacturing efficiency and boost competitiveness for UK exporters: “Deploying more automation will fill lowerskilled roles – and thus create more skilled jobs. It’s a chance to upskill our workforce and encourage more young people into manufacturing.”
However, he says this depends on buyin from the government, which needs to support businesses by reviewing schemes such as T-levels and apprenticeships. In addition, tax incentives – such as higher capital allowances – will help overcome the ongoing reluctance to invest in robotics.
Another factor is the ability of vision systems to enhance robot productivity. It’s become increasingly common for robots to incorporate a vision system – allowing them to raise their performance. Assembly, packaging, inspection and many other industrial processes now rely on the seamless integration of robots and vision systems.
“The benefit of adding a vision system is
that you effectively provide the robot with a ‘human’ sense, so it can carry out certain repetitive or low-skilled tasks,” added Peter. “Correct deployment of robots with vision systems will increase productivity, reliability and accuracy.”
Creating more synergy between robots and vision is the thinking behind a new joint event in Coventry this year. It sees UKIVA’s annual Machine Vision Conference (MVC) co-located with a new show from BARA –called Automation UK – on June 20-21.
This will give end users an opportunity to assess how these two critical technologies – independently or in conjunction – might be applied to their own businesses.
“Suppliers of robotics and vision systems must continue to offer viable solutions for SMEs, in terms of cost, and ease of installation and use,” Peter concluded. “These smaller organisations will be the drivers of our economy.”
NCC
8-pole bayonet locking
> 5000 mating cycles
Panel mount parts unplugged IP67
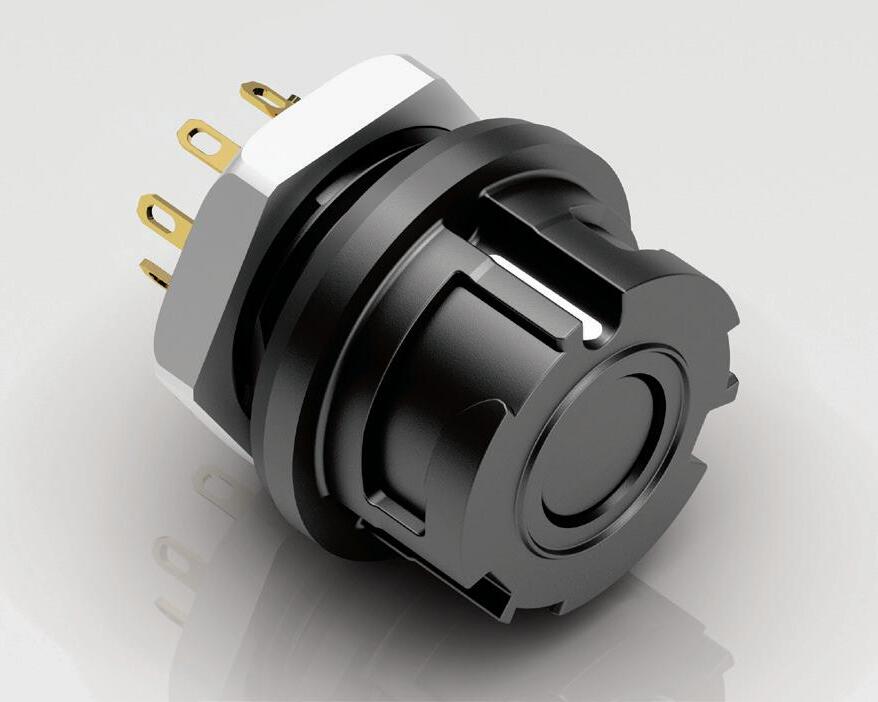
Solder and dip solder contacts
www.binder-connector.co.uk
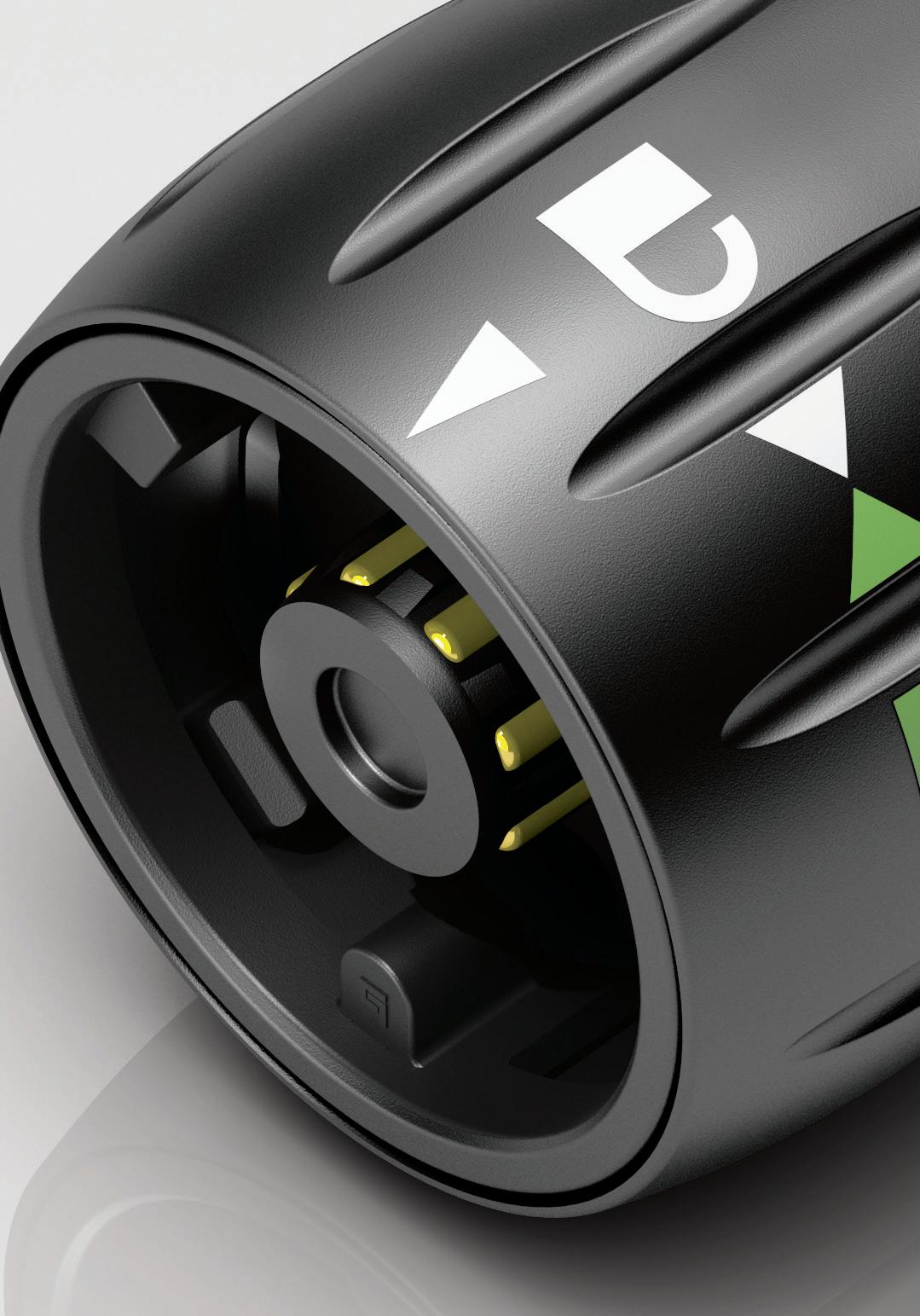
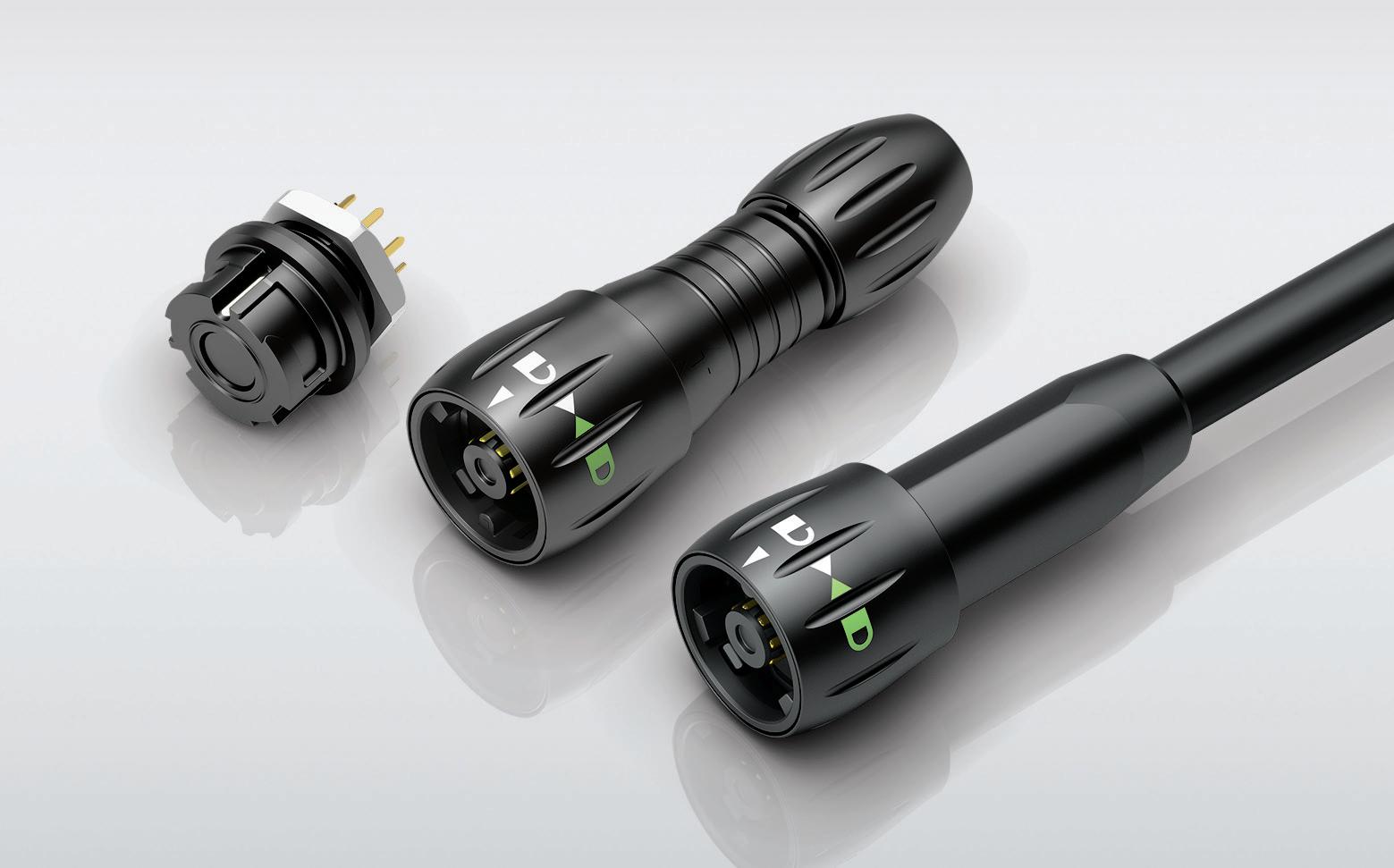
IO-Link from ifm delivers big benefits for Monk
The innovative automation and digitalisation solutions specialist, ifm electronic, explains how one of its longstanding customers, Monk Conveyors, benefitted from
devices and connections.
With more than 25 years of experience in developing and manufacturing automated handling systems, Aldershot-based Monk Conveyors is constantly seeking ways of providing its customers with solutions that are more efficient, more flexible and more cost-effective. Spurred on in this quest by Covid-era restrictions, the company has now adopted IO-Link, using products from ifm electronic, as the basis for field wiring in all but the smallest of its projects.
While Monk had been aware of IO-Link for some time, the company had continued to use traditional field wiring, not least to meet the preference of some of its customers. When Covid restrictions came into force, however, the situation changed. It was now difficult for Monk’s engineers to visit customer sites, so the promise that IO-Link could reduce the time needed for installation and commissioning was increasingly attractive.
As a result, Monk engineers designed a small project using IO-Link sensors and devices, with IO-Link connections in place of conventional field wiring. All of the IO-Link equipment was supplied by ifm electronic.
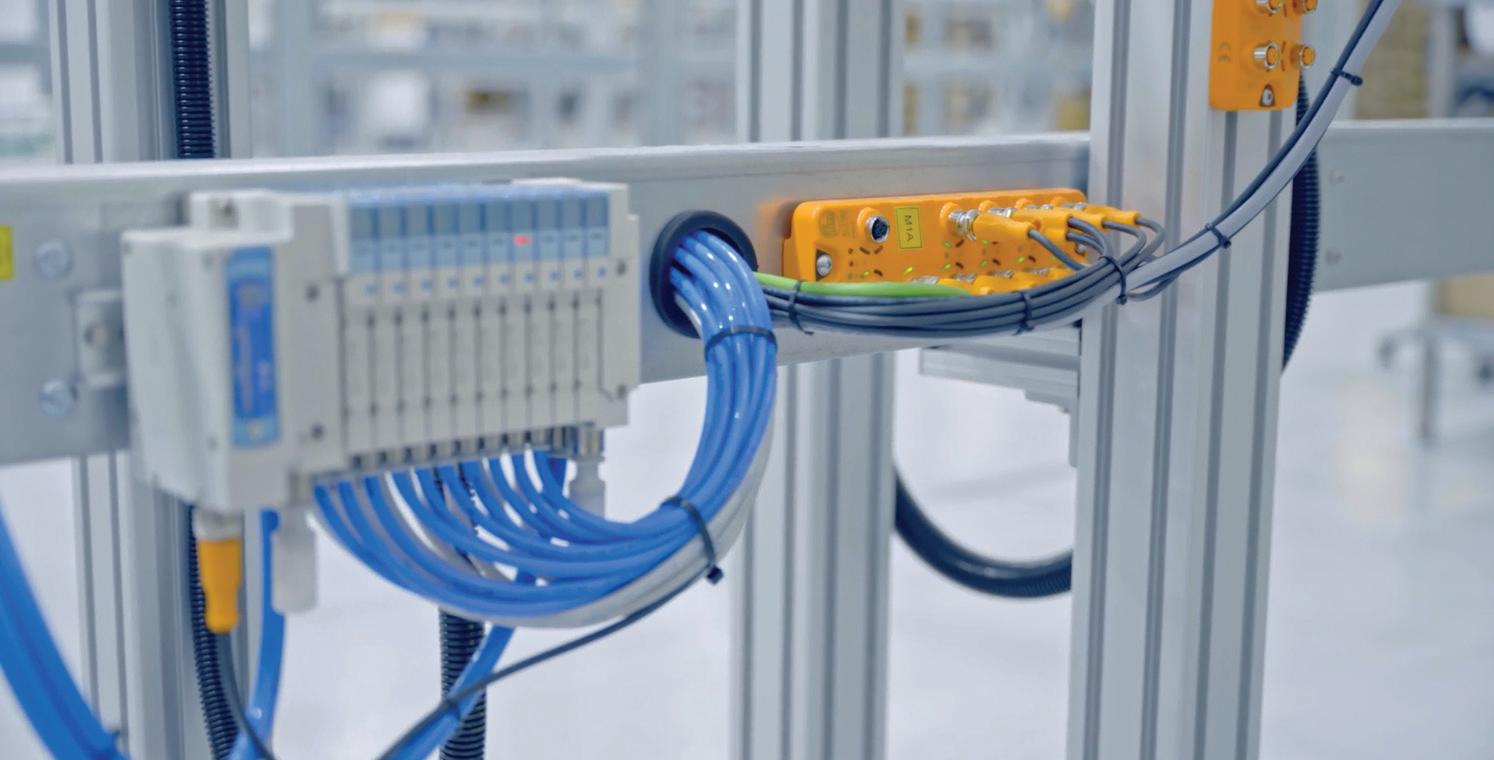
“At the design stage, we found moving to IO-Link was straightforward,” said Phil Monk, Technical Director of Monk Conveyors. “To be fair, our engineering team has excellent software skills, but these were hardly called upon because IO-Link is very easy to configure and work with. Of course, we also had excellent backup from ifm on the few occasions when we did have queries.”
Experience with this initial project showed that there was a large reduction in the time required to install field wiring, and because many of the field connections used preterminated cables, lower levels of skill were required. In addition, wiring errors
were almost eliminated, which meant that commissioning was faster and easier. The success of this initial project led Monk to use IO-Link for further projects and, ultimately, to adopt it as the company’s standard approach.
Monk has now used IO-Link based on equipment from ifm electronic in eight major projects. The largest incorporates almost 500 field-mounted devices, including sensors, reed switches, encoders and RFID readers. This is a complex automated rubber moulding line that covers a large area, so the cost savings associated with IO-Link are particularly notable.
“This production line makes 180 different mouldings, all of which are similar in appearance, so RFID product tracking is very important,” continued Phil. “Fortunately, with ifm’s IO-Link-capable RFID readers, the product tracking was easy to implement. Interfacing the IO-Link system with the Siemens PLCs used on this project was also straightforward.”
A further benefit of using IO-Link is that it makes it easy for Monk to set up remote access to control systems it has supplied, which means that the Monk engineers can check system status and carry out fault
a move to IO-Link
finding without leaving their desks. This is more convenient and less costly than making a site visit to resolve queries.
“Even customers who were initially reluctant about making a move from conventional field wiring are now appreciating the benefits of IO-Link,” added Phil. “Certainly, fault finding on an IO-Link system is different from fault finding on conventional systems, but thanks to the diagnostic features built into IO-Link, it’s actually easier and faster. A further advantage is that if a sensor or other field device does need to be replaced, IO-Link automatically downloads the parameters into the replacement, so set up is almost instant, with a consequent reduction in plant downtime.”
Monk’s experience with IO-Link using products from ifm electronic is that it not only provides technical benefits like remote access, but it also reduces site wiring time by as much as 50% and cuts costs as savings on cable outweigh the small extra cost of IO-Link enabled devices. In short, as Monk has found, IO-Link opens a new era in automation, which delivers valuable benefits for system suppliers and end users alike.
www.ifm.com
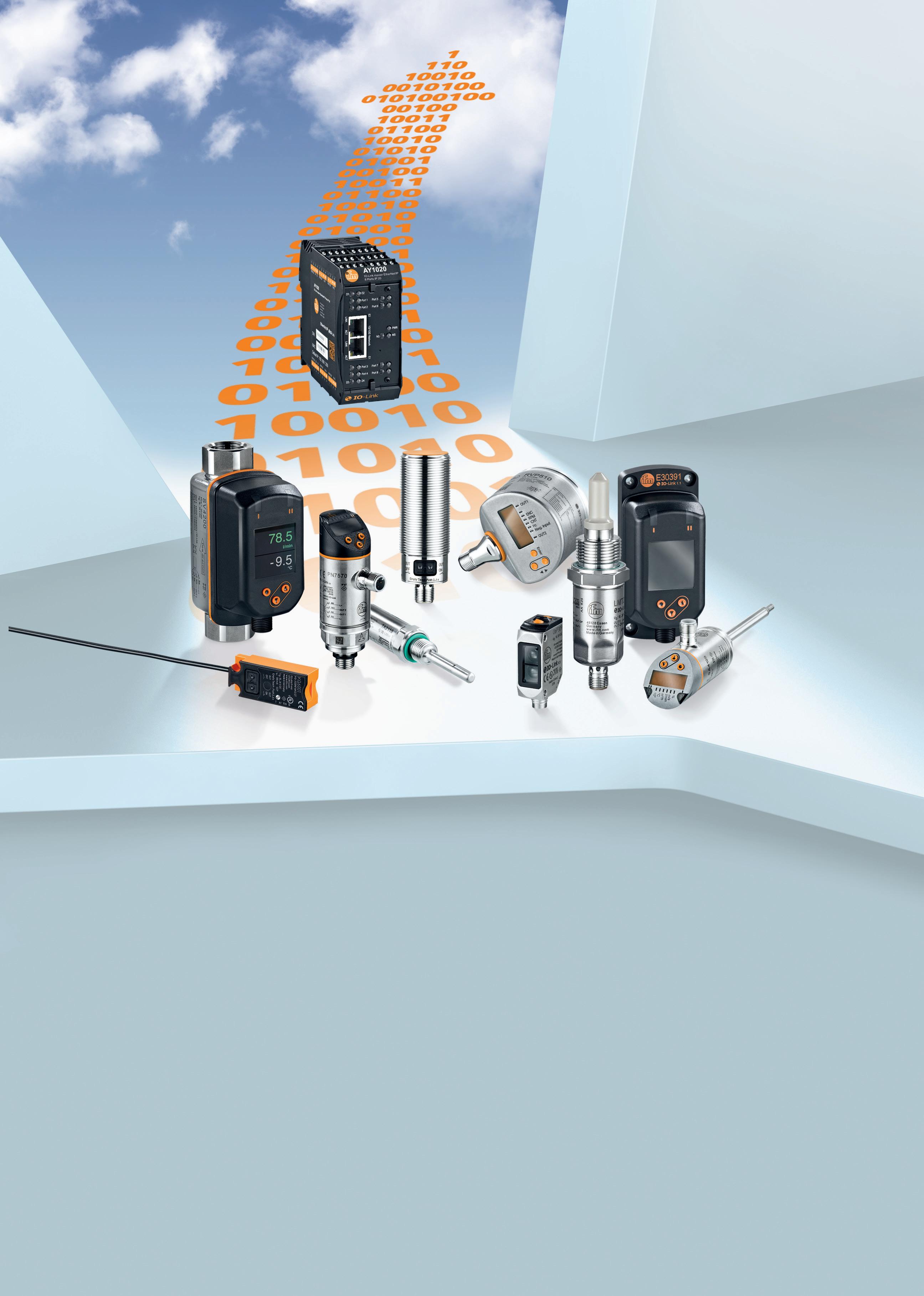
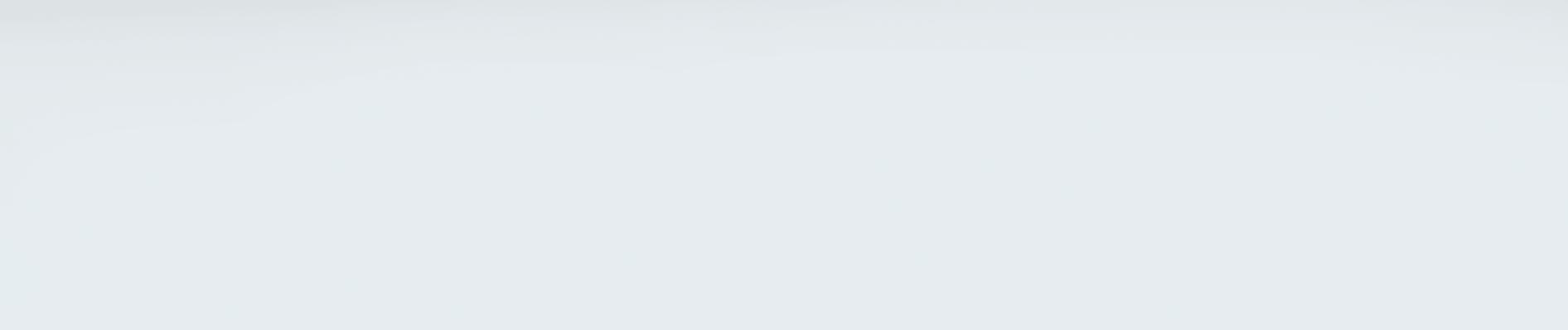



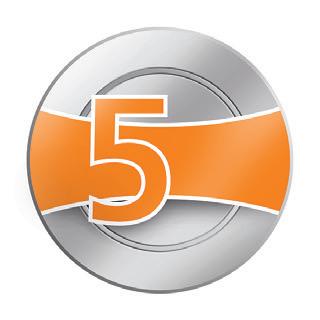
Changing the game for HMLV manufacturers
Adnan Khan, Business Development Manager at Beckhoff Automation UK, discusses how manufacturers can leverage technology to manage their supply chain effectively, save on costs, and deliver products to customers on time and in the way they want.
In recent years, the manufacturing industry has undergone a significant transformation, driven in part by advances in high-mix, low-volume (HMLV) manufacturing. This trend has impacted the entire supply chain operation, from procurement to sales.
HMLV manufacturing involves producing a variety of products in small quantities. This approach allows manufacturers to cater to individual customer needs and preferences while minimising inventory costs. However, it also presents significant challenges to supply chain operations. Each product requires unique components, which can make it difficult to manage inventory and track products throughout the process.
To meet the evolving demands of their customers, numerous HMLV manufacturers are embracing increased automation. However, conventional fixed automation products can be excessively costly or lack flexibility. Automation suppliers are now addressing this gap in the market with solutions that provide flexibility, modularity, a small physical footprint, and mobility. This is made possible by onboard software intelligence, more lightweight and responsive hardware, and low-code/no-code applications.
The Beckhoff XTS linear transport system is an instance of such a solution. It is a flexible conveyance technology that empowers manufacturers to handle diverse product combinations and packaging formats on a single line, without requiring any mechanical changeovers.
The XTS comprises configurable motor modules that are assembled into a continuous track, which can take on various shapes such as circular, rectangular, or complex, curved geometries based on the requirements of the specific application. The movers on the XTS have the ability
to operate autonomously, allowing them to accelerate, brake, and adjust their speed independently. They can also form groups and synchronise with other equipment such as conventional conveyors.
Manufacturers can process a larger variety of products without needing to expand their facilities due to the XTS’s configurable track, which conserves floor space and facilitates software-based changeovers.
Manufacturers in the global confectionery industry face numerous trends that can change rapidly, necessitating the production of many different products that require packaging in a wide range of packages and pack sizes.
Cereal bars are a prime example of the diverse range of products in the confectionery industry. They are available in various flavours and packaging formats, such as single-serve portions, variety packs, multi-packs, and family packs, with different numbers of bars in each pouch. The bars themselves can differ in length and width and may require packaging in various box sizes and shapes based on retailers’ needs. To meet these demands, highspeed packaging systems with rapid format changeover capabilities are essential.
Traditionally, supply chains require individual and manual changeovers of movers for each packaging format. However,
with the XTS, this can be done at the push of a button through its corresponding software functionality, resulting in significant time savings and improved overall machine efficiency.
The trend of HMLV manufacturing has brought about new challenges and opportunities for manufacturers, particularly in managing their supply chains effectively. However, with the development of innovative automation solutions like the XTS, manufacturers can address these challenges while also providing more customised products and reducing inventory costs.
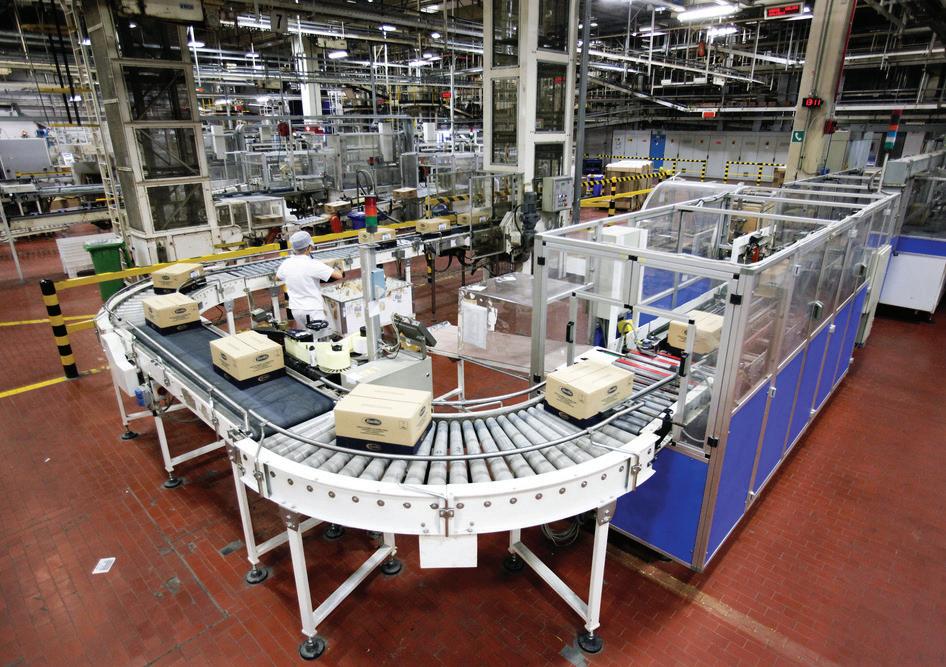
Linear transport systems allow manufacturers to handle diverse product combinations and packaging formats on a single line, resulting in improved efficiency and time savings. As the manufacturing industry continues to evolve, the adoption of these advanced automation technologies will likely become increasingly essential for manufacturers looking to stay competitive and meet the changing demands of their customers.
www.beckhoff.co.uk
Focus On: Connectivity
MEPCA explores a range of topics looking at plant wide connectivity and communications

Industry 4.0-ready smart safety
The proliferation of automation in production is placing new demands on machinery safety and the associated safety engineering, while connectivity is becoming all the more important as manufacturing heads towards the factory of the future. As a force for innovation in industrial safety engineering and automation, Euchner continues to develop practical, pioneering products that perfectly fit the IIoT world. Euchner’s Hollie Dixon discusses some technological innovations saving time and helping keep our factories running safely.
Fieldbus networks have been around for many years and have evolved from simple communication systems to more advanced solutions that now include safety protocols. Historically, the most widely used fieldbus networks were DeviceNet and Profibus. These protocols were reliable and allowed control of machines with some obvious limitations. However, these limitations became more evident as greater-complexity machines with multiple axes, higher speeds, and increased safety requirements were developed.
The development of fieldbus safety networks such as PROFIsafe and Safetyover-EtherCAT (FSoE) allows the oftencomplex logical safety solutions required on modern machinery to be easily implemented through fieldbus-connected hardware and configurable software. As a pioneer in this sector, Euchner develops future-oriented safety switches and safety systems to meet today’s IoT requirements.
For example, ‘key in pocket’ solutions such as the CKS2 from Euchner are now possible to prevent unintentional start-up of machinery when an operator is within a danger zone.
Maximum personalisation
The highly flexible MGB2 Modular door locking system from Euchner is another example of a safety solution that can easily be implemented when using a safety fieldbus network such as PROFINET or EtherCAT P.
The MGB2 protects machine and installation safety doors and fences during
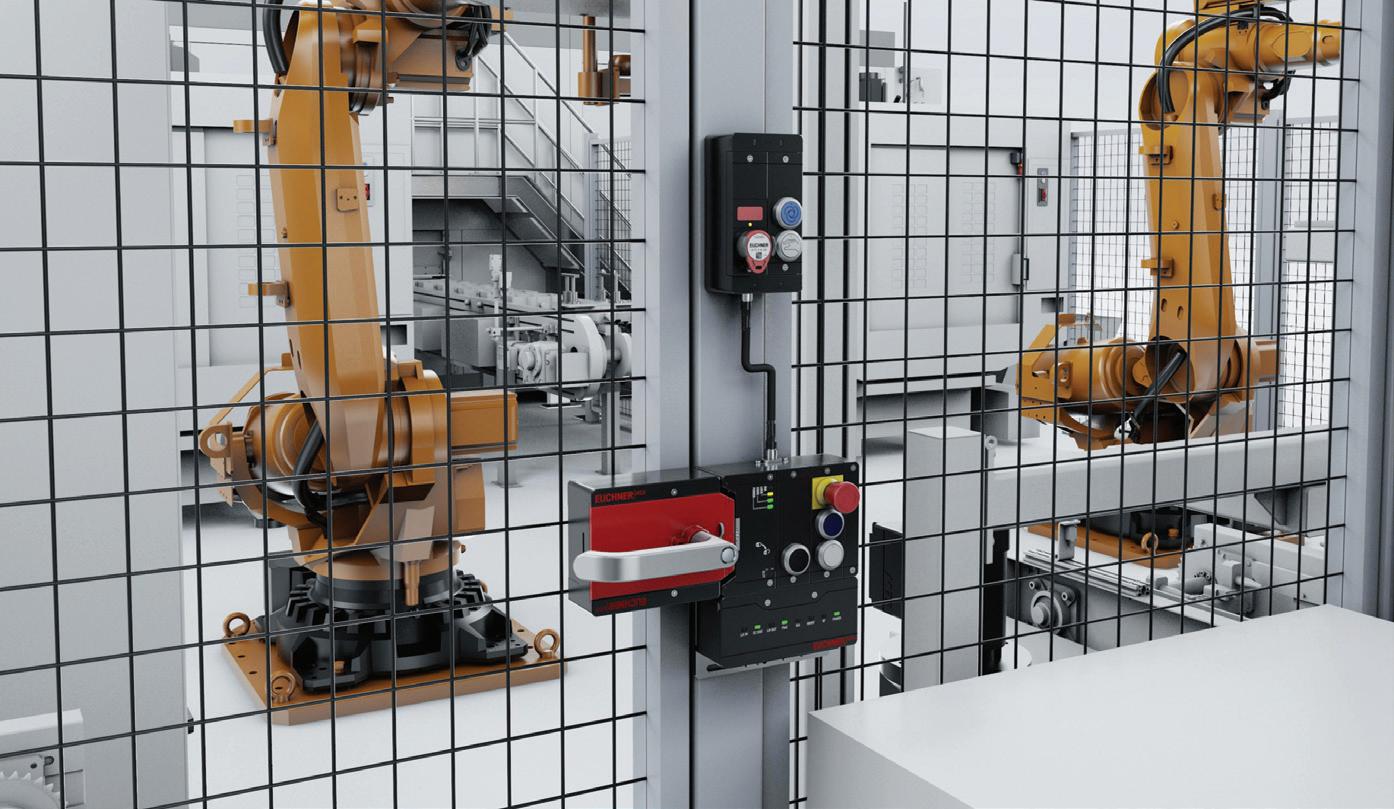
hazardous machine movements and combines a safety switch, bolt and door locking mechanism into one, reducing the amount of additional engineering required to secure a guard door. Its modular design is perfect for customisation and can be easily configured to meet individual requirements.
The interface consists of a guard locking module, the contained submodules for controls and indicators, optional expansion modules and the bus module for connecting to PROFINET/PROFIsafe – and now also to EtherCAT P/ FSoE. The MGB2 Modular is the world’s first guard locking device for safe EtherCAT.
The MBM bus module acts as the system’s ‘head’. All information from the connected modules comes together and is transferred to the installation’s control system via the fieldbus. In addition to the safety signals, comprehensive diagnostic
and communication functions in the form of EtherCAT or PROFINET messages and the integrated web server provide a fast and detailed overview of the device status. The control system, in turn, sends its signals via the bus module to the connected system modules to control guard locking or activate a lamp, for example.
Apart from the obvious benefits of drastically reduced installation time and simplified field wiring, the modular MGB2 features a wide range of safety functions through the readily available function modules that include not only the more common operating elements such as emergency-stop pushbuttons and selector switches but also variants for the connection of enable devices or hold-to-run controls and additional OSSD Safety devices.
The system can be configured to suit a wide range of applications, and the safety
functions can be easily customised using software. The MGB2 can also be supplied with the embedded CKS2 RFID key system module, providing an additional layer of safety and security.
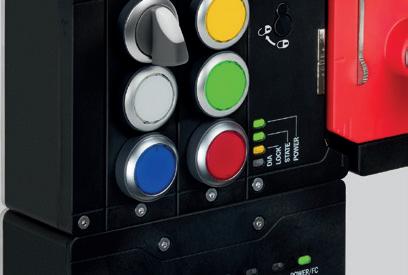
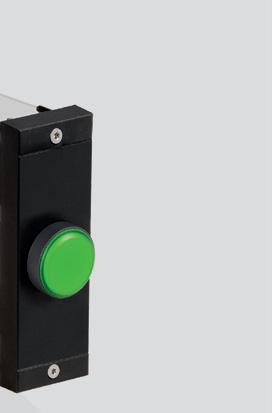
Modern key-exchange
Safety tasks, such as ensuring access restriction, safe installation lockout and starting, and operating mode selection, play an important role in modern facilities. These tasks are often complex, but solving them can be simple. The CKS2 from Euchner is a new, safe key system that is simple to integrate into the overall control system and can be used in a wide range of applications.
Whether for machine and installation lockout and starting, for assigning authorisation to select an operating mode, or as a trapped key system – the new CKS2 safe key system is versatile. It is available as a compact system with integrated evaluation electronics and as a submodule for installation in the MGB2 Modular safety door system. The CKS provides a straightforward solution for many tasks without all the laborious programming.

One key can be assigned to several key adapters in different installations. The CKS2 is also flexibly scalable regarding the number of keys, and the system can therefore replace complicated key exchange boxes and key distribution stations.

Thanks to highly coded, transponderbased RFID keys, the system always guarantees maximum protection against tampering and a safety level in accordance with category 4/PL e. The system is easy to integrate into the overall control system. Configuring the key is simply a matter of teaching it in on the key adapter.
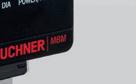
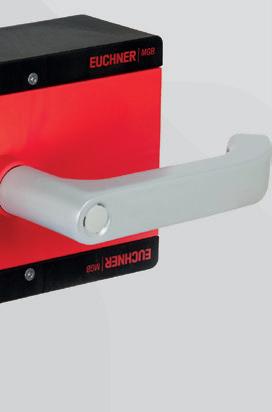
This compact system can be connected to IO-Link via Gateways from Euchner to provide relevant diagnostic and device data to the higher-level control system. This enables users to read the key that was used to operate the installation, for example.
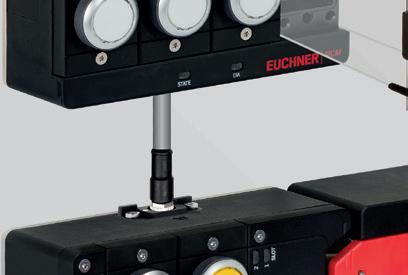
As a submodule, the key system is integrated into the MGB2 door protection system and thereby linked directly to the bus module. Together, these two systems are a powerful combination delivering a wealth of new application options in the digital Industry 4.0 era.
Overall, the development of safety fieldbus networks such as PROFISafe and Safetyover-EtherCAT (FSoE), combined with safety solutions such as the CKS RFID key system and the MGB2 safety door system from Euchner, has enabled complex logical safety solutions to be easily implemented through existing hardware and software solutions that are not only safer but also more efficient and cost-effective, making them an ideal choice for modern facilities with a focus on productivity and OEE.
As technology continues to evolve, we can expect to see even more innovative solutions that will further improve the safety and efficiency of industrial machinery.

Automated processes call for innovative safety engineering in line with modern communication requirements for machines and installation. Safety technology company Euchner is driving innovation in this field by developing safety solutions and systems for all commonly used fieldbus systems and for communication via IO-Link and AS-i Safety at Work.
www.euchner.co.uk
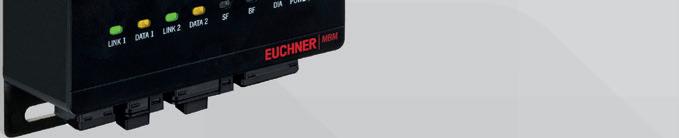
u Safety system with guard locking device
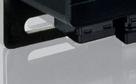
u Modular layout for maximum flexibility during operation
u Bus module with PROFINET/ PROFISAFE/ EtherCAT with FSoE

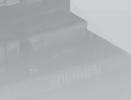

u Expansion module MCM for even more functions
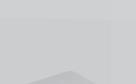
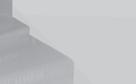


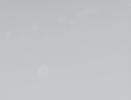

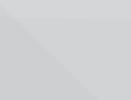
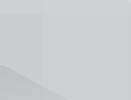
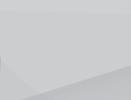

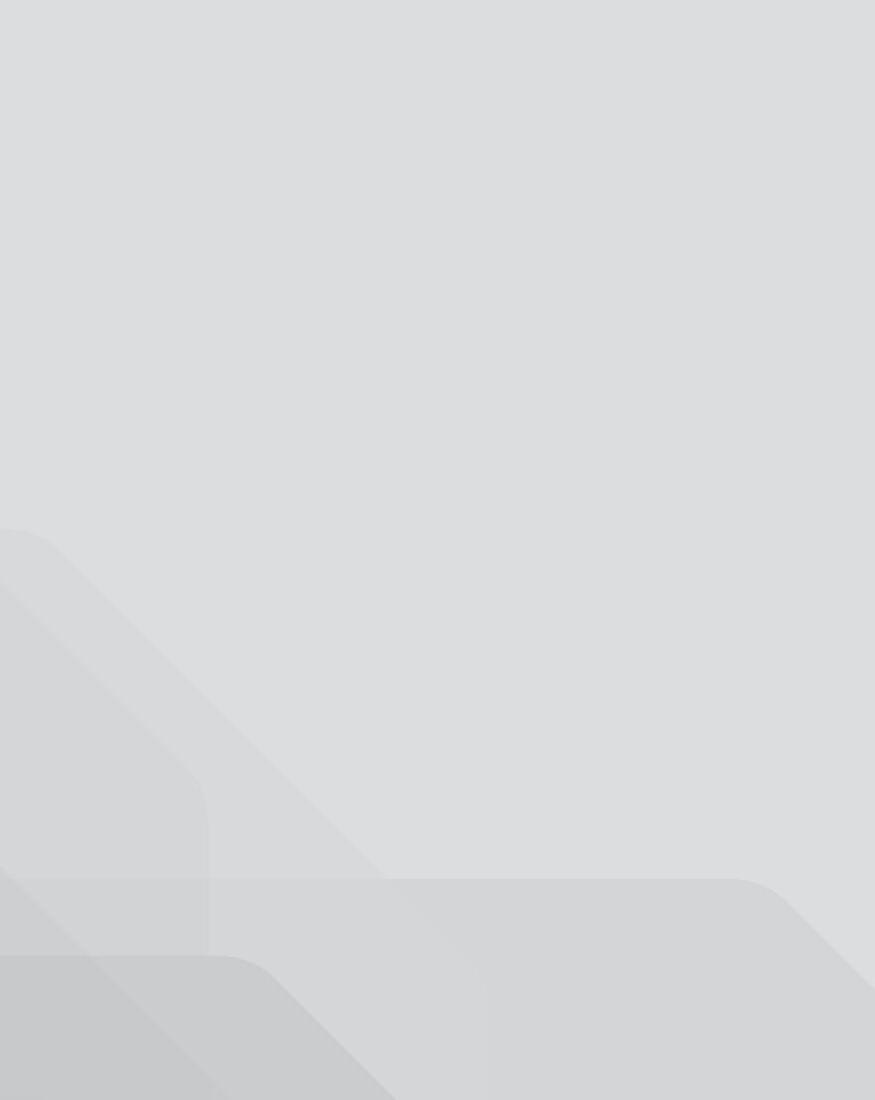
u Category 4 / PL e according to EN ISO 13849-1

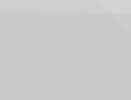
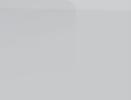
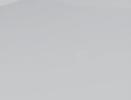
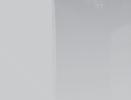
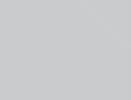
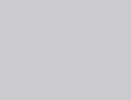
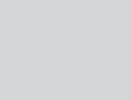

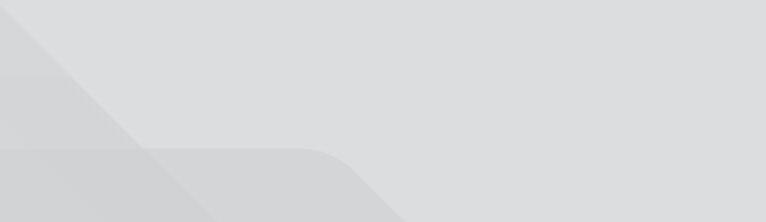
Data from the deep
Communication device developer, Brainboxes, explains how its Ethernet switches are being used in vital work monitoring subsea cable links in extreme environments.
Subsea cables are responsible for carrying telecommunication signals between different continents and servicing offshore wind farms. Therefore, it’s vital that installed subsea cables are accurately mapped to carry the data. By monitoring the installation of the cables, operators can quickly observe any changes or breaks in the intercontinental communications system.
North Sea Systems is dedicated to developing and operating systems for extreme marine environments. Dave Rigg, the founder of North Sea Systems, is keen to support the marine renewables industry through innovative design solutions. ROVs (remotely operated vehicles) are manoeuvrable underwater and can be used to explore ocean depths, however, ROVs are complex and expensive to operate, and the limited remote-control range doesn’t allow for precision accuracy.
North Sea Systems developed Cablefish, a tool that monitors the installation of subsea cables in shallow or high flow environments. The Cablefish system consists of a mechanical carriage, a fibre optic umbilical and an electrically driven winch. Within the carriage, there is an electrical enclosure containing two cameras and lights. The electrical enclosure also contains an altimeter to control the height of the carriage above the seabed, a depth sensor to measure the depth below the sea surface, a roll and pitch sensor, a sonar system and a USBL beacon.
Brainboxes Ethernet switches in the winch cabinet on the surface and in subsea pods enable connection to the Cablefish network, and support the successful operation of the mission-critical equipment. The Brainboxes receive reliable Ethernet data from the video cameras and sensors, and in more murky conditions, they can also receive data from sonar, allowing operators to monitor altitude, depth, live video and sonar.
The system also monitors the roll and pitch to keep track of the performance of the motor of the carriage and umbilical tension. This data is transmitted up to the
fibre optic umbilical cable, which runs the telecommunication signals, meaning North Sea Systems aren’t limited by running Ethernet from a point-to-point basis.
“There is a job in Taiwan starting in May, another job going out in the States and another one in the North Sea, so it’s really important that the kit is reliable,” explained Dave Rigg.
The remote functionality of the Ethernet switches enables the system to be controlled and monitored via a PC over an Ethernet connection or a wireless tablet on the Cablefish network. This procedure provides the operators with GPS coordinates of the cable touchdown point. Additionally, continuous video recordings of the cables enable the operators to visually monitor the product landing on the seabed in real time. The video recording also helps contractors show their clients that they’ve correctly installed the subsea cables. This leads to less downtime because operators can clearly observe any faults with the subsea cables and quickly jump into action.
Once deployed, switches allow the system to be operated in automated mode, programmed so that the carriage automatically maintains a set position relative to the seabed. Therefore, during operation, only a single operator is required to monitor the system. By implementing the automated functionality of the Brainboxes, North Sea Systems can reduce the manning costs required for 24-hour operations.
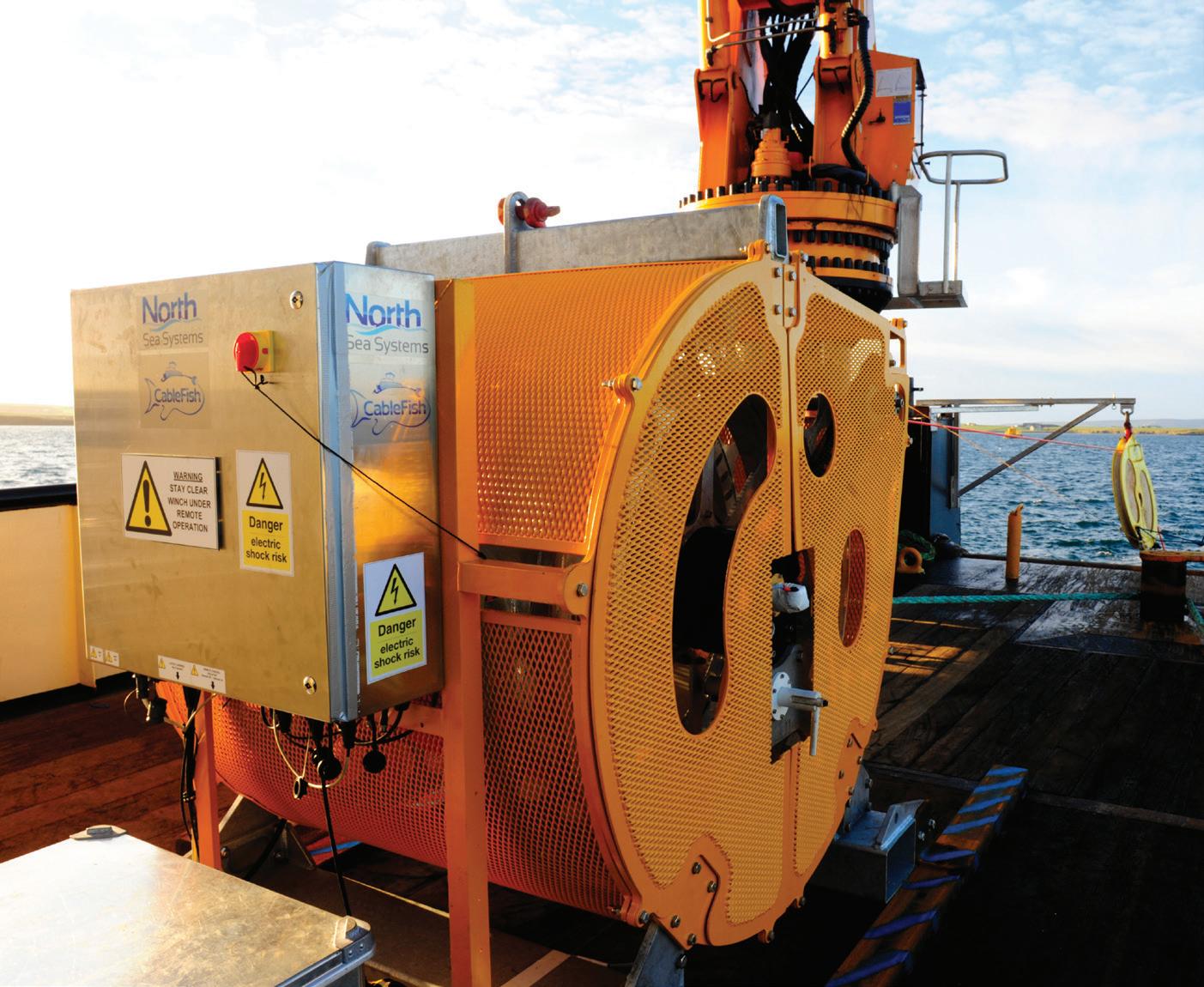
“You can’t send a man in a van to go and buy a new bit; you’ve got to deploy with everything you need,” added Dave.
The trusted reliability and availability of Brainboxes’ devices means North Sea Systems can reliably deploy their systems offshore without the challenging need to constantly find new parts. If the switches fail, the operators will not be provided with any data, causing the whole operation to stop. Therefore, it’s vital that North Sea Systems select a product that is proven to be reliable and robust for working in extreme environments.
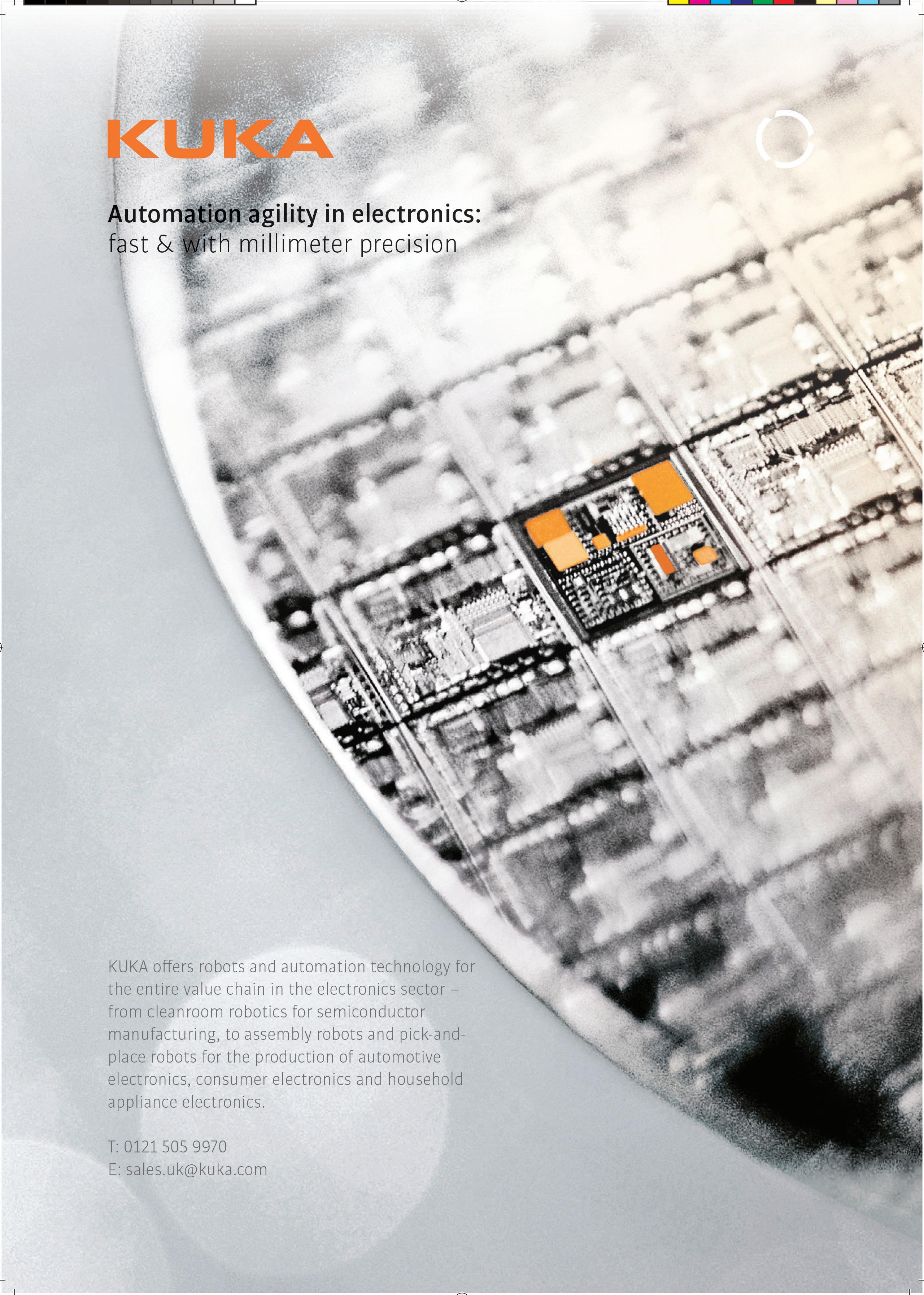
Unlock cutting-edge applications with TSN
General
Continuous development and breakthrough technologies are advancing industrial communications, enabling them to reach new heights and ultimately writing the next chapter of the digital era. One key innovation unlocking significant opportunities and cutting-edge applications is Time-Sensitive Networking (TSN).
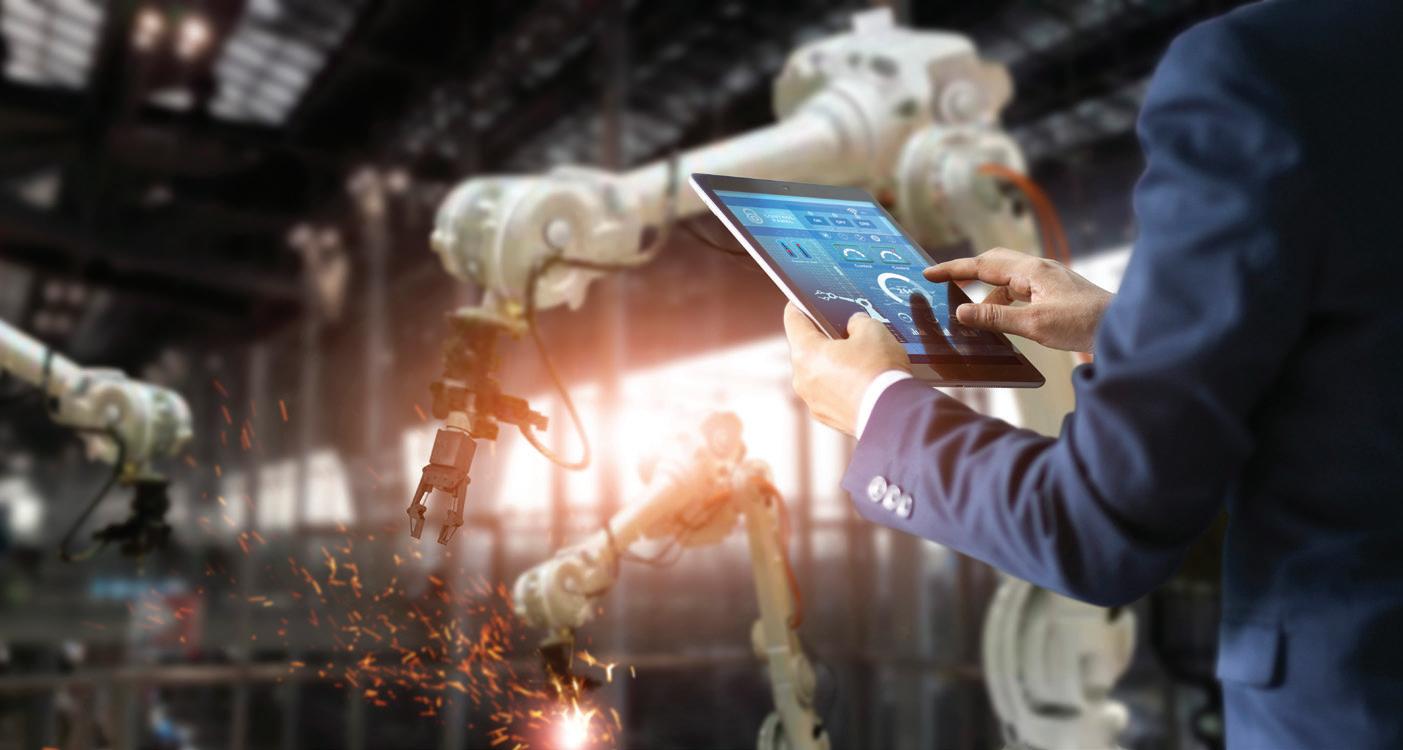
Control engineers worldwide now have more tools than ever available to create seamlessly interconnected plants – and the best is yet to come, thanks to TSN. In effect, this technology complements standard industrial Ethernet to offer extremely accurate synchronisation, traffic prioritisation and scheduling. Thanks to these functions, TSN can handle multiple types of data and their different priorities over a single network infrastructure. As a result, it is possible to share information and generate more holistic business intelligence while reducing cabling requirements, which can reduce network complexity, capital expenditure and operational expenses.
Therefore, we can confidently state that adopting TSN marks the first crucial step in creating unified, comprehensive network architectures that serve all types of automation. Even more, the power of TSN to drive convergence enables engineers to implement many more future-oriented industrial communications technologies, even beyond Ethernet. These provide a pathway to the realisation of the Connected Industries of the future as well as the creation of smart, flexible and proactive supply chains where all players can share key insights with their partners and end users.
Cable multitasking
For example, reducing the number of cables required to create factory or enterprise-wide networks will continue and
at the CC-Link
may even lead to the complete transition towards wireless technologies. These are evolving to support industrial applications, in addition to the information technology (IT) world, the consumer marketplace, and home automation systems.
Expanding the use of wireless technologies in the operational technology (OT) domain, the latest 5G and 802.11 Wi-Fi standards can support ultra-reliable low-latency communications (URLLC) to meet the need of manufacturing facilities. Adding TSN functions can lead to communications with bounded low latency, low jitter and extremely low data loss. TSN-wireless hybrids may be the key to creating network architectures with unprecedented levels of flexibility while increasing data accessibility and availability to support a wide range of activities, such as enhanced remote monitoring.
What the future holds doesn’t end here. While 5G adoption is still underway, work to develop the next-generation wireless solution, i.e. 6G, has already begun. These networks are expected to support even more heterogeneous applications, such as virtual and augmented reality,
artificial intelligence (AI) infrastructures and the metaverse.
Driving change
All these communications technologies can help companies advance the digital transformation of their businesses and even their entire supply cycles. Given this will also be enabled by TSN, forward-looking businesses that want to keep up with the latest, most promising trends to drive their competitiveness should look at adopting new frameworks that are compatible with the technology.
CC-Link IE TSN, the earliest open industrial Ethernet to combine gigabit bandwidth with TSN functions, offers the ideal platform to support this transition. In addition to being the first of its kind, developed by an organisation committed to delivering innovative solutions to its users, CC-Link IE TSN provides a reliable system that leverages proven protocols and technologies. The open industrial network is already being used in readily available automation devices, empowering companies to set up futureproof machines and facilities now. eu.cc-link.org
CC-Link IE TSN Class A & B certified switch






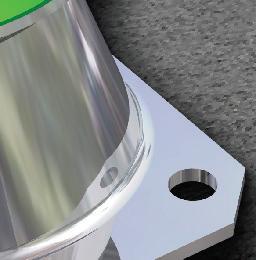
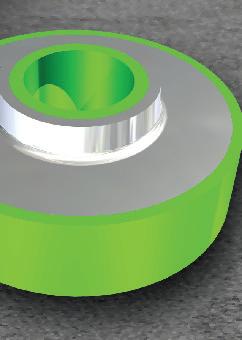


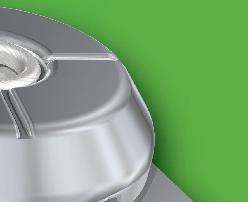
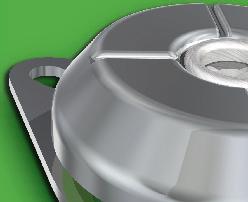

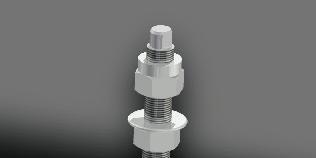



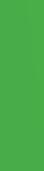

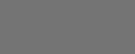
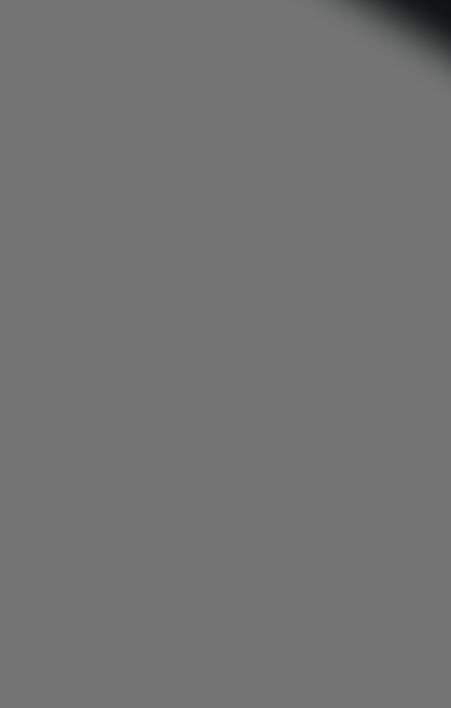

Advantech, the industrial communication solutions provider, has launched the EKI-8510G Time Sensitive Networking Ethernet switch.
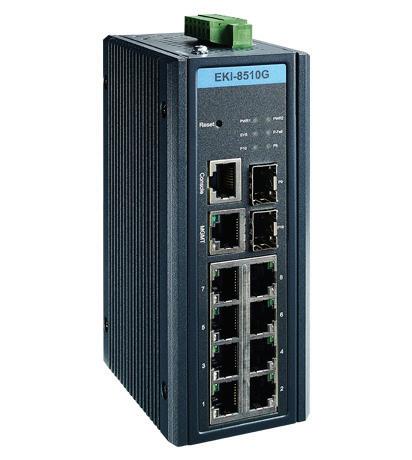
Advantech has proactively participated in the CC-Link Partner Association’s (CLPA’s) initiatives, promoting CC-Link IE Time-Sensitive Networking (TSN) applications to various industries.
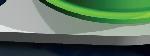

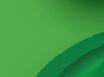
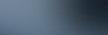

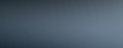

EKI-8510G obtained CC-Link IE TSN Class A & B certifications, enabling a wide variety of applications in industrial environments. TSN is the industrial communication technology that realises the integration of information technology (IT) and operation technology (OT), bringing the benefits of time synchronisation, high bandwidth, and reduced transmission latency.
The EKI-8510G is the next generation of industrial Ethernet switch which supports real-time communication through TSN




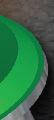
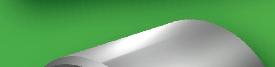
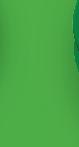



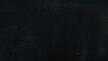
technology, providing determinism over Ethernet-based networks to guarantee data delivery for critical time-sensitive
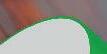




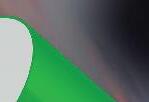
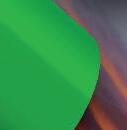



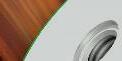
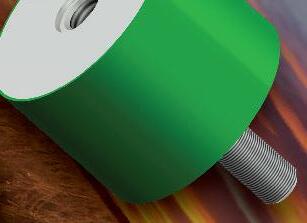














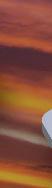






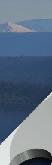





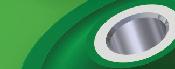
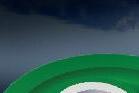


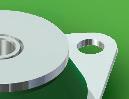
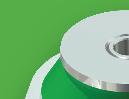

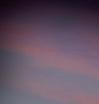
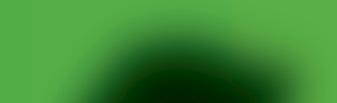



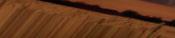




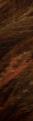

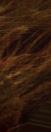

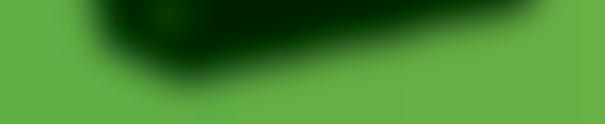



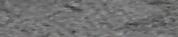

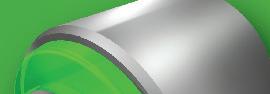
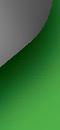

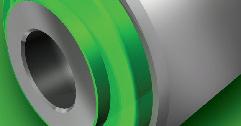



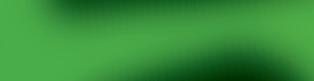

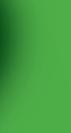
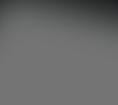





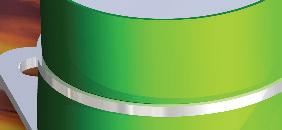


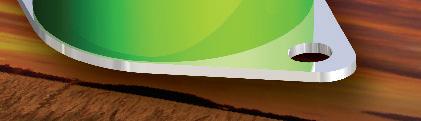


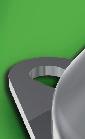




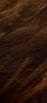





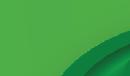



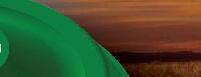
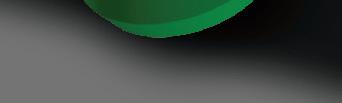
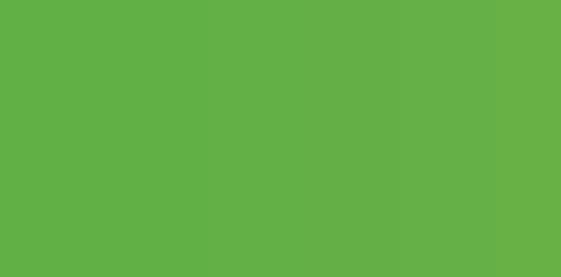
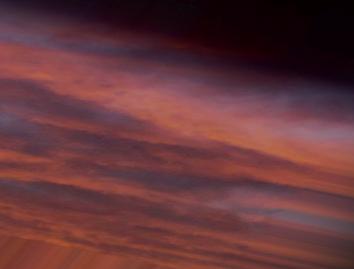



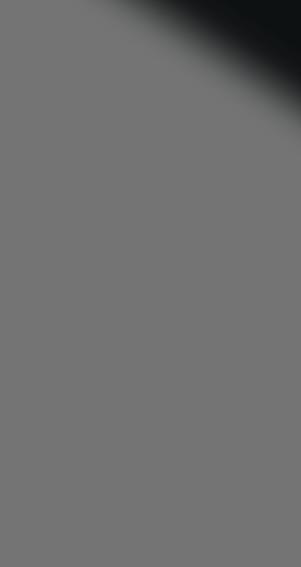
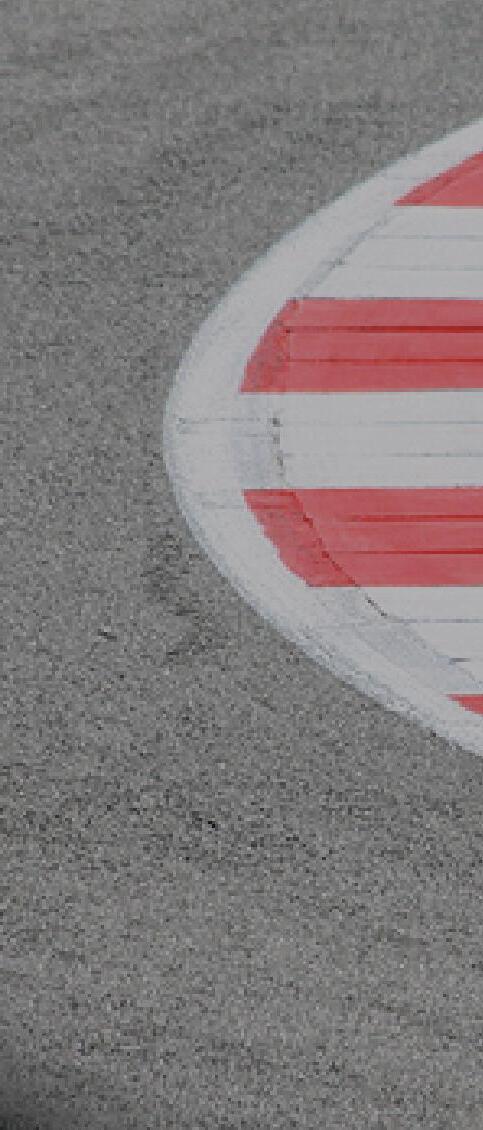
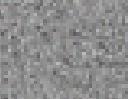
applications. Designed with industrial use cases in mind, EKI-8510G supports full layer 2 managed functionality and complies with EN 50121-4 transportation regulations for approval for railway track use. Equipped with 8 Gigabit ports and 2 Gigabit SFP ports, EKI-8510G offers high-speed transmission and an SFP socket for easy and flexible fiber connectivity.
The TSN technology framework is empowered by the development of interoperability and stability, enabling industrial operators to enhance industrial communication automation, timing accuracy, and realising the blueprint of the Industrial Internet of Things (IIoT).
www.advantech.com.
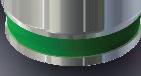

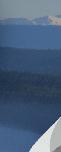
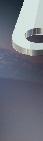
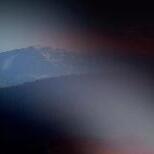

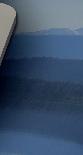



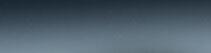


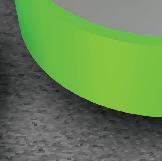
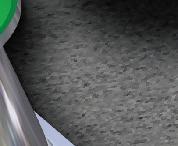
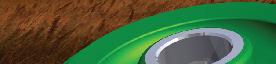
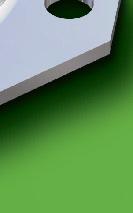
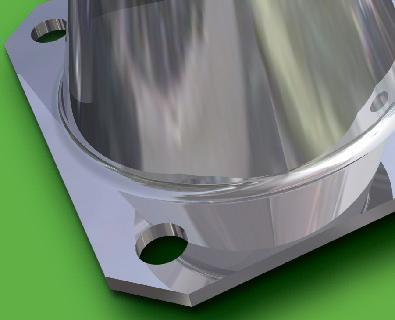

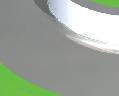
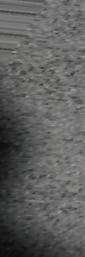


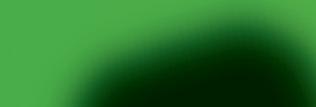
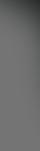


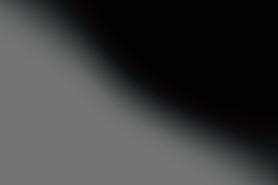
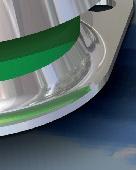
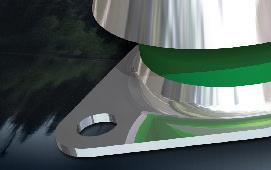
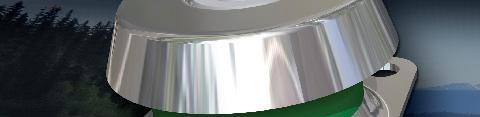


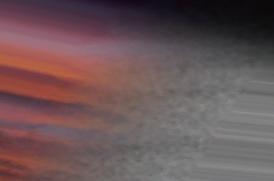

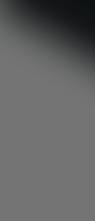
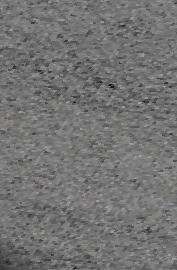
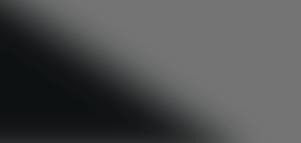


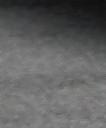

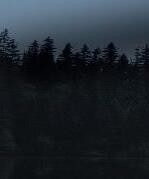
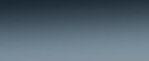
Safety and cleanliness in food production
Automation24 is expanding its portfolio in the food industry field with the addition of switch cabinets featuring a hygienic design from Rittal to the company’s online shop.
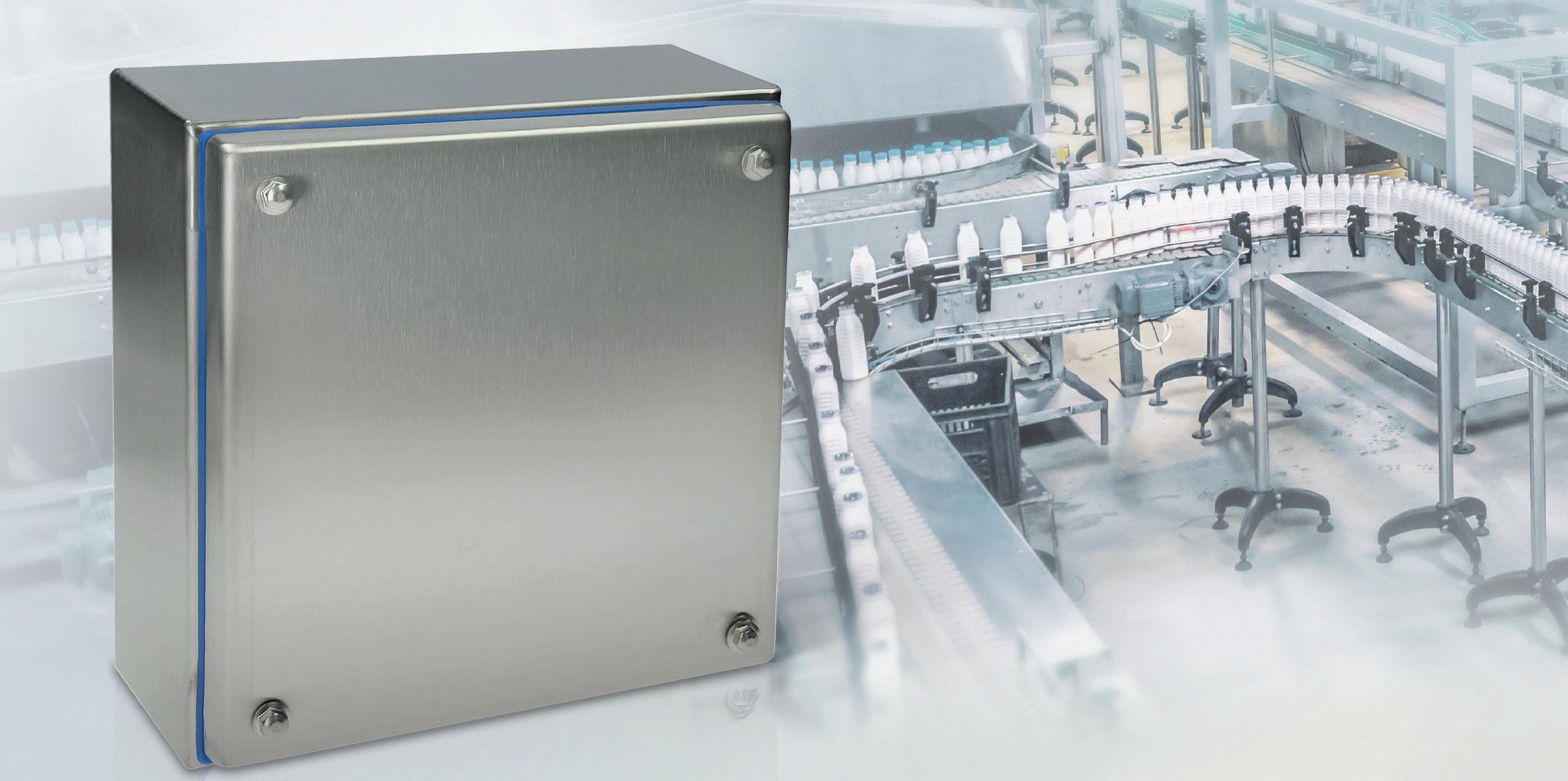
Food production is an industry with high requirements when it comes to quality and hygienic production processes. For some time now, Automation24 has been offering suitable components and devices for process optimisation and monitoring. With the HD (Hygienic Design) switch cabinets from Rittal, the online retailer is expanding its range in the area of food production with a functional and hygienically safe product series, which contributes to ensuring a contamination-free workspace.
Hygienic design
Many processes within the food industry can be simplified using high-quality automation technology. As such, as of recently, Automation24 has been offering high-quality control cabinets by Rittal, thus providing protection for components for optimal control and monitoring to prevent potential contamination during the production process, and to protect against water and chemical cleaning agents. The enclosure solutions made
of stainless steel are available in various sizes. They have an IP66 protection rating, and thus offer a high level of protection against water and dust. With a top panel at a 30° angle, the cabinets are designed in such a way that all liquids immediately flow off when cleaning. In order to prevent the penetration of moisture, the doors have an external, continuous silicone seal that runs the whole way around. Thanks to their blue colour, contamination with food is quickly recognisable. Using a provided mounting plate, various elements can be securely integrated into the switch cabinet.
“Industrial food production is, first and foremost, all about consistent product quality, adherence to hygiene regulations, and a high level of efficiency,” said Thorsten Schulze, who, as Managing Director of Automation24, is responsible for product range management in particular. “In order to support our customers in selecting the right process instrumentation, the products are marked with the corresponding protection class. Furthermore, using the configurator, the most varied of options can be put together -
thus, custom solutions can be adapted to suit conditions in your own plant.”
A comprehensive range
Inductive and capacitive sensors from various brands are available for reliable position detection alongside light barriers and light sensors. For process measurement and control, customers can find pressure, temperature, and level sensors featuring corresponding protection ratings and a hygienic design. For example, the Liquiphant FTL33 vibronic point level detector from Endress+Hauser can reliably measure the fill level of liquids, regardless of your media properties. Reliable and long-lasting seals can be created using various connection technologies. In the field of process analytics, Automation24 offers conductivity sensors, pH sensors, and analysis transmitters. Using data loggers such as the Ecograph from Endress+Hauser, processes can be recorded and visualised.

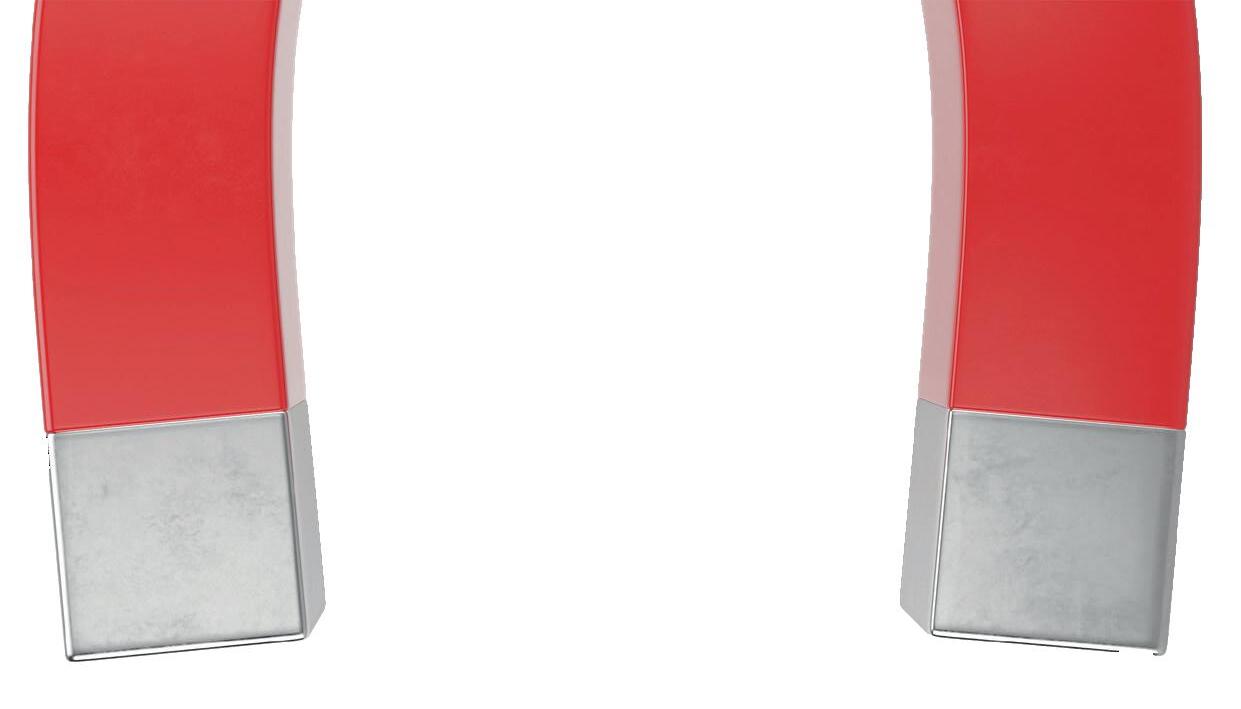
Metal and X-ray detectable 3D printed components
Foreign body contamination in food products is a major area of concern for food processors and manufacturers. Until recently, it has meant the benefits offered by 3D-printed machinery components were out of reach. Thanks to the development of detectable polymer additives, this is no longer the case, as Radical Materials explains.
Examples of foreign body inclusions are fragments of metal, bone and glass, as well as plastics and rubbers, which find their way into the food production chain from products, equipment or machinery used as part of the processing line. Should such foreign bodies pass through into the consumer chain, then there is a significant risk to consumer health as well as huge financial and reputational implications to the manufacturers.
Standard plastics and rubbers are used extensively in machinery and products within food production lines and, as foreign body particles, are often totally undetectable by conventional metal and X-ray detection systems.
The manufacturing technique is also a consideration when it comes to plastic components utilised on food production lines. Components can, for example, be injection moulded or machined from solid, but it is often desirable to have such components manufactured by 3D printing. This can offer a range of benefits, including:
• A rapid development process and easy transition from prototype to production.
• A high design freedom and the opportunity to continuously change and optimise the design.
• The ability to produce complex geometries, which would not typically be possible using traditional manufacturing methods.
• No requirement for expensive tooling and the elimination of the waste associated with machining from a solid form.
Radical Materials was approached by the Danish Technological Institute (DTI) to facilitate a specific customer’s requirement for metaldetectable 3D-printed nylon parts for the food processing industry. For this to be taken to a successful outcome, Radical Materials was required to supply a detectable additive to

DTI, which would need to meet the following requirements:
• It had to be highly metal detectable, such that the final printed components achieved high levels of detectability whilst utilising the lowest addition rate possible into DTI’s base nylon powder.
• It had to be compatible with DTI’s 3D printing process used to manufacture the nylon components.
• It had to be capable of meeting the food contact regulations required of the final components.
Working together on this global issue, DTI successfully mixed and processed detectable powder from Radical Materials with its base polymer. The organisation subsequently developed the parameters in its process, ultimately offering the production of metaldetectable 3D-printed nylon parts to the customer.
The resulting material was tested and reported on by Radical Materials for both metal and X-ray detectability.
As a further enhancement to the offering, and responding to demands from the wider industry, there was a requirement for DTI to be able to offer nylon-printed components, which were not only strongly detectable by metal detection systems but also by X-ray detectors.
Radical Materials subsequently developed and supplied a special additive blend, which DTI mixed with its base nylon powder and used to successfully print nylon parts with both metal and X-ray detection performance. An additional benefit of this additive blend is that, due to the specific materials utilised, colouring of the final components is easily achieved, and DTI was able to offer products in a bright and bold blue.
Mads Østergaard, Team Manager at the Danish Technological Institute, commented: “We first became aware of metal detectable
powder through experiences from the injection moulding industry, and we believe that it has great potential in 3D printing as well. With the detectable additives and blends from Radical Materials, we can explore new business opportunities, develop new types of products, and enter new markets where we can demonstrate the potential of 3D printing.
Chris Vince, Technical Director at Radical Materials, added: “As a company, we already offered leading solutions for imparting metal and X-ray detectability to polymer products manufactured by techniques such as moulding and extrusion. We were aware of the advantages of 3D printing and the benefits of utilising this technique to produce components for the food processing industry. We are therefore happy to have been able to support DTI in its successful venture to offer the best of both worlds.”
www.radicalmaterials.com
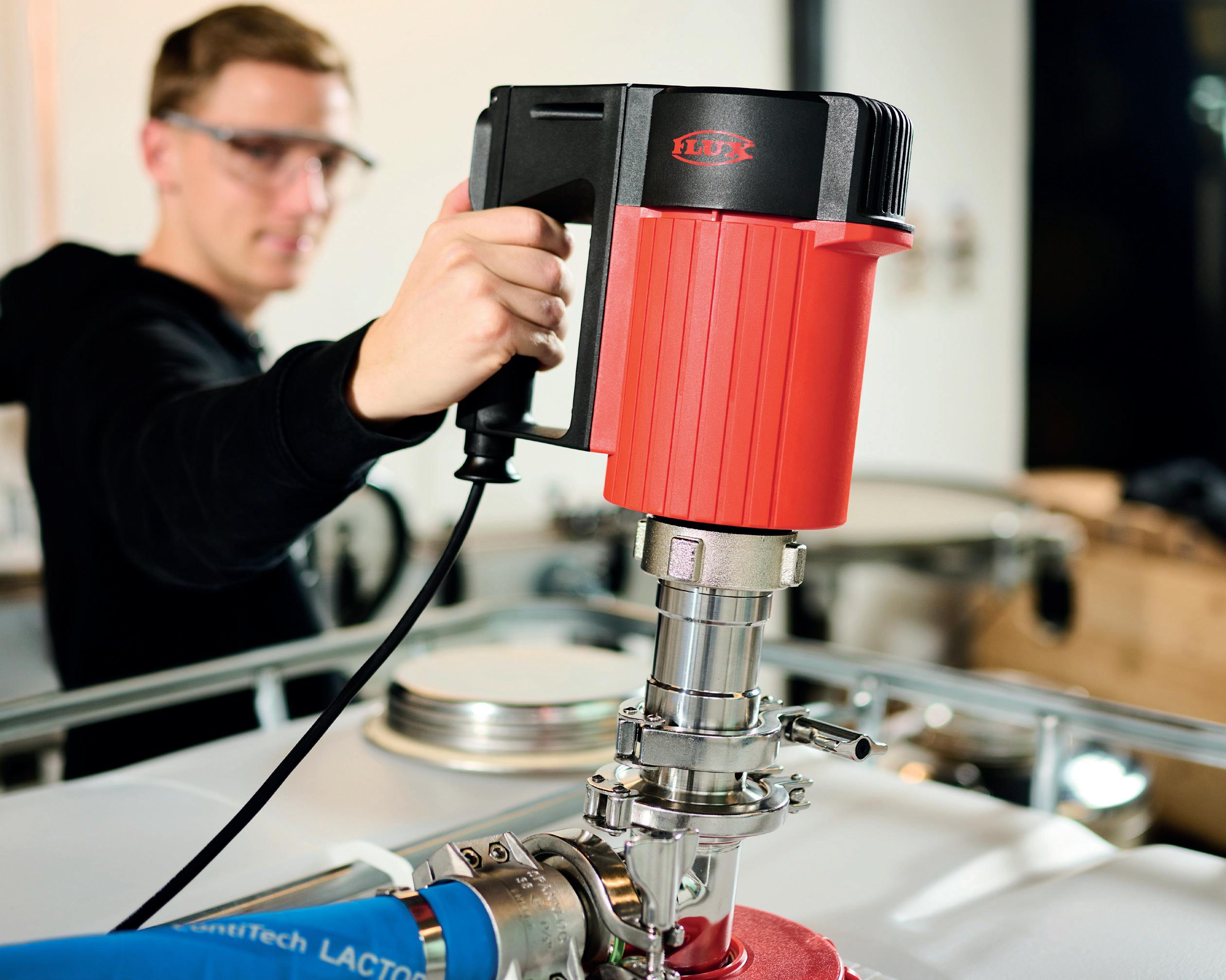
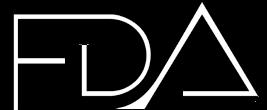
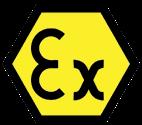

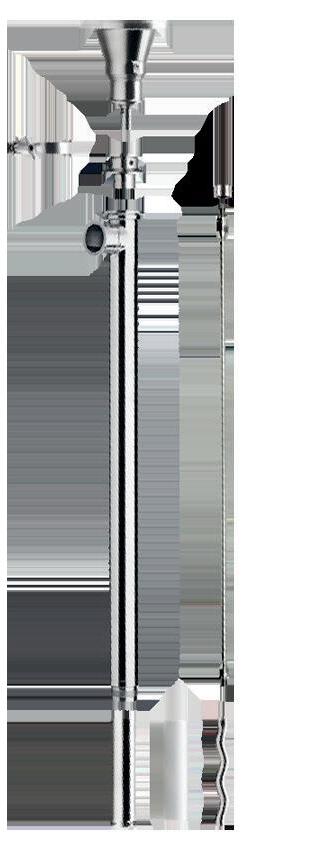
Kawasaki Robotics launches agile cobots
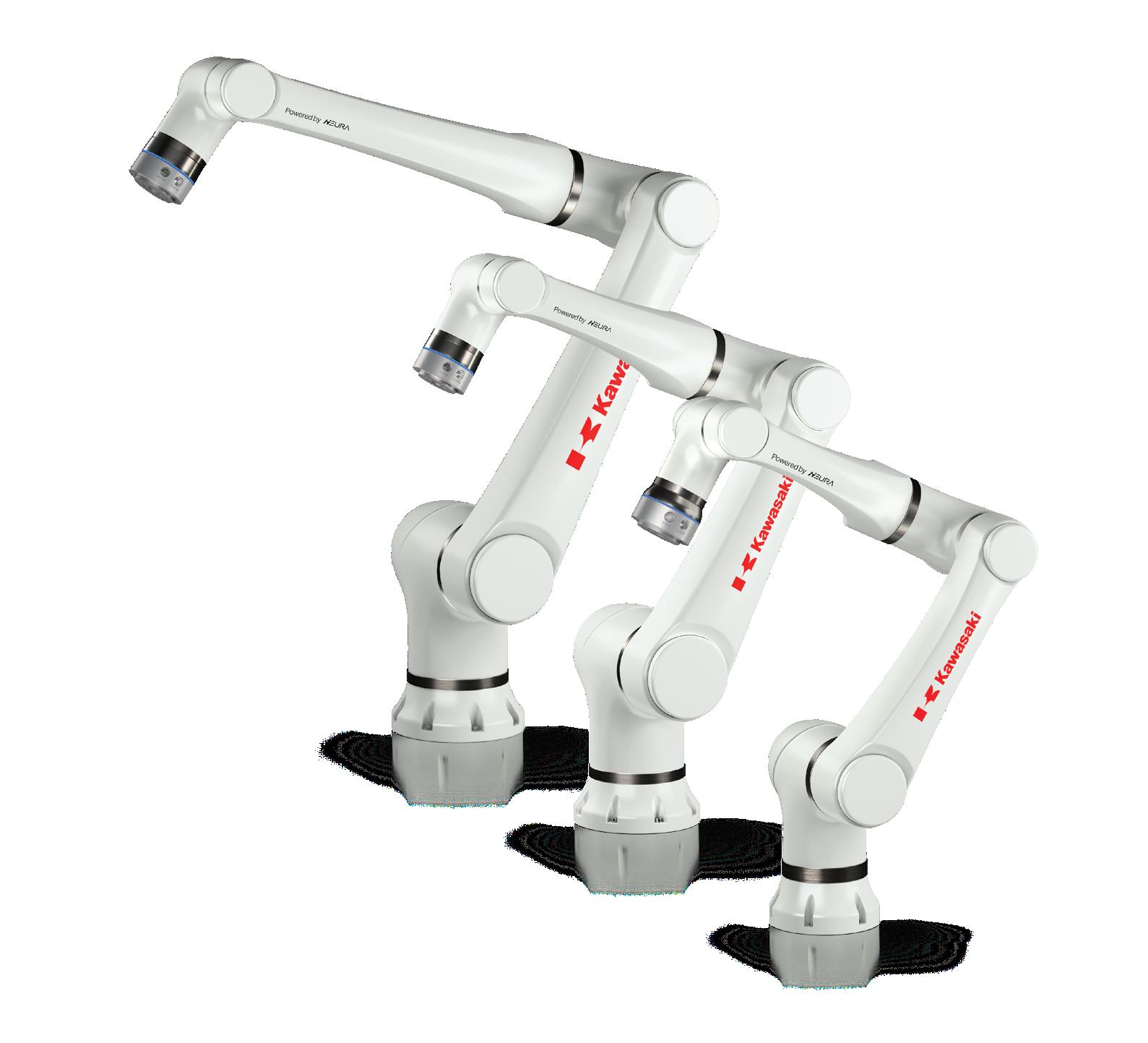
With its new CL Series, Kawasaki Robotics provides an entirely new and agile approach to collaborative robotics – powered by a partnership with Neura Robotics. Mepca found out more.
A50-year history of robotics expertise and leading technology made in Japan meets automation innovation made in Germany. With its newly launched CL Series and a variety of payloads and reaches, Kawasaki Robotics provides an entirely new and agile approach to collaborative robotics – powered by a partnership with Neura Robotics. The joint venture brings together two companies with a like-minded desire to challenge the current understanding of cobots in industry – entering a new era of collaborative automation.
No compromise
The CL Series offers the best of both worlds, with full-on industrial scale performance and speed paired with maximum protection and all the advantages of collaborative robotics. Combined with an intuitive user interface, the CL Series makes automating production lines easier than ever before. With payloads and reaches of 3kg/590mm, 5kg/800mm, 8kg/1300mm and 10 kg/1000mm, the four models of the CL Series offer the perfect solution for every scenario. Free mounting orientations, extremely small footprints and IP66 classification provide additional flexibility – for all models. Its proprietary safety architecture and many features for safety positions, speed, torque, zones, limits and collision detection allow the CL Series Cobots to operate alongside human workers.
Designed and made in Germany
The CL Series brings together an industryleading speed of 200°/s, with repeatability of ±0.02mm for all models. The collaborative robot line is the perfect choice for
automating simple and repetitive tasks –effectively saving costs and maximising revenue. Designed and made in Germany, the CL Series offers excellent performance through high-quality components, such as the integrated 24-bit encoders, which are among the highest-resolution on the market, and extremely light-weight yet with a reliable construction. Thanks to its compact and robust design and IP66 rating, the CL Series can be used in all kinds of harsh environments that may not be suitable for other collaborative robots.
kawasakirobotics.com/uk
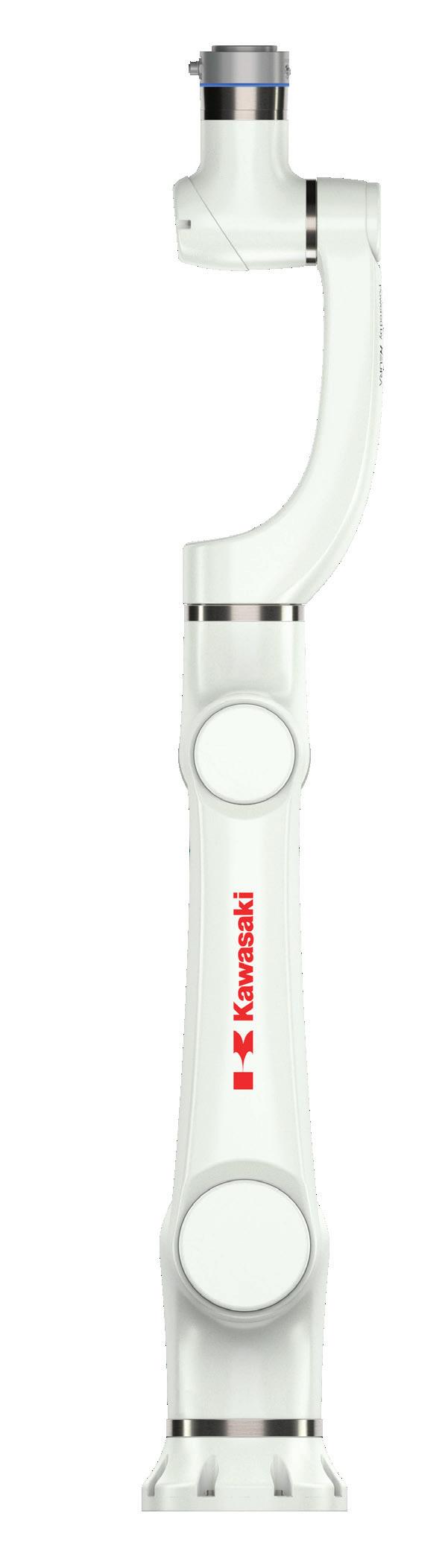
On Demand Failure Analysis


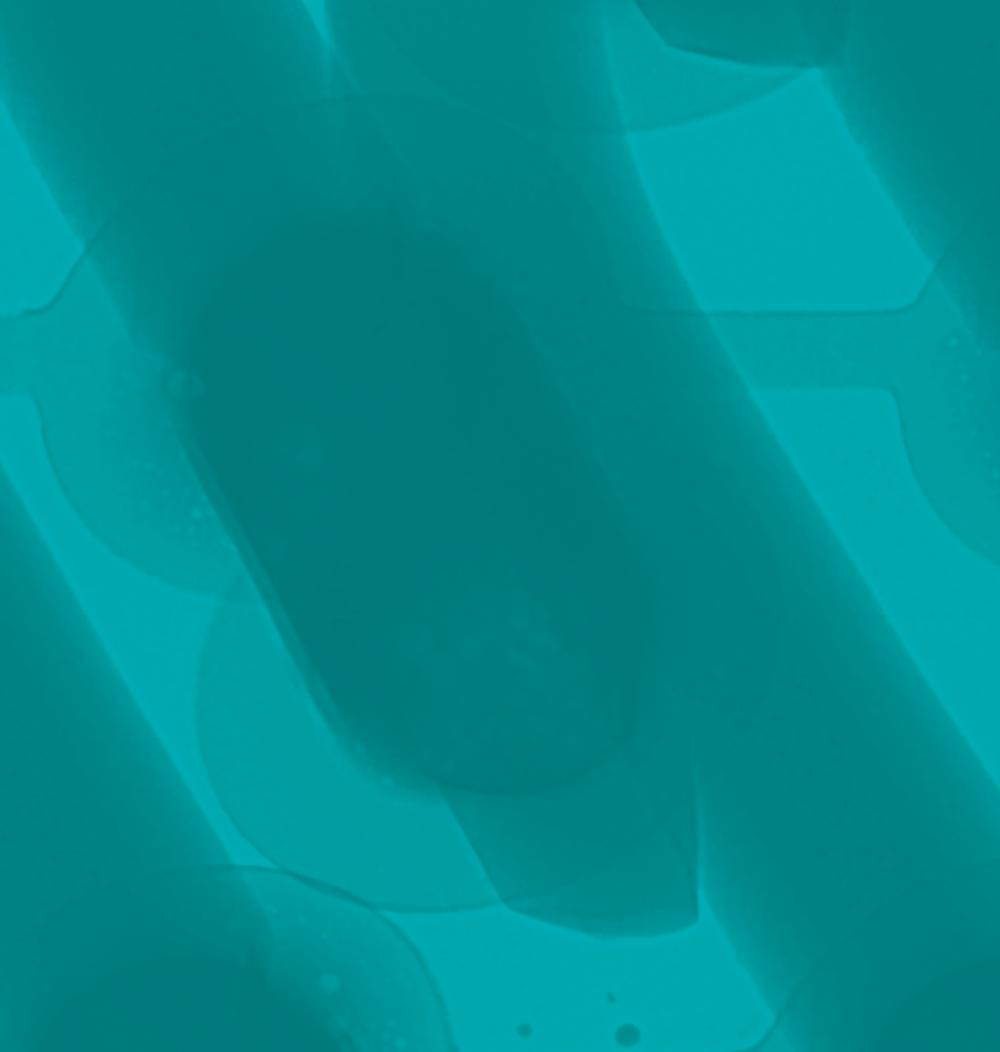
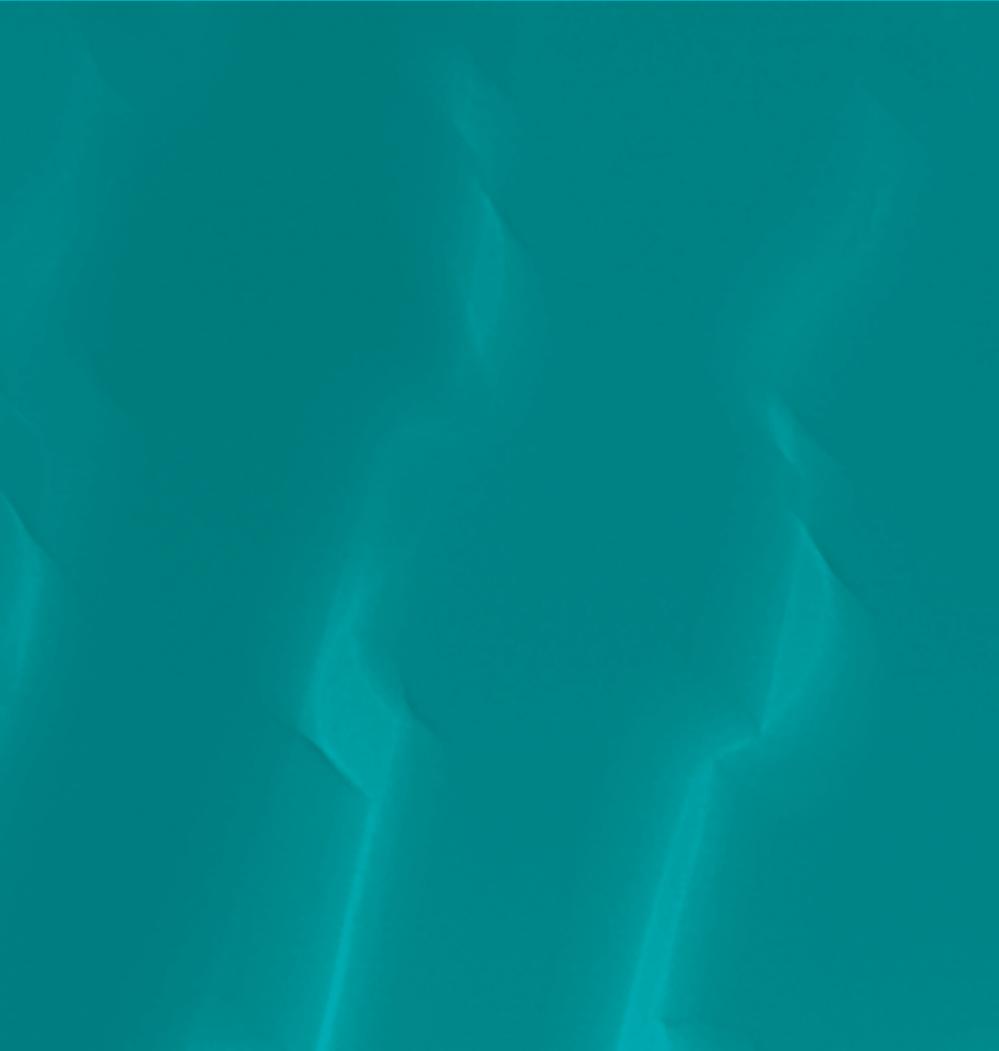

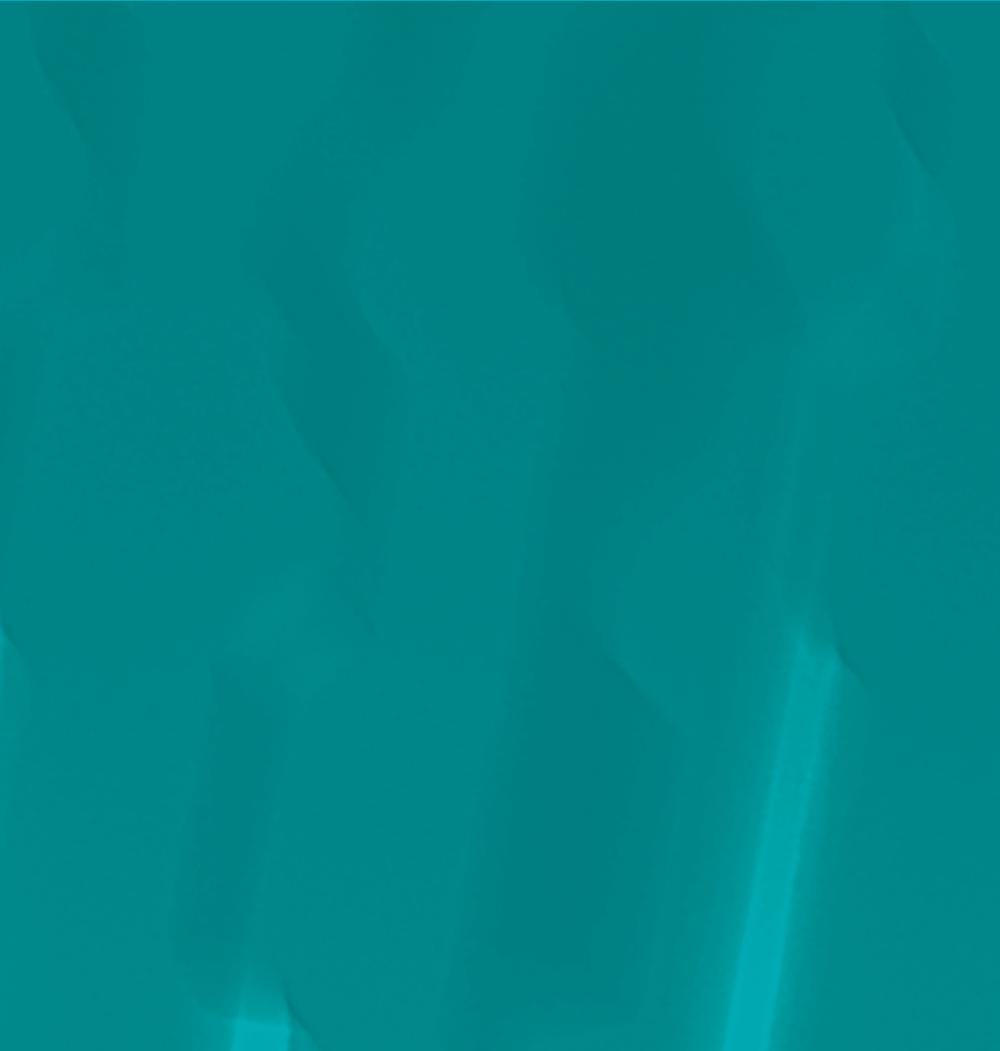
and In-Depth
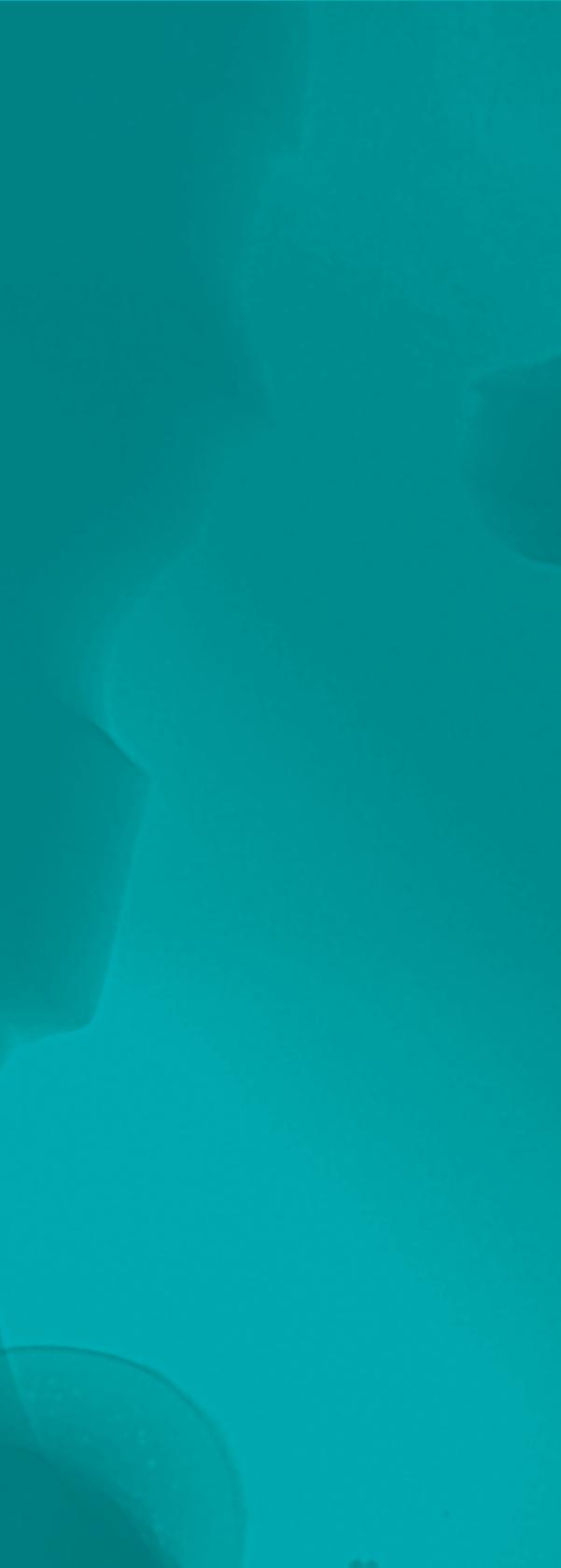
Non-Destructive Inspection
Cupio Services provides x-ray, acoustic, optical and electronic test, inspection and analysis services.
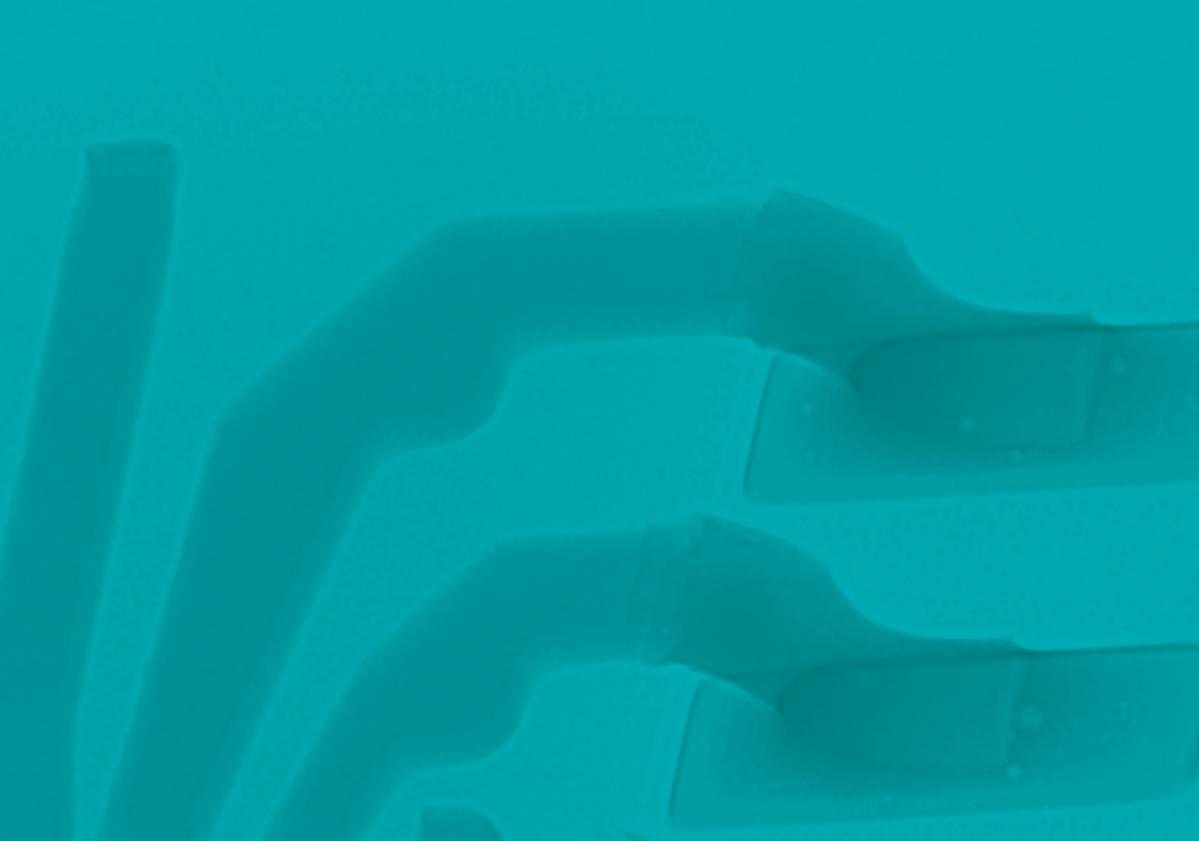


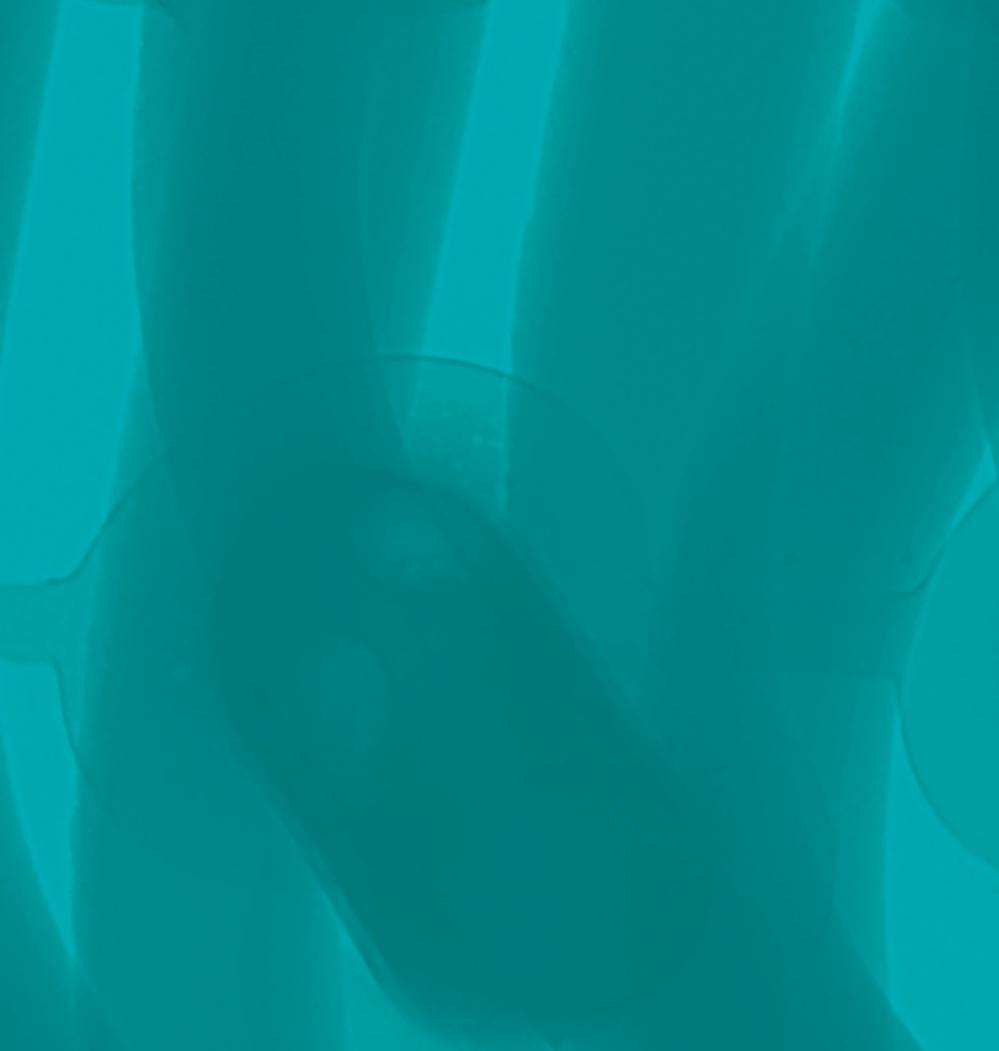
If you only require inspection, test or analysis services occasionally throughout the year, the requirement to purchase our equipment may not be necessary, this is where Cupio Services is the answer.
• Cutting-edge inspection and test equipment
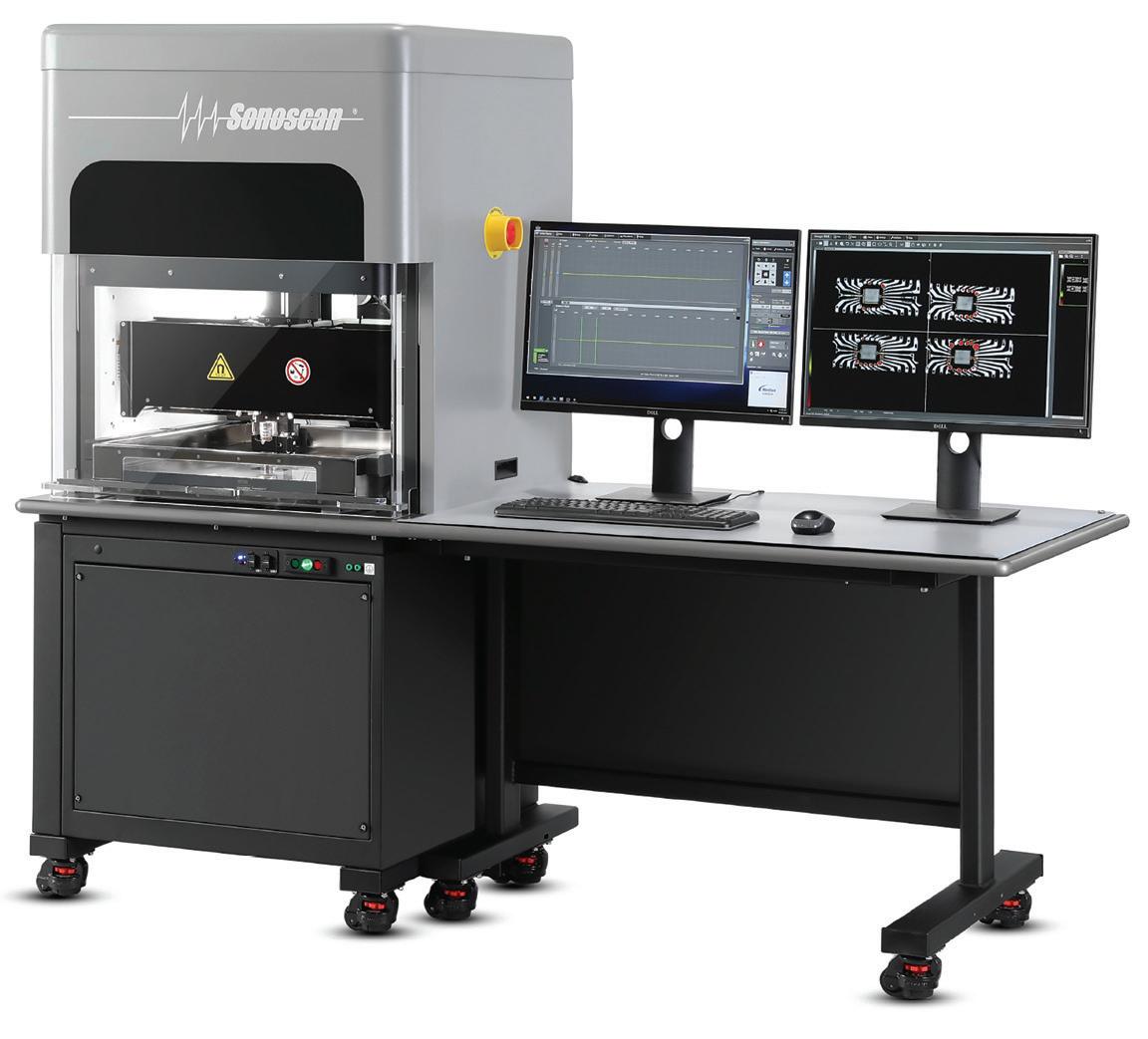
• Functional testers and counterfeit part detection
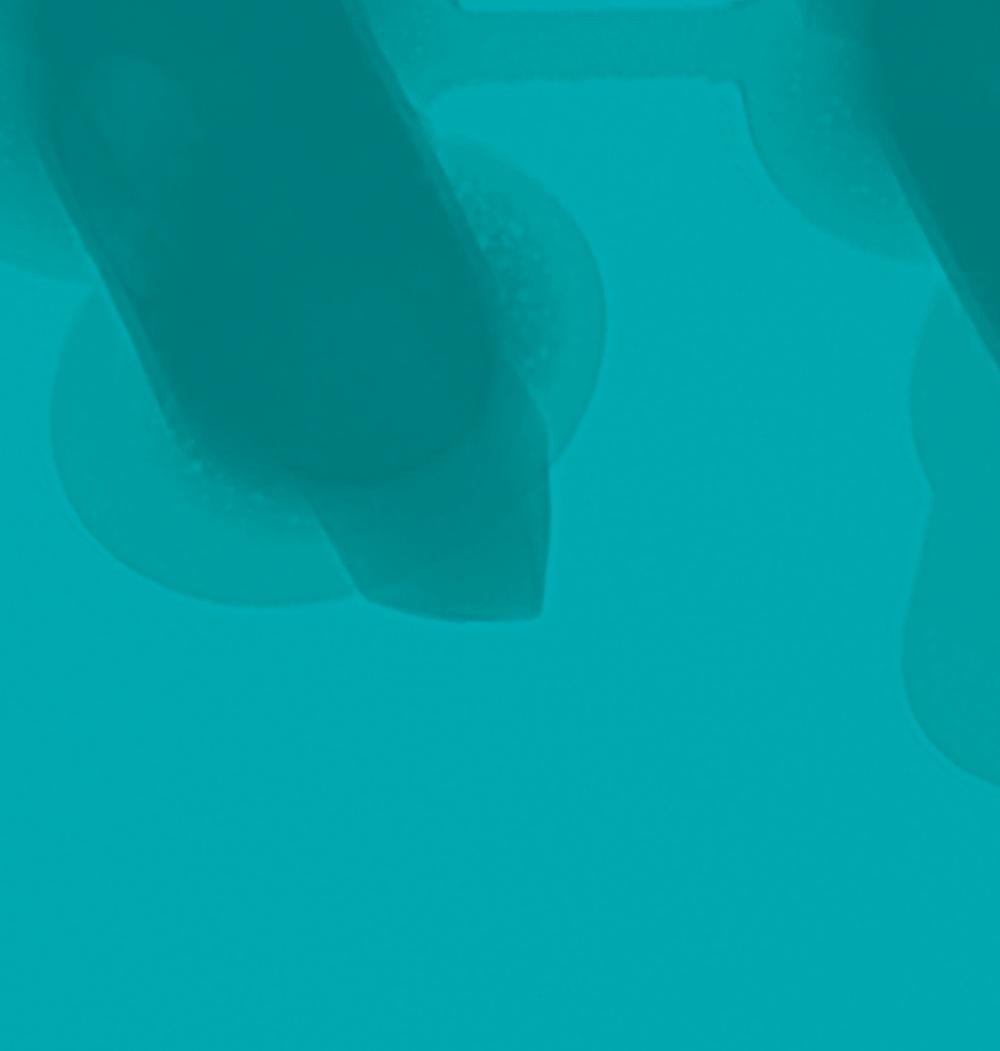

• High resolution x-ray with multiple CT imaging options

• Acoustic microscopes for delamination detection within boards or complex devices
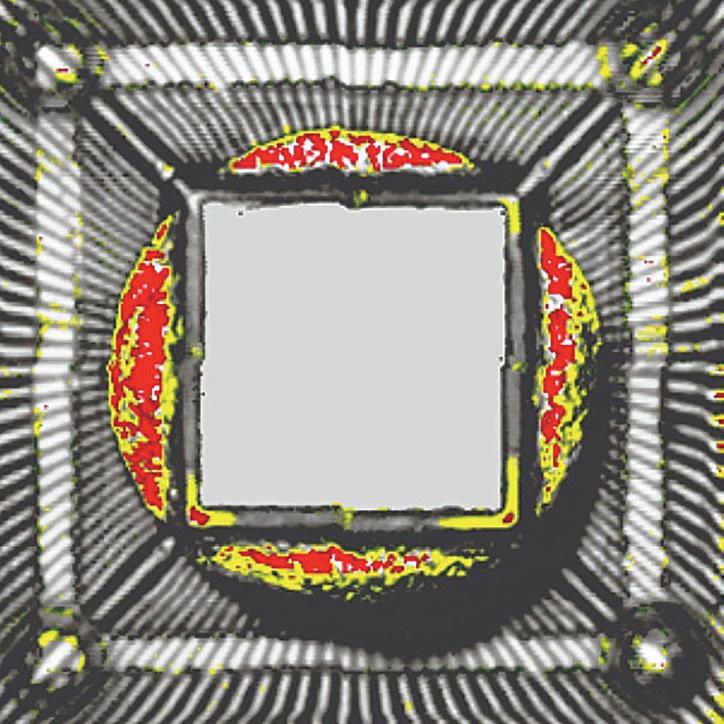
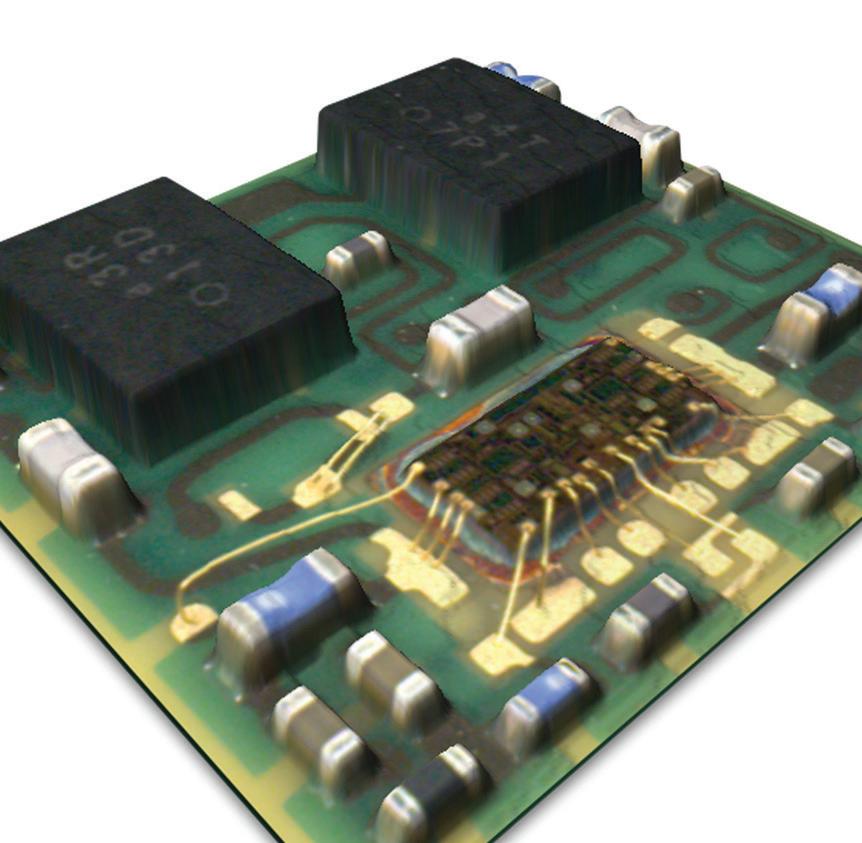
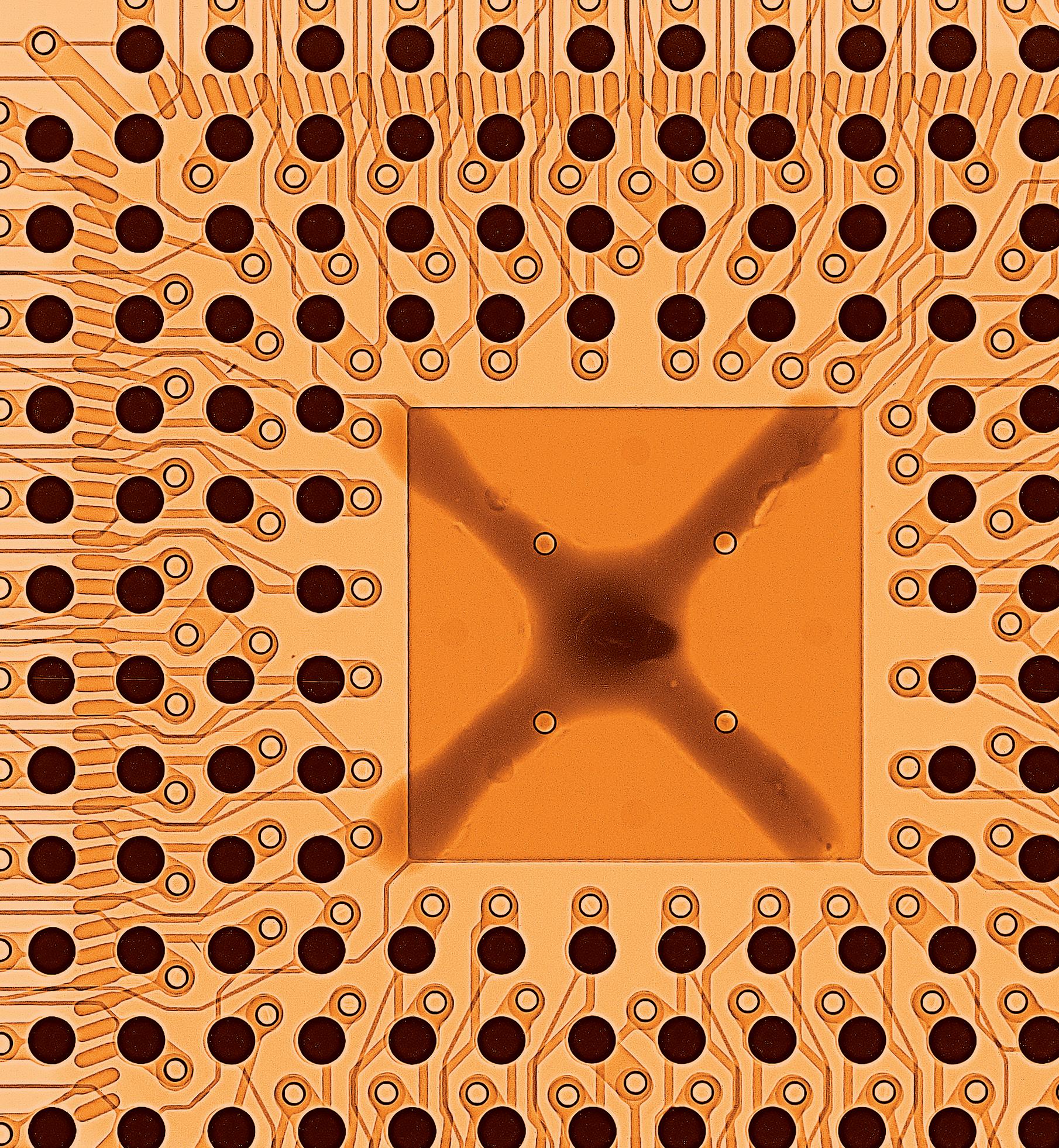
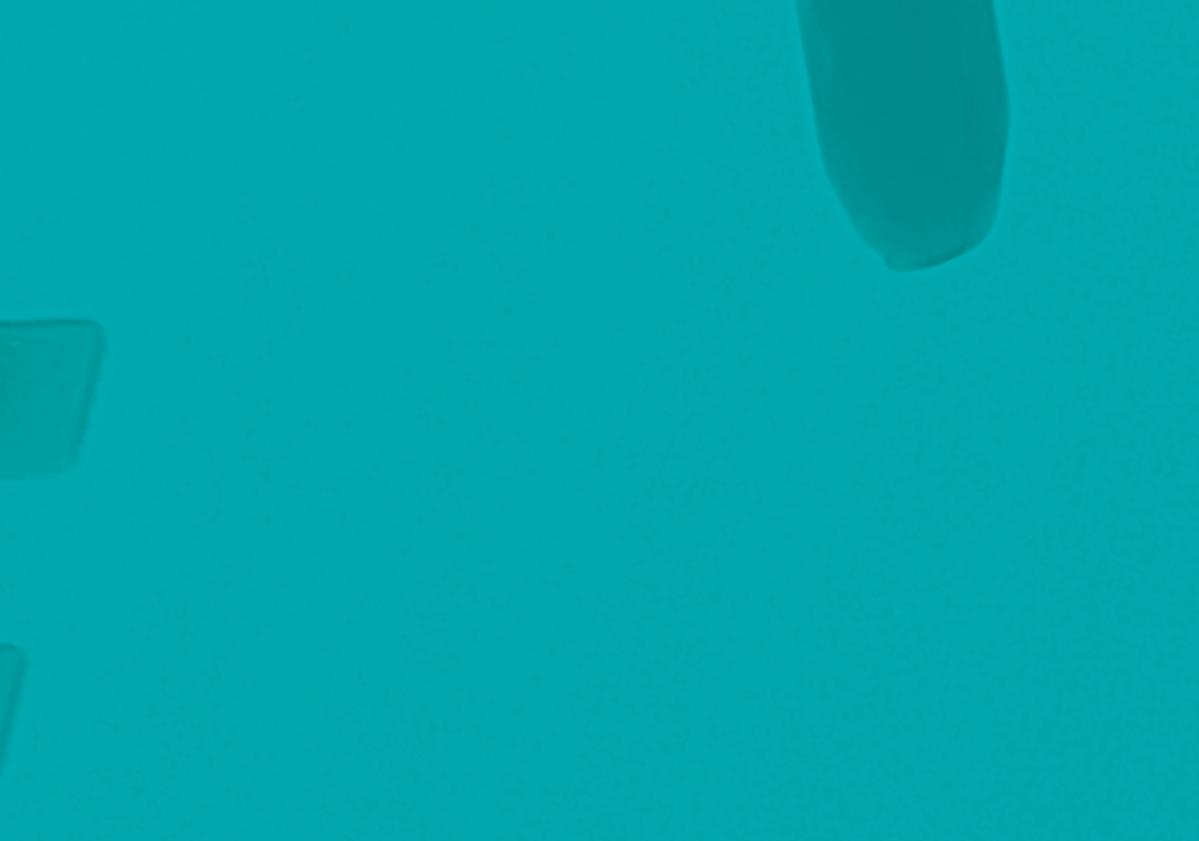
• Full failure analysis reports.
Speak to one of our experts today:
Powering AGVs and AMRs in cleanrooms
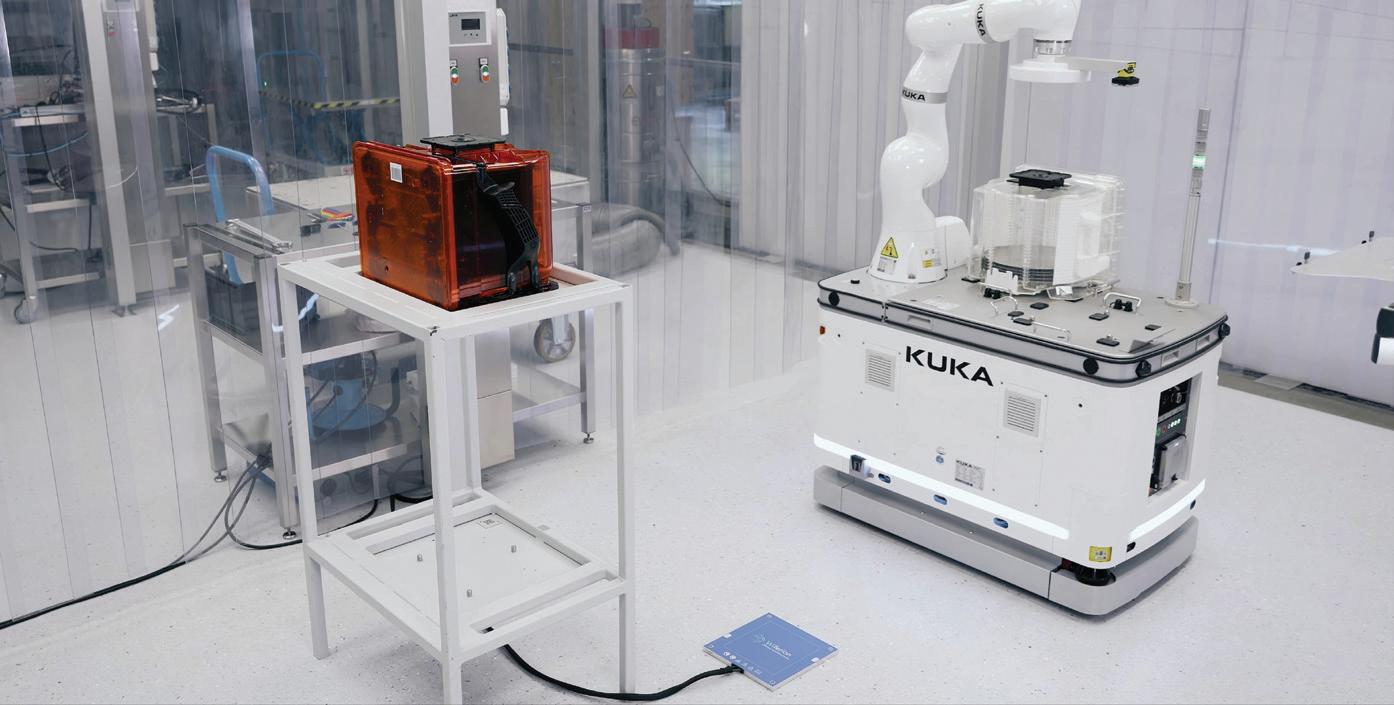
The market for Automated Guided Vehicles and autonomous mobile robots for the process industry is growing continuously. In semiconductor production, pharmaceuticals or medical technology, robots can efficiently automate material transport in sensitive production environments. But in higher ISO cleanroom classes in particular, the installation of the systems has generally been time-consuming and expensive because of the introduction of particles during mechanical power supply. Wiferion explains how inductive charging systems can overcome this.
The pressure to automate transport processes efficiently and reliably is increasing in the process industry partly due to a lack of skilled workers and interruptions to delivery chains. Increasing numbers of companies are therefore choosing automated guided vehicles (AGV) and autonomous mobile robots (AMR). However, where the transport of production resources needs to meet the most stringent cleanliness requirements, any contamination of the production environment can lead to downtimes. Particles floating in the air that pollute a batch of medicines or damage highly sensitive semiconductor substrates (wafers) can cause significant issues. Therefore, every component of automated transport vehicles must be designed with a view to cleanliness. A sticking point here has been the supply of power to the transport robots.
Until now, AGVs and AMRs have been charged automatically with sliding contacts. With this charging method, a robot travels across copper contacts set into the floor. The transmission of power begins when direct contact is made with the charging contacts on the underside of the vehicle. The problem is every charging process creates copper abrasion, which pollutes the environment. In addition, there is a risk that employees could trip over the charging points, and this is a danger to process safety. Traditional contact charging plates sit several centimetres above the floor so that the power supply works despite a robot being clear of the floor. Finally, the systems require considerable maintenance, as broken or dirty contacts have to be replaced.
Inductive power supply
For this reason, AGV and AMR manufacturers are increasingly turning to inductive point charging systems where the transfer of power is contactless, following the principle of magnetic induction. As soon as a vehicle has reached the loading pad of an inductive point charging unit, the charging process starts automatically at full power within a second. Battery fast charging systems such as Wiferion’s etaLINK are encapsulated and can operate without mechanical components. In this way, Wiferion enables charging to take place with minimal particle generation. Additional reliability is provided by PohlCon’s Wireless Charging Protection System (WCPS), specially designed with a double bottom system for use in cleanroom environments. This means that the toughest cleanroom requirements can be met.
In addition, the charging technology allows production to be maintained without interruption for charging the battery. Instead of moving to permanent charging stations,
the robots are provided automatically, at frequently used stations such as processing machines, with the quantity of energy they need for their transport tasks through “inprocess charging” during their workflow – so no time is wasted. The vehicles can thus carry out their transport tasks in a continuous 24/7 operation without needing to interrupt their transport work for charging breaks. This increases the productivity of a fleet of robots by up to 32% in comparison with traditional charging technologies.
The etaLINK charging pads can be installed completely flush with the floor, at the side or like a tile. The charging station does not impede the flow of work, and there is no longer any risk of tripping. Another plus point is the flexibility of the application. If the production layout is changed, the charging points can be relocated in a few quick steps. In addition, no maintenance is required due to broken or dirty contacts.
www.wiferion.com
Robot contract supports high-tech kitchen factory
MEPCA learns how ABB Robotics has been selected by Nobia – a European kitchen specialist – to supply robotic automation solutions for the company’s new factory in Jönköping, Sweden.
By securing the contract to supply robotic automation solutions, ABB Robotics is furthering its expansion into new industry segments, helping to make production more efficient and sustainable.
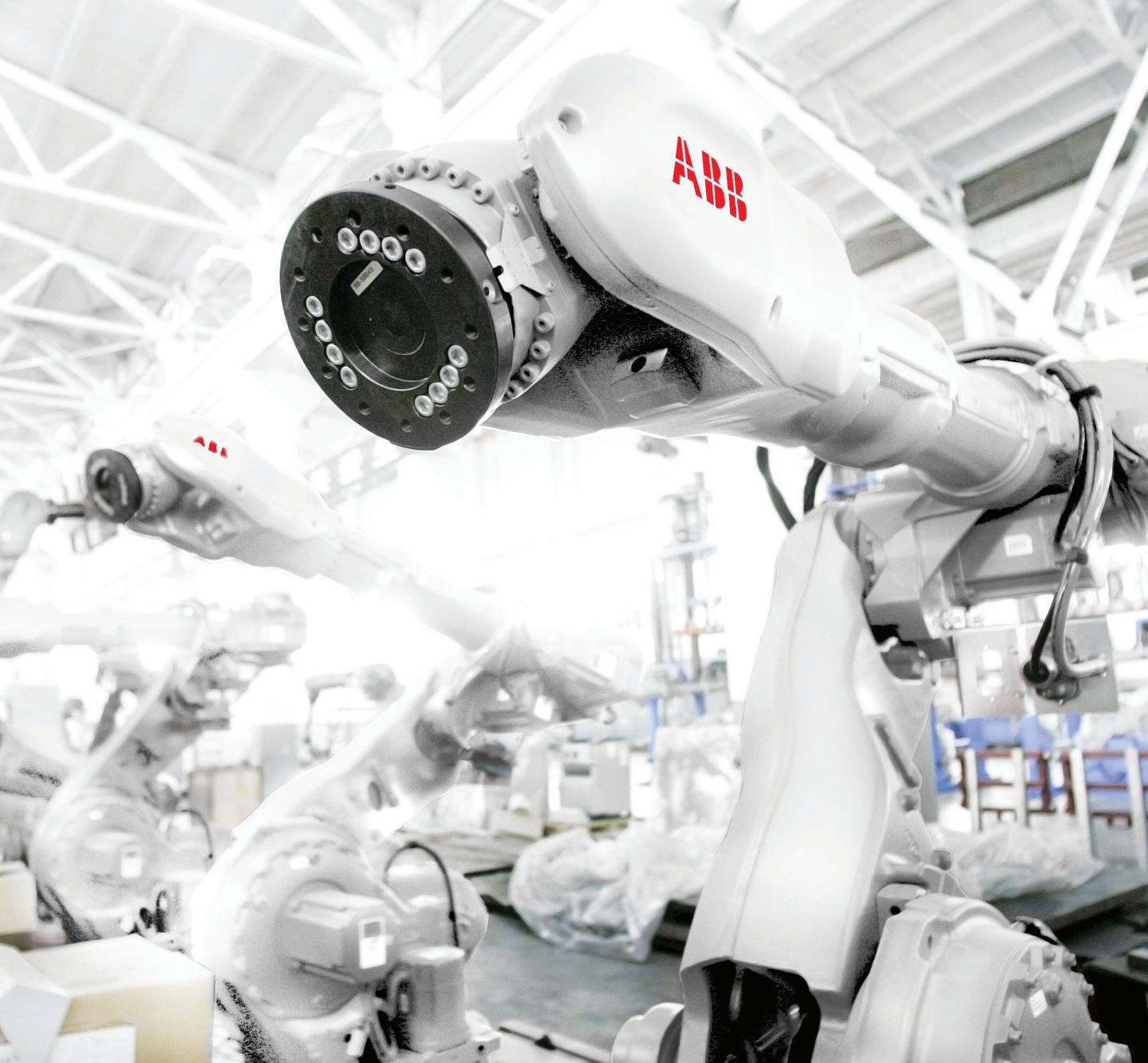
“ABB’s contribution to Nobia’s new stateof-the-art factory clearly illustrates how we are helping companies unlock flexible automation to transform their business, supporting with unique global industry expertise and innovative, tailormade products,” said Andrea Cassoni, Managing Director, General Industry at ABB Robotics. “Working with Nobia, our robotics solutions will enable fast massproduction of customised kitchens, meeting consumers’ increased demand for tailored and personalised product choices”.
The supply of ABB robots will enable Nobia to achieve its vision for more flexible and more automated manufacturing that’s capable of producing customised products at scale. By taking on the dull, dirty and sometimes dangerous tasks, the range of robots will enable Nobia’s workers to take on safer, more rewarding work. The robots included are the IRB 7600, ideal for heavy applications; the IRB 4600, a general-purpose robot that increases production capacity and improves productivity; and the IRB 6700, the highestperformance robot in the 150–300kg class which, on average, takes about 2.5 tons per day off the shoulders of an employee. The robots will enable the factory to produce customised cabinets with 75-80% higher efficiency (time) in comparison to nonautomated processes.
Combining ABB’s technological leadership in automation with Nobia’s segment insights and knowledge of its customers’ needs, the relationship will lead to more flexible and digitalised manufacturing processes. Together, the companies strengthen the
competence development within automation for the region around Jönköping. In the local area, ABB Robotics will support and educate Nobia’s existing and future employees as well as students at Jönköping University and neighbouring Linköping University. The training will be held in ABB Robotics’ recently opened training centre in Jönköping.
“We are very excited about this partnership with ABB. We are building a future-proof, high-capacity factory that will support our leading position. It is a real game changer for the whole industry. The factory will manufacture customised, made-to-order kitchens at the highest speed and at the same time highest possible quality. The unique combination of technology solutions
combined with our expertise will enable us to offer kitchens with leading design and sustainability performance to customers in the Nordic region. To achieve this, we will utilise ABB’s market-leading technology for highly automated and flexible processes, and extensive logistics consolidation,” said Jon Sintorn, CEO at Nobia.
The region around Jönköping is characterised by extensive know-how and expertise in manufacturing, with ABB Robotics further enhancing this through its work with Nobia. The factory will be fully operational in 2024, becoming one of Europe’s most modern kitchen factories.
go.abb/robotics
X-ray inspection opens up new markets
A Nordson DAGE Quadra 3 X-ray inspection system supplied by inspection, production and test solution specialist Cupio is facilitating FermionX’s extension into demanding military and defence applications – and improving the company’s operational efficiency too.
As a family-run company with nearly fifty years of expertise, FermionX offers both contract electronic manufacturing and design for manufacture services. It tailors its solutions to customers ranging from established companies seeking to outsource their work, to innovative product brands that need industry expertise. Long experience with the company’s own two international brands gives it deep insight into the pressures on product manufacturers endeavouring to meet their customers’ requirements.
The company’s contract manufacturing services include supply chain management, PCB assembly, and box build. All services are operated with a rigorous quality control regime meeting ISO 9001:2015, ISO 14001:2015, RoHS and CE compliance.
Demand for inspection quality
The electronics manufacturing industry has always required X-ray testing of assembled PCBs, and, until recently, FermionX outsourced this. However, the company has been growing and is now branching into military and defence – and customers in these markets only use suppliers with inhouse X-ray inspection capability, because they cannot risk deploying products that have not been fully inspected.
Meanwhile, as components continue to shrink, manufacturing problems will become impossible to spot with the naked eye, so even companies working in less unforgiving environments are increasingly seeking the peace of mind that X-ray inspection provides. FermionX regards X-ray inspection as the only technology that can assure their end users of their quality and compliance with industry standards. Also, bringing
the service in-house creates cost savings that can be passed on to customers – a crucial benefit in the current economic climate.
The right choices
Having identified the need for in-house X-ray inspection capability, FermionX had to decide on which system would suit them best, and who best to purchase it from. From the outset, Cupio – with its Nordson product lineup – appeared as the most likely choice as a supplier, as they had previously delivered a Nordson YESTECH FX940 automated optical inspection (AOI); the experience had turned out well in terms of both Cupio’s support and Nordson’s product.
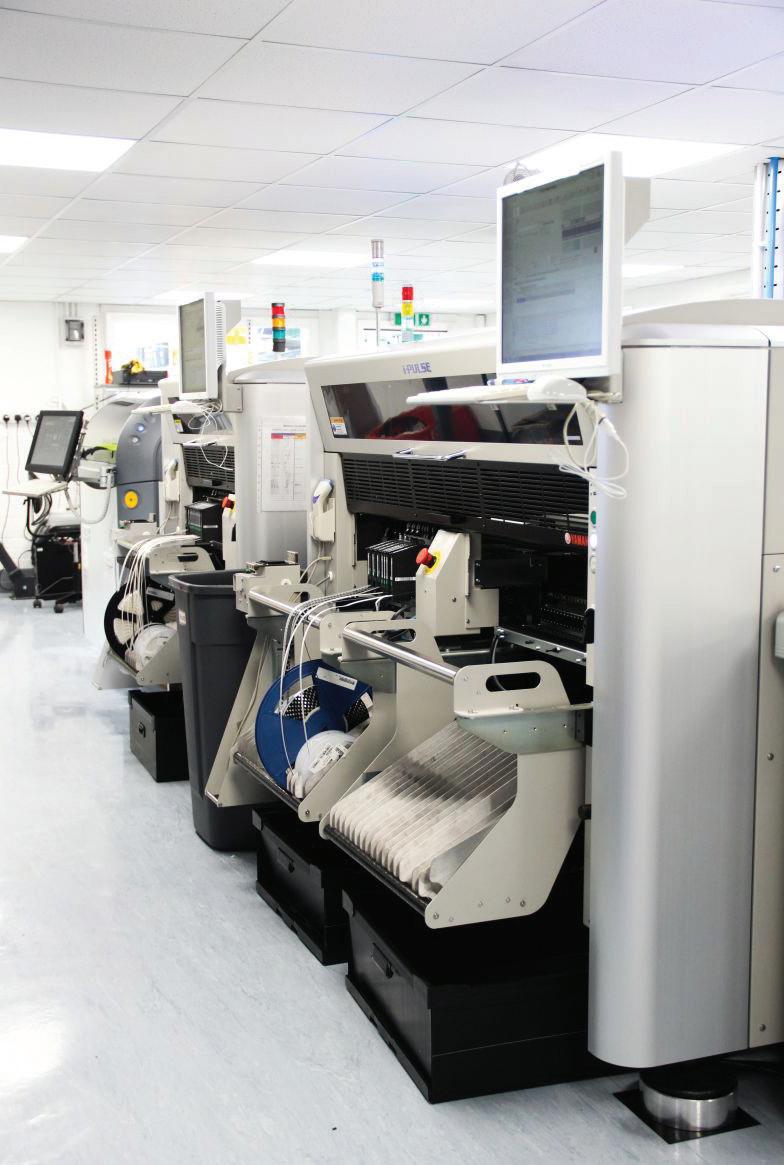
Accordingly,
FermionX chose the Nordson DAGE Quadra 3, which is ideal for high-quality X-ray inspection in production line quality control. They liked the Quadra’s ability to change viewing angles and see every detail from all sides at high magnification, without having to rotate the PCB under inspection. Being able to view BGA pads from side angles as well as from above means they can check for interfacial faults, or if the ball is not touching the pad or the board.
The software allows for void checking,
giving not only the total void percentage, but also roundness, diameter and largest single void. Additionally, the Quadra’s X-ray source uses proprietary filament-free technology; this requires no regular maintenance or filament changes, while the inspection imagery remains clear and repeatable.
This assures FermionX and their customers that their boards are compliant with standards such as IPC-A-610G.
“We have had nothing but positive experiences with Cupio throughout the
whole process from enquiry to installation and training,” commented Samantha Lane, HR, HSE & Business Process Improvements Manager at FermionX. “After our initial enquiry, we were invited to Cupio’s Basingstoke facility to see a live demo of the machine – we even inspected one of our own boards.
“Seeing the machine gave us a far better understanding of what we wanted and needed, and allowed us to make an informed choice when deciding on which company and machine to proceed with.
“Following our purchase, Cupio was always on hand to answer the preinstallation questions – and there were a lot.
“When the machine arrived, it was installed with no issues, making the process as easy and stress-free as it could be. Cupio’s trainer Ben Seviour joined us for the installation and training. He has a wealth of knowledge which is evident when he describes what the machine is doing and how to operate it. His training was well received, and gave our staff the skills and knowledge needed to start operating the machine as quickly as possible.”
Integration
FermionX has now added the Quadra’s X-ray inspection capability to the Nordson YESTECH FX-940 AOI and many other items of inspection and QA equipment. It loads all its ‘first offs’ into the machine as it provides a quick and accurate way to identify any fine voiding in the BGA, and if it is interfacial.
If they identify voids in the BGA, they can slightly increase the time above liquids during reflow by a few seconds, allowing the gas to escape and reduce future voids. This method allows them to instantly report to the surface mount team if there are any faults, and prevent the whole batch from running incorrectly.
As well as being an important pass/fail check for individual boards, voiding is also a good indicator of the overall production quality.
While using the Quadra to raise production efficiency and make quality improvements, FermionX also sees it as a tool for component failure analysis, reducing the amount of unnecessary repair. Time saved in inspection allows their hand
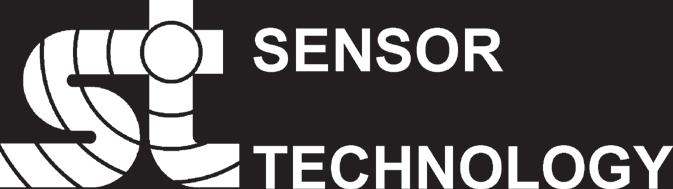

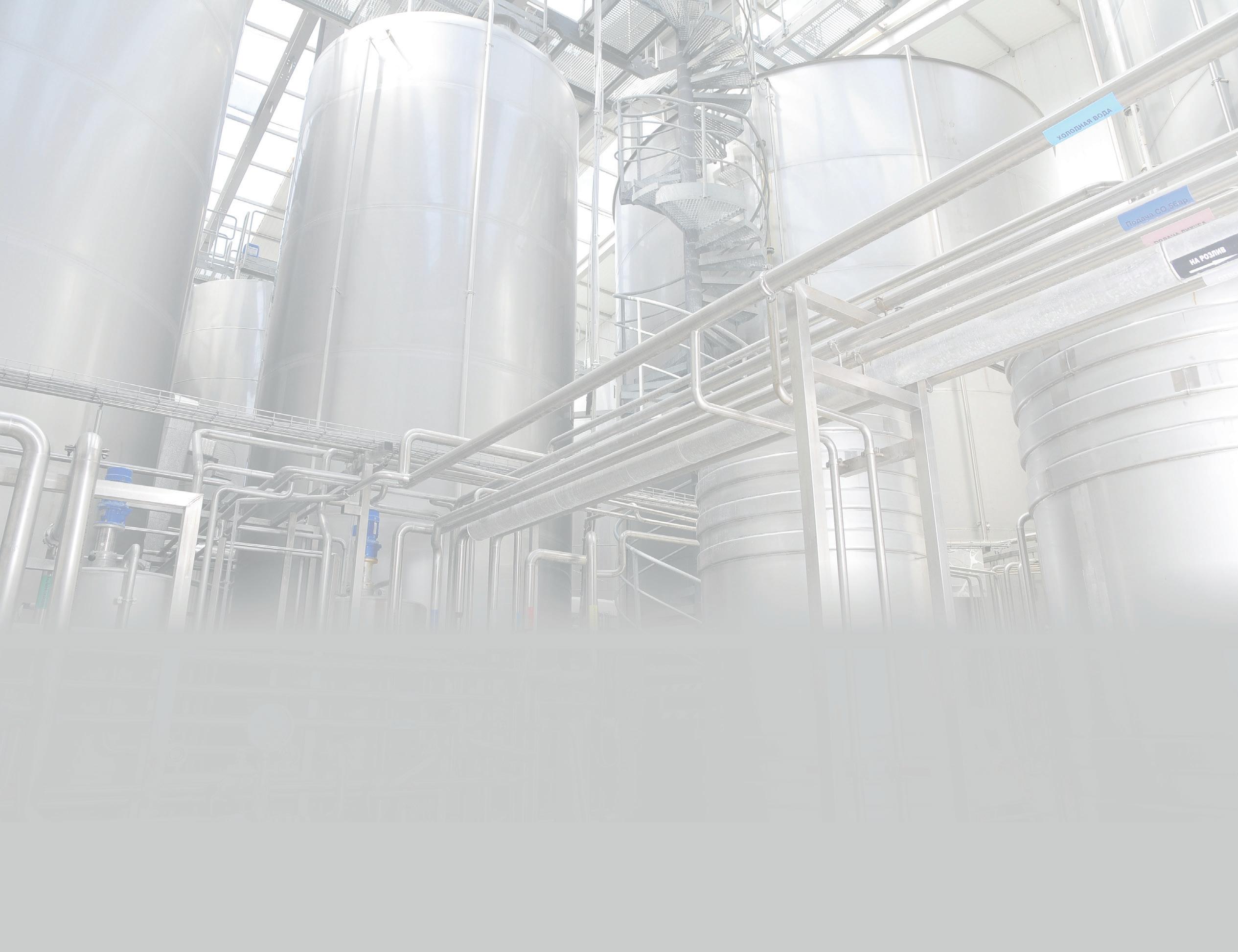
assembly team to build a batch of boards more efficiently and the surface mount team to run the machines for longer.
FermionX will also offer the Quadra’s X-ray inspection capability to OEMs seeking to outsource this activity. The machine can provide them with video reports giving a complete view of all boards inspected. Equally, FermionX’s customers can utilise X-ray inspection when running a first time design, or if they experience repeated issues in their manufacturing process.
“Although our quality has always been very high, the Quadra reduces the likelihood of returns or failures in the field, by checking our boards prior to despatch,” added Samantha. “Should the worst happen, we will be able to investigate the boards as soon as we receive them. This will significantly reduce the turnaround time and gets the products back to our customers quickly – complete with a report to explain the issues and how they were rectified, to give them peace of mind.”
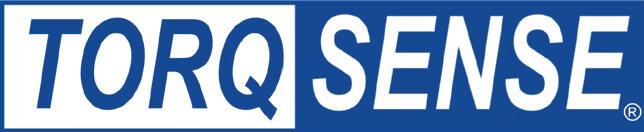
Machine Vision Conference: free tickets now available
Delegates can now register to attend UKIVA’s Machine Vision Conference, taking place on 20-21 June 2023 at the Coventry Building Society Arena, to discover the very best in machine vision and industrial technology.
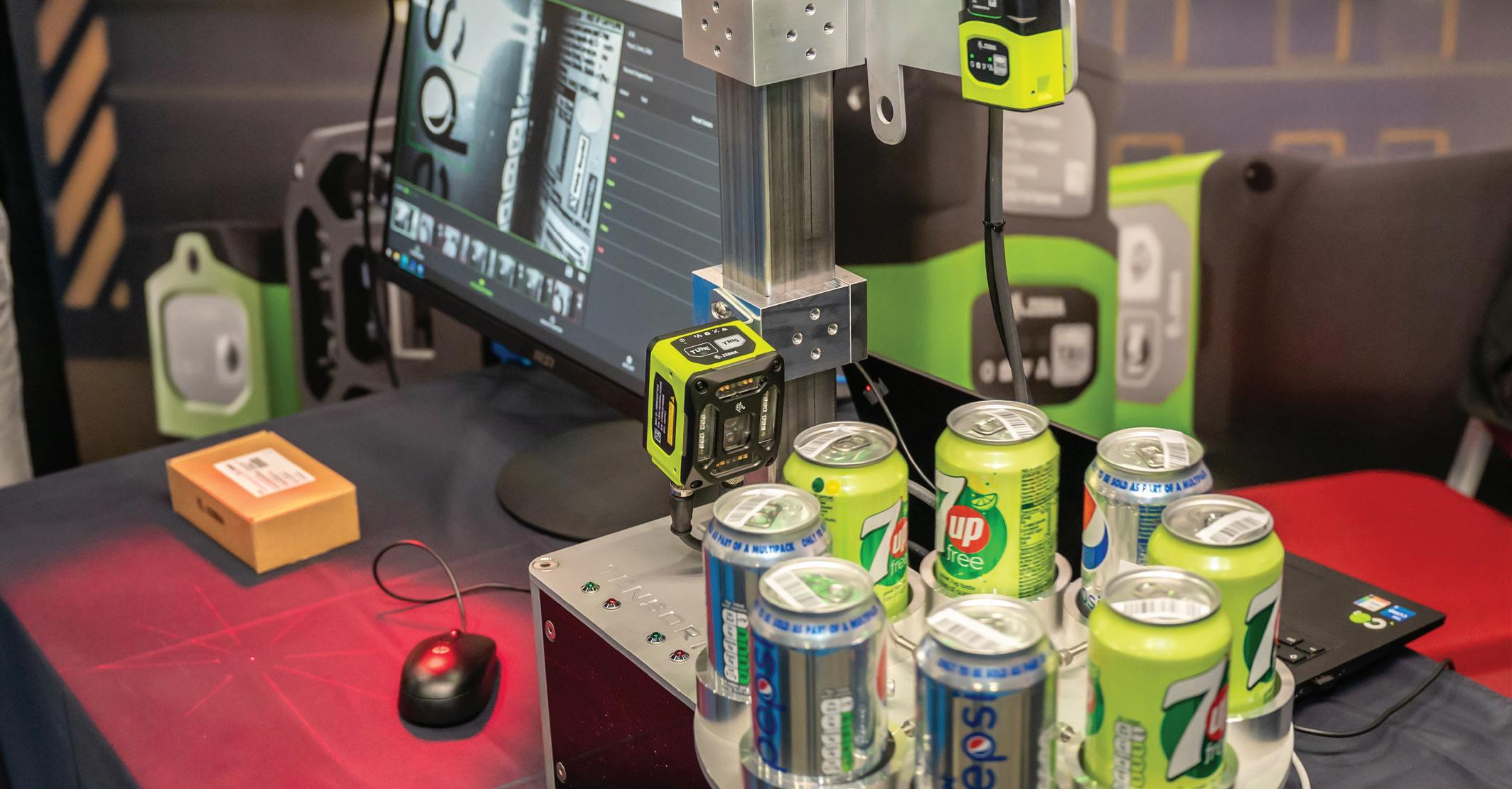
With its wide-ranging conference programme, this live, two-day event will once again act as a focal point for the latest vision trends and technologies and their uses in real-life applications, as well as offering the opportunity to see the latest vision products in action.
Now in its seventh year, the Machine Vision Conference (MVC) has established an impressive reputation for its far-reaching educational and technical conference programme. This year’s seminar programme, delivered by experienced and knowledgeable vision specialists, will focus on eight specific themes: Vision in Robotics; Understanding Vision Technology; Deep Learning & Embedded Vision; 3D Vision; Optics & Illumination; Camera Technology; Systems & Applications; and Vision Innovation.
Content has been designed for a range of skills, from experienced practitioners who are keen to explore the latest developments and innovations to those new to the industry who want to learn more about the fundamentals of vision technology. Visitors can tailor their own programme from the multiple technical seminar theatres that run in parallel throughout the day.
An essential component of MVC 2023 is a focus on new product development and the latest vision technology. New image sensors with exciting new capabilities have been developed, new illumination sources have emerged, AI capabilities have improved, and image processing toolkits have been enhanced.
MVC 2023 will represent an excellent cross-section of the industrial vision industry, with many world-renowned manufacturers, leading vision technology suppliers,
distributors, and vision systems integrators available to demonstrate their products and then discuss how their specialist expertise can help solve vision problems.
The conference theatres are conveniently located around the exhibition space, with plenty of opportunities for visitors to visit all the stands in between seminars.
MVC 2023 is an ideal event for anyone actively involved in the design or implementation of a vision system, or who has a problem that might be solved using industrial vision. With relevance to a host of industries, including food, beverage, pharmaceutical, healthcare, automotive, aerospace, medical devices, packaging, solar energy, electronics, semiconductor, sport, traffic & transport and more, this event is the perfect opportunity to investigate the latest vision technology on offer.
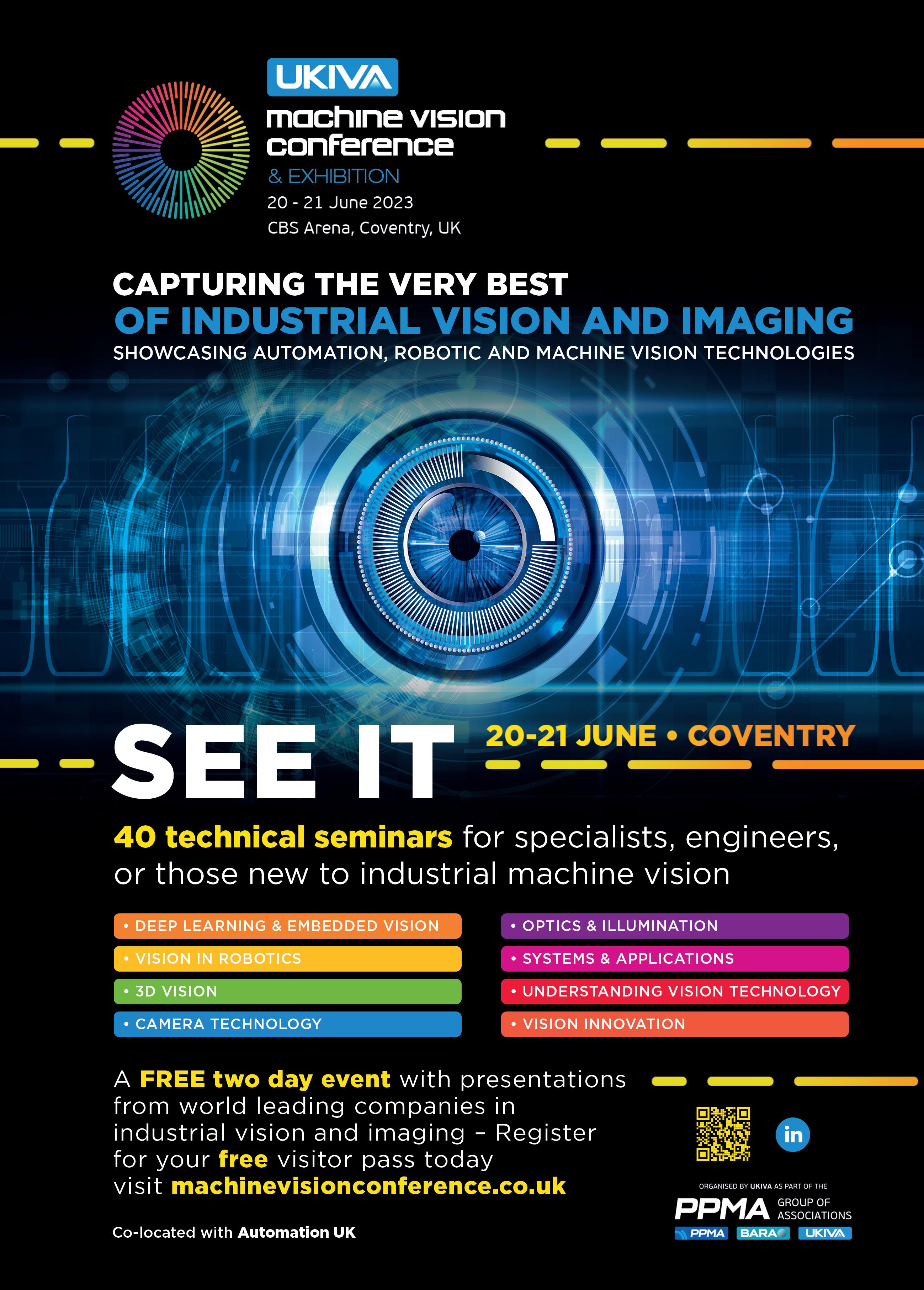
Registration is open for Automation UK
Visitors can now register for the UK’s newest exhibition highlighting the importance of robotics and systems integration to the future growth of the UK economy.
This new event is owned by BARA (British Automation & Robot Association), the respected advocate of the UK robotics and automation industries. BARA promotes the use of and assists in the development of Industrial Robots and Automation in British industry. It provides strong support to assist with the growth of the automation sector in the UK, as well as having a presence overseas.
The event will shine a spotlight on the latest technologies and highlight their true value to the wider economy. Co-located with UKIVA’s (the UK Industrial Vision Association) Machine Vision Conference (MVC), it will be the largest annual gathering of industry experts under one roof in the UK.
The event has been specially designed for businesses operating in the automation and robotics markets. Showcasing live demonstrations of the latest products and services, exhibitors will span a range of sectors, including:
• Robots / Robotic Systems
• Automated Assembly Machines and Systems

• Parts Handling Equipment / Conveyors and Materials
• System Integrators
• Industrial Automation Control
• Manufacturing Sensors and Sensor Integrated Systems
• Automatic Identification and Data Collection (RFID)
• Machine Safety
• Education and Skills
Mark Stepney, Managing Director of Schubert UK, a board member of the PPMA (Processing and Packaging Machinery Association), said: “Automation UK and the co-located Machine Vision Conference will be the largest annual event in the UK to showcase leading robotic and vision suppliers. Its legitimacy is underlined by the backing of two leading industry associations
– BARA and UKIVA – and will be an event
not to be missed. Aside from being able to view live demonstrations of the latest machines, talk to exhibitors face-to-face and gain the latest market intelligence from industry experts, we have a very competitive offer for exhibitors and one we believe they will find very attractive, not least because the show is open to all suppliers and prospective purchasers.”
Both BARA and UKIVA are part of the PPMA Group, a coalition that spans the breadth of the automation and robotics sector. The PPMA itself represents and lobbies on behalf of suppliers of processing and packaging machinery to both the domestic and overseas markets. The PPMA group comprises more than 550 member companies, and its unique structure enables it to be the authoritative voice of the automation and robotics sector, which is why it delivers such a compelling offer to this new event.
www.automation-uk.co.uk
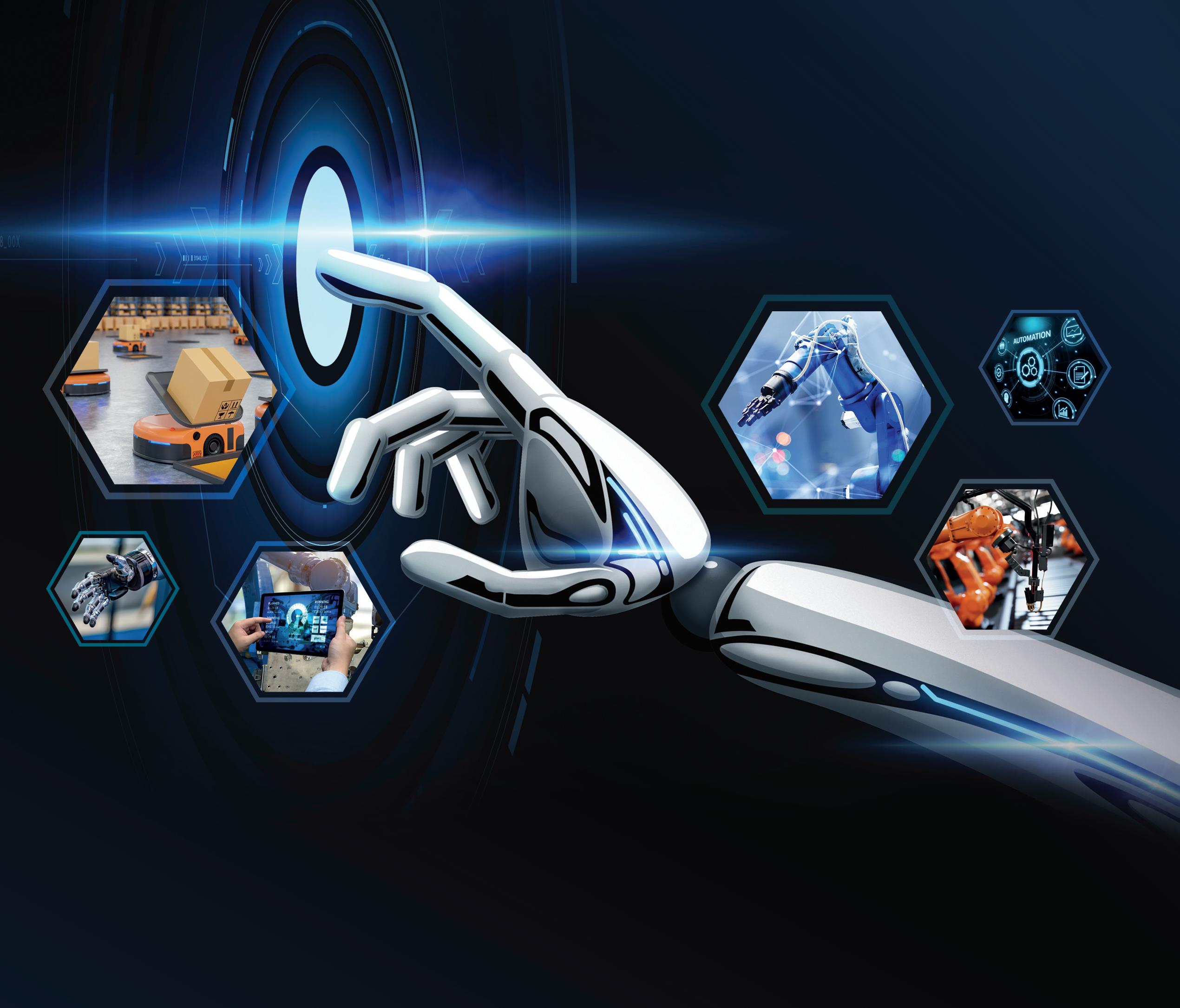
Join the conversation at Subcon 2023
At Subcon 2023, which runs on 7 and 8 June at the Birmingham NEC, the Chatty Hatter Media and Marketing team will actively engage with exhibitors and visitors to capture their insights and opinions for their live podcast series, ‘THAT Engineering Chat’. With so much to see and do, the Chatty Hatter team will act as your friendly guide to help you navigate through the highlights and personalities of this dynamic industry event.
Subcon, in collaboration with Chatty Hatter, launched the live podcasting experience at last year’s 45th-anniversary edition of the show, which saw a variety of attendees take part in the podcast, including Phillip Anthony, sales and marketing director at DP Engineering, who discussed the different industry career routes to introduce young talent and how high tech machinery could challenge the image of engineers’ covered in oil’.
Amongst other guests on last year’s podcast was Subcon regular DVR Ltd. David Hellings, Managing Director, used the platform to praise the exhibition, saying he values the opportunity to connect with colleagues and create new leads and opportunities. Tom Parr, Project Manager at WLR Precision Engineering, echoed this sentiment, stating that while virtual communication has its place, Subcon offers a unique opportunity to connect with key suppliers and customers face-to-face.
During his guest appearance on the podcast last year, Paul Smith, Managing Director of Omnidex, said: “We’ve always found the show to be very useful to connect with existing customers. We have targeted conversations with decision-makers, looking for specific things”. At the same time, he added, the show is an opportunity to encourage new customers to talk to the manufacturing and outsourcing company to enhance their supply chains.

The Subcon team is delighted to facilitate more meaningful conversations by providing this fantastic platform once again. A podcast can showcase a company’s expertise or be a vibrant platform to explore issues. Whether it is discussing AI in automation, how to
manage supply chain issues or nurture engineering talent, they are an effective, informative, relevant and entertaining medium.
The THAT Engineering Chat podcast series host, and owner of Chatty Hatter, Nicole Piesse Turner, has said: “We are excited to be returning to Subcon this year; there is nothing like meeting exhibitors and visitors and sitting down with them to get closer to the personalities and issues in our industry today”.
Nicole and her team will also be conducting real-time interviews on Instagram live that will be posted on LinkedIn, allowing you to stay up to date with all the latest news and highlights from the UK’s largest subcontract manufacturing supply chain show. Additionally, Chatty Hatter is collaborating with other media partners,
exhibitors, and speakers for a Subcon Special pre-show episode airing on YouTube and across all podcast platforms before Subcon in June.
If you are interested in being featured on the podcast as a special guest, Chatty Hatter would be glad to speak with you. You can discuss your company’s news or highlights and share your expertise on current industry topics. All interviews conducted at the show will be streamed and made available to the Subcon database after the event. To learn more about this opportunity, please contact the Subcon team directly.
In the meantime, register your place for the 2023 Subcon show and discover the complete manufacturing ecosystem.
bit.ly/Subcon23
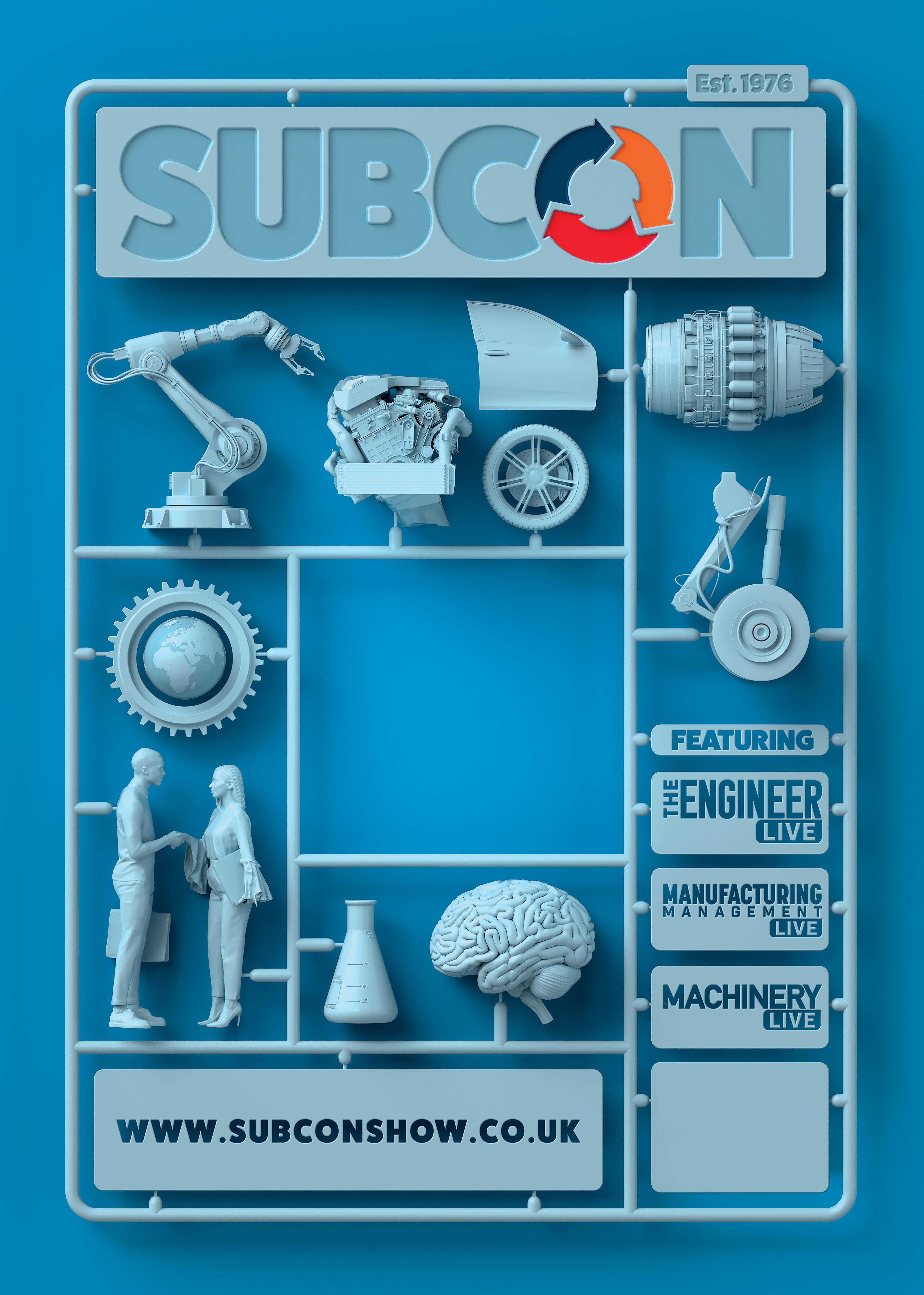
A festival of innovation
Manufacturing and Engineering Week 2023 continues to live up to its promise of becoming ‘the festival of industrial innovation’ with a number of new events added for 2023, including Smart Factory Expo and the Drives & Controls zone.
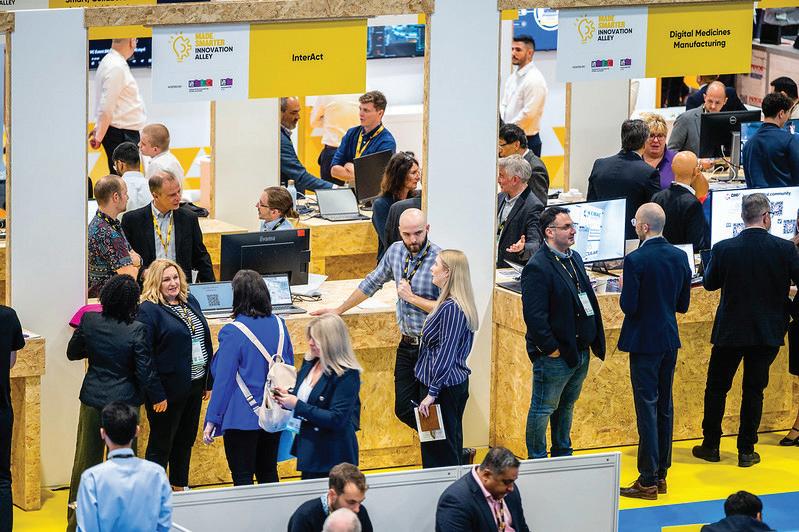
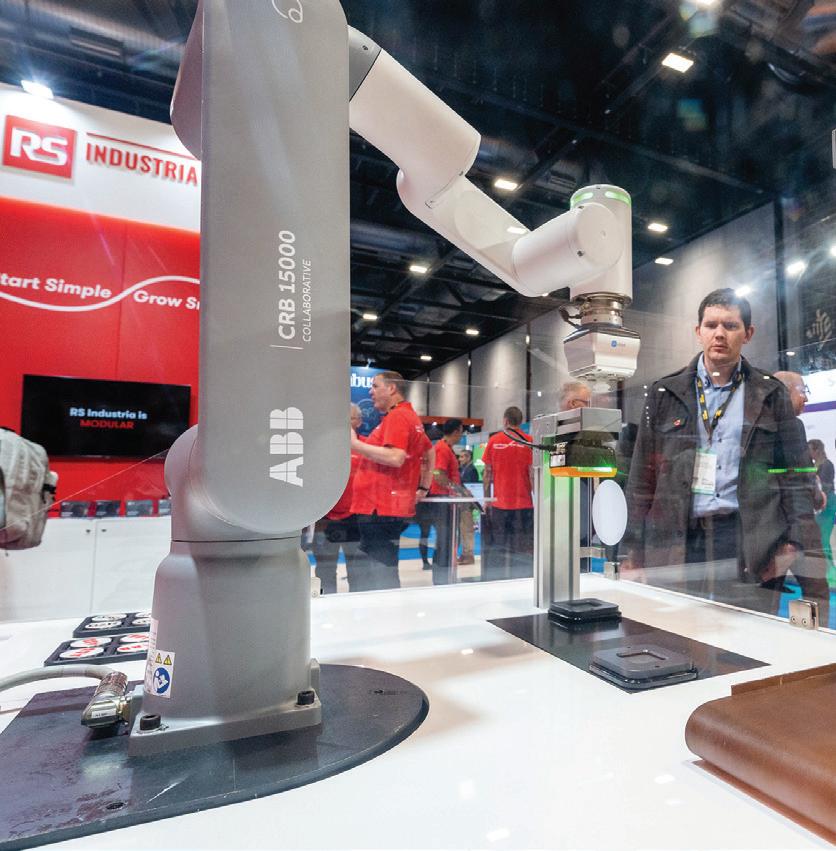
The week beginning 5 June 2023 is Manufacturing & Engineering Week, with the centrepiece exhibitions Design & Engineering Expo, Smart Factory Expo, Maintec and the Drives & Controls zone taking place at Birmingham’s NEC on 7 and 8 June. Other exhibitions are also taking place at the NEC during the week, and these include Automechanika, run by Messe Frankfurt; Med-Tech Innovation Expo and TCT 3Sixty from Rapid News Group and Subcon from the Mark Allen Group.
A major part of Manufacturing & Engineering Week 2023 is the free conference programme that will take place across two keynote conferences and six solutions theatres. Emphasising the importance of M&E Week is the fact that on day one, the keynote address in the main theatre will come from the Government on the topic of their plans for supporting UK manufacturing, while on day two, the shadow government will talk on the same subject. The conference agendas include topics including What next for UK manufacturing? Led by former Siemens UK CEO Juergen Maier and The Story of a British Engineering Icon that looks at the history of Triumph Motorcycles.
Highlighting innovation is at the forefront
of M&E Week. Made Smarter’s Innovation Alley, for example, will showcase all the new and developing technologies that will change the landscape of manufacturing over the next five to ten years. Similarly, the Innovation Village, run by the seven High Value Manufacturing Catapult research and technology centres, will be an immersive and interactive demonstration area that will take visitors on a journey from fossil fuels to renewables, demonstrating the technological advances that will transform industry for a sustainable world.
As well as looking to manufacturing’s future, M&E Week will also celebrate its current leaders be they businesses, individuals or products. A Best of British showcase will celebrate domestic manufacturing, featuring world-beating new designs, innovative modes of manufacture, products that redefine categories and export successes that plant the flag in overseas markets. Continuing the theme of best in class, each year, The Manufacturer magazine celebrates the achievements of 100 inspiring individuals from the UK’s manufacturing sector at its Top 100 awards ceremony. The winners will be announced at a ceremony on the evening of 7 June.
Manufacturing and Engineering Week strives to offer something different. An
example of this is a focus on engineering and music with a number of activities for the music fans in attendance. Visitors will get the chance to win a 3D-printed guitar from sponsors Nexa3D as part of the Guitar Legends competition. Entrants will put their names forward in advance (via an online entry form) to be in for a chance to enter the M&E Week soundproof booth and record a classic song intro and a solo in a musical genre of their choice. Not only will the winner receive a brand-new 3D printed guitar, but the winner on day 1 (7 June) will also have the chance to join the band entertaining both visitors and exhibitors alike at the after-party.
The major differentiator of M&E Week 2023 is that it brings together all aspects of manufacturing and engineering. Due to this wide focus, it’s suitable for a business to bring their whole team from operations, safety and maintenance to design and more. This connectivity encourages cross-functional teams to attend together, despite the fact that they are responsible for different parts of the projects they work on. Multiple divisions, be that from a small or large business, can get value from attending because there are elements that are specifically created for them.
www.mandeweek.co.uk
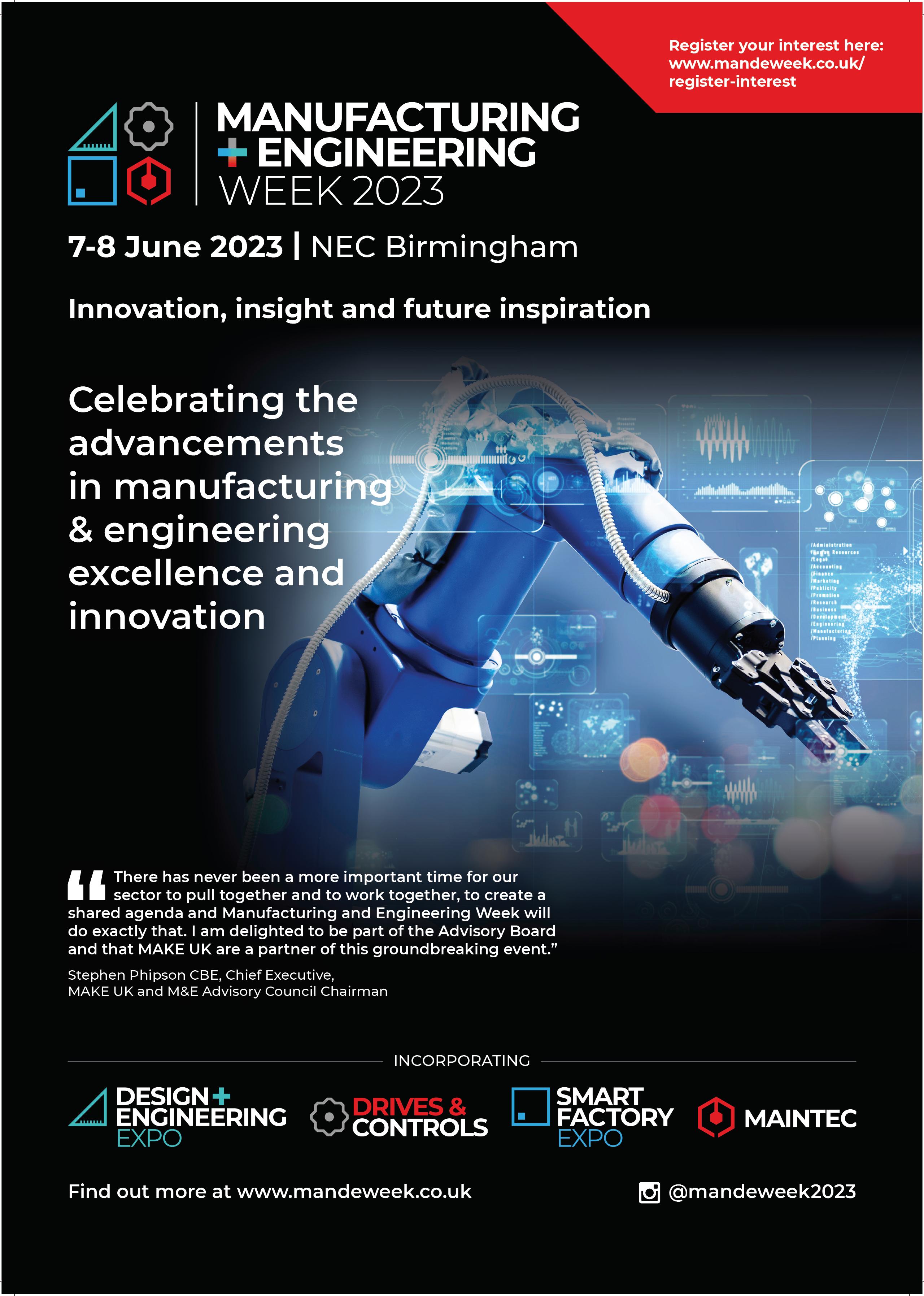
CKI adds Clipacore to its product portfolio
Carl Kammerling International (CKI) has purchased the Clipacore brand, a revolutionary tool system designed to eradicate a common and dangerous problem for users of core drills. Its purchase by CKI means that Clipacore will quickly become widely available to tradespeople across the UK.
Clipacore is a clip release system which allows users to change and remove core bits from drills quickly and effortlessly. Dismantling a core drill after use often requires physical strength and brute force, as torque tension locks components together. Clipacore was conceived by a heating engineer who broke his hand hammering a wrench to change a bit. Another problem which has been solved with the Clipacore system is waste concrete becoming wedged in the tool.
The Clipacore system is now distributed into the plumbing and heating sector through CKI subsidiary Nerrad Tools, available for purchase in-store this Spring. It will also soon be available as part of the CKI portfolio of brands alongside C.K Tools, C.K Magma, avit and Kasp Security, with wider distribution anticipated later in the year.
Protecting tools from damage and tradespeople from injury, the Clipacore system has been rigorously tested, is produced with high-quality materials, and holds its own against CKI’s impressive range of quality tools.

www.carlkammerling.com
Performance-driven manufacturing execution system

International supply chain solutions provider
TouchPath is launching ‘TouchMES’, a performance-driven manufacturing execution system that records and displays machine control and other shop floor data in real time. TouchMES continuously monitors the status of all production processes, including downtime, to enable leaner manufacturing at lower cost and with less waste. It can also be integrated with any ERP or related system, for example, Quality Control.
TouchMES gives production staff and managers instant access to key performance indicators (KPIs) for efficiency and productivity, as well as work centre schedules, inventory location and availability, downtime, waste and other metrics.
www.touchpath.com
120dB of sound power with the SE120 alarm sounder
Distributed by Switchtec, Sirena’s SE120 new alarm sounder offers one of the highest levels of sound propagation available on the market, allowing the installation of fewer units to cover a larger area. It is also available in different voltages, functionality, and colour versions.
The SE120 features 64 pre-configured sounds, each with eight volume levels and a power range of up to 120dB. Thanks to internal memory integrated into the PRO version, it is also possible to use customised messages on the four available channels, allowing the sounder to be fully configured to individual needs.
With a protection rating of IP66 / IP69K and an impact resistance rating of IK08, the SE120 is ideally suited to factory and industrial settings.
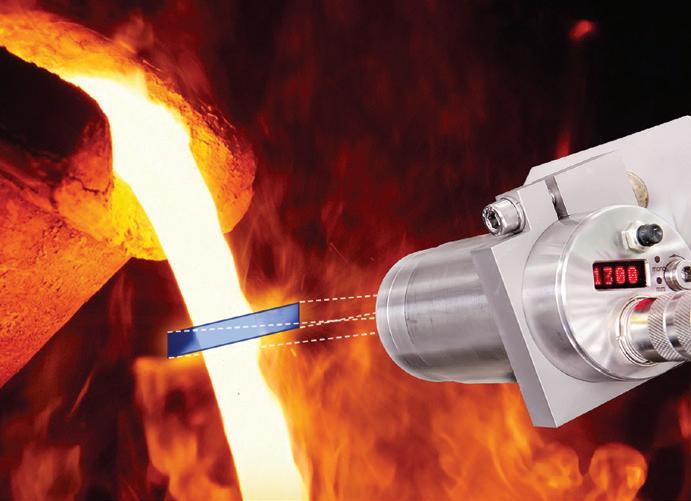

www.switchtec.com
Line optics for infrared temperature measurements
The Impac ISR 6 and IGAR 6 pyrometers from Advanced Energy are available with integrated line optics as an option, which offer significantly wider measurement spots in the shape of a line. This enlarged measurement field provides advantages for steel applications, especially for wire production or pouring stream measurements.
The line-shaped spot guarantees that a pouring stream does not move out of the pyrometer’s target spot. The pouring stream needs to be aligned diagonally to the line-shaped spot allowing a wider field for accurate infrared temperature measurements.
bit.ly/AEThermal
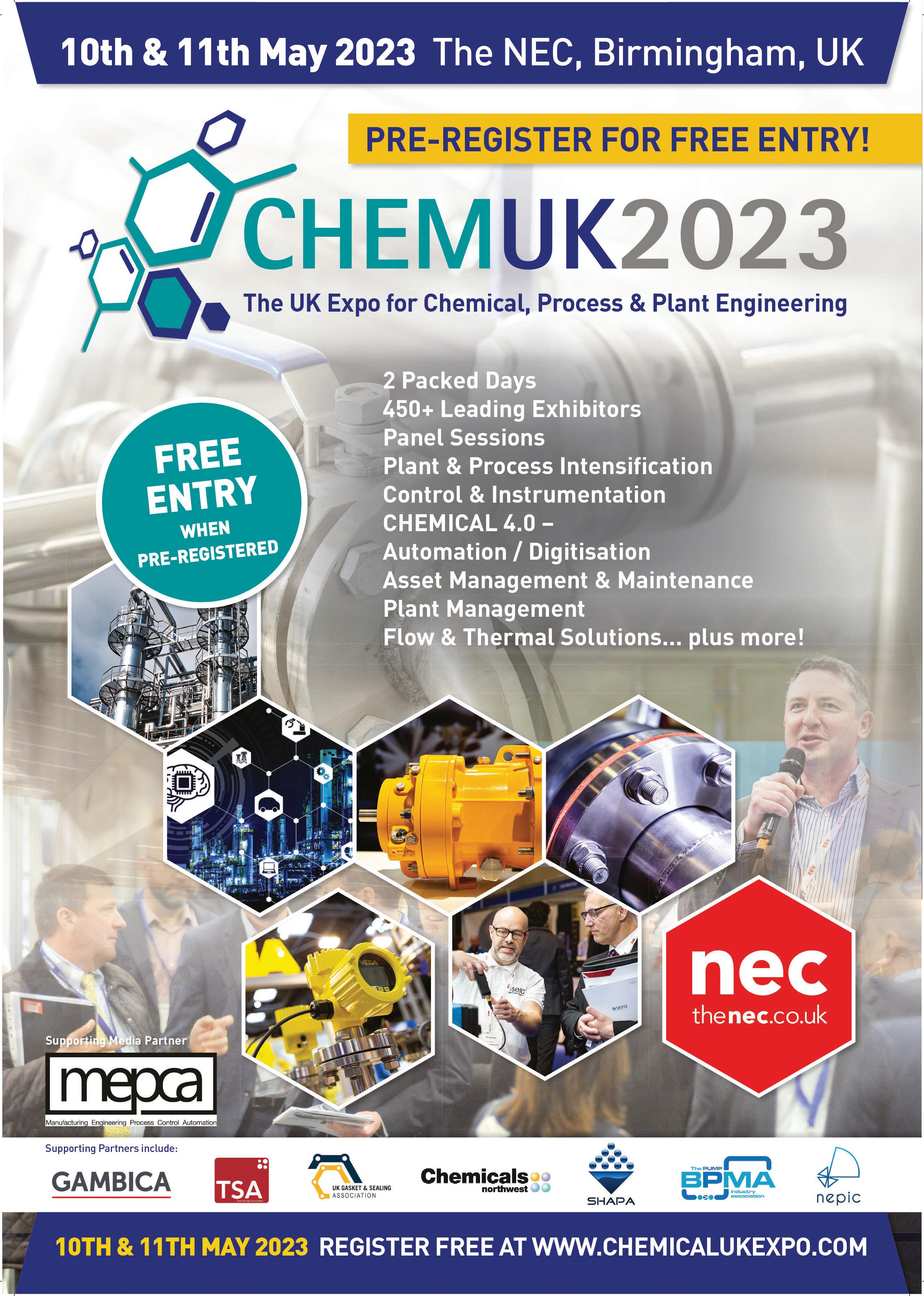
CONNECTIONS
3D Print Manufacturing
Midlands 3D Printing
Units 6-7 Emerald Way, Stone Business Park, Stone, Staffordshire, ST15 0SR
T: 01785 594389
E: sales@midlands3d.com
W: www.midlands3d.com

Anti Vibration Products, Mounts & Bushes
Fibet Rubber Bonding (UK) Ltd
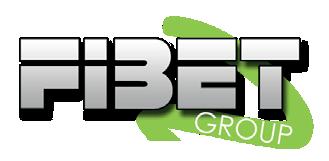
Unit 9 Dale Mill, Hallam Road, Nelson, Lancashire, BB9 8AN
T: 01282 878200
E: sales@fibet.co.uk
W: www.fibet.co.uk
Control Systems
Beckhoff Automation Ltd
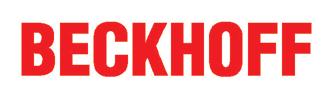
The Boathouse, Station Road
Henley-on-Thames, Oxon RG9 1AZ
T:+ 44 (0)1491 410539
E: info@beckhoff.co.uk
W: www.beckhoff.co.uk
Dust & Fume Solutions
Impact Technical Services
3 Kingsley Street, Leicester, LE2 6DY
T: 0116 244 8855
E: enquiries@impactts.co.uk
W: www.impacttechnicalservices.co.uk
Flow Meters
Titan Enterprises Ltd Unit 2, 5A Cold Harbour Business Park, Sherborne, Dorset, DT9 4JW
T: +44 (0)1935 812790
E: sales@flowmeters.co.uk
W: www.flowmeters.co.uk
High Shear Mixing Equipment
Silverson Machines Ltd
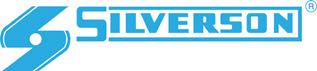
Waterside, Chesham, Buckinghamshire, HP5 1PQ
T: +44 (0)1494 786331
E: sales@silverson.co.uk
W: www.silverson.co.uk
Industrial Communications
Brainboxes
T: + 44 (0) 151 220 2500
E: sales@brainboxes.com

W: www.brainboxes.com
Industrial Fans
Axair Fans UK Limited Lowfield Drive, Wolstanton, Newcastle-under-Lyme, ST5 0UU
T: 01782 349 430
E: aj@axair-fans.co.uk
W: www.axair-fans.co.uk
Machine Safety
Schmersal UK Ltd
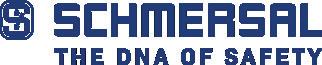
Sparrowhawk Close, Malvern, Worcestershire, WR14 1GL
T: 01684 571980
E: uksupport@schmersal.com
W: www.schmersal.co.uk
Pipework Systems
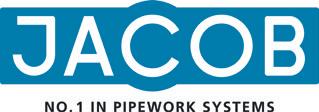
Jacob UK Ltd
Laundry Bank, Church Stretton, SY6 6PH
T: 01694 722841
E: sales@jacob-uk.com
W: www.jacob-group.com/uk
Robotics & Automation
KUKA Robotics UK Ltd

Great Western Street, Wednesbury, West Midlands, WS10 7LL
T: 0121 505 9970
E: sales.uk@kuka.com
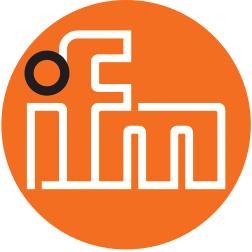

W: www.kuka.com
Rotation Monitoring Equipment
Rotech Systems

Unit 57, Canal Bridge Centre, Ellesmere Port, Cheshire, England, CH65 4EH
T: +44 (0)151 356 2322
E: sales@rotechsystems.co.uk
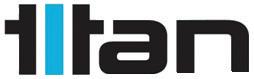
W: www.rotechsystems.co.uk
Sensors
Carlo Gavazzi UK Ltd

4.4 Frimley Business Park, Frimley, GU16 7SG
T: 01276 854110
W: www.carlogavazzi.co.uk
IFM Electronic
Efector House, Kingsway Business Park, Oldfield Road, Hampton, Middlesex, TW12 2HD
T: 020 8213-0000
E: enquiry.gb@ifm.com
W: www.ifm.com
Test & Inspection
Cupio Services Ltd
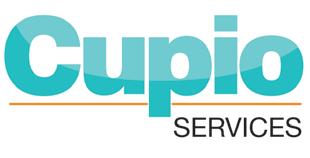
T: 01256 262800
E: info@cupioservices.co.uk
W: www.cupioservices.co.uk
Interested in advertising within future issues of MEPCA?
Please call 01795 509105 or email hannah@cimltd.co.uk for more details.
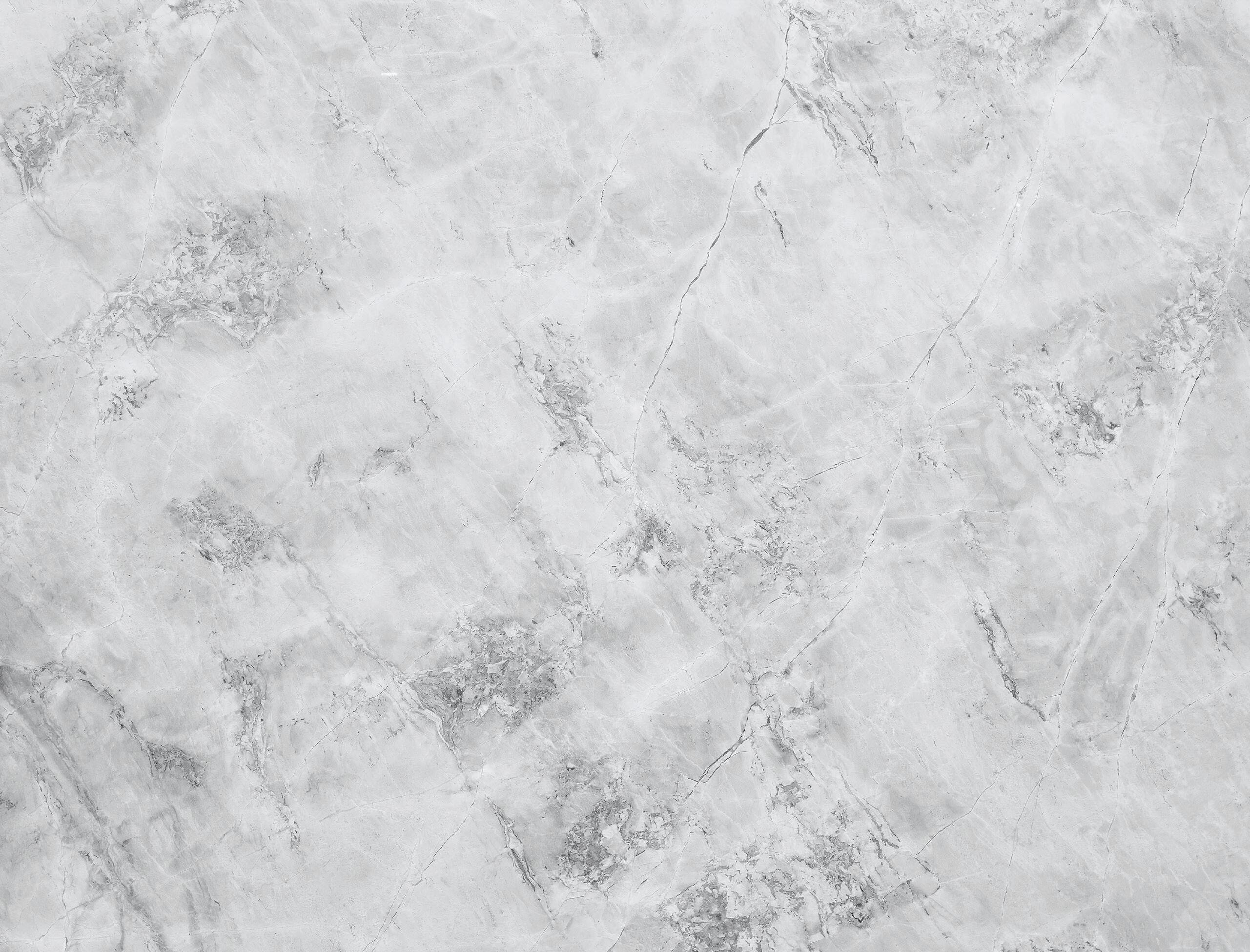
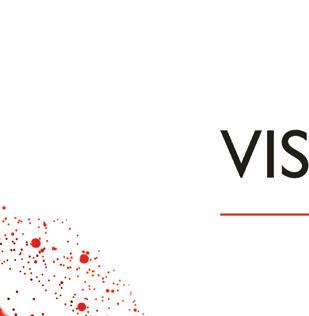
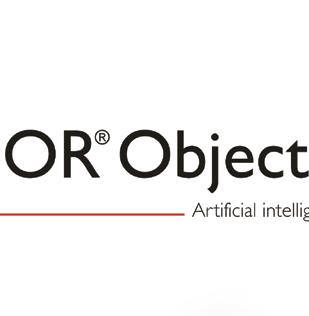
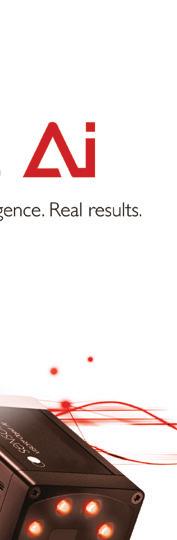
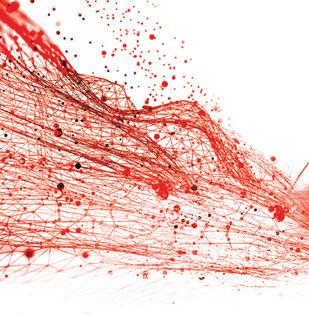
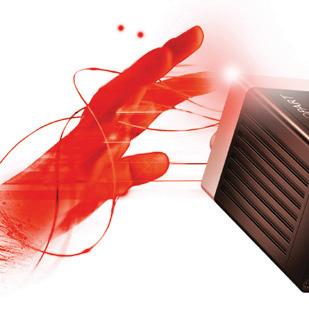

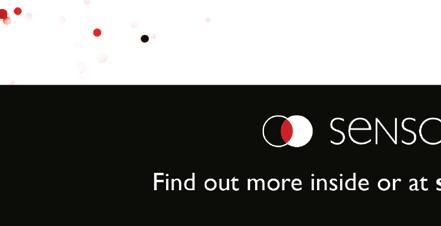
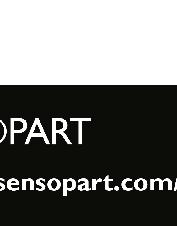
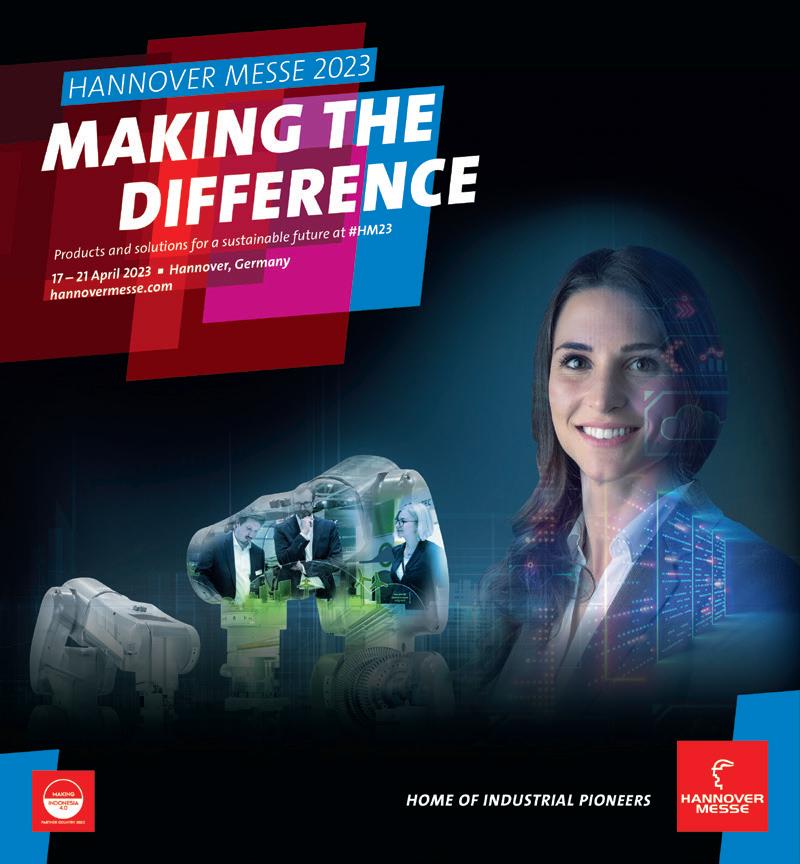
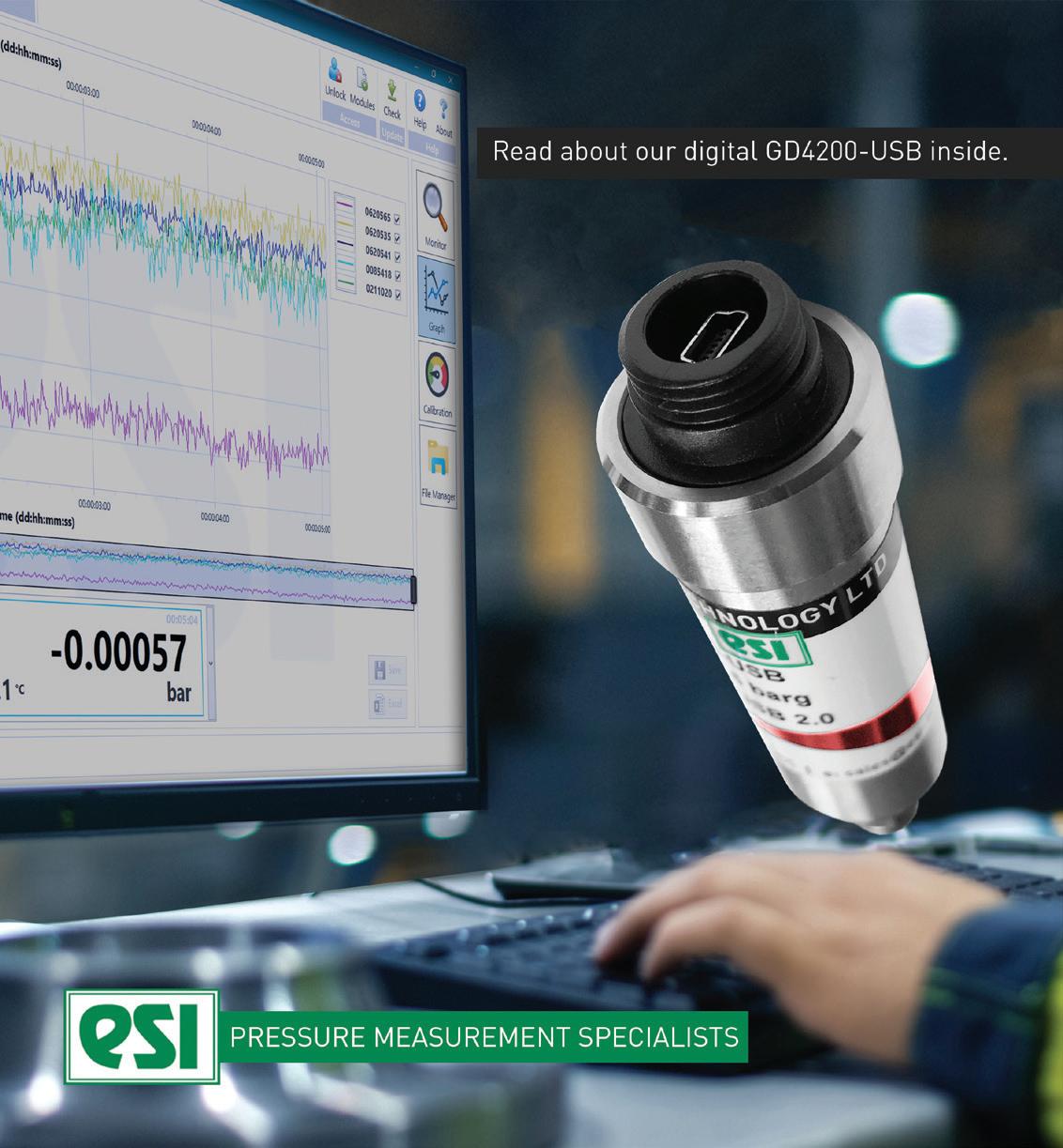
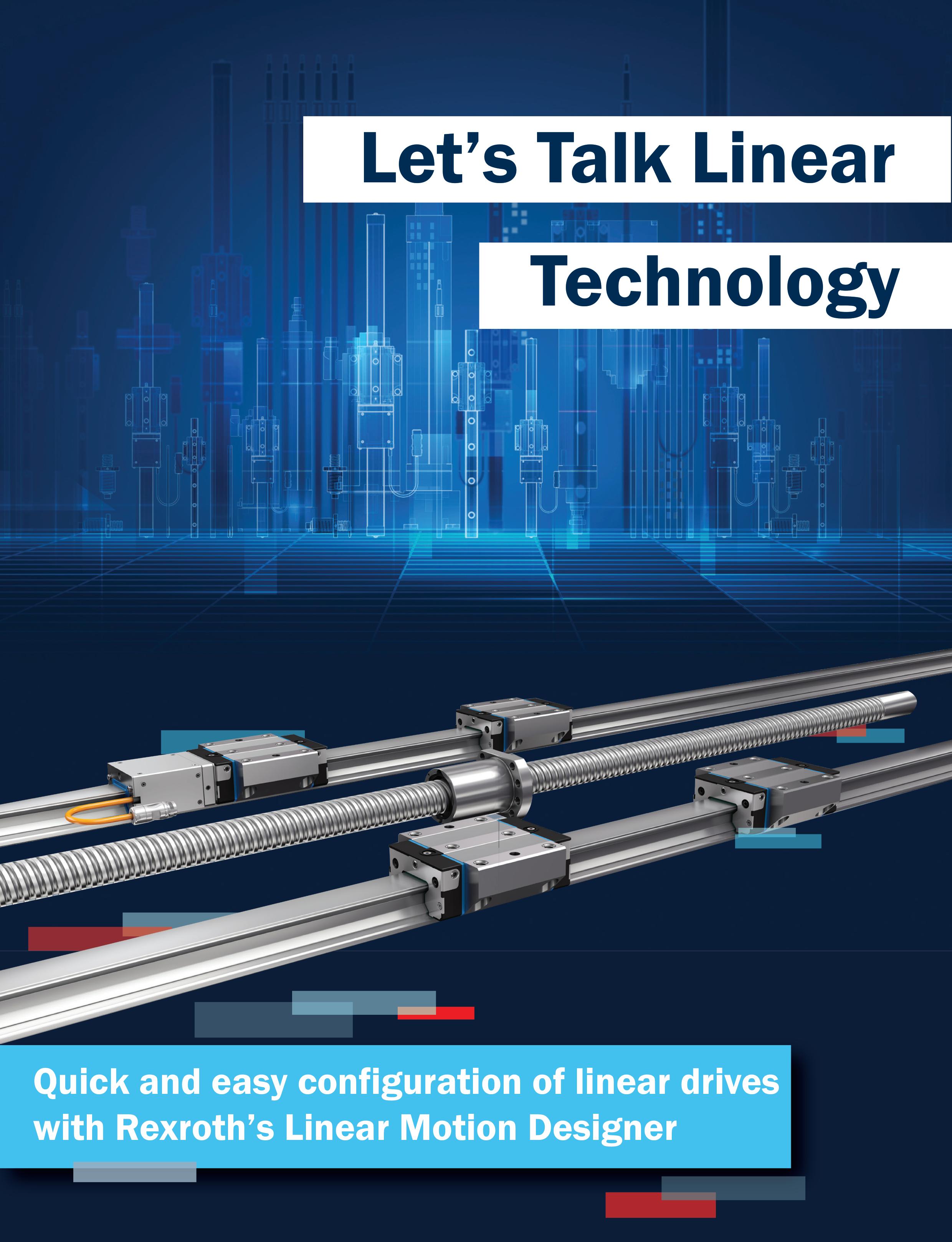
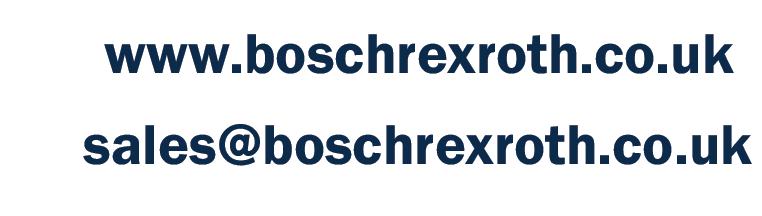
