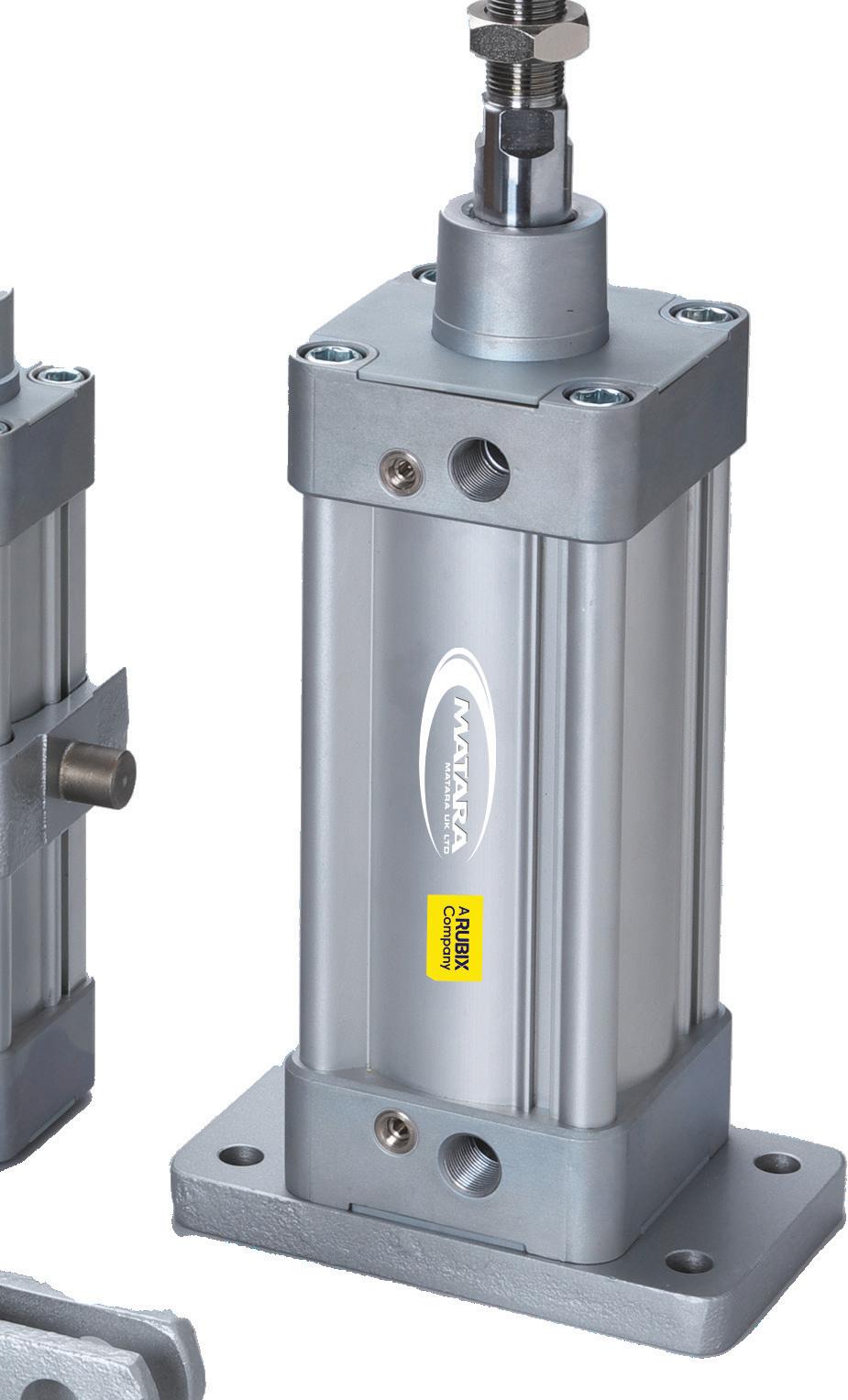
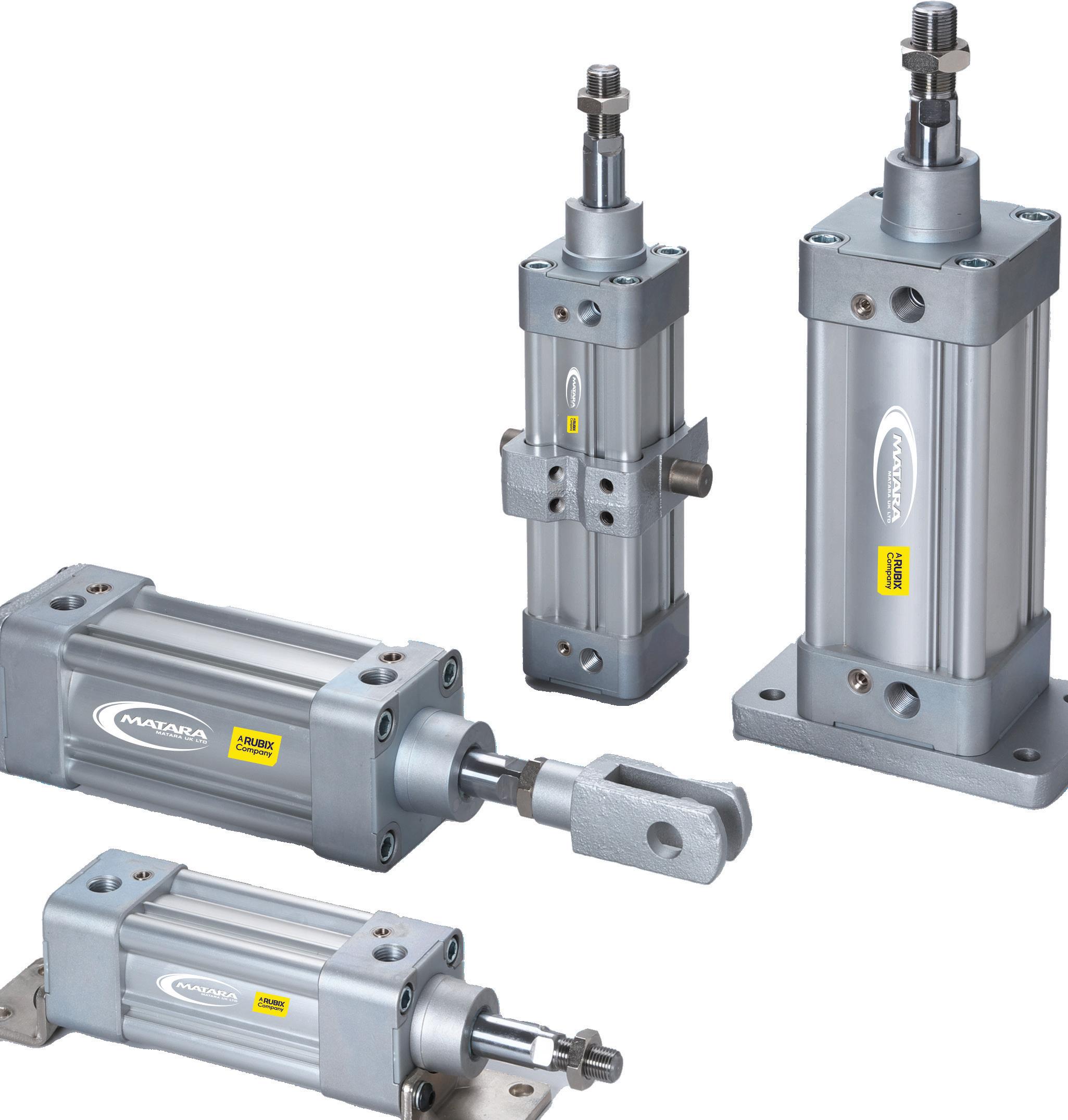
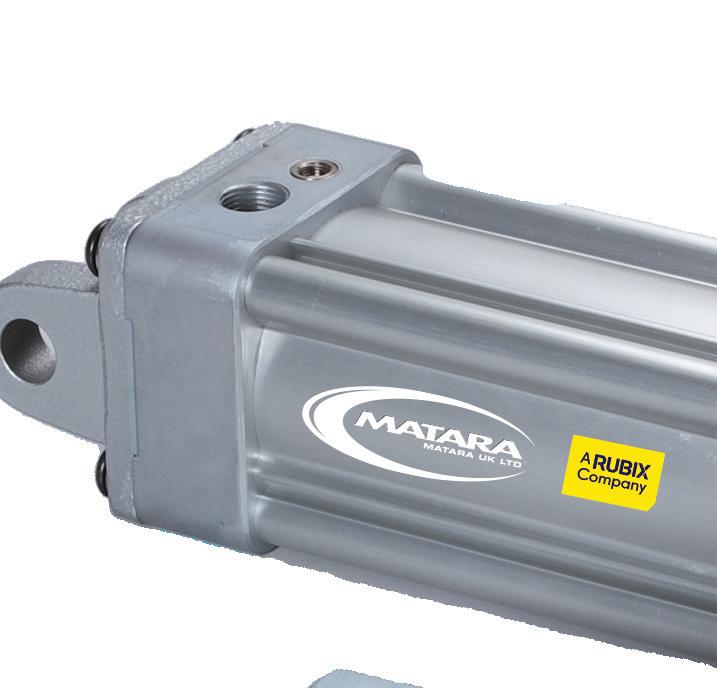
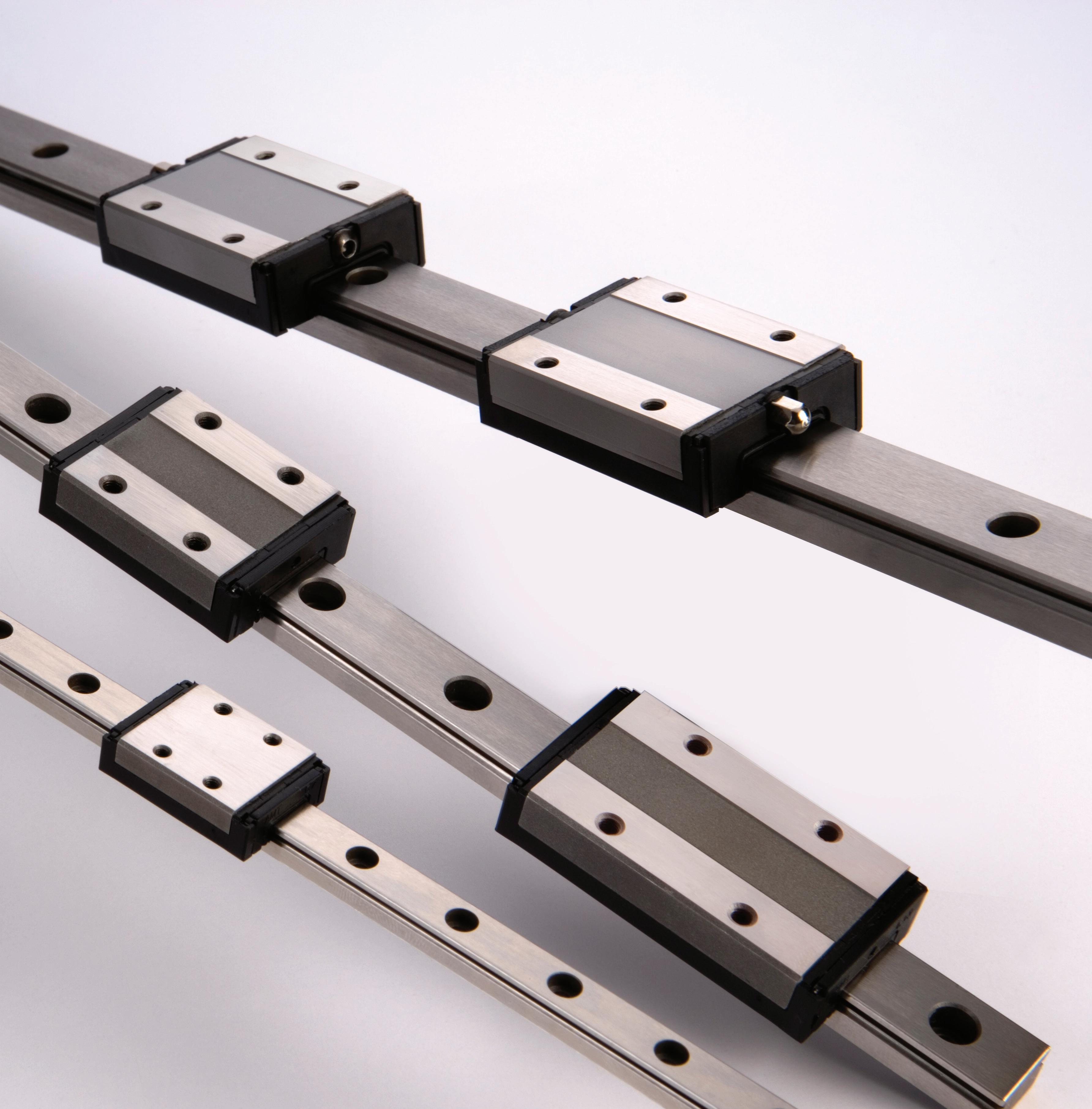















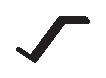

With 50 years of innovation in sensing solutions, ifm has the experience and the team that you need.
ifm operates in more than 85 countries, selling directly, one or a million products to over 165,000 customers, generating €1 billion turnover. We have 10 manufacturing and development facilities worldwide producing over 22 million products annually.
We have specialist support teams and highly trained application engineers on the ground, covering the entirety of the UK.
All of this, plus we offer a 5 year warranty on all ifm products.
Editor
Oliver Batt oliver@cimltd.co.uk
Publication Manager
James Burke jb@cimltd.co.uk 01795 509105
Account Managers
James Davies jamesd@cimltd.co.uk 01795 509105
Jim Bearden jim@cimltd.co.uk 01795 509105
Design & Production
Grant Waters grant@cimltd.co.uk
James Taylor james@cimltd.co.uk
Administration Manager
Natalie Murray admin@cimltd.co.uk 01795 509103
Credit Facilities Manager
Gwen Lee creditcontrol@cimltd.co.uk 01795 509103
Marketing Manager
Lucas Payne lucas@cimltd.co.uk
Sales Director
Tom Woollin tom@cimltd.co.uk
Chief Executive
John Denning
© 2024 TGM Publishing Limited,1st Floor, Saphir House, 5 Jubilee Way, Faversham, Kent, ME13 8GD. No part of this magazine may be reproduced or stored in a retrieval system or transmitted in any form – electronic, mechanical or physical – without express prior permission and written consent of the publisher. Contributions are invited and when not accepted will be returned only if accompanied by a fully stamped and addressed envelope. Manuscripts should be typewritten. No responsibility can be taken for drawings, photographs or literary contributions during transmission or in the editor’s hands. In the absence of an agreement the copyright of all contributions, literary, photographic or artistic, belongs to TGM Publishing Limited. The publisher accepts no responsibility in respect of advertisements appearing in the magazine and the opinions expressed do not necessarily represent the views of the publisher. The publisher cannot accept liability for any loss arising from the late appearance or non-publication of any advertisement.
elcome to our November issue. In this bumper issue of MEPCA, we delve into one of the most exciting and fast developing fields of technology: robotics.
We begin our robotics focus with a forward look at 2025 in five predictions, before taking an in-depth look at the common myths and misconceptions surrounding robotics. This would not have been possible without the support of our robotics experts, who highlighted just how crucial robotic automation will be for the future of UK manufacturing.
While it is all too easy to focus on the marvel of new technological solutions, to forget about the human element of manufacturing and engineering would be a gross oversight. In this this issues’ Editor’s Choice, we highlight the important role apprenticeship schemes play in combating the growing skills shortage.
In this month’s Cover Story, Matara addresses the meaning of quality when it comes to pneumatic cylinders. Also in this issue, we announce our Manufacturing Champion of the Month, chosen from amongst the heavyweights of the automotive industry.
While putting this issue together, I took a trip to Birmingham to attend this year’s excellent PPMA Show at the NEC, where I had the pleasure of meeting our readers and contributors. For our full account of the event, read our PPMA Show Review.
We hope you enjoy this issue.
@Mepca-magazine
To subscribe to MEPCA visit our website www.mepca-engineering.com or scan the QR code.
As part of a nationwide campaign to find the next-generation of automotive engineers, YASA has partnered with Formula Student 2025.
YASA, the wholly-owned subsidiary of Mercedes-Benz, is partnering with Formula Student 2025 as part of its ambition to inspire the next generation of automotive engineers.
Launched in 1998, Formula Student is Europe’s most established educational engineering competition, having inspired thousands of students to take up a career in engineering. With more than 100 university teams taking part every year, the Formula Student competition provides real-world experience combining practical engineering skills with broader business competencies, such as logistical planning, budgeting and project management.
Simon Odling, YASA’s Chief of New Technology, said, “Formula Student holds a special place in my heart – it’s a competition that has shaped the careers of so many engineers, myself included, in the automotive and motorsport industries. At YASA, we’re thrilled to be involved with next year’s event, and we can’t wait to meet the talented young engineers who could be the future of YASA, joining our exceptional engineering placement programmes in 2025.”
In celebration of this new partnership, YASA has launched its latest campaign to recruit students to take part in its highly sought after engineering placement programmes at its sites in Yarnton near Oxford and Bicester.
Founded in 2009, YASA is redefining the future of electric vehicle performance. It designs and manufactures high performance electric motors and power electronics for the premium automotive sector, with current high profile customers including Ferrari and McLaren. YASA’s revolutionary axial-flux electric powertrain technology brings the highest power and torque densities in its class for the smallest size and weight dimensions.
The world-leading axial flux electric motor innovator is looking for up to 10 university students who have a clear passion for engineering and innovative technology to take part in its placement programmes. Starting in July 2025, the three- and 12-month placements offer students real-world, hands-on experience within YASA’s fast-paced and high-tech design, development and manufacturing environment.
The placements are available across the company’s engineering functions including development, design, testing, manufacturing, and innovation. Students will be given the opportunity to work on current and future electric motor and e-propulsion projects as well as work on current tech and engineering challenges.
Chris Jeffcock, Recruitment Manager, said, “Being a University of Oxford start-up success story, we have tried to consistently
support many placement students across our engineering functions, and several of them have subsequently returned to work for us as graduates.
“As a lean, agile company, we can offer students an unrivalled level of hands-on experience working on some of the most innovative projects in today’s automotive industry.”
Danae Topi, former Industrial Placement Student at YASA, commented, “With the support of my manager, I had the opportunity to collaborate with the Innovation Team on a year-long project involving electromagnetic design, simulations, and motor control software development. Throughout my placement, I have developed my practical engineering skills through component testing alongside learning more about materials, manufacturing, failure analysis, and microscopy.” yasa.com/careers
Frankfurt am Main, October 16, 2024 — Takayuki Ito has been elected as the new President of the International Federation of Robotics. Mr Ito will represent the IFR alongside his newly elected Vice President, Jane Heffner.
Takayuki Ito of Fanuc Corporation, who previously held the position of Vice President, succeeds Marina Bill of ABB who has served the rotating post since 2022. “I am proud to continue the work of my predecessor, Marina Bill, who has been a great ambassador for the world of robotics. We are witnessing rapid change in the automation of industrial and service sectors around the world. Together with Jane Heffner of Mobile Industrial Robots as the new Vice President of the IFR, I look forward to our mission,” said Takayuki Ito.
More than 40 years of experience in robotics
Takayuki Ito has a track record of more than 40 years in the robotics industry. He currently holds the position of Chief Technical Advisor at the Japanese robot manufacturer Fanuc Corporation based in Oshino, Japan. Since 1981, Takayuki Ito has worked at the Japanese robot manufacturer in various positions: In 1997, he became Executive Vice President for Fanuc Robotics in North America. He returned to the Fanuc headquarters in Japan in 2002, taking on the role of General Manager for the Robot Technology Center.
New Vice President Jane Heffner
The IFR’s new Vice President, Jane Heffner, has more than 20 years of experience in technology-driven industries, including automation, robotics, automotive, and aerospace. She currently serves as Vice President Global Sales at Mobile Industrial Robots (MiR), a leading manufacturer of autonomous mobile robots. In this role,
based in Detroit, Heffner oversees the company’s global sales strategy and execution. Before joining MiR, Heffner held leadership roles at ABB Robotics and other major industrial companies. ifr.org/
Ateam representing the UK’s finest young robotics talent, and supported by factory automation specialist FANUC UK, has been honoured at WorldSkills Lyon 2024, known as the ‘skills Olympics’.
Jason Scott and Charlie Carson, both from Northern Ireland, were awarded the Medallion for Excellence in the category of Robot Systems Integration, in which they competed against teams from 18 different countries. The duo attended Northern Regional College and Jason now works at AES Global while Charlie attends the University of Ulster. They began their WorldSkills journey back in 2022, competing against teams from across the UK in a series of robot challenges set by FANUC and
ably supported by representatives from the automation company. After being selected by WorldSkills to represent the UK in the international finals in Lyon, the pair were delighted to be recognised by the judging panel for their hard work and talent, with teams from China and Korea jointly named as the overall winners.
Over 1,500 young people from 69
countries competed over four days of tough competition in 62 different skills at WorldSkills Lyon, which was watched by over 250,000 spectators.
FANUC UK is now turning its attention to supporting the next crop of young robotics enthusiasts. The final of the 2024 WorldSkills UK Robot Systems Integration competition will take place at the FANUC UK Open House event in Coventry on 12-14 November 2024, where the country’s most talented teams will battle it out in a series of automation challenges set by FANUC’s in-house robotics experts. Winners will have the chance to represent Team UK at the next WorldSkills competition, which takes place in 2026 in Shanghai, China.
www2.fanuc.eu/uk/en
This month, we celebrate Andreas Lehe, Member of the Board for Manufacturing at Bentley Motors, as our Manufacturing Champion.
Andreas joined Bentley Motors in September 2023 and has since been instrumental in Bentley’s transformation plans; particularly the development of the new, sustainable manufacturing facilities at the company’s zero-carbon headquarters in Crewe. Prior to his role at Bentley, Andreas served as Head of Strategic Planning at Audi AG, where he furthered the company’s production, digitisation and logistic strategies.
In the following Q&A, Andreas provides MEPCA magazine with an insight into his work at Bentley, helping the company to achieve a more sustainable future for automotive manufacturing.
Since joining Bentley, you have played a pivotal role in the company’s ambitious Beyond100 strategy. What key challenges must the industry address to achieve its sustainability and carbon neutral goals?
I believe that Bentley, and the entire industry, is at a point of fundamental transition. The future of mobility is open to innovation –even redefinition – and Bentley is perfectly positioned to grasp this opportunity and lead the way in shaping the future of sustainable luxury mobility. We are committed to real change across our value chain and although the scale of the opportunity is significant, we have clear plans to make this a reality. The biggest challenge is delivering a true circular economy approach to future battery electric vehicles, from green steel and aluminium, the circular approach to minerals and other materials, to environmental paint methods and even customer touchpoints. It’s not straightforward and certainly won’t be linear,
but the speed of change is lightning, and we are confident Bentley will be a much-evolved company in the years that follow.
The new Paint Shop at Crewe is shaping up to be a truly ground-breaking facility. What features of the site are you most proud of and why?
We are in the middle of a site transformation that is evolving an 85-year-old factory into a new age of electrification, while at the same time confirming our commitment to the UK. The new facility supports our aim for a benchmark position in new innovative technologies, skills and facilities to enable a truly digital, highly-flexible benchmark for
luxury car manufacturing. I think what I am most proud of, and continues to make Bentley unique, is the sheer scale of optionality that we can deliver. Every customer has nearly 100 different paint colours to choose from as our ‘standard’ palette, and that is before we consider Mulliner personalisation. That is extraordinary capability, in our facilities, and from our valued colleagues.
How has your career to date, which has included working in Europe and South America, prepared you for your role in the development of Bentley’s Dream Factory?
I feel very privileged that I have had the opportunity to lead a number of very complex factories around the world in some of the most successful automotive companies, including Volkswagen and Audi. My previous roles align well with the upcoming opportunities for expansion at Bentley, not least where I was responsible as Head of Strategic Planning to evolve the production strategies for every Audi factory around the world, and advancing the digitisation across the global network. Before this, I was Executive President of Audi’s newest global plant, Audi Mexico, which offered the latest advances in manufacturing processes and was firmly committed to ecological, social and economic stability, a shared belief with Bentley. Having also delivered one of the most successful modern paint shops across the Volkswagen Group, the production, sustainability and commercial insights gained, and working closely with our fantastic team, will help deliver a ground-breaking, state-of-the-art paint shop for Bentley. bentleymotors.com/en
ifm has unveiled its latest innovation, moneo Cloud. Designed to enable companies with unprecedented efficiency, scalability, and data-driven decision-making capabilities. This cutting-edge platform not only simplifies complex processes but also delivers actionable insights in real-time.
ifm simplified the user experience by removing the need for customers to manage server infrastructure and constant software updates. Now, from unboxing to retrieving essential data from the cloud, can be accomplished in under 30 minutes. moneo Cloud is accessible online from any location with just an internet connection, an edgeGateway device, and a moneo Cloud subscription, you can start improving your manufacturing processes.
The moneo Cloud platform offers a straightforward route to collecting machine or process data to provide actionable
insights for the business. The moneo Cloud allows users to effortlessly configure sensor parameters, analyse and visualise data on user-friendly dashboards. Making process data quickly and easily visible, alongside the option to provide alerts to the user, allows businesses to make quick decisions based on data.
moneo Cloud, paired with the innovative Edge controller, simplifies the integration of data whether it’s sourced from existing sensors, PLCs, or new devices like power meters, making the onboarding process seamless. It provides a comprehensive suite of features designed to enhance machine performance, ensure process reliability, and reduce energy consumption. With flexible subscription plans based on information points that refresh data to the cloud every 60 seconds, and options for more frequent updates, it caters to varying needs. Its versatility, supported by expert
advice and assistance from ifm’s system sales team, positions moneo Cloud as a critical tool for industries aiming to leverage digital transformation and fully exploit the advantages of IIoT.
As an add-on component of our cloud solution, moneo remoteConnect offers a comprehensive solution for remote maintenance. This function allows you to access moneo and various plant components. Adapt access configurations precisely to your individual requirements and maintain control over your remote maintenance processes.
ifm.com/gb/en/shared/industry-4-0moneo/overview
The Euchner MGB (Multifunctional Gate Box) Fieldbus is a state-of-the-art safety solution designed for safeguarding access points in automated industrial systems. It integrates seamlessly with fieldbus systems such as PROFINET and EtherNet/IP, offering enhanced communication between safety devices and a machine’s control network.
One of its key strengths is flexibility. The modular design allows users to customize the MGB with various components such as emergency stop buttons, lock monitoring, and control elements. This modularity enables tailored safety configurations for specific machine areas, making it ideal for complex or evolving environments.
The MGB Fieldbus enhances efficiency through its integration with PROFINET and EtherNet/IP. These protocols provide highspeed, real-time data exchange, ensuring that safety-critical information is transmitted
instantly. This fast communication allows for better system coordination, minimizing response times to faults or issues. Additionally, it enables centralized monitoring, which simplifies diagnostics and reduces downtime by allowing operators to address problems quickly, before they escalate. Designed to meet the highest safety standards, the Euchner MGB Fieldbus complies with ISO 13849-1 Performance Level (PL) e. These certifications ensure the system provides reliable, advanced
protection for both personnel and machinery in hazardous environments.
In summary, the Euchner MGB Fieldbus with PROFINET and EtherNet/IP offers a versatile, high-speed, easily integrated safety solution. Its real-time diagnostics, fast communication, and flexible configuration make it an invaluable asset in industrial automation, boosting both efficiency and safety while ensuring regulatory compliance.
euchner.co.uk
Bosch Rexroth offers a range of engineering tools for automation, designed to simplify the process of configuring, designing, and implementing automated systems. Among these, LinSelect stands out as an efficient tool for engineers working with linear motion technology. LinSelect streamlines the selection of linear axes and actuators, which are essential components in modern automation systems, providing a userfriendly interface that makes the design process faster and more accurate.
One of the main advantages of LinSelect is its ease of use. Engineers often face complex decisions when selecting linear motion systems, such as load capacity, speed, and precision requirements. LinSelect simplifies this by guiding users step-by-step through the selection process. The tool prompts users to input basic parameters
like stroke length, load, and dynamics, and then generates the most suitable linear system configurations based on these inputs. This eliminates guesswork and reduces the risk of errors, ensuring that engineers choose the optimal solution for their application.
Another key benefit is its integration with Bosch Rexroth’s extensive product portfolio. It is specifically designed to work with Bosch Rexroth’s broad range of linear modules, motors, and controllers. The tool not only offers detailed product specifications but also provides real-time updates on product availability, enabling faster decision-making and project turnaround times.
engineers can reduce power consumption and material costs, improving the overall efficiency and sustainability of their projects.
Additionally, LinSelect supports cost and energy optimisation. By selecting the most efficient combination of components,
Overall, Bosch Rexroth’s engineering tools, particularly LinSelect, enable engineers to enhance precision, efficiency, and ease of implementation in automation systems. This results in quicker project completion, lower costs, and optimised performance – key factors in modern industrial automation.
boschrexroth.com/en/gb/
Designers are still missing out on the efficiency and cost benefits of using standard parts in product development, according to global parts provider norelem. Many designers are still relying on custom-made parts to create their prototypes. However, this comes with hidden costs and is a drain on productivity.
Marcus Schneck, CEO of norelem, comments: “Like every other facet of manufacturing, product development is always looking for ways it can create efficiencies. Using more standard parts from a full line manufacturer like norelem makes design work significantly easier, quicker, and more cost-effective.
“Standard parts can make an exceptional difference.”
The savings quickly add up. Even for a relatively simple component like a locating bolt, a designer needs an average of 15
minutes for a production-ready drawing, including dimensions. Along with the costs incurred for manufacturing, this is an expensive and time-consuming process compared to ordering a standard part.
In-house manufacturing also means reliance on a supply chain for raw materials, booking in production time and allowing time for changeover of tooling. In addition, custom parts production can lead to inaccuracies in tolerance limits, meaning that either reworking is required or sometimes the entire process needs to start over.
Conversely, designing with standard components has many advantages. Parts like locating pins, bushings and ball bearing housings are significantly less effort to procure than produce - and assembly is also faster. This is because standard parts are manufactured precisely, eliminating the need for reworking. Typically, it also means
a shorter development phase, especially in mechanical engineering, meaning that you get your product to market faster.
Another advantage is the quick and easy replacement of parts. If a standard part becomes worn or damaged, it is simple to re-order, rather than going through the entire manufacturing process once again for a custom part. At norelem, for example, costeffective locating bolts are readily available worldwide. norelem.co.uk
Providing improved data streaming, field evaluation, object detection and robustness, SICK’s range of customisable LiDAR sensors now perform better than ever.
The sensor expert has unveiled new models in its extensive LiDAR portfolio, the multiScan and picoScan devices, with faster data streaming and a series of enhancements including excellent light performance and greater accuracy.
Based on SICK’s common user environment and development platform, both the multiScan and picoScan come with a wide range of add-ons, including some onboard software tools. They are configurable to suit a huge array of different applications and scenarios, ranging from robotic guidance and mobile outdoor automation to security and interactive art installations.
With a ruggedised design and vibration resistance, both multiScan and picoScan sensors provide outstanding measurement performance in real conditions, making them ideal for outdoor automation and harsh environments.
The multiScan range is based on time of flight (ToF) technology and delivers high quality 3D data. The multiScan 100 platform currently includes the multiScan 136 and the multiScan 165, with different coverages depending on the model. These include 65° coverage at 360° for the multiScan 136 and ranges of up to 60 m for the multiScan 165.
SICK’s compact picoScan 150 sensor is the natural progression of the popular TIM sensor, providing faster data streaming and more precise localisation in a high angle LiDAR device. It comes in three variants –Core, Prime and Pro, with a working range from 0.05m up to 120m.
Nathaniel Hofmann, SICK UK Market
Product Manager, says, “At SICK we are continually pushing the boundaries of what sensors can do and how they can be used. These are two great product lines that now take performance to a higher level, even in the most challenging conditions.” sick.com/gb/en/
Many manufacturers and engineers find their online presence to be increasingly important for attracting clients. Sarah West of Full Mix Marketing looks at the key areas of digital marketing.
Customers may look you up online so your website needs to be good. The tests for a good website are:
• Is it immediately obvious what you deliver?
• Is it clear where someone must click?
• Does your website explain how you satisfy customer needs?
• Is your website modern and up-to-date?
Search Engine Optimisation ensures your website appears in Google results. Website content is therefore critical, and you should include text, images and video that address your customers’ needs. Backlinks from other websites show search engines that your website is respected. Sharing your content
with trade websites increases the chances of them linking to your website. Google is ‘mobile first’, so ensure your website works on all devices.
Pay-Per-Click advertising can also help you appear in search results. Identify the search terms your target audience uses to improve this. The most effective ads highlight features and benefits and use an active voice to encourage clicks. Specify landing pages that relate closely to the keywords targeted, and concentrate your campaign on working hours to attract businesses who are ready to buy.
Content can demonstrate your expertise, engage clients and improve SEO. Busy professionals’ attention space is limited, so split articles into chunks with subtitles. Genuine news can be shared as a press release. Sharing content on social media and via email marketing are powerful tactics.
50% of senior professionals are active on LinkedIn, making it an important medium. Successful posts report something new, like an achievement or a project.
To boost your reach:
1. Ask staff to like and share your company posts
2. Request senior staff to invite individuals to connect
3. Once connected, invite contacts to follow your company page fullmixmakreting.co.uk
Effective and safety compliant high-pressure submitter technology can mitigate the risk of inaccurate measurements, equipment failure, and much worse. Read on for why companies operating in dangerous settings should employ such pressure measurement solutions.
Operating in environments with hazardous dust and gas poses significant risks, and these dangers are compounded when dealing with very high pressures. Industries such as oil and gas extraction, chemical processing, and pharmaceuticals often work under these extreme conditions, where even minor lapses can lead to catastrophic events.
The key challenges in such settings include the risk of explosions, equipment failure, and maintaining accurate measurements under pressure fluctuations. The high-pressure HP1000 transmitter from ESI Technology is designed to address these challenges, ensuring safe and reliable pressure measurement in hazardous environments.
1. Explosion Risk: High-pressure systems in environments with flammable gases or combustible dusts are particularly prone to explosions. A small leak or a failure in the pressure containment system can introduce high-pressure streams of gas or dust into the surrounding area, which can ignite upon contact with a spark or heat source.
The HP1000 from ESI Technology is specifically designed to operate safely and reliably in these high-pressure hazardous environments. Several features make this device an ideal choice for such demanding applications:
2. Equipment Failure: High-pressure systems exert immense stress on equipment. Valves, seals, and pipes must withstand these pressures without deforming or failing. In hazardous environments, any failure can lead to the release of dangerous substances, creating a significant safety hazard.
3. Measurement Accuracy: Maintaining accurate pressure measurements at such high levels is challenging. Inaccurate readings can lead to improper handling of pressure systems, which may result in overpressurisation or under-pressurisation, both of which pose safety risks.
1. Robust Construction: The HP1000 is built with high-strength materials that can withstand pressures up to 5000 bar. This robust construction ensures that the transmitter maintains its integrity even under extreme conditions, minimising the risk of equipment failure.
2. ATEX and IECEx Certification: These certifications are critical for equipment used in hazardous environments. The HP1000’s compliance with ATEX and IECEx standards means it has undergone rigorous testing to ensure it does not ignite explosive atmospheres, either through sparks or heat. This certification provides confidence
that the device can be safely used in environments with explosive dust and gas.
3. Accurate and Reliable
Measurements: The HP1000 offers precise pressure measurements, essential for maintaining safe operating conditions. Its advanced sensing technology ensures that even at extremely high pressures, the readings are accurate and reliable. This accuracy is crucial for operators to make informed decisions and maintain safe pressure levels.
4. Durability and Long Life: Designed for longevity, the HP1000 can endure the harsh conditions typical of hazardous environments. Its durability reduces the frequency of maintenance and replacements, which is particularly important in environments where equipment downtime can be dangerous and costly.
5. Integrated Safety Features: The HP1000 incorporates features that enhance its safety profile. These include overpressure protection, which prevents the transmitter from being damaged by unexpected pressure spikes.
The high-pressure HP1000 pressure transmitter from ESI Technology is an essential tool for industries operating in hazardous dust and gas environments. By combining robust construction, advanced safety certifications, precise measurement capabilities, and durable design, the HP1000 addresses the unique challenges posed by high-pressure operations in such settings. Its ability to provide reliable and accurate pressure readings while ensuring safety helps prevent accidents and maintain efficient and secure industrial processes.
esi-tech.com
AI is rapidly transforming how businesses operate, particularly in manufacturing. Nikesh Mistry, Sector Head at Gambica, addresses the hesitancy of UK businesses to adopt this technology.
AI, with its ability to analyse vast datasets, learn from experience, and make intelligent decisions, offers immense potential to enhance competence and productivity in UK manufacturing. One of the primary ways AI can benefit UK manufacturing is through analysing sensor data from machinery to predict potential failures before they occur, allowing for proactive maintenance and reducing downtime. This not only saves costs but also improves overall equipment effectiveness. Moreover, AI-powered quality control systems can identify defects in products more accurately and efficiently than traditional methods.
AI can also optimise production processes by analysing historical data and real-time information to identify bottlenecks and inefficiencies. By suggesting adjustments to production schedules, inventory levels, and resource allocation, AI can help manufacturers streamline their operations and reduce costs. These benefits are not brand new; engineers have been utilising machine learning (ML) in manufacturing for a while. Whereas ML uses algorithms and data to enable computers to learn and improve from experience without direct instruction, AI has the ability to mimic human cognitive functions, such as learning, problem solving, and decision making.
Despite the numerous benefits that AI can offer, many UK manufacturing businesses remain hesitant to adopt this technology. One common fear is job displacement due to task automation. However, it is important to note that AI is not a replacement for human workers but rather a tool that can
augment their capabilities. By automating routine tasks, AI can free up human workers to focus on higher-value activities, such as innovation and problem solving.
Another concern is the potential for AI to make mistakes. While AI algorithms are becoming increasingly sophisticated, they are not infallible. If not properly trained or implemented, AI systems can make errors that have significant consequences. For example, a faulty AI-powered quality control system could lead to the shipment of defective products, damaging a company’s reputation and bottom line.
Beyond these practical concerns, the widespread adoption of AI in manufacturing also raises significant ethical questions. For instance, there are concerns about the potential for AI to exacerbate existing inequalities. If AI is used to automate jobs in certain industries or regions, it could lead to job losses and economic hardship for those who are unable to adapt to the changing workforce. Additionally, there are concerns about the potential for AI to be used in ways
that are harmful or discriminatory. For example, AI-powered algorithms could be used to profile individuals based on their race, gender, or other personal characteristics, leading to unfair treatment or discrimination.
The widespread adoption of AI in manufacturing will also have significant implications for machinery and OEMs (Original Equipment Manufacturers). As AI becomes more integrated into manufacturing processes, there will be a growing demand for machines and equipment that are AI-compatible. This will require OEMs to invest in research and development to develop new products and technologies that can be easily integrated with AI systems.
Furthermore, the increasing reliance on AI in manufacturing will also necessitate new cybersecurity standards. AI systems are vulnerable to cyberattacks, and a successful attack could have devastating consequences for a manufacturing business. To protect themselves from cyber threats, OEMs and manufacturers will need to invest in robust cybersecurity measures, including regular software updates, strong passwords, and network monitoring.
Of course, AI offers immense potential to enhance efficiency, productivity, and profitability. However, it is crucial to approach AI adoption with a balanced perspective, recognising both its benefits and potential risks. By addressing the ethical implications of AI and investing in responsible AI practices, UK manufacturing businesses can harness the power of this transformative technology while minimising its negative consequences.
gambica.org.uk
Process improvement is like sailing. With an experienced partner, you can achieve more.
Optimizing processes and maximizing efficiency is important to remain competitive. We are the partner that helps you master yield, quality, and compliance. With real-time inline insights and close monitoring of crucial parameters, we support manufacturers to optimize processes, reduce waste, and increase yield.
While replacing an industrial motor with a modern equivalent can reduce energy costs and emissions, it is not always practical. Thankfully, as Thomas Marks, General Manager and Secretary of the Association for Electrical and Mechanical Trades (AEMT), explains, there are other options.
With the attention on global carbon emissions and the increasing pressures on energy prices in recent years, it’s clear why the focus on industrial energy use is at an all-time high. When you also consider that electric motors are widely reported as using half of the electricity generated globally, it is easy to see why motor efficiency is well and truly under the spotlight.
The minimum efficiency requirements of newly-supplied industrial motors have been mandated by governments and standards setting bodies in a growing number of categories.
Motor manufacturers are rising to the challenge admirably, with many, if not all, able to supply new and replacement motors offering greater efficiency than the minimum requirements set.
Replacing a motor with a modern alternative can improve the energy consumed in many scenarios, but it’s not always that simple – in some situations, replacing an industrial motor with a modern alternative is not practical.
Some older motors are customdesigned for specific applications, making it challenging to find a modern replacement that matches the exact requirements. These motors may have unique dimensions, mounting configurations, or operating conditions that modern standardised motors can’t replicate without modifications. In addition, integrating a modern motor into an existing system may require significant re-engineering of adjacent components,
such as drives, control systems, or mechanical couplings, which could be cost-prohibitive or time-consuming. For example, different electrical characteristics can cause compatibility issues with existing electrical protection systems, circuit breakers, or variable frequency drives (VFDs), necessitating upgrades to the entire electrical system.
Also, in industries with tight capital budgets, the upfront cost may not be justifiable, especially if the existing motor is still performing adequately or operating at a low-duty cycle. Plus, in some cases, the procurement and delivery of custom or large high-efficiency motors can take considerable time.
There are, however, some circumstances under which the efficiency of a motor can be improved by refurbishment and rewinding, particularly with older, less efficient motors. Generally, the most effective way to
improve a motor’s efficiency is to add more copper to its coils, or, more specifically, increase the copper cross-sectional area. This is achieved through the tight tolerances modern coils can be manufactured to, as well as the ability of state-of-the-art CAD systems to optimise coil design.
In addition, advancements in insulation materials mean that less insulation is required, freeing up further space in the coils for copper. However, it is worth noting that this will affect the motor’s electrical characteristics.
Efficiency can also be improved by repairing a motor to tighter tolerances than it was originally designed to meet. Higher efficiency bearings and more accurate stator and rotor alignment and balancing can reduce energy losses. Resurfacing elements such as the rotor core can reduce what is referred to as ‘windage losses’. While improving the motor’s cooling system via the fan design or improved heat dissipation techniques can also lead to energy savings as lower operating temperatures improve a motor’s efficiency, while better magnetic design and winding techniques can reduce losses from harmonics, stray flux, and leakage.
This is not exhaustive, but it shows there are ways a motor’s efficiency, and in turn the operating cost and environmental impact, can be reduced through refurbishment. If you have motors that need attention, a good starting point is to talk to a reputable electromechanical service centre that can advise you of the options open to you. AEM have a comprehensive list in its member directory.
theaemt.com
Mike Bacon, Internal Technical Applications Engineer at Matara, addresses the issue of quality when it comes to pneumatic cylinders: what constitutes quality, why does quality matter and, just as importantly, when does it matter.
From their origins in the first part of the 19th Century, pneumatic cylinders have been used in countless industrial processes around the world to move something along a linear path. A relatively straightforward mechanical device, the pneumatic cylinder uses compressed air to drive a piston inside a cylinder; the piston rod then transfers the force it develops to the object to be moved.
Although it depends on the application at hand, pneumatic cylinders are often preferred to hydraulic cylinders as they don’t come with the associated risks of leakage and cross-contamination. Furthermore, they are quieter and, overall, take up less space as there is no requirement to store fluid.
Over the years, a wide array of pneumatic cylinders has been developed to meet specific needs, including roundline, guided, precision slide, compact, clamp and stopper cylinders. Rodless pneumatic cylinders are also available – and becoming more popular – which have been designed to perform as a self-contained linear actuator for improved flexibility.
As with all mechanical devices, quality differs between types of pneumatic cylinders and between manufacturers.
While ideally quality always matters, the reality is that quality matters more in certain applications than others.
When it comes to miniature ‘brown’ cylinders, typically used in moving items off a conveyor belt, for example, these are generally low-cost items that don’t tend to be long-lasting. You could invest in better quality versions, but the return on investment doesn’t add up, mostly because they are
very low cost so it’s not worth repairing them, and they are incredibly easy to replace – you swap out the broken one with the new one in ten minutes.
Where quality most certainly does matter is when it comes to the bigger cylinders –125, 100, and 160 bore cylinders – which are lifting heavy weights. Replacing a big pneumatic cylinder is costly and rarely quick, as they generally aren’t stock items and therefore have to be machined and cut, which could easily take several days. At Matara, we have a large UK-based machine shop and can build many pneumatic cylinders in-house, which means we can frequently deliver a replacement cylinder in two to three days, but that isn’t the case for all suppliers. Time is also required for
the on-site engineers to fit the replacement, which will take several hours, not minutes. All this time is disrupting the process at hand. That’s why you want these larger cylinders to be reliable, repairable (where possible) and long-lasting.
Then, of course, you have the health and safety implications to consider, especially if the cylinders are lifting several tonnes of machinery or items vertically. The last thing anyone wants in this scenario is for the cylinder to fail and everything to plummet. If this did happen, other machinery could be damaged and you would probably have to shut down the whole area, which could last for days. To skimp on the cylinder, saving a few pounds, really wouldn’t be a good idea here.
Pneumatic cylinders are simple devices in that they’re composed of just three or four parts. This makes it quite straightforward to tell when they’re not good quality by just looking at them. Typically, there will be gaps, such as around the seals, and they may not quite line up.
Other important aspects to consider when assessing the quality of a pneumatic cylinder need you to probe a little further.
Let us start with the materials used in the construction of the cylinder. Aluminium, steel, and stainless steel are essential. When it comes to the rods, chromed rods are ideal if the cylinder will be lifting heavy weights, as these are far less prone to breaking. The seals are the items that are most likely to go wrong on a cylinder as they can be easily damaged, especially in dirty, dusty sites. In harsher environments, it pays to invest in better-quality seals. In food environments, for example, corrosive-resistant stainless-steel seals would be a good option, but there are also PTF, PTFE and wiper seals.
To ensure you end up with a pneumatic cylinder that meets the demands of your site and application, it’s important that the manufacturer can offer a range of accessories. These include external accessories, such as mountings and crevices, and accessories fitted within the cylinder itself, including scrapers and bellows to protect the rod from dust and
debris. Not every manufacturer will have a comprehensive range of accessories, but the better-known, better-quality ones will. At Matara, we produce a range of accessories including clevises such as male/female, rear and offset variations, as well as flange mounts, flow controllers, foot brackets, and reed switchers.
Next, check that the pneumatic cylinder adheres to the relevant standards: ISO 15552, ISO 21287 and ISO 6432. All reputable companies manufacture to those international standards, so that shouldn’t be an issue. What is an issue though is how those manufacturers test their products. Avoid batch-tested products as you cannot be sure your specific cylinder has been tested. At Matara, we test each cylinder we manufacture in-house, which means we very rarely have any returned.
Lastly, what level of support can the manufacturer bring? This is a muchundervalued area, but one that impacts the overall quality of the product and service. Is the manufacturer willing to visit the site and provide advice on the cylinder? Maybe it can be repaired rather than replaced. Would a high-temperature seal solve any issues?
No matter how good quality the pneumatic cylinder is, regular maintenance will help reduce unexpected downtime. This will generally involve checking the cylinder, tube, and rod seal for damage and applying
lubricant where necessary. As the seals are most prone to damage, pay particular attention to these and replace them where necessary. Matara supplies seal kits which make this process very straightforward. Keeping the pneumatic cylinder clean also pays dividends. In particularly dusty environments, it’s worth considering an easy clean cylinder where the surfaces are smoother all around, so they don’t collect dust and debris in the first place and can be easily cleaned. Tie rod cylinders are also slightly easier to clean as well.
Ultimately, the nature of the site and the cost implications of repairing or replacing a pneumatic cylinder are the determining factors in just how much you are willing to invest in them. If it’s a hostile environment or one where hygiene is paramount, such as food or pharmaceutical, then quality does matter. Choose well and your pneumatic cylinder should perform reliably and consistently for a long time. We were asked to replace a Matara cylinder recently that had been operational for over 13 years, which is an astonishing length of time to be fully operational. Quality counts! matara.com
MEPCA explores the latest news, innovations and applications in robotics
P24: MEPCA examines some of the myths and misconceptions surrounding robotics.
As demonstrated this year by astounding progressions in technology, a great deal can happen in a year in the field of robotics. MEPCA consulted with renowned robotics programming specialist Vanessa Loiola for a forward look at the industry trends for 2025.
The global robotics market is expected to reach a value of $147.26 billion in 2025* and Tesla’s eagerly awaited ‘Optimus’ humanoid robot** is also scheduled for release. Other anticipated developments include improvements to AI and Machine Learning, with natural language processing replacing traditional code, and an expected increase in robotics solutions in healthcare.
Vanessa works at the forefront of robotics in manufacturing and production and has become one of the most influential women in the sector. With 2025 looking to be a fundamental year for the industry, Vanessa has shared her predictions for 2025.
Artificial intelligence will continue to revolutionise robotics, with AI-driven robots capable of learning and adapting in real time. We will witness robots performing increasingly complex tasks, using machine learning to optimise performance. This will dramatically reduce the need for manual programming, allowing robots to adjust their actions based on the environment or task at hand, thereby improving efficiency and reducing downtime in various industries.
Industrial robots will offer unprecedented levels of flexibility, driven by advancements in
software and AI. Manufacturers will be able to quickly reconfigure production lines with minimal downtime, allowing robots to handle a wider variety of tasks and product types. This flexibility will be key as industries shift toward mass customisation, reducing lead times and enabling manufacturers to adapt to rapidly changing market demands.
Predictive maintenance will become a cornerstone of industrial automation. AI-driven robots equipped with advanced sensors and data analytics will be able to monitor machinery continuously, detecting wear and tear before failures occur. These
robots will autonomously predict and schedule maintenance tasks, reducing downtime and increasing operational efficiency. This proactive approach will save companies significant costs by extending equipment lifespan and preventing unexpected breakdowns.
The integration of robots and human workers will reach new heights in industrial settings. Advances in collaborative robots (cobots), safety systems, and AI will allow robots and humans to work side by side more seamlessly. Rather than replacing human jobs, robots will take on repetitive, dangerous, or physically demanding tasks, enabling human workers to focus on higherlevel problem-solving and decision-making. This collaboration will drive innovation, improve productivity, and create safer and more ergonomic workplaces.
Sustainability will be a key driver in industrial automation, with a growing focus on green technologies and energy-efficient robotics. Manufacturers will integrate automation systems that minimise energy consumption, reduce waste, and optimise the use of resources. Robots will be designed with energy-efficient motors, power-saving modes, and the ability to work in low-energy environments. They’re also using lightweight, durable materials to minimise resource use and carbon footprints. Modular designs allow for easier upgrades, extending the lifespan of robots and reducing electronic waste.
valoy.ie
*www.transparencymarketresearch.com/ robotics
**www.bbc.co.uk/news/articles/ cz5reve8476o
When it comes to utilising robotics, UK manufacturing is still trailing behind its closest competitors in Europe. In this feature, MEPCA examines the misconceptions and myths that might prove to be a barrier to the wider adoption of robotics in the UK.
Despite UK manufacturing continuing to be in a strong position, it has remained slower in its adoption of robotics than many of its key competitors. According to the International Federation of Robotics (IFR) in 2023, the UK’s robotics density was considerably lower than other Western European countries. The IRL measure robotic density in terms of the number of operational units a country has. The operational stock of robotics in the UK reached 28,831 units in 2023, while Germany had nine times as many at 269,427 units.
While the super deduction encouraging
investment in capital expenditure significantly drove up the number of units in the UK going into 2024; with this is now ending, the uptake is predicted to drop once again before recovering in 2025.
There are, of course, many, many contributing factors to why UK is trailing behind countries such as Germany, including parts and materials procurement post-Brexit, the destabilising impact of ongoing global conflicts on the UK’s supply chain, as well further socioeconomic and infrastructure differences between the two countries. Mercifully, this is not intended as an exhaustive examination of these contributing factors; the purpose is instead to gain an
understanding of what may discourage decision makers from embarking on small or large-scale robotics transformations at their manufacturing facilities.
To assist us in understanding and, hopefully, helping to dispel some of the key myths and misconceptions that are contributing to the UK’s reluctance to adopt robotics technology, we have sought and consulted with six people working at the forefront of robotics.
Our panel consists of Vanessa Loiola, Robotics Programming Specialist and CEO of Valoy Automation; Professor Mike Wilson, Chief Automation Officer, MTC and Visiting Professor of Robotics & Automation,
Loughborough University; Erik Verebely, Junior Robotics Installation Specialist at Peak Analysis and Automation; Neil Mead, Marketing & Strategy Director KUKA Robotics UK & Ireland; Oliver Selby, UK Sales Manager at FANUC; Marc Segura, President ABB Robotics Division.
Common myths and misconceptions about robotics in the UK:
This is prevalent concern in the manufacturing industry and one that arises repeatedly in discussions on robotics and automation. While it is true that robots are, and will increasingly, undertake certain tasks in place of their human counterparts, it does not necessarily follow that they will replace workers.
As Vanessa Loiola explained: “While robots can automate repetitive and dangerous tasks, they are meant to complement human skills, not replace them.”
Further to this, Professor Mike Wilson believes that rather than taking jobs, the opposite is the case: “Tasks may be automated, and staff redeployed to often more rewarding roles, but the improvements to the company normally lead to increased orders, growth and more and better paid employment.”
Neil Mead expanded on this idea: “The myth that robots will take our jobs also persists in the public consciousness despite evidence to the contrary… As robots take on the mundane and repetitive tasks, human workers will be released to do more interesting and creative jobs where thinking, creativity and dexterity are required. These up-skilled operatives will have the opportunity to take on new roles, such as control engineers, data analysers, system designers and robot programmers to name just a few.”
Discussions around job replacement may ultimately become redundant for a simple reason: if a manufacture cannot remain competitive, it has no jobs to offer. As Neil Mead highlighted: “We have no choice but to automate to remain competitive, so workers are going to have to get used to the idea of operating alongside smart machines and robots.”
Another important dimension to this topic is that the UK is facing labour shortage, which robotics can alleviate. Rather than taking a person’s job, often
“The operational stock of robotics in the UK reached 28,831 units in 2023, while Germany had nine times as many at 269,427 units.”
a robotics solution is filling a position that the manufacturer has struggled to place a human in.
Professor Mike Wilson explained: “We have a significant labour shortage in UK manufacturing caused by a number of issues including both the pandemic and Brexit. According to Make UK there are currently 61,000 vacancies leading to a lost opportunity of £6Bn.”
Marc Segura: “In the UK, skilled manual labour is becoming increasingly harder and more expensive to find, increasing the demand for such skills. By using robots, you can reduce the amount you spend retaining and employing staff. With robots you can improve working conditions of your staff.”
It is also important to point out that there is distinction between the automation of a task and the replacement of an employee; an employee’s expertise is worth more than the sum of the tasks they complete.
There may be a root cause to this misconception about robotics, as Erik Verebely explained: “The most common misconception with robots is their nature. From an outside perspective, many people view robots as mostly humanoid in nature. Which our media has some influence over.”
Our tendency to associate robotics in manufacturing with the humanoid robots could be part of the problem. Humanoid robots readily capture our imaginations, but
in reality, this type of robot would rarely, if ever, be used in manufacturing. If this is what robotics means to us, it is understandable that we conjure a human replacement as the likely outcome of a robotics implementation.
For manufacturers, particularly SMEs, looking to make an investment in robotics technology it can be an understandably daunting task. However, a reluctance based on factors such as cost, ROI and installation complexities does not necessarily reflect the reality experienced by many manufacturers, as addressed in the following commentary.
Professor Mike Wilson: “The most common misconceptions, particularly within the smaller businesses, relate to the cost and complexity of robot automation. Most business leaders are aware, and recognise the value, of the widespread use of robotics in the automotive sector but do not see it as appropriate for their companies. Robots have significantly reduced in cost over the last 10 years, and they are also much easier to implement and operate, making them very applicable to smaller businesses.”
Vanessa Loiola: “A common myth is that robotics are too expensive and complex for most manufacturers, particularly small- and
medium-sized enterprises. Many companies believe that implementing robots requires a massive upfront investment and extended downtime. In reality, advancements in technology have made robotics more affordable and adaptable. Scalable solutions exist, which can be customised for specific needs, reducing the time and costs associated with implementation.”
Oliver Selby: “For certain, the biggest barrier to automation uptake in the UK is the belief that it’s prohibitively expensive. The key here is to look longer term in measuring the result of the automation deployed. Focusing on the total cost of ownership (TCO), rather than just the initial purchase price, allows not only for the tangible benefits to be measured, but also the intangible benefits that offset the capital cost by means of the value they bring to the business.”
According to Marc Segura, there is a belief amongst UK manufacturers that the ROI of investing in robotics is low or problematically slow: “Short term expectations of ROI can prohibit investments in robotic automation in favour of other solutions such as fixed machinery. In fact, experience has shown that an ROI on robotic automation can often be achieved quickly, with examples of fast payback within months depending on the application.”
In Neil Mead’s opinion: “The technology is now highly developed, and the investment required to automate a process is relatively low, considering the positive impact it can have on productivity, with a reasonably short payback.”
A consideration related closely to cost and ROI, is the perceived complexity of implementing these technological solutions in existing manufacturing facilities, including programming the robots to perform the desired function.
Neil Mead: “Another misconception we come across is that robots are complicated to program and operate. While this may be true for some complex operations, thanks to advances in operating systems and software packages, programming for basic applications is now relatively easy and intuitive.”
After addressing some of the common myths and misconceptions, a selection of our contributors had advice to offer any UK manufacturers considering taking the plunge
“We have a significant labour shortage in UK manufacturing caused by a number of issues including both the pandemic and Brexit. According to Make UK there are currently 61,000 vacancies leading to a lost opportunity of £6Bn.” –Professor Mike Wilson
to invest in robotics solutions of any kind.
Vanessa Loiola: “For companies considering robotics, my advice is to start with a clear understanding of the specific challenges you aim to solve. Identify the areas of your operation where automation can bring the most benefit. It’s important to not only focus on the short-term costs but also on the long-term return on investment (ROI), including increased efficiency, reduced labour costs, and improved safety. Collaborating with a knowledgeable integrator and staying up-to-date on the latest robotic technologies will also help to maximise your investment.”
Erik Verebely: “Always make sure to look for the more suited robot for your needs. Robots are expensive to install but make their value back over time. The robot maintenance can heavily eat into the profitability of robots in the long run.”
Professor Mike Wilson: “Firstly, it is important to identify the appropriate application. This is not necessarily the major challenge in the factory, which may be difficult to automate. There is a learning curve associated with any new technology, and it is therefore important to select a
reasonable application to make steps along that learning curve. A comprehensive business case needs to be developed to justify the budget to buy the correct solution. This is not just about labour savings but other factors that should be included.
“Most importantly, a requirement’s specification must be developed to convey the necessary information to the potential vendors. This also helps to provide a consistent basis for comparison of the vendor’s proposals. Selection of the most appropriate suppliers is critical and, given the large choice, can be a challenge.
“My key advice, particularly for businesses implementing robot automation for the first time, is to seek independent guidance. Organisations, such as the MTC, can guide companies through this journey to help them ensure their investment delivers success.”
MEPCA are grateful to all those named in this piece for providing their invaluable insight and encouragement to UK manufacturers interested in robotics. This is by no means an end of the discussion, and we encourage anyone interested in this topic to contact us to share their opinions.
Kawasaki Robotics
Tel:+44-1925-713-000
www.kawasakirobotics.com/uk/
OnRobot, provider of hardware and software solutions for collaborative applications, addresses the hesitancy of SMEs to implement automation solutions and explains how automation can simplify growth.
Automation’s benefits extend well beyond large industries like automotive manufacturing or logistics.
Sectors such as small-scale manufacturing and warehousing can also significantly benefit from automation by increasing productivity, reducing costs, and encouraging innovation. Yet, many smaller businesses hesitate to embrace automation due to its perceived complexity and high costs.
For SMEs, challenges arise not only from the initial investment but also from the expertise and time required for installation and operation. Concerns about potential disruptions to existing workflows, extensive training needs, and long setup periods further delay adoption. These concerns slow down the implementation of automation, preventing businesses from tapping into its potential to drive productivity and, by extension, economic growth.
OnRobot focuses on making automation accessible to SMEs by offering solutions that are easy to use, scalable, and affordable. The company’s approach eliminates technical complexities, allowing businesses to adopt automation rapidly. Key elements of its strategy include:
1. Plug-and-Play Solutions: Off-theshelf systems that are easy to install and operate. For example, the AA:PALL palletizing system, developed with Applied Automation, and OnRobot’s CNC Machine Tending solution, created in partnership with Olympus Technologies, are designed for quick setup. Businesses can install these systems and start reaping benefits within a single day.
2. Scalability and Affordability: Solutions designed to be scalable, allowing businesses to start small and expand their automation capabilities as needed. This flexibility reduces the risks associated with automation and ensures affordability for
smaller businesses.
3. Comprehensive Support: To ensure businesses make the most of OnRobots automation solutions, it provides comprehensive training and support. This minimises disruption to operations and helps employees quickly adapt to new systems, allowing businesses to fully capitalise on the benefits of automation.
Simplifying automation makes it easier for businesses to adopt technologies that provide tangible economic benefits. Automating repetitive tasks allows workers to focus on more complex, value-added activities, which increases productivity and operational efficiency.
Automation also enhances competitiveness. It enables businesses to reduce costs, improve quality, and deliver consistent results. As a result, SMEs that adopt automation are better positioned to compete on both a local and global scale. Additionally, automation opens new opportunities for innovation by enabling the
development of advanced products and optimising processes.
Christian Lyth, Area Sales Manager at OnRobot, emphasizes how removing barriers to automation is key: “Our goal is to eliminate the hurdles that have traditionally hindered automation adoption. With solutions like the AA:PALL palletizing system and CNC machine tending technology, businesses can automate with minimal disruption and achieve immediate benefits.”
James Taylor, Chief Commercial Officer at OnRobot, adds: “Our off-the-shelf solutions, which can be implemented in a single day, make automation both feasible and indispensable for UK businesses, helping them stay competitive in an increasingly automated global economy.”
Automation is essential for UK businesses to thrive in the future. By simplifying the process, OnRobot is enabling businesses of all sizes to adopt automation easily, driving growth and ensuring competitiveness in a rapidly changing economy.
onrobot.com/en
Multifaceted, configurable, efficient and maintenance-friendly - Eta has become the worldwide standard.
Find out more at www.ksb.co.uk - 01509 231872 - sales@ksb.com
MEPCA; 180x126; September 2024.indd 1
Manufacture products of the highest quality with inspection and automation solutions designed to set you apart.
#MakeitExcellent
HELUKABEL’s production site in Windsbach, Germany was already at the height of modernity. Now, the company has gone even further on its smart manufacturing journey by making the decision to integrate a cobot into the facility.
The decision to add a collaborative robot (cobot) into the production of high-performance cables is one of many on the road to multi-faceted optimisation. Efficiency, production, agility, safety, sustainability, quality control, and savings. Each is a pillar of smart manufacturing that robotic innovations continually improve upon.
For years, robotics have been the solution to enhancing productivity and precision. The by-products of this include reduced production costs and increased output. By powering up on the latest innovations in robotic technology, HELUKABEL can maintain its ability to meet demands while focusing on the safety of its staff and the sustainability of its business.
HELUKABEL’s Project Lead, Peter Bluhm, gives his insight: “Manually handling [cable] spools was not only monotonous but made keeping up with increasing production speeds exceptionally difficult [...] With the new cobot, our teams operating the braiding machines can work more ergonomically and more efficiently [so] we can save a lot of time and effort.”
The story of robots in manufacturing is a familiar one. In the early ‘60s, it was General Motors that integrated the first robotic device into an assembly line. Since then, strides in robotic innovation have paved the way for widespread adoption.
Today, industrial robots have a firm place in smart manufacturing. They are one of
the core components of fully integrated production systems with real-time response rates to changing conditions and global demand. As these devices face constant evolution, they become more efficient, more precise, and more cost-effective across various industries. Industrial robots are no longer only suitable for the General Motor assembly line; they are omnidirectional.
With approximately 15 categories of manufacturing robot in the modern market and thousands of specifications within each, the move to integrate a cobot in HELUKABEL’s production facility was highly deliberated.
In the company’s mission to administer smart manufacturing processes, existing processes and wider goals were carefully considered. For example, Peter Bluhm highlighted the monotony of spool movement; the ergonomic challenges staff faced could have led to the development of chronic pain. Then, there are human
speed limitations that robotic arms bypass. Finally, there was the need for the robotic integration to work in the same space or “cell” as HELUKABEL’s staff without risk of injury.
While the company already has a fleet of robotic technologies operating throughout their production, testing, and warehousing facilities, the specific spool movement process required something new. Hence, the cobot. This robotic device is designed to work alongside humans and ensure it doesn’t cause harm when they come into contact. For example, they feature lightweight materials, rounded contours, padding, sensors, and defined speed and force thresholds.
Modern robots, like the cobot, move in 3D space within a single cell. They complete repetitive tasks with continuous precision while maintaining quality; to do this, the cables inside the robots need to meet the highest of standards. For example, they must withstand rapid acceleration, rapid deceleration, torsion, tensile loads, bending movements, and more. Some also need to withstand mechanical, chemical, and thermal factors depending on the application.
HELUKABEL’s ranges of ROBOFLEX® , industrial ethernet, and BUS cables are specially designed for robotic integration with properties matching every application. For example, HELUKABEL designed its ROBOFLEX® range with resistance to oil, abrasion, notches, welding spatters, extreme bending radii, and more. shop.helukabel.com
Automate UK delivered an exceptional PPMA Show this year with an excellent turnout.
PPMA is a seminal 3-day platform for showcasing the latest in technological solutions, live demonstrations, product launches and expert seminars. MEPCA were delighted to attend PPMA this year. As always, it provides us with the perfect opportunity to catch up with our regular readers and contributors, and, of course, meet new ones.
Alongside the MEPCA team were 8,000 attendees and 350 exhibitors, as well as entrepreneur broadcaster Gregg Wallace who received a warm welcome at the event, with many visitors trying to spot him as he did the rounds.
From going through security and collecting our tickets to navigating the exhibitions and refreshments, the attention to detail and care put into curating this event was clear. New to PPMA this year was the app provided by Automate UK, which, as well as holding ticket information, boasted additional features such as the floor plan and a QR code function that enabled attendees to retrieve exhibitor information.
The first day started more quietly than expected due to travel disruptions that had affected attendees and exhibitors alike. However, as the first day progressed, that initial quietness soon passed and PPMA was in full swing. While overshadowed by the array of impressive technology on show and in operation, many of the event stands were themselves marvels.
Our initial stop-off was within additive manufacture. At Markforged/Mark3D’s stand, we witnessed the ease at which even complex components can be 3D printed to order and saw (and felt) the superior surface quality achieved by their technology, before then discussing the successes of their industrial installations, which is revolutionising machinery repair.
Later, it was a pleasure to meet with Apex Dynamics, who talked us through the
evolution of planetary gearboxes, explaining how they facilitate torque in a wide variety of applications, including in autonomous mobile robots, and at the other end of the scale, industrial scale energy turbines. The enthusiasm the Apex Dynamics team have for their products was clear as they unveiled their latest releases: the MG and MGH ranges of planetary gearboxes, designed for high radial and axial loads and rack and pinion applications.
Catching up after the show, we got Mike Gulliford, Apex Dynamics’ Managing Director, provided us with his impressions of this year’s event:
“PPMA is always a great show to go to. Not just for sales – though these are important – but also learning from our peers and other industry experts. This is an industry in which everyone knows each other, so every show feels like a reunion. As one of the six largest gearbox suppliers in the world, with the biggest capacity of
any manufacturer for servo gearboxes, PPMA helps us touch base, easily, with the specific needs of our existing and potential customers.
“For these reasons and more, we knew PPMA was an excellent platform for showcasing our new planetary gearbox ranges and our first-ever range of elastomer/ disc coupling, which were very well received by visitors to our stand at the show.”
Armaguard exhibited at PPMA for the second year, exhibiting their range of protective enclosures for hygienic environments. Their food-grade 316 stainless steel enclosures for printers, PCs, and displays drew attendees’ interest.
“The PPMA organisers provided great support in preparation, with thoughtful touches like complimentary badge scanners and the added boost through the 360° virtual tour. While the first day started off slowly, the show gained momentum, allowing us to connect with exceptional
prospects and discuss exciting projects.”
The following day, we visited Fortress Technology, who were showcasing their metal detecting and X-Ray equipment, as well as the monitoring software that allows for diagnostics, which facilitates intelligent maintenance. Fortress highlighted to us the importance of traceability.
“Phil Brown, Sales Director of Fortress Technology Europe, found the PPMA Show, to be a resounding success, particularly as attendees had the opportunity to engage directly with cutting-edge inspection technologies, a vital aspect that Brown emphasises as irreplaceable. Fortress Technology showcased its groundbreaking Halo Automatic Testing, offering manufacturers an efficient approach to inspection that aligns with real-time processing needs. This innovation earned recognition at the Automate UK Awards 2024, held during the event. Fortress also unveiled its latest development, the Icon X-ray, demonstrating the benefits of both metal detection and X-ray inspection systems.”
Our next stop was Endoline Automation. The family run company are a long-standing PPMA Show participant. Endoline’s “Pack For The Future” exhibit captivated audiences, highlighting the evolution of packaging. This included the debut of Endoline’s sustainable Wet Paper Taper Case Sealer and the versatile Four-in-One Robotic System from Endoline Robotics.
Andrew Yates, Managing Director of Endoline Automation commented: “Our presence at the PPMA Show not only enabled us to connect with new and existing clients, but also served as the perfect stage to launch systems that align with the industry’s dynamic needs. We were honoured to be recognised at the Automate UK Awards 2024 for our ground-breaking 407 High-Speed Random Case Gluer, solidifying our commitment to engineering pioneering sustainable and efficient end-ofline solutions.”
The Omron stand was notably impressive and had a steady stream of visitors for the duration of the event. Stuart Coulton, Omron’s Marketing Manager provided us with an in-depth look at the company’s solutions, highlighting the importance of data and traceability in the move towards flexible manufacturing, and beyond that, to operational excellence. Among the products demonstrated were several impressive AI-
visualisation technologies capable of picking out defects in situations that would challenge other solutions.
At this year’s PPMA show, Lindum Packaging showcased their new product, Kontrol4.0. This IoT monitoring device can be retrofitted to any pallet wrapping machine, providing real-time insights into film consumption and machine performance through an easy-to-use online dashboard.
As Arrio Wade, Lindum’s Marketing Manager, explained: “Our main goal was to introduce Kontrol4.0 to the market and connect with interested prospects. Although the first day started slowly, the turnout improved, and we had some great interactions, including connecting with companies like Diageo. Overall, it was a fantastic opportunity to meet relevant industry contacts and generate interest in our new innovation.”
Silverson Machines debuted their new range of small-scale mixers at this year’s show. On the stand were the 150 UHS Ultra Hygienic small-scale In-Line mixer, the 088/150 Multistage UHS In-Line mixer and the FMX10, a small-scale powder/liquid mixer. The FMX10 was demonstrated on the stand as part of the daily live demonstrations drawing a large crowd.
Catching up with Silverson after the even, they explained that this was an
incredibly successful product launch for, with customers already booked in to trial the new mixers for their applications, as well enquiries for other high shear mixing equipment from new and existing customers.
We were honoured to attend the awards ceremony this year, which was held at a brand new venue, Vox, inside the NEC. On entrance, guests were greeted with cocktails and pop songs given a classical spin courtesy of the exceptional harpist in the foyer.
The awards celebrated those making a real difference in the industry, and among the winners were Endoline Automation and Fortress Technology. Attendees were treated to a night of exceptional food and entertainment, including an energetic set by comedian Russell Kane and music from Boney M.
MEPCA would again like to congratulate all the winners and nominees, and thank everyone we spoke to at PPMA, as well as those that joined us on the dancefloor postawards. A special mention for Automate UK who delivered an excellent show. We look forward to seeing you all next year.
ppmashow.co.uk/awards/2024-awardswinners
ABB’s Steve Hughes, Strategic Marketing & Sales Manager – Motion Service, explains how new approaches to drive servicing are opening up more options to extend asset lifetime and improve energy efficiency.
If a drive is no longer working as it should, or is approaching the end of its useful life, then in the past there were typically two options: repair or replace. The right option for a particular drive would generally be based on running hours, cost to repair/replace, and total running costs, although other factors such as criticality or ease of access may also be considered.
As approaches to drive care and maintenance have grown more sophisticated, new options have opened up beyond repair and replace. There are now a wide number of additional options, ranging from preventative maintenance and reconditioning all the way up to hardware upgrades. The right solution can be tailored to the individual drive and the facility in which it runs, taking into account the device’s life cycle status, service history and operating environment.
For instance, reconditioning (for functioning drives) and Premium Repair (for non-functioning drives) are now viable options for drive users in the UK thanks to ABB’s specialist Drive Workshop facility in Coalville. Reconditioning and Premium Repair involve replacement of all agesensitive components according to the relevant maintenance schedule, as well as any others that may need replacing early due to the drive’s environment and load characteristics. Drives are then fully load tested and leave the workshop with a twoyear warranty.
An additional option may be to retrofit, whereby the complete drive module within a panel is replaced. This is carried out on site, reducing carbon footprint by retaining the drive enclosure and other ancillary components. In the case of retrofitting, internal components can be upgraded, taking the drive out of its classic life cycle
phase and putting it back into an active phase. In ABB’s case, this can quite literally mean taking an older ACS800, ACS600 or SAMI drive and replacing the drive or module to turn it into a newer ACS880.
Extending the useful life of a drive asset can delay the carbon impact of replacing it. ABB estimates that Reconditioning or Premium Repair services use between 55 and 80 percent less carbon compared to buying a new drive and disposing of the old one.
Knowing what level of service a drive needs at a given time isn’t always easy. Many drives are installed and then left to run for long periods without being regularly inspected. As such, it can be difficult to know their true condition. Any undetected issues, if not dealt with, can turn into sudden failures and unexpected downtime further down the line. This is why lifecycle management goes hand-in-hand with maintenance. Keeping a simple spreadsheet
cataloguing drive assets, their age, and when they were last serviced can provide a much better understanding of what the drives need in the way of servicing at a given time, or what they are likely to need in the future based on typical preventive maintenance schedules linked to their duty levels. This data can then be used with ABB’s Life Cycle Audit tool to prepare a detailed report allowing for financial and project planning.
Data should also be embraced as part of any circular approach, and this can provide additional insights into the performance and condition of a drive asset. Monitoring assets digitally is now easier than ever. The data generated provides useful insights to aid decision-making on repairs and upgrade pathways.
There are now more options than ever to find the right level of service to support a drive’s needs throughout its life. new.abb.com/service/motion
In the following case study, AdaptTech Manufacturing Solutions (the UK & Ireland distributor for the mk Technology Group) demonstrates how a mechanical engineering company utilised the mk conveyor range to achieve a customised solution for its material flow requirements.
Amachine manufacturer that builds dosing systems for foaming a wide variety of products with sealing, casting and adhesive compounds sought a partner that could provide the conveyor technology and the corresponding know-how for its material flow.
The manufacturer required a tailored individual conveyor line for transporting large plastic lids in different shapes and dimensions, automatically cleaning them and then foaming them at a dosing station. To ensure that the cleaning and dosing systems could be aligned properly, the lids needed to be positioned with a repeat accuracy of +- 1 mm. The changeover time that needed to be observed was four seconds.
For this application, the solution provided required two parallel conveyor lines. Each line comprised of two belt conveyors at the infeed and outfeed of the line. In between, were timing belt conveyors that serve as a centring station. The customer attached the cleaning and dosing systems to an overhead gantry above the conveyor lines.
The transitions between the conveyors were equipped with rolling knife edges for problem free transfer. Guides were also attached to the belt conveyor as stops to ensure that the lids are placed and removed in the correct position.
The lids move against a pneumatic stop for both process steps – cleaning and application – while a second pneumatic stop clamps the lid from behind. The square lids were also pneumatically clamped from the sides. This allowed the significantly different formats to be positioned securely. The lines were designed so that the varying
configurations can be processed without retooling and without changing parts.
An mk timing belt conveyor was a key component of the above application, consisting of a conveyor system with a timing belt for cycled transport of piece goods. The conveyor’s fast, precise and flexible nature made it the perfect choice for this mechanical engineering company.
The mk belt conveyor range is extensive and incorporates a wealth of standard modules and accessories that can be adapted to meet a customer’s bespoke requirements. It has a large number of options for lightweight and medium weight products, and it is both sturdy and versatile. There is even a free online configurator available for customers to use to quickly and easily create their own custom belt conveyors. QuickDesigner provides a no obligation quote alongside a CAD model for reference.
It is this knowledge and adaptability that
has led to a long-term relationship with this customer, and has given them the confidence to put their trust in mk conveyors to provide the solution. AdaptTech is the only UK & Ireland distributor of the mk conveyors. adapt-tech.co.uk
Choosing a safety coupling for your air system used to mean sacrificing performance, but that’s no longer the case with the next generation eSafe safety couplings from CEJN. These couplings prevent hose recoil, provide the highest flow and lowest pressure drop on the market, and reduce energy consumption by up to 30%.
Experience the benefits of eSafe with a free on-site flow test. Call to book.
The CEJN 208 Detect blow gun is the first FDAapproved metal and X-ray-detectable plastic blow gun on the global market. This innovative product reduces contamination risks, product rejections, recalls, and waste. It offers high blowing force, chemical resistance, lightweight design, and high-precision flow control.
The new 209 Series blow gun from CEJN is suitable for compressed air or fluid use. It provides high blowing force and precise flow control. The blow gun has an ergonomic grip and is available in classic blue or a new high-visibility, safety-focused version. Specialist nozzles comply with OSHA noise safety standards.
CEJN ‘s compressed air hose reels now feature high-visibility hoses for added safety. Their new Hi-Vis Safety Reel retains the same great features found in all CEJN hose reels, including high flow rate, low-pressure drop, ease of use, slow retraction, and a stop ball design to prevent trip hazards.
A one-stop solution for Fluid Power
Offering engineering apprenticeships could help alleviate the growing skills shortage in the UK. Carter Manufacturing shares the inspiring story of one of its apprentice engineers.
The current demand for skilled engineers across all sectors of UK industry is well documented and constantly features in engineering and manufacturing media. It was one of the key topics discussed at the recent Farnborough International Airshow (FIA), showcasing an industry that generates income to the UK economy estimated to be £13bn per annum and predicted to grow exponentially. It was also an ideal platform for the new UK government to announce ‘Skills England’, a body that aims to provide valuable opportunities for ambitious young individuals, particularly those interested in apprenticeships. With the world of work evolving faster than ever, it’s never been more important to secure and nurture the best new talent in engineering, so the availability of apprenticeship opportunities is crucial.
A good example of where apprenticeship opportunities can be effective is at precision bearing and tooling specialists Carter Manufacturing, who was delighted to share the experience and success of one of its apprentice engineers, 19-year-old Jake Hopgood. Jake attended Abingdon and Witney College, studying for a Level 2 Engineering Diploma one day a week, along with his hands-on, practical experience 4 days a week at Carter. He recently completed his 2-year apprenticeship at Carter. Below, he answers questions about his role and experience at Carter, perhaps helping to inspire others hoping for a career in engineering.
What was the main inspiration for Jake to pursue a career in engineering?
“From a young age, I actually wanted to be
a builder following in the footsteps of my father, although he always used to tell me, it’s not a great job and I think you could be doing something better!” Another family influencer was Jake’s grandfather who told Jake about engineering and told him to look it up and find out more about what engineers actually do. “Ever since then engineering is all I wanted to do.”
“The sectors I’m most interested in are machining, assembly and inspection, mainly because I really enjoy using the CMM machine”.
role, job function did Jake fulfil?
“As an Apprentice Engineer at a precision bearing specialist company I fulfilled quite a few things, for example: bearing and tooling
assembly, machine operating, a little bit of SolidWorks/CAD, MD coating, programming and operating a riveting machine. Also, programming and operating the CMM machine, cryogenic testing bearings using Liquid Nitrogen and using the RIC rig to find out the radial internal clearance of bearings. In addition, fire warden and health & safety training”.
Most importantly, Jake’s experience included a first-hand insight into Carter’s acknowledged specialist expertise as a leading precision bearing and tooling supplier to many of the UK’s leading high-technology companies. This meant he needed to be involved in assembling hybrid bearings for cryogenic applications, lightweight slewing bearings for the defence sector, titanium bearings for highly competitive yacht racing and aluminium thrust bearings for the medical sector.
Why has your time spent at Carter been a success story?
“I wanted to share my positive experience as an apprentice at Carter. I feel like it’s been a great success story because I joined a specialist bearing and tooling company knowing next to nothing and in the last 2 years I have learnt so much. I now know how to do things I never imagined I would know”.
Jake concluded, “Hopefully, I can go onto bigger and better things and keep building myself up, step-by-step and achieve great things in engineering”.
ucas.com skillsforcareers.education.gov.uk carterbearings.co.uk
You think their product knowledge is poor. Ours is revolting.
You heard us correctly. We’re revolting - changing the rules of the game, breaking the mould. Response times that take some companies days, only take us minutes. Pre-sales and after-sales support is based around your needs not theirs. Our job is to empower you. So as they say in Stoke, viva la revolution! Join us now. Axair. Revolutionary Fan Experts Causing A Complete & Dramatic Change.
The way materials are made, moved, packed, stored, and shipped has been revolutionised by Automated Material Handling (AMH) and innovations in robotics, AI, machine vision, and RFID (Radio Frequency Identification) technologies. Circular connector specialist Binder explains more.
AMH optimises manufacturing and logistics, increasing efficiency, with faster, more precise material movement, increased accuracy and enhanced safety. AMH and Warehouse Management Systems (WMS) offer real-time data on operational performance, material flow, and inventory benefitting the whole organisation.
Mechanical elements include check-in machines, sorters, conveyors, stackers, bins, and trolleys. Conveyors utilise, rollers, or chains to move goods and can be straight, curved or inclined, making them customizable to the material.
Robots and cobots have the torque to move large loads for applications like palletising, while having the speed, and accuracy for delicate tasks such as pick and place. Automated Guided Vehicles (AGVs) navigate autonomously along predefined paths or by using mapping technology.
Automated Storage and Retrieval Systems (AS/RS) combine cranes, shuttles, and conveyors, as well as software to control movement and maximizes storage density. WMS control the flow of materials throughout the facility, optimising the entire AMH process through real-time inventory management.
Connectivity links the network of systems, components, and devices used to power, control, and communicate. It is essential for ensuring efficient operations, plus enabling data exchange for control monitoring, and power optimisation, playing a critical role in enhancing productivity, safety, and overall performance.
Sensors detect objects, measure distance, and monitoring conditions. While connectivity enables their integration with the central control system, allowing real-time
data and decisionmaking. Actuators perform physical actions based on control signals, and are interconnected to execute various tasks, such as opening gates, activating brakes, or controlling robots.
PLCs (Programmable Logic Controllers) are the centre of electrical connectivity, controlling and automating processes based on sensor inputs; coordinating the movement of materials, managing traffic flow on conveyors, and synchronising the operation of different machines to enhance overall efficiency. Presenting information on HumanMachine Interfaces (HMI), they provide a Graphical User Interface (GUI) allowing operators to interact with the system.
minimise loss and ensure efficient energy transmission. Connectors should prevent signal interference to maintain reliable data communication and employ electromagnetic shielding as required.
AMHs depend on communication networks for high-speed data through industrial ethernet protocols such as Profibus or PROFINET, plus wireless technologies enable seamless data exchange, supporting real-time monitoring, diagnostics, and optimisation.
Connectors are the essential backbone to keep data and power transmission running. They should be robust to withstand extreme temperatures, moisture, dust, vibration, and mechanical stresses. Manufactured from corrosion-resistant materials they must provide protection to IP67 or higher to guard against contaminants. Reliable locking mechanisms are required to prevent accidental disconnection, ensure stable and secure electrical connections. They must provide low resistance and impedance to
Compatibility of the electrical and mechanical specifications of the equipment is important to ensure easy integration and interchangeability. Industrial M12 and M8 automation connectors and cord sets produced by binder are a good choice offering IP67, IP68 & IP69K with coded variants for signal, power (AC & DC) plus high-speed data up to 10Gbit/s for Ethernet and PROFINET.
Robotics, machine vision, and RFID continues to make AMH even more efficient, cost effective, and sustainable. Industry 4.0, AI, and big data will transform systems with real-time data and intelligent decisionmaking allowing predictive maintenance, optimised workflows, and increased efficiency.
With continued advances in technology, reliable and efficient circular connectors, vital for successfully operating AMH systems, will play an increasingly significant role in enabling intelligent, data-driven, and sustainable material handling processes. binder-connector.com
8-pole bayonet locking
> 5000 mating cycles
Panel mount parts unplugged IP67
Solder and dip solder contacts
With AI and automation booming, Keith Tilley, CEO of digital workflow specialist Intoware, discusses how the key to digital transformation success is to put your human workforce – not just technology – at the heart of the process.
When companies consider embarking on a digital transformation journey, they all too often focus solely on the technology they choose to use.
Of course, this is vitally important. Factors such as robust security, data privacy and ease of use need to be considered, but one of the most important areas firms need to consider when making the transition to a more digital operation is the workforce itself.
Rather than asking what workers can do with technology, companies need to start their digitalisation journey by asking what the technology can do for workers, instead.
But, where’s the best place to start?
A good starting point is identifying the pain points of your workforce and working closely with staff to understand their needs. Common issues may include inefficient reporting tools or excessive paperwork. By addressing these challenges, you can streamline processes that have been left behind in many modern smart factories, using the right technology to digitise workflows.
This approach often leads to improved job satisfaction and retention, both crucial in today’s competitive market where attracting and retaining skilled talent is a challenge. Younger, tech-savvy employees expect workplaces to integrate digital technologies into their roles, such as video learning or hands-free devices, rather than relying on outdated manuals or clipboards.
Technologies like assisted reality (AR) devices can meet these expectations, but they must be aligned with workforce needs. For instance, AR devices can be integrated with digital workflow software and attached to safety helmets, allowing employees to use
voice commands to access training videos, manuals, mechanical drawings, and other essential materials.
By working with your team to identify the right technologies, you can add real value to workers while boosting productivity.
With the rapid rise of artificial intelligence (AI), capturing your organisation’s data and documenting employees’ daily workflows is more crucial than ever for leveraging AI effectively.
By recording how processes are carried out by staff, businesses can gain valuable insights into bottlenecks and capture the expert knowledge of experienced workers, ensuring it is passed on to future generations. This data becomes a key resource, ready to guide and shape the company’s digital transformation journey.
As AI becomes part of the industry’s daily operations in the near future, having evidence-based insights will be essential for identifying and addressing further areas for improvement, ensuring your business stays
competitive and innovative.
Employees are sometimes hesitant about digital transformation, but it doesn’t need to replace workers. When implemented with their involvement, it can empower teams by providing easier ways of working and actionable insights to enhance performance.
For example, Intoware’s digital workflow platform, WorkfloPlus, enhances health and safety with digital checklists, streamlines compliance tasks with consistent digital guidelines, and breaks down maintenance tasks into step-by-step workflows. Training certifications can also be kept up to date with alerts and qualification checks.
We are on the brink of significant digital change, not just in manufacturing and engineering, but across society. The companies that will succeed are those already embracing digital transformation, using the wealth of data within their organisations to drive progress and innovation.
intoware.com
For today’s manufacturers, the pressure to remain competitive while improving quality, efficiency, safety, and sustainability is relentless. That is where Prodigy SCADA steps in, as the following case study demonstrates.
Continuously improved over the past 40 years and fully developed in the UK by Tascomp, Prodigy SCADA provides a tailored, reliable, and highly flexible solution for all manufacturing facilities –regardless of size.
Prodigy SCADA will detect whether the temperature in a process is going up at the right rate or that the pressure is within tolerance. If it isn’t, it will produce a warning straight away, so you don’t get to the end of the process and then say, “Those parts don’t look right”.
Tascomp: “Some processes that we control might involve £200,000 worth of product, so you need to ensure that the process is right. First time. Every time.”
What truly sets Prodigy SCADA apart from other automation systems is its flexibility. The system is designed to meet the unique needs of any industrial process. Whether you need advanced process monitoring, end of line testing, batch data collection, or complex control capabilities, Prodigy SCADA delivers.
Prodigy’s support structure also differentiates it from the competition. Not only do you get a reliable system that helps improves operations, but you also gain direct access to a dedicated team of engineers and programmers. This means you get realtime support from experts who understand your system inside and out. No vapourware promises – just practical, real-world solutions from a UK-based team that’s been refining its approach for decades.
In an age where data is key to competitive advantage, Prodigy SCADA offers robust data recording, reporting and analysis tools that empower businesses to make informed decisions.
A large producer of malted ingredients has seen significant benefits from Prodigy’s advanced data capabilities, stating, “We predominantly use the [Prodigy] systems for process control, however, with a business focus on sustainability and process improvement, the use of trend data has been invaluable”.
Using Prodigy SCADA to deep dive into trend data and create automated, insightful reports, has revealed areas for significant improvement.
While Prodigy SCADA excels in complex, large-scale DCS environments, it’s also perfectly suited for smaller, niche applications.
A major supplier of cooking oil to one of the UK’s most iconic industries, fish and chips, needed to track their IBCs
(intermediate bulk containers).
Prodigy monitors tank levels, valve states, contents, IBC locations and IBC conditions. Utilising barcodes, scanners, and detailed reporting tools, Prodigy SCADA helped them reduce costly waste, maintain health and safety standards, and track IBCs throughout their entire journey –from cleaning to transportation and return.
Prodigy SCADA delivers results that count, right down to the last drop of oil in the fryer. The ability to improve processes and cut costs makes Prodigy an invaluable tool for manufacturers in all sectors, from pharmaceuticals, aerospace, automotive, textiles, metals, to plastics.
While many SCADA systems offer standard process control and monitoring features, Prodigy goes a step further. Its seamless integration with systems like PlantRun and ERP / MES allows businesses to combine their data sets effortlessly.
Prodigy also brings a host of features, including energy monitoring, audit trail logging, automated proof of process reporting, real-time thermal imaging, and, with its flexible licensing options and UK-based development team, Prodigy ensures manufacturers receive tailored, fully supported solutions designed to grow with them. With over four decades of development, Prodigy SCADA remains a trusted partner for manufacturers in the UK and beyond, continually evolving to meet ever-changing demands.
prodigyscada.com
The renowned Belgian brewery Chimay, known for its traditional Trappist beer, relies on maintenance-free spherical bearings from igus® in its bottling plant. The following case study demonstrates how switching to lubricant-free polymer bearings benefited the brewery.
The Chimay Brewery is one of thirteen breweries in the world that produces Trappist beer, made by monks. Interestingly, the majority of their profits are intended for social and environmental projects. Chimay have pledged to invest in reducing their ecological footprint installing 1200 photovoltaic panels and generating wind power with the wind turbine erected in 2020, creating a more energy-efficient bottling line.
Brewed at Notre-Dame de Scourmont Abbey in the Belgian province of Hainaut, Chimay produced around 18.5 megalitres of beer in 2018. The high production requirements posed special challenges for the bottling plants, especially due to frequent failures and the seizing of conventional metallic ball bearings to shafts.
The replacement of a defective ball bearing could take up to one and a half days, which unfortunately led to production losses. As part of a project to optimise the filling lines, Chimay turned to igus® to find a permanent solution to this problem. After an extensive series of tests and optimisations, the igubal H3 bearing proved to be the optimal choice and since the changeover in September 2022, these bearings have shown very little wear. By replacing rusty, seized ball bearings with lubrication-free igubal H3 bearing inserts, the brewery was able to increase efficiency and reduce maintenance.
Lubrication-free, safe and easy to clean
The igubal H3 bearings offer many advantages that significantly improve the brewery’s production process. They are made of tribologically optimised highperformance plastics. This makes them lubrication-free, maintenance-free and corrosion resistant. Even at speeds of 200 rpm, the bearing material is working well
within design limits. The igubal bearing inserts are much easier to install and replace than metal ball bearings, which drastically reduces maintenance times. In addition, there is no longer any wear-related shaft damage, which extends the service life of the entire system. Another advantage is the high resistance of the igubal H3 bearing inserts to chemicals. Despite regular cleaning processes, they show no signs of damage. Due to these characteristics, the line achieves an impressive speed of 55,000 bottles per hour. After a successful test phase on three different production conveyors, Chimay has already ordered 150 additional bearing inserts to replace the remaining ball bearings. “With the igubal H3 bearings, we have been able to solve the most important problem on our conveyor systems and significantly extend the service life of our systems,” says Vivien De Schryver, maintenance technician at Chimay.
This improvement in the efficiency and reliability of their bottling process will positively impact customer satisfaction. With fewer production interruptions and a more consistent output, Chimay can now better meet the demands of their customers with timely delivery of their renowned Trappist beer.
The use of lubrication-free igubal H3 bearings removes the need for lubricants, which are often petroleum-based and can be harmful to the environment. By eliminating the need for these lubricants, Chimay Brewery is not only enhancing the efficiency of their bottling process but also contributing to environmental sustainability, something that aligns with the brewery’s commitment to social responsibility and environmental stewardship.
igus.co.uk
• EC+ AHU efficiencies of 85%
• Energy savings of 20-50%
• Product lifetimes of 20+ years
• Recyclability rate of 98%
• Complete plug-and-play
• Ultra-low sound levels
• Low maintenance costs
• ROIs between 12-18 months
• EC+ AHU efficiencies of 85%
• Energy savings of 20-50%
• Product lifetimes of 20+ years
• Recyclability rate of 98%
• Complete plug-and-play
• Ultra-low sound levels
• Low maintenance costs
• ROIs between 12-18 months
Andrew Jones, Technical Sales Director at Axair Fans UK Limited, provides his candid take on the importance of respecting technical buyers during the sales process.
I’ve previously discussed the impact of complacency and frustration in technical industries and how looking at things differently can aid competitive advantage and open the door to new opportunities. Customers deserve more than they get from industry giants, regardless of spend or size, interactions should be frictionless and foster a collaborative work environment. Business leadership teams constantly talk about how they can improve their processes and systems, but how many spare a thought for customers buying solutions for organisations?
As the technical head of an engineering company, I speak to many buyers of industrial fans, and the positive feedback following the first interaction is often overwhelming. The thing is, buyers have a long, arduous, and heavy process that sales teams really don’t appreciate. Only after they’ve conducted extensive self-serve research, becoming subject matter experts in many niche components or applications themselves, do they think they can clearly and confidently express what they need. They want to speed this process up of course, but, admittedly, none of us like to speak to a salesperson who doesn’t add value or understand our specific requirements; it’s a painful experience, especially when we feel we know more about the component than the very people who are meant to be the experts. The biggest issue for these buyers isn’t finding suppliers, it’s trusting the information available, the people giving that information, and mitigating the risk associated with the solutions or suppliers offering them. Today’s
buyer journey, made more difficult by the vast amount of information online, has reached a point where it’s now difficult to navigate without a significant amount of help.
Our buyers don’t want more information, they want the right, relevant information to help them to pinpoint the right solution. Reports show that 84%* of technical buyers prefer purchasing from a company that understands their goals – they clearly want to be understood. I‘ve spoken about the benefits of collaborative working in previous articles, but this statistic really resonates with me. Our company, Axair Fans, has a set of values that every employee embodies in their everyday activities. A key value we live by is that “We Understand, Apply and Give Back”. This means that we focus on understanding
our customers’ needs before offering a solution. Our team are taught and reminded regularly that listening starts and ends with respect. It means we’ll actually hear and digest our customers points before offering our take. In an antiquated industry such as ours, there are lots of old school salespeople who are keen to speak, talk about product features or ask the next question, but they forget to listen. This creates a huge gap in communication at a stage that is highly significant to the buyer, who wants to ask questions about specifications, implementations, and the expected challenges of transitioning to our solution.
You must be genuinely interested in your clients’ challenges to operate in this way, because, ultimately, customers don’t buy products; they buy the results that the product gives. To appreciate this, you must show empathy for the customer’s plight and build an authentic and trusted relationship. In my experience, giving the buyer the control in the selection process ensures they can focus on their goals rather than being swayed towards the supplier’s own objectives. This doesn’t only help the buyer to navigate to the right decision using their own goals as the compass, it benefits the supplier, too.
In an economy where one of the most popular measures businesses are taking to remain solvent is improving efficiency, reducing friction in the purchasing journey and speeding up selection times makes a significant contribution.
axair-fans.co.uk *salesforce.com/uk/resources/articles/ customer-expectations/
In the age of Industry 4.0, the rapid expansion of interconnected devices presents discrete manufacturers with a growing set of challenges. Aerco, a long-established stockist and distributor of electrical components, details the benefits of Belden’s industrial automation solutions.
As more sensors, cameras, and actuators connect to factory networks, the demands for faster data speeds, increased bandwidth, and stronger security measures become ever more pressing. Discrete factories must not only keep pace with these changes but also future-proof their operations to remain competitive in a quickly evolving landscape.
Belden, industrial automation specialist, offers a comprehensive suite of solutions designed specifically for the unique requirements of discrete manufacturing. These solutions combine scalable technology, robust security, and flexible configuration options to ensure manufacturers can adapt to the changing needs of their networks.
One of the primary challenges facing discrete manufacturers is the ability to handle an ever-increasing amount of data traffic. As more devices become part of the production process, the demand for bandwidth grows. Belden’s solutions provide the flexibility and scalability to meet current demands while also preparing for future growth.
At the heart of this strategy is the BEETLE Lite Managed Switch from Lumberg Automation. This switch supports Single Pair Ethernet (SPE) technology, which allows for future-ready networks while addressing space and weight constraints. The BEETLE Lite simplifies infrastructure by reducing cable complexity, making it ideal for applications where space is at a premium.
For manufacturers looking to upgrade their network backbone or aggregation layers, Belden’s Hirschmann GREYHOUND 105/106 Ethernet switches provide a
powerful, future-proof solution. These multipurpose switches offer fast and secure connectivity, with up to 30 ports in a compact form factor. The GRS105 model features 2.5 Gigabit uplink ports, while the GRS106 model includes 10 Gigabit uplink ports. This versatility ensures that manufacturers can select the appropriate model based on their specific needs. Both models utilise HiOS switch software, which provides high performance, network redundancy, and robust security features to safeguard data flow across industrial networks.
These switches are designed to handle the harsh conditions of industrial environments, offering protection against extreme temperatures, dust, and vibration. With their compact size and ability to be mounted in control cabinets, they seamlessly integrate into existing infrastructure without the need for powerful cooling systems.
As the number of connected devices grows, so does the risk of cyberattacks. Belden’s Hirschmann EAGLE40 series firewalls deliver advanced multi-layer cybersecurity to protect against these threats. These firewalls are compliant with key industry standards, including NERC CIP, IEC 62443, and NIST, ensuring that
manufacturers are equipped with the latest in cybersecurity protections. The EAGLE40 firewalls support IT/OT convergence, making them a critical component in the seamless integration of enterprise and factory networks. Built for the rigors of industrial environments, these firewalls help ensure network uptime and provide comprehensive protection against cyber threats, keeping sensitive data secure.
Belden’s commitment to reducing complexity and optimising network performance is further demonstrated through its DataTuff Single Pair Ethernet (SPE) cables. These cables enable fast data communication and power delivery to the network edge, minimising cable footprints and simplifying network architecture. When paired with Belden’s switches and firewalls, DataTuff cables contribute to a streamlined, efficient network design that meets both current and future operational needs.
Belden’s portfolio offers a range of interoperable hardware and software solutions tailored to meet the specific needs of each manufacturing operation. aerco.co.uk
Long-duration weather balloons have become instrumental in monitoring the impacts of climate change. Brainboxes, leading communications device developer, explains how Pure Embedded Ethernet switches can transform atmospheric data collection at high-altitude.
According to the National Oceanic and Atmospheric Administration (NOAA), the global average atmospheric CO2 level reached 422.99 parts per million (ppm) in August 2024, setting a new record high* and highlighting the critical importance of ongoing atmospheric monitoring to understand and address the impacts of climate change.
Against these global climate challenges, weather balloon missions have taken on unprecedented importance in gathering critical meteorological data at various altitudes within Earth’s atmosphere. By installing Brainboxes’ compact and highperformance Pure Embedded Ethernet switches, weather balloon missions can transmit data more reliably, in real-time, while significantly minimising the impact on payload weight and size.
matter, allowing maximised use of limited payload space, and enabling the inclusion of additional scientific instruments without compromising on networking capabilities.
in the market between traditional embedded boards and chips, offering a cost-effective solution that doesn’t compromise on performance. This is particularly valuable in weather balloon applications, where budget constraints often compete with the need for high-quality data collection. For telemetry systems, where choices are often limited by factors such as altitude restrictions for cellular systems or the high costs of satellitebased solutions, Brainboxes Pure Embedded switches offer boardto-board and board-to-cable connection options, providing the flexibility needed for different requirements and budgets.
Recent technological advancements have led to smart, long-duration weather balloons capable of flying hundreds of times longer than traditional weather balloons to circumnavigate the globe collecting critical weather data from areas previously undersampled or missed altogether. Brainboxes Pure Embedded Ethernet switches, available in both 10/100 and Gigabit versions, allow optimised data transmission in weather balloon applications in several key ways.
Pure Embedded switches stand out for their exceptionally compact and lightweight design, crucial for weather balloon payloads, which have strict space and weight limitations. Measuring just 55x55x10mm – smaller than a standard business card –these switches are the perfect solution for applications where every millimetre and gram
Despite their small size, Pure Embedded switches are expertly engineered to withstand extreme conditions, operating reliably in temperatures ranging from -40°C to +85°C. This durability is essential for weather balloon missions, which expose equipment to harsh environmental conditions including rapid temperature changes and high-altitude pressures.
Advanced weather telemetry systems can save over 500 megatons of carbon emissions by improving ship and plane routing and accelerating the transition to renewable energy. Innovative designs, such as automatic valves that release helium at set pressures for controlled descents below 10 m/s, not only increase measurement quality but also enable data collection from the same air column twice. The high data throughput of Brainboxes Pure Embedded Gigabit switches ensures real-time transmission of this increased data volume, preserving all valuable information.
Pure Embedded switches fill a crucial gap
Brainboxes offers a 10-year stability guarantee for its Pure Embedded switches, meaning the design will remain available and unchanged for at least a decade from launch. For industries relying on futureproofed, consistent performance this guarantee is invaluable
Brainboxes Pure Embedded Ethernet switches represent a significant advancement in networking technology for weather balloon telemetry and beyond. Their compact and lightweight design, robust performance, and long-term stability makes them an ideal solution for a wide range of applications where space is limited but data transmission demands are high. As we continue to face environmental challenges, such innovative technologies will be crucial in our efforts to monitor, understand, and address the impacts of climate change brainboxes.com
*National Oceanic and Atmospheric Administration (NOAA), Global Monitoring Laboratory. “Trends in Atmospheric Carbon Dioxide.” Updated 2024.
The adhesives industry has a poor sustainability track record. Permabond, an adhesives manufacturer with a keen eye on the future, is looking to change this. MEPCA discovers how.
Sustainability in adhesives is becoming an issue of ever greater concern for design engineers and manufacturers. Most adhesives are generally not environmentally friendly, being either petrochemically derived and/or solventbased. Synthetic adhesives don’t break down in nature and, if not disposed of properly, can cause harm to water and plant life. The adhesives industry as a whole has been slow to react to changing customer demand for ‘greener’ products, partly hindered by the inherent nature of adhesives themselves, as well as the higher cost of renewable raw materials.
A fascinating development in the world of adhesive sustainability is the use of cashew nut shells as a sustainable, renewable and affordable product. More specifically, the cashew tree produces a resin called cashew nut shell liquid (CNSL), which contains compounds such as anacardic acid that provide adhesive properties. CNSL has thermosetting properties, making it very well suited as a wood adhesive and for coatings. It’s also great as an epoxy resin, as it’s able to form strong bonds on a wide variety of substrates such as metals and plastics. Permabond has recently developed new two-part epoxies, Permabond ET5393 and ET5164, which contain CNSL in their hardener component. ET5393 bonds well to a wide variety of substrates and is particularly effective on stainless steel, while ET5164 offers both FDA and EU food grade conformity.
Another area of sustainability that the company have been working on is adhesive cartridges made from recycled plastics. Permabond’s ET5393 epoxy comes in postconsumer recycled (PCR) polypropylene cartridges, as does its ET5164 food-grade epoxy. These cartridges create 38% fewer CO2 emissions during production compared to cartridges made of conventional, nonrecycled plastic, without any compromise in quality and strength.
Permabond has also been looking at ways to reduce potential hazards, both to health and to the environment, when using its products. Businesses and manufacturers, particularly those based in Europe, are actively looking for ways to reduce their environmental footprint and create a safer workplace for their staff. EU REACH regulations and the ever-growing list of substances of very high concern (SVHCs) necessitate forward and flexible thinking in
this area to meet customer demand. To this end, creating new formulations that bear fewer GSH hazard symbols, including those with none (socalled ‘white label’ adhesives) has become a higher priority. Permabond will soon be exhibiting at Advanced Engineering at the NEC in Birmingham. A point of interest for anyone at the show who’d like to pay Permadbond a visit is a bike provided by Field Cycles, a company in Sheffield specialising in making handmade bikes. Permabond have been working on a wheel hub application for Field Cycles, bonding titanium to carbon fibre using a two-part epoxy adhesive.
Before using its adhesive, the carbon fibre was experiencing substrate failure. Since carbon fibre is such a lightweight material, mechanical fastenings were out of the question due to the added weight they would impart, as well as the fact that they would ruin the structural integrity of the composite and concentrate stress in weak areas. Welding is not possible as carbon fibre won’t melt. Adhesives, on the other hand, are lightweight, aesthetically pleasing and also ensure better overall stress distribution across the entire bike – they really are the only reliable, effective solution for bonding carbon fibre.
Attendees of Advanced Engineering interested in learning more about sustainability in the world of adhesives should visit Permabond at stand Q120 in hall 3.
permabond.com
Innovating sustainable adhesives to help you achieve your green ambitions
With Advanced Engineering 2024 a matter of days away, Hamamatsu Photonics is preparing to welcome attendees to its stand. Read on for reasons to visit the company this year, including a preview of its technology.
Hamamatsu Photonics is a global leader in photonics technology, offering cutting-edge light-based solutions that transform not only industrial manufacturing, but also diverse sectors such as healthcare, scientific research and environmental monitoring. The company’s comprehensive range of advanced photonic devices is designed to enhance precision, improve efficiency and ensure superior quality control. At Advanced Engineering 2024, the company will showcase technologies that cater to a broad range of industries, helping businesses stay competitive in an era driven by automation and scientific advancement.
In manufacturing, the company’s photonic solutions help industries such as electronics, automotive and semiconductor wafer fabrication achieve high levels of accuracy and efficiency. Hamamatsu’s high-speed optical sensors detect defects in real time, preventing costly errors and ensuring smooth production. From laser heating systems for plastics welding, to area image sensors capable of hyperspectral imaging for material inspection, Hamamatsu’s technologies offer reliable, high-performance solutions.
With the increasing demand for automation and Industry 4.0 technologies, Hamamatsu’s photonic components, encompassing both detectors and light sources, are essential for the development of intelligent inspection and detection systems. These systems not only optimise operations, but also enable manufacturers to implement predictive maintenance strategies and increase throughput.
Hamamatsu’s expertise in imaging
allows us to offer solutions tailored to each industry’s unique challenges. For example, in materials analysis, the company’s equipment enables detailed examination of raw materials and finished products, ensuring the highest standards of quality. For machine vision systems, its sensors enable automated inspection, providing the greatest levels of speed and accuracy.
Beyond industrial manufacturing, Hamamatsu Photonics’ versatile technologies extend its reach into multiple sectors. For scientific research, it provides photodetectors and spectroscopy systems in fields ranging from quantum physics to environmental science. Additionally, the company’s technologies for optical coherence tomography (OCT) and fluorescence imaging serve medical and research applications, highlighting the flexibility of its photonic technologies across disciplines.
Customers encounter a variety of challenges when selecting products, including performance requirements, operating environments, size and shape. The
Hamamatsu customisation process begins with in-depth consultations with its team of specialised engineers to accurately identify the specifications, encompassing everything from material selection to the initial design phase.
The company prioritise understanding the specific challenges customers face to ensure that its solutions are not only effective but also sustainable and compliant with industry standards. Leveraging its advanced technologies and extensive expertise, the company is committed to delivering tailored solutions that precisely meet unique needs.
Join Hamamatsu at STAND J120 during Advanced Engineering 2024 to explore their latest innovations in industrial manufacturing and beyond. Learn how their latest technologies can streamline production processes, enhance product quality, and support your business goals in today’s fast-evolving landscape. Attendees will also have the opportunity to participate in Hamamatsu’s “Light Speed Racing” competition for a chance to win fantastic prize bundles. hamamatsu.com
Undetected thermal anomalies can have disastrous consequences in steel production, but achieving reliable, real time temperature monitoring can be challenging in this environment.
Quantum Design UK and Ireland, distributer of high-tech instrumentation, highlights the benefits of thermographic monitoring.
Steel production and processing are accompanied by numerous thermal processes. For quality assurance purposes, the temperatures of the steel itself are recorded and evaluated during production.
Careful attention must also be paid to the tools and equipment needed for production, including the cranes used to transport the ladles of pig iron. The crane ropes are exposed to great heat when filling the converter (known as “charging”). If the ropes become thermally overloaded and simultaneously subjected to strong mechanical stress, they can break, causing molten steel to leak into the production hall. In order to reliably eliminate the likelihood of such a disastrous scenario, a thermographic camera provides a continuous real time temperature measurement and threshold alarming. This allows the reliable early detection of weak points through noncontact monitoring of the temperature of the crane ropes.
Requirements for a thermographic system are very high in this environment. Thermal anomalies must be detected from a great distance despite dust and steam on the very small structures of the rope. Furthermore, the ropes themselves are in front of a hot background.
InfraTec provides a solution to this task with the VarioCAM® HD head. The camera is protected from adverse environmental conditions by a special protective housing with cooling and air purge and equipped with special tele-optics as well as an interface to the control system of the steelworks. Temperature measurement is carried out fully automatically with two cameras on each converter – one for monitoring directly during
charging and one for a repeat inspection after this process.
The data is transmitted to the control system where it is displayed on a screen. If the pre-configured temperature thresholds are exceeded, an automatic warning is issued by the system and then, if necessary, an alarm is issued for each crane. The special software required was especially adapted for this process and its demands and is based on the INDU-SCAN 4.0 software from InfraTec.
The benefits of thermographic crane rope monitoring:
• Full automatic operation without stopping the crane
• Monitoring and thermal characterisation of the crane rope even under difficult visibility conditions for the safe prevention of accidents or damage
• High-resolution thermographic camera technology in a robust protective camera housing that protects against dirt and heat
• Reliable alarm release at defined pre and main alarm limits
• Customised system alignment and adjustment
• Software for parameterisation, supervision, operation, display, evaluation and playback
• Easy to operate data presentation in the steel plant network
• Remote access available
Employing advanced thermographic monitoring technology, such as InfraTec’s, can mitigate the risk of crane ropes breaking unexpectedly. The technology achieves this through the contactless measurement of temperature distributions and profiles with industrial thermographic cameras. Leading examples of thermographic technology – like that detailed above – also permit efficient monitoring and control of temperaturedependent processes and procedures within a system-integrated quality assurance programme.
Thermographic monitoring is suited for many other areas of application within metal production and processing, where even minimal deviations in temperature can have serious impacts on production. InfraTec products are available through Quantum Design UK and Ireland.
qd-uki.co.uk
Warehouse modernisation can increase performance and service life. Edward Hutchison, Managing Director of BITO Storage Systems asks: have you considered retrofitting existing pallet racking?
As logistics operations and warehouses grow older, not only does the technology contained within wear out, incurring more regular downtime, it also naturally becomes outdated – unable to keep pace with modern requirements driven by omnichannel logistics, e-commerce, the demand for small order sizes and handling faster order picking speeds.
It makes sense to plan modernisation before a system or equipment reaches service life expiry. Those concerned about the cost and convenience of a major replacement or modernisation programme should consider retrofitting.
Modernisation offers the opportunity to adapt intralogistics systems to meet new requirements and to make them more efficient and reliable. This means maintaining the basic structure of a warehouse in terms of storage zones, layout, conveyor and storage systems, but modernising individual items of materials equipment and creating new processes. This will increase performance, improve overall warehouse system availability and can even avoid the expense of constructing a new building or extending an existing facility.
A retrofit is a refurbishment and modernisation of existing intralogistics systems. The advantages of retrofitting include lower planning and implementation costs compared to a new purchase or new installation. The risk of failure is also reduced compared to completely new systems. Not only is modernisation in this way resource-
friendly, but also employees can continue to work in the existing facility for as long as possible.
Many individual areas can benefit from retrofitting; one important area to focus on is picking operations. If a picking system no longer proves efficient and ergonomic, a company must be able to react quickly to adapt their existing storage system to the new conditions. Given that most warehouses have pallet racking as their major item of materials handling equipment, this presents a great opportunity for modernisation, with a number of picking options that can be retrofitted in pallet racking at ground level –the prime order picking area.
BITO pallet racking has been designed to allow fast adaptation to different needs, providing customers with a maximum amount of flexibility. The vast range of accessories and ancillary products allow many easy-to-implement reconfiguration variants. For example, by fitting flow levels at
floor height, pallet racking can be adapted for picking individual packaging units or single items whereas the pallet storage levels on top are used as a buffer store.
Retrofitting options for pallet racking include drop in sections of roller tracks for unit or piece picking, push-back roller track levels also for unit or piece picking, full-width roller lanes for pallets, container pick walls, shelving, drop-on wire shelves, chipboard panel decking, inclined shelving and steel panel decking.
The advantages include a substantially higher number of reference lines, shorter travel routes, reduced pick times, maximum configuration flexibility and excellent ergonomic conditions for strain-free working.
Of course, modernisation does not result in a new warehouse, but it will bring it up to date and extend its service life. The project will involve investment, a detailed concept and preliminary planning. The new components have to be coordinated with the existing ones. It is also important to ensure that existing components are not overloaded by the performance of the new ones, risking failure. The implementation of retrofitting measures during ongoing operation must also be planned in detail so that warehouse operations are not disturbed or even interrupted.
It is worth seeking out a storage system supplier, such as BITO, to ensure the modernised system is designed to fit a given space, maximising the potential for improved picking efficiency and material flow. bito.com
The Silverson product range boasts the largest capacity range from a single manufacturer, from mixers capable of mixing volumes as small as 1ml, up to 30,000 litres. With Silverson having now also launched a small-scale mixing range, MEPCA looks at the company’s extensive catalogue.
High shear mixing involves intense mechanical agitation and shearing forces to achieve superior blending, dispersion, and particle size reduction. Unlike conventional mixers or agitators, high shear mixers utilise specialised rotor/stator technology to generate extremely high shear rates, creating a powerful suction effect that continuously draws materials into the high shear zone. This enables faster processing times and increased production throughput, finer and more uniform dispersions and particle size distribution, as well as improved product quality, consistency and stability, batch-afterbatch.
The popularity of Silverson Laboratory multipurpose Laboratory mixers can be attributed to their versatility; they can be used to mix, emulsify, homogenise, disintegrate and dissolve, with an efficiency and flexibility unmatched by other machines.
A range of over 40 workheads, screens and assemblies makes these Laboratory mixers even more versatile. The easily interchangeable workheads enable any machine to perform a wide range of mixing operations; this allows one mixer to perform duties that in the past may have required several different pieces of processing equipment.
As well as the workheads supplied as standard with the mixer, this range offers an In-Line assembly for the L5 Series. This assembly converts the L5 mixer to an In-Line mixer/homogeniser with a throughput of approximately 20 litres/minute. The Duplex mixing assembly converts the L5 series into a small-scale version of the production scale Duplex machine, ideal for disintegration and solubilisation of solids, high viscosity mixes, or the incorporation of powders with a tendency to float. Other assemblies include Tubular units for narrow-necked containers, Sealed Units for sterile materials and an
Ultramix powder/liquid mixing assembly. The Silverson Verso, a bench-top In-Line mixer, and the Silverson FMX5, a laboratory-scale powder/liquid mixer, are also available. One of the key benefits from using Silverson laboratory equipment is the accuracy with which the performance of the production-scale mixers can be predicted based on laboratory trials. Silverson’s laboratory mixers are designed and built to the same tolerances as the production units; comparable rotor tip speed and shear rates across its entire product line means scalable results, every time.
The company has just launched a new range of mixers for small-scale production designed to bridge the gap between laboratory mixers and full-scale production machines. The range includes an “Ultra Hygienic” specification In-Line mixer, an InLine mixer suitable for higher viscosity mixes, a small-scale Multistage In-Line mixer and a Powder/Liquid mixer, the FMX10. These new mixers complement the different types of laboratory and production models already
available from Silverson, but also offer customers more options in terms of batch sizes and processing requirements. They are particularly useful in applications where the smallest production-scale mixers may be too large, but laboratory equipment may not offer sufficient capacity.
All mixers available at laboratory or smallscale in the Silverson product range have a production scale equivalent. Laboratory mixers can be scaled-up to in-tank mixers such as Silverson Batch, Ultramix or Duplex models.
Silverson’s line of production-scale high shear In-Line mixers offers a great many advantages – speed, versatility, aerationfree mixing, and guaranteed efficiency. Capable of self-pumping throughputs of up to 200,000 litres per hour, these mixers are ideal for continuous mixing. These mixers can be supplied as General Purpose, Ultra-Hygienic, Multistage, High Viscosity and as Jacketed models, depending on the application. Information on other models is available on Silverson’s website. silverson.co.uk
As a leading supplier of precision motion control products for over 40 years, we have a commitment to technical excellence and customer service and adopt a partnership approach to business. We offer our customers a professional specification and design & build service, backed up with qualified and experienced technical sales and applications support staff.
• Cost-optimised, microstepping 2-phase, 1.8° stepper motors in NEMA sizes 08 through 34
• Aimed at the unique demands of OEM users
• Stock availability for standard products and fast turnaround for application customisation
• Extended torque performance and smooth operation, suiting dynamic motion positioning and speed control applications
• Microstepping drives: 3, 6 and 10 Amps/Phase
• Optimal use for automation and motion control systems where Industrial Ethernet is preferred
• EtherCAT, EtherNet/IP, CANopen, Modbus, Ethernet (UDP & TCP), and RS-485
• Command streaming or store complete programs for multi-axis synchronisation
Ian Kelsall, Technical Specialist, Respiratory Protection Equipment (RPE), Draeger Safety UK, explains the significance of inclusivity in respiratory protection.
Providing respiratory protection equipment (RPE) for employees is a wellrecognised and generally well-understood requirement for employers to comply with the Health and Safety at Work Act 1974 and the Management of Health and Safety at Work Regulations 1999. Supplying equipment that truly fits, such as Filtering Face Piece (FFP) disposable masks that provide critical respiratory protection from solid or liquid particles including dusts, mists and fumes is a more complex area, however.
One of the reasons for this is the increasing diversity of colleagues in workforces, which is leading to greater representation across age, ethnicities and religions. Despite this evolution, protective
equipment design is largely unchanged.
Historically, respirator mask certification has been based on standardised adult head shape panels, using a model developed in the 1960s from studying white male military personnel in the US Airforce. This approach provided very little accommodation for those who fall outside of these specifications. However, facial dimensions vary significantly between genders, ethnicities and with age, as well on an individual basis.
Today, in the UK BSI standards are based on the 50th percentile of four dimensions – face length, face width, face depth and mouth width, originally of the adult white male face shape, but more recently a more ethnically diverse sample group has been used.
To focus on healthcare as an example,
the NHS is the largest employer in the UKi., and also one of largest employers globally.
The Kings Fundii. estimates that nearly three quarters of the NHS’s employees (74%) are women and nearly a third (31%) are from an Asian background. Both of these groups are – on average – genetically inclined to be smaller-framed than the average white male. A study carried out in NHS hospitalsiii. in 2023 involving 5,604 healthcare workers concluded that female and nonwhite ethnicities were less likely to have a successful respirator fitting, while male and white ethnicity healthcare workers were most likely to achieve RPE fit test success.
Whilst this is perhaps not wholly surprising, it is concerning, and illustrates that a standard design FFP mask will typically not accommodate the variety of
face shapes and facial features present across industries in the UK. While not all of these industries will have the significant diversity present in the NHS, the fit of respiratory protection needs to be suitable for all face shapes to accommodate all.
The HSE states that there are two essential questions when specifying respiratory protection equipment. The first, which is usually given greater focus, is the question ‘Is the equipment adequate?’ I.e., is it appropriate for the hazard and does it reduce exposure to the level needed to protect the health of the worker? However, the second question is equally important to ask, ‘Is the equipment suitable for the wearer, the task and the environment?’ This can be more challenging as it includes the suitability for an individual.
Employers are legally required to carry out fit testing for all their employees who wear tight-fitting respirators, and to find a mask that will fit and is suitable for every individual. This is where problems arise.
Fit is clearly an essential component to ensure safety across all workplace environments, but when it comes to respiratory protection, safety of the workforce can also be affected by employees not complying with wearing the equipment. Once again fit is also relevant here, as poor fitting respiratory equipment will be uncomfortable, or the mask simply ‘won’t feel right’ and therefore workers may wear the RPE incorrectly, or not at all.
When it comes to the fit of a mask, design plays a crucial role and is key to creating RPE that meets the changing requirements of today’s diverse workforce. By understanding the needs of different workers, designers can create PPE that is both functional and comfortable (i.e. adequate and suitable). It is therefore important to consider factors such as fit, weight, and breathability of the mask, as well as the specific hazards that workers may face.
As a leading global manufacturer of RPE, Dräger has wide-ranging experience across a broad portfolio of air purifying respirators from FFP masks to Powered Air Purifying Respiratory Protection (PAPR).
When it came to developing Dräger’s FFP3 1930, a high-performance, singleuse dust mask which is used to provide protection from fine dust and particles, designing a mask which provides a good fit
for as many different face shapes and sizes as possible was the priority.
Customer research was conducted with thirty six customers across seven countries, benchmarking sixteen products, with fifty participants in total, looking at a wide range of face shapes and sizes. The faces of the participants were mapped using a grid system, which looked at the face width, length, depth and mouth width.
Analysis of this information found that by employing an innovative design approach, which focused on a pioneering three-fold model, greater flexibility in both height and width is achieved. This, combined with easy-adjustment capabilities, ensures that the mask stays in place – something that is particularly important in allowing the wearer to speak while maintaining the all-important protective seal for a perfect fit. At the same time, the use of a flexible nose clip and soft wide nose pads enables the mask to be effectively positioned and securely sealed in the nose area. In addition, it was found that developing masks in two sizes would accommodate the majority of different face shapes and sizes, and extensive testing by Dräger showed a 96% pass rate in face fit test procedures using this design.
Of course, a wide range of other questions also affect whether a particular mask is suitable for the individual wearer. Do they have wrinkles, moles, warts, deep cuts or scars, or struggle with a tight fit for medical reasons? Does the wearer have facial hair, or stubble?
For these groups a mask is often not an option, so a different approach is needed.
In these scenarios, a Powered Air Purifying Respirator (PAPR) would be a more appropriate solution. When fitted using a loose-fitting headpiece that covers the entire head, it negates the need for a tight fit and a face seal, allowing a wider range of workers to remain safe in the workplace. Therefore, many employers specifying RPE for a diverse workforce are turning to PAPR as a solution.
Finally, once the fit and specification have been addressed, it is essential that the equipment be used correctly. Wearers must be trained on how to use masks, the importance of fitting them to their faces and getting a seal every time and education on topics such as why being clean-shaven is essential. Added to this, instructions on how to store and maintain masks appropriately must be explained by the employer and followed by the employee.
In conclusion, equipment that is functional, comfortable and suitable for the needs of the workforce, used and maintained properly, will keep those at risk of respiratory hazards safe: both from the hazards present today and from those that may be experienced in the future. Central to this is equipment that is appropriate for all.
draeger.com
i. Nuffield Trust, The NHS Workforce in Numbers, February 2024
ii.The Kings Fund, The NHS Workforce in a Nutshell, Saoirse Mallorie, May 2024
iii. Retrospective evaluation of factors affecting successful fit testing of respiratory protective equipment during the early phase of COVID19P Worsley et al, BMJ 2023
As online purchasing continues to gain popularity, even within specialised sectors like the food machinery industry, the importance of clarity and transparency cannot be overstated. Industrial Auctions, the leading online auctioneer, explains why.
Buyers are increasingly turning to online platforms to procure machinery, attracted by the convenience and broad selection available. However, this shift also underscores the need for clear information to build trust and ensure satisfactory transactions.
In the realm of online auctions, transparency is not just a virtue but a necessity. It forms the bedrock of trust, ensuring that bidders have confidence in the process, and in the items they are bidding on. Industrial Auctions, the online auctioneer to buy or sell your food and beverage machines, recognises the importance of transparency and strives to uphold it in every aspect of its operations.
Firstly, detailed and accurate descriptions of auction items are paramount. Each item listed in the company’s auctions comes with comprehensive information, including clear, high-quality images, precise specifications, any known history or issues, and, when available, even videos of the machines in working condition when available. This level of detail helps bidders make informed decisions, knowing exactly what they are purchasing. By providing thorough descriptions, the auctioneer eliminates guesswork and enhances bidder confidence.
Secondly, Industrial Auctions believes in clear communication throughout the auction process; its customer service team is readily available to answer any queries, provide additional information, and assist with any concerns that may arise. An open line of communication ensures that potential buyers feel supported and valued, further reinforcing
trust in the auction platform.
From the knowledge Industrial Auctions has gained over the years in the food and beverage industry, it knows that attention to detail, a strong commitment to providing a highly valued service, and maintaining toplevel professionalism from start to finish is what buyers require.
The auctioneer does organise viewing days for each and every auction. If potential buyers would like to inspect the machinery or equipment from up close, they are always welcome to make an appointment and pay a visit to the auction location.
Transparency also extends to the bidding process. The bidding process is straightforward and all bids are visible to participants in real-time. If a bid is placed in the last 5 minutes before the closure of a lot, the closing time will be extended. This process continues until no more bids are made in the last 5 minutes before the closing
time, which ensures fair competition and gives everyone an equal chance in winning the lot.
The company also provides clear terms and conditions, so that bidders understand the rules and expectations from the outset. Moreover, the auctioneer is committed to post-auction transparency. Winning bidders receive detailed invoices, and the company provides full disclosure of any fees or additional costs. The goal is to ensure there are no surprises and that buyers feel they have received fair value for their purchases.
In summary, transparency builds trust, fosters confidence, and ensures a positive experience for all participants. Industrial Auctions is dedicated to maintaining their level of transparency in its online auctions, ensuring that every bidder feels informed, confident, and valued. This commitment to transparency not only distinguishes the company in the marketplace but also ensures that its clients can participate in its auctions with complete peace of mind. industrial-auctions.com
On 28th November, Newcastle will host Manufacturing and Engineering North East (MENE) 2024, the region’s premier event for the manufacturing and engineering community.
As the final major trade show of the year, MENE is set to bring together over 800 professionals for a day of innovation, collaboration, and growth. Held at the Vertu Motors Arena, the event will feature 80+ exhibitors, live product demonstrations, expert-led sessions, and the launch of a dedicated Careers Corner.
MENE is designed not only to showcase the latest innovations but also to strengthen connections within the region’s industrial community. Unlike many industry shows that are concentrated in the Midlands or further south, MENE provides a unique opportunity for engineering professionals to gather in Newcastle. As David Harrison from Newcastle College University remarked at last year’s show, “It’s quite hard for the people of the North East to get to engineering exhibitions, so it’s great to see it.”
companies such as Advanced Adhesives, MEC Machine Tools, and Starrag will be showcasing their cutting-edge solutions.
With over 80 exhibitors, covering the entire supply chain, from automotive and aerospace to 3D printing, electronics, adhesives, motion control, and machine tools. Top suppliers from across the sector will showcase their latest products, technologies, and services, providing attendees with valuable insights and opportunities. Whether you’re seeking new partners or aiming to stay ahead of industry trends, MENE has you covered. Exhibitors will include both local and UK-based industry leaders, offering a strong mix of expertise and innovation. Major Newcastle-based
This year, Manufacturing and Engineering North East is partnering with the Advanced Manufacturing Forum (AMF), a prominent membership network for the manufacturing and engineering community in the North East. AMF connects local professionals to promote collaboration and drive business growth. By facilitating knowledge exchange and networking opportunities, AMF supports its members in navigating the challenges of today’s industrial landscape.
The Student Engineer is a new initiative from The Engineer UK, aimed at supporting students and graduates as they start their careers in engineering. This programme features a newsletter and an online channel
that offer a lively mix of news, careers advice, and interviews with leading employers. With inspiring profiles of successful graduate engineers and information on the latest job opportunities, The Student Engineer seeks to help students navigate their path into the profession while fostering better communication between industry and the engineers of tomorrow. At MENE 2024, The Student Engineer will host drop-in advice clinics, providing students with the opportunity to seek guidance from industry experts.
Alongside the exhibition and product demonstrations, MENE will once again host a series of expert-led conference sessions. Attendees can gain valuable insights from industry leaders and engage in discussions on key topics such as Industry 4.0, skills shortage, supply chain challenges, and sustainability. These sessions will explore the latest trends and innovations in manufacturing and engineering, providing practical solutions to pressing industry issues. The interactive format encourages participants to ask questions, share ideas, and engage in meaningful dialogue with thought leaders and peers.
Registration is now open, and with so much to offer, MENE 2024 is an unmissable event. Join the North East’s top manufacturing and engineering professionals in Newcastle this November and celebrate the best of Northern England’s industrial sector.
menortheast.co.uk/MENE2024
Attend
Watch
Explore
Easyfairs, the new owner of the Southern Manufacturing & Electronics exhibition, is delighted to announce that the 2025 show will be the biggest in its 28-year history.
This year’s event will boast more than 500 stands, split approximately equally between companies operating in the mechanical engineering and electrical/electronics sectors. To be held at the Farnborough International Exhibition & Conference Centre from 4th to 6th February 2025, it is the most important annual trade fair in the UK calendar. It is certainly the most comprehensive in terms of not only the products and technology on show, but also the breadth of subcontract manufacturing and support services on offer.
Having such a large variety of exhibitors in the same place makes the event ideal for anyone involved in design, manufacture, procurement, training or management to carry out comprehensive market research and address multiple purchasing requirements efficiently. The organisers operate an open access policy to firms of all sizes, which gives the exhibition a unique quality that encourages networking and makes it an ideal place to do business. Technology Trails grouping firms with expertise in specific areas help to guide visitors around the stands.
This year’s show will reflect the ongoing growth in digitalisation of production, as well as an increase in manufacturing systems that may be interconnected via Industry 4.0 protocols. On the mechanical engineering side, there will be all the latest in machine tools, tooling, workholding and other production hardware, plus suppliers of castings, plastic injection and rubber mouldings, fasteners, pressings, wireforms, springs and gaskets. On the electronics side, featured will be PCB design, box build services, cables and connectors. Spanning both disciplines will be mechatronics assembly, electro-mechanical components and systems, controls, displays, HMIs and data acquisition systems, sensors,
drives and encoders, neatly illustrating how intertwined the two engineering sectors are.
Testing, inspection and measurement serving all industry sectors will be in evidence throughout, as will production planning systems, engineering and business software, materials and consumables. Additional products and services essential for the smooth running of businesses will include oil and coolant, waste recycling, environmental control equipment, packaging and storage, labelling, hand tools, adhesives, and diverse services from freighting to financial consultancy.
Although it will be business as usual at the show, people will notice some important changes that will take the user experience to the next level. Leveraging the latest developments in digital marketing technology, there will be new Smart Badge technology for visitors featuring an embedded NFC chip that may be slid over an exhibitor’s unique EasyGo badge reader. The person will then receive an email containing a list of all stands that have been visited and details of what they were displaying. Likewise, without any effort, the exhibitor will have a record of who has
visited. There will also be a Visit Connect app for sharing information.
Throughout the three days, visitors will be able to take advantage of an extensive programme of free-to-attend technical seminars covering a wide range of topics to give visitors and exhibitors alike valuable learning opportunities, with a particular focus on the technical, managerial and environmental issues facing manufacturers today. The Institute for Interconnecting and Packaging Electronic Circuits (IPC) hand soldering competition returns in 2025, as does AutoAero, a specialist thread that runs through the main programme concentrating on matters important to automotive and aerospace engineering.
Register today via Southern Manufacturing & Electronics website to receive your free entry ticket with code 1027. A regular, complimentary bus service runs between Farnborough’s two railway stations and the showground, which is also easily accessible by road. Car parking is free and very close to the exhibition. The current exhibitor list is also available to view on the website. southern-manufacturing-electronics. com
Advanced Engineering, the eagerly awaited engineering and manufacturing event, has announced this year’s keynote speakers. The premier show promises to treat attendees to an inspiring lineup this October.
The six industry leaders — and 150 plus other speakers — will share their expertise and insights on critical industry issues during talks across several different forums. The two-day show will take place at the NEC in Birmingham on October 30 and 31, 2024.
The first of this year’s keynote speakers, Brian Holliday, is a leading figure in industrial technology and digital manufacturing. As the head of Siemens Digital Industries for the UK and Ireland, he oversees advanced automation, industry software, systems integration and R&D. He is an expert on productivity, digital manufacturing and industrial strategy, often contributing to media discussions.
The next speaker Matthew Atkinson, lead research engineer at Jaguar Land Rover, is an expert in automotive engineering, specialising in replacing metallic structures with injection-moulded composites. His work focusses on interior mechanical commodities like cockpit, seating and loadspace features and his innovative approach has earned him multiple patents, including for the Range Rover 18MY Executive Seating.
Next, Shaun Harris CBE is currently director of support and chief engineer at the Royal Air Force. With a distinguished 37-year career in the RAF, Shaun has held numerous leadership roles. His extensive experience spans engineering, logistics and information warfare. Shaun has served around the world, from the UK and USA to Afghanistan and Iraq.
Also set to speak are Solange Baena, UK lead for the aviation environmental roadmap at Airbus, and Leonie Moffat, laser radar sales account manager at Nikon. Last but most certainly not least is Stefan Lawrenson, senior polymer chemist at Scott Bader, who specialises in sustainable technology and
polymer chemistry. His research focusses on enhancing nanoparticles and synthesising eco-friendly materials.
What’s more, the Composites Forum will feature a range of industry experts discussing crucial topics. Among the speakers is Dr. Sue Halliwell, operations manager at Composites UK, who is organising the forum, which will feature insights from other industry leaders in what is an impressive lineup. Along with Brian Holliday and Stefan Lawrenson, the forum will also feature Jen Hill, director at B&M Longworth Ltd, Ian Jenner, director of control systems at Busch UK and Tony Lloyd, principal research engineer at GKN Aerospace.
A notable session will focus on workforce development, addressing key issues such as skills gaps, equity, diversity and inclusion, in alignment with the #mindtheskillsgap campaign. This session will be led by Matt Bradney from Prodrive, who chairs the Composites UK Workforce Development Group, alongside Dr. Halliwell.
“This year’s speaker lineup brings together
some of the brightest minds in the industry,” said Alison Willis, CEO of the show’s organiser, Easyfairs UK & Global. “Their diverse expertise will provide deep insights into pressing issues like Industry 4.0, supply chain management and sustainability.
“This lineup highlights the spirit of innovation that Advanced Engineering is all about, and our commitment to fostering knowledge exchange within the engineering community. I’m sure the knowledge and inspiration they’ll bring to the event will be of value to all visitors.”
Advanced Engineering brings together industry leaders and professionals to explore the latest innovations across multiple sectors, including aerospace, automotive, defence and security, marine and more. Attendees can expect presentations on a wide range of topics, from digitally enabled supply chains to advanced propulsion technologies.
For more information on the full speaker program and to register online, please visit the Advanced Engineering UK website. AdvancedEngineeringUK.com.
Midlands 3D Printing
T: 01785 594389
E: sales@midlands3d.com
W: www.midlands3d.com
Anti Vibration Products, Mounts & Bushes
Fibet Rubber Bonding (UK) Ltd
T: 01282 878200
E: sales@fibet.co.uk
W: www.fibet.co.uk
Connectors & Cabling Solutions
CEMBRE Ltd
T: 01675 470 440
E: sales@cembre.co.uk
W: www.cembre.com/en
Drives, Motors & Gears
Flow Meters
Nord T: 01235 534404
E: GB-sales@nord.com
W: www.nord.com
Schmersal UK Ltd
T: 01684 571980
E: uksupport@schmersal.com
W: www.schmersal.co.uk
Marking Solutions
T-Mark T: 0330 153 8320
E: sales@t-mark.co.uk W: www.t-mark.co.uk
Pipework Systems
Jacob UK Ltd
T: 01694 722841
E: sales@jacob-uk.com
W: www.jacob-group.com/uk
Pressure Measurement Specialists
Titan Enterprises Ltd
T: +44 (0)1935 812790
E: sales@flowmeters.co.uk
W: www.flowmeters.co.uk
Silverson Machines Ltd
T: +44 (0)1494 786331
E: sales@silverson.co.uk
W: www.silverson.co.uk
Industrial Communications
Brainboxes
T: + 44 (0) 151 220 2500
E: sales@brainboxes.com
W: www.brainboxes.com
Intoware
T: 0115 977 8969
E: hello@intoware.com
W: www.intoware.com
Industrial Fans
Axair Fans UK Limited
T: 01782 349 430
E: sales@axair-fans.co.uk
W: www.axair-fans.co.uk
ESI Technology Ltd
T: +44 (0)1978262255
E: sales@esi-tec.com
W: www.esi-tec.com
Robotics & Automation
KUKA Robotics UK Ltd
T: 0121 505 9970
E: sales.uk@kuka.com
W: www.kuka.com
Sensors
IFM Electronic
T: 020 8213-0000
E: enquiry.gb@ifm.com
W: www.ifm.com
PLUS Automation Ltd
T: 0121 58 222 58
E: Sales@PLUSAutomation.co.uk
W: www.PLUSAutomation.co.uk
Storage Solutions
BITO Storage Systems Ltd.
T: 02476 388 852
E: Info.uk@bito.com
W: www.bito.com
Test & Inspection
AMETEK Land (Land Instruments International)
T: +44 1246 417691
E: land.enquiry@ametek.com
W: www.ametek-land.com
8-pole bayonet locking
> 5000 mating cycles
Panel mount parts unplugged IP67
Solder and dip solder contacts