TIER 1 UNIVERSITY TRANSPORTATION CENTER (UTC)
Sponsored by the Office of the Assistant Secretary for Research and Technology in the U.S. Department of Transportation
VOL. 8 | ISSUE 2 | FALL 2024
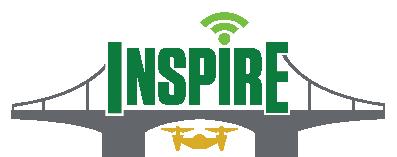

Sponsored by the Office of the Assistant Secretary for Research and Technology in the U.S. Department of Transportation
INSPIRE-UTC Biannual Publication
Message
Awarded in December of 2016 by the U.S. Department of Transportation, the five-year INSPIRE UTC is a Tier 1 University Transportation Center with a research priority of preserving the existing transportation system as part of the UTC Program (https://www. transportation.gov/utc/2016-utc-grantees) that was authorized under the Fixing America’s Surface Transportation Act.
CONSORTIUM MEMBERS
I am pleased to share with you the last edition of our regular INSPIRE UTC newsletter. This edition begins with the 2025 American Society of Civil Engineers (ASCE) Charles Pankow Award for Innovation for INSPIRE UTC’s Bridge Inspection Robot Deployment Systems (BIRDS). It highlights seven milestone research achievements in five categories of emerging technologies: flying and crawling robots, artificial intelligence, 3D reconstruction and digital twin, probability of detection evaluation, and advanced technology training.
This edition also highlights the first National Summer Transportation Institute at Missouri S&T, which motivated 15 high school students to explore careers in STEM education in 2024. Robotic solutions for automated bridge inspection and smart shear key solutions for bridge resilience are presented at the inaugural 2024 USDOT Future of Transportation Summit. Their hands-on demonstration attracted about 30 visitors and received positive responses on technology novelty and potential impact. The expanded robotic solutions for steel weld defect and concrete crack inspections will be exhibited at the 2025 TRB Annual Meeting.
This edition further highlights significant technology transfer efforts. Three patents were granted to INSPIRE investigators. The novel BIRDS helped collect more and higher quality data to meet the latest National Bridge Inspection Standards (NBIS) requirements. They continue to be tested and evaluated at bridge sites through the pooled-fund study no. TPF-5(395). Artificial intelligence tools are developed to improve work efficiency in video analytics for element segmentation and defect classification.
INSPIRE quarterly webinars (29 total) engaged 5,012 people from 50 U.S. States and 57 different countries. On average, 40% of the participants are from academia, 19% are from industry, 14% are from Government, and 27% are unknown. INSPIRE outreach events (56 total) reached approximately 5,012 participants and covered 220 contact hours. In addition, with the INSPIRE UTC support, the Kaleidoscope Discovery Center reached over 2500 K-18 students through robotics and engineering programming.
The INSPIRE UTC grant is the impetus of establishing Missouri S&T’s Center for Intelligent Infrastructure (CII) to expand and sustain intelligent infrastructure research and education at Missouri S&T. CII aims to overcome the world’s increasing challenges with aging infrastructure for a safe, sustainable, and resilient community and environment.
While this INSPIRE UTC funding cycle expired on September 30, 2024, the translation of the developed technologies into applications is just beginning. To further automated infrastructure inspection and achieve data-driven asset management, CII will organize a national workshop on digital twins in the built environment on May 14-16, 2025, to harness academic, industrial, and governmental interests, develop national digital twin initiatives, and further realize the value of INSPIRE technologies.
We remain committed to advancing our research, fostering educational excellence, and engaging our community. We invite you to explore the featured articles and summary achievements in this edition and encourage you to visit our website at https://inspire-utc.mst.edu for more information about our upcoming events.
Genda
Chen, Ph.D., P.E., F. ASCE, F. SEI, F. ISHMII, F.SPIE, F. TGI Professor and Robert W. Abbett Distinguished Chair in Civil Engineering
Director,
INSPIRE University Transportation Center
Director,
Center for Intelligent Infrastructure
Drs. Genda Chen, Hung La, and Yang Wang at the INSPIRE UTC are the recipient of 2025 ASCE Charles Pankow Award for Innovation. Founded in 1852, ASCE represents more than 150,000 members of the civil engineering profession in 177 countries. The ASCE Charles Pankow Award for Innovation (https://www.asce.org/career-growth/ awards-and-honors/asce-charles-pankow-award-for-innovation) was established by the Civil Engineering Research Foundation (CERF) in 1996. Named for industry visionary Charles J. Pankow, the award recognizes the contributions of organizations working collaboratively to advance the design and construction industry by introducing innovation into practice. It was instituted as a Society award on December 17, 2008.
Entitled “Bridge Inspection Robot Deployment Systems (BIRDS),” this innovation includes a multifunctional robotic system of uncrewed aerial vehicles (UAVs) and structural crawlers (SCs) that are interactive with bridges to support high-quality data collection using close-distance sensing (e.g., visual or thermal imaging) and near-surface nondestructive testing. The BIRDS innovation consists of a hybrid UAV and SC system and a wireless communication and control system. The hybrid system, called BridgeBot, is designed to enable a close-distance under-deck inspection of girder bridges using RGB, infrared, and hyperspectral cameras. The BridgeBot has two driving systems, one for flying like an octocopter and the other for traversing like a ground vehicle on four wheels that are fixed on two arms with adjustable spacing and angles. The BridgeBot can fly to the underside of a bridge deck, self-attach to a steel or concrete girder, and traverse along the girder. It has four unique advantages:
(1) A stationary traversing platform for high-quality imaging and nondestructive testing,
(2) A carrier and launching ramp of a bicycle SC to the attached girder,
(3) A dual-mode operation with an elongated duration, and
(4) An emergency landing gear on water.
A BridgeBot prototype weighing less than 4 kg was tested on girder bridges for visual and thermal imaging. It overcomes the challenges encountered by commercial drones, including platform vibration during measurement, limited capabilities for close-distance inspection, and limited flight time when deployed at bridges. While the BridgeBot can fly for about eight minutes only, it can traverse for more than 60 minutes along bridge girders. The resolution of an image from a GoPro Hero11 camera installed on the BridgeBot is 0.015 mm when taken at 0.3 m distance or 0.14 mm at a girder spacing of 2.75 m. This level of pixel resolution is sufficient for the detection of any structural features on the bridge surface.
A bicycle-like crawler consists of two magnetic wheels, visual-inertial odometry, an onboard computer, and an iPad robot controller. The crawler weighing about 2.2 kg can swiftly maneuver around different shapes of steel members. It is equipped with a Martlet wireless sensing device that contains an ultrasonic transducer for metal thickness measurement. To perform each ultrasonic test, a miniature pump applies couplant gel on the surface of a steel member to ensure that a solid wave propagates into the metal. The robotic system was deployed on Missouri, Georgia, and Nevada highway bridges to measure the thickness of steel girders. The Martlet motherboard includes a daughter board to enable ultrasonic testing at up to 80 MHz sampling rate. The ultrasonic board consists of a high-speed analog-to-digital converter (ADC) chip, a memory chip, and a shift register. It transfers the sampled signal to the Martlet motherboard through a serial peripheral interface protocol. Using a 2.25 MHz dual element transducer and a sampling rate of 50 MHz, the ultrasonic board measured the thickness of a 25.4-mm-thick steel plate and an 8-mm-thick rusty steel plate with an error of less than 0.01 mm.
VICE CHANCELLOR OF RESEARCH
It is with great pleasure that I take a moment to recognize the many achievements of the INSPIRE UTC in its final newsletter. Since the beginning, this center has committed to knowledge creation and deployment of innovative technologies dedicated to automated bridge preservation. These achievements will support Missouri S&T’s strategic initiative in geospatial engineering and intelligence with new interdisciplinary talents in robotics, virtual/augmented reality, and artificial intelligence/machine learning; and new research infrastructure in training facility for tele-inspection in a unity game engine and digital twins for infrastructure preservation. At Missouri S&T, the mission that has started with INSPIRE UTC will continue through the Center for Intelligent Infrastructure, a multi-disciplinary university research center. This reflects the importance of the center to further advance research, workforce development, and outreach and technology transfer in the vital field of transportation infrastructure. We are very grateful for US DOT for the opportunity to lead INSPIRE Tier-1 UTC.
Dr. Kamal Khayat PROFESSOR & VERNON & MARALEE JONES CHAIR CIVIL ENGINEERING
The BIRDS innovation, both BridgeBot and crawler version, were controlled via a mini computer (CPU) that is empowered by artificial intelligence (AI) and machine learning for bridge element segmentation and defect classification. A semi-supervised learning paradigm was developed to automatically and efficiently process a large volume of videos and/images from which important frames were selected to quantify the essential elements and main defects according to the 2019 Manual for Bridge Element Inspection. The semi-supervised framework was based on cooperative artificial and human intelligence, taking temporal correlation into account. Specifically, a domain expert (i.e., senior inspector) is working along with a multishot machine from training through testing to validation so that the expert knowledge is distilled into the learning algorithm of the machine and the machine segments elements and classifies defects to the inspector's satisfaction and understanding. The so-trained machine is a natural extension of the expert's ability and thus easy to be adopted in engineering practices, compared to other black-box AI algorithms developed in the published literature.
The BIRDS innovation results from collaborative research and implementation among academic, governmental, and industrial partners coordinated by the INSPIRE UTC, which was funded by the U.S. Department of Transportation. In the development phase, Missouri University of Science and Technology (INSPIRE UTC PI: Dr. Genda Chen), the University of Nevada, Reno (INSPIRE UTC Co-PI: Dr. Hung La), and Georgia Institute of Technology (INSPIRE UTC Co-PI: Dr. Yang Wang) collaboratively designed, tested, and evaluated a hybrid UAV and SC system, a bicycle SC, and a wireless communication and control system, respectively. In the application phase, the three universities designed, tested, and evaluated an optical and thermal imaging system, a couplant gel dispensing system, and an ultrasonic metal thickness measurement system, respectively, and collaborated with Missouri (Dr. Bryan Hartnagel), Nevada (Mr. Michael Premo), and Georgia (Mr. Donn Digamon) Departments of Transportation on steel bridges for both robot locomotive functions and imaging/testing capabilities.
In 2016, the INSPIRE UTC was awarded to Missouri University of Science and Technology (S&T) by the U.S. Department of Transportation. The INSPIRE UTC includes four major research partners: University of Nevada-Las Vegas, University of Nevada-Reno, Georgia Institute of Technology, and City College of New York. Since 2017, the INSPIRE UTC has marked seven milestone achievements toward automated bridge inspection as highlighted in the following figure. These achievements were made through 28 multi-phased research projects as detailed in their final reports posted at Missouri S&T’s INSPIRE UTC Website (https://inspire-utc. mst.edu/researchprojects/). They are grouped into five emerging technologies as briefly summarized below.
Federal Highway Administration and Rutgers University developed and deployed world’s first autonomous RABITTM bridge deck inspection tool in 2008-2015. To enable automated inspection for entire bridges, the INSPIRE UTC developed and demonstrated a suite of new Bridge Inspection Robot Deployment Systems (BIRDS) in 2017-2024. The BIRDS consists of hybrid flying and traversing vehicles and structural crawlers that can access difficult-to-reach areas on bridges, particularly steel and concrete-girder bridges. They can be equipped with lightweight nondestructive testing devices to enable rapid data collection along the surface of bridge elements. For example, a microscope can provide a detailed view of defects in steel weld connections and machine learning can help detect weld debonding as illustrated below.
Artificial intelligence (AI) can aid engineers in rapidly detecting and quantifying defects and damage occurring on bridges. The INSPIRE UTC focused the development of AI in its explainability in engineering applications. To this endeavor, the INSPIRE UTC developed and demonstrated AI at three levels: individualized, domain-specific, and domain-independent. Trained with individual knowledge and experience, the Individualized AI represents inspector-in-the-loop, semi-supervised deep learning for bridge element segmentation defect classification. Representative to a group of professionals, the Domain-specific AI symbolizes unsupervised domain adaptation learning. The Domain-independent AI represents supervised deep learning with complete interpretability, which is transferable to other engineering fields.
In 2022, the INSPIRE UTC launched a new task for the 3D reconstruction of bridges. At beginning, a manual Light Detection And Ranging (LiDAR) scanner was used to scan the 10th street highway bridge in Rolla, MO, and reconstruct the virtual bridge with smooth surfaces. In 2023, vision-based 3D reconstruction started using the photogrammetry technique. Later, drone-based images were collected and Gaussian splatting approach was adopted to conduct the 3D reconstruction of bridges from RGB images only. The Gaussian splatting is a point based approach that uses simple neural networks. This approach starts with capturing videos of a bridge ensuring full coverage with 80% overlapping. It then extracts frames and apply a Structure-from-Motion technique to extract point cloud and RGB information. Lastly, it applies Gaussian splatting to reconstruct a 3D model of the bridge.
In 2023, the 3D reconstruction was transformed into a digital twin when sensor and nondestructive test data were used to update information in real time and computational/informational models were introduced to predict the behavior of bridges. A novel multidimensional digital twin was developed and implemented for the Missouri S&T campus to enable rapid, consistent campus management for infrastructure assets, landscapes, energy, security, flood, etc.
Probability of Detection (POD) determines the ability of an inspection as a function of defect type and size. For data taken from independent, repeated tests, such as ultrasonic measurement for crack length, traditional statistical methods work as summarized in existing handbooks such as the 2009 MIL-HDBK-1823A. For sensors that are fixed and acquire data over time as cracks grow, the acquired data could be partially correlated. The traditional statistical methods are thus invalid for in-situ sensor data processing. The INSPIRE UTC developed two new POD analysis methods: the Size of Deterioration at Detection (SODAD) model and Random Parameter (RP) model. The SODAD model is based on the statistics of the measured deterioration sizes at a measurable threshold signal. The RP model considers each sensor as a sample of a sensing system and randomizes the parameters of sensor’s calibration equation. The RP model is more robust in corrosion detection applications than the SODAD model.
With the advent of robotics, AI, and augmented reality, bridge inspectors need to receive proper training in order to make these advanced technologies be adopted to their full exploit in applications. The INSPIRE UTC developed a three-day training and evaluation program for trainees to master the skills of using the advanced technologies. This program starts with an introduction to AI, mixed reality, robotics, and remote sensing. It is then followed with three-phase hands-on practice on automated bridge inspection. The first phase of training helps understand bridge elements, defects, materials, reporting requirements, and master the skills of maneuvering a robot (drone + crawler) in simulations. The second phase operates a physical drone that is interactive with a virtual highway bridge and be monitored with psychological stress. The third phase operates a physical robot (drone + crawler) surrounding a physical steel frame, representing a bridge pier, and quantify defects for inspection reporting. Once all three phases are passed successfully, trainees are paired to conduct a two-member collaborative inspection on a mock-up steel-girder bridge. The trainees receive the certificate of completion at the end of successful training.
The INSPIRE UTC was awarded in 2016-2024 by the Office of the Assistant Secretary for Research and Development (OST-R) in the U.S. Department of Transportation. It developed and advanced emerging technologies such as robotics, remote sensing, robot-assisted nondestructive testing, virtual/augmented reality, digital twin, and artificial intelligence for their applications in automated bridge inspection and maintenance. To provide administrative support to external centers such as the INSPIRE UTC, sustained leadership, research infrastructure, and broader visions in intelligent infrastructure, Missouri University of Science and Technology (S&T) established the Center for Intelligent Infrastructure (CII; https://cii.mst.edu) in 2019 based on the 2019 University of Missouri Strategic Investment funds and the Missouri S&T’s strategic plan.
CII creates, conveys, and applies knowledge and intelligence that help solve the world’s increasing challenges with aging infrastructure for a safe, sustainable and resilient community and environment. It aims to develop faculty and research infrastructure resources to transform currently disparate design, construction, and operation phases into an integrated, open-source, cloudbased, digital twin of cyber-physical infrastructures.
CII provides staff services and infrastructure support to members to boost interdisciplinary research and scholarly activities. Intelligent infrastructure represents an integration of informatics, automation, and actuation into the management of civil and power infrastructure assets. It involves measurement science, intelligent built environment, intelligent asset operation, and smart cities.
CII currently has one full-time administrative staff and six technical staff. It provides support to 25 faculty members in Chemistry, Civil/Architectural/Environmental Engineering, Computer Science, Economics, Electrical and Computer Engineering, Engineering Management and Systems Engineering, Geological Engineering, Mechanical Engineering, Nuclear Engineering, Philosophy, and Research Technical Services.
To support research and education activities, CII has developed and managed four unique spaces:
• Collaboration Office for Research and Education (CORE)
• Robotic Engineering, Application, and Learning (REAL) Lab
• Visual Inspection Research & Training Using Augmented Learning (VIRTUAL) Lab
• Bridge Inspection Robot Deployment Systems (BIRDS)
On August 13-15, 2024, INSPIRE UTC inspection team (Drs. Zhenhua Shi, Son Nguyen, Woubishet Taffese, and Joel Runji) demonstrated novel concepts for automated bridge inspection at the 2024 USDOT Future of Transportation Summit, Washington DC. Participation at the Summit is by invitation only. The specific objectives of the Summit are to
• Enhance coordinated research among the USDOT University Transportation Centers and the broader transportation community,
• Highlight the most impactful projects completed, aroundthe-corner, and over-the-horizon, and
• Identify gaps, challenges, and opportunities, both in intermodal and multi-modal research.
The Center for Intelligent Infrastructure (CII) was invited to present and demonstrate the emerging technologies developed at Missouri S&T on behalf of the INSPIRE UTC and the Mid-America Transportation Center (MATC). Specifically, Dr. Genda Chen, INSPIRE UTC Director and MATC Associate Director, delivered two lectern presentations entitled:
1. Automated Bridge Inspection and Maintenance as part of the INSPIRE UTC Program
2. Resilient Design of Bridges under Multiple Hazards as part of the MATC Program
The first presentation gave an overview of the challenges of current practices in bridge inspection and maintenance and identified the gaps and opportunities to create the future of automated infrastructure preservation by inventing Bridge Inspection Robot Deployment Systems (BIRDS). BIRDS involved robots that are interactive with bridges, multi-inspector collaboration in mixed reality, and artificial intelligence and machine learning for data retrieval, fusion, and analysis to support decision-making. Interactive robots included a structural crawler equipped with an ultrasound testing device for metal thickness measurement of corroded elements, drones that enable maintenance tasks, such as washing, drilling, and valve turning in air, and a hybrid uncrewed vehicle that can fly to the underside of a bridge and attach to a girder like a "traveler platform' currently in use for the inspection and maintenance of river-crossing bridges. A two-inspector collaboration platform was developed in mixed reality to enable beyond-the-visual-line-of-sight flight and inspection with robots. Explainable artificial intelligence
algorithms were developed to enable good understanding of the predicted results for adoption in engineering practices. This presentation concluded with a summary of future research needs.
The second presentation overviewed the development and deployment of sliding, modular, adaptive, replaceable, and two-dimensional (SMART) shear keys as fuse elements between superstructures and substructures. The SMART shear keys enable an adaptive control of both the force and displacement of bridges under different types of loads. The performance of SMART shear keys under tsunami loading was investigated through a 1/5-scale six-girder concrete bridge model.. The shear keys were prestressed to represent flexible, medium, and fixed superstructure-substructure connections, respectively. The test results indicated that the residual displacements of the SMART shear keys were less than 1 mm in the vertical direction and zero in the horizontal direction. The energy dissipated by the SMART shear keys was up to 32.5% of the input energy that the bridge received from the tsunami loading. The natural frequency and energy dissipation of the bridge were respectively modified up to 18% and 14.2% by changing the prestress level of the SMART shear keys from 0 to 200 MPa.
During the Summit, the four INSPIRE crew demonstrated, for the first time, a structural crawler that is launched off a ramp on a hybrid flying and traversing vehicle. The team also demonstrated the concept of operation with collaborative field inspection using two Hololens. These hands-on demonstration peaked the interest of about 30 visitors as seen in the following photos (courtesy of the USDOT). Some visitors even tried hardware and had the firsthand experience.
The Transportation Needs: Artificial intelligence (AI) has been increasingly applied into bridge design and inspection. This integration involves interdisciplinary knowledge in computational intelligence and domain expertise (e.g., materials and structures). In computer science, AI algorithms can be treated as a black box and are mostly evaluated for accuracy and computational cost in their predictability and generalizability. Their adoption in civil engineering is likely pre-conditioned on the explainability of AI predictions. Civil engineers design, construct, and maintain capital infrastructure that are costly and, equally important, critical to the function of a society. Failure of engineering structures bears significant social, economic, and environmental consequences. To make informed and responsible decisions, civil engineers must know how AI derives segmentation, classification, and evaluation results.
The Key Innovation: The INSPIRE UTC introduces three approaches of increasing degrees of AI explainability in application to civil engineering, specifically materials and structures. The first approach is to develop a semi-supervised, AI and human collaborative learning protocol to enable researchers to incorporate the knowledge of a domain expert during AI training, validation, and test so that the developed AI serves as an extension of the expert’s capability in executing potentially multiple AI-targeted engineering tasks. This multi-tasking protocol involved an iterative process to improve the accuracy of AI predictions by implanting more and more domain knowledge, resulting in a relevant AI to the domain expert involved during the AI development. It was demonstrated for elements segmentation and defect classification in highway bridges.
Fig. 1 Overview of the proposed semi-supervised self-training method with human-in-the-loop (https://doi.org/10.1177/14759217211010422)
The second approach is to develop an unsupervised domain adaptation technique in multishot deep learning. This study proposed a class-wise histogram matching-based data augmentation technique that seeks to complement the domain adaptation strategy, leading to a significantly improved adaptation in situations where no labeled data are available from the target domain. The proposed framework was validated with a case study of bridge inspection but can be extended to other relevant application areas, including but not limited to autonomous vision-based bridge defect detection and post-disaster structural reconnaissance.
Fig. 2 Bridge component segmentation from the multishot archtecture based on four input frames (https://doi. org/10.1016/j.engappai.2024.108297)
The third approach is to develop a neural additive network by establishing one-to-one highly nonlinear relations between each input and an output and minimizing false prediction of the overall output from the combined effect of the inputs. As demonstrated in Fig. 3, this approach is significantly more accurate than the design equation in the AASHTO design specifications in the determination of concrete-concrete shear strength.
The Outcomes: The first approach results in an AI platform that is transparent to the specific expert that is involved during the development. The second approach is transparent to a group of domain experts in disciplines, such as bridge engineering, through domain adaptation. The third approach is completely transparent to all experts in civil engineering as it mimics the traditional statistical regression yet incorporates the learning approach in establishing highly nonlinear functions.
The Impacts: The semi-supervised approach will reduce tremendous labor hours of a specific inspector in image labeling and processing for critical defect type and size. The unsupervised approach will enable knowledge transferring between engineers, for example, for concrete vs. steel girder bridges. The learning-based regression approach results in a concrete-concrete shear strength design equation that is recommended to the AASHTO for potential adoption as the new design equation is much more accurate than that in the AASHTO LRFD Bridge Design Specifications.
Fig. 3 Prediction accuracy of (a) AASHTO LRFD equation and (b) Learning-informed Design equation: experimental (vn,test) and predicted (vn,pred) interfaciaial shear strengths, respectively (https://doi.org/10.1177/03611981231183718)
Led by Dr. Ruwen Qin, Associate Professor in Engineering Management and System Engineering at Missouri University of Science and Technology, this project on A Training Framework of Robotic Operation and Image Analysis for Decision-making in Bridge Inspection and Preservation is part of the INSPIRE (INSpecting and Preserving Infrastructure through Robotic Exploration) UTC Research Program.
Led by Dr. Genda Chen, Professor and Abbett Distinguished Chair in Civil Engineering and Director of the INSPIRE (INSpecting and Preserving Infrastructure through Robotic Exploration) UTC at Missouri University of Science and Technology, the Bridge Inspection Robot Deployment Systems project is part of the INSPIRE UTC Research Program. For more information on this INSPIRE UTC project, please contact Dr. Chen at inspire-utc@mst.edu or (573) 341-6114.
Genda Chen, Ph.D., P.E., F. ASCE, F. SEI, F. ISHMII, F.SPIE, F. TGI
Professor and Robert W. Abbett Distinguished Chair in Civil Engineering Director, INSPIRE University Transportation Center Missouri University of Science and Technology
gchen@mst.edu
The Transportation Needs: The primary goal of bridge inspection is to ensure that structures are safe for the traveling public. In recent years, inspection data have been increasingly used to support a more proactive approach of asset management such that structures are not only safe but also maintained for a minimal life-cycle cost. The broadening of inspection scope requires a significant shift in practice from fully visual inspection to partially visual inspection supplemented with advanced technologies such as remote sensing and nondestructive evaluation. These technologies enable the implementation of objective decision-making processes in asset management and the understanding of infrastructure resilience.
In current practices, human inspectors (or divers for underwater operation) are required to be physically close (e.g., 0.5 m) to potential defect and damage areas. At close distances, they can tap members for concrete delamination, scrape/cleanse surfaces for steel corrosion, conduct nondestructive tests for steel crack, and examine bridge foundations for flow erosion.
The Key Innovations: To support new data collection as stipulated in the 2022 National Bridge Inspection Standards, INSPIRE (INSpecting and Preserving Infrastructure through Robotic Exploration) University Transportation Center (UTC) at Missouri University of Science and Technology has developed a mobile, automated bridge inspection facility, referred to Bridge Inspection Robot Deployment Systems (BIRDS). The BIRDS include a series of novel robots that are interactive with bridges for high-quality inspection tasks following four strategies.
First, a hybrid flying and traversing vehicle is attached to the bottom flange of an I-shaped girder as a steady measurement and observatory station for bridge deck, girder, and pier inspection. Fig. 1 shows the prototype of an octocopter, which was tested on June 18, 2024, at the Roubidoux Creek Bridge in Waynesville, MO. The octocopter weighs approximately 40 N, flies for seven minutes or traverses for 40 minutes, and is collision-resilient with a protective square composite box. When equipped with RGB and infrared cameras as well as a LiDAR scanner, the octocopter rapidly takes consistent high-fidelity images in an automated, cost-effective way.
Second, an unmanned aerial vehicle (UAV) carries and launches a lightweight structural crawler to inspect steel members and connections in great details through a microscope or a crack probe. Fig. 2 illustrates a mini bicycle climbing robot that is launched off the ramp of a hexacopter. The small robot can travel to crowded areas, inaccessible to the hexacopter, to detect and localize defects such as cracks in welded connections and non-redundant tension members in steel bridges.
The third approach is to develop a neural additive network by establishing one-to-one highly nonlinear relations between each input and an output and minimizing false prediction of the overall output from the combined effect of the inputs. As demonstrated in Fig. 3, this approach is significantly more accurate than the design equation in the AASHTO design specifications in the determination of concrete-concrete shear strength.
The Outcomes: The BIRDS can be used to automate bridge inspection following one or more of the three phases:
1. Screening Inspection – Inspectors walk around the bridge when accessible or fly an UAV equipped with RGB and infrared cameras when inaccessible to the inspectors.
2. Probing Inspection – UAV-assisted imaging or near-surface imaging while the hybrid flying and traversing vehicle is attached to an I-shaped girder.
3. Verifying Inspection – Severe damage/defects determined during the probing inspection are confirmed with inspectors’ engineering judgment based on visual inspection using augmented reality or crawler-assisted nondestructive evaluation. Depending on the interest and in-house capability, interactive robots-assisted nondestructive testing can be moved to Probing Inspection.
The Impacts: The BIRDS will have significant impact on future bridge preservation of over 617,000 bridges in the U.S. as approximately 60% of them by deck area are girder types. For inspection, the INSPIRE UTC inventions will overcome several challenges facing current visual inspection, such as physical accessibility, human interaction, results inconsistency, and cost effectiveness. For maintenance, the inventions will enable local refurbishment and repair, such as surface painting, bolt screwing, and crack sealing, without requiring the setup of a scaffolding platform.
Led by Dr. Genda Chen, Professor and Abbett Distinguished Chair in Civil Engineering and Director of the INSPIRE (INSpecting and Preserving Infrastructure through Robotic Exploration) UTC at Missouri University of Science and Technology, the Bridge Inspection Robot Deployment Systems project is part of the INSPIRE UTC Research Program. For more information on this INSPIRE UTC project, please contact Dr. Chen at inspire-utc@mst.edu or (573) 341-6114.
Genda Chen, Ph.D., P.E., F. ASCE, F. SEI, F. ISHMII, F.SPIE, F. TGI Professor and Robert W. Abbett Distinguished Chair in Civil Engineering Director, INSPIRE University Transportation Center Missouri University of Science and Technology
gchen@mst.edu
INSPIRE UTC research resulted in three patents. These innovations represent the novelty of the INSPIRE UTC research. Once transferred to practices, they have potential economic impacts.
Miniature 3D Position-to-Optical Displacement Sensor, U.S. Patent No. 12,025,438, Awarded on July 2, 2024 to Genda Chen, Jie Gao, and Chuanrui Guo
A miniature, micrometer-accuracy, three-dimensional (3D) position-to-optical displacement sensor that has at least one extrinsic Fabry-Perot interferometer (EFPI) in Z direction and a series of plasmonic metasurface reasonators with distinctive wavelength-selective characteristics in X and Y directions. The interferometer comprises at least one single mode optic fiber for light propagation, and a substrate mirror to create a light interference fringe as a function of distance between the mirror and distal end of the optic fiber. Each plasmonic resonator is capable of modifying the substrate mirror and comprises an array of multiple unit nanostructure unit cells that are arranged in a two-dimensional (2D) square lattice or array in the X-Y plane. The nanostructure unit cells are preferably inscribed in the top layer of a three-layer thin film via the focused ion beam (FIB) technique.
Object Manipulator and Payload Management System for Un-
manned Aerial Vehicles (UAVS), U.S. Patent No. 17,348,453, Awarded on July 24, 2024 to Dongbin Kim and Paul Oh
A parallel manipulator with six degrees of freedom may include a base that attaches to an unmanned aerial vehicle (UAV) and a movable gripper element that may be positioned below the UAV. The positioning of the gripper element may reduce impact of the center of gravity of the attached UAV. The gripper element may include a geometric shape that complements objects routinely used in high-throuhput screening (HTS) laboratories, such as microplates. The parallel manipulator and gripper element may be used to quickly, safely, and securely move objects in HTS laboratories and/or the like.
, U.S. Patent No. 12,103,232 B2, Awarded on October 1, 2024 to Chenglin Wu, Genda Chen, Dimitri Feys, Guirong Yan, and Bryce Tyler Tafolla
A three-dimensional printing system for reinforced concrete and a nozzle therefor. The system employs an extruder for extruding unreinforced concrete and a concrete reinforcement feeder is for feeding one or more elongate reinforcement members. The nozzle has an outlet and is operatively connected to the extruder and the concrete reinforcement feeder to receive the unreinforced concrete from the extruder and to receive the one or more elongate reinforcement members from the concrete reinforcement feeder. The nozzle combines the unreinforced concrete from the extruder and the one or more elongate reinforcement members fom the concrete reinforcement feeder into a reinforced concrete extrusion and impacts the reinforced concrete extrusion through the outlet.
The goals of this pooled-fund study are to engage closely with seven state Departments of Transportation (DOTs) in the early stage of technology development in the INSPIRE UTC, and leverage the center resources to develop case studies, protocols, and guidelines that can be adopted by state DOTs for bridge inspection with minimum or no impact on traffic. The objectives of this initiative include, but are not limited to:
• Development of inspection/operation protocols for various types of bridges with the robotic system integrated into current practice.
• Comparison and correlation of bridge deck inspections from the top and bottom sides of decks to understand the reliability of traffic disruption-free bridge inspection from the underside of decks.
• Design and technical guidelines of measurement devices on a robotic platform for the detection of surface and internal damage/ deterioration in structural elements, and for the change in lateral support of foundations.
• Data fusion and analytics of measurements taken from various imaging and sensing systems for consistency and reliability.
• Development of best practices on bridge inspection using the robotic system.
To achieve the above objectives, eight tasks were proposed and are currently at approximately 85% completion. Technical progresses and/or system integrations of each task are briefly described as follows:
A selection protocol of bridges was developed to enable comparison and contrast between manual and automated visual inspections and/or between visual inspection and nondestructive evaluation (NDE). The main parameters considered in this selection include span length, bridge type, years of service, accessibility, and importance. For example, river-crossing bridges may be inspected in great depth with advanced technologies, while simple highway bridges with easy access may not require any robotic platform during inspection. Other specific criteria include state owned bridges, maximum span length between 10 to 50 m, two to four lanes, average daily traffic of less than 50,000, and less than 50 years of service. The bridges within the Long Term Bridge Performance (LTBP) database are considered for potential long term study.
Three age groups were determined to take the difference and importance of deterioration into account: 15-20 years, 25-30 years, and 35-40 years. Two common girder materials were focused: prestressed concrete and steel girder bridges. They were clustered in convenient locations for work efficiency. A total of 72 highway bridges were selected, including nine bridges in each of New York, Virginia, Georgia, Wisconsin, Texas, and California states and 18 bridges in the state of Missouri. One or more long-span bridges over the Mississippi River will be selected for testing in consultation with Missouri DOT.
A mobile test facility, referred to as Bridge Inspection Robot Deployment Systems (BIRDS), was developed to support a crew of 2-4 inspectors and field operation/remote tests at bridge sites. The overall robotic system includes commercial drones and custom-built robots. These robotic vehicles are equipped with multiple remote sensing and nondestructive testing devices.
A 11-seat Nissan van was procured to house the mobile test facility. To date, the BIRDS include a diverse profile of commercial drones (Skydio 2+, Elios3, Parrot Anafi, and DJI Phantom4), custom-designed drones (Headwall-integrated DJI M600 and Geodetic-integrated DJI M600), and custom-built uncrewed vehicles (hybrid flying and traversing vehicles and structural crawlers). Multimodal remote sensing systems include RGB cameras, infrared cameras, hyperspectral cameras, and Light And Detection Range (LiDAR) scanners. Nondestructive testing systems include microscope for surface defect inspection, crack probe for crack depth measurement, impact echo device for concrete delamination/voids, and ground penetrating radar for substrate structure and condition.
3. Correlation of Top and Bottom Deck Inspections
Due to gravity, deterioration on the bottom surface (a safety issue) is more critical than that on the top surface (a serviceability concern). On the bottom side of a bridge deck, deterioration such as concrete cracking, concrete delamination, and reinforcement steel corrosion are easier to detect from underside of the deck.
The detection results derived from inspections above and below a pedestrian bridge deck on Missouri S&T campus were compared to understand their correlation or complementary nature. Microwave, impact echo, and ground penetrating radar tests were conducted in detail.
4. NDE and Sensing Integration into Visual Inspection
NDE devices for surface features and subsurface corrosion condition of steel rebars was conducted. In-line fiber optic sensors were tested for simultaneous measurement of strain, temperature, and mass loss in cross section of the reinforcing bars. Their capabilities in detecting structural damage and deterioration were compared. Laboratory tests for NDE and fiber optic sensing were conducted on concrete specimens and rebar samples. Their relative merits in qualitative and quantitative condition assessments were contrasted. Together, they were compared with visual inspection for surface distress to understand their potential for being integrated into the current practice of visual inspection. More systematic evaluations of NDE and sensor capabilities in defect/damage detection will be done through the probability of detection.
5. Case Studies with a Representative Bridge Inventory
To date, 54 of the 72 selected bridges in the state of Virginia, Georgia, Wisconsin, Missouri, and Texas were tested. The remaining bridges in New York and California were not yet tested due to coordination challenges. In addition, one pedestrian bridge on Missouri S&T campus was tested with NDE devices and inspected from dronebased images. Additional bridges in the state of Missouri were also tested for scour monitoring.
A case study was conducted on the pedestrian bridge to implement and demonstrate NDE devices and multimodal remote sensing systems for the detection of surface and internal damage and deterioration in structural elements. More case studies were conducted on highway bridges to implement and demonstrate UAV-based remote sensing with and without field agents (i.e., smart rocks with embedded magnets for scour monitoring).
6. Protocol and Guideline Modification
The protocols and guidelines of field tests for bridge inspections are developed and improved after multiple field visits. Imaging and sensing data are fused to improve the detectability of problem areas with reduced capacity.
Best practices for using drone-based remote sensing were drafted and summarized in automated bridge inspection guidelines. Preliminary test results and corresponding visual inspection results were evaluated and summarized in a mid-term report. Once successfully completed in Task 4, efforts will be made to introduce the probability of detection of nondestructive testing, remote sensing, and visual inspection reporting for structural damage/ deterioration with the intent of improving the consistency of visual inspection practice.
A beta version rollout of the protocols, guidelines, and performance criteria will be conducted in collaboration with the Missouri Local Technical Assistance Program (LTAP). As part of this roll-out, a Missouri S&T workshop or in-house workshops in the participating state DOTs will be conducted with the use of developed protocols, guidelines, and field demonstration technologies.
Once further developed and reviewed, the preliminary guidelines will be released to limited reviewers in the participating state DOTs for feedback and improvement.
A final report will be prepared and published on the protocols, guidelines, and performance criteria of field tests with the novel robotic system developed by the INSPIRE UTC. It will be expanded from the mid-term report and organized to highlight the process of inspection and reporting in practices. This process includes pre-inspection scoping and planning, during-inspection execution and decision-making, and post-inspection analysis and reporting.
Due to COVID-19 interruption, most activities were delayed for one year. Currently, the pooled-fund study is in its no-cost extension period. At its completion, robot-based sensing and nondestructive testing technologies developed at the INSPIRE UTC will be evaluated and validated at bridge sites.
Example optical and thermal imaging from the BIRDS platform is presented below. During these tests, the hybrid flying and traversing robot successfully collected RGB and thermal visual data, demonstrating its ability to perform inspection in real-world conditions.
With the financial support of $8.4M from the U.S. Department of Transportation and $8.4 match funds from various nonfederal sources, the 2016-2024 INSPIRE UTC research projects directly contributed to 28 final project reports, three patents, 49 archival journal papers, and 61 books and conference papers. In addition, the INSPIRE UTC projects also resulted in 12 educational modules that will provide INSPIRE UTC’s minor partners (e.g., community colleges) with wealthy instructional materials (power point slides) on diverse STEM subjects.
The final project reports are grouped into five research topics: autonomous survey (AS), inspection and maintenance (IM), sensing and nondestructive evaluation (SN), retrofit and resilience (RR), and workforce development (WD). The first three topics aimed to explore, develop, validate, and demonstrate standardized-integrated measurement technologies, decision-making tools, data analytics, and autonomous systems to facilitate the field inspection and maintenance of bridges. The fourth and fifth topics aimed to develop, validate, and demonstrate methods of robot-enabled resilience analysis and intervention technologies of bridges and to develop innovative tools and methods for the next-generation transportation workforce training and public education. Each project is designated by a consecutive project number prefixed by each research topic.
REPRESENTATIVE PARTICIPATING COUNTRIES
Australia, Austria, Brazil, Canada, China, France, Germany, India, Italy, Japan, Portugal, Serbia, Sweden, Taiwan, United Kingdom, and USA.
Missouri S&T hosted the very first National Summer Transportation Institute (NSTI) in the state of Missouri. The NSTI program aims to promote the Science, Technology, Engineering and Math (STEM) disciplines in transportation-education and career opportunities among middle and high school students. This program was sponsored by Federal Highway Administration through the Missouri Department of Transportation (MoDOT). Coordinated by the Kummer Center for STEM Education, the program was directed by Dr. Jenny Liu and co-directed by Drs. Xiong Zhang, Grace Yan, and Genda Chen. All of them are faculty from the Department of Civil, Architectural, and Environmental Engineering (CArEE).
On July 21-26, 2024, Missouri S&T welcomed fifteen 10th -12th grade high school students from Missouri, Illinois, and Oklahoma. The students were immersed in transportation activities through this five-day well-designed program and enjoyed interactive technical seminars with transportation professionals, field trips, research facility tours, hands-on laboratory experience, and collaborative team projects. The program received tremendous support from MoDOT, the National Museum of Transportation, the College of Engineering and Computing, Wind Hazard Mitigation Laboratory, the Center for Infrastructure Engineering Studies, and the Office of Admissions in addition to the CArEE Department and the Center for Intelligent Infrastructure (CII). CArEE faculty, staff, students, and alumni enthusiastically made this program diverse, comprehensive, and exciting. The program planted transportation engineering seeds in the mind of the participating students when choosing their professional careers. Following is a gallery of selected photos to reflect some of the program activities.
On July 9, 2024, the Center for Intelligent Infrastructure (CII) at Missouri S&T hosted 26 junior high school students for a 1.5-hour session aimed at sparking their interest in STEM (Science, Technology, Engineering, and Math). The event began with a PowerPoint presentation showcasing the center’s cutting-edge research, followed by a tour of three state-of-the-art labs. Students were then introduced to handson activities that included operating drones used for bridge inspections (such as the Tello, Phantom 4, Skydio 2 Pro, Elios 2, and BIRDs), interacting with augmented reality (AR) technologies to explore virtual bridges, experimenting with 3D printing, and testing advanced robotics. Their excitement was palpable as they asked about flying the large geodetic drones, navigating the Tello drones, using AR glasses, and operating a commercial driving simulator. The hands-on activities, particularly with the Tello drones, the driving simulator, and the HoloLens 2 glasses, were met with great enthusiasm, with many students eager to retake the activities whenever possible. Led by team members Mohammad, Zhenhua, and Joel, and guided by CII Director Professor Genda Chen, the event provided an inspiring glimpse into STEM fields while energizing both the students and the center’s team.
On June 17, 2024, the CII welcomed and hosted 71 middle school students.. The intent of this event was to get the students excited with STEM education by demonstrating what a future STEM professional could mean for them. Specifically, the students got familiarized with infrastructure inspection aided by robotic exploration and Augmented Reality (AR) visualization. Two separate introductory and walk-through sessions and a combined demo session were organized. The campers' curiosity led to a wide range of questions, such as whether a hyperspectral camera could detect snakes or be used for hunting, why the robot’s electronic components were exposed, what materials were used to cage the Elios 2 and 3 drones, whether the simulator cars could crash or simulate collisions, how sensitive the driving simulator was, and whether 3D printing could use materials other than plastic. They also asked if drones could drill through stones, and whether passengers in the prototype driving car could face each other.
On June 4th, 2024, Missouri S&T’s Center for Intelligent Infrastructure (CII) hosted an iSTEM outreach event, engaging 18 high school students in STEM-related activities. The event included a PowerPoint presentation, a tour of three advanced lab facilities, and hands-on activities. Students explored diverse research areas such as bridge inspection using commercial and custom drones, augmented reality (AR) with virtual bridges, 3D printing, and advanced robotics. The students’ interests ranged from questions about how the large GEODETICs drone was transported and powered, the payload capacity of commercial drones, the cost of AR headsets and Alienware PCs, to the materials used by 3D printers. They also inquired about test flights of drones. Students eagerly interacted with hands-on activities, including flying Tello drones, using a driving simulator, and experimenting with HoloLens 2 glasses, with many participating in all three.
As of April 30, the Kaleidoscope Discovery Center has supported robotics and engineering programming in our region and across the state that has reached over 2500 K-18 students through the FIRST Lego League and the Missouri Future City Competition. Continuing this level of outreach and engagement would simply not be possible without the generous sustained support from the INSPIRE UTC grant. The past year has further expanded robotics programming options which now include preK – age 18 on site and in the community. Additionally, Missouri was selected to pilot a high school Future City program, the first of its kind in over 30 years!
The preK-1st grade Robotics Discover program ran multiple times last year in five-week program sessions and the Kaleidoscope just completed its twelfth FIRST Lego League Explore cycle bringing 1-4th grade students from around the area to Rolla to celebrate and show off their creative designs at the April 6 Expo at Missouri S&T! The Lego League Challenge group which reaches 4th-8th grade students expanded from three to six competition-ready teams, one of which advanced to the Missouri State Competition. Additionally, through the assistance of the UTC grant, robots for this older class were updated from EV3s to Spike Primes allowing our rural area students to use the most current technology available for this level competition. And the newly formed FIRST Tech Challenge high school team won both the INSPIRE and Robot awards regionally earning a position at the state competition.
The Kaleidoscope received additional grant funding from AmeriCorps for a final year of robotics outreach support through the VISTA program which includes visits to area libraries, 4-H Camp Clover Kid presentations, Scouting robotics merit badge sessions, and Girl Scout STEM projects.
The Missouri Future City competition was held on January 20 in the Butler Carlton Hall on the Missouri S&T campus. Teams of five-ten 6th – 8th grade students presented their visions of “Energizing Your Future” to panels of professional engineer judges from across the state. Each team researched the current year’s theme and created a solution presented orally, in writing, and through the visual representation of a 50”x25”x20” model which contained at least one moving part, generally with a battery-powered robot mechanism. Die Gruenestadt, the Missouri team from St. Clair Middle School, was named our Missouri state winner and competed at the international competition in Washington, D.C. during the National Engineers Week in February. This year saw a record increase in the number of students participating in this engineering competition. Additionally, national Future City piloted a high school program and selected Missouri as one of 19 teams across the country. Delann, a combined team of students from Herculaneum and Rolla represented Missouri well place fourth internationally for their innovative design solutions. While the Missouri representatives competed in Washington, DC, the top five teams represented at the St. Louis Science Center’s ASCE STL private screening of #Cities of the Future opened by Marcia Geldert-Murphy, national ASCE president, and Martina Hahn-Baur, Missouri State Future City Coordinator. Over 250 people were present at this event!
We are thrilled to see this expanded programming capturing and encouraging the interest in STEM in our rural area and also our students across the state. Thank you INSPIRE UTC for your support in reaching these STEM outreach goals with us!
May 14-16, 2025
“… Digital twins can be a critical tool for decision-making based on a synergistic combination of models and data. The bidirectional interplay between a physical system and its virtual representation endows the digital twin with a dynamic nature that goes beyond what has been traditionally possible with modeling and simulation, creating a virtual representation that evolves with the system over time … Digital twins have the capacity to revolutionize scientific research, enhance operational efficiency, optimize production strategies, reduce time-to-market, and unlock new avenues for scientific and industrial growth and innovation” – an excerpt from the 2024 report on Foundational Research Gaps and Future Directions for Digital Twins by the National Academy of Science.
R&D Needs:
Multidimensional digital twins in city or regional scales can address multiple models, functions, and values to justify their capital investment. Such a large-scale initiative surely requires the integrated use of physics-based and data-driven methods, such as computational and experimental mechanics, machine learning, geospatial computing, virtual/augmented reality, and quantum computing.
As an example of modeling in the built environment, building and civil infrastructure assets have been managed using databases since 1970 and with the aid of Building Information Modeling (BIM) since 1992 for value engineering and as-built information. The imperative for embracing digital twinning becomes evident in the aftermath of the 2007 Minneapolis Interstate 35W Bridge Collapse, a catastrophic event that claimed 13 lives and injured 145. This tragic incident underscores deficiencies not only in extracting overlooked design information from BIM but also in the incapacity of BIM alone to assess the design capacity of bridge members.
The urgency to adopt multidimensional digital twins to support informational, computational, and behavioral modeling is amplified as our nation's infrastructure is aging, requiring more frequent condition assessment and maintenance, particularly in the face of accelerating climate changes and increasing natural disasters.
-To brainstorm and develop a research and development (R&D) roadmap for community-driven national digital twin initiatives in the built environment, which will potentially advance and improve infrastructure engineering, living environments, and emergency responses.
-To harness the interest and opportunity in the U.S. to explore frontier research and innovation using digital twins as a platform to drive economic development, citizens’ wellbeing, environmental sustainability, and infrastructure resiliency.
National Steering Committee:
-Dr. Sreenivas Alampalli, Senior Principal – Transportation, Stantec
-Dr. Carolina Cruz-Neira, Agere Chair Professor in Computer Science and Director of VARLAB, University of Central Florida
-Mr. Jon Hotra, Chief Engineer of High Fidelity Digital Twins and Visualization, Boeing
-Dr. Kaan Ozbay, Professor and Founding Director of the C2SMART, USDOT Tier I University Transportation Center, New York University
-Dr. Kenichi Soga, Donald H. McLaughlin Professor in Mineral Engineering and Director of the Berkeley Center for Smart Infrastructure, University of California, Berkeley
-Dr. Billie F. Spencer, Nathan M. & Anne M. Newmark Endowed Chair in Civil Engineering and Director of Smart Structures Technology Laboratory, University of Illinois, Urbana and Champaign
Distinguished Guests:
-Dr. Mohammad Dehghani, Missouri S&T Chancellor
-Dr. Firas Ibrahim, Director in the Office of Research, Development and Technology, Department of Transportation
-Dr. Daniel G. Linzell, Director of NSF Division of Civil, Mechanical and Manufacturing Innovation
-Mr. Brandon Meinert, Acting Chief, Installation Readiness Branch, Construction Engineering Research Lab, Engineering Research and Development Center
Keynote Speakers:
-Dr. Burcu Akinci, Department Head and Hamerschlag University Professor of Civil/Construction Engineering, Carnegie Mellow University, United States
-Dr. Carolina Cruz-Neira, Agere Chair Professor in Computer Science and Director of VARLAB, University of Central Florida, United States
-Dr. Daniel G. Linzell, Director of NSF Division of Civil, Mechanical and Manufacturing Innovation, United States
-Dr. Jennifer Schooling, Professor of Digital Innovation and Smart Places, Anglia Ruskin University, United Kingdom
-Dr. Jiaqi Ma, Associate Professor and Director of FHWA Center of Excellence on New Mobility and Automated Vehicles and Associate Director of UCLA Institute of Transportation Studies, University of California-Los Angeles, United States
Working Group Leaders:
-Dr. Soheil Sabri, Assistant Professor in Urban Planning and Geospatial Science and Director of Urban Digital Twin Lab, University of Central Florida (Group 1)
-Dr. Yang Wang, Professor of Civil Engineering, Georgia Institute of Technology (Group 2)
-Dr. Zhiqiang Chen, Professor of Civil Engineering, University of Missouri-Kansas City (Group 3)
-Dr. Necati Catbas, Lockheed Martin St. Laurent Professor of Civil, Environmental, and Construction Engineering, University of Central Florida (Group 4)
-Dr. Fernando Moreau, Associate Professor of Civil Engineering, The University of New Mexico (Group 5)
-Dr. Sreenivas Alampalli, Senior Principal - Transportation, Stantec (Group 6)
Workshop Format:
Participants (capped at 50) will collaborate in six thematic working groups:
1. Data Acquisition: Collecting and analyzing remote and in-situ sensing data and engineering metadata.
2. Data Transmission: Enabling secure, wireless transfer of information through data infrastructure.
3. Model Analysis: Creating virtual representations and predictive models.
4. Feature Mapping: Extracting and updating features and 3D geospatial distribution.
5. User Collaboration: Enabling access and navigation through dashboards, interfaces, and visualizations.
6. Policy and Impact: Evaluating information privacy, user equity, and values of decision-making.
Join academic, industry, and government leaders to shape the future of digital twin research. Poster submissions are due by March 1, 2025. Accepted posters will be printed for the event (dimensions: 3 ft. by 4 ft.). Please contact Natalie Hankinson at ngc6z@mst.edu for poster requirements and Dr. Genda Chen at ghen@mst.edu for any technical assistance.
Since 2017, the INSPIRE UTC has conducted research on emerging technologies such as robotics, remote sensing, robot-assisted nondestructive testing, and artificial intelligence. For the first time, the INSPIRE UTC will showcase some of the latest technologies to support automated bridge inspection at the 2025 Transportation Research Board Annual Meeting, Washington DC, on January 5-9, 2025. The INSPIRE UTC Booth #538 is located next to the FHWA demonstration area as indicated in the following floor plan. Specific technologies that will be displayed and demonstrated in the TRB Exhibition Hall include:
• Magnetic-wheeled hybrid drone that combines the flying and traversing capabilities for steel-girder bridge inspection.
• Mechanic-wheeled hybrid drone that can operate on both steel- and concrete-girder bridges for detailed inspection and launch a structural crawler on steel bridges.
• Palm-size crawler equipped with a microscope, which can traverse to crowded areas for detailed inspection of steel weld connections.
• Structural crawler equipped with a crack depth probe, which can measure the depth of cracks on steel welds.
• Drone equipped with a microwave heater and an infrared camera for concrete crack detection.
INSPIRE University Transportation Center
Missouri University of Science and Technology
112 Engineering Research Laboratory, 500 W. 16th St. Rolla, MO 65409
Connect with INSPIRE UTC:
• FACEBOOK: www.facebook.com/inspireutc
• X: www.x.com/inspire_utc
Connect with CII:
• FACEBOOK: www.facebook.com/MSTCII
• X: www.x.com/MST_CII
Newsletter Editors
Genda Chen, INSPIRE UTC Director
Natalie Hankinson, INSPIRE UTC Program/Project Support Coordinator
Contact Us
Phone: 573-341-6114 | Email: inspire-utc@mst.edu | Web: inspire-utc.mst.edu
Visit our website to follow us on social media.
January 5 -9, 2024
104th TRB Annual Meeting https://trb-annual-meeting.nationalacademies.org/
March 17-20, 2025
SPIE Smart Structures + NDE 2025 https://spie.org/conferences-and-exhibitions/smart-structures-nde
May 14-16, 2025
U.S. Workshop on Digital Twins in the Built Environment https://cii.mst.edu
May 19-22, 2025
15th Americas Conference on Wind Engineering https://15acwe.mst.edu
September 1-5, 2025
13rd International Conference on Structural Health Monitoring of Intelligent Infrastructure https://www.tugraz.at/events/shmii-13/general-information
September 9-11, 2025
15th International Workshop on Structural Health Monitoring https://iwshm2025.stanford.edu/
inspire-utc.mst.edu/events