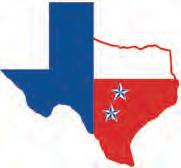

The Citation jet, named Cloudkisser II, is as clean and slick as the new 100-foot by 100-foot hangar where it resides. Owned by Gary and Sondra Bertrand of Ataraxis Holdings LLC, the hangar is equipped with a remote opening 80-foot by 22-foot liftstrap/ autolatch bifold door wind-rated at 115 mph. Inside the hangar is a 25-foot by 55foot pilot and tenant office, a main central TV lounge, galley, restrooms and storage and utility rooms, with a mezzanine overlooking it all.
The 11,375-square-foot hangar is finished with Proliner insulation, yielding
an R-38 rating for the roof and an R-30 for the walls and bifold door.
After they moved in, the Bertrands sent a letter of thanks and praise to the builder, Norm Paulson of Paulson Kimball Construction.
“We celebrate the completion of our hangar and the wonderful job that was done by Paulson Kimball Construction and the many excellent subcontractors and everyone’s ability to work in harmony with Greg Cullen and his fine folks at the Regional Airport,” they wrote. “I must hasten to say that as we arrived on Cloudkisser, it was, and will continue to
be, an exceptional feeling of gratitude to approach and pull into our beautiful hangar for the first time. Thank you for making that happen!”
Paulson says the staff at Schweiss Doors was helpful and the installation crews are always good. “We’ve done five of these big bifold doors and it always amazes me when we run one up for the first time,” Paulson says. “It was my recommendation to go with the Schweiss bifold door on this project. I originally found out about Schweiss Doors through my Behlen Buildings district manager and from talking to people and browsing
Othe Internet. We had the Schweiss crew come out and install the door. That always goes well, that’s why there is no reason to reinvent the wheel. With us, the guy that makes the door is always the guy that is going to put it in. They are in and out in a couple of days.
“The Schweiss door is overall a nice, simple, quiet-running door. From a GC point of view, the upfront overall complexity of the building makes installation easier versus the lot more labor-intensive sliding door system with a track and drain system that needs to be put in.”
n May 24 BakerTriangle hosted their 17th Annual Charity Golf Tournament. The event was held at the beautiful Canyon Springs Golf Course. Proceeds went to Roy Maas Youth Alternatives (RMYA) where they raised over $56,000.00. BakerTriangle has proudly donated more than $429,000.00 over the course of all their tournaments.
A huge thank you to all sponsors from the construction community that helped make this day a huge success.
Darin Thomas Larson, Business Specialist at Lone Star National Bank in San Antonio, grew up in the industry. Born and raised in San Antonio, he has fond memories of going to Luaus hosted by SpawGlass, where his father worked. His mom, who worked the front desk at Lynwood Building Supply, was a friendly and familiar face to many in the local industry. Darin spent summers behind the desk with her as she worked, and got a first-hand look at what top notch customer service really looks like. She was the receptionist, placed orders, and always found the answers if someone had questions. His dad taught him a lot about construction, and he learned from him the value of hard work.
Growing up around all these people who are so deeply connected in the construction industry in San Antonio has given Darin the desire to help them grow their businesses and protect their financial futures. Seeing so much behind the scenes of the industry has given him a unique understanding of the needs of the people in the community. Now that he’s in banking, he knows the best way he can help them is to share his financial knowledge with them and show them what Lone Star can do to help them grow.
Lone Star is focused on building long term relationships with their clients. They pride themselves on being a local bank that Texans can trust. Darin says, “When a small business comes into my branch they’re going to meet with me, and they’re going to have a banker that they can call directly. We take a lot of pride in our ability to bring banking to them. I think that’s really what sets us apart from everyone else. Lone Star prioritizes building relationships, and we have the ability to be flexible enough to go to our clients for whatever they need, they can call me and I’ll come to them. We can
do everything the big banks do, but we can also do things smaller banks can’t.”
Eric Canupp, a financial advisor at Lone Star, says he’s proud to work for an institution that truly feels like family. “When you start building a relationship with a banker like Darin, it’s not foreign for him to introduce you to me or to the lenders we have relationships with. In fact, some of us share offices in the same branch. It’s not like we’re going to pass you on to a different building across the nation, and you’re going to have to retell your story again. We’re going to work together to reach your goals and even sit in on loan meetings or insurance meetings, doing whatever needs to be done to make sure that the client’s taken care of. We very much pride ourselves on not just bringing the bank to you literally, but also having that family feel where you’re going to be greeted and treated warmly. You can just go from office to office and get exactly what you need taken care of without feeling like you’re just another name or another number being drawn out,” Eric says.
Lone Star National Bank has many locations throughout South Texas, including 5 locations in San Antonio to serve you. If you have any questions, just give them a call or stop in to meet one of their bankers. They’re ready to shake your hand, and start building relationships that build strong futures. -ndw
Congratulations to the Joeris General Contractors team for winning Best in Show at Bark + Build Design/Build Competition! Joeris partnered with Stantec and Allan Commercial Millwork to create this unique cat condo.
Vermeer Texas-Louisiana, the authorized dealer for Vermeer construction equipment in Texas and Compact Construction Equipment, LLC, the authorized Bobcat dealer in south, central and west Texas have opened a new, co-branded facility in Buda, Texas. The branch officially opened for business in late April.
Located on just under five acres directly off of Interstate 35 in Buda, the branch is conveniently located between Austin and San Antonio in the rapidly growing I-35 corridor. The full-service location offers equipment sales, parts and service for Vermeer and Bobcat construction and grounds maintenance equipment. Equipment is also available for short or long-term rental.
In addition to the two primary equipment brands, the parts department
stocks tree and arborist products from Sherrill, Inc., underground locating products from Digital Control, Inc., and a wide selection of mud mixing fluids for directional drilling. Attachments from manufacturers including Belltec, Virnig, Blue Diamond and Fecon are also available for purchase or rental.
The store operating hours are Monday through Friday from 7am to 5pm. A grand opening event is scheduled for Thursday, October 3rd from 11am –1pm at the branch.
“We are excited to open this new branch location in Buda. The central location between Austin and San Antonio will allow our customers to save time and money when they need equipment, parts or service” said Chief Operating Officer of the Southern Region, Brian Harris.
Beth
(Chief Financial Officer at JE Dunn), Sara Harwood (Chief Development Officer of YMCA Austin), Kathy Kuras (President and CEO of YMCA of Austin), Christy Paoli (Chief People Officer at JE Dunn), Brian Haulotte (Vice President and Regional Director of Construction Operations at JE Dunn) Chuck Lipscomb (Sr. Vice President - Austin Office Leader at JE Dunn)
row,
Shaquan Brown (Chief Operating Officer of YMCA of Austin), Tad Hatton (Chief Financial and Administrative Officer of YMCA of Austin), Greg Lorei (South Central Region President at JE Dunn), Gordon Lansford (President, Chief Executive Officer at JE Dunn), Tom Whittaker (Chief Legal Officer at JE Dunn), Nancy Phelps (Community Impact Director at JE Dunn)
The Greater Austin YMCA is the proud recipient of a $100,000 gift from JE Dunn Construction. In honor of its Centennial celebration, JE Dunn is extending its community impact by choosing ten worthy organizations to receive a gift of $100,000 to further their important work. This community impact program, Building a Legacy: A Century of Generosity, will be honoring nonprofit organizations from across the country. The Greater Austin YMCA, which works to provide access and help people of all backgrounds improve their total wellbeing and quality of life, received this grant on Thursday, May 23, in a surprise ceremony at JE Dunn Construction’s Austin headquarters.
“JE Dunn has been a longstanding supporter of the Greater Austin YMCA, and especially YMCA Camp Moody,” said Kathy Kuras, Greater Austin YMCA President & CEO. “This Centennial Grant will help us fulfill the long-term vision for YMCA Camp Moody and enable us to deliver transformative camp experiences to kids. One in four kids at Y camp benefits from assistance provided by donors like JE Dunn. We are very grateful and extremely humbled by the generosity of all our supporters.”
The Greater Austin YMCA will use the money to build an airnasium as part of the upcoming expansion of Camp Moody – a summer camp that was constructed by JE Dunn in 2020. The open-air gym will provide a multipurpose space for multiple sports and recreational activities. This 5,153-squarefoot area will offer court spaces for various sports including basketball, volleyball, pickleball, dodgeball, archery tag, and more. The space will provide campers, members, school groups, and families a safe area for play and recreation.
“This donation is an incredible opportunity to celebrate more than a decade of partnership between our two organizations while supporting the great work being carried out by the Greater Austin YMCA,” said Brian Haulotte, Vice President and Regional Director of Construction Operations at JE Dunn. “I cannot wait to see the airnasium become a staple of Camp Moody and be enjoyed by residents in Central Texas.”
According to an Impact Report from 2020-2022, YMCA Camp Moody has served: over 1,000 families through campouts, adventure days, and special
events, 350 students in outdoor education programs and field trips at camp through area school districts, 800 members in health & wellness and group training programs, and 1,200 kids through swim teams and swim lessons.
At the start of the year, JE Dunn employees nominated and voted on a variety of nonprofits to settle on the final 10 recipients. In addition to the Greater Austin YMCA, $100,000 gifts have been made to Colorado Youth Outdoors, Kanbe’s Markets in Kansas City, Missouri, and Our Kids Center in Nashville, Tennessee. The other seven $100,000 donations will be made over the remainder of the year.
“It’s our goal to celebrate the Centennial and the incredible impact JE Dunn has had on the communities where we live and work,” JE Dunn Community Impact Director Nancy Phelps said. “It’s an incredible honor to recognize these amazing organizations and help them further their mission.”
To learn more about this historic milestone, go to www.centennial. jedunn.com to read stories about JE Dunn’s legacy, projects, impact on the community, and more.
huge congratulations to the Alterman Austin division for earning the National AGC Safety Award for Zero Incidence Rate in 2023! At Alterman, safety is both a core value and a daily commitment to ensuring their team goes home just as they arrived. This achievement is a testament to the hard work and dedication of the entire Alterman team. Kudos to the Austin division for upholding their values and continuously striving for a safer work environment.
3 – Eloina Benavides, Tone Custom Sounds
3 – John Tezel, Tezel & Cotter
3 – Lauren Mandel, AGC SA
5 – Amy Ronek, A&B Automatic Doors
6 – Rhonda Piel, Robinson General Contractors, Inc.
8 – Andi Mathews, Construction News
11 – Adam Matthys, Chamberlin Roofing & Waterproofing
12 – James Ellison IV, Keller Martin Construction
13 – Bill Sommers, Langley & Banack
13 – Brett Schropp, Chamberlin Roofing & Waterproofing
23 – Bill Dawley, Markel Surety
25 – Brian Carroll, Sanderford & Carroll
27 – Jacquelyn Bustillos, Robinson General Contractors, Inc.
28 – Greg Kanning, Dumas Hardware
30 – Becky Rodriguez, Turner Construction
Know someone celebrating a birthday next month? Let us know! Email Andi Mathews, andi@constructionnews.net
The 2024 Austin Build Expo is Austin’s premiere regional building and construction event. Held this year on May 22 and 23 at Palmer Events Center, the Expo was a great success and memorable experience. Construction News Owner, Haley Mathews and Staff Writer Nicole Wyatt had the honor to attend as exhibitors. The two-day event was packed with lots of great networking opportunities, and a chance to learn
about new and innovative construction products and services. The opportunity to shake hands with people from all sectors of the Construction Industry was invaluable. We also enjoyed meeting and talking to people who have been loyal readers of Construction News for many years, as well as getting to spend some time with the founder of Construction News, Buddy Doebbler.
This annual event features hundreds of booths, featuring everything from
equipment manufacturers, general contractors, stone masons, business services and so much more. The two days were absolutely necessary to take everything in. Every year, this highly anticipated event includes a dynamic schedule of classes, lectures and demonstrations. Many exhibitors also provided free snacks, merchandise and the chance to win prizes like a propane BBQ or a Yeti Cooler. Many of the local trade organizations were in attendance
as well, giving them a chance to connect with people in their specific community. Build Expo travels the country, with annual events in Austin, Atlanta, Charlotte, Dallas, Houston, Los Angeles, South Florida and Tampa. Next year’s Austin Build Expo will be held again at the Palmer Events Center, on March 19th and 20th, 2025. Registration is open now for exhibitors. Don’t miss your chance to build your business with Build Expo! -ndw
The Texas concrete industry came together on April 25, for the annual Texas State Concrete Industry Management (CIM) Scholarship Gala. The event, held to honor and support the future leaders of the concrete industry, saw a remarkable turnout, with more than 250 industry professionals and supporters in attendance.
The evening was a celebration of academic excellence and industry dedication. A highlight of the gala was the recognition of 42 current CIM student scholarship recipients for the 2023-2024 academic year. These students were acknowledged for their hard work and commitment to their studies, setting the
stage for their future contributions to the concrete industry.
Attendees enjoyed a delightful dinner followed by an electrifying concert from country music artist Clay Hollis, whose performance added an extra layer of enjoyment to the evening. The atmosphere was filled with camaraderie and shared enthusiasm for the advancements in the concrete industry.
One of the evening’s most anticipated moments was the presentation of the inaugural Distinguished Patron award. Dr. Earl Ingram of Ingram Ready Mix was honored for his unwavering support of
the Texas State CIM program since its inception. Dr. Ingram’s contributions have been instrumental in the growth and success of the program, making him a well-deserved recipient of this prestigious award.
The gala also served a critical fundraising purpose, with more than $40,000 raised to fund scholarships for the upcoming academic year. This generous support ensures that more students will have the opportunity to pursue their education and become the future leaders of the concrete industry.
Since graduating its first class in 2012, the Texas State CIM program has been dedicated to educating students and
preparing them for successful careers in the concrete industry. The program’s success is evident in the strong network of alumni and the continuous support from industry partners.
The Texas State Concrete Industry Management Scholarship Gala was a resounding success, highlighting the commitment of the Texas concrete community to fostering education and excellence within the industry. The funds raised and the recognition given at the event will undoubtedly have a lasting impact on the students and the industry as a whole.
Lake life Pioneers
Since 1981, Ken Milam has been guiding fishing trips for striped bass on Lake Buchanan in the Texas Hill Country. You can hear Ken on the radio as follows:
The Great Outdoors:
5-8 am Saturday on 1300, The Zone, Austin and The Great Outdoors:
5-7 am Saturday on 1200 WOAI San Antonio
The Sunday Sportsman:
6-8 am Sunday on 1300, The Zone, Austin All on IHeart Radio
It’s kind of funny to think about because it just seems so natural now, but do you realize that once upon a time here in Texas we really didn’t know what to do with a lake?
According to www.brazos.org, there was only one natural lake in Texas, Caddo Lake and it was formed by an accidental log jam. In Texas the usual way of water is for it to get dumped from the sky and you better catch it quick before it runs off.
Here in the Hill Country of Texas in the 1930s a grand experiment was underway, just like the one in the Tennessee Valley. People always had a love – hate relationship with their rivers. The water brought life and possibility and an avenue for travel and trade. The flip side though was the nasty fact that rivers also brought deadly floods that had a bad habit of washing away towns and anything else that tried to get too close. Finally someone had the idea that it was time to tame the rivers with dams to control the flooding, hold the extra water for dry times and make the water that did pass through churn out a new commodity that the nation was suddenly so hungry for, electricity.
Before long a lot of farmers and their families were standing on the shorelines of new lakes instead of in the fields that had supported them for so long. Some of them moved to the cities to find work and build new lives and some stayed put and adapted to lake life becoming a new kind of pioneer. The old boys who didn’t leave knew from living near the river how to
build simple wooden boats and how to river fish. The lakes were wider and rougher, but they were learning and newfangled outboard motors were getting more common.
It wasn’t long before World War II ended and our country welcomed home our returning heroes. We no longer needed to manufacture a stream of war planes, but we had companies with aluminum and the workforce who knew how to meld it into the sleek aerodynamic lines for flight. To stay in business and help people keep their jobs, they turned to making boats. Wonderful boats that were just the welcome diversion so many servicemen dreamed of enjoying if they ever got to come home to fish again. That is the beginning of the spectrum of boats you see today.
Think about what it was like for our lake pioneers. Before them there were no water skis, wakeboards or fancy specialized boats. They were just a bunch of river rat farm boys looking for fun and having to figure out things as they went along. That’s what makes talking to any of these old timers so interesting. Nobody did this stuff before, no one could teach them, it just all started with, “What if we…”
Next time you are at the lake with the jet skis whizzing past and the wake boats thumping by and the center-consoles cruising along, think about the humble farm boys who had lost their way of life and found a way to channel their loss and confusion into the boating lifestyles we still love to this day.
In Memory of Max Alexander, 1932 - 2018
The white bass fishing on Choke Canyon is on fire right now! It’s not uncommon for the clients to boat well over a hundred fish on a 4-hour trip. If you start early, you might be able to catch the white bass schooling on main lake flats near ledges or in the backs of creek channels amongst the hard woods. Casting square bill crank baits, spoons, white grubs or swimbaits on jig heads, and small jerk baits will get you bit. As the sun starts to get overhead, the white bass start to settle down after chasing shad and move back out to deeper water. The best offshore bite has been later in the day between 10 a.m. and 3 p.m. We have been focusing on rocky ledges and humps with hard bottom. 3/8 oz and 1/2 oz Jigging spoons have been the go-to tactic. Jigging the spoons while the fish are suspended or bouncing them off the bottom amongst the schools. If you’d like to get in on some of this action, give me a call at 210-831-4679. Be safe out there and tight lines y’all. Give me a call at 210-831-4679, and let’s go catchin’!
Rising temperatures and the month of June signal the arrival of the dog days of summer. With heat-related illnesses on the rise, Texas State Parks is sharing seven tips to help Texans beat the heat and enjoy their time in the outdoors safely.
Last year, 48 state parks reported 156 heat-related illnesses in humans and pets, but this year could well eclipse that. State parks have already fielded 51 heat-related incidents since Jan. 1, compared to 32 reported by this time last year.
Here are the top seven heat hacks recommended for park visitors:
Hydrate: It’s important to drink at least 16 ounces of water every hour to prevent dehydration. Don’t forget to bring enough for your four-legged family members too.
Block the Rays: Apply a generous amount of sunscreen or sunblock before heading outdoors. Be sure to reapply every couple of hours, and after swimming or sweating.
Dress Smart: Wear light, loose-fitting, breathable clothing; a hat, correct shoes, sunscreen and wet bandanas to keep you cool while in the sun. For pets, protect paws against blistering by hitting the trails during cooler times of the day when the ground isn’t hot or by putting booties on pets to help shield paws from the hot ground. Touch the pavement or ground with the back of your hand. If you cannot hold it there for five seconds, the surface is too hot for your dog’s paws.
Stay Salty: Food helps keep up energy and replace salt lost from sweating. Eating snacks such as jerky, granola, trail mix, tuna and dried fruit is a fantastic way to nourish your body while on the trails.
Buddy System: Two brains are better than one. It’s beneficial to have someone with you in hot conditions so you can look after each other on the trail. With high temperatures hitting Texas, heat-related illnesses are common and having a friend around to help recognize the early symptoms can save you from getting sick.
Plan Ahead: Study the map and have it with you. Avoid relying on your phone for maps since service may be unavailable in back-country areas. Average hikers move at two miles per hour, so allow yourself plenty of time to avoid hiking in the heat of the day. Make sure to rest in a cool or shaded area to recover from the heat if necessary. It is also a good idea to let someone know your plan before you hit the trails and what time you should be back. That way, if you become lost, people know where to look.
Pup-Safety: Dogs are as susceptible to heat as their humans are, so it is good practice to ensure that you bring enough water and snacks for four-legged hiking buddies to last the entirety of the trip.
Additionally, visitors should heed notices posted at trailheads about site-specific conditions before setting out for the day. The park websites and staff are also a valuable resource for folks wanting to know about trail and forecasted conditions before starting their walk. Park alerts on the website are updated regularly and are a valuable resource for visitors prior to arrival at the park.
Statewide deer carcass disposal regulations were adopted by the Texas Parks and Wildlife Commission last month. They will go into effect for the upcoming hunting season.
Commission officials said the regulations are an effort to reduce the risk of transmission of chronic wasting disease (CWD) across the state and that the new regulations will not change how most hunters currently care for their deer after harvest.
“Proper disposal of all potentially infectious material is critical for reducing the risk of disease transmission,” said Blaise Korzekwa, Texas Parks and Wildlife Department (TPWD) White-tailed Deer Program leader. “These new regulations provide hunters more options when it comes to processing their deer to reduce that risk. If CWD is not managed and efforts are not made to mitigate potential spread of the disease, the implications for Texas and its multibillion-dollar ranching, hunting, wildlife management and real estate economies could be significant.”
The new regulations will allow hunters to debone a carcass at the site of harvest, provided proof of sex and tags are maintained until the hunter reaches the final destination. By leaving the unused parts at the site of harvest, the chance of spreading CWD to other parts of the state is greatly reduced, TPWD said.
Meat from each deboned carcass must remain in whole muscle groups (i.e., not chopped, sliced or ground) and maintained in a separate bag, package or container until reaching the final destination. These disposal measures apply only to unused carcass parts from native deer, such as white-tailed deer and mule deer, harvested in Texas that are being transported from the property of harvest. If carcass parts from native deer species are not being transported from the property of harvest, these carcass disposal rules would not apply, TPWD said.
Since many hunters take their harvest to a commercial processor, TPWD noted it will be the processor who then properly disposes unused parts for them. For hunters processing deer at home, disposal in a commercial trash service is preferred, but other options are available.
Acceptable disposal options include:
• Directly or indirectly disposing of the remains at a landfill permitted by the Texas Commission on Environmental Quality to receive such wastes,
• Burying the carcass at a depth of no less than three feet below the natural surface of the ground and covered with at least three feet of earthen material, or
• Returned to the property where the animal was harvested.
Texas Parks and Wildlife Commission unanimously passed a proposal to prohibit canned hunting of mountain lions and implement a 36-hour trap check for the species last month.
For the first time in 50 years, the Texas Parks and Wildlife Commission has updated the standards for hunting and trapping mountain lions, marking an early step in moving the state toward more modern wildlife management practices.
In the May 23 meeting, the commission unanimously voted to ban canned hunting of mountain lions and implemented new rules for trapping the large wild cat species.
The recent decision came after a period of public comment that largely supported the new regulations. More than 91% of the 7,531 comments supported the prohibition of canned hunting and implementation of a 36-hour trap or snare check for the species, according to a news release from the Texas Parks and Wildlife Department.
“It was inspiring to see ranchers, trappers, hunters, hippies, outfitters, biologists and wildlife advocates from across the state all converge to support more respectful management of our cats. We are grateful for the Texas Parks and Wildlife Commission’s leadership on this issue and for the thousands of people who chimed in supporting these changes.”
Canned hunting is a type of trophy hunting that many do not consider a “fair chase.” It is the practice of capturing and later releasing a mountain lion for the sole purpose of hunting or pursuing with hounds. The species is confined in a fenced area, making it easier prey for the hunter.
Many people also take issue with trapping, as some cases involve mountain lions being trapped and left to perish, according to the parks department’s release. In response, the wildlife commission voted to adopt a 36-hour trapping standard for mountain lions, ensuring that live animals are not held in traps or snares for longer than that duration.
Initially proposed during the commission’s meeting in March, the regulation included an exemption to the 36-hour trapping standard for snares equipped with a breakaway device. However, the proposed regulation was revised after public feedback received during the comment period. The breakaway device exemption was removed and replaced with a blanket exemption for snares set vertically with a maximum loop size of 10 inches or less.
Consequently, if a mountain lion is inadvertently captured in a vertically set snare with a loop that cannot exceed 10 inches in diameter, the 36-hour requirement does not apply.
“The passage of these regulations is an important step toward better management of mountain lions in the state,” said Richard Heilbrun, the parks department’s wildlife diversity program director, in the release. “The regulations support ethical hunting and trapping practices while continuing to provide flexibility for landowners to manage mountain lions.”
Before last month’s decision, Texas was the only one of 16 states with mountain lion breeding populations that did not have protections for the species.
This year’s National Women in Construction Conference (NAWIC) will be held in Houston, on August 14th-17th. “The Keys to the Future” will be the association’s 69th annual conference. This important event will connect women in the industry, as they lead, inspire and encourage each other in all aspects of construction life.
The event will host many important speakers, focusing on topics like Safety, Marketing, Company Culture and Leadership. In addition to meetings and classes, fun events like a welcome reception and brunch will be there to be enjoyed. Awards ceremonies will also be held to celebrate those who have made their mark on the industry in the last year. Awards to be given include: OSHA Project Partnership Recognition, Chapter Leadership and Champions of Progress Award, Act. Achieve. Inspire Award, Emerging Professional Award, 2024 Tradeswoman Of The Year Award, and the Carol A Kueker Construction Education Visionary Award.
NAWIC began as Women in Construction of Fort Worth, Texas. Sixteen women working in the construction industry founded it in 1953. Knowing that women represented only a small fraction of the construction industry, the founders organized NAWIC to create a support network for women working in a maledominated field. Women in Construction of Fort Worth was so successful that it gained its national charter in 1955 and officially became the National Association of Women in Construction.
Today, NAWIC is still based in Fort Worth and has over 115 chapters throughout the United States that provide its members with opportunities for professional development, education, networking, leadership training, public service and more. NAWIC continues the vision of its founding members by advocating for the value and impact of women builders, professionals and tradeswomen in all aspects of the construction industry. -ndw
KDC , one of America’s leading commercial real estate development and investment firms, announced today an agreement to market and develop Taylor HQ, a 150-acre site in Taylor, Texas. The acreage fronts Farm-to-Market Road 973 and is next to Samsung’s $17 billion, 2,000-acre Central Texas semiconductor plant near U.S. Highway 79.
KDC will pursue build-to-suit opportunities for manufacturing, office, logistics, warehousing, data center and other uses. In addition, KDC and Transwestern have joined forces to market and capture these opportunities.
“Taylor HQ offers a one-of-a-kind opportunity for companies working with Samsung or that are interested in having a high-profile neighbor next door,” said Bill Guthrey, KDC senior vice president of land development. “Our build-to-suit experience allows us to pivot quickly and develop this acreage for a company seeking any number
of uses on this prime spot.”
Samsung has demonstrated its commitment to Central Texas with its semiconductor plant, which will generate at least 2,000 direct jobs when it opens in mid-2024. Additionally, Samsung recently signed a memorandum of agreement with the U.S. Department of Commerce to receive $6.4 billion in direct funding under the CHIPs and Science Act. In return, Samsung will invest more than $45 billion for additional development in Taylor and Austin. Samsung’s efforts are anticipated to generate at least 21,500 jobs in the area.
“We look forward to working with KDC and Transwestern as they help further job creation and economic development in Taylor and the Central Texas region,” said Taylor Mayor Dwayne Ariola. “We’re delighted that Samsung selected Taylor for its semiconductor plant and look forward to welcoming its new neighbor to Taylor HQ.”
Content submitted by Associations to Construction News
ABC CTX
Associated Builders & Contractors
Central Texas Chapter
Jul. 9-10: Construction Estimating Principles & Application
Jul. 9: Updated Safety Best Practices During Public Events
Jul. 10: Microsoft Outlook - English
Jul. 10: Construction Executive’s 2024 MidYear Construction Economic Update & Forecast
Jul. 10: Exploring the 2023 Tech Report
Jul. 11: Bluebeam Baseline Basics - July
Jul. 11: Learn About the IRS’ Final Rule’s Controversial PLA, Prevailing Wage and Apprenticeship Policies on IRA-Funded Clean Energy Projects
Jul. 12: First Aid/CPR Training - July
Jul. 16: A Conversation About Addiction: The Faces You Know and The Faces You Wouldn’t Expect
Jul. 17: Bluebeam Basic Material Takeoffs & Estimates - July
Jul. 18-19: OSHA 10 - July
Jul. 18: Bluebeam Advanced Material Takeoffs & Estimates - July
Jul. 18: FEA Wine Tasting and Fundraiser
Hosted by Tommy Meserole, Bastrop, Exact address will be emailed to attendees when they register. Crystal Smith, csmith@ abccentraltexas.org
Jul. 23: Bluebeam for Administrative Professionals - July
Jul. 24-25: Reading Construction Documents - July
Jul. 25: STEPping Stones: Leading IndicatorEmployee Participation
ACEA
Greater Austin Contractors & Engineers Association
Jul. 11: July Luncheon, Speaker: Casey Moore, 11:30am-1pm, Norris Conference Center, 2525 W. Anderson Lane, Austin
Jul. 29: Summer Classic Golf Tournament, Star Ranch, 7:30am Registration, 9am Shotgun Tee Time, 2pm Awards Reception
AGC
Associated General Contractors Austin
Jul. 18: Construction Leadership Council (CLC) School Supply Drive Happy Hour, Parlor & Yard, 4:30 -7pm
AIA
American Institute of Architects Austin
Jul. 30: Early bird pricing ends for 85th Annual Conference & Design Expo, October 3–5 in Houston. 85th Annual Conference & Design Expo, October 3–5 in Houston. 70 continuing education sessions, 25 exclusive architectural tours, three inspiring keynote speakers, and 130+ hours of CE credit texasarchitects.org/conference
CLC
Construction Leadership Council
Jul. 18: Back-to-School Drive, 4:30-7pm, Parlor & Yard, 601 W 6th St, Austin
CTRCA
Central Texas Roofing Contractors Association
Jul. 16: Lunch & Learn, Topic What the HECK is EOS, 11am-1pm, Spare Time Texas, 1724 FM 685, Pflugerville
CTSA
Central Texas Subcontractors Association
Jul. 25: Sales Tax in Construction Seminar: Presented by Kathy Mayeux with The Sales Tax Team, 11pm - 3pm, Springhill Restaurant, 2505 W. Pecan Street, Pflugerville, Registration includes Buffet Lunch & Printed Materials, Register at www.ctsaonline.org. Contact Carrie Buckley 817-983-6244
DACA
Drywall Acoustical Contractors Association
Jul. 17: Member Educational Meeting, 11am1pm, Maggiano’s at the Domain
HBA
Home Builders Association Greater Austin Jul. 9: Government Relations Committee Meeting, 12-1pm Jul. 16: Young Professionals Council Happy Hour & Panel, 4:30-6pm, Classroom at HBA Offices, 7800 Shoal Creek Blvd., Ste. 225E, Austin
NARI
National Association of the Remodeling Industry
Jul. 24: Austin NARI Social at Wilsonart Social, 4-7pm, 19101 N. Heatherwilde Blvd. Bldg. 4, Ste. 100, Pflugerville
TAB
Texas Association of Builders
Jul. 9: Chip Dence Memorial Golf Tournament, Shotgun start 8am, Cowboys golf Club, 1600 Fairway Dr., Grapevine
TCA
Texas Construction Association
Jul. 17: CIAC Summer Luncheon, 11:30am2pm, Norris Conference Centers, 2525 West Anderson Lane, Austin
oeris General Contractors loves watching projects come to life, literally! On Jun. 5 Joeris joined Soli Organic Inc. for their ribbon cutting, unveiling its most technologically advanced facility yet in San Antonio’s mixed-use Brooks Community at the site of former Brooks Air Force Base. This new indoor vertical farm builds on the state’s rich agricultural traditions, boosts the local economy, enhances regional food security with locally grown produce, and creates an array of employment opportunities. Constructed by Joeris General Contractors, the facility is one of Soli’s three facilities in Texas and 10 throughout the U.S. It has four indoor farms, but its largest is located at Brooks.
Pro-Line Paving did the site work, concrete and asphalt paving, and pavement markings for this project located on the Wagner High School campus.
Construction News owner Haley Mathews recently had the opportunity to sit and talk with Craig Noto, the founder of Quality Fence and Welding, which has now branched out into a new venture - Quality Steel Fabrication. Having first entered the structural steel industry in 2009, Quality is now doubling down on the market with the purchase of a new, top of the line piece of fabrication equipment, and the implementation of Tekla PowerFab. Chris Loeffler, a longtime Quality employee and now General Manager of Quality Steel Fabrication, will head up the new venture as it looks to take the firm’s structural steel division to the next level.
Craig Noto started his journey in the industry in 1980, starting out with a painting and remodeling business. At age 19, with no financial backing, his drive and work ethic put his career on the fast track to success. It started with building a fencethen another fence, and another… until the chain link supply company he used wasn’t able to keep up with the demand he had for gates. So Craig went out and bought his first welder. Craig remembers, “The first guy that could come in and weld that thin tubing with that cracker box welder got the job, and he just celebrated his 39th anniversary here with the Company.” Since then Quality Fence and Welding has continued to grow and diversify their services. From automation of custom wrought iron gates to custom fences, all the way up to commercial steel fabrication, Craig recognized the need to create a separate entity and with that, Quality Steel Fabrication was born. He and Chris Loeffler have set focus on growing Quality Steel. Readers may remember that Craig recently sold the Quality family of businesses to TRTF Community House, a local nonprofit that
reinvests the organization’s earnings into the community.
In 2017, Chris Loeffler was working full time and finishing his Mechanical Engineering degree. Under the mentorship of Steve Gooden, former owner of Empire Steel and project manager at Quality, he got his first structural job and was positioned to take over the steel division. After graduation, he thought he’d have a few years at least to absorb more of Steve’s wisdom and experience, but unfortunately Steve got diagnosed with cancer and retired 3 months after his graduation, Chris then became the only Project Manager.
Chris and Steve originally met and bonded over playing a golf arcade-style game called Golden Tee at a dive bar in Helotes. Chris, being what some might call an old soul, was a young man who honestly preferred more mature company. His background, based in the farming community, had provided him a hard work ethic, and he had no trouble relating to people in the industry who were many years his senior. Majoring in Mechanical Engineering while working at a Feed Store, it was Steve who convinced Chris to come on board with him to the structural steel business. He needed someone who had the engineering education and project management ability, and he knew Chris was the man for the job.
In order to really get to the next level in the Steel Fabrication industry, a major investment was made by Quality Steelthe purchase of a new Python Robotic CNC Structural Fabrication System, a machine worth over $1 Million. Made in North America by Lincoln Electric, this behemoth is a steel fabricator’s dream. The exploding commercial construction industry in our region demands fast
turnaround time, efficiency and accuracy for steel fabrication. This robot will help Quality Steel meet the ever increasing tight deadlines. In addition to this incredible machine, they have implemented the use of Tekla PowerFab, a comprehensive software suite providing a systematic, collaborative approach for managing steel fabrication projects. Craig explains, “When they detail the project, they also make the files that run through this new robot, and it also creates all the mark numbers. So when the erector gets it on site, he knows right where that piece goes. And it actually monitors those pieces and gives you a 3D model of what’s being built. It shows what you can load on the truck, and what the exact weight is. Then when it gets out there and the project manager can send a report and show me them exactly what’s being built in the shop and what’s been delivered to the job in a live 3D model. This resource is free for our customers because we pay for it.”
Chris understands the importance of standing out in this extremely fast paced business, using technology such as Tekla PowerFab and the PythonX Robot are what’s going to make Quality Steel do just that. “You know, the hardest part of this job is communication. We’re trying to do things that separate us from the rest and make our customers’ jobs easier. When our customers issue a Division 05 contract, or PO, they already know that with us, they could put a PM on the project that’s not really Division 05 savvy- they don’t have to have a specialist because they know I’m going to help them. That’s what we’re offering.”
With this new machine, and embracing the latest technology available, Quality Steel has hit the ground running with record sales and production capacity. The efficiency of this incredible
new machine means less waste, more accuracy, and time saving capabilities that are lightyears ahead of the old ways of steel fabrication. This means bigger jobs for Quality, with better and faster results for their clients. “We have a good team. It’s not just me, we’ve got a team that surrounds us that we’ve created over the years. And the cool thing about Chris is, he took the stuff that Steve, his mentor was doing on a piece of paper, and he excelled it to the max, using the latest programs, and really made it to where you could do three times the estimating. It’s about how many numbers you throw at the wall, you’re gonna get some, and that was where he really was the game changer,” Craig says proudly.
Craig’s decades of experience and business acumen, along with Chris’s knowledge of the latest technology and desire for perfection in all he does, makes them a powerhouse duo. When you combine that with their team of loyal employees- Quality Steel Fabrication is built to last. -ndw
In 1995, BakerTriangle opened their first Texas branch in Austin. Jerry Smith, then a Vice President in the Dallas office, was appointed president of this new office by Steve Baker, and the rest is history. These images represent some men and women that make BakerTriangle great in Austin!
The Texas Aggregates & Concrete Association (TACA) welcomed
more than 600 attendees to its 70th Annual Meeting June 12 - 14 at the JW Marriott San Antonio Hill Country Resort & Spa. The theme this year was “Preserving a Strong Foundation” – to support an enduring commitment to the environment, as well as fostering a workforce that will carry the industry far into the future.
Outgoing TACA Chairman Kevin Kipp, Few Ready Mix Concrete Co., noted the thinking behind the theme. “‘Preserving a Strong Foundation’ pays homage to those who have committed to preserving the environment – well before conservation was in the spotlight,” said Kipp. “And it underscores one of our most important assets: our people, who will lay the foundation for the next 70 years.”
A highlight of the conference was the keynote from Aaron Witt, “Chief Dirt Nerd” of BuildWitt, a marketing, media and software business dedicated to helping the Dirt World overcome its workforce challenges, which are real, considering that 40 percent of the construction industry and 50 percent of the mining industry are now retiring.
“Rather than view this as a catastrophe, we can think of this as the biggest opportunity we’ve had in a long time,” said Witt. “By focusing on being a ‘Best in Class’ company that attracts the right workforce, we can perform better and serve humanity better. ‘Best in Class’ companies take an active role in their future. When needed, they are not reluctant to change course,” he said.
Witt outlined the characteristics of a winning company. 1) They train all day long. It is worked into their cultures…brick by brick by brick. They train their front-line leadership, and their front-line leadership has great attitudes. 2) They have non-stop communication. They talk to each other all day long, not just a 40-minute safety meeting in the morning. 3) They take pride in every single detail of their business – from how it looks to how it performs. 4) Their teams have a genuine sense of humility. They care about their workers and are not afraid to show it. But they can also say, “Maybe there’s a better way to do it. Let’s pivot.”
TACA President & CEO Josh Leftwich agreed that workforce development is essential to the industry’s success. “Workforce development is not just about individual skill-building; it is also about nurturing a resilient, adaptable and forward-thinking workforce that serves as the backbone of a thriving aggregates industry,” said Leftwich. “Robust workforce development is sculpting a future where every stone of potential is meticulously honed to ensure a strong, resilient workforce everready to build a strong Texas.”
TACA members also heard from Vance Ginn, Ph.D., Vance Ginn Economic Consulting, on how policy uncertainty drives economic volatility in an election year; Robert Mineo II, PE, LEED AP, Managing Director, FMI Capital Advisors, on the impact of economics and drivers for construction materials on the current market; Aaron Demerson, President & CEO, Texas Economic Development Corporation, on how Texas is an economic powerhouse; and Libby Pritchard, Director, Occupational Health, Safety and Sustainability, National Stone, Sand & Gravel Association, on total worker health.
Amy Teykl has never been afraid to get her hands dirty. With a broom in her hand and ambition in her heart, she had a vision to become one of the leading woman-owned construction cleaning companies in Austin. Amy has been cleaning construction sites in Austin and the surrounding area for over 20 years, and founded ATX Construction Clean in 2016. Her willingness to do the “dirty work” means she never asks her crew to do anything she hasn’t done herself. She has awareness of what it takes to get the job done right the first time, and her attention to detail is impeccable. Her experience and ability to lead her team gives her the unique ability needed to become an industry leader in the construction site cleaning sector.
ATX Construction Clean can do it all.
Their services include:
WINDOW CLEANING:
• Interior/Exterior Window Cleaning
• Low, Mid, & High Rise Window Cleaning
• Exterior Final Cleaning
• Construction Window Cleaning Skylight Cleaning
• Atrium Cleaning
• Awning & Canopy Cleaning
Commercial TPO Roof Cleaning
• Customized Cleaning Programs
ALL FLOOR CARE:
• Grout Haze Removal
Polished Concrete
• Strip and Wax VCT
• Carpet Cleaning and Stain Removal
COMMERCIAL SERVICES:
• Final/Progress/Composite Cleans
Make Ready & Move Out Cleans
• Maintenance Cleans
• Year-Round Scheduling
Emergency Cleanings
• ATV Site Clean Up and Light Hauling
• Pressure Washing
Parking Lot and Garage Striping
• Sweeper Truck
• Graffiti Removal
HYDROMULCHING:
• Temporary Irrigation Erosion
Control Blankets
• Silt Fence
From multi-million dollar buildings, shells, hospitals, schools and more, ATX Construction Clean is a single source provider in all phases of your construction project. ATX Construction Clean can create customized solutions to fit your company’s needs. -ndw
For more information, please visit: www.atxconstructionclean.com or contact Amy directly: 512-947-9817 | amy@ atxconstructionclean.com
YSteven Bankler, CPA, PFS, Cr.FA, CFF, CGMA Senior Partner Steven Bankler, CPA, Ltd.
Gina Valorz,
CPA,
PFS, CGMA Managing Partner Steven Bankler, CPA, Ltd.
our accounting method can impact your tax bill, cash flow, and much more. With so many methods used in construction—cash, accrual, percentage of completion, and completed contract—how do you know what’s right for your business?
We all know how complicated the construction business can be. You’re constantly adapting to cost fluctuations, material or supply setbacks, delays, labor costs, and inconsistent workflow. Accurate estimates and reliable forecasting can feel like a pipe dream.
The accounting method you choose can either help or hinder these efforts. At the most fundamental level is the cash basis of accounting or cash-in/cash-out accounting (recording revenue and payments as they occur). You may have kept your books this way when you were first starting out or specializing in projects that could be completed and paid for within a short period. It’s the most straightforward method, and it can offer tax advantages, like allowing the ability to accelerate end-of-year billing or defer it to the following year.
However, cash-basis accounting has concerning drawbacks for contractors. The IRS doesn’t allow larger businesses to use it, and banks and other financial institutions don’t trust it to reflect financial performance over time reliably. Therefore, cash-based accounting can be a significant stumbling block for businesses seeking financing, investors, buyers, or partners.
Enter accrual accounting, which larger contractors are required to use. This method recognizes work when it occurs or transactions when they’re agreed upon, not necessarily when payment happens. It allows businesses to provide a better snapshot of workflow by recognizing revenue and expenses within the same period. In other words, it gives a more accurate picture of the company’s financial health at any given time. This is important for decisionmaking, securing financing, and tax planning, among other reasons.
The Percentage of Completion (POC) method is a form of accrual accounting that’s popular with contractors. It can satisfy revenue recognition requirements for larger businesses and allows income and expenses to be recognized throughout the lifespan of a long-term project, rather than waiting until the entire project is finished (completed contract). Spreading out reporting this way offers some tax deferral opportunities and can provide a decently reliable financial performance snapshot because it allows you to match revenue with project progress. It also aligns with more realistic billing cycles for improved cash flow management, which can make or break your business.
While the POC method offers advantages, it’s not without complexities. It relies on accurate project completion estimates, which can be challenging due to scope creep, delays, and disruptions. Allocating costs can also be highly complex. POC depends upon the allocation of costs to different stages of
construction, which can be a headscratcher for large-scale projects with various materials and labor involved. Implementing and maintaining this accounting method requires skilled personnel who can understand and interpret the data accurately. It also involves subjectivity. Different project managers might have slightly varying interpretations of progress, which could lead to inconsistencies.
Despite these complications, the benefits of POC for construction contractors can outweigh the challenges. However, contractors might not have the staff to dedicate to this specialized accounting approach. A qualified CPA could be a valuable resource for:
Guidance: It’s essential to set up a system tailored to your needs, including defining your cost categories, establishing procedures for estimating completion, and ensuring compliance with Generally Accepted Accounting Principles (GAAP).
Estimating: Many contractors admit that, despite their best efforts, their estimates are troublesome. A CPA can investigate and help remedy any underlying issues, which can be a massive barrier to successfully implementing a POC method.
Calculating: There are several different ways to calculate the POC, including cost-to-cost, efforts-expended, and units of delivery. Balancing best practices with what works for your situation is important.
Internal Controls and Outside Reviews: Strong internal controls help to minimize errors in cost tracking and completion estimates. Regular outside reviews can identify and address any discrepancies or potential issues.
Representation: CPAs are uniquely qualified to represent taxpayers during audits, including face-to-face interactions with the IRS. They can be instrumental in understanding and discussing complexities and adherence to GAAP during the audit process.
Another valuable reason to seek help is for clarity. If you’re a small contractor, you may be able to utilize a small-business taxpayer accounting method like the cash method, but there are numerous other ways you could be excluded from eligibility. For instance, manufacturing and non-home construction contracts spanning more than two years must use the accrual method. Those with related businesses or a flow-through business with losses allocated to passive investors may be questionable candidates. Your personal Alternative Minimum Tax (AMT) rate may also affect your ability to use a simplified accounting method.
Don’t underestimate your accounting method’s impact on your business’s current and future health. And don’t wait until you’re facing financial challenges to address the method you’re using. Choosing the correct accounting method can mean the difference between a thriving business and one struggling to maintain cash flow, secure financing, or answer to the IRS.
Sarah Houser-Kean Commercial Producer
The Nitsche Group Insurance Agency Giddings, TX
weather safety and heat illness prevention is more important than ever.
As the Central Texas region continues to experience rapid, exponential growth, the demand for new construction shows no signs of slowing down. Retail and commercial development projects are booming, but along with that surge of activity comes increased risk— especially in the extreme Texas heat.
While Central Texas and surrounding regions are no strangers to working through sweltering summer heat, the average number of heat advisory days is on the rise, as are the numbers of reported heat-related employee injuries.
In the summer of 2023, the U.S. saw the highest number of heat-related deaths since recording began 45 years ago. Of those deaths, 450 were in Texas.
According to the National Weather Service, heat now ranks as the deadliest weather threat with the most linked fatalities each year. In addition, workers are at a 6% to 9% higher risk of injury and accident occurrence during days with temperatures above 90° F. The risk of injury jumps even further to 10% to 15% on days above 100° F.
Beyond the medical impact and safety risk to employees that heat poses, it is also costly. An analysis by OSHA found that heat-related workplace incidents resulted in approximately $35,000 per injury in worker’s comp claims alone.
That estimate doesn’t include the indirect costs from heat-related illness incidents, which could include lost productivity, training for replacement employees, implementing corrective measures, lower employee morale, reduced employee retention, and the impact on reputation.
People like doing business with companies that invest in the well-being of their employees. Today’s customers/ clients increasingly demand that their contractors invest in effective health and safety practices supported by a strong safety culture.
While you may not be able to avoid the heat in Texas, employers can play a crucial role in safeguarding their workforce by creating a strong culture of safety within the workplace to mitigate heat-related risks. This approach protects your company’s reputation and bottom line by preserving your workforce’s safety, bolstering morale, and increasing employee retention.
Creating a Culture of Safety
Building a strong safety culture means going beyond the minimum requirements.
Most companies understand the importance of providing the “big three” heat prevention measures: rest, shade, and hydration.
Unfortunately, those simple measures can fall short in especially hot, humid, or heavy work conditions. It is crucial for your workers, your safety program, and your company’s bottom line to go beyond the basics by implementing a comprehensive heat illness prevention program.
Creating a heat illness prevention program that promotes education and encouragement will benefit your workers, overall safety, and your company’s bottom line.
Start with a Review
Begin by reviewing your current safety measures and how effective they are. Next, look for low-hanging fruit that will be easy to implement but will make a big impact. These opportunities can include changes like a modified work schedule to help avoid exposing employees to the hottest parts of the day.
These risk control steps might seem obvious, but too often they aren’t enforced. Give a clear indication to employees that you care about their safety, not simply keeping a jobsite open and finishing a project on time.
Companies should also review their current training to see if their workforce is receiving the right kind and level of information. Without proper training from company leadership, workers may be unaware of the symptoms of heat stress beyond recognizing that they’re feeling hot and sweaty.
Additional early symptoms of heat stress and exhaustion that employees may be unaware of include disorientation, stumbling, lethargy, fumbling with tools, confusion, or slurred speech.
Imagine what could happen if an employee who is untrained and unaware of the symptoms of heat stress becomes disoriented on the jobsite or while operating heavy machinery. The outcome could be devastating.
Employee Training & Education
With especially high temperatures scorching Central Texas, now is a great time for a refresher and additional training on heat safety.
Companies should provide employees and supervisors training on how to work safely in hot and humid conditions, as well as how to identify the signs of heat exhaustion in themselves and their coworkers. Training should include topics like: identifying the signs and symptoms of heat-related illnesses, how heat can affect the body, steps to prevent heatillness, and what to do if a co-worker is experiencing symptoms of a heatrelated illness.
Construction workers in the U.S. are 13 times more likely to die from a heatrelated illness compared to workers in other industries. By offering proper training, outdoor workers can greatly reduce the risk of heat-related dangers.
Safety is Everyone’s Responsibility
Ultimately, it’s crucial for your entire team to be trained and aware of what to do when it comes to heat safety and prevention. Companies that don’t create a safety program from the top down inevitably fail their employees and, in turn, lose business. By integrating safety into every step of your organization, you ensure a successful future for your employees and your business.
R. Carson Fisk Construction Attorney Andrews Myers P.C. Austin, TX
exas law provides for a process by which contractors, including subcontractors and suppliers, can secure their right to payment for work performed on a property by following required steps and recording a “mechanic’s lien” with the applicable county clerk. The governing statutes are notoriously complex, with numerous books and guides devoted to explaining the processes and offering practical tips. Properly perfected lien claims can offer immense benefits for parties seeking to be paid for work performed. However, they also can be prone to abuse, with legitimately disputed claims, or even entirely invalid claims, being made the subject of a lien claim. Issues with upstream payment, lender financing, and conveyance of title may follow, causing strife among project participants that may be preferably avoided.
There are various processes by which parties can negate the impact of a lien claim. One of those is obtaining a bond to pay liens or claims. Such a bond is statutorily framed as being “for the benefit of [lien] claimants” working under an “original contractor” (i.e., a contractor who has a direct contract with a property owner). But it also affords benefits to the original contractor, as well as the owner. For example, if a valid bond is filed, a lien claimant may not file suit against the owner or the owner’s property, and the owner is relieved of obligations to hold “reserved funds” (commonly referred to as statutory retainage). Basically, the bond supplants the property as security for a debt—presuming that the bond is properly prepared and filed with the county clerk.
Texas law is clear as to the impact of a valid bond being filed. Specifically: “A purchaser, lender, or other person acquiring an interest in the owner’s property or an insurer of title is entitled to rely on the record of the bond and contract as constituting payment of all claims and liens … incurred by the original contractor as if [such person] were the owner who approved, accepted, and endorsed the bond and as if each person furnishing labor or materials for the work performed under the original contract, other than the original contractor, had filed a complete release and relinquishment of lien of record.”
But the bond, which has to be provided by the original contractor, must meet specific requirements. In general, it must: (1) be in an amount at least equal to the contract price of the contract between the owner and
original contractor; (2) be “in favor of the owner;” (3) include the written approval of the owner; (4) be signed by the original contractor as principal and a qualified surety; (5) be conditioned on “prompt payment for all labor, subcontracts, materials, specially fabricated materials, and normal and usual extras not exceeding 15 percent of the contract price;” and (6) “clearly and prominently display” contact information for the surety. The bond, along with a copy of the contract between the owner and original contractor (excluding any “plans, specifications, and general conditions”) or a memorandum of that contract, must be filed with the county clerk of the county where the applicable property is located.
Any failure to meet these requirements may open the door to an argument that the bond is invalid, and that a lien claim remains viable. In practical terms, that means that a lien claimant can sue the owner and seek foreclosure of the property to satisfy the debt, which negates the entire purpose of obtaining the bond in the first place.
While the best practice is certainly to comply with the necessary steps, Texas law does not require perfect compliance. A non-conforming payment bond is to be treated as a conforming one as long as there is “attempted compliance” or the bond “evidences by its terms an intent to comply” with these steps. However, this alters the interpretation of validity from a theoretically objective assessment to a more subjective one (e.g., what the intent was in providing the bond). Such matters can easily lead to time-consuming and costly litigation as that interpretation is made by a judge, jury, or arbitrator, again negating part of the purpose of obtaining the bond.
Statutorily-permitted bonds to pay liens or claims bonds are commonly used as a means to protect all parties involved in a construction project. But their validity hinges on the required steps being met. Thus, for any project owner or contractor, ensuring that a bond includes the necessary components is prudent. For example, some standard forms may omit key information and required signatures or attachments may be easily missed. Those issues should be identified as soon as possible, and preferably before filing. For any lien claimant, a detailed review of any bond is equally important, as a missed step may allow for additional or different security for a debt in connection with a lien claim.
Michael Middleton Compliance Safety Officer OSHA Austin, TX
rench collapses, or cave-ins, pose the greatest risk to workers’ lives. When done safely, trenching operations can reduce worker exposure to other potential hazards include falls, falling loads, hazardous atmospheres, and incidents involving mobile equipment.
OSHA standards require that employers provide workplaces free of recognized hazards. The employer must comply with the trenching and excavation requirements of 29 CFR 1926.651 and 1926.652 or comparable OSHA-approved state plan requirements.
Trench Safety Measures: Trenches 5 feet (1.5 meters) deep or greater require a protective system unless the excavation is made entirely in stable rock. If less than 5 feet deep, a competent person may determine that a protective system is not required. Trenches 20 feet (6.1 meters) deep or greater require that the protective system be designed by a registered professional engineer or be based on tabulated data prepared and/or approved by a registered professional engineer in accordance with 1926.652(b) and (c).
Competent Person: OSHA standards require, before any worker entry, that employers have a competent person inspect trenches daily and as conditions change to ensure elimination of excavation hazards. A competent person is an individual who is capable of identifying existing and predictable hazards or working conditions that are hazardous, unsanitary, or dangerous to workers, soil types and protective systems required, and who is authorized to take prompt corrective measures to eliminate these hazards and conditions.
Access and Egress: Keep heavy equipment away from trench edges.
Identify other sources that might affect trench stability. Keep excavated soil (spoils) and other materials at least 2 feet (0.6 meters) from trench edges. Know where underground utilities are located before digging Test for atmospheric hazards such as low oxygen, hazardous fumes and toxic gases when > 4 feet deep. Inspect trenches at the start of each shift. Inspect trenches following a rainstorm or other water intrusion. Do not work under suspended or raised loads and materials. Inspect trenches after any occurrence that could have changed conditions in the trench. Ensure that personnel wear high visibility or other suitable clothing when exposed to vehicular traffic.
Protective Systems: There are different types of protective systems.
1. Benching means a method of protecting workers from cave-ins by excavating the sides of an excavation to form one or a series of horizontal levels or steps, usually with vertical or nearvertical surfaces between levels. Benching cannot be done in Type C soil.
2. Sloping involves cutting back the trench wall at an angle inclined away from the excavation.
3. Shoring requires installing aluminum hydraulic or other types of supports to prevent soil movement and cave-ins.
4. Shielding protects workers by using trench boxes or other types of supports to prevent soil cave-ins. Designing a protective system can be complex because you must consider many factors: soil classification, depth of cut, water FactSheet content of soil, changes caused by weather or climate, surcharge loads (e.g., spoil, other materials to be used in the trench) and other operations in the vicinity.
It all began with a simple social media post- a man offering his services for free to the elderly and disabled in the community of New Braunfels on a local Facebook page.
That man turned out to be Michael Boggs, the owner of MK Ultra Renovations . He had a few free days and decided that he wanted to do something helpful for someone in the community. Whether someone needed some simple repairs, yard work or help hauling away something too heavy for them to move, Michael was ready to help. Cue the dozens of messages pouring into his DM’s within an hour. He had to stress to everyone contacting him that his offer to help was for someone who was elderly or disabled, someone not able to do it themself. He ended up in contact with an elderly gentleman who said he could really use some help with yard work, and so that’s where Michael went, on his rare few days off, ready to get it done.
Construction News reached out to Michael to express our admiration and gratitude for his desire to help the community. In that conversation, we got to know a little bit about Michael and his company, MK Ultra Renovations. Michael recently returned home after nine years away, five of which he spent in the US Army, including two combat missions in Iraq and Syria. He and his Wife, Dakota, are both from New Braunfels, they even went to elementary, middle, and high school together! After High School, Michael enlisted in the Army and he and Dakota started talking more often. Dakota said she wanted to come visit him sometime, and Michael agreed and said he’d love that. After a whirlwind romance, the pair were married. A little over a year later, their first child was born, and a year after that- they found out they were expecting twins! Suddenly, this young couple was about to be parents to three children under the age of three. They knew it was time to come home to their families, so they could have their village surrounding them on their parenting journey. As anyone who has braved the “3 under 3” club knows, you need all the love and support you can get. Michael says he’d be lost without his wife, “Dakota is definitely the foundation of our family, and that is the foundation of my business. If she wasn’t doing all she does for us, there’s no way I could do what I do.”
The Boggs Family had been living in Maine, where Michael and some of
his Army buddies had settled with the intention of living somewhere new, and getting into construction together. They were coming back to the States after serving their country, and they were ready to work on building their futures. Michael had loved his time spent in the military, but he desired to be home with his family, so he knew it was time for a new career. After some time working in new and commercial construction, he found his niche doing renovation work. A natural problem solver, he learned a lot from renovating centuries old houses in New England, where each job was a new puzzle, and no job was like the other. He enjoyed the creative aspect of bringing new life to spaces. When he and his wife made the decision to come back to Texas, one of his friends decided he would come along for the journey as well. So together with his friend and fellow Army Vet, Kobe Andrews, they started MK Ultra Renovations. They look forward to growing their business and creating relationships with their clients. With most of his job references being from New England, Michael jokes, “I have to always find a way to mentionI’m a local! I was born here!” He says he and his family are thrilled to be home in Texas, and look forward to what the future holds.
MK Ultra specializes in quality renovation work. Whether you need a new deck, a bathroom or kitchen overhaul, new flooring or a new coat of paint, they can do it all. If you’d like to support this veteran-owned business, you can contact Michael Boggs at mkucarpentry@gmail.com or call him directly at (830)-221-8637.
Welcome home to Texas, and from all of us at Construction News, we are so deeply grateful for your service! -ndw
JT Magen , a national construction firm specializing in preconstruction, construction management, designbuild, and general contracting across a variety of industries, has completed a full office renovation for JBGoodwin REALTORS®, a residential real estate brokerage, at 1613 S. Capital of Texas Highway in the Westlake neighborhood of Austin, TX.
JT Magen served as construction manager for the project, overseeing all aspects from budgeting, procurement of materials, managing subcontractors and conducting the final handover upon completion. JT Magen collaborated with the JBGoodwin team and Seventh Spectrum Studios, who led the interior design for the project.
“We’re pleased to announce the completion of this office refresh for JBGoodwin,” said Dan Longshore, Southwest Regional Director at JT Magen. “The space has significantly enhanced the day-to-day environment for the brokers and staff, providing them with several flexible work and training areas. By removing several private offices, we were able to
welcome more natural light and access to greenery.”
Established in 1972, the full-service brokerage specializes in the Austin and San Antonio real estate markets, and helping homebuyers, sellers and renters find homes that fit their needs. The company has eight branch offices in Texas. JBGoodwin has occupied the 8,000-SF space at the building for more than 40 years and was looking for a complete refresh that would allow the firm to best serve the needs of brokers and clients.
JT Magen built out an open, modern office space for JBGoodwin that features increased natural light and via floor-to-ceiling windows, refreshed materials, a variety of functional spaces for staff training and hosting clients, as well as added desking areas. Luxury vinyl tile in a light wood tone spans the well-traveled paths around the office, while carpeting was placed near the workstations and conferencing areas. A selection of wallcoverings in the conference and sign rooms help create a sense of warmth. Furniture in a variety of muted colors and wood tones reflect the natural landscape of the Texas region. Accents of yellow are incorporated across the office as a nod to JBGoodwin’s signature color.
“This renovation will allow for the continued expansion of JBGoodwin as a brokerage, as well as the attraction and retention of talent,” said J.B. Goodwin, CEO of JBGoodwin REALTORS®. “Looking back on our more than 50 years in business, I am humbled to see how the company has grown to become one of the top names in Texas real estate. JT Magen has helped make our space a home and ensure our longevity in the market.”
JT Magen’s Austin office is one of the region’s leading general contractors and construction managers. Led by Dan Longshore, the team has been involved in number of projects across the retail and commercial interiors sector for clients such as the University of St. Augustine, Owlchemy, The Roarty Law Firm, Oak Point Real Estate, TAWA, and UNIQLO.
Cokinos | Young knows Austin construction and commercial real estate law – it’s what we do. With over 100 of the nation’s most knowledgeable legal professionals, we’ll guide your disputes and transactions and back you every step of the way. We are renowned for our experience and success across commercial, industrial, pipeline, offshore, heavy highway, civil, and residential sectors. For over 30 years, clients have depended on us across Central Texas. Savvy. Tough. Dedicated. And Austin to our core. That’s Cokinos.
COKINOS | YOUNG
Las Cimas IV, 900 S. Capital of Texas Hwy, Suite 425 Austin, Texas 78746
512-476-1080 CokinosLaw.com
Don’t let a single faulty component take down your operation. Bring your machine in or we can come to you. Either way, you get the best hydraulic technicians and parts in Texas.
FULL HYDRAULIC SERVICES INCLUDE:
Assessment of all hydraulics
Disposal of old components
Custom fit hoses
Custom manufactured cylinders
New, high quality couplings
Complete quality assurance review