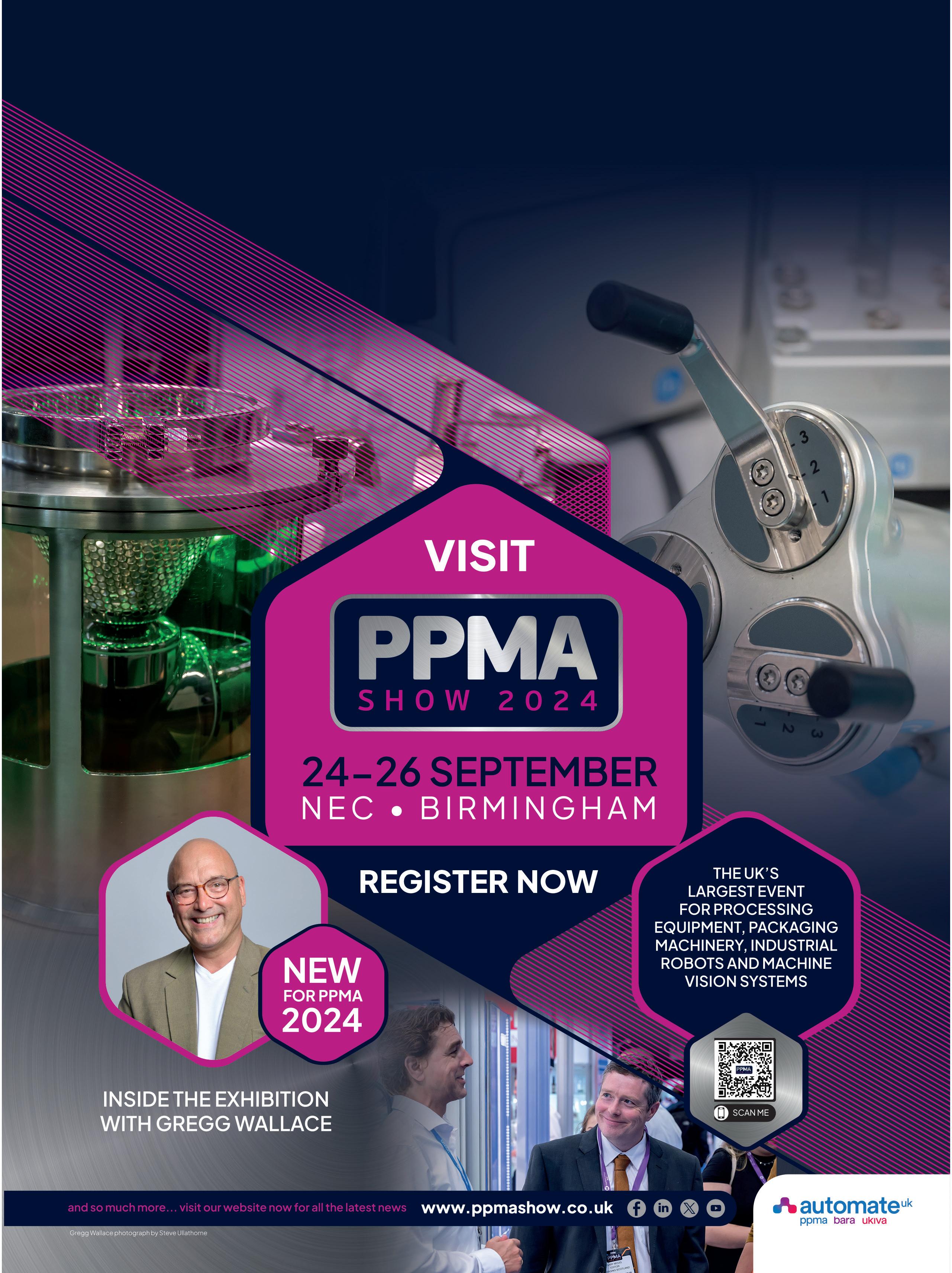
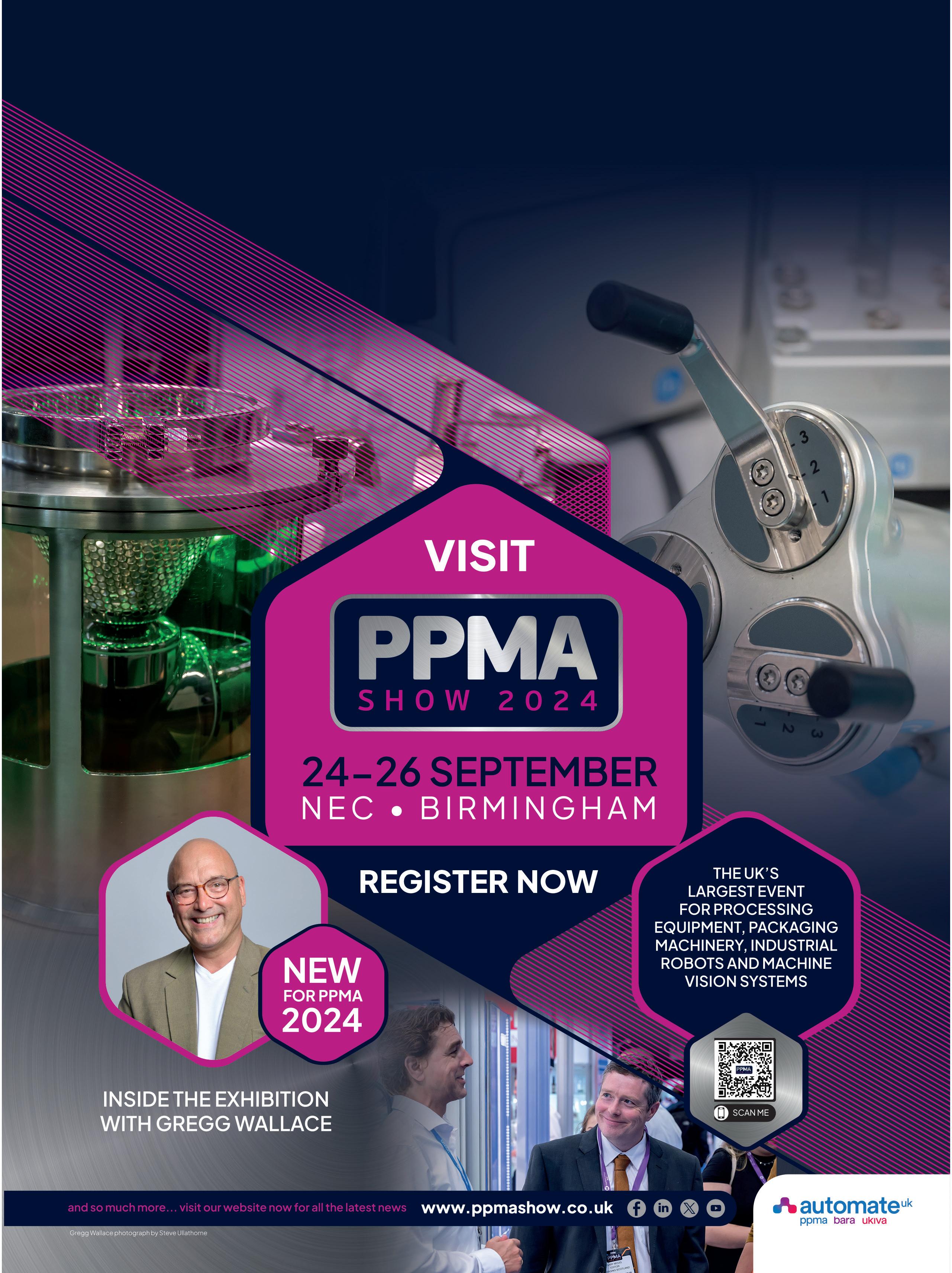
A team you can rely on

With more than 30 employees visiting companies in the UK similar to yours, ifm does more than you might think.
Software engineers remove the hassle of integrating automation solutions and ensure that you are getting all the usable data you can, providing actionable efficiency insights.
Condition monitoring specialists can analyse your plant to give you options for protecting critical assets.
Automation solution engineers will advise you on any aspect of your plant, from a single sensor to a complete Industry 4.0 factory.
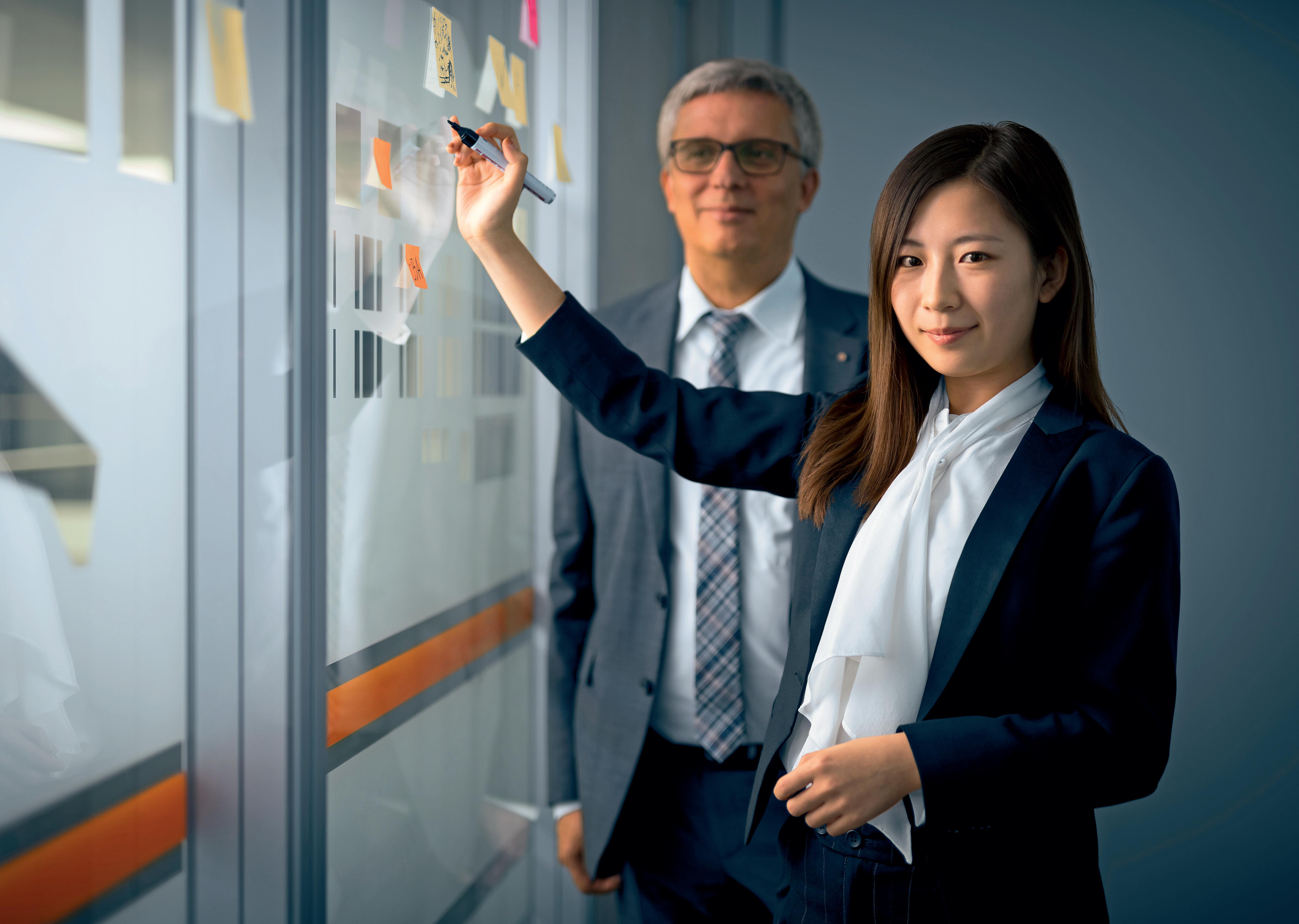

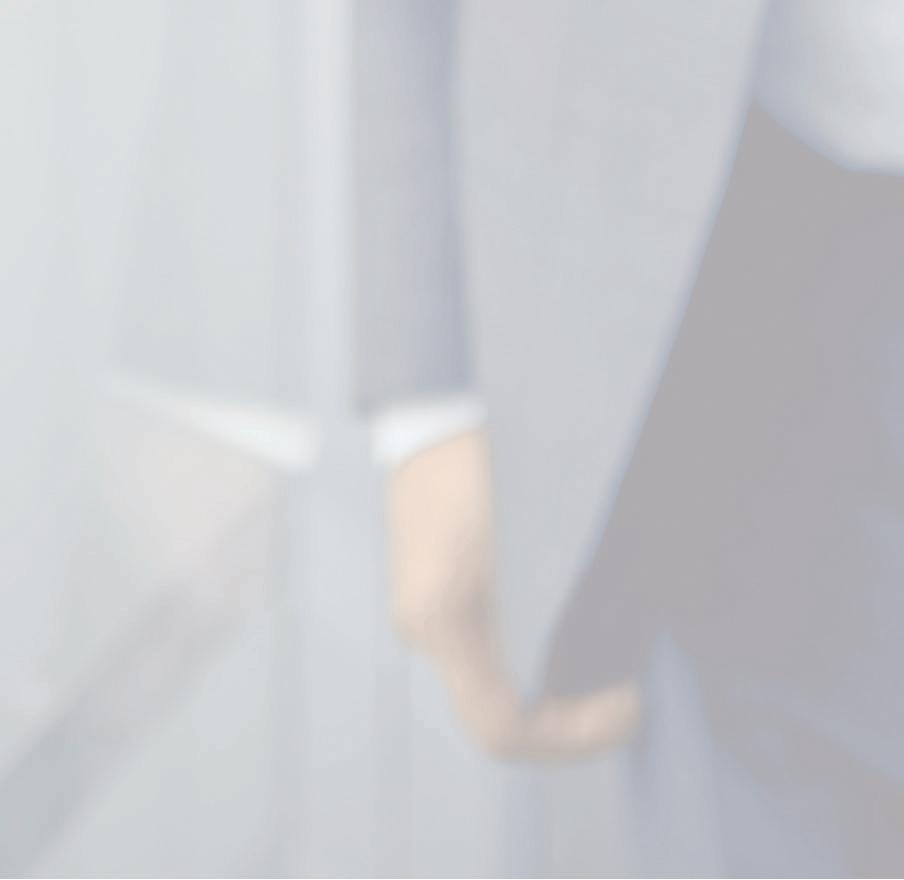
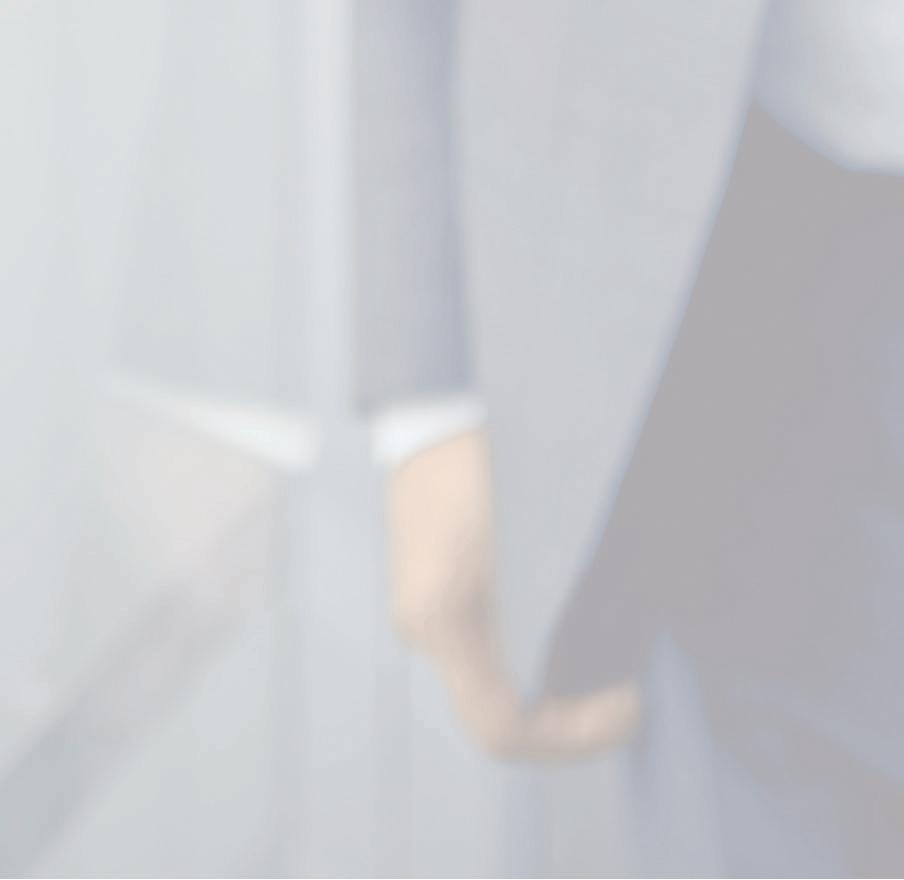


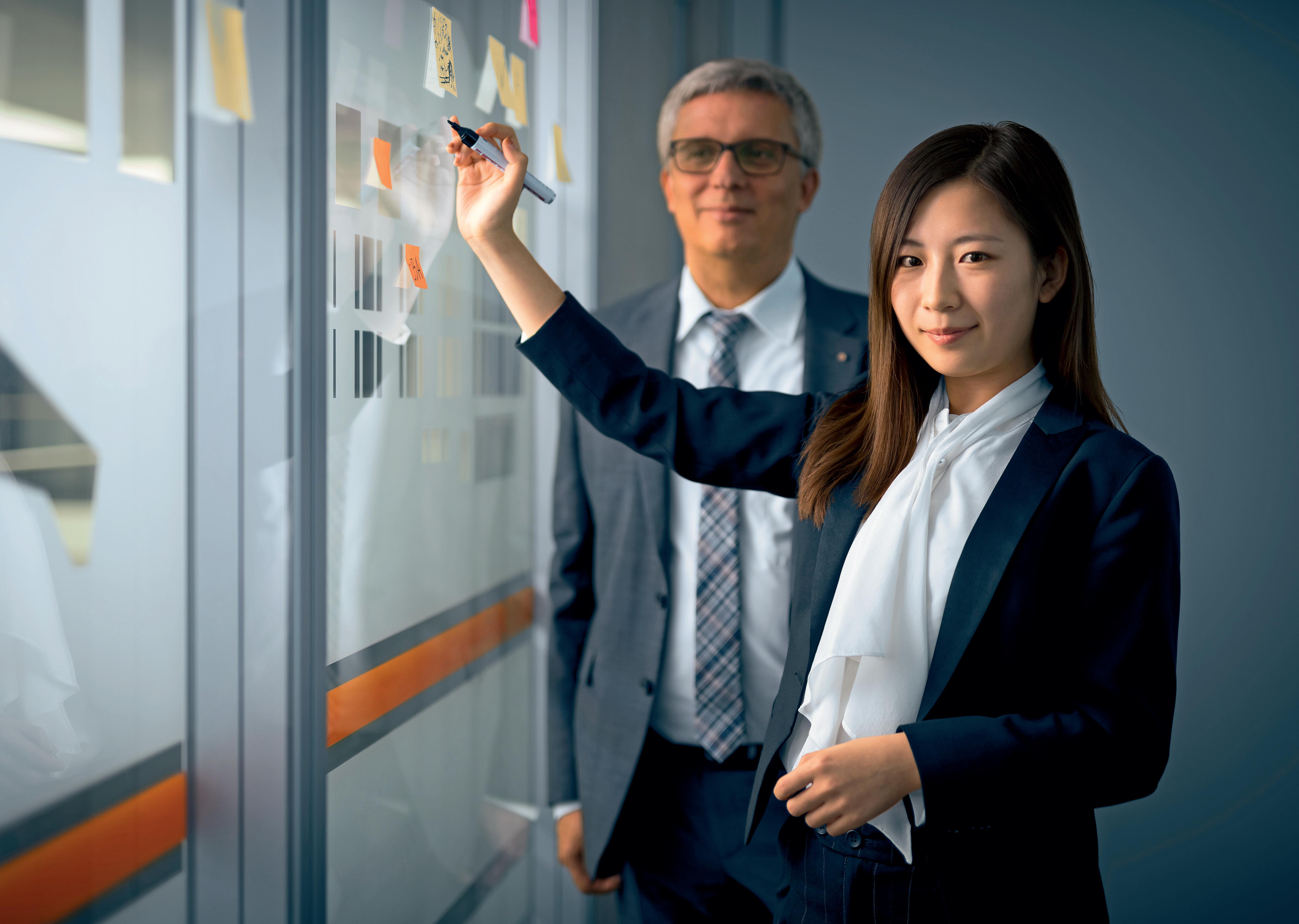
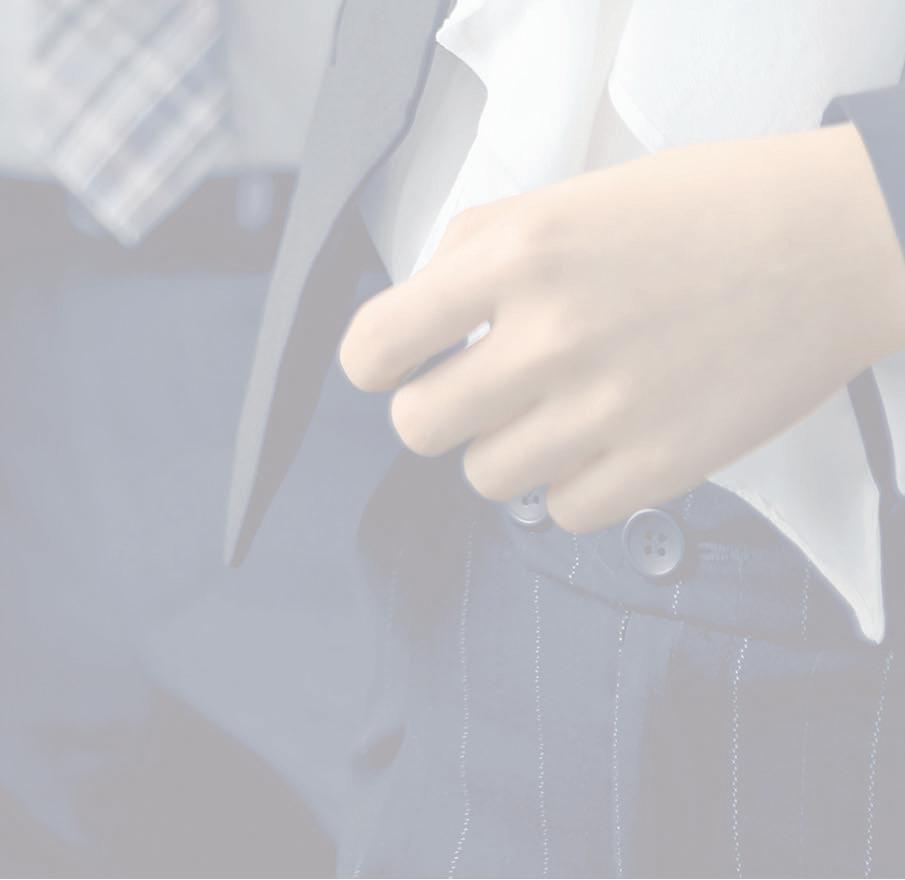
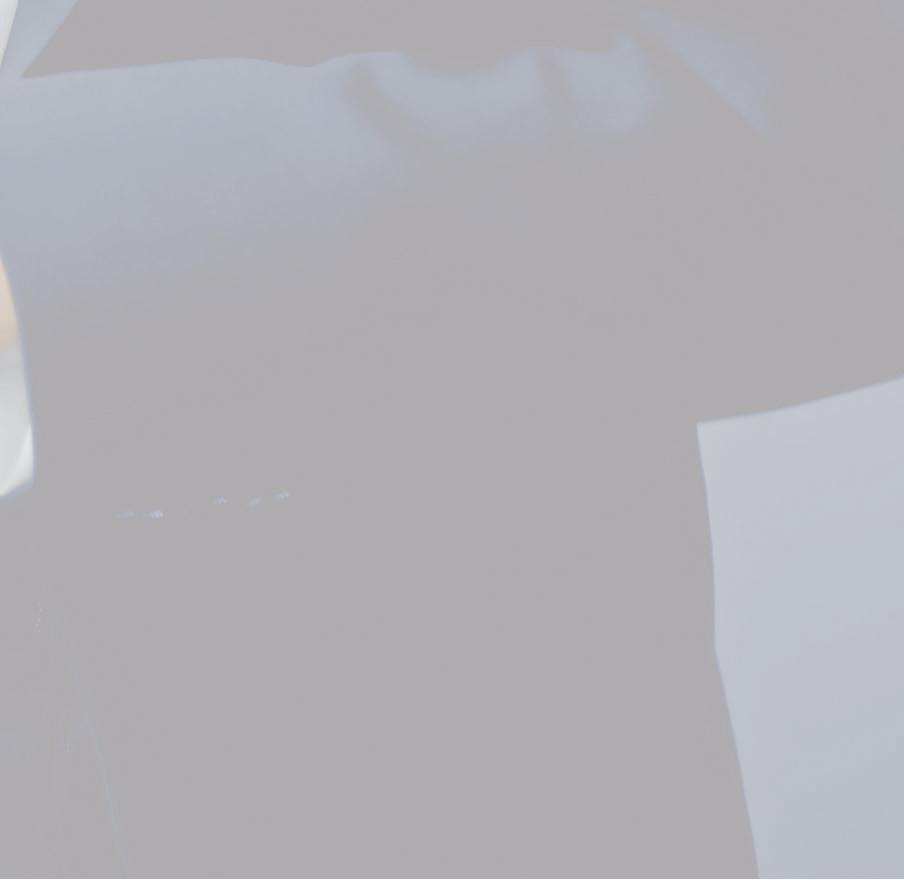
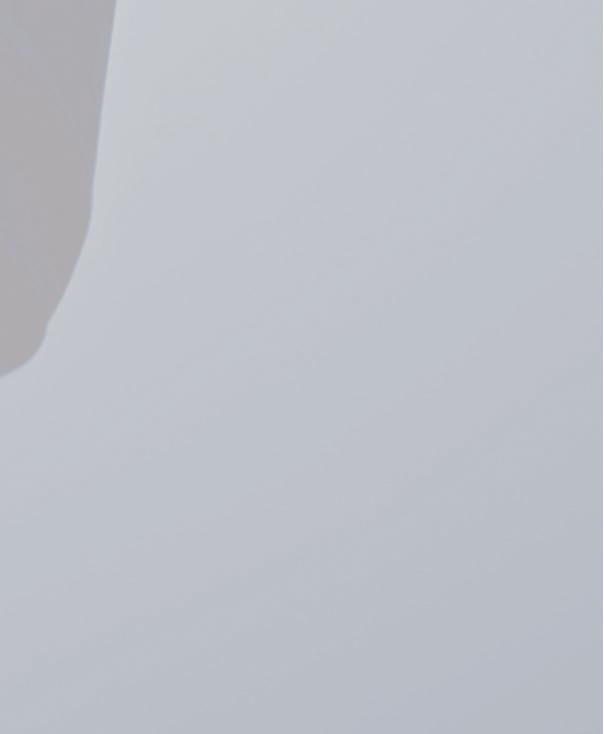

Editor
Chris Callander chrisc@cimltd.co.uk
Publication Manager
James Burke jb@cimltd.co.uk 01795 509105
Account Managers
James Davies jamesd@cimltd.co.uk 01795 509105
Jim Bearden jim@cimltd.co.uk 01795 509105
Design & Production
Grant Waters grant@cimltd.co.uk
James Taylor james@cimltd.co.uk
Administration Manager
Natalie Murray admin@cimltd.co.uk 01795 509103
Credit Facilities Manager
Gwen Lee creditcontrol@cimltd.co.uk 01795 509103
Marketing Manager
Lucas Payne lucas@cimltd.co.uk
Sales Director
Tom Woollin tom@cimltd.co.uk
Chief Executive
John Denning
© 2024 TGM Publishing Limited,1st Floor, Saphir House, 5 Jubilee Way, Faversham, Kent, ME13 8GD. No part of this magazine may be reproduced or stored in a retrieval system or transmitted in any form – electronic, mechanical or physical – without express prior permission and written consent of the publisher. Contributions are invited and when not accepted will be returned only if accompanied by a fully stamped and addressed envelope. Manuscripts should be typewritten. No responsibility can be taken for drawings, photographs or literary contributions during transmission or in the editor’s hands. In the absence of an agreement the copyright of all contributions, literary, photographic or artistic, belongs to TGM Publishing Limited. The publisher accepts no responsibility in respect of advertisements appearing in the magazine and the opinions expressed do not necessarily represent the views of the publisher. The publisher cannot accept liability for any loss arising from the late appearance or non-publication of any advertisement.
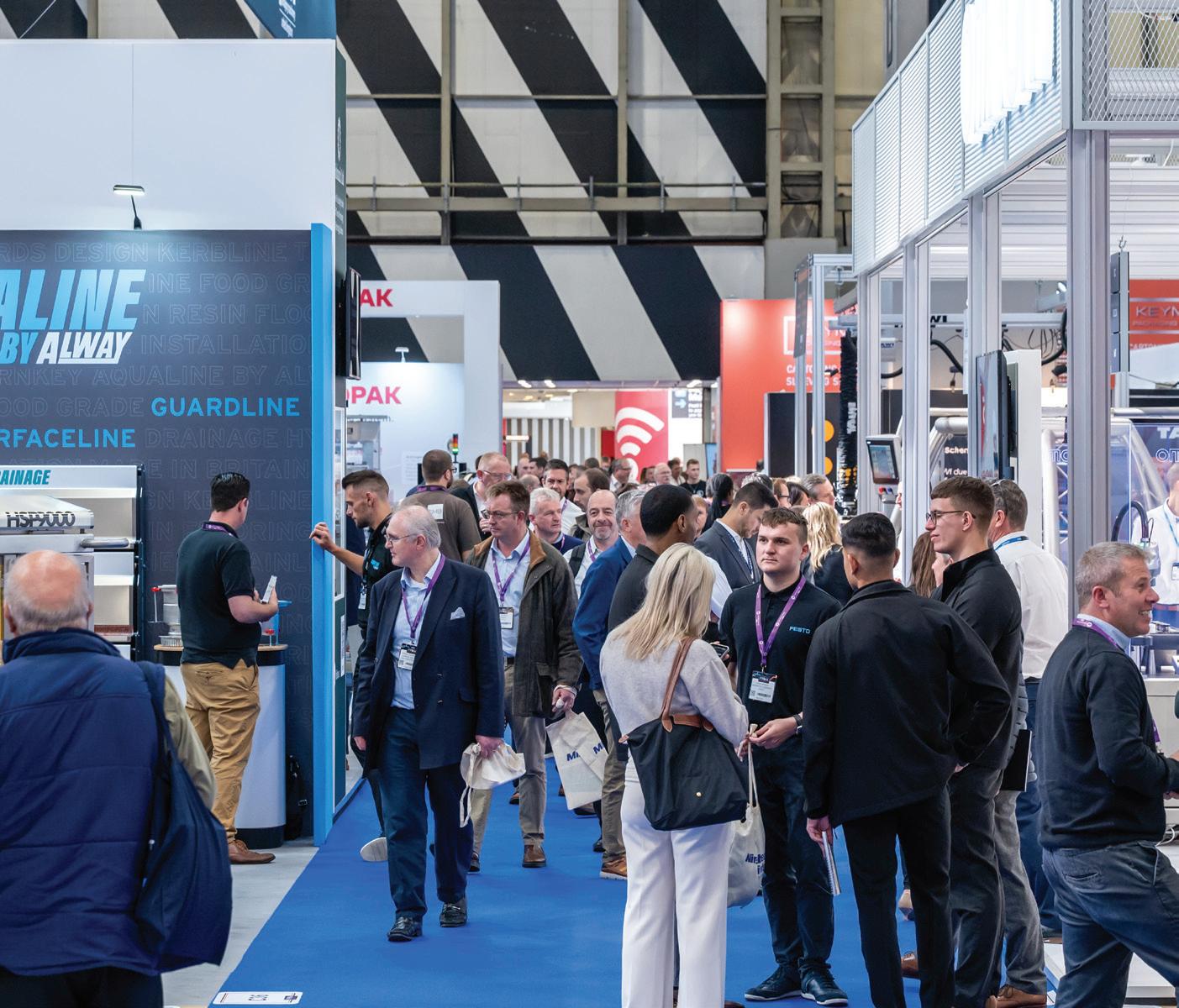
September 2024
The one thing that manufacturers need to embrace above all else has to be change. A manufacturer that doesn’t embrace change and tries to compete will stagnate and will be left behind by its competitors.
Although change is important it is rarely easy to implement. In life change is often seen negatively. Generally, that comes from a total lack of understanding about what the change will mean.
For manufacturers looking to implement change in their business the one area that is probably the most important, therefore, is communication. Large numbers of projects fail because staff are not on board and resist the change. Keeping everyone in the loop and ensuring they understand how the change will affect them is something which is, therefore, vital for success.
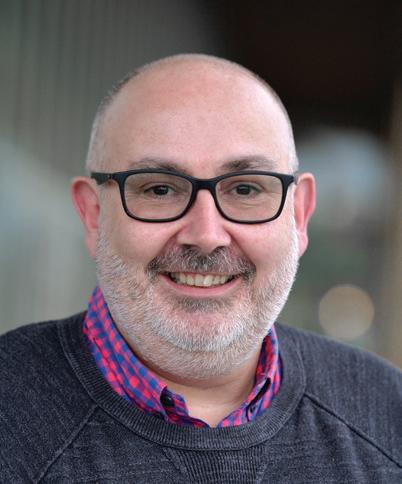
And on the subject of change, this is my last issue in the editor’s chair at MEPCA. I wish you, our reader, all the best for the future and may all your change projects be a success.
So for the last time... Enjoy the issue!
To subscribe to MEPCA visit our website www.mepca-engineering.com or scan the QR code. @Mepca-magazine
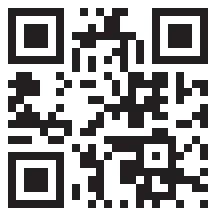
Chris Callander, Editor
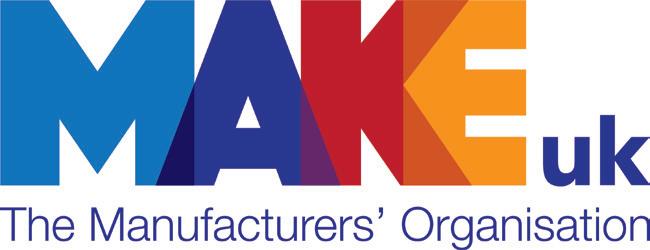
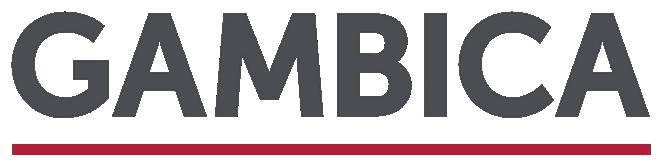
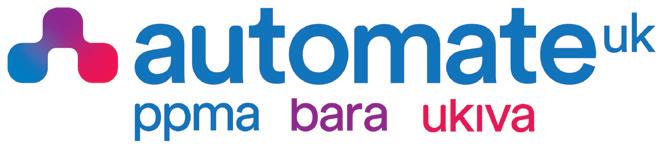

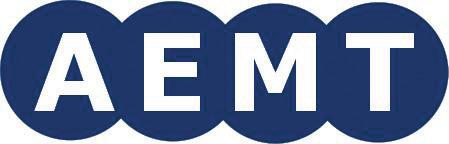
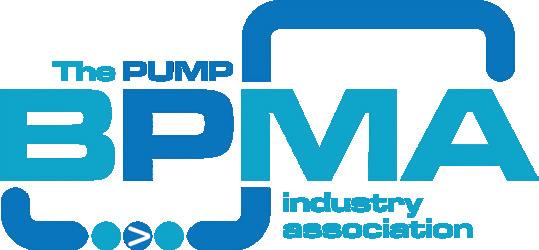
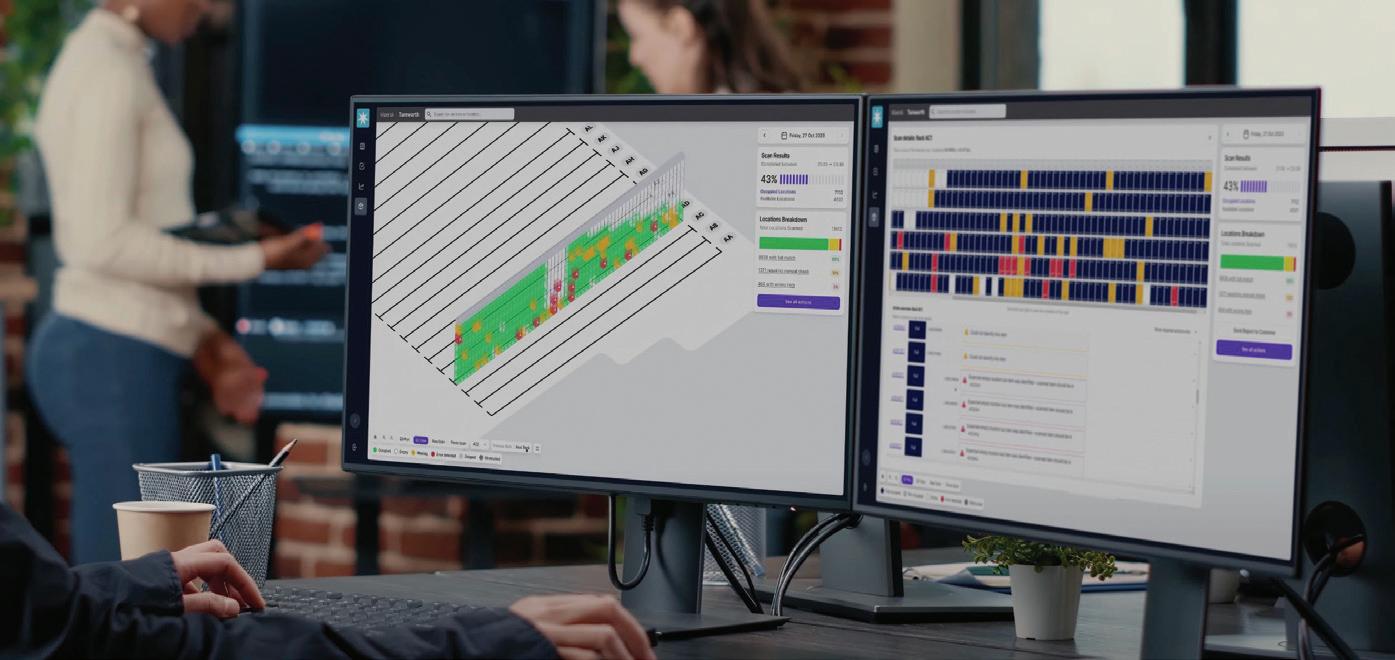
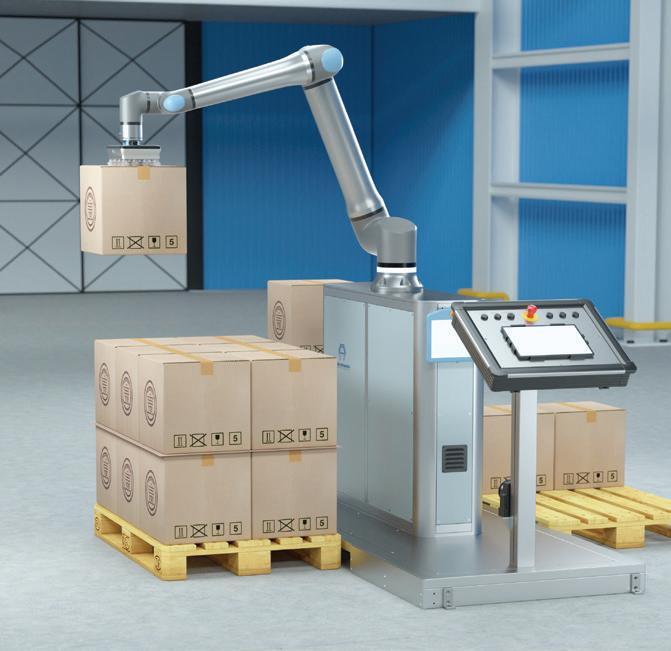
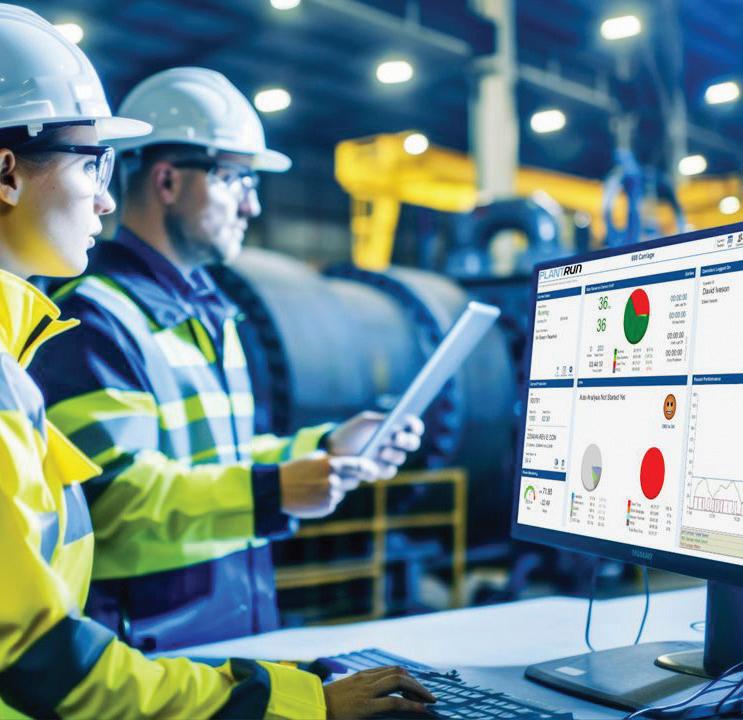
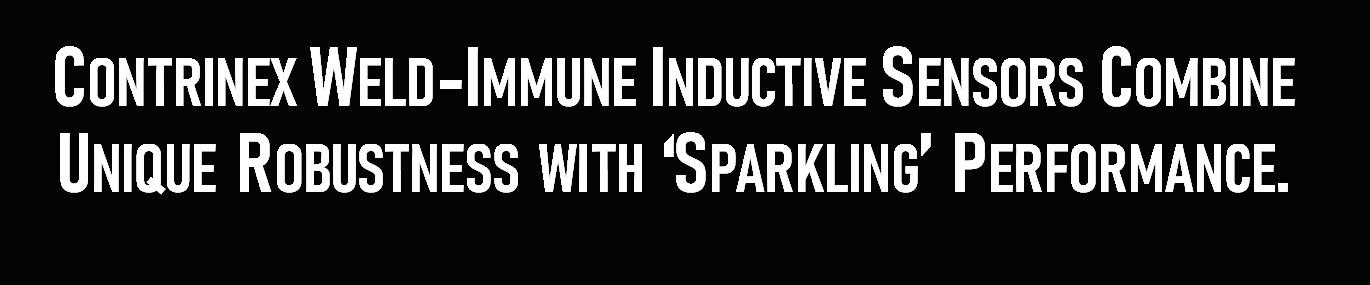





Global precision gears market forecast for 10% growth in 2025
The landscape of the global precision gearbox and geared motor market is undergoing significant transformation and is expected to grow by over 10% in 2025, as it recovers from an earlier than anticipated dip in 2023 and 2024. According to the latest data from market intelligence specialist Interact Analysis, strong demand will generate a compound annual growth rate (CAGR) of 7.9% - with the market increasing from $3.29 billion to $4.8 billion - between 2023 and 2028.
The precision gearbox and geared motor market has not been immune to the broader economic challenges of the last two years. The slowdown for the market made an early appearance in 2023 and 2024 due to global economic and socio-economic unrest, including inflation and high interest rates.
The Americas region is expected to show the highest rate of growth over the period from 2023 to 2028, with a CAGR of 10.4%, while the APAC region, excluding Japan, is forecast to be the fastest-growing market in 2024. This latter growth is attributed to the region’s manufacturing sector and the rise of local precision gearbox suppliers catering to
the burgeoning number of collaborative robot manufacturers in China.
At the heart of the precision gearboxes market’s resilience is innovation. The emergence of new industries, such as battery manufacturing and humanoid robots, will present fresh opportunities for growth.

The industry projected to see the strongest growth in demand during the forecast period is mobile robots (CAGR of 45.9%), where precision gearboxes are commonly used in the drivetrain of the robot, and the second largest predicted increase in demand is in battery manufacturing (CAGR of 13%).
With over 150,000 mobile robots shipped globally in 2023, the sector is experiencing substantial growth due to increasing demand for more automated fulfilment and warehouse automation resulting from the continuing trend towards e-commerce.
Despite strong growth in mobile robotics,
the industrial and collaborative robot markets remain the largest consumers of precision gearboxes worldwide. Regional variation exists, but overall, these markets experienced a slowdown in market growth in 2023, but demand is expected to pick up again worldwide fairly quickly. In 2023, the market value of gearboxes sold into the industrial and collaborative robots segment was just over $1 billion, making up 31% of the total precision gearbox market. By 2028, this segment is expected to grow to $1.33 billion.
Schneider Electric Training launched in the UK & Ireland
Schneider Electric has announced the launch of its Schneider Electric Training programme in the UK and Ireland (UK&I).
Schneider Electric’s vision in the UK&I is to create a best-in-class approach to training, unifying specialist academies, courses, and digital campuses into a holistic offering.
The move is in response to the chronic skills gap in engineering and the vital role that training plays in addressing the growing complexities associated with digital transformation.
The extensive programme covers everything from AI and the automation of machinery and equipment, to innovations in
power and energy management, and safety standards and regulations.
Schneider Electric Training will provide customers, partners, and engineers with a single point of access to the vast array of training options and resources available, covering Schneider Electric solutions, industry-focused courses and professional accreditations.
It will be delivered via several specialist academies for in-person courses and a digital campus offering on-demand courses for Continuing Professional Development (CPD) via the mySchneider portal.
Two academies are already up and running, with three more due to be launched by the end of the year.
The Safety Academy in Telford offers a range of Schneider Electric and professional training courses to ensure the safe operation of electrical equipment and site safety, including Competent Person certification and City & Guilds assured Authorised Person training.
The Automation Academy in Coventry offers a comprehensive curriculum covering Schneider Electric’s automation portfolio. It is designed to take students from basic product understanding through to advanced programming of both legacy and current technology, including Programmable Logic Controllers (PLC), Variable Speed Drives (VSD), Human Machine Interfaces (HMI), Motion Control and Robotics.
UK manufacturing slips to twelfth in world rankings
The UK’s manufacturing sector has dropped out of the top ten world rankings, falling to twelfth according to the latest official figures available published by Make UK.
The figures are contained in the latest annual ‘Manufacturing – The Facts’ which contains a wide variety of data about the contribution of manufacturing to the economy including exports, sectoral breakdown, how the UK compares to other nations and salary levels.
The data shows that in 2022 (the latest year for which global comparisons are available), UK manufacturing output was worth $259bn. This is behind Mexico (£316bn), which has climbed to seventh on the back of an already strong manufacturing base but also Chinese investments made in the first Trump Presidency to counter tariffs, while Russia has climbed to eighth place ($287bn) on the back of substantially increased defence production which is now worth 6% of GDP. Both these countries have also leapfrogged Italy ($283bn) and France ($265bn), respectively, who have dropped in the world rankings as a result to ninth and tenth, respectively.
Taiwan has also edged very slightly ahead of the UK on the back of its global dominance of semiconductor manufacturing where demand has risen substantially in recent years.
China remains the largest manufacturing nation with output worth $5.06trn (almost a third of global production) followed by the United States $2.69trn and Japan $850bn. Germany remains the biggest manufacturing nation in Europe by some distance ($751bn) and retains its position as the world’s fourth largest manufacturing nation, followed by India and South Korea who have swapped places in fifth and sixth respectively.
According to Make UK the data reinforces the need for the UK to adopt a long term industrial strategy as those countries who have such a strategy are clearly seeing the benefits on economic output. A report by Make UK last year found that eight in ten manufacturers feel they are at a competitive disadvantage compared to other nations with industrial strategies.
The analysis of official data also shows that the United States remains the dominant export market for UK goods worth £60.1bn in 2022. Germany is the second highest destination (£33bn) while The Netherlands is
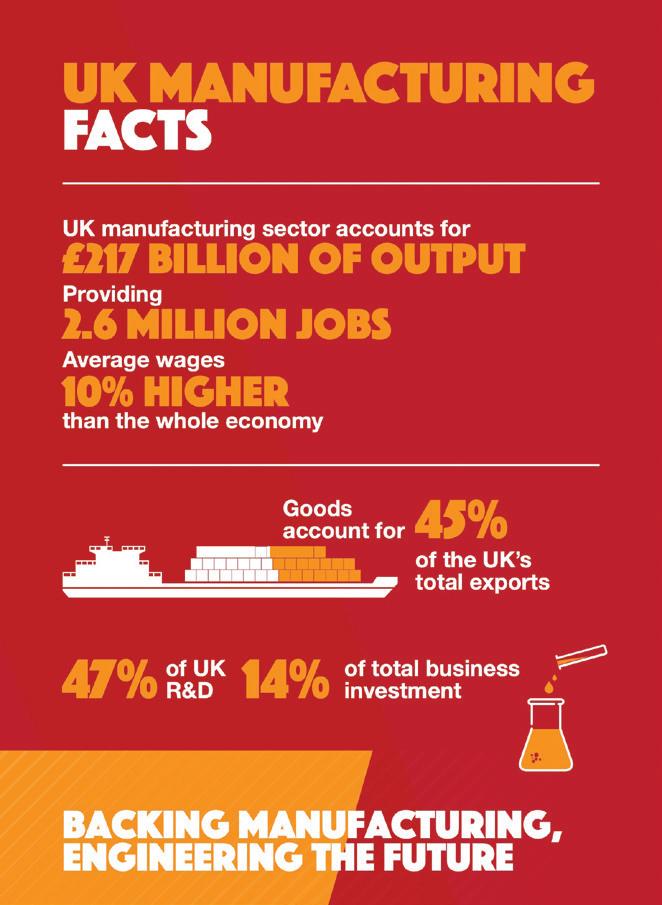
third (£31bn). However, Make UK cautioned that trade with the Netherlands could be inflated artificially by goods being routed through Rotterdam for onward travel to other destinations. Ireland is the fourth largest export market (£28.2bn).
Six of the top ten export markets are in the EU, worth approximately £150bn, which is almost three times the exports to the US and around eight times the amount to China (£21.4bn). According to Make UK, this highlights the continued importance of the EU for UK goods and the need for the new Government to smooth out trade barriers with what overwhelmingly remains the UK’s dominant export market.
Made Smarter launches peer network to accelerate digital adoption
Made Smarter North West has launched a new peer-to-peer network to accelerate digital adoption among SME manufacturers.
The Digital Champions Network brings together businesses who have engaged with Made Smarter’s adoption programme, including graduates of its Leading Digital Transformation and Leading Change for Digital Champions programmes.
The initiative will connect those employees actively engaged in digitalisation, from the top floor to the shop floor, at different stages of technology adoption. In-person and online
events will be facilitated throughout the year to enable participants to share learning and experience, forging longlasting connections.
A launch event at the Manufacturing Technology Centre (MTC) in Liverpool attracted North West businesses from across industries. It kicked off with a panel discussion about digital transformation featuring Max Barnett, digital champion for CNC Robotics, Made Smarter’s technology adoption specialists Will Kinghorn and Claire Scott, and Mark Sutherberry from the MTC.
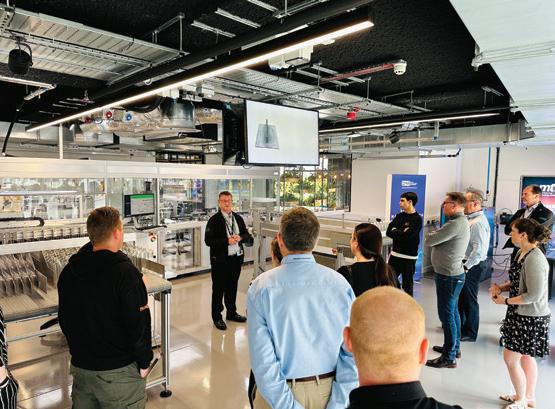
This was followed by a workshop session, led by Karen Lancaster from the Centre for People-Led Digitalisation, exploring the role of dignity at work and how this can be affected by technology.
The event finished with a tour of the MTC, a demonstrator backed by the High Value Manufacturing Catapult which showcases how advanced manufacturing equipment can be applied to industry to support skills, productivity and growth across UK manufacturing.
Customised pumps for Montréal’s water supply
KSB has supplied six singlestage horizontal split case double suction pumps, each with a 2500HP motor, to support Montréal’s water supply infrastructure. These pumps operate at 1580l/sec with a head of 73m. The project faced challenges, including maintaining plant operations during installation and dealing with two separate electrical power systems.
In 2018, Montréal launched a tender for six new motor pump sets to replace ageing pumps at the Atwater plant. The project required custom-designed centrifugal pumps to fit the existing infrastructure. KSB, with a history of collaboration with Montréal, won the contract. The pumps had to meet specific hydraulic and mechanical criteria and were custom-made in Germany.
Montréal’s Water Department operates six water treatment plants, including Atwater and Charles-J.-Des Baillets, which extract
water from the St. Lawrence River. The water is purified through filtration, ozonisation, UV treatment, and chlorination before distribution. The plants are interconnected to ensure continuous water supply even if one plant is shut down.
The Atwater plant, built in 1868, is a significant part of Montréal’s heritage. It has undergone numerous upgrades, including the replacement of steam pumps with electric ones in 1923. Recent investments have increased its capacity to 700,000 cubic meters per day. The plant has been crucial for public safety and health.
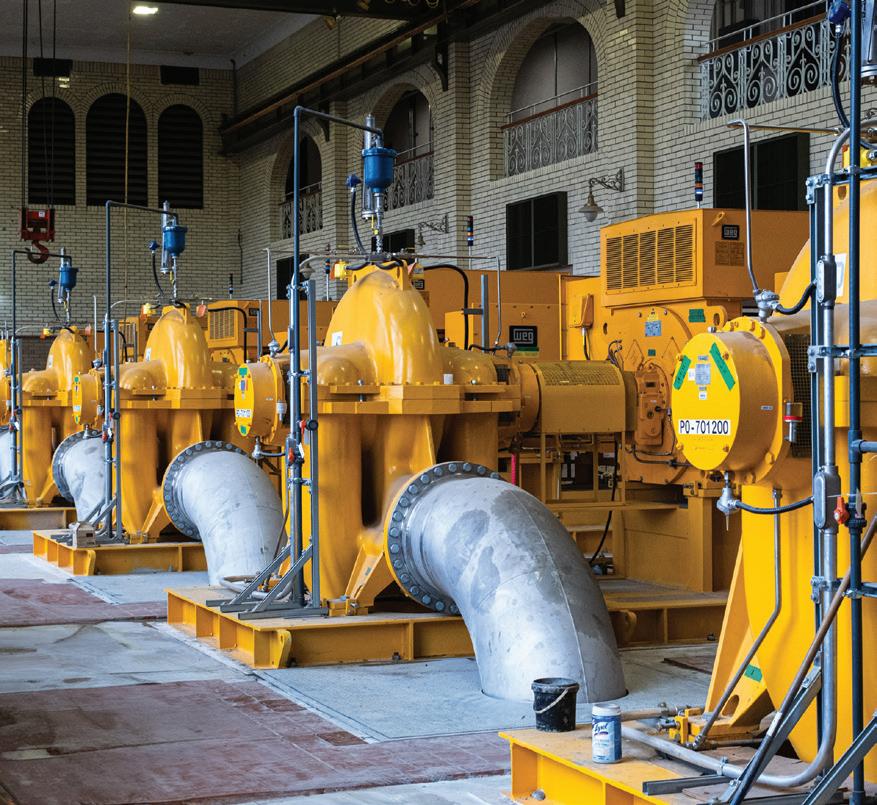
remaining four installed in 2023. KSB ensured proper installation and integration of all components.
Despite the COVID-19 pandemic, KSB completed the fabrication and testing of the pumps on schedule. Remote participation was used for factory tests. The first two pumps were installed in 2022, with the
KSB successfully delivered and installed the new pumps, ensuring a continuous water supply for Montréal. The project overcame significant challenges, including maintaining operations and adapting to existing infrastructure.
www.ksb.com/en-gb
Inductive sensor delivers reliability in harsh environments
Industrial sensor expert SICK has unveiled the IMG inductive sensor, designed specifically to provide stable detection in harsh environments.
With machinery manufacturers and system integrators increasingly being called out to sites to carry out minor maintenance and repairs, the reliability, robustness and repeatability of components is crucial.
As rising skills and labour shortages continue to affect the manufacturing industry, particularly among maintenance technicians, OEMs and equipment suppliers are receiving more requests for site visits from field service engineers. Ensuring parts are robust and reliable can reduce the burden on equipment suppliers, as well as enhancing their reputation by preventing costly stoppages.
SICK’s IMG inductive proximity sensor for metal detection is designed specifically for industrial machines that require precise switching points and a high level of repeatability in harsh environments. For
example, IMG sensors are perfect for the machine tooling industry, where they can be used for detection of tool turret position, tool detection on the turret or to determine the lock/ unlock position of the turret.
The SICK IMG inductive sensor family operates in environments where many inductive sensors fail to perform. Suitable for end position and home position detection, as well as simple speed detection tasks, the robust device is impervious to shocks, vibration, oil, cooling lubricants, and weather effects such as rain, snow, mud and frost.
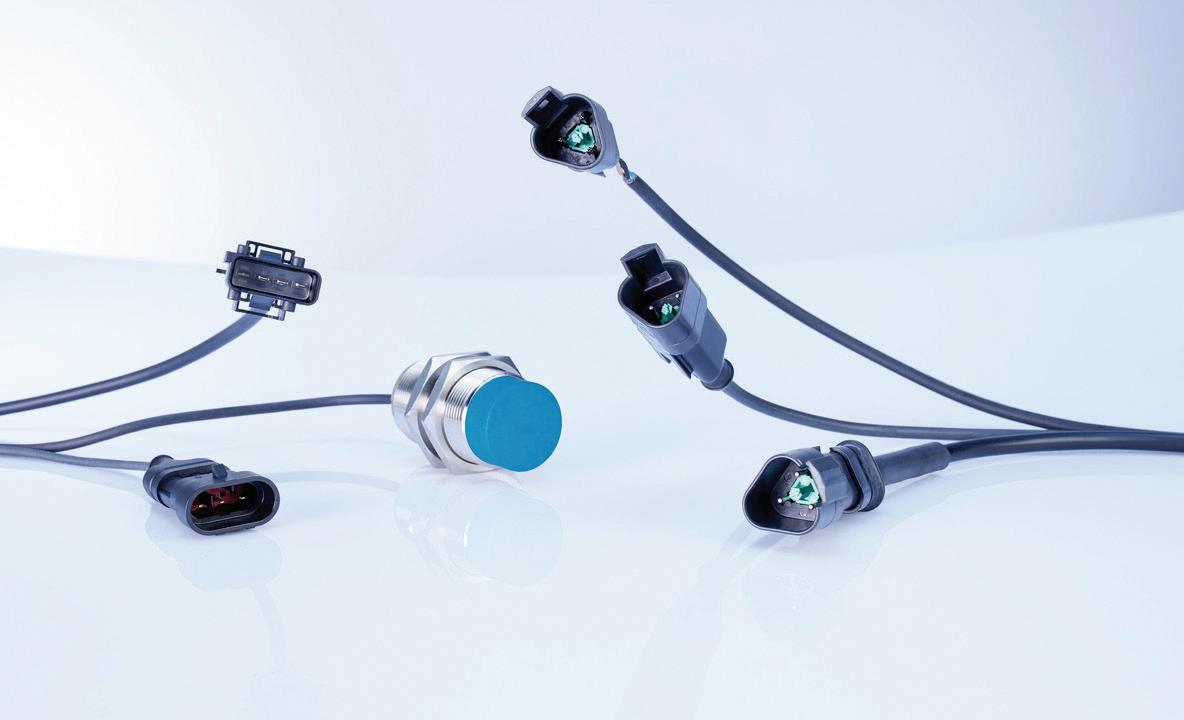
SICK UK Market Product ManagerPresence Detection, David Hannaby, said, “IMG combines robustness and stable
detection in a great value product. We know that industrial machinery manufacturers are experiencing added pressures as a result of labour and skills shortages in manufacturing, including additional callouts. The tough IMG sensor family is designed for machines operating in harsh environments where reliability and stable detection is critical.”
sick.com
New electronic key system offers simple set-up and operation
The new Electronic-Key-System
EKS2 developed by Euchner is the latest generation of its key systems. The new product has achieved three objectives: it is simple to implement, simple to operate and simple to adjust.
The new generation of products is a logical development of the successful EKS system and has many advantages in terms of digital access control and the selection of a safe operating mode. Template projects with predefined functions and data fields have minimised the programming work needed to integrate the system. Current requirements, including security factors, for example, have been taken into consideration right from the start.
Euchner uses Profinet for communication purposes, together with reliable, safe semiconductor outputs. The Profinet switch that forms part of the system makes
integrating it into an extensive bus system very simple. The 1-of-n safety outputs are directly connected to a safe control system and evaluated there. This allows for the selection of a safe operating mode on the highest safety level, PL e, for example.
Instead of programming the entire selection of safe operating modes in the control system, as was the case in the past, customers can now select a suitable project and simply configure individual parameters via the GSDML file in their configuration software. Other benefits include compact dimensions, industrial keys and a hygienically designed read unit.
“The development process was based on more than 20 years’ experience of the existing EKS system and many discussions with customers,” said product manager Marc Wiederoder. “Sometimes, only a few improvements
are needed to make an already good system even better. Our main objective was to design a system that is as simple as possible for customers to use.”
www.euchner.co.uk

Advancing X-ray inspection with deep learning de-noising technology
X-ray inspection plays a pivotal role in the food and nondestructive testing industries, ensuring optimal quality and safety. To improve contaminants and defects detection, it is crucial to reduce the amount of noise in the acquired images. Addressing this, Hamamatsu Photonics has developed a new de-noising technology based on deep learning algorithms and an innovative X-ray simulation method.
Deep learning, a method of artificial intelligence (AI) that mimics how humans think and learn, relies on ‘artificial neural networks’. These computational models are constructed with several hidden layers that perform complex operations. Training the AI is the most challenging part, requiring significant computational power and a vast dataset. Images with as little noise as possible are captured, and various types of noise parts are artificially added to create
expected measured images. Using these structure-plus-noise images as input data, and the noise images as the teacher dataset, the neural network learns how to discriminate noise.
The proprietary X-ray simulation technique developed by Hamamatsu Photonics simulates four main components: X-ray emission spectrum, X-ray transmission through the object, scintillator response, and sensor response. The performance of the simulation is verified by comparing simulated images with empirically measured ones. The applications of Hamamatsu X-ray simulations offer support in defining optimal inspection parameters and developing new cameras. During the training phase, conventional training images can be replaced with simulated ones. The X-ray simulation software generates training images under various conditions, structures, and noise
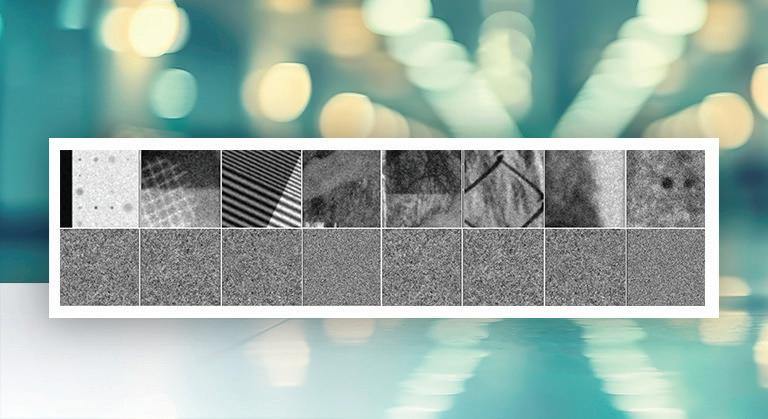
levels. A neural network that extracts noise from real captured images is obtained, selectively subtracting the noise component without removing structural details. This approach improves contaminants detection. The simulation-plus-AI de-noising tool is suitable for real-time image processing during inline inspection. Initially available for X-ray line scan cameras, future developments aim to extend compatibility to flat panel sensors.
www.hamamatsu.com.
AERZEN provides increased efficiency resulting in significantly lower OPEX
Operational efficiency and reliability should be priorities in wastewater treatment plants (WWTP).
Consequently, there has been a prominent focus on being more efficient and reducing carbon footprint.
A WWTP recently supported by AERZEN treats wastewater for over eight million people. The plant was working with three energy-intensive blowers that no longer met today‘s standards, this is where AERZEN was consulted on a replacement solution.
For this replacement, a detailed calculation of profitability showed potential energy savings.
All three blower units were showing significant signs of wear. Therefore, instead of an extensive and costly refurbishment, it was decided that these old units should be replaced with three new efficient AERZEN Turbo Blowers.
AERZEN consulted with the company Air Technology to determine the current load requirement. A detailed profitability calculation indicated energy savings of over 20% could be made.
AERZEN supplied three Turbo G5plus blowers (3 x AT150 0.8S DN250), which modernised the plant as they replaced the competitor’s aging blowers that were consuming a lot of energy.
While these works were going on, the client involved AERZEN Rental who supplied two BVO 55000 skid mounted assemblies to avoid downtime.
The space-saving installation of the new turbo technology from the G5plus series enabled an efficiency gain of approximately 21% for the aeration of wastewater tanks, which ultimately led to savings in operating costs.
Additionally, in comparison to the earlier ventilation systems, the noise emissions were
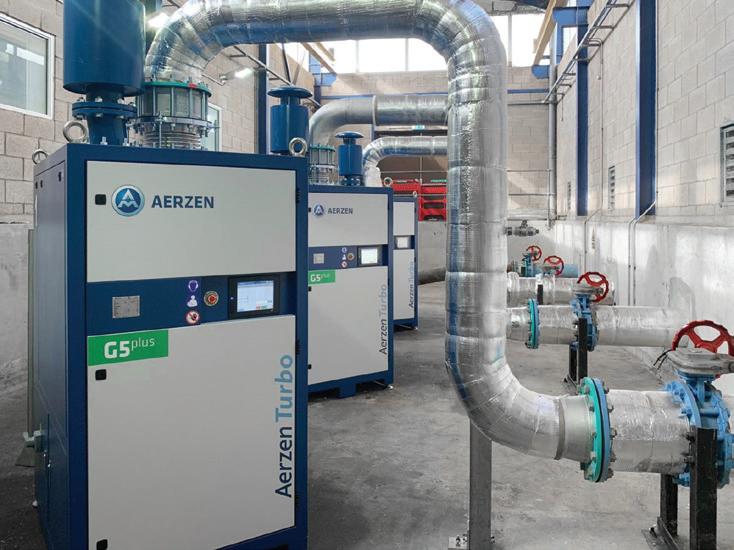
significantly decreased.
This wastewater treatment facility can save over £21,000 by utilising state-of-the-art technology from AERZEN.
The calculation assumes an amortisation period of about three years. And, the cost and energy savings coincide with the customer‘s desire to reduce their carbon footprint.
www.aerzen.com
Vision Engineering enhances EVO Cam,
Lynx EVO, and Swift PRO
lines
Vision Engineering, a UK designer, manufacturer and exporter of ergonomic microscopes and measuring systems, has announced advancements across its EVO Cam, Lynx EVO, and Swift PRO product lines. These enhancements broaden the appeal and applications of these powerful tools, making them more accessible to a wider range of industries and users.
The EVO Cam series now boasts a wider range of configurations, offering even greater flexibility for digital inspection tasks. With the launch of a new, simplified ICON model, users can now choose from multiple software configurations and ergonomic stands to perfectly tailor their EVO Cam system, enabling effortless image comparison, capture, measurement, and reporting.
The latest iteration of the Lynx EVO builds upon its reputation for ergonomic design
and stunning 3D stereo imaging. A new, simpler, non-zoom configuration variant extends the range to appeal to a more price conscious market. This makes the benefits of Lynx EVO accessible to a much wider audience who have applications demanding exceptional image quality and clarity, useable working distance, and exceptional user comfort.
Vision Engineering has further refined the Swift PRO metrology line, its flagship range of benchtop optical measuring systems. The new Swift PRO EDGE features a 6.5x zoom, allowing quick, precise measurement of a wide range of part sizes and features without lens changes. The new configuration reduces setup time and operator intervention by eliminating the need to manually change lenses for different measurement tasks. This
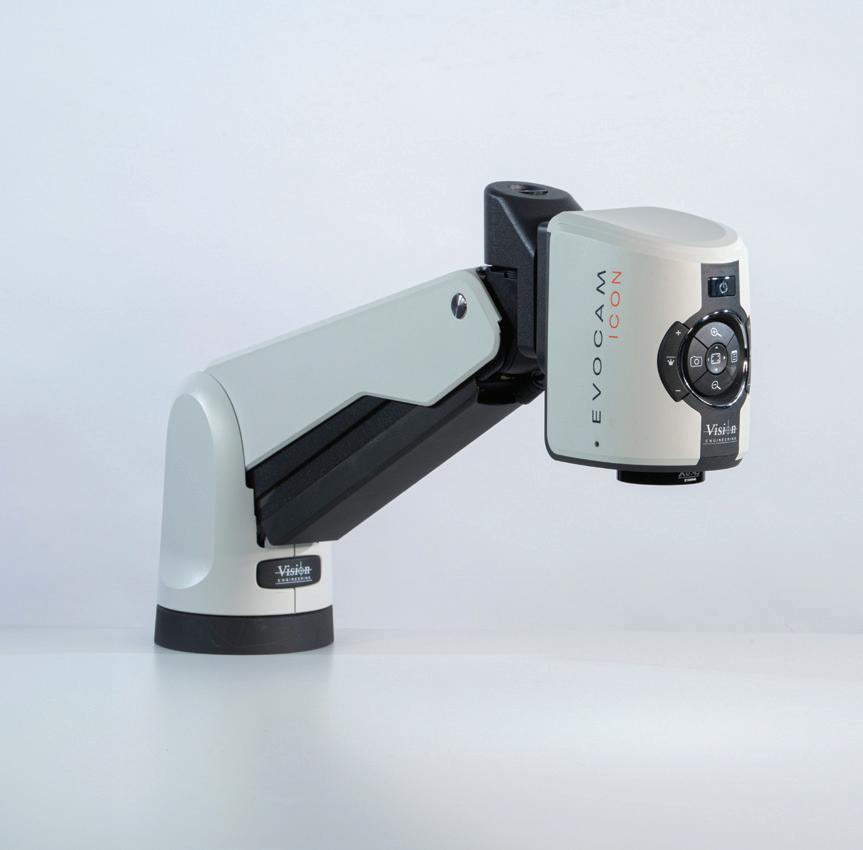
enables operators of all skill levels to use the metrology system in a more efficient way, thereby boosting productivity.
www.visioneng.com
AVPE Systems achieves a 30% factory uptime increase with FourJaw smart technology

AVPE Systems, a manufacturer of components and assemblies for the aerospace industry, has achieved a 30% increase in shop floor uptime since implementing FourJaw Manufacturing Analytics.
Part of the Broadway Group, AVPE supplies aerospace customers in the UK, Europe and Asia with complex machined components. It specialises in airframe and landing gear parts and machining castings, forgings and 3D printed parts.
AVPE introduced FourJaw’s plug-andplay analytics platform in 2023 as part of a broader business transformation programme to enhance productivity, eliminate process inefficiencies and gain capacity. Data gathered using FourJaw has enabled it to identify and address the top causes of downtime across its factory, boosting overall production uptime by almost a third.
The manufacturer has also used data gathered with FourJaw to improve the accuracy of its planning processes. Armed with a real-time view of production schedules across its factory and a more precise understanding of how long each production run takes to complete, AVPE can provide more accurate lead times to customers and unlock additional capacity by finding more space in its schedules for urgent incoming jobs.
Sean Thomas, Head of Operations at
AVPE Systems, said: “FourJaw has delivered a significant and sustained improvement in the productivity levels we’re getting from our manufacturing centres. Monitoring downtime, eliminating the various causes of waste in our processes, and deploying colleagues to where they are needed most has helped achieve a 30% overall increase in uptime.”
“We used to focus on fixing the most irritating things rather than the issues that are now proven to have caused the most downtime and lost productivity. In some areas, even without additional resources, we’ve seen a 10 to 15% increase in productivity by addressing the true causes of downtime with FourJaw.”
Chris Iveson, CEO at FourJaw Manufacturing Analytics, commented:
“Manufacturers have recognised the importance of using business intelligence and analytics technologies such as ours in recent years, as the race to become more productive and competitive has picked up. This is particularly evident in sectors such as aerospace, where there is huge pressure on the supply chain to meet demand.
“AVPE is achieving fantastic results with FourJaw, improving uptime and productivity, supporting investment decisions and aligning its processes perfectly with the OEMs and tier-one customers it serves in the global aerospace industry.” fourjaw.com

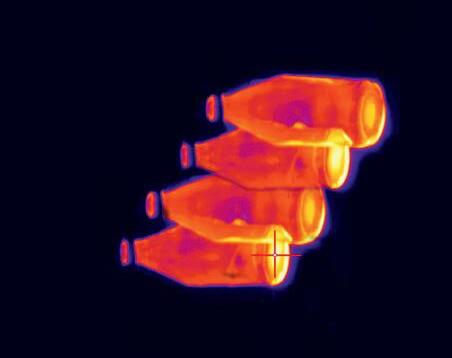
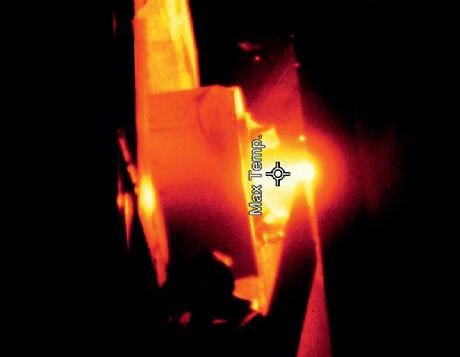
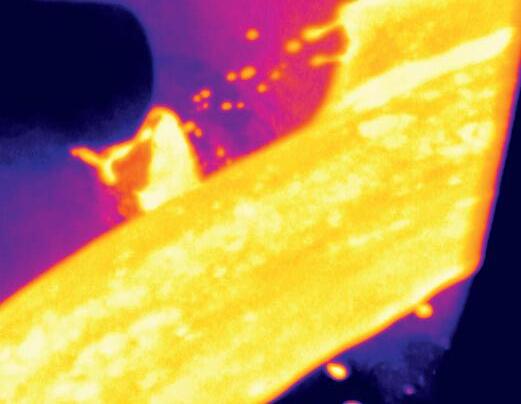
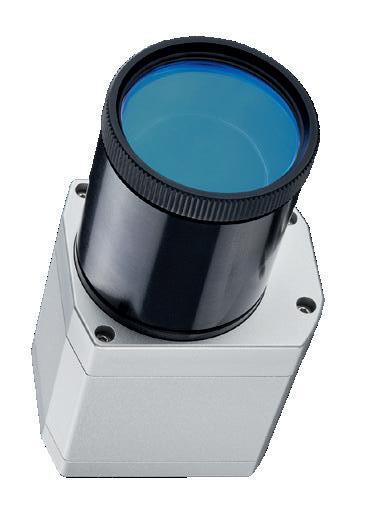
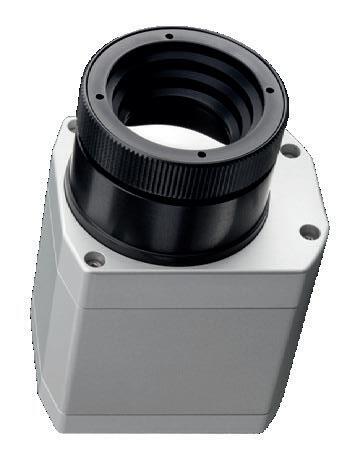

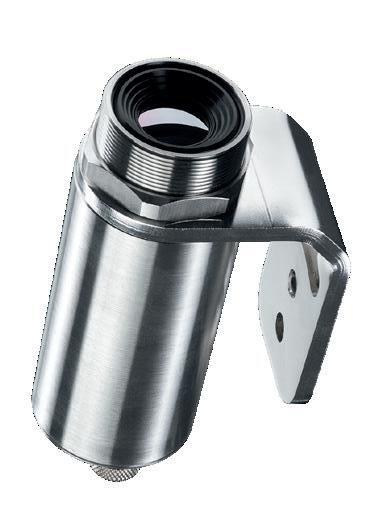
Changing of the guard
George Thompson, Chairman of BARA, the British Automation & Robot Association, reflects on the Association’s achievements over the last three years.
This is the article that I have been dreading… Before I get into why, I need to ask where have the last three years as BARA Chair gone? As with most business endeavours I had such big plans, some of which have been realised, some are still in progress and some just weren’t possible to achieve.
In my opinion, one of our greatest achievements during my tenure as BARA Chair was the creation of the Automation UK exhibition, which had its inaugural event in 2023. Having attended both years of the event, I personally think that it feels like no other event that I have attended. Could there have been a higher footfall? Maybe… That being said, the people who attended were all looking for solutions for specific manufacturing challenges. The show attendance has grown in the second year when compared to the first year, and the show doubled its footprint at the same time. For 2025, the Machine Vision Conference will also fall under the banner of Automation UK, which we think will benefit both Automation UK and MVC as vision and automation work hand in glove.
We have also continued to develop the format for our BARA Roundtable events, which have predominately been held as online webinars. We did hold a Live Roundtable at Automation UK back in June, which was such a resounding success, we are repeating it on 25 September at the PPMA show. The panel all agreed that it was such a broad and important topic, that we all could have spoken for hours on the subject.
So, if you haven’t guessed it by now, my time as BARA Chair is at its end. On 1 October, I will hand over the reins to Oliver Selby, who is also the Head of Sales for Fanuc UK. I have known Oliver for quite a while and can safely say that he will do an outstanding job and will drive the Association forward with his unwavering drive and passion for Robotics and Automation. I know that he will want to introduce himself properly in his first article, so I will leave that bit to him. I will say that, like me, he thinks
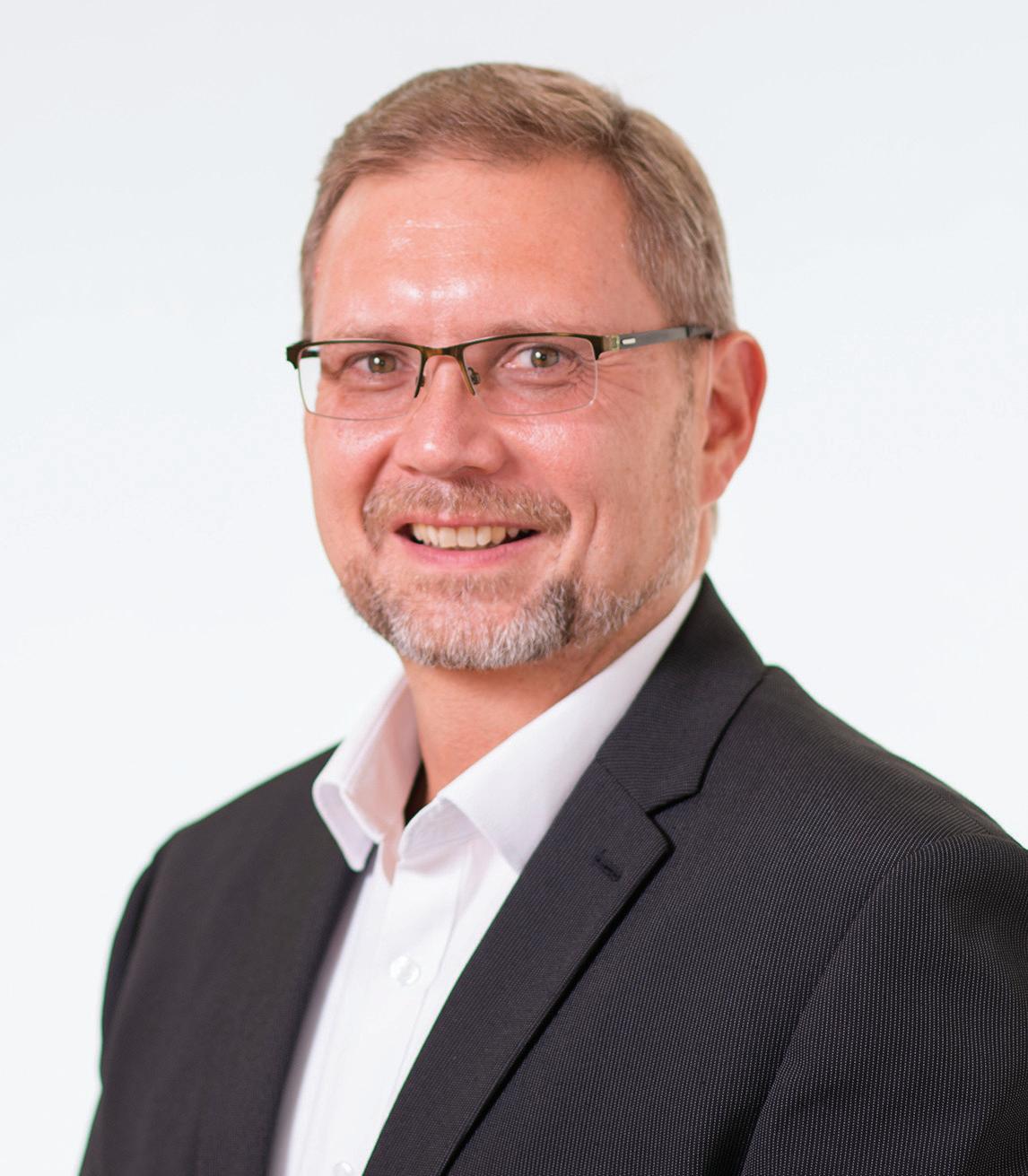
that the key to making our economy stronger is reliant on making our manufacturing sectors more efficient and cost-effective on the global stage. The key to this is to automate more dull, dirty, and dangerous applications, which will assist in enabling UK companies to reshore their manufacturing and, in turn, create more jobs.
We all know that there is a skills shortage here in the UK, and I know that Oliver is passionate about how we can potentially overcome this. Again, I do not want to preempt anything he may or may not promote, so I’ll fade quietly into the background – to some extent, anyway. Don’t worry; I’m still going to be on the Council and hope to be able to take part in Roundtable discussions
in the future. If you’re around PPMA 2024 or Automation UK 2025, I’m sure I’ll be found somewhere around the events.
I guess the only thing left is for me to thank you for reading my ramblings over the last three years. Thank you for giving me the opportunity to express my opinions and hopefully get you to think more about how automation can help your business grow, become more efficient and, most importantly, become more sustainable for the good of us all.
If you would like to start your automation journey but don’t know where to start, I would highly recommend visiting the BARA website.
www.automate-uk.com


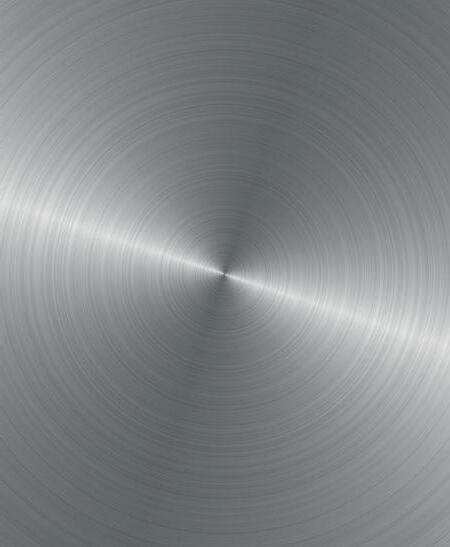

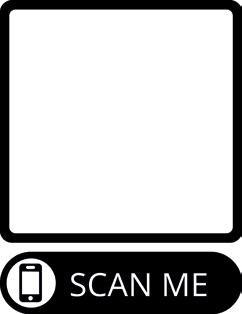
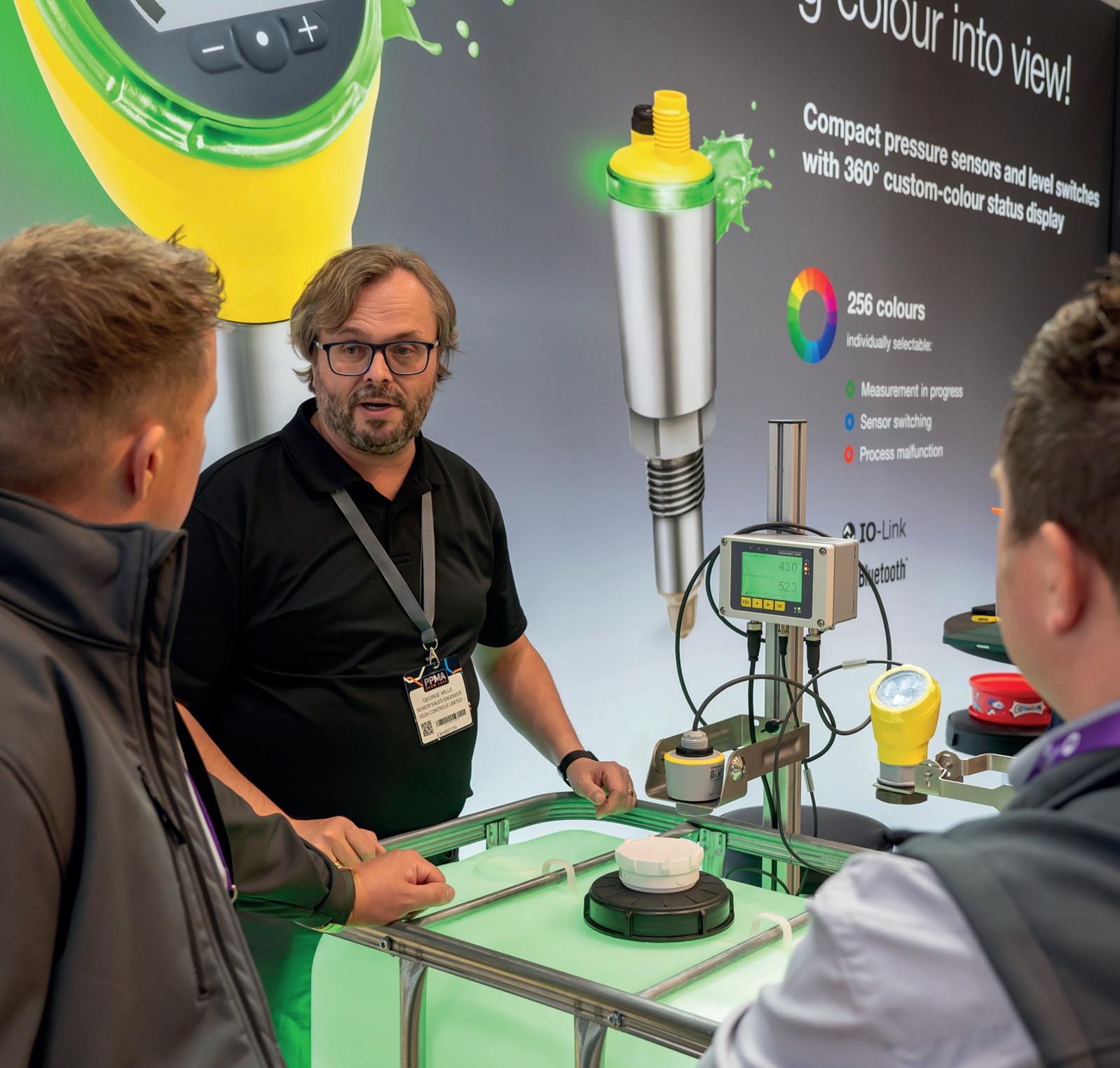

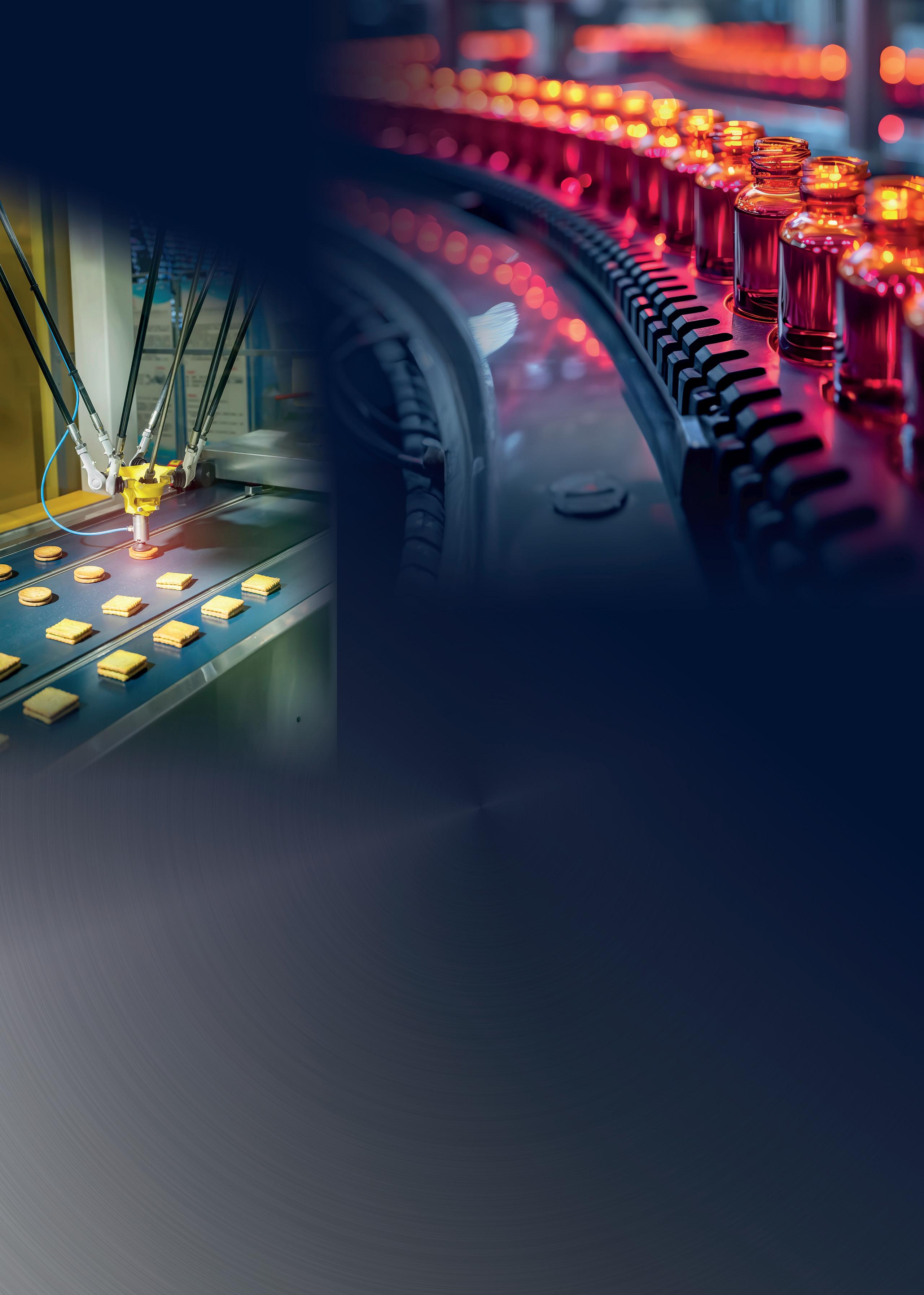
The 2024 PPMA Show is fast approaching
For over 35 years, the annual PPMA Show has been a highlight of the processing and packaging industry’s calendar. This event, taking place this year between 24-26 September at the NEC in Birmingham, is renowned for bringing together thousands of visitors and exhibitors from the FMCG sector. It is expected that Hall 5 will once again be filled with excitement and anticipation, providing visitors with a perfect platform to network with well-known exhibitors and learn about their latest state-of-the-art technologies and solutions.
Owned and organised by Automate UK, the PPMA Show is recognised as the industry-leading event. It brings together the very best suppliers of processing and packaging machinery, robotics and industrial vision systems with the capability to deliver significant benefits to a wide range of businesses. These include cost reductions, increased efficiency, quality improvements, and reduced downtime and turnaround, all of which can deliver a healthy return on the investment in these technologies.
The show provides a unique opportunity for visitors to experience a complete production line with every aspect of it being represented, from labelling, filling and packaging to processing, robotics, automation and industrial vision systems.
Visitors will be able to see the latest innovations from an impressive line-up of over 350 exhibitors, comprising over 1,500 brands. These exhibiting companies will be showcasing their latest cuttingedge solutions for the full spectrum of the manufacturing industry, including pharmaceuticals, food and beverages, building materials and suppliers, pet care, and microbrewers and distillers.
The show floor is expected to be vibrant, with live demonstrations and product launches, along with experts on hand to help the visitors find the right solutions for their needs. It is anticipated that the show will deliver impressive results, with many business transactions taking place during the three-day show.

Talking about the 2023 PPMA Show, Aaron Moore, Asset Maintenance Manager at Nestle, said: “Fantastic day here at the PPMA Show, lots of suppliers that we work with. Some really innovative solutions and a lot of relatable things for us, so we are taking lots of lessons home.”
Technology
Here are just some of the hundreds of exhibitors taking part in the show: Reiser (D110) has been a leading supplier of processing and packaging equipment for the meat, food, pet food, bakery, and cheese industries for over 60 years. From single machines to complete process-to-
packaging production lines, their solutions combine specialised equipment, custom engineering, and in-depth expertise to meet customer challenges.
Videojet (E30) is one of the world-leading manufacturers of coding and marking systems. The company’s portfolio includes its full end-to-end suite of primary, secondary and tertiary equipment, including printing date or batch codes onto a food package and labelling full traceability information on a pallet.
ULMA (B20) provides the most extensive selection of packaging machinery and applications on the market. ULMA’s product range also includes fully automated
solutions encompassing crate/case loading, product handling, pick and place, palletising, end-of-line, and comprehensive turnkey project management.
Ishida (B50) is a world leader in the design, manufacture and installation of end-to-end weighing, packing and safety solutions for the food industry. The company helps manufacturers increase automation and compliance, reduce cost and downtime, increase operational efficiencies and brand protection, and maximise profits.
The comprehensive exhibitor listing is available online to help visitors plan their visit at www.ppmashow.co.uk/ exhibitors-2024#/exhibitors/
Seminars
One of the show’s highlights is its informative and inspiring expert talks, which provide visitors with a wealth of knowledge to take with them and help them consider how they can apply this knowledge to improve their businesses. This year’s keynote speakers are:
Jessica Sansom from Huel on the subject of ‘The manifestations of climate change - rising to the challenge and adapting to a new normal’.
The food industry is responsible for more than a quarter of all global greenhouse gas emissions. Without significant change in this industry, it will be impossible to limit global warming to under 2 degrees.
One hundred thirty-four countries at COP 28 signed a declaration on sustainable food systems, meaning that they must now include food in their national climate action plans, including a commitment to shift from higher greenhouse gas-emitting practices to more sustainable production and consumption approaches.
Jessica’s presentation explores what needs to happen in the processing equipment and packaging machinery sector in order to meet those targets.
Stefan Casey from Nestlé will be exploring ‘The digital transformation of FMCG industry: How digital technology is bringing both challenges and opportunities in packaging across the whole value chain’.
Stefan’s talk will focus on affordable personalisation and customisation in packaging design through to production. His presentation will cover points such as the need for more flexible packaging production solutions, cost-effective solutions by optimising end-to-end from design through to manufacturing, and quality control and safety.
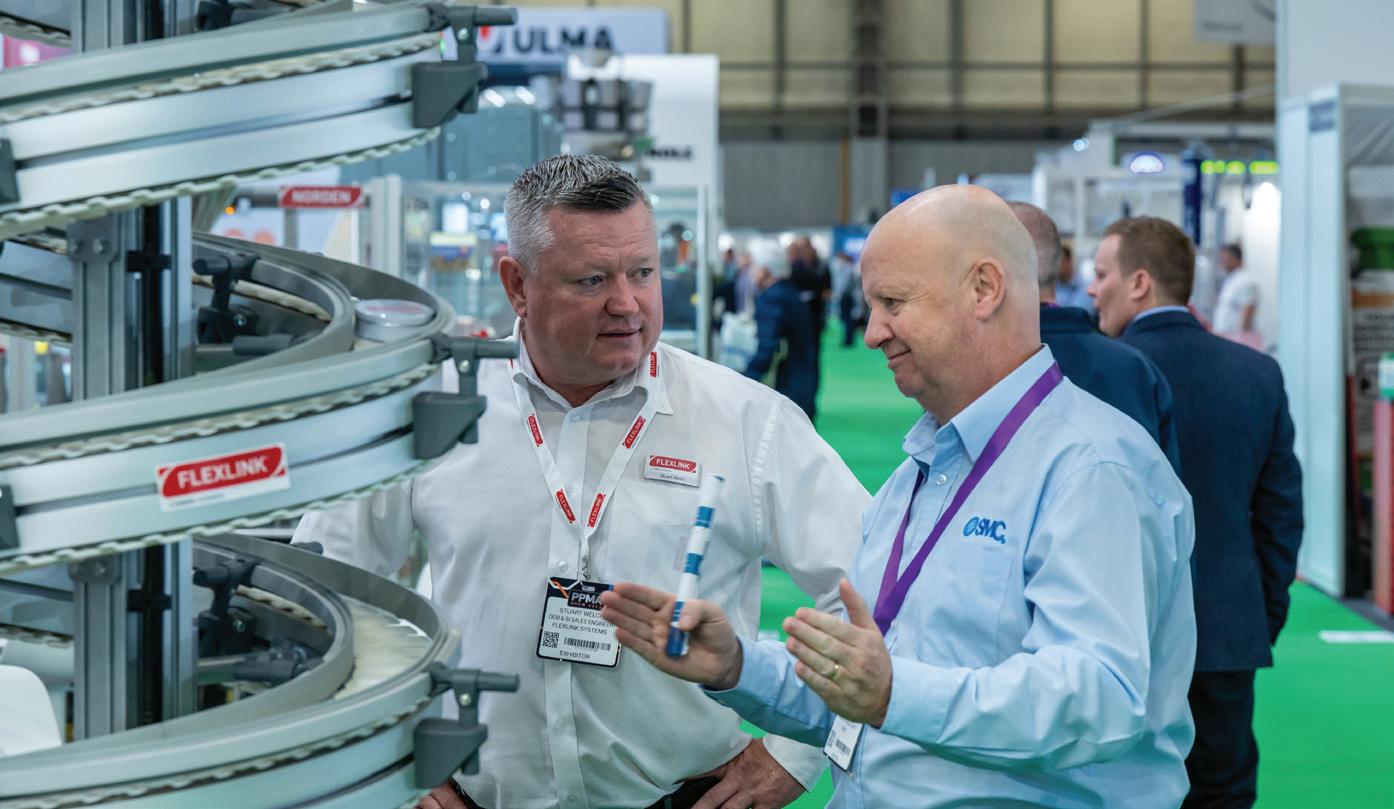
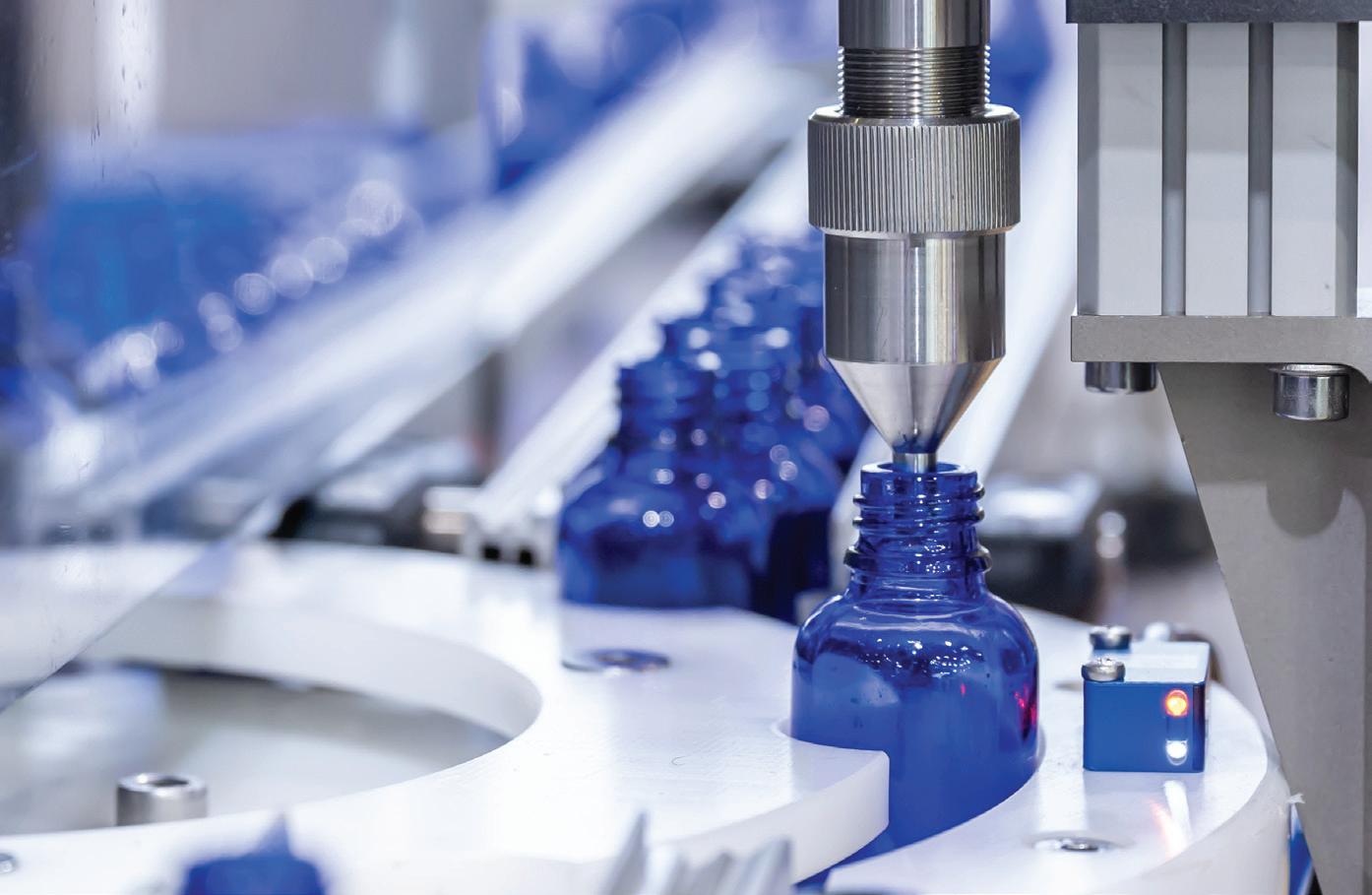
Visitors will also have an opportunity to hear from leading industry speakers, including Dr Martin Kidman – SICK UK Ltd, Adam Dickins - AD Frameworks Ltd, and Chris Whyborn - Thornton Tomasetti. The seminars will provide a wealth of valuable insights covering a wide range of topics, such as industry standards, CE and UKCA marking, automation to reduce carbon footprint, and many more inspiring subjects.
Discussion
The discussion will focus on the positive impact that adopting automation can have on the sector, as well as share advice and learnings that can help deliver successful outcomes.
In addition to discovering and exploring various innovations and solutions, experiencing live demonstrations, seeing product launches first-hand and learning at seminars, visitors will have plenty of opportunities to make new business
connections and network with industry peers.
Automate UK wants to ensure that visitors have a standout show experience; one of the new features at this year’s show is the free PPMA Show app. This will allow visitors to plan their day, have easy access to their entry ticket and discover all aspects of the show, from exhibitors and products through to a complete list of seminars and speakers.
Scott McKenna, Chief Operating Officer at Automate UK, said: “We’ve been working hard to ensure that the PPMA Show continues to live up to its reputation as the UK’s largest event showcasing innovative technology from the processing and packaging industry. Our aim is to ensure that the show continues to evolve, and as such, we’ll be introducing new features to enhance the show experience for both visitors and exhibitors.”
www.ppmashow.co.uk
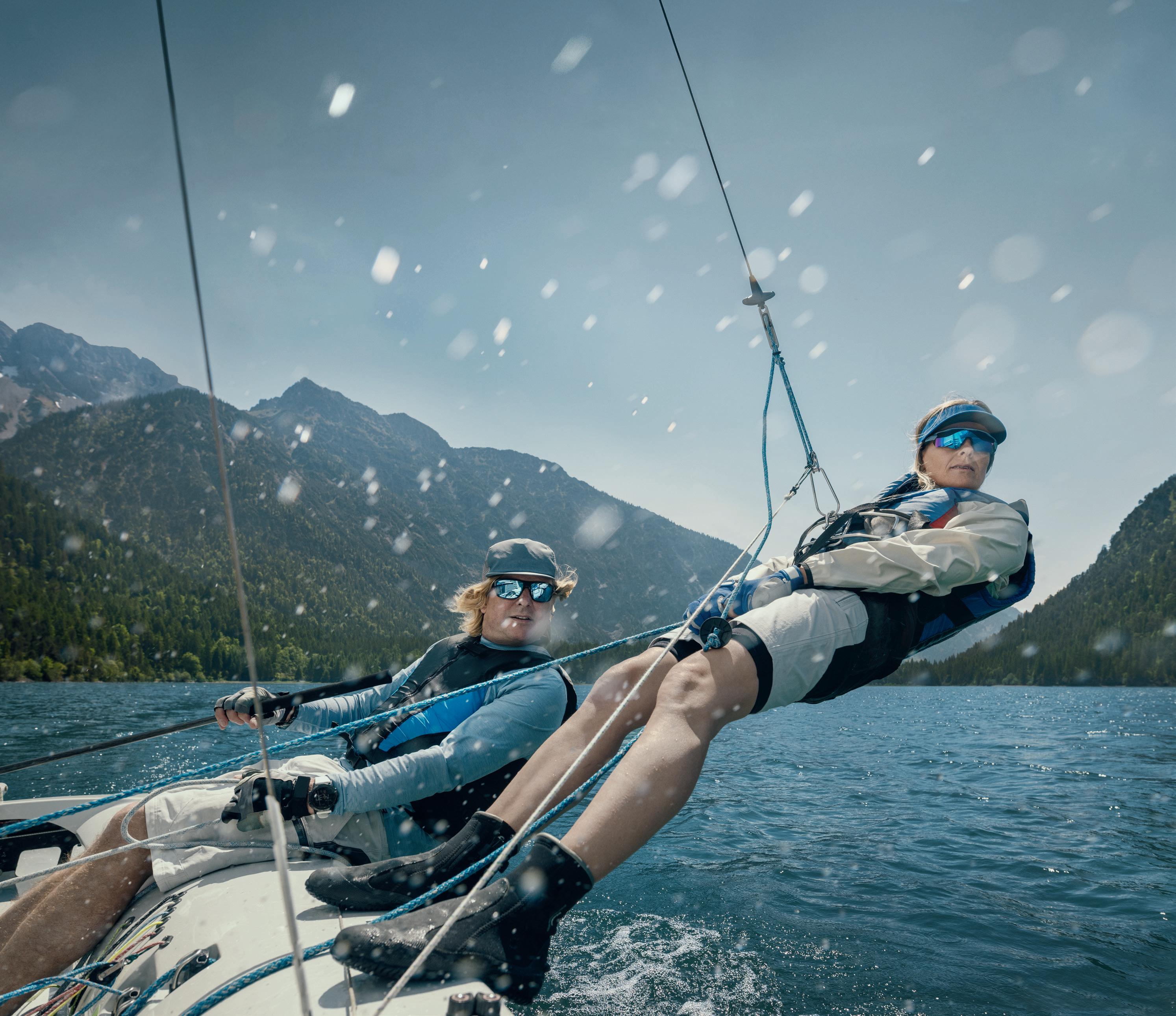
Process improvement is like sailing. With an experienced partner, you can achieve more.
Optimizing processes and maximizing efficiency is important to remain competitive. We are the partner that helps you master yield, quality, and compliance. With real-time inline insights and close monitoring of crucial parameters, we support manufacturers to optimize processes, reduce waste, and increase yield.
Focus On: Machine Building
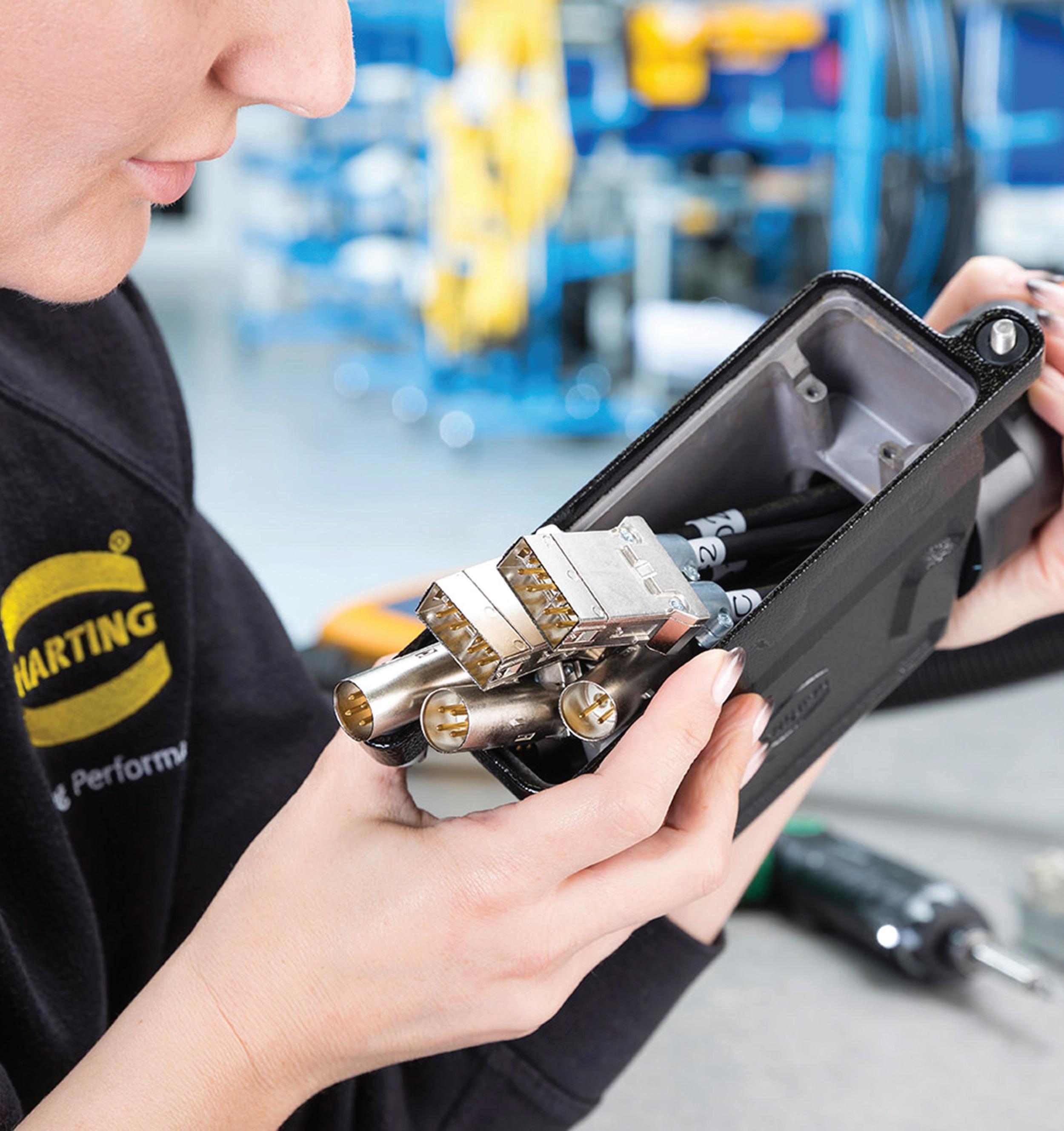
MEPCA explores the latest news, innovations and applications in machine building
The advantages of t-slot extruded aluminium profiles
Adaptech Manufacturing Solutions, the UK and Ireland distributor of the mk Technology Group aluminium profile range, explains how using t-slot extruded aluminium profile is a convenient and cost-effective way to build a machine framework.
Using T-Slot extruded aluminium profiles for building machine frames offers numerous advantages over traditional steel welding methods. Here’s an in-depth look at why this method stands out.
Eliminates welding and surface preparation
• No welding required: T-Slot extrusions can be connected using various fasteners and connectors, eliminating the need for welding.
• Anodised finish: The profiles come preanodised, providing a superior and durable surface finish compared to traditional paint jobs. This also eliminates the need for messy and toxic painting processes.
Ease of use and flexibility
• Easy cutting and assembly: Aluminium profiles are much easier to cut and handle compared to steel. The assembly process is straightforward, requiring simple tools.
• Modular design: The t-slot system allows for easy modifications and adjustments. Frames can be dismantled and reassembled if design changes are needed, providing flexibility during the build process.
Precision and reduced rework
• No distortion: Unlike welding, which can cause distortion due to heat, t-slot assemblies maintain their precision and alignment, reducing the need for rework.
• Consistent tolerances: The precision machining of t-slot extrusions ensures that all components fit together accurately, maintaining consistent tolerances throughout
Cost and time efficiency
• Reduced labour costs: By eliminating welding, grinding, and painting, labour costs

are significantly reduced.
• Quicker turnaround: Preparation and assembly times are reduced, leading to faster project completion.
Safety and environmental benefits
• No hazardous processes: The absence of welding, grinding, and painting reduces the exposure to hazardous fumes and materials, creating a safer working environment.
• Environmentally friendly: The anodised aluminium finish is more environmentally friendly compared to traditional painting processes that involve solvents and chemicals.
Durability and strength
• High strength-to-weight ratio: Aluminium profiles provide a strong and lightweight solution for machine frames, ensuring durability and ease of handling.
• Corrosion resistance: The anodised surface of the aluminium provides excellent corrosion resistance, ensuring the longevity of the frame.
Conclusion
Switching to T-Slot extruded aluminium profiles for machine frames can greatly enhance the efficiency, precision, and flexibility of the build process. The elimination of welding and painting not only reduces costs and time but also improves safety and environmental impact. With the added benefit of modularity and ease of assembly, T-Slot extrusions offer a superior alternative for highquality machine frame construction. Whether you are a seasoned builder of complicated machinery or a complete novice, building a frame with T-Slot Aluminium extrusions is easy.
www.adapt-tech.co.uk

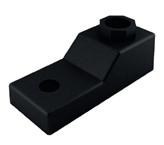
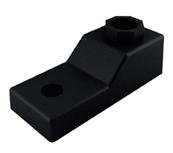

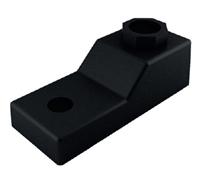

Why continue to give away your profits?
Process and control specialist Harford Control, exhibiting on stand B46 at this year’s PPMA show, explores strategies to address underfilling and overfilling while remaining legal and reducing wastage.
Billions of packages are being filled in factories around the world, and two common challenges that factories often struggle to overcome are underfilling and overfilling. Both issues can lead to significant consequences for businesses, including product defects, recalls, wasted raw materials and packaging, customer dissatisfaction and brand damage.
When we conducted research, we found that some factories in other countries deliberately underfill to save on the cost of raw materials. Customers end up paying more than they receive. While most people may overlook this, some choose to take action against such practices.
Two customers in the US filed a lawsuit against a potato chips company for consistently underfilling their chip bags. Although nitrogen gas may contribute to keeping the chips fresh and damage-free during delivery, the net weight of the chips was 58% to 75% lower than the information labelled on the packages. The lawsuit gained widespread coverage on news and social media platforms, leading to even more customer complaints and causing serious damage to the brand.
Bringing it closer to the UK manufacturing industry, there were still some underfilling incidents happening, even though Average Quantity has been the law for most prepackaged consumer goods produced and sold in the UK since 1979. A leading dairy plant pleaded guilty due to T2 failures within the Weights and Measures Act. This was attributed to inadequate testing procedures that had been in place for over 15 years. Though the underfilling was unintentional, it caused huge damage to the brand, and the manufacturer was fined.
We can’t just assume that what was ‘good’ yesterday will be good enough tomorrow. Manufacturers need to revisit every aspect of
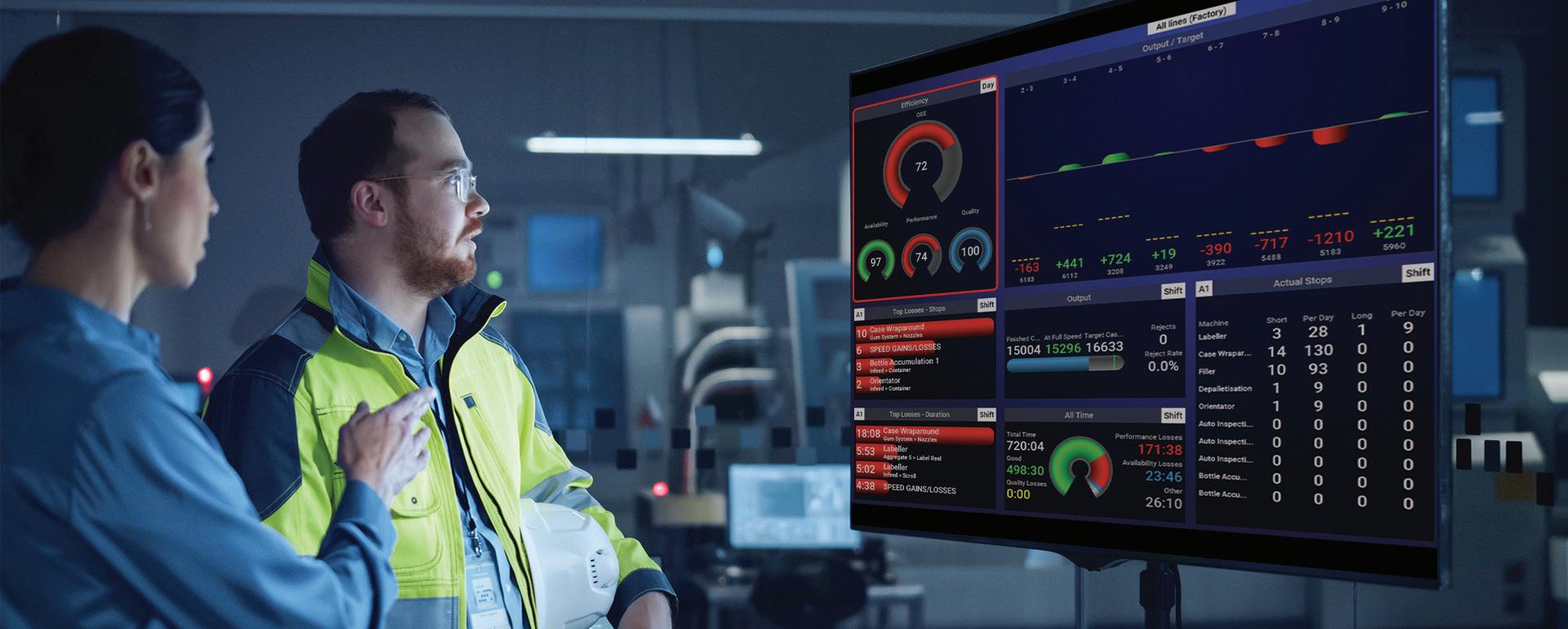
the manufacturing processes and ask: Why? What? Where? When? Who? and How? ‘We have always done it this way’ is no longer good enough.
Knowing the consequences of underfilling, many factories decided to take action to be compliant. With the introduction of Average Quantity Law, there was no longer a Minimum Quantity Law for most pre-packaged goods. However, some companies continued to pack to what they called ‘Minimum Quantity.’ This simply meant that they were giving more product away in overfill, whilst gaining no greater legal protection.
Let’s have a look at some numbers. Imagine you are a medium-sized whisky bottler producing, say, 10 million cases per annum. The industry standard for a case is 9 litres (based on 12 x 750ml bottles).
Ten million cases at 9l per case equals 90 million litres. With just 1ml of overfill on average, this amounts to giving away 90,000l per year. As whisky must be matured in oak casks for at least three years before it can truly be called whisky, it has to be worth at least £1 per litre at the time of bottling (three years later). Thus, this must represent a giveaway cost of around £90,000 per annum on such a volume, per average of 1ml in overfill.
What’s even worse, HMRC could raise an estimate as they are entitled to the excise duty on overfill, which could be traced back through the previous six years.
Tackle underfilling and overfilling
Being stuck between rising input prices and little or no opportunity to pass on these rising costs to retailers, manufacturers need to do everything to protect consumers, their financial health and brand reputation. Optimising the filling process should not be an option but a necessity – why give it away?
Preventing underfilling and measuring and controlling overfilling can significantly reduce production costs. Many manufacturers are unaware that technologies are available to help ensure optimal control of the filling level, with real-time data collection and analysis, feeding back to the management team. Managers can, therefore, take immediate action to ensure legal compliance and reduce the wastage of overfills.
To better control your filling processes, we suggest three key strategies you could implement for your factory. Choose a reliable and trusted technology partner with a proven track record to work with to help you remain compliant and reduce giveaway. In your choice of partner, make sure that they fully understand and can effectively communicate the benefits of process control and legal compliance, and ask your chosen partner to come to your site and prove their claims.
www.harfordcontrol.com
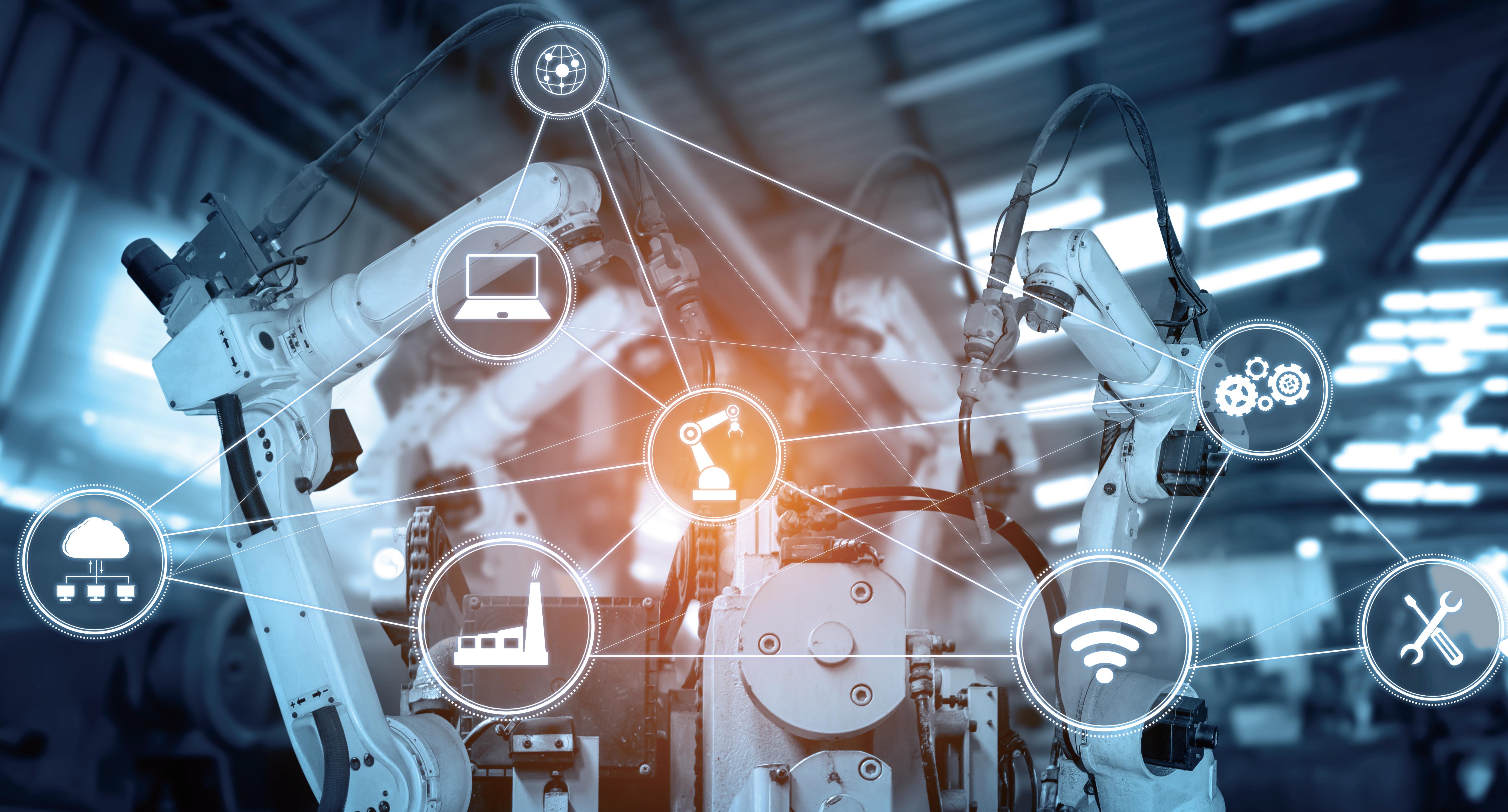

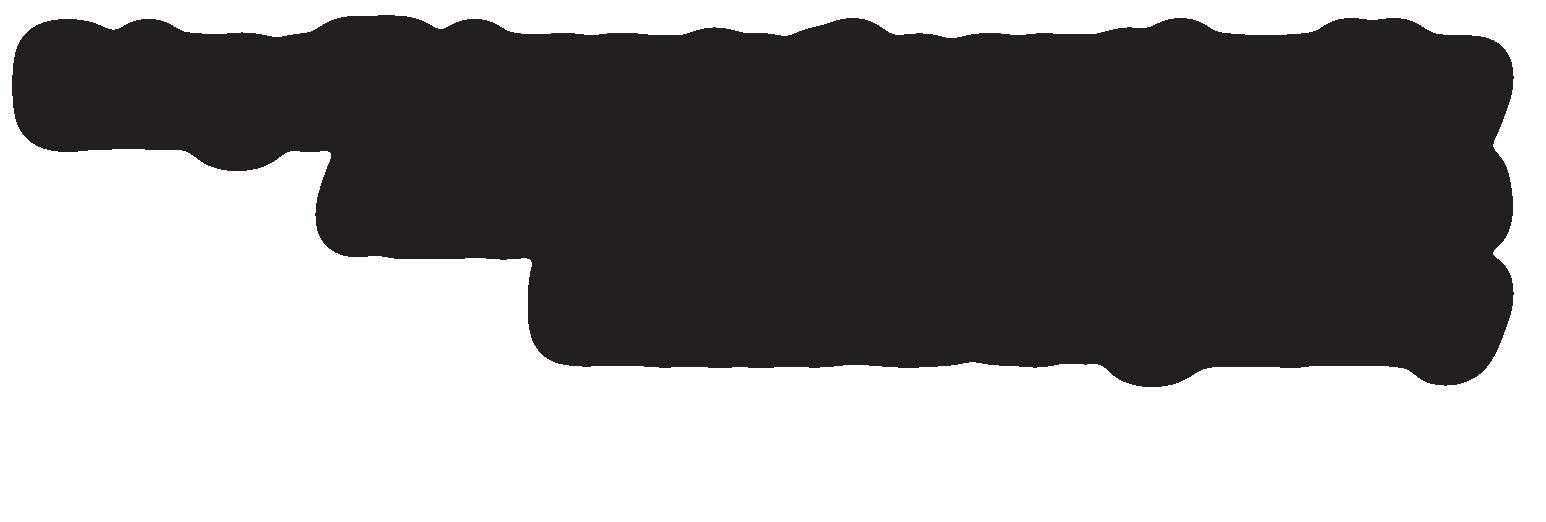
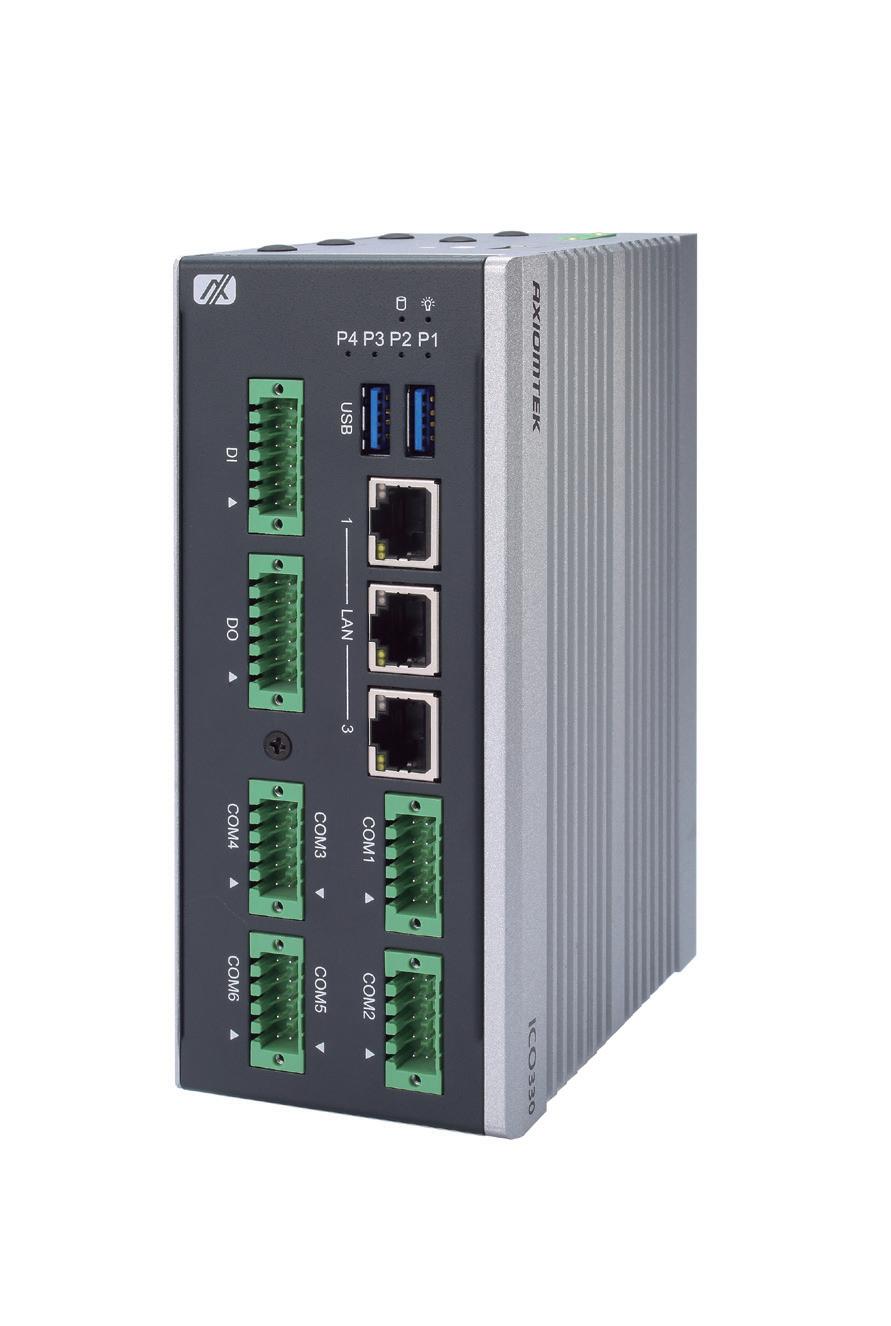
DIN-Rail Fanless Embedded System with Intel Atom® x6212RE or x6414RE Processor, 3 2.5GbE LAN, Isolated COM, and Isolated DIO
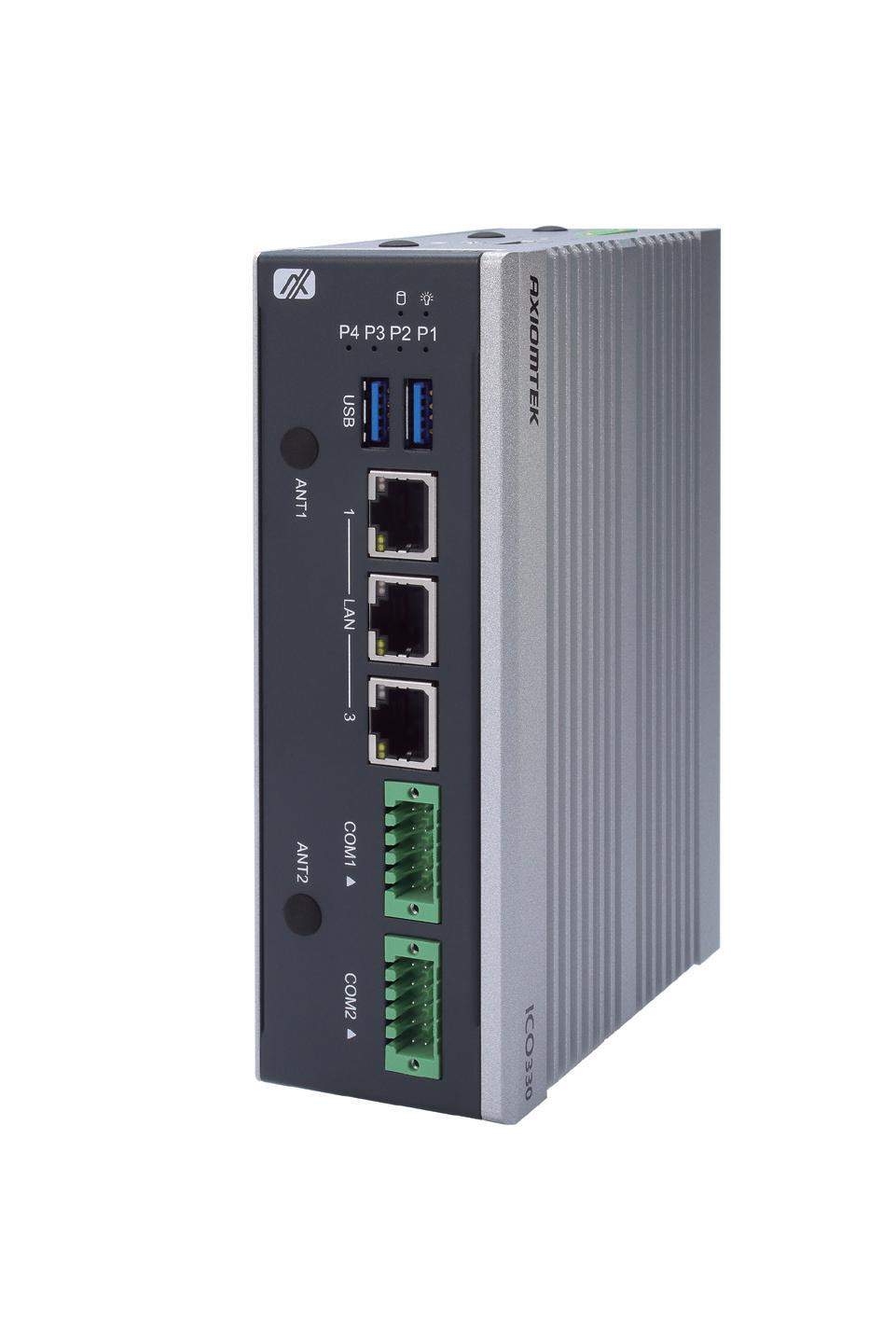
3-D volume measurements on conveyor belts
The Volume3D volume acquisition system from Pepperl+Fuchs enables non-contact and reliable volume measurements in mining applications, as MEPCA discovered.
In mining, a wide variety of bulk materials, such as different types of ore and soil, are transported over long distances by conveyor belts to loading silos and other areas of the plant. It is necessary to calculate the material volume with dynamic measurement systems along the routes. The control of produced material is carried out by these systems at strategic points along the conveyor belt, and knowing how much ore has been extracted and handled is directly related to the company’s profits. However, the harsh environmental conditions pose a particular challenge for the sensor solution used.
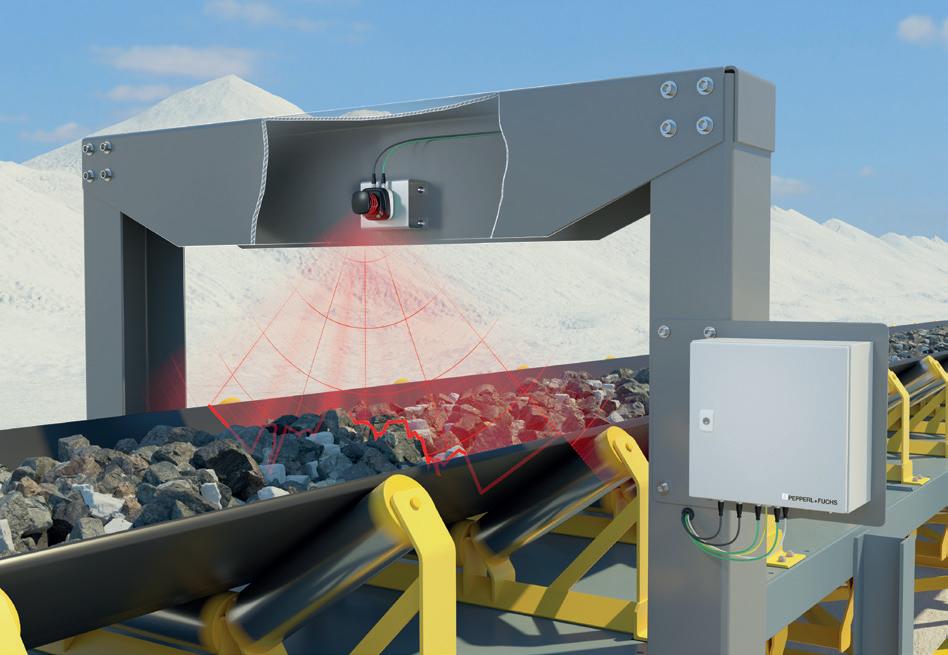
conveyor belt and can measure the volume without coming into contact with the ore.
The challenge is to measure the volume of material on the conveyor belt without coming into physical contact with the material. In addition, a device that performs reliable measurements and requires less maintenance compared to conventional volume measurement systems is required. The corresponding sensor solution must have a range of more than 5m, be equipped with software filters that make it possible to filter the environmental influences on the measuring data, and also provide information about the presence of dirt on the lens. Communication with an industrial PC via an Ethernet switch would enable the product to be operated with different types of controllers.
The solution
The Volume3D volume acquisition system from Pepperl+Fuchs, which consists of an R2000 2-D LiDAR sensor, a multiscan evaluation unit (MSEU), an ENI58IL incremental rotary encoder, and all the required connection cables, is the ideal solution for this application. Equipped with a flexible measurement data filter, the R2000 is positioned on a gantry facing the
The ENI58IL incremental rotary encoder with BlueBeam precisely captures the speed and direction of the conveyor belt, while the MSEU processes the sensor data and allows the volumetric scan data to be transmitted directly to other controllers to obtain variables such as flow rate. In addition, the maximum and mean height of the loaded materials on the conveyor can be output.
The R2000 sensor offers a number of technical features including easy mounting above the conveyor belt without major adjustments to the system, precise monitoring of wide belts with a width of over 5m, through high angular resolution and an integrated lens contamination monitor (LCM) which evaluates the degree of contamination of the lens. It also offers Pulse Ranging Technology (PRT) for measurement precision and highly accurate contour detection with a high angular resolution of 0.042° and a scan rate of up to 50 Hz.
The technical features within the ENI58IL encoder include BlueBeam technology for high measuring quality, interlocked bearings that withstand high loads for reliability and durability and special EMC circuit protection, which prevents damage from electromagnetic interference. It also achieves
rotational speeds of up to 12,000 rpm, includes a blue emitter LED and provides high shock and vibration resistance.
Finaly the MSEU has a robust IP66 housing with integrated industrial PC, offers easy integration due to easy-to-use data output, and intuitive Windows software for commissioning and monitoring. Simple commissioning is possible in three steps: installation, configuration, and initialisation with applicationspecific adaptations possible due to its own flexible software platform.
The Volume3D volume acquisition system offers the most efficient solution on the market for this application: the minimal installation effort and fast commissioning make the sensor system a particularly economical solution for conveyor technology. The noncontact concept also contributes directly to a reduction in maintenance costs in terms of the time required for maintenance and the avoidance of unexpected downtimes. The R2000 2-D LiDAR sensor guarantees maximum precision through a very high angular resolution of 0.042° and a scan rate of up to 50Hz. The intelligent software, which is integrated into the MSEU of the volume acquisition system, subsequently filters out invalid scan points and, therefore, ensures correct measurement results.
During operation, the Volume3D volume acquisition system outputs the volume in m3, the flow in m3/s, a height profile along the belt’s width, as well as the length, width, and height dimensions for separated and aligned objects. In addition, measurement filters can be created and data on the presence of dirt on the lens is received to enable timely cleaning.
www.pepperl-fuchs.com

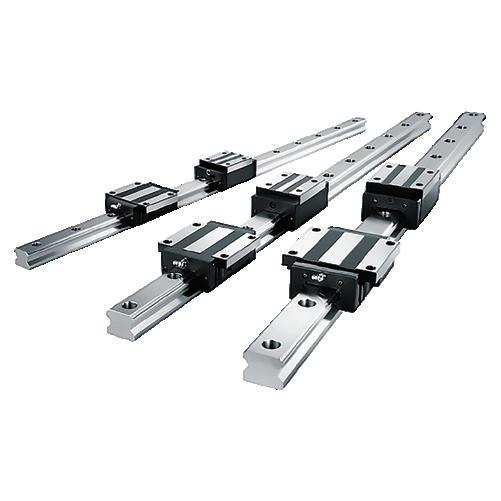
Linear Motion
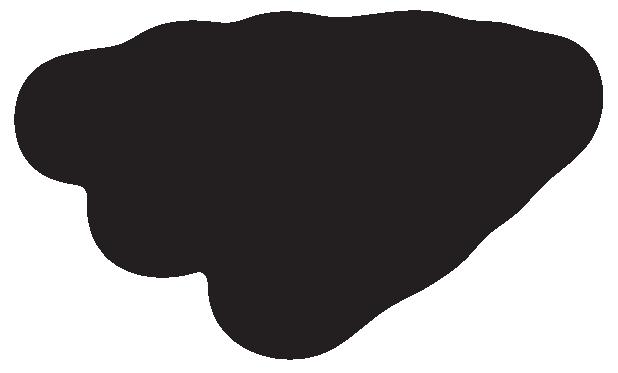

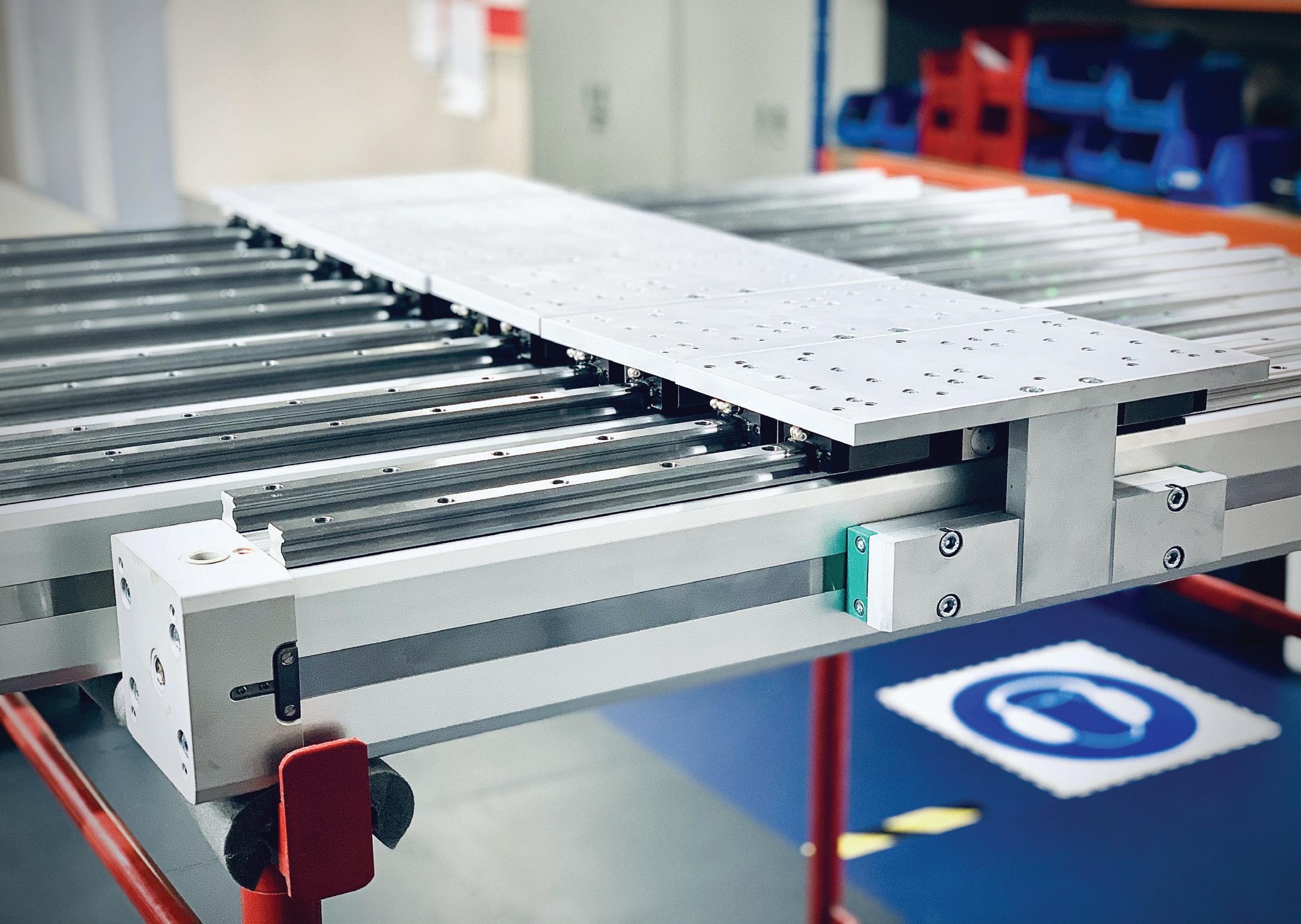
Over 25 years of experience: With a quarter of a century in the industry, Matara has the expertise to help you select the right components for your application.

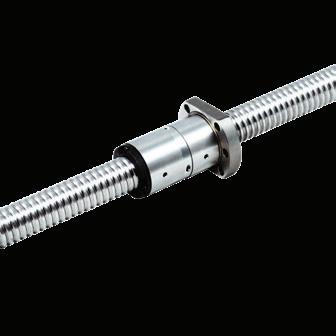
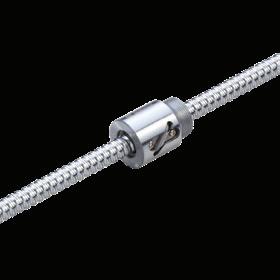
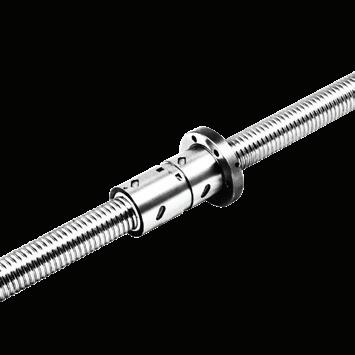
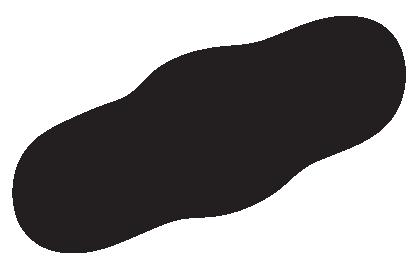
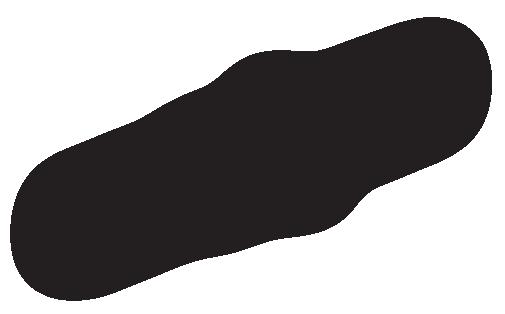

















Wide range of products: We offer a comprehensive selection of motion control components to suit a variety of needs.
Customisable solutions: We can cut linear rails to specifications and machine ball screws to meet your specific requirements.
Precision engineering: Our products are precision-engineered to provide smooth, accurate, and reliable motion control.
Powering Precision in Linear Motion

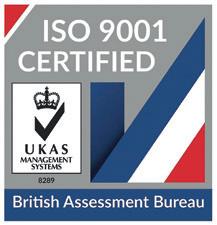
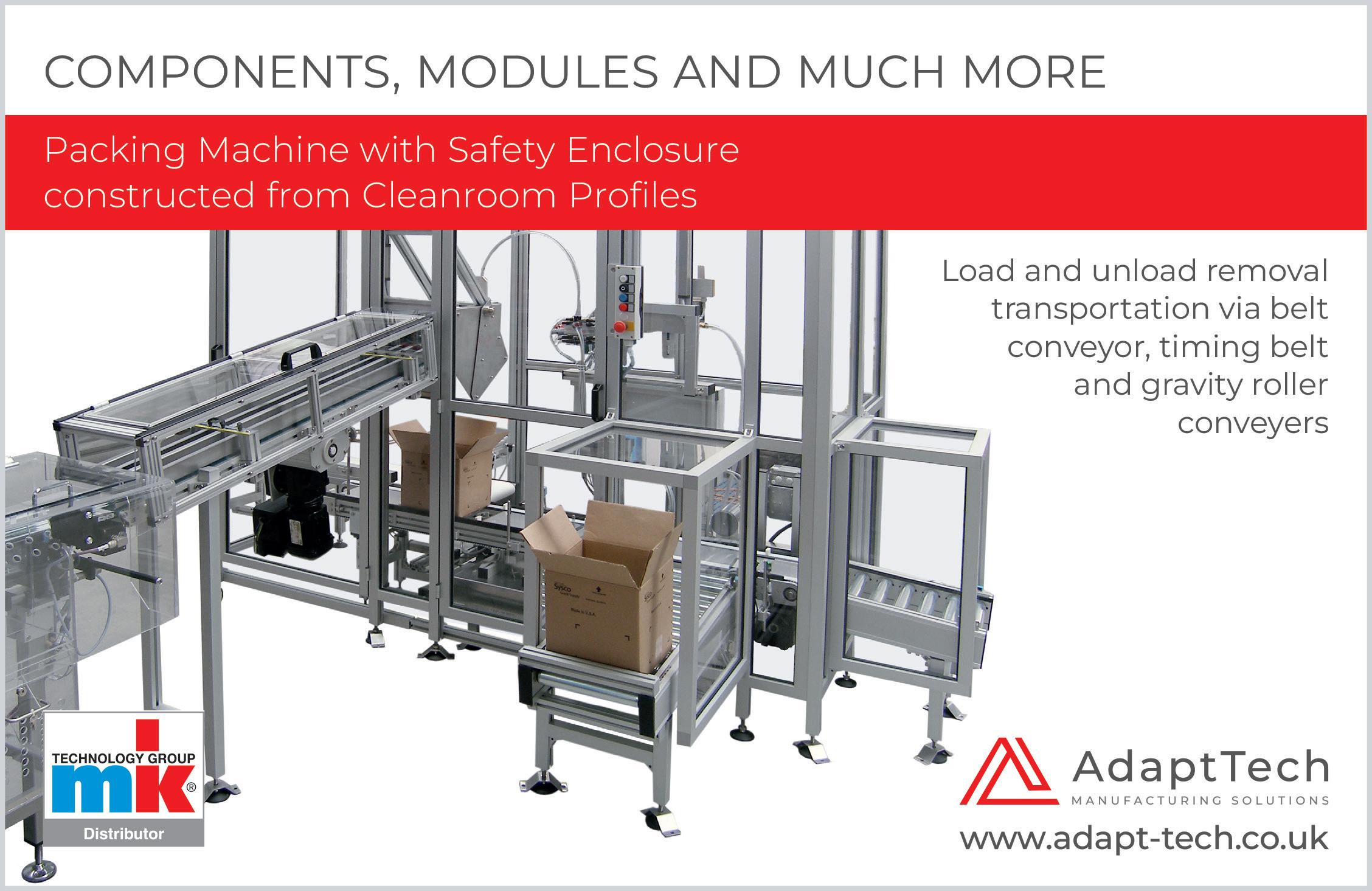
Linear Rails
Ballscrews
Actuators
Specifying a linear actuator: Three key factors
Mike Bacon, Internal Technical Applications Engineer at Matara UK, looks at three key areas to consider when selecting the right linear actuator for an application.
Linear motion systems are crucial across various industries, from food processing to semiconductor manufacturing and packaging. These systems enhance automation while reducing production costs, making them indispensable. At the core of these systems are linear actuators, which combine linear guides and power-transmission components into one unit. Although machine builders can create these elements, most prefer ready-made linear actuators to cut costs and benefit from their reliability and accuracy, which are essential for production and automation.
Selecting the right linear actuator – beltdriven, ball screw-driven, or electric rodtype – is vital. Three key factors significantly influence the performance of a linear motion system: speed, stroke length, and load capacity.
Factor one: Speed
The process’s speed affects the actuator’s efficiency and lifespan. Ball screw linear actuators typically operate at 0.35 to 1.5m/s for stroke lengths under one metre, with higher speeds achievable with additional supports. However, ball screw actuators may experience ‘screw whip’ at high speeds, causing vibrations that can lead to wear and reduced lifespan. While no universal speed limit exists for ball screw actuators, achieving speeds up to 3m/s might require a belt actuator, which performs better at high velocities and long strokes.
Factor two: Stroke length
Stroke length is the distance the actuator needs to move a load in one direction. Ball screw actuators are designed for around 1000mm stroke lengths, though variations exist. However, for lengths over 5400mm, belt-driven actuators are preferable. Matara,
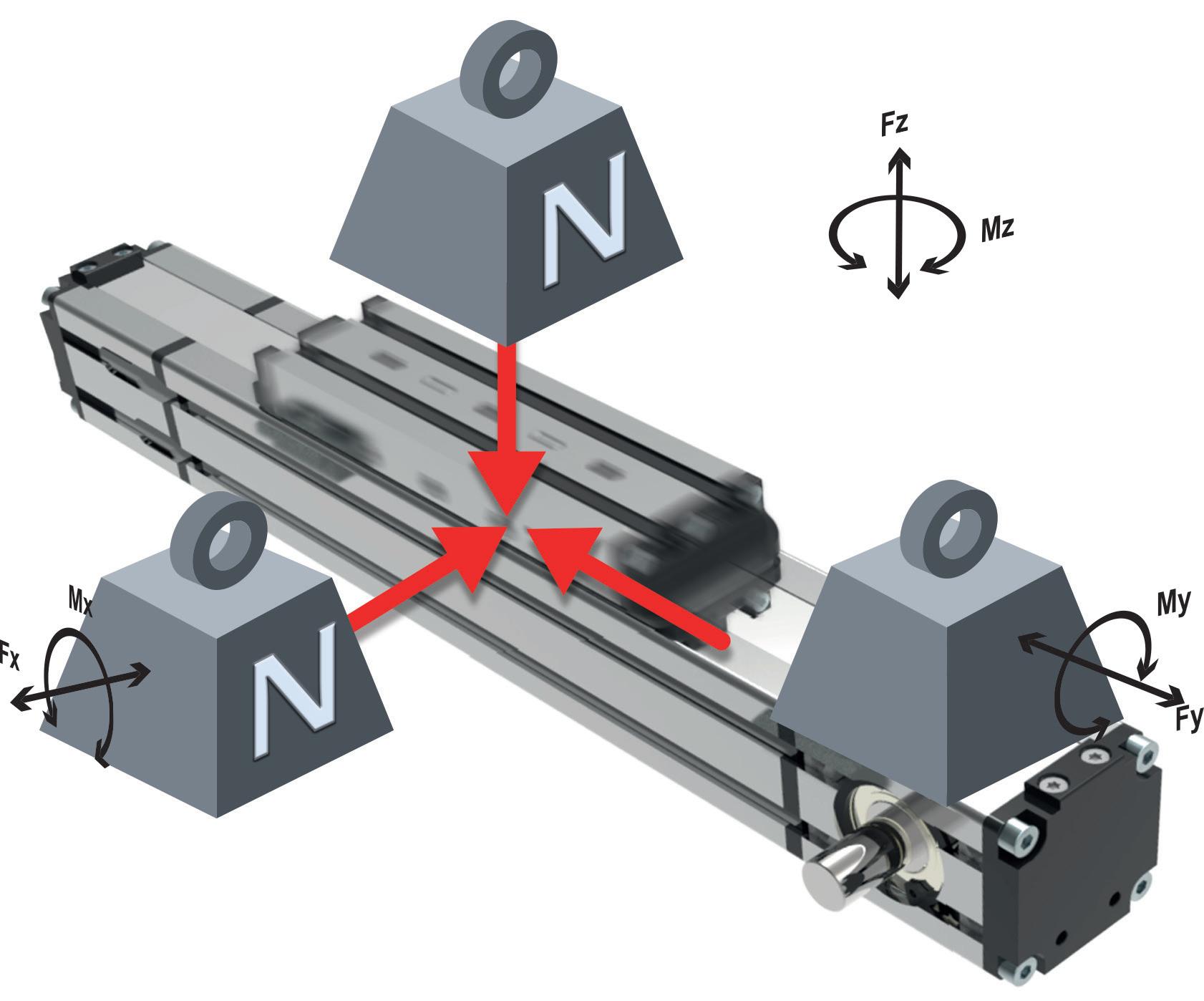
for instance, manufactures actuators with stroke lengths from 100mm to 6700mm.
A critical consideration for stroke length is the safety stroke, which allows the actuator to stop safely during an emergency, preventing damage. To calculate the safety stroke for belt-driven actuators, specify a distance equal to two motor turns at each end of the actuator. For ball screw actuators, use twice the pitch of the ball screw as a starting point.
Factor three: Load
Load impacts both speed and stroke length, and its calculation must consider dynamic load capacity, not just static load. Misjudging the load can lead to loss of precision or catastrophic failure, posing safety risks. Calculations should include radial and axial load capacities and the moment capacity of the support carriage. The load’s size, overhang, and orientation are also important.
Ball screw actuators can handle higher loads and are commonly used for vertical movements, such as in gantry robots. Belt actuators, less suited for vertical movement due to tension risks, can achieve higher load ratings by using linear rails and carriages as external guides. Linear rails, with two parallel tracks and rollers, support various load sizes, from light electronic components to heavy industrial loads.
Ultimately, choosing the right linear actuator depends on prioritising speed, stroke length, and load capacity based on the specific application. Other factors, such as mounting direction, accuracy, maintenance, and environment, also play roles. However, none of the others will matter without optimising the primary factors— speed, stroke length, and load capacity.
bit.ly/MataraLin

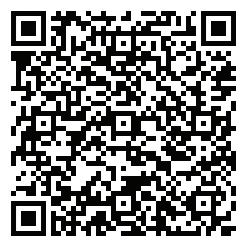
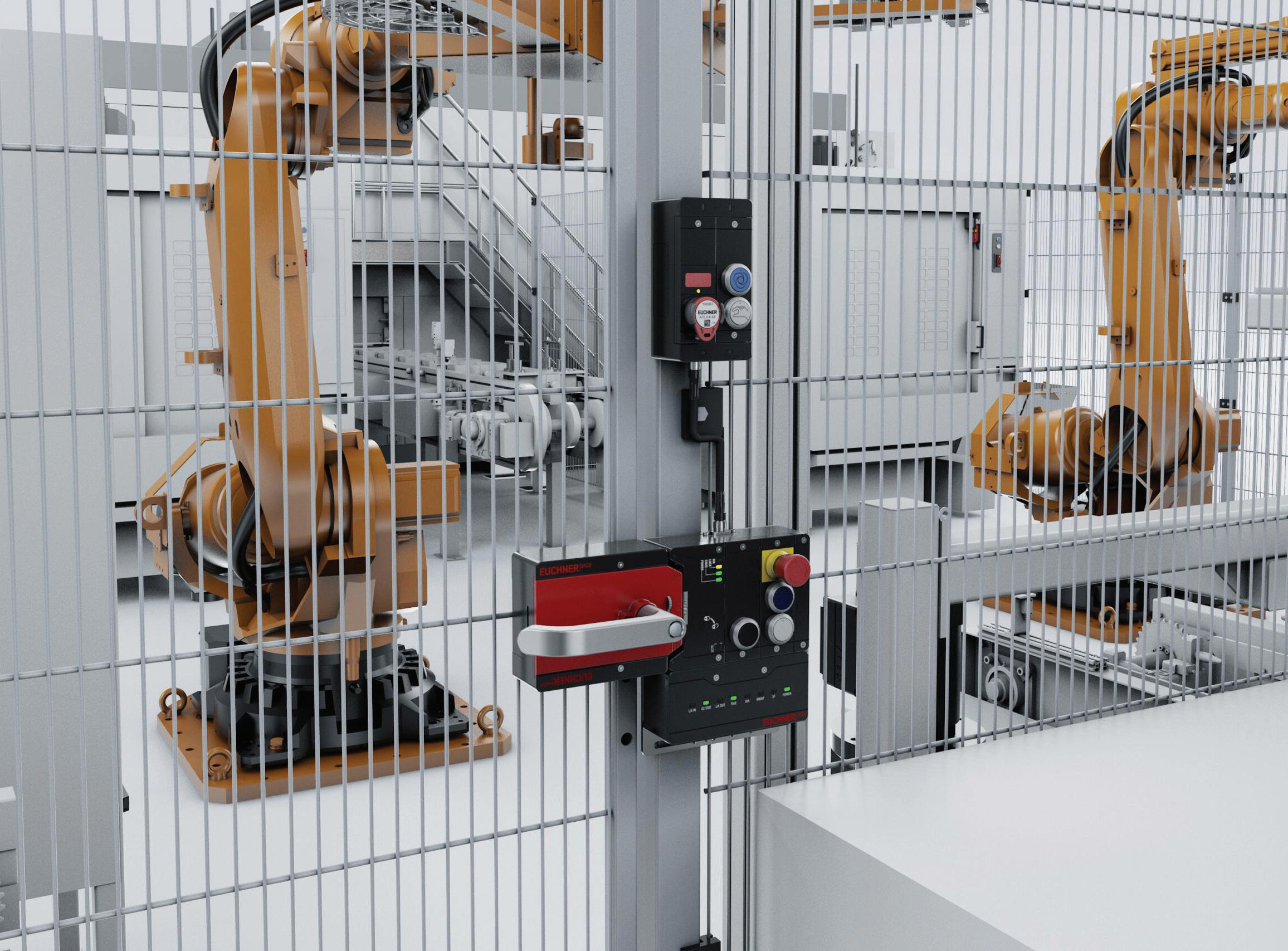
Euchner MGB2 with safety over EtherCAT and PROFISAFE
• Modular design with submodules
• Up to six MGB2 on one bus module
• Easy to expand
• Submodule replacement in operation
• For doors hinged on the right as well as on the left


Industrial enclosures for today’s challenges
In an era where industries are under increasing pressure to optimise efficiency, ensure safety, and withstand environmental challenges, the right equipment can make all the difference. Enter the Hercules range from CamdenBoss, a new line of industrial enclosures and electrical cabinets designed to meet and exceed the demands of today’s industrial landscape.
Crafted from fibreglassreinforced polyester (GRP/ SMC), the Hercules range offers exceptional durability, security, and customisation, making it the ideal solution for modern industrial challenges.
Industries such as manufacturing, utilities, transportation, and telecommunications are the backbone of modern society, driving progress and innovation. However, these industries face a host of challenges:
1. Environmental extremes: Equipment must operate reliably in diverse and often harsh environments, from extreme temperatures to high humidity and corrosive conditions.
2. Security concerns: As industries become more interconnected, the risk of unauthorised access and vandalism increases, necessitating robust security measures.
3. Operational efficiency: Downtime and maintenance disruptions can significantly impact productivity and profitability, making reliable and easy-to-maintain equipment essential.
4. Customisation needs: Industrial applications vary widely, requiring solutions that can be tailored to specific operational needs and integrate seamlessly with existing systems.
5. Regulatory compliance: Adhering to stringent industry standards and regulations for safety, environmental impact, and operational efficiency is crucial.
The Hercules range is engineered to meet these challenges head-on, providing a robust solution that excels in durability, security, versatility, and compliance.
Manufactured from fibreglass-reinforced polyester, the Hercules range of enclosures
is built to last. These enclosures are UVstabilised, allowing them to withstand temperatures from -30º to 70º Celsius, making them suitable for both indoor and outdoor use. This durability ensures that the enclosures can protect electrical components from environmental extremes, reducing the risk of damage and prolonging the lifespan of critical equipment.
Security is a paramount concern for industries, and the Hercules range delivers with its advanced locking mechanisms. Featuring 90º quarter-turn keyed locks and options for triple lock systems, these enclosures offer robust protection against unauthorised access. These security features provide peace of mind, knowing that valuable equipment is protected from tampering and theft.
Operational efficiency
Designed with ease of maintenance in mind, the Hercules range facilitates operational efficiency. Tool-free assembly and a hinged door that opens up to 180º allow for quick and easy access to internal components, reducing downtime during maintenance. The optional UV-stabilised window provides visibility for monitoring equipment without the need to open the enclosure, further enhancing efficiency.
Industrial applications are diverse, and the Hercules Range offers the flexibility to meet specific needs. With a variety of accessories, including modular chassis, plinths, windows, locking systems, cable glands, wall brackets, and air vents,
these enclosures can be customised to fit any operational requirement. CNC machining capabilities ensure precise customisation for cable entry and exit points, enabling seamless integration with existing systems.
Meeting industry standards and regulations is crucial, and the Hercules range is designed to comply with key requirements. The IP66 water resistance and IK-10 impact resistance ratings ensure that these enclosures can withstand environmental hazards and physical impacts, safeguarding equipment and ensuring operational safety.
In a rapidly evolving industrial landscape, the Hercules range stands out as a solution designed to tackle the most pressing challenges. Its combination of durability, security, operational efficiency, and customisation makes it an invaluable asset for industries striving to optimise performance and protect their investments. With the Hercules Range, industries can unlock new levels of reliability and resilience.
www.camdenboss.com
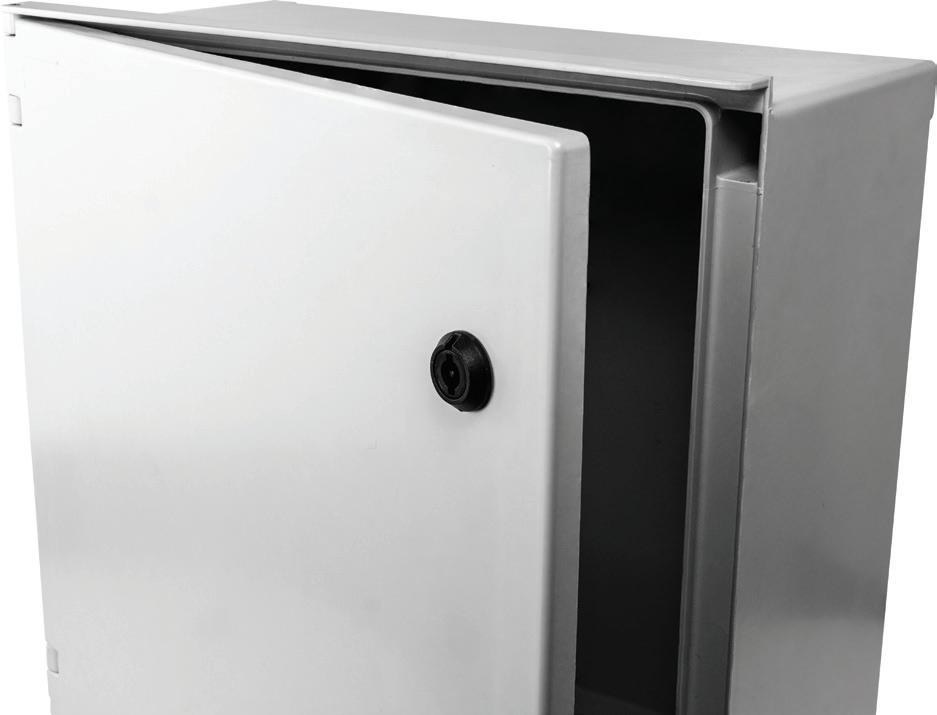
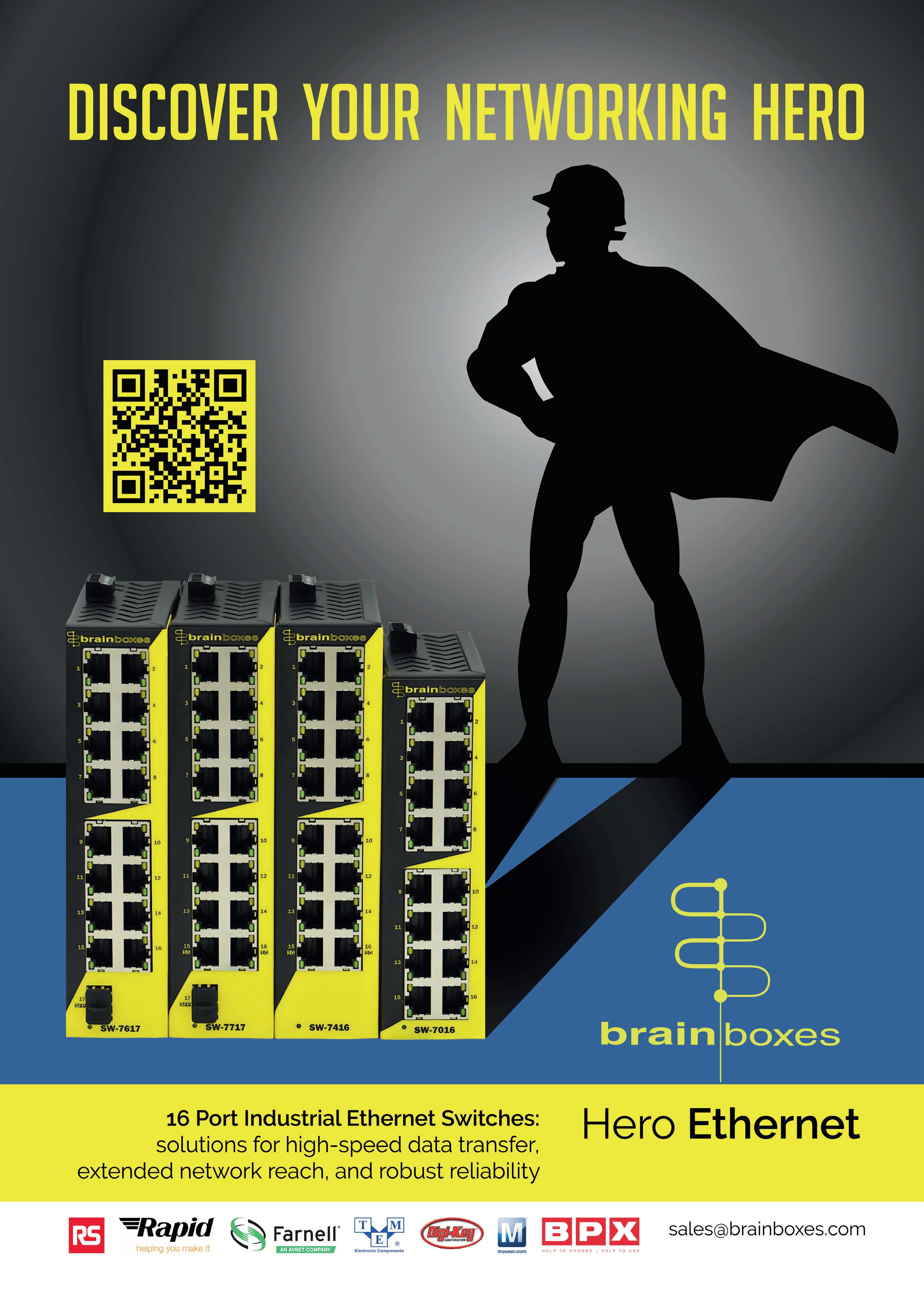
Custom-made connector and cabling solutions
HARTING has been designing and manufacturing industrial connectors for the last 75 years, with a focus on developing products which are easy to handle, durable and adaptable. However, as markets and industries continue to evolve, customers are increasingly seeking bespoke, custom-made products, as MEPCA discovered.
With specialisms including box builds and inter-car jumpers for the rail market, HARTING designs and creates custom solutions that meet exacting requirements. The company can also support customers with thorough in-house testing of cabling and wiring.
No matter what the degree of complexity, HARTING has the capacity to produce bespoke box builds and project-specific assemblies to suit customer needs, including installing components, efficiently routing cable harnesses and fabrication. To further assist, its design team can create a 3D CAD visualisation of a build beforehand to ensure absolute accuracy before manufacturing begins.
HARTING also has forty years’ experience of building cable assemblies for the UK market and can offer standard or custom cable lengths and a range of plastic or metal housings. All its customised products are built at its manufacturing facility in Northampton and are based on market-leading connectors from the extensive HARTING range, including M12, RJ45 and modular solutions.
Using these standard products, HARTING designs cable assemblies for the transmission of data, signals and power. Its expertise has allowed it to create solutions for a wide range of markets, including transportation, mechanical and plant engineering, automation technology, data centres, and energy distribution.
For example, the company offers a wide range of all-purpose M12 circular connectors, available with a traditional screw connection or the new, fast PushPull locking mechanism. The two connector sections are clicked into place by hand, a tool-free
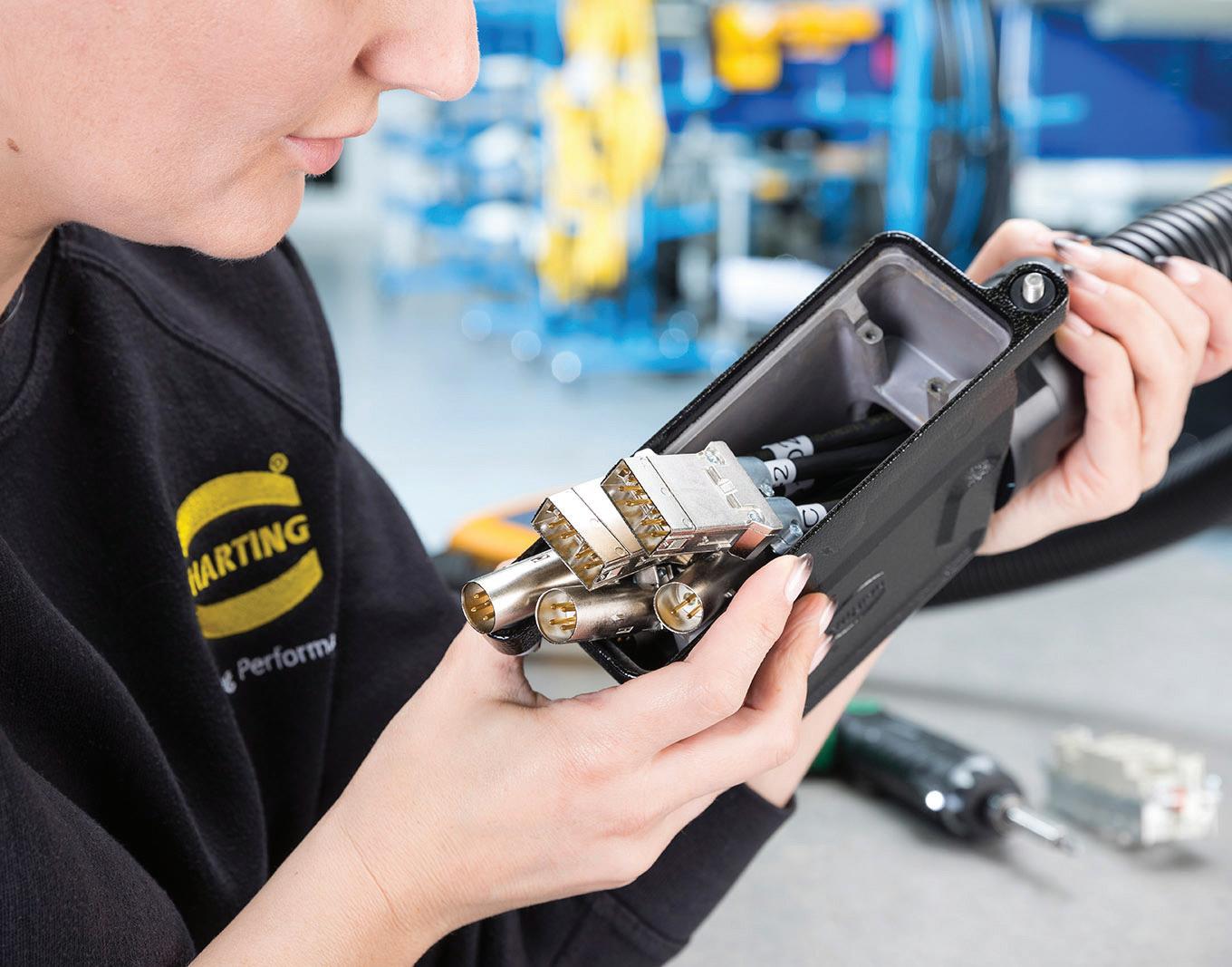
installation method which simplifies tricky installations and means the assembly density can be significantly increased, helping to save valuable space.
Other cable assembly options include RJ45, the perfect solution for transmitting high data rates in harsh industrial environments. Like the M12, they are available with PushPull connection technology for installations where space is at a premium. HARTING also offers the innovative ix Industrial, which is the answer to the challenges presented by Industry 4.0 and the IoT. This solution is suitable for the next generation of miniaturised products as the PCB jack is 70% smaller than the RJ45 socket. In addition, the ix combines both data transmission and power supply into a single interface.
Inter-car jumpers are designed to run connections between train carriages, including roof or underfloor systems, ensuring a reliable supply of data, signals and power along the train. The Han-Modular series allows users to create a flexible and versatile solution by combining individual inserts for different transmission media into standard-sized industrial connector housings. The series offers over a hundred different inserts, enabling a wide range of customisable combination options.
The HARTING manufacturing facility holds ISO 9001 certification for Quality Management, the ISO 14001 Environmental Standard, and UL certification for Wiring Harnesses ZPFW2 / ZPFW8.
bit.ly/HartingCS

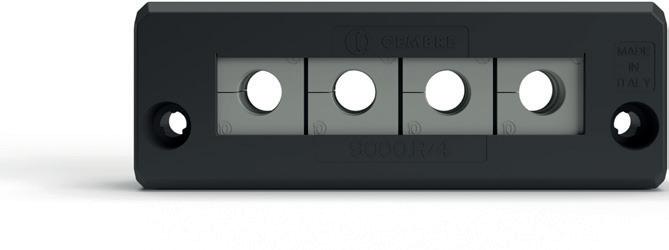
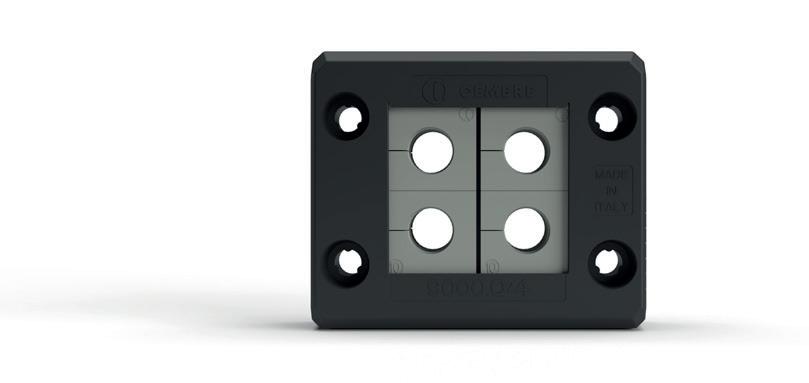
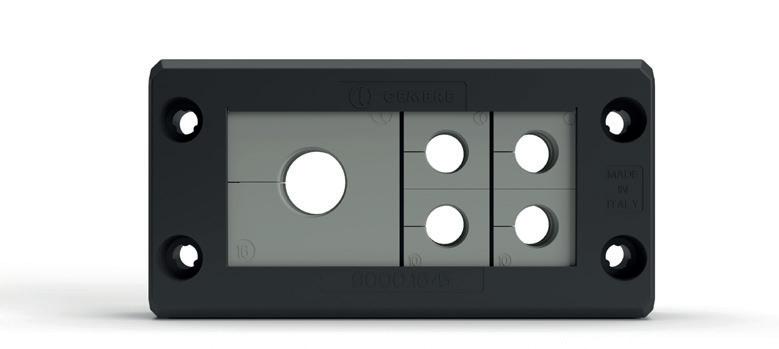
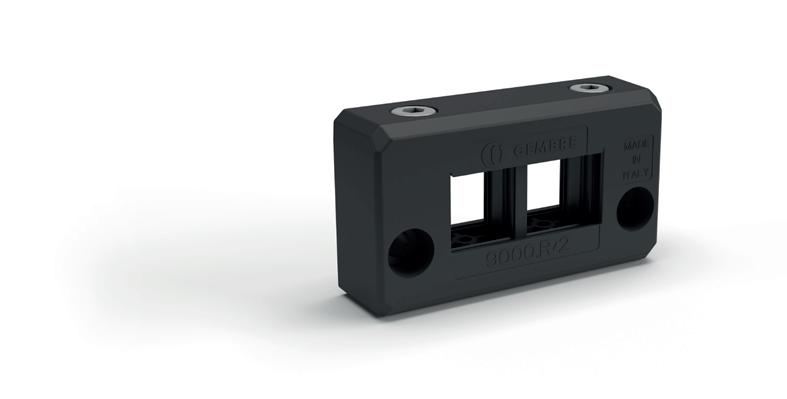


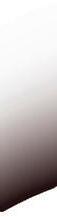


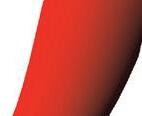

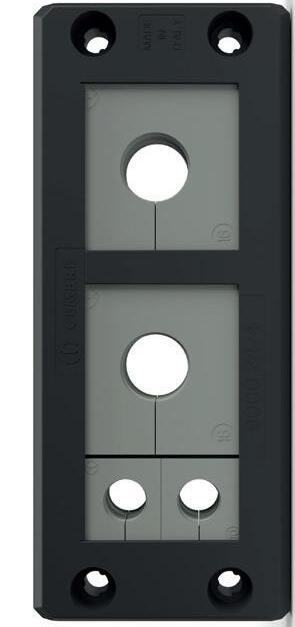
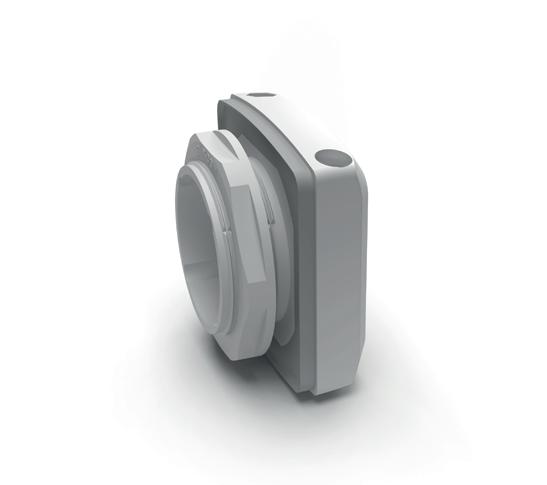
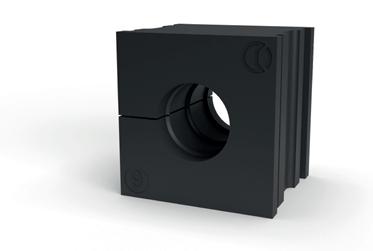
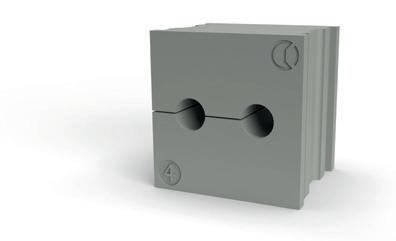

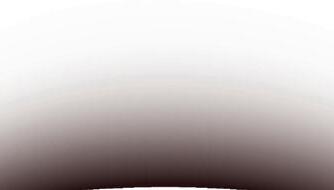


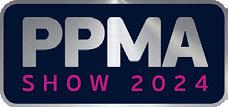
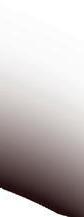


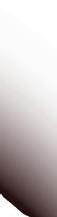



The role of encoders in vision systems
British Encoder Products Co outlines some of the key ways encoders support the effective performance of vision systems.
Machine vision systems typically consist of a digital camera, a light source, and a computer processor that analyses the captured images. To obtain an image of sufficient quality, the distance from an object to a lens, lighting intensity, and exposure duration all need to be synchronized. Two synchronization methods are used, either time-based, when object speed is constant, or distancebased, when object speed can vary. While a variety of sensor types can be used for time-based synchronization, incremental encoder feedback is almost always required for distance-based timing. A key function of encoder feedback within vision systems is to trigger image capture at the appropriate time. As an example, in an inspection application for parts transported on a conveyor, the edge of an approaching object is detected by a photoelectric sensor. The system counts encoder pulses from the point of detection, with each pulse representing an interval of distance travelled. The light and camera are triggered when the desired count is achieved, indicating the part is in the correct position for image capture. The encoder pulses are also used to time the camera exposure.
Line scan cameras
be distorted by compression or extension. This is another area where encoders play an important role in the vision system.
Since the line scan camera creates an image of a moving object one row of pixels at a time, the interval between exposures must be timed precisely to avoid distortion from too many or too few pixel lines. The key encoder attribute that creates successful
measuring wheel, such as the Model TR1 Tru-Trac, is a common means of obtaining accurate belt speed feedback. The EPC Model TR1 is an easy-to-use, linear measurement solution that is readily integrated with vision sensors for conveyor speed feedback.
Typically, the pixel dimension for each image line dictates encoder resolution. For example, if an inspection process requires a minimum of 5 pixels per mm to identify a defect, the pixel dimension is 0.2 mm/scan. Each encoder pulse will trigger a scan, so encoder resolution should be 5 pulses per mm of belt travel. With a measuring wheel circumference of 200 mm, the desired TR1 Tru-Trac encoder resolution would be 1000 CPR.
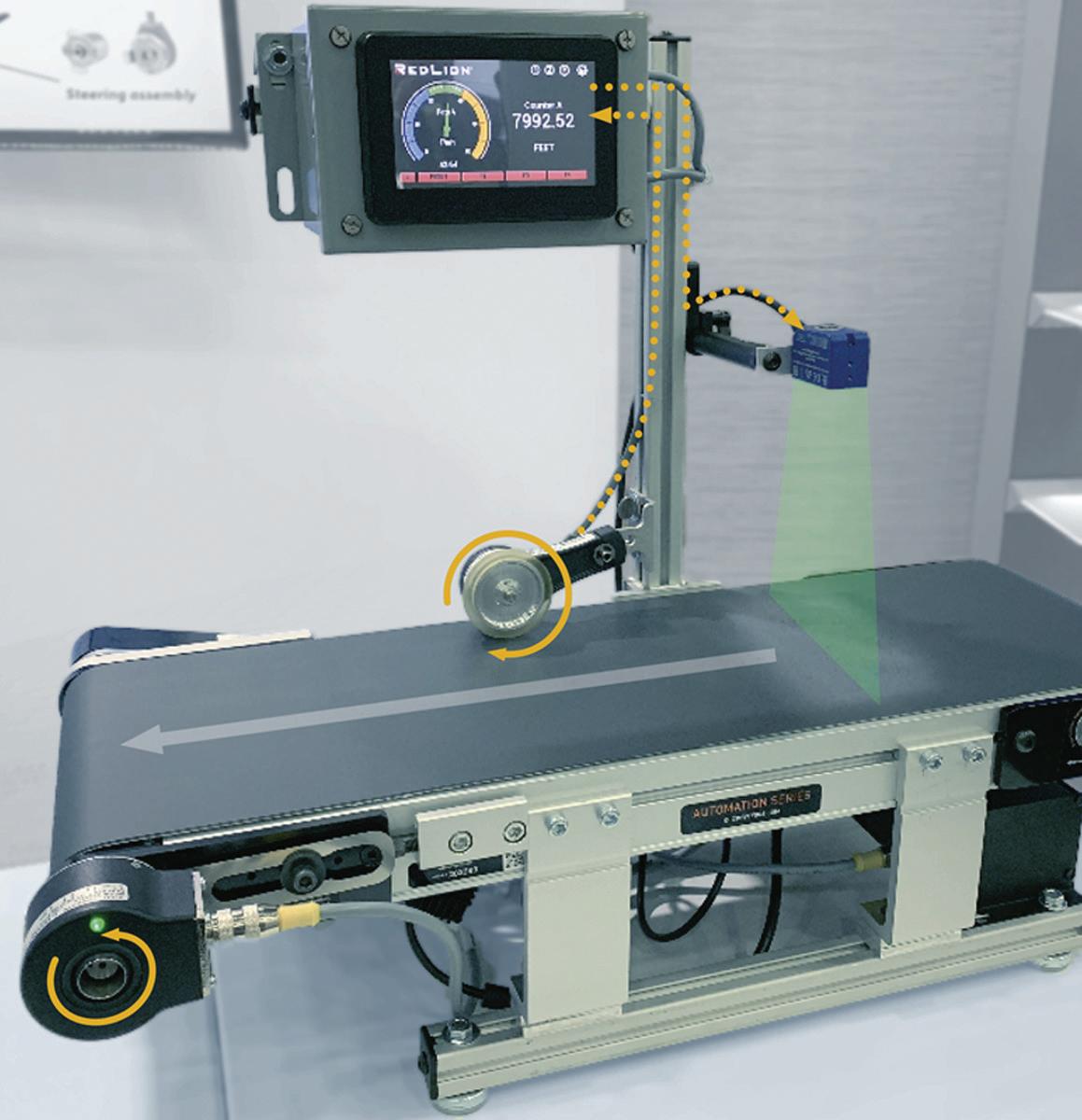
Line scan cameras capture a single line of pixels, with each exposure occurring as the object moves past the camera. The successive pixel lines are then digitally assembled to render the complete image. With line scan cameras, it’s important that the camera’s frame rate is synchronized with the object’s travel. Otherwise, images can
imaging is encoder resolution, which is stated as Cycles Per Revolution or CPR. Factors dictating encoder resolution are image size, image resolution, frame rate, and transport speed. The image acquisition card or camera software may include scaling capabilities that allow the user to correlate a line of pixels with a certain number of encoder pulses.
For encoder transport applications, the speed of the conveyor belt must be measured accurately to ensure the image is free of distortion. An encoder with a
Some installations can benefit from a programmable encoder, such as Model 58TP or Model 25SP, that offers resolutions from 1 – 65,536 CPR. For example, to compensate for changes to other system components (conveyor, lighting, image field, etc.) or inspection attributes, the encoder resolution may need to be tuned to an optimal CPR to eliminate image defects. For an OEM of inspection equipment, a programmable encoder can facilitate the installation of devices on a wide range of customer applications and operating environments. Examples of motion feedback for machine vision systems include those used in conveying, autonomous vehicles and robots, object detection, part counting and verification, automated vision testing and measurement, bar code reading/ scanning, defect detection, and pick and place.
encoder.co.uk
Automating and optimizing intralogistics processes is a key success factor in the factory of the future. The product family ctrlX FLOW, with the planar system for contactless high-performance conveying and the linear motion system for high-speed transportation and and positioning, the ctrlX FLOW family offers easy-to-integrate solutions for highly efficient material and goods flows.
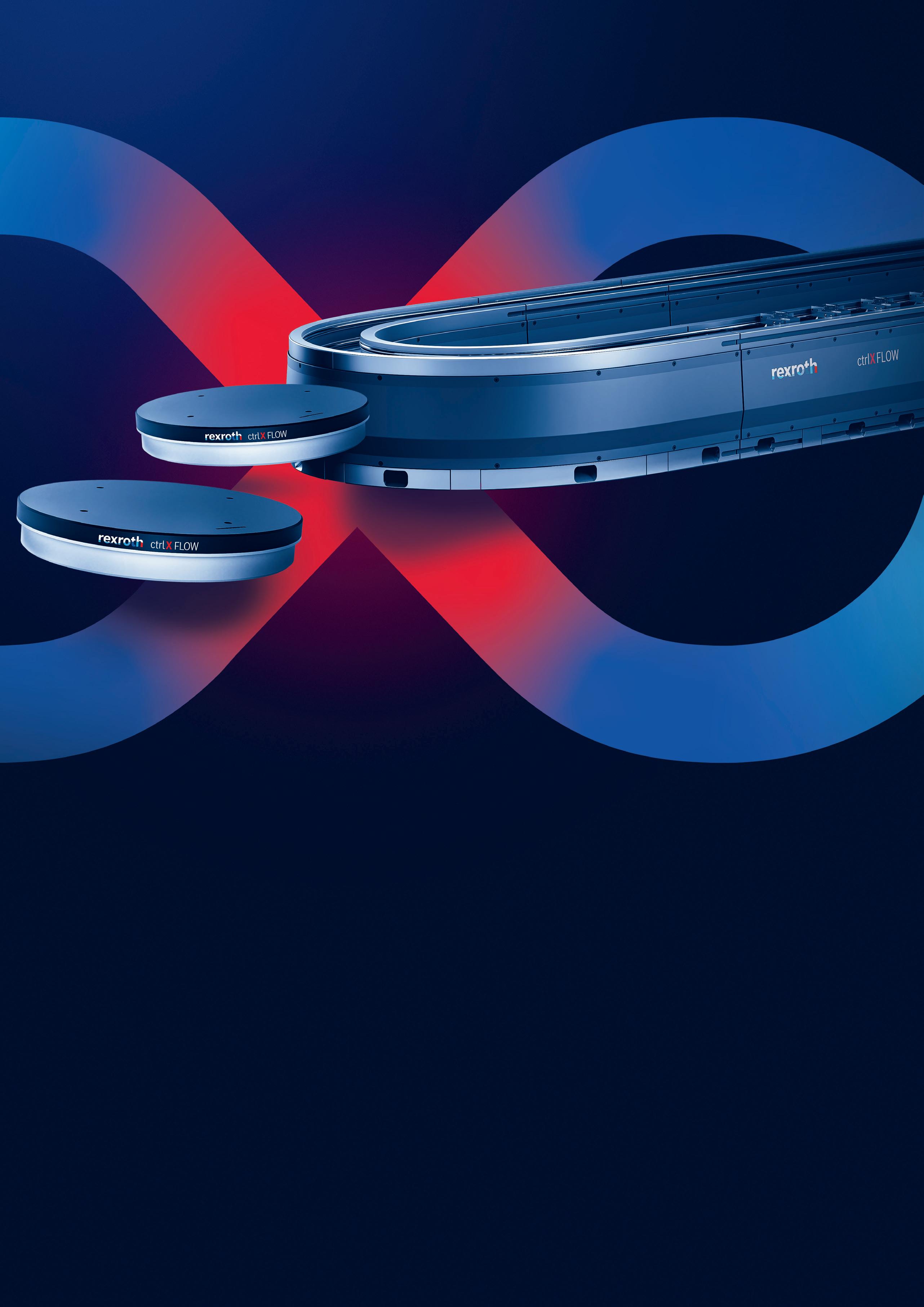

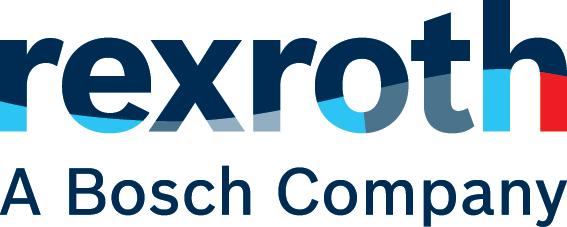
Optimising gas flow in semiconductor fabrication
MEPCA discovered how Pivotal Systems utilises Brainboxes Pure Embedded Ethernet Switches in its precision gas management systems to optimise gas monitoring and control systems in semiconductor fabrication plants, ensuring efficient and accurate chip manufacturing processes.
The dawn of the CHIPS Act means that many new semiconductor fabrication plants (fabs) are being built across the USA and beyond. As chip technology advances, these fabs are becoming increasingly complex, with a critical focus on wafer processing. Precise monitoring and control of gas flow during the reactions that transform silicon wafers into chips is essential for reliable production.
Wafer processing is a crucial step in semiconductor manufacturing, where thin slices of semiconductor material, typically silicon, are transformed into integrated circuits. This process involves multiple stages of depositing, removing, and patterning materials on the wafer surface to create complex electronic components. Wafer processing is essential because it enables the production of increasingly smaller, faster, and more efficient microchips that power our modern electronic devices, from smartphones to supercomputers.
Wafer processing demands exceptionally precise, consistent, and reproducible gas flow management as semiconductor technology advances. With chip features shrinking to 3 nanometres – roughly the width of 30 hydrogen atoms – even the most advanced mass flow controllers face significant hurdles. These devices must meet exacting standards for accuracy, rapid stabilisation (settling time), and consistent performance (repeatability) to ensure uniform results across all production equipment and maximise the yield of functional chips produced. The challenge is intensified by the need to control minute gas flows, accommodate brief processing windows, and maintain stability during continuous plasma-based manufacturing processes. This level of control is crucial for creating the intricate structures that enable modern electronic devices to be smaller,
faster, and more energy-efficient.
Pivotal Systems, a leading supplier to the global semiconductor industry, builds advanced Flow Ratio Controllers (FRC) to improve wafer uniformity for manufacturers. This includes providing highly accurate, continuous monitoring and control of the most critical, difficult-to-control parameters in wafer processing today. Controlling the gas flow in semiconductor manufacturing is crucial for effective wafer processing.
Pivotal Systems searched for a compact solution using Ethernet for real-time communication between five PCB boards inside of the Flow Ratio Controller (FRC), considering various small, embedded switches from offshore manufacturers. These switches were reasonably priced and maintained the small size that they required. However, these manufacturers couldn’t provide the company with the traceability, degree of customer service, or technical support that it needed, whilst other compact, embedded switches had expensive price tags.

needs into the small space required for its system, ensuring that space efficiency is maximised without compromising on Ethernet connectivity. And unlike commercial products, Brainboxes guarantees that the PE-505 will be available for a minimum of ten years, which is essential for industrial applications.
“The price of other switches was prohibitive, and for the mass market, it would be too much,” explained Igal Sokolov, Principle Systems Engineer at Pivotal Systems
This search identified a gap in the market for a solution that balanced size, affordability, and dependable support. To fill this gap, Brainboxes developed the Pure Embedded Ethernet range, which offered Pivotal Systems a small, ready-to-use solution that sailed through reliability testing at an economical price. Using a board-to-cable connection to connect Brainboxes PE-505 to the Flow Ratio Controller (FRC), all of the data was transferred between the valves and the main controller.
With its mega-compact form, the Pure Embedded switch resolves Pivotal System’s challenge of fitting all of the connectivity it
The reliability of the Pure Embedded Switch also allowed Pivotal Systems to comfortably integrate industrial communications into its system. To assess reliability, the PE-505 was tested using ovens and was power cycled 113,000 times. The device was proven to be ultra-reliable, providing Pivotal Systems with a reliable and reputable supply chain source.
Brainboxes Pure Embedded switches allow Pivotal Systems to provide customers with a high-speed, accurate, and reliable flow control solution, resolving the challenges of regulating system-critical parameters within wafer production. Miniaturisation of control systems in space-constrained environments is made possible, supporting the trend towards more compact and efficient industrial equipment and providing an affordable way to integrate Ethernet and enable fast, dependable communication.
www.brainboxes.com
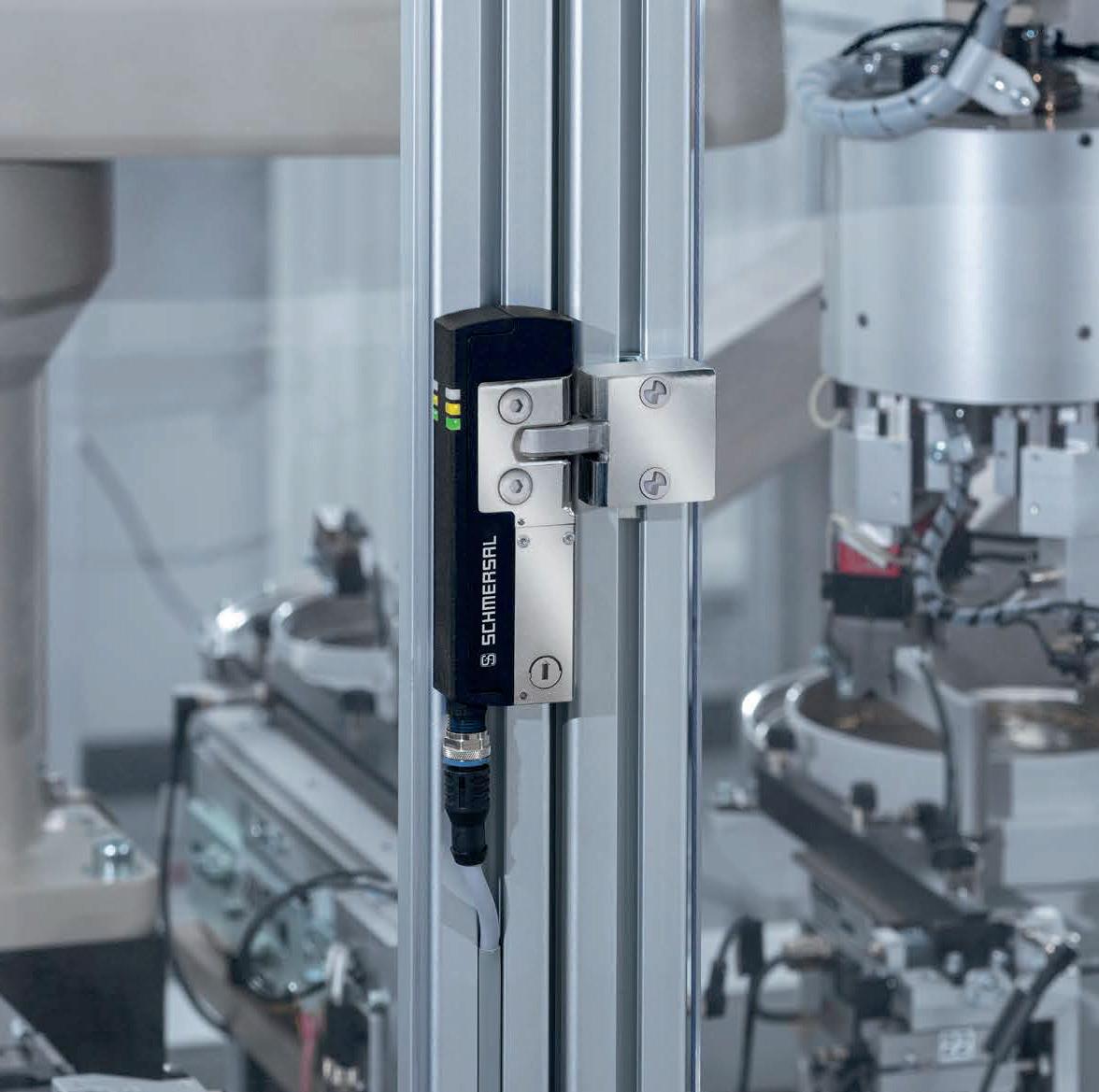
THE WORLD’S SMALLEST ELECTRONIC SOLENOID INTERLOCK
With dimensions of just 119.5 x 40 x 20 mm, the AZM40 is the smallest electronic solenoid interlock in the world. This makes it especially suitable for small safety doors and flaps. Despite its compact size it has an amazing 2000 newton interlocking force and 25 Newton latching force.
Thanks to the 180° angle flexibility of the actuator, it can approach the AZM40 on a stepless basis, making the interlock also suitable for flaps which do not close at 90° or those that open upwards to a 45° angle. This means the angle flexibility helps the interlock easily fit into compact spaces and difficult to access areas.
In the event of a power cut, the AZM40 retains the current position. This ensures safe operation, whatever the status of the machine. Even if there are hazardous run-on movements, the safety door remains locked in the event of a power failure. Another advantage of the bistable principle is the consistently low energy consumption, as the interlock only requires power when the door is to be locked or unlocked.
SCHMERSAL | Enigma Business Park Malvern, Worcestershire, WR14 1GL
www.schmersal.co.uk
uksupport@schmersal.com

Durable, high-quality motors for all industrial segments
Cantoni Group has a longstanding history of manufacturing and supplying electric motors and associated equipment in its native Poland and the wider EU, but it is perhaps less well known in the UK. MEPCA magazine spoke to the company to find out more about its history, its values and how it meets its customer exacting requirements.
MEPCA: In case our UKbased readers are not familiar with your brand, can you tell us a little about Cantoni Group?
Cantoni Group: Cantoni Group is a worldwide leader in manufacturing and supplying electric motors, brakes, and tools, and it has an almost 150-year-long tradition.
100% of the products are manufactured in Poland using highquality materials and components of European origin.
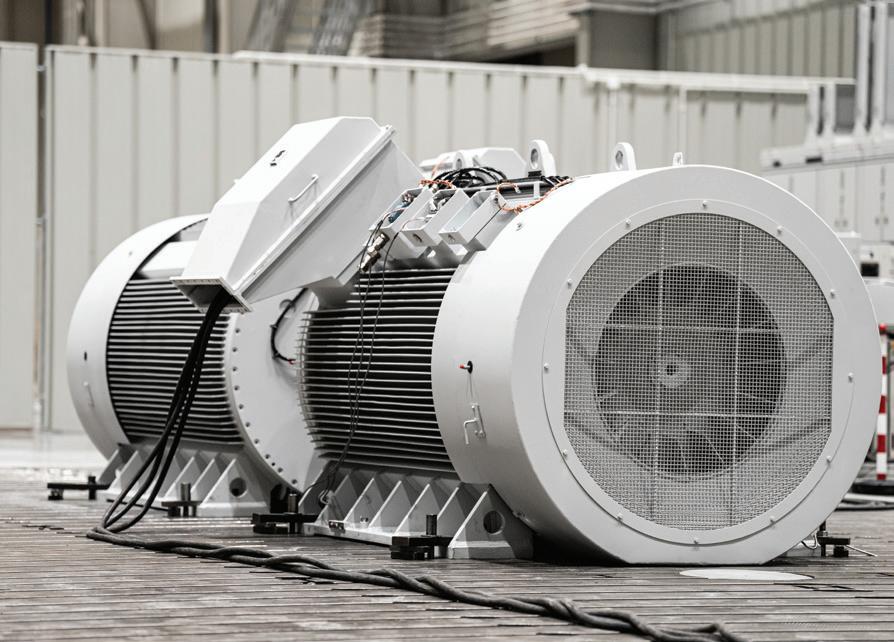
Cantoni Motor, as the International Sales Office and Headquarters, coordinates among others the sales and purchasing for the whole Cantoni Group.
The Group produces and exports industrial electric motors in the range from 0.04kW up to 7,000kW in standard and special executions.
Our production plants have a rich experience in design and production, therefore, we have developed a reputation for durable, high-quality products which can operate in almost all industrial segments.
Our wide range of products includes low-, medium- and high-voltage asynchronous induction electric motors for single-phase and three-phase applications. Customers can also find brake motors, motors with forced ventilation, explosion-proof motors, NEMA motors or traction motors. While a wide range of electromagnetic brakes and releases is equally impressive.
M: What sectors do you supply motors to, and are there any where you are particularly active?
CG: Cantoni Motor supplies electric motors to a broad range of sectors including marine,
oil and gas, mining, chemical, energy, paper or food industry. We are also active in the industrial manufacturing sector, where our motors are used in machinery and equipment for production lines.
Our motors are produced with the aim to be flexible and adaptable, thus, they can operate in many different applications e.g. pumps, fans, compressors, conveyors, theatre, concert halls, lifts, platforms, traction vehicles, coal or paper mills, woodworking machines or food processing devices, etc.
M: What are the key factors you see driving your customers’ purchasing decisions, and how does Cantoni Motor meet those customer requirements?
CG: From our experience, the qualities our customers value the most are flexibility, quality, durability, genuine authenticity and support.
Turning raw materials into electric motors: It is important to emphasise that all the Cantoni Group production facilities are located in Poland and that the entire production process takes place in our facilities, ensuring top quality.
Each factory, with its R&D department
and experienced engineering staff, is engaged in advanced research and development projects, and as a result, our technical support is at the highest level. One of our new Research and Development Centres located in ychlin enables comprehensive tests of motors in the power range from 50kW up to 6MW and is open for our customers and other interested parties. This approach gives us a very strong control over the process and, thus, remarkable flexibility in fulfilling customers’ needs.
Customisation is our standard: Apart from standard motors which are our main product, we offer customised motors adaptable to many different applications. As we control our whole manufacturing process, such special executions of motors can be tailored according to customer’s specific needs.
European origin only: In order to ensure high quality in our products, we pay particular attention to the materials used for production, which are delivered only by qualified suppliers, exclusively from the European Union. Cantoni Motor’s short and secure supply chain is becoming increasingly important to our customers, particularly in the context of global supply chain disruptions.
As a family owned Group, with Italian ownership and Polish production experience and thoroughness, we treasure long-term partnerships, loyalty and individual approach to our business partners.
Cooperation with Cantoni Group gives our customers not only a wide variety of good quality products, but also an opportunity to cooperate with a stable and reliable partner.
www.cantonigroup.com
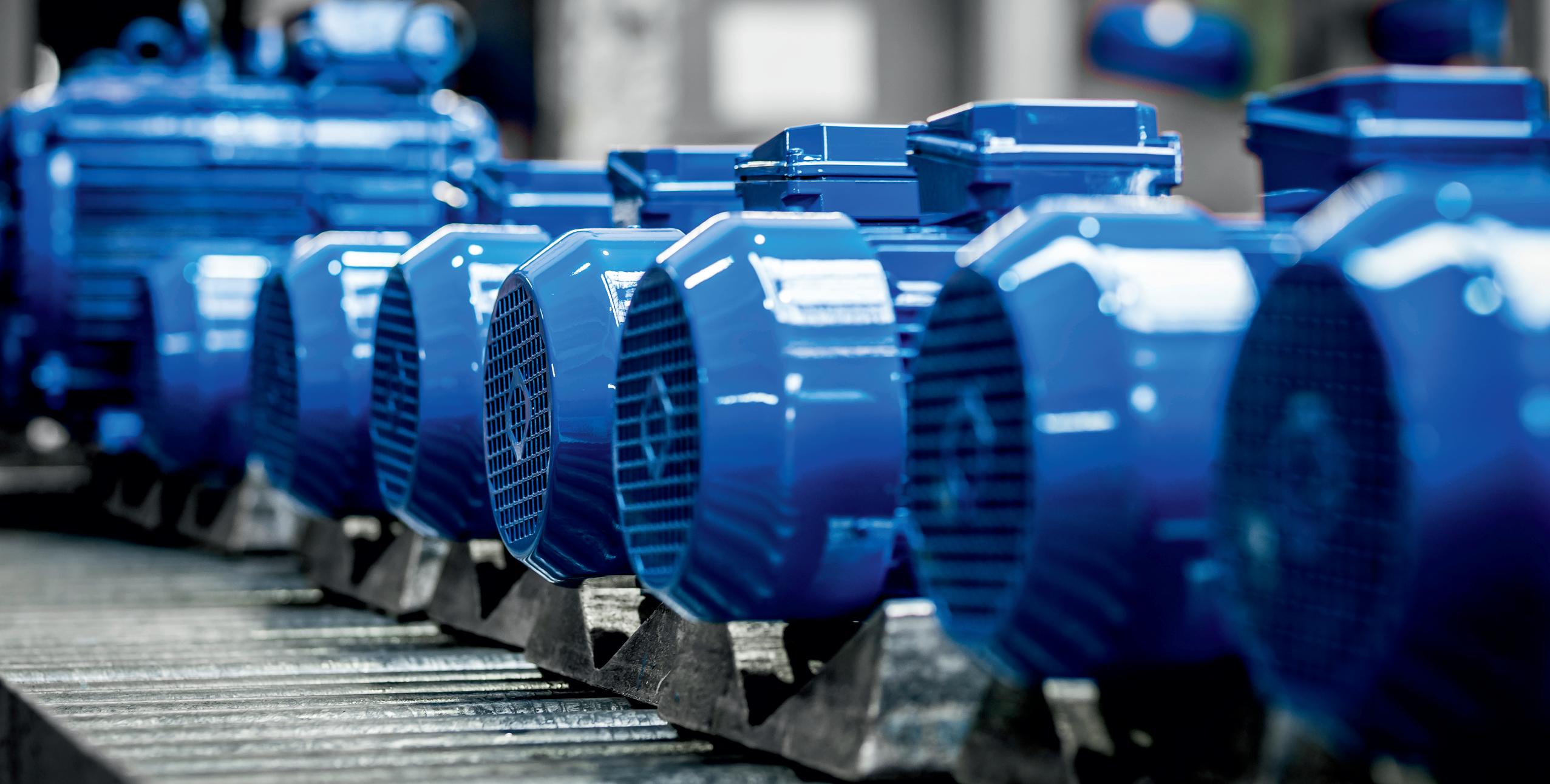

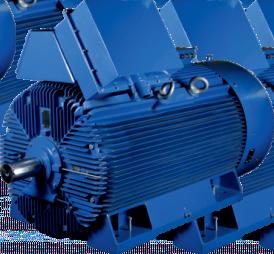

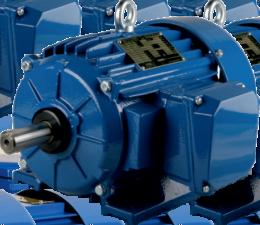

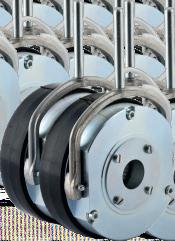
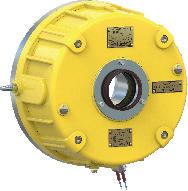
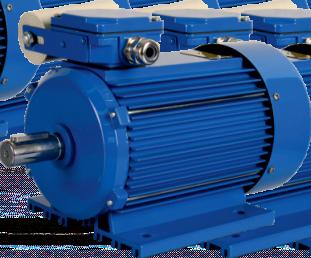
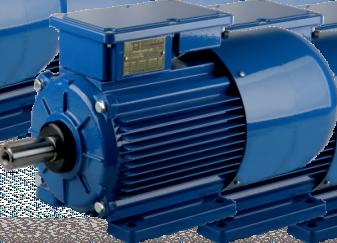
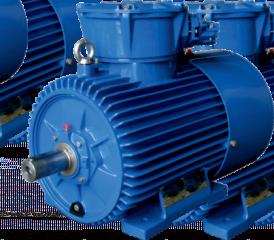
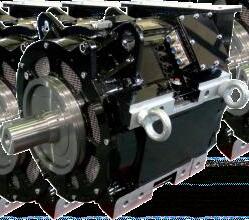
A new generation of cable entry systems
The EWO series is CEMBRE’s innovative family of split cable entry systems, marking a global leap forward in quality for this product category.
Thanks to the work and study of its technical team, CEMBRE has been able to design a new generation of cable entry systems. They are characterised by an ergonomic split frame, equipped with an over-moulded seal and compatible with grommets with a high degree of protection against the ingress of solid foreign bodies and the penetration of water.
Thanks to their compact design, they are slim and space-saving. The absence of an outer seal makes EWO cable entry systems the ideal choice for countless applications, especially those in the field of industrial automation. CEMBRE cable entry systems are available in square, rectangular and circular shapes to meet all installation requirements and allow them to manage, easily and with precision, the passage of cables on switchboards, panels and machines.
Thanks to the efficiency and widespread coverage of the CEMBRE distribution network, EWO cable entry systems are the ideal solution because they are easily and quickly available to anyone, anytime, anywhere.
The frame of the EWO cable entry system is made of glass-fibre-reinforced PA6.6. With its slim and compact design, it is equipped with an innovative over-moulded seal, which allows EWO to achieve a high level of IP66 protection without the need for an external seal. The CEMBRE cable entry systems prove to be a versatile and practical product, suitable for every operational requirement.
The EWO cable entry systems can also be equipped with an additional external seal, which is suitable for supporting the fastening of the frame on particularly rough surfaces and those damaged by irregular drill holes, thereby guaranteeing maximum tightness and protection against weathering.
The Stop Plinth technology, which

characterises the frame structure, protects the over-moulded seal from any risk of compression, ensuring effective IP66 protection at all times.
The demountable frame structure of the EWO cable entry system ensures great freedom and versatility in every wiring operation. Through the opening side of the frame, it is possible to conveniently insert the protective grommets, modulating and configuring them according to the various installation requirements.
Designed to be as functional and versatile as possible, the EWO cable entry system can be conveniently fixed using galvanised stainless-steel screws, deep-drawn holes or rivets. The anti-fall system allows cable entry systems of the EWO series to be secured quickly and easily, even if the installed frame is pointing downwards. The accessory fitting of a snap-on bracket increases the installation options of the EWO cable entry systems, satisfying every configuration requirement.
The EWO cable entry systems are equipped with the modern Plug&Fix system, which reduces wiring time and simplifies the entire installation process. The demountable side of the frame can be opened and closed easily by means of the convenient galvanised stainless-steel screws, implemented with an anti-fall system. This allows the grommets to be positioned and cables to be inserted at
any time with great ease.
EWO cable entry systems are tested to certify a high level of safety and complete IP66 protection against dirt and water. The Cembre-designed over-moulded seal no longer requires the installation of a traditional external seal, thereby considerably reducing space requirements and installation time.
Because of the double side shaping of their design, the EWO grommets adhere perfectly to the frame, positioning themselves inside it without ever protruding, ensuring full IP66 protection against dirt and water and an effective cable seal in accordance with EN 62444.
EWO cable entry systems meet all installation requirements with versatility because of the wide variety of grommets, designed to create as many combinations as possible and adapt to every configuration.
EWO cable entry systems are designed to reduce installation time and costs.
Not only that. The revolutionary interchangeable faces of the EWO grommets have been specifically developed by the CEMBRE technical team to allow the grommets to be positioned without having to worry about the direction of installation, thereby offering a valuable and unique advantage in terms of time and convenience.
www.cembre.com
The next level of modular industrial connectors.
Han-Modular ® Domino ModulesRobust technology for industrial transformation.
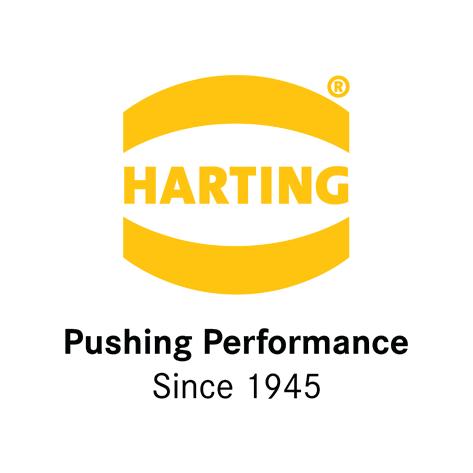
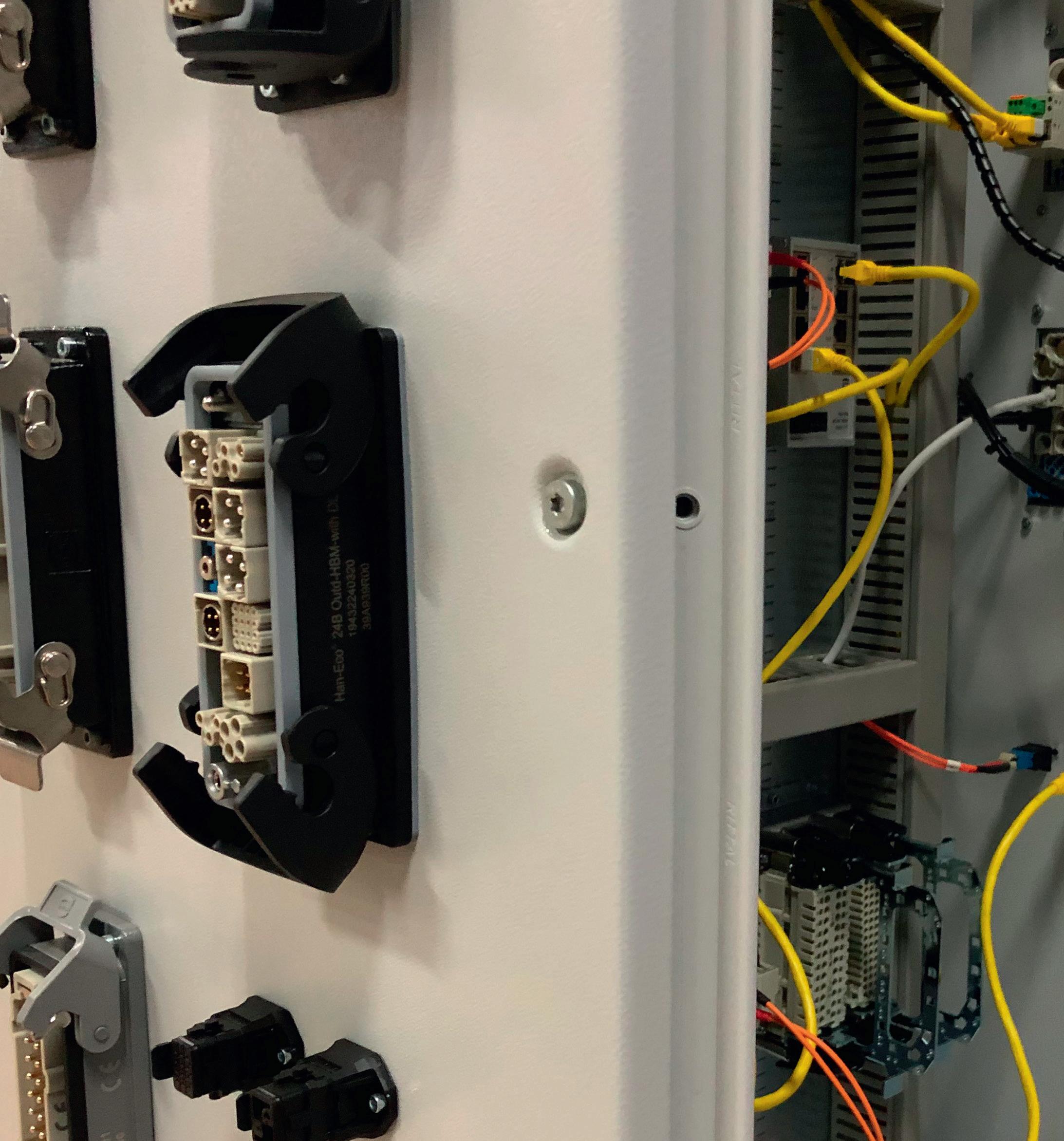
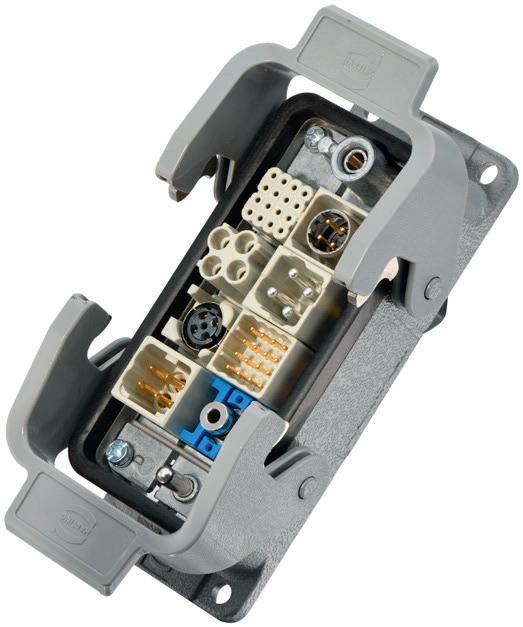
The first modular connector with a hybrid module configuration
■ Smaller and lighter connectors allow space savings of up to 50%
■ Compatible with components of the Han-Modular ® series, the market standard for modular industrial connectors
■ Flexible and scalable to the respective need
■ Sustainability through consistent modularisation
■ Reduction of installation times by combining several individual connections
One Range. No Limits: www.HARTING.com/domino
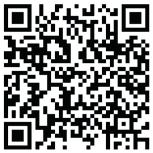
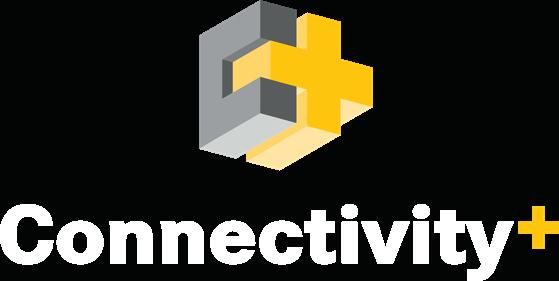
What more could your drive do for you?
Most people know that a drive can help to reduce energy usage in motor-driven applications.
But even entry-level drives have a lot more to offer to OEMs, as ABB’s Liam Blackshaw, Product Manager – LV Drives, explains.
Motors are often among the most energydemanding pieces of equipment in a typical industrial environment. Adding a drive to control the motor’s speed can significantly reduce the amount of energy that the motor uses. In applications like pumps and fans, it can reduce energy consumption by up to 50%.
However, there’s more to a drive than just saving energy. Modern drives now incorporate an ever-increasing array of features designed to provide utmost efficiency, reliability, safety, and precision control. Application-specific drives may also include software functionality for specific applications, such as pumping, or enhanced communication features for integration with other systems.
Energy saving is increasingly being asked for by customers who have a keen eye on the machine’s sustainability, forcing machine builders to consider the energy efficiency of their products from the design stage. However, while adding a drive can significantly reduce a motor-driven system’s energy and carbon emissions, it also takes up vital space in the panel.
When looking to make a machine as compact as possible, balancing form with functionality is a major challenge. However, energy saving is not the only benefit of using a drive. For smaller and simpler machines, a smaller, entry-level drive can still provide energy-saving performance while also contributing in other ways to improved machine operations.
For instance, ABB’s ACS180 drive includes Safe Torque Off as standard rated to SIL3, which removes the need for an additional safety relay and contactors. Even if the drive has failed, the motor defaults to a no-torque state, and no power will be

able to reach it. In addition to improving the overall safety of the system, this can also free up valuable panel space by shifting functionality previously carried out by discrete components to within the drive.
Adaptive programming allows the drive and, by extension, the motor’s operation to be customised beyond the standard factory parameters, allowing it to intentionally trip or provide specific faults or warnings under certain conditions. Conversely, it could instead be programmed to override such conditions. In essence, this enables the drive to take on limited PLC functionality without the need for an actual PLC. For simple applications, this can not only save money but free up valuable space that would have been taken up by a separate device. The ACS180 also features Modbus connectivity to allow communication with wider control systems, again reducing the need for
additional devices, gateways and cabling. Saving energy is one of the number one selling points a drive offers, but this in itself has benefits beyond the actual energy saved. Running the motor at a lower speed and reducing heat losses can substantially reduce strain on components, particularly for applications with long hours of operation. Ultimately, this means lower maintenance requirements for the motor and a longer lifetime.
Drive technology may have advanced significantly in recent years, but sometimes, the bells and whistles associated with the latest generations simply aren’t needed. Smaller, less complex drives can still save energy, improve performance, and deliver value while also helping to keep unit costs down.
bit.ly/ABBACS180


Premium Quality Hydraulic Fittings with Next-Level Corrosion Protection
• Tom Parker Ltd is an authorised UK Distribution Partner
• Large Stock Available for Same-Day Despatch
• Unique protective corrosion-resistant coating
VOSS Hydraulics, a market-leading company with over 80 years of experience, is known for providing exceptional fluid-system connection technology. The company operates globally from its HQ in Germany and has authorised distribution partners, including Tom Parker Ltd in the UK.
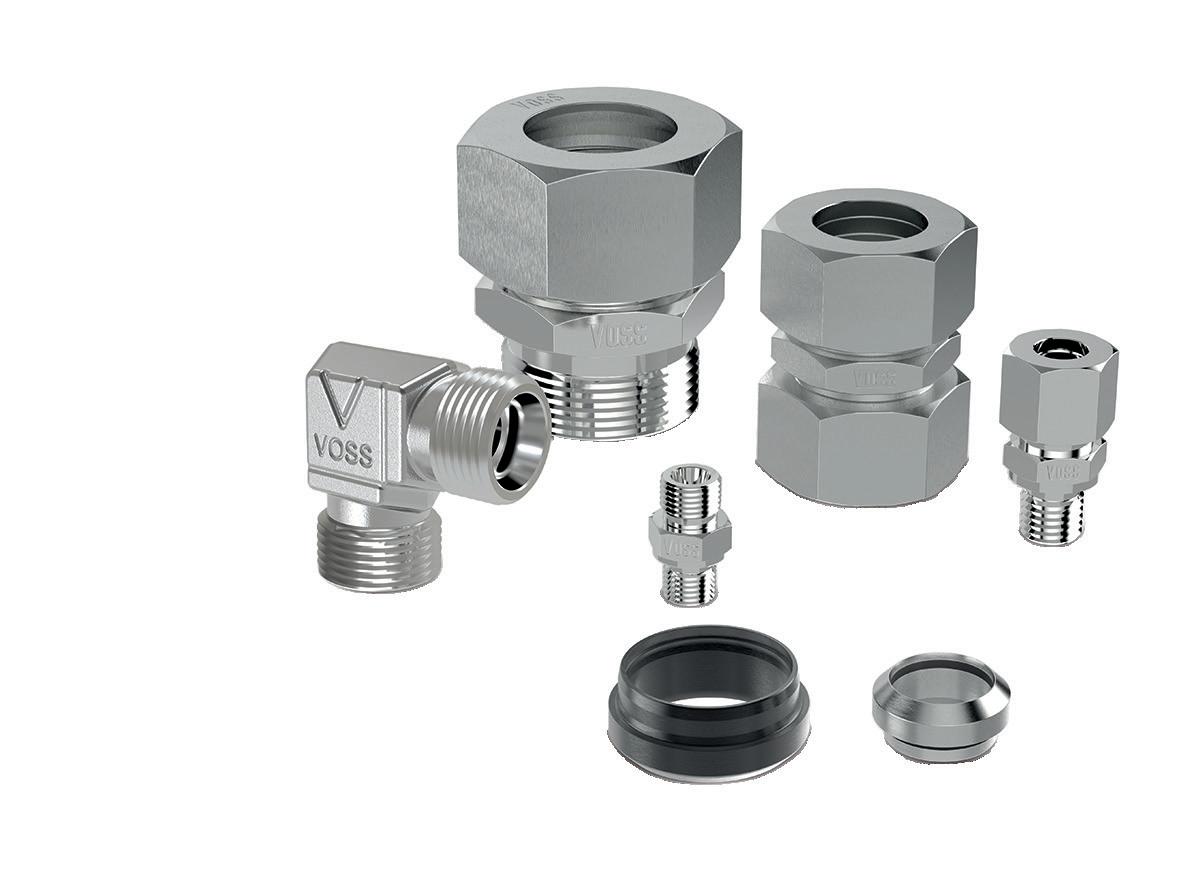
All VOSS fittings are equipped with an innovative VOSS coat, which provides superior, reliable, and long-lasting corrosion protection in hydraulic systems. Their products are certified to withstand 1,000 hours of corrosion and undergo rigorous testing to ensure consistent quality.
Explore the range of premium, durable, and secure VOSS hydraulic components in the Tom Parker Ltd 2024-2025 catalogue and online. Contact their expert technical support team today to find the perfect VOSS connection solution for your specific fluid power application.

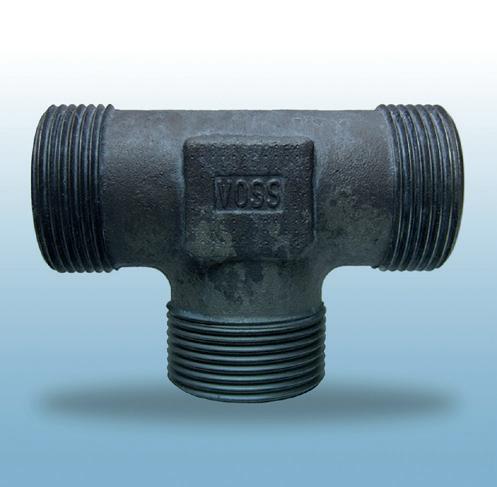
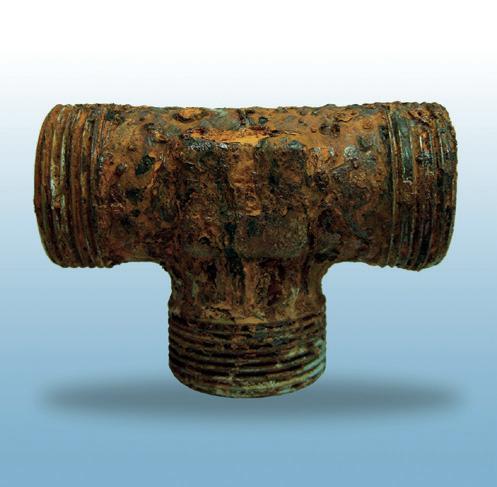
Solving modern intralogistics challenges
Automation solutions specialist Bosch Rexroth introduces its ctrlX FLOWHS linear motion and ctrlX FLOW6D planar systems, which together can meet today’s demanding intralogistics requirements.
In connected factories, everything must interact dynamically, seamlessly and quickly. The same applies in intralogistics too. The aim is to ensure short throughput times in production by optimising material flows.
ctrlX FLOWHS is the key here; a linear motion system which brings flexibility and high speed to manufacturing, with maximum precision and reduced space requirements.
Recent supply chain disruptions have prompted companies to overhaul their logistics, focusing on automation, efficiency, and increased throughput in complex production lines combining robots, highspeed machines, and manual stations. This shift, alongside increased product individualisation and smaller production runs, necessitates flexible, reliable transport solutions that can adapt quickly to changes. The goal is to streamline production processes, reduce complexity, and integrate multiple functions within single machines.
ctrlX FLOWHS addresses these needs. This linear high-speed motion system enhances production processes and provides the flexibility to adapt to new requirements swiftly. Fully integrated into ctrlX AUTOMATION, it benefits from the system’s openness, security, and extensive ecosystem, offering users a comprehensive range of functions.
The system’s modular design allows for flexible configuration across various applications, both inside and across machines. One typical application is the direct feeding of products into production lines, eliminating the need for complex robots to remove and place components. Additionally, power ovals in the machines can easily combine with conventional conveyor systems to perform tasks like forming product stacks, requiring high
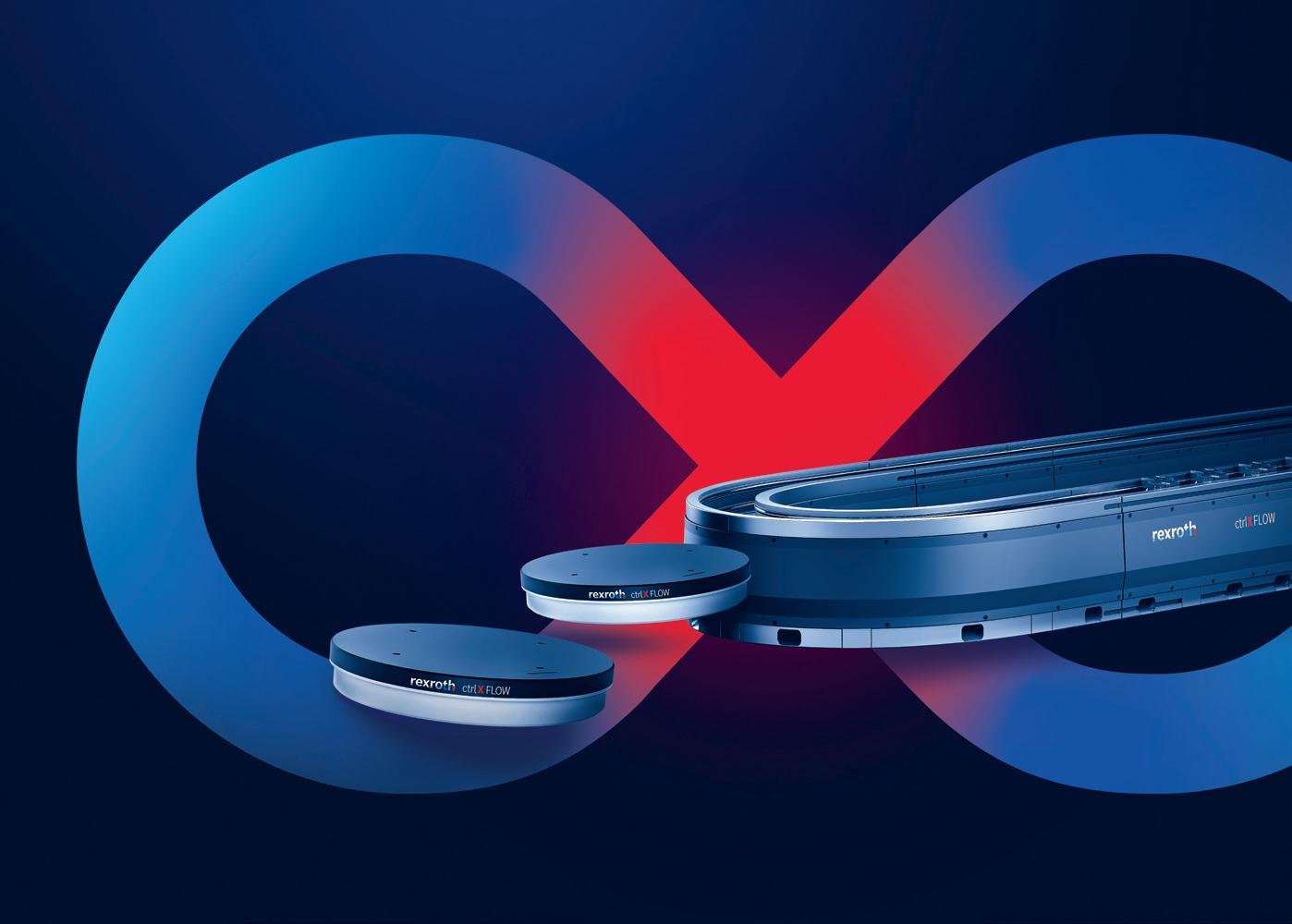
power, speed, and precision. ctrlX FLOWHS meets all these requirements.
Using the linear motion system, the internal machine transport processes between the workstations can be easily expanded to additional applications, for example in bottling lines. Bottles are gripped between two movers, transported to filling stations, labelled in another, inspected in another, checked in a third and bundled together at the last. Adjusting for different bottle sizes is simple, requiring only software changes.
ctrlX FLOWHS also optimises product transport between machines, moving products swiftly and flexibly through the factory. The system can use diverters to avoid queues by providing parallel routes, enhancing overall efficiency. This adaptability and versatility underline the system’s capability to meet diverse intralogistics challenges.
Complementing ctrlX FLOWHS, the ctrlX FLOW6D planar system further
boosts throughput and flexibility. It offers contactless, high-performance transport and positioning, with free-floating transport platforms (movers) operating on horizontal, vertical, or overhead surfaces. Each mover operates in six degrees of freedom with high speed and precision, without friction or pollution.
This innovative approach replaces traditional production lines with a selfsufficient area where products can move individually. The system also allows for re-testing or removal of products that fail quality checks. This highly adaptable production line has the potential to fundamentally transform conventional production methods.
Combining ctrlX FLOWHS and ctrlX FLOW6D harnesses the strengths of both systems, resulting in highly flexible, efficient production processes that meet modern intralogistics demands effectively.
www.boschrexroth.co.uk
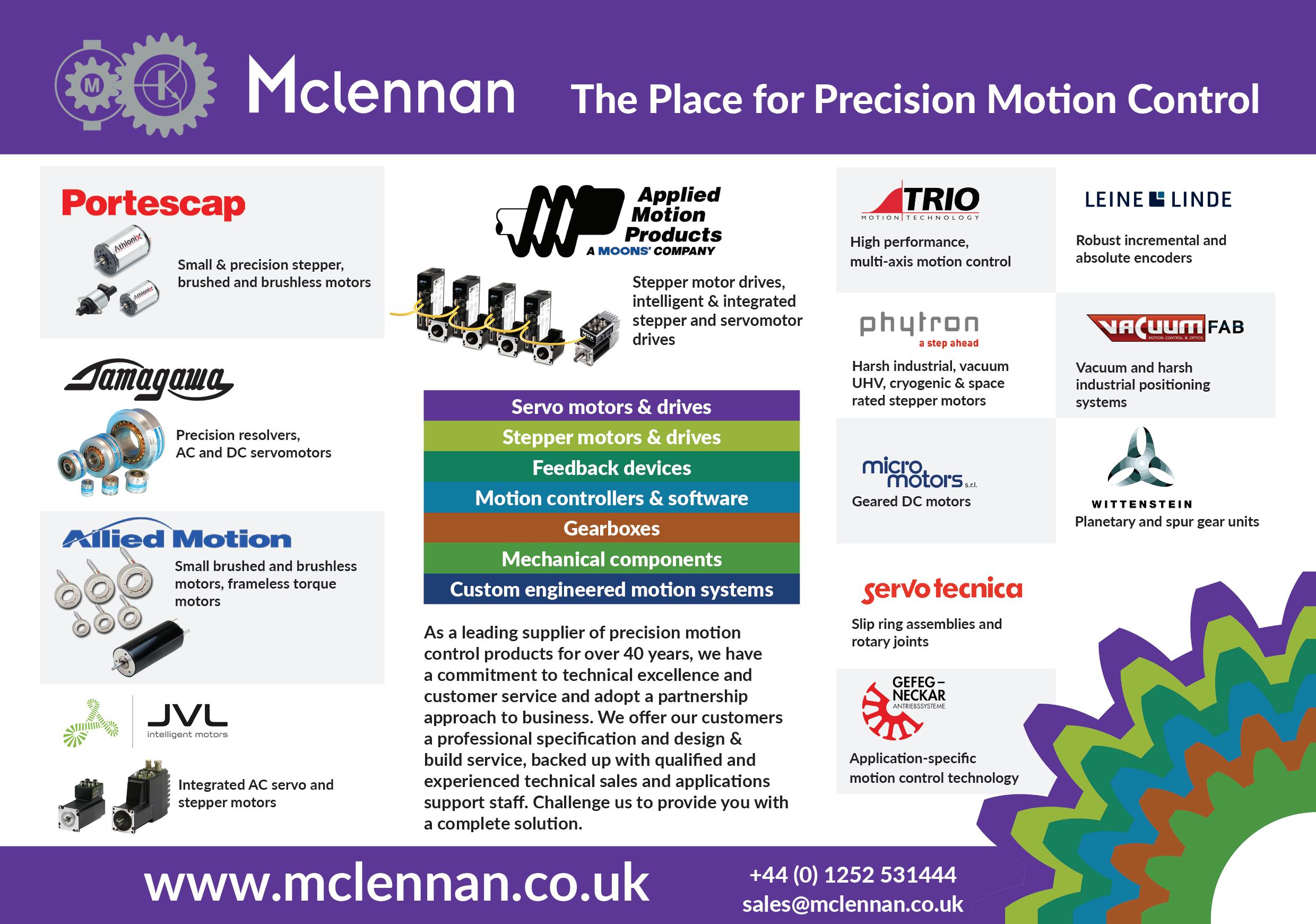
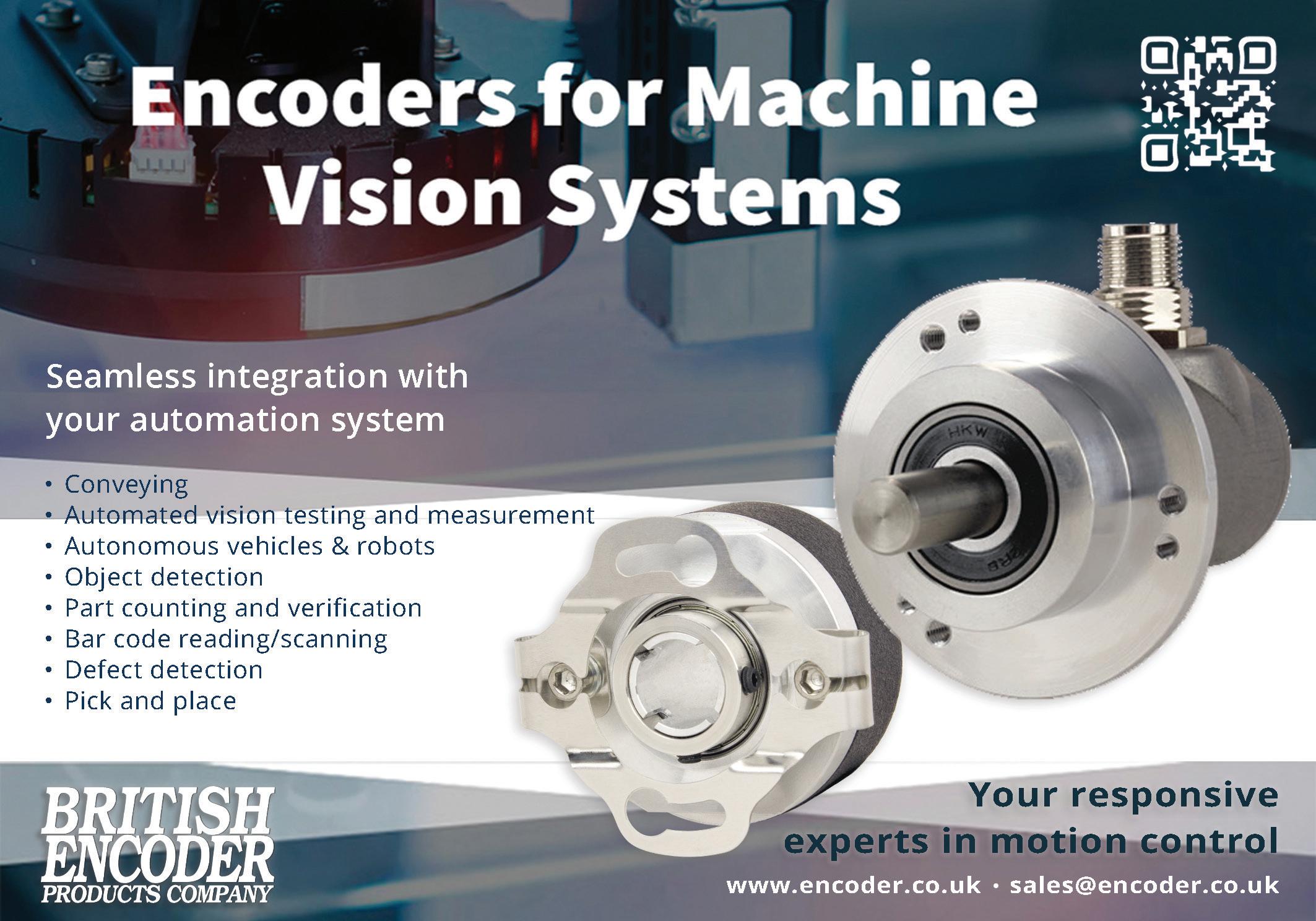
Photo firm focuses on exports
MEPCA found out how Lloyds Bank helped an SME camera film manufacturer to develop a new product range with international appeal and expand its export markets.
Harman Technology has an international reputation for its black and white photographic films. With the backing of Lloyds Bank, it’s now exporting its new colour film to photographers around the world.
The Cheshire-based business is one of a very small handful of companies in the world that still manufacture camera film at scale since the technology was overtaken by digital photography. Harman’s products have an unrivalled reputation among black and white photographers around the world; its ILFORD-branded films are sold in more than 85 countries.
However, Harman had never made colour film, which Managing Director Greg Summers felt was a missed opportunity as analogue photography was enjoying a revival. The global film camera market was set to reach almost £311 million by 2030, growing by 5.2% each year from £223.2 million in 2023, according to research and market consulting company Cognitive Market Research. The timing seemed right for Harman to make its move, so Greg challenged his team to develop Harman’s first ever colour film. The secret project soon paid dividends.
A global growth opportunity
Greg said: “We are so well known for our black and white films that we are regularly asked why we don’t make colour films. It was initially an experiment to explore what was possible, but what we achieved in such a short space of time is quite remarkable.”
Harman didn’t have the machinery to manufacture the potentially transformative new product, so Greg turned to Anthony Tsui, Associate Director – Trade and Working Capital, at Lloyds Bank.
Convinced by Greg’s business case, Anthony arranged a £multi-million funding package, including capital import financing
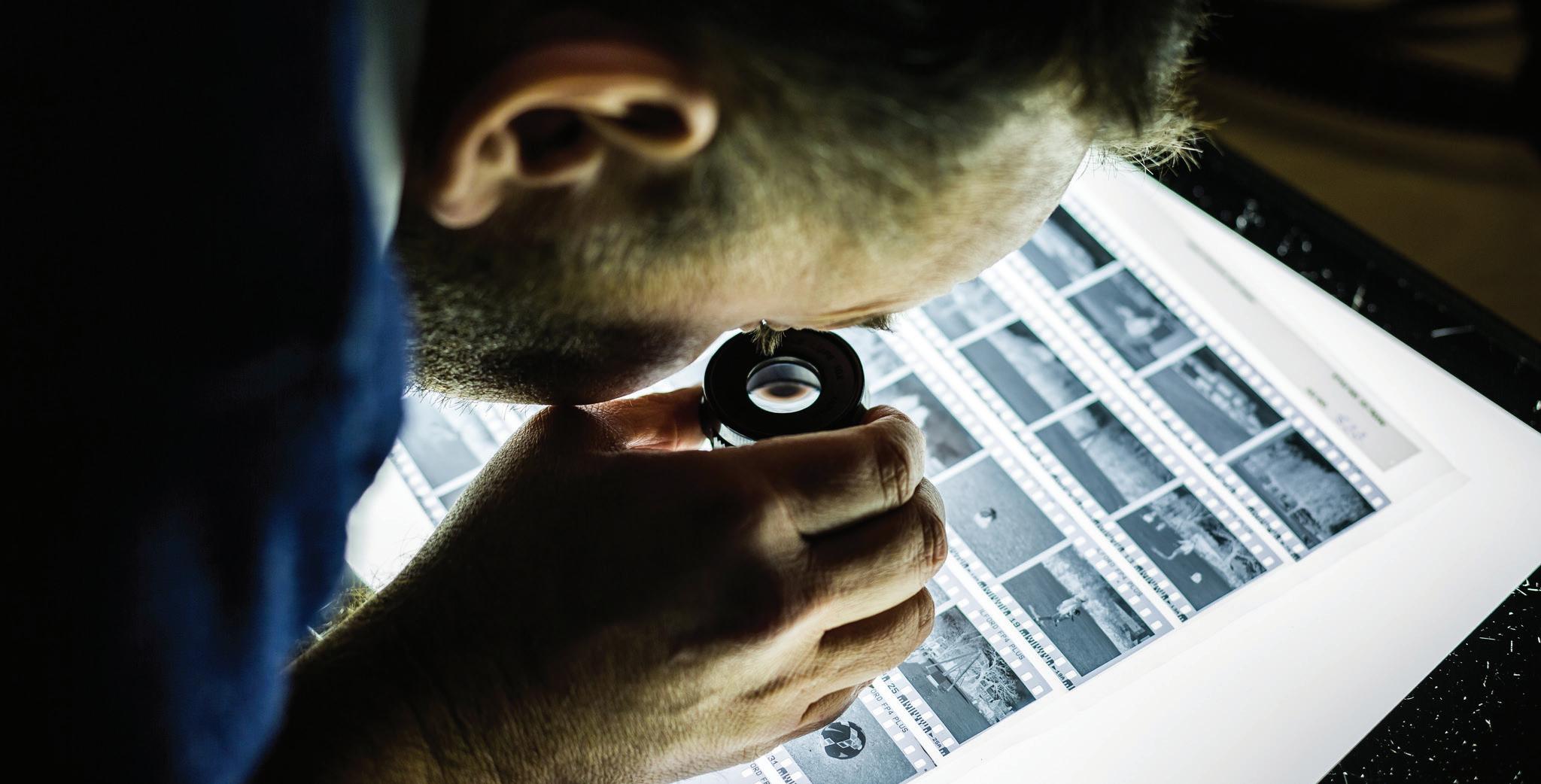
and export financing, as well as investment to double Harman’s manufacturing capacity.
The capital import finance supported its capex investment and mitigated the risk of upfront payments to overseas suppliers. While the export financing helped fund the transport of its goods to market once they were manufactured. As a result, Harman commissioned two custom-built finishing machines – the first to be built since before the millennium – to manufacture its new colour film cartridges.
Strategic support
“Lloyds Bank’s tailored approach to supporting firms’ global ambitions starts with understanding how the client trades and all the associated risks and opportunities they face. We have supported a diverse range of businesses’ export plans, which means we are well positioned to provide those meaningful conversations,” said Anthony.
“Harman – like so many British brands –enjoys an international reputation for quality and excellence, and it was clear its latest innovation presented an outstanding growth opportunity.”
The new film represented a rebirth for the business, and so was christened Phoenix. It was a big leap. But Phoenix launched in early
2024, making waves with photographers around the world and opening up a whole new market for Harman for the first time in its 145-year history.
The future of film
“We’re seeing new people fall in love with film photography every day. So, it’s a better time than ever to push resources into our team and build on the market’s momentum. The backing of Lloyds Bank’s International Trade team not only means that we can take this amazing opportunity, but also that we can manage the risk that comes with it.” said Greg.
And it means Harman has been able to invest in its R&D team’s commitment to advancing film research, so more innovative products could soon be on the way.
Anthony added: “Any business that is considering entering new markets overseas should get in touch as early as possible so that we can work with you to support your strategy. Identifying the market is, of course, key, as is understanding any trade controls in that country, which may include licencing requirements. We take a straightforward approach to how we can best support you, your supply chain and buyers.”
lloydsbank.com/manufacturing
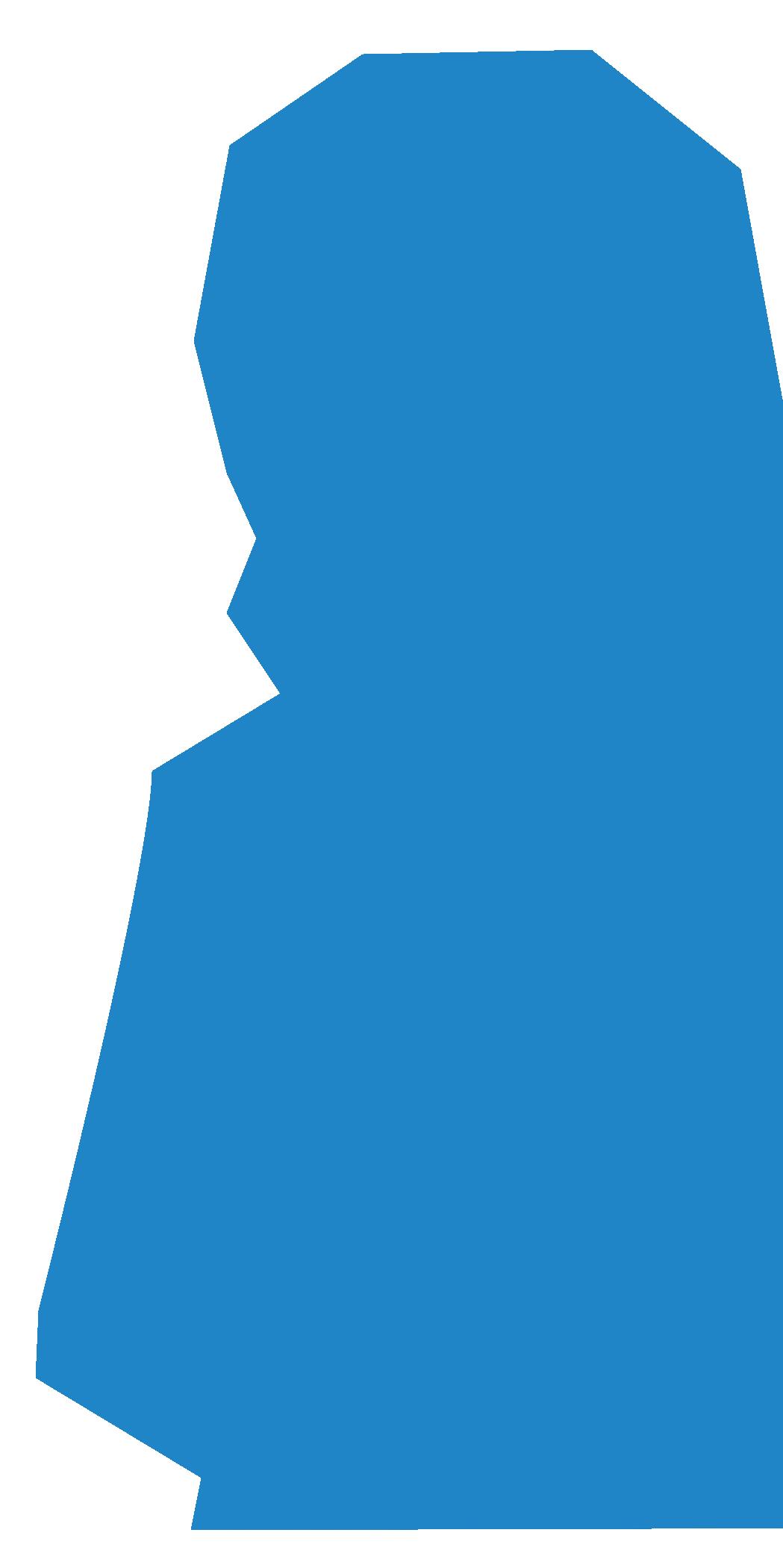
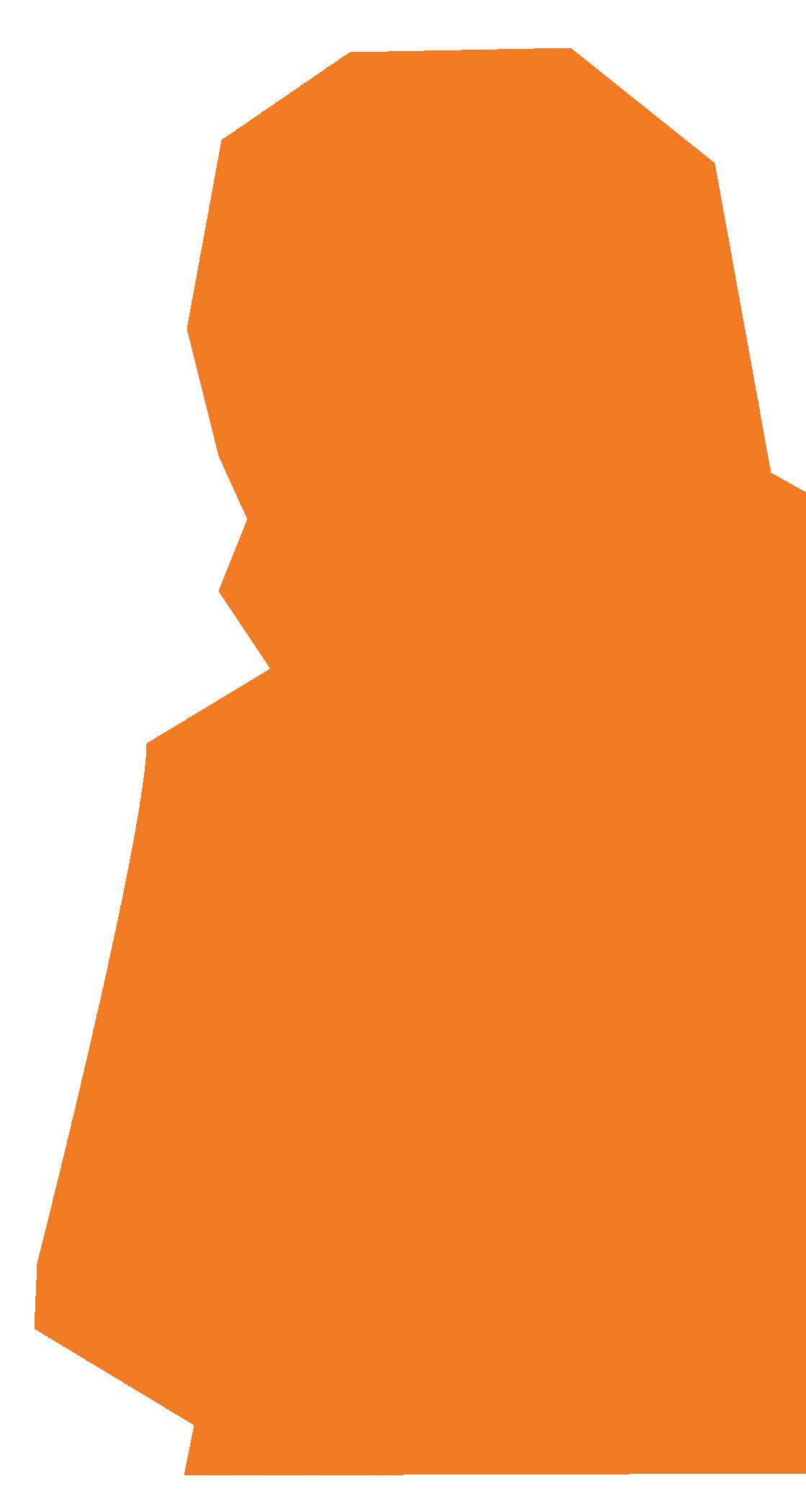

Accurate daily inventory counts made easy
Warehouse data intelligence specialist specialist, Dexory, explores how automated solutions can make daily counts easy and essential.
Accuracy and efficiency of inventory management can make or break a business.
Traditionally, inventory counts were done manually on a set schedule – like weekly, monthly, or even yearly. But now, with technological advancements, automated cycle counting has become a preferred solution.
Imagine a world where inventory errors are a thing of the past. In this world, the tedious and error-prone process of manual counting in warehouses and distribution centres is replaced by a system that’s both precise and efficient. Manual counting, which often only reaches an accuracy rate of 65% to 70%, is no longer a concern, and discrepancies that are used to disrupt operations and impact customer satisfaction are eliminated.
Errors and their compounding effect
Daily inventory counting is key for several reasons, but one is more important than others for maintaining accurate stock levels.
If an error occurs on day one and isn’t corrected, it will indeed compound over time. For instance, if an extra 100 units of a product is mistakenly recorded, that incorrect count will lead to erroneous stock data. This error can affect subsequent inventory decisions, such as ordering and stock allocation. By the time anyone realises there’s an issue, the impact of that initial error could be significant and can cause a cluster of mismatched inventory figures and disrupted supply chains.
It’s no secret that regular daily counting helps catch these errors early, preventing them from escalating and causing widespread problems. And this is where automated solutions, especially robotics, step in.
Autonomous mobile robots (AMRs) can effortlessly move through warehouse aisles, scanning barcodes and keeping inventory records up to date. These robots work
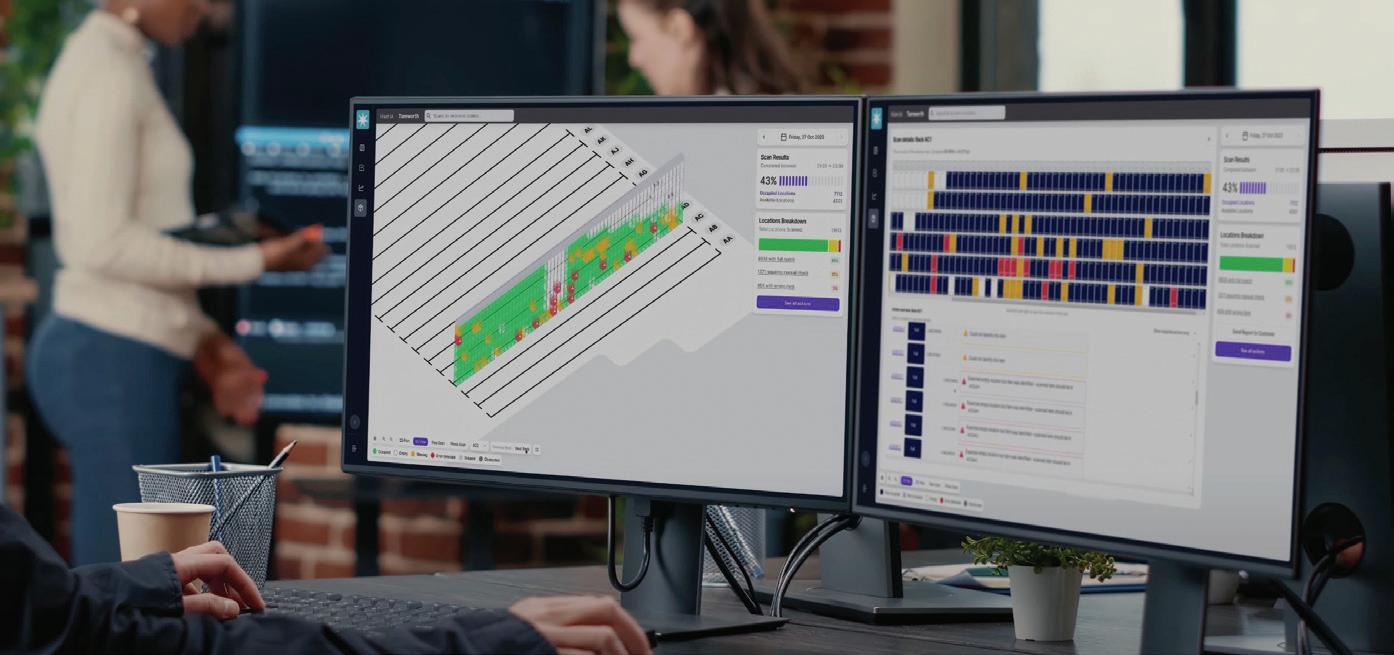
seamlessly with a user’s WMS, providing real-time updates and valuable insights into operations. This means users get unmatched visibility and control, making warehouse operations smoother and more efficient.
Here’s how automated solutions can transform operations:
• Improved accuracy and real-time insights: Automated inventory counting with robotics and AI achieves incredible accuracy, often hitting 99.9%. Daily counts keep users updated on inventory levels, reducing the risks of stockouts or overstocking.
• Enhanced operational efficiency: Automated systems can scan large areas and thousands of locations in hours, freeing up teams from manual counting and allowing them to focus on more strategic tasks, while real-time data will help logistics managers adjust inventory and improve supply chain processes.
• Cost reduction and waste minimisation: Daily inventory counts help catch discrepancies early, reducing stock loss and financial waste. By addressing issues like misplacements or picking errors promptly, users can cut operational costs and increase profitability. Plus, with new subscription models, adopting automated systems is more affordable than ever, avoiding the need for hefty initial investments.
Utilising real-time data
But it doesn’t stop there. Daily inventory counts are crucial, but integrating them with advanced technologies like AI, Machine Learning, or IoT can significantly enhance operations, allowing real-time data action and quick recovery of potential revenue losses. They ensure accuracy in inventory levels, reducing errors and improving order fulfilment rates. Plus, they streamline the put-away process. Real-time monitoring keeps production lines running smoothly by maintaining optimal stock levels and reducing downtime. And let’s not forget space optimisation – automated solutions analyse storage patterns to make sure every inch of a warehouse is used efficiently. With real-time data from automated solutions, users can manage their warehouse proactively and easily meet, or even exceed, their KPIs.
In a nutshell, automated inventory cycle counting is a game changer for the logistics and warehousing world. Instead of sticking with the traditional manual checks every day or week, or only counting now and then, switching to automated daily inventory processes can make a big difference. It helps businesses keep their inventory spot-on, run more smoothly, and stay flexible.
www.dexory.com

Explosion-proof lifting for hazardous environments
Lifting equipment specialist, Konecranes, has launched a range of EX C-series electric chain hoists, engineered for explosion proof lifting in hazardous environments.
The new EX C-series range of electric chain hoists is suitable for a wide range of industrial applications where gases, flammable substances, dust and other ignition sources create the potential for explosions. The range has been designed and tested specifically to fulfil ATEX and IECEx requirements for use in Zone 1, 2 and 21 explosive environments.
EX C hoists offer inherently safe workplace operation. In addition to their explosion proof characteristics the models feature a slipping clutch which activates automatically providing protection in the event of an overload. They also incorporate a travelling limit switch and a geared hoisting switch. Ingress protection is rated at IP66.
Ergonomics, operational efficiency, versatility and ease of use have been the driving factors in the development of the hoists. The compact design and low headroom allow maximum use of available workspace. Inverter-controlled trolley movement and two-step hoisting facilitate smooth and accurate load handling with a lifting ratio of 6:1 for operational efficiency.
EX C models are available with SWLs from 320kg to 2,500kg. As standard, the ambient operating temperature is +5 to +40°C with -20 to +55°C available to order. A comprehensive range of options and accessories may be supplied, allowing hoists to be tailored to specific applications.
Smart engineering techniques have been employed in the manufacture of the EX C-series with the use of Konecranes’ ‘Core of Lifting’ components, including a purpose-built motor, gearbox and controls. The hoisting brake is designed for lifetime operation with two friction linings and no need to adjust the brake gap. The chain is available in galvanised (DAT) or stainless steel options. The robust and durable hoists provide reliable performance over
extended periods, ensuring maximum operational availability, reduced maintenance requirements and extended life cycle.
EX C-series hoists are fully compatible with the company’s online customer portal, yourKONECRANES, facilitating prompt and easy access to comprehensive intelligence on performance, maintenance history, asset condition, usage data and agreement details. Information is updated in real time during service visits by IT-enabled technicians, providing customers prompt access to the latest and most comprehensive data, reports and recommendations.
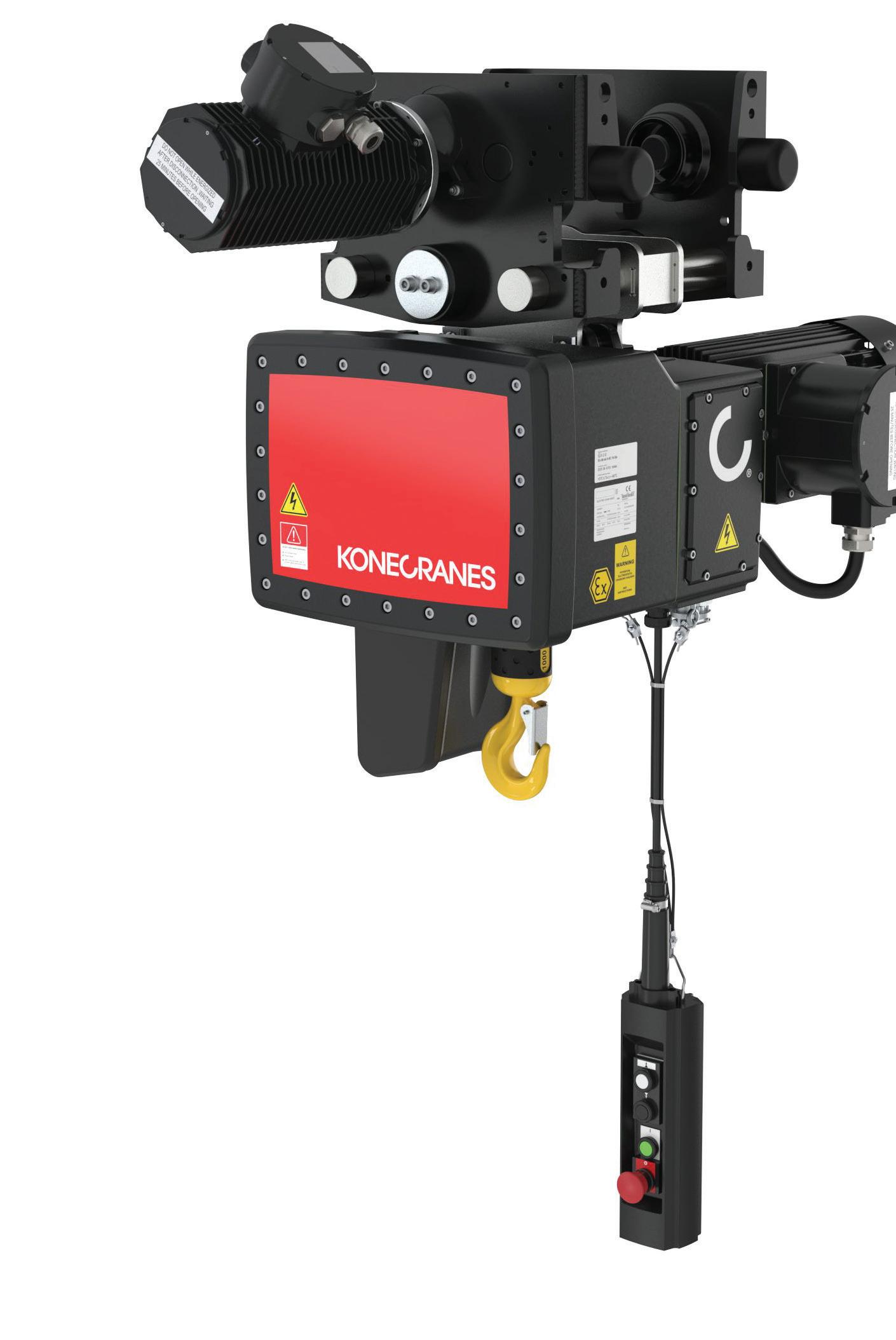
Konecranes’ Customer Experience Manager, James Bow, commented: “The fact that the EX C-series is certified for use in Zone 1, 2 and 21 explosive environments means that they are a versatile material handling solution for a wide range of industrial and manufacturing applications. The models are an important addition to our comprehensive portfolio of explosion-proof lifting equipment. We are well placed to provide cranes that meet the requirements of customers in a broad variety of hazardous
environments, including chemical, pharmaceutical, oil and gas, wastewater treatment and process industries.”
www.konecranes.co.uk


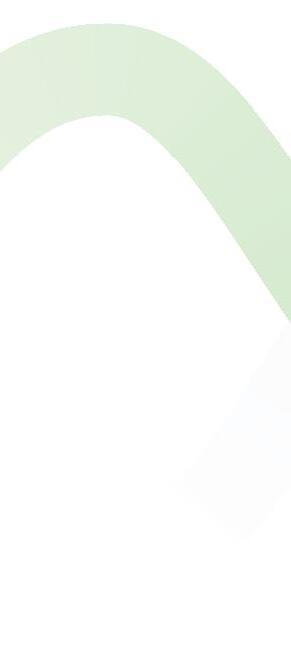
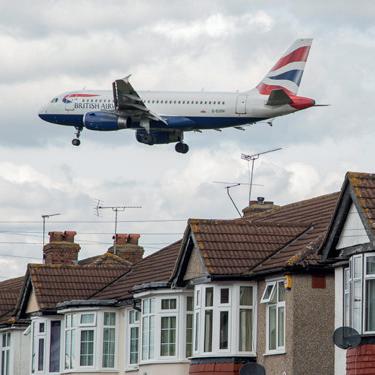

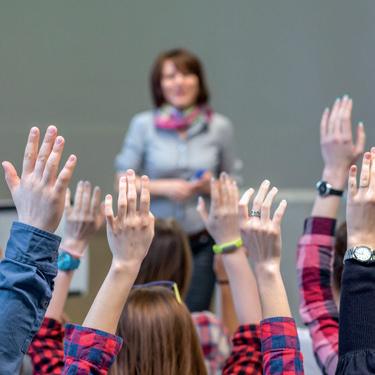

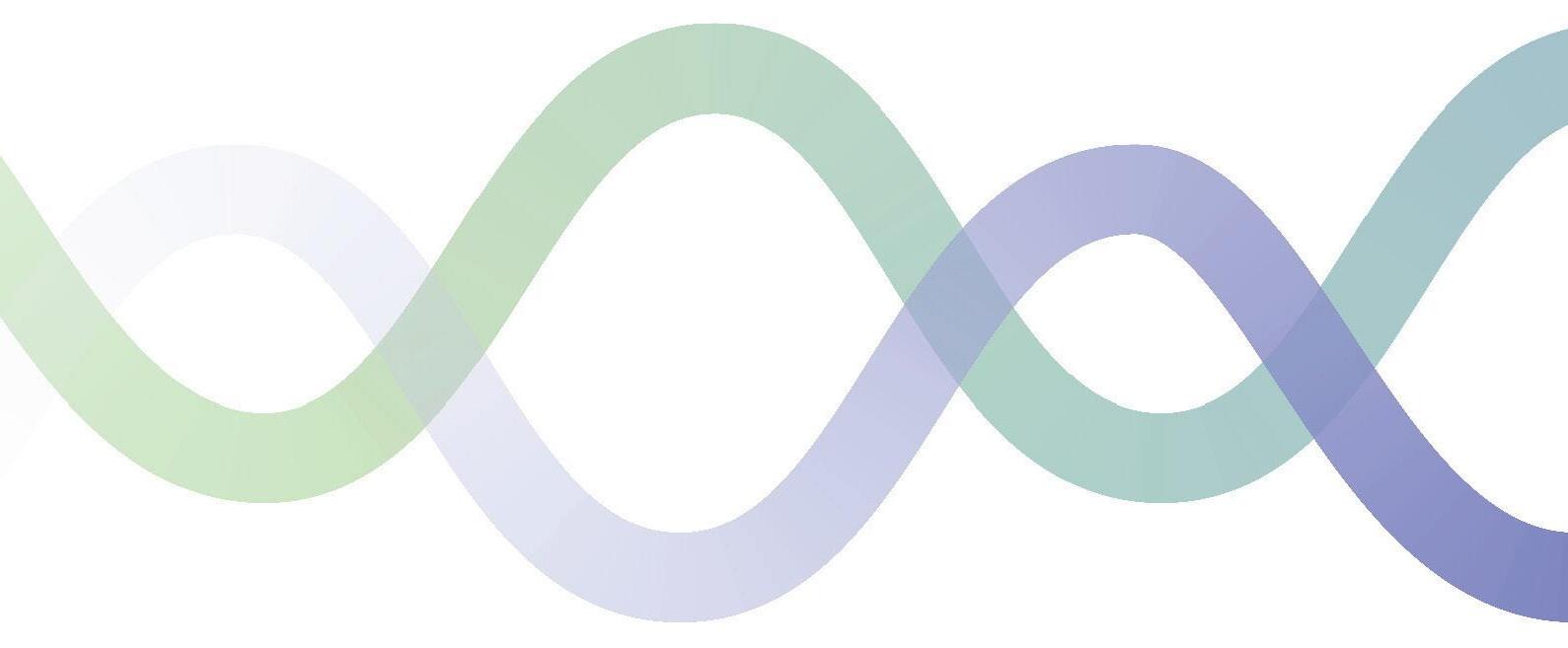
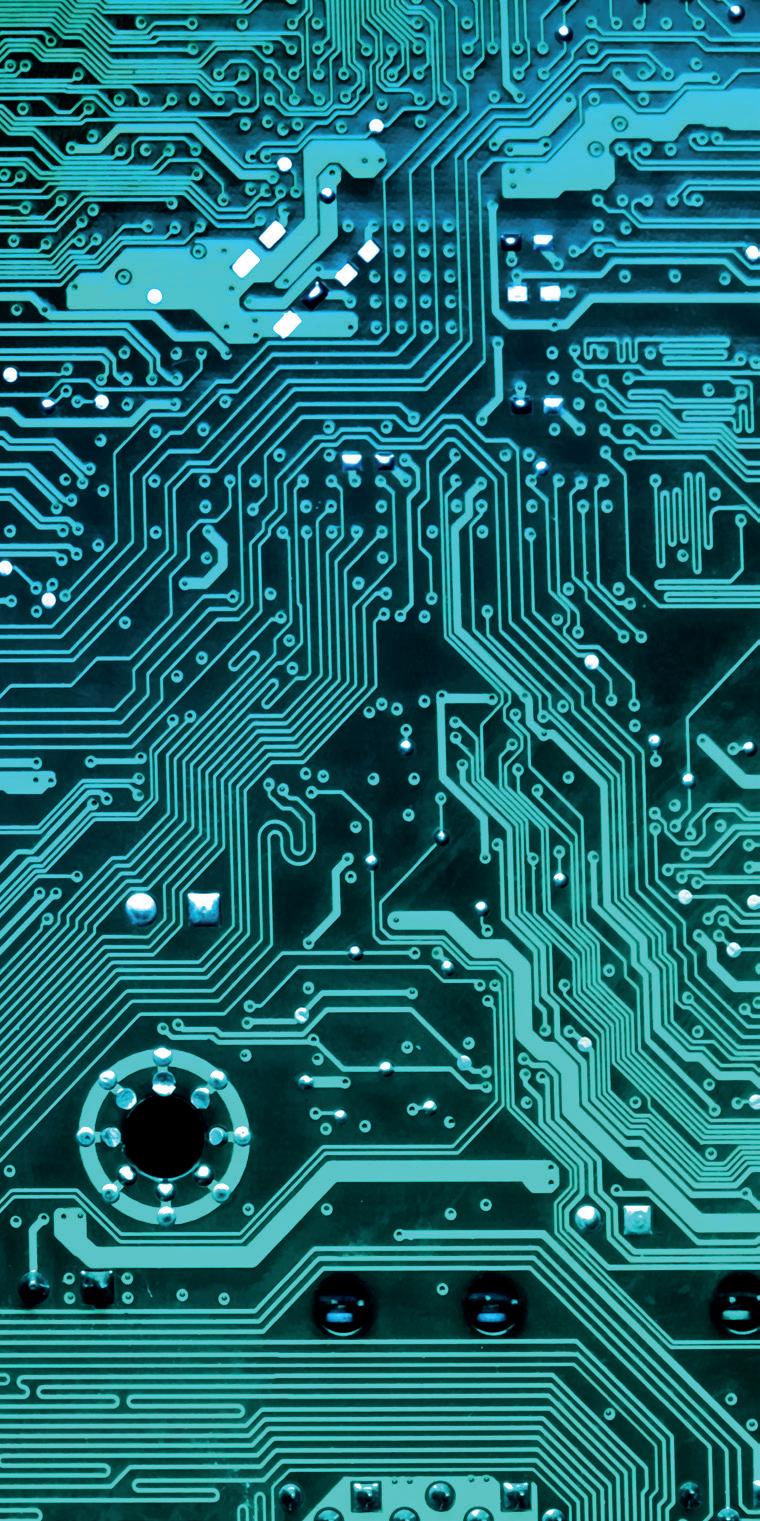
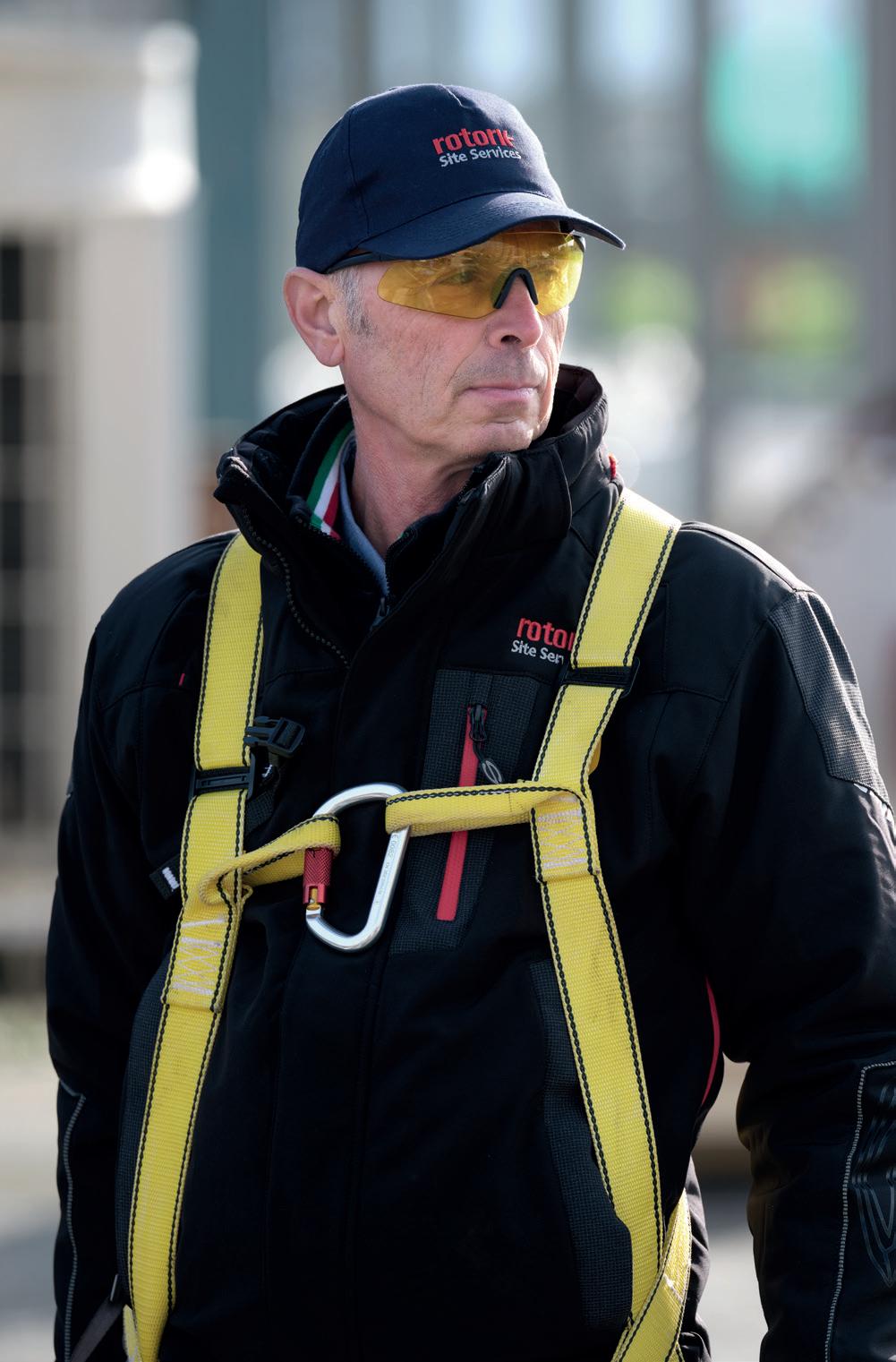
Off-the-shelf collaborative palletiser makes automation more attainable
Visitors to stand C24 at the PPMA Show, taking place at the NEC Birmingham from 24-26 September, will be able to find out how a new off-the-shelf collaborative palletiser, developed through a partnership between OnRobot and Applied Automation, will enable them to swiftly implement a comprehensive, cost-effective, and flexible solution on their production floor.
OnRobot, a turnkey provider for collaborative applications, has partnered with UK-based robotics company Applied Automation to introduce an off-the-shelf collaborative palletiser for SMEs. This industry-first solution offers same-day installation, requires no programming and can be re-deployed within minutes.
“OnRobot has successfully introduced end-of-arm tooling and sensors for robotic automation to the market by ensuring seamless integration with all major robot brands and providing a simplified and consistent user experience,” said James Taylor, Chief Commercial Officer for OnRobot.
“With D:PLOY, we are taking the next logical step in simplifying the overall application rather than just focusing on individual components within the robot cell.”
Founded in 2018 in Denmark, OnRobot identified a need for quality cobot hardware. “With so many cobot manufacturers coming onto the scene, we recognised a need for a reputable manufacturer that could provide all the complementary physical hardware required.”
The missing piece of the puzzle is D:PLOY, the industry’s first automated software platform for building, running, monitoring, and re-deploying collaborative applications.
“Our goal is to ensure that no matter what robots customers choose to use, they will always have a consistent OnRobot experience,” James added. “We recognise the fact that the end-user has a desired outcome. Their challenges are centred around time and cost – and more specifically when it comes to changing box sizes.”
The ultimate peace of mind lies in D:PLOY’s same-day installation, changing an application or box size within minutes and the quick changeover of a production line. “Most
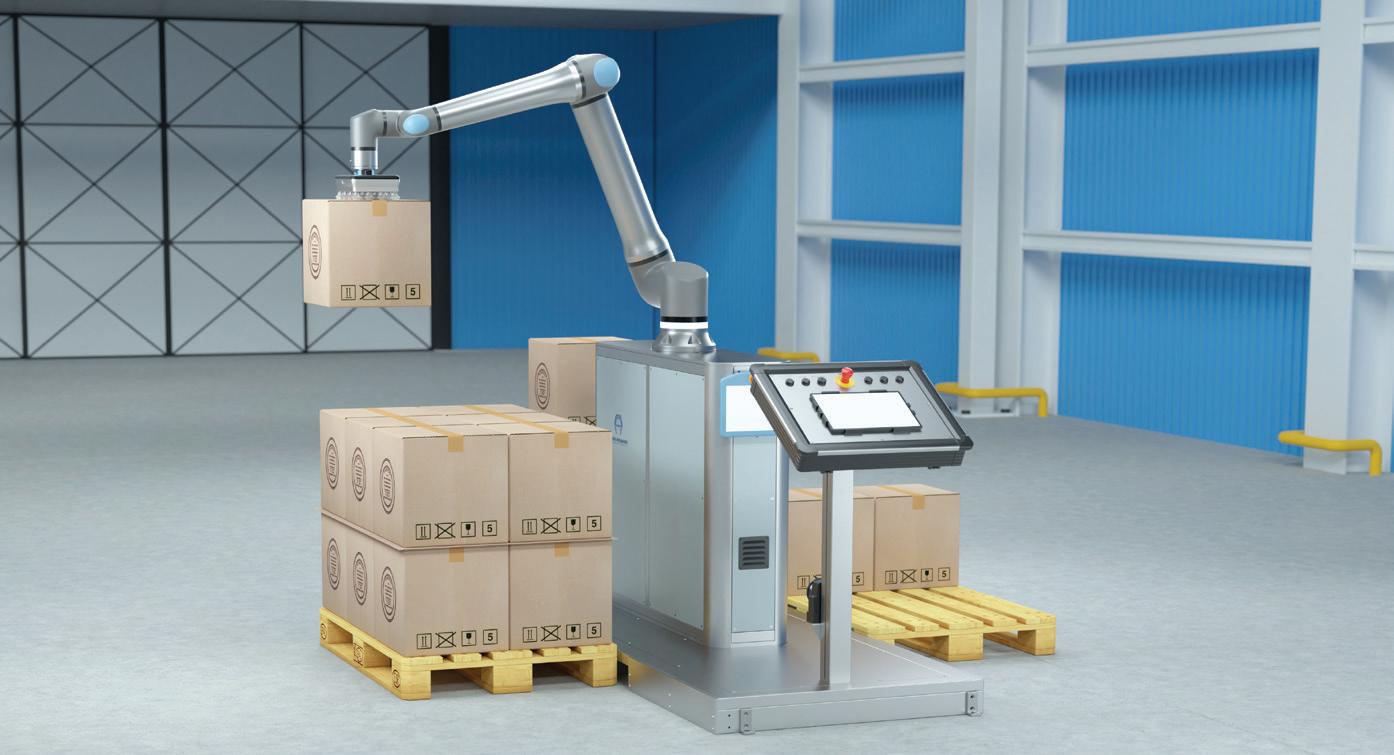
palletising is done manually due to the highmix nature of production lines with frequent changes in productions or box sizes. With D:PLOY, changeover can now be reduced to a few minutes, making automating tasks with robots achievable and affordable since the application cell can automate multiple palletising tasks,” explained James.
Speaking of OnRobot’s investment in the UK, James highlighted the fact that many SMEs face workforce challenges and require a cost-effective solution for high-mix palletising applications.
OnRobot’s partnership with Applied Automation provides a unique advantage. “We partner with local companies who can best serve the local market – this is our tried-and-trusted global model. Applied Automation is an industry expert, and we support it and its customer offering, including a flexible, quick-to-deploy, always-available solution.”
David Rowe, owner of Applied Automation, believes that the launch of AA:PALL, in conjunction with OnRobot’s D:PLOY, will reduce the barriers to entry – particularly for SMEs.
“SMEs often face challenges in automating their processes due to high costs and complexity associated with traditional industrial robots and automation systems. Our AA:PALL palletiser solution aims to provide an affordable and accessible automation option specifically tailored for SMEs,” David said. “Thanks to its functional, easy-to-use, and fast installation design, among others, the AA:PALL significantly lowers the barriers to entry for automation, making it an accessible and practical option for SMEs looking to enhance their operational efficiency and competitiveness.”
Commenting on the partnership, David explained that integrating OnRobot’s D:PLOY with AA:PALL will reduce the complexity of deploying a robotic palletising solution, making automation more attainable for SMEs.
The AA:PALL is a UR20 equipped with an OnRobot VGP20 gripper, OR:Base Controller and D:PLOY software license. It comes complete with Applied Automation’s compact palletising base, training, installation, set-up and delivery across UK.
bit.ly/4dzcDvL
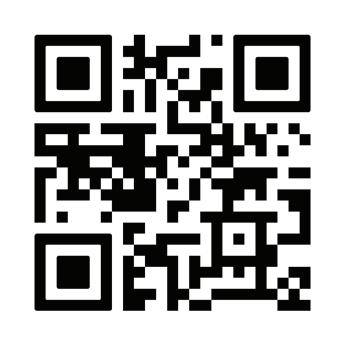

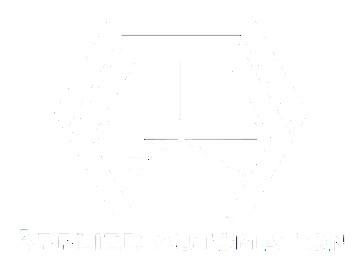
Automated battery disassembly makes EVs more sustainable
Electric vehicle sales have been booming over the last few years, but what happens to the tons of used batteries? The Fraunhofer Institute for Manufacturing Engineering and Automation has successfully evaluated how industrial battery disassembly works using a KUKA KR QUANTEC robot, with the goal of making electric cars even more sustainable.
In March 2023, the European Union (EU) made the decision to only newly register zeroemission passenger cars and vans starting in 2035. Since making that decision, it has been clear that the future of the automotive industry is in e-mobility.
There are, however, two problems with electric vehicles. With increased consumer demand, the mountain of used batteries grows. This is because they currently only have an average service life of around ten years. At the same time, raw materials for their production are becoming increasingly scarce and expensive. One solution for both is recycling, which is where the KUKA industrial robot – or, more specifically, the KR QUANTEC industrial robot – comes into play.
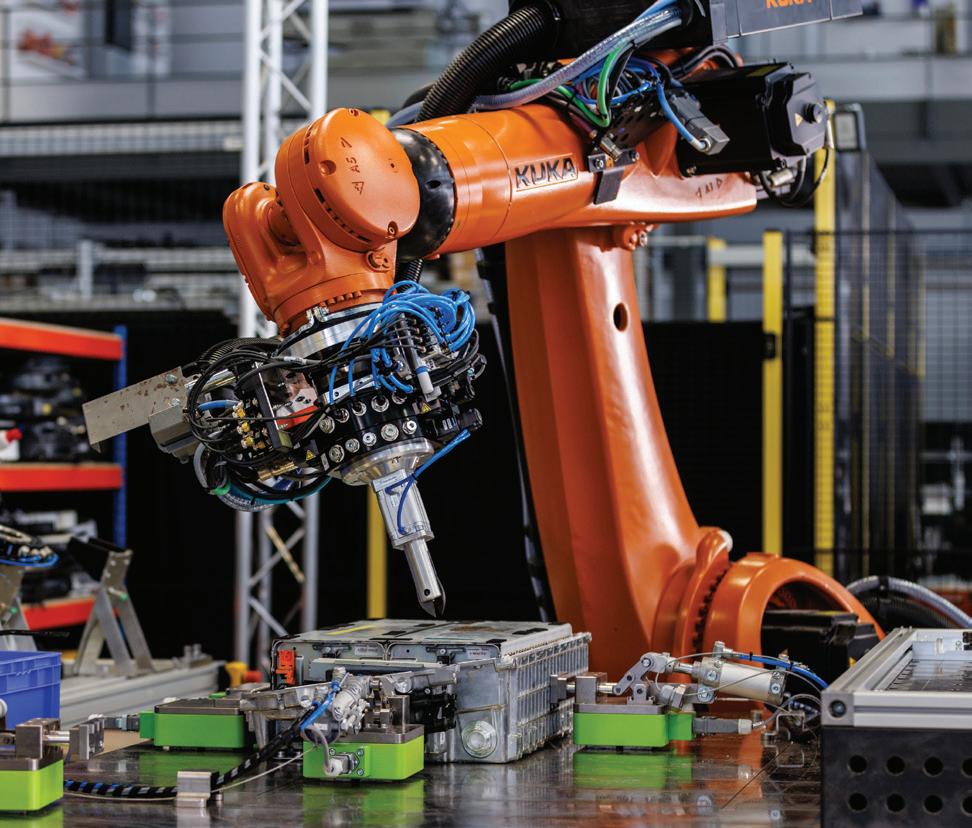
With the robot’s help, the Fraunhofer Institute for Production Technology and Automation IPA in Stuttgart, Germany, proved how recycling can work efficiently through the ‘DeMoBat’ - an abbreviation that loosely translates to ‘Industrial Disassembly of Electric Motors and Batteries.’ The research partners investigated how to recondition batteries from electric cars in both sustainable and economically viable ways. In this project, a total of eight robotic applications were set up as demonstration and testing tools that could be used for continuous industrial operation.
Battery disassembly
The focus was on the disassembly of electric car batteries since the prerequisite for recycling these components is a clean separation into their component parts, which is no easy task. “The disassembly of batteries presents three major challenges,” explained Anwar Al Assadi, Group Leader at
the institute. “First, you need highly qualified specialists because working with high-voltage technologies requires time-intensive training. Second, manual disassembly is associated with a health risk due to the high voltage and hazardous gases. In the worst case, spontaneous ignition may occur. And thirdly, disassembly by hand takes a long time and is very costly. The trio of difficulties often makes recycling seem unprofitable.”
The three challenges are ideal for a robotbased solution. A KUKA KR QUANTEC robot with a payload capacity of 270kg is operated entirely by the ‘pitasc’ software developed at Fraunhofer and controlled with KUKA. RobotSensorInterface, which facilitated connection to external sensors. Researchers were able to control important disassembly steps in real time and thus automate various operations that previously had to be done manually.
KUKA’s technology solved three problems at once: it reduced the shortage of skilled labour, minimised the safety risk for employees and, with efficiency, ensured that battery recycling is also economically profitable.
The KUKA robot conducted a wide range of work steps: unscrewing screws, opening sealing joints and disconnecting cables. “The complex thing is that there are an incredible number of different battery systems on the market,” added Anwar, “and each one looks different inside.” He further notes that, at times, manufacturers change the structure of the battery systems within a singlevehicle model. As a six-axis robot, the KR QUANTEC leverages its six degrees of freedom. The jointed-arm robot can optimally adapt to the different dimensions and geometries of the battery system, and thanks to its payload, it can also cope with high torques.
In conjunction with the hardware, the ‘pitasc’ software recognises what needs to be done regardless of the battery model.
Supporting image processing systems for the automatic detection of screws as well as other components made it unnecessary to manually teach the KR QUANTEC for each individual step.
“Because of its streamlined geometry and small footprint, the KR QUANTEC can be used to build a flexible and future-oriented system,” said Thomas Schmidberger, Global Business Development Manager for Electronics at KUKA. “Like all KUKA robots, it is also ESD-certified as standard to ensure safe handling of components that are sensitive to electrostatic discharges.”
“We have built Europe’s largest test facility for battery disassembly,” concluded Anwar proudly, “and we have demonstrated how automation solutions can play a definitive role in making e-mobility even more sustainable.”
www.kuka.com/en
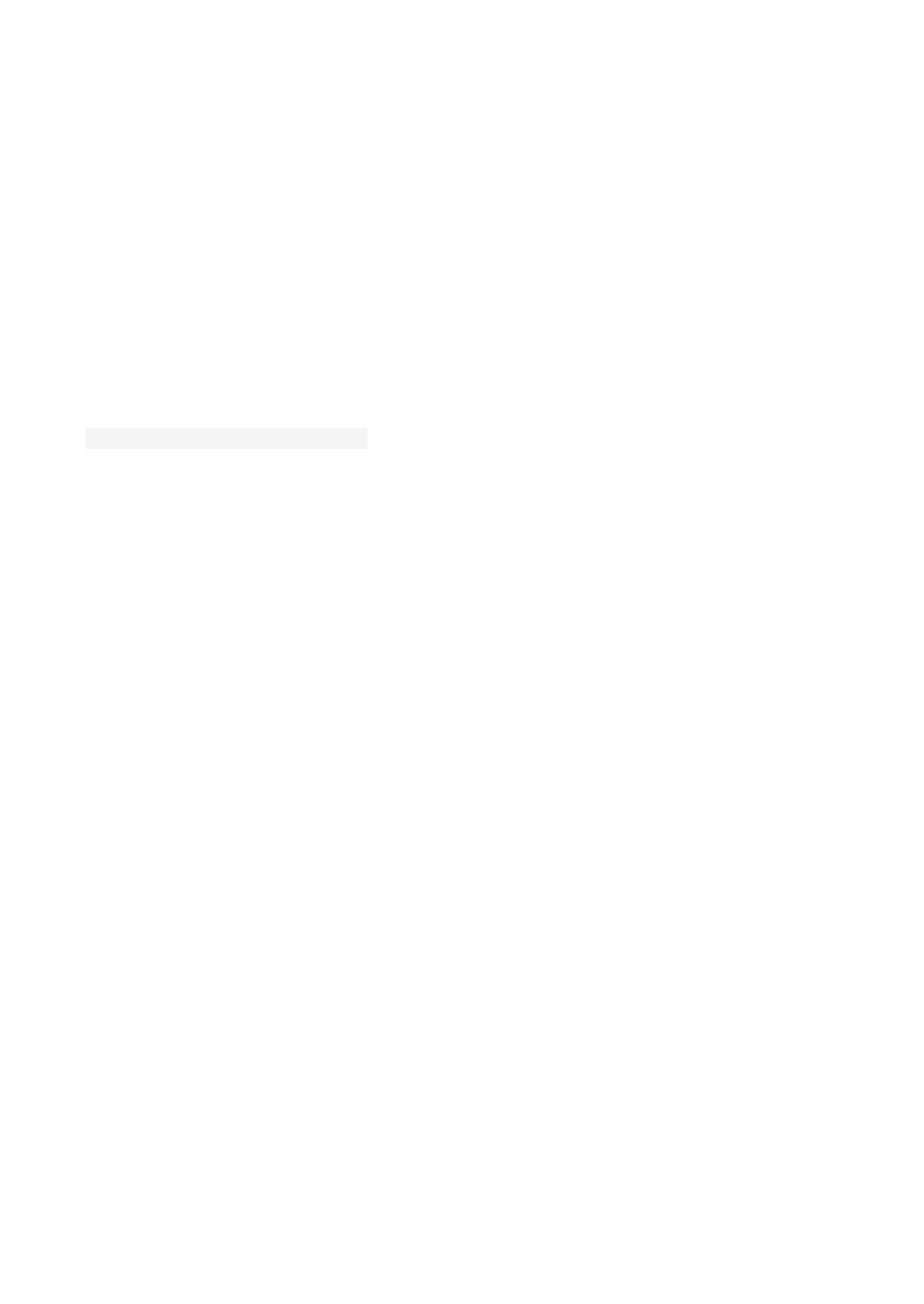
Smarter automation with visionguided robotics in Industry 4.0
SensoPart explores the fundamentals of vision-guided robotics, its applications, and the benefits it offers to modern industries, with a focus on how the company’s VISOR Robotic sensor exemplifies these advancements.
In the rapidly evolving landscape of Industry 4.0, automation is key to maintaining competitiveness and efficiency in manufacturing and production. Vision-guided robotics, an innovative integration of vision sensors and robotic automation, is transforming how industries operate. This technology allows robots to ‘see’ their environment, adapt to changes, and perform complex tasks with greater precision.
Vision-guided robotics refers to the use of camera systems and sensors to enable robots to identify, locate, and manipulate objects within their operational environment. This capability is crucial for tasks requiring high precision and adaptability, such as sorting, assembly, and quality inspection. Unlike traditional robotic systems that rely on fixed coordinates, vision-guided robots use real-time visual data to navigate and interact with their surroundings, providing significant flexibility and accuracy.
Applications in industry
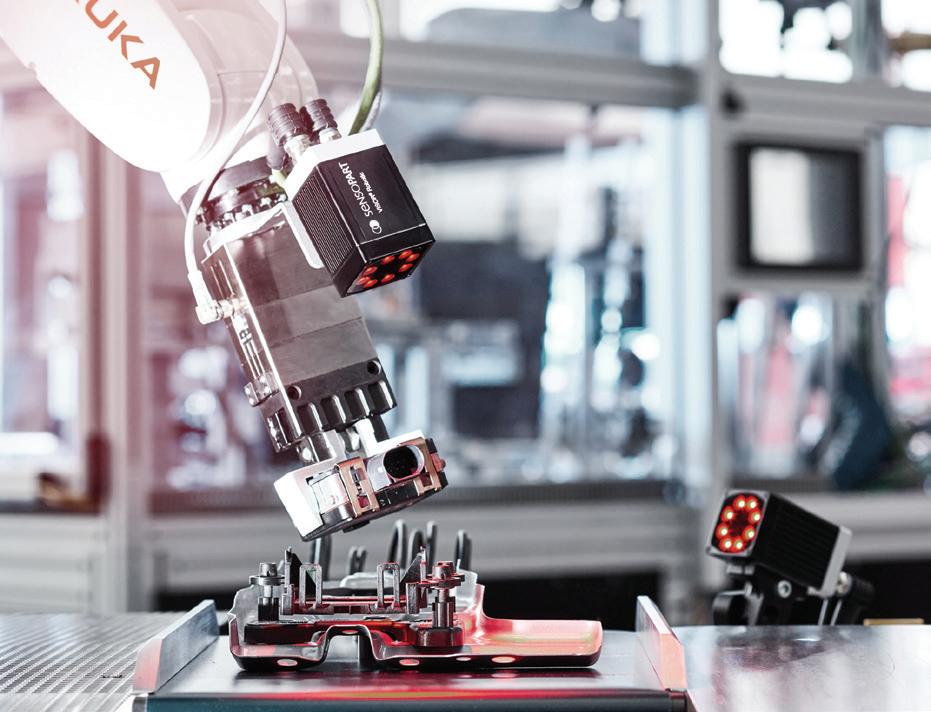
object detection and manipulation, even in complex scenarios.
The versatility of vision-guided robotics makes it suitable for various industrial applications:
In the automotive sector, robots equipped with vision sensors can precisely position and assemble components, conduct inspections, and perform tasks like welding and painting. This not only enhances the quality of the final product but also speeds up production lines.
In electronics manufacturing, visionguided robots are integral to the assembly of components, where precision is paramount. They can handle delicate components, inspect circuit boards, and ensure that assemblies meet strict quality standards.
In logistics, vision-guided robots assist in sorting and packing goods, optimising space usage, and ensuring accurate order fulfilment. They can adapt to different packaging types and sizes, significantly enhancing efficiency.
Vision-guided robotics offers significant advantages, enhancing flexibility, quality control, and cost efficiency. One of the key benefits is increased flexibility. Vision sensors enable robots to adapt to different tasks and environments without extensive reprogramming. This adaptability is particularly valuable in industries that deal with a diverse range of products or frequently alter production lines. Improved quality control is another major advantage. By integrating vision sensors, robots can conduct detailed inspections, identify defects, and ensure that products meet stringent quality standards, which helps in reducing waste and improving customer satisfaction. Although the initial investment in vision-guided robotics can be substantial, the technology proves to be costefficient in the long run. The savings stem from reduced labour costs, lower error rates, and accelerated production cycles, making it a wise investment for forward-thinking manufacturers.
SensoPart’s VISOR Robotic sensor represents a significant advancement in visionguided technology. It integrates seamlessly with existing robotic systems, offering a user-friendly interface and advanced machine vision capabilities. The sensor’s award-winning Target Mark 3D technology enables precise
For organisations struggling with the high costs and complexities of 3D robotics tasks, SensoPart’s Target Mark 3D technology, paired with VISOR Robotic 2D-Vision Sensors, represents a breakthrough in enhancing robotic accuracy and efficiency. This innovative approach is crucial for applications like machine tending and material handling, where precise positioning and part placement are critical. With Target Mark 3D, positional variations are dynamically adjusted and corrected within the robot’s programming, ensuring smooth and accurate handling processes.
Typical applications include material feed from a carrier. Components are often supplied in load carriers, and the precision of positioning these carriers is vital for a stable, robot-assisted handling process.
When part of a mobile workstation, mobile robots offer flexibility in machine tending processes, but this can result in imprecise robot positioning. Target Mark 3D ensures that the robot’s movements align accurately with the machine, enabling successful and efficient operations.
Conclusion
Vision-guided robotics is at the forefront of modern automation, providing industries with tools to enhance productivity, flexibility, and quality. As technology continues to evolve, the capabilities of these systems will expand, offering even greater benefits to manufacturers. SensoPart’s VISOR Robotic sensor, with its advanced Target Mark 3D technology, is a prime example of how companies can leverage cutting-edge vision technology to stay competitive in an increasingly automated world.
bit.ly/SPVisor

• EC+ AHU efficiencies of 85%
• Energy savings of 20-50%
• Product lifetimes of 20+ years
• Recyclability rate of 98%
• Complete plug-and-play
• Ultra-low sound levels
• Low maintenance costs
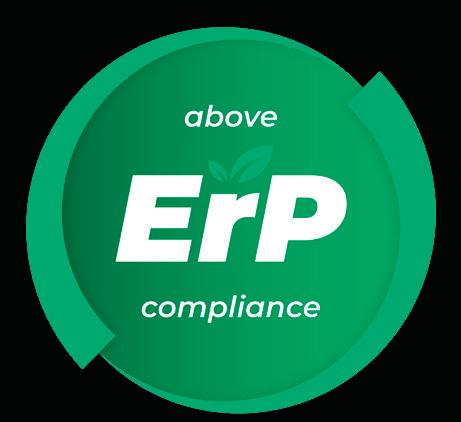
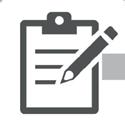
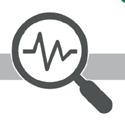

• ROIs between 12-18 months

• EC+ AHU efficiencies of 85%
• Energy savings of 20-50%
• Product lifetimes of 20+ years
• Recyclability rate of 98%
• Complete plug-and-play
• Ultra-low sound levels
• Low maintenance costs
• ROIs between 12-18 months
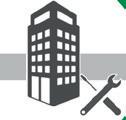
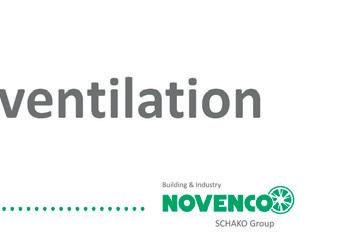
Unlock next-level productivity using cobots
Collaborative robots are fast becoming the benchmark in industrial automation, thanks to their ability to deliver higher productivity while working safely alongside human workers. Collaborative robots, a.k.a. cobots, are compact and lightweight, making them easy to deploy as requirements grow and change. Julian Ware, UK & Ireland Sales Manager for ABB Robotics, explains.
For today’s manufacturing companies, cobots offer many benefits that add value at every step of the production process. Their ability to work safely alongside humans without the need for physical guards, greatly reducing their overall footprint. This makes them ideal for applications where users want to maximise productivity without compromising on safety. Applications can include both continuous and intermittent collaboration, such as final trim and assembly in automotive manufacturing where some human interaction is needed.
Cobots also provide the flexibility to manage the shift towards low-volume/highmix production because they can swap between products and be trained to work with new products quickly and easily. With people and robots working side by side, users can benefit from the problem-solving capabilities, insights and adaptability to change of human operators, as well as the tireless precision and tolerance of repetitive tasks provided by robots.
Big potential, small size
The global collaborative robots market was valued at US$1.23 billion in 2022 and is expected to expand at a compound annual growth rate (CAGR) of 32.0%, from 2023 to 2030, according to Grand View Research. The analyst suggests that a combination of two factors is driving that growth.
First is the penetration of cobots into SMEs as they become more accessible in terms of price and ease of use. While robotic automation technology has evolved to meet the growing demands for high-volume industrial production, it has also led to the creation of smaller collaborative robots, such as ABB’s YuMi and GoFa cobots, which

are designed to fit easily into existing production lines, thanks to their flexible mounting options. With their smaller size and reduced reliance on peripheral equipment, collaborative robots can also reduce the investment needed for a robotic work cell to under $50,000 in many applications.
Second, technological advances are enabling robots to tackle more varied applications. An example is ABB’s cobot welding package, which uses a GoFa cobot equipped with a simplified auto-generated program selector tool to enable users to create welding sequences in less than 30 seconds. By eliminating the need for a teach pendant, the package cuts programming time by 70% and removes the need for operators to have prior experience in using a robot.
Plug the talent gap
Many manufacturers find it difficult to recruit experienced workers. Many young people who have grown up in the digital world see manufacturing as dirty, dull, dangerous, and repetitive. Also, with shorter product lifecycles, small manufacturers operating in high-labourcost countries cannot simply outsource to low-cost countries like large corporations do. In these conditions, collaborative robots not only reduce the need for manual labour, but can work tirelessly to deliver higher quality.
Hit the ground running
The plug-and-play qualities of modern cobots mean they can be installed much
more quickly, minimising interference with production processes. Their small footprint and portability make cobots suitable not only for automating existing production lines, but also more diverse applications.
Technological advances have made collaborative robots far more intuitive than their conventional counterparts. Features such as lead-through programming and a user-friendly touchscreen interface allow operators with no programming experience to quickly program the robot. Offline simulation tools such as ABB’s RobotStudio also allow operators to simulate an application on a PC. This helps reduce the time taken to get the robot running, which is ideal for organisations that have short product cycles.
More companies are looking towards the possibilities offered by robotic automation in general, and collaborative robots in particular, as a way of shoring up their workforce. These possibilities are likely to expand as robot manufacturers and their partners work to develop enhanced software features such as cloud connectivity, artificial intelligence and machine learning that increase their functionalities and make them safer, more adaptable, flexible and easier to use.
bit.ly/ABB_Collaborative
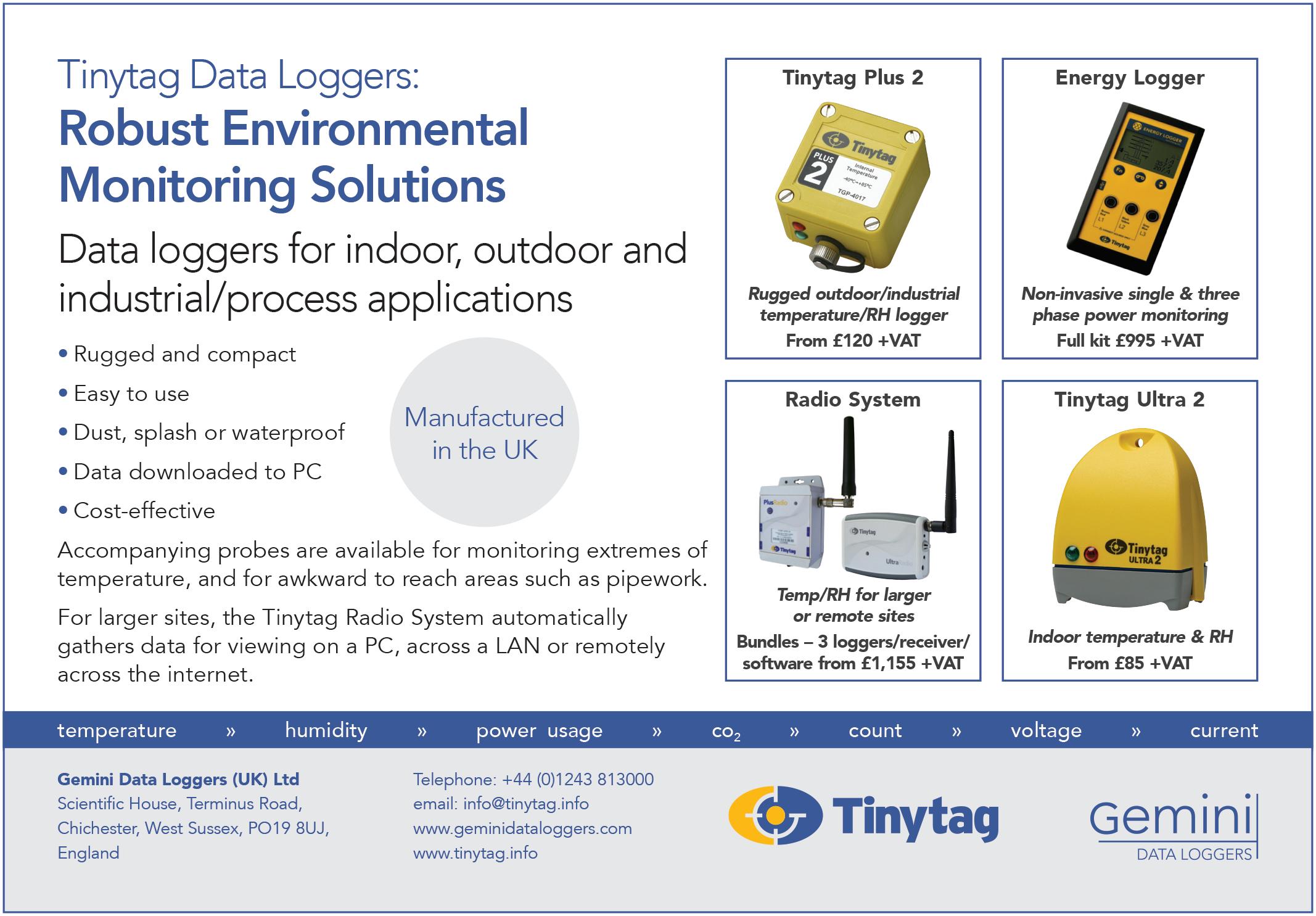

Real-Time Location Systems.
The next step in warehouse efficiency.
• Track the position of forklift trucks and other transport vehicles.
• RFID tags on individual products or pallets.
• Forklift reads all the tags on a pallet.
• Combine height data from forks with location data and RFID data.
• Software automatically tracks every movement of products.
• Integration with ERP and WMS systems.
• Real time reporting.
• Fulfills Auditing requirements.
• Operator guidance.
Turck Banner Ltd. Blenheim House, Blenheim Court, Wickford, Essex SS11 8YT Tel: 01268 578888 rfid@turckbanner.co.uk

Industrial robots and their human counterparts
Eric Halvorson, Marketing Technology Manager - Automation and Control at DigiKey, looks at how robotics is integrating with the traditional workforce in manufacturing settings and how fears around roles being replaced can be offset by opportunities for roles to be enhanced.
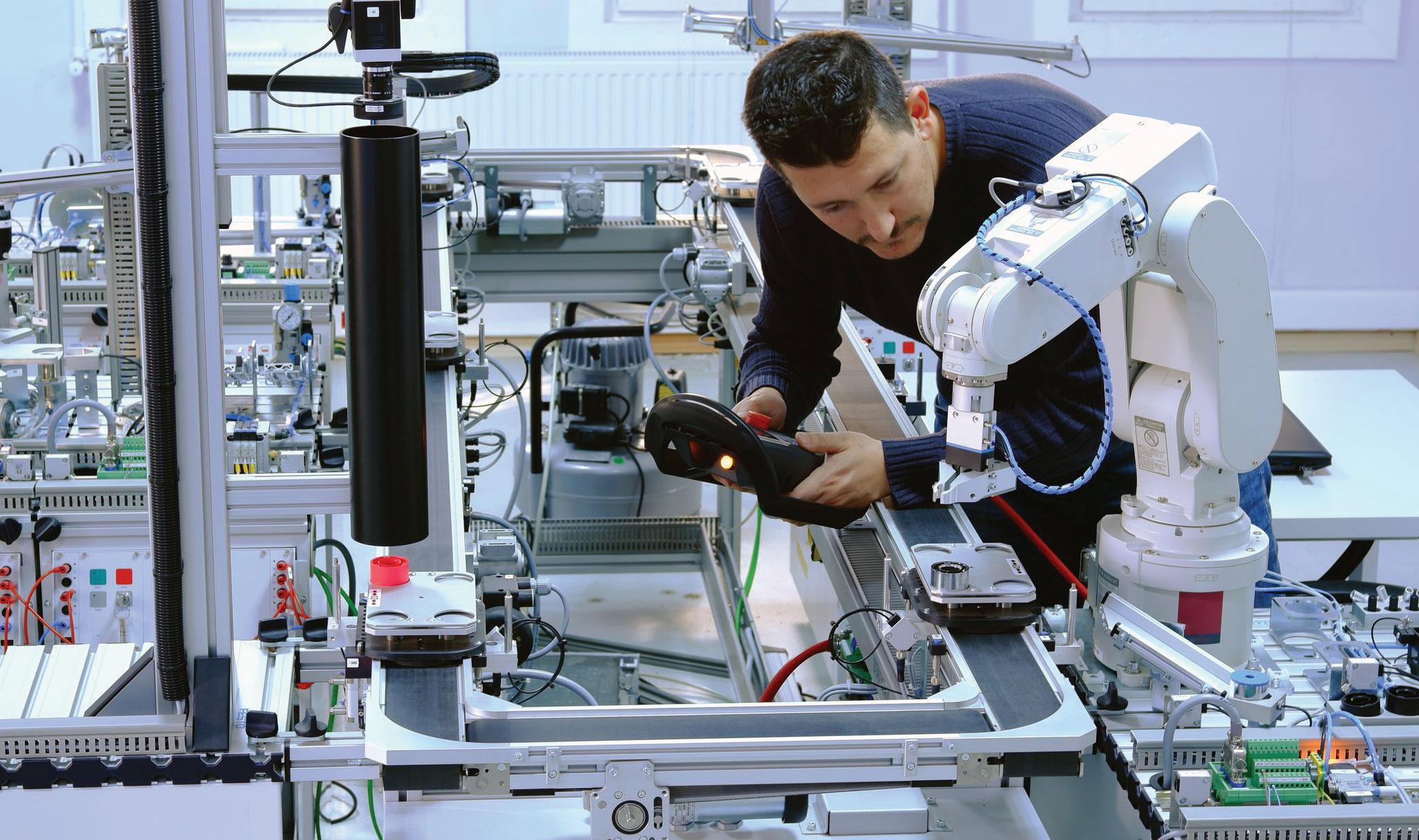
The conversation around robots and their use in manufacturing has long been controversial.
Many fear that the introduction of robots into the workplace will displace human jobs. In some respects, yes, robots will replace some jobs, but it’s not that simple. Yes, robots will replace some lowerlevel jobs. These jobs are the more menial and tedious jobs. These are jobs such as quality control on a factory line.
I can fondly remember the opening scene of an American television comedy show from the 1980s that took place in a brewery. While the antics on the plant assembly line are funny and over the top, in today’s manufacturing world, the demands for quality are quite high.
The need to ensure those bottles are properly filled and meet customer expectations is more important than ever. With the use of robotics and machine vision, we can now inspect every bottle as it passes at breakneck speed. From ensuring the liquid is filled to the proper level and colour accuracy to checking labelling applications and caps being sealed correctly, all aspects of the product’s quality are checked and made to meet specific tolerances. People have offdays and are subject to fatigue, illness, and complacency. Robots and machines do not. But the question is, what happens to those employees after their jobs are made obsolete? This is where the employee benefits. Now, those employees who were underutilised in
the past can move into better quality jobs, including jobs that require problem-solving or jobs that require more job fulfilment. These are higher-quality jobs. Many of these jobs are in concert with robotics. These are called collaborative robots, or cobots for short.
As I said earlier, there is quite a bit of fear about the implementation of cobots in the workplace. Yes, some jobs will be made obsolete. However, what many will experience is a shift in their job roles. There will be a need for robot designers, programmers, and maintenance workers. Others will need to be upskilled; basically, they will need to upgrade their skill set. This means better pay, better benefits, and greater job satisfaction. There are also things that humans are inherently
good at where their robot counterparts are not, such as problem-solving skills, critical thinking, and creativity.
Cobots have come a long way over the past decade. With safety in mind, these robots work right alongside their human counterparts. These cobots are capable of handling the heavy lifting for humans, allowing them to focus on the more mental workload. For example, at Amazon, cobots are used to move products to pickers rather than the picker going to the shelf, pulling the product, and returning it to their station. This saves the worker time, steps, and possibly a lot of heavy lifting. The cobot saves the worker’s energy and reduces the daily wear and tear on their bodies.
But how do we ensure human safety around cobots? Today’s safety standards for cobots are exceptionally stringent, as they should be. There are numerous safety features on cobots as defined by ISO/TS 15066, which provides guidelines for the design and implementation of collaborative workspaces. This enables shop managers and manufacturers to safely incorporate
humans and their mechanical counterparts. Some examples:
1. Maximum Allowable Speed. This is set at the point of the EOAT (end-of-arm-tooling). These speeds are in line with human equivalent speeds.
2. Speed and Separation Monitoring. Defines the minimum safety distance between the worker and the robot system to prevent contact between the robot and the human. This can be achieved by utilising safety scanners, light curtains, and operator presence mats.
3. Power, Force, and Torque Limits. Cobots are designed to measure torque at every joint in case of excessive torques or forces and monitor for sudden impacts, including soft obstructions.
4. Redundant Checking Systems Diagnostics. If the robot detects an anomaly or error at any point, the robot will disable motor power instantly.
5. Safety Rated Stop Modes. Cobots are required to act based on the level of risk. That could be a full emergency stop if a safety mishap has occurred, or it may be a protective
6. Ergonomic Design. In six axis robots, there are a number of potential pinch points. By designing those joints ergonomically, the worker can avoid injury should their hand, fingers, or even loose clothing get trapped in a joint.
7. With the installation of any robot in a production setting, great care must be taken to ensure a truly safe workspace. This is particularly true in an overlapping workspace that will be shared by humans and their robot counterparts. Consulting a professional installer or integrator will help you to do a full risk assessment and ensure you meet all applicable safety codes and regulations with regards to cobots.
Cobots have the ability to reduce worker fatigue, increase production rates, and increase quality, all while reducing waste. In truth, they can be a force multiplier for your production force. In today’s world, where we all face labour shortages, increased competition, and high consumer demand, cobots can be an equaliser while creating higher-quality jobs.
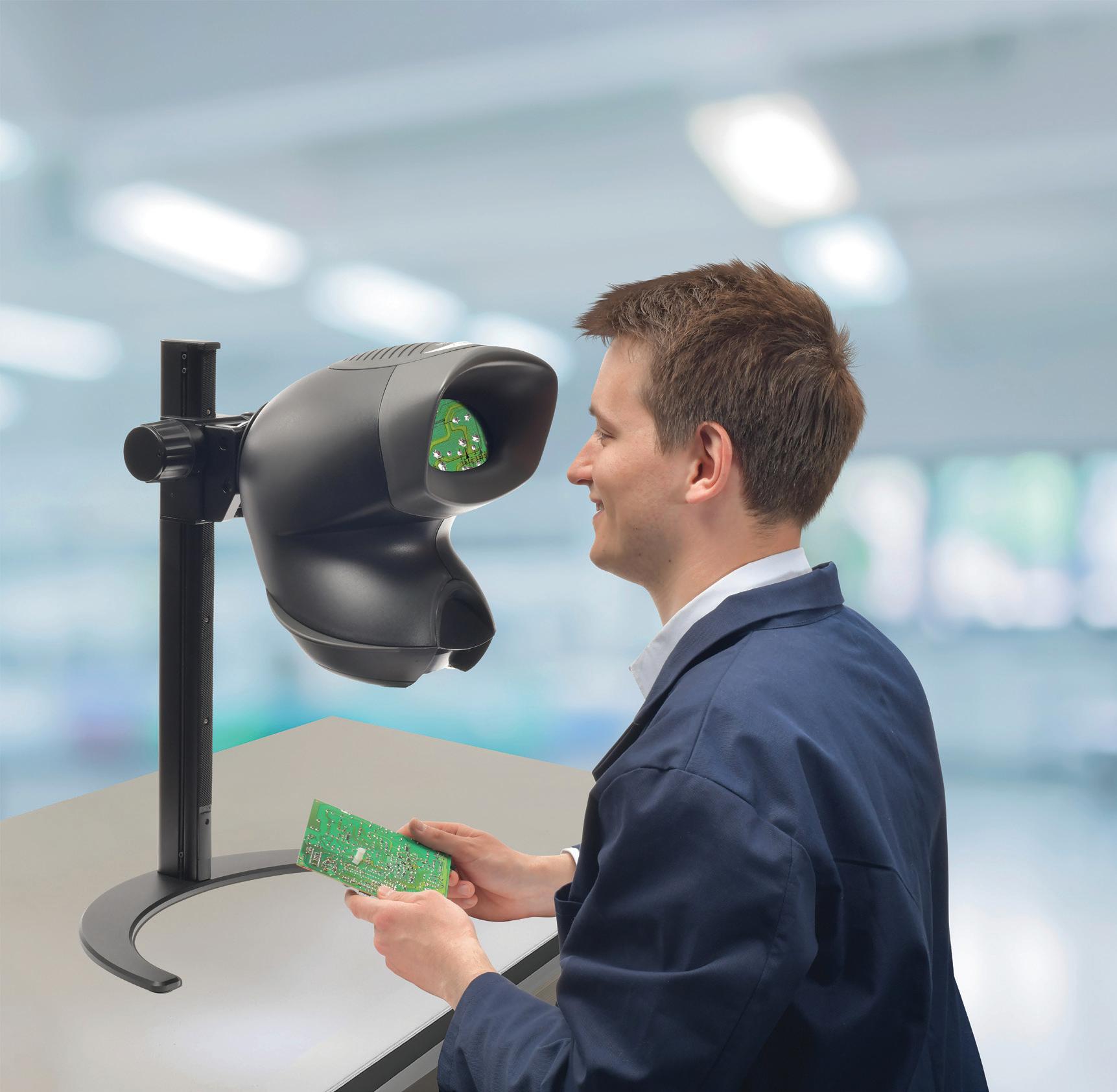



www.digikey.co.uk


Partnership automates airframe drilling
An automated drilling solution comprising a FANUC cobot uses pre-qualified tools and process parameters to speed up aircraft production in response to booming order books and a record backlog within aerospace manufacturing.
The ADUbot has been developed in conjunction with aerospace automation specialist Electroimpact and Luebbering, a leading manufacturer of high-precision fastening and drilling tools and technology. By automating the traditionally manual task of drilling thousands of holes in airframes –and using tools that have already been qualified – the ADUbot will assist aircraft manufacturers to rapidly achieve high levels of drilling autonomy, freeing up human employees to take on more value-added tasks.
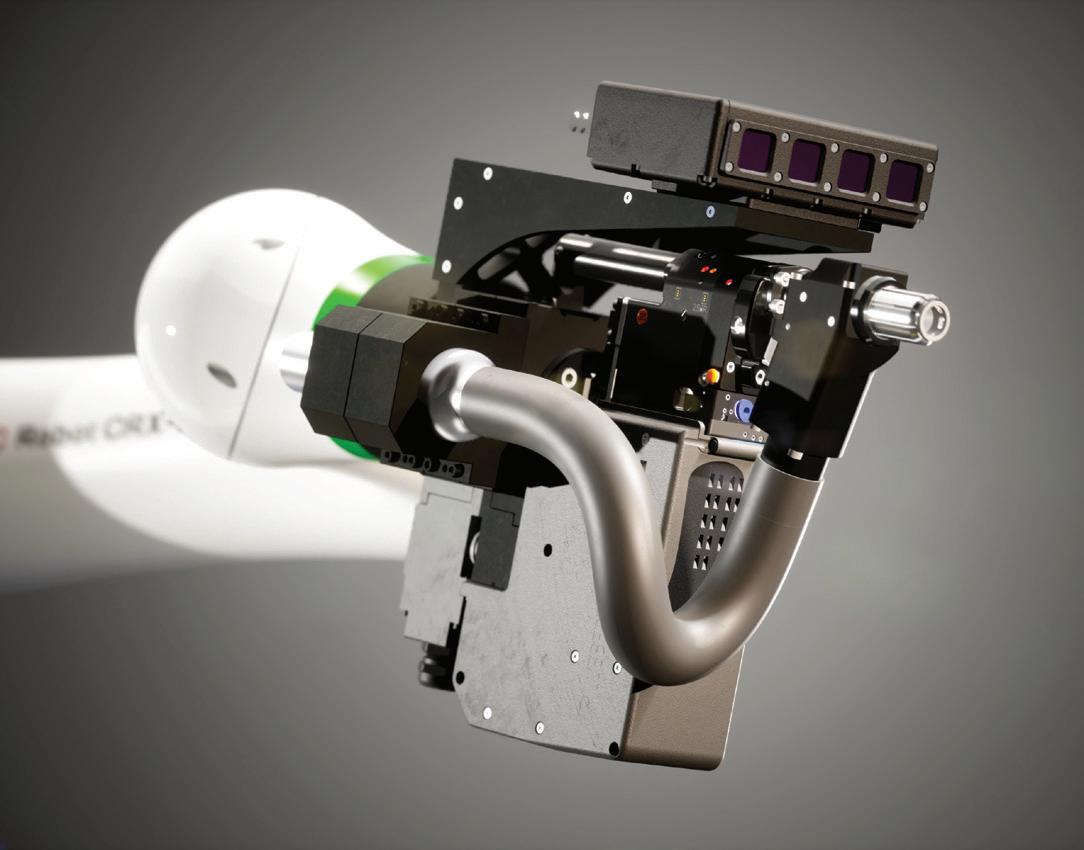
“The record number of orders for aircraft over the next decade means that manufacturers and suppliers, across the whole supply chain, are having to streamline operations and cut cycle times while, at the same time, maintaining the highest standards of quality and safety,” said Oliver Selby, Head of Sales at FANUC UK.
In a bid to help aircraft manufacturers increase production rates without impacting on quality, the FANUC/Electroimpact/ Lueberring partnership identified drilling as a key application that would benefit from being automated.
“Traditionally, operators rely on a standard aerospace hand tool that uses a concentric collet locking interface to metallic drill templates or drill jigs that are attached to the wing. These drill tens of thousands of holes in aircraft every day – yet they are all operated by hand,” explained Robert Brownbill, Senior Mechanical Engineer for Deeside-based Electroimpact. “The operator must locate the end of the drill unit into the drill jig, then activate the locking collet to
begin the process, drilling an incredibly hightolerance hole into the structure. The collet is then unlocked, and the operator moves to the next hole.”
Accurate, fast and safe
By contrast, the ADUbot developed by FANUC, Electroimpact and Luebbering, sees a FANUC CRX-25iA cobot take over the manual aspects of this drilling process.
As a collaborative robot, it is designed to operate safely with human personnel in close proximity. It can be quickly programmed for the task at hand and equally quickly be reprogrammed for the next job. It is mobile and can be moved easily from one location to another, making it especially suited to aircraft assembly operations.
Accuracy is also crucial – each hole has to be drilled to a very tight tolerance in terms of location and dimensions. “The use of FANUC’s Force Control routines allows us to utilise the existing manual drill jigs to locate ADUbot into the drill jig, and then we can command the ADU to drill the hole,” said Robert. “The ADUbot still requires some
manual support in fixing the drill jig to the structure. However, once that’s done, ADUbot can be wheeled into place, the jig resync targets can be scanned, and the system can be left alone to complete the drilling processes. The major benefit to this process is that one operator can now operate many ADUbots, making it much more efficient.”
Overcoming hurdles
A particular challenge for any new process within the aerospace industry is that it often requires qualification before it can be used on a flying aircraft. The validation process can be lengthy, which can discourage the adoption of even the most innovative new ideas and processes. Return on investment (ROI) usually has to be high to overcome this hurdle. FANUC, Electroimpact, and Luebbering have turned that situation on its head by offering a solution that can be deployed immediately and with low capital investment.
“The beauty of the ADUbot is that it uses tools that have already been validated,” says Oliver Selby. “As end-users won’t have to go through the validation process, we can save them months in getting up to speed on automation. It’s a very cost-effective solution with a fast ROI.”
Drilling may appear to be a straightforward process to automate, and in many ways, it is. However, achieving the precision required for aerospace tolerances presents significant challenges. The simplicity of using a pre-qualified tool makes this the perfect application for automation.
www.fanuc.eu/uk/en
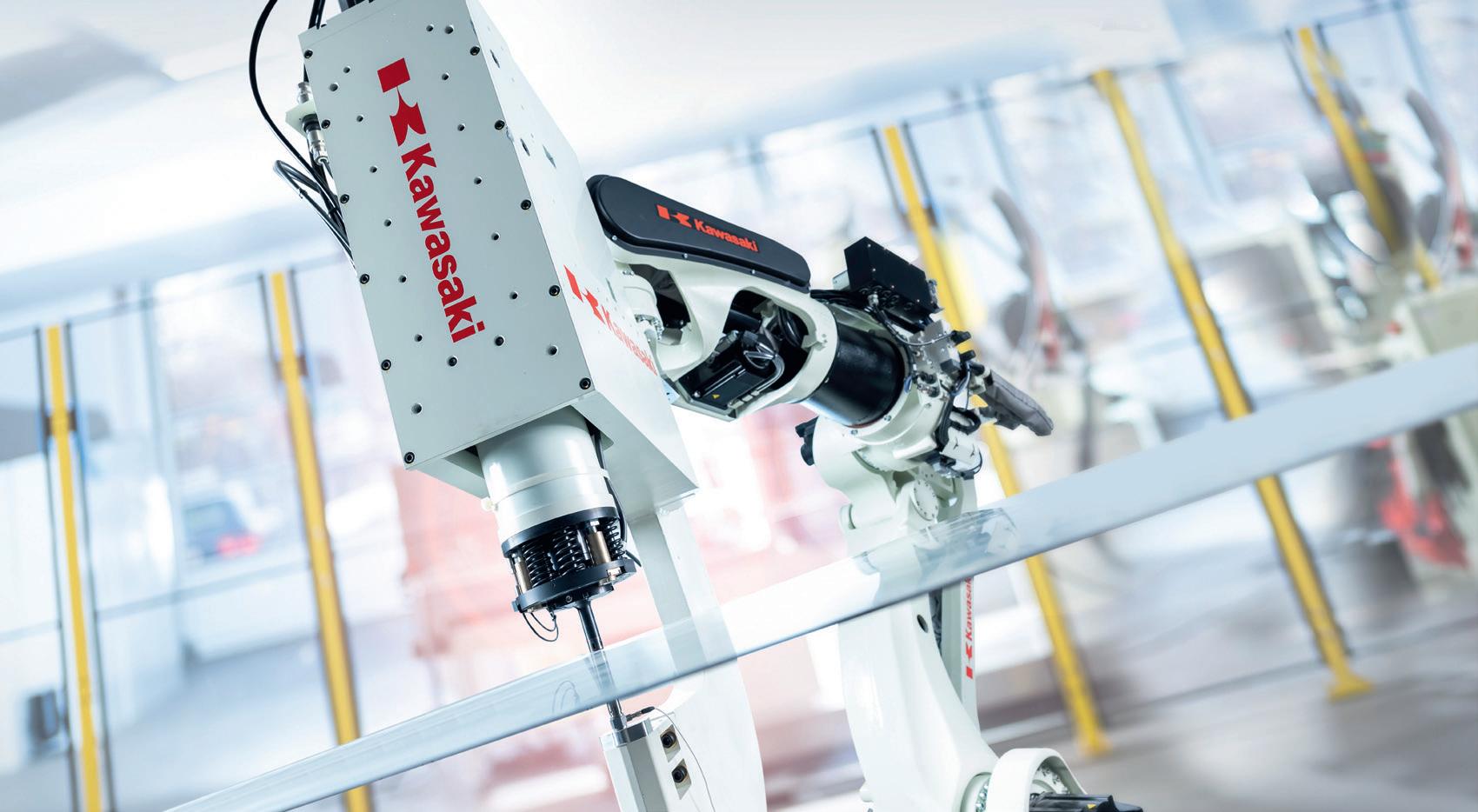
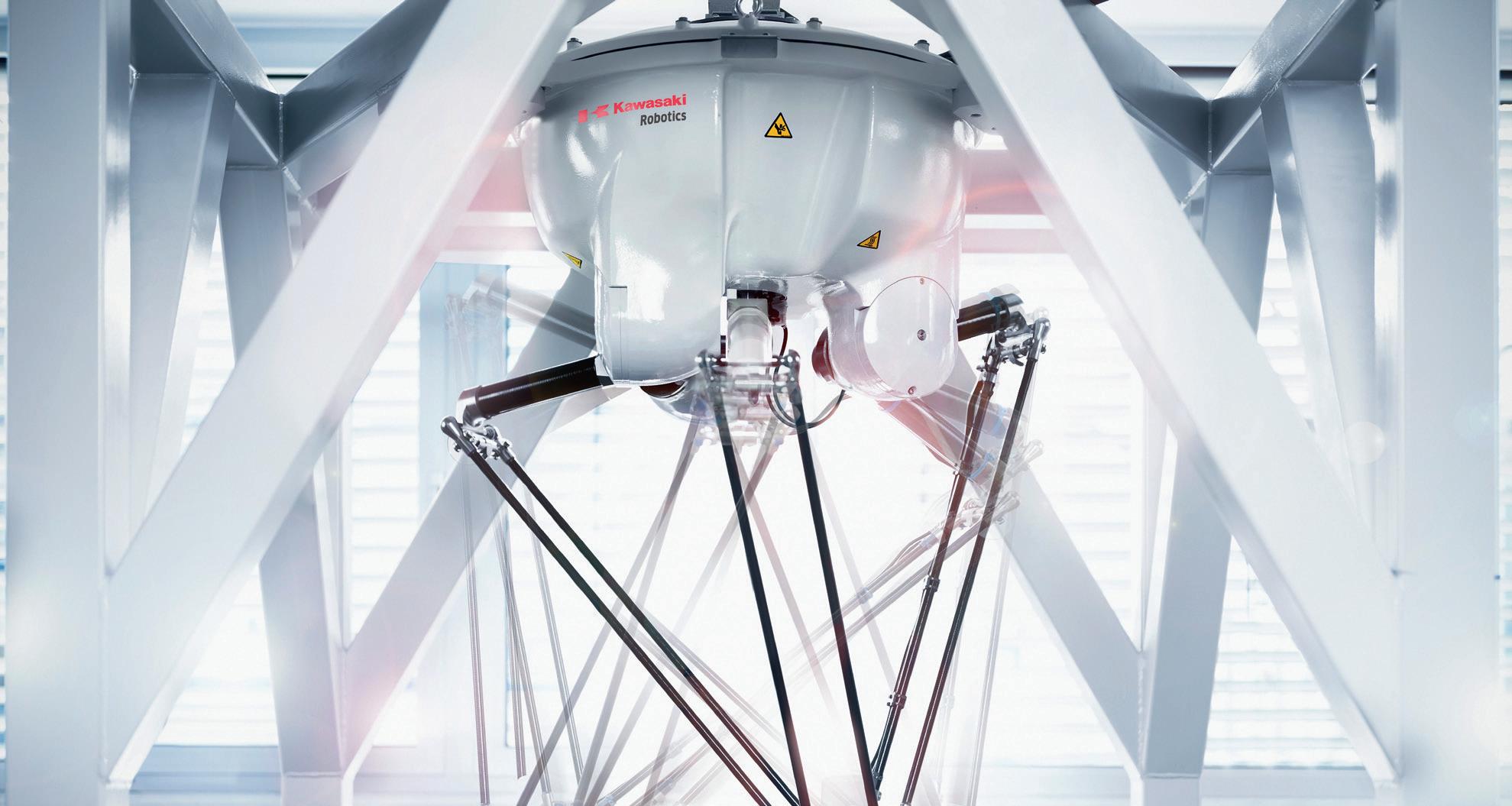
Kawasaki Robotics
Tel:+44-1925-713-000
www.kawasakirobotics.com/uk/
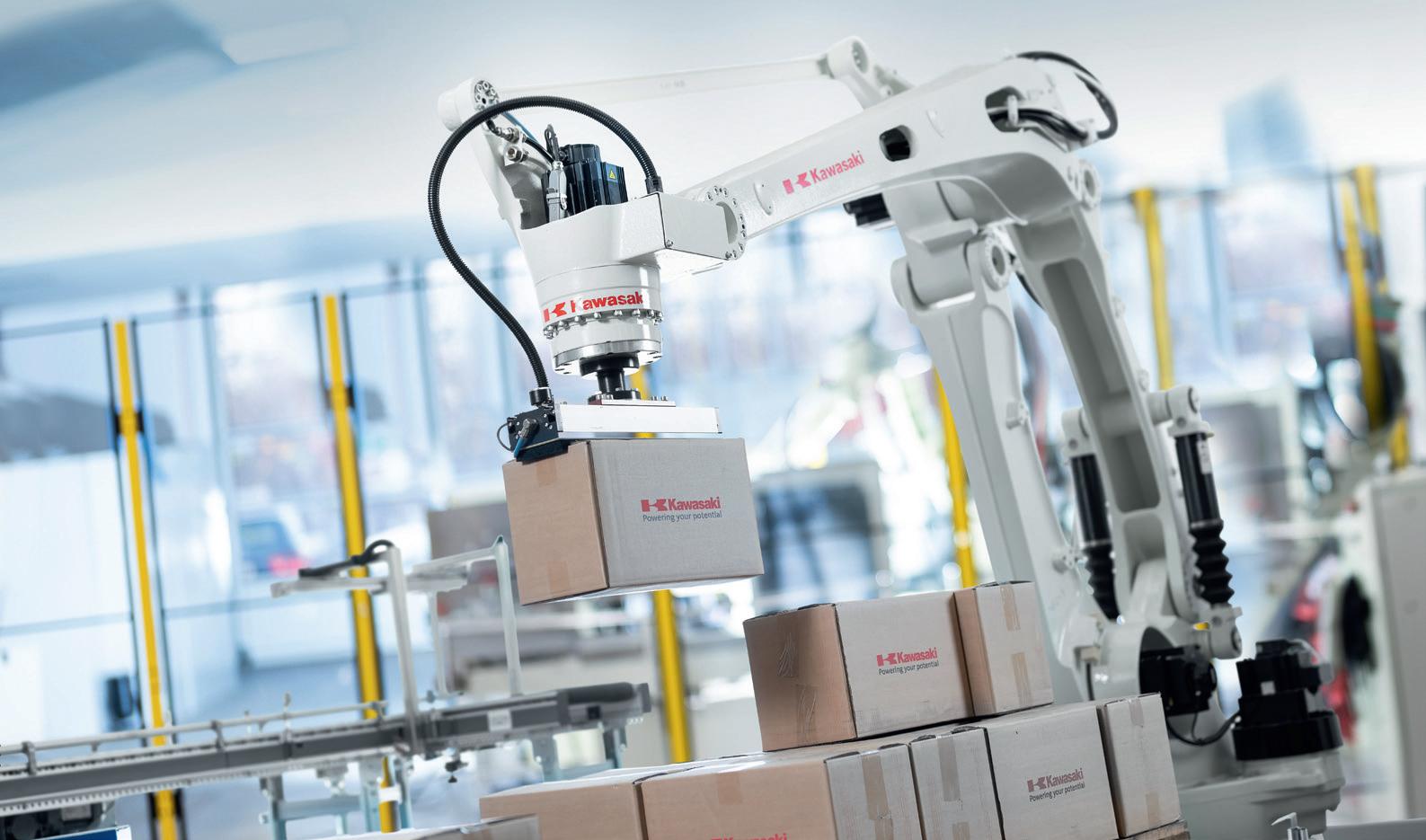
Digitising with open standards
Tim Foreman, European R&D Manager at OMRON Europe BV, explores how open standards can maximise the performance optimisation benefits that digitisation can deliver.
In a manufacturing context, the purpose of digitisation is to help factory managers sleep soundly at night. Can we commit to the predictions I have made? Will we be able to deliver to the deadline? Do I have enough insight to know for sure? How is the factory doing in terms of QCDE (quality, cost, delivery time and environmental impact) against our targets and compared to the competition?
These are some of the concerns that keep factory managers awake at night, concerns that can be addressed through digitisation. In a digitised production environment, factory managers don’t have to worry about the unknowns, the risks and the might-happens. Digitisation eliminates uncertainty and enables performance-driven optimisation. It provides insights that can help factory managers improve quality, reduce cost, shorten lead times and reduce environmental impact. The manager of a digitised factory shouldn’t wake up worrying in the middle of the night, but if they do, a brief glance at their mobile phone should reassure them that everything is running as it should be.
However, moving from a state of anxiety-induced insomnia to one of blissful somnolence is not easy. Put bluntly, digitisation can be quite tedious. Project leaders rarely have the luxury of working with a blank canvas; most of the time they are working with a patchwork quilt of old technologies sewn together; they are trying to digitise production lines incorporating machines that have never logged data and were built before data communication protocols even existed. This all adds up to a sizeable OT and IT integration challenge.
Aim for 80%
My advice would be to accept that you are not going to be able to digitise every square metre of your factory (unless you are lucky
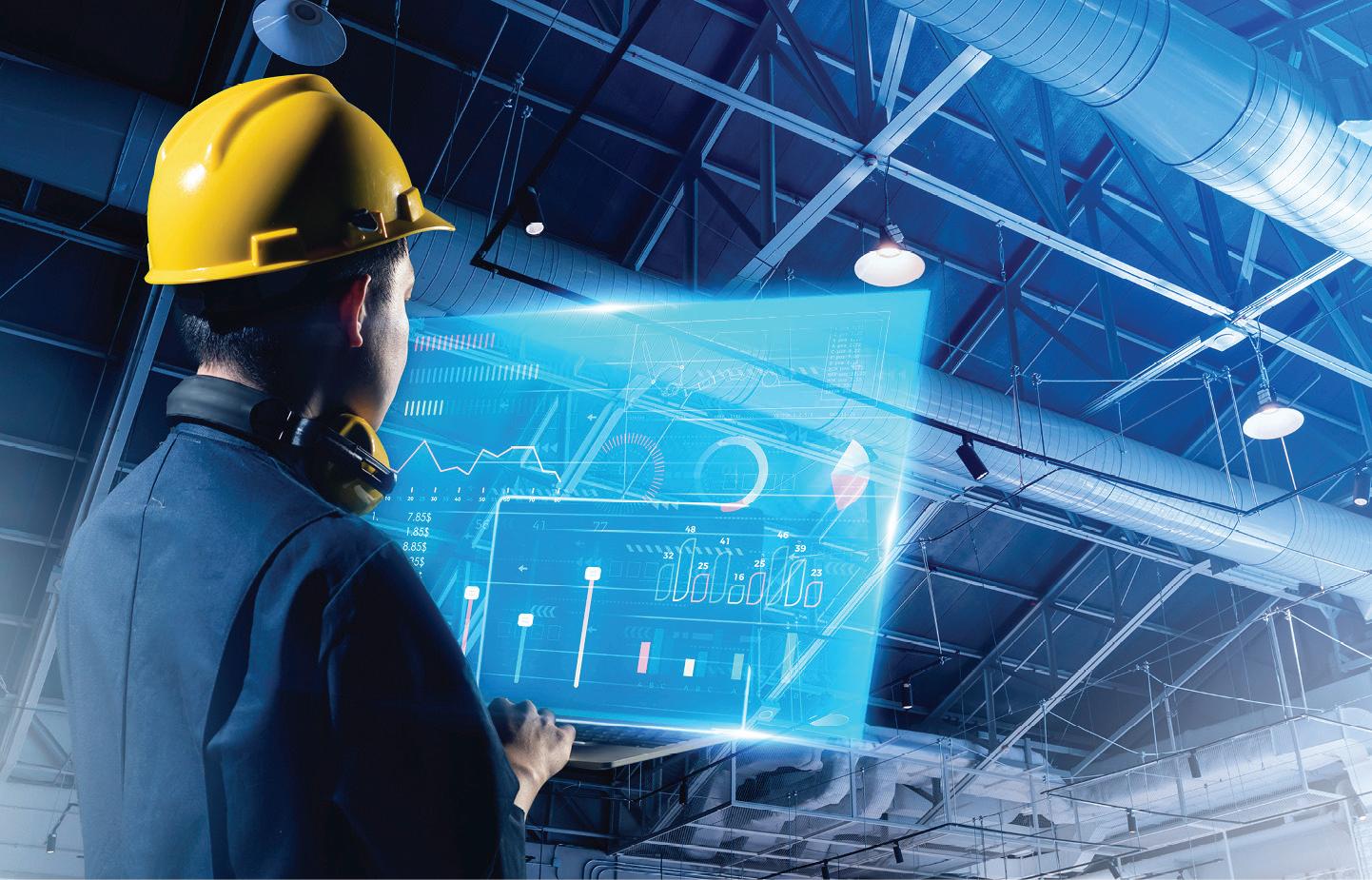
enough to be digitising a brand-new facility). To do so would be way too expensive and complex. Most factories built in the last five years can expect to be able to digitise at least 80% of their workflow, and the key to this is establishing standardisation. That means standardising the type of data being generated and collected, the metadata that is used to document data and the way in which data is exchanged and communicated.
You can use non-open standards, but ultimately this will limit your ability to fully capitalise on the performance optimisation opportunities that digitisation presents and to communicate beyond the factory walls, which is why we advocate an open standard digitisation approach.
For collecting real-time machine and process data, a common modelling language such as PackML will achieve standardisation. Successful digitisation also requires a standardised communication protocol so that machines can talk to one another and other Industry 4.0 components. OPC UA, a protocol that originates from the IT domain,
is increasingly crossing over to the industrial automation sphere, and OMRON is part of an automation industry-led steering committee that is extending OPC UA to industrial fieldlevel devices called UPC UA FX.
The analogy I often use is with the English language, the universal language of business. If you speak English, you can do business with most people. The same principle applies to OPC UA FX in an industrial context.
This open standard supports complete interoperability within a factory. Not only does it allow machines to talk to each other in data terms, it also enables machines to talk to IT systems such as ERP and MES systems, as well as data analytics systems that you may be running on a local or virtual cloud.
Opening up opportunities
However, its real potential lies in its ability to support mutual information sharing and communication across multiple sites and in the supply network. With open standard digitisation, manufacturers can
compare multiple factories to drive further improvements, and can duplicate ways of working across production sites. They can even use data from their supplier processes to inform their manufacturing schedules, telling them when a particular part is going to be delivered, for example.
Open standard digitisation is also key to deriving value from Digital Product Passports (DPPs). As well as being a legal requirement from 2027 for some industries, DPPs, which provide a digital record of a product’s composition, origin and lifecycle, are a useful Industry 4.0 tool. For example, DPPs could be used to improve the quality and reduce waste in the production of batteries for electric vehicles. Combining components of the same quality has been found to result in a better battery. The reason this doesn’t always happen is because of variation that occurs within set tolerances. Using DPP data communicated via OPC UA, warehouses could pick individual components with similar characteristics and thereby reduce the risk of batteries failing factory tests and having to be scrapped.
One of the questions I am often asked
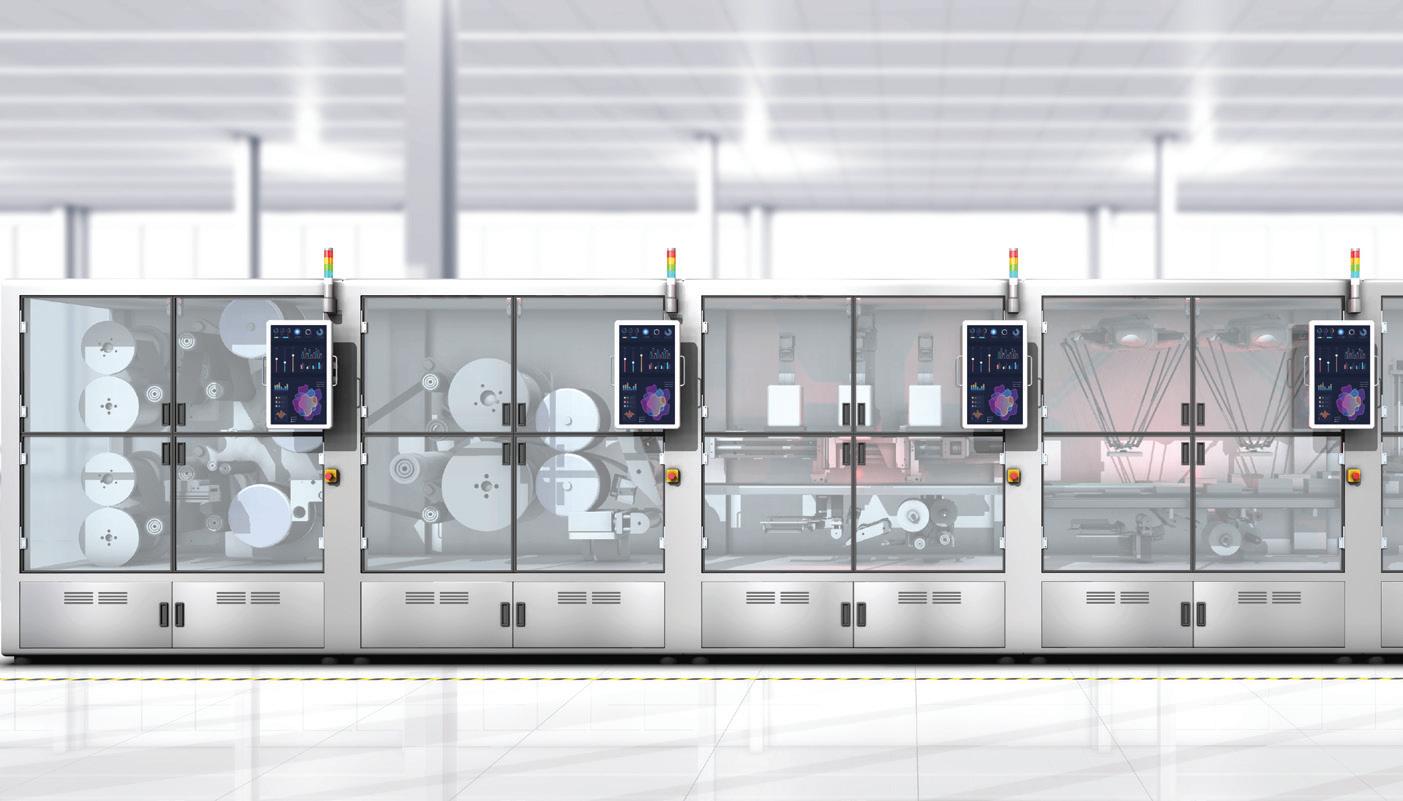
about open standard digitisation is whether it is ‘retrofittable’. I’m going to bring in another language-themed analogy here, this time with Google Translate. OMRON has developed an edge data controller that translates data from older machines into the latest language and data types. Effectively, it is a gateway box that can be used to make older machines open standard.
Digitisation is gaining momentum with growing awareness of the real-world
Sustainability for a net zero future
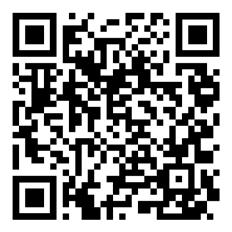
benefits that data-driven insights can bring. However, standardisation – in terms of the type of data being collected and the way in which that data is communicated – is a major challenge for factories looking to digitise industrial automation. By adopting an open standards approach, manufacturers can succeed at digitisation, and factory managers can sleep easy.
industrial.omron.co.uk

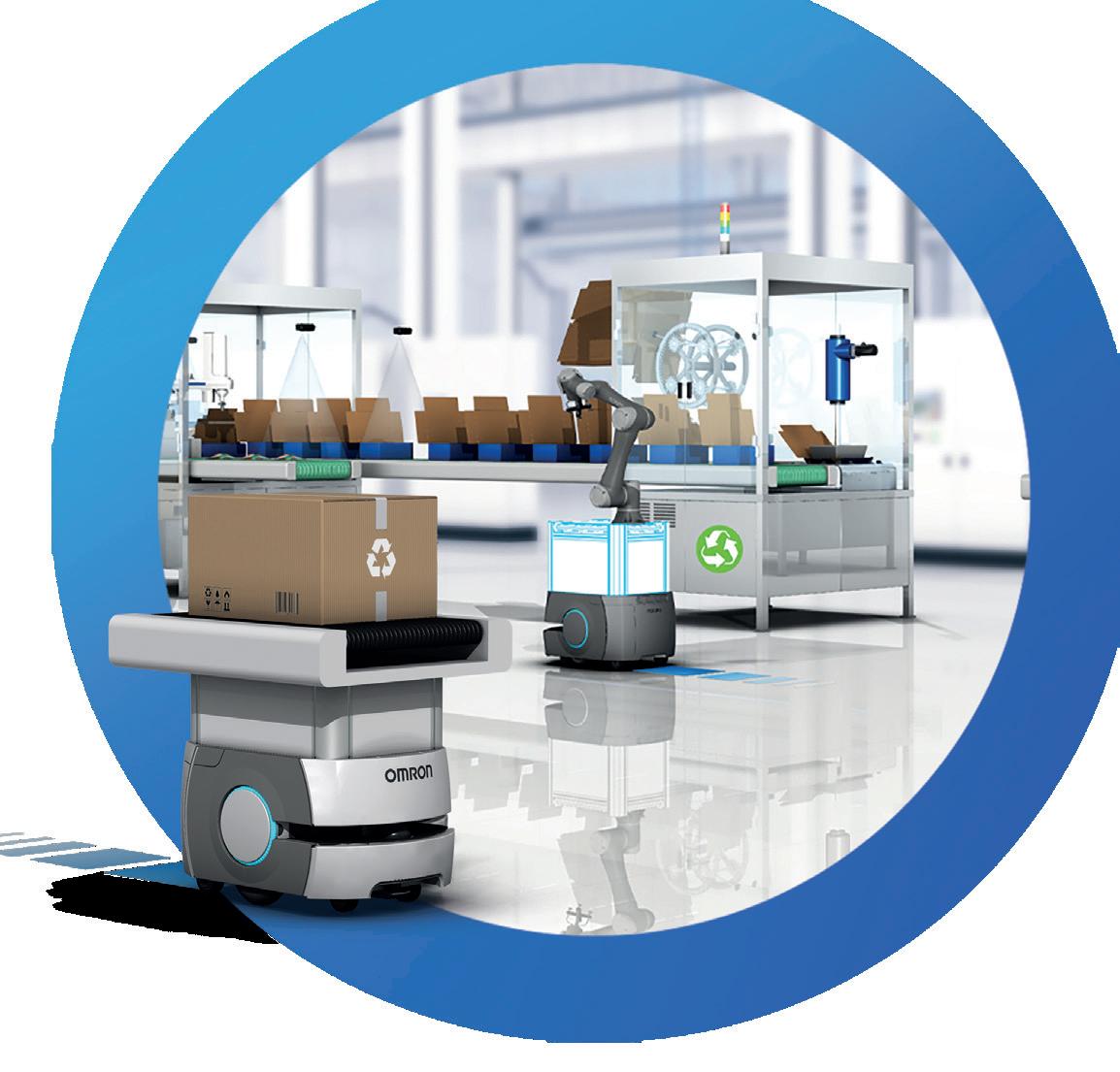
Manufacturing Information Systems: A clear strategy is key
Tascomp, the company behind the PlantRun OEE, machine downtime and manufacturing information system, looks at how and when to implement a manufacturing information system to achieve the greatest benefit.
There is no value in implementing a system unless it is done strategically and with clear objectives.
Many companies rush to adopt new technologies without fully understanding their needs, leading to wasted resources and disappointing results. The key to a successful implementation lies in knowing when and when not to introduce a new Manufacturing Information System that provides real-time KPIs such as overall equipment effectiveness (OEE), shopfloor dashboards and automatic reporting.
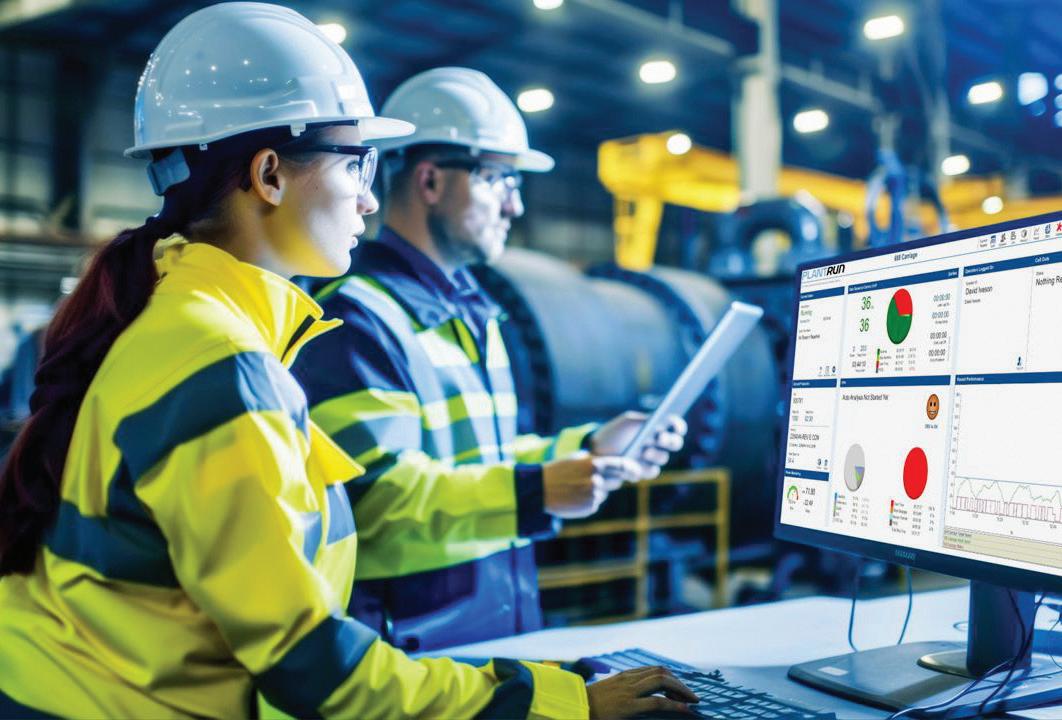
information drives continuous improvement initiatives, with adjustments in processes and lean strategies based on realtime insights.
Engage your team in these efforts by sharing findings and involving them in problemsolving. When employees see the tangible benefits of the system, such as reduced downtime or improved product quality, they are more likely to support and actively participate in its use.
When not to implement
Implementing a system without a clear purpose or plan is a recipe for failure.
If your organisation lacks specific goals, such as reducing downtime or improving production efficiency, the system will likely become an expensive, under-utilised tool. Additionally, if the resistance to change within your team is not managed, or there is insufficient training, the new system may cause more disruption than improvement. Data alone does not drive improvement. Without a commitment to analyse and act on the information collected, even the most advanced system will not deliver a return on investment. Systems like PlantRun provide valuable insights, but their benefits are only realised when this data is used to make informed decisions and drive process improvements.
When to implement
The best time to implement a system is when there is a clear understanding of the goals you want to achieve and a
commitment to use the data effectively. Start with specific, measurable targets. Identify key performance indicators (KPIs) that align with your business objectives, such as reducing cycle times, increasing throughput, or improving product quality. Systems like PlantRun can track these metrics and provide the data needed to monitor progress and make adjustments.
One of PlantRun’s customers, a printing company, aimed to reduce reprints, each costing them time and money. By halving their yearly reprint figure, they saved £75,000, paying for their system multiple times over.
To truly maximise the return on investment, it is crucial to involve operators and managers in the implementation process. Ensure they understand how to use the system and the benefits it provides. Engaged employees are far more likely to utilise the system effectively and contribute to its success.
Making data work for you
Once the system is in place, you should establish a routine for reviewing the collected data. Regular analysis will help identify trends and areas for improvement. Using this
PlantRun does more
PlantRun can seamlessly integrate with existing ERP and MES systems, providing a holistic view of operations. This integration ensures that data flows smoothly across different platforms, enhancing overall efficiency and decision-making.
From one machine to hundreds of processes across multiple sites, PlantRun has been used across every manufacturing industry and scales to meet the user’s needs. PlantRun offers a range of modules, from energy and condition monitoring to digital work instructions and setup checklists. Tailoring the system ensures that it addresses the user’s unique challenges and objectives.
Implementing a Manufacturing Information System like PlantRun can transform a business’s operations, but only if done thoughtfully and with a clear strategy. Users must understand when and why to implement, set measurable targets, involve their team, and use the data to drive continuous improvement. By doing so, it’s possible to ensure that the investment pays off and leads to significant gains in productivity and efficiency.
www.plantrun.com
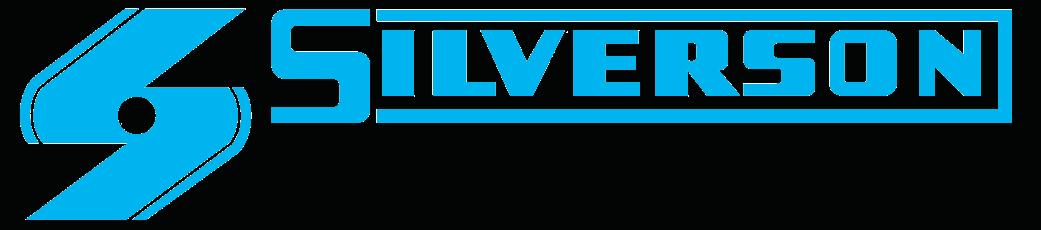
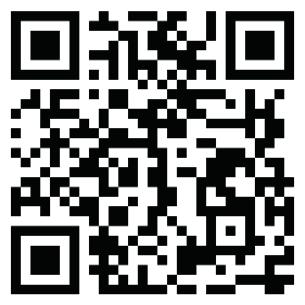

High Shear, High Impact
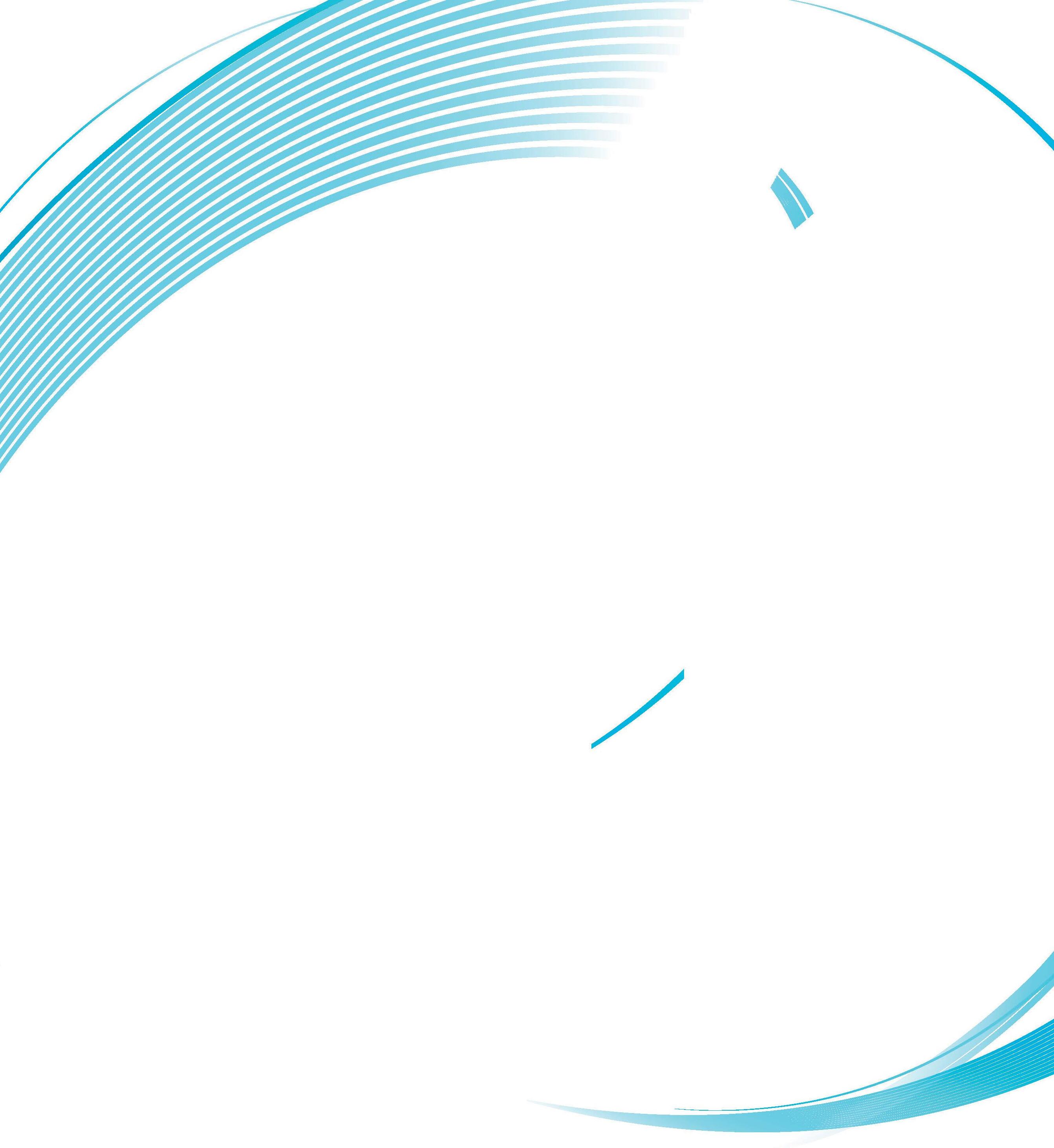
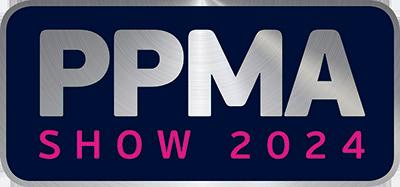
Maintaining excellence through a connected workforce
Digital transformation is revolutionising maintenance tasks by creating a connected workforce empowered with advanced tools and technologies such as real-time data, wearable devices, and digital workflows. Keith Tilley, Chief Executive of Intoware, explores the benefits this transformation offers maintenance teams.
In today’s fast-evolving industrial landscape, the concept of the “connected workforce” is becoming increasingly important, driven by digital advancements that streamline operations, enhance productivity, and foster a collaborative working environment.
But what exactly is a connected workforce?
A connected workforce refers to employees who are seamlessly integrated with digital tools and systems, enabling real-time communication, data sharing, and collaborative problem-solving.
This connectivity is not just about having access to the internet or mobile devices, but utilising tools and technologies such as digital workflows to boost productivity and reduce downtime.
In the context of maintenance tasks, creating a connected workforce through digital transformation can lead to significant improvements in several key areas:
• Preventive maintenance involves regular inspections, servicing, and upkeep of equipment to prevent breakdowns and prolong lifespan. A centralised digital platform allows maintenance teams to access equipment manuals, standard operating procedures, and maintenance histories, enabling efficient performance of routine tasks.
• Corrective maintenance is required to restore functionality when equipment malfunctions or breaks down. Accessing digital work instructions using a tool such as Intoware’s WorkfloPlus, which outlines stepby-step procedures for diagnosing issues and repairing components, minimises downtime and maximises productivity.
• Predictive maintenance leverages real-time data to forecast machine failures, enabling proactive maintenance and better resource management. Digital transformation facilitates easy access to this data.
• Condition-based maintenance relies on real-time monitoring and analysis of equipment condition. Digitalisation allows maintenance teams to assess equipment health, trigger tasks based on actual conditions, and take proactive measures to prevent failures.
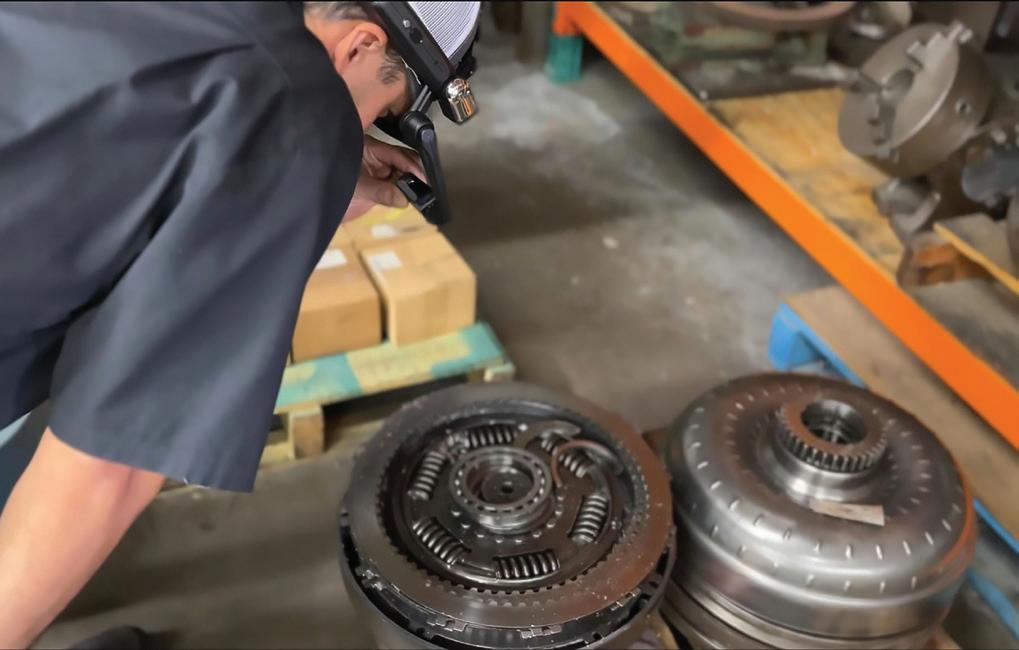
• Shutdown maintenance during planned shutdowns involves comprehensive inspections, overhauls, and major repairs.
A connected workforce utilising digital tools transforms this process by providing a centralised place for equipment information, work instructions, and safety guidelines, ensuring compliance and efficient task execution.
Case study
Centranz, which specialises in remanufacturing transmissions for off-highway equipment, including Volvo, ZF, Allison, Funk and Fuji, introduced WorkfloPlus to simplify and streamline its reporting process. The Centranz team uses the technology during component failure evaluations, disassembling and maintaining transmissions to identify root causes and potential future failures.
The company captures details and communicates findings to customers through failure analysis reports, including detailed descriptions and images/videos that clarify solutions.
Previously, this process used pencil and paper illustrations, mobile phone photos, and verbal or email communication.
Now, as David Crowther, Sales Representative at Centranz, explained, WorkfloPlus ensures consistent and clear
reporting: “Now, with WorkfloPlus, we’re able to put all our findings into one format, with pictures and descriptions of each image of the failures, in one file which can be shared with our customers.
“Rather than an email with descriptions of the failures within, and sending random pictures, everything is condensed within this file for your product that helps the customer get a bigger picture and a better understanding of what all our team’s findings entail.
“It’s a simplified process that has helped all aspects here within Centranz, for us to communicate properly and professionally with our customers on a much higher level compared to the way we were doing things.”
Maintaining excellence
The connected workforce is not just a futuristic concept but a practical and necessary evolution in today’s industrial environment.
And, when it comes to maintenance tasks in particular, digital transformation provides the tools and technologies needed to enhance performance, leading to greater efficiency, reduced downtime, and cost savings through the creation of a better equipped, more informed and highly connected team.
www.intoware.com
Streamline maintenance operations to reduce asset downtime and increase production
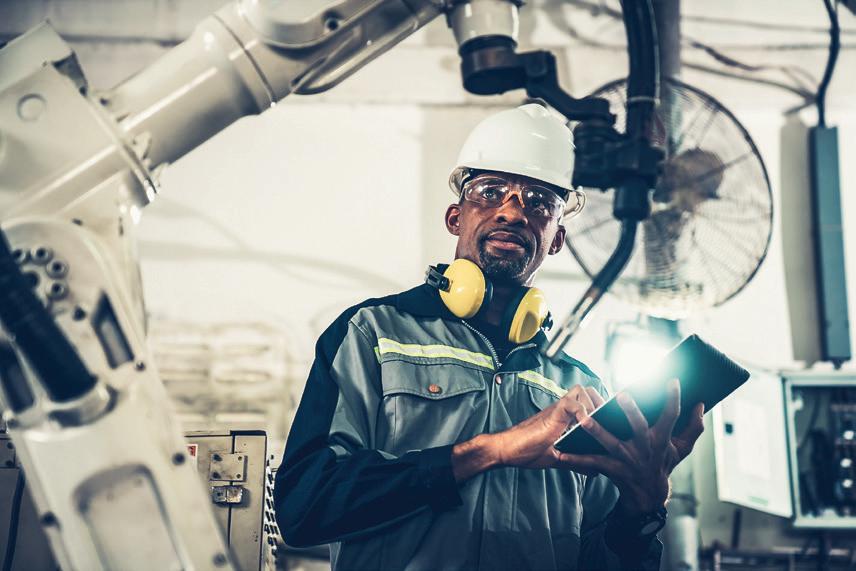
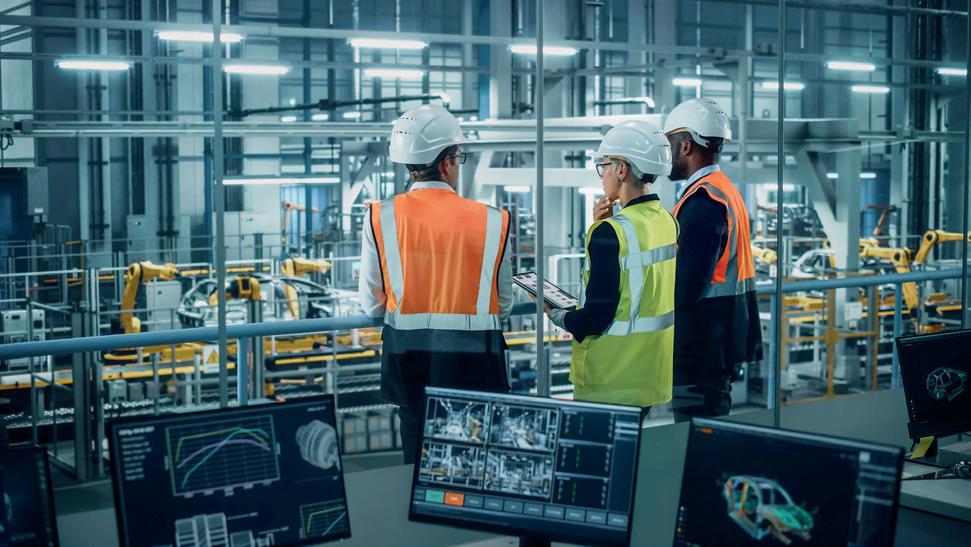
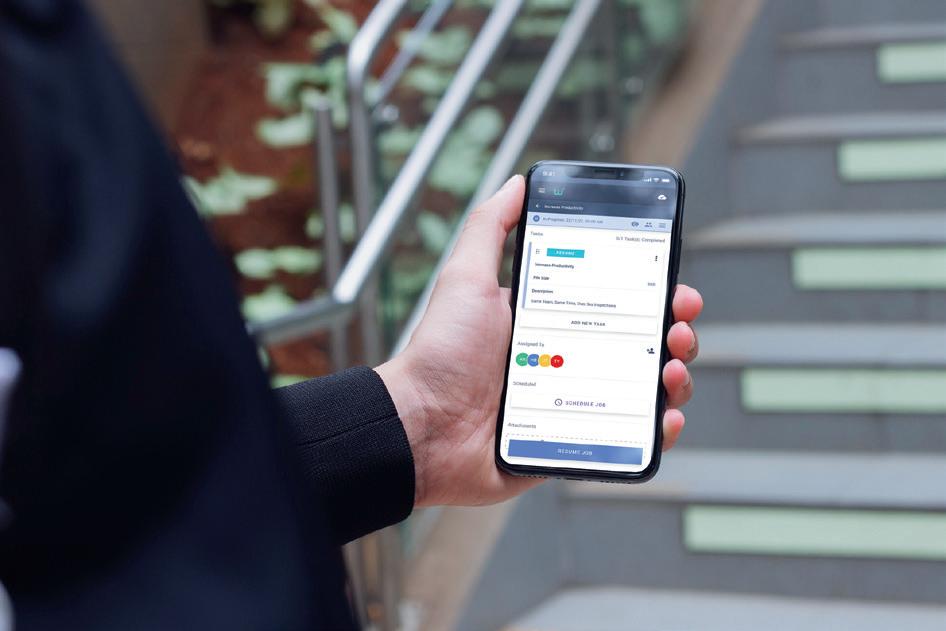
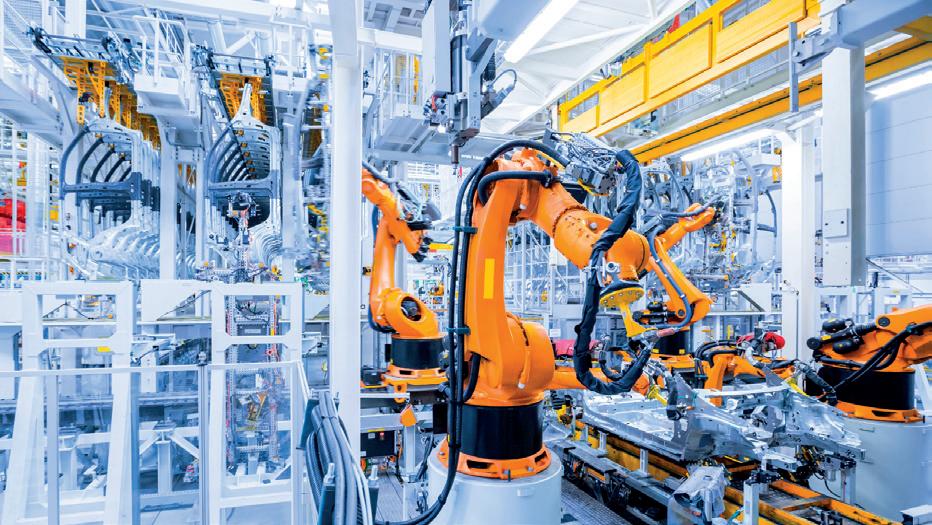


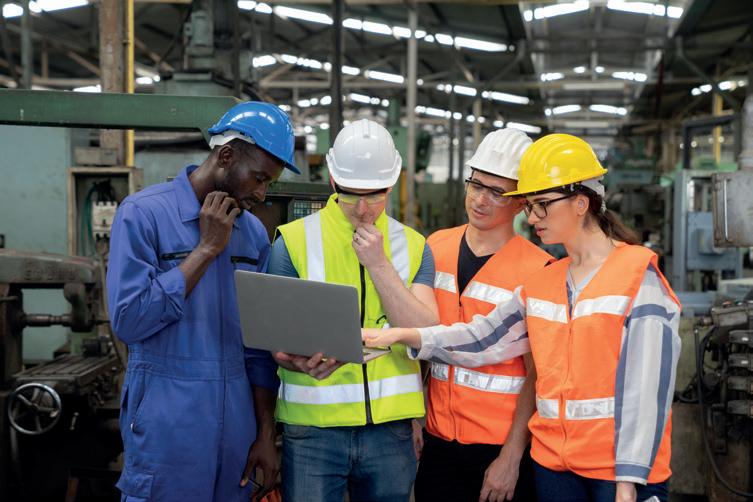
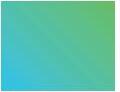
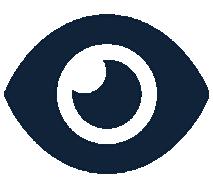
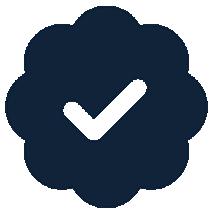
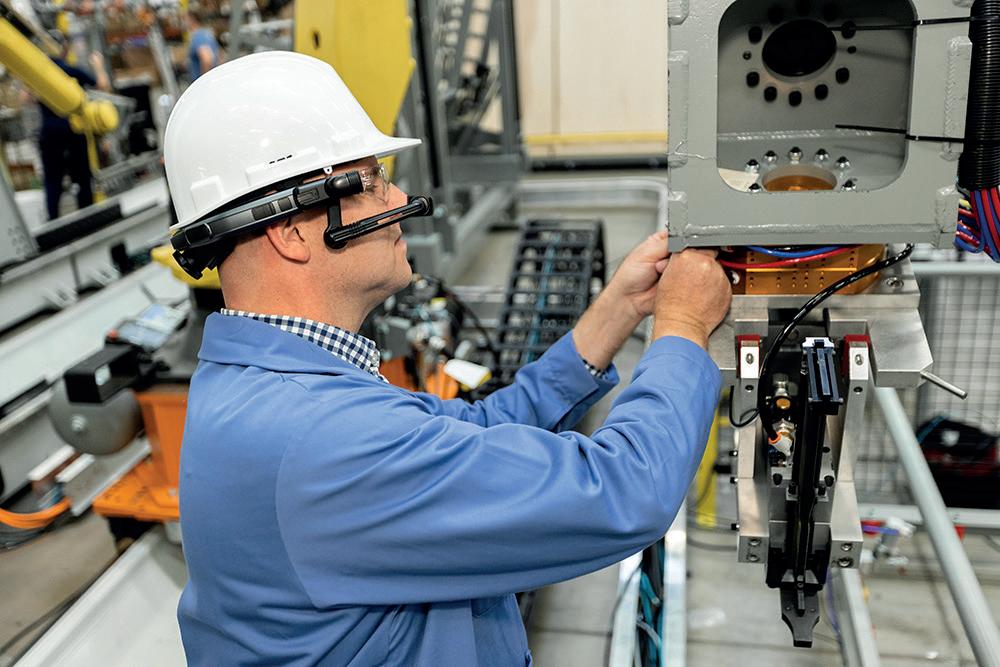

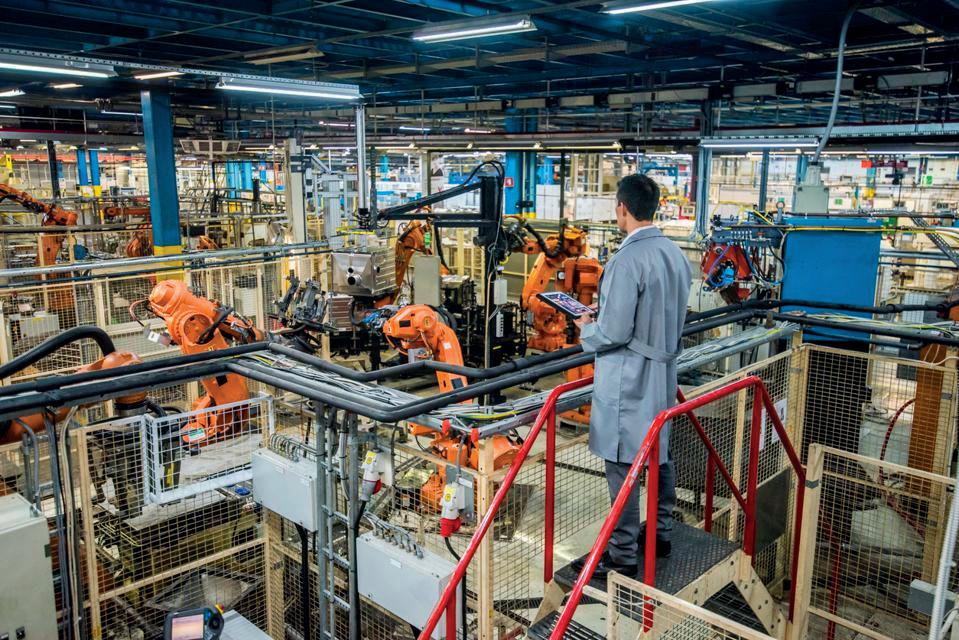
Equip your maintenance team with the digital tools they need to perform their best work - safely and effectively.
Reduce downtime and improve productivity by implementing thorough, easy-to-follow, step-by-step maintenance procedures with WorkfloPlus. The platform’s digital workflows ensure that every task is completed correctly and timely, minimising the risk of equipment failure.
Eliminate information delay by removing the need to manually enter paper-based logs into centralised systems. WorkfloPlus allows workers to instantly submit job data, ensuring accurate and up-to-date maintenance records. This real-time data can be used to schedule preventive maintenance, predict potential failures, and optimise resource allocation, to extend the lifespan of your equipment and reduce costly downtime.
A new way to manage a vast field device installed base
Accurate, reliable measurement in industrial applications is vital to enable organisations to fine-tune their process performance and ensure their operations are meeting the latest regulations. ABB explains how its Ability SmartMaster platform can help do just that, with a host of resulting benefits.
Ensuring that field devices and instrumentation such as flow meters, level meters, temperature sensors, pressure sensors and valve positioners are operating at peak performance can be very challenging for industrial operators. With many sites having potentially thousands of devices installed, it can be difficult to obtain an accurate picture of how each one is performing or when it needs to be maintained. This can be further compounded on sites where devices may be hard to reach or located in dangerous areas, preventing regular access.
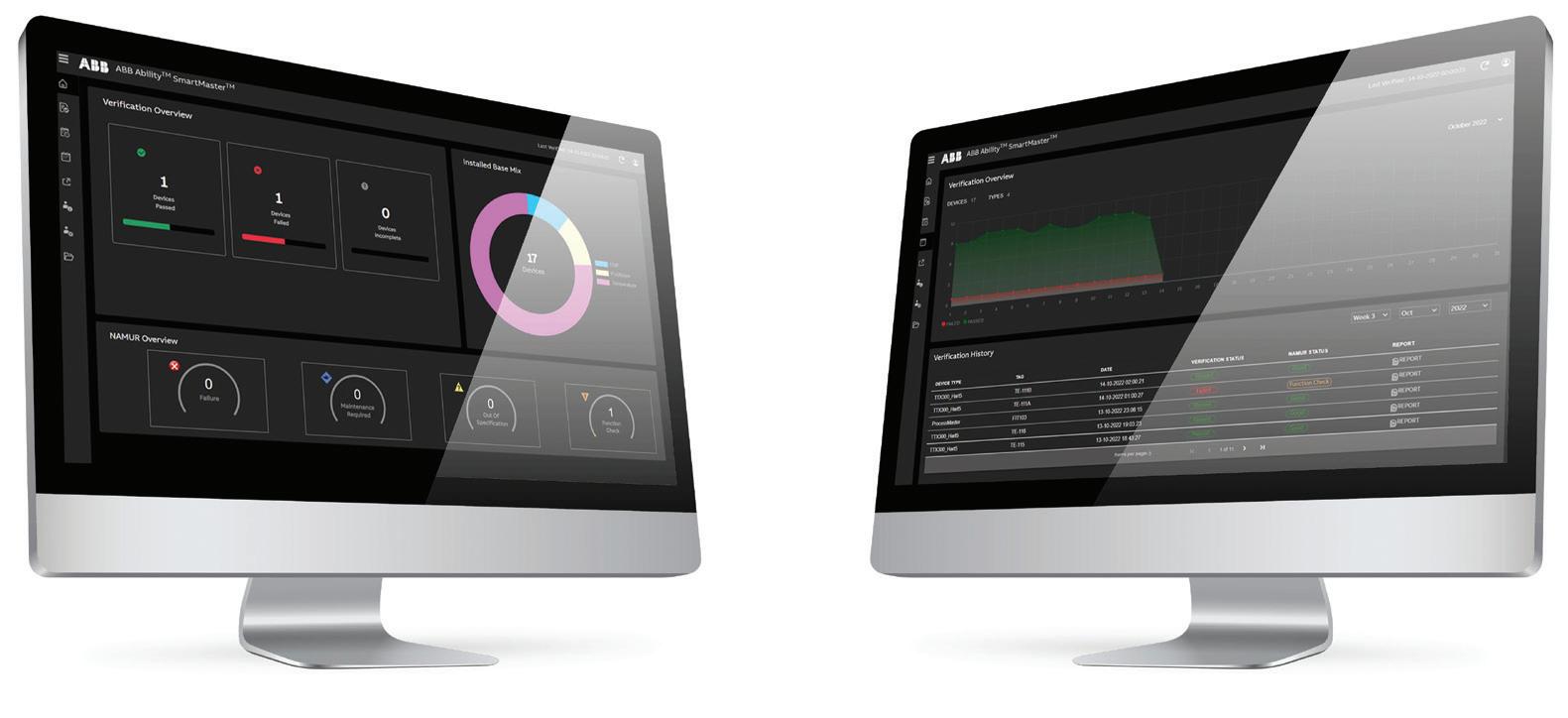
shutdown of the plant if problems are not identified in time to prevent them, leading to productivity losses due to unplanned failures of instrumentation assets.
Managing large installed bases
As well as quantity, problems can also be presented by the diverse operating principles, sophistication, and ages of instruments. This diversity can pose major challenges in managing them and ensuring that every device is delivering optimum performance.
Some of the challenges include gaps in the instruments’ historical performance data or the inability to access relevant documents about the asset. Applications and data will also often run in disconnected silos, limiting the insights that can be gained and the efficiencies that can be achieved.
Gaining a clear insight into the installed base can also be hampered due to legacy technology or procedures, manual operations and systems that cannot work together. This lack of insight in turn risks
A lack of a comprehensive management system can also lead to an incomplete inventory of the assets – with unknown or undermanaged assets, there can be unpredictable and unexpected failures leading to potential plant shutdowns.
There is also the danger that the process system could fail due to misdiagnosis of system issues that could lie either within the process itself or be due to non-optimal behavior or performance in the instrument. Failure to adequately deduce the root cause of problems can lead to their constant recurrence, with all the risks of process interruptions this carries.
Another risk is a lack of plant optimisation through inefficient running of the instrumentation installed base. These inefficiencies can lead to a low availability of instruments and analysers, interrupting production. This, in turn, ramps up the number of unscheduled maintenance
events, leading to increased costs, and also increases the risk of non-compliance with safety and environmental legislation due to failing to manage these instruments in the best way.
Failure to manage and optimise the performance of instruments can lead to reduced confidence in their readings, possibly leading operators to guess what the process is doing according to their own experience and leading to control inputs that are not based on objective evidence.
Lack of instrument management can also lead to poor communication between operations and maintenance, possibly resulting in uncoordinated and conflicting goals and activities.
Merging the physical with the digital
The challenges can be overcome by developing an Asset Performance Management (APM) solution that gives comprehensive access to asset data.
The ABB Ability SmartMaster is a platform designed to manage large installed bases
of field devices. Based on a prescribed schedule, SmartMaster collects data remotely from field devices to conduct condition monitoring.
The solution uses data from the verification tests performed on devices before they leave the factory. The SmartMaster software enables the operator to choose whether to use the factory fingerprint or to create a new fingerprint based on real site conditions after product commissioning. All verifications performed in the field can then be compared with the fingerprint data and previous tests to ensure device performance has not degraded.
During verification, the health of the device is verified, and its NAMUR status is read to provide an overview of the installed base. This knowledge enables users to plan service operations, as well as order spare part orders and device replacement. If there is a pattern of device failures, a calendar view analysis and an analytical report provide more insight into the failure scenarios.
With the licensed software version, test reports can be generated and stored locally for further analysis. Results can also be compared with historical measurements
using a trending function.
SmartMaster can be sited locally or in the cloud:
• On-premise: remote monitoring support. Collected data is managed within the customer network
• Dedicated cloud: dedicated link to each customer for monitoring. Collected data is man-aged securely in ABB’s dedicated infrastructure for customers
• Shared cloud (coming soon): global link to all customers for monitoring. Collected data is managed securely in ABB’s common cloud infrastructure for all customers
With remote access, costs are lowered as remote experts can carry out precompliance activities, reducing routine visits to site by an engineer.
Often, measurement devices are deployed where connection is difficult. In such cases, field device integration (FDI) technology connects the devices without additional wiring or disturbing operations. SmartMaster can also connect via 3G/4G and NB-IoT.
Essentially, SmartMaster connects the physical and digital world and sends
valuable information from the field straight to a phone, tablet or other device. As such, it empowers instrumentation users to improve efficiency, maintain their installed base and drive innovation.
The result is greatly enhanced management of instruments and the data they produce, resulting in increased uptime, greater efficiency and maximised flexibility and production time to meet the demands of ever-changing markets.
Summary
By connecting the physical and digital world and unlocking the power of instrument and analyser data, SmartMaster provides operators with the assurance that their measurement data is as accurate as possible, enabling them to make informed operating decisions that will transform the way they manage their plant. By presenting new opportunities for gathering and sharing maintenance data, the technology also opens the way for new ways of working, making engineering teams more productive.
new.abb.com
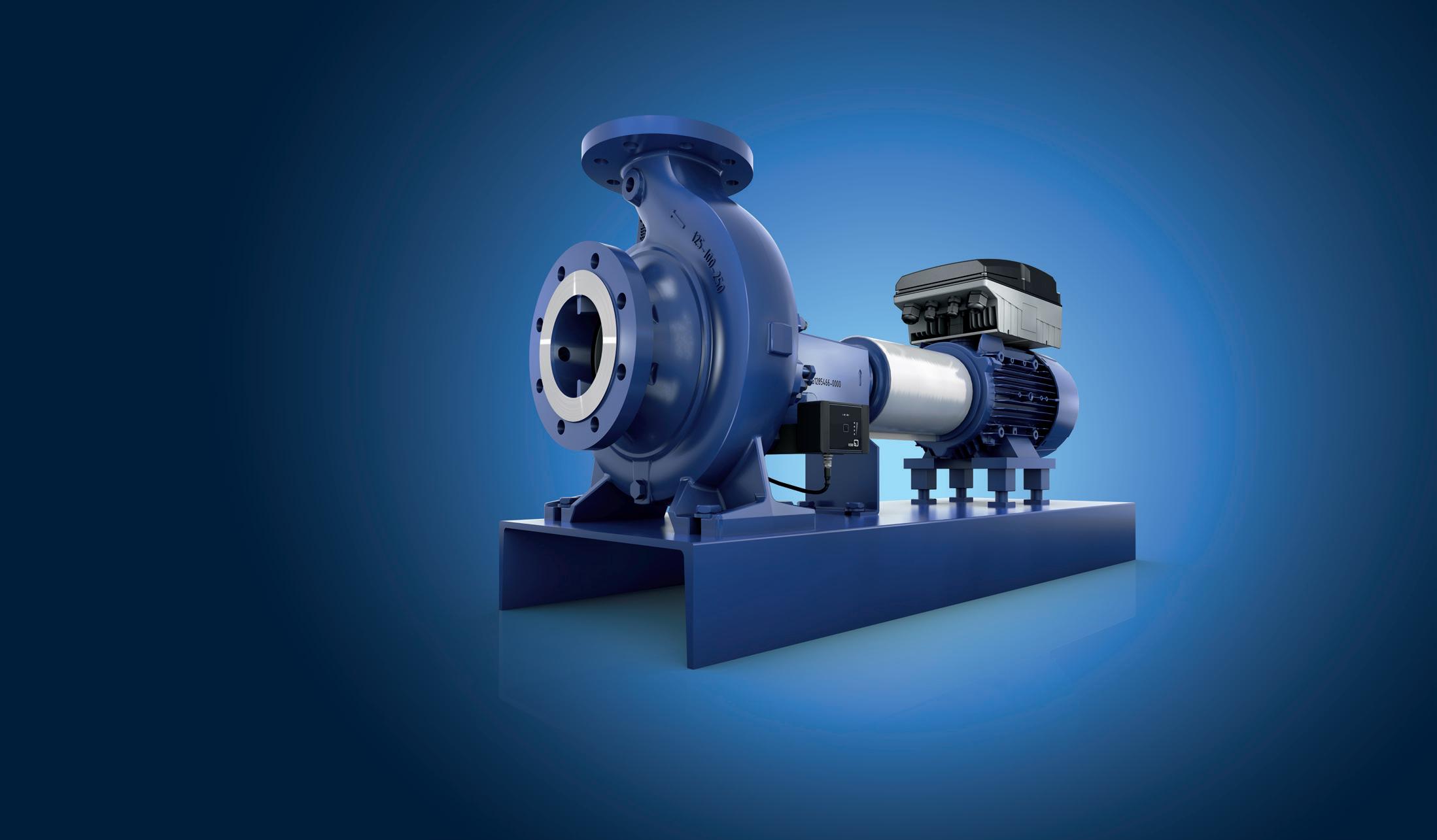
Calibration for flow meter accuracy
Flow meters are the silent workhorse of many industries helping maintain process quality and accurate system performance. However, to maintain their accuracy, regular calibration is essential, as iCenta Controls explains.
Flow meters measure the rate and total consumption at which fluids flow, this can be in open or closed pipe work. Applications are vast and so are the industries, from oil and gas fiscal meeting to high purity pharmaceuticals production. More common applications can be found in food, chemical processing and the water networks which pump water across the country. Even the most modern sophisticated flow meters can drift from their original accuracy over time. This is where consistent and repeated calibration comes into play.
Calibration is the process of comparing a measuring instrument to a known standard to determine its accuracy. For flow meters, this involves comparing the meter’s readings to a reference flow meter or a calibrated system. The goal is to identify any discrepancies and, if applicable, adjust the flow meter accordingly.
The frequency of calibration depends on several factors. Some types of flow meters are more susceptible to drift. Those designed for corrosive fluids may also require more frequent calibration. In addition, operating conditions, environments or extreme temperature fluctuations may necessitate more frequent calibration, such as:
• Wear and Tear: the physical components of a flow meter can wear out, leading to decreased accuracy.
• Corrosion: Corrosive fluids can damage meters, impacting their performance. Contamination: Particulate matter or can coat and contaminants can obstruct flow meters,
• Temperature and pressure fluctuations: Changes in temperature and pressure can influence flow meter accuracy.
• Installation errors: Incorrect installation can lead to inaccurate flow measurements.
• Industry standards: Some industries have specific calibration requirements.
Calibration methods
Master meter calibration is where a highly accurate flow meter is used as a reference standard to calibrate other flow meters. It’s essentially the gold standard in flow measurement.
Gravimetric calibration is a highly precise method for determining the volume of a container or the volume delivered by a measuring instrument. It involves measuring the mass of a known liquid (typically water) that is contained or delivered by the instrument being calibrated. Piston prover calibration is where apiston prover – a highly accurate device used to calibrate flow meters – is used. It operates on the principle of displacing a known volume of fluid using a piston of precise dimensions. This displaced volume is then compared to the volume measured by the flow meter being calibrated.
Uncertainties

ensure consistency and reliability, calibration should adhere to recognised standards and be traceable to national or international standards. This ensures that calibration results are comparable across different facilities and industries.
As part of iCenta Controls goal to achieve accreditation to ISO/IEC 17025 in the very near future, the company has reassessed its measurement uncertainties for one of its calibration setups. By understanding and applying measurement uncertainties, the company can ensure that calibration results better reflect the true accuracy of an instrument and precise measurement in practical applications. An added benefit of this process is that it can identify and quantify potential sources of errors in the calibration process. By understanding these uncertainties, steps can be taken to minimise systematic errors, improve measurement methods, and enhance the overall accuracy of measurements.
The combined standard uncertainty needs to be multiplied by an appropriate factor. To
To maximise the benefits of calibration, follow best practices such as developing a Calibration Plan to outline calibration procedures, frequency, and responsibilities. Use qualified personnel to ensure that calibration is performed by certified technicians. Calibration records, which document all calibration activities, including dates, results, and corrective actions should also be kept. It is also important to analyse calibration data, using the data to identify trends and potential issues. While calibration procedures should be regularly reviewed to stay up to date with industry standards and technological advancements.
By prioritising calibration, customers can enhance efficiency, improve product quality, reduce costs, and minimise environmental impact. It is an investment that pays dividends in terms of overall operational excellence.
www.icenta.co.uk

Why is SOS the best choice for measuring pressure?
To understand why Silicon on Saphire has been ESI’s pressure sensor technology of choice for 30 years, the company explains what it actually is and the key advantages it offers.
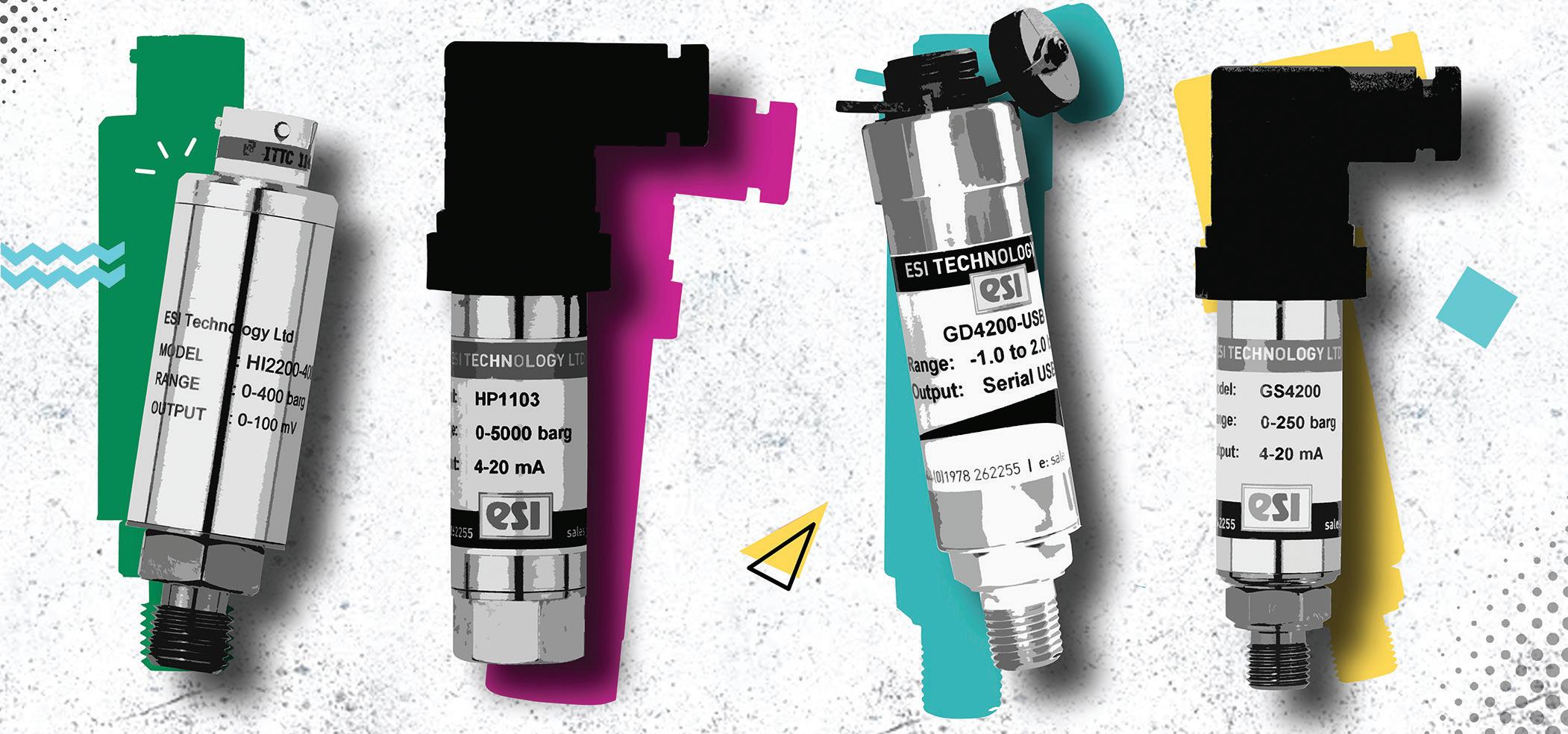
Silicon on Saphire (SOS) technology consists of high-purity, artificially grown sapphire crystals. The substrate is cut from a singlecrystal sapphire ingot, but not along what might be the traditional axis. It’s cut at an angle along what is called the r-plane. In a remarkable phenomenon of nature, the r-plane of sapphire has oxygen atoms spaced at a distance that is close to the spacing of the atoms in the (100) plane of a silicon crystal. Via a process called epitaxial growth, the silicon becomes an atomic extension of the sapphire itself.
Strain gauges are precisely etched from the silicon to form Wheatstone bridge structures. These strain gauges are free from any residual stresses that may add to hysteresis and non-repeatability errors, which decrease long-term stability. Additionally, as the silicon is grown on to the sapphire substrate, there are no bonding agents required that may age and
cause instability.
Because of this unique composition and method of manufacture, SOS technology offers several advantages that make it a superb choice for pressure sensors. Firstly, SOS sensors offer exceptional accuracy and precision in pressure measurements due to the stable substrate provided by sapphire and the precise manufacturing processes involved. This high accuracy is crucial in various industries, such as automotive, aerospace, and medical, where precise pressure readings are essential for ensuring safety, efficiency, and optimal performance. Additionally, SOS pressure sensors exhibit low hysteresis and drift, maintaining consistent and reliable measurements over time, even after prolonged use or exposure to changing environmental conditions. This characteristic ensures the long-term reliability and stability of pressure readings, which is critical for applications requiring continuous monitoring and control.
Furthermore, SOS provides excellent resistance to temperature variations, chemical corrosion, and mechanical stress, making SOS pressure sensors suitable for use in harsh and demanding environments. The sapphire substrate offers inherent thermal stability and resistance to chemical corrosion, enhancing the durability and longevity of the sensors. Moreover, SOS sensors are robust against shock and vibration, ensuring reliable operation in industrial, automotive, and aerospace applications where mechanical stress is common. Combined with low power consumption and wide temperature operation, SOS pressure sensors offer a versatile solution for a wide range of applications – from industrial process control and automotive systems to oil & gas, aerospace and environmental monitoring – where accuracy, reliability, and resilience are of foremost importance.
tinyurl.com/SOS-technology
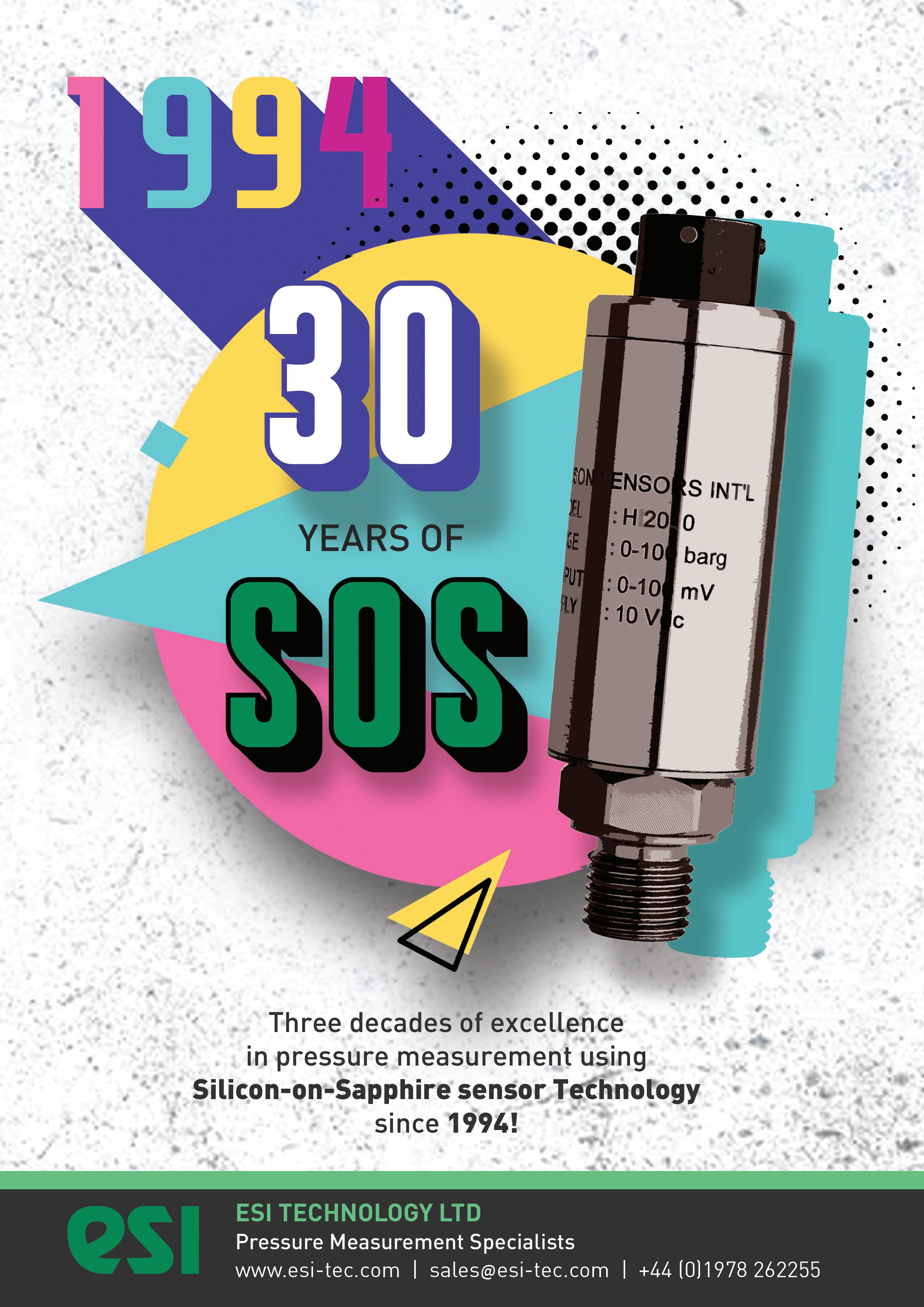
Reducing time-to-value: A win-win solution
In a time where customers are inundated with options, providing value is crucial to success, and providing value in the quickest time is key. With a new generation brought up on the instant gratification of likes, shares and follows, Andrew Jones, Technical Director at Axair Fans, discusses how the tolerance of customers has changed.
Time to value defines the time it takes for your customers to see the value they get from you as a provider. From the moment they first interact with you or use the product they buy from you for the first time, for example. Time to exceed value is a deeper level and signifies the moment the customer discovers benefits they didn’t expect initially, and it’s a particular focus that is missing in the technical industry we operate in as we’re all so busy that it’s often a rush to quote rather than a rush to have an attentive discussion.
Customers can quickly get overwhelmed in our industry if they’re not technically astute in the physics of air movement, so they must quickly hand over their trust to an expert who talks them through the application and potential component solutions. At this point, they realise the cultural value of the offer; by cultural value, I mean the way they’re spoken to, listened to, and understood. It goes beyond the product value. Fan products are becoming more of a commodity, a crucial commodity for systems to work, but still something they can get from multiple suppliers with very little difference in features and benefits. Cultural value is different. A crucial element all our team possess that makes our culture foster the right relationships is curiosity, learning what the enquirer wants to accomplish and why. Customers are passionate about their work, so they want to talk about what’s preventing them from moving forward; they
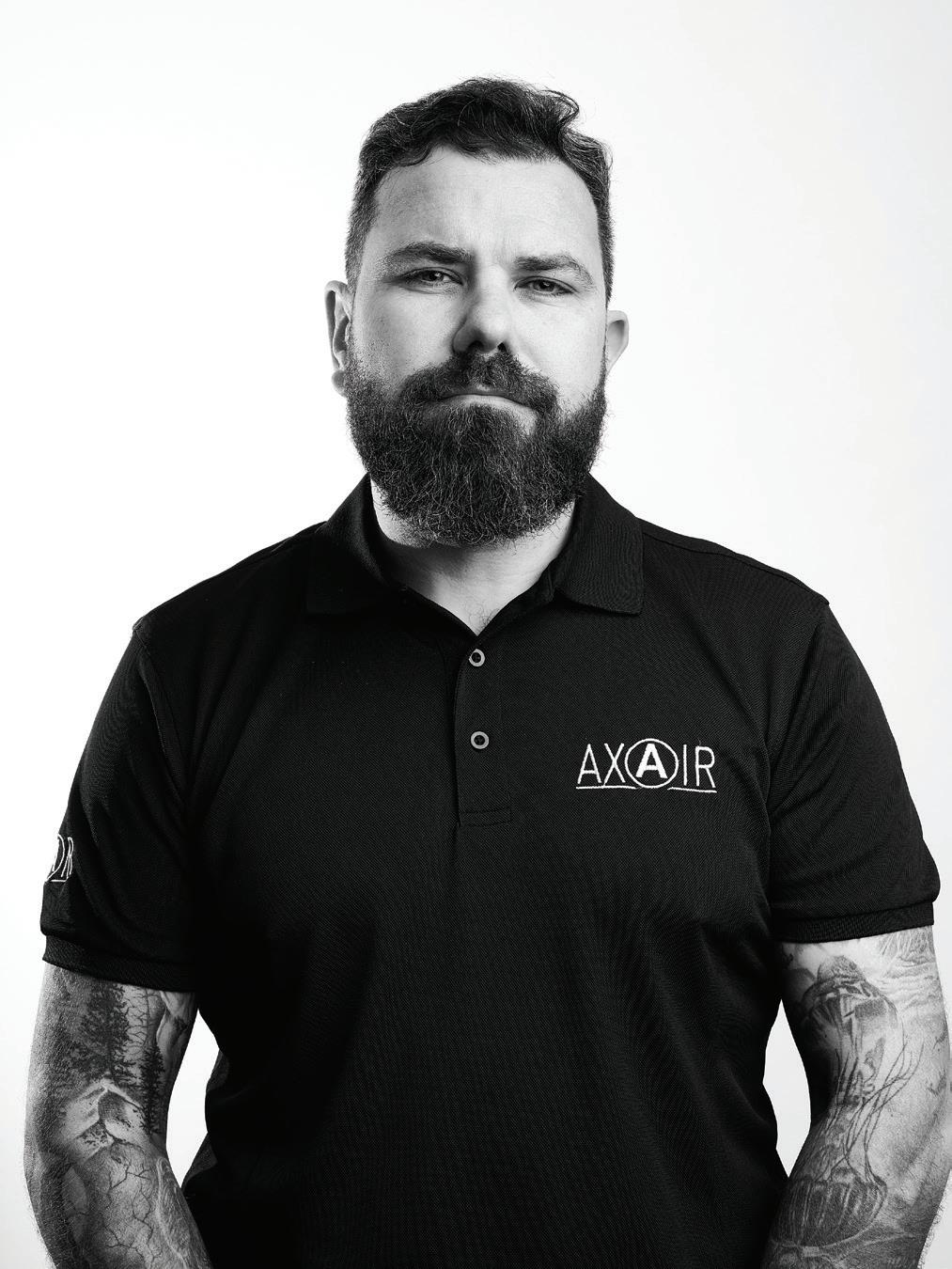
want to be challenged and are, most often, open to suggestions on alternative ways that may improve efficiency and more. Being curious about the customer’s application earns their respect and motivates them to contact us in the first place. The journey doesn’t end with curiosity; we want our customers to know they can turn to us when they have an integration challenge, so they’ll share their pain points and their high points. The less friction a potential customer experiences initially, and going forward, the better; it’s a win-win situation for both parties by building a level of trust that allows
considerably more room to test out new ways to offer solutions, delivering better outcomes and high-quality service.
Recognising the value you can elevate within your industry starts with the question of why your company exists. For us, we exist to help our customers create better systems, and it’s embedded throughout the company in our customer-centric values. These values were created collaboratively with our entire team a few years ago. We help our customers create better systems by working with them, listening, being attentive to their needs and showing resourcefulness in finding the right industrial fan components that make their systems the best. Challenging the status quo by offering a culture value leads to that ‘aha moment’ much faster than they would have when compared to the antiquated responses in the industry we work in. It’s said that companies that implement shorter time-to-value times have reported an increase in customer satisfaction by 20%.
Business moves fast, and there is pressure for results in every industry. While manufacturers and suppliers might be experts in products and components, it is important to remember that our customers may not be. By prioritising people and sharpening focus on customer needs, we protect the team’s focus from less pressing matters. That’s the key to maximising a customer-centric approach.
www.axair-fans.co.uk

James Croxton aka The Joker Head of OEM
UV curing print solutions for difficult surfaces
Inkjet printing has long been available to manufacturers who need to mark their products with traceability information. Industry standard large character printers and continuous inkjet (CIJ) printers produce a dot-matrix print effect suitable for batch and date codes and basic product information. Developments in the technology saw high-resolution printers allow the addition of fine detailed information, such as machine-readable codes and logos. The latest innovation in inkjet printing has opened up further opportunities, particularly on surfaces that are notoriously difficult to print such as PE pipes, as marking systems specialist, T-Mark, explains.
T-Mark offers printers with integrated UV curing modules. By plasma treating the surface to be printed and UV curing the ink, the latest printing systems can produce a mark that is scratch resistant and solvent resistant.
Doncaster-based egeplast UK approached T-Mark, looking to improve the quality of its printing on the wastewater and drinking water PE pipes it manufactures. It had been using a continuous inkjet (CIJ) printer to print information on the PE pipes, but the manufacturer wanted to improve the quality of the mark and include its company logo. In addition, the print needed to be solvent – specifically petrol–resistant.
T-Mark used 32mm piezo printheads from its supplier, Yeacode, to solve the problem. Using UV-curing white ink onto a plasma-treated pipe, egeplast was able to achieve all its objectives and print its logo and product specification information on both sides of its PE pipes.
In the egeplast installation, the printer and UV curing module are mounted 1mm away from the curved surface of the pipe, producing a sharp print in white against the dark surface of the pipe. Non-contact marking is an essential feature of the system due to the risk of any pressure on the pipe leading to squashing and ‘ovality’.
This technology is also being used by a new customer that specialises in subsea engineering to mark its ocean floor cables at 1m intervals with product information and a logo.
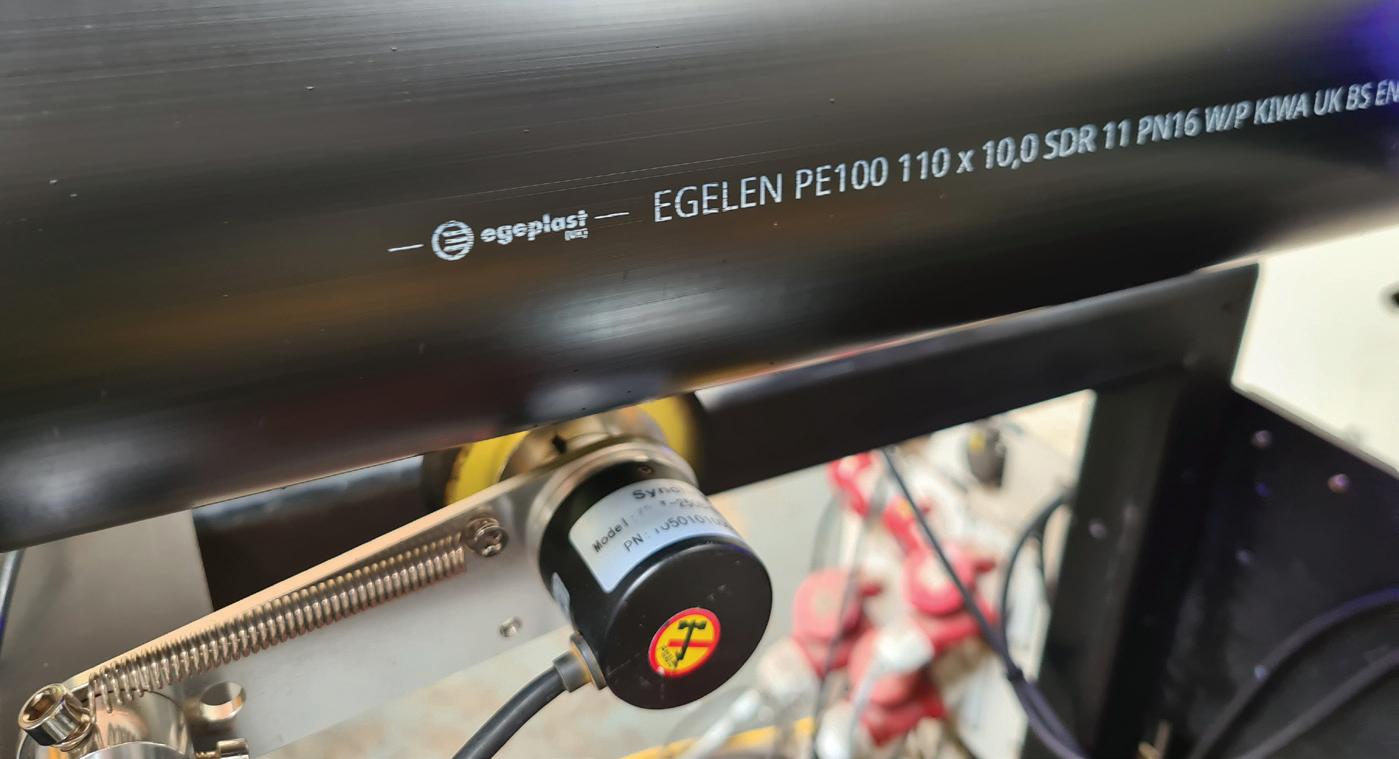
The customer had been using a combination of laser marking and CIJ printing in an attempt to make a permanent, clear mark on the product.
However, the CIJ dot matrix effect print quality was not as sharp as was desired and the print was rubbed off during the haul-off part of the production process, leaving a mark that was blurred and illegible.
T-Mark constructed a frame that incorporates a UV plasma treatment module, a Yeacode piezo inkjet printer, and a UV curing LED so that the customer can print and cure a clearly legible mark that won’t rub off with the application of either solvent or pressure.
UV curing inks are also available for T-Mark’s thermal inkjet (TIJ) printers, which have the advantage of being low cost and requiring zero maintenance. The easy-to-use cartridge system means that any problems with print quality or requirement to change
ink colour can be easily addressed by simply swapping out the ink cartridge. The printhead is incorporated in the cartridge, so there is no need to flush through a cleaner if wishing to change from printing in black, say, to white.
While shown to its best advantage printing onto plastic surfaces, UV-cured inks are also suitable for timber applications, producing a mark that is darker than standard, which does not fade when exposed to sunlight.
Industrial printing has come a long way since the first CIJ printers were introduced. The new technologies produce a higher resolution mark allowing for greater variety of printed content, including machinereadable codes. And being able to UV cure the latest generation of ink types onto a plasma treated surface means that manufacturers are able to apply a mark that, once printed, is there for good.
t-mark.co.uk/applications
PE pipe manufacturer, egeplast UK, prints product specification information and its logo onto water pipes, which are plasma treated, printed and then UV cured to make a mark that is solvent and scratch resistant.
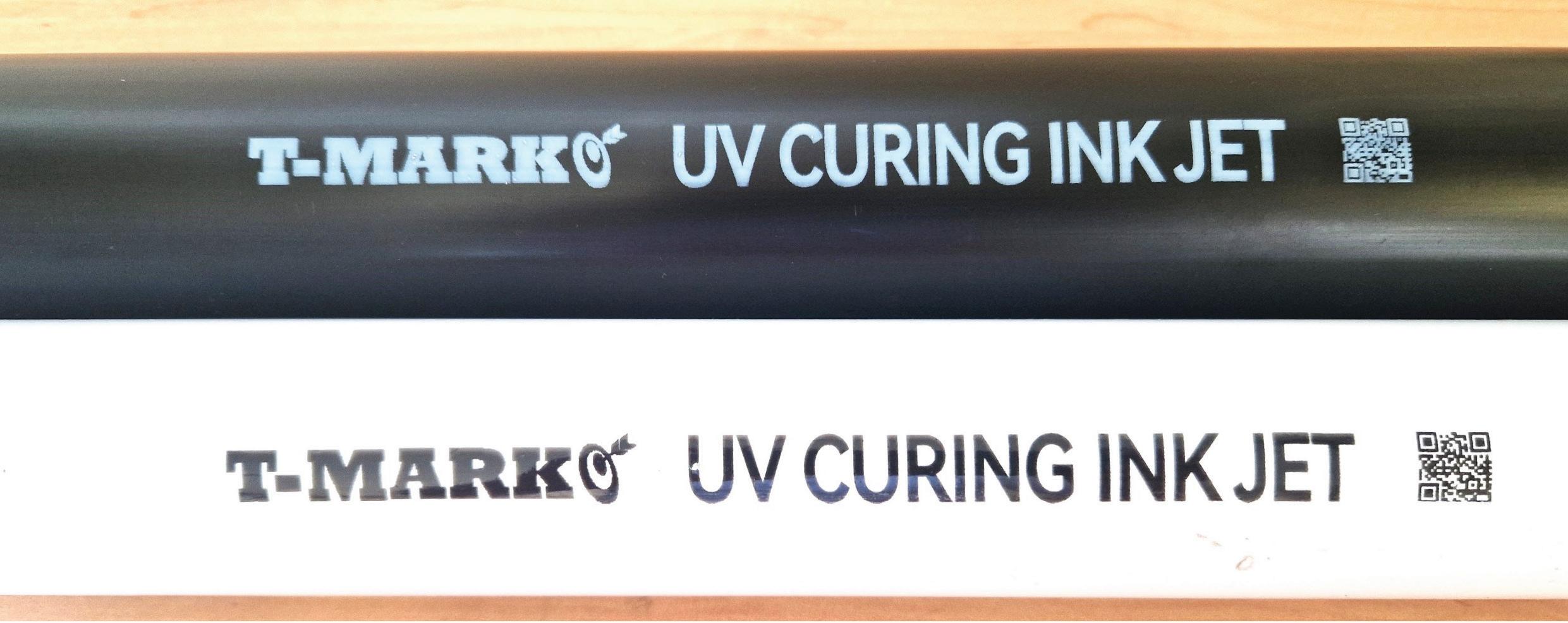

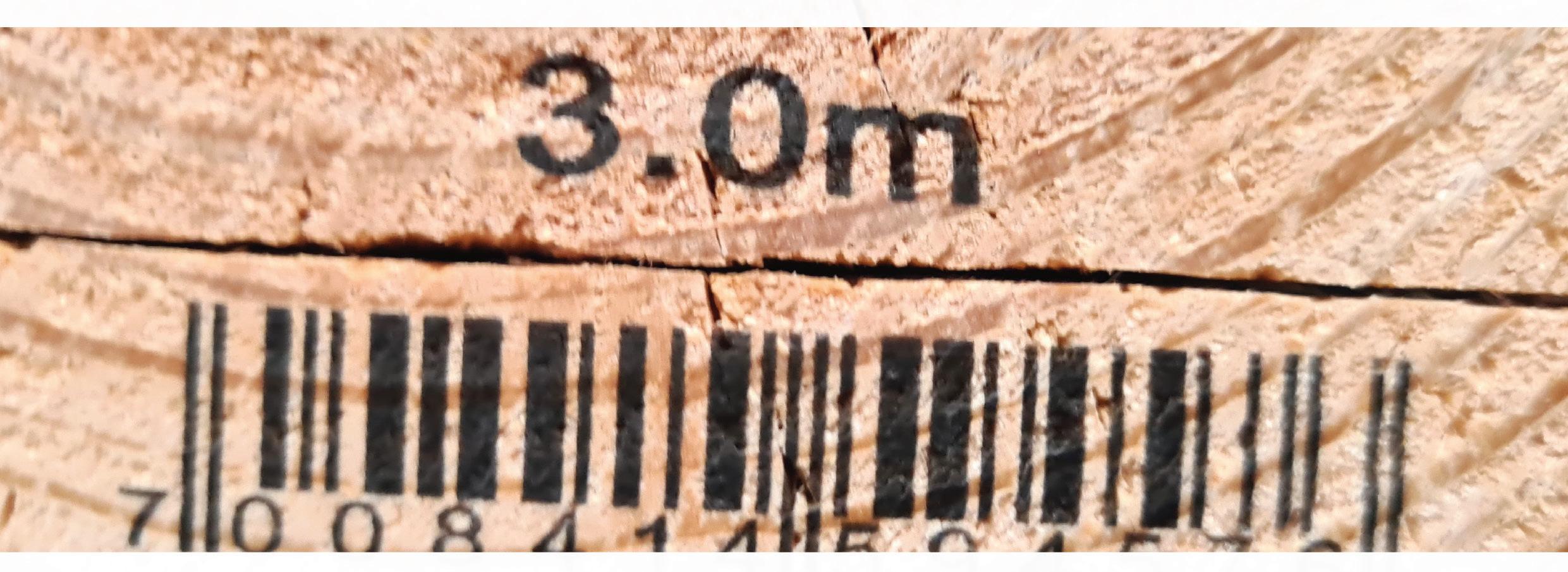


Container emptying pumps: Get the flavour for productivity
Castle Pumps explains how it met the needs of a customer looking for specialist container emptying solutions to support production growth.
Amanufacturer of vape liquids and flavours contacted Castle Pumps, looking to upscale its production. Part of this involved improving the efficiency of transferring the concentrated flavours from the IBCs where they are stored.
The company was looking for a number of container emptying solutions for fitting onto the IBCs and dispensing the favours without manually handling the fluid, which takes up more operator time, is less accurate and is more likely to result in waste and spills. It wanted to be able to remove these when not in use and store them away and it needed them to be food-grade due to the final product being for human consumption.
A solution that fits
When it comes to container emptying, Castle Pumps’ first port of call is to consider a Flux barrel pump. All Flux drum pumps benefit from being lightweight and easily fitted to a container and removed just as easily. With various immersion tube lengths available to suit the container size, a 1200mm downtube would be able to be selected for use on the vape liquid manufacturer’s IBCs.
The good news was that this customer already had Flux pumps on site for another process, which meant it was a natural option as the company was already familiar with their maintenance and operation.
Given the low viscosity and clean nature of the product, Castle Pumps knew that the Flux F400 impeller-style pumps were suitable as they could handle up to 1200cP. The F430 model with mechanical seal was specified to protect the pump’s inner tube from the fluid and prevent cross-contamination between

flavours. To ensure that they last with the aggressive nature of the concentrated flavours, the seals were upgraded to FFKM to prevent them from being eaten away.
The Flux F430 selected was ATEXapproved, fully food grade, constructed of stainless steel and supplied with tri-clamp fittings for a hygienic connection. Castle Pumps supplied a full solution for dispensing the vape flavours from the customer’s IBCs, including a motor, pump with 1200mm immersion tube, screw cap, compression gland, earthing wire and clip, trigger nozzle, hose and swaged fittings.
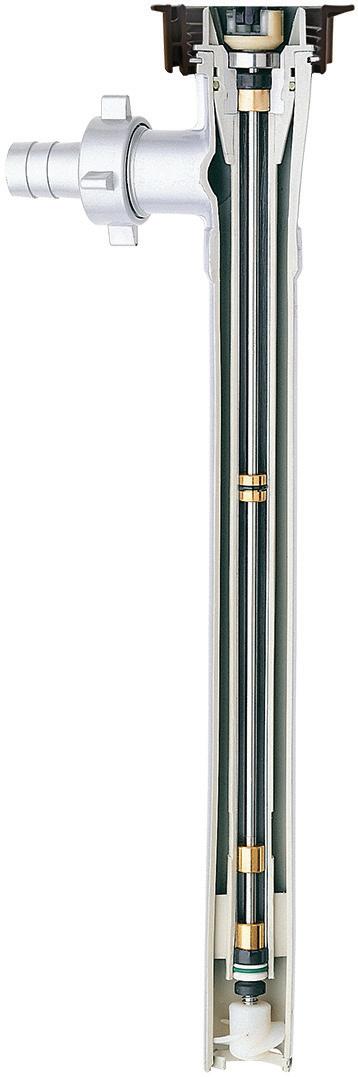
The customer ordered three of these food grade pumps for use and one to hold on site as a spare to prevent any risk in production downtime when maintenance is required. These solutions have been in use for several months now and are successfully delivering the customer’s process.
Getting the wrong pump for your process can result in inconsistency in the finished product, crushed solids, clogging, excessive wear, loss of productivity, waste of costly product or, at worst, contamination. Always trust technical experts to specify the right pump for your application.
www.castlepumps.com
ENVIRONMENTAL MANAGEMENT SOLUTIONS
Work with EMMA to understand your company’s environmental impacts, highlight opportunities for improvement, create achievable targets, track progress and fulfill documentation and reporting requirements
BUILD A FLEXIBLE BESPOKE SOLUTION:
Book the number of days per month required and adjust these each month in line with your business requirements
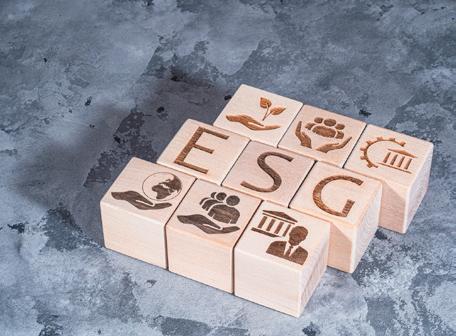
ASSESSMENTS TO UNDERSTAND BUSINESS IMPACTS
COMPLETION OF CERTIFICATION REQUIREMENTS
FACILITATION OF STAFF ENGAGEMENT ACTIVITIES
COMPLETION OF CLIENT REPORTING REQUESTS
CREATION OF CONTINUAL IMPROVEMENT PLANS
DATA ANALYSIS AND PERIODIC MANAGEMENT REPORTING

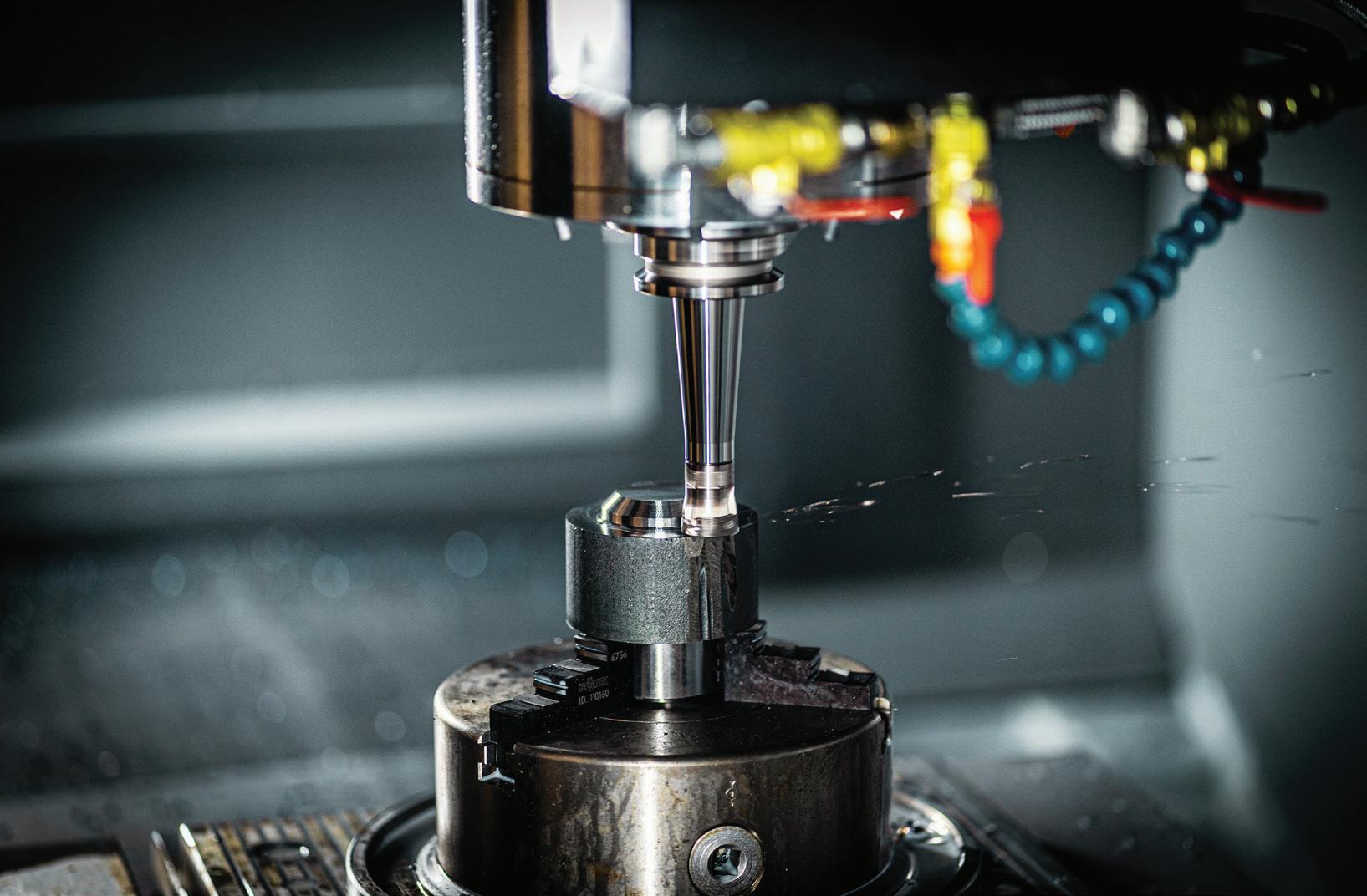


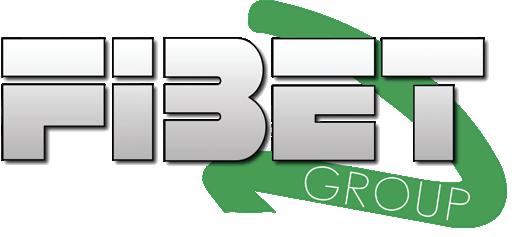
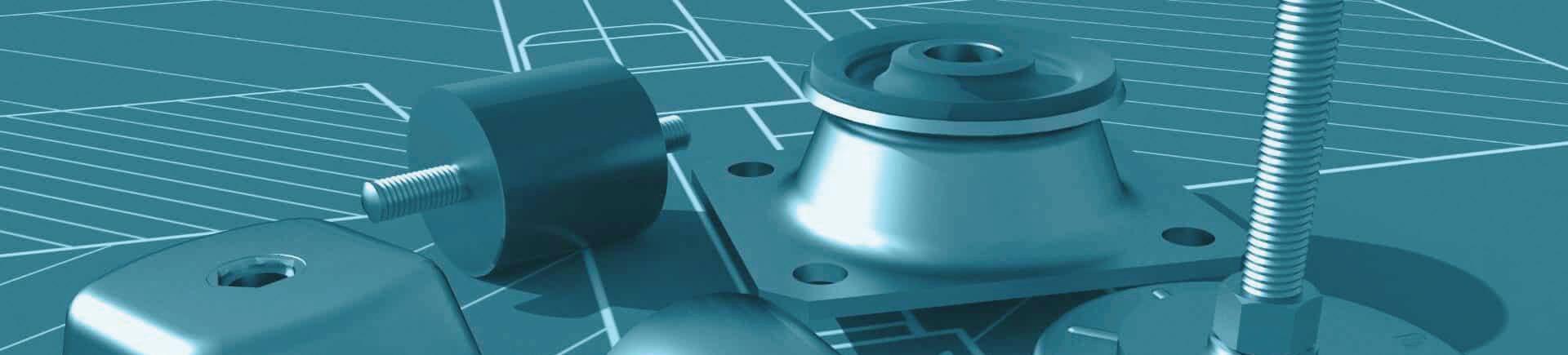
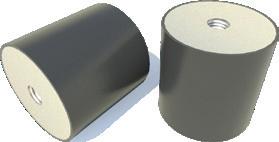
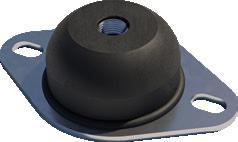
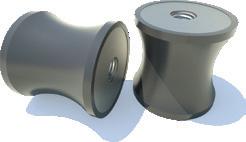

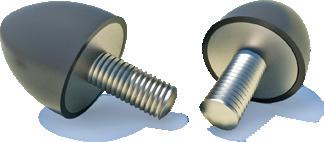


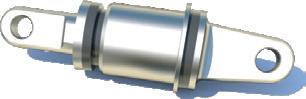

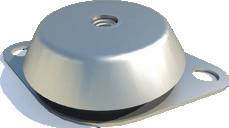
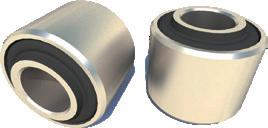
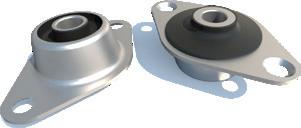
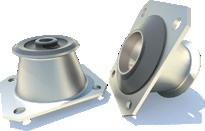
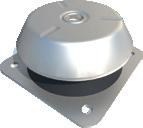

How to successfully manage major online auctions
The online auction of assets of The Family Butchers in Vörden (Germany) is already in full swing and will conclude on the auction platform on September 3 and 4. With more than 2,500 lots going under the hammer, this is one of the largest food machinery auctions of the year organised by Industrial Auctions.
From grinding and mixing lines to injectors, slicers, cutters, and tumbler installations, this auction includes a wide range of equipment. It features pasteurising tunnels, vacuum installations, slicing and thermoforming lines, smoking and cooking chambers, cooling and drying systems, packaging machines, transporting lines, and complete sausage production lines.
Industrial Auctions knows what they are doing, which is evident from the positive reviews from satisfied clients in the food and beverage industry. However, organising an auction of this magnitude requires significant dedication and efficiency. So, how does the auctioneer manage this feat?
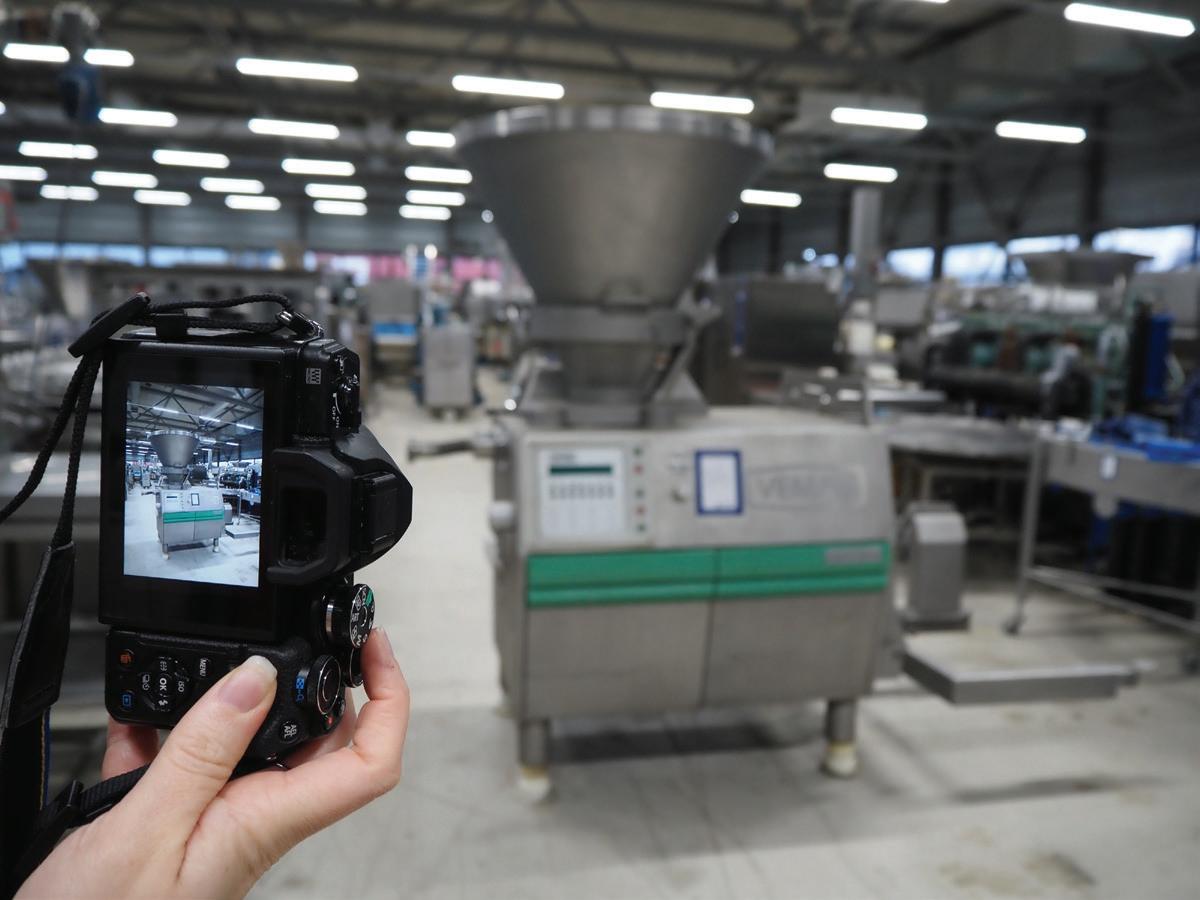
scale is a significant undertaking. Inventorying a standard auction takes a few days, but with over 2,500 lots, the process extends to several weeks. With our well-coordinated team, we are able to navigate the challenges and deliver a successful auction.”
First of all, Industrial Auctions specialises in auctioning machinery used in the food and beverage industry. This focused approach, combined with years of experience, gives the company in-depth knowledge of the machines being auctioned.
Every auction begins with the project managers inventorying the assets to ensure optimal presentation. They meticulously photograph each machine and provide detailed descriptions, helping potential buyers make informed decisions while maximising the lot’s selling potential. To further enhance transparency, viewing days are organised, enabling buyers to inspect assets up close.
Project manager Bas Schellekens explained: “I can tell you that organising an event of this
Before the auction goes live, an extensive marketing campaign is launched, both offline and online. Media partners are carefully selected, and newsletters are sent to Industrial Auctions’ extensive global customer database, reaching thousands of industry professionals. This step is essential for effectively bringing supply and demand together, optimising opportunities for both parties.
“Our work continues long after the auction goes live online”, said Bas. “We strive to present each lot accurately and comprehensively, but questions from interested parties inevitably arise. Our team is dedicated to addressing these inquiries promptly and thoroughly, ensuring clear and
transparent communication. This helps maintain trust and satisfaction throughout the auction process.”
After the auction ends, lots are collected as early as a week after the closing date, with options for transport and dismantling arranged by the auctioneer. With ample manpower provided, the auctioneer manages every detail to ensure a hassle-free experience for all parties involved. As a final touch, the auction location is left in broom-clean condition.
Project manager Bas summarised: “Our commitment to highquality support is key to delivering a successful auction experience. The hard work pays off when we see the satisfaction on everyone’s faces at the end.”
Last but not least, it’s experience that matters. With over 1,500 auctions organised, Industrial Auctions has collaborated with renowned companies such as Danish Crown, Homann, FrieslandCampina, Struik, Nestlé, and Vion, continuously enhancing their expertise, improving efficiency, and forging new relationships.
In addition to organising on-site auctions, like the one for The Family Butchers in Vörden, the company also holds auctions at its own premises, allowing contributions of fewer machines. Whether handling a few surplus machines, a complete production line, or an entire factory, Industrial Auctions has the expertise and experience to manage it all.
www.industrial-auctions.com
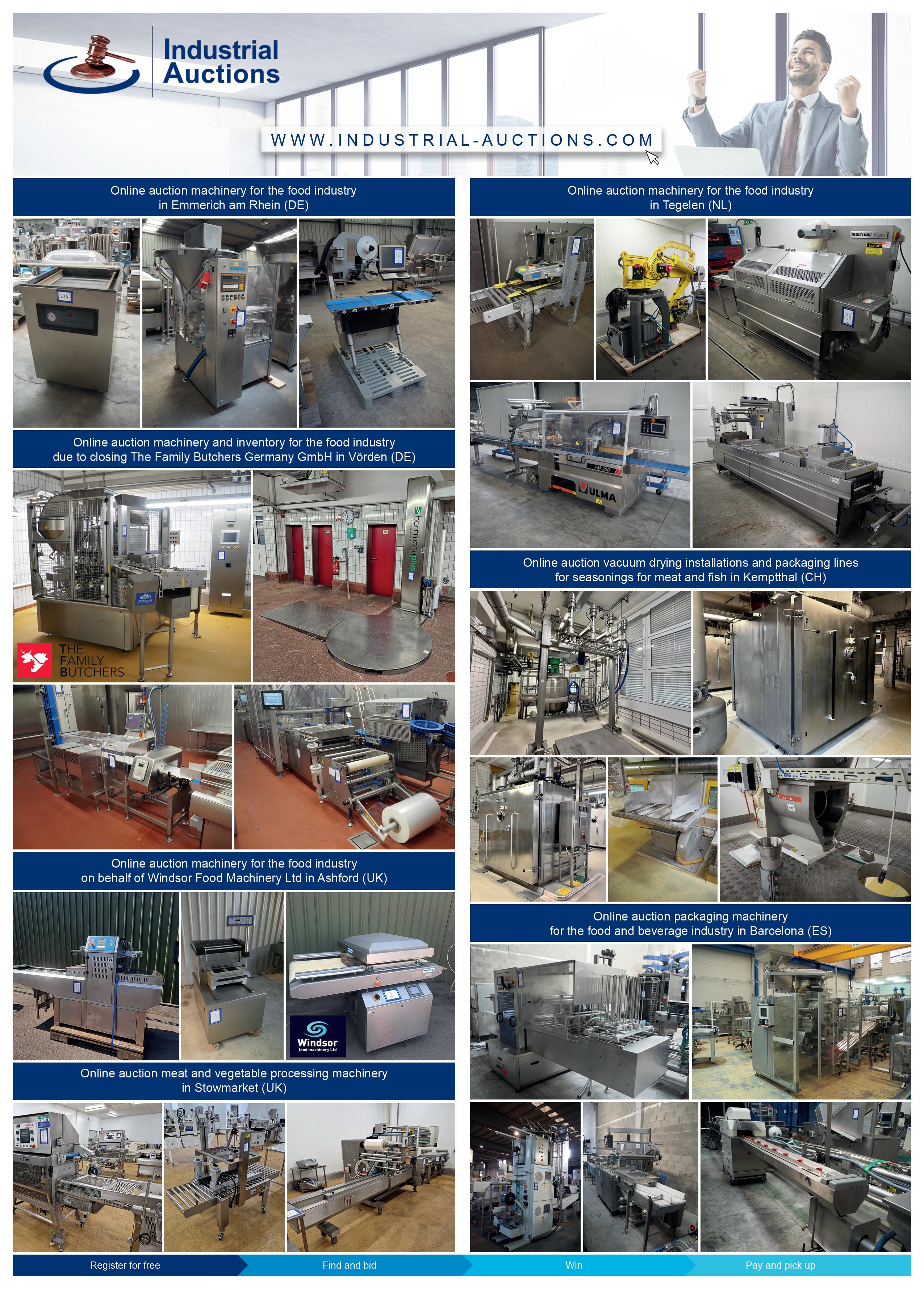
The Industrial Automation Technology Exhibition
Industrial automation components and solutions provider OEM Automatic has announced the launch of IATECH, an event which aims to provide a platform for industry professionals to connect and innovate which takes place in Leicester on 23 October.
This new exhibition will showcase OEM Automatic’s extensive product range and broad business areas, featuring over 50 leading suppliers under one roof.
OEM Automatic’s decision to launch IATECH stems from a desire to create a unified space where industry professionals from all sectors of industrial automation can gather. From machine builders and control panel builders to system integrators and strategic distributors, the event aims to foster valuable relationships and provide networking opportunities.
Expertise and innovation
IATECH is designed to highlight OEM Automatic’s commitment to industry-led knowledge and various technologies. Attendees will benefit from tech talks and live product showcases, gaining insights into the latest advancements in surge protection, 3D vision and robotics, AI, automotive manufacturing, and more.
With over 30+ manufacturers represented, IATECH will cover five key product areas:
• Control panel components
• Pressure, flow, and level instrumentation
• Sensor and safety equipment
• Machine vision
• Electric motors and drives
Visitors will be able to experience the latest innovations and technologies from brands such as CONTA-CLIP, Emerson, Agro, Senseca, Suco, Georg Fischer, Legrand, Photoneo and more.
In addition to these areas, OEM Automatic’s Bespoke Solutions service and logistics capabilities will be prominently featured. A cornerstone of OEM Automatic’s offering, its Bespoke Solutions Service is
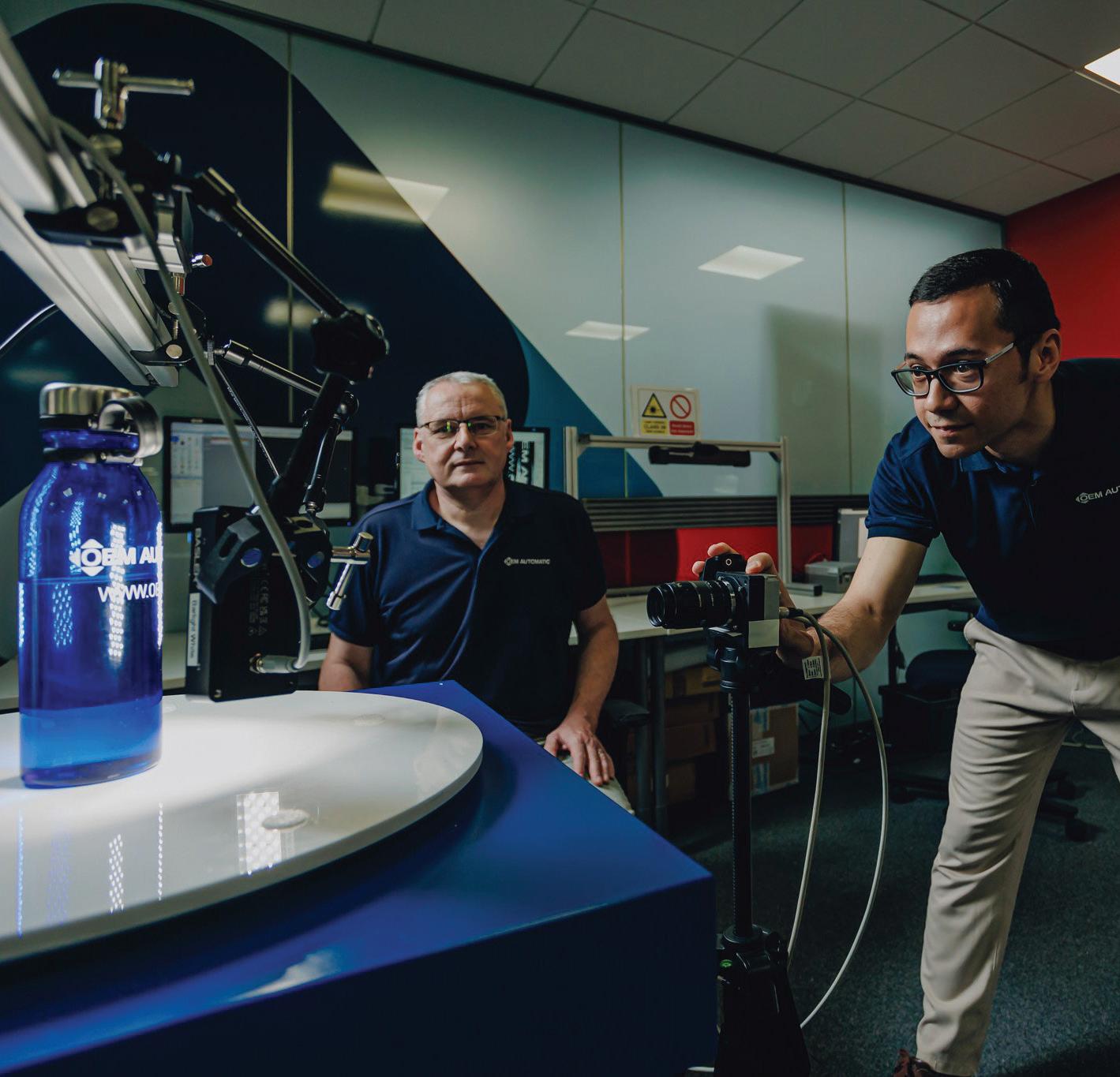
rapidly growing and provides a wide range of flexible, in-house solutions. The service includes assemblies, customisations, specifying, purchasing, and kitting parts, ensuring that each solution is meticulously crafted to meet specific customer needs.
Application examples include DIN rail terminal assemblies, cam switch assemblies, custom pressure switch settings, electric actuator modifications, and more.
The main goals of the bespoke solutions are to simplify customers’ production and purchasing processes, save time and resources, and optimise production efficiency. Customers benefit from custom products that fit within their existing systems, allowing
them to focus on other critical aspects of production. The service also addresses stock availability issues, making the purchasing process smoother and more efficient.
Don’t miss the opportunity to experience IATECH and explore how OEM Automatic is adding value to the customer buying journey.
The IATECH Exhibition will be taking place at the Leicester Marriott Hotel, Leicester, on Wednesday, 23 October 2024, between 9:30 and 16:30.
With less than three months to go, register to secure your space at IATECH on the OEM Automatic website.
www.oem.co.uk/iatech
AN OEM AUTOMATIC EXHIBITION
• CONTROL PANEL COMPONENTS
• PRESSURE, FLOW, AND LEVEL INSTRUMENTATION
• SENSOR AND SAFETY EQUIPMENT
• MACHINE VISION
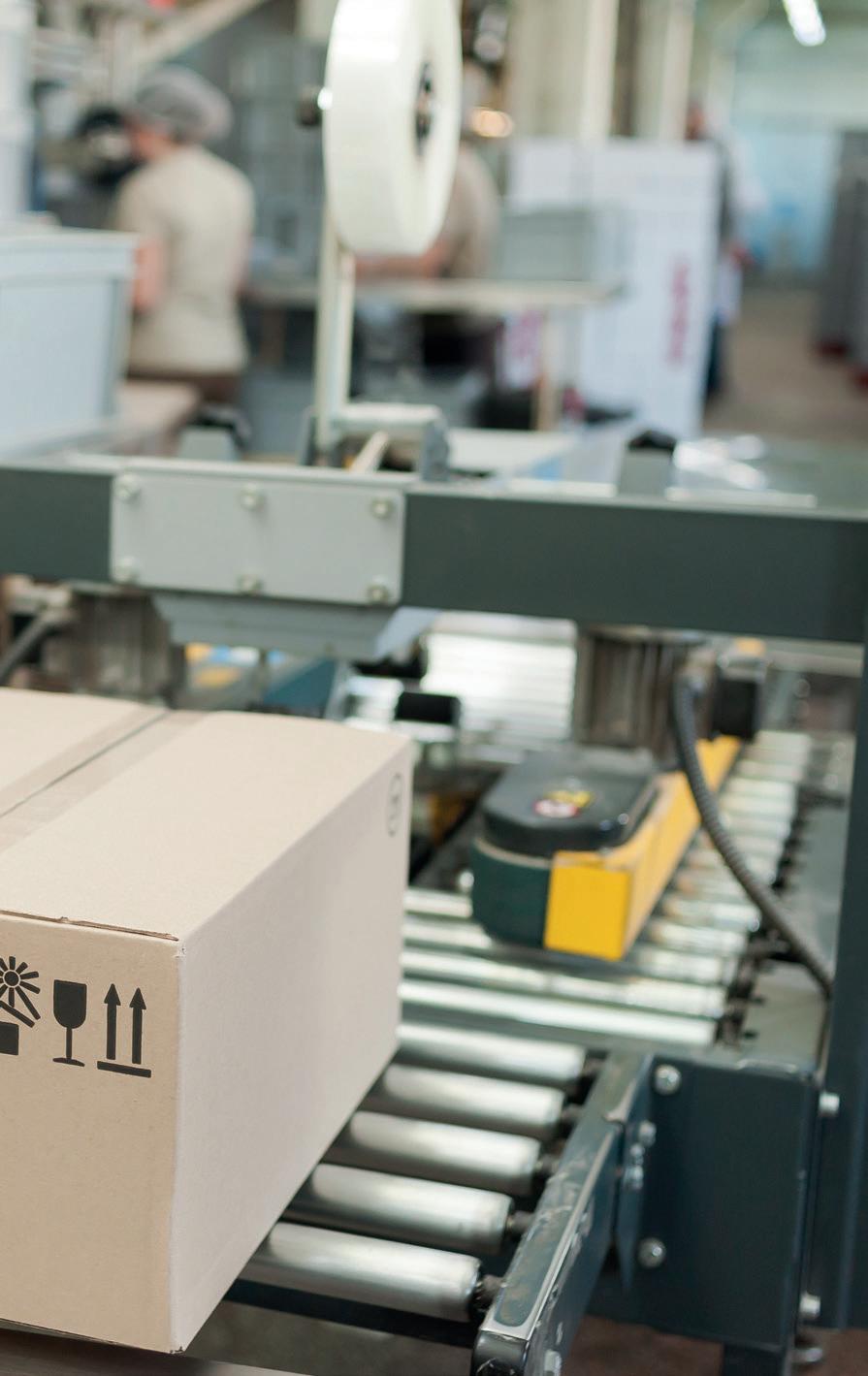
• ELECTRIC MOTORS AND DRIVE SOLUTIONS
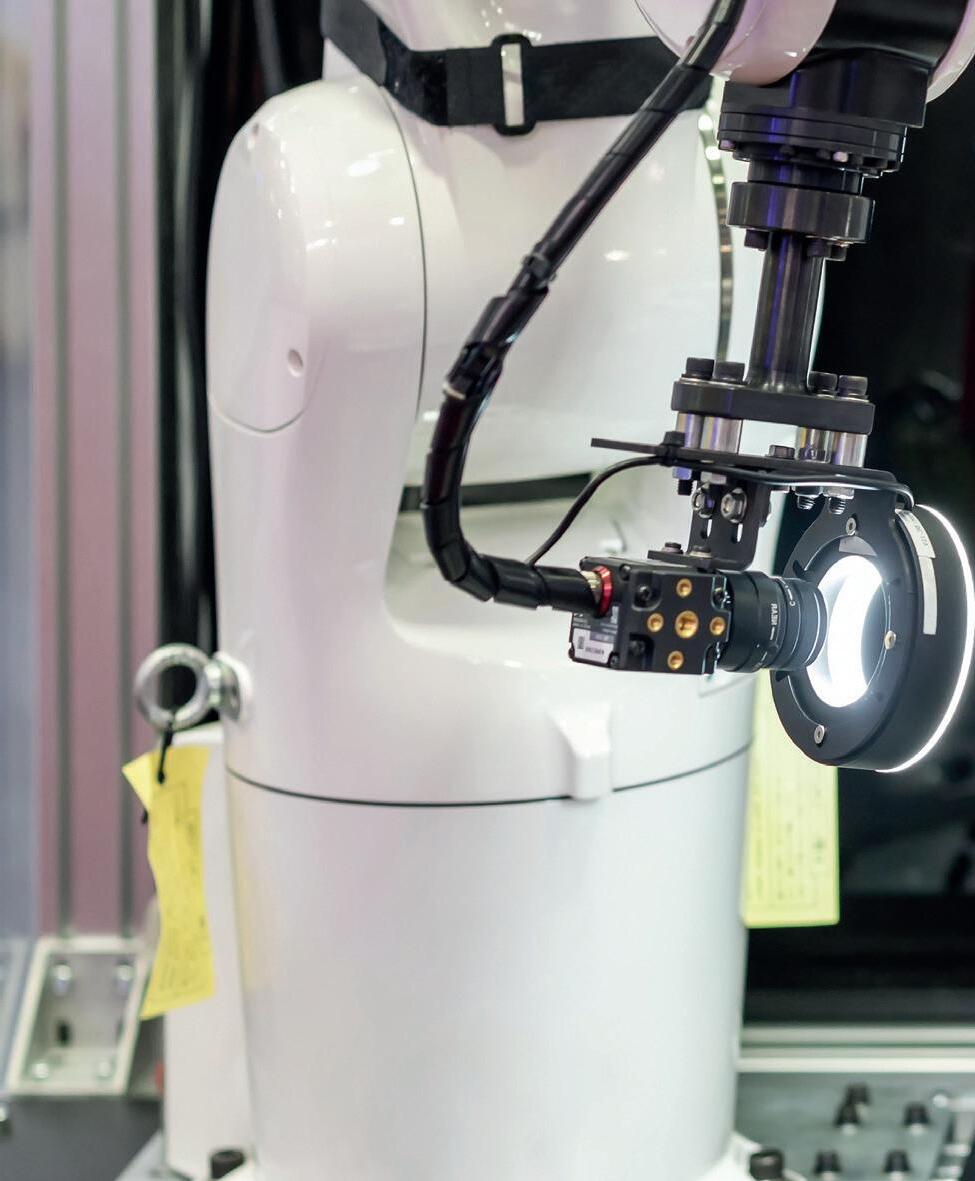
IATECH is a one-day event showing the latest advancements and technologies in industrial automation. From computer vision to control panel components, you’ll find solutions to fit a wide range of applications.
#IATECH
JOIN US ON 23RD OCTOBER
9:30 - 4:30
Leicester Marriott Hotel, Grove Park, Smith Way, Leicester, UK, LE19 1SW
Register to attend or find more information at www.oem.co.uk/iatech
Bringing the metals supply chain together
Visit the UK Metals Expo, the leading trade show for metal engineering solutions, which opens on 11 and 12 September at the NEC, Birmingham.
UK Metals Expo is the leading event that brings together the entire metals supply chain with the world of manufacturing and engineering on 11 and 12 September 2024 at the NEC Birmingham.
This free-to-attend exhibition and conference will showcase a wide range of innovative products, services, and interactive sessions from companies such as Kasto, Code a Weld, AMG Critical Materials, Bodycote, Spectro, Hitachi, Behringer, Tata Steel, Marcegaglia, Outokumpu, LIBERTY Steel, Norsk Hydro, CELSA Steel UK, EMR Group, ArcelorMittal, British Steel, the MTC, Make UK, United Autosports, Celtic Freeport, ADS Group, Volvo Cars, Boeing, JLR, Rolls-Royce, and many more. The full exhibitor list is available at www.ukmetalsexpo.com.

Winning Combination’ and ‘Scrap Shake-Up: The New Era of Scrap and Raw Materials in the UK Supply Chain’.
UK Metals Expo 2024 will feature over 300 exhibitors from 18 countries, presenting the latest technologies and methodologies designed to enhance efficiency, sustainability, and productivity. Attendees will have the chance to explore state-of-the-art machinery, cutting-edge materials, and innovative processes that are shaping the future of metal production.
The event’s comprehensive seminar programme, which is spread across four dedicated theatres, will feature 50 seminars led by 100 industry leaders, practitioners, and experts. These sessions will cover a wide range of topics, from primary metal manufacturing and supply chain management to surface finishing and recycling. Key themes will include the integration of Industry 4.0 technologies, advancements in automation, and strategies for achieving net-zero emissions.
“We find ourselves at a pivotal moment for our country and the metals industry. The UK is not only the birthplace of the industrial revolution; it’s also where the next chapter of the industry is being written. With a new government comes new hopes, new directions, and new opportunities. Together, we will help shape the future of the UK metals supply chain and drive transformative change across many industrial sectors,” emphasised UK Metals Expo Chair Lord Rupert Redesdale.
One of the highlights of the UK Metals Expo 2024 will be the focus on sustainable practices in metal production. Exhibitors will present solutions that drive energy-efficient production and promote the use of recycled materials, ensuring a more sustainable future for the metals sector.
Day 1 of the expo, on 11th September, will begin with a keynote by Tata Steel UK’s CEO, who will share the vision of Tata Steel’s sustainable steelmaking future in the UK. Following this, a panel on sustainable practices in the automotive, aerospace, and wind sectors will feature experts from NMIS, Boeing, and Renewable Parts Ltd, discussing innovative approaches to extending product lifecycles and enhancing resource efficiency. Other sessions include ‘Culture + Robots =
Day 2 will continue to showcase the industry’s commitment to sustainability, innovation, and strategic growth. Experts from Make UK (UK Steel), Cbamboo, CarbonChain, and Tata Steel UK will discuss CBAM’s implications on importers and exporters, focusing on practical advice. Another significant session, ‘Aluminium Manufacturing with Recycled Scrap’, will cover sustainable aluminium production, with insights from EMR Group, Brunel University, Innoval Technology, Frog Bikes, and Volvo Cars. Later, the ‘Meet the Funder + Networking’ session will offer a platform for stakeholders to connect with potential investors.
The expo also offers unparalleled networking opportunities, allowing professionals to connect with peers, industry leaders, and potential business partners. Make the most of your day by arranging meetings with colleagues and clients in the event’s Central Networking Area, co-sponsored by Tata and British Steel. Head to the Café des Arts – the dedicated speaker corner ¬– wherevisitors can continue conversations from the seminars they have attended.
Plus, experience the thrill of motorsport with a racing car from United Autosports, the 2024 Le Mans winner. The company’s Commercial Director will deliver a must-see keynote on Day 1 – an unmissable moment for any motorsport enthusiast.
For the full conference agenda, exhibitor list, floor plan, and to receive afree badge, please visit the event’s website.
www.ukmetalsexpo.com

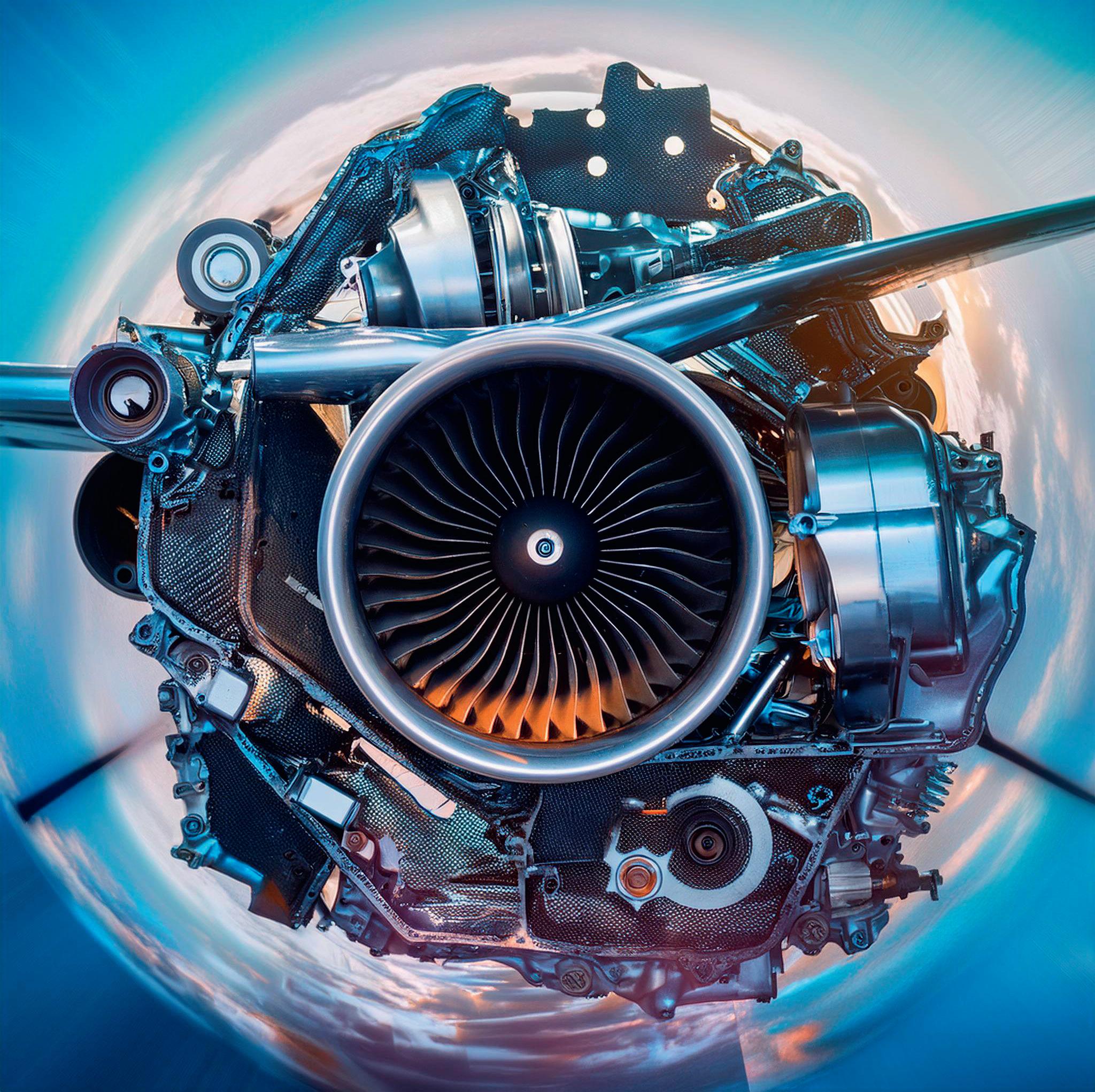


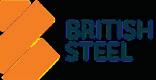

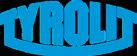
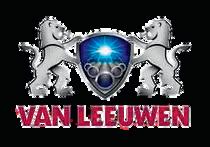


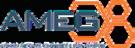

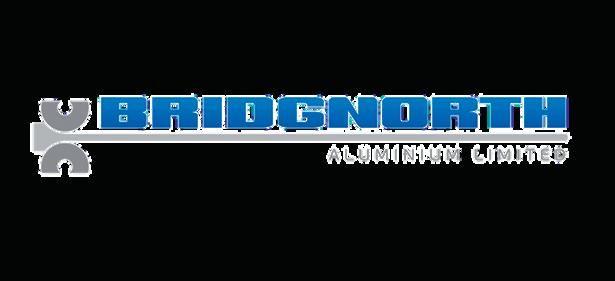

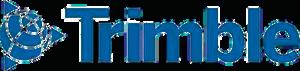
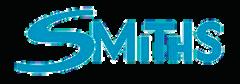
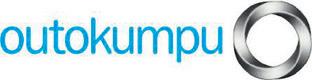
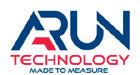
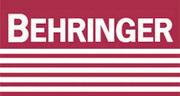
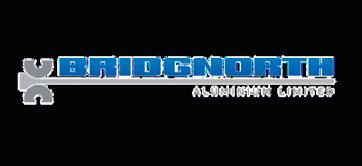
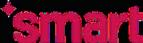


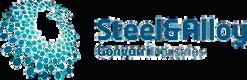
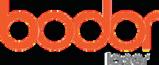
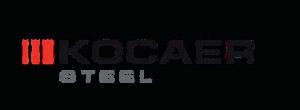
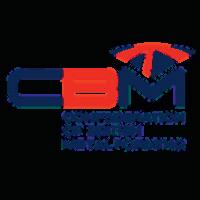
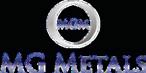

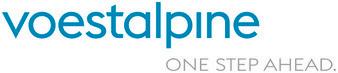
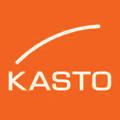

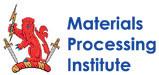
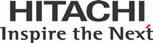
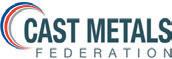

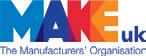
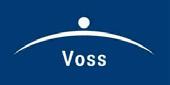
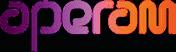
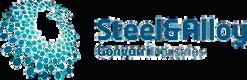
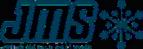
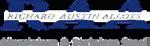
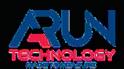
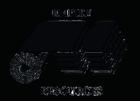
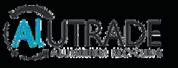

Boost lifting safety and productivity at LiftEx 2024
LiftEx 2024, the flagship event of the Lifting Equipment Engineers Association (LEEA), will take place on 16-17 October 2024 at the new West Hall at Olympia in London.
The free-to-attend show is an essential visit for lifting safety professionals in manufacturing, engineering and anyone involved in using or procuring lifting equipment or vital supporting services such as inspection, maintenance and training.
Crucially, a visit will contribute to improving safety and best practice with advice from experts on the LEEA stand, while free training sessions and presentations will be delivered at the LEEA Accredited Training Scheme (ATS) seminar sessions, held across both days in the show floor theatre.
These will begin with Barrie Mordue, Managing Director of Tensology, conducting a seminar titled ‘Crane ropes – what the eye can’t see’, which will lead attendees through a thorough examination of crane ropes and inform them about indicators of internal degradation and MRT as an aid to inspection.
Visitors can learn about safe system fundamentals, equipment application and rescue planning in ‘Working at height and rescue’, which will be delivered by Arco’s Training Manager Steve Dawson, Technical Sales Specialist Rosie Webb and Senior Technical Sales Specialist Nerys Knight.
In ‘Know your sling calculations’, Elevation Training & Development Managing Director Steve Mohammed and David Middlemiss, Instructor at ETDL, will explain mode factor calculations, types of ton/tonne and sling angles.
In his presentation titled ‘Slinging vs lashing – the critical difference’, Andy Cartwright, Technical Manager of Mentor, will look at the common mistakes and assumptions between slinging and lashing, how to read a sling and ratchet strap and what can go wrong if a sling and ratchet get mistaken for each other.
The ‘Importance of pre-use checking equipment’ seminar will see Geoff Burkill, Training Manager at Carl Stahl, presenting the importance of pre-use checking, legal requirements and practical Inspections.

‘The role of an Appointed Person and the importance of planning a safe lift’ session delivered by Matthew Bowden, Lead Trainer at Certex, describes the role of an Appointed Person, the importance of planning a lift safely, and the fundamentals of planning a lift.
The option to attend the ATS Seminar is included as part of your visitor ticket, but you must pre-register for the sessions you wish to attend. Check for details and times at events.leeaint.com/liftex-london-2024/ ats-seminar
Lifting innovation
The show floor at Olympia will be packed with exhibitors demonstrating innovations to improve productivity, efficiency and safety. They will include a broad array of lifting equipment solutions from companies such as Atlas Winch & Hoist Services, Britlift, Cromax, George Taylor Lifting Gear, Green Pin (Royal Van Beest), Hird, JD Neuhaus, Lifting Gear UK, Modulift, Reid Lifting, RHC Lifting, Rope and Sling Specialists (RSS) and Worlifts. Visitors interested in materials handling equipment will find GGR Group, Lift Turn Move and Probst.
Chains, ropes and accessories will be featured by companies including Bridon Bekaert, Codipro, Dolezych, Lift Turn Move,
Marlow Ropes, RUD Chains, Pewag, Sahm Splice, Talurit and William Hackett Chains. There will be slings and rigging from Aberdeen Web, Crosby Group, Dolezych and PMS Industrie.
Exhibitors displaying height safety equipment include Delphini, RidgeGear, SafetyLiftinGear, Safehold, SpanSet, Tiger Lifting and YOKE Industrial Corp. There will be load monitoring equipment from Dynamic Load Monitoring (DLM), Load Monitoring Systems (LMS) and Red Rooster Lifting. A range of IT solutions will be shown from companies, including Core Inspection Software, RiConnect and Tele Radio. Lifting and safety training will be featured on the stands of Carl Stahl and Elevation Training & Development Ltd (ETDL).
Stands featuring logistics lifting solutions include Redtrail and there will be hire solutions from Speedy Hire. Test machinery can be seen from Staht and Tensology. And, finally, LEEA will have its usual prominent stand for visitors to meet and engage with the Association’s team.
To see these and many other exhibitors at LiftEx 2024 and to attend the ATS seminar sessions, register now.
bit.ly/LiftEx24
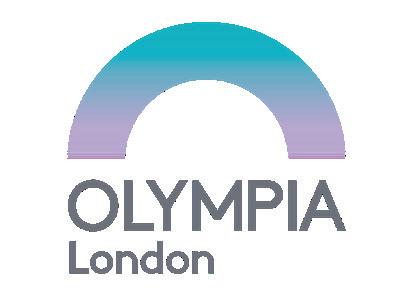
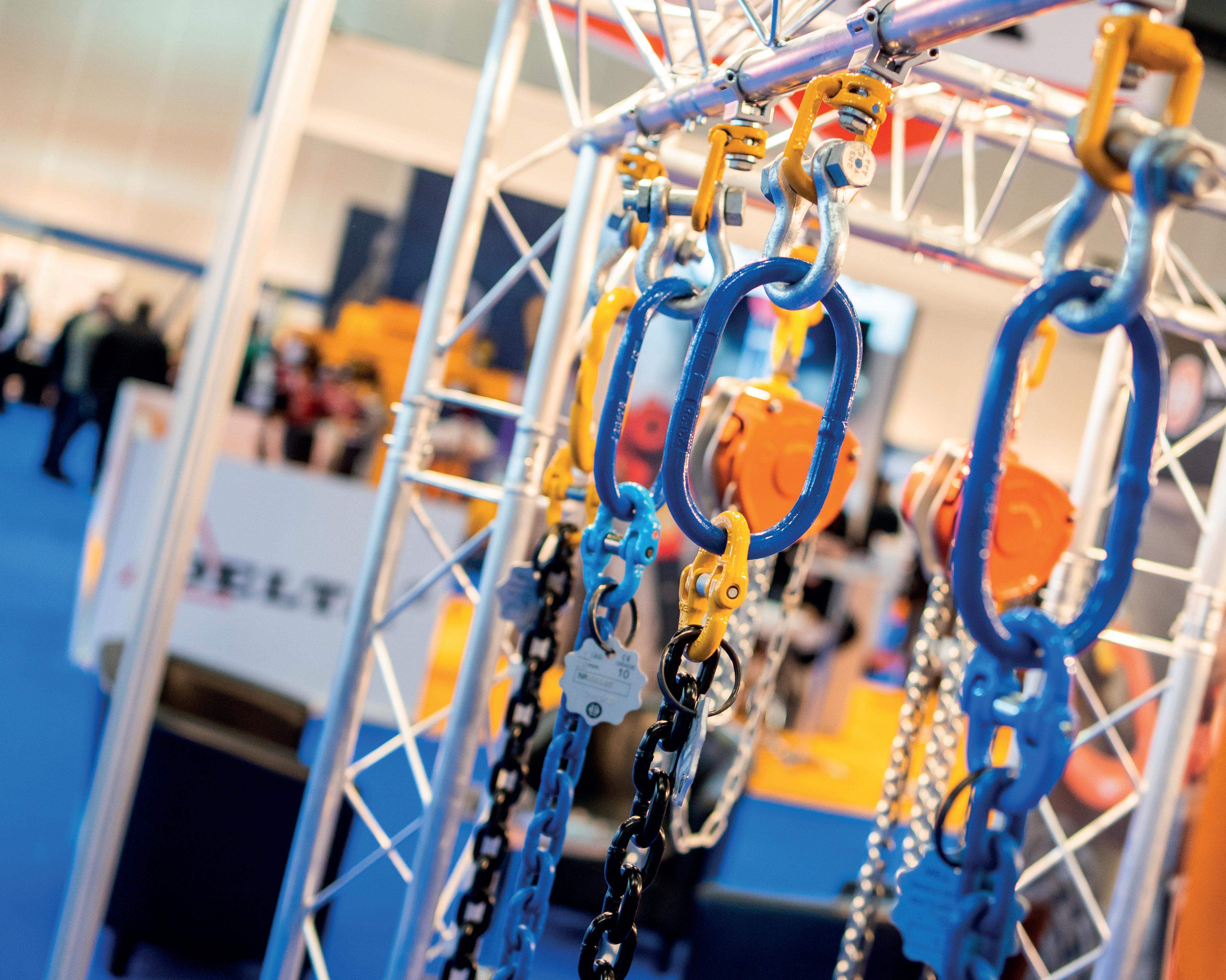
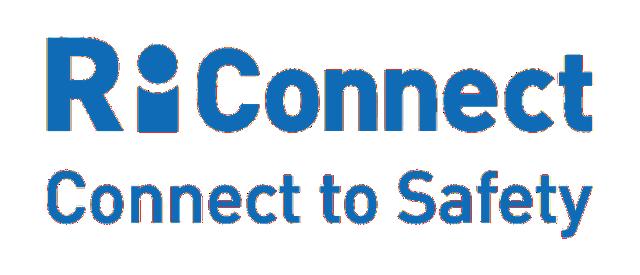
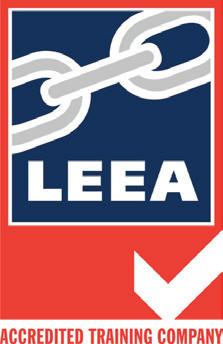
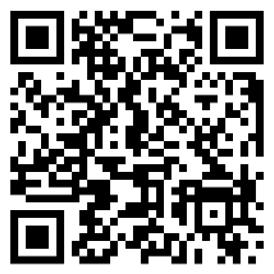
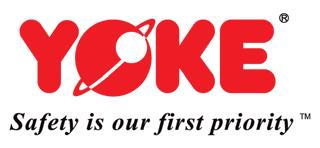
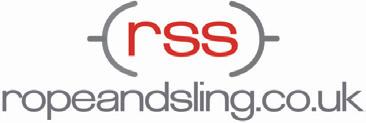
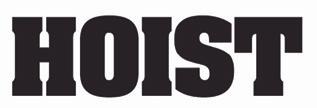
Discover your next supplier at The Engineering Design Show
With a sold-out exhibition floor, EDS 2024 – The Engineering Design Show ¬– is back on 9 and 10 October at The Coventry Building Society Arena. MEPCA readers are invited to join thousands of engineers at the UK’s number one free exhibition of mechanical, electronic and embedded design.
Headline Sponsors Powell Electronics, Solsta and Wurth Electronics return to the show for two unmissable days. They will be joined by Dassault Systemes, sponsors of The Engineer Conference Theatre, QRA, sponsors of the verypopular EDS Party and ConeX, sponsor of our new Start-Up Zone.
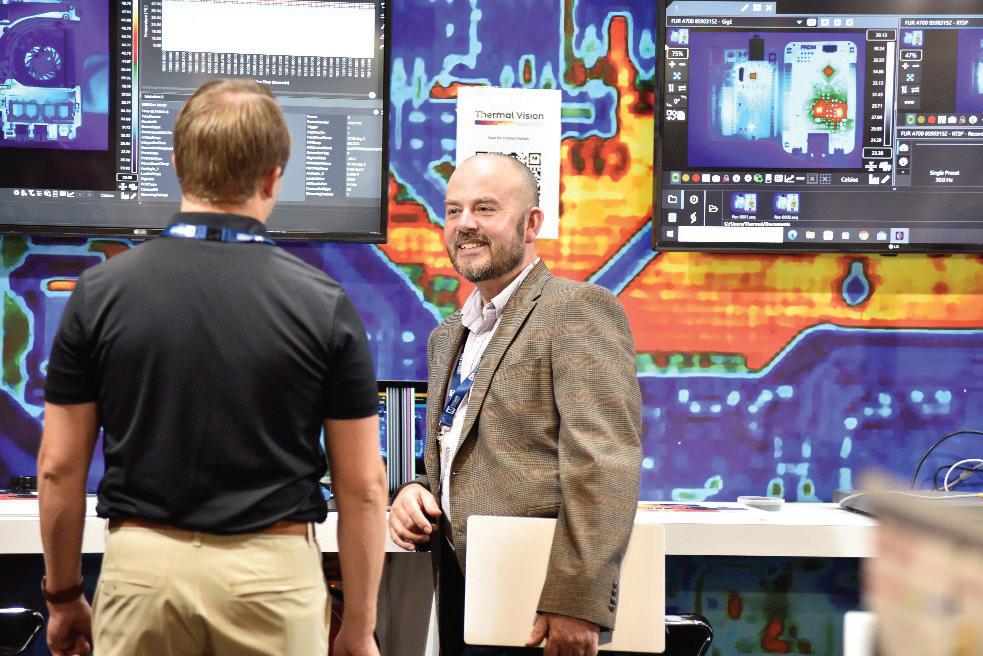
Visitors can expect to meet with 200+ exhibitors covering everything from 3D printing, fasteners and adhesives, design software, drives and controls, embedded systems, labelling, laser marking, motion control, PCB manufacture and assembly, and much more.
Visit the website (www. engineeringdesignshow.co.uk) for the full list of exhibitors, and read below to hear about everything else you can’t afford to miss.
Unlock 50+ hours of free learning across the three conference theatres. Highlights include ‘Socially assistive robots and the UH Robot House’, with Patrick Holthaus, Senior Research Fellow and Robot House Manager, University of Hertfordshire / The Robot House, ‘Protecting intellectual property in the age of AI’, with Katy Sayer, UK and European Patent Attorney at Venner Shipley, ‘British Olympic track bike development’, with Ben Collins, Lead AM Applications Engineer at Renishaw and ‘The Fight to Repair: why you don’t truly know your product until someone else has tried to repair It!’, with Jude Pullen, Creative Technologist at RS DesignSpark.
Visitors can also join practical workshop sessions. Takeaway inspiration to apply to your business from sessions that include
‘How high-speed data communication is used on industrial machinery’, with Ryan Milligan, Director Business Development at Powell Electronics, ‘How to maximise the potential of multiphysics simulation’, with Dr Ross Hubble, Technical Manager at COMSOL Ltd, ‘Realising productivity and innovation through inclusive working environments’, with Poppy Harrison, Engineer, Maira Bana, CFD Manager and Laura Hoang, Human Factors Engineer at SheCanEngineer, and ‘The devil is in the detail’ with Martin Dinmore, Distribution Channel Manager at Pico Technology
Nottingham Trent University will be showcasing the next generation of over 25 product designers. Featuring graduates from 2024 who have exhibited recently at New Designers in London, whereby their work has secured outstanding recognition from prestigious brands such as Dyson, Kenwood and Unilever.
Additionally, second-year product design students will be exhibiting their collaborative project with industry partner Trampboards showcasing the use of the VESC power system. The Trampaboard team will be on hand to describe the innovative VESC system and how students have applied their
technology in their robots.
The Innovation Zone will be displaying an exciting selection of design work. This includes Creative Hubb Limited’s EOD Bomb Disposal Suit, a complex garment made up of multiple layers of meta and/or para aramid materials required per panel/area to achieve the specified level of protection.
At the Start-Up Zone visitors can meet with an exceptional line-up of companies. Explore new products from Structural Evolution, Electrogear solutions Infinicity and HAL Robotics. Plus, 3D printers and scanners from Construct 3D, Nexa 3D, Central Scanning.
There are plenty of other exciting things visitors won’t want to miss.
Stop by The Robot House from the University of Hertfordshire, where the ground floor has been adapted into a unique research facility for human-robot interaction. Enjoy the immersive F1 racing simulators, take your shot on the basketball shoot the hoop, or check out our other fun games and activities. Take a break at the Chill and Charge Zone, which offers a quiet spot to relax and recharge both yourself and your devices. Enter the free EDS raffle, and join the party between 4:30 and 6:00 pm on 9 October, where visitors, exhibitors, and speakers can enjoy complimentary drinks, nibbles, and live music.
There is no better opportunity in the UK for design engineers to source the latest products and suppliers, find inspiration and network. Use the link below to register for your free ticket now.
bit.ly/3M0kd6r
9-10 October 2024
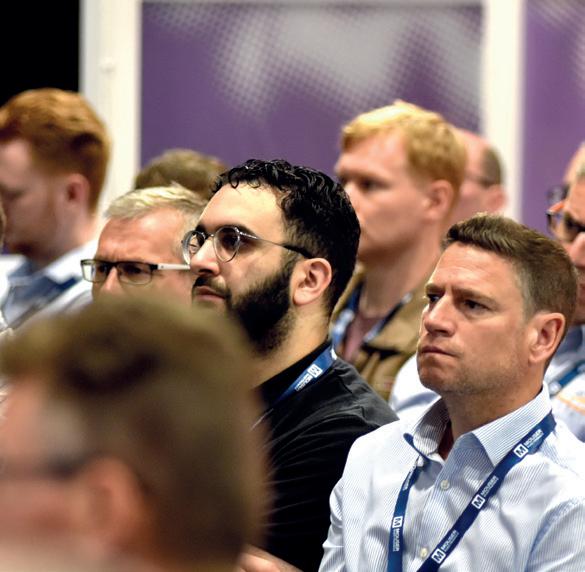
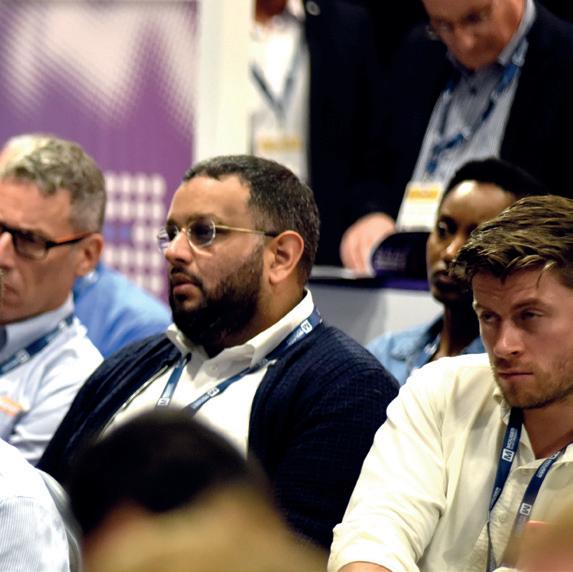
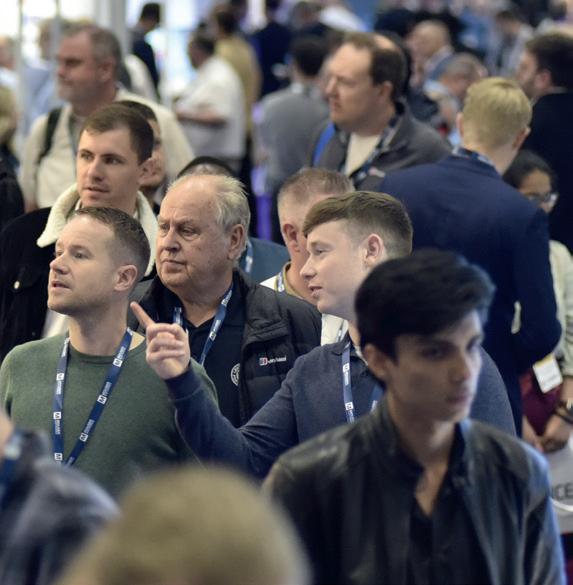
The UK’s biggest event dedicated entirely to engineering, electronic and embedded design
Coventry Building Society Arena HEADLINE SPONSORS @EngDesignShow #EngDesignShow www.engineeringdesignshow.co.uk
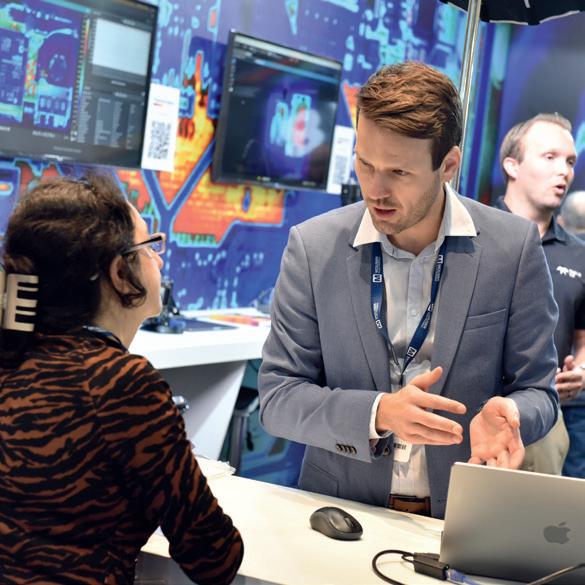
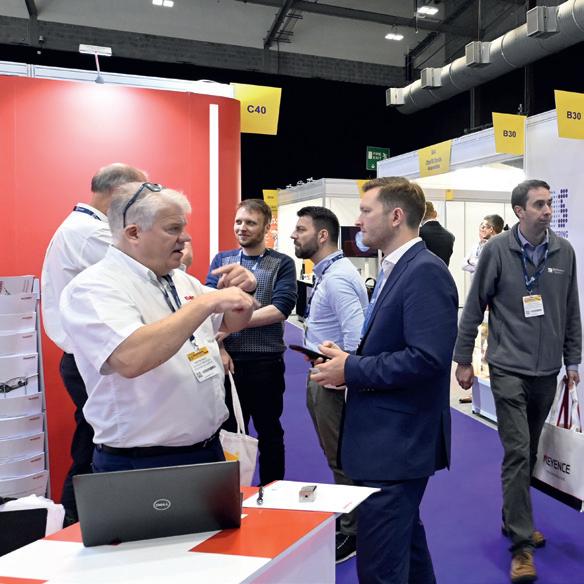
Join thousands of design engineers this October! Source the latest products, services and innovations available to the sector. Register today.


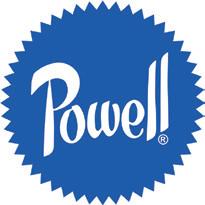
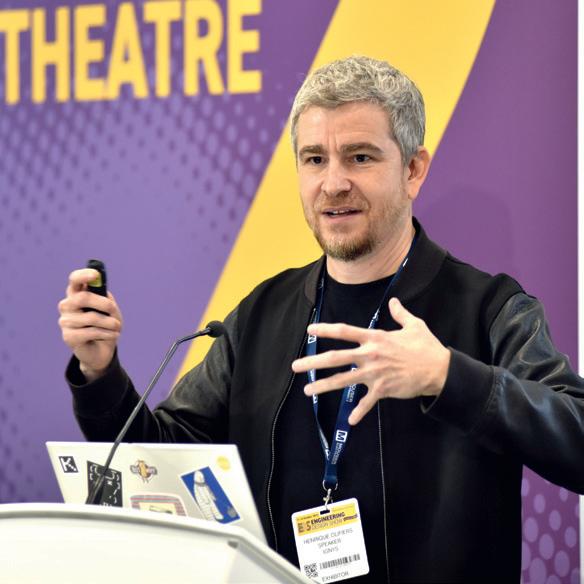
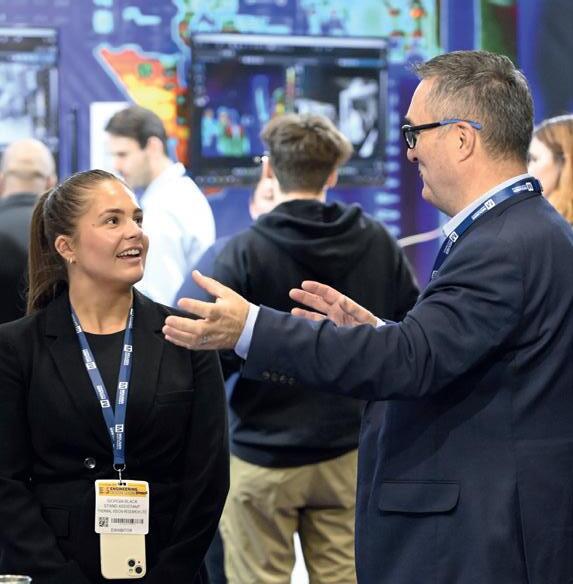
Robust cables for currents up to 16 Amperes
The EVCA range, ifm electronic’s latest product line, pairs innovation with unparalleled durability. These cables have been expertly designed to handle currents up to 16 Amperes, redefining excellence in power transmission technology.
Designed for the modern world where reliability is paramount, the EVCA cables boast exceptional durability, making them ideal for high-intensity applications across various industries. Whether it’s powering industrial machinery, supporting high-power electronics, or facilitating efficient energy transfer, the EVCA range delivers unmatched performance under demanding conditions.
The EVCA range is designed for superior performance, offering a high current capacity of up to 16 Amperes for reliable power delivery. Its robust construction ensures long-term durability, while its versatility
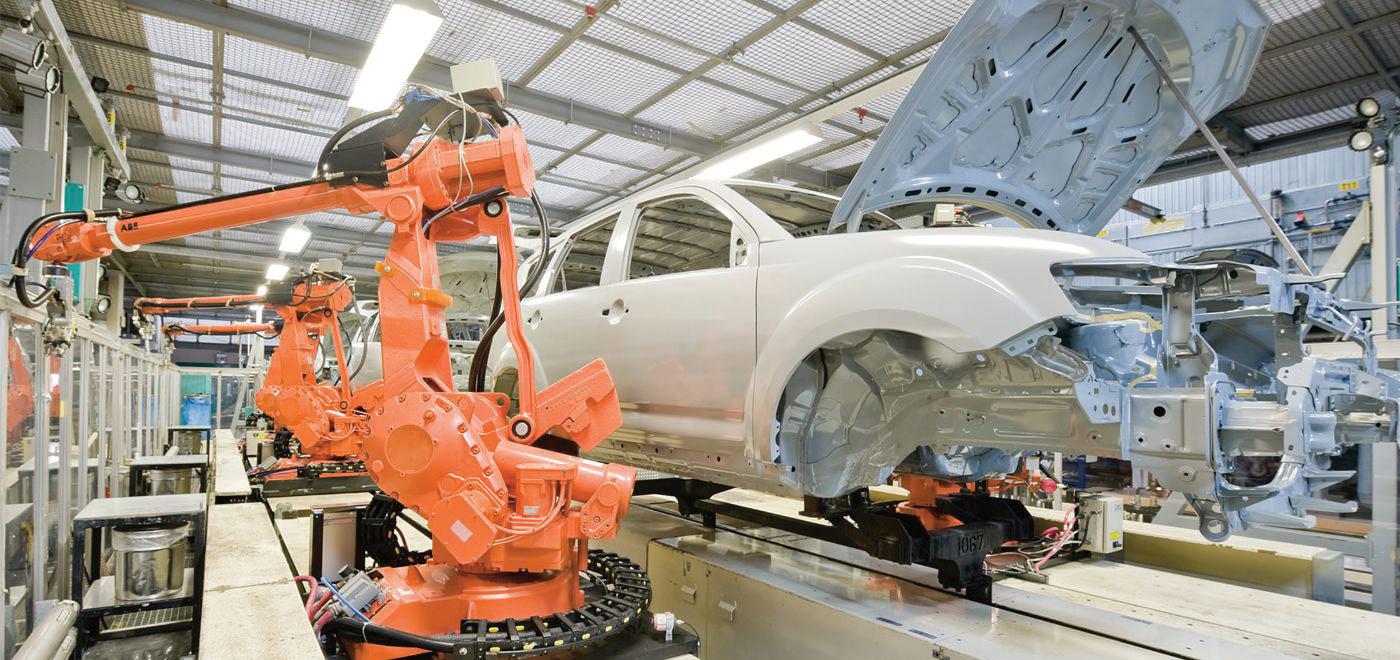
makes it suitable for a wide range of applications, from automotive to industrial settings. The range is also compatible with various devices, enhancing system efficiency. Additional advantages include a low voltage drop across extended cable lengths, attributable to a 2.5 mm² cable cross-section. Featuring a standard L-code connector and equipped with proven ecolink technology, it guarantees a safe and errorfree connection, making it ideal for powering
IO-Link masters. Additionally, it’s engineered to withstand the rigorous stress factors typical in industrial environments.
In a competitive market saturated with standard offerings, the EVCA range stands out for its unparalleled strength and reliability. Its ability to sustain high current ratings without compromising on quality makes it a game-changer for businesses seeking toptier electrical solutions.
ifm.com
New AC stepper drives provide a boost to industrial automation
Motion Control and Drives specialist MOONS’ Industries has introduced a new generation of AC Pulsed Stepper Drivers, the SRXAC Series. Efficiency, ease-ofuse and reliability are among the key requirements for many of today’s motion control applications and the SRXAC series is an excellent example of MOONS’ commitment in developing drives and motors which help enhance productivity, whilst maintaining exceptional quality.
Designed to meet the increasing demands and challenges of factory automation, logistics and other similar industry applications, these AC Pulsed Stepper Drivers offer important features and benefits. For example, Versatile Voltage Support ensures single-phase 85-265V AC input with maximum current
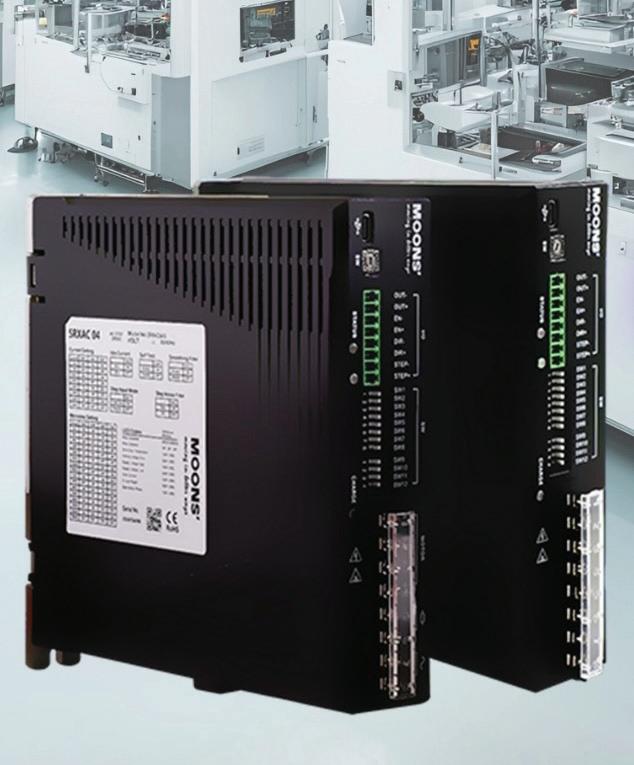
options of 4.5A, 8A and 12A, which means the drives are ideally suited to a wide range of applications that demand various
torque requirements. Additional features combine to provide a user-friendly configuration; for example, a Type-C interface which helps to simplify tuning, a 16-bit motor selector which enables easy matching and a 12-bit DIP switch for motor current interpolation with antiresonance functions.
Additionally, the drives meet the demand for enhanced performance because they offer higher continuous torque output at up to 1200rpm which significantly surpasses the performance of 750W servo motors in low speed applications, helping to improve factory production line efficiency and stability.
The SRXAC series is designed for applications requiring low control accuracy and high torque at low speeds, so it will excel in factory assembly lines, logistics conveyor belts, the food industry and many more. bit.ly/3SMn8TR
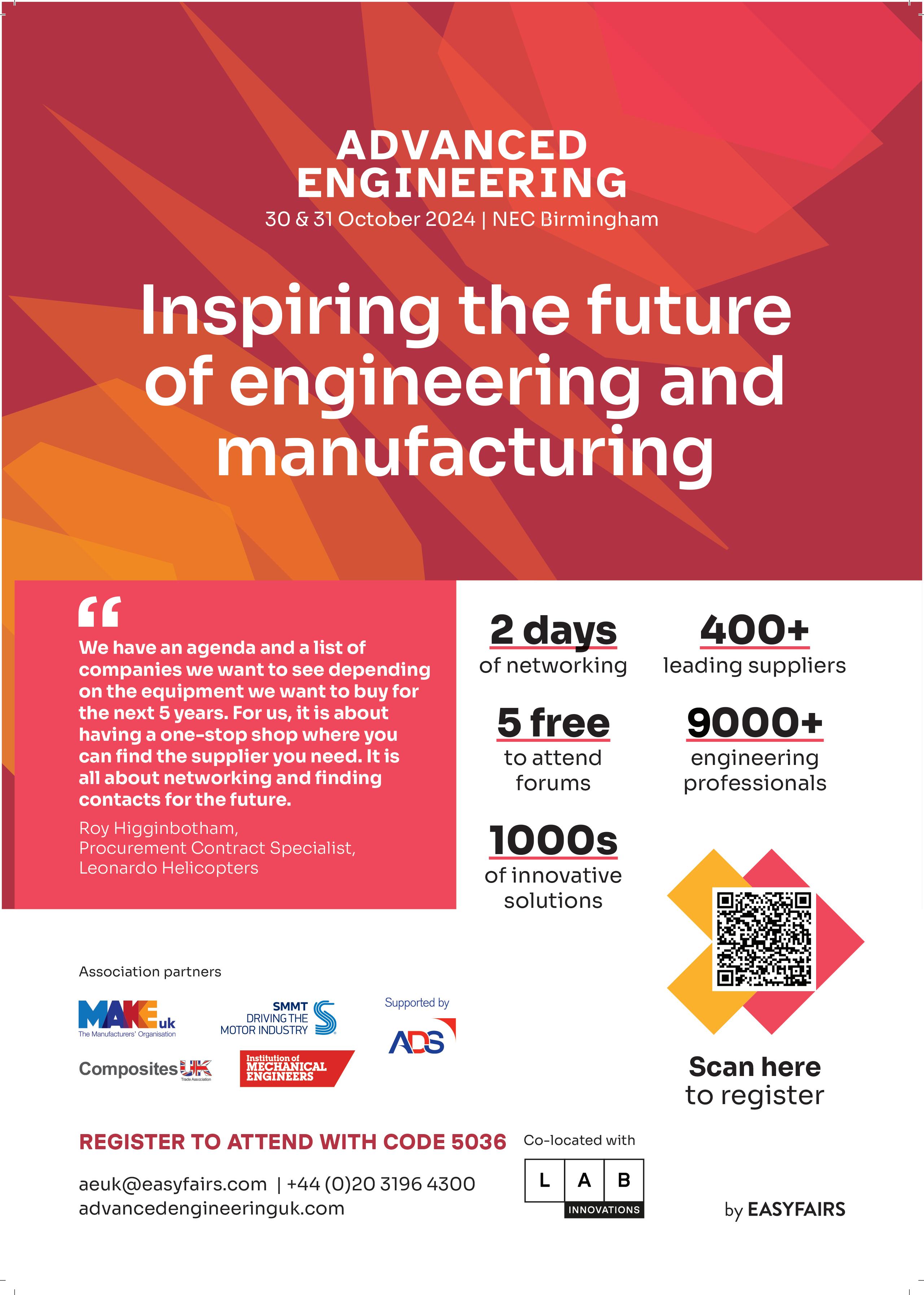
CONNECTIONS
3D Print Manufacturing

Midlands 3D Printing
T: 01785 594389
E: sales@midlands3d.com
W: www.midlands3d.com
Anti Vibration Products, Mounts & Bushes
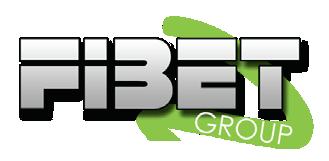
Fibet Rubber Bonding (UK) Ltd
T: 01282 878200
E: sales@fibet.co.uk
W: www.fibet.co.uk
Connectors & Cabling Solutions
CEMBRE Ltd
T: 01675 470 440
E: sales@cembre.co.uk
W: www.cembre.com/en
Drives, Motors & Gears
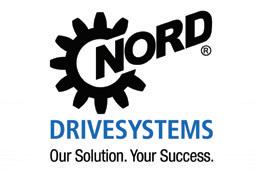
Flow Meters
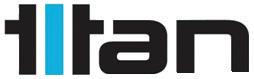
Nord T: 01235 534404
E: GB-sales@nord.com
W: www.nord.com
Titan Enterprises Ltd
T: +44 (0)1935 812790
E: sales@flowmeters.co.uk
W: www.flowmeters.co.uk
High Shear Mixing Equipment
Silverson Machines Ltd
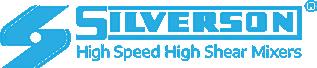
T: +44 (0)1494 786331
E: sales@silverson.co.uk
W: www.silverson.co.uk
Industrial Communications
Brainboxes

T: + 44 (0) 151 220 2500
E: sales@brainboxes.com
W: www.brainboxes.com
Intoware

T: 0115 977 8969
E: hello@intoware.com
W: www.intoware.com
Industrial Fans
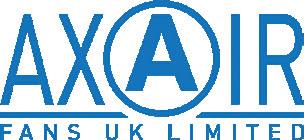
Axair Fans UK Limited
T: 01782 349 430
E: sales@axair-fans.co.uk
W: www.axair-fans.co.uk
Machine Safety
Schmersal UK Ltd
T: 01684 571980
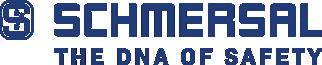
E: uksupport@schmersal.com
W: www.schmersal.co.uk
Marking Solutions
T-Mark T: 0330 153 8320
E: sales@t-mark.co.uk W: www.t-mark.co.uk
Pipework Systems
Jacob UK Ltd
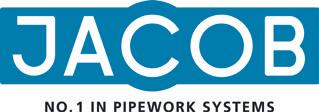
T: 01694 722841
E: sales@jacob-uk.com
W: www.jacob-group.com/uk
Pressure Measurement Specialists
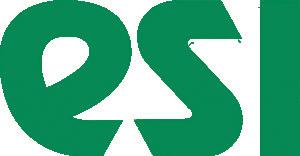
ESI Technology Ltd
T: +44 (0)1978262255
E: sales@esi-tec.com
W: www.esi-tec.com
Robotics & Automation
KUKA Robotics UK Ltd

T: 0121 505 9970
E: sales.uk@kuka.com
W: www.kuka.com
Sensors

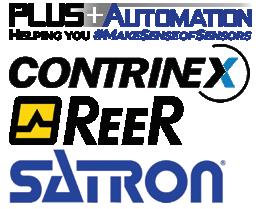
IFM Electronic
T: 020 8213-0000
E: enquiry.gb@ifm.com
W: www.ifm.com
PLUS Automation Ltd
T: 0121 58 222 58
E: Sales@PLUSAutomation.co.uk
W: www.PLUSAutomation.co.uk
Storage Solutions
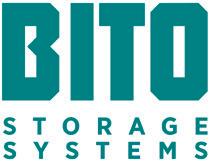
BITO Storage Systems Ltd.
T: 02476 388 852
E: Info.uk@bito.com
W: www.bito.com
Test & Inspection
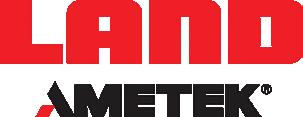
AMETEK Land (Land Instruments International)
T: +44 1246 417691
E: land.enquiry@ametek.com
W: www.ametek-land.com
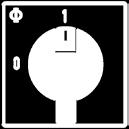
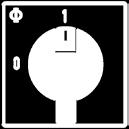
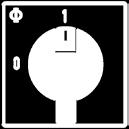
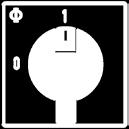
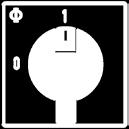
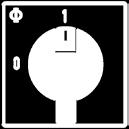
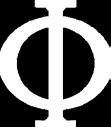
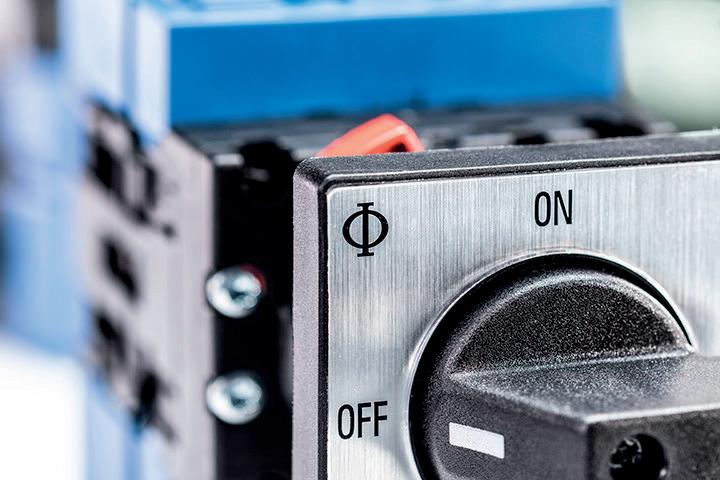
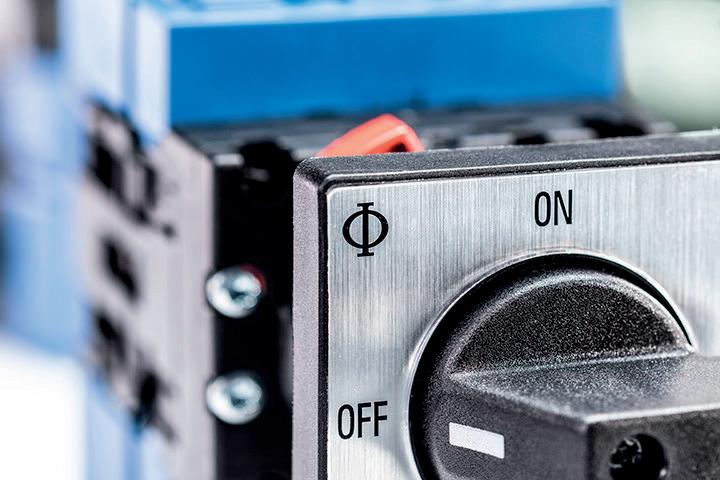
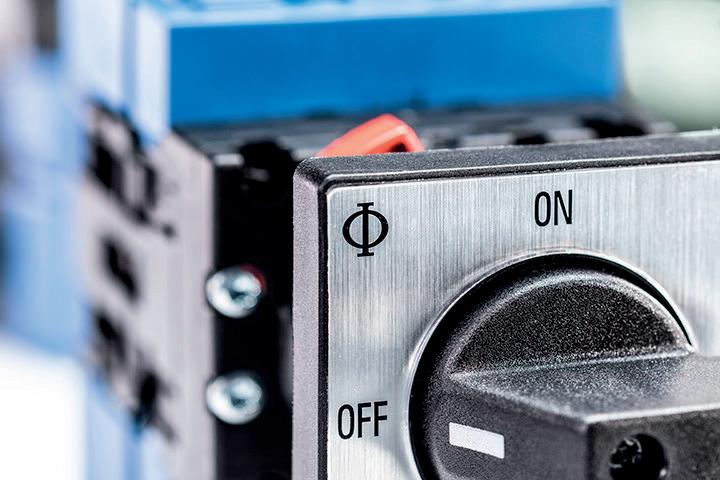
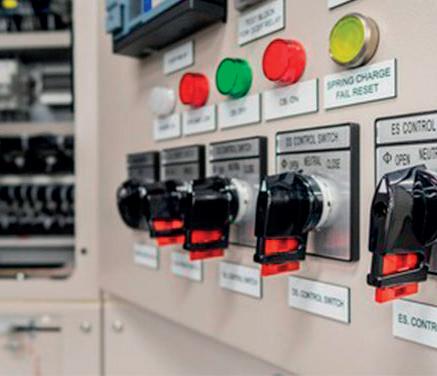
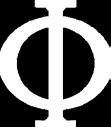

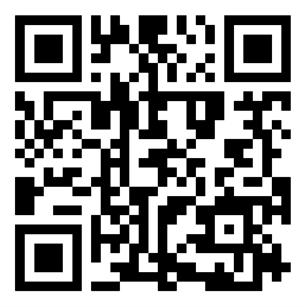
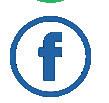
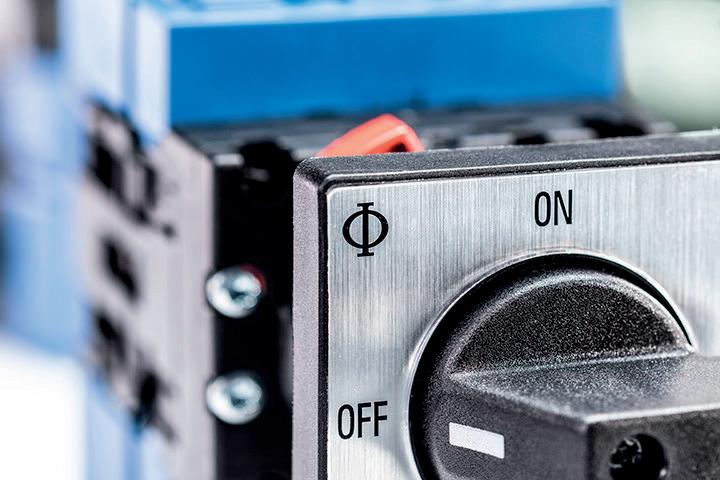
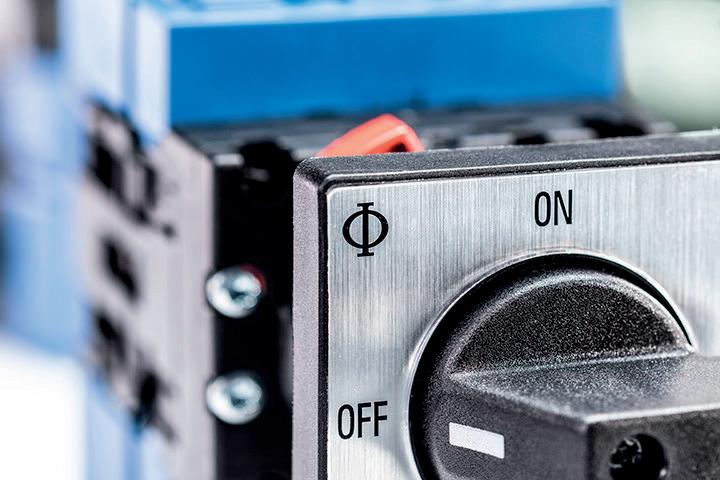
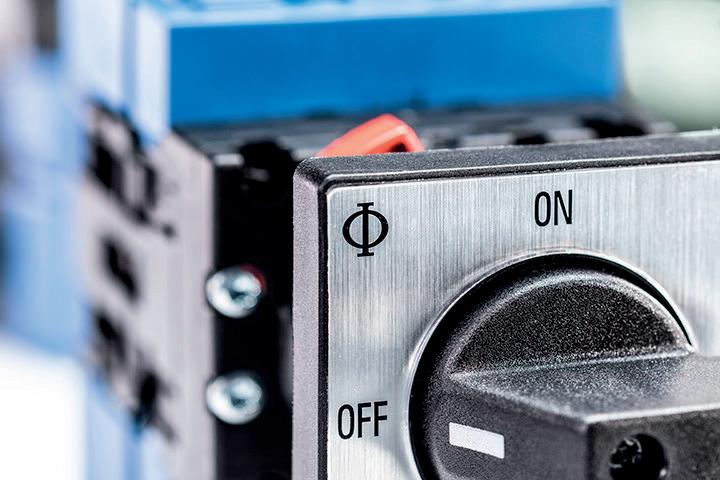
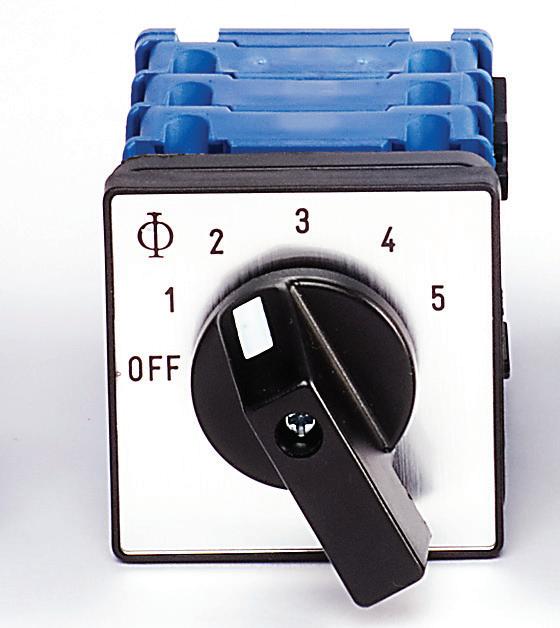
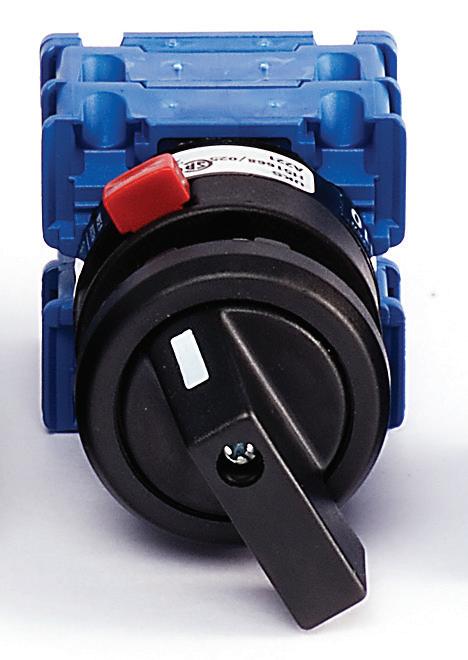
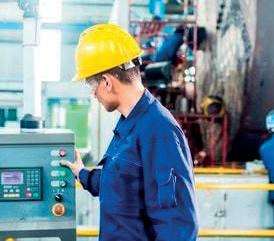
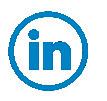
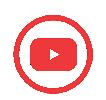
Sensors. Software.
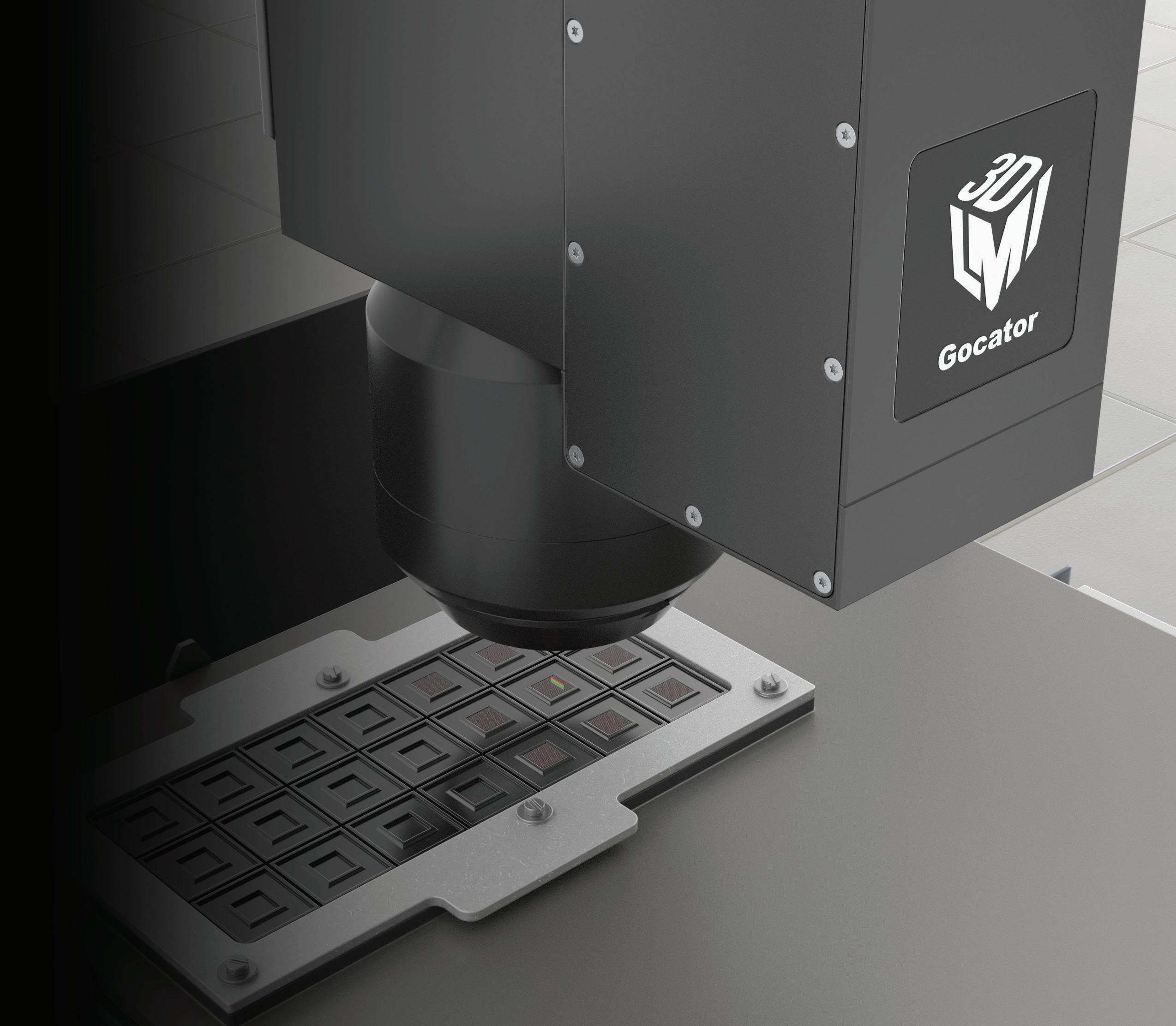
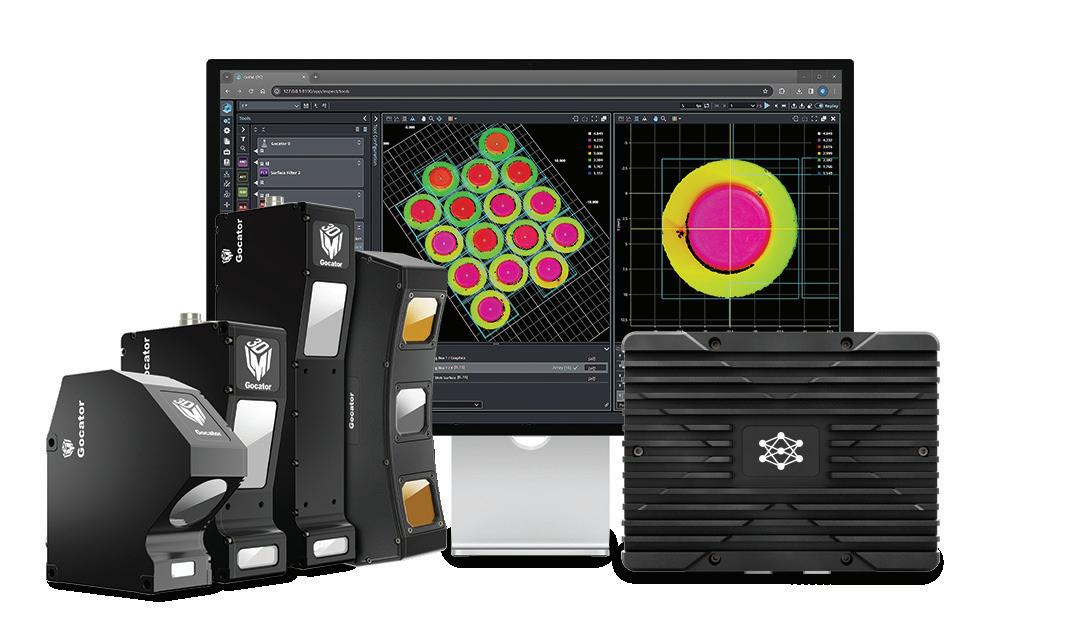
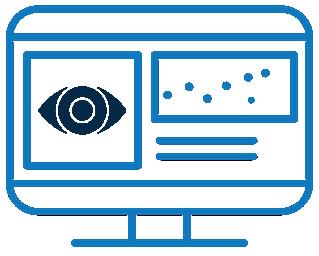
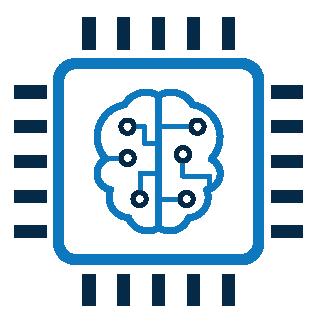
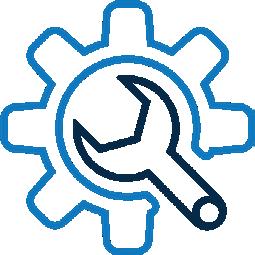