
6 minute read
Load Cases?
By Glenn Traylor
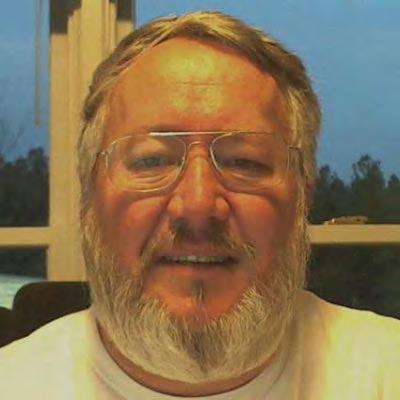
Years ago, truss design was focused on a simple calculation that determined the final forces that would be considered to be imparted on a truss component. These simple forces were used to determine the design. Things like snow, wind, and building materials weights were generally the only considerations made. Very quickly, however, the truss industry became more sophisticated and analyzed additional forces including seismic and long-term considerations. The main equation used is Newton’s Second Law:
F = Ma ; and we desire a = 0 ; so the sum of the forces on a truss are equal to zero or
∑F = (F1 + F2 + … + Fn) = 0 , where F is the forces on an object, M is the mass of the object, and a is the acceleration of the object. In truss design, we desire “a” acceleration to be zero except when dealing with seismic—but is that always the case?
Consider the active delivery of trusses from the roll-off trailer in this video posted on YouTube. The trusses even pick up speed as they slide downhill!
When trusses experience acceleration, a.k.a. movement, the forces acting upon these trusses can be tremendous. Potentially, the forces are a hundred times more than intended. More importantly, the truss designer would not calculate this sort of dynamic loading. But, how important is it to understand this situation? Is there any way to address this type of loading? How can we try to eliminate the “delivery load case”?
It’s a fact that truss delivery can be dramatic. Years ago, we used to deliver trusses with Barnes Trailers, which were pole trailers better designed for poles than trusses—talk about scary. But it’s also a fact that truss delivery doesn’t have to be traumatic. Today’s roll-off trailers are much improved from the olden days, and one of their advantages is being able to “sit” the trusses on the ground “gently” without the trauma.
Therefore, the question becomes: is it worth investing in more sophisticated equipment such as roll-off trailers? If you do, is additional training necessary? Example of a modern roll-off trailer
From the perspective of loads, both those loads acting on trusses and a load of trusses themselves, these are some items to consider.
1. When trusses experience acceleration, a.k.a movement, the forces acting on these trusses can be tremendous, potentially a hundred times more than an intended design.
2. Dynamic action can stress members and components past yield points, causing damage to your product.
3. Investing in decent delivery equipment will greatly increase your chances of eliminating dramatic deliveries.
4. Drivers should be trained to exercise extreme care when making deliveries.
5. Different types of lots, soil, and weather require different protocols.
6. Deliveries should be coordinated with the building contractor to designate a suitable drop area.
7. Customers should be informed of the need for a level area for the delivery.
8. When banding your trusses, keep the delivery in mind and use more banding than just what was necessary at the plant.
9. Consider nailing trusses together at tails with a 10d brite nail to help prevent sliding.
10. Use tools within your design software to upsize connectors to account for handling considerations or minimum tooth bite requirements for certain types of trusses.
11. Consider providing crane services to those clients with special situations.
12. Deliver only on very dark nights without moonlight—if you can’t see it, it didn’t happen.
13. Reread point #12 as an attempt at humor.
14. Create skid packages that bind trusses together so they are more likely to come off intact and together.
The most difficult part of a truss’s life is making it from the manufacturing plant to the roof. Let’s help the truss make the trip with as little drama as possible.
An ANSI/TPI 1 3rd Party Quality Assurance Authorized Agent covering the Southeastern United States, Glenn Traylor is an independent consultant with almost four decades of experience in the structural building components industry. Glenn serves as a trainer-evaluator-auditor covering sales, design, PM, QA, customer service, and production elements of the truss industry. He also provides project management specifically pertaining to structural building components, including on-site inspections and ANSI/TPI 1 compliance assessments. Glenn provides new plant and retrofit designs, equipment evaluations, ROI, capacity analysis, and CPM analysis.
Glenn Traylor Structural Building Components Industry Consultant http://www.linkedin.com/in/glenntraylor
“I would encourage other component manufacturers to attend the workshop because it is an opportunity to gain a better understanding of MSR and how it can be used. That makes you a more responsible customer because you know how to maximize its use in the design of your product.”
—Porter Clark, Hiwassee Builders Supply Inc., Athens, TN
“Unless they can say they have their business running perfectly, I believe there’s something any CM can take back from the workshop to improve their business. I know our business will be better because we attended.”
—Adam Beck, Drexel Building Supply, Campbellsport, WI
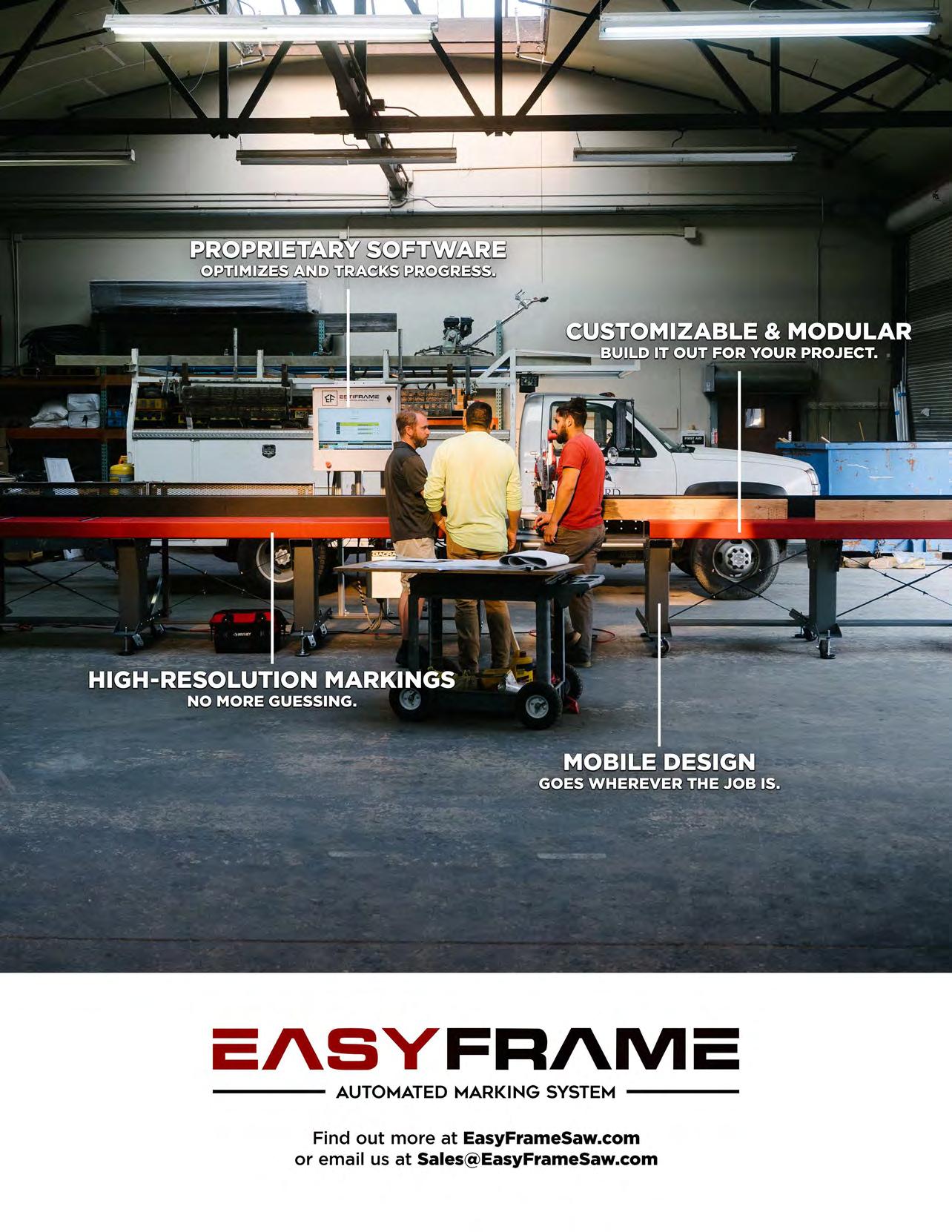
Component Saw
2002 Auto Omni 5 blade automated component saw includes shaker waste conveyor with factory side pans, [3] 20 inch blades, [1] 30 inch blade and [1] 12 inch blade. Fully automated setup with full power length and all axis angulation, single sided setup from operator console, 2×3 through 2×12, 22’ to 3′ @ 90°/90°, and spare blades. 208/240/480 volt, 3 phase, 100 Amp and 120 vac, 90 Amp electrical required.
Price: $19,990 FOB PA Wood Tech Systems 765-751-9990 www.woodtechsystems.com
2008 Alpine PF90 Wall Panel Saw

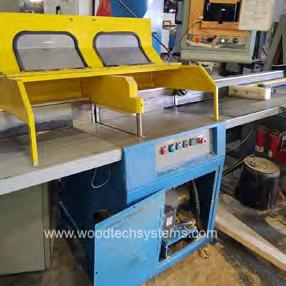
2008 Alpine PF 90 wall panel cutting and marking system. 3.5″ x 12″ maximum cutting profile, Inkjet option, cuts to 16 ft long. From the OEM’s literature, “Effortlessly handles two of the most critical and difficult processes in any wall panel operation – plate cutting and panel layout. At the rate of 1,000 linear feet per hour or more, uses data from the design software and accurately marks stud, cripple and jack locations, job and panel number, subcomponent and window/door locations, and even sheathing locations on both top and bottom plates simultaneously with ink-jet printing.
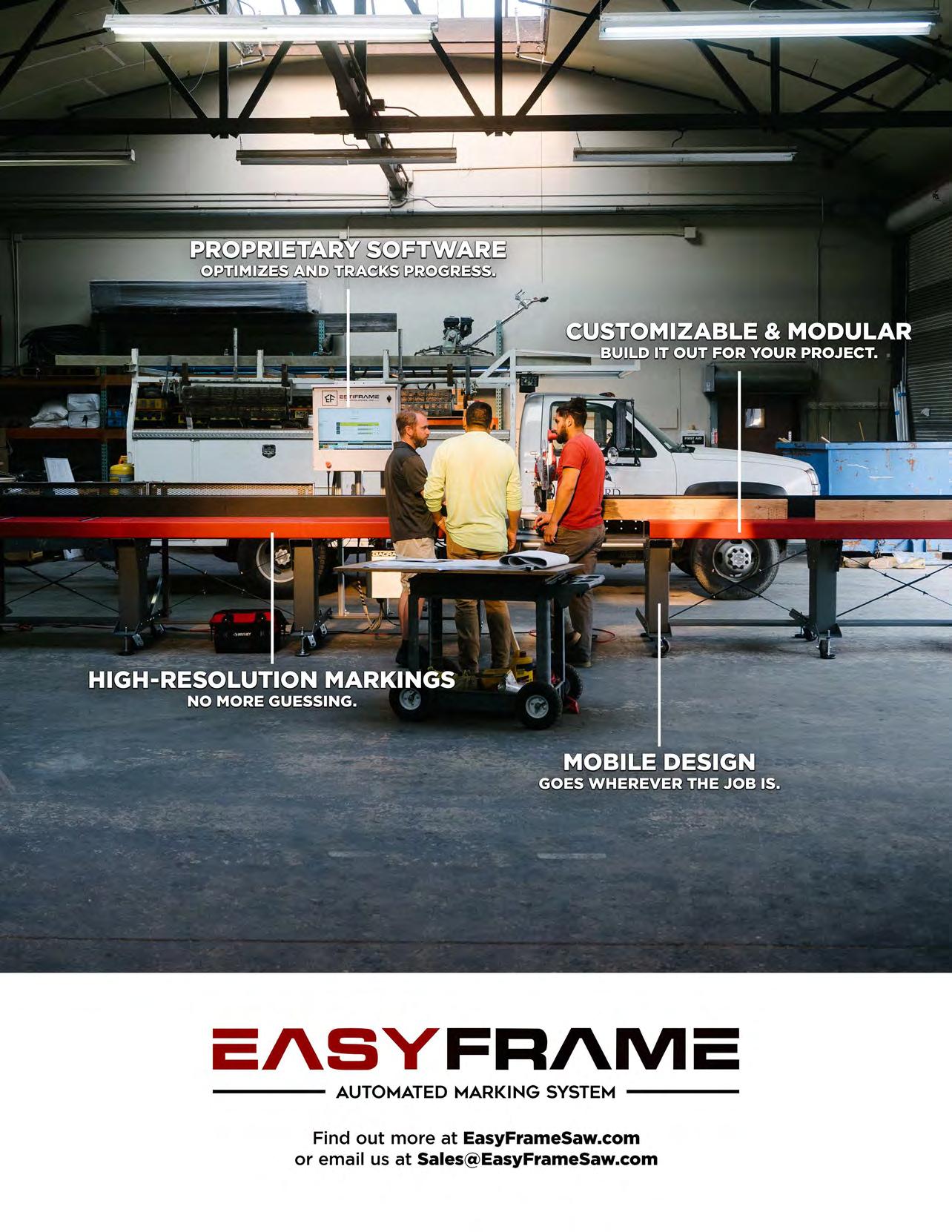
$8,499 FOB NY Wood Tech Systems 765-751-9990 www.woodtechsystems.com
Electrical Supply: 110 VAC
Motor: 1/4 HP, 110 VAC, Linear Actuator
Highly Accurate: +/- .010 Inches
Stop Rail: 2 x 4 x 1/4 Aluminum Extrusion

Stops: Jig Bored Steel
Stop Blocks: Machine Billet Aluminum
Internal Components: Hardened, Ground and Polished Steel and Billet Aluminum
Dimensions:
Length: 5 feet (60”) to 60 feet (720”)
Height: 12 inches
Depth: 12 inches
If you are looking for the fastest, most consistent way to measure and cut your product, then the Hain Measuring System (MEA) is your answer. The MEA changes from one length t any length instantly, up to 60’, without changing the operator’s position on the line. It is also highly accurate (+/- .010) and quickly moves from one length to the next in seconds. The MEA is designed for quick and easy setup and is simple to use. Even a first time user will be productive with little or no training required. It can adapt to any saw and can be mounted to any surface so that you can integrate the MEA with your existing setup. The MEA is versatile allowing “left” or “right” handed operation and measurement in “feet and inches” or “inches” depending on your preference. The MEA is also available in a “Skid Mounted” version.
4,001,398
That’s the total trigger count from all six nail guns combined on an installed Terminailer.® For a machine that was a little over two years old, that is a big number; a real tribute to the durability of the machine’s components and engineering.
Yes, that number represents a pretty darn impressive mechanical milestone to be sure, but what is really impressive is that human hands were saved from millions of repetitive motions and potentially costly nailing accidents.
With just a sole operator, Terminailer drives a whole lot of improvement in efficiency and output. This amazing sub-component assembler quickly and precisely drives 30% to 70% of the framing nails in any wall panel job—be it batch, or just–in–time production. All with no complicated training, software or set-up time required when switching configurations. Add increased safety and easy maintenance with off-the-shelf parts, and you can see why Terminailer should be driving greater productivity in your plant.
Put things together like never before.
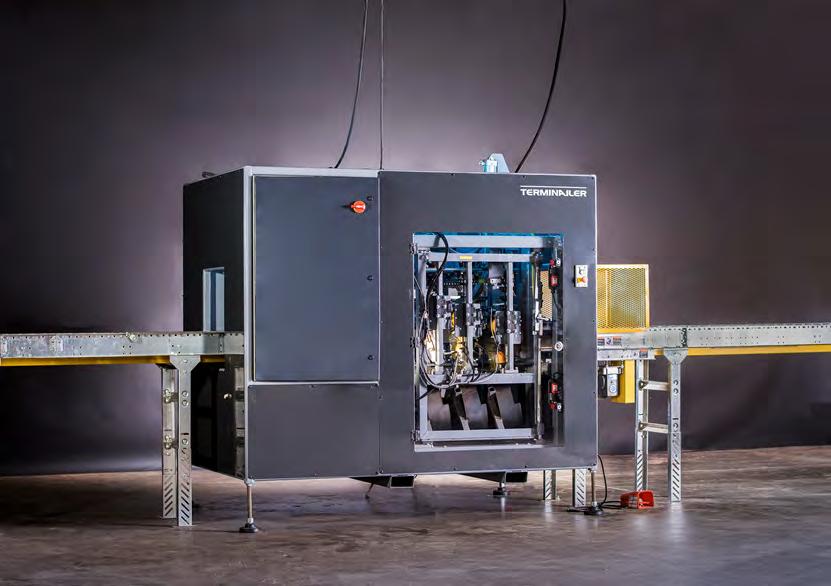
Safety Speed Manufacturing Model 6400 Panel Saw
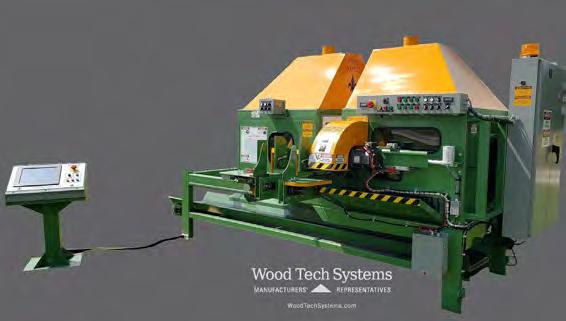

Safety Speed Manufacturing model 6400 vertical panel saw, 3 HP worm drive motor, 64 inch crosscut, 1 3/4" inch maximum thickness, accuracy within 1/64th of an inch, 10 foot welded steel frame with integrated stand and linear V-guides, enclosed counterweight system, adjustable vertical and horizontal rules. Quick changes from vertical to horizontal cutting. Includes machined aluminum material rollers, hold down bar, wheels, quick stop gauges and material hold downs. Dust collection ready. Options available include lower frame extensions, digital readouts, laser guide, stop bar, vacuum and midway fence. 120 volt. Starting at $5,169 FOB MN.
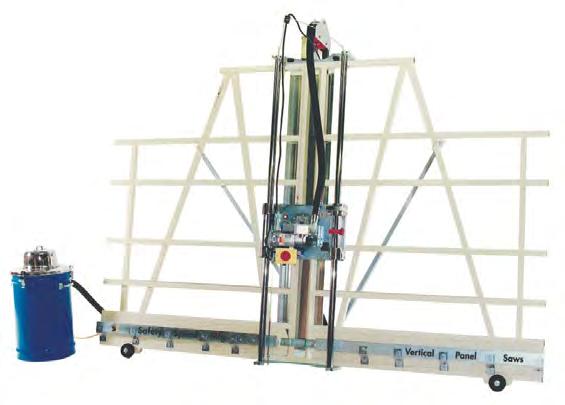
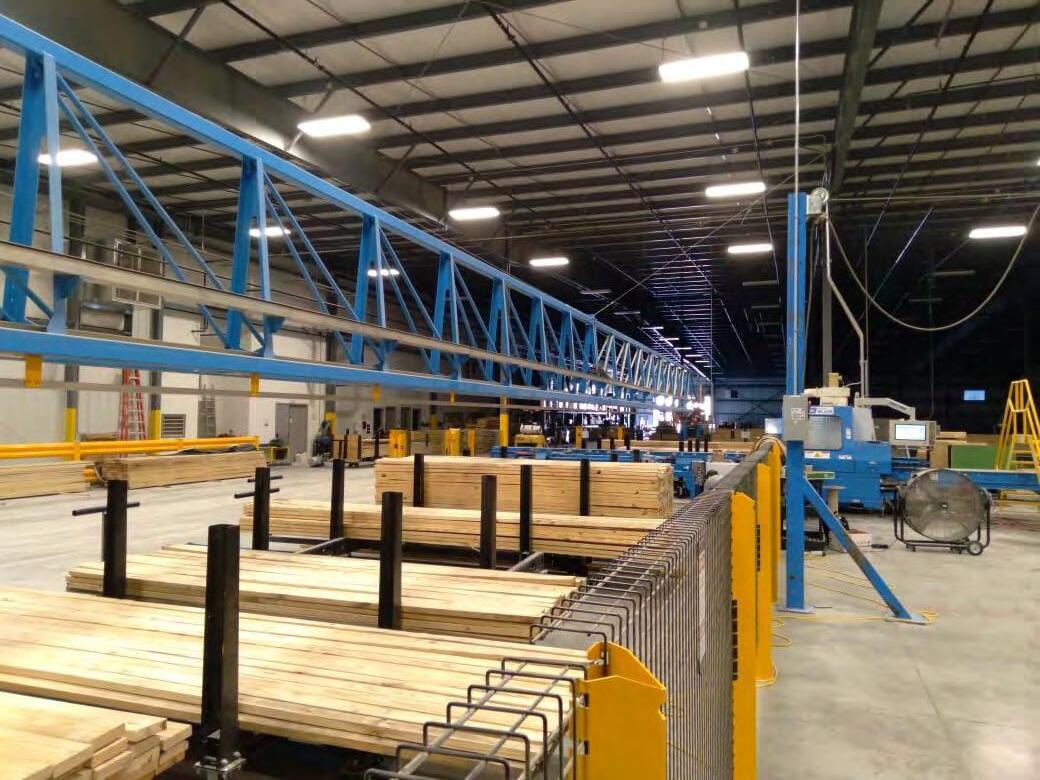
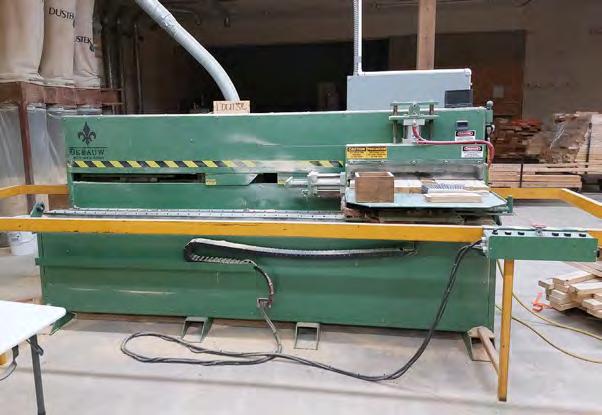
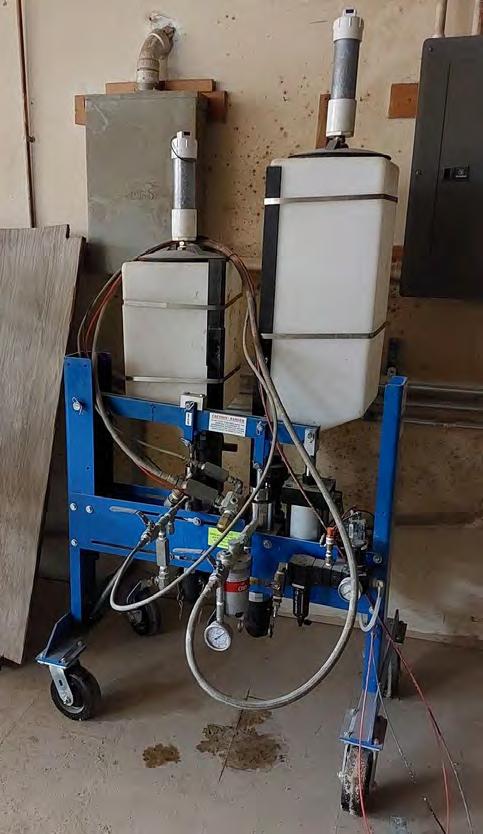
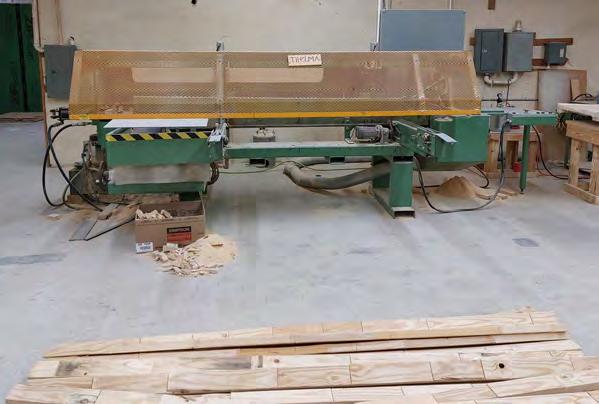
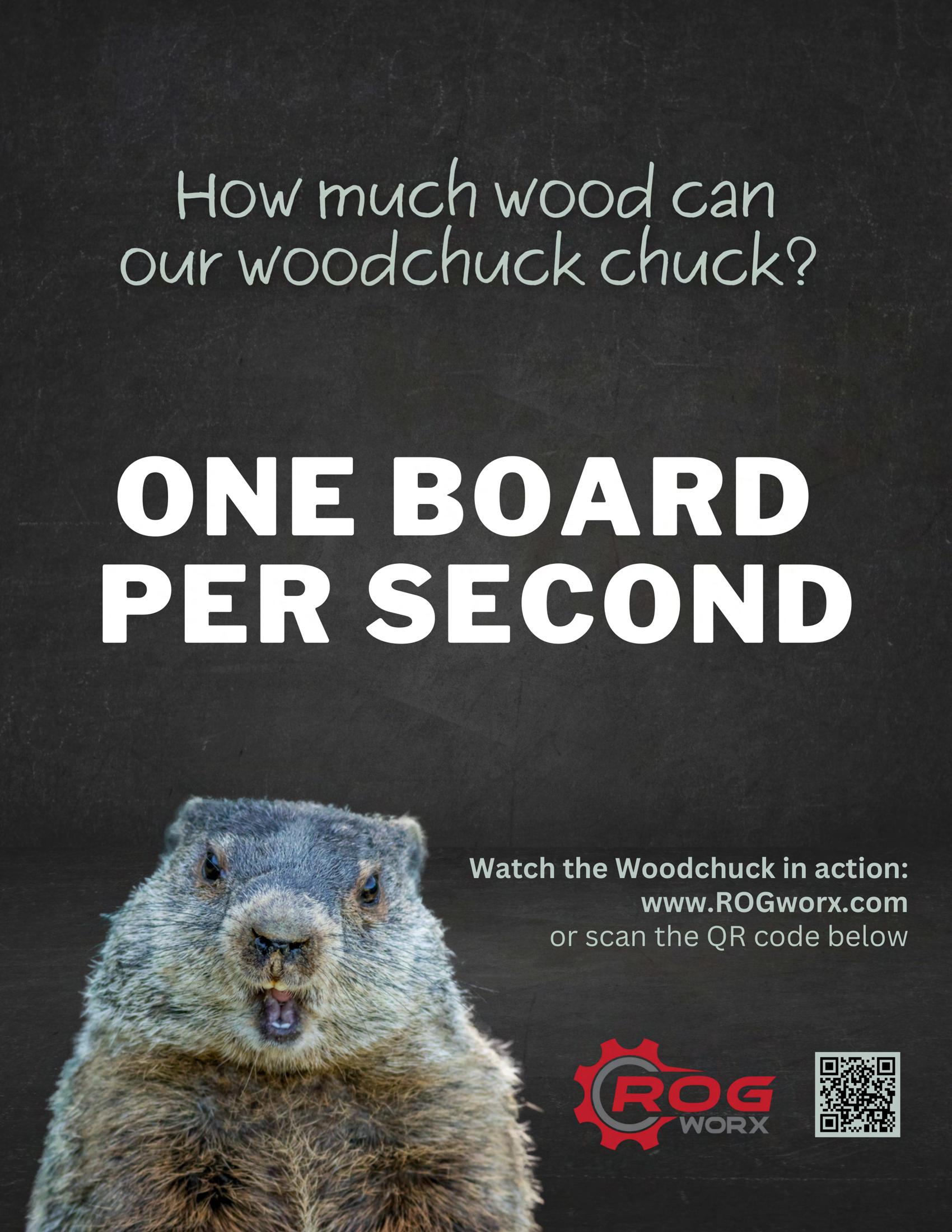

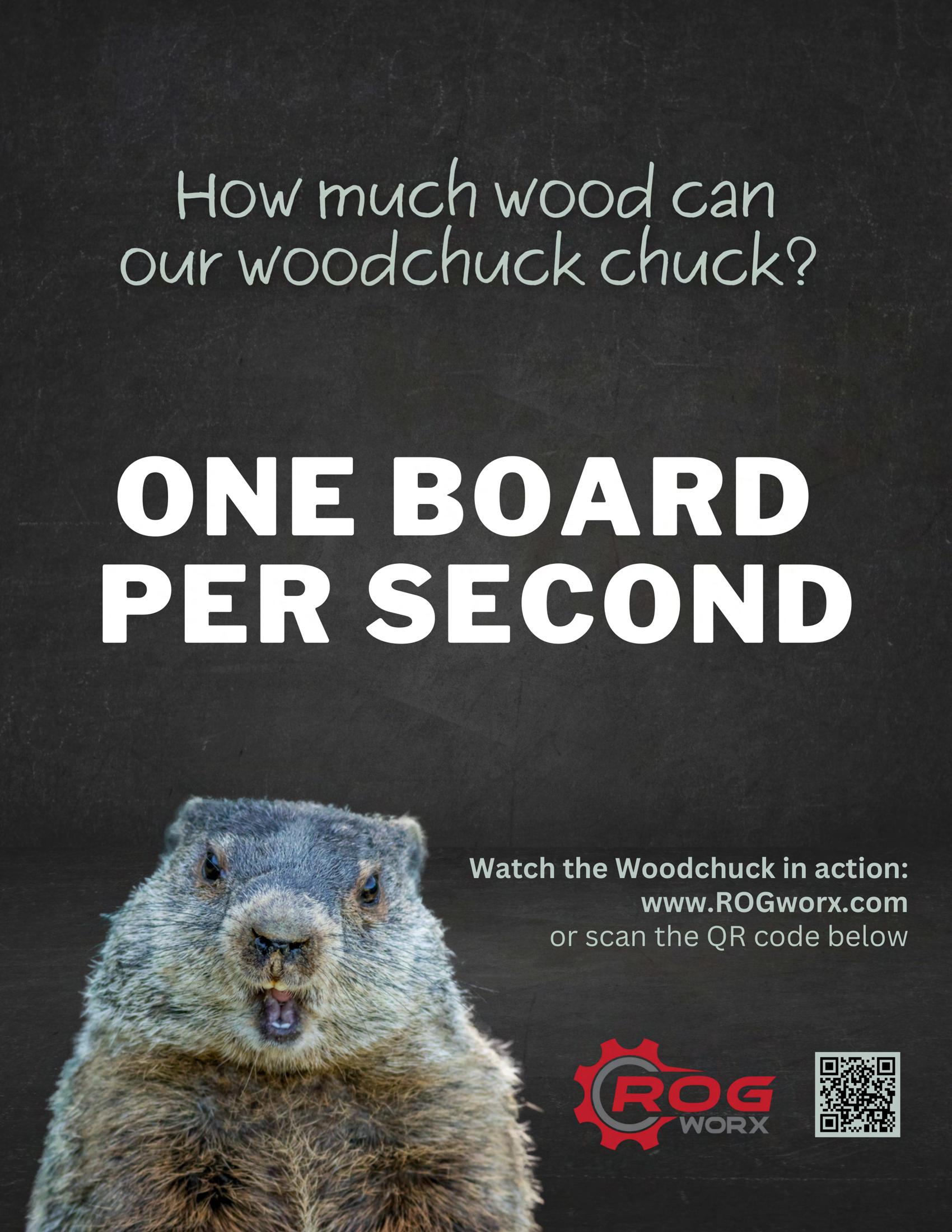

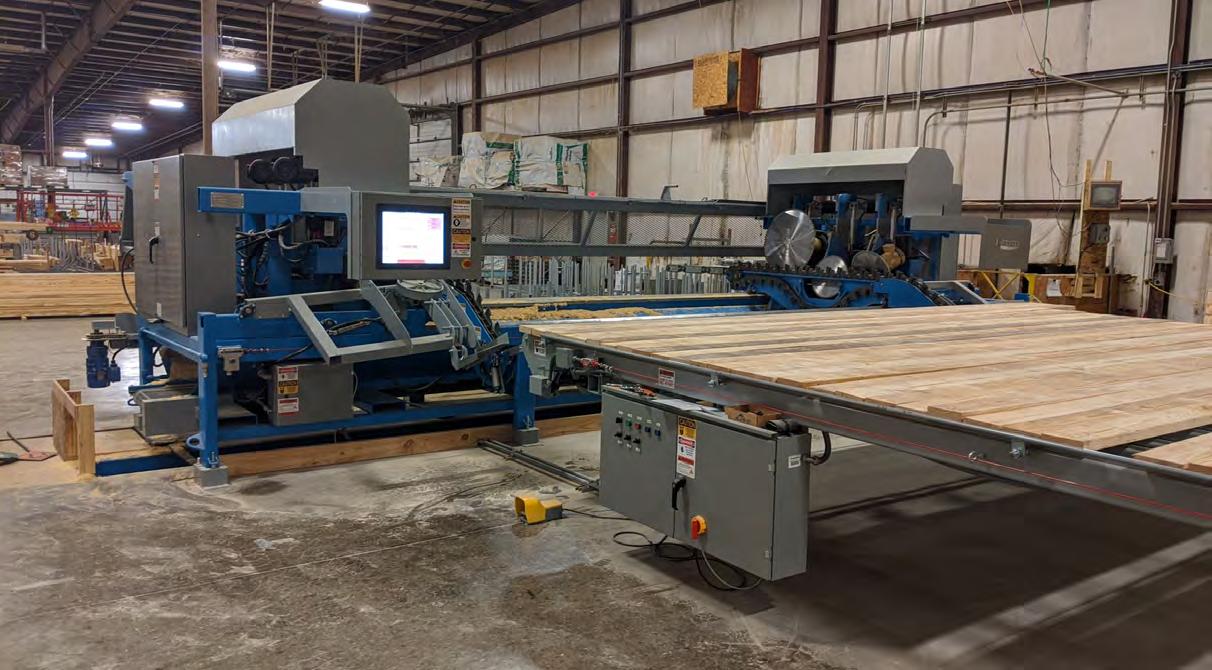
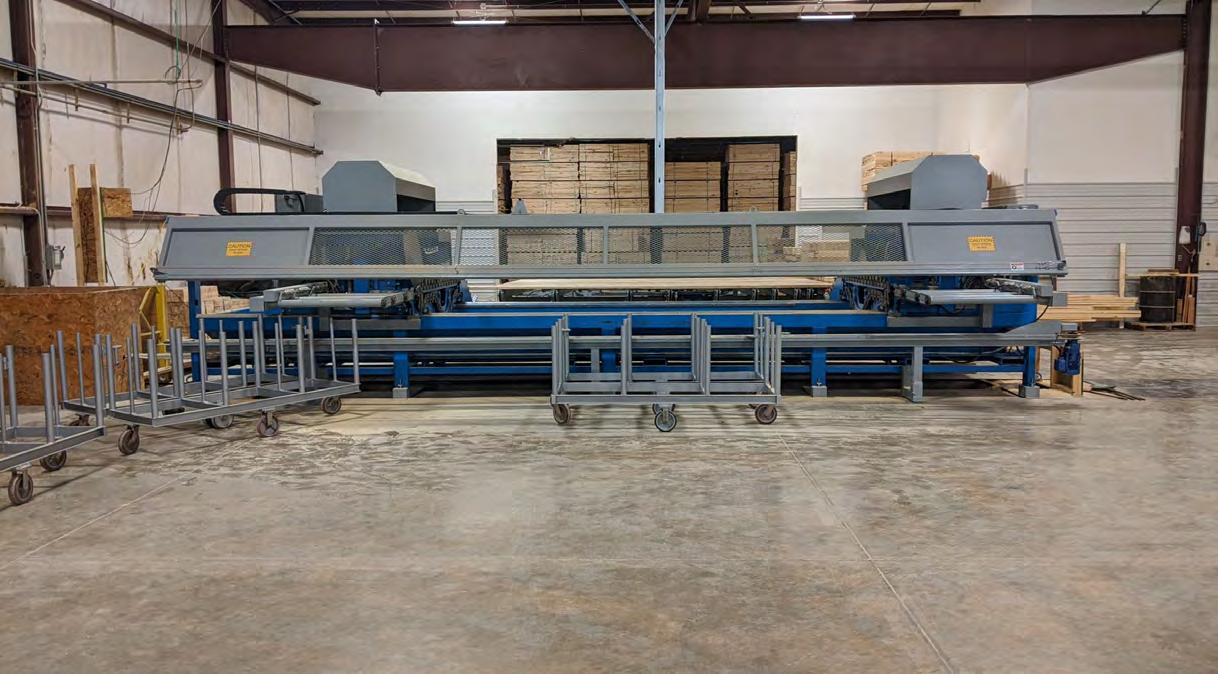
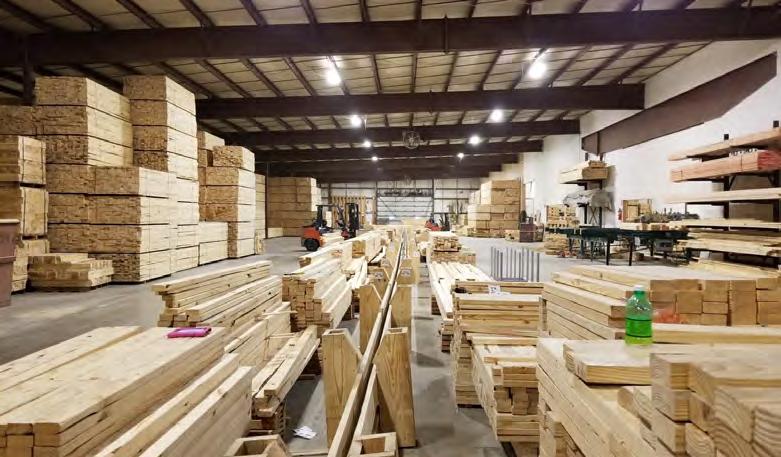
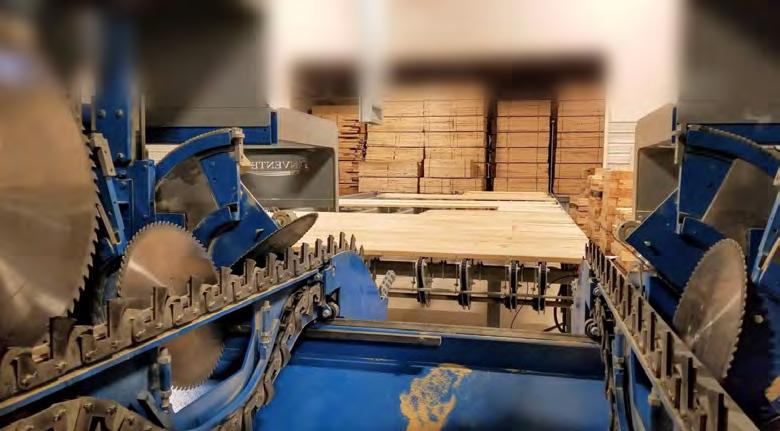