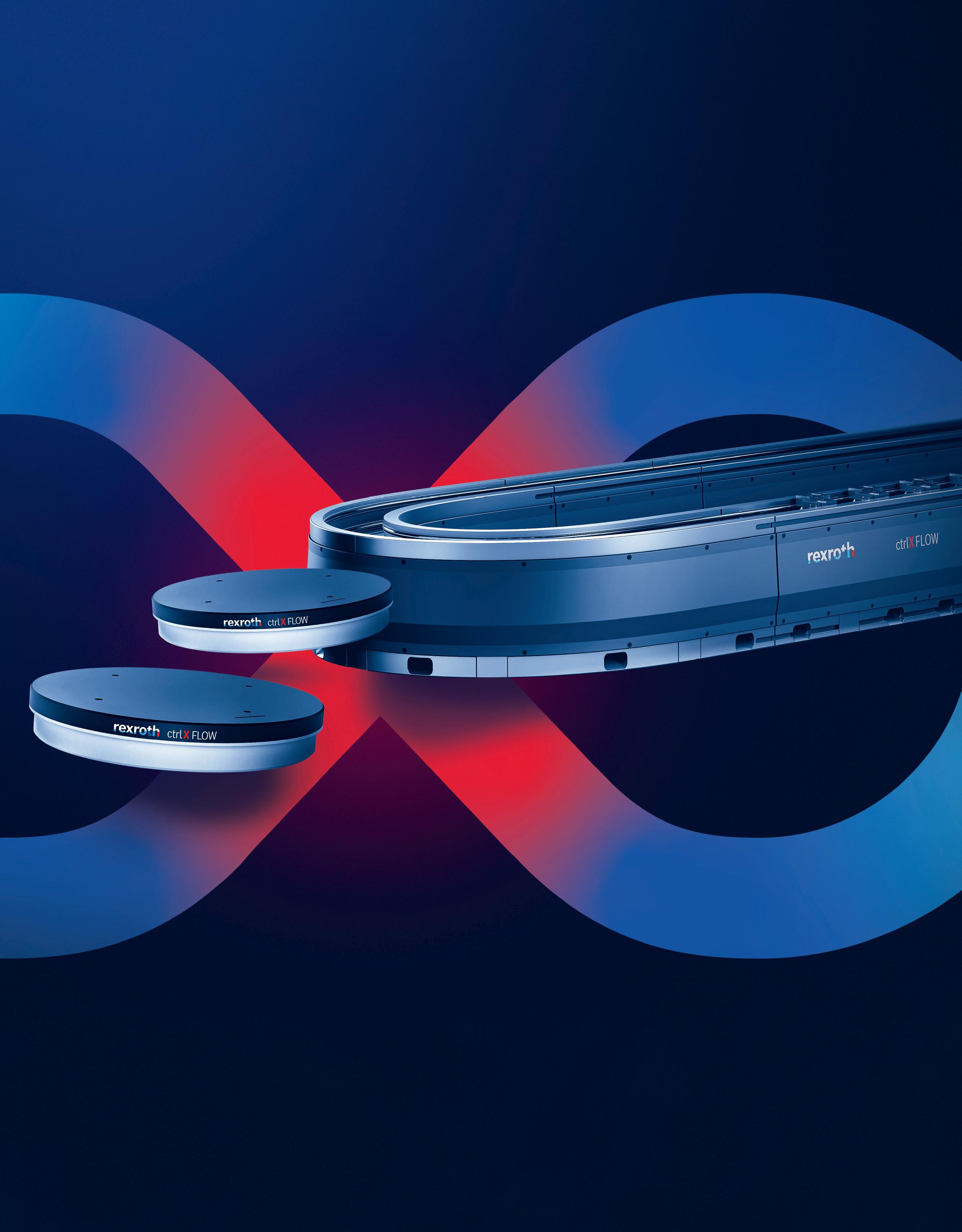

a highly flexible control cabinet-free automation solution robust, water- and dust-proof design (IP67 protection rating)
plug-and-play with pluggable function modules for IPC, coupler, I/O, drive, relay and system standardized connectors for transmission of data and power
EtherCAT communication
tried-and-tested connector for the field level reduces engineering work high time and cost savings integrated diagnostic functions
Editor
Oliver Batt oliver@cimltd.co.uk
Publication Manager
James Burke jb@cimltd.co.uk 01795 509105
Account Managers
James Davies jamesd@cimltd.co.uk 01795 509105
Jim Bearden jim@cimltd.co.uk 01795 509105
Design & Production
Grant Waters grant@cimltd.co.uk
James Taylor james@cimltd.co.uk
Administration Manager
Natalie Murray admin@cimltd.co.uk 01795 509103
Credit Facilities Manager
Gwen Lee creditcontrol@cimltd.co.uk 01795 509103
Marketing Manager
Lucas Payne lucas@cimltd.co.uk
Sales Director
Tom Woollin tom@cimltd.co.uk
Chief Executive
John Denning
© 2024 TGM Publishing Limited,1st Floor, Saphir House, 5 Jubilee Way, Faversham, Kent, ME13 8GD. No part of this magazine may be reproduced or stored in a retrieval system or transmitted in any form – electronic, mechanical or physical – without express prior permission and written consent of the publisher. Contributions are invited and when not accepted will be returned only if accompanied by a fully stamped and addressed envelope. Manuscripts should be typewritten. No responsibility can be taken for drawings, photographs or literary contributions during transmission or in the editor’s hands. In the absence of an agreement the copyright of all contributions, literary, photographic or artistic, belongs to TGM Publishing Limited. The publisher accepts no responsibility in respect of advertisements appearing in the magazine and the opinions expressed do not necessarily represent the views of the publisher. The publisher cannot accept liability for any loss arising from the late appearance or non-publication of any advertisement.
Welcome to our October issue. With the evenings drawing in and the weather becoming unsettled, it’s not typically a period associated with new beginnings, but it does evoke change. This being my very first issue as the editor of MEPCA exemplifies both. I’m proud to join this remarkable magazine and excited for what we have planned for MEPCA over the coming months.
In this issue, we have our own sensing faculties honed in on sensors & sensing systems and machine vision technology. Whether used in robotics for navigation, in production lines for quality assurance, or for a host of other measuring and monitoring applications, the importance of these solutions cannot be overstated.
This is especially true when it comes to the prevention and management of unplanned down time, a dreaded but sometimes unavoidable occurrence, and one of particular concern in the compliancedriven recycling industry, as addressed in this issue’s Cover Story featuring Bosch Rexroth.
In addition to our usual wealth of industry news, thought leadership, expert analyses and technology focuses, I’m delighted to introduce a new regular segment of MEPCA magazine – the Manufacturing Champion of the Month. Every month, we will select and celebrate an individual who has gone above and beyond, be they familiar stalwarts of the industry or unsung heroes.
By the time this issue goes to print, I will have attended the first of many industry events with MEPCA: PPMA at the NEC in Birmingham, where I will have had the opportunity to meet many of our regular readers and contributors.
We hope you enjoy this issue.
To subscribe to MEPCA visit our website www.mepca-engineering.com or scan the QR code. @Mepca-magazine
Oliver Batt, Editor
The metals sector has made an overwhelming call for a ‘Minister for Manufacturing’ to back its vital role in supporting jobs and the UK economy.
More than 62% of companies who took part in the State of the Metals Industry in the UK’s annual report called on the government to introduce a dedicated political power to represent their interests in Whitehall, with more than half throwing their considerable weight behind the introduction of the
“The message is clear from the companies we represent…they want real political power in the corridors of Whitehall that understand our sector and will fight for it. This is stark message yet also a clear opportunity for Labour,” explained Rachel Eade MBE, Chair of the UK Metals Council.
“Despite all the supply chain pressures, energy instability and changes in political power, metals firms are showing unbelievable resilience with nearly half feeling optimistic about growth.
“We want the launch of the report to
deliver six key asks to government, ranging from introducing a Minister of Manufacturing and providing support to smooth trading with our continental neighbours, to better engagement with industry to review the Apprenticeship Levy and eligibility of learning for funding.
“These are all important messages that need to be acted on and we will use the UK Metals Expo to start the lobbying, alongside hundreds of companies from our sector.”
The second State of the Metals Industry in the UK Report provides a sector snapshot of the opportunities and challenges faced by the domestic metals industry and the prospects for future growth and sustainability.
It will be officially available from Wednesday September 11th at the UK Metal Expo and all the findings will be discussed at a high-profile panel debate.
ukmetalscouncil.org
Donna Edwards, director of trailblazing North West Adoption Programme at Made Smarter, warns that tackling change in the wrong way risks wasted time and money.
Businesses are hesitant to commit to change because they lack the confidence with technology and digital skills among leaders and employees. But, delaying digital transformation risks being left further behind, or wasting time, effort and money, Edwards cautioned.
The stark warning features in the foreword of Made Smarter’s new white paper – Digital Transformation: A Made Smarter Roadmap for SME Manufacturers.
The free-to-download guide aims to help makers looking for a place to start, explaining the concepts and steps to a successful digital transformation.
Crucially, it explains the Made Smarter process, the services available, and
showcases some of the hundreds of businesses who have benefited in the North West, the North East, Yorkshire and Humber, and the Midlands.
Donna Edwards said: “Ask a hundred SME manufacturing leaders what digital transformation means to them, and you’ll likely get a hundred different answers. But the common view is that it is daunting and confusing. SMEs, while aware of the benefits technology brings, lack the resources and skills to approach digital transformation in the right way. Many hesitate or become paralysed, risking being left behind, or wasting time, effort and money.
“The Made Smarter Adoption Programme is a tried and tested approach that offers businesses access to fully funded support so they can improve their understanding of what steps they need to take, to arm them with the tools and strategy to take
those steps, and accelerate them towards the multitude of benefits and growth opportunities.”
madesmarteruk/resources/digitaltransformation-a-made-smarterroadmap-for-sme-manufacturers/
Vapourtec is investing in the future of flow chemistry through a partnership with the organic chemistry team at the University of Bristol’s Centre for Doctoral Training (CDT), headed up by Professor Varinder K Aggarwal.
Over the next five years a minimum of 70 PhD candidates will have access to Vapourtec’s R-Series and E-Series flow chemistry systems in the first year of their doctorates as part of a scheme that is supported by the Engineering and Physical Sciences Research Council (EPSRC).
Professor Aggarwal explained: “Vapourtec are leaders in the field of flow chemistry, having developed user-friendly and versatile equipment that can be used for different types of chemistry from cryogenic chemistry with reactive intermediates to photoand electrochemistry. That makes them ideal for use in our department where we can explore a range of different chemistry in flow and we are looking forward
to training the next generation of students on this state-of-the-art equipment.”
Vapourtec founder and MD Duncan Guthrie commented: “We are delighted to be playing our part in ensuring the chemists of the future discover the incredible potential and scope of flow chemistry.
“For the duration of the agreement Vapourtec will also loan an R-Series system featuring two acid resistant piston pumps and the latest software.
“The R-Series RS-200 is a highly flexible system that can be combined with the E-Series system to configure a platform of five pumps and six reactor positions.
“The modularity of the R-Series also means it can be expanded at a later stage with the addition of an autosampler or fraction collector, a UV detector (or other in-line analytical tools) and any of Vapourtec’s 16 reactor options. We will support research activities at the CDT with some of these add-ons over the duration of this partnership” added Duncan. vapourtec.com
According to Epicor’s new “Future of Work in Manufacturing” report, a significant gap exists between how manufacturing managers and frontline workers perceive workplace morale. In 2024, 57% of managers rated their morale as high compared to only 45% of workers, highlighting a potential disconnect in understanding and addressing employee engagement.
Bridging this morale gap to ensure alignment between managers and workers is especially critical given the projected 3.8 million manufacturing employee workforce shortage, and the need for leaders to address current challenges and prepare for future demands.
Separately, the report found there is a disconnect in upskilling efforts, with 91% of managers but only 70% of workers
recognising it as a priority.
Epicor surveyed more than 1,400 manufacturing leaders and 1,200 manufacturing workers worldwide to uncover critical trends and strategies that will shape the industry’s future. These findings are meant to inform and guide C-suite leaders, operations managers, manufacturing supervisors, IT leaders, and HR leaders.
Key findings:
• Technological gap: While 52% of managers considered their workplace very modern in 2024, only 39% of workers agreed, suggesting a mismatch in perceptions of technological advancement.
• Sustainability priorities: Only about half of the companies prioritise sustainability, with 61% of managers and 45% of workers viewing it as crucial, pointing to the need for
stronger, more visible sustainability initiatives.
• Supply chain challenges: Despite 75% of managers recognising the critical importance of supply chain resilience and sustainability, issues like cost, regulatory hurdles, and technological shortcomings remain obstacles.
• Automation’s impact: A growing awareness of automation’s role shows 73% of managers and 53% of workers expect job changes due to automation, with decreasing immediate concerns among workers.
• Turnover trends: Worker-reported turnover dropped by 6% in 2024, while managerreported turnover rose by 25%, reflecting varying experiences and viewpoints on workforce stability.
epicor.com/en-us/resources/library/ manufacturing/future-of-work-inmanufacturing/
In the first of a regular feature of MEPCA magazine, we are delighted to be celebrating Maria Chacon Cubo, Site Director of Taw Valley at Arla Foods, as our October Manufacturing Champion of the Month.
For the past 9 years, Maria has played an integral role at Arla Foods, the leading dairy manufacturer, where she has helped to shape future direction of its Taw Valley site with her forwardthinking leadership.
We had the pleasure of speaking with Maria, who provided us with an insight into her continuing achievements at Arla Foods.
What has been your proudest achievement during your time at Arla Foods?
One of the proudest moments in my 9-year journey at Arla has been having the opportunity to create the CAPEX strategy for the upgrade of the Taw Valley Creamery. This project was especially meaningful because it allowed the site, which is 50 years old this year, to continue producing incredible cheeses.
In addition to this, we secured a massive commitment from the business to invest 210 million euros into producing mozzarella using ground-breaking technology. Being trusted with one of Arla’s largest-ever investments was incredibly humbling. It not only marked a significant mile-stone for the site but also validated the hard work and dedication of every single member of the team. Seeing the team rise to the challenge and knowing that our collective efforts will have a lasting impact on the future of the site makes this moment one of the highlights of my career.
Can you share a specific example where you overcame
a major challenge in manufacturing, and how your leadership played a key role in turning the situation around?
In FMCG (Fast-Moving Consumer Goods), every day can bring a new challenge, but a specific example that comes to mind was last year when we undertook the replacement of a large part of our downstream equipment in our continuous production line. This line is highly dependent on a steady flow, and any disruptions can lead to considerable frustrations, cost of downgrade, and impacts on quality and safety.
Here’s how we tackled the challenge:
1. Steady Drumbeat of Meetings: We established a regular cadence of meetings focused on the top three critical issues impacting the production line, ensuring visibility and accessibility.
2. Dedicated Problem-Solving Team: A specialised team was assembled to analyse data, identify root causes, and brainstorm solutions.
3.Visible Actions and Progress: We made the actions and progress from these meetings highly visible for the whole factory, fostering a sense of involvement and empowerment.
4. Enhanced Communication: Communication was a cornerstone of our strategy. We kept the lines of communication open, addressing employee concerns and managing their frustrations.
How have you contributed to sustainability or environmental initiatives within your manufacturing operations, and what impact have these efforts had on the company and industry?
Sustainability and Digital are key pillars in Taw Valley’s site strategy. We were amongst the first sites to deliver and implement Arla’s sustainability program, targeting the creation of a roadmap to reach Arla’s target of 63% reduction in carbon emissions for scope 1 and 2 by 2030.
Our current projects include exploring anaerobic digestion (AD) plants, solar energy, and wind energy.
Dairy manufacturer Arla Foods – employer of our Manufacturing Champion of the Month – is committing £300 million to enhance key sites across the UK. The strategy will extend the cooperative’s UK production capabilities and bolster its prominent position in UK manufacturing.
Britain’s biggest dairy company has given a major boost to UK manufacturing and the future of British dairy by pledging to invest tens of millions in its production sites.
From Scotland to the West Country, new investments across Arla’s sites bring its total UK investment commitments in 2024 to over £300 million.
The investments will see significant upgrades that secure the future of its sites, including Lockerbie, Stourton, Aylesbury, Westbury and Taw Valley. These investments ensure Arla can continue producing worldleading products whilst adding the most value possible to the milk from its farmer owners.
Arla announced in March that it will invest £179m in state-of-the-art technology at its Taw Valley Creamery, under the leadership of Site Director, Maria Chacon Cubo. The strategy will create 100 new jobs and enable the business to export mozzarella that can be used for the likes of pizza toppings around the world. Further export opportunities will also be explored thanks to a new investment at Westbury that will see milk turned into powder for consumption in countries across the globe.
New technology and significant upgrades will be implemented at Lockerbie Creamery to allow the site to expand and grow over the coming years. The investments illustrate the cooperative’s long-term commitment to producing cheddar at the Lockerbie Creamery and to continuing to produce award-winning cheese.
At Arla’s site in Stourton, the upgrades will expand Arla’s capabilities in extended shelf life (ESL) milk, particularly the Arla Cravendale® and Arla B.O.B® brands, as well as introduce a capability to supply
milk in cardboard cartons. ESL is a filtered milk that stays fresher for longer, helping shoppers to reduce their food waste. As a result of the investment, the site will produce enough additional milk to fill the equivalent of 560 million bowls of cereal.
Aylesbury, which is the UK’s biggest fresh milk site producing more than 1 million bottles of milk daily, will get additional automated box packing capabilities, allowing customers to have greater flexibility with packaging formats.
Bas Padberg, managing director of Arla Foods UK, comments: “What this means is that our farmer owners are investing in UK food security – as they are not only producing our milk, but they are backing this investment in our production sites. Dairy plays a significant role in the UK economy, with sales of dairy products exceeding £8bn*. We are delighted to set out plans for continued vital investment in our business worth tens of millions of pounds, ensuring the UK remains at the forefront of food
production and keeping the nation’s favourite dairy products on our supermarket shelves.”
Fran Ball, vice president for production at Arla Foods, comments: “We are wholly committed to UK manufacturing to ensure we continue to produce the nutritious dairy products that are a staple in millions of fridges across the country. The investments will allow us to make significant upgrades across our portfolio, making our facilities fit for the future of dairy production here in the UK.”
Mobile machines such as aerial work platforms, loader cranes and other construction vehicles and equipment with tough motion control applications demand robust sensors that deliver high precision and optimum reliability. To meet these challenges, sensor specialist BAUMER continues to expand its range of options with the introduction of a new safety compliant inclination sensor – the GIM600R.
The GIM600R sensor has been specifically designed to ensure maximum robustness combined with high measurement accuracy according to the latest standards (ISO13849-1:2023). The result is outstanding robustness and durability, helping engineers simplify machine design and enabling higher
performance in construction vehicles thanks to reliable measured values for static stability control.
Proof of this exceptional resistance was the result of demanding endurance tests resulting in an IP69K rating and guaranteed corrosion protection up to CX,
along with further resistance to shocks, vibrations, dust, dirt and salt-spray ingress. Easy integration into machinery is assured thanks to redundant standard interfaces, including CANopen and SAE J1939, along with an ultra-compact housing measuring 72mm W x 24mm H x 64mm H.
The freeware Baumer Sensor Suite can also be used for the GIM600R to provide parameterisation via an intuitive dashboard, saving even more engineering time.
OEM’s who have previously relied on the proven Baumer inclination sensors GIM140R or GIM500R can simply replace them with the new GIM600R, and so benefit from enhanced performance safe in the knowledge that their systems are compliant with the very latest safety standards.
baumer.com/gb
Vision Engineering, UK designer, manufacturer and exporter of ergonomic microscopes and measuring systems, today announces a new sub £1k entry point for its patented optical stereo microscope technology with the global launch of OPTA.
Available for only £900, with a choice of three stands and two lenses, OPTA redefines the entry point for users to benefit from Vision Engineering’s exceptional image quality, ergonomic design and ease of use.
Additionally, Vision Engineering announces exciting advancements across its popular EVO Cam, Lynx EVO, and Swift PRO product lines.
The EVO Cam series now boasts a wider range of configurations, offering even greater flexibility for digital inspection tasks. With the launch of a new, simplified
ICON model, users can now choose from multiple software configurations and ergonomic stands to perfectly tailor their EVO Cam system, enabling effortless image comparison, capture, measurement, and reporting.
Building upon its reputation for unparalleled ergonomic design and stunning 3D stereo imaging, the Lynx EVO series has been extended to include a simpler, non-zoom variant to appeal to a more price-
conscious market.
Vision Engineering has enhanced the Swift PRO metrology line, its flagship range of bench-top optical measuring systems, with the release of the new Swift PRO EDGE. Featuring a 6.5x zoom, the EDGE enables quick, precise measurements of a wide range of part sizes and features without timeconsuming lens changes for different measurement tasks.
Commenting on the upcoming product launches, Paul Newbatt, Group Sales and Marketing Director at Vision Engineering says “These products are the combined result of listening to our customers and continuously developing our innovative products … This enables a much wider range of customers in existing and new markets to better achieve their inspection and measurement objectives with Vision Engineering solutions.”
visioneng.com
Following the acquisition of DCT by the Babcock Wanson Group in 2022, industrial process heating equipment and solutions specialist Babcock Wanson UK has expanded its range of regenerative oxidisers to offer complete solvent recovery systems to help reduce customers’ carbon foot print and meet increasingly stringent emission limits for solvents and volatile organic compounds (VOC).
DCT solvent recovery systems feature activated carbon adsorption, using steam or inert gas for the regeneration. A distillation section (batch or multi-columns) allows for a very high level of purity – frequently exceeding international standards – for the recovered solvents to then be reused in production, making for a rapid return on investment. These solvent recovery systems are easy to use and, because they are modular, can be expanded and reconfigured to meet changing site requirements. With its compact size, plug and play design, plus easy maintenance, the latest solvent recovery system, the X-CSR, has been specifically designed for printers using smaller solvent quantities (as little as 300 tons/y), extending this valuable technology beyond the traditional, large-print plants.
Babcock Wanson UK has been providing oxidisers for many years, but with the addition of DCT regenerative and recuperative oxidisers, it can now meet a wider range of industries and requirements than ever before. DCT regenerative oxidisers enable up to 99% VOC abatement by increasing the polluted air temperature to over 750-800°C with a high efficiency (up to 95%) heat recovery system based on the use of ceramic material; all whilst minimising energy consumption. DCT regenerative oxidiser capacities range from 3.000 to 300.000 Nm3/h and also boast low maintenance costs and consistency of performance during their life time.
Additional DCT products supported by Babcock Wanson UK include VOC Concentrator Units for the purification of polluted air with low solvent concentration; Catalytic Oxidation to treat waste air or gases; and Scrubber and Filter Treatment Systems for inorganic polluted fumes.
The DCT range has already proven extremely popular in the UK and Babcock Wanson is currently working on a number of high profile projects, including its largest ever oxidation project, with a building materials manufacturer.
The DCT range of oxidisers and solvent recovery systems are one of the latest additions to Babcock Wanson’s comprehensive range of products and services for boiler houses and other process heating needs, including fire-tube boilers, coil type steam generators, thermal fluid heaters, hot water boilers, VOC and odour treatment by thermal oxidation, water treatment and process air heating solutions. The company aims to not only help optimise customers’ energy production but to also be the European leader in environmental solutions for industry.
babcock-wanson.com
Automation technology specialist ifm continues to set the standard in delivering innovative solutions that drive industrial advancement with the release of the new PQ series. This groundbreaking pressure sensor, which sets new standards in performance, reliability, and versatility, is poised to revolutionise various industrial applications.
The PQ is engineered to deliver exceptional precision and performance across diverse sectors. Its advanced design integrates state-of-the-art sensors and automation technologies, making it ideal for use in manufacturing, automotive, food and beverage, pharmaceuticals, and more. The PQ’s cutting-edge sensor technology
ensures real-time data accuracy and rapid responses, enabling industries to optimise their processes and enhance productivity seamlessly.
Alongside its high-precision sensing capabilities for accurate data collection and process optimisation, the PQ offers enhanced connectivity for seamless system integration, allowing it to interface
effortlessly with existing systems and infrastructures. Its robust construction ensures it can withstand the harshest industrial environments, providing longterm reliability and reducing maintenance costs. The PQ is exceptionally adaptable, suitable for applications such as quality control, process automation, and safety monitoring, where precision and reliability are paramount.
The PQ’s intuitive user interface simplifies setup and operation, minimising the learning curve for operators and technicians. This user-friendly design allows businesses to swiftly leverage the full capabilities of the PQ, enhancing operational efficiency and productivity from the outset.
When it comes to driving industrial efficiency, inspection vision systems regularly play a key role in enabling reliable and effective robotics and automated solutions, giving you an ‘all-seeing-eye’ for automated process or robot application. Once considered to be a ‘dark art’, resulting in excessive costs compared to conventional methods, vision inspection was often pushed, but not developed to its full potential.
With the rapid growth of AI and machine learning, along with cost-effective, userfriendly image sensors, vision inspection has become more affordable and attainable. A perfect example is SICK’s powerful and compact Visionary-T Mini camera, combined with their easy-to-use Nova 3D Presence Inspection toolset.
The SICK Visionary-T Mini uses snapshot Time-Of-Flight (TOF) technology to set new
standards of data accuracy for detailed environmental perception at rapid production speeds. With a low-weight and no moving parts, the Visionary-T Mini’s IP65/67 housing makes it ideal for installation in compact robotics and automation solutions. Even in situations where shocks and vibrations could present a problem to other vision systems, the SICK Visionary-T Mini performs reliably. Cutting out the ‘black magic’, SICK’s Nova software is an intuitive common development software platform across a range of 2D and 3D cameras. Nova doesn’t need programming skills – this allows a user to quickly create and deploy different inspection tasks depending on their needs.
The combination of the 3D TOF Visionary-T Mini with the intuitive Nova software makes a well-suited solution for continuous 3D fill level monitoring, or identifying the presence of parts in a bin/box/ tote, or of ingredients in a vessel.
bpx.co.uk
Invertek Drives, manufacturer of variable frequency drive (VFD) technology, has announced a significant enhancement to its warranty programme.
Effective for all new Optidrive VFDs manufactured from 1st June 2024, the company is now offering a standard three-year warranty, with an optional “Warranty Plus” extension that provides coverage for up to five years.
Every Optidrive VFD is manufactured in Invertek’s state-of-the-art facility in Welshpool, UK. This ensures that each drive undergoes rigorous testing and that every component can be traced back to its origin, guaranteeing superior product quality across the entire Optidrive range.
The extended warranty applies to all models, including the Eco, E3, P2, Coolvert, Compact, and Elevator Core series, available in IP20, IP55, and IP66/NEMA 4X enclosures.
Rhydian Welson, Sales and Marketing Director at Invertek Drives, emphasised the company’s emphasis on quality. “Our commitment to quality is ingrained in our culture,” he said. “We work closely with our suppliers, invest heavily in research and development, and utilise advanced manufacturing techniques at our UK-based global manufacturing facility. This results in drives that are not only easy to use and set up but also deliver lasting value to our customers.”
Rhydian highlighted the significance of the warranty extension, stating, “For over 26 years, we have focused on delivering VFDs that not only meet but exceed industry standards. This warranty extension is a testament to the durability and reliability of our Optidrive range. We want our customers to have complete peace of mind knowing that their Optidrive VFDs are backed by one of the most comprehensive warranties in the industry.”
The Optidrive range’s user-friendly design ensures ease of setup and operation, minimising downtime and maximising productivity. With its versatility across various applications and industries, the extended warranty further strengthens the Optidrive range’s value proposition, providing customers with long-term peace of mind and return on investment.
Chris Newson, Make UK Environment, Health and Safety Director, explains the crucial steps a business should take when developing cultural change, without which it risks undervaluing its most important but often overlooked asset – its people.
Many organisations talk about ‘building a culture’ that enables them to become high achievers and more successful. The Royal Marines pride themselves on being elite and set certain standards of individual and collective performance, along with ways of measuring it, that take them beyond other regiments. Their ethos is all about the collective and not the individual, and officers take responsibility for showing leadership and the development of both individuals and teams.
Similarly, the most successful businesses also build a company culture that might not involve such physical extremes but will similarly invoke feelings of teamwork, pride, being made to feel valued, rewarded and recognised. This allows employees to become high achievers and best performers in their own fields, with their own ways of measuring success which takes them beyond their competitors. As a result, the companies that take this approach and embed it in their organisation are far more likely to have better productivity, employee morale, lower sickness absence and better prospects for recruitment and retention of key staff.
So, how do you go about creating a ‘culture’ in an organisation that will drive behavioural safety, with the aim of achieving zero accidents and upholding an effective and transparent practice of accident reporting, whilst taking responsibility for near misses?
Make UK has developed a four step
process for developing culture change. Firstly, building such a culture of change within an organisation comes from the very top. Senior leaders have both a collective and personal responsibility for developing a positive workplace culture from the CEO down, to the extent that it runs through the DNA of the company and its everyday operations at all levels. This leadership involves being honest about how positive or negative the current culture is and then following through a desire to innovate, which then becomes a business priority at all levels, whether it be in the field of productivity,
skills development, marketing or, effective Environmental, Health & Safety (EHS) management. Such leadership ensures that any senior management team has a buy in and becomes a positive asset to building such a culture, rather than a negative obstacle to organisational change.
Most importantly, the desire to innovative in cultural change is driven by people at all levels of an organisation who have a positive attitude and a desire to improve. There are many factors that go into keeping your workforce happy that are nothing to do with legal compliance, though that along with effective monitoring is vital, with people being given effective tools and trained to do the job. It comes from an approach which is often intangible but can yield huge results, so qualities such as respect, selfesteem, teamwork, making people feel rewarded and recognised and, ensuring that everyone else throughout the organisation knows they are recognised and their contribution is valued.
Essentially, this is building a culture of innovation by making the most of a company’s most important asset – its people. This isn’t just a moral imperative to ‘do the right thing’ by employees and making sure they are working in a safe environment, critically important though that is; it is about creating a workplace culture that can make a real difference to people’s performance. Time and again history has shown that, whether large or small, the most economically successful companies are organisations that create this ethos by making the most of their human capital.
Process improvement is like sailing. With an experienced partner, you can achieve more.
Optimizing processes and maximizing efficiency is important to remain competitive. We are the partner that helps you master yield, quality, and compliance. With real-time inline insights and close monitoring of crucial parameters, we support manufacturers to optimize processes, reduce waste, and increase yield.
Unplanned downtime is the bane of many industries, but it can be catastrophic for recycling companies that incur hefty penalties as a result. Investing in digital solutions for predictive maintenance can help mitigate this issue, as the following case study from Bosch Rexroth illustrates.
At its Heilbronn site, TSR Recycling GmbH uses databased analyses to avoid potential downtime costs and have found that the moderate fees for the digital service adopted can quickly recoup themselves.
Recycling companies are highly dependent on the availability of their equipment. If hydraulically-driven shredders, scrap shears or presses fail, there is a risk of severe penalties. If trucks, trains or ships wait in vain for their cargo, the follow-up costs
can reach five to six figure sums. To prevent this, TSR Recycling GmbH is breaking new ground with the digital service CytroConnect PREDICT from Bosch Rexroth. The rule- and data-based analyses using machine learning can not only prevent production downtimes, but also reduce maintenance costs and extend the service life of the equipment.
Established in 1890, TSR Recycling is based in Lünen in North Rhine-Westphalia and
employs 4,100 people around the world. The company processes ferrous and non-ferrous metals at its German site in Heilbronn. “The output and purity of our products can be further improved only with a high degree of innovation along the entire process chain can,” explained Sebastian Bischof, Technical Manager in the Shears and Presses division. “The predictive analysis and maintenance of our production machines plays a central role here.”
With a premise of finding the most energyefficient solution possible that minimises both
CO2 emissions and production costs, TSR Recycling opted for a predictive analytics solution from its long-standing hydraulics partner Bosch Rexroth. “After a detailed market analysis, the overall package from Bosch Rexroth won us over,” said Sebastian Bischof.
A pair of scrap shears from Metso was the first machine at TSR to be prepared for data analysis. The inventory and the necessary hardware update were carried out by Hydrobar, a Rexroth Certified Excellence Partner based in Sindelfingen. The company equipped the process-critical system parts with suitable sensors and installed a DAQ box (data acquisition) with an integrated gateway. This records sensor data which is then pre-processed by the IoT (Internet of Things) Gateway and transferred in encrypted form to the cloud. Here, the data streams are verified, decrypted and evaluated with the help of self-learning algorithms.
If the measurements deviate significantly from the learned comparison data, the system recognises an anomaly and reports it to the supervising expert team at Rexroth. The experts verify the situation and make a predictive maintenance recommendation to those responsible at TSR. The recycling company then has enough time to plan and prepare the measure without productivity suffering. By recognising and correcting anomalies early on, damage and unplanned downtimes can be avoided.
There was a four-week learning phase before operations started in August 2021. During this phase, the analytics team at Bosch Rexroth first identified suitable models and parameters for the scrap shears. The algorithms selected for the analysis are improved on an ongoing basis, as a result of which the predictions become more and more accurate over time.
“Predictive analyses require a high degree of expertise and a comprehensive network that processes huge quantities of data from a giant pool of anonymous comparative data,” explained Marcello Miceli, Senior Manager Service Sales Support at Bosch Rexroth. “It’s virtually impossible for companies to set up such a solution on
their own, but as a rental service predictive analytics becomes attractive for many users.”
Marcello Miceli knows from experience that for most failure-critical hydraulic applications CytroConnect PREDICT pays for itself within the first year. How much the failure of a hydraulic component actually costs depends on how long it takes to procure spare parts. “Generally speaking, the avoided downtime costs exceed the monthly fees by a factor of five or more,” said the Rexroth expert. “If just one or two downtimes a year are avoided, the technical investments will have paid for themselves within a few weeks or months. The peripheral costs should also be borne in mind. For example, damage to other components can be avoided by monitoring the oil cleanliness.”
It is still too early for TSR in Heilbronn to draw a final conclusion on cost and energy savings. However, Sebastian Bischof already has one or two successes to report: “With the newly introduced system, we were able to identify several failure-critical anomalies early on. For example, worn valves would have disrupted production in the foreseeable future. We’ve achieved our
main goal,” said the Technical Manager. “Predictive maintenance protects against unplanned downtimes and also helps us to minimise maintenance costs at the Heilbronn site. Because certain hydraulic components are no longer replaced on a regular basis, in certain cases excessively early, the maintenance staff have much less work to do. This also helps to alleviate the shortage of skilled workers. At the same time, condition information and predictions increase energy efficiency and equipment uptime, which in turn saves money.”
CytroConnect PREDICT monitors not only the cylinders, the pumps and the motors in the scrap shears but also the cleanliness of the hydraulic oil and the tank parameters.
Sebastian Bischof is also hoping to improve production further with the data obtained. “By assigning specific hydraulic data to particular scrap types, we’re able to analyse and adjust processes. We’re very happy with the result because of these many benefits too,” said Sebastian Bischof. “If this extremely positive impression proves correct, we’ll retrofit further production systems with the predictive maintenance system from Bosch Rexroth.”
Predictive analytics in recycling prevents unplanned downtimes, reduces maintenance work and extends equipment uptime. The data can also help to improve production on an ongoing basis. boschrexroth.com/en/gb/
The increasing use of automation is leading to highly individualised mobile robotics applications and the need for more flexible sensor solutions. Universal solutions provider SICK explains the benefits of using modular sensor technology.
The rapidly expanding use of automation has generated an array of technologies and applications, creating a critical need for high performance solutions for autonomous mobile robots (AMRs) and autonomous guided vehicles (AGVs) that can adapt to different scenarios.
SICK has developed its modular series of sensors to do just this – meeting and exceeding industry needs for adaptability, safety and precision to provide long-term solutions.
SICK’s modular sensor technology enables manufacturers and users of mobile robots to select precisely the modules they require and combine them to create the ideal solution for their application.
The benefits of a modular sensor solution:
• A modular system of sensors allows for individual modules to be easily customised, combined or changed without having to redesign or reconfigure the whole system. This saves time and effort when developing and designing, expanding the ways in which mobile robots can be adapted and used.
• The components are simple to integrate, customise and change, allowing mobile robots to be adapted to specific, individual requirements. Each sensor device is designed and standardised with easy integration in mind. Plug-and-Play eliminates the need for technical knowledge, manual configuration and minimises user intervention.
A versatile, scalable system can bolster many aspects of mobile robots’ performance, some of which are outlined below.
Mobile robots must perform highly precise, complex movements in very different, and sometimes dangerous, environments.
Modular sensors and LiDAR technology can enhance the localisation and navigation of mobile robots.
The Optical Line Sensor (OLS) and Magnetic Line Sensor (MLS) offer precise navigation through line-based tracking. They use luminescent or magnetic tapes on the floor, that are unaffected by light and dirt, to guide mobile robots around factories and warehouses. Additionally, 2D and 3D LiDAR technology can detect any sharp bends in the environment, while LiDAR-LOC application software seamlessly links and exchanges information with other sensors – ensuring the highest accuracy for mobile robot navigation.
SICK blazed a trail with the world’s first safety rated 3D, time-of-flight camera. Coupled with 2D and 3D image processing, it provides completely new, adaptive
solutions for automation applications that control positioning, environmental perception, and robot guidance.
3D cameras increase safety through:
• Ensuring high levels of safety for human workers, such as preventing collisions between forklifts or identifying safety hazards such as cable clutter.
• Low latency, meaning that the computing system can respond to any stimuli or danger in the environment with minimal delay. Access to real-time data is vital in dangerous and rapidly changing environments.
• Quick and precise detection of objects and far-ranging distance measurements. 3D cameras are even able to detect objects beyond the protective layer of a safety laser.
Matt van den Braak, Robotics and Mobile Platforms Sales Specialist, says: “We realised that the answer isn’t a one-size-fits all solution. Rather, what was needed was a modular system – a chain of individualised, standardised sensors to solve complex challenges and suit different environments.”
“With automation growing so rapidly and creating the opportunity to bridge gaps within industrial and logistic operations, our modular sensor range ensures humans and robots can operate seamlessly in factories, warehouses and across industrial sites.”
There is no single mobile robot or sensor that can address the many challenges this industry faces, both now and into the future. But SICK is using its expertise to develop a modular range of sensors that can be combined to suit each task and application.
For more information, please visit the SICK UK Website. sick.com/de/en/
The BLUEline Nova sets new standards in pump technology. With or without protection plates and liners – the BLUEline Nova achieves unrivaled volumetric efficiencies.
Made for one another – the newly developed DIUS rotors in combination with the flow-optimized pump chamber ensure perfectly smooth running at pressures of up to 12 bar.
In the first of a two-part turbine series, Titan Enterprises explains the working principles of the Pelton wheel and other turbine flow meters to MEPCA.
Turbine flow design has changed little since their invention in the eighteenth and nineteenth centuries due to the simplicity and power of these devices to extract energy from the movement of a flowing water source.
Turbine flow meters are one of the most commonly used and simplest methods of measuring liquid flow, from water and beer to aggressive chemicals, including ultra-pure water. The variety of turbine flowmeters are based on the mechanics – the physical orientation of the turbine in relation to the fluid flow.
Turbine flowmeters work in two primary ways:
1. Analogous to a propeller or windmill –axial turbine
2. Analogous to a water wheel – radial turbine
Turbine flowmeters measure the flow rate of a fluid within a pipe or process line by utilising a rotor or turbine that rotates on an axis as the fluid moves across its blades.
As the turbine rotates, each blade of the turbine passes a sensor which outputs a pulse signal. The speed at which the turbine rotates is directly proportional to the volumetric flow rate and the number of pulses the total volume passed.
In an axial turbine, the fluid flows along the rotation axis where the fluid enters and exits in the same direction, the fluid striking the angled turbine blades.
In contrast, fluid flowing through a radial
turbine strikes the plain blade in the direction of the tangent or 90° to the rotational axis (hence it is also referred to as tangential flow).
Titan Enterprises released its first flowmeter sensor in 1981, a turbine device based on the Pelton wheel design and working principles of the radial turbine.
The Pelton wheel, conceived by Lester Pelton in the 1870’s, is an energy extraction device. Its working principle and design
are simple: characterised by a series of distinctive reaction cups, to extract as much energy as possible from the moving liquid, typically to generate electricity. These cups or buckets efficiently capture the momentum of high-velocity water jets, inducing an impulsive force. This force makes the turbine rotate and the rotating shaft runs a generator to produce electricity. As the energy available is only kinetic energy, the Pelton wheel is an example of an impulse turbine.
Such impulse turbines do not require an enclosed case, whereas radial flow turbines have very different requirements; they must operate in an enclosed pressure chamber and have a linear velocity to flow rate characteristic. Early flowmeters were designed using radial flow onto blades (without reaction cups) with single or multi-jets of liquid. In the last seventy years or so, as accurate measurement of lower flow became a requirement, smaller meters were produced and became known as the generic Pelton wheel flow meter we know today where a single jet impinges a flat blade in an enclosed chamber. There are many design variations of these devices to ensure the best overall performance is attained. The most common system is to simply point a jet radially at a turbine and place the outlet directly opposite the inlet. The turbine has multiple flat blades, from 3 to many more. Titan has utilised up to 12 blades in order to increase the resolution on custom-designed OEM (Original Equipment Manufacturer) turbine flowmeters, thus improving the accuracy of low volume dispense.
Titan’s small turbine flowmeter range use the radial flow principle based on the Pelton wheel technique. This well proven method is the ideal way of measuring low rates of flow of low viscosity liquids. For these mini flowmeters, a jet of fluid is directed at a turbine that is mounted on robust low friction sapphire spindle and bearings. The geometry of the turbine and the fluid chamber ensures that the rotational speed of the rotor is proportional to the flow rate through the device. The use of this radial arrangement allows more energy to be imparted into the turbine, so the bearing drag is far less important. Furthermore, because more energy is available the bearings themselves can be a lot stronger, increasing the life of the flowmeter. For larger flows, some of the liquid can bypass the turbine chamber, which then behaves as a “shunt” to the metered fluid. As a result, accuracy is still maintained and the output
remains linear.
Axial flow turbines are typically larger and have a higher flow throughput. Generally more efficient at moving large volumes of air or fluid at lower pressures, they are more suitable for large-scale, high-speed applications where high flow rates and low pressure drops are of prime importance. As such conventional axial turbines are commonly used in thermal power plants, propulsion aircraft engines, wind turbines, and cooling fans for electronics and HVAC (Heating, Venting and Air Conditioning) systems. Complex designs, manufacture and maintenance of axial turbines can be costly and challenging, becoming increasingly difficult to manufacture as size is reduced and bearing drag becomes more significant.
On the other hand, radial turbine flowmeters are better suited for applications requiring low flow rates, typically seen in medical applications and laboratory work.
Whilst offering many advantages and ideally suited to handling clean fluids, the
turbine flowmeter has one Achilles’ heel: it is very sensitive to changes in the liquid Reynolds number (used to give a measure of the ratio of liquid inertia forces to liquid viscous forces); a product of viscosity and density, therefore temperature and, for gas fluids, pressure. Turbine flow devices perform most efficiently with turbulent flow of liquid through the meter. Laminar flow and viscous drag can disrupt the dynamic behaviour of this type of flowmeter, which ultimately affect the accuracy of flow measurements. To mitigate this effect, Titan use a hexagonshaped chamber, which permits the formation of vortices that reduce the drag and assist the linearity into the laminar flow region.
Titan Enterprises Ltd is a leading UKbased manufacturer and supplier of highperformance liquid flow measuring solutions with over 40-years’ experience in flow meter innovation. Part 2 of this series will feature in the December issue of MEPCA and will cover the critical design features of turbines. flowmeters.co.uk/turbine-flow-meters
SensoPart, leading manufacturers of photoelectric sensors, explains the nuances of red light sensors and BlueLight sensors, and how the advantages offered by the technology can improve automation processes.
In the world of industrial automation, the reliable detection of objects is paramount. Traditionally, red light sensors have dominated this field, offering a range of capabilities for various applications. However, in recent years, SensoPart has revolutionised the market with its BlueLight sensors, providing enhanced process security and flexibility. But what exactly are BlueLight sensors, and how do they differ from traditional red light sensors?
SensoPart introduced BlueLight technology in 2014, specifically to address the challenges of detecting solar wafers. Traditional red light sensors were ineffective because solar wafers are designed to absorb red light to convert it into electrical energy. BlueLight sensors, however, utilise a different wavelength that solar wafers reflect more effectively, ensuring reliable detection. This technology is based on a precisely tuned transmission and reception system, optimised for the blue light wavelength.
1. Enhanced Flexibility and Robustness
BlueLight sensors offer significant advantages over traditional red light sensors, particularly in detecting challenging surfaces. They are highly reliable, even when dealing with objects at steep angles. This makes them versatile for both standard and problematic applications, allowing companies to streamline their sensor inventory and save storage space.
2. Superior Detection Capabilities
The primary advantage of BlueLight sensors lies in their ability to detect dark or lowreflectivity objects more effectively than red light sensors. This capability is particularly valuable in applications where the target objects are black or highly absorbent, which are traditionally challenging for other sensor types.
1. Packaging Industry
In the packaging industry, BlueLight sensors excel in detecting difficult-to-see objects, such as transparent or reflective films. This ensures greater accuracy and reliability in the sorting and packaging processes, enhancing overall operational efficiency.
2. Medical and Laboratory Automation
In the medical field, these sensors are crucial for the precise sorting and analysis of laboratory samples and containers. Their accuracy ensures that only the correct items are processed, minimizing errors and increasing throughput.
3. Automotive Industry
The automotive industry benefits significantly from BlueLight sensors’ ability to detect both plastic and metallic components. They
are particularly effective in reliably identifying screws, clips, and various shiny or dark car body parts. This precise detection ensures that components are correctly positioned and secured, thereby enhancing the overall quality and safety of the final vehicle.
The Challenge
In automotive manufacturing, clips are essential for securing door panels. If these clips are incomplete, they can lead to issues like vibrations or noise, compromising the vehicle’s quality. These clips are often small and vary in shape, colour, and structure, making detection challenging.
The BlueLight Solution
BlueLight sensors with background suppression can reliably detect these clips, regardless of their characteristics. Thanks to their blue LEDs, these sensors can even detect shiny or black materials effectively, ensuring that only the correct parts are recognised and processed.
SensoPart’s BlueLight technology represents a significant advancement in industrial object detection. With its ability to detect a wide range of materials and surfaces, even under challenging conditions, BlueLight sensors set a new standard for process security and flexibility in various industries. As the technology continues to evolve, it promises to further enhance the efficiency and reliability of automation systems across the globe.
info.sensopart.com/en/bluelighttechnology
• Tom Parker Ltd is an authorised UK Distribution Partner
• Large Stock Available for Same-Day Despatch
• Unique protective corrosion-resistant coating
VOSS Hydraulics, a market-leading company with over 80 years of experience, is known for providing exceptional fluid-system connection technology. The company operates globally from its HQ in Germany and has authorised distribution partners, including Tom Parker Ltd in the UK.
All VOSS fittings are equipped with an innovative VOSS coat, which provides superior, reliable, and long-lasting corrosion protection in hydraulic systems. Their products are certified to withstand 1,000 hours of corrosion and undergo rigorous testing to ensure consistent quality.
Explore the range of premium, durable, and secure VOSS hydraulic components in the Tom Parker Ltd 2024-2025 catalogue and online. Contact their expert technical support team today to find the perfect VOSS connection solution for your specific fluid power application.
Leading temperature sensor manufacturer have been awarded grant funding and innovation support to assist them in solving efficiency challenges. David Holcombe, Key Account Manager at Labfacility, provides insight into the process.
Labfacility is a South Yorkshire, familyowned, manufacturer of temperature sensors and related products, with a rich history spanning 53 years. Operating from Dinnington, the company is ISO:9001 accredited and has grown substantially since its inception – now boasting an 18,000 square foot facility, employing over 40 members of staff and selling its products to over 120 countries.
Labfacility reached out to the Made Smarter Yorkshire & Humber programme, delivered by Oxford Innovation Advice and engaged with Digital Manufacturing Advisor Marcus Pearson, to address workload management and strategic plans while tackling issues affecting efficiency and operational performance.
The primary challenges identified were:
• Data Analysis Improvement: A need to improve their in-house data analysis capabilities using the existing operating software.
• Packaging Operation Efficiency: A need to increase the capacity and throughput of their manual and costly inhouse packaging operations.
With the support of Made Smarter, the Digital Manufacturing Advisor and £27,500 grant funding Labfacility implemented the following solutions to overcome those challenges:
• Qlik Software: A software which allows quicker and detailed analysis across all operations, including sales, purchasing, and stock management. Seven staff members at Labfacility were trained in using Qlik software for in-depth data analysis.
• Automation in Packaging: Labfacility invested in a fully automated packaging machine with a hopper, significantly improving efficiency by increasing output and reducing manual input. This change allowed staff to refocus on more productive and profitable operations.
The assistance from Made Smarter Yorkshire & Humber has been instrumental in enhancing various aspects of Labfacility’s operations, improving efficiency, reducing costs, and solidifying its market-leading position in the temperature sensing field.
According to David Holcombe, Key Account Manager at Labfacility, the primary benefits of implementing Qlik software and packaging automation were:
“Qlik software is invaluable for my data analysis. Its easy-to-use interface allows me to visualise and explore data quickly,
connecting multiple data sources for a comprehensive view. This integration enhances our ability to gain deep insights, make better decisions, improve operational efficiency, and ensure our business processes are streamlined and data-driven.”
Additional benefits seen across the company as a result of working with the Made Smarter programme were:
• Improved Purchasing Efficiency: Tony Mitchell, Procurement Officer, highlights the benefits, stating, “Previously, manual reporting and analysis of supply lines were time-consuming. Qlik has automated these tasks, enabling alerts and providing regular reports. This has significantly reduced the time needed for analysis and freed up time for other tasks, allowing us to stay on top of more suppliers and lines efficiently.”
• Packaging Efficiency: The new packaging machine, excluding the hopper which will be operational by June 2024, has made the packaging process at least twice as efficient with less manual input.
Thanks to their ongoing investments in digital technology and the company infrastructure, and driven by their excellent,
determined and hardworking staff, Labfacility is on track to achieve its highest sales level in its 53-year trading history.
Along with securing a new contract with worldwide distributor DIGIKEY, Labfacility has created seven new skilled jobs and plans to create another twelve within the next twelve months.
Marcus Pearson, Digital Manufacturing Advisor, said, “The support provided to Labfacility by Made Smarter is a perfect example of how building and developing a strong relationship with key local agencies and intermediaries is crucial to the delivery of aligned business support that adds real impact to the recipient SME.
Martin Riddett was introduced to me by David Grimes, his Key Account Manager from Rotherham’s local authority. The fact that I have worked with Dave for many years and been able to demonstrate that I would ensure that his clients’ needs were handled efficiently, professionally and in a way that would minimise the level of bureaucracy and paperwork so that they could focus on their business critical issues, ensured that when he set up my initial contact with Labfacility,
he had already got Martin and the senior teams buy in to what we were all about. Without the trust of the local business support and advice community – and having their commitment to recommending the company’s that they work should be accessing Made Smarter – there is a real risk that the programme doesn’t maximise its reach, its why we invest so much time building solid relationships and ensuring that the work that we do not only enhances the growth prospects of the business, but also endorses the reputations of our local partners.”
Labfacility is committed to ongoing development in operational efficiency and digital improvements, including investigating barcoding and capacity increases through possible mezzanine installation. The company is also focused on new product research and development, which will require additional tools and machinery.
labfacility.com
Utilising the cloud to make better use of deep learning machine vision technologies can overcome data and factory site silos to enhance the volume and variety of data in high value workflows, such as testing and quality control. Donato Montanari, VP and GM of Zebra Technologies, explains more.
When it comes to developing new and existing factories and procuring solutions, the focus is at site level, with input and sign-off shared at site and corporate level. But there’s always the possibility of different sites using different solutions for similar workflows, and the risk of expertise and data not being shared across sites, including when using newer artificial intelligence (AI)-powered solutions where data quality is essential. This can also be true for visual inspection teams using machine vision systems for quality and compliance.
According to this Zebra report examining AI machine vision in the automotive industry, almost 20% of automotive machine vision leaders in Germany and the UK say their AI machine vision could be working better or doing more.
Machine vision teams across manufacturing industries need new ways to leverage deep learning machine vision, which should include using the cloud. A cloud-based machine vision platform would allow teams to securely upload, label, and annotate data from multiple manufacturing locations across site, country, and region. A larger, more diverse range of pooled data in a cloud-based platform from across sites and environments is better for deep learning training. Such a platform would allow defined users to work together in real time, collaborate on annotation, training and
testing projects, and share their expertise. With a cloud-based platform, users with defined roles, rights and responsibilities could train and test deep learning models in the cloud. Powered by much better training and testing data, they may deliver much higher levels of visual inspection analysis and accuracy beyond conventional, rules-based machine vision for certain use cases. These outcomes are sought by manufacturers in the automotive, electric battery, semiconductor, electronics and packaging industries, to name a few.
A cloud-based solution also delivers scalability and accessibility of computing power. With traditional systems, select employees get powerful GPU cards to perform training. With the cloud, every user can access the same high computing power from their laptops. While cloud solutions cost, through a payas-you-go subscription model, it may still be more beneficial than investing in servers and additional hard-to-find IT personnel.
A software as a service model would give machine vision teams the flexibility and ease of investing in a cloud-based platform with a subscription while new features, models, and updates are seamlessly added by the technology partner. Deep learning cloud-based platforms allow for model edge deployment on PCs and other devices to support flexible, digitised workflows on the production line, wherever a user is located.
54% of manufacturing leaders in Europe (61% globally) expect AI to drive growth by 2029, up from 37% (41% globally) in 2024, according to Zebra’s 2024 Manufacturing Vision Study; while 26% (27% globally) believe one of today’s most significant quality management issues is integrating data. With these AI and data goals, the time is ripe to look at the potential of the cloud to leverage data and extend the benefits of deep learning machine vision.
zebra.com
• EC+ AHU efficiencies of 85%
• Energy savings of 20-50%
• Product lifetimes of 20+ years
• Recyclability rate of 98%
• Complete plug-and-play
• Ultra-low sound levels
• Low maintenance costs
• ROIs between 12-18 months
• EC+ AHU efficiencies of 85%
• Energy savings of 20-50%
• Product lifetimes of 20+ years
• Recyclability rate of 98%
• Complete plug-and-play
• Ultra-low sound levels
• Low maintenance costs
• ROIs between 12-18 months
Upholding compliance standards and eliminating abnormalities is a crucial aspect of semiconductor production. As the industry evolves, so too must the technology underpinning quality assurance practices.
Gocator Smart 3D Coaxial Line Confocal Sensors are at the forefront of nextgeneration machine vision technology for automated inline quality control, providing robust 2D intensity and 3D shape inspection of complex details in precision-manufactured semiconductor components and assemblies.
Central to the Gocator 4000 Series’ effectiveness in semiconductor applications is its outstanding resolution performance.
Achieving X resolutions down to 1.9 microns, these sensors enable meticulous inspection of key features like BGA (Ball Grid Array) ball bumps (as illustrated), silicon wafer dies, and IC (Integrated Circuit) wire bonds.
Such precision allows engineers to adhere to rigorous quality standards in semiconductor production, where even the smallest deviations can have a profound impact on device performance and reliability.
Speed is another area where the Gocator 4000 Series excels. Capable of scanning at rates up to 16 kHz within limited measurement ranges and 4 kHz at full measurement range, these sensors ensure that inspection processes keep pace with the rapid throughput requirements of semiconductor production lines.
The Gocator 4000 Series’ coaxial optical design is also an advantage over competing vision solutions. The coaxial optical approach effectively eliminates shadowing effects — a common drawback of dual-axis confocal scanning technologies that can obscure details in steep-angled or deep-
grooved features. By offering unobstructed visualisation of complex semiconductor surface topologies, coaxial line confocal scanning enhances measurement accuracy and reliability. This is especially beneficial for inspecting challenging features such as steep PCB (Printed Circuit Board) chip angles and deep wafer die grooves, where shadowing can otherwise result in missed defects or inaccurate readings.
The Gocator 4000 Series has an impressive angular range, boasting a Maximum Slope Angle of up to +/- 85 degrees. This ensures superior performance on highly specular and curved surfaces that include machined-metal components and cell phone display glass. In addition, versatility in scanning and measuring a wide array of materials and geometries underscores these sensors’ adaptability to various inspection applications, from semiconductor components to consumer electronics.
Finally, the Gocator 4000 Series provides excellent ease of use and seamless system
integration. Equipped with a web-based user interface, on-sensor measurement tools, built-in input/output connectivity, and standard mounting options, these sensors are designed for seamless implementation into existing production lines for rapid deployment and pre-calibrated measurement out-of-the-box. Their smart, streamlined design minimises setup times and simplifies operator training, ensuring a smooth transition to advanced inspection capabilities.
The Gocator 4000 Series Smart 3D Coaxial Line Confocal Sensors represent a significant advancement in semiconductor inspection technology. Combining high resolution, exceptional speed, shadow-free imaging, and a large angular range, these sensors meet the dynamic needs of today’s demanding semiconductor manufacturing environments. As the semiconductor industry continues to evolve, integrating these state-of-the-art sensors into production lines is pivotal for upholding the highest standards of quality and reliability.
lmi3d.com
3D printing for mass production has come a long way in a short time. It’s now so mature it has become a commodity purchase in many industries. However, some manufacturers are still reluctant to adopt it, which could be a mistake, as Paul Moloney, Midlands 3D’s founder and MD, explains.
Not so long ago 3D printing was confined to hobbyists, prototypes and tiny runs of custom parts, but ground-up printing systems, new materials and the rapid growth of 3D print manufacturing services changed all of that.
Manufacturers that are not using 3D printed components as end-use parts alongside processes like injection moulding and CNC machining are more than missing a trick; they’re missing an evolution in manufacturing capability and the commercial benefits that come with it. Here are three mini case studies, and one change to procurement thinking to illustrate the point:
Air quality monitor makers, Synetica, 3D print both chassis and case for their outdoor monitors. If they suffer component shortages they are able to flex their chassis design to accommodate available part variants – even within the same production batch. Any other process would inevitably lead to excess stock holding of incompatible parts and incomplete final products.
Bringing a new product to market can be a massive challenge, especially before the market and/or design are fully proven.
Motorbiking accessory innovators BullShift had this very problem, almost committing to a design too early and risking being locked into an expensive, and what could have been wasted, injection mould tool. Adopting 3D printing has allowed them to “stay lean” - building batches of final products, testing and adapting their design, while still bringing a cost-effective, and highly functional product quickly to market.
In the design, testing and final production of their pipeline measurement and inspection products, OMS applies production ready technologies such as HP Multi Jet Fusion (MJF) to validate both design and durability characteristics. The confidence of going to full production with 3D printed components identical to those used in product development, gives assurance the product will perform in the often harsh applications their equipment ultimately encounters. Simpler, low-cost technologies such as large format Fused Deposition Modelling (FDM)
are also used to develop full scale test rigs for particular client applications.
In their eBook, Midlands 3D lists 5 ways 3D printing can transform your procurement strategy. Here is just one:
Unlike the two dimensional build plate constraints of FDM printing, the three dimensional build volume nature of powderbased printing introduces a new perspective relevant to both you and your 3D print manufacturing partner. The more parts of varying sizes required, the greater their ability to optimise the use of available space in every print run, and the more cost effective the production run becomes. Unlike FDM or Selective Laser Sintering, a MJF print run takes the same amount of time whether there’s one part or a thousand parts in the build.
With this new thinking in mind, and applying it to your own requirements, smaller components like brackets, spacers, etc., which may be overlooked could be printed cost effectively alongside larger product specific parts. The printer is going to run the job for your larger parts regardless. Now imagine ordering ‘sets’ of multiple printed parts on-demand, quickly translating to far less capital tied up in your supply routes and warehouse shelves from parts waiting for products.
To read the full case studies and get free access to the eBook “Five Principles that Unlock 3D Print Manufacturing”, visit the website below.
midlands3d.com/mepca
Equip your maintenance team with the digital tools they need to perform their best work - safely and effectively.
Reduce downtime and improve productivity by implementing thorough, easy-to-follow, step-by-step maintenance procedures with WorkfloPlus. The platform’s digital workflows ensure that every task is completed correctly and timely, minimising the risk of equipment failure.
Eliminate information delay by removing the need to manually enter paper-based logs into centralised systems. WorkfloPlus allows workers to instantly submit job data, ensuring accurate and up-to-date maintenance records. This real-time data can be used to schedule preventive maintenance, predict potential failures, and optimise resource allocation, to extend the lifespan of your equipment and reduce costly downtime.
UltiMaker is a renowned manufacturer of 3D printing machinery that enables on-site production across a wide range of industries. Vicki Bromley, Product Specialist at Laser Lines, explains how the UltiMaker Factor 4 improves on prior iterations of the technology.
When UltiMaker Factor 4 shipped in August, it topped out an impressive line-up from the European 3D printer manufacturer. It has much in common with the existing S7, including a flexible PEI-coated build plate and identical build volume, but in every other respect, it marks a significant step up.
It’s as much at home on the factory floor as it is in the office or lab – as its name would suggest – because alongside a rigid chassis and steel gantry, it’s got a dualgeared feeder and modular design. That makes it more durable and, in the unlikely event it needs spares or to be repaired, it will be easier and quicker to get back up and
running.
“In almost every way, we’re seeing this as an upgrade from the UltiMaker S7,” says Laser Lines’ Vicki Bromley. “But the S7 isn’t going anywhere. The two will be sold side by side, with the Factor 4 aimed squarely at the most demanding users.”
Factor 4 is tailored for high-end production of end-use parts. Its dual-gauge feeder has been reinforced for use with robust engineering-grade consumables, including the new PPS-CF (carbon fiber reinforced polyphenylene sulfide filament), which is flame retardant and resistant to temperatures over 230°C (a good alternative to steel/ aluminium). Working with these is only
possible at higher temperatures, so the HT core (an abrasion resistant print core) has been designed to reach 340°C, the heated bed to 120°C and the build chamber to achieve 70 degrees.
The five-degree increase on the maximum chamber temperature is a significant improvement that required an end-to-end redesign of the UltiMaker S7. The chamber is now fully sealed, and triple insulated to control the airflow and achieve consistent temperatures to ensure reliable part quality.
UltiMaker has taken advantage of this design requirement to give the machine a thorough refresh. The black facing and metal sides look great in any environment. It really is a printer you’ll be proud to have on display.
Internally, the material’s climate control is integrated, rather than having a separate unit as is the case with the UltiMaker S7, and here, it helps keep humidity below 15%.
That’s a ten percentage-point improvement on the 25% cut-off seen in the S7. Again, this may sound marginal, but it’s a significant change that’s testament to the Factor 4’s strengths as a high-performance production unit. Materials are highly sensitive to moisture, after all, so humidity is a significant consideration that can’t be ignored when working at this level.
Laser Lines has been running a Factor 4 in its customer demonstration room for a while and the team has already noted that its dimensional accuracy is second to none. Officially, this stands at 0.2mm or 0.2% in either direction.
The machine has a built-in physical analytics system, which tracks the extruder’s motion throughout the production process to grade the finished product with reference to its input data. For companies wanting to monitor and improve their 3D printing process, the new Print Process Reporting feature is available via activation of a premium software licence.
“It’s called Onboard Structural Integrity Validation,” says Vicki. “This delivers an in-depth report on the overall extrusion parameters and any deviations from nominal values, their locations in the 3D model, and severity. If you’re producing end use parts with fine tolerances, we reckon that this alone is reason enough to put Factor 4 on your shortlist.”
Better yet, despite all these additional features, the finer tolerances, and the analytics system, UltiMaker Factor 4 is around 50% faster than the S7 which, as Vicki points out, will help it to more quickly offset the purchase price in throughput and time saved.
UltiMaker Factor 4 is a stock item. Vicki adds: “Anyone who places an order can expect delivery in about a week. In the meantime, we’re more than happy to show one in action to any prospective customers – or produce a free benchmark or sample part. Come and see the printers at our HQ in Banbury – we’d love to see you.”
You have two options for obtaining a sample: you can either choose from the samples provided by the manufacturer or
submit your own CAD design to Laser Lines. Vicki, their product expert, will guide you through the process, ensuring your project is properly prepared and helping you select the most suitable material for your specific printing needs. Once your sample is ready, you can either pick it up in person or have it delivered directly to your office.
Laser Lines, based in Oxfordshire, is a trusted UK reseller of additive manufacturing technologies with over 30 years of experience. Known for their expert advice, outstanding customer service, and comprehensive support, they work closely with clients to understand their unique business requirements and workflows. This allows them to recommend tailored additive manufacturing solutions that maximise
efficiency and value.
Their product portfolio includes not only FDM (Fused Deposit Modelling) 3D printers from UltiMaker but also Stratasys 3D printers, which offer a variety of advanced printing technologies. Additionally, Laser Lines provides DyeMansion post-processing machines for finishing 3D-printed parts, and Xact Metal printers for precise metal printing.
Beyond hardware, Laser Lines offers a full range of consumables and accessories, ensuring customers have everything they need to keep their systems operating at peak performance. Their commitment to ongoing customer support means they are there every step of the way, from initial consultation to post-installation service, helping businesses fully integrate additive manufacturing into their operations. 3dprinting.co.uk
The Honeywell BW™ MicroClip Series has earned its reputation as the world’s most popular multi-gas portable detector, offering a reliable, long battery life, and user-friendly operation. This series is a top choice for industry professionals who require robust and efficient gas detection solutions.
1. Simultaneous Multi-Gas Detection:
The BW™ MicroClip Series can monitor up to four gases at once, including oxygen (O2), hydrogen sulphide (H2S), carbon monoxide (CO), and combustibles. This comprehensive detection capability is essential for maintaining safety in environments with multiple gas hazards.
2. Extended Battery Life: With a battery runtime of up to 18 hours in normal temperatures and a cold weather guarantee of at least 12 hours, the BW™ MicroClip Series ensures continuous operation throughout an entire work shift, even in extreme conditions.
3. Compact and Lightweight Design:
The detectors are designed to be compact and lightweight, making them easy to carry and use. The one-button operation simplifies usage, reducing the need for extensive training and allowing workers to focus on their tasks.
4. Unmatched Water Protection: The BW™ MicroClip Series boasts an IP68 rating, providing maximum protection against dust and water. The device can even withstand being immersed in water up to a depth of 1.2 meters for 45 minutes.
5. IntelliFlash™ and Reflex™ Technology:
The IntelliFlash™ light provides a quick visual confirmation of compliance, while Reflex™ Technology ensures sensor responsiveness. These features enhance safety by maintaining device readiness and worker confidence.
6. Device Management with Honeywell Safety Suite: The BW™ MicroClip Series integrates seamlessly with the Honeywell Safety Suite, allowing for efficient device management and data analysis. This
capability helps organisations maintain compliance and optimise safety protocols.
7. Cost-Effective Ownership: The BW™ MicroClip X3 model offers a threeyear warranty and an all-new O2 sensor, extending the expected service lifetime to five years. This long-term reliability reduces overall maintenance costs, making it a costeffective solution.
By providing reliable detection of multiple gases, the BW™ MicroClip Series helps protect workers from potential hazards, ensuring a safer work environment. The simple one-button operation and intuitive design reduce training time and make the device accessible to all workers, regardless of their technical expertise. The IP68 rating and rugged construction ensure the device can withstand harsh environments, while features like the IntelliFlash™ light and Reflex™
Technology help ensure that the device is always ready and compliant with safety standards.
Rockall Safety have been providing specialist safety equipment since 1995. They are committed to providing a safer working environment for employees across numerous industries. By partnering with industry leaders like Honeywell, Dräger, Blackline Safety and Crowcon, Rockall Safety have reaffirmed their commitment to quality, affordability, and exceptional customer service. So confident are they in the affordability of their pricing, that if you find their products available at a lower price elsewhere, they pledge not only to match that price but to surpass it (where possible), ensuring you receive the best deal possible. rockallsafety.co.uk/the-honeywell-bwmicroclip-series/
Dr Karen McDonnell, RoSPA’s Head of Global Relations, discusses the importance of controlling noise in the workplace. With 11,000 workers in the UK suffering from hearing problems, what impact does noise exposure have on your employees?
Most people recognise the direct effects that noise can have on the auditory system, resulting in noise-induced hearing loss, tinnitus or hyperacusis (sensitivity to loud noise). Even though these risks are often understood, the debilitating, disabling and isolating results of these permanent effects are greatly underestimated.
Less well-appreciated are the other known implications for health related to noise exposure – resulting in cognitive decline, coronary and circulatory problems and depression or stress. We know that exposure to noise at work can cause irreversible hearing damage, but is it preventable?
According to the Health and Safety Executive (HSE), the industries most likely to involve high levels of noise are construction, demolition, woodworking, engineering and manufacturing.
Across all industries, noise-induced hearing loss is responsible for the highest number of work-related personal injury claims. ‘Occupational deafness’ has been a prescribed disease under the Industrial Injuries Disablement Benefit scheme since 1975. In the last 10 years, it has consistently been one of the top three reasons (excluding lung conditions) for benefit awards under the scheme.
Instant noise-related hearing damage can occur from one episode of loud noise, but most often, workrelated harm is caused by prolonged exposure and is gradual.
All employers need to be
aware of their duties under the Control of Noise at Work Regulations (CNWR) 2005, under which employers are required to:
• Conduct a risk assessment to identify if there is a noise risk to employees and to identify who may be affected
• Introduce control measures if needed to reduce noise exposure to comply with CNWR
• Identify any employees who need to be provided with health surveillance (hearing checks) due to noise exposure
• Provide employees with information, instruction and training about noise risks and any control measures being taken Under the regulations, employers need to take specific action once noise levels (action values) set out in the regulations are reached. The action values relate to average noise exposure over a working day or week, and to the maximum noise (peak sound pressure) to which employees are exposed in a working day.
The lower exposure action values are:
• Daily or weekly exposure of 80 dB(A)
• Peak sound pressure of 135 dB(C)
The upper exposure action values are:
• Daily or weekly exposure of 85 dB(A)
• Peak sound pressure of 137 dB(C)
When considering what control measures to introduce, clear advice is provided in HSE’s guidance on the regulations (L108), which is now in its third edition. The regulations set out a hierarchy of control measures, with eliminating the noise at the source at the top and providing ear protection at the bottom.
Personal ear protection should only ever be considered after engineering controls and organisational measures (such as limiting the time spent in noisy areas) have been considered; the ideal is to design the noise out at source.
Damage to hearing is preventable if employers take the relevant action to assess and control the risks and provide health surveillance for all staff who are regularly exposed to noise above the upper exposure level, as well as for other employees who may be at risk of hearing damage.
For their part, workers need to take responsibility for their hearing by using any noise control devices or hearing protection provided to them, following prescribed working methods, attending any hearing checks, and reporting any concerns about noise to their employer or safety rep. Employers can mitigate risks by buying quieter machinery, controlling noise at source, and managing the condition, use, fit and fitness for purpose of the hearing protection they provide.
rospa.com
Mislabelled allergens can still be found on shop shelves despite a heightened awareness of allergies and dietary requirements. Harford Control questions why this problem persists and highlights the benefits of employing a technology-based solution.
Food recalls due to allergen mislabelling are still very common in the UK. Food Standard Agency data shows that 314 allergy alerts were issued in the reporting period for 2022/23.*
The consequence of food recalls not only leads to tragic loss of life, but also causes serious damage to a brand’s financial health.
Pret a Manger set aside £10m to cover legal costs after Natasha Ednan-Laperouse died from consuming mislabelled baguettes in 2016 and Celia Marsh suffered from a fatal reaction to a ‘vegan’ wrap in 2017.
Whilst efforts are made to ensure allergens are properly labelled, some food and drink manufacturers are not fully aware of the allergen labelling guidance. Some choose not to invest further and instead opt to ‘hope for the best’. Others have integrated ineffective solutions, such as print rooms.
Print rooms cannot be solely responsible for ensuring that products are accurately labelled (that the right label goes on the right product), as workers may overlook allergens or ingredients. Besides, the print rooms may not have access to all the necessary information.
From raw materials to finished products, it’s the manufacturers’ responsibility to ensure allergen control and provide clear and safe products to retailers and consumers. Allergen control must include, but is not restricted to:
• Supplier verification: Verify that suppliers provide accurate information about allergens present in their ingredients and adhere to appropriate safety standards.
• Allergen testing: Implement regular testing of both ingredients and finished products to verify the absence of allergens and
detect any contamination. This can include laboratory testing as well as on-site testing methods such as swabbing for the presence of allergens.
• Accurate labelling: Review and improve their labelling and inspection procedures regarding allergen declarations to ensure clear and accurate labelling of all known allergen ingredients.
Harford Autocoding Solutions help manufacturers ensure 100% verification of packaging accuracy, to avoid inaccurate label information and unnecessary wastage. The solutions can be integrated into production lines to send real-time actionable data directly to those who need it. At the start of each production run, the system will ensure that label printers are set up accurately and in-line barcode scanners
are configured to check that the correct packaging materials and labels are used –on each individual product, case or pallet. In some instances, on-line integrated cameras may also be required to ensure that the pre-printed packaging displays the correctly highlighted allergens.
Though this is a huge, essential step towards ensuring compliance, it must also be said that no automated system can ever guarantee total compliance, and full training and operator engagement are also essential to provide world class due diligence.
Harford Control Ltd have enormous experience in helping food and drink manufacturers ensure greater accuracy of labelling for control of allergens, date coding, quality and much more. With Harford Autocoding, the company have provided a reliable method for eliminating risk and improving labelling accuracy.
harfordcontrol.com
*Incidence and Resilience Report 2022/23
The company that introduced the world’s first modular design cam switch (making it possible to manufacture tailor-made products) and created the world’s smallest cam switch help to ensure safer flying in the world of avionics.
At Kraus & Naimer product quality is tightly and reliably controlled at every stage. This is made possible by a vertically integrated process. Since its foundation in 1909, Kraus & Naimer has kept manufacturing of all components in-house. This requires great understanding of every single step of the process and enables the company to:
• maintain absolute quality control on all production & distribution processes
• manufacture even the smallest switch components in-house
• be able to quickly react to fluctuations & respond to market demands
• customize products to meet customer needs
After more than 100 years, this has been one of their main ingredients for success.
Another is their flexibility, one of their core competences. Knowing that many applications have unique requirements, they don’t only offer standard switches but also tailored solutions that fit specific needs, enabling the personalisation of the switch with a variety of add-ons, door clutches, auxiliary contacts, padlock devices, shaft extensions, key-lock devices … and many more.
The team at RS Flight Systems develop and produce avionics devices for 2- to 4-seater aircraft and helicopters.
Safety in the aviation industry is of course the top priority, but when it comes to functionality, a lot has to be covered in a small space: overlapping areas when switching from one fuel pump to the other, for example.
In addition, highly efficient injection
engines for small aircraft, such as those from the market leader BRP-Rotax from Austria, have complex components and require a whole series of switching operations, as testing all functions is a necessity before starting the engine.
The brief was to produce a control panel that meets those switching requirements but is also able to fit into a confined space and withstand the inevitable vibrations within the aircraft.
The result is the intuitive & tidy iS Engine Panel V3. It has Kraus & Naimer CHR10 switches coupled on the back; on the left with a socket wrench device for powering the aircraft, on the right with a gate lock for testing the engine control units and starting the engine. When flying, it is of course crucial to ensure that no part comes loose due to vibrations. For this reason, all cables are securely connected to the switches
using ring connectors and the unique switch terminals ensure they cannot come loose.
“Our switches are generally installed in industrial applications, machinery or in the logistics sector. “That’s why a project of this kind was an interesting challenge,” sums up the Kraus & Naimer Sales representative Rauh.
The CH switch range (used in this instance) are designed for universal applications and are ideally used as control switches, instrument switches and motor switches. They are compact in design, have a built-in screwdriver guide for easier installation, and modifications are available using quick-connect terminals. krausnaimer.com
Nord Drivesystems, provider of innovative drive solutions, has made a breakthrough in versatile control cabinet technology with its new inverter, offering a control standard for numerous applications.
With the NORDAC PRO SK 500P, Nord Drivesystems possesses a control cabinet inverter for virtually every drive application. It is available in variants with a power range of 0.25 to 22 kW, which can be assigned to different requirements in different industries. At present, the system supplier is working to extend the power range.
A control standard across several applications – the objective Nord has set itself when developing the NORDAC PRO SK 500P. The result is a control cabinet inverter, whose features allow for a high level of versatility and intelligent communication with system components. This way, Nord users can reduce the number of inverter variants and rely on a system in the long term.
As with all NORDAC PRO inverters, the integrated multi-protocol Ethernet interface is one of the key elements. It can be used to integrate the control component into different networks without retrofitting. This includes the Profinet, EtherCAT, EtherNet/IP and POWERLINK protocols. Further protocols are covered depending on the model. A USB interface also allows for the voltage-free parameterisation of the inverter.
The integrated PLC (Progammable Logic Controller) responds independently to process changes in the system. It can thus relieve the load on the higher-level control. The POSICON positioning function implements various positioning tasks. It is equally able to control relative or absolute positioning using incremental or absolute encoders. Parameter set switching even allows for the sequential positioning of up to four axes.
With NORDAC PRO SK 500P, users can implement a wide range of industry-specific drive applications. The control cabinet inverter has a vector regulation with an overload reserve of 200%. It is thus suitable for the control of geared motors in heavyduty applications or lifting systems. Its PI (Proportional Integral) controller and its integrated compensator control makes it the most suitable frequency inverter for pumps and winding systems. At the same time, the frequency inverter in its book-size format requires very little space in the control cabinet and allows for direct side-by-side installation without gaps.
With NORDAC PRO SK 500P, it is possible
to control all motor types with and without encoder feedback. To make its advantages available in a wider power range, NORD currently works on new sizes for the inverter.
Nord Drivesystems is part of the Nord Group, which has 48 subsidiaries in 36 countries and further sales partners in more than 50 countries. Founded in 1965, all companies within the group share a single ethos. Thanks to their global service network, Nord guarantee worldwide service. This includes simple organisation and handling of repairs, spare parts deliveries and on-site support in the customer’s country. Nord Drivesystems provides on-site consulting, assembly centres, technical support and customer services.
nord.com/en/home-uk.jsp
• quality linear rail and carriages.
• Long-term partners with TBI, which produces high-quality rolled ballscrews and ball nuts.
development experience and represents the state of the art in linear actuator designs
- Rails cut to specification In-House
- Ballscrews machined In-House
- Bespoke Belt Driven Actuators
- Precision Ballscrew Driven Actuators
Adhesives are a silent but crucial partner in countless engineering projects and are utilised in nearly every industry. The more effective the adhesive, the less likely it is to be noticed or appreciated. This month MEPCA shines a light on Permabond, a foremost manufacturer of engineering adhesives.
Permabond has been providing adhesive solutions to engineers and product designers since the 1960s.
Many of our readers have likely used Permabond’s adhesives whether they are aware of it or not – their product range is exhaustive, and the industries they provide solutions to includes Aerospace, Automotive, Electronics, Marine and Medical, to name but a few.
Since establishing themselves in industry, Permabond have gained extensive experience in providing adhesive solutions and product innovation, enabling them to help with all manner of bonding and sealing challenges, no matter which materials are involved. Permabond provide solutions to companies of all sizes and have a global reach thanks to their extensive worldwide network of distributors, and offices in Europe, the US and China. Permabond continues to grow year-on-year and is constantly looking to create the next breakthrough in adhesion technology.
We are delighted to have had the opportunity to ask Permabond some questions and highlight their continued efforts to provide industrial adhesive solutions to a multitude of industries.
What are the key benefits our audience can expect from utilising your engineering adhesives?
Permabond adhesive products offer engineers and product designers a wide range of benefits. Firstly, our adhesives are ideal for replacing more traditional bonding methods such as mechanical fastenings and welding. In the case of fastenings, our anaerobic threadlocking and threadsealing
adhesives provide a stronger bond that is far more resistant to vibration and impact, and thus prevents loosening of parts.
In the case of welding, adhesives are a safer, more aesthetically pleasing and affordable choice. We offer products that bond almost any substrate, from plastics (including nylon) to metals, composite materials, glass and many others, thus increasing the design flexibility of engineers.
How committed are Permabond to innovation and new technology development?
As a company, we pride ourselves on innovation and product development. We are constantly looking to create new products that provide solutions to the challenges faced by engineers across many different industries. For example, Permabond has pioneered a breakthrough adhesive technology for the reliable bonding of nylon, a substrate known for being very difficult to bond due to its low surface energy.
In addition, we’ve recently launched structural acrylic adhesives that are able to bond through greasy or oily surfaces, allowing for major time savings in surface preparation. A final example is our commitment to developing greener product solutions, which includes sourcing our raw materials from sustainable sources and developing cartridges using biological compounds.
Do you offer customised adhesive solutions at request, catering to specific industry requirements?
A part of Permabond’s unique service
is our ability to provide customers with individualised adhesive formulations to meet their specific needs. We are able to customise an adhesive based on a wide range of factors, including viscosity, thixotropy, curing mechanism and cure speed, product colour, and so on. We will work with a customer at every stage to tailor a product best suited to their individual needs and demands, from conception all the way through to product testing and fine tuning.
permabond.com
Instead of completely replacing factory workers with robots, some manufacturers are looking to integrate collaborative robots, cobots for short, which work in harmony with human workers.
The idea of autonomous robots taking overall work in a factory or assembly line was seen as progress – replacing workers to perform tasks on assembly lines to improve overall efficiency with a high price tag – but has come to be seen as a threat to the job security of factory workers. Much has been debated over the years about this topic and the current trend of collaborative robots has emerged as an alternative.
The collaborative robot concept has gained popularity in recent years. It has the potential to help smaller operations to be more competitive, as well as enhance productivity and efficiency in large factories. Experts are predicting a strong growth potential for cobots, with an expected 22% increase predicted for 2024 and similar levels of growth expected year on year to 2028. The price of these cobots is expected to continue to fall, hence the increased adoption rate for use in automation. Mid- to small-size companies are soon expected to be able to enjoy their use and expanded applications. Newer available technologies, i.e., vision sensors and 3D sensors, have also helped widen the uptake of cobots. One thing is for certain: cobots will be used in many more new applications as technology progresses and the associated costs drop.
The majority of recent cobots take the form of simple robotic arms. They are programmed to perform specific tasks that may include: inspection for outliers, lifting heavy items, assembling parts, monitoring specific functions of other machines or tasks, moving items and more. These robots can handle heavy loads beyond human
capabilities. They can be programmed for specific movements that a human’s anatomy is incapable of performing. Most cobots are safe to work alongside humans and can navigate around them using sensors to avoid potential injuries.
Cobots and Other Advanced Computer Hardware Technology for Automation
The real brains behind these collaborative robotic arms are the industrial embedded motherboards, PC-based controllers and touch panel PCs that are used to control cobots, factory assembly line equipment including sensors and actuators and other robotics in factory automation. Axiomtek’s compact, industrial-grade Pico-ITX embedded motherboards can be integrated into cobots to control a variety of their functionality and task performance. Axiomtek’s Pico-ITX product line offers scalable CPU options including the advanced 6th generation Intel® Core™ family
and Celeron® processors, high expandability, rich I/Os including USB, DIO, PCI Express and Gigabit LAN ports with great graphical capabilities and Intel® AMT support for remote management.
Advancements in embedded computer hardware is constantly pushing the limits of factory improvement. The evolving landscape of the automation industry depends largely on availability and the cost of adopting of emerging technologies. Who knows – maybe the future of automation will be truly evolutionary innovations, where collaboration between machines and humans results in the highest quality products, efficient operations and optimum values for the manufacturers, workers and consumers.
axiomtek.co.uk
DIN-Rail Fanless Embedded System with Intel Atom® x6212RE or x6414RE Processor, 3 2.5GbE LAN, Isolated COM, and Isolated DIO
According to new research, most UK manufacturers have been adversely affected by rising business costs. Anton Nebbe of Close Brothers Asset Finance, the corporate financing experts that commissioned the research, provides MEPCA with an analysis.
Recent research commissioned by Close Brothers Asset Finance has revealed the significant impact of rising costs on businesses across the UK, including those in the manufacturing sector, with a majority of respondents reporting adverse effects on their operations and financial health.
According to the research, 75% (UK total: 71%) of businesses have been affected by the rising cost of doing business, while 25% (UK total: 19%) reported no impact, and 5% (UK total: 6%) were unsure.
Among those experiencing increased costs, 56% (UK total: 56%) of manufacturers indicated it has negatively impacted their cashflow. Conversely, 32%
(UK total: 27%) reported no negative impact on cashflow, and 10% (UK total: 15%) have not noticed an increase in costs.
The survey also identified the top five primary inflationary cost pressures affecting manufacturing businesses – in order of most impactful:
1. Energy (gas, electricity)
2. Supplier costs
3. Fuel (petrol, diesel)
4. Interest rates
5. Rent
This list matched exactly that of the other sectors polled, clearly demonstrating that firms across the board are sharing common cost pressures, regardless of industry or location.
Additionally, 71% (UK total: 67%) of businesses have seen their business insurance costs rise in the past 12 months, while 20% (UK total: 26%) have not, and 9% (UK total: 7%) are unsure. In response to these increased costs, 23% (UK total: 24%) of businesses have fully passed price increases onto customers. A further 66% (UK total: 61%) have partially passed on the cost increases, while 11% (UK total: 15%) have chosen to absorb the additional cost entirely. Regarding employee wages, 59% (UK total: 54%) of businesses reported wage increases in the past six months, 30% (UK total: 34% did not), and 7% (UK total: 6% were unsure).
These findings underscore the challenges faced by UK businesses in the current
economic climate, highlighting the need for strategic planning and support to navigate these pressures.
In order, businesses felt they would benefit most from:
• Economic stability - 24%
• Lower interest rates - 13%
• Subsided energy bills - 13%
• Easier access to finance - 12%
• Supply chain stability - 12%
• Tax cuts - 11%
• Better access to skilled workforce - 9%
“The rising costs of doing business are presenting significant challenges for many enterprises across the UK,” said Anton Nebbe, Head of PR and Communications, and responsible for commissioning research at the firm. “Our research highlights the critical areas where businesses are feeling the pinch, from energy and supplier costs to increased insurance premiums.
“At Close Brothers Asset Finance, we are committed to providing the support and resources businesses need to navigate these pressures and continue to thrive. By understanding these challenges, we can better assist our customers in developing strategies to mitigate these impacts and ensure long-term success.”
Cost of living increases were also among the factors considered: five in four manufacturing business owners reported that the increased cost of living had impacted their employees, aligning with national sentiment. While this option wasn’t available for everyone, working from home had reduced living costs for 57% of employees.
closeassetfinance.co.uk
Schneider Electric to invest £42 million in new manufacturing site in Scarborough, North Yorkshire. It will create 200 jobs. The New 16,500 sq m site will be a blueprint for sustainable design and operations.
Schneider Electric, the leader in the digital transformation of energy management and automation, is investing £42 million in a new manufacturing facility in Scarborough, North Yorkshire.
More than 200 jobs will be created to meet the increased demand for electrical equipment to drive the UK’s move to cleaner energy including renewable energy sources, electric vehicles, and intelligent, energyefficient buildings.
The site, which is almost triple the size of Schneider Electric’s existing Scarborough facility, is a blueprint for sustainable design and operations in the manufacturing industry. It is poised to become a net-zero plant and will use modern technology to reduce energy waste and maximise the use of renewable energy. It is expected to be net-zero in Scope 1 and 2 emissions when it opens in early 2025.
• 30% of the facility’s energy will be produced by a state-of-the art solar energy system, with solar panels covering 50% of the roof, to ensure the building harnesses solar energy efficiently
• Any energy consumed on site from the national grid will be “renewable certified”
• An intelligent Building Management System, based on Schneider Electric’s EcoStruxure platform, will ensure energyefficient operations including light sensors, automated heating and cooling.
• It will feature one of the first fully electric paint lines in Europe to support decarbonised operations
• It is targeting a BREEAM ‘Excellent’ rating, setting it apart in terms of sustainable construction standards.
The site is designed to be environmentally friendly, with sustainable transport options for employees.
• Employees will have access to 30 EV
chargers on site
• There will be dedicated cycling racks, shelters, and showers on site for bike riders
• Work is underway with Natural England to create a habitat for protected species
• It will promote biodiversity by retaining as many of the existing trees and natural features as possible
Scarborough is a long-established manufacturing base for Schneider Electric, currently employing 450 people. It specialises in the manufacture of low-voltage switchgears which protect and distribute electricity and are crucial to the rollout of sustainable and energy-efficient operations such as EV charging infrastructure and netzero buildings.
“Sustainability is at the core of our purpose, culture and business. We’re proud to be investing in and developing innovative solutions which will deliver immediate and lasting decarbonisation in the UK, while bolstering the creation of local, green jobs in
Yorkshire.
“The region has long been part of our operational presence in the UK, and we’re excited to expand this as part of our commitment to investing in the UK’s green economy. The new facility in Scarborough represents a pillar of innovation in netzero, and one which will be an industry benchmark for the transition to sustainable, energy efficient buildings.”
“This is a marvellous example of how sustainable manufacturing can be achieved, creating many highly skilled jobs in the process. Green technologies are going to be the solution to many of the challenges that we face and Schneider should be applauded for pioneering this facility. It is an exemplar model for other manufacturers to follow when they build new facilities.”
The investment in Scarborough is in addition to a £7.2 million facility upgrade to Schneider Electric’s site in Leeds, announced in October 2023, meaning the company will create more than 300 jobs in Yorkshire over the next ten years.
se.com
8-pole bayonet locking
> 5000 mating cycles
Panel mount parts unplugged IP67
Solder and dip solder contacts
The design of heavy outdoor machinery and equipment is transitioning from mechanical and hydraulic components to sophisticated, computer-controlled electronics and telematics systems. Such innovation has increased the need for “Harsh Environment” connectors to suit these difficult conditions.
Harsh environment connectors are vital links for power and signal transmission in outdoor and harsh conditions, where materials and designs are tested to their limits – the reliability of these connectors is therefore critical. These connectors must have unique characteristics and meet stringent requirements to ensure the reliability of applications across demanding sectors.
Engineered to perform reliably under the most challenging conditions, they withstand extreme temperatures, humidity, chemical exposure, dust, vibration and shock. They are crucial in industries such as industrial automation, agriculture, automotive, heavy machinery, renewable energy, aerospace, military, and marine.
flexibility and sealing capabilities, ensuring effective ingress protection and long-lasting durability.
connectivity solutions designed to endure extreme conditions. The HEC series 696 (Harsh Environment Connector) is the top choice for robust outdoor connectors. Available in square flange and cable versions with an integrated protective conduit, this power connector offers protection up to IP67, and up to IP69K when mated. It is uniquely UV-resistant and has VDE and UL approvals. The high mechanical load capacity is demonstrated by over 500 mating cycles for the 12-pole version and more than 1,000 mating cycles for the 5- and 8-pole versions.
The diverse types of harsh environment connectors are designed to meet specific application. Circular connectors, for example, are known for their ease of connection and frequent use in industrial settings. Other types include rectangular connectors, which offer high density; fibre optic connectors, which enable high-speed transmission in telecommunications; and coaxial connectors, which are used in communication systems.
Durability is crucial in extreme conditions, requiring robust materials and construction to withstand physical and environmental stresses. Material choice is vital: stainless steel, aluminium, and brass for strength and corrosion resistance and polymers such as PEEK and PTFE provide excellent chemical resistance and mechanical properties. Rubber and silicone are used for their
Sealing is important in achieving high IP ratings IP67, IP68 or IP69K to protect against water, dust, and other contaminants. These connectors must also offer high resistance to chemicals, damp heat and extreme temperatures ranging from -40°C to 100°C, and other mechanical impacts. Above all, reliability is essential, ensuring consistent performance under continuous use and extreme conditions for long-term functionality.
In explosive environments, classified as “Class 1, Division 2” (C1D2) according to international standards, it is crucial for harsh environment connectors to ensure safety, durability, performance, and compliance. These connectors are often installed in areas where flammable gases, vapours, or liquids might be present under abnormal conditions. Additional standards focus on material resistance to salinity.
As a specialist in circular connectivity, binder provides harsh environment
The rapid growth in use of sensors in outdoor harsh environments means the “go-to” industrial standard M12 connectors are increasingly being used for outdoor applications. Given binder’s long history in being a market leading manufacturer of M12 for indoor applications it is no surprise that there is an M12 connectors specifically designed for outdoor use in harsh conditions. These connectors feature stainless steel locking mechanisms, with options for either stainless steel or UV-resistant plastic housings and offer protection up to IP69K. The M12 also has a protective cap, which ensures resistance to dust and water when unmated.
With innovative design and the careful selection of materials, connector manufacturers like binder are meeting the ongoing challenge in providing ever more reliable connector solutions for signal, data and power no matter how tough or demanding the conditions.
binder-connector.co.uk
Flexible, modular range of high efficiency, robust gearboxes with output torques up to 250kNm.
Available on short delivery times, same
Dust zone 21 cat 2D and zone 22 cat 3D
Gas zone 1 cat 2G and zone 2 cat 3G
IEC Ex, EAC Ex, CCC Ex, UKEX and specifications for North American market
When it comes to marketing, being direct is often the best policy for manufacturers and engineers. To understand why, it’s important to consider the nuances of direct and indirect marketing. Sarah West of Full Mix Marketing provides her insight.
Marketing can sometimes be criticised for being too general – adopting too much of a scatter gun approach. But it does not have to be. In fact, being direct and targeted often delivers the greatest results for manufacturers and engineers hoping to grow sales.
Sarah West of B2B experts, Full Mix Marketing, takes a look at the difference between direct and indirect marketing and which is best:
For most, the best possible outcome from marketing is that it attracts customers actively looking for what you do – something often called ‘pull’ marketing.
It’s the basis of many aspects of digital marketing, including search engine optimisation (SEO), paid search (PPC) ads and other online advertising. They all rely on someone first expressing an interest in what you deliver.
Indirect marketing can be very effective, especially if there is a ready supply of customers who need what you deliver.
However, if what you do is a little more niche – or your customers prefer a closer relationship with their chosen suppliers – it can have its limitations.
From experience, most manufacturing and engineering businesses can describe who their ideal customer is. Perhaps there’s a local company who has always evaded their charms – or a major player for whom they’re sure they could do a better job than their competitor.
Often, this can be expanded into a lengthy list of either specific companies or a certain type of business in a given industry or location.
As the name suggests, direct marketing (sometimes called ‘push’ marketing) is the tactic of approaching them directly, rather than waiting for them to react to your general
marketing.
In its purest form, direct marketing means making an approach by email, letter or even in person. However, direct marketing can also include hanging out in the same places as your ideal customers – such as at trade events, on social media or by appearing in the press and websites they read.
Most businesses get the greatest results from a mix of both direct and indirect marketing – push and pull.
However, when resources are limited, it is the direct approach which may often offer the greatest potential for transformational results.
In a noisy world – with many companies competing for our attention – direct marketing can cut through and ensure your name is the one customers turn to.
Direct marketing is more straight forward to
deliver than some might think. A database of businesses and decision-makers can often be easily sourced, all within GDPR rules. Email software and low-cost postage services make it simple to send carefully designed messages.
Social media can be used to connect with important individuals and quickly increase awareness of what you can deliver for them.
Your expertise can be highlighted in content marketing sent to press and websites who are keen to share articles with their readership.
Firstly, be specific but make sure your target list is large enough to deliver the results you need.
Secondly, be persistent and consistent. It can take several exposures to your direct marketing before potential customers feel comfortable to respond.
fullmixmarketing.co.uk
• High resolution and speed
• Shadow-free scanning
• Maximum versatility
• Outstanding angular range
Automate. Inspect. Optimize. Explore
The new and highly configurable Borger jet-mixing pump system can reduce costs while improving efficiency and providing greater redundancy, as Moove discovered at its site in Gravesend.
Anew jet-mixing pump system has significantly reduced capital, installation, maintenance and energy costs at Moove, global lubricants manufacturer and distributor, in the UK.
For a closed-top 50m3 tank used in the manufacturing process of quality lubricating, engine, hydraulic and gear oils, Moove wanted to trial a set-up that would not only be better economically, but also provide more redundancy.
Ian Lowe, Moove’s Manufacturing General Manager, explained; “A motor failure on a blender could mean as much as four days impact on production, so it was important for us to take the opportunity to prove a different technology.”
He added: “The performance of our existing paddle mixers has been good, but Borger were recommended as a company that would work with us to provide a better option; one that could be easily replicated.”
The team at Moove drew up a logic for Borger to examine, outlining their objectives, which ultimately resulted in a pump (plus two nozzles), for a 3-bar application with a flowrate of up to 60m3/hr. To meet the space requirement at the Gravesend site in Kent, Borger also provided the system as a skidmounted unit, working closely with Moove to supply a customised control panel with a specially written program.
“The fact that Borger were able to deliver a complete, all-in-one package was a real bonus,” continued Ian.
“It was also a big advantage to go to Borger for a site test, running different
configurations to determine the best operating modes for us. This clearly worked very well, because apart from one very minor tweak, we haven’t had to make any changes since the pump was installed.
“With a 9kW motor (compared to 12kW for the paddle mixers), we are automatically saving on energy, but one of the other main benefits is that the Borger equipment is so simple to look after. There’s easy access to the pump-head, and no special tools required. Retrofit to an existing tank is also very straightforward.
“We’re very pleased with solutions provided by Borger that allowed us to achieve the goals of our project.” boerger.com
Unused or depreciating equipment represents untapped capital that could be reinvested into new production opportunities. Industrial Auctions, a globally operating online auctioneer, explains why auctioning machinery online is the smarter choice.
In a rapidly evolving manufacturing landscape, businesses must often reassess their equipment to stay competitive. Whether it’s due to the closure of a production site, to create space for new machinery, or changing production demands, selling food and beverage machines can be a strategic move. By auctioning surplus equipment, manufacturers not only maximises returns but also contributes to a more sustainable industry by reusing machinery.
Auctioning the machines online through Industrial Auctions provides a seamless and efficient auction process. Companies can focus on optimising production and meeting business goals, while the auction platform handles every aspect of the sales process for their machinery. From listing and marketing to finalising the sale, the platform ensures a smooth and efficient transaction, allowing manufacturers to unlock the value of their unused equipment without diverting attention from core operations.
Over the years, Industrial Auctions has successfully organised more than 1,500 online auctions in the food and beverage industry, for renowned companies like Vion, Nestlé, FrieslandCampina, Homann, Refresco, Danish Crown, 2 Sisters Food Group and many more. With a growing number of auctions across Europe and a worldwide buyer network the online auctioneer has proven invaluable to the industry.
Specialising in online auctioning used machinery for the food and beverage industry, Industrial Auctions’ focused approach and years of experience have provided them with deep industry and machinery knowledge. They weekly add new auctions to their platform, offering machinery for all segments in the food and beverage industry, including various
kinds of packaging machines. Think about thermoformers, packaging robots, vacuum machines, traysealers, vertical forming, filling and sealing machines, flow wrappers, bottling and filling machines, carton erectors, labelling machines, checkweighers and metal detector systems from brands such as Multivac, GEA, Ishida, Krones, Mettler Toledo, Ulma and Bosch.
Selling food and beverage machines via online auction has several advantages. “The shortage of qualified personnel in the food industry presents significant challenges for food producers and traders. We aim to alleviate this burden by taking the entire sales process off their hands. Additionally, we have a large international database, which allows us to reach a wide network of professionals within the industry, effectively connecting supply and demand”, explains Jeroen van Kollenburg, the CEO of Industrial Auctions.
The “no cure, no pay” model means sellers only incur costs if their item is actually sold, minimizing financial risk. “Our approach ensures a hassle-free experience, with our
commitment to handling the entire process smoothly. We prioritize customer satisfaction and relationship building, guaranteeing prompt financial settlement and a thorough cleanup of the location within the agreed timeframe” the CEO explains.
“Whether handling a large auction or a smaller-scale event, we are always committed to making each auction a success. The hard work pays off when we see the satisfaction on everyone’s faces at the end. Working closely with a committed team not only makes the process more enjoyable but also drives us to achieve even greater results.”
In addition to organising online auctions on location, the company also holds auctions at its own premises. For these auctions, parties can contribute a smaller number of machines. Whether dealing with a few surplus machines, a complete production line, or an entire factory, a business can benefit from the service.
industrial-auctions.com
The Southern Manufacturing & Electronics show returns in February under new management, but long-term attendees will be glad to learn that the defining characteristics of the show have been retained, maintaining the versatility of exhibitors. Read on for a wealth of reasons to save the dates.
The well-publicised skills shortage in the UK is fuelling an increase in the adoption of automated manufacturing solutions across industry. It will be a prominent theme at the forthcoming Southern Manufacturing & Electronics show, which will open its doors from 4th to 6th February 2025. It moved to its present location in 2008 and was the first event to be held in the world-class Farnborough International Exhibition & Conference Centre when it was built in 2018.
The show returns under different ownership and management, having been bought earlier this year by specialist exhibition company Easyfairs, which runs more than 100 events across Europe. The new organisers say that early stand bookings and visitor registrations suggest that the show will be the biggest yet.
manufacture, plastic packaging, hand tools, waste removal and recycling, training and financial consultancy.
The event is divided approximately equally between mechanical engineering and the electrical/electronic sector. However, there is no physical separation between the stands, allowing cross-over between the different disciplines. Visitors say this is a defining feature of the show, as it often results in the discovery of products and services not on their original shopping list.
SM&E appeals to all sectors of industry thanks to the incredible range of suppliers taking part. It is the ideal place to see the latest production machinery and hardware in action, and meet suppliers from across the UK, continental Europe and beyond.
The comprehensive exhibitor profile covers virtually every aspect of engineering, from mechanical, electrical, electronic, electromechanical, hydraulic and pneumatic components and assemblies to PCBs, connectors, sensors, drives and encoders, and on to fasteners, pressings, springs, mouldings, castings and more. Hightechnology production cells with Industry 4.0 interconnectivity, 3D printing, test and inspection systems, metrology equipment, business and manufacturing software, and a wide range of subcontract services will also be well represented.
Other offerings include controls, displays, human-machine interfaces, data acquisition systems, virtual reality, robotic machine tending and additional automation solutions. Items for day-to-day business operations will include workshop essentials, dust and fume extraction, humidity control, workplace storage systems, bespoke case and foam
Although SM&E is an important event that attracts big-name manufacturers, it is also very accessible to small and medium size enterprises. Easyfairs stresses that it will continue to operate the current policy of open access, which discourages larger firms from dominating the space to the detriment of smaller vendors. The exhibitor mix has given the show a unique, vibrant atmosphere that is unlike that of similar exhibitions. Testament to this, and to the effectiveness of the show as a business forum, is the very high rate of return bookings. A large percentage of participants are regular returnees and many have been with the show since it started in 1997.
Over the three days, there will be a series of free technical seminar programmes to give visitors and exhibitors alike valuable learning opportunities, with a particular focus on the technical, managerial and environmental issues facing manufacturers today. As usual, the specialist AutoAero theme, devoted to aerospace and automotive engineering, will add extra value for people involved in those sectors.
There is ample free car parking and the site is well served by road and public transport links. A regular, complimentary bus service runs between Farnborough’s two railway stations and the showground. Admission to the exhibition is also free. southern-manufacturing-electronics. com
Howay! Newcastle is calling. After a successful relaunch last year, Manufacturing and Engineering North East (MENE) returns on the 28th of November, bringing the best in design and manufacturing to Newcastle.
As the go-to event for the North East, MENE is designed not only to showcase the latest innovations but also to strengthen connections within the region’s industrial community. Building on last year’s success, MENE is expanding in exciting new ways, with an increased live product demonstration and the introduction of a brandnew Careers Corner.
This year’s event will welcome over 80 exhibitors, covering the entire supply chain. Exhibitors will include both local and UK-based industry leaders, offering a strong mix of expertise and innovation. Major Newcastle-based companies such as Advanced Adhesives, MEC Machine Tools, and Starrag will be showcasing their cutting-edge solutions, alongside renowned UK businesses like Tri-Tech 3D, European Springs & Pressings, Sunpower Electronics, and TDK, making this a must-attend event for anyone involved in manufacturing and engineering.
MENE 2024 is also expanding its Live Product Demonstration programme, giving attendees the chance to experience the latest advancements in manufacturing and engineering technology first-hand. This year’s demos will feature more companies than ever before, showcasing groundbreaking products and solutions that are driving the industry forward.
In addition to the exhibition and product demonstrations, MENE will once again feature expert-led conference sessions, providing insights from industry leaders and discussions on the latest trends and innovations in manufacturing and engineering. These sessions will cover various topics, from emerging technologies and best practices to industry challenges and solutions. The interactive format allows attendees to ask questions, share ideas, and engage in meaningful dialogue with thought leaders and peers.
The new Careers Corner is an exciting addition to this year’s exhibition, offering a dedicated space for engineers looking to advance their careers. Featuring advice clinics run by recruitment experts, CV assistance, and recruitment guidance, this dedicated area delivers everything an engineer needs to elevate their career.
MENE is also thrilled to be collaborating with The Student Engineer, who will host
a special feature area within the Careers Corner. This partnership will bring extra resources and tailored insights specifically for aspiring engineers and students. More information about this collaboration will be released shortly. The Student Engineer is a new careers resource from The Engineer UK. With its lively blend of news, careers advice, interviews with leading employers, inspiring profiles of successful graduate engineers and –of course – information on the latest job opportunities, The Student Engineer hopes to help students and recent graduates map out a clearer route into the profession, while also allowing industry to communicate more effectively with the engineers of tomorrow. Another highlight of MENE 2024 is the opportunity to connect with the In2ScienceUK team. This vital initiative is dedicated to unlocking young people’s potential and addressing the skills shortage in STEM fields. By breaking down barriers to STEM careers, In2ScienceUK is helping to empower the next generation of professionals and build a brighter future for the industry.
The event takes place on the 28th of November at Vertu Motors Arena, Newcastle Upon Tyne. Join the region’s top manufacturing and engineering professionals in Newcastle this November and be part of an event that celebrates the best of Northern England’s industrial sector. Register on MENE’s website. menortheast.co.uk
Attend
Watch
Explore
Advanced Engineering has announced this year’s keynote speakers. The six industry leaders will share their expertise and insights on critical industry issues during talks across several different forums.
The first of this year’s keynote speakers, Brian Holliday, is a leading figure in industrial technology and digital manufacturing. As the head of Siemens Digital Industries for the UK and Ireland, he oversees advanced automation, industry software, systems integration and R&D. He is an expert on productivity, digital manufacturing and industrial strategy, often contributing to media discussions.
The next speaker, Matthew Atkinson, lead research engineer at Jaguar Land Rover, is an expert in automotive engineering, specialising in replacing metallic structures with injection moulded composites. His work focusses on interior mechanical commodities like cockpit, seating and loadspace features; his innovative approach has earned him multiple patents, including for the Range Rover 18MY Executive Seating.
Next, Shaun Harris CBE is currently director of support and chief engineer at the Royal Air Force. With a distinguished 37-year career in the RAF, Shaun has held numerous leadership roles. His extensive experience spans engineering, logistics and information warfare. Shaun has served around the world, from the UK and USA to Afghanistan and Iraq.
Also set to speak are Solange Baena, UK lead for the aviation environmental roadmap at Airbus, and Leonie Moffat, laser radar sales account manager at Nikon. Last but most certainly not least is Stefan Lawrenson, senior polymer chemist at Scott Bader, who specialises in sustainable technology and polymer chemistry. His research focusses on enhancing nanoparticles and synthesising eco-friendly materials.
“This year’s speaker lineup brings together some of the brightest minds in the industry,” said Alison Willis, CEO of the show’s organiser, Easyfairs UK & Global. “Their
diverse expertise will provide deep insights into pressing issues like Industry 4.0, supply chain management and sustainability.
“This lineup highlights the spirit of innovation that Advanced Engineering is all about, and our commitment to fostering knowledge exchange within the engineering community,” concluded Willis. “I’m sure the knowledge and inspiration they’ll bring to the event will be of value to all visitors.”
Advanced Engineering brings together industry leaders and professionals to explore the latest innovations across multiple sectors, including aerospace, automotive,
defence and security, marine and more.
Attendees can expect presentations on a wide range of topics, from digitally enabled supply chains to advanced propulsion technologies. The full speaker program will be announced soon.
The two-day show will take place at the NEC in Birmingham on October 30 and 31, 2024 and will include talks from over 150 industry experts. For more information and to register online, please visit the Advanced Engineering UK website at AdvancedEngineeringUK.com.
Midlands 3D Printing
T: 01785 594389
E: sales@midlands3d.com
W: www.midlands3d.com
Anti Vibration Products, Mounts & Bushes
Fibet Rubber Bonding (UK) Ltd
T: 01282 878200
E: sales@fibet.co.uk
W: www.fibet.co.uk
Connectors & Cabling Solutions
CEMBRE Ltd
T: 01675 470 440
E: sales@cembre.co.uk
W: www.cembre.com/en
Drives, Motors & Gears
Flow Meters
Nord T: 01235 534404
E: GB-sales@nord.com
W: www.nord.com
Titan Enterprises Ltd
T: +44 (0)1935 812790
E: sales@flowmeters.co.uk
W: www.flowmeters.co.uk
Silverson Machines Ltd
T: +44 (0)1494 786331
E: sales@silverson.co.uk
W: www.silverson.co.uk
Industrial Communications
Brainboxes
T: + 44 (0) 151 220 2500
E: sales@brainboxes.com
W: www.brainboxes.com
Intoware
T: 0115 977 8969
E: hello@intoware.com
W: www.intoware.com
Industrial Fans
Axair Fans UK Limited
T: 01782 349 430
E: sales@axair-fans.co.uk
W: www.axair-fans.co.uk
Machine Safety
Schmersal UK Ltd
T: 01684 571980
E: uksupport@schmersal.com
W: www.schmersal.co.uk
Marking Solutions
T-Mark T: 0330 153 8320
E: sales@t-mark.co.uk W: www.t-mark.co.uk
Pipework Systems
Jacob UK Ltd
T: 01694 722841
E: sales@jacob-uk.com
W: www.jacob-group.com/uk
Pressure Measurement Specialists
ESI Technology Ltd
T: +44 (0)1978262255
E: sales@esi-tec.com
W: www.esi-tec.com
Robotics & Automation
KUKA Robotics UK Ltd
T: 0121 505 9970
E: sales.uk@kuka.com
W: www.kuka.com
Sensors
IFM Electronic
T: 020 8213-0000
E: enquiry.gb@ifm.com
W: www.ifm.com
PLUS Automation Ltd
T: 0121 58 222 58
E: Sales@PLUSAutomation.co.uk
W: www.PLUSAutomation.co.uk
Storage Solutions
BITO Storage Systems Ltd.
T: 02476 388 852
E: Info.uk@bito.com
W: www.bito.com
Test & Inspection
AMETEK Land (Land Instruments International)
T: +44 1246 417691
E: land.enquiry@ametek.com
W: www.ametek-land.com
Schmersal’s innovative DHS door handle system combines the functions of a robust door handle with the signalling of machine status via illuminated handle or push-button.
The door handle system is designed for use with the AZM40 solenoid interlock or with safety sensors from the RSS36 and RSS260 series or as a stand-alone solution. The illuminating handle signals various machine conditions over its area using seven different colours, enabling the user to control the colours individually to signal the machine status.
In addition, a push button is available, which can be individually adapted to customer requirements using the coloured push button caps. The pushbutton can be used for tasks such as a reset function or a request to open the guard door.
SCHMERSAL | Enigma Business Park Malvern, Worcestershire, WR14 1GL
www.schmersal.co.uk
uksupport@schmersal.com